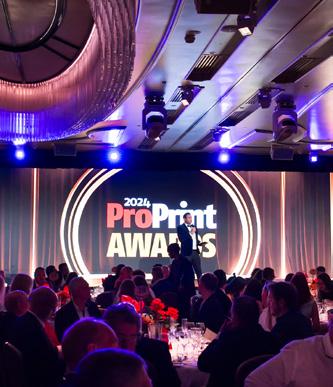
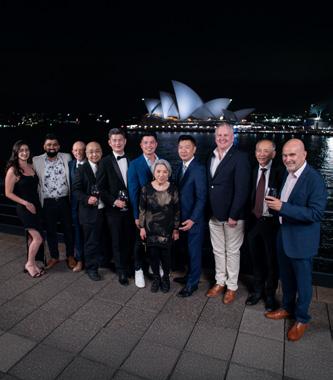


6-16 Update
A news roundup from the world of print
17 Downtime
Record turnout for recent ASGA SA social bowls event
18 Star Business: Next Printing
How Next Printing is harnessing the power of data for its sustainable practices
20 Cover story
Pack & Print installs a Komori A1 Lithrone G437 sheetfed press at Newcastle-based WHO Printing
24 2024 ProPrint Awards overview
A recap of the industry’s night of nights
26-39 2024 ProPrint Awards winners gallery
Photo highlights of senior print leaders, industry suppliers, and rising stars
40 2024 ProPrint Awards post-event trophy recipients
ProPrint visits winners who were unable to collect their trophies
42 Case study
IVE Group sets new performance standard with recent Zünd installs
44 How automation will evolve labels and packaging
HP Industrial Print’s Haim Levit shares his observations and predictions for the year ahead
46 Automation at the heart of Kodak’s solutions
Kodak’s commitment to enhancing and expanding the automation capabilities of its production digital workflow solutions
50 Comment: Charles Watson
How to take to mitigate the risk of wage theft in your business
51 Comment: Andrew Ash
Tips for passing the torch to the next generation
52 ProPrint Diary
Keep up-to-date with the latest industry events
Welcome to the first edition of ProPrint for 2025. The start of a new year is always a good opportunity to reflect on the year that was and set goals for the year ahead.
The new year is also a chance to examine the trends shaping the industry and how to prepare for them. As we enter 2025, businesses are faced with an increasingly dynamic and rapidly changing landscape. From advancements in technology such as AI and automation, to shifting consumer behaviours and sustainability demands, the print industry is on the cusp of significant transformation.
One company that has continued to set itself apart is Next Printing. Next, which recently celebrated its 20th
anniversary, has led the way in sustainability. In this edition, the Sydney-based printer shares the next evolution of its sustainability journey and how it’s increasingly harnessing the power of data to support its sustainable practices.
A new year also brings with it new reforms and regulations. As of 1 January, new criminal offences for intentional wage theft commenced. Previously, the consequences of intentional wage theft attracted only civil penalties if an employer was found guilty of such deliberate conduct.
However, amendments to the Fair Work Act last year mean that from 1 January this year, employers who intentionally underpay their employees may now face criminal charges. These new laws are in addition to the existing legislative framework dealing with underpayment related matters.
In this issue, Visual Media Association’s Charles Watson reviews the new wage thefts laws and outlines steps employers can take to mitigate the risk of wage theft.
Editor Claire Hibbit, chibbit@intermedia.com.au
Editor Hafizah Osman, hosman@intermedia.com.au
Design and Production Manager Sarah Vella, svella@intermedia.com.au
Managing Director James Wells, james@intermedia.com.au
Subscriptions (02) 9660 2113, subscriptions@intermedia.com.au
Printed by Hero Print Alexandria, NSW, 2015
Mailed by D&D Mailing Services Wetherill Park, NSW, 2164
Redefine Commercial Printing Standards and elevate production with Next-Gen High-Speed Inkjet
PRODUCTIVITY
•High productivity
•560mm paper width
•High machine uptime
QUALITY
•New Inkjet 1200dpi PHs
•New saturated ink SC2
•Enhanced image quality
USABILITY
• Energy-efficient drying
•Easy operation
•Offset-coated papers
AGILITY
•Optimised integration
•Precision paper sensing
•Complete New Platform
The former local head of EFI, Brett Addison, has joined Durst Oceania as sales manager.
Prior to Christmas, ProPrint confirmed Addison’s departure from EFI after five years, ahead of a new role to be announced in early 2025.
Addison has since confirmed his appointment and explained his reasons for joining Durst.
“I have always wanted to work for the best and that is why I have now decided to join Durst. I believe Durst is not only the best at this point in time, but they are going to best in the market until I retire, which is probably 20 years from now. I doubt anyone is going to top Durst for a very long time,” Addison told ProPrint
“When it comes to high end technology and innovation, you cannot argue with the investment that Durst has made into its equipment and its commitment to future products.
“For me, I am excited about the ability to directly access people within the business that design, develop, and manufacture the machines that are going to be purchased by my local customers. By having these direct conversations with the product development team, I will be able to understand the technology thoroughly and the tolerances of the machines which is invaluable.
“Durst is also a family-owned business and not owned by private equity. This means from Australia we have direct access to the owner who makes all the decisions.
“Durst also has its own in-house ink laboratories as well as the ability to create its own components, meaning there is only a very small amount of its manufacturing supply chain that is outsourced – and there is no one else like this currently in the market,” said Addison.
“What has also been crucial for me in making this decision is that Durst is the only company able to entirely manage its customer satisfaction process. Durst is the only one that controls customer satisfaction completely in-house from manufacturing, delivery, warehousing, sales, service, and implementation.
“Durst has a greater control over its costs because there is no third party. In a world where things are so volatile, customers need to be able to partner with a manufacturer they can trust.
There is a Durst customer in Australia that needed a small modification to their machine to make it slightly wider for their printing needs – and it wasn’t a problem. No other business can offer the ability to control innovation. Companies that do not own their end-to-end processes don’t have any control over their costs and the customer experience.”
Durst Oceania managing director Matt Ashman said Addison is the perfect fit for the local team based on his previous experience as well as his personal attitude to sales and the industry.
“I’m so pleased to have Brett on board. I have been watching his work for several years, not only as a competitor but professionally as a great sales guy and advocate for the industry. His passion and motivation for customers’ needs aligns with the Durst philosophy. Brett will enjoy great success as the latest Durst’ler down under,” Ashman told ProPrint.
Reflecting on his career to date, Addison said his decision to join Durst at this point in his career represents the next stage in his evolution as an executive in the local print industry.
“In 2012 I joined Viatek – a regional provider of industrial Fuji Xerox equipment – and I was in charge of half of the Victorian market. After initial success, NSW was added to my territory. I then worked for Fuji Xerox direct, reporting to Craig Walmsley and one of the biggest deals I closed at the time was selling iGens into ABC Photosigns. I then met my wife and moved to Adelaide where I worked for Ricoh, reporting to Mark Morrow,” he said.
“I came back to Victoria and worked for
Andy Cocker at Océ. I enjoyed my time working with Andy but Océ was a small business and so I moved to EFI. For the last five years I was in charge of Australia and New Zealand as well as managing its distributor Currie Group and won some big accounts over that time.
“Since Durst Oceania was formed by Matt Ashman and the team five years ago, the business has expanded significantly. Matt and I have always had a healthy respect for each other as competitors.
After talking to Matt on and off for the last three years the opportunity presented itself, and I jumped at it.
“When you decide to switch companies – you are making a career choice. When I weighed up the options, I realised there is only one company that has complete control of their destiny and for me this is not a job – it is about my future. Job security and certainty over what the next 20 years of my professional life is important to me and my wife and five children aged from 12 to 15 years.
“For my future Durst customers, this means there is a strong likelihood that I will be there for the entire lifetime of that product journey, with one person to sell it and look after their entire service and satisfaction journey and that is exciting for me.”
Assets from the sale of Sydney-based large format printer Blow Up Imaging have been acquired by Next Printing.
The administrator of Tricol Pty Ltd, Cameron Gray from DW Advisory, told ProPrint “certain business assets were purchased by Next Printing”.
Romeo Sanuri, managing director of Next Printing, confirmed the company has acquired key assets from Blow Up Imaging, including its trading name and customer list.
“This partnership brings together two high-quality printers, creating an incredible synergy. Blow Up Imaging has built a stellar reputation working with leading cosmetic brands, museums, and global giants, delivering exceptional results every time,” Sanuri told ProPrint.
“At Next Printing, we’re committed to continuing this legacy of excellence while introducing our innovative sustainability solutions. Together, it’s a win-win for customers and the environment.”
Blow Up Imaging entered voluntary administration in November 2024, with
Fujifilm Business Innovation and Konica Minolta have announced further details for the joint venture.
Effective from January 31, the companies have completed all review and approval procedures under overseas competition laws.
In addition, the companies have named the joint venture company Global Procurement Partners Corp, which will be located in Yokohama, Japan with capital of ¥50m ($575,000).
Fujifilm Business Innovation will have a 75 per cent share ratio and Konica Minolta 25 per cent.
President Masaharu Furukawa, corporate vice president and director at Fujifilm Business Innovation will oversee 192 employees – 137 from Fujifilm Business Innovation and 55 from Konica Minolta.
The venture’s business description has three layers:
• Development of procurement strategies and deployment to the procurement function divisions at each production site.
administrators confirming at the time that the business was for sale.
Blow Up Imaging was established in 1993 and is owned by Tricol Pty Ltd (incorporated in 1976) and forms part of the WK Family Investments Group.
Blow Up Imaging described itself as “a leading supplier of large format digitally printed images, image manipulation and lenticular solutions offering complete
in-house service from the initial consultation, artwork setup, printing to installation”.
On the company’s website, Blow Up Imaging listed its range of equipment as consisting of true digital photographic, aqueous, UV and eco-solvent inkjets.
Blow Up Imaging claims to have the first Lambda in Sydney and first production Inca Spyder with white ink in the world.
“Quality is at the forefront of the work we produce. We offer a complete in-house service from the initial consultation to installation. We have the staff, expertise and specialist equipment to enhance, retouch and manipulate your imagery as requested,” the company states on its website.
“Our staff are all highly trained professionals and will ensure the quality of your work. Our finishing department will mount, wrap edges and laminate to all kinds of substrates with the greatest of care and craftsmanship. If you require installation our staff and trade professionals are selected for their experience and capacity to fulfill your project requirements.”
Blow Up Imaging’s work has covered museum graphics, fine art photography, lenticular, giclée, large scale public artworks, office fitouts, retail graphics, fashion and cosmetics graphics, lightboxes and exterior signage.”
