LIGHTWEIGHT STRUCTURES FROM THE PERSPECTIVE OF FORM-FINDING GEOMETRY SABAH SHAWKAT Sabah Shawkat©
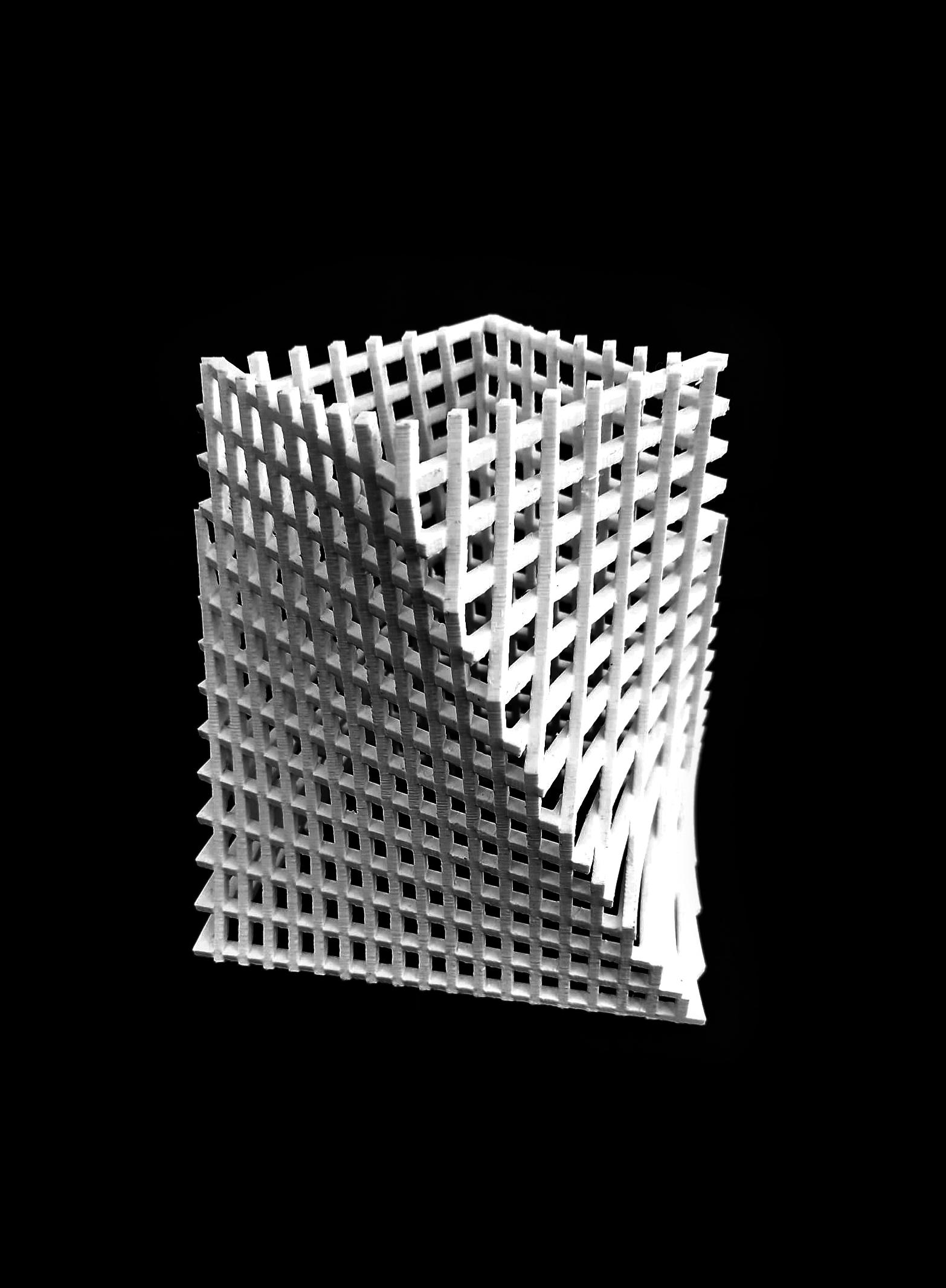
Sabah Shawkat©
Sabah Shawkat LIGHTWEIGHT STRUCTURES FROM THE PERSPECTIVE OF FORM-FINDING GEOMETRYSabah Shawkat©
Reviewer: Dipl.-Ing. Dr. Robert Roithmayr Prof. Ing. Ján Brodniansky, PhD Cover: Sabah Shawkat, Richard Schlesinger Software Support: asc. Applied Software Consultants, s.r.o., Bratislava, Slovakia Publisher: Sabah Shawkat, Brigádnická 56, 841 10 Bratislava Printed and Bound: Tribun EU, s.r.o. Cejl 892/32, 60200 Brno, Czech Republic LIGHTWEIGHT STRUCTURES FROM THE PERSPECTIVE OF FORM-FINDING GEOMETRY © Assoc. prof. Sabah Shawkat Bratislava1.edition 2022 ISBN 978-80-570-3676-0 All rights reserved. No part of this book may be reprinted, or reproduced or utilized in any form or by any electronic, mechanical or other means, including photocopying, without permission in writing from the author.Find me on Pinterest Find me on Issuu Sabah Shawkat©
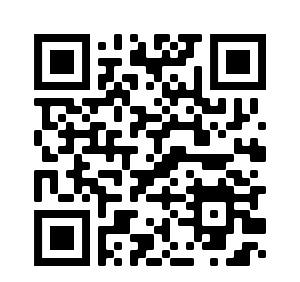
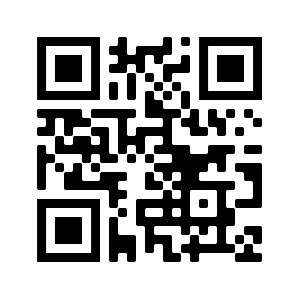
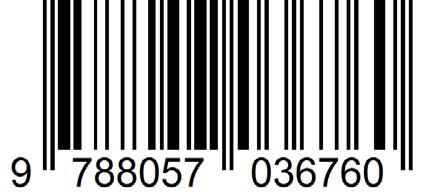
Sabah Shawkat
Sabah Shawkat is a structural designer, specializing in lightweight structures, such as tensile structures, tensile integrity structures, grid shells and reciprocal frames. He focuses on transforming these beautiful structures into design components such as chairs, tables, illuminated lamps or hammocks for interiors, gardens or public spaces.
Sabah Shawkat©
Sabah Shawkat is also a passionate expert in traditional fibre reinforced and prestressed structures. He has published numerous articles in professional journals and has written several books. He teaches students of architecture and building engineering. Moreover, he regularly organizes workshops for students and exhibitions of his own as well as student projects and construction models. He is also actively involved in projecting and building constructions as well as reconstructions and modernizations of buildings.

LIST of LIGHTWEIGHTWORKINTRODUCTIONPREFACEILLUSTRATIONSGOALSTRUCTURES 1 1. TENSEGRITY STRUCTURES 6 2. ANTI-GRAVITY TENSEGRITY STRUCTURES 22 3. TENSILE STRUCTURES 25 3.1 MEMBRANE STRUCTURES 27 3.2 TYPES OF MATERIAL OF MEMBRANE STRUCTURES 36 3.2.1 PTFE (Polytetrafluoroethylene) 37 3.2.2 ETFE (Ethylene Tetrafluoroethylene) 37 3.2.3 PVC (Polyvinylchloride) 38 3.2.4 SILICONE 38 3.3 FORM FINDING 38 3.3.1 THE FORCE DENSITY METHOD 39 3.3.2 ADVANTAGES and DISADVANTAGES OF MEMBRANE STRUCTURES 46 3.4 LINEAR THREE NODE TRIANGLE ELEMENT 47 3.5 THE PLANE STRESS PROBLEM 58 3.6 PLAN STRESS STATE and PRINCIPAL STRESSES 59 3.7 HOOKE LAW for THE PLANE STRESS STATE 61 4. ELASTIC GRID SHELLS 66 5. GEODESIC DOME 73 6. CATENARY CURVE 83 7. MÖBIUS BAND 92 8. RECIPROCAL FRAME 99 9.HYPERBOLIC PARABOLIC MODEL-GRID SHELL STRUCTURE 108 Sabah Shawkat©
LIST of ILLUSTRATIONS
Fig. 1. Pedestrian Tensegrity Bridge (Shawkat, 2019) Fig. 2a. Pedestrian Tensegrity Cable-stayed Bridge (Shawkat, 2019) Fig. 2b. Pedestrian Tensegrity Cable-stayed Bridge (Shawkat, 2019) Fig. 2c. Pedestrian Tensegrity Cable-stayed Bridge (Shawkat, 2019) Fig. 1.1a, b. Tensegrity Tower and Geodesic Tensegrity Dome (models created by the author) Fig. 1.2. Tensegrity Land (models created by the author) Fig. 1.3. Orthogonal Triangular Tensegrity Prism (Shawkat 2019) Fig. 1.4. Process of Thinking in the Grasshopper Programme Fig. 1.5. Process of Thinking in the Grasshopper Programme Fig. 1.6a. Tensegrity Icosahedron (model created by the author) Fig. 1.6b. Expanded octahedron” or “Icosahedron” Physical model Tensegrity Icosahedron (Shawkat) Fig. 1.6c. Process of Thinking in the Grasshopper Programme Fig. 1.7. Physical model Diamond T- Tetrahedron (model created by the author) Fig. 1.8. Physical model - Double-Layer Tensegrity Dome Fig. 1.9. Physical models – Tensegrity (models created by the author) Fig. 1.10. Table Lamp (Model created by the author) Fig. 1.11. Tensegrity as a Chair (Shawkat, and co-authors 2019) Fig. 1.12. Tensegrity art -Design systems- Parametric Modelling (models created by the author) Fig. 1.13. Tensegrity art - Parametric Modelling (models created by the author) Fig. 1.14. Parametric Tensegrity Form Finding-Physical models (models created by the author) Fig. 1.15. Parametric Tensegrity Form Finding-Physical models (models created by the author) Fig. 2.1 a, b. Tensegrity Anti-Gravity Tea Table (models created by the author) Fig. 2.2 a, b. Anti-Gravity Tensegrity Tea Table (models created by the author) Fig. 2.3a, b. Anti-Gravity Tensegrity Tea Table (models created by the author) Fig. 2.4 Anti-Gravity Tensegrity (models created by the author) Fig. 3.1. Membrane Models, Small Scale Counts (Shawkat, 2021) Sabah Shawkat©
Fig. 3.2. Form Finding of Membrane Structures (Shawkat, 2021) Fig. 3.3. Typical shapes of membrane structures Fig. 3.4. Conical surface Fig. 3.5. Process of Thinking in the Grasshopper Programme Fig. 3.6. Process of Thinking in the Grasshopper Programme Fig. 3.7. Process of Thinking in the Grasshopper Programme Fig. 3.8. Process of Thinking in the Grasshopper Programme Fig. 3.9. Process of Thinking in the Grasshopper Programme Fig. 3.10. Rectangular Plan with Parallel Curvatures in x and y Fig. 3.11. Membrane Roof Construction Fig. 3.12. The general area of a hyperbolic paraboloid Fig. 3.3.1. Base Forms of Membrane Structures Fig. 3.3.1.1. Force Density Method (Bletzinger, 2014) Fig. 3.3.1.2. Detail of Cable Network (Bletzinger, 2014) Fig. 3.3.1.3. Cable Element in the Global Coordinate Frame Fig. 3.4.1. Linear triangle element. Nodal coordinates and displacements. Fig. 3.4.2. Linear Triangle Element Fig. 3.4.3. Dimensions of Fabric Membrane Structure Fig.3.7.1 Compression: Plane Stress-Plan Strain Fig.3.8.1. Principal Stress Fig.3.8.2. Principal Stress-Mohr’s Circle of Stress Fig.3.8.3. Plane Stress State Fig.3.8.4. Analytical Solution of Stresses Fig.4.1. Plane flat Elastic flat grid plan members (models created by the authors) Fig. 4.2. Elastic deformation, reversible deformations, and form finding of E.G.SH, (models created by the authors) Fig. 4.3. Grasshopper Script created by the author, physical form-finding Fig. 4.4. Form Finding of the elastic geodesic dome using grasshopper inside Rhino, (models created by the authors) Fig. 4.5. Parametric Physical Form-Finding of EGG Shells (models created by the author) Fig. 5.1. Tensegrity as a Geodesic Dome (Shawkat, 2020, Shawkat, 2021) Sabah Shawkat©
Fig. 5.2. Process of Thinking in the Grasshopper Programme Fig. 5.3. Process of Thinking in the Grasshopper Programme Fig. 5.4. Physical model of the multi-geodesic dome Fig. 5.5. Process of Thinking in the Grasshopper Programme Fig. 5.6. Segment =6, Pressure 0.05, Edge factor 2.20, Radius =12 Fig. 5.7. Segment =8, Pressure =0.05, Edge factor= 2.20, Radius =12 Fig. 5.8. Segment =10, Pressure= 0.05, Edge factor= 2.20, Radius =12 Fig. 5.9. Segment =6, Pressure= 0.05, Edge factor =1.10, Radius =12 Fig. 5.10. Segment =6, Pressure= 0.05, Edge factor =0.05, Radius =12 Fig.5.11: Eden design project as a beautiful global garden landscape Fig. 5.12. FEM joint analysis and the final version of the joint after the application of the surface treatment Fig.5.13. Traditional Geodesic Dome 1:1, physical form-finding Fig.5.14. Grasshopper Script created by the author, physical form-finding Fig. 6.1 Physical Model as a Design Tool Fig. 6.2. Catenary Curve-Determination of Forces Fig. 6.3. Shapes for the circular, pointed, parabolic and elliptical arches Fig. 6.4. Vertical and Horizontal Forces of Catenary Cable Fig. 6.5. Transformation of Catenary Curve to the Horizontal Direction Fig. 6.6. Catenary Curve-Form Finding, Grasshopper Script created by the author Fig. 6.7. Grasshopper Script created by the author Fig. 6.8. Grasshopper Script created by the author Fig. 7.1. Möbius Strip Rotations of Other Geometric Shapes (models created by the authors) Fig. 7.2. Möbius Strip Structure of Rectangle Geometric Shape Fig. 7.3. Mobius Band with Various Degrees of Twist Fig. 7.1.1. Process of Thinking in the Grasshopper Programme (Variant a) Fig. 7.1.2. Deformations and Animation of Möbius Band ( = - 0.1 to 0.1) Fig. 7.1.3a, b. Deformations and Animation of Möbius Band, for a = - 0.1 to 0.1, for b = - 0.3 to 0.3 (Variant a) Fig. 7.1.4. Process of Thinking in the Grasshopper Programme (Variant b) Sabah Shawkat©
Fig. 7.1.5. Möbius Bands with Various Degrees of Twist with Constant Floor Level (Variant b) Fig. 7.1.6. Process of Thinking in the Grasshopper Programme (Variant c) Fig.7.1.7. Möbius Bands with Various Degrees of Twist with Constant Floor Level (Variant c) Fig. 7.1.8. Process of Thinking in the Grasshopper Programme (Variant d) Fig. 7.1.9. Process of Thinking in the Grasshopper Programme, the script created by the author Fig. 8.1. Physical Model of Temporary Bridges, (Shawkat, 2021) Fig. 8.2a. Self-Supporting Structures - Reciprocal Frames (Shawkat,2021) Fig. 8.2b. Self-Supporting Structures - Reciprocal Frames (Shawkat,2021) Fig. 8.3. Process of Thinking in the Grasshopper Programme Fig. 8.4. Platonic Tetrahedron Fig. 8.5. Platonic Octahedron Fig. 8.6. Platonic Cube Fig. 8.7. Platonic Dodecahedron Fig. 8.8. Platonic Icosahedron Fig. 8.9. Model Created by Shawkat 2022 Fig. 9.1. Hyperbolic Paraboloid Model (Shawkat, 2021) Sabah Shawkat©
The revolutionary progress in science and technology pushes the boundaries of technical unfeasibility. Construction and technological methods now often determine the architecture of the building. New technologies allow us to realize structures that have larger spans and are more and more light. The differences between design, construction, and its characteristic form are disappearing.
The concept of lightweight structures has also initiated a new discussion in our educational activities, and we aim to increase the interest and popularize this topic among students of architecture and other related study fields.
Sabah Shawkat©
Architects and engineers are studying, improving, and discovering. They are the creators of new spaces, forms, and structures. These structures developed over the years and together with advances in material engineering and technology they continue to progress. Lightweight structures may be internal, external, permanent, temporary, large, small, supported, etc. Their unique forms have played an important role in contemporary architecture and design since the time they first appeared in the 1967s, pavilion at the world exposition Montreal, as part of the work of the world-famous German architect and engineer Otto Frei. A typical feature of today’s architecture is the unity of function, structure, and form. Contemporary buildings are a synthesis of two concepts: Art and structure. A construction designed logically, in conformity with the principles of structural engineering, is at the same time an aesthetic construction, one that we tend to call "nice architecture".
Designing lightweight structures is a complex task. Meeting all the technical criteria while bringing beauty and elegance to the space requires the unification of the role of an architect and an engineer. Every part is visible and constructive, relying on the proper functioning of all parts. At present, lightweight structures are an integral part of architectural creation. They transform the space with their untraditional solutions, exceptional shape, as well as subtle and elegant quality.
Lightweight structures can be seen in various forms and variations in a broad spectrum of use in architecture, engineering as well as building construction. They are highly appreciated for their subtle aesthetic appearance and their innovative character.
PREFACE Lightweight construction is one of the popular architectural forms of today's building and design, they appeal mainly to their untraditional solutions and exceptional shape. The concept of lightweight construction is particularly interesting for the needs of architects or designers from Form-finding.
All the models shown in this book have been made by the author.
Sabah Shawkat©
Free Form; Form Finding; Computation Design; Parametric Design; Lightweight Structures; Pedestrian Tensegrity Bridge; Membrane Structures; Anti-gravity; Tensile Integrity Structures. Elastic Grid Shells; Geodesic Dome; Catenary Curve; Möbius Strip; Hyperbolic Parabolic Grid Shell; Reciprocal Frame, Biomimicry design.
The virtual models and their transformation into the real design were incorporated by means of both physical form-finding and numerical/digital models.
Keywords:
The study began with an experimental and numerical form-finding process including different fabrication methods on (Tensile integrity structure, reciprocal systems, elastic grid shells, tensile structures, geodesic dome, and Biomimicry design). At the same time, physical models and their transformations into real forms served and at the same time were tools for students to develop a critical approach to modeling. Physical models have been designed to demonstrate the power and beauty of mathematics, physics, and architecture, to show their interactions in design and in real design principles, emphasizing that some degree of speculation and inconsistency in process of thinking among all activities in this field is legitimate.
Current patterns in architecture began to develop in the second half of the 20th century when architects started to center on observing nature more than functionality. Because Linear measurements have a limited ability to capture the three-dimensional curvature of the body.
Shaped the freedom that architects have gained after liberating themselves from linear conventions is now leading to "geometric anarchy", which is manifested in the design of so-called "freeform" structures geometry, which presents in contemporary architecture the modern mathematics of curved Free-formsurfaces.shapes have no analogy in nature, and they can’t be exactly described mathematically.
The idea of teaching designers the principles of form improvement is the most creative way because it encourages experimentation and makes the relationship between structure and forms easily clear.
During this period, Le Corbusier's "Form follows function" changed to Otto's "Form follows force", which means the form is subject to the course of forces. Most of us are familiar with Euclidean geometry during our studies, but we never learned non-Euclidean geometry unless we started studying math or science. Evolution in nature, which optimized its structures (animal skeletons, plant, and tree shapes), has also become a major source of inspiration for building structure shapes.
Nowadays, an attempt to free objects from shapes that are based on straight lines or Euclidean geometry is starting to develop. By considering nature and the surrounding world, the spectator may discover that the only straight lines that surround him are those that the man himself established. The perfection of the time of straight lines and straight forward geometric shapes or Euclidean geometry in design was the period of cubism design, constructivism, and functionalism. The main representative of this current was the Swiss Le Corbusier with his celebrated quote “Form follows function”, that is the form subordinated function.
Complex object geometries have begun to require a new approach in the engineering part of their design. Form improvement provides a very interesting approach between artistic expression and structural engineering. A particular task of construction form of the non-conventional structures is form finding. Physical modeling of structures was used in their work by builders such as António Gaudi, Heinz Isler, and Frei Otto. With the development of computer technology, numerical methods based on finding the shape and modeling of the equilibrium state have also begun to develop geometrically nonlinear problems. Physical models (form-models) are used to describe the power of the variability and beauty of these structures to achieve the fine art of non-traditional structures.
Sabah Shawkat©
INTRODUCTION
Designers in our field, such as structural designers together with artists and architects analyze, discuss, and improve to create new forms, whether traditional or parametric to invent progressive construction processes as well as production technologies and thus enrich our society with new designs. They have continued to progress over the years, together with advances in material engineering and technology, and are considered an integral part of architectural creation.
Working with physical modeling is a very powerful tool for the exploration of three-dimensional structural forms and the designers will certainly profit from it. This type of experimentation opens a new space and makes the relationship between structure and form easily comprehensive.
Sabah Shawkat©
Experimentation with small to larger physical modeling is a very important characteristic of this idea.
The objective of this excursion is to show the designers how to create several physical models of nonconventional structures such as tensegrity systems, tensile membrane structures, reciprocal frames, Möbius band, and grid shell structures simply and stylishly way. The amazing advantage of these structures is that we can design various models to demonstrate their structural and physical beauty and at the same time they can have an additional creative function. Our examples of non-conventional structural models serve as beautiful architectural components such as chairs, table lamps, sculptures, tea tables, or hammocks designed for interiors or public spaces.
Evolution in nature, which optimized natural structures, has also become a major source of inspiration for the shapes of structures in construction and architecture. However, as we mentioned that the "Free Form" shapes have no analogy in nature, and it is impossible to describe them exactly mathematically. We want to choose our approach to the issue of shape search and optimization of the so-called free-form membrane constructions of synclastic and anticlastic shapes. We have set goals for the creative design of the free form geometry and estimating a useful design procedure with integrated form and topology optimization of the free form geometry in architecture. Our examples of non-conventional structural models serve as beautiful architectural components such as chairs, table lamps, sculptures, tea tables, hammocks, or geodesic domes designed for interiors or public spaces. Investigating, small, medium, and large scale of free form geometry to serve the people. finding a feasible form finding geometries process of free form geometry in architecture with high ultimate limit state respectively serviceability limit state serving as a universal design work method, which can be adopted in the realization of similar structures to reach shape stabilization. Minimizing the negative friction in nodes during the installation of structures. Parameterizing the geometry using improving the detail of the node joints and increasing the numbers of equal elements for industrial prefabrication. Improving and simplifying the creation and easy installation of the boundary conditions of anchors and connecting the members. create a script using the grasshopper inside the rhino program for better analysis, parameterization of free-form geometry, and comparison with real physical models
WORK GOAL
This work aims to present our approach to the problem of finding the shape and optimization of "free form" geometry in architecture. We will create virtual and subsequent real models creatively by physically searching for a form and applying numerical methods based on finding the shape and modeling the equilibrium state of geometric nonlinear shapes. We will aim to free constructions from shapes that are based on straight lines. The "Form Finding" method allows you to search for shapes regardless of traditional compositional, static, or constructional principles using a virtual, so-called trans-architecture.
Sabah Shawkat©
Sabah Shawkat©
Physical models of bridges in Fig. 1. and Fig. 2. a,b, and c are nice examples showing the relation between art and structural engineering. The advantage of lightweight structures is that all forces are nicely visible. Forces are a mechanical concept useful for engineers who want to size their structures and they are by nature visible. By differentiating cables and struts, the model of the footbridge provides information on whether tension and compression are present. Therefore, the dimensions of the components such as tubes and size, and the arrangement of cables depend upon the material properties as well as on the level of tension resp. compression state. As seen in the figures, lightweight tensegrity structures are fascinating as the gravity seems to be absent and the structure looks as if floating in the air. The stability of the entire system ensures that the whole is in equilibrium which ensures its stability.
The potential of lightweight structures in the future for designers is very significant, so the tensile integrity structure as it is called tensegrity is of great importance for construction under tension. And that is why we were dealing with parametric models in this section that we expressed the benefits of this system for pedestrian bridges. In general, a tensile structure is a type of construction involving the use of elements in which tensional forces are implied, with no compressive forces action, or bending, giving it great construction advantages. That is the quality that offers possibilities of large spanning and utilizing a variety of free-standing forms.
Sabah Shawkat©
1
LIGHTWEIGHT STRUCTURES
From an ecological, social, and cultural perspective, lightweight structures have never been more contemporary and necessary than today. Moreover, lightweight structures can bring beauty and elegance to the space, and they are seen in various forms, shapes, sizes, and variations in a wide range of applications. They transform the space through their unconventional solutions, unique shape, as well as subtle and elegant quality. Lightweight structures, in place of stiffness of the material, derive their resistance from their shape and may therefore be denoted as shape active. One of the main design steps of lightweight constructions is therefore the design of a shape that is controlled by the required stress state. According to their characteristics, lightweight structures can be divided into several subgroups, one of them being tensegrity systems.
The smaller the ratio between a structure’s dead load and the supported live loads, the “lighter” the structure (Schleicher, S., Lienhard, J., Fleischmann 2010). Designing and forming lightweight structures is not an easy task due to the small ratio of the structure's self-weight to the live load compared to traditional structures where the ratio is much higher. Each part is clear and useful and relies on the proper functioning of all parts.
Fig. 1. Pedestrian Tensegrity Bridge (Shawkat, 2019) Fig. 2a. Pedestrian Tensegrity Cable-stayed Bridge (Shawkat, 2019)
2
We attempt to create light and slender structures quickly set a high standard for structural design. Steel and prestressed concrete enabled us to embody the lightweight ideal in structural design. This type of parametric bridge is a wonderful example of this. The structural system of the cable-stayed bridge or suspension bridge is well suited to this desire: by decreasing the distance between the cable supports, the deck can be made slenderer as the bending moments are reduced. Therefore, the structural designer's greatest goal was to make the deck as slender as possible. Cable-supported bridges, which can be built in a great variety of forms and with considerable elegance, have undisputed potential.
Sabah Shawkat©
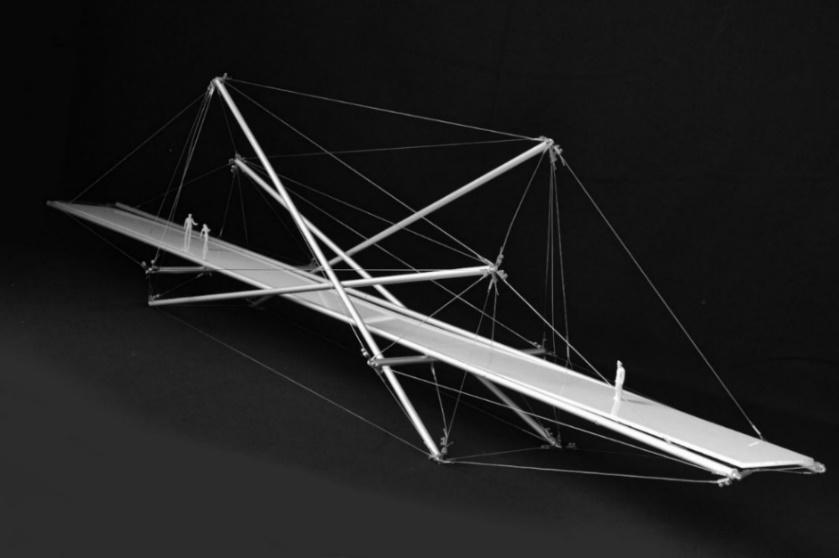
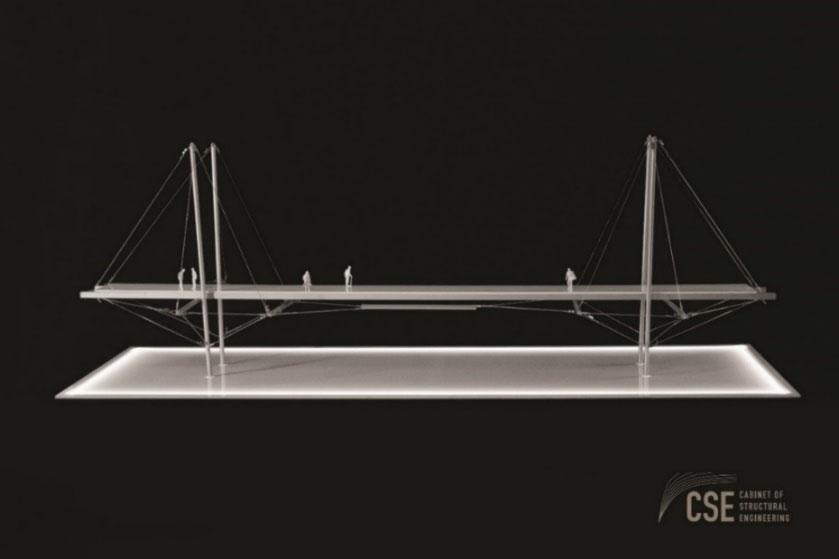
3 Fig. 2b. Pedestrian Tensegrity Cable-stayed Bridge (Shawkat, 2019) Sabah Shawkat©

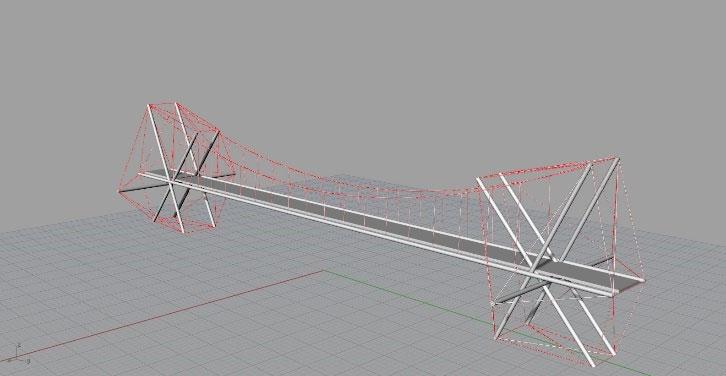
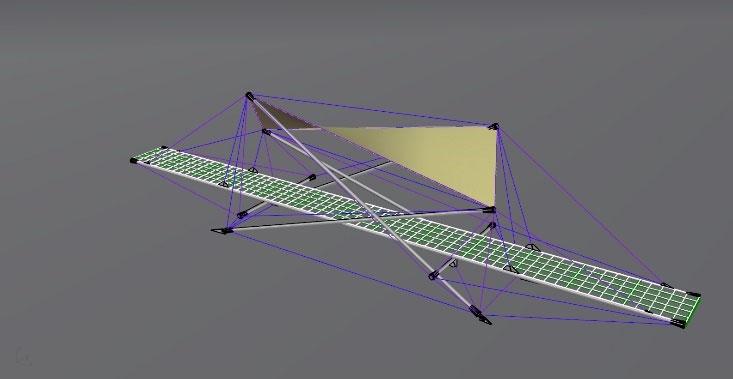
4 Fig. 2c. Pedestrian Tensegrity Cable-stayed Bridge (Shawkat, 2019) Sabah Shawkat©
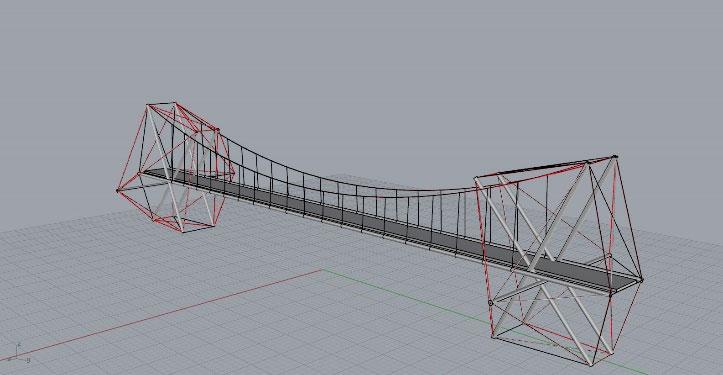
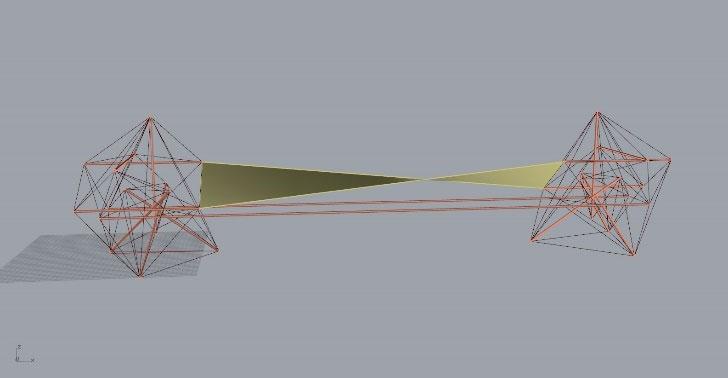
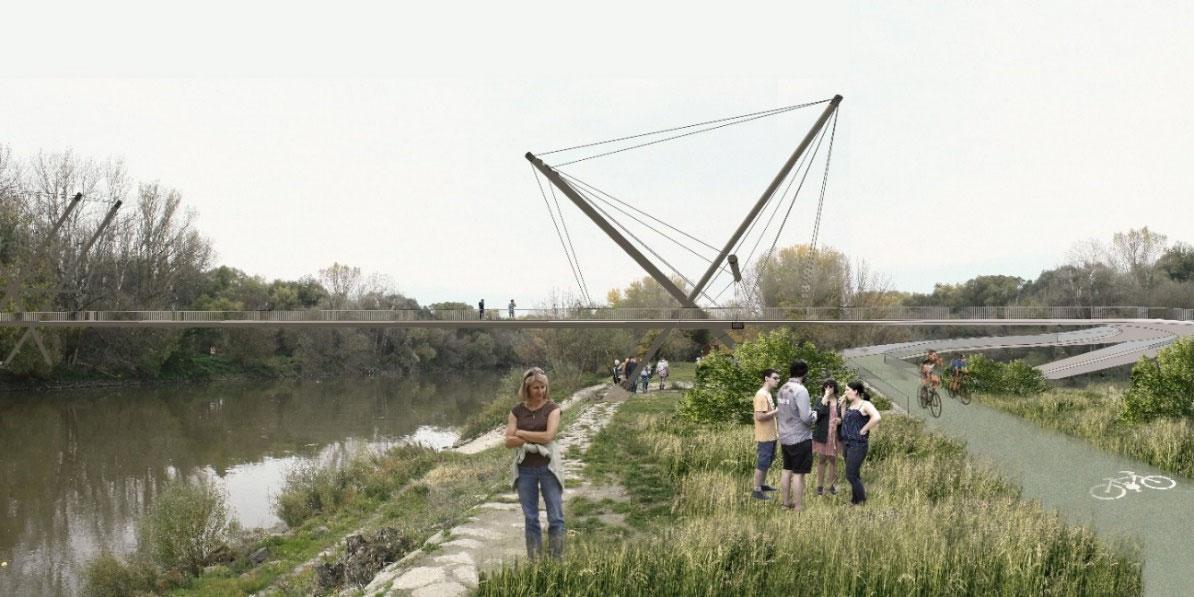
The question of whether it is necessary to consider the load of the structure as quasi-static or accidental is usually solved by comparing the time of loading the load and load time, with the largest period of natural vibrations of the structure. If the time of the load is less than half of the largest period of the natural frequency, the loads must be considered accidental. if the load time is more than three times the period of the natural frequencies, the loads can be considered quasi-static. In the case of accidental load, it is necessary to consider not only the value of the load but also the time during which this load reaches the final value, as well as the impulse, which represents the area under the curve of the load-time diagram.
In the case of quasi-static loads, they arise in the structure in different ways. the load is created by a rapidly moving load, created for example by the movement of a train on a bridge.
when solving the load-bearing capacity of structures as the Pedestrian Bridge, it is necessary to solve the problem of how stresses and de formations arise when the structure is suddenly loaded, which are in many times greater than when the load is slowly applied to the structure. Such rapidly applied forces or displacements are usually referred to as impact respectively accidental or impulse loads.
Once it takes place at the reinforcement point of the structure, for example at the connection point of the support plate to the heat exchanger tubes, accidental forces may cause abrasion due to small transverse displacements caused by transverse deformations or small transverse components of the speed of the sliding impact, i.e. there is a risk of failure in the form of abrupt friction. It should be noted that due to accidental loads, the load increase, and the properties of the material can change significantly in comparison to quasi-static loads, it can be noted that the values of yield strength and elasticity under accidental load significantly differ from their values under static or quasi-static loading.
Sabah Shawkat©
5
Kenneth Duane Snelson (1927 – 2016) was an American sculptor and photographer. He was one of the first to build tensegrity sculptures and he defined tensegrity as a closed structural system composed of compression struts within a network of tension tendons. He liked to describe his tensegrity sculptures as floating compression. Snelson considered tensegrity as a connection between architecture and art.
Sabah Shawkat©
The first patented definitions of tensegrity are very general. Fuller described tensegrity systems as “Islands of Compression in a Sea of Tension”. Snelson patented the system which he called “Continuous Tension, Discontinuous Compression Structures”. Richard Buckminster Fuller (18951983) was an American engineer, architect, inventor, and futurist. He developed the famous Geodesic dome – a spherical form in which lightweight triangular or polygonal facets consisting of either skeletal struts or flat planes, largely in tension, replace the arch principle and distribute stresses within the structure itself.
Kenneth Snelson, after completing lectures and Fuller's practice at Black Mountain College in North Carolina, created a catalytic contribution to understanding the construction of tensegrity when he collected his X-Piece statue.
The Tensegrity concept offers a high level of geometrical and structural efficiency when the external load acting on construction is transmitted to all elements of the structure in the same way. Once the external force is removed the elements will return to their original shape. Vibration in one part of the structure causes vibration in all other parts (Motro, 2003). The mechanical stability of structures does not depend on the strength of individual parts but the whole structure distributing and balancing mechanical strain. Tensegrity is a relatively new design principle that applies when a discontinuous set of compression elements is opposed and balanced by a continuous tensile force, thereby creating an internal prestress that stabilizes the entire structure. Tensegrity structures are a particular class of lightweight structural systems. Tensegrity is based on the use of isolated components in compression inside a net of continuous tension, in such a way that the compressed members (usually bars or struts) do not touch each other, and the prestressed tensioned members (usually cables or tendons) delineate the system spatially. Tensegrity systems were introduced in structures approximately in the middle of the 20th century within the work of Fuller and Snelson. They can also be defined as a set of compressed bars inside a continuum of tense cables, the whole being in a stable self-stressed state. The tensegrity system can effectively use compression and tensile elements, which allow significantly reducing the weight of the structure. The word tensegrity was coined by Richard Buckminster Fuller in the 1960s, by combining the words tension and integrity (R.B.Fuller, 1962, and K. Snelson, 1965).
6 1. TENSEGRITY STRUCTURES
7
In other words, in a tensegrity structure the two types of forces in nature, tension, and compression are completely separated and you can see them in their pure state. Where there is a strut, there is pure compression; and where there is a cable, there is pure tension.
French architect and engineer David George Emmerich (1925 – 1996) added the condition of a selfstress state: Tensegrity structures consist of rods mounted in such a way that the struts remain physically isolated in a continuous set of cables (D.G. Emmerich, 1964). However, according to some sources, structures based on the princi ple of tensegrity were explored and identified as early as in the 1920s by the obscure Latvian artist Karl Ioganson whose physical models were destroyed by the Soviet regime (D.G. Emmerich, 1964). Fig. 1.1a, b shows physical models of two tensegrity structures: a high-rise building of rectangular shape Figure 1.1a and a shell geodesic dome based on the idea of Fuller Fig. 1.1b. “Geodesic” means the shortest distance between two points. The geodesic structure consists of as many struts of the same length as possible as well as congruent surfaces. It is a network of equal triangles whereby the cross points are always situated on the surface.
Then we can describe the characteristics of a tensegrity structure as follows: The structure is free-standing, without any support.
The structural members are straight.
Sabah Shawkat©
The main shortcomings and problems of the practical application of tensegrity technology for the practice these artists have identified are:
2. The complexity of the production of details - spherical and domical structures are complicated to produce details of joints as well as the selection of suitable material for their realization, these factories can lead to production difficulties.
Fuller's basic model of tensegrity patent has quotes of element length, but no indication of how lengths would be proposed. Probably the lengths were then calculated and parameterized, as measured by the length of the elements of the finished structure
There are only two different types of structural members: struts carrying compression and cables carrying tension. The struts do not contact each other at their ends. The response to the loads is nonlinear.
1. Low Load Response - "Relatively high deformation and low material efficiency compared to conventional, geometrically rigid structures."
I think that part of the reason that the beauty and construction of tensegrity did not come into practice, even in circles where there was a strong interest in the practical application of tensegrity, is the clear lack of professional and intelligent workers as well as the precise tools for realizing their design and creation.
Sabah Shawkat©
8
This triangulation guarantees the strength and rigidity of the ball-shape d structure. There is no direct contact between the compression elements as seen in Fig. 1.1a, b. The struts are combined into triangles, pentagons, or hexagons, whereby each strut is aligned in a way that each connection point is held in a firm position. This guarantees the stability of the whole structure. Tension is distributed equally to all parts of the whole construction. Increased tension in one part provides increased tension in all parts. A global increase in tension is balanced by an increase in tension in various parts. Whilst tension is thus distributed evenly in the whole system, only individual parts are balanced by compression. There is a balance between tension and compression, we can define the system as “stable self-equilibrium”. It is a self-stabilizing whole system. The tensegrity network is a stable, at the same time adaptable construction. The whole system reacts to an outside force with an adaptive tension distribution. Both types of structures depicted in Fig. 1.1a, b use separate elements for tension and compression as we can nicely see in this visual example. The tensegrity systems can be defined as spatial structures consisting of compression (struts) and tensile (cables) components that stabilize each other through pre-stress, tension, and compression work together to resist the applied load. In our models, struts are made of aluminum or wood and nylon or steel fibers represent cables or tendons.1.1a
1.1b
Fig. 1.1a, b. Tensegrity Tower and Geodesic Tensegrity Dome (models created by the author)
There are several problems associated with tensegrity systems, and the primary one is the geometry of the structure. The self-stressed equilibrium of the structure is determined by the form-finding method. Since much of the ideas on tensegrity structures have been developed based on existing identification with nonlinear geometrical behavior, it also follows that the challenges identified are also on the same track. Firstly, analytical form-finding methods need to be developed.
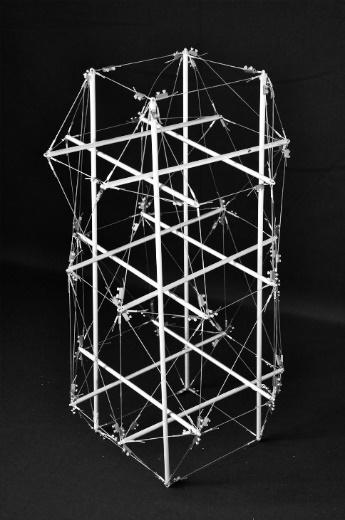
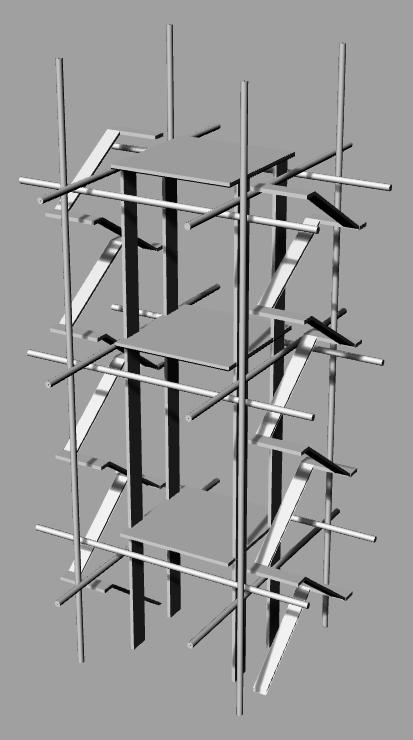
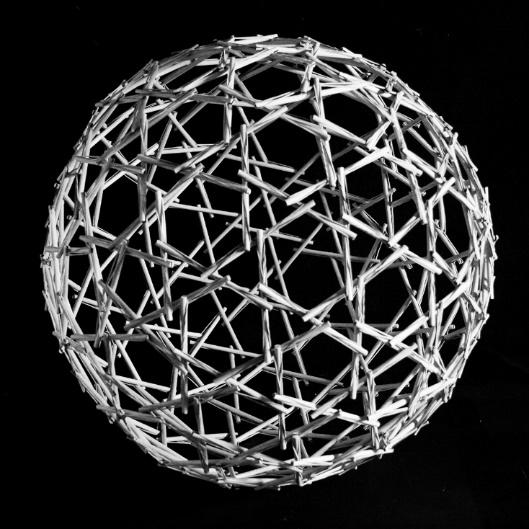
Without the proper analytical form findings methods, it would be impossible to understand high order tensegrity structures. Secondly, form-finding for arbitrary tensegrity structures is seen to involve only a little knowledge of structure. This is especially the case with structures such as spheres, cylinders, and others. There are challenges in simultaneous form-finding, also there are constraints in understanding the member length and axial stiffness parameters. Sometimes, the advancement in the context of parameter identification poses a challenge as well. In form-finding of assemblies, there are difficulties in identifying the known tensegrity units and the unknown tensegrity grids. Contrary to developing and optimizing structures using intuition and experimentation, form-finding is the determination of the design of the tensegrity geometrical configuration analytically. The configuration found should also keep the tensegrity structure in a state of equilibrium. Form finding studies have been carried out on tensegrity structures from the early research studies of Fuller and Snelson. The tensegrity structures that they formed were mostly convex polyhedron based. They used this geometric research to understand the existing structure and understand how to formulate newer configurations if possible.
Tensegrity structures can be seen as “internally pre-stressed, free-standing pin-jointed networks, in which the cables or tendons are tensioned against a system of bars or struts.” This description introduces the fact that the system is pre-stressed and pin jointed. This implies that there are only axial forces present in the system and there is no bending or torsion. The tensegrity concept offers a high level of geometrical and structural efficiency and results in modular and lightweight structures. When the external load acting on construction is passed on from one element or place to another element of the structure finds a new form. Once the external force is removed the elements will return to their original shape. Vibration in one part of the structure affects vibration in all other parts. Fig. 1.2 shows the author´s physical models of the series called “Tensegrity Land” which were presented at an exhibition in Prague, in 2019. These tensegrity structures serve as table lamps. One of the most elegant tensegrity forms is a three-struts T-prism Fig. 1.3: nine tendons, three struts single layer, twist element that rise to the open space. A triangular tensegrity prism was probably first made either by a Lithuanian artist K. Ioganson around 1920 or by a student of R. B. Fuller at the University of North Carolina in the early 1950s named Ted Pope (Snelson, 1965, and Emmerich, 1964).
Sabah Shawkat©
9
The tension of the cable is applied to each strut (compression) element. As it is a threedimensional system, at each end of the strut we should have at least three cables in tension attached to the node to ensure the stability of the entire structure. Based on this principle, we created a triangular tensegrity prism that can serve as a nice hammock for public space which is depicted in Fig. 1.3. Fig. 1.3. Orthogonal Triangular Tensegrity Prism (Shawkat 2019)
Sabah Shawkat©
10 Fig. 1.2. Tensegrity Land (models created by the author)

