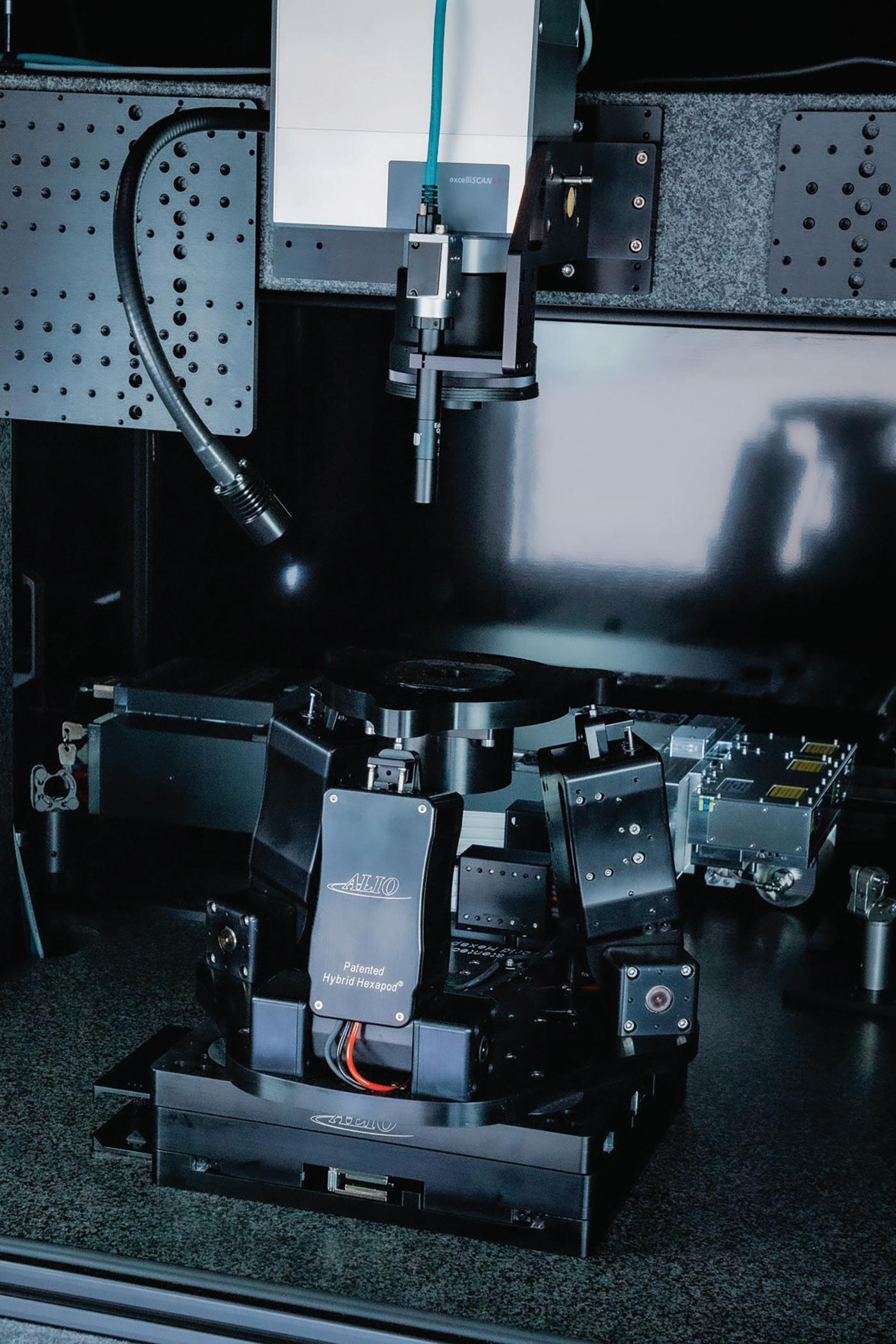
3 minute read
Design for Industry
Laser processing machines can achieve highly accurate positioning with sub-micron-level precision and repeatability. This level of precision is crucial in many industries, such as aerospace, automotive, and medical device manufacturing, where the accuracy of laser processing can have a significant impact on the quality and safety of the final product. They enable manufacturers to produce high-quality, intricate parts with speed and precision. Today, laser processing machines can cut complicated shapes but they are typically limited to working in two dimensions. This means that when more complex geometries or cuts are needed, it is necessary to cut in one dimension, turn the part, and cut again. This often makes the process prohibitively time-consuming and expensive. Therefore, motion control systems for laser processing can benefit from 6D repeatability performance validated by the 6D Point Precision performance specification.
“Laser processing is often faster and more cost-e ective than traditional machining methods, and with increasing demand for miniaturization, customization, and automation, laser processing technologies are poised to play an even more significant role in the future, driving innovation and improving productivity in various industries,” said Bill Hennessey, president of Alio Industries.
