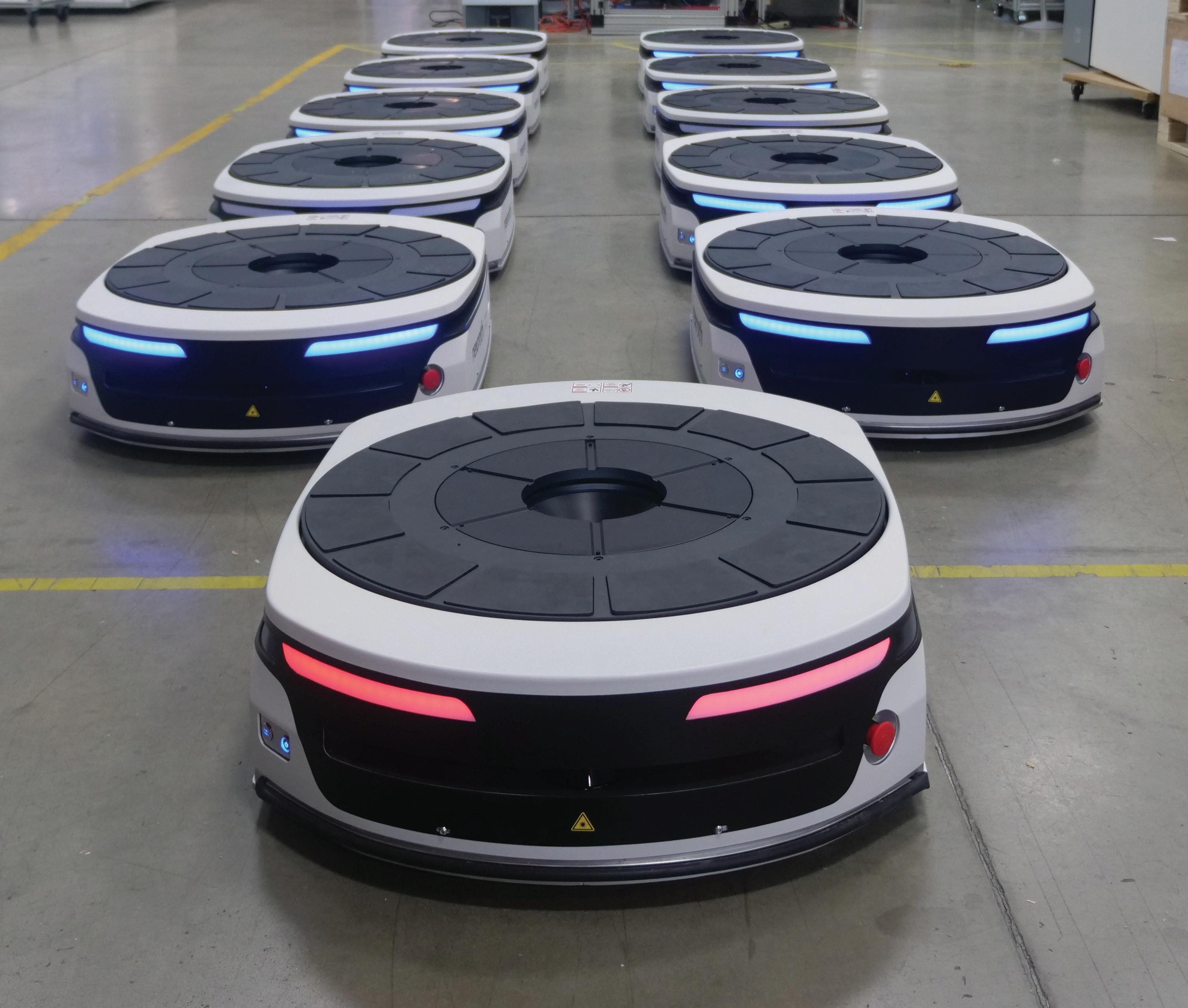
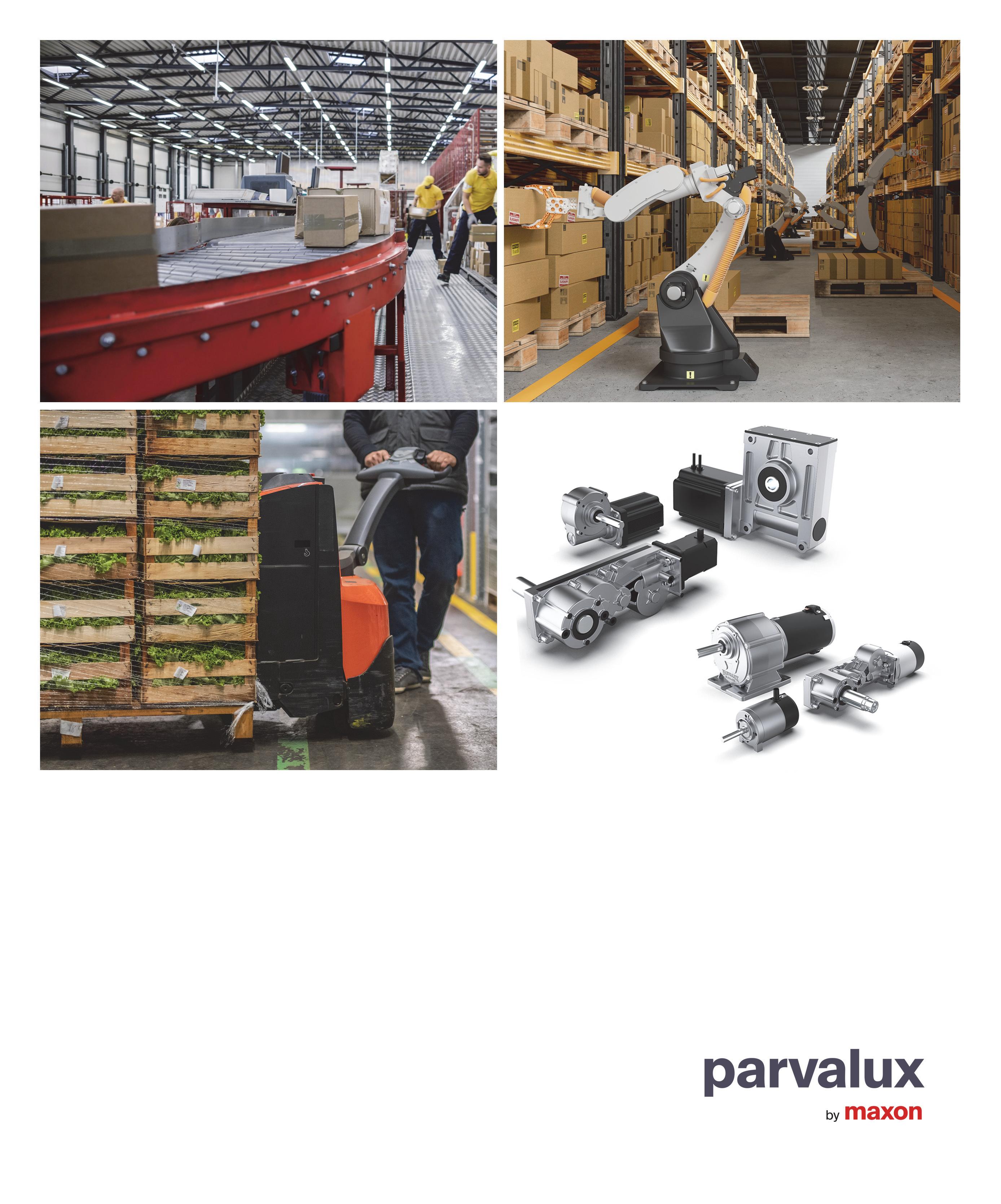



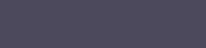
80
How real-time data can increase uptime
Today in automation, predictive and preventive maintenance are constantly in the conversation.
86
SLAM technology improves AMR autonomy
Dynamic warehouses seek robots that can adapt to change with minimal human intervention. With localization and mapping software, AMRs can build facility maps, orient themselves, detect di erences, and share changes with their fleet for uninterrupted and safer operations.
92
Top five robot trends in 2023
Why did the global stock of operational robots hit a new 3.5-million-unit record? Why did the value of installations reach an estimated $15.7 billion? The IFR analyzed five key things shaping robotics and automation.
98
What’s the difference between an AMR and an AGV?
Despite the growing popularity of warehouse automation, confusion remains around the various acronyms and technology. For those in the discovery phase of an automation journey, here’s an overview of two of the most talked about warehouse solutions.
Today in automation, predictive and preventive maintenance are constantly in the conversation. While the ideas may be clear, the implementation and advantages are not. Is this a fad that will fizzle out soon?
By Gerry Paci, Marketing Manager — Material Handling, Pepperl+FuchsFFor many years in the material handling industry, warehouse operators have strived to achieve minimal downtime and optimal operation. There are countless ideas and aspects for attaining this milestone within the warehouse.
In this era of intralogistics, the requisite for automation has become apparent. While some automate more than others, the necessity has proven clear. Managing automated equipment and potential downtime is crucial to production and intralogistics.
When a machine is down, the alarm will sound, reminding those on the floor that time and money are paramount. It is one thing to fix the issue quickly so that the process can continue, but understanding when this type of issue or downtime could occur again is the real prize. Moving from reactive to proactive maintenance in the warehouse can be the di erence between a streamlined process and a chaotic event within intralogistics.
The industry has learned over the years that regularly scheduling maintenance helps minimize problems with automation. A planned approach involving inspecting and repairing equipment to prevent failures has proved successful. Based on history, the warehouse maintenance team may understand that a motor controlling the conveyor needs to be inspected once per quarter
for potential loosening due to vibration. This tactic helps extend the equipment’s lifespan and identify and address problems before they cause downtime. Nonetheless, if the maintenance team had access to the motor’s vibration velocity and temperature over time, they could predict when a failure could occur, streamlining their maintenance process.