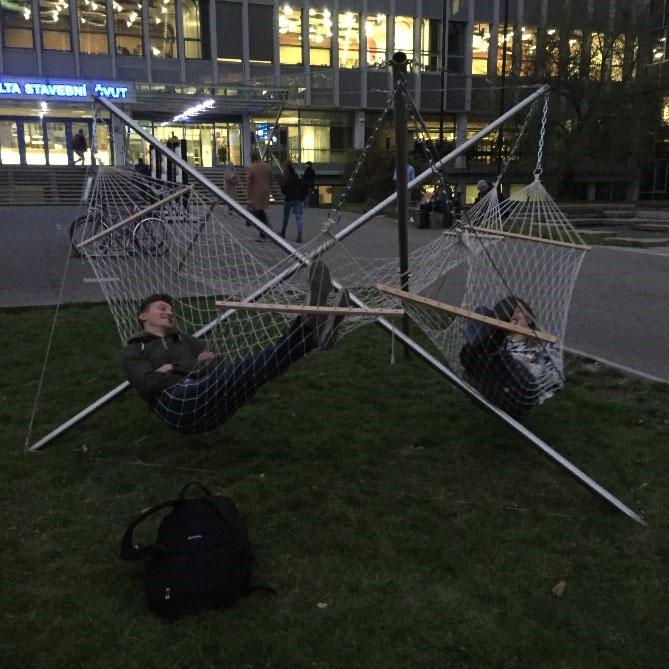
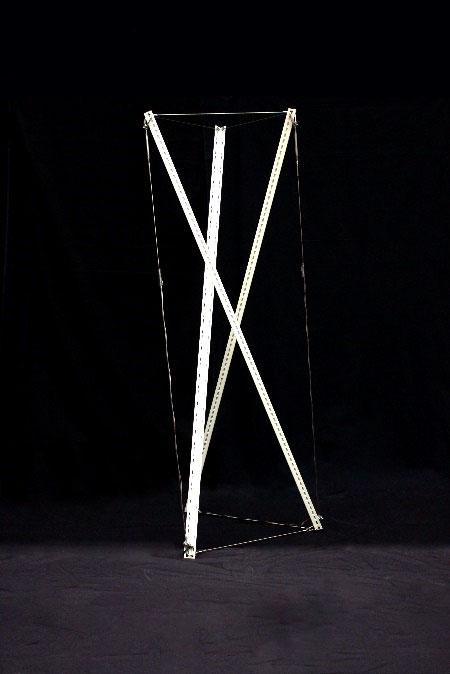
Kangaroo refined in terms of goals and kind of other things, so the idea is like there are different features that you want to adhere for example to behave as a hinge or to behave as a minimal like surface as a soap film. It’s going to try to create a form that is based on that but what it is not looking at is like, what the object is made from you know it’s not considering cross-section or materiality, and specific things like bracing or like pins as well as verses hinges. If you are looking at form and you know kind of computation this is a very quick way of resolving some things and kind of making some progress and they are based on the structural principles which I think are interesting.
Sabah Shawkat©
Orthogonal Tensegrity Prism: It is the most elegant tensegrity one can conceive, three struts Tprism, nine tendons, twist an element, 3 struts single layer, rise to the open space, this 3 strut T prism was probably first made either by a Lithuanian artist Karl Ioganson around 1920 or by a Fuller student at the University of North Carolina in the early 1950s named Ted Pope. But both Karl's and Ted's contributions helped the development of the tensegrity stops here. We are not even sure they indeed build this principal tensegrity. Each strut is acted upon by the tension of the cable. As it is a threedimensional system, at each end of the strut we should have at least three cables in tension attached to the node. This is also observed by Snelson: “I know I need a minimum of three cables on any end of any stick” (Snelson and Von Baeyer, 1989). The resultant of each triad of forces at each node, added to the relatively small weight of each component, must be in line with the axis of the strut because otherwise the rod would be affected by a bending moment and would not be in equilibrium, i.e. there is a three-dimensional equilibrium of tensions and compressions at each node. From this analysis, we can understand that the definition of tensegrity structures as internally pre-stressed, freestanding pin-jointed networks, in which the cables or tendons are tensioned against a system of bars or Tostruts”.make a parametric design for Tensile integrity structure, we create algorithmic editors that ordinarily consolidate visual programming dialects using Grasshopper inside Rhino Fig. 1.4 and Fig. 1.5, to overcome the imperatives of the interface, and to design specifically, overseeing not the form, but the code that produces the shape. Parametric, in mathematics, is a set of quantities expressed as an explicit function of several parameters, according to the set of results determined from the parameters (string length, anchor point location, birdshot weight).
All members of a Tensegrity structure are axially loaded. Generally, members that experience deformation in two or three dimensions are much harder to model than members that experience deformation in only one dimension. Hence, increased use of tensile members is expected to yield more efficient structures. let me now present some small scaling models for illustration, to give the idea of tensegrity to the readers in a simple way.
11
Fig. 1.5. Process of Thinking in the Grasshopper Programme
As you can see in Fig. 1.6a, this construction is made of one tensegrity spatial 3D element consisting of six X-shaped modules (six strut elements of equal length and shape). The strut elements are oriented in three mutually perpendicular axes, each having the same length, and eighteen cable elements. Three cables pass through each node. The assembly of triple-X shapes provides structural morphology of tensegrity systems and adding tension cables to the components gives a stable state to the structure, therefore, preventing a motion of the triple X-shapes out of their plane.
Sabah Shawkat©
12
Fig. 1.4. Process of Thinking in the Grasshopper Programme
The same reasoning could be applied to the wires, which are attached to the ends of two struts and influenced by, at least, the other two cables in each node. As a result, each join is in equilibrium if it is put under a particular tension, which is usually a pre-tensioning force.
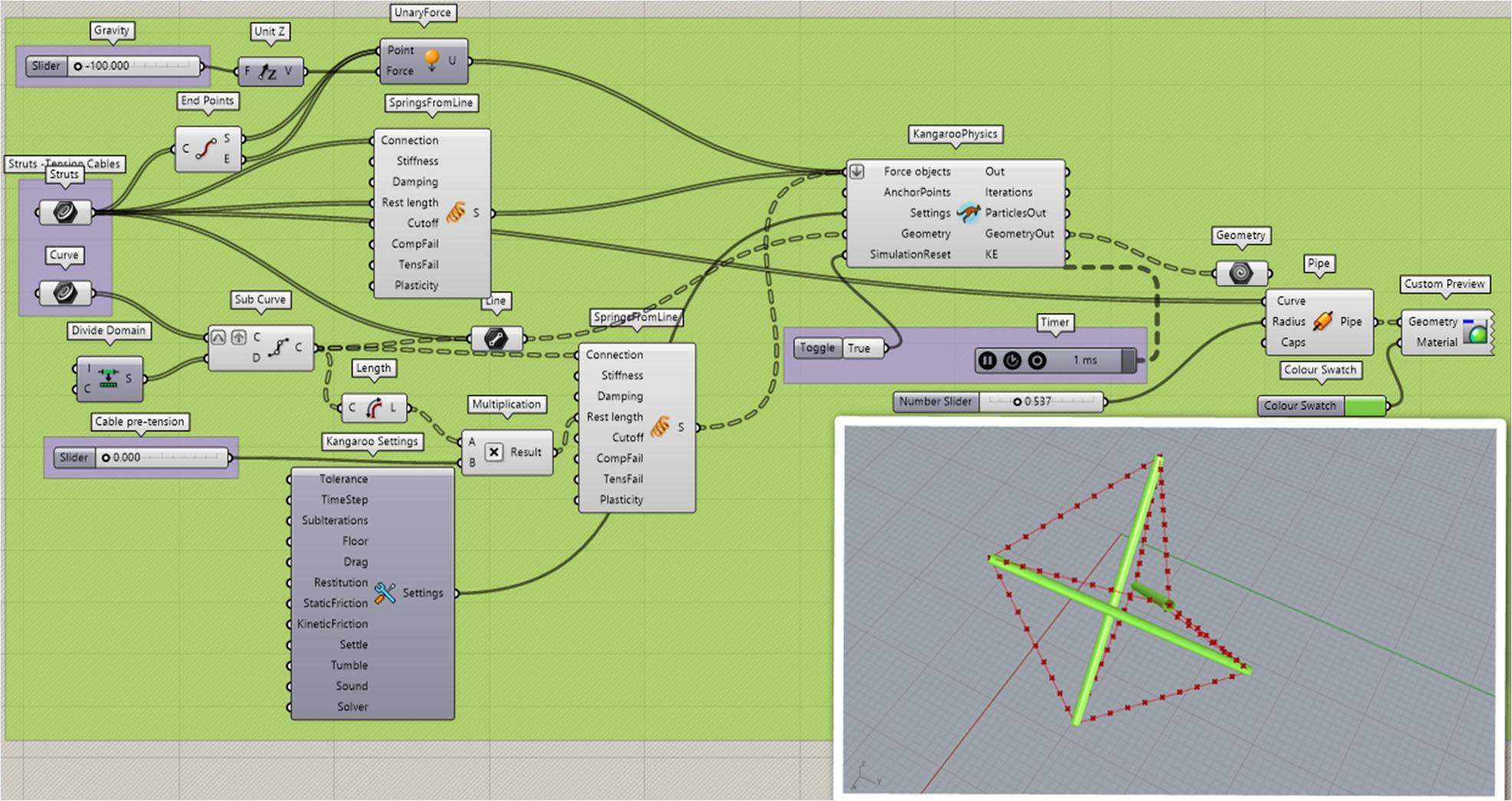
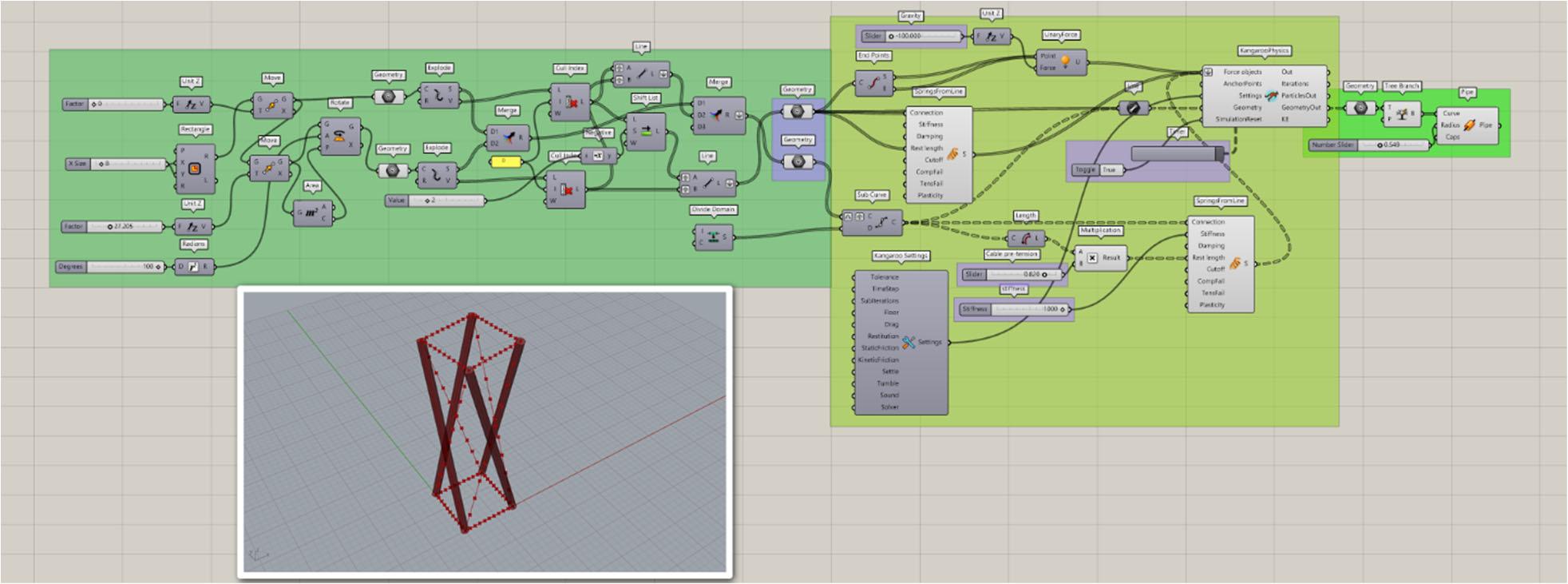
Fig. 1.6a. Tensegrity Icosahedron (model created by the author)
Sabah Shawkat©
13
The tensegrity as a pin-jointed network they are more flexible under light loads, but their stiffness increases rapidly as the load is higher, like a suspension bridge (Kenner, 1976; Smaili, 2003; Wang In2003).the absence of externally applied loads, tensegrity, as a type of form-active structure, needs selfequilibrium configuration as determined in the process called form-finding.
Fig. 1.6a presents our physical models of triple-X shape tensegrity showing their structural beauty. We have transformed them into interior components, namely table lamps to show some of the other possible functions of this creative tensegrity design. The weight, thickness of the elements, and the use of the same material in all directions influence the stability of the structure.
The process is started with a simple system and next, more and more struts and cables are added step by step, however, the strut elements must not touch together. The upper edge of the struts must be connected to the lower edge of the other elements. The properties such as weight, the thickness of the elements, and the use of the same material in all directions have an influence on the stability, and equilibrium of the structure (Snelson,1965, and Motro,2003).
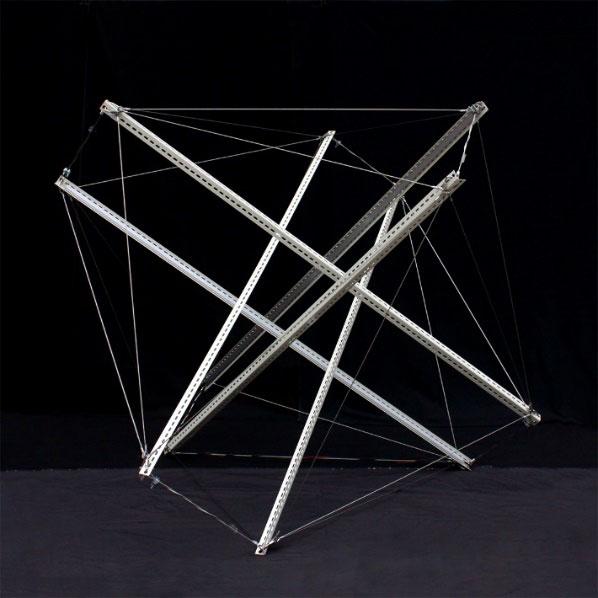
Fig. 1.6b. Expanded octahedron” or “Icosahedron” Physical model Tensegrity Icosahedron (Shawkat)
The form-finding state determines the self-equilibrated configuration in the absence of externally applied loads, but they are not always defining other characteristic features of tensegrity structures. Tensional forces naturally transmit themselves over the shortest distance between two points, so the members of a tensegrity structure are precisely positioned to best withstand stress. For example, if the configuration of an “expanded octahedron” is changed and the cables are fixed following the zigzag pattern Fig. 1.7 the result is a “truncated tetrahedron”. As Motro (2003) remarked, it is not always possible to attain a balanced geometry and, therefore, sometimes the figures do not have a perfect definition of the polyhedron in question. Due to the orientation of the struts that converge in each face, it can be appreciated that a certain distortion of the regular polygons can arise.
Fig. 1.6c. Process of Thinking in the Grasshopper Programme
Sabah Shawkat©
14

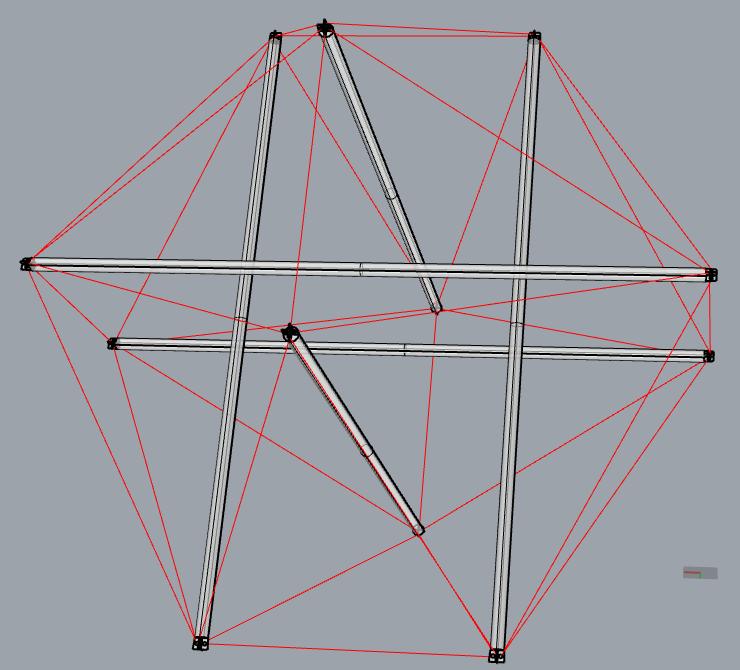
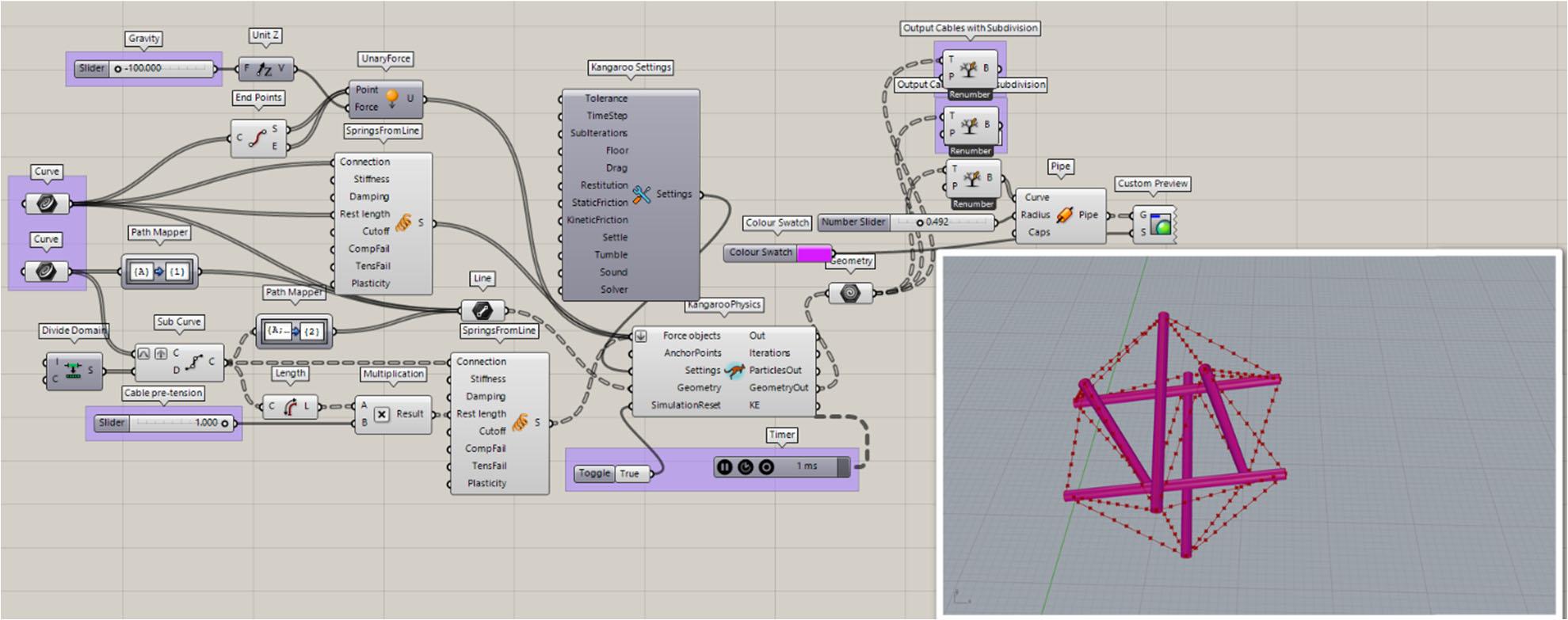
15 The potential of the tensegrity concept has inspired new metamaterials. Metamaterials are artificially invented materials that have properties that are not observed in nature. These are composite structures with extremely unusual mechanical properties. In recent years increased interest in the research of metamaterials has been observed.
We also proposed one interesting model, Fig. 1.8 this is a geodesic tensegrity dome inspired by the author, where the tendons could be substituted by a plastic skin that took the role of the continuous tension component. The adjacent figure shows the model is a dome fragment that can be used as the roofing of different spaces: representative, indoor, and exhibition. It is constructed from aluminium tubes (struts) and nylon fiber (rods). The struts do not touch each other. The model consists of 15 basic modules that are mutually connectable and detachable. The base module has three struts’ bars with a diameter of 6mm and a length of 166mm. The upper base rods are 140 mm long, the bottom base rods are 80 mm long. The rods connecting the lower and upper bases are 115 mm long. The top base of the base module is 1.75 times larger than the bottom base, ensuring a dome-shaped curvature when bonded. In practice, it would be appropriate to use a smaller ratio for a larger dome span. The basic modules and the whole structure are removable thanks to the rods. The joint is a cut slit into the aluminium tube into which the rods are inserted. The rods are terminated at the end with a node that is larger than the slot to avoid the collapse of the structure. In practice, it is advisable to use solid joints.
Fig. 1.7. Physical model Diamond T- Tetrahedron (model created by the author)
Sabah Shawkat©
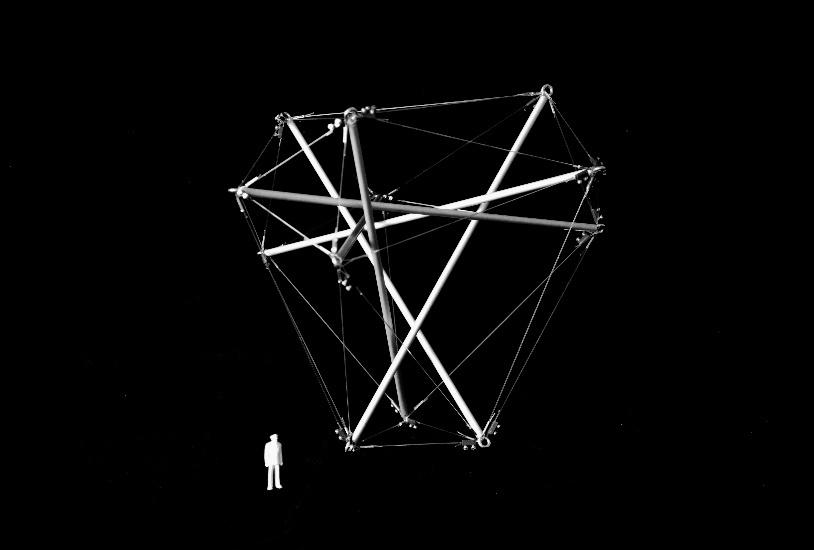
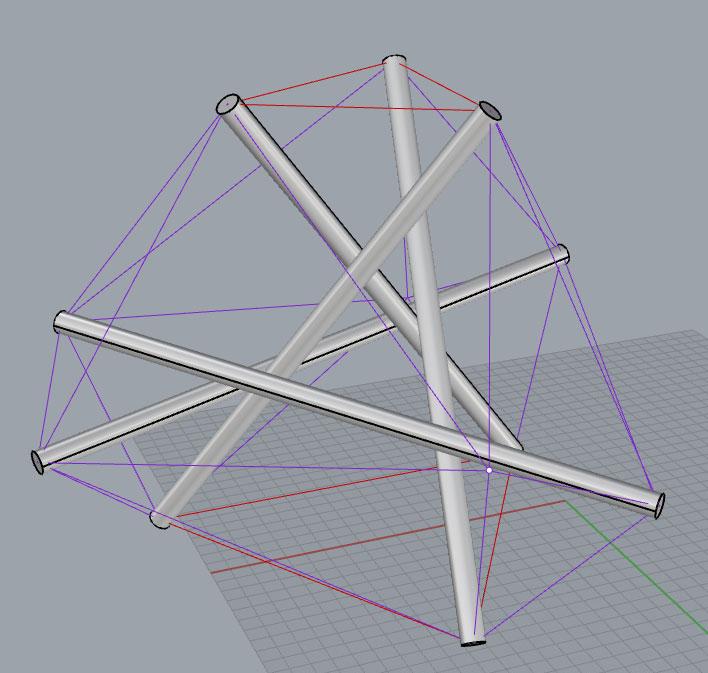
16 Fig. 1.8. Physical model - Double-Layer Tensegrity Dome Fig. 1.9. Physical models – Tensegrity (models created by the author) Fig. 1.10. Table Lamp (Model created by the author) Sabah Shawkat©
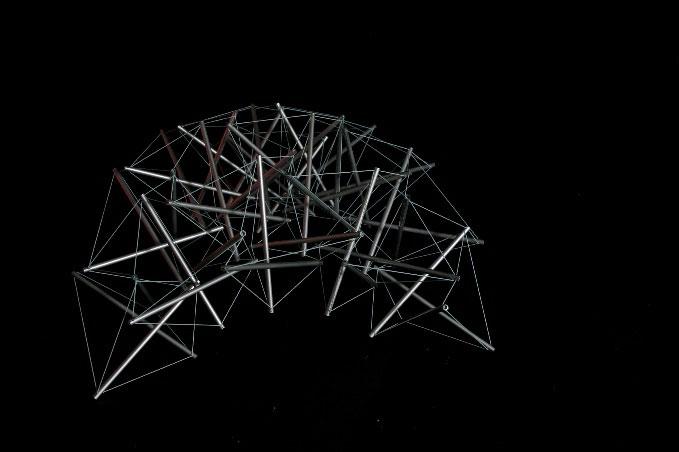
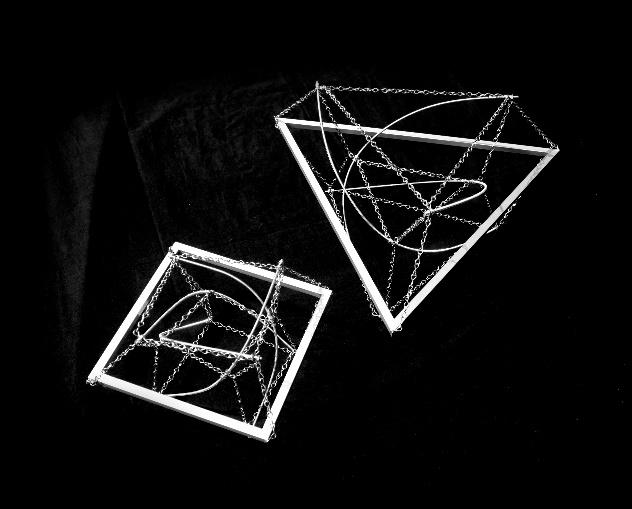
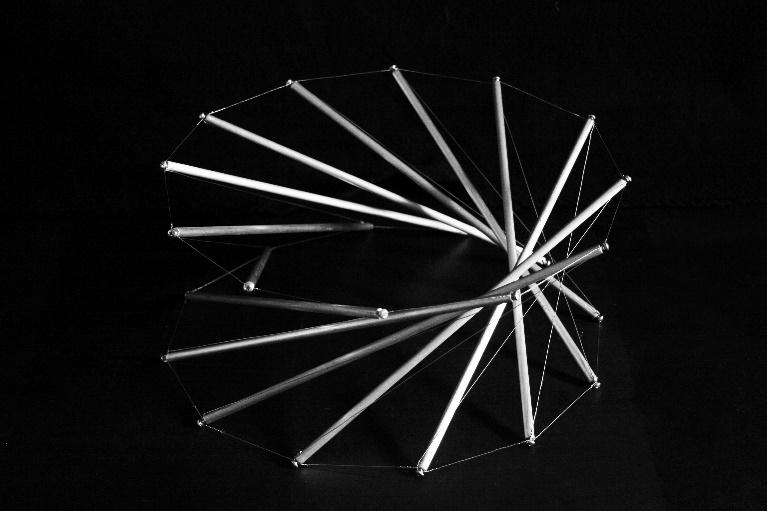
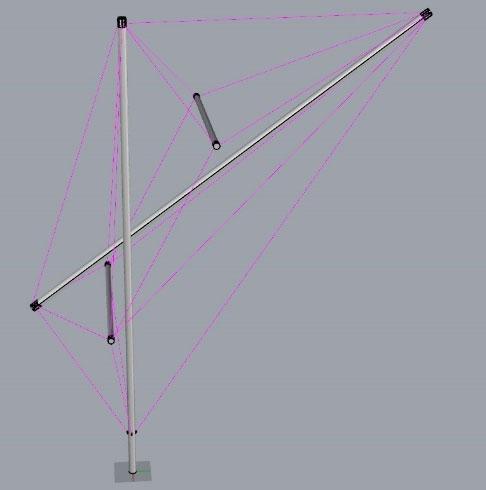
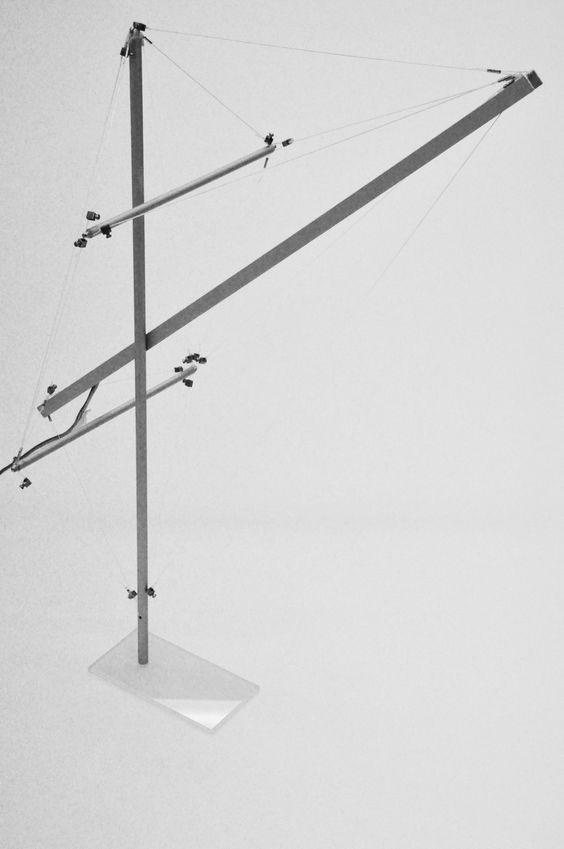
All tensegrities are prestressed under tension; they are self–supporting and independent of gravity. But the weight of the structure also adds to the prestress. All components are dynamically linked such that forces are translated instantly everywhere; a change in one part is reflected throughout the whole Thestructure.stability of prismatic tensegrity structures is not only determined by the connectivity manner of the members but also sensitive to the height/radius ratio and the stiffness/prestress ratio.
17
Each node of the structure is connected by two horizontal cables within its horizontal plane and is connected by one vertical cable and one strut to nodes in the other plane. The thick and thin lines denote, respectively, cables that can only carry tension, and struts that carry compression. These structures are called super stable. In the model structures shown in this chapter, the tensile members are usually cables or rods, while the compression members are sections of tubing. The tensile members can be thought of as cables that pull two points together, while the compression members can be thought of as sections of rigid tubing that maintain the separation of two points. The tensile members are continuously connected to the ends of the compression members while the compression members are only connected to tensile members and not to other compression members.
The results of our design process are presented also graphically. To determine the equilibrium position the lengths of the struts are specified, which are assumed to be all the same, together with the stiffness of the top ties (assumed equal), bottom ties (assumed equal), and connecting ties (assumed equal).
Sabah Shawkat©
Our team of structural designers started to deal with this kind of fine art of structure in the year 2008. Together with the students, we try to bring fresh ideas into the field and create different models of tensegrities. In this chapter could be found various models used for living and pleasure as furniture, table lamps, and toys. We pay attention not only to the structure itself, but also to details, aesthetics, and the elegance of the models.
One of our physical tensegrity models is an amazing chair shown in Fig. 1.11 We can use it to clarify the main ideas of tensegrity and demonstrate the entire concept for educational purposes and at the same time, it serves as an unusual chair. Our experience and way of thinking are conditioning the quality of our proposal. Similarly, training conditions are also very important, and common training with other professions may contribute to increasing the level of our art of engineering.
18 Fig. 1.11. Tensegrity as a Chair (Shawkat, and co-authors 2019) Fig. 1.12. Tensegrity art -Design systems- Parametric Modelling (models created by the author) Sabah Shawkat©
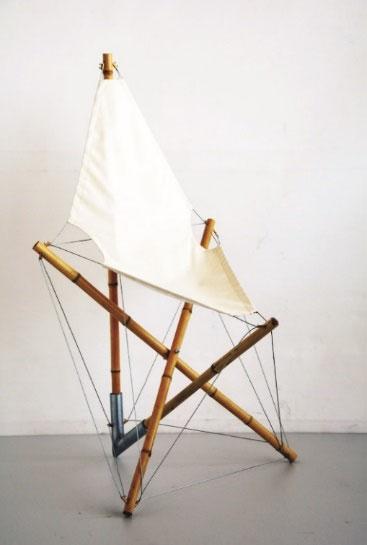
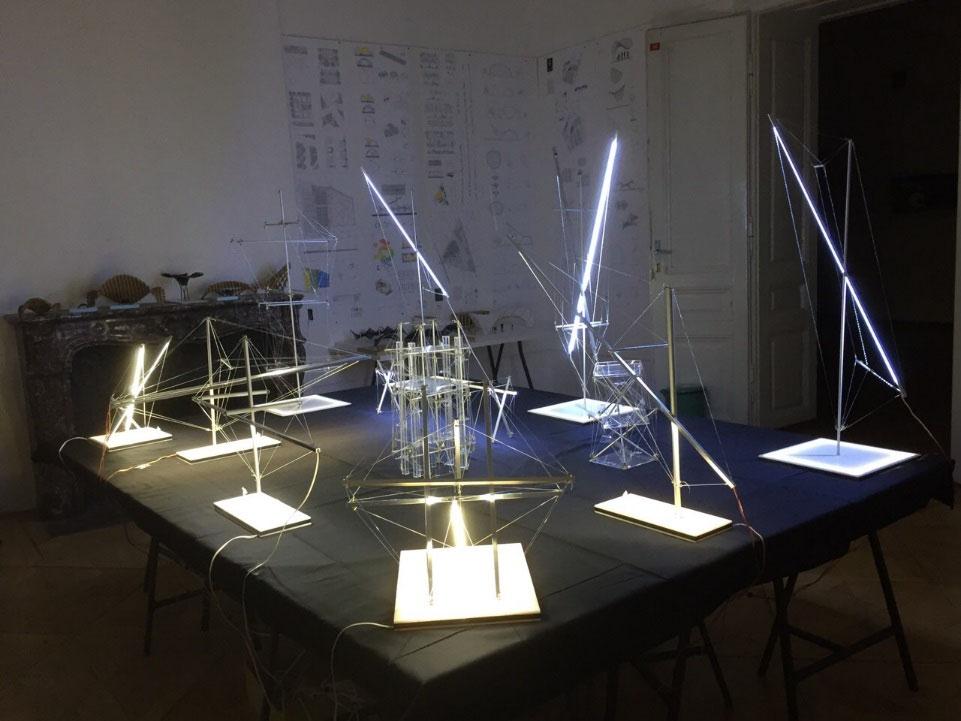
19 Fig. 1.13. Tensegrity art - Parametric Modelling (models created by the author) Sabah Shawkat©
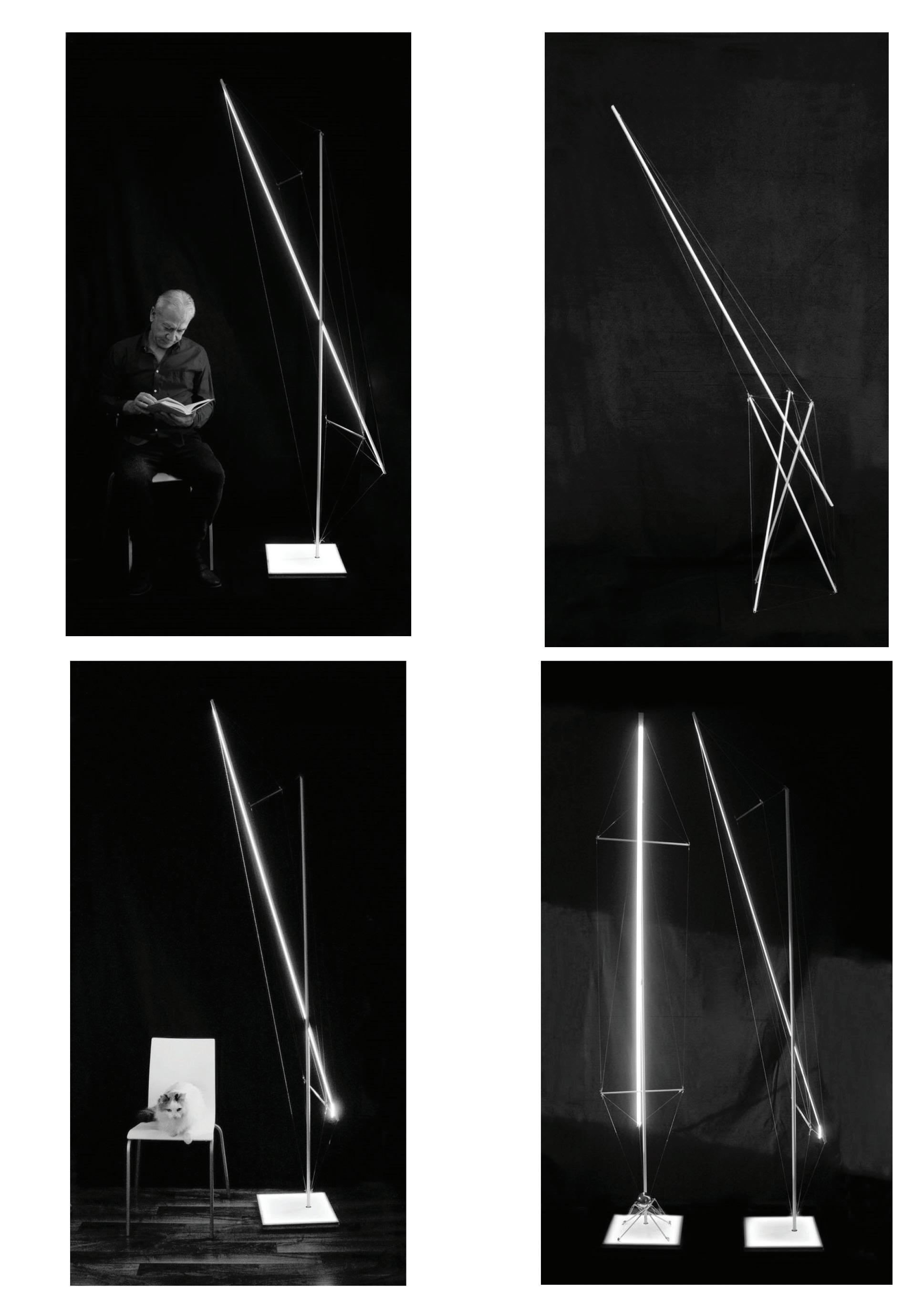
20 Fig. 1.14 Parametric Tensegrity Form Finding-Physical models (models created by the author) Sabah Shawkat©

21 Fig. 1.15 Parametric Tensegrity Form Finding-Physical models (models created by the author) Sabah Shawkat©
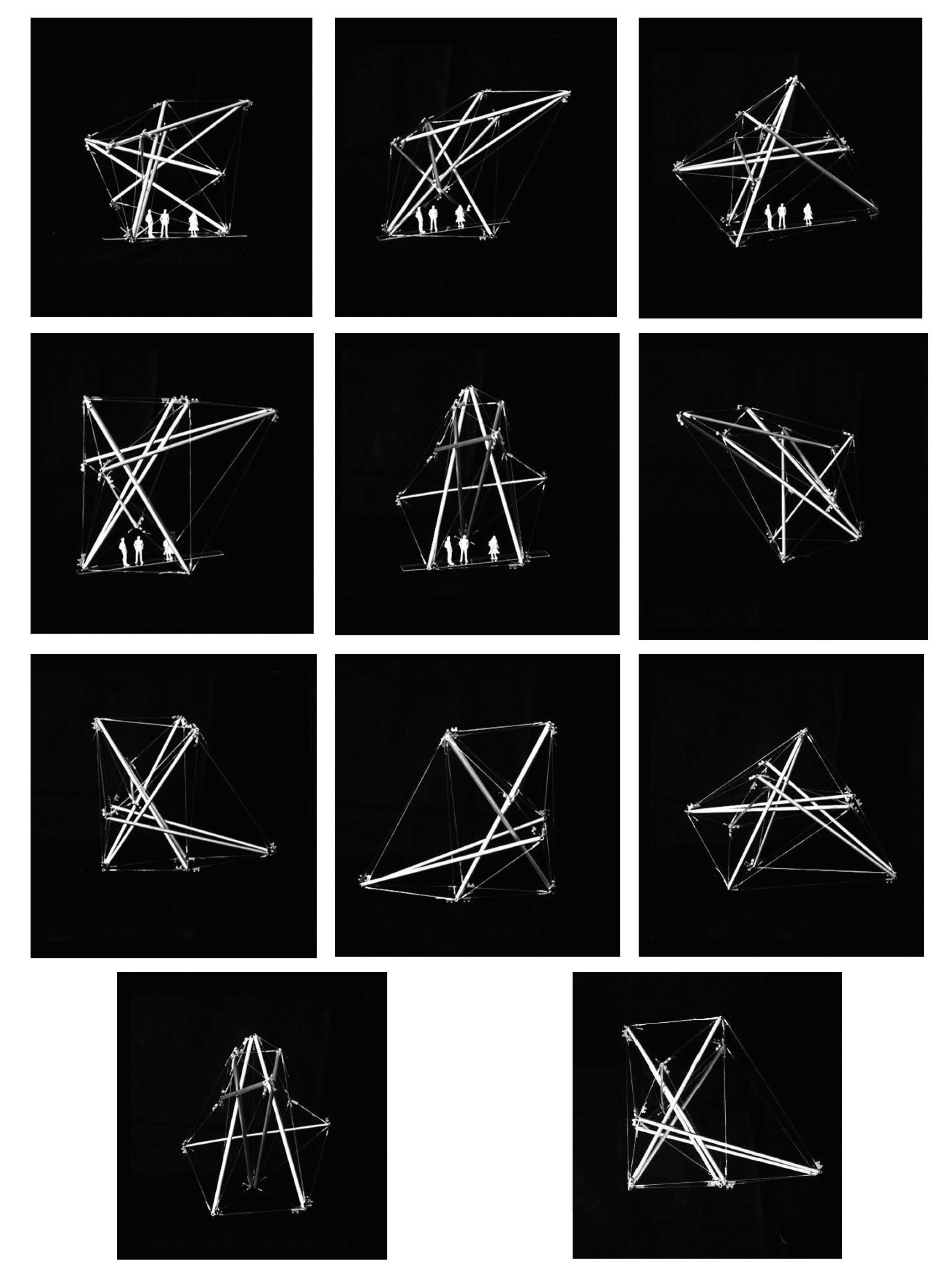
Our team of structural designers started to deal with the fine art of lightweight structures in the year 2008. Together with the students of architecture and design, we work on bringing fresh ideas into the field by creating various novel models of tensegrities, e.g., design structures used for living and pleasure as furniture, table lamps, or toys. We pay attention not only to the structure itself, but also to details, aesthetics, and the elegance of the models. New subgroups of these unique forms include anti-gravity tensegrity structures which play an important role in today's architecture and interior design. Our passion for creating beautiful and innovative solutions in the field of tensegrity lightweight structures led us to design “magical floating” tea tables Fig. 2.1a, b - 3 a, b. The structures of our models are constructed of simple materials, mostly wood and aluminium. The floating anti-gravity models represent a nice application of the basic tensegrity structure; simple in principle, finicky to build. Anyone can try to create them relatively easily, without using any complex materials. A result is an object that seems to defy gravity and physics. In one group of anti-gravity tea table models, the load-carrying capacity of the structure is equal to the tensile capacity of the string. It is just a matter of achieving the right tension strings to center the structure and then connect them in place. The center string provides tension, and the other strings provide balance Fig. 2.2a, b. Therefore, all strings are necessary, not just the center one. By taking any of them out, the whole model falls apart. However, the center string is the most important and the most elegant one. It seems that the tables fly in the air providing an intriguing sense of freedom. In another type of anti-gravity tea table, the main element (the center string) was replaced with two opposite magnets which ensure the stability of the entire system Fig. 2.3a, b. The resulting optical illusion is our favorite demonstration of the charm of physics and the elegance of tensegrity. The main shortcomings of the practical use of tensegrity technology for common practice belong to the relatively high displacements
Sabah Shawkat©
TENSEGRITY STRUCTURES
Snelson constructed tensegrity structures whereby the stability is based on pre‐stress because pre-stress induced stiffening. Before an external force effect, the structure of the system including all structural parts is under tension or compression. This way even opposed forces are kept in balance. The simple tensegrity models were criticized because, if one or two cables or struts are damaged, the whole system would collapse immediately. All elements are an innovative way of interconnection so that the force is immediately distributed throughout the entire structural system; the change in one part is reflected in the whole structure, which meets the condition of light construction, the whole construction system, and the shape of the object works on the principle of form follows force. (F. Otto, 1967, and R. Motro, 1992).
22 2. ANTI-GRAVITY
Sabah Shawkat©
23 in nodes and low ultimate limit stat of material efficiency compared to traditional, geometrically rigid structures and the difficulty to create the details of joints as well as the selection of suitable material for their realization.
Fig. 2.2 a, b. Anti-Gravity Tensegrity Tea Table (models created by the author)
Fig. 2.3a, b. Anti-Gravity Tensegrity Tea Table (models created by the author)
Fig. 2.1 a, b. Tensegrity Anti-Gravity Tea Table (models created by the author)

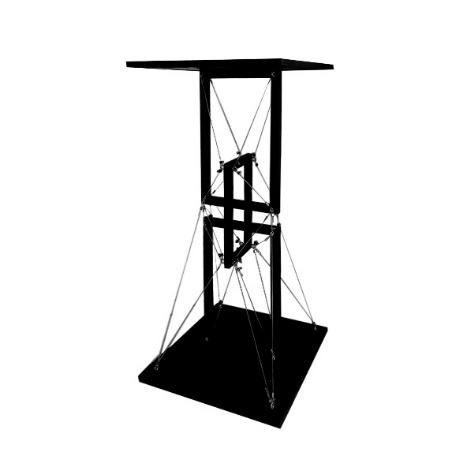
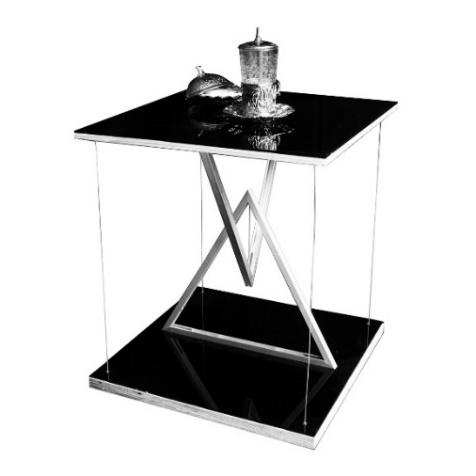
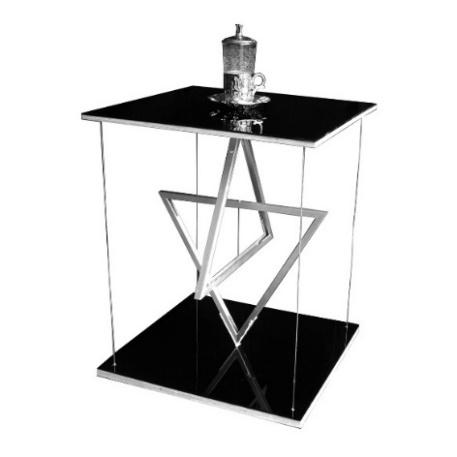
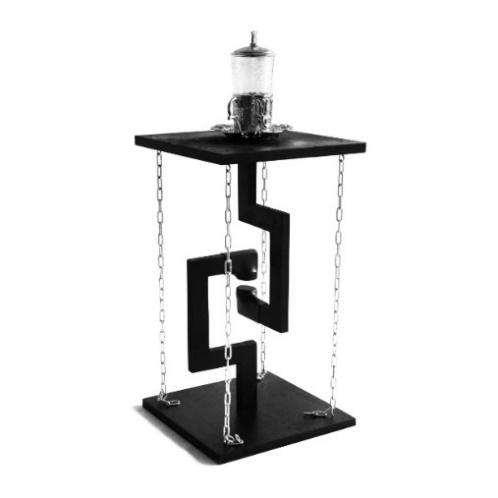

