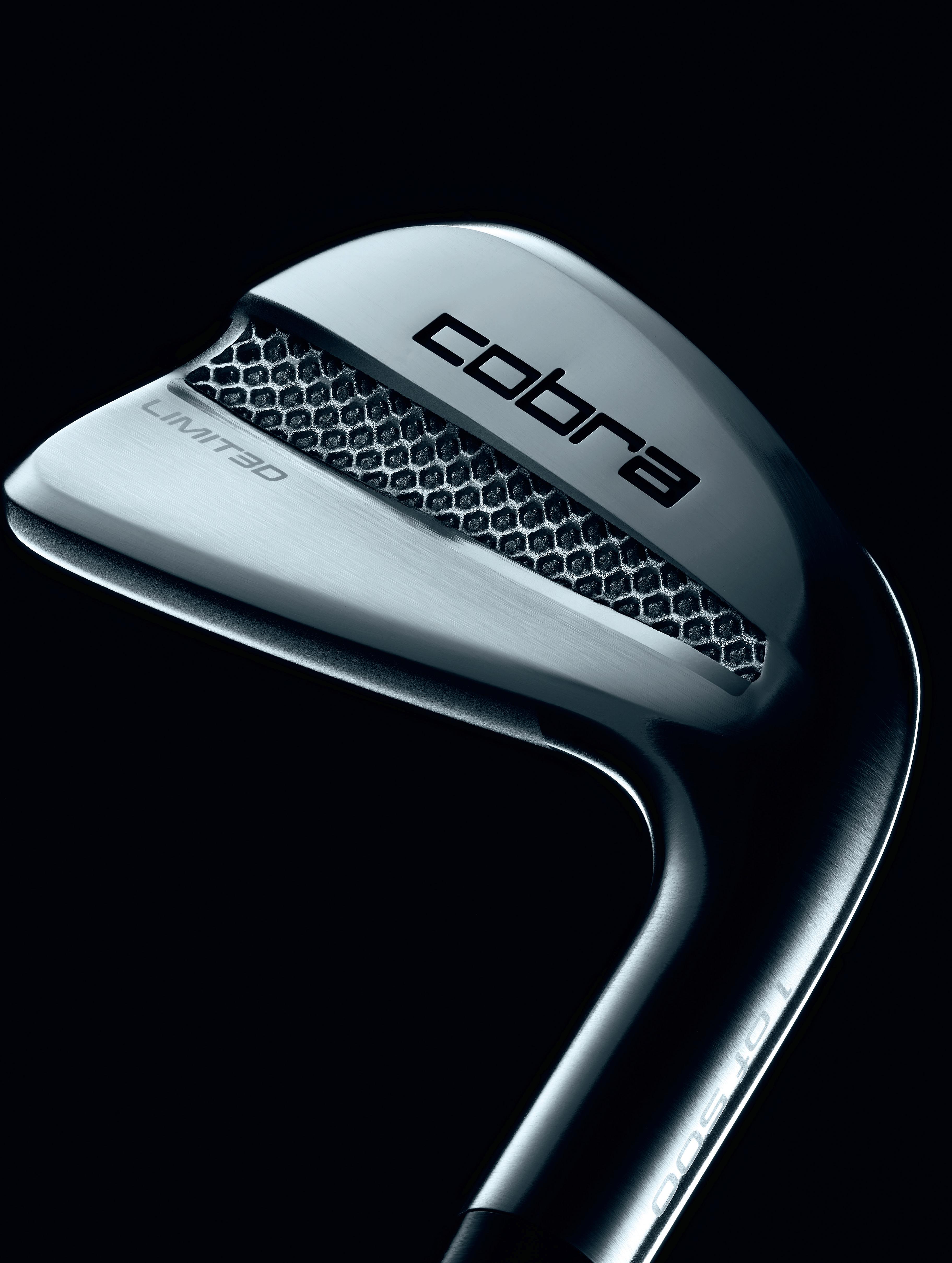
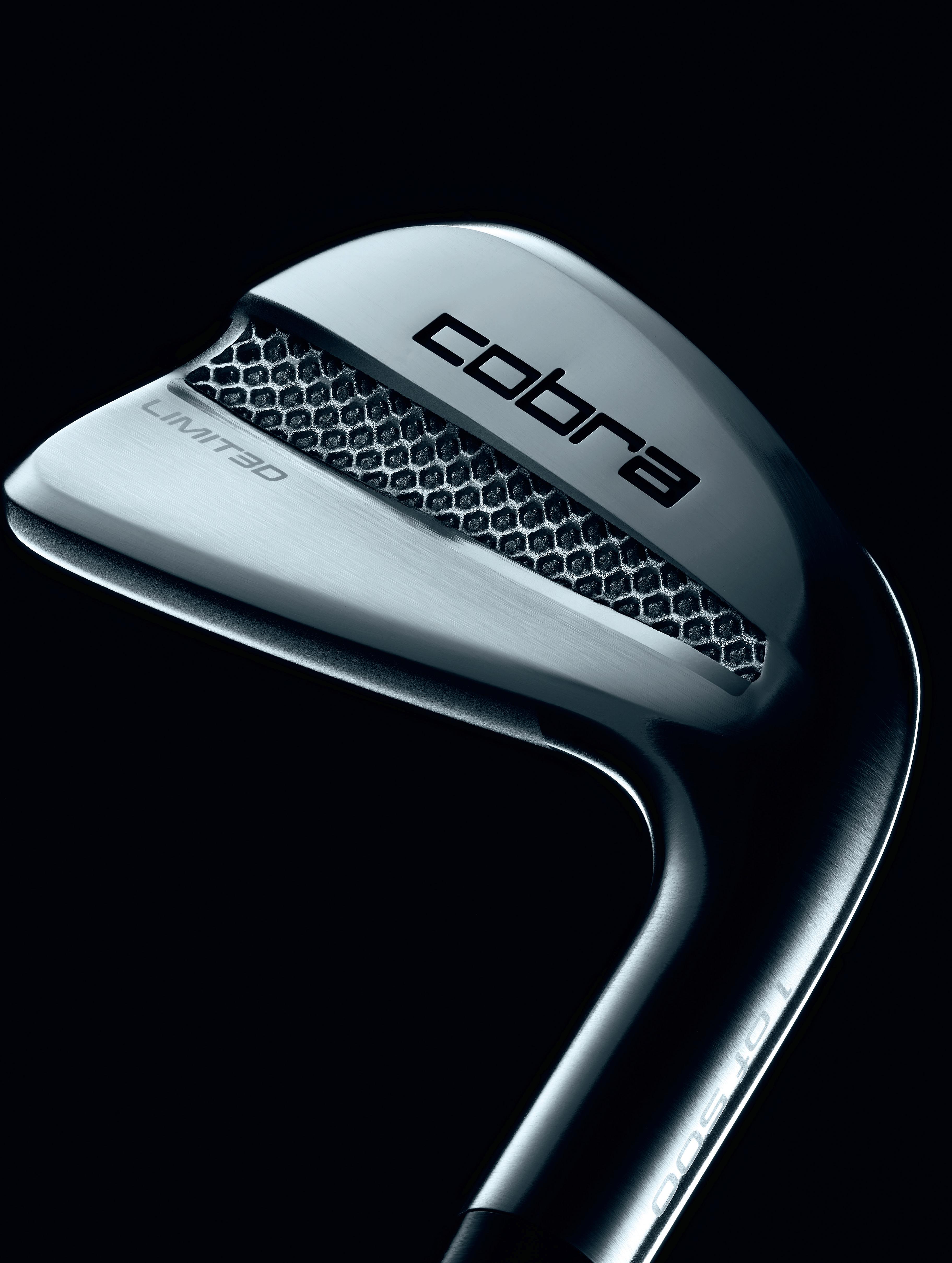
IN THE BAG
Cobra Golf puts the power on the inside with world’s first 3D printed irons

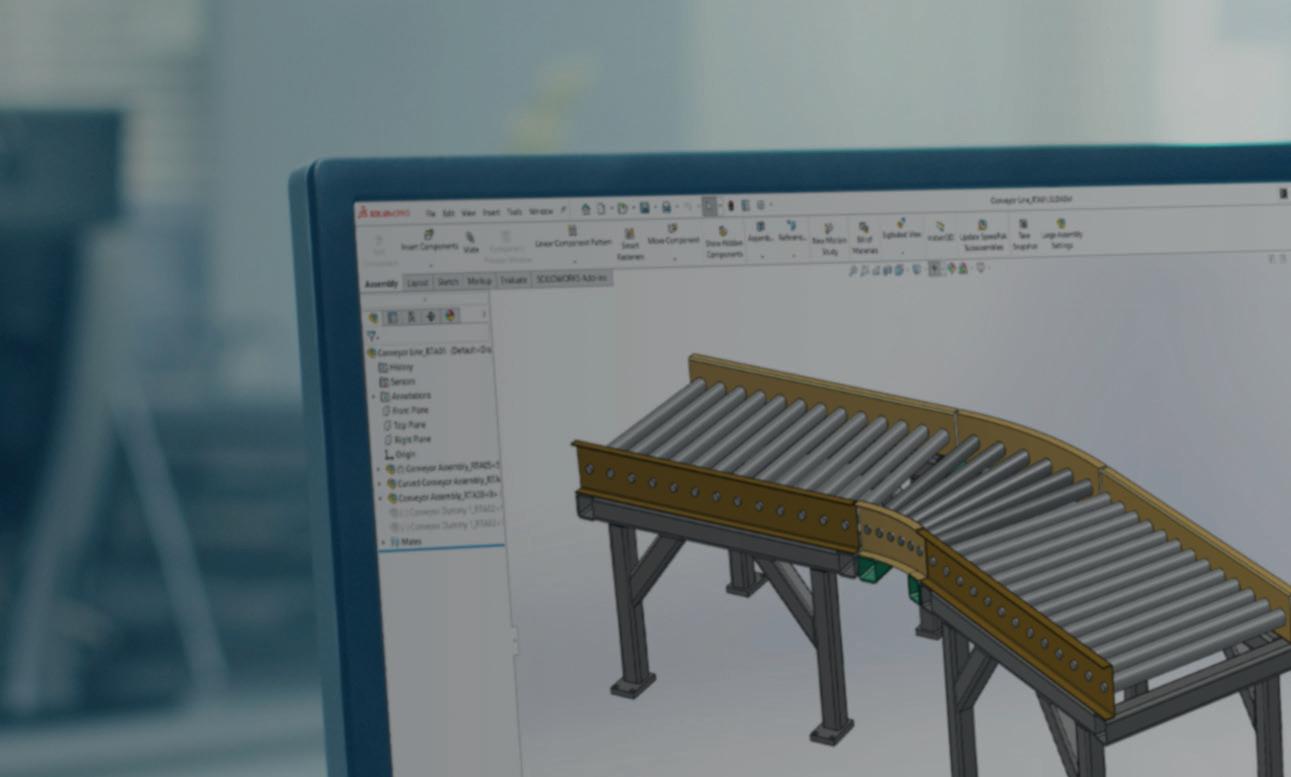
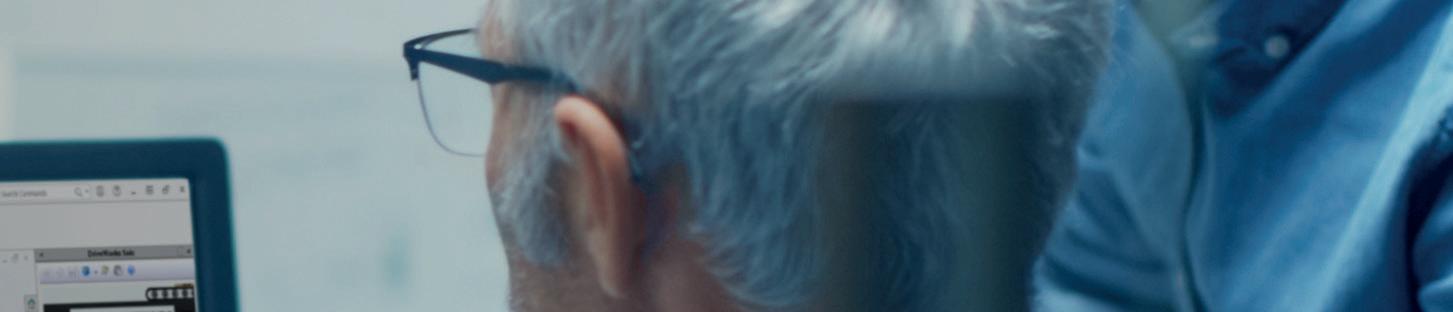
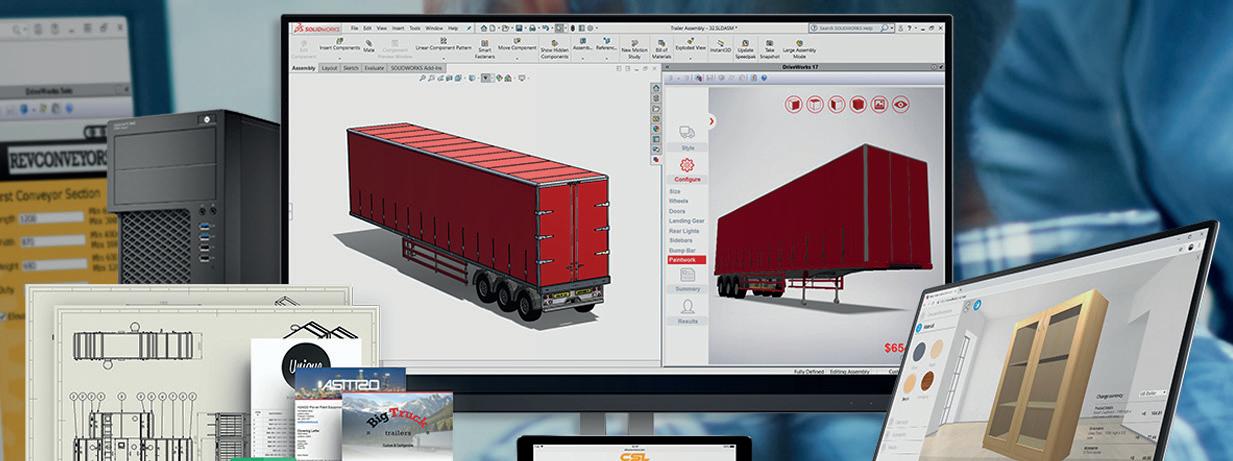

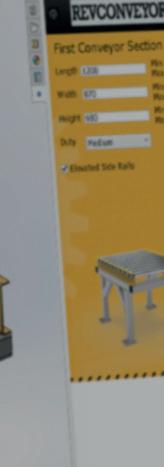
Automate
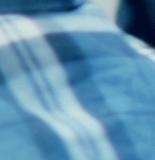

SOLIDWORKS manufacturing processes & sell digitally using DriveWorks
DriveWorks is flexible and scalable. Start for free, upgrade anytime. DriveWorksXpress is included free inside SOLIDWORKS or start your free 30 day trial of DriveWorks Solo.
DriveWorks Pro
30DAY FREETRIAL
DriveWorksXpress
Entry level design automation software included free inside SOLIDWORKS®
Entry level SOLIDWORKS part and assembly automation
Create a drawing for each part and assembly
Find under the SOLIDWORKS tools menu
One time setup
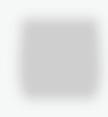
Modular SOLIDWORKS® automation & online product configurator software
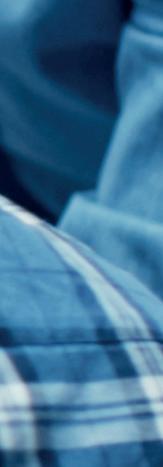

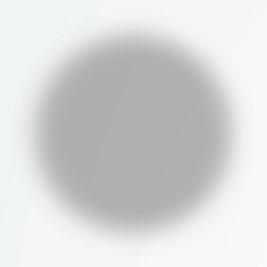
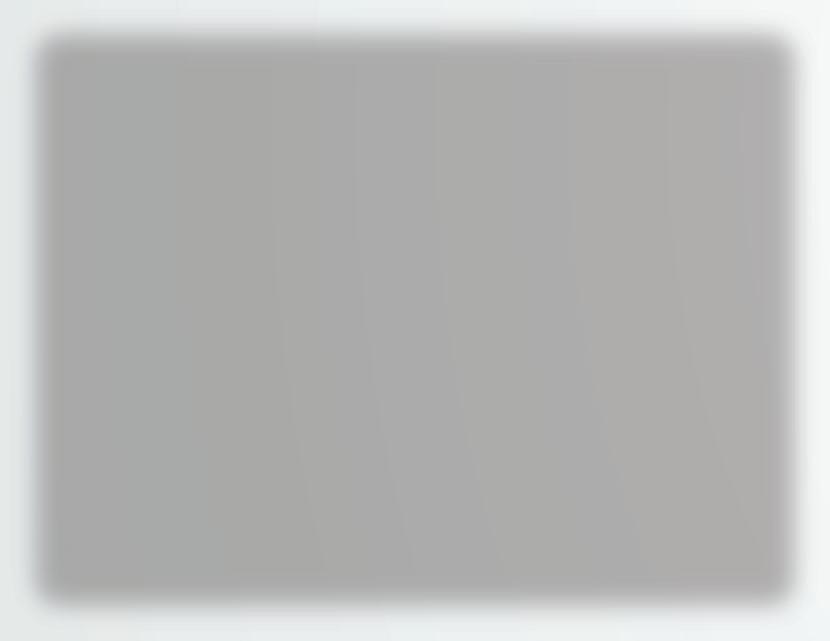
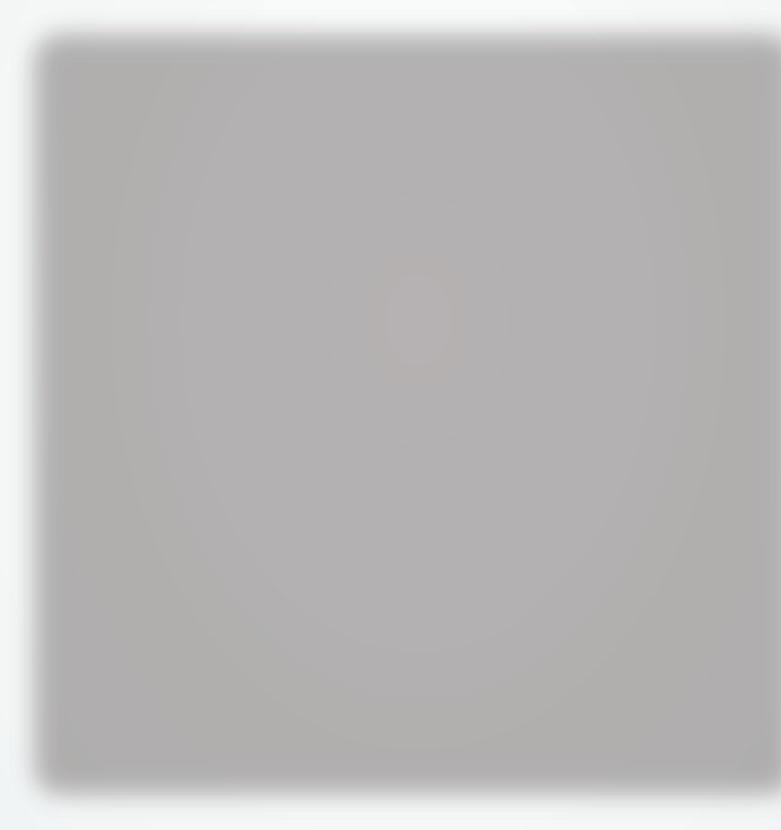
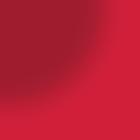
DriveWorks Solo

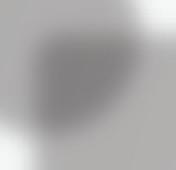
SOLIDWORKS® part, assembly and drawing automation add-in
Automate SOLIDWORKS parts, assemblies and drawings
Generate production ready drawings, BOMs & quote documents automatically Enter product specifications and preview designs inside SOLIDWORKS
Free online technical learning resources, sample projects and help file
Sold and supported by your local SOLIDWORKS reseller
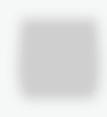
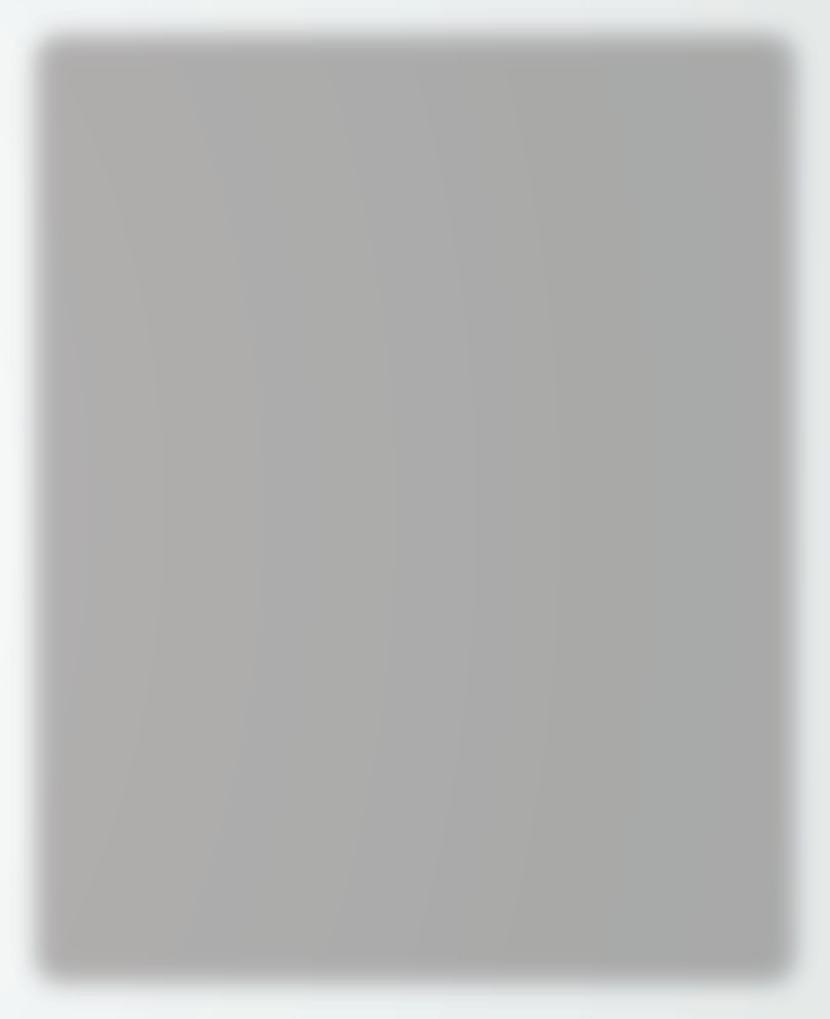
Complete SOLIDWORKS part, assembly and drawing automation
Automatically generate manufacturing and sales documents
Configure order specific designs in a browser on desktop, mobile or tablet
Show configurable design details with interactive 3D previews
Integrate with SOLIDWORKS PDM, CRM, ERP, CAM and other company systems
Scalable and flexible licensing options
Sold and supported by your local SOLIDWORKS reseller
Set up once and run again and again. No need for complex SOLIDWORKS macros, design tables or configurations.
Save time & innovate more
Automate repetitive SOLIDWORKS tasks and free up engineers to focus on product innovation and development.
Eliminate errors
DriveWorks rules based SOLIDWORKS automation eliminates errors and expensive, time-consuming design changes.

Connect sales & manufacturing
Integrate with other systems
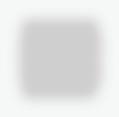
Validation ensures you only offer products that can be manufactured, eliminating errors and boosting quality.
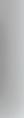
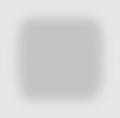
DriveWorks Pro can integrate with other company systems, helping you work more efficiently and effectively.
Intelligent guided selling
Ensure your sales teams / dealers configure the ideal solution every time with intelligent rules-based guided selling.
EDITORIAL
Editor
Stephen Holmes
stephen@x3dmedia.com
+44 (0)20 3384 5297
Managing Editor
Greg Corke
greg@x3dmedia.com
+44 (0)20 3355 7312
Consulting Editor
Jessica Twentyman jtwentyman@gmail.com
Consulting Editor
Martyn Day martyn@x3dmedia.com
+44 (0)7525 701 542
Staff Writer
Emilie Eisenberg emilie@x3dmedia.com
DESIGN/PRODUCTION
Design/Production
Greg Corke greg@x3dmedia.com
+44 (0)20 3355 7312
ADVERTISING
Group Media Director
Tony Baksh tony@x3dmedia.com
+44 (0)20 3355 7313
Deputy Advertising Manager
Steve King steve@x3dmedia.com
+44 (0)20 3355 7314
US Sales Director
Denise Greaves denise@x3dmedia.com
+1 857 400 7713
SUBSCRIPTIONS
Circulation Manager
Alan Cleveland alan@x3dmedia.com
+44 (0)20 3355 7311
ACCOUNTS
Accounts Manager
Charlotte Taibi charlotte@x3dmedia.com
Financial Controller
Samantha Todescato-Rutland sam@chalfen.com
ABOUT
DEVELOP3D is published by
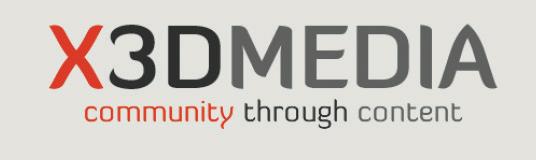
X3DMedia 19 Leyden Street
London E1 7LE, UK
T. +44 (0)20 3355 7310
F. +44 (0)20 3355 7319
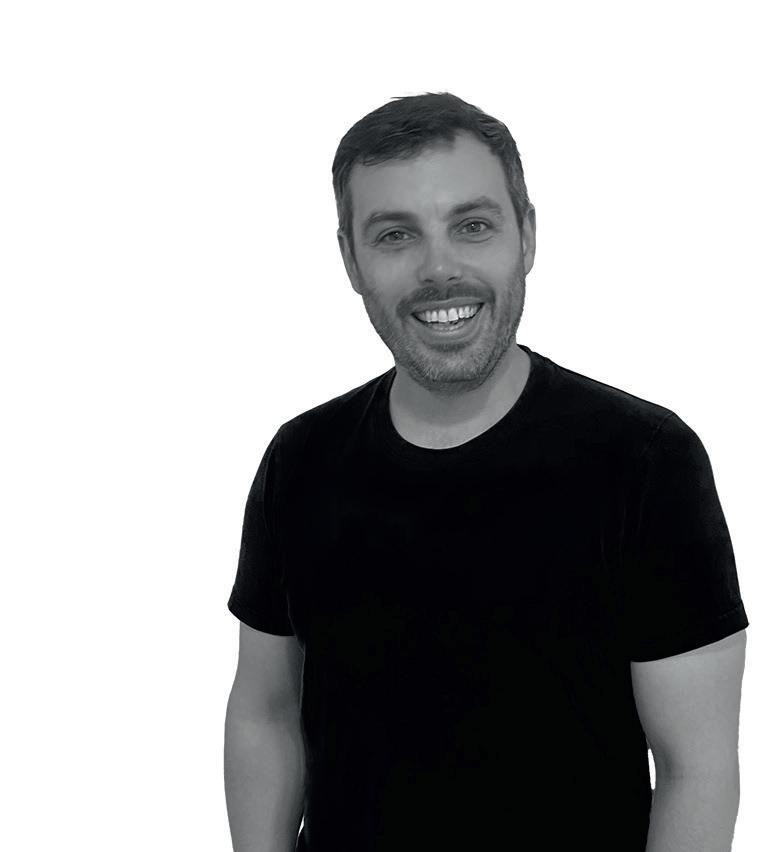
As autumn is ushered in, we turn our attention to the industry’s season of future manufacturing. The world of modern production methods is now accommodating more and more additive technology; 3D scanning is a staple tool on shop floors and new AI software is transforming machining. For designers, keeping abreast of how products can be manufactured is a constantly evolving task, so this issue we hope to keep you covered and provide a little inspiration.
As this issue’s cover story demonstrates, technology moves fast. Metals 3D printing may still be something of a rarity, but for Cobra Golf, it’s a proven way to get cutting-edge golf clubs into the hands of regular Joes and Joannas, as well as the professionals who win millions on the fairways. The company’s latest set of irons combine generative design and additive manufacturing in a sleek and highperformance design.
Elsewhere, we look in on the Red Bull Formula 1 team, to hear how its partnership with Hexagon is helping to advance 3D scanning technology across the board. We see how a new temporary road sign design is helping local councils to ditch sloppy and unsustainable sandbags for recycled polymers.
Large format additive manufacturing is a fast-maturing technology that sits somewhere between FDM 3D printing and robotic welding, but to better understand its nuances we spoke with two of the sector’s leading companies to learn the industries and workflows where it can make a difference. And we take a closer look at the latest Lotus concept car, the Theory 1.
We’ve also got in-depth reviews of the benchtop Formlabs Form 4 3D printer and the pocket-size Ratta Supernote Nomad tablet – both products that, in terms of sheer capability packed into compact footprints at reasonable cost, are something of a manufacturing miracle.
So read on – it’s the season to make something!
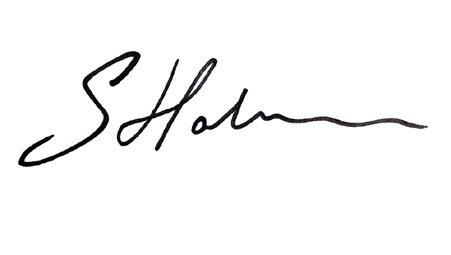

Stephen Holmes Editor, DEVELOP3D Magazine, @swearstoomuch
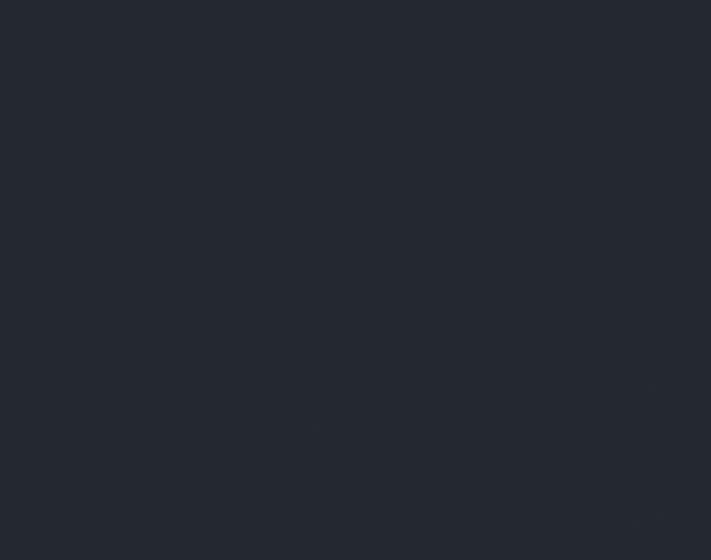

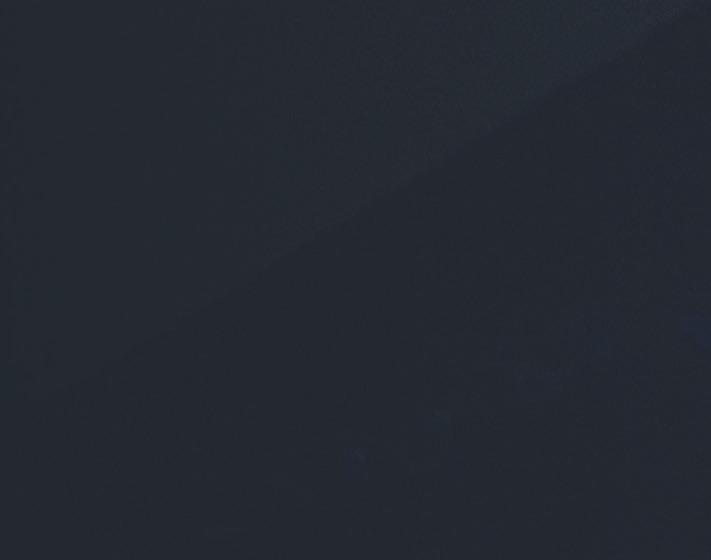
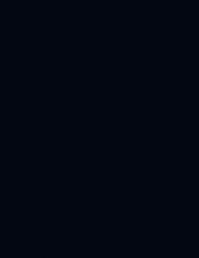
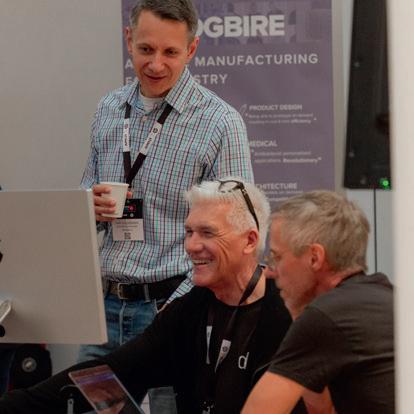
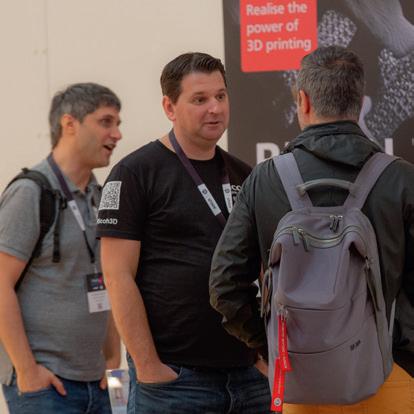
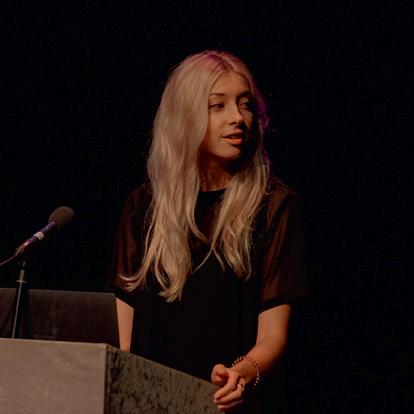
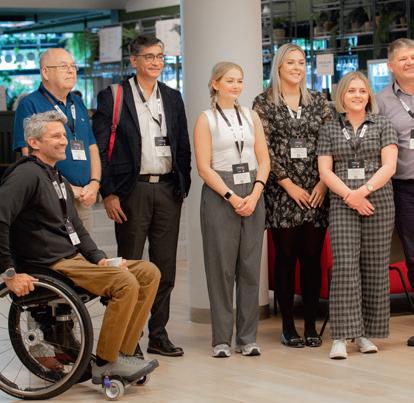

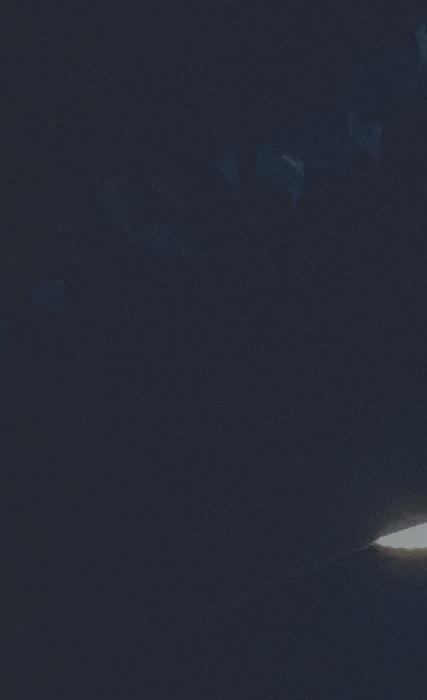
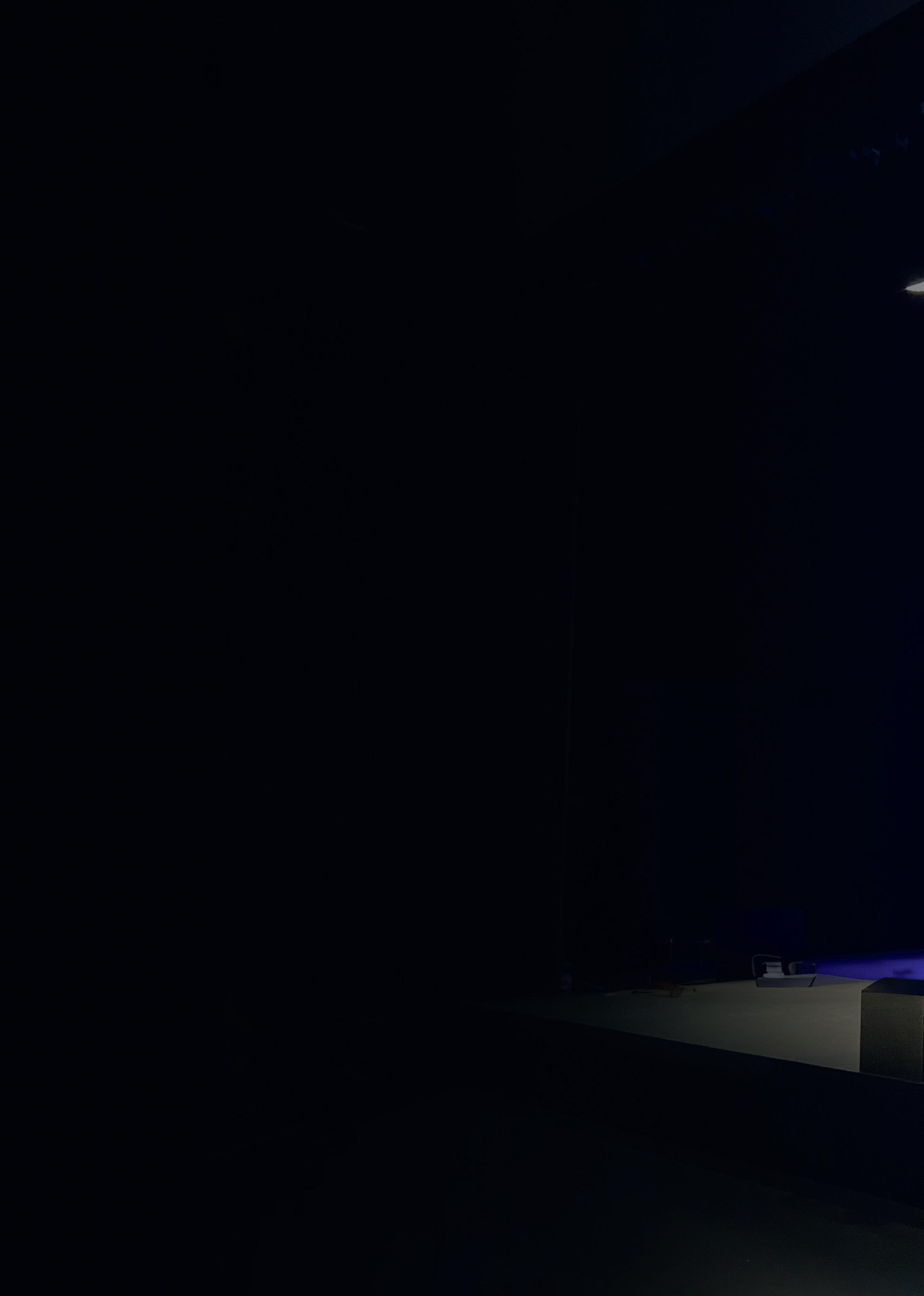
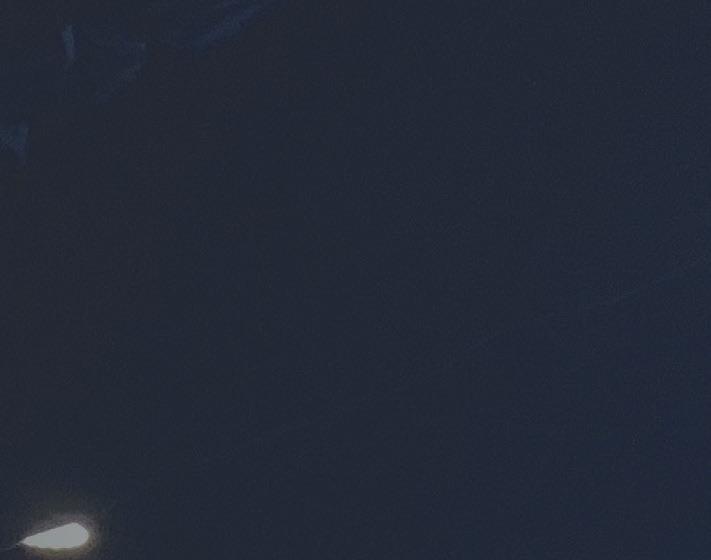
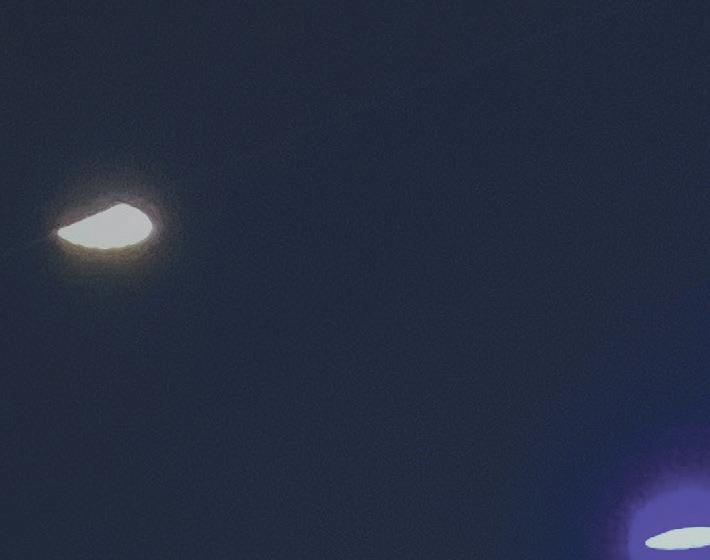
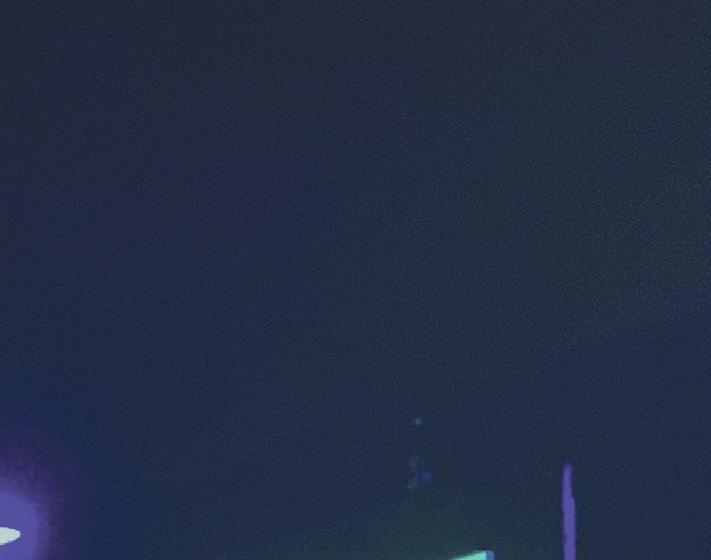
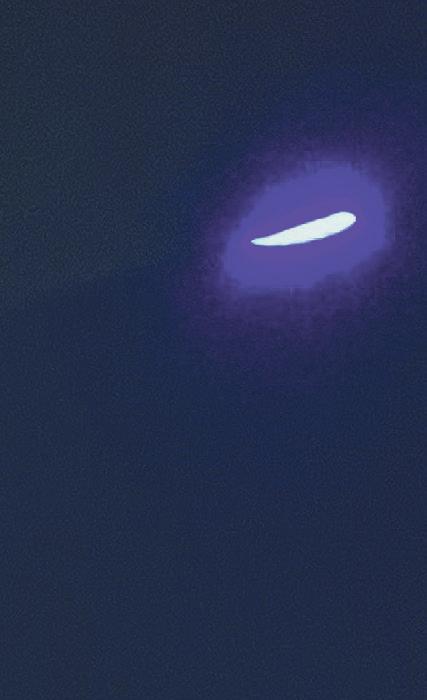
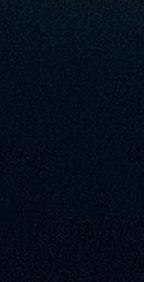
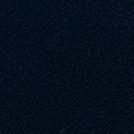
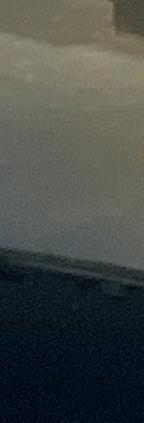
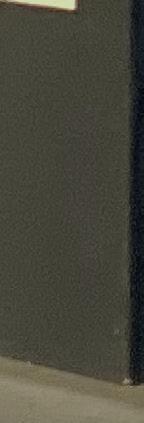
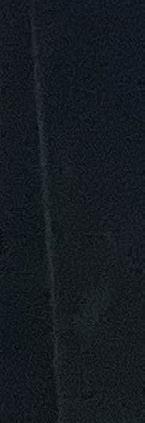
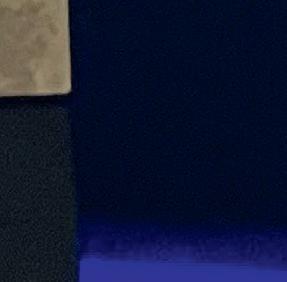
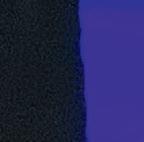
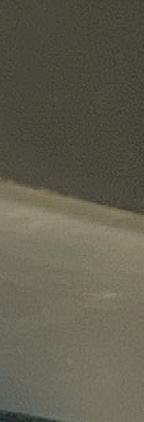
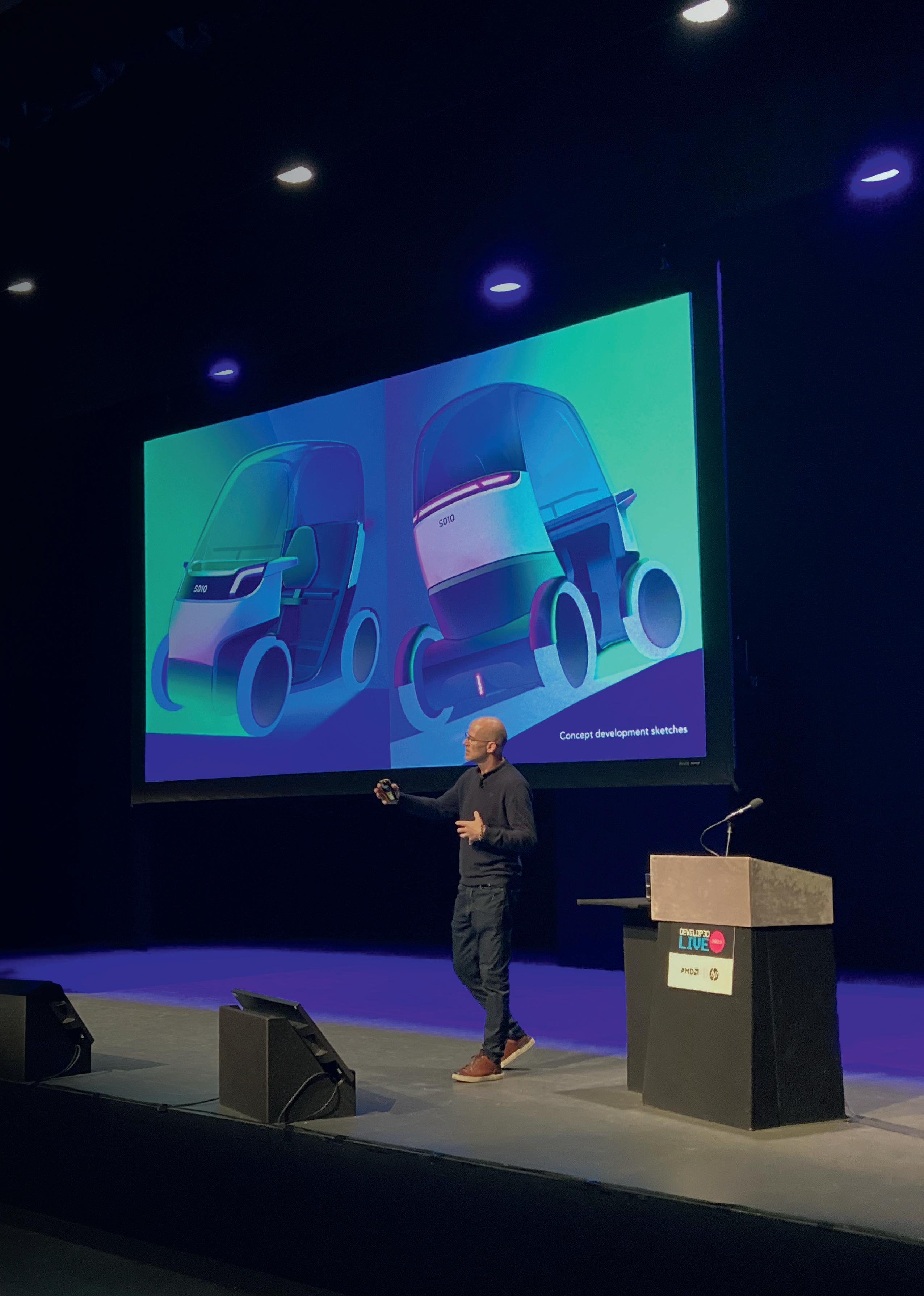
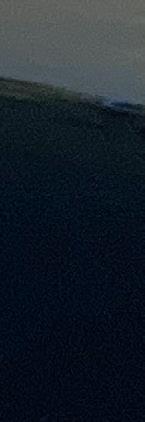
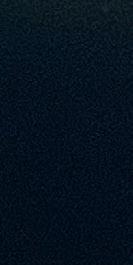
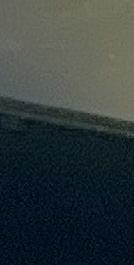
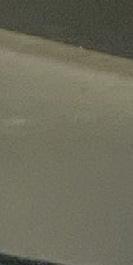
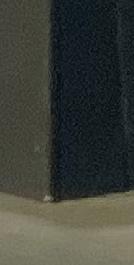
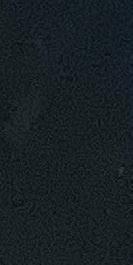
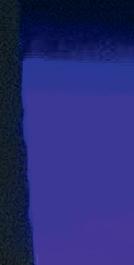
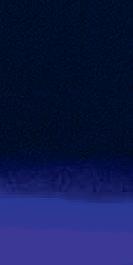
Full Colour 3D Print
It’s All Over
Your search for a 3D printer capable of producing complex & creative models in up to 10,00 0,00 0 colours is over . T he new Mimaki 3DUJ-22 07 delivers extraordina r y detail in full colour.

