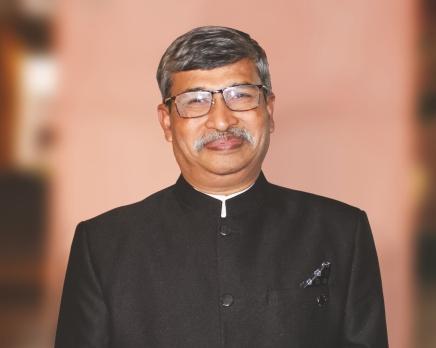



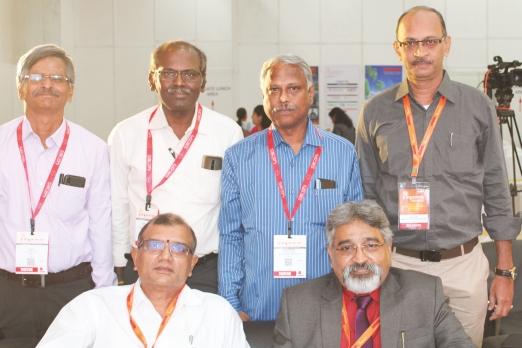
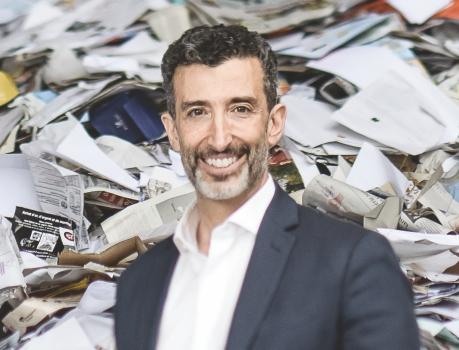






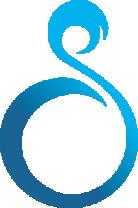



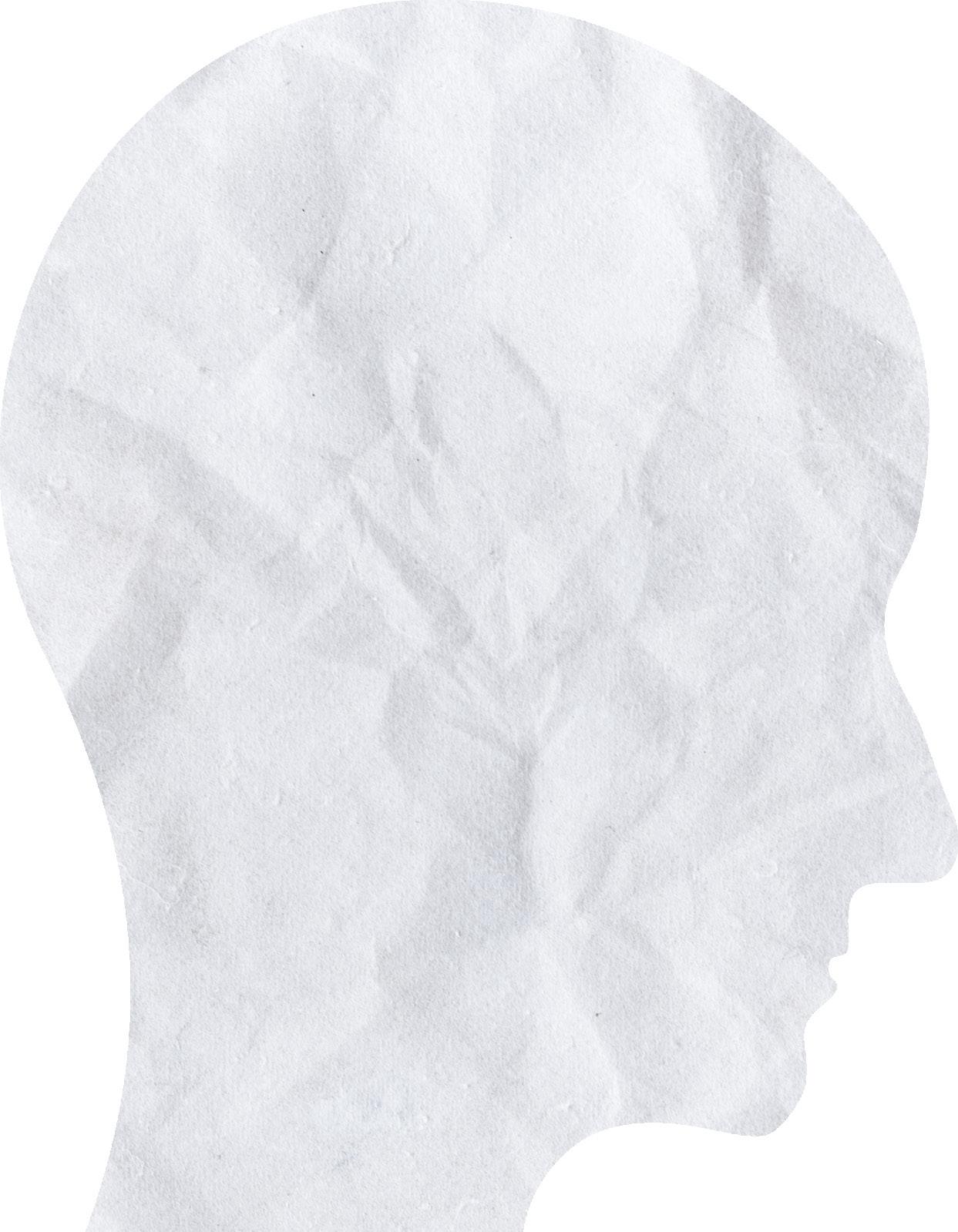

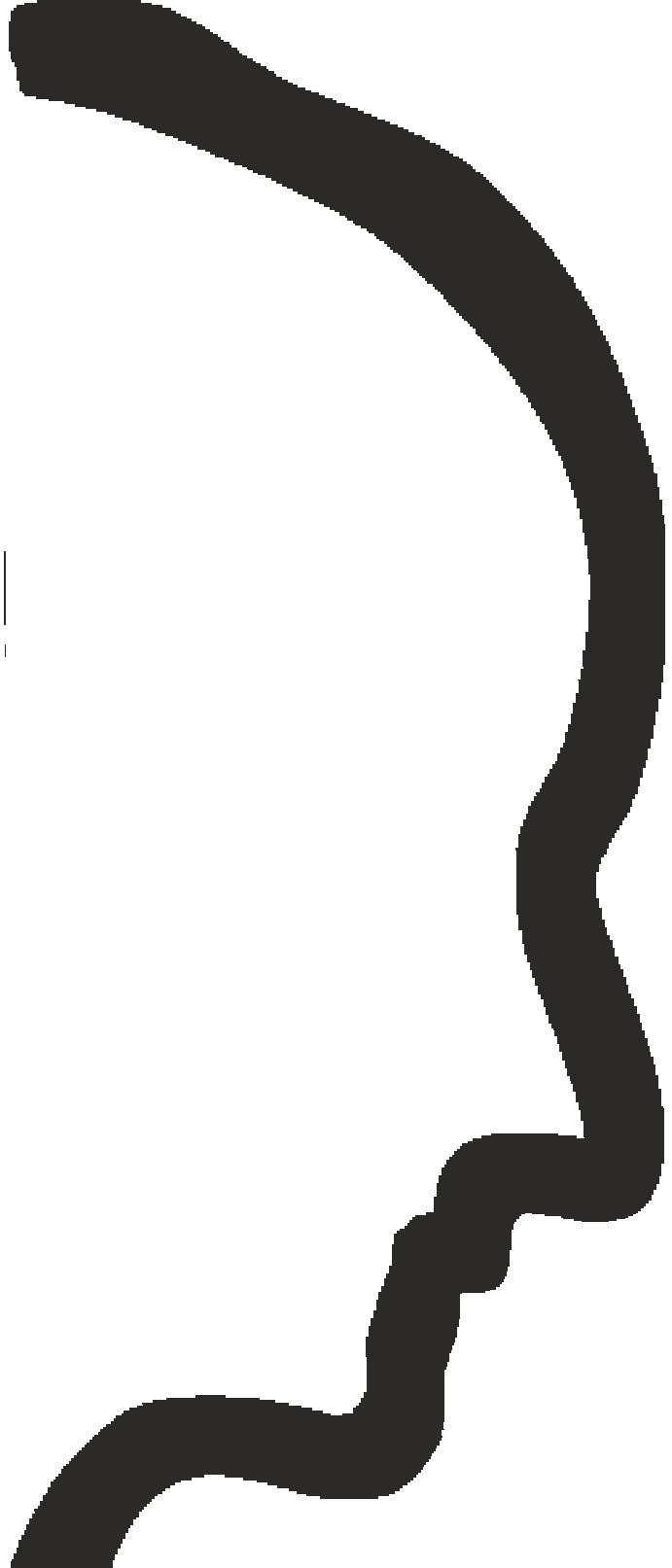

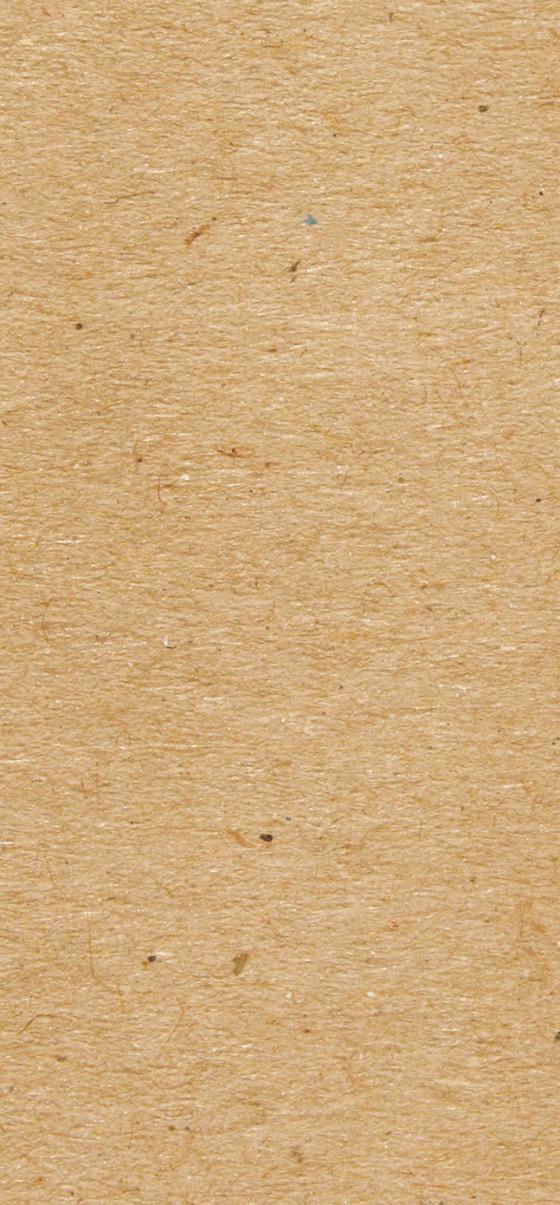


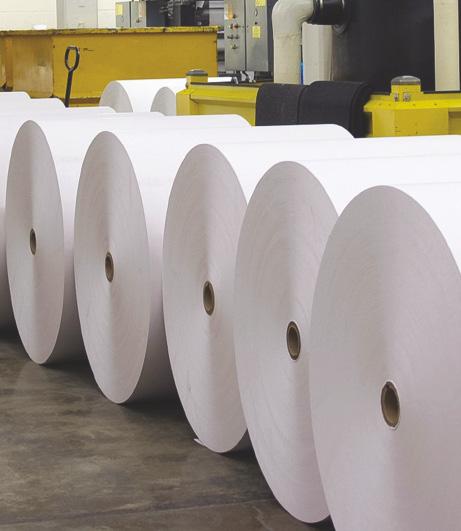
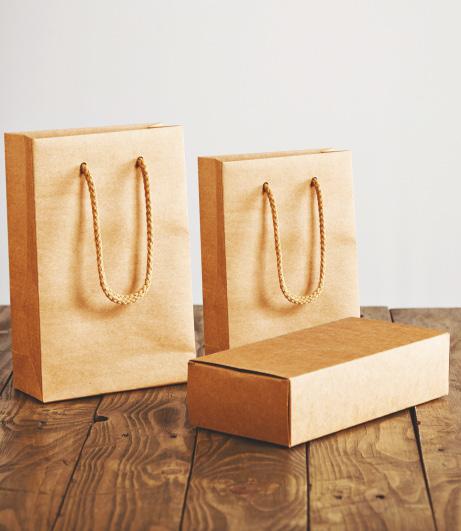
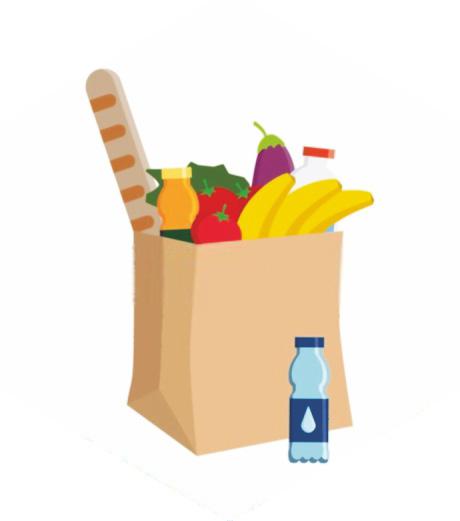
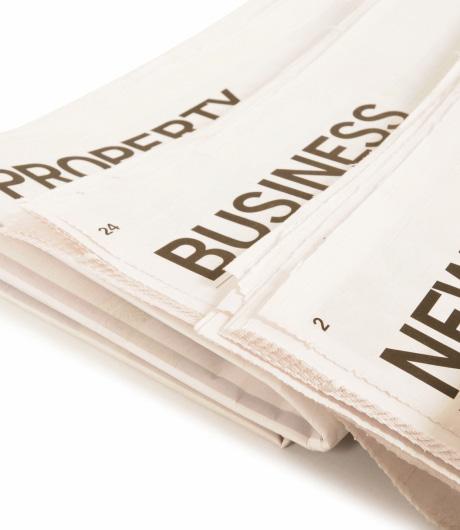
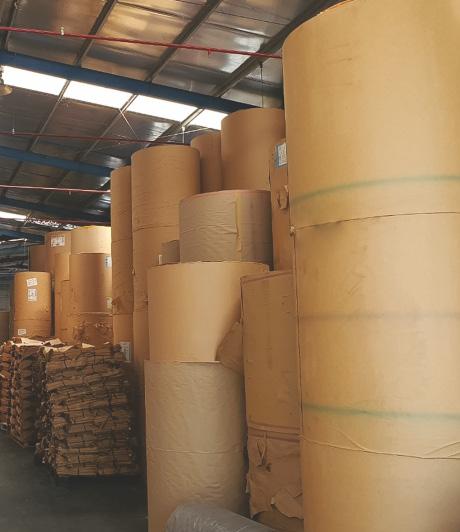
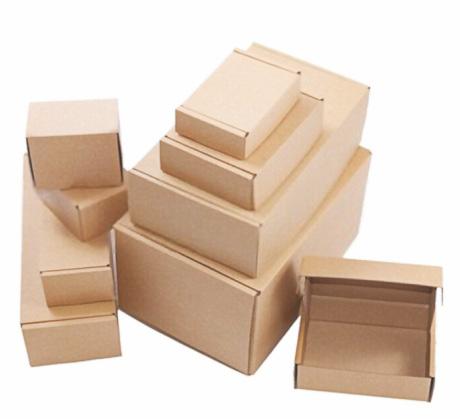
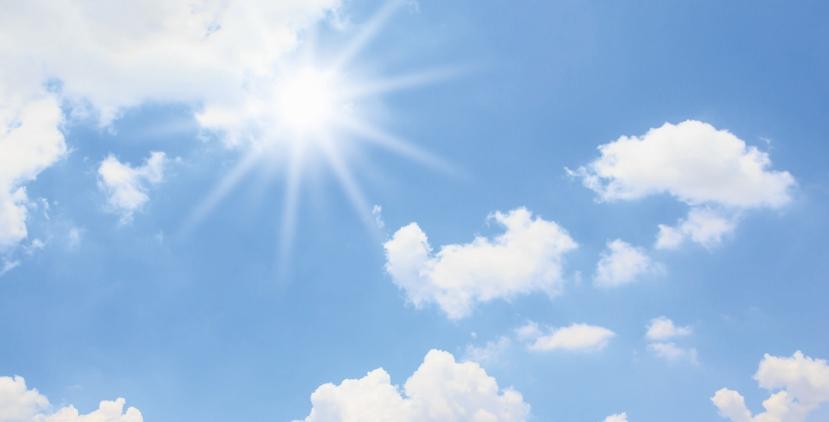




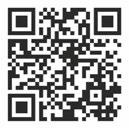

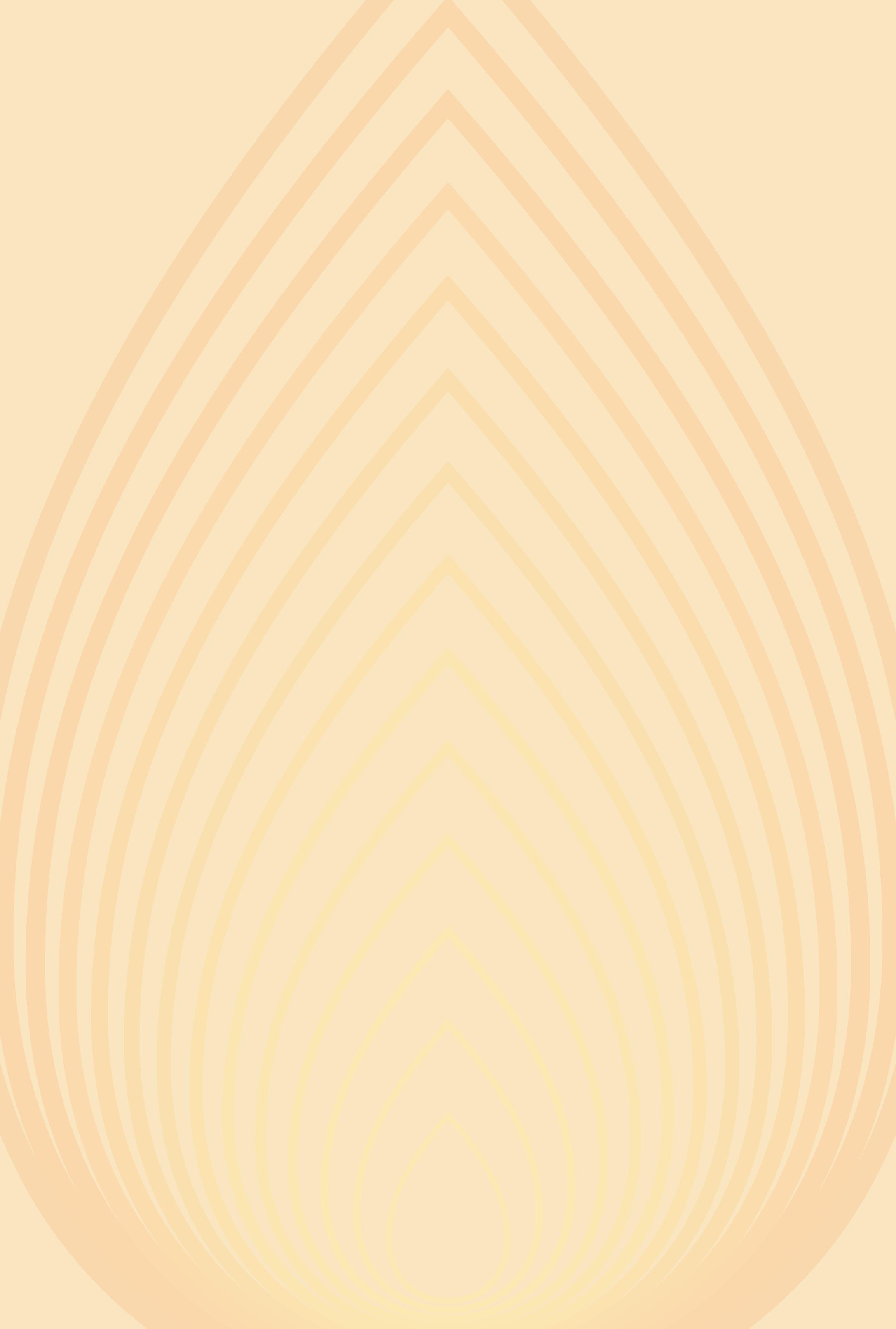
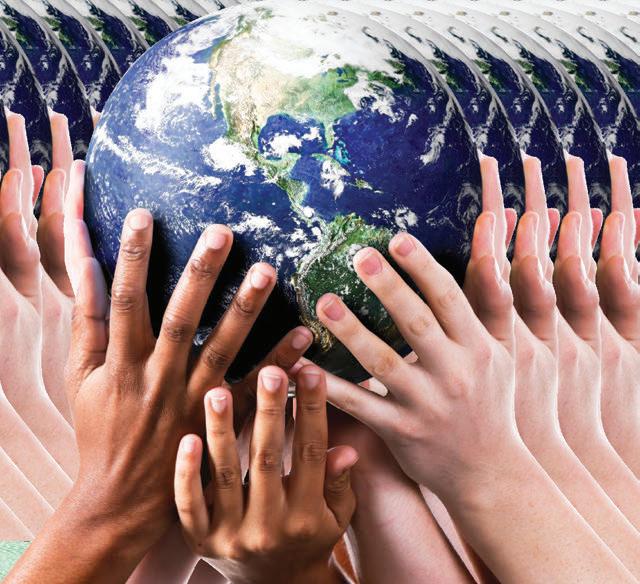
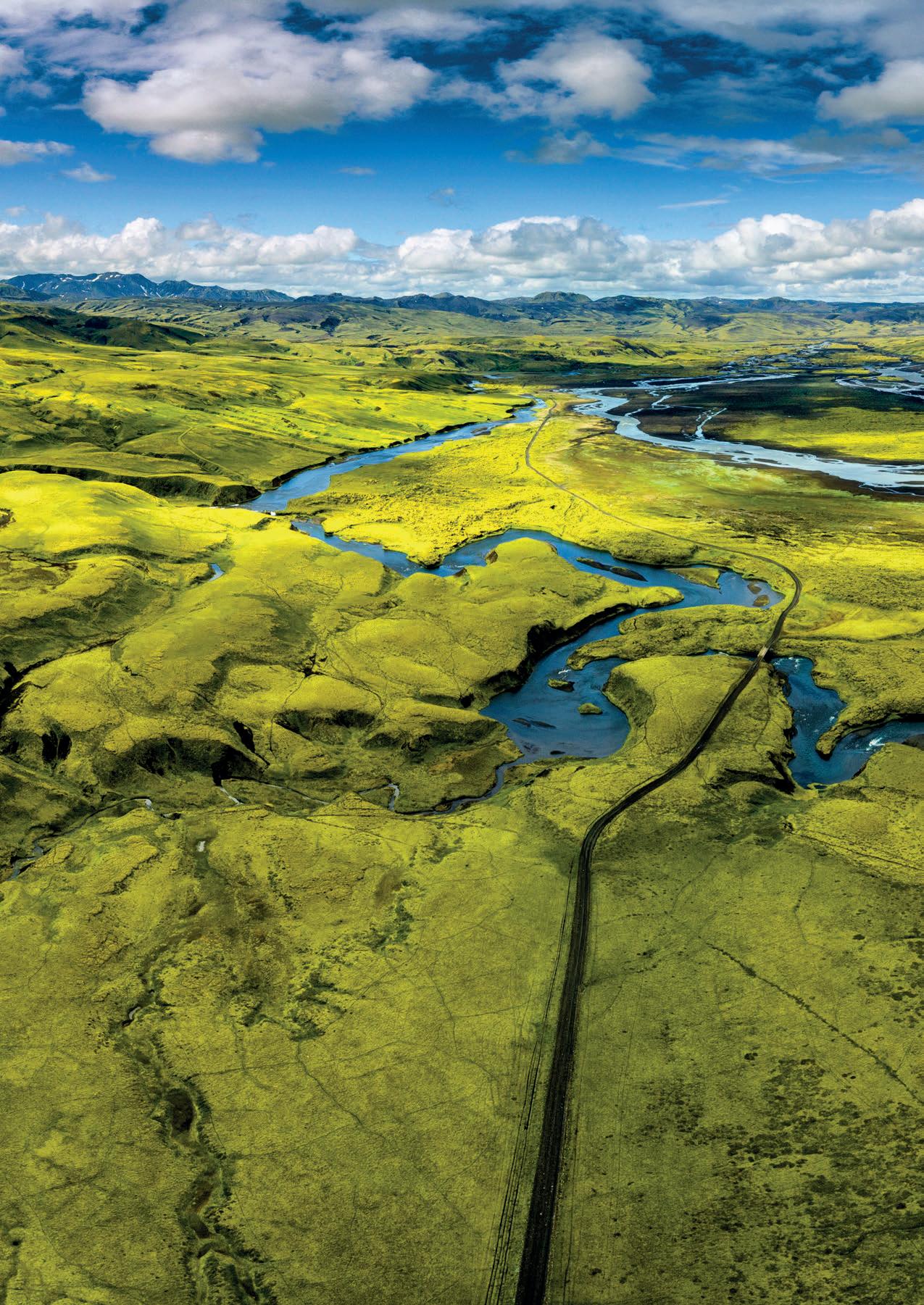
ALLIANCE INTERNATIONAL
Sales / Service Agents
Alliance International is a leading supplier of consumables, components, assemblies and new and used paper machinery. We representwell-knownmanufacturersinthepulpandpaperindustry who are known for their quality and reliable products. This enables ustoprovidecosteffectivesolutionstothepulp&paperindustry.