24 Fig. 2.4 Anti-Gravity Tensegrity (models created by the author)
The capacity of a structure increases with the minimal mass design for a given set of stiffness properties. Tensegrity structures use longitudinal members arranged in a very unusual pattern to achieve maximum strength with a small mass.
Sabah Shawkat©
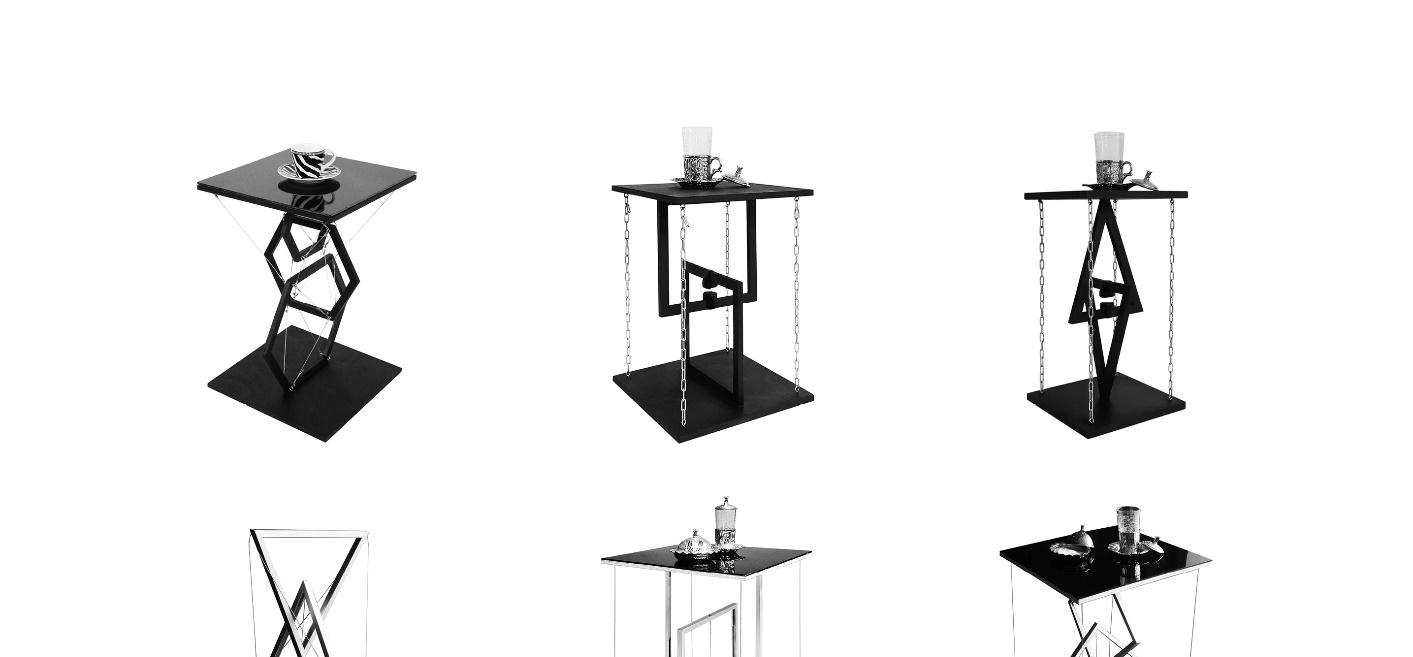
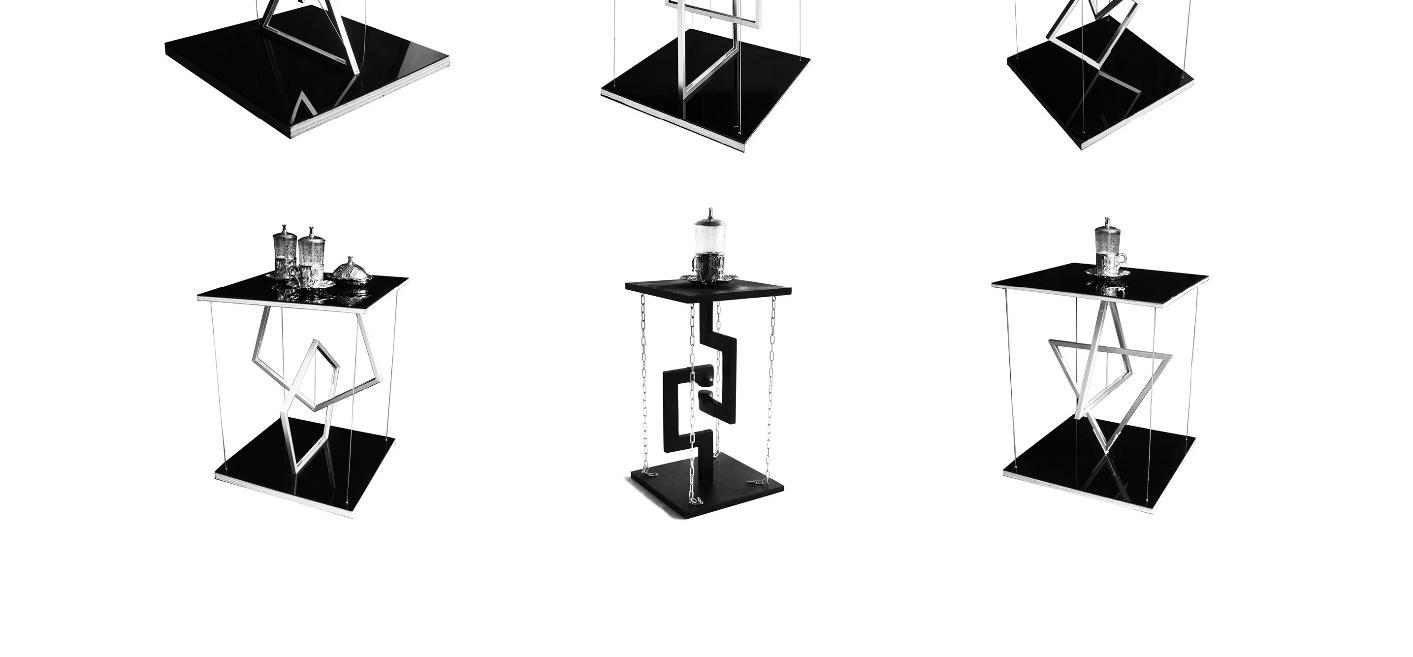
Fabric reinforced membranes are a class of lightweight materials that are important for many different engineering branches. They can be used to efficiently cover big areas or enclose large volumes with a minimum of structural weight.
Tensile structures often have irregular shapes and low self-weights which may give rise to unforeseen effects such as very high snow loads and flutter instability due to wind. To Sabah Shawkat©
Membranes lend themselves to different kinds of work or adaptation, in fact, they often provide different solutions to practical problems that frequently occur on the building site, and which must be solved even in the phase of realization.
The shape of a tensile structure, which very much depends on internal forces, also governs the load-bearing capacity of the structure. Therefore, the process of determining the initial equilibrium configuration calls for the designer’s ability to find an optimum compromise between shape, load capacity, and constructional requirements.
Membranes become the protagonist and represent the new trend in design: construction with the minimum amount of material, thanks to many qualities and features that make possible a correct functionality for different architectonic spaces, and they can give a particular meaning to places where they are installed. As is well-known, the primary advantage of tensile members over compression members is that they can be as light as the tensile strength permits.
25 3. TENSILE STRUCTURES
Due to the negligible flexural stiffness of cables and membranes, the initial configuration of these structures must be stressed, even if the self-weight is disregarded. Thus, before the analysis of the behavior of the structure to external loads can be performed; the initial equilibrium configuration must be found.
Tensile structures have always fascinated architects and engineers, mainly because of the aesthetic shapes they produce. Despite this, very few tensile structures have been built. From the works we have described here, we can derive some considerations about special aspects of textiles, about their adaptability and their facility to furnish, as well as their reversibility. So we can say that membranes are very easy to adapt to different spaces and at the same time they can modify these spaces because of given needs, for instance expanding or restricting delimited spaces, in height or depth. Moreover, membranes can be included with lightness in contexts that are yet full of values and strong signs, without any volumetric invasion in consolidated spaces; furthermore, membranes are easily usable so they make places recognizable and perceptible in a direct way, avoiding disorientation as it could happen in places which are not well designed.
These features require special care in the design, for example, an error in the distribution of the pre-tensioning forces may lead to damage to the cladding under large loads.
It is no surprise that experience and good engineering judgment are frequent characteristics among famous designers of tensile structures: Fritz Leonhard, Jorge Schalch, Frei Otto, Horst Berger, and David Geiger, to mention a few.
26 ensure the safety of the structure, experimental tests must be undertaken together with statistical analyses to find the magnitudes of the snow and wind loads.
If the numerical analysis of building structures is concerned, the finite element method is the dominating tool. In this method, the structural characteristics and external loads are described by matrices and vectors. The sought parameters, e.g. displacements and internal forces, are found by matrix operations. The first step in the analysis process is the definition of the geometry of the structure, which generally is known as a priori. However, this is not the case for tensile structures.
Sabah Shawkat©
Applications such as membrane roofs, airship skins, or sail materials demonstrate their capabilities.
Nevertheless, if confronted with cases in which failure occurs, in the civil engineering application usually in the erection and pre-stressing process, numerical models using the limited homogeneous material representation could not at all help further in explaining or avoiding the damage.
This lack of accuracy on the analysis side is usually counterbalanced by the experience of the engineers and the application of testing and a trial-and-error type of approach.
The same need for high accuracy strength predictions is evident in aerospace applications in which the material capabilities must be fully exploited to allow minimum weight configurations. In this sense, it is even more surprising, that modelling of failure in fabric reinforced membranes did gather only a little attention in engineering science in the last decades
The vastly expanding numbers of architectural applications underline the aesthetic value of these types of lightweight structures.
The modelling approaches frequently used for the design and dimensioning of membrane structures do not or only partially consider these effects, as the numerical cost of the analyses would drastically increase.
In addition, a more detailed description of the material would also require a deeper knowledge of the material at hand, which is costly and impractical for realistic engineering applications underlying strict cost and time constraints.
Instead of the term Membrane Structures, we can also come across designations such as Tensile Structures, Architectural textiles, Fabric Architecture, or Textile Membranes. All these names refer to the same concept.
Sabah Shawkat©
One of the extremely popular architectural forms of contemporary architecture and design represents the membrane structures Fig. 3.1. They appeal especially with their non-traditional solution, innovative design, unique shape, and great flexibility (Otto, Trostel, 1967 Bach, 1988). Compared to traditional rigid structures they allow larger spans with a minimal number of support members.
27 3.1
Membrane structure has always enjoyed the great interest of students. Many different models of textile structures can be produced as physical miniatures of the static-structural system with large spans as shown in Fig. 3.2. The advantage of such models versus virtual 3D models is the possibility to verify the structural scheme.
Fig. 3.1. Membrane Models, Small Scale Counts (Shawkat, 2021)
MEMBRANE STRUCTURES
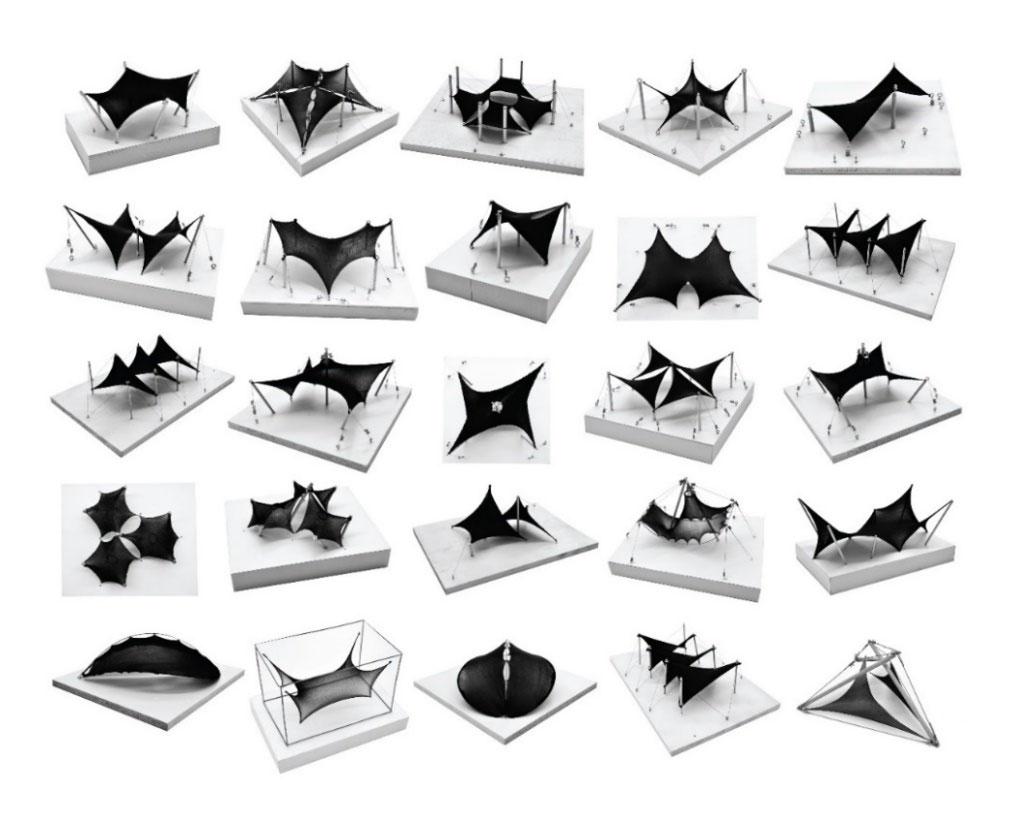
The idea of making objects using a minimum of material is as old as humanity itself. With frequent population transfers for water and food, it was vital to be able to build a shelter for temporary housing and protect people from the weather or predatory beasts. From ancient times, people used textile constructions made of animal skins or fabrics, for example, to create temporary dwellings or sails. With the general shortage of raw materials, the first lightweight structures were developed that could be rebuilt, decompose and transport. The first tent constructions appeared in various variations in all cultures throughout the world.
the technology used by today's lightweight membrane constructions was not developed until the 19th Century. With the advent of the industrial revolution, looms were automated, which had a significant contribution to lower prices and higher availability of fabrics.
As part of modern permanent structures, membrane structures began to be used in the 1960s, mainly due to the development of new technologies (Otto, Trostel, 1967). The process of designing the shape of the membrane is called the "form-finding" process. It is an iterative process in which the designer adjusts the boundary conditions (support geometry, external load, structural stress) based on the suitability or unsuitability of the equilibrium state. The geometry of the minimum surfaces is thus unique for each set of boundary conditions. A change in their geometry has a global effect on changing the geometry of the minimum surface.
The main characteristic of the minimum surfaces from the construction point of view is that they are curved in two directions, their mean curvature is equal to zero, and uses the minimum amount of potential energy. It should also be noted that minimum areas also have their physical limits and cannot be created between each set of boundary conditions. The final form of the construction depends mainly on the position of the fixed points. or the magnitude of the prestress force. Due to the continuous three-dimensionality, the design and shape analysis is practically impossible to perform with conventional design procedures. Several techniques of their physical and numerical modeling have been developed over the past decades to study the shape, control the collision of
Sabah Shawkat©
28
During our era, tents and similar light structures were used to temporarily accommodate people on war expeditions, discovery, and hunting expeditions, to isolate the sick during epidemics, and increasingly also to shield and temporarily protect the weather during military parades or knightly However,battles.
29 surfaces with surrounding structures, accurately describe the geometry for static analysis, and create production drawings of elements and membranes.
Physical models serve to refine the idea of the shape of the surface in space, allow to study and simulate the interior space and allow the designer to observe global changes in the shape and rigidity of the structure with local changes in boundary conditions.
Sabah Shawkat©
Fig. 3.2. Form Finding of Membrane Structures (Shawkat, 2021)
Today, membrane constructions are a common (and at the same time very aesthetic) part of various interior and exterior constructions and are used in every type of design. Exterior membrane constructions made of technical textiles are used as temporary (often mobile) or permanent light roof constructions of stadiums, arenas, cultural stands, shopping centers, exhibition halls, airports, amphitheatres, or as effective dominants of selected spaces. In interiors, textile membranes fulfil an aesthetic function and can also function as thermal or acoustic insulation. In general, the design process of membrane and shell structures is inverse to the procedure used in traditional architecture. While the shape of the structure is known in advance when designing conventional structures, the state of stress and strain is unknown, the determination of which is subject to static calculation. In the case of lightweight structures, the state of stress, or the magnitude of the deformation, from which the equilibrium geometry is determined, is known in advance (designed by the designer). This inverse procedure makes static analysis and the architectural shape of the structure inextricably linked, and the cooperation of the engineer and architect is necessary for the pre-project preparation.
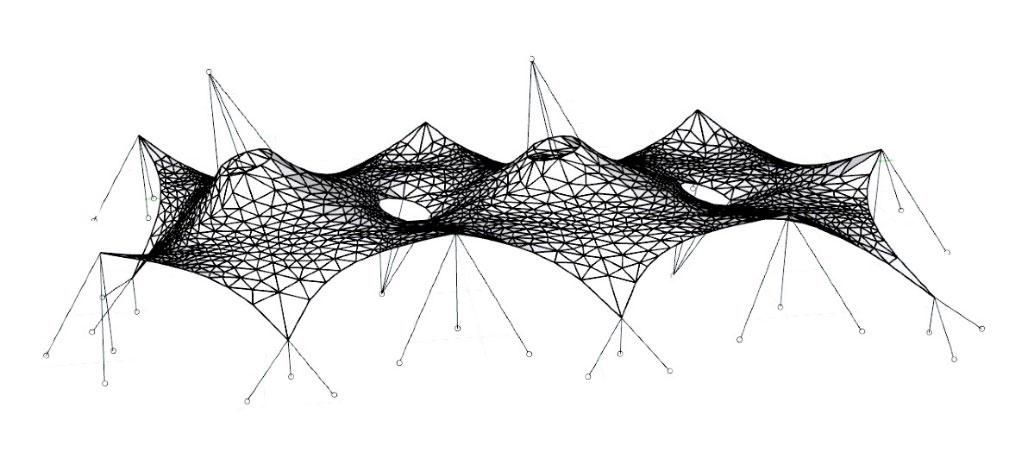
30 Numerical models prepare geometry data for static analysis and production documentation. Due to the already mentioned interdependence of architecture and the static behavior of the structure, it is appropriate to combine the knowledge gained from both approaches to their design. Membrane structures are often referred to as textile structures. However, the actual membrane construction is far removed from the classic tent. The main difference is its exact geometric shape. For the functioning of the membrane structure, the exact geometric criteria must be computed. The basic criterion is to maintain the concavity and convexity of the main directions of the membrane surface. Following this principle, we can talk about the basic four types of membranes: • saddle-shaped (hyperbolic paraboloid) • conical shape, • Wave shape, • vault shape. Fig. 3.3. Typical shapes of membrane structures Sabah Shawkat©
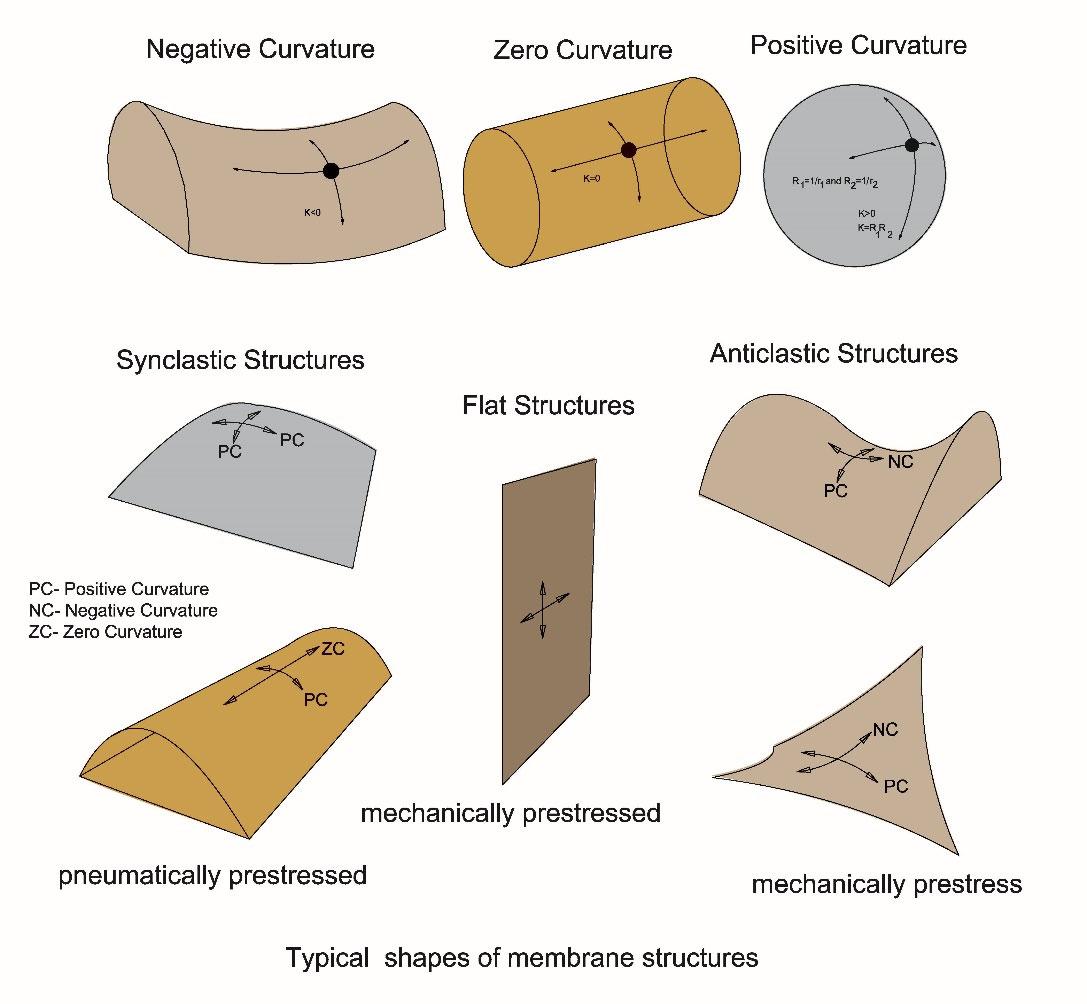
Fig. 3.5. Process of Thinking in the Grasshopper Programme
Fig. 3.4.: Conical surface
Sabah Shawkat©
Another criterion of lightweight membrane construction is its prestress. The correct geometric shape and prestress guarantee its stability, stiffness, and dynamic resistance. At the same time, it allows the structure to resist the effects on which it was designed, rain, wind, and snow.
The displayed area can be constructed by introducing a non-constant prestress in the direction of the main curves. However, the resulting area is no longer minimal. Two-way curves that meet or roughly meet the minimum area criteria can carry external loads by their shape, not by the built-in mass. The smallest area between the specified boundary conditions reduces the material costs of the supporting structure and in combination with its effective shaping, it is possible to achieve a significant redistribution of internal forces during load transfer, which predestines these structures for roofing large spans.
31
In the case of a conical surface, the boundary conditions which do not allow the formation of a minimum surface, the imbalance is evident from its unequal curvatures. In this case, at points A and B on one meridian section, r, is constant and r2 is variable, which means that r1/r2 is not equal to r1/r2

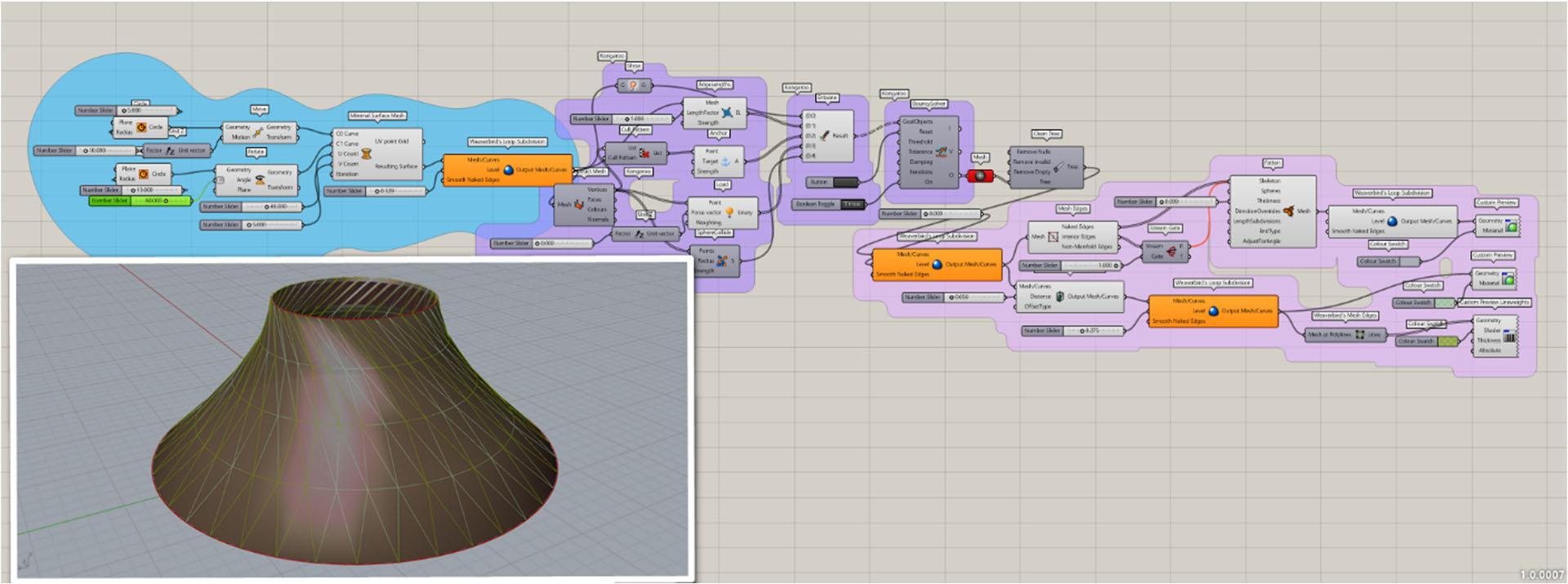
Various curvatures as positive, negative, and a mix of them have been shown and analyzed. Due to graphical software programs that can produce new, irregular, non-standard forms under the principles of digital design.
32 Frei Otto, the only true precursor of Parametricism, free-forms, as organic, nonstandard, irregular shapes, are the deformation of these mentioned earlier by changing the amount and direction of the depth. Architects, with novel imagination and digital tools, use both forms and shapes with their potentialities to represent the new. Hyperbolic paraboloid shape can be transformed into geometry by double curvature with twisted straight lines.
Fig. 3.6. Process of Thinking in the Grasshopper Programme
The first modern building in the 20th century was the Raleigh Livestock Arena in North Carolina, USA, designed by architect Matthew Nowicki and engineered by Fred Severud. The saddle shape of the Raleigh Arena consisted of a rope net anchored on opposite arches, which were made at an inclination of 20 degrees from the horizontal. The rope net had a maximum span of 95 m and its geometry pointed out the importance of the method of laying. Appropriately selected boundary conditions (2 boundary arcs) can transfer the load and at the same time allow the structure to have a double curvature. This aspect was often used later, and several other similar designs were made over the next 10 years, following the example of the Raleigh Arena.
Also during the 1950s, German architect Frei Otto began extensive research into the geometry of membrane structures. Inspired by natural laws, and the study of the shape of plants and animals, he laid the foundation for the current method of design. In collaboration with tent manufacturer Peter Stromeyer, many membrane structures of various sizes and purposes were created during the 1950s and 1960s, from exhibition pavilions to elements of small architecture to iconic works.
Sabah Shawkat©
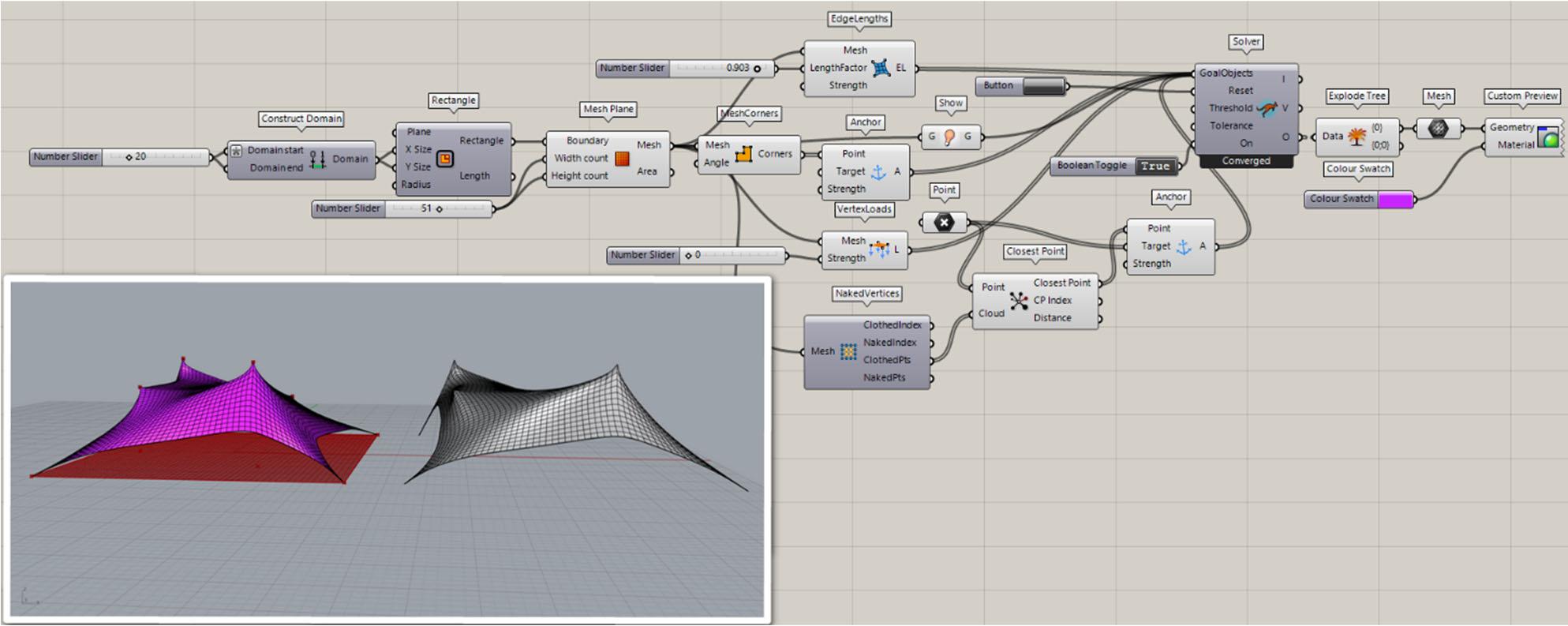
33
The German pavilion at the EXPO '67 exhibition in Montreal was the first object made of a rope network and a membrane of world importance. For the first time, it was constructed with the so-called free-form shape, which was created by a combination of elevation and valley points. Following the success of the German Pavilion in 1967, Frei Otto was commissioned to design a sports complex for the 1972 Olympic Games in Munich. He collaborated on this project with professors Klaus Linkwitz, Fritz Leonhardt, Gunter Behnisch, engineers Wolfhart Andrä, Jôrg Schlaich and Rudolf Bergerman. During the design of the German Pavilion and the Olympic Complex, mathematical models were built to generate a shape suitable for rope and membrane structures, thus beginning a smooth transition from physical to numerical object modeling.
Fig. 3.7. Process of Thinking in the Grasshopper Programme
Usually, we use the Kangaroo tool when a quick form-finding procedure is needed in conceptual design. Fig. 3.8 - First, a simple NURBS surface has been divided in u,v grid, and then used as the reference geometry for a form-finding test.
Sabah Shawkat©
- The setup of the model we start to constrain and anchor the number of points at corners, and the simulation of a hanging model will be run by a kangaroo solver plug-in.
Each completed construction was another of his experiments, on which the shapes were tested, materials, method of construction, and introduction of prestress.

34 Fig. 3.8. Process of Thinking in the Grasshopper Programme Fig. 3.9. Process of Thinking in the Grasshopper Programme GEOMETRIC SHAPES of MEMBRANE The basic geometric shape of the membrane system emerges from the surface of the hyperbolic paraboloid. We can describe this area by mathematics: For an area with parallel curvature margins and a rectangular plan, we can define the following dimensions of the areas Lx, Ly, fx, and fy. Under marginal conditions: then they result zxy () x2a2 y 2 b 2 zfx for x Lx2 y 0 Sabah Shawkat©
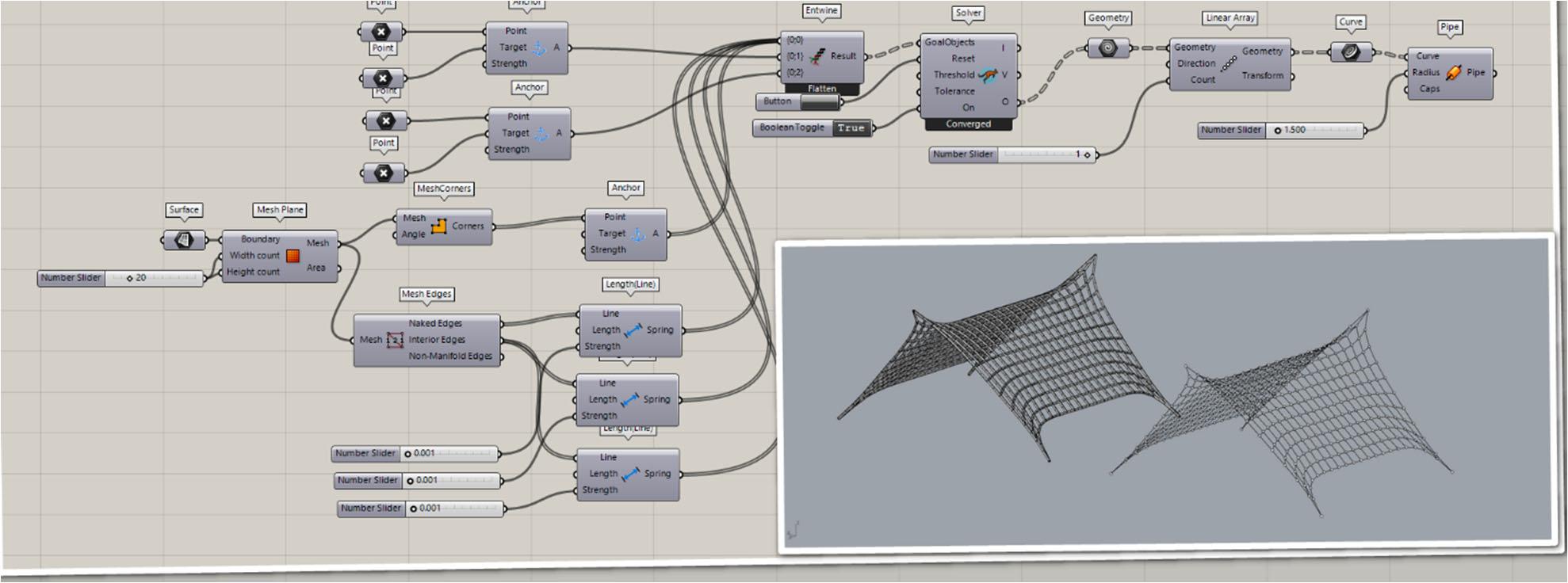
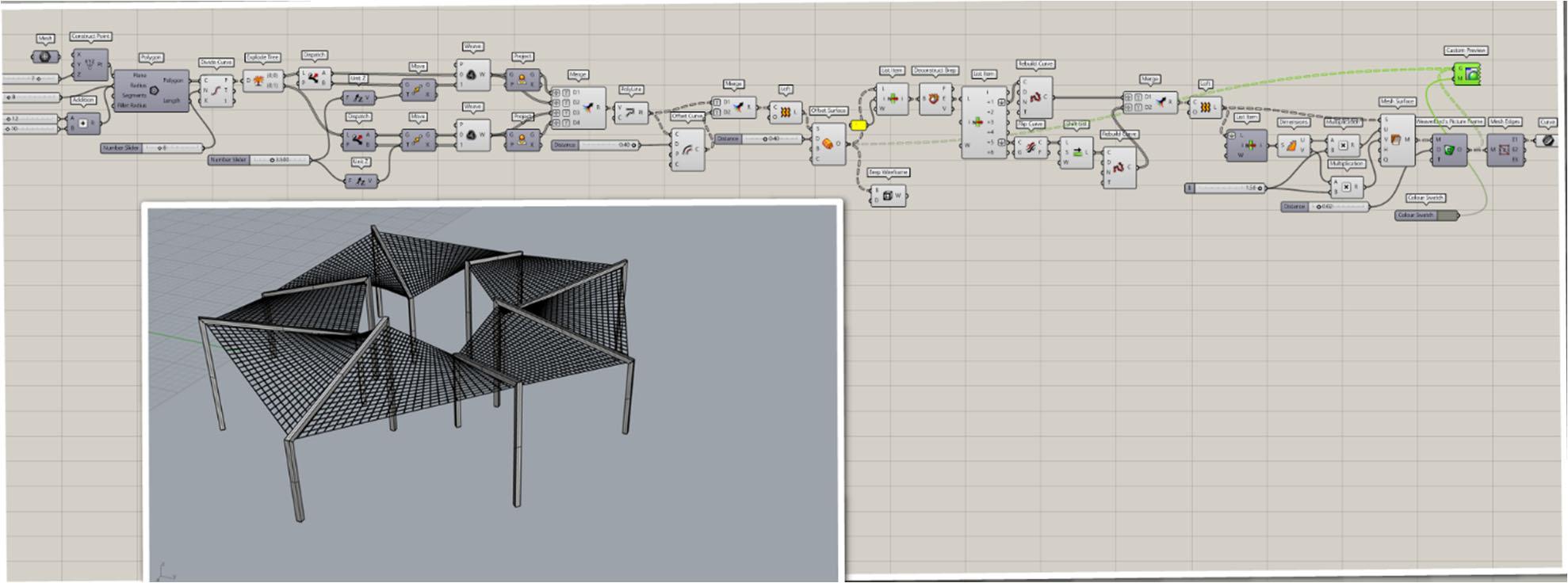
35 then coefficients result after fitting we get: Let's look at the length coordinates that will then: After simplifying the expression we get: Fig. 3.10. Rectangular Plan with Parallel Curvatures in x and y Modern membrane systems are manufactured from different types of textile membranes. These are produced as composite materials and almost always consist of a bearing woven core and a surface film. The supporting core has a bearing function and therefore transfers the force to the membrane. The surface film has a protective function, ensuring waterproofness and tightness of the membrane. zfx for y Lz2 x 0 a2 4fLx2x b 2 Ly 2 4fy zxy () 4fxLx2 x2 4fyLy2 y 2 Lxx2 Lyy2 z ()fx 2 fy 2 Sabah Shawkat©
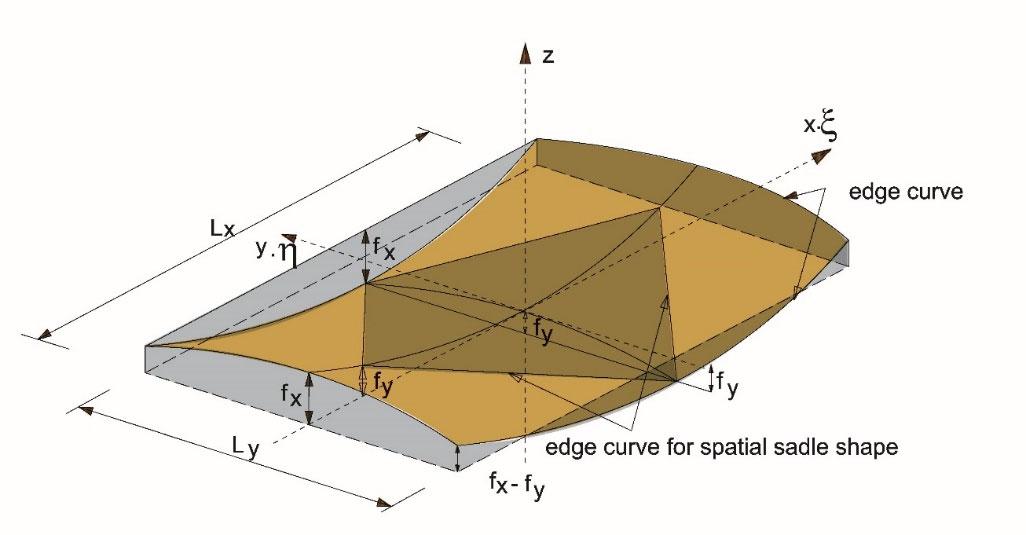
36 Fig. 3.11. Membrane Roof Construction 3.2 TYPES OF MATERIAL OF MEMBRANE STRUCTURES
Sabah Shawkat©
A great challenge for today's architects is global warming and membrane structures are increasingly seen in our territory as an integral part of sustainable climate solutions for public spaces and parks.
Membranes usually must fulfil both a load bearing and a roofing function at the same time and are therefore made of high-strength technical textiles. The tensile strength of the membrane material depends directly on the structure of the base fabric. The fabrics are usually made of glass fibers or of polyester, polyamide, polyvinyl alcohol, and polyaramid fibers. To achieve higher strength and durability, the fabrics are coated and laminated with synthetic materials. The most used materials include polyvinyl chloride (PVC) laminated or coated polyesters and woven glass fibers coated with polytetrafluoroethylene (PTFE), known under the trade name Teflon or ethylene tetrafluoroethylene (ETFE). The coatings form protective layers of fibers and ensure that the membrane is impermeable to water (Foster, and Mollaert, 2004).
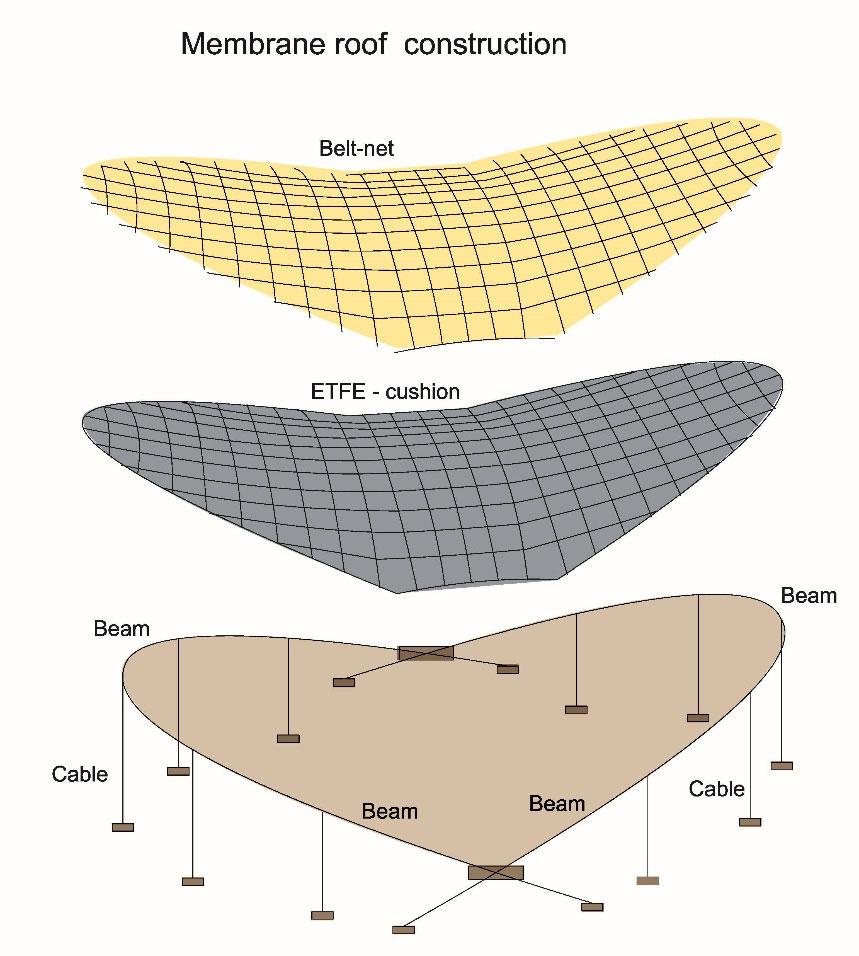
Sabah Shawkat©
37
Teflon is a synthetic fluoropolymer, that has a very wide application in industry and construction. It has a high resistance to chemicals and an extremely low friction coefficient. The most famous PTFE membrane material is Gore-Tex. The largest PTFE construction can be termed the "Hubert H. Humphrey Metrodome" roof in Minneapolis with an area of approximately 80,000 m2 where a double-layered membrane with a glass fiber construction is used. The strength of the PTFE membrane in tension is 2,300-4,500 N / 5 cm. If glass fibers are used as the support material, the tensile strength of such a membrane will be 3,500-7,500 N / 5 cm. Fig. 3.12. General area of hyperbolic paraboloid 3.2.2. ETFE (Ethylene Tetrafluoroethylene)
ETFE is a fluorocarbon - a basic polymer (fluoropolymer) type of plastic. It has been designed as a material with high corrosion resistance and resistance over a wide range of temperatures. It was used for example for the pneumatic panels of the "Allianz Arena" football stadium, or for the "National Water Sports Centre" - the world's largest construction made of ETFE membrane. Also on panels of "Tropical Island" 20 000 m2 in Germany. Because ETFE has excellent mechanical stiffness and chemical resistance with which it can compete with polytetrafluoroethylene (PTFE). In addition, ETFE has high energy radiation resistance and can withstand moderately high temperatures for a long period of time. The strength of the ETFE membrane in tension is about 1200 N / 5 cm and ETFE foil is 430-500 N / 5 cm.
3.2.1. PTFE (Polytetrafluoroethylene)
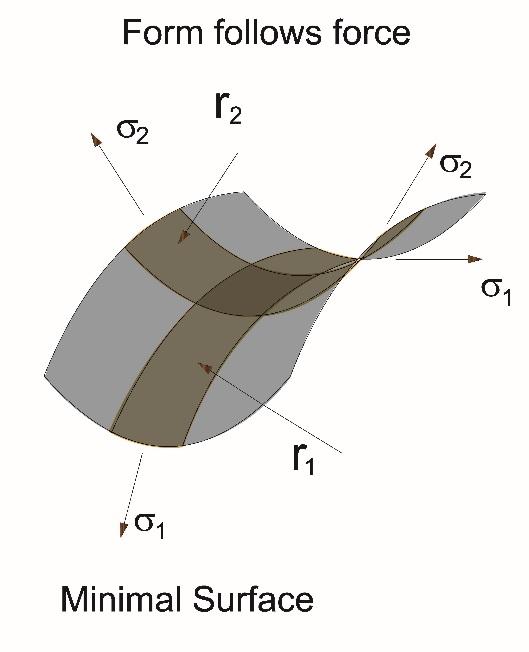
Fig. 3.3.1. Base Forms of Membrane Structures
Sabah Shawkat©
3.2.3. PVC (Polyvinylchloride)
Form finding is the process of determining the equilibrium state of a membrane structure at a given level of prestressing and selected boundary conditions. For the membrane structure to be able to efficiently transmit the corresponding effects of any loaded vector, its spatial surface must have the shape of a double curvature (Otto, 1988). It can be achieved in three basic ways, which characterize the three most used types of membrane roofing Fig. 3.3.1: 1. hyperbolic paraboloid, which is achieved by fixing the membrane to four points, two of which are always at different levels. The flatter the saddle, the smaller the height distance between the upper and lower points, the greater the force effects arising in the corners of the system, 2. conical shape, which is achieved by fixing the membrane to the top of the column and at the bottom to the circular support ring, 3. arch - the membrane hanging between the arches situated in the transverse direction and in the lower longitudinal part is connected to the end ropes (Foster, and Mollaert, 2004).
38
3.3. FORM FINDING
PVC is less rigid and more deformable but also more resistant to mechanical deformations. It has a lower lifetime compared to PTFE material. The carrier material of these membranes is polyester or aramid fiber. The advantage is the lowest price of all materials used and lower flammability. Strength of PVC membrane in tension in combination with polyester carrier fibre is 3,000-9,800 N / 5 cm and aramid carrier fibre 7,000-24,500 N / 5 cm. Silicone is a very progressive material, used in combination with a glass fiber construction. It has a high service life of over 30 years, a third of the PTFE material, and, as with the only material used, its smoke is not toxic. Silicone is mainly used in combination with glass fiber and the tensile strength of such a membrane is 3,500-6,000 N / 5 cm.