This information and data have become widely available from the software and sensor technology intertwined with the automation process. From a simple photoelectric sensor that detects whether an AS/RS shuttle has entered the proper level of the rack to a 2D LiDAR system looking down over a conveyor to understand the flow of parcels over time, real-time data is constantly surging into a PLC, IPC, or data collection tool within the warehouse. How this real-time data
is used is one of the most interesting portions of the process.
As with any newer process or idea in a long-standing industry, challenges and speculation will arise. The transition from preventive to predictive maintenance is not free of these challenges. Where the data comes from, how to process it, and how much upfront implementation time it takes are all common questions during development.
In many cases, some of these questions can be answered using the data from the sensors already living in the warehouse. For example, it is becoming more difficult to walk into a warehouse without seeing the major use of automation, which requires sensors. To implement preventive maintenance, the data from an IO-Link capable sensor can be used as an analytical tool to understand when the machine could fail.
Vibration sensor data extends automation equipment’s lifespan and helps maintenance teams identify and address problems before they cause downtime.
Now that the data is located and available, networking technology such as a managed Ethernet switch can transfer the data to the next step. A gateway can also be added if the data needs to be converted to a different programming language. The final step is employing a digital transformation strategy to examine the information in a centralized repository.
It is essential to remember that not every problem has a standardized solution, and a new solution can create a new silo of data. The strategy must ensure that every portion of the warehouse with data — from the AGV that carries a tote to the conveyor that transfers the tote to the production worker — behaves as one system.
After this convergence is coordinated, valuable preventive maintenance and condition monitoring analysis solutions can finally occur. A digital dashboard is a simple way to make informed decisions using the available data. To avoid making data
For most of my life, I pushed myself while working out at the local gym. I used my feelings to balance reasonable rest periods between exercises while keeping my heart rate elevated. After training sessions, I self-evaluated and asked myself if I had trained hard enough or could have pushed a little more. Then, I adjusted the next training session’s intensity, higher or lower, based on my feelings. Over time, I saw gains, which convinced me that my method was successful.
However, was the method optimal? Was there a more efficient path to success or progress? The answer is yes.
Now, instead of using my feelings, I use a smartwatch to record my heart rate and manage rest between exercises. Instead of guessing whether I’m having a rigorous training session, I check my calories burned and make informed decisions based on real-time data.
This example is how I like to think of preventive maintenance compared to predictive maintenance. Preventive maintenance allows me to make decisions based on my feelings. Predictive maintenance allows me to make more accurate assessments based on real-time data and a simple dashboard.
Automated warehouses use many facets of automation, such as autonomous storage and retrieval systems, moving conveyor systems, palletizing and sorting systems, and automated guided vehicles and robots. Found throughout industries such as automotive, machine building, food and beverage, material handling, logistics, and e-commerce, warehouse automation is a fixture in today’s industrial environment. HELUKABEL offers a wide array of flexible and continuous-flex control, data, VFD/servo power and feedback cables, as well as the guidance and protection systems to ensure the transmission of power and data remains constant so materials stay on the move and arrive at the right place in your facility just in time.
analysis difficult, an open architecture solution can converge the data from the various systems to produce a much clearer view in the digital dashboard. When analytics highlight a problem, data sources can be analyzed to detect which system generates the issue, from micro-stops to AGVs receiving incorrect instructions.
In the end, a process analysis can be overlaid on top of the productivity metrics to get a picture of the overall health of the operation and a clear understanding of where the process can improve or where the next bottleneck or failure will occur.
A critical component of this datadriven, preventive maintenance solution is to share all the data sources from the smart sensors and machines to constantly evaluate the health and condition of the process. This is typically managed in the background of the operation in a non-time-sensitive fashion. The advantage is that rather than having the maintenance team periodically or regularly check the systems, the software-driven solution queries the smart sensors for their IOLink-provided health diagnostics. This data can be shared to help operations, engineering, and management understand the warehouse’s long-term health. This requires the previously mentioned methods of converging systems and the technology connectivity that provides the data to be analyzed.
As we continue to debate which diagnostic approach is right for each specific warehouse organization, there are two aspects most may agree on today: having the ability and resources to prevent downtime and failure is strongly desired, and it’s a very interesting problem to solve. l WH
Pepperl+Fuchs
pepperl-fuchs.com
| Courtesy of Pepperl+Fuchs
For an effective preventive maintenance program, all data sources from smart sensors and machines should be shared to constantly evaluate the process and equipment’s health and condition.
| Courtesy of Pepperl+Fuchs
analytical tools to predict potential machine failure and provide health diagnostics.
Realize your vision with Festo’s approach to smart automation for food processing and packaging. Partner with Festo today.
Industry Leadership
Superior Quality Products
Global Training & Support
Dynamic warehouses seek robots that can adapt to change with minimal human intervention. With localization and mapping so ware, AMRs can build facility maps, orient themselves, detect di erences, and share changes with their fleet for uninterrupted and safer operations.
When people were building warehouses 10 or 15 years ago in the U.S., few considered employing robots over human labor. In time, autonomous guided vehicles (AGVs) proved useful, and workers gradually appreciated their help. Yet AGVs need tape on the floor, magnets, or some sort of infrastructure, which requires well-thought-out strategies and sometimes permanent facility designs.
