

NEW OSMO® F1 Concealed Cistern
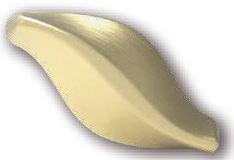
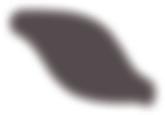
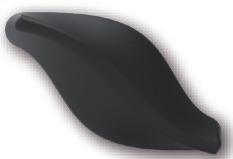
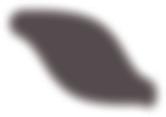

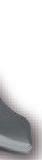
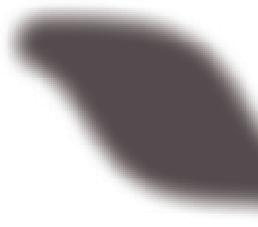
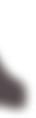
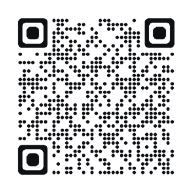
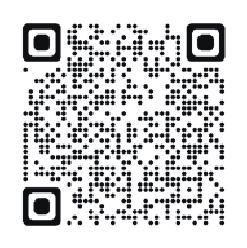


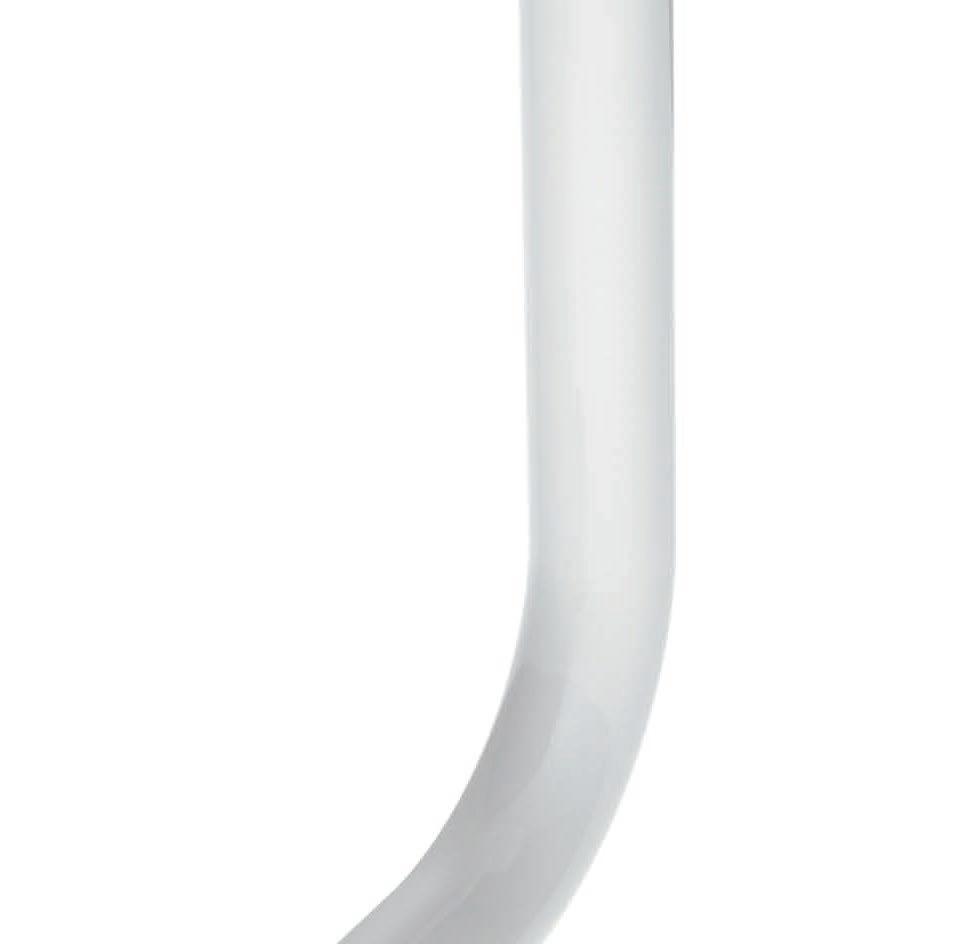
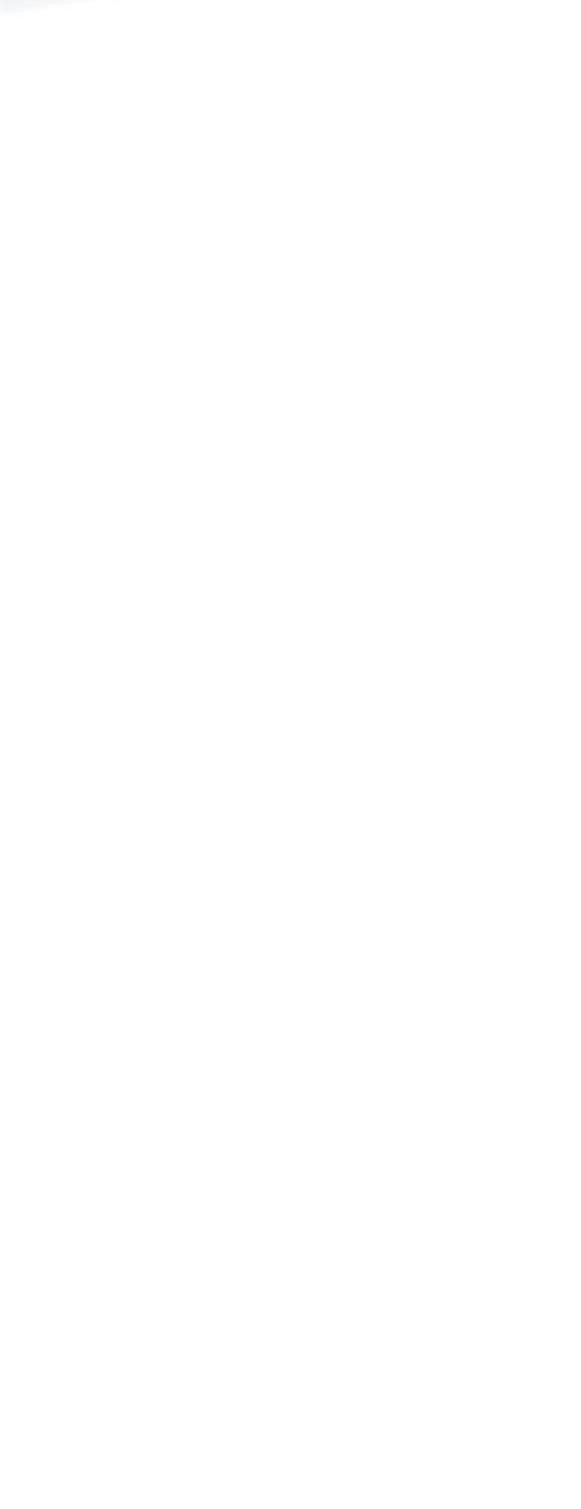
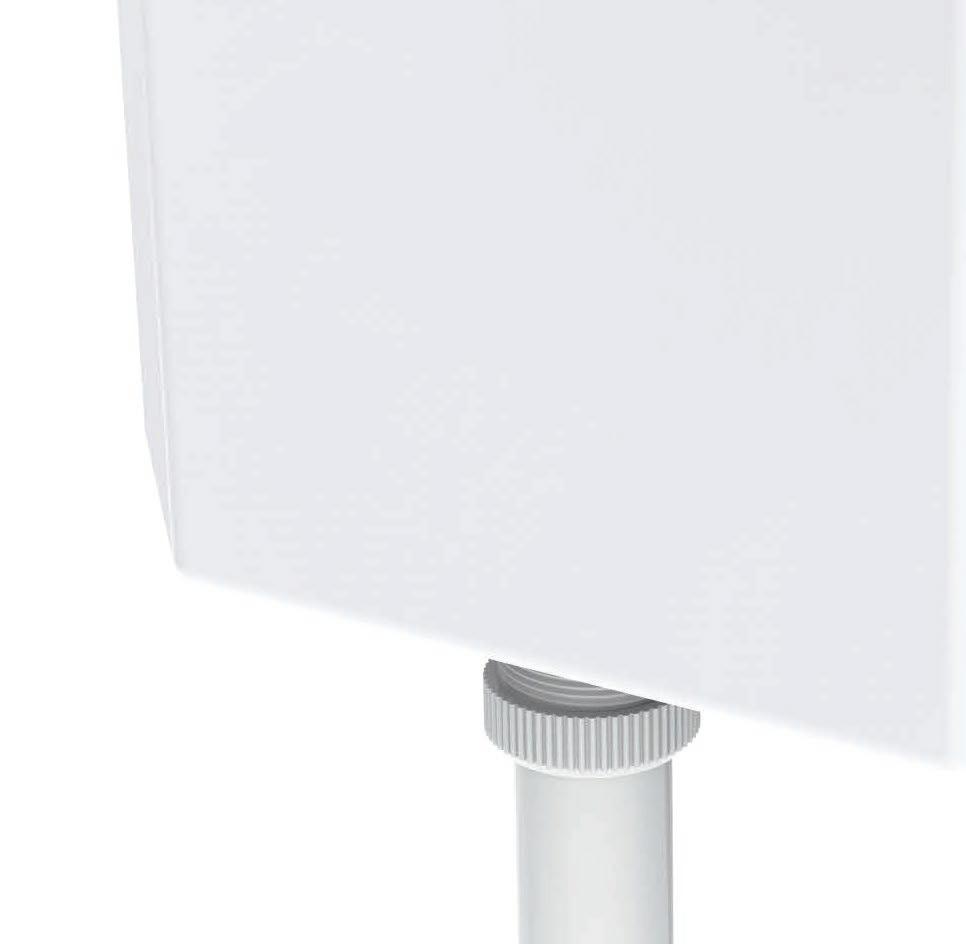
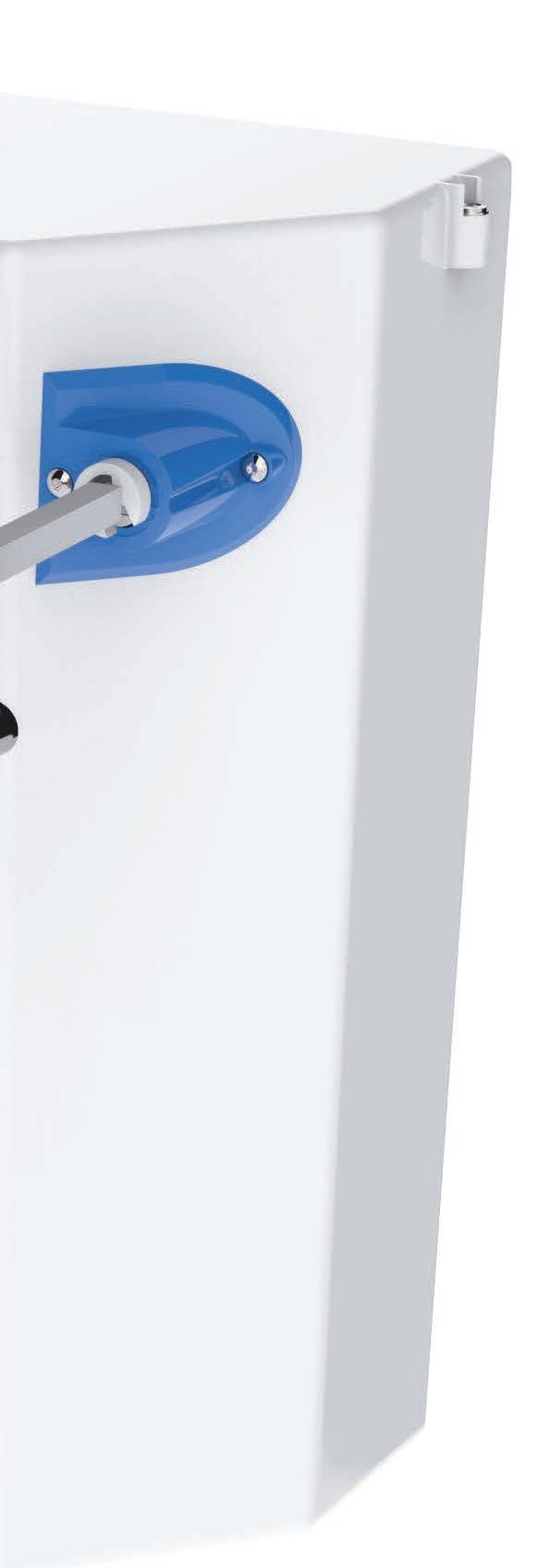
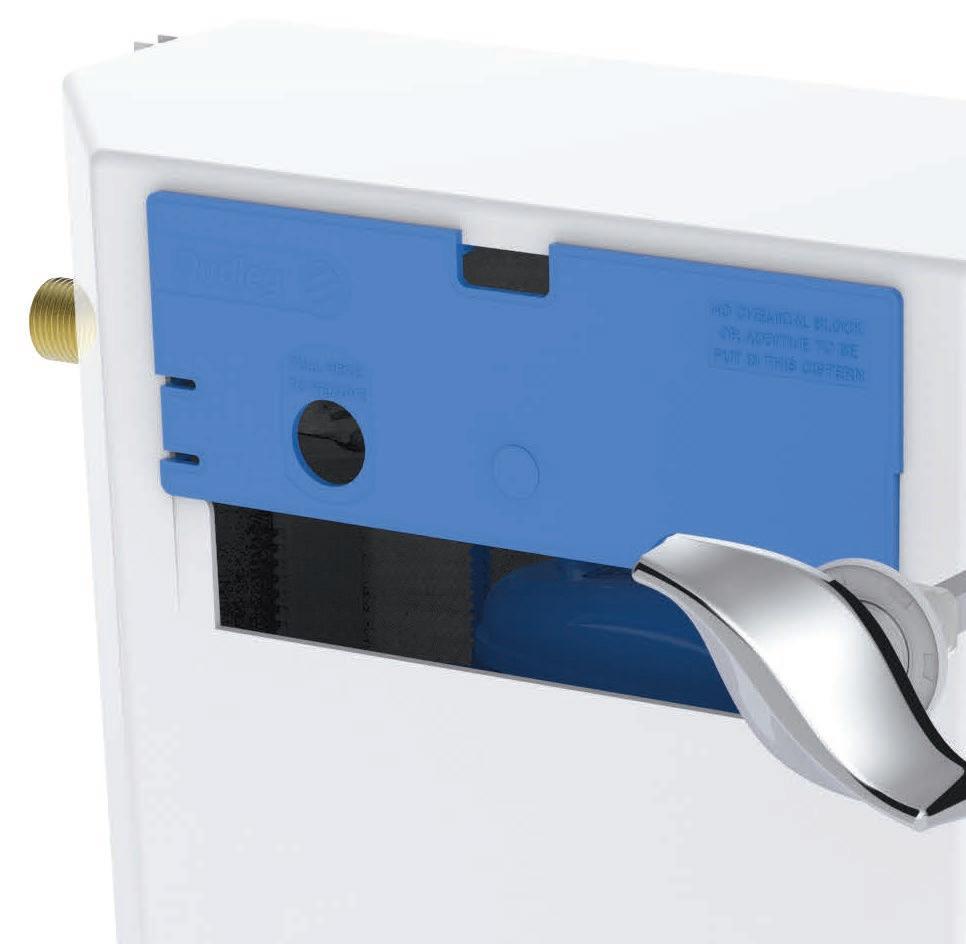
Manufactured in the UK, OSMO ® F1 is a new innovative concealed category 5 cistern designed to be stylish, versatile and easy to fit and service with minimal disruption to WC furniture or panelling.
Fitted with Turbo Edge® & Hydroflo® , the world’s most compact syphon & guaranteed to be leak-free & quiet fill type AG Inlet Valve.
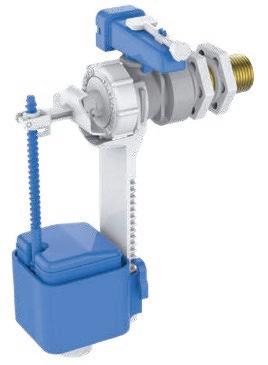
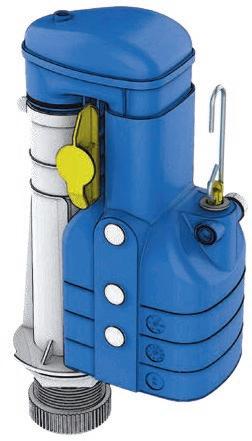
Welcome
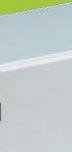
The housing industry is continuing to pour through the latest changes to Building Regulations and assess the detail of the Future Homes Standard as the Government pushes through more legislation.
NHBC Foundation has published a new report that gives advice and guidance to housebuilders on unlocking the full potential of the Future Homes Standard. The report considers the challenges that may arise from energy saving measures in new homes and how these could be overcome.


While construction principles and technology largely exist to enable new build homes to be future-proofed with low carbon heating and world-leading levels of energy efficiency by 2025, work still needs to be done on bridging gaps in the house-building industry’s knowledge, skills and practices to deliver these homes reliably and at volume.
Future Homes - Avoiding unintended consequences has three key themes – heating, ventilation and design considerations – and covers issues that are fundamental to homeowners, including comfort, usability and resilience to climate change.
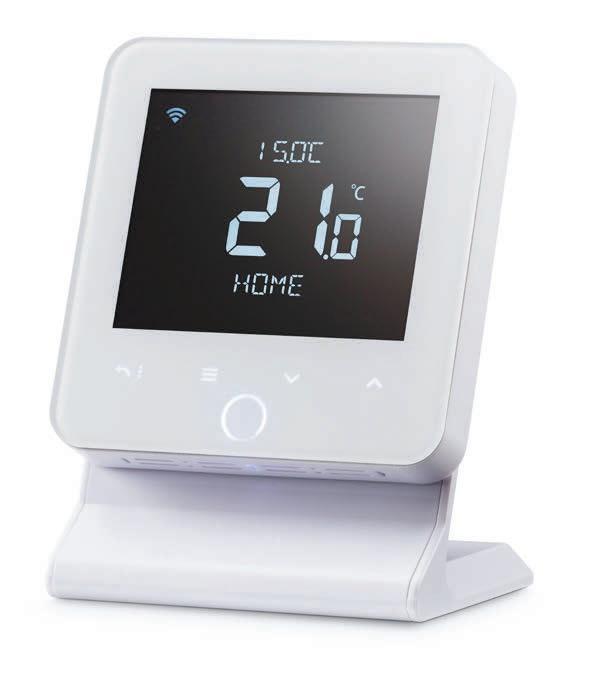
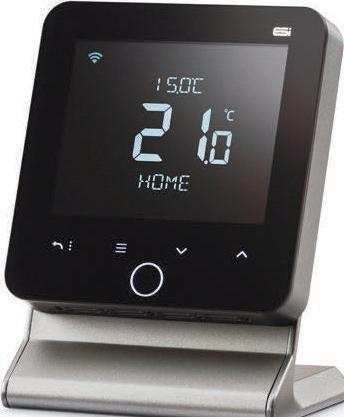

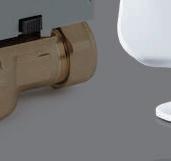
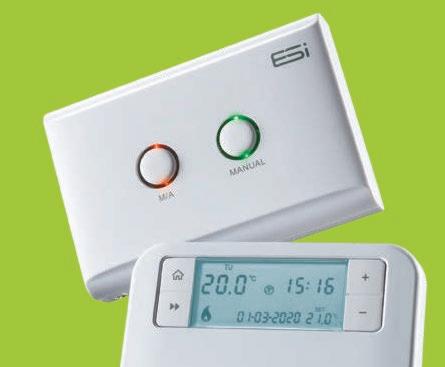
This free report, in association with Studio Partington, is available in a new, interactive, digital format, on its own
dedicated website. Designed to act as a resource for the industry, this website will also signpost users to other guides and learning.

Richard Smith, NHBC’s Head of Standards, Innovation and Research, said: “The Future Homes Standard will set the UK in the forefront of global ambitions to achieve net-zero homes. We want this ongoing project to become a forum for knowledge and a stimulus for thinking about the home in use, as well as its design for future homeowners. Our aim is for it to prompt discussion, identify the scale of the challenge and be a reminder of lessons from the recent past.
“Over the coming months, we will continue to identify the challenges and anticipate possible consequences, thinking particularly of homeowners’ needs and the things that should be in place to allow our homes to function efficiently.”
Groves Group Editor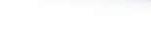
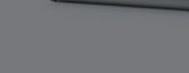
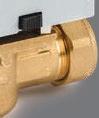



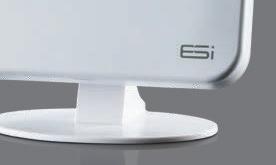
paul.groves@tspmedia.co.uk



THINK VISIBLE
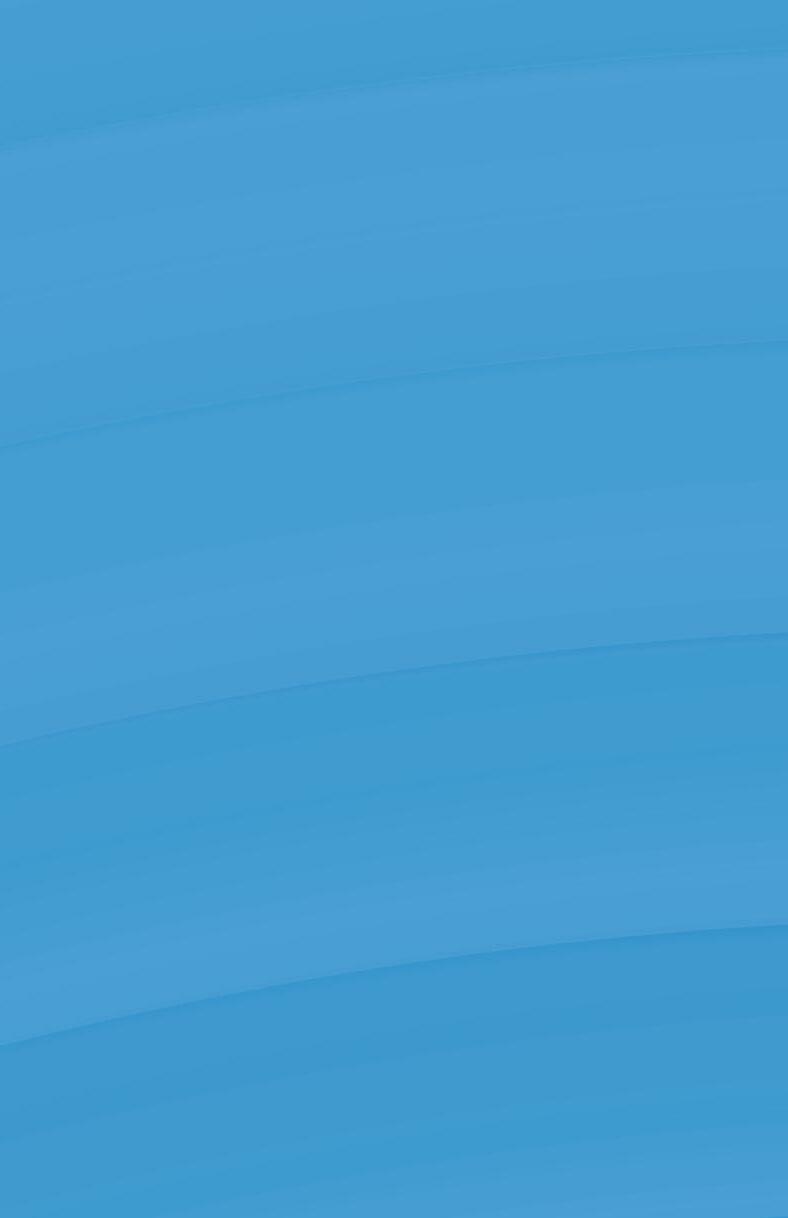




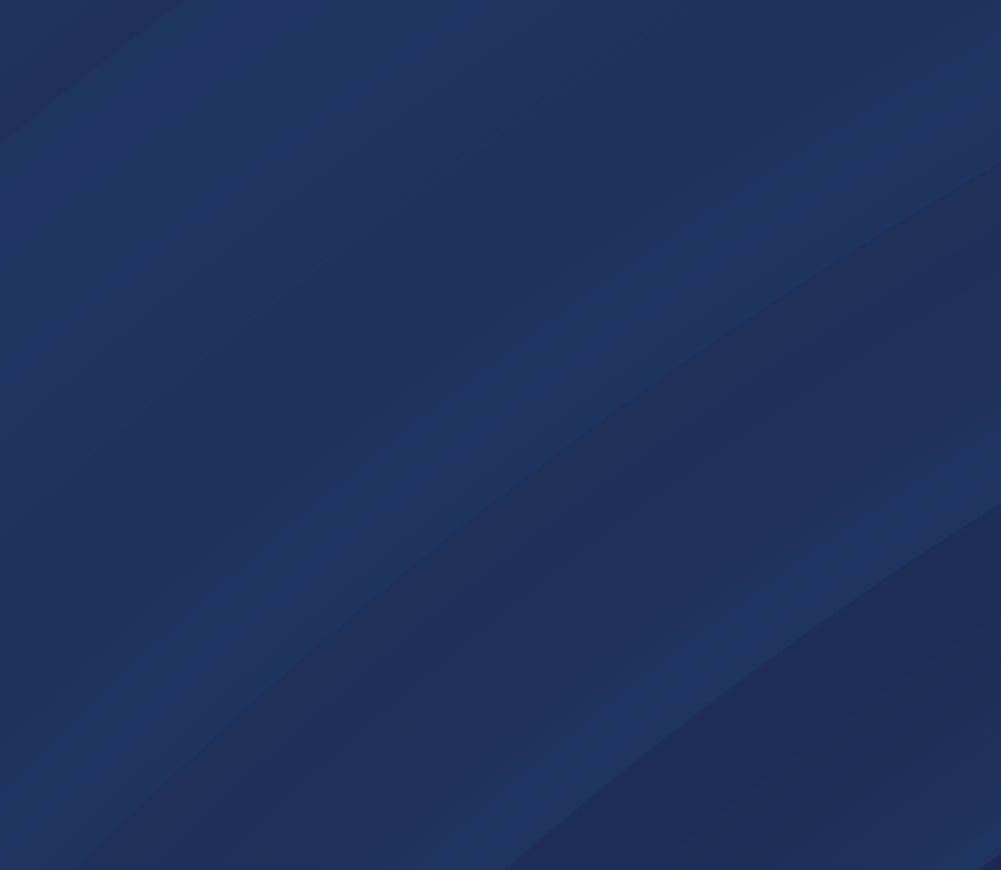

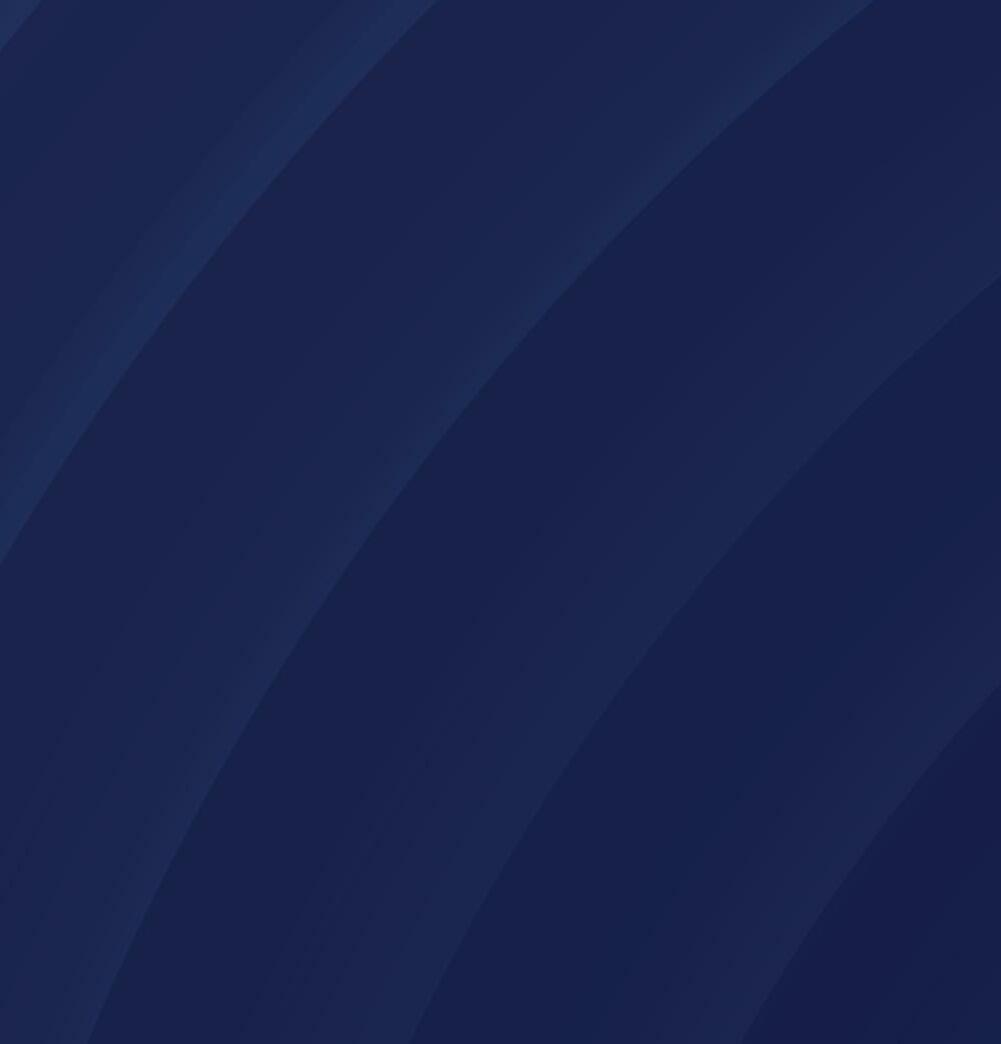
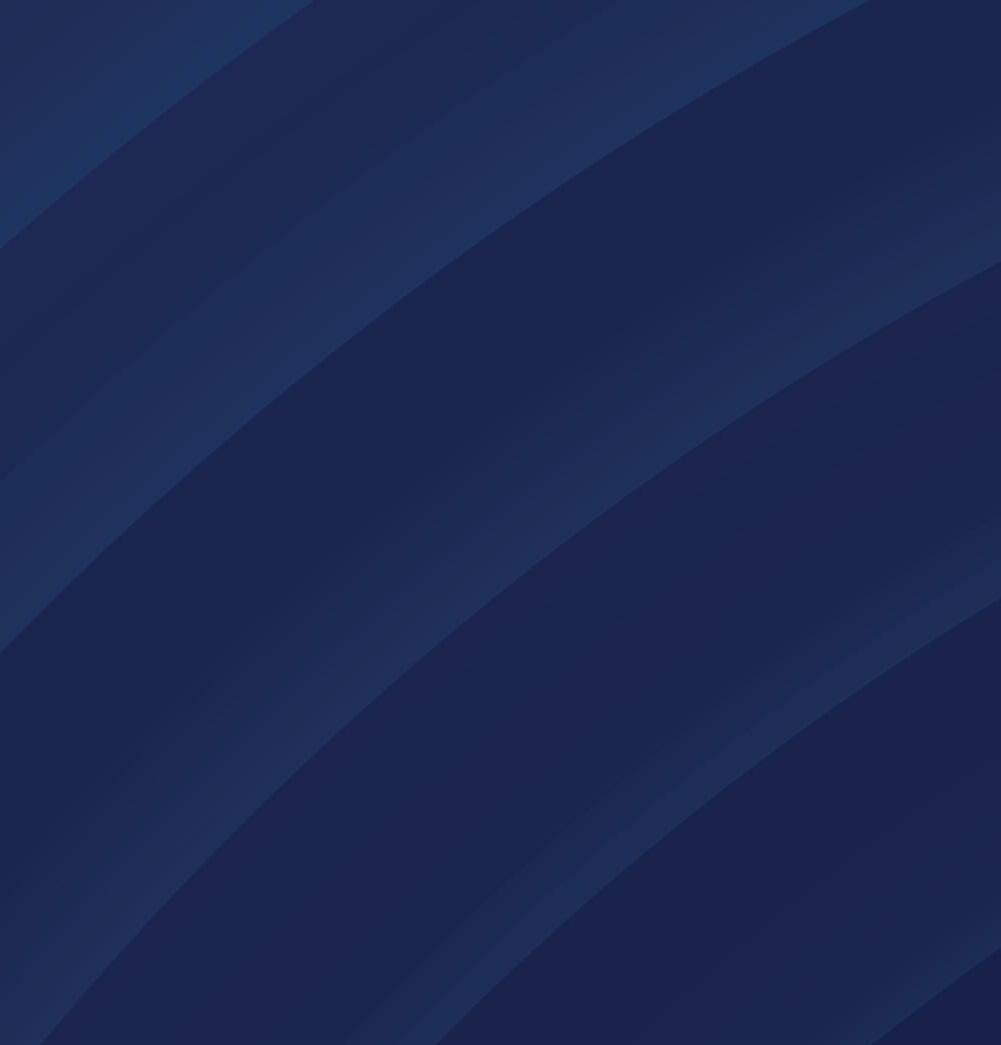
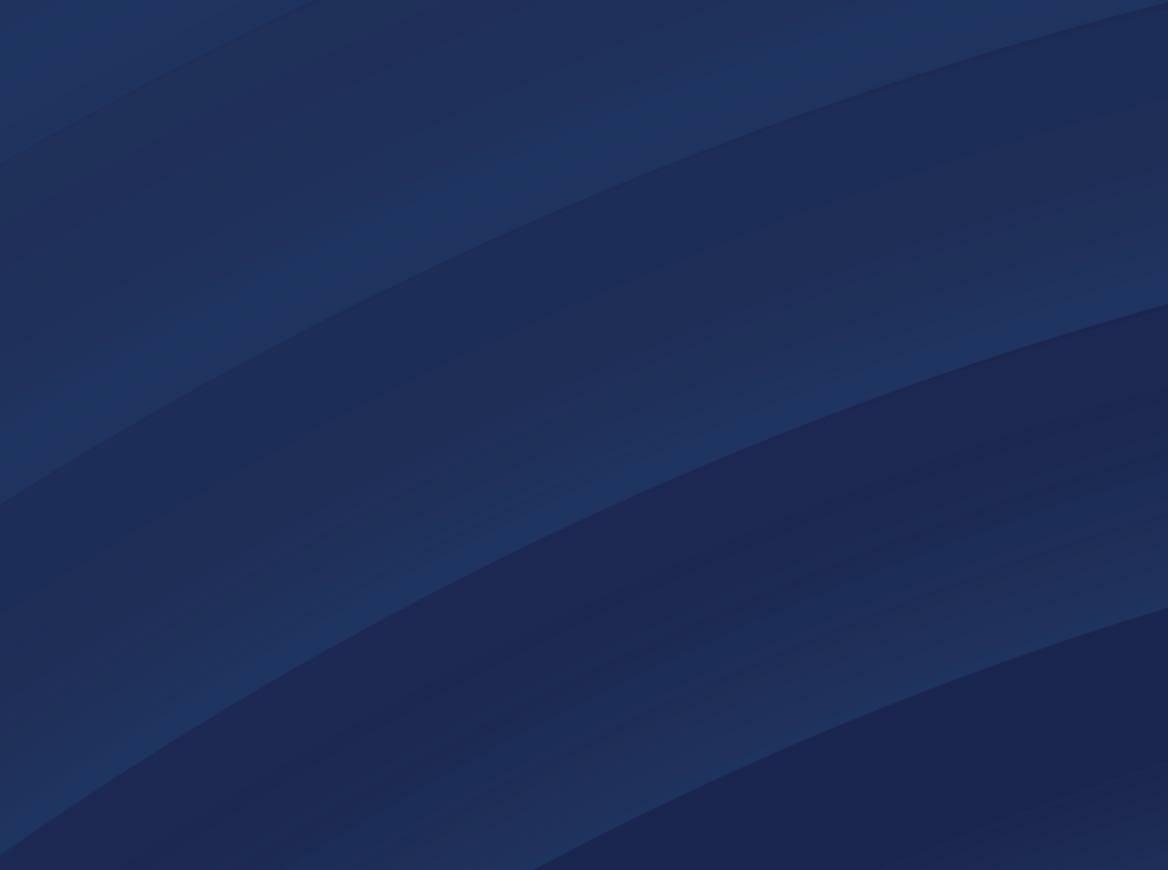
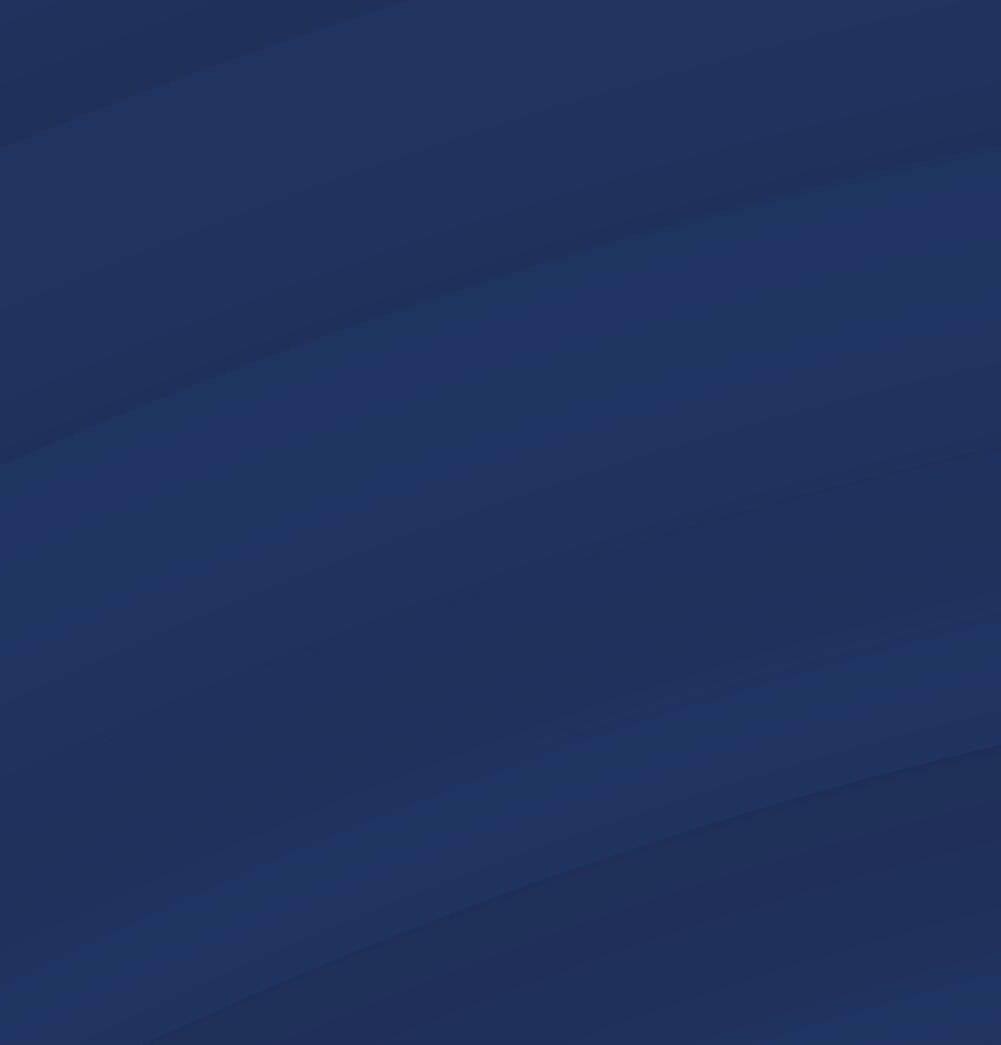
The SC-03 isn’t just a point of access. It’s a wireless solution that promises an advanced user experience, with scrollable functionality and a vandal resistant, durable and full colour screen. Better visibility with its light sensor and excellent functionality with its online remote management system.
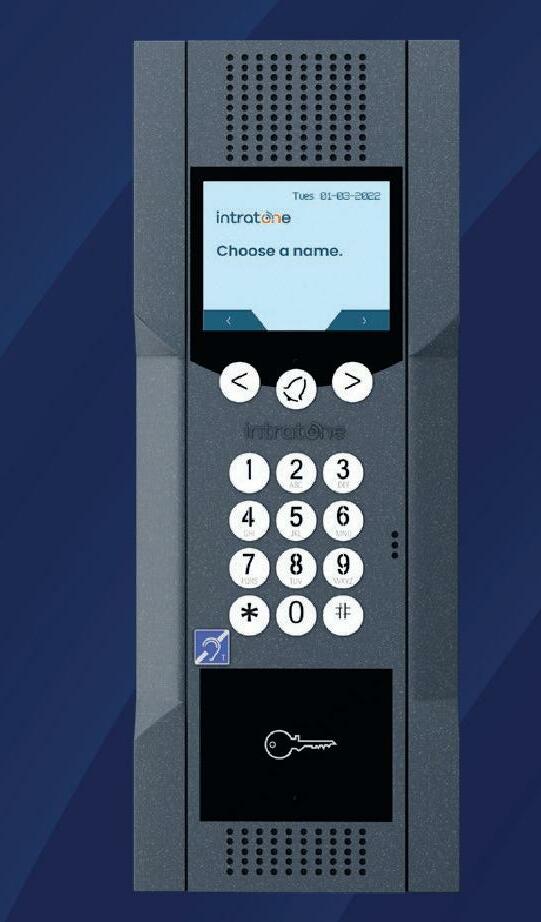
The quality you are used to with new features you won’t want to miss. Discover Intratone’s SC-03 wireless intercom. www.intratone.uk.com
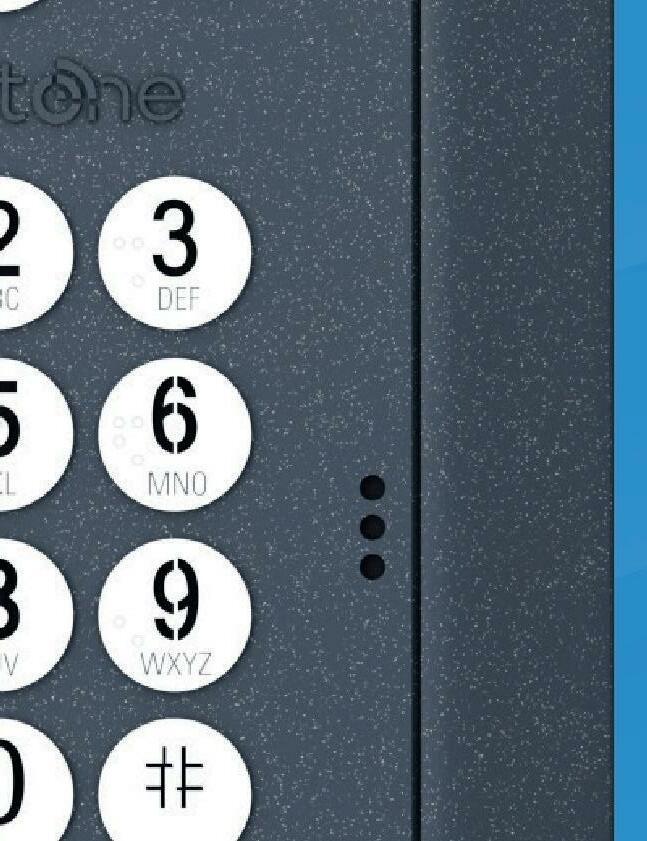
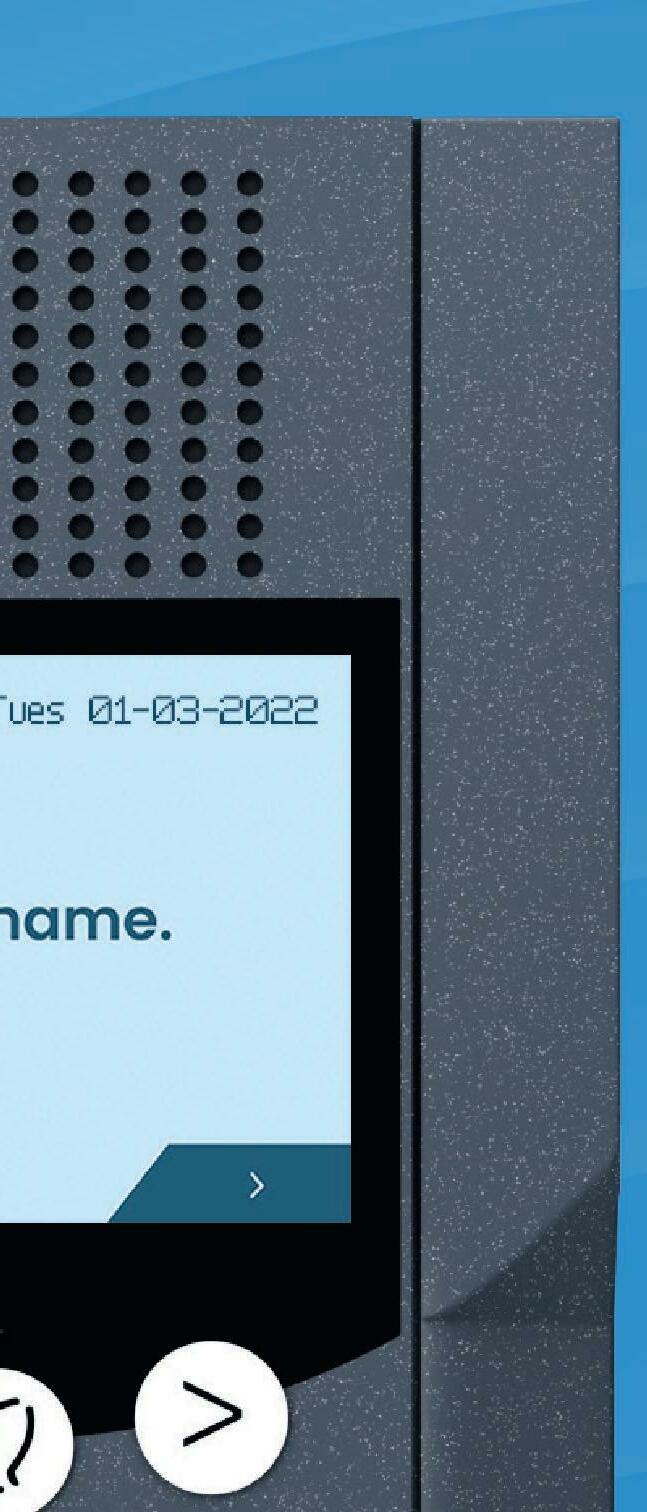