PRESS & DRYER PART
• Press Felts
• Dryer Fabrics
• C. I. Dryers / MG
• C. I. Press Rolls
• C. I. Pope Reel Drum
• Granite Rolls
• Suction Press Rolls
• Calendar & Calendar Rolls
• Pocket Ventilation & Hood
• Online Felt / Screen Cleaners
STOCK PREPARATION
• Drum Pulper
• Centri Cleaners
• High Pressure Screens
• Baskets Slotted / Perforated
• Screw Press
• Hot Disperser
• Poly Disc Filter(PDF)
• Chest Agitators
ALLIANCE INTERNATIONAL
PAPER MACHINE
• Forming Fabrics
• Head Box- Pressurised
• Suction Boxes & Ceramic Covers
• Suction Couch Rolls
• Doctor Blades & Systems
• Shower System & Nozzles
• Vaccum Pumps
G-32, Suite No. 201, Hansraj Sethi Marg, New Delhi-110019 (INDIA)
• Ph.: 011-41315501/02/03
• Fax : 011-41315506
• E-mail : aneja@allianceint.co, info@allianceint.co
• Website: www.alliancepapermachinery.com
FINISHING HOUSE SHEETER
• Rewinder
• Simplex Sheeter
• Reel Handling System
• Complete Warehousing Solutions (ASRS)
• Mob.: +91 9810102608
Also available used Equipments & Machines from Europe / USA
Vipa Group: Extensive Recycling Can Fulfill Recovered Fiber Requirements in
RC Paper Machines: “We are known for our quality, efficiency, accuracy, and performance”
Indian Paper Manufacturers Association (IPMA) hosted the Annual Session and Awards Function on January 13, 2023, at Hotel Le Meridien, New Delhi.
Indian Paper Manufacturers
Association (IPMA) conducted its 23rd annual session & awards function in Hotel Le Meridien, New Delhi. Themed 'India's Paper Industry: Towards Global Competitiveness & Sustainability', the session witnessed the participation of many stalwarts from the industry. The apex body for the paper industry also announced its new office bearers at the event.
Mr. Pawan Agarwal, Managing Director, Naini Papers Ltd., and Mr. Vadiraj Kulkarni, Divisional Chief Executive, ITC Ltd. (PSPD) have been elected as President and Vice President of the Indian Paper Manufacturers Association (IPMA) respectively.
The event began with a welcome speech by Mr. AS Mehta, President & Director, JK Paper Ltd. He further discussed the scenario of the Indian paper industry. “Raw material security is going to be one area where we all need to be concerned. Unless we do extensive plantation activities, we may suffer. Thankfully, some of the players have been investing heavily in the plantation and clonal R&D activities but we need to do much more so that
very well with double-digit growth. With all the demand drivers in place, the only thing that we need is to be far more competitive and agile so that we can take full advantage,” he added.
still growing in India, though the outlook for segments within printing and writing i.e. newsprint and cream wove is not positive. These grades have shrunk from a 50% share in FY 2010-11 to about 32% in FY 2021. On the other hand, grades like copier and maplitho are continuing to grow. The packaging segment has increased from 47% to 62%. The pulp & paper industry is witnessing extraordinary challenges, and to emerge as the winner, we are required to transform, adapt, and innovate”.
we have the right kind of material at the right price and a competitive price,” said Mr. AS Mehta.
“Another area that is impacting the industry is waste paper. We should change this nomenclature and call it recovered fiber. How do we improve the collection system, what kind of infrastructure is needed and how can the industry help so that the fiber is recovered are some of the things we need to focus on. More than 55% of the fiber is recovered fiber today; hence, we can't ignore this area. The industry will have to play a very effective role in the fiber recovery segment.
On the various consumption parameters, whether it is power consumption, water consumption, or other environmental-related parameters, the industry has done a fantastic thing. Water consumption is just one-fourth of what it used to be, and energy consumption has come down by 30%, but we need to continuously do this.
Although the writing & printing segment is not growing globally, it is growing consistently in India due to the emphasis on the education sector. The packaging sector is also doing
The welcome address was followed by a speech by the chief guest Mr. Harsh Pati Singhania, Vice Chairman & Managing Director, JK Paper Ltd. Emphasizing the plantation activities of the industry, Mr. Singhania said, “The Indian paper industry is a shining example of a domestically created industry (Aatmanirbhar); it caters to the domestic market, produces domestically and uses largely domestic raw materials and inputs.”
He further pointed out that sustainability is going to be another very important aspect of the industry. Elaborating on the current scenario of the paper industry, he added, “On one hand, you're observing structural changes in the form of consolidation and shift in the product portfolio. On the other hand, the industry is preparing itself to address issues such as climate change, sustainability, biodiversity, etc. The global paper market continues to grow at a CAGR of 0.5% to 1%, pivoting strongly on the packaging segment. However, there has been a decline in the printing and writing segment. Large global players such as Stora Enso and Sappi have carved out their printing and writing businesses and are now focusing on the packaging segment. The Indian paper market remains the fastergrowing market, globally led by growth in the packaging segment. The printing and writing segment is
Talking about the near future, Mr. Singhania said, “In the coming decade, 2020-2030, there is a need to transform, adapt, and innovate”, adding that sustainability has three key pillars, environmental, social and economic. He further informed that environmental sustainability has two dimensions. The process needs to be resource efficient, and the product should either be easy to recycle or a substitution for fossil-based materials.
“Companies are responding with bold declarations, mainly towards reduction of plastics and carbon emissions. Top FMCG companies have made declarations towards adopting sustainable packaging, focusing on increased recycled content, reducing the use of plastics by eliminating plastic peripheries such as single-use bags, reducing packaging weight, and innovating plastic substitutes. Likewise, several large corporates have made declarations towards becoming carbon neutral by adopting a hundred percent renewable energy strategy. The good news is that for the pulp & paper industry, thisshift towardssustainability is actually an opportunity rather than a challenge. The pulp & paper industry inherently has sustainability, at the core, because wood products such as pulp and paper are renewable, biodegradable and recyclable. Pulp & paper making is an integrated process and recovered paper can be recycled multiple times to produce various papers and boards, therefore increasing the lifetime value of paper. Thus, the industry is truly at the heart of the circular economy,” he said.
The inaugural session was followed by the presentation of IPMA Awards: 2019-20 and 2021-22. JK Paper Ltd. won the IPMA Paper Mill of the Year Award for 2021-22. Seshasayee Paper and Boards Limited (SPBL) bagged two awards -- IPMA Paper Mill of the Year Award for the year 2019-20 and the IPMA Energy Conservation Award for 2021-22. ITC Ltd. (PSPD) was conferred with the IPMA Energy Conservation Award for 2019-20. Meanwhile, IPMA Environment Award for 2019-20 and 2021-22 were presented to Tamil Nadu Newsprint & Paper Ltd. and Bilt Graphic Paper Products Ltd. respectively.
industry players, and everyone for their guidance and unwavering support.
I would like to end my vote of thanks session with a couplet in Hindi –'Raah Kathin ho Jitni, Sankalp Majboot ho Mera.. Nazar Kamzor pad Jaaye, Nazariya Mazboot ho Mera'. For our overseas friends, I would like to translate this as 'The road could be difficult but my resolve should be strong. The eyesight could be weak, but my vision should be strong'.”
for sustainable choices in their consumption patterns and behaviours. These factors, in turn, impact retailers and mega/large-scale corporations and top brands to adopt sustainable packaging materials. Since a product needs to be protected in transit and storage and the packaging should display the branding, paper and paperboards as packaging materials are quite unique. Besides conventional packaging materials, pulp molding is a new form of packaging.
Presenting the vote of thanks at the session, Mr. Pawan Agarwal, Managing Director, Naini Papers Ltd., asserted, “I would like to start from a quote of Ralph Waldo Emerson, which goes, 'Whatever you do, you need courage. Whatever course you decide upon, there is always someone to tell you 'you are wrong'. There are always difficulties arising which tempt you to believe that your critics are right. To map out a course of action and follow it to an end requires some of the same courage that a soldier needs.'
I would like to congratulate Mr. Vadiraj Kulkarni of ITC Ltd. for being elected as the Vice President of IPMA. It would be my privilege to work with him at IPMA for the next two years. Both of us look forward to the support of all of you who are present here. I would like to express my sincere gratitude to all the past presidents, office bearers & members of the IPMA committee, CEOs of the paper
Talking about the Indian paper industry, Mr. Andreas Endters, President & CEO, Voith Paper GmbH said, “India is a huge market. If we look into the future to talk about trends and opportunities, it is difficult to assess in the world of unreasonable challenges due to the volatility and unprecedented situations, and a scientific approach might fail.
The good thing is that paper has been quite important in the past; it is still a key product today and will be even more important in the future because 'sustainability' as a key characteristic of paper is a unique aspect. Paper is produced from renewable fibers, is recyclable, and biodegradable, making it very different from other materials and providing you with good opportunities. When we talk about these opportunities, it includes – legislation pressure; consumer packaging becoming sustainable (particularly in Europe and the USA markets); and the restriction on single-use plastics around the world. In fact, it is not just the legislation but the interests of consumers all around the world to go
When we talk about the substitution of plastic, this also means that paper has to substitute the functions of plastic, which means it should be resistant to grease, humidity, vapour, or smell. Earlier, these parameters were not easy to fulfill. However, there is a huge development around barrier coatings that are fulfilling all those considerations. In just a couple of years, there have been significant developments made in the segment of paper-based packaging. Today, technology is advanced enough to make such solutions possible. Also, there is a huge push from the consumers in this regard. This is one of the major growth opportunities for the paper industry. To achieve futuristic transformations, any industry needs to adapt and keep pace with the growth opportunities. In our understanding, thereisapositivegrowth story for paper production globally.
The Indian paper industry is growing, which is great news. Also, we think that there are huge growth opportunities for the graphic papers segment in the country. Amongst the major demand factors in the paper and paper-based packaging industry are the growing education sector and the demand in consumer packaging. In the Indian paper industry, the share of paperboard as a segment is increasing and is expected to increase in the future.
Also, there is a good growth potential for segments such as tissue paper, speciality papers, and so on. And as mentioned, if we want to grow the production of paper and paperboards, the availability of fiber will be the key consideration. Interestingly, the share
of virgin fiber, in the overall fiber consumption, is decreasing while the demand for recovered/recycled fiber is increasing. At the same time, there are large-scale plantations of Eucalyptus trees in South America that are actually fulfilling the requirements of a large part of the world, with China occupying a lion's share of the production.
In addition, using the data by artificial intelligence, we are being able to develop algorithms that help us to optimize the paper production process. This enables us to conserve fibers, energy, maintenance costs, and human labour. Thus, on an overall basis, one gets around savings with digital and intelligent solutions. We have developed algorithms that equip us with a virtual sensor for getting the real-time strength of the paper at any minute. This, in turn, allows optimizing the paper production at the site.”
Concluding his presentation and emphasizing sustainability, Mr. Endters, said, “The industry should increase their dependence on renewable energy instead of fossil fuel. For instance, the electrification of the processes is one of our major focus areas. We are working on intensive things in order to increase our consumption of renewable energy. Also, the use of hydrogen as a fuel is going to increase, replacing some of the fossil fuels that are currently being used. Thus, thoseare two majoraspects that will become very important in the future. The industry should be more sustainable in the future in order to ensure that we make our world better and we have opportunities to do that!”
Management Consulting said, “The size of the global paper and paperboard market is about 430 million tonnes and the growth has been quite consistent. In the past two-three years, there have been certain disruptions like the financial crisis and COVID-19 when the market temporarily declined. However, it has been a steady growth. There was a slowdown certainly in a few segments of the industry.
There are many mega-trends that are influencing the development of the paper industry, such as urbanization, increasing disposable incomes, and sustainability trends. Also, the bid to push plastic substitution is favouring sustainable products such as paper. On the other hand, it is also providing huge growth opportunities for paperbased packaging in the e-commerce sector around the whole world. Thus, it is clearly the packaging sector, which is leading the growth of the paper industry. For instance, if we look at the European folding boxboard segment, just less than 10 years ago, there used to be a situation wherein Europe was supplying to the regional markets. However, with these new conversion and expansion projects, Europe has become dependent on exports and high hopes are being set for North American opportunities. Also, there are huge investment opportunities in the North American market. Thus, it now looks like the packaging board segment is burgeoning in both Europe and North America.
In recent years, India has become one of the largest consumers of paper and paperboard with a demand of about 20 million tonnes. It seems that there are huge growth opportunities in the Indian market. Our view at the moment is to expect robust growth to continue in the market for the upcoming 10-15 years. Also, we are expecting above-average growth for certain specific segments such as virgin fiber-based paperboards, container boards from recycled sources, and so on. The writing &
printing paper segment is also proliferating due to increasing business activity, and the development of education sectors while the market size is still reasonably good but not as big as the packaging segment. Thus, the domestic market opportunities are quite promising and healthy. However, beyond the domestic market, there are other significant market opportunities from other parts of the world. As a matter of fact, in recent years, exports have been going up and are showing an upward trend with the exception of the COVID-19 pandemic.
Thus, to conclude my presentation with some of the key takeaways, the mega-trends are the increasing demand & consumption of different paper grades and the surge in the packaging sector which has a mixed market outlook depending on the region. The paper producers have undertaken strategic transformations of many of their traditional business models. From a market perspective, this has been an interesting time period bringing a series of opportunities for Indian paper producers.”
The discussion included a questionand-answer session with the audience. Meanwhile, Mr. Vadiraj Kulkarni, in his concluding remarks, thanked all the participants. “India is on a road trajectory and in the industry, we go through a lot of ups and downs, but in the long-term, we have a good growth story,” he concluded.
Indian Pulp and Paper Technical Association (IPPTA) organized a zonal
seminar on 'Energy Conservation, Cost Reduction and Developing Alternate Source of Energy' at Vapi, Gujarat from November 17 to November 18, 2022. The seminar aimed at addressing the current challenges being faced by the paper industry regarding energy efficiency. Mr. Sunil Agrawal, Chairman-Programme Committee & President of Gujarat Paper Mills Association gave the welcome address and Mr. M.K. Goyal, Honorary Secretary General, IPPTA, presented the outline of the workshop.
The event commenced with a lamp lighting ceremony by the Chief Guest Shri Kanubhai Desai, Finance Minister, Government of Gujarat, Mr. Sunil Agrawal, Chairman-Programme Committee & President, Gujarat Paper Mills Association, and CMD, Shree Gajanan Paper & Boards Pvt. Ltd., Dr. TG Sundara Raman, Technical Advisor (BD & Tech), Enviropool Engineers Pvt. Ltd., Mr. Ganesh Bhadti, President, IPPTA & Director (Operations) Seshasayee Paper and Boards Ltd., Mr. MK Gupta, Director, CPPRI, and Commodore Saurav Deb, CMD, NEPA Ltd.
Addressing the leaders of the paper industry, Shri Kanubhai Desai said, “Vapi has improved a lot in the last five years and paper has turned out to be a profitable business. The industry has performed well even during the pandemic. The theme of the seminar 'Energy Conservation, Cost Reduction and Developing Alternate Source of Energy' is extremely important for the industry. If you work on that, your profit will definitely increase because when you become energy efficient and control environmental problems, your waste reduces and you get the maximum out of your business”.
environment and emission'. Through his presentation, he showed that uses of alternate sources of energy in paper mills could be solar thermal coupled with waste heat radiation (lime kiln) conversion, solar concentrating parabolic trough collector with tracking, solar drying of fossil fuel, and solar thermal for hot water generation at 90°C for VAM deaerator steam consumption reduction. He further emphasized that the industry needs to move from segment (isolation)/block practice to an integrated approach.
Elaborating on energy conservation approaches by Nepa Ltd., Commodore Saurav Deb said, “Conservation of energy will give us cost reduction and that's how we not only save the planet but also save ourselves. As long as the smoke gushes out of the chimney, keeping all the environmental parameters in mind, Nepa is a beacon of hope for the people in the area, and I can assure you that we will not let you down.”
Along the same lines, Mr. Ganesh Bhadti added, “A religious approach is needed at the moment because once we change our approach or the attitude toward the natural resources, we can avoid this depletion”. He further said, “There are some changes expected in the energy consumption pattern of the pulp & paper industry by 2030. The coal consumption is expected to reduce by 18.2% and gas will be coming down by 15%. Electricity would go up by 12% and bioenergy will go up by 23%. Further, paper production will go up to 20 million tonnes and net energy consumption will come down by 16%. Sustainable consumption is required to ensure that this energy is available all the time.”
The inaugural session was followed by a panel discussion moderated by Mr. Tushar Shah, Director, Daman Ganga Board Mills Pvt. Ltd. Sharing his views on the paper industry, Mr. Abiali Jani, Director of Jani Sales Pvt.
‘Paper has turned out to be a profitable businessʼ
‘The three Es important in the paper industry are energy, environment and emissionʼDr. TG Sundara Raman shed light on the three Es that are important in the paper industry, i.e. 'energy,
‘There are some changes expected in the energy consumption pattern of the pulp & paper industry by 2030ʼ
‘Conservation of energy will give us cost reductionʼ
‘We've got good potential in terms of the availability of infrastructure and manpowerʼ
Ltd., said, “There is a lot of development in the e-commerce sector which has opened a plethora of opportunities for the packaging industry. Apart from this, education is also a booming sector in India and an important factor for the growth of the paper industry. However, you need to study what kind of project you want to put up. As an industry, we've got good potential in terms of the availability of infrastructure, labor, and manpower. We are far better than the Western countries.”
increase your efficiencies, increase your control methods, and work on the kaizen system, which is rolling off your processes, rechecking, and then evaluating. That will eventually lead to your decrease in power consumption and increase in your efficiency.”
power. By 2030, our target is to meet 30% of our total energy requirements from renewable energy. Besides investing in solar and wind power, we have a waste-to-energy boiler at our mill, which is under commissioning. We are using sludge (the deinking sludge) as one of the fuels for the boiler which essentially reduces the coal consumption by about 15 tonnes per day. With the boiler, we expect to save about 10 tonnes of coal per day in the near future” he said.
Talking about the ways to increase efficiency in the paper industry, Mr. Varun Shah from Shree Ajit Pulp and Paper Ltd. said, “The power cost is always going to go up. All you can do is bring about new technology or
Meanwhile, Mr. Pritesh Shah Joint Managing Director, Shah Paper Mills Ltd., shed light on the strategies taken at his company. “We take action today to make our future generation better. So we need to work across all the aspects, like saving water, saving energy, saving steam, and, also our fossil fuel. We need to work in each and every direction to make more efficient and cleaner production. This will also help in bringing our profitability better. At Shah Paper Mill, we already invested in wind and solar
Mr. Prince Shah from Best Paper Mills Pvt. Ltd. added, “Our country has a lot of potential and we've been actively investing in paper mill plants and other technologies. We are not looking here to improve, increase or decrease our production, but to make profits. We all should look at the varied products that we can make on
‘All you can do is bring new technology, increase efficiencies, increase control methods, and work on the kaizen systemʼ
‘By 2030, our target is to meet 30% of our total energy requirements from renewable energyʼ
‘We need to expand our horizon towards the international marketʼ
Clyde Industries is the world's leading Boiler Cleaning operations expert. Our equipment, technology, field service and knowledge is unmatched in the industry,creatingsignificantvalueovertheentirelifecycleofyoursootblower.
Heavy
Minimize Downtime Maximize Efficiency
89 or 102 mm OD
High Yield Strength Lance Tube 70 mm OD
Hardened ArmorGlide Feed Tube High
Externally Adjustable Poppet Value (For ease of setting the steam pressure)
Gearbox Separate from Spindle Keeps Head Away
Seal Pack Packing Cartridge
Having Boiler plugging or clinker formation issues? Want to avoid 3 days forced outages?
Nowwe servein INDIA
Sealed Bearings in Separate Lower Spindle Housing
Heavy Duty Chain Drives Lance Rotation
TM
Here we come with our SMART Clean Intelligent Sootblowing System for Pulp and paper recovery boiler. Clyde industries customers realize an average yearly plant savings of $1.56 million and avoid 3 days of forced outages.
l Clyde have good record in reducing the Sootblower steam consumption to a level below 5% of the boiler steam generation while increasing the recovery boiler throughput.
l Increase Throughput and Reduce Operating Costs.
the same machinery. Secondly, we are facing a lot of competition domestically; hence, we need to expand our horizon towards the international market. Our qualities are great, and we have made good CapEx investment. I truly believe that we should be competing on an international platform and not within ourselves. So that will be our key for going forward in the next coming few years,”
Mr. Kunal Dharia, Director of Revival Paper Mill Pvt. Ltd. emphasized that “Quality development, sustainability and profitability should go hand in hand. Sustainability is increasing machine efficiency, reducing your cost, making it affordable, and at the same time, providing good quality products to the clients.”
Mr. Aditya Gupta, Director at Narsingh Dass Group added that “In India, we have the capability of producing very good quality of paper. By the good quality of paper, I mean efficiently producing it with the best of the cost parameters that exist for the industry. The paper mills should increase that capacity within their unit to compete internationally and reduce the import of the paper to serve that application.”
When asked about the possibility of paper replacing plastics in the near future, he said, “I have tried combining paper with each and every kind of material that exists right now as a choice of material in the packaging line. Plastic offers a functional barrier property, which is generally moisture barrier and oxygen barrier, which gives the shelf life to the product. These two things are the most challenging thing
for paper. But paper with suitable properties can definitely replace plastics in that application where the commercial sense of the final product makes brand owners accept the paper as a choice of material such as molded fiber products. The cutlery made out of paper is getting exported from India. Similarly, the sachet business, like the e-commerce bags, is happening in a big way. Paper tape is the third such product, which is a big wave right now in India. If a systematic collection system of waste paper gets in place, there is no stopping. People can really go ahead and just replace plastic in a big way. The issue of 'barrier' might also be addressed in the coming times because people are working day in and dayout to bring in this barrierproperty.”
‘Quality development, sustainability and profitability should go hand in handʼ
‘Paper with suitable properties can definitely replace plasticsʼ
‘As the larger industries come in, they bring lower costs and better quality productsʼ
Mehali Papers Pvt. Ltd., says, “The scale of production is directly dependent on the cost of production and high-end technology. Some of the small and medium-scale industries might not be able to afford those and, that possibly is a bottleneck for them to give up the required quality in that product. A lot of factors need to be considered. In the past, there have been a lot of small paper mills in China and in the US that are being closed down and replaced by some of the largest mills in the world. As the larger industries come in, they bring lower costs and better quality products, so it becomes very difficult for the smaller ones to compete with them. However, I should add that there could be some advantages, like location which offers specific advantages for people in remote areas in India where they could use the agriresidue as fuel and that would be advantageous in times like today when the coal prices have shot up almost three times.”
Talking exclusively to Paper Mart, Ms. Fazilah Nathani says, “I would love to see more women participation in the paper industry. We do have a lot of women in the administration side of it, but I want to see them in the factory side and for that, I think, we as an industry should change our mindset and empower women.”
The first panel discussion was followed by a second panel discussion moderated by Mr. Ashraf Nathani, Managing Director, Mehali Papers Pvt. Ltd where many young leaders of the industry shared their interesting
journey in the paper industry. The participants were mostly the renowned suppliers of machines and technology to the paper mills.
