VALMET: A sustainable investment for the next half-century
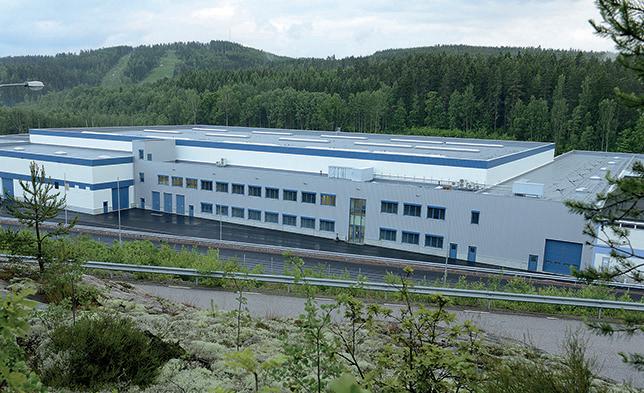
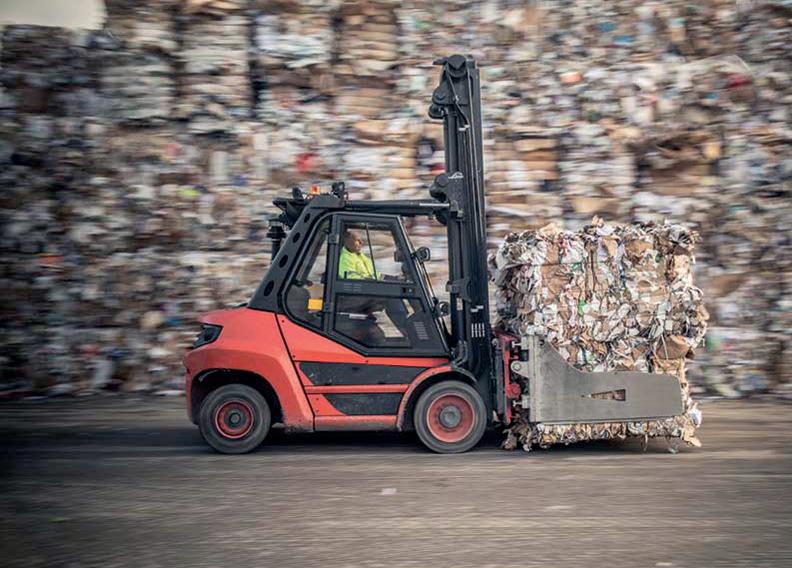
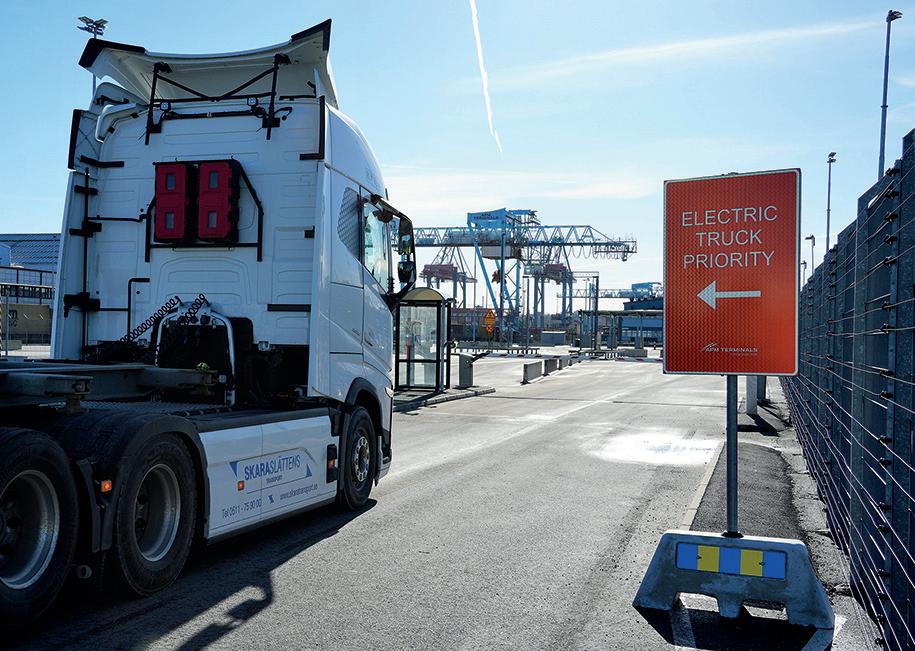
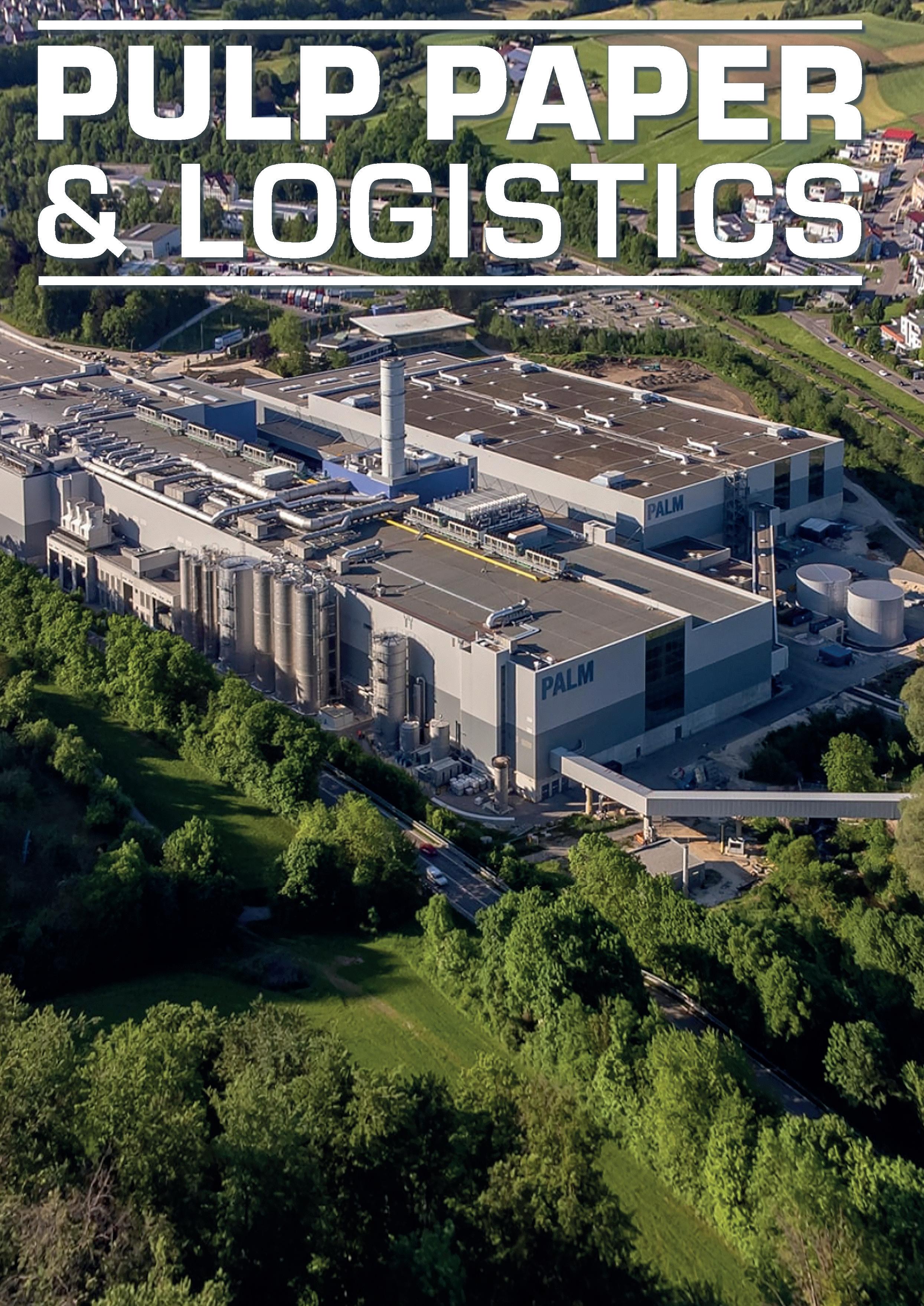
VALMET: A sustainable investment for the next half-century
Regularly maintaining equipment is the best way to maximize efficiency of tissue, paper and board machines. Analysis confirms that regular scheduled maintenance can reduce downtimes by as much as 75%.
To ensure effective maintenance, as well as increase the lifetime of critical
components, it is essential to have the right partner. ANDRITZ Novimpianti has over 30 years’ experience of designing, installing and servicing technology for all kinds of paper and board, MG and tissue installations around the world.
ANDRITZ Novimpianti provides an array of dedicated packages for
scheduled maintenance programs of critical components and processes, including burners, steel and cast-iron Yankees and complete steam systems for paper machines.
For further information, please contact us at novimpianti@andritz.com
Welcome to the March-April issue of Pulp Paper & Logistics.
With continuing uncertainty about the security of energy supplies, paper mills worldwide have been forced to search for ways to optimise their operations and to meet environmental targets.
Energy diversity and the move away from fossil fuels to power from renewable sources are key issues for those companies supplying machinery and equipment to the pulp and paper industry. Solutions and technology to reduce energy consumption are continuingly being developed to help mills in their transition to a more renewable and sustainable future.
As an example in this issue we report on collaboration between Voith and Essity that promises to make huge savings in water and power consumption in paper making processes, along with moving towards enabling lines to be carbon neutral by 2030.
But meeting environmental targets and legislation is an increasing, but necessary, burden on mill owners as they try to maintain profitable production. Flexibility and alternative energy sources are all areas that PPL will be looking at in coming issues, plus much more.
The May-June issue will include the annual shipping, ports, handling and warehouse focus (including cranes and forklifts), the production, management and saving of energy plus drying technology. Contributions should be sent to me by email at pulppaperlogistics@virginmedia.com to arrive no later than 12 May.