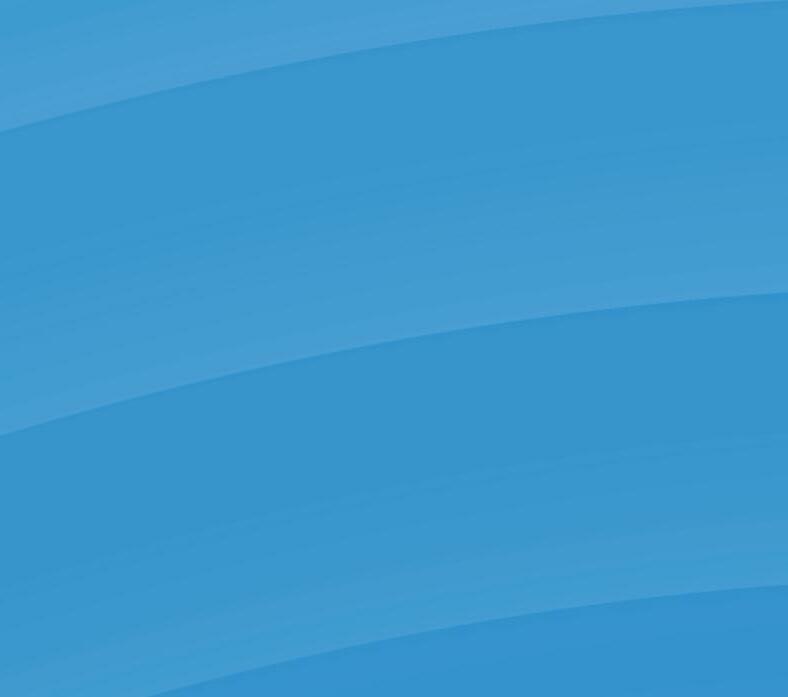
Deceuninck has invested in one of the world’s most advanced PVC-U recycling and compounding facilities. This gives it the capability to reprocess up to 45,000 tonnes of post-consumer and post-manufacturing PVC-U per year –the equivalent of preventing 3 million windows from going to landfill annually.
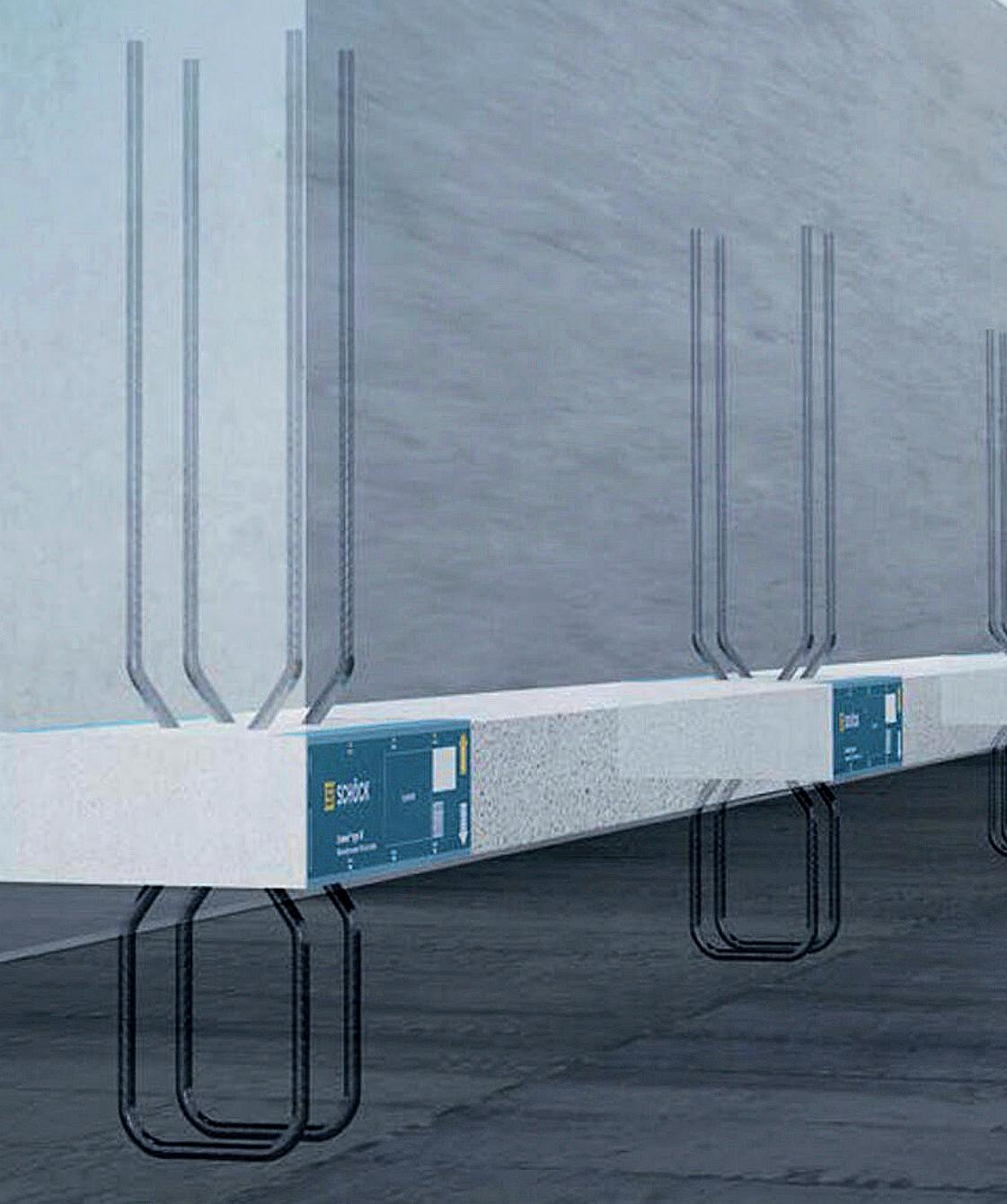
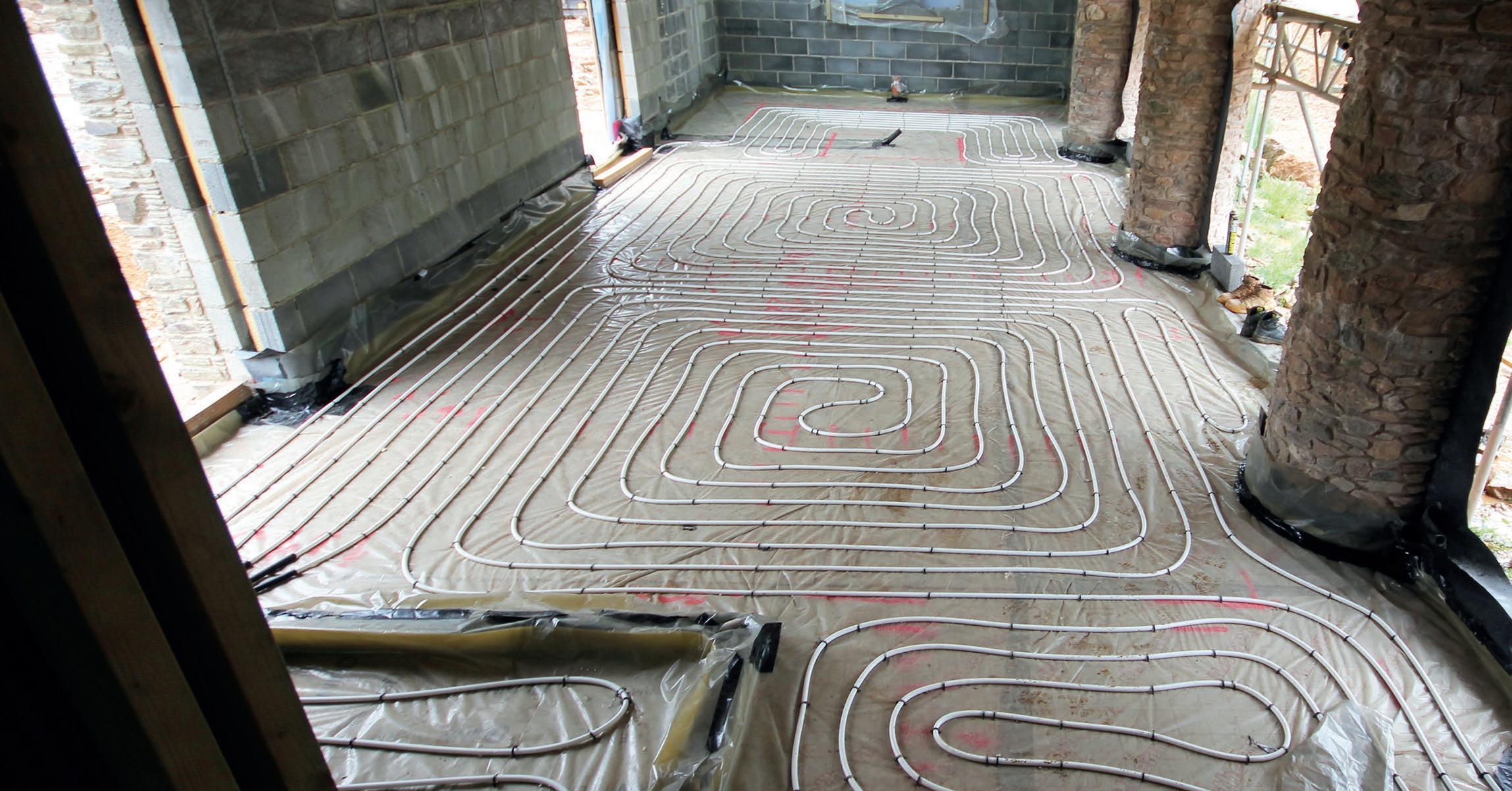
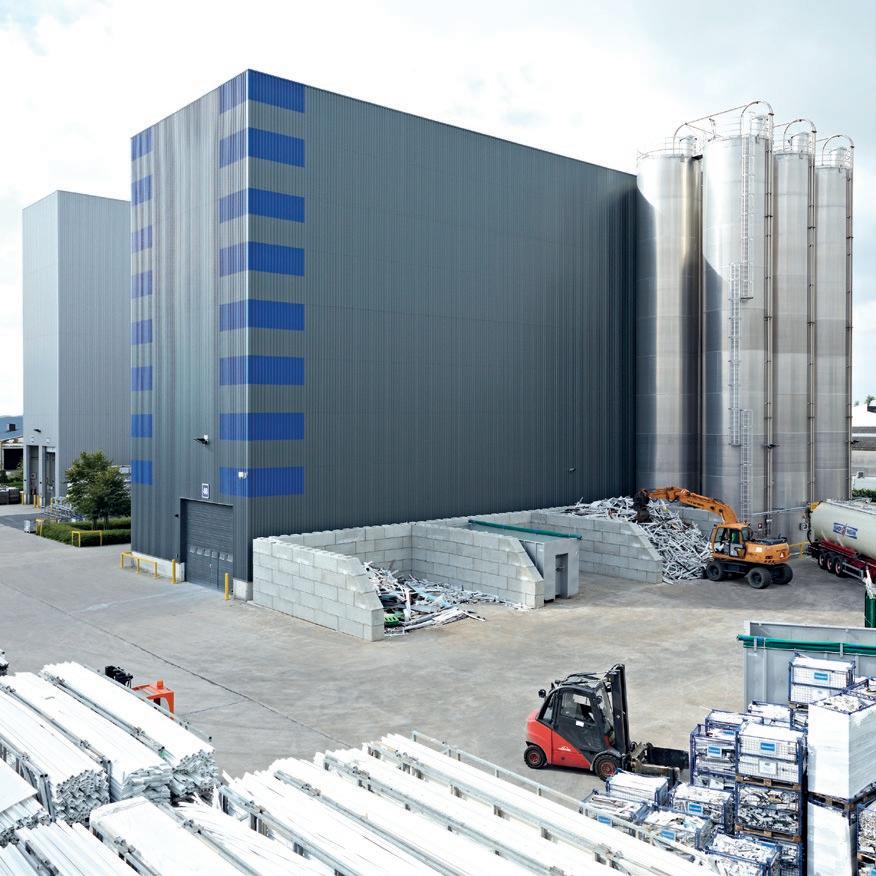
Its own research shows more than twothirds of end-users (68%) would choose windows and doors with a higher recycled content over and above products that
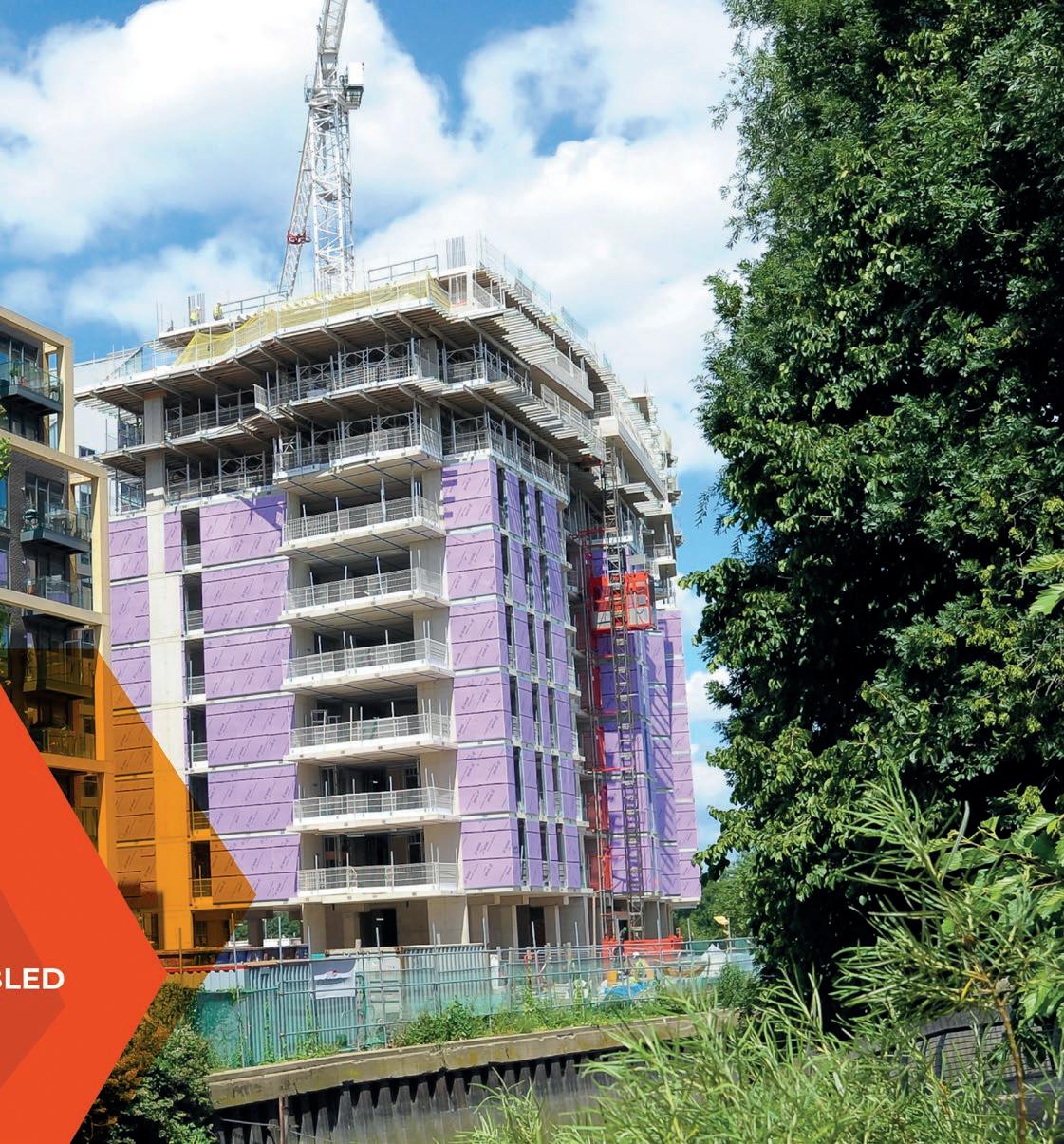
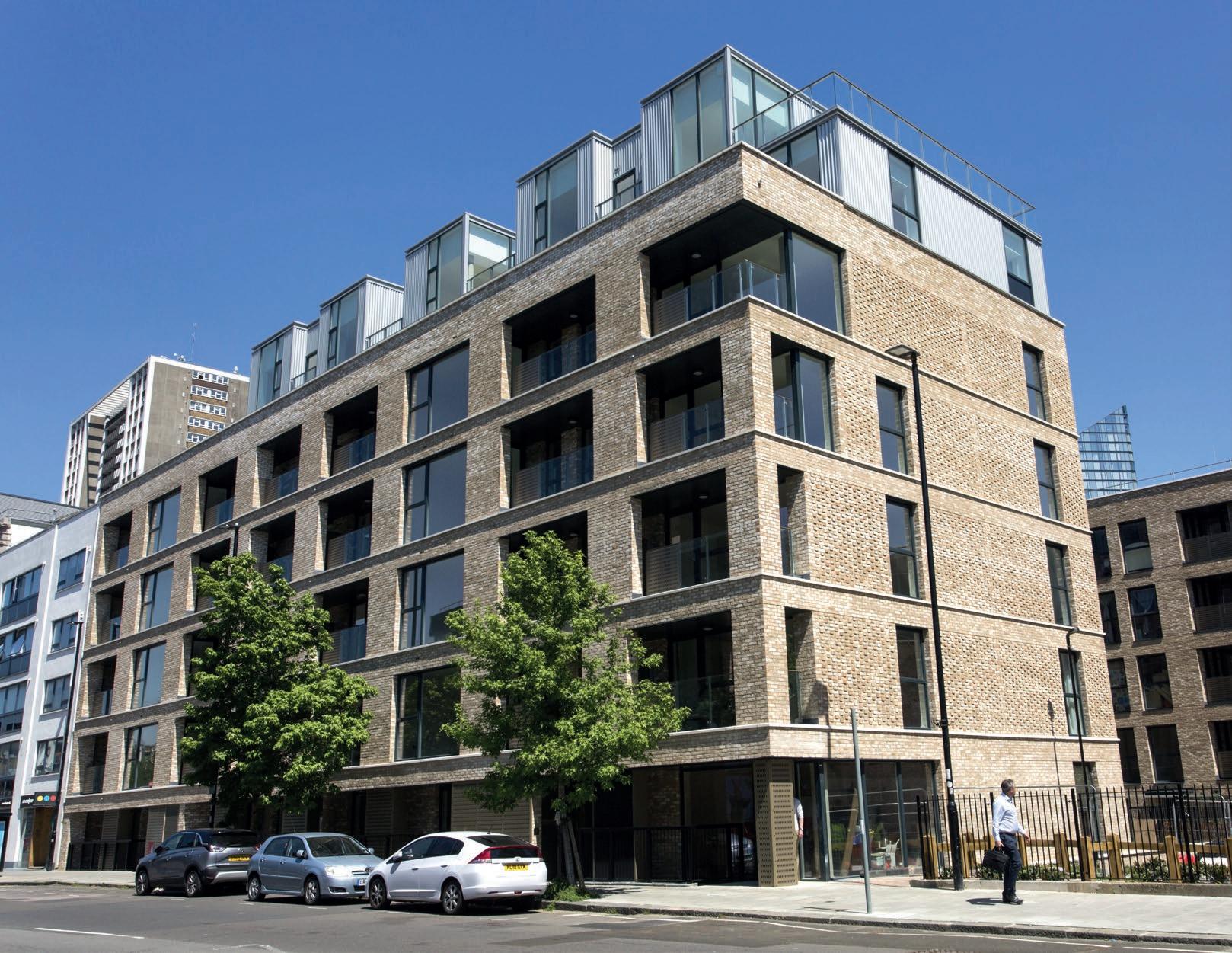
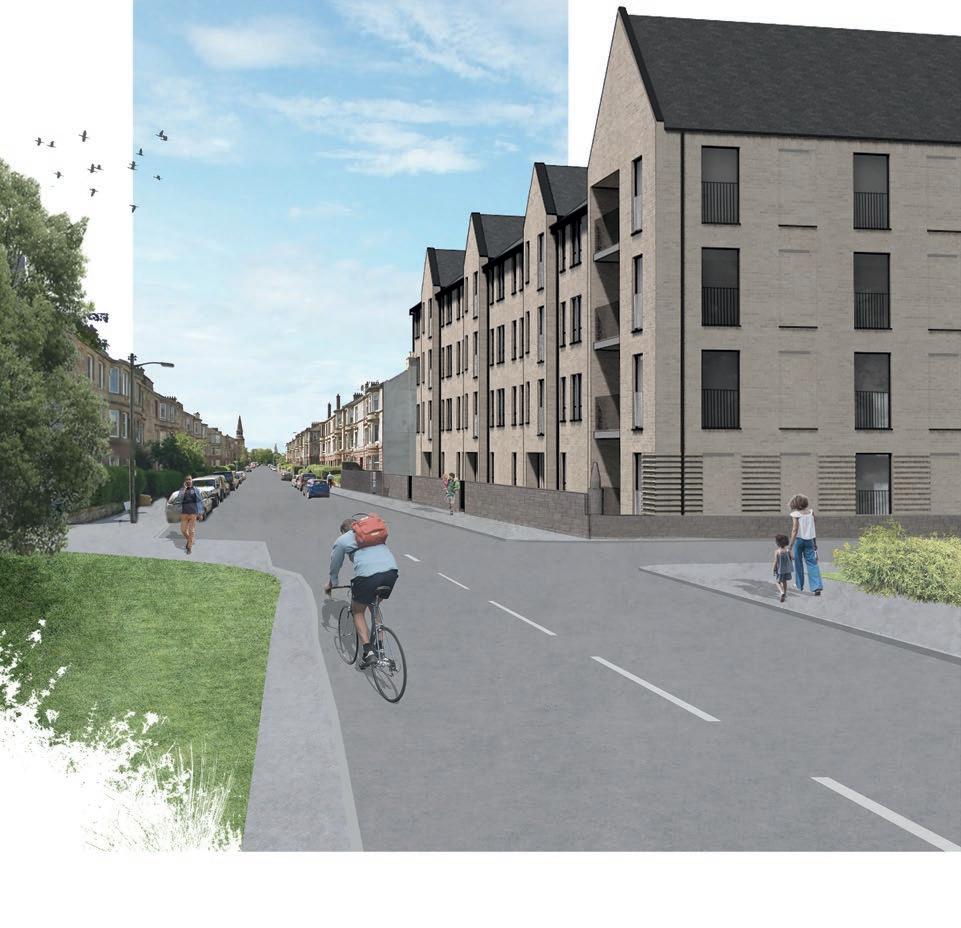
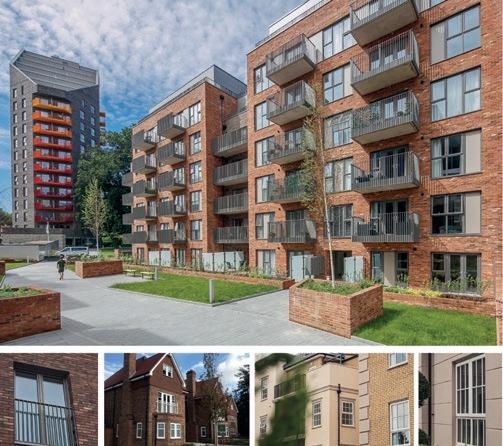
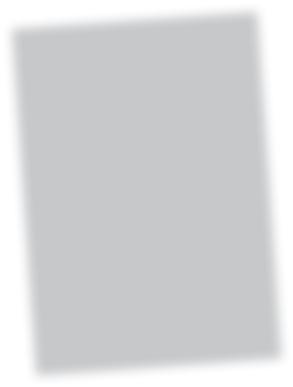
Better flood protections for new homes
New homes will be better protected from flooding following changes to planning guidance, the government has announced. Updated planning guidance published today will help councils make sure developments meet strict criteria in locations at risk of flooding before they are approved, to ensure local communities aren’t negatively impacted as a result.
The move aims to ensure that developers across England can adapt to the challenges of a changing climate and that new homes are sustainable. Levelling Up Secretary Greg Clark said: “We have all seen how flooding is becoming all too frequent. This new guidance will strengthen councils’ ability to require better flood resilience in new developments.
“Councils will need to demonstrate that the development will be safe from flooding for its lifetime, will not increase flood risk elsewhere, and where possible will reduce flood risk overall. This will help make sure our homes and neighbourhoods are built to last for generations to come.” Floods Minister Steve Double said: “As climate change
makes extreme weather events such as flooding more likely, we must do all we can to make sure that people’s homes and businesses are kept safe.
“This guidance will help ensure new developments are designed with flood resilience in mind and do not increase flood risk elsewhere. This will build on our record £5.2 billion investment to build around 2,000 flood schemes by 2027 and level-up defences across England.” Caroline Douglass, Executive Director of Flood and Coastal Risk Management at the Environment Agency, said: “It’s vital that we plan for a changing climate by avoiding unsafe new development in flood and coastal risk areas.
“The Environment Agency plays an important role in working with planning authorities to ensure new development is both safe and sustainable. The new guidance provides vital advice to planners and developers to encourage the use of more sustainable drainage systems to reduce surface water flood risk as well as how to plan and adapt to coastal change.” Under the changes to the planning practice guidance developments, councils
Affordable homes at former academy site
Groundwork has officially started for the development of 36 affordable flats in Bellahouston by AS Homes (Scotland) in partnership with Home Group.
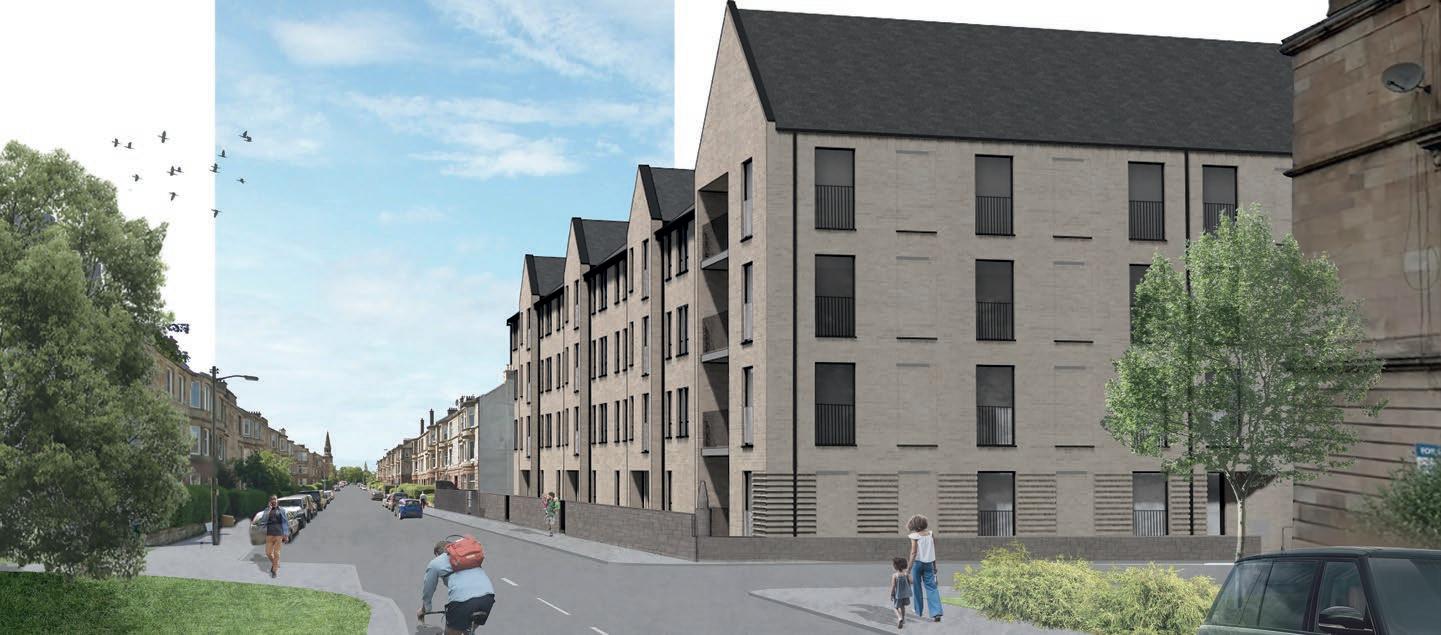
Located at the former Bellahouston Academy site, the new development will see the transformation of the school’s former gymnasium and swimming pool facilities to build a mix of sustainable one-bedroom and two-bedroom flats. Spanning a 0.7 acre site, the vibrant new development has been designed to
compliment the local surroundings and bring a fresh yet well-suited ambience to the area, including an on-site car park, cycle stores and a community playpark for families and children to enjoy.
The development has been Secure By Design Gold Accredited and modelled to accommodate varying occupier needs. Supporting the area’s wider net zero ambitions, the energy-efficient homes meet Glasgow’s gold hybrid standard for suitability.
will be better placed to apply government policy, where new homes in areas at risk of flooding, should meet recommended standards on flood resilience – for example, using flood resilient building materials or moving plug sockets higher up walls.
Local areas will also have access to better guidance on how to control surface water run-off, with the use of sustainable drainage systems to enhance the quantity and quality of water in the region, as well as local biodiversity. The guidance also highlights the opportunities new development can bring to reduce the causes and impacts of flooding through the use of natural flood management techniques.
The new planning guidance forms part of the government’s mission to level up and regenerate communities by delivering sustainable and lasting homes. It will also support delivery of the government’s policy statement on flood and coastal erosion risk management and help to achieve our long-term goal to create a nation more resilient to flood and coastal erosion risk.
Fruit Market development given the go-ahead
A unique townhouse development in Nottingham City Centre is due to start construction this summer. Fruit Market, which will be delivered by Blueprint, specialists in the development of sustainable homes and workspaces, will begin with the first phase of 13 townhouses and follow a low-energy, design-led ethos. The new homes will be completely gas-free, with air source heat pumps and underfloor heating, making the scheme one of the most energy-efficient, future-proofed housing developments in the city.
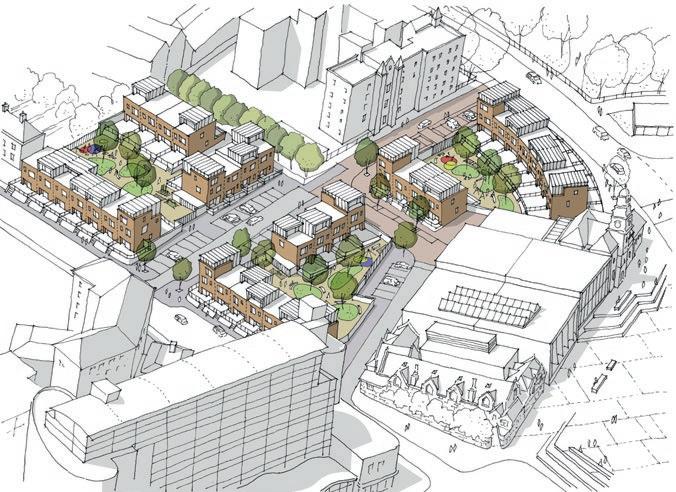