In comparison, emerging autonomous mobile robots (AMRs) live on the wild side and don’t necessarily need such infrastructure. They can navigate a facility’s current layout without adjustments to aisle widths or flooring. They’re characteristically flexible and can be less costly to implement.
However, the AMR market is still maturing, with new vendors popping up every day. And there’s a sustained resistance to change and an underlying fear that robots will steal jobs and be a headache to deploy and maintain. Many still ponder who will get the call at 3 a.m. when the robots aren’t working — and whose career will be on the line if the automation fails.
It’s fair to say that AMRs are only as e ective as the people who commission them. So, the robots need a little human support during and after deployment to ensure they fulfill their intended purpose and function correctly.
“We make deploying robots sound really simple, but it’s a change. It’s an automation project and a people-change project,” said Chris Mercurio, sales product manager for AMR solutions in North America at Bosch Rexroth. “Once people get a chance to work with the robots, they realize they don’t have to walk all the way across the floor to get more supplies. They can just press a button.”
But make no mistake, warehouse robots aren’t servants that make people lazy. Sure, they can take over mundane, repetitive tasks, but they can also spare people chronic back pain, reduce trips and falls, and mitigate common safety risks.
“There are a lot of accidents involving forklifts and other industrial trucks. So, we let the robots take the strenuous and unsafe jobs and reserve people for critical thinking, problem-solving, and handling complex tasks. Everything else, we can automate,” said Mercurio.
Post-pandemic labor shortages and supply chain issues drive reshoring and automation efforts to recover from setbacks and prepare for new waves of uncertainty. Over the past few years, more companies have welcomed automation to fill vacancies long-term and move remaining people toward value-add operations. Hence, more AMRs are being deployed with no signs of slowing down.
AMRs’ popularity is intertwined with the advancements of their underlying technologies. For example, scanning and sensing technology improves
alongside increased AMR demand and subsequently improves affordability. Similarly, the electric vehicle industry drives battery technology forward, and the AMR industry can take advantage of longer life and more uptime.
Additionally, software advancements have made AMRs more intelligent, and open-source solutions lower the barriers to entry. Manufacturers can use open-source technology, libraries, and development tools as a base to build upon without reinventing the wheel.
AMRs usually need three pieces of software: (1) a fleet manager that manages tasks and traffic, (2) a navigation piece that plans the paths and controls the robot’s motion, and (3) a localization piece that tells the robot where it is and where it’s going. The localization software is a key differentiator that makes AMRs more independent.
For instance, Bosch Rexroth’s Rokit Locator software is a simultaneous localization and mapping (SLAM) technology that determines the robot’s position and orientation based on an environment’s natural features, such
as the building columns, walls, and machines.
“Rokit Locator creates a map based on the natural environment, and then it’s able to understand where it is on that map and navigate the facility,” said Mercurio. “It’s scanner agnostic and uses existing scanners on the robot to constantly scan the environment, draw a map, and position itself. An algorithm constantly compares the map to what the robot sees so it knows where it is.”
This type of software is special because it’s a standalone solution that AMR manufacturers can use to upgrade their systems. They can also use it for other vehicles, such as forklifts, so that all mobile equipment uses the same map as the robots. This improves real-time location tracking to manage warehouse traffic better. Plus, it’s really easy to use.
“It helps our implementation engineers when they can show up, take the robot out of the box, turn it on, and start mapping the facility with a couple of clicks,” said Mercurio. “Just by driving the robot around, it can create that map of the facility. It almost looks like a video game.”
When the robot comes out of the box for the first time, a user will connect the robot to the facility’s wireless network and software. Then, the user manually drives the robot around with a controller, joystick, or interface, such as a tablet. Many safety features are turned off during the manual run-through, which can take as little as one hour or more than three hours, depending on the facility size. Once the initial map is
| Courtesy of Bosch Rexroth
In dynamic warehouses, AMRs must understand their location as shelves, pallets, and carts move around.
AMRs use simultaneous localization and mapping (SLAM) software to map a facility, orient themselves, and respond to layout changes.
created, the robot can move around autonomously, and personnel must be coached on interacting with the robots to ensure everyone’s safety.
Many warehouses are dynamic environments. Some have wide-open spaces with few landmarks, while others constantly move pallets and carts, making it difficult for robots to orient
Users can monitor AMR locations and pathways along the SLAM-generated map in real time.
themselves. Over weeks or months, enough small changes can throw off a robot such that personnel must redraw the map periodically or deal with the robot getting lost. Most likely, personnel will grow frustrated and stop using the robots.
However, when localization software is deployed to a robot fleet, the fleet
records all detected changes. Then, the software modifies the base map and distributes the changes back to the fleet.
“It doesn’t matter how good your fleet management software is or what kind of robot you have. If the robot can’t localize itself, you’re going to have problems,” said Mercurio.
Rokit Locator can use up to two
During initial setup, a user manually drives an AMR to create the base map. Then, the AMR can operate autonomously and update the map with detected changes.
lasers and the wheel odometry for location accuracy. In the near future, Bosch Rexroth will also include a navigation solution to help plan paths. With localization, the robots know where they are; with navigation, they’ll chart an optimal course and respond to obstructions and traffic more intelligently.
