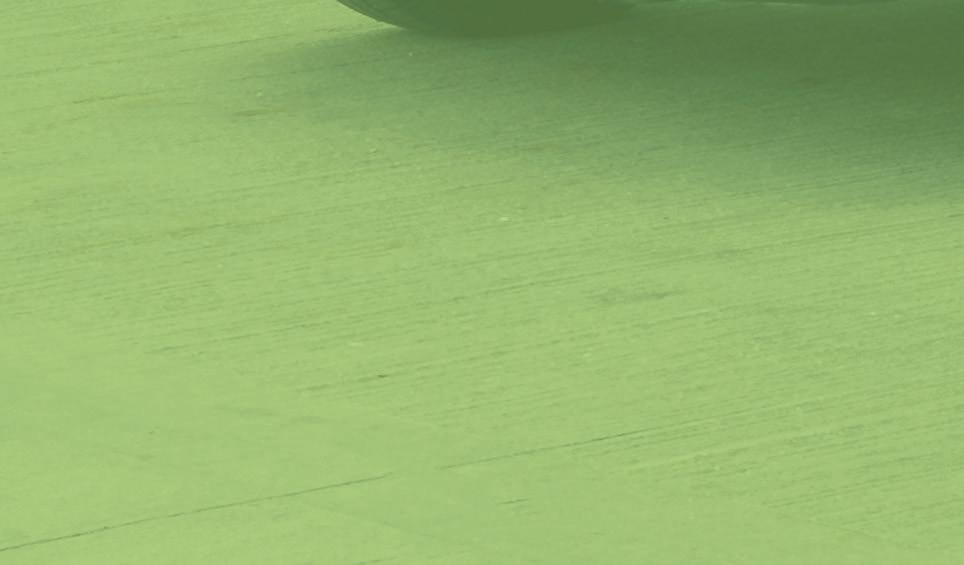
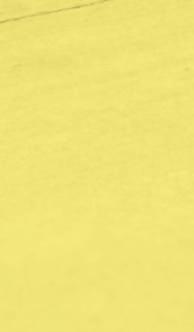
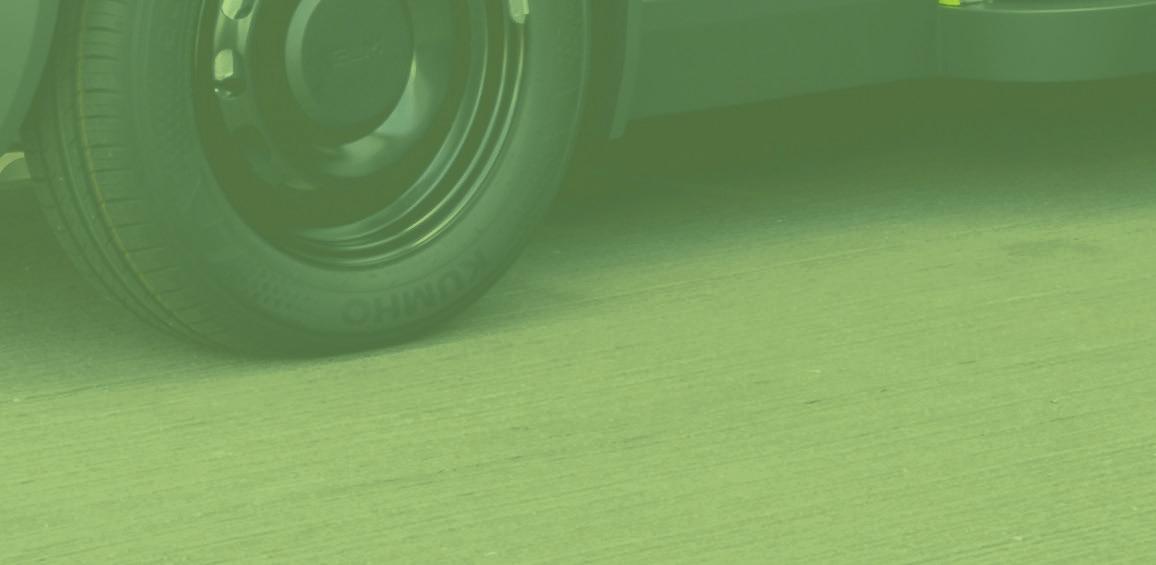
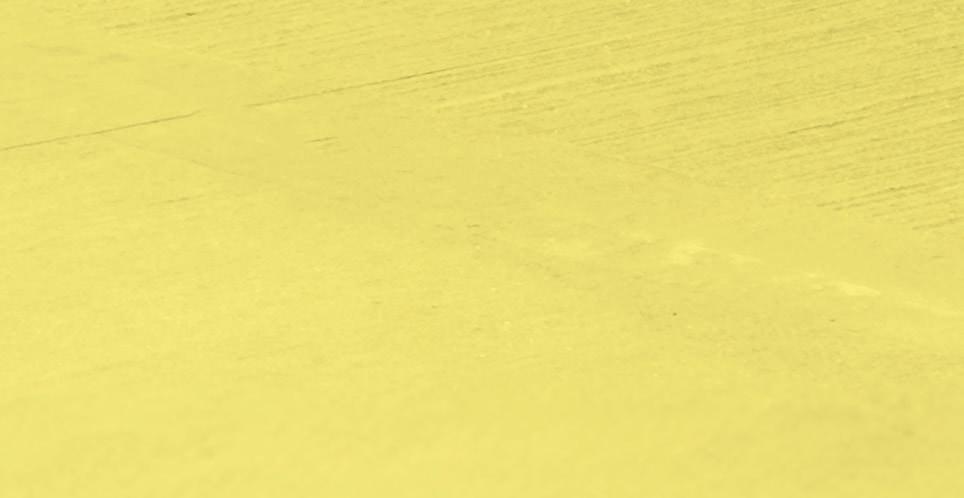
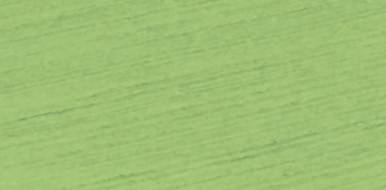
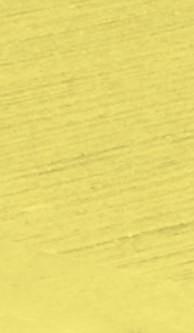
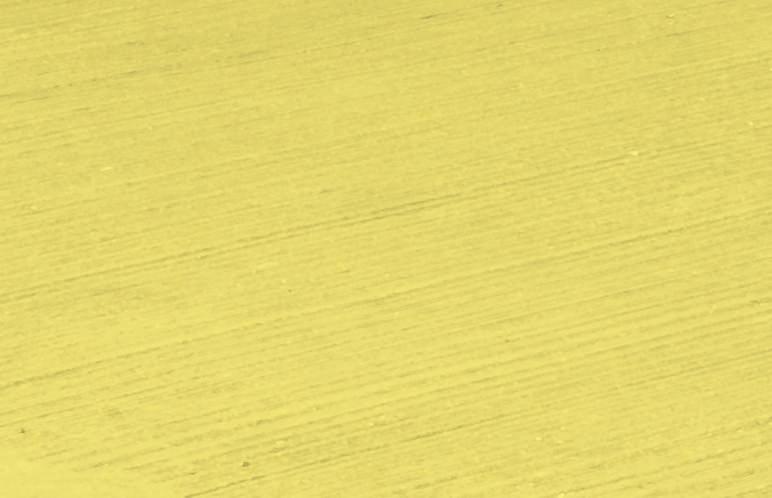

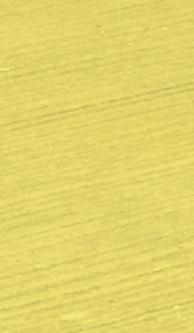
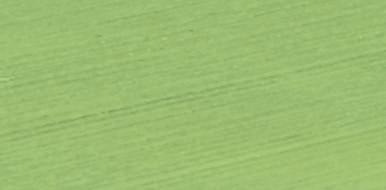
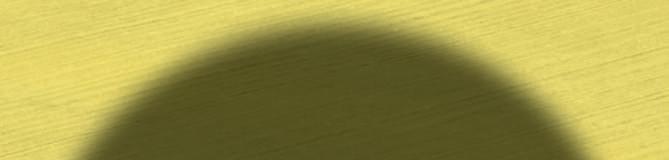
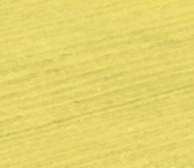

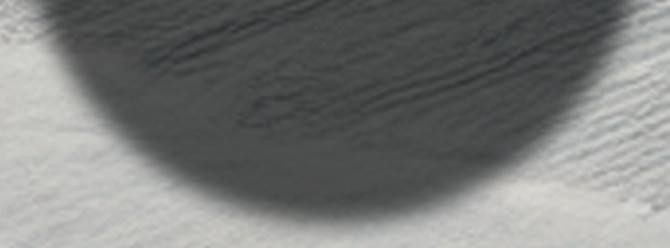
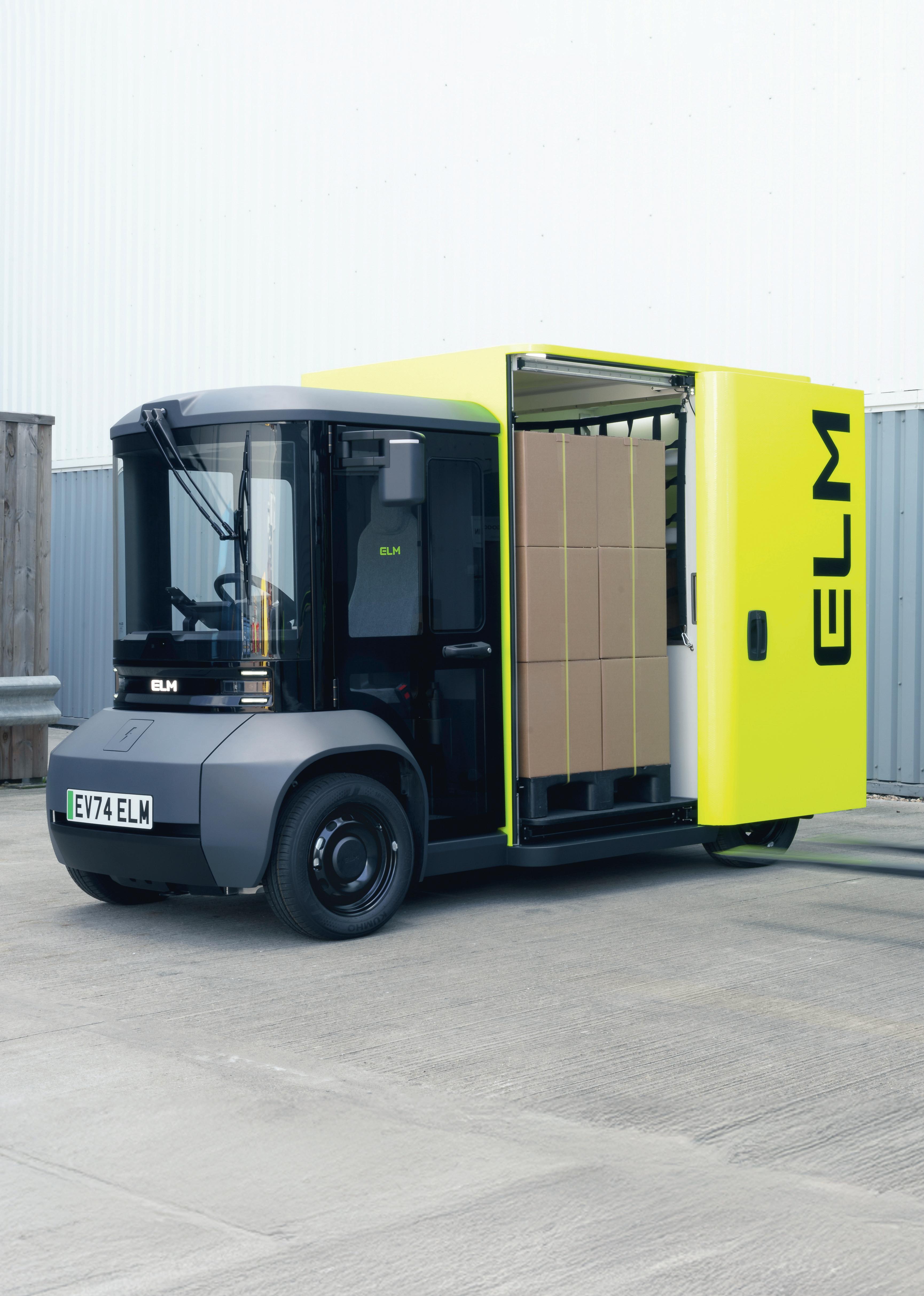
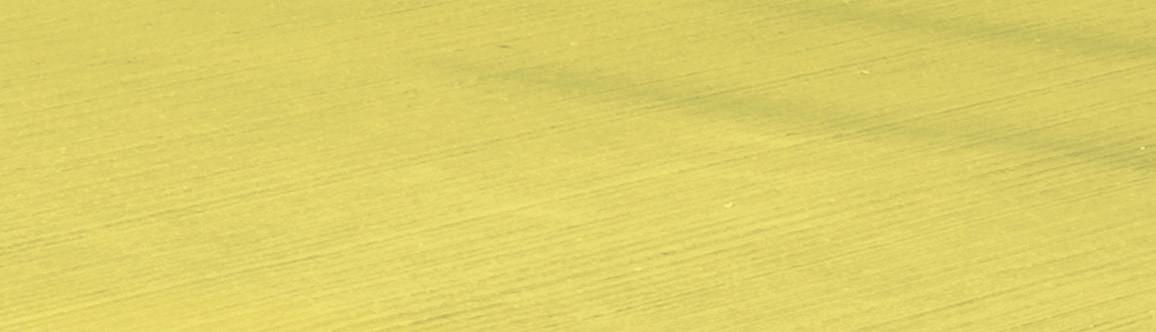
Your search for a 3D printer capable of producing complex & creative models in up to 10,00 0,00 0 colours is over T he new Mimaki 3DUJ-22 07 delivers extraordina r y detail in full colour.