‘There is going to be a lot of engineering and a lot of studiesʼ
other people are doing. That should be the solution in the paper industry, at least because of the competition, that we are facing now. Every manufacturer should focus on their expertise, what they can make.”
Mr. Amit Mistry, Managing Director, CAD Paper Machines Pvt. Ltd. said, “I see this journey of last 50 years as very memorable, a lot of learning in this and coming 50 years, which I see is going to be just as beautiful and as wonderful, as what the past has been. I would like to also add to this part that, it's not only past and the present which we're looking at but, we should also emphasize and focus on our future. There is going to be a lot of engineering and a lot of studies. Every mill is different and every idea is different. We are just looking ahead and we are seeing what best opportunities will come to us and we can give back.”
‘In the last three years, we have supplied a good number of headboxes in the marketʼ
Mr. Dipak Panchal, CE-Marketing, Honest Iron & Engineering Works added, “We have to focus on specialization on the making of certain types of machinery. In the last few years, we have been going on making all the things together and it is not the solution. We have to follow certain models like what other countries or
Talking about his journey, Mr. Kunal Rana, Managing Director, Micro Fab Industries said, “I joined Micro Fab in 2018 after completing my engineering. And then personally, I developed pressurized headbox. I saw a lot of potential in the market, and also we started doing some of the projects after that. In the last three years, we have had a good number of headboxes supplied in the market. And our main target was small and medium-scale industries, which were facing a lot of problems with their head boxes. So we developed a high-quality head box
‘We have to focus on specialization on the making of certain types of machineryʼ
basically for the kraft paper industry, which was the major potential market. Most of the mills in Gujarat are facing huge issues with their GSM range. We have started working on it, and we are also developing hydraulic head boxes.”
Saloni Sharma, Executive Director, Saloni Paper Machines Pvt. Ltd. added, “It has not even been two decades that we have been a part of the paper industry. Although short, the journey has been a rollercoaster ride. We never thought that we will be coming up as a manufacturer and supplier of the paper machine. We were basically the erectors - commissioning and installing the paper machines. Seeing the opportunity at Vapi, we thought to have a small workshop for the maintenance purpose of all the paper mill owners. Eventually, with the support and trust of all our valued customers, we have now started taking up turnkey projects. Till now, we have been giving machines to the kraft paper industry, from headbox to the rewinder for around 300 TPD capacity. If I talk in terms of speed, we have already commissioned 750-800 mpm machines, and are currently working on 1000 mpm machines.”
Elaborating on the milestones achieved by JMC Paper Tech Pvt. Ltd., Dr. Yesha Patel, CEO of the company said, “As our generation enters the pulp and paper industry, it's important for us to recognize the journey of our companies because they will influence our personal journeys in the industry as well. JMC started by supplying drying cylinders. And at the time, the idea of supplying a full-scale paper machine was just a distant dream for JMC. But not long after, JMC commissioned an 80 TPD kraft paper machine to Sripathi Paper & Boards Pvt. Ltd. in Sivakasi, making JMC's dream a reality. And now, almost 30 years later, we continue to break barriers and reach new heights as one of the leading paper machine manufacturers with the first-ever integrated pulp mill and paper plant with a capacity of 200 TPD. And this is just the beginning at JMC. Our strategy, while approaching future developments is to be critical, yet creative, curious, yet capable. JMC's journey toward the future includes innovations to increase energy efficiency within each step of the manufacturing process. Our focus remains on the development of energy-efficient technologies, research and development and digital transformation in
the paper machine manufacturing process. The area with the highest potential for energy efficiency improvements is the drying process, which accounts for about 70% of the total energy that's used for pulp and paper making. Research shows that there are three areas for innovation having high-efficiency potential.”
“First is the superheated steam; the superior heat capacity and thermal conductivity of superheated steam allow for higher drying rates, shorter process times, and more homogenous drying. The second is water removal without evaporation through using electric forces like electro-osmosis, this method would avoid the most energy-intensive part of the drying process leading to up to 90% energy savings during drying. And third is paper making without water. There is research being done to eliminate water from the pulping process, providing the potential to remove the use of heat for drying completely to increase energy efficiency. JMC has adopted several technologies with highefficiency potential, such as our new design steel dryers. The use of steel allows for higher heat transfer rates throughout the cylinder, leading to higher evaporation rates. This helps increase the production rate while reducing drying capacity. Additionally, steel dryers include grooving inside the shell, which allows for better conductivity and lower total energy consumption. Steel dryers provide a better and quicker response to any changes, which provides more efficient control, better quality, and better consistency of paper. JMC is also in the process of completing a hydraulic head box, which is designed for a high-speed modern paper machine with operating speeds above 500 meters per minute.”
‘We are currently working on 1000 mpm machinesʼMs.
‘The area with the highest potential for energy efficiency improvements is
the drying process, which accounts for about 70% of the total energyʼ
Mr. Mihir Mistry, Managing Partner of Scan Engineering said, “Engineering in the paper industry has come a long way from complete mechanical systems to sophisticated systems, which have more electronics in them. Scan engineering, as a manufacturer of equipment which enhances the productivity of the basic paper machine, also believes in that same value. We have installed CNC machines, and are continuously upgrading. We are moving from a conventional setup to a complete CNC workshop and we are also adding more and more products.”
‘Our vision for the coming years is to develop tech-
tapping new engineering methods of creating economical, better machinery, bringing something new to the table as we move ahead.”
‘Around 80% of our business is from the pulp and paper sectorʼ
Discussing the history and vision of the company, Mr. Keyur Panchal from Panchal Engineering Works, said, “We begin our industrial journey under the guidance of Ruby Macons. We were one of the first manufacturers to introduce an MG cylinder with a 12-foot diameter during a time of limited resources and untapped technology. Our vision for the coming years is to develop technology in waste management. As we all know, there's a lot of waste being created in paper mills. In the interest of generating a more sustainable and environmentally friendly procedure, this would be our main focus as a paper mill machinery manufacturer, another main focus, is to improve and advance the quality of paper by
Talking about the scope of robotics and automated guided vehicles in the paper industry, Mr. Ashish Chokhawala, Partner, CN Automation LLP, says, “Around 80% of our business is from the pulp and paper sector because we have been born and brought up in the paper industry. The sector has been a blessing for me.”
The panel discussions were followed by various technical sessions that can benefit the industry in terms of adopting new technologies, improving existing operations and investigating the value of specific technology tools.
‘Engineering in the paper industry has come a long wayʼ
“The quality of our paper board is well-accepted in the Domestic & Overseas Markets. Seeing the rising demand for our Paper Board, we have decided to come up with one more packaging board line soon,” says Mr. SVR Krishnan, Executive Director, Tamil Nadu Newsprint and Papers Ltd.
Today, bagasse has established itself as a well-known fibrous raw material for the Pulp and Paper industry. However, the situation was not always the same. Although the industry had recognized the advantages of bagasse long ago, setting up a newsprint manufacturing facility using bagasse was considered a high-risk and the project was not very successful commercially. However, Tamil Nadu Newsprint and Papers Ltd., (TNPL) took up the challenge of making Newsprint using bagasse as the primary raw material and became India's first bagasse-based Paper Mill at that point in time.
The Bagasse pulping facility was commissioned by TNPL in 1985. Over the years, it has perfected pulping technology, right from its storage to preservation of quality. Starting with an initial capacity of 90,000 tonnes
per annum (TPA) on a single Paper Machine to producing 6,00,000 TPA of Paper & Board, and serving 60 countries, TNPL has come a long way.
Recently, the company took up a Mill Expansion Plan (MEP) at Mondipatti in Tiruchirapalli which is to be implemented in two phases. The first phase of the project, covering the installation of a modern Hardwood ECF Pulp Mill along with a Chemical Recovery Island, has commenced trial production. Sharing the details about the expansion plan with Paper Mart, Mr. SVR Krishnan, Executive Director(Operations), Tamil Nadu Newsprint and Papers Ltd., says, “We commissioned the Hardwood Fiberline with a capacity of 400 TPD and a Chemical Recovery Boiler with a capacity of 950 TPD. All the Machineries have been procured from
reputed global suppliers. Besides these, Chipper, Chlorine Dioxide Plant, Oxygen Generation Plant, Recovery Boiler, Evaporator and Recausticizing were under Phase-I of the Project. The trial production in Pulp Mill was also commenced and stabilised.” Talking about the future plans, he revealed, “We are now embarking on the Mill Expansion Phase 2 activities, which will be an addition of 200,000 tonnes per annum packaging Board Plant.”
Tamil Nadu Newsprint and Papers Ltd., (TNPL) has a long history of prioritizing the sustainability of its business operations and the viability of its products. The company has commissioned a 300 TPD Deinking plant which added a new source of raw material — recovered Paper or used Paper — to produce pulp –Deinked Pulp (DIP).
“Currently, the paper produced in unit-I is a combination of Hardwood, Bagasse and Deinked pulp. Hence, our Papers are eco-friendly and have superior surface and strength along with consistent quality. We are a reliable and preferred Paper supplier from Tamil Nadu. As one of the integrated pulp and bagasse-based Paper Mills in the world, our products are an extension of our commitment to sustainability – in production and conversion processes with Innovation.,” Mr. Krishnan adds.
TNPL stands uncompromised when it comes to sustainable practices. To eradicate single-use plastics, the Company is working towards developing the base Paper for carry bags, straws and beverage cups etc., In a bid to positively impact the environment, TNPL practices water conservation with a vision to reduce any dependency on freshwater.
Talking about the market presence, he reveals, “Besides Tamil Nadu, we are supplying Paper to neighbouring states like Telangana, Andhra
Pradesh, Karnataka and Kerala as well. Our exports account for 18% to 20%. The Paper Board is also wellaccepted in the Domestic & Overseas Market and seeing the rising demand for our Paper Board, we have decided to come up with one more packaging Board line soon.”
The core competency of the company is its adoption of the latest technology and adaptation to sustainability for a Circular Economy Model. TNPL excels in the selection of the best-in-class contemporary technology, with a clear focus on delivered quality at competi-
tive cost combined with the lowest water and Energy consumption.
“Currently, we need to focus more on how to be flexible and agile on the manufacturing front and how to leverage the digitalization part of it. That will take the industry a long way. All along we all have been trained for looking “inward-out”, but now, the “outward-in” perspective is more important.
By “outward-in” perspective, I mean that we need to have the focus centered on the customer and then develop everything internally,” Mr. Krishnan concludes.
Tamil Nadu Chief Minister M K Stalin inaugurated TNPL Unit II at Mondipatti village in Tiruchirapalli district. The project was implemented at a capital outlay of INR 1385 crore.
The second unit of Tamil Nadu Newsprint and Papers Limited (TNPL) with state-of-the-art infrastructure was inaugurated at Mondipatti village in Tiruchirapalli district by Tamil Nadu Chief Minister M K Stalin. At a capital outlay of INR 1385 crore, the unit has a hardwood pulp plant with a capacity of 400 MT and a chemical recovery boiler with 20MWTG.
TNPL had proposed a Mill Expansion Plan (MEP) at a capital outlay of INR 2520 crore, to be implemented in two phases. While phase 1 has commenced its production, phase 2 consisting of the board machine would be taken up after financial closure.Themillwasabletoproduce good-quality pulp during the trials.
With unit II, TNPL aims to remain competitive by reducing its dependency on the import of hardwood pulp and the overall cost of production. The project will also create job opportunities for around 500people.
According to a statement released by the company, TNPL unit II has transformed into an integrated pulp andpaperboardmill.Theinauguration ceremony was attended by Mr. Gangadhar Bandi, IPS, chief vigilance officer, Mr. Nishanth Krishna (IAS), executive director, SIPCOT, Ms. E Sundaravalli (IAS), Managing Director, SIPCOT, Mr. SVR. Krishnan, Executive Director, and Dr. M Sai Kumar (IAS), Chairman and Managing Director, TNPLamongothers.
Saurav Deb: We restarted our plant on 23 August 2022 and started production on 5 October 2022. We are still streamlining and fine-tuning our processes to ensure that we give the best product to the market. After the modification, the production capacity of Nepa increased from 88,000 metric tonnes to 100,000 metric tonnes per annum. With the machines running at the optimum levels, the capacity might further go up.
Nepa Limited, regarded as the
first newsprint paper mill in India, was inaugurated in 1956. Situated in Nepanagar, an industrial township located in the Burhanpur district of Madhya Pradesh, Nepa Limited used to be the only newsprint production unit in the country. Closed in 2016; the mill resumed its commercial operations a few months ago. In an exclusive interview with Paper Mart, Commodore Saurav Deb (Retd), Chairman-cum-Managing Director, Nepa Limited talked about the revival journey and more.
Paper Mart: Tell us about the present status of Nepa and its new developments.
We would be taking about a month more to be operational at full capacity. Once the final trials are completed, on-the-job training would be given by the vendors who have supplied new machines and equipment. At present, we are manufacturing newsprint, and soon we plan to enter the writing & printing paper segment as well. We have a new de-inking plant and the paper machines are refurbished, modernized, and automated. Hence, I think, we can make a major mark in the writing and printing segment.
PM: Do you have any plans to add to your capacity soon?
SD: We have enough space and we might look at the expansion subsequently but right now, we are still taking baby steps. And I strongly believe when you take such a step, it should be a firm and sure-footed step. Currently, we are focused on meeting the market challenges and the competition. Till the time we don't settle down on that sort of strategy, we can't talk about adding new capacity. Moreover, it depends on the
“Paper is here to stay; it is an industry that can never die.”Commodore Saurav Deb (Retd), Chairman-cum-Managing Director, Nepa Ltd.
decision of the government. We have just come out of our revival plan.
PM: What challenges did you face during the renovation of Nepa? Also, talk about the bottlenecks of the industry.
SD: Our paper machines are old - one is of 1950s vintage and the other is of 1960s vintage, and that is a challenge. Another major issue that is being faced by the industry is the lack of skilled and experienced manpower. As
we are in the hinterland, it is more challenging for us to get manpower at the salary that we offer. Currently, we are trying to train local people. As the paper is a niche industry, the product depends on the process engineer. The non-availability of paper tech as a subject at a graduate level at many institutes has affected the industry. Other bottlenecks include the cost and availability of raw materials, chemicals, and steam. Being a government entity, we must go through the Government eMarket place and that makes the sourcing of raw materials more challenging at Nepa. We have been in dialogue with all our vendors to ensure that we get the best price. Today, we are purchasing raw materials at higher prices but we hope to have a definite improvement in the coming months. In the future, the energy crisis will also affect
the industry. We need to think of an alternate source of energy source.
PM: What opportunities do you see foresee for the paper industry?
SD: Paper is here to stay; it is an industry that can never die. Initially, the newsprint segment was facing a hurdle, but today it's picking up once again. People want to get up in the morning and want to hear the crispiness of the newspaper with a hot cup of tea. Though schools and colleges switched to virtual classrooms, they have now shifted back to textbooks.
If you see the other segments, whether paperboard or tissue - it is seeing an upward trend. Tissues were in huge demand during the COVID-19 times. Now that plastic is banned, the paper seems to be an eco-friendly alternative.
“ We have a new deinking plant and the paper machines are refurbished, modernized, and automated.
Headquartered in Lausanne, Switzerland, Vipa Group was founded in 1965 by Michel Ehrlich. Today, the group is based on two differentactivities:thecollection&sortingofallkinds of waste and the trading of recovered paper, prime paper, stock lots, other recyclable raw materials, and recycling services. With a pre-established market presence in Europe, the United States, India and Southeast Asia, Vipa Group handles more than 3 million tonnes of materials annually. The family-owned company is now managed by CEO Marc Ehrlich, son of Michel, who joined the company in the late 1990s. In an exclusive conversation with Paper Mart, Mr. Marc Ehrlich, CEO, Vipa Group, talks about the principal vision of the group, an overview of the recycled fiber industry,anoutlookontheIndianmarket,andmore.
Paper Mart: Please present the core philosophy and vision of Vipa Group. Also, briefly take us through the role of the organization and its contribution to the recycled fiber industry.
Marc Ehrlich: Vipa Group, a family-owned enterprise, was established by myfatherMichel Ehrlichin1965.Rightfromitsinitial beginnings,thegroup has been a purpose-driven organization. In view of the collection of paper fiber from waste streams, there should be an outlet and paper mills are considered to be appropriate outlets. However, more often than not, paper mills are in different places than the regions where the fiber is collected because the fiber can be found in highly populated places while the paper productionsitesareinremoteandsecludedareas.
Recently, India is becoming a production giant for the world. This has given risetothedemand forpackaging needs fortheproductsto beexported from India. Buttheproductsareactuallyconsumed inthewestand hencewasteis alsogenerated inthewest. Now,thereisadoubleimbalanceinthiscontext–firstly, the fact that the recycled fiber needs to reach its destination, for instance, India,andthesecondaspectisthetransport.Thecontainersfrom Asia totheWestern partof theworld areusually filled tocapacity but most of the containers are unoccupied while coming back. With the rising concerns over CO emissions, the containers, if shipped back empty to 2 Asia,would beatotalwasteof transportandotherresources. Hence, filling
the containers with recycled fiber is a very good way to addressthischallenge.
PM: Shed some light on the significant milestones and the key strengths of VIPA.
ME: In the beginning, Vipa Group was solely a trading company, which meanswe had tofind thespecific material forthecustomeralong with the best logisticsolutionas per therequirements. Subsequently,we'vetriedtoassesswhere we could bring additional value to other sectors. For example, since we are based in Switzerland, we discerned that it would be a great idea to start our own collection, sorting,and recyclingof paperdomestically. Inashortspan of time, we became the biggest recycling company, especiallyintheFrench-speakingpartof Switzerland.Since thisoperational model ispractical, wearedoing exactlythe same in another country where we have a substantial presence,i.e.,Greece.
In Greece, we have three recycling facilities and we aspire to expand further because we feel that recycling can be improvedinthiscountry,thinkingabouthowtoexpandto other businesses where we can bring value. A few years back, we started discussing with our customers and we realized that there was a need for them to export their products. Besides, Vipa had the right platform with best logistics, expertise on the products, and culture of internationalrelations.
PM: Give us an overview of the recycled fiber industry with respect to demand, price, trends, various challenges & opportunities globally, and also the perspective for the Indian market.
ME:Thefiberrecyclingmarkethasseenmajorupheavalsin the last three years due to the COVID-19 pandemic which hasdramaticallychangedconsumerbehaviour. Consumers used to largelydepend on physical retail for theirshopping needsbutthepandemicledtoasurgeine-commercedueto pandemic-induced restrictions and lockdowns. The consequence was such that there was an even greater need for packaging while lesser waste was collected since the retail shops and markets are adept in the waste collection but not the households. To sum up, there was a lack of availability of recovered paper while the packaging needs surged exponentially. This led to a distressing scenario where many paper mills lacked raw materials. We've seen oneof the mostdramaticincreases inpricesof wastepaper. ThesecondshockfortheindustrywastheRussian-Ukraine warwhichledtoaglobaleconomicturmoil.Theperception that recession would hit us while the exact opposite sentimenthappenedwiththesamepsychologicalexaggerations. In justafewdays,wesawthehighestpeak inpricesto oneofthebiggestfallswehaveseeninourhistory.
Now,we'vetofindanewbalancebetweenthecollectionof recovered paper and the subsequent use of recovered
“
paper by the paper mills. I think this balance will be reached somewhere in Q2 of 2023, when we would better understand the cycle we belong to for the next years. It is importanttoencouragethemassestomaketheireffortsin recycling at home so that any crisis in the paper industry and the recovered paper segment doesn't affect the households. Weshould continue to push to have fiberout of landfill and incineration because many countries have recycling ratesclose to 5-10 percentwhen there isa lack of resources,energy,andfiber.
PM: India relatively has a very low rate of recovery of waste paper as compared to other developed nations. Please suggest what could be some relevant strategies to increase the recovery rate in India.
ME: The only strategy that works is education. When the kids go to school, they learn how to recycle at home and persuade their parents to do the same. As long as the general public doesn't recycle, there is no infrastructure thatcan be helpful. If you paythe infrastructuretorecycle and the population is not recycling at home, then the investmentis idle. Thus, togetoutof this 'chickenand the egg' argument, you need to go step-by-step with pushing education. While this might take one generation more; it isnothingwhenyouthinkaboutthefuture.
In India, therearesomegood initiatives. A fewyears back, ITC was developing the 'Wealth out of Waste (WOW)' program. Similarly, in Switzerland, many years back, recycling was based solely in schools where the kids were takingthewastepaperfromtheirhomestoschool,andthe school was responsible to sell the waste paper. The funds generated while selling the waste paper were paid for the classes and excursions. It is quite heartening when a kid pushes forrecycling at home; this becomes the firstsocial step in his/her life as well as the first thing he/she can do for the community. In India, there are big cities as well as small villages; hence, the strategy cannot be the same for everylocation.
PM: According to you, what should be the strategy of papermillstoenhancetheir'sustainability'quotient?
ME: The global trend is to have large-scale paper
When the kids go to school, they learn how to recycle at home and persuade their parents to do the same. As long as the general public doesn't recycle, there is no infrastructure that can be helpful.
“The quality of our paper board is well-accepted in the Domestic & Overseas Markets. Seeing the rising demand for our Paper Board, we have decided to come up with one more packaging board line soon,” says Mr. SVR Krishnan, Executive Director, Tamil Nadu Newsprint and Papers Ltd.
Today, bagasse has established itself as a well-known fibrous raw material for the Pulp and Paper industry. However, the situation was not always the same. Although the industry had recognized the advantages of bagasse long ago, setting up a newsprint manufacturing facility using bagasse was considered a high-risk and the project was not very successful commercially. However, Tamil Nadu Newsprint and Papers Ltd., (TNPL) took up the challenge of making Newsprint using bagasse as the primary raw material and became India's first bagasse-based Paper Mill at that point in time.
The Bagasse pulping facility was commissioned by TNPL in 1985. Over the years, it has perfected pulping technology, right from its storage to preservation of quality. Starting with an initial capacity of 90,000 tonnes
per annum (TPA) on a single Paper Machine to producing 6,00,000 TPA of Paper & Board, and serving 60 countries, TNPL has come a long way.
Recently, the company took up a Mill Expansion Plan (MEP) at Mondipatti in Tiruchirapalli which is to be implemented in two phases. The first phase of the project, covering the installation of a modern Hardwood ECF Pulp Mill along with a Chemical Recovery Island, has commenced trial production. Sharing the details about the expansion plan with Paper Mart, Mr. SVR Krishnan, Executive Director(Operations), Tamil Nadu Newsprint and Papers Ltd., says, “We commissioned the Hardwood Fiberline with a capacity of 400 TPD and a Chemical Recovery Boiler with a capacity of 950 TPD. All the Machineries have been procured from
company has recently bagged a prestigious project from Abu Dhabibased Star Paper Mill Paper Industry LLC. In conversation with Paper Mart, Mr. Chaitanya Nighoskar, Managing Director, RC Paper Machines Private Limited talks about the journey, product portfolio, key projects, and gives his outlook on the Indian pulp & paper industry.
Paper Mart: Could you please present an overview of RC Paper Machines along with your product portfolio?
Established in 2000, RC Paper
Machines is one of the leading manufacturers and suppliers of pulp & paper machinery and related equipment. Over the past 23 years, RC Paper Machines has grown on the basis of good quality products and remarkable after-sales service. The
Chaitanya Nighoskar: Based in Saharanpur, Uttar Pradesh, RC Paper Machines is a renowned manufacturer and exporter of paper machines and paper machine equipment. We develop high-tech production systems and industrial process solutions. Our product portfolio includes components like headbox (open & air cushioned), wire part (double/triple/four fourdrinier), press part (jumbo presses up to 400 Kg linear loads), size presses (inclined and horizontal), calenders (single nip/double nip with crown control), doctoring systems (oscillating and air tube loaded), dryer sections, sizer kitchens, pope reels, rope feeding, auto tensioners, stretchers, approach
system equipment - centricleaners, chest agitators, stock pumps, pressure screens, power pack and control panels and bi-nip & tri-nip presses. Besides providing technical solutions to the industry, we also offer consultancy services to industrialists who plan to set up paper/board plants.
PM: Kindly cast some light on the infrastructure, machinery and manpower at your facility along with the USPs.
