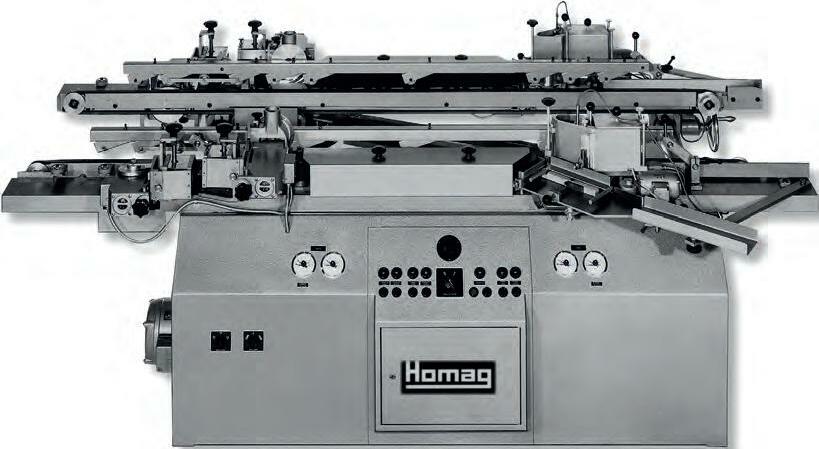
28 minute read
HOMAG GROUP
TECNOLOGIE
SESSANT’ANNI DI BORDATURA
Advertisement
UNA RICORRENZA DI GRANDE SIGNIFICATO PER IL PERCORSO DI HOMAG IN UNO DEI SUOI AMBITI TECNOLOGICI PIÙ RILEVANTI.
Homag Group celebra un anniversario: sessant’anni fa l'azienda di Schopfloch (Germania) lanciò la prima bordatrice in esercizio continuo secondo il processo caldo-freddo. E quello fu un vero e proprio punto di svolta. Nel corso degli anni successivi è stato un continuo susseguirsi di innovazioni e sviluppi, con i quali Homag si è dimostrata, fino a oggi, pioniera e leader nel campo della tecnologia per quanto riguarda la bordatura. Homag Group è leader mondiale nella produzione di macchine e impianti per l'industria del legno e dei mobili nella lavorazione dei pannelli. Questa gamma di prodotti ha anche permesso al gruppo di consolidarsi nel settore artigianale, svolgendo un ruolo di primo piano nel campo delle costruzioni di case in legno. In qualità di Global Player, Homag Group è presente in oltre sessanta paesi e detiene una quota di mercato superiore al trenta per cento. Per la produzione di mobili e componenti nonché per le costruzioni di case in legno, il gruppo offre soluzioni perfettamente adattate ai clienti, dalla macchina singola alle linee di produzione fino alle attrezzature complete di fabbrica. I servizi completi nell'ambito delle macchine e degli impianti completano l'assortimento di prodotti, accuratamente organizzato in termini di larghezza, complessità e prestazioni. primo brevetto per una bordatrice automatica, la KH 2/18, una macchina di serie con magazzino per strisce di impiallacciatura, gruppo di incollaggio, zona di pressione e gruppo refilatore. Questa tecnologia diventerà il punto di partenza per quasi tutti gli ulteriori sviluppi di Homag in questo segmento. Lo stesso anno, nel 1962, l'azienda ha presentato alla fiera di Hannover una nuova bordatrice con il processo caldo-freddo, con la quale l'incollaggio dei bordi avveniva in modo molto più rapido e meno costoso rispetto alla concorrenza. Fu una vera e propria rivoluzione. In seguito, l'ottimo rapporto qualità-prezzo ha portato a un'enorme domanda, tanto che dal 1962 Homag ha cominciato a focalizzarsi interamente sulla produzione e sullo sviluppo di questa tecnologia di incollaggio», spiega il Dr. Sergej Schwarz, Member of the Board. «Il processo è stato accelerato in particolare da una nuova tecnologia di incollaggio: la colla termofondente». Dopo che nel 1965 Homag è riuscita a presentare un'altra bordatrice doppia con basamento di nuova concezione e regolazione della larghezza, nel 1967 l'azienda ha sviluppato la KH 12, la prima bordatrice monolato. I successivi sviluppi per un trasporto preci-
ECCELLENZA NELLA BORDATURA
«La gamma di prodotti per l'industria del legno e dei mobili per la lavorazione dei pannelli, che copre tutta la catena di lavorazione dei clienti, comprende da sessant’anni anche sistemi per la bordatura. Ancora oggi, Homag continua a essere pioniera di nuovi processi e leader nel campo della tecnologia in questo segmento. Nel 1962, appena due anni dopo la creazione dell'azienda, è stato depositato il
Sopra, nel 1962 la bordatura si rivoluziona: la prima bordatrice che utilizza il processo caldo-freddo. A destra: la bordatrice combinata KF 60 è diventata rapidamente un modello di successo nella produzione di mobili negli anni Settanta.