Vince Maynard, publisherVol. 13 Issue No. 77, March/April 2023
ISSN 2045-8622 (PRINT)
PUBLISHER & EDITORIAL DIRECTOR
Vince Maynard
Tralee, Hillcrest Road, Edenbridge, Kent, TN8 6JS, UK
Tel: +44 (0) 1732 505724
Mobile: +44 (0) 7747 002286
Email: pulppaperlogistics@virginmedia.com
CONSULTANT EDITOR
David Young
Tel: +44 (0) 1737 551687
Mobile: +44 (0) 7785 796826
EDITOR
John Nutting
Email: johnnutting47@gmail.com
REGIONAL REPRESENTATIVE
Einar Johansson
Tel: +46 8 540 255 15
Mobile: 0046 70 234 80 85
Email: einar.lennart@gmail.com
PRODUCTION
Anthony Wiffen
ASTAC Business Publishing Ltd
Tel: +44 (0) 1460 261011
Mobile: +44 (0) 7557 280 769
Email: anton_print_1@mac.com
Port of Gothenburg gives priority to electric trucks
Time to trust the (blending) process
Synthesised gas offers dramatic reductions in carbon emissions
A sustainable investment for the next half-century
PRINTER
Brown Knight and Truscott
Tunbridge Wells, Kent, TN2 3BW
United Kingdom
Tel: +44 (0)1892 511678
What is being described as a ‘ground-breaking’ and ‘disruptive’ paper making concept that will be carbon neutral, and dramatically save water and energy, is being developed in a collaborative project between global hygiene and healthcare company Essity and engineering group Voith Paper.
Successful tests have been carried out on the process – which doesn’t use fossil-based fuels, reduces consumption of fresh water by 95 per cent and energy by 40 per cent – and now the results are being transferred to a pilot production line at Voith’s Heidenheim site in Germany. This new set-up will enable testing under conditions close to production in a mill.
Voith has agreed an exclusive
partnership with Essity to further develop the process. This will incorporate Essity’s expertise in the tissue industry and Voith’s knowledge as a leading technology supplier.
“As the full-line supplier to the paper industry, we have set ourselves the ambitious goal of being able to realise carbondioxide-neutral paper production
by 2030,” says Andreas Endters, chief executive of Voith Paper.
“The fact that we have developed this new process is an important milestone in the industry and demonstrates our high level of innovation. We are very pleased to have found a suitable partner in Essity, who shares our objective of climateneutral paper production.”
The sale of the Maxau paper mill at Karlsruhe in Germany to Schwarz Produktion was completed at the beginning of March by Finland’s Stora Enso as it continues to focus on growth in renewable products in packaging, building solutions and biomaterials innovations.
Schwarz Produktion produces packaging and high-quality food for Schwarz Group retailers Lidl and Kaufland, all part of the diverse Schwarz Group, which employs 550,000 people in 32 countries and has sales of more than €130 billion a year..
The €210 million deal, originally
announced in September 2022, is part of Stora Enso’s plan to divest four of its five paper mills in Europe.
The plan was concluded earlier this year when it signed an
agreement to sell its paper mill at Hylte but discontinued the Anjala mill divestment process. The sale of the Nymölla paper mill in Sweden was completed in January with ownership transferred to
Magnus Groth, chief executive of Essity, adds: “Sustainability is integrated into Essity’s strategy for long-term profitable growth. We are committed to reducing our environmental footprint and achieving net zero emissions by 2050. This partnership with Voith is yet another concrete example of this.”
PPL asked Naomi Keitel, global communications manager at Voith Paper, for more information about the processes being developed. Keitel said that the pilot machine will cover the entire paper making process from raw material processing up to the reel, allowing full development of the opti-mised process. “Due to non-disclosure agreements, it is not possible to describe the concept in more detail at the moment. Further information will follow,” she said.
Sylvamo. Stora Enso said the Maxau divestment would reduce its yearly sales by about €385m.
The Maxau mill has capacity to produce 530,000 tonnes of SC (supercalendered) paper a year. In 2022, there were plans to connect the mill’s combined heat-and-power plant to the local district heating system that would generate 50,000MWh a year, providing a carbon dioxide reduction of 11,500 tons a year. Other Stora Enso mills have similar arrangements.
In addition to mineral water and soft drinks, Schwarz Produktion companies also produce chocolate, dried fruit, baked goods, coffee and ice cream. It operates three plastic and recycling plants that are central to a PET materials cycle.
Aglobal research and development (R&D) centre for the pulp and paper industry has been officially opened by ABB in Dundalk, Ireland.
The new multi-million-dollar R&D Centre is at the heart of ABB’s automation and digital products for the sector and will be home to the ongoing evolution of the ABB Quality Control System (QCS).
ABB says its vision for the centre is to develop solutions that respond to global trends and will meet the sustainability goals of the rapidly-evolving industry. A QCS, for example, has the potential to reduce annual production losses by 2 per cent or more per paper machine. This is able to impact a mill’s sustainability goals by also reducing annual emissions for each machine by the same amount, or 1,100 tons of carbon dioxide, using the assumption of 57,000t of carbon dioxide emissions for a typical paper, board or tissue machine.
The project is supported by the Irish Government through IDA Ireland, which was originally created to help attract foreign investment into the country and has links to ABB that go back to the 1980s.
Dara Calleary TD, Ireland’s minister for trade promotion and digital transformation, said at the opening: “ABB’s new centre here in Dundalk will support technology advancement in the pulp and paper industry with the creation of up to 30 new highly-skilled jobs to the area. The new R&D facility will provide an exciting space for innovation to help papermakers in areas such as waste reduction, reducing
emissions including finding new ways of reaching sustainability goals.”
The centre will take advantage of modern technologies such as additive manufacturing (3D printing), collaborative robots and Augmented/Virtual Reality for training and field service delivery to better meet the needs of ABB’s pulp and paper development team. The site will also include a new training hub that will provide skills development support for ABB and its customers, enabling more cross-industry partnerships and collaboration.
Joachim Braun, division president of process industriesat ABB, commented: “ABB’s Pulp and Paper business grows year on year, and this investment into our Quality Control Systems development will allow us to sustain our global market leadership and push the industry forward for the next generation of paper makers.
“With Ireland ranked in the top 10 EU countries for innovation and boasting the fourth-highest international share of workforce in the EU, it is the perfect location for our new R&D site. From this base, we will continue to advance the future of the industry and pioneer new technologies to meet the evolving needs of our customers.”
Michael Kerley, global technology manager for ABB Pulp & Paper, and a Dundalk local, added: “This new centre represents ABB’s proud heritage and presence in Ireland, which is extremely important to us.
“In addition to being a hub for technological innovation in the pulp and paper industry, the new centre will play a vital role in creating up to 30 high-level job opportunities over the next three to five years, thereby bolstering the talent pool in Ireland and supporting the local economy.”
Dundalk is one of ABB’s four main global Pulp and Paper R&D centres, along with Bangalore, Singapore, and Stockholm.
Sales at Smurfit Kappa jumped by more than a quarter in 2022 to reach €12.8 billion with chief executive of the Ireland-based paper packaging maker Tony Smurfit saying that “against a year of extraordinary circumstances, 2022 was another highly successful year”.
While sales were up 27 per cent, ebitda increased 38 per cent to €2.36 billion with a margin of 18.4 per cent.
Smurfit continued: “Our performance reflects the ongoing benefits of our investment programme together with our customer-led innovation and sustainability initiatives. SKG’s integrated model, together with our geographic footprint, continues to deliver for all stakeholders.
“For the full year, box volumes
were down less than 2%. This slowdown was particularly evidenced in the latter part of the year, especially in the month of December, where we saw stock reductions and downtime taken by customers.
“In 2022 we invested close to €1 billion to support our customers and capitalise on long-term demand growth drivers. We also continue to make progress towards our sustainability goals with investments to reduce our carbon footprint, reduce our impact on the environment and help our customers achieve their own carbon reduction and sustainability goals.
“The Group continued to expand its geographic footprint and product portfolio through acquisitions in 2022. In Europe, we purchased operations in Spain and the UK, while in the Americas we acquired operations in Argentina
and Brazil.
l Smurfit Kappa has also completed its withdrawal from the Russian market as originally announced in April 2022, and subsequently agreeing to sell the operations to local management, with the approval of the Russian authorities.
The operations include a bagin-box facility and two corrugated plants in St Petersburg, and a corrugated plant in Moscow. They contributed to 1 per cent of SKG’s global operations.
l Smurfit Kappa has again been recognised as a top ESG performer by leading research and analytics company Morningstar Sustainalytics. Following an analysis of global companies, Smurfit Kappa’s 2022 ESG Risk Rating improved, with the company positioned in the list of Top Rated companies both for the
industry and regional categories.
Morningstar Sustainalytics is a leading global independent ESG research, ratings and data firm that supports investors around the world with the development and implementation of responsible investment strategies. It rates more than 15,600 companies worldwide and many industries.
Commenting on the rating, Garrett Quinn, chief sustainability officer at Smurfit Kappa, said: “It’s an honour to receive recognition from Sustainalytics for a second year which includes improved rankings and recognises our work in the field of sustainability by awarding us top rated both in the geographies and industry we operate in.”
Production has started at Mondi’s new greenfield plant at Tangier in Morocco, which is capable of producing 100 million paper bags a year for the building industry.
The €16 million plant has increased Mondi’s capacity in West Africa to 500m bags a year, helping to meet the growing customer demand for paper bags in the
region. This plant is Mondi’s fourth site in West Africa (in addition to two other plants in Morocco and one in Ivory Coast).
The sack kraft paper used by these sites is produced by Mondi’s own mills, ensuring security of supply of packaging materials to the region. In addition, Tangier is ideally located within a free economic trade zone making it well positioned to supply to neighbouring countries.
Hicham Jalal, Mondi’s regional manager for West Africa Paper Bags, comments: “It is really exciting to see the growth in the West African building industry. Mondi is uniquely positioned to deliver paper-based packaging materials
directly to customers in the region, who benefit from a reliable supply of high-quality paper bags and local services.”
Claudio Fedalto, operations chief for Paper Bags at Mondi, adds; “This investment illustrates our commitment to growing our offering of sustainable packaging through our integrated value chain. Thanks to the excellent work and spirit of the local team, we secured, progressed and turned this project around incredibly quickly. Work on the ground started in January 2022, and we have already started production at our new plant. This excellent achievement was only possible thanks to the highly motivated local team.”
More and more companies aim to increase the autonomy of their mill or plant operations. In an autonomous mill or plant, an autonomous system can monitor its own performance, which brings several benefits, like improved safety and efficiency, lower costs and reduced environmental impact. Digitalization and more autonomous operations also mean that there is less need for human intervention. The role of people will continue to be important, evolving towards supervising and ensuring that different process areas perform well together, and towards managing exceptions. Operations and maintenance work will become more collaborative in the future as well.
