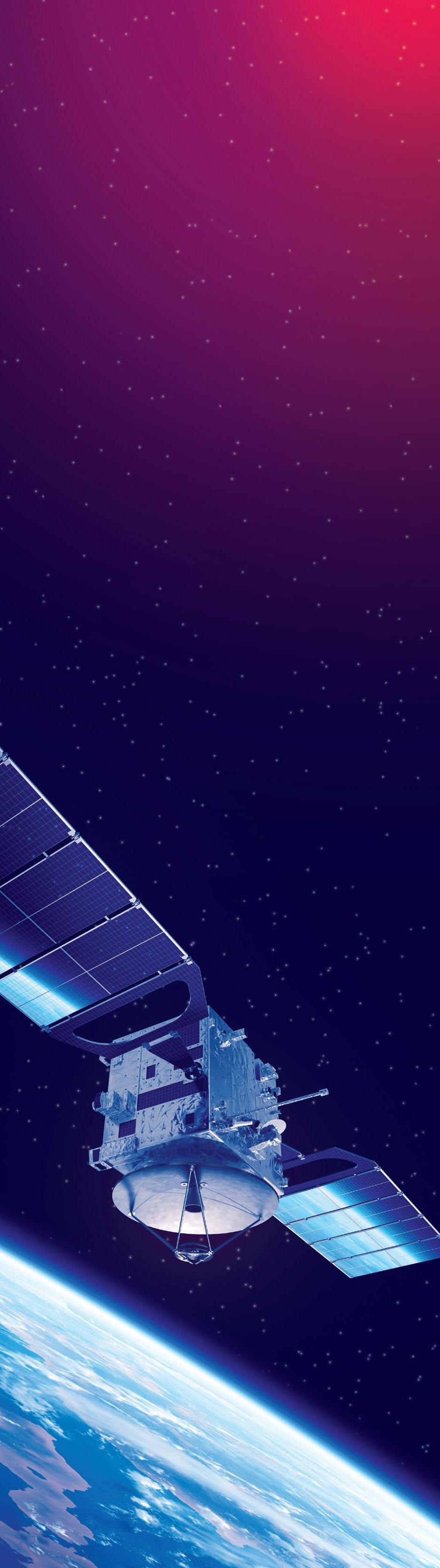
1 minute read
CONNECT TECHNOLOGY WITH CONFIDENCE
3D-printed valves with identical quality and performance characteristics were additively manufactured in six different locations to demonstrate how AM can quickly deliver complex parts on a global scale.
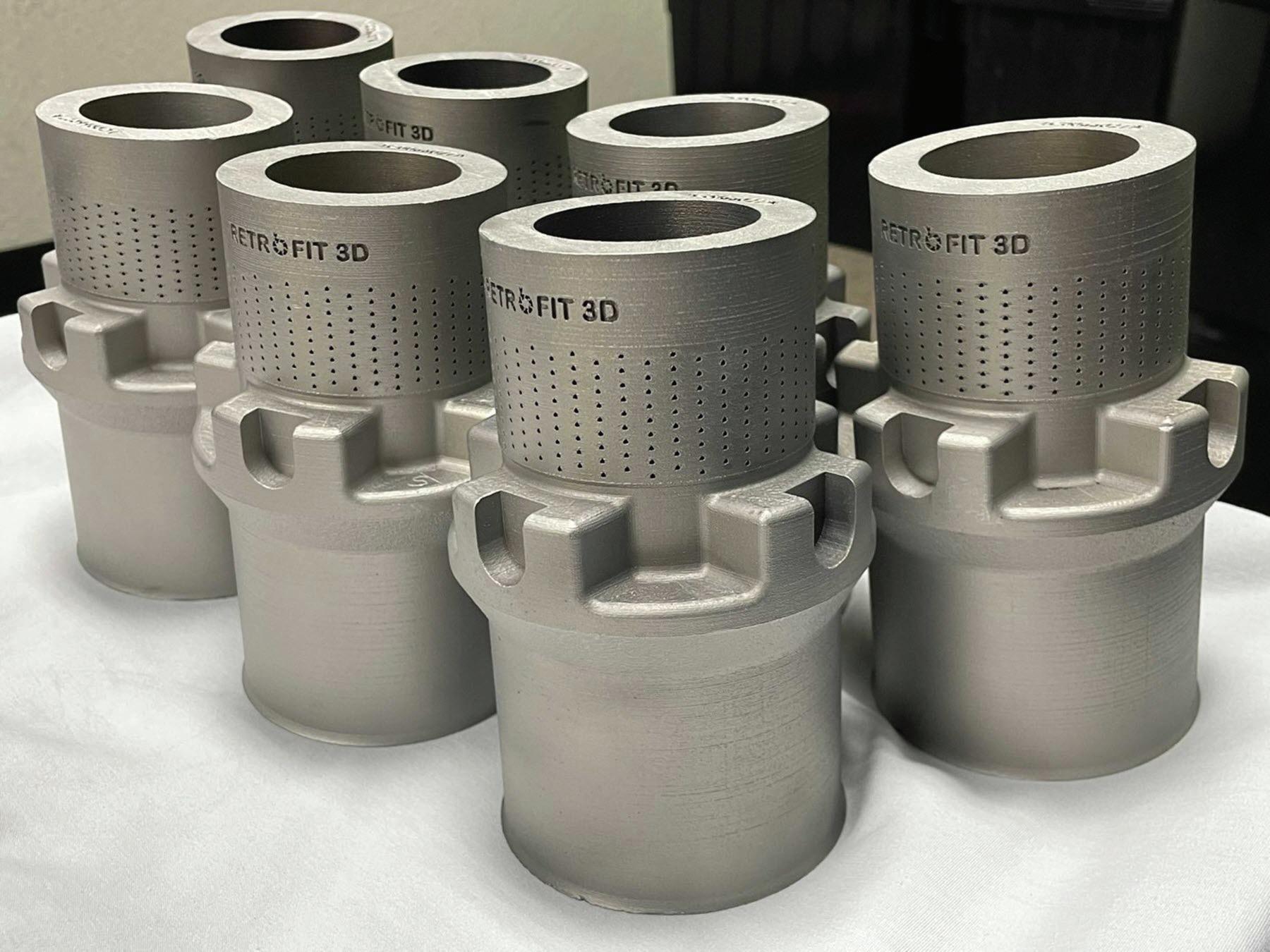
| courtesy of Velo3D and IMI Critical
Turbines discovered these benefits firsthand when it engaged with metal AM experts early in the design process, allowing the team to consolidate 61 discrete parts into a single unicore design. Doing so cut the overall part count almost in half without sacrificing quality or performance. It also increased power density by a factor of 10, the time between overhauls (TBO) by 20, and overall e ciency by 40-fold.