E xplore a wor ld of colour for just
£ 3 4,995
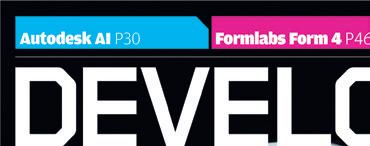
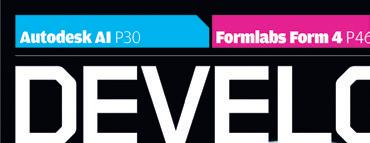

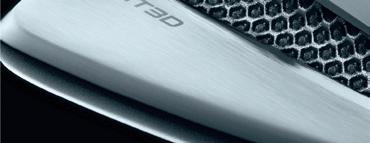
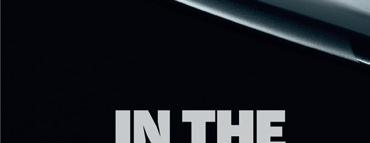

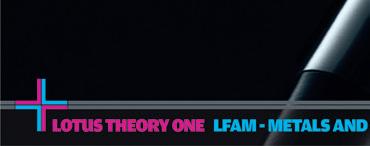
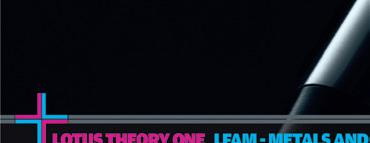
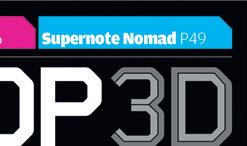

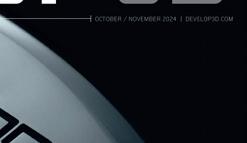

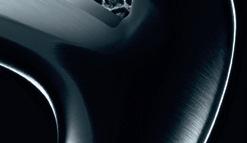
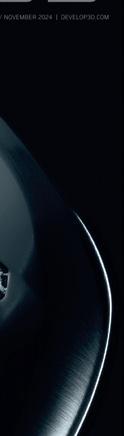
NEWS
Autodesk delivers AI features, Solidworks gears up for collaboration, PTC and AWS partner for Onshape, Nano
Dimension to acquire Markforged, and lots more
FEATURES
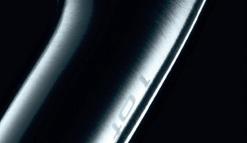
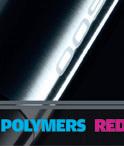
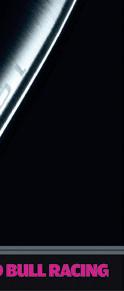
Comment: SJ on the maturity of additive technologies
Comment: Theo Saville on traditional manufacturing
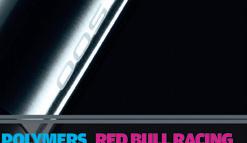
Visual Design Guide: Lotus Theory 1
COVER STORY Cobra Golf embraces 3D printing
Music to go: AlphaTheta’s portable DJ system
Next steps: Elastium’s hybrid 3D printed shoes
Autodesk charts its AI future
All that glitters: AM transforming jewellery at Progold
Large Format Additive Manufacturing 101
Smart & strong: Materials for Vuzix Shield smart glasses
Race to victory: Hexagon MI and Red Bull Racing
Keep it clean: Proclaim Healthcare boosts oral health
Sign of the times: Ross Atkin updates Britain’s road signs
REVIEWS
Formlabs Form 4 3D printer
Ratta Supernote Nomad
THE LAST WORD
20 September 2023
Organisations that engage with local communities not only help them thrive but also gain unexpected ideas and expertise. Stephen Holmes encourages collaboration: “Get the kettle on and get together.”
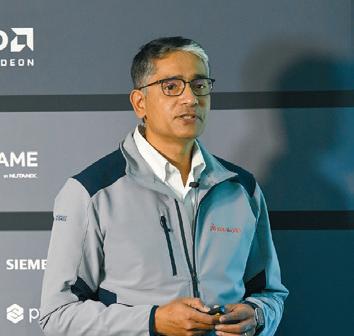
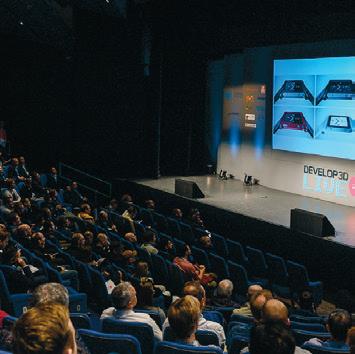
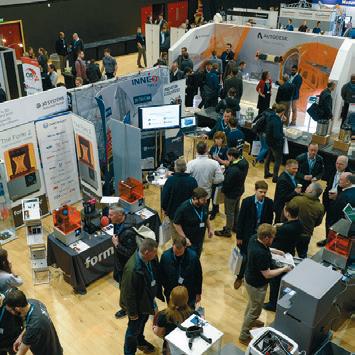
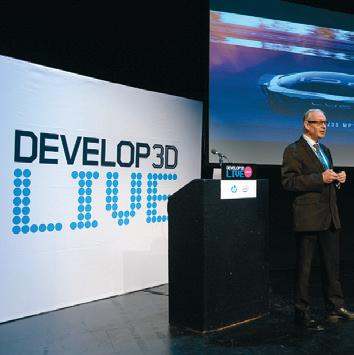
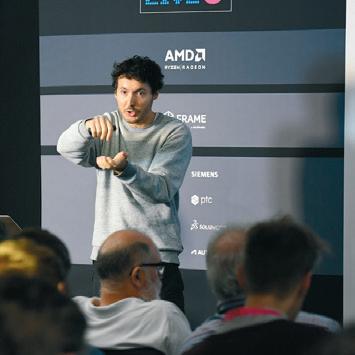
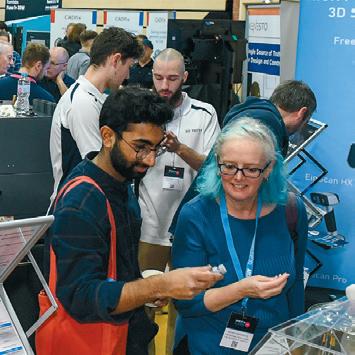

AUTODESK FUSION AND ALIAS GET AI BOOST TO SPARK INSPIRATION AND PRODUCTIVITY
» Executives outlined the myriad benefits they believe AI will bring to customers at the company's annual conference, held this year in San Diego, California
Autodesk has announced updates to Fusion and Alias that take advantage of Autodesk AI, with the stated goal of increasing inspiration and helping users cut through complexity.
Announcing the new AI capabilities at Autodesk’s user event in San Diego, California on 15 October 2024, executives from the software giant said that they will help save significant amounts of time, while augmenting the creative processes of the product designers and engineers responsible for manufacturing today’s increasingly complex products.
A new AutoConstrain function will analyse project sketches to detect intended spatial relationships between parts of a design and relationships between parts. It will then suggest dimensional constraints to maintain design intent through the entire project, adapting as the user works. Automating this process saves time that a designer might otherwise waster in manually defining drawings.
Drawing Automation in Fusion will examine 3D models and generate the 2D drawings and dimensions required to manufacture parts. Autodesk AI will now accelerate and streamline this process even more by laying out drawing sheets for each component in a model, applying
a style, and identifying and removing fasteners that don’t need to be included.
Autodesk’s platform sees the launch of a new Manufacturing Data Model API, so that partners and customers can build powerful cloud-to-cloud and desktop-tocloud connections into Fusion workflows.
With the new API, authorised thirdparty apps can feed their data into Fusion models, better integrating it into existing workflows, connecting it to cloud and desktop tools used across the industry.
For example, tools that can be implemented include OpenBOM, which automates bill of materials (BOM) workflows, and Cideon, for creating a twoway connection between Fusion and SAP. This provides greater clarity about the components specified in a design, giving everyone up-to-date BOMs and common ground for follow-up ERP processes, such as calculating costs and ordering parts.
Integration of the Paperless Parts platform into Fusion adds more manufacturing abilities, allowing estimators to quickly generate quotes from the CAD models they receive from customers, regardless of file format.
Additionally, Autodesk says that Fusion has now been equipped with the horsepower necessary for complex projects with thousands of parts in their assemblies.
At the same time, it has increased its speed, with company executives publicly stating that many workflows now take less than half the time they used to and some take less than 10% of the time they took previously.
Autodesk’s 2023 investment in Blank.AI also sees its first mainstream application, with the launch of Form Explorer in Alias. The tool will enable automotive stylists to explore new design forms and shapes in seconds using generative AI. Autodesk explained that it will have the ability to learn from a brand’s historical styling language, generating designs that maintain those styling cues.
Autodesk has also signed a definitive agreement to acquire Navasto, which will bring a plug-in to enable wind tunnel simulation in Alias, letting designers predict and optimise the drag co-efficient over an automotive exterior, reducing the likelihood of redesigns during engineering. Finally, an add-on for Inventor from Makersite is set to bring sustainability insights to the product design phase. Designers can use it to calculate the environmental and cost impact of designs, to view material replacement recommendations, and to track progress toward sustainability goals as design changes are made.
www.autodesk.com
Drawing automation is a big part of the AI picture, turning 3D models into 2D docs that can be used by manufacturing
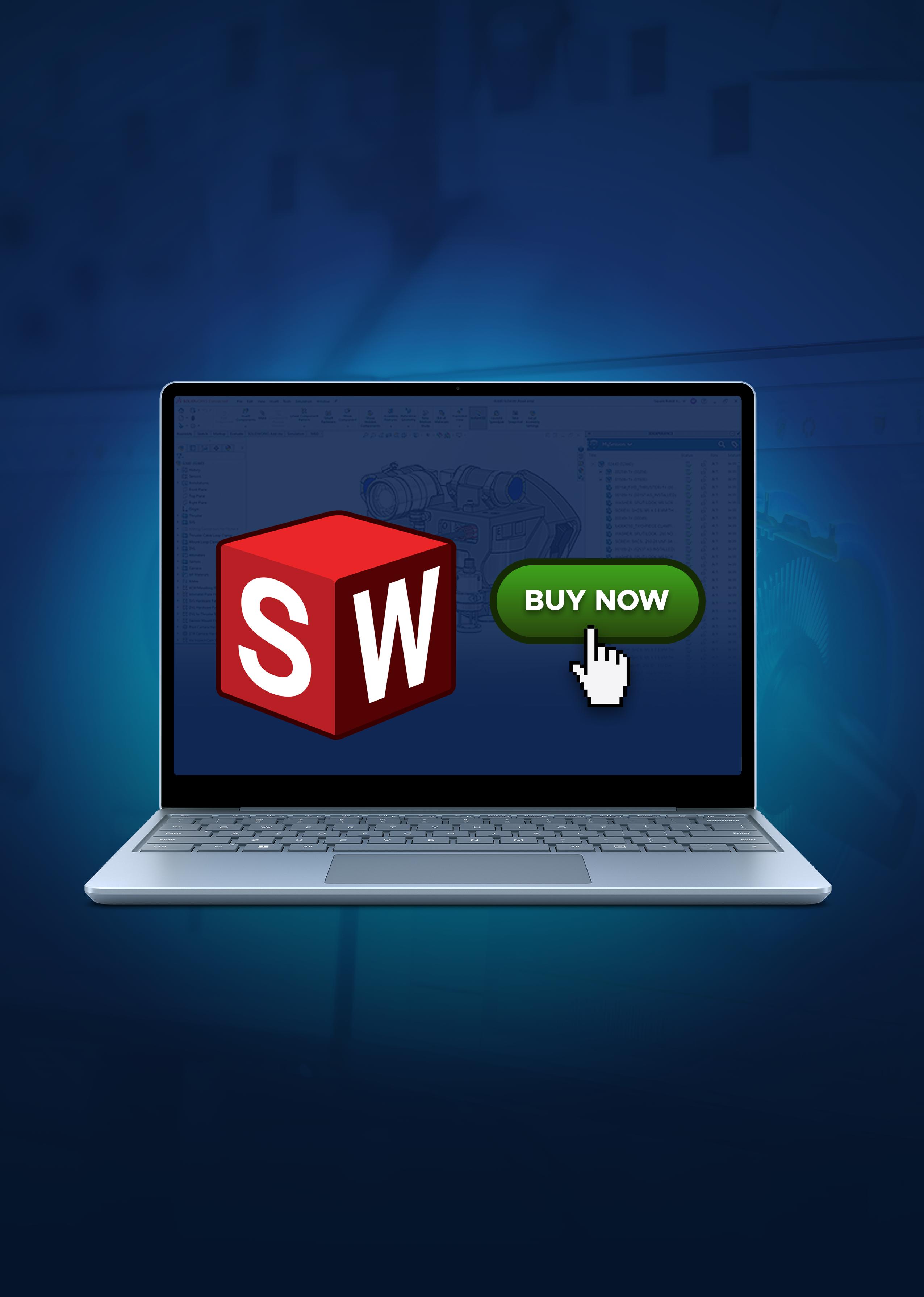
SOLIDWORKS 2025 GEARS UP FOR SEAMLESS COLLABORATION
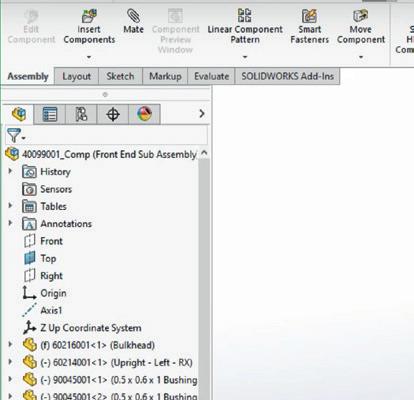
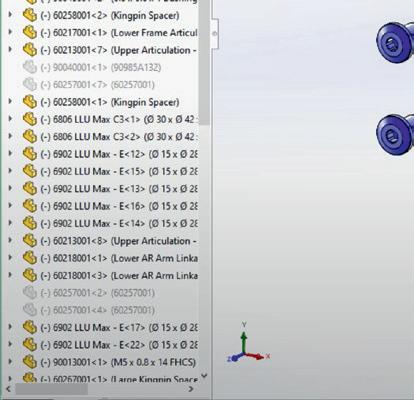
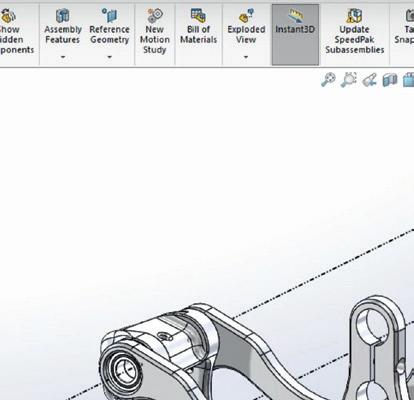
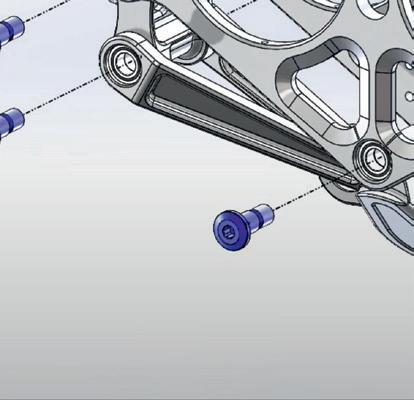
Dassault Systèmes has officially launched Solidworks 2025, introducing enhanced collaboration and data management capabilities, as well as more streamlined workflows, to help users quickly design and develop products.
One example of improved support for collaboration is multi-approval timestamps, which help enforce company rules on drawings. Anyone who is part of the approval workflow can easily log in from a web browser, review a drawing, and approve it, from anywhere and at any time. The approval timestamp appears automatically on the drawing, alleviating the need for manual work.
Part modelling sees some interesting updates to selection tools. The new
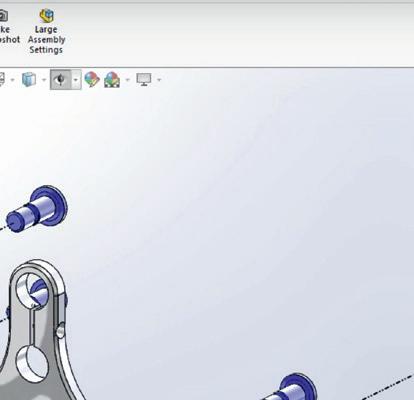
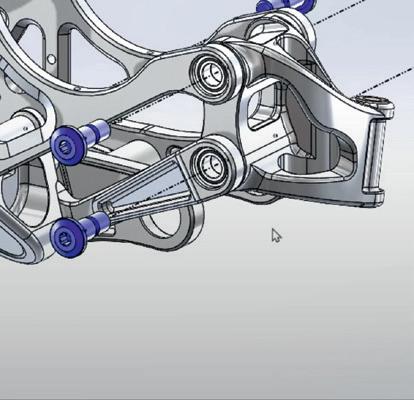
release looks to create the exact geometry needed for a design more efficiently.
Tools like the Chamfer command now help to select edges, there’s a new option to continuously blend fillet edges for smoother variable size fillets, and users can automatically create customisable bend notches on the flat pattern bend line of a sheet metal part.
“We believe in empowering companies to deliver not only the best possible product, but also an unforgettable customer experience,” said Solidworks CEO Manish Kumar.
“That’s why we enhanced platform collaboration, enabling users to easily share models with industry peers, inside and outside your organisation, by accessing communities directly from Solidworks.”
www.solidworks.com
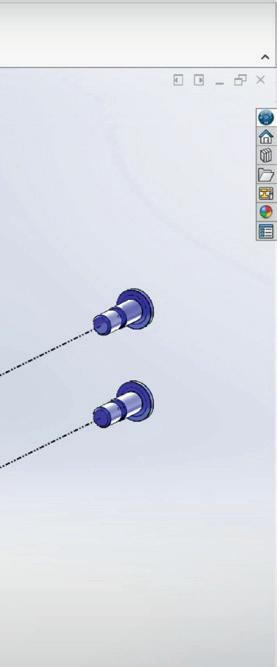
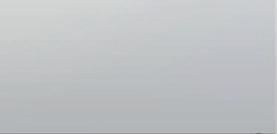
Enhancements in Solidworks 2025 include a focus on helping designers collaborate with both internal colleagues and external partners
Nano Dimension in deal to acquire Markforged
Nano Dimension is to acquire Markforged, adding to an expanding portfolio of 3D printing technologies and software that executives at the company hope will enable it to take on industry heavyweights Stratasys and 3D Systems.
Having signed a definitive agreement, Nano Dimension will acquire all outstanding shares of Markforged in an all-cash transaction for $5 per share, putting the final value around $115 Million.
Nano Dimension has its roots in micro 3D printing. Under the stewardship of CEO Yoav Stern, it has broadened its horizons.
Recent acquisitions include Admatec/ Formatec, a specialist in 3D-printed ceramic and metal end-user parts (in 2022) and multi-material AM optimisation software Additive Flow (2023).
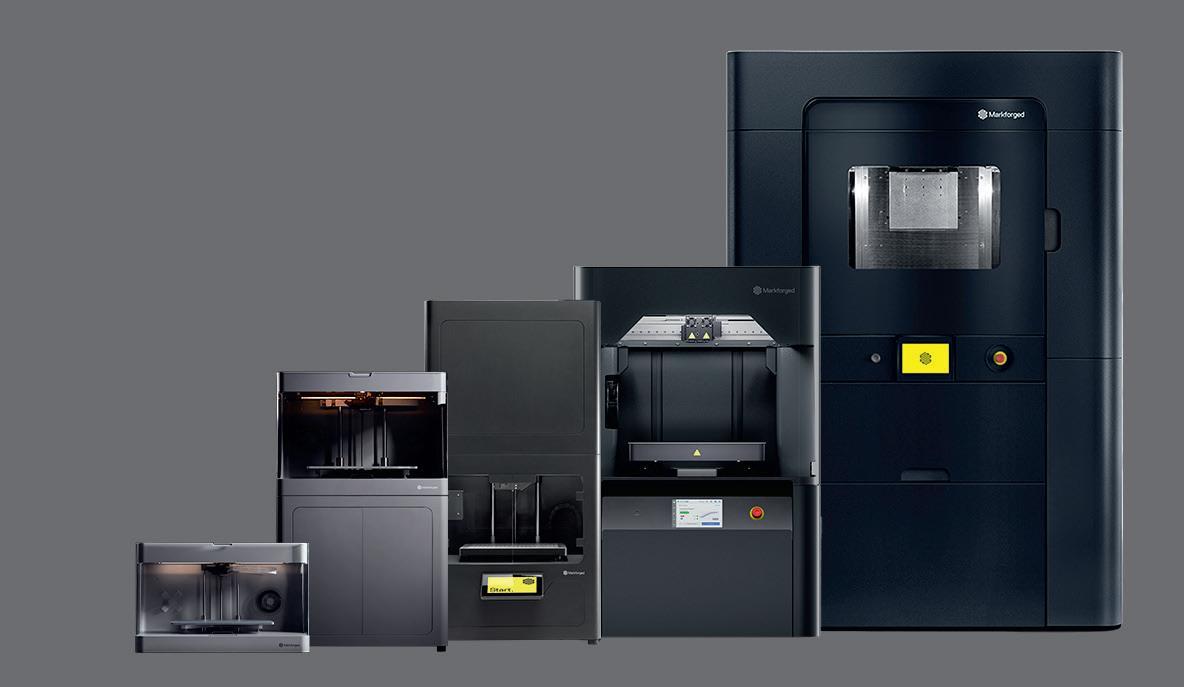
In 2023, Nano Dimension made a bold move to acquire Stratasys, triggering a fierce bidding war.
In July 2024, it acquired Desktop Metal, which combined with technologies from Markforged, gives it an enviable portfolio of additive manufacturing technologies. www.nano-di.com
Markforged 3D printers are set to join the Nano Dimension stable
HTC launches Vive Focus Vision H
TC has announced the Vive Focus Vision, its latest XR headset for the enterprise with 5K per eye resolution and numerous updates.
DisplayPort mode for PCVR enables lossless visuals by connecting the headset directly to a workstation graphics card. Offering up to 120-degree FOV and a 90Hz refresh rate, support for 120Hz refresh rate via DisplayPort mode is intended as an upgrade later in 2024.
The bundle, which costs $999 / £999 inc. VAT/€1,199 inc. VAT, includes head mounted display (HMD), two controllers, headset battery, charger and cables. www.htc.com
Two new scanners from Artec 3D
Artec 3D has released two new scanners: the Artec Spider II, a target-free handheld 3D scanner; and the Artec Point 3D scanner, its first target-based laser scanner.
The Spider II features multiple improvements on the previous iteration, including greater depth and field of view, capture speed and resolution.
The Artec Point is designed for metrology use and has an accuracy of 0.02mm. It features metal casing for suitability in industrial conditions and an ergonomic grip for easier measuring. www.artec3d.com
Maxon gives ZBrush an update
ZBrush is now available for use on the go, with Maxon reimagining its user interface, maintaining a stacked brush system and adding touch-based controls on the Apple iPad.
Available for iPadOS 17 or later, and on iPad models with A12 Bionic or later, the digital sculpting software offers many of the same tools and features found in the desktop version. These include its collection of proprietary digital sculpting brushes, created with real-world sculpting techniques in mind.
ZBrush and Maxon One subscribers can also share ZTool (ZTL) and ZProject (ZPR) files between iPads and desktops. www.maxon.net
SIEMENS DEBUTS CLOUD SOFTWARE SOLID EDGE X
As part of its Solid Edge 2025 software release, Siemens Digital Industries Software has annouced a new cloud version, Solid Edge X.
Part of the Xcelerator SaaS portfolio — alongside NX X, Simcenter X and Teamcenter X — it will enable new AI tools, simplified IT admin and greater options for collaboration in Solid Edge.
Siemens executives say that the AIpowered functionality will be available in 2025 and will offer real-time assistance to users and help minimise workflow disruptions.
With cloud-enabled built-in data management, based on Siemens Teamcenter software and infrastructure, users can collaborate across engineering and manufacturing disciplines wherever and whenever it is needed.
“The release of Solid Edge X delivers on Siemens’ strategic goal to bring our industry-leading software to customers as a service. This release delivers toolsets that are open, accessible and as scalable as our customers demand,” said John Miller, senior vice president mainstream engineering, Siemens Digital Industries Software.
“Solid Edge delivers transformative technologies that bring together the innate collaborative capabilities of the cloud combined with cutting-edge AI-based tools, allowing our customers to innovate at the accelerated pace that today’s manufacturing industry mandates.”
More certain is what’s new in the latest on premises version of Solid Edge 2025, which immediately offers a range of

enhancements to increase modelling speed, improved etch and bend features for sheet metal design, and simplified Model Based Definition (MBD) creation.
A new hybrid annotation capability in Solid Edge 2025 allows engineers to insert dimensions and feature control frames into designs with an efficient, all-in-one workflow that supports Model Based Definition and provides the tools to quickly and accurately detail 3D models. New Feature control frames and updated Surface Texture symbols help users adhere to ever-changing standards, while automatic dimensioning will maintain consistency and reduce errors.
Users are now able to tailor their Solid Edge experience with a personalised design environment, including redesigned and enhanced toolbars. solidedge.siemens.com
PTC and AWS partner to accelerate Onshape
PTC and Amazon Web Services (AWS) have announced that they have entered into an agreement to accelerate the growth of PTC’s Onshape CAD and product data management (PDM) solution.
The partnership will focus on advancing cloud-native Onshape product enhancements, customer adoption programmes and supporting artificial intelligence (AI) initiatives.
According to executives at PTC, this will assist product designers and engineers in creating new and better products, faster and more efficiently. This includes those users enrolled in the Onshape Discovery Program, which allows them to try Onshape Professional at no cost for up to six months.
The two companies will also work
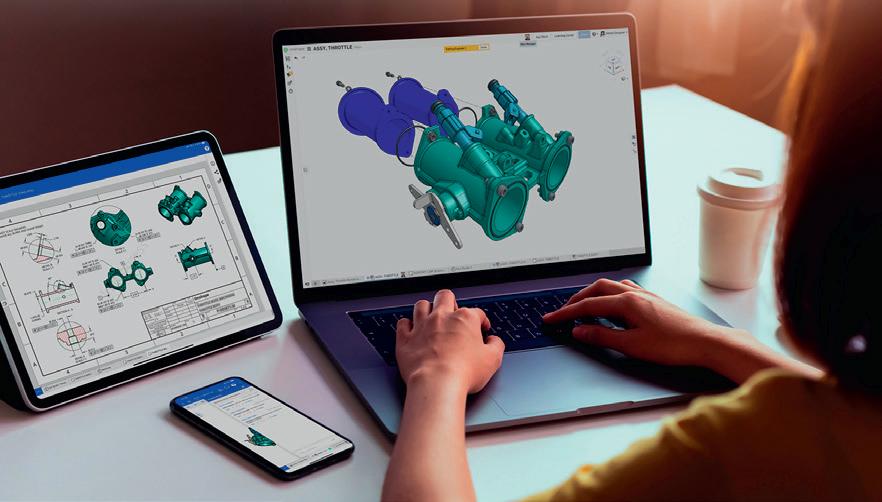
together on Onshape AI Advisor, which looks to boost product design by cataloguing the Onshape resource library, allowing users to type in a question and receive the correct result from the library. Other features will include CAD and PDM conversion tools. www.ptc.com
ROUND UP
Arburg has announced the launch of its latest Freeformer pellet-fed 3D printer, the Freeformer 550-3X, which is equipped with two discharge units, a 230 x 230 x 203 mm build chamber, and ease-of-use that promises to make 3D printing simple for workers of all skills levels www.arburg.com
Infinitive, a new configuration platform, is looking to revolutionise how companies design, sell and produce modular or build-to-order products, by enabling their customers to build personalised and unique configurations of those products directly in their browsers www.infinitive.io
Xact Metal and PanOptimization are partnering with the goal of expanding access to affordable metal 3D printing to small and medium-sized companies. By employing PanOptimization’s PanX software, Xact Metal is able to lower the cost of metal powder-bed fusion systems www.xactmetal.com
Having received investment from the Nvidia NVentures VC fund, executives at nTop have rushed to support technology solutions from the new investors, integrating ray tracing and Omniverse technologies into nTop's own computational design software www.ntop.com
PTC and AWS will team up on helping cloudnative Onshape to broaden its horizons
Cooksongold has announced a new industrial division, Cookson Industrial, which will be based at HM Precious Metals’ facilities in Birmingham, UK and provide services to precious metal additive manufacturers, including consultancy, R&D and new product development www.cooksongold.com
New cloud SaaS to offer AI productivity enhancements, simplified IT admin and better collaboration

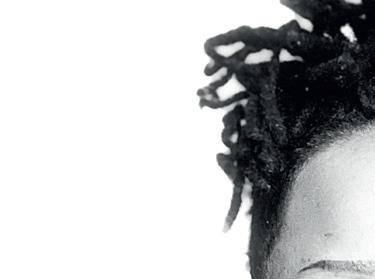
As the development of metals 3D printing approaches the end of its second decade, its maturity is still in question – but like many twentysomethings, writes our
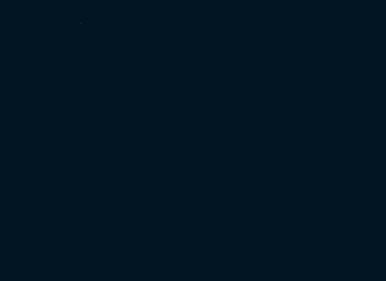


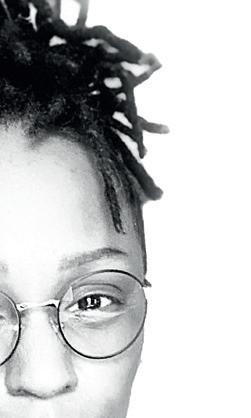

columnist SJ, it still needs a little more time to find its true purpose
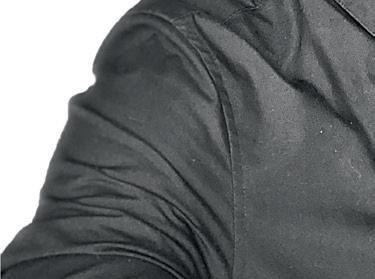

It’s just not the compliment I believed it to be back when I was a child: “You’re really mature for your age!”
It was a remark I heard frequently as I navigated raising my younger brother while my mother worked multiple jobs to keep a roof over our heads. I continued to hear it when I started to work odd jobs to afford school lunches, and later, when I worked three jobs to get through university.
Now that I’m in my thirties and better at pretending to be an ‘adult’, I’m more likely to hear that remark targeted at the additive manufacturing technology I love so much.
Additive evangelists will be quick to tell you about how mature the technology is, given its timeline, but providing a bit of context never hurts. Compared to more traditional methods of manufacturing –subtractive, brazing, forging, injection moulding and so on – additive is still young.
The 3D printing of polymer materials has only been around since the mid-1980s. The 3D printing of metals only started around 2004/2005. For comparison, CNC machining has been around since the 1940s. Brazing has been in use for some 5,000 years!
ROARING TWENTIES
When it comes to 3D printing in metals, additive is still very much in its roaring twenties. Your twenties are supposed to be a magical time, characterised by plenty of exploration and soul searching, a time when you’re more accepting of making mistakes as you learn how to navigate this thing called adulthood.
But that brings me to a hard question: Is additive ready to grow into a fully mature technology?
Let’s break it down. What does it mean for a technology to be ‘fully mature’? In my world, we define maturity in levels. A technology readiness level (or TRL) is a measure of how close a technology is to being fully developed and used in a realworld application.
Is AM being used for real world applications? Sure! See, for example, SpaceX rockets, Airbus landing gear, the GE fuel nozzle, and Siemens Energy industrial gas turbines. Need I go on? The technology has definitely proven itself in real-world applications, reducing development time, increasing design flexibility, improving part performance and/or efficiency, and supporting better cooling and heat transfer.
All of these are impressive accomplishments for a technology still ripping through its twenties. But as this era comes to a close, more and more companies are struggling to be enthusiastic about a ‘mature-for-its-age’ technology. What they’re seeking instead is a technology with a bit more stability and purpose.
THIRTY AND THRIVING?
The next level that AM must achieve is manufacturing readiness level, or MRL. This describes how close to ready a manufacturing process is to make products efficiently, reliably, and most importantly, at scale.
As additive enters what some would call the ‘dirty thirties’, it still has so many challenges to address before it reaches that final MRL level and full-rate production.
For one, the AM process still contains a fair amount of variability and inconsistency, which make it less predictable.
Predictability is a sure-fire sign of a mature adult. Predictability is safe, and it keeps costs low and projects on schedule.
But since we’re talking schedules, AM is typically slower compared to traditional processes when it comes to mass production of parts. The technology is more suited to lower volume or custom/bespoke pieces. So considering it mature on a scale where maturity is so closely tied to mass production doesn’t seem fair.
The AM industry is so young and often leans on the knowledge of more established manufacturing processes to help make informed decisions about its
The next level of maturity that additive technologies must achieve is manufacturing readiness level, in order to build products reliably, efficiently and at scale
future growth. Metal additive, for example, leans a lot on the field of welding to help create acceptable standards and certified processes. As helpful and insightful as that has been, metal 3D printing is not welding. The thermal history of parts – although similar in methods of fabrication – is drastically different. These discrepancies and tiny nuances, combined with how rapidly the technology accelerates and changes every day, makes it incredibly difficult to establish universal standards and certification processes for AM parts.
Who wants a quality control and regulatory compliance nightmare in their thirties? Nobody does. So, we’ve got to stop comparing AM to other processes and let it stand on its own as a new and unique, fully formed adult.
So, to summarise, is AM technologically mature? Yes. Is it mature enough for fullrate production manufacturing? Well, it’s getting there.
As someone who has poured literal blood, sweat and tears into this industry, into getting parts and machines qualified, and has helped to serve on boards and committees to advance the maturation of the technology, I have a lot of hope for the future.
ABOUT THE AUTHOR: SJ is a metal additive engineer aka THEE Hottie of Metal Printing. SJ’s work involves providing additive manufacturing solutions and 3D printing of metal parts to help create a decarbonised world.
Unleash Your Design Potential with Creo
Power Your Innovations with Creo
From concept to creation Creo is the CAD software trusted by industry leaders
Whether designing groundbreaking electric motorbikes or the next big thing in your field, Creo provides the precision and flexibility you need to bring your ideas to life.
What will you create?
Visit our Creo page today and elevate your design process

Honorary sponsor
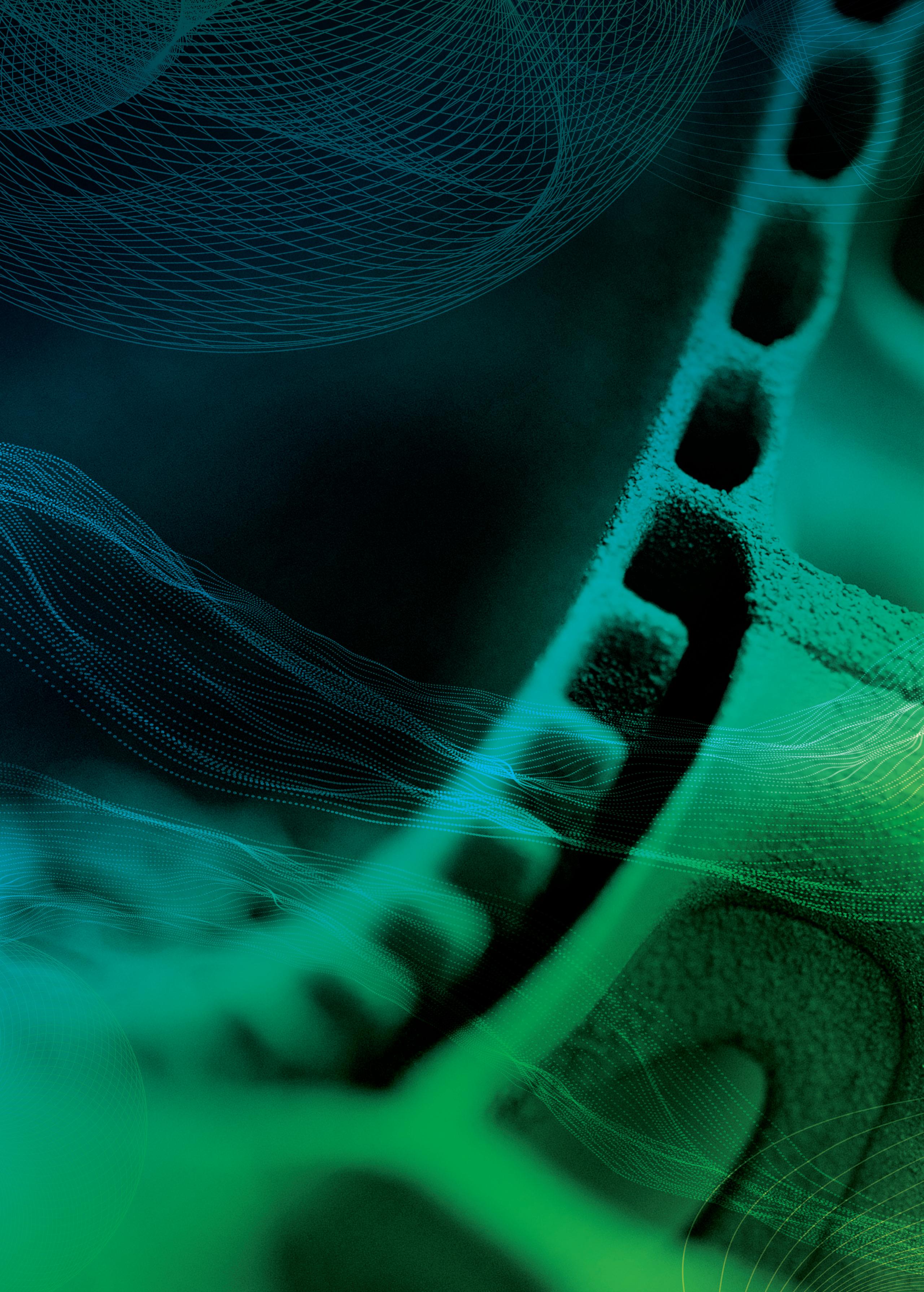
Demand for more complex, customized parts is rising fast. Product cycles are shortening, traditional supply chains are evolving, and the importance of sustainability continues to grow.
Additive Manufacturing offers you the solutions to meet these challenges and inspire your customers.
Stay ahead of the competition! Visit Formnext, the international expo and convention for Additive Manufacturing in Frankfurt am Main.
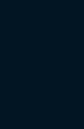
Overhyped and failing to deliver, 3D printing hasn’t lived up to its promises.
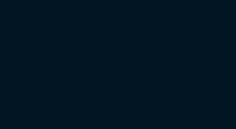
Automation of more traditional manufacturing methods is where the real potential for big progress lies, writes Theo Saville of CloudNC
It’s time to get real: 3D printing sucks. Or rather, it sucks at delivering what we were promised, which was a method for making everything.
As it transpires, 3D printing can’t deliver that. We need to accept not only that 3D printing cannot replace traditional manufacturing processes, but also that the dream of producing what we need to produce with 3D printers, on demand and autonomously, is over.
The issue with 3D printing is simple: market hype has outpaced reality, and while the technology is innovative, it was never the all-encompassing solution it was made out to be. Even as the technology advanced, in fact, fundamental limits remained, which I’ve witnessed first-hand during my career as an engineer and entrepreneur.
Yes, 3D printing offers the advantage of creating complex geometries that traditional methods can’t achieve – but there aren’t as many benefits from creating those kinds of parts as we expected. They just aren’t needed all that often.
In addition, every 3D printing process – whether it’s FDM, stereolithography, or metal printing – comes with significant drawbacks, especially when compared to mainstream manufacturing techniques.
FDM produces parts with poor surface finishes and weak bonds between layers. Stereolithography and PolyJet parts may be detailed, but they are often brittle and costly. Metal printing is immensely expensive, slow and unreliable. All of these methods are pretty inaccurate, no matter what the manufacturers claim. They all involve trade-offs, and those trade-offs are problematic.
SO WHERE NEXT?
Today, some 40 years on from its invention, 3D printing remains slow, expensive, and ineffective for mainstream manufacturing – that is, the production of things you actually use day to day.
The use of 3D-printed parts is still limited to niche applications, where the added cost of development and certification can be justified by long-term benefits such as weight reduction or enhanced functionality. However, most organisations aren’t shooting something into space or around a Formula 1 circuit every day.
Even the biggest fleet of 3D printers would not capable of producing the diverse components that make up most products, which require various specialised techniques and materials. That’s why we won’t be 3D printing car doors or consumer electronics anytime soon. The complex multi-step (and, often, multi-company) manufacturing processes that already produce these items are far more efficient and cost-effective at scale.
So, if 3D printing isn’t the future of manufacturing, what is? In my opinion, the answer lies in automating traditional manufacturing processes like CNC machining, injection moulding, punching and pressing, forming, welding and so on.
At my company, CloudNC, we’ve taken a major step towards this goal with CAM Assist, an AI solution that automates 80% of the CNC programming process, and is now in use in hundreds of workshops across the United States.
SIGNIFICANT POTENTIAL
Unlike 3D printing, which is autonomous by design but limited in practical application, CNC machining has the potential to become just as automated, while retaining the precision and accuracy needed for mainstream manufacturing.
The challenge with CNC machining today is its complexity. Setting up a CNC machine requires skilled labour, from selecting the right tools to programming toolpaths manually. The process is time-consuming, and even small mistakes can lead to scrapped parts and expensive crashes. We envision a future where much of this set-up work is automated. CAM Assist is