Whether you are just beginning your digital transformation journey or you’re further along in the process, Valmet’s framework helps you recognize the necessary steps and building blocks. Our experts are there to support you as you move towards more autonomous and optimized operations.
More on valmet.com/autonomousoperations
Andrew King, group chief executive of packaging and paper maker Mondi, has called on the industry to play its part in creating a better future for the planet.
In a keynote speech at the 25th Fastmarkets Forest Products Europe Conference in Prague in March, King addressed opportunities for the packaging and paper industry to contribute to building a more sustainable future through partnership and innovation. He cited some of the world’s biggest sustainability challenges, including food loss, plastic pollution, biodiversity loss and climate change as key areas where the packaging value chain can accelerate change.
He encouraged delegates to think about what he called “the big question – for all of us”.
“It’s a question my children ask
me and I’m sure your families and friends are asking you,” he said. “It’s one we are rightly asked by any talented people thinking about joining our industry, and of course the communities we work with. It’s a question for all of us here – and for our industry more broadly: How can we play our part in creating a better future for our planet?”
To drive the change the planet needs and move forward as an industry, he highlighted that connec-tion across the value chain has never been more important – “to develop ideas, technologies and solutions at scale”.
Two other areas King considers vital to making progress are engaging with complexity and changing people’s perceptions of the paper and packaging industry. “There are no simple answers,” he said. “We need to manage a
variety of trade-offs like material efficiency and durability in terms of reuse and recyclability… and use a variety of solutions involving different materials if we want to make progress.”
On perceptions, he said the industry needs to tell its story better: “We’re an industry focused on doing the right thing, full of incredible innovation, with real commitment to tackling our
planet’s biggest sustainability challenges. We should be an industry of choice for anyone passionate about sustainability, technology, innovation and partnership working on a global scale.”
As part of the conference, attendees had the opportunity to tour Mondi’s Štětí kraft paper mill. The tour came after news of a €400 million investment in a new 210,000 tonnes per year kraft paper machine at the mill, announced in October 2022. The decision forms part of Mondi’s capital investment programme of more than €1 billion to accelerate growth and meet the growing demand for sustainable paperbased packaging.
Mondi’s global sales for the 2022 year were €8.9 billion, up by 28 per cent on the previous year. Profit before tax more than doubled to €1.56bn.
To help minimise the use of single-use plastic bottles in the food, drink, consumer health and fmcg industries, the Bottle Collective has been formed by PA Consulting and PulPac, the Swedish R&D company behind the Dry Molded Fiber proprietary production process.
PA’s mechanical engineering, design, automation, and material sciences teams, along with PulPac, have already developed the first functioning Dry Molded Fiber bottle prototypes. A number of leading brand partners have already joined the Collective to continue developing and scaling-up fibre bottle production by 2025.
produce low-cost, high-
less carbon dioxide than plastic and conventional wet moulding options. Almost no water is used in manufacturing to create a highly versatile container mould for consumer companies.
Sanna Fager, commercial chief at PulPac, said: “Plastic bottles are the holy grail of plastic replacement. They have an estimated annual production volume of up to 500 billion pieces and are a significant source of plastic pollution worldwide. We are proud to share some of our patent-protected advances with PA Consulting, combining Dry Molded Fibers’ forming versatility, broad barrier applicability, and high production efficiency.”
Aleading pulp and paper maker in Europe will soon use ‘decarbonised’ steam produced with energy from a large high-temperature heat pump installed by Turboden, which is part of the Mitsubishi Heavy Industries group.
The heating upgrade system, based on the integration of a Turboden Large Heat Pump and a mechanical vapour compressor, will exploit low-grade heat ranging between 10 and 20 deg C to produce electricity from renewable sources, and generate 12 MWth of superheated steam at the 170 deg C needed in the paper production
process. The heat upgrade system has been developed by Turboden and its customer to match with the production process’s needs.
“This project is an important milestone for establishing Turboden leadership in large heat pump solutions for customers with high demand of steam or high temperature heat in industrial process-es,” says Paolo Bertuzzi, chief executive of Brescia, Italybased Turboden SpA, which has a non-disclosure agreement with the paper maker.
The project is also an example of corporate synergies within Mitsubishi Heavy Industries Group. The Turboden LHP system
uses a compressor from Mitsubishi Heavy Industries Compressor Corporation (MCO).
“MCO is very pleased to provide our compressors to Turboden for the realisation of this innovative large heat pump. Thanks to our long experience in the market, we will provide a cutting-edge proven technology in order to achieve outstanding performances with the highest reliability,” said Masahiro Kobayashi, director of Mitsubishi Heavy Industries Compressor Corporation.
The move into the paper industry follows Turboden’s development of LHP systems for the Italian steel industry.
A joint working group between members of the European paper and heat pump industries has calculated that potential energy savings in paper drying of more than 50 per cent are possible by using heat pumps. A joint paper published by the Confederation of European Paper Industries and the European Heat Pump Association details how heat pumps could be integrated into paper mills.
Italia Technology Alliance (ITA Holding), whose best-known company is A.Celli, has acquired Taiprora Srl, a wellestablished company based in Abruzzo that has been developing Software and Automation systems for production and intralogistics for 30 years.
Taiprora was identified by ITA Holding as the ideal company to integrate its knowledge for the supply of fleets of vehicles and stacker cranes for automatic warehouses, as well
as development of software for internal logistics flows.
Mauro Celli, who owns ITA Holding, said: “Our development model is based on the acquisition of new skills to create more value for our customers, ensuring proven solutions and measurable results with the best practices of the global market. We invest in leading companies in their sector that have a history of reliability and good reputation.
“The entry of Taiprora corresponds exactly to these
success criteria and complements the group’s digital offering: from the user interface of the production line to logistics and warehouse management, to IoT and Big Data analysis.”
Francesco Alfieri, president of Taiprora, added: “The operation is the result of the integration of two different worlds and sectors, but which share an extremely wide and interesting area of contact. The basis of the agreement with ITA Holding is the common factor of a great aptitude towards innovation
and internationalisation.
“Our goal is to continue growing by valuing the identity of Taiprora. We want to increase research and focus on creative innovation to achieve ambitious goals in a future full of opportunities and challenges for us and our territory.”
The impact of high energy prices and of declining EU and global economic growth have been revealed in the latest preliminary statistics for 2022 from Cepi, the Confederation of European Paper Industries.
The sector can however capitalise on positive long-term trends, which the EU Green Deal Industrial Plan could accelerate, says Cepi.
Consumption of paper in Europe remained stable in 2022, despite Europe’s current economic slowdown. At same time, production of paper and board decreased to 84.8 million tonnes, a fall of 5.9 per cent compared to the previous year. A decrease in production was also seen in other global regions, including most of the EU’s main competitors in the sector.
The combined developments of a decreased production and a stable consumption led to a decrease in the sector’s trade balance in the context of increased global competition: a situation which
Cepi has repeatedly brought to the attention of EU Institutions. The weakness of the paper production recorded during the second part of the year is to a major extent explained by Europe’s high energy and raw material costs, which have led to temporary shutdowns.
The slowing of the EU economy in the second half of 2022 and the paper industry openness to global markets, where
growth is also stalling, have also contributed to this downward shift and the temporary drop off in competitiveness. However, Europe’s paper sector is traditionally a strong exporter, and its trade balance remains positive.
Packaging paper and board, increasingly replacing fossil-based alternatives, remains one of the sector’s main drivers for growth.
While paper packaging production
in Europe has decreased by 4.6 per cent in 2022 compared to 2021, the output of packaging paper still remains well above pre-Covid levels. The figures, calculated by tonne of paper produced, do not take into account notable advances realised in reducing the weight of individual paper packaging solutions, in line with the industry’s commitment towards sustainability.
Continuing from the previous three years, new consumption patterns following the Covid pandemic have also resulted in a growing demand for sanitary and household grades, gaining 3.6 per cent compared to 2021.
Director of Cepi Jori Ringman commented: “Long-term trends for our industry show that we can be ambitious about our future. Now we need the EU Green Deal Industrial Plan to be equally ambitious. We are confident that a transition towards a greener economy is in the long-term an oppor-tunity for the European paper industry.”
Electric trucks are being are being granted priority passage and handling in the container terminal at the Port of Gothenburg in Sweden, the biggest of its type in the Nordic region.
Terminal operator APM
Terminals is favouring haulage firms that have already started to convert their vehicle fleets, while at the same time giving an additional incentive to those considering investing in electrification.
It means that electric trucks will be fast-tracked through APM Terminals’ gate 4 with a reserved lane, and also enjoy prioritised handling within the terminal area. This creates efficiency gains and planning ability that is particularly important for electric trucks, as there are strict demands on optimisation, given the limited range of electric vehicles.
Brian Bitsch, commercial manager at APM TerminalsGothenburg commented: “We’re seeing more and more haulage firms starting to electrify parts of their vehicle fleets, and we know that more are considering investing in a green transition of heavy goods traffic.
“We hope that supporting these initiatives by offering the fastest possible passage and handling will serve as an incentive and be one small step along the way. Our own container handling operation has been fossil-free for several years, and this solution is fully in line with APM Terminals’ work on sustainability, in which collaboration with our customers is an important key.”
Of the one million vehicles that pass through the port each year, a third – about 1,000 a day – use APM Terminals, but only fraction –
so far – are electric.
But from the beginning of March logistics firm DFDS introduced 20 electric trucks, some of which are used within the port. Also, Sweden’s biggest container road transporter recently deployed three electric trucks in flows to and from the container terminal. The new priority for electric trucks has contributed to the haulage firm’s recent decision to invest in two more electric trucks, which will be put into service in May.
“Electric trucks are a major investment, so the fact that we now have priority in the container terminal is really important to us. It means that we can perform more assignments every day, which benefits both us and our customers. It also means that we can recoup the investment more quickly,” says Johan Söderström, commercial chief at Skaraslättens Transport.
Including the priority measures at APM’s terminals, there are now three that have a priority system in place for electric trucks. Between them, these terminals handle around 90 per cent of the port’s total truck flows. The other two terminals are operated by Gothenburg Roro Terminal and Stena Line.
“It’s a really important initiative by the terminal operators, which literally paves the way for the transition. With a priority system in place for the terminals that handle the most trucks, and the growing infrastructure for charging in the area around the port, the conditions for electric trucks are better here than at any other port. This is a development we’re incredibly proud of, but there’s still work to be done,” says Martin Adeteg, head of decarbonisation, health and safety at the Gothenburg Port Authority.