• Procurement lead function, including negotiation with suppliers and procurement management.
• Procurement services to ensure quality, cost, delivery, and environmental compliance of externally purchased goods.
Fujifilm Business Innovation and Konica Minolta first announced plans to explore a “potential strategic alliance” in multifunction printer and printer areas in April 2024.
“Sharing a common understating of the challenges facing the business, the two leading companies will be able to mutually maximise strengths through this alliance,” Toshimitsu Taiko, president and CEO, Konica Minolta, Inc, said at the time of the announcement.
“I am looking forward to working together to improve investment efficiency and cost-competitiveness, strengthen capabilities for stable supply, environmental initiatives, and business continuity plans (BCP), and pursue the potential for enhancing business resilience as global manufacturers.”
Naoki Hama, president and CEO, Fujifilm Business Innovation Corp, said: “The ongoing discussions for this business alliance are of immense importance as we strive to strengthen our competitiveness and expand our global presence to make a significant leap forward. We are confident that this partnership will create a new framework to enhance our supply chain and build a robust business foundation.”
Agfa country channel manager, Phillip Burns, has announced his retirement from the industry after 26 years.
In a letter shared with ProPrint, Burns reflected on his journey within the printing industry.
“I was introduced to the digital print industry over 26 years ago when it was just beginning to take shape. Working at a sublimation textile printer I was tasked with finding a solution for producing short-run colour tests for customers. In my search, I discovered inkjet technology, which was still new at the time, as well as electrostatic printing,” Burns wrote.
“In late 1998, I took a bold step and invested everything into a Raster-Graphics Electrostatic Dye Sub printer and a Lemaire Calendar (names that might ring a bell for some). Over the next eight years, I grew a business and witnessed four significant technological shifts in ink technology. Unfortunately, I wasn’t able to keep pace with the required investment, leading to the eventual end of the business.
“My love for the technology and the industry soon saw me emerge in a technical sales role with the Australian Vutek distributor, focusing on new business development, where I built many lasting friendships that have remained with me throughout my career.
Metamark appoints new APAC MD to support regional growth
Self-adhesive material manufacturer
Metamark has hired Pravin Krishnan as its new managing director for Asia Pacific and Middle East, following recent business growth in these regions.
Krishnan’s responsibilities include strengthening Metamark’s distribution partnerships, expanding into new and existing markets, and building representation through new collaborations. Metamark is distributed locally through Ball & Doggett.
Krishnan brings more than 20 years of senior leadership experience in the graphics and allied industries, with a strong track record in marketing, brand development, and channel management. He joins Metamark from CCL Design,
“After six years, I transitioned to HP, where I worked for eight and a half years as a business development manager with the HP Scitex products. During that time, I had the privilege of witnessing incredible technological advancements and growth in the industry and the major transition from analogue to digital output.
“In 2020, I made a move to Fuji Xerox, stepping away from wide format inkjet printing, but by 2021, the wide-format industry beckoned me back, and since mid-2021 I’ve enjoyed being part of the Agfa team. I’m grateful to Agfa for the opportunity to work with its industry leading product range, especially in the past year when we saw Smartech appointed as the Australian reseller taking the products to a larger market share.
“Looking ahead, I’m excited to focus on new personal ventures, for many who know my passion this will include restoring vintage cars, working on my holiday house, and some travel including
walking the Camino De Santiago. I won’t be idle as I have recently started a Hydroblasting business, assisting motorbike and car restorers in bringing parts back to OEM condition.
“To everyone I’ve had the pleasure of meeting over the last 26 years, thank you for the opportunity to be part of an industry that continues to amaze me with its innovations. It’s been a privilege to work in an industry that truly feels like one of my happy places.”
Burns worked with Agfa since 2021 and prior to this worked for Fuji Xerox (Fujifilm Business Innovation) during Covid, had eight years with HP as business development manager and two years prior to this with DES. Burns was managing director of Full Impact Australia from December 1998 to 2006 including during the time of the company’s acquisition by AA Wade Screen Printers and worked for textiles company Brush Fabrics from 1992 to 1998.
In March 2024, Burns enthusiastically welcomed Smartech Business Systems as the exclusive distributor for wide format inkjet printing solutions in Australia.
“By partnering with Smartech, we are confident our customers in Australia will have unparalleled access to our wideformat printing portfolio. Smartech’s industry expertise and extensive presence across Australia make them the ideal partner,” Burns said at the time as he became country channel manager –liaising between Agfa in Belgium and Smartech locally.”
Burns has confirmed Agfa service manager Rashed Chugtai is remaining with the business following his retirement.
where he most recently served as ASEAN vice-president and managing director for three years. Prior to that, he was ASEAN managing director for about 1.5 years and the ASEAN sales and marketing director for about a year at the company.
Krishnan also worked at Avery Dennison for almost 11 years across several roles including senior commercial director North Asia Pacific, Asia Pacific graphics segment director and South Asia graphics business director.
Metamark said this key appointment comes at an “exciting time” as its business continues to grow across the APAC and Middle East regions.
Metamark international vice-president Shaun Dobson said, “Our business is growing on all geographical fronts. Pravin’s appointment will help us reach our potential in APAC and ME, and his expertise further strengthens our talented international team”.
Krishnan said, “I am genuinely excited to join Metamark at this pivotal moment of international growth. I look forward to working with our customers and teams to drive sustainable growth”.
The Visual Media Association (VMA) has announced the reappointment of CEO, Kellie Northwood, across a five-year agreement to continue leading the association.
Kevin Pidgeon, president, VMA, said Northwood has been a pivotal leader in the industry.
“As the board looked to building our strong strategic focus for members and the broader industry into the next chapter of the association’s history, we saw no better leader than Kellie to appoint,” Pidgeon said.
“From her lobbying and advocacy achievements to member growth and improvement of the financial performance of the association throughout the merger, Kellie is someone recognised by our members who truly fights for them whilst building commercial programs to assist their businesses. I am proud of the board’s endorsement across this contract and am confident it will be welcomed, by not only our members, but our industry.”
Northwood has worked across the industry in sales, sustainability, and strategic roles beginning her career with Moore Business Systems, Finsbury Green, and GEON, before moving into association roles campaigning for the environmental credentials of paper and print with retailers, government and brands under Two Sides Australia. Following this was the
Coritex has announced the appointment of Edward Cristia as the new business development representative for South Australia. Based in Adelaide, Cristia will be responsible for introducing Coritex’s digital print media solutions to new clients and supporting the growth needs of existing clients across the state.
According to Coritex, Cristia brings a wealth of experience and a proven track record in business development and client relationship management. His extensive background in the print media industry, combined with his passion for innovation
catalogue and publishing sector representation with her appointment as executive director for the Australasian Catalogue Association and Australasian Paper Industry Association.
Northwood has achieved a Treasury Consultation across paper billing fees, implemented incentive discounts with Australia Post during Covid, launched the only industry-led promotional campaign of print media (VoPP), reinstated the Sustainable Green Print standard providing a compliant and affordable environmental scheme for the industry and successfully lobbied against waste paper export bans and fibre-based packaging regulations for industry as well as merged four entities together with the recent PVCA and TRMC being the final catalyst to a clear vision of a united industry.
“I am delighted to have the opportunity to continue working with the industry association. I thank the board for their endorsement and support, however most importantly for their inspirational and
and customer satisfaction, makes him an ideal fit for this role.
Daniel Watts, managing director of Coritex, said, “We are thrilled to welcome Edward to our team. His local knowledge and experience will be invaluable in supporting local businesses and further ingraining Coritex in the South Australian market. We are confident that Edward will help us build on our strong relationships with our clients and drive significant growth.”
In his new role, Cristia will focus on
brave vision for the association,” Northwood said.
“To our members, your support and insights are what drives and assists me in building strong outcomes and deliverables for your businesses. Ours is an innovative, resilient, and intelligent industry which I believe is stronger when we stand together as the largest manufacturing employer across the country. I feel privileged to have the opportunity to ensure your industry body is delivering for you.”
Following Northwood’s appointment, the VMA also announced it is returning to its head office in Mulgrave, Melbourne. Set to open this year, the Mulgrave head office will not only house the VMA team, however further, offer training and meeting room facilities to host information sessions for members, emerging talent, graduates, apprentices, and more throughout the year. It is believed the facility will also provide VMA members access to hot desks and sales spaces, facilitating greater member engagement.
“The relocation is more than a physical location, it’s about creating a ‘home’ for the industry once more – a place where members can connect, collaborate, and share knowledge. Returning to the Mulgrave facility symbolises a commitment to utilising association assets for the best outcome for members and industry,” Northwood said.
“We welcome our fellow industry associations also to utilise the facilities, whether as office spaces, industry events, meeting rooms or hot desks. VMA firmly believes working together, united and not duplicating expenses, to strengthen delivery for members and industry is key to all our future successes.”
engaging with potential clients to introduce Coritex’s advanced digital print media offerings, building and maintaining strong relationships with existing clients to ensure their continued growth and satisfaction and collaborating with the Coritex team to develop tailored solutions that address the unique needs of each client.
South Australia represents a key market for Coritex. Cristia’s appointment underscores Coritex’s commitment to fostering strong client relationships and delivering exceptional value in this dynamic region. By leveraging Cristia’s local expertise and contacts, Coritex aims to enhance its market penetration and support the growth objectives of businesses throughout South Australia.
Cristia said he is honoured to join Coritex and lead the business development efforts in South Australia.
“I look forward to working with our clients in Adelaide and beyond, helping them discover the unparalleled benefits of Coritex’s digital print media solutions.”
Victoria-based ADS Australia has expanded its capabilities and ability to take on more complex projects following its recent install of a Canon Colorado M5W printer from Currie Group.
The printer was purchased to enhance the company’s production efficiency, print quality, and overall customer satisfaction.
ADS Australia managing director Dean Wright since the installation was finalised, the Canon Colorado M5W has exceeded all expectations.
“Since we integrated the Colorado M5W into our operations, we’ve seen significant improvements in both efficiency and productivity,” he said.
“The advanced features of the Colorado, such as its high-speed printing capabilities and exceptional print quality, have allowed us to take on more complex projects while reducing turnaround times.
“Additionally, the versatility of the machine has enabled us to expand our service offerings, attracting new clients and helping us better serve existing ones.”
The machine has also delivered on superior print quality, especially in fine text and high-end imagery, which has been particularly appreciated by clients requiring high-resolution art prints and smooth UV images without raised textures.