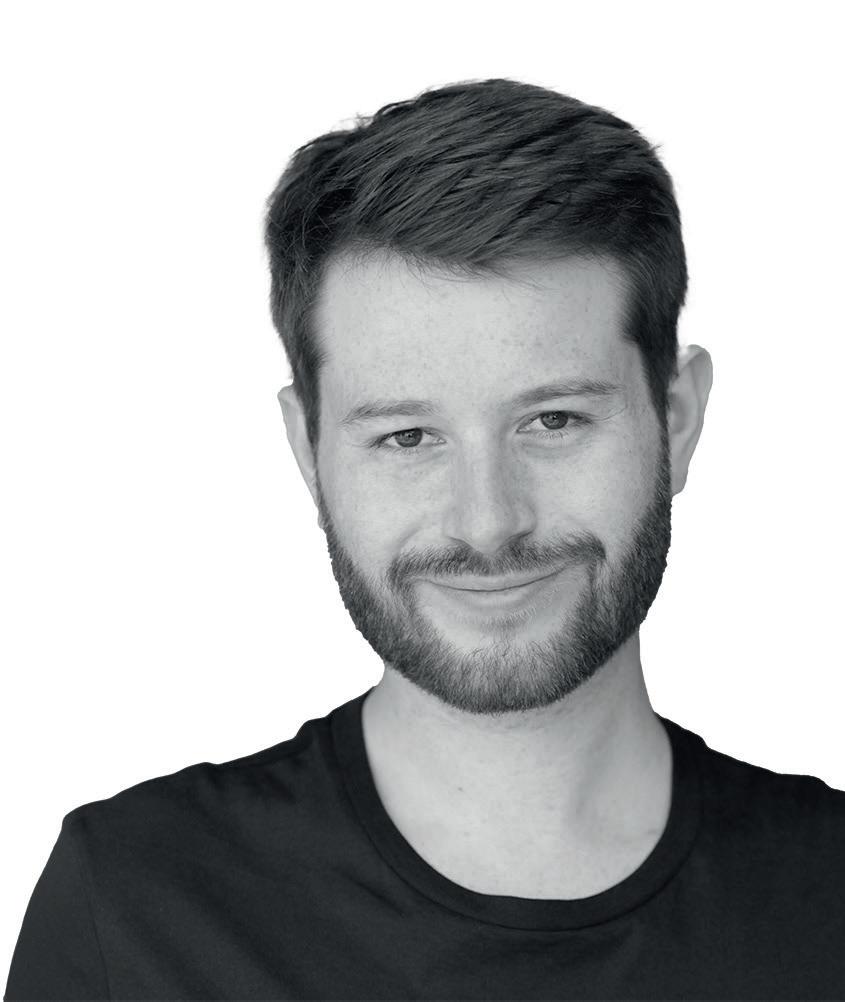
Even the biggest fleet of 3D printers would not be capable of producing the diverse components that make up most products today, which require various specialised techniques and materials
already bridging the gap, making it possible to streamline CNC machining to reduce expertise requirements and improve efficiency.
Imagine a machine with hundreds of tools, flexible workholding and software capable of autonomously programming and optimising most of the machining process. Such technology would allow manufacturers to achieve tight tolerances and perfect quality with minimal human intervention, delivering parts the next day that with today’s practices might take weeks or even months.
We’re not there yet, but we’re making progress. We’re working on automating multi-axis machining, handling complex materials and integrating automatic feeds, speeds and in-process inspections.
In short, the next great leap forward lies in the autonomous CNC machine, not the 3D printer.
It’s may not be as neat. It may not capture the public imagination with cool images of wacky designs. But it will have an extraordinary and practical impact on modern manufacturing – or, at least, on those ‘boring’, multi-trillion-dollar aspects of modern manufacturing.
ABOUT THE AUTHOR: Theo Saville is co-founder and CEO of CloudNC, a UK-based technology company on a mission to enable single-click manufacturing. CloudNC has raised over $75m in VC funding and is aiming to reinvent the precision manufacturing sector through the use of artificial intelligence technologies. www.cloudnc.com
VISUAL DESIGN GUIDE LOTUS THEORY 1
» The latest experimental concept car from the famous British marque has been built with intelligent performance and driver engagement in mind
DOOR DESIGN
A proprietary door system allows all three occupants easy, step-in access to the cabin, with a reverse-opening, wrap-over design that creates the smallest footprint possible when the doors are open
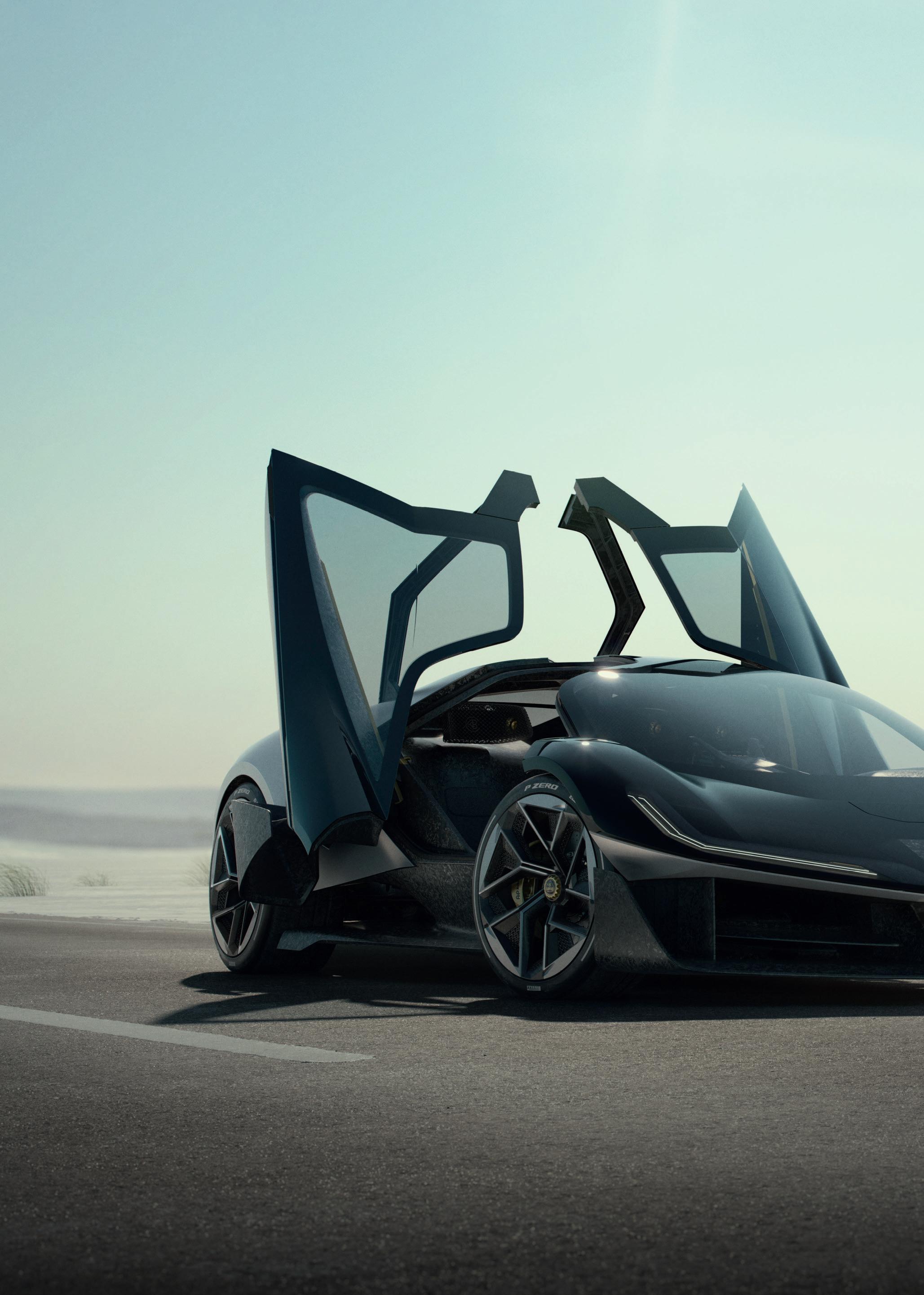
INNOVATIVE CHASSIS
Inspired by the revolutionary Lotus 49 Formula 1 car, Theory 1 has been engineered to use its motor and battery assembly as a stressed member that takes forces directly from the suspension, reducing chassis complexity and weight
SUSTAINABLE MATERIALS
ADVANCED LIGHTING
A Kyocera SLD Laser advanced lighting system drastically reduces component size and weight using ‘laser wire’ technology less than one millimetre in diameter, with main and dippedbeam functions delivered through 7x35mm lenses
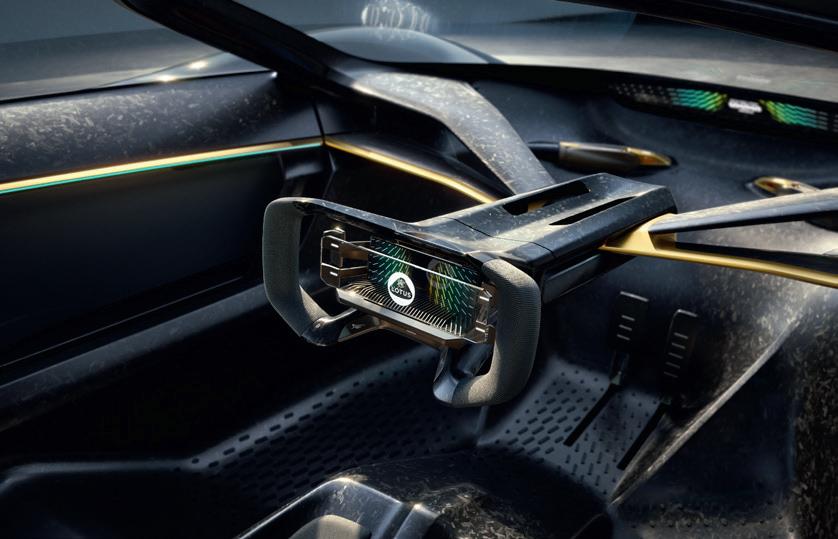
RESPONSIVE INTERIOR
The vehicle interior is shaped around the human body and responds to it, moving the pedals and steering wheel closer to the driver, for example
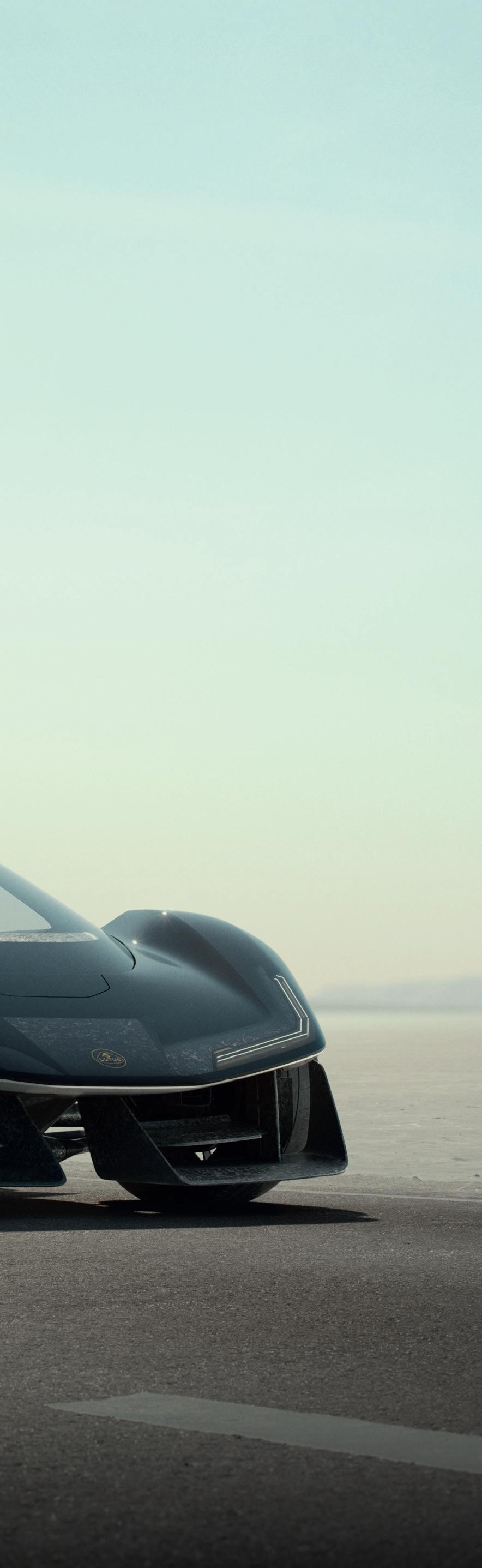
AVAILABILITY
The Theory One concept car is currently on view in the Lotus London showroom at 73 Piccadilly in Mayfair. Technologies derived from this concept car will directly impact future Lotus models www.lotuscars.com
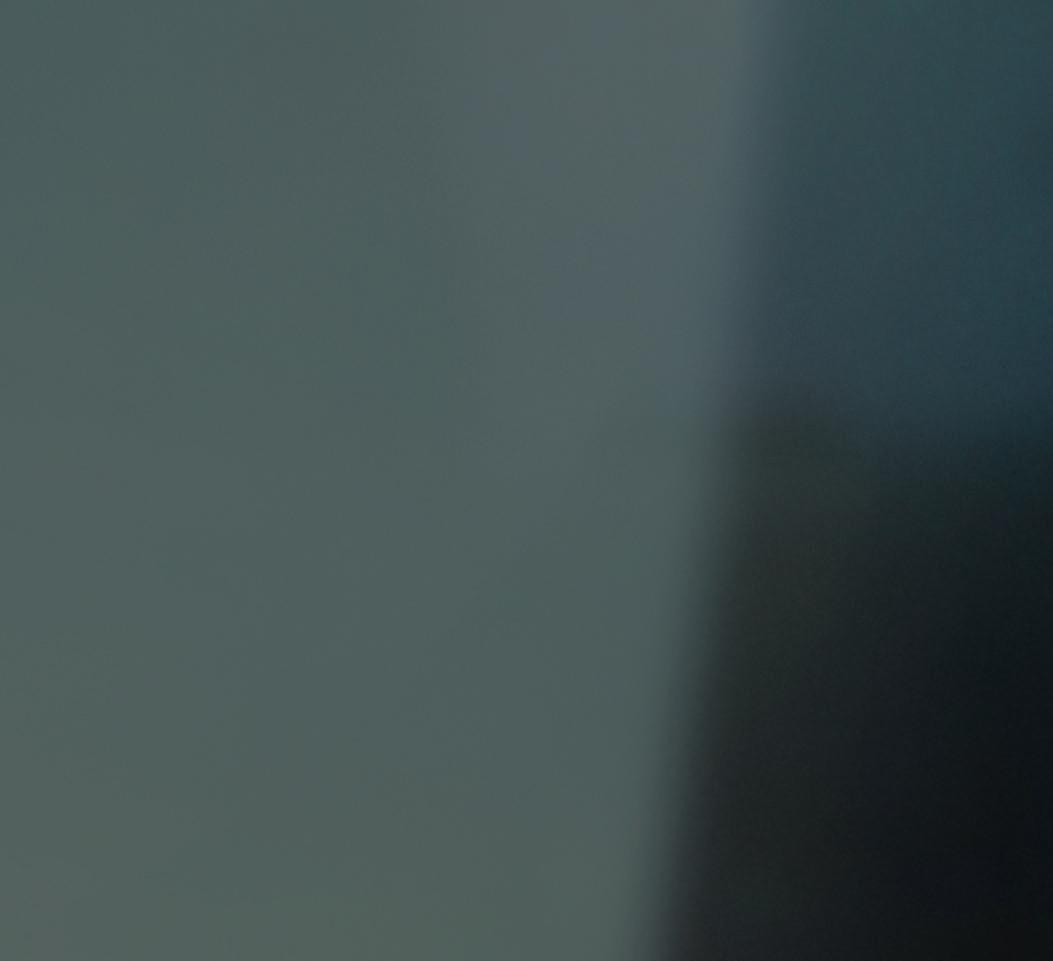
LIGHTWEIGHT HEADRESTS
The Theory 1’s 3D-printed lattice headrests were built using Carbon’s L1 3D printer and EPU46 material and house audio drivers from sound expert KEF. They offer each occupant maximum comfort along with a bespoke soundscape, while reducing overall weight
VEHICLE STATUS
Integrated OLED technology displays multiple functions of vehicle status to the driver and occupants, as well as other road users and pedestrians, including detecting the presence of an object or person close to the vehicle
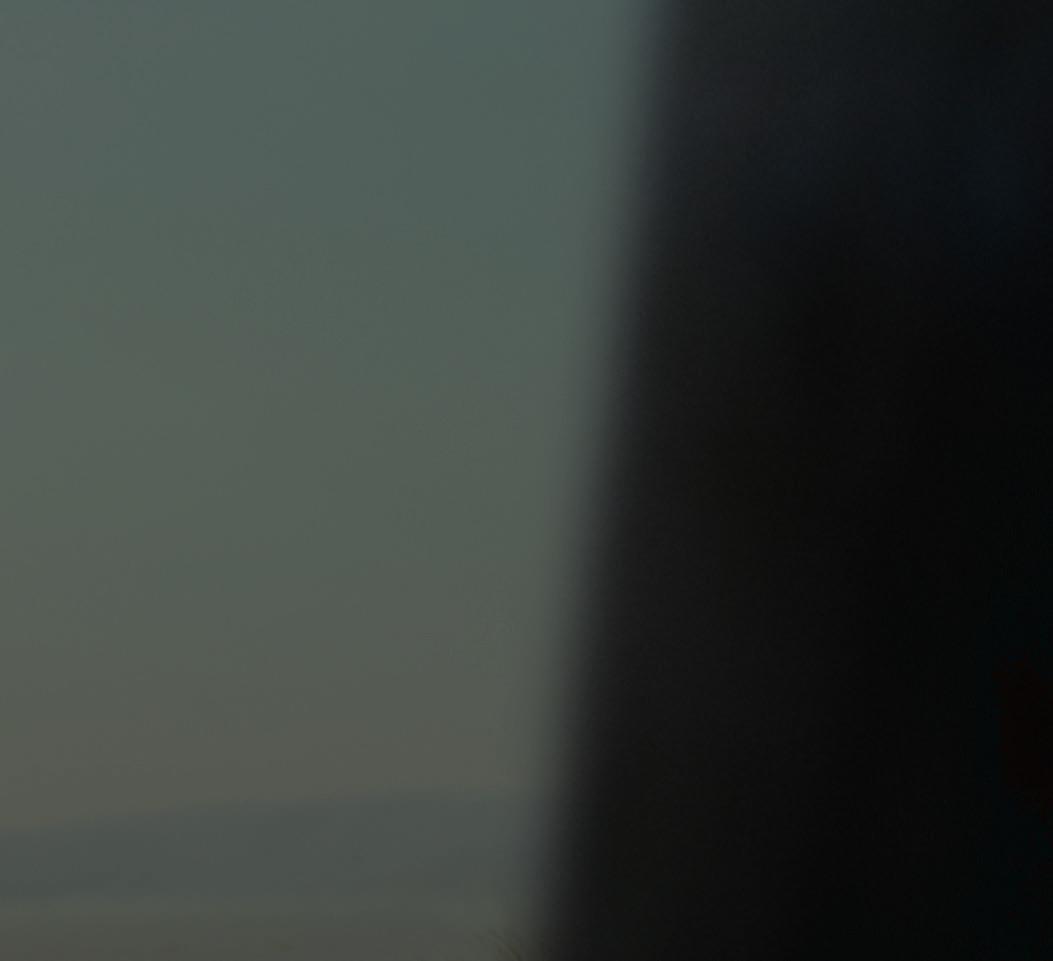
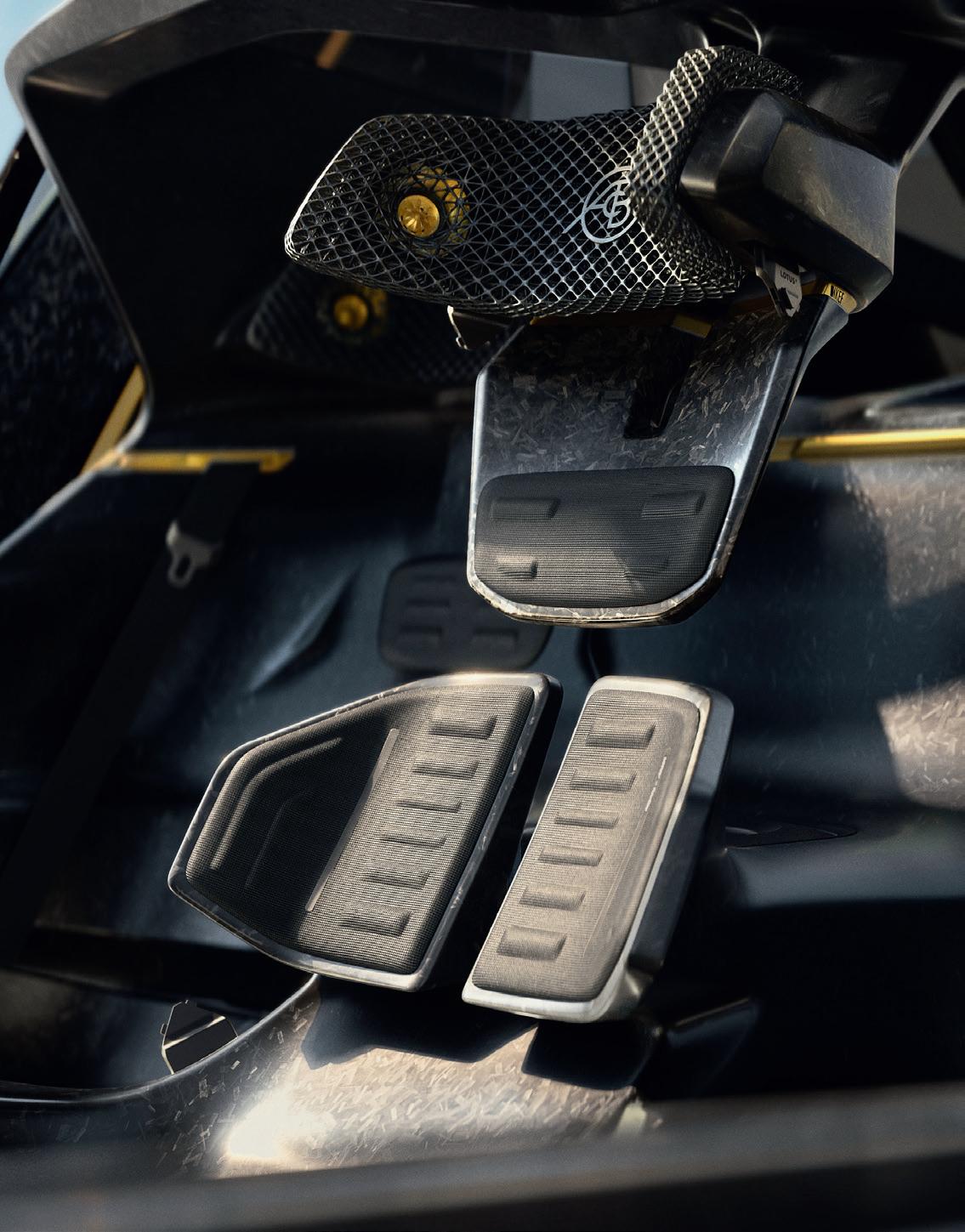
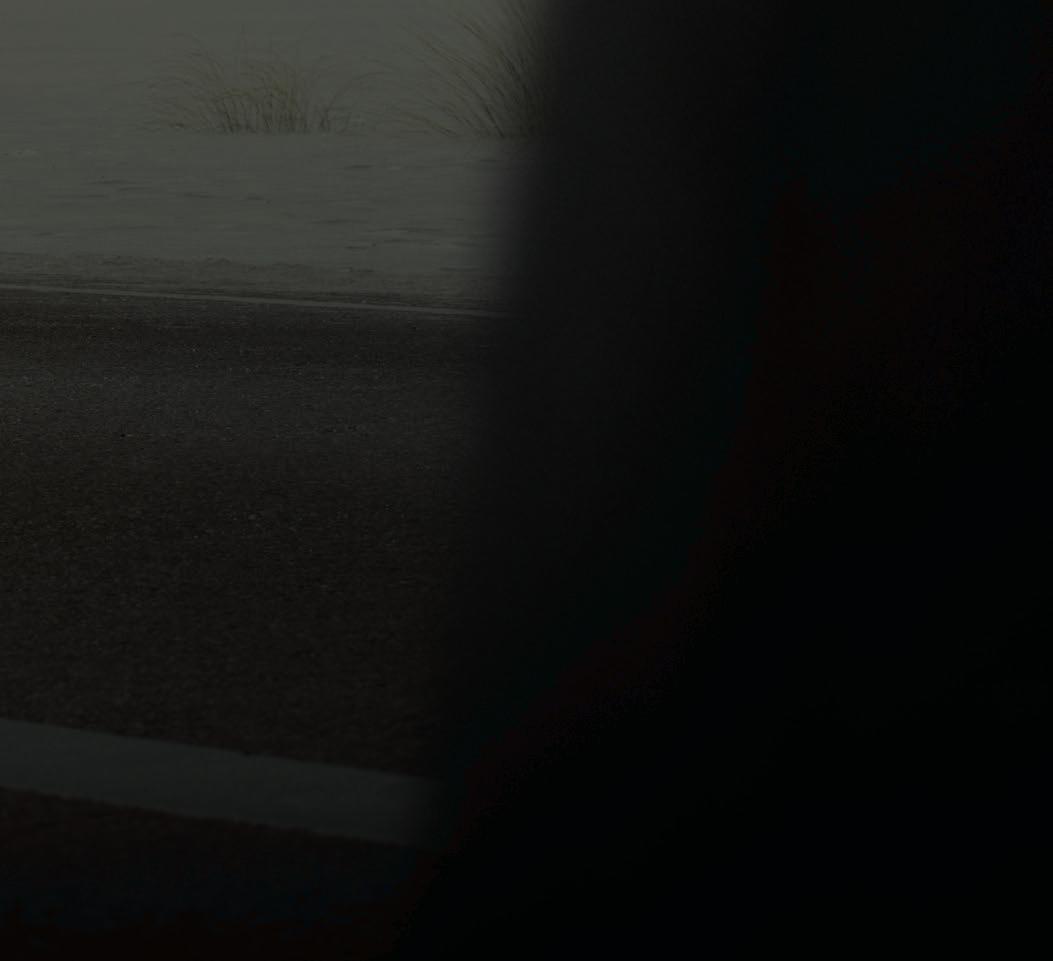
ROBOTIC TEXTILES
The soft, lightweight robotic textile used for the seats and steering wheel of the Lotus Theory 1 was developed by Motorskins and reacts in real time to offer drivers more support, better grip and haptic prompts
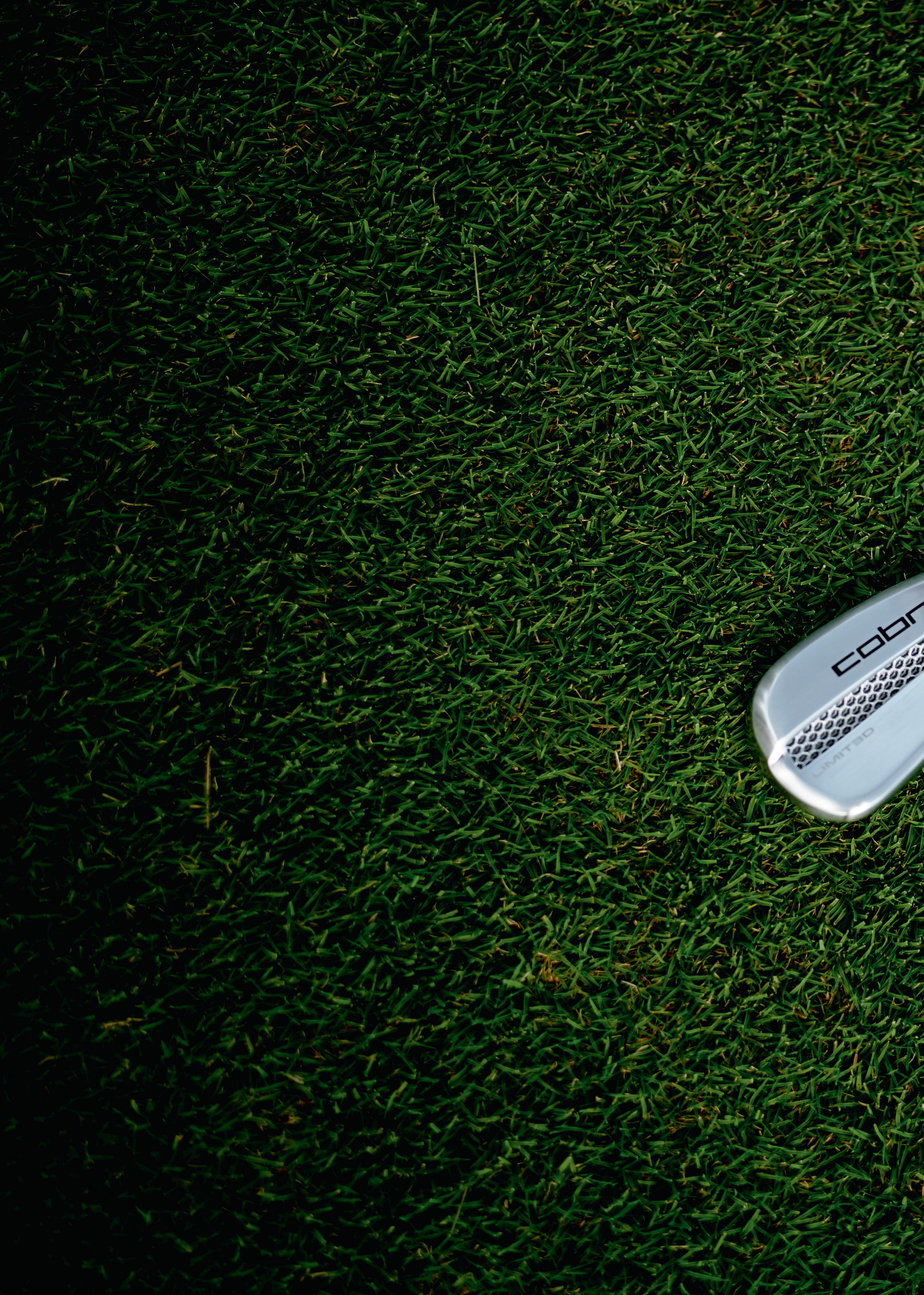
HOLE IN ONE
» The first golfing irons to be built using 3D printing are no gimmick. These clubs offer a unique design and a level of performance that are making both amateurs and pros fall in love. Stephen Holmes speaks to the team at Cobra Golf about the work that went into its Link3D range

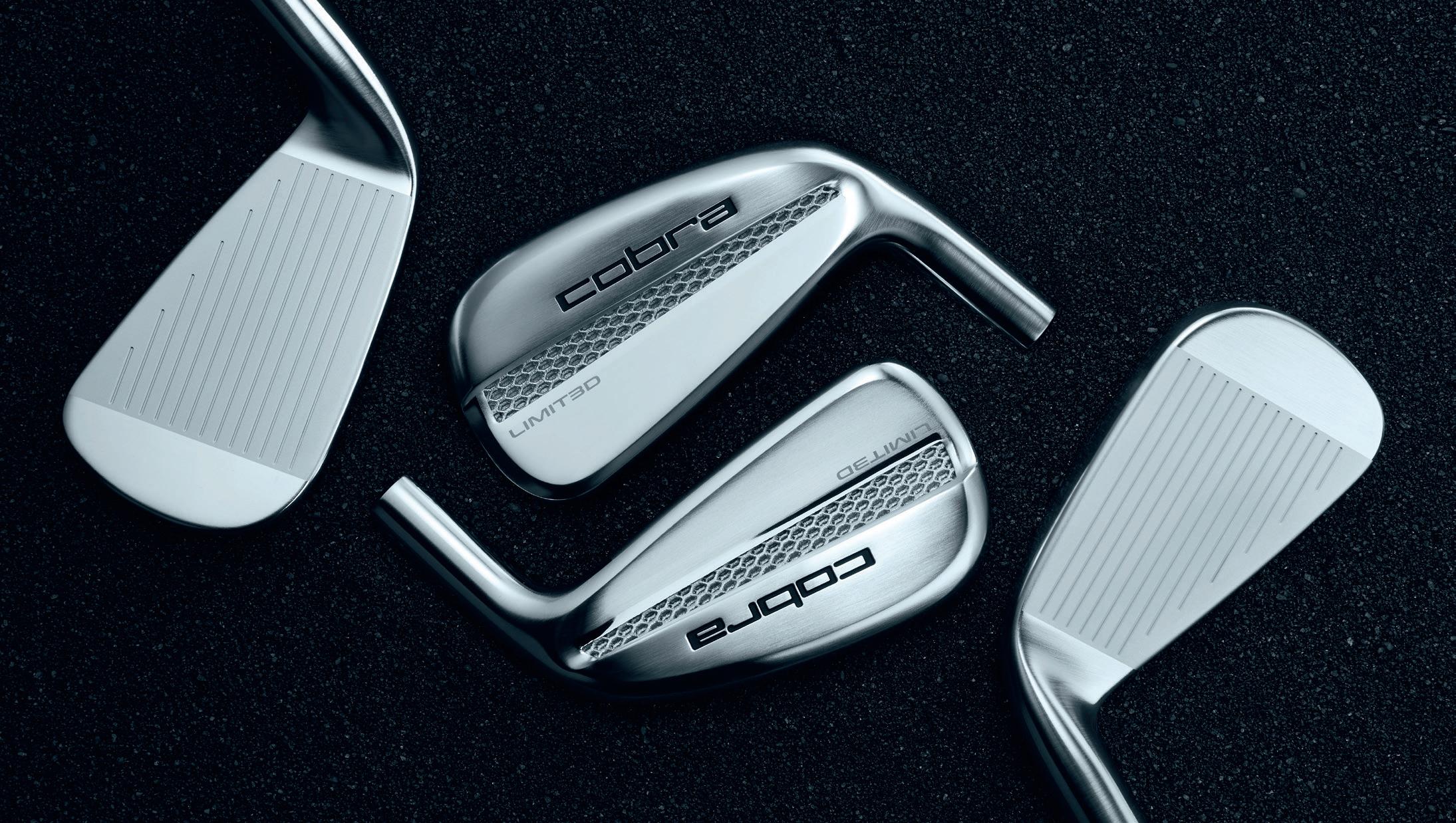
While drivers are expected to deliver big hits off the tee, and putters must finish the job on the green, it’s irons that enable players to navigate some of the most challenging areas of the golf course.
Each iron has a unique angled loft design, designed to enable a golfer to hit the ball a specific distance with greater accuracy. This comes with a caveat: the ball needs to be struck in the centre of the club face, otherwise the club’s promised performance may end up in the bunker.
Some players choose more forgiving clubs that add bulk to make this sweet spot bigger. More skilful pros typically look to the power and rigidity of defter clubs.
And plenty of enthusiasts want to emulate their heros, regardless of their own skill level, according to Ryan Roach, director of innovation at Cobra Golf. “They want to play something that looks like what the pros play – but they just aren’t good enough to hit the ball with it.”
The Carlsbad, California-based company has a robust presence in the global golf market through innovative club design, with many products using metals 3D printing. But the team were still looking for the best application of additive manufacturing for the sport.
Roach and Cobra’s vice president of innovation Mike Yagley had already helped develop putters that take advantage of 3D-printed club heads, but irons looked likely to attract more market demand.
“There are an awful lot of golfers out there – some really accomplished golfers and some golfers that are, let’s say, average – for who we could make an iron that in some way, either in feel, distance, consistency or forgiveness, was going to be substantially better than anything they’d ever played. That got me super-excited,” says Yagley.
The ability to marry the forgiveness of a development club to the look and feel of a pro model led the team at Cobra Golf to develop its Limit3D irons.
BUILT DIFFERENT
Cobra has been using 3D printing for many years now, initially with polymer models being used for shape validation and iteration, and metals printing added in around 2015 to build prototypes faster as club designs became more complex.
“Where, in the past, we would just go out to our machine shop and machine up a prototype, the designs were becoming more complex, and so it became a steeper task to actually make that and stay true to the design,” explains Roach.
The harder it became to remove materials, the more clubs had to be produced in multiple pieces and assembled, adding time and expense to prototyping.
Cobra shifted to 3D printing which, while still costly, proved cheaper than making tooling for five test designs.
“You’re using one alloy to print the entire head, whereas you might have been using all sorts of different parts to try and do this. Before, it’d be expensive. You’d have to join it, then you’d have to worry about the joints, and would it stay together?” says Yagley.
The team soon began to view additive manufacturing as a chance to manipulate the material inside the clubs, in order to lightweight designs and develop new properties.
Roach explains that, when it began to deal with the structures additive manufacturing allows, the team quickly found a rather unappealing workflow.
“We tested out a lot of software,” he reflects. From lattice add-ons in its CAD software Siemens NX, to recommendations like Materialise and Autodesk, Roach found the process to develop an internal club lattice “too cumbersome”.
The team then began to investigate specialist latticing software, and were immediately taken with the implicit modelling of nTop. “The barrier to entry with nTop was a little bit higher than, say, NX, because we knew NX and we knew the workflow and how to use it. But the functionality of the NX lattice software was not up to par, compared to what nTop offered us,” says Roach.
● 1 Cobra’s Limit3D line of irons is designed to be played by both golfing amateurs and pros alike 1
‘‘ Engineers can look at it and go, ‘That’s a hell of a solution for what was a fairly complex problem!’ That’s the beauty of what we’re doing
Mike Yagley, Cobra Golf VP of Innovation
“Once we got going, it was really eye-opening how intuitive it is once you get over that initial barrier to entry. And if you’re of an engineering mindset – not that we’re all computer programmers over here – and you’ve had some exposure to coding, I think that the workflow works more like a coding slant than, say, a traditional CAD creation slant. It allowed us to iterate very fast.”
The bulk of the design and surfaces of the Limit3D irons are still produced with NX, but the interior lattice has been developed using nTop, which has led to a lot of twists and turns in development.
By using a lattice, 100 grams of steel – some 33% of overall club weight – could be removed from the main club head design. This gave designers the ability to add that weight back in strategically. To do this, high-density tungsten inserts are added in the lowest heel and toe points of the club, dropping the centre of gravity and spreading the weight to allow for a higher moment of inertia, but without changing the shape of the head.
“So you’ve still got this nice, players-looking head, but you’ve got the mass properties – meaning centre gravity and moment of inertia – that you’re used to experiencing, but with something that’s a way diff erent shape,” says Roach.
“The old adage of ‘form follows function’? Well, with additive, it doesn’t necessarily have to. We’ve been able to separate them.”
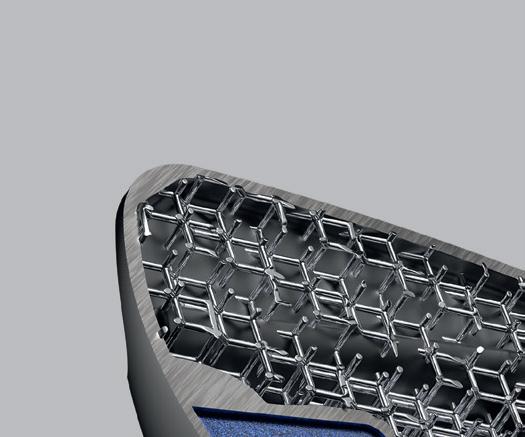
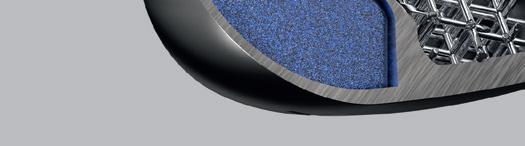
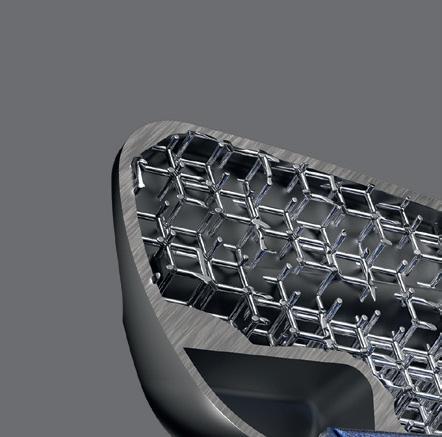

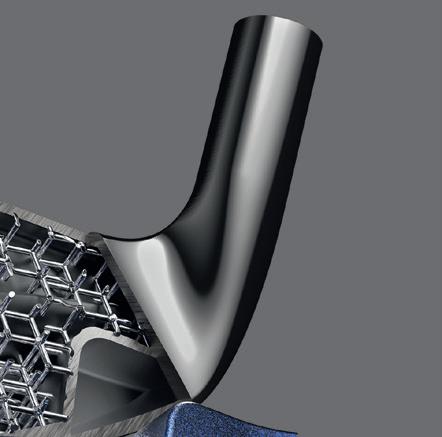

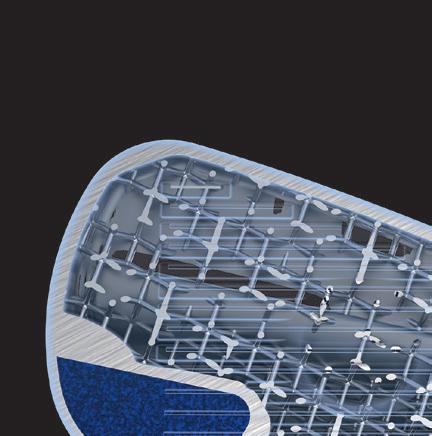


Yagley reflects on watching players, of all abilities, using the clubs for the first time. “It’s really interesting when, given the shape, they hit it and they have what we call this paradoxical reaction, like, ‘Wait a minute, this thing in the shape it’s in shouldn’t do what it just did’. Both the less accomplished players and the really accomplished players have the same reaction, for different reasons,” he says.
“It’s like, ‘Wow, I can play this if I’m not that good. Or, holy crap, I’m really good and this thing is doing things I want it to do and more. We’re able to shift that curve because of 3D printing, the removal of mass, but still making it stiff, because you’ve got the lattice putting the mass down low and wide.”
The beauty of what Cobra Golf is doing comes down to this, he concludes: “Engineers can look at it and go, ‘That’s a hell of a solution for what was a fairly complex problem!”
BIG SWING
The development entailed a lot of physical testing to ensure durability. The team’s typical simulation set-up for club impact simulations, comprising Ansys LS-Dyna and Altair Hyperworks, needed validating for the new lattice internal structures.
Long before club heads are shafted up and swung, the method of choice is shooting balls at the face of the club at varying speeds using an air cannon. The number of hits and their speed are varied, allowing the test team to check for cracks or issues like face deflection.
FEA analysis for clubs like drivers is now pretty mature in terms of understanding the modal analysis, stresses and the performance of a ball off a club face, says Yagley.
With drivers subjected to forces in the region of 3,000G and irons around 1,000G, it’s a huge load – the reason why all club designs are still subjected to physical air cannon tests.
“Things can happen that you just don’t pick up in normal FEA analysis,” explains Yagley. “There’s nothing wrong with that. We’re using the tools for what we can, but we still have to make and break our clubs.”
Cobra has already simulated its designs statically in nTop, for stress and for modal analysis, the latter proving particularly interesting to the designers, because it enables them to achieve a vibration signature similar to that of other solid, professional irons.
Vibration, and in particular, the noises made when the club strikes the ball, began to be a factor as driver heads grew in size and materials shifted from wood to steel and then to titanium, impacting the feel of the club and making what Roach describes as “some pretty weird sounds!”
He comments: “Even with irons, when you start making cavity back irons, you get that face really thin, it changes the acoustics and the feel of the club.”
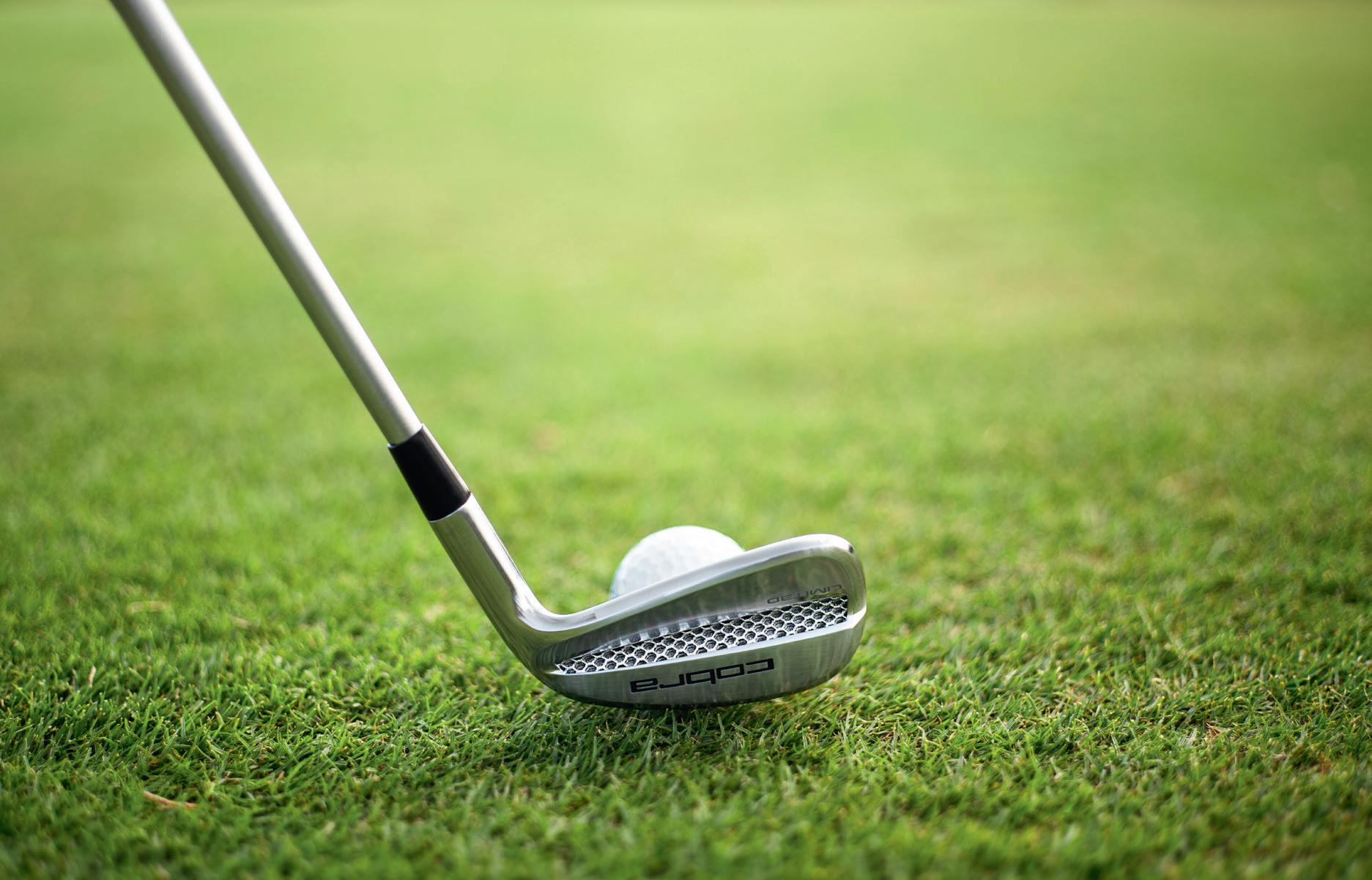
The standard fix is to stick something on the back of the face to act as damping and help dissipate the vibration. Or, if it’s hollow, it might be filled with a foam or TPU to help mitigate the sound.
“You’re just putting band-aids on a problem there,” says Roach. “In some cases, there’s some advantage to having that thin face, because you get maybe a little more face flex, which translates into ball speed. But the clubs that are designed for the better player, they’re pretty stiff overall, and you don’t hear the club as much as you hear just the ball compression sound. So that’s what we were going for with the Limit3D. We put the lattice in there to save a bunch of weight and maintain that stiffness to make it as close to what that solid structure would be.”
A QUICK ROUND
Cobra’s development cycle for its Limit3D irons, with ability to design, print and test iterations on demand, meant progress was swift.
Working with an additive production supplier, as it does with casting and forging houses, Roach explains that while earlier 3D printed putters were built using HP Metal Jet Fusion, the Limit3D clubs are produced in 316L stainless steel using SLS 3D printing.
This process allows for 16 club heads to be produced on a single build plate, and the unsintered powder supporting the internal lattice to be removed through two small openings.
“If those truly were 16 different versions that required different tools for forging or for casting, we’d probably look at it and go, ‘Okay, we’re never going to do this’. It could take years to make all those tools, to make the waxes, to make the investment casting, or to make the tools, to make the forged part, and that’s too expensive,” he says.
“So you can literally do 16 different variants on one build. Imagine the design experiments, or just the variations you could achieve, which you just wouldn’t do with forging or casting!”
Using nTop allowed the team the ability to adjust designs very quickly, almost on the fly, and to fix
problems when found, says Roach. “That’s coupled with the fact that there’s no tooling, so when we did make a design change, it was ‘Okay, now go print it, and then we’ll deal with it’. So that got the project over the finish line in such a fast manner relative to our traditional process cycle.”
Cobra calculates that the Link3D clubs were developed in a little over 18 months – from the start of innovation to having a product in the market. That’s cutting the typical three year process by around half.
“This alone is exciting, and as we are trying to proliferate the use of this approach when we have a good case that works, it’s the speed with which we can do stuff I think will be a big advantage for our company.”
The process allows the club’s steel surfaces to be machined and polished, while a small segment of sintered lattice on the back of the club is exposed.
Initial prototypes didn’t feature any lattice at all. “They just look like a standard club, and some of the tour pros that we tested with preferred that,” Roach confides.
“But I think we struck a really good balance with making sure that we were able to show it, so that people understood that there’s something different about this club,” he says.
“We have an amazing industrial design team, and so we want to make sure we evoke the look of technology, but it’s there for the aesthetics. It does save a little weight, but it’s inside where the performance is really happening.”
The visible section is structurally different to the lattice inside the iron, which the team describe as a functional lattice unit cell, with a specific unit cell size and type to achieve the necessary stiffness.
Outside, the lattice is a marriage of art and science, says Roach, “which golf clubs are to a lot of people!”
A BETTER WAY
The next step will be for Cobra to integrate more additive manufacturing into its process, in order to support both new ways of incorporating new materials such as titanium and more means of testing dynamic simulation analysis.

