Most gums and thickening agents are prone to forming agglomerates when added to liquid: As soon as the gum get wet, it forms a gel, trapping dry powder particles inside an outer gel coating. Turn to

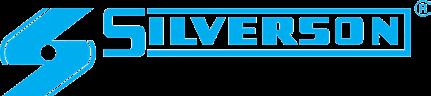
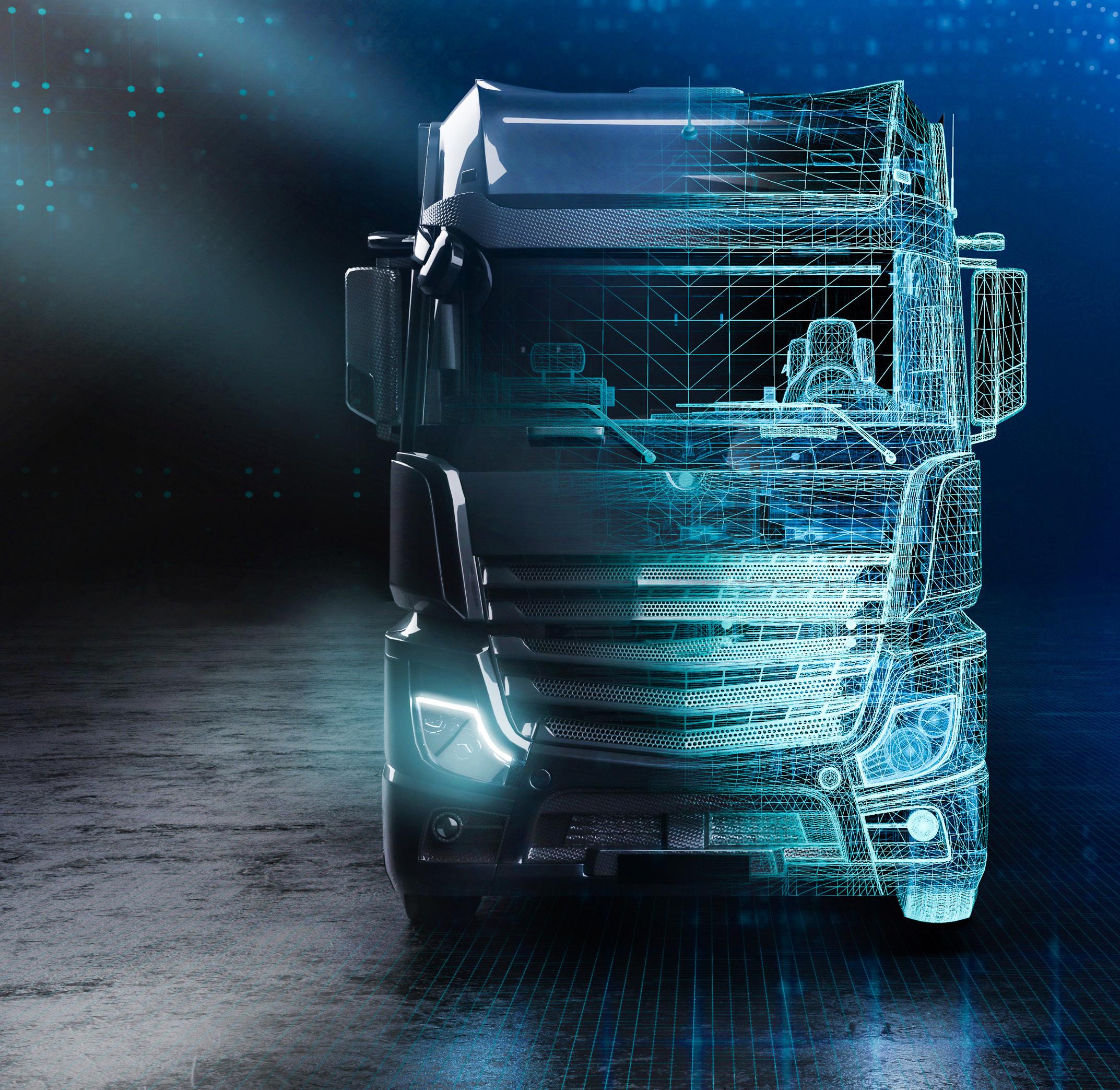
May
June
July
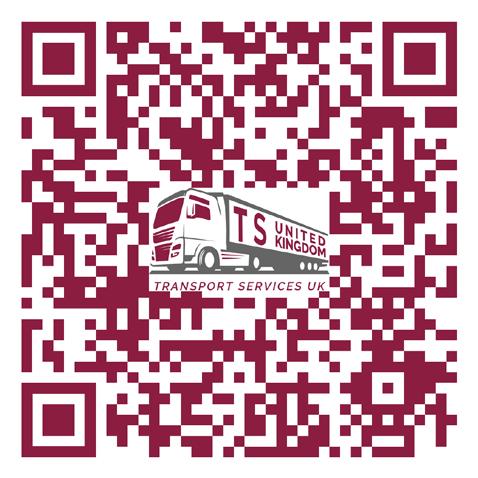
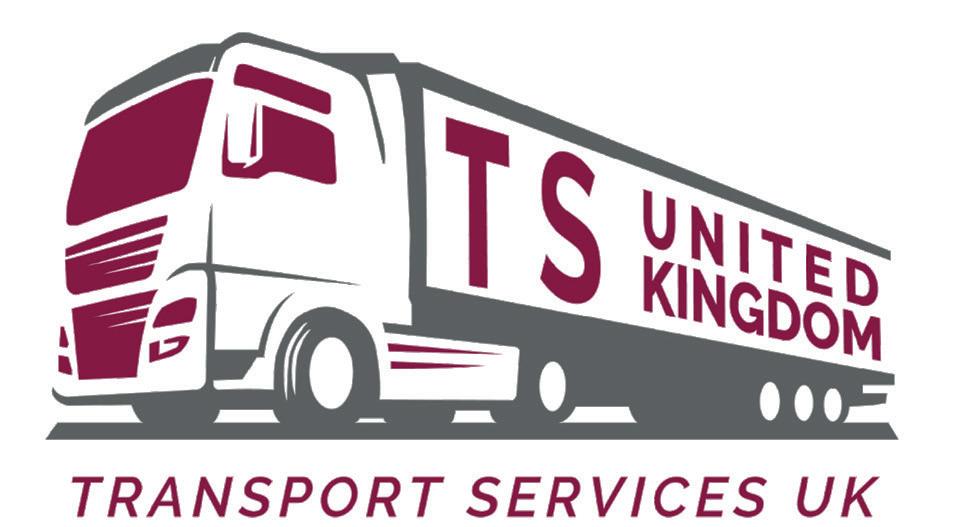
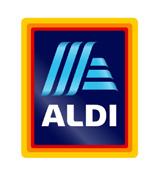

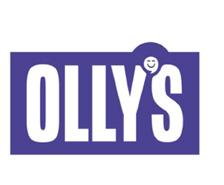
Most gums and thickening agents are prone to forming agglomerates when added to liquid: As soon as the gum get wet, it forms a gel, trapping dry powder particles inside an outer gel coating. Turn to
May
June
July
EDITORIAL:
Multimodal
PPMA
Automate UK
Harford control
Neo PR
RSK Group
ADVERTISEMENT SALES:
KIMBERLEY READ (Advertisement Sales Manager) GINA MADDISON
AMANDA WALMSLEY
EVELYN WOOLSTON
STUART TURNBULL - Studio Manager
RACHEL RILEY - Designer
WALTONS PUBLICATIONS LTD 46 HENEAGE ROAD, GRIMSBY N.E. LINCOLNSHIRE DN32 9ES
Kimberley Read at: kimberley@ foodanddrinknetwork-uk.co.uk or Gina Maddison at: gina@foodanddrinknetwork-uk.co.uk
foodanddrinknetwork.co.uk
Meet the positive new meat and dairy free burger from food procurement expert allmanhall Less than 6% emissions* compared to a standard beef burger.
As part of allmanhall’s commitment to challenging food systems and supply, and encouraging change that is responsible, sustainable and nutritious, alongside the growing trend for reduced or meat-alternative foods, the concept of a new burger has evolved. Leading this development was allmanhall’s procurement and sustainability director, Mike Meek in collaboration with partners Redefine Meat, Wildfarmed, Bidfood, Applewood Vegan and Rubies in the Rubble.
To create a tasty meat-free alternative burger there has been considerable research into what ingredients can be used, with the challenge to not just ensure a similar tasting product but also create something that is nutritionally beneficial. The result was the The Brighter Burger. With Redefine Meat’s premium patty, coupled with vegan mayo from Rubies, all held within the Wildfarmed bun, they’ve created one of the best meat alternatives in taste, texture, look and smell.
Following a recent audit, leading warehousing and distribution specialist Bretts Transport has been awarded a BRCGS AA grade for Storage and Distribution.
The BRCGS is a globally recognised food safety and quality certification program that sets the benchmark for food manufacturers and suppliers –ensuring that they are compliant to the Global Food Safety Initiative. As one of the UK’s most experienced operators for food packaging and distribution, the coveted AA grade is a significant achievement for Bretts, which last year celebrated 90 years in business. Over the decades the business has stood the test of time priding itself on continually demonstrating a high level of commitment to providing a best-in-class service to its customers, with the BRCGS AA accreditation being a testament to this longstanding ethos. In order to help achieve the BRCGS AA standard, Bretts took the strategic decision to appoint Jo Doyle as its new HSEQ Manager – who arrived with an extensive track record in achieving BRCGS and ISO standards at her previous places of employment. Hitting the ground running, Jo managed to support the team in obtaining the AA grade within just 3 months of her joining. Along with implementing and maintaining quality management standards, in her new role Jo has been tasked with ensuring the well-being and progression of all staff, as well as being responsible for driving forward solutions to reduce the company’s carbon footprint.
Simon Brett, Managing Director at Bretts Transport commented:
“The importance of achieving a AA grade cannot be overstated. In line with our long-standing ethos of delivering excellence in every aspect of the business we felt obtaining the standard was fundamentally important in order to reflect that commitment and dedication to new and existing customers.
“In order to comply with the accreditation, we placed huge emphasis on cleanliness and hygiene within the warehouse where we both store and handle ambient, packaged food products, bulk ingredients and packaging materials. In an environment where retailers demand precise adherence to quality, consistency, and service, our BRCGS AA offers customers the assurance that we are committed to maintaining high operational standards.
“A significant thanks must go to Jo Doyle, our HSEQ Manager, who played an integral role in increasing our BRCGS rating to AA standard. Her expertise and experience in supporting the business with the implementation of HSEQ processes and initiatives, will enable us to not only ensure a safe and healthy working environment but also to maintain all-important standards such as the BRCGS AA as well as enhance the best practice of our team members.”