so dei pezzi puntavano a disporre nella zona di entrata della macchina anche gruppi di squadratura. «In questo modo, con la KF è nata un'altra pietra miliare nella produzione di mobili: la prima macchina combinata per la squadratura e la bordatura», sottolinea Matthias Volm, Senior Director Product Development. «Il modello di successo nella produzione di mobili è stato soprattutto il modello KF 60. Infatti, questa macchina, originariamente concepita per la bordatura e la refilatura, ha presto potuto integrare anche gruppi intestatori e levigatori». Oggi su tali macchine sono installati fino a quindiici gruppi che consentono di lavorare i pezzi fino a essere pronti per l'installazione. Per poter offrire in futuro una bordatrice adatta anche alle piccole aziende produttrici di mobili, nel 1973 Homag ha progettato la serie KH 10-13. Già allora le macchine erano disponibili con due diverse stazioni di incollaggio in modo da lavorare materiale in rotoli, bordi in legno massello e bordi prerivestiti. Due anni dopo, alla fiera Ligna del 1975, Homag ha presentato per la prima volta agli specialisti il processo di attivazione di colla a freddo (procedimento KA), una tecnologia per l'incollaggio dei bordi con colla PVAc. Nel 1976 ha acquisito una quota di maggioranza dalla Heinrich Brandt Maschinenbau GmbH, successivamente Brandt Kantentechnik GmbH, anch'essa produttrice di bordatrici e molto conosciuta per i lavori con bordi prerivestiti. Ciò ha rafforzato non solo la posizione di mercato di Homag nel settore dell'artigianato, ma anche la presenza al centro dell'industria tedesca dei mobili, nella Renania SettentrionaleVestfalia. Nel 1982, in occasione della fiera dell'artigianato di Monaco, è stata presentata una nuova generazione di bordatrici, la KL 70, in cui sono state implementate le innovazioni fondamentali per la costruzione, la versatilità e la sicurezza sul lavoro. «Un'innovazione fondamentale è stata la rimozione meccanica dei trucioli con supporto ad aria, integrata nel supporto, che ha ridotto del 70% la potenza di aspirazione
60 YEARS OF HOMAG EDGE BANDING MACHINES
■■ The Homag Group is celebrating a birthday: 60 years ago, the company from Schopfloch in Germany launched the first throughfeed edge banding machine using the hot-cold application process onto the market. The machine was an immediate hit. What followed over the years was a constant series of innovations and further developments that have allowed Homag to regularly prove itself as a pioneer and technology leader in edge banding right up to the present day. The Homag Group is the world's leading manufacturer of machines and systems for the panel-processing wood and furniture industry. With this diverse and wide range of products, the group has also established itself strongly in the woodworking shops sector and plays a leading role in timber house construction. As a global player, the Homag Group is present in more than 60 countries and has a market share of more than 30%. The group offers solutions precisely tailored to the customer for furniture and component production, as well as for timber house construction – from individual machines through production lines to complete factory systems. Comprehensive services in the area of machines and systems complete the product range, which is carefully graded in terms of breadth, complexity and performance. HITTING MILESTONES FROM THE VERY BEGINNING
For 60 years, the product range for the panel-processing wood and furniture industry, which covers the entire process chain of customers, has also included systems for edge banding. To this very day, Homag has repeatedly proven itself to be a pioneer in new processes and a technology leader in this segment. For example, in 1962, just two years after the company was founded, it registered a patent for the KH 2/18, the first automatic edge banding machine – a series machine with veneer strip magazine, gluing unit, pressure zone and flush trimming unit. This technology was to become the starting point for almost all further developments by
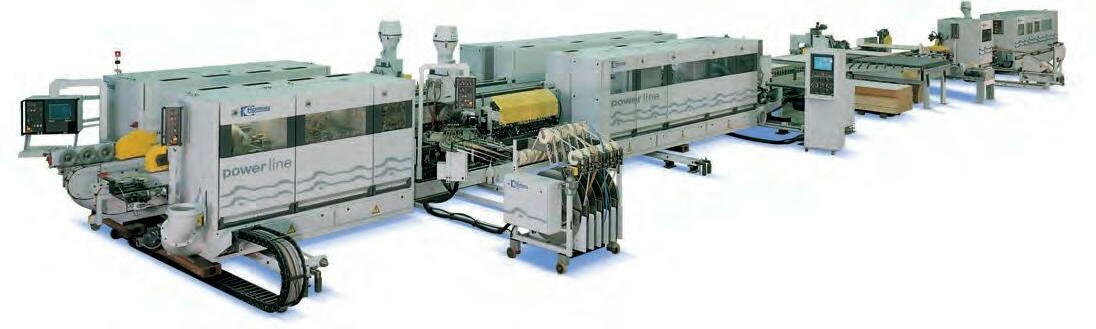
necessaria», afferma Christian Schürle, Senior Director Product Management. Nel 1995 la macchina è stata ulteriormente elaborata con il nome di KL 70 Optimat. A PIENO RITMO
«Nel 1999, con la serie powerLine, concepita come macchine doppie per la produzione in serie, Homag è riuscita ancora una volta a passare a una nuova classe di prestazioni», sottolinea Achim Homeier, Senior Director Global Marketing&Product Management. «L'obiettivo del programma powerLine, con una prestazione superiore del cinquanta per cento e costi aggiuntivi solo del trenta per cento, è stato raggiunto grazie a velocità di avanzamento più elevate, a intervalli e tempi di conversione più brevi e a disponibilità più lunghe». Poiché negli anni successivi la produzione di piccole serie e di pezzi singoli è diventata sempre più importante, nel 2001 Homag ha presentato una nuova generazione altamente automatizzata di powerLine per la produzione in lotto 1. Oltre alla produzione in lotto 1, l'utilizzo di pannelli leggeri ha acquisito un'importanza sempre maggiore nell'industria dei mobili, a cui nel 2004 Homag ha risposto con le prime soluzioni per la bordatura di pannelli leggeri. Da allora il gruppo offre non solo macchine e impianti per la loro produzione, ma anche per la lavorazione e la bordatura. Homag ha potuto celebrare con un'altra prima mondiale alla Ligna 2009: le bordatrici della serie Ambition, sotto forma di sei serie di Brandt e Homag, sono entrate sul mercato. «Le serie hanno coperto già nella loro versione base più del 90 per cento di tutte le applicazioni nell'industria e nell'artigianato», sottolinea Christian Schürle. Nel 2014 è stata la volta della nuova generazione della serie Ambition, con nuove tecnologie dei gruppi e modelli in diverse classi di potenza. Una novità sulle macchine è stata, tra l'altro, la ormai consolidata tecnologia airTec. A partire dal 2016, gli utenti hanno anche potuto contare sull'Ambition 2482, dotata come bordatrice
Progettare per la produzione in serie: dal 1999, le macchine a doppia faccia della serie powerLine hanno consentito il passaggio a una nuova classe di prestazioni.
completa con un ritorno TFU 521 edition e una posizione di accatastamento.