E xplore a wor ld of colour for just
£ 3 4,995
EDITORIAL
Editor
Stephen Holmes
stephen@x3dmedia.com
+44 (0)20 3384 5297
Managing Editor
Greg Corke
greg@x3dmedia.com
+44 (0)20 3355 7312
Consulting Editor
Jessica Twentyman jtwentyman@gmail.com
Consulting Editor
Martyn Day martyn@x3dmedia.com
+44 (0)7525 701 542
Staff Writer
Emilie Eisenberg emilie@x3dmedia.com
DESIGN/PRODUCTION
Design/Production
Greg Corke greg@x3dmedia.com
+44 (0)20 3355 7312
ADVERTISING
Group Media Director Tony Baksh tony@x3dmedia.com
+44 (0)20 3355 7313
Deputy Advertising Manager Steve King steve@x3dmedia.com
+44 (0)20 3355 7314
US Sales Director Denise Greaves denise@x3dmedia.com
+1 857 400 7713
SUBSCRIPTIONS
Circulation Manager
Alan Cleveland alan@x3dmedia.com
+44 (0)20 3355 7311 `
ACCOUNTS
Accounts Manager Charlotte Taibi charlotte@x3dmedia.com
Financial Controller
Samantha Todescato-Rutland sam@chalfen.com
ABOUT
DEVELOP3D is published by
X3DMedia
19 Leyden Street
London E1 7LE, UK
T. +44 (0)20 3355 7310
F. +44 (0)20 3355 7319
Time moves quickly, and just like that, DEVELOP3D LIVE is back and scheduled to take place on 26 March at the Warwick Arts Centre. In this issue of DEVELOP3D, we offer you a preview of this exciting event, the finest around for showcasing both the talents of designers and engineers and the power of the latest technologies at their disposal.
For our cover feature, we speak to a previous D3D LIVE main stage speaker, Carsten Astheimer, about his design studio’s role in ELM Mobility and its electric last-mile delivery vehicle, EVOLV. In a world where many vehicles are repurposed for new tasks – from vans to bicycles – Astheimer Design has partnered with auto-engineering experts Prodrive to create a custom design fit for purpose in urban environments.
Last-mile delivery is a cut-throat market, governed by tight margins and an overwhelming need for efficiency, so creating this clean-sheet design required designers to immerse themselves in an unfamiliar world, even going out themselves to drive vans and deliver pizzas.
We also hoist sails with Rigging Projects, a company looking to protect its 5-axis machining hardware investment with some slick software as it strives to build more products in-house and stay close to customer needs.
You will also find the key news points from the 3DExperience World event in Houston, Texas where, along with other attendees, I got an introduction to Aura, Dassault Systèmes Solidworks’ first AI tool. Given that Solidworks has some 8 million users globally, by the end of 2025, Aura could prove to be the most ubiquitous – and therefore most important - AI tool being used in product design and engineering. It’s worth finding out more about what it does and what’s on the horizon when it comes to developing this tool further.
On that note, Solidworks CEO Manish Kumar will also be heading to D3D LIVE to give attendees a better idea about what all this means and what’s in store for them, so it’s definitely worth checking out.
See you there!
Stephen Holmes Editor, DEVELOP3D Magazine, @swearstoomuch
DriveWorks is flexible and scalable. Start for free, upgrade anytime. DriveWorksXpress is included free inside SOLIDWORKS or start your free 30 day trial of DriveWorks Solo.
Modular SOLIDWORKS® automation & online product configurator software
Entry level design automation software included free inside SOLIDWORKS®
Entry level SOLIDWORKS part and assembly automation
Create a drawing for each part and assembly
Find under the SOLIDWORKS tools menu
One time setup
SOLIDWORKS® part, assembly and drawing automation add-in
Automate SOLIDWORKS parts, assemblies and drawings
Generate production ready drawings, BOMs & quote documents automatically Enter product specifications and preview designs inside SOLIDWORKS
Free online technical learning resources, sample projects and help file
Sold and supported by your local SOLIDWORKS reseller
examples
Set up once and run again and again. No need for complex SOLIDWORKS macros, design tables or configurations.
Save time & innovate more
Automate repetitive SOLIDWORKS tasks and free up engineers to focus on product innovation and development.
Eliminate errors
DriveWorks rules based SOLIDWORKS automation eliminates errors and expensive, time-consuming design changes.
Complete SOLIDWORKS part, assembly and drawing automation
Automatically generate manufacturing and sales documents
Configure order specific designs in a browser on desktop, mobile or tablet
Show configurable design details with interactive 3D previews
Integrate with SOLIDWORKS PDM, CRM, ERP, CAM and other company systems
Scalable and flexible licensing options
Sold and supported by your local SOLIDWORKS reseller
Connect sales & manufacturing
Validation ensures you only offer products that can be manufactured, eliminating errors and boosting quality.
Integrate with other systems
DriveWorks Pro can integrate with other company systems, helping you work more efficiently and effectively.
Intelligent guided selling
Ensure your sales teams / dealers configure the ideal solution every time with intelligent rules-based guided selling.
Dassault Systèmes welcomes ‘age of Univ+rses’, Twinmotion unveils tyre and tree options, Wacom launches Intuos Pro tablets, and more
Comment: Julien Vaissieres on why AM needs AI
Comment: SJ on the importance of workplace allies
Visual Design Guide: Roborock Saros Z70
COVER STORY ELM Mobility’s special delivery
Event Preview: DEVELOP3D LIVE 2025
Event Report: 3DExperience World 2025
Take a seat: 3D printing the Nozzle office chair
Navigating 5-axis CNC machinging at Rigging Solutions
Quick fix: AI puts repairs back in consumer hands
PNY Nvidia RTX A1000 workstation GPU
As the 2025 red carpet season draws to a close, Stephen Holmes would like to nominate the stars of our own industry when it comes to committing 100% to a role – product designers
» Launch of virtual assistant Aura for Solidworks at 3DExperience World 2025 signals the beginning of a new chapter in advanced product design technologies
Dassault Systèmes has announced new generative experiences and virtual assistants for Solidworks as part of its new ‘Univ+rses’ environment for combining virtual twins, training AI engines and protecting customers’ intellectual property (IP).
At its 3DExperience World user event in Houston Texas in February 2025, thousands of designers and engineers were introduced to Aura, the company’s first virtual assistant to be made public.
Taking the form of a chatbot within the 3DSwym collaboration tool, Aura is trained on Solidworks training guides, bestpractice guides and help docs. Initially, users will be able to ask Aura questions and request guidance, but its skillset will expand in future updates to include generative AI tasks such as creating drawings from 3D CAD models, rendering CAD models and producing scene visualisations based on user text prompts.
While Aura will have access to user data stored on the 3DExperience Platform, all AI responses are specifically tailored for the user organisation, with no data used to train Aura capabilities for other companies, reinforcing Dassault’s pledge to keeping customer IP secure.
Solidworks CEO Manish Kumar explained that Aura will be available on the platform on any device from July 2025 and is the first ‘virtual companion’ to be announced as part of the overarching Dassault Systèmes ‘3D Univ+rses’ plan to embed multiple generative AI technologies at the core of what it calls IP Lifecycle Management (IPLM).
Executives say that this evolving architecture will enable its large client base to fully exploit rich, highquality 3D design, virtual twin and PLM data, providing the “premier digital environment to train new categories of Experience as a Service (XaaS)", namely: Generative Experiences (GenXp), Virtual Companions, and intelligent Virtual Twin Experience as a Service (VTaaS).
“All our longtime loyal clients are expecting us to protect their ‘gold mine’ of virtual assets and reveal the invisible. In order to generate and protect the most valuable intellectual property, it is of critical importance to create virtual twin experiences of everything for everyone that harmonise product, nature and life,” said Bernard Charlès, executive chairman of Dassault Systèmes “Dassault Systèmes is committed to becoming the most trusted partner to provide ‘3D Univ+rses,’ as the ultimate source of knowledge and
know-how, for our mutual benefit and human progress.”
Also announced at 3DExperience World was Solidworks CPQ, a new configure, price and quote solution on the 3DExperience platform. The new CPQ software integrates generative AI capabilities to accelerate the order and delivery of customised products by connecting product portfolio management, development, manufacturing and sales. By linking product configurability rules to a virtual twin on the platform, design teams can use CPQ to explore material selection, structural integrity, availability, cost and other factors, and select the optimal choices. Based on these selections, it can help technical sales engineers to quickly generate an accurate quote as well as a 3D configured product that can be explored in a VR experience that fully immerses the customer in the completed project, facilitating final decisions.
Finally, Dassault announced its 3DLive VisionOS app to allow users to view and interact with models stored on its 3DExperience platform in XR using Apple’s Vision Pro headset. The 3DLive app will be available this summer.
Read our full report from 3DExperience World on page 38. www.3ds.com
Twinmotion 2025.1 has launched with an array of new features and updates to its real-time visualisation and animation capabilities.
Specific lighting and rendering enhancements include Projector Lights, perfect for visualising live events or installations, or for simulating effects like caustic reflections on the hull of a boat, for example.
There’s now also an optional method for rendering shadows in real-time rendering mode based on Virtual Shadow Map (VSM) technology.
Extra controls are added to camera animations, with a new Orbit cam rig revolving the camera around its specified central pivot within the scene, making it easier to present a 360-degree view of an
object or point of focus.
A new Tyre base material textures and automatically creates UVs for flat cylindrical objects, such as tyres. Four tyre materials have also been added to the Library in the Materials category.
In addition, there are new controls for pearlescent scale, clear coat roughness and imperfections – including dust, fingerprints, and scratches – to the Car Paint material, together with new coated carbon fibre materials in the Metals category.
Twinmotion 2025.1 also brings with it a forest of new foliage options, with a new collection of 62 photorealistic tree species examples from different parts of the world. These are added to the Twinmotion Library, with each tree available in three stages of maturity, giving a total of 186 new trees. www.twinmotion.com
Wacom has launched the Intuos Pro, a graphics tablet with updated design features and its new Pro Pen 3.
The Wacom Intuos Pro is available in three sizes, with the small size intended for fully portable use with dimensions of 8.5 inches by 6.4 inches. The medium and large sizes are designed for use across several monitors.
The tablet features a new chip set which slims down form. Changes compared with previous versions include the ExpressKeys and touch buttons being moved to the top of the tablet, and two dials on the medium and large sizes of the tablet, with one dial on the small size.
All models are Bluetooth-enabled with a wireless operating time of up to 16 hours. Up to three devices can be connected, one
using a USB and two wireless, and users can switch between each device using a switch on the tablet.
Prices at launch see the small, medium and large editions costing £229.99, £339.98 and £469.99 respectively. www.wacom.com
oland DG has announced new industrial binder-jet 3D printing technology, along with the Brightorb ‘artificial ceramic’ material, which the company claims reduces shrinkage during sintering to 1%.
Best known for its wide-format inkjet printers and compact 3D modeling machines, Roland’s two new powder 3D printer models are the PB-600 and PB400. The PB-600 has a maximum build area of 595 x 600 x 250mm, while the PB-400 has a maximum build area of 390 x 290 x 200mm, with Roland providing proprietary slicing software. www.rolanddg.com
HCLSoftware has announced the release of HCL CAMWorks 2025, now integrated with 3DExperience Solidworks to enable data management and crossdiscipline collaboration in the cloud. The new version is compatible with CAMWorks and Solidworks CAM data from the Solidworks desktop version, so companies have the flexibility to coordinate CNC part programming across multiple platforms and enabling users to share data between cloud and onpremise versions. www.hcl-software.com
Creaform has revamped its Creaform.OS platform, formerly known as VXelements, along with the Creaform Metrology Suite, a portfolio of application software modules designed for metrology. The Creaform.OS platform provides users with scan, probe and photogrammetry modules. Features exclusive to the platform include a new workflow-oriented interface and customisable toolbar placement, menu structure and homepage. Additional tools aim to improve user experience (UX) and make the software, which connects hardware to software during the scanning process, user-friendly and streamlined. www.creaform3d.com
Backflip has announced a new AI foundation model that automatically creates parametric CAD from 3D scans. A plug-in for Solidworks and a web app are available, enabling users to transfer scan data into editable CAD in seconds.