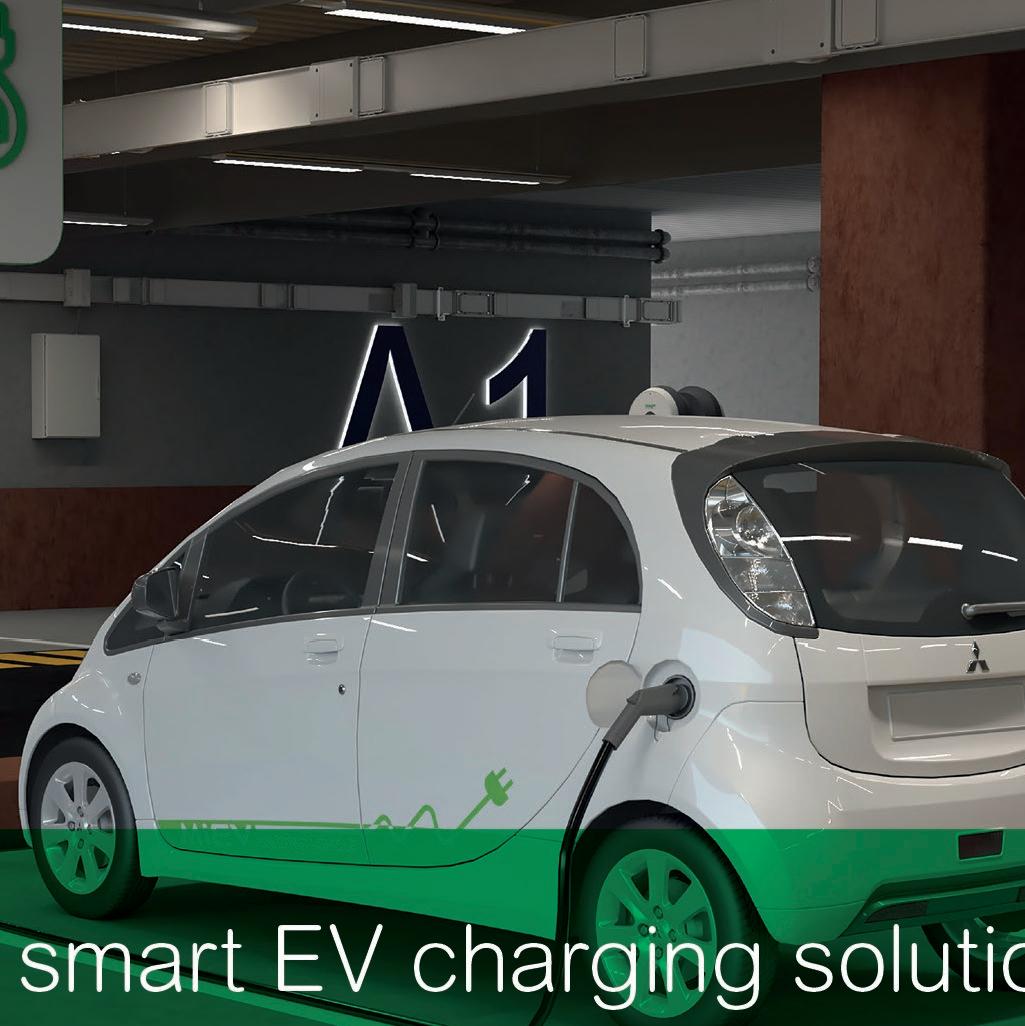

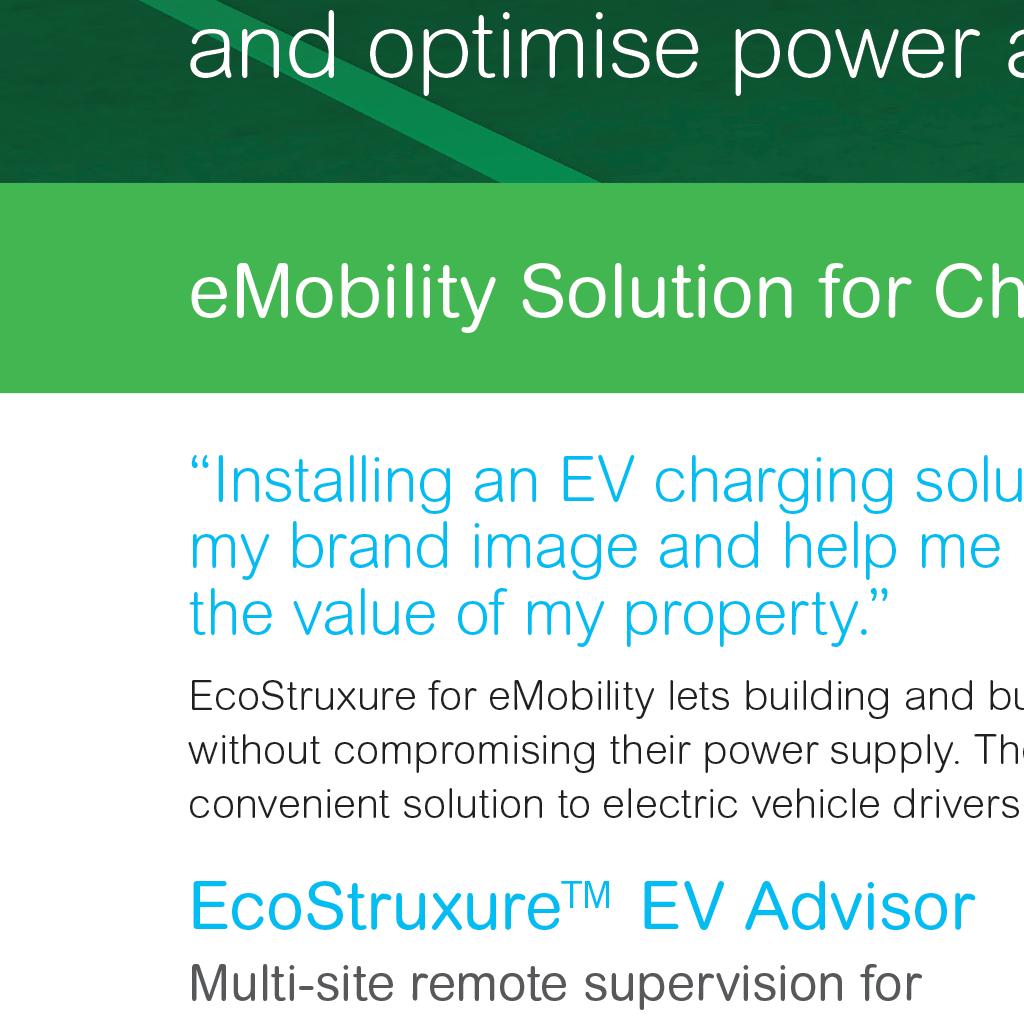
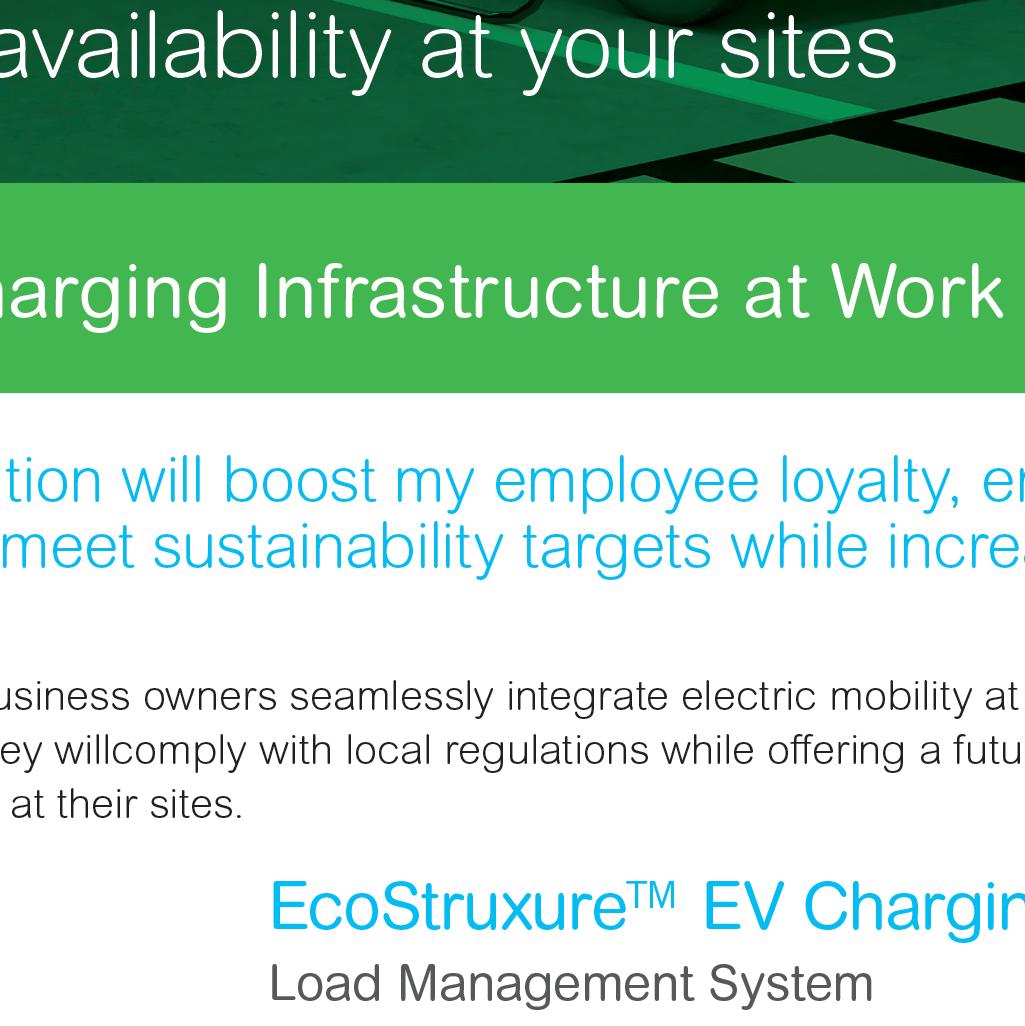
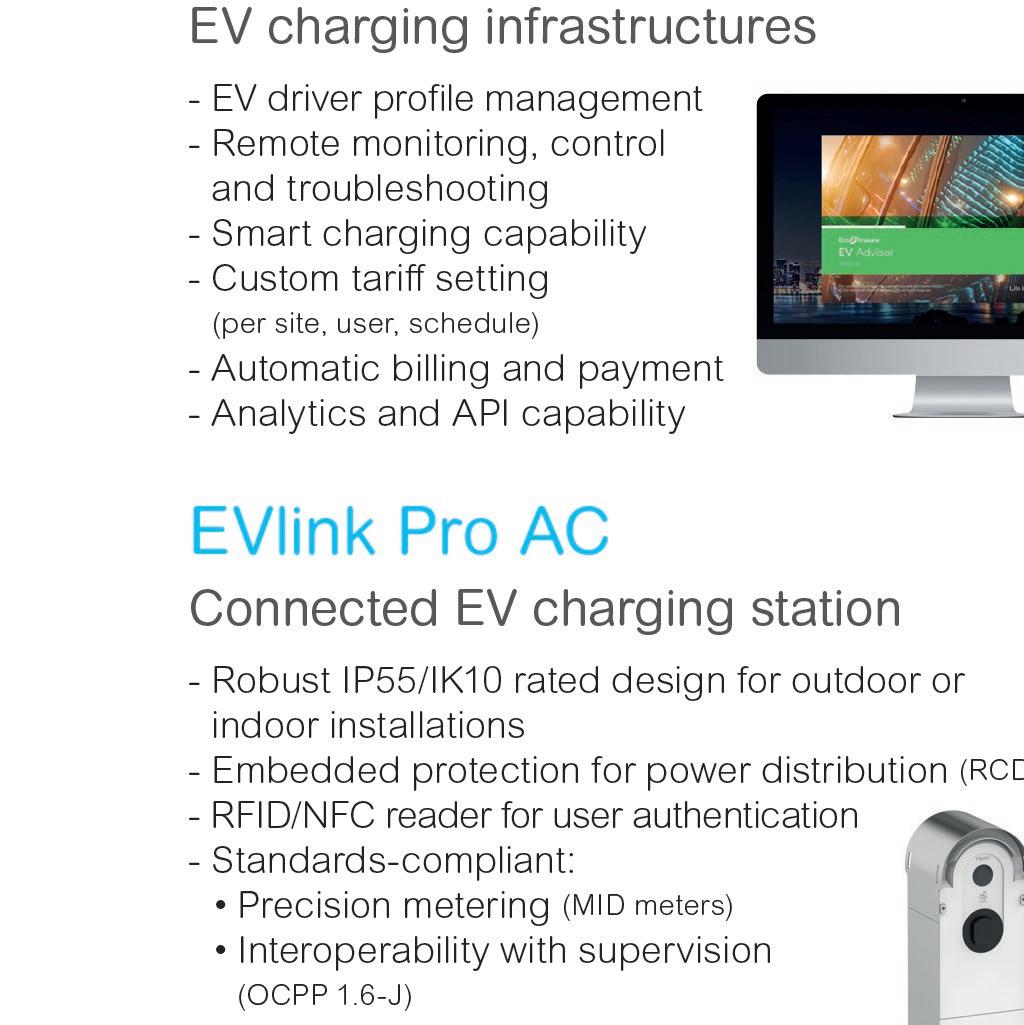
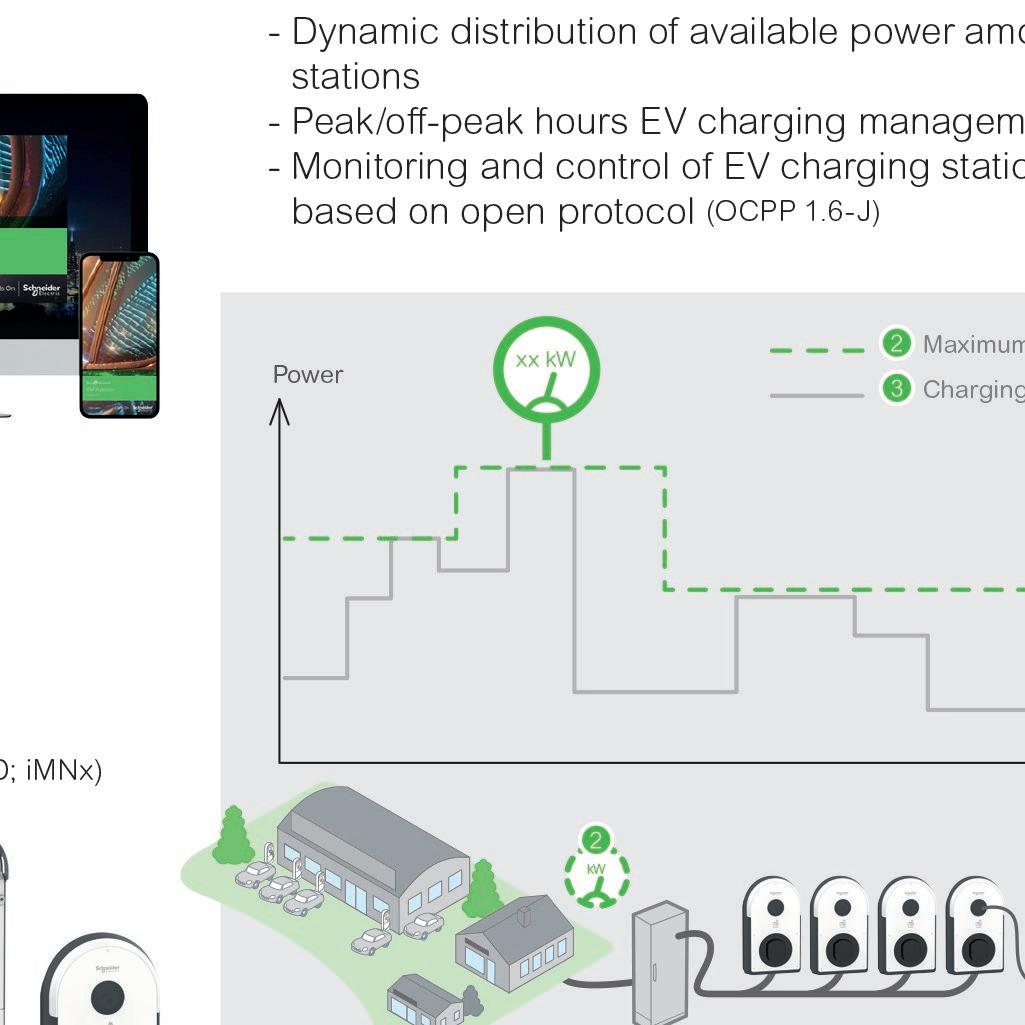


Levelling Up Bill lacks clarity and funding needed to transform communities
The Levelling Up, Housing and Communities Committee has written to Secretary of State for Levelling Up, Housing and Communities, Greg Clark MP, setting out the Committee’s initial findings following scrutiny of the Levelling-up and Regeneration Bill.
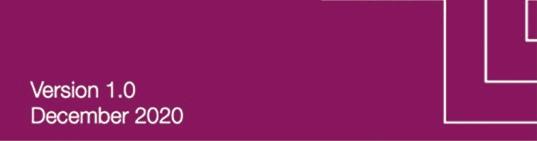
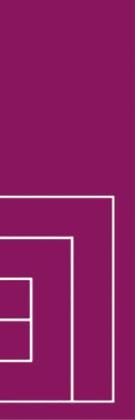
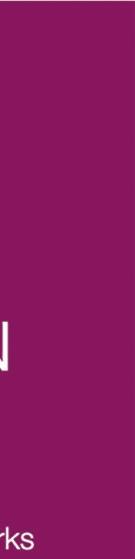

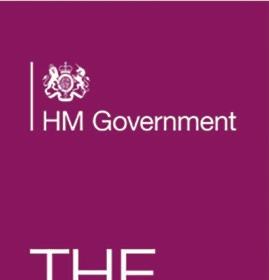
The Committee’s inquiry has focused on the planning provisions in the Bill. However, the main tool to achieving levelling up will be ensuring there is appropriate funding going to the areas that need it most.
The Bill will do little to ensure improvement in key areas such as transport, skills training or digital connectivity, which would make a significant contribution to improving local communities. In the letter, the Committee expresses concern about the Bill’s lack of detail on planning provisions amid fears of a move to a more centralised approach to planning decisions. It warns that while the Committee had not heard significant criticism of the proposals, much of the substantive detail will come in secondary legislation or after further consultation,
leaving people guessing as to the direction of the Government’s planning agenda.
With the Government still committed to its target of delivering 300,000 homes a year, the Committee finds that more clarity is needed on how the Government plans to achieve this level of building. The Bill would mean that a level of affordable housing provision will have to be met by local authorities but it is not clear if this a set target or merely a guideline.
Chair of the Levelling Up, Housing and Communities Committee, Clive Betts MP said: “In its current form, the Bill does little to reassure that levelling up will prove to be more than just a slogan and that we will have meaningful change in local communities across the country. In key areas, it is unclear how the Government intends to drive change and they are yet to commit to the spending that is necessary to level up the country. Our inquiry has focused on the planning provisions in the Bill, which can be described as loosely connected proposals to tinker with the current system, hopefully achieving
Nautical centrepiece completed at new estate
A bespoke piece of steel art, positioned within a new, affordable housing estate in Staithes, has been preserved for years to come thanks to a sustainable choice.
Funded by charitable donations, York Housing Association and Karbon Homes, commissioned local artistblacksmith, Katie Ventress, to create a sculpture of a Humpback whale tail. Standing at 1.8m tall and approx. 1.73m wide, it was constructed using an internal steel skeleton to form the shape and strength, with 2mm panels of sheet steel then welded to it to replicate the whale’s skin.
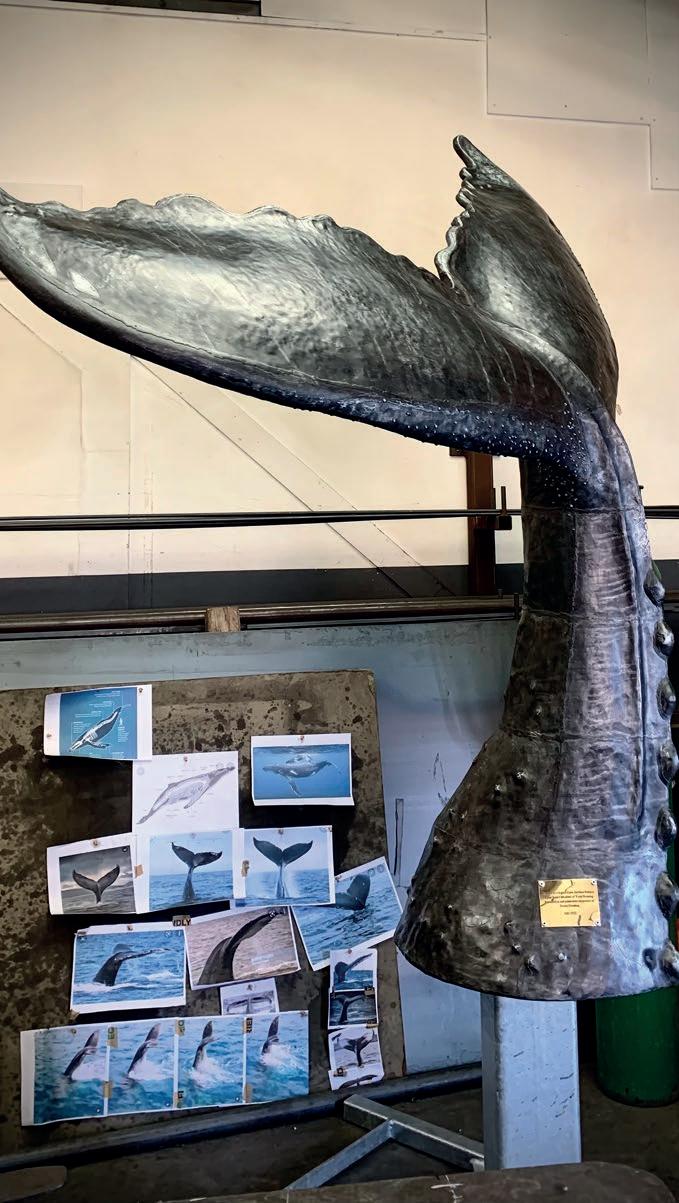
With the piece to be permanently based outdoors, Katie sent the structure to Humber Galvanizing Ltd to be hot-dipped in molten zinc – a treatment that produces a coating which is bonded metallurgically to the steel. No other coating process has this feature and, as a result, galvanized steel has by far the greatest resistance to damage, and offers long-term protection against corrosion.
some improvement. It has been difficult to conduct scrutiny due to a lot of the detail of the provisions having not yet been published. We were asked by the Secretary of State to give our view, and our advice is that more information is provided on what the Government’s intentions are, and that the Government states unambiguously that it is not seeking to centralise planning decisions.”
BSI supports decarbonisation of construction
As the UK’s new Prime Minister, Liz Truss, takes the helm and forms a new government, revisions to the UK’s Construction Playbook, the official document which lays out the public sector’s approach to building and infrastructure works, has been published.
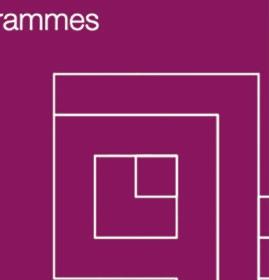


The Construction Playbook has been updated to include enhanced guidance on net zero carbon and environmental performance so that it is easier to ensure the sustainability of building and infrastructure projects. In particular, the government has included clear statements that whole life carbon assessments should be undertaken for all HMG construction projects, supporting best-in-class procurement standards. government.

MINDFULNESS AND CRAFTSMANSHIP
AT ITS BEST
wedi has always understood the importance of supporting sustainability through innovation, and is already well known for its innovative solutions for showers and bathrooms, but perhaps it is less known that wedi is a certified EcoProfit operation and has been for almost 17 years.


The brand’s responsibility to people and the environment is second to none in the construction industry and especially amongst XPS manufacturers.
Manufactured with at least 25% recycled foam material and 100% renewable/green
energy, wedi building boards as well as wedi Fundo shower systems have their own Environmental Product Declarations (EPDs) confirming their environmental footprint throughout their entire lifecycle, making sustainable bathroom construction all the more easier.
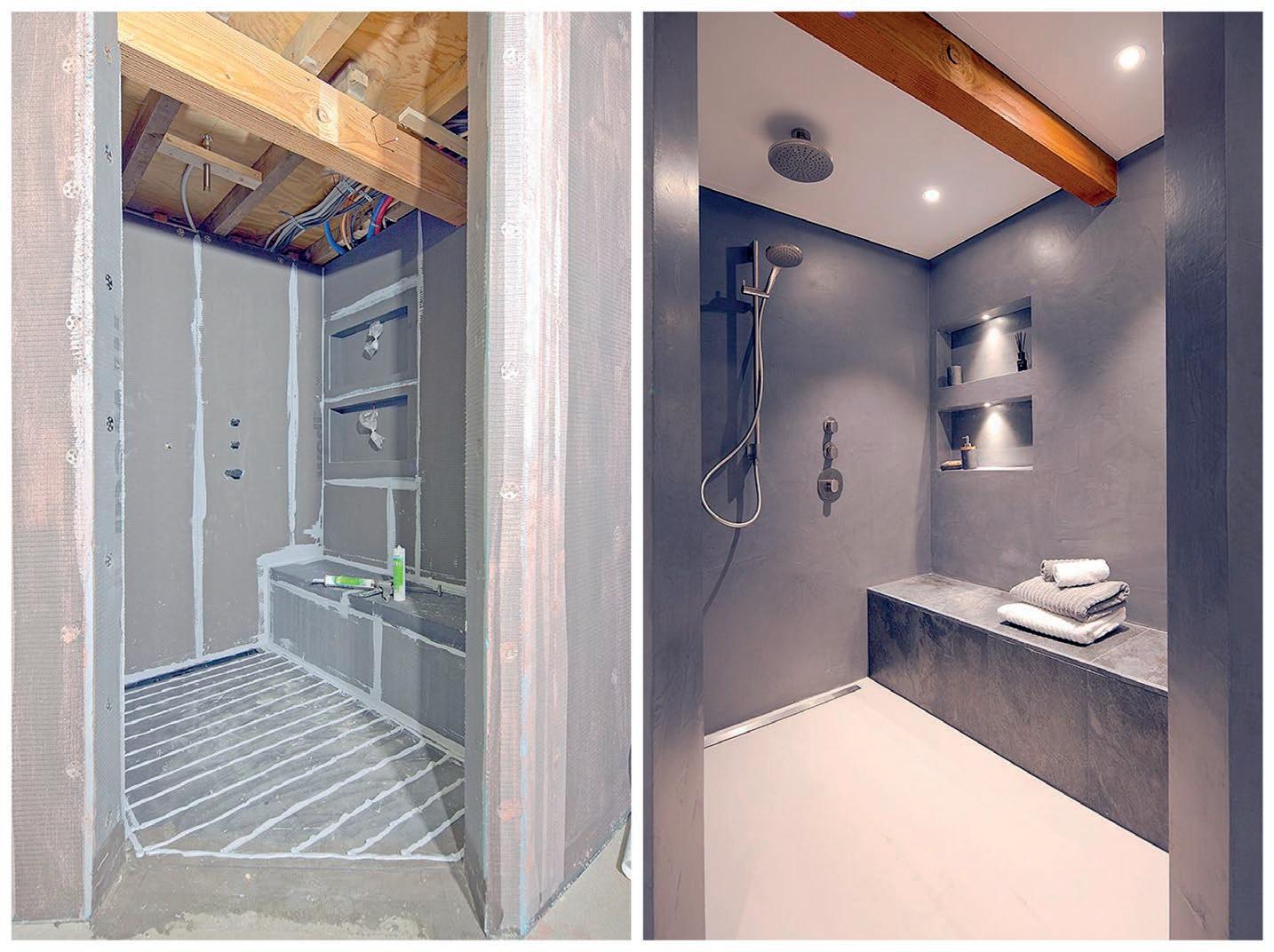
However, wedi’s precision engineered XPS solutions are not only eco-friendly, 100% waterproof to their core or have the best thermal (0.036 W/mK) and vertical loadbearing (133 kg/m2) properties amongst foam tile backers, but also, produce very little, non-hazardous dust when worked on and therefore also contribute to a healthier working environment on the construction site. What’s more, thanks to their low U-value, they reflect the heat back into the room and so, when used underneath underfloor heating (electrical or hot-water), they improve the heating system response time by up to 70% - contributing towards the energy efficiency of the building.
The good thing about wedi is that the brand offers so many individual product variants that it’s always possible to find a solution. Behind every product, there is mindfulness & craftsmanship –thanks to their modular design, perfectly
coordinated wedi components allow for unlimited freedom in design whilst providing all-round protection against mould and fungi at substrate and now also at surface level.
wedi’s newest product line of seamless Top design surfaces is comprising minimalism and environmental awareness - as groutless, ready-to-use design elements, they do not only provide a sleek, modern finish but are made of a unique mineral composite: a mixture of 50% resin and 50% stone powder derived of recycled materialsmeaning that they can be fully recycled at the end of their life. What makes the wedi Top Line stand out even further, is that these surfaces have a pleasantly warm feel representing underfoot comfort and thermal insulation equipped with slip-resistance and antibacterial protection.
Furthermore, the wedi range is characterised by its products’ extremely light weight paired with straightforward and fast installation – cutting back on labour and time, and at the same time, offering unrivalled system security. As an innovation driver in the construction industry for bathrooms and wet rooms, the brand continues to develop its range and improve the products, while remaining true to the guiding principles that started its sustainable journey.
Sustainability is not a new concept at wedi, it is in fact embedded into the core of the business, but the brand continues to explore new strategies to reduce and recycle.
Cost of living crisis causing rethink about retrofitting
as being able to maintain a constant temperature in the home, as well as increasing the desirability of your property - the December 2019 Residential Market Survey, prior to the energy crisis, cited almost two thirds of the survey’s respondents believed that the willingness to pay for energy efficient homes would rise in the next three years.
However, the latest consumer research from RICS and YouGov shows that homeowners are unsurprisingly looking to concentrate spending on escalating household costs.
RICS and YouGov survey shows homes therefore less likely to be able to cope with climate impacts or to mitigate rising energy costs.
The cost of living crisis, has cast new doubt on the progress towards the United Kingdom’s Net-Zero ambition.
Previous research from RICS had found that homeowners were citing cost of retrofitting as a barrier, but despite new policy measures, new research from RICS and YouGov shows that consumers are now concerned about paying for the cost of living above upgrading their homes. Retrofitting has obvious benefits, such
First homes delivered to new affordable housing site
Vital progress was made on a new, low-carbon and affordable homes site in Peacehaven, East Sussex, as the first factory-built homes were craned into place.
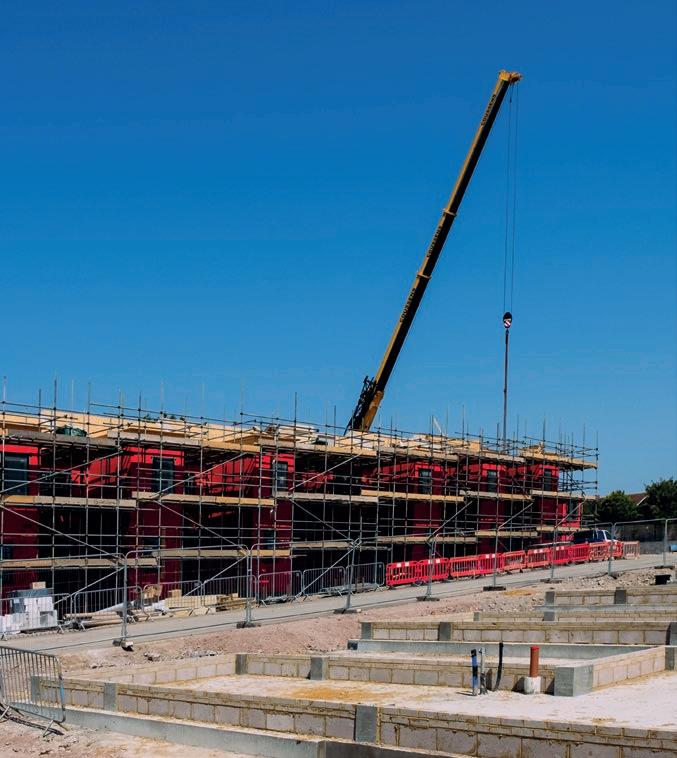
The scheme is being delivered in partnership by social housing provider Stonewater and Boutique Modern, the UK’s first certified B Corp modular construction company, and is being delivered with the support of Lewes District Council and Baily Garner. The site, which upon completion will comprise of 40 homes that are constructed using modern methods of construction (MMC) from Boutique Modern’s factory in Newhaven — just 5 miles from the development, which was formerly home to a plant hire company and derelict residential property.
Consisting of three one-bedroom flats, six two-bedroom flats, 20 two-bedroom houses and eleven three-bedroom houses, all the modular homes will be available for affordable rent and have been constructed to high energy-efficiency standards. Boutique Modern’s B Corp certification
means that the company uses the highest social and environmental performance standards in the industry. Furthermore, each home’s energy performance will be optimised to maximise the potential fuel and energy efficiency for each resident, and with the homes being factory built three miles from their final location, carbon efficiency is also amplified.
The new research backs up previous calls made by the institution in 2020 for more policy measures to incentivise industry and consumers to retrofit the UK housing stock. The research found that while 34% of homeowners said they would invest in green technology to lower bills in the future, 45% would be focusing on using any savings to pay for their existing living expenses, meaning more incentives and cheaper options must be made available if the country is to stay on track to meet target and green 15 million properties.
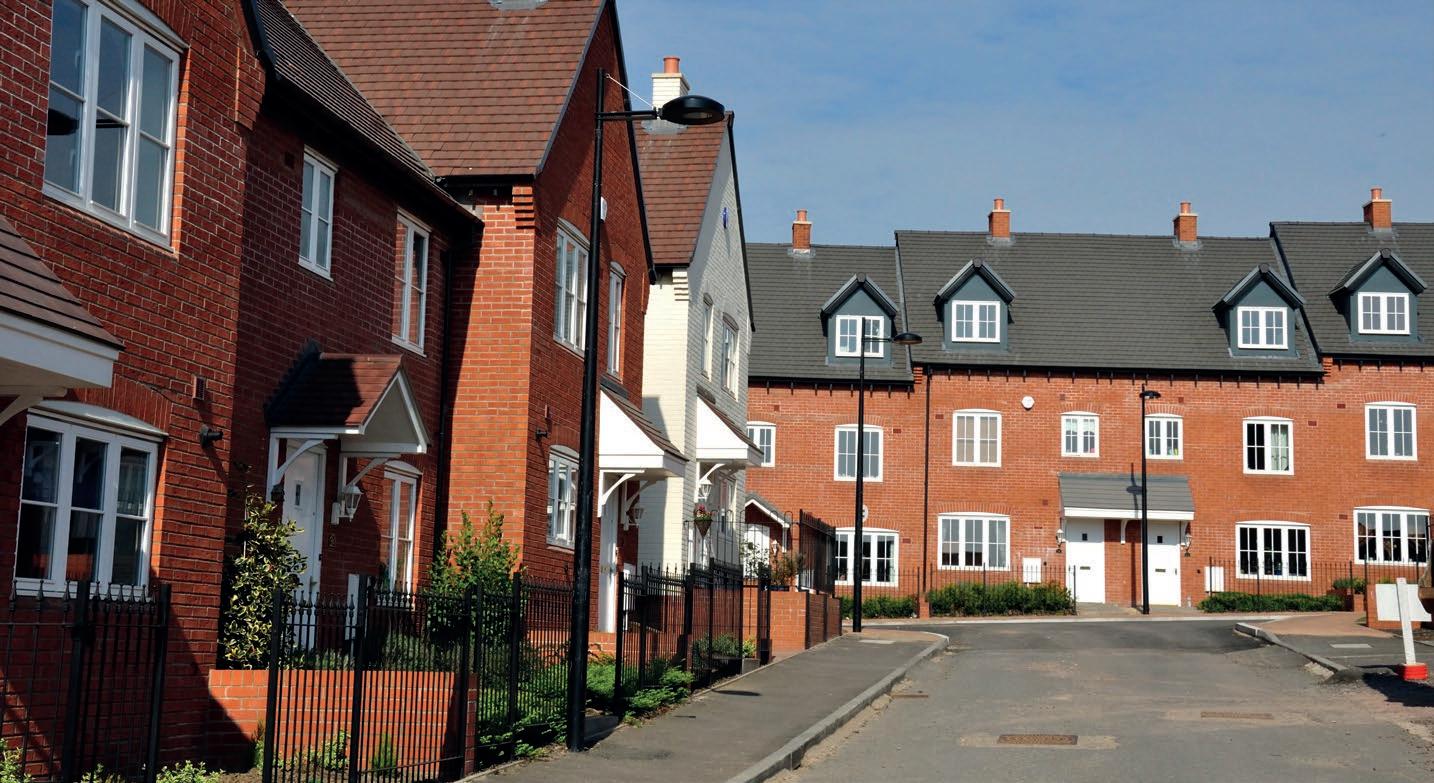
This latest research follows the RICS January 2020 Residential Market Survey where members operating in the residential sales and lettings market stated that without strong market driven incentives, regulation was the policy lever with the greatest potential to improve energy efficiency outcomes. Alternatively, a tax policy could achieve a similar effect through a mix of stamp duty and a reduction of VAT on home improvements.
Currently, the Government’s ambition to hit Net-Zero carbon emissions requires significant numbers of private homeowners to retrofit their properties to make them greener. Fifty-one per cent who confirmed they hadn’t already installed new energy saving measures in their homes but would know how to, said it was because of the costs involved. And of the same group, even those who would consider it to make their home more attractive to prospective buyers, 40% said they’d only consider spending around £1000 to £5000 on energy improvements, which could pay for some solar panels but wouldn’t cover the heat-pump.
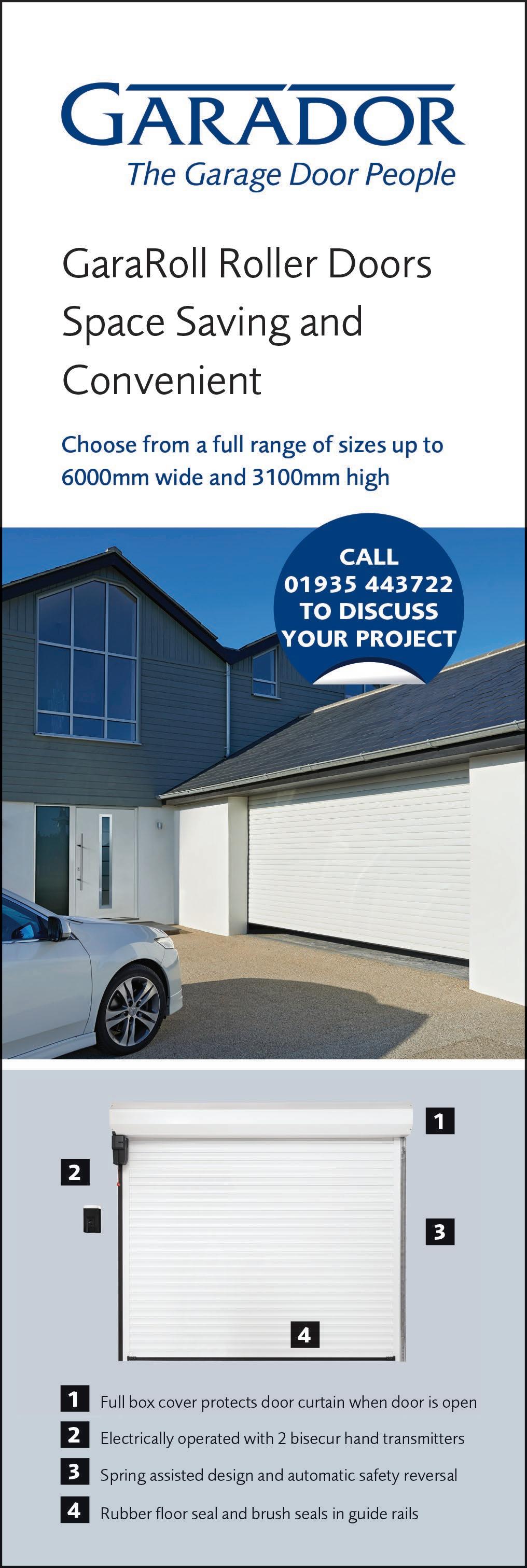