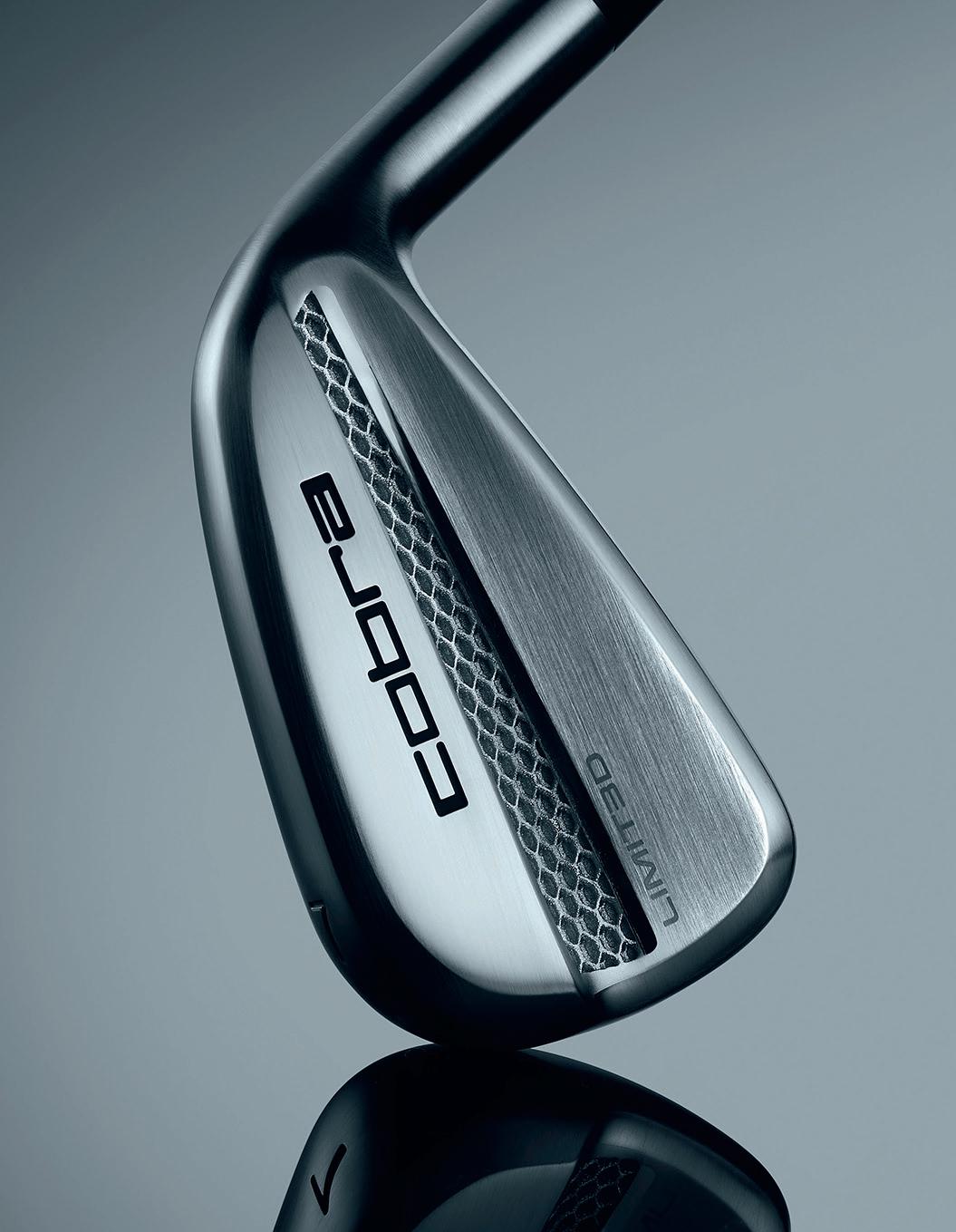
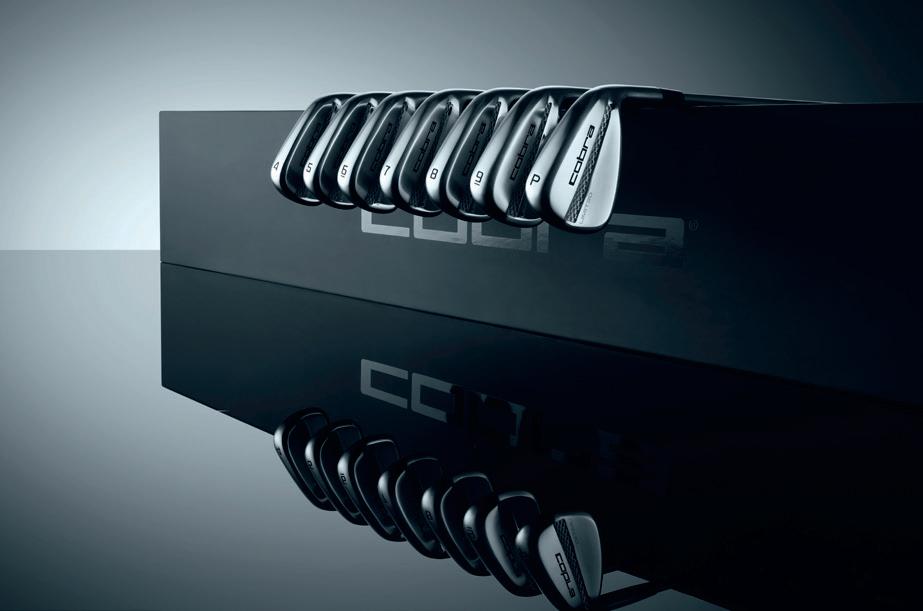
Additive, alongside casting and forging, looks set to form a key pillar of Cobra’s future manufacturing, with much of this about finding cost-effective ways to bring new designs to market – especially when it comes to levels of post-processing.
“It’s got to look like a piece of jewellery for most golfers,” says Roach, walking us through the transition of a metal club head through the factory.
Regardless of how it was made, each head is subjected to the necessary grinding, polishing, PVD coating, chroming, painting and application of decals.
“If you went to a golf club factory right now, you might be surprised at just how many people are in there and how many times a golf club head is touched by a human,” says Roach.
“I’ve heard that a driver, from cast titanium body to a finished head, can be touched 300 to 400 times, depending upon the product and the factory.”
Yagley adds: “If you look at an iron, it’s a very complex surface. Our being able to print it and turn it into something that’s acceptable from a looks standpoint, and doing it cost effectively, is one of our great quests.”
For now, the combination of exciting, high-performance lattice structures and unique 3D printed parts is producing a brand new approach to club design for the centuries-old sport.
The Limit3D summer release was limited to 500 sets of the clubs. At $3,000 a set, the price still had amateur players clamouring to buy them, eager to play with irons that look like the hard-to-play pro clubs.
With the real professionals now well into the test season, Cobra is seeing its tour players look at the clubs from a different perspective. “August to November is when they get to test all this stuff,” explains Yagley, whose phone lights up throughout our interview as yet more feedback from the brand’s stars arrives.
“Now they’re testing and they’re saying, ‘Wow, this thing’s the best I’ve ever hit in my life. Why wouldn’t I play it?’ So, you’re going to see more players switch over.” www.cobragolf.com
‘‘ We wanted to make an iron that in some way, either in feel, distance, consistency or forgiveness, was going to be substantially better than anything they’d ever played Mike Yagley, Cobra Golf VP of Innovation ’’
SendCutSend makes manufacturing easy and accessible for everyone
It all started in a garage…” is the beginning of many, well-known origin stories for successful entrepreneurs and companies. It’s also true for SendCutSend CEO Jim Belosic who uncovered his passion for design and manufacturing in a garage—and a huge business opportunity that came along with it.
Belosic had always tinkered with and fabricated parts for boats and vehicles over the years. While running a software company, he realized how the actual making of a physical object was important to him. As his projects in the garage became more complex, he realized he couldn’t make parts at the quality level he wanted with the hobby-level tools he had on hand.
“I started exploring local resources and machine shops, and I found no one wanted to do one part for someone in his garage,” Belosic says. “They wanted to do a thousand parts, or it was a very high price. And all I really wanted was something like a custom dashboard for a car.”
Then the light-bulb moment happened. Accessible, affordable, small-batch manufacturing was a major hurdle for many. Belosic realized there was a business opportunity to manufacture that one part or product for one person. Little did he know at the time that larger customers wanting larger quantities might also have a similar need. SendCutSend was born soon after in 2018 with the purchase of its first machines, including a high-end AMADA fibre laser cutter.
Since then, it’s grown to produce over 1500 tons of products annually, 200 employees, a 70,000 square-foot headquarters and manufacturing site in Reno, Nevada, a 40,000 square-foot site in Paris, Kentucky, and a third location soon to be announced.
Building a manufacturing business with a few clicks
The business started out serving people who didn’t have access to a high-tech manufacturer, such as someone building a one-off telescope or a kit aircraft or making a replacement part for a classic car. Part of the business appeal for these customers was— and continues to be—the simplicity and affordability SendCutSend offers.
“We’ve worked really hard to make sure you can get something like a car part you can’t find anywhere else, cheaper and faster than you can even get the raw material to your house,” says Jake Holland, vice president of manufacturing, SendCutSend.
To get a part or product started, a customer simply uploads a DXF or STEP file for an instant quote on
the website, then adds on options like CNC bending, powder coating, or PEM hardware, and then previews a 3D model. The final step is just a click to purchase, and it’s manufactured and shipped within a couple of days.
It turns out that this simplicity is equally attractive to Fortune 500 companies who began increasingly using SendCutSend within the first year. Now SendCutSend does anywhere from one-off, custom pieces to orders that have upward of 10,000 units.
“Fast forward to today and we do a big chunk of the Fortune 500, private space companies, defence, and everything in between,” Belosic says. “I always say my mom can make a sign for her kitchen that says ‘Live, Laugh, Love,’ but, at the same time, we have parts that are in orbit.”
SendCutSend’s manufacturing itself is also democratized. There’s no discrimination on order type. Everyone—from individuals and mom-and-pop shops to global manufacturers—uses the same web interface, receives the same service and machines, and the same quality, tolerance, materials, and certifications, no matter the run size.
Autodesk Fusion powers customers’ designs, manufacturing evaluations, and in-house innovations
Autodesk Fusion is an integral tool for the majority of SendCutSend’s customers. When SendCutSend receives an especially complex or difficult-tomanufacture order, they can quickly and easily evaluate the manufacturability in Fusion and provide any advice or guidance, when necessary, back to the customer. At the same time, SendCutSend uses Fusion to create custom designs for their own shop floor.
“We’re always building little gadgets to improve our work and efficiency,” Holland says. “We move a lot of orders around our shop. We have a tug system instead of a conveyor system because everything moves so differently. With Fusion, we were able to build a full train trailer setup, similar to what airlines use to move luggage.
“Having the CAM software built-in with the CAD software is essential,” he continues. “I don’t have to go back and forth between two different things. It’s just easy to use and, with the cloud, I can just open my computer at home, too. I use it every single day.”
To leverage SendCutSend’s business model and Fusion even further, the company recently developed a new plugin that enables customers to seamlessly review and order parts directly in Fusion itself.

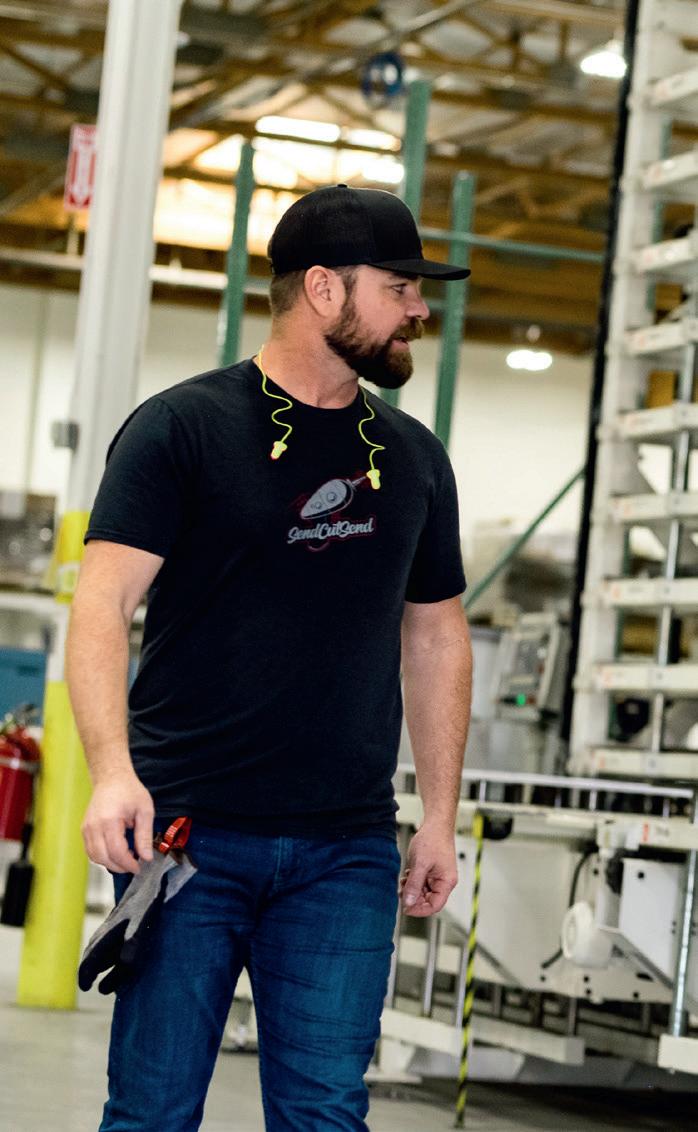
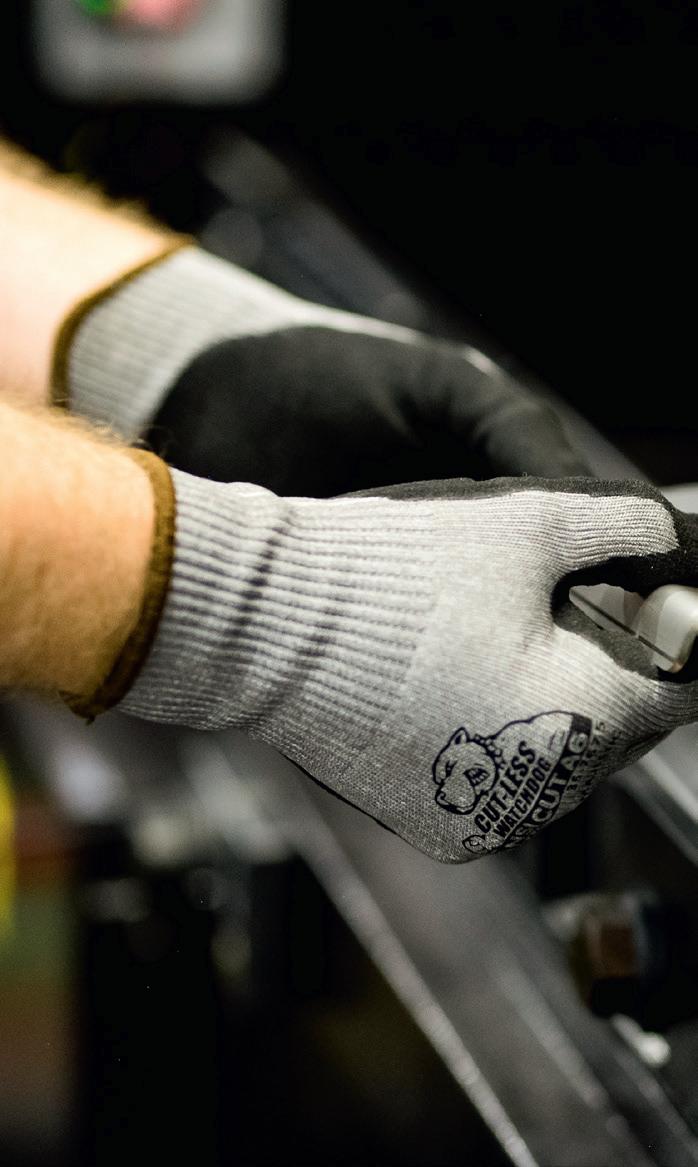
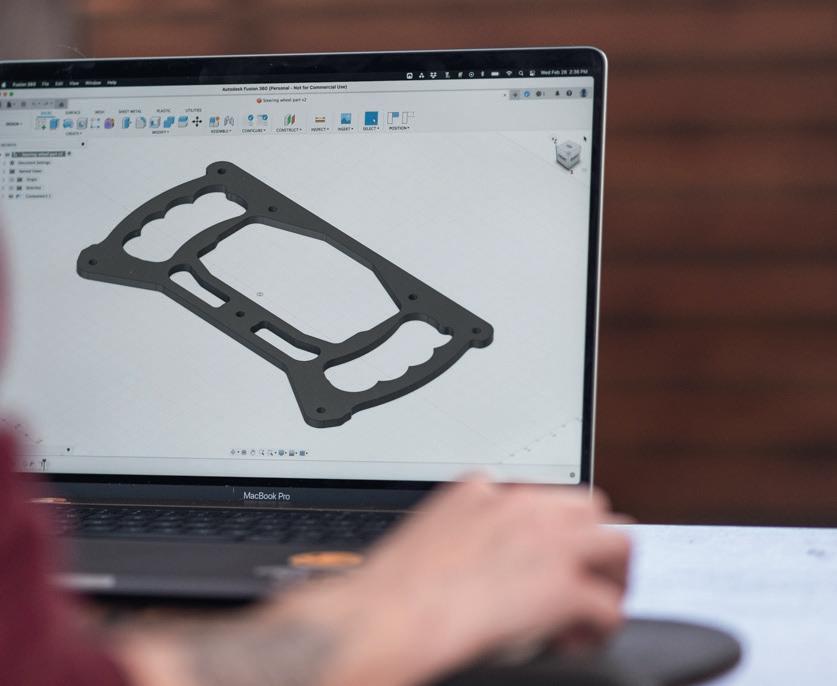
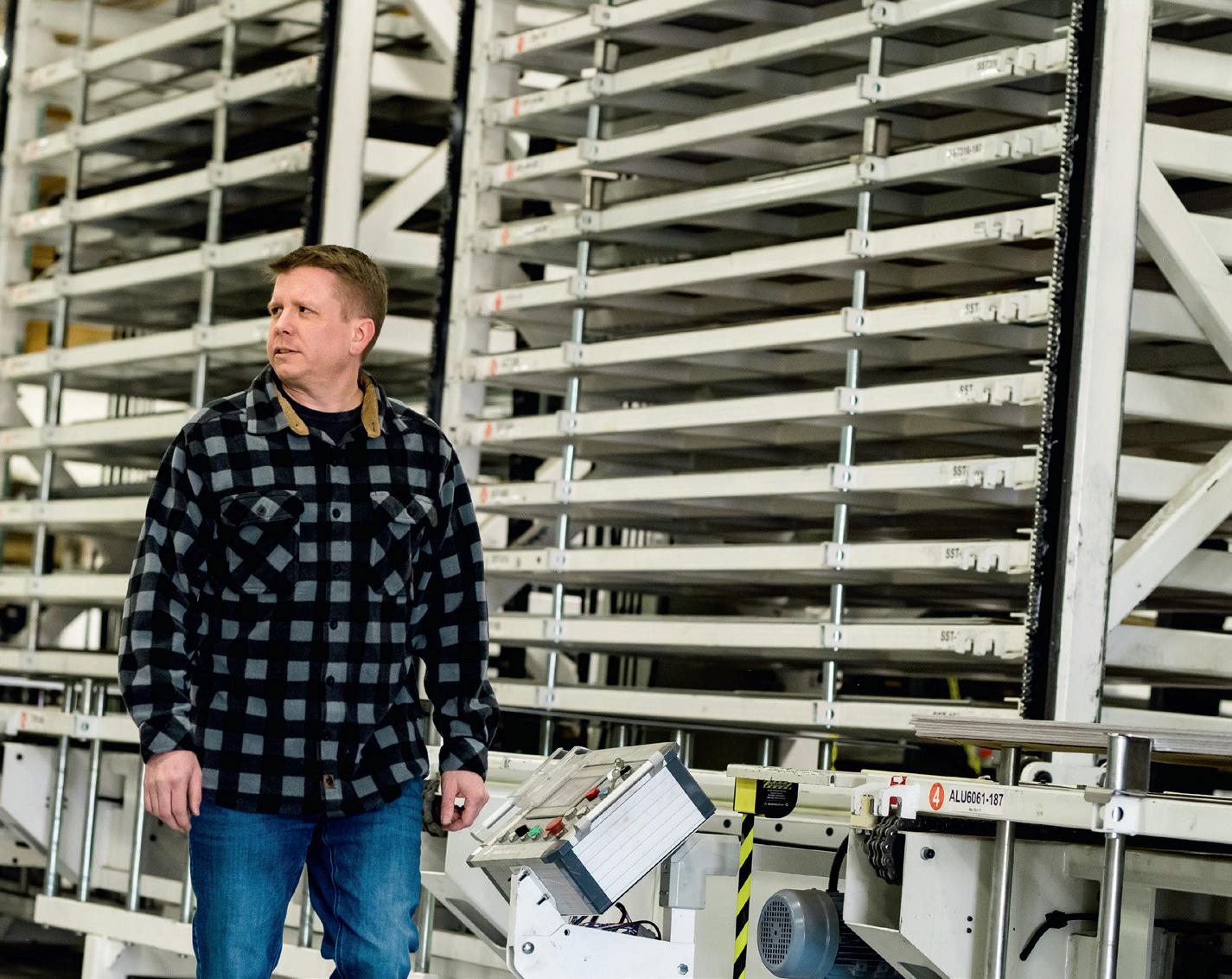
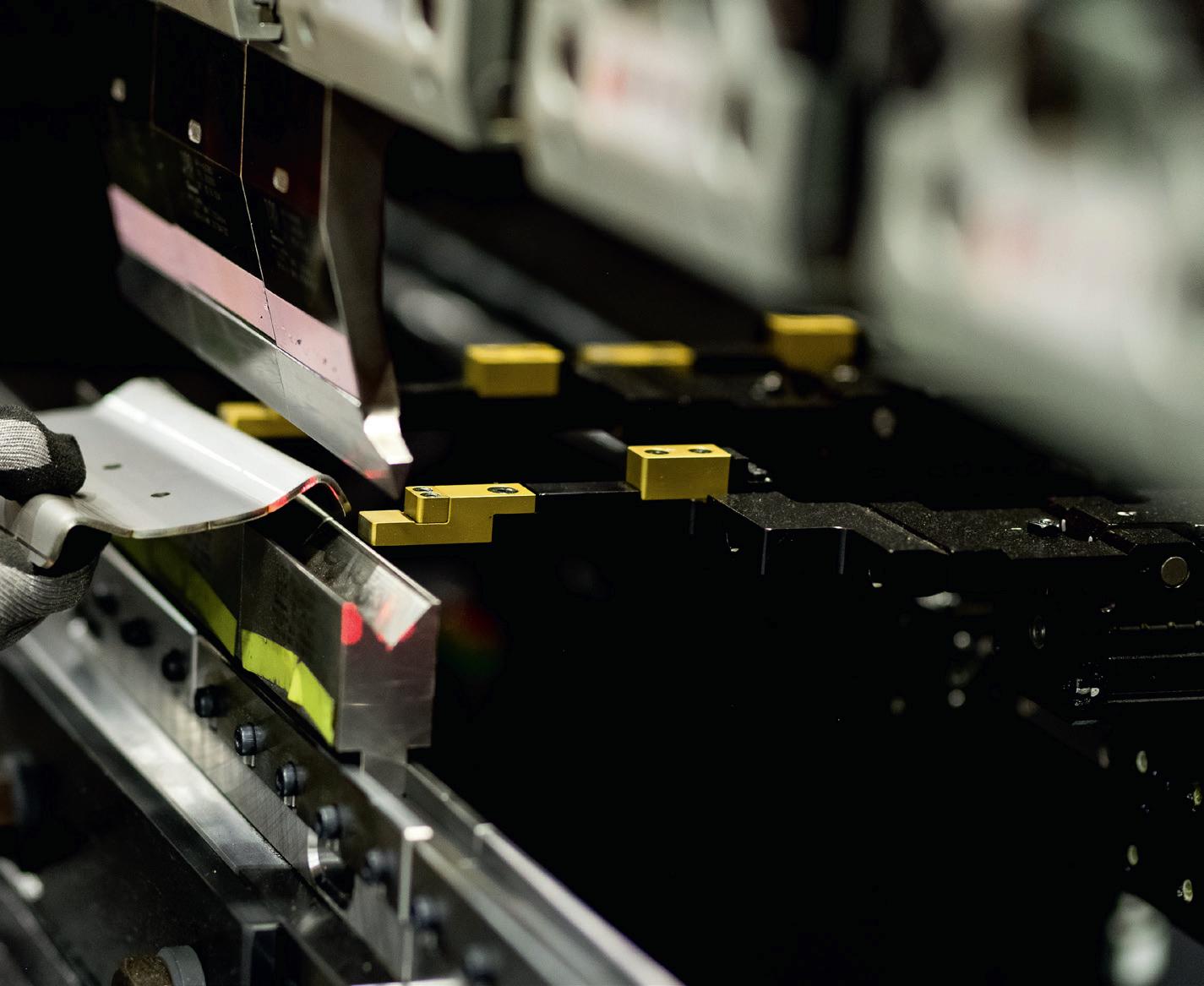
SendCutSend’s data is available for anyone to adjust their designs based on material, price, and other priorities directly in the software before placing an order. Accessing data within Fusion is transforming how customers can not only improve designs but also experience better outcomes.
“We can start to do more Design for Manufacturing (DFM) directly in Fusion and access its bend or material libraries for the plugin,” Belosic says. “You can get a ‘go’ or ‘no go’ right there in the software. It’s exciting to leverage this data and automation. It gives our customers the ability to make even better design and cost decisions before anything is ever cut.”
Embracing the future of manufacturing
As a company, SendCutSend is focused on taking a sustainable approach as much as possible. 99.99% of all waste metal from its manufacturing processes is recycled and sent to a mill to repurpose into future projects. Even a special dust-collection system is used to capture even the smallest specks of metal that result from laser cutting. To reduce their carbon footprint, they are diversifying manufacturing locations across the country to reduce shipping impact—and improve delivery times even further.
With SendCutSend’s growth, they are always looking to adopt Industry 4.0 practices even further. As AI continues to bring new innovations every day, the team is developing new approaches to incorporate throughout the company and its services.
“Where I want to go in the future is live recommendations and leveraging machine learning and AI,” Belosic says. “We’d love to give those recommendations of how to open a bend relief or prevent a collision in manufacturing. It’s complex, but it’s a lot of fun. It keeps me coming back.”
N.B: SendCutSend currently exclusively ships to the US and Canada
Scan the QR code to see how Autodesk Fusion can improve your design and manufacturing workflow.

MUSIC TO
» For today’s DJs, parties, festivals and rehearsals can happen any time, anywhere. The need for spontaneity has led AlphaTheta to develop a new wireless, battery-powered system with a new aesthetic to match
Deep indigo, the matte colour chosen for the Omnis-Duo controller from AlphaTheta, softens the edges of this state-of-the-art piece of DJ kit, making it look and feel more tactile than any of its predecessors.
“We dedicated considerable time and effort to perfecting the colour, materials and finish,” says Muneki Sugita, product designer at AlphaTheta.
“We aimed to create an appearance that would encourage customers to take the product outside, while also considering practical aspects such as portability and operability. The colours, materials, and finishes were carefully selected and adopted to achieve this balance.”
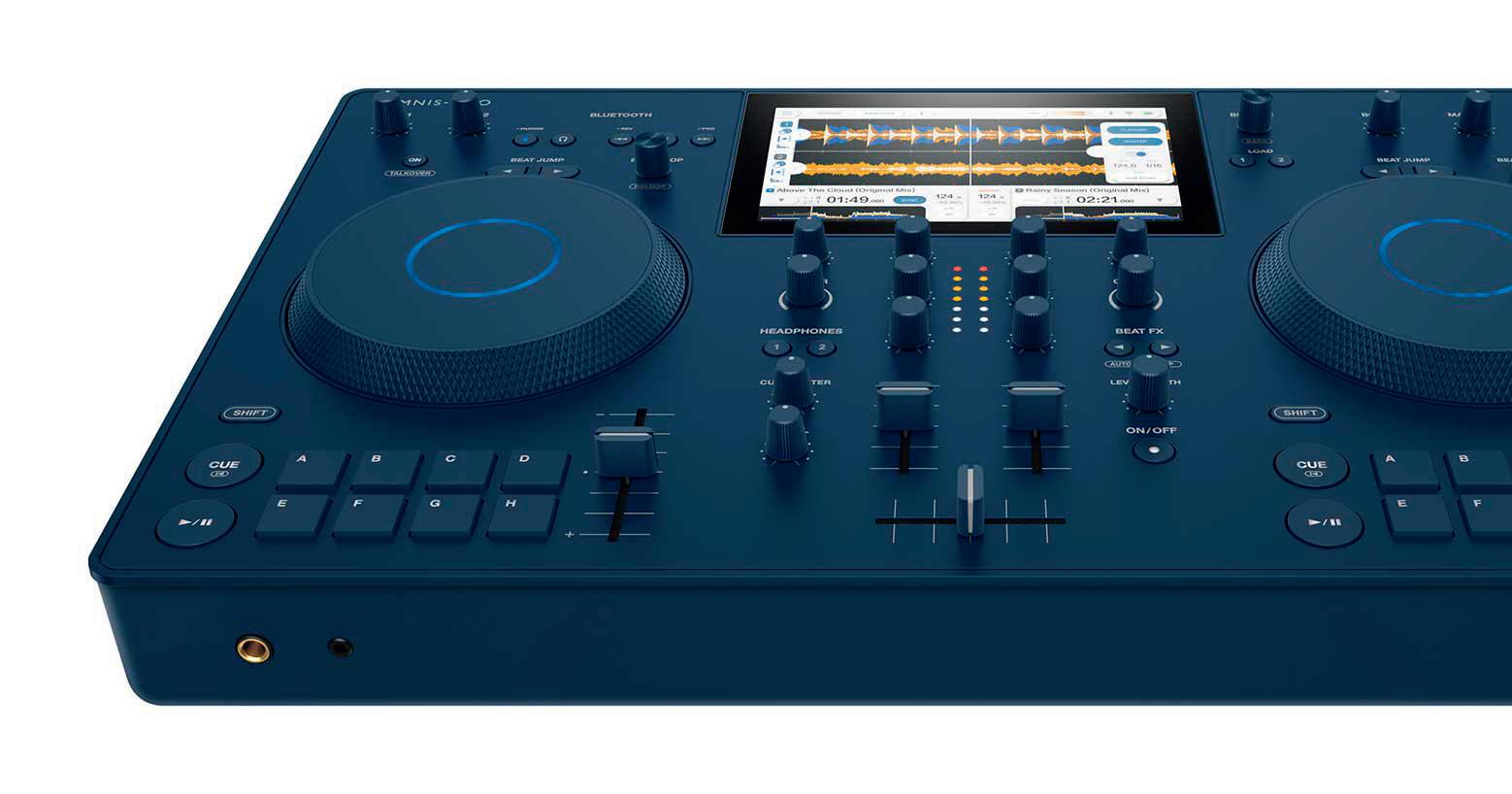
INSIDE OUT
The controller’s designers proposed many ideas in their concept sketches, to match a variety of scenarios, he adds. The decisive factor in the final selection process?
“Choosing an idea that aligned with our initial goal of ensuring that anyone can enjoy DJing at any time and place, including day, night and outdoor environments.”
AlphaTheta is the evolution of the Pioneer DJ brand, a well-respected name in professional audio equipment and DJ controllers. As performances begin to shift from dark nightclubs to daytime parties held on beaches and in parks, it is looking to reshape the way that DJs plan and play their sets.
The goal for the Omnis-Duo, in particular, was to create a product that could entertain in any surrounding, at any time and in any place. Visually and technically, it’s a radical departure from the traditional ‘black box’ designs typically associated with DJ equipment.
Battery-powered, and with Bluetooth audio output and ultra-low-latency wireless connectivity, it even enables users to take requests by quickly recording a track from an app on a phone, for example, and then allowing the DJ to add it to a set.
The Omnis-Duo was designed from the start with the idea of encouraging customers to take it outside, while also considering practical aspects such as portability and operability, says Kazuhiro Ohnuma of the AlphaTheta hardware design management division.
Early 3D models were built in Rhino 7, while crisp visualisations were created in Keyshot, with colour chips carefully matched to give accurate renders even in the earliest stages of the design process.
The Omnis-Duo also includes many functions that the team behind it were implementing for the first time. That meant starting from scratch in terms of design knowhow and evaluation methods and conducting thorough preliminary research and benchmarking against other companies’ products.
With the expectation that the Omnis-Duo will spend much of its life being carried around, target values for product rigidity, weight and the durability of each control component were considered well in advance. The team used Autodesk Fusion to develop the 3D model, allowing them to perform stress analysis and select appropriate materials.
For AlphaTheta’s first battery-powered product, the team also used thermal analysis tools to address concerns around internal temperature rises when the
● 1 The Omnis-Duo is looking to reshape the way that modern DJs plan and play their sets
design goal was to create a DJ controller that could be used to entertain in any environment and still look the part
GO

product is used in different environments, such as on a bed or outdoors.
“We needed to consider various potential accident scenarios, such as user misuse and component failures,” states Ohnuma. “We dedicated the most time to developing and structuring safety mechanisms that would prevent accidents under any misuse or defect condition.”
This in-depth virtual testing was matched by the amount of physical prototyping, which proved invaluable for designing and verifying the product’s safety.
“It also helped us clarify specifications for our Bluetooth-equipped products,” Ohnuma adds, helping verify connectivity with the OmnisDuo’s partner product, the WaveEight Bluetooth speaker.
SOUND AND COLOUR
Another initiative in the design of the Omnis-Duo was a collaboration with the development department of a paint manufacturer to develop new paints. Since the newly developed colour offered low weather resistance, not ideal for outdoor use, the team worked with this partner on improving weather resistance and conducted accelerated degradation analysis to assess the pace and extent of deterioration over time.
Achieving a consistent deep indigo finish across the entire product also created a challenge, given that various components were manufactured by different suppliers.
“Ensuring colour uniformity was a critical aspect of quality control,” says Sugita.
Through collaboration with the parts management departments of each manufacturer, and multiple trials that were carried out alongside the paint manufacturer, the AlphaTheta team was able to achieve the necessary colour grading across the Omnis-Duo for mass production.
The resulting product blends all the familiarity of a professional controller with new levels of fun and portability, enabling the music to go wherever the party takes it.
www.alphatheta.com
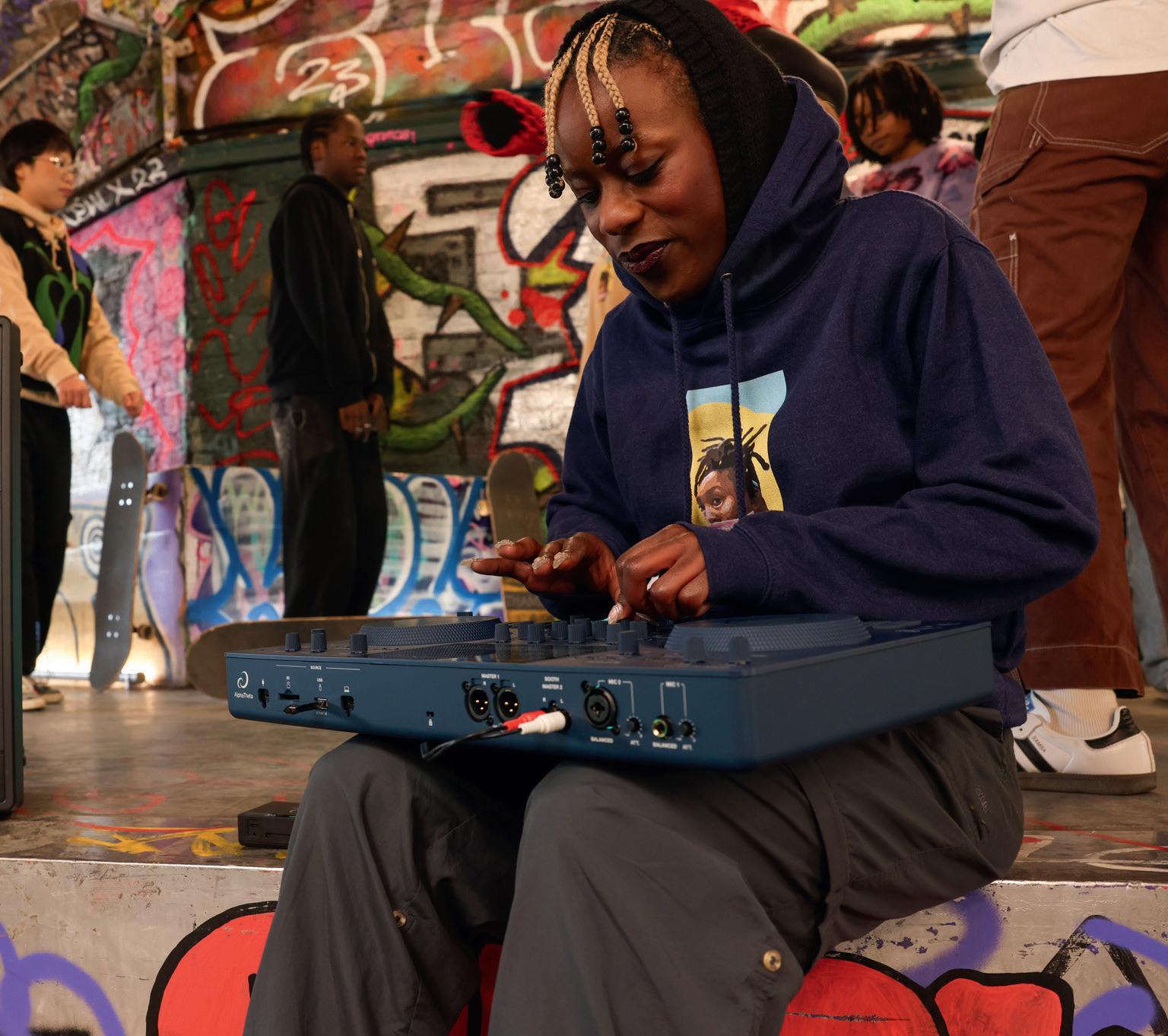
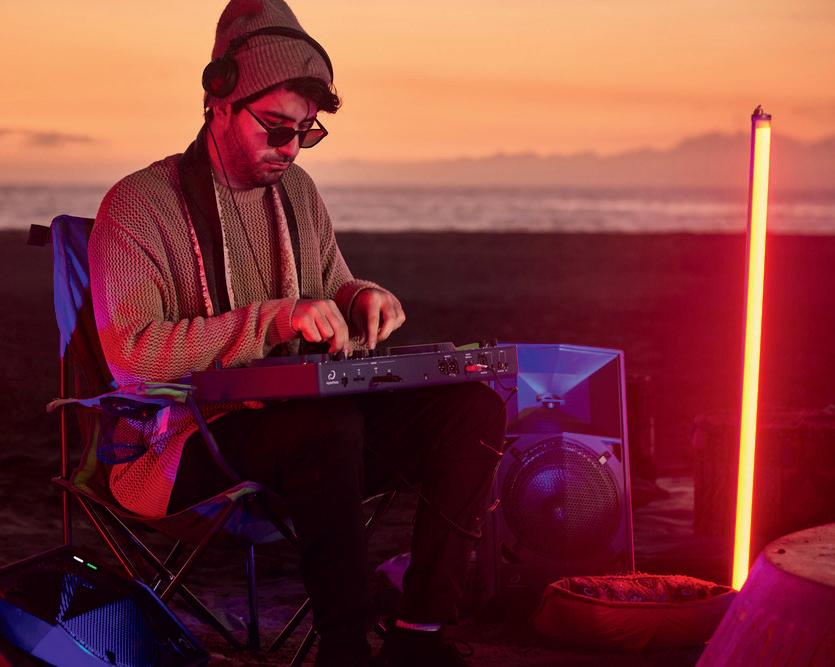
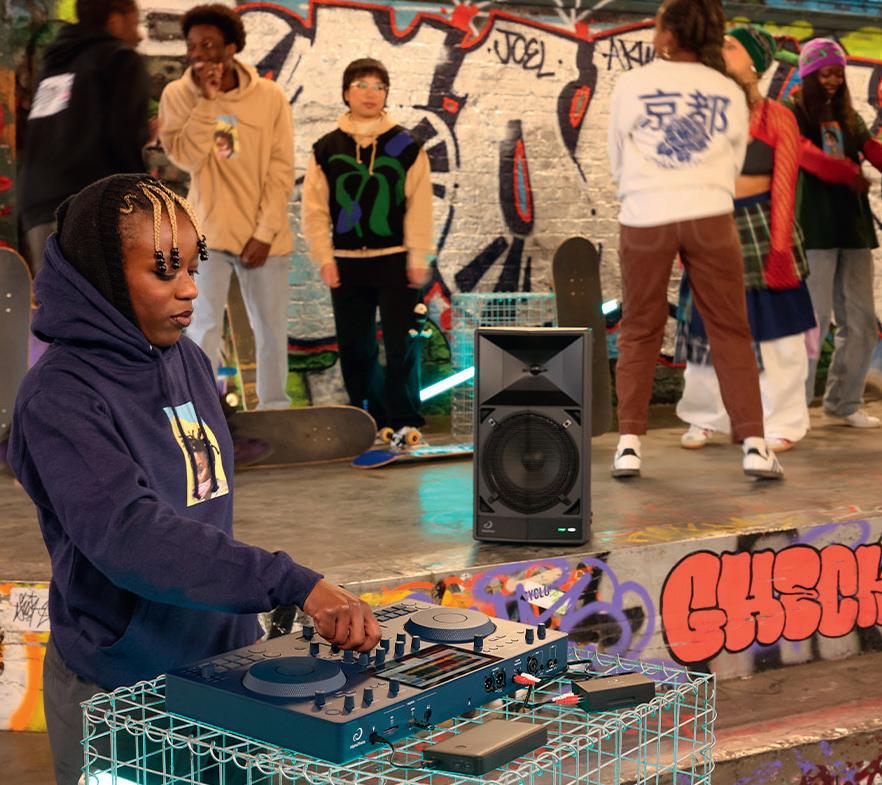
NEXT STEPS S
Karklinsh knows more than most about this subject. His company Elastium is best known for developing a fully 3D-printed shoe that was launched in Spring 2023. The experience of launching a challenger footwear brand with a focus on a new manufacturing technology appears to have been a sobering one.
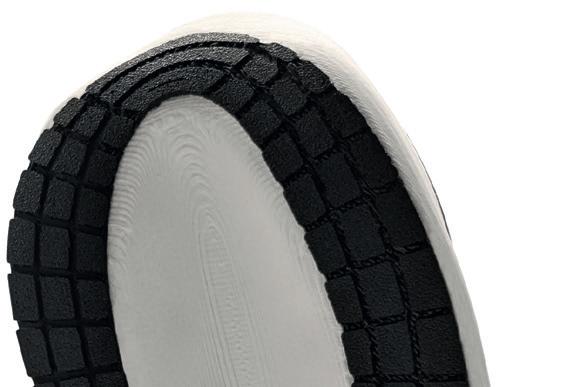
» The footwear industry is rushing to adopt additive manufacturing, with a host of new 3D-printed shoes being launched. Elastium, by contrast, believes in a hybrid approach and is looking to use 3D printing to drive a lasting change in footwear manufacturing
ince Adidas first revealed its 4D range back in 2017, the 3D-printed shoe has taken giant strides forwards and now enjoys an established foothold in the world of sports apparel.
Cut to the present day, and barely a fashion week passes without another 3D printed running shoe, clog or slip-on being launched. The reasons for that –beyond aesthetics – are clear.
Footwear brands have long grappled with complex supply chains and traditional manufacturing challenges. Logistical overheads, heavy upfront investments, stockpile accumulation and growing geopolitical risks have intensified the demand for more localised and more sustainable production.
Moves to disrupt this market with new technologies such as 3D printing have typically put themselves in opposition to traditional manufacturing alternatives.
However, examples of additive manufacturing for footwear, although fast and easy to localise, tend to sacrifice scalability and impose limitations on the types of products that can be produced.
“For me as an engineer and designer, the idea of 3D-printed shoes grown like potatoes in 3D printer farms is fascinating,” says Robert Karklinsh. “But the market doesn’t move on what engineers or designers think. It moves on what consumers demand. And consumers demand far beyond fully 3D-printed ‘potato shoes’, which are seen as just another trend, rather than a revolution.”

