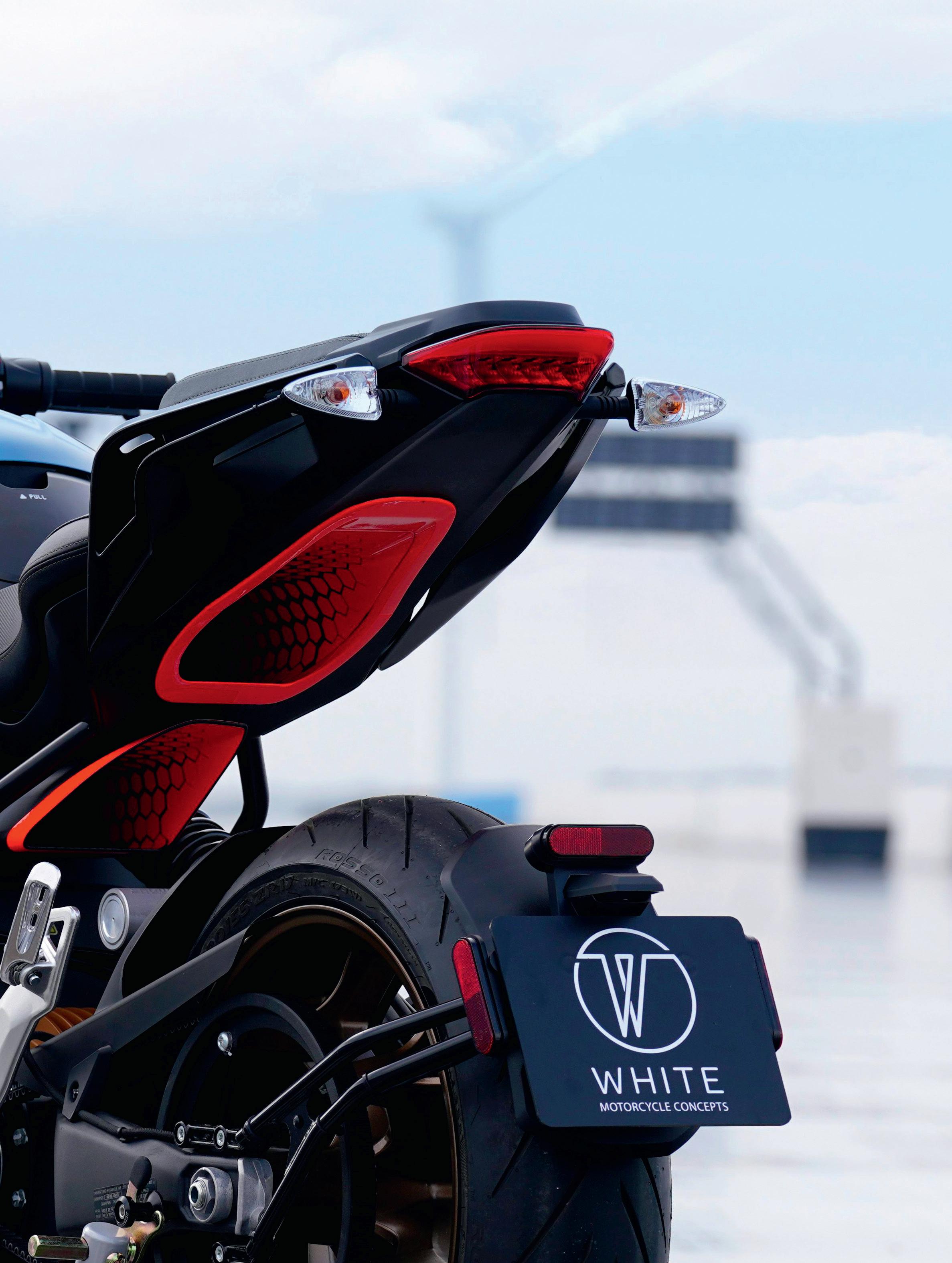
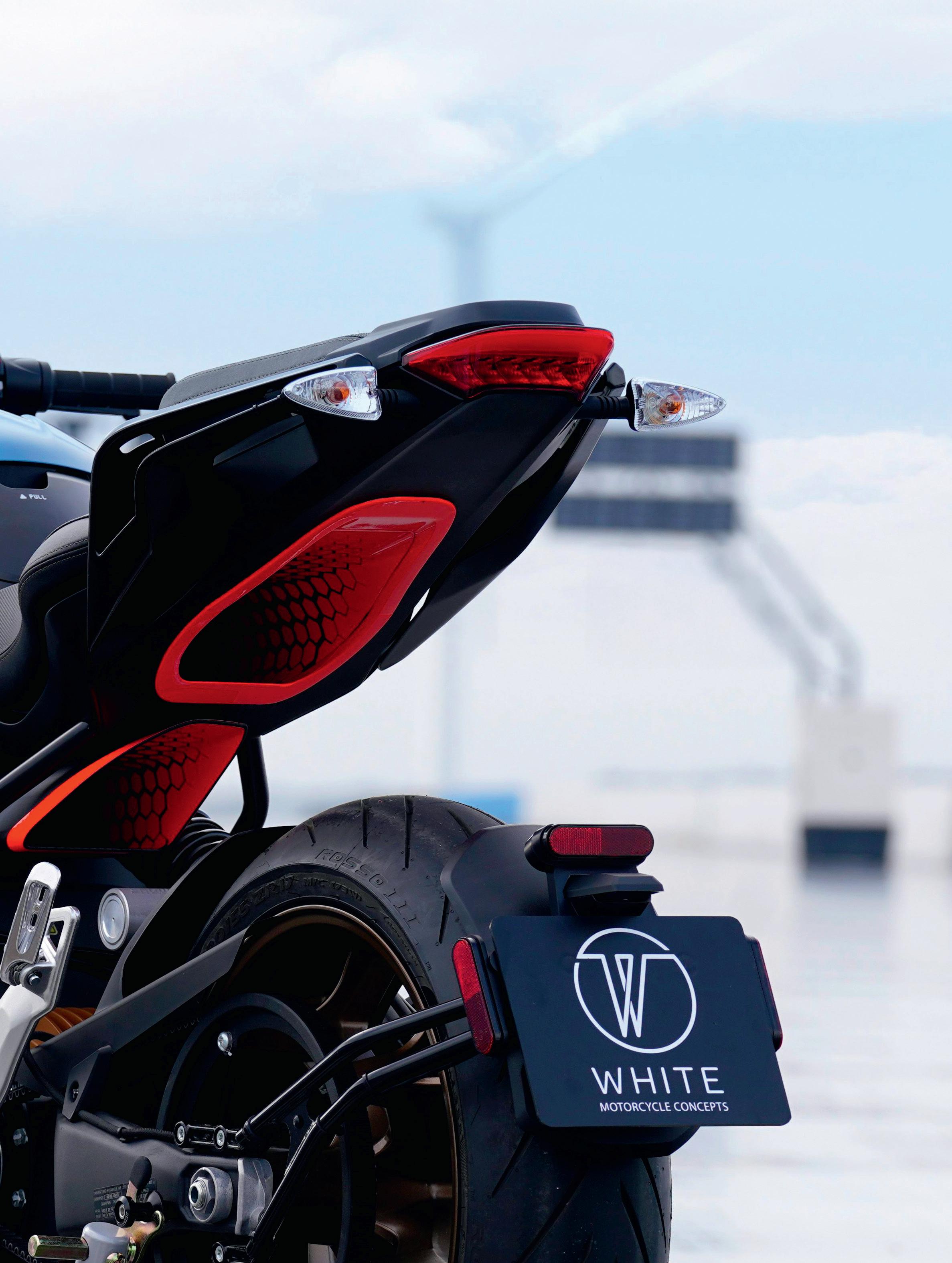
FIGHTING THERESISTANCE
White Motorcycle Concepts blends aerodynamics and innovation to take EVs further
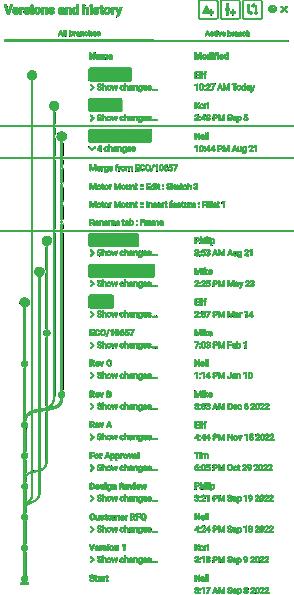

From the founders who created SOLIDWORKS, Onshape is the most widely used cloud-native CAD & PDM system on the market with over 3 million users.

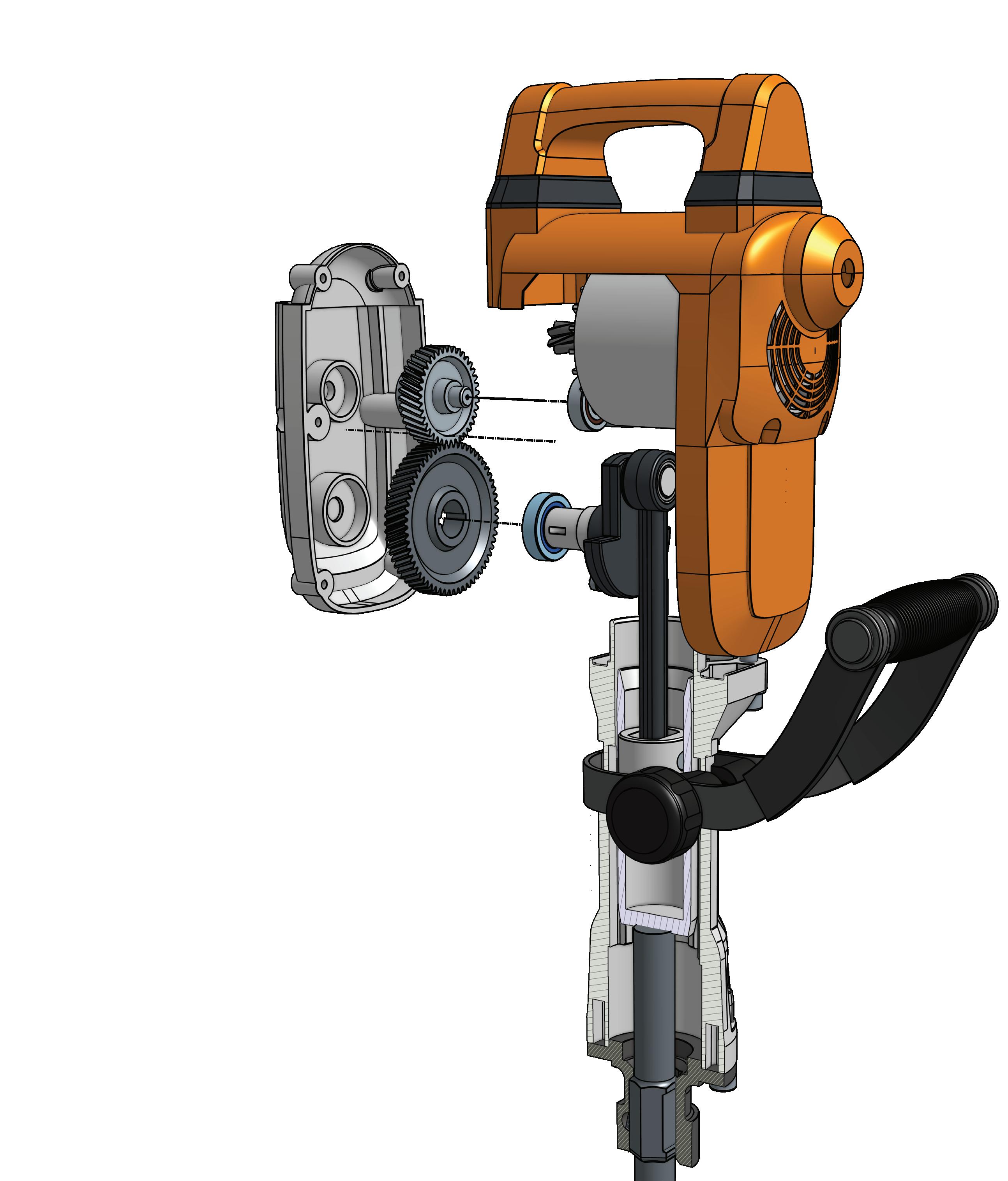
Built-in PDM - a single source of truth for design data with robust version control.
Real-Time Collaboration - users across the globe can simultaneously view and edit parts, assemblies, and drawings.
Zero IT Overhead - Onshape runs in a browser anytime, anywhere, and on any device. No costly workstation required.
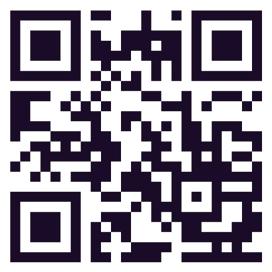
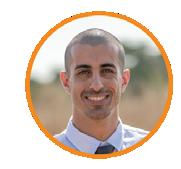
EDITORIAL
Editor
Stephen Holmes stephen@x3dmedia.com
+44 (0)20 3384 5297
Managing Editor
Greg Corke
greg@x3dmedia.com
+44 (0)20 3355 7312
Consulting Editor
Jessica Twentyman jtwentyman@gmail.com
Consulting Editor
Martyn Day martyn@x3dmedia.com
+44 (0)7525 701 542
Staff Writer
Emilie Eisenberg emilie@x3dmedia.com
DESIGN/PRODUCTION
Design/Production
Greg Corke
greg@x3dmedia.com
+44 (0)20 3355 7312
ADVERTISING
Group Media Director Tony Baksh tony@x3dmedia.com
+44 (0)20 3355 7313
Deputy Advertising Manager Steve King steve@x3dmedia.com
+44 (0)20 3355 7314
US Sales Director Denise Greaves denise@x3dmedia.com
+1 857 400 7713
SUBSCRIPTIONS
Circulation Manager
Alan Cleveland alan@x3dmedia.com
+44 (0)20 3355 7311
ACCOUNTS
Accounts Manager
Charlotte Taibi charlotte@x3dmedia.com
Financial Controller
Samantha Todescato-Rutland sam@chalfen.com
ABOUT