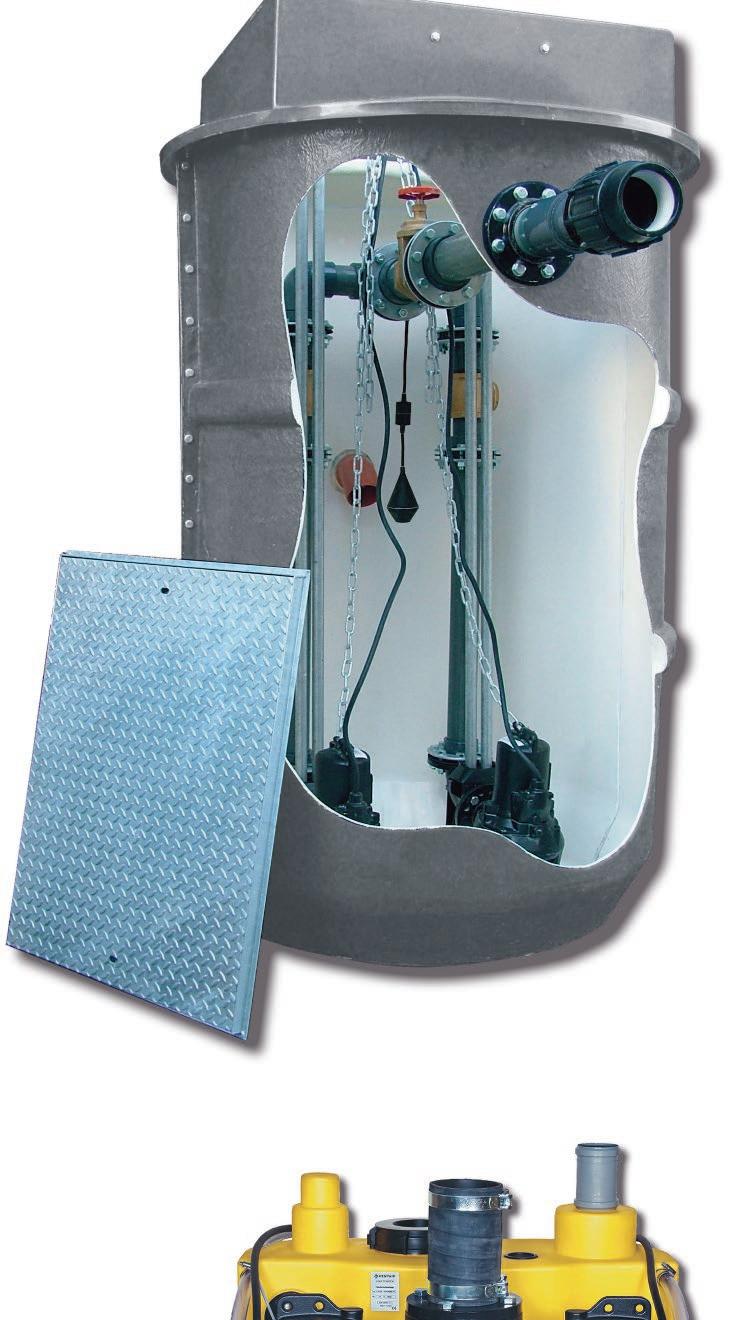

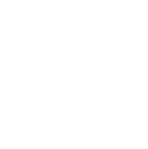
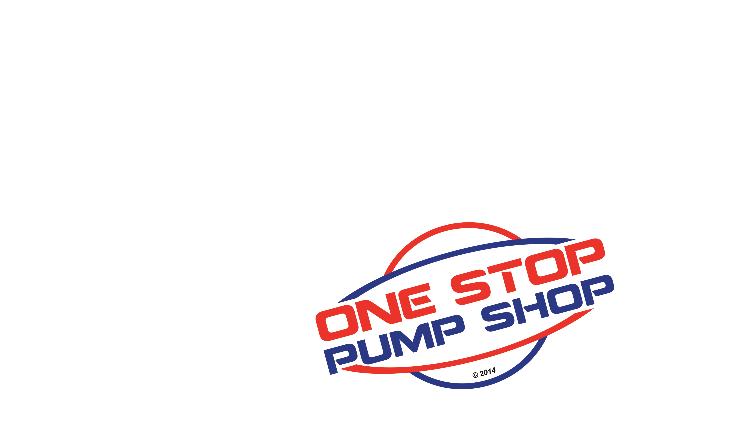
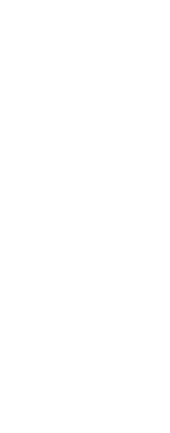
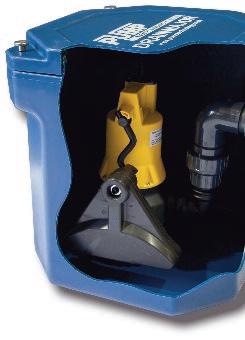
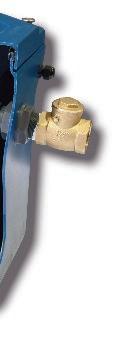

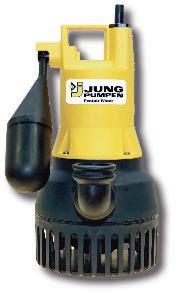

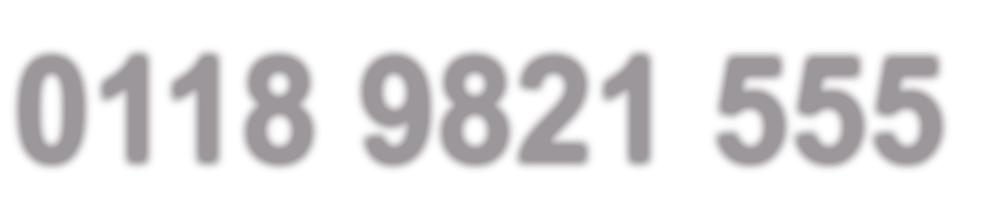
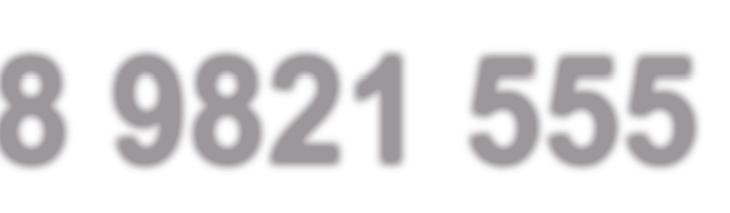
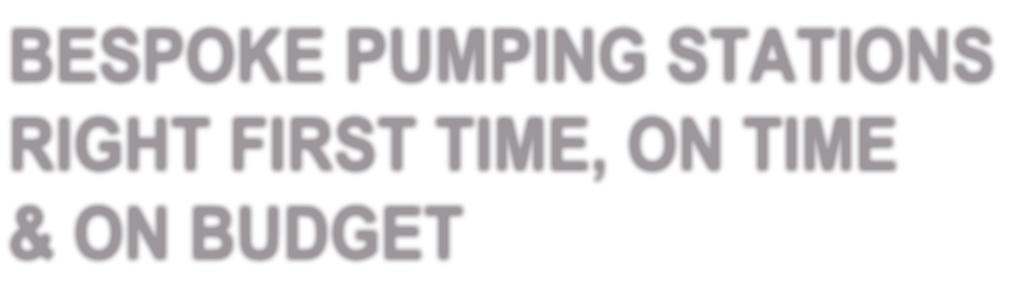
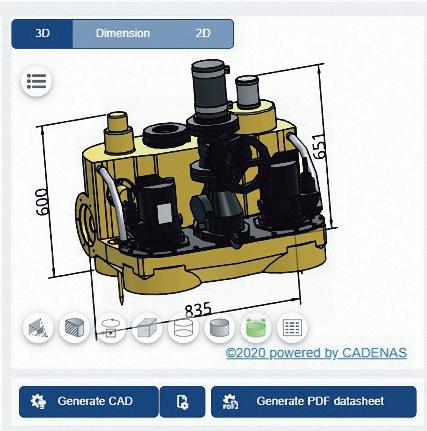
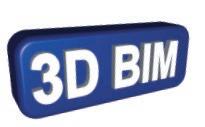
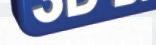
NEW FUTURE HOMES AND BUILDING STANDARD STARTS TO TAKE EFFECT
One of the first steps in a major new government initiative to cut carbon emissions - which will involve sweeping changes for the construction industry - was taken in June when various changes to building regulations were introduced ahead of the Future Homes and Building Standard.
The first sector where the new Standard appears to be having an impact on tendering arrangements is social housing work for councils and housing associations. Glenigan data shows some significant new frameworks currently being let are including features such as ground and air sourced heat pumps and solar panels which will become part of the new Standard.
The new Standard is set to come into full effect in 2025 with a goal of dramatically cutting carbon emissions in new homes by 75-80% on current levels.
Inevitably, this will mean new homes built by both private and public developers will have to meet more demanding and potentially costly standards. But the new Standard will also extend to existing homeowners who are undertaking extensions or renovations involving thermal upgrades, says industry analysts Glenigan.
The non-residential construction sector will also be impacted. Developers of new offices, retail premises and public authorities will be obliged to meet new standards with a target to cut emissions by 27% over coming years.
The timing and broad scope of the new Standard means it could have a significant influence on workloads in various sectors – particularly new private housing and commercial work – over coming years.
Already, there are signs that commercial developers have brought forward the start of some new schemes this spring to avoid some of the new regulations which came into force in June. In the medium term, contractors working in the housing renovation and refurbishment sectors
should see stronger demand for their services as clients are obliged to meet more exacting standards.
Suppliers of energy efficient building insulation materials and productsparticularly for products such as heat pumps and window replacements units - will stand to benefit.
Yet in an era of rocketing fuel costs, the significant savings on energy bills enjoyed by buyers of new homes could give a boost to demand for private housebuilders.
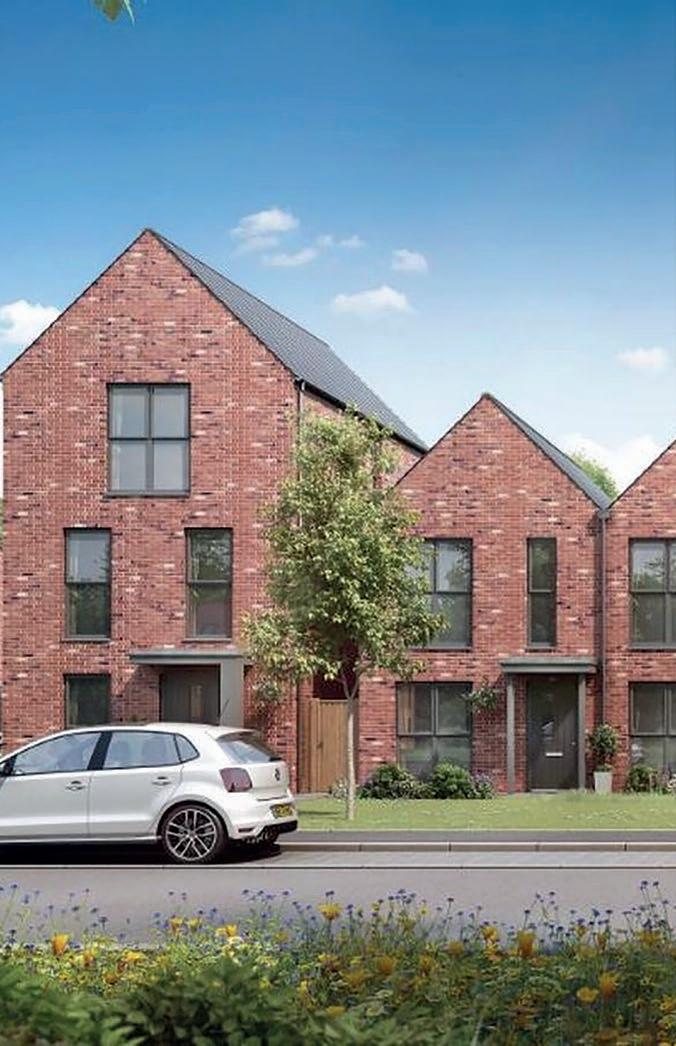
The new standard could also bolster demand for newly built commercial and office space. The rise in fuel costs has moved energy efficiency increasingly onto the radar of both major private developers and landlords as well as occupiers of business space. It has been reflected in the growing number of new projects built using the sustainable BREEAM route and will be reinforced by the new Standard.
According to Allan Wilen, economics director at Glenigan, “This marks a major change as it means businesses are looking at a broader environmental platform. By moving energy efficiency up the agenda, it will help to reduce their footprint and will have a direct benefit on costs and on the bottom line.”
For example, a £1 billion renewables servicing & maintenance framework for Hastoe Housing Association in Kingston-on-Thames - where applications to tender are currently invited - involves firms providing various services which will be commonplace under the new Standard.
Work on energy efficiency for social housing linked to the new Standard - on both new and renovation schemes - should provide a useful support to the pipeline of work in the sector over coming years.
free
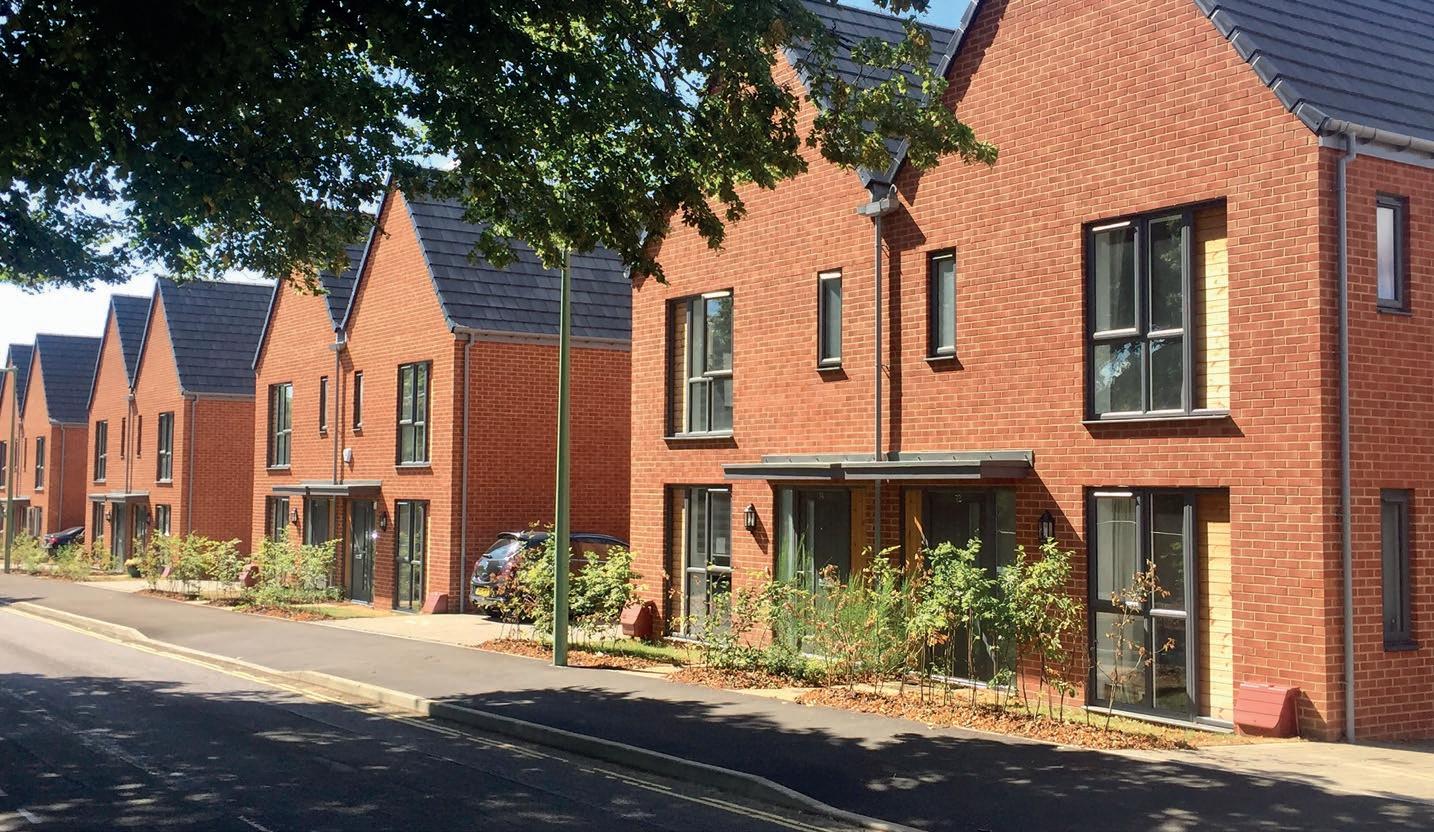
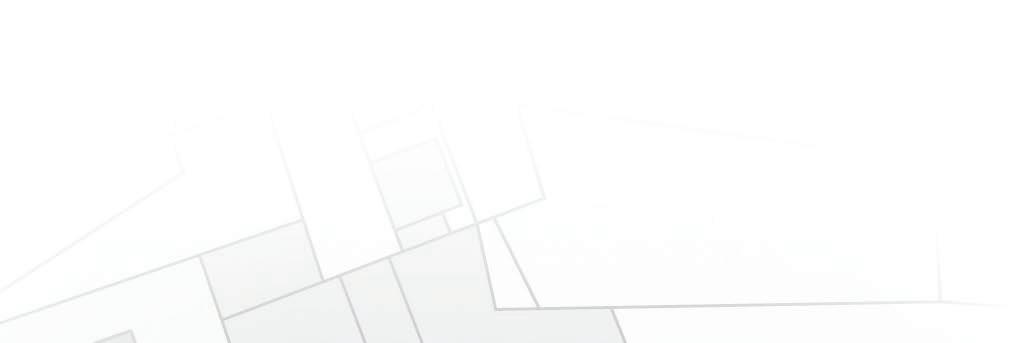
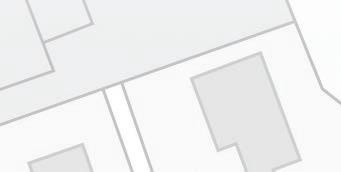
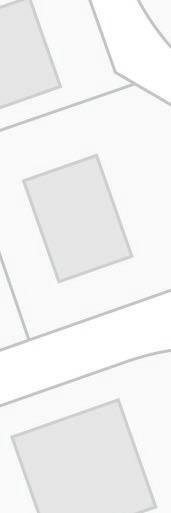
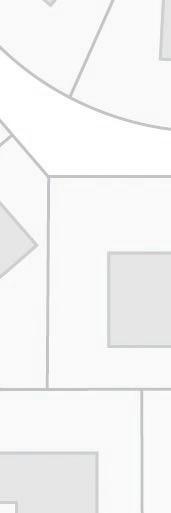
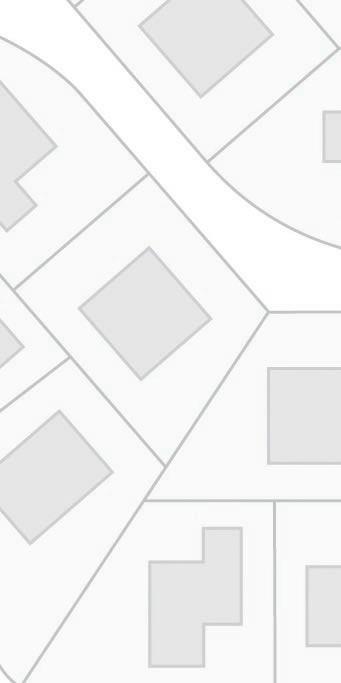


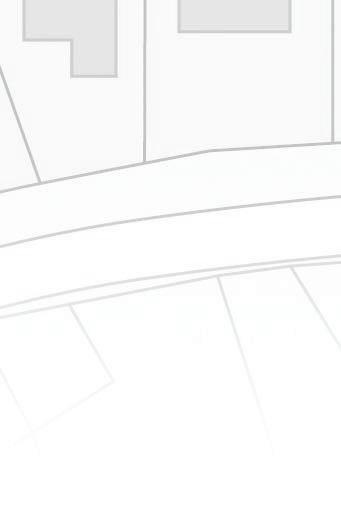


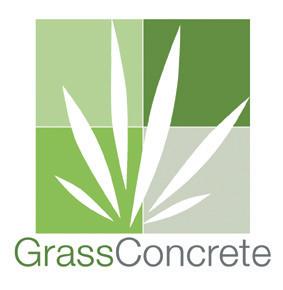
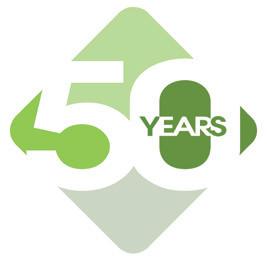




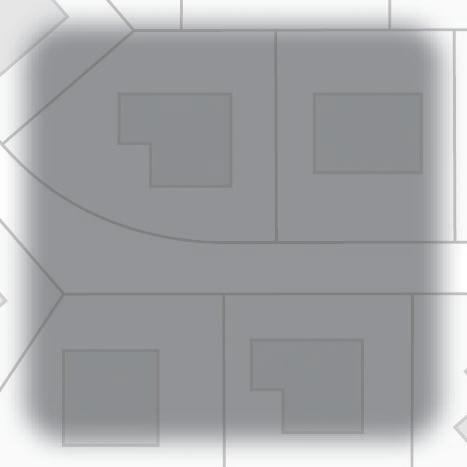
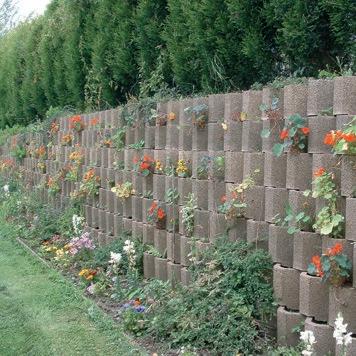
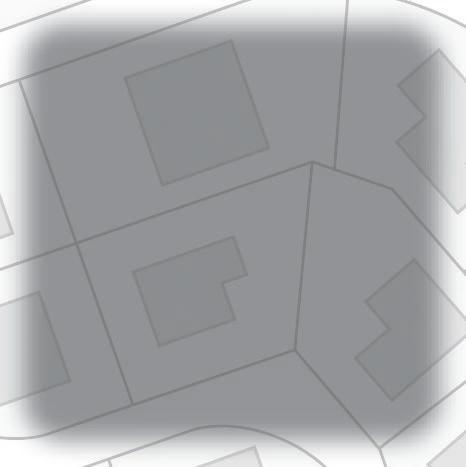


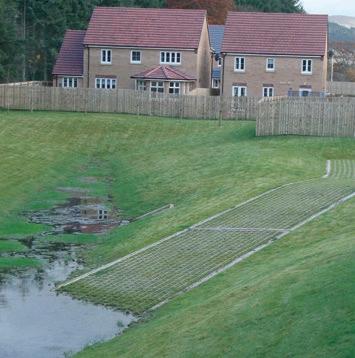
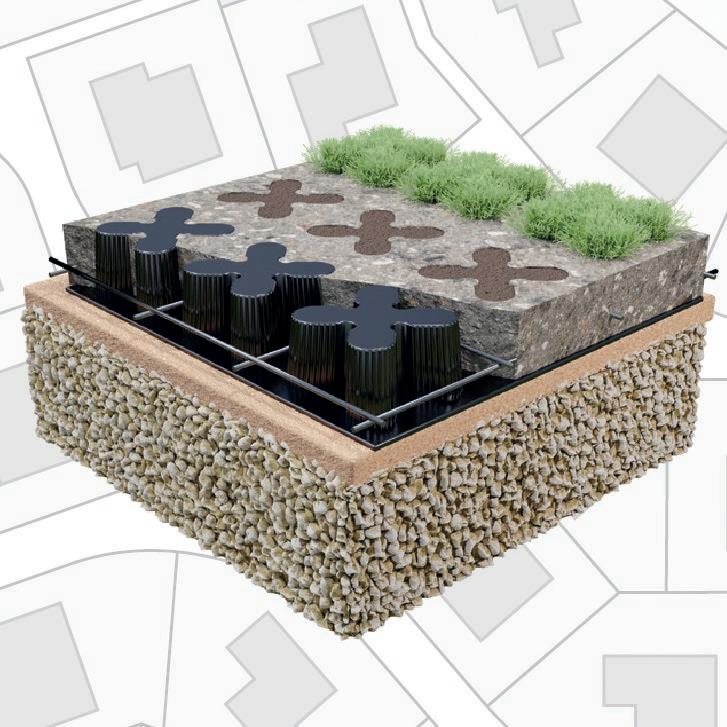

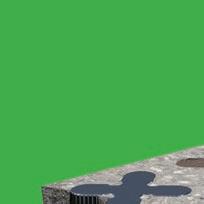
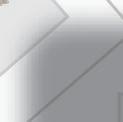
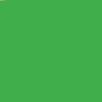
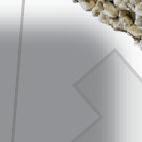

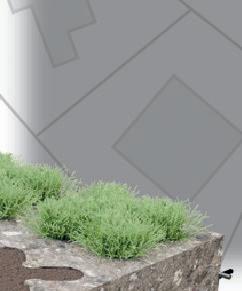
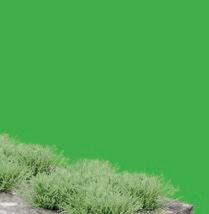



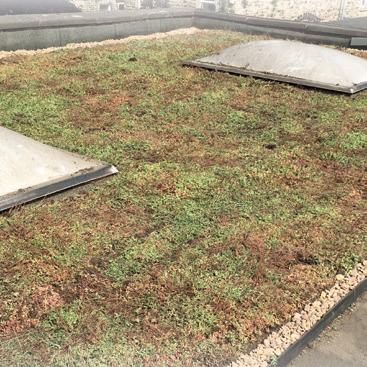
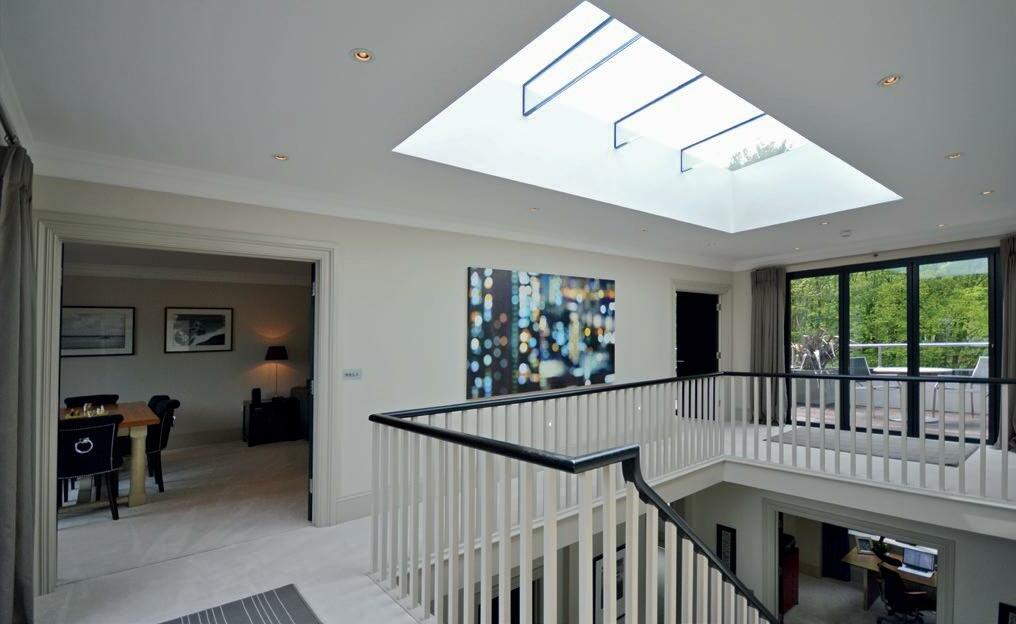
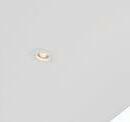
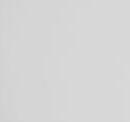

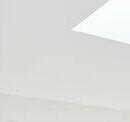
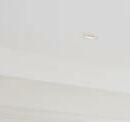
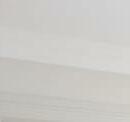
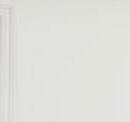
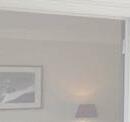
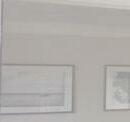