CN: RC Paper Machines has fully equipped in-house designing and drawing infrastructure with high end CAD & CAM facilities. We have a steel casting facility and a separate roll manufacturing division. Some of the prominent machines in our facility are lathe machines, VMC, CNC, plano miller, shapers, radial drill, pug cutting, plasma cutting machines, boring machines and portable grinders among others. With CNC machines, we assure good accuracy and precision in component-making. Talking about our USPs, we are known for our quality, efficiency, accuracy, and performance. We use highquality raw materials and offer turnkey solutions to the industry. Our team comprises experienced engineers and personnel, and this team meets frequently with a supervisory committee to review schedules, safety procedures, budgets and technical status. The overall strategy is to become the leading service and technology provider for all types of paper and pulp manufacturing processes.
PM: Share information about some of the prestigious projects executed by you?
CN: RC Paper Machines has delivered over 70 complete projects in the past 23 years. Apart from this, it has completed over 250 machine rebuilds, modifications or upgrades. A dominant player in Northern India, RC Paper Machines is a technology-centered company with global operations. We have recently been awarded a prestigious project by Star Paper Mill Paper Industry LLC, Abu Dhabi (UAE) to install a 400 TPD multiwire kraft paper mill with a finish deckle of 5200 mm. This project is undertaken by us on a turnkey basis & will be helpful for us in emerging markets of the Middle East & GCC countries. Apart from this, we have supplied 250 TPD machine in Nigeria and 70 TPD machine in Kenya.
Talking about the domestic market, we have supplied 400 TPD kraft paper machine around six years ago with a finished deckle size of 4900 mm to Paswara Paper Mills Ltd. It was the biggest machine of that time and had a speed of 400 mpm. We have also supplied tissue/specialty paper machine with a deckle size of 5000 mm to Shree Bhageshwari Paper Mills Ltd. Specifically designed for lower GSM ranges (1840 GSM), the high-speed machine had the sole plate centre of 5650 mm. We have also supplied an indigenously made pressurized headbox which was an alternative to Chinese machinery. Besides being more efficient, it was also more economical.
PM: Could you tell us more about the expansion plans and product range of Star Paper Mill Paper?
CN: This is a significant order for us. Star Paper Mill is expanding its existing capacity with an investment of AED 200 million in a 59,000 square metre site in KEZAD. The company is expected to manufacture recycled
“
RC Paper Machines has delivered over 70 complete projects in the past 23 years. Apart from this, it has completed over 250 machine rebuilds, modifications or upgrades.
kraft paper jumbo reels to be used to manufacture corrugated cartons and papers for carry bags. If all goes as planned, the new facility would have an installed capacity of 135,000 tonnes to manufacture recycled semi-kraft liner, white top liner, testliner, fluting and bag paper.
PM: Please name some of the other renowned clients you have served with your product range.
CN: Besides Star Paper Mill Paper Industry, Paswara Paper Mills, and Shree Bhageshwari Paper Mills, we have supplied machines to Krishna Tissues Pvt. Ltd., Disha Industries Ltd., Tehri Pulp & Papers Ltd., Gangotri Paper Millls Pvt. Ltd., Subam Paper Pvt. Ltd., Rana Papers Ltd., Maruti Papers Ltd., Mohit Paper Mills Ltd., Devrishi Paper Pvt. Ltd., Chandpur Enterprises Ltd. and many others.
PM: Share your outlook on the pulp & paper industry. Moving ahead, what would be your business roadmap?
CN: The paper industry has been rapidly evolving over the last two decades. The competition in global pulp & paper markets is intensifying. The pandemic and postpandemic eras have been particularly challenging and there is a growing need for modernization and energy-efficient technologies. RC Paper Machines has continued innovating and supplying state-ofthe-art machinery. It is our mission to expand our global footprint, support local operations, embrace the skill of emerging workforces and provide greater value & prosperity to the world.
“
We have recently been awarded a prestigious project by Star Paper Mill Paper Industry LLC, Abu Dhabi (UAE) to install a 400 TPD multiwire kraft paper mill with a finish deckle of 5200 mm.
Essity's mission to produce more-from-less drives an effort to integrate more “circularity” into its business: from responsible raw material sourcing to more efficient production with a smaller climate footprint. The latest example is its innovative project to convert agricultural residue into a bleached pulp and utilize it in high-quality tissue products. ANDRITZ is a technology partner in making this happen.
Essity's Mannheim mill is the company's largest tissue facility in Europe with a capacity of 283,000 t/a. The mill, which was founded in 1884 as a producer of packaging products, has a long and storied history. The mill has for decades produced sulphite pulp onsite, which is unique in its own right. Adding to its uniqueness, the mill has recently started up a new pulping process that will convert 70,000 t/a of regionally sourced wheat straw into 35,000 t/a of bleached pulp.
“Wheat straw pulping is certainly not new,” says Mr. Jim Haeffele, Essity's Vice President Technology, Material Breakthrough. “What is unique here is that this is the first large-scale use of bleached wheat straw for tissue production in the world.”
The wheat straw pulp is blended with the 220,000 t/a of long- and short-
fiber wood pulp to produce a full range of tissue and towel grades, including the company's Zewa brand which is a leading brand in Europe.
Tissue and towel products are manufactured on Mannheim's five tissue machines (four conventional and one TAD machine).
Sustainable Fiber Source
Essity signed a license agreement granting exclusive rights with an American company, Sustainable Fiber
Technologies (SFT). SFT developed a proprietary process (the Phoenix Process™) for pulping non-wood raw materials in a way that is environmentally friendly and delivers quality comparable to the wood-based pulp at a competitive cost. In this way, Essity can reduce its climate footprint and utilize a material formerly considered to be waste.
ANDRITZ has been working with SFT for a number of years, supplying equipment for SFT's pilot plant and some of the company's commercial applications. As Mr. Markus Pichler, Vice President for Mechanical Pulping Systems with ANDRITZ's Paper, Fiber and Recycling Division, explains, “We have done extensive lab trials with SFT for various alternative raw materials at our pilot plants in Austria and the USA. That has led us to exclusively employ the Phoenix Process for pulping non-wood raw materials.”
That is why it was a “natural choice” according to Mr. Martin Wiens, Factory and Project Manager for Mannheim's wheat straw plant, to select ANDRITZ to supply the main equipment.
This includes screening, cleaning, dewatering, chemical mixing, heating, bleach tower discharge, and refining
“By converting agricultural residue into high-quality bleached pulp, we become more circular and can offer our consumers a tissue product with less climate impact”, says Mr. Jim Haeffele, Vice President Technology, Essity.Image Credit: Essity.
systems. Mechanical installation, commissioning, and start-up supervision were also the part of the scope of supply.
“We have developed unique processing technology that does not exist anywhere else in the world,” Mr. Wiens says. “The design is based on the SFT/ANDRITZ pilot work and together we managed to go from concept to reality in a little over two years. That is really impressive!”
For the uninitiated, wheat straw is considered an “agricultural residue” –cellulosic material that remains in the farmer's field after a grain harvest. Up to about one-third of the residue can be tilled back into the field to maintain soil integrity, but what to do with the rest? A portion is used for such things as animal bedding.
Mr. Haeffele and his colleagues began discussions with SFT in 2017 because
“The raw material is so different from wood fibers that it behaves differently in every machine from what was expected. We had to confirm our assumptions about pulp properties and fiber development for each process step,” says Mr. Markus Pichler, Vice President for Mechanical Pulping Systems with ANDRITZ's Paper, Fiber and Recycling Division.
with our Phoenix Process has characteristics comparable to virgin hardwood pulp and superior to recycled fiber. The process uses significantly less energy, water, and chemicals than conventional wood pulping and is sulfur-free.”
“The design is based on the SFT/ANDRITZ pilot work and together we managed to go from concept to reality in a little over two years. That is really impressive!,” says Mr. Martin Wiens, Factory and Project Manager, Essity Mannheim mill
Essity was looking to secure wheat straw pulp to replace OCC due to instabilities in the recycled market at that time. “Unbleached wheat straw pulp was being produced at commercial scale primarily for packaging grades, but the more that we discussed the process with Mr. Mark Lewis (Founder and CEO of SFT) the more we began thinking about installing our own line for bleached wheat straw pulp,” he says.
Lewis was excited by the idea. “We looked forward to working with Essity and ANDRITZ to prove out the pulping and bleaching processes on a large-scale,” he says. “Pulp produced
The €40 million investment in the wheat straw plant was approved by Essity's board of directors in 2019 and construction began in May 2020. The plant started up in August 2021.
Project activities were performed in parallel, Mr. Wiens explains, to keep to an aggressive schedule. “We already had started erection while we were still finalizing procurement of some of the equipment such as piping, equipment, etc.,” he says.
As with virtually every project, there were daily surprises in erecting and starting up Mannheim's straw pulp plant. “This mill has been in existence since 1884 and in excavating the site chosen for the wheat straw plant, we found old foundations, tunnels, and other structures which had to be removed and filled in,” Mr. Wiens says. “Construction occurred during the hottest summer and the coldest winter that we had experienced in Germany in many decades. Just to add to the challenge, we worked through the COVID-19 pandemic as well. Throughout it all, we prevailed and ANDRITZ was a very professional and flexible partner.”
is not wood chips” In the run-up to the project, several trials for dewatering, refining,
bleaching and the mixing behaviour of wheat straw were conducted at ANDRITZ's fiber preparation pilot plants in Austria and the USA. Mr. Pichler of ANDRITZ notes, “We were of course familiar with the SFT process, but most of our trial work was at small scale. We needed to do extensive testing of the wheat straw to specify the correct machine sizing. We had to confirm our assumptions about pulp properties and fiber development at 100 t/d scales.”
“The raw material is so different from wood fibers that it behaves differently in every machine from what was expected,” Mr. Pichler explains. “We had to confirm our assumptions about pulp properties and fiber development for each process step.”
Straw pulp was shipped from SFT's pilot plant in the USA to Graz (Austria) to run dry-crepe and structured (TAD) tissue trials at ANDRITZ's PrimeLine Tissue Innovation and Application Center, the world's most modern tissue pilot plant. “This facility brings together customers, suppliers, and R&D institutes in a very special way to create solutions,” Mr. Haeffele says. “ANDRITZ's approach to R&D is very sophisticated and professional.”
Even with the trials and pilot plant work, there have been surprises –some positive and some challenging. “Producing bleached wheat straw pulp of tissue-grade quality is complicated,” Mr. Haeffele explains. “Achieving wood-like characteristics for brightness and drainage from wheat straw is not a simple matter. It sounds simplistic, but straw is not wood chips. It has been a learning curve for sure.”
One of the most positive learnings so far is that the wheat straw pulp has excellent strength characteristics. “We originally thought that it would be more of a hardwood replacement,” Haeffele explains, “but because of the high tensile characteristics, it is a suitable softwood replacement.”
The new cellulose made from straw is as soft, tear-resistant and highly absorbent as conventional cellulose
made from wood fibers. The pulping process uses less water, chemicals, and energy than wood fiber pulping.
A byproduct of the wheat straw processing at Mannheim is lignin (minus the sulfur that is present in wood-based lignin which is produced via standard pulping technologies) that is valuable as a feedstock to produce biopolymers. These biopolymers can replace oil-based chemicals in dust abatement, corrosion inhibitors, binders, feed, cement additives, and other speciality chemicals.
“This fits our more-from-less philosophy completely,” Wiens says. “We don't waste anything. We take what used to be agricultural waste and make tissue. From the byproducts, we could even make the packaging for our products – bio-based, biodegradable, compostable, and recyclable. This is a real circular economy.”
In developed countries, there is significantly more agricultural biomass available than wood biomass. In Europe, Essity estimates there exist about 15 million tonnes of wheat straw each growing season.
Mannheim is receiving its raw material from about a 300 km radius around the mill, the same radius that they source their wood fiber, according to Wiens. “Since this is a new fiber
source for us, and since the fiber procurement is done once per year, we had to develop our own infrastructure for the centralized purchasing, gathering, storage, and transport of wheat straw,” he says.
The mill keeps about 1500 tonnes (5day supply) at the mill site. The remaining supply is stored at special facilities nearby.
“There are many benefits to this project in terms of having an alternative fiber source that meets our sustainability ambitions while reducing our climate footprint and improving our cost efficiency,” Mr. Wiens says. “Adding to our existing expertise in processing sustainable wood-based fresh fiber and recycled fibers, our growing expertise in processing alternative fibers gives us much more security and flexibility in sourcing. This will allow us to capitalize on fiber availability and pricing in the future.”
“Globally, half of all straw goes unused,” Mr. Haeffele adds. “By converting agricultural residue into high-quality bleached pulp, we become more circular and can offer our consumers a tissue product with less climate impact. Mannheim is showing that there is an alternative way to produce tissue. The world needs alternatives to meet the increasing consumption demands in developing countries.”
Haber is a well-known provider of automated AI-
driven solutions which helps in bringing accurate and real-time insights, enabling the industries in their process management activities. In interview with Paper Mart, Mr. Felix Sahayaraj, Vice President – Sales, Haber, shares how the sizing process can be improved by eLIXA®. Further, he explains how Artificial Intelligence (AI) has the potential to optimize chemical consumption while discussing thepossibilitiesautomationbringsforthtothepulpandpaper industryasawhole.
Paper Mart: To start off our interaction, could you shed some light on the sizing process?
Felix Sahayaraj: Sure. As we all know, sizing refers to the method by which additives are introduced to the pulp stock to improve the water-repellency of the paper produced. External sizing done at the size press influences the end product quality by varying the sheet strength, which is improved by controlling the resistance of paper to stress or penetrationbyliquids.
With, Haber's eLIXA®, we use Artificial Intelligence (AI) & Machine Learning (ML) to optimize the process, helping to achieve Wax Pick, Cobb Values, and other target properties withminimalfluctuation.
PM: Take us through the eLIXA® platform and its key advantages.
FS: eLIXA®'s platform provides real-time AI/ML-based closed-loop control catered towards optimizing the surface sizing of the paper. Key process variables like starch solids, starch viscosity, pH, temperature, and the surface size addition rateare measured and uploaded to thecloud in real time. The big dataanalysis iscarried out in thecloud and the closed-loop control ensures that sizing and strength propertiesaremaintainedwithinthetargetrangeatalltimes. Thus, the implementation of AI/ML through eLIXA® can optimizethisprocessand result ina marked improvement in thequalityof thepaper. Infact,atoneofourcustomers, itwas able to reduce their surface starch addition from 4% to 3.2% withnochangeinstrengthproperties.
PM: So, can we say that automation is the next step in improving process performance?
FS:Yes,absolutely! Havinggrownandadaptedovertheyears, itisimportantweembraceIndustry4.0. –real-timemonitoring and communication between machines which will reducetheworkload on human labourwhichcan bedirected towards tasks of higher importance. The automation of repetitive tasks would also aid in improving the overall effectivenessofprocessesintheindustry.
Data-driven decision-making and actions carried out with the implementation of AI ensure accuracy in decisions and timely action to improve system performance and endproduct quality. It has the potential to transform the entire industry,rightfromthesourcingof rawmaterials,tothestage ofdeliveringtheendproducttothecustomers.
“Data-driven decision-making and actions carried out with the implementation of AI ensure accuracy and timely actions to improve system performance and endproduct quality.”
Designer, Manufacturer & Exporter of Testing Equipments
Bursting Strength Tester
Microprocessor Based
Manual Sheet Former with Table
Basis Weight Valve
Tensile Tester (Vertical) Microprocessor Based
Photovolt Brightness Tester with Printer
Palm Sensing Assembly
Pneumatic Die Punch Cutter
Digital Stiffness Tester
Photovolt Type Brightness
Opacity & Gloss Tester (Microprocessor Based )
SPS Tester (Bendsten)
Technibrite Type Brightness (Opacity Color Tester)
Digital Ply Bond Tester
C-506, Gurushikhar Apartment, Post-Bilwa, Jaipur-302022, (Raj.), India
www.paptechengineers.com / www.paptechinstruments.com follow us: @paptechofficial
Incorporated in 1995, Best Paper
Mills Private Limited is a manufacturer of machine-glazed kraft paper, used in manufacturing corrugated boxes and packaging material for industrial, consumer, and agricultural products. The company's two units in Vapi (Gujarat) have a combined capacity to produce 170,000 tonnes of kraft paper per annum. In a conversation with Paper Mart, Mr. Prince Shah, Director, Best Paper Mills Private Limited, talks about the journey, product portfolio, and his outlook on the Indian pulp & paper industry.
Paper Mart: To begin with, could you please give us a walkthrough of the business journey of Best Paper Mills?
“It is our endeavour to add another 100,000 MT of volume to our existing capacity by setting up another kraft paper plant. Consistent growth and improvement to further set a 'best'-in-class standard in the industry is and would continue to be our prime area of focus for the future.”
Prince Shah: Best Paper Mills Private Limited is a third-generation of a family-owned business engaged in manufacturing recycled kraft paper based out of Vapi, Gujarat. In 1997, we started with a humble capacity of producing 40 MT a day. It is through the business acumen, hard work and strategic decisionmaking of our promoters Mr. Keshavji Shah, Mr. Ramesh Shah and Mr. Ketan Shah, that today we are the largest manufacturers of kraft paper in Western India with an annual capacity of producing 170,000 MT. We are growing towards a better tomorrow; the core strength of our business is sustainability. We recycle, reuse and reproduce kraft paper. We understand the pulse of this industry - whether it pertains to our suppliers, dealers, customers, or end consumer; there is a reason why we call ourselves 'Best'.
PM: Shed some light on the unique strengths of your product range.
PS: Kraft paper can be easily recycled, reused, and decomposed completely. As a result, kraft paper is widely utilized in numerous packaging applications, including envelopes, bags, sacks, composite cans, pouches, cartons, etc. The majority of the paper we produce is used for making corrugated cartons, paper bags and core pipes. We are able to suffice our customers' requirements completely with our broad product category from producing 16 to 35 BF range and 115 to 250 GSM range. We believe in continuously upgrading ourselves - be it our machinery, human resources or our after-sales support to clients.
PM: Could you please outline the recent developments at Best Paper Mills?
PS: The paper industry today is very different from what it used to be. Even a few years ago, there used to be an equilibrium between demand and supply. Today, we see a massive oversupply due to a large number of mills expanding and new mills coming into foray. The paper industry is facing turbulent times. It is the
need of the hour to have an innovative approach to our business. As an organization, we have taken steps to keep up with new technological advancements in our product quality. Rather than competing with one another, we have set new goals to expand our horizons and grow in international markets.
PM: What is the market footprint of your company? What, according to you, are the key trends driving the growth and demand in the coming times?
PS: We established our first plant in the year 1997 and added another one in 2003. Our plants together have a combined capacity of 550 MT per day. Although we are located in the western belt of India, we supply all over the country and in international markets as well.
The growing usage of compostable and sustainable packaging materials owing to the increasing awareness regarding the detrimental impact of plastic and other non-biodegradable variants is primarily propelling the growth of the Indian kraft paper market. Furthermore, the escalating
demand for highly technical saturated kraft paper in the construction sector to meet unique needs related to countertop, partition, and flooring applications is acting as another significant growthinducing factor. Apart from this, the expanding utilization of kraft paper in the e-commerce industry for packaging solutions on account of various associated benefits, such as folding resistance, toughness, and high-strength compression performance, is further augmenting the market growth. Moreover, the rising focus of the Indian government authorities on banning the use of plastics is also creating a positive outlook for the kraft paper market across the country.
For instance, in June 2022, the Central Pollution Control Board (CPCB), a federal agency under the Ministry of Environment, issued a list of steps to be taken to prohibit the use of specific single-use plastic products.
Numerous other factors, such as the inflating popularity of kraft paper in the printing and publication sectors and the introduction of advanced packaging solutions are anticipated to stimulate the Indian kraft paper market. We expect to grow our capacity and market reach hand in hand with the industry.
PM: What are your future plans?
PS: The Indian kraft paper market reached 8.50 million tonnes in 2021. It is expected that the market will reach 14.49 million tonnes by 2027, exhibiting a growth rate (CAGR) of 9.3% during 2022-2027. There is tremendous potential to grow in the kraft industry if we keep performing consistently. It is our endeavour to add another 100,000 MT of volume to our existing capacity by setting up another kraft paper plant. Consistent growth and improvement to further set a 'best'-in-class standard in the industry is and would continue to be our prime area of focus for the future.
Established in 2013, Shripaper Product (Indore) Private Limited is one of the leading paper manufacturers in Central India. The company produces kraft liner and coloured kraft paper in the 18-28 BF ranges and is known for its excellent quality and timely delivery.
“Quality is our first commitment and we do not compromise on this. We plan to set up a machine with a finished deckle size of 4500 mm in the second unit,” says Mr. BD Patel, Managing Director, Shripaper Product (Indore) Private Limited
Talking to Paper Mart about the journey and expansion plans, Mr. BD Patel, Managing Director, Shripaper Product (Indore) Private Limited said, “Located in Pithampur, Shripaper has been producing high BF and high RCT papers for almost ten years. We produce paper from indigenous and imported raw materials and have pulp machine, headbox and dryers from wellestablished suppliers that help us produce superior-quality papers. Quality is our first commitment and we do not compromise on this. We are about to set up the second unit at the same location. In the second unit, we plan to set up a machine with a finished deckle size of 4500 mm.”
He added, “Besides a good market presence in Madhya Pradesh, we also ship our products to different states including Maharashtra and Rajasthan. From packaging requirements to supply chain, we minutely check every angle of our paper-making process. We might expand our business and enter into the plyboard business soon. While the industry is facing various challenges at the moment, I am sure that good times will come soon. With schemes like 'Make in India' and the export scenario, the country's GDP is likely to grow by 7% in FY23. Every product that is exported needs to be packed; hence, there are endless opportunities for the kraft paper segment.”
Located in the industrial area of
Pithampur in Madhya Pradesh, Incohub Papers Pvt. Ltd. has an installed capacity of 250 TPD, and currently achieving a production level of around 150 TPD. While Incohub Papers was incorporated in 2016, the production started two years ago. It manufactures paper in the range of 150-250 GSM and 18 to 28 BF which is suitable for carton and box production. Talking to Paper Mart about the infrastructure and market footprint of the company, Mr. Virendra Patel, Managing Director, Incohub Papers Private Limited said, “Incohub Papers has a double wire plant and machinery procured from DS Pulp and Paper. The finished deckle of the machine is 4.2 meters. Parason Machinery delivered the entire pulp mill section, while all wire part sections were imported from Germany. With Parason Confiner CR-45 and an experienced team of technicians, we are able to manufacture paper of superior quality and ship to various states including MP, Rajasthan, Chhattisgarh and Maharashtra.”
“With the ban on single-use plastics, the demand for paper has increased. To meet the rising demand, we plan to increase our production by 50 TPD and produce 200 TPD from 2023,” said Mr. Virendra Patel, Managing Director, Incohub Papers Private Limited
“Incohub Papers has installed a wastewater treatment plant which was procured from Ishan Paryavaran Pvt. Ltd. The company has also installed a 12-tonne boiler from Industrial Boilers Limited. The company has invested approximately INR 60 crore in this project,” Mr. Patel added.
Talking about the future plans, he said, “With the ban on single-use plastics, the demand for paper has increased. To meet the rising demand, we plan to increase our production by 50 TPD and produce 200 TPD from 2023. Paper has a bright future and the industry will witness growth in the coming years.”
“After India imposed a ban on single-use plastics to tackle the country's increasing levels of plastic pollution, the opportunity for kraft paper has substantially increased, especially in the packaging industry,” says Mr. Parag Patel, Director - Marketing, Skywin Paper Industries Private Limited
Located in Surat and spread across 20 acres, Skywin Paper Industries Private Limited started its operations in 2021. The company has a capacity of 250 TPD and manufactures kraft paper for corrugation boxes in the 100-400 GSM range and 16-32 BF range.
Talking to Paper Mart about the infrastructure of the company, Mr. Parag Patel, Director - Marketing, Skywin Paper Industries Private Limited said, “We have taken pulp machinery from Parason and customized paper machine from reputed global suppliers having finished deckle size of 4250 mm. Effluent treatment is from Krofta Engineering Ltd. We produce high-quality and odour-free papers that are suitable for FMCG and pharmaceutical industries. Our primary raw material is imported waste paper. In the near future, we might introduce paper in lower GSM ranges and set up a duplex board plant. We rely on Finor Piplaj Chemicals for water treatment and ensure that there is zero liquid discharge. We have technically qualified staff and that is our strength.”
Revealing more on the idea behind establishing the mill, he added, “After India imposed a ban on single-use
plastics to tackle the country's increasing levels of plastic pollution, the opportunity for kraft paper has substantially increased, especially in the packaging industry. People's inclination towards the e-commerce sector has acted as a catalyst in this growth. Witnessing this trend, there are many new entrants. However, one has to be competitive, qualitative and service-oriented to remain in the industry.”