Elastium’s Shoe 1 design was a fully 3D-printed TPU design, with a ‘generative design’ organic aesthetic, but niche appeal.
The company’s latest product, Orca, features a more traditional-looking upper-on-sole design, and has involved enlisting the skills of LaLaLand, a footwear and accessories manufacturer in California. Having worked with brands like LVMH Group, Diadora and Amiri, its 60,000 square foot manufacturing facility in Los Angeles will combine existing technologies with new additive processes.
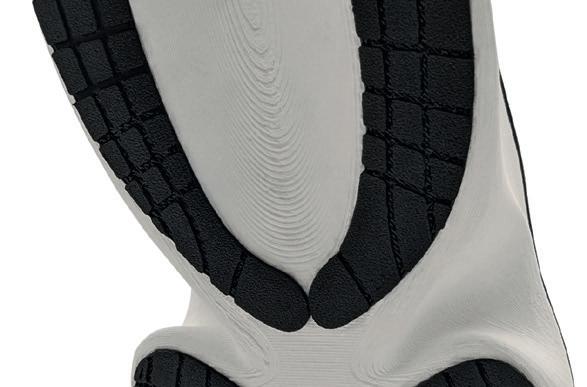
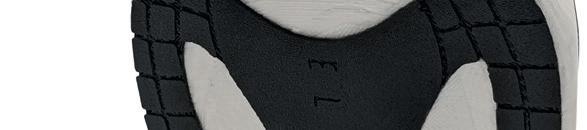
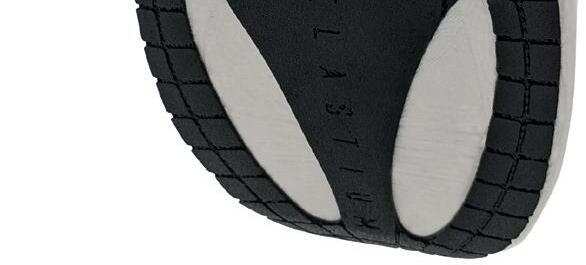
The goal, Karklinsh says, is to empower traditional manufacturing instead of declaring war on it.
HYBRID PRODUCTION
To begin, Elastium is introducing a hybrid production model, with no minimum or maximum order quantity, with “massive shortcuts” enabled by 3D printing technology.
With this, brands will be able to launch new designs with as few as one pair through advanced manufacturing, with the scope to ramp up to mass production without compromising on quality or cost.
Elastium says that this flexibility is enabled by bridging the gap between 3D-printed and moulded shoes using its proprietary TPU material.
The company says that its pellet-based 3D printing technology creates a foam that needs no alterations to designs – whether 3D-printed or moulded – and allows for similar production costs. It’s a move that the company claims will allow for the transition between 3D printing and traditional moulding techniques.
The midsole of the Orca is crafted from TPU foam and features internal lattices that contribute to its 75% energy return and cushioning performance. The outsole is 3D-printed from slip-resistant TPU.
The manufacturing of this shoe still involves some traditional techniques, such as stitching to attach the laceless upper, which is made from a breathable mesh composite of an elastane inner and 3D-printed outer TPU shell for all-around tight fit.
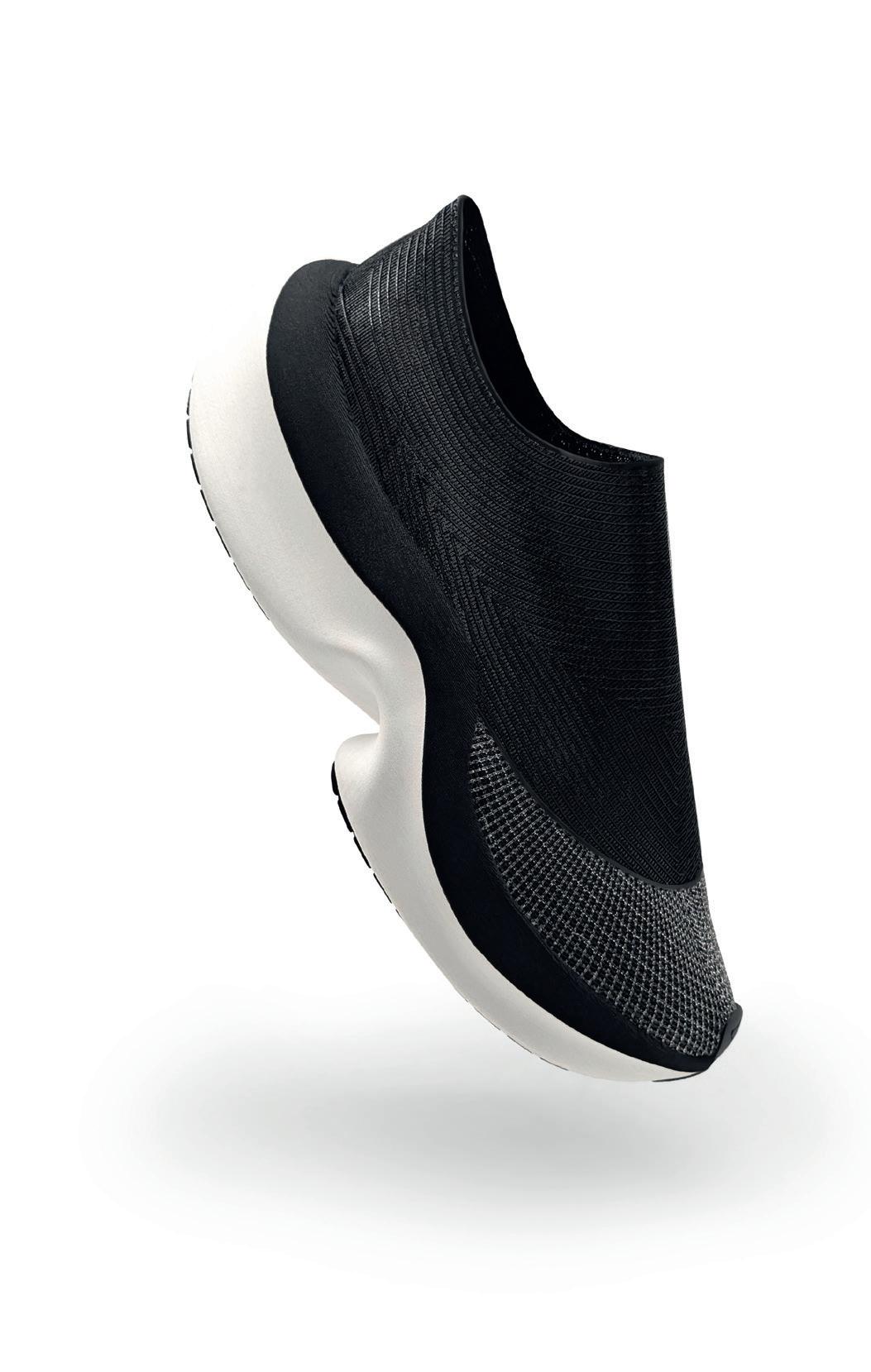
The process, according to Karklinsh, enables designs to move from concept to market in weeks rather than months and reduces initial investment costs by up to 80%, which can only serve to grab the attention of footwear designers. However, Karklinsh suggests that design iteration is only the starting point.
“The actual revolution towards localised production can be only achieved by putting the consumer in the centre of it and integrating all kinds of technologies and craftsmanship into breakthrough products that fascinate consumers rather than designers,” he says.
Fast, scalable and sustainable onshoring are all promised, along with enabling designs that are more familiar to consumers. It certainly sounds like a step in the right direction.
www.elastium.io

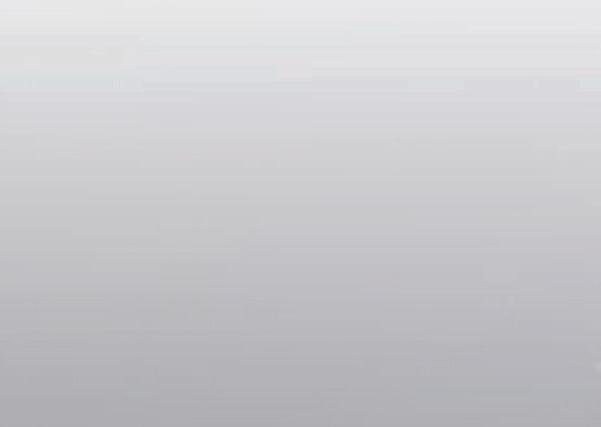
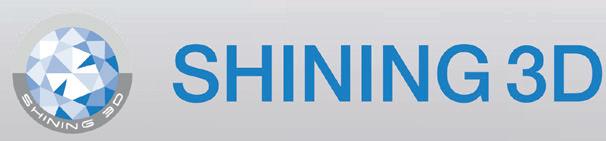
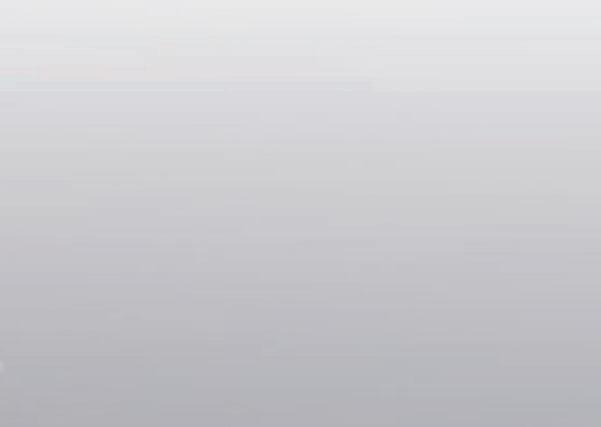
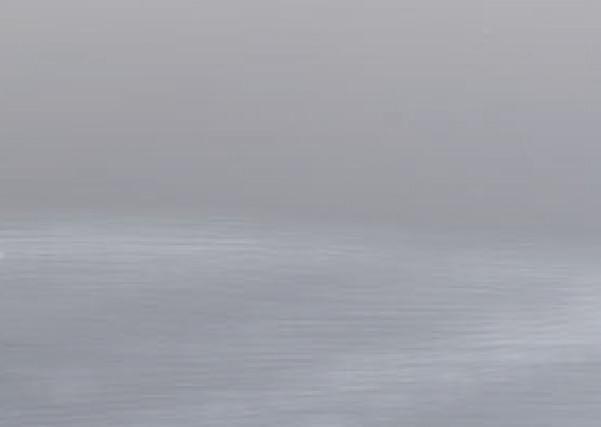
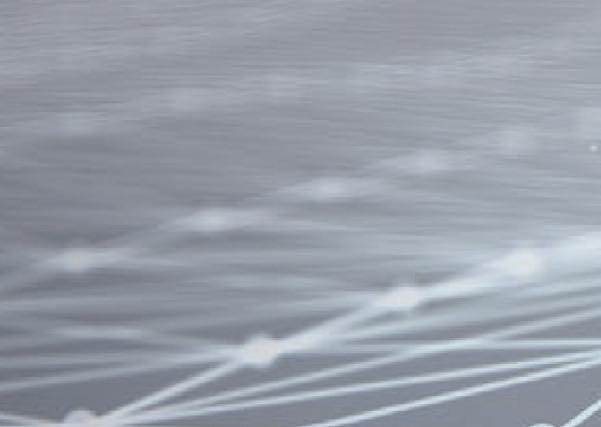
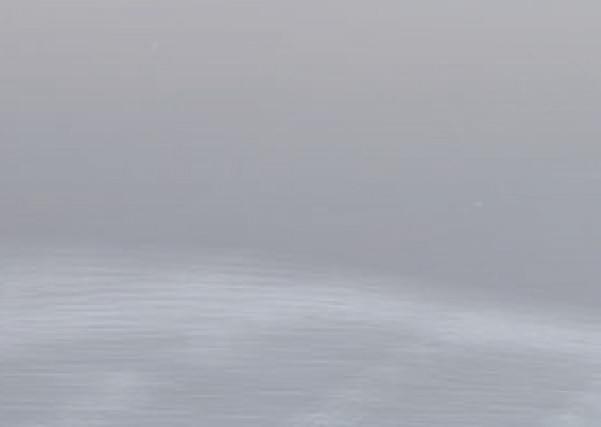
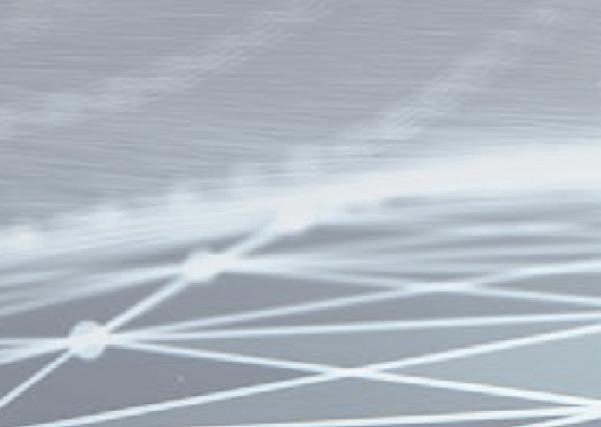
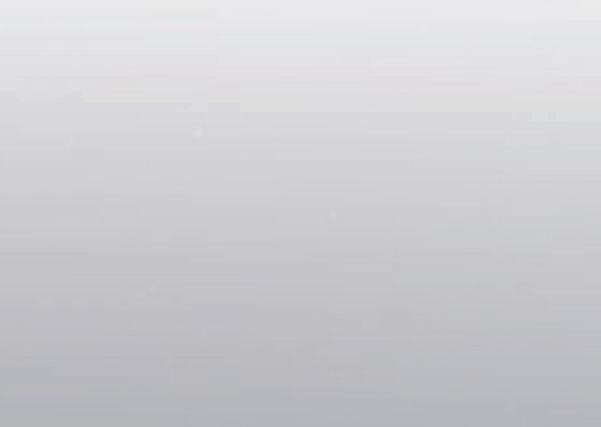
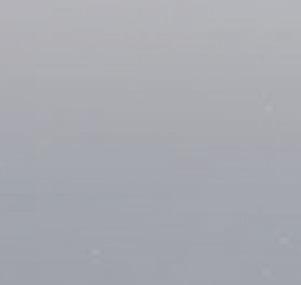
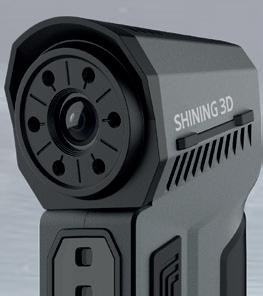
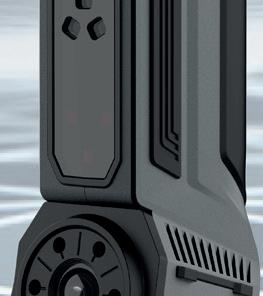
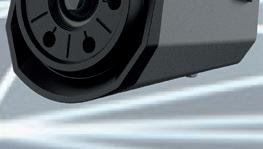
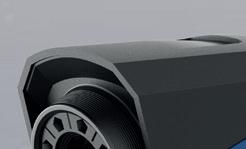

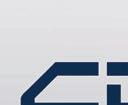
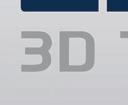

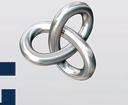
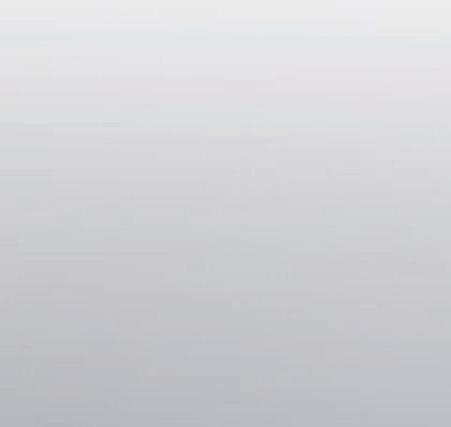

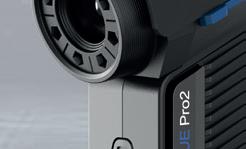
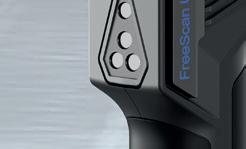
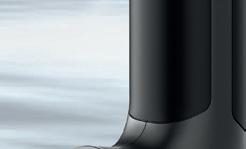
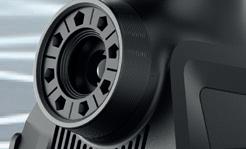

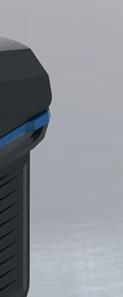
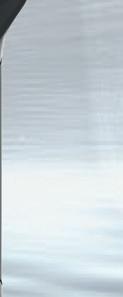

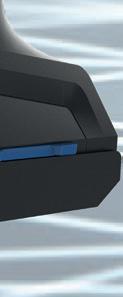


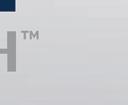
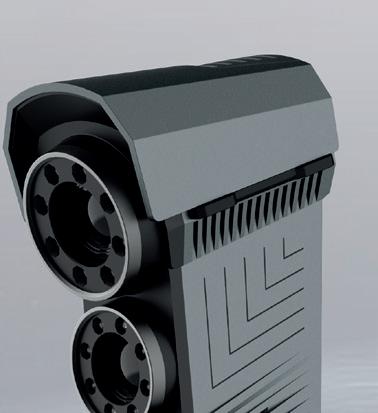
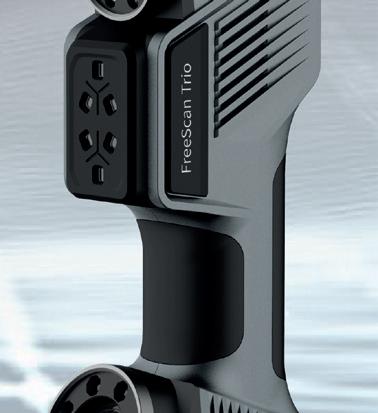


AUTODESK CHARTS
» If 2023 was the year that Autodesk announced its ambitions for AI, 2024 was when it fleshed out some of the details. But, as Greg Corke reports, there’s still a long journey ahead
The Autodesk AI brand debuted in Las Vegas last year at Autodesk University, but the launch lacked any real substance. Despite a flashy logo there were no significant new AI capabilities to back it up. The event seemed more like a signal of Autodesk’s intent to add greater focus on AI in the future — building on its past achievements. It came at a time where ‘AI-anything’ was increasing share valuations of listed companies.
Fast forward 12 months and at Autodesk University 2024 in San Diego the company delivered more clarity on its evolving AI strategy — on stage and behind the scenes in press briefings. Autodesk also introduced a sprinkling of new AI features with many focused on modelling productivity, signalling that progress is being made. However, most of these were for manufacturing with little to excite customers in Architecture, Engineering and Construction (AEC).


to maintain design intent through the entire project. This, said Hooper, eliminates the need for your designer or engineer to spend hours adding relationships to a sketch.
Automatically constraining sketches is just the starting point in Autodesk’s broader vision to use AI to optimise and automate 3D modelling workflows. As Anagnost indicated, the company is exploring how AI models can be taught to understand deeper elements of 3D models, including features, constraints, and joints.
With the click of a button, the AI examines 3D


In his keynote CEO Andrew Anagnost took a cautious tone, warning that it’s still early days for AI despite the growing hype from the broader tech industry.


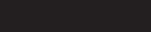
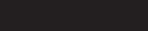


Anagnost set the scene for the future. “We’re looking at how you work. We’re finding the bottlenecks. We’re getting the right data flowing to the right places, so that you can see past the hype to where there’s hope, so that you can see productivity rather than promises, so that you can see AI that solves the practical, the simple, and dare I even say, the boring things that get in your way and hold back you and your team’s productivity.”
One of those ‘boring things’ is sketch constraints, which are an essential part of 3D modelling and govern a sketch’s shape and geometric properties.

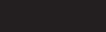



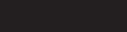
As Stephen Hooper, Autodesk VP D&M product development, explained they are timeintensive to create and must be maintained as the design evolves. “As a result, this step is often skipped,” he said. “That leads to manual rework if you ever change the orientation or size or position of the sketch.”



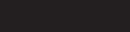
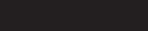
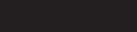
Autodesk Fusion’s new AI-powered sketch auto-constrain feature streamlines this process. It analyses sketches to detect intended spatial relationships between aspects of a design, such as symmetry, relative scale, and relationships between parts. It will then suggest dimensional constraints
days for AI despite the growing hype from the if symmetry, relative scale, and relationships between parts. It will then suggest dimensional constraints
Another ‘boring’ task ripe for automation is the production of drawings. This labour-intensive process is currently a hot topic in CAD (read this AEC Magazine article - www.tinyurl.com/auto-drawings). With Drawing Automation for Fusion, Autodesk is using AI to automate the process, down to the precise placement of annotations. With the click of a button, the AI examines 3D models and does the time-consuming work of generating the 2D drawings and dimensions required to manufacture parts. The technology has evolved since its initial release earlier this year and now accelerates and streamlines this process even more by laying out drawing sheets for each component in a model and applying a style. Early next year, the technology will be able to recognise standard components like fasteners, remove them from drawing sets, and automatically add them to the bill of materials for purchase.
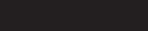
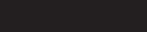
technology has evolved since its initial release earlier this year and now accelerates and streamlines this process even more by laying
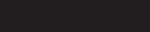
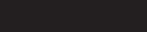
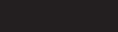





Both these new AI-powered features are designed to automate complex, repetitive, and errorprone processes, significantly reducing the time that skilled engineers spend on manual tasks. This allows them to focus on more critical, high-value activities. But, as Anagnost explained, Autodesk is also using AI to fundamentally change the way people work.
‘‘ You have to teach the computer to speak a certain language We’re creating training methods that understand 3D geometry in a deep way. Those training methods are data independent Autodesk CEO Andrew Anagnost ’’
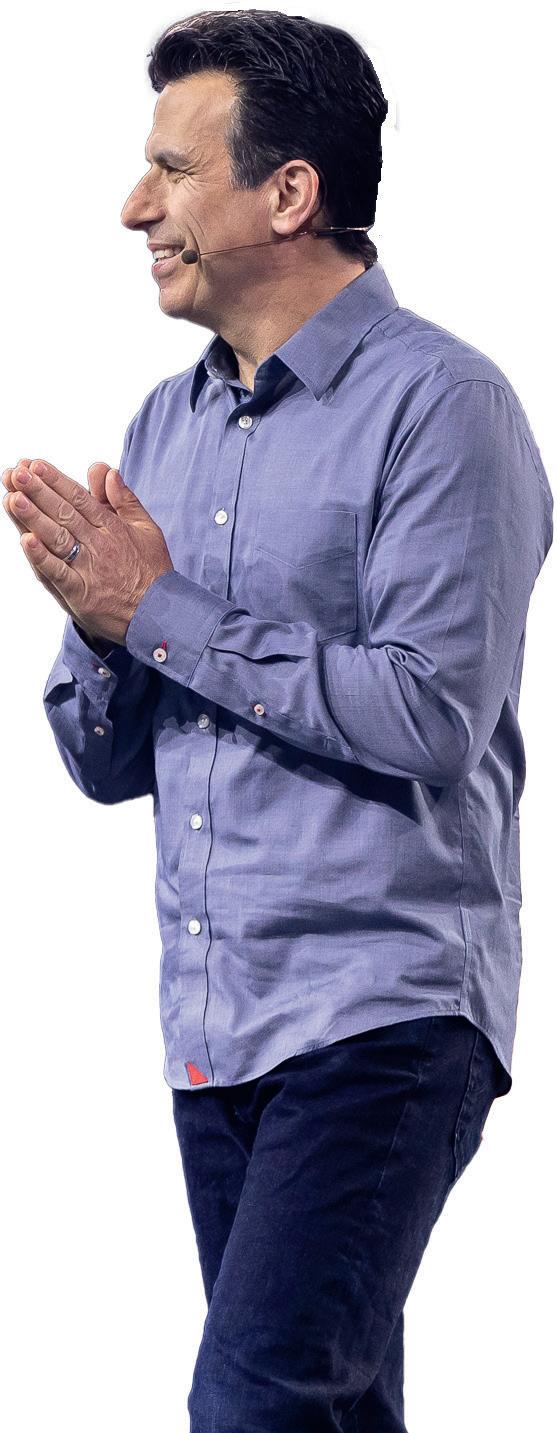
● 1 Autodesk CEO Andrew Anagnost on stage at AU 2024

One approach is to enhance the creative process. Form Explorer is a new generative AI tool for Autodesk Alias, designed to bridge the gap between 2D ideation and traditional 3D design. Emerging from Autodesk’s 2023 acquisition of BlankAI, it allows designers to ‘rapidly generate, modify, and explore 3D concepts in real-time’ without the need to manually edit complex 3D geometry.
traditional 3D design. Emerging from Autodesk’s 2023 acquisition of generate, manually edit complex 3D geometry.
● 2 Project Bernini is designed to generate models that are ‘functionally correct’, so a pitcher, for example, will be empty inside
CHARTS ITS AI FUTURE
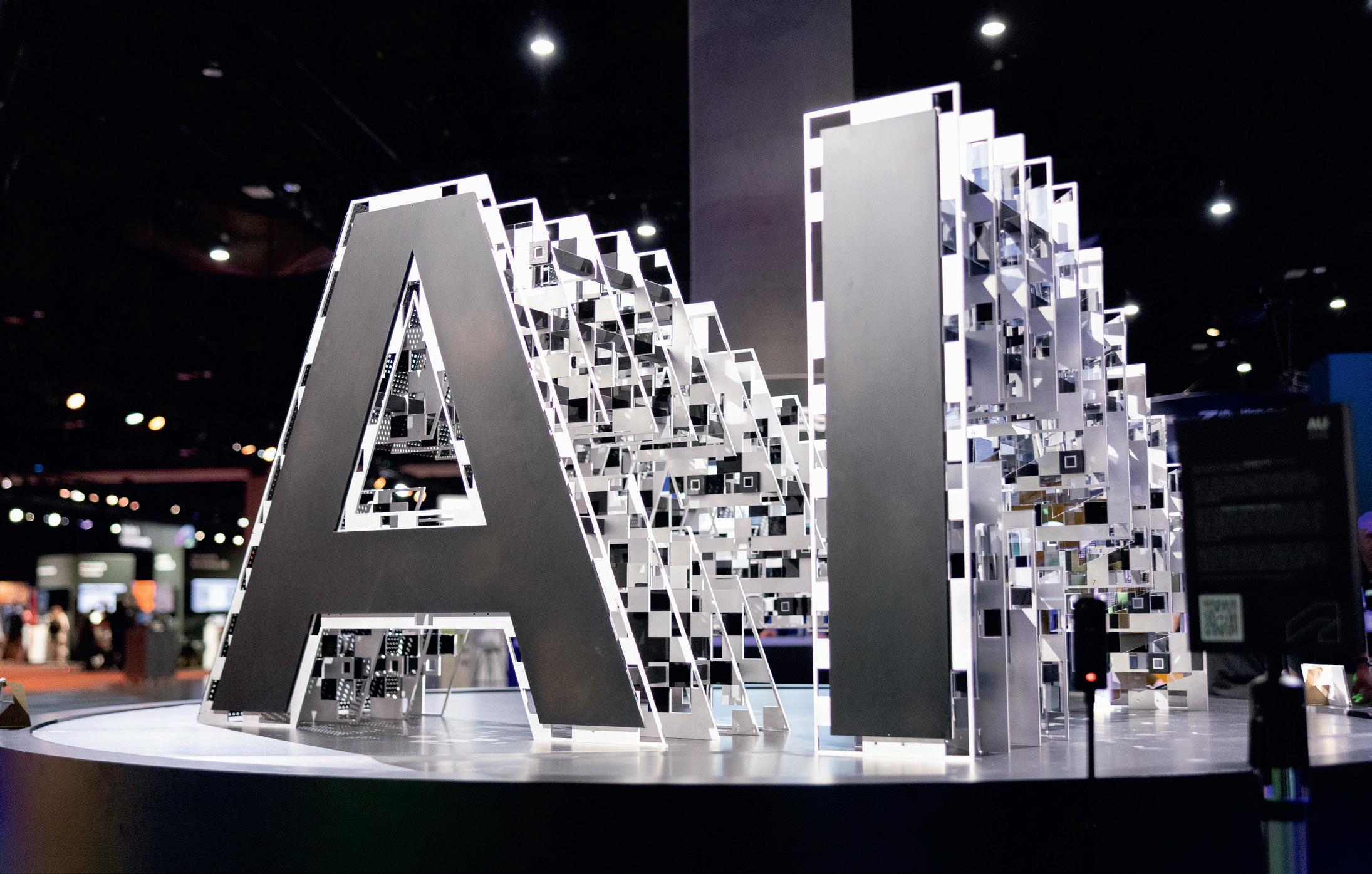
As Hooper explained, the software accelerates creative development by leveraging a company’s historical designs to understand and apply its unique styling language. For each individual firm, the generative AI algorithm is trained on its past 3D models and their associated metadata.
Lessons learned from Form Explorer are also helping Autodesk augment and accelerate creativity in other areas of conceptual design.
Project Bernini is an experimental proof-of-concept research project that uses generative AI to quickly generate 3D models from a variety of inputs including a single 2D image, multiple images showing different views of an object, point clouds, voxels, and text. The generated models are designed to be ‘functionally correct’, so a pitcher, for example, will be empty inside. As the emphasis is on the geometry, Bernini does not apply colours and textures to the model.
Project Bernini is not designed to replace manual 3D modelling. “Bernini is the thing that helps you get to that first stage really quickly,” said Mike Haley, senior VP of research at Autodesk. “Nobody likes the blank canvas.”
Project Bernini is industry agnostic and is being used to explore practical applications for manufacturing, AEC and media and entertainment. In manufacturing, one of the ultimate aims is to learn how to produce precise geometry that can be converted into editable geometry in Fusion. On stage at AU, Jeff Kinder, executive VP of product development and manufacturing solutions
showed a prototype example of how the technology could be applied to conceptual design, taking a pair of sunglasses generated with Bernini into Fusion where the designer can continue to iterate on the concept.
However, there’s a long way to go before this is practically possible. There is currently no established workflow for this, plus Bernini has been trained on a limited set of licensed public data that cannot be used commercially.
AI is also being used to rapidly accelerate engineering simulation and next year Alias will gain new AI capabilities through Navasto, an Autodesk acquisition announced at AU.
The German firm uses AI to bring Computational Fluid Dynamics (CFD) up front in the design process. Formula 1 teams use its technology to train AI models on CFD data, enabling them to ‘instantly predict’ results for geometries that haven’t been previously analysed. Other customers include Audi, General Motors and Volkswagen.
With a forthcoming Navasto plug-in for Alias, wind tunnel simulation will be brought into the early creative design process. The idea is that designers will be able to predict and optimise the drag co-efficient over an automotive exterior and its aerodynamics, while they craft high-quality, aesthetically pleasing surfaces. The ultimate aim: to reduce the likelihood of major redesigns during engineering.
Autodesk is also working on general purpose AI through the application of Large Language Models (LLMs). With Autodesk Assistant, customers can use natural language to ask questions about products and workflows.
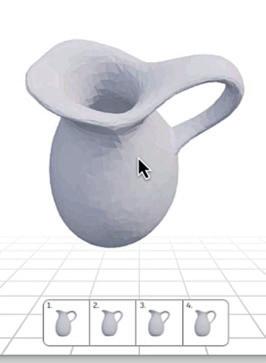
Autodesk Assistant has been available on Autodesk’s website for some time and is now being rolled out gradually inside Autodesk products. Autodesk Assistant in Fusion is billed as an ‘on-demand expert’ trained with both Autodesk-specific knowledge, such as Fusion’s capabilities, as well as general industry knowledge.
“The important thing about the system, is it’s going to be context-aware, so it’s understanding what you’re working on, what project you’re on, what data you’ve run, maybe what you’ve done before, where you are within your project, that kind of thing,” said Haley.
According to Autodesk, users of Autodesk Assistant in Fusion will be able to prompt it with questions like, “How can I program my toolpath to avoid slot milling?” or “What manufacturing methods should I consider for this part?”. Autodesk Assistant will then respond with Fusion-specific answers, or answers specific to manufacturing, and share hyperlinks to original sources.
GETTING CONNECTED
Like most software developers Autodesk is harnessing the power of LLMs or vision models, such as ChatGPT and Gemini. “We can use them, we can adapt them, we can fine tune them to our customers’ data and workflows,” said Haley, citing the example of Autodesk Assistant.
But, as Haley explained, language and vision models don’t have any sense of the physical world, so Autodesk is focusing much of its research on developing a family of foundation models that will eventually deliver CAD geometry with ‘high accuracy and precision’.
Autodesk’s foundation models are being trained to understand geometry, shape, form, materials, as well as how things are coupled together and how things are assembled.
“Then you also get into the physical reasoning,” added Haley. “How does something behave? How does it move? What’s the mechanics of it? How does a fluid flow over the surface? What’s the electromechanical properties of something?”
According to Anagnost, the ultimate goal for Autodesk is to get all these foundation models talking together, but until this happens, you can’t change the paradigm.
“Bernini will understand the sketch to create the initial geometry, but another model might understand how to turn that geometry into a 3D model that actually can be evolved and changed in the future,” he said. “One might bring modelling intelligence to the table, one might bring shape intelligence to the table, and one might be sketch driven, the other one might be sketch aware.”
AI MODEL TRAINING
Model training is a fundamental part of AI, and Anagnost made the point that data must be separated from methods, “You have to teach the computer to speak a certain language,” he said. “We’re creating training methods that understand 3D geometry in a deep way. Those training methods are data independent.”
With Project Bernini Autodesk is licensing public data to essentially create a prototype for the future. “We use the licence data to show people what’s possible,” said Anagnost.
For Bernini, Autodesk claims to have used the largest set of 3D training data ever assembled, comprising 10 million examples, but the generated forms that were demonstrated — a vase, a chair, a spoon, a shoe, and a pair of glasses — were still primitive. As Tonya Custis,
senior director AI Research, admitted there simply isn’t enough 3D data anywhere to build the scale of model required, highlighting that the really good large language and image models are trained on the entire internet.
“It’s very hard to get data at scale that very explicitly ties inputs to outputs,” she said. “If you have a billion cat pictures on the internet that’s pretty easy to get that data.”
The billion-dollar question is where will Autodesk get its training data from? At AU last year, several customers expressed concern about how their data might be used by Autodesk for AI training.
This was a hot topic again this year and in the press conference Anagnost provided more clarity. He told journalists that for a generative AI technology like Bernini, where there’s a real possibility it could impact on intellectual property, customers will need to opt in.
But that’s not the case for so-called ‘classic productivity’ AI features like sketch auto-constrain or automated drawings, “No one has intellectual property on how to constrain a sketch,” said Anagnost. “[For] that we just train away.”
This point was echoed by Hooper in relation to automated drawings, “Leveraging information that we have in Fusion about how people actually annotate drawings is not leveraging people’s core IP,” he said.
To help bring more transparency to how Autodesk is using customer data for training its AI models, Autodesk has created a series of Autodesk AI transparency cards which will be made available for each new AI feature. “These labels will provide you a clear overview of how each AI feature is built, the data that is being used, and the benefi ts that the feature off ers,” said Autodesk CTO Raji Arasu.
●
3 To help build trust in AI, Autodesk AI Transparency Cards are designed to explain how each AI feature is built, the data used, and the benefits it offers
● 4 Autodesk Assistant in Fusion will provide ‘expertlevel’ answers to questions about completing tasks in Fusion, and best practices in manufacturing
●
5 AutoConstrain in Fusion Automated Sketching helps maintain a designer’s intent throughout project iterations by detecting and suggesting dimensional constraints between aspects of a design
●
6 Drawing Automation in Fusion automates the time-consuming process of creating 2D drawings from 3D models of parts and assemblies
●
7 For automotive exterior designers, Navasto’s AI-based wind tunnel performance and aerodynamics analysis predictions are coming to Autodesk Alias 3
Of course, some firms will not want to share their data under any circumstances. Anagnost believes that this may lead to a bifurcated business model with customers, where Autodesk builds some foundational intelligence into its models and then licenses them to individual customers so they can be fine-tuned with private data.
AI COMPUTE
AI requires substantial processing power to function efficiently, particularly when it comes to training. With Autodesk AI, everything is currently being done in the cloud. This can be expensive but, as Anagnost boasted: “We have negotiating power with AWS that no customer would have with AWS.”
Relying on the cloud means that in order to use features in Fusion like auto constraints or drawing automation, you must be connected to the Internet.
This might not be the case forever, however. Arasu told DEVELOP3D that AI inferencing [the process of using a trained AI model to make predictions or decisions based on new data] could go local. She noted some of Autodesk’s customers have powerful workstations on their desktops, implying that by using the cloud for compute would mean a waste of their own resources.
AN ITERATIVE FUTURE
Autodesk is beginning to add clarity to its AI strategy. It is addressing AI from two angles: bottom up, bringing automation to repetitive and error prone tasks, and top down with technologies like Project Bernini that in the future could fundamentally change the way designers and engineers work. The two will eventually meet in the middle. Autodesk is keen to use AI to deliver practical solutions and the automation of drawings and constraints in Fusion should deliver real value to many firms right now, freeing up skilled engineers at a time when they are in short supply. Meanwhile, it’s clear there’s still a long way to go before the AI foundation models being explored in Project Bernini can deliver CAD geometry with ‘high accuracy and precision’.
While Bernini is starting to understand how to create basic geometry, the 3D models need more detail, and Autodesk must also work out how they can be of practical use inside CAD. With rapid advances in text-to-image AI, one also wonders what additional value text-to-CAD will bring to concept design. One could also ask whether product designers or engineers would even want to use something like this to kickstart their design process. As the technology is still so embryonic it’s very hard to tell, and it’s important to remind us all that this is a proof-of-concept to explore what’s possible, rather than a practical application.
Meanwhile, as Autodesk continues to develop the complex training methods, there’s also the challenge of sourcing data for training. It will be interesting to see how Autodesk’s trust relationship with customers plays out.
While Autodesk’s long-term plan is to get multiple foundation models to talk together, this doesn’t mean we are heading for true design automation any time soon.
At AU Anagnost admitted that the day where AI can automatically deliver final outcomes from an initial specification is further away than one might think. “For those of you who are trying to produce an epic work of literature with ChatGPT, you know you have to do it iteratively,” he said. That same iterative process will apply to AI for design for quite some time.

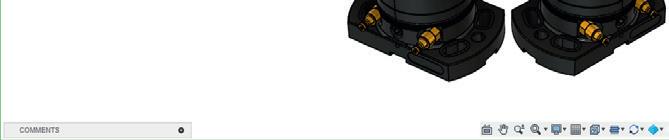
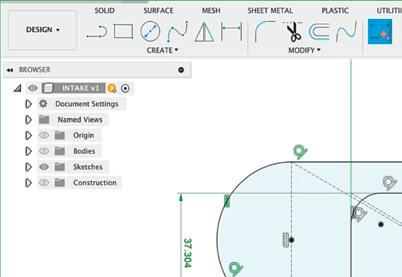
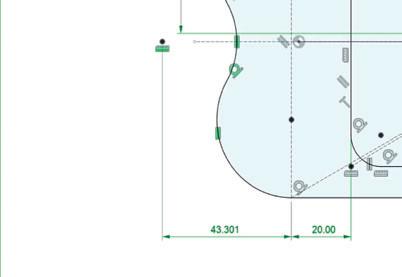
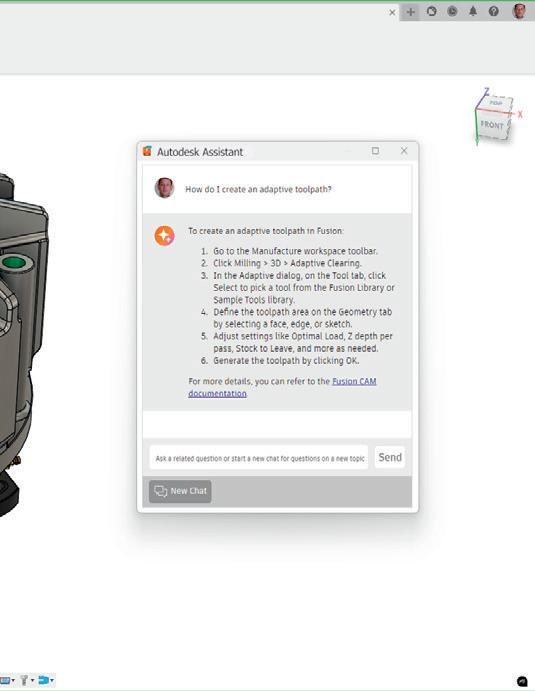
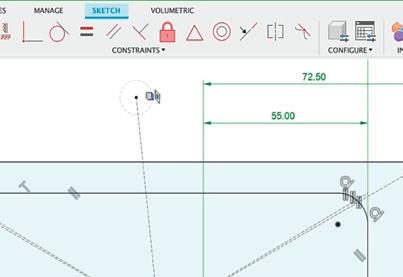
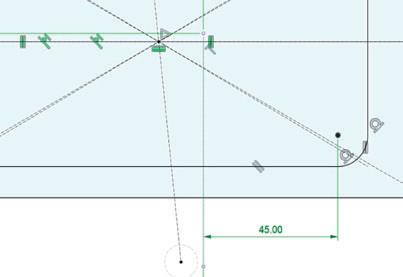

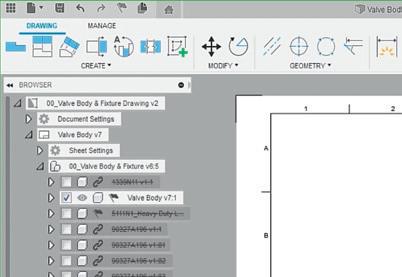
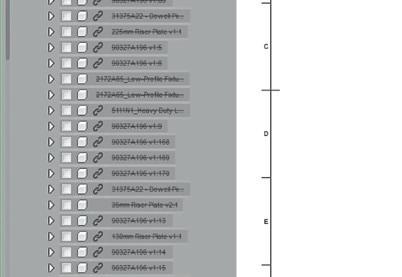
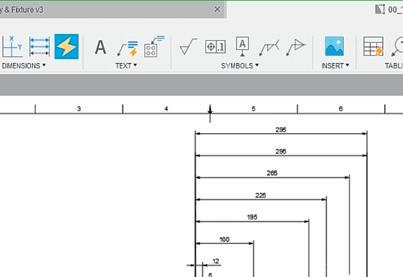
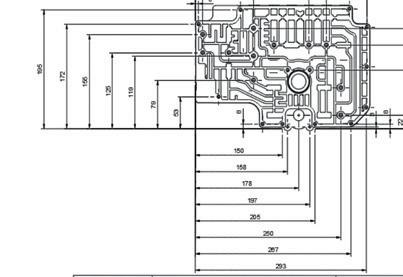


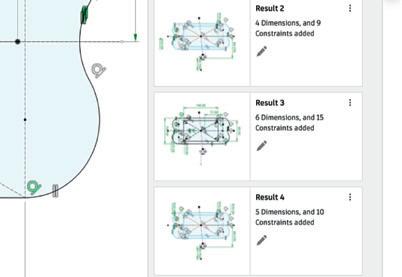
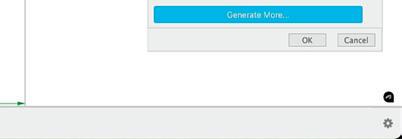