As a younger man, I always imagined that the year 2025 would be far more futuristic than the present-day reality suggests. However, having lived through the drudgery of the Millenium (25 years ago – drink that in, kids!), we’re at least now living in a world of electric cars, renewable energy, high-level simulation and generative design. By a wonderful coincidence, these are all topics covered in this issue of DEVELOP3D.
White Motorcycle Concepts is bringing aerodynamics to motorcycles, an industry that has barely touched the subject since the first motor was strapped to a bicycle frame. To achieve its goals, it’s running optimised air ducts through a bike’s structure. It’s a unique challenge, and one that promises benefits that will only grow as other technologies advance.
Key to all this is the use of simulation software, which as many of you know, is a sector undergoing some seismic shifts. With multi-billion-dollar acquisitions of some of the biggest software companies in this area during 2024, we look at what new tools are beginning to bleed through into workflows in 2025. More specialist simulation software is starting to rub shoulders with huge GPU-powered and AIenabled accelerators, a shift that should see more analysis capabilities added to product development workflows.
Late 2024 saw the return of one of the most important global trade shows for additive manufacturing, Formnext, and from that event, we bring you some of the most interesting trends to keep an eye on in 2025.
While the business side of the additive manufacturing industry is as much of a jumble as ever, the technology continues to advance, presenting designers and engineers with some thought-provoking new materials and capabilities.
And, to combine all of the above, we bring you a special story from Airbus, showing how its concept for lightweighting an aircraft air separator with 3D printing became a reality via an end-to-end software workflow from Hexagon.
The goal was to not only to optimise the huge part so it could be 3D printed in titanium, but also to show – via simulation and new compensation software – how a new design might be successfully created before a 3D printer was switched on.
It’s a move that executives at both Hexagon and Airbus hope will enable even more pioneering parts to be built, without the worry of costly failures, and more sustainable parts being used in all kinds of transportation.
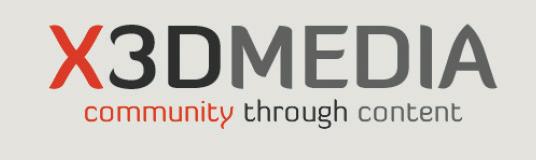
DEVELOP3D is published by X3DMedia 19 Leyden Street London E1 7LE, UK
T. +44 (0)20 3355 7310 F. +44 (0)20 3355 7319
With these processes and tools maturing rapidly, maybe by the time we get to 2030, my youthful hopes of jetpacks and flying cars will no longer be pipedreams. So, welcome to the future – it’s a bit like yesterday, only better.
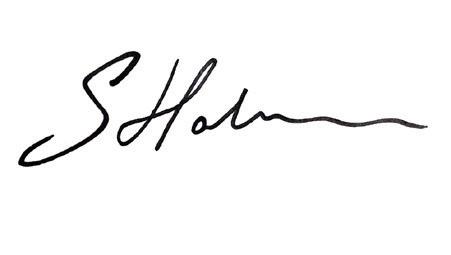

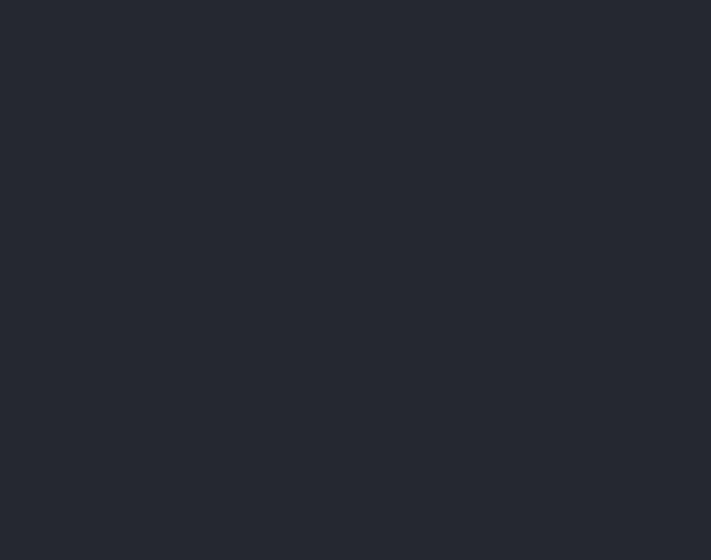
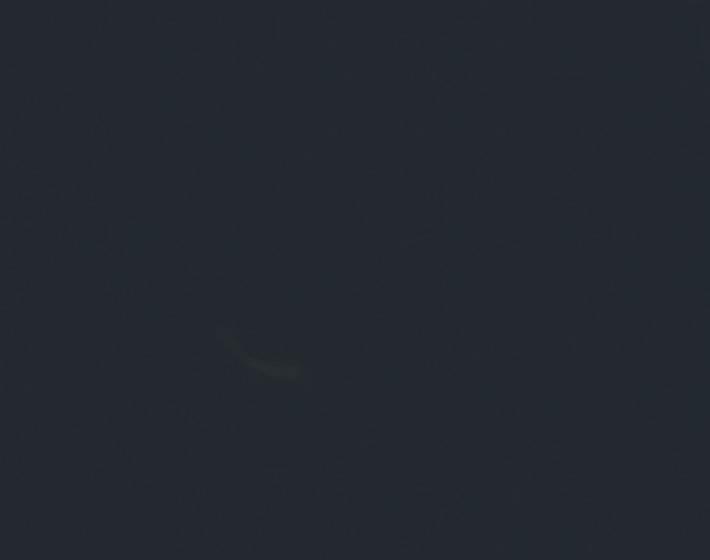

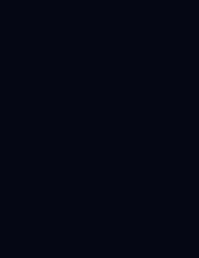

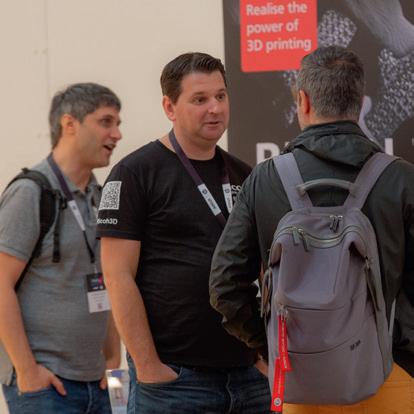
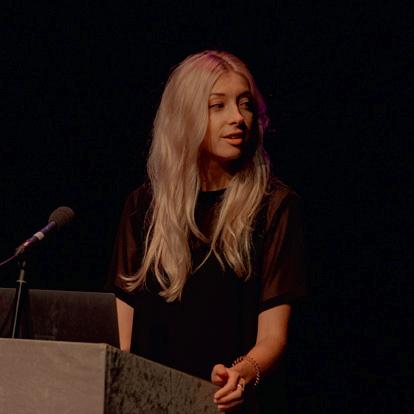

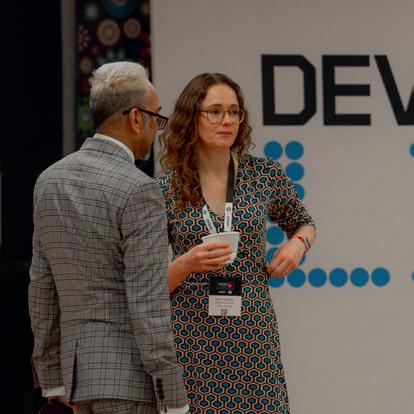

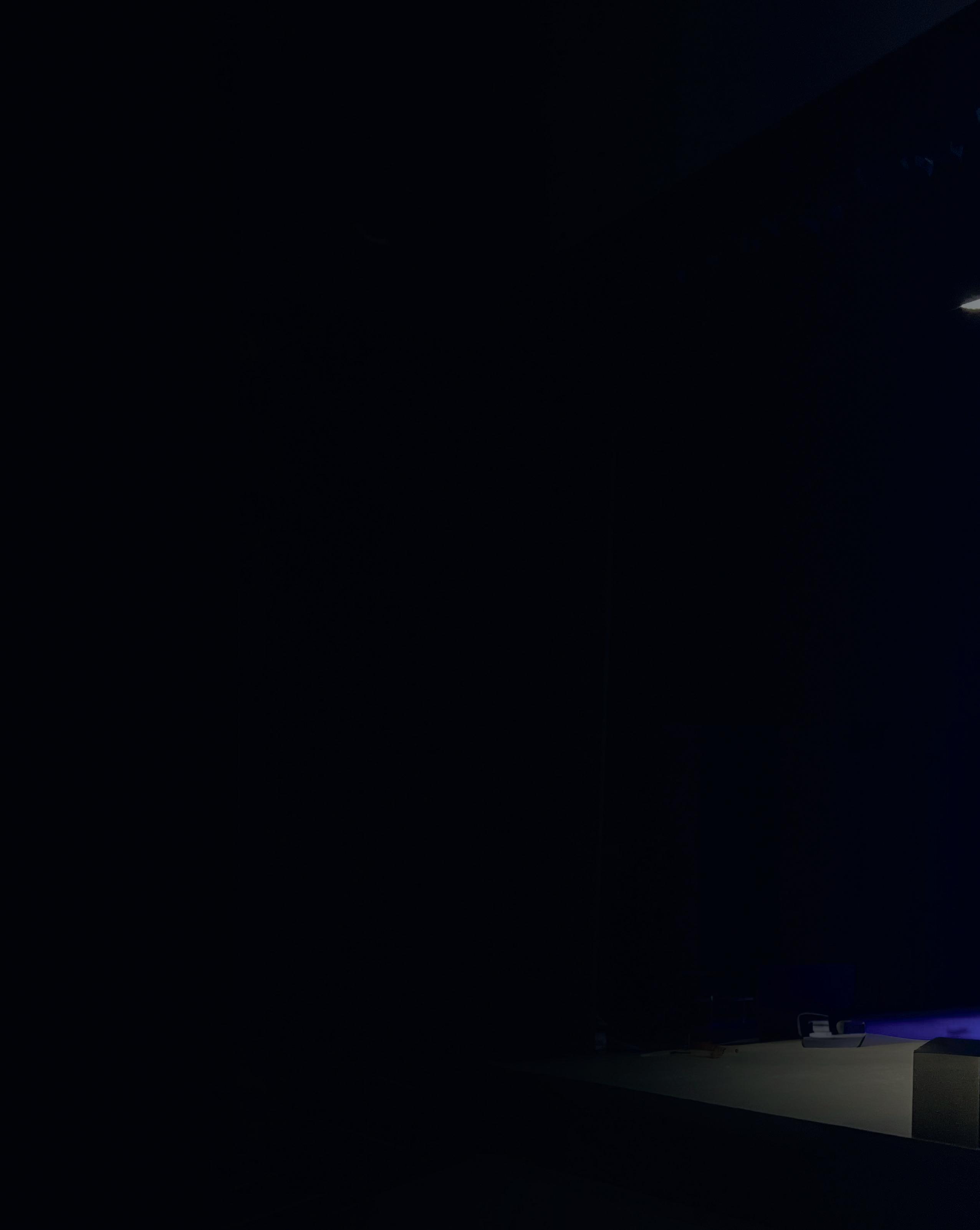
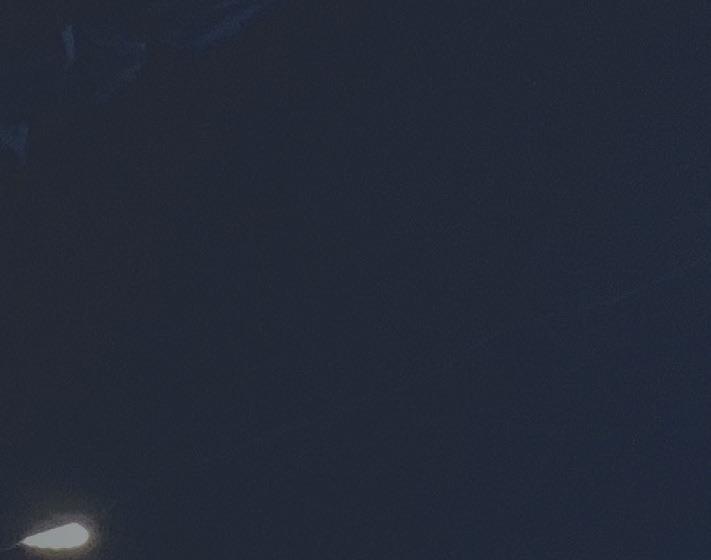
The future of product development technology
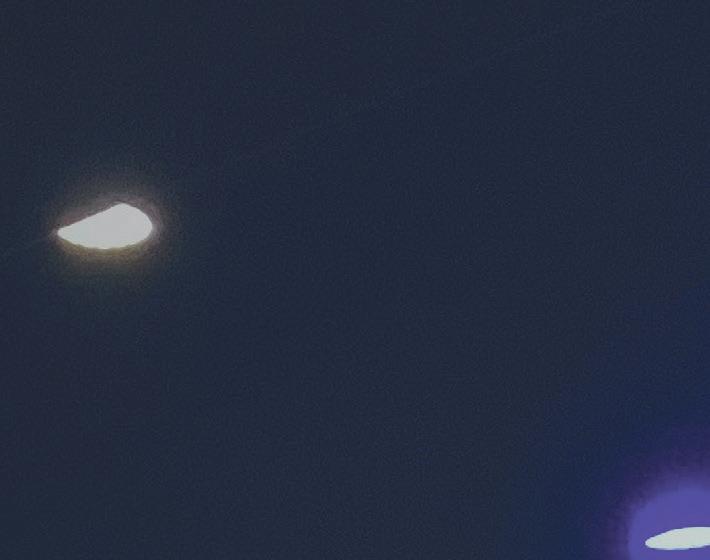
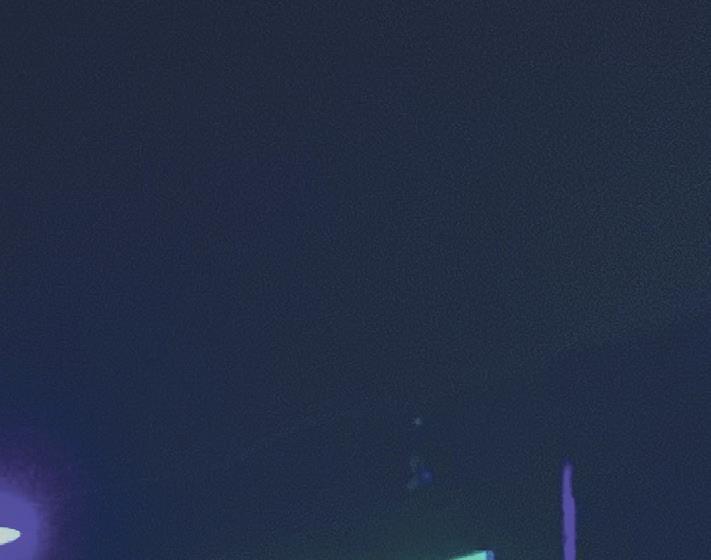
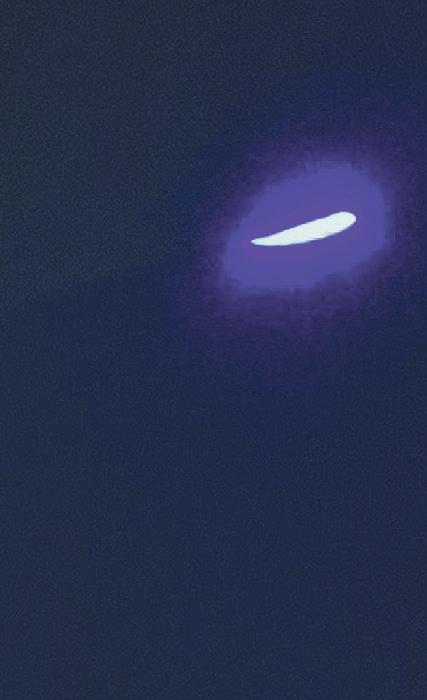