As a manufacturer of high-precision motion control systems, Alio uses 6D Point Precision to validate the 6D repeatability performance of its single and multi-axis motion control systems used in laser processing applications. The 6D Point Precision methodology involves measuring six different points in space, including X, Y, and Z position, pitch, yaw, and roll. By taking measurements at these six points, the company ensures its motion control systems can achieve high-precision positioning and repeatability across all six degrees of freedom.
NIST has now produced the ASME B5.64 standard “Methods for the Performance Evaluation of Single Axis Linear Positioning Systems,” which advocates a new method for defining the precision of advanced motion control solutions, similar to suggestions made by Alio moving away from conventional planar methodologies.
By validating its motion control systems using 6D Point Precision, Alio can provide its users with a high level of confidence in the performance and reliability of its products.
The company also offers a range of linear motion control stages, including air-bearing and mechanical-bearing stages, that can provide high-precision linear motion control for laser processing. These stages offer a variety of features, including sub-micron level precision and repeatability, long travel ranges, and high load capacity, and are designed to provide a high level of accuracy and reliability, even in harsh industrial environments. They can be customized to meet the specific needs of each laser processing application. Its Hybrid Hexapod, for example, is a multi-axis motion control system that combines the precision and accuracy of a hexapod with the long travel range of a linear stage.

“We have also developed True Nano precision rotary motion stages with a sub-arc-second resolution, making them ideal for a variety of laser processing applications where nanoscale precision is required, such as laser cutting, welding, and marking, and can also be integrated into larger motion control systems to provide multi-axis control, further expanding their applications,” said Hennessey. DW
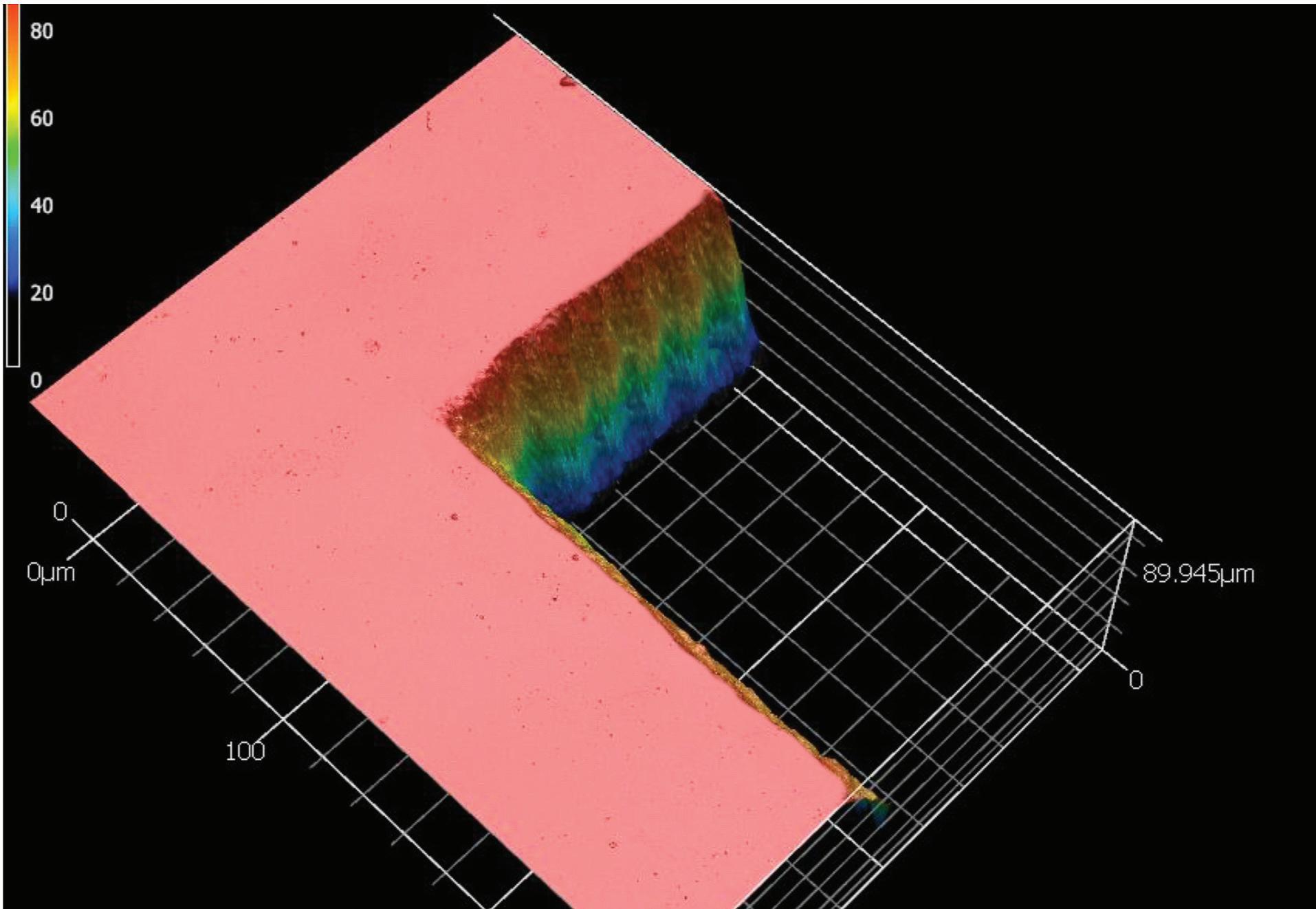
Alio Industries www.alioindustries.com
TOOL-LESS ADJUSTMENT COMPONENTS
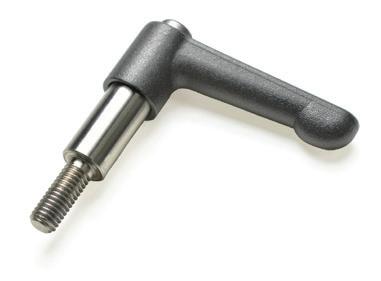
• Adjustable handles and knobs replace standard hardware and can be used to torque components without tools.