“The next big trend in the AMR space will be interoperability — robots from different manufacturers being able to work together in the same environment,” said Mercurio. “And as the adoption rate goes up, warehouses might want to diversify providers to accomplish different tasks. That will push manufacturers to find ways to add value. I’m sure we’ll see all kinds of integrated solutions around robots.”
As AMRs evolve, we may see more 3D vision and more efficient motors and wheels. We may also find more mobile robots outside factories and warehouses, as they’re already in hospitals, grocery
stores, and restaurants. And just as other industries advance warehouse automation technology, hardware and software improvements in warehouses influence applications and make robotic solutions more available and affordable.
l WH Bosch Rexroth boschrexroth.comAutonomous mobile robots safely and efficiently transport different payloads in manufacturing and warehouse logistics operations.
Why did the global stock of operational robots hit a new 3.5-million-unit record? Why did the value of installations reach an estimated $15.7 billion? The IFR analyzed five key things shaping robotics and automation.
Robots play a fundamental role in securing the changing demands of manufacturers and warehouses worldwide. The International Federation of Robotics describes how five robotics trends attract users from small enterprises to global OEMs.
Energy e ciency is critical to improving companies’ competitiveness amid rising energy costs. In many ways, adopting robotics helps lower energy consumption in manufacturing and warehouses. Compared to traditional assembly lines, considerable energy savings can be achieved through reduced heating. At the same time, robots work at high speed, increasing production rates so that manufacturing becomes more time- and energy-e cient.
Today’s robots are designed to consume less energy, which leads to lower operating costs. Companies use industrial robots equipped with energy-saving technology to meet sustainability targets for production. For example, robot controls can convert kinetic energy into electricity and feed it back to the power grid. This technology significantly reduces the energy required to run a robot.
Another feature is the smart powersaving mode that controls the robot’s energy supply on-demand throughout the workday. Since industrial facilities must monitor their energy consumption, such connected power sensors will likely become an industry standard for robotic solutions.
Resilience has become an essential driver for reshoring in various industries. For example, car manufacturers invest heavily in short supply lines to bring processes closer to their customers. These manufacturers use robot automation to manufacture powerful batteries cost-
effectively and in large quantities to support electric vehicle projects. Such investments make shipping heavy batteries redundant, and more logistics companies refuse to ship batteries for safety reasons.
Relocating microchip production back to the U.S. and Europe is another reshoring trend. Because most industrial products nowadays require a semiconductor chip to function, placing the supply close to the customer is crucial. Robots play a vital role in chip manufacturing, as they fulfill extreme precision requirements, and specifically designed robots automate silicon wafer fabrication, take over cleaning and cleansing tasks, or test integrated circuits. Recent examples of reshoring are Intel’s new chip factories in Ohio or the chip plant in the Saarland region of Germany run by chipmaker Wolfspeed and automotive supplier ZF.
Robot programming has become easier and more accessible to non-experts. Software-driven automation platforms let users manage industrial robots with no prior programming experience. Original equipment manufacturers work with low-code or even no-code technology partners, allowing users of all skill levels to program a robot.
The easy-to-use software paired with an intuitive user experience replaces extensive robotics programming and creates new robotics automation opportunities. Software startups are entering this market with specialized solutions for small and medium-sized companies. For example, a traditional heavy-weight industrial robot can be equipped with sensors and new software for collaborative setup operation. This makes it easy for workers to adjust heavy machinery for different tasks. Companies
will thus get the best of both worlds: robust and precise industrial robot hardware and state-of-the-art cobot software.
Easy-to-use programming interfaces that allow customers to set up the robots themselves also drive the emerging new segment of low-cost robotics. Many new customers reacted to the pandemic by trying out robotic solutions. Robot suppliers acknowledged the demand for easy setup and installation and preconfigured software to handle grippers, sensors, or controllers for lower-cost robot deployment. Such robots are often sold through web shops, and programs for various applications are downloadable from an app store.
Propelled by advances in digital technologies, robot suppliers and system integrators offer new applications and improve the speed and quality of existing ones. Connected robots are transforming manufacturing and will increasingly operate as part of a connected digital ecosystem, where cloud computing, big data analytics,
or 5G mobile networks provide the technological base for optimized performance. The 5G standard will enable fully digitalized production, making cables on the shop floor obsolete.
Artificial intelligence holds great potential for robotics, enabling a range of benefits in manufacturing. AI’s main aim in robotics is to better manage variability and unpredictability in the external environment, either in realtime or offline. Consequently, AI and machine learning play an increasing role in software, for example, where running systems benefit from optimized processes, predictive maintenance, or vision-based gripping.
AI technology helps manufacturers, logistics providers, and retailers deal with frequently changing products, orders, and stock. The greater the variability and unpredictability of the environment, the more likely it is that AI algorithms will provide a cost-effective and fast solution — for example, for manufacturers or wholesalers dealing with millions of products that change regularly. AI is also helpful in environments where mobile robots must distinguish between the
objects or people they encounter and respond differently.