While there is no denying the march towards more sustainable practice in the paper and packaging world, we do need to acknowledge the elephant in the room when it comes to reclaimed fibre inclusions: For many the word ‘recycled’ paper is synonymous with imperfection. It is still a challenge for luxury brands to put their trust in the quality of upcycled fibre. In a world of unboxing videos and a thriving resale market for the packaging from luxury goods, it is understandable that packaging needs to reflect the craftsmanship and quality of the product itself. Brands are desperately trying to strike the balance between creating packaging which delivers both experience and eco credentials, but concerns over the aesthetic and functional quality of reclaimed fibre may hold some brands back from really exploiting the sustainable options available. The environmental opportunity is meaningful. Paper is one of the most widely recycled materials in the world. In 2021, 71.4% of all paper and board consumed in Europe was recycled and the total amount of paper and board collected and recycled increased by 2% to 57.1 million tonnes. Giving a second life to that recycled fibre as luxury packaging is a wonderful story and one which we know consumers want to hear. So, what is holding the luxury market back from doing more?
At James Cropper we often get questions about the integrity of reclaimed fibre because of the degradation which happens over time and reuse, resulting in a
loss of strength. This is a bit of a misnomer: in our established supply chains the fibre we use is typically being recycled for the first time, and as such is pretty much indistinguishable in terms of strength from fresh fibre. Likewise, there are questions around imperfections that might be visible in the final sheet. These visible imperfections may be specks of dirt or a phenomenon known as ‘shive’. When processing fibres, some can be pressed and compacted and these small clumps of fibre are generally more
visible in darker grades, and often attributed to processing recycled content.
While these functionality concerns have until recent years been founded, the dedicated FibreBlend Upcycled Technology team at the James Cropper mill is committed to perpetual sustainable fibre innovation, and we know that things have changed. From the world’s first technology to upcycle used coffee cups to the industry-leading incorporation of used denim jeans into fully-recyclable paper
for packaging – transforming waste into beautiful paper and packaging is at the core of our mission. But it doesn’t begin and end with recovered fibre. We believe that the perfect balance of paper performance, a sustainable story and visual appeal lives in the unique blend of virgin and recovered fibre.
Crucial to this is the process of fibre selection, specific to every brief. Taking a bespoke approach to each project means that we are able to select the perfect blend of fibres to ensure the desired outcome is achieved. Being selective of the supply chain is key: our team conducts rigorous tests to validate the quality of the fibre stream, testing for levels of contamination, optical brightening agents, mechanical content, long-fibre to short-fibre ratio, and more.
Stringent fibre selection takes us a long way to achieving the same results as offered by virgin fibre. However, the key to zero compromise in terms of quality and environmental impact is absolutely in the blend of virgin and reclaimed.
This can create fantastic results. Recently, a long-standing luxury packaging customer wanted to move to a 40% recycled UK office waste fibre composition. The project posed some challenges, which the team overcame through its bespoke approach, rigorous fibre selection and testing. The trial was a complete success. Not only did the move give new life to a waste stream and reduce the
carbon footprint of the product through local sourcing, it also did so without compromising the appearance of the paper.
Trusting the process paid dividends for this client, and has done so for many more. But what about colour? How do we allay concerns about reclaimed fibre affecting the ability to colour match or produce clean finishes without visible inclusions?
There are two parts to the answer. First, there is an argument to say that consumers are increasingly happy to see that recycled fibre has been used; perhaps there is a change in mindset that needs to happen in order to accept imperfections which can sometimes be seen, especially in lighter shades.
In fact, James Cropper’s range of Wainwright Colours from Nature was created by fully embracing the natural origins of paper and the associated aesthetic. Made with 100% recycled fibre and dyed with natural ingredients, our first two shades, Limestone and Herdwick Brown, are both derived from Rosemary extract. The natural
dyes are sourced from renewable origins that can be replenished responsibly, including food waste and inedible plant sources.
Some are ready to embrace the aesthetics of reclaimed fibre and natural dyes and their brands allow for this transition; but what is the answer if colour perfection is a must? Again, it’s all in the blend of fibres. Recycled fibres can
be highly fibrillated and so accept colour very well. Fibre that has more visual impurities would be used for darker colours, while we need to be more selective with recycled sources or might need to increase the percentage of virgin fibre for white.
James Cropper’s destination for fibre expertise is bolstered by its passion for colour. its onsite colour
laboratory holds 2,000 live shades that the mill regularly produces, with some 200,000 colours stored electronically. With this industryleading colour matching capability, the inclusion of recycled fibre in premium paper need not impact colour options and can also build on the story of the packaging.
While brands were understandably concerned about the move towards packaging which contributes to the circular economy in recent years, what we now know about fibre innovation really has put paid to those concerns. There are answers for every brand: Answers which promise that aesthetics and performance need not be sacrificed at the altar of circularity. It’s time to trust the blending process.
* Joanne Storey is R&D Programme Leader at James Cropper, a specialist manufacturer of wood and paper-based products with headquarters at Burnside in the UK’s Lake District, around 20 sites around the world and customers in 50 countries.
The burning of fossil fuels in industrial applications to generate heat and power is one of the greatest contributors to global greenhouse gas emissions, according to the United Nations’ Intergovernmental Panel on Climate Change (IPCC).
Process heat used in manufacturing represents around 25 per cent of the world’s energy consumption. Action to reduce this source of carbon dioxide (CO2) is therefore one of the main targets under the European Commission’s ambition for climate
neutrality by 2050.
Leading global tissue producer Sofidel is the second-largest tissue producer in Europe and well-known for its Regina brand, among others. The Italy-based company takes its responsibility to reduce its environmental impact very seriously. A pillar of its strategy is to achieve a 40 per cent reduction in its CO2 emissions per tonne of paper produced by 2030 compared with
the base year 2019.
The Science Based Target Initiative (SBTi), which promotes best practices in line with climate science, has approved this target as being consistent with limiting global warming to well below 2 Centigrade degrees.
As part of this commitment, and with the help of Andritz Novimpianti, gasification technology specialists Meva Energy, and the University
of Pisa, Sofidel has identified an opportunity for an annual reduction in CO2 emissions of 8,500 tons through a project at its Kisa tissue mill in south east Sweden, a project that was first reported in Pulp Paper & Logistics for May-June 2022 as part of a hood upgrade by Andritz Novimpianti. In common with many tissue plants, Kisa uses liquid petroleum gas (LPG) to generate process heat for tissue
A ground-breaking method for cutting fossil fuel out of tissue drying is being developed by Andritz Novimpianti and tissue maker Sofidel. PPL reports
drying – for now.
Now more details of the project’s potential can be revealed. Through a 10-year agreement between Meva Energy and Sofidel Sweden, Meva Energy will operate a thermochemical conversion plant with the capacity to generate at least 4.2 MW of gas on site at Kisa, using locally-sourced woodchips as biofuel. During the first half of 2023, the renewable gas production will replace fossilbased LPG for a substantial part of Kisa’s tissue drying needs.
According to Meva Energy, onsite generation in combination with not having to refine the gas to pure methane is the basis for reaching a high conversion efficiency along with CO2 reductions that are more substantial than with conventional
types of biofuel. The Meva Energy system also produces biochar, a stable form of renewable carbon that creates a carbon sink and can be used for soil improvement.
A paper-drying first Bio-syngas is not a direct substitute for LPG however. With its lower energy density, bio-syngas requires significant downstream modifications to enable the Andritz 3.4m CrescentFormer PM3 tissue machine at Kisa to perform to its potential. This is where Andritz Novimpianti has played a vital role with its long experience in air and energy systems for tissue, paper, and board.
Managing director of Andritz Novimpianti Luca Linari explains: “This is the first time that syngas or bio-syngas has been used to dry paper – any type of paper. Andritz has several current CO2-reduction initiatives across its portfolio but this project shows particularly interesting potential. It is a significant step for the whole paper industry and for sustainability but also a stimulating technical challenge.”
The different characteristics of bio-syngas when compared with LPG mean it is necessary to replace the burners and upgrade the combustion chamber in the hood of Kisa PM3, to ensure the uniform flow of gas and therefore heat that is essential for effective and consistent tissue drying. PM3 will be 100 per cent reliant on bio-syngas for paper drying while PM4 at the same mill will be partially fed by bio-syngas. It is also possible to use bio-syngas to generate electrical power using a turbine, but the Kisa project is focussed on heat for now.
This specific application at Kisa of burners within the hood for tissue drying based on bio-syngas
is also a world first for the paper industry.
“The volume of gas is bigger with syngas compared with LPG, which has an impact on the flow, so the main challenge is to keep combustion even,” continues Linari. “In addition, the combustion chamber and
fans are integrated within the hood on PM3 at Kisa, which means we have less space to work with. But we are confident that the combination of the specially-designed burners and modifications within the hood itself will enable a strong drying performance combined with the
crucial environmental benefits which are the main motivation behind this project.”
Before Sofidel and Andritz Novimpianti could be confident that the proposal for Kisa would perform in practice on the scale of a commercial tissue machine, it was necessary to perform detailed modelling.
This is where the Department of Civil and Industrial Engineering at the University of Pisa stepped in as an essential contributor to a collaborative feasibility study with Sofidel and Andritz Novimpianti. The university’s Professor Chiara Galletti takes
up the story: “We developed a model for operating the hood that would reflect the change in gas composition from LPG to bio-syngas. The composition of bio-syngas makes it challenging for combustion and thermal power, so using computational fluid dynamics (CFD), we could verify that the new fuel would provide a stable flame and flow of heat without excessive production of CO2 or pollutants such as carbon monoxide and nitrogen dioxide.
“This was a complex and detailed modelling scenario, involving dozens of processors and numerous simulations that each ran for 10 days or more. But we needed to be rigorous to be
Syngas, short for synthesis gas, is produced by the gasification of a carbon-containing fuel such as coal or, in the case of Sofidel at Kisa, biomass, when it is known as bio-syngas. A challenge with using syngas is its relatively low energy density but it brings benefits of lower carbon emissions and the ability to generate renewable power.
sure the combination of Meva Energy’s gasification and Andritz Novimpianti’s hood technology could produce a stable flame, acceptable emissions, and effective drying performance. The results were very encouraging and not only for this single project. We were also able to simulate other biofuel inputs and establish the scalability of the technology, too.”