Jo Doyle is looking forward to the challenge ahead. She said: “We have so far managed to make significant inroads in achieving the BRCGS AA grade, as well as to streamlining the company’s HSEQ processes and policies.
“Ultimately, the business is passionate about doing things in the correct manner and understands both the short term and long-term benefits in investing in health and safety, staff training, sustainably and various standards, which is hugely refreshing. Over the coming months I will now set my sights on fine-tuning Bretts’ processes and policies in order to deliver improvements for the business as well as further develop its much-valued staff.”
For more information visit: www.brettstransport.co.uk
At the heart of The Brighter Burger is the Redefine Meat patty. When Tess Warnes, allmanhall’s dietitian, reviewed this before the pilot trials, she was impressed with it’s nutritional content. It is fortified with vitamins and minerals including 3mg B12, and 4.2mg Zinc. As well as offering 11g protein it also impressively contains 5g fibre, a key compound not found in animal proteins, which helps keep digestive systems healthy.
Find out more and see all emissions claims* and nutrition data here: https://allmanhall.co.uk/starting-a-burger-revolution Understand more about allmanhall: https://allmanhall.co.uk/
Europe’s packaging one-stop shop, H-Pack Packaging is adding to its line of white, paper souffle pots with a kraft version. With no other catering disposables supplier offering alternative colour souffle pots, this addition places the popular packaging expert firmly ahead of the competition once again.
Both the kraft and the white pots are available in a full range of sizes, from one ounce through to 5.5 ounce, in cases of 20 x 250 and 15 x 200, depending on product size. The souffle pots are expected to appeal to those caterers and ‘to go’ outlets that already use kraft disposable food boxes and bags and want the pots to complement the rest of their packaging offering.
Head of merchant sales for H-Pack, David Martin comments: “We are aiming to introduce products that offer valid alternatives to our customers and their customers; challenging what is available elsewhere in the market so that H-Pack maintains its pole position as a market leader with vision.” H-Pack is the UK arm of leading, global food packaging brand, Hotpack and, as such, can offer bespoke custom products, working with pioneering new materials and state of the art machinery and technology, along with its internationally recognised, premium lines.
To order the souffle pots, email sales@h-packglobal.com For further information and for details on the products H-Pack manufactures and supplies, visit https://h-packglobal.com/ or call +44(0) 1978 855595.
If you would like to see your Newsworthy articles , regarding the Food & Drink Industry, published in the next issue of ‘Food & Drink Network UK’ email:
graphics@waltonspublications.com
Your release will also be placed on our website: foodanddrinknetwork.co.uk
...and on our Social Media and online Platforms
Jangro, the largest network of independent janitorial distributors in the UK and Ireland, is proud to present its new Catering & Hospitality Supplies 2024/25 catalogue. Boasting a fresh new look, the latest edition is the ultimate caterer’s companion, offering a wide range of quality brands and choice at competitive prices.
Enabling establishments to keep up to date with trends, the catalogue offers all the equipment and supplies required to stir up positive customer experiences. From front of house to back of house, casual to fine dining, the latest crockery and table presentations to environmentally friendly catering disposables, Jangro’s new Catering & Hospitality 2024/25 catalogue has it all. Jangro is committed to becoming a more sustainable business and helping its customers reach their own green goals. This new edition, therefore, offers a plethora of eco-conscious products, from food packaging containers, which are recyclable, compostable, and fully bio-degradable, to Jangro’s award-winning and innovative ntrl range of vegan cleaning solutions. The ntrl portfolio comprises 13 products ideal for cleaning surfaces in a variety of environments, from kitchens through to washrooms. Registered
The BCMPA – The Association for Contract Manufacturing, Packing, Fulfilment & Logistics, is helping US food producers from the state of Colorado find their ideal outsourcing partners in the UK for a range of manufactured food and drink goods.
Faced with distribution issues for their products in overseas markets, the Colorado Department of Agriculture’s (CDA) International Marketing & Business Development Team initially contacted the BCMPA to help build better relationships in the UK. Colorado’s farmers, ranchers and food processors grow, process and market over $15 billion worth of products each year, with goods marketed to more than 115 countries around the world. However, when exporting packaged products directly from the United States, producers often experience problems in effectively getting their goods to market. Following their introduction, conversations were held between the BCMPA and CDA at the IFE Manufacturing exhibition, with the Association showing how it could help US brands find effective third-party outsourcing partners in the UK.
“We were very impressed with the BCMPA’s resources, in particular its comprehensive website which has the capability to search for contract manufacturers according to specific requirements,” explained Ashley Warsh, part of the CDA’s International Markets & Business Development team. “It is also reassuring that all members are known by the BCMPA, which confirms that businesses are operating to the highest standards. Having a collaborative approach between industry associations and governing bodies is proving to have great benefits to trade for both sides.”
The partnership is already bearing fruit, with a Colorado sauce manufacturer Thunder Snout due to launch a new barbeque sauce into the UK later this year thanks to BCMPA member Sauce Shed. In addition, the CDA team is spearheading a visit for UK contract manufacturers to Colorado, Wyoming and New Mexico in June. The objectives of the trip are for US food manufacturers and brands to meet the UK companies and discuss opportunities for establishing manufacturing and distribution in the country. At the same time, the visitors from the UK will be able to meet their US counterparts to identify synergies and develop cross fertilisation of ideas and products, potentially helping them to extend their manufacturing overseas.
BCMPA CEO Emma Verkaik commented: “This is a very exciting initiative, and we are delighted to be working with the CDA and promoting the many benefits of UK contract manufacturing for US food producers. Working with a reputable supplier can make all the difference to successfully launching products and as an Association we work hard to help overseas companies find their perfect outsourcing partner in the UK market. We are very much looking forward to building on the initial successes with the CDA and building a long-term partnership that benefits our members. This is a great example of collaboration and one we are keen to continue developing.”
For more information visit: www.bcmpa.org.uk
Email: info@bcmpa.org.uk
with The Vegan Society’s Vegan Trademark, all formulas are 100% biodegradable, contain zero petrochemicals, and can reduce the product’s carbon footprint by up to 85%.
The catalogue features all the essentials required for catering, leisure and hospitality businesses – including kitchen hygiene, utensils and equipment, cleaning chemicals, tableware and glassware, washroom supplies, work wear, janitorial and waste management.
For more information, or to order a free copy visit Jangro.net or call 01204 795 955.
The Artist Collection initiative by ABK6 celebrates the alliance between art and cognac, the two passions of Francis Abecassis. Since 2019, this collection has annually showcased the talent of a local artist, offering a unique and creative inter-pretation of the ABK6 spirit and its Single Estate Cognac.
These bottles are genuine limited edition works of art, illustrating the authenticity and modernity of ABK6 Cognacs. This collection provides a unique sensory experience, where visual pleasure merges with palate satisfaction. Each edition of the Artist Collection tells its own unique story — a true delight for art and Single Estate Cognac enthusiasts.
A work centered around the Charente region and its treasures. To echo her artistic work on the heritage of the Charente region, Audrey Sedano has reinterpreted the building of the Vaisseau Moebius, emblematic of both the city of Angoulême and the comic strip, for the “Reserve” bottle. The typography “Cognac ABK6” as a motif refers to the art of calligraphy used in the cellars on the barrels of cognac. The colors symbolize the territory: the blue of the Charente River, the green of the vineyards, and the orange of cognac. Lastly, the blend of linocut for grounding in tradition and craftsmanship (a nod to Angoulême’s papermaking past), and digital work, a reference to the decidedly modern present of the Cité des Valois (between comics and animation), encapsulates the richness of the region.
• Shiny and luminous amber colour.
• Intense and elegant aromas combining notes of apple, pear, candied plum, cinnamon and vanilla with delicate woody touches.
• Beautiful balance between roundness and structure, spicy, vanilla and woody aromas revealing lingering fruity notes.
Vocation Brewery announces a new visual identity and packaging system which is set to roll out this month.
UK-based Vocation Brewery, which is known for its range of bold and flavourful craft beers, has unveiled a brand refresh that signals a major step in the next phase of its future growth.
Brewing a breadth of beers, including exemplary IPAs, pale ales, stouts, and barrel aged beers, Vocation Brewery crafts distinctive beers with interesting aromas and flavours that invite conversation.
Vocation Brewery was founded in 2015 by John Hickling, who left his job to follow his calling and brew the big, flavourful beers that he loves. From its humble beginnings in an old chicken shed high up on a hill, 1000 feet above sea level, Vocation Brewery has grown strongly and now brews over 10 million pints a year which are sold nationally in the UK and throughout the world.
Its range of popular brews include its original Classic IPA ‘Life & Death,’ the Everyday Hazy Pale Ale ‘Crush Hour’ and Gluten Free Session IPA ‘Heart & Soul,’ as well its modern take on a British classic ‘Bread & Butter’. The new visual identity and packaging system brings to life the personality and style of creative illustrations that celebrate the process of crafting bold and beautiful beer.
Vocation Brewery’s brand refresh aims to increase on-shelf standout whilst building a distinctive, recognisable brand which is accessible to a wide range of consumers who are seeking something new and exciting. The new look is underpinned by the brewery’s belief that great tasting, quality beer should be for the many and for every occasion.
Vocation Brewery has reintroduced its eye icon which pays homage to the brand’s heritage and looks to the future. The eye is prominent on the packaging to make it stand out on shelf in supermarkets and in bars, symbolising Vocation Brewery’s focus on crafting beers of substance.
Created by Turner Duckworth in partnership with illustrator Brian Steely, the new visual identity and packaging makes use of a bold and vibrant colour palette and illustrations to aid visual appeal and showcase the personality of each beer, whilst also establishing a clear and consistent brand identity that stands out from the crowd.
Tom Holmes, Head of Marketing at Vocation commented: “In today’s competitive landscape, standing out on-shelf and in bar is key, and our new creative direction boldly and distinctively positions Vocation Brewery’s desire to brew bold and flavourful beer for the many.
“Our brand refresh marks the start of an exciting new chapter for our business; it reflects our bold and flavourful beers and how we are continuing to push the boundaries to redefine the craft beer landscape. We’ve invested in the brewery to brew flexibly at scale, and it’s an exciting time for the business as we position ourselves for our next phase of growth, backed by an experienced team and a fresh new look that will stand out on shelf and is worthy of the bold and beautiful beer inside.”
Vocation Brewery’s rebrand is the latest phase in the business’s plans to lead the next phase of growth and development in craft beer in the UK under the leadership of beer industry veteran Gail Lumsden as Chair and CEO and experienced senior team with strong beer and drinks credentials.
Vocation’s new branding is set to roll out in May in major retailers and bars across the UK.