UNA NUOVA ERA PER LA BORDATURA
«Per quanto riguarda il punto di svolta alla Ligna 2009, in quel caso è stata messa in risalto soprattutto la presentazione del processo laserTec, che avviava una nuova era per la bordatura», sottolinea Matthias Volm. «Fondendo la superficie da incollare con un raggio laser e quindi pressandola direttamente sul pezzo, il processo garantisce una qualità di lavorazione costantemente elevata quasi senza giunture. Inoltre, con laserTec è possibile lavorare tutti i tipi di bordi tradizionali come PVC, ABS, PP, PMMA, impiallacciatura o melamina». Nel 2010 la tecnologia è
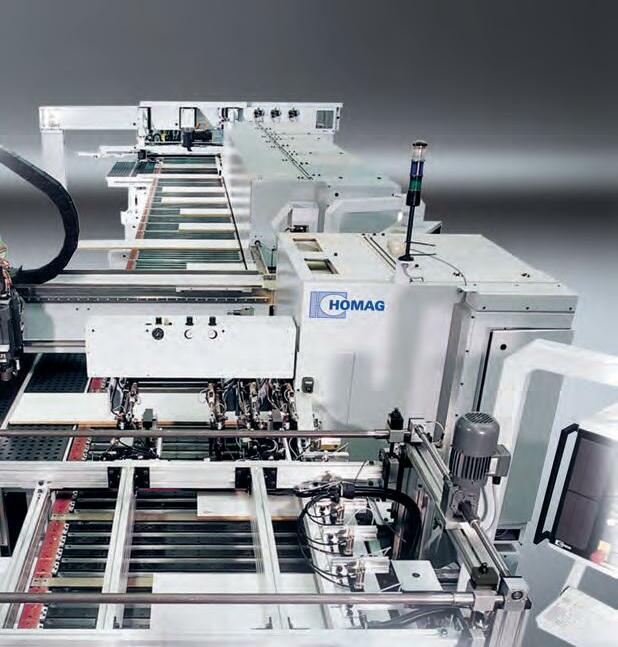
Homag in this segment. In the same year, 1962, at the Hanover trade fair, the company showed a new type of edge banding machine using the hot-cold process. In comparison to the competition, this machine allowed edges to be glued much faster and more economically. This was a revolution. "As a result, the favorable price-performance ratio led to immense demand, meaning that from 1962, Homag concentrated entirely on the production and further development of this gluing technology", explains Dr. Sergej Schwarz, member of the board. "The process was driven in particular by an innovative glue technology: hot-melt glue". In 1965, Homag was able to present a further doublesided edge banding machine with a new base frame and width adjustment device. Following this, in 1967, the company developed the first single-sided edge banding machine: the KH 12. The subsequent further developments for precise workpiece transport would soon allow for sizing units to be arranged in the infeed area of the machine. "With the KF, another milestone in furniture production was thus reached: the first combined sizing and edge banding machine", emphasizes Matthias Volm, Senior Director Product Development. "The KF 60 was a particularly successful model in furniture production. This machine, which was originally designed for edge banding and flush trimming, was soon able to use snipping and sanding units". Today, up to 15 units are installed on these types of machines, allowing workpieces to be processed in a way that makes them ready for installation. In order to be able to offer a suitable edge banding machine to smaller furniture companies in the future as well, in 1973, Homag designed the KH 10-13 series. Even then, the machines were offered with two different gluing stations to allow coil material, solid edges and pre-coated edges to be processed. Two years later, at Ligna 1975 trade fair, Homag presented the cold-glue activation process to the experts for the first time – a technology for edge gluing with PVAC glue. In 1976, a majority stake was acquired in Heinrich Brandt Maschinenbau GmbH, which later became Brandt Kantentechnik GmbH, a company that also built edge banding machines and that had also made a name for itself by working with pre-coated edges. This strengthened not only the market position of Homag in the woodworking shops sector, but also its presence in the center of the German furniture industry, in North Rhine-Westphalia. In 1982, a new generation of edge banding machines, the KL 70, was shown at the trade fair for the wood craft in Munich. Fundamental innovations in construction, versatility and work safety were implemented in these machines. "A decisive innovation here was the mechanical air-supported chip removal, which was integrated into the stand and reduced the suction power needed until then by 70%," reports Christian Schürle, Senior Director Product Management. The machine was further developed to become, for example, the KL 70 Optimat in 1995. ONE THING FOLLOWED ANOTHER
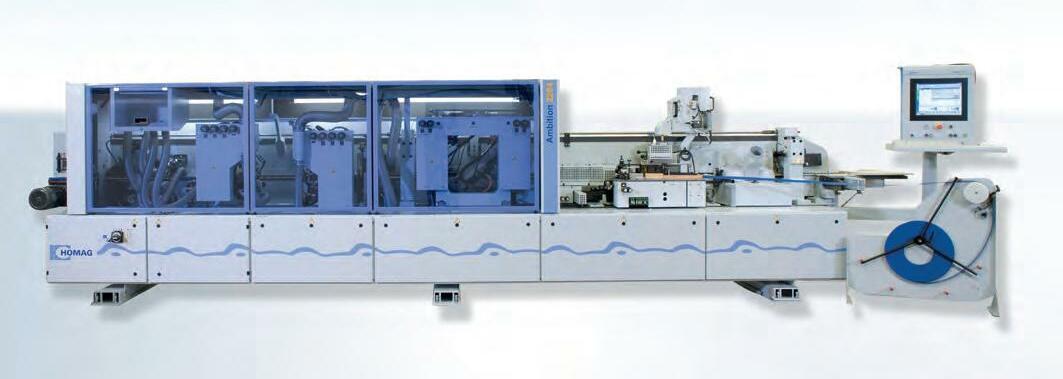