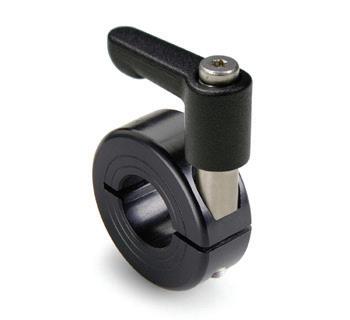
• Levers can be used with Ruland shaft collars for quick installation and adjustment.
Slit And Controlflex Couplings
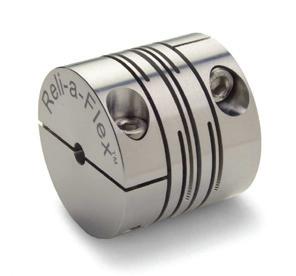

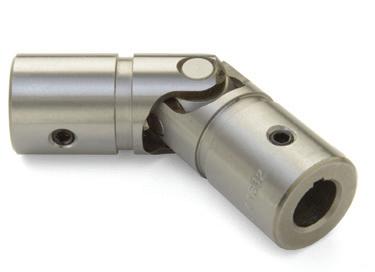
• Slit couplings are available in short and long styles giving designers a variety of body sizes to choose from to t application envelope and performance requirements.
• Control ex is a highly exible encoder coupling designed for applications with high speed, low torque, and wide differences in shaft sizes (up to a 4:1 small to large ratio).
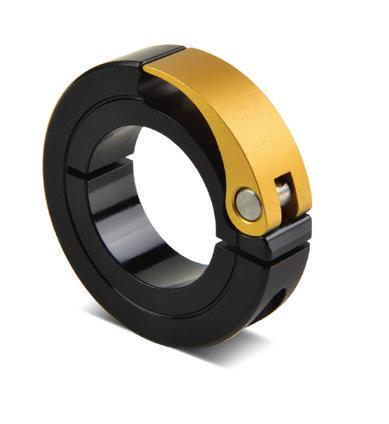
• Slit couplings are available in bore sizes from 1.5mm to 12mm (1/8” to 1/2”) and control ex couplings are available in sizes from 6mm to 40mm (1/4” to 1-1/2”).
Ruland Manufacturing is proud to support the FIRST Robotics Competition as a Gold Supplier of precision shaft collars & couplings.
Mountable Shaft Collars
• Available with OD ats and holes for direct mounting of the collar to other components.
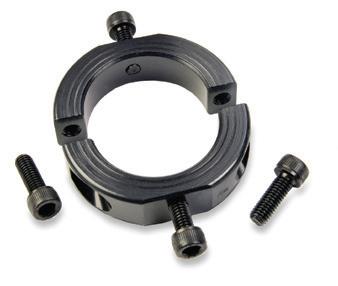
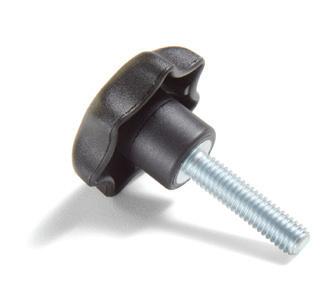
• Proprietary manufacturing processes ensure superior t, nish, and holding power.
• Manufactured in a variety of sizes, styles, and materials.
Universal Joints
• Widest selection in the industry: over 3000 standard single and double universal joints to start your next design with.
• Available from Ruland in 2 weeks or less for the shortest lead times in the industry.
• Yokes, pins, and blocks are precision machined, ground, and selectively heat treated for smooth operation at high operating angles.
Modular Mounting Systems
• Assortment of components that allow users to build small assemblies for mounting sensors, conveyor rails, machine guards, and more.
• Optional pre-designed kits make it easier to select the right system for your application.
Quick Clamping Collars
• Hand operated: no tools required to install, remove, & adjust.
• Best suited for systems that require frequent adjustments.application.
All products available directly on RULAND.COM www.ruland.com |