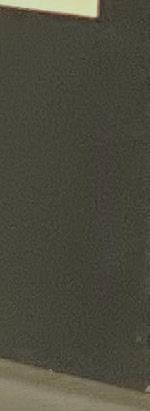
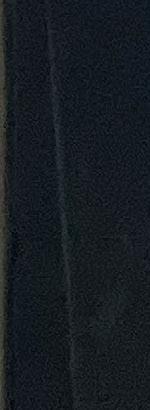
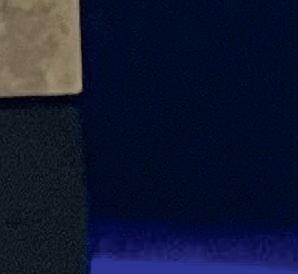
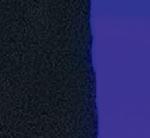

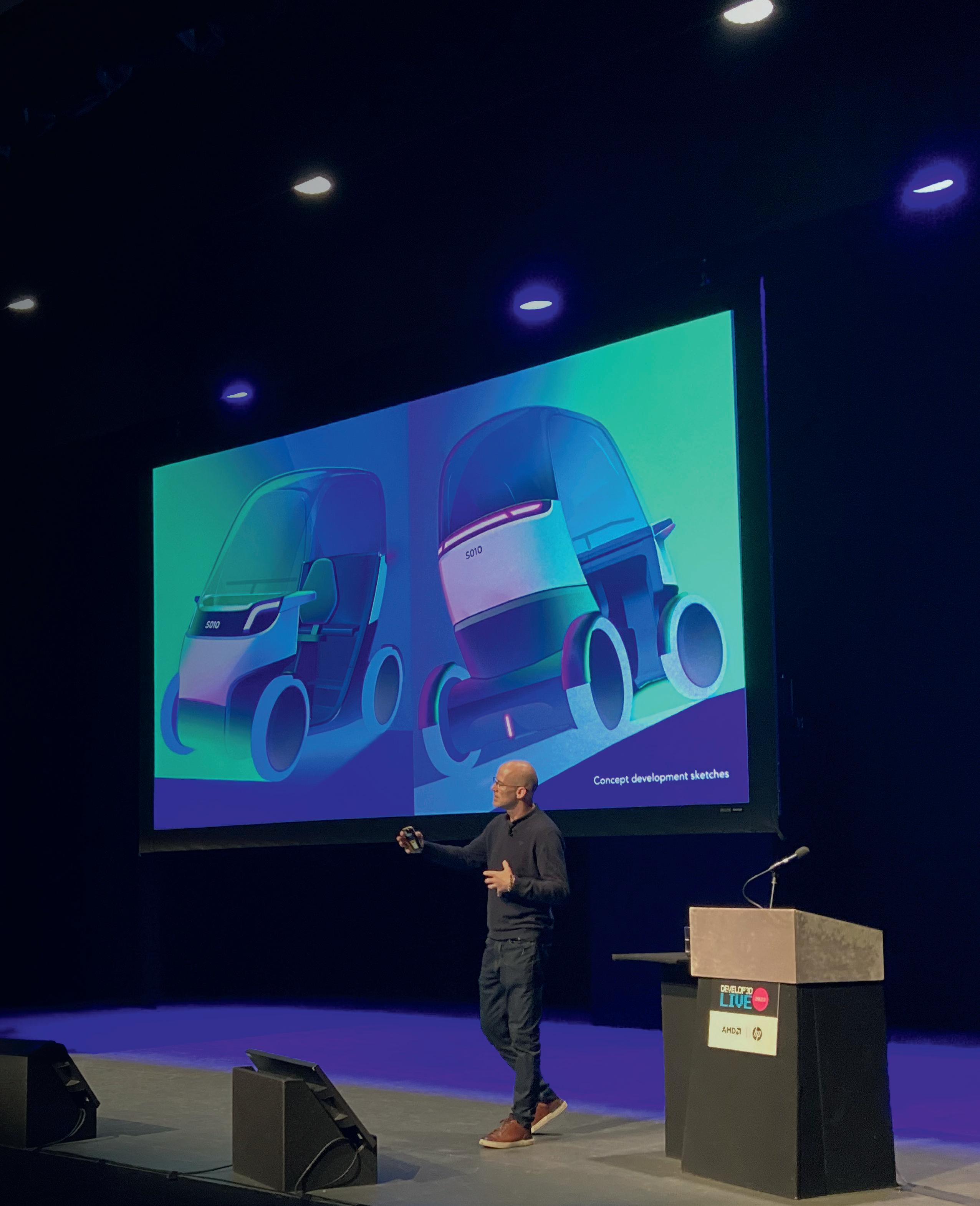

Gold sponsors Silver sponsors
Bronze sponsors

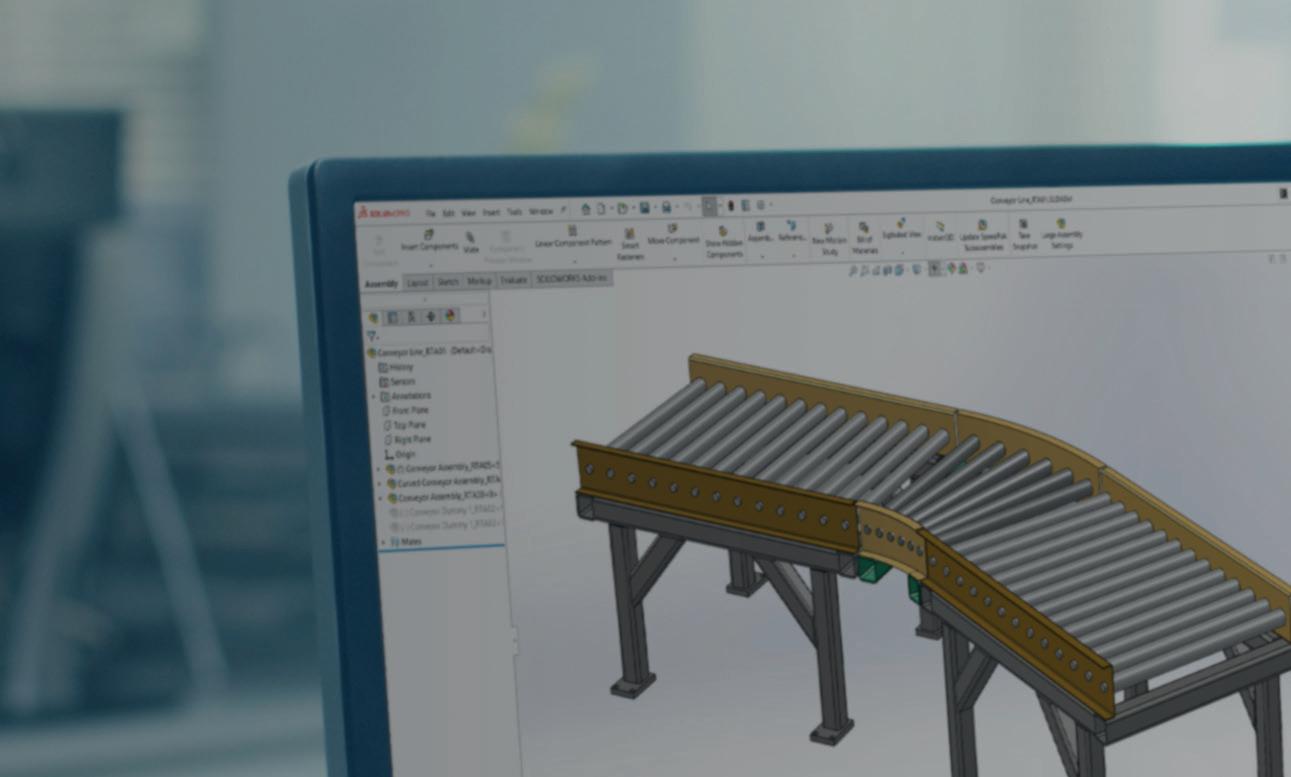

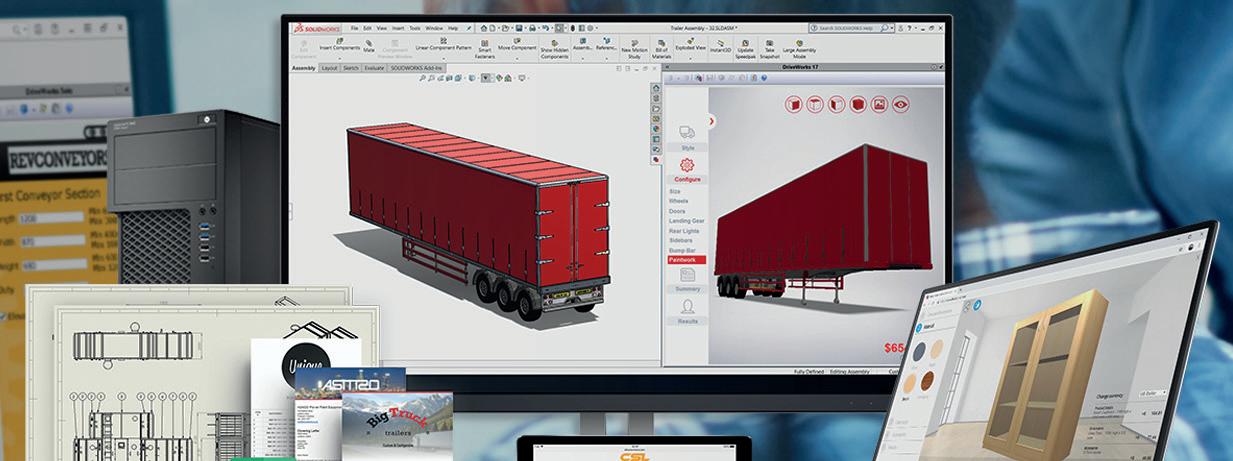




Automate SOLIDWORKS manufacturing processes & sell digitally using DriveWorks
DriveWorks is flexible and scalable. Start for free, upgrade anytime. DriveWorksXpress is included free inside SOLIDWORKS or start your free 30 day trial of DriveWorks Solo.
DriveWorks Pro
30DAY FREETRIAL
DriveWorksXpress
Entry level design automation software included free inside SOLIDWORKS®
Entry level SOLIDWORKS part and assembly automation
Create a drawing for each part and assembly
Find under the SOLIDWORKS tools menu


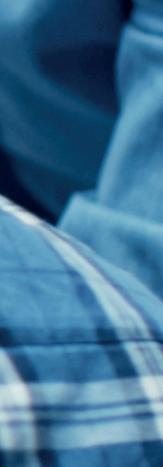
One time setup
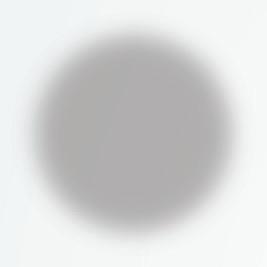
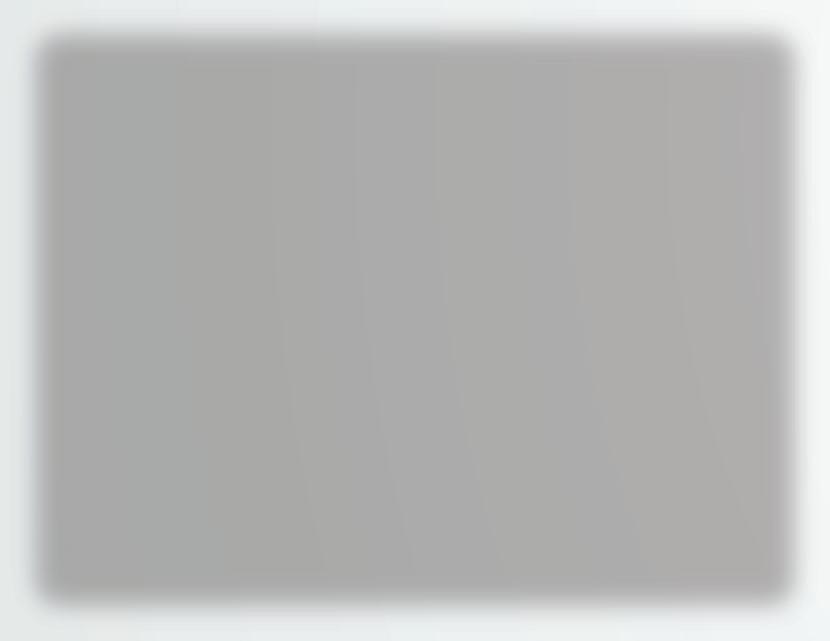

Modular SOLIDWORKS® automation & online product configurator software
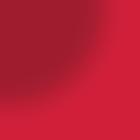
DriveWorks Solo

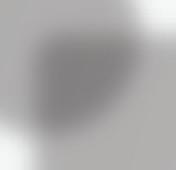
SOLIDWORKS® part, assembly and drawing automation add-in
Automate SOLIDWORKS parts, assemblies and drawings
Generate production ready drawings, BOMs & quote documents automatically Enter product specifications and preview designs inside SOLIDWORKS
Free online technical learning resources, sample projects and help file
Sold and supported by your local SOLIDWORKS reseller
examples online
Set up once and run again and again. No need for complex SOLIDWORKS macros, design tables or configurations.
Save time & innovate more
Automate repetitive SOLIDWORKS tasks and free up engineers to focus on product innovation and development.
Eliminate errors
DriveWorks rules based SOLIDWORKS automation eliminates errors and expensive, time-consuming design changes.