SPRAYING SOLUTIONS
AN ISO 9001:2015 CERTIFIED COMPANY
Prioritising Top-Notch Quality & Reliability.
Wire online cleaning (Actual Picture)
Dryer Screen Online Cleaning (Actual Picture)
OURPRODUCTS:•SHOWERS•OSCILLATORS•SPRAYNOZZLES•WEDGEFILTERS•ROBOCLEANERS
Compound33/16,Site-2,IndustrialArea,HindonAirForceLoniRoad,P.O.-MohanNagar,Sahibabad,Ghaziabad-201007UPIndia Contact:09810636863,09899889855,09910320682,09999070778|E-mail:rahul_basra21@rediffmail.com,spraying.solutions@gmail.com, Info@sidhuindustries.com,sanjivbasra03@gmail.com|Website:www.sidhuindustries.com
Amrit Papers Private Limited
has been a paper trading company since 1989, with offices in Indore, Bhopal, Delhi and Ahmedabad. The company supplies various types of paper including newsprint, writing & printing papers & packaging boards. A dealer and distributor for various paper mills, Amrit Papers is all set to put up a kraft manufacturing unit in the Dhar district, around 91 km away from Indore, with a capacity of 350 TPD.
“We plan to manufacture kraft paper between 1835 BF range. In the future, we intend to produce paper in the 40 BF range as well,” said Mr. Satish Dave, Executive Director, Amrit Papers Private Limited
Talking to Paper Mart about the infrastructure and the product range of the upcoming mill, Mr. Satish Dave, Executive Director, Amrit Papers Private Limited said, “We plan to manufacture kraft paper between 18-35 BF range. We have the pulping section from Voith, paper machine from Saloni Paper Machines, ETP from Krofta Engineering, QCS & DCS from Valmet, and rewinder from The Globe Radio Company. We are going to start our production in this financial year. In the future, we intend to manufacture paper in the 40 BF range as well.”
When asked what convinced them to come up with the kraft paper plant Mr. Manoj Bahety, Director added, “During the COVID-19 pandemic, the writing & printing segment suffered but it picked up quickly. However, the packaging industry which is the kraft paper segment performed well even during the pandemic due to people's inclination towards the e-commerce sector. According to the estimates, the packaging segment is witnessing a year-on-year growth of 22-25 percent.”
Om Sree Papertek Private
Limited is a kraft paper manufacturing plant based out of Hyderabad. It manufactures around 300 tonnes per day (TPD) of kraft paper ranging from 120-250 GSM and 18-35 BF. Talking to Paper Mart about the technology, Mr. Hardik Patel, Director, Om Sree Papertek Private Limited said, “The twin-wire installed gives us an edge over others in terms of technical parameters like good ply-bond and high RCT paper. We are catering to the entire south India and intend to give a new dimension to the paper industry by catering to the specific needs of corrugators. We make high BF kraft papers that are well-accepted in the market.”
“Currently, we are producing 9,000 tonnes of kraft paper per month, and our target is to scale it up to 12,000 tonnes by the end of 2023”, says Mr. Hardik Patel, Director, Om Sree Papertek Private Limited
“We have recently launched a new shade of paper which is predominantly for packaging of white goods such as refrigerators, TV and laptops. The product is getting good traction in the market. Currently, we are producing 9,000 tonnes of kraft paper per month, and our target is to scale it up to 12,000 tonnes by the end of 2023,” he added.
Om Sree Papertek has a presence in Goa, Kerala, Maharashtra, Andhra Pradesh, Telangana, and Tamil Nadu. When asked if the company is willing to expand in the other parts of the country, Mr. Patel said, “In the kraft paper segment, it is very difficult to market your product beyond a point because the freight is a concern. Hence, we want to restrict to South India as of now. However, if we get an opportunity, we might think of establishing a unit in the northern part of the country to cater to other states.”
Elaborating on the opportunities and challenges of the industry, Mr. Patel
said, “The paper industry promotes sustainability by recycling. With every tonne of paper that we recycle, we save around 370 gallons of water. The future of the paper industry is bright and I encourage young entrepreneurs and large corporates to invest in this sector and make it more organized. At present, the market is in turmoil. The Russia-
Ukraine war and the volatility in the market have put pressure on our costs and supply chain. As India imports most of its waste paper and hence, worst affected. Overall it is a tough situation right now. While the next six months are challenging; the market scenario is expected to improve thereafter. There is light at the end of the tunnel!”
“The company manufactures copier paper under the brand name 'Ecomate' and we are currently focusing on the brand development strategies,” says Mr. Ram Srinivasan, General Manager-Marketing, Danalakshmi Paper Mills Private Limited.
Established in Tamil Nadu in
the year 1982, Danalakshmi Paper Mills Pvt. Ltd. is a recycled paper plant capable of producing 150 TPD of various grades of paper such as MF white varieties, colour wove, newsprint, MG kraft and poster varieties. Talking about the mill and its recent developments, Mr. Ram Srinivasan, General ManagerMarketing, Danalakshmi Paper Mills Private Limited said, “We are an FSC-certified mill with experienced operational team and quality control as well. The company manufactures copier paper under the brand name 'Ecomate' and we are currently focusing on the brand development strategies.”
Elaborating on future plans, Mr. Ram Srinivasan added, “We already have a state of art double loop deinking plant installed from Andritz, and are having plan to commission it by the end of this financial year. Surface sizing operation is also on the cards.” When asked about his outlook on the paper industry, he replied, “The industry is in turbulent times and is going through a lot of ups and downs. Due to uncertainty, people are not able to take decisions. Even on the raw material front, we don't know if the prices would increase or decrease in the coming times. However, I hope that the coming year would be better and we can expect market consolidation after the pandemic.”
Ram Srinivasan, General ManagerMarketing, DanalakshmiPaper Mills Private
Limited
“
“The future of the paper industry is bright and I encourage young entrepreneurs and large corporates to invest in this sector and make it more organized.”
Bell Multi Kraft is one of the leading manufacturers of kraft liner boards in west India spread over 65,000 sqm. Equipped with state-of-the-art production lines, the company offers kraft liner, test liner, and fluting in 140-250 GSM ranges & 18-35 BF ranges.
Talking to Paper Mart about the journey of the company, Mr. Kishan Kaila, Managing Director, Bell Multi Kraft Private Limited said, “Incorporated in 2018 and situated in Morbi, Bell Multi Kraft had the initial capacity of around 250 TPD but now we are achieving the capacity of 300 TPD. In the beginning, we faced trial issues pertaining to quality. Gradually, we were able to improve in each and every aspect. We are already in the process of installing a hot disperser system in our plant to improve our quality.”
Apart from the paper and board, the Group is into diverse sectors including duplex, ceramics tiles, sanitary wares, and laminates. Their sister concern company - Bell Impex - is also a provider of paper machines and industrial products.
“We have supplied paper machinery to various mills such as Apollo Paper Mills, Golden Yellow Paper, Spento Papers India, Edicon Paper Products, and Lemit Papers,” he added.
Elaborating on the opportunities and challenges in the paper industry, Mr. Kaila concludes, “Many mills are coming up; there is going to be a growth in the production of paper as well as the competition in the market. However, at present, price fluctuation is the biggest challenge in the paper industry. We need to stick together in this tough period and better days will come soon.”
“Many mills are coming up; there is going to be a growth in the production of paper as well as the competition in the market,” says Mr. Kishan Kaila, Managing Director, Bell Multi Kraft Private Limited
HenanJingxinFabricTechnologyCo.,Ltd.,foundedin2011,isoneprofessionalmanufacturerandtechnicalservicerofpaper machineclothingandchemicalproductsforpulpandpapermills.
Initspapermachineclothingproductionbase,factoryhas33000squaremeters,annualproductioncapacitycanget 1000000sqm.JingxinfabricʼsformingfabricallusedtheGerman“Perlon”brandhighqualityimpomonofilament,andDryer screenwillusedPortugal“Filkemp”brandmono-filament.InJingxin,toproducehighqualityproducts,weintroducedthe mostadvanced5setsSwedenTEXOfullyautomaticrapierloom,14.5metershotsettingmachine,16metersGerman Jürgensweavingmachine,AustrianWISfullautomaticseamingmachine,etc.
ThecoreproductsforpapermachineclothinghasFormingFabric,DoubleWarpFlatWireDryerFabric,SingleWarpFlatWire DryerFabric,SpiralDryerFabric,PlainWeaveDryerFabric,SludgeDewateringFabric,etc.
Initspapermakingusedchemicalproducts productionbase,factoryhas44000squaremeters, annualproductioncapacitycanget400000tons.
ThecoreChemicalproductsare:SurfaceSizingAgent GS,SurfaceSizingAgentWS,WetStrengthAgent,Dry StrengthAgent,Defoamer,etc.
JingxinmanagementhaspassedISO9001qualitymanagementsystem,ISO14001environmentalmanagementsystem,ISO 18001occupationalsafetymanagementsystemcertification.
Duetothereliableproductquality,theproductssellwellalloverthecountry,andhavereachedlong-termcooperative relationswithmanylistedpapercompaniesinChinaandthepulpandpapermillsfromRussia,India,Vietnam,Pakistan,Iran, Indonesia......morethan15countries.
Tel.:+863945228866
Mobile:008618838386818
Fax:+863945106388
E-mail:info@jingxincorp.com
HENANJINGXINFABRICTECHNOLOGYCO.,LTD
Website:www.jingxincorp.com
SHENQIUNORTHINDUSTRYZONE, HENAN,CHINA
“As the government has imposed a ban on single-use plastics, people are getting inclined towards paper bags. We are trying to get into lower GSM ranges and targeting 70 GSM odourfree paper,” says Mr. Mahesh Gandhi, Director (Tech), Tirumala Venkateshwara Paper & Board Private Limited
Established in 2009, Tirumala Venkateshwara Paper
& Board Private Limited is a Hyderabad-based mill with a capacity of 65 TPD. Talking to Paper Mart about the mill's journey, Mr. Mahesh Gandhi, Director (Tech), Tirumala Venkateshwara Paper & Board
Private Limited says, “We started with 15 to 20 TPD of kraft paper production and have now reached the capacity of 65 TPD. Although we have grown over the years, the location of our mill doesn't allow us to go beyond a particular capacity. Hence, we are trying to create a niche wherein now, we are manufacturing paper of lower GSM ranges, i.e. fluting medium of 80 GSM. As the government has imposed a ban on single-use plastics, people are getting inclined towards paper bags. We are trying to get into even lighter varieties and targeting 70 GSM odour-free paper. We also have plans to put up a barrier coating plant.”
Talking about the corrugation sector, Mr. Gandhi says, “Over the last 15 years, corrugation has undergone a huge change. Earlier, it was dominated by semi-automatic and manual plants and now, it is dominated by automatic plants. And hence consistency in quality parameters, runnability have become more important quality aspects for any kraft paper mill.”
Sharing his outlook on the paper industry, he adds, “Paper is the most sustainable material and has a bright future. However, at present, there's a global recession. As India seems to be less hit by the recession, the domestic market seems better than the export market. Things will be better in the coming times. Let's keep our fingers crossed!”
Established in 2012, KKT
Shakti Hitech Private Limited is one of the leading manufacturers and exporters of water ring vacuum pumps and systems. Talking to Paper Mart, Mr. V Narsinga Rao, Director, KKT Shakti Hitech
Private Limited said, “KKT Shakti Hitech has an experience of more than 35 years in designing, manufacturing and installing vacuum pumps. Since 2012, we have established ourselves in the Indian market and replaced almost all other make vacuum pumps in the country with their energy-efficient models. It is our pride to say that as of today, we are the single largest & biggest capacity vacuum pump producers in India in cone design.”
“Currently, we are producing vacuum pumps, having a 3 capacity of 600 m per minute and 20,000 CFM which is biggest vacuum pump in India” said Mr. V Narsinga Rao, Director, KKT Shakti Hitech Private Limited
Elaborating on the features, he added, “the internal design is entirely different from others, though the outside features are the same. Due to this, we have an edge over others. Currently, we are producing vacuum pump, having a 3 capacity of 600 m per minute i.e. 20,000 CFM.”
“At present, we have a good market footprint, and are planning to further expand across the country.
Considering the present scenario, power is the main criterion as the vacuum pump is power-consuming equipment. We are developing and changing some internal designs by which the customers should get the benefit out of it with the power efficiency,” he concluded.
“Ecosure has successfully installed more than 150 machines. We have fourteen plants running and very soon, we aim to finish another six,” says Ms. Kritika Tripathy, CEO & Co-founder.
Ecosure Pulpmolding Technologies Limited offers sustainable solutions to produce in-house pulp fiber from non-wood resources using chemicalfree patented technology & to produce molded fiber pulp products. Talking to Paper Mart about the company's background and achievements, Ms. Kritika Tripathy, CEO & Co-founder, Ecosure
Pulpmolding Technologies
Limited said, “The journey of the company began in 2016 when we had collaboration with a Chinese company called BST. With time, we planned to completely turn into an Indian company and that is when we started Ecosure. Since 2019, Ecosure has been in the market and we have successfully installed more than 150 machines. We have fourteen plants running and very soon, we aim to finish another six.”
Elaborating on the product range and USPs, she added, “We are the first company to bring a machine that is completely made in India. There are companies who are either making machinery in India by bringing in some parts from China or refurbishing the machines brought from China. However, in our case, every part is
coming in from India and it is getting fabricated in-house. Starting from 2019 till now, we have been offering semi-automatic machines and recently, we launched fully-automatic machines in India. We have already received the order for 34 such machines in India.”
When asked about the future plans, she revealed, “We are getting into pulp mill also and very soon, Ecosure will have its own set up in Goa and in Noida running. We will be manufacturing paperware products. The paperware plant will act as a demo plant. We don't intend to sell products but to show the entire production process. Our primary focus continues to be on machines.”
Speaking on the opportunities and challenges of the industry, Ms. Kritika Tripathy said, “There is a need for pulp for the paperware manufacturing sector, which can be fulfilled by the paper mills. The paper mills should cater to this upcoming demand of pulp for the paperware sector.”
“At Ecosure, we keep on re-investing by investing into building infrastructure and further product developments,” she concluded.
PAPER ONE SHOW
“Biodegradable and compostable products are the future. It is important to save the Earth!” says Mr. Tapas Kumar Das, Director –Marketing, Fomex Group.
Established in 2012, Gujarat-based Fomex Group is a
manufacturer of high-quality recyclable and biodegradable products catering to both domestic and international markets. Brimming with the zeal to establish the epitome of client satisfaction and to achieve excellence with every effort, Fomex Group has three established business units – Fomex Packaging, Fomex PetPack, and Fomex PulpPack – each catering to various dynamic needs of the market.
Elaborating on the product development process and infrastructure, Mr. Tapas Kumar Das, DirectorMarketing, Fomex Group said, “We manufacture biodegradable tableware from sugarcane pulp. The fully automatic reciprocating tableware machine is mainly applied for producing pulp molding one-time-use tableware, premium egg packaging, medical care items, highend industrial packaging products and so on.
Reciprocating system provides uniform distribution of raw material. Because of hot-pressing - the surface of the product becomes smooth. Auto trimming can give a better edge to the products. Also, our products are oil and waterproof.”
Talking about the recent developments and future plans, Mr. Das added, “We would soon be coming up with some exclusive products wherein we might also introduce different industrial packaging molds. Currently, we are the only suppliers to Pizza Express for customized products. We have recently developed some products which are used in pregnancy and COVID-19 tests. Apart from that, we are the only company to manufacture coloured bagasse products in the Indian market, though around 80 percent of our products are exported. By 2025, the company is targeting revenue of INR 500 crore.”
“Biodegradable and compostable products are the future. It is important to save the Earth!” he concluded.
Robo Cleaners - an advanced cleaning system by Sidhu Engineering Works - has been developed for the cleaning of the wire and felt part of the paper machine. Until now, the manufacturer has installed 35 systems which stands testament for the effective performance of the cleaning system.
Apaper machine performs three major functions through its different sections - formation of sheet/dewatering of the pulp sheet (wire part); pressing of the paper sheet (press part); and drying of the paper sheet (dryer part). All these functions require some kind of a belt structure to carry the pulp sheet to move forward to other sections. The formation of pulp sheet from pulpiscarriedoutbywirewheredewateringonwire(forming fabric madeof polyamide). Thepressing of thepapersheet is performedonthepresspartwherethefeltisusedforpressing and absorptionof waterand thedryerpart forthepressing of the web firmly with the dryer to enhance the heat transfer withthehelpof SLDF(CFM).
Although these fabrics require periodic cleaning, in case of pressand wire part, there iscontinuouscleaning iscarried out with conventional showers. These conventional showers use ample amounts of water for cleaning the wire and press sections.Thereareafewsolutionsforthecleaningof SLDF but these are very costly and less effective. With the current increaseintheuseoftheOCC/recycledfiber,theimportanceof cleaningisbecomingmoreandmoreimportantbecauseof:more finesgeneration;stickiesformation;andothercontaminants.
An advanced cleaning system has been developed by Sidhu Engineering Works. The Company has already been providing solutions for wire and felt cleaning with the Robo Cleaning system. So far, they have installed 35 systems, wherein the Company claims that they were are able to decrease water consumption drastically and were able to increaseimproveCDmoistureprofile.
The recently developed SLDF cleaner - Robo Dryer Screen Cleaner - is being used successfully on many machines. It is continuous and advanced machinery which is one-of-itskindandapioneering'MadeinIndia'product.
RoboCleanershavearoboticheadwhichoscillatesinalinear manner. We've tweaked thedesign of the robotic head in the Robo Cleaners with several nozzles and a different open area in the same head. A jet from nozzles hits the SLDF with high pressureandsimultaneously, thevacuumsucksthecontaminants and removes these from the system. An air knife is also providedforenhancedcleaning.
In case of wire and felts showers being in continuous or intermittently operational, the conventional showers enable the paper mills to maintain the normal operative conditions and in meeting the optimum process levels. Due to the inadequatecleaningof SLDF,anumberof problemscanarise suchas - stickies, deposits, etc. whichcan lead topapersheet breaks. On the other hand, with SLDF Robo Cleaners, the cleaning is much better, resulting in the reduction of paper breaks. Thus, this eventually reduces the downtime in production and achieves the maximization in production levels. Furthermore, the bettercleaning outcomes also paves wayforbetterdryingrates.
To sum up, there are several advantages offered by the Robo DryerScreenCleanerssuchas:
l Reducingthecleaningtimeandofflinecleaning.
l Tremendous increase in the life of the SLDF due to the
enhancedcleaningof theSLDF.
l Reduction in the steam consumption as the CFM remains asdesignedandsuppliedbythemanufacture.
l Increase in the evaporation rate of the moisture in the papersheet.
l There will be lesser breaks on the paper machine in the dryerpartsinceallthestickiesandothercontaminantswill beeradicatedoutof thesystem.
Robo Cleaners will provide all the aforementioned benefits and havingaveryhighpaybackbecausethesteameconomics will be betterwhich implies thatanyunwanted expensesdue to improper cleaning wouldn't arise. In addition, a new fuel policy - regarding the use of unapproved fuels - is being implemented in Delhi-NCR, around 150 paper mills are affected by it. Thus, it becomes imperative to use the maximum amount of heat from the dryer since the cost of steamhasincreased.
Established in 2013, CN
Automation LLP was founded by Mr. Ashish R. Chokhawala and Mr. Arshad Nathani to explore industrial applications using automation with the core intent of contributing to the advancement of pulp and paper industry. The Company is engaged in providing turnkey EPC solutions to the pulp and paper industry in the area of electrical and automation systems. In an interview with Paper Mart, Mr. Ashish R. Chokhawala, CoFounder & Director, CN Automation LLP, talks about their journey, product portfolio, expertise in developing process-centric solutions, and the future roadmap.
Paper Mart: Could you please present an overview of CN Automation - the business journey,
specializations, and some notable accomplishments?
Ashish R. Chokhawala: CN Automation LLP was established in 2013. In the following year, we started commercial operations in Pardi, Gujarat, which is situated in the vicinity of Vapi - regarded as an engineering hub for pulp and paper machinery.
I, along with another new-generation technocrat - Mr. Arshad Nathani (ExDirector, M/S Ruby Macons Ltd.), went on to establish the Company with the aim to provide value-added and cost-effective automation solutions to the industry. Previously, I was the partner for M/S Kinetic Engineering Systems. Mr. Nathani was engaged in the machinery division of Ruby Macons which was into the manufacturing of value-
added and highly precise consumable components of various equipment such as - screen baskets, rotors, internal parts of suction rolls and other peripheral equipment of paper plant and machines.
On the other hand, my experience has been in supplying automation solutions to various industry segments, namely pulp & paper and plastic processing. Having a vast experience in design and know-how of manufacturing processes, Kinetic Engineering had supplied a number of rugged and reliable low-cost systems to the pulp and paper industry through Ruby Macons Ltd. Thus, we have a collective experience of more than 35 years in machinery manufacturing and automation business. Our venture - CN Automation has never looked back in terms of achieving excellent growth since the very beginning.
To date, we have provided automation solutions, ranging from micro to mega-scale, to reputed paper mills, namely, Mehali Papers, Shah Paper Mills, Binjusaria Papers, The South India Paper Mills, Binjusaria Papers, etc. At CN automation, we are specialized in providing turnkey automation solutions to the pulp and paper industry.
PM: Talk about your expertise in creating highly efficient and productive automation solutions and machinery for the pulp and paper industry.
ARC: Since both partners have achieved exponential growth in the pulp and paper industry, we have developed our own unique understanding and expertise of pulp processing and operations of paper machines. Across our entire product portfolio, we've developed many modular small to medium and large-
scale automation solutions to optimize the performance of various processing equipment and plants such as:
l Air cushioned/hydraulically pressurized headboxes, coarse screening, fine screening, pulping system, high-density cleaners, deinking cell, disperser, refiners, steam & condensate system, press section operation, size press and size kitchen, pope reel, twin drum rewinder with or without break generator.
l Medium to large-scale plant-wide automation solutions based on the DCS system for Mehali Papers, Shah Paper Mills, NR Agrawal Industries Ltd., Binjusaria Papers, The South India Paper Mills, and many more to come viz. Shree Ajit Paper Mills Ltd., Kuantum Papers; Nigeria, Uniglobal Papers.
l Sectional drives solutions to Mehali Papers, NR Agrawal Industries (Unit 5; Wire Part), The South India Paper Mills Ltd., Binjusaria Papers, etc.
PM: What are the strengths of the product portfolio of CN Automation? Since process efficiency is core to profitability, how do you design process-centric solutions which can achieve process optimization for pulp and paper manufacturers?
ARC: CN Automation has established its reputation for supplying systems which performs satisfactorily and ensures trouble-free operations. Presently, we've been working in the direction of providing turnkey EPC solutions to the pulp and paper industry in the area of electrical and automation systems.
We are using devices made by leading brands like Siemens, ABB, Phoenix,
Mitsubishi, etc. for the development of all our automation solutions. As a matter of fact, we don't make any compromises in the selection of components for the design of control panels. Also, we abide by European standards for the programming and documentation of our solutions, leading to minimize downtime for the end customers. This has helped in keeping the rate of service inquiry calls to a minimum level.
One of our major USPs is the understanding of process applications thoroughly which enables us to develop value-added solutions that are long-lasting and highly efficient. For instance, in our solutions of sectional drives, we use a common DC bus with 12 pulse application. This helps in maintaining the level of 5th and 7th-order harmonics to almost at par or lesser than the standards of various electrical institutions.
PM: What is the future roadmap of CN Automation?
ARC: We are in the process of development and integration of multi-axes robots and robotic applications for material handling systems. Further, we are looking forward to imparting to the development of finished goods handling using automated guided vehicles with artificial intelligence. These kinds of solutions will be quite helpful in large capacity mills having a variety of product grades of higher volumes.
We would like to emphasize that we've been consistently growing in our business. By adopting the latest state-of-the-art technologies and with continuous development of our automation solutions range, we would continue to strive to scale new heights and grow gracefully.
“We make energy efficient and maintenance free pulp stock pumps and process pumps for paper and allied industries,” says Mr. K L Narayanan, Chief Executive, Abirami Engineering Company.
Abirami Engineering Company
is in the field of pump manufacturing for more than two decades. The Company will be celebrating its silver jubilee year in the year 2024. They manufacture centrifugal pumps for water, chemical, pulp stock, slurry, petrochemicals, etc.
Talking to Paper Mart, Mr. K L Narayanan, Chief Executive of Abirami Engineering Company said, “We make energy-efficient and maintenance free pulp stock pumps and process pumps for paper and allied industries. We have supplied pumps to more than 350 paper
companies in India and are exporting to more than 20 countries. In India, around 50% of the paper industries are using Abirami Pumps.”