39 3.3.1.
THE FORCE DENSITY METHOD
The Force Density Method is popular among space structure designers and the method was developed at the end of the 1960s by German engineers Linkwitz and Schek for the determination of cable net structures or for the initial equilibrium problem of the cable roofs at the Olympic Games in 1972 hosted by Munich (Bletzinger, Wüchner, Daoud, Camprubi, 2005, and Bletzinger, 2014). Their goal was to determine a geometry that would be sufficiently rigid without the addition of load ballasts, a geometry that would be built easily and would efficiently carry the loads over long distances using subtle elements. This method became very popular rapidly and designers began to work on research from various countries, which caused expansion and variation. Prestressed cable-nets structure and textile membranes are characterized by the inherent interaction between their geometry and stress distribution. This relationship between the form and forces makes it impossible to directly design such structures as is the case with conventional structures. The assumption for using this method is that, that the creating elements of the analyzed structure, must be straight and must be pin joined to each other or to the supporting structure Fig. 3.3.1.1-2, which is fulfilled in this case (Bletzinger, 2014).
Looking at the geometric model of a typical node of the net, this node will be in a steady position, if the resulting force effect of the members will be in equilibrium with the external load in the node. On this basis, it is possible to construct the equilibrium rule for the node as follows: The element between the nodes i and j will be denoted by (i, j). The nodes that are linked with elements by node i will be called "neighbors" to node i, and the set of their labels will be denoted by Ni.
Sabah Shawkat©
First, a graph of a network is drawn, and all nodes are numbered from 1 to Ns, and all the elements are numbered from 1 to m. The Nf nodes which are to be fixed points are taken at the end of the sequence. All the other nodes N are considered free. Thus, the total number of nodes is Ns= N + Nf. Then the connectivity matrix Cs is constructed with the aid of the graph. Each element j has the node numbers k and l (from k to l).
Nf ∪ Ns means the set of those elements which are either in Nf, or in Ns, or in both Nf ∩ Ns means the set that contains all those elements that Nf and Ns have in common
40 Fig. 3.3.1.1. Force Density Method (Bletzinger, 2014)
By defining the positioning vectors xs, ys, zs which are again based on the partial vectors related to the free node x, y, z and related to the fixed node xf, yf, zf , we can calculate the vector displacement of each node, in all directions of the global coordinate system, Sabah Shawkat©
Fig. 3.3.1.2. Detail of Cable Network (Bletzinger, 2014)
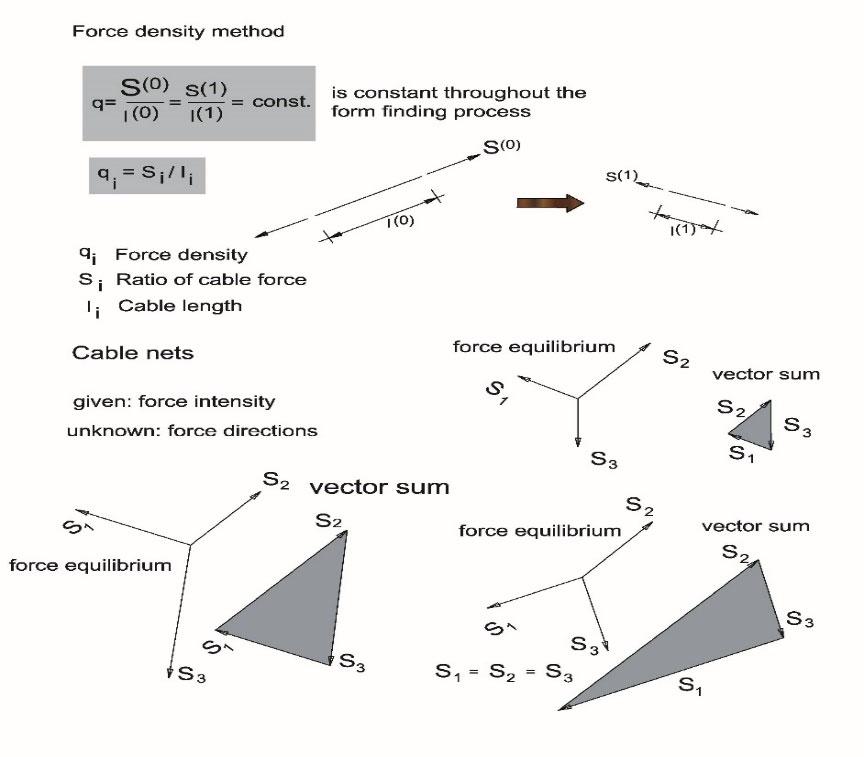
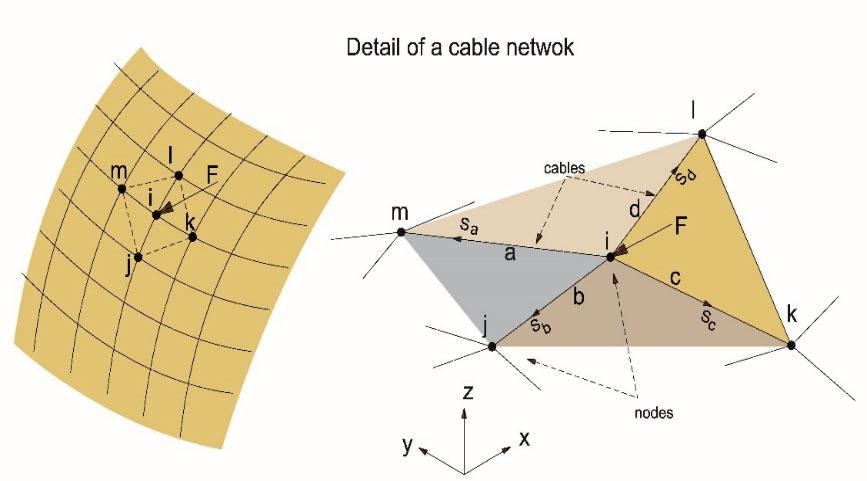
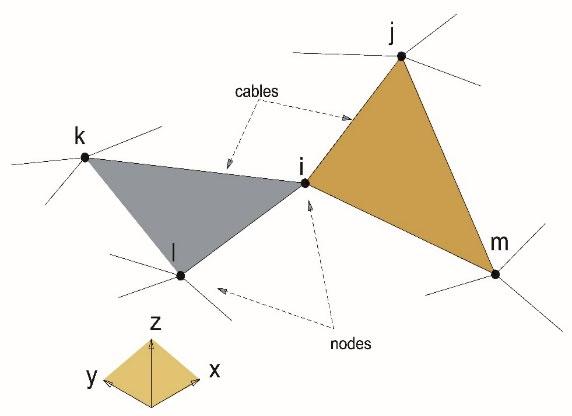
41 where C and Cf contain the free and fixed nodes, respectively. Denoting the vectors containing the coordinates of the n free nodes y, z, and similarly for the Nf fixed nodes xf, yf, zf, the coordinate differences for each element can be written as: The equilibrium equations for the free nodes for the x-, y-, and z-directions are written as By using the force-to-length ratios for the elements, i.e. the force densities, are written as: where the vector q, of length m., is described as: Modeling and analysis of membrane structures is a relatively demanding issue, especially when it comes to combining several element types, such as tension surface material with elements support structures. Only a model that will consider the real situation is relevant to the design of the real Weconstruction.writedown the matrix expression of the equation of equilibrium to the shape: can translate equations of equilibrium into shape: after the introduction of substitution
we
C s CC f uC s xs Cx C f xf vCs ys Cy Cf yf wCs zs Cz Cf zf ()C T ()U ()L 1 S F x ()C T ()V ()L 1 S Fy ()C T ()W ()L 1 S Fz ()C T ()U q Fx ()C T ()V q Fy ()C T ()W q Fz ()Lq() 1 ()S ()qU ()uQ() ()qV ()vQ() ()qW ()wQ() ()CT ()Q ()C ()x ()QC() Cf xf Fx ()C T ()Q ()C ()y ()QC() Cf yf Fx ()C T ()Q ()C ()z ()QC() C f zf Fx ()C()DT ()Q ()C Df ()C T ()Q Cf Sabah Shawkat©
x,
42 continue to shape from which we express the node's final position
The essential ideas are as follows. Pin-joined network structures assume the state of equilibrium when internal forces S and external forces F are balanced
For the compilation of a computational program, equations of equilibrium can be converted into the following Equilibriumform:offree node i j ∈ Ni means j is an element of the set Ni
The equilibrium equations described above represent the linear system of equations, after the solution, we obtain the equilibrium of the position of the nodes. By introducing a force density coefficient (q) a set of otherwise non-linear equations was modified to allow its solution in one computed step. However, this method of solution is highly difficult for programming.
The force density method (FDM) is commonly used in engineering to find the equilibrium shape of a structure consisting of a network of cables with different elasticity properties when stress is applied.
The properties of the force density method were subsequently studied thoroughly, and the method could be implemented in an efficient way by applying special sparse matrix techniques for solving the resulting equations. It proved to be a powerful tool for setting up and solving the equations of equilibrium for prestressed networks and structural membranes, without requiring any initial coordinates of the structures.
While shape analysis of tensile structures is a geometrically non-linear problem, the FDM linearizes the equations analytically by using the force density ratio for each cable element, q = S /L, where S and L are the force and length of a cable element respectively. The method relies on the assumption that the ratio of tension force to the length of each cable can be constant, transforming a system of non-linear equations to a set of linear equations which can be solved directly.
()xD() Fx Df xf ()yD() Fy Df yf ()zD() Fz Df zf ()Fxx Df xf ()D 1 ()Fyy Df yf ()D 1 ()Fzz Df zf ()D 1 j Ni Sij cos ij 0 j Ni Sij cos ij 0 j Ni Sij cos ij 0 Sabah Shawkat©
43 Si,j is the force value in the element (i, j), with positive orientation from the node i toward the node j, αi,j, βi,j, γi,j are angles between coordinate axes and axis of the element (i, j), oriented from i toward j, Fig. 3.3.1.3. Cable Element in the Global Coordinate Frame cos ij xj xi l ij cos ij yj yi l ij cos ij zj zi l ij lwhereij () lxi yi zi xj yj zj xj xi 2 yj yi 2 zj zi 2 j Ni Sij zj zi l ij 0 j Ni Sij xj xi l ij 0 j Ni Sij yj yi l ij 0 Sabah Shawkat©
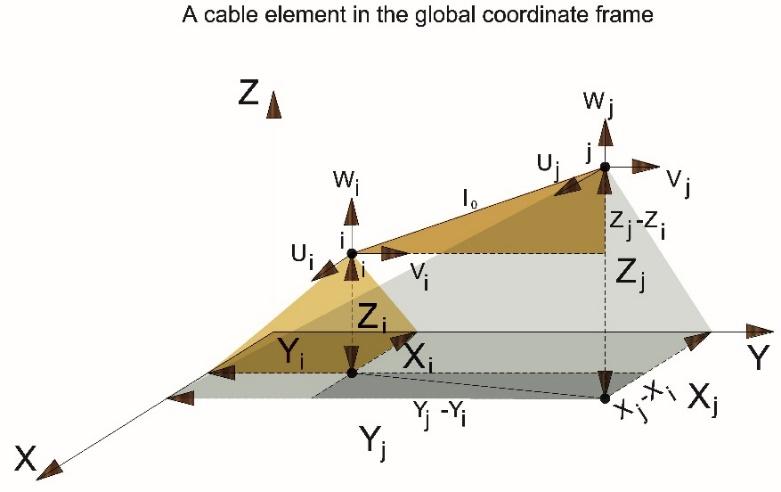
44 li,j is the length of the element (i,j). The nonlinear algebraic equation system will be obtained i ∈ Nf means i is an element of the set Nf If the relationships Si,j / li,j in the equilibrium system are denoted qi,j, the system becomes j Ni Sij xj xi xj xi 2 yj yi 2 zj zi 2 0 j Ni Sij yj yi xj xi 2 yj yi 2 zj zi 2 0 j Ni Sij zj zi xj xi 2 yj yi 2 zj zi 2 0 Sabah Shawkat©
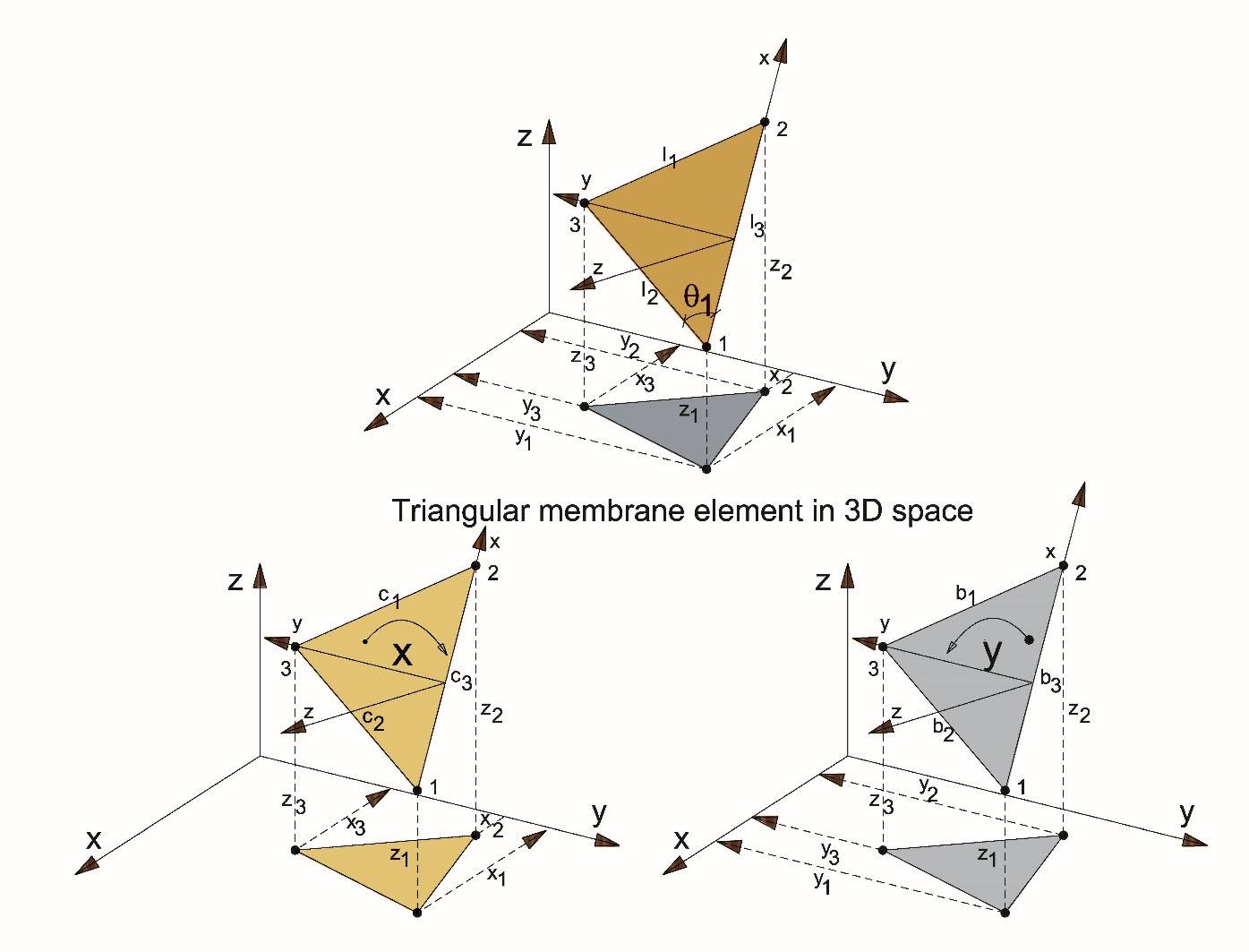
45 are called force densities Force densities qi,j can be set instead of force values Si,j what is possible for the general network topology write as follows: This suggests that the equilibrium position of each node in the space is a function of the average position of its neighbors, where the great coefficient is the force density of the bristles seizing the solved nodes. q ij () Sij xj xi 2 yj yi 2 zj zi 2 j Ni q ij zj zi 0 j Ni q ij xj xi 0 j Ni q ij yj yi 0 qij. xj xi qik xk xi qil xl xi qim xm xi Fxi 0 qij xj qij xi qik xk qik xi qil xl qil xi qim xm qim xi Fxi 0 xi qij qik qil qim qij xj qik xk qil xl qim xm Fxi 0 xi qij qik qil qim qij xj qik xk qil xl qim xm Fxi xi qij xj qik xk qil xl qim xm Fxi qij qik qil qim xi 1 n j xj qij Fxi 1 n j qij yi 1 n j yj qij Fyi 1 n j qij zi 1 n j zj qij Fzi 1 n j qij Sabah Shawkat©
The latest materials have sufficient durability and permeability, as evidenced by their use in various climatic regions, from the Arctic winter to the desert heat. Some materials perfectly reflect sunlight, which can save a lot of electricity for cooling. Their unique light properties can also be used cleverly: during the day, thanks to their high transmittance, they make ideal use of daylight, and conversely, during the night, artificial lighting from the interior provides interesting exterior luminescence.
It turns out that the introduction of state of modern technologies in connection with membrane structures allows this "light" concept to be promoted in others in areas where until now only heavy construction has dominated (Foster, Mollaert, 2004). For example, when creating an air-conditioned large space and a protected urban environment. Many buildings based on the principle of membrane structures belong not only to the original and creative in terms of architectural form, but they are also top technical works with a high level of technical detail.
Sabah Shawkat©
When using membranes as a building material, it is important to pay attention to the long life and functionality of the membranes. Several problems that may occur include e.g., uneven thickness of the protective layer on the surface of the fibers, change in colour due to the aging process, different elongation of the warp fibers, or penetration of water into the fabric.
The main advantages of constructions made of textile materials include their lightness (therefore they are also called lightweight structures), airiness, and enormous flexibility. Compared to traditional rigid constructions, they make it easier to cover large spans with a minimum number of support elements (such as columns). Another plus is their design variability, providing almost unlimited possibilities for finding non-traditional elegant forms (Foster, and Mollaert, 2004).
The most important factor in large-span structures is the relationship between sufficient distance and membrane joints. The largest span and the lowest stress on the anchoring and connection of membranes allow greater economy of the structure. A very important factor is the quality of the joint.
The more indeed adapted the design details are to the real demands, the more durable the whole construction is, and the less maintenance required.
Economically, membrane constructions are less demanding because they require only minimal maintenance compared to conventional constructions of similar dimensions.
46 3.3.2. ADVANTAGES AND DISADVANTAGES OF MEMBRANE STRUCTURES
In 2010, the independent association Tensinet, which covers universities, scientists, designers, material manufacturers, and light construction contractors, tasked its members with finding and describing the shape and geometry of a cone and hyperbolic paraboloid between given support points and with a given internal prestress. This task aimed to gather information on the method of analysis
3.4. LINEAR THREE NODE TRIANGLE ELEMENT
47 and procedures for finding the shape from all globally relevant organizations. Although the tasks had an exact solution, the results varied by up to 200% between organizations [Tensinet].
We
xe T x1 y1 x2 y2 x3 y3 e T 1 1 2 2 3 3 Sabah Shawkat©
The linear triangle element (Turner triangle), which is often called the triangle membrane element or constant strain triangle (CST) element is depicted in Fig. 3.4.1. At each node there are two degrees of freedom. Consequently, the degrees of freedom is equal to six for the whole element. The arrow in the center point of the element refers to the orientation of the element, i.e. for each element we have a direction, which means how the nodes are followed by each other. Interpolation of the displacement field collect the nodal x, y coordinates and displacement components in vectors: The nodal x, y coordinates Displacement components in vectors Fig. 3.4.1. Linear triangle element. Nodal coordinates and displacements.
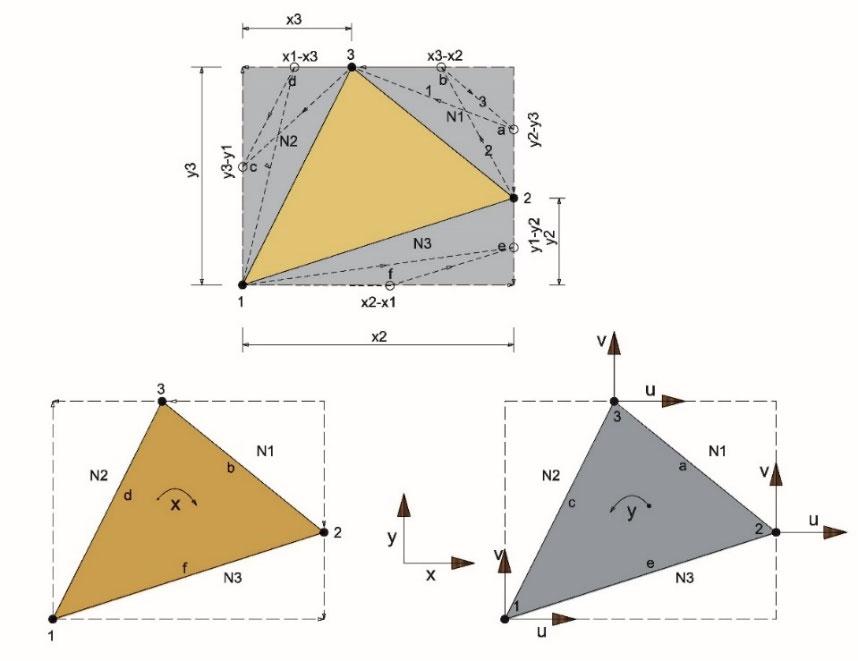
48 Fig. 3.4.2. Linear Triangle Element The triangle area can be expressed as a determinant: The u and v components of the displacement field are formulated as the linear function of x and wherey:a0, a1, a2, b0, b1, and b2 are unknown constants. The vector of strain components is: we Thehave:nodal displacements must be obtained if we take back the nodal coordinates into the u (x, y) and v (x, y): 2 Ae 111 xxx123 yyy123 x2 y3 x3 y2 x3 y1 x1 y3 x1 y2 x2 y1 1 2 3 xy ()a 0 a 1 x a 2 y xy ()b 0 b 1 x b 2 y T x y xy xy y x a2 b1 x x a1 y y b2 1 a0 a1 x1 a2 y1 1 b0 b1 x1 b2 y1 2 a0 a1 x2 a2 y2 2 b0 b1 x2 b2 y2 3 a0 a1 x3 a2 y3 3 b0 b1 x3 b2 y3 Sabah Shawkat©
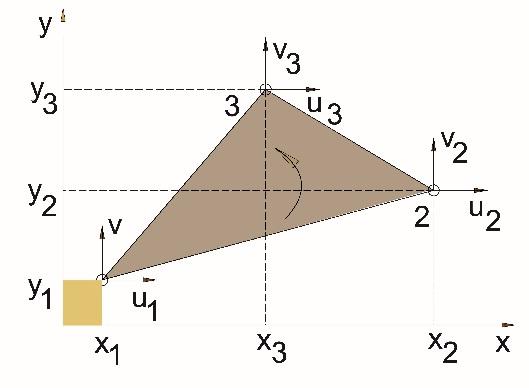
49 The solution of the system of equations above results in: where:Substituting the solution above back into the components of the displacement field, we obtain: Because for the triangle element we have three interpolation functions we can write that: The interpolation functions can be derived in the following form: a0 1 1 2 2 3 3 2 Ae a1 1 1 2 2 3 3 2 Ae a2 1 1 2 2 3 3 2 Ae b0 1 1 2 2 3 3 2 Ae b1 1 1 2 2 3 3 2 Ae b2 1 1 2 2 3 3 2 Ae 1 x2 y3 x3 y2 1 y2 y3 1 x3 x2 2 x3 y1 x1 y3 2 y3 y1 2 x1 x3 3 x1 y2 x2 y1 3 y1 y2 3 x2 x1 xy ()a 0 a 1 x a 2 y xy ()b 0 b 1 x b 2 y xy () 1 2 Ae 1 1 x 1 y 1 2 2 x 2 y 2 3 3 x 3 y 3 xy () 1 2 Ae 1 1 x 1 y 1 2 2 x 2 y 2 3 3 x 3 y 3 xy ()N 1 1 N 2 2 N 3 3 1 3 i N i xy () i xy ()N 1 1 N 2 2 N 3 3 1 3 i N i xy () i N i xy () i i x i y 2 A e i 1 2 3 Sabah Shawkat©
50 Based on the relation of x, yx, y the matrix of interpolation functions becomes:
The definition of the element stiffness matrix is: the previously mentioned strain-displacement matrix
becomes: N N01 N01 N02 N02 N03 N03 AeAe AN 1i N 2j N 3k d ij k ij k 2 () 2 Ae K e yxB T C T B d d B N 0x y 0 y x N01 N01 N02 N02 N03 N03 N 1 0x N 1 y 0 N 1 y N 1 x N 2 0x N 2 y 0 N 2 y N 2 x N 3 0x N 3 y 0 N 3 y N 3 x Sabah Shawkat©
The parameter lines of the interpolation function, which implies the following properties: - at the nodes: (N1 N2 N3), (1,0,0), (0,1,0), (0,0,1), - at the midpoints of the triangle sides: (N1 N2 N3), (1/ 2,1/ 2,0), (1/ 2,0,1/ 2), (0,1/ 2,1/ 2), - at the centroid: (N1 N2 N3), (1/ 3,1/ 3,1/ 3), - i.e., it is seen that at every point: (N1 N2 N3),Parameterfinally: lines of the interpolation functions of linear triangle element. of the stiffness matrix
where
Calculation
51 This formulation implies that the elements of the matrix are independent of the x and y variables, they depend only on the nodal coordinates. Therefore, the stiffness matrix can be written as: B where Ae is the element area, Ve = Aev is the element volume, respectively. Consequently, the stiffness matrix of the linear triangle element can be computed in a relatively simple way and in closed form. Definition of the loads Body force or volume force. Let the vector of body forces be equal to: from which we have: Utilizing the special properties of the interpolation functions, e.g., if i= 1, j = 0 and k = 0, we have: Consequently, we have: B N 1 2 Ae 01 1 0 1 1 02 2 0 2 2 03 3 0 3 3 K e BT CT B Ae BT CT B Ve q qqxy Fab yxN T q d d AeAe A N NN012030 NNN010203 qqxy d AeAe A N 1 qx N 1 qy N 2 qx N 2 qy N 3 qx N 3 qy d AeAeAN 1 d 31 Ae FebT 31 Ae qx qy qx qy qx qy Sabah Shawkat©
52 To illustrate the properties of the linear force densities a simple example will now be given. Consider the structure below with all fixed nodes in the x-y plane. The initial position of free nodes The initial position of fixed nodes (supports): Fig. 3.4.3. Dimensions of Fabric Membrane Structure A simple cable structure with zero external loads. The arrows indicate the directions of elements. Fig. 3.4.4 Form Finding Geometry x 21010 y 10021 z 00000 xf 2200 y f 0202 zf 2002 Sabah Shawkat©
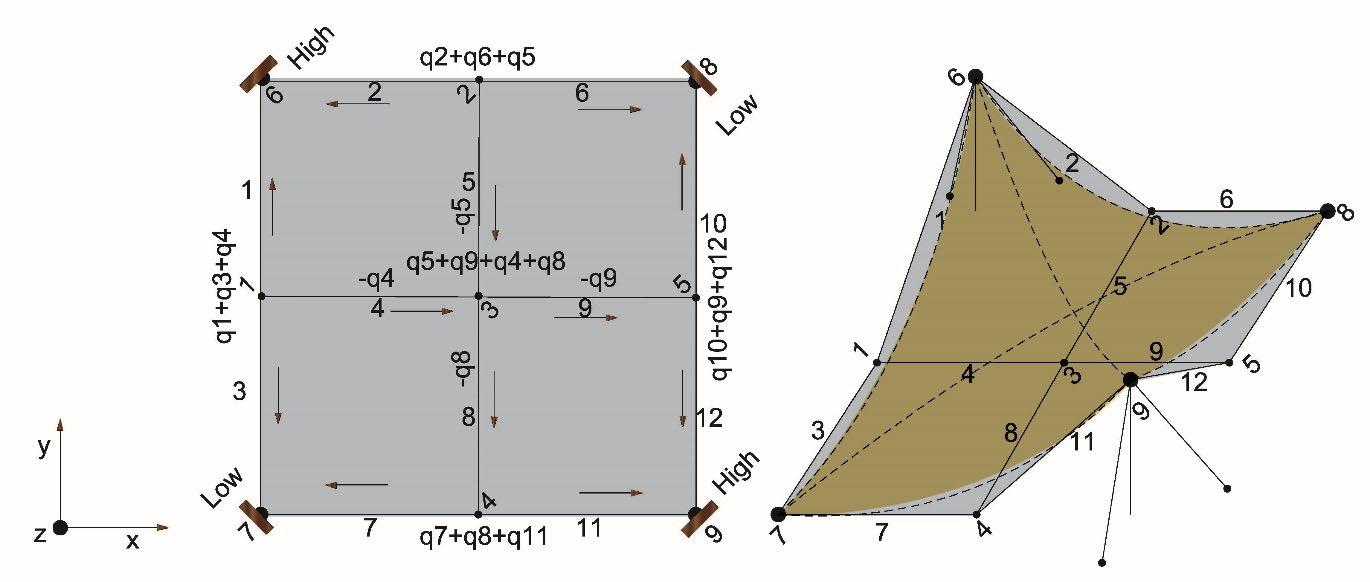
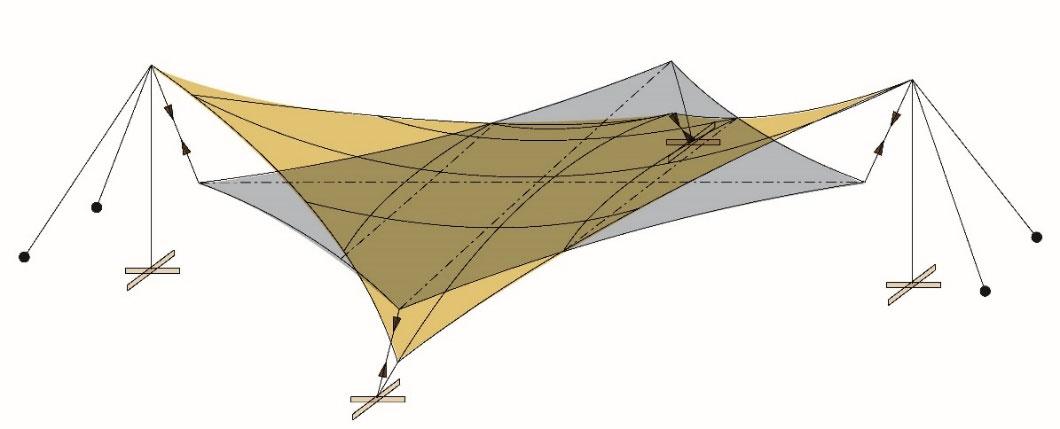
53 Matrix of continuity External Load of Free Nodes: Force Density Coefficient of Prestress: C 000000001101 000000110010 000110011000 100000010010 000000001101 Cf 000000000011 001000100000 000001000100 000000000011 Fx 00000 Fy 00000 Fz 00000 Q 000000000001 000000000010 000000000100 000000001000 000000010000 000000100000 000001000000 000010000000 000100000000 001000000000 010000000000 100000000000 Sabah Shawkat©
54 Design stiffness matrix: Calculation of new position of free nodes: Design stiffness matrix DCT Q C 00031 30100 41111 03001 30001 Df CT Q Cf 00011 00011 00011 00011 xD 1 Fx Df xf 1.6670.333111 yD 1 Fy Df y f 0.3331.667111 D 1 Fz Df zf 11111 i112 q i 1 df q1 q2 000 q3 q007 0 q06 q0010 q00011q12 d q 1 q 3 q 4 q0 4 00 0 q 2 q 5 q 6 q 5 00 q 4 q 5 q 4 q 5 q 8 q 9 q 8 q 9 q00 8 q 7 q 8 q 11 0 q00 9 0 q 9 q 10 q 12 d 00031 00301 41111 00130 30001 d f 00011 00011 01001 00011 Sabah Shawkat©
55 Calculation of new position of free nodes For different force density values, we get different resulting shapes of this structure. it is seen that for a single element an increase in the force density relative to the others results in the construction of that element. the opposite holds for the decrease in the force density, even more, emphasized with negative values. For elements 1-3, 5-12 have q = 1 and element 4 has q = 9 Calculation of new position of free nodes xd 1 Fx d f xf 1.6670.333111 yd 1 Fy d f y f 0.3331.667111 zd 1 Fz d f zf 11111 d f q 1 q 2 000 q 3 q00 7 0 q0 6 q0010 q00011q12 d q 1 q 3 q 4 q0 4 00 0 q 2 q 5 q 6 q 5 00 q 4 q 5 q 4 q 5 q 8 q 9 q 8 q 9 q00 8 q 7 q 8 q 11 0 q00 9 0 q 9 q 10 q 12 d 110900 00301 121911 03001 30001 d f 00011 00011 00011 00011 xd 1 Fx d f xf 1.5780.9110.7330.9110.6 yd 1 Fy d f y f 0.3331.667111 zd 1 Fz d f zf 11111 Sabah Shawkat©
56 For elements 1-3, 5-12 have q = 1 and element 4 has q = -0.2 Calculation of new position of free nodes For interior elements 4-5, 8-9 have q = 1 and edge elements 1,2,3,6,7,10,11,12 have q = 6 d f q 1 q 2 000 q 3 q00 7 0 q0 6 q0010 qq0001112 d q 1 q 3 q 4 q0 4 00 0 q 2 q 5 q 6 q 5 00 q 4 q 5 q 4 q 5 q 8 q 9 q 8 q 9 q00 8 q 7 q 8 q 11 0 q00 9 0 q 9 q 10 q 12 d 0.21.8000 30100 2.80.2111 00130 00103 d f 00011 00110 01001 00011 xd 1 Fx d f xf 1.8331.1671.1670.1671.5 yd 1 Fy d f y f 0.3331.667111 zd 1 Fz d f zf 11111 d f q 1 q 2 000 q 3 q00 7 0 q0 6 q0010 qq0001112 Sabah Shawkat©
57 Calculation of new position of free nodes d q 1 q 3 q 4 q0 4 00 0 q 2 q 5 q 6 q 5 00 q 4 q 5 q 4 q 5 q 8 q 9 q 8 q 9 q00 8 q 7 q 8 q 11 0 q00 9 0 q 9 q 10 q 12 d 130100 130100 41111 130010 130010 d f 00066 00660 06006 00066 xd 1 Fx d f xf 1.9230.077111 yd 1 Fy d f y f 0.0771.923111 zd 1 Fz d f zf 11111 Sabah Shawkat©
xx , yy and xy zz yz xz 0 xx yy zz yz zx xy 0001 0001 0001 000 1 00 0000 1 0 00000 1 xx 000yy xy xx yy xy E1 10 01 000 xx yy xy xx yy xy E 1 2 1 0 01 00 1 xx yy xy xx yy xy xx yy xy xx 0.015 yy 0.025 xy 0.022 0.4 E0.200 mmkN2 xx yy xy E 1 2 1 0 01 00 1 xx yy xy xx yy xy 3.1437.3815.952 MPa Sabah Shawkat©
The plane stress analysis refers to the problems where the thickness of the structure is very small compared to other dimensions of the structure in the XY plane. The plane stress problem is a 2D problem. The stresses in the z direction are negligible.
The stress-strain compliance relationship for an isotropic material becomes: The three zero stress entries in the stress vector indicate that we can ignore their associated columns in the compliance matrix (i.e. columns 3, 4, and 5). If we also ignore the rows associated with the strain components with z-subscripts, the compliance matrix reduces to a simple 3x3
and
58 3.5. THE PLANE STRESS PROBLEM
Thematrix,stiffness matrix for plane stress is found by inverting the plane stress compliance matrix, is given by, in-plane stress field forms a tensor defined by three independent components:
Stresses:If: The
Material
membrane
The
(Hint:
A is subjected to shear deformation. material itself can be assumed to behave linear elastic (the stress-strain relationship can be described with the Hooke law for the plane stress state.) parameters: Strain state at point P referring to the given local coordinate system: configuration Determine the stress state at point P referring to the given local coordinate system Evaluate the principal stresses and their Determine the principal strains A principal strain state is defined by vanishing shear deformation. can use the inverse relationship of the Hooke law to determine the principal strains from the principal Extrastresses)question: realistic? the characteristic mechanical behavior of membranes) Hooke law for the plane stress state:1. Determine stresses: C is the so-called constitutive or elasticity matrix (in general it is a fourth-order elasticity
59 3.6. PLAN STRESS STATE and PRINCIPAL STRESSES
directions 3.
Are they
(Consider
Etensor)represents Young´s modulus ν the poisons ratio 11 0.01 11 22 22 0.02 0.05 2 12 12 21 0.4 E0.200 mmkN2 11 22 or 11 22 2 12 C E 1 2 1 0 01 00 1 2 11 22 12 C 11 22 12 E 1 2 1 0 01 00 1 2 11 22 11 22 12 3.5715.7144.286 MPa Sabah Shawkat©
2.
You
reference
1.
60 The inverse relationship is as follows: The strain in the thickness direction can be determined as: 2. Determine principal stress: 3. Determine principal stress directions: C 1 11 22 2 12 C E1 01 01 00 21 () 11 22 12 33 E 11 22 1 11 22 det 0 I 11 0 21 12 22 0 02 11 22 0 11 22 122 02 tr0 det 0 02 11 22 0 11 22 122 0 B 11 22 C 11 22 122 B10MPa C11.735MPa 2 01 BB2 4C 2 02 BB2 4C 2 01 8.642MPa 02 1.358MPa 01 8.642MPa 11 4.286MPa 22 5.714MPa 12 3.571MPa 11 12 12 22 01 01 10 n 1 n 2 00 11 12 12 22 01 01 10 3.5714.356 3.5712.928 MPa n 1 1 4.356 MPa n 1 3.571MPa n 2 0 n 2 4.356MPa n 1 3.571MPa () n 2 1.22 n 01 1 n 12 n 22 n 1 n 2 n 01 0.7730.634 n 02 0.6340.773 Sabah Shawkat©
61 Fig.3.6.1 Compression: Plane Stress-Plan Strain 3.7 HOOKE LAW FOR THE PLANE STRESS STATE 1. Determine stresses: C is the so-called constitutive or elasticity matrix (in general it is a fourth-order elasticity Etensor)represents Young´s modulus ν the poisons ratio The inverse relationship is as follows: 11 22 or 11 22 2 12 C E 1 2 1 0 01 00 1 2 11 22 12 C 11 22 12 E 1 2 1 0 01 00 1 2 11 22 11 22 12 3.2147.3815.952 MPa C 1 11 22 2 12 C E1 01 01 00 21 () 11 22 12 Sabah Shawkat©
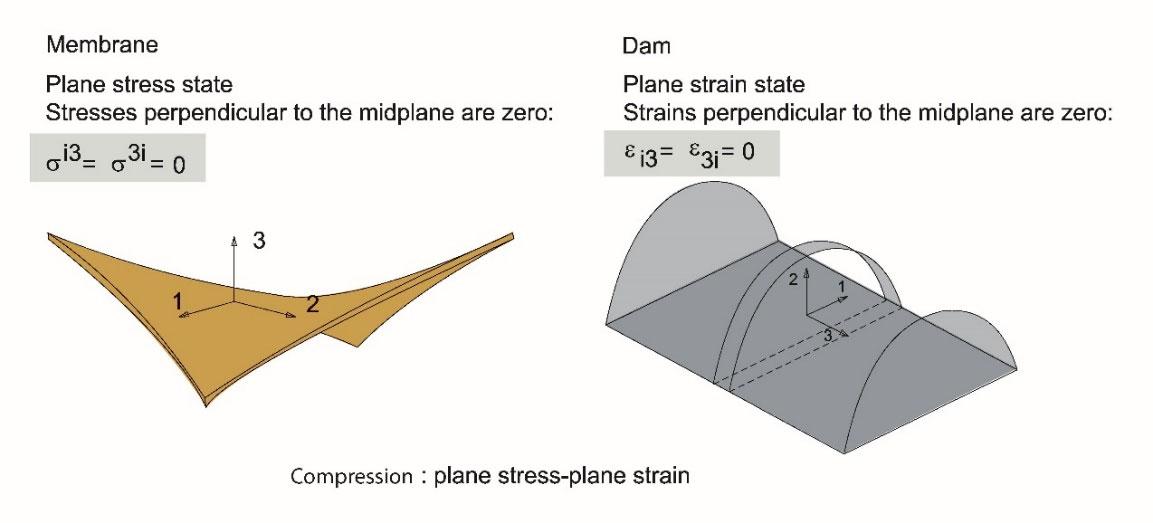
62 The strain in the thickness direction can be determined as: 1. Determine principal stress: Fig.3.7.1 Principal Stress 2. Determine principal stress directions: 33 E 11 22 1 11 22 det 0 I 11 0 21 12 22 0 02 11 22 0 11 22 122 02 tr0 det 0 02 11 22 0 11 22 122 0 B 11 22 C 11 22 122 B13.333MPa C33.603MPa 2 01 BB2 4C 2 02 BB2 4C 2 01 9.959MPa 02 3.374MPa Sabah Shawkat©
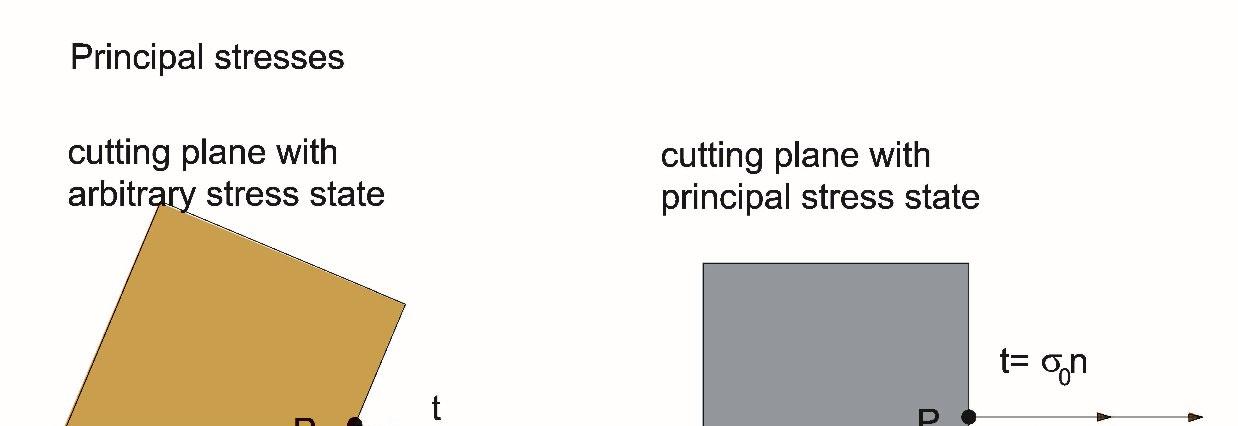
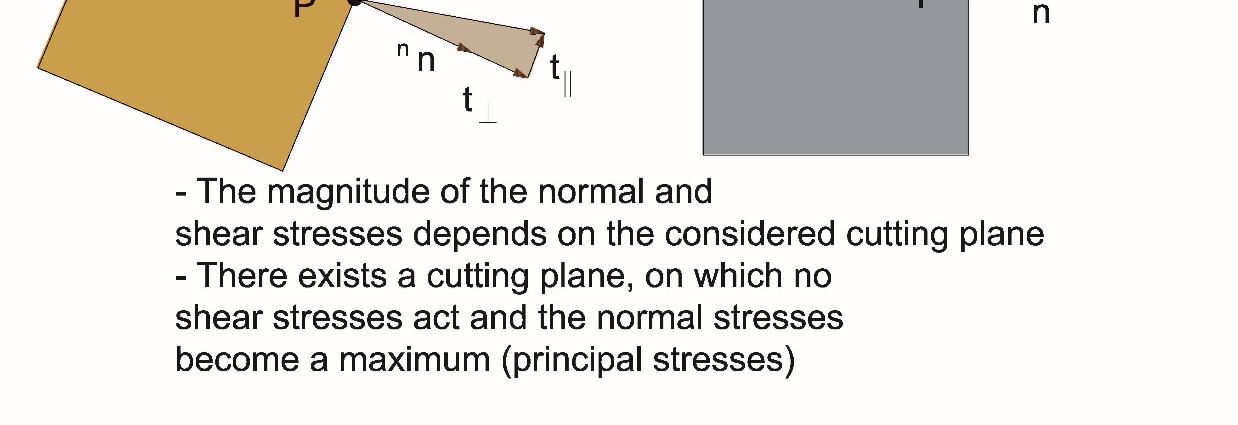
63 Mohr´s circle of stress Fig.3.7.2. Principal Stress-Mohr’s Circle of Stress Solution of the principal stress eigenvalue problem: Characteristic polynomial: 01 9.959MPa 11 5.952MPa 22 7.381MPa 12 3.214MPa 11 12 12 22 01 01 10 n 1 n 2 00 11 12 12 22 01 01 10 3.2144.007 3.2142.578 MPa n 1 1 4.007 MPa n 1 3.214MPa n 2 0 n 2 4.007MPa n 1 ()3.214MPa n 2 1.247 n 01 1 n 12 n 22 n 1 n 2 n 01 0.6260.78 n 02 0.6260.78 0 I n 0 n 1 n 00 11 2 22 6 122.5 12 12 21 12 det ()0I 11 0 21 12 22 0 0 2 11 22 () 0 11 22 ()12 2 0 2 11 22 () 0 11 22 ()12 2 0 2 tr0 det 0 Sabah Shawkat©
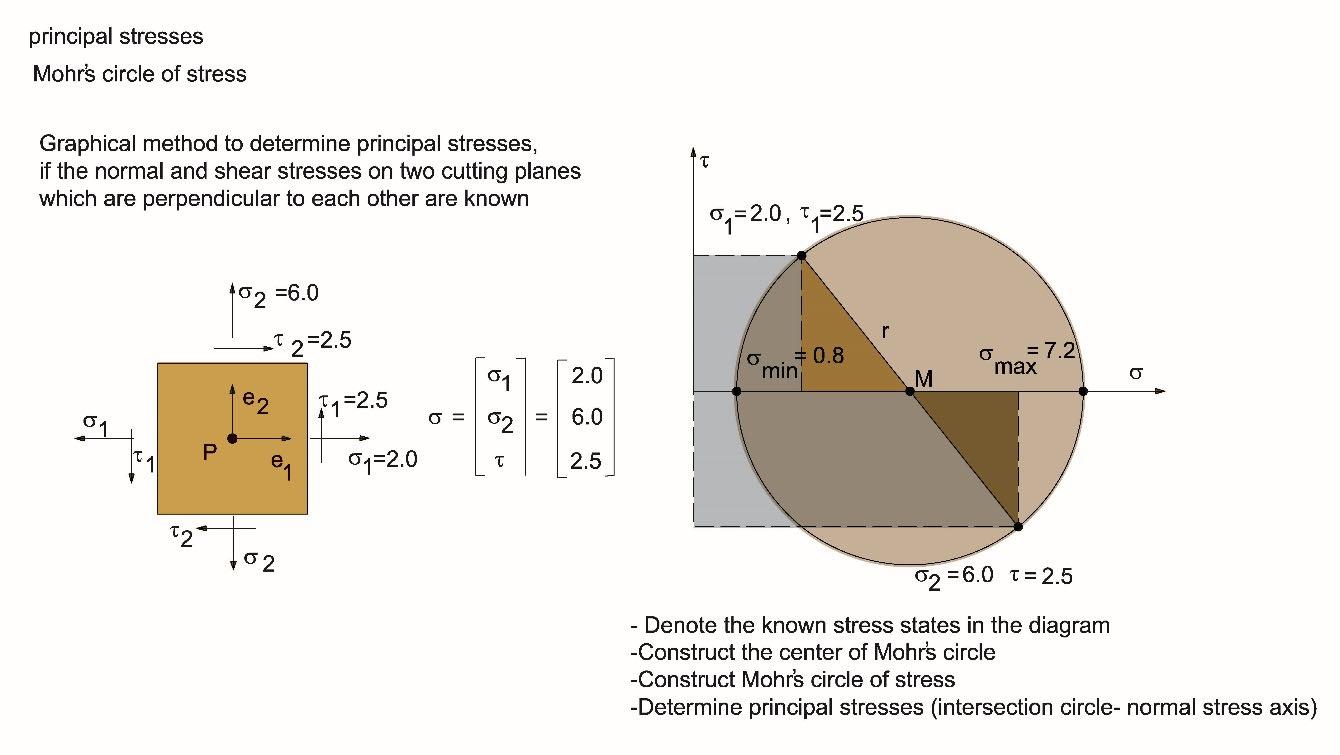
64 Analytical solution. Principal stresses: Characteristic polynomial of the eigenvalue problem: Fig.3.7.3. Plane Stress State Analytical solution. Principal stress directions: det ()0I det 11 21 12 22 0 0n n0 I 0n n0 b 11 22 () b8 11 22 ()12 2 c 11 22 ()12 2 c5.75 max bb 2 4c 2 max 7.202 min bb 2 4c 2 min 0.798 Sabah Shawkat©
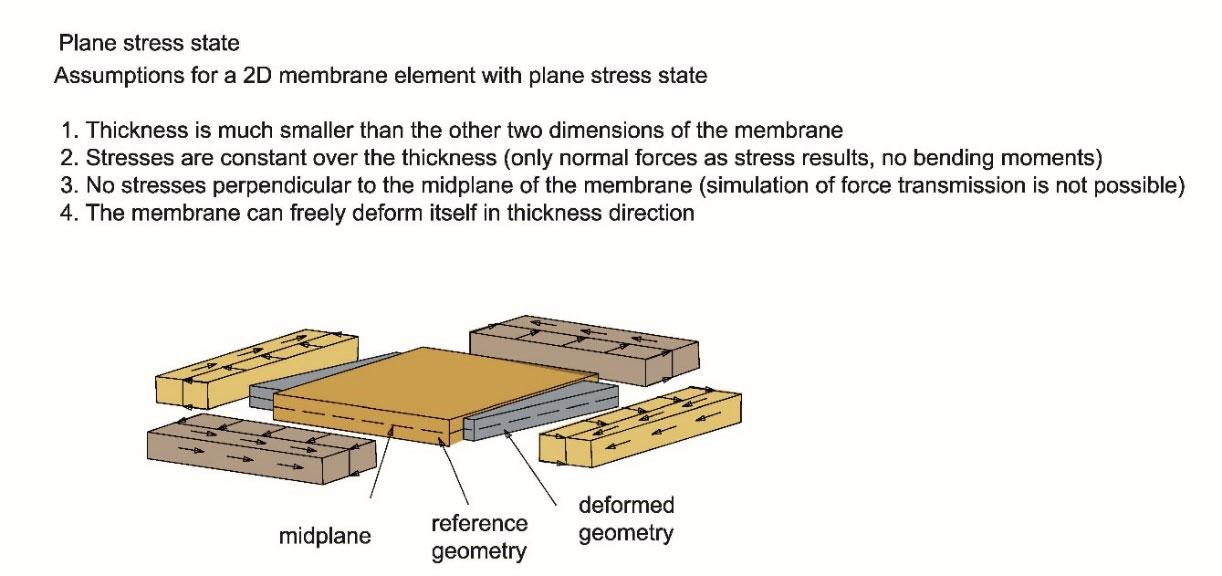
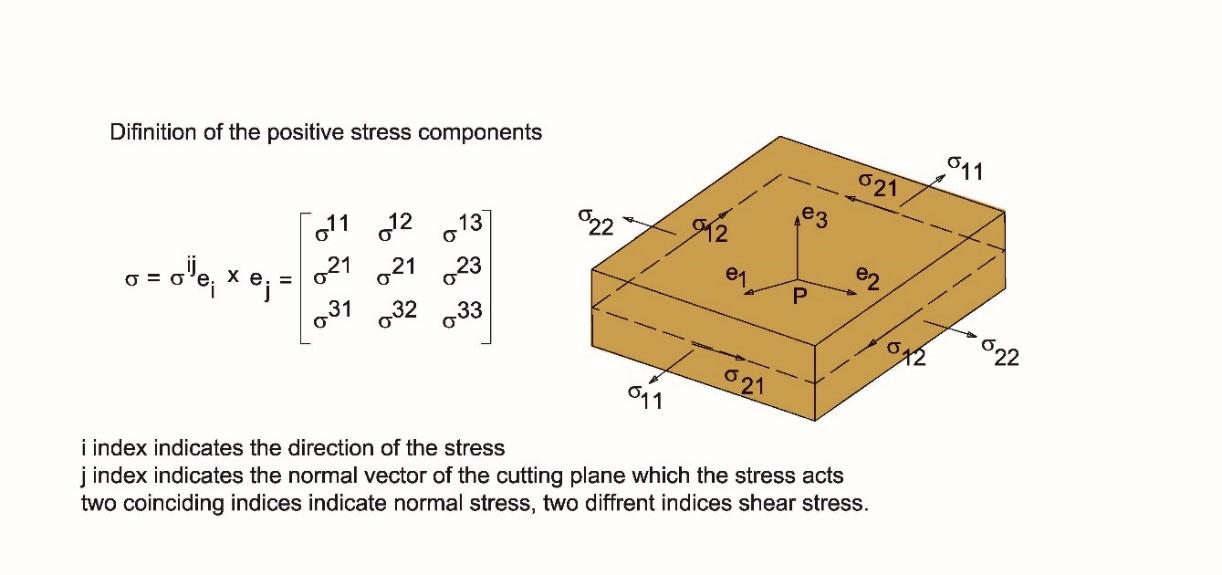
65 Fig.3.7.4. Analytical Solution of Stresses 0 I n 0 min 0.798 I 0n n0 min I n 0 11 21 12 22 min 01 10 n 1 n 2 11 21 12 22 min 01 10 1.2022.5 5.2022.5 n 1 1 ()1.2022.5 n12 0 1.2021 2.5n 2 0 n 2 1.2022.5 n 2 0.481 n min 1 12 n 2 2 n12 a 1 12 n 2 2 a0.901 b 1 12 n 2 2 n 2 b0.433 n min 0.9010.433 n max ba or n max 0.9010.433 Sabah Shawkat©
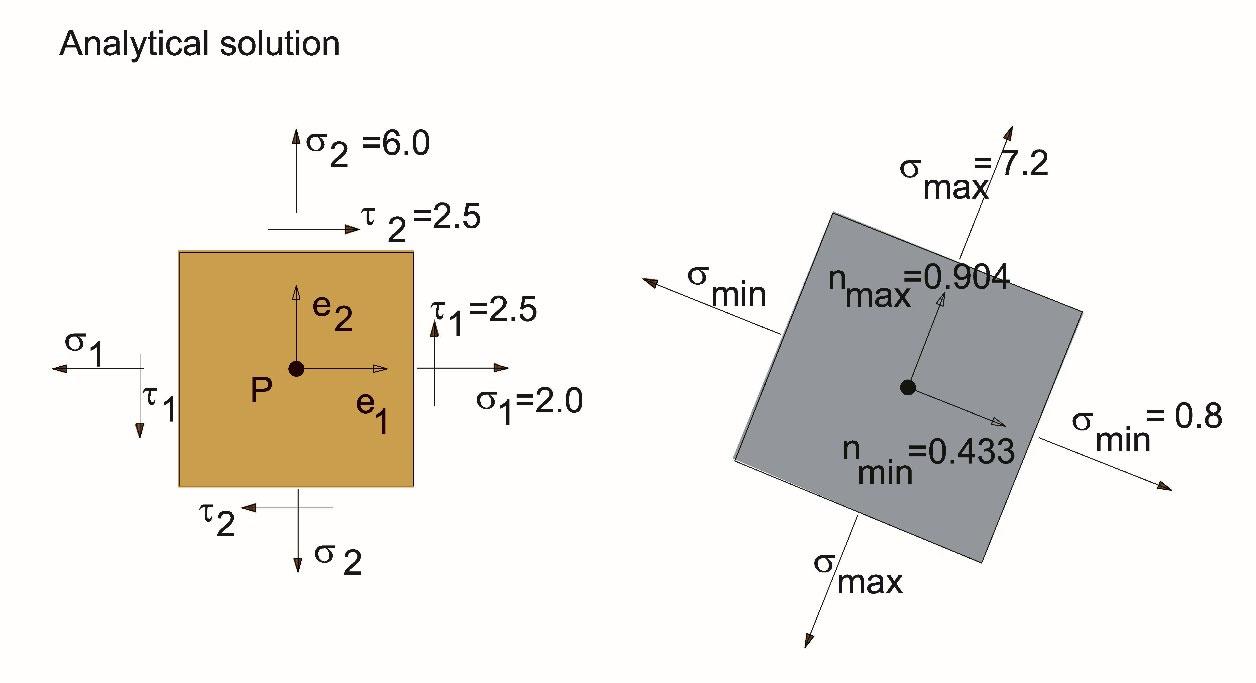
66 4. ELASTIC GRID SHELLS
An elastic geodesic grid (EGG) is one of the subgroups of lightweight structures that can be freely used to unfold the free-form spaces and make the application of the grid movable. Furthermore, their installation does not need complicated instructions. Lightweight grid constructions are especially needed for realization where large spans and low weight are required and do not have to be straight, at the same time the satisfactory curved shape for the designer is based on iteration.
Static shapes are often straight with horizontal lines and may appear quiet and active shapes are diagonal with orthogonal lines. This behavior of traditional interpretation of geometrical design was caused by a lack of the existence of computational and material characteristic tools. The principles behind this “computation” have also been computationally recreated and are now in principle available to designers.
The proposed task aims to continue research into applications of resistant membrane structures. We will create virtual and subsequent real models creatively by physically searching for a form and applying numerical methods based on finding the shape and modelling the equilibrium state of geometric nonlinear shapes.
Sabah Shawkat©
We will aim to free constructions from shapes that are based on straight lines. As it is known, the basic elements of standard shapes are line and plane, positive-curved line guides the spherical geometry, while a negative-curved line guides hyperbolic geometry. The "Form Finding" method allows searching for shapes regardless of traditional compositional, static, or constructional principles using a virtual, so-called trans-architecture. Evolution in nature, which optimized natural structures, has also become a major source of inspiration for the shapes of structures in construction and architecture. However, the "Free Form" shapes have no analogy in nature, and it is impossible to describe them exactly mathematically. We want to choose our approach to the issue of shape search and optimization of the so-called free-form membrane constructions of synclastic and anticlastic shapes. This problem requires designers to understand and analyze sets of relationships between parameters and components. One of the useful tools for producing architectural designs is to convert aims into abstract shapes. In its long history, algorithmic plan as a form-finding strategy, permitted designers to oversee complex non-standard associative geometries, recommending a move from the computerized representation of frame to its efficient representation into a parametric demonstration through code. Modern geometry became more attractive in the architectural design process with great innovations from form-finding stages to the final fabrication.
To create a spatial surface, we select a simple way using sheet plat for its perfect characteristics, which is closely related to the Japanese art of origami. Recently besides architecture diagrams, there has been developed digital graphic investigation support with visual programming such as grasshopper inside rhino using the kangaroo solver plug-in for parametrizing the geometry of the folding structure.
An elastic grid shell is a system “consisting of flexible members”. The required geometry is achieved through the progressive elastic bending of originally in-plane grid members Fig. 4.1. The erection process can be completed on initially plane flat grid disposition or through gradually bent of single members (gradually erected).
As we show the structure in Fig. 4.1, the grid system is 2d, with the dimensions x,y including spaces between the strips in u,v distances. The transformation of this flat surface in 2d to 3d we achieve via induced curvature to the structure, applying to bend or twisting the grid elements. The materials used for this type of construction are available and common ones are available on the market.
67
The new position of the form-finding grid system is usually found geometrically, which is the function of networks of elastic grid geodesic curves. This elastic-kinematic mechanism for Set up the free-form finding substructure offers a non-Euclidian form simply call it a curved shape surface during the installation of geometry, therefore we realize the boundary conditions of the anchors.
The main purpose of this presentation is to build a regulation method for elegant temporary structures, which can be realized shortly by inexperienced builders or workers.
The variety of a geodesic dome and elastic grid shell structural system is motivated by its amazing budget, clearness of structure and high install ability potential, continue the ongoing research in the Sabah Shawkat©
Our goals are to analyze how the virtual design of such a structure becomes real according to elastic deformation and to use it in different scaling for public spaces.
Yet we used a small physical model with a small budget for a better understanding of the kinematic behavior of such free form finding substructure, to serve for further development and their easy installation, and expansion at various scales in the future. This setup procedure makes the doubly curved surface more easy, quick, and more material efficient. The creation of such constructions is aesthetic, functional, and special, in addition, they are nice because the form finding of the surface is curved, which brings us closer to nature and gives us a sense of freedom with its parametric design. The creativity of elastic geodesic grids is the transformation analysis of the structure that the input data come for the planar surface design, where the output data are achieved from a 3d curved surface grid, this can be set up simply by pulling at least the two corners at the planar state with applying some additional bending.
Sabah Shawkat©
The reason for the creation of our EGG was based on cutting plastic lamellas in the width of 2cm, the thickness of 2mm, and in 1m length for both directions x, y, while the lamellas will be mounted at a distance of 100mm in both directions u, v, which will eventually create an area of 1m x1m Fig. 4.1. Practical lamellas are deformable but after the creation of curved shape based on curvature in both directions which controls the shape and therefore ensures the stability and safety of the entire structure. In all nodes, we have created notches in the x, y-axis directions, for ease of node movement in the x-direction and y-direction, respectively, so that the design will be able to provide us with different types of shapes in the form-finding process which is the function of iteration.
Fig.4.1: Plane flat Elastic flat grid plan members (models created by the authors)
68 field of their structure concept, design, and analysis, set up the work procedures and Potential development are still open.
Fig. 4.2: Elastic deformation, reversible deformations, and form finding of E.G.SH, (models created by the authors)
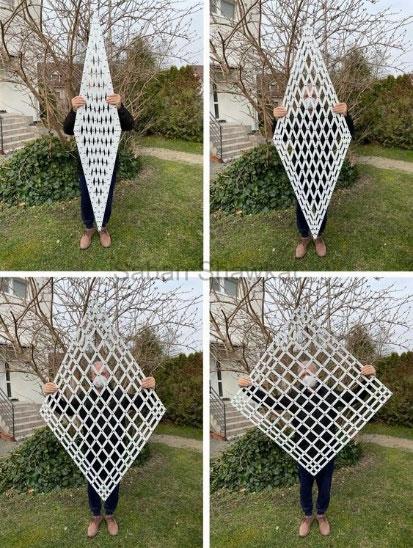
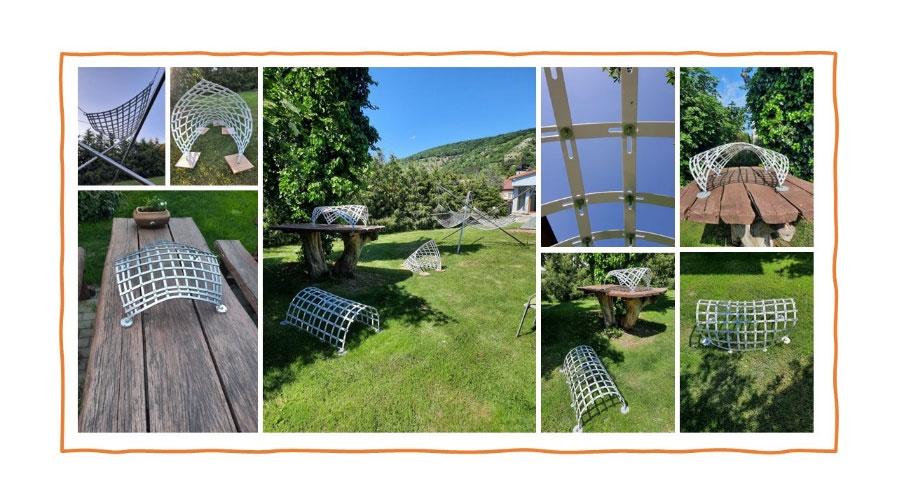
As we show the initial grid flat plan in Fig. 4.1, the grid system is 2d, with the dimensions x,y including spaces between the strips in u, and v distances. The transformation of this flat surface in 2d to 3d we achieve via induced curvature to the structure, applying to bend the grid elements. The materials used for this type of construction are available and common ones are available on the Themarket.new
Elastic grid shell is one of the subgroups of lightweight structure that can be freely used to unfold the free-form spaces and make the application of the grid flexible as well as movable. Furthermore, their installation does not need complicated installation. Lightweight grid constructions are especially needed for realization where large spans and low self-weight are required and do not have to be straight, at the same time the satisfactory curved shape for the designer is based on iteration during the state of the form-finding process. Our goals are to analyze how the virtual design of such a structure becomes real according to elastic deformation Figure 4.2 and to use it in reality with different scaling for public spaces.
Yet we used a small physical model with a small budget for a better understanding of the kinematic behavior of such free form finding substructure, to serve for further development and their easy installation, and expansion at various scales in the future. This setup procedure makes the doubly curved surface more easy, quick, and more material efficient. The creation of such constructions is aesthetic, functional, and special, in addition, they are nice because the form finding of the surface is curved, which brings us closer to nature and gives us a sense of freedom with its parametric design. The creativity of elastic grid shells is the transformation analysis of the structure that the
Sabah Shawkat©
We try to understand the conceptual design of elastic grid shells in all its difficulties, and we try to find a solution for their theoretical, structural, and technical concepts. An elastic grid shell is a freeform non-Euclidean structure, generally doubly curved, but formed out through the reversible deformation of a normal and originally flat structural grid. This type of grid shell, known as an elastic grid shell, offers a very elegant method to create freeform shapes from an originally flat and proper grid Fig. 4.2, which indeed has many practical advantages: planar initial geometry, ordinary connection nodes, modular cross-sections, and so on. Note that the term rigid shell is often opposed to the term elastic grid shell to indicate net structures that behave like shells but are not formed in an active-bending process.
69
position of the form-finding grid system is usually found geometrically, which is the function of networks of elastic grid geodesic curves. This elastic-kinematic mechanism for Set up the free-form finding substructure offers a non-Euclidian form simply call it a curved shape surface during the installation of geometry, therefore we realized the boundary conditions of the anchors.
Both Grasshopper and Generative Components are based around graphs (a mathematical name for a type of flowchart) that map the flow of relations from parameters, through userdefined functions, usually concluding with the generation of geometry. Changes to parameters or the model’s relationships cause the changes to propagate through the explicit functions to automatically redraw the geometry. Usually, we use the Kangaroo tool when a quick form-finding procedure is needed in conceptual design. First, a simple NURBS surface has been divided in u,v grid, and then used as the reference geometry for a formfinding test. In the setup of the model we start to constrain and anchor the number of points at corners, and the simulation of a hanging model will be run by a kangaroo solver plug-in.
70 input data come for the planar surface design, where the output data are achieved from a 3d curved surface grid, this can be set up simply by pulling at least the two corners at the planar state with applying some additional bending.
The bending and twisting behavior of the strips can be analyzed by using different characteristics of materials and cross-sections. A parametric model is special not for what it does but rather for how it was made. In this way, the utilization of parametric models in the computerized plan permits architects to depict the geometry of their model with adaptability and make conditions between the components of the model, using particular rules and limitations.
Parametric models, using grasshopper inside Rhino using kangaroo plugin to find physical Form finding, which is one of the most powerful designs in contemporary architecture today, leads to creating forms, gravity, tension, minimal surfaces, compression, relaxation, and optimization are known in the realm of physics Fig. 4.3.
To make parametric models, designers utilize algorithmic editors that ordinarily consolidate visual programming dialects (like Grasshopper inside Rhino3d,), to overcome the imperatives of the interface, and to design specifically, overseeing not the form (with the plan devices given by common program packages), but the code that produces the shape. In this way, the designer can define the associations of the parts of the parametric model into code, so that an alteration within the parameters that depict it'll, cause a facilitated general upgrade in this way by watching the varieties of the created comes about. Visual programming involves representing programs not as text but rather as diagrams (https://www.slideshare.net/HaneenFraihat/parametisim).
Sabah Shawkat©
Fig. 4.3: Grasshopper Script created by the author, physical form finding
Fig. 4.4: Form Finding of the elastic geodesic dome using grasshopper inside Rhino, (models created by the authors)
71
As we observe from Fig. 4.3, how the code produces the shape, changing the parameters of an initial rectangle or in Triangular remesh of the model relationships cause the changes of the entire form of physical form finding. In this way, the designer can define the associations of the parts of the parametric model into code. These relationships between the parameters and the components offer one useful tool for producing architectural designs converting aims into abstracted shapes, this modern geometry became more attractive in the architectural design process with great innovations from form-finding stages to the final fabrication.
Sabah Shawkat©
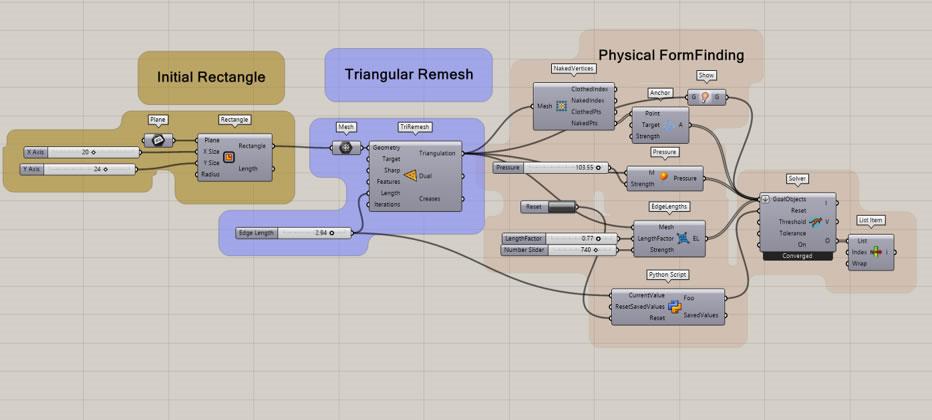
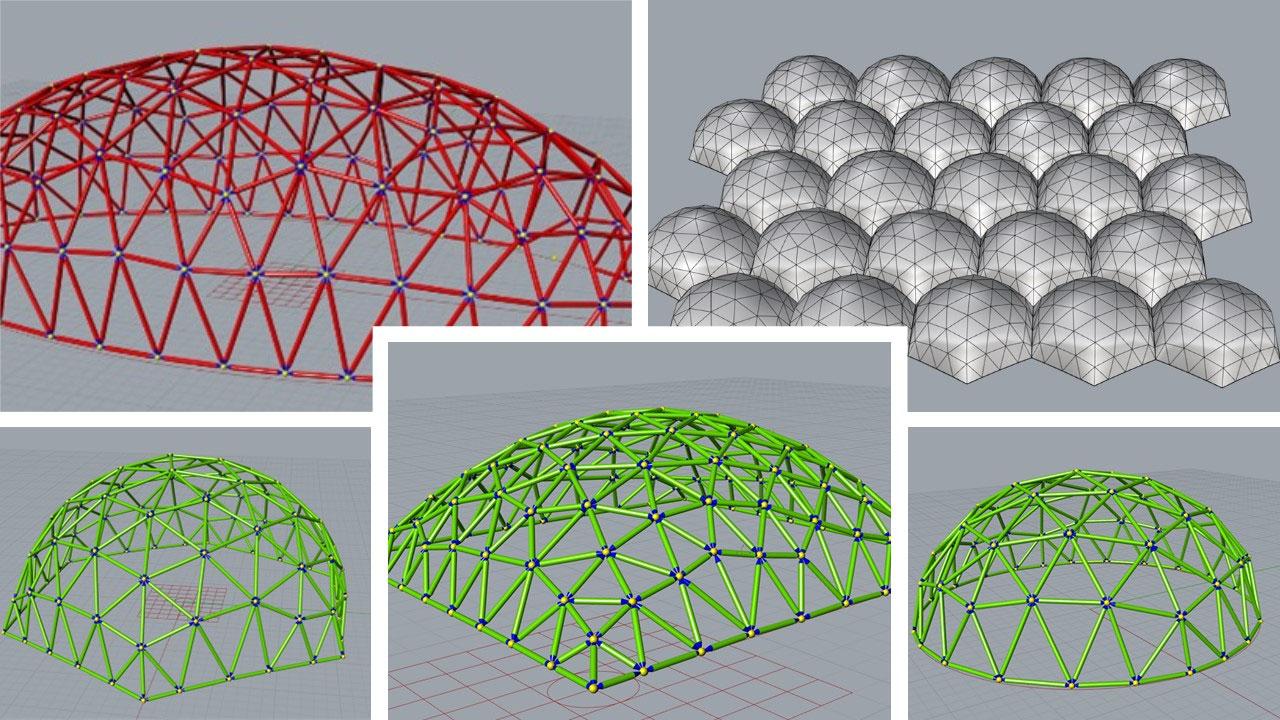
72 Fig. 4.5.: Parametric Physical Form-Finding of EGG Shells (models created by the author) Sabah Shawkat©
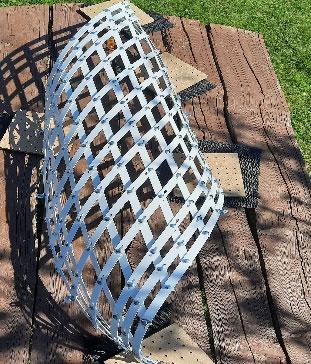
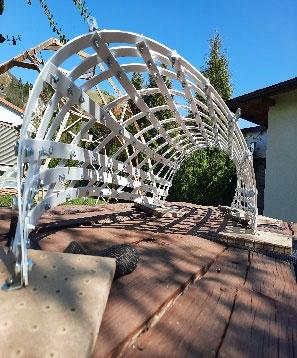
Both types of structures depicted in Fig.5.1 use separate elements for tension and compression as we can nicely see in this visual example. These tensegrity systems can be defined as spatial structures consisting of compression (struts) and tensile (cables) components that stabilize each other through pre-stress, tension, and compression work together to resist the applied load.
The term “geodesic” can be understood as the shortest distance between two points (Fuller,1962).
The geodesic structure consists of as many struts of the same length as possible as well as congruent surfaces. It is a network of equal triangles whereby the cross points are always situated on the surface. This triangulation guarantees the strength and rigidity of the ball-shaped structure. There is no direct contact between the compression elements as seen in the models in Fig. 5.1. The struts are combined into triangles, pentagons, or hexagons, whereby each strut is aligned in a way that each connection point is held in a firm position. This guarantees the stability of the whole structure. Tension is distributed equally to all parts of the whole construction. Increased tension in one part provides increased tension in all parts. A global increase in tension is balanced by an increase in tension in various parts. Whilst tension is thus distributed evenly in the whole system, only individual parts are balanced by compression. There is a balance between tension and compression, we can define the system as “stable self-equilibrium”. The tensegrity network is a stable and at the same time adaptable construction. The whole system reacts to an outside force with an adaptive tension distribution.
The dome is an architectural art element, it may be positive synclastic structures or negative anticlastic Structures. Domes are said to be those whose structure is in a state of compression. We know the dome as a corbelled dome, compound domes, cross arched dome, onion dome, oval dome, Parabolic dome, geodesic dome, sail dome, saucer dome, umbrella dome, glass domes, transparent plex glass domes, bamboo domes, fractal dome.
Sabah Shawkat©
73 5. GEODESIC DOME
The dome as an art that was made by the author of this book is the geodesic dome.
Domes have a long architectural lineage that extends back into history, and they have been constructed from mud, stone, timber, brick, reinforced concrete, steel, glass, and plastic over the centuries. The symbolism associated with domes as a structural system was an evident case starting from Mesopotamia.
The formation of rod shells was caused by the need to lighten the surface shell structures and simplify their construction. By replacing the full material with discrete rods, it is also possible to illuminate the roofed building and eliminates the need to build a complex formwork, reinforcement binding, and demanding concrete. The first reed shell was the already mentioned Šuchov exhibition pavilion from 1896. In the 20th century, the first buildings were the Zeiss Planetarium in the German city of Jena in 1925, the roof of the market in Frankfurt in 1927, and the E l Frontón Recoletos theatre in Madrid in 1935. In the next 30 years, several rod shells were made on a smaller scale. In the case of all these constructions, these were simple structures that were mathematically definable. The first free-form rod shell was the Multihalle in Manheim in 1975. It was a wooden structure with a maximum span of 60 meters and a maximum height of 20 m. The shape of the building was determined using a suspended model and the supporting structure consisting of a square net of wooden slats with a cross-section of 2x50 / 50 mm. At the Belarusian exhibition in 1896, the Russian engineer V.G. Šuchov built several exhibition pavilions, which went down in history as ground-breaking and thus indicated the trend that the 20th century will follow. One of the constructions was the first-rod shell, which was curved in two directions and therefore its rigidity did not depend on the amount of built-in material but its shape. The second was a rotunda, the conical shape of which was formed by crossed sheet metal lamellas that passed from the central upper ring to the circumferential lower ring. The geometry of the rotunda was curved in two directions and its forming lamellas were prestressed by their weight. This construction was the predecessor of the Sabah Shawkat©
74 Fig. 5.1. Tensegrity as a Geodesic Dome (Shawkat, 2020, Shawkat, 2021)
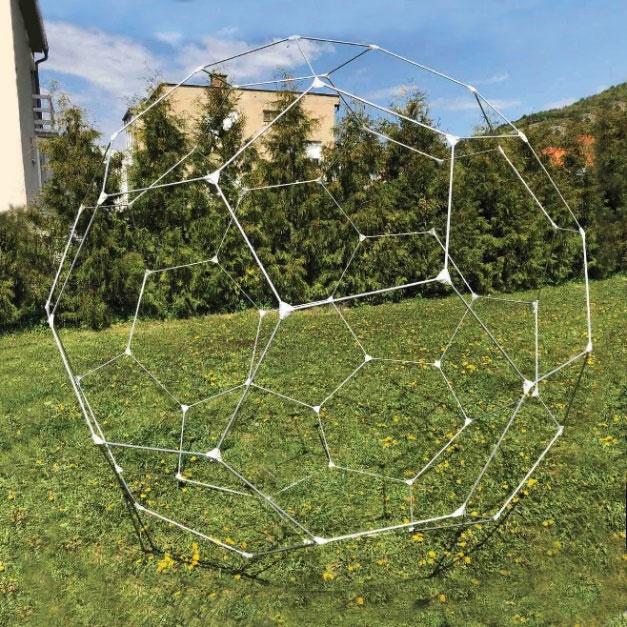