For Sofidel, Kisa represents a landmark installation. Says Sofidel’s technical chief Davide Mainardi: “There are many elements to achieving our target of a 40 per cent reduction in emissions by 2030 compared with 2018. Cumulative changes throughout our operations are important: a shoe press, for example, can reduce the energy requirement of a tissue machine with consequent carbon-reduction benefits. But we also need to be ready to take more radical steps and the adoption of bio-syngas at Kisa, which will achieve an annual reduction in CO2 emissions of 8,500 tons, is a major feature on our roadmap towards 2030 and beyond.
“The ultimate goal of carbon neutrality will not happen without huge commitment and unprecedented levels of innovation from us and our suppliers. We are looking at many potential solutions to achieve the CO2 reductions we need, but SBTi has helped define our goals
in relation to specific climate targets. As an approach to tackling Scope 2 emissions, this initiative with Andritz Novimpianti, Meva Energy, and the University of Pisa brings concrete benefits which will yield results within a relatively short timeframe. It will also help give us confidence that our interim goal of a 40 per cent reduction in CO2 emissions by 2030 is achievable with available technology.”
With the help of Andritz Novimpianti, Meva Energy, and the University of Pisa, Sofidel’s Kisa mill is set to be a reference point for best practice in tissue mills as the tissue sector strives to reduce, and ultimately eliminate, fossil-based CO2 emissions. The project represents not only a tissue industry first but is pioneering for all process industries. The Meva Energy plant is the first in the world to use bio-syngas (or any form or syngas) for industrial process heat and Andritz Novimpianti has harnessed this capability with an unprecedented solution applicable to tissue manufacturing, which is flexible according to local biofuel sources.
“Science-based targets require a scientific approach,” says Linari. “It’s a privilege to be involved in such a landmark project where analysis and innovation can help significantly towards a reduced environmental footprint for a world-class tissue producer.”
Improve your press section efficiency! SmartScan™ contactless sensor accurately measures paper web dryness after the press section 24 hours a day, 7 days a week. Using a proprietary microwave technology, it is developed to overcome the typical limits of the NIR (near-infrared) sensors. SmartScan™ is available both for fixed point positions or traversing web scan. To save hundred of thousands of Euros in energy costs, stop collecting samples, choose the safe accuracy of SmartScan™ technology.
The world’s widest containerboard line, at the Aalen-Neukochen mill in Germany, represents an investment by Papierfabrik Palm that will pay off with sustainable high-quality product for the next 50 years. Report by Marika Mattila and Pauliina Purola.
The PM5 containerboard line at Papierfabrik Palm’s mill at AalenNeukochen in Germany is the largest of its type in the world. Delivered and started up by Valmet in July 2021, it is 10.9 metres wide, runs at up to 2,000 metres per minute and
has capacity to yearly produce 750,000 tonnes of very lightweight corrugated case material made from 100 per cent recycled fibres.
The location of the line is significant for Papierfabrik Palm, which operates five paper mills, 29 corrugated board plants and two recycling plants in Europe.
The Aalen-Neukochen mill is where Palm was established in 1872 when Adolf Palm laid the foundation stone for the family business on the Kocher River.
The PM5 production line comprises many novel paper making innovations, including a mill-wide automation system.
It is a true showcase of carbon dioxide-efficient board production. The new production line replaced three old machines at the mill.
“There’s a clear trend – even pressure – to be more sustainable in everything we do in the
The Palm mill is located at Aalen-Neukochen, the headquarters of the family-owned company in Germany. Valmet’s scope of delivery for PM5 included a complete containerboard production line from headbox to winder, with a wide scope of automation
market. If we didn’t react to these demands, we’d probably quickly go out of business. I strongly believe that PM5 has a sustainable lifetime that is much longer than 50 years,” says Dr Wolfgang Palm, owner and chief executive of Papierfabrik Palm. “Corrugated boxes only have
a great future as a packaging material if you can reduce carbon dioxide emissions further in the production process. One way to do this is to reduce the basis weight. We worked closely with Valmet to design a board machine that could produce more lightweight containerboard
than any other board machine in the world,” continues Dr Palm.
“PM5 features many technological innovations, which were tested and proven at Valmet’s pilot plants in Finland,” says
Stephan Gruber, managing director and chief technical officer of Papierfabrik Palm. “An outstanding highlight is Valmet’s Sleeve roll technology in the forming section, which enables high water removal capacity without using any vacuum. We’ve already reached our dryness 4
target, and we would absolutely install this unique technology again.
“We selected a three nip press concept with Transfer beltsystem to remove open draw from the press to the drying section with an excellent dryness level.
This has proved an excellent combination with the OptiDry Twin impingement dryer, which increases dryness and sheet temperature before entering the drying section.
“OptiDry Twin enables a very low deposit level at the beginning of
the cylinder drying, and the drying section’s runnability components stay absolutely clean. There are no stickies or dusting at the pre-dryer section. In the drying section, the reliable and compact geometry of the Valmet Hirun Compact runnability system works
very well to even further improve both runnability and cleanliness. We believe that selecting these innovations was the right decision.”
PM5 features novel OptiSizer Hard surface sizing technology for improved runnability, higher strength properties, the cleaning of starch in the recirculation, and lower operating costs than conventional film sizing.
“The hard nip sizing is working really well, with excellent runnability. This is the right solution for low basis weight production with a low draw, high sheet stability and savings in starch consumption. Because the spray size application is contactless, the recirculated starch is never in contact with recycled fibres,” continues Gruber.
“The reel and winder area are streamlined and highly automated, and roll movement is minimised, making it very operator friendly. The winder is like a robot that performs better and better every day. There
aren’t any quality issues with the finished rolls.”
Industry-leading control systems for distribution (DCS), quality (QCS), machines (MCS), analysers and measurements were selected for PM5 to improve process performance and achieve savings in fibres, chemicals and energy.
Dr Palm explains: “We’ve had very good experiences with the Valmet DNA Automation System, which is utilised mill-wide from the power plant and wastewater treatment system through to the stock preparation and paper machine to the winder.
Gruber adds: “We see clear advantages for both operators and maintenance getting the mill-wide automation system from one supplier. The Valmet platform is very reliable, and there’ve been no issues with the start-up.”
The PM5 line was started up during the Covid-19 restrictions. Valmet’s data-driven Industrial Internet applications with remote connections worked as a valuable support to achieve a
world-class start-up.
“Industrial Internet applications help us a lot, because Valmet’s specialists can very quickly connect to our process directly from Finland.
Industrial Internet solutions are part of our daily routine – for example, in-strength
development with Valmet experts,” says Gruber.
High-quality ultralightweight packaging material with low operating costs
The market for recycled containerboard has good
prospects, especially due to its sustainability as a packaging material: it is renewable and recyclable.
Containerboard production needs to deliver high efficiency and advantages in sustainability. Producing packaging grades with a low basis weight while maintaining high strength and excellent printing properties is always a challenge for board makers. Palm overcame this challenge with Valmet’s experts and the right solutions.
“If you produce ultralightweight board, you must achieve two things: you need to produce it efficiently and – even more important – economically. This means you have to increase the board machine’s speed much further. Our target was simply to have the fastest running containerboard machine in the world,” says Dr Palm. “We’ve seen strong demand for ultra-lightweight containerboard, much higher than we anticipated. Our ultralightweight board strategy really is a major success.”
Gruber concludes: “We produce ultra-lightweight high-quality containerboard for strong packaging purposes, which means the same strength properties and more square metres in a roll than in conventional containerboard grades.
“The whole value chain starts from PM5 and ends in households through e-commerce, for example. This means a much more sustainable supply chain.”
More information from: Tomi Tissari, project manager. Tel: 358 4076 5392. Email: tomi. tissari@valmet.com
Winders and their development have a long history at Valmet. The engineering company has already delivered more than 1,000 winders and 50 Dual Unwind systems, but their development is far from complete. The 1,000th winder delivered to Papierfabrik Palm PM5 showcases all the great features it offers.
Palm values its gigantic winder: “It’s not just a winder for us – it’s a robot. Just one winder manages all the paper from PM 5,” says Stephan Gruber, managing director and chief technical officer of Papierfabrik Palm. Having just one winder is a clear benefit for Palm: “It has reduced our investment cost compared to two winders, and it also reduces our personnel costs, because we need only two winder operators,” Gruber continues.
“The two key features of the winder at Aalen are the Valmet Industrial Internet (VII) and the Dual Unwind system to achieve high throughput,” Gruber says. Valmet developed the Dual Unwind system more than 10 years ago with the idea of having two unwinds at the winder. The innovation reduced the parent roll change time from ten to six minutes, improving winder capacity by as much as 50 per cent. More than 50 Valmet customers are already enjoying the benefits
of their Dual Unwind systems. The VII provides completely new opportunities to optimise winder production and maintenance. For example, it can give detailed insights into winding performance, with data-driven analytics to avoid unplanned stops and increase end product quality.
Automation has always been an important part of improving winder capacity, usability and roll quality. When combined with a reel and automatic transfer rails, the entire reeling and winding process can be operated with a minimum of personnel safely and effectively, while providing higher production levels. The winder at Aalen is equipped with a Valmet DNA automation system to maximise its high performance.
Although Valmet is proud of its past and the 1,000 delivered winders, this is not the end of the story. Valmet’s two pilot winders are used to continually develop new innovations. And the culture of innovation will drive Valmet to create even better winding solutions in the future.
Valmet offers several technologies that enable
the production of lighter board products without compromising on quality or visual properties. This is achieved with light weighting, which allows board and packaging producers to optimise raw material use, board quality and production capacity. The benefits of light weighting expand to each stage of the value chain: Packaging producers need less board for their products; transporting lighter products decreases the environmental impact, less energy is needed at every stage; and less waste is created thanks to recycling.
Palm’s PM5 produces ultra-lightweight board in basis weights down to 60 grams per square metre, which means a raw material reduction of at least 15 per cent, with comparable performance. In addition, old corrugated containers as 100 per cent recycled raw material contributes to the conservation of natural resources.
The PM5 replaces three old production machines, and it is equipped with the latest energy-efficient technological solutions, enabling substantial energy savings.
Further environmental benefits are achieved through mill-wide automation, which improves process performance while enabling savings in fibres, chemicals and energy.