“3D scanners map the surface of an object with incredible precision, quickly generating millions of
data points, but they produce micro surface
while walking new users through how a part was created in the first place, and thus flattening the learning curve for designing in 3D.
Backflip hopes that the new technology will help in industries like manufacturing, where broken parts on production and assembly lines can cause expensive, lengthy downtime. Backflip executives claim that its new technology helps manufacturing teams
textures that can’t be manufactured with traditional
tools,” said Backflip CEO Greg Mark. “Our technology automatically converts these intricate surfaces into clean geometries designed for existing 3D CAD and manufacturing software.”
Backflip’s Solidworks plug-in displays each step in the process used to build a part, generating a native feature history that users can modify. This lets designers finetune a generated 3D model,
Following the discontinuation of HoloLens 2 in October 2024, Microsoft has now officially announced the product line's end, issuing a final major software upgrade for its headset, which from now until 2027 will receive only minor security updates www.microsoft.com
compress the time from broken parts to digital 3D models without need to remodel a part that is
literally in front of them, helping them to manufacture a new part quickly and without using the time of a CAD designer.
Backflip says that its two new tools will be available to interested users soon. DEVELOP3D readers can sign up for the 3D scan-to-CAD wait list on the company’s website. www.backflip.ai
Cloudfluid, a specialist in computational fluid dynamics (CFD) software, has been acquired by nTop, in a bid to revolutionise how engineers design high-performance products.
Users will be able to couple Cloudfluid’s GPU-native solver technology, which accurately predicts fluid flow without the difficulty of creating complex conformal meshes, with nTop’s implicit geometry kernel to iterate on designs in near realtime and create breakthrough products.
While CFD simulation typically involves labour-intensive meshing and lengthy run times, particularly for complex computationally designed products, it is impractical to use for rapid design iterations. With the addition of Cloudfluid, nTop now offers what it says is the ‘most advanced and complete platform’ for
computational design.
In particular, the integration of Cloudfluid with nTop expands the platform’s applications in aerospace, defence, and turbo machinery, where fluid dynamics are crucial. www.ntop.com
EOS has announced that its EOS Aluminium AlSi10Mg material is now produced with 100% recycled feedstock, resulting in a 77% CO2e reduction when compared to its predecessor and an 83% CO2e reduction compared to AlSi10Mg made from 100% virgin raw material www.eos.info
Authentise has announced that its Flows software now integrates with Autodesk Fusion Industry Cloud, so users can check design quality, generate support structures and create machine-specific build files directly from the Flows interface and operating directly on live Fusion Data www.authentise.com
Materialise has achieved EN 9100 certification for its metal AM processes for aerospace, confirming the quality of its metal parts and its reliability in producing metal parts for aerospace OEMs, suppliers and providers of maintenance, repair and overhaul (MRO) services www.materialise.com
ESI has unveiled BM-Stamp, an automotive stamping solution that integrates with a user's CAD software, offering simulation capabilities for all skills levels. The first release focuses on validation for cold-formed stamped components with line/ transfer die processes www.esi-group.com
It feels as if we’ve reached a critical juncture for manufacturing, one where traditional moulds and traditional mindsets no longer fit. As CEO of Batch.Works, I’ve seen first-hand how the drive for local, circular production collides with realworld manufacturing challenges.
We’re producing thousands of end-use parts every day at our London hub, working with small studios right through to large UK retailers, all looking to push beyond prototyping into on-demand, consumerready products.
But with AI rapidly transforming additive manufacturing (AM), and with government initiatives such as the UK’s new Circular Taskforce, ongoing reshoring efforts, and initiatives for AI adoption and supply chain resilience, there’s now a genuine opportunity to overcome those barriers and unlock unprecedented potential for designers and end users alike.
Many of traditional manufacturing’s entrenched production models are increasingly misaligned with net-zero targets and local, sustainable supply chains.
Designers and engineers crave agile, small-batch production with minimal waste, but often face cost constraints, long lead times and a shortage of domestic suppliers. That’s precisely what Batch.Works has set out to tackle with a technology platform that merges AI-driven additive processes with circular material flows, printing every part locally using recycled or renewable feedstock, and then recovering it for reprinting at end of life.
This resonates with a wave of new UK government measures, from Extended Producer Responsibility rules holding producers accountable for packaging waste, to the forthcoming Deposit Return Scheme arriving in 2027, aimed at boosting plastic recycling rates.
Put simply, there’s mounting institutional support for practical, low-carbon production solutions that don’t rely on shipping vast volumes of products across oceans.
But to ensure such visions truly scale, we need AI to boost efficiency, reliability and speed, empowering designs that are as green as they are feasible.
Part of the solution lies in addressing the siloed nature of how we design, develop and manufacture products. Typically, there’s a cycle between a designer and an AM engineer, who painstakingly tinkers with slicing parameters and toolpaths. If something goes wrong, the cycle repeats. This is neither time-efficient nor scalable.
AI can streamline the process, by spotting potential structural weaknesses, predicting print failure rates and automating slicer settings. In practice, such tools drastically reduce the trial-and-error loop. Designers can be confident that their concept will print flawlessly and efficiently, while also tracking its carbon footprint from day one.
As 3D printing rapidly expands into highvolume, end-use territory, the question is how to ensure consistency, reliability and cost-effectiveness at scale. That’s where AI and data analytics come into play.
Imagine an AI engine that has learnt from tens of thousands of print jobs how to continually finetune parameters such as extrusion temperature, infill density and print orientation. It slashes the time from concept to production-ready part, while driving down scrap rates. It can also optimise material flows, ensuring that reprocessed polymers or bioplastics remain consistent in quality after multiple cycles, crucial for functional end-use parts where safety and regulatory compliance matter.
An ever-growing dataset on real-world mechanical performance will let designers and engineers confidently specify 3D-printed components for everything from consumer electronics to retail fixtures,
As 3D printing rapidly expands into high-volume, end-use territory, the question is how to ensure consistency, reliability and cost-effectiveness at scale. That’s where AI and data analytics come into play
knowing they can be repaired on-site or recycled entirely.
From my perspective at Batch.Works, bridging design and manufacturing to meet net-zero and circular targets is impossible without AI. We cannot rely on guesswork or on the old approach of sending containerloads of identical items across the globe.
The UK has Europe’s largest design economy, worth over £100 billion, and we’re seeing that talent channelled into more sustainable, digitally powered processes.
With AI-driven AM, the results can be profound: localised, on-demand microfactories, near-zero-waste production, and products designed from the ground up for repair and re-use.
At Batch.Works, we’re already demonstrating this in our London facility, backed by over £3 million in government grants and a major partnership with E3D to scale our technology globally. We aim to make our platform accessible by the end of the year, enabling more designers to embed net-zero principles into their work.
In many ways, this feels like a new industrial revolution, merging local resilience with global collaboration and powered by the belief that we can both dream and deliver.
ABOUT THE AUTHOR: Julien Vaissieres is CEO of Batch. Works, a London-based tech company pioneering scalable, circular and sustainable 3D printing innovation and actively contributing to the achievement of the UK’s Net Zero ambitions www.batch.works
SJ. Here’s what a recent encounter with an Engineering Fellow taught them about vulnerability, acceptance and forging strong bonds in workplace environments
Igrew up reading tales of Camelot, spellbound by stories about King Arthur and his Knights of the Round Table. I was particularly obsessed with stories in which women masqueraded as men, in order to be treated as equals on the battlefield. I was obsessed with the idea that the gender of the person wielding a sword didn’t matter, only their heart and determination.
In the big engineering organisations of today, we also encounter knights, although they are more commonly referred to as Engineering Fellows. Like their Camelot counterparts, they sit at special tables, serving as technical advisors and supporting the business with engineering expertise.
Until recently, I hadn’t met a Fellow myself. I had only heard of them from others, who reverently whispered about Fellows as if they were legends from a bygone era. Then I crossed paths with one of these knights, and our quest began.
The background to that meeting was my request to a colleague about to leave the company to nominate me as his replacement and give me the chance to work with an Engineering Fellow. At first, he was hesitant and I couldn’t understand why. Eventually, he admitted: “It’s your gender.”
I was floored. I had only been ‘out’ as non-binary for three years. I was struggling to find my footing on the battlefield. So I pushed my colleague to elaborate. After all, our organisation is known for championing diverse leadership.
“He’s a good man, but a religious one. He’s from a different time than you and I. It’s your pronouns. I don’t want you to get hurt if he’s callous with his language,” my colleague explained.
At this, a giggle burst from my lips. I was born in the swampy backwaters of the southern United States. I’m no stranger to callous language. “Put my name forward for consideration,” I told my colleague. “I promise you, I can handle it.”
My advice to anyone starting out on a quest like this is to know three key things: what you want, why you want it, and how you’re going to get it.
When fatigue sets in, understanding these points is what will carry you through in any battle. I wear that understanding like armour into every meeting.
For me: I wanted political connections, so I could have the power to create change within my organisation; I wanted that power and influence, so that I could foster the growth and adoption of a technology that I fundamentally believe will be revolutionary for our business. And I knew in my engineering gut that the support from this Fellow for additive manufacturing could cement it as a strategic technology for the organisation.
How did that pan out? It wasn’t easy at first. In one of our early meetings, the Fellow in question turned to me as I was reviewing my slides. “Hey SJ,” he said, “I’m sorry. I hope you know I’m trying.”
I was confused. Trying? Fortunately, he continued. He told me that he had been trying hard in meetings to respect my pronouns. He told me it was a challenge for him, as this was so new and different from the engineering world in which he grew up. He was afraid of offending me, and others like me, in these meetings, but the concept of gender identity was still foreign to him. He was struggling to adjust.
His vulnerability floored me. I stammered out a response, indicating that trying was enough. It was enough to make me feel like he cared about me as a person. That no one is perfect. That I wouldn’t get mad, or cry, or ‘cancel’ him if he slipped up occasionally.
“Good, very good!” he said, relief in his voice. “I think we work well together as a team, and at the end of the day, I really care about this technology, and I think it’s critical to our future success.”
And there it was: his ‘why’ and my ‘why’ were now in alignment.
My advice to anyone starting out on a quest is to know three things: what you want, why you want it, and how you’re going to get it
For anyone else out there struggling to show up authentically at work, especially those in marginalised or underrepresented minority groups, here are a few tips that I’ve found helpful as a squire in training.
First, keep your cool. If someone says something untoward, don’t let their behaviour provoke you into a reaction. Keep interactions polite, focused on the topic at hand and, where possible, brief.
I recognise that my experience with this knight could have gone awry. I was lucky that he was vulnerable early on, which allowed me to address the issue directly, which brings me to my second tip: if it’s safe for you to do so, address problematic behaviours head-on and as early as you can. For example, “I noticed you [insert behaviour]. Is there a reason for that?”
If you do find yourself in a Knightmare situation, my advice is to document everything, especially where behaviour crosses a line into discrimination, harassment or straight-out sabotage. Finally, build strong working bonds with your fellow squires and knights. If others notice signs of prejudice, they may back you up or work as an intermediary during conflict. After all, we all need allies on the battlefield.
ABOUT THE AUTHOR: SJ is a metal additive engineer aka THEE Hottie of Metal Printing. SJ’s work involves providing additive manufacturing solutions and 3D printing of metal parts to help create a decarbonised world.
» The Roborock Saros Z70 is a robotic vacuum cleaner with super-smart navigation abilities, a foldable five-axis mechanical arm to retrieve stray items from floors and an ultra-thin design that enables it to infiltrate dusty, hardto-reach corners
A built-in weight sensor prevents the Saros Z70 from lifting items weighing more than 300g and the grip can be manually reversed to gently drop objects without damaging them
This smart vacuum connects to the user’s phone and uses AI-powered customisation to learn about what it encounters in its working environment. It’s pre-programmed to recognise 108 objects, and up to 50 more can be added using the app, including pets, cables and children’s toys
The FreeFlow main and side brushes feature an anti-tangle system, ideal for sweeping pet hair and other debris from carpets, wood flooring and other surfaces. The FlexiArm Riser Side brush boasts a 0% hair tangling rate
An emergency button and child lock makes the Saros Z70 safe for household use, enabling operations to be paused either from a button on the side of the vacuum or the user’s connected device
The Roborock Saros Z70 will be available for purchase in the first half of 2025. Retail prices are yet to be confirmed www.roborock.com
The Saros Z70’s omnidirectional wheel comes with a brush attachment that cleans the wheel as it operates, reducing the need for maintenance
The Roborock Saros Z70 boasts an OmniGrip five-axis mechanical arm, enabling it to move objects out of its path, accurately relocate them and clean the areas they were blocking using its FlexiArm mop
VertiBeam lateral obstacle avoidance technology enables the Saros Z70 to navigate rooms with ease and improving accuracy when it comes to recognising unfolded cables, uneven floors and irregularly shaped furniture
» With last-mile delivery booming, translating the specific demands placed on the transport types involved into purpose-built designs is key to delivering success. Stephen Holmes speaks to ELM Mobility about the creation of its compact and capable EVOLV vehicle
Online shopping promises the consumer convenience and simplicity: a click, a wait and then a knock at the door.