According to a grasshopper, we design by means of the weaverbird plugin, how you can use it to produce much of the mesh model as you can see here below, and to use this plugin to produce smooth mesh for the curve, points, or surfaces, as well as we use plugin Cocoon with kangaroo too to create easily 3d model by means of curves and points, changing the position of curves and points will change the form and position of the entire structure.
The blob (meta-ball) system gives much more morphogenetic scope to algorithmic selforganization, it is at the same time more versatile and complex organizational logic than NURBS modelers that are manipulated via pulling control points Fig. 5.3. It is an approach to building design that attempts to view architecture in bits and pieces and may seem to have no visual logic.
75 first cable networks. The magnitude of the external load in the case of modelling shell structures only shapes its shape formally.
Blob geometries, as a new type of free-form architecture, became noticeable landmarks with the progress and the developments of spatial structures. These irregular forms need innovative design processes and advanced technological and structural systems that vary from traditional and familiar systems. Blobs, which are distinguished as irregular geometry, are not instituted on euclidean principles of plane surfaces.
Sabah Shawkat©
Fig. 5.2. Process of Thinking in the Grasshopper Programme
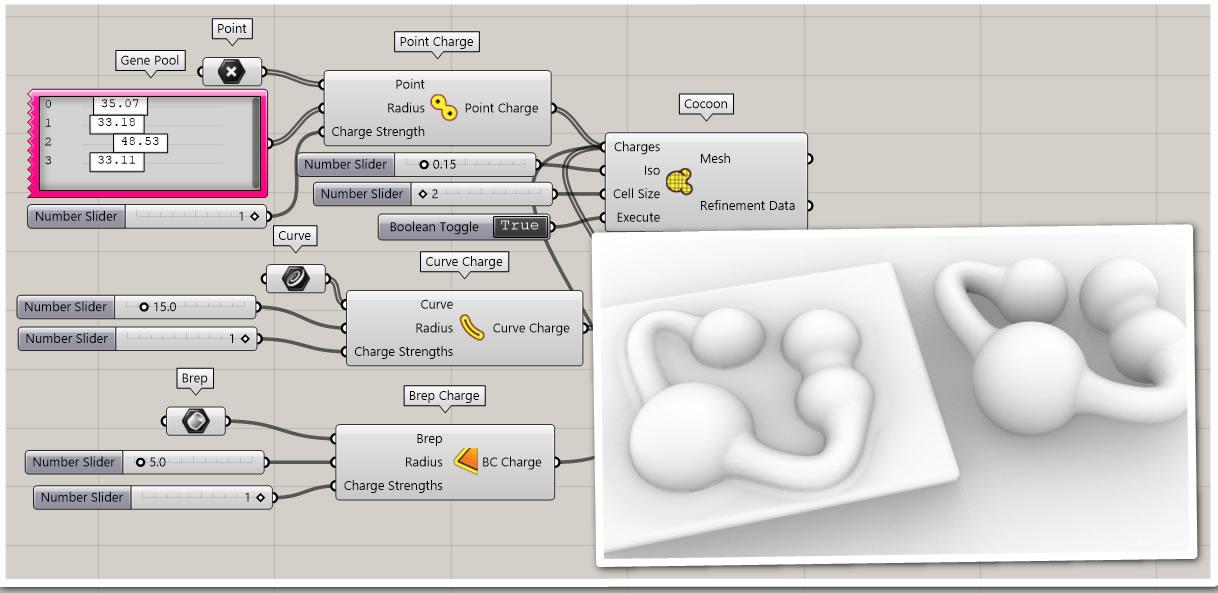
76 Fig. 5.3. Process of Thinking in the Grasshopper Programme Fig. 5.4. Physical model of multi geodesic dome Fig. 5.5. Process of Thinking in the Grasshopper Programme Sabah Shawkat©
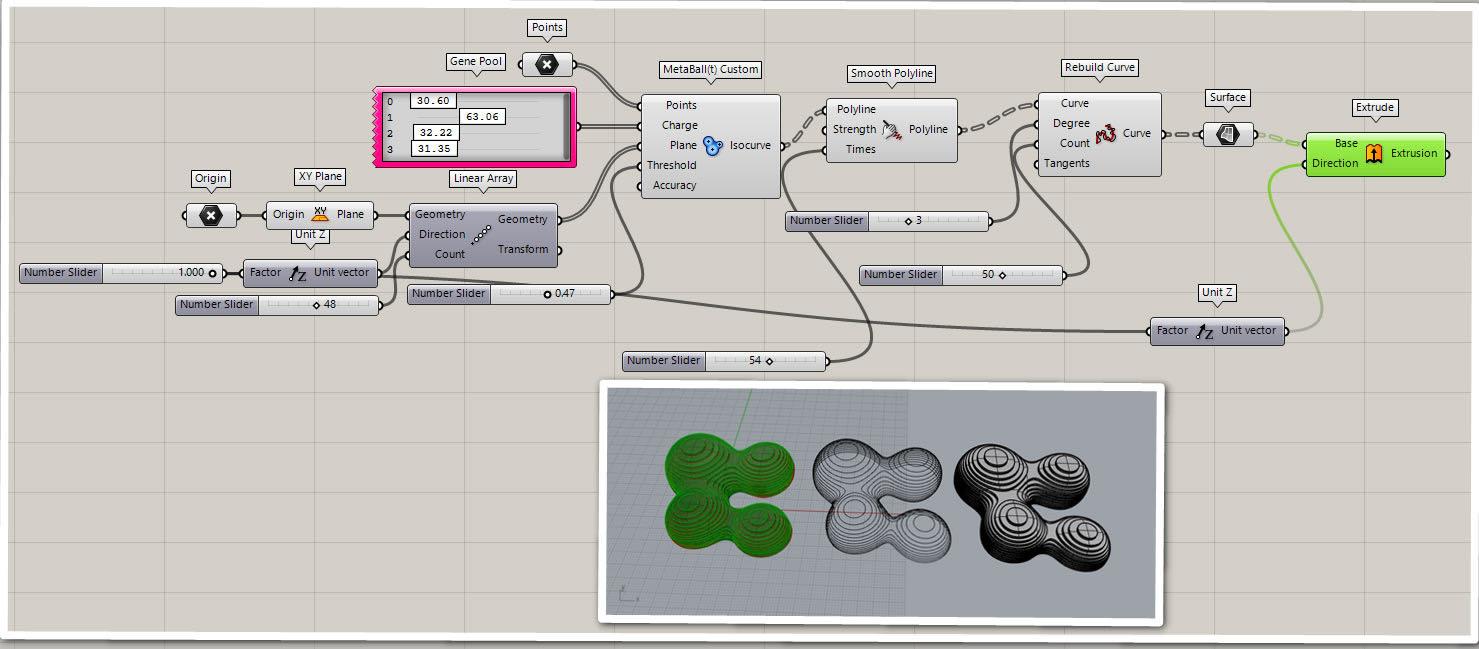
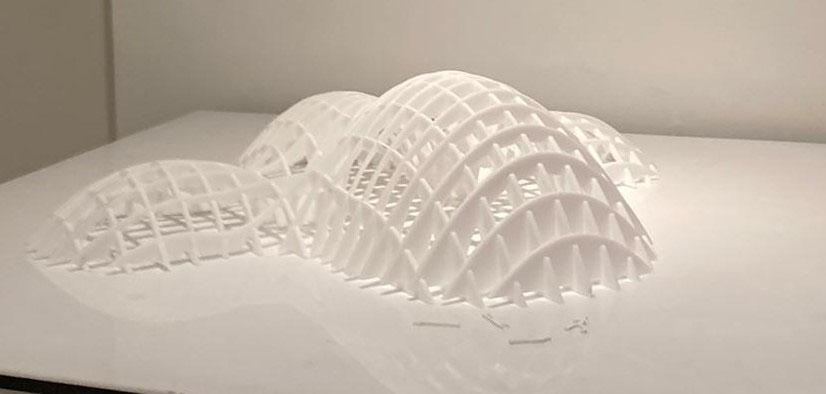
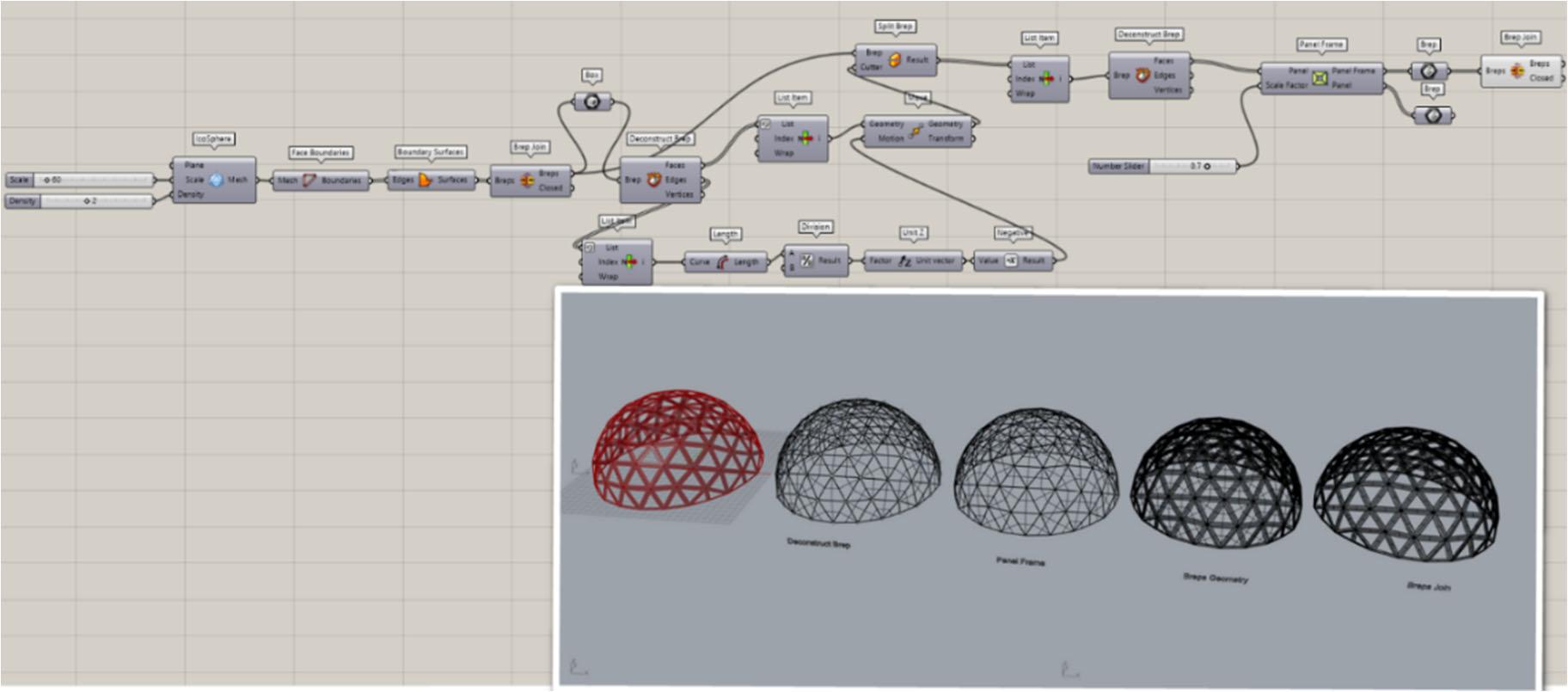
77 Fig. 5.6. Segment =6, Pressure 0.05, Edge factor 2.20, Radius =12 2 iterations 3 iterations 4 iterations 5 iterations 6 iterations 7 iterations 8 iterations 9 iterations 10 iterations 11 iterations 12 iterations 13 iteration 14 iterations 15 iterations 16 iterations 17 iterations Fig. 5.7. Segment =8, Pressure =0.05, Edge factor= 2.20, Radius =12 2 iterations 3 iterations 4 iterations 5 iterations 6 iterations 7 iterations 8 iterations 9 iterations 10 iterations 11 iterations 12 iterations 13 iterations Sabah Shawkat©
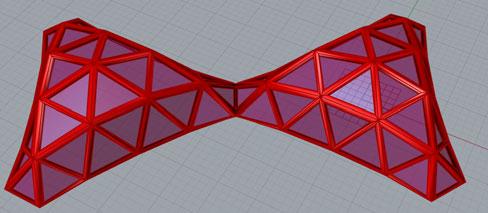
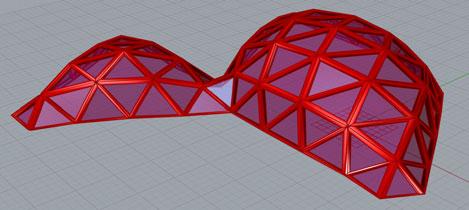
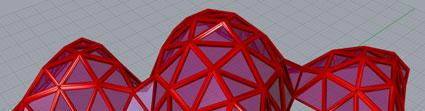
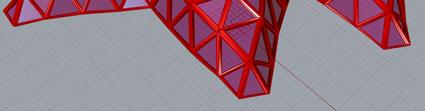
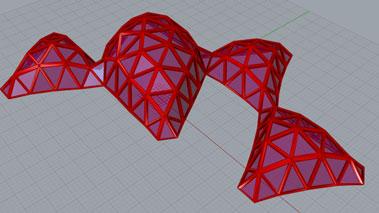
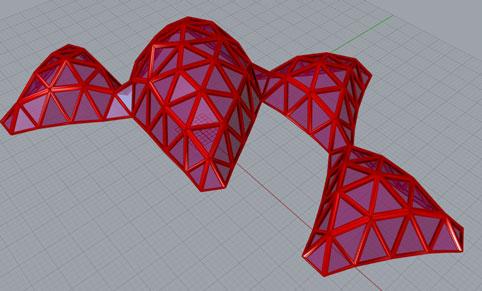

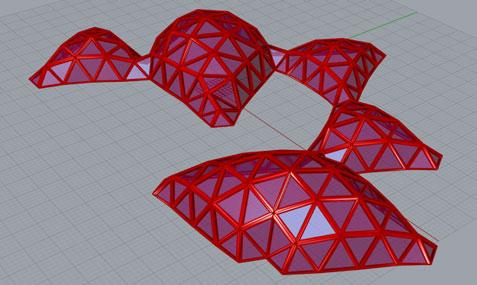
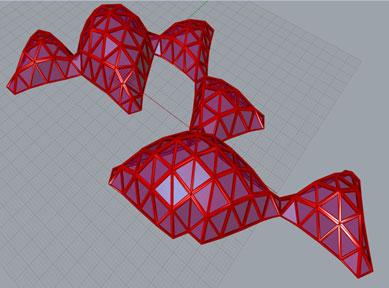
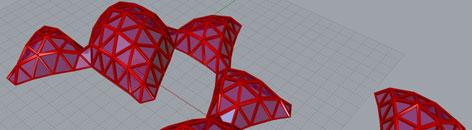
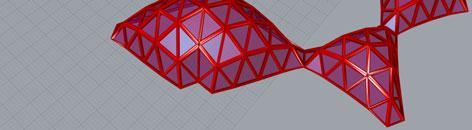
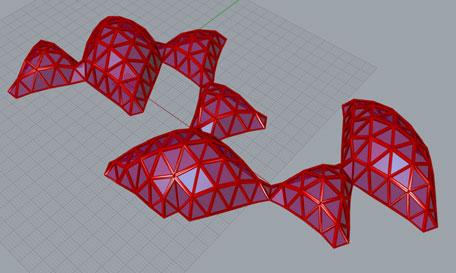
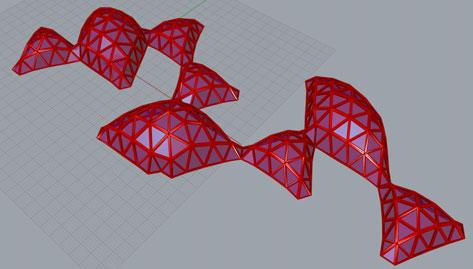
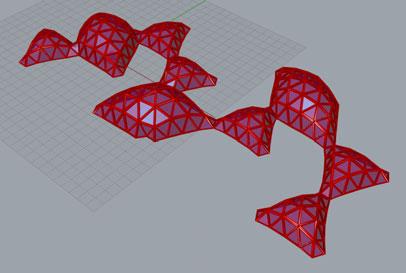

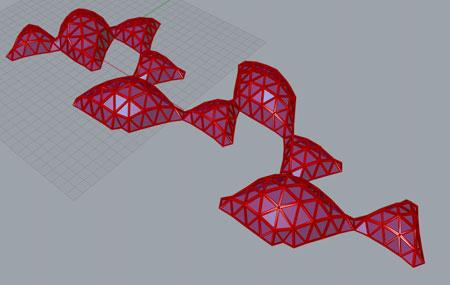
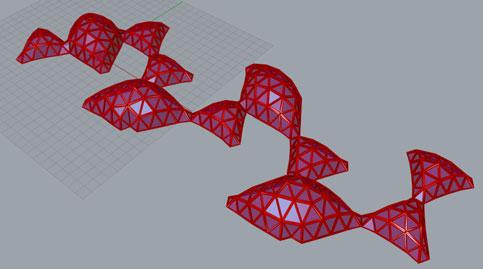
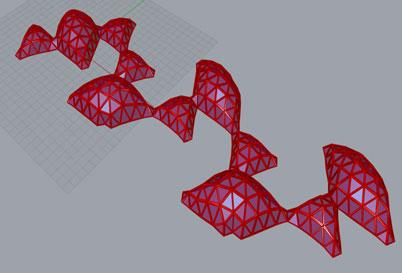
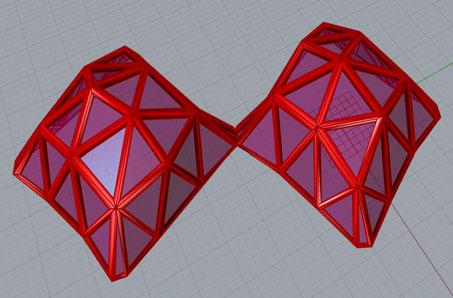
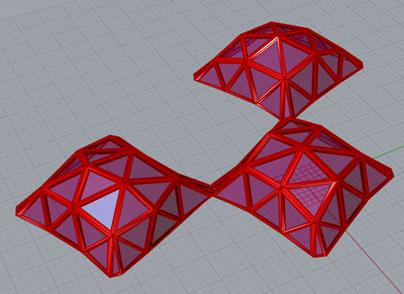
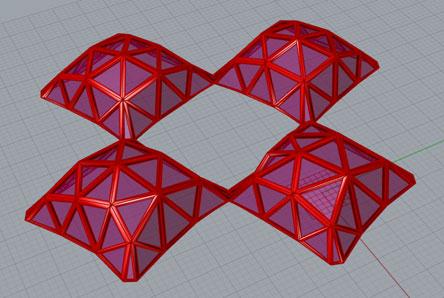

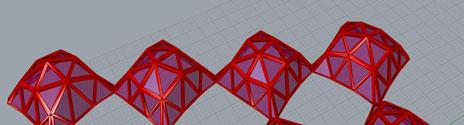
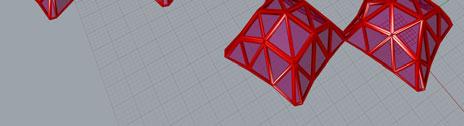
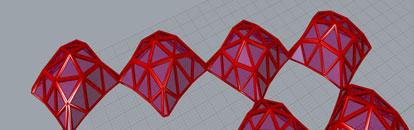
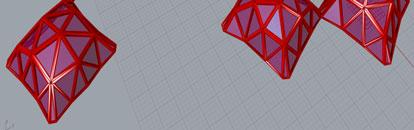
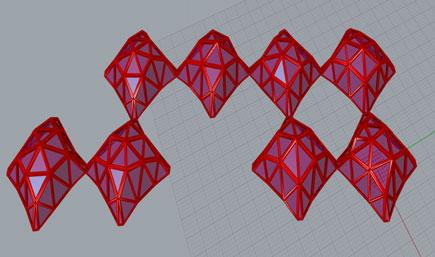
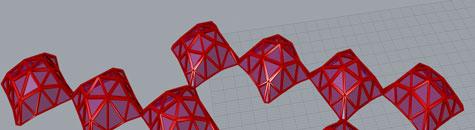
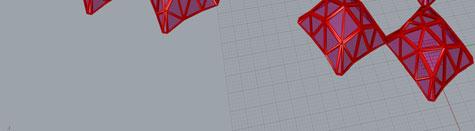
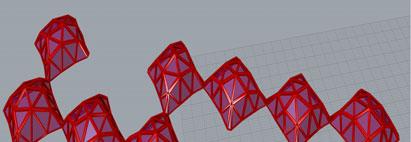
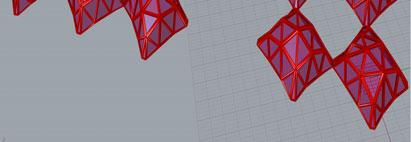
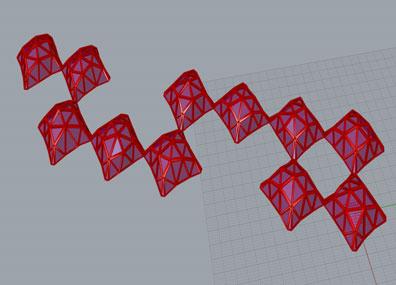
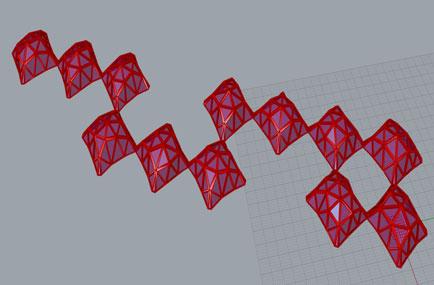
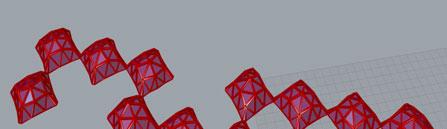
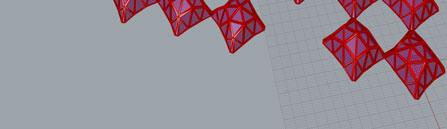
78 Fig. 5.8. Segment =10, Pressure= 0.05, Edge factor= 2.20, Radius =12 2 iterations 3 iterations 4 iterations 5 iterations 6 iterations 7 iterations 8 iterations 9 iterations 10 iterations 11 iterations 12 iterations 13 iterations 14 iterations 15 iterations 16 iterations Fig. 5.9. Segment =6, Pressure= 0.05, Edge factor =1.10, Radius =12 2 iterations 3 iterations 4 iterations 5 iterations 6 iterations 7 iterations 8 iterations 9 iterations 10 iterations 11 iterations 12 iterations 13 iterations Sabah Shawkat©
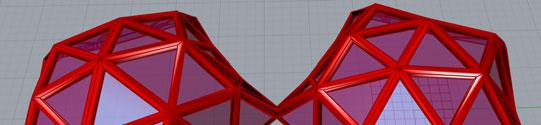
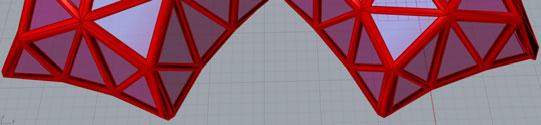
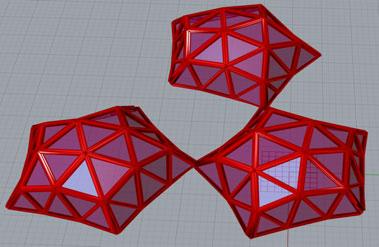
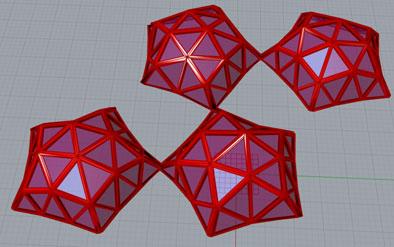
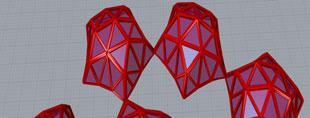
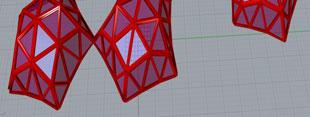
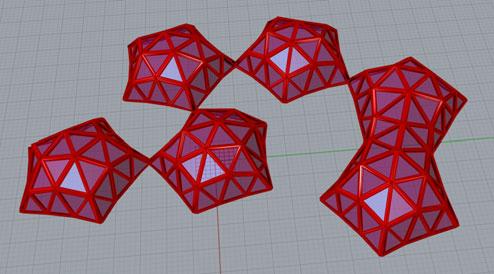
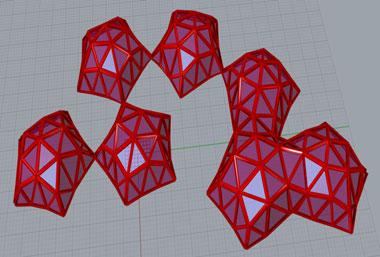
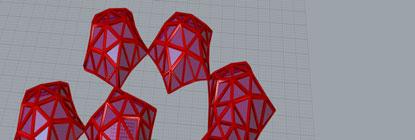
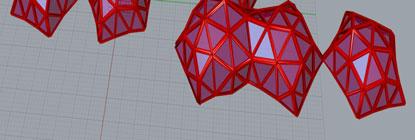