Palm PMS: a showcase of carbon dioxide efficient board production
Pneumatic cylinders are an efficient, reliable and clean solution for moving loads in a linear direction (back and forth or up and down), with good levels of force and speed.
In the paper industry, they are in widespread use and can be found in machinery such as presses and knife gate valves that enable pulp and other products to flow. In fact, you are likely to find a pneumatic cylinder in any location where lifting, stopping or pushing is required as part of the production process.
Pneumatic cylinders use compressed air as the input source to move a load. There are various pneumatic cylinder types, including single-acting, doubleacting and rodless. Most contain
a piston inside the cylinder, and the compressed air enters at one end and acts upon the piston within the contained environment to translate the energy into movement, using a rod to move the external load. In the case of rodless cylinders, these are engineered to perform as a selfcontained linear actuator with the piston moving within a cylinder bore, for improved flexibility. Unlike a hydraulic cylinder which uses fluid and therefore comes with a risk of leakage or cross-contamination, a pneumatic cylinder relies solely on air, making
them suitable for use in a wide range of mechanical applications.
Cylinders are often the most important component of a linear motion system. If the cylinder fails, the linear motion system is unable to function and, in most instances, the machine it is part of and even the entire production line is out of action until the cylinder is replaced. This downtime is undesirable in any setting, but in a harsh environment where contaminants
are heavily present, standard cylinders are going to fail all the more frequently, resulting in more downtime.
Cylinders can be contaminated internally from the air supply or externally from the operating environment. In the latter case, seals become damaged from particles and corrosive elements in the immediate atmosphere, which are then able to enter the main workings of the cylinder, reducing the effectiveness and life of that cylinder.
Airborne particles in the form of dust are the most obvious threat to cylinders. If this penetrates a nose seal, it builds up and sits in seals and bearings with a similar effect to sandpaper. In a normal environment, with regular preventative maintenance, standard cylinders can cope well with basic levels of dust, but where these contaminants are prevalent, such as in a paper mill, a more robust cylinder must be considered.
Water may not be deemed a contaminant in the usual sense, but when it comes to pneumatic cylinders it is very much a problem as where there is compressed air, there is water vapour. Furthermore, in the paper making industry where water is used extensively, it has the potential to collect within system components
Many of the operations in a paper or pulp mill are actuated pneumatically. Japh Humphries* explains how to the ensure the reliability of the cylinders and their longevityStainless steel bodies offer better abrasion and corrosion protection than aluminium
where it can block the flow of air through orifices, dilute or adulterate lubricants, corrode the barrel or rod finish and, of course, freeze in cold weather.
Contamination from synthetic oils used to lubricate the air compressor can have a similar impact on cylinders to water, in that it can block orifices, as well as causing seals to swell. In harsh environments, higher volumes of lubricant are often used, which makes the contamination situation worst.
So, these are the problems, but what are the solutions?
First and foremost, invest in cylinders that are manufactured and sealed to a high quality from a well-established, recognised manufacturer. You really do get what you pay for.
However, in the paper production industry, which would be considered as a harsh environment, you will need to look to a more customised cylinder. The good news is, most of these customisations are relatively straightforward and represent a
good return on investment.
Let’s start with the cylinder seals, these being one of the most important means of preventing the ingress of dirt and water. Standard seals can be replaced with specialist versions to meet the needs of a specific application. Viton – a fluoropolymer elastomer and synthetic rubber compound –seals, for example, have been designed for use in some of the harshest environments. These can readily be used in Matara’s standard rod-type pneumatic cylinders and rodless pneumatic cylinders.
Moving further into the cylinder’s construction, with rodtype pneumatic cylinders a rod seal or wiper can be incorporated to both stop contaminants from entering the inner body of the cylinder, with the wiper removing larger particulates from the rod. For added protection the rod can be fitted with a rod bellow or gaiter which keeps contaminants away from the piston rod. When it comes to corrosion prevention, then consider going further than just swapping seals
for tougher versions. For corrosive environments, including those where large amounts of water are used, the choice of rod material may need to be reconsidered. Standard rods are mostly manufactured from chrome-plated steel, but swapping to stainlessexercised rods and fasteners, or even a stainless-steel rod, will provide extra protection against corrosion. This will impact the cost, usually by an additional 10 per cent of the overall cost of the cylinder. For complete corrosion protection, Matara offers a range of 100 per cent stainless steel pneumatic cylinders. The other option is to stay with existing materials but use specialist coatings or epoxy paints. There are a good range of options here, including Armoloy TDC coating, which Matara uses on its linear rail and ballscrews for maximum longevity in demanding applications and locations.
Armoloy TDC is a hard (78Rc), thin, hard chromium coating with a micro-nodular surface texture which provides corrosion protection equal to 440 series stainless steel.
Having selected the right cylinder type for your environment, it’s important to conduct basic preventative maintenance to a regular schedule. This should include the regular cleaning of external parts of the system so that visual inspection of seals and other parts is straightforward; inspection for wear and tear; draining of airline filters and checking that the water traps are operating as they should; lubrication of the cylinder, rod seal, piston seals and surfaces; checking for air leaks and resealing where required; and last, but not least, replacement of air filters. Paper mills make for difficult operating conditions, but by selecting quality pneumatic cylinders customised to your specific site, you can costeffectively prolong the service life of a cylinder and reduce costly downtime.
*Japh Humphries is UK sales & commercial manager at Matara UK Ltd. More information from www.matara.com, email at sales@ matarauk.co.uk or by telephone at 44 1684 850000.
As a cornerstone of its sustainability programme called ‘Papermaking for Life’, Voith has set a goal of reaching a 90 per cent recycling rate by 2030 through new fibre streams and an optimised recycling process.
Part of this is an innovative pulping concept that reduces energy consumption by more than 30 per cent compared to conventional systems. In particular it is designed for pulping special raw materials.
At German paper manufacturer Papierfabrik Palm, Voith’s pulping technology is already operating profitably as a pilot project. The stock preparation system is designed to produce 500 tons per day and enables Palm to
save 1,000 MWh of energy per year. In addition, high accept consistencies are possible, which leads to advantages in downstream processes.
Stephan Gruber, technology chief at Palm, is impressed by the new process: “Voith’s innovative stock preparation system has started up very well. Thanks to Voith’s tailormade concept, expertise and professional support, we were able to achieve and even exceed the performance targets within a very short time. In the area of sustainability, the technology takes a top position and is a good tool to further increase our resource efficiency and achieve our goals.”
The idea behind the optimised recycling process links two
pulping technologies. This involves continuous HC pulping in a trough with a horizontal pulping shaft and downstream screening section. At Palm, it is installed in a separate line for pulping processing waste and reject rolls and is already in continuous operation. The pulping of standard raw materials with increased dirt loads has already been successfully tested. Sustainability gets special emphasis in all such projects at Voith. Wolfgang Mannes, Voith’s senior expert for R&D in Fiber Processes, explains: “In various load tests at Palm, we had very positive experiences with the pulping result and the robustness of the concept. The specific pulping energy is also more than 30 per cent lower than in
conventional dissolution systems – a big step towards improved sustainability.”
Steffen Bassmann, director of product management for Fiber Systems at Voith Paper, summarises the achievements: “In the light of limited raw material availability and challenging sustainability targets of the entire paper industry, we are already seeing clear interest from the market.
“Palm’s results are promising,” adds Bassmann. “We are further optimising the concept, especially with regard to its use for difficult-to-dissolve and coated recovered paper grades, for which mostly discontinuous HC pulpers are used today.”
l More about paper manufacturer Papierfabrik Palm: see page 16.
The L&W Bending Tester produced by ABB has been enhanced with new features to deliver easier and more reliable operator-independent measurements of bending resistance and stiffness.
The tester, which measures resistance to bending in paper and packaging, is a benchtop instrument with a large touchscreen interface and improved post-processing for instrument checking and calibration.
The new features enhance the ease-of-use for operators and help them to overcome challenges associated with older, complex or difficult-to-operate instruments:
l A test piece is clamped automatically and precisely with a support for easy sample
loading, aiding the operator and leading to a repeatable measurement process
l A new ergonomically-placed start button is pressed, and the testing sequence starts
automatically with an improved auto-touch function
l A large touchscreen with customisable programs, options for instrument check and calibration, and adjustable
testing speed and bending angle makes it easy for the operator to select the right options and program settings.
In addition, bending length is automatically detected, which ensures that the correct settings are selected every time. On-screen results include an overview of the measurement series and a graphical display of the bending curve with break angle/force. This model also accommodates bending lengths from 1mm to 50mm.
Integration with other ABB products, such as L&W Lab Management System (LMS), also means connectivity to the full Quality Data Management module within the larger Manufacturing Execution System (MES), enabling greater visibility of data across the mill and enterprise.
As an addition to its OceanCoat roll cover, Voith has now developed the OceanCoat P.
The new coater backing roll cover is design specifically for high-demand locations in blade coaters. With its new polyurethane chemistry and a unique filler, OceanCoat P is optimised to meet the requirements of stable profile conditions and the highest wear resistance.
Voith says that OceanCoat P has been confirmed as very resistant to over pressing. Due to the resistant polymer matrix enhanced with fillers, a constant
cover surface including very high abrasion resistance can be ensured. This is an important advantage in coater backing roll applications, as paper breaks may lead to over-pressing on standard covers which can shorten the cover’s life. Another advantage of
OceanCoat P is its high chemical resistance. All features increase the running time of the roll, simplify work processes, and thereby increase the machine’s productivity.
“We are extremely satisfied with the OceanCoat P,” said Markus
Krall, production manager on Coating & Finishing Line 4 at Norske Skog’s Bruck paper mill in Austria. “After six months in operation, the roll is still in very good condition. The runtime, which is usually 180 days in this position and shows wear especially in the edge area, was achieved without difficulty. OceanCoat P shows no wear and is used without regrinding.”
When combined with ceramiccoated high-performance blades, OceanCoat P offers the potential to reduce overall production costs for the customer, says Voith.
Anew type of drying hood with electric heating for use in tissue mills has been launched by Andritz .
The hood, which produces no carbon dioxide emissions in the mill, offers better energy efficiency and productivity, and enables tissue machine operators to avoid the use of fossil fuels and to progress towards their sustainability goals.
Andritz says it already has an order for the electric hood with startup expected before the end of 2023.
George Nowakowski, vice president of tissue drying at Andritz Canada, commented: “We developed the new hood in close cooperation with customers. It perfectly matches today’s need for sustainable
and especially carbon dioxide reduced high-quality tissue production. Having received the first order right after the market launch is the best proof that we are meeting our customers’ needs.”