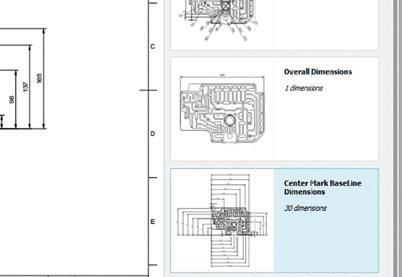
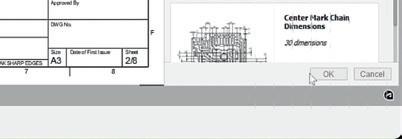
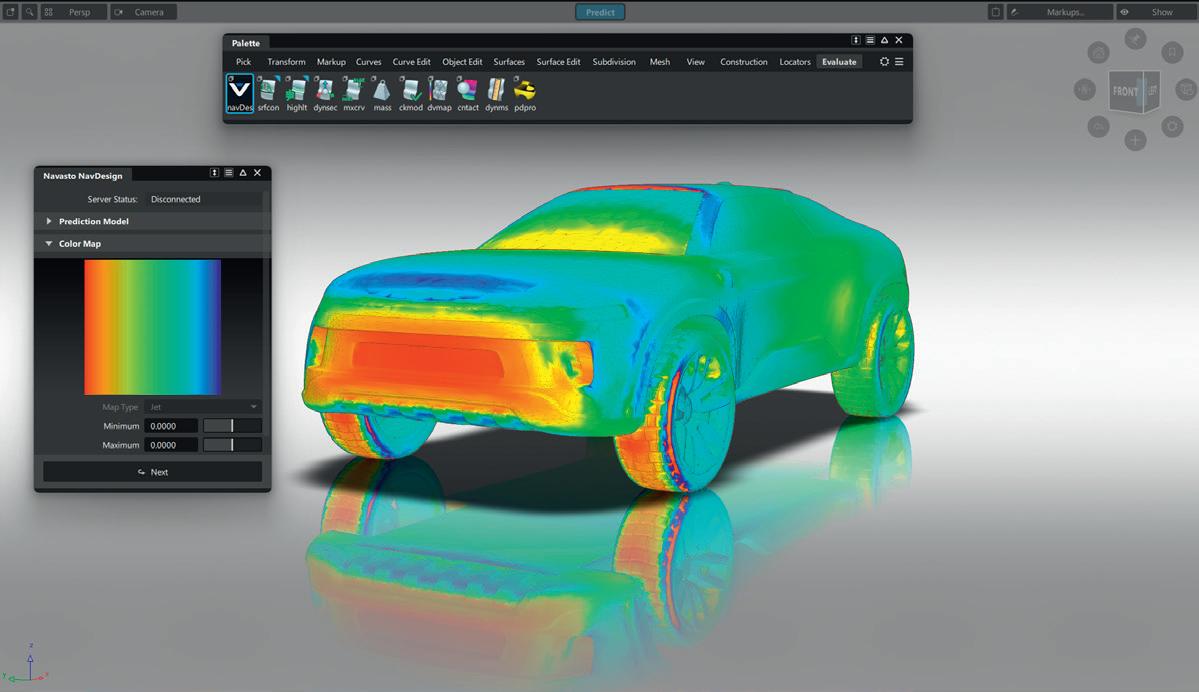
www.autodesk.com
ALL THAT GLITTERS
» Additive manufacturing is transforming jewellery, and Progold is at the forefront of the movement, producing perfect parts that require little polishing, reports Emilie Eisenberg
Damiano Zito, CEO of Progold, is far too discreet to disclose client names, but he assures DEVELOP3D that they include brands operating in the highest echelons of the fashion world.
“We are not talking about mass [produced] fashion accessories, or mass jewellery,” he says. “We are talking about brand jewellery and brand fashion accessories. People pay several thousand euros for a bag or several thousand euros for jewellery. People need perfect, and they are not open to paying these amounts for something that is not perfect.”
Zito took over the reins at Progold from his father back in 1997. A distributor of gold, silver and platinum alloys to jewellery manufacturers around the world, the company began to explore metal powders for 3D printing in 2008, investing in powder bed fusion (PBF) technology. Having promoted these technologies and its feedstocks to their clients, in 2015, Progold spotted a gap in the market and began its own in-house service bureau, using its own PBF 3D printers to produce precious metal parts.
The company currently has ten printers in-house that can produce precision parts using 18K yellow, red and white gold and platinum, which it delivers to clients to be finished by skilled craftsmen.
METALS EXPANSION
As fashion houses have expanded their lines, there has been a concomitant increase in the number of metal parts needed, too, from handbag clasps and buckles to jewellery items. The traditional approach of using electroplated copper and brass hardware has shifted to stainless steel parts, coated with a thin layer of precious metal using the PVD (physical vapour deposition) method.
The plating is often just a few microns thick, but requires no extra coatings to maintain the kind of smooth, long-lasting finish favoured by the biggest brands in luxury goods.
This shift has created another opportunity for Progold, allowing it to produce non-precious metal additive parts to be plated. However, the thinner coating is less capable of hiding the rougher surface blemishes of the PBF process.
“You can print whatever you want with a 3D printer, but you can polish only some of it,” says Zito. “If it’s a mechanical component, no problem. But if it’s an aesthetic piece? Would you go to buy an expensive piece of jewellery if, in some of the holes, it was rough? No!”
This led Progold to explore new additive technologies that require less post-processing, while still allowing
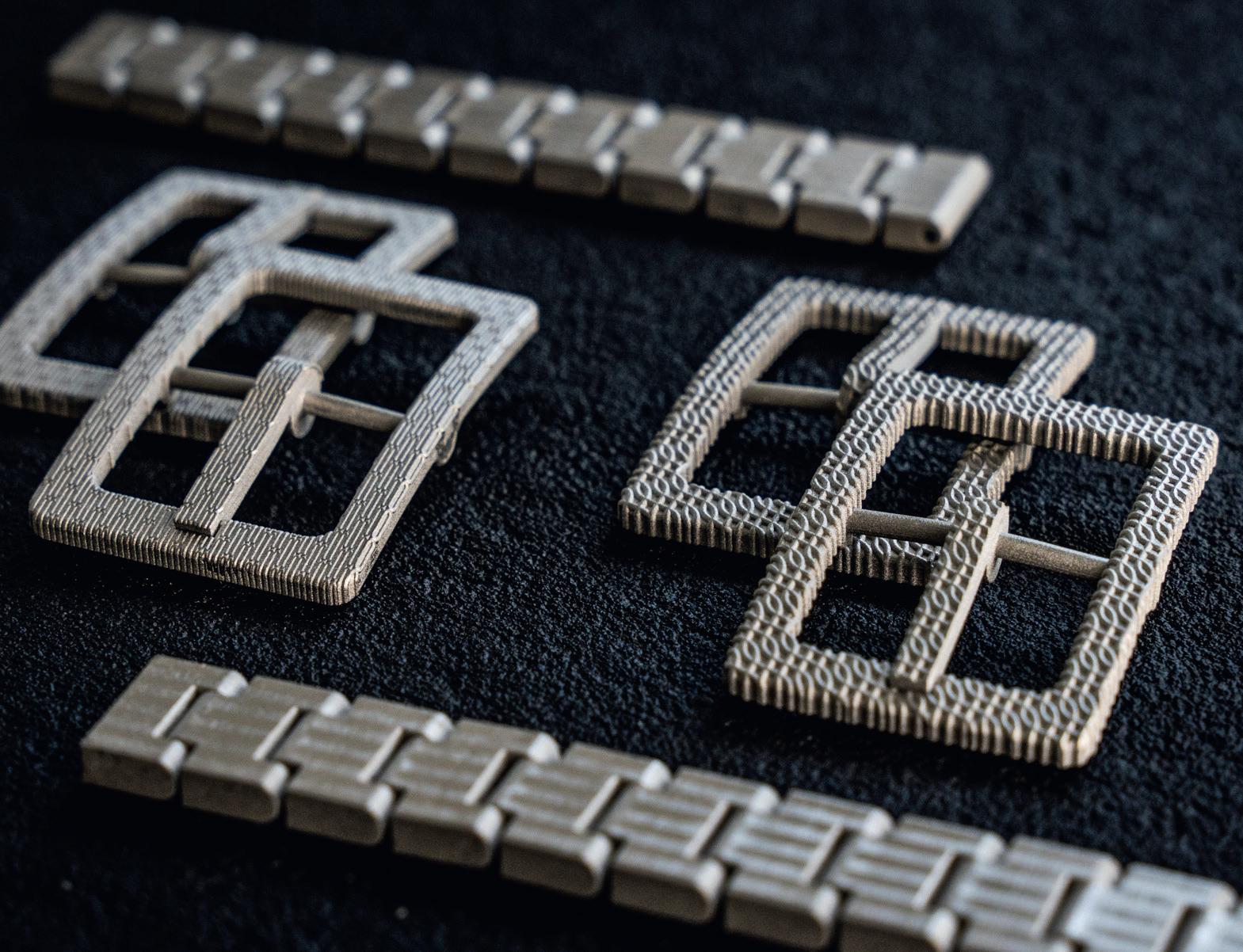
design freedom when it comes to additive parts.
A partnership founded in 2021 with NanoParticle Jetting (NPJ) expert XJet saw Zito’s team bring an XJet Carmel 1400 M Metal System to its headquarters in Trissino, Italy.
The technology sidesteps some of the issues associated with 3D printing with powders and lasers, by instead suspending metal or ceramic particles in a solution, before layering it (along with a support material) from high-resolution print heads.
A 300C build chamber evaporates the liquid ‘ink’, fusing the part into a solid. The soluble support material is removed easily once removed from the printer, before the green part is finished in a kiln.
Boasting an accuracy of 50 microns on dimensions up to 5mm, the surface finish of 316L stainless-steel part, once sintered, is so good that it requires minimal postprocessing before a PVD coating can be applied to give a beautiful high-end finish.
For Progold, this has been a resounding success, leading to the company to produce a wide range of hardware, jewellery and watch cases using the process.
METALLURGY KNOW-HOW
Progold’s CEO says that, in addition to its production capabilities, the Italian company’s background in metallurgy and cutting-edge laboratories sees it lending its knowledge to global brands, acting primarily as consultants on 3D printing. This is helping to steer some of the biggest brands towards using the right 3D printing technology for their particular designs and getting the best results.
“With PBF, there is the issue of the support system that is not only holding the parts but transferring the melting heat from the laser. Support systems are very complex, and we need to work side-by-side with the customer. With nanoparticle jetting, it’s different. Much more is on the side of the sintering phase, and we have all the know-how to do all the sintering phase in a very scientific way. It is very important.”
It is scientific prowess like this that Zito is keen to emphasise when discussing his company, over its manufacturing capabilities. “One advantage that we believe we have over any other [company] is that we are really able to fix the parameters not by experience or by superficial understanding, but because we are able to go into the material and understand the material,” says Zito.
“We approach every single problem in a very scientific way,” says Zito, confirming that even high fashion has its basis in the elemental.
www.progold.com
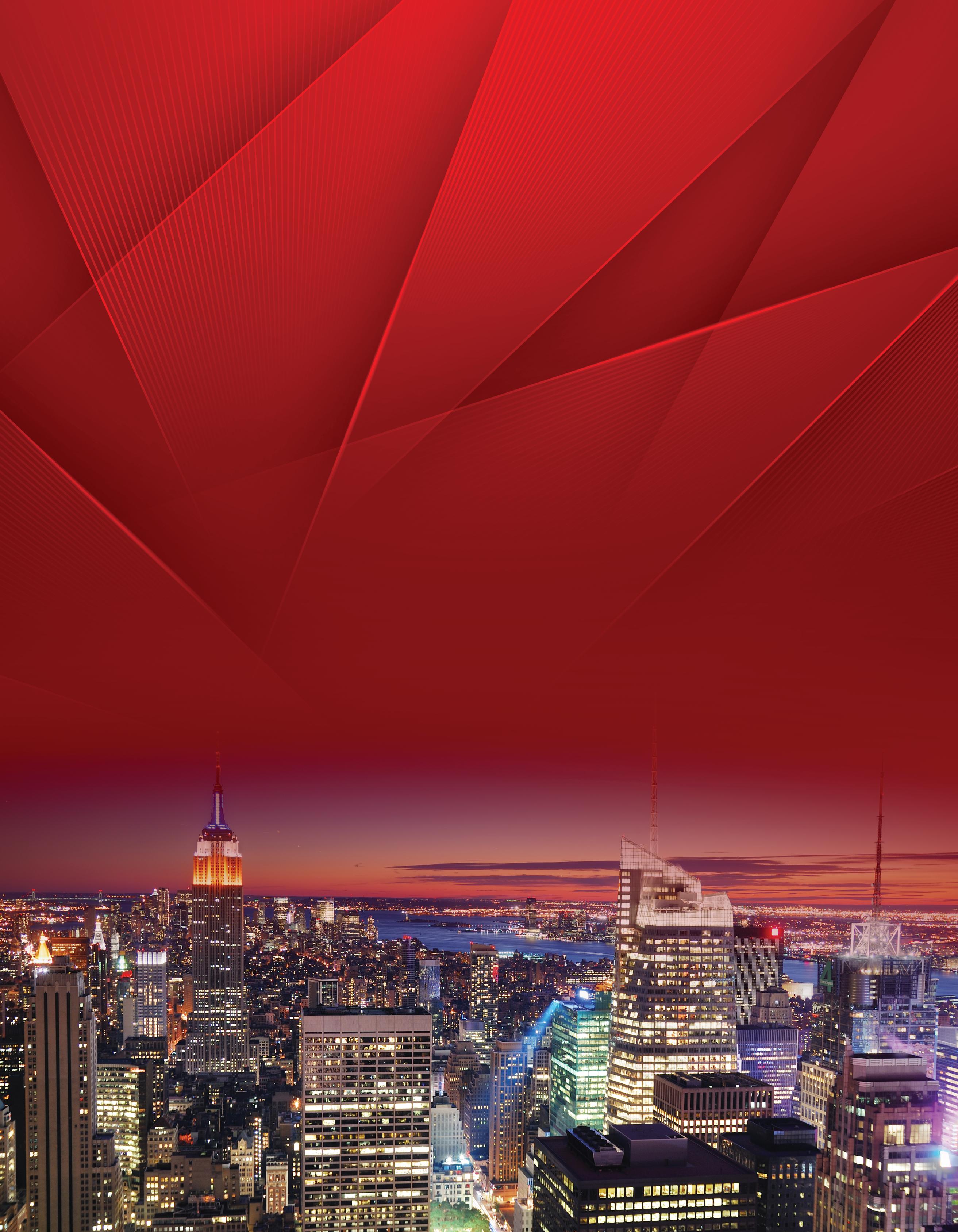
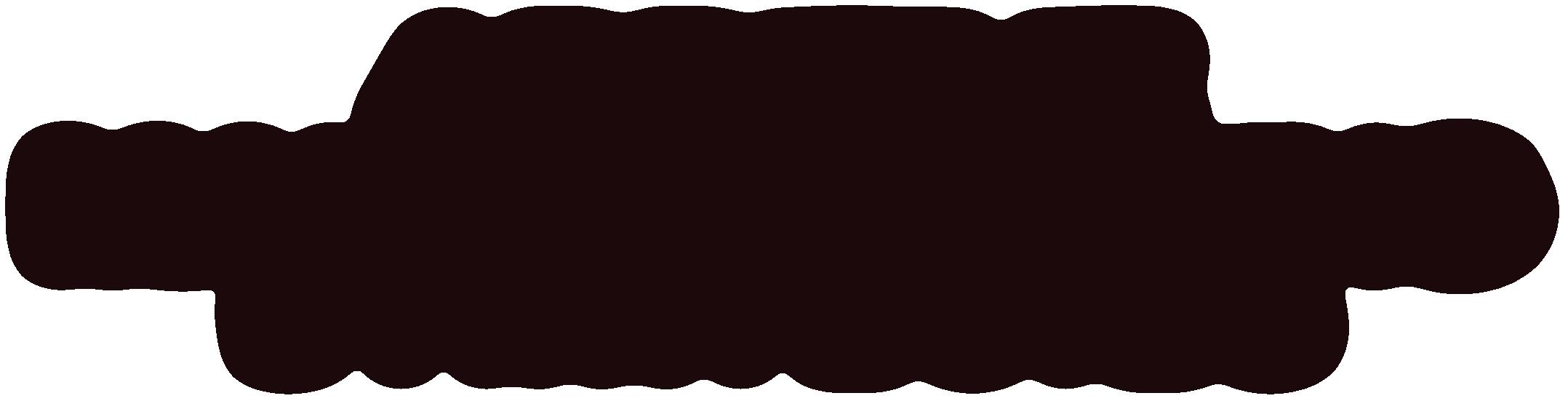

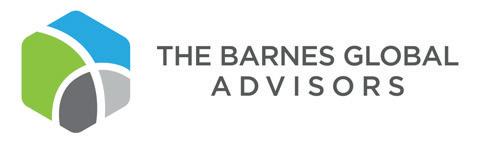
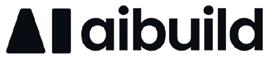
LARGE FORMAT ADDITIVE
» Large format additive manufacturing, or LFAM, has evolved rapidly in recent years, with technologies from companies including Caracol and MX3D enabling users to take giant steps forwards, thanks in part to custom software and robotic arms equipped with printheads. DEVELOP3D spoke with executives from both companies about current use cases and smart approaches to adoption
CARACOL: LFAM WITH POLYMERS
Q (D3D): What would you say are the overall benefits of your company’s LFAM technology?
A (Caracol): Caracol’s Heron AM platform is a 6+ axis platform that works with pellet thermoplastic composites, from high temperature resins to recycled and bio-based options. With an average bounding box of 3 cubic metres, it can be extended to 12 cubic metres, and robotics give the ability to print multi-planar, non-planar, conformal, 45-to-60-degree printing and more.
Q: And if you had to pick out a key benefit, which one would you say best represents your company’s unique selling point?
A: Simplicity for the user. Heron AM is a turnkey solution developed following years of experience working on applications across sectors, and looks to simplify a company’s manufacturing processes providing flexibility, efficiency and sustainability.
Q: From which industry sectors are you seeing the most adoption?
A: We’re seeing systems adopted in the aerospace and automotive industries - for tooling, jigs, fixtures, moulds, mock-ups and custom parts development – and in the marine industry, where it is used for finished parts or boat hulls, prototypes and pre-series.
Q: And in which industry sectors would you say your company’s LFAM technology is having the biggest impact?
A: The biggest impact often combines benefits in terms of lead times with cost efficiencies, as well as more sustainable processes. For example, for tooling in aircraft manufacturing, LFAM can on average reduce costs by 30% and lead times by 50%, creating tools that are 50% lighter.
Q: Is Caracol attracting interest from any areas that have come as a surprise to you?
A: LFAM has gained unexpected interest in the marine and construction industries, which usually adopt very traditional and manual methods. However, the need to improve efficiency and sustainability and sometimes the safety of their highly customised production processes has driven them towards LFAM adoption.
Q: What type of robot arms does Caracol’s technology work with?
A: Heron AM can be set up with several robotic arms, such as models from Kuka, Fanuc and ABB. On average, the chosen robotic models have a reach of around 3 metres, easily extendable with booster frames or plinths, as well as with rails as additional axis. All of Caracol’s systems are supplied with enclosures, which can be either plexiglass protections, or closed rooms or enclosures to control humidity, temperature and so on. This is fundamental to guarantee safety to operators as well as for best performance.
Q: What design constraints need to be considered early on for LFAM parts?
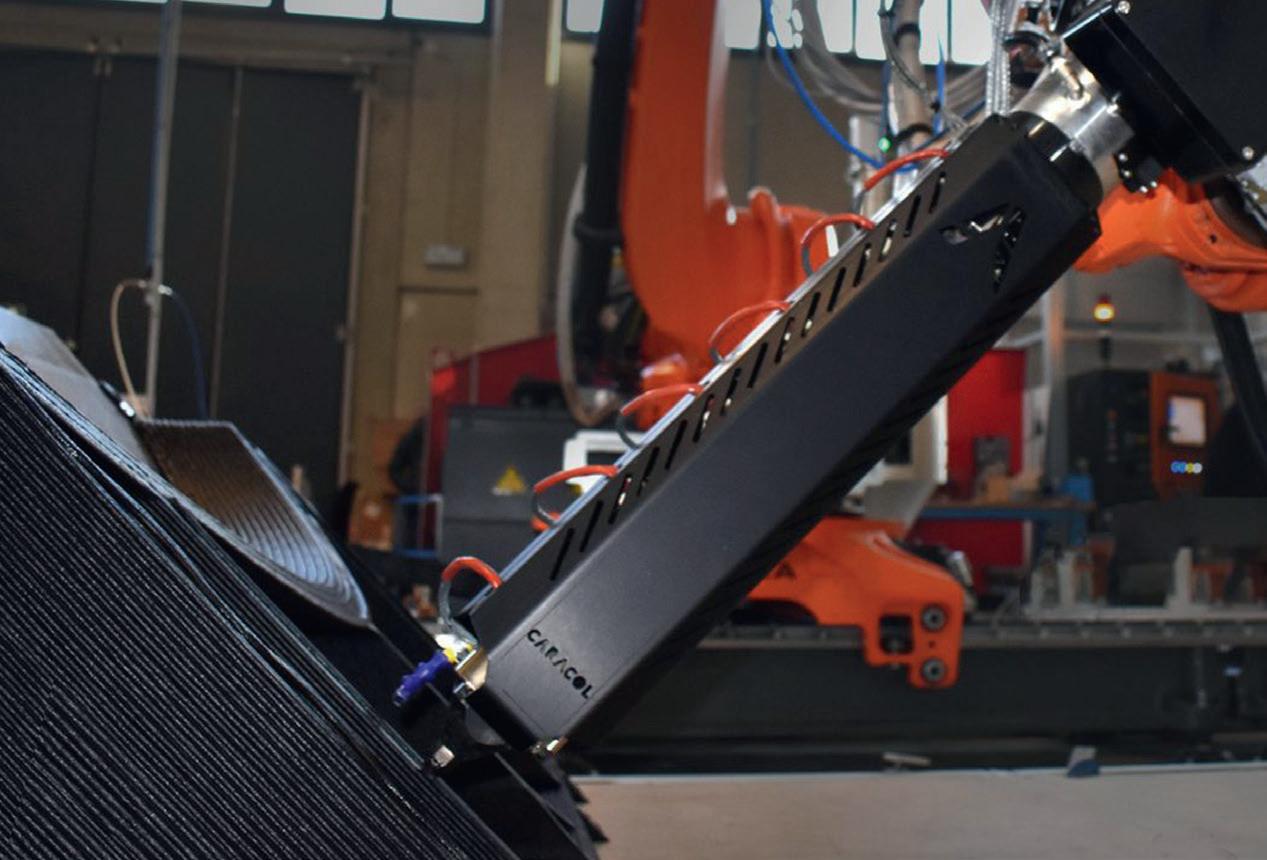
A: LFAM means having a lot of freedom, but requires some understanding of a few key aspects. In some cases, these are like other AM technologies, and in other ways, very different. Some aspects to look into closely when designing parts include aspects like overhangs and descents, to avoid material collapse and delamination, toolpath settings, offsets and walls to ensure wall runs, support and ribs, bed positioning to avoid warping.
Q: How does your software communicate with 3D CAD packages and how do you help address issues with models in terms of editing them, building simulation and so on?
A: Caracol’s Eidos Manufacturing software suite can import standard CAD files and other formats into its libraries, analyse them with a 3D mesh editor, assess and even adjust some issues in the
files. After this first check, it’s possible to set up parameters and path planning, to generate a 3D printing file. The software seamlessly integrates with Heron AM and allows users to accurately simulate the printing programme. It is possible to simulate robot kinematics, process inverse kinematics and perform collision checks and singularity analysis etcetera with an intuitive interface that clearly reports the simulation’s feedback.
Q: In your opinion, is a background in working with robotics necessary for getting the best out of LFAM?
A: A background in robotics is not needed to operate a robotic LFAM platform and Caracol provides comprehensive training, ensuring users are well-equipped to utilise the system effectively. We are seeing a lot of excellent work from customers that didn’t
have any previous robotics experience. The best users usually already had some capabilities in AM, but we’ve been working well also with companies with more traditional manufacturing capabilities that are completely new to 3D printing.
Q: What would you say are some of the limiting factors of LFAM?
A: The major criteria to keep in mind are: production volumes (ideal for on-demand or small batches); geometrical complexity (difficult to obtain with traditional technology); materials (from part production to postprocessing needs); technical and mechanical requirements; technical advantages achievable (eliminating assemblies and enabling lightweight structures); supply chain and logistics (ability to localise production, print on demand, and more).
www.caracol-am.com
MANUFACTURING 101
MX3D: LFAM WITH METALS
Q (D3D): What would you say are the overall benefits of your company’s LFAM technology?
A (MX3D): Using a type of metal 3D printing called Wire Arc Additive Manufacturing (WAAM), we stand out from other AM technologies for our high deposit volume and cost effectiveness, with excellent mechanical properties. This makes MX3D’s WAAM ideal for producing large, complex metal parts - think over 5 tons and measuring over 5 metres.
Q: And if you had to pick out a key benefit, which one would you say best represents your company’s unique selling point?
A: Lead time reduction. The key reason why clients need our help is to reduce lead times compared to casting and forging processes. We sometimes reduce lead times by over a year!
Q: From which industry sectors are you seeing the most adoption?
A: The energy, maritime and aerospace sectors have lately been active in increasing their use of WAAM, due to its ability to produce large, complex metal parts meeting highperformance requirements, with great lead times. Defence and AEC are next in line.
Q: And in which industry sectors would you say your company’s LFAM technology is having the biggest impact?
A: WAAM is currently making the biggest impact in the energy industry. The technology has proven it can
comply with that industry’s strict standards. Several successful pilot projects have increased the industry’s belief and appetite for WAAM. Lead time is their biggest pain and our biggest advantage.
Q: Is MX3D attracting interest from any areas that have come as a surprise to you?
A: The nuclear sector. After many years of research and convincing the market, we finally saw increased confidence in the quality of WAAM prints in recent years. Still, we were surprised by the fact that even nuclear and space are now big fans of WAAM. Those industries are risk averse –and for good reasons.

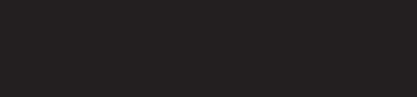

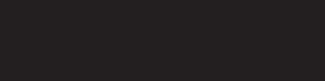
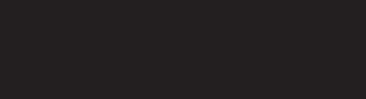

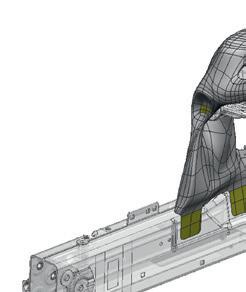


The fact that these industries, based on empirical research, now invest in MX3D’s WAAM definitively proves the potential of this technology.
Q: What type of robot arms does MX3D’s technology work with?
A: Currently, we work with ABB and Kuka robots, 6-axis arms and additional positioners. Our software workflow, however, is suitable to work with most types of industrial robots. We kept it ‘agnostic’. But as we have a small team, we try to keep hardware variables as low as possible for now.
Q: What design constraints need to be considered early on for LFAM parts?
A: General FDM printing design guidelines often apply for our

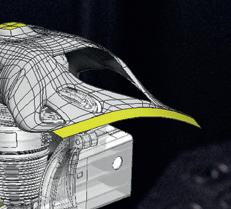




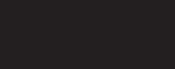
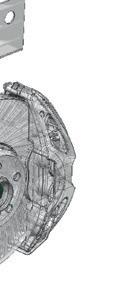

technology. As mentioned, the technology works best with relatively large metal parts. We can start printing parts or segments mid-air. WAAM wall thickness typically starts at 3mm, but no maximum wall thickness applies. We typically say that parts, especially more complex ones, need a minimum size, say, of 15cm by 15cm and more than 5Kg before this technology makes sense. Furthermore, WAAM does not print large flat surfaces well, due to distortion caused by heat input. With a flat surface, we can add support ribs.
Q: How does your software communicate with 3D CAD packages and how do you help address issues with models in terms of editing them, building simulation and so on?
A: One of our differentiators is that MX3D has its own WAAM-dedicated software called MetalXL. It provides an end-to-end workflow for industrial WAAM, starting at a CAD file, creating CAM for WAAM, active control loop and all the way to a complete print report for the qualification officer. Our software signifies CAD issues. Certain CAD issues can be repaired by MetalXL, while for others, tips are given to the user to improve the file. Furthermore, the user is given a review of the WAAM printability of the part, including tips to improve this. With our partners, we are working on a beta add-on that helps with identifying and solving problematic distortions.
Q: In your opinion, is a background in working with robotics necessary for getting the best out of LFAM?
A: Surprisingly not! We solved the robotics part. It’s always an advantage, but in practice, our software and robotic systems do not require a robotics background. We provide on-site training to designers, engineers and operating teams to ensure a smooth start with WAAM technology. In our case, we advise operators who have at least basic or better welding knowledge.
Q: What would you say are some of the limiting factors of LFAM?
A: Thermal distorting from high heat might be limiting, but it is not all that serious, as users are getting around it by optimising designs to minimise heat accumulation, allowing for post-processing like machining to improve surface finish, and using advanced control systems to enhance precision and material properties. www.mx3d.com
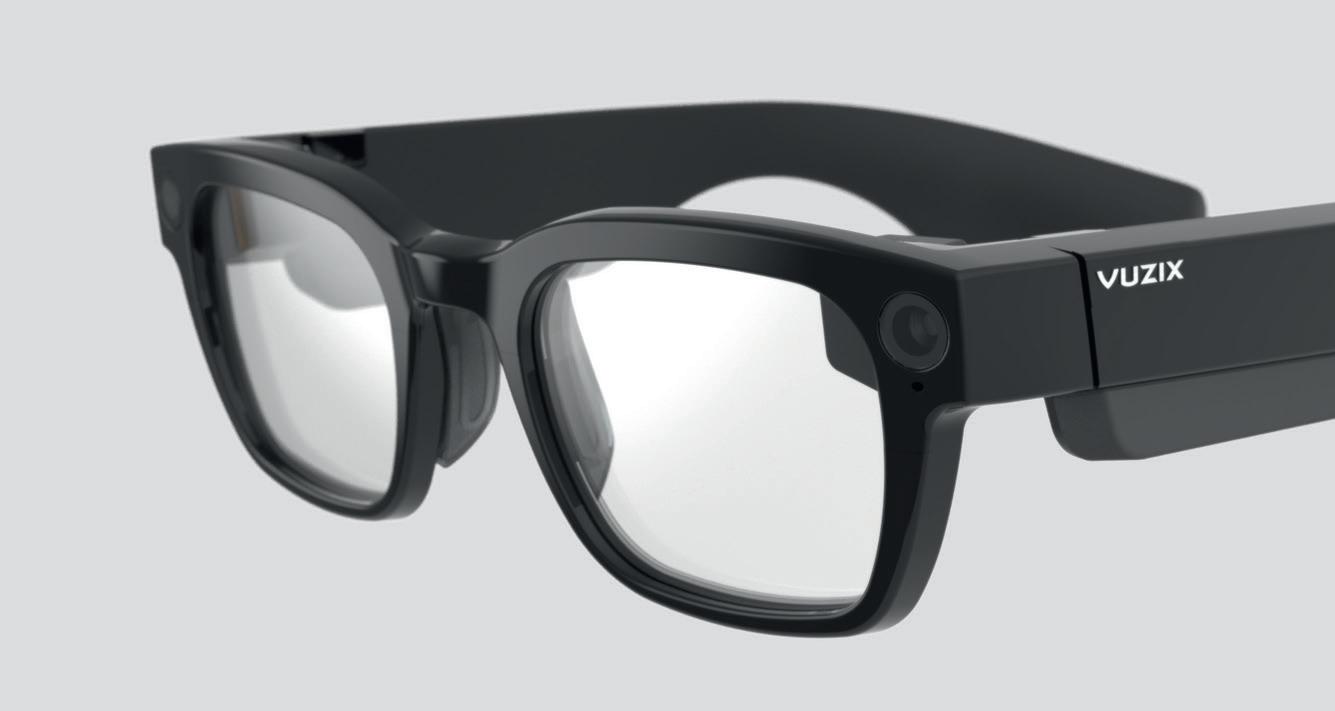
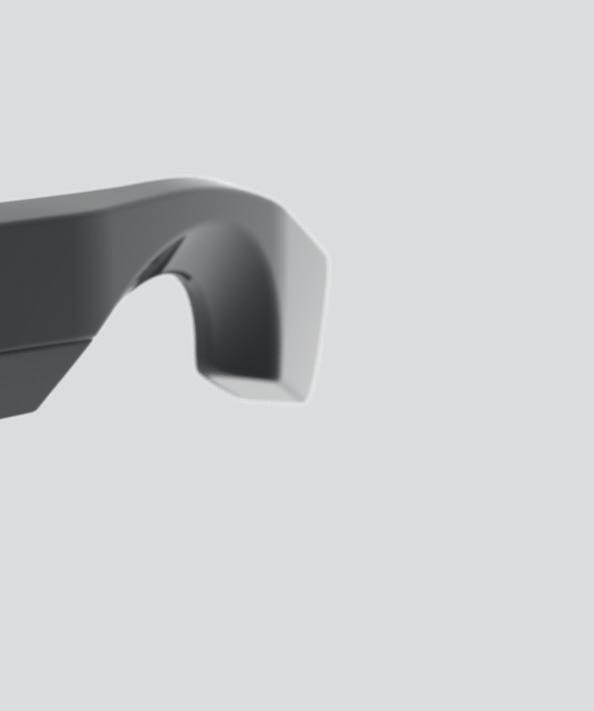
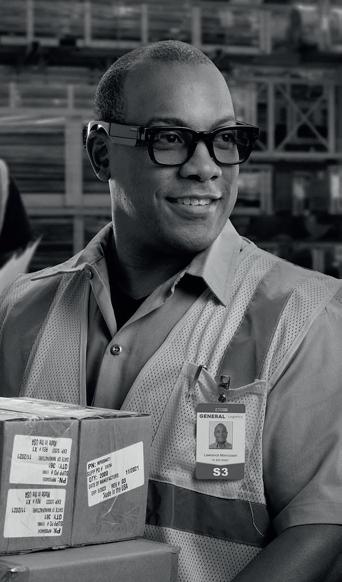
SMART & STRONG
» In design, the right material choice can make all the difference. In the case of Vuzix’s Shield smart glasses, expert advice from Materialise gave this piece of kit the rigidity to operate in tough working conditions while still remaining stylish
At first glance, Vuzix’s Shield glasses are a pair of safety work glasses with a stylish titanium frame. Wear them, however, and their onboard 8-core CPU puts some unexpected capabilities within view. Cut to the present day, and barely a fashion week passes without another 3D printed running shoe, clog or slip-on being launched. The reasons for that – beyond aesthetics – are clear.
These smart glasses connect their wearer to a world of IT sensors, instructions and live remote guidance, via miniature uLED stereo displays. Codes can be scanned with an advanced reader and video can be streamed from the field, with all functions enabled through voice or touch.
For Vuzix, it was important for all of its technology to be incorporated in a traditional eyewear form factor. In turn, this eyewear had to meet the requirements laid out by the ‘three Fs’ – fashion, function, and fit.
In other words, it was crucial that these smart glasses looked as good as they worked, so that they would appeal to a broad audience, while also taking into account the science around how the human eye works, and also how consumers wear their glasses.
But in designing the Shield, the biggest challenge came down to stability. With the twin displays sitting in a fixed component within each temple, keeping the frame rigid was key, explains Shane Porzio, vice president of engineering at Vuzix.
“If anything’s out of alignment, especially on binocular systems, you literally can’t use the images. So, from user to user, taking them on and off , beating them up, these things all have to stay aligned within a pixel for rotation and vertical and horizontal positioning. That means we can’t aff ord any twisting, rocking or ratcheting across the front frame.”
STIFF CHALLENGE
Prototypes built using injection moulding with both carbonand glass-filled polymers failed to provide the necessary stiffness, according to Porzio. “No matter what the industrial design was, we couldn’t get the support rigid enough. If you were just wearing the glasses on their own, they were fine. But if you connected a cable to the battery in your pocket, for example, it could put just enough torque on the glasses to cause a slight misalignment from right to left.”
Having identified the rigidity of the top of the frame as the key issue, the design team partnered with 3D printing experts Materialise to evaluate other materials, eventually turning to 3D-printed titanium.
The Shield’s temples contain the CPU and batteries, meaning that they’re already a little thicker than average. But by ensuring the newly designed 3D-printed front connects easily to the remaining components, other materials could be used in that area. As a bonus, a hybrid frame design further reduces the weight, increasing comfort and wearability.
“In a situation like this, if you think about how we’re trying to get this just right, there’s a lot of iteration that has to happen,” says Porzio, adding that 3D printing with the aid of Materialise helped the team’s iterative design process, allowing for lightning-fast prototyping.
“If you were doing that with injection-moulded parts, it would be incredibly expensive and time-consuming, because of tooling changes and the like.”
For production, Materialise and Vuzix combined their expertise to identify the tight tolerances required. Together with post-processing capabilities, the titanium parts were finished to an accuracy within 0.1mm. The high-quality surface, meanwhile, gives Vuzix Shield an extra touch of luxury, ensuring that the frames don’t just function as intended but also look great, too. www.vuzix.com
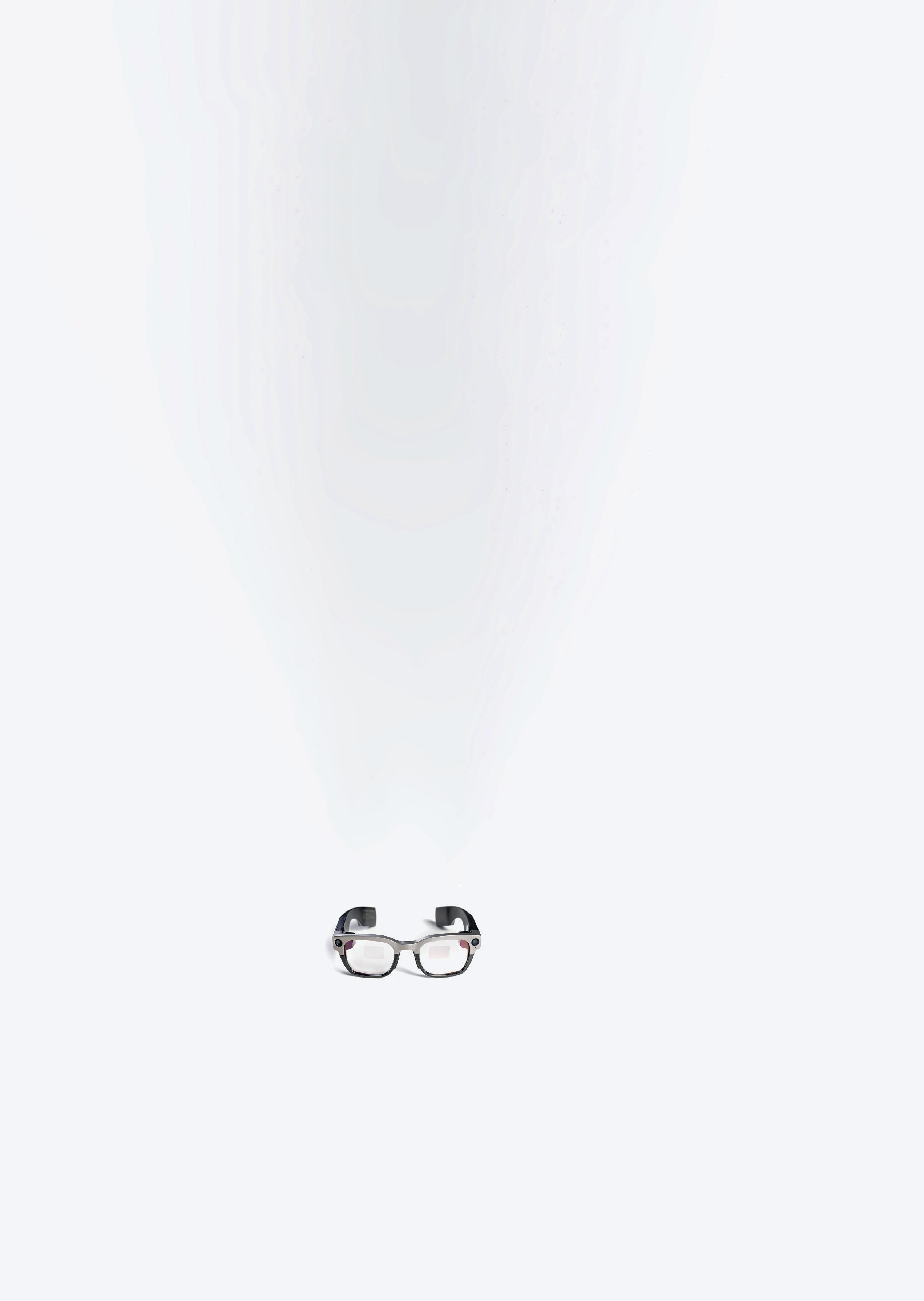
● 1 Style and safety work closely together in Vuzix’s design for its Shield glasses
● 2 3D-printed titanium provides the stiffness needed for rigid support
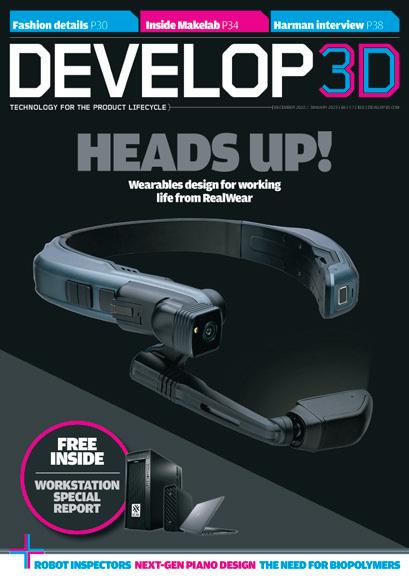
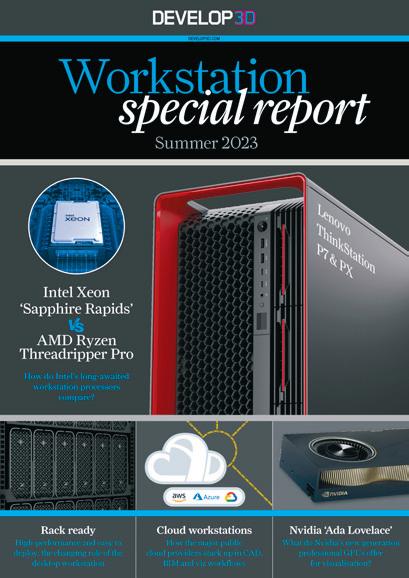
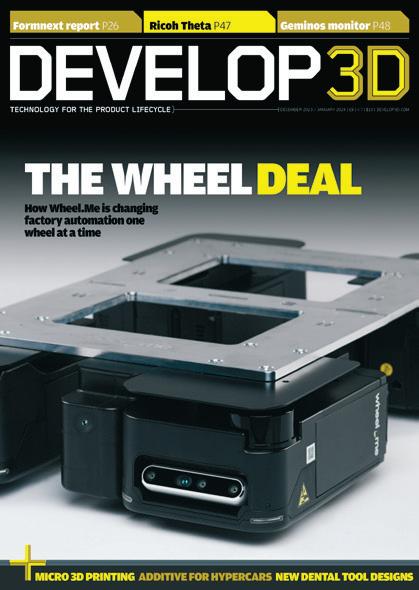
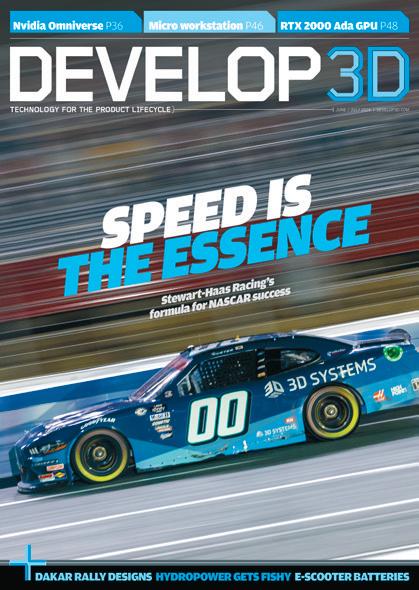
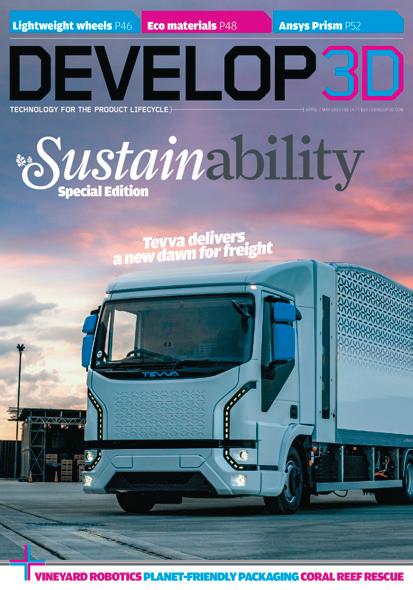


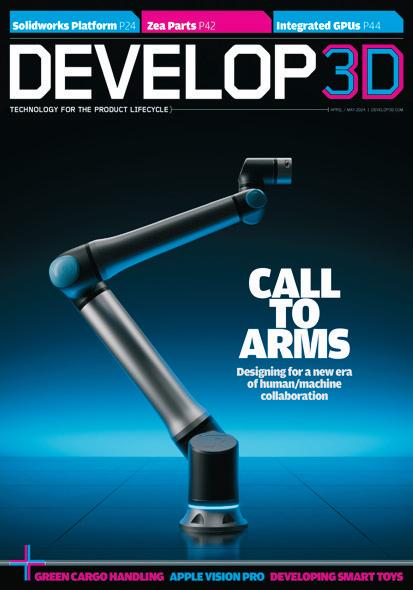
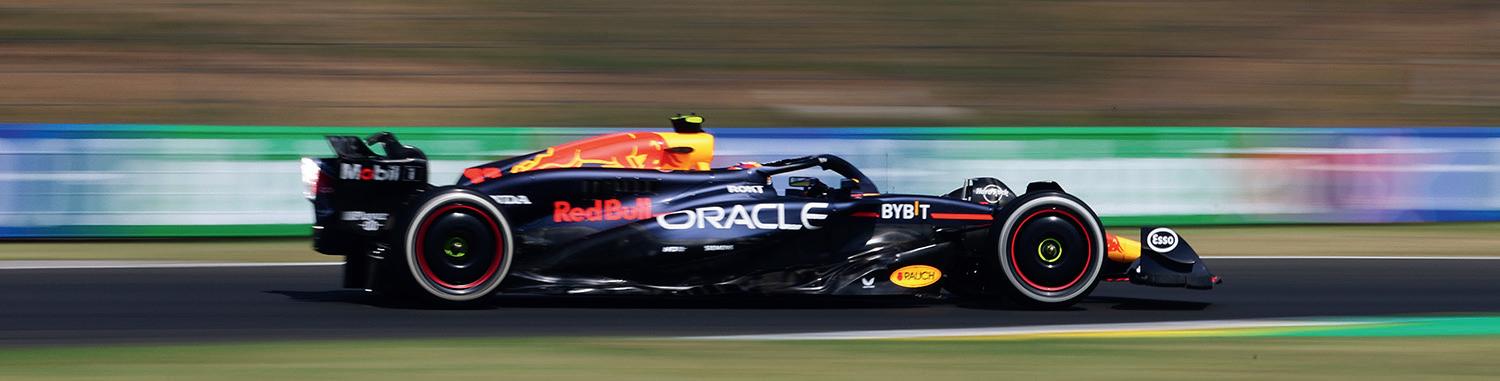
RACE TO VICTORY
» In the two-way relationship between Hexagon MI and Red Bull Racing, Hexagon provides the technology and Red Bull puts it through some pretty fierce paces. Emilie Eisenberg hears how this team effort is paying off for both partners
Red Bull Racing’s RB19 car can boast the highest percentage of wins in any Formula 1 season. With a win rate in the 2023 season of over 95%, Red Bull is showing good pace in the current 2024 season.
At least some of its success can be attributed to Red Bull Racing’s partnership with Hexagon Manufacturing Intelligence (MI). This sees Red Bull using Hexagon’s 3D scanners, laser trackers, portable measuring arms and coordinate measuring machines (CMMs) to help build, edit and test cars to exacting tolerances.
As Hexagon’s sole innovation partner, Red Bull Racing acts as its guinea pig, testing state-of-the-art 3D scanning technology at the Red Bull Technology Campus in Milton Keynes, UK. The partnership works to both sides’ advantage.
Hexagon provides novel new technology to Red Bull, which finds ways to use the technology to its full advantage, both when building cars and in real time on the sidelines of Grand Prix races. In return, Hexagon gets to take home new learnings about how Red Bull engineers use its technology.
“For us, it is useful to see our technology being used at the very pinnacle of the industry,” says Ignazio Dentici, vice president of global automotive and e-mobility at Hexagon. “Hexagon’s customers know that our technology is suitable for the highest possible end of the industry, and so it will be able to fulfil what they are requiring.”
The obstacles involved in manufacturing cars suitable for motorsport – short development cycles, reduced design, prototyping and manufacturing costs – are similar to those faced during the manufacture of road cars, making Red Bull an ideal test subject for Hexagon’s technology.
MAKING CHANGES
Red Bull makes over 20,000 design changes to each car over the course of a season, and every change must be measured, checked and verified to ensure that it is compliant with both the original measurements and with the FIA’s regulations.
Hexagon’s technology is beneficial for completing full scans of a car before and after these changes are made, in order to remain within regulations. Since introducing Hexagon’s technology to the design change process, Red Bull claims it has experienced 50% fewer faults in its cars.
Red Bull was the first Formula 1 team to use Hexagon’s technology in the pit lane during races, starting with the Leica Absolute Tracker AT960 back in 2012.
Paul Monaghan, chief engineer of car engineering at Red Bull, recalls the experience: “We were able to measure things we’d never measured before. We were able to see where things were on the car which we couldn’t before. And then we realised how much more accurate it was than other technologies.”
Hexagon products are now used by almost all Formula 1 teams. “Did we change Formula 1 a little? Perhaps,” Monaghan says. “I suspect, given our time with Hexagon kit, we may be a little bit better [than other teams].”
TWIN CHALLENGE
The digital twin model – referred to at Hexagon as a ‘digital reality’ – is especially beneficial for Red Bull. Before Formula 1 introduced a budget cap of $135 million per team in 2021, the wealthiest teams were spending upwards of $400 million per season on their cars. Now that there is no bottomless fund to spend on prototype vehicles, using a digital twin to test the car in as many scenarios as possible is essential.
Instead of making multiple prototypes, Red Bull makes one and replicates it with multiple digital realities, which can be tested in a virtual wind tunnel. Tests can be run simultaneously, allowing for a higher number of tests within the tight time frame of each season, and for a significantly lower cost.
The FIA is anticipated to make significant changes to sustainability rules in Formula 1 racing within the next few years. By 2026, the cars will lean less on fuel and more on power units, and Red Bull is anticipating the change already. Its Red Bull Powertrains subsidiary has been manufacturing engines in collaboration with Honda since 2021 and is now working to develop a power unit that will comply with new regulations, and will be completely designed and manufactured in-house, an industry first.
Jonathan Crankshaw, supply chain director of Red Bull Powertrains, says “With new regulations come new opportunities. By 2026, our first in-house designed, built and operated power unit will be on track. We’re trusting in Hexagon to help us on that journey.”
For the two companies, extending the collaboration into the manufacturing of powertrains is anticipated to bring yet more success for both sides. As the automotive industry moves increasingly towards sustainable solutions, Red Bull and Hexagon are utilising the best of the best to show manufacturers how it can be done. www.redbullracing.com