“Our pumps are known for their heavy-duty, energy efficiency and reliability and user-friendliness. Development is a continuous process for us. Recently, we have launched underwater submersible pumps of different RPMs up to the capacity of 150 HP that can handle any liquids, i.e. pulp, paper and sludge. Apart from this, we also have leak-free pumps with special design,” added Mr. Narayanan.
“We have recently implemented 100 TPD-project in Angola and 80 TPD-project in Sri Lanka,” says Mr. Hareram Pandit, Consultant, Amit Paper Consultants and Engineers.
Established in 2013, Amit Paper
Consultants and Engineers is engaged in the manufacturing and export of a wide range of paper & board machines ranging from 10 TPD To 400 TPD. The company supplies a customized range of stock prepara-
tion equipment, paper machine equipment, tissue paper-making machines and kraft paper-making machine, etc.
Sharing a brief history of the company with Paper Mart, Mr. Hareram Pandit, Consultant, Amit Paper
Consultantsand Engineers said, “Initially, we started our journey with trading of machines but soon, we set up our own manufacturing unit in Ahmedabad where we are continuously expanding our production. We provide complete end-to-end turnkey solutions for the paper industry and have
implemented around 11 projects abroad. Recently, we have implemented 100 TPD-project in Angola and 80 TPD-project in Sri Lanka. Besides these international projects, we have also signed a contract with Chennaibased Nandi Paper Industries Private Limited to supply paper machine with
the capacity of 200 TPD.”
“In India, a project takes around 12-14 months to get completed while it takes 6 months in other countries. Our experienced team has a proven track record when it comes to the erection and commissioning of plants,” he concluded.
“We will continue to expand our market position in future by developing innovative and market drive products and services”, says Mr. Guna Sekaran, Regional Director - Marketing, Risansi Industries Limited
Risansi Industries Limited is headquartered in the promising industrial city of Kanpur, India. The company develops, manufactures, and globally markets progressive cavity pumps, magma massecuite pumps, and online blind / actuators for delivering low to highly viscous, aggressive & abrasive media. With a wide network of branch offices and agencies, the manufacturer is currently being represented successfully in more than 10 countries.
For more than 42 years, Risansi has been offering optimum and economical solutions based on low life-cycle costs, to its customers across the chemical, paper, food, petroleum, mining, sugar, distillery, and numerous other industries. India has an inherent advantage of low-cost technological advancements which are being replicated through in-house research & development by experi-
enced engineers, resulting in innovative product designs that differentiate Risansi from the competition.
Mr. Guna Sekaran, Regional Director - Marketing, Risansi Industries Limited shares with Paper Mart, “Mr. Vipul Agarwal founded the company in 1979 after graduating as a Metallurgical Engineer (B.Tech) from the Indian Institute of Technology, Kanpur. He was the first to introduce 'Progressive cavity pumps', in the sugar industries in India. And the Company commands 90 percent of business in the domestic sugar market as of date. Risansi Industries Ltd. has an expertise in providing fluid handling solutions that are techno-economical to a wide range of industries including pulp and paper.”
He further added, “We entered in the paper industry around 15 years ago
and supplied our pumps to several mills in pan-India for various applications. Our vision is to provide optimum & cost-effective pumping solutions; products customized to the client's need; service network, and technically the best of quality-driven products to our clients.”
Risansi Industries Ltd. offers the installation of requisite pumping solutions for moving pulp slurry to be fed into the wet end of the paper-
forming machine. During the dilution process whereby, water is added to the pulp slurry to make a thin mixture and distribution of fiber slurry uniformly over the width of the paper sheet to be formed, the Risansi Highflow progressive cavity pumps play a pivotal role.
Mr. Guna Sekaran, again says that “There can be various companies but the quality & after-sales service of Risansi Industries cannot be com-
pared with others. We manufacture tailor-made pumps for various industries including sugar, distillery, sludges, effluent water treatment, dairy, cattle feed, and chemicals industries. Continual improvement of the products based on customer feedback is the policy of the Company. We will continue to expand our market position in future by developing innovative and market drive products and services.”
“Carl Bechem Lubricants offers specialty lubricants for the wet and press section and dry-end processes that involves high-alkaline water exposure, high-temperature areas and high load conditions,” says Mr. Kaushik Trivedi, Business Manager - Special Lubricants, Carl Bechem Lubricants India Private Limited
Carl Bechem Lubricants India
Private Limited develops a wide range of specialty lubricants for various industries including automotive, food processing, cement, steel, textile and paper etc. The German multinational company manufactures highperformance greases and oils for paper processing applications.
Talking to Paper Mart about the products specifically for the paper industry, Mr. Kaushik Trivedi, Business Manager - Special Lubricants, Carl Bechem Lubricants India Private Limited said, “Paper processing is one of our core segments in which we have more than 80 customers across India. In
paper processing, presence of alkaline water, heavy loads, chemical exposure and high temperature areas are the biggest challenges for lubricants. Carl Bechem Lubricants offers specialized products for all the critical applications starting from wood processing, pulp and soda recovery and paper machine.”
“In recent times, we have been focusing more on providing solutions for applications where high waterresistant grease is required against conventional lubricant, for example, wet and press section in paper machine. Apart from that, we have urea-based, high temperature resistant greases which are an excellent solution for hightemperature applications,” he added.
An upcoming media company, Tulip 3P Media brings out publications for different B2B verticals. Theactivitiesofthecompanynowembraceeventsandmarketresearchaswell.Tulipiscurrently on its way to further expanding its publication portfolio through publications for other business verticalsandarichofferingofothernichemediaservices.
“We have introduced the Yearly Extended Care (YEC) pack for our customers, where we take care of the equipment, the laboratory, the calibrations and the preventive maintenance,” says Mr. Vishal Malhotra, Director, Presto Stantest Private Limited.
From a humble beginning in 1983, Presto Stantest Private Limited has become one of the leading testing instrument manufacturers in the Indian subcontinent. The company is known for its innovation, perseverance and close attention to customer needs. Presto Stantest has its own manufacturing plant and three units for manufacturing of testing instruments with latest technology.
Talking to Paper Mart about the company, its product portfolio and USPs, Mr. Vishal Malhotra, Director, Presto Stantest Private Limited said, “We manufacture laboratory testing equipment for packaging, corrugation, flexible packaging industries and have a very comprehensive range for the paper industry. Our laboratory equipment is equivalent to the European brands. All our machines are computer compatible and some of them are even IoT driven. We are using the latest technology at one-tenth the cost of European brands and that's our biggest USP.”
Elaborating on the recent developments and future plans, he added, “We have launched two new modelsone is a box compression tester (HMI model) and the other is a fully-
automatic bursting strength tester (HMI model). 'Profitable box code' boom was launched by us last year to create knowledge and value for the paper and packaging industry. Also, we have introduced the yearly extended care (YEC) pack for our customers, where we take care of the equipment, laboratory, calibrations and preventive maintenance, so that they are able to focus on their work. The last experience center which we opened was at Ahmedabad. Our next target would be opening an experience centers in Chennai and Hyderabad. In total, we would be opening about 12 experience centers across the country. We want to be closer to our customers and serve them in a more effective manner.”
Presto Stantest was conferred with the National Award for quality products by the government of India in 2017. The company was also featured in the Outlook magazine for being one of India's top 10 test and measurement instrument manufacturers.
Sharing his views on the paper industry, Mr. Malhotra said, “The paper manufacturers have to look at how they can improve their quality and increase their efficiency.
Innovation is one of the key things they need to focus on.”
“Manufactured using advanced technology, our products are known for their user-friendliness, durable finish standards, high operational efficiency, longer service life and low power consumption,” says Mr. MK Agarwal, CEO, Global Engineering Corporation.
Mr. MK Agarwal, CEO, Global Engineering Corporation
Global Engineering
Corporation manufactures and supplies quality testing equipment used in pulp, paper, printing, packaging, converting, and other industries. It has a wide gamut of machines consisting of paper testing instruments, printability
testers, environment testing instruments, pulp testing instruments, plastic testing instruments, corrugated testing equipment and packaging testing instruments.
Talking to Paper Mart about the company and its future plans, Mr. MK Agarwal, CEO, Global Engineering Corporation said, “We are a designer and exporter of quality control and process control machines. Our vision is to become a prominent player in quality testing equipment. We are committed to total customer satisfac-
tion through continuous improvement. Apart from this, we deliver products at a very economical price. Manufactured using advanced technology, our products are known for their userfriendliness, durable finish standards, high operational efficiency, longer service life and low power consumption. Currently, our turnover is around INR 30 crore and we are aiming to make it INR 50 crore.” Sharing his views on the industry, he added, “Many paper mills are ignoring quality control and that is a big issue. The paper industry should focus on quality.”
The NovaTech Automation Process Solutions business will be integrated to Valmet's Automation Systems business line. The acquired business specializes in process control and optimization solutions for batch, continuous and hybrid processes.
January3,2023
Valmet has completed the acquisition of the US-based NovaTech Automation's Process Solutions business. The acquired business specializes in process control and optimization solutions for batch, continuous and hybrid processes.
The NovaTech Automation Process Solutions business will be integrated to Valmet's Automation Systems business line. The acquired business will be included in Valmet's financial
reporting for the first time in Valmet's first quarter 2023 financialreporting.
"The acquisition was completed as planned and we are very happy to welcome the new colleagues as well as the former NovaTechprocesssolutions'customerstoValmet.Theacquired business complements our automation offering well, bringing new synergies and opening the opportunity to serve both companies' current and future process automation customers with a wider offering," says Emilia Torttila-Miettinen, President, AutomationSystemsbusinesslineatValmet.n
Paperex South India 2022, held from 23-25 November 2022, witnessed the participation of 165 leading exhibitors from 5 countries. The event was organized by HYVE INDIA Pvt. Ltd. in association with Indian Agro & Recycled Paper Mill Association (IARPMA).
Held from 23rd to 25th
November 2022, Paperex South India 2022 was inaugurated by Mr. Nandikeshwaran, South India Kraft Paper Mills Association, and Chairman & Managing Director, Vishnu Paper Products Pvt. Ltd. in presence of various eminent personalities in the paper industry.
The 6th edition of Paperex South India 2022 was a great success with the support of all major industry associations, and the participation of
165 exhibitors from 5 countries. Organized at Chennai Trade Centre, India, the event was organized by HYVE INDIA Pvt. Ltd. in association with Indian Agro & Recycled Paper Mill Association (IARPMA). The prestigious sponsor of the event was Saloni Paper Machines. The event provided paper manufac-
turers with an opportunity to explore new technology, machinery & equipment and raw material for paper & board manufacturing. Also, the mass audience of paper traders, printers, publishers, converters and paper packaging companies came together to explore the vast variety of papers & paper processing technolo-
gies at the show.
A high-level concurrent Conference on “Indian Paper Industry: PostPandemic Growth Prospects” was also organized by IARPMA and an Open Seminar on “Paper, Corrugated Packaging & Printing: Rapid Industrialization & Sustainable Development”.
ANDRITZ will deliver high-consistency (HC) pulping, high-density (HD) cleaning and deflaking for processing the special type of broke.
December1,2022
Sappi Austria Produktions GmbH & Co KG has ordered key components for a new broke handling system from ANDRITZ for its mill in Gratkorn, Austria. The broke handling will be part of the production line PM9 producing high-quality wet-strength paper, such as label paper in the future. ANDRITZ will deliver high-consistency (HC) pulping, high-density (HD) cleaninganddeflakingforprocessingthespecialtypeofbroke.
Specific trials on pulping and deflaking of wet-strength paper were conducted at the ANDRITZ stock preparation pilot plant in Graz, Austria in advance. The trials were carried out with comparable raw materials from Sappi and confirmed the pulp properties and operating characteristics required by Sappi for thefuture.Start-upisscheduledforthethirdquarterof2023.
Talking about the development, Mr. Flavio Froehli, VP Marketing & Sales at Sappi Europe says, “We are very pleased that we will also be able to produce wet-strength label paper at ourGratkornmillinthefuture.Thisinvestmentunderscoresour strategy to establish Sappi as the leader within the label sector,
adding to the supply of value-adding products across our entirebusiness.”
SappiAustriaispartoftheSappiGroup,aleadingglobalprovider of sustainable wood fiber products and solutions, in the fields of dissolving pulp, printing papers, packaging and specialty papers, castingandreleasepapers,biomaterialsandbio-energy. n
Indonesia-based Sinar Mas will set up a paper manufacturing unit in Raigad district's Dherand village. The project will entail an investment of INR 20,000 crore in two phases.
December01,2022
The Maharashtra government has allotted 287-hectare land for an INR 10,500-crore project by Sinar Mas Pulp & Paper. One of Indonesia's largest conglomerates, Sinar Mas Pulp & Paper, would be setting up a paper manufacturing unit in Dherand village in the Raigad district. The project will entail an investment of INR 20,000 crore in two phases. The land allocationpaperswerehandedovertothecompanyofficialsby Chief Minister Eknath Shinde and Deputy Chief Minister DevendraFadnavisinMumbai.
According to a press statement issued by the State government, the Indonesian company will invest another INR 10,000 crore in the second phase after the investment of INR 10,000 crore in the first phase. Chief Minister Eknath Shinde further said that all kinds of facilities and support would be provided bythegovernmenttothecompany.
The project is expected to generate around 7,000 direct and indirect jobs. Meanwhile, around 600 hectares of land in the same district has been earmarked for the second phase. State
Industries Minister Uday Samant said that the flow of investment is increasing in the State and MoUs of around INR 40,000 crore would be signed in the coming days. He also added that special status has been given by the State government to the SinarMasproject.n
The supply comprises key stock preparation and fiber recovery equipment, Toscotec's patented TT SAF® DD (Short Approach Flow System with Double Dilution) for superior energy efficiency, and two OPTIMA 2200 slitter rewinders.
Gayatrishakti is entering the tissue market with this new line slated for start-up in 2024.
December16,2022
Gayatrishakti Tissue, a subsidiary of Gayatrishakti Paper & Boards Ltd. (GSPBL) has ordered a complete AHEAD 1.8 tissue machine from Toscotec for its mill in Vapi, Gujarat. The Indianmanufacturerisenteringthetissuemarketwiththisnew line slated for start-upin 2024. Established in 1996, it has a head office in Mumbai and three manufacturing facilities with a combined installed capacity of 300,000 MTA in Vapi & Sarigam GIDC,Gujaratstate,India.
The AHEAD 1.8 tissue machine has a sheet trim width of 2,850 mm, an operating speed of 1,800 m/min, and production of over 35,000 TPA. It features Toscotec's best-in-class drying configuration including an upgraded design shoe press TT NextPress, a third-generationdesignTT SYD SteelYankee Dryer andahigh-efficiencyTTHood.
The supply comprises key stock preparation and fiber recovery equipment, Toscotec's patented TT SAF® DD (Short Approach Flow System with Double Dilution) for superior energy efficiency, and two OPTIMA 2200 slitter rewinders.The service package includes erection supervision, commissioning, training programs, YESCONNECT-VISION Augmented Reality on remote assistance system, and start-up support.
Talking about the development, Mr. G.N. Agarwal, Managing Director, Gayatrishakti Paper & Boards, says, “We selected Toscotec because we wanted to invest in state-of-the-art tissue-making technology. We value their solid experience in guiding and sharing their expertise with newcomers in tissue.
Gayatrishakti is a well-established board manufacturer in India and based on our strong background in Paper and Board, we understand the importance of choosing the right partner for thisnewmarketentry.”
Mr. Marco Dalle Piagge, Sales Director of Toscotec, adds, “Toscotec is committed to providing Gayatrishakti with firstclass support to ensure their successful penetration of the Indian tissue market. Thanks to Voith's global presence, they canalsobenefitfromlocalservicesofferedbyVoithPaperIndia. With this new project, Toscotec strengthens its presence in Southeast Asia where we received two new orders of complete tissuelinesin2022.”n
Toscotec will design the new line to operate with a gas turbine that produces the electricity and the steam required for the mill.
Saudi Paper Group has placed an order with Toscotec for a second tissue line for its Dammam facility in Saudi Arabia. The new AHEAD 2.2L machine (PM5) will be a full-on turnkey project and it follows Toscotec's supply of a complete AHEAD 2.2S line that is currently undergoing erection at the same tissue mill. The start-up of PM5 is scheduled for 2024.
The new AHEAD 2.2L line has a sheet trim width of 5,600 mm, a maximum design speed of 2,200 m/min, and a production capacity of over 60,000 tonnes per annum (TPA). Designed for superior performance and energy efficiency, the tissue machine is equipped with TT NextPress upgraded design shoe press, a third-generationdesignTT SYD SteelYankee Dryer, and high-efficiencyTTHood.
The scope also includes two OPTIMA 2600L slitter rewinders devised to preserve bulk and softness while ensuring optimal windingperformance.
In order to guarantee superior energy efficiency, Toscotec will design the new line to operate with a gas turbine thatproduces the electricity and the steam required to meet the mill's needs. A full-service package with detailed mill engineering, erection, training, commissioning, and start-up assistance completes Toscotec'sturnkeysupply.
In the words of Mr. Yousseri Abdel Hamid Abdel Aziz El Bishry, CEO of Saudi Paper Group (SPG), “Progressing on the path of strong expansion we have set for SPG, we selectedToscotec for this second tissue line, because we value both their ability to deliver first-in-class technology and their proven history of
successfullymanagingcomplexturnkeyoperations.”
About the partnership, Mr. Alessandro Mennucci, CEO of Toscotec, says,“AtToscotec, we strongly believe in partnerships as the basis for success. Therefore, we look forward to continuing our close partnership with Saudi Paper Group. AsToscotec's fourth tissue order in the fast growing Middle Eastern region, this major project represents the perfect opportunity to strengthen our market leadership as supplier of turnkey tissue projects.” n
The association between Naini Papers and Valmet has been quite longstanding and the new order further strengthens their partnership.
January11,2023
Mr. Pawan Agarwal, Managing Director, Naini Papers Limited, has announced on LinkedIn the signing of an agreement with Valmet for the supply of a Speciality Paper Machine.The order is for a Brownfield paper project coming up inUttarakhand.
Naini Papers has a long-standing relationship with Valmet. In 2022, Naini Papers and Valmet signed an agreement for the supply of the headbox and a service agreement for improved machine efficiency, etc. With the new order, the association between the paper manufacturer and the technology supplier isfurtherstrengthened.
Naini Papers Limited, which was started in 1995, is one of the few leading paper manufacturing facilities in India with a production capacity of 120,000 tonnes per annum. The papermaker offers high-quality writing and printing papers
with improved physical and optical properties. Naini is a leading player in producing single-layer cup stock (for making papercups)andsaturatingkraft(formakinglaminates). n
The board machine at Lemit's mill manufactures whiteback and grayback coated duplex board in a basis weight range of 200-450 g/m2.
January12,2023
Lemit Papers, one of the largest and finest quality duplex board manufacturers, has started its commercial production of the board production line in Morbi, Gujarat. The board line,atthenewGreenfieldsite,hasaproductioncapacityof450 TPD.
In September 2022, the trial production on the board production line commenced while the actual production began in December 2022. The board machine at the mill produces whiteback coated duplex board and grayback coated duplex 2 board in a basis weight range of 200-450 g/m. It has a productioncapacityof160,000TonnePerAnnum(TPA).
Asinformedinarelease,LemitPaperprocuresRecoveredPaper (RCP) for the unit's feedstock domestically and from the USA, Europe, and the Middle East, says Mr. Jayesh Patel, Chairman, LemitPapersLLP.
The board line was provided by China-based Qinyang Pingan Light Industry Machinery. Moreover, France-based Kadant Lamorthaddevelopedtheintegratedpulpproductionlineand approach flow system and the automation system was
deliveredbyValmetGlobalfortheboardunit.
Mr. Patel added that in addition to serving the domestic packaging sector, the output of the board production line will also be considered for exports to the Middle East, Europe, Africa,theUSA,Bangladesh,andVietnam. n
The upgradation project of Andhra Paper for the cooking, fiberline and evaporation plant at its Rajahmundry unit is scheduled to take place in December 2023.
January12,2023
Andhra Paper Ltd., one of the largest integrated pulp and paper manufacturers in India, has selected Valmet to rebuild the cooking, fiberline and evaporation plant of its Rajahmundry unit, Andhra Pradesh. The order is scheduled to take place in December 2023 while the start-up is planned for thefirstquarterof2024.
The order is included in Valmet's orders received for the fourth quarterof2022-23.Thevalueoftheorderwillnotbedisclosed.
Speaking about the rebuild project, Mr. NageswaraGadde,Vice President, Project of Andhra Paper Ltd., says, “With this investment, we will be able to improve our cost competitiveness and profitability as well as increase production at our Rajahmundry mill. In line with Andhra Paper's commitment to sustainable development, the processes will be based on the best available technology and the use of state-of-the-art
equipment, such as Valmet TwinRoll press and Valmet Tube Evaporatoreffectwithventcondenser.”
In the words of Mr. Varun Jain, Director – India Region, Valmet, “Valmet's excellent references and continuous drive for technical development convinced Andhra Paper that the solution proposed will help them meet their goals.The aim is to increase the pulp production while reducing the chemical and waterconsumptionandtheeffluents.” n
Around 90,000 square meters of land in Jubail 2 would be used to produce tissue jumbo rolls and other related paper products.
January6,2023
Crown Paper Mill has acquired 90,000 sq m of land in Jubail 2, for building a paper complex to cater to future needs in Saudi Arabia. The land would be used to produce tissue jumbo rolls and other related paper products. The new paper machine, with an annual production capacity of 65,000 MT jumbo roll, will be in operation during the last quarter of 2024.
The mill houses one of the most advanced de-inking plants that convert waste paper into industrial high-quality tissue paper.
Established in 1996, Crown Paper Mills LLC (CPM) is a producer of jumbo tissue paper rolls.The mill covers a total area of 50,000 sq m, with an annual production capacity of 100,000 metric tonnes. Headquartered, in the Industrial city of Abu Dhabi (ICAD), the mill's “Prime Quality” Jumbo Rolls come in various grades such as facial, toilet, kitchen towel, napkin, C-fold, and carriertissue.
All high-quality tissue grades are produced from the highest virgin pulp grade sourced from all over the world. Since its inception, the mill has built a reputation for producing worldclasstissuepaperfromthehighest-gradevirginpulp. n
The closure of Canfor's Prince George Pulp and Paper will bring in a reduction of 280,000 TPA of market kraft pulp. While the speciality paper facility would sustain its operations.
January13,2023
Vancouver-based Canfor Pulp Products Inc. is going to permanently shut down the pulp line operations at its Prince George Pulp and Paper Mill. This closure will result in a reduction of 280,000 Tonnes Per Annum (TPA) of market kraft pulp. However, the speciality paper facility at the site will continuetooperate,aspertheirofficialrelease.
Mr. Kevin Edgson, President and CEO, Canfor Pulp, says, “In recent years, several sawmills have permanently closed in the PrinceGeorgeregionduetoreductionsintheallowableannual cut and challenges accessing cost-competitive fibre. This has had a material impact on the availability of residual fibre for our pulp facilities and we need to right-size our operatingplatform. As a result, we have made the very difficult decision to shut down the pulp line at Prince George Pulp and Paper Mill and willcontinuetooperatetheSpecialtyPaperfacility.”
Inthenextfewmonths,themillwillbefollowinganorderlywind downprocess.Thepulplineisprojectedtoshutdownbytheend of the first quarter of 2023.This is anticipated to impact approximately300positionsacrosstheorganizationbytheendoftheyear.
Mr. Edgson further added that, “We greatly appreciate our valued team members who have been helping to navigate a very challenging business environment. We understand and regret the impact today's announcement has on our employees, their families, the businesses that support our operations, andthelocalcommunity.”
Under this collaboration, Shah Paper Mills and IIT Roorkee will set up an Advanced Packaging Research Laboratory and introduce a skill development program at the Department of Paper Technology (DPT), Saharanpur.
January9,2023
Shah Paper Mills Ltd. has signed an agreement with the Indian Institute of Technology Roorkee (IIT Roorkee) for a collaborative project aimed at setting up an Advanced Packaging Research Laboratory and introducing a skill development program at the Department of PaperTechnology (DPT),SaharanpurCampus.
According to the official statement, IIT Roorkee is fostering collaboration with the Indian paper industry, with a focus on providing cutting-edge innovation research and skill development. In this regard, IIT Roorkee Development Foundation (IITRDF) strives to bridge the gap between industry and academiatopromoteR&D.