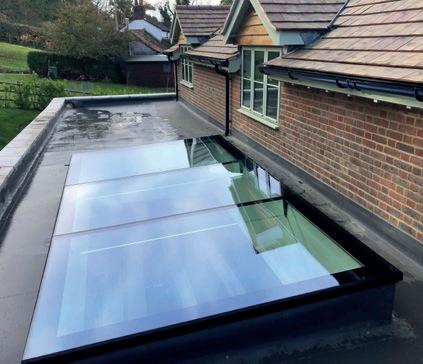

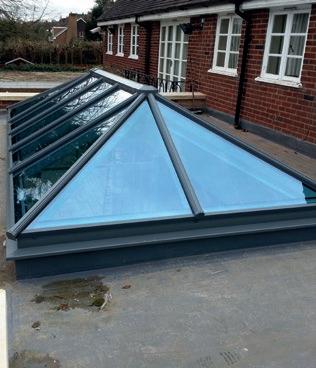
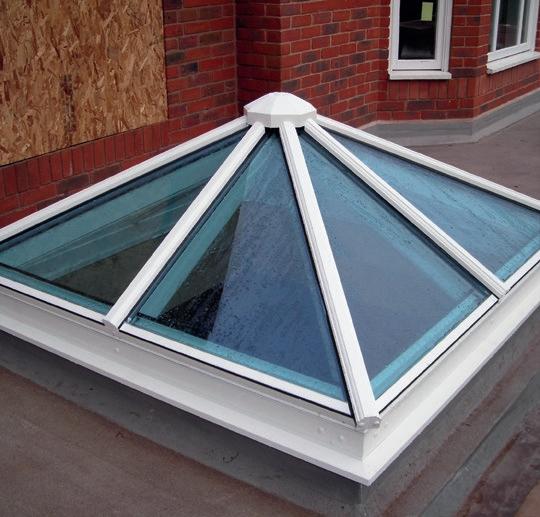
TECHNOLOGY AND INNOVATION HELPS TO KEEP RESIDENTS SAFE AND SECURE
As a leading London Borough Council, Islington has made the transition to a PAC cloud solution across its housing network, delivering improved security for residents.
Initially, PAC pilot tested the system across six blocks chosen by the council’s capital works team. The pilot was successful in working around residents to ensure a seamless transaction of fobs and secure access to communal areas. The works have now been extended to more locations across the borough.
With the ongoing programme, Islington Council is committed to safe and secure housing for residents across the borough. The PAC security system can accommodate the high frequency movement of residents and operators who may need controlled access to communal areas. Overall, the PAC installation offers greater peace of mind and safe audit control.
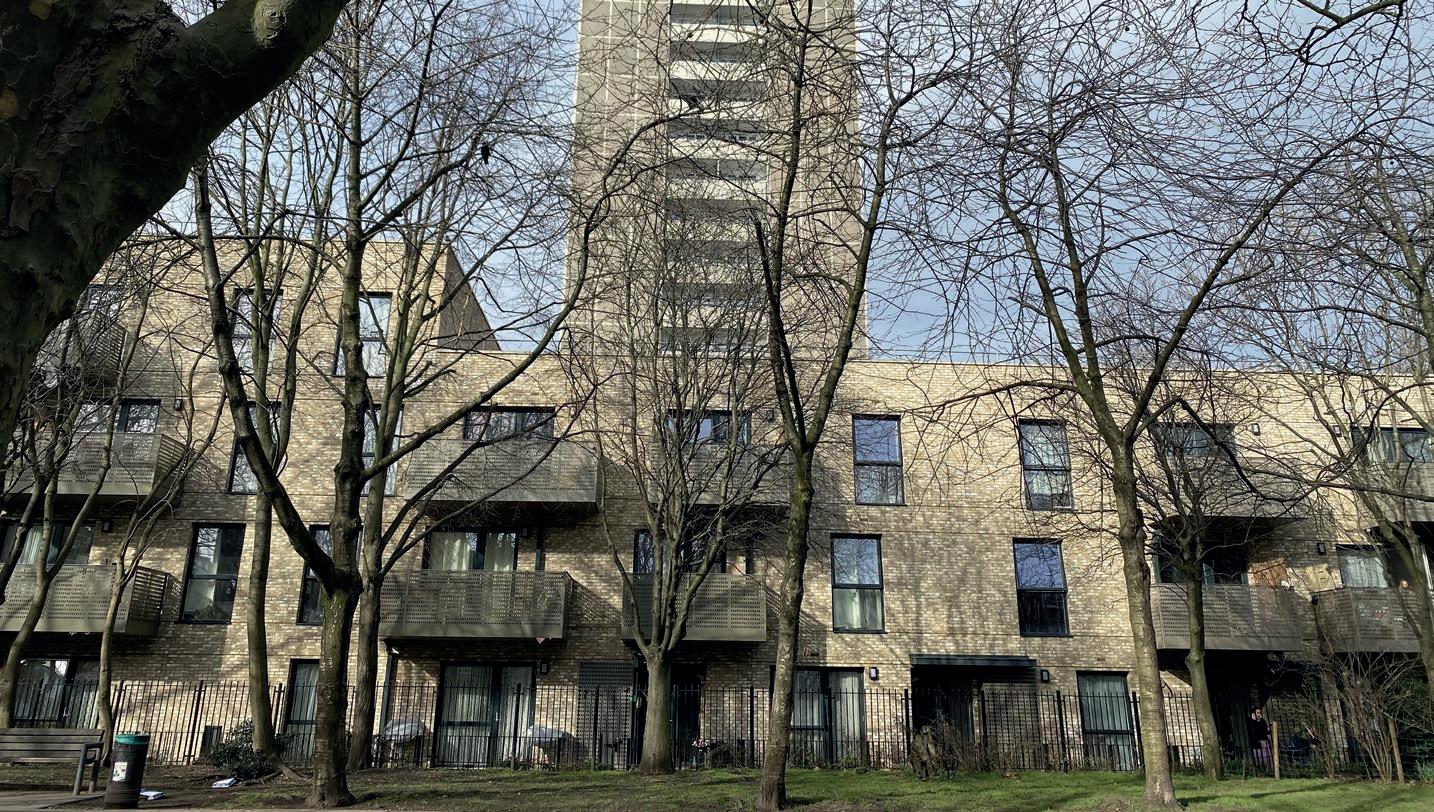

The London Borough of Islington has been using PAC systems for over
25 years, with the team working closely with technical services from specification to installation, ensuring a seamless transition from the existing standalone system to the smart cloud based solution.
From the borough’s perspective, the remote capability enables a much
more efficient approach to managing access throughout our properties, enabling resident instant access, and old resident details can be removed and replaced as necessary.
At the same time, Islington has peace of mind that data captured is secure in the cloud, in compliance with latest
Islington Council has worked with Comelit-PAC to create a cloud based door entry solution for managing access control to communal residential developments across its housing portfolio.standards. Paul Scott, Sales Manager at Comelit-PAC added: “The benefit of the long term relationship we share with The London Borough of Islington, is that we understand their requirements, from a technical and operational perspective. We also have come to know their processes to ensure resident safety across its housing network.
“The new cloud system enables the Homes and Neighbourhoods team to operate more efficiently, especially with the new focus on hybrid working. It also comes with the assurance that all data is safely stored and backed up, secure and accessible, even remotely when they are not on site. This means they can respond quickly to resident’s needs for new or replacement fobs, and ultimately secure access to their home.”
Concealed multipoint locking
Recent development work carried out by Steel Window Association member company, Steel Window Fittings, means it is now possible to specify concealed multipoint locking on virtually all the different door and window systems available in the sector.
Where steel frames traditionally only offered a single point of locking, or the traditionally admired duplex locking, which featured surface mounted rods and noses, the modern alternative houses all the components within the perimeter sections.
Not only can this be aesthetically much more appealing, but it further enhances steel fenestration's renowned
strength and security, while helping improve weather-tightness. And having debuted on the W30 system back in 2013, further development work by Steel Window Fittings and the SWA's Technical Committee has enabled the advancements to be offered across the range from the benchmark W20 suite of sections through to the highest performing, thermally broken options.
Multipoint locking systems are available for the W20, W30, W40 and thermally broken W50 systems in five different styles of lever handles and seven choices of finish, as well as custom finishes where required.

New and improved app
Seeking to empower residents to create safer and healthier homes, Aico, the European Market Leader in Home Life Safety, has launched the third iteration of the HomeLINK App for Residents.

The app provides an innovative solution to some of the housing sector’s biggest challenges, such as damp and mould and poor indoor air quality, allowing residents to take the first steps in improving their home’s health.
The app is a complementary addition to Aico’s HomeLINK Internet of Things
(IoT) platform, which includes a network of fire and carbon monoxide alarms, environmental sensors and the Ei1000G Gateway that connects them all.
Designed to provide residents with detailed information about the health and safety of their home, the app provides users with hints, tips and recommendations to better their home’s indoor environmental conditions, in turn, improving their own health and wellbeing. For example, with the improved core features, residents will receive notifications and recommendations, detailing how to reduce the risk of allergens, mould and indoor air pollution besides fire alarm testing reminders.
Through real-time information, residents will see a breakdown of carbon dioxide, temperature and humidity conditions within each room, followed up by educational information to understand their home better.
A game-changing new feature with the opportunity for enhanced care provides residents with the ability to invite others to app, so that their family members, carers or friends can also access the information to support the resident in following the healthy home recommendations.
HOW SUSTAINABLE IS YOUR SUPPLY CHAIN?
Inflation and disruption is putting massive pressure on the construction supply chain. That can’t be at the expense of supply chain integrity. We report.
A study published by the Chartered Institute of Procurement & Supply (CIPS) found that 48% of supply chain managers did not believe their organisations were transparent enough with clients and regulators about sustainability.
A further 19% admitted not even knowing how sustainable their products were themselves, despite marketing claims about commitments made to sustainability.
The CIPS suggested a lack of procurement involvement in setting corporate sustainability strategy in the UK is at least partly to blame.
Much of the UK’s carbon footprint is generated abroad, several tiers down the supply chain in the extraction of raw materials, manufacturing of products and transportation. It argues the procurement function has a crucial role in understanding, measuring, and addressing the sustainability of this supply chain.
“If you don’t know where something is coming from then you run the risk of making claims which aren’t true”, says John Duckworth, Head of Commercial Sales, Deceuninck.
“Whether that’s intentionally or unintentionally greenwash is something contractors need to be very careful to avoid - that includes throughout their supply chain”, he continues.
He argues the launch of the Green Claims Code by the Competitions and Market Authority at COP26 last year is a precursor to more aggressive prosecutions for false or unfounded claims on sustainability.
This is based on existing law but makes it clear that firms making green claims “must not omit or hide important information” and “must consider the full life cycle of the product”.
“This is one of the points that is always a bone of contention for us as a PVC-U window and door systems company”, continues John. “There’s no point us pretending to be something we’re not. PVC-U windows are essentially
manufactured from a polymer made from hydrocarbons – oil - and chlorine derived from salt. There’s a lot of the latter about, less of the former.
“If we’re going to use oil as a finite resource, surely it makes more sense to put it into a high value and infinitely recyclable product, than to burn it in heating and our cars, especially when those products deliver significant through life energy savings.
“That’s a sustainable way forward –recycling something, over and over. It’s not only about renewables.” Deceuninck has invested more the €15million in one of the world’s most advanced PVC-U recycling and compounding facilities.
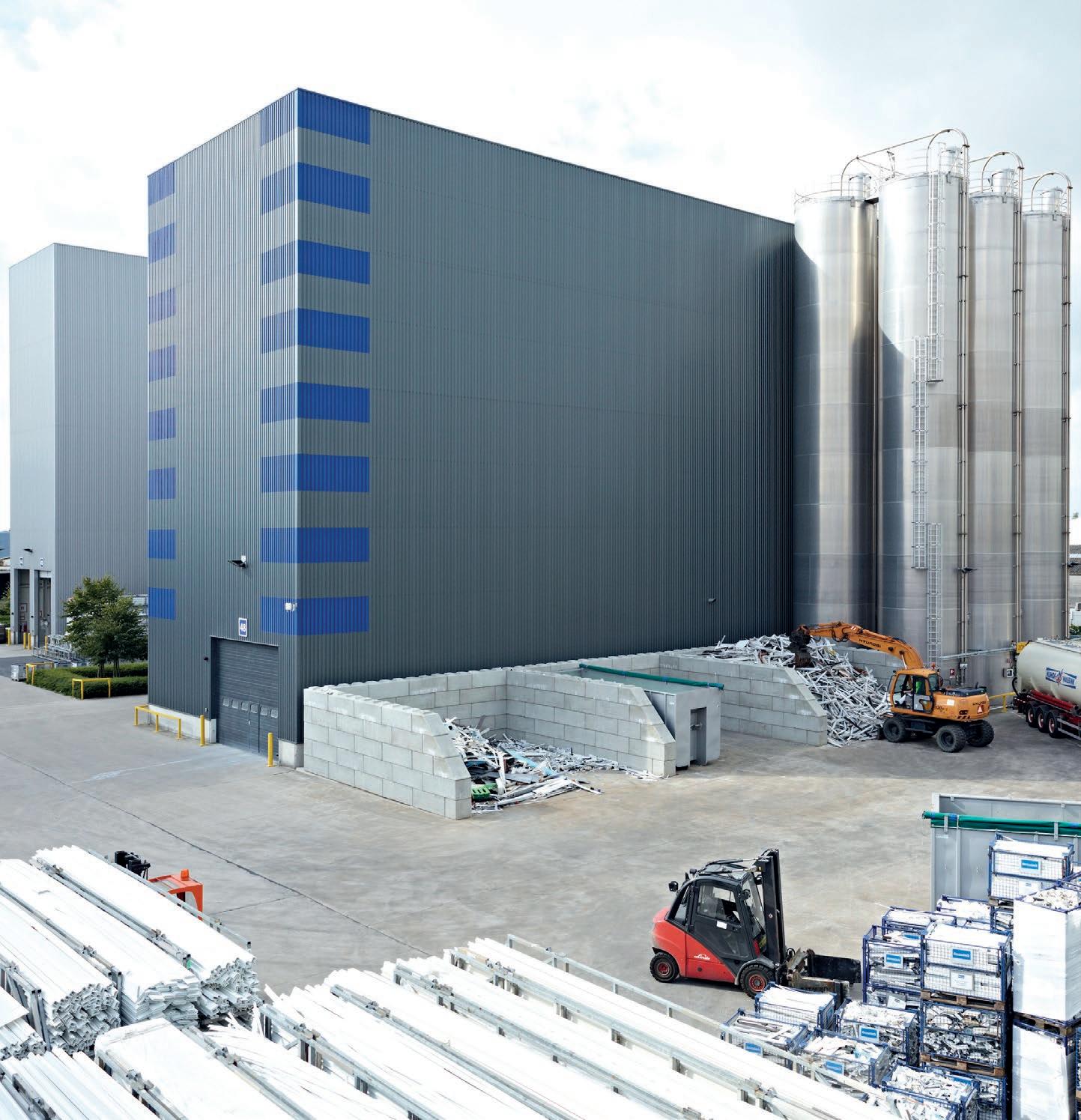
This gives it the capability to reprocess up to 45,000 tonnes of post-consumer and post-manufacturing PVC-U per year – the equivalent of preventing 3 million windows from going to landfill annually. Use of recycled material also delivering
a reduction in CO2 emissions of 90,000 tonnes compared to virgin feedstocks as well as a 90% energy saving.
The focus the PVC-U building products industry has applied to sustainability, supporting its BRE Green Guide A+ rating.
“The PVC-U supply chain is comparatively short and most importantly, it’s transparent”, John continues. “Critically, it is recyclable. Each window can be recycled up to 10 times without degradation of performance.
“Given an average reference service life of around 30 years for each window, it means that the raw materials used in each product could still be making homes warmer and more energy efficient 300 years from now - as long as they are recovered and recycled.” This is something the PVC-U industry has committed to drive forward. Deceuninck is one of a number of leading PVC-U window and door systems companies to
have signed up to Vinyplus, a voluntary 10-year commitment to drive a circular economy in PVC-U manufacture.
“We know through figures from Vinylplus that collectively the industry has recycled more than 6.5million tonnes of PVC-U since 2000. That’s roughly 27.5% of the PVC-U ‘waste’ material that we could recycle, so we have more to do, but it is nonetheless a very significant figure.
“We expect the inflationary pressure that we’re now seeing on oil prices, to drive higher rates of recycling across Europe”, John said. Deceuninck offers an extensive commercial window and door range, working with commercial window and door manufacturers specialising in modular builds as well as other specialisms including steelframe construction.
Its’ flagship commercial system is the 5000 series, which extends the design potential of PVC-U using patented glass fibre technology, removing the requirement for steel reinforcement,
increasing thermal efficiency and reducing weight.
Available in Standard, Slim and the ultra-energy efficient Neo option, as a leading edge, tilt-and-turn window it achieves U-values of as low as low as 0.84W/m2K, air permeability is 600Pa, watertightness of up to 600Pa and wind resistance is 2000 Pa.
“It’s about the circular economy. Creating next generation products from old ones which deliver a better level of performance through-life and which are being and can be recycled more easily at end-of life”, John argues.
Its own research also evidences just how important sustainability is to end-users with more than two-thirds of end-users (68%) stating that they would choose windows and doors with a higher recycled content over and above products that don’t contain recycled content, or which did so at lower levels. The independent survey conducted by YouGov during COP26, also found that 63% of homeowners
said that they would be more likely to purchase home improvements which they saw as being more ‘sustainable’. Of these, 38% would be prepared to pay more for home improvement products that had higher recycled content and reduced impact on the environment.
“PVC-U is energy efficient, it’s low maintenance, recyclable and far easier to be recycled than many other products which are seen to be sustainable – for example timber.
“What we have to do is get better at capturing that material and that requires a change in the way that we see it and in the way that specifications are drawn up to increase focus on not only whole-life costs but also end of product life and a circular value chain.”
For more information about Deceuninck’s product and service offer please call 01249 816 969, email deceuninck.ltd@deceuninck.com or visit www.deceuninck.co.uk
Deceuninck - Enquiry 10
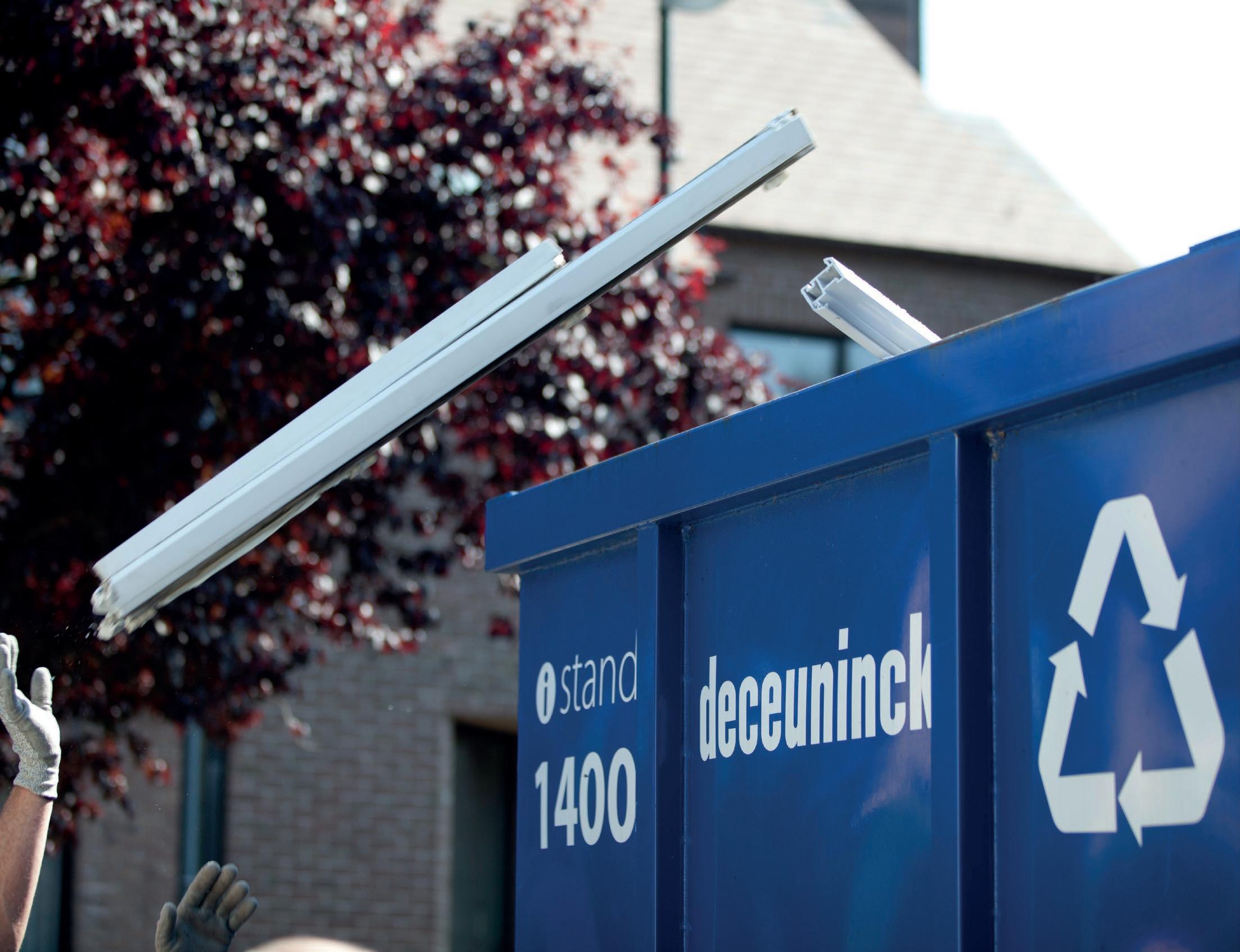
COVERING YOUR FIRE SPRINKLER SYSTEM INVESTMENT
Residential fire safety continues to be a primary focus for housing associations and local authorities, particularly in tower blocks where the retrofitting of fire sprinkler systems is an essential part of an ongoing multi-million pound investment in fire protection upgrades. Peterborough based, Encasement, is one of the key manufacturers and suppliers of fire sprinkler pipe boxing systems and they have provided an insight into the cost benefits of pre-formed boxing solutions.
With HAs and LAs investing significantly in fire safety improvement packages, questions regarding best value and cost effectiveness are inevitable considerations while also ensuring that quality and safety are not compromised.
As sprinklers need to be located within individual flats and communal areas to suppress fires and aid escape, incorporating them in new builds is comparatively simple, as they can be integrated at the building design stage and pipework can be hidden within wall cavities and ceiling voids. For retrofitted sprinkler installations, however, it’s not as straightforward, as in most cases the pipework will need to be surface mounted.
Once sprinkler system is installed, the pipework is concealed to provide a more aesthetic finish and avoid potential tenant complaints, as well as covering sprinkler system components and acting as a visible barrier to potential tampering.
Covering up
A key advantage of surface mounted pipework is the simplicity and speed with which it can be installed by skilled contractors. Clearly, the fitting of pipe boxing also needs to be quick and easy to ensure the associated costs are effectively managed, which are key considerations on any sprinkler project.
These are key reasons why pre-formed and pre-finished solutions, such as Encasement’s Versa pipe & fire sprinkler system boxing, are increasingly specified by sprinkler contractors and installers.
Versa ‘L’ shaped boxing is manufactured, from 5mm or 8mm thick UKTR compliant plywood and is available in a range of sizes and profiles to meet various sprinkler pipework configurations.
A range of dedicated accessories is also incorporated as part of the Encasement system, including internal and external corners, as well as stop ends, fixing battens, screws and caps. These help create an integrated and consistent finish within each flat whilst also simplifying the sprinkler installation project.

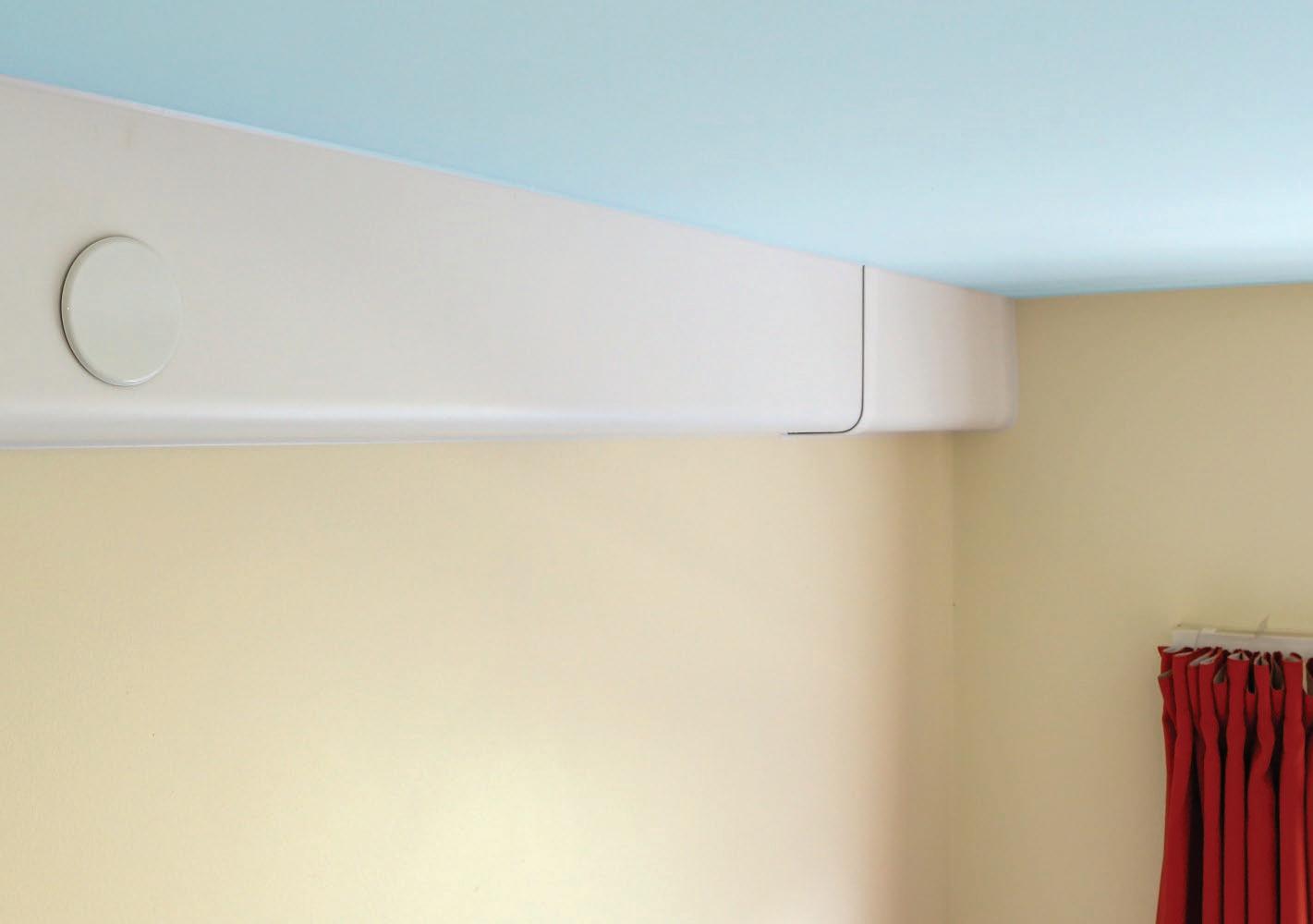
Time and cost benefits
Experience of working with contractors across the UK on countless social housing projects where pipework needs to be concealed, has shown that Versa pipe and fire sprinkler boxing can typically be fitted in less than half the time of site made alternatives.
In addition, as it is pre-finished with durable white melamine, there’s no painting required on site, which further helps to save time and cost. This time saving provides several advantages. For contractors, local authorities and housing associations, not only can fire safety upgrades be completed within a shorter timescale, but they also help minimise disruption for tenants while the work is being carried out.
Potentially the most important benefit is that costs can be reduced, not by ‘cutting corners’, but by cutting the time taken on the project without compromising the quality or integrity of the installation.
The focus, rightfully, is on improving fire safety in high-rise residential buildings and Versa can contribute to that process, in terms of effectiveness, ease of installation and economics, by effectively concealing sprinkler pipework and ‘covering’ the significant investment in sprinkler systems.
Encasement - Enquiry

NO WELDING FOR LUXURY APARTMENTS
St Edwards has
Ensuring safety, performance, and quality, developer Berkeley St Edwards has specified the Viega Profipress system for one of their latest residential projects. The high-quality pipework installation for heating and drinking water sits at the heart of the prestigious West End Gate apartments in central London.
The priority was a system for delivering both potable and heating water without any risk to hygiene. The piping system must guarantee this quality and above all, it had to be faultless, future proof and guaranteed to last.
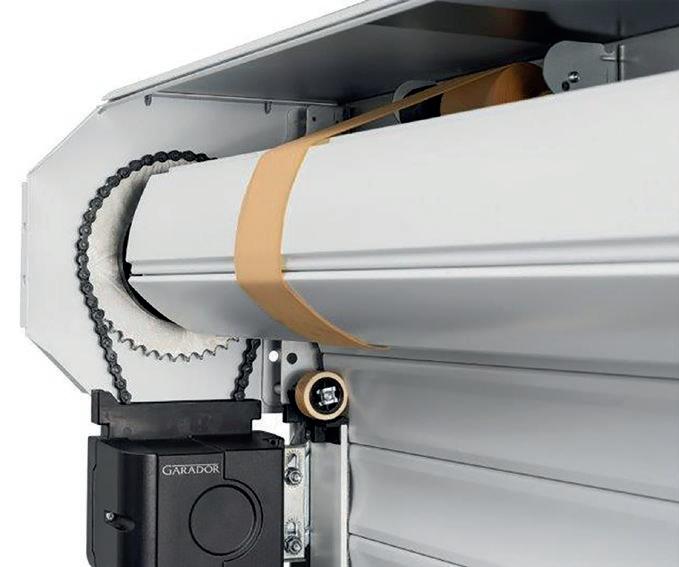
Kevin Guiry, Senior MEP Manager for Berkeley St Edwards, said this on the choice: “Quality
Viega Profipress
was our top priority, both in terms of the water system and the products used. With all the heating and chilled distribution pipework running in a closed system, we needed a solution to guarantee clean and safe water without contamination. The copper Profipress system delivers this alongside real on-site benefits.” Kevin continued.
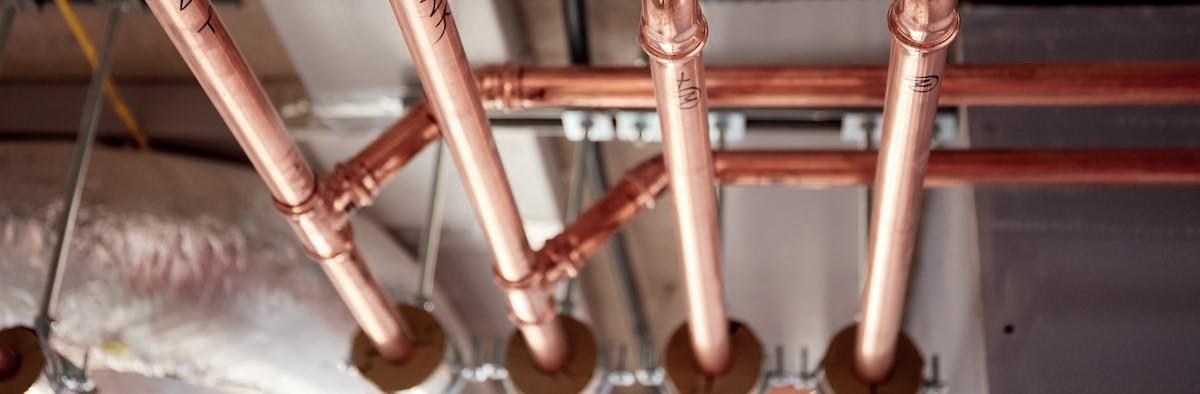
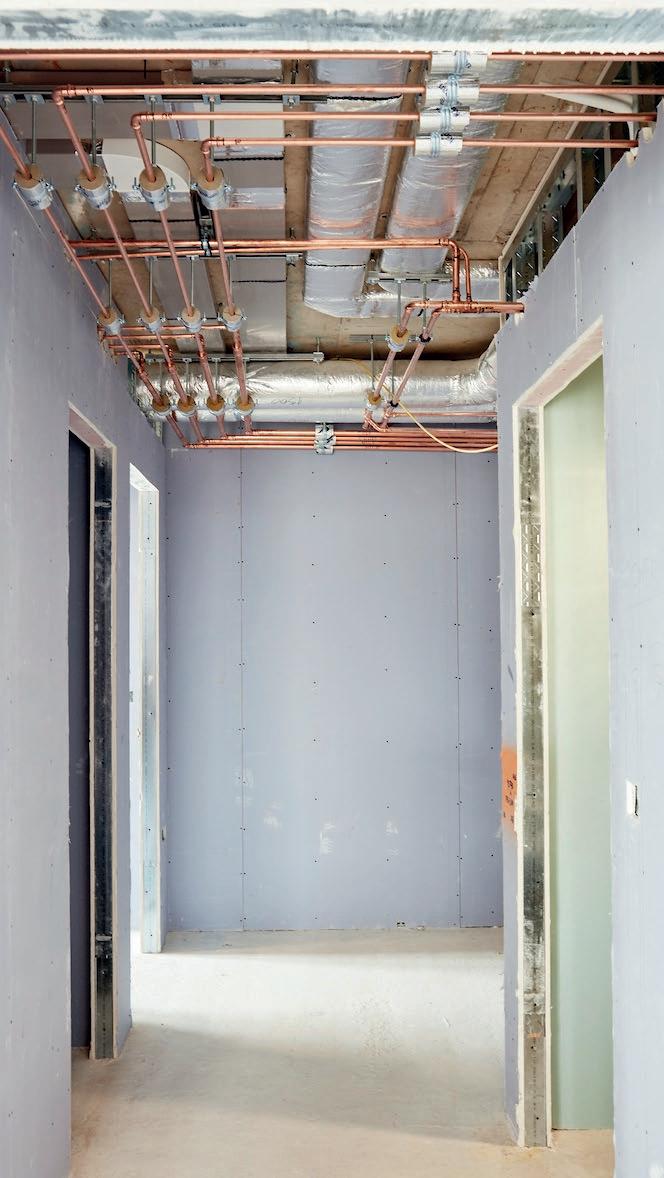
“I’m a big believer in quality and with this system we’re getting the best quality fittings for this premium development. We didn’t want to risk any further maintenance or damage and the Viega Profipress system achieves this.” Kevin summarised.
Viega - Enquiry 12
A prestige housing project in New Romney, Kent, has seen a leading developer make extensive use of the prefabricated wall niches which have recently been added to the range of bathroom and wetroom specialist, Marmox: saving time and cost while facilitating the completion of luxurious interiors for the properties’ new occupants.