The Canon Colorado M5W is the fourth generation of the Canon Colorado, underpinned by Canon’s UVgel technology. It offers a modular, configurable
upgrade platform, enabling customers to add new features to base models. Additional upgrades include white ink, FLXfinish+ for gloss and matt, or a combination of both in a single pass, double-sided printing, and a magnetic media kit.
As the reseller for Canon Production Printing Australia, Paul Whitehead, sign and display business unit manager for Currie Group said the new Canon Colorado M-series offers a whole new dimension to its sign and display offering.
“Not only does it add brand-new applications to our existing customer base, but it is also allowing us to introduce Currie Group to new customers. With our national service coverage and ability to supply consumables and service with market leading turnaround times, Currie Group differentiates itself from other distributors.”
Currie Group, in its first 12 months of its partnership with Canon Production Printing Australia, has quickly established a large install base of Colorados across Australia.
“Working with Currie Group and Paul Whitehead has been a game-changer. Their support and expertise have ensured a smooth installation, and their ongoing customer service has been instrumental in maximising our operational capabilities,” Wright added.
FESPA
FESPA Global Print Expo and its co-located events, European Sign Expo, and Personalisation Experience, will be held from 6-9 May 2025.
FESPA Global Print Expo 2025 and its co-located events will return to Berlin, Germany, serving as a connection point for all future-thinking industry specialists and experts who attend.
FESPA Global Print Expo and co-located events will enable visionaries to meet and discover a wealth of products and solutions for use in speciality print, signage and personalisation.
As FESPA marks its return to Berlin for the first time in three years, organisers look forward to welcoming its global exhibitor and visitor bases, many of whom are familiar with the host city.
FESPA Global Print Expo head Michael Ryan said, “We’re thrilled to be back in Berlin this year with our new strapline: ‘Where Visionaries Meet’. This year’s message shines the spotlight on our futuristic and forward-thinking FESPA community, including our visitors, exhibitors, award winners, association heads and more.
FESPA Global Print Expo and its co-located events, European Sign Expo and Personalisation Experience, will be held from 6-9 May 2025
“It also highlights that our events serve as a meeting point for these visionaries, empowering them to discover new opportunities and make impactful decisions for the future of their business.
“In an ever-evolving industry like ours, it is vital that we are consistently looking forward. How can we guarantee a sustainable future? How is AI impacting the sector? The possibilities for our community are endless and we look forward to highlighting them at our 2025 events.
“FESPA, as an organisation, is delighted to welcome visionaries from our community to the Messe Berlin in May to not only discover the range of solutions being displayed, but to share their thoughts on what the future holds too.”
Visitors to FESPA Global Print Expo 2025
and its co-located events will be able to explore an array of technologies, media, services and consumables from confirmed exhibitors including: 3M, Brother, Caldera, Canon, Durst, EFI, EFKA, Epson, Fujifilm, Kit Builder, Kongsberg, Optimus Group Limited, Roland, Ricoh, and swissQprint.
More than 500 exhibitors are expected at the events, with several (18 per cent) being returning exhibitors who were not able be present at the 2024 events in Amsterdam, and a selection (17 per cent) being first-time FESPA exhibitors.
The highly anticipated World Wrap Masters competition is also set to return to Berlin. Following a series of regional competitions over the first two days of the event, vehicle wrappers from across Europe will go head-to-head to wrap a variety of special objects and vehicles.
This will be followed by the allimportant final, where regional champions will battle it out to be crowned the World Wrap Masters 2025 champion.
The FESPA Awards are also returning this year and will celebrate innovation and creativity across 18 different categories, including print, sign and display, vehicle wrapping, garment and textiles, and special effects.
Visitors will have the opportunity to see entries to the FESPA Awards 2025, first-hand, throughout the duration of the exhibition. The winners will be announced during the awards ceremony on 7 May.
With just months until PacPrint25 opens its doors in May 2025, industry professionals are eagerly anticipating the event’s dynamic showcase of innovation, collaboration, and sustainable growth.
PacPrint25 organisers say 2024 marked a period of rapid evolution for the sector, driven by technological breakthroughs and shifting market demands, adding that with skilled labour a primary concern across the industry automation is a focus for all.
Rhe integration of digital and traditional print technologies paved new paths for creativity and efficiency, while ecofriendly practices gained traction in response to consumer demand and regulatory pressures.
“2024 has been a remarkable year of innovation and growth for the print industry,” PacPrint25 chair Kirsten Taylor said.
“Businesses have embraced change, leveraged new technologies, and demonstrated that sustainability and profitability can go hand in hand. PacPrint25 will provide a platform to celebrate these achievements while looking ahead to the opportunities and challenges of the future.”
Scheduled for 20-23 May 2025 at the Sydney Showgrounds, PacPrint25 aims to be the year’s premier event for the print, sign, and graphic communications industry.
With a focus on digital transformation, sustainability, and the latest industry trends, the event will feature:
New technology: Exhibitors will showcase their latest tools, from manufacturing automation, cloud-based workflows, energy-efficient solutions and more.
Thought leadership: Seminars and panels led by industry experts will explore topics including sharing of business knowledge, innovation, sustainable practices, and strategies for thriving in a competitive landscape.
Networking opportunities: Attendees can connect with peers, partners, and potential clients, fostering collaborations that drive growth and innovation.
PacPrint25 invites industry professionals to participate actively, whether as exhibitors, speakers, or attendees. Applications for speakers and panellists remain open, with opportunities to share insights and shape the conversation around the industry’s most pressing issues.
“Collaboration and knowledge-sharing are essential for the future of our industry,” Taylor said.
“PacPrint25 will bring together the brightest minds to explore how we can harness technology, improve sustainability, and build a stronger future for print.”
For more information about exhibiting at PacPrint25 contact exhibitions@visualconnections.org.au or call +61 2 9868 1577. For more information about the show and all the latest news, go to www.pacprint.com.au
Canon, Heidelberg make partnership in sheetfed inkjet printing official
Following the announcement of a global co-operation agreement in sheetfed inkjet printing between Heidelberg and Canon at drupa 2024, members of both companies’ senior management recently met for the official contract signing at the WieslochWalldorf site of Heidelberg in Germany.
At the time of the announcement, both companies stated that the collaboration aims to “support commercial print businesses striving to establish hybrid offset/digital production to meet changing print buyer needs and increase their capability to handle shorter runs of more diverse jobs”.
Heidelberg will sell the new Jetfire 50 B3 inkjet printing system with Prinect connection worldwide and incorporate it into an ecosystem for a hybrid production environment that also includes offset printing solutions. A B2 version – the Jetfire 75 – will also be added to the portfolio in the future.
Heidelberg CEO Jürgen Otto and CSO Dr. David Schmedding additionally gave the representatives from Canon an overview of the new Jetfire 50 industrial B3 inkjet
printing system’s positive market launch.
“The digital printing collaboration with Canon marks a milestone in the growth strategy for our core business,” said Otto.
According to Heidelberg, customer interest in the solutions making up the Jetfire 50 ecosystem remains high following drupa. Potential users particularly appreciate the option of integrating the system into a hybrid and AI-controlled production environment together with the Heidelberg portfolio for offset printing.
“The digital printing collaboration with Canon marks a milestone in the growth strategy for our core business,” said Otto.
“Besides selling the Jetfire 50 itself,
we will also benefit from recurring sales from services and consumables throughout the press’s lifetime. In commercial printing, too, that means we can share in the growing digital printing volume and significantly strengthen our market position.”
Schmedding said the first Jetfire 50 presses will be installed in Germany, Austria, and Switzerland mid-year.
“Users will benefit from our application know-how, our in-depth understanding of the market’s needs, and the most comprehensive service network in the entire sector,” explains Schmedding.
The next phase will be to make the press available in all Heidelberg regions.
Koenig & Bauer recently invited existing and prospective customers from all over the world to an exclusive event under the banner ‘Post-press Solutions Experience’ at Koenig & Bauer in Radebeul.
More than 150 guests from 12 countries were given the opportunity to learn more about the latest solutions for even greater profitability and efficiency at the postpress stages of folding carton production.
The objective of the event was to present innovations in the field of postpress technology and to share comprehensive insights into the future of folding carton production.
It addressed both potential customers and current users who wish to further optimise their production processes and are therefore interested in learning about the latest trends in the industry.
A highly varied agenda allowed the international post-press experts to gather a wealth of information on
Bernhard Gansert demonstrated highperformance die-cutting production, job changes and technical highlights on the
Thomas Grübner, Elbe-Leasing,
current and future developments in folding carton production.
Ralf Sammeck, member of the executive board of Koenig & Bauer and CEO of Koenig & Bauer Sheetfed, used his keynote presentation to explain the post-press strategy and digital orientation of the company. He positioned Koenig & Bauer as a leading partner in the field of folding carton production. Subsequent breakout sessions offered the participants additional, more detailed information on
commercial, packaging and label printing Heidelberg has outlined its growth strategy as the company enters a milestone year in 2025.
March 11, 2025, will mark the 175th anniversary of the founding of Heidelberg, when it began as a bell foundry in Frankenthal in the Palatinate region of Germany.
According to the company, it sees growth potential of more than €300 million in sales for all strategic initiatives by the 2028/2029 financial year, while at the same time consolidating performance and increasing efficiency.
“To expand our market position, we are increasingly tapping into growth potential in our core business in packaging and digital printing as well as in the software and lifecycle business,” said Jürgen Otto, CEO of Heidelberg.
“We will also continue to expand our offering in the growing green technologies market. This includes key areas such as high-precision mechanical engineering, the automotive industry, charging
infrastructure and software, and new hydrogen technologies.”
Heidelberg said it is benefiting from the constantly growing global demand for packaging. The end customer market for packaging has grown by more than 60 per cent worldwide over the past 10 years.
In cooperation with Solenis, Heidelberg is responding to the global trend away from plastic and foil towards paper-based packaging and will in future offer solutions for printing recyclable packaging, particularly for the food industry. The company already generates more than 50 per cent of its turnover in the packaging segment.
Heidelberg also sees a lever for more sales growth in its strong international presence in around 170 countries worldwide. The company will continue to expand this internationalisation, particularly in growth markets such as
topics such as the service experience, performance management and expanding post-press options. Practical demonstrations with live production runs and job changeovers presented a broad spectrum of innovative solutions with which Koenig & Bauer is shaping a forward-thinking and efficient future for folding carton production. Machines and solutions demonstrations included the CutPRO Q 106 SB, the CutPRO X 106, Ipress 106 PRO SB, Omega Allpro 110, and myKyana.