The PrimeDry Hood E uses electric elements to heat the air
flow. As a result, overall carbon dioxide emissions are cut by about 70 per cent compared with conventional gas-heated systems. Without the need for combustion air, energy efficiency for the drying system is said to improve by up to 4 per cent compared to gas-heating. With its ability to
achieve air temperatures of up to 450 deg C, the hood contributes to higher productivity compared to steam-heated systems.
The Hood E is also available as a hybrid model, with an air system that combines electric heating with natural gas burners working in tandem.
Accurate data regarding the cationic demand and zeta potential of fibres in the wet end of the papermaking process helps with its smoother running and achieving higher product quality, says Emtec Electronic GmbH. With this end in mind, the company has developed a pair of instruments – the CAS touch! Charge Analyzing System and the FPA touch! Fiber Potential Analyzer – to specifically measure both parameters.
Data gathered from the systems enable technicians to determine the correct dosage of chemicals to add to achieve desired product
properties and reduce resource waste.
The compact and lightweight
devices also make it easy to transport in a carry-on suitcase, which is helpful for
technicians providing onthe-go measurements and troubleshooting.
Emtec Electronic demonstrated the instruments at the ExpoAcotepac conference and trade show held in February at Cali in Colombia.
Other instruments from Emtec Electronic include the EST, which is specifically designed to resolve issues with gluing, coating and printing that arise during conversion, and the TSA which is said to provide objective and reliable data on the haptic parameters softness, smoothness, and stiffness.
Austria’s MM Board & Paper has successfully re-started the KM3 board machine at its Frohnleiten mill after Andritz completed a major rebuild. The rebuild included several upgrade measures to improve the machine’s performance in line with the customer’s targets.
Mag. Gernot Schleiss, managing director of MM Frohnleiten, explains: “The main objective of our investment was the modernisation of the KM3 to enhance the quality of the end product, to reduce specific energy consumption and to increase productivity across the entire product range. We are convinced that ANDRITZ’s innovative PrimeLine technology will help us reach our targets.”
KM3 has a design speed of 800 metres per minute and a wire width of five metres. It produces folding boxboard (chromo duplex quality) in a range from 230 to
450 gsm. The rebuild comprised the modernisation of the wire section including approach flow systems, headboxes and hybrid former. In addition, Andritz’s scope included a new press section, the rebuild of the pre-
dryer section, an upgrade of two under-machine pulpers, machine clothing and roll covers, adaption of the automation system, as well as assembly, start-up and production assistance.
MM Board & Paper is Europe’s
Graphic Packaging International (GPI) has ordered a coated board machine from Valmet for its Waco mill in the United States, similar to the one that was delivered to GPI’s Kalamazoo mill in 2022. The start-up of the Waco machine is scheduled for early 2026.
“Valmet has offered us innovative yet proven
technology to reach our high product quality targets. We have had a long and good cooperation with Valmet. Our relationship is based on mutual trust, which is very important in large projects like this one,” says Rusty Miller, senior vice president for engineering and technology at GPI.
The project includes
equipment for stock preparation, approach flow systems, a board machine with extensive process ventilation scope, a wide Valmet DNA automation package and a winder. The delivery will also include Valmet Industrial Internet services.
The board machine will produce white line chip board
largest board producer (excluding liquid packaging board). With a capacity of 540,000 tons per year, the Frohnleiten mill in Austria is Europe’s largest recycled cartonboard mill.
(WLC) grades, with an annual capacity of 456,000 metric tons. Atlanta, Georgia-based GPI produces paper-based packaging for a variety of products for the food, beverage, foodservice, and other consumer product sectors. With more than 130 sites worldwide and 24,000 employees its sales in 2022 were about $9 billion.
Aformer paper machine at Stora Enso’s Oulo mill in Finland is to be converted by Voith from the production of graphic papers to high-quality folding boxboard and coated kraft back (CKB).
With a capacity of 750,000 tons per year, the line, estimated to represent an investment of €1 billion, will be the largest board machine in Europe when it startsup in early 2025. Stora Enso said it was important that the converted line offers optimum production efficiency while meeting the highest environmental standards, especially in heat recovery. With the converted line, the company will be able to achieve the highest production capacity in Europe for high-quality packaging made of folding boxboard and CKB.
“We are very pleased that Stora Enso has chosen our full-line solution,” says Dr Michael Trefz, president of projects at Voith Paper. “The order builds our existing partnership with Stora Enso further. After the conversion, the board machine will be a high-tech plant with the latest
standards to produce high-quality board packaging.”
To achieve the high production volume, Voith collaborated with Stora Enso to develop a tailormade design that maximises both efficiency and sustainability throughout the entire paper machine. The scope of supply includes a new, three-layer wire section with the DuoFormer D II. The high-performance Triple NipcoFlex shoe press will enable maximum production output at the highest quality level. At the same time, the technology will
minimise specific energy and production costs. The machine will also feature maximum flexibility and top product quality with the use of a SpeedSizer system and four DynaCoat AT coating units with JetFlow F applicators. The SpeedSizer as well as the DynaCoat AT are partly made of carbon fibre to ensure stable cross sections at all grades and speeds. In addition, Voith’s bulksaving EcoCal HiBulk calender will provide excellent stiffness, outstanding smoothness and printability.
To achieve ideal energy efficiency, Voith experts are also extensively rebuilding the existing dryer section. The high operating dew point of up to 65 deg C in the Eco Hood 65 dryer lowers the supply and exhaust air volumes and thus reduces power and steam consumption. The CombiDuoRun dries the web on both sides, preventing curl even at high operating speeds. Finally, two VariFlex Performance winders will be installed. In addition, Stora Enso relies on Voith’s leading digitalisation and automation expertise. Thus, Voith will implement an OnControl.Machine MCS for the automation of the board machine, the OnQuality quality control system, and an OnCare. Health condition monitor. The dataPARC cloud serves as the IIoT platform.
In 2019 Stora Enso started the conversion of the Oulu paper mill to packaging production. The €350 million investment included converting the mill’s PM7 to produce virgin-fibre-based kraftliner and the closure of the PM6 and a sheeting plant.
At its Oulo mill in Finland, Stora Enso is having a bleached chemi-thermo mechanical pulp (BCTMP), evaporation and non-condensable gas (NCG) technology installed by Valmet.
Valmet will also deliver an extensive automation package as part of the project to convert the mill to produce consumer
board in high-volumes.
The deliveries will carried out in phases and the upgraded mill is scheduled to be in operation in early 2025.
Sami Riekkola, pulp and energy business line manager at Valmet, said: “With Valmet’s process technology and automation, we enable Stora
Enso to produce carton board with excellent environmental performance and optimised fiber properties. Our leading BCTMP technology is built on Valmet’s strong ‘Fiber to Board’ knowledge. With the extensive automation package, we are able to offer Stora Enso a good visibility to the mill processes
and excellent operability to maximize the performance of the whole mill.”
In addition, Valmet had already earlier agreed on a recovery boiler rebuild delivery for the Oulu site. The rebuild includes an electrostatic precipitator upgrade to ensure the required capacity for future production.
Visy Paper is to install the first Andritz FibreFlow Drum pulping system in Australia at its Coolaroo recycled paper mill in Victoria.
The drum pulper will offer a maximum feed capacity of 1,400 tons per day with a range of fibre cleaning equipment, and a spray water treatment system for the production of various board grades.
“The drum pulper is the first of its kind in Australia,” says Jean Yves Nouaze, executive general manager of Pulp & Paper at Visy. “This upgrade will increase our capacity to process up to an additional 95,000 tonnes of waste
paper per year, to be made into new products here in Victoria. We thank Andritz for partnering with Visy and working collaboratively on this critical project.”
The drum pulping system enables Visy Paper to process a
demanding special raw material mix consisting of household wastepaper and old corrugated containers (OCC) with a reject content of up to 25 per cent.
The project features a number of technological highlights:
● A FibreFlow Drum with longer and reinforced design to ensure gentle pulping of the demanding
raw material mix and efficient removal of coarse contaminants at minimum fibre loss
● A PrimeScreen X for spray water treatment
● A new RB450 cleaner to enable better removal of glass fragments.
Visy’s paper mill in Coolaroo is part of the Visy Group – a global leader in packaging and resource recovery – and produces plasterboard liner for the building industry as well as white and brown liner grades from 100 per cent recycled content.
Pulp and paper maker Stora Enso has contracted ABB to upgrade two of its mills in Sweden with the latest manufacturing execution systems (MES) to manage and streamline endto-end production and improve overall efficiencies.
Migrating to ABB’s Ability MES will offer new functionalities and customised features that meet Stora Enso’s specific site requirements.
Most importantly, says Stora Enso, the system will interface with the mill’s ERP, DCS, QCS, WIS, laboratory devices for true integration and greater visibility over systems and processes throughout the
manufacturing chain.
This will give operators, supervisors, production engineers and plant managers the insights to act and optimise, in turn improving productivity and end-product quality while reducing waste.
The contract covers two of Stora Enso’s sites. The modern Skoghall Mill produces renewable and recyclable premium board, with some one-in-six of all liquid packaging board cartons in the world originating from there. Skoghall also produces bleached and unbleached kraft pulp using a single fibre line with continuous cooking, and ChemiThermoMechanical Pulp (CTMP).
The Forshaga barrier-coating site, situated 30km north of Skoghall, manufactures and develops a wide range of barrier products and laminates that are required in certain packaging to keep food fresh and extend shelf life.
“Stora Enso’s upgrade to ABB’s MES has been carefully planned to meet their requirements and ultimately improve production efficiency and quality management at their mills,” said Jyrki Juvonen, business development manager for ABB Ability MES. “ABB’s MES provides the key elements that will give Stora Enso a competitive advantage by enabling higher plant efficiency and productivity,
as well as greater flexibility throughout the production processes.”
The delivery includes layering ABB’s Production Planning, Production Management, Quality Data Management, Overall Equipment Effectiveness (OEE), Diary and Operative Reporting modules with interfaces to ABB and third-party systems. All will be supported by a global service contract, going live after start-up in 2023. The integration will streamline management and provide seamless orchestration and synchronisation of all the parties involved in mill operations while also mitigating cyber security risks.