Mulberry Place is a beautifully landscaped development of 150 new properties by Pentland Homes, creating a mix of two, three and four bedroom houses, located just a mile and a half from the sea and close to the Romney Marshes. As a highly experienced contractor and developer, Pentland is always
seeking to adopt new technologies which can help deliver schemes on time and to budget and is installing more than 250 of the Marmox units in two different size options.
This figure includes 238 of the manufacturer’s 305 x 305mm option and a further 29, 305mm wide by 711mm tall niches: with both being built into the internal timber studwork of the mainly masonry constructed homes.
The Site Manager for Pentland Homes, Glynn Pogue, commented: “The Marmox niches are being well received by the purchasers who like the appearance and the usability of the recesses for storage. They have definitely been a success from that point of view.”
Along with a Corner Shelf, the niches are new additions to the Marmox range, which can fit any bathroom or even inside a shower cubicle. Each niche is formed from 112.5 mm thick XPS and can be installed into 100 mm deep wall cavities or between standard Multiboards to maintain the integrity of the insulation. Both products are fully waterproof, ready to tile and create useful storage for toiletries. Marmox additionally manufactures solutions for pipe boxing, curved walls and bath panel kits as well as other products.
Garador
Garador has developed an innovative new roller door concept that will lift its range of GaraRoll roller doors into an exciting new era. Roller doors are one of the most popular designs for modern garages, but over time a build-up of dust and dirt on the surface of the door can cause abrasion on the paintwork which can lead to scratches and unsightly markings. To combat this problem, Garador has developed DuraBelt. This is new technology based around microcellular polyurethane elastomer which which provides a protective layer between each lath as it rolls up, reducing scratching and prolonging the life of the door curtain.
Garador - Enquiry 14
online: www.enquire2.com or post our free Reader Enquiry Card
launches new and improved Gararoll, with durabelt technology
Ensuring safety, performance, and quality, developer Berkeley
specified the
system for one of their latest residential projects.Pentland homes purchasers
praise appearance of Marmox niches

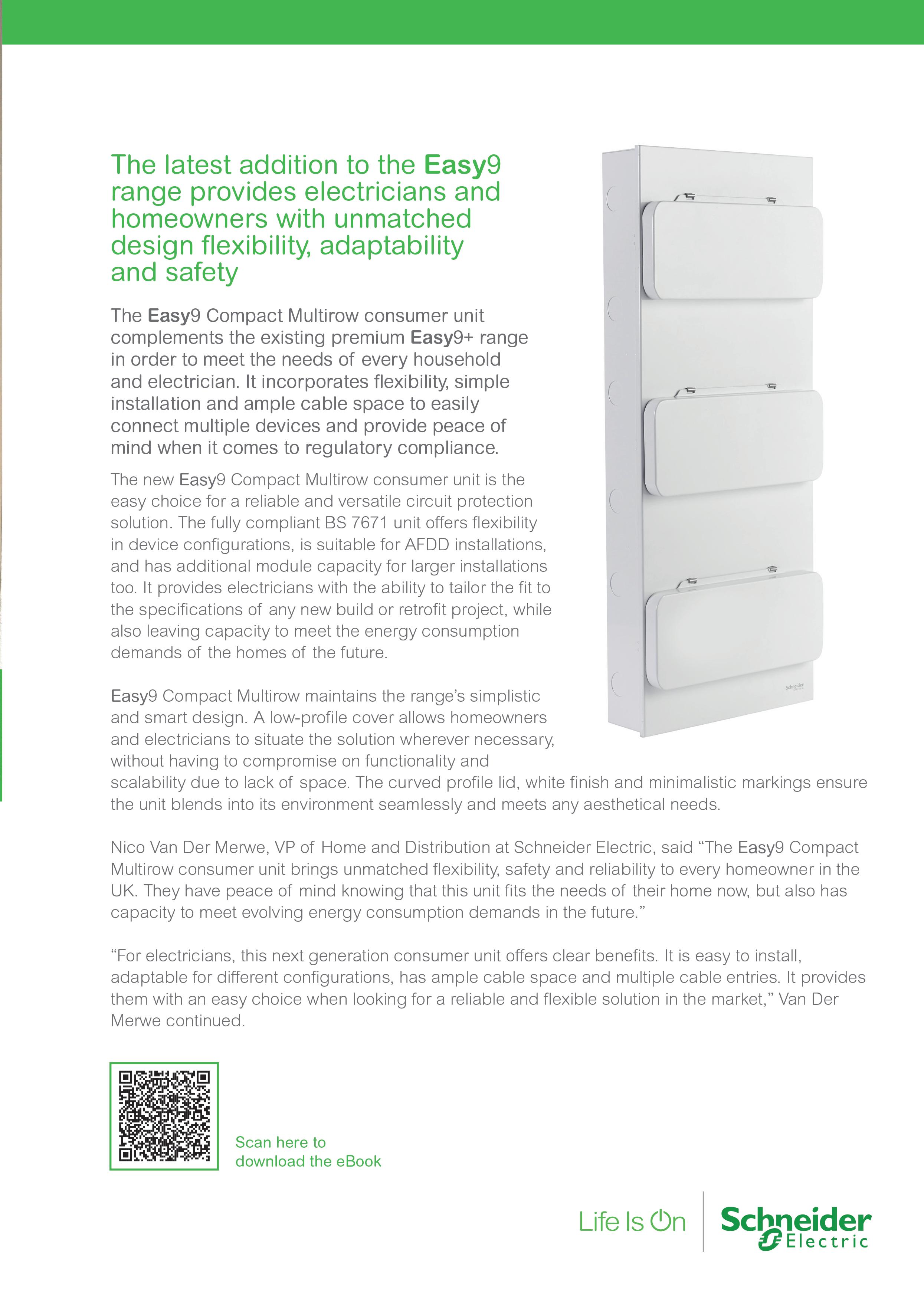
NEW SCHÖCK SCONNEX FOR MAJOR PASSIVHAUS SOCIAL HOUSING SCHEME
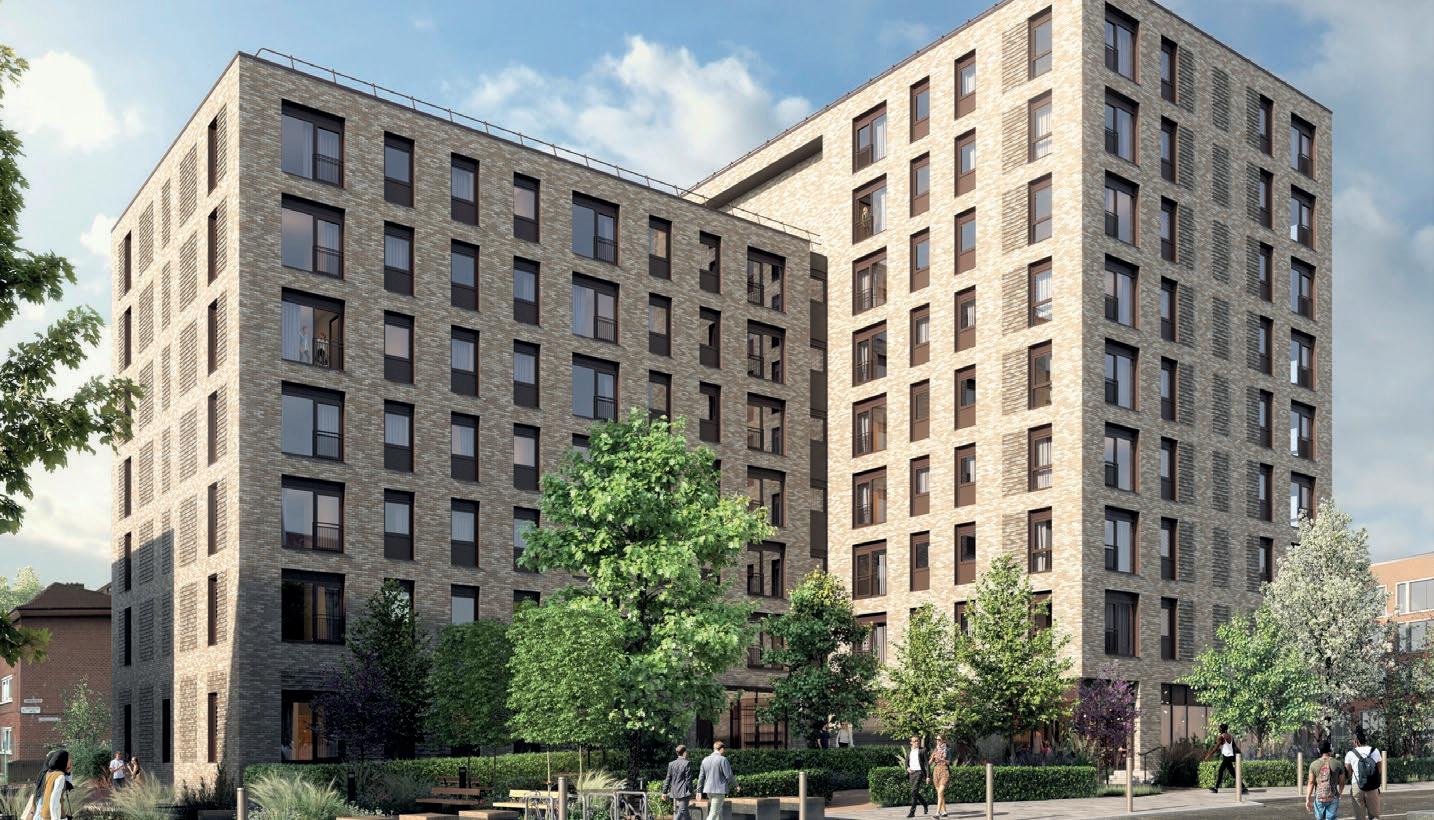
Minimising thermal bridging at the wall connection to the floor, or floor slab, is an ongoing problem with reinforced concrete construction. However, a dedicated new solution – the Sconnex type W – has been developed by Schöck and is being installed in what is currently the largest Passivhaus accredited social housing scheme in the North of England.
Eric Wright and Salix have key roles
Greenhaus forms part of ECF’s wider £1bn, 50-acre, Salford Central masterplan transforming former surface car parks and derelict buildings into a vibrant and diverse community. John Hartnett, managing director at Eric Wright Construction, comments: “We are proud to be supporting not only a green future for Salford, with the delivery of high efficiency buildings built to Passivhaus standards, but also supporting Eric Wright’s own journey to net zero carbon. These new homes will deliver valuable social housing in partnership with Salix Homes.“
The ‘Greenhaus’ nine-storey development of 96 affordable homes in Chapel Street, Salford, is part of the 50-acre Salford Central regeneration and the result of a collaboration between The English Cities Fund (ECF) – a national development partnership between Muse, Legal & General and Homes England –contractor Eric Wright Construction and Salix Homes.
The scheme focuses on sustainability and is designed to reduce the energy consumption of the building. With Passivhaus, energy savings can be as much as 90% compared with the average building stock and more than 75% compared to average new builds.
Thermal losses are greatly reduced The unique Schöck Sconnex type W makes a major contribution to achieving this initiative and is a product based on derivative technology from Schöck. Sconnex utilises the company’s longstanding expertise in structural thermal breaks for balconies and other cantilever constructions and applies it to reinforced concrete wall and support applications.
By installing the Sconnex product in Chapel Street, thermal losses are greatly reduced and the surface temperature in the rooms increases to considerably more than the critical dew point temperature. Heating costs are lower, a pleasant room climate is created and the linear thermal
transmittance (Psi) of the connected reinforced concrete wall is reduced by as much as 80%.
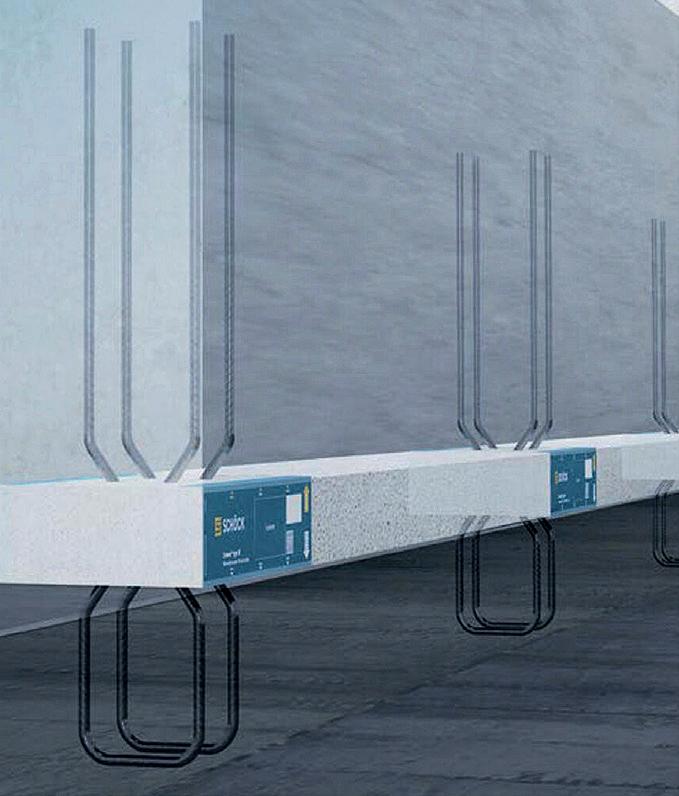
This outstanding insulation performance is combined with an excellent load-bearing capacity. It transmits very high pressure, tensile and shear forces, in the longitudinal and transverse direction, made possible by the use of a pressure buffer consisting of ultra-high performance fibre reinforced concrete. Compressive strength levels in excess of 175 N/mm2 are achieved, with extremely good flexural strength. A further important benefit is the significant cost reduction involved when compared to installing insulation beneath the floor slab.
Sue Sutton, chief executive at Salix Homes, also adds: “Chapel Street enjoys an incredibly rich history and the innovative Greenhaus development marks the next exciting chapter for this historic part of Salford.
“At a time when affordable housing is in such short supply, we’re very proud to work alongside our partners to deliver these high quality, sustainable, eco-homes of the future, and we look forward to seeing this ambitious development take shape on the Salford skyline.”
For further information on the new Sconnex type W product contact Schöck on 01865 290 890; or download the brochure at www.schöeck.com
- Enquiry 16
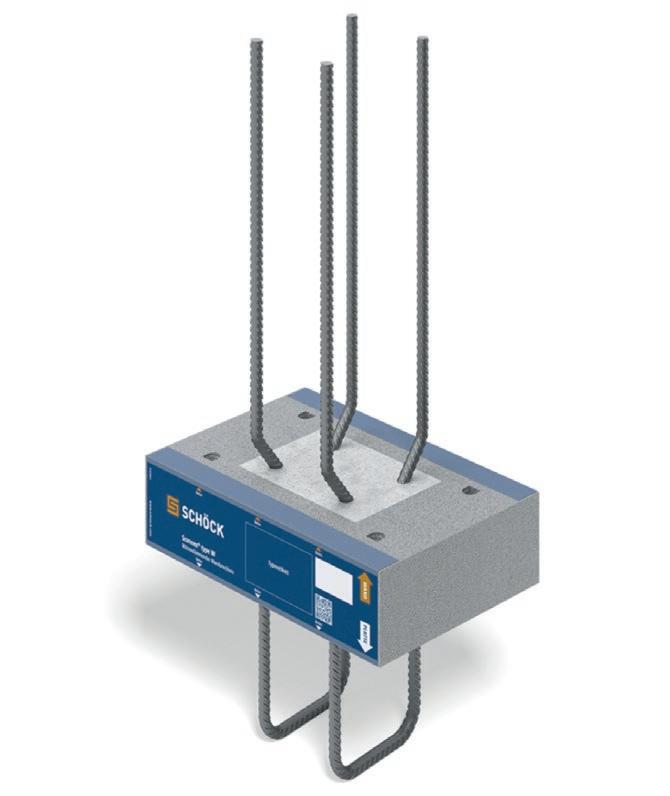
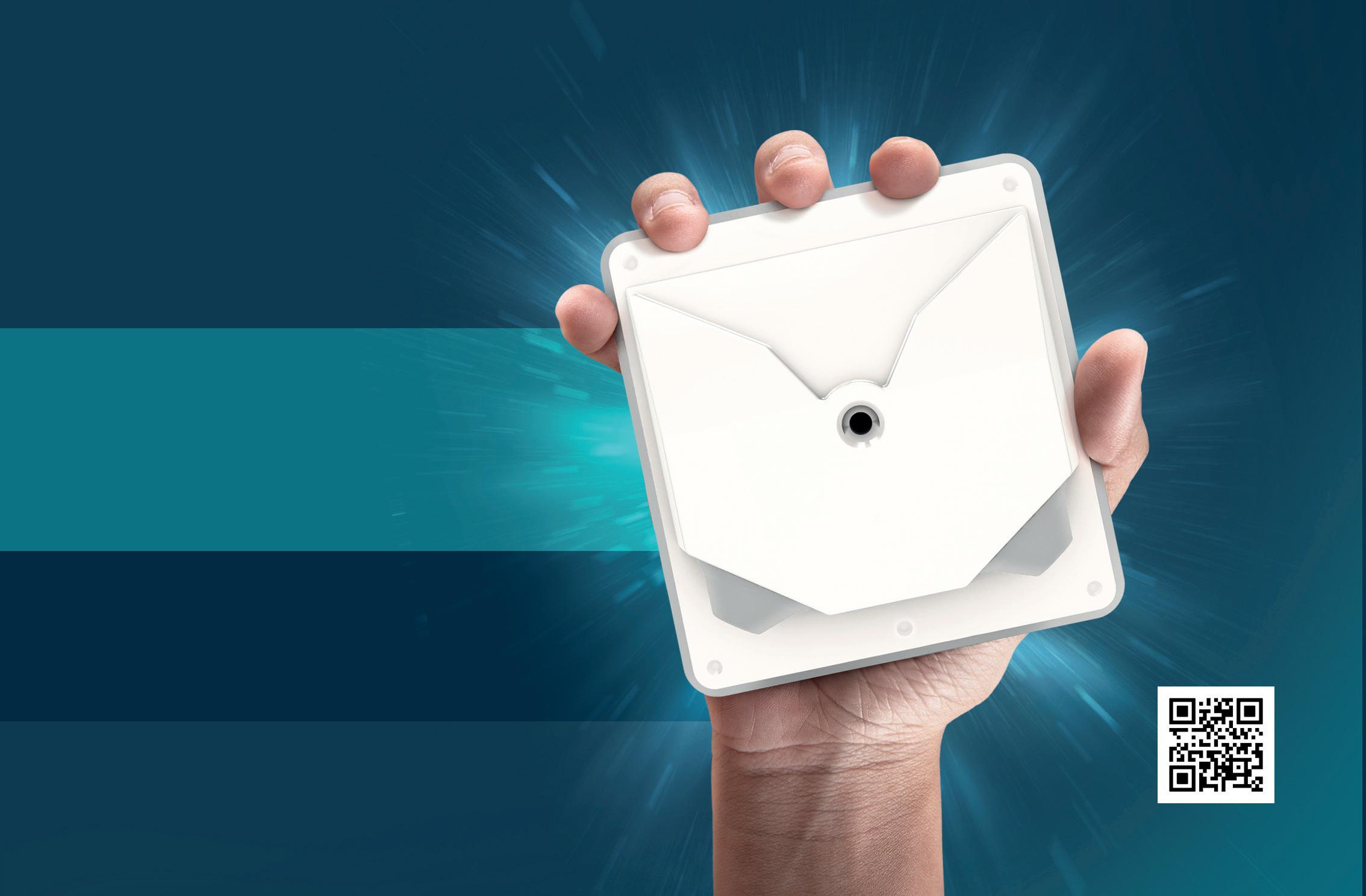
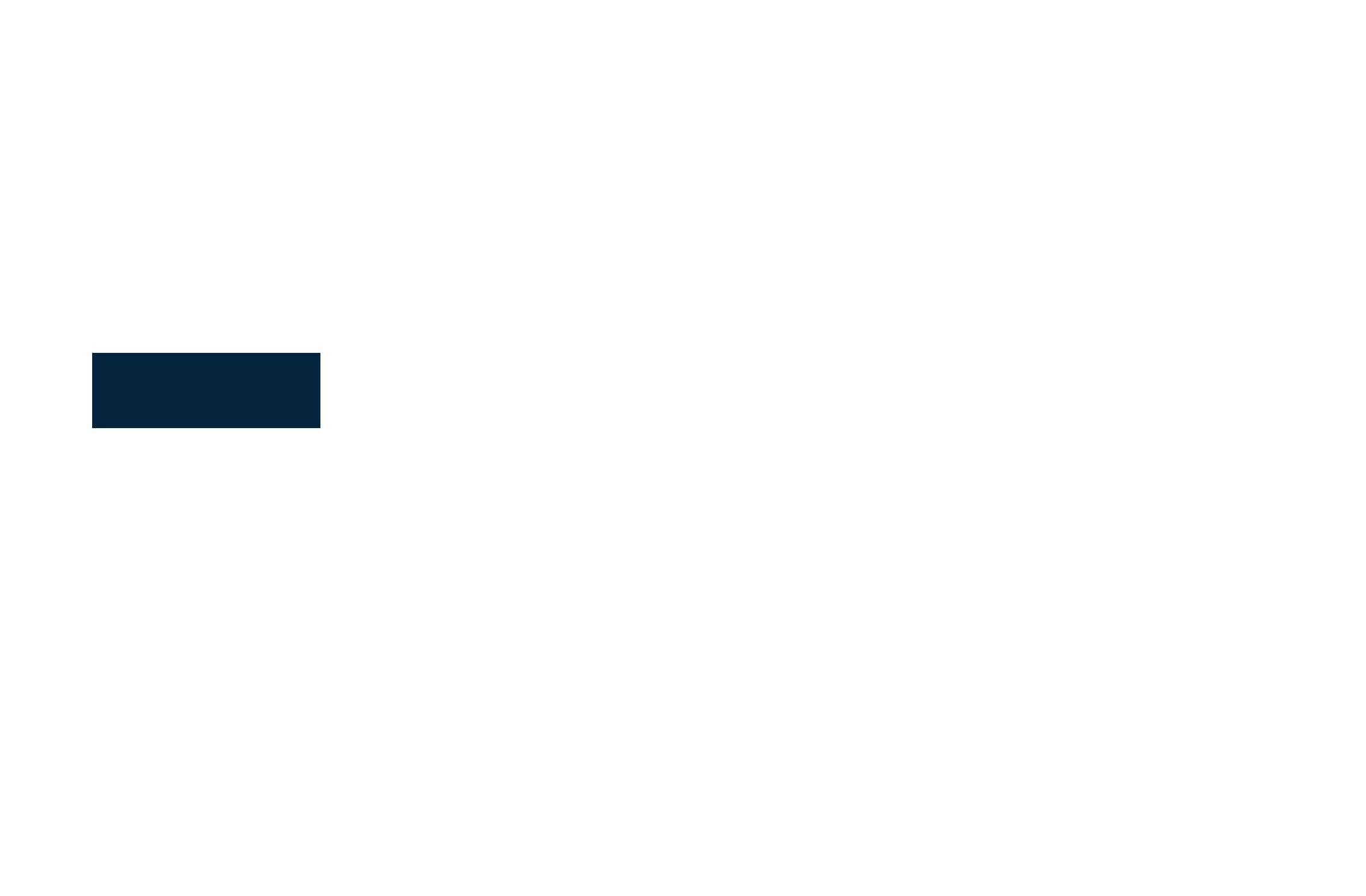
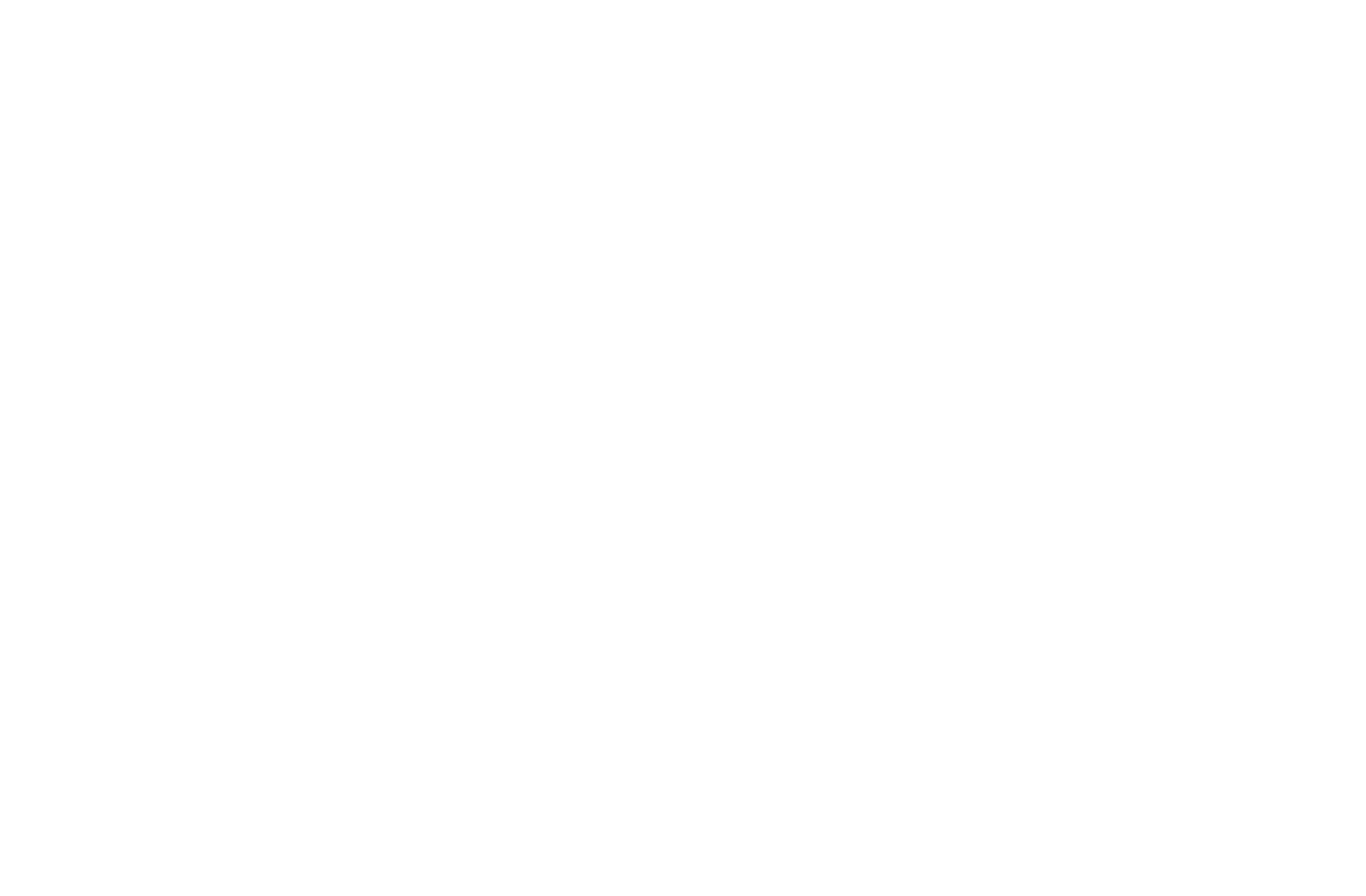
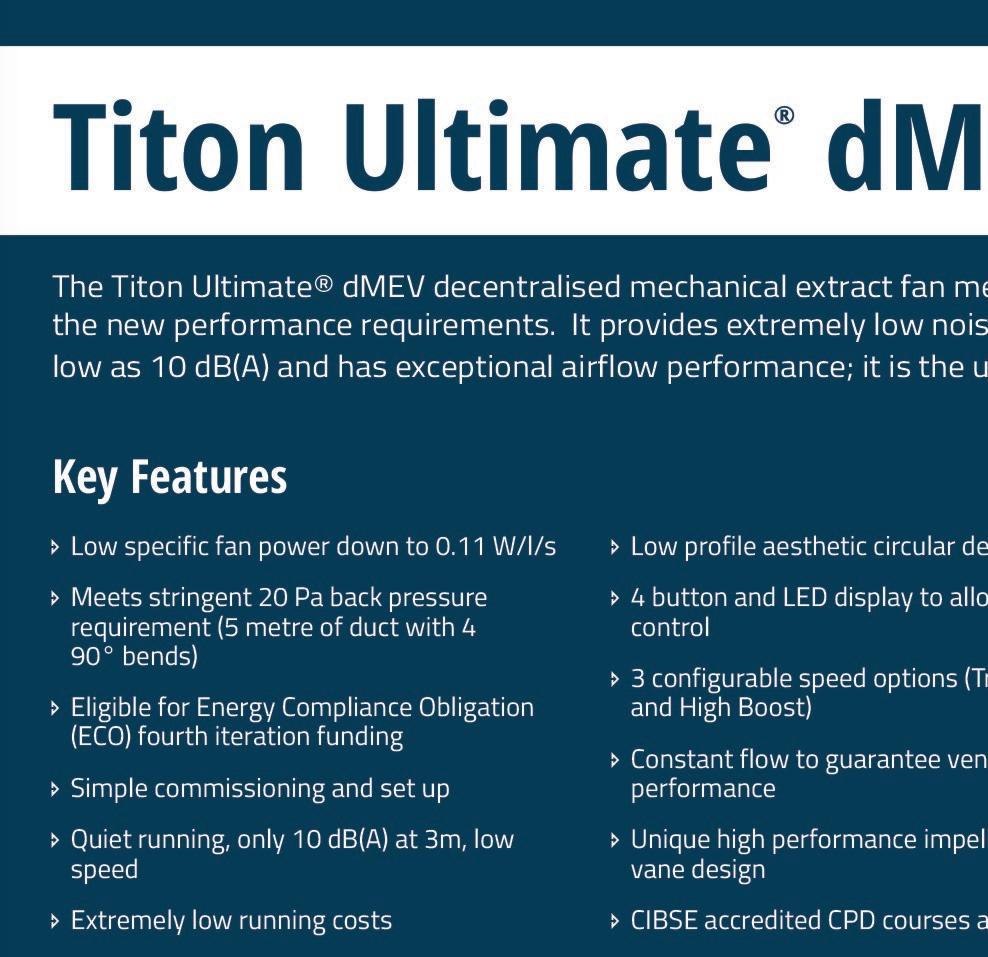