“At our recent event, we didn’t just talk about our technology; we showcased it live,” Rayne Simpson, sales manager, ANZ – Koenig & Bauer, told ProPrint.
“Customers had the chance to experience our cutting-edge die cutters and folder gluers first-hand. We demonstrated the CutPRO Q106 the SB die-cutter, and the CutPRO X 106 rotary die-cutter, alongside the OMEGA Allpro 110 folder gluer.
“During the demonstrations, we ran production jobs, including make-readies, allowing everyone to see how these machines operate in real-time.
“This hands-on experience gave customers a clear understanding of our capabilities and the quality of our equipment. It was an exciting opportunity to engage with our experts, witness the machines, and see their efficiency in action.”
Asia, the USA, and emerging markets.
Another focus is on Heidelberg’s industrial business to expand into new product areas, markets, and industries. The company said it already has extensive skills, expertise, and resources that are currently already being used outside the printing industry, particularly in the fields of high-precision mechanical engineering, the automotive industry, electromobility and hydrogen.
The company is also increasingly offering its expertise and installed capacities to other companies in order to efficiently industrialise or manufacture their products.
“175 years of Heidelberger
Druckmaschinen is a strong testimony to consistency, as well as innovative strength and thus future viability,” said Otto.
Together with customers, employees and partners, Heidelberg will celebrate its anniversary year with numerous events and activities. In the summer, for example, there will be a week of celebrations at the Wiesloch-Walldorf headquarters in the newly designed demonstration centre –the Home of Print – including an anniversary ceremony with guests from all over the world. Family days are planned for employees at individual locations. In addition, there will be an anniversary magazine in which the history of the company will be presented, and the future will be directed.
Melbourne-based stationery and gifts brand Greenigo is pursuing local print partners ahead of its expansion into the US later this year.
Greenigo, a Melbourne-based company known for its unique, eco-friendly stationery products, is seeking local print partners ahead of its expansion into the US later this year.
Founded in Melbourne in 2014, Greenigo’s proprietary technology enables its products to be printed on maple wood veneer to create wood gifts and stationery.
“Environmental sustainability is at the core of our business,” Greenigo director Vivek Panchakshari told ProPrint.
“We print only on sustainable harvested wood veneers and use recycled paper in our products.”
The business is the brainchild of Vivek. While working at his father’s print and copy business in India while studying engineering before moving to Australia, Vivek developed an interest in designer stationery. However, according to Vivek, while the stationery brands he admired developed products that were beautiful in style, he believed they were lacking an ecofriendly element.
Following his acquisition of a Melbournebased printer, and after more than five years of research, and searching for an alternative stock to paper, Vivek established an exclusive trade deal with a US-based manufacturer of wood veneer. Wood veneer is made from FSC controlled wood logs. It is biodegradable, and the veneering process uses less water and chemicals compared to the paper making process.
“I started the business printing greeting cards and wedding invitations on timber. However, when COVID hit and severely affected the events industry we decided to pivot into gifts and stationery.”
Since then, the business expanded into gifts and stationery including bookmarks, journals, and calendars. The company now sells its products in several major Australian airports, tourist centres, souvenir shops, boutique gift shops, and online. The business has also become a family affair with Vivek’s wife Priya and son Dhruv joining the business.
“After a decade in the business, my wife joined our team in 2023 to lead digital marketing and enhance our market presence through trade expos. Even our son Dhruv is enthusiastic about our marketing efforts, attending trade expos and generating numerous leads.”
Vivek is planning to expand to the US market later this year.
“Now that we are more established, we are focused on scaling the business. Expanding into the US market is a significant step toward achieving that goal and introducing more people to the beauty and functionality of our maple wood gifts and stationery,” Vivek said.
“We are also actively seeking investors to scale our operations globally, including the acquisition of other established sustainable brands in the giftware industry.
“The timber is from the US so we can easily set up a print hub there and offer this globally,” Vivek told ProPrint
“We have already started to expand the gift and stationery side of the business through our e-commerce platform, and we have a consultant who is working with us to enter the US market next year.”
Vivek said he is open to conversations with suppliers and online web-to-print platforms, with the aim to be “the Vistaprint of timber printing”.
“We are open to conversations with potential partners to be able to have a bigger impact on the industry.”
“Our aim is to specialise only in timber printing, and we want to offer more personalised stationery such as business cards, flyers, event invitations, as well as expand our range of merchandise such as photo frames.
“As a business, we do everything possible to keep the product as sustainable as possible and local. We manufacture locally. We don’t want to compete with overseas because we follow ethical practices.
“We believe our products offer a unique combination of sustainability, functionality, and aesthetic appeal that will resonate with consumers in the US and other international markets.
“We are excited to introduce more people to the Greenigo brand and our commitment to eco-friendly, premium gifts and stationery which are made in Australia.”
Epson Australia has released its inaugural Sustainability Impact Report, the first-ever documented step that highlights and details the company’s continued commitment to driving sustainable progress across Australia and New Zealand.
The report showcases and details the company’s dedication to operating responsibly, while fostering positive relationships with people and communities and striving for continuous improvement across industries.
Epson A/NZ managing director Craig Heckenberg said Epson is committed to integrating sustainability across its operations and products, helping reduce environmental impact while supporting partners and customers in achieving their own sustainability goals.
“While we acknowledge that we don’t have all the answers yet, this Impact Report is a significant step forward and particularly important as we openly highlight both our progress and the challenges we face,” Heckenberg said.
Auckland-based PrintLounge has ordered a second AB Graphic International (ABG) digital converting machine: the Digicon Lite 3 Series.
Supplied through Currie Group, ABG is a global leader in innovative labels and packaging solutions.
PrintLounge director Steve Sheppard said, “PrintLounge is extremely excited about the acquisition of our second ABG machine. We’ve been so impressed with our first one, that it seemed like the only logical step.
“Although I have investigated other options, I feel that the ABG is exactly the right fit for our needs, fulfilling our current requirements as well as being future proofed for further endeavours in the label and packaging markets. Currie Group has been excellent to deal with and provides us with all the service and support we need.”
Currie Group A/NZ labels and packaging director Mark Daws said Currie Groups is thrilled to see PrintLounge invest in its
Epson’s inaugural Impact Report, a first for Australia and New Zealand, comes after decades of work in the area of sustainability by Epson globally, where underpinning everything the company does is the firm belief that that energy saving solutions, space saving innovation and ultrahigh precision help to protect the natural environment and enrich communities.
Epson Australia’s Impact Report is based on the company’s initiatives and operations from April 2023 to March 2024 and highlights key achievements during this time.
These include how the company transitioned to 100 per cent renewable electricity across all of its offices in Australia and New Zealand and how it
initiated the measurement and reporting of their carbon emissions with a commitment to establishing local reduction targets –aligned with Epson’s global Science-Based Targets Initiative goals – aiming for carbon negativity by 2050.
Epson A/NZ also achieved a 50 per cent reduction in landfill waste at its main sites and further contributed to the circular economy through the continuation of long-established recycling programs for ink cartridges and e-waste. The company also launched partnerships with Botanic Gardens of Sydney, First Nations Fashion + Design, and the Australian Fashion Council to support environmental, social and economic development.
second ABG digital converting line.
“This decision reflects its commitment to innovation and quality in the evergrowing digital labels and packaging market,” said Daws.
“Our partnership with PrintLounge continues to strengthen, and its investment is a testament to the value it sees in our technology. It was clear from their time spent at Labelexpo Americas that they thoroughly explored the best solutions to drive their business forward. We look forward to supporting its ongoing
success in the future” said Daws.
The Digicon Lite 3, a compact digital finishing system built to the same exacting standards as the larger Digicon Series 3, can run at 64 metres per minute in semi rotary.
Currie Group New Zealand country manager Craig Paul added, “It provides an excellent solution for day-to-day applications, and can provide additional capacity at busy times. The Digicon Lite 3 is easy to use and can be specified with a wide range of options”.
The Australian Sign and Graphics Association (ASGA) recorded its most successful social bowls event to date, with more than 35 industry people recently gathering at the Adelaide Bowls Club in Kent Town.
The networking event is part of a series of bowls events hosted around the country following a successful pilot, first started by ASGA’s South Australian committee, three years ago.
Attendees of the third annual event included ASGA SA members, nonmembers, and suppliers.
Lisa Michalanney, SA chair for ASGA, said the record turnout was a fantastic demonstration of the strength and enthusiasm of the SA industry.
“It was wonderful to see such a large turnout for what a really enjoyable evening and a great chance was to catch up with industry colleagues and make new connections,” said Michalanney.
“It was not only the largest registration and attendance we’ve ever enjoyed here in SA, but we believe we are now leading the other states with the best turnout for any ASGA bowls event this year.”
Honours were hotly contested, and the final result came down to a final matchup between the ‘Lagerfields’ – Derek Michalanney from Signageworld, Lestyn Young-Roberts from Spicers, Terry Smith from Kwikstripe Sign Shop and Jarrod White from Spandex – and the ‘Awesome Foursome’ comprising Dennis La Rosa, Heather La Rosa and Matt La Rose from Signarama Norwood and Julie Rochester from Sign Language SA.
In the end, it was team Awesome who came out on top to take home the top prize – bottles of SA Shiraz and Adelaide Bowling Club stubbie holders.
Sustainability, talent, and automation are set to shape the future of Next Printing.
Next Printing recently celebrated its 20th anniversary, marking two decades as a pioneer in print.
First started as a photographic lab, Next Printing has continued to pivot throughout its 20-year history, becoming a leader in wide format printing, and more recently, entering the labels market.
The milestone was recently marked with a celebration at Sydney’s Quay Restaurant, with staff, customers, and suppliers gathering to reflect on the company’s history.
“You often hear the phrase that people are the most valuable assets, but at Next Printing, we see it differently. Our people aren’t assets, they are family,” Romeo Sanuri, managing director of Next Printing
told attendees at the 20th anniversary event in Sydney.
“We have had our share of setbacks, but that doesn’t keep us from continuing to innovate. They are our stepping stones that have taught us incredible lessons,” Sanuri said.
“Looking around this room, I see more than colleagues and partners. I see family. I see fellow travellers that have shared this incredible journey with us. Through challenges and triumphs, through innovation and transformation, thank you for being a part of our story.”
Sustainability has been at the forefront for Next throughout its history, with
the Sydney-based printer one of the first in Australia to introduce eco-friendly solutions, such as Swedish cardboard product, Re-board, and biodegradable materials to the local market.