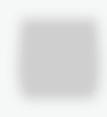
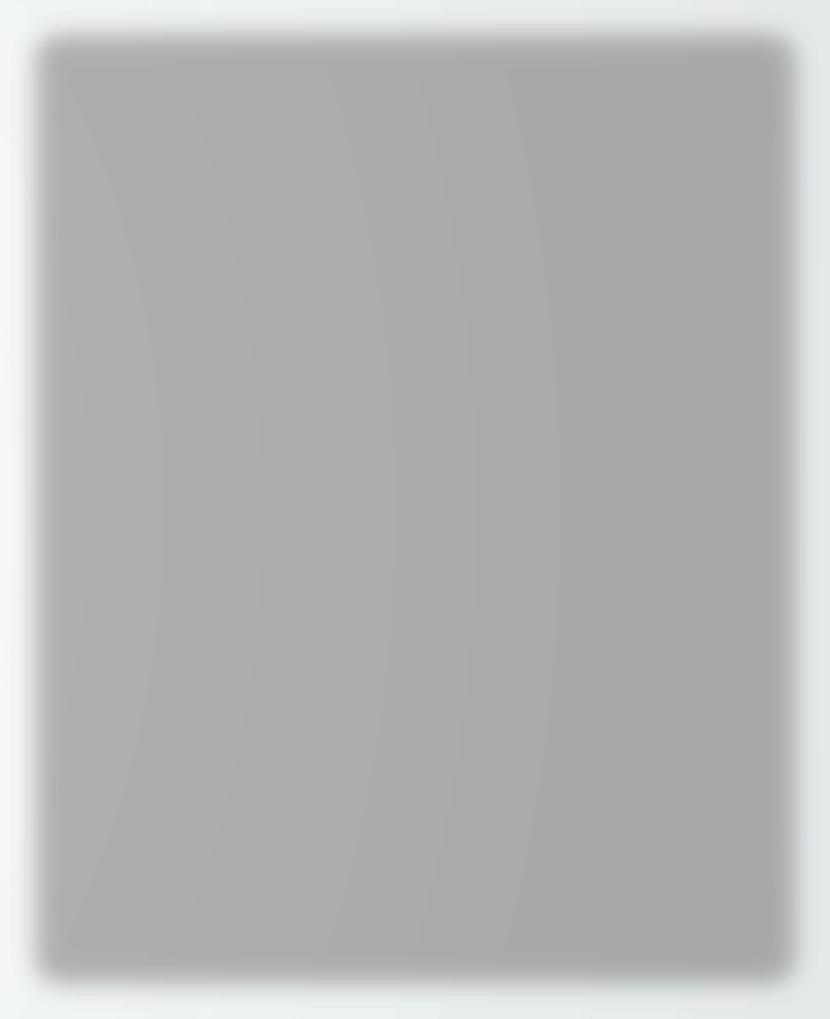
Complete SOLIDWORKS part, assembly and drawing automation
Automatically generate manufacturing and sales documents
Configure order specific designs in a browser on desktop, mobile or tablet
Show configurable design details with interactive 3D previews
Integrate with SOLIDWORKS PDM, CRM, ERP, CAM and other company systems
Scalable and flexible licensing options
Sold and supported by your local SOLIDWORKS reseller

Connect sales & manufacturing
Validation ensures you only offer products that can be manufactured, eliminating errors and boosting quality.
Integrate with other systems
DriveWorks Pro can integrate with other company systems, helping you work more efficiently and effectively.
Intelligent guided selling
Ensure your sales teams / dealers configure the ideal solution every time with intelligent rules-based guided selling.
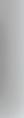
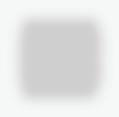
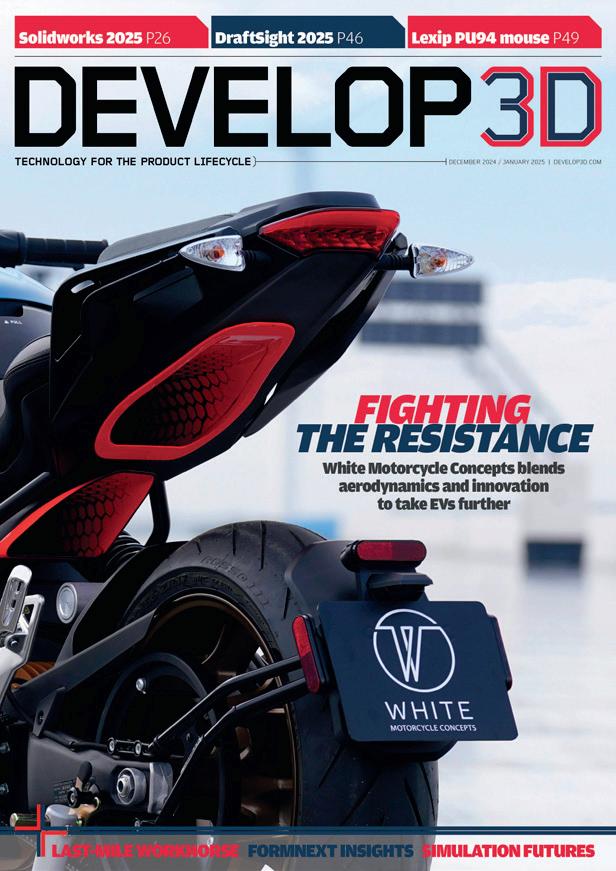
NEWS
Siemens snaps up Altair, Geomagic tools join Hexagon’s portfolio, PhysicsX trains AI tool on Simcenter datasets, and more
FEATURES
Comment: Marleen Vogelaar on a better future for AM
Comment: Mazen El Hout on boosting engineering with AI
Visual Design Guide: Vayve Mobility’s Eva
COVER STORY Free flowing aerodynamics at WMC
Q&A: DS’s Stephen Endersby on SolidWorks 2025
Laurence Marks on up-and-coming simulation tools
Light as air: A new way to build parts at Airbus
Event report: Five insights from Formnext 2024
Turning point: 3D printing at Gulf Wind Technology
Beast of burden: Workhorse electrifies delivery vans
Best foot forward: Customisation at ASICS
Think Tank’s approach to sustainable packaging
REVIEWS
DraftSight 2025
Lexip PU94 mouse
THE LAST WORD
The total kerfuffle sparked by Jaguar’s recent rebrand says a great deal about the automotive industry as a whole, writes Stephen Holmes – but has the sector got its priorities straight on the journey to electrification?
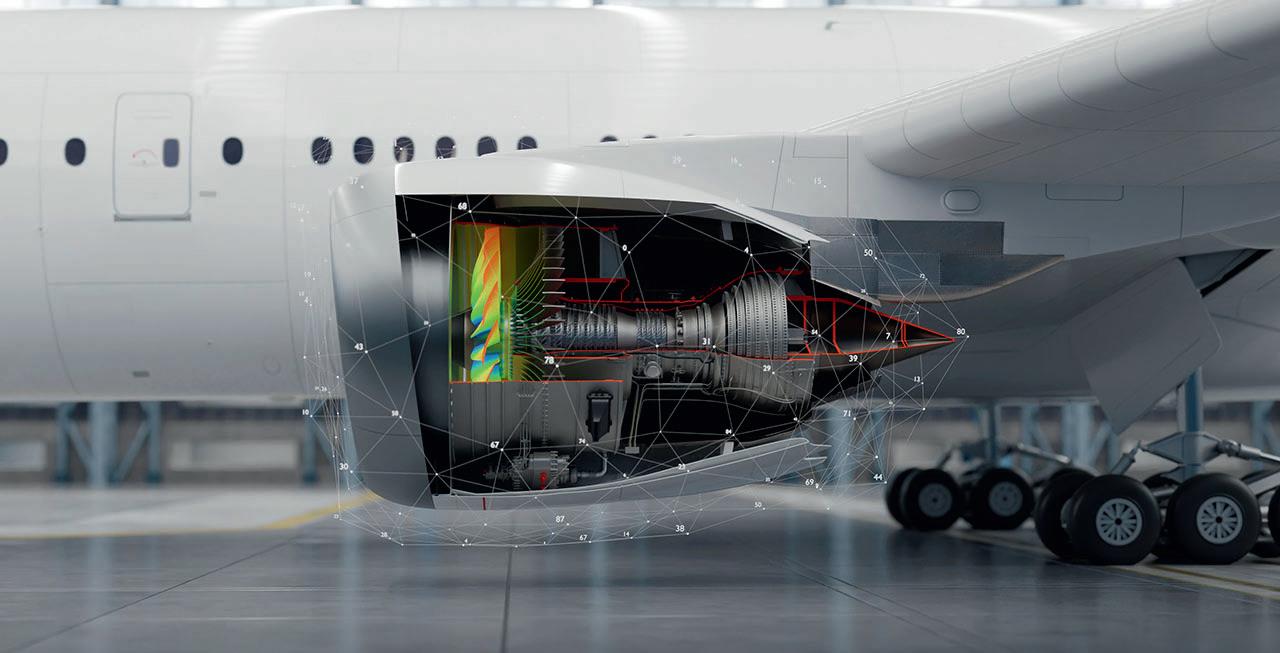
SIMULATION SPECIALIST ALTAIR IS SNAPPED UP BY SIEMENS IN $10 BILLION DEAL
» The recent acquisition by Siemens aims to boost its industrial software strategy and, in particular, its focus on digital twin technology
Siemens is to acquire Altair Engineering in a deal worth around $10 billion. The deal provides a significant boost for Siemens' design and engineering software portfolio.
Roland Busch, president and CEO of Siemens AG, said that acquiring Altair marks a significant milestone for Siemens. “This strategic investment aligns with our commitment to accelerate the digital and sustainability transformations of our customers by combining the real and digital worlds,” he said.
“The addition of Altair’s capabilities in simulation, high performance computing, data science, and artificial intelligence together with Siemens Xcelerator will create the world’s most complete AI-
powered design and simulation portfolio.”
Busch called the acquisition the “logical next step” in Siemens’ software arm’s evolution. “We have been building our leadership in industrial software for the last 15 years, most recently, democratising the benefits of data and AI for entire industries.”
Altair founder and CEO James Scapa said that the acquisition represents the culmination of nearly 40 years, in which the company has grown from a startup in Detroit to a global software and technology company.
“We have added thousands of customers globally in manufacturing, life sciences, energy and financial services, and built an amazing workforce and innovative culture,” he said.
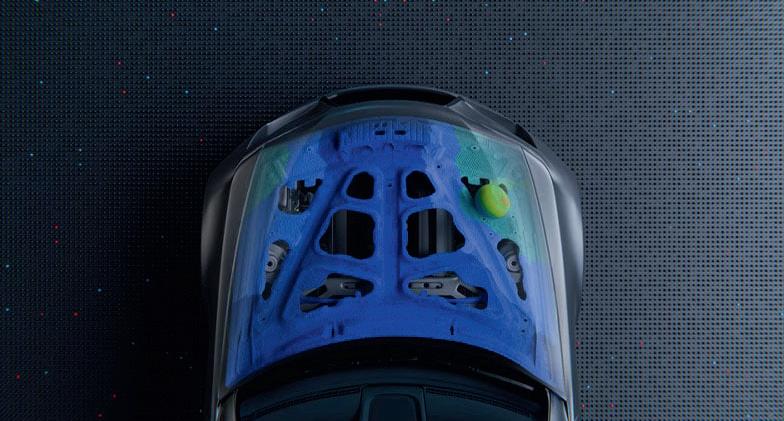
“We believe this combination of two strongly complementary leaders in the engineering software space brings together Altair’s broad portfolio in simulation, data science, and HPC with Siemens’ strong position in mechanical and EDA design.”
He added: “Siemens’ outstanding technology, strategic customer relationships, and honest, technical culture is an excellent fit for Altair to continue its journey driving innovation with computational intelligence.”
Siemens executives claim that Altair’s simulation portfolio, with its strength in mechanical and electromagnetic capabilities, will enhance the company’s own capabilities to produce comprehensive digital twin technology, to deliver a fullsuite, physics-based, simulation portfolio as part of Siemens Xcelerator.
Speaking with German newspaper Handelsblatt, Siemens Digital Industries CEO Cedrik Neike added that this would not be the last software acquisition for the company, which has the financial strength to do further deals.
He also suggested that the move makes business sense in terms of growing the reach of both companies: “In simulation Altair is very strong in the United States and we are very strong in Asia and Europe. We can increase growth through cross-selling.”
The transaction, which was unanimously approved by the Altair Board of Directors, is expected to close in the second half of 2025. www.sw.siemens.com
Altair has over 40 years of experience and expertise in enabling engineers to perform mechanical and electromagnetic simulations
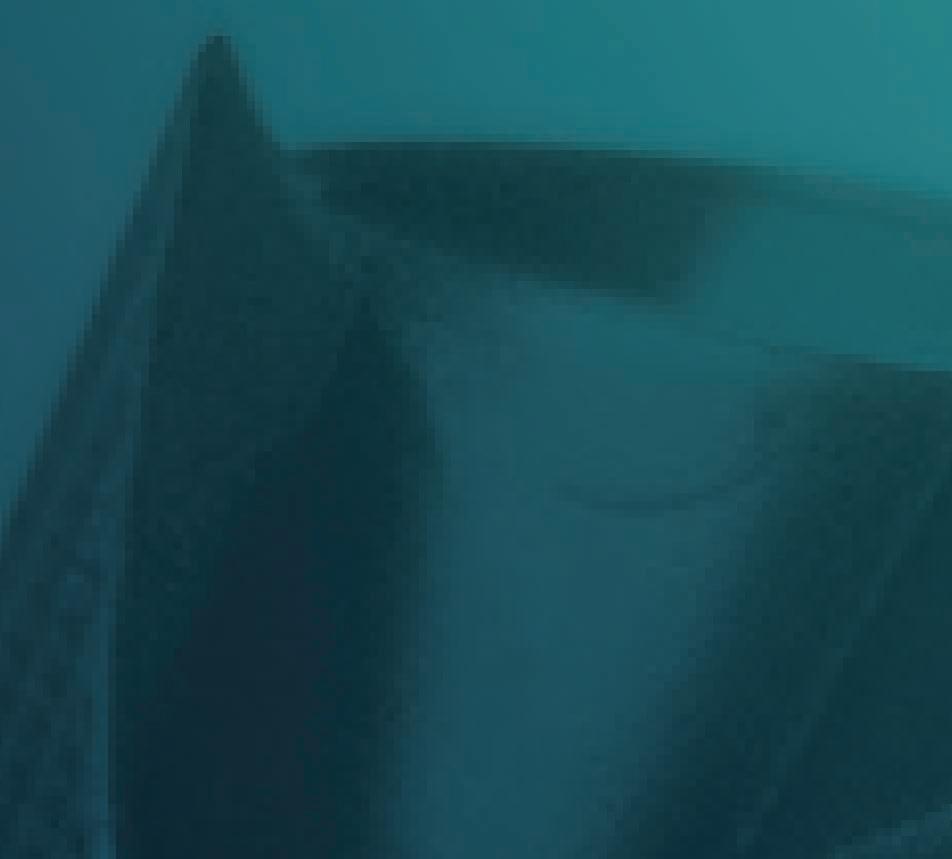
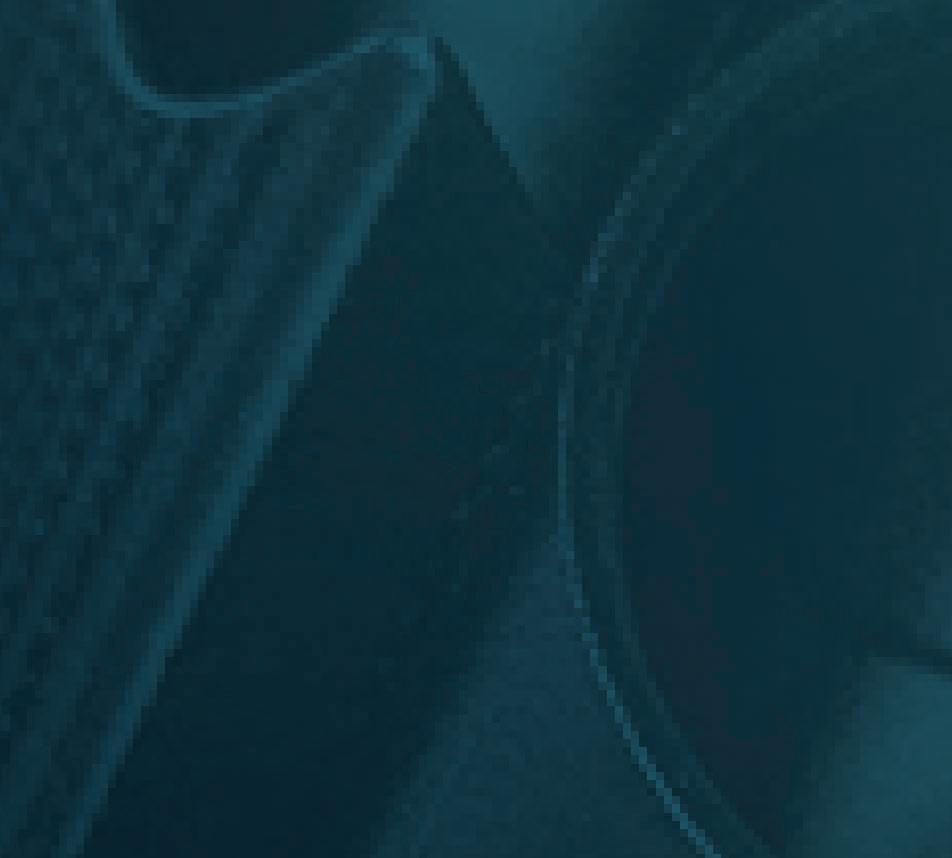
• MAXIMIZE ROI
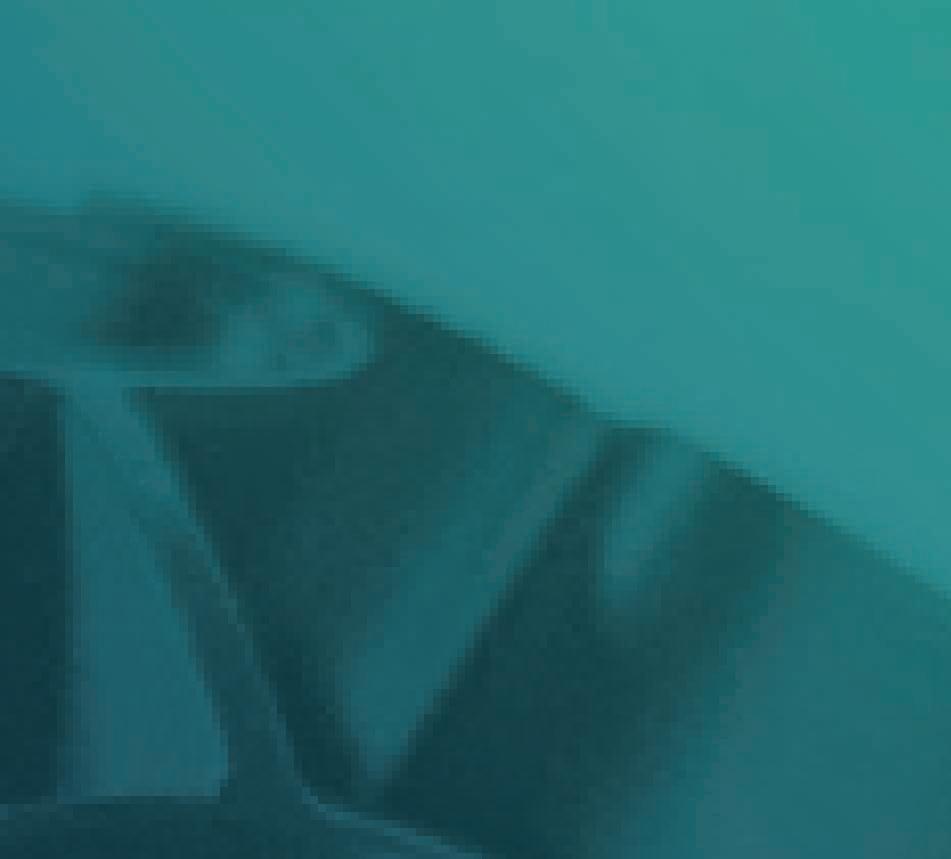
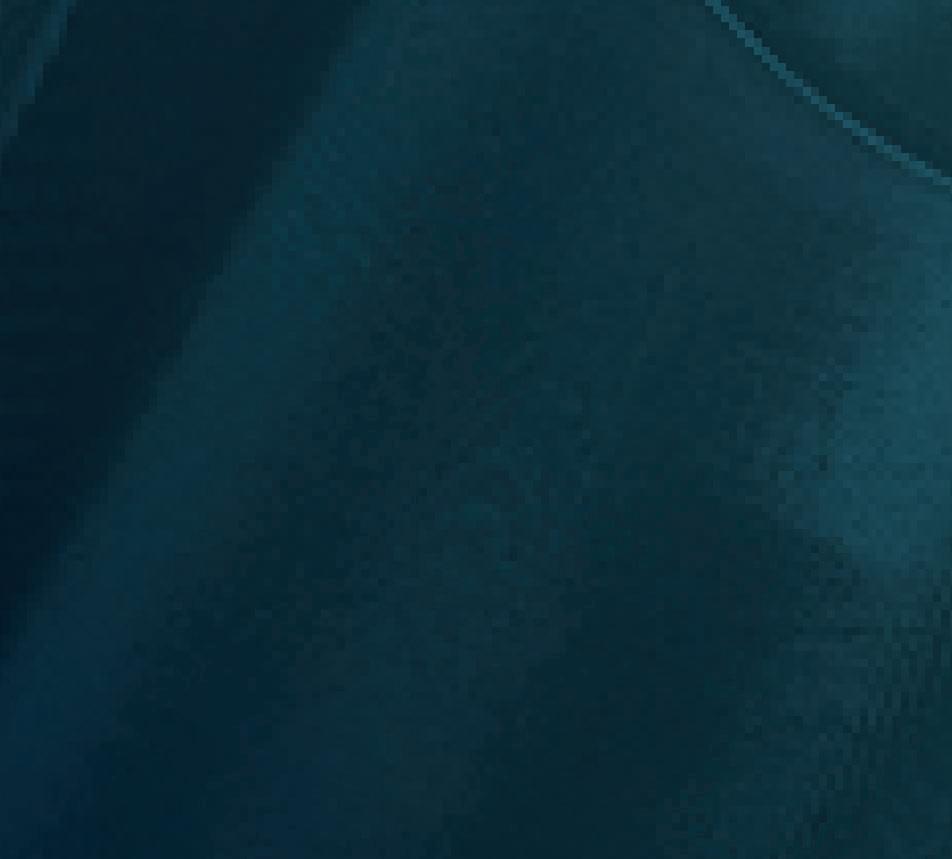
Streamline work ows with minimal reliance on specialized personnel. Its cost-e cient design ensures a quick payo while delivering highquality results.
• SPEED & VERSATILITY