"In 1999, with the powerLine series, a range of doublesided machines designed for series production, Homag once again managed to move into a new performance class", emphasizes Achim Homeier, Senior Director Global Marketing & Product Management. "The goal of the powerLine program – a 50% increase in performance at only 30% additional costs – was achieved through higher feed speeds, shorter gaps and changeover times, and longer availability". Small series production and individual production became more and more important in the following years, so in 2001, Homag presented a new, highly automated generation of the powerLine series for batch size 1 production. In 2004, with its first solutions for the edging of lightweight panels, Homag responded to the growing importance of the use of lightweight panels in the furniture industry as well as batch size 1 production. Since then, the group has offered machines and systems not only for the production of lightweight panels, but also for the further processing and edging of such panels. Once again, Homag was able to celebrate a world premiere at Ligna 2009: the Ambition series of edge banding machines was launched on the market in the
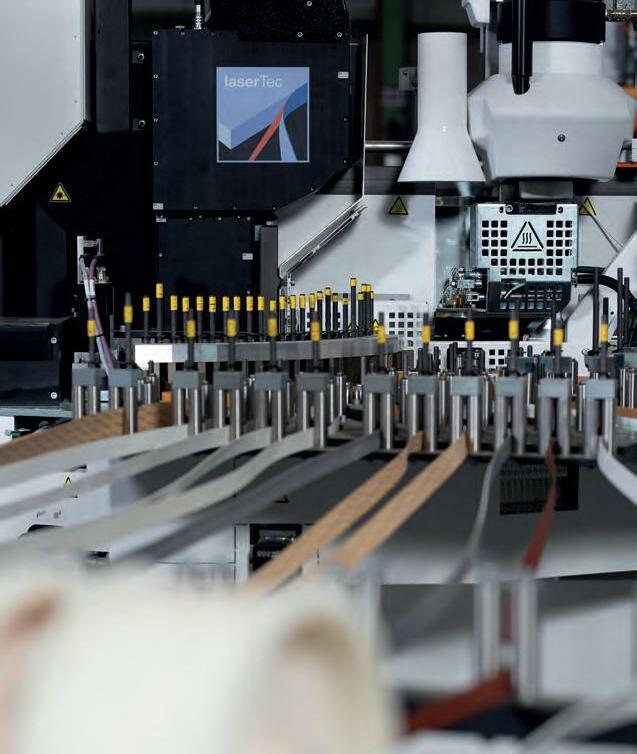
stata messa a disposizione solo per l'artigianato, per poi consolidarsi nel 2011 anche nei centri di produzione. Secondo Matthias Volm, la Ligna 2017 ha avviato la nuova fase del processo laserTec «dove con laserTec – Next Generation l'utente riceve una nuova generazione più robusta, più piccola e ottimizzata in termini di prestazioni». Il gruppo era ora disponibile in due classi di potenza e offriva all'industria una qualità con giunzioni a zero sia nella produzione in lotto 1 sia in serie. Nel 2013 è seguito il lancio di airTec per la giunzione a zero a regola d'arte, «un processo che collega bordo e pannello tramite aria calda», spiega Christian Schürle. «Si utilizzano bordi speciali costituiti da uno strato decorativo e da uno strato funzionale. Lo strato funzionale viene fuso a temperatura uniforme e flusso volumetrico costante e viene collegato in modo affidabile alla superficie stretta». Dal 2016 è disponibile il gruppo airTec con un generatore di aria calda rotativo, che lo ha reso ancora più potente e silenzioso. Nel 2017 il processo si è consolidato nella produzione di porte, dove da allora è possibile realizzare una giunzione ottica a zero con bordo in ABS/PP.
SOTTO UN UNICO MARCHIO
L'anno 2017 è stato un anno molto speciale per Homag Group e per tutte le sue aziende: da quel momento in poi il motto "One" Homag si riferiva solo al marchio Homag e a un logo. «Questo valeva anche per le bordatrici di Brandt Kantentechnik, che già dal 2012 appartenevano al cento per cento a Homag in qualità di specialista del segmento entrylevel e che ora si chiama Homag Kantentechnik», sottolinea il Dr. Sergej Schwarz. «Dal 2017, gli stabilimenti di Homag Group lavorano in qualità di associazione internazionale di produzione con standard, metodi e processi uniformi. Da allora i prodotti sono stati costruiti in modo ancora più modulare. E il cliente ottiene tutto da un unico fornitore». Sulla base di questa fusione, negli anni successivi il gruppo ha presentato una serie di nuove generazioni di macchine che coprivano tutta la catena di processo e combinavano un nuovo design funzionale e un nuovo nome. Da quel momento in poi le bordatrici presero la denominazione Edgeteq e si continuava ad andare avanti a ritmo costante sul piano tecnologico: nel 2018 venne lanciata la macchina entrylevel Edgeteq S-200, modello 1130 FC, seguita dalle nuove serie Edgeteq S-500 e Edgeteq S-800. L'evoluzione del mercato verso sistemi di produzione autonomi e automatizzati è stata realizzata da Homag nel 2021 con un nuovo concetto. In occasione di Live.Homag, l'azienda ha messo a disposizione due soluzioni di isole con bordatrici: una
Nel 2009, il processo laserTec ha inaugurato una nuova era nell'applicazione dei bordi. Da allora è stato spesso utilizzato in combinazione, ad esempio con la tecnologia PUR.
Edgeteq S-380 con ritorno Loopteq O-300 è ideale per la produzione di elementi di costruzione e una Edgeteq S-500 con ritorno Loopteq O-600 e nuovo sistema di alimentazione pezzi per pezzi particolarmente su misura. Homaq ha inoltre presentato una squadratrice doppia, con la quale è possibile realizzare elementi di mobili che vengono assemblati nel sistema a clic grazie alla tecnologia a clic per mobili Threespine dell'azienda svedese Välinge. Se necessario, i gruppi per il sistema a clic per mobili possono essere integrati anche direttamente nelle bordatrici.