“Ten years ago, we were one of the first to introduce Re-board,” Pranil Chandra, general manager of Next Printing, told ProPrint.
“Back then, people didn’t know what it was, so it was a hard slog educating customers about it.”
More recently, Next has harnessed the power of data to support its sustainable practices, introducing comprehensive carbon studies and life cycle assessments of the materials and production processes used for customers’ displays and activations.
“The data has made a big impact and has really resonated with our customers,” Chandra said.
In collaboration with internal and external stakeholders, including experts in environmental studies, Next produces a ‘cradle to grave’ sustainability comparison between Re-board and MDF. This data provides a comprehensive understanding of the harmful effects of MDF at all stages, including its disposal to landfill post-event – the point at which the material does its most harm.
By showing the emissions comparison between sustainable materials and MDF and how these carbon savings equate in the real world – such as the number of kilometres a car travels or the number of days used by an average household – customers can see how green their initiatives are.
The studies analyse emissions at a job level and provide comparisons against more traditional methods of completing a project, along with the associated energy savings. This emissions data can then be converted into clear and simple messaging. For example, ‘this stand is made from Re-board and reduces emissions by 50 per cent, the equivalent of one flight from Sydney to Melbourne’.
“We recently had a job where the savings was a car travelling 18,000km – that’s one whole year of car travel saved in one job,” Chandra said.
Using the data provided by Next to back up their sustainability claims, customers can go one step further and produce relatable
and persuasive messaging around it that’s concise, digestible, and informative.
“There are a lot of brands that are doing the right thing, but they can’t properly communicate it with their customers, but this messaging helps make it very clean and succinct for them,” Chandra said.
Chandra said Next has only “scratched the surface” of migrating customers away from MDF to other materials such as Re-board.
“Four years ago, we decided to focus on educating our existing database on alternative materials, which we have had great success with. The focus for us over the next 12 to 18 months will be talking to other potential business partners about Re-board,” he said.
“It is not so much about selling to them but educating them. Increasingly, millennials want to buy from brands that have the same ethos and belief systems as them. Therefore, we want to empower customers with as much information as possible so they can make better business decisions.”
Another key area of growth for the company is its labels business, Next Labels, which was first started in 2019. At the time of the business’ launch, Next purchased a HP Indigo 6900 Digital Press, setting it up in its own room at Next Printing’s factory, along with an ABI Digicon cutter and laminator system, all sourced through Currie Group.
“Alongside Re-board, labels is one of the fastest growing segments of our business,” said Chandra.
“Re-board represents about 35 per cent of the business and labels is around 30 per cent. Both are continuing to grow quite rapidly, and we expect this growth to continue for the next two to three years.”
Chandra said Next Labels’ strategy is to apply a “b2c mindset in a b2b environment”.
“Before we started Next Labels, we saw a massive increase in small businesses who were printing smaller label runs overseas. We learnt a lot from one of our business partners overseas about how they go about printing labels cost effectively.
“We are putting significant focus on our platform to ensure small businesses don’t go offshore and instead go businesses like ours here in Australia. We’re investing heavily in automation and in our e-commerce platform, and we are already seeing significant growth.”
Attracting new and young talent to the print industry is also a key priority for Next this year, with plans to expand its project management team and production team.
“As an industry, we generally look to hire people that are already in print, whereas we’ve taken a different approach,” said Chandra.
“We want to get younger people into our business that don’t come from a print background, but instead are enthusiastic about what we stand for as a business.
“We are looking for talent who have the same mindset and ethos about sustainability as the business does. We recently hired two new people without any print experience and they’re kicking goals. We’ll continue to add more young people in our business, and instead of telling them to come and work for a printing business, we will say to them to come and make a difference.
“Young people care about sustainability and their perspective on the environment and their social conscious is a lot stronger than older generations, so it challenges us in a good way. We are genuinely very excited about the young people that we have coming into our business,” he said.
“While there is a bit of a softening in the industry at the moment, we are confident the industry will continue to grow, and Next Printing will continue to grow with a focus on its people and sustainability.”
Scan the QR code to watch some of the highlights from Next Printing’s 20th anniversary event.
Ahead of its 40th anniversary this year, Newcastle-based WHO Printing has upgraded to a Komori A1 Lithrone G437 HUV-L sheetfed press, sold and installed by Print & Pack.
WHO Printing has expanded its operations with the purchase of a Komori A1 Lithrone G437 HUV-L 37-inch sheetfed press – the fourth Komori press in its history.
Founded on Christmas Eve in 1985 by husband-and-wife team Wayne and Helen Ogle at their family home in Macquarie Hills on the NSW Central Coast, as a simple laminating and photocopying service, WHO Printing has evolved into a dynamic print group, delivering services across the Hunter region.
WHO Printing has remained family-owned and operated throughout its history, with Wayne and Helen’s son Daniel joining the business in 1991 as a laminator.
In 2017, Daniel and his wife Melanie took over the business. In October 2024, Daniel and Melanie’s daughter Keziah also joined the team.
Over the decades, WHO Printing has worked with Komori offset printing machines and enjoyed a long-standing relationship with Komori’s local distributor, Print & Pack.
“We’ve been in offset printing for 27 years, and this will be our fourth Komori press,” Daniel Ogle, Managing Director of WHO Printing, told ProPrint
Installed in August 2024 by Print & Pack, the A1 Lithrone G437 HUV-L replaces an older 5-colour Komori A2 press.
“Our very first Komori press was secondhand. However, since then we have purchased two brand new Komori presses: a 4-colour Komori A3 press and a 5-colour Komori A2 press,” Ogle said.
“Our most recent machine prior to the G437 HUV-L, the 5-colour A2 press, was 18 years old when we decided to replace it. The machine was still printing well, and we were still winning national print awards, which is a testament to the longevity of the machine, but it was starting to date.
“The main efficiencies we were looking for from a new press was decreased makeready time, decreased makeready waste, decreased overall job time, and increased colour consistency. These were
all the main deciding factors to go with the A1 Lithrone G437 HUV-L.
“There were other brands that we looked at before purchasing the A1 Lithrone G437, but I wasn’t confident in the resale value or the longevity of some of the other machines in comparison to Komori. Also, the fact that we had purchased two other
brand-new Komori presses with Print & Pack and had minimal issues gave us the confidence to buy another one.”
The 37-inch HUV-L offset press is aimed at magazine and general commercial printers looking for a cost-effective A1 capable upgrade. The press is designed to address the critical needs of short
turnaround. The Lithrone G437 HUV-L offers a 640 x 940 mm maximum sheet size and is also equipped with UV printing for on-demand jobs. The press can print at 15,000 sheets an hour and with HUV-L it provides instant drying.
“I was initially hesitant about UV machines. I wasn’t sure of the quality of them,” said Ogle.
“However, prior to purchasing, we visited the team at Prism Imaging in Victoria. They are also a small operation like us, and they had recently upgraded their A2 Komori to the G437 HUV-L. Talking to them and seeing the quality of work produced put my mind at ease about UV.
“We have a regular job that is a short turnaround. We print it, let it sit for 24 hours, and then fold it and stitch it – all within a week – so timing can be quite tight on occasions. With the new machine, we’re able to halve the printing time, halve the folding time, and we can fold it straight away. We don’t have to wait for it to dry like before.”
The purchase of the new printing machine is not only a significant milestone for WHO Printing, which will celebrate its 40th anniversary in December this year, but it’s also a testament to the company’s commitment to staying at the forefront of the printing industry.
With the added capacity and improved efficiency, the company is now poised to handle more business and expand into new markets.
“Before, with the A2 machine, we could print four A4s on a sheet. Now, with the new A1 Lithrone G437 HUV-L we can print eight A4s on a sheet. Because of this, we now don’t require an afternoon shift to produce the same amount of work,”
Ogle said.
“There’s also scope to print on other materials as well as produce larger-sized prints. Before, we would outsource A1 posters as we previously couldn’t do those in-house but we’re now able to do those with this new machine. We also recently produced some wrapping paper for a customer before Christmas. Previously, we were limited to around A2 size, but they wanted A1, which we able to do for them with the new machine.”
WHO Printing initially began discussions regarding the purchase of a new Komori with the Print & Pack team three years ago.
The installation was led by Print & Pack’s national Komori demonstrator, Steve Harper.
“We always had a good long-standing relationship with Steve,” said Ogle.
“Before we bought the new machine, we were talking to Steve for about three years. I knew we needed a new machine at some stage, it was just a matter of when. We worked together with our other Komori presses as well, so we had a lot of confidence in Steve and in the product itself.
“Peter Tidswell, who was the chief engineer for the install, was also excellent throughout the entire process, as well as Greg Johnson. Nothing was a drama. It was a smooth process the entire way through.”
According to Print & Pack sales manager Miro Williams, the Komori range offers a
wide range of options for specialists in the printing and packaging category looking to invest in an offset solution.
“The beauty of Komori is its broad range of products that are suited to all types of printing businesses – whether you are a multi-site large organisation, or a small print shop working with small to medium suppliers, Komori has something for you,” Williams said.
Williams also credits the experience and knowledgeability of the Print & Pack team.
“Steve Harper has been with the company for 35 years and he is an integral part of the Print & Pack business. His experience with Komori is just invaluable and there’s not too many guys out there now in the industry with that type of experience,” he added.
“The automation and the technology in the machine is also second to none and is key to Australian business at the moment. Return on investment in today’s climate is critical. Everyone is wanting to decrease the manpower while increasing productivity – and Komori offers that.
“Businesses are also looking to be kinder to the environment and minimise waste, so the environmental benefits of Komori are also significant.
“For printers that are wanting to grow their business, Komori is a great solution to deliver a return on investment while also offering quick makeready times and stable running capacities. We have seen a larger number of companies investing in Komori offset printing solutions as we can offer everything printer needs.”
* Model in photograph includes optional specifications.
Handling sheet thicknesses up to 0.8 mm and configured in 6 or 7 colors with in-line coater, this press features extraordinarily high print quality and productivity to flexibly deliver high added value printing for packaging, labels and cards. The Lithrone G37 provides compact size and energy saving in a packaging press. An environmentally friendly strategic machine aimed directly at higher earnings.
The ProPrint Awards, the largest awards event in the Australian printing industry, grew again for the sixth consecutive year in 2024, with a sell-out crowd at the Shangri-La Sydney.
The ProPrint Awards, now in its 14th year, has become the industry’s premiere event, showcasing leaders, innovators, and the best emerging talent in the Australian print industry.
Hosted by Australian comedian Sam McCool, the 2024 ProPrint Awards reported record sponsorship and attendance, with more than 365 guests.