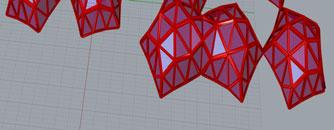
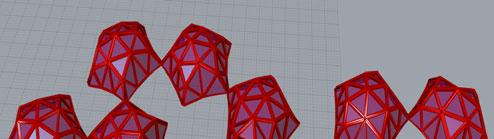
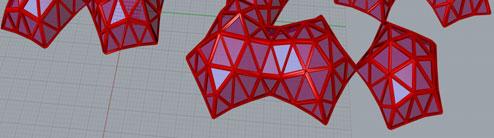
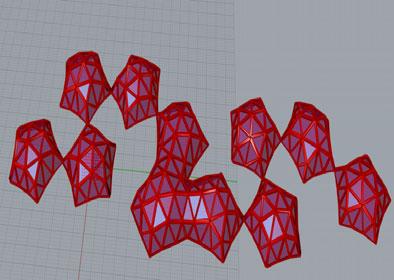
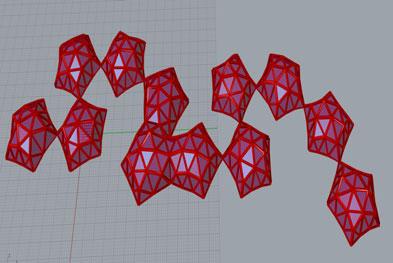
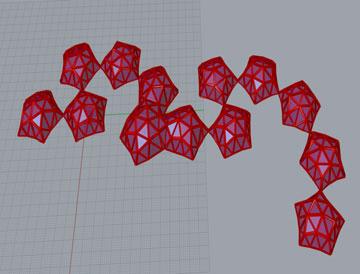
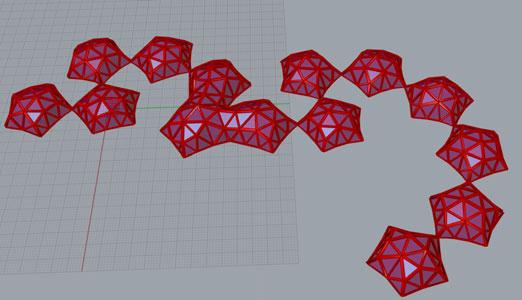
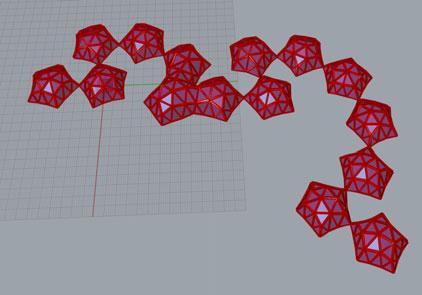
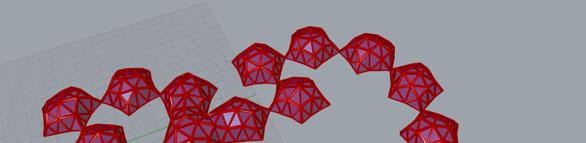
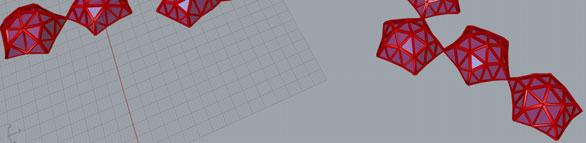
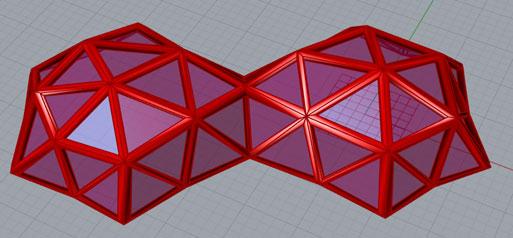
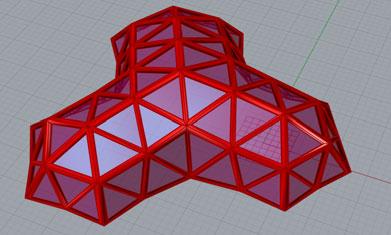
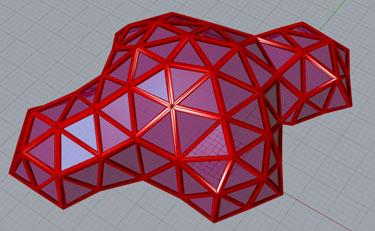
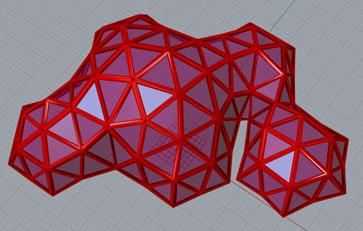
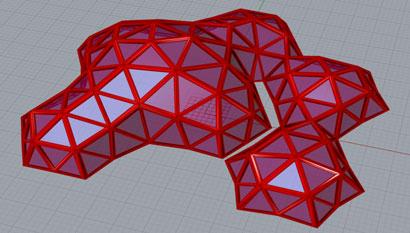
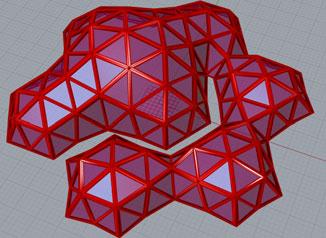
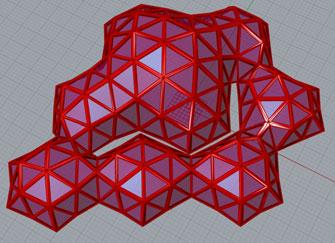
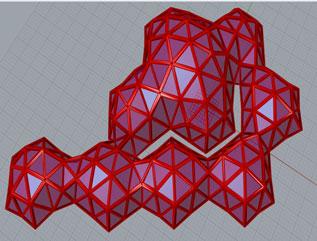
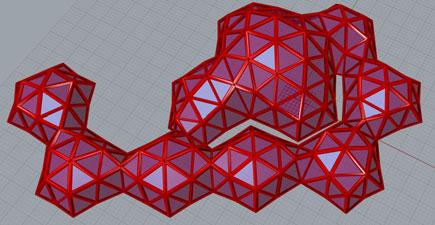
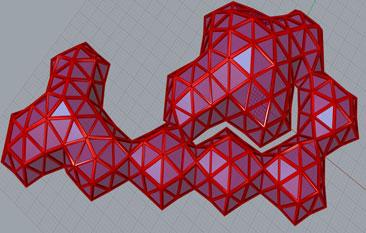
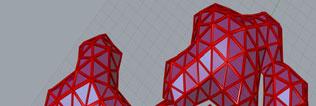
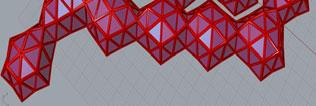
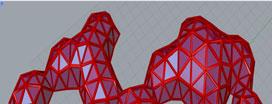
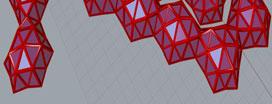
The potential use of membrane structures in the future regarding anticipated climate change is the Eden Project in Cornwall, the UK by Grimshaw Architects Fig. 5.11, which has been open to the public since 2001.
79 14 iterations 15 iterations 16 iterations Fig. 5.10. Segment =6, Pressure= 0.05, Edge factor =0.05, Radius =12 2 iterations 3 iterations 4 iterations 5 iterations 6 iterations 7 iterations 8 iterations 9 iterations 10 iterations 11 iterations 12 iterations 13 iterations 14 iterations 15 iterations 16 iterations Light geodesic dome structures are particularly suitable for applications where large spans and low weight are required. This makes them potential candidates for architecture purposes.
Sabah Shawkat©
The Eden project is a complex of botanical gardens and two large artificial biomes, which consist of several intersecting domes. Thousands of plant species from different climatic regions of the world are gathered in the so-called "biomes" for research, but also for ordinary visitors. The forest biome, a tropical and humid greenhouse, was built in the second phase of the Eden Project. This
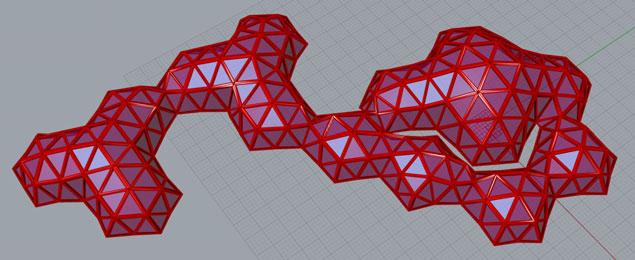
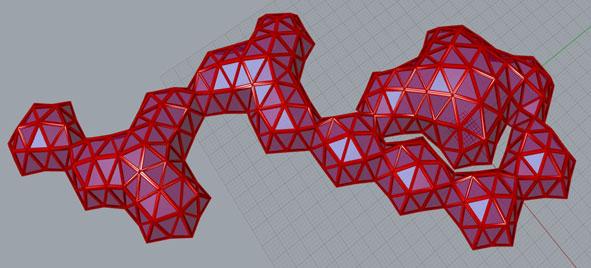
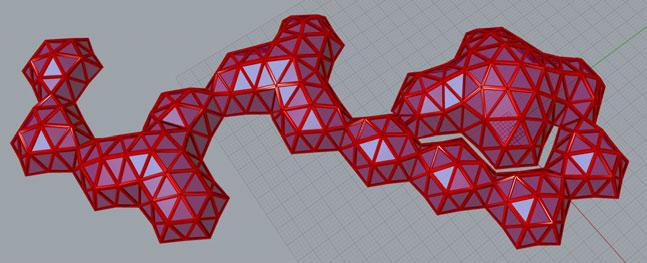
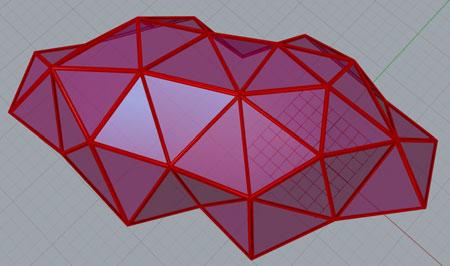
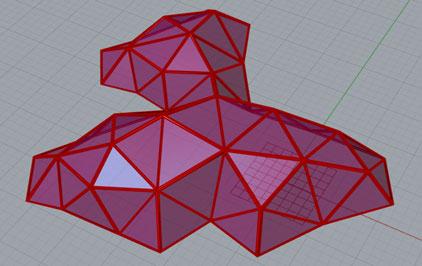
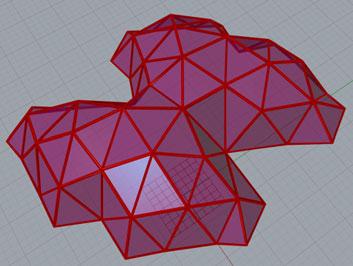
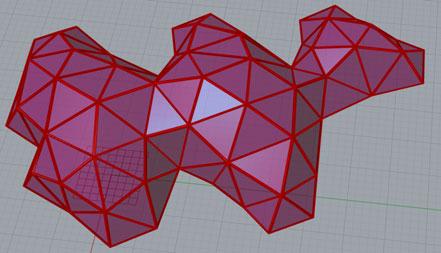
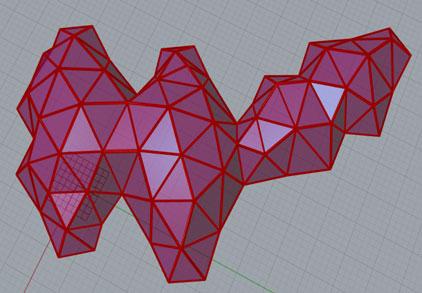
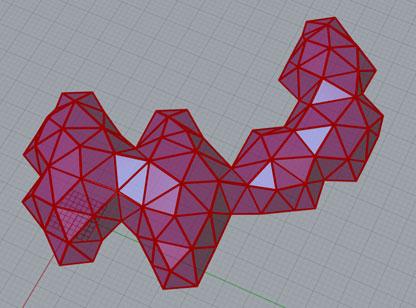
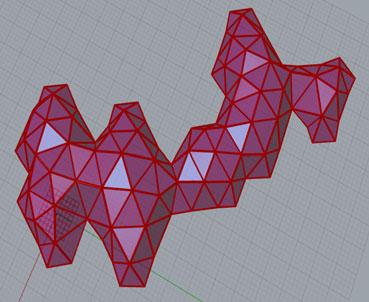
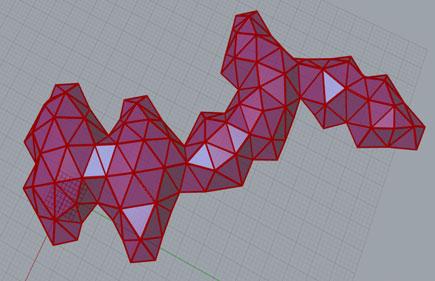
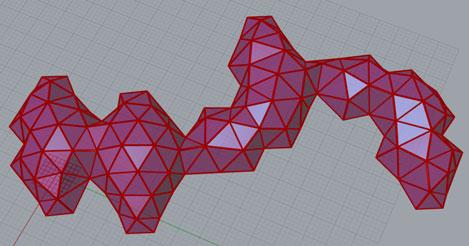
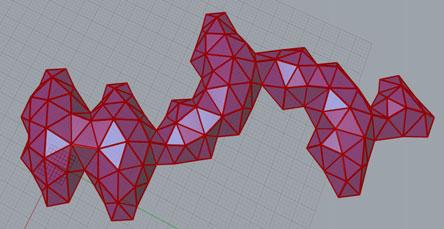
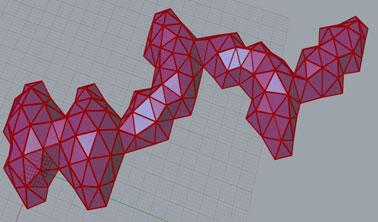
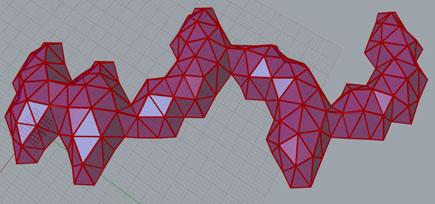
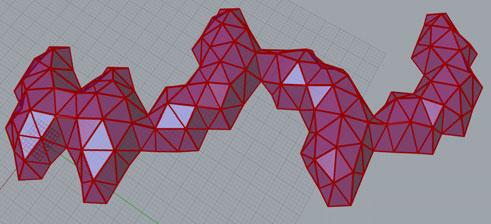
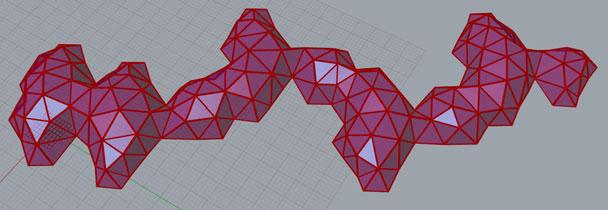


80 greenhouse mimics the natural environment of the tropical rainforest and hides more than a thousand species of tropical plants. The project is also interesting in the fact that it was created on a modified surface kaolinite quarry, which succeeded in re-creating a "green zone" with its irreplaceable functions in an environment destroyed by mining.
membrane constructions in a similar way could in the future make it possible to create "green oases" even in an inhospitable environment or to secure crops in such areas. In the example of the Eden project, we can also see innovations inspired by nature, currently known as biomimicry. The use of the hexagonal shape as a solid, naturally occurring structure together with EFTE foils led to solid construction, but at the same time very light. Biomimicry idea is a relatively new scientific discipline that examines "nature's best ideas" and they then try to emulate and solve many environmental problems associated with the production and consumption of products. A good example of architecture is the Eastgate in Harare, Zimbabwe. Termite buildings were the inspiration for this building. Efficient ventilation and cooling system allow the termite press to maintain a stable temperature and humidity throughout the colony's life. Similar principles as ventilation chimneys, massive stone elements protecting windows from the sun, heat exchangers, etc. were also used in the construction of Eastgate. Thanks to this, the temperature in the building, even without air conditioning, thus shows a pleasant distance from the outside environment all year round only with the help of a system observed from termites. Eastgate consumes less than 10% of the energy of a common building of the same size. Inspirations of this nature can also be found in nature in the case of future development and the use of membrane structures in connection with the impact of climate change. The construction of a dome - a "geodesic dome" of acceptable size in terms of the possibilities and properties of building materials proved to be a demonstration output of the need for partial fulfilment of the goal in the field of material testing. We attempted to change all proposal requirements into shapes and spaces by adopting processes and a series of aimoriented steps. However, a proper design means that it has an identity where all components agree with the context and requirements of modern and future times.
The success of the whole project also lies in the fact that the originally uninteresting and miningmarked area has become a place of multifunctional use, as evidenced by the huge number of visitors (almost two million visitors in 2001, the second most visited place in the UK outside London).
Sabah Shawkat©
Biome domes are made of steel structures made of interconnected steel tubes forming hexagonal cells. The cladding is made of inflatable cushions of three layers of ETFE foil, which maximizes ultraviolet sunlight, and allows you to maintain the necessary climate for tropical plants.
Fig.5.11. Eden design project as a beautiful global garden landscape We attempted to change all proposal requirements into shapes and spaces by adopting processes and a series of aim-oriented steps. However, a proper design means that it has an identity where all components agree with the context and requirements of modern and future times. As we used form-finding process the digital program grasshopper inside rhino helped us to parameterize the geometry and make a quick decision on the final shape of the geodesic dome Fig.5.14, we further assessed the final modified nodes using FEA. The joints prototype was selected for FEM analysis of structural elements. It is characterized using 11 375 steel and consists of a total of four parts. The middle, axial part consists of a tube with an outer diameter of 20 mm and three arms, fired by laser technology from sheet metal with a thickness of 2 mm Fig. 5.12. Fig. 5.12. FEM joint analysis and the final version of the joint after the application of the surface treatment Sabah Shawkat©
81
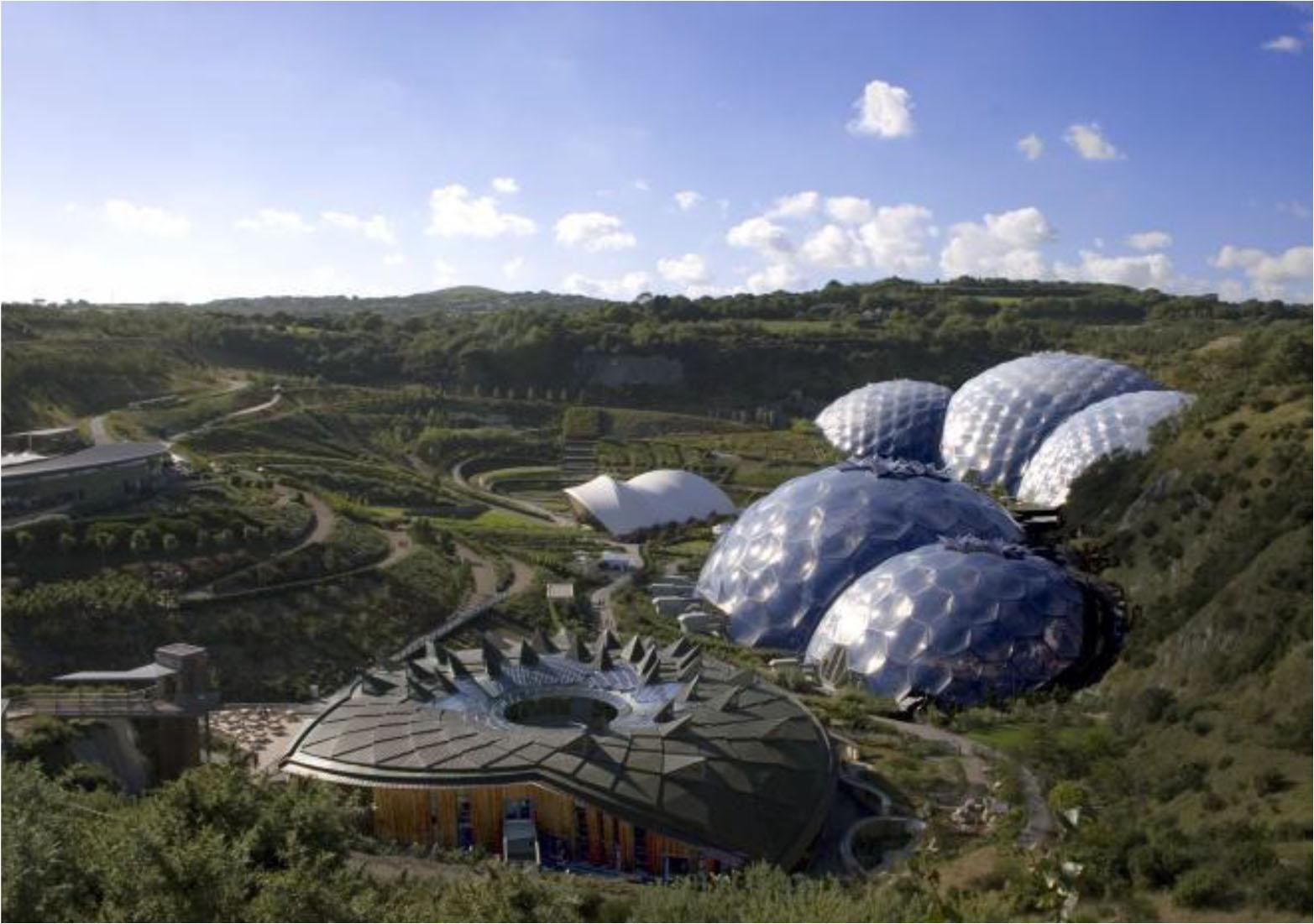
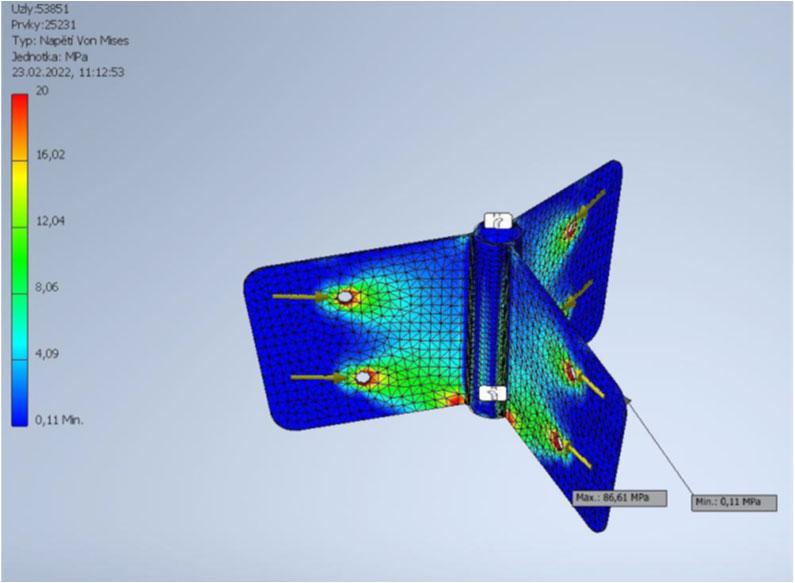
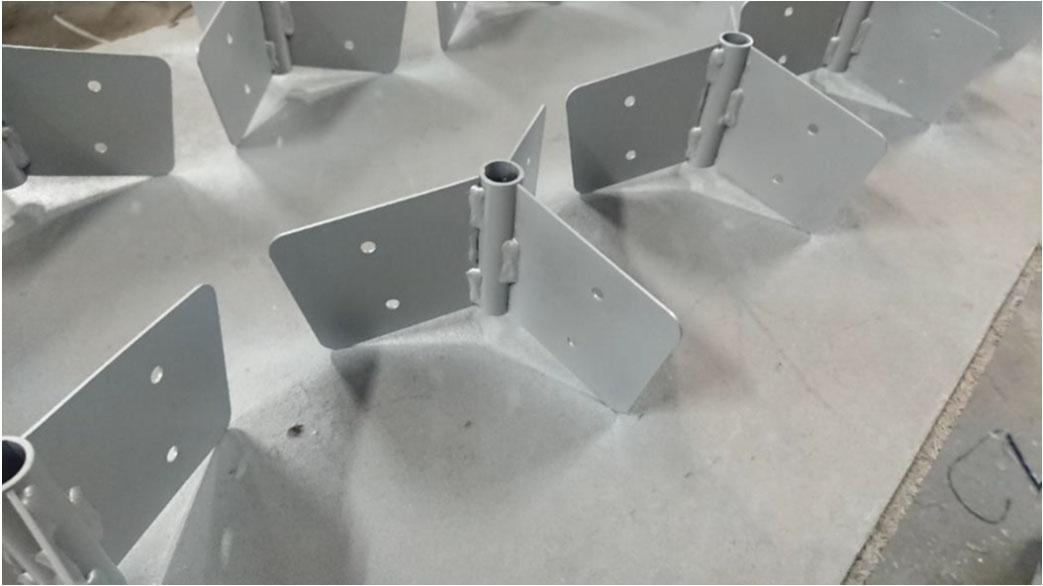
Sabah Shawkat©
Fig.5.14. Grasshopper Script created by the author, physical form finding
82 From the obtained data it can be clearly stated that the solution is satisfactory and the production of 30 pieces was started. Fig. 5.13. Fig.5.13. Traditional Geodesic Dome 1:1, physical form-finding
It follows from the above that this is a multidisciplinary project, which requires a targeted and responsible approach. To increase safety during construction and the duration of the installation, ground screws as well as punch holes in individual segments are prepared. Their task is to open under the influence of strong winds and thus prevent the collapse of the membrane by direct wind passage without the effect of a "sailboat".
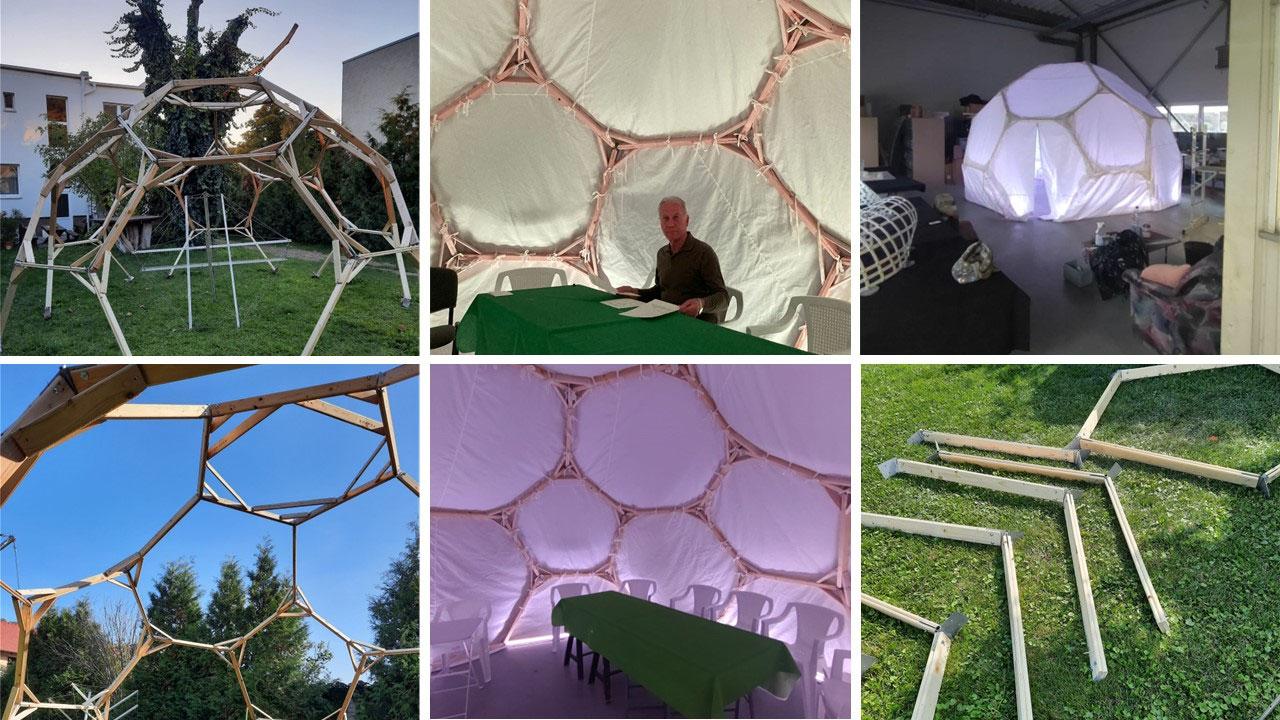
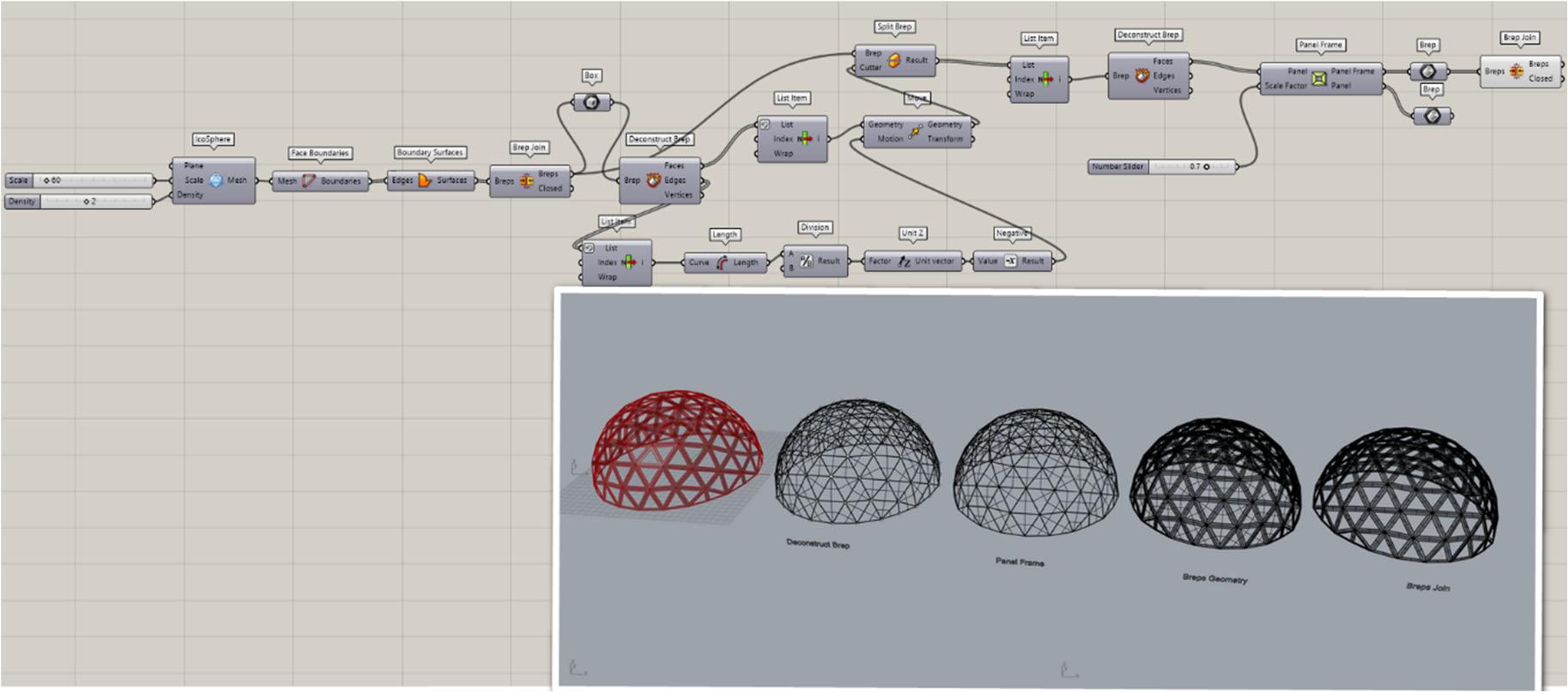
x. Both distances are measured from
We also include the arch among the planar structures. Nowadays, they are most often used as supporting elements (e.g., bridge girders), but it also serves as an architectural element - the shape of a parabola, which has the highest load-bearing capacity from a static point of view. Arches have already appeared in architecture in the ancient past, in Mesopotamia, then in Ancient Greece and Rome in the form of triumphal arches and aqueducts. What we get at the end of this, is not a surface, it’s a boundary representation because each one of these curves is slightly different in the way that it's drawing with its parametrized. If we want to get a surface, we had to make these curves as similar as possible, so we rebuild those curves to have the same parameters. With panel tools, we create the surface using u and v. Catenary, in mathematics, which means a curve that describes the shape of a flexible hanging chain or cable. Any freely hanging cable or string assumes this shape, also called a Chinetti, if the body is of uniform mass per unit of length and is acted upon solely by gravity. This type of geometry curve is strong because they redirect the vertical force of gravity into compression forces pressing along the arch's curve The equation for the catenary can be written in the form we now call the hyperbolic cosine (R. Osserman, 2010). = cosh = ½
(ex + e-x)
The published equation of the centreline of the St Louis arch, so with a = 0.01, our arch equation becomes, with the constants rounded to three digits, is Fig. 6.1. Physical Model as a Design Tool, created by the author
y
axes. y68.8cosh0.01()1() coshax() eax e ax 2 y68.8 e0.01x e 0.01x 2 1 Sabah Shawkat©
83 6. CATENARY CURVE
An arch consists of two weaknesses which, leaning one against the other, make a Leonardostrength.daVinci
y
x
A determination of the equation of the arch will give the height of any point on the arch at a given horizontal distance chosen
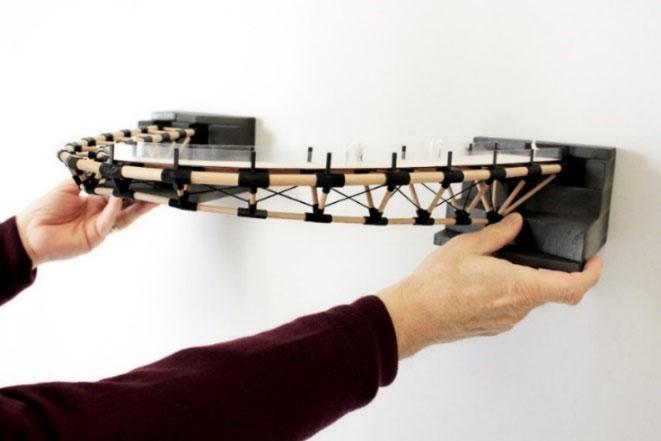
84 Fig. 6.2. Catenary Curve-Determination of Forces
A determination of the equation of the arch will give the height y of any point on the arch at a given horizontal distance x. Both distances are measured from chosen axes. An equation is, of course, meaningless unless one knows the x and y axes, and the origin, the point where they intersect (P. Calter Assume2006).auniform string of constant linear density. Given these physical parameters, determine the equation of the catenary y(x), and the string length is fixed (P.Calter, 2006). W is the total weight of the cable, and w is the united weight of the cable, y is the distance from the origin to the top of the cable, c is the distance from the origin to the bottom of the cable, s is the length of the cable T is a force in tangent, T0 is tension force in the horizontal direction. We need the equations to relate all these unknown values, to do that we need to know We want to consider one more thing, we go to start with the case when the two attach points are in the same elevation when the cable is supported on two exact same vertical heights, which means we have another constantly called sag of the cable.
Objective: Relate T and T0 to a, find dx in terms of ds
cosh 2x()sinh 2()x 1 a T0 c T0 TT02 2 s 2 T T02 2 s 2 T a2 s 2 Sabah Shawkat©
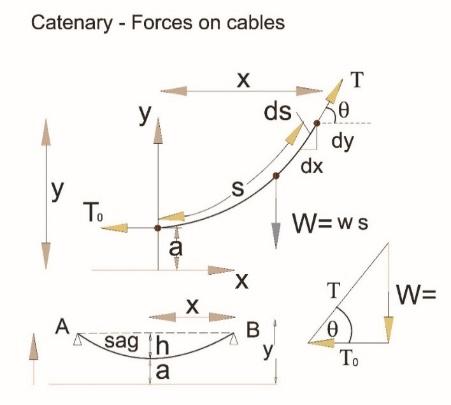
85 Objective: Relate x to s Objective: Relate y to x and a T a 1 s a22 TT 0 1 s 2 a 2 dxdscos dxds T0T dxds a T0 1 s a22 dxds T0 T0 1 s a22 ds 1 s a22 W s a T0 T a2 s 2 sinh0() 0 sinh 1()0 0 cosh0() 0 cosh 1()10 0xx1 d 0s s 1 1 s a22 d xcsinh 1 cs ax sinh 1 as as sinh ax sasinh ax xasinh 1 as 0 a T0 Twa2 s 2 sasinh ax tan () dydx dytan ()d()x dy TW0 dx s a dx asinh ax a dx sinh ax dx cyy1 d 0x xsinh ax d ya acosh ax cosh0() ya acosh ax a yacosh ax Sabah Shawkat©
By such a detailed procedure we found three unknown quantities to express the equation for the catenary curve.
One side of Pointed:
y and h
2 yh a hy a a T0 T a2 s 2 sasinh ax sasinh ax yacosh ax cosh 2x()sinh 2()x 1 y 2 s 2 a2 a2 cosh 2 ax a2 sinh 2 ax a2 cosh 2 ax sinh 2 ax a2 T0 a T a2 s 2 y 2 y T y yr 2 x2 yr 2 x2 yb 1 ax22 ykx2 Sabah Shawkat©
86 Objective: relate y,, and s, then relate
One of the most amazingly realized projects in the world as a catenary curve is Ero Saarinen's Gateway Arch in St. Louis has the shape of an Arch are parabola, catenary, and weighted catenary., that is, the form taken by a suspended chain. A catenary is a shape assumed by a hanging chain or a flexible cord of uniform density. A weighted catenary is a shape assumed by a hanging chain whose links vary in size or weight, or by a flexible cord of variable width, or variable density material. The Arch is designed to sway and can withstand an earthquake, however, under normal conditions, the Arch does not sway. I would like to mention just for a better understanding of the catenary curve, we show the equations, for example, here are the equations for the circular, pointed, parabolic, and elliptical arches Fig. 6.3.Circular: Elliptical: a y s
Parabolic:
2
– As the vertical force decreases, the angle θ of the resultant decreases, as the horizontal force H is Theconstant.hyperbolic functions, some basic information, and definitions
– The vertical force V is equal to half the weight of the cable below that point, the other half being supported on the right-hand side.
87 Fig. 6.3. Shapes for the circular, pointed, parabolic, and elliptical arches
Let us look at the forces on a small section of cable Fig. 4. Fig. 6.4. Vertical and Horizontal Forces of Catenary Cable
Sabah Shawkat©
The two horizontal forces H must be equal and opposite, as there are no other horizontal forces acting on this section of cable.
-
– As we go lower along the cable, the vertical force V decreases a constant amount for each foot of cable.
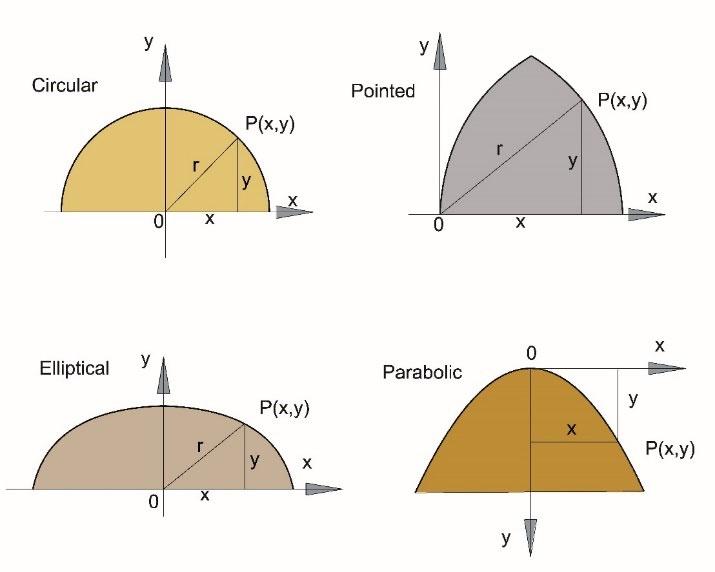
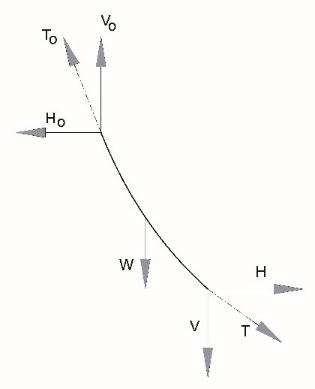
sinhx1() sechx() coshx1() cothx() coshx()sinhx() Sabah
To make form finding with kangaroo 2 in grasshopper. parametric models, permit us to depict the geometry of the model with adaptability, and make conditions between the components of the model, using particular rules and limitations Fig. 6.7. Using sinhx() cschx() Shawkat©
88 Fig. 6.5. Transformation of Catenary Curve to the Horizontal Direction, created by the author If you hang something physically from two points and then flip it upside it creates a structural arch, so to make Catenary Curve you need two points and a length of chain this length of the chain matters because it gives you the kind of hang. Catenary slack you create by hanging two points and pulling down the chain when you want to flip gravity and to manage vector to make it whatever negative gravity to get catenary arch. Then we copy this catenary curve four-time, and plugin each point to create four catenary arches. Create the surface from the curves to get B- rep surface.
e x e x 2 coshx() e x e x 2 tanhx() coshxsinhx()()
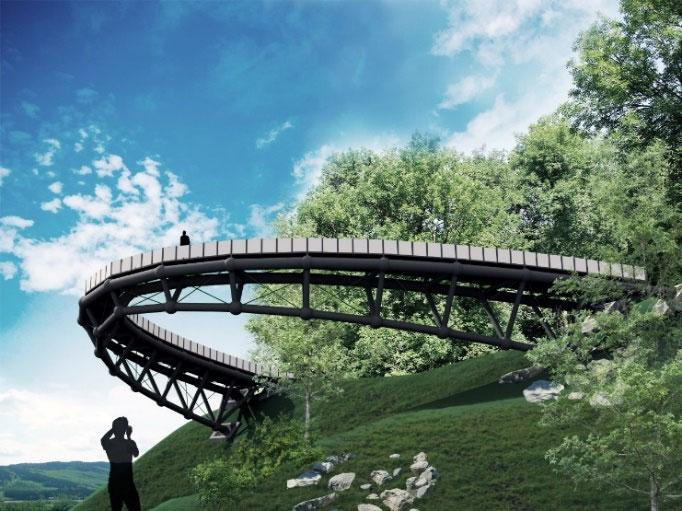
Grasshopper inside Rhino with Kangaroo plug-in Bouncy solver helped us to parametrize our model for better understanding the process of thinking and to show the power of visual
Kangaroo works on meshes, the mesh is not the same as the surface, the surface is a mathematical thing it always has perfect curvature, bouncy solver helps to find form finding consequently to reach equilibrium using the gravity load, force vector in z-direction because its gravity, the weight factor is not very big and strength which is kind of meaningless. Boolean toggle is going to say whether we reset the simulation or not, in the true state it means it’s not operating, in the false state it’s going to run. We anchor the start and end points, to have a proper simulation the anchors should be fixed. Deconstruct the mesh take all the vertices and plug them in for loads, we basically going to create a catenary across every line. Weaverbird WB plug-in will give you the mesh, it’s just an easy way to visualize the catenary. Convert the mesh to a surface in a couple of different ways, easy one is using a lunchbox and going to mesh reduce, we plug our mesh into that, and we get rid of mesh edges.
programming using changing the parameters of the catenary curve. Kangaroo is a physicsbased solver that is now included with Rhino and is embedded in grasshopper like a plugin for grasshopper. Using physics to create forms, gravity, tension, minimal surfaces, compression, relaxation, and optimization are known in the realm of physics. How to create Catenary Curve, using Bouncy Solver Component?
Sabah Shawkat©
89
First, we set a point, 0,0, define the distance of the line, define the start and end point, the direction will be in the x to get the length. Use component to divide the curve and Bouncy solver from Kangaroo 2, it is the simulation engine that is going to attempt to create a relaxed state of the system which it’s going to continue the input and receive feedback until the system reaches equilibrium.
Using physics to create forms, gravity, tension, minimal surfaces, compression, relaxation, and optimization are known in the realm of physics.
How to create Form- Finding of parametric shell in architecture?
90 Fig. 6.6. Catenary Curve-Form Finding, Grasshopper Script created by the author
We begin with three different plans, using the xz plan component, plugin xz plan to plane component with defining the values x and y, this step gives us one surface plan with xy values in xz direction Fig. 6.7. We copy this xz plane twice in the y direction, to get three surfaces’ planes after that we have to reparametrize the surface, this step allows us to pick one point on the first surface which is on direction xz. Creating three different points on the xz geometry plan as surface number one, the first point is going to be on the bottom plane xz, the next point is going to be in the middle of the upper chord edge of plan xz, and the third point is going to be on the right side on the bottom corner of the xz surface plan. This step allows us to move freely all three points on xz surface plan, Then we get three different designs, after that, we interpolate the curves during this step we get the arch curve on each of the three surface planes, lofting all three arches together we get subsurface then we use hexagon component, with this component we can create a wireframe into subdivision u,v, then we use pipe component to define the dimensions of hexagon wireframe.
Sabah Shawkat©
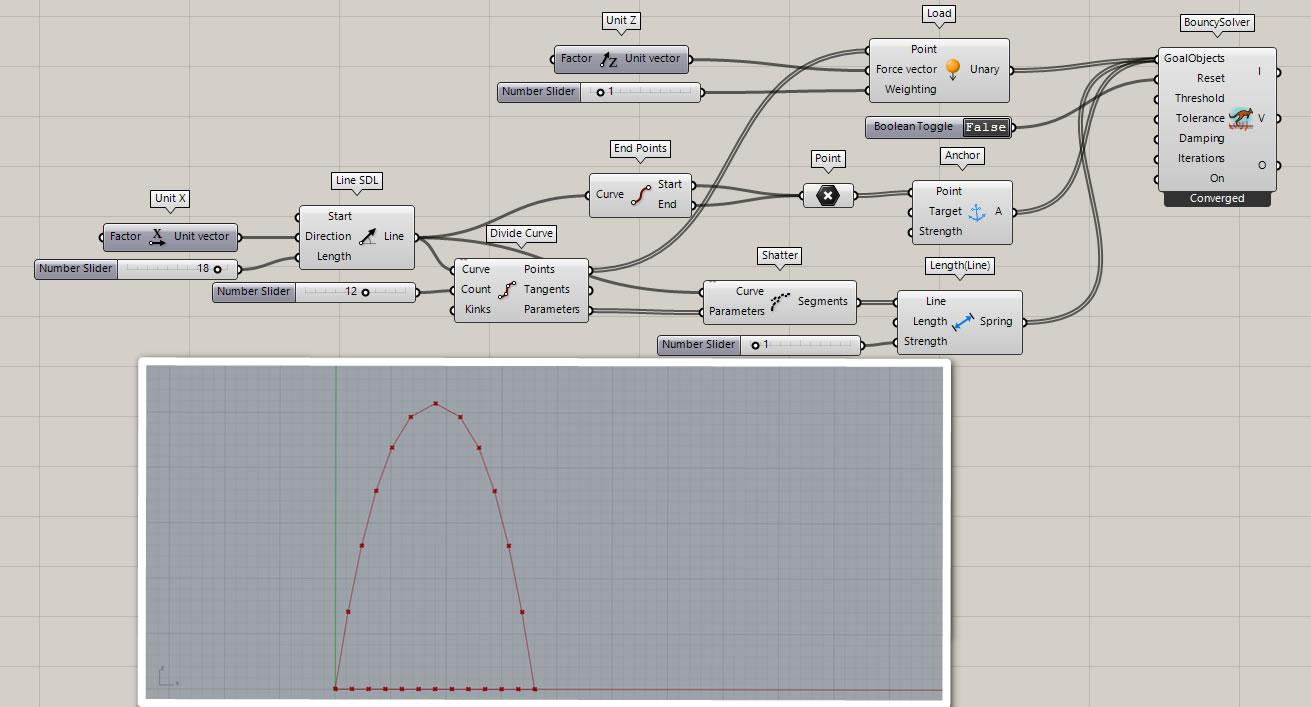
91 Fig. 6.7. Grasshopper Script created by the author Fig. 6.8. Grasshopper Script created by the author Sabah Shawkat©
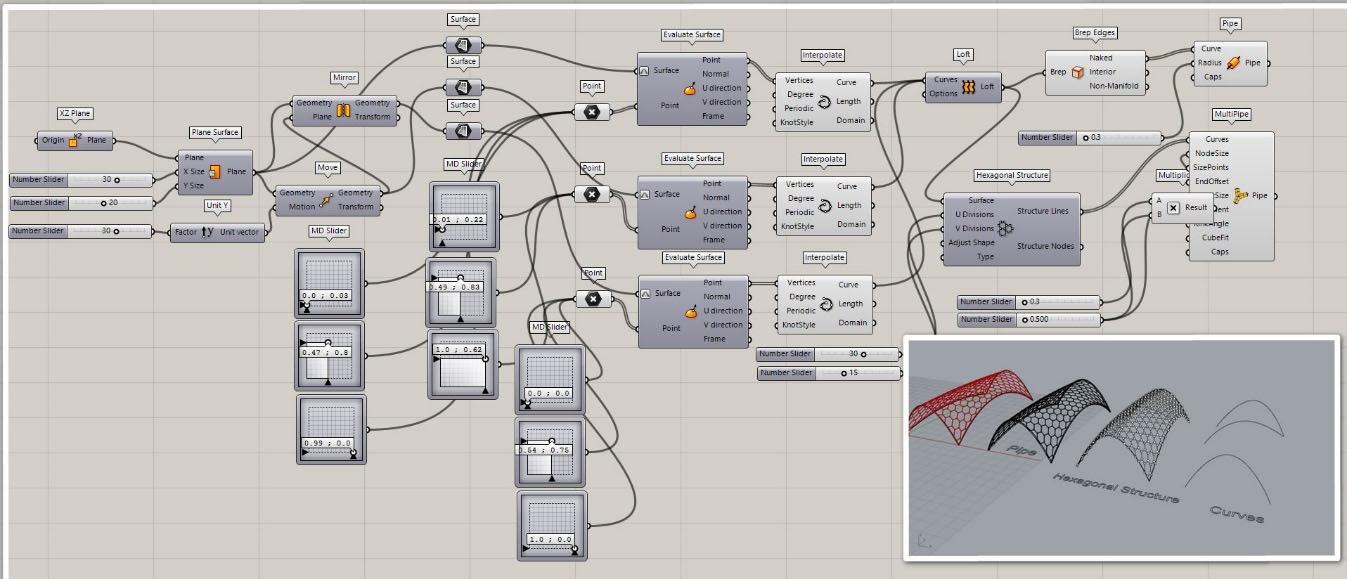
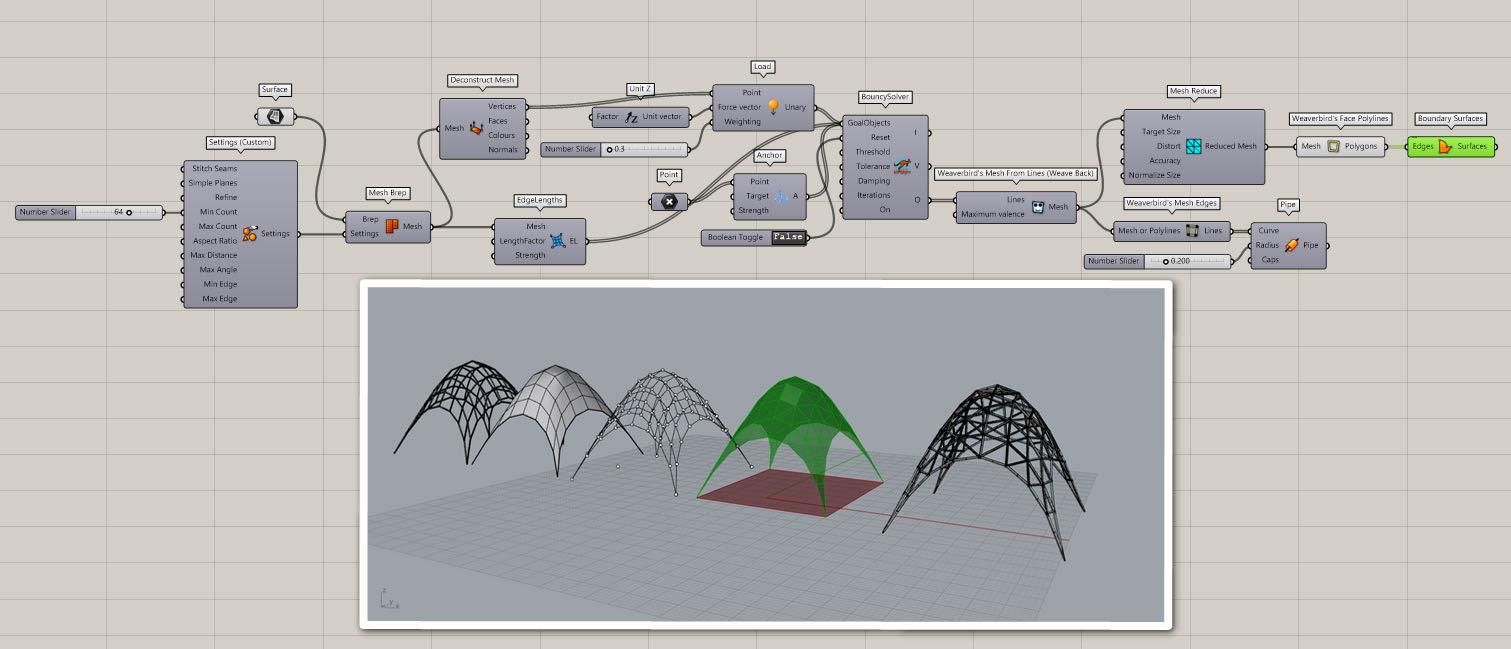
92 7. MÖBIUS BAND
Sabah Shawkat©
to the development of computer technology and available professional programs that consider the non-linear properties of materials in the process of our thought and design, we can analyze and investigate parametric surfaces to realize long-span’s structures based on pure mathematical descriptions. This modern way allows us to easily design unimaginably mathematical curves to create real architectural spaces (V. Petresin, and R. Laurent-Paul, 2002). The so-called fluid topological architecture is the result of a set of new ideas of space. In topology, there is no longer difference between two places, you can move from one space to the other space using a continuous deformation with neither leap, tear nor cut. This is the case of Möbius geometry which plays an important role in modern architecture and design.
The interest of the authors in applying topology to virtual architecture led to the creation of a project called the Observatory based on the Möbius band. The outside of the structure becomes the inside, where horizontal bearing members become vertical members and then they transform into the horizontal again.
The well-known single-sided Möbius strip has inseparable properties that can be expressed in architectural form, surface, and space. Analyzing the way of transforming the 2D of the Möbius band into 3D enables the creation of a new property for architectural space based on the human Thanksscale.
In 1858, the astronomer and mathematician August Ferdinand Möbius was the first to define a surface in three-dimensional space at the Paris Academy of Sciences, a surface we know today as the Moebius band. But history reveals that the true discoverer was Johann Benedict Listing, who came across this surface in July 1858 (I. Peterson, 2001). The strip twisted is called a ribbon of Möbius or Möbius strip, also Mobius or Moebius band.
Topology is a mathematical study of the properties that are preserved through the deformation, twisting, and stretching of objects. Its relatively recent discovery by architects led to an interesting transformation of the art of understanding and building space. The Möbius band or strip is a structure that represents the progress of a two-dimensional plane into a three-dimensional space. By integrating the inside space with the outside surface, it creates a single continuously deformed curved surface.
Non-orientability of the Möbius strip means that in the process of motion of a plane notsymmetrical figure inside a Möbius strip, this figure, having returned to the initial point, transforms into its own mirror image.
93
The introduction of the Möbius strip into architecture is a unique phenomenon by which we can achieve the spatial feeling of a person walking and still twisting, without having to walk up or down. The Möbius strip offers new possibilities for design space, where the interior of the building becomes external and vice versa just as the horizontal elements of the space become vertical elements, it becomes a horizontal element again or where the space is turned into another space. However, the shape creation of the Möbius band has great potential as an architectural form that is difficult to visualize and investigate without the aid of digital technologies (I. Peterson, 2001). The creation of architectural space as well as an understanding of the idea of space within a walk inside the building resulted in two projects: First, the realization of multi Möbius strip Fig. 7.1 and second, as a single Möbius band. Both objects were designed to be located on the banks of the river Danube Fig. 7.2. Fig. 7.1. Möbius Strip Rotations of Other Geometric Shapes (models created by the authors) Fig. 7.2. Möbius Strip Structure of Rectangle Geometric Shape
Sabah Shawkat©
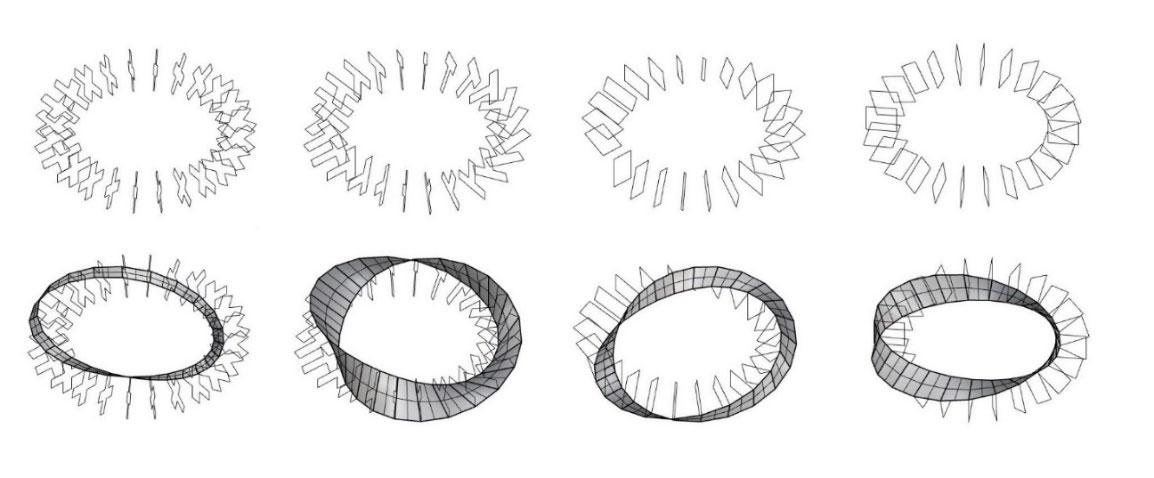
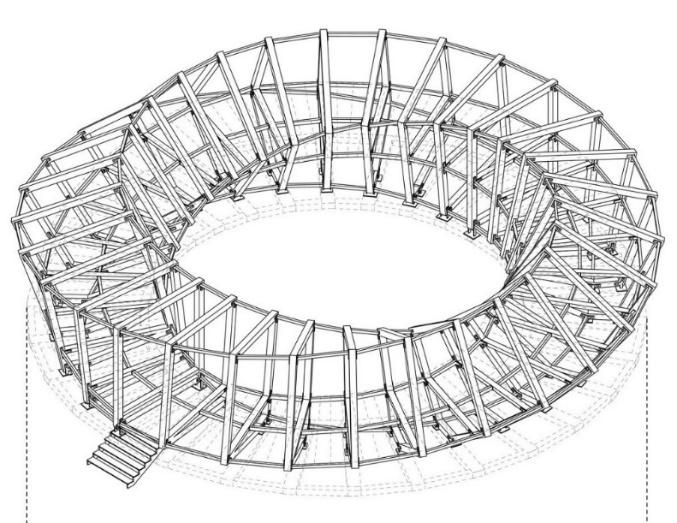
94 Fig. 7.3. Mobius Band with Various Degrees of Twist Imagine surfaces or spaces with continuous rotations without interruption along the entire length of a certain material resulting in a new form with completely different properties. Our construction design depicted in Fig. 7.2 consists of 30 timber frames in a shape of a square 4 x 4 meters. Each one of them rotates on a circle every 12 degrees and on its axis - 6 degrees. On top of these two kinds of frame rotation, the wooden floor gradually elevates, starting from 0.60 m and reaching a height of 2.15 meters, which is why the visitors enter the observatory’s ramp by 6 stairs.
When the frame concludes it is 90-degree rotation, the floor rises by 1.5 meters compared to the beginning of the walkway, thus creating a different volume and height of space within each frame, ranging from 2 meters to 3.6 meters.
Sabah Shawkat©
From this height is derived the width of the walking part of the ramp, which adjusts its width so that the height of the space is never less than the mentioned 2 meters, allowing fluid movement through the space. The ramp is therefore 4 meters at the widest point and 2.76 meters at the narrowest. The volume of the space thus gradually decreases, but even in its smallest configuration, it is large enough for a comfortable transition. This space created by the rotation allows the visitors to enjoy unique vistas, thanks to the continual change of heights and widths of space.
As for the construction details, a solution to all joints is steel plates, which are visible on purpose, so that the visitors can better understand how the structure works. There are two types of foundations possible – the first one is the concrete footing for permanent placement of the observatory and the second solution is full wooden frame foundations, which add mobility and variability of placement. The second variant is located on a supported concrete podium raised above the river Fig. 7.2.
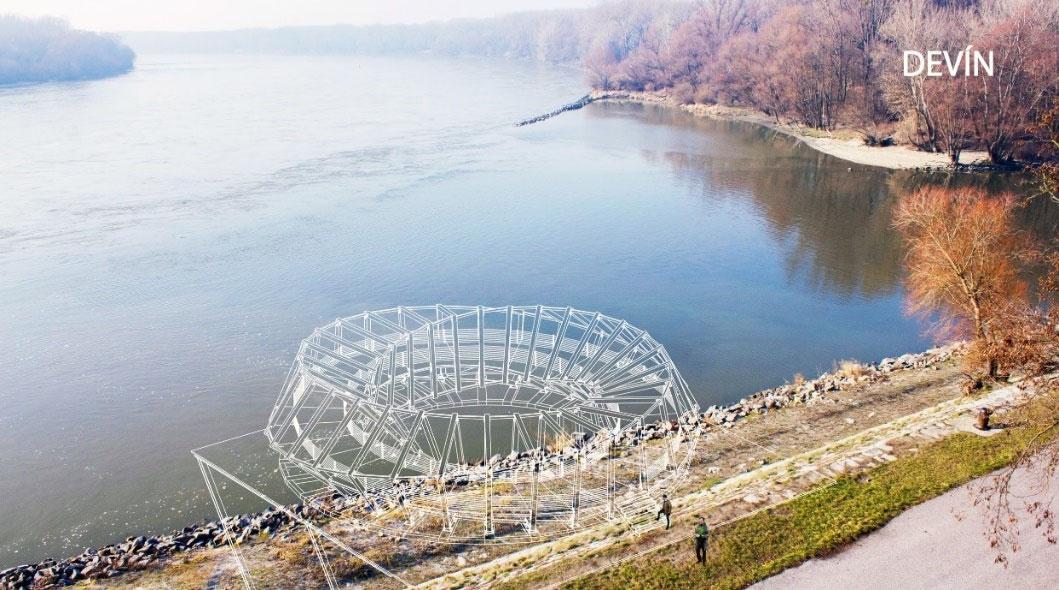
����� ���� ���� � = ⎣ ⎢ ⎢ ⎡������������������ ������������������������������������������������� ������������������������������������������������������������������� ������ �����������������/����� ⎦ ⎥ ⎥ ⎤ where ranges from 0 to 2*π and ranges typically from - 0.4 to 0.4 Fig. 7.1.1.
As we know, the Möbius strip is the simplest geometric shape which has only one surface and only one edge. It can be created by taking a strip of paper, giving it a half twist along it, and then joining the two narrow ends together. If the curved profile of the structure following the path of the Möbius surface has a positive concavity direction at the starting point of the translation, it will have a negative convexity direction after having completed the path and revolving to the starting point.
95 7.1 FORMS, DEFORMATIONS AND ANIMATION
Creating the Möbius strip is a complicated task when using a physical model, but the current technology such as using Grasshopper, which is virtual visual programming Inside Rhino, enables us to create several different models and reconfigure them in a digital environment (J. Thulaseedas and R. J. Krawczyk). This virtual tool shows the power of parametric modeling for the design phase of the project and integrates it with Rhino. The following explanation shows the process of creating the Möbius strip structure in different ways. Creating the Möbius Strip due to Mathematical Equations Here we investigate the basic mathematical equations of the Möbius Band and its extension to a geometry. If we slit a Möbius strip along its long axis, then we shall have an oriented strip twisted at 2π. Fig. 7.1.2 and Fig. 7.1.3 demonstrate the usual elliptical Möbius strip, when the value of the integer equals 1. The Möbius strip in 3 dimensions can be represented parametrically f (����, ����) as follows:Parametrical equations: Process
of Thinking in the Grasshopper Programme (Variant a) Sabah Shawkat©
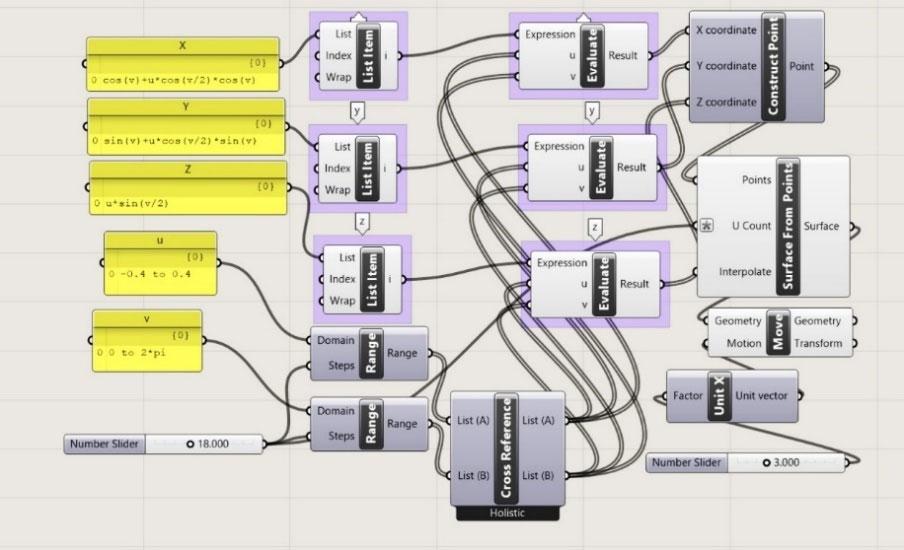
The generation of a curve representing the path of an ellipse or circle form is determined by the number of segments which will be distributed uniformly at equal distances, inclinations, and the center of the individual segments defining the axes of rotation from which the edge points are calculated. Connecting the edges of the segments to each other generates the shape of the Möbius band.
a. Using Curve for Creating Mobius Band
96 Fig. 7.1.2. Deformations and Animation of Möbius Band ( = - 0.1 to 0.1) 7.1.3a 7.1.3b Fig. 7.1.3a, b. Deformations and Animation of Möbius Band, for a = - 0.1 to 0.1, for b =0.3 to 0.3 (Variant a)
Fig. 7.1.4. Process of Thinking in the Grasshopper Programme (Variant b) Sabah Shawkat©
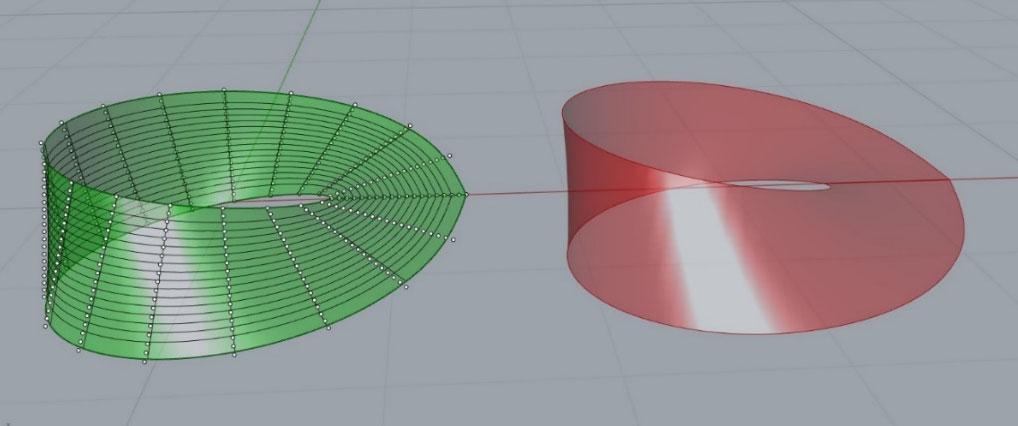
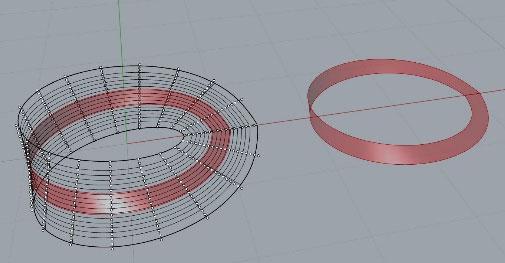
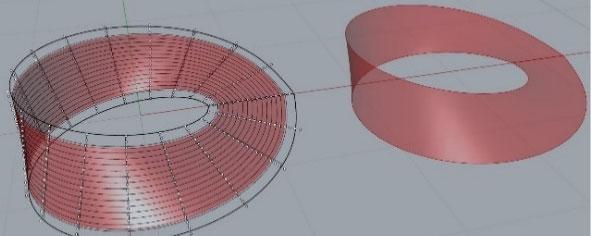
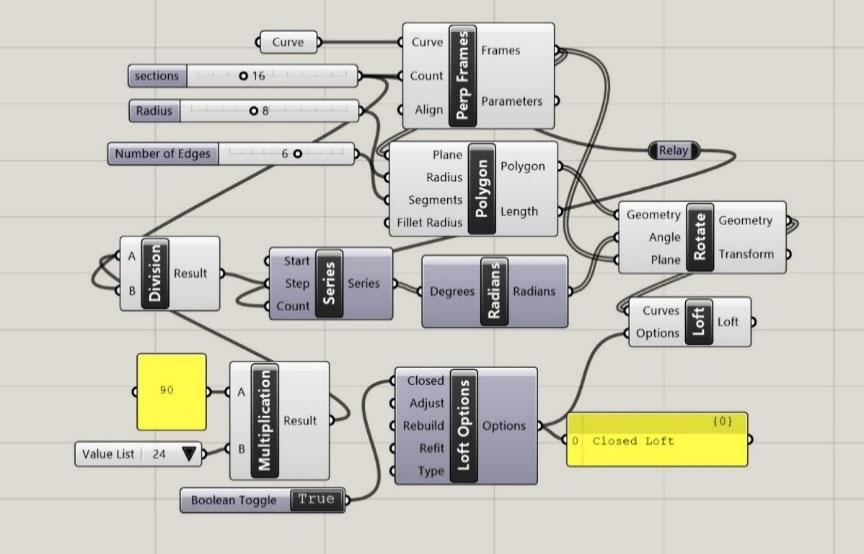
The Parametric form of the definition of a Möbius strip this an elliptical plan that shows the Möbius strip twisted several times when the value of the integer is more than 1 Fig. 7.1.7. Fig. 7.1.6. Process of Thinking in the Grasshopper Programme (Variant c) Fig.7.1.7. Möbius Bands with Various Degrees of Twist with Constant Floor Level (Variant c) Shawkat©
Sabah
97 Fig. 7.1.5. Möbius Bands with Various Degrees of Twist with Constant Floor Level (Variant b) b. Using Circle for Creating Mobius Band
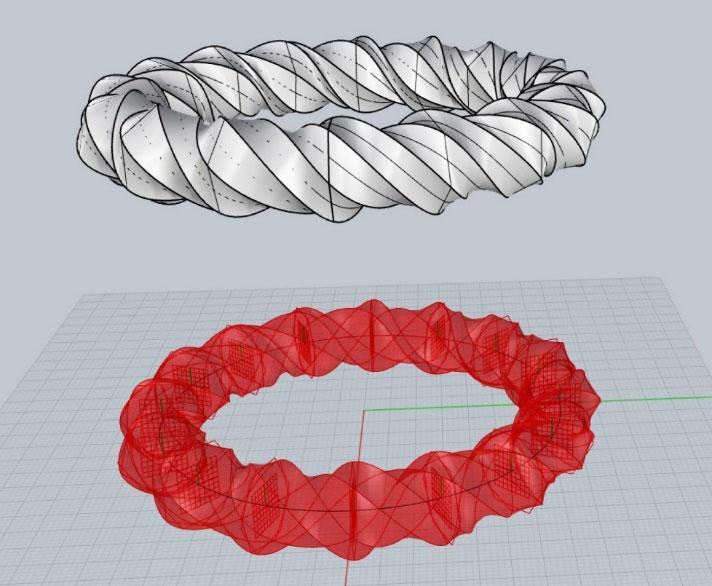
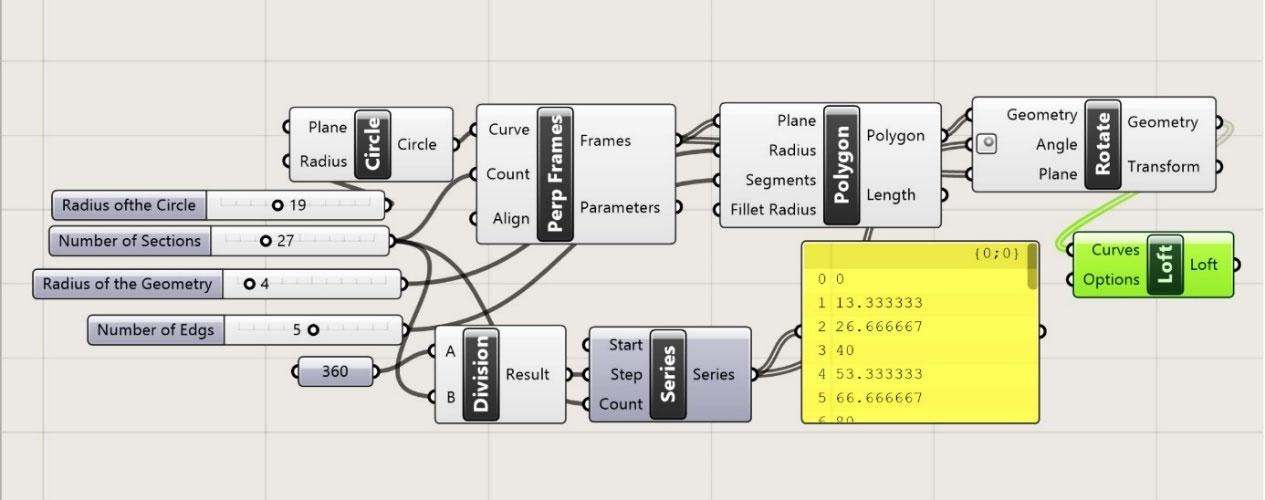
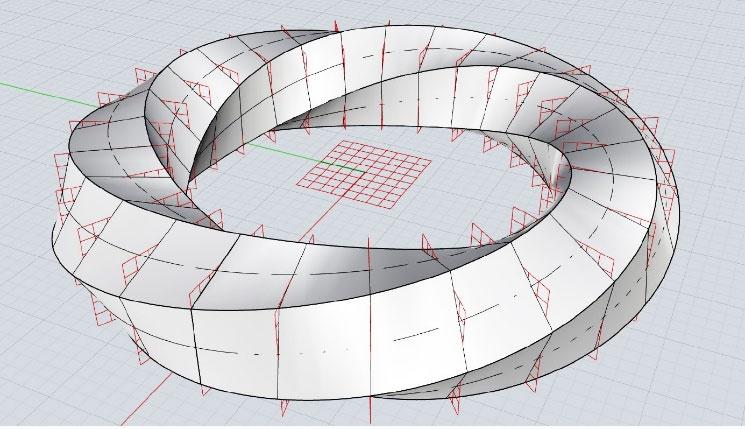
Baking-exporting geometry from GH back to Rhino Fig. 7.1.8. Process of Thinking in the Grasshopper Programme (Variant d)
Process of thinking according to program GH, for creating Mobius strip Fig. 7.1.8:
Grasshopper
To conclude, the conceptual design of structures is a specific part of the design process when the most fundamental and influential decisions are made. It is an area where all the parameters such as experience, intuition, tradition, and technical skills of designers come together.
Create a geometry that will rotate around the curve at 180 degrees Sequences of frames, parallel to rotation around the curve
Creating a surface from frames, the function of connecting curves and lines
Sabah Shawkat©
Drawing the basic curve of Rhino, Loading geometry from Rhino to GH Input parameters, side length, number of profiles, rotation angle, floor height Divide the curve into equal parts
98 inside Rhino is the newest technology that seems to have the potential of finally solving the compatibility issues with Rhino, as we mentioned before in the example of virtual designing of Möbius strip by parametric modeling. In our short example, we have explained in detail the process of thinking with a step-by-step approach, so as to better understand the process of creating the conceptual form improvement of the Möbius band in different ways. We used the perp frames tool that allow us to create our structure, this comprehensive plugin helped us to fulfill our purpose in a simple way. Once we have finished the overall shape in Grasshopper, we baked the geometry and continued with the creation of details directly in Rhino. In the end, we sorted the geometry based on layers and materials.
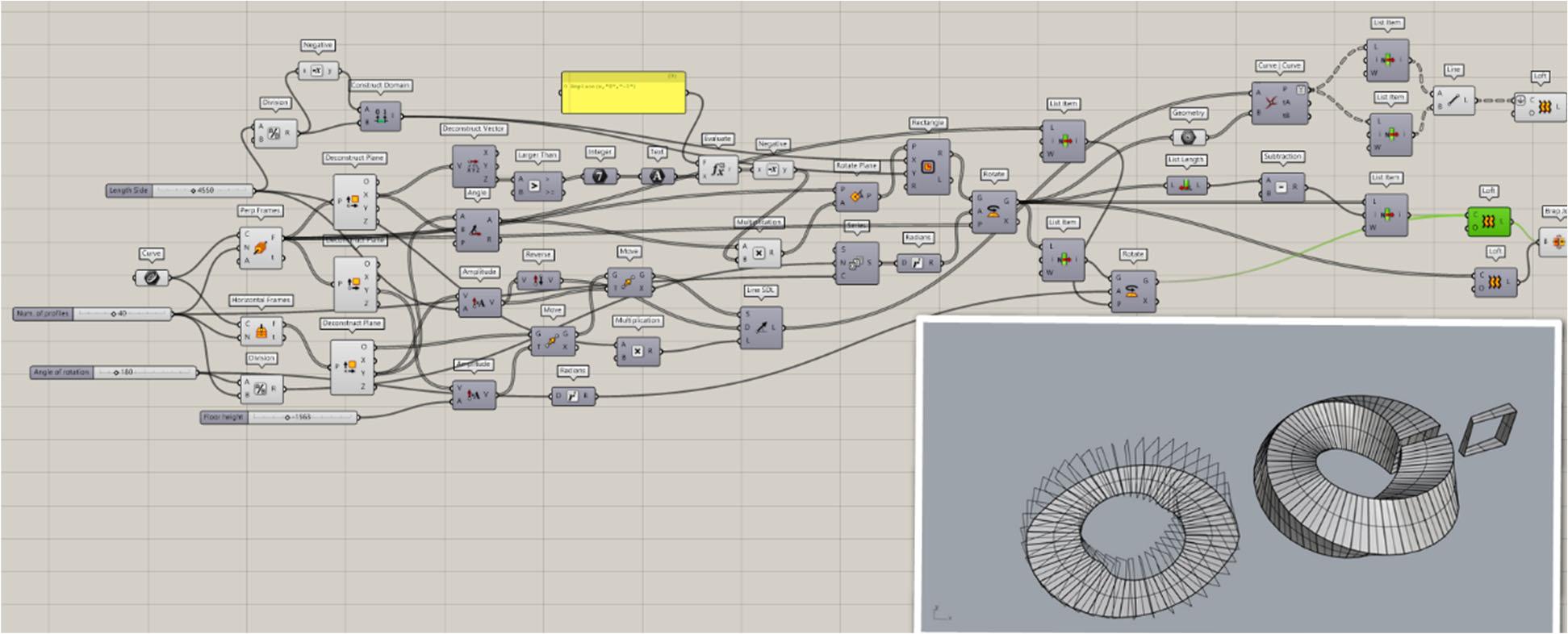
Generally, it is always useful to begin with physical models, because it is the best way to understand the complexity of the design with all implied parameters. Here we try to present some of the opportunities the reciprocal frame offers, however, like any structural form, the reciprocal frame structure has its limitations too. Fig. 8.1 is depicted a small-scale physical model of Leonardo da Vinci’s proposal for temporary bridges. The arched form is created by using short timber elements of simply supported interlocking beams.
Sabah Shawkat©
The name “reciprocal frame” comes from Graham Brown, who developed this type of structure and used the term “reciprocal” because of the way the beams mutually support each other. A reciprocal frame is a three-dimensional structure with complex geometry, consisting of linear straight members which are mutually supported and interlocking, forming either a flat, horizontal structure or a pitched three-dimensional frame system (Chilton, Choo, and Popovic,1995). The key point was how you solve in a proper way spanning distances longer than the length of the available beam. this problem helped the constructors to find a such structure which was therefore called short beams or reciprocal systems. Reciprocal frames and structures similar to them have been built by many cultures throughout history. Villard de Honnecourt provides us with information on how to deal with the problem of beams shorter than the span, but he gives no information on the spans. His solution to this problem was a planar grillage and it adopts similar principles to the reciprocal frames, for spanning long distances with shorter beams (Chilton, Choo, and Yu,1994).
99 Fig. 7.1.9. Process of Thinking in the Grasshopper Programme, script created by the author 8. RECIPROCAL FRAME
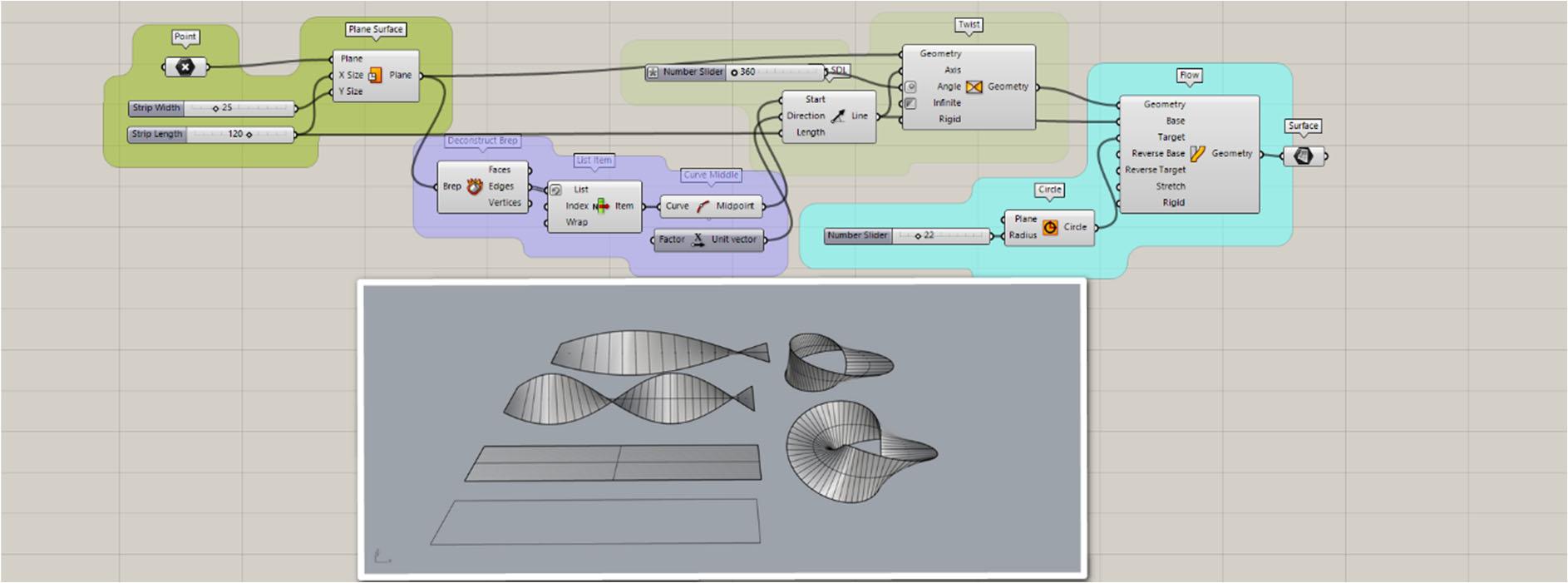
Sabah Shawkat©
Fig. 8.2a. Self-Supporting Structures - Reciprocal Frames (Shawkat,2021)
100
Fig. 8.2a, b shows different morphology forms of classical self-supporting structures (reciprocal frames). All these physical models are made of one type of rectangular wooden beam with a length of 30 cm. Traditionally, reciprocal frames were used as roofs but due to their beauty we can consider them also as art. “a reciprocal frame is a structure on the use of load bearing capacity of elements which, supporting one another along their span and never at the extremities, construct a spatial configuration without any clear structural hierarchy” In this framework, a study of reciprocal frames based on the use of 1D short timber beam with 30cm is proposed. We provide several morphological classifications of reciprocal beams based on 1D elements, which have been divided according to elements’ shape and growth possibilities.
Fig. 8.1. Physical Model of Temporary Bridges, (Shawkat, 2021)
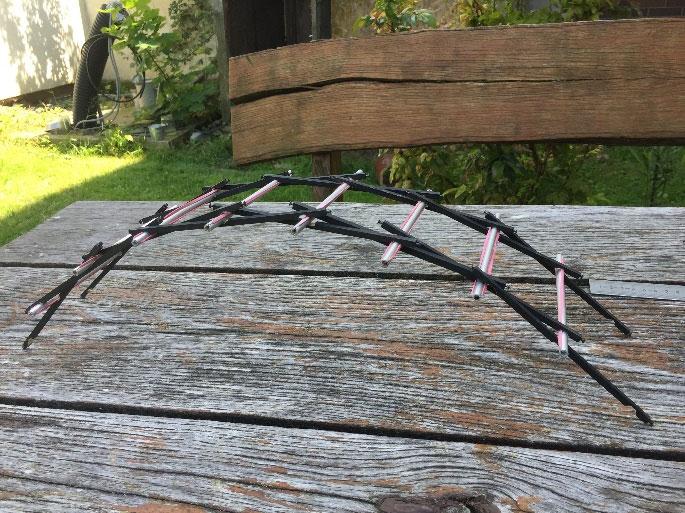
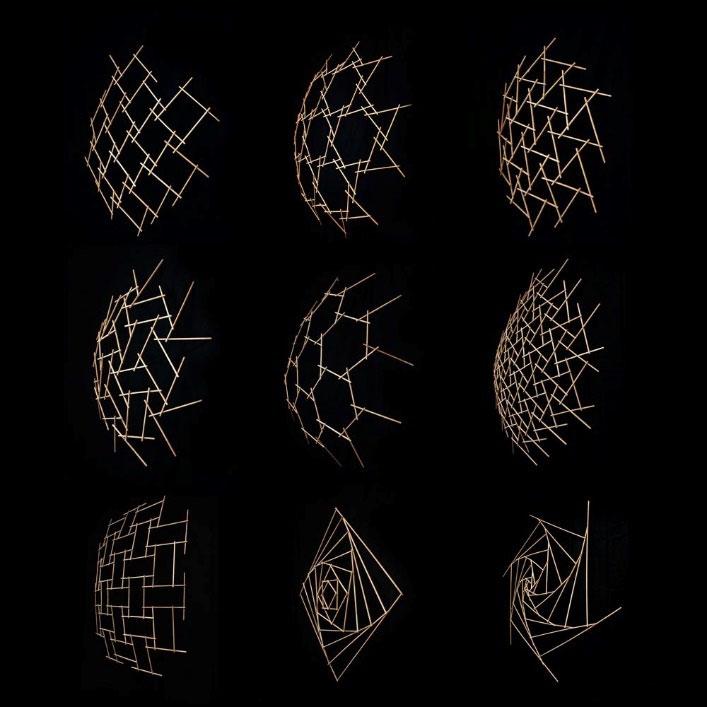
101 Fig. 8.2b. Self-Supporting Structures - Reciprocal Frames (Shawkat,2021) Fig. 8.3. Process of Thinking in the Grasshopper Programme Sabah Shawkat©
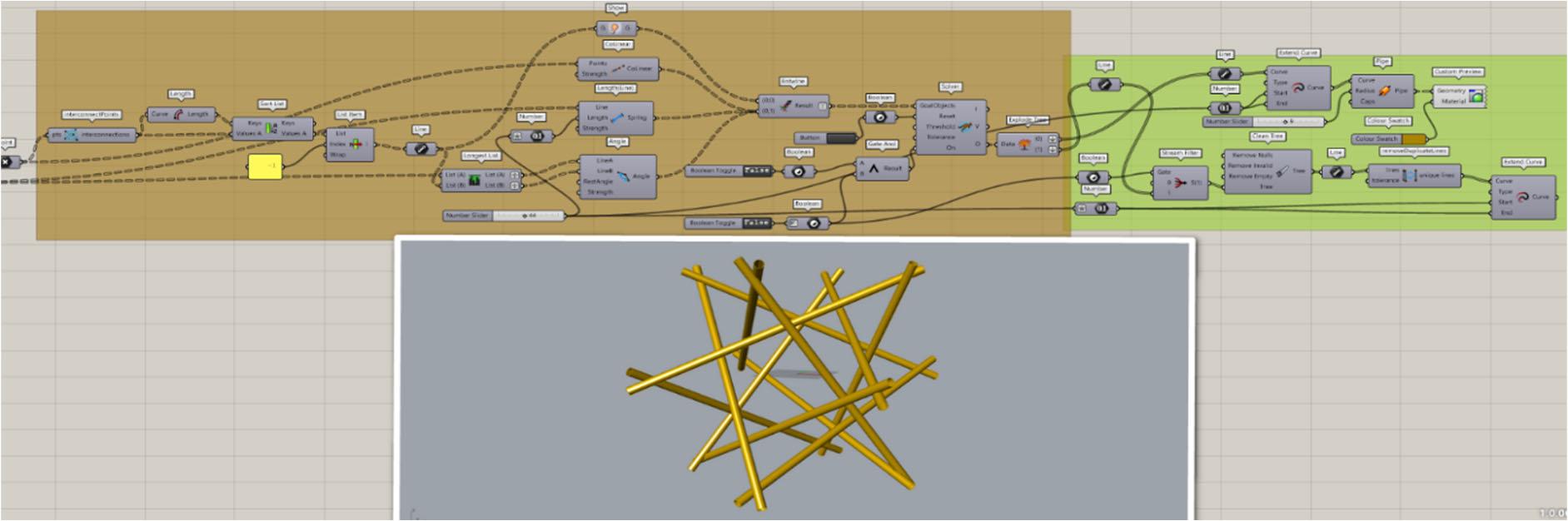
102 Platonic Tetrahedron – Rotate the Geometry in Degrees 1 degree 4 degrees 11 degrees 14 degrees 43 degrees 46 degrees 48 degrees 77 degrees 80 degrees 87 degrees 89 degrees 89 degrees Fig. 8.4. Platonic Tetrahedron Sabah Shawkat©
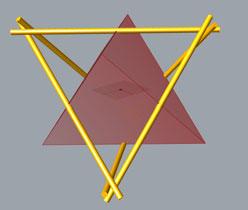
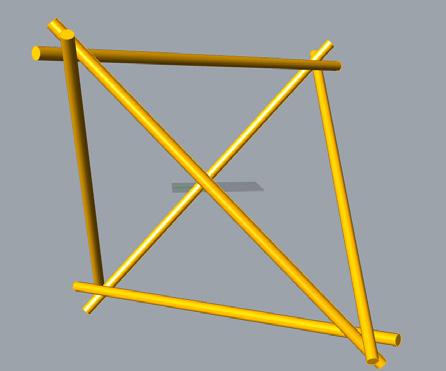
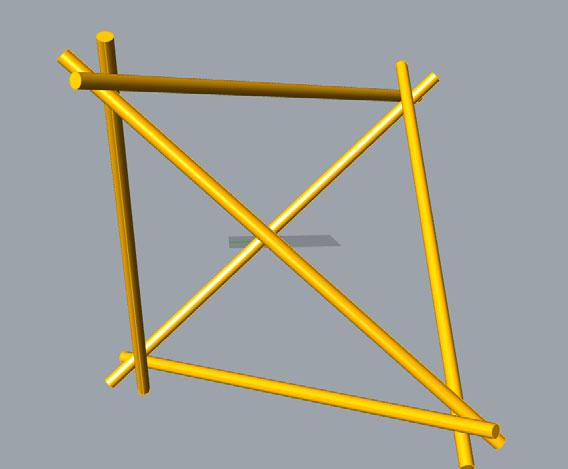
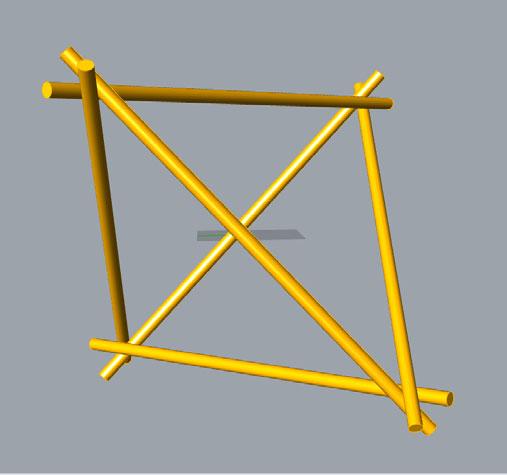
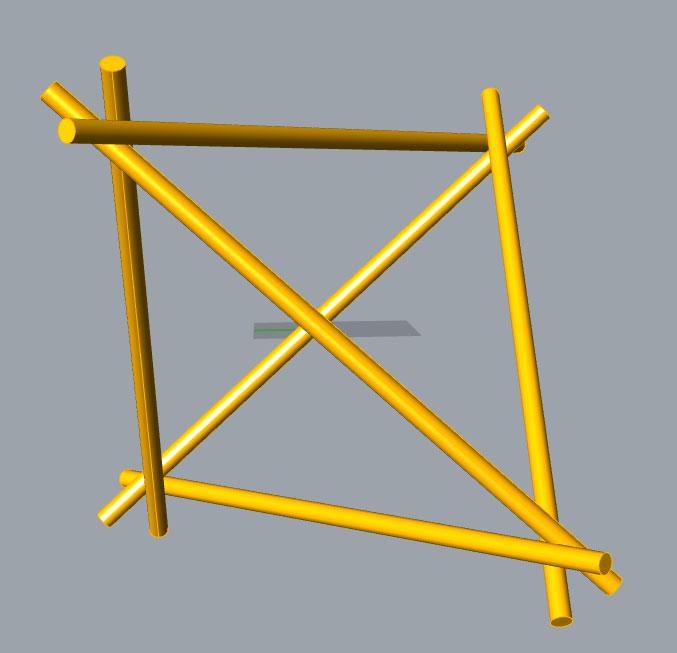
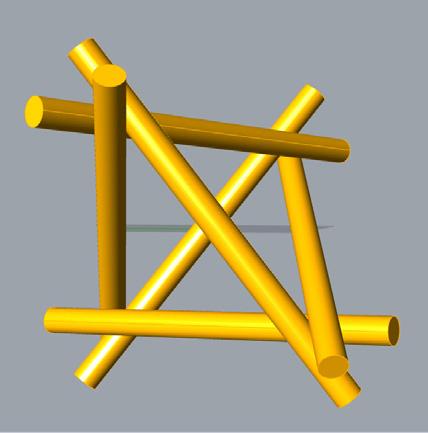
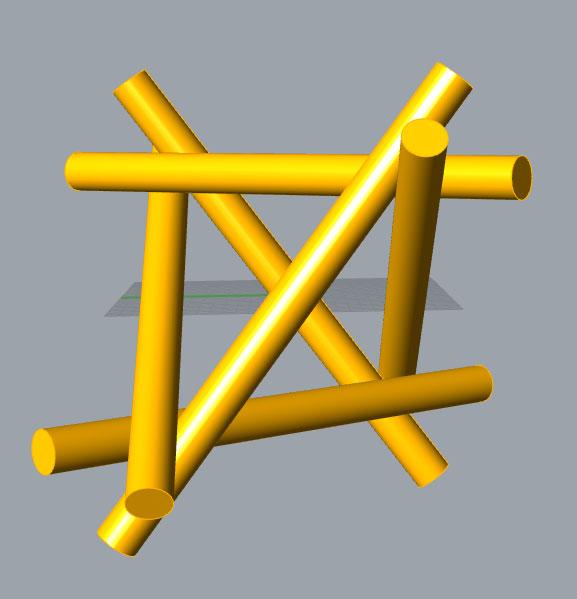
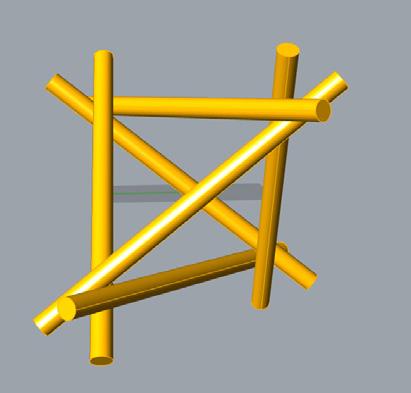
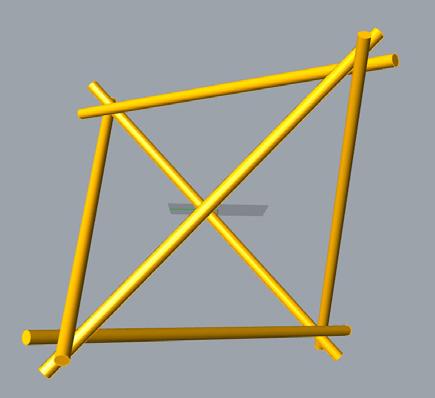
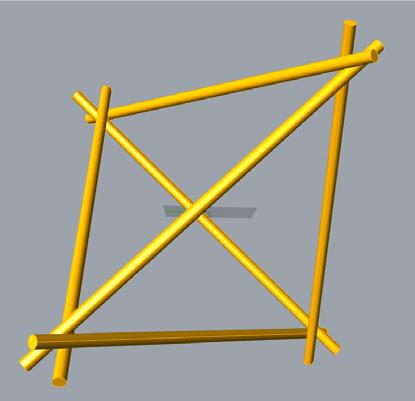