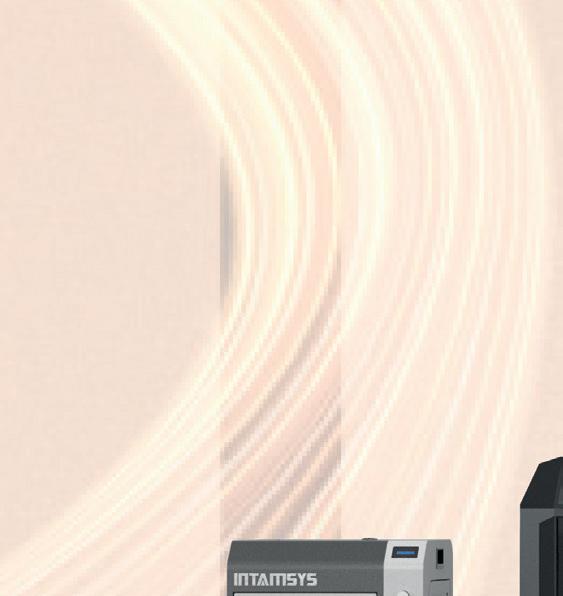
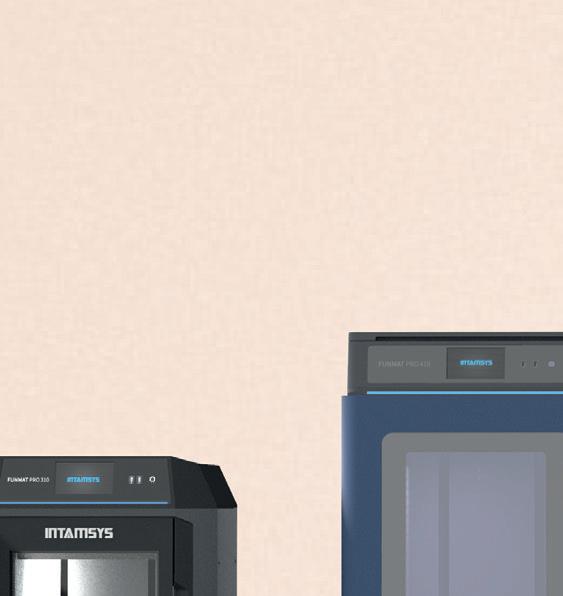



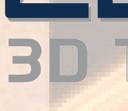
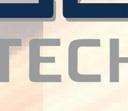

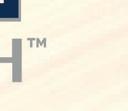
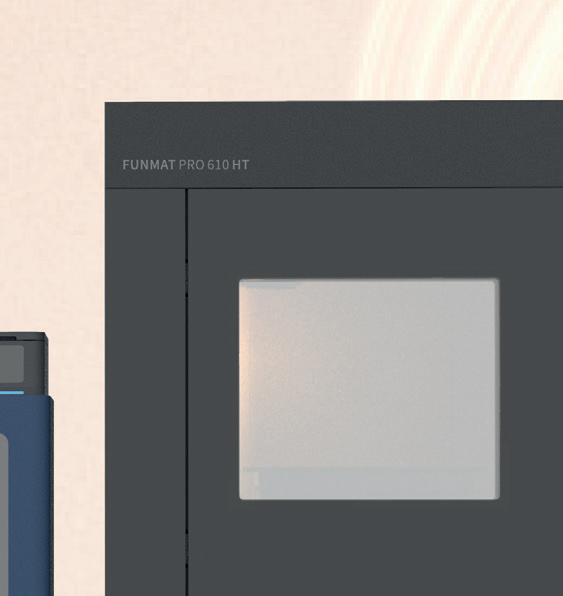




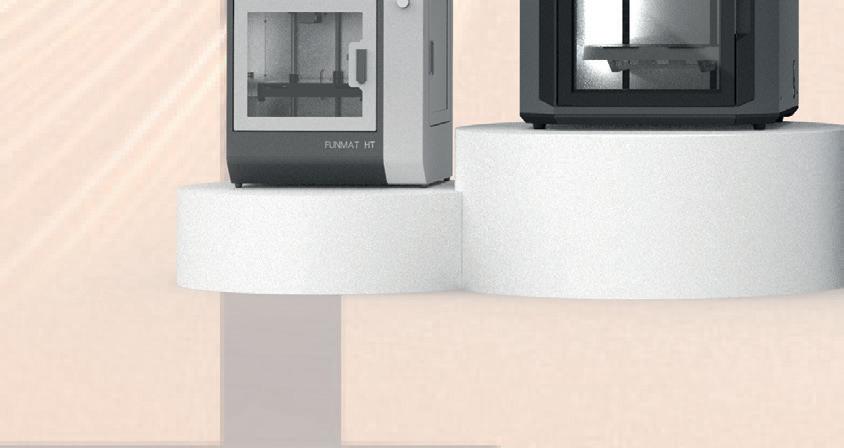


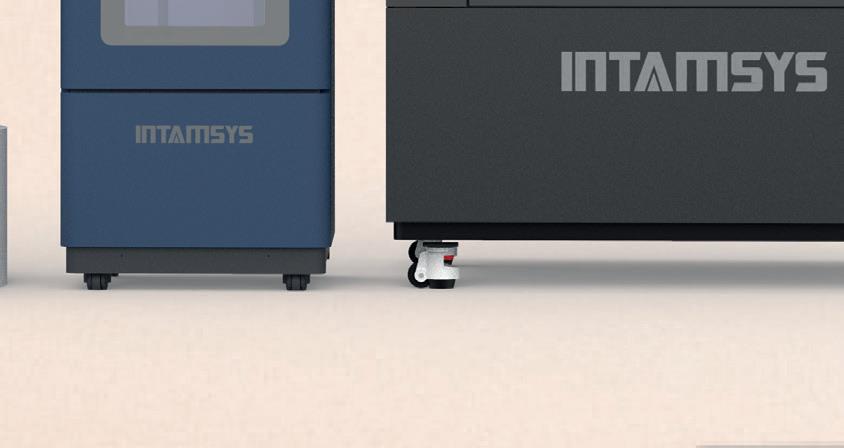
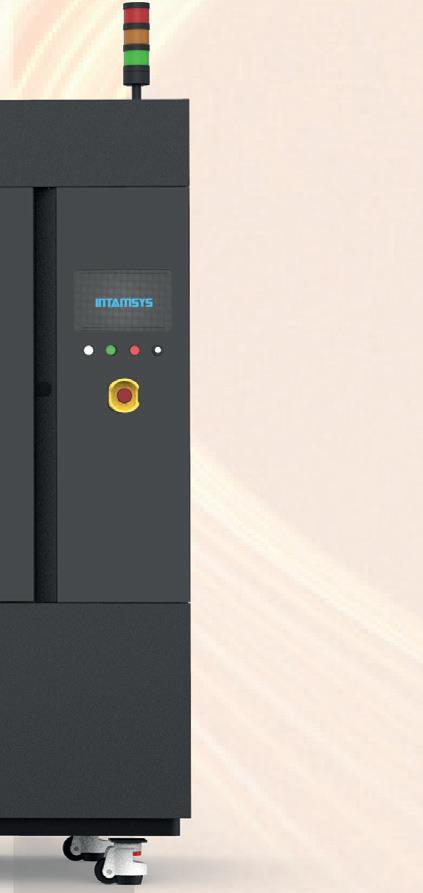
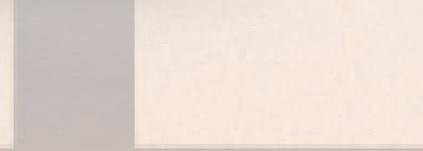
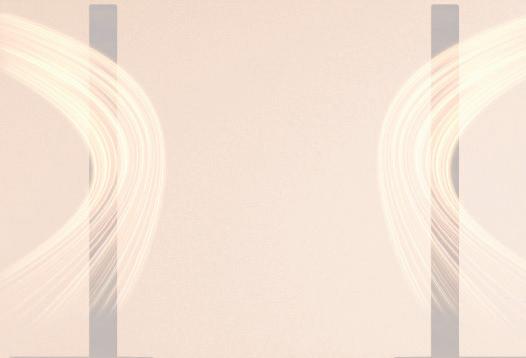
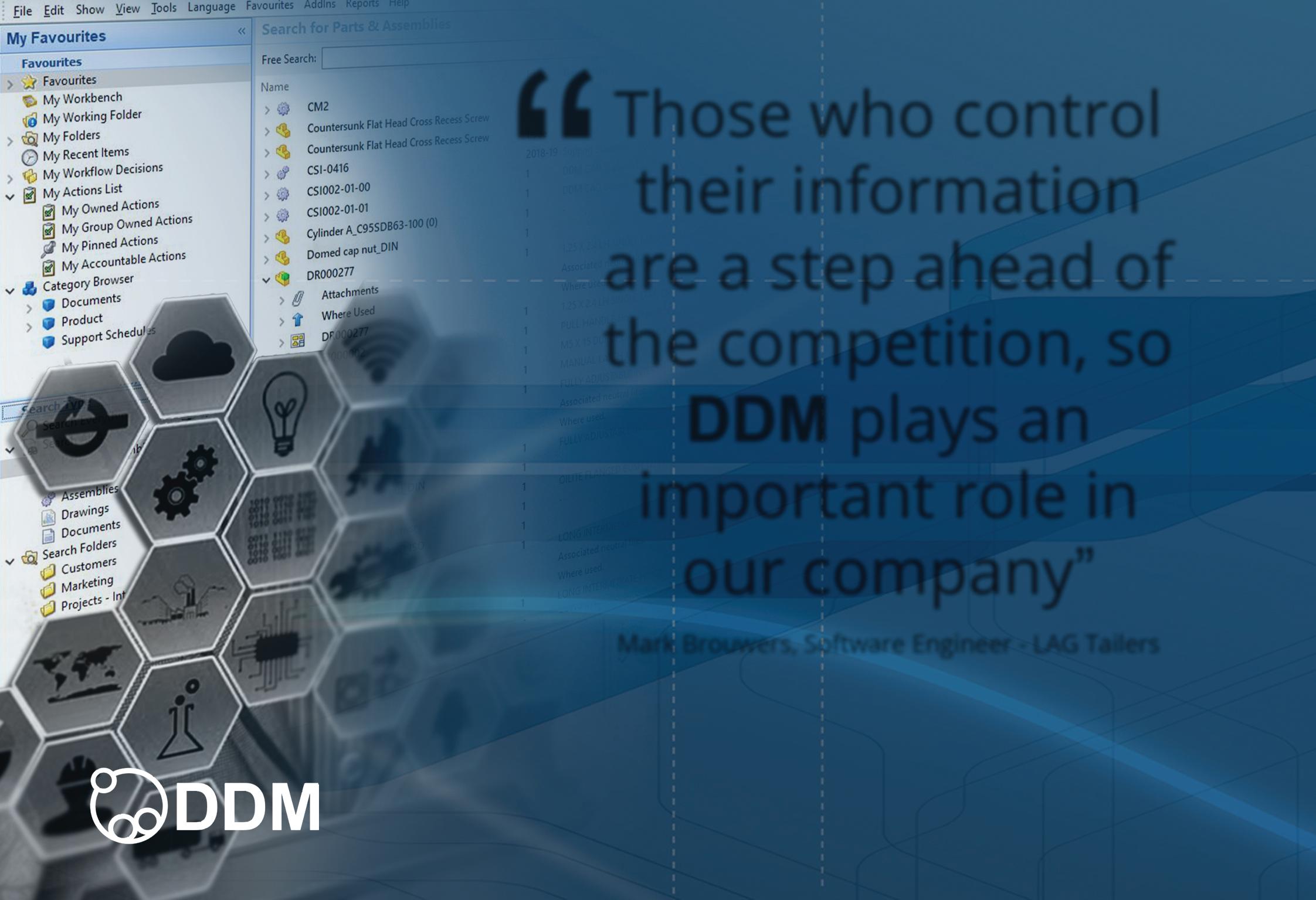

KEEP IT CLEAN
» Proclaim Healthcare is testing the limits of 3D printing with a new oral health tool that looks to boost the efficacy of flossing via custom-made mouthpieces, as Emilie Eisenberg reports
For many people, flossing their teeth is a dreary task, often avoided until their dentist remonstrates with them. For Proclaim Health, it’s a gap in the market that the company is hoping to clean up.
According to Proclaim Health marketing director David Hood, most people don’t floss effectively or don’t bother at all – but there are clear links between gum disease and other conditions including cardiovascular disease and diabetes.
To help patients tackle such concerns, Menlo Park, California-based Proclaim set out to create a tool that would make better tooth and gum health easier. The Proclaim Custom-Jet Oral Health System is customised to the individual user’s mouth and can pressure-wash a full mouth of teeth in just 7 seconds, entirely eliminating the need for traditional flossing.
Proclaim states that a clinical study of the Custom-Jet’s performance has shown a reduction in gum bleeding by up to 82% and a reduction in gum inflammation by up to 41% after 30 days of use.
SAY CHEESE
“We start with a dental scan and create each system to fit a person’s mouth and get the jets pointed in the right spots, with just the right pressure,” says Brent Goldstein, vice president of software and digital-customised medical products at Proclaim. “There’s nothing else like it in the world today.”
In part, this is because traditional injection moulding doesn’t allow for custom designs to be manufactured for each user or for the insertion of targeted fluid lines within each mouthpiece.
The team at Proclaim realised that 3D printing would enable it to best optimise their design’s functional requirements, which included surface quality, biocompatibility, translucency and cost per part. From there, they turned to 3D Systems’ Application Innovation Group (AIG) for advice.
The AIG team at 3D Systems worked alongside Proclaim’s engineers to manufacture a mouthpiece with eight manifold capillaries running through it. Each tube breaks off into multiple nozzles capable of accurately focusing up to 60 water jets at exactly the right points in the user’s mouth.
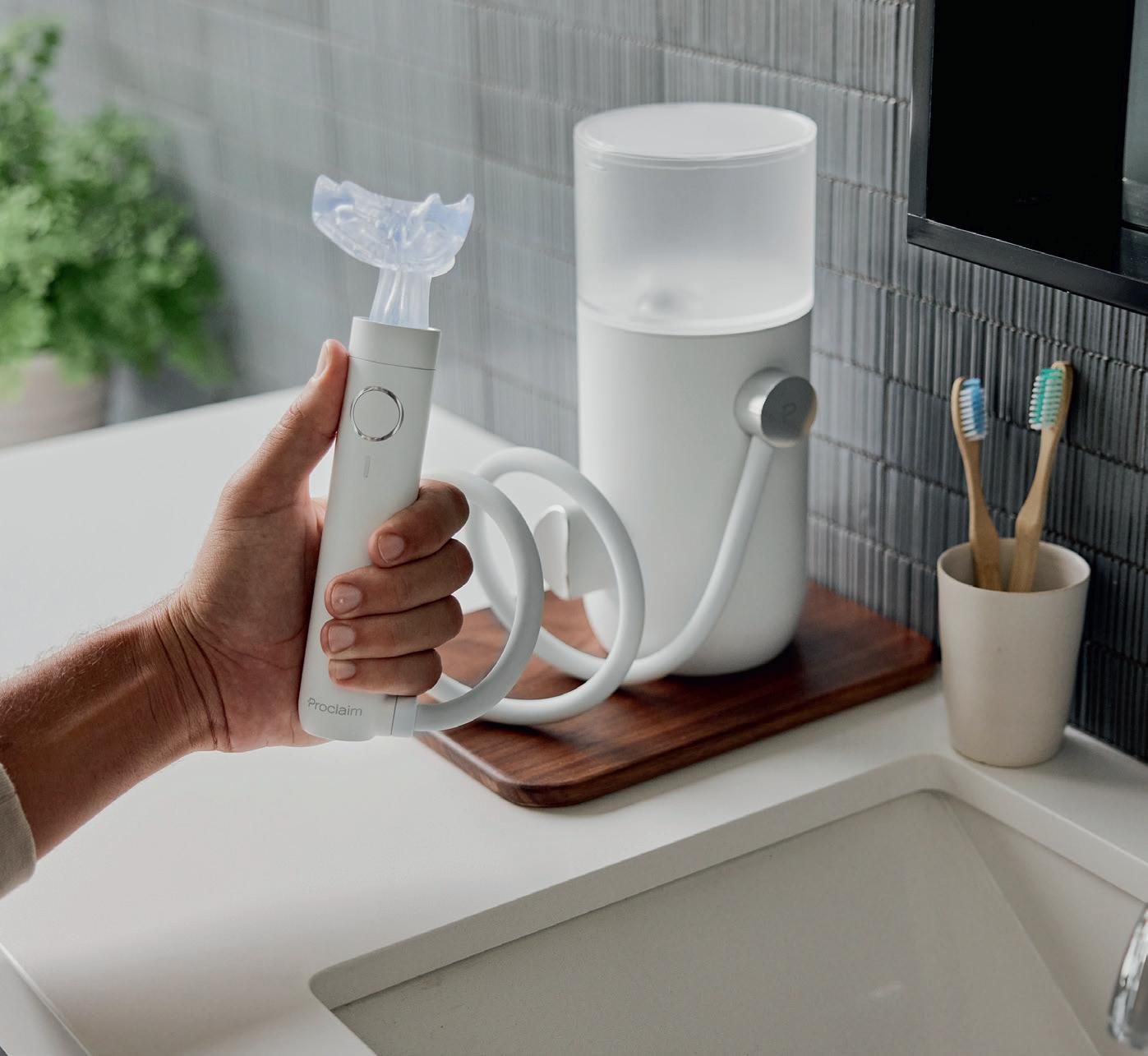
The design is powered by a single pump unit, the Hydro Station, which pulses nearly 650ml of water through to the mouthpiece during each 7-second session. Each custommade mouthpiece is interchangeable within the Hydro Station, so multiple members of a household can use the device with their own mouthpiece.
ALL CLEANED UP
Once confident that the mouthpiece design met its technical feasibility requirements, Proclaim embarked on a beta testing phase, bringing a 3D Systems SLA 7000 3D printer in-house in order to produce multiple prototype units.
With satisfactory early results under its belt, the Proclaim team then moved to the next stage of industrial scaleup and mass production. For this, it turned to additive manufacturing production house In’Tech Industries, based in Minnesota and home to a fleet of 3D Systems SLA large-format printers.
First, Proclaim’s learnings and optimisations from the SLA 7000 had to be transferred to fit In’Tech’s large-format SLA approach. In’Tech has extensive experience of mass producing medical-grade products, including custom hearing aids and orthodontic products.
Over the course of three months, In’Tech performed 3D printing, post-processing, assembly, hydrotesting, and both high- and low-tolerance testing for the mouthpiece.
Using its experience and the resources available in its tooling, engineering and moulding facility, In’Tech enhanced the product further, developing finishes for the bottom section of the mouthpiece and adding plastic elements so that it attaches better to the main device.
With FDA clearance achieved, In’Tech began scaling up production. Now, when each online order is received, the company prints the mouthpiece, post-processes and assembles the parts, before hydrotesting and further cleaning. Then the device is packed and shipped to Proclaim’s fulfilment centre, from where it is sent straight to the user.
With the Custom-Jet becoming part of everyday routines in bathrooms around America, it’s also a healthy sign that more custom products are being enabled by additive manufacturing.
www.proclaimhealth.com
‘‘ We start with a dental scan and create each system to fit in a person’s mouth, with the jets pointed in the right spots and with just the right pressure ’’

SIGN OF THE TIMES
» A project to update Britain’s temporary road signs presented a good opportunity to divert design work in a better direction for pedestrians and workers alike. Designer Ross Atkin spoke with Stephen Holmes about creating more inclusive designs from recycled materials
They’re hidden in plain sight, part of the everyday street furniture that you might pass by without noticing, but Britain’s temporary road signs are evolving Working with PF Cusack, a major supplier of road traffic management products, designer Ross Atkin has developed a new Highway Sign System that offers benefits for everyone that uses and works on the roads.
Compared with traditional metal A-frames anchored by sandbags that hold up temporary signs, the new design is made entirely from plastic, including its injectionmoulded, recycled base.
Eliminating the need to use heavy sandbags is a big bonus from the get-go. These sandbags need to be filled, any spillage must be managed, and they must be transported from place to place. Getting rid of them means that vehicles used to transport signs can accommodate more units and these units also feature hand grips that make possible safer lifting and manoeuvring.
Atkin’s experience in designing signage for visually impaired people also impacted the project. “Many years ago, I worked on something called Sight Line, which involved a whole load of small tweaks to the barriers and signs placed around roadworks to make them much easier to navigate, primarily for people with sight loss, but also other disabled people,” he explains, speaking from his studio in Hackney, East London.
Sight Line was deployed on London’s streets by a construction firm for a trial period. Impressed by the results, they reported their findings to PF Cusack.
With that connection made, Atkin was soon asked by PF Cusack to explore a new design for temporary road signs, a regular feature on the pavements and streets of the UK capital.
According to Atkin, this is a good example of a marginally more expensive product gaining adoption because of changing circumstances. The official body that oversees London’s roads was clear that it wanted to ban sandbags from being used to weigh down signs. “So everyone could see a future where sandbags were banned, and that this product was the thing that would be used instead,” he says.
BASE CONSIDERATIONS
Without sandbags, Atkin faced the design challenge of creating a base that could stand up to forces such as strong winds. The new base, which weighs in at 27kg, is made from the weighted bases of recycled traffic cones and road barriers, which are themselves made from recycled PVC carpet tiles and other postconsumer waste.
The neat footprint of the base, meanwhile, is defined by the Presma rotary injection moulding machine used to manufacture such hefty parts. Atkin jokes that it was

‘‘ Everyonecouldseeafutureinwhich newsandbagswerebannedandthatthis productwouldbethethingthat wasusedintheirplace ’’
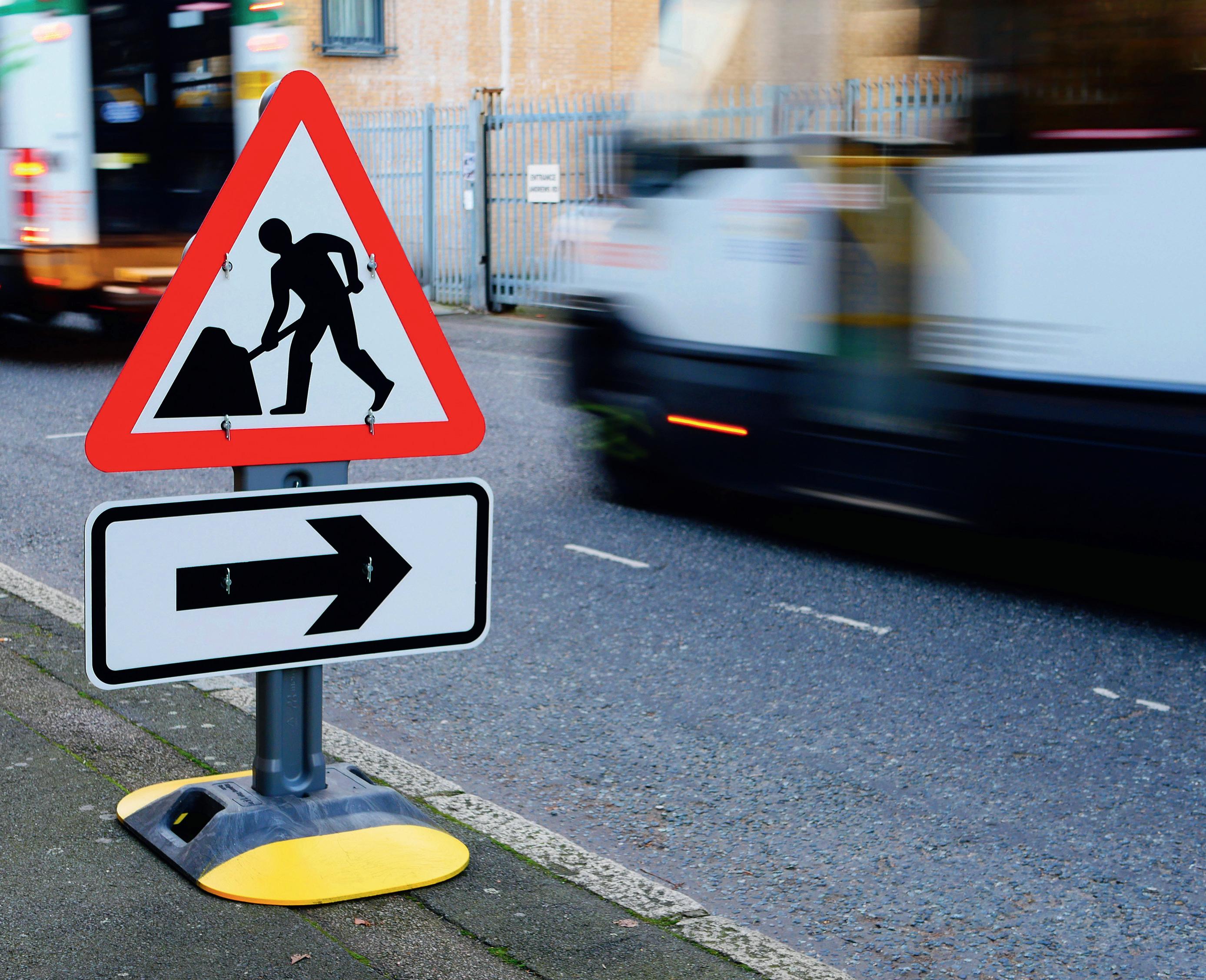
strange having to maximise the amount of material being used in an injection moulded part, instead of keeping it to the minimum.
The rotary injection moulding machine allows for multiple tools to be filled, revolving on a carousel post-injection, allowing twelve of the heavy bases to be produced in a faster cycle time. It’s a process that Atkin refers to as ‘high-entropy recycling’.
“It’s quite tolerant of different kinds of materials”, he adds, explaining that the material isn’t super dependable, as it lacks the consistent mechanical properties of virgin plastic, meaning that the design needed to be quite rugged to avoid weird things happening when parts were demoulded.
The base design did, however, allow Atkin to implement more design considerations for different street users, reducing the risks of people tripping and making signs more detectable to pedestrians with sight-loss using long canes to navigate, this being a problem associated with metal A-frame signs.
“I’ve been really aware of the long cane trap between the feet of these things ever since I was working on the research for Sight Line, where I’d always been trying to get them to change the design,” he says.
trip people over, but you also don’t want it so tapered that you the cane just runs over it.”
TESTING TIMES
Atkin’s designs for the injection moulded bases, created in Autodesk Fusion, were immediately successful. However, the intricacies of designing the centre posts for the blow moulding process required further iterations.
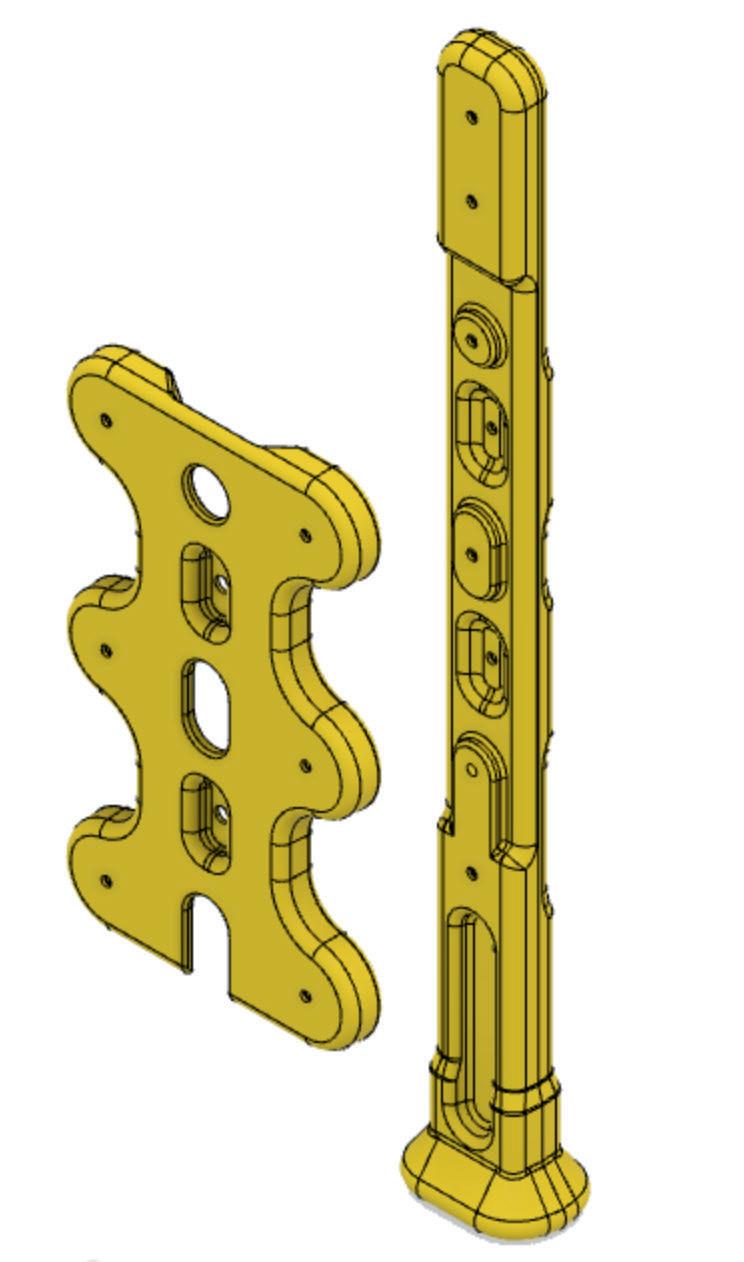
“There’s a bit of a trade-off [with the new base], because you want to make it as fl at as possible to not
Working alongside factory engineers, Atkin updated his design to make it easier to reliably blow mould and to support volume production, in line with the expectation of producing thousands of parts each week.
Updated parts were assembled and underwent wind tunnel testing at the Building Research Establishment, before they were pilot tested for eight weeks in early 2024. These tests saw the signs set up in a high footfall area and major bus corridor and coincided with two major storms. Only one sign out of the 40 deployed was toppled by strong winds.
The contractor that managed the trial described the new design as a “game changer” and praised the ease with which signs could be quickly assembled and dismantled on large job sites.
Today, Atkins’ Highway Sign System is widely deployed across London and further afield, signalling a positive change for the better.
www.rossatkin.com | www.cusack.co.uk
● 1 The new design eliminates the need for sandbags to anchor temporary road signs
● 2 The base of the new system has a smaller footprint and is more sustainable
● 3 Models were built in Autodesk Fusion for eventual injection and blow moulding
Formlabs Form 4
» The Form 4 is billed as Formlabs’ fastest 3D printer yet, but that’s not just down to its new, lighter engine. Matt Batchelor puts the machine through its paces and finds that every aspect of its design shaves off time and makes set-up a breeze
S»
ince 2011, inverted stereolithography (SLA) pioneer Formlabs has grown from a Kickstarter-funded spin-out from MIT Media Labs to an established manufacturer of smallerscale, low-cost SLA machines, with over 100,000 products out in the field. Its new Form 4 SLA 3D printer marks a transition from using a scanned laser beam to cure resin layers to a projected light source, a shift that Formlabs executives claim contributes to the 3D printer being between two and four times faster than the Form 3. That’s primarily because each layer is exposed in one go, rather than being scanned line by line.
The new machine is also claimed to warm the resin up to operating temperature more quickly and to perform pre-print calibration faster, too. New resins optimised for the printer are said to further accelerate the user’s workflow.
With a brand-new Form 4 3D printer and v2 Form Wash station installed in the workshop at Instrument Product Development in South-East London for long term testing, it was time to check out these claims and to gauge the advancements achieved with the Form 4, especially when compared to the Form 3 sat on the workbench nearby.
FIRST IMPRESSIONS
The machine arrives well-packaged in several boxes. In addition to the printer,
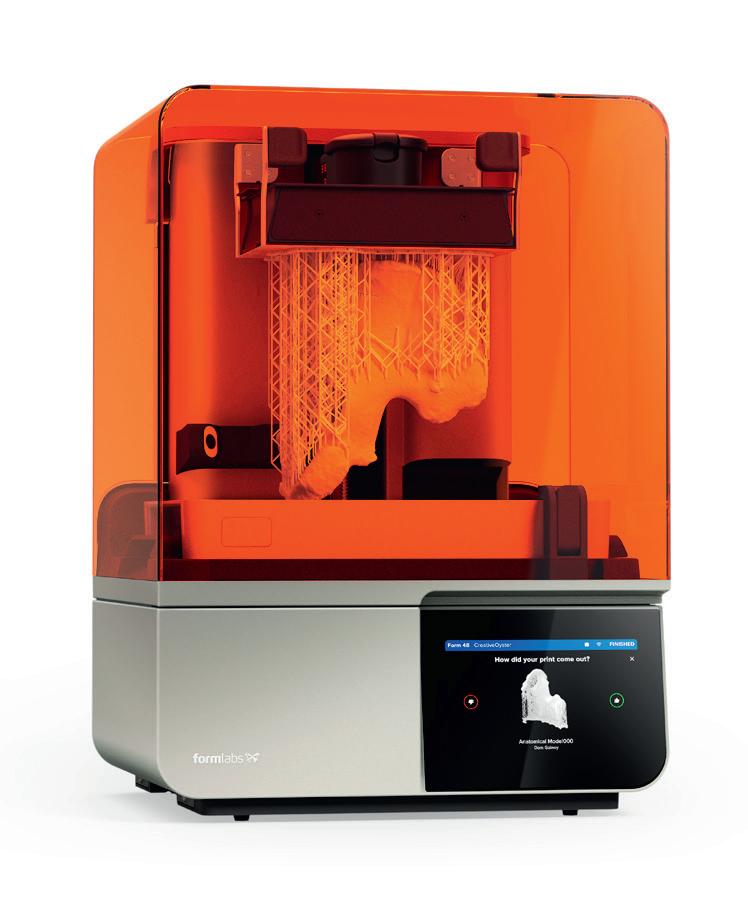
Formlabs sent us three resin trays, three mixer arms (now a separate SKU), a Form Wash v2 and three litres of grey and clear v5 resin and Elastic 50 Shore Resin.
With no transit screws to mess with, it’s simple to pull the product out of the box, power it on and run the built-in levelling routine, which uses an on-screen ‘spirit bubble’ and a handy wrench disc to turn the four threaded feet.
There is now a metal frame around the base of the acrylic hood to provide stiffness and the optics are sealed behind a glass panel with a 3D ‘wave’ surface that Formlabs calls a Release Texture.
While the Form 3 performs some kind of electromechanical movement in order to detach a freshly built layer from the film of the resin tray, the Form 4 just lifts the build platform. This texture must help break the suction somehow.
A fine resolution (50 microns per pixel) LCD mask sits under the panel, while a beefy mechanical drive for the new mixing arm runs in a track under the splash guard. By contrast, the Form 3 has a vulnerable open space where the scanning optics transit.
A physical power switch now lets you power down the machine to save energy while it is not in use, which is a nice addition.
Formlabs now offers polyurethane and silicone rubber resins (although these were not tested). To accommodate these more hazardous chemistries, there is now
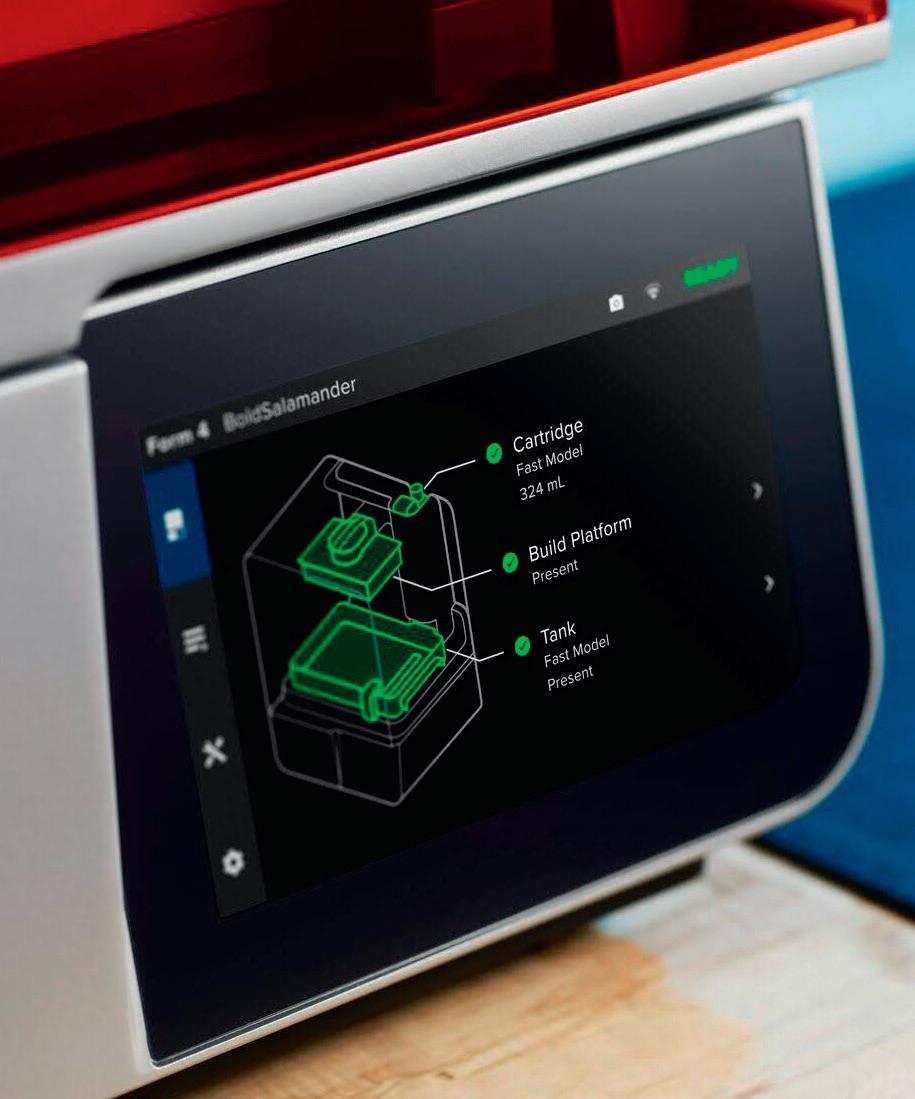
a fume extraction port at the back. This is sealed by a 3D-printed plug, built on a Form 3 in Tough 1500 resin, according to the embossed text.
Additional 3D-printed elements on the new machine include a small tool caddy printed on a Fuse 1, which clips in the top of the frame. The resin tanks are now clamped in place by two large over-centre latches on each side.
The resin cartridges are now a different shape – more square in cross-section than Form 2 and 3 cartridges. This is supposedly to save material and support improved thermal efficiency, although it comes at the expense of backwards compatibility.
The resin is still dosed out by a ‘burp’ valve, but the valve on the newgeneration tanks is much bigger. We have not experienced any issues with the valve clogging on the Form 4, which we did see with several resins used in the Form 3 and the older cartridge.
Filling happens so fast that it took us a few prints to figure out when it actually happens – right at the start of the process, semi-obviously.
The resin trays themselves no longer have a full protective box for storage. The actual tray is now a more rigid component, and the new base film seems harder – identical to a mylar drum head. Unlike lower cost machines, this film is not user replaceable, as the metal carrier frame that tensions the film is heat-staked into the resin tray frame.
As far as I can tell, there are no life restrictions on the tray with certain resins, so maybe it will prove durable enough to not need replacing, whereas we did have to retire a couple of Form 3 trays where the softer film had delaminated.
A thermoformed lid is provided, which keeps light and dust out of your precious resin when not in use and facilitates a stable stack of trays.
One important detail to note is that the mixing arm is now a separate purchase from the tray. Formlabs say that this is to avoid unnecessarily having to replace both when one wears out. You could clean and reuse the arm between several resins, but it would be a pain and Formlabs doesn’t recommend it.
The new tray and arm together cost £99 plus VAT (£20 + £79) whereas the Form 3 tank including a mixer is £120 plus VAT, so at least they have not used the two SKUs as an excuse to bump the price.
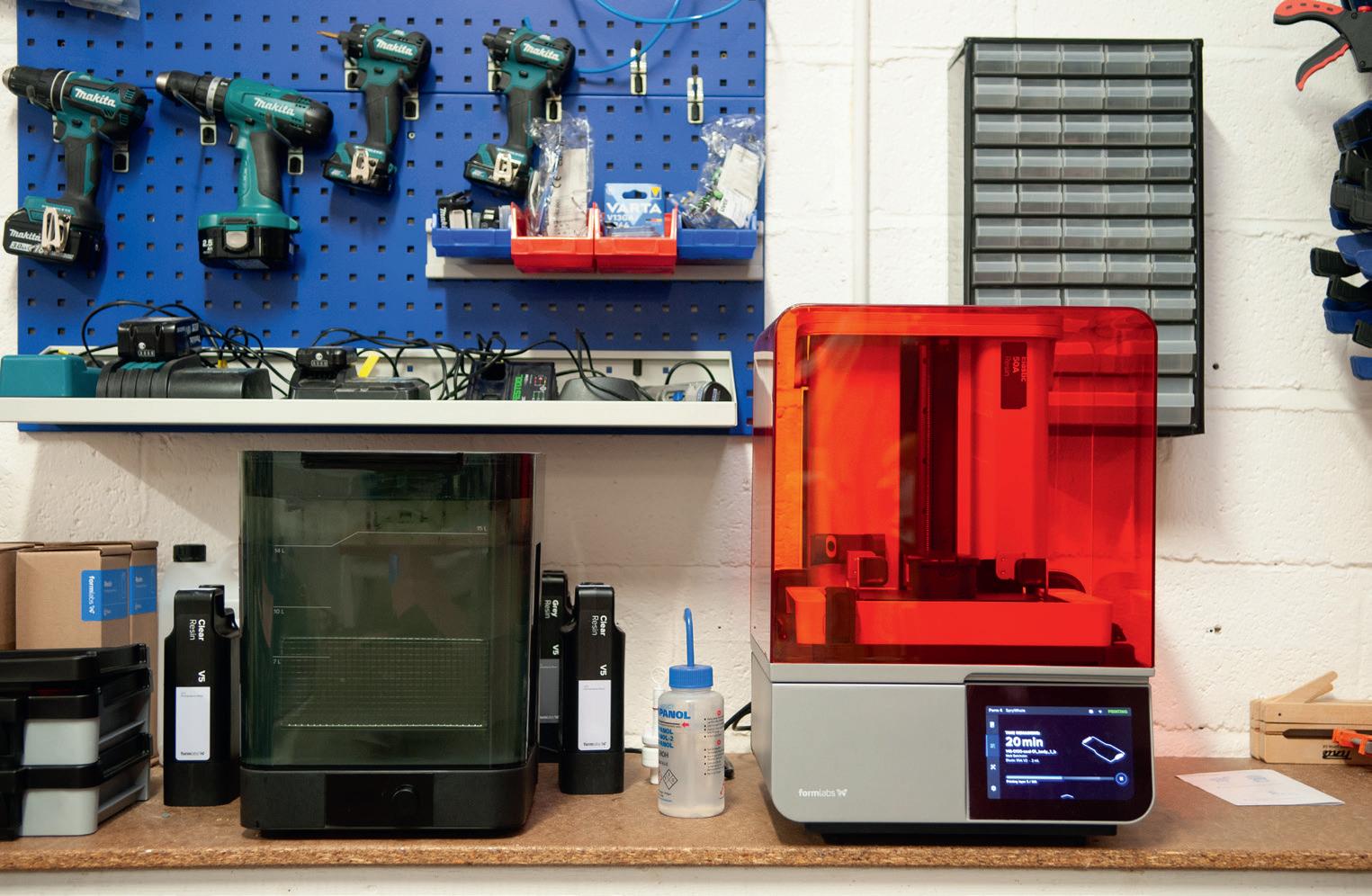
3
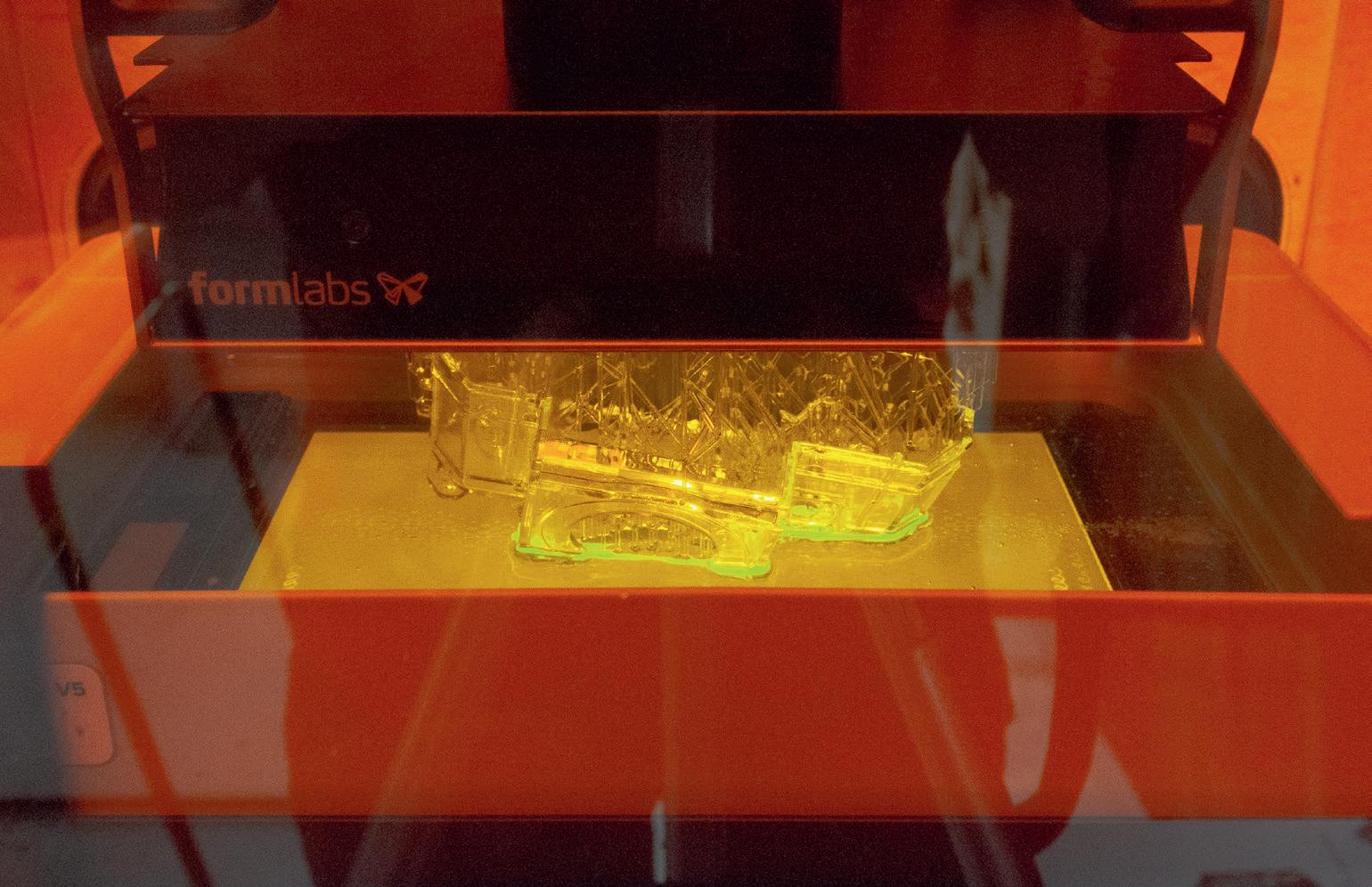
(Though it’s worth noting that this is an improved version of the Form 2 design, which is just £50 all-in.)
Finally, the build platform is more rectangular, at 200 x 125 mm versus 145 mm square on the Form 2 and 3, and offers a maximum build height of 210 mm (versus 193 mm).
Formlabs claims an average print speed for the Form 4 of 40 mm of height per hour, versus 11 mm/h with the previous generation.
Our Form 4 was provided with the ‘Flex’ build platform with a flexible stainlesssteel sheet to help peel models off. This costs £110 more than the standard rigid aluminium plate (£209 versus £99), but enables much easier part removal and the possibility of printing directly onto the build plate.
The same flexible set-up is also available in the old Form 2/3 form factor.
Pleasingly, for anyone with previous Formlabs machines, the new Form Wash – a large tank of solvent with an agitating rotor in the base and a lift mechanism that holds the build platform and print with a mesh basket for loose components – is backwards-compatible with the Form 2 and 3 build platforms, with support arms that can be relocated to suit the differently sized baseplate.
The Cure UV oven, meanwhile, remains the same.
PRE-PROCESSING PARAMETERS
As with its other printers, Formlabs’ proprietary (but free-to-download) software Preform is used to set up a print job with the requisite support structures and resin curing parameters.
Mesh files in .stl, .obj and .3mf files are supported and jobs can be saved as .form files.
No neutral ‘analytic’ formats – such as .step or .iges – are supported, requiring some form of import and conversion to mesh in order to work.
Formlabs’ pitch is that everything works appliance-style using built-in validated presets. As a result, the interface is very geared towards clicking auto-generate and then uploading via a local network (WiFi or good ‘ol Ethernet), or over the web if you have enabled remote printing on your printer.
Preform is pretty good at the automatic flow, with warnings of possible print errors, but it would still be good to be afforded more manual control, since the support structure algorithm often puts support points on functional or hard-topost-finish feature edges.
There is a ‘brush’ tool to scatter points in a somewhat controlled fashion, but the ability to axially pattern a manually generated layout would be a huge time-saver.
There is an option for an ‘Open Material’ mode with more settings (this starts at £1,699 plus VAT), but presumably this intended either for bureaux that use so much resin that they want to use a thirdparty material with their own settings, or researchers building their own materials. It certainly isn’t a money-saving option for more moderate users, and if you need it, then you probably know more about materials and their uses than us.
TIME TO PRINT
First impressions of the Form 4’s print performance are dominated by how fast it runs. Because of the layer-by-layer process, there is no time penalty for filling the bed, and you can almost watch the build platform ease its way out of the resin bath. If you are printing in a clear resin, you can see the cross-sections being exposed through the UV filtering orange cover.
4
● 1 The Form 4’s primary USP is a dramatic increase in speed over the Form 3
● 2 The big, bright user display is another example of the overall build quality of the machine
● 3 Form 4 is at home on the workbench and partners with the Form Wash V2 (left)
● 4 Compared to Form 2 and 3, the 200 x 125mm build platform of the Form 4 is more rectangular
We did have some issues with autogenerated supports becoming detached in the clear resin, but we fixed the issue by adding a few more support points.
Like many SLA printers – or any manufacturing process involving a phase change – we did see some warping on more complex parts, but were mostly able to fix this by printing in a completely vertical orientation. The prints were crisp and accurate, in line with Formlabs’ suggested tolerances, to the point where some small (#10-32 UNF) threads just needed a tidy-up with a plug tap.
There is even a camera built in for checking on prints remotely, which is easily turned off during set-up if your security policies require it. This is accessed via Formlabs’ online dashboard.
The camera can take a time-lapse sequence of parts emerging from the resin, but doing so slows the print down, as it requires the printer to hold still for each frame. We did it once for the Terminator reference and then turned it off.
WASH AND CURE
The new Form Wash (£579 plus VAT) moves solvent noticeably more vigorously than the previous model. With the resins we tested, wash times were down from 20-40 minutes to 5-10 minutes and with less ‘snot’ to wash off manually when using the new v5 resins.
Using our Form 3, we would normally take the worst off in a tub of IPA before putting a print in the original Form Wash. Even then, we sometimes need to take the parts off of the build platform and perform another wash in the ‘chip basket’ to get the last of the primordial goo out from around the supports.
This improved washing workflow is a massive time-saver. It also becomes backwards-compatible with the Form 3 build platform by moving the supports inwards, and is able to run only part-filled with solvent for those who never use the full height of the printer’s build envelope. That potentially saves on solvent usage, which is a nice bonus. There is now a seal under the lid, but it did not seem to ease the rate of evaporation of the alcohol.
Our printer came with the ‘Flex’ build platform (£209 plus VAT). I liked it, having spent too much time levering prints off the original rigid platforms on our Form 3.
A flexible stainless steel sheet is fixed to two steel brackets that form a magnetic pivot with two grooves in the build platform. When a print is washed and ready to cure, you squeeze the pads on the top of the brackets together, flexing the sheet and releasing the print. This is much more elegant than trying to pry a print off the more basic aluminium blocks still available for £99 plus VAT.
The Form Cure oven, meanwhile, has not been replaced. The new v5 resins can be cured at room temperature and for shorter periods than v4 equivalents – five minutes for Grey v5, versus 30 minutes at 60C for Grey v4.
We have sometimes gone off-menu and cured our parts at room temperature to avoid warping issues on certain parts, but it’s nice to be working closer to the ‘official’ recommendation. It also saves more time as the curing unit does not have to warm up to temperature.
CONCLUSION
It would be fair to say we expected more of an incremental improvement over the previous Form 3, but the faster cycle time of the Formlabs Form 4 has genuinely changed how we use it.
The time investment demanded by a Form 3 print means that some bigger jobs present an overnight or even over-theweekend challenge, with a few hours needed afterwards for post-processing. The Form 4, by contrast, is fast enough to turn around some simple parts in a couple of hours or to perform multiple runs in a day for more complex jobs.