The ProPrint Awards recognised rising stars, suppliers, as well as the most influential printers.
The highly coveted Printer 50 is a peervoted award recognising the senior
leaders and innovators of the Australian printing industry, with the 2024 awards receiving a record number of nominations.
Christoph Gamper, CEO and co-owner of Durst Group, platinum sponsor of the 2024 ProPrint Awards, said attending the awards and presenting the Printer 50’s top 10 was a tremendous honour.
“These awards celebrated the best in print and highlighted young talent and outstanding suppliers,” said Gamper.
“A huge thank you to the incredible Australian print community and the organisers who made this event so special.
“Your warmth, passion, and commitment to excellence are the driving force behind the success of the ProPrint Awards.”
The 2024 ProPrint Awards could not have been possible without the ongoing support of the event’s sponsors: Platinum sponsor, Durst Oceania; Gold sponsors, Ball & Doggett, FUJIFILM Australia, HP, IVE Group, Omnigraphics, and Pozitive Sign & Graphic Supplies; and Silver sponsors, ABC Copiers, Böttcher Systems, Cactus Imaging, EFI, Graph-Pak, Konica Minolta, Kurz Australia, Lamont Print + Signs, Lamson Paragon, Mimaki Australia, PAKKO, Ricoh Australia, Spicers Australia, and Xeikon.
The Printer 50 recognises the senior leaders and innovators of the Australian printing industry. The top 25 leaders are ranked, and the remaining 25 leaders are announced alphabetically. The 2024 Printer 50 category received a record number of nominations, with the top honour awarded to Keith Ferrel, co-founder and general manager of operations of Sydney-based grand format production company, Cactus Imaging.
one-stop destination for printable materials, press consumables, and printing equipment.
Our commitment to quality, sustainability, and innovation sets us apart.
Explore ecoporium, our online platform for eco-friendly packing solutions, and experience i_Consignment for e icient stock management.
Our Print & Packaging Consumables team boasts technical mastery, cutting-edge ink lab blending, and converting facilities. We're not just products; we're your partner in
Embrace new possibilities with an unbeatable white ink printing experience, easily.
Shining a spotlight on the industry’s rising stars, winners in the Emerging 50 category represented a broad and diverse range of print industry talent.
Get ready for an even bigger and better experience than in 2024!
FRIDAY 17 OCTOBER, 2025
6. 30 pm, Shangri-La Sydney
INDUSTRY AWARD ACHIEVEMENT GEOFF SCHOLARSHIP SELIG
INDUSTRY AWARD ACHIEVEMENT GEOFF SCHOLARSHIP SELIG
The Supplier 50 recognises those who service and supply the industry and people committed to providing quality service and advice.
Proud Gold Sponsor of the ProPrint Supplier 50 Award from World War I. The Link was Oscar’s way of creating a sense of connection in the local community. And since those humble beginnings, IVE has grown to become Australia’s largest diversified marketing company. From creative, content and brand activations through to print, uniforms and 3PL, we continue to create connections across the marketing mix.
ivegroup.com.au
The Acuity Ultra R2 is a modular system with scalable architecture, meaning it can grow and change as your business evolves.
Multi-roll capability maximises productivity for smaller jobs
Auto media thickness and position measurement
Our Acuity Range is known for its excellent high quality, productivity and reliability on a massive industrial scale. Engineered with the operator in mind, LED configurations work in harmony with specialist inks to support the printing of exceptional near-photographic interior graphics and the high speed printing of banners and PVC signage.
With a throughput of over 600 m² per hour, the machine has the potential to produce huge volumes of work when printing on three rolls simultaneously, as well as printing superwide format graphics up to five metres in width.
The Acuity Ultra R2 is equipped with a media detector mounted on the carriage. This is used to determine the position and thickness of the media.
To discover more, scan below:
The 2024 ProPrint Awards honoured individual achievements including Outstanding Achievement in Sustainability, Industry Achievement, and the inaugural Geoff Selig Scholarship in honour of former IVE Group chairman, Geoff Selig.
Climate One, an Australian initiative aimed at reducing PVC waste, received the Outstanding Achievement in Sustainability Award.
The award is given to a company that is undertaking sustainable practices within their organisation, using sustainable materials, or has achieved specific sustainability benchmarks or improvements over the last 12 months.
Officially launched in 2024, Climate One was created to avoid putting PVC into landfill by recycling end of life soft PVC. Utilising world-first technology, Climate One’s mechanical separation recycling process, located at its Queensland factory, the company is able to recycle billboards printed on PVC banner and save them from going into landfill.
The Industry Achievement Award recognised former Visual Connections CEO Peter Harper was recognised for his contribution to the industry over a
50-year career in the print, sign, and graphics sector.
Now in its third year, the Industry Achievement Award honours an industry legend with more than 25 years of experience. The winner is judged by the 2023 Printer 50 Top 10 and platinum sponsor, Durst Oceania.
Jacinta Allen, graphics prepress co-ordinator at Breen Printing, was named the recipient of the inaugural Geoff Selig scholarship.
Geoff Selig, who tragically passed in early 2024, was the former executive chairman of IVE Group. The scholarship is dedicated to Selig’s passion for encouraging emerging talent within the industry, and his desire to see people grow and thrive as well as the enjoyment he received from seeing people develop and succeed.
The scholarship provides a financial value of up to $10,000 for personal and professional development and is funded jointly by ProPrint and IVE Group. All 2024 ProPrint Awards Emerging 50 finalists were invited to enter the scholarship (excluding
IVE employees who will have two additional scholarships made available to them).
Jacinta Allen said “I’m delighted to have been chosen for such a special award. I’m passionate about helping evolve the print industry through latest innovations and new practices to keep us relevant and competitive. I’m also keen to further explore the effects our industry has on the environment and how we can implement more sustainable practices moving forward. I plan to visit industry leaders in Japan like Fujifilm, Konica Minolta, and Canon to learn more about the technology and machinery they’re using, what they’re planning on introducing, and where they stand on sustainability. It means a lot to me to now be able to bring back information and knowledge on their practices to benefit both my workplace and the wider industry.”
Matt Aitken, managing director of IVE Group said: “Jaz is a truly deserving recipient of the Geoff Selig Scholarship. She’s truly passionate about the print industry and being part of driving its evolution which is something Geoff played a pivotal role in his time at IVE. We’re excited to see where Jaz takes this opportunity, we know good things are coming!”
The ProPrint team recently visited several Printer 50 and Emerging 50 winners around the country who were unable to collect their trophies on the awards night.
1. Stuart Gittus, head of operations at IVE Brand Activations, proudly received his Printer 50 award at IVE Group’s state-of-the-art production facility in Braeside, Melbourne.
2. The ProPrint team visited Studio Labels graphic reproducer/typesetter and two time Emerging 50 winner Christine Gardiner at the Studio Labels office in Adelaide.
3. Evan Gill, owner of Kwik Kopy Eagle Farm, proudly accepted his Emerging 50 trophy in Brisbane.
4. Talbot Press apprentice Chloe Ford received her Emerging 50 award from the ProPrint team in Brisbane. Ford is pictured alongside Talbot Press managing director Gavin Keily.
5. Bright Print Group joint managing directors John Bright and Debbie Burgess were thrilled to receive their trophy. The duo ranked 12 in the peer voted top 25 of the Printer 50.
6. Aaron Lusch, general manager of Brisbane-based Platypus Print Packaging placed 24 in the highly coveted Printer 50.
7. Ellisha Venz, internal account manager at MMT Print in Brisbane collected her Emerging 50 award from the ProPrint team. The Emerging 50 recognises talent from all parts of print with five years or less experience.
The recent Zünd D3 3XL-3200 and BHS150 installs at IVE Brand Activations in Melbourne has allowed the company to enhance its cutting power and automation.
IVE Brand Activations has ramped up its production capabilities following the recent installation of a new Zünd D3 3XL-3200 and BHS150 at its production facility in Braeside, Melbourne.
“The D3 3XL-3200 and BHS150 have been amazing, and there has been a lot more upside than we expected,” Stuart Gittus, head of operations at IVE Brand Activations told ProPrint
The new machine was installed by Zünd Australia in September 2024. IVE already operates three G3 Zünd digital flatbed cutters in Melbourne and one G3 model at its facility in South Granville, Sydney.
“Due to their productivity and size, the existing Zünd G3 3XL-3200 cutters have been the workhorses for IVE’s digital cutting needs, cutting a range of materials from flexible materials such as SAV, banner, and Yupo, through to carton, corrugated, foam board, and honeycomb board,” said Gittus.
The conversation with IVE around enhancing its cutting power and automation initially commenced in early 2023. At the time, IVE was looking to expand its carton and corrugated POS business and move work from traditional die cutting, resulting in the need for additional digital cutting production.
IVE performed extensive market research into available solutions to meet the company’s needs. This involved a proofof-concept component involving a series of material handling and cutting and creasing processing speed tests.
IVE provided 30 different files on E-flute and B-flute for the cutting and creasing speed testing. After running the tests and the numbers, IVE was convinced the Zünd D3 3XL-3200 and BHS150 systems delivered the best productivity in the market for its needs.
“There was a lot of due diligence around this machine and other competitor machines. We have a broad range of customers, and our corrugated displays are not cookie cutter – there’s a lot of theatre and intricacies. We did test files
and ran simulations but, in the end, we knew Zünd was the right choice for us,” Gittus said.
The D3 3XL-3200 sets new performance standards with its innovative dual-beam system and twin tool sets, enabling IVE to cut and crease each sheet in half the time it did before.
The D3 model also provides significant cutting speed advancements over IVE’s existing G3 machines. Additionally, the cutting table width of 3200mm and length of 3200mm enables IVE to load two standard size boards onto the cutting bed and cut both sheets simultaneously.
Configured with the BHS150 automatic board handling system, this converts the digital cutting system into a pallet-topallet production system, resulting in significantly longer uninterrupted operating time, or the need for down time, as it automatically loads two boards and cuts and creases and unloads and stacks simultaneously. It also provides IVE with ‘lights out’ cutting production, leaving the machine operating unattended at night, which Gittus says has been a game changer.
“The increased capacity with no labour has been a massive win for us,” he said.
The machine also operates with the latest version of Zünd Cut Center (ZCC). ZCC is the command centre for production and also controls the material-handling systems operators use for loading and unloading.
ZCC Version 4 supports operators with smart, intuitive digital-cutting functions throughout the production workflow. Version 4 also offers further capabilities for flexible, automated file preparation, and efficient digital cutting via touchscreen.