But much like a graceful swan gliding across a pond, the logistics involved with achieving this seamless experience are the furiously paddling feet below the water’s surface.
From flexible warehousing and pick-and-pack robotics to logistical software and a complex mix of delivery stages and vehicle types, technology is involved at every touchpoint on a package’s journey to your home.
Yet for the consumer awaiting their parcel, the only element that really matters – and that provides any visible experience – is the successful last-mile drop-off at the end of the supply chain.
From beat-up old vans to cycle couriers, cities are home to a multitude of options for these final steps, although most transport types have a ‘sweet spot’ when it comes to the kinds of loads they can carry. Many are frankly unsuitable for general use.
To solve this problem, ELM Mobility was formed as a collaboration that brings together the styling and userdriven insights design approach of Astheimer Design, and the automotive and electrical engineering expertise of Prodrive. The first vehicle produced by this partnership, the EVOLV, is a last-mile, L7e quadricycle-class electric vehicle built to be compact, capable and safe.
A clever dual bay allows class-leading storage of 60% of overall vehicle volume, with the EVOLV main cargo bay able to handle a 1.6m tall, 300kg Euro pallet payload, and a secondary area able to accommodate a 1.2m tall Euro pallet and 200kg payload.
Despite the considerable consignment in the back, the EVOLV is capable of quick manoeuvring in congested streets, with a turning circle comparable to that of the famed London black cab.
At its heart is a 20kWh battery with the potential to meet the demands of daily deliveries, offering an ample 100-mile range and capable of a top speed of 50mph.
The unique set-up means EVOLV offers approximately twice the load box volume of other L7e vehicles, and is half the weight of a compact van with a similar load volume, making it the most efficient vehicle in this class, both in terms of cost and energy consumption per unit volume of goods per mile.
Founded in 2009 by Carsten Astheimer with Russell Gillott, Astheimer Design is a studio based in Warwick, UK, which despite a wide range of clients, has gained a reputation as a specialist in sustainable mobility.
Having worked on several commercial electric vehicle (EV) projects large and small, including the 16-tonne Volta Zero, the world’s first purpose-built, all-electric commercial vehicle designed for city-centre deliveries. At the other end of the scale is the Deliver-E demonstrator, which was created to help showcase Warwick Manufacturing Group’s battery technology capabilities, and sees a Renault Twizzy converted into a capable goods vehicle.
“That was a six-week project and it was completely nuts,” Carsten Astheimer says of Deliver-E. It was also the studio’s first foray into last-mile logistics. The success of the project led to companies as far afield as Singapore contacting him, hoping to buy small fleets of the vehicle. He describes this as the ‘first bell’ to ring, with the second bell chiming during work on the Volta Zero and the industry feedback.
Speaking with logistics company heads at the launch of the Zero, the positive feedback came with the caveat that the companies in this industry need more than a single truck. They require a full ecosystem of vehicles to handle different types of delivery in the optimum way possible.
Having seen funding become available from UK Research & Innovation for a feasibility study, the Astheimer team quickly put together a brief, which having proved successful sparked the initial concepts for EVOLV.
A positive market response to the concepts saw Astheimer approach Prodrive, a company that had already
‘‘ It’s really in the inner-city areas that we are the most efficient, but as you go into the outer town areas, we’re also very applicable
Carsten Asteheimer, Astheimer Design
assisted in the feasibility study, about collaborating – and that led to the creation of a new entity, ELM Mobility.
From here, the project took shape over 12 months, quickly moving from a blank sheet to a functional prototype.
Astheimer describes the EVOLV as three very distinct volumes. There’s the cabin volume, which wraps around the driver. Then there’s the front bumper volume, which houses the impact zone and the front wheels, adding protective stability. Finally, there’s the big box in the back, which is the purpose of the vehicle.
For Astheimer, capacity for 150 packages – roughly the maximum number of deliveries that a driver would complete in a day – was the magic number. He goes on to explain how the initial concepting stages were as much a volume packaging exercise as a clean-sheet automotive exercise.
“We knew we wanted to stay in the L7e [powered light vehicle] category, and there are dimensional limitations – 1.5m width and 3.5m length. We knew we didn’t want to go over 2.1m in height. And so, within that package, we wanted to maximize the load volume to allow for 150 parcels,” he says. “And the other thing that we wanted was to be able to get a full-height Euro pallet in.”
This last factor would make the EVOLV more attractive to urban logistics companies. These dimensions would
allow them to transfer bulk parcel loads or single large products while easily competing with traditional vans that weigh double the weight. By requiring half the energy to make each delivery, the EVOLV is considerably more environmentally friendly and cost efficient, but there were other practicalities to consider.
EVOLV needed to be compact, so as to be easier to park than a compact van or a 4.25-ton van. Astheimer explains that, in downtown areas, cargo bikes will always be the most efficient form of transport, because of infrastructure elements like cycle lanes and their ability to park on pavements. However, they’re simply not suitable for all goods.
“It’s the inner-city area where we’re really the most efficient, and as you go into the outer town part, we’re also very applicable, but that’s where the bigger van then becomes slightly more efficient. So I think we’re able to really define where our efficiencies come,” states Astheimer.
The initial design phase involved increasing the load volume by as much as possible, while shrinking the driver cabin – but not by too much. The team found through its research that driver experience is fundamental to the success of a logistics vehicle. If drivers aren’t happy with the vehicle, then their employers won’t buy them, says Astheimer. So driver comforts that make their lives as easy as possible – driving position, ease of entry and egress and so on – are critical.
That last point is fundamental for users who will climb in and out of a vehicle over 100-times a day. “Our seat height is quite high and the H-point (hip point) of our seat is about the same height as when you’re stood next to it. So, it’s more of a slide-in translation horizontally. You’re not dropping down into the seat or climbing up into it, and that is quite intentional,” explains Astheimer. Access on either side of the vehicle and extended all-round visibility also help with safety when it comes to getting in and out in busy urban environments. The design team also focused on helping drivers maintain focus on their work, by making the operation of the vehicle and the navigation to their next delivery extremely simple. Here, they created user interfaces influenced by video gaming, such as the layout of the dash and steering wheel, with scrolling menus and intuitive physical buttons.
When asked about the technology used in the design of the EVOLV, Astheimer responds: “More and more we’re using something through the whole process to a much later phase in the development of the design. It’s only when we really get down to splitting the model into panel parts and having to create offsets for panel thicknesses and A and B surfacing that we go into NURBs modelling.”
This can take the form of sub-D or T-splines in Blender or Geomagic Freeform. Blender is increasingly ELM’s
software of choice in the early stages, as it covers the whole process, explains Astheimer, adding that the team are allowed to work in whichever software they find most familiar and comfortable.
“Then we’ll move into Rhino or Alias as we go into the final surfacing – but we only go there when we’re really, really sold on exactly what the design is. Otherwise, it just takes too long.”
This same flexibility applies to creating renders necessary to building out the design. “Some of our designers will use KeyShot, others will use Blender, because they’re working in Blender. We use VRED for virtual reality, and we’re using Unreal now as well. Chaos V-Ray seems to give really nice soft interiors. I lose track of the amount of software that we’re using!”
From initial designs, Astheimer explains that the project moved quickly into a rudimentary mock-up to test ergonomics, analyse proportions and better understand the volumes and architecture of the proposed vehicle.
Once design intent had been established, a more precise ergo buck with moveable components was built to help define seating, control and pedal positions.
From this model, ergonomics could be tested on a wide range of people. GoPro cameras were fitted into the buck to capture people getting in and out of the vehicle, while an AI motion-tracking software captured their movements, helping to finetune cabin boundaries and shave off precious millimetres of space.
All of this work took place over the first three months: defining the concept for driver and cargo volumes, and the placement of key infrastructure like the motor and the batteries.
Astheimer explains that it was by the end of month three that the team had the basic concept down, before having pivot to building a working prototype. Deciding on the familiar drive train from a readily available Renault Twizzy, the process involved working hand-in-hand with
Prodrive to align it in an architecture, commission the parts and get it ready to assemble in time for launch.
Robustness and reliability are as fundamental to logistics companies as they are to motorsport teams, where Prodrive has a strong foothold. Based in Banbury, UK, the company develops engineering solutions from a blank sheet through to low-volume production for businesses across the transport sectors. Previously, it helped Ford create its first plug-in hybrid electric Transit van and bring Volta Trucks’ vision of a fully electric midsize truck to life by exploiting the electric powertrain.
The EVOLV was split into two halves, with Astheimer Design focusing on the top half, with its body, cabin and user touchpoints, and Prodrive on the lower half, with its skateboard chassis, drive and electrical systems.
“We had to work extremely closely together to get everything in the right place, both when we were working virtually and when we were starting to build a prototype,” says Astheimer.
Relying on Microsoft Teams, Prodrive’s in-house project management tools and in-person meetings, collaboration on such a fast-paced project demanded a clear definition of responsibilities and good communication at every stage.
With the vehicle developed, the project then moved into further testing and verifying of the prototype, while working towards manufacture and developing the business model.
The next stage will be to simulate the details and efficiencies of the EVOLV, using what Asteimer calls a ‘digital twin of the urban environment’. This means a deep-dive into the detail of practical elements. How long does it take to park the EVOLV? What is its manoeuvrability like? How long does it take to get out and unload a delivery? How should a driver organise the trolleys and pallet loaders?
●
5 A VR model was created in Autodesk VRED to help explore the design
● 6 Early concept sketches focused on maximising the EVOLV’s load volume
●
7 The design comprises three distinct volumes: front ‘bumper’, cabin and load space
● 8 Members of the ELM Mobility team assess the ergo buck positioning
Key to understanding these demands – and knowing how to slot them into existing architectures and set-ups – has been one of the biggest learning curves. As part of this, Astheimer is keen to acknowledge London-based Mango Logistics. Operating an entirely electric fleet, as well as managing warehousing solutions, Mango’s CEO Daniel Levan-Harris has given ELM invaluable insights into the nuances of last-mile delivery from the start of the project and has since joined the ELM advisory board.
Astheimer says he has learnt a lot along the way. “I’ve done a day on a cargo bike. I’ve been in their vans. I’ve delivered pizzas for my brother-in-law! And, in previous projects, we sent designers out with DPD, so we’ve now got quite a bit of knowledge and data from this world,” he says. “We’ve become quite specialised in delivery, and in last-mile delivery in particular.”
Next comes tackling all the other aspects of the business: manufacturing, sales, distribution and maintenance. With further investment and discussions with manufacturing partners underway, the goal is for EVOLV to reach production in 2028, with prices starting at around £25,000 per vehicle.
“As an ideas company – and as an ideas person –coming up with ideas and creating new ideas is almost the easy part. The difficult part is designing that for cost and getting traction in a market, especially a market that’s very competitive and subject to huge pressures in cost and complexity, like last-mile delivery,” he explains. “It’s essential that our vehicle is a solution that saves money and doesn’t cost the earth.”
With some market analysts projecting the value of the UK last-mile delivery industry to be worth over £7 billion by 2030, and some £200 billion globally, a design that can glide through the urban landscape with the least environmental impact and greatest efficiencies looks destined to be one that will deliver the goods.
‘‘ Ideas are almost the easy part. The difficult part is designing for cost and getting traction in a market, especially a market that’s very competitive Carsten Asteheimer, Astheimer Design ’’
Thinkerbell Labs’ Annie helps users learn to read, write, and type in Braille
At the age of three in 1812, Louis Braille lost his eyesight after an accident while playing in his father’s leather workshop. When he was 10 years old, he was awarded a scholarship to attend the first Institute for Blind Children (Institution des Enfants-aveugles) and left his family and small village behind to further pursue his education in Paris.
hinge on this core knowledge. However, access to learning Braille can be incredibly challenging and requires a tremendous investment in time and resources both for educators and students. With a new innovative device, Thinkerbell Labs is on a mission to transform how Braille is learned by making it easy, accessible, and, yes, even fun.
At school, Braille was intrigued when he discovered night writing—a raised-dot alphabet created by an officer in Napoleon’s army and used to communicate without words or light on the battlefield. When Braille was 13, he began innovating his own version of it, reducing the complexity from a 12-dot system to a sixdot cell that is now the standard today.
For the blind and visually impaired, Braille literacy is a critical component for future success. Positive educational outcomes and employment
Thinkerbell Labs’ flagship innovation, Annie, is the world’s first Braille selflearning device that helps users learn to read, write, and type in Braille on their own. Named in honor of Helen Keller’s teacher Anne Sullivan, it offers interactive and audio-guided lessons that allow students to independently learn, practice, and be assessed on Braille literacy.
Annie provides a tactile learning experience with real-time audio
feedback that helps children build Braille literacy in an engaging and self-paced manner. The device speaks in a friendly voice, and students note that she even sounds like a friend.
The device speaks in a friendly
“The content on Annie is available in 14 localized languages,” says Sana Dhawan, Marketing Associate, Thinkerbell Labs. “With Annie in schools, students can independently learn Braille without constant hand holding from educators, reducing the learning time significantly. It’s also a fun and gamified way to teach Braille with the combination of lessons, games, and vocabulary-building activities.”
