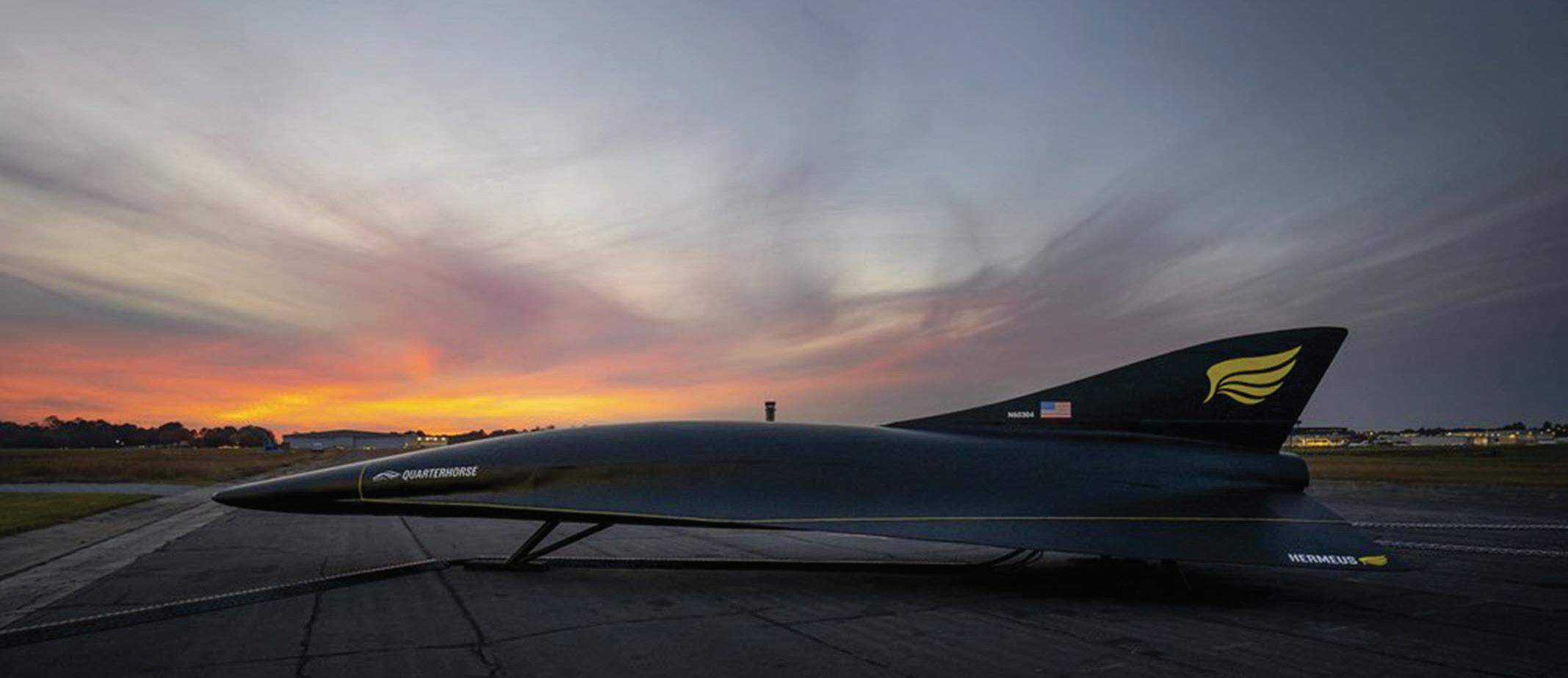
1 minute read
Design for Industry Supporting warfighter readiness with advanced metal AM
Whether responding to shifting budget priorities or the urgent need to assist an ally, the U.S. military must be flexible and adaptive. Chief among these requirements is battlefield superiority in potential future global conflict. How the defense sector responds to such challenges is therefore critical, and the U.S. must use every tool at its disposal to encourage military innovation, particularly in the field of hypersonics.
Advanced metal additive manufacturing (AM) is one of these tools. With it, manufacturers can produce components with thin-walled parts, intricate internal channels, and complex lattice structures — qualities that can be particularly transformational for hypersonic systems.
Hypersonic propulsion and vehicle developers have taken notice and turned to metal AM for the design, rapid iteration, and production of mission-critical components. While much of the defense-focused development remains out of the public eye, one example with good visibility is Hermeus, an Atlanta-based company developing reusable hypersonic aircraft for defense and commercial applications. Hermeus recently began using advanced metal AM to dramatically reduce lead times on components for its dual-mode ramjet Chimera engine.
According to CTO Glenn Case, this has allowed Hermeus to “increase performance, consolidate components, reduce weight, and minimize external dependencies” in the Chimera-equipped Quarterhorse, a remotely piloted aircraft with a goal of briefly hitting Mach 4+ speeds and demonstrating reusability. Its concept proven, Hermeus will then expand its hypersonic e orts to Darkhorse, a UAS (uncrewed aerial system) designed for defense and intelligence missions with the ultimate goal of delivering a human-crewed commercial hypersonic aircraft — dubbed Halcyon — by 2029.
In addition to cutting-edge technologies such as hypersonic propulsion, there is a parallel push towards shrinking, simplifying, and reducing the cost of gas-turbine engines. As these engines become smaller, it is important to optimize features to drive higher e ciencies, potentially at lower costs. The units feature dozens of highly complex individual components that have long been fabricated using a combination of casting, five-axis machining, brazing, and welding to produce a completed assembly. This process, however, presents numerous logistical hurdles, including long lead times and costly, often di cult manufacturing steps that require significant technical skill.
Advanced metal 3D printing, with its ability to consolidate assemblies of multiple components into a single, monolithic structure, greatly simplifies this process. California-based Sierra
The cross-section (le ) of Sierra Turbines’ microturbine shows fine inner details of the unicore design (right) made possible with metal AM.
| courtesy of Sierra Turbines
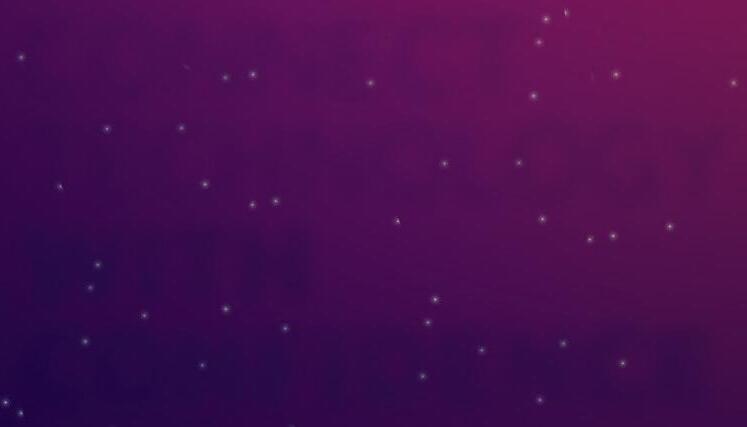