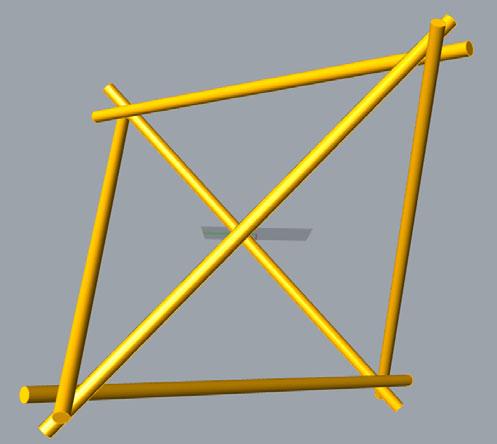
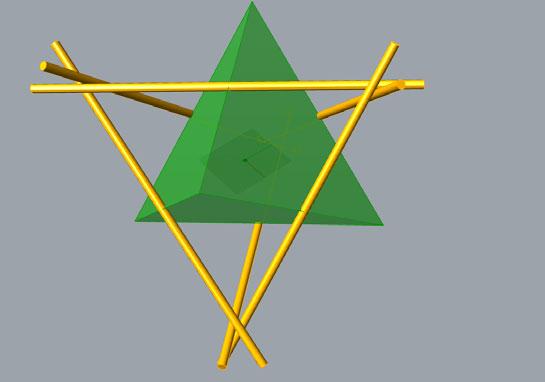
103 Platonic Octahedron – Rotate the Geometry in Degrees 1 degree 4 degrees 11 degrees 14 degrees 43 degrees 46 degrees 48 degrees 77 degrees 80 degrees 87 degrees 89 degrees 89 degrees Fig. 8.5. Platonic Octahedron Sabah Shawkat©
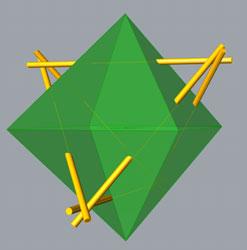
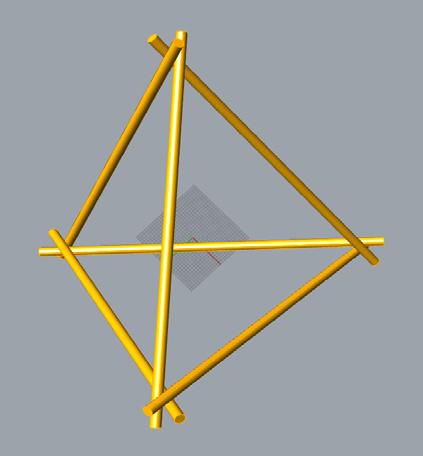
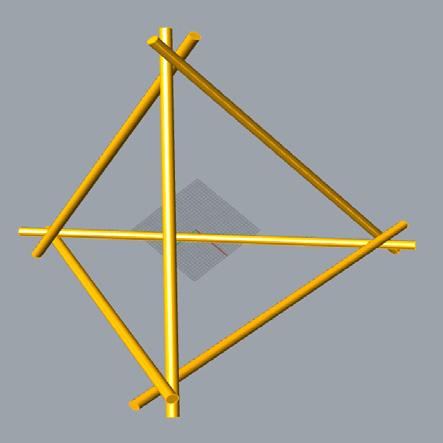
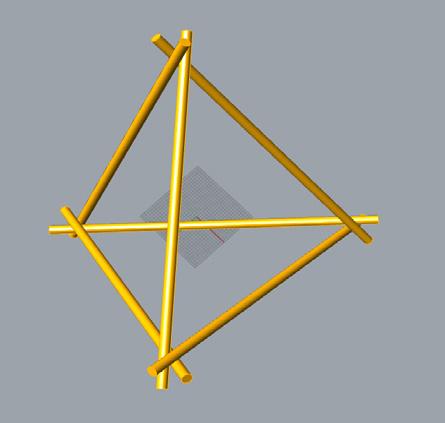
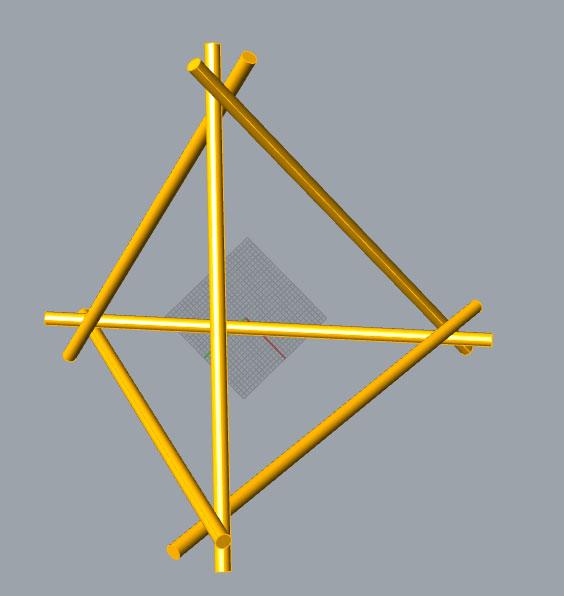
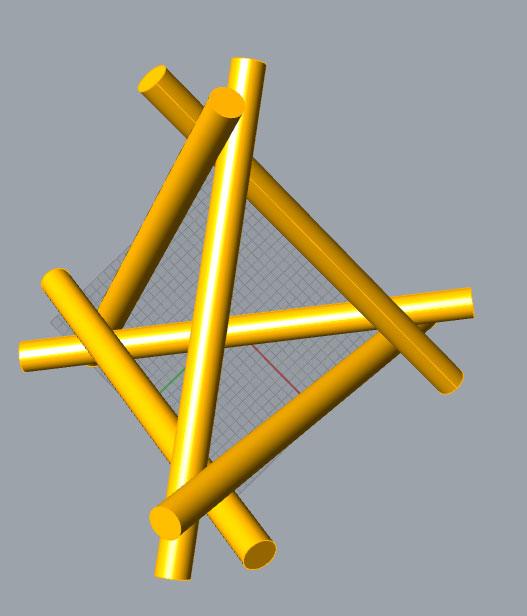