Labs. “With Annie in schools, students can
learning time significantly. It’s also a fun and
Initially launched in India and with an investment from the popular TV show Shark Tank India, Annie gained global recognition. The company quickly grew, thanks to partnerships with organizations including American Printing House for the Blind (APH) in the U.S. for the distribution of the Polly version of the device and HumanWare in the UK.
Innovating the next generation of Annie
The next version of Annie is currently in development to address user feedback and incorporate even more features. The team is using
Foranyonelookingtoscaleuptheir manufacturingprocesses,Fusion Operationsisaperfectfit.Itchecks alltheboxesthatwewanttotick.My adviceisverysimple:Youdon’tneed toreinventthewheel.It’salreadybeen inventedwithFusionOperations
SaiSachitPathak,HeadofBusiness Operations,ThinkerbellLabs
Autodesk Fusion for advanced modeling tools to create more ergonomic and user-friendly designs and taking advantage of global collaboration in the cloud for partners in the U.S., UK, and other regions to review and contribute in real time. By adopting Fusion, Thinkerbell Labs can focus on enhancing the user experience, such as improving the tactile feedback in Annie’s Braille display. Based on this user feedback, the team adjusted vibration intensity. They also reduced operational noise by 70% to enable better learning. Fusion allowed them to rapidly prototype and implement these changes quickly and efficiently. Gupta also moved to Fusion Electronics for their electrical designs. Annie contains hundreds of components. In addition to the precision of selecting and placing components, frequently updated libraries available in Fusion transformed his process. “It was very easy for me to make the shift,” he says. “I’ve reduced the time I spend on designs by 50%.”
“There are many small benefits that deliver big benefits as well,” adds Yashasvi Yadav Mechanical Design Engineer, Thinkerbell Labs. “Things like the ability to have multiple tabs open, autosave, or even auto-generating gears and other components through community-developed Python scripts have
drastically reduced my manual design effort. With Fusion, about 50% of my overall design time has been reduced. My productivity has also increased because I don’t need to think about any other stuff while designing. I can be in the zone and just design.”
To scale and streamline operations, meet growing demand, and keep affordability of the device first and foremost, Thinkerbell Labs turned to Fusion Operations. “Before Fusion Operations, our production data was scattered across multiple spreadsheets,” says Sai Sachit Pathak, Head of Business Operations, Thinkerbell Labs. “Tracking inventory, sourcing raw materials, and managing production was cumbersome and time-consuming.”
After evaluating different options, the team decided to move forward with Fusion Operations, and it has transformed their manufacturing and supply chain processes. Centralized data, real-time inventory tracking, and automated alerts via Slack deliver unseen levels of accuracy and efficiency. Access to data is available across the organization in real time. Fusion Operations has also brought new opportunities to efficiently scale production with the new demand for both Annie and Polly.
“Today, generating an inventory report with Fusion Operations now takes us five minutes instead of a week,” Pathak says. “We’ve also automated alerts for production issues, enabling faster problem resolution. This shift to Fusion Operations allows us to meet critical deadlines, such as fulfilling a recent contract for 2,100 Polly units.”
Making a difference—one device at a time
For the Thinkerbell Labs team, working on Annie and Polly is more than just a job—it’s a mission to make education inclusive worldwide.
“It’s an incredible journey working with the company, and it doesn’t feel like work,” Gupta says. “It feels like we’re truly helping someone when we see kids and even adults learning how to read and write in Braille. It’s an amazing feeling that you get to see the product that you have designed and made is making a difference in the world.”
» As we gear up for DEVELOP3D LIVE 2025 at Warwick Arts Centre on 26 March, Stephen Holmes takes a look at some of the highlights planned for the bumper one-day event, packed with design and engineering technology and know-how
Big things are afoot in the world of technology, with product design and engineering tools undergoing fundamental changes.
The big guns are readying their products for a new world of AI enhancements. New players are popping up regularly, with capabilities boosted by GPU and cloud compute power.
This is the lull before the storm – the time to figure out where you, your team and your organisation stand in terms of the tools at your disposal. Stick or twist, you need to decide.
But how are you going to choose which path to take? At DEVELOP3D, we believe there’s nothing more valuable than getting up close and personal with the companies behind the tech and hearing what they have planned directly from senior executives. Add to that the opportunity to kick the tyres of a product on the exhibition floor and to chat to your peers about their own experiences, and you’re looking at an event that will help you cut through the hype and confidently take the driving seat.
That’s why you should head to DEVELOP3D LIVE on
26 March 2025 at the Warwick Arts Centre, UK. Our conference programme will give you all the information you need to make sound decisions that will give your organisation a competitive edge over its competitors.
This is the only event where all the leading software companies that matter to product designers and engineers come together to engage directly with their most important audience: end users, corporate decisionmakers, and key influencers.
We’ve spent months finding exactly the right speakers to inspire you. So come and meet incredible designers doing wonderful work and technology suppliers truly pushing back boundaries. Come and explore the innovations that will transform your own workflows.
Be part of the changes underway. Don’t miss out. We look forward to seeing you at DEVELOP3D LIVE on 26 March.
Stephen Holmes Editor DEVELOP3D
www.develop3dlive.com
You’ll find Goodwin Hartshorn's work in products that look and perform with equal brilliance, from Bowers & Wilkins’ Hi-Fi equipment to medical devices, wearables and more.
The co-founders — Richard Hartshorn and Edward Goodwin — both have a background in engineering, before shifting to industrial design. This is amply clear from their ability to find beauty in details. Learn how the team at Goodwin Hartshorn approaches projects and uses technology to develop award-winning products.
Your everyday CAD tool of choice is now part of a platform, a growing ecosystem, and in some cases, a ‘universe’ of exploratory design software enabling you to design anything from a spoon to a spacecraft.
Get the very latest news from the likes of Solidworks, Catia, Siemens Digital Industries, Autodesk and Shapr3D as executives from these companies appear in back to back sessions on our main stage. They’ll give you insights into how their products stand today and what customers achieve using them, not to mention a tantalising glimpse of what the design software you use today might look like tomorrow.
The design of luxury watches regularly gets compared to the styling and engineering of cars, planes, trains and boats – so how about incorporating the same 3D-printed lattices into a watch that you might also find in a next-generation spacecraft?
Apiar is on a mission to combine cutting-edge technology and materials with exclusive designs, and to make it all in the UK. Join Apiar founder Matt Oosthuizen to find out more.
Generating power from flowing water is nothing new, but Energyminer is looking to do it more locally to areas of energy demand, without dams or weirs to impact on nature.
Hear from Energyminer CTO, Dr. Chantel Niebuhr, about how CAD and simulation technology enables the company to test its Energyfish power plants in a fraction of the time that it might otherwise take.
Parent company of retail brands including B&Q and Screwfix, Kingfisher is pivotal in the UK’s building, home improvement and gardening sectors. Behind the stores and the e-commerce websites lies a team of in-house industrial designers, developing everything from power tools capable of handling the toughest jobs to beautiful bathroom sets.
Join industrial designer Liam Donnelly and head of design Tom Jarvis as they reveal how Kingfisher brings its products to life.
Do you love your lattices or are you jumpy about gyroids? Our panel of experts are here to put computational design in the frame and offer you insights into how you can transform your products with structures impossible to build by hand. There’ll be plenty of real-world examples, built with the power of these tools. Panellists include executives from Synera, ToffeeX, 3D Systems and Carbon.
Computational Design
With hardware from established consumer brands such as Apple and Sony regularly turning up in workplaces, the spatial computing sector now has fresh impetus and new accessibility. Join experts from Siemens, Shapr3D, Tech Soft 3D and Threedy to explore the potential gains for designers and engineers from working in extended reality (XR) to elevate concepting, visualisation, exploring assemblies and more.
House building is in trouble. The industry has tried to copy automotive, but in the UK nearly all offsite manufacturers have crashed and burned. Bruce Bell from Facit Homes will present an exciting alternative. His innovative architecture firm has partnered with Tharsus to build a robot system to take the housing factory to the worksite in two shipping containers. The potential to have these robots in every city and county, ready to manufacture buildings through CNC cut box sections could solve the housing crisis, helping overcome the skills shortage endemic in the industry.
The Landr 500 is a new FDM 3D printer for industrial use. Developed by experts in their field and battle tested preparing parts for some of the most demanding clients in automotive, it is a sign that 3D printing is fast maturing for end use components.
Hear from Landr CEO Mitchell Barnes how the product was developed to meet the needs of users.
Nvidia GPU-powered CAE platform, Neural Concept, is a name the software you’re already using is racing to collaborate with.
Neural Concept’s platform aims to bring together data scientists, CAE and CAD designers on a single platform for deep-learning simulation capabilities. Learn how it can accelerate your workflow with HPC power.
Beyond the design of the product and the engineering to optimise production, there are management level issues which impact the whole business of producing manufactured goods.
This year DEVELOP3D LIVE features a new track looking at more strategic issues which face 21st Century businesses; desktop and cloud tech stacks, business process change using Artificial Intelligence (AI), PDM and PLM, factory design, Intellectual Property (IP), Patents, accessing grants for R&D innovation and working with Catapult institutions.
We are working with industry analyst Cambashi, Innovate UK (part of the Government's UK Research and Innovation) and various departments of Warwick University.
As part of this track, Peter Harman, CEO of Infinitive, creator of a configuration platform for product development, will share strategy and tips for SMB success for accessing grants as routes for technology development.
Infinitive has a great record in securing various grants and Harman will show how these have helped accelerate the in house development of its technology.
Industrial designer Henrik Svanvig has worked at Vital Auto and interned at Chinese Automotive giant SAIC Design Advanced in London.
He has a deep interest in mobility for the elderly and how many of today's designs seem to alienate the target demographic.
Svanvig will present some of his ideas on elderly friendly vehicles and explain how he has incorporated the use of cutting edge tools like Gravity Sketch and VR in his design process.
Focused on low to mid volume batch production runs, 3DPRINTUK bridges the gap between additive manufacture and injection moulding for plastic items. The company explains that the viability of using SLS as an alternative to injection moulding really kicks in with smaller items; there are no set-up fees only a unit cost, so for small parts with volumes of up to 10,000 units, it’s a no brainer. The more complex the part the higher the viability as equivalent tooling cost becomes astronomical, it adds.
3DPRINTUK offers price breaks for higher quantities and free samples for production runs if a qualifying order is placed. It can do the CAD work and offers a free polishing service for finished parts so they are near injection mould quality. www.3dprint-uk.co.uk
3DRP works exclusively with 3D Systems in the UK and Ireland. According to the company, it offers the most comprehensive additive manufacturing solutions in the 3D printing industry, as well as expertise across a wide range of applications and partner industries.
3DRP's range of commercial 3D printers can be used to produce both plastic and metal parts on demand, in a fraction of the time compared to traditional manufacturing.
At DEVELOP3D Live delegates can explore 3DRP's extensive and versatile portfolio of 3D printing solutions designed for precision in additive manufacturing, featuring a wide range of engineering materials including plastics, elastomer, composite, wax, and more. www.3drp.co.uk
Additive-X has 30+ years' experience of building relationships and knowledge bases with the best manufacturers. The company doesn’t just sell 3D printers; it provides 'best-in-class' additive manufacturing solutions with full certified technical support, training, brand specialists and unbiased advice.
Additive-X's experienced staff are able to give impartial advice on the wide range of technology the company offers and its technical support, sales and customer service teams have developed a wealth of experience in many industries.
Additive-X is an authorised reseller and trusted partner of Formlabs, Lynxter, Bambu Lab, Markforged, Builder and AMT. www.additive-x.com
For more than 50 years AMD has driven innovation in high-performance computing, graphics and visualisation technologies. Billions of people, leading Fortune 500 businesses and cutting-edge scientific research institutions around the world rely on AMD technology daily to improve how they live, work and play. AMD employees are focused on building leadership highperformance and adaptive products that push the boundaries of what is possible. www.amd.com
Advent 3D is a UK based reseller dedicated to the supply and support of Formlabs and UltiMaker 3D printers. According to the company, its background in engineering and design gives it a deep understanding of the requirements of these industries.
The Form 4L DLP Low Force Display (LFD) printer offers larger parts, and is compatible with more than 12 different materials. Where robust parts are required for functional prototypes or end use production parts, Advent 3D recommends the the Formlabs Fuse One +30w SLS printer. Advent 3D offers UltiMaker's range of FDM printers from the low-cost Sketch Sprint to the industrial grade performance printer, the UltiMaker Factor 4. www.advent3d.co.uk
Carbon helps people make radically better products with a fusion of tools for manufacturing, professional expertise, and your imagination.
Global organisations, including adidas, PUMA, Riddell, Vicis, Ford Motor Company, and Becton Dickinson choose Carbon to produce applications with a wide range of functional, high-performance properties, at scale. Carbon’s exceptional production partner network produces parts reliably wherever and whenever they’re needed. Carbon is a venture-backed company headquartered in Redwood City, CA. www.carbon3d.com
Since 2012, the purpose of Dassault Systèmes has been to provide business and people with virtual universes to imagine sustainable innovations capable of harmonising product, nature and life. Since its inception, and at every stage in its history, the company has been committed to contributing positively to society through its sustainable business practices and solutions.