The installation was led by Zünd Australia’s technical sales and applications manager, William Berlowitz.
“The commitment by the Zünd Australia team was A1,” Gittus said of the installation process.
Building on its fleet of Zünd machines, IVE NSW also recently updated its cutting fleet with a new Zünd G3 3XL-3200 and front extension table.
IVE NSW had been operating two older model PN series Zünds and decided it was time to update to deliver more cutting power and functionality.
Zünd Australia is a wholly owned subsidiary of Zünd Switzerland and commenced business in March 2024, with Dale Hawkins at the helm of the new organisation.
“We have a highly experienced technical team with a long association with Zünd products. Our technicians are all factory trained,” Hawkins said.
This year, Zünd is looking to continue to expand across the local market. The company recently moved into its new headquarters with dedicated showroom in Cheltenham in Victoria, with an official open house to launch the new premises slated for March.
“We look forward to inviting customers, both new and existing, to our showroom to demonstrate the latest in Zünd technology and provide training and hints to get the best from their Zünd across a wide range of applications,” Hawkins said.
Haim Levit, senior vice-president and division president, HP Industrial Print,
shares his observations and predictions for
industry after a drupa year.
In 2024, we saw a shift in labels and packaging. Key challenges such as labour shortages, rising energy costs, waste, and idle machines came into focus. However, at drupa 2024, the industry’s transformation – foreseen by HP more than two decades ago – became clear. Our vision for intelligent automation, as revealed at drupa, will guide the industry for decades to come and HP remains committed to supporting converters on their digitalisation journey.
Alongside this clear vision for the future are some significant developments across the industry. Inventories are down, inflation has eased, and optimism is cautiously returning. Market consolidation continues across all industry segments. Over the next few years, packaging will embrace automated job management and pre-press, dynamic job batching and scheduling combined with flexible pricing.
There is also a strong focus on data collection and processing, powered by AI, to help printers execute faster. Multi-site operation will require software and workflow standardisation.
And, of course, sustainability remains critical. Converters are prioritising low-energy and waste-reducing production lines. Digitalised workflows will measure and cut CO2 emissions while still enabling shorter runs and faster turnarounds.
Brand owners’ dynamic requirements are driving the need for fully integrated and standardised printing equipment, connected with global MIS solutions and ERP systems. Additionally, as consumers and brands seek more than just information from labels and packaging, security and track-and-trace capabilities are becoming essential.
Labels: The adoption of digital printing, reaching more than 10 per cent of the pressure sensitive label volume, will intensify. The HP Indigo technology quality – now available up to 120 m/min on the HP Indigo V12 – offers the most complete and proven printing portfolio.
As printing is not enough, HP presses are developed to operate within the largest community of printing solution partners such as ESKO, Hybrid Software, CERM, Label Traxx, ABG, and Infigo. With these partners and more, HP guarantees the highest level of automation across the largest range of substrates. Today, more than 1,800 presses are the go-to digital technology for brand owners.
Flexible packaging: Digital adoption is still at an early stage and accounts for less than 1 per cent of the sector. HP Indigo started the journey of digitally printed flexible packaging 10 years ago. We ended 2024 with 400 HP Indigo 25K and 200K digital presses installed. Digitally printed flexible packaging is the fastest growing segment in print, with a growth rate in 2024 of above 20 per cent. This trend will continue as more conventional flexible packaging converters require more agile production capabilities.
The HP Indigo 200K helps converters to deliver non-minimum quantities in a very short time across a breadth of products, which are becoming more and more popular. The complete HP Indigo solution also helps to reduce converters’ overall carbon footprint by reducing waste in setups.
Folding carton and corrugated: The HP portfolio, which combines HP Indigo LEP and inkjet technologies, is addressing similar converter painpoints. The ‘fibrebased’ printing sector is not only facing the growing demand for short-runs, but also a tremendous pressure on substrates and energy costs.
Globally, digital adoption has been lower than initially anticipated; however, 2024 showed positive signs, especially during drupa. Pre-print adoption remains higher than post-print and folding carton remains of high interest.
In an industry where substrates represent most of the total costs, digital printing is critical. The recently announced HP PageWide T700 streamlines processes, improves productivity, and helps reduce costs for digital single-face lamination, corrugation, and folding carton applications.
With more than 100 HP Indigo presses installed in folding carton and the most complete line-up of pre-print and postprint water-based corrugated presses – HP PageWide T400, T700, T1195, C550 – HP provides proven printing technologies and solutions to increase flexibility, enhancing profitability of the entire production floor.
2024 was a turning point for the industry. drupa demonstrated digital printing is core to the labels and packaging industry. HP Inkjet and Indigo LEP are driving the shift to fully automated, lights-out production sites where machines, software, and robots will take care of the entire production workflow.
Across labels and packaging and beyond printing technologies, new services are emerging to accelerate customer growth. In 2024, HP began testing AI capabilities to expand the functionality of its xRServices, with a full roll out expected this year. HP’s AI-enhanced mixed-reality service environment will elevate the entire customer journey, streamlining ramp-up, production, diagnostics, issue resolution, and system availability to maximise overall performance.
The key to this future lies in seamlessly integrating machines, software, and robots with partners under cloud-based workflows. Some may think, ‘that’s impossible for my shop’, but the challenges ahead demand more intelligence, and step by step, with HP, it will happen. Together, we will unlock profitable growth.
Kodak is committed to continuously enhancing and expanding the automation capabilities of its production workflow solutions with the Kodak Prinergy Platform.
The prepress workflow is a central production component at any print shop. The level of workflow automation ultimately determines how efficiently and profitably production runs from white paper to the final printed product.
The Kodak Prinergy Platform provides an integrated and future-proof workflow automation solution for streamlining production from end-to-end, across digital and analog printing processes, and offers efficient collaboration between printers and their clients.
The Prinergy Platform offers support for offset, flexo, digital, gravure, and wide format printing. It offers multiple deployment options including on premises, in the Cloud, or as a hybrid solution, with subscription bundles giving printers ultimate value and cost savings.
Prinergy boasts compatibility with virtually all third-party software and equipment, and connectivity with the broadest range of digital presses. As an integrated end-to-end workflow for all production needs of the printing industry, it eliminates the need to manage multiple software investments and reduces manual touchpoints to a minimum.
Prinergy also maximises ink savings, improves quality, reduces waste, and maintains consistent and accurate colour across all printing processes.
Prinergy’s Rules-Based Automation (RBA) software allows printers to create powerful automation rules for any existing manual event, business process, or daily step in their production workflow.
The use of RBA minimises labour expenses and decreases costs arising from errors. RBA also provides a framework in which the user can instruct Prinergy and other third-party software and equipment how to react when certain events occur – giving printers the opportunity to systematically eliminate manual touchpoints and errors.
Preflight+ is another efficiency-boosting automation component within the Kodak Prinergy Workflow. It automatically
Prinergy Access 2.0 is a digital workflow solution enabling printers to maximise customer value and business productivity through embedded, end-to-end automation
verifies incoming files against selected preflight profiles, correcting and reporting errors based on industry standards or predefined user-based criteria. Additionally, when integrated with RBA, Preflight+ can automatically alert the job owner that file optimisation is needed to address a critical issue.
Prinergy 11.0 brings a host of
The recently launched Kodak Prinergy Workflow 11.0 has been designed to provide even more efficient support for digital, analog, and hybrid print production in addition to greater security and usability.
Prinergy 11.0 features enhancements to RBA, including improved usability for the Virtual Proofing Software Plus (VPS+), seamless import of Harmony calibration curves into Kodak COLORFLOW Software and many more functional and performance improvements. Direct connectivity to Kodak PROSPER Inkjet Presses is another significant new feature.
Kodak Prinergy Business Solutions is a comprehensive solution that goes beyond the production workflow to cover all of a print shop’s processes, bringing together proven, print-specific applications in a single, completely cloud-based platform.
From e-commerce and MIS/ERP to collaboration tools, Prinergy Business
Solutions seamlessly integrates all aspects of a print shop, enabling end-toend automation at the highest level of performance. With Kodak Prinergy Business Solutions, printers can focus on delivering exceptional results while streamlining their operations for enhanced productivity and profitability.
Completely secure and fully managed by Kodak, Prinergy Business Solutions does not require a print shop to make multiple investments for the acquisition and maintenance of different software solutions. Likewise, no high initial investment with corresponding capital costs for high-performance IT infrastructure is required.
The powerful Kodak Prinergy Access 2.0 SaaS Digital Workflow Solution combines Prinergy’s high-performance automation and portal tools with the versatility of connectivity to any digital press and any on-premises workflow. Prinergy Access 2.0 includes proprietary intelligent layout technology, which dynamically imposes files for any production line.
Intelligent layout reduces waste by automating complex tasks and reducing manual touchpoints. The browser-based solution offers a feature-rich customer portal with Smart Review as well as Kodak’s advanced Preflight+, colour management, file management, backup, trapping and routing software.
Prinergy Access 2.0 stores files securely on the Microsoft Azure cloud platform. It can automatically receive and process customer job files 24/7 according to their specific production requirements. Access 2.0 processes files and fixes issues on the fly or indicates corrections to be made. Once processed, a printer’s customer can proof, annotate, edit and approve the job. The approved file is ready to be sent to print.
With all these features, Prinergy Access 2.0 is an innovative digital workflow solution enabling printers to maximise customer value and business productivity through embedded, end-to-end automation.
Discover how Ricoh’s digital services can revolutionise your business operations. With decades of experience in workplace technology, we provide comprehensive solutions that free you up to focus on what you do best – delivering exceptional products and services to your customers.
From cloud and security solutions to managed IT services, Ricoh has the expertise to keep your business running smoothly and efficiently.
Learn more about how Ricoh can support your digital transformation.
Visual Media Association’s Charles Watson reviews the new wage thefts laws and outlines steps employers can take to mitigate the risk of wage theft.
Previously, the consequences of intentional wage theft attracted only civil penalties if an employer was found guilty of such deliberate conduct.
However, amendments to the Fair Work Act last year mean that from 1 January 2025, employers who intentionally underpay their employees may now face criminal charges.
These new laws are in addition to the existing legislative framework dealing with underpayment related matters. This article reviews the new wage theft laws and provides steps employers can take within their businesses.
Essentially, the new laws mean an employer will commit an offence if:
• They are required to pay an amount to an employee under the Fair Work Act or an industrial instrument such as an Award or enterprise agreement; and
• They intentionally engage in conduct resulting in a failure to pay these amounts to the employee on or before the due date.