Since an industrial robot has a service life of up to 30 years, new technology is an excellent opportunity to give old robots a second life. Industrial robot manufacturers such as ABB, Fanuc, KUKA, and Yaskawa run specialized repair centers close to their customers to refurbish or upgrade used units in a resource-efficient way. This prepare-torepair strategy for robot manufacturers and their customers also saves costs and resources. Offering long-term repair to customers is an essential contribution to the circular economy. l WH
An automated guided vehicle (AGV) is a type of unmanned guided vehicle (UGV) that moves throughout a facility by following a set of predetermined paths. An AGV is not a sub-class of a mobile robot. Instead, AGVs are the predecessors to mobile robots and have been in operation since the 1950s. However, they still have a variety of uses within a modern manufacturing or warehouse environment.
An autonomous mobile robot (AMR) is a di erent class of UGV that has more capabilities than an AGV. AMRs are capable of free-movement and real-time path planning, enabling them to collaborate in material handling tasks with humans.
In addition, while AGVs are all-wheeled vehicles, AMRs come in various locomotion configurations. This includes wheeled vehicles, tracked vehicles, bipedal robots, quadruped robots, and multi-legged robots.
Despite the growing popularity of warehouse automation, confusion remains around the various acronyms and technology. For those in the discovery phase of an automation journey, here’s an overview of two of the most talked about warehouse solutions.
The best analogy for understanding one of the primary di erences between an AGV and an AMR is that an AGV is like a railroad train engine, constrained only to operate on its train tracks. On the other hand, an AMR is like a taxi, able to freely move between any two points and replan a route when tra c is too dense.
The term industrial mobile robot (IMR) was introduced in the recent safety standard ANSI/RIA R15.08. Although it was widely debated by industry experts and voted on within the new standard, IMR has yet to reach broad usage as of the writing of this article but may emerge to replace the term AMR in future years.
In addition to UGVs, there are also unmanned aerial vehicles (drones) and unmanned marine vehicles (autonomous boats or ships).
Similarities between AGVs and AMRs
AGVs and AMRs perform similar functions in different applications. Both types of vehicles can:
• Move material from one point to another within a facility.
• Avoid collisions with objects that might come into their path.
• Operate collaboratively and safely with humans within their workspace or intended paths.
• Carry cargo between 2 kg and 1500 kg.
Differences between AGVs and AMRs
It’s not that one technology is better than the other, but their differences make them useful for specific applications and environments. Such differences include:
Simplicity and cost: AGVs have simpler control systems and sensors than AMRs. In some cases, AGVs are a less expensive solution than AMRs.
Paths and infrastructure: AGVs follow paths along a fixed infrastructure, such as magnetic tape or wire, painted lines, QR code stickers, or laser targets, and they remain within the confines of their lanes or paths. Contrarily, AMRs freely navigate their operational space and between a starting point and a destination. They can also operate outside of a building and follow humans around in a “follow me” application.
Payload: AGVs can be designed to carry extreme payloads, such as locomotive engines and airplane fuselages.
The best analogy for understanding one of the primary differences between an AGV and an AMR is that an AGV is like a railroad train engine, constrained only to operate on its train tracks.
On the other hand, an AMR is like a taxi, able to freely move between any two points and replan a route when traffic is too dense.
AMRs are best suited for unstructured environments, creating more opportunities for warehouse flexibility.
| Courtesy of ABB
AGVs can be designed as carriers, scissor lifts, forklifts, or other variations and include modules such as box carriers.
| Courtesy of Jungheinrich.
Obstacles: AGVs may become “stuck” if they encounter an object in their intended path. This often requires the help of an operator to move the object and restart the AGV on its mission. AMRs not only avoid obstacles but actively navigate around obstacles to continue toward a mission goal. However, AMRs can become “lost” if they can’t recognize their surroundings. This often occurs when crossing large expanses of floor space without any recognizable infrastructure, such as airplane hangars or large meeting spaces. AMRs can also become lost in repetitive environments, such as similar-looking warehouse aisles or chaotic work areas, such as loading docks. AMR manufacturers have a variety of methods to keep their machines “localized.”
Applications: AGVs work best in welldefined conditions and applications, such as material handling or WIP in a manufacturing facility. AMRs work best for applications in unstructured environments, such as security, deliveries, and person-to-goods and goods-to-person intralogistics.
Unfortunately, some AMR manufacturers have adopted the term AGV to describe their autonomous machines. This is unfortunate, as it causes confusion within the market. Remember, the primary requirement of an AGV is that it needs some infrastructure within the vehicle’s workspace to enable navigation and cannot navigate around obstacles. l WH
The Spinea DriveSpin brushless DC servo rotary actuators come packed with several impressive features that make them stand out from the competition. First and foremost, these actuators offer high precision and repeatability, thanks to their integrated high-resolution encoder and zero backlash integrated TwinSpin cycloidal reducer technology. This makes the DriveSpin actuators ideal for a wide range of applications that require high positioning accuracy and tight tolerance control.