Dassault Systèmes has always been a global player when it comes to knowledge and knowhow for the industries and clients it serves; this is one of the reasons why so many market leading organisations have joined Dassault Systèmes for the ride. www.3ds.com
For decades, HP has been a trusted hardware partner for designers and engineers around the world. The HP Z Workstation portfolio offers high performance laptops, desktops, and solutions engineered to drive the most demanding professional workflows. From conceptualisation and 3D modelling to real-time rendering and simulation— Z Workstations are tested, optimised, certified and engineered to outperform standard PCs. The devices are highly reliable and undergo up to 360,000 hours of rigorous testing, maximising productivity with solutions built to last.
www.tinyurl.com/HPZ-PDM
IMSCAD Services will be showcasing its (WaaS) ‘Workstation as a Service’ offering, which recently launched globally.
The company has partnered with Lenovo Workstations and Equinix Data Centres to offer Private Cloud solutions and rentable machines on a month by month basis
According to IMSCAD, its WaaS offering delivers the Lenovo range for AI, HPC tasks and gives users the most powerful remote working solution on the market — up to 6.0 GHz CPUs, up to 24 GB GPU per user and up to 40% cheaper than high end instances from the Public Cloud. www.imscadservices.com
ITI began in 1983 with a mission to help manufacturers drive innovation and time to market by applying computer-aided product development to engineering problems. Today, the company specialises in conversion, integration, validation, and migration solutions for product data and related systems. It is a wholly owned subsidiary of Wipro Limited, a leading global information technology, consulting, and business process services company.
ITI's solutions include CADfix (3D CAD model translation, repair, healing, defeaturing, and simplification), Proficiency (feature-based CAD conversion), and CADIQ (model validation). www.iti-global.com/CADfix
LANDR 3D is setting a new benchmark in industrial 3D printing with the LANDR 500, a UK-designed and manufactured large-format FFF (Fused Filament Fabrication) production machine. Engineered for businesses that demand scalability, speed, and reliability, the LANDR 500 is a true production-ready additive manufacturing solution—delivering exceptional output at an accessible price point. Designed to bridge the gap between prototyping and full-scale production, the LANDR 500 is ideal for manufacturers looking to reduce costs, streamline workflows, and scale operations with precision engineered parts and high-performance materials with functional prototypes, end-use parts, or batch production. www.landr3d.com
KeyShot, the Product Design-to-Market Suite, revolutionises 3D design with its real-time rendering technology. The KeyShot suite enables 'seamless collaboration' from sketch to market launch, helping businesses of all sizes design with precision, align processes with clarity, manage workflows with efficiency, and deliver impactful products. KeyShot facilitates a faster and more streamlined journey from concept to customer and also unleashes the power of 3D visualization to captivate audiences with stunning product experiences.
KeyShot Studio is a cutting-edge 3D rendering tool that brings your design to life with photorealistic accuracy. www.keyshot.com
Integrated PLM has been providing services in PLM for nearly a decade. The company supplies PLM strategy, deployment and support services across the UK, Europe and internationally.
Integrated PLM has small team of highly specialised engineers with a with vast experience in many engineering fields from automotive to pharmaceutical, focussed on technology driven change for dynamic organisations.
Integrated PLM is also a provider of Vertex, a solution that offers 'instant access' to CAD geometry. Vertex allows you to view and collaborate with 'unlimited' assembly sizes - no software to download and maintain, all with just a browser. www.iplm.co.uk
Lexip is a leading brand in the gaming peripherals market, recognised as one of the top peripherals makers in the world by the CES Innovation Awards. The company pushes the boundaries of performance, comfort, and durability.
Lexip offers patented mice, controllers, and headsets. The Lexip PU94 mouse, as reviewed in DEVELOP3D Magazine, supports Autodesk Fusion and Inventor, Dassault Systèmes Solidworks and Catia, and Siemens Solid Edge.
One of Lexip standout innovations is the use of Titanium in its devices, which not only enhances durability but also ensures a premium, lightweight feel. www.lexip.co
Lenovo Workstations, powered by NVIDIA are said to be the most trusted and reliable products in the industry. With a wide range of options, Lenovo Workstations give designers, engineers and manufacturers the flexibility to power through any demanding product function – from CAD, CAM and Computer Aided Engineering to rendering and animation. Lenovo believes in the creative power of passionate people. That power is amplified when they have the best tools to transform their imagination into reality. Tailored to the needs of specific users, Lenovo’s NVIDIA Workstations combine hardware, software, and technical expertise to help unleash the user’s potential. www.lenovo.com/gb/en
Since 1971 Malcolm Nicholls Limited (MNL) has been a expert within Rapid Prototyping, 3D Printing and Low Volume Manufacturing. According to the company, its reputation for excellence is based upon a superb blend of high-tech 3D printing machines and materials, expert knowledge along with high-quality traditional craftsmanship.
MNL is home to two of the largest 3D printers with build platforms of 800 x 800 x 600mm. It also offers large format SLA, small intricate SLA, superior finish SLS, FDM, 3D colour printing and traditional model making, and vacuum casting. The company can manufacture from 1 – 1,000s of parts bridging the gap from prototype to mass production.
www.mnl.co.uk
Mimaki is redefining what’s possible in full-colour 3D printing. With a heritage in industrial inkjet technology and a reputation for innovation, Mimaki’s 3D solutions deliver what the company describes as unmatched colour accuracy, fine detail, and exceptional print quality. At DEVELOP3D Live, Mimaki reseller R A Smart will be showcasing Mimaki's full-colour 3D printers, including the 3DUJ-553 and the compact 3DUJ2207, demonstrating how they enable designers, engineers and creatives to bring their concepts to life with 'vibrant, photorealistic precision'. The printers utilise UV-curable inkjet technology to model in over 10 million colours with high definition and fine gradients. www.tinyurl.com/RA-Mimaki
OR3D specialises in providing 3D solutions and consultancy. The company states that, as the UK’s largest Geomagic partner for hardware and software, it is well placed to offer the right solution. OR3D offers a range of laser scanning equipment that covers long range scanning, to non-destructive testing with its CT machine. For high precision manufacturing and engineering applications, the company is able highlight the capabilities of sub millimetre accurate scanners and laser trackers from API. Using Geomagic Design X the OR3D can demonstrate complete scan to CAD workflows, including the creation of native parametric CAD models in SolidWorks, Inventor, NX, Creo and CATIA. www.or3d.co.uk
PNY celebrates over 35 years of success as a provider of electronic solutions for several high growth markets.
As a long-standing leader in the field of memory, the company has further expanded its offer with storage products such as USB sticks, memory cards and SSDs.
For over 20 years, PNY has fostered a special partnership with NVIDIA and supplies the latest GPU technologies for the embedded and gaming markets, as well as professional applications, including NVIDIA Professional Visualisation.
PNY proposes a full spectrum of high value-added solutions in HPC and Artificial Intelligence environments. www.pny.com/en-eu
Scan delivers hardware, workstations and cloud solutions to the AEC, CAD, manufacturing and product development industries. According to the company, its 3XS workstations are meticulously designed to deliver exceptional performance, reliability and responsiveness. As an NVIDIA Elite partner, Scan explains that it has been at the cuttingedge of AI and cloud advancement, both for solutions and as a consultant to some of the UK’s most important thought-leaders. www.scan.co.uk/pro-graphics
Siemens Digital Industries Software and Siemens Xcelerator are seeking to transform the everyday by giving companies the agility, flexibility and adaptability to turn ideas into innovation with greater efficiency and speed. Discover the wide portfolio of products that will help transform the everyday for everyone:
• Designcenter, a software suite of NX X and Solid Edge X for product development
• NX X Essentials - design anytime, anywhere on any device on this affordable, web-based engineering platform that combines CAD, CAM and CAE tools.
• Immersive Engineering with NX CAD - visualise, simulate and interact with designs in a virtual environment www.siemens.com
Synera believes that engineering deserves an efficiency boost. Engineers should be creative once again, the company explains, instead of being trapped in tedious, manual processes and routines.
Synera enables engineering organisations to create and deploy collaborative AI agents that double as engineering experts – to supplement engineering teams and autonomously address product development tasks around the clock.
The company's easy-to-use builder allows firms to automate at multiple levels – from simple automated engineering workflows to fully fledged multi-agent-systems that combine workflows with the scalability and reasoning of AI. The platform is said to seamlessly integrate with existing CAx tools and processes. www.synera.io
Tech Soft 3D is a provider of engineering software development toolkits (SDKs) and end-user applications for CAD/CAE data conversion, visualization, and data publishing.
For developers, it offers a range of software development toolkits, including HOOPS for CAD data translation, visualisation, photorealistic rendering, and 3D PDF publishing.
CEETRON toolkits are available for CAE data, meshing and solver support, while Theorem, SpinFire and Tetra4D provide CAD translation, publishing, viewing, 3D PDF, extended reality (XR) and more.
Partners include Adobe, Autodesk, Dassault Systèmes, Trimble, 3D Systems, Bentley, Ansys and more. www.techsoft3d.com
T3DMC is an expert in 3D scanning services and provider of the latest innovations in handheld 3D scanning and portable CMM equipment.
The company will show its latest range of portable, lightweight, easy to use 3D scanning laser equipment incorporating unique features such as dual scanning mode (red and blue laser) in the Prince scanner and red laser with incorporated photogrammetry in the AXE scanner.
T3DMC also has a new range of portable CMM 3D scanning equipment which uses camera positioning to enable wireless functionality over large areas, and operates without reference markers or spray.
www.t3dmc.com
Threedy GmbH is looking to revolutionise how businesses access, visualise, and collaborate with 3D data. The company's cloud-native platform, instant3Dhub, enables 'seamless interaction' with complex 3D models in real time—regardless of scale, format, or infrastructure. instant3Dhub delivers instant streaming, high-performance visualisation, and multi-user real-time collaboration without hardware or software limitations. It optimises resource use across on-premise, private, and hybrid cloud environments and integrates seamlessly with PLM, ERP, AI, and enterprise security systems like Teamcenter and SSO. It supports all major CAD formats (JT, NX, Catia, etc.). www.threedy.io
»
At Dassault Systèmes’ annual user event, Solidworks celebrated three decades of software excellence by treating attendees to a glimpse of its next big thingits AI tools, beginning with Aura. Stephen Holmes reports from Houston
Dassault Systèmes’ annual global event for its Solidworks software opened with one eye on the past and the other fixed very much on the future. Its achievements as a leading 3D CAD software vendor over the past 30 years are impressive. But it’s what comes next that has the potential to be truly remarkable.
“We’re ready to change the game – again!” proclaimed Gian Paolo Bassi, senior vice president of 3DExperience Works, addressing attendees gathered at the Houston, Texas-based event. The main sessions and exhibitor halls certainly had a lively feel, despite the in-person experience being somewhat pared back, while slick video production was hard at work to bring the event to absent members of the 8-million-strong global Solidworks customer base.
The key announcement was that the Solidworks platform is now moving into its ‘Gen 7’ phase, with a stream of Dassault Systèmes executives over the three days explaining the company’s vision to the crowd.
Much of the event was spent deciphering the latest branding slogans and marketing buzzwords. The virtual twin decade of the 2020s, it seems, looks set to be followed by the ‘Gen 7’, ‘3D UN+VERSES’ and ‘Metamorphosis’ era of the 2030. And the goal behind that shift? “Elevated human know-how.”
If customers are a little confused, it seems that Solidworks executives are also feeling a lack of clarity in all this. In a lengthy FAQ on the Solidworks website, the company attempts to clarify the situation, addressing a stack of questions: Is 3D Experience Solidworks the same
as Solidworks 3D CAD? Is 3DExperience Solidworks the same as Solidworks Cloud?
That said, the 3DExperience World crowd – mostly made up of passionate, veteran Solidworks users with years of experience under their belts – know that Solidworks gets work done for them. The Suits at company HQ in Vélizy-Villacoublay may continue to tinker with products and product names, but the core tools on which these users remain functional, familiar, and reliable.
The event’s general sessions were heavy with explanations of new AI features. “AI is not just an add-on to our platform. It’s at the core of how we’re transforming your workflow,” proclaimed Dassault Systèmes CEO Pascal Daloz, who spoke of forthcoming ‘generative experiences’ and ‘virtual companions’, the first of which, will appear in Solidworks this July, in the form of AI assistant Aura.
Trained on a variety of Solidworks training guides, best practice information and help docs, Aura will take the form of a chatbot embedded in the 3DSwym collaboration tool.
Solidworks CEO Manish Kumar explained that Aura will be available to web-connected Solidworks, and will learn from your data to provide AI responses specifically for your organisation. This learning and data will remain within your company’s 3DExperience platform and not be accessible by others, or be used by Dassault to train Aura for other 3DExperience platform users – a message
The excitement around new AI tools in Solidworks looks set to continue as CEO Manish Kumar heads to DEVELOP3D LIVE to give us some exclusive insights into what the future holds. Kumar is returning once again to our free UK event aimed at product designers and engineers, where attendees can expect to find out more about the latest features in Solidworks as it moves to embrace Dassault Systèmes’ Gen 7 vision.