Shah Paper Mills, one of the leading paper manufacturers based inWapi(Gujarat),hastwomanufacturingunitswithstate-of-theartproductionlinesdesignedtomanufacturepaperutilisingthe wastepaperbyrecyclingandthetwo-stagedeinkingprocess.
This project is a part of the Corporate Social Responsibility (CSR) initiative of Shah Paper Mills, as outlined in the Memorandum of Understanding (MoU). The MoU signing event, which was held onDecember15,2022atIITRoorkee,wasgracedbythepresence ofMr.PriteshShah,JointManagingDirector,ShahPaperMills;Mr. Kanu Mehra, representative on behalf of the President of the Gujarat Paper Mill Association; Mr. Shreyas Bahety, Executive Director, Shah Paper Mills; Board of Directors IITRDF – Prof. K. K.
Pant, Prof. Akshay Dvivedi, Prof. Bhola Ram Gurjar, Prof. Manish Shrikhande, DORA office representatives, Mr. Santosh Kumar (Chief Executive Officer, IITRDF), Prof. Sanjay Palsule (Acting Dean, Saharanpur campus), Prof. Dharm Dutt (Head Paper Technology),andProf.MilliePant.
Gujarat Paper Mills Association, a representative body of paper manufacturers based in Gujarat, aims to provide a collective platform to achieve excellence in paper manufacturing and solveissuesrelatedtoitsmemberpapermills.
As mandated by GOI, with this project, Shah Paper Mills along with IIT Roorkee will be help youths aspiring to grab employment by showcasing their skill empowered with the training providedbyIITRoorkee.
Prof. K.K. Pant, Director, IIT Roorkee, said,“IITRDF will enable the Institute's pursuit of excellence by serving as a liaison between the Institute and donors. Our partnership with Shah Paper Mills Ltd. is a second such partnership in this direction. The vision shared by Joint Managing Director shows a strong commitment of the Company towards sustainability by implementing best practices of circular economy and sensitivity towards the environment. With IITRDF as an Industry-Academia partnership arm of IIT Roorkee, we're looking forward to creating and
nurturing moresuchpartnershipstomeetglobalaspirationsof CorporateSocialResponsibility.”
In the words of Mr. Pritesh Shah, Joint Managing Director, Shah Paper Mills,“As a part of our strong commitment to Corporate Social Responsibility (CSR), Shah Paper Mills Ltd. is delighted that both IIT Roorkee and students from the region will benefit from this program. With the growing potential of paper and pulp industries to absorb the young workforce, this initiative will prove fruitful for the region. Shah Paper Mills is looking forward to working closely with IITRDF to pave out new potential collaboration opportunities to strengthen our partnership further. Collaboration with IIT Roorkee will help industries to solve technical problems by engaging students andfacultiesknownfortheirtechnicalacumeninIndia.”
Mr. Santosh Kumar, Chief Executive Officer, IIT Roorkee Development Foundation, said, “This MoU signing event has opened avenues for strategic partnership between IIT Roorkee Development Foundation and Shah Paper Mills Ltd. The mandate of IITRDF is to raise funds to meet the growth aspirations and promote scientific and engineering innovation at IIT Roorkee. IITRDF will closely work with our donors to build and nurture relationships to make a positive impact on IIT Roorkeeandsociety.”n
The event, themed 'Being Future Ready: Water for All', recognised companies making significant strides in water conservation. Yash Pakka has introduced a number of water conservation initiatives.
Yash Pakka Ltd., a pioneer in the sustainable packaging industry, has been named the NoteworthyWater Efficient Unit at the National Awards for Excellence in Water Management 2022 by the Confederation of Indian Industry (CII). The stellar accolade was presented at the 8th CII Water Innovation Summit organised by CII-Triveni Water Institute alongwiththeMinistryofJalShakti,Govt.ofIndia.
Yash Pakka's win was backed by its several water saving initiatives. This includes a Micro Plate Settler (MPS) & Sedicell which makes machine backwater reusable by removing suspended fibres, thereby reducing freshwater use and effluentgeneration.
Further,thecompanyhasinstalledsettlers(save-all)initspaper machines which essentially reuse effluents and suspended solids from water in the manufacturing process. With these initiatives, the Yash Pakka saves 750 million litres of water each year.
Speaking on the win, Mr. Jagdeep Hira, Business Head – Yash Pakka Ltd. said, “We are honoured to receive this recognition from the prestigious CII. Yash Pakka is determined to make all
efforts towards a cleaner planet, and saving naturalresources is our primary focus. We have taken our total water consumption 3 3 down from around 50 m/ton to 37 m/ton in the last 4 years of hard work and commitment towards the environment which means savings of around 750 million litres of water annually. But we didn't stop here, we have set a challenging target of 25 3 m/ton of water consumption by the end of FY 2023-24, and we arealreadyonit.”
November28,2022
Qifeng Group, a leading company in the production and sales of decorative paper, will install the rewinder in its No 27 special paper production line located at the Guigang plantintheGuangxiAutonomousRegion.
The A.Celli solution, equipped with spool parking, automatic core gluing and dust removal system has been designed and manufactured to process jumbo rolls of decorative paper with a diameter of 2800 mm and a width of 3860 mm at a design speedof2000mpm.
In the words of Mr. Li Andong, General Manager, Qifeng group, “The collaboration between Qifeng Group and A.Celli began in 2009 with the supply of an AC842 rewinder. We are very honoured to have received the support of this important partner for more than ten years.The establishment of a new production line in Guangxi is an important regional strategy of Qifeng Group and,thankstoit,wewillachieveevenhigherachievements.”
The business partnership between A.Celli Paper and Qifeng Group, which began more than 10 years ago, will be strengthened with the order placed in October for a new E-WIND® P100 PaperRewinder,thesixthpurchasedovertheyears.
Qifeng Group, founded in 1976, has 46 years of papermaking history and 22 years of experience in the production of special papers. Its main products are decorative base paper, wearresistant paper, and nonwoven wallpaper base paper. A special mention goes to the production of latex impregnated paper, for which Zibo Oumu is the leading producer in China. The company currently employs 1,500 people and was listed on the ShenzhenStockExchangeinDecember2010.n
The Voith XcelLine paper machine will produce 725,000 tonnes of high-quality kraftliner per year with basis weights between 100 and 200 GSM. Compared to the old line, it has increased SCA's production capacity by 270,000 tonnes.
November30,2022
Swedish forest industry company SCA's new kraftliner machine at its Obbola site is up and running.The machine started up by Voith at the beginning of November is touted to be the world's largest kraftliner machine. The state-of-the-art machine features a design speed of 1,400 meters per minute and a wire width of 10,200 mm. The Voith XcelLine paper machine will produce 725,000 tonnes of high-quality kraftliner per year with basis weights between 100 and 200 GSM. Compared to the old line, the new machine increases SCA's productioncapacityby270,000tonnes.
Talking about the new machine, Mr. Per Strand, Project Director at SCA said, “Thanks to the excellent cooperation with Voith, the start-up of the most modern kraftliner machine took place
Qifeng Group relies on A.Celli Paper's technology for the sixth time by ordering a new rewinder for special papers.Image Source: A.Celli
ahead of schedule. With this high-tech plant, we are setting new standards in the market. We are very pleased to have chosen Voith as our full-line supplier. The highly efficient solutions reduce our resource consumption and enable maximum productivity with the lowest overall production costs.”
As the leading full-line supplier to the paper industry, Voith supplied the complete line, the heart of which is a highly efficient XcelLine paper machine. In addition,Voith is responsible for all relevant auxiliary systems, from hall ventilation to roll transport, and together with Meri for a highly efficient water and wastewater management system. The XcelLine paper machine will be supplemented by a new BlueLine stock preparation system, which is scheduled to replace the existing systemnextyear.
Voith's BlueLine stock preparation plant will save up to 40 kWh per tonne of paper compared to conventional plants. In
addition, the freshwater requirement is around 30 percent lower than the previous production. Upon completion of the project, SCA will take a big step towards a fossil-free industrial process.
Intelligent automation and digitalization solutions also ensure an optimal and thus more sustainable process. As the most modern kraftliner machine in the world, a range of applications from the Voith Papermaking 4.0 portfolio are used along the entire paper machine. “We are very proud to have successfully set up this major project with SCA.The plant sets new standards in terms of resource efficiency, productivity, safety and quality. We were only able to achieve this through our joint commitment, very good cooperation and the highest demands on both sides. PM 2 shows how the latest technologies in combination with innovative automation and digitalization solutions can lead to significant efficiency advantages,” added Dr. Michael Trefz, President Projects atVoith Paper. n
The expansion of the backpressure turbine and generator at the biopower plant will further increase Kyro mill's fossil-free electricity generation, enabling the board mill to reach its sustainability goals.
November
Metsä Board's Kyro mill is investing to enhance its fossilfree electricity generation. The paperboard manufacturer will invest in a new backpressure turbine and generator at its biopower plant at the Kyro mill. Presently, the biopower plant generates one-third of the electricity consumed by the mill.
After the said investment in the new turbine, the share of captive power produced will rise to 50 percent. The Kyro mill is self-sufficient in heat. Moreover, 85 percent of the mill's electricity consumption is fossil-free. Since the share of fossilfuel-based electricity would further decrease after the investment, the mill would become more fossil-free in terms of electricity.
About the investment, Mr. Petri Huiko, VP Metsä Board Kyro, says, “By increasing the share of fossil free electricity, we are becoming more climate sustainable. The investment will also improve the safety of electricity work in the mill area and the predictabilityofthemill'selectricitycosts.”
The expansion of the biopower plant is projected to be completed by the end of 2024. In this modernisation and expansion project, the electrical equipment will also be replaced. Due to this, electricity production will be interrupted
for about three months at the unit but heat production and the runningoftheboardmachinewillsustainitsoperations.
Metsä Board Kyro mill produces high-quality fully coated folding boxboards for packaging and printing segments. The mill only uses its own pulp in its production: BCTMP pulp from Metsä Board's Joutseno and Kaskinen mills, and chemical pulp is sourced from Metsä Fibre's mills. The recent investment is significant for Metsä Board's vision of achieving completely fossil-freemillsandproductsbytheendof2030. n
For both the tissue machine rebuild projects, Toscotec upgraded the wet and the dry section of the two respective production lines.
November28,2022
On 11 November 2022, Toscotec started up two tissue machinerebuildsattheproductionfacilitiesoftwomajor producers in North and South America. On both projects, the scope of the modificationswasextensive, covering the wet and dry section of the two lines.The tight periods of machine stops havebeenexecutedaccordingtoschedule.
In the words of Mr. Andrea Paganucci, Toscotec Project Manager, “One of the most challenging aspects on this large rebuild was the integration ofToscotec's key components with the existing equipment. Creating an effective interface between different systems requires strong multi-stakeholder coordination. We are happy that the machine is now running efficientlyasexpected.”
About the rebuild projects, Mr. Flavio D'Orlando, Toscotec Site Manager, says,“After the rebuild, the machine started producing sellable paper right away. We are now fine-tuning the new
equipment, which is already meeting the mill's product quality requirements. The on-site operations, including dismantling, erection,commissioning,andstart-up,allwentverysmoothly.”
For its multi-year contracts with Mehali Papers and Urvashi Pulp and Paper Mills, SKF India will provide a wide range of products and remote diagnostic services and onsite training programs.
December30,2022
One of the leading technology and solutions providers of bearings andservicesinthecountry–SKFIndiahasinked multi-year performance-based agreements with two renowned pulp and paper manufacturers – Mehali Papers Pvt. Ltd.andUrvashiPulpandPaperMills.
These performance-based contracts are aimed at improving productivity, reducing downtime, and raising profitability, as stated in media reports. Moreover, the contracts are a component of the Rotating Equipment Performance (REP) offering, with which the customers are enabled to increase the machine's reliability and outcome while reducing the Total CostofOwnership(TCO).
Within the agreement,SKF India will be responsible for offering a thorough range of products such as – bearings, lubrication systems, onsite vibration analysis, dynamic balancing and alignment, connected condition monitoring units as well as remotediagnosticservicesandonsitetrainingprograms.
In the words of Mr. Sujeeth Pai, Director – Industrial Market, SKF India and Southeast Asia,“As a customer-centric organization, SKF develops innovative products and solutions that meet its
customers' objectives. With our performance-based REP contracts, customers can gain valuable insights to maximize their equipment's productivity, reliability, and efficiency while reducingtheiroverallcostofmaintenance.”
Speaking about the agreements, Mr. Sundeep Shah, Managing Director, Urvashi Paper said, “With fast-growing paper market in India, paper machine uptime & OEE are primary growth drivers for UrvashiPaper to cater the market demand for higher quality paper. Partnering with SKF will help us achieve the desired Rotating Equipment Performance and improve productivity, with greater flexibility on mechanical maintenancecostandoptimization.”
In addition, SKF India has developed a fee-based business
model around the customer's needs and productivity targets. Thus, the Company offers an appropriate combination of products and services to help customers improve the competitivenessoftheirmachines.
Mr. Ashraf Nathani, Managing Director, Mehali Paper, said,“The pulp and paper sector is transitioning towards Industry 4.0 for more flexible & efficient manufacturing process. Continuous innovation can not only improve processes, products, and services, but also have a positive impact on business models, workforce training, and environmental compliances. With the long-term performance-oriented REP contracts, we are confident of improving the efficiency of our maintenance strategy by leveraging SKF's digital solutions and application engineeringknowledge.”n
Smurfit Kappa's investments in the two plants include installing state-of-the-art equipment for capacity augmentation in view of the rising consumer demand for paper-based packaging solutions.
November24,2022
Europe's leading paper-based packaging producer Smurfit Kappa has infused significant investments in its Olomouc plant in the Czech Republic and Obaly Štúrovo site in Slovakia. The previous year, the Company had announced investments of more than EUR 20 million in expansion in line with the commitment to strengthen operations in Central and Eastern Europe.
With the investments, there were significant upgradations in the two plants including the installation of state-of-the-art equipment for capacity augmentation in view of the rising consumer demand for paper-based packaging solutions. A new converting equipment has been installed which will enhance the converting capacity by more than 100 million regularandoffsetprintedboxesperannum.
Additionally, the investments are aimed at further enhancing Smurfit Kappa's positioning in the Czech Republic and Slovakia so as to further target specific industries, most notably the FMCGandelectro-technicalsectors.
Mr. Tony Smurfit, Group CEO of Smurfit Kappa and Mr. Saverio Mayer, CEO of Smurfit Kappa Europe, attended the official launch of the upgraded plants during which customers were givenadetailedwalk-throughoftheenhancedcapabilitiesand SmurfitKappa'sdeep-rootedsustainabilitycredentials.
Commenting at the official unveiling of the two upgraded plants, Mr. Zdenek Suchitra, CEO of Smurfit Central & SouthEast Europe, said,“I am delighted to announce that both of our
investments at the Olomouc (Czech Republic) and Obaly Štúrovo (Slovakia) plants have finished on time and within our original budget in a time when there is a scarcity of all kinds of materials. These investments, along with the investments we made in two additional sites in the Czech Republic, demonstrate our commitment to our customers and operations in CentralandEasternEurope.”
Mr. Suchitra further explained that they have transformed their plants into state-of-the-art facilities through these investments. The group is assured of its positioning to satisfy their well-establishedcustomerbase.n
Metsä Board's current development programme, which is a EUR 67 million investment, will increase the production capacity of the mill's coated white kraftliners by 40,000 tonnes.
December15,2022
Metsä Board's Kemi mill has been a forerunner in the product development of coated white kraftliners. Production of brown kraftliner started in 1971 and the capacity was 180,000 tonnes per annum. In 1975, the mill's bleaching plant was completed, and the production of mottled liner began soon after. Following investments, the production of white top kraftliner began in 1986. In 1990, the degree of upgrading was further raised with the launch of coating, followed by investments made in double-coating in 2011. From January 2023, Kemi mill's full focus will be on the development and enhancing the availability of coated white kraftlinerstomeetthegrowingdemand.
Presently, there are three different coated grades in the product range and, as a result of continuous process development and numerous investments over the years, the production capacity of the mill has more than doubled to 425,000 tonnes per year. Metsä Board's current development programmeisaEUR67millioninvestmentthatwillincreasethe production capacity of the mill's coated white kraftliners by a further40,000tonnesandhelpimprovethemill'ssustainability performance.
“The basis for the development of the coated grades has from the very beginning been meeting the most demanding customer needs and anticipating future trends of the end user industry”, says Panu Räsänen, Product Manager WKL, Metsä Board.
Owing to an experience spanning many years of systematic development,Kemimill'scurrentproductrangehasanoptimal coated krafliner grade for each printing method. Metsä Board's aim is to support circular economy by premium and lightweight paperboards produced resource-efficiently, helping customerstoreducetheircarbonfootprint.n
December29,2022
The HYFLEXPOWER consortium and Smurfit Kappa have announced the successful completion of the first stage of the HYFLEXPOWER project, an innovative research project on renewable energy. This project located at the Smurfit Kappa Saillat paper mill in France is the first in the world to introduce anintegratedhydrogengasturbinedemonstrator.
The highly innovative project involves significantcollaboration across several industries, academic bodies and research institutes, including ENGIE Solutions, Siemens Energy, Centrax, Arttic, German Aerospace Center (DLR), and four European universities.
The hydrogen pilot was successfully trialled last month with a mixof30percenthydrogenand70percentnaturalgas.Theaim of the HYFLEXPOWER project is to clearly demonstrate that
renewableenergy can be converted to hydrogen and serve as a flexible means of storing energy which can then be used to poweranindustrialturbine.
The project officially marks the implementation of the world's very first industrial-scale power-to-X-to-power demonstrator
The HYFLEXPOWER project is aimed at demonstrating that renewable energy can be converted to hydrogen and serve as a flexible means of storing energy. This is an important first step forward in the journey to a carbon-free industry.Image Source: Smurfit Kappa
with an advanced hydrogen turbine. In 2023, trials will continuetoincreasethehydrogenratioupto100percent.
Garrett Quinn, Chief Sustainability Officer of Smurfit Kappa, commented, “We are focused on reducing our emissions with the best available technology today, but equally this announcement demonstrates how we are focused on looking beyond 2030 and trialling new technology, such as hydrogen, today.This project will allow us and our partners to understand the technical feasibility of using hydrogen with a lot of our existing energy infrastructure. This is an exciting project for us, and industry in general, as we progress on our journey towards netzero.”
The project was inspired by the European Commission's (EC) 'Hydrogen Strategy for a Climate-Neutral Europe' report, which outlines the essential role that hydrogen will play within the European Green Deal carbon neutrality and energy transition initiative.
Commenting on the end of the initial testing phase, Gaël Carayon, Director of Subsidiaries at ENGIE Solutions, said, “Ambitious projects like this one require taking partnerships to the next level and being united in a joint mission to make decarbonisation a reality. Hydrogen will play a crucial role in
the interaction between renewables and electricity storage and generation. ENGIE Solutions is proud to participate in this uniqueproject.”
Bertrand Muguet, Smurfit Kappa Saillat Paper Mill Manager, added, “We are delighted that the initial testing phase of the project was completed successfully at our Saillat paper mill. Smurfit Kappa is proud to be collaborating with our partners on this project which tests new technologies that we believe willformpartofournetzerodelivery.”
Dr. Ertan Yilmaz, HYFLEXPOWER Global Director at Siemens Energy, said, “With the HYFLEXPOWER project we are showcasing that carbon-neutral and reliable power supply is possible - even for energy-intensive industries. Hydrogenready turbines will play a decisive role in climate-neutral energy, so it is very exciting to be looking forward to the next phaseoftesting.”
The project, first announced in 2020, involves significant funding by the EC, with two-thirds of the EUR 15.2 million investment coming from the EU's Horizon 2020 Framework Programme for Research and Innovation.The next trials for the HYFLEXPOWERprojectarescheduledforspring2023.n
December24,2022
Together with booming online shopping, the role of ecommerce packaging is growing. This means retailers are fighting for consumers' attention while striving to make the unboxing process as smooth as possible for their busy customers.
This surge in e-commerce behaviour also means that items must be packed in a shock-proof way. Cushioning is an essential part of protecting fragile goods from shock and vibration. However, the expanded plastic foams used in cushioning are currently made of crude oil and are hard to recycle. At the same time, national and global policies are underway to prevent the use of plastics that could potentially end up polluting the environment. How can we respond to
thesetwoclashingmegatrendsinonego?
“The idea for recyclable cushioning foam arose in a research group led by Professor Lars Wågberg at the Royal Institute of Technology in Stockholm,” says Ms. Paula Martirez, business developeratStoraEnso.
In the wake of this research, a company called Cellutech was established in 2013, serving as a link between academia and the industry. The idea was to bring cutting-edge materials to the market by developing innovative, renewable products usingrawmaterialsfromtheforest.
The group was able to use wood pulp in making stable foam that could be dried in an efficient way. The result was a light and strong material with good mechanical properties. Thanks to thorough research and development work, Papira® became
Stora Enso's Papira® is entirely bio-based and recyclable, consisting of pulp and a small part of bio-based additives.
entirely bio-based and recyclable, consisting of pulp and a small part of bio-based additives. It is also delivered as sheets in thesamewayaspolyethyleneandpolyurethane.
“Sheets are laminated on top of each other to build up the structure around the intended product held by the packaging. This production method enables complex packaging solutions foranyshapeofproduct,”Ms.Martirezexplains.
Acquired by Stora Enso in 2018, Cellutech joined the Stora Enso's Biomaterials division. After the development breakthrough, a pilot plant was built at the premises of Stora Enso's first fossil-CO₂ emission free board mill in Fors, Sweden. The new facility enabled the development, optimisation, and markettestingofPapira®.
“Themainpurposeofthepilotistovalidateboththeprocessand theusageofPapira®indifferentapplications.Withfeedbackfrom customers and different actors in the value chain we can preparefordifferentscenariosforthefuture,”sheadds.
Since the pilot plant has been up and running, the learning curvetooptimizetheprocesshasincreased.
“It is also the pilot's purpose that we learn how to scale the production to full commercialisation. All operationsof the pilot plant run completely fossil free, a fact that we take great pride in,”sheadds.
Currently, Stora Enso is working with multiple customers on performing tests and validation of the material and its properties in various applications. These projects include a variety of potential and current customers from different productssegments.
The idea is to make Papira® the new standard in protective packaging.To make this our reality, Stora Enso will gradually scale up operations while developing this material. Potential customers for Papira® include all who need to protect fragile products such as electronics, household appliances, furniture, industrial products,andexpensiveconsumerproductsduringtransport.
Inadditiontothetissueline,A.CellihadalsoprovideditsDCSprocesscontrolsystem andanIndustry4.0-readyautomationplatformforIntertradeHellas'plant.
January13,2023
Intertrade Hellas has successfully started up an A.Celli tissue line at its plant in Inofyta, Viotia (Athens). The startup of the operations has been achieved in tandem with the stipulated timelinesoftheagreementbetweenthetwocompanies.
As per their press release, A.Celli turnkey tissue line delivered has produced its first batch of jumbo rolls on a timely basis. Moreover, the production operations are equivalent to the expectedspeedandproductquality.
The tissue production line is designed to manufacture topquality tissue paper from virgin fiber in view of Intertrade Hellas' specific request in terms of layout and desired productioncapacity.
The supply includes the following solutions: stock preparation line; A.Celli iDEAL® Master 2000L tissue machine with a web width of 5600 mm, design speed of 2100 MPM, and working speed of 2000 MPM; 16” Forged Yankee Dryer, with a width of 6085 mm; 5600 mm wide three-ply E-WIND® T200 slitter rewinder, with a speed of 1800 MPM; and R-WAY® automatic reel handling system composed of conveyor belt, wrapper, upenderandlabellingsystem.
A.Celli also provided its exclusively designed DCS process control system and an Industry 4.0-ready automation platform, developed to integrate the numerous systems implemented in IntertradeHellas'plant.
The tissue line is expected to reach a production capacity of 244 TPD or 221 TPD, respectively for tissue paper with a basis
weightof20GSMand16GSM.
In the words of Mr. Ioannis Delidimos, CEO of Intertrade Hellas S.A.,“The A.Celli iDEAL® Master 2000L combines high efficiency and superb tissue quality with minimum energy consumption. Over the last 2 years A.Celli has been proven a valuable partner in every stage of the process. We are indeed very happy with our decision: A.Celli fulfills the highest standards in tissue machines.”