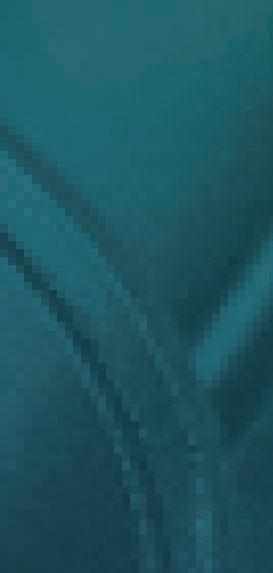

Enhance your production capabilities with a large build area, 5x faster layer cure times versus laser technology, and material changeovers in minutes.
• PREMIER PARTS

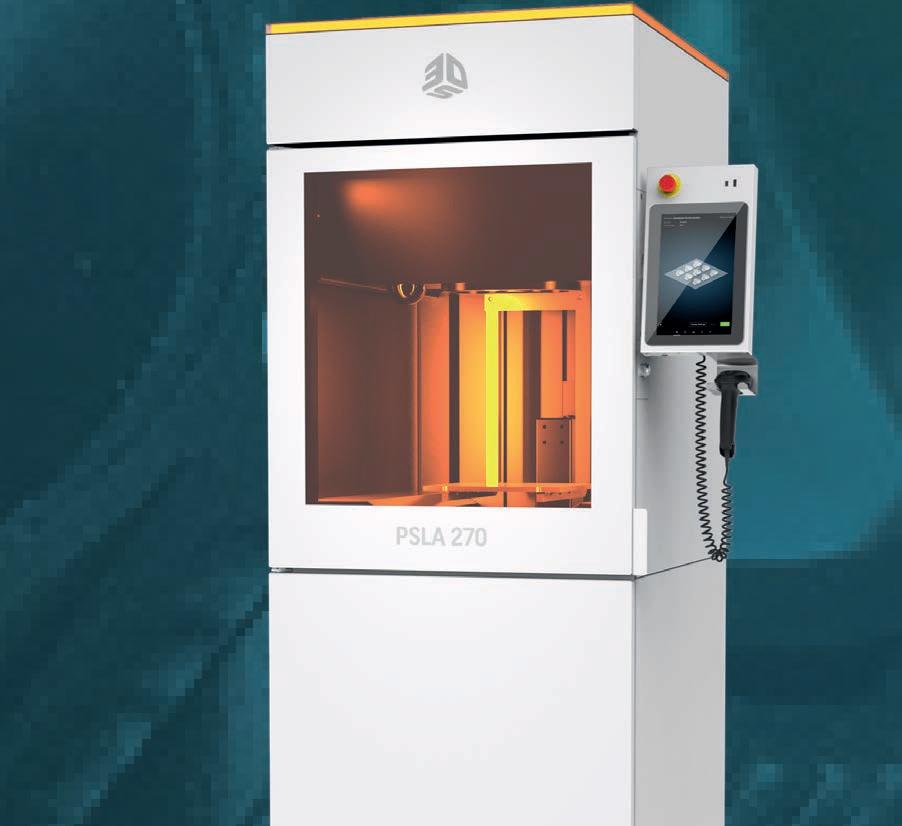
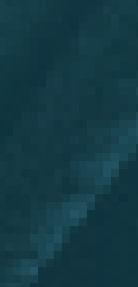
Leverage the breadth of the Figure 4 Materials Portfolio for professional prototypes, functional end-use parts, and indirect production applications.

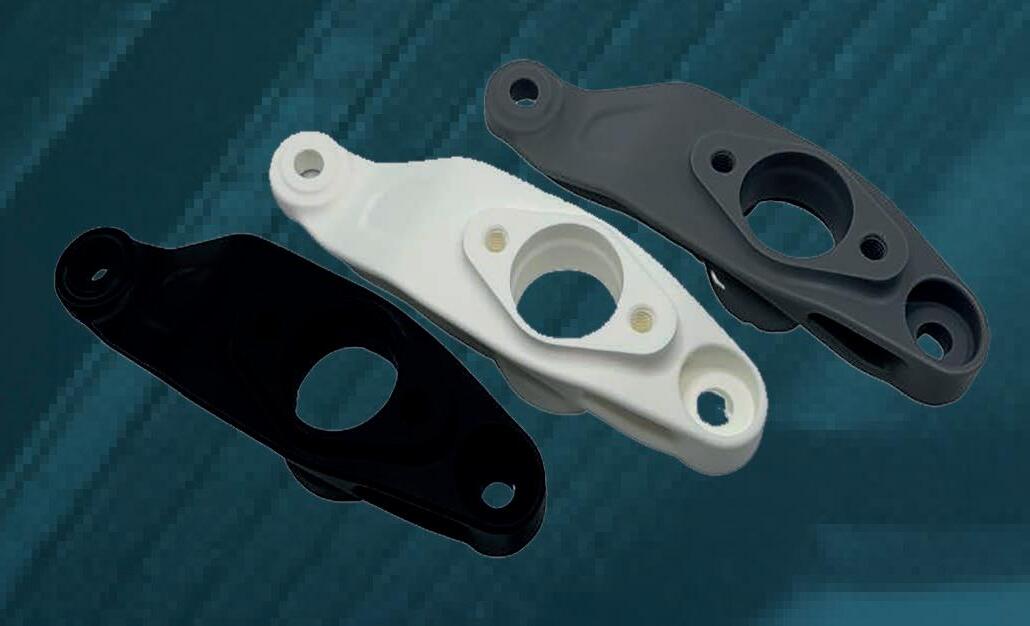


Discover the PSLA 270 at www.3dsystems.com/3d-printers/psla-270 and meet with us at Develop3D Live at stand A33 with our partner 3DRP.
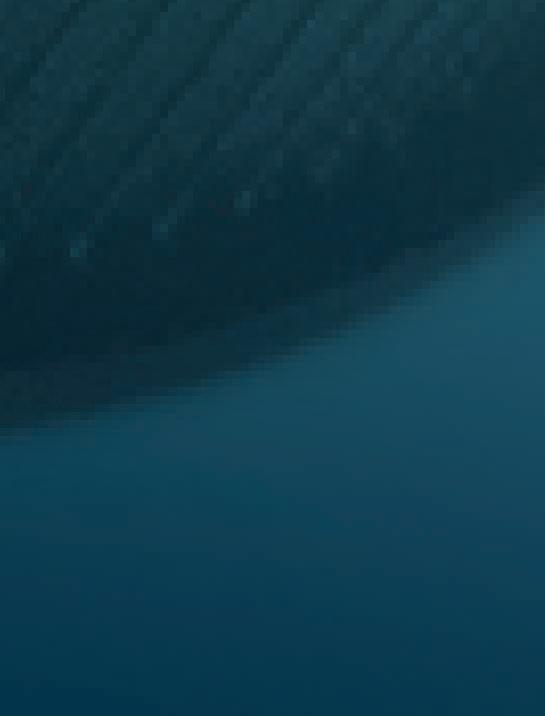
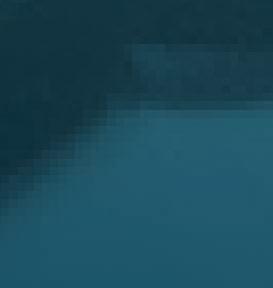
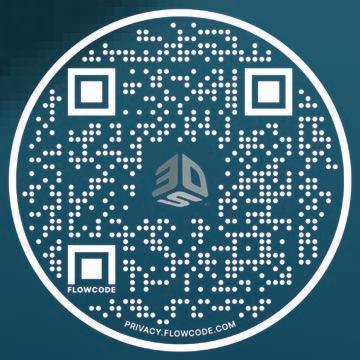
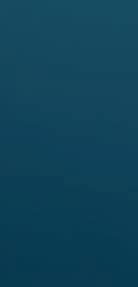