Top of the list of exciting new developments will be Solidworks’ new AI tool Aura. Kumar has already hinted at some future capabilities for Aura, including AI drawings, assemblies, mesh-to-CAD and visualisation. On 26 March, we hope to hear more about what will make it into the launch version of Aura, due in July, and what other features and functions might be confirmed before the end of 2025.
There’s also the chance to learn about the wider 3DExperience ecosystem and hear from an exciting Solidworks customer, speaking on stage alongside Kumar, who uses the software to design incredible new products.
Sign up online for your free event pass and join us at Warwick Arts Centre on 26 March 2025: www.develop3dlive.com/ register-now-2025/
that was constantly reinforced as Solidworks looks to reassure users about how their valuable intellectual property is protected.
Kumar went on to explain that the three primary tasks of Aura are learning from users, teaching users, and taking actions on behalf of users. But there are plans for it to offer much more.
The second day of 3DExperience World 2025 showcased potential enhancements for Aura, currently in development. These included some pretty low-hanging fruit (such as creating drawings using AI), but also some more ambitious uses of AI.
For example, Kumar demoed one such capability, Perform Task. Here, we saw Aura presented with the layout design for a new factory floor and asked to bring that layout up to standard with current safety protocols. In response, Aura, having consulted publicly available and company-specific standards and practices, introduced guard rails into the model where needed.
There were also teasers for mesh-to-CAD tools that can take a mesh file and make it an editable parametric model in Solidworks. “Whether you are working with 3D scan data, imported mesh files, or legacy CAD models, this feature - once fully developed, I must say - will provide a seamless way to transition from complex mesh geometry to native parametric features,” Kumar said.
Also shown was a clip of how Aura can be asked to quickly render a product visualisation of the model on screen from a simple prompt.
And the ability for Aura to build an assembly from parts – many of which are already in Solidworks Toolbox – was described by Kumar as representing the point where: “AI becomes incremental. You do something, and once you have achieved it, then you realise that it can. You can achieve even more.”
On watching the AI assemble component parts from a
user’s files, and mating connectors and fasteners using intelligence rather than user-defined automation, you could see his point.
While some or all of these capabilities will eventually reach users, one thing was clear: the desire to keep users tied to the 3DExperience platform user interface and well away from the clutches of emerging start-ups. The message here is that customers don’t need to buy AI, because they already have AI at home.
However, getting its customers to use these tools will be the challenge for Dassault, something acknowledged by Daloz in a press conference. This gave some insight into the frustration felt by Dassault Systèmes executives over the market’s slow adoption of the cloud technology that these new AI tools will require to function.
“The cloud is already ready. I mean, if you look at our portfolio, we have more applications available on the cloud than we have on-premise,” said Daloz. Earlier that day, he said, he’d delivered that same message at a partner session.
“I said, ‘Guys, you are not yet embracing everything we do for you.’ And the problem is, I’m coming with a Gen 7 where, if you are not on the cloud yet, you will not get the benefit of it,” Daloz said.
“So why I’m saying this is because the vision is in place. Most of the technology and the products are already available, but we know [that] to transform the companies is taking time – and why? Because the most difficult part to change is really the human side.”
This longing for the existing Solidworks customer base to shift to the 3DExperience platform is understandable. That shift, after all, would enable customers to use a wider range of advanced tools from its stable and allows Dassault not only to consolidate a confusing product list but also stop developing tools on someone else’s geometry kernel.
So it must have been a punch to the guts for Solidworks executives when the biggest cheer from the crowd was elicited by functional updates extending how the escape key can be used to cancel out actions, rather than in response to shiny new generative AI tools.
Still, what we’ve been able to see of the ‘Gen 7’ Solidworks looks great, with pragmatic and functional solutions to speed up workflows and create a clear security cordon around intellectual property.
Key to the company’s success will be getting these capabilities to market quickly and ensuring that Aura becomes a tool that is used regularly by customers. That will put some pressure on Dassault’s software developers, but there were also mentions of acquisition activity later this year that may bring new expertise to the software development effort.
This was an event with a genuinely positive message, in contrast to predecessors of recent years, which often felt too weighed down by lengthy sales pitches for the 3DExperience platform that never seemed to hit their target.
More users are finally shuffling over to the platform now. So a bunch of new AI tools that promise to make their lives simpler and more productive, as well as the allure of Aura, might be the bait needed to get others into the saddle.
The event returns to Houston in 2026, a city that loves rodeo. By then, we’ll have a clearer view of how many Solidworks customers have taken up the 3DExperience reins and are blazing a trail with Aura. www.3ds.com
● 1 A 1995 edition of Solidworks was on display to celebrate the 30th anniversary
● 2 Main stage announcements included the launch of Solidworks CPQ
● 3 The annual event brings together a wide range of users to share their experiences
Solidworks CPQ, a new configure, price and quote solution, will integrate generative AI capabilities to enable businesses to accelerate order and delivery of customised products, and quickly produce precise quotes
With SkillForce, Dassault Systèmes will provide Solidworks licences to students on internships and placements, helping the companies that host them by removing barriers to software access
Dassault Systèmes 3DLive visionOS app will be available this summer, enabling users to view and interact with models in XR using Apple’s Vision Pro headset (pictured right)
Dassault Systèmes is to join Mosaixx , the cloud platform from robotics company Kuka, with a view to developing more efficient and adaptable solutions for virtual twins and simulations for robotic manufacturing and assembly (pictured far right)
» Nozzle has put 3D scanning and 3D printing to work in its mission to deliver seating tailored to the needs, preferences and proportions of every customer, providing them with optimum ergonomic support, as Emilie Eisenberg reports
Before Aline Ollevier founded Nozzle, she was an occupational therapist working in a rehabilitation department. Firsthand, she witnessed the multitude of issues that sitting in a generic office chair can trigger: back, neck and shoulder pain, muscle stiffness and poor circulation. This inspired the creation of Nozzle and its Up chair, a custom ergonomic office chair.
The customisation of the Up chair begins with the Nozzle App, which uses 3D scanning technology to give Nozzle information about the customer’s posture, measurements and preferences. After a full 3D scan has been conducted, the 3D model is automatically cleaned and processed to create the most ergonomic design possible.
With the information captured by the app, Nozzle then begins the manufacturing process. This starts with designing each chair in Autodesk Fusion, adapting the design to both the customer’s preferences and their workspace requirements. The company then uses Simplify3D to convert the design into a printable file with the most efficient material usage possible.
Nozzle uses Modix 3D printers for the manufacturing of the Up chair as a result of its collaboration with OMD3D, a Belgian reseller of Modix printers. OMD3D assists the Nozzle team with technical drawings, strength calculations and technical support.
The seat shell and backrest are printed with upcycled rPP made from old fishing nets, while armrests are
printed from biodegradable composite materials. Connection elements and structural supports are also custom-printed. Nozzle sources its recycled materials from Reflow, an Amsterdam-based provider of sustainable 3D printing materials.
The seat cushions are handmade by Studio KUIT in Bruges using sustainable materials, and the chair base is manufactured from recyclable materials. It was important for Nozzle to choose materials that are both sustainable and durable, so that a chair can withstand years of consistent use, says Ollevier.
Once a chair is complete, it can be shipped to anywhere in the world, either directly to a customer or to a reseller. Thanks to this smart application of Ollevier’s rehabilitation expertise, the chair is intended to reduce a user’s muscle pain and stiffness and make sitting at their desk for long periods a less physically uncomfortable process.
Nozzle plans to expand its product line in 2025 with the release of the Flex Desk Chair, a chair designed specifically for shared desk environments; and the High-Mobility Chair, designed for dynamic office set-ups with wheels and increased mobility. The company is also working on a range of 3D-printed ergonomic office accessories, including laptop stands, back support cushions and foot rests, all to be made from upcycled materials.
Nozzle’s goal is two-fold: to reduce the epidemic of back pain and health issues that come as a result of desk working, and to minimise the impact on the planet. The Up chair achieves both, comfortably. www.nozzle.be
» Rigging Projects, a specialist in marine hardware, is making waves in machining efficiencies as it welcomes its first in-house, five-axis CNC machine
For centuries, the southern coastline of England has been a place where seafaring adventures begin. It’s also an area rich in expertise when it comes to building vessels for the high seas.
Based on the outskirts of Southampton, Rigging Projects is an end-to-end design and consultancy services provider that works alongside designers and builders of race yachts and superyachts to produce a wide array of deck hardware built to handle sails and lines.
Rigging Projects was founded by Tobias Hochreutener in 2014 and has since grown from a tiny home-office operation to a high-tech manufacturing facility. The impressive centrepiece of the company’s machine shop – and a new addition to its kit – is a Matsuura MAM7252V, a colossal, high-speed, five-axis vertical machining centre for variable-part/variable-volume production and extended unmanned operation.
Standard features of the Matsuura MAM72-52V include 130 tools on a 330-tool magazine base, a tower pallet system for extended lights-out manufacturing, and a chip-removal system.
“Prior to investing in our new Matsuura five-axis machine, we relied on three-axis machining centres and Y-axis lathes,” explains Ian Foss, CNC programmer and machine shop supervisor at Rigging Projects.
“We could make complex parts, but it would require multiple set-ups, nine or ten in extreme cases. As we make most of our parts in small quantities, set-up was costing us a lot of time.”
The five-axis Matsuura ensures Rigging Projects can make almost all of its components in a single set-up, saving significant time and cost.
“In terms of complexity, the Matsuura is another level entirely,” says Foss. “It was clear in my mind that, with such a high-value [piece of equipment], we needed verification software to provide us with confidence during machining.”
Complex parts are par for the course at Rigging Projects. Components that handle a line or sail cannot feature sharp corners, but must also meet the high expectations
● 1 Rigging Solutions builds deck hardware for racing yachts and superyachts
● 2 The Matsuura MAM72-52V is a new arrival on the factory floor at the company
● 3 Almost all Rigging Solutions components can now be built in a single set-up
● 4 Parts are designed in Autodesk Fusion and readied for manufacturing in Vericut
● 5 Handling lines and sails requires designs that offer rounded edges and curves
of yacht owners. Aesthetic appearance is vital. The company’s parts feature many radii, rounded edges, curves and freeform surfaces – so its designers need to be pretty handy with 3D surfacing tools.
Every part is programmed for the Matsuura using Autodesk Fusion. Rigging Projects then uses Vericut to ready the parts for machining, including optimising and verifying multi-axis machining, machine simulation and auto-diff capabilities.
The Fusion cascading post-processor integrates with Vericut to transfer manufacturing data, a capability that allows users to simulate and optimise NC programmes in Vericut while continuing to work in Fusion.
“Fusion offers simulation, but it’s a pre-post process and takes twice the time of Vericut. Moreover, while Fusion will flag up potential collisions, there’s no tolerance-setting option. It won’t send an alert if the tool or spindle gets within 5mm of the table, for example,” says Foss. “In contrast, Vericut will let me know if we get within whatever tolerance I set. I can subsequently refine the gap as confidence grows.”
Foss stresses that his team is much more about ‘rightfirst-time’ machining and safety, rather than saving every second in cycle time. “The Matsuura has driven huge savings in set-up time, so now we just want to stay safe and avoid scrapping expensive workpieces. Vericut is a massive help in that regard.”
The value of avoided collisions involving expensive machine tools should not be underestimated. Repairs to hardware such as spindles are extremely costly, as is the machine downtime it entails. Furthermore, a company like Rigging Projects would be forced to create new programmes for other machines while waiting for the repair.
“We’ve already had an incident where Vericut saved the day,” reveals Foss. “We encountered an isolated issue with the Matsuura post-processor, where it failed to pick up the work coordinates after a homing routine to reorient the table. It used the machine coordinates instead, which means it would have tried to machine itself!” he explains.
Vericut alerted Foss to the situation, enabling him to rectify the issue, saving the company a lot of time and avoiding a potentially dangerous situation.
“With such a large, fast, five-axis machine like our Matsuura, Vericut is an insurance policy. Moreover, with its pallet-change capability, we often leave the machine running overnight,” says Foss.
With CNC simulation, Rigging Projects now has a safety net for its in-house development and production, allowing the company to continue making waves in an industry that consistently demands flawless products for its adventures.
www.riggingprojects.com
• MAXIMIZE ROI
Streamline work ows with minimal reliance on specialized personnel. Its cost-e cient design ensures a quick payo while delivering highquality results.
• SPEED & VERSATILITY
Enhance your production capabilities with a large build area, 5x faster layer cure times versus laser technology, and material changeovers in minutes.
• PREMIER PARTS
Leverage the breadth of the Figure 4 Materials Portfolio for professional prototypes, functional end-use parts, and indirect production applications.
Discover the PSLA 270 at www.3dsystems.com/3d-printers/psla-270 and meet with us at Develop3D Live at stand A33 with our partner 3DRP.
» Can we fix it? AI-Fixer reckons we can, and its creator aims to revolutionise at-home repairs, putting consumers back in charge and providing designers with the feedback they need to make better products in the first place
We’ve all thrown away a broken device and bought a replacement, just because tackling a repair looked to be too timeconsuming or complicated.