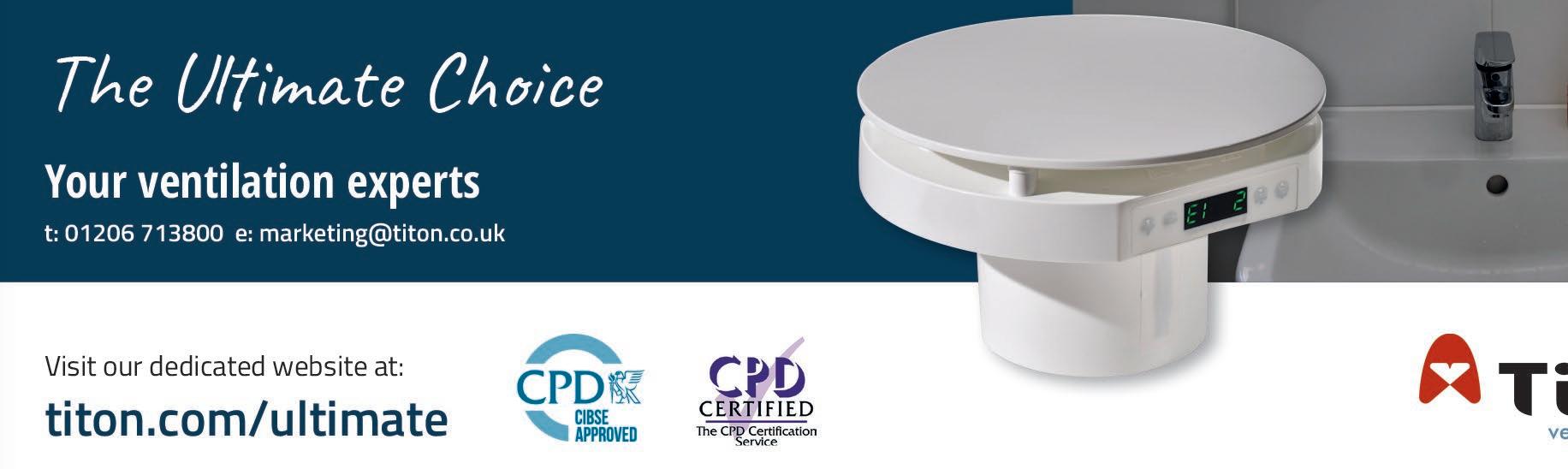
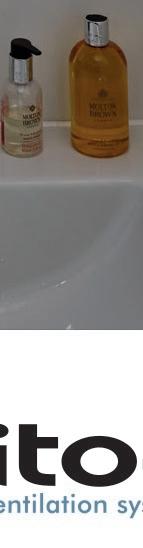
TITON REACHES A GOLDEN MILESTONE
Incorporated in 1972 following the creation of the first Titon product, a window casement stay, John Anderson created Titon Hardware from his garden shed in Feering, Essex.
Fifty 50 years later, Titon Hardware has gone from strength to strength and is now a market leader of window and door hardware and ventilation products. Titon manufactures and supplies
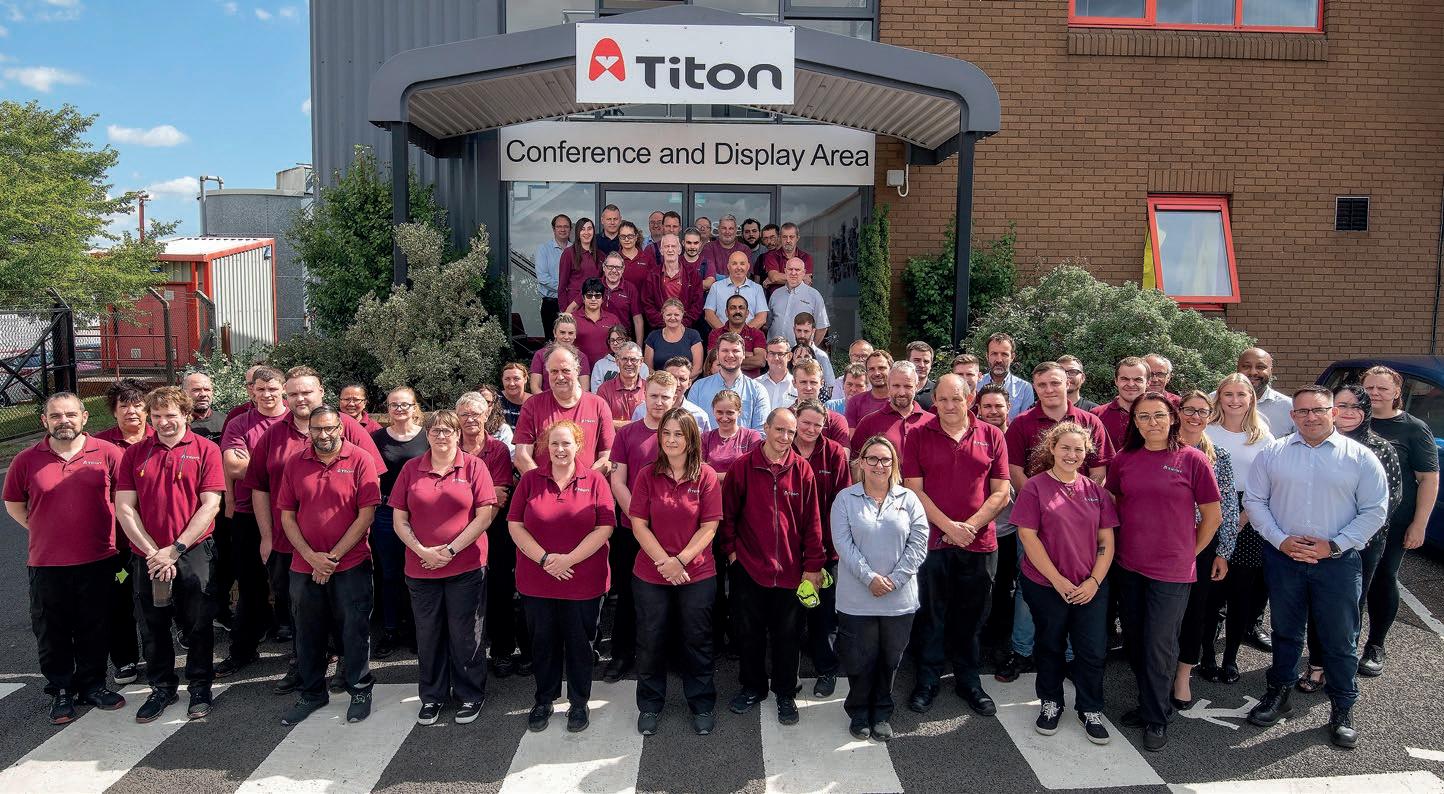
ventilation and window and door products – ranging from its signature Trimvent background ventilator (first made and patented by John Anderson in 1973) to window handles, locking
systems and hinge systems as well as powered ventilation products including whole house systems and extract fans. Tyson Anderson, the firm’s Sales & Marketing Director and the son of John Anderson, said the firm’s original ethos was still evident.
“That initial ‘family feel’ permeated to every new employee and is reflected in the fact that anyone who left the business always reported back that they missed that Titon ethos and friendly approach,” he explained.
“I have seen Titon progress from its initial inception all those years ago and I’m very proud of what has been achieved from its humble beginnings. We have always been grateful to our staff, who have moulded and developed the company in to the successful organisation it is today.”
Titon Hardware - Enquiry 19
ISO Chemie’s thermal insulating and load bearing bracket support system and sealing tapes have been specified for a new energy improvement initiative being carried out by a northern housing association.
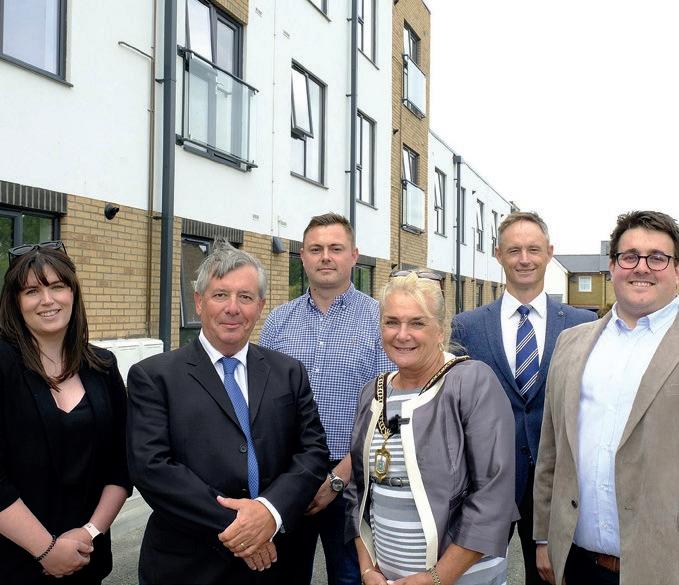
The move sees WINFRAMER units being retrofitted at three 1940s–1960s built houses in Northallerton and Stokesley as part of Yorkshire-based Broadacre Housing Association’s (BHA) pilot project. This will eventually bring hundreds of poorly insulated properties up to zero carbon ready standards and provide improved housing for BHA customers along with long-term cost savings. Passivhaus certified and fire rated to up to
30 minutes, WINFRAMER is a prefabricated installation frame, manufactured to accommodate cavities up to 250mm that allows windows to be supported independently from the face of the wall regardless of any external cladding being in place.
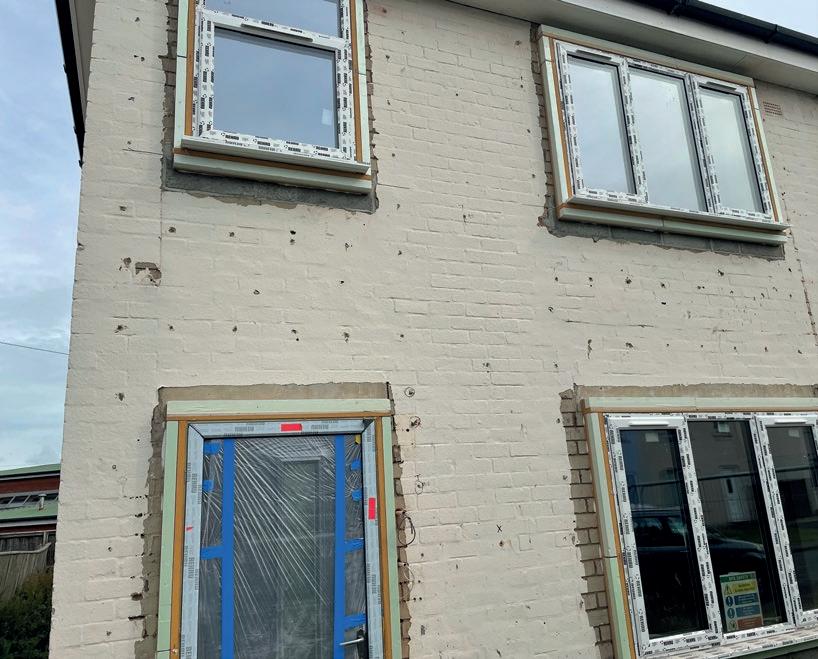
Quick and easy to install, the product’s application at The Crescent, Northallerton has been integrated alongside ISO Chemie’s ISO BLOCO One sealing tapes to achieve Passivhaus certified window perimeter sealing performance. The flexible humidity variable sealing foil ISO-CONNECT VARIO SD and ISO-TOP FLEX tape have also been chosen to deliver greater internal air tightness around wall, floor and ceiling joints.
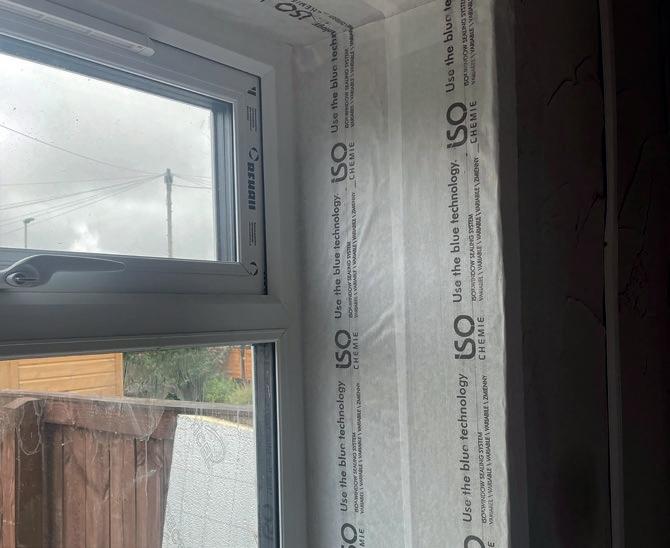
ISO Chemie - Enquiry 20
Specialist offsite contractor M-AR has completed the first of three new housing schemes in partnership with Bromley Council, all designed to provide ‘Bromley Homes for Bromley People’. By utilising offsite construction two crucial operations of the build were caried out concurrently, with the groundworks/ foundations installed as the modules were manufactured offsite – reducing disruption to the local community during construction. The housing development has recently been shortlisted for several industry awards, including Social Housing Project of the Year in the Offsite Awards.
M-AR - Enquiry 21
M-AR delivers new affordable housing
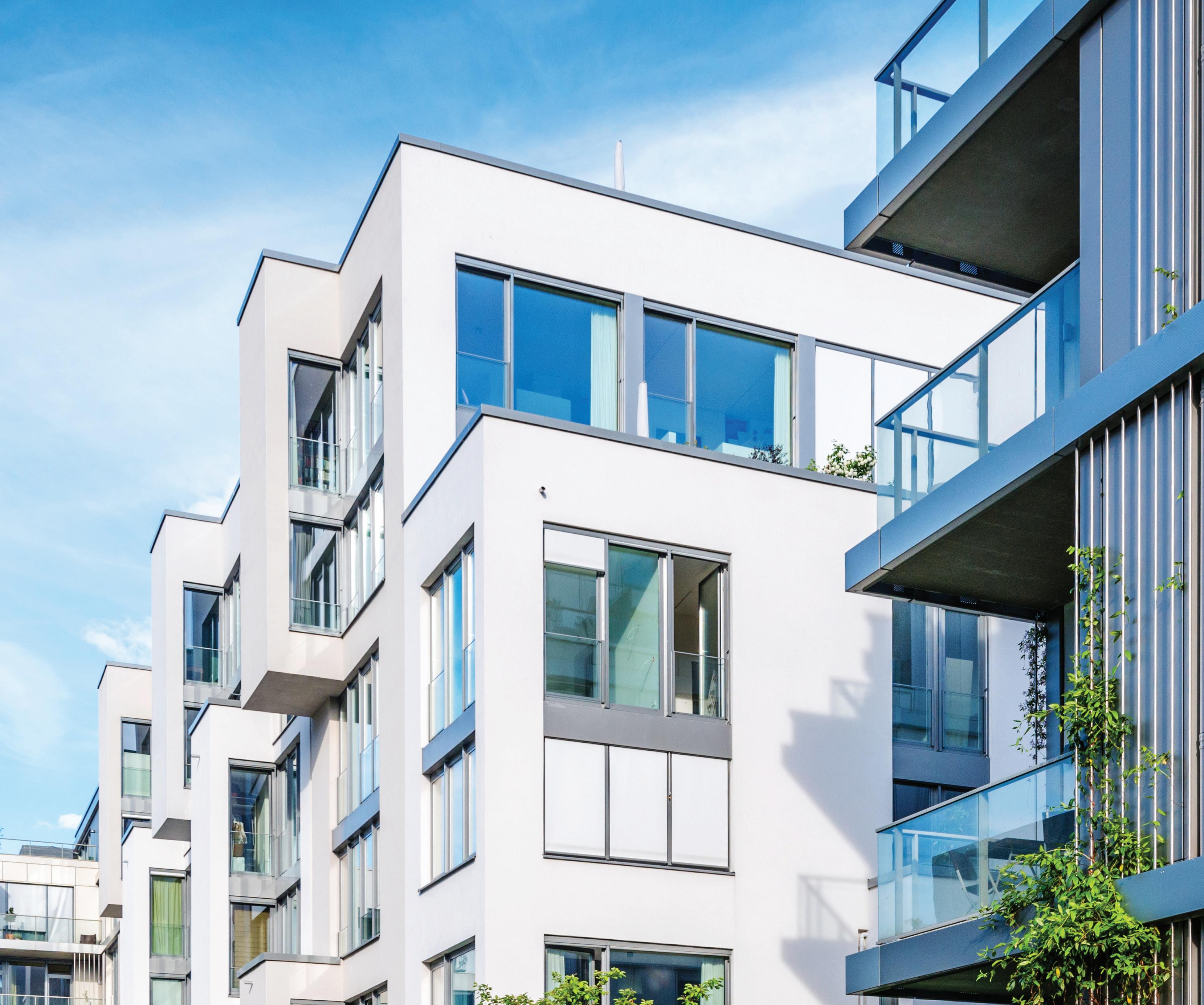
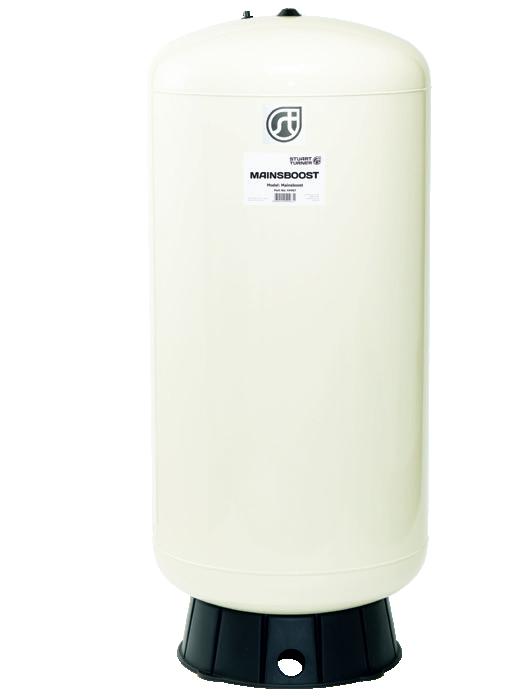
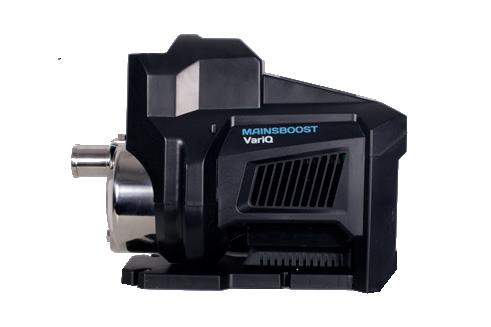
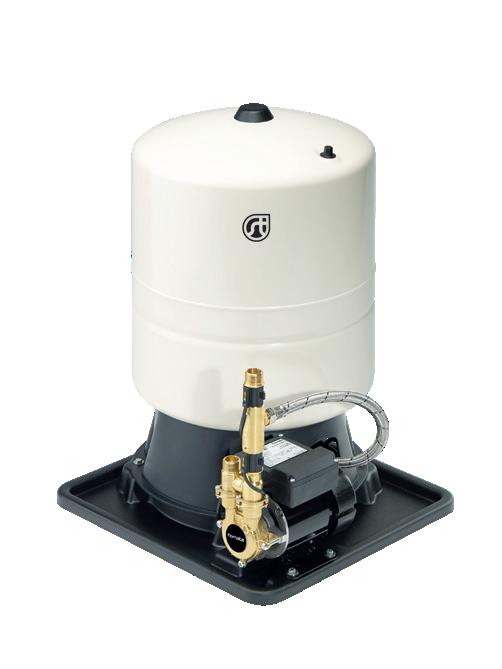
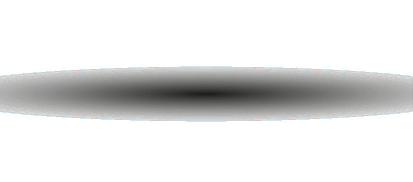
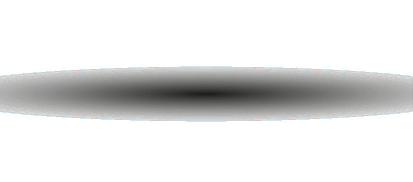
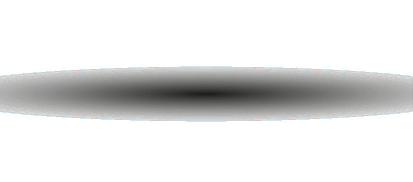
IT’S OFFICIAL –EOS GAIN BOPAS ACCREDITATION
Following on from the announcement that EOS Framing has reached the finals of the Construction News Specialists Awards and has an unprecedented seven entries shortlisted in the Offsite Awards, the leading steel framing innovators have reported that the company has been awarded Buildoffsite Property Assurance Scheme (BOPAS) Accreditation.
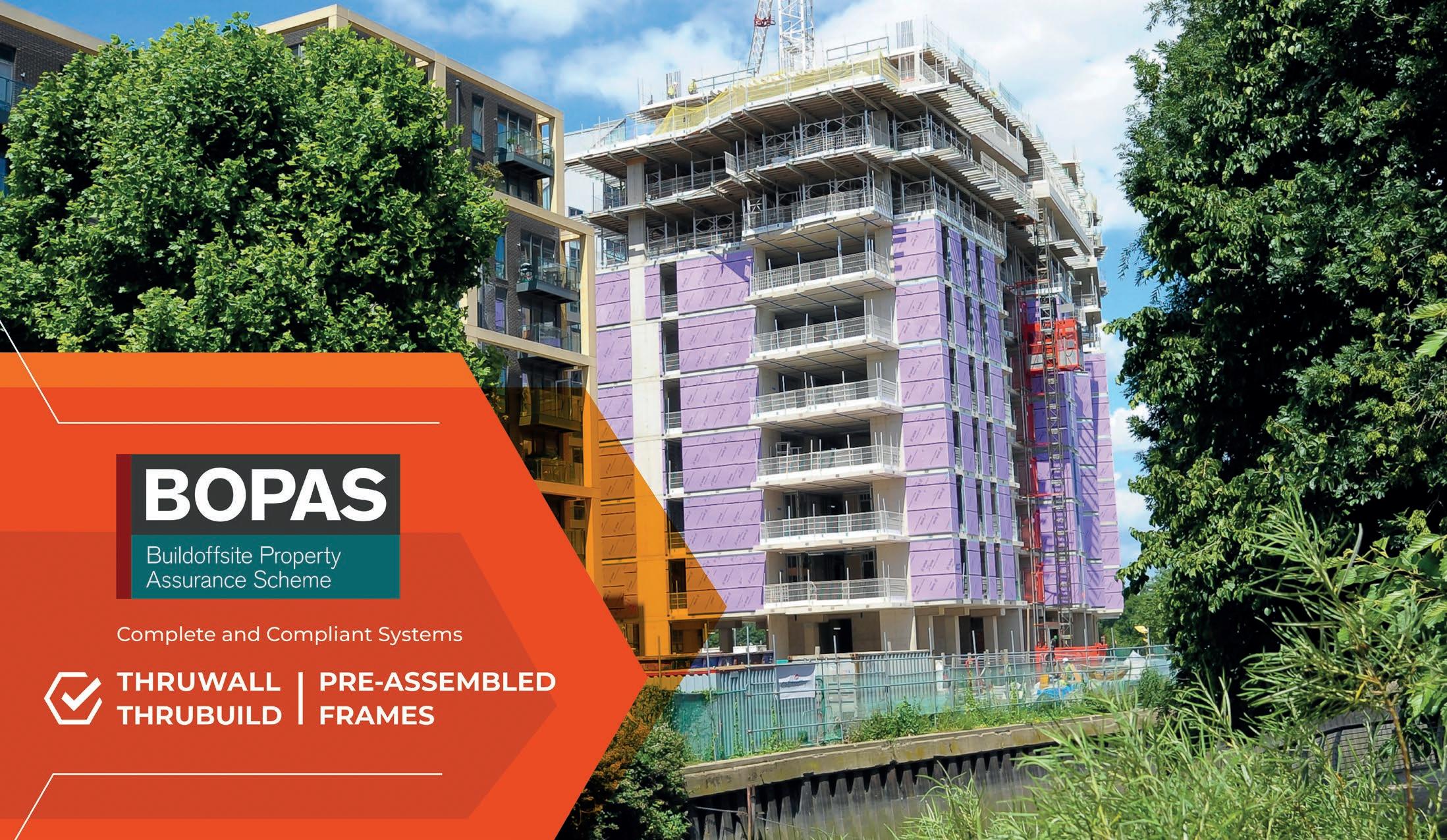
BOPAS Accreditation is recognised by principal mortgage lenders as providing the necessary assurance underpinned by a warranty provision that the property will be readily mortgageable for at least 60 years.
Why is this important?
For funders and lenders BOPAS provides assurances that EOS Framing’s light steel systems are fit for purpose and eliminates the uncertainty surrounding the construction for valuation purposes.
It also removes the risk for developers of mortgages being declined on construction grounds and improves business opportunities for EOS as a manufacturer of offsite systems.
BOPAS demonstrates to funders, lenders, valuers and purchasers that homes built from non-traditional methods will be durable, delivered to high quality
standards and stand the test of time. Managing Director of EOS, Steve Thompson stressed the importance of certification and accreditation: “We take our responsibilities as a manufacturer extremely seriously. Our light steel frame systems are rigorously tested, manufactured under ISO 9001:2015 quality management standards and are now backed by BOPAS Accreditation.
“Our aim is to deliver confidence and certainty in the construction process and empower specifiers to be technical forerunners in the offsite sector. This achievement has only been made possible by our dedicated team who share our vision and values. My thanks and appreciation goes out to all those involved.”
Against a backdrop of government targets to build 300,000 homes a year combined with increasing construction costs and poor quality conventionally constructed houses as well as a huge shortfall in
traditional skills – the demand for innovative offsite construction methods has never been greater.
Complete and Compliant Systems
Specialising in advanced light steel framing technologies, EOS is taking the construction industry forward by pioneering a new certified systems approach, helping specifiers to comply and compete in challenging markets.
EOS are committed to technical competence and as part of Etex, have some of the best building performance experts in the UK on their team. They work closely with certification bodies to jointly develop and design advanced technical solutions.
To discover how EOS systems are delivering certified, predictable and warrantied performance, go to: www.eosframing.co.uk EOS - Enquiry 23

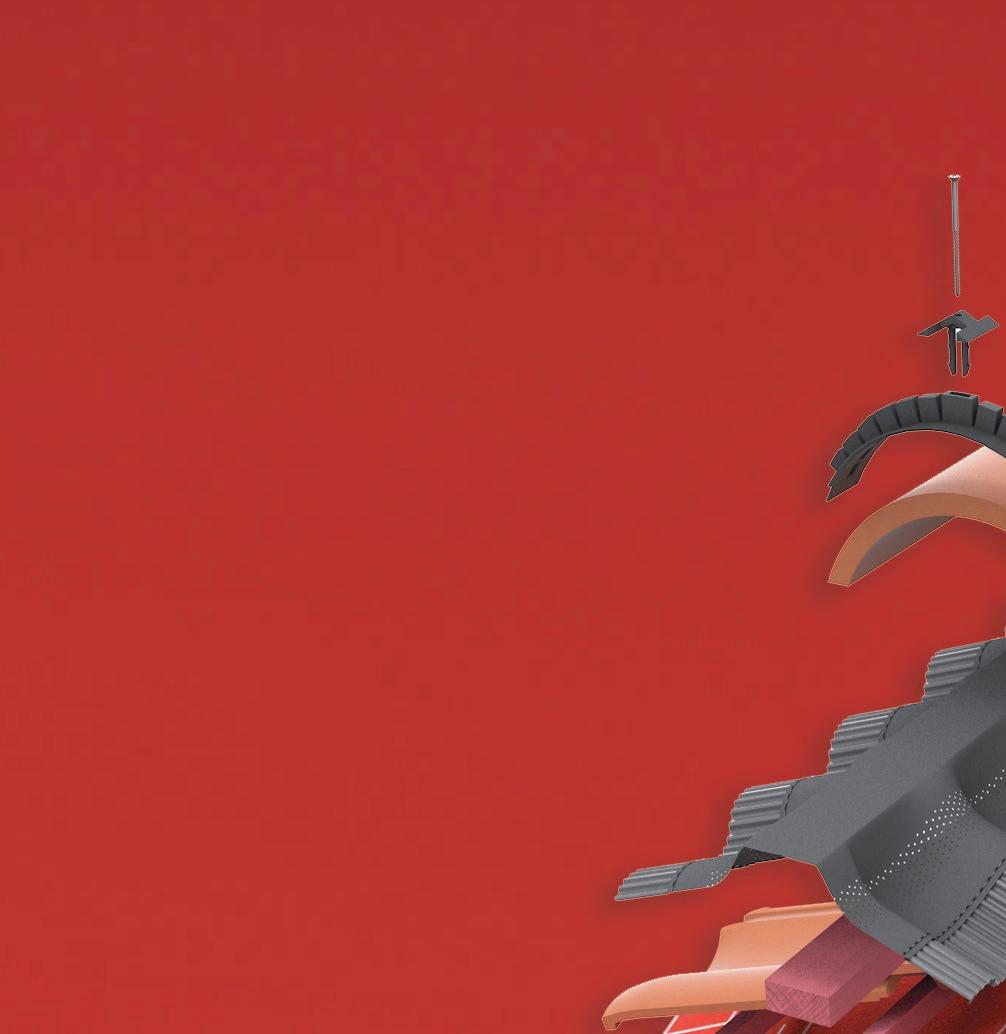
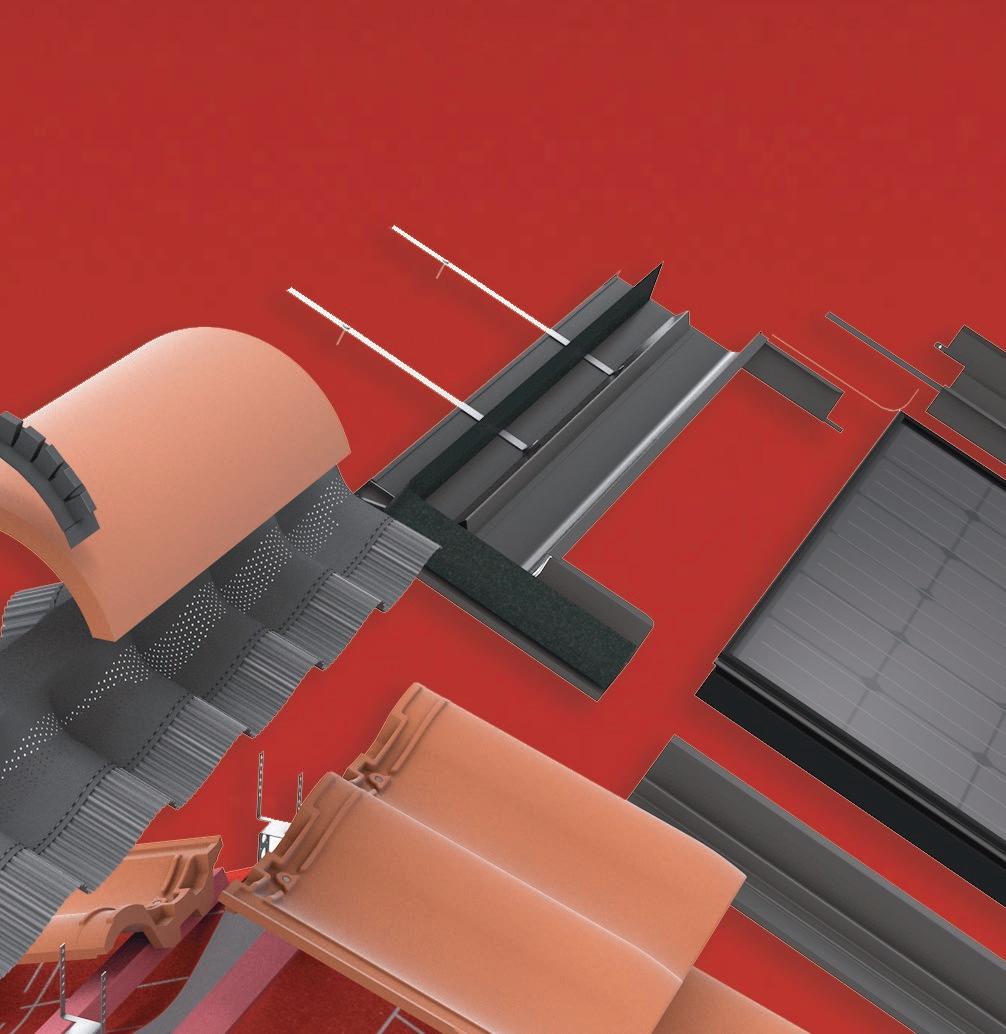
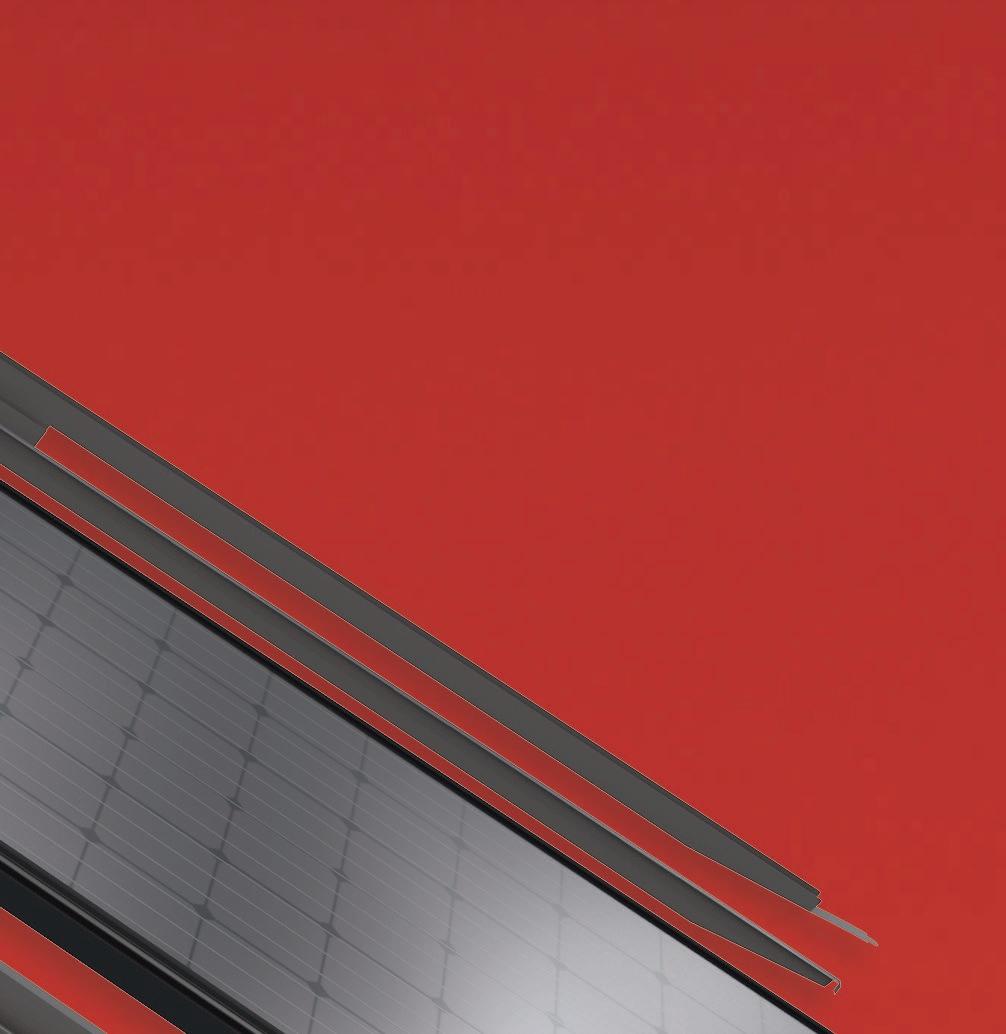


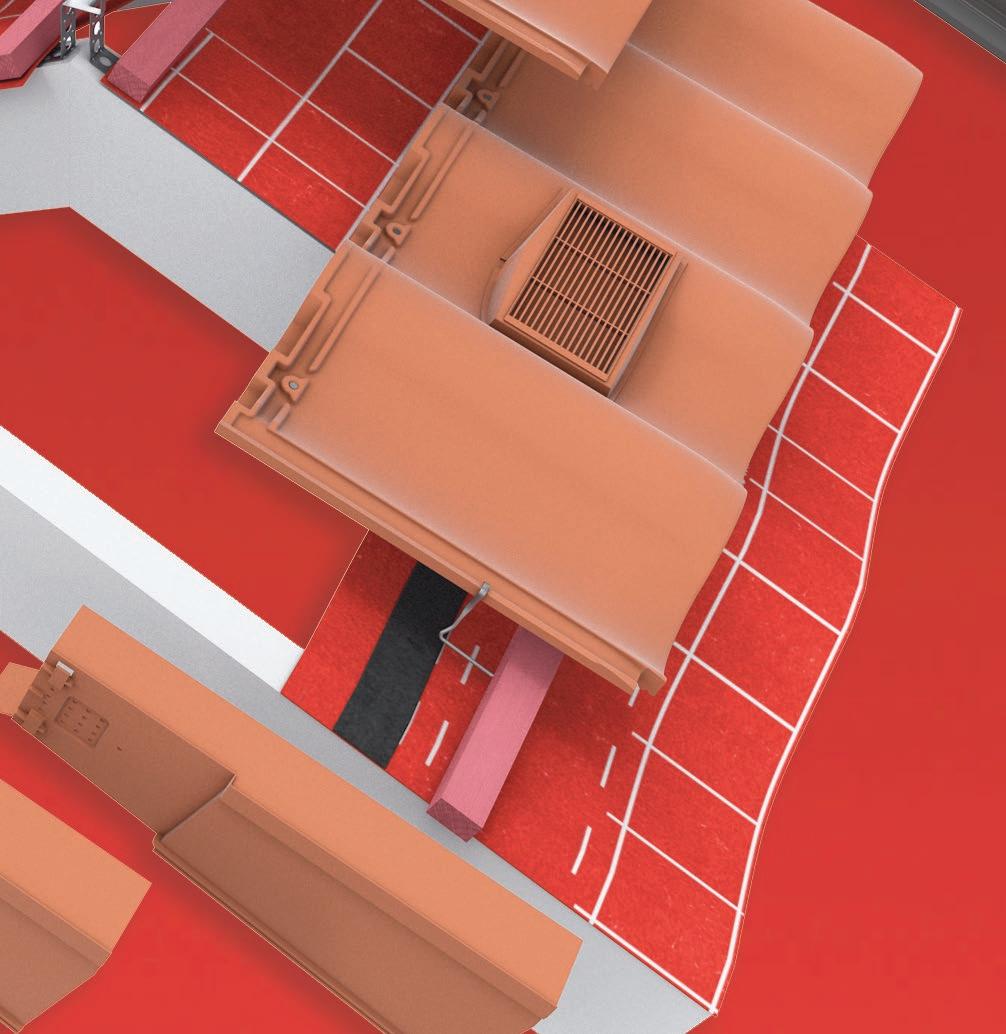
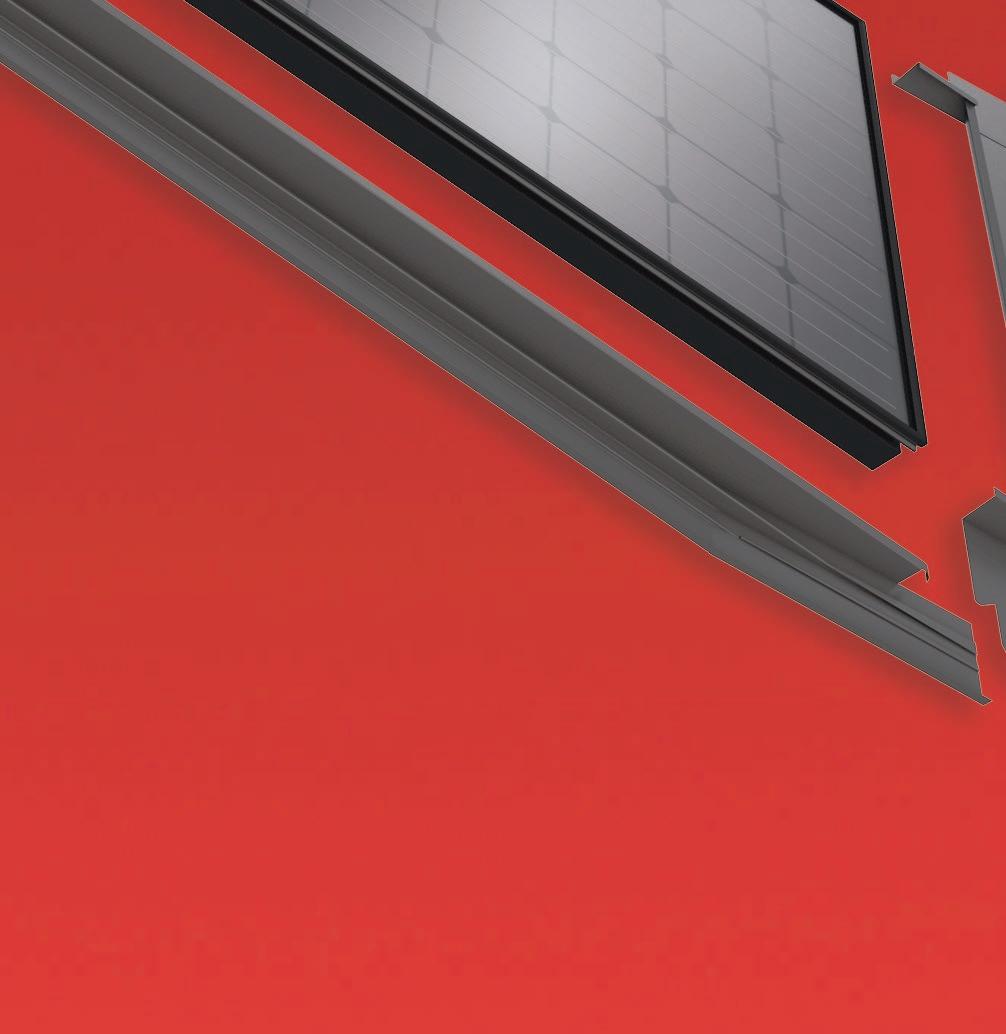
MEETING BUILDING REGULATIONS WITH FASSA BORTOLO’S QUALITY RENDER
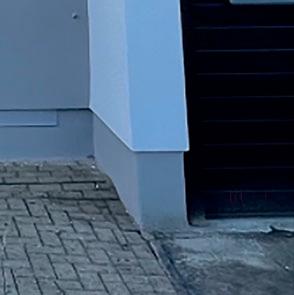
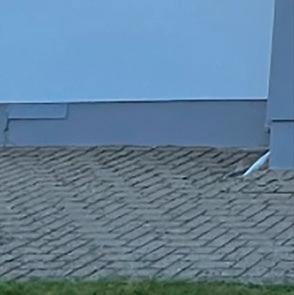
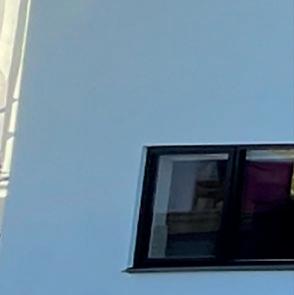

The team at Fassa Bortolo were recently contacted by award-winning building, surveying, architectural and property management specialist, 3Sixty Real Estate, to provide a solution that would protect and weatherproof a high-end, luxury home in Bristol. The property was originally designed by renowned Bristol-based architect, Hartland Thomas in 1935 and was in need of modernisation.
Following the specification process, cycle 3C from the Fassarend system was selected to ensure a quality finish.