The intention of a body corporate may be established by:
• Proving the board of directors intentionally, knowingly or recklessly carried out the relevant conduct, or expressly, tacitly or impliedly authorised or permitted the commission of the offence; or
• Proving a senior manager intentionally, knowingly or recklessly engaged in the relevant conduct, or expressly, tacitly or impliedly authorised or permitted the commission of the offence; or
• Proving that a corporate culture existed within the body corporate that directed, encouraged, tolerated or led to non-compliance with wage and entitlements legislation laws; or
• Proving that the body corporate failed to create and maintain a corporate culture that required compliance with
Under the new laws, a company found to have committed ‘wage theft’ will be subject to a fine of up to $7.825 million or three times the amount of the underpayment
- Credit: iStock.com/enjoynz
wage and entitlements laws (unless it can prove it exercised due diligence to prevent the conduct).
For a person to be guilty as an accessory:
1. Their conduct must have in fact aided, abetted, counselled or procured the commission of the offence by the other person; and
2. The offence must have been committed by the other person; and 3. The person must have intended that:
(a) their conduct would aid, abet, counsel or procure the commission of the offence; or
(b) their conduct would aid, abet, counsel or procure the commission of the offence and was reckless about the commission of the offence.
The Fair Work Ombudsman will continue to investigate wage theft issues. However, the prosecution of offences under the Criminal Code Act will be handled by the Director of Public Prosecutions or the Australian Federal Police, with cases assessed based against the criminal standard of ‘beyond reasonable doubt’.
Under the new laws, a company found to have committed ‘wage theft’ will be subject to a fine of up to $7.825 million or three times the amount of the underpayment. For individuals who engage in intentional wage theft, the offence will carry a maximum of up to 10
years’ imprisonment and/or a maximum fine of the greater of either $1.565 million or three times the amount of the underpayment.
There are practical steps employers can take to mitigate the risk of wage theft, including:
• Ensure all statutory entitlements are paid, and when they are due
• Regularly review payslips and payroll systems for compliance
• Ensure employee records are accurate and up to date
• Seek advice if you are unsure about obligations
• Train boards and management about the importance of paying employee wages and other statutory entitlements
• Create and maintain a corporate culture that requires compliance with wage and entitlements laws
• Exercise due diligence to prevent noncompliance with wage and entitlements laws.
Compliance with the complexities of the workplace relations system is challenging and underpayments can and do happen. These new laws do not seek to criminally prosecute accidental, unintentional, or honest mistakes, but rather seek to prosecute deliberate actions by companies and individuals.
If an employer becomes aware they are underpaying employees, they should act immediately to address the issue and make any necessary payments to the affected employees. They should also get advice on whether they should self-report to the Fair Work Ombudsman.
Charles Watson is GM – IR, Policy, and Governance at the Visual Media Association
This article is of a general nature and guidance only and does not constitute legal advice.
Andrew Ash shares how businesses can continue to thrive, innovate, and grow, regardless of who is at the helm.
Every great business starts with an idea – a spark of inspiration that drives the founder to pour everything they have into building something from the ground up. Whether it’s creating an innovative product, providing a unique service, or solving a problem no one else has tackled, the founder’s initial drive and passion are what sets a company apart from the rest. But what happens when that founder isn’t around anymore? How can a successor maintain that same energy, vision, and determination that was there at the beginning?
As a family business advisor and fractional CFO, I’ve had the privilege of helping many businesses navigate this exact question. Here’s what I’ve seen work well:
1. Connecting the past, present, and future
When transitioning the founder’s mentality to the next generation, it’s essential to continually refer to the company’s origins and connection to where the business is in terms of the founder’s vision. This reinforces the sense of continuity, ensuring that the next generation understands the ‘why’ behind the company’s culture and decisions while aligning them towards a shared vision.
Tip: As a family business advisor, I use the power of financial history as a tool to make those connections. For example, I show how decisions made 10 or 15 years ago have shaped the company’s current financial health. When decisions were made, identify what principles have been followed to make decisions and how we think current decisions are going to help the business achieve its vision. By doing so, the founder can provide a framework for the next generation to build upon while ensuring they don’t lose sight of what made the business successful in the first place.
2. Relentless focus on innovation
Founders don’t just create businesses; they revolutionise industries. The founder mentality is rooted in constant innovation, asking ‘what’s next?’ and challenging the status quo. As businesses grow, it’s easy for
operational pressures to stifle creativity. But maintaining that innovative spark ensures that the business remains competitive, adaptable, and relevant.
Tip: Even as the business transitions to new hands, it’s essential to keep fostering an environment where creativity thrives. The next time the business is reviewing its strategy, get the future leaders involved in coming up with new innovative ideas and encourage them to ask questions.
As the founder, you may have a unique skill set that made the business successful. However, your successors will need to develop their own skills to manage the business moving forward. Investing in leadership development and training ensures they’re equipped to take over the business.
Tip: A useful strategy for cultivating leadership and accountability in successors can be through involvement in management and business discussions. Encourage the next generation to have conversations with external advisors and the CFO. Bring them into advisory board and management meetings and give them responsibility to run one or two agenda items. Gradually assign them specific responsibilities, starting with small tasks and expanding their role over
time as they gain experience and confidence, ensuring they also have a deep understanding of how the business works from the ground up.
Founders build businesses based on an intimate understanding of their customers’ needs. They are driven by a passion to serve and create value for those who matter most – their customers. As businesses grow, it’s easy to lose sight of the customer experience. However, passing on the founder’s mentality can ensure that the business stays rooted in the customer-first approach.
Tip: The next generation of leaders must continue the founder’s commitment to understanding the customer, staying attuned to their changing needs, and ensuring the business remains responsive. Try introducing them to clients early on in their journey and quiz them on how well they know their customers. This can be a useful way to encourage the next generation to get closer to businesses customers.
The founder mentality isn’t just for the original creator of the business. It’s a mindset that can – and should – be passed down to future generations of leaders, employees, and stakeholders. By encouraging this mentality at every level of the organisation, companies can ensure that they continue to thrive, innovate, and grow, regardless of who is at the helm.
Ultimately, the founder mentality is about more than just staying true to the past; it’s about ensuring the future of the business is as bright as its beginnings. When the original vision, passion, and commitment to excellence are woven into the fabric of the company, the business can continue to make an impact for generations to come.
Andrew Ash is a business advisor, fractional CFO, and tax agent. He can be contacted at pfbconsulting@outlook.com or 0412 055 814
FESPA Australia BBQ
FESPA Sydney Social
CCE International
FESPA Global Print Expo 2025
PacPrint 2025
Print4All 2025
Labelexpo Europe 2025
Pack Print International
Melbourne, Australia
Sydney, Australia
Munich, Germany
Berlin, Germany
Sydney, Australia
Milan, Italy
Barcelona, Spain
Bangkok, Thailand
Hosting an event? Send an email to ProPrint magazine managing editor – Claire Hibbit chibbit@intermedia.com.au with the details
• Near total coverage of roller requirements for the graphic arts sector
• Wide range of rollers for printing and packaging, laminating, gluing, transport and nip
• Specialised services for non-standard applications
• In-house expertise to help you achieve your production goals
Mimaki JFX 200-2513
CMYK + WWClCl Inks
Max Print 2500x1300mm In great working order MAKE AN OFFER
Mimaki CF-22 Cutting Table 2500x1220mm Plotting Area
Single Phase 240V In excellent condition MAKE AN OFFER
Autobond Mini 52SD-T
Max sheet size: 52 x 74 cm 150 gsm to 650 gsm
Small footprint (10’ x 4’) MAKE AN OFFER
2010 Isuzu NLR 200 205,000kms, Electric Windows, Tinted Windows, Freshly painted cab.
$22,000 + GST Call Print Storm on (02) 6372 7599 or email paul@printstorm.com.au
US T O M LAB E L SP E CI A LIST S 24- 4 8 HO U R P RO D U CTIO N
G E T Y O U R R E SE LL E R S A M P L E P A C K T O D AY
HOT METAL PRINTING SET-UP & FINISHING EQUIPMENT
• Ludlow: 2 cabinets of mats (up to 72pt)
• Heidelberg Platens: 2 units, 14 x 10
• Full Finishing Equipment: All necessary equipment for finishing available
• Number Machines to Skip 6-2 up
• LP Gas Melting Pot: Ideal for ingots or bars
Location: Sydney West
Contact: Peter 0427 063 094, Formerly of Astute Typesetters
Revolutionise Your Bookbinding with Our State-of-the-Art Hard Case Solutions.
Print Logistics is proud to offer cutting-edge, hard case binding technology that delivers a new level of durability and sophistication. Our innovative process involves expert casing of the hardcover, resulting in a final product that exceeds the competition in both robustness and elegance.
Elevate your publications, specialty books, and projects to new heights with our superior hard case binding solutions, perfect for customers who refuse to compromise on quality.
• Fast turnaround times
• Competitive trade-only pricing
• Privileged communication
• Family owned and run
• Variety of customisation options to meet your specific needs
“We’ve relied on Print Logistics for years and couldn’t be happier with their service. Their professionalism, precision, and dedication to confidentiality make them invaluable partners. We highly recommend Print Logistics for exceptional printing and binding services.” Principle Design
Print is perception and we treat it accordingly.
Contact Us Today
Phone: 1300 659 029
Email: contactus@printlogistics.com.au Visit: www.printlogistics.com.au
No odor
No Ozone
No spray powder
No set-off
No loss time
• Instant dry
• Instant ON/OFF irradiation
Reduce CO2 emission
No large peripheral equipment
No need for overprint varnishing
Reduce electrical consumption
• Up to 91%
No VOC (Volatile Organic Compounds)
Reduce heat generation
Long life span
• Up to 15 times
Printing on film and cardboard
Just like your conventional offset press ...without the cons.
The RMGT 1060TP series is the Gold Standard for perfecting printing. This innovative tandem perfector on which the reverse-side printing units are connected to a straight printing press via a special translink unit. After printing the reverse side, the front side is printed without the need to reverse the printed sheets, eliminating various limitations typically associated with perfecting. This also makes it possible to perform perfecting on folding cartons, such as for blister packaging. LED-UV perfecting printing is also possible by equipping both the translink unit and delivery with a LED-UV dry-to-dry printing system, providing an instantly dry, high-quality printing solution. Achieving printing quality equivalent to that of a straight press with highly accurate front to back registration. In addition, the translink unit does not flip the sheets thus perfecting printing can be done with only 1 grip edge. Eliminating the need to make plates differently for front side and back side printing units and can handle pallets of sheets with irregular length just like a straight press.