Another key feature of the Spinea DriveSpin rotary actuators is their high torqueto-weight ratio, which makes them incredibly powerful despite their compact size. With torque capacities ranging from 18 Nm to 460 Nm, these actuators can handle heavy loads with ease, making them suitable for use in industry 4.0 and automation applications, such as robotics, packaging, and assembly systems.
In addition to their wide range of features, the Spinea DriveSpin rotary actuators also offer many benefits to users. These benefits include reduced maintenance requirements, long service life, and high efficiency. Unlike hydraulic or pneumatic systems, these electric actuators do not require regular maintenance, resulting in significantly lower operating costs over time. Furthermore, they boast a long service life, thanks to their robust construction and high-quality materials. With an efficiency rating of up to 95%, DriveSpin actuators also help users conserve energy, further reducing their overall operating costs.
Advantages:
• low lost motion
• low moment of inertia
• high reduction ratio
• high kinematic accuracy
• high moment overload capacity
• high capatity of the integrated radial-axial output bearings
• high dynamic performance
Applications:
• Robotics: 6-axis robots, gantry robots and manipulators
• Machines: CNC machine, grinding machine, lathe machine
• Special machines: bending machine
• Medicine equipment
• Aerospace applications
• Flight simulators
• Defense industry
• Semiconductor industry
• Radar and monitoring systems
In the last decade, the e-commerce industry has become a facet of modern society and has fundamentally changed how we view retail today. The ability to purchase anything online and have it delivered to your door in a matter of hours has become vital to both individual consumers and businesses alike.
This change from traditional retail environments has been good for consumers but challenging for retailers and suppliers to keep both prices and delivery times down. It has spurred on significant changes in warehousing, from the way they’re managed all the way to where and how they are built.
As an intelligent motion company, Dorner gets an inside peek at many different industries. These are a few of the areas we see growing in warehousing development and management in the future.
Automation has had exponential growth in recent years, and with continued improvements in AI and adaptive machine learning, automation is the way of the future. Not only can automating manufacturing and logistics help companies maintain productivity through staffing shortages and other unforeseen challenges, but it can also improve lead times and accuracy in operations.
In warehousing, automation can help speed up the picking and packing process, while also improving accuracy and efficiency. The popularity of e-commerce means retail suppliers have moved away from shipping large quantities of the same product to brick-and-mortar stores, to shipping individual items directly to consumers. Rather than staff locating and picking several different products that may be across the warehouse for one order, the use of an automated picking system, such as AGVs, vertical storage systems, or a network of conveyance lines, can speed up order processing and packaging while still maintaining a high level of accuracy.
To aid in tracking products throughout the picking and packing process, as well as managing warehouse inventory, some companies are turning towards innovative warehouse management software and Industry 4.0 technology. With RFID tags or other unique product IDs used throughout warehouse inventory, automation tools such as scanner-integrated conveyors can index, sort, and monitor product as it moves throughout the warehouse and shipping process.
Some of the leaders in warehousing and consumer goods distribution are already utilizing full automated warehouse management systems to track product, monitor inventory, and even measure machinery performance. A completely integrated system like this puts important data in one place so it’s easy to put the data to work towards meaningful development and growth of the facility.
Finally, with available commercial space shrinking every day, sprawling warehouses are becoming more difficult to achieve. However, retailers still need to maintain a huge range of products in their warehouse inventory to keep up with consumer demand. The solution to this challenge is a growing adoption of vertical storage systems.
Offering a compact solution to sorting and storing product, automated vertical storage can be easily integrated within a warehouse to make moving product from the shelves to conveyors and through packaging simple, accurate, and fast.
Automating warehouse operations can help improve throughput, efficiency, and accuracy. Whether it’s switching over the entire warehouse to a completely automated system or automating small processes, it can make a significant difference for companies.
Dorner is here to help you design and build custom conveyor systems to automate your warehouse and logistics processes. Our team will work with you to help determine what system will meet your needs and improve product throughput in the warehouse. Contact us to learn more and get a free quote.
In today’s automated warehousing industry, Amazon and Walmart have distinctly established themselves as the household names of global consumers. How did they achieve such a demand of consumer usability and market share? They designed an infrastructure so that their customers at the push of a few buttons, could quickly purchase and receive almost anything they want or need without having to step outside their house, except maybe to grab the package they ordered just a few days earlier.
The brilliance of this application is its simplicity and ease of access to its users. What is not so simple is the actual infrastructure itself. Warehouse automation involves so many moving and programmable components that if any of those components are not functioning properly, it disrupts the entire flow of the automated process. From the automated storage and retrieval system and the conveyor system down to the pick and place center, getting inventory sorted, packaged, labeled and shipped properly is a very complex process. Even the cable and electrical system solutions being specified for these components add another level of complexity to ensure the longevity of the system itself and safety for its users. Designing a robust, efficient and competitive automated system is a delicate balance for everyone involved. Once the system is commissioned, the facility operations become almost completely self-sufficient with just ongoing routine maintenance and control station monitoring oversight.
As conveyors and automation components require significant technical aptitude and focus from both designer and supplier, pairing artificial intelligence and robotics with your warehouse automation moves things to another level. Automated guided vehicles can interoperate algorithms, and independently move inventory to and from dedicated areas around the clock. Traditional multi-axis robots pick, sort and place products as well as handle heavier products that employees can’t manage without assistance. This improves not only efficiencies but safety as well.