L’INNOVAZIONE NEL MOBILE
Tutte queste tecnologie di bordatura, tuttavia, non hanno avuto solo uno sviluppo proprio, ma queste innovazioni hanno anche inaugurato una serie di novità regolari per quanto riguarda il design dei mobili. Tra questi figuravano i pezzi sagomati, per la cui produzione nel processo continuo Homag ha sviluppato macchine per il soft e il postforming, in particolare le KL 70/KL 80, VF 78/79 e VF 88/89. Tali sviluppi, a loro volta, hanno dato impulso al design dei mobili.
form of six series from Brandt and Homag. "The basic version of the series already covered more than 90% of all applications in industry and woodworking shops", emphasizes Christian Schürle. In 2014, the next generation of the Ambition series followed, with new unit technology and models in various performance classes. Among the new features of the machines was the airTec technology, which had already become established. From 2016, users then had access to an Ambition 2482, which, as an all-round edge cell, was equipped with a TFU 521 edition return conveyor and a destacking station. A NEW AGE IN EDGE PROCESSING
"The presentation of the laserTec process, which was intended to herald a new age in edge application, was the most important feature of Ligna 2009", stresses Matthias Volm. "By using a laser beam to melt the surface to be glued and then pressing it directly onto the workpiece, the process guarantees a consistently high processing quality with almost no joints. What's more, laserTec can be used to process all standard edge types such as PVC, ABS, PP, PMMA, veneer or melamine". In 2010, the technology was first made available to woodworking shops, to then become established for use on processing centers in 2011. The next step in the laserTec process was marked by Ligna 2017, "where the more robust, smaller and performance-optimized successor generation was handed over to the user with laserTec Next Generation", says Matthias Volm. The unit was now available in two performance classes and offered the industry zero joint edge quality in both batch size 1 production and series production. In 2013, airTec was launched on the market for invisible joints tailored to the needs of woodworking shops. "A process in which the edge and panel are connected by hot air", explains Christian Schürle. "Special edges consisting of a decorative layer and a functional layer are used. The functional layer is melted at a constant temperature and constant volume flow and securely connected to the narrow surface". Since 2016, the airTec unit has been available with a rotation air heater, which has made it quieter and even more powerful. In 2017, the process was established in door production, therefore allowing the manufacture of optical zero joints with ABS/PP edge material. ONE BRAND, ONE LOGO
The year 2017 was to become a very special one for the Homag Group and all its companies: From that point on, under the motto "One" Homag, there was only the Homag brand and one logo. "This also applied to the edge banding machines from Brandt Kantentechnik, which, as a specialist for the entry-level segment, had been a 100% subsidiary of Homag since 2012 and is now called Homag Kantentechnik", emphasizes Dr. Sergej Schwarz. "Since 2017, the plants within the Homag Group have therefore been working as an international production association with uniform standards, methods and processes. Since then, products have been built in a much more modular way. And the customer gets everything from a single source". In the years following this consolidation, the group presented a whole series of new machine generations that covered the entire process chain and combined a new functional design with a new name. From that point on, the edge banding machines bore the name Edgeteq and the technology continued to develop step by step: for example, in 2018, the entry-level Edgeteq S-200 machine, model 1130 FC, was launched on the market, followed by the new Edgeteq S-500 and EDdgeteq S-800 series. In 2021, the company kept up with the market development toward autonomous, automated production systems by introducing an advanced concept. At Live.Homag, the company unveiled two cell solutions with edge banding machines: an Edgeteq S-380 with Loopteq O-300 return conveyor, ideal for the production of construction elements, and an Edgeteq S-500 with Loopteq O-600 return conveyor and a new workpiece infeed system for workpieces requiring a particular sizing accuracy.

Fin dall'inizio, un sistema di controllo integrato in tutte le macchine è stato l'obiettivo di Homag. Dal 2013 powerTouch ha assunto questo compito.
Macchine entry-level con equipaggiamento completo: la serie Edgeteq S-200.
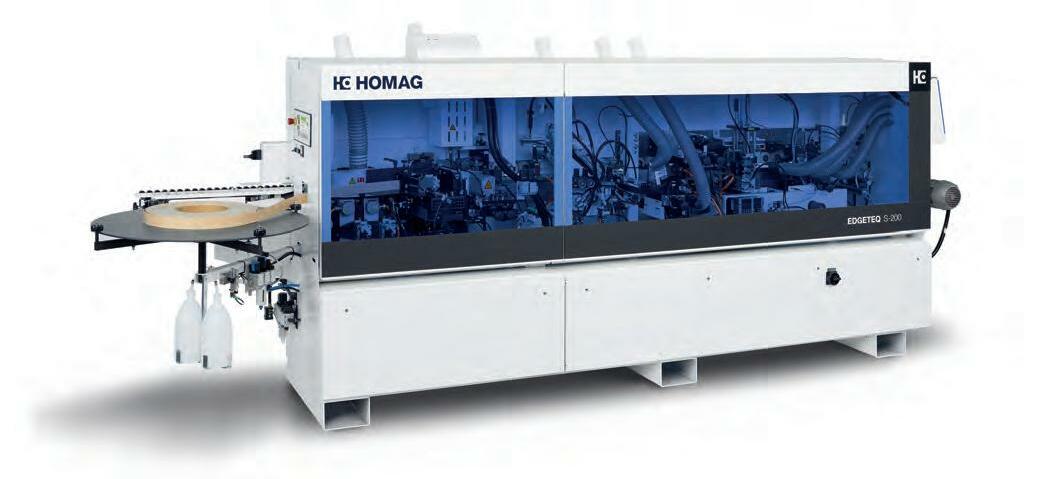
Oltre ai concetti di soft e postforming, Homag ha presentato sempre più soluzioni di concatenamento, automazione e movimentazione a un'industria dei mobili in piena evoluzione, come ad esempio i trasferimenti angolo o le stazioni di rotazione. «A metà degli anni Ottanta Homag ha poi costruito anche i primi impianti per porte per l'applicazione di bordi alle porte pieghevoli», ricorda Ernst Esslinger, Director Systems Project Execution. «Nel 1987 sono seguite le macchine in continuo per pezzi sagomati, che hanno soddisfatto le esigenze dell'industria dei mobili per quanto riguarda la produzione in un unico passaggio di pezzi sagomati o curvi a partire da pezzi rettangolari. Fino a quel momento, ciò era stato possibile solo con un enorme lavoro e in seguito a due o tre operazioni». Homag ha contribuito sempre in modo decisivo nello sviluppo del processo di postforming, raggiungendo un ulteriore risultato nel 1990: l'ulteriore sviluppo del processo diretto di postforming ha permesso all'utente di organizzare in modo semplice la procedura, senza dover più profilare, spazzolare, incollare, posizionare e pressare separatamente. BORDATURA A CICLO CONTINUO
Anche al di là della semplice lavorazione dei bordi, Homag Group ha sempre presentato nuove tecnologie.