International paper maker
Smurfit Kappa has ordered an energy-efficient debarking line for its Yumbo paper mill in Colombia from Andritz . Start-up is scheduled for the fourth quarter of 2024.
The order is part of Irelandbased Smurfit Kappa’s goal to replace the fossil fuels currently used with range of organic waste
types to generate cleaner energy at the mill and is another step towards Smurfit Kappa’s goal of achieving net-zero carbon dioxide emissions by 2050.
The organic waste, processed in the Andritz debarking line, will comprise pine and eucalyptus bark from Smurfit Kappa’s own forestry plantations and waste from its wood treatment plant, among other materials.
The project includes a new debarking line with rubber-tire supported debarking drum which is said to provide excellent results with very low wood losses. The capacities of the new line are 333 cubic metres of hardwood and 370 cubic metres of softwood solid-over-bark per hour. The scope also includes chip screening equipment and a bark handling system with
Greek paper maker Unipakhellas has ordered complete paper packaging line for its Pelasgia mill in the Fthiotida region.
Operated by Unipakhellas Central (UHC), the line will deliver highquality test liner and fluting grades to Greek and export markets, and is expected to start up soon.
The new machine has a wire width of 3.0 metres and will produce corrugated paper in the range of 90 to 200 gsm at a maximum operating speed of 800 metres per minute, processing 100 per cent recycled paper.
The machine features a twolayer Fourdrinier configuration with a hydraulic TT Headbox-SL. It is equipped with a TT Xpress shoe
press, along with TT SteelDryers, a steam and condensate system, and stabilisation boxes in the dryer section.
The delivery also includes a hard nip calender, a hydraulic pope reel and the tail threading system. The scope is completed
by mechanical drives, an enclosed hood, and air and ventilation systems. Unipakhellas selected a comprehensive service package with engineering, erection supervision, commissioning, training, and start-up assistance. Fayssal Frem, chairman of
Andritz BioCrusher BSX.
With capacity to produce 7.7 million tons a year, Smurfit Kappa is one of the leading providers of paper-based packaging in the world, with operations in 23 European countries and 13 countries in the Americas.
Unipakhellas, which is part of the Indevco Paper Making group, says, “Our decision to invest in Greece testifies to our belief that Greece is an actively growing market due to its geography and most importantly its human talents. The choice of Pelasgia’s strategic location not only makes commercial sense, but it is primarily driven by Indevco’s philosophy of furthering community development. We are confident that Toscotec will deliver on our expectations of high performance.”
Unipakhellas operates a number of mills in Greece, including at locations in Athens, Pelasgia, Thiva, Thessaloniki and Crete.
Asecond paper making line at Sappi’s Skowhegan mill in Maine, USA, is to receive and extensive rebuild by Valmet.
The order, to rebuild the PM2 line, follows the successful rebuild of the PM1 line. The project is expected to represent an investment of between €90 million and €120 million.
As a result of the PM2’s conversion from coated woodfree
graphic paper to solid bleached sulphate board, its capacity will be increased from 240,000
The start-up of a FibreFlow drum pulping system and reject handling equipment has been successfully completed by Andritz at Asia Honour Paper’s mill in Mentakab, Pahang Darul Makmur, Malaysia.
Andritz installed a new drum pulper as well as reject handling equipment to upgrade the PM21 production line, processing a
mixture of recycled fibre grades for manufacturing of newsprint, printing and writing paper (P&W) and low basis-weight board (LWB).
Asia Honour Paper Industries (M) was established in 1999 as newspaper manufacturer and nowadays produces a broad range of high-quality paper products based on recycled fibre mainly for the Asian and global markets.
to 470,000 tons per year. The start-up of the rebuilt machine is scheduled for mid-2025.
“Valmet has proven to be a trusted supplier to Sappi over the years and we’re pleased to work with them again on our PM2 project. This investment is fully aligned with our Thrive25 strategic focus to reduce our exposure to graphic paper and transition our portfolio to packaging and speciality papers, pulp and biomaterials,” says Michael Haws, chief executive of Sappi North America.
An energy-saving LimeCool system has been installed and commissioned by Andritz at Stora Enso’s Imatra pulp mill in Finland.
The system is designed to use the heat of the processed hot lime in the lime kiln. This enables higher energy efficiency to be achieved in the white liquor plant and an increase in the production of high-quality lime
when compared to conventional separate satellite coolers.
Mika Varis, project manager at Stora Enso, says: “We selected the LimeCool system due to the stateof-the-art technology combined with Andritz’s flexibility and fast response. This was the complete package that met our needs.”
Metsä Tissue has ordered a new tissue production line from Valmet for its Mariestad mill in Sweden. The delivery will include a package of stock preparation, automation and service systems. The order is part of Metsä Tissue’s Future Mill development programme, which aims for world-class environmental and technological performance in tissue production. The value of the order was not revealed.
Valmet and Metsä Tissue have a long history of cooperation. Recently the PM10 machine at the Metsä’s Mänttä mill in Finland was successfully rebuilt. In the past few years Valmet has also supplied a series of energy saving and efficiency upgrades to Metsä Tissue’s other mills, including Advantage ReDry energy saving
solutions, Advantage ViscoNip presses, refiners and automation controls.
“With the new tissue machine, we will increase the offering of locally produced sustainable virgin fibre-based tissue paper to the Scandinavian market. It enables reliable local deliveries of high-quality tissue to the consumers. The new technology brings big environmental benefits. In addition to the energy savings, we can reduce the process water
Hubei Xianhe New Materials Co in China has ordered a chemithermomechanical pulping line with a capacity of 350 admt/d from Andritz for its mill at Jingzhou City in Hubei Province. With this contract Andritz says it is consolidating its strong market position for low-energy hard wood mechanical pulping technology focusing on production of highquality fibres at lowest operating cost.
Established in 2021, Hubei Xianhe New Materials is active
in a number of business fields including the pulp and paper industry.
in the paper making process by 50 per cent,” says Esa Paavolainen, vice president for projects at Metsä Tissue.
The new tissue machine – which will be optimised for low energy consumption and product quality – will have a design speed of 2,200 metres per minute and increase the mill’s tissue capacity by 70,000 tons to 145,000 tons a year.
The line will be based on a Valmet Advantage DCT 200 TS tissue machine with the latest
technology for high efficiency, low energy and water consumption and reduced carbon dioxide emissions.
Valmet will also supply a quality control and monitoring system, complete engineering, installation supervision, training, start-up, and commissioning.
Start-up clothing as well as master maintenance data services and remote support from Valmet’s Performance Center are included.
Procter & Gamble (P&G) has ordered a tissue machine from Andritz for its Box Elder Family Care mill in Utah, USA.
Delivery of the PrimeLineTAD machine is scheduled for 2024. The machine will be supplied with state-of-the-art energyefficient equipment to meet the global FMCG giant’s demanding sustainability targets.
Andritz and P&G have been strong business partners for many years. In 2007, Andritz supplied
and started up a TAD tissue/towel machine at P&G’s mill at Green Bay in Wisconsin that was said to fully meet P&G’s expectations. This was followed by another TAD tissue/towel machine P&G’s Box Elder mill, which started up successfully in 2011.
P&G, one of the largest manufacturers of premium consumer bath tissues and paper towels in North America, produces brands such as Charmin, Puffs, and Bounty.
Daniella Dahlbom has been appointed as chief people & culture officer at PulPac, the Sweden-based fibre-forming technology specialist.
It is an executive team role at PulPac for Dahlbom, who has been HR manager since 2021. She brings more than ten years of experience in human resources, recruitment, and people operations. She will lead the HR, recruitment, culture and people team.
“We are thrilled to have Daniella on our executive team,” said chief executive Linus Larsson. “She is a true leader that helps us foster a culture of belonging and connection, empowering employee success. The team is
at the core of everything we do and empowering our people to shape the future of packaging is the foundation of our success. With her skill set, we are confident that Daniella will help elevate and strengthen PulPac as we step into this next exciting chapter of our journey.”
Dahlbom commented on her appointment, saying: “This is a fantastic company with a unique opportunity to make a real impact for a more sustainable future. And the road to success goes through our people.
“I’m excited to help drive the company forward by elevating and
advocating for our employees. It’s a joy to work with and serve this talented team. My contribution is to create an environment where they can do their best work. Together we will show how thriving companies can drive successful business outcomes”.
PulPac is scaling up operations and has grown its workforce rapidly to meet increasing demand for its fibre-forming technology worldwide. In her role, Daniella will lead the human resources team, drive continued growth, and help scale all elements of the organisation, including culture, organisational design, talent acquisition, engagement, training and development, employee experience, and infrastructure.
Rob Tilsley has been appointed as fibre operations group lead at James Cropper, the UK-based paper maker.
Tilsley’s role drive growth of upcycled fibre within the company’s paper products to 50 per cent by 2025, both increasing the capacity and the quality of recovered fibre available to the James Cropper business.
In addition, he is responsible for the day-to-day management of the on-site upcycled fibre facility, baler house and wastewater plant at the mill in the Lake District; as well as the introduction of new fibre streams and the standardisation of recovered fibre use.
The appointment comes after
the creation of James Cropper’s destination brand for its fibre activities: The FibreBlend model organises the fibre blending options available to customers.
Tilsley has worked at James Cropper for 18 years and has extensive experience of speciality paper making processes, capabilities and products.
Richard Burnett, head of technology and innovation at James Cropper said: “Rob’s extensive knowledge of the industry and our business coupled with his commercial mindset and passion for innovation make him the perfect fit to drive our ambitions for FibreBlend Upcycled Technology.
“At a time when consumer
demand for paper and packaging which tirelessly pushes the boundaries of sustainable solutions continues to grow at
pace, it is an exciting time to take on this role.
Speaking on his appointment
Tilsley said: “From the world’s first technology to upcycle used coffee cups to the industry leading incorporation of used jeans into fully recyclable paper for packaging: transforming waste into beautiful paper and packaging is at the core of the FibreBlend Upcycled Technology mission. Having honed my knowledge of papermaking within the James Cropper family, I am over the moon to be involved in continuing this mission and reaching our goal to have a balance of fresh and recovered fibre across our portfolio of paper products by 2025.”
Evolving market demands require agility and efficiency for mills to deliver products on spec and on time. Trust ABB and our MES specifically designed for pulp and paper to help you deliver the best operational results. Our comprehensive and modular solution covers all the core MES functionalities across the value chain, helping you achieve new levels of operational efficiency.
Learn more: abb.com/pulpandpaper