The beverage industry and food producing sector are intricate ecosystems that require sophisticated technology to ensure efficiency, quality, and safety in production processes.
One of the critical components in these industries is the filling and bottling technology, which includes a wide range of equipment and systems designed to handle various container types while maintaining product integrity.
Krones, a leader in this field, specialises in providing cutting-edge solutions for bottling lines, aseptic systems, block synchronised systems, and conveyors, addressing the diverse needs of these industries.
BOTTLING LINES FOR PET
Food and Drink Network UK, 133 x 186 mm, Intralogistik, CC-en33-AZ001 05/24
Bottling lines are crucial in the beverage and food producing sector as they determine the efficiency and quality of the packaging process. Krones offers advanced bottling lines tailored for different container types, including PET containers, glass bottles, and cans. Each of these container types has unique requirements and challenges, and Krone’s technology addresses these with precision:
Streamlined routing and processes combined with agile material flows that can be flexibly matched to changing production and dispatch requirements: System Logistics is the Krones Group’s expert team for innovative, fully automated solutions geared to optimising your intralogistics, warehousing and material-flow technology. krones.com
PET CONTAINERS:
Lightweight and Versatile: PET containers are popular due to their lightweight nature and versatility. Krone’s bottling lines for PET containers ensure high-speed filling while maintaining the structural integrity of the containers.
Customisation: These lines offer flexibility in terms of shape and size, allowing manufacturers to meet market demands effectively.
GLASS BOTTLES:
Quality and Aesthetics: Glass bottles are often chosen for premium products due to their perceived quality and aesthetic appeal. Krone’s technology ensures precise filling and capping to maintain the product’s premium quality. Durability: The robust design of these bottling lines handles the delicate nature of glass bottles, reducing breakage and wastage.
CANS:
Efficiency: Cans are preferred for their convenience and recyclability. Krone’s canning lines are designed for highspeed operations, ensuring minimal downtime and maximum output.
Consistency: Advanced systems ensure consistent filling volumes and secure sealing, crucial for maintaining product quality and shelf life.
In an evolving landscape of the beverage and food producing sector, advanced process and filling technology are crucial for maintaining a competitive edge and ensuring product quality.
Krones stands out as a specialist in this field, offering state-of-the-art solutions for bottling lines, and conveyors.
Rotronic, part of Process Sensing Technology (PST) and the specialised manufacturer of humidity and temperature instrumentation, has launched a combined Bluetooth Water Activity meter with smartphone and tablet app.
Called the AwEasy, the new stand-alone instrument is advanced, lightweight and compact, and is designed to produce extremely accurate reading simply and quickly – up to ten times faster than traditional devices. This makes it ideal for use by laboratory analysts, quality control teams and production staff who need to take spotwater activity measurements in the food, pharmaceutical, cosmetics and chemical industries.
The new AwEasy is the most recent addition to Rotronic’s existing range of water activity analysers, meters and probes. The company believes that it is the first of its type to offer both Bluetooth connectivity with the ability to use a smartphone or tablet app, to store and analyze data and then automatically output reports as pdf documents, for use in quality control and traceability regimes.
The AwEasy features a robust stainless steel and aluminum housing, measuring just 65mm tall and 68mm in diameter, with a topmounted color LCD display, indicator ring and single control button. The instrument also incorporates Rotronic’s latest humidity and temperature sensing technologies. These are capable of providing levels of accuracy to within plus or minus 0.008aw, which is far better than competing devices in the same price range, while ensuring exceptional repeatability and stability.
Set-up and operation is carried out via the iOS or Android compatible app, with measurement simply requiring a test name and batch number. Analysis is automatic and can be displayed in detail, as raw data or on a choice of charts, with reports being exportable as pdf or csv files.
The AwEasy has also been designed to minimize the time required for water activity measurements. These normally take up to 50 minutes, but with the AwEasy in Quick Function mode this time can be significantly reduced to around 5 minutes. Combined with the in-depth analysis reports, this enables the new AwEasy to offer considerable improvements in productivity, quality control and traceability.
In areas such as factory environments, where connectivity may be an issue, or where the use of Smartphones is prohibited, the new AwEasy can be used on its own. Control of each analysis can be carried out directly from the front panel, with data being displayed on the LCD control panel and then automatically uploaded once the smartphone is back within range.
As part of the PST group, Rotronic is able to provide a comprehensive range of technical and sales support services, including training, sensor calibration and repairs.
Compact, lightweight and mobile
• AW Quick for results in 4 – 5 min.
• Easy to use with display
• Also measures humidity and temperature
•
• Free smartphone app
Auto-report nction
The new AwEasy complements our range of water activity measurement devices perfectly. Measurement probes, penetration probes, laboratory benchtop and handheld devices can be combined flexibly according to your requirements. Bene t from the highest accuracy, e ciency, and easy calibration to optimize processes and ensure product quality. ProcessSensing.com
We human beings consume over 30,000 species of plants and animals. However, for the most part, we don’t know much about what’s in them. The Rockefeller Foundation initiated the Periodic Table of Food Initiative (PTFI) project with the aim of documenting the extensive variety of biomolecules present in food. Its longterm objective is to support enhancing agriculture, nutrition and health (Science Organisation).
It was great to see organisations helping to improve the transparency and traceability of food products for consumers. As consumers, however, we fortunately don’t need this level of detail before we eat or drink – we just need to know that it’s safe.
Which?, the consumer rights pressure group, has uncovered a surprising amount of inconsistent and misleading labelling. According to a survey of 2,011 UK adults, only 51% of shoppers considered the current origin information displayed on groceries to be useful (Food Manufacture).
For example, Aldi’s Crestwood bacon and cheese wraps are labelled as ‘made in Britain,’ while Lidl’s sausage rolls are made
with a mix of UK and non-UK pork, so these could contain port from anywhere, worldwide. The information on food labels is confusing and conflicting, leaving consumers struggling to obtain clear information about the origin of their food, especially in ultra-processed foods. Most of us would be more interested to know which parts of the animal are contained within our highly processed food, than where it came from.
Ultra-processed foods (UPFs) scored worse on food package labelling. UPFs typically contain more than five ingredients and have been linked to obesity and heart disease (BBC). Despite being perceived as
less healthy, these convenient options are chosen by consumers at least once a week, largely because they are convenient, readily available and taste good.
The research conducted by the EIT Food Consumer Observatory revealed that 67% of European consumers express discomfort when their food contains unfamiliar ingredients while 40% do not trust that ultra-processed foods are regulated well enough by authorities to ensure these foods are safe and healthy in the long term (The Grocer).
There is a clear knowledge gap between how manufacturers present ingredients and how consumers identify useful information on food labels. Whether it’s identifying potential allergens, verifying product origins, or understanding nutritional content, clear and reliable labelling is essential to support consumers in making informed and healthy decisions about the food they consume.
With increasing trends in healthy eating, more consumers might shy away from ultraprocessed foods, especially when they can’t obtain clear information on the food label. Providing consumers with clear labelling and guidance could help them better understand the food they eat and regain confidence in minimally processed foods. Packaging should indicate whether a food item is high in fat, salt and sugar, which are largely flavour enhancers, become addictive and contribute hugely to obesity and other long term health problems.
To ensure accurate and consistent labelling, we suggest that ultra-processed food manufacturers implement a systematic approach and adhere to regulatory guidelines. Here are a few steps manufacturers can take to achieve this:
• Ensure that your SKU master data is always up to date.
• Conduct regular audits: Periodically audit labelling practices and procedures to identify any deviations or non-compliance issues. Address any discrepancies promptly and implement corrective actions to prevent reoccurrence.
• Verify ingredient information: Conduct thorough checks to verify the accuracy of ingredient information before labelling. Cross-reference ingredient lists with supplier documentation and ensure that any allergens are correctly identified and highlighted.
• Utilise technology for accuracy: Consider implementing technology solutions such as barcode systems and automated label verification software, to minimise human error and ensure accurate labelling. These systems help streamline the labelling process, improve efficiency, minimise risks to consumer health and costly batch rejections.
At Harford Control, we always encourage Quality and Compliance first. Harford Compliance Solutions empower manufacturers to ensure consistently accurate labelling, precise product identification and matching. The safety and quality of products is ensured, whilst maintaining allergen control. Our compliance solutions include barcode inspection, vision inspection, autocoding, machine
integration and ERP/SAP connectivity, dependent upon the risks and needs of each application.
To maintain competitiveness in the food and beverage market, it’s crucial for UPFs manufacturers to take proactive steps to improve their labelling, ensuring the provision of accurate and consistent information on their packaging.
Where food and drink manufacturers face consumer health risks, product withdrawals, costly batch rejections or encounter any label compliance or appearance challenges, our specialists are here to offer guidance, provide the necessary audits and technology to enhance their quality control processes and install system solutions for ease of control and sustained product confidence.
As one satisfied client said,
“We now have the confidence to know that what goes out, stays out.”
Please reach out to us at info@ harfordcontrol.com or give us a call on +44 (0)1225 764461.
Multimodal 2024 celebrates 17 years of bringing together shippers and cargo owners with exhibitors and sponsors who can offer products and services to help them make their supply chains more efficient and more cost effective. Visitors attend to meet new suppliers, compare new routes and modes, source new products and ideas to improve their efficiency and to network with the industry.
Bigger and better than ever, Multimodal 2024 is already smashing records with over 275 exhibitors already signed up, including industry giants such as Amazon, CEVA Logistics, DP World, Hapag-Lloyd, Kuehne+Nagel, Maersk, Maritime Transport, Malcolm Logistics and Samskip Services. With expectations to exceed 300 exhibitors, this year’s event will offer unparalleled networking and business opportunities for the 12,000+ visitors over the three days of the show.
Multimodal is the one-stop shop for shippers and cargo owners to discover ways to move their goods more sustainably, efficiently and more cost effectively. The three-day show between 11-13 June 2024 at the Birmingham NEC, offers unique opportunities to make valuable face-to-face contact with new prospects and existing companies.
It’s free to visit Multimodal 2024, registering in advance is recommended, to save time on arrival, at www.multimodal.org. uk All the conference sessions are free to attend too and with 4 theatres there is something of interest to everyone.
You’ll be in great company as already registered are representatives from Sainsbury’s, Aldi, Whitworths, Nestle UK&I, Diageo, Lovering Foods, Rowan International, Bunzl Catering, Glanbia Nutrition, Crops UK, Kingsland Drinks, AB World Foods and Poundland to name just a few.
Multimodal works in partnership with the leading trade associations ensuring all aspects of the industry are served, also ensuring that relevant topics are covered in the free to attend conference sessions. Partner associations include Logistics UK, the Cold Chain Federation, the Rail Freight Group, The Chartered Institute of Transport and Logistics, the British International Freight Association, Institute of Export and International Trade, the United Kingdom Warehousing Association, and the Road Haulage Association.