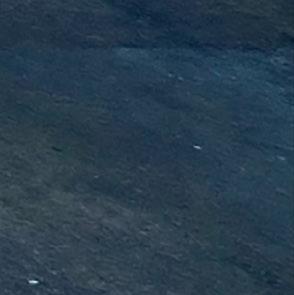
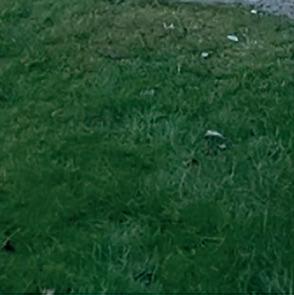

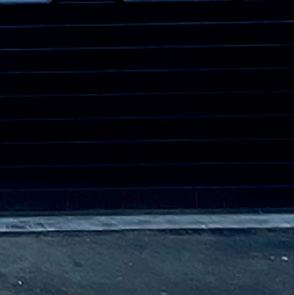
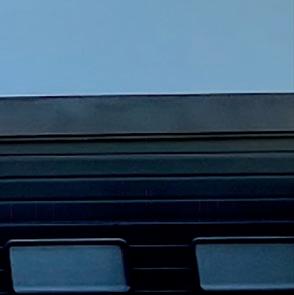

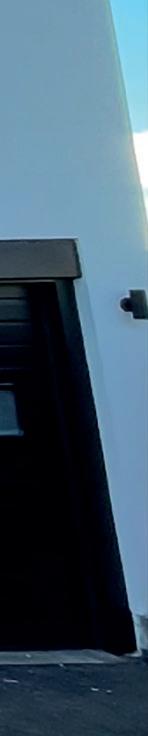
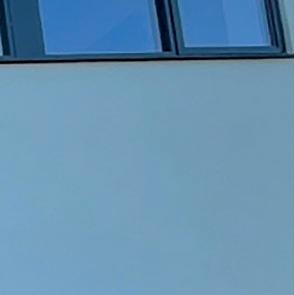
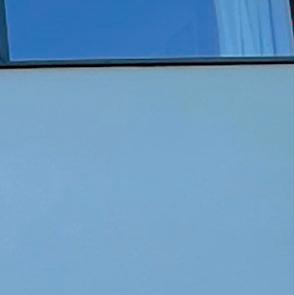
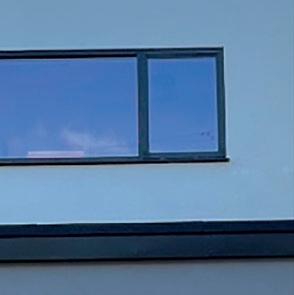
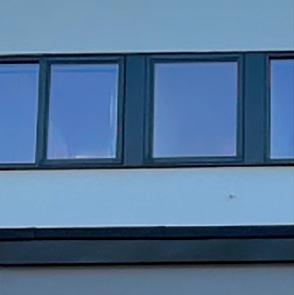
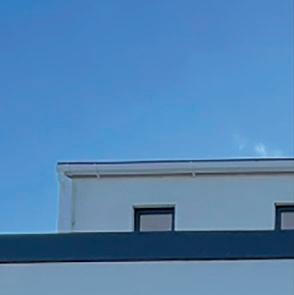
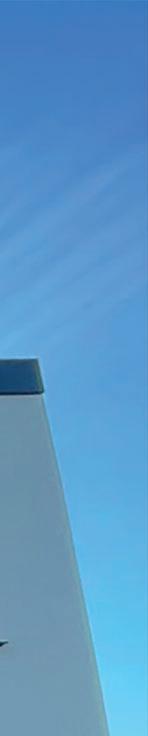
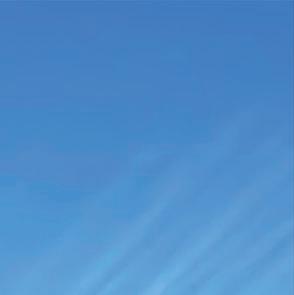
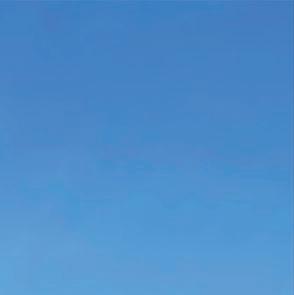
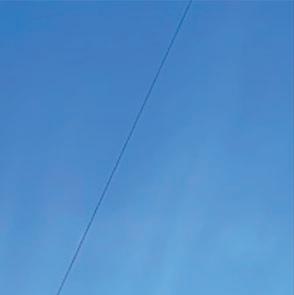


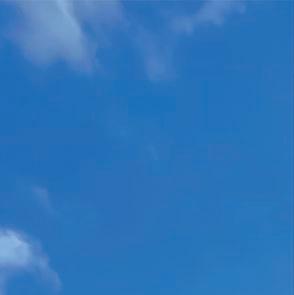
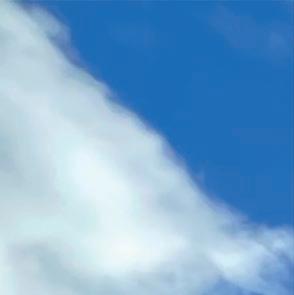
This cycle includes a cement undercoat (SP22), followed by a lime and cement base coat (KC1), Fassanet reinforcing mesh and a primer (FX26) with a texture coat (RX561).
The nature of the raw materials used in the formulation gives the surface a rustic appearance, which well suited the aesthetic of the property.
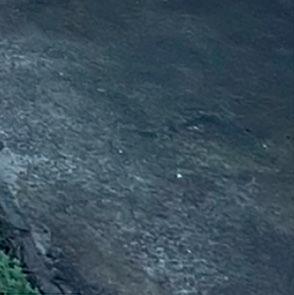
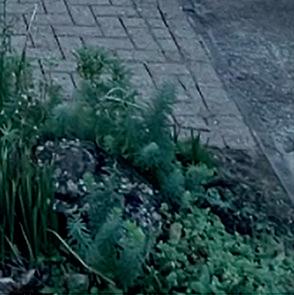
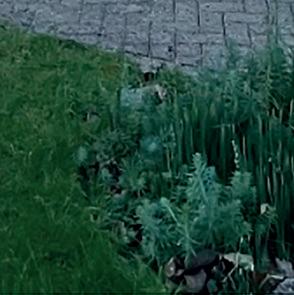
DE Price Plastering was contracted for the project, who chose to work with local distributor, Woodman Brothers Construction Supplies Ltd, who has 25 years’ industry experience and is a dedicated supplier of Fassa Bortolo products.
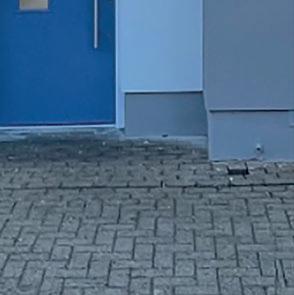
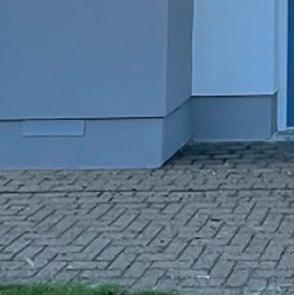
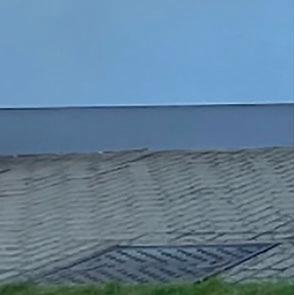
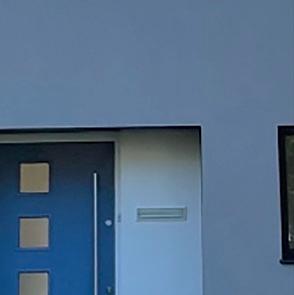
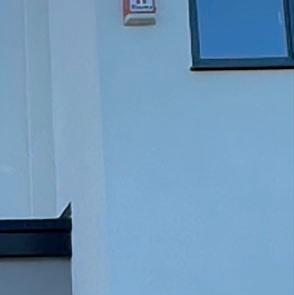
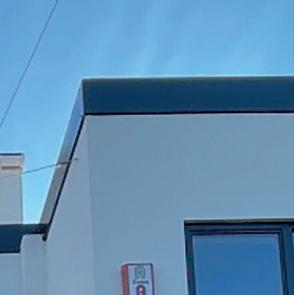
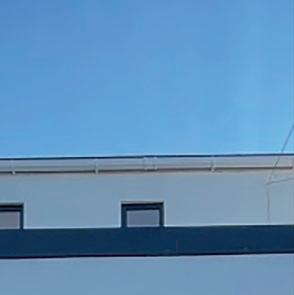
Darren Price, director DE Price Plasterings, commented: “ We’ve worked with Fassa Bortolo on many projects as the company offer a great range of products which are all extremely easy to use no matter what
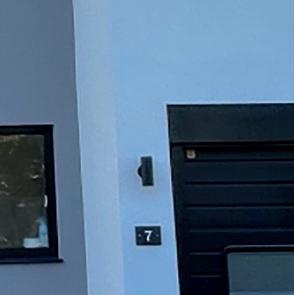
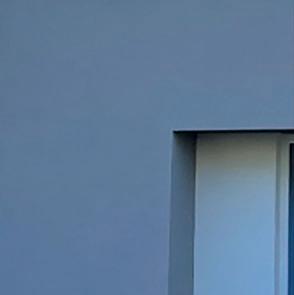
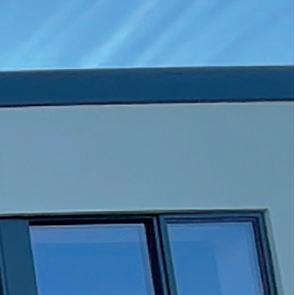

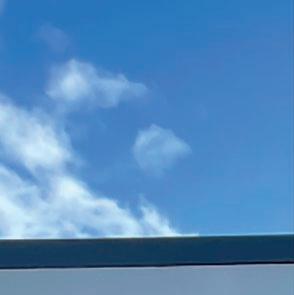
the requirements are. As well as this, the customer service is excellent and there is always someone available to contact who is willing and able to meet our requirements.”
He added: “ Woodman Brothers have a good knowledge of the render industry combined with a vast stock of Fassa Bortolo products, making them the go-to distributor for all of external façade related jobs.”
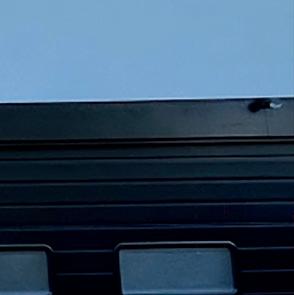
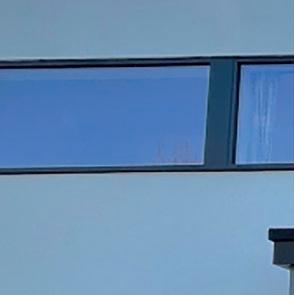
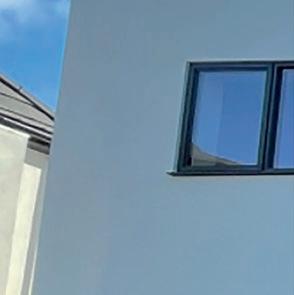
Fassa Bortolo - Enquiry 25
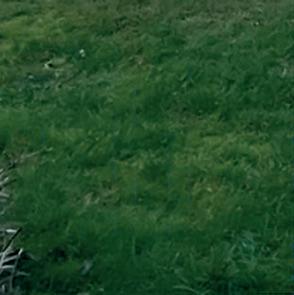
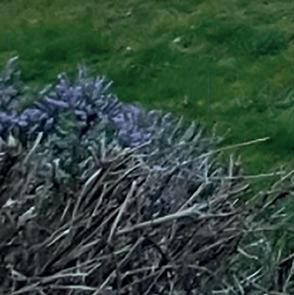
SENIOR BRINGS LIGHT TO LAMPWICK QUAY
Senior Architectural Systems has completed its fourth project for client Manchester Life after supplying the full aluminium fenestration package for the developer’s new Lampwick Quay apartment scheme.

A mix of Senior’s aluminium windows, commercial doors and curtain wall solutions have been used extensively throughout the development and installed by supply chain partner Aire Valley Architectural Aluminium for main contractor John Sisk & Son Ltd.
To help reduce heat loss and energy costs, Senior’s low U value and Part L compliant PURe® aluminium casement windows have been installed to each of the apartments to create a comfortable living space. The stylish window system also provides the perfect frame for the development’s views of Manchester’s New Islington Marina.
Energy-efficiency has also been addressed in the communal, retail and ground floor areas through the use of Senior’s thermally-enhanced SF52 aluminium curtain wall system which
maximises the controlled use of use of natural light.
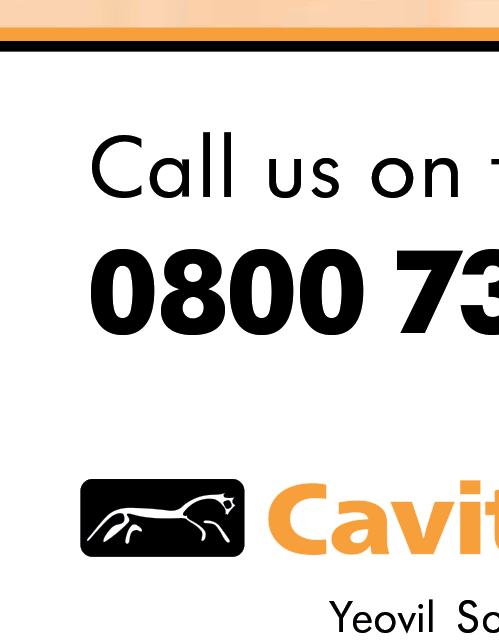
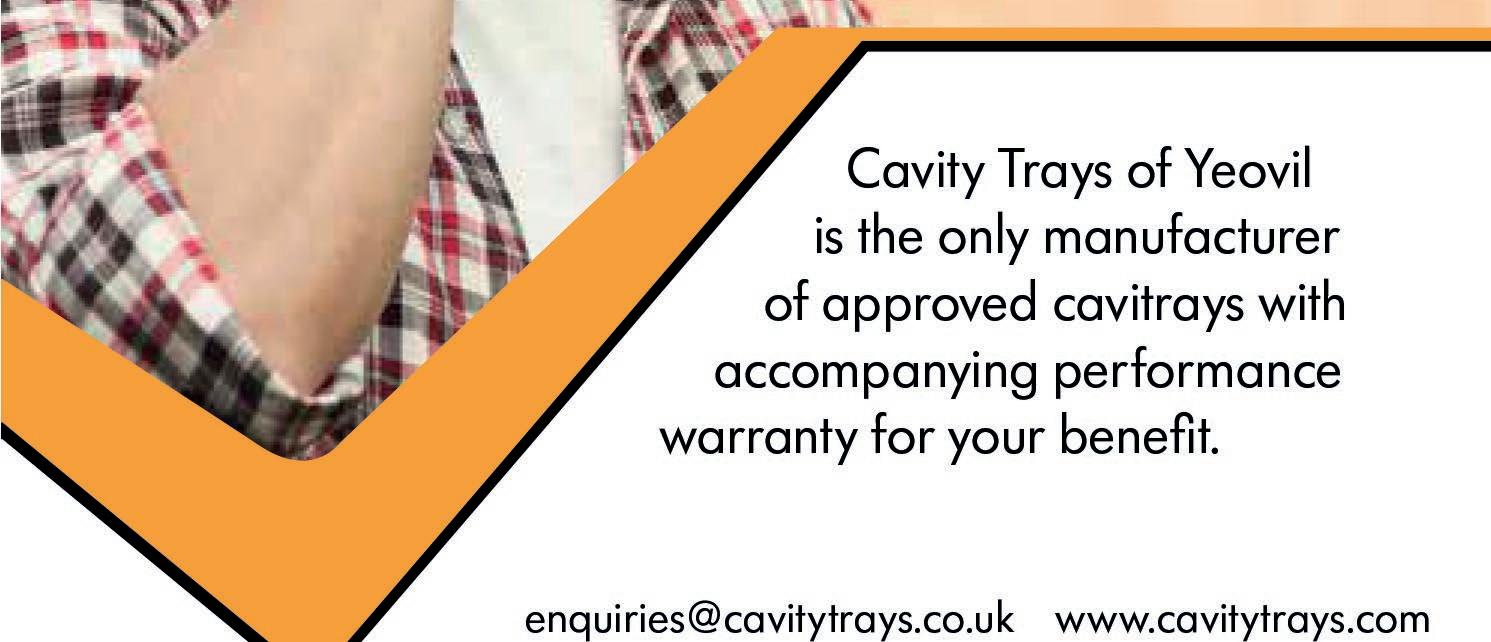
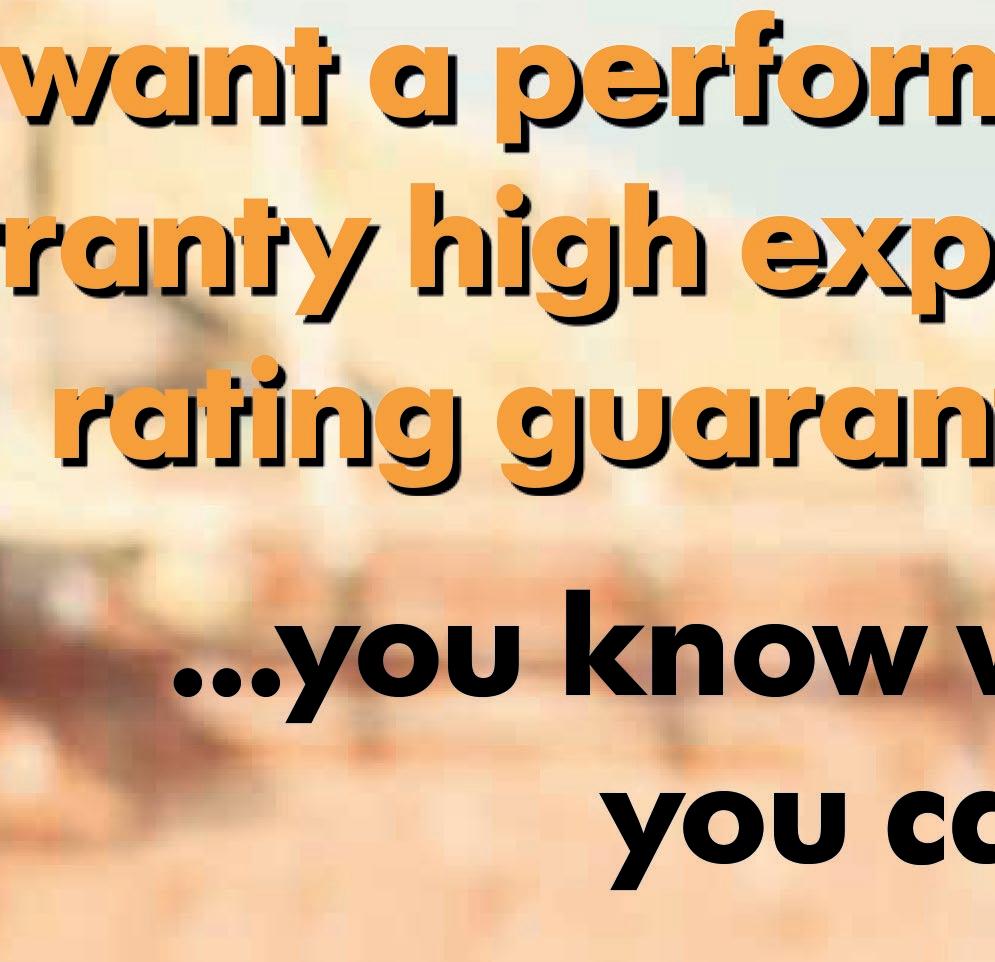
To meet the scheme’s stringent safety and security requirements, Senior’s robust SPW501 aluminium commercial doors were installed to the main entrance and exit points. The SPW501 commercial door system is ideally suited to high pedestrian use and meets the requirements of Secured By Design. Key elements of the fenestration package have also been designed to work as part of the scheme’s overall passive fire protection strategy, with the use of Senior’s SPW600automatic opening ventilation (AOV) aluminium windows in the communal areas and stairwells.
Although visually similar to Senior’s popular SPW600 system, these AOV windows are fitted with a smart actuator which allows for quick and automatic
ventilation in the event of a fire, helping to remove smoke from the air.
Senior Architectural Systems - Enquiry 26
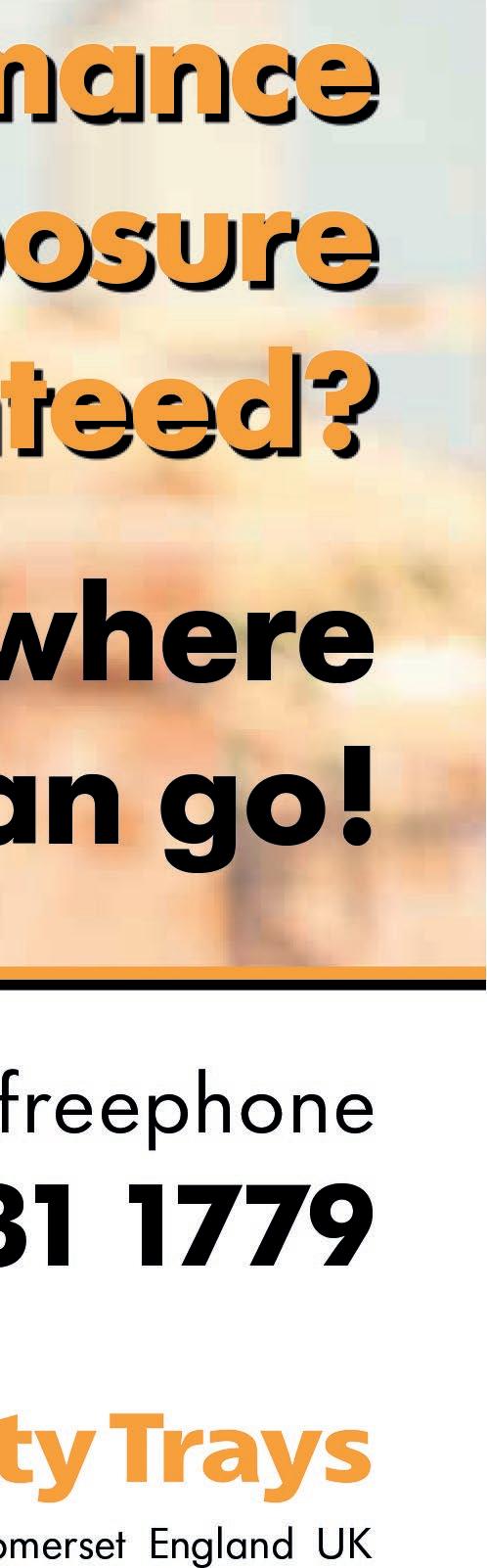

IDEAL HEATING UPGRADES FLAGSHIP LOGIC BOILER RANGE

Leading heating appliance manufacturer, Ideal Heating, has upgraded its Logic boiler range to enhance its ease of installation, servicing and maintenance for installers, while delivering more helpful features for homeowners.
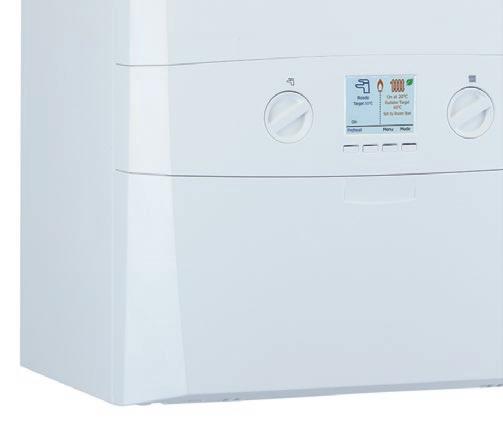

The development of the new Logic2 MAX follows Ideal Heating consulting with installers through focus groups across the UK.
The company also polled more than 1,100 of its installer base by questionnaire to identify and deliver on areas where Ideal can enhance its flagship range.
The company says the new design makes installation even easier, with a new fixed flue turret seal that prevents it being dislodged when fitting the flue.
A push-fit pressure relief valve (PRV) pipe connection also removes the need for compression fitting, and an improved wiring centre with more space and larger grommets accommodates different sizes of electrical cable. Moving
the condensate outlet also supports a tidier installation.Servicing and maintenance have also been enhanced with changes to the internal layout of the boiler.
Fewer gas connections allow for a quicker strip down of the system. Access to the PRV has also been made even easier, with the unit fully serviceable from the front as with previous models.
The new boilers are also fully compatible with greener technologies such as solar thermal and hybrid systems, and are ready to run on a natural gas blend containing up to 20% hydrogen. The combi models deliver an A+ efficiency rating when fitted with a Halo Combi WiFi thermostat.
Ideal Heating - Enquiry 28
whole-house solution for barn conversions
The conversion of three stone-built agricultural buildings near the beautiful Devon town of Totnes is employing a full selection of renewable and low-energy technologies from the range of Exeter based manufacturer, OMNIE, to create a comfortable living environment for the new occupants.
Each of the luxury homes is to be heated by an LV air source heat pump, which will be connected via multi-branch manifolds to OMNIE’s Staple underfloor heating system across the ground floors with the company’s LowBoard being specified to warm the upper levels.
Then to maximise fuel efficiency and help guarantee a healthy indoor living environment, a constant supply of pre-warmed and filtered
fresh air will be supplied via one of OMNIE’s Zehnder ComfoAir mechanical ventilation with heat recovery (MVHR) units.
The Totnes conversions vividly demonstrate how high efficiency heat pumps, combined with underfloor heating developed to bring the best performance from them, can heat any home and keep fuel consumption to a minimum.

Coupled with the ComfoAir MVHR units, the development also illustrates OMNIE’s capabilities to design and deliver its WholeHouse” concept, with a nationwide specification and sales service able to assist clients with any type of application.
OMNIE - Enquiry 29
Consort Claudgen launches Consort Connect app

Consort Claudgen have launched Consort Connect app which allows users to have complete control over their heating remotely via their smartphone or tablet. The app is free and downloadable from Google Play or Apple Store. It can control Consort’s Wi-Fi enabled heaters and SL heaters connected to an SLPBWIFI wireless controller. Features a 7-day timer with 24 heating periods per day, lock function, open window tracking and response capability, and custom automations. Also, the SLPBWIFI and Consort ‘MWIFI’ heater models have a selflearning control ability utilising occupancy and temperature sensors.
Consort Claudgen - Enquiry 30
www.housingspecification.co.uk | To make an enquiry - Go online: www.enquire2.com or post our free Reader Enquiry Card

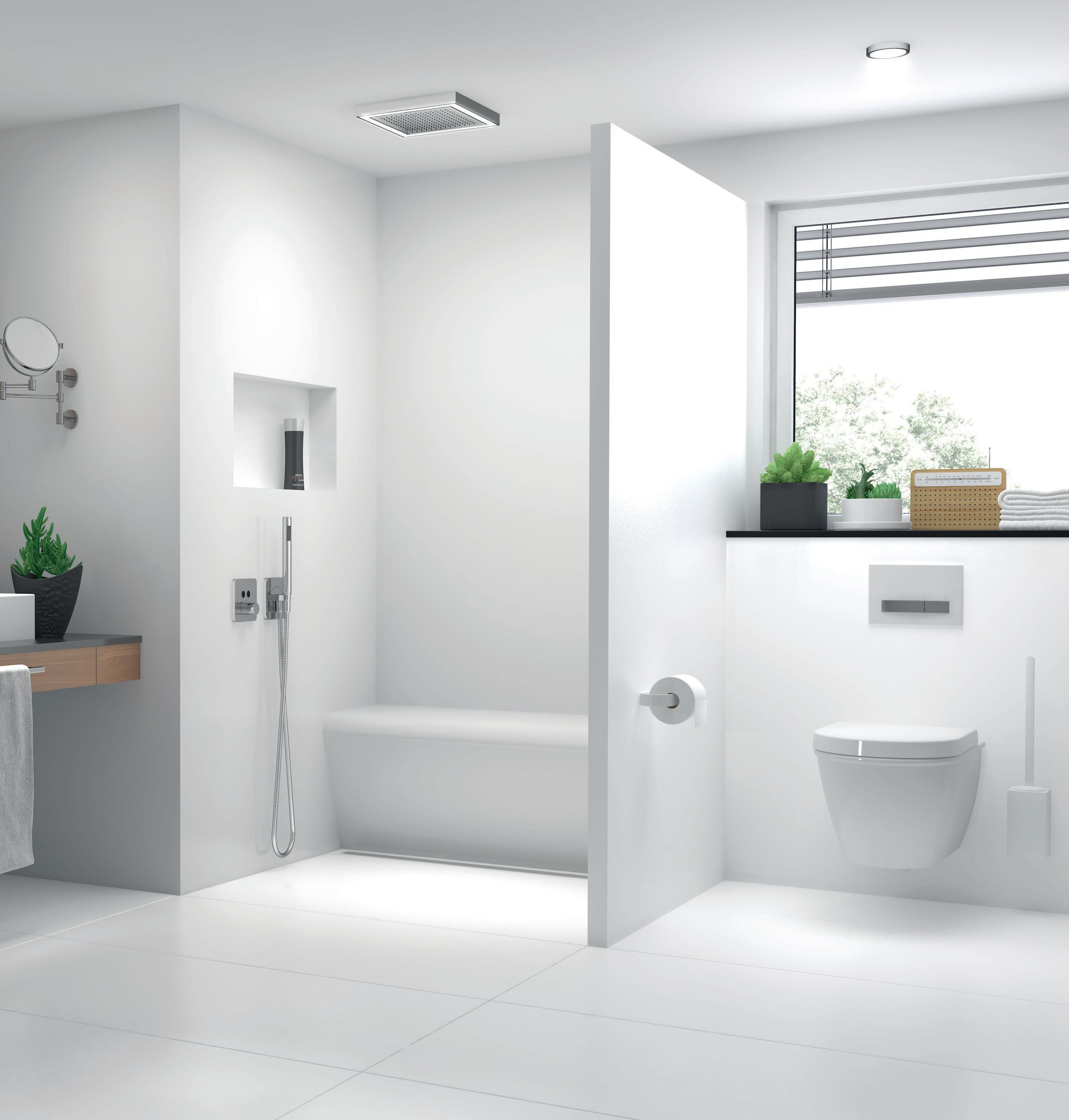
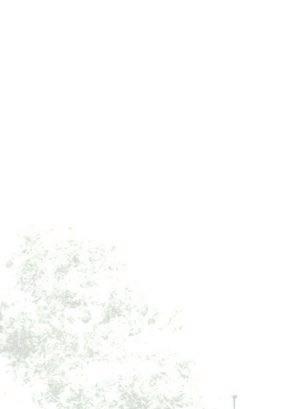
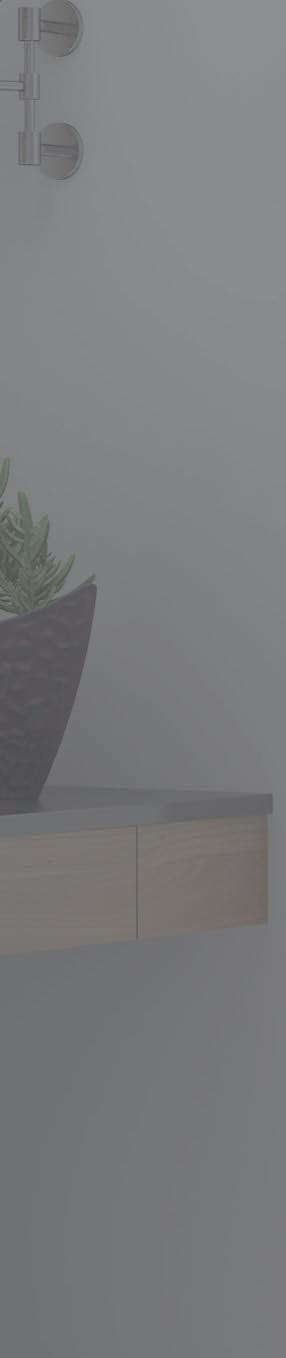
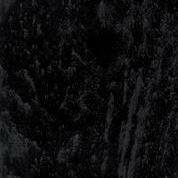
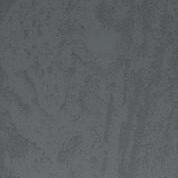
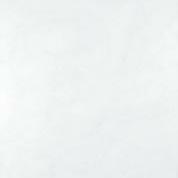
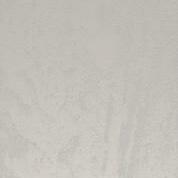
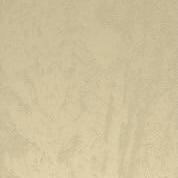
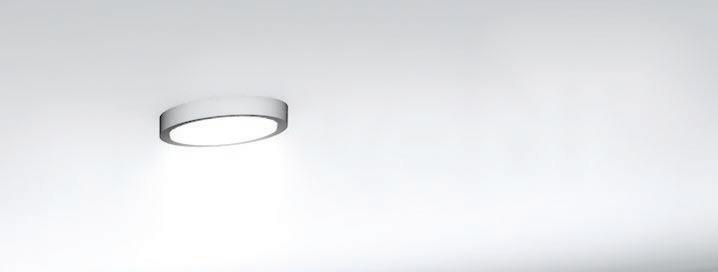





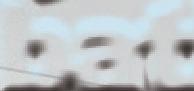


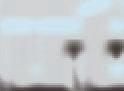


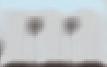

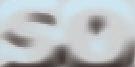
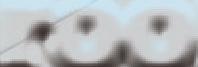






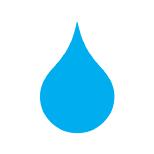
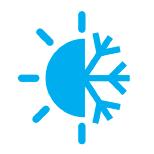
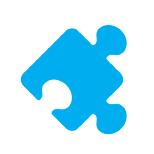

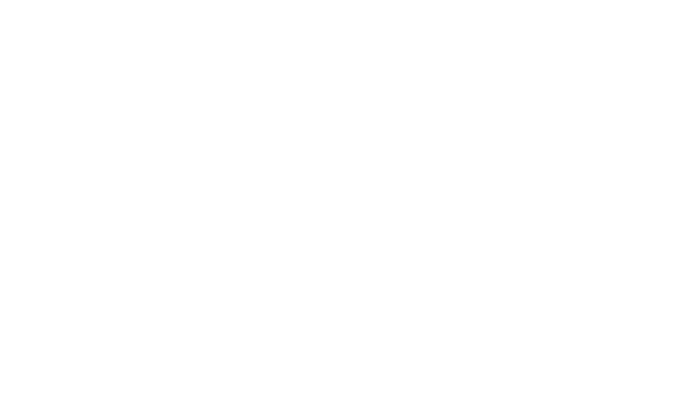
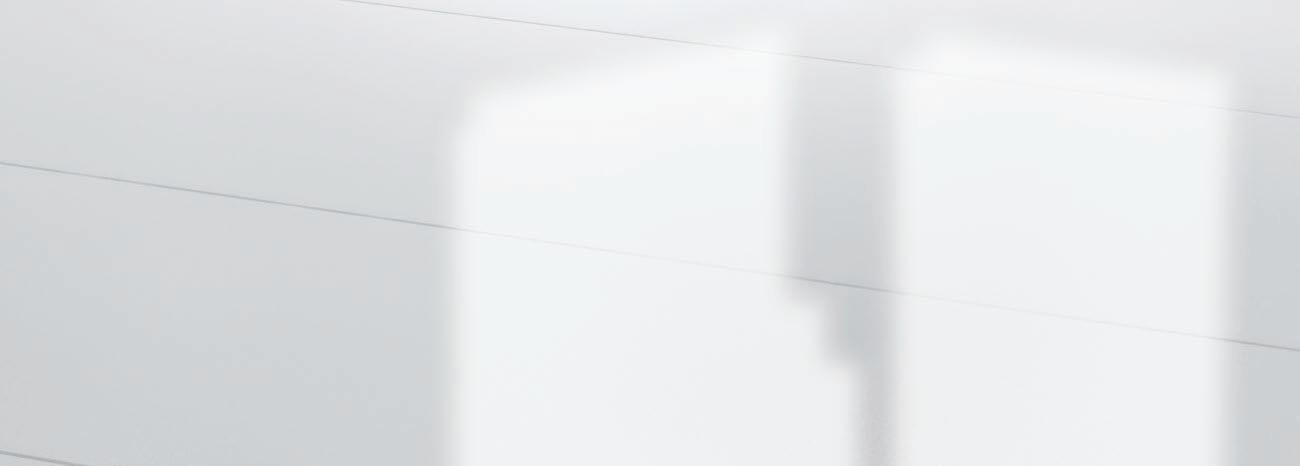
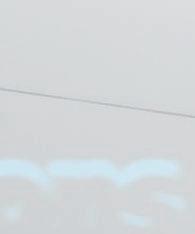
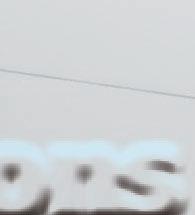




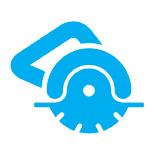
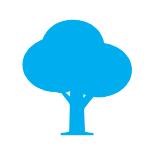
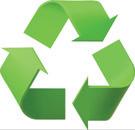
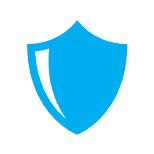

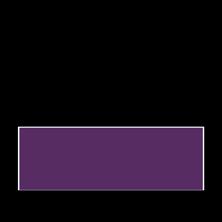