Success stories such as these extend beyond aerospace and defense. Consider IMI Critical, a world leader in flow-control solutions that was tapped by a major oil and gas operator recently to validate metal AM’s potential to reduce lead times on critical components. One of these was a choke valve cage, which the company aimed to produce in a scalable, predictable manner using a global supply chain.
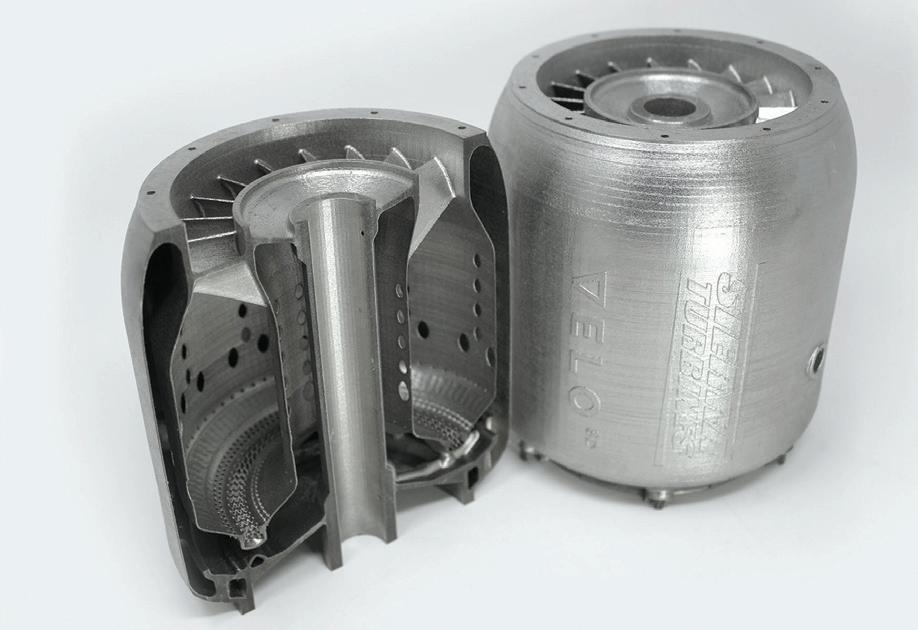
Partnering with metal AM solution provider Velo3D, IMI Critical redesigned the choke valve cage and locked it into a set of unique printing instructions that could be delivered to any certified, in-network printer anywhere in the world. Parts of identical quality and performance were printed at six di erent locations, several of them overseas.
Each of these examples used metals that most machinists would recognize. Inconel 718 and 625, Haynes 282, and titanium Ti-6Al-4V are just a few of the