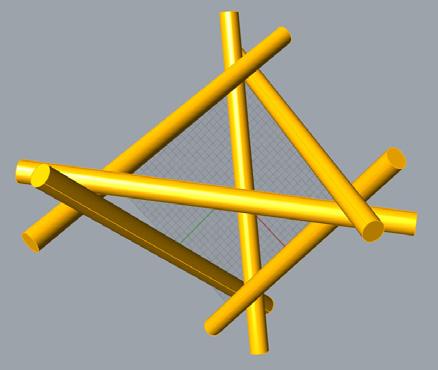
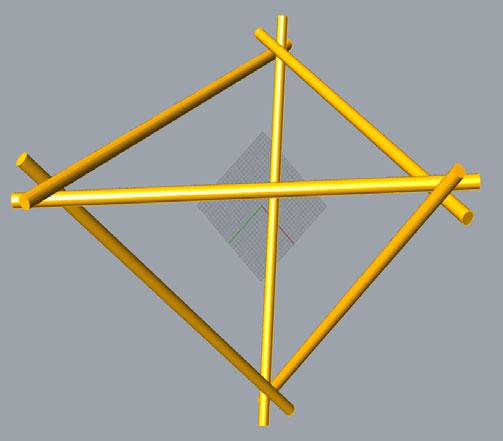
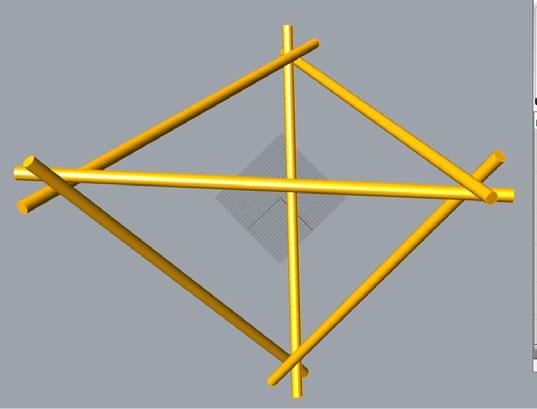
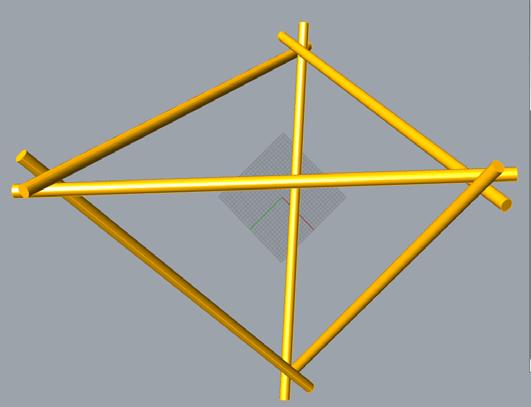
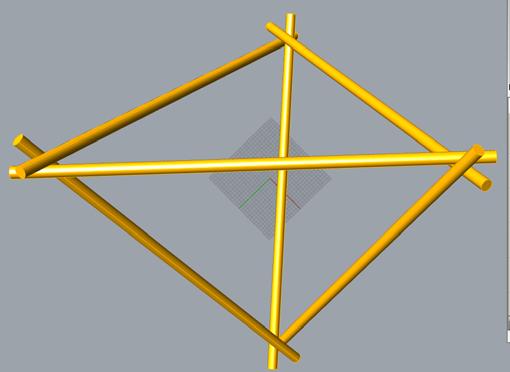
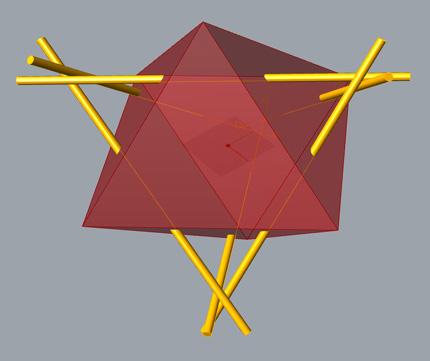
104 Platonic Cube – Rotate the Geometry in Degrees 1 degree 4 degrees 11 degrees 14 degrees 43 degrees 46 degrees 48 degrees 77 degrees 80 degrees 87 degrees 89 degrees 89 degrees Fig. 8.6. Platonic Cube Sabah Shawkat©
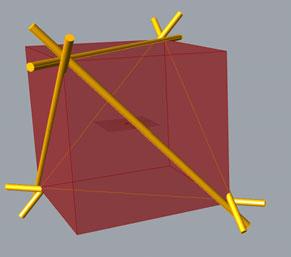
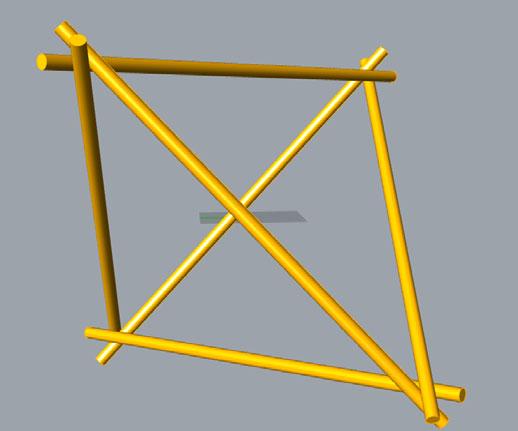
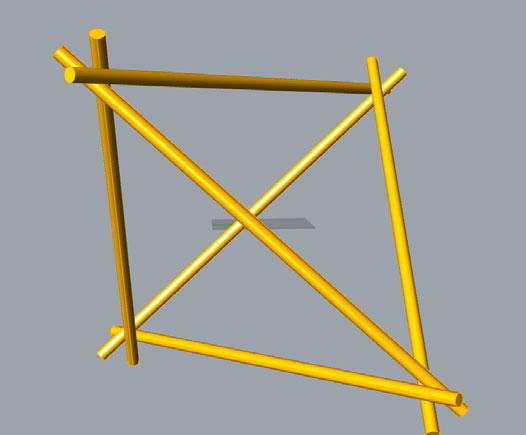
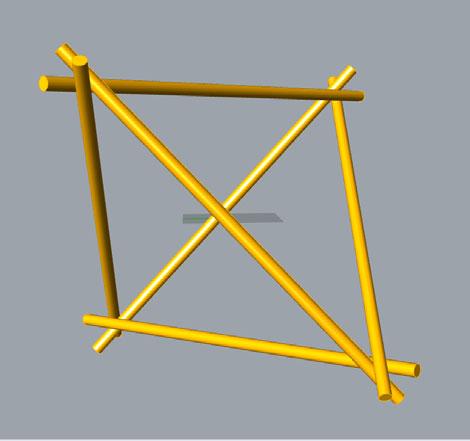
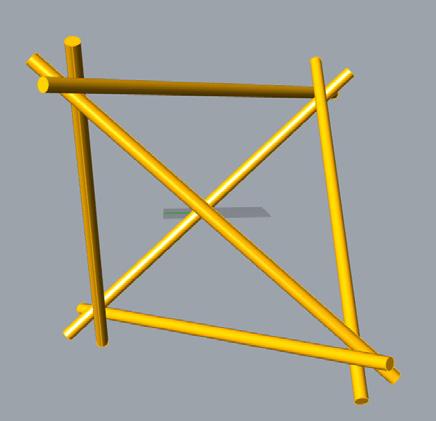
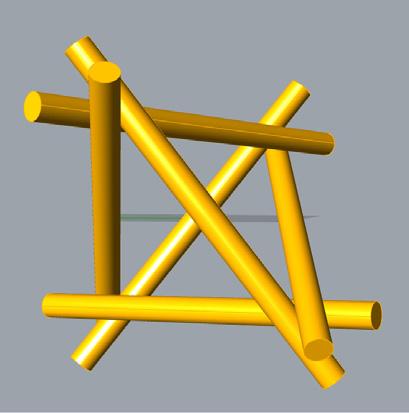
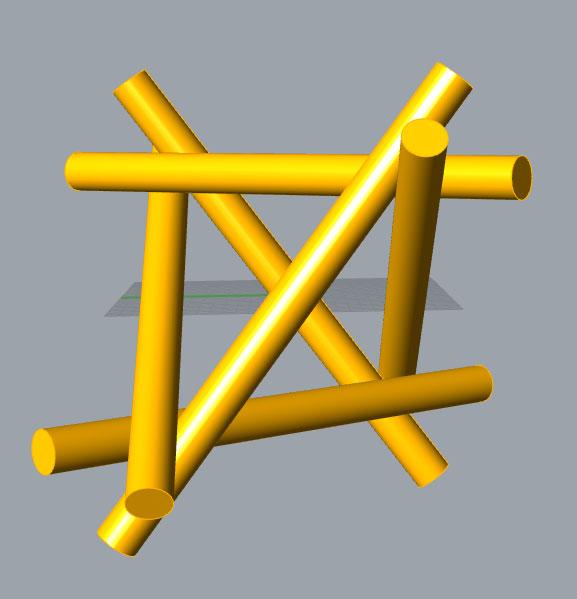
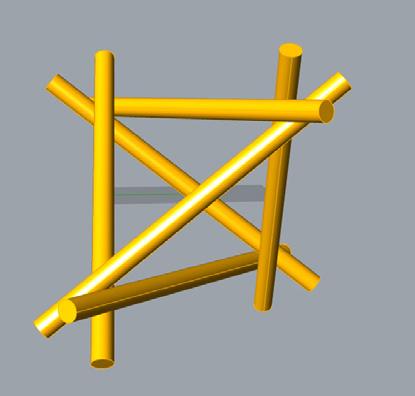
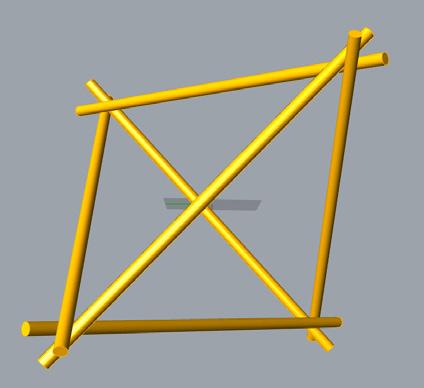
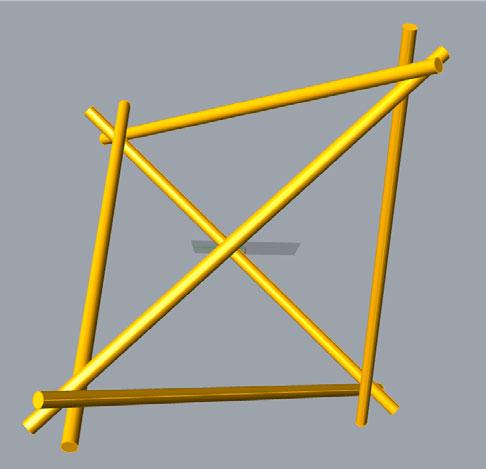
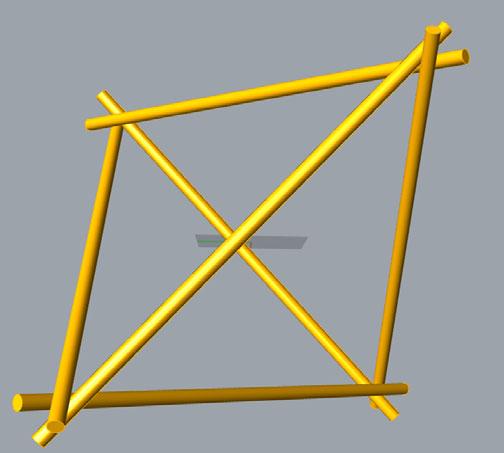
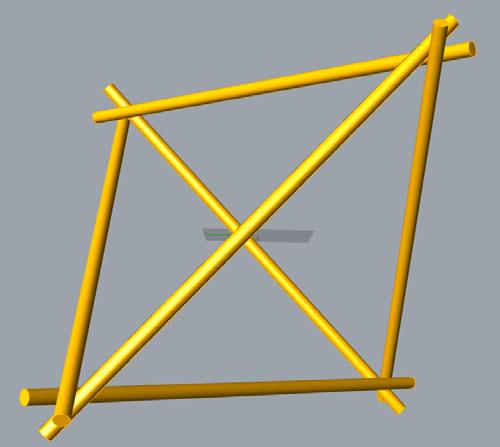

105 Platonic Dodecahedron – Rotate the Geometry in Degrees 1 degree 4 degrees 11 degrees 14 degrees 43 degrees 46 degrees 48 degrees 77 degrees 80 degrees 87 degrees 89 degrees 89 degrees Fig. 8.7. Platonic Dodecahedron Sabah Shawkat©
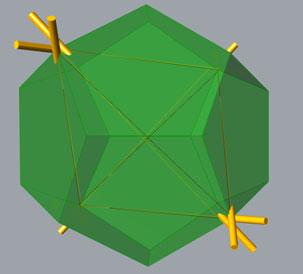
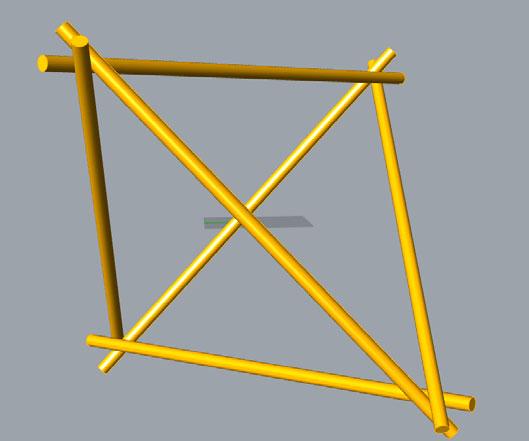
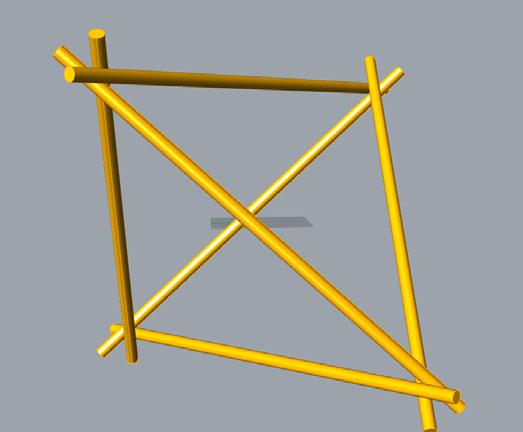
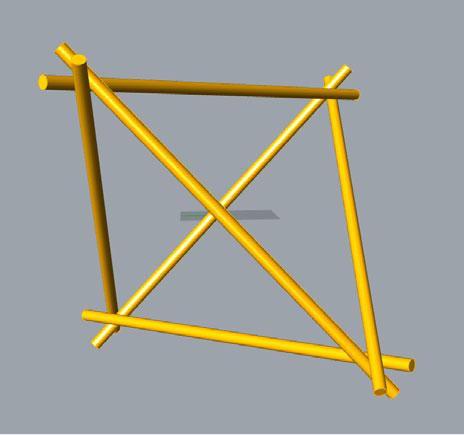

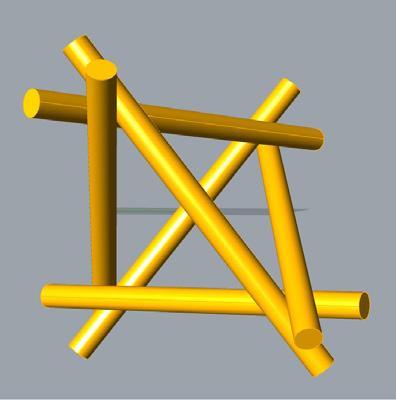
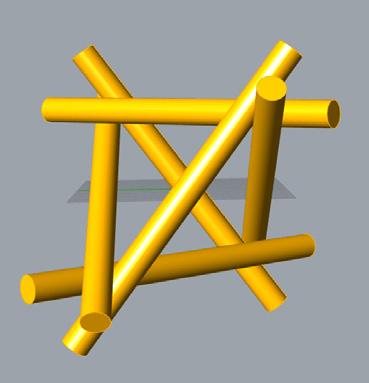
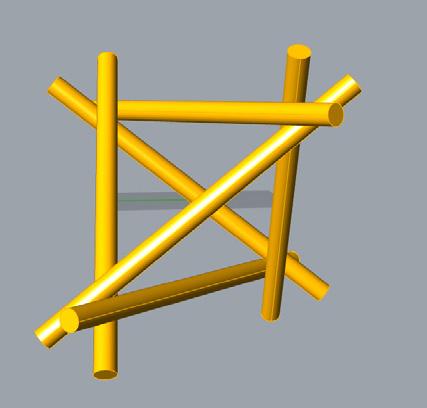
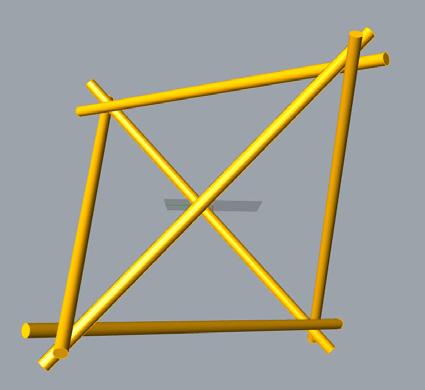


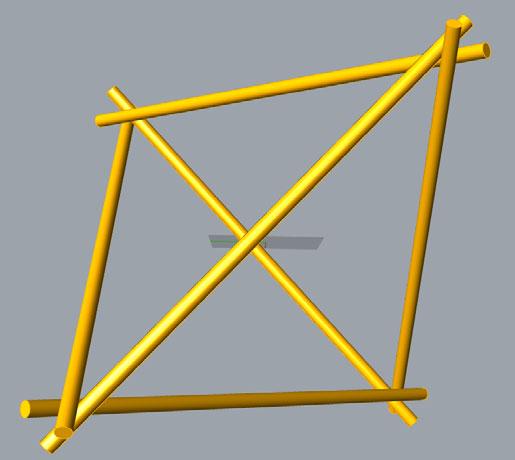
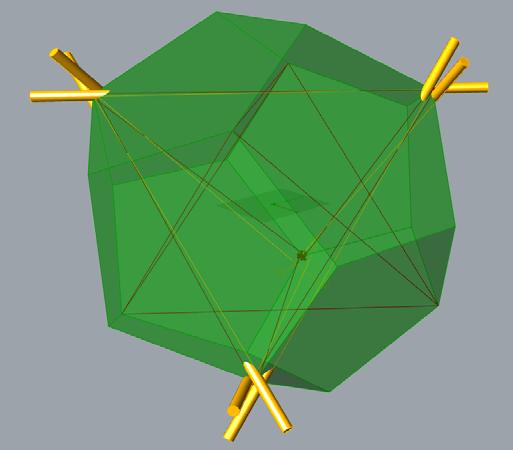
106 Platonic Icosahedron– Rotate the Geometry in Degrees 1 degree 4 degrees 11 degrees 14 degrees 43 degrees 46 degrees 48 degrees 77 degrees 80 degrees 87 degrees 89 degrees 89 degrees Fig. 8.8. Platonic Icosahedron Sabah Shawkat©
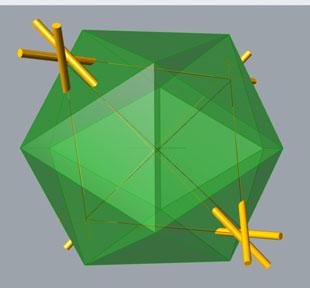
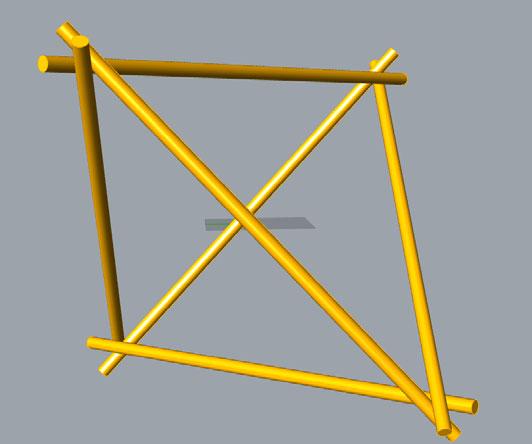
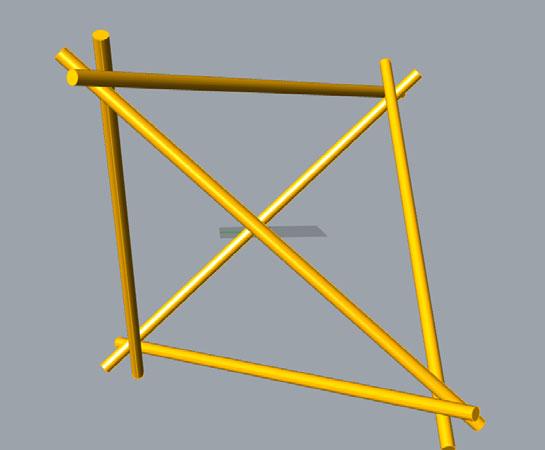

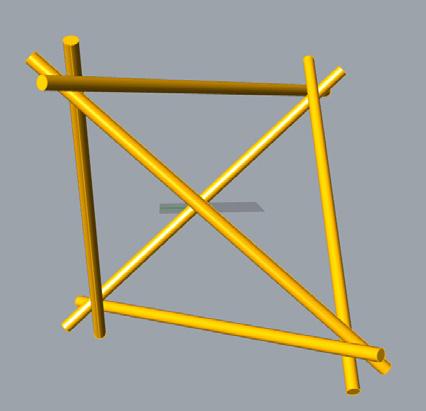

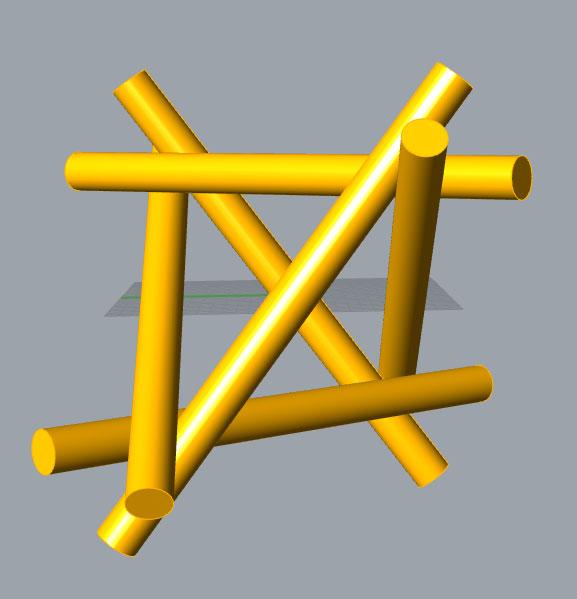
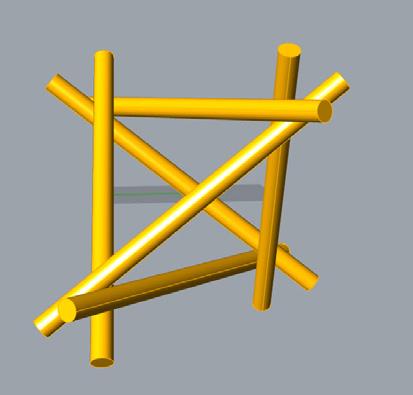
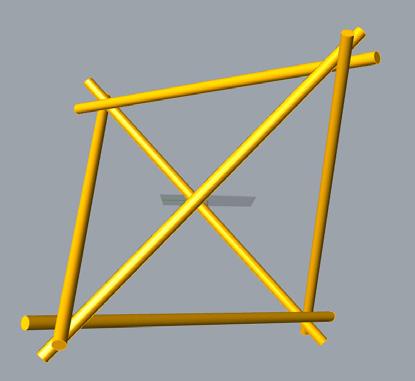
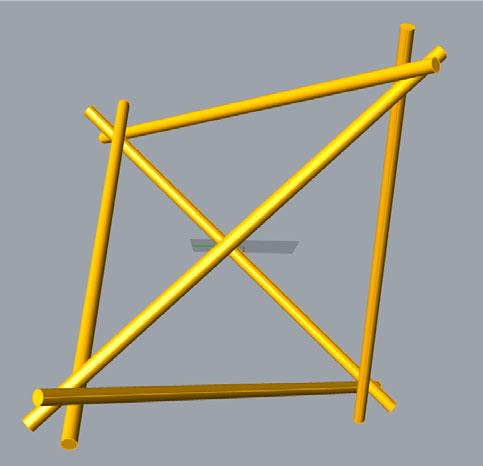
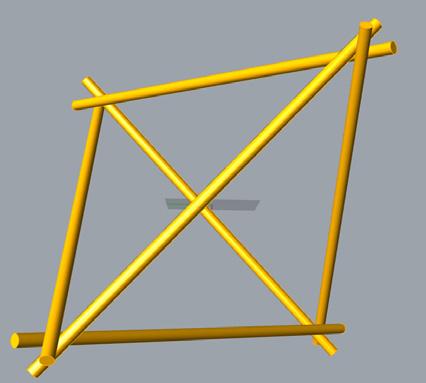
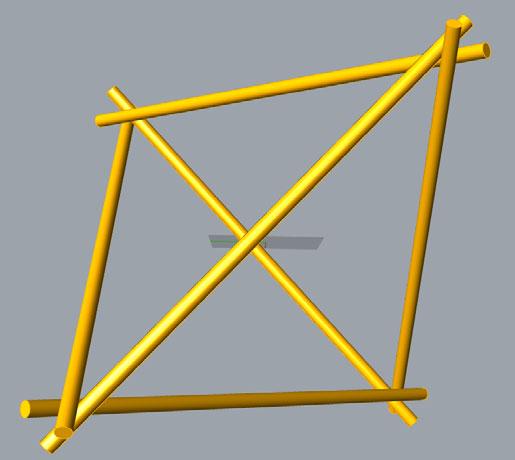
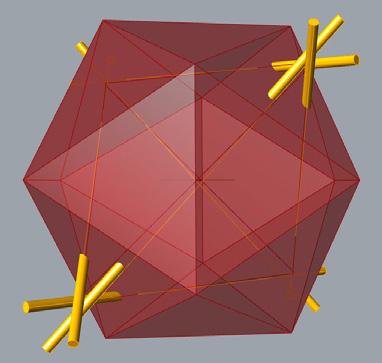
107 Fig. 8.9. Model Created by Shawkat 2022 Sabah Shawkat©

Fig. 9.1. Hyperbolic Paraboloid Model (Shawkat, 2021)
As we know from mathematical diagrams, the hyperbolic paraboloid is a ruled surface, which means that we can create it using only straight lines even though it is curved. Fig. 9.1 shows our models of a hyperbolic paraboloid made of fifteen straight 30cm and 90cm long wood elements. First, we created an equilateral triangle using three elements of our straight timbers. Then we used this triangle as a template to form two skewers at a 60-degree angle, completing 2/3 of another equilateral triangle. Connecting the first triangle by one skewer to the second triangle, created together a regular tetrahedron shape. Further, we marked the edges of the tetrahedron in regular 4 cm intervals to connect the skewers between the marks. Then we connected a skewer to the first marks on each of the edges. In another step, we created another layer of skewers so that they would overlap. We kept connecting skewers by moving one interval mark on each edge. The overlap got greater each time. To reach the goal we had to use two of the other edges to form the other ruling lines.
Sabah Shawkat©
108 9. HYPERBOLIC PARABOLIC MODEL-GRID SHELL STRUCTURE
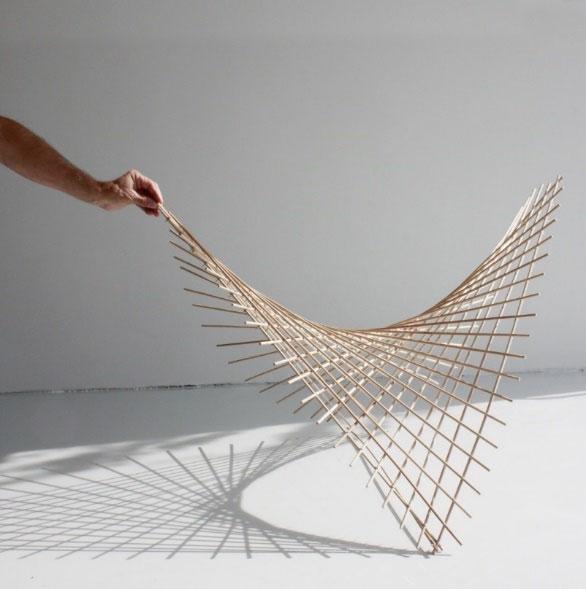
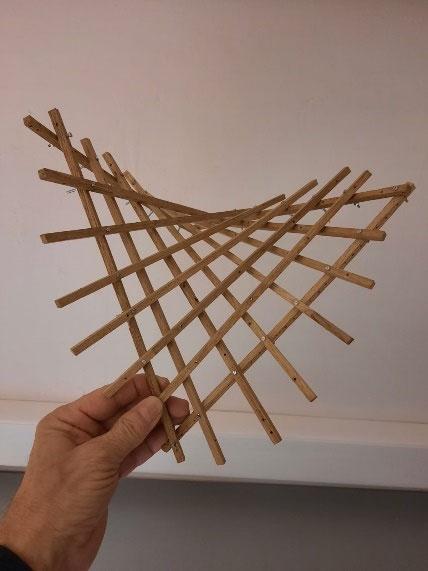
Tensile-Integrity Structures. U.S. Patent 3,063, 521, 13 November 1962. K. Snelson, Continuous Tension, Discontinuous Compression Structures. U.S. Patent 3,169, 611, 16 February 1965. D.G. Emmerich, Construction de Reseaux Autotendantes. French Patent 1,377, 290, 28 September Shawkat,1964. S. (2019). The Art & Engineering of Lightweight Structures. Tribun EU, Brno, 308 pp. Shawkat, S. (2021). Structural icons for architects, Tribun EU, Brno, 840 pp. Shawkat, S. (2021). Time Space Existence 2021, European Cultural Centre, Grafiche Veneziane Venice, Italy, pp. 550. Shawkat, S. (2019). Behavior of Steel Structures. Tribun EU, Brno, 312 pp. Bach, K., Burkhardt, B., Otto F. (1988). IL 18, Seifenblasen, Karl Kramer Verlag,Stuttgart, 400 Foster,pp.
B. (1998). The Integration of Large Fabric Structures within Building Projects including the Significance of Design and Procurement Methods. Proceedings of IASS – LSAA Symposium Foster, B., Mollaert, M. (2004). European Design Guide for Tensile Surface Structures. Tensinet, Schleicher,Brussels. S., Lienhard, J., Fleischmann, M. (2010). Forschungspavillon ICD/ITKE, Detail, online: http://www.detail.de/artikel forchungspavillonuniversitaet- stuttgart 26600 De.htm Bletzinger, K.U., Firl, M., Linhard, J., Wüchner R. (2008). Optimal shapes of mechanically motivated surfaces. In Computer Methods in Applied Mechanics and Engineering. Bletzinger, K.U., Wüchner, R., Daoud, F., Camprubi, N. (2005). Computational methods for form finding and optimization of shells and membranes. In Computer Methods in Applied Mechanics and Engineering, Vol. 194 Bletzinger, K.U. (2014). Structural Optimization, Lecture Notes, TU Munich, Bletzinger, K.-U. Ramm, E. Structural optimization as tool for shape design, in: Hirsch, C. et al., (Eds.), Numerical Methods in Engineering 92, Elsevier, Amsterdam, New York, 1992 Motro, R. (1992). Tensegrity systems. The state of the art. Int. J. Space Struct. 1992, 7, 75–83.
Sabah Shawkat©
109
REFERENCES Otto, F., Trostel, R. (1967). Tensile Structures, vol 2, MIT Press R.B. Fuller, R. Marks, The dymaxion world of Buckminster Fuller, New York, Anchor Books, R.B.Fuller,1973.
Chilton, J. C., Choo, B. C. and Yu, J. (1994). Morphology of reciprocal frame 3-dimensional grillage structures. In Spatial Lattice and Tension Structures, Proceedings IASS-ASCE (Abel, J. F., Leonard, J.W. and Penalba, C. U., eds), Atlanta, GA, pp. 1065–1072. Chilton, J.C., Choo, B. S. and Popovic,O. (1995). Reciprocal frames past, present and future. In Proceedings of the International Conference in Lightweight Structures in Civil Engineering (Obrebski, J. B., ed.), Warsaw, Poland, September, pp. 26–29. Magat-Magdalena Burska, Warsaw, I.Poland.Peterson, Fragments of Infinity, A Kaleidoscope of Math and Art, John Wiley & Sons, 2001, p. V.138-141.Petresin, R. Laurent-Paul, “The Double Möbius Strip Studies”, Nexus Network Journal, Vol. 4, 2002. Z. Hadid, The Complete Buildings and Projects, Thames, and Hudson, 1998, pp. 110-115. J. Thulaseedas and R. J. Krawczyk, Möbius Concepts in Architecture, College of Architecture Illinois Institute of Technology Chicago, IL, 60616, USA, info on https://arch.iit.edu/ Kolar, V., Nemec, I., Kanicky, V. (2001). FEM principy a praxe metody konecnych prvku, Computer Press, Brno, 401 pp. Sabmeethavorn A. (2013). Studio Detailing and Patterning, IMS Dessau, Germany Senk, P. (2018). Capsules: a typology of other architecture, Routledge, London, 207 pp. Pottmann H 2007 Architectural Geometry Bentley Institute Press 1st edition Meades J. (2008). “Zaha Hadid: The First Great Female Architect”. Intelligent Life Magazine. Accessed April 18th, 2012. http://moreintelligentlife.com/story/zaha-hadid. Michaud J. (2011). “Zaha Hadid: The Lady GAGA of Architecture”. The New Yorker. Accessed June 25th, 2012.
J. Thulaseedas and R. J. Krawczyk, Möbius Concepts in Architecture, College of Architecture Illinois Institute of Technology Chicago, IL, 60616, USA, info on https://arch.iit.edu/ C. J. Mathews, Some Novel Möbius Strips, Mathematical Teacher, Vol. 65, 1972, p. 123-125. R. Osserman, How the Gateway Arch Got its Shape, Nexus Network Journal 12 (2010) 167–189. P. Calter, Gateway to Mathematics Equations of St. Louis Arch, Nexus Network Journal. https://www.danieldavis.com/a-history-of-parametricOct.2006 Sabah Shawkat©
110 Motro, R. (2003). Tensegrity. Structural Systems for the Future; London, UK. Imprint: Butterworth-Heinemann, ISBN: 9780080542348
111 1. Design of reinforced concrete members (2000) 2. Železobetónové konštrukčné sústavy (2002) 3. Deformation behaviour of reinforced concrete beams (2011) 4. Konštrukčné projekty (2014) 5. Structural design I (2014) 6. Structural design II (2015) 7. Architektonika (2015) 8. Structural design III (2015) 9. Structural projects (2016) 10. Element design to shape a structure I. (2016) 11. Element design to shap e a structure II. (2017) 12. Inžinierske drevené konštrukcie (2017) 13. The art of structural design (2017) 14. Lightweight steel structures (2018) 15. The art and engineering of Lightweight Structures (2019) 16. Art in/of Nature (2020) 17. Application of structural system in building design (2020) 18. Structural icons for architects (2021) 19. Construction in architecture (2022) 20. Lightweight structures from the perspective of formfinding geometry (2022) 21. Free Form Geometry in Architecture (2022) Other books by Sabah Shawkat Sabah Shawkat©
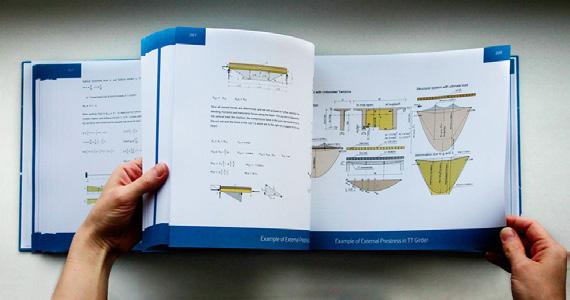
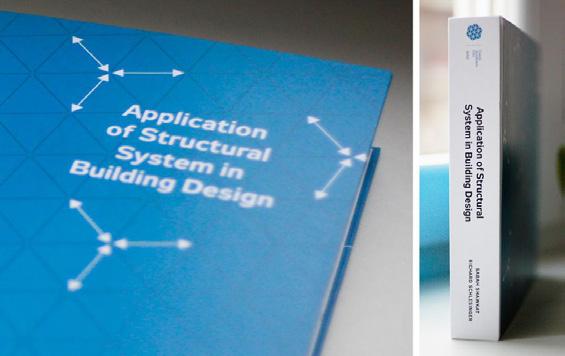
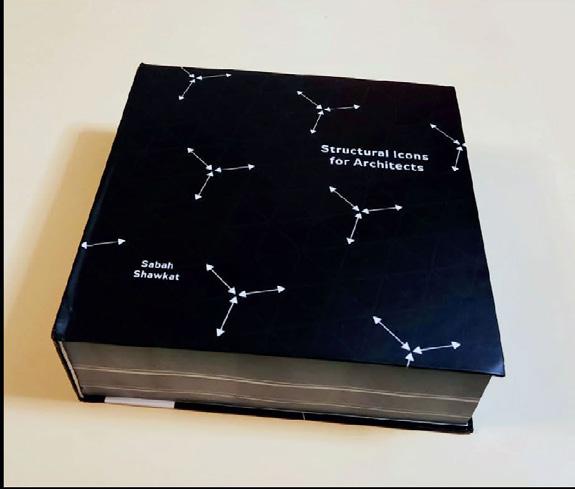
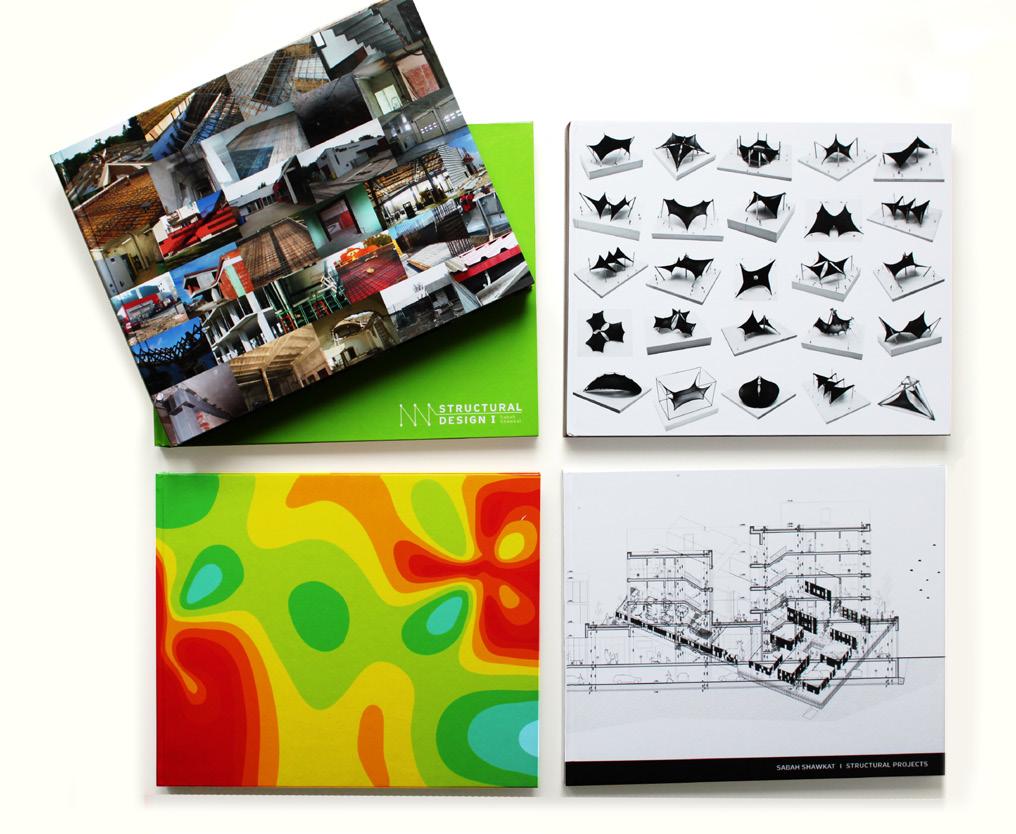

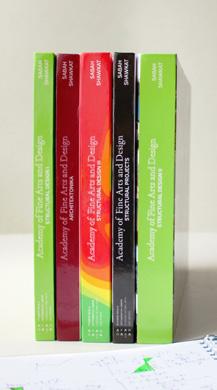
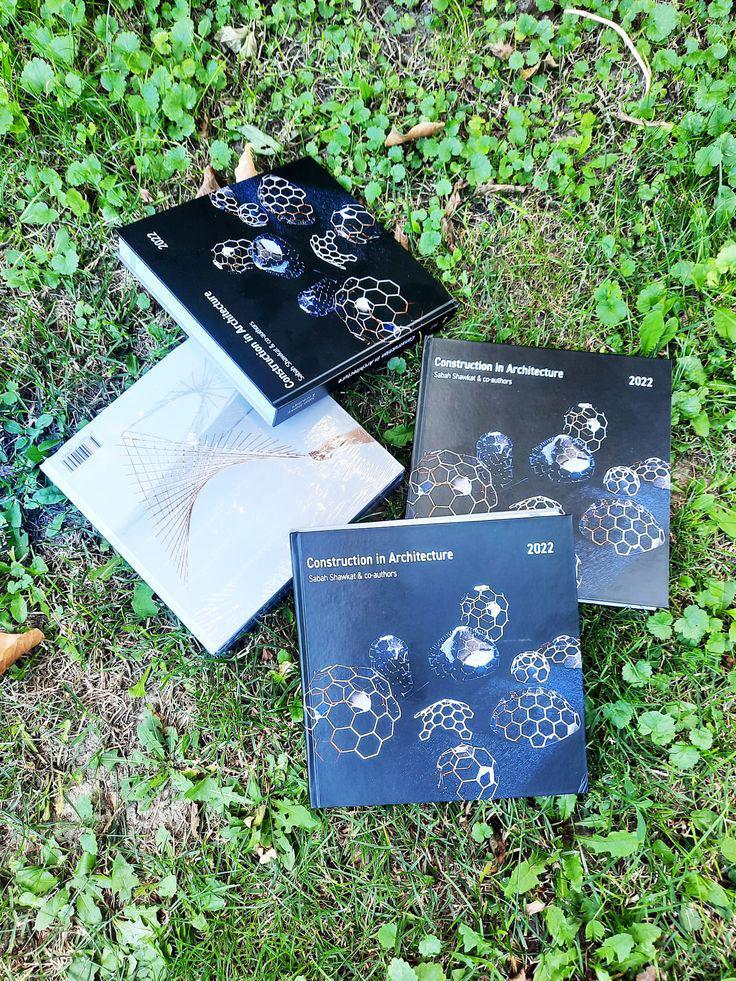
LIGHTWEIGHT STRUCTURES FROM THE PERSPECTIVE OF FORM-FINDING GEOMETRY © Assoc. prof. Sabah Shawkat 1. edition Bratislava 2022 ISBN 978-80-570-3676-0 Sabah Shawkat©
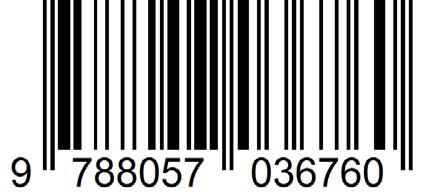
Sabah Shawkat©
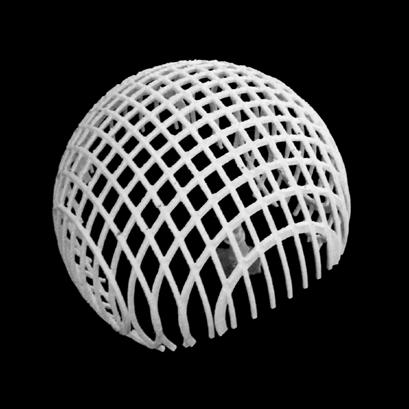
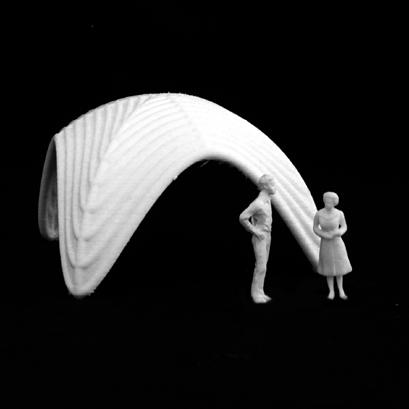
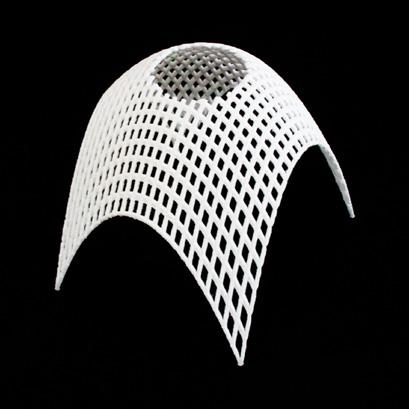
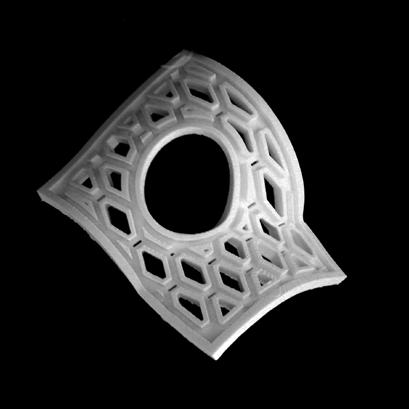
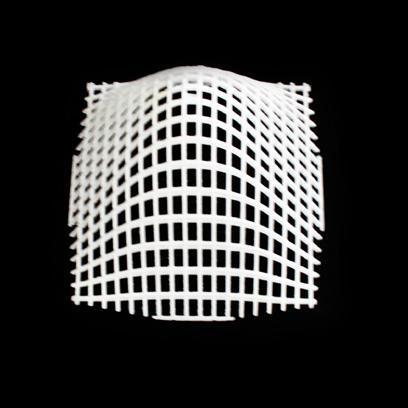
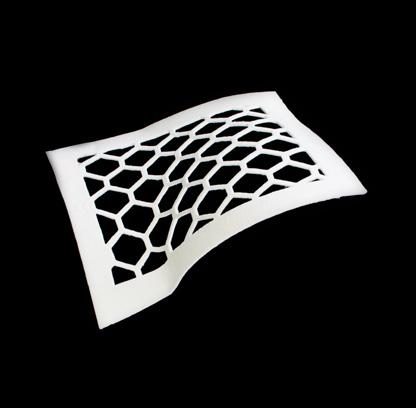
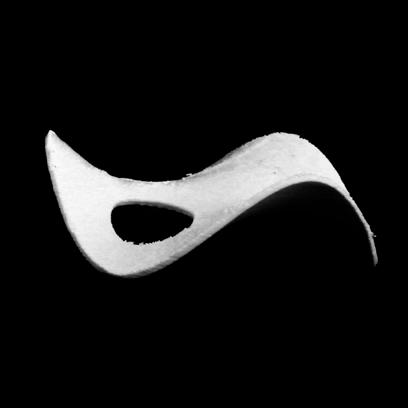
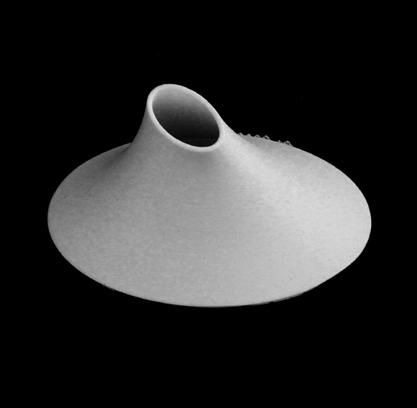
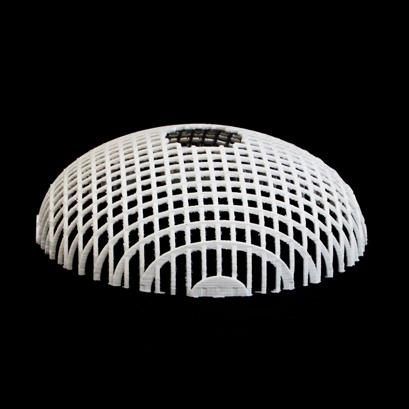
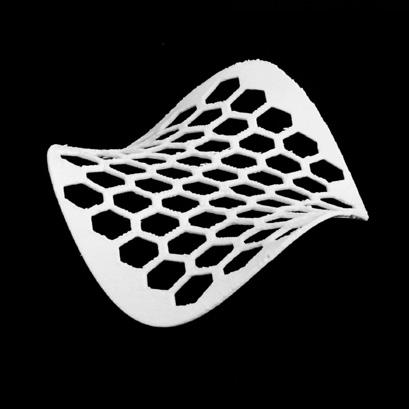
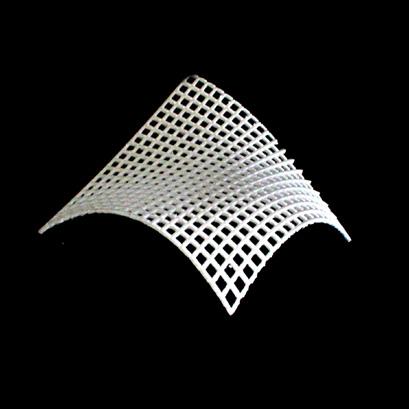
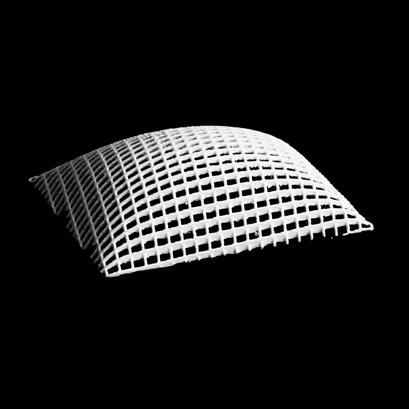
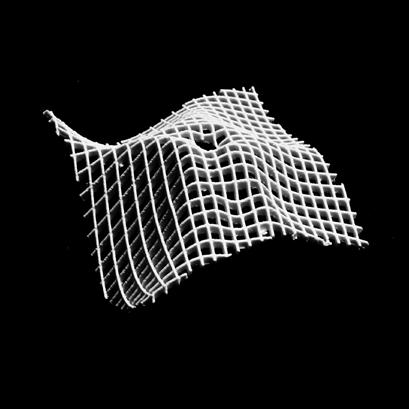

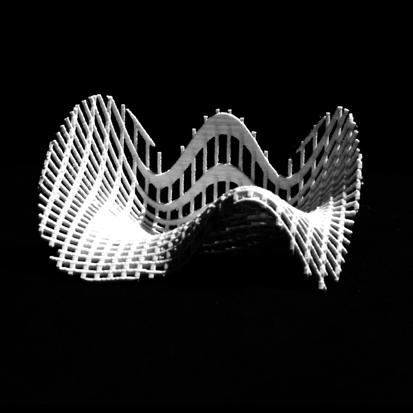
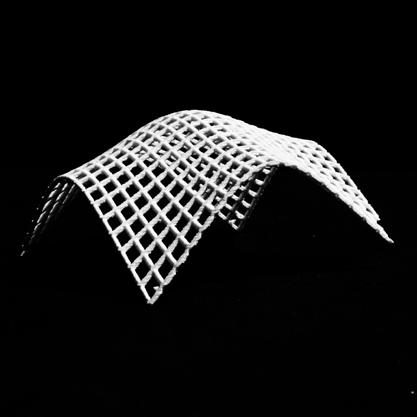
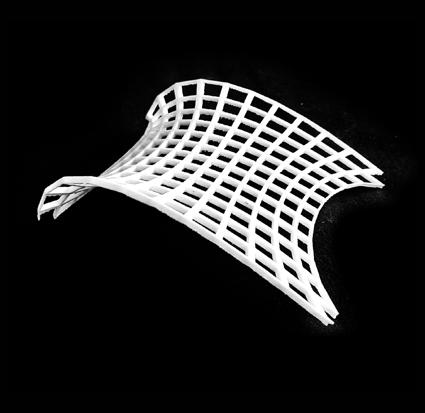


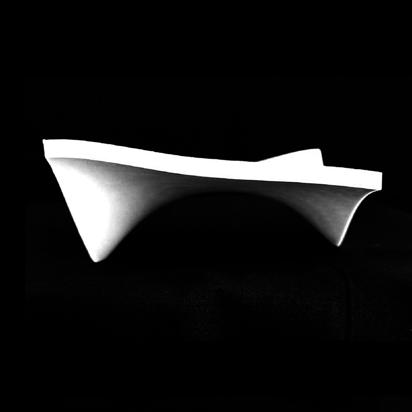
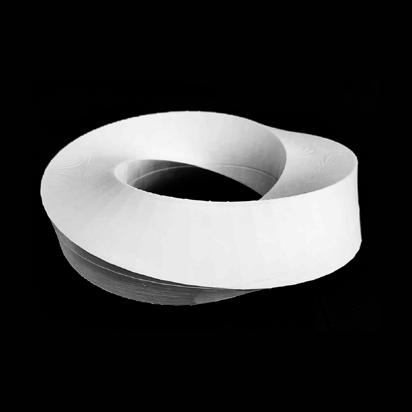
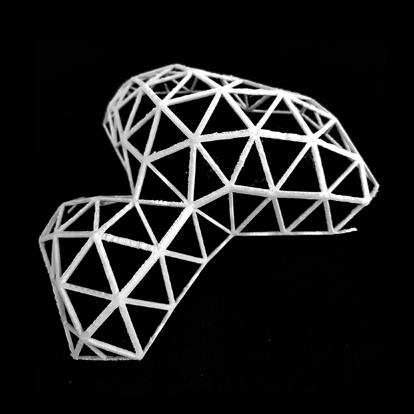
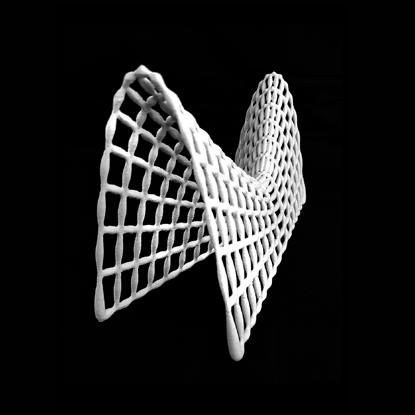
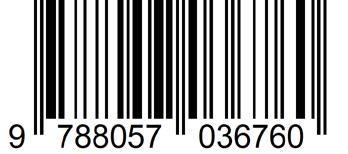