GEOMAGIC JOINS HEXAGON'S 3D SCANNING PORTFOLIO
Hexagon has announced that it is to acquire 3D Systems’ Geomagic suite of interoperable software tools in a deal valued at $123 million.
The Geomagic suite is used to create history-based parametric 3D CAD models, typically from 3D scan data, for use in product development. It includes products such as Design X, Control X, Freeform and Wrap.
The deal does not include the 3D printing-specific software product 3D Expert, nor the Oqton platform.
In particular, the Geomagic tools are typically used to repair issues with scan data – adding in surfaces that the scanner cannot capture, for example, or removing artefacts. They are also used to undertake initial free-form design, modify existing CAD models, and to accurately measure
and inspect parts for quality control purposes when finished.
The deal also includes the popular Geomagic for Solidworks reverse engineering plug-in, which allows direct scanning into the Solidworls environment, with advanced mesh and PMI editing tools.
“The combination of Geomagic and our existing solutions will further strengthen our market leadership in 3D metrology and reengineering, demonstrating our commitment to deliver increasingly user-friendly tools capable of executing complex tasks, so our customers can bring innovative, high-quality products to the market at speed and with confidence. We look forward to welcoming the Geomagic team to Hexagon,” said Norbert Hanke, interim president and CEO at Hexagon. www.hexagon.com
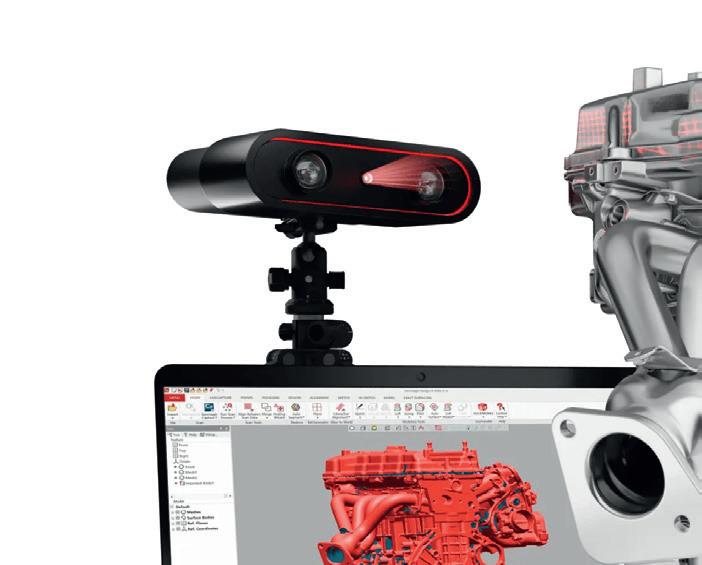
Geomagic will help in Hexagon's mission to provide user-friendly tools for performing complex tasks
New PSLA 270 from 3D Systems
The new PSLA 270 from 3D Systems promises the speed of light projection technologies with the quality and reliability of SLA and combines the latest 3D printer with Wash 400 and Cure 400 stations.
The PSLA 270 is a high-speed, projectorbased, mid-size 3D printer, designed to make use of the existing Figure 4 materials portfolio.
Able to pass through a standard doorway, using standard power, and with a levelling system that can be set up rapidly, it’s a versatile machine intended for production spaces and workshop floors. www.3dsystems.com
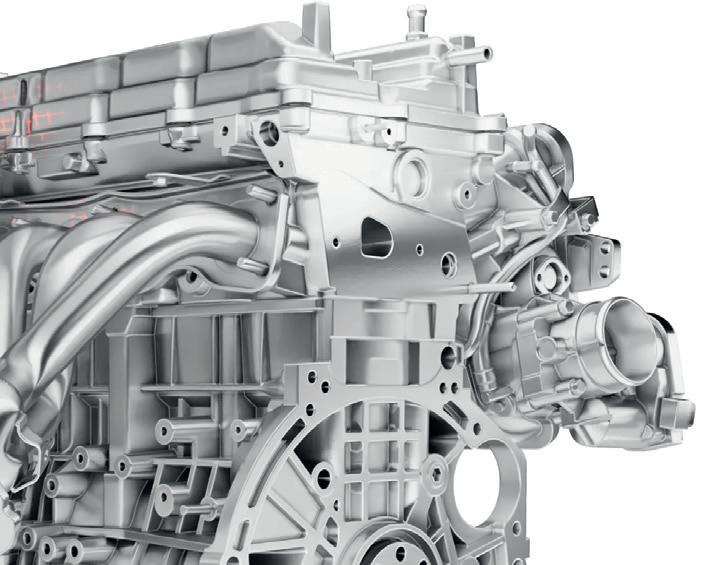

PhysicsX trains AI tool on Simcenter datasets
PhysicsX is building its latest pre-trained deep physics model for aerodynamics on high-fidelity simulation data generated using the Siemens Xcelerator portfolio.
This ongoing collaboration between Siemens Digital Industries Software and the start-up aims to create the next generation of AI-based deep physics simulation technologies for accelerating performance predictions and optimisation.
PhysicsX says that its LGM-Aero tool is trained on a corpus of more than 25 million geometries and associated physics simulations. The training data involved contains tens of billions of mesh elements and tens of thousands of computational fluid dynamics (CFD) and finite element analysis (FEA) simulations

using Simcenter STAR-CCM+ software and Simcenter Nastran software.
This should allow users to fine-tune deep learning models for use in their own applications with as little as “a few tens of simulations”, according to executives at PhysicsX. www.physicsx.ai
PhysicsX's LGM-Aero tool is a generative AI model for aeroelastic applications
Meltio unveils its Engine Blue tech
Meltio has launched its Engine Blue technology, which opens up its wire-fed directed energy deposition (DED) 3D printing capabilities to new materials, greater speed and simpler operations. Meltio’s blue lasers melt metal materials – such as stainless steel, titanium, copper, aluminium and nickel – making it possible to print metal parts with high reliability and optimal density.
The Engine Blue 1.4 kW blue laser head is compatible with a wide range of vertical machining kit and robotic arms. www.meltio3d.com
Start-up Backflip launches AI tool
Backflip has announced its first product, an AI-powered design platform that can take a range of user inputs and translate them into high resolution, 3D-printable models.
The company’s founders claim its software can produce real parts from a simple text description, for example, or even by uploading a photo of a broken part that needs to be replaced.
Led by the original founders of 3D printing company Markforged, Greg Mark and David Benhaim, Backflip has been joined by a team of AI researchers from MIT and has received $30 million in funding from VC firms NEA and Andreessen Horowitz. www.backflip.ai
SOLID EDGE X CLOUD SOFTWARE DEBUTS IN 2025 RELEASE
The 2025 release of Solid Edge introduces the cloud-enabled Solid Edge X, which brings to the package new AI-enabled tools as well as simplified IT administration, a personalised user experience and more options for collaboration.
Executives at Siemens Digital Industries Software says that the AI-powered functionality will be available in 2025 and will offer real-time assistance to users and help minimise disruptions to workflows.
With cloud-enabled built-in data management, based on Siemens Teamcenter software and infrastructure, users can collaborate across engineering and manufacturing disciplines wherever and whenever needed.
A new hybrid annotation capability in Solid Edge 2025 allows engineers to insert dimensions and feature control frames into designs with an efficient, all-in-one workflow that supports model-based definition and provides the tools users need to quickly and accurately detail 3D models.
New Feature Control frames and updated Surface Texture symbols help users to adhere to ever-changing standards, while automatic dimensioning helps to maintain consistency and should reduce errors.
Users are now able to greater tailor their own Solid Edge experiences with a personalised design environment. This includes features such as redesigned vertical command bars and enhanced context toolbars, so that the user experience can be streamlined to suit an individual’s own habits and workflows and offer them greater flexibility.
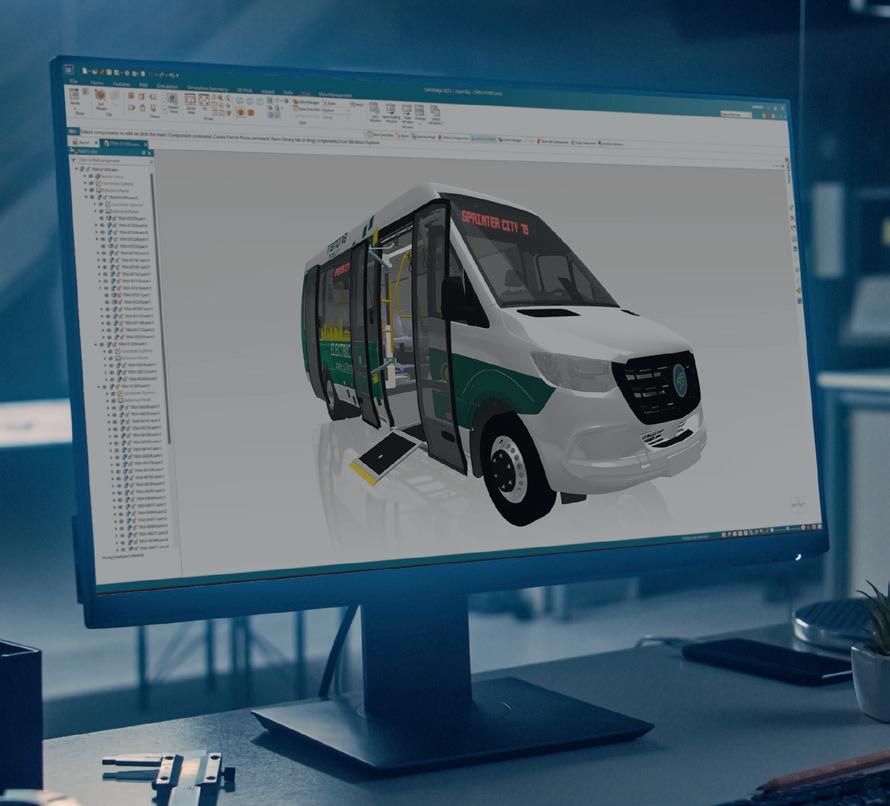
hub where users can access a wide range of resources, learning materials and free trials from directly within the product. Improved integration with Simcenter FLOEFD for Solid Edge allows direct imports of complex CAD models for analysis, saving time in the simulation setup process. Simplified fluid flow and heat transfer analysis make it easy to evaluate product performance under a wide variety of conditions.
Interoperability between Solid Edge and NX software allows engineers to reuse data and work with the software that best meets their needs. Transferring section views, advanced PMI, kinematic data and more between Solid Edge and NX is said to be a smoother process now. solidedge.siemens.com
Nano Dimension introduces new Ataru resin
Nano Dimension Ataru is the latest material to be launched by the company which, following months of hardware acquisitions, is keen to position itself as a leading provider of materials.
Ataru is a UV-curable resin material, engineered for temperature resistance in excess of 300C and high-tensile strength, and suitable for injection moulding and demanding environmental conditions.
The cream-coloured material also boasts low dielectric loss property, making it suitable for high-frequency electrical applications.
Perhaps one of Ataru’s more notable qualities is the surface finish it offers, which is excellent, even on parts produced on entry-level DLP 3D printers. As a result, the material is a versatile and accessible