Amazon has over 520,000 robots working in unison with their automated warehouses and have added over one million jobs worldwide to transform their business. Walmart recently partnered with Symbotic to deploy and retrofit all 42 of its regional distribution centers over the next 10 years with robots. These industry leaders are paving the way in industrial automation, which is starting to see smaller type companies with sizeable warehouses follow suit as it relates to warehouse automation and efficiencies just to stay competitive. The importance of factory floor space,
fulfillment process flow, reducing idle and/or downtime, and improving employee safety and efficiencies is critical to these types of business models.
With these factors in play and more within the infrastructure of an automated facility, you also have to be fully prepared to respond to any electrical, mechanical or software issues that can create significant delays to consumers or end users and revenue loss. Robust and sustainable cable systems are key to the life of the automated warehouse, so qualifying and selecting the right component manufacturer and/or electrical system supplier becomes more important than ever. Suppliers who control not only the design quality and manufacturing of their products, but also provide the added value of complete component and electrical system solutions for automated applications quickly rise to the top.
HELUKABEL is a global cable system solutions provider specializing in the production of cables, wires, accessories, cable assemblies, and guidance and protection systems found in equipment used throughout today’s automated warehouses. HELUKABEL offers a wide array of flexible and continuous-flex control, data, network and bus, VFD/servo power and feedback cables to reliably transmit power and data to keep materials on the move.
Our ability to provide cable solutions from bulk cable to complete, plug-and-play cable sub-assemblies makes us the one-stop shop for complete electrical system solutions within the automated warehouse ecosystem.
In true WAGO fashion, the manufacturer is continually innovating and improving its product offering. WAGO’s 221 Series Lever Nuts are an excellent example of this, representing the company’s answer to the twist-type splicing wire connector. This termination device quickly and easily connects different wire sizes and types, using 2, 3, and 5-wire connectors.
“A few years ago, WAGO developed the original 222 Series LEVER-NUTS®, which has been effective and successful,” shares Evan Syens, Product Manager, Electrical Splicing Connectors with WAGO Corporation. “However, innovation doesn’t stop for us just because a product has hit the market. We never settle for ‘good enough’ and are always striving for better. WAGO is all about ongoing advancements.”
To this end, WAGO created their newest version wire-connector solution, the 221 Series LEVER-NUTS®— and they’ve quickly become one of the company’s top-grossing products.
“The biggest difference between the original 222 and the latest 221 Series is the size, as the newest version is smaller,” says Syens. “But, perhaps, the most notable feature of our 221 Series LEVERNUTS® products is their transparent housing, which is significant.”
This is because with a typical twist-type connector, it’s impossible to know how secure the wire connections are for each terminal, which is a maintenance and safety concern.
“The clear housing completely takes the guesswork out of the installation process,” Syens explains. “Without it, how would you know how many twists are ideal for a secure connection? There’s room for error. In fact, installers will often secure wires with electrical tape to maintain the twist-type connection. But that’s unnecessary, thanks to WAGO’s innovation. Simply pull the orange lever up, insert a stripped conductor (according to the strip-length gauge on the side of the 221) and push the lever back down. That’s it. You’re done.”
Since every 221 Series LEVER-NUTS® also includes CAGE CLAMP® technology (the spring-pressured connection technology that WAGO pioneered back in the ’50s), installers can also ensure a secure a reliable connection. The CAGE CLAMP® is starting to become the industry standard for electrical interconnection technologies.
What’s more, is WAGO has incorporated test slots in the LEVERNUTS® Series for additional safety — one in the direction of wire insertion and one on the opposite side. This allows an installer to insert a test probe into the slots to determine if a wire is live.
“Another unique feature about these products is that they’re reusable, without any added steps. For example, there’s no need to re-strip the wires. Simply lift the lever and connect the new wires,” he says. “Again, it’s that simple.”
WAGO offers two different versions of the 221 Series:
• The original variant: 24-12 AWG
• The 10 AWG variant: 20-10 AWG
“The 20 to 10-gauge version also has three variants — a 2, 3, and 5-conductor, which goes up to 600 volts and 30 amps. And, as for the operating temperature, each variant is approved to 105° C,” says Syens.
Along with these innovative connectors, WAGO also offers a line of mounting carriers that can be mounted onto a DIN Rail or chassis, easily cleaning up your cabinet, panel, or junction box.
“It’s really about peace of mind because with CAGE CLAMP® technology, you can be confident in a secure connection for your application,” says Syens.
Whether for an electrical contractor, DIY home projects, lighting applications or use in hazardous locations, WAGO’s 221 LEVER-NUTS® Series offers fast, safe, and dependable connection technology.
“Now when people see the orange lever, they associate it with WAGO and know the product can be trusted.”
• Terminate conductors from 24–10 AWG (with two models: 24-12 AWG and 20-10 AWG)
• Connect solid, stranded, and fine-stranded conductors
• Combine different wire sizes and types
• Install devices with higher levels of power consumption
• Save time connecting wires without the use of tools