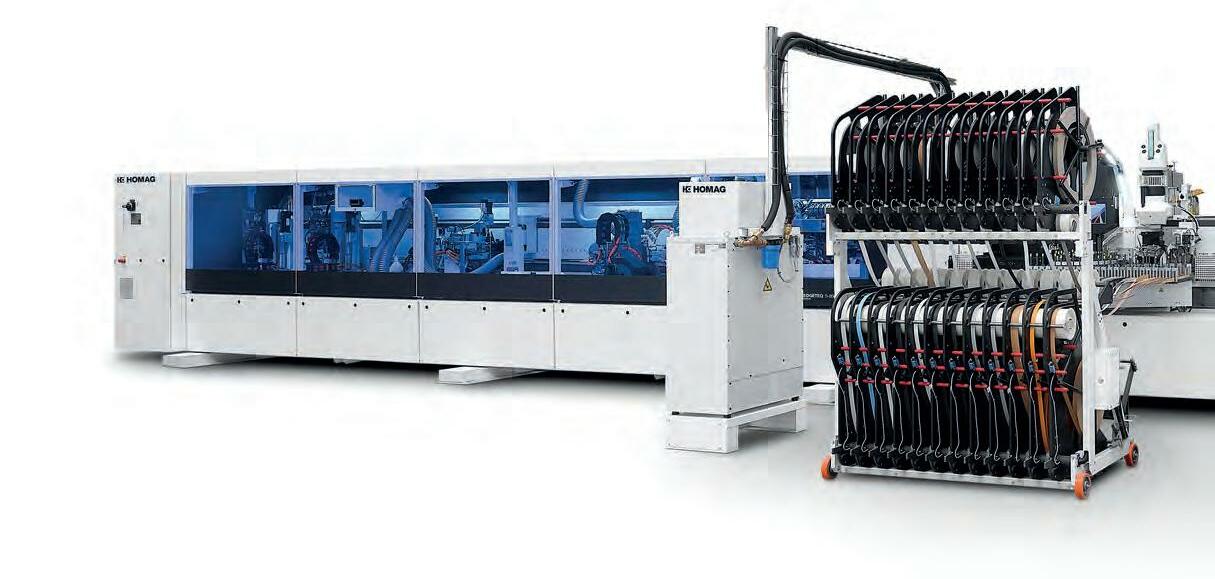
Precisione e prestazioni nel lotto 1: la serie Edgeteq S-800 con sistema di alimentazione del pezzo WZ24.
Homag also presented a double-end tenoner that can be used to produce furniture elements that are assembled using a click system with the Threespine furnitureclick technology from the Swedish company Välinge. If necessary, the units for the furniture click system can also be integrated directly into edge banding machines in the future.
FURNITURE AS A DRIVER OF INNOVATION
However, all of these edge banding technologies were driven not only intrinsically – new features in furniture design also regularly initiated innovations. These included shaped parts, with Homag developing soft-forming and postforming machines for the production of such parts in throughfeed operation – specifically, the KL 70/KL 80 and VF 78/79 and VF 88/89. In turn, such developments spurred on furniture design. In addition to soft-forming and postforming concepts, Homag has increasingly presented interlinking, automation and handling solutions, such as angular transfers or rotary stations, to a furniture industry that was undergoing change. "In the middle of the 1980s, Homag also built the first door systems for attaching edges to rebated doors", recalls Ernst Esslinger, Director Systems Project Execution. "In 1987, shaped part throughfeed machines followed, meeting the demands of the furniture industry to produce curved or shaped parts from rectangular workpieces in one throughfeed. Up until that point, this was possible only with great effort and two to three process steps". The fact that Homag always had a decisive influence on the expansion of the postforming process paid off once again in 1990: The further development into the postforming direct process now enabled the user to organize processes easily, without having to profile, brush, glue,
overlay and press separately. THROUGHFEED AND STATIONARY COATING
The Homag Group has also repeatedly introduced new technologies outside the scope of pure edge processing. In 1982, this included the completeLine process, which is used to coat unprocessed chipboard on three and four sides in one throughfeed. For this purpose, the "narrow surface is compressed with a mass, which gives the edges a higher quality and makes them more resilient, even with large-pored panel material" explains Ernst Esslinger. "In this context, the FKF 200 flat laminating machine with reacTec nozzle application was introduced in 2015 in the completeLine process. The machine can be used to laminate the wide and narrow surface with rolled material in one process step. The narrow surface is then finished by a casing line and a post-processing unit". In 1989, with the increasing change in furniture design and the increasing demand for shaped parts, Homag decided to use CNC stationary technology for processing these types of parts. As a result, significant further developments were presented and the possibilities for use and processing were continuously expanded. One milestone in particular was the integration of edge banding and processing units, for which the machine control unit had to meet high demands for dynamic response and positioning accuracy. "Today, stationary machines can be used to perform almost any complete processing", explains Frederik Meyer, Executive Vice President, CNC Processing. "As the equivalent of the throughfeed technology, they represent an important, future-oriented pillar of the group. Combined with feed and stacking equipment, complete production cells that also enable unmanned processing are produced".