For Nazlı Tergiozlu, a research tutor at the Royal College of Art (RCA), London, that wasteful habit represented an intriguing challenge. To tackle it, she has designed a chatbot based on artificial intelligence (AI) called AIFixer, which aims to help consumers carry out device repairs with confidence. This embodies much of her expertise in product repair for circularity, a topic in which she’s long taken a keen interest, beginning with research in 2011 into why appliances break down.
This exploration led Tergiozlu to realise that, while most broken appliances are repairable, they don’t get fixed. For her PhD research, she looked into the reasons why and identified no fewer than nineteen of these. They included the time that a repair might involve; users’ lack of confidence in being able to carry out the repair successfully; and their frustration and embarrassment about not knowing where to start.
With the release of OpenAI’s chatbot GPT-4 in 2023, Tergiozlu began considering how AI could help consumers with repairs, figuring that they might feel more comfortable asking a chatbot questions than a human expert.
“During my PhD, I realised that there are people who want to repair their products. I don’t need to convince everyone. There are so many people who want to repair their products, who want that knowledge, who want products to be more repairable,” she says. “I thought a chatbot could help them ask the questions they need to.”
Tergiozlu partnered with smartphone manufacturer Fairphone, a company that prioritises product sustainability and the circular economy. The partners then held workshops in which repair novices and experts alike used the bot to guide them through repairing devices. As Tergiozlu discovered, it was complete beginners that got the most from it.
Expert fixers with more knowledge and experience preferred to go straight to ifixit.com, find the right manual, understand it in seconds, and solve the problem. Yet, with AI-Fixer’s help, those less experienced managed to successfully repair Fairphone devices in the workshops, and many wanted to provide feedback to Fairphone about parts of the process.
Tergiozlu was aware that although a lot of feedback is posted online about manuals and the repair process
of devices, it rarely gets back to the designer from community forums like Reddit or ifixit.com. Now that designers are beginning to integrate AI tools with their websites and digital manuals, Tergiozlu theorises, it may get easier to send feedback directly to designers.
Originally, the aim with AI-Fixer was to replace repair manuals. After all, they are notoriously difficult to read and hard to scan for exactly the right piece of information. But, as the workshops continued, Tergiozlu noticed that people did not only want an easier instruction manual. They also wanted more interactive materials, ones that included photos of each stage of a process and instructional videos. This, she believes, is what AI can provide.
“I imagine [AI-Fixer] being part of the manual, and then you can chat and ask certain questions to that AI tool when you start reading the manual,” she explains.
“People are already using this kind of web page, for example, for Phillips shavers. The menu – I checked – has been visited over 150,000 times. If companies implement chatbots with their websites and provide proper knowledge, they’d receive the benefit of feedback about which parts of the information fail.”
This technology could be applied to all sorts of products, not just consumer electronics, Tergiozlu reckons. Although many manufacturers recommend repairing and maintaining devices, few of their customers actually know how to do this. How many of us neglect changing the filter on their washing machines, for example? AI-generated videos created for each different model of washing machine, Tergiozlu argues, could get us changing those filters without wasting time researching how to do so.
Looking ahead, she wants to work with designers of different appliances to see how AI-Fixer might help a wide variety of consumers.
“In the next five years,” she says, “I want to develop my research in different scenarios. Maybe I will look at 20 scenarios and select a couple of them, and then implement those scenarios, create the tools and test them with the companies. I want to focus on electrical and electronic equipment appliances at home. I want to provide something that people will use.”
From washing machines to shavers to smartphones, Tergiozlu’s research all points to the same conclusion: that with the help of AI, our gadgets might well prove simpler to repair than we thought, and the insights we gain from fixing them might prove just as valuable to designers.
www.ecologicalcitizens.co.uk/ec-projects#ai-fixer.com
» Nvidia’s entry-level workstation GPU is a notable upgrade from the Nvidia T1000, but could the slightly pricier Nvidia RTX 2000 Ada Generation be the better option for those looking to future-proof their investment? writes Greg Corke
Nvidia RTX redefined professional graphics when it debuted in 2018. With dedicated RT cores, it cemented the role of the GPU as a ray tracing powerhouse, while the Tensor cores made AI an integral part of many visualisation workflows.
Nvidia RTX workstation GPUs were initially limited to Nvidia’s mid-range 4000 series and high-end 5000 and 6000 series. Over time, the technology trickled down, reaching a significant milestone last year with the debut of the first entrylevel Nvidia RTX cards—the RTX A400 (4GB) and RTX A1000 (8GB).
The RTX A1000, the focus of this review, features 8 GB of GDDR6 memory and four Mini DisplayPort outputs. Unlike most of Nvidia’s current pro graphics lineup — the RTX 2000 Ada, RTX 4000 Ada, RTX 4500 Ada, RTX 5000 Ada and RTX 6000 Ada — all of which are based on the Ada Lovelace architecture, the RTX A1000 uses the older Ampere architecture, introduced in 2020. That means its RT and Tensor cores are one generation behind.
Like its predecessor, the Turing-based Nvidia T1000, the Nvidia RTX A1000 is a low-profile card, making it compatible with compact workstations like the HP Z2 Mini G9 and Dell Precision 3280 CFF. However, with an optional ATX bracket, it can also be installed in standard desktop systems. With a peak power consumption of 50W, it draws all its power directly from the motherboard’s PCIe slot.
As expected for a GPU in this class, the RTX A1000 handles most CAD and BIM workflows with ease. In Solidworks 2024, it delivered a perfectly smooth viewport at 4K resolution when navigating a large 2,300-part, 49-million-triangle snow bike assembly—even with RealView enabled for realistic lighting and materials.
Eighteen second-gen RT cores also provide a level of futureproofing for CAD. We anticipate ray tracing techniques will become integrated with traditional rasterisation to create more realistic CAD viewports. The idea is that users will be able to switch to ‘ray traced’ mode just as they do now with shaded, shaded with edges, and realistic view modes.
Visualisation demands significantly more GPU power than CAD. Here, the RTX A1000
offers an entry point, and noticeably faster ray tracing than its predecessor, the Nvidia T1000, which relied solely on generalpurpose CUDA cores.
For example, in Twinmotion 2024, we could navigate the Snowden sample project smoothly at FHD resolution. However, the RTX A1000 falls significantly behind when compared to the Nvidia RTX 2000 Ada Generation (16 GB), which delivers far better performance for just £157 more (£509 vs. £352). Rendering six standard 4K images took nearly four times as long, while five 4K path-traced images took twice as long. Similar slowdowns were observed in Lumion, D5 Render, and V-Ray.
This performance gap isn’t just due to the RTX 2000 Ada’s more powerful processor; memory also plays a crucial role. With only 8 GB of VRAM, the RTX A1000 struggles with larger visualisation models. When a scene exceeds 8 GB, the card must borrow from system memory via the PCIe bus, significantly reducing performance. In some cases, such as with our 12 GB Enscape dataset, this limitation even caused the software to crash. We explore this in more detail in our “Workstations for arch viz” article [www.tinyurl.com/d3d-arch-viz].
With 72 third-gen Tensor cores, the RTX A1000 brings AI capabilities to the entrylevel segment. In visualisation workflows, this could be beneficial in three key areas: Nvidia DLSS for improving 3D performance, AI-powered denoising for reducing noise in low-pass renders, and AI image generators like Stable Diffusion. We did not test DLSS directly, but we expect the benefits with this card may be limited due to relatively low Tensor performance and the fact that the Ampere architecture only supports older versions
of DLSS (2.0 and below).
In Stable Diffusion 1.5, the RTX A1000 was about twice as slow at generating images as the RTX 2000 Ada. However, in the more demanding Stable Diffusion XL, performance plummeted, as 8 GB is insufficient to run the software effectively. Nevertheless, it remains significantly faster than the Nvidia T1000, which lacks Tensor cores altogether. While we did not test the T1000 directly, Nvidia claims the RTX A1000 is up to three times faster. Beyond visualisation, the RTX A1000 supports a range of AI workflows, including inferencing for large language models (LLMs) and AI assistants—some of which are not particularly demanding computationally.
For example, reality modelling software like Leica Cyclone 3DR uses machine learning to ‘intelligently classify’ point cloud data. It requires an RTX GPU, but in our tests the RTX A1000 was not that much slower than the RTX 4500 Ada Generation, trailing the high-end GPU by just 29%.
The Nvidia RTX A1000 marks a significant leap forward for Nvidia’s entry-level workstation GPUs. With dedicated RT cores and Tensor cores, it enables ray tracing and AI workflows that simply weren’t viable on the Nvidia T1000. However, potential buyers must consider whether the RTX A1000 provides enough value compared to the RTX 2000 Ada Generation. For only £157 more, the RTX 2000 Ada delivers significantly better RT and Tensor performance and, crucially, twice the memory, which can be a limiting factor in some workflows.
With software evolving so quickly, especially in the area of AI, spending a bit more now could be the smarter way to future-proof your workstation.
carpet
Afew days on from the Oscars ceremony, I’ve been keeping an eye on the press whirlwind that inevitably follows. This year, the Academy Awards for Best Actor and Best Actress were awarded to actors in demanding roles that deviate significantly from their own life experiences.
Look away now if you’ve not seen the results. Best Actress was won by Mikey Madison, who plays a sex worker in the movie Anora. Adrien Brody, meanwhile, took home Best Actor for his role in The Brutalist, picking up the gong a second time for playing a passionate creative that survives the Holocaust (with the first time being The Pianist back in 2003).
Both in the build-up to the Academy Awards and on the red carpet, both talents were pressed about the process of ‘finding’ their roles, identifying with them and getting into character.
Madison took up new skills, learning Russian and pole dancing in order to portray her character. Brody meanwhile lent on his artistic talents and his family’s history and experiences in migrating from Europe to influence his portrayal.
This shape-shifting ability to fully embody another human, their life and their experiences, and channel that through mimicry, emotions and speech is part of what defines acting. Much is made of this, and aside from undercover spies and some dubious salesmen and politicians, few other people get paid for these skills.
However, the more time I spend around product designers, the more of these skills I see in their work. The traditional role of ‘The Designer’ has always been as an observer and an interpreter.
Like a nature documentary maker, they sit watching gorillas in their natural habitat, analysing their behaviours. There are
also those who find and create a product for themselves, for a family member or colleagues, based on their observations of those around them.
The more designers I meet, the more I find them embracing a ‘method acting’ approach. In other words, they’re attempting to live as if they themselves were the end user. I see it regularly, the designer who is ‘always on’ – either obsessed with a project already underway or on the hunt for a new problem to tackle.
As I learnt while putting together this issue of DEVELOP3D, it’s one thing to speak to a delivery driver and maybe shadow one for a couple of hours in a sterile setting. It’s another thing entirely to send your team out to graft like one, lugging boxes in and out of a van, eating lunch behind the wheel, and engaging in not-so-diplomatic negotiations with traffic wardens.
This hands-on approach applies to multiple projects I’ve seen over the years, predominantly at design studios that serve a multitude of different markets. Much like actors, these designers are guns for hire, chasing the next paycheck.
Versatility as a leading man or lady is all very well, but for me, it doesn’t come close to most agency designers, who might on one day be developing a life-changing surgical tool and on the very next day sculpting beautiful Class-A surfaces for a piece of high-end audio equipment. The following week, they might be designing a kitchen gadget that they, the client and (deep down) the consumer knows will languish in the bottom of a kitchen drawer, unused, for a decade or so. (I look forward to receiving your Spiralizerrelated hate mail.)
Much like the movies, AI is about to change our industry, and much of this could be linked to how designers get further into their research. There are already apps to filter through video
draws to a close, Stephen Holmes reflects on the ‘method acting’ approach increasingly favoured by some product designers and applauds their willingness to commit to the role of end user
The more designers I meet, the more I find them embracing a ‘method acting’ approach, attempting to live as if they themselves were the end user
footage and capture the ergonomics of drivers getting into and out of vehicles. Now imagine this at scale, with years of cabin data logged, every button pressed, every gear change made and every Wagon Wheel eaten on the road.
Suddenly, all this real-world activity becomes the stuff of endless metrics influencing the design of products, similar to how the reaction of test audiences to plotlines and characters in movies are keenly watched by studio executives.
In short, a survey is no longer enough. At this new level of data capture, delving into the minute details of human experiences should in theory create hit after hit when it comes to new products – yet it still makes many creatives uncomfortable. We feel it reduces some of the art, as though imperfection is something that makes a product more human.
Personally, I think most mainstream products will become homogenised to a point. Just look at all the similar SUVs on our roads, all with designs based on broadly the same regulations and constraints around safety, drag co-efficients and manufacturing capacity.
Yet some still vehicles still manage to stand out, guided by brilliant visionaries and supportive producers. Hollywood is far from dead, and neither is the human skill in design. But as ever, only the best efforts will take home an award.
GET IN TOUCH: Thanks to several recent long-haul trips, Stephen has rediscovered the joy of watching five movies back to back. Sadly, Kong was not among the options available for his in-flight entertainment. On Twitter, he’s @swearstoomuch