A special highlight of the three days is the Multimodal Awards, which recognise outstanding industry-leading supply chain businesses and individuals. With seats for the awards have now sold out for the 11 June evening ceremony.
The 2024 Awards include some new judged Awards to continue the development and evolution of the event. The evening will be hosted by Kevin Keegan, an incredible host who brings enormous professionalism and fantastic humour. More information about the awards can be found at www.multimodal.org.uk/awards
The networking event you won’t want to miss! Be there for the Multimodal Mixer on 12 June. It’s a fun relaxed drinks reception open to all visitors and exhibitors, hosted by DP World on their stand in the Hall from 5pm, giving everyone a chance to mingle in a relaxed and fun atmosphere.
To find out more about attending, the awards, exhibiting, or sponsoring, visit www.multimodal.org.uk, or contact Robert Jervis, Director on +44 (0) 20 7384 7760 or robert.jervis@clarionevents.com
In less than 2 months time the two-day Automation UK opens its doors at the Coventry Building Society Arena in Coventry. The show, on 18-19 June, provides a fantastic platform for visitors to explore a wide range of the most up to date cutting-edge automation and robotics technologies and solutions. The content led seminar programme will be packed with thought-provoking presentations from leading industry experts which will provide visitors with a wealth of knowledge and inspiration for use in their businesses. There will also be an abundance of networking opportunities with over a thousand peers and experts which are expected to attend in June.
British Automation & Robot Association (BARA), organisers of Automation UK, are excited to reveal a leading industry expert as a keynote speaker.
Vanessa Loiola, the founder of Valoy Automation will talk about ‘Enhancing Robotic Cell Performance with Strategic Programming Solutions’ which explores those manufacturing companies that face the challenge of inefficient processes caused by outdated programming methods. Vanessa highlights the importance of modern solutions that can optimise robot functionality, reduce downtime, and increase productivity. She shares exciting benefits that implementation of strategic programming techniques can deliver to manufacturers. These can revolutionise their operations, achieving peak efficiency and competitiveness in today’s ever-evolving market.
BARA will soon be sharing more information about further inspiring speakers and sessions that will be part of the Automation UK seminar programme.
The two-day show, including the seminar programme, will act as a catalyst to motivate and encourage visitors to take the necessary steps to invest in these technologies and solutions. As well as this investment being important for the growth of the UK economy there are a number of other significant benefits to businesses, such as increased productivity delivered by automation and robotics performing repetitive and manual tasks. In addition, they can create a safer working environment and help solve labour and skills shortages. These benefits can ultimately deliver improvements in the financial performance of a business who commit to invest in automation and robotics.
“The real highlights have been seeing some of the newer technology, both in automation robotics side of the business and the vision side of the business, really giving that flexibility to the customers.”
Steve Banton, Global ProgramManager – Social Selling & Inside Sales, ABB Robotics
This comprehensive show will provide plenty to explore and experience. The show will be buzzing with around 50 well-known brands showcasing their latest innovative products and services, including robots, robotics systems, systems integration, automation control parts and systems, and sensor and machine safety. Visitors will be captivated by the live demonstrations and fascinating new product launches. These exhibitors will be keen to engage and interact with visitors about understanding their requirements and the benefits of adopting a particular solution as well as sharing their technical expertise.
Some of the founding exhibitors include ABB, Fanuc UK, Festo, Piab, KUKA Robotics UK, Schubert UK, and RARUK Automation.
The Automaton UK event will also provide plenty of exciting networking opportunities with leading industry experts, exhibitors and peers which provides a platform to develop sustainable and mutually beneficial business relationships.
One of the visitors to the Automation UK 2023, Shreyansh Agrawal, Founder at Kairos Diagnostics said:
“Coming to this event will help you grow your business, network and automate your way to the future.”
For more information, please visit: https://www.automation-uk.co.uk/
The annual Machine Vision Conference is renowned worldwide as the principal event that captures the very best in machine vision technology, from the latest cutting-edge industrial vision to innovative imaging technologies. This year’s MVC will be held between 18-19 June at the Coventry Building Society Arena where the MVC visitors will also have the unique opportunity to visit the co-located Automation UK which showcases the latest automation and robotics all under one roof.
Machine vision solutions have already been applied to many industries, from food, beverage and pharmaceutical to healthcare, automotive, traffic and transport. Implementing these solutions has been recognised as offering significant benefits to various businesses by enhancing process efficiency, which often results in improved financial performance.
The versatility and adaptability of machine vision technology can be used for automated inspection, object recognition and defect detection, which will in return minimise errors and reduce wastage. Through incorporating these solutions, businesses can streamline their operations, improve quality control and boost productivity. It is proven that in fast-growing industries, businesses who embrace and take advantage of these innovative machine vision solutions will benefit from improving their overall performance and competitiveness.
The MVC’s reputation to provide an impressive and comprehensive machine vision event attracts a diverse range of visitors, including those from big global brands. These companies are keen to discover the latest innovative solutions to enhance their businesses. The 2023 visitors included: Airbus, BMW, DeBeers, Jaguar Land Rover, McVities Cake Company, Mercedes AMG F1, Mitsubishi Electric, Morrisons, Nestle UK, Nissan, Ocado, Panasonic, Rolls-Royce, Siemens, Sony,
Tata Technologies, Tesco, The Co-Op, Unilever, Vodafone, and Warbutons.
The event organisers, UK Industrial Vision Association (UKIVA), which is part of Automate UK alongside British Automation and Robot Association (BARA), is anticipating over a thousand visitors during the two-day event. MVC will host more than 50 wellknown brands exhibiting their state-of-the-art products, services and solutions and over 40 technical presentations from leading industry experts. MVC is a ‘must attend’ event for visitors to expand their knowledge on machine vision.
Andrew Mark Peacock, Director at Peacock Technology Ltd visited the 2023 MVC and described it as: “A unique opportunity to meet suppliers and industry experts covering the full machine vison stack.”
There are many other compelling reasons to visit MVC which provides a perfect combination for existing vision users and engineers as well as educating those new to the world of machine vision. Visitors can explore the content packed event with plenty of opportunities to meet and connect with industry peers, talk to exhibitors who can directly help their businesses, see live demos, hear from industry experts about new machine vision technology, and captivating product launches.
Scott McKenna, Deputy Chief Operating Officer at Automate UK said:
“Last year’s Machine Vision Conference was a huge success. Co-located with the brand new Automation UK exhibition, and capitalising on the synergies that exists within these sectors, visitor numbers were at an all-time high. We very much look forward to growing the event this year, with even more informative content and innovative technology on display.”
Irrespective of visitors’ level of expertise in machine vision, the event will have something for everyone. Anyone planning to attend MVC in June can register for a free pass by visiting: https://www.machinevisionconference.co.uk/
In just five months’ time the UK’s largest processing and packaging machinery exhibition, PPMA Show, will return to the NEC in Birmingham between 24-26 September 2024.
This pre-eminent show is renowned for bringing together a broad range of innovative technologies and solutions, delivering an abundance of inspiring content rich seminars as well as providing plenty of networking opportunities. All of which provides a superb platform for visitors to be inspired and expand their knowledge and understanding of the latest developments in the processing and packaging industry.
Many businesses are already reaping the benefits of incorporating cutting-edge processing equipment, packaging machinery, industrial robotics and machine vision systems into their operations.
Automated solutions can transform operations in many businesses. For example, in food industries some of the fantastic benefits achieved include reduced costs, increased efficiency, quality improvements, and reduced downtime and turnaround. These benefits go a long way to delivering the necessary returns on the original investment costs.
In addition to the food industry, there are a number of other sectors where businesses take advantage of adopting some of these advancing technologies and solutions into their operations. These include pharmaceuticals, beverages, confectionery, micro-brewery and distilleries, pet food, baking, luxury goods, chemical processing, and building materials and supplies.
Regardless of the industry sector that visitors are in, PPMA Show delivers outstanding opportunities for them to explore the latest advancements in production, manufacturing and packaging
amongst over 300 well-known brands. These companies will be showcasing their most up to date cutting-edge innovative solutions and offering live demonstrations of their most up to date technology. This provides visitors with a great chance to see, experience, explore, review and assess products and services before making any investment commitments.
Visitors will also have a unique opportunity to discover a complete production line in action from start to finish, from labelling, filling and packaging to processing, robotics, automation and industrial vision systems.
One of last year’s visitors from Nestle said: “Fantastic day here at the PPMA Show, lots of suppliers that we work with. Some really innovative solutions, and a lot of relatable things for us, so we are taking lots of lessons home.”
The PPMA show organisers, Automate UK, are pleased to announce that Richard Allen, Senior Applications Engineer at Mitsubishi Electric and Janet Bellamy from Lincoln University National Centre for Food Manufacturing are guest speakers as part of the seminar programme at the three-day show.
The show features a thought-provoking seminar programme delivered by leading industry experts. These fascinating seminars will provide visitors with a wealth of information, ranging from innovative technologies and solutions to current and future industry trends. All of which they can take away and consider for use in their business.
PPMA Show provides visitors with plenty of face-to-face meeting opportunities with exhibitors, experts, new contacts and peers. These are invaluable in that they can be mutually beneficial for sharing knowledge, industry insights, problem solving and developing new and existing relationships.
Established over 35 years ago, PPMA Show takes centre stage when it comes to showcasing processing and packing machinery. The organisers of the show have indicated that this year’s show will include some exciting new developments which will be revealed nearer the date…
For more information, please visit: https://www.ppmashow.co.uk/visit
Julian Ware, UK & Ireland Sales Manager for ABB Robotics, looks at how robotic automation can tackle some of the key global challenges faced by the food and beverage industry.
The article also looks at how some of the latest developments are helping to overcome traditional barriers to adoption. The global food business is worth over $9 trillion U.S. dollars in 2024, according to Statista*, and is expected to continue growing at a CAGR of 6.58% every year until 2028.
The main factors behind this rise are the dual drivers of increasing population and urbanisation. At present, the Worldometer population counter reads at over 8.1 billion and it is expected to reach 9.7 billion by 2050**. The most explosive growth will be heavily concentrated in emerging markets like India and Mexico, where up to 70 percent of the population are under 30 years old.
The global population is also increasingly urban, with more than half of us now living in cities***. That includes over 80% of people in high-income countries and between 50 and 80% in middle income markets, Lower-middle and lower-income populations have yet to hit the 50% urban mark, but that is changing fast. This shifting population is most obvious in the world’s largest cities, the vital engines
of economic growth and where millions of former rural inhabitants arrive each year. For instance, Delhi had a population of 30.29 million in 2020 and is projected to reach 43.35 million by 2025.