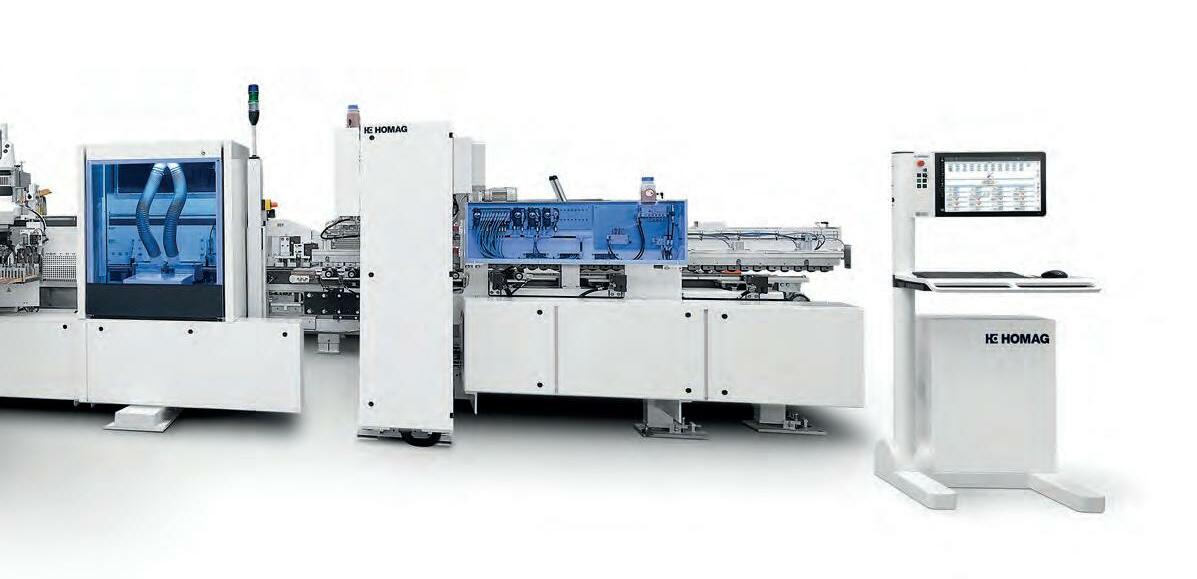
GRANDANGOLO HOMAG GROUP WWW.HOMAG.COM Nel 1982 è stato incluso il processo completeLine, che consente di rivestire pannelli truciolari grezzi su tre e quattro lati in un unico esercizio continuo. Ernst Esslinger spiega che la «superficie stretta è compattata con una massa che rende i bordi di qualità superiore e più resistenti anche nel caso di materiale per pannelli con pori grossi». «Nel 2015 è stata quindi presentata la macchina per il rivestimento piatto FKF 200 con applicazione ad ugello reacTec nel processo completeLine, con la quale è possibile rivestire la superficie larga e stretta con materiale a rulli in un unico ciclo di lavoro. La finitura della superficie stretta viene quindi realizzata da una linea di rivestimento e da un'unità di finitura». Con la crescente modifica del design dei mobili e la crescente richiesta di pezzi sagomati, nel 1989 Homag ha deciso di utilizzare anche la tecnologia CNC fissa per la lavorazione di questi pezzi. Di conseguenza, sono stati presentati sviluppi significativi e le possibilità di impiego e di lavorazione sono state costantemente ampliate. Una pietra miliare è stata in particolare l'integrazione dei gruppi di lavorazione e incollaggio dei bordi, con il comando della macchina che presentava requisiti elevati per la dinamica e la precisione di posizionamento. «Oggi con le macchine stazionarie è possibile realizzare quasi tutte le lavorazioni complete», spiega Frederik Meyer, Executive Vice President, CNC Processing. «Come equivalente alla tecnologia a esercizio continuo, esse rappresentano un importante pilastro del gruppo orientato al futuro. In combinazione con dispositivi di carico e di impilamento, si creano isole di produzione complete che consentono anche lavorazioni senza operatore». L’ETÀ DELLA DIGITALIZZAZIONE
Gli sviluppi nel settore della lavorazione del legno e dei mobili sono oggi caratterizzati da enormi megatrend come l'automazione e la digitalizzazione. Ciò si riflette in particolare nelle tecnologie di comando e di computer, le quali essendo tecnologie cruciali determinano lo sviluppo di tutta la produzione e di singoli processi di lavorazione. «Come quasi nessun'altra azienda, Homag è stata in grado di riconoscere questi aspetti precocemente e ha continuamente presentato soluzioni. Un comando unificato per tutti i processi del gruppo è stato quindi un obiettivo strategico fin da subito», sottolinea Matthias Volm. Nel 1985, con la denominazione Homatic, l'azienda ha introdotto un nuovo comando, seguito dallo sviluppo di un comando linea di produzione che consente di seguire i pezzi attraverso diverse macchine che lavorano insieme. Dal 2005 il successore, il comando "powerControl", ha dominato il processo di decentramento dei comandi e degli armadi elettrici. Alla Ligna 2013 Homag ha infine presentato con powerTouch un concetto di comando touchscreen che combina design e funzionalità e che, insieme al comando powerControl, offriva un elevato vantaggio per il cliente. Elementi di comando e componenti software unificati hanno fatto sì che da quel momento tutte le macchine Homag venissero utilizzate nello stesso modo. La generazione successiva, powerTouch2, è seguita nel 2019. Con ServiceBoard Homag ha lanciato un altro potente strumento nel 2014. «Questa app consente agli utenti di trasmettere tramite video i casi di assistenza sulla macchina al ServiceCenter, dove un dipendente mette a disposizione immediatamente informazioni quali istruzioni, filmati o piani, consentendo così di eliminare rapidamente il guasto», spiega Achim Homeier. Per ridurre il tempo di esecuzione del progetto, dal 2016 è inoltre possibile mettere in funzione virtualmente le macchine e gli impianti Homag prima della consegna. Ciò avviene in tempo reale e utilizzando componenti software e di comando reali. Dal 2019, i gemelli digitali consentono inoltre ai dipendenti e ai clienti di realizzare corsi di formazione digitale sulle macchine. Due anni prima, infatti, alla Ligna era stato presentato in anteprima mondiale tapio, una piattaforma basata su cloud che comprende prodotti digitali e servizi basati sui dati per l'intera catena di valore dell'industria del legno.