In real terms, this marks a change from the Form 4 being a high-resolution ‘verification’ machine to something that can be used for process models to help figure out details during a design process.
For existing Form 3 owners, the backwards compatibility – or lack thereof – will complicate the decision to upgrade, as they will likely have several hundred pounds already invested in resins and print trays and may be reluctant to buy a new washing device.
In fairness, Formlabs has kept a decent level of commonality between the Form 2 and Form 3, which together represent some 10 years’ worth of development. Plus, the new changes do make sense, unless your work absolutely requires the squarer proportions of the older build envelope.
All moving parts on the Form 4 (and the Fuse 1) are now field replaceable units, with spare parts available for purchase from Formlabs. This is a huge boon, enabling businesses to keep assets in use for as long as they work.
The Formlabs team does not provide definitive end-of-life dates for the Form 3, 3L, 4 or Fuse, but at time of publishing, parts for the Form 2 (launched in 2015) are still available, even if it is no longer ‘officially’ supported on a service plan.
The Form 4 is a really good machine, built with the needs of professional users clearly in mind. The big selling point of increased speed aside, it manages to make the SLA 3D printing slick and straightforward, allowing users to better use time previously spent messing around on set-up and post-processing tasks.
●
The Form
from
machine’s
●
The resin tray of the Form 4 is more rigid and its base film seems tougher
4 mixing arm is now purchased separately
the
tray
Ratta Supernote Nomad
» This A6-size E-ink display has many charms to offer those who rely on sketching and note taking, writes Hannah Devoy, who finds that its diminutive form still packs all the digital essentials for modern working
Sketching and note-taking by hand remain essential elements of the modern designer’s process. While the device of choice for some will be an iPad or graphics tablet such as Xencelabs’ Pen Display 16, many others still find the humble pen and paper hard to beat. This is the group for which Supernote’s Nomad e-notebook promises to deliver.
With its compact 7.8-inch screen, the Nomad is comparable in size to an A6 notepad and thus perfect for slipping into a bag or large pocket. Weighing just 266g, versus the 444g of the 11-inch iPad Pro, it’s an easy and super portable companion to a laptop, packing an impressive feature set despite its diminutive size.
Once we had selected our device on the Supernote website, the product soon arrived in neat recycled packaging. Each element of the Nomad – the e-notebook itself, the stylus and the folio case – was tucked in its own compact drawer, ready for unboxing.
We opted for the Crystal edition of the Nomad; its clear casing allows the user to see the under the hood when the device is not encased in its canvas folio. For the stylus, we selected the standard push-up pen, the lightest option at 12.5g. Other options include Heart of Metal and LAMY models, for users who prefer something that looks a little more expensive.
A major selling point for the Supernote Nomad is its promised longevity. Even for an E-Ink display, it consumes far less power than you would expect, needing to be recharged only twice during the hours spent using it over several weeks. Supernote bills itself as a supplier of “the only sustainable e-notebook”; the Nomad is modular by design, so you can easily replace the battery yourself and upgrade memory via micro-SD card up to 2TB.
Unlike many other tablets on the market, the stylus’s 0.7mm ceramic nib doesn’t need to be replaced, which saves the hassle of having to carry replacements.
USER EXPERIENCE
If you’re a lover of pen and paper, the Nomad’s writing and drawing experience will be the first thing to win you over. Its E-Ink display and FeelWrite 2 Self-recovery Soft Film surface deliver natural writing akin to the analogue experience and without the backlit glare of a typical tablet.
Product
» Ratta Supernote Nomad
From £299 (Ex VAT) www.supernote.com
Specifications
» 7.8” Glass EPD (ePaper display), 300 PPI (1,404 x 1,872) display
» Weight – 266g
» Dimensions - 191.85 mm x 139.2 mm x 6.8 mm
» 32 GB, expandable via microSD (up to 2TB) storage
» RK3566 Quad-Core 1.8GHz processor
» 4 GB memory
» 2,700 mAh battery
» 2.4 GHz / 5 GHz
WIFI, Bluetooth 5.0, USB-C 2.0
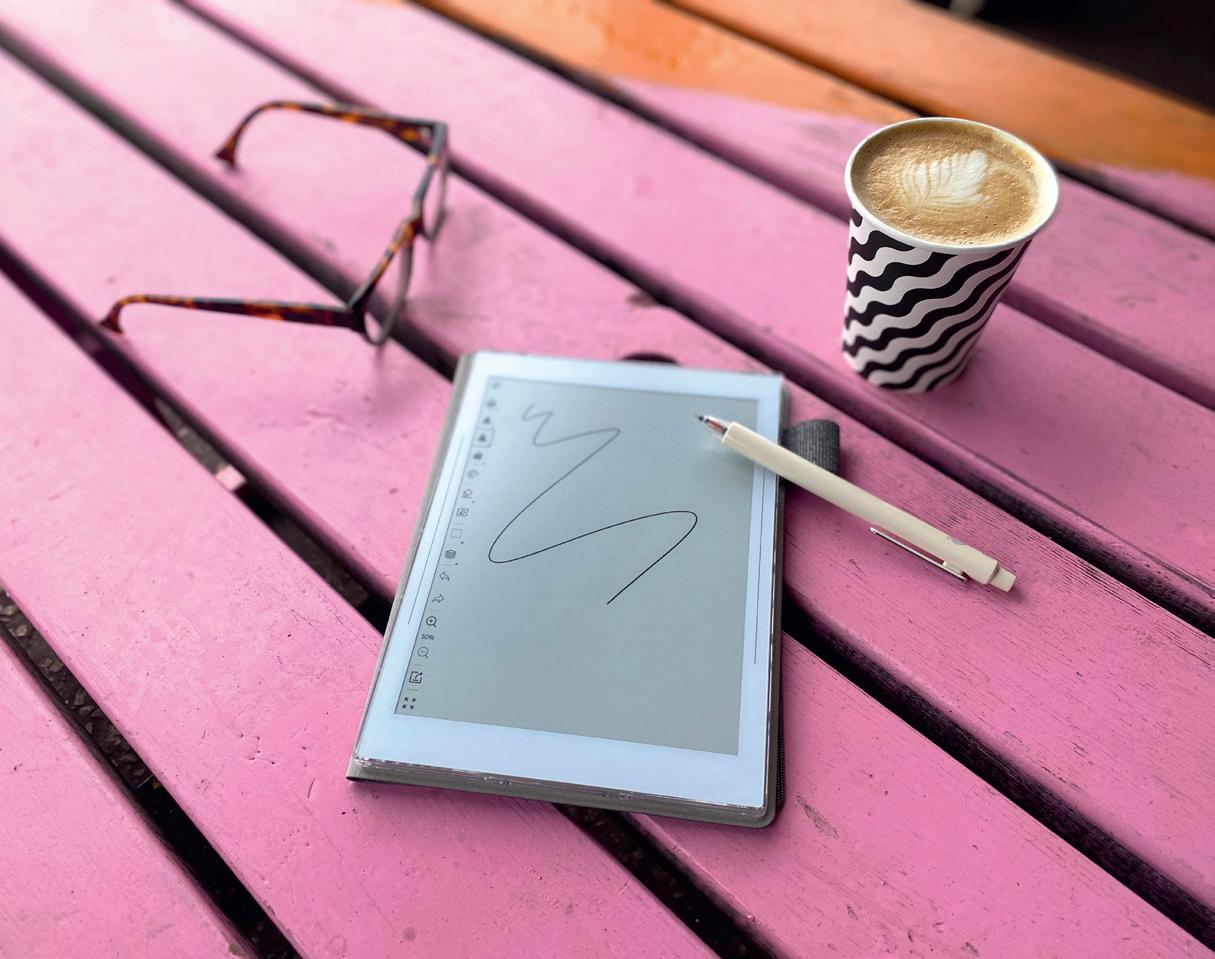
During our testing, we were impressed by the sensitivity of the interface, which enables you to really work with the grayscale levels. In fact, we enjoyed being able to lighten our drawing style to reduce pressure after previously using a less sensitive device.
For drawing, the Nomad really comes into its own with its Atelier app, which is free to download from Ratta via the apps section in the device settings.
Atelier offers a wide array of different pencil and pen weights, with pressure sensitivity that mimics the experience of drawing with a real pencil on paper, allowing accurate shading and crisp lines.
Unlike paper, Atelier allows you to use up to five different layers, although these can be compressed to add more. Drawings can be exported in PNG format, with an export to Photoshop feature currently in development.
With a RK3566 Quad-Core 1.8 GHz processor, we found the Nomad to be responsive, with less lag when writing and drawing than other e-notebooks that we’ve tested.
Gesture controls, swiping in different directions across the screen with one or two fingers, help to make navigation within and between documents faster and more efficient. However, we found this sometimes a little slow, so tended to fall back on clicking with the stylus.
The Nomad stands out for its ability to elevate note taking, enabling users to set headings and keywords to make it easy to organise and search through notes.
With the option to write straight into a new Word document or link into email, you can convert handwriting into text as you go along, which is particularly useful if you want to share your scribblings with others.
The offline ability for handwriting recognition, meanwhile, adds another dimension, useful when on the move or temporarily without WiFi access.
Documents can be downloaded in PDF, Word or JPG format, and edited or annotated on the move, and the Nomad can also double up as an e-reader with the option to install Amazon’s Kindle app.
Files can be backed up and shared across platforms via Supernote Cloud without having to fork out for a subscription, or you can connect to OneDrive, Google Drive or Dropbox. You can also share screens in Zoom and Google Meet for easy collaboration.
The Supernote Nomad promises users a solid digital alternative to old-fashioned pen and paper. While you won’t be able to watch Netflix on it, if you crave the familiar sensation of putting ink on paper, the Nomad offers exactly that, but with all the digital capabilities you need to make your notes fit for modern working.
Organisations that build bridges with local
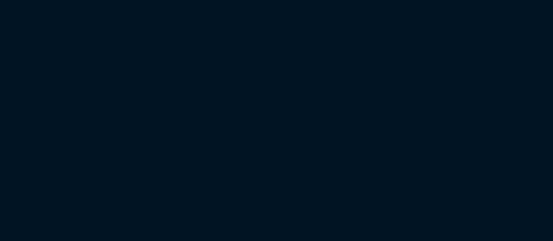
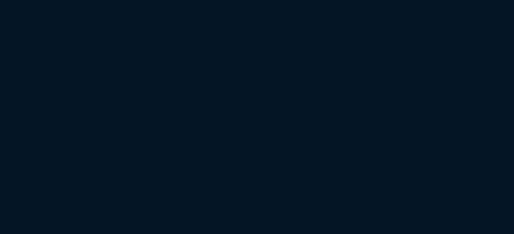
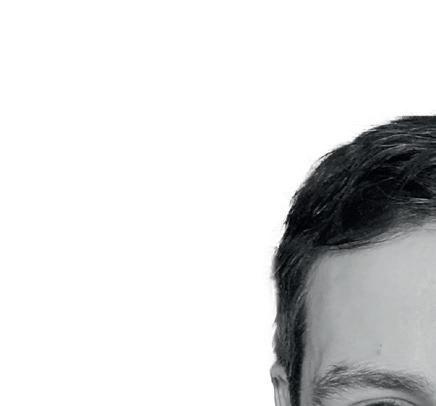
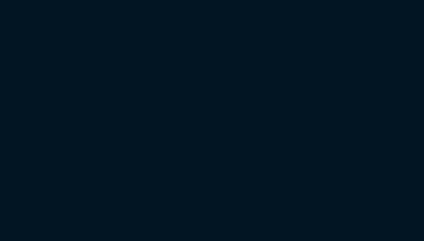
Ialways find it heartening to hear about the contributions that design studios and engineering companies make in their local communities.
In the case of some big businesses, it’s a part of their wider ESG (environmental, social and governance) programme, helping them connect to the local area – or perhaps dodge a bit of scrutiny. In other cases, that work is much more hands-on.
This past month, I’ve been to networking sessions taking place at opposite ends of England, but both located in areas that might generously be described as ‘left behind’ when it comes to economic prosperity. Yet in both these locations, people are trying to build on the local population’s drive for change, in ways that clearly involve technology.
On a trip to my hometown in the North West, I dropped in at Barclays Eagle Labs in Whitehaven. A repurposed former bus station situated in the town centre is now a co-working space in the stereotypical style, complete with glasspartitioned offices, bare brick walls, meeting rooms and even a small workshop.
It takes a lot to bring something of its ilk to West Cumbria, an area so deeply post-industrial that its coal, steel and shipping legacy still hangs over it like a thick mist. The huge nuclear decommissioning operation happening at nearby Sellafield is the reason behind the laboratory’s arrival, as various parts of the giant operation look to attract new talent and suppliers.
of the noise about this cutting-edge, energy-sector engineering gets drowned out by fearful chatter of oozing toxic waste (Spoiler: it’s rarely oozing), and many groundbreaking projects are created solely for that site, meaning nobody shouts about them to the wider world.
The Bus Station in Whitehaven is hoping to change that, offering a hub for new businesses, many with connections to engineering projects taking place at Sellafield, but also acting as a focal point for others to meet and interact.
BRIDGE BUILDING
Having arrived for one of its regular breakfast networking sessions, I chatted with bio-engineers hoping to develop new materials from agri-waste, hydro-power inventors and some of the engineers that had set up base in the building.
If you’re thinking that there’s no meeting place like this near you, then maybe it’s something you could start, in your own little act of giving back
Sellafield is the site of some incredible engineering, including the development of unique robotics technologies designed for deeply hazardous environments. Much
The workshop has been a valuable asset for businesses in the local area, helping those with bright ideas to 3D print parts, build prototypes for start-ups and even create laser cut signage for established businesses.
Networking was equally diverse at my second meet-up, this time in Hastings on the South East coast. It’s a similar tale of a redundant and decrepit local structure in a hardhit coastal town. This time, it’s an old newspaper office that has been redeveloped as a home for new businesses, along with the now-familiar co-working and workshop spaces.
The Observer Building offers monthly tech coffee meet-ups, typically attended by creative industry types who have fled London in their droves in recent years.
The north-south hospitality divide means there were no bacon sandwiches
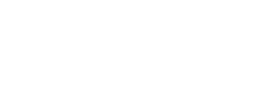

communities not only help their regions to thrive, but also get access to ideas and expertise they never knew existed. Get the kettle on and get together, urges Stephen Holmes
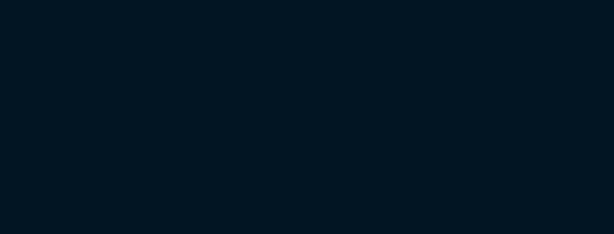
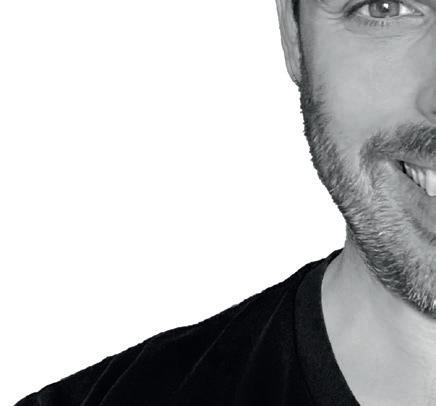
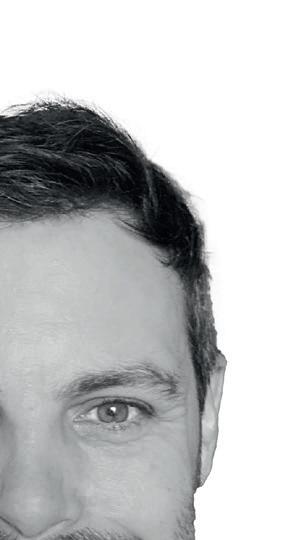
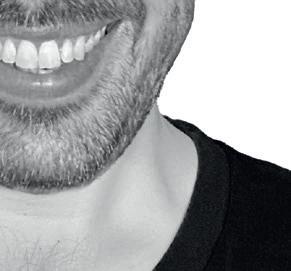
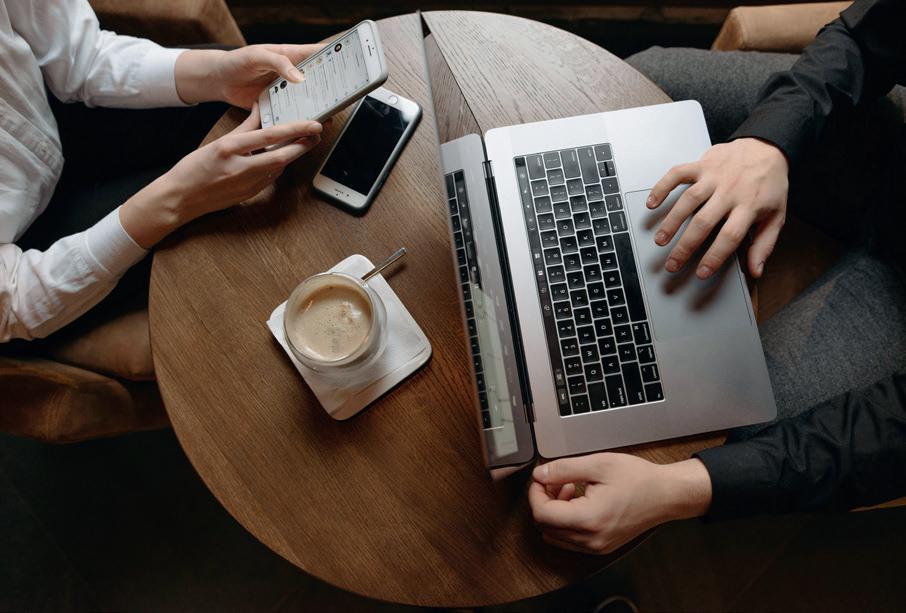
in Hastings, but there were jewellery designers, experts in embedded electronics for garments, and creatives simply looking for help developing websites.
By offering up space, hot drinks and the chance to network, both venues, north and south, hope to attract new businesses to set up shop in their buildings.
However, they’re also playing an important role in building a network around them that can help the broader community.
Everyone that has bootstrapped a startup tells me that any help at all in those early stages can have huge consequences, even if it’s just making a new connection with someone who might be able to answer a question for you.
Having banged the drum for flexible working in the last issue, a focus point for your area, once a month, might be a location that’s not just a great place to work, but also to chat, share ideas, or meet new suppliers and collaborators.
If you’re thinking that there’s nothing like that near you, then maybe it’s something you could start, in your own little act of giving back. My tiny piece of advice: don’t skimp on the bacon.
GET IN TOUCH: After a 24-hour round trip by car between Whitehaven and Hastings, Stephen is grumpily wondering where else he might have travelled in that timeframe. St Lucia? Mumbai? Miami? Answers on a postcard. On X, he’s @swearstoomuch
What bright idea or useful connection might a cup of coffee and a chat bring you?
DEVELOP3DSERVICES

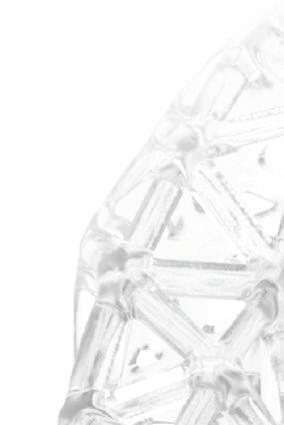
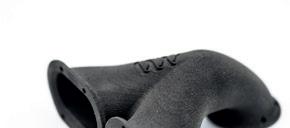
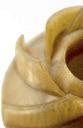
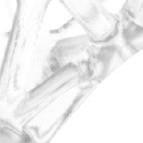
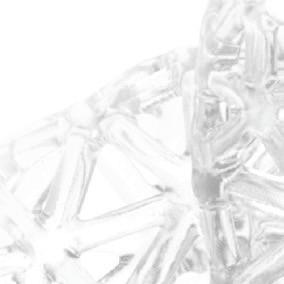
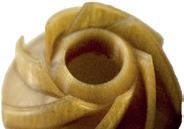



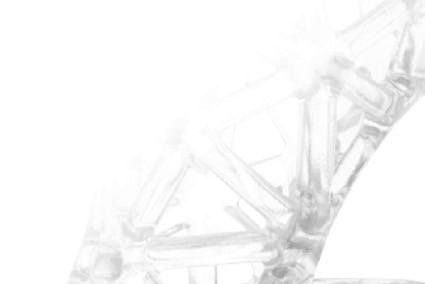

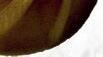
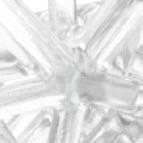
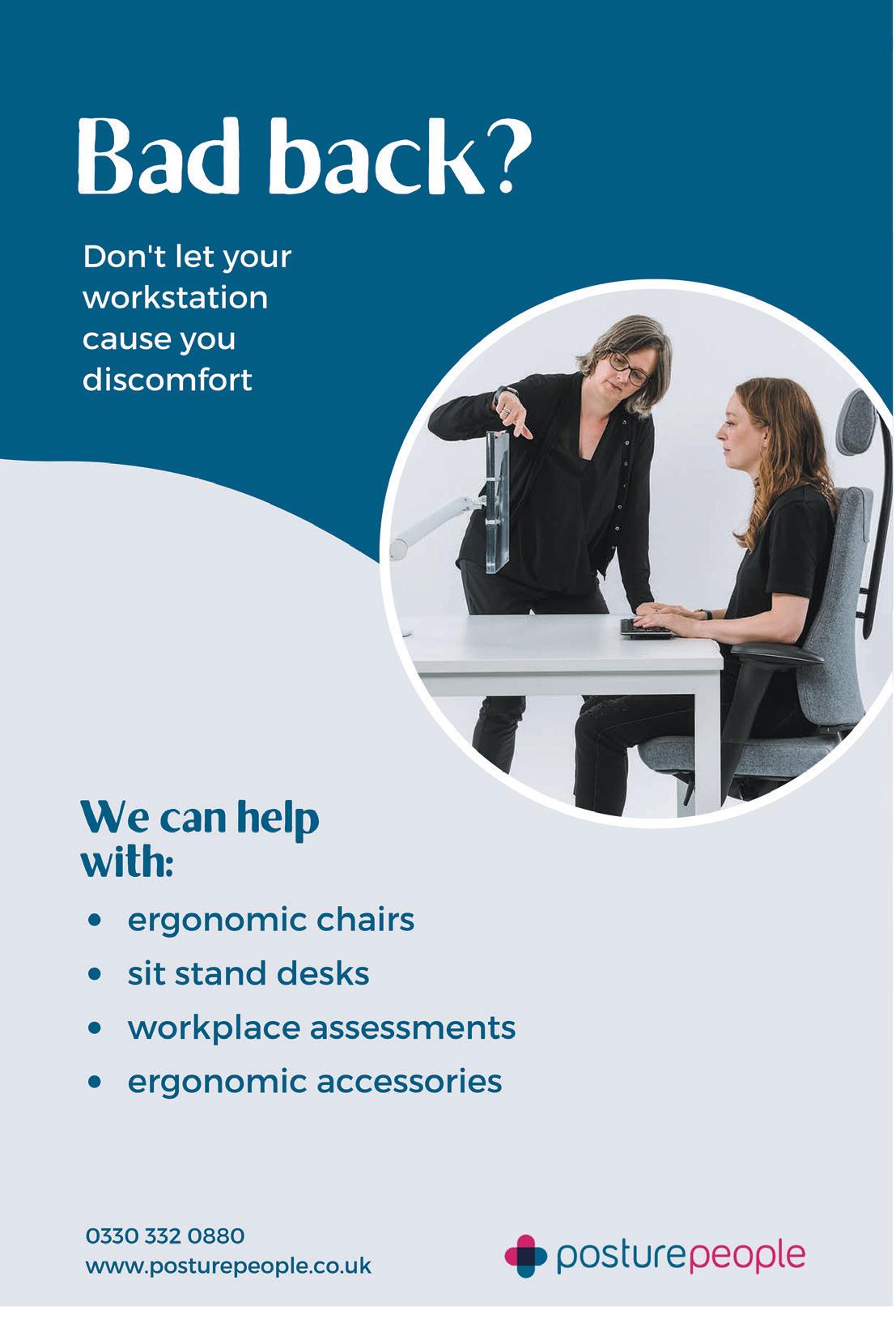
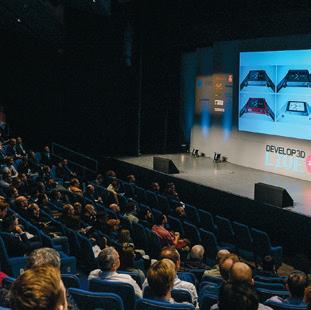
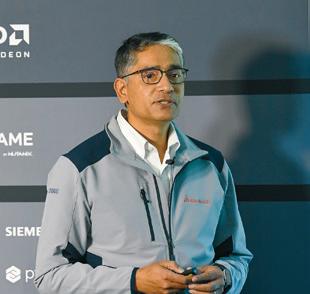
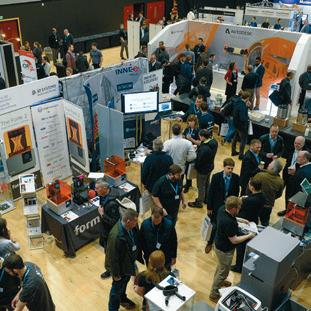
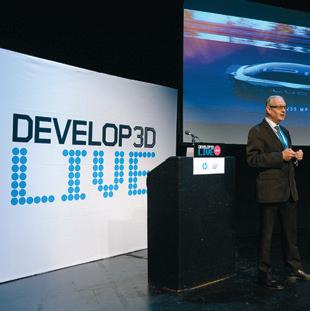

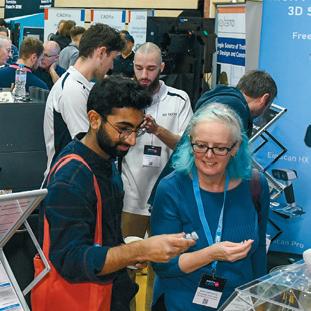
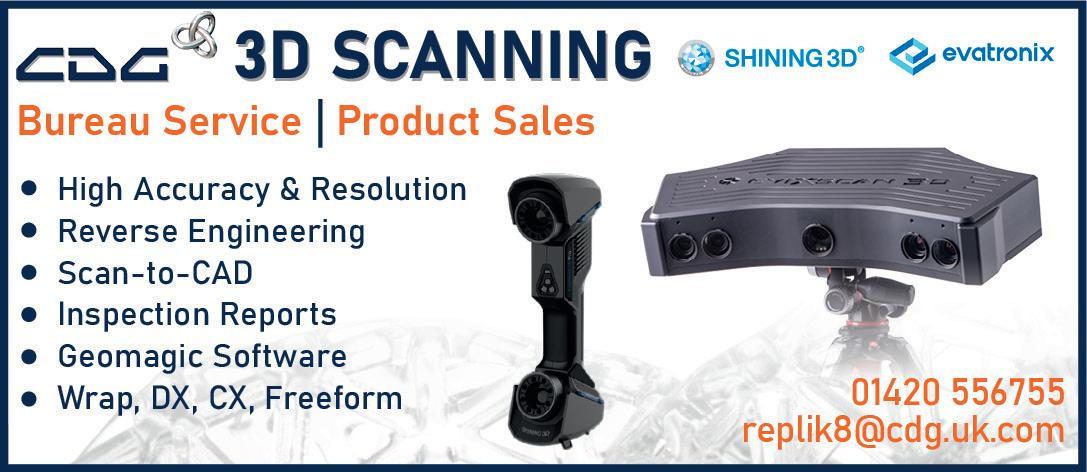
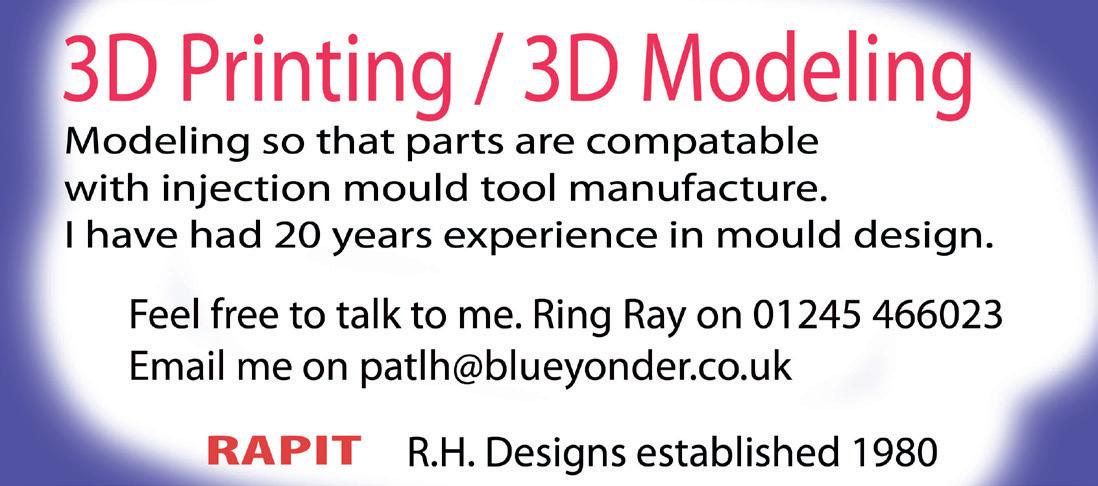

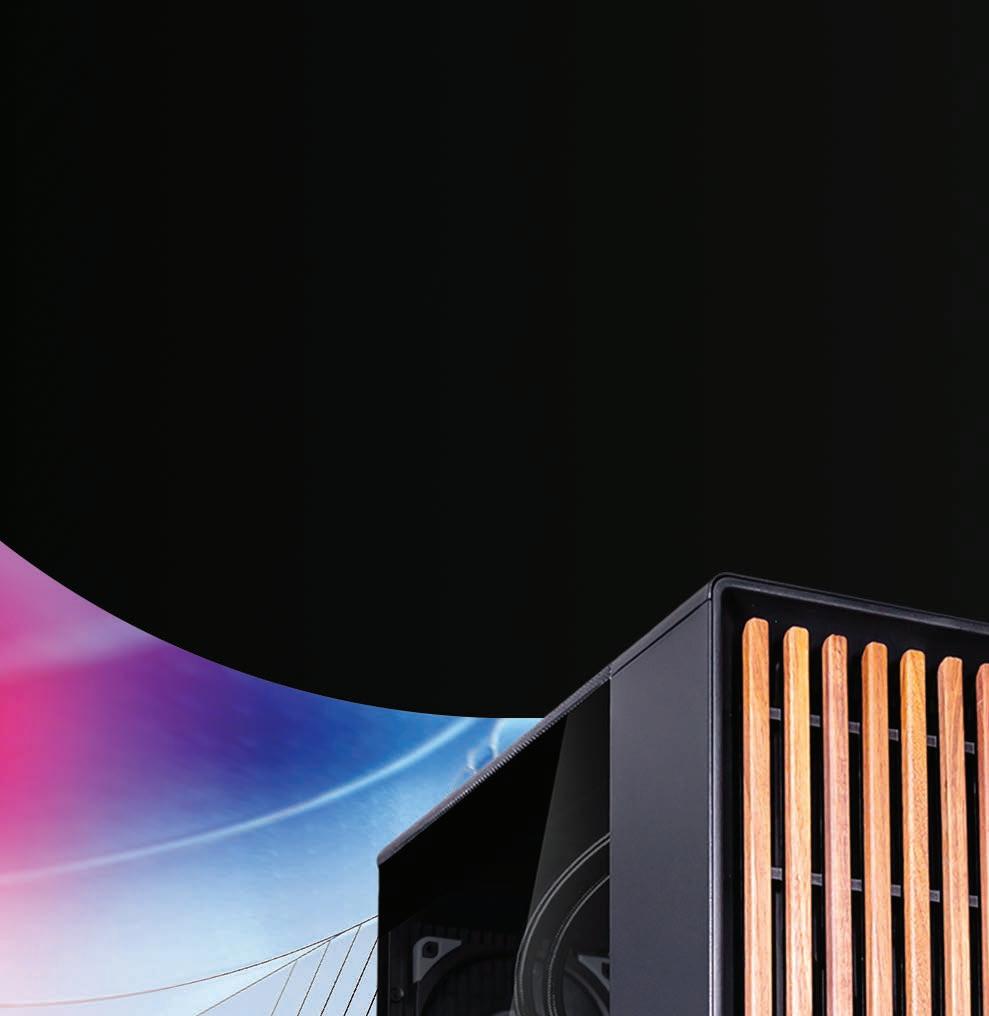
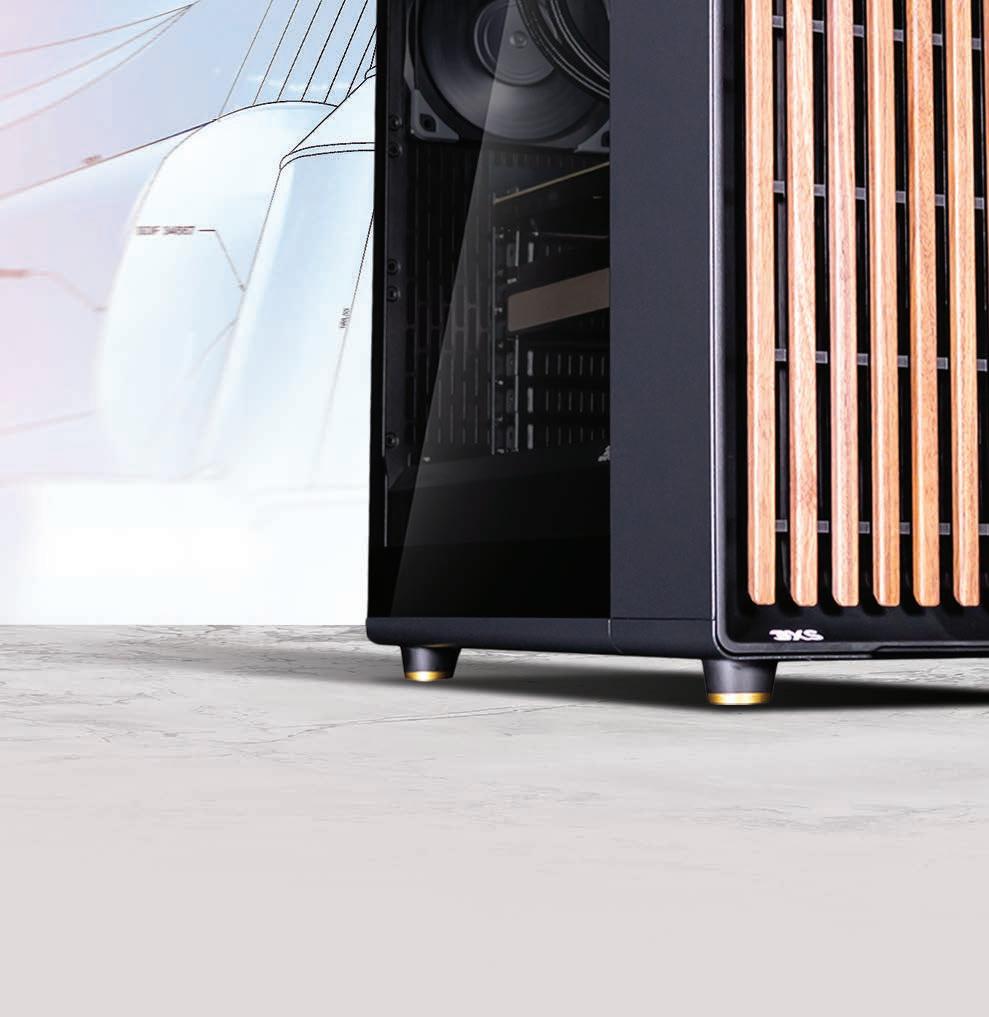
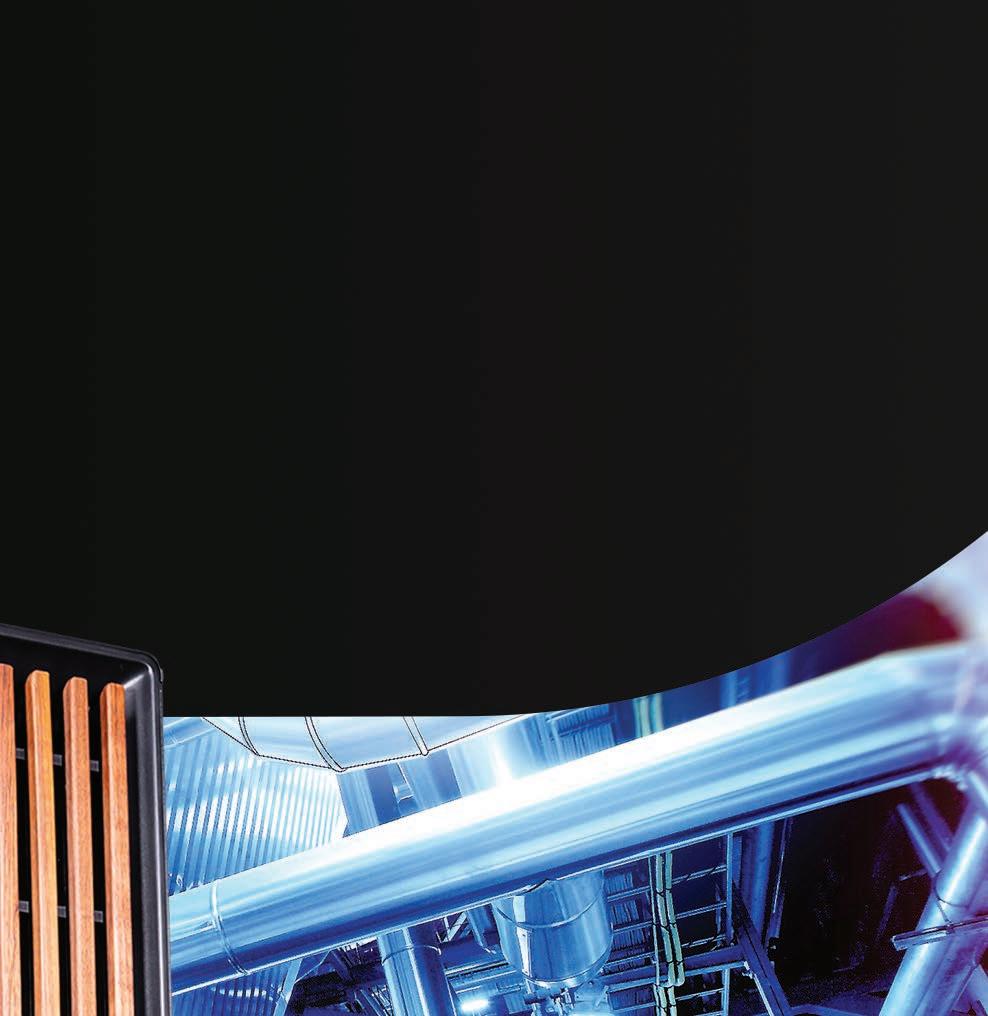



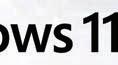

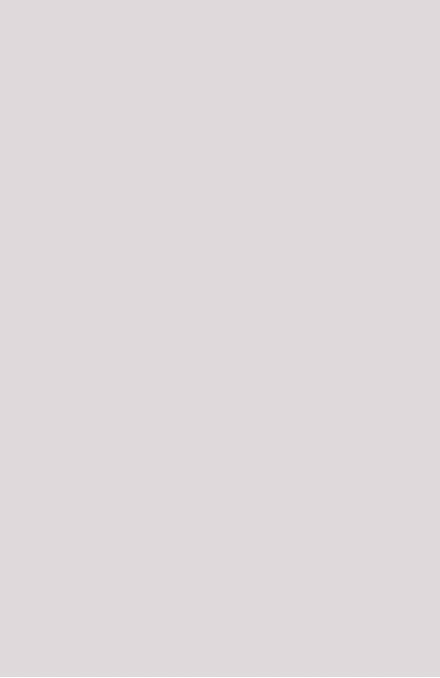