Mr. Alessandro Celli, Member of the A.Celli Paper Board of Directors,says,“Thisprojectstartedinfullspirit ofcollaboration with Intertrade, defining all the guidelines together. The successful start-up of the supplied line, which includes our exclusive forged Yankee Dryer, an automatic reel handling system and innovative Industry 4.0 solutions, is the result of the excellent collaboration between our two companies and trust placedbyIntertradeinourknow-howandtechnology.”n
December24,2022
Turkey-based Essel Kâğıt's new AHEAD 2.2L tissue production line, supplied by Toscotec, has exceeded its guaranteed production by a significant margin and surpassed bulk and softness parameters. The order, which was delivered on a turnkey basis, made PM3 as online at Essel's Osmaniye mill in October2021.
Mr. Ahmet Temuroglu, Production Coordinator and Mr. Burak Ipek, Maintenance Manager, Essel Kâğit, says,“The target of our performance test was successfully accomplished with a production of 290.5TPD on a 23 GSM towel grade at the speed of 1,810 m/min. We are now fully reaping the benefits of Toscotec's first-in-class technology across our entire product rangebothfortissuequalityandconsumptions.”
Mr. Nicola Fontana, Senior Papermaker at Toscotec, says, “This double-width AHEAD line is delivering a high and stable performance. TT NextPress is offering good results of bulk and hand-feel even at maximum load on low basis weights, exceedingEsselKâğıt'sstrictqualitystandards.”
Once the startup was completed, Toscotec has been providing consistent assistance to fine-tune the whole plant and achieve topperformance.
In the words of Mr. Andrea Rossi, Toscotec's Commissioning Manager,“The performance test confirmed the machine's low energy usage we had been monitoring including at the speed of2,000m/min.Thetotalenergyconsumptioniswellbelowthe guaranteed figure. The cooperation with Essel's team was extraordinary and they did a fantastic job in getting the machinereadytoachieveitstopefficiency.”n
The European Commission's revised proposal for packaging and packaging waste is based on the EU industry's recycling model for paper and board packaging.
December12,2022
Aproposal for a revised Packaging and Packaging Waste
Regulation which has been tabled by the European Commission builds on the performance of the EU industry's recycling model for paper and board packaging. The paper industry now calls for a science-based evaluation of recyclable andreusableoptions.
Recycling is today the first source of fibres for the pulp and paper sector and 'circularity' is part of a business model that places Europe as the global recycling champion. In the EU, paper and board packaging is recycled more than all other materials combined. Paper and board also already far exceed legal recycling targets set for 2025, which are the most
The paper and board industry acknowledge that the EU could achieve higher circularity by supplementing the recycling model with reuse systems.
After the completion of startup, Toscotec has been providing consistent assistance to fine-tune the whole plant and achieve top performance to Essel Kâğıt.
stringent among all materials. Nevertheless, paper producers and recyclers have pledged to reach a 90 percent recycling rate by 2030, which is higher than the current legal requirement of 85 percent. To achieve this, one prerequisite would be to improve the separate collection of paper and board throughoutEurope.
The paper and board industry recognises that recyclable and reusable options are complementary and that the EU could also achieve higher circularity by supplementing its successful recycling model with reuse systems. But the performance of reuse systems will now have to match that of the paper and board industry's recycling model. Notably, targets set in the
new proposal should concentrate on markets where circularity performance needs to be improved, and decisions to go for either recyclable or reusable packaging should be based on independent science-based proof of their respective environmentalbenefits.
“It is important to understand that we are not against reuse. Independent environmental impact evaluation, as established in theWaste Framework Directive, should be how we decide to go for recycling or reuse. Neither recyclers or 're-users' would want to bear responsibility for a failing environmental model,” says Mr. Jori Ringman, Director General – Cepi (Confederation oftheEuropeanPaperIndustries). n
Through this paper, Cepi expressed its willingness to contribute to a methodology for the certification of carbon storage in products, to be included in a specific act in the European Commission's proposal.
December9,2022
The proposal for a regulation on carbon removal certifica-
tion released today by the European Commission recognizes several essential principles preventing such mechanisms to devolve into greenwashing. The upcoming regulation builds on the synergies between the potential of carbon storage products and the development of a circular bioeconomy.
In a circular bioeconomy, CO is naturally removed from the 2 atmosphere and stored in growing forests. Before ageing trees starttodecayandreleasegreenhousegases,woodisharvested tobetransformed intowoodproductsandby-productssuchas pulp and paper, and the lifetime of fibres is further extended by well-established recycling systems. They store carbon for as long as their wood fibres are re-used, before re-entering biogenic carbon cycles. Carbon goes back from the atmospheretoplants,thenproducts,cyclically.
This has been coined under the term of 'renewable biogenic carbon', defined in international standards. Cepi, the Confederation of European Paper Industries, has recently published a position paper explaining how the concept of renewable biogenic carbon relates to the proposal tabled today.
Other 'carbon cycles' are based on the capture and re-use of carbon from finite, fossil resources. While these can also be sustainable under certain conditions, Cepi welcomes that the EU Commission's proposal for the certification of carbon removal allows for a clear differentiation between fossil and renewablebiogeniccarbon.
The proposed regulation plans for the further definition of
different types of certification schemes via several delegated acts. As a precursor in the measurement of product-embedded carbon, and with extensive expertise in the field, Cepi is ready to contribute to a methodology for the certification of carbon storage in products, to be included in a specific delegated act mentionedintheEuropeanCommission'sproposal.
Forest-based products, together with forests' carbon sink, already have an overall positive net climate effect of -806 million tonnes of CO equivalent annually. This corresponds to 2 avoiding 20% of all EU fossil emissions. An expansion of carbon removals via the substitution of fossil carbon by“recycled […] carbon from sustainable sources of biomass”, foreseen by the newregulation,couldfurtherincreasethispositiveeffect.
“If we are ready to leave a fossil-based economy behind us, EU regulation supporting renewable biogenic carbon would have to offer a predictable framework, enabling investments needed to reach climate neutrality. This, together with avoiding fossil emissions in the first place, would bring EU closer to reaching its ambitious 2030 and 2050 goals,”says Mr.
“It would also make bio-based 'made in Europe' industries an essential part of the EU's climate policy and would allow
Europe to make the best of its home-grown raw materials, in a way that is compatible with our suppliers' as well as our own efforts to continuously increase carbon storage in forests,”adds Mr.Ringman.n
Presently, Voith's R&D team is working on new possibilities with the help of Life Cycle Analyses (LCAs).
December23,2022
Voith has a range of specific solutions for sustainable paper production, the advantages of which are proven by many positive customer references. A German graphic papers manufacturer, for example, reported that Voith's SolarPress roll covers have enabled energy savings due to a 1.5 percent point higher dry content after the press section. Efficiency add-ons for press fabrics are another example. In particular, +Peak technology, a specially developed elastomer material, optimizes nip dewatering and increases the service life of a press fabric. For one paper producer, +Peak resulted in higher dry content in the tandem press and reduced the average amount of steam by 11 percent, from 1.6 t/ton to 1.43 t/ton. In addition to energy savings, significant water savings are also enabled. For example, customers worldwide benefit from HydroSeal, the modern version of sealing strips for suction rolls. At a board mill in the USA, HydroSeal reduced water usage by 80 percent and saved the papermaker more than USD 30,000 per year in sealing strip lubrication.
“In addition to production that conserves resources as much as possible, it is important that the products themselves are also manufactured sustainably,” says Ms. Lidia Loskan, R&D Project ManagerSustainabilityatVoithPaper.
Here, it is important to be able to offer the same product propertiesaswithpetroleum-basedrollcoversandfabrics.
To further optimize the product portfolio in terms of sustainability,Voith's R&D team is working on new possibilities with the help of Life Cycle Analyses (LCAs). As an example, Dr. Robert Hilbing, Senior Vice President R&D FRS at Voith Paper, mentions the newly launched roll cover AiroGuideTune Green. The innovative roll cover is certified according to the international DIN CERTCO standard for bio-based products. The fiber composite roll cover is manufactured with bio-based raw materials and was specially developed for the wet-end section.
Italsohasimprovedcorrosionpropertiesandalongservicelife. This makes AiroGuide Tune Green the first DIN CERTCOcertified sustainable roll cover on the market with the same performancedataasthepetroleum-basedalternatives. Furthermore, Voith is increasingly focused on the entire manufacturing process of wear parts.The company has already been systematically measuring its own energy, water and waste volumes since 2012 and reducing them in a targeted manner.
In the words of Dr. Robert Hibling, “As part of Voith Paper's sustainability program Papermaking for Life, Voith is working intensively on sustainable solutions to strengthen the circular economy and reduce its carbon footprint. Our goal is to offer our customers an optimal portfolio of fabrics and roll covers that increases performance and sustainability while reducing operatingcosts.”
As part of the innovation and development offensive "Papermaking for Life,"Voith Paper presents versatile technologies and initiatives that lead to more efficient and sustainable processes in papermaking. The emphasis is on the topics of water, energy and fiber savings as well as digitalization, innovations and partnerships as levers for more sustainable production.n
Well-known confectionery and chocolate brands – Snickers, Milky Way, and Mars Bar, owned by Mars Corporation, will now come in a paper-based packaging film.
December24,2022
Mars Wrigley Australia has announced its plans to transition to paper-based packaging wrappers for its chocolate product.This marks a pioneering move for Mars and is aligned with the increasing trend for consumer brands to switch to sustainable or paper-based packaging which is curbsiderecyclable.
According to media sources, Mars Corporation will introduce the new paper-based packaging for its range of candy and chocolate products including Mars Bar, Snickers, and MilkyWay from April next year. Moreover, the confectionery manufacturer intends to bring in a transition of its complete chocolate barportfoliotosustainablepackaging.
The new packaging will include the Australasian Recycling Label (ARL) to elucidate clear recycling instructions to consumers. Once Mars Australia's chocolate bar portfolio is fully transitioned to paper-based packaging, the Company will be able to strengthen its plans related to the circular economy and achievethe2025NationalPackagingTargets.
As part of the company's commitment to its USD 1 billion Sustainable in a Generation plan, Mars Wrigley says it is “committed both in Australia and globally to supporting and creating a circular economy where packaging never becomes waste.”n
Voith's FastFormat offers a return on investment of only a few months and helps paper manufacturers avoid capacity losses due to frequent format changes.
December20,2022
Voith has introduced an integrated service offering which will increase winder performance in all applications, besides FastFormat – a new solution for automatic format changes. The performance of the winder is crucial for the efficiency of the paper machine, because winder operation that is not optimal can lead to capacity bottlenecks across the entirepaperproductionprocess.
With this, the paper technology group provides an integrated technology service for higher winder availability. FastFormat, a new product for automatic format changes, also increases winderperformanceandensuresgreatersafetyforoperators.
An extensive winder service enables quick identification of bottlenecks and increases capacity, paper quality, and safety. Customers benefit from comprehensive technology service to improve winder availability, increase productivity and cut costs. The scope and content of the service offering are individually adapted to the respective requirements of each customer. Thus, key production figures, such as set change time and acceleration, can be demonstrably improved. An
Image Source: Voith
important part of the service offering is a 24/7 hotline support that provides customers with rapid assistance and solutions to problems. At its PM1 in Munksund, Sweden, forest industry company SCA already relies on Voith's winder technology service.
“The biggest benefit of our winder service partnership with Voith is the fact that it can't be simply narrowed down to a
single advantage,” says Mr. Urban Marklund, Production Technician at SCA Munksund AB in Sweden.“It's the complete package that makes it so valuable to us. It's everything from Voith's unrivaled expertise in the areas of automation and technology to the annual on-site visits and 24/7 hotline support. Allthisaddsuptoadealthatisveryusefulandimportanttous.”
“With our comprehensive service offering, we support our customers even better in continuously improving the performance of their winder,” adds Mr. Sven Franke, Senior AutomationEngineeratVoithPaper.
In FastFormat,Voith brings its first product for fast and safe format changes. It has a return on investment of only a few months and
particularly helps paper manufacturers avoid capacity losses due to frequent format changes. Further, it also allows the winder's engaging edge slitters to be moved at crawl speed and the web width to be changed, enabling automated format changes without operator intervention. This not only increases safety for theoperatorbutalsoboostswinderproduction.
“Approximately one minute can be saved per format change, which really makes a difference, especially for customers with frequent format changes,”says Fabian Köberle, Global Product Manager atVoith Paper.“In addition, FastFormat eliminates the need for operator interventionpreviously required on a regular basis.”n
In January 2022, Mondi expressed its commitment to Net-Zero Greenhouse gas emissions' reduction and is amongst the first companies in the paper and packaging industry to have confirmed Net-Zero targets from the SBTi.
December16,2022
Mondi Group has announced that the Science Based
Targets initiative (SBTi) has given its approval to the science-based Net-Zero targets. The targets covering Greenhouse gas emissions from the group's operations and supplychain(Scopes1,2,and3)areconsistentwithareduction required to keep global warming to 1.5°C, stated in their official pressrelease.
In January 2022, Mondi expressed its commitment to Net-Zero GHG emissions reduction. Further, it is amongst the first companies in the paper and packaging industry to have confirmedNet-ZerotargetsfromtheSBTi.
The global paper and packaging leader has asserted its
commitment to reduce absolute Scope 1 and 2 GHG emissions by 46.2 percent and Scope 3 GHG emissions by 27.5 percent by 2030. However, its long-term goal is to reduce absolute Scope 1,2,and3GHGemissionsby90percentby2050.
Since 2015, Mondi Group has made a number of strategic energy-related investments across its pulp and paper mills of more than EUR 650 million. Thus, these investments are directedtowardsfulfillingtheenergy-relatedrequirementsonsiteanditspulpandpapermills.
In the words of Mr. Andrew King, CEO, Mondi Group, “The approval of our science-based Net-Zero targets according to SBTi's Net-Zero Standard underlines our long-term commitmenttotakingactiononclimate.”n
The complete line order includes the stock preparation system with lowconsistency refiners, a PrimeLineTM W 2000 tissue machine and the automation system. The tissue machine has a speed of 1,900 m/min and a width of 5.65 m and produces high-quality tissue in 11-42 GSM range.
January3,2023
Asia Symbol (Guangdong) Paper Co., Ltd. has started up its
tissue production line delivered by ANDRITZ for its mill in Xinhui district, Jiangmen City, Guangdong Province, China.The complete line order includes the stock preparationsystem with low-consistency refiners, a PrimeLineTM W 2000 tissue machineandtheautomationsystem.
The tissue machine has a speed of 1,900 m/min and a width of 5.65 m and produces high-quality tissue in 11-42 GSM range. It is equipped with a PrimePress XT Evo shoe press, a PrimeDry Steel Yankee and a steam-heated PrimeDry Hood ST to enable energyefficienttissueproduction.
To speed up the process of production, both ANDRITZ and Asia Symbol'steamcollaboratedcloselyanddedicatedlyduring the whole stage of installation and commissioning. As a result, the firstpaperonreelwasachieved16daysaheadofschedule.
Talking about the project, Mr. Steven Hung Ching Lung,
General Manager of Asia Symbol (Guangdong) Paper Co., Ltd. says, “With the new TM13 we enter the tissue business. It is essential for our expansion strategy to provide our customers with high-quality tissues that have minimum impact on the environment. We have a vast experience in the production of high-quality printing and writing papers. Now we want to achievethesamesuccesswithANDRITZinthetissuemarket.”n
The tissue machine will enable the production of high-quality tissue grades made of either 100 percent virgin or 100 percent deinked pulp (DIP).
November30,2022
Xuan Mai Paper Co. Ltd. has ordered a PrimeLineCOMPACT S1800 tissue machine from ANDRITZ for its production line PM2 at its mill located in Ho Chi Minh City, Vietnam. The tissue machinewillhaveadesignspeedof1,800m/min,awidthof2.85 m and a design capacity of 72 admt/d and the suction pressure roll will be covered with a polysoft polyurethane cover for highperformance dewatering. The PrimeDry Steel Yankee (16 ft. diameter) in combination with a steam-heated COMBO hood enableshighlyefficientdryingwithsubstantialenergysavings.
The tissue machine will enable the production of high-quality tissue grades made of either 100 percent virgin or 100 percent deinked pulp (DIP).While start-up is scheduled for 2024, ANDRITZ will also deliver stock preparation and automation equipment, aswellasprocess-,fan-andmultistage-pumpsandauxiliaries.
Mr. Pham Van Dung, Vice President of the Board of Xuan Mai Paper, says, “ANDRITZ's innovative tissue solutions offer both economic and ecological benefits. Professional service offers
perfectly complement the technology. Since 2012, we have established a long-term cooperation that is built on mutual respect and trust. Our joint projects are in the areas of old corrugatedcontainerboardlines,deinkedpulplines,andtissue production lines.” In 2020, ANDRITZ already started up a complete tissue production line at Xuan Mai Paper. This would beafollowuporder.n
For the new corrugated sheetfeeder plant spanning 28,000 sq m, Progroup has invested around EUR 72 million.
January13,2023
Progroup has commenced operations at PW14, which is its new28,000sqmcorrugatedsheetfeederplantinStrykow, Poland. The new plant will produce up to 200,000 tonnes of corrugated sheetboard annually. Along with the PW07 plant situated nearby, the new unit will have an annual production capacity of 825 million sq m. This makes Stryków as one of the world's largest sites for corrugated board production. Progroup has invested around EUR 72 million in the project at the site, which covers around 28,000 sq m, and created 50 new jobs.
Almost all standard grades of the corrugated board can be produced at the PW14 plant, with a working width of 3.35 metres and a production speed of 400 metres per minute. At the heart of the corrugator machine is the Modul Facer MF-A concept which was developed by BHS Corrugated Maschinenund Anlagenbau GmbH. It has been used for the first time anywherewithaworkingwidthof3.35metresatProgroup.
Due to the modern combined cooling, heat and power plant, carbon emissions are now as lowest as possible. The state-ofthe-art plant utilises waste heat from its own power generation either in an absorption chiller to“produce”cold, or feeding the
heat into the heating circuit, as and when required. This will enableinthesavingofasignificantquantityoffossilfuels.
The plant also has a 32-metre-high, fully automatic high-bay warehouse with more than 14,000 storage spaces and four automatic storage and retrieval machines. It will be able to store up to two days of corrugated sheetboard production, enabling perfect just-in-time deliveries by decoupling the time between the manufacture of the corrugated board and the productionofpackagingbythecustomer.
Based in Landau, Germany, Progroup AG is one of the leading European manufacturers of containerboard and corrugated boards.n
ANDRITZ will supply key equipment for two RCF lines, featuring a total capacity of 150 t/d and processing LOCC (Local OCC) and MOW (Mixed Office Waste) as raw material for production of testliner, writing and printing paper.
December24,2022
Bangladesh-based Lipy Paper Mills Ltd. has placed an order with ANDRITZ for wastepaper processing systems. ANDRITZwillsupplykeyequipmentfortwoRCFlines,featuring a total capacity of 150 TPD and processing LOCC (Local OCC) and MOW (Mixed Office Waste) as raw material for production of testliner, writing and printing paper. This would be first ANDRITZRCFlinesforBangladesh.
Talking about the project, Mr. Shahiar Hasan Khan, Deputy Managing Director, Lipy Paper Mills says, “ANDRITZ convinced us because of its energy-saving technology for screening and flotation and its focus on minimum fiber loss. In addition, with the Ultra High Dispersion we'll be able to keep steam demand atalowlevel.Allthesetopicsarestrategicdevelopmenttargets foranaspiringcompanylikeLipyPaperMills.”
The processing systems would be delivered to the mill in Changine, Modonpur, Kanchpur, Sonargaon. Start-up is scheduledforthethirdquarterin2023.n
ABi-monthly Magazine for Pulp, Paper & Converting Industries in INDIA
Please choose the following subscription plans: India Rest of World
o 1year(6issues) Rs.1000 USD200
o 3year(18issues) Rs.2000 USD350
o 5year(30issues) Rs.3000 USD500
*Including Mailing Cost & GST
*Including Mailing Cost & GST
Company Details (PleasecompleteinEnglishusingBlockletters&attachyour Business Card)
Pay Online
First Name_______________________________________________ Last Name___________________________________
Company Name___________________________________________ Designation_________________________________ Delivery Address______________________________________________________________________________________
City__________________ State___________________ Zip code___________ Country______________________________ Tel._________________________________Mobile_______________________________Fax________________________ Email______________________________________________Website__________________________________________
Business Activity______________________________________________________________________________________ Cheque/DDNo.__________________Dated________________ForRs______________Drawnon_________________________ GSTNo._________________________BillingAddress___________________________________________________________
Favouring “TULIP 3P MEDIA PVT. LTD.”
Transfer from Abroad (Please mail the duly filled subscription form along with Bank Remittance copy to info@papermart.in)
Bank Details for Payment Transfer:HDFC BANK (Swift Code: HDFCINBB)
IFSC Code: HDFC0000287
Credit: TULIP 3P MEDIA PVT. LTD., A/C No.: 02872560002186
Branch: Ashok Vihar, Ph.-II, New Delhi-110052 (INDIA)
Please fill & return to : TULIP 3P MEDIA PVT.LTD., 501-502, ABW Tower, MG Road, IFFCO Chowk, Sector-25, Gurugram-122002, Haryana, INDIA Ph: +91-0124-4250148, Mobile : +91 99999 35011 / 22 / 44, Email: info@papermart.in, info@tulip3pmedia.in
Signature / Stamp
* Due to COVID-19 event status could change. Please check with the organizers before visiting.
Papertech Expo 2023
2 - 4, February 2023
Dhaka, Bangladesh
www.papertechexpo-bd.com
Paper One Show 2023
21 - 23, February 2023
Sharjah, UAE
www.paperoneshow.net
IPPTA 58th AGM and Seminar
17-18 March 2023
Hyderabad, India
https://ippta.co/seminar-details
TAPPICon
22-26 April 2023
Atlanta, Georgia (USA)
www.tappicon.org
Paper-ME
2-4 September 2023
Cairo, Egypt
www.papermideast.com
MIAC 2023
11 - 13 October 2023
Lucca, Italy
www.miac.info/en
Paperex 2023
6 - 9, December 2023
Greater Noida, India
https://india.paperex-expo.com
Paperex South India
5 - 7 December 2024
Chennai, India
https://southindia.paperex.in
A Bi-monthly Magazine for PULP, PAPER & CONVERTING INDUSTRIES in INDIA
Vol.: 23 / No.: 05 Dec-Jan, 2023
Editor & Publisher
Parveen Kumar Jain – pkj@tulip3pmedia.in
Deputy Editor Geetika Jain – gjain@papermart.in
Associate Editor Anurima Mondal – desk@tulip3pmedia.in
Sub Editor Soumya Ojha – desk3@tulip3pmedia.in
Graphic Designer
Ravi Thakur – ravithakur@tulip3pmedia.in
Advertising & Marketing Puneet Dua – mktg@papermart.in
Akansha Tiwari – mktg3@tulip3pmedia.in
Priya Thapar – mktg2@tulip3pmedia.in
Support Team Kushagra Mehrotra
Sandeep Kumar Rahul Kumar admin@tulip3pmedia.in
Chief Executive Officer Priyank Jain pj@tulip3pmedia.in
Editorial & Publisher's Office : Paper Mart, Tulip 3P Media Pvt. Ltd. 218, Sanjay Nagar, Gulabi Bagh, New Delhi-110007, INDIA
Correspondence Address: Tulip 3P Media Pvt. Ltd. 501-502, ABW Tower, MG Road, IFFCO Chowk, Gurugram, Haryana-122003, INDIA, Tel.:0124 425 0148
Mob.: +91 99999 350 11 / 22 / 44, E-mail : info@papermart.in / info@tulip3pmedia.in
International Sales : RNP
Nicolas Pelletier
16, rue Bannier 45000 Orleans, France
Tel.: +33 682 25 12 06, Fax: +33 238 422910
Chinese Representative: China Pulp & Paper Industry Publishing House No. 101, Gongyenan Road, Jinan Shandong, China Tel.: +86 531 88522949
Owned, Published & Printed By : Parveen Kumar Jain, Published at 218, Sanjay Nagar, Gulabi Bagh, Delhi-110007, INDIA. Printed at: Pankaj Paper Mart, 218, Sanjay Nagar, Gulabi Bagh, Delhi-110007, INDIA.
All disputes regarding this magazine will be settled in Delhi (India) Jurisdiction Only.
The views expressed in the columns of Paper Mart are not necessarily those of the editor or the publisher & they accept no responsibility for them.
CAUTION: No part of this magazine including advertisements designs, prepared by us or through us should be copied, reproduced or transmitted by any one without prior written permission of the publisher.
Paper Mart Partner magazine: I
www.papermart.in