To meet the demands of a growing global population, food production needs to almost double by 2050. Clearly that implies producing more, but the hidden issue is really food waste. If the root causes of waste across the production and distribution process could be tackled, there would be enough food to comfortably feed a global population of nine billion.
A Circular Economy, suggested by some as part of the solution, would address 30-40% of global food production lost or wasted every year. In direct contrast to the traditional economic model of take, make and waste, the Circular Economy approach seeks to minimise waste and pollution. Efforts are concentrated on maximising product value, re-purposing at the end of use and optimising water usage by driving supply chain resiliency.
Digitalisation is increasingly offering a
potential solution to the problem of food waste. The capabilities of Big Data mean that when sources as varied as consumer buying patterns and smart sensor readings provide manufacturers with huge datasets, the data can be collated, analysed in detail and used to create actionable insights. This can have a significant impact in optimising food production and minimising waste by ensuring that supply more closely matches demand.
Beyond data and analytics, the food and beverage industry is being further transformed by digital culture, with consumers playing an increasing role in shaping new trends. Consumers are sharing their food on social apps such as Instagram and Pinterest, pursuing authentic dining in and out of the home, and reading food blogs to discover the latest products and dining experiences. Social media has also transformed public accountability. Businesses are used to seeing consumers ‘calling out’ food and beverage brands on Twitter, their complaints occupying the same space as traditional digital marketing. As a result, manufacturers are having to become more responsive, both in terms of replying to complaints and factoring
feedback into their production to help improve customer satisfaction.
Consumer tastes
While mega-trends such as population growth and food waste will have a fundamental impact on the future of the food and beverage industry, recent consumer trends are having a more immediate impact on the sector.
Meat free
Euromonitor reports that consumers in a number of key markets are continuing to reduce meat consumption, with Europeans showing the strongest shift****. Globally over one fifth of consumers are now trying to limit their meat intake. The rise of alternative meat consumption is a prime example of a win-win scenario, benefitting both consumers and the planet. As flexitarian, vegan and vegetarian diets increase, this clearly reflects consumers’ growing awareness of the environmental impact of livestock farming, coupled with health concerns surrounding excessive red meat consumption.
A focus on health
Consumer interest in health and wellbeing has led to the rise of so-called functional foods.
Products like these are typically marketed as being rich in nutrition with ingredients beneficial for health. This is in direct contrast to ‘free-from’ products which remove ingredients like gluten, lactose or sugar to address consumers needs like weight loss, allergies and intolerances.
Changing priorities
There are significant structural changes occurring at the retail stage of the value chain. Global consumers are challenging ‘Big Food’ and the hyper/supermarket model and moving towards eCommerce and convenience formats. As well as this, consumers are demanding authentic alternatives alongside their convenience purchases.
Put simply, consumers will buy products that feel true to the story they tell about themselves. While this change is directly driven by factors like changing lifestyles, connected technologies, and urban living, it is also linked to a growing consumer sophistication and awareness of practices that are perceived to be either unethical or unsustainable.
How is robotic automation helping?
Taken together, all these factors will increasingly require food and beverage producers to put in place flexible production processes that can respond quickly to shifts in consumer tastes and demands. From farm to fork, robotic automation can help to address this challenge. Correctly implemented, robotic automation can help to deliver several benefits including adaptability, improved production output, consistent quality and reduced wastage, and – importantly, with growing shortages of people wanting to work on food and beverage lines – improved
quality of work and job satisfaction.
In terms of worker performance, the COVID-19 pandemic had a fundamental impact across all industries, none more so than the food and beverage sector, where it led to a step-change in levels of automation. For example, the British Automation and Robot Association (BARA) found that, while overall industrial robot sales during 2020 in the UK were up 7.5 percent on 2019 figures, sales to food and beverage businesses rose by 35 percent. Though food manufacturers are often portrayed as laggards in the adoption of robotics, compared with other sectors, this performance took the food and beverage industry to second place - in terms of the number of robots installed - behind the high-investing automotive sector.
More recently, the widening recognition of automation benefits is continuing to drive increased adoption across the food industry. Growth in the adoption of food industry robotics looks set to be particularly marked, with a forecast compound annual growth rate of 6.16% from 2024 to 2028, according to BARA*****. There’s also expected to be a rise in the integration of AI and machine learning systems for such purposes as product scanning and issue identification.
Supporting the move to automation
While many companies are realising the benefits of robotic automation, there are barriers to some businesses fully embracing this technology. In a recent survey of UK food producers undertaken by ABB, the main barriers to adoption were cited as:
• My employees would prefer to work with people – 42%
• Belief that robots are too expensive and therefore the investment isn’t justified – 42%
• Uncertainty / lack of knowledge about how robots or automation can be used in food and beverage production –33%
Regarding employee hesitancy, it’s important to remember that the best robotic automation projects are ones that combine the inherent benefits of robots such as speed, flexibility, accuracy, and consistency, with the adaptability, imagination, and intelligence of people. When introducing robotic automation, it is important to see how robots could be used to address both the strengths and weaknesses of the workforce. The chosen solution should ideally augment their capabilities and empower them, giving them both a tool that they can use to do their job more effectively and a potential avenue for improving their skills, such as through programming the robot or working on other tasks.
Addressing the cost of investment has been a major focus of the automation industry as of late. Where hardware is concerned, this has seen the development of specific dedicated options for the processing, handling and packing of food and drink products. Specifically designed to meet both the hygiene and fast handling requirements inherent in food and beverage production processes, options such as fast picking Delta robots and robots for operations such as slicing and handling of raw meat are opening new options for faster, more efficient production.
In terms of uncertainty and concerns around the complexity of robotic automation, robot manufacturers have devoted considerable efforts on developing technologies and approaches focused on ease of use, with particular attention devoted to creating easy user interfaces that can be used by those with little or no experience of robots. ABB’s Wizard easy programming software for its cobots and small IRB 1100 industrial robot, for example, uses Blockly, an open-source visual coding method that presents programming language or code as interlocking blocks, which can be used to quickly create robot application programs without the need for specialised training or expertise in robot programming. Finally, in terms of technical knowledge, robots are continuing to evolve through AI, enabling robots to learn as they work on the job in hand. Some automation companies, ABB included, are also enhancing their training and support offerings to assist with lack of in-house expertise.
The challenges of meeting the future food and beverage demand to sustain a growing population are vast and multifaceted. However, the good news is that these challenges are increasingly being matched by developments in robotic automation that are already allowing companies to take a huge stride forward in terms of increasing productivity while minimising waste.
go.abb/robotics
ABB’s new FlexBuffer™ answers your wishes for fast, flexible and efficient order handling. Discover how FlexBuffer™ can help you transform your order processing and delivery in a wide range of industries and applications including food and beverage, logistics, healthcare, restaurants, consumer packaged goods and retail applications. Find out more here: https://bit.ly/ABBFlexBuffer
This technical paper discusses the unique advantages offered by electromagnetic vibratory feeders in the context of scale feeding applications. A comparative analysis is presented, drawing parallels between electromagnetic feeders and alternative technologies--particularly bucket elevators, belt conveyors, and mechanical vibratory feeders-to emphasize the superiority of electromagnetic feeders for scale feeding.
In this issue we discuss the unique advantages offered by electromagnetic vibratory feeders in the context of scale feeding applications. A comparative analysis is presented, drawing parallels between electromagnetic feeders and alternative technologies--particularly bucket elevators, belt conveyors, and mechanical vibratory feeders-to emphasise the superiority of electromagnetic feeders for scale feeding.
This technical paper discusses the unique advantages offered by electromagnetic vibratory feeders in the context of scale feeding applications. A comparative analysis is presented, drawing parallels between electromagnetic feeders and alternative technologies--particularly bucket elevators, belt conveyors, and mechanical vibratory feeders-to emphasize the superiority of electromagnetic feeders for scale feeding.
Importance of Scale In-feed Systems in Industrial Operations
In diverse industrial settings, precise control and maintaining a consistent material flow are fundamental requisites. Scale feeding systems are purposefully designed to fulfill this role, ensuring a controlled and dependable on-demand supply of bulk material to the scale. The significance of scale feeding is evident in industries such as food processing, pharmaceuticals, agriculture, and others where uniform material delivery is crucial. Scale feeding serves as a vital component for upholding product quality, meeting capacity requirements and minimizing waste.
In diverse industrial settings, precise control and maintaining a consistent material flow are fundamental requisites. Scale feeding systems are purposefully designed to fulfill this role, ensuring a controlled and dependable on-demand supply of bulk material to the scale. The significance of scale feeding is evident in industries such as food processing, pharmaceuticals, agriculture, and others where uniform material delivery is crucial. Scale feeding serves as a vital component for upholding product quality, meeting capacity requirements and minimizing waste.
In diverse industrial settings, precise control and maintaining a consistent material flow are fundamental requisites. Scale feeding systems are purposefully designed to fulfill this role, ensuring a controlled and dependable on-demand supply of bulk material to the scale. The significance of scale feeding is evident in industries such as food processing, pharmaceuticals, agriculture, and others where uniform material delivery is crucial. Scale feeding serves as a vital component for upholding product quality, meeting capacity requirements and minimizing waste.
Selecting the right scale feeding equipment hinges on properly identifying the unique needs of the application.
Electromagnetic vibratory feeders, renowned for their swift and steady control over material flow, emerge as optimal choices. While valid alternatives like bucket elevators, conveyor belts, mechanical feeders, and augers exist, the ultimate decision centers around the importance of maximising scale packaging and operational efficiencies.
Selecting the right scale feeding equipment hinges on properly identifying the unique needs of the application. Electromagnetic vibratory feeders, renowned for their swift and steady control over material flow, emerge as optimal choices. While valid alternatives like bucket elevators, conveyor belts, mechanical feeders, and augers exist, the ultimate decision centers around the importance of maximizing scale packaging and operational efficiencies. Bucket Elevators and Belt Conveyors: A Traditional Choice for Scale Feeding
Selecting the right scale feeding equipment hinges on properly identifying the unique needs of the application. Electromagnetic vibratory feeders, renowned for their swift and steady control over material flow, emerge as optimal choices. While valid alternatives like bucket elevators, conveyor belts, mechanical feeders, and augers exist, the ultimate decision centers around the importance of maximizing scale packaging and operational efficiencies.
Often adopted for scale infeed applications, bucket elevators and belt conveyors serve as mechanical conveying systems, facilitating the transport of bulk material through a production line and elevating product to the top of a vertical form fill and seal (VFS). Operating in various configurations, including vertical, inclined, or horizontal, bucket elevators and belt conveyors can be found across light industries such as food processing, agriculture, and chemicals. However, this type of equipment has clear limitations which include cycling on/off rapidly, as is typical for scale infeed applications. For efficiently handling large-scale feeding applications that involve elevating materials to a weighing scale, a best practice is to employ either a bucket elevator or a belt conveyor to transfer the materials to the electromagnetic feeder for discharge.
Often adopted for scale infeed applications, bucket elevators and belt conveyors serve as mechanical conveying
Often adopted for scale infeed applications, bucket elevators and belt conveyors serve as mechanical conveying
The vibratory action of the feeder will help even out the surges of
material as is typical from the discharge of a bucket elevator or belt conveyor. By cycling the feeder on and off, materials can be promptly and uniformly supplied on-demand, resulting in an increase in scale efficiency and weight accuracy.
Mechanical or motor driven vibratory feeder or conveyor designs are periodically utilized for scale in-feed applications. While these units may have the same sanitary tray designs of electromagnetic feeders, they are challenged by the rapid on/off cycling often required for scale infeed applications.
By: Rob Yandrick Eriez® Global Product Manager—VibratoryMotor driven designs typically utilize eccentric shafts or out-ofbalance motors that rely on centrifugal force to vibrate the feeder tray. Instantaneously starting or stopping the supply of material is not feasible due to the inherent inertia of the rotating shaft, which requires a gradual acceleration or deceleration process. Therefore, achieving immediate material supply or halting the material infeed is not possible. An electromagnetic feeder bypasses this challenge altogether. Upon supplying or cutting off power to the feeder, it promptly initiates or ends the feeding process without delay.
When employed in scale feeding operations, electromagnetic vibratory feeders offer several distinct advantages over alternative technologies:
This technical paper discusses the unique advantages offered by electromagnetic vibratory feeders in the context of scale feeding applications. A comparative analysis is presented, drawing parallels between electromagnetic feeders and alternative technologies--particularly bucket elevators, belt conveyors, and mechanical vibratory feeders-to emphasize the superiority of electromagnetic feeders for scale feeding.
these units offer full customisation options to cater to specific needs, such as incorporating longer tray lengths, screens for fines removal, enclosed or covered trays, screens, and extended tray overhangs, enabling them to feed even the largest radial scales in a highly sanitary manner, among other features.
5. Advancements in Design: Ongoing technological advancements have propelled vibratory feeding solutions, particularly in the food processing sector, to unprecedented levels of sophistication. Manufacturers are consistently adapting to address industry demands and overcome sanitary challenges, thereby providing both safety and efficiency in feeding operations.
Manufacturers are consistently adapting to address industry demands and overcome sanitary challenges, thereby providing both safety and efficiency in feeding operations.
Feeder
The table below provides a comprehensive side-by-side analysis of the advantages and disadvantages associated with electromagnetic feeders and bucket elevators in the framework of scale feeding operations.
In diverse industrial settings, precise control and maintaining a consistent material flow are fundamental requisites. Scale feeding systems are purposefully designed to fulfill this role, ensuring a controlled and dependable on-demand supply of bulk material to the scale. The significance of scale feeding is evident in industries such as food processing, pharmaceuticals, agriculture, and others where uniform material delivery is crucial. Scale feeding serves as a vital component for upholding product quality, meeting capacity requirements and minimizing waste.
The table below provides a comprehensive side-by-side analysis of the advantages and disadvantages associated with electromagnetic feeders and bucket elevators in the framework of scale feeding operations.
• Offers rapid on/off cycling, which enhances operational efficiency and process control
• Delivers a uniform product feed and precise feed rate control
• Little to no maintenance required with proper care
• Opportunity to screen and remove fines prior to scale
• Provide versatility in handling various materials, from the powders to large granules
• Offer the most sanitary
1. Highly Controlled Flow: Electromagnetic vibratory feeders are designed to deliver a highly controlled flow of materials on-demand into downstream processing and packaging equipment, ensuring the scale systems attain maximum accuracy and efficiency. The material feed rate of electromagnetic feeders is adjustable from 0-100% with the feeder controller. This offers another means of controlling the flow of material to the scale.
Conclusion
Making informed decisions between electromagnetic feeders and alternative technologies in scale feeding operations requires a comprehensive review of your expectations and overall process. Electromagnetic feeders, distinguished for prioritizing consistency, precision, and adaptability, emerge as the most robust option overall for scale feeding. However, it's crucial to acknowledge that there is no one-size-fits-all solution. For a complete understanding of the optimal solution for your application, consider collaborating with a trusted manufacturer like Eriez. Their team is ready to assess your unique needs and offer tailored support.
2. Swift and Precise Material Flow: These feeders propel material utilizing an upward and forward motion. The extent of the motion is adjustable and effectively regulates the material flow on the tray. Advanced electromagnetic feeders, such as those offered by Eriez, excel in adjusting feeding rates to meet dynamic demands
3. Wide Range of Material Handling: Electromagnetic feeders can handle virtually any bulk material, from micron-sized particles to bulky chunks. Operated with precision controls, they ensure accurate and reliable control in various applications. The versatility of electromagnetic feeders in accommodating a wide array of material types makes them particularly well-suited for packaging lines that deal with diverse products, such as those found in co-packing companies.
4. Customis able Options: Manufacturers like Eriez provide standard electromagnetic feeder models that are capable of handling a wide range of feeding applications. Furthermore,
In the face of evolving industrial requirements, this analysis advocates for a continuous and all-inclusive reassessment of industrial processes. More often than not, departing from conventional approaches proves to be the best strategy for sustaining progress and enhancing process efficiency.
Making informed decisions between electromagnetic feeders and alternative technologies in scale feeding operations requires a comprehensive review of your expectations and overall process. Electromagnetic feeders, distinguished for prioritizing consistency, precision, and adaptability, emerge as the most robust option overall for scale feeding. However, it’s crucial to acknowledge that there is no one-size-fits-all solution. For a complete understanding of the optimal solution for your application, consider collaborating with a trusted manufacturer like Eriez. Their team is ready to assess your unique needs and offer tailored support.
For technical inquiries and personalized guidance on selecting the ideal vibratory equipment for your specific application, reach out to Eriez' dedicated technical team at (814) 835-6000 or via email at sales@ eriez.com.
About Eriez®
In the face of evolving industrial requirements, this analysis advocates for a continuous and all-inclusive reassessment of industrial processes. More often than not, departing from conventional approaches proves to be the best strategy for sustaining progress and enhancing process efficiency.
Selecting the right scale feeding equipment hinges on properly identifying the unique needs of the application. Electromagnetic vibratory feeders, renowned for their swift and steady control over material flow, emerge as optimal choices. While valid alternatives like bucket elevators, conveyor belts, mechanical feeders, and augers exist, the ultimate decision centers around the importance of maximizing scale packaging and operational efficiencies.
Established in 1942, Eriez is a global leader in separation technologies. Our commitment to innovation has positioned us as a driving market force in several key technology areas, including magnetic separation, flotation, metal detection and material handling equipment. The company’s 900+ employees are dedicated to providing trusted technical solutions to the mining, food, recycling, packaging, aggregate and other processing industries. Headquartered in Erie, Pennsylvania, USA, Eriez designs, manufactures, and markets on six continents through 12 wholly owned international subsidiaries and an extensive sales representative network. For more information, visit www.eriez.com.
For technical inquiries and personalised guidance on selecting the ideal vibratory equipment for your specific application, reach out to Eriez’ dedicated technical team at (814) 835-6000 or via email at sales@eriez.com.
The Advantages of Electromagnetic Feeders for Scale In-feed Applications | 3
Often adopted for scale infeed applications, bucket elevators and belt conveyors serve as mechanical conveying
Most gums & thickening agents are prone to forming agglomerates when added to liquid:
As soon as the gum gets wet, it forms a gel, trapping dry powder particles inside an outer gel coating. These agglomerates are sometimes called fish eyes because of their gelatinous appearance.
In using traditional mixing equipment such as conventional agitators due to their low shear mixing capability. Their inability to ‘break’ into these agglomerates can leave material undiluted or partially hydrated in the mixture and needing to be removed. This may have to be done by filtration, but this is wasteful and time consuming, and as a result, many formulations contain unnecessarily high levels of gums to compensate for the poor yield. This not only increases raw material costs, incorrect dispersion of these functional ingredients can also adversely affect the appearance, texture and shelf life of the finished product. Premixing the gum with other powdered ingredients before adding to the water is often carried out to reduce the formation of agglomerates, but this is only partially successful and in itself adds to process time.
However, if you can disperse the agglomerates, rather than filtering them out, then you will achieve the full yield from your ingredients and reduce processing time and costs.
This can be done by using a high shear rotor/stator mixer. The positive mixing generated by the high shear workhead will rapidly disperse agglomerates, ensuring all the powder is exposed to the surrounding liquid, resulting in an agglomerate-free dispersion within minutes.
This is achieved by the multi-stage mixing/ shearing action of the rotor stator workhead: The high speed rotation of the centrifugaltype rotor creates a powerful suction which draws the gum and liquid into the workhead, eliminating rafting on the surface of the vessel. The powder and liquid are intensely mixed inside the workhead and then forced out through the holes in the stator, which subjects the materials to intense but targeted mechanical and hydraulic shear. Any agglomerates which may have formed are broken down as they are forced through the precision engineered gap between the rotor and stator. The mixture is projected back into the body of the mix.
In a short mixing cycle all of the material passes many times through the workhead, progressively reducing the particle size and exposing an increasing surface area to the surrounding liquid, accelerating the hydration process, maximising yield of the raw materials. This means the filtration stage can be eliminated. Using this method of mixing, many products can be reformulated with reduced gum content, cutting raw material costs.
Silverson offers a range of High Shear mixers from laboratory to full scale production which are ideal for rapid and efficient hydrating gums and thickeners, producing an agglomerate-free dispersion batch after batch.
The offering from Interfood Technology’s Bakery Division has been extended with a staple piece of equipment for the production of baked goods – the oven.
Interfood has signed a partnership deal with world renowned oven manufacturer Salva to represent the San Sebastian based family-owned company in the UK. This will cover the whole range of deck, rotary and fixed rack convection ovens, along with ancillary equipment including retarder provers, mixers and blenders.
The range offers options to cover the requirements of retail craft bakeries through to semi-industrial operations, with electric ovens which are characterised by their low energy use, realising typical savings of £700 per year, per deck. The modular ovens are custom built, with the potential to configure individual decks for different applications.
Consistency of bake is a fundamental focus in the manufacture of the ovens on site at Salva’s factory in the Basque region of Northern Spain. The deck ovens feature ceramic heaters which hold the temperature, resulting in a loaf with a crusty finish all over. The convection ovens use a heated and static air circulation system that achieves uniform baking by avoiding hot and cold spots. The controls are also designed to enable high quality baking time and time again, with the smart touch control panel developed by Salva to be user-friendly and intuitive, offering useful information such as energy consumption data, warnings and alarm screens.
James Fitch, Interfood’s Bakery Divisional Manager, comments –
“the build quality was one thing that struck us when we visited Salva to discuss a potential partnership. Salva have focused on building well made, robust, energy efficient ovens, with a high quality appearance, and their experience and heritage in this area allows them to have a complete understanding of the requirements of the baking process. Their range offers an oven for all product types. In recent years they have focused on adding a range of ancillary equipment to support their offerings in this area, to become a complete one stop shop for bakers. We are delighted to be working with Salva, their company spirit and commitment to putting customers first mirroring our own, and we look forward to discussing how we can offer bespoke solutions based around one of the most important pieces of equipment in the production of quality baked goods.”
Salva has been manufacturing ovens since 1943 and was the first to launch a modular oven into the Spanish market. It is now one of Europe’s ten largest manufacturers and is in its third generation of operation by the Llordés family.
Frank Teixeira (left), Salva’s Export Area Manager for UK and Ireland, finalises the new partnership with James Fitch, Interfood’s Bakery Divisional Manager.
Commenting on the new partnership, Frank Teixeira, Export Area Manager for UK and Ireland of Salva, said –
“We are thrilled to partner with Interfood, a company that shares our commitment to delivering topnotch solutions tailored to the needs of bakeries. Our ovens, built with precision and innovation, are designed to elevate the baking experience, ensuring consistency and quality every time. Together, we look forward to empowering bakeries across the UK with our state-of-the-art equipment.”.
In a new packaging development partnership, SN Maschinenbau and Südpack have developed an overall concept for the in-house production of stand-up pouches with spouts, which is designed for the packaging of paste and liquid products. The concept is aimed at food manufacturers and bottlers who previously use premade spout bags and will be presented at Anuga FoodTec 2024.
makes handling much easier and allows staff to process a larger number of pouches more efficiently, for example because there is no need for timeconsuming separation of the rails. The low-maintenance machine works highly efficiently and, thanks to its compact design, can also be used in production environments with limited available floorspace. This means it can be set up flexibly either directly on the filling machine
“TNA’s case packing systems have enabled us to improve operational efficiency, redistribute manpower and future-proof our operations.”
Andrew McManus, Manufacturing Manager, Majans
Majans’ partnership with TNA solutions delivers 140% throughput increase in 12 months with the TNA ropac®
Building on its ongoing relationship with TNA solutions, Majans leveraged the all new tna ropac® 5 technology to automate its case packing operations. At a capacity of 200 bags per minute, and featuring a bag conditioner, case packer, case erector and checkweigher, it is the fastest case packing system on the market today, with the smallest footprint. Since its deployment it has helped to deliver an impressive 140% throughput increase in just 12 months.
Established in 1984, Majans produces over 2 million cases of snacks each year across a range of 53 products. The company has ambitious growth plans, and with a tough labour market and volatile supply chains to navigate, it needed a trusted partner to help increase throughput and reliability, enhance uptime and mitigate risk. Manufacturing Manager Andrew McManus had already experienced TNA solutions in operation during his time at Mars and was reassured when Majans’ owner, Kam Raniga, selected the company to help futureproof operations.
“I’d seen TNA baggers working perfectly after 40 years of service, and I knew we were on track when we made the decision to partner with TNA at Majans. With a TNA flavouring system and tna robag® baggers already in place, we knew we would benefit from the interchangeable aspects of a TNA solution for case packing - particularly from an electronics perspective, and also the consistency of the HMI interface for our technicians. Introducing tna ropac® 5 systems has enabled us to improve operational efficiency, redistribute manpower and future-proof our operations as we look to continue our growth path.”
Majans currently uses around 70% of the TNA ropac® capacity
of 200 bags per minute, but through working with TNA solutions the company has ensured that future increases have been firmly factored into the equation. Since its introduction in February 2023, throughput performance has increased by 140% and uptime by 15%. From a sustainability perspective, the tna ropac® 5 is also able to accommodate the company’s plans to move to paper-based packaging in 2024, supporting its sustainable development plans without impacting production speeds.
“Just five years ago, Majans regularly had between 28 and 35 people on a single shift, bagging, mixing and case packing,” continued Andrew.
“Today, with the help of TNA solutions, that same factory operates with just 10-11 people per shift at outputs up to 6.9 times greater than before the automation process began. Casual jobs have been transformed into stable, full-time employment contracts, and technicians and maintenance crews have also been upskilled to effectively service and support these systems at a higher technology level.”
Speaking about the strategic partnership between the two companies, Thiago Roriz, Chief Operating Officer at TNA solutions said:
“In recent years, we have further strengthened our market leadership through sustained innovations, delivering true business value to our valued customers, such as Majans. We are extremely grateful to Majans for choosing us as their trusted partner, to support their goals as they focus on their expansion strategy.”
To read the full case study on TNA solutions’ partnership with Majans, visit www.tnasolutions.com.
Amcor has opened its European Innovation Center in Belgium. The facility will partner with brands and retailers from across the region to design packaging that delivers better results for consumers and the environment alike.
Amcor (NYSE: AMCR, ASX: AMC), a global leader in developing and producing responsible packaging solutions, has expanded its packaging innovation hubs around the world. In addition to existing centers in the US, South America and Asia Pacific, the company has now opened its Amcor Innovation Center Europe (AICE) in Ghent, Belgium. The AICE will pioneer new material technologies to make packaging more sustainable and performant, while focusing on designs that stand out in shops and increase ease-of-use for consumers.
“The opening of the Amcor Innovation Center Europe is a significant investment towards more sustainable, circular, and innovative packaging,” said Michael Zacka, President Amcor Flexibles Europe, Middle East, and Africa “The center brings together the brightest minds in packaging design, material science and state-of-the-art technology to offer our customers a complete brand solution, from concept to commercial launch.”
In its Innovation Center Europe, Amcor supports brands from concept to shelf using its Catalyst™ approach. This flexible, collaborative, and creative co-development methodology creates packaging solutions that take into account a brand’s market, consumer needs, sustainability and recyclability requirements, and customers’ existing production lines.
To support this end-to-end collaborative process, the AICE facilitates a range of activities:
• The Material Science Center creates innovative packaging materials that can drive down packaging’s carbon footprint; for instance, by introducing recycle-ready mono-material solutions that can match the performance of common mixed-material solutions; or switching to bio-based and recycled polymer alternatives. The centre also supports developments in high-barrier paper packaging and vapor-deposited nanocoating. In the analytical labs, new materials are tested using the most advanced techniques.
• The Customer Engagement Center supports collaborative sessions and boasts an observation room for consumer focus groups. Packaging appeal and usability can be tested in an on-site retail simulation area, plus in kitchen, living room and bathroom settings where consumers and marketers alike can interact with packaging. The on-site prototyping lab can quickly create different packaging solutions for test participants to try out.
• The E-Commerce Lab tests and certifies packaging according to ISTA 6 standards, to validate packaging for shipment through Amazon and other ecommerce distribution chains.
• The soon-to-be-added Packaging and Recycling Test Center will house small-scale packing lines which mimic brands’ own packing lines for in-house machine trials. Recycling equipment will allow Amcor to evaluate packaging for ease of recyclability in the real world.
“We want to create packaging that consumers like, and that is better for the environment,” said Noemi Bertolino, Vice President Research & Development. “The packaging needs to look appealing, and be easy to open, portion and close. It also needs to be suitable for current and future collection, sorting and recycling infrastructure. At the AICE, we can test packaging against these requirements. For example, in our Customer Engagement Center, we can test whether a child-resistant push-through blister pack for pharmaceuticals is easy for an adult with arthritis to open.”
Amcor has set ambitious sustainability goals for itself. It has pledged to develop all its packaging to be recyclable, compostable or reusable by 2025, and to significantly increase its use of recycled materials. In line with this sustainability commitment, the Amcor Innovation Center Europe is housed in a building that is designed and built according to BREEAM sustainability certification standards.
Site photo Christeyns Food Hygiene facility at Winwick Quay, Warrington
Christeyns Food Hygiene has been awarded the prestigious EcoVadis Gold Medal for its commitment to sustainability and responsible business practices.
EcoVadis is the world’s largest and most trusted provider of business sustainability ratings, creating a global network of more than 130,000+ rated companies. It evaluates companies’ sustainability performance across various criteria. This Gold Medal achievement for Christeyns Food Hygiene underlines the firm’s dedication to environmental stewardship, labour practices, ethical conduct, and sustainable procurement.
As part of the evaluation performance, the business is meticulously assessed across these categories, with evaluation of company policies, procedures, and key performance indicators (KPIs).
This award places Christeyns Food Hygiene in the top 5% of companies worldwide that are recognised with this esteemed Gold Medal.
Warrington-based CFH manufactures premium hygiene products and along with its partners supplies solutions for the safe cleaning and disinfection of food and beverage plants and food retail businesses across the country. Recognising the critical role that cleaning and disinfection protocols play in upholding food safety
management systems, the firm is committed to enhancing clients’ operations whilst leading the sector in sustainable business practices.
“At Christeyns Food Hygiene we have long been conscious of the impact that our products and services have on the environment and on our customer’s operations,” states Chris Bayliss, CFH UK Sales Director.
“This award is recognition and validation of the long-term efforts we have in place to ensure and support food safety and hygiene in our customer’s sites in a sustainable way for now and the future.”
Christeyns Food Hygiene is part of the international hygiene group, Christeyns, with headquarters in Ghent, Belgium. The group has subscribed to the Responsible Care Global Charter committed to a corporate leadership culture that safeguards people and the environment, strengthens chemicals management systems, influences business partners, promotes safe management of chemicals, engages stakeholders and contributes to sustainability. The company has also signed up to the UN Global Compact initiative.
www.christeyns.com
As the UK appears to be moving towards mandatory food waste reporting coupled with a focus on landfill diversion (and a Scottish landfill ban on biodegradable municipal waste next year), the food and drink sector could be well served by investing in anaerobic digestion, says Synergie Environ Sector Director Gavin Ramsey.
This, he says, ensures that waste becomes a valuable resource, powering renewable energy and driving greater self-sufficiency and compliance.
The food and drink industry is one that has evolved to gain a much greater appreciation of the waste it creates and it has achieved considerable success in minimising this. However, despite the achievements and greater clarity, challenges remain. This is particularly evident in the dairy and distillery sectors. What is true across the entire food and drink industry, however, is that producers, their clients, consumers and shareholders have a strong preference for a process that puts any waste that cannot be avoided to work, generating renewable energy. These are enviable green credentials to highlight on any annual report or tender document.
Anaerobic digestion is a process that enables carbon-rich biodegradable wastes to be broken down into a less degradable solid or semi-solid matrix (known as digestate). The technique involves degradation of the waste with the use of bacteria in a low-oxygen environment, which in turn produces heat and biogas.
Biogas is a methane-rich gas that can either be cleaned and injected into the national gas grid network as a non-fossil-fuel gas or used directly onsite to generate renewable electricity. When used for the latter, this enables some or all of the electricity and heat requirements for manufacturing or industrial processes that produce high-organic-content wastes or by-products to be met, as well as significantly reducing the costs of waste disposal to landfill. This is, of course, not the only benefit of the digestate created. It is also valued, depending on the original feedstock, as an agricultural improvement and renewable fertiliser. It is equally important to note that digestate from feedstock that has been segregated at source (such as organic waste from a food manufacturing process or spent lees from whisky distillation) is capable of achieving a recognised quality standard (PAS 110), meaning that it is no longer considered a waste but rather a fully recycled product, opening up its use to a much wider range of applications.
Creating an on-site green waste management system with such an anaerobic digestion plant has many benefits, especially for businesses in more remote areas, such as distilleries, that wish to process their waste close to the source. This is, of course, also in line with the European Waste Framework Directive. But regardless of location, the legislative direction of travel strongly indicates greater regulatory attention to how all food waste is managed and, in an industry with significant energy requirements, it makes sense to invest in technology that can deliver in this way. Should
future regulatory change close the door to biodegradable waste at municipal and other landfill sites and introduce mandatory food waste reporting, the investment offers a future-proof and compliant resource management system. The beauty of anaerobic digestion feedstock is that it can accommodate a range of materials – meaning one plant can offer cross-sector use, such as the food and drink and agriculture industries –with the power generated offering self-sufficiency, multi-business shared use or an injection of power to the grid.
Suitable feedstocks that can be co-digested in an anaerobic digestion plant include the following:
• Agricultural slurry/manure
• Sewage sludge
• Municipal food waste
• Dairy manufacturing wastes
• Organic chemicals and solvents
• Biomass/energy crops.
In the case of one anaerobic digestion plant designed to serve the needs of a distillery in the Scottish Highlands, the facility diverted 20,000 tonnes of waste from landfill each year, while generating 95% of the business’s annual heat and energy requirements (1.2 GWh of electricity, which is the equivalent of that required to power 100 homes, and 1.4 GWh of heat).
This was achieved on a 0.1 hectare site staffed by one person with an eight-year return on a £2.8 million investment. The co-located plant also helped the business to achieve a £600,000 saving on waste disposal costs annually. Subsidies are available as part of the introduction of anaerobic digestion and this avenue should be fully explored as part of the project planning process.
Food and drink businesses are in a unique position to lead the energy transition for the manufacturing sector, owing to the nature of the wastes and by-products they produce and the requirement for heat and power in production processes. By harnessing the benefits of anaerobic digestion, companies in this sector can create their own circular economy of producing their own heat and power, reducing their waste disposal costs and minimising their carbon emissions.
Gavin Ramsey is the anaerobic digestion, waste and circular economy sector director for decarbonisation and energy efficiency specialists Synergie Environ, part of the PD&MS Group, and has 23 years’ experience in delivering environmental and sustainability solutions across numerous industries. A Chartered Resource & Waste Manager, Gavin has held key roles across the waste management, construction, minerals and utilities sectors.
The food and drink industry, a critical component of the global economy, is increasingly focusing on sustainable practices to reduce environmental impact and operational costs.
A breakthrough in this endeavor is the integration of Ecofill technology with benchtop autoclaves, exemplified by the AMB benchtop autoclave with Ecofill. This innovation marks a significant step towards eco-friendly and cost-effective sterilisation processes in the industry.
THE ECOFILL ADVANTAGE
At the heart of this technological leap is the Ecofill system, a cutting-edge solution designed to capture and reuse water and heat energy. Traditional autoclaves require significant amounts of water and energy for sterilisation processes, often leading to high operational costs and environmental strain. The Ecofill system
This means they need refilling less often and use
addresses these challenges by enabling the autoclave to recycle water and heat, drastically reducing waste and energy consumption.
The AMB benchtop autoclave, when combined with the Ecofill system, becomes a powerhouse of efficiency and sustainability. This autoclave is engineered to require less frequent refilling, thanks to the Ecofill’s water recycling capabilities. This not only saves water but also reduces the labour and downtime associated with refilling the unit.
Moreover, the Ecofill technology’s heat recovery feature plays a crucial role in reducing electricity consumption. By capturing and reusing the heat generated during sterilsation cycles, the AMB benchtop autoclave with Ecofill requires less electrical energy to maintain operating temperatures. This translates to lower energy bills and a reduced carbon footprint, aligning with the industry’s growing commitment to environmental stewardship.
The economic benefits of using the AMB benchtop autoclave with Ecofill in the food and drink industry cannot be overstated. Reduced operational costs are a direct consequence of lower water and electricity usage. Businesses can expect a noticeable decrease in utility bills, contributing to improved profitability in an increasingly competitive market.
From an environmental perspective, the reduced consumption of water and electricity signifies a substantial decrease in the industry’s ecological footprint. By embracing this technology, businesses in the food and drink sector can actively contribute to global efforts in combating climate change and promoting sustainable resource usage.
The integration of Ecofill technology with autoclaves like the AMB benchtop model is more than just an innovation in sterilisation - it’s a testament to the food and drink industry’s potential to lead in sustainability. As businesses continue to seek environmentally friendly and cost-effective solutions, technologies like Ecofill will play a pivotal role in shaping a more sustainable future.
In conclusion, the adoption of the AMB benchtop autoclave with Ecofill represents a significant stride in the food and drink industry’s journey towards sustainability. By capturing and reusing water and heat energy, this technology not only enhances operational efficiency but also exemplifies the industry’s commitment to environmental responsibility and economic viability. As this technology gains wider adoption, it sets a precedent for other industries to follow, marking a new era of eco-conscious industrial practices.
In the ever-changing world of the food and beverage industry, trends are constantly changing, shifting priorities and introducing new technologies. But how can manufacturers within this industry respond to these trends quickly and effectively?
Establishing a valuable long-term relationship with buyers and contractors are the starting points of our core values: specialized, sustainable, transparent, and service-oriented.
We are talking to Lina van Loon, marketing employee at Industrial Auctions. Industrial Auctions is the auction platform specialized in the online auctioning of used food and beverage machinery. We will discuss the main trends and explore how this company can assist producers in this rapidly changing market full of new developments.
While automation is now indispensable in the food and beverage industry, it remains a continuous trend that is constantly evolving. More and more factories are relying on advanced machines and robots to perform tasks that were previously done manually. This not only improves efficiency and productivity but also combats waste and ensures product quality. Additionally, it contributes to a safer working environment, enhancing the sector’s image. This is becoming increasingly important given the current challenges in terms of labor force, where producers must compete to attract and retain qualified personnel. Industrial Auctions addresses this by offering high-quality, used machinery that producers can use to further automate their production processes.
A noticeable shift in consumer needs is emerging within the food and beverage industry. “We see a growing demand for plant-based options, sustainable packaging and an increase in convenience products, but also an
increasing awareness on both our health, animal welfare and the impact of food production on the environment.” In response, manufacturers are focusing on reducing their carbon footprint by, among other things, adopting more sustainable packaging and minimizing food waste. However, Van Loon also contends that deploying new machinery isn’t always necessary. “For example, a plantbased burger can be produced with the same forming machine as a burger made of meat, and existing packaging machines can also accommodate more environmentally friendly alternatives.”
Everything is getting more expensive, so too for producers in the food and beverage industry. “To remain profitable, cost increases need to be offset, and secondhand machines offer an affordable solution. They are significantly cheaper than buying new ones, allowing producers to maintain profit margins even with rising inflation. By purchasing used machines, manufacturers contribute to a circular economy and reduce the need for new raw materials.” States Lina.
All in all, an industry that is constantly subject to various trends, which presents challenges. Despite these challenges, Industrial Auctions maintains a positive outlook, emphasising how the company can assist producers in addressing these challenges. Trends are closely monitored and emphasized. Competitors in production are already taking action, so being left behind is not an option.
Borne from a passion for wholesome ingredients and a commitment to conscious living, their company offers a range of delectable treats that nourish the body and delight the senses. At the heart of their offerings are their Vegan Collagen Bars – a game-changer in the world of plant-based nutrition.
Originally founded by Jade, Jade & Joy has now evolved into a team of women, who through qualitive research and personal experiences, understand the unique challenges that women face in maintaining balance and vitality.
Their aim is to help support a healthy lifestyle through considered ingredients. Via the fusion of science and nature, their products aim to enhance overall wellness, uplift moods, support hormonal balance, promote radiant skin/hair/nails, and provide sustained energy.
At the core of their philosophy is a belief in the power of plant-based nutrition to nourish the body and support overall well-being. Their Vegan Collagen Bars are a shining example of this ethos. Made with a blend of carefully selected ingredients such as almonds, dates, and natural plant extracts, these bars are packed with nutrients to support healthy skin, hair, and nails – all without compromising on taste.
Finding the right packaging for packing collagen-filled bars is crucial for several reasons. Preserving freshness and quality, maintaining collogen integrity, preventing contamination, and enhancing shelf appeal are just some of the areas that need to be considered, and with our expertise in packaging, that’s where we could help.
Working together, Jade & Joy and our team at National Flexible produced a packaging material composed of two layers: 20 microns Matte Oriented Polypropylene (MATT OPP) and 20 microns Metallised Oriented Polypropylene (MET OPP). Both MATT OPP and MET OPP films provide excellent barrier properties, protecting the contents of the packaging from environmental factors that can
In a world where wellness and indulgence often seem at odds, Jade & Joy is rewriting the script.
degrade quality and freshness. These films are also recyclable, making them environmentally friendly packaging options, contributing to sustainability efforts, and reducing environmental impact.
By investing in high-quality packaging solutions, Jade & Joy can effectively protect and promote their collagen-filled bars, whilst attracting and retaining loyal customers and we’ve loved being able to help with their project.
What sets Jade & Joy apart from the competition is their unwavering commitment to quality, taste, and transparency. Unlike many collagen bars on the market, theirs are 100% vegan, crueltyfree, and free from artificial additives and preservatives. They believe that what you put into your body matters, which is why they source only the finest ingredients from trusted suppliers.
But don’t just take our word for it – their Vegan Collagen Bars speak for themselves. With their irresistible texture, satisfying sweetness, and 4 indulgent flavours, they’re sure to become your new favourite snack.
If you would like to discuss your packaging needs, we’d love to help. Contact our team to find out more 01274 685566 marketing@nationalflexible.net
Last year, we prevented over 40,000 tonnes of surplus food from going to waste. That’s thousands of great quality meals our Company and Community Shop members bought at massively discounted prices. It’s what we do. Helping local communities and businesses by unlocking value from surplus that would otherwise end up in the bin.
Change begins with what iff...
Watch our film to find out more