option for open-source DLP 3D printer users, with uses that range from creating moulds and tooling for composites to creating radio frequency antennas.
Ataru’s low viscosity, meanwhile, ensures compatibility with a wide range of DLP systems.
www.nanodimension.com
Nano Dimension's new Ataru UVcurable resin is compatible with a wide range of DLP systems
ROUND UP
Following its July 2024 bankruptcy, 3D printing service Shapeways is back in business with a new management team led by two of its original co-founders, both of whom have been out of the business for a decade, and a new, sustainable business model www.shapeways.com
Ametek has announced the acquisition of Virtek Vision International, a manufacturer of laserbased projection and inspection systems, which will join Ametek as part of its Electronic Instruments Group, which focuses on monitoring, testing, calibration and display kit www.ametek.com
Solukon’s new SFMAT1500-S machine is designed to handle the depowdering of extra-large parts by vibrating them and is built to accommodate parts built from metals SLM technologies that weigh in excess of two tons with dimensions of either 600 x 600 x 1,500 mm or 820 x 820 x 1,300 mm www.solukon.de
Revopoint has announced the Revopoint MetroX 3D Scanner, which features a hybrid multi-line laser and full-field structured light to capture small and medium objects and a variety of textual details with an accuracy of up to 0.3 mm and a precision of up to 0.01 mm www.revopoint3d.com
Authentise has launched ThreadsDoc, a generative AI extension to its Threads engineering collaboration platform, developed with the support of Boeing and designed to automate the generation of templated documents using rich data from engineering collaborations www.authentise.com
Solid Edge 2025 also offers a new Discovery Center, a centralised
Solid Edge 2025 gives access to a range of new cloudenabled tools
A decade of eager but often failed investments suggests that the AM industry needs to redefine its core value proposition and build more sustainable solutions, writes new Shapeways CEO Marleen Vogelaar
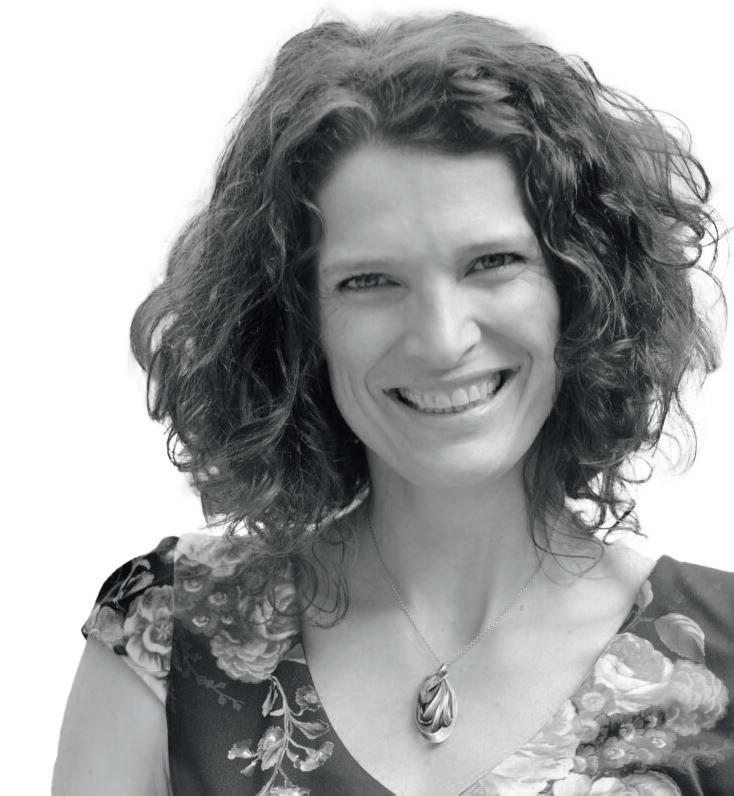
In the last decade, the 3D printing industry has been on a journey marked by groundbreaking innovations, bold promises and sobering realities. Like many people, I’ve watched the euphoria of sky-high valuations and the subsequent reckonings when promises and unrealistic expectations met the demands of the real world.
At the peak of the hype cycle, 3D printing seemed almost fantastical: a world where mass customisation was the norm, supply chains were transformed overnight, and production was as simple as pressing a button. The topic of 3D printing was on every conference agenda, regularly appeared on mainstream TV and even made it into President Obama’s 2013 State of the Nation address. Investors, wooed by the possibilities, flocked to fund the future.
But unlike the digitally-focused ‘unicorns’ (those elusive privately owned startups that achieve a $1 billion valuation), manufacturing is in the business of creating real, tangible, physical products. That means supply chains, trained workforces, warehousing, big capex budgets, regulations, and so on. In short, it’s just not as easy to scale manufacturing as it is a SaaS model.
That didn’t stop management teams from trying, of course. But we often see companies ‘get ahead of their skis’ with the relentless push of investment. Eventually, the numbers can’t be massaged. Growth isn’t there and overheads become too large to carry, resulting in losses. At this point, investment vanishes, which in turn, makes it harder for companies to realise the genuine opportunities before them.
In Shapeways’ case, being a pioneering brand brought in early investment and early challenges. Being first to market in any given niche requires you to build the market as you go. There are no quick wins to be had by stealing market share from the competition. There is no competition,
because there is no market! Building a market takes time, patience and money –not something for which eager investors have much patience.
A further challenge for 3D printing, seen directly within Shapeways, was the disconnect between the technologies’ abilities and long-standing consumer expectations.
For many, the fact that they can realise their digital designs in a physical way is enough, and these people quickly adopted 3D printing. Mass-market consumers, however, are not interested in the manufacturing process, and care only about the part. And the parts coming off 3D printers – even those designed for the process, processed by trained technicians and highly finished – often failed to meet their expectations.
CHOICES AND CONSEQUENCES
Unfortunately, our industry has learnt – and is still learning – what happens when visionary promises fail to align with market adoption, user expectation and investor demands. Bankruptcies, customer frustrations, and disillusionment have become part of the narrative.
It is worth remembering that the challenges facing the 3D printing industry are not unique. Every transformative technology goes through a cycle of hype, correction and maturation. The important thing, in terms of the future of this industry, is how companies respond.
As a brand, Shapeways has experienced these cycles first-hand, rapidly expanding in response to ever-increasing demand. When growth slowed and operating margins increased, Shapeways should have adjusted its overhead costs, but doubled down on them, investing in a new digital business model that was pleasing to its investors, but which failed to achieve the growth projections made for it.
But as someone who has returned after a decade away, I can confidently say that
It’s tempting to chase every headline, every next big thing, but longevity is rooted in staying true to your strengths
the core of Shapeways – the heart of what made it special – has remained strong. That’s where resurrection begins.
For businesses in this industry, the key is to focus on the core value propositions, but be flexible in their application, providing value, serving real customer needs and building sustainable solutions. It’s tempting to chase every headline, every next big thing, but longevity is rooted in staying true to your strengths.
The market today is massively different to 2007/8. First, there is already an existing market. Second, technology has moved quickly and today’s consumers have access not only to vast libraries of ‘printables’, but also to the software they need to more easily realise their design in 3D.
Creators are driving massive consumer buying trends nowadays, and not just niche purchases. For the B2B business, adoption of 3D printing has been steady and the number of opportunities for smallto-medium sized 3D printed production runs has increased proportionally. People now ‘get it’, whether they are personal or business users.
By getting back to core values and capabilities, adapting to changing market realities and learning the lessons of the past, we can ensure the future of 3D printing proves to be just as transformative as we imagined.
ABOUT THE AUTHOR: Marleen Vogelaar is an original co-founder of Shapeways and part of the new management team that has bought the company out of bankruptcy. She is a US-based Dutch serial entrepreneur with a passion for manufacturing, a keen eye on sustainability, and a wealth of knowledge and expertise in on-demand manufacturing. www.shapeways.com
Full Colour 3D Print
It’s All Over
Your search for a 3D printer capable of producing complex & creative models in up to 10,00 0,00 0 colours is over . T he new Mimaki 3DUJ-22 07 delivers extraordina r y detail in full colour.
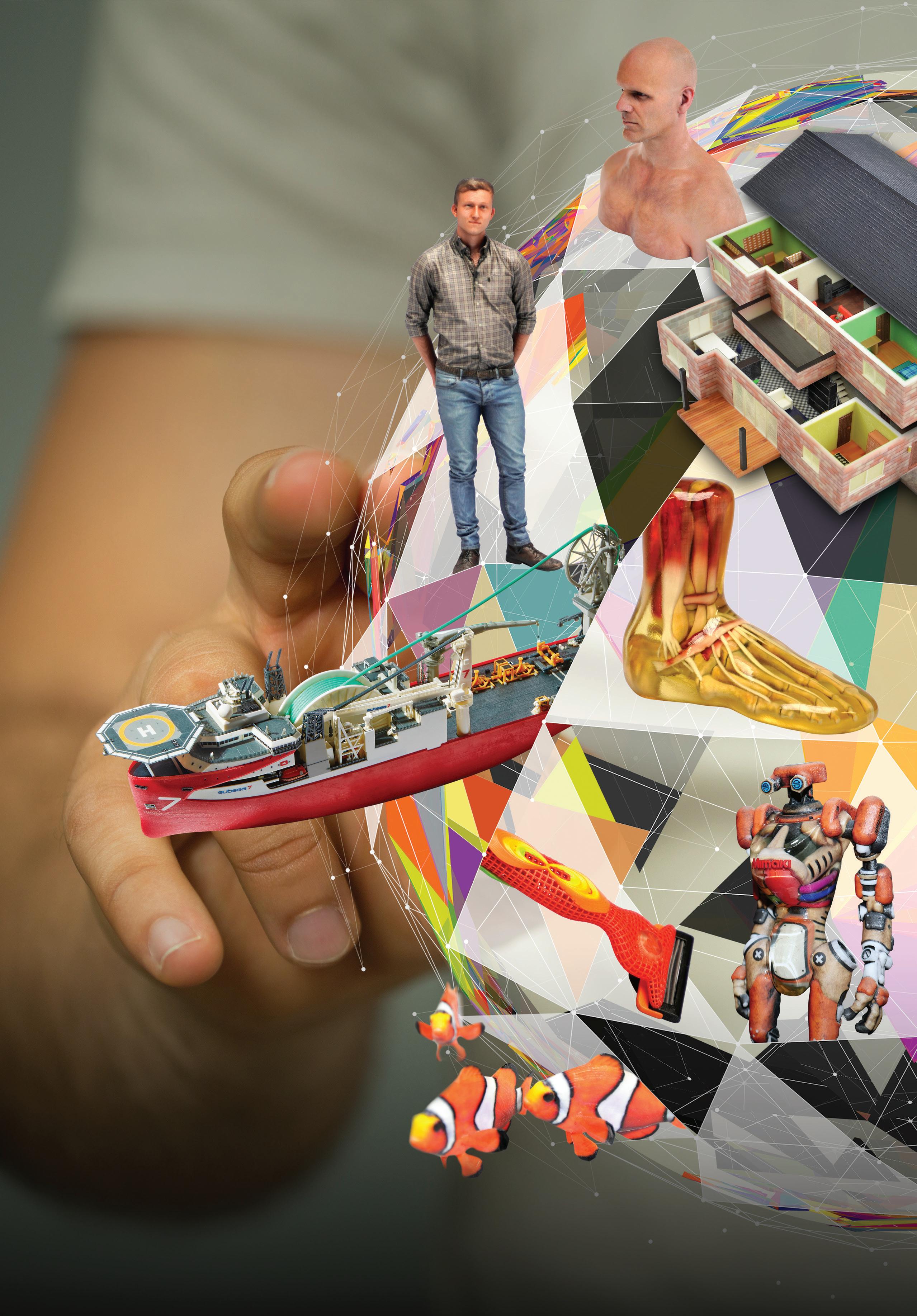
E xplore a wor ld of colour for just
£ 3 4,995
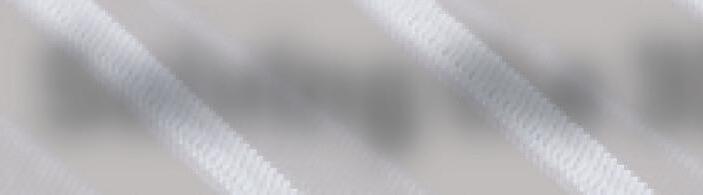

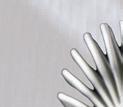
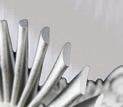


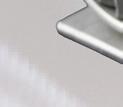
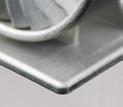
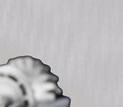
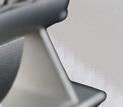
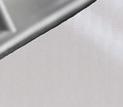
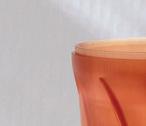
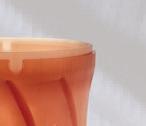
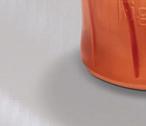

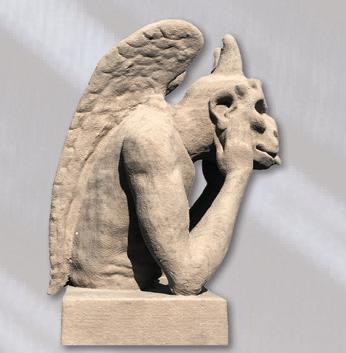
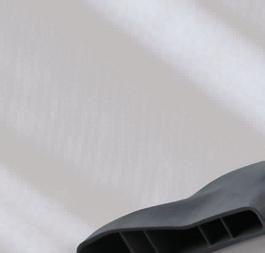

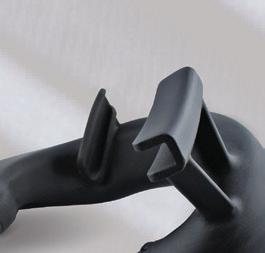
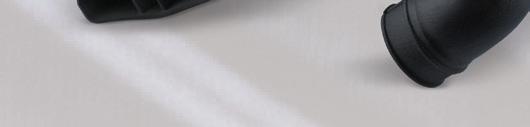



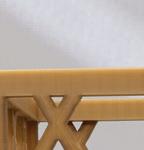
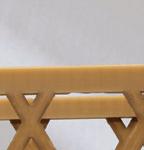
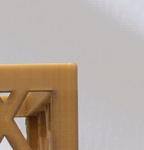

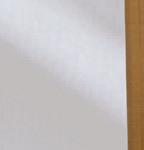
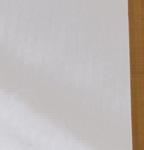
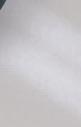
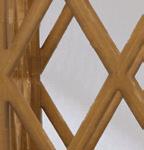
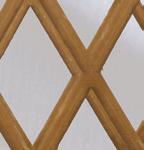
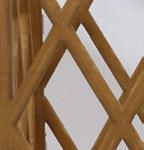

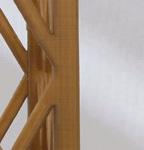
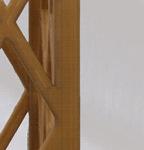
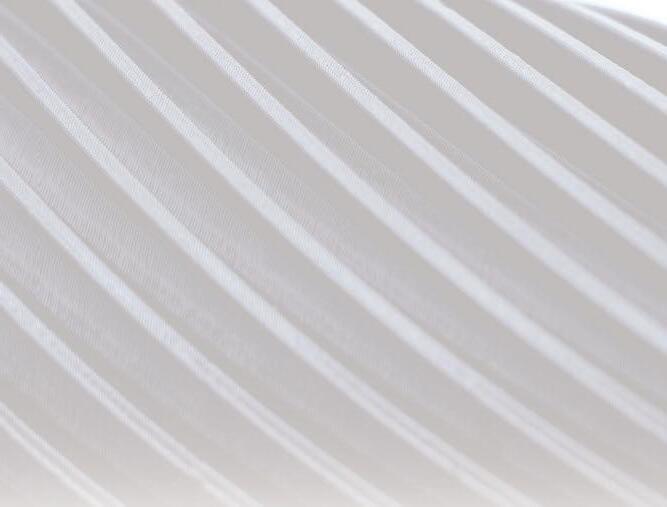






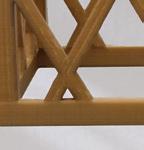
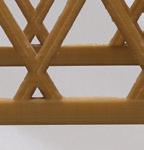
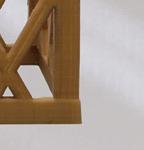
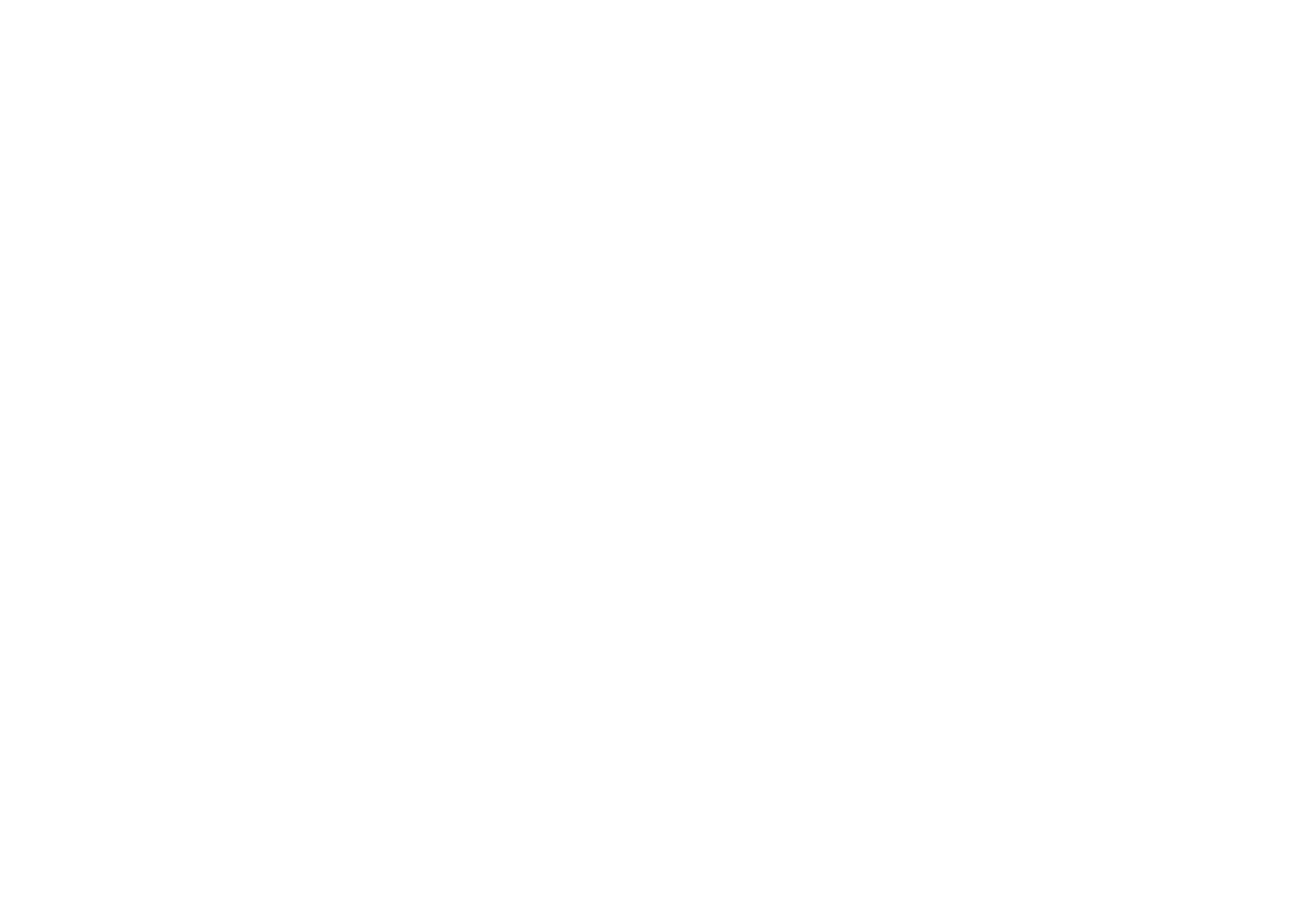

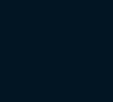
For those who rely on simulation, AI can add speed to the power already on offer
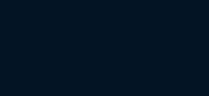
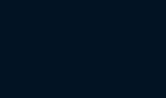
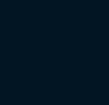
and, as a result, support a more iterative engineering approach that comes with fewer limitations,
writes Mazen El Hout of Ansys
The advantages of AIenhanced simulations are substantial, particularly when it comes to making rapid predictions that optimise the design processes. Training AI models accelerates this process, by enabling faster, datadriven insights that can be used to refine product development.
AI’s transformative potential is wellknown, especially for engineers, designers and other professionals who rely on simulation technologies to create innovative solutions. Integrating AI into simulation workflows can dramatically speed up design and optimisation, which is especially beneficial in industries where precision and efficiency are paramount, such as high tech, automotive and aerospace.
AI-enhanced simulations offer four key advantages. First, they bring speed: AI can analyse past simulations to quickly identify complex patterns while incorporating new data to uncover meaningful relationships. Second, AI can democratise simulation, making advanced tools accessible to non-technical users through easy-tonavigate, web-based platforms. Third, AI simulations also allow for the integration of multiple models to create comprehensive representations of complex systems, providing greater insight into product designs. Finally, AI-powered simulations enable a more iterative engineering approach, allowing designers to refine their work with fewer limitations.
EXPLORING AI
With these benefits in mind, let’s explore some real-world examples where AI and simulation are enhancing product design and driving innovation forward.
Designing optical systems that perform well under diverse environmental conditions – such as fog, haze, or varying weather – requires precise and efficient methodologies.
By integrating simulation datasets with AI-driven technologies, it becomes possible to predict illuminance fields with exceptional accuracy. For example, using just 10 optical simulation results as input, Ansys’ AI model demonstrated only a 2% error when calculating the maximum illuminance for unseen designs.
This approach drastically reduces the need for extensive simulation runs, empowering engineers to evaluate designs under numerous operational conditions quickly. By optimising optical system performance with AI, designers can accelerate development timelines while maintaining accuracy, ensuring products meet real-world demands efficiently.
Integrating AI into simulation goes beyond thermal analysis; in aerospace, structural analysis and design validation are essential to ensure an aircraft’s safety for take-off. This applies not only to large components, but also to smaller parts like jet engine brackets, which bear the engine’s weight and must be exceptionally strong.
As aircraft designs evolve, developing new jet engine brackets that meet both weight and structural strength requirements can be challenging. Engineers often start with prior design iterations that have been thoroughly simulated and validated. Building on this, they can incorporate an AI model trained on a diverse set of bracket designs. By retaining data from previous simulations, the model can quickly predict the behaviour of new shapes and can be updated with additional sample designs over time, allowing it to continually refine its predictions.
Using AI-driven simulation in structural analysis not only minimises material waste, but also turns failed designs into learning opportunities. Each iteration provides valuable insights, helping both the model and engineers to identify best practices in jet engine bracket design. This ultimately enables them to develop an optimised, reliable product.
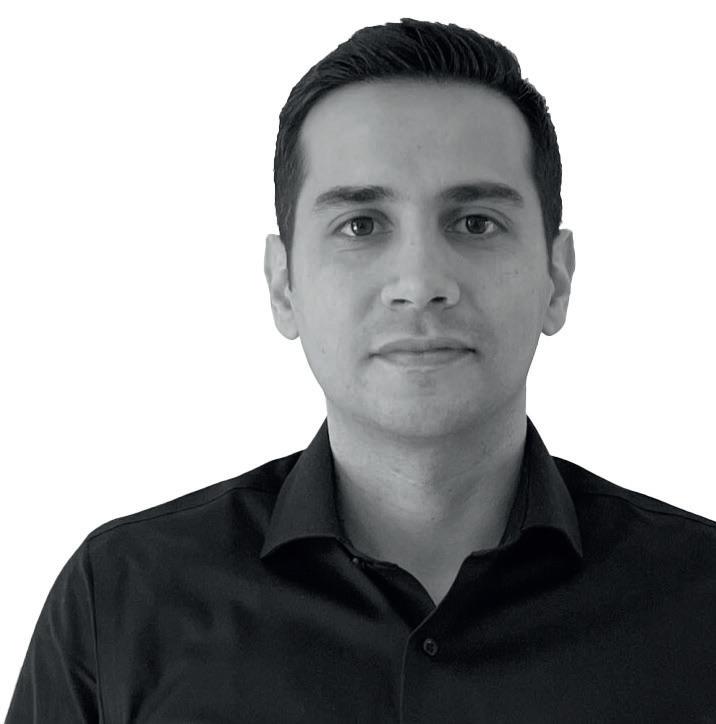
Using AI-driven simulation in structural analysis not only minimises material waste, but also turns failed designs into learning opportunities
BACK TO EARTH
AI simulations are just as valuable for ground applications. In the automotive industry, environmental regulations on emissions – such as Euro 7 – are a top priority for manufacturers, requiring them to assess and demonstrate vehicles’ aerodynamic performance.
While engineers can rely on physical wind tunnel testing, this can be costly and time-consuming. Instead, they can turn to simulation for quick and costeffective assessments. AI enhances this by analysing variations in vehicle shape and topological changes, like rear mirrors, ski racks or spoilers, to predict aerodynamic performance and optimise designs.
Incorporating AI simulations early in the design process allows engineers to generate rapid, meaningful aerodynamic predictions at every stage and produce a better, compliant product in less time.
AI and simulation each offer significant benefits. Combining them to amplify their impact is a logical progression. This integrated approach enables engineers to tackle complex physics and engineering challenges, while organisations benefit from increased workforce efficiency, reduced costs and faster development timelines, ultimately bridging the gap between design and reality.
ABOUT THE AUTHOR: Mazen El Hout, senior product marketing manager at Ansys, has a Master’s degree in Systems Engineering, a decade of experience in the software industry and extensive knowledge of AI, model-based systems engineering (MBSE) and embedded software and systems optimisation. www.ansys.com
VISUAL DESIGN GUIDE VAYVE EVA
» As India’s first solar electric car company, Vayve Mobility is aiming to redefine city travel with its new two-seat micro EV
FULLY CHARGED
For Eva, Vayve has developed a 14 Kwh modular battery pack with active liquid cooling. This can be fully charged in four hours using a standard home socket, or 80% charged in 45 mins using a DC CCS2 charger. An optional solar panel adds six miles of free driving per day, pushing total range to over 150 miles
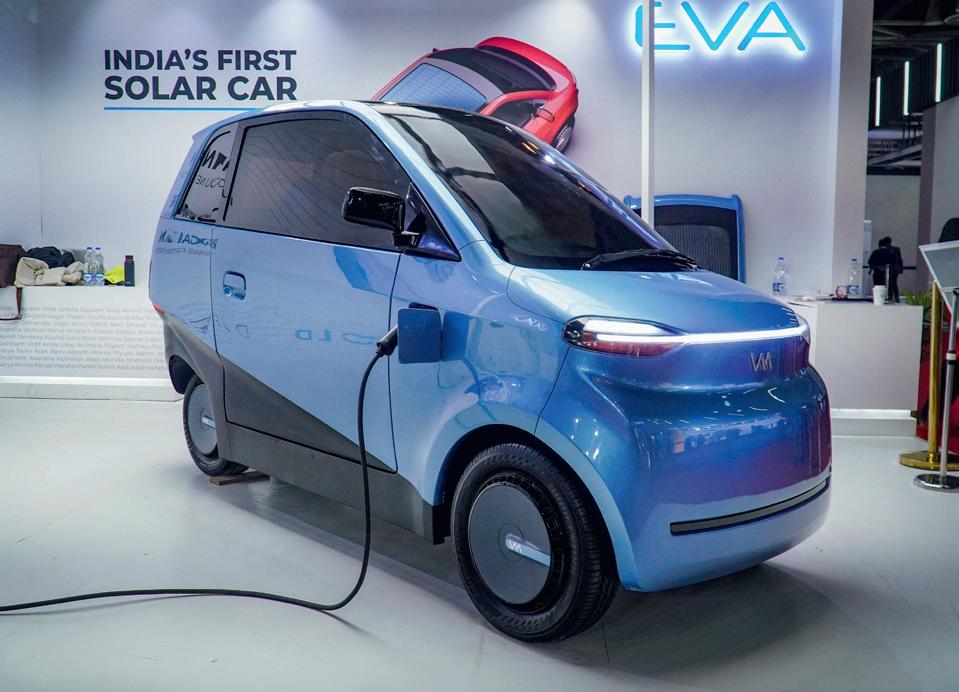
PREMIUM COMFORT
Offering the wide driver visibility, six-way adjustable seating, air conditioning and in-car apps and connectivity that you might associate with a much larger vehicle, Eva is a driver-focused premium product and will likely serve as a second car for many families
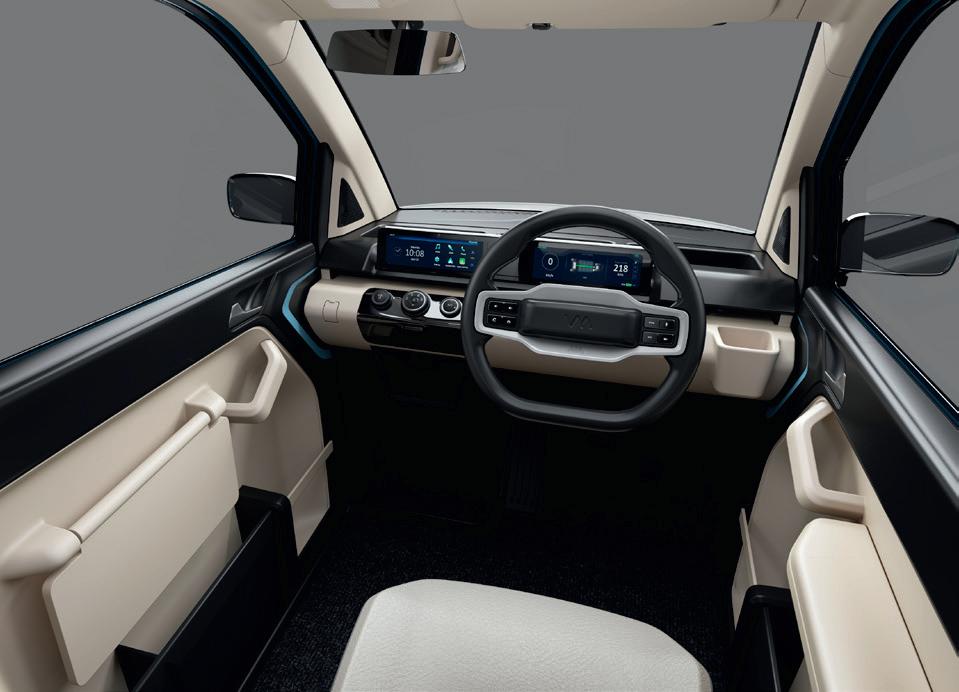