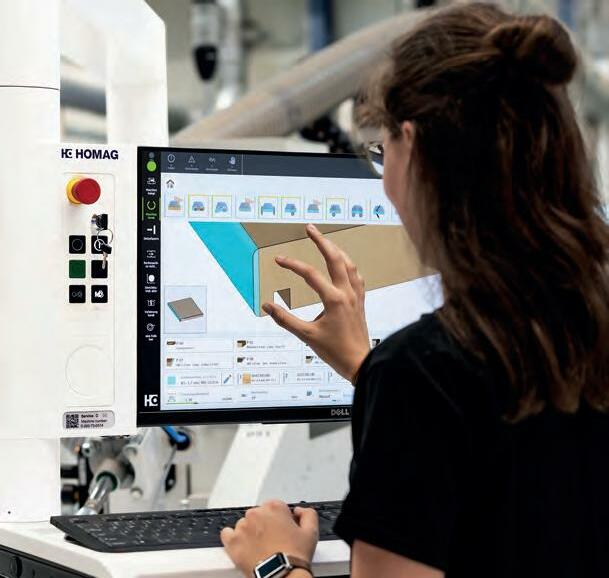
Da quel momento tutte le nuove macchine di Homag Group erano pronte a fornire dati nel cloud di tapio. Nel settore software, il woodCommander 5 segna l'attuale traguardo raggiunto nel 2022 con Edge Data Plugin sulle bordatrici Edgeteq S-500. Consente di selezionare rapidamente programmi di lavorazione e materiali per i bordi, nonché di registrare in modo sicuro i parametri di produzione e di creare programmi macchina orientati al pezzo. Inoltre, costituisce il collegamento diretto tra la macchina e l'app "materialAssist", che gestisce il materiale del bordo in rotolo.
UN CONTRIBUTO DETERMINANTE
Nella lavorazione dei bordi, come in tutte le altre tecnologie per la costruzione di mobili e la produzione di componenti, la gamma di prestazioni di Homag spazia oggi dalla macchina singola nel segmento entrylevel, medio o high-end, alla progettazione e all'installazione di complesse linee di produzione e impianti, fino alla soluzione completa del settore, inclusi consulenza e software, nonché allo sviluppo e all'implementazione di sistemi. Grazie a questo programma di macchine e servizi perfettamente armonizzato, Homag Group offre al suo gruppo di clienti una gamma completa di prodotti con un elevato valore aggiunto per i clienti. Il Dr. Sergej Schwarz: «le tecnologie di bordatura contribuiscono in modo significativo al rafforzamento della competitività industriale e artigianale, e i loro sessant’anni di storia lo dimostrano in modo molto chiaro».
DIGITALIZATION AND ITS TOOLS
Today, developments in the wood processing and furniture industry are heavily influenced by mega trends such as automation and digitalization. This is particularly reflected in control system technology and computer technology, which are key technologies that determine the expansion of the entire production as well as individual processing methods. "Like almost no other company, Homag recognized this at an early stage and continuously presented solutions. A uniform control system for all the group's processes was therefore a strategic goal from a very early point", emphasizes Matthias Volm. In 1985, for example, the company introduced a new control system called Homatic, which was followed by the development of a production line control unit that allows workpieces to be tracked across several machines operating in a network. Since 2005, the successor, the "powerControl" control system, which is accompanied by the decentralization of the control systems and switch cabinets, has dominated. Finally, at Ligna 2013, Homag presented powerTouch, a touch-screen operating concept that combined design and function and offered a high customer benefit in combination with the powerControl control system. Since then, uniform operating elements and software modules have ensured that all Homag machines can be operated in the same way. The next generation – powerTouch2 – followed in 2019. In 2014, Homag launched another powerful tool on the market with ServiceBoard. "With this app, users can transfer service cases on the machine to the ServiceCenter via video. An employee then immediately provides information such as instructions, films or diagrams, enabling the error to be resolved quickly", explains Achim Homeier. In addition, since 2016, machines and production lines from Homag can be put into operation virtually before delivery to reduce project processing time. This is done in real time using real software and control system components. Since 2019, digital twins have also enabled digital machine training for employees and customers. Two years earlier, tapio, a cloud-based platform with digital products and data-based services for the entire value chain of the wood working industry, had already celebrated its world premiere at Ligna. From that point on, all new machines from the Homag Group were ready to deliver data to the tapio cloud. The current milestone in the software sector was marked in 2022 by woodCommander 5 with Edge Data Plugin on the Edgeteq S-500 edge banding machines. This enables quick selection of processing programs and edge materials as well as reliable recording of production parameters and the workpiece-oriented creation of machine programs. In addition, it forms the direct connection between the machine and the "materialAssist" app, which manages the edging material. SIGNIFICANT CONTRIBUTION
In edge processing, as in all other technologies in furniture construction and component production, the range of services offered by Homag today extends from individual machines in the entry-level, medium or high-end segment, through the engineering and installation of complex production lines and systems, to complete industry solutions, including consulting and software, as well as system development and implementation. With this closely coordinated machine and service range, the Homag Group offers its customers a comprehensive product range with high customer benefits. Dr. Sergej Schwarz: "Edge banding technologies make a very significant contribution to strengthening competitiveness in industry and woodworking shops – as their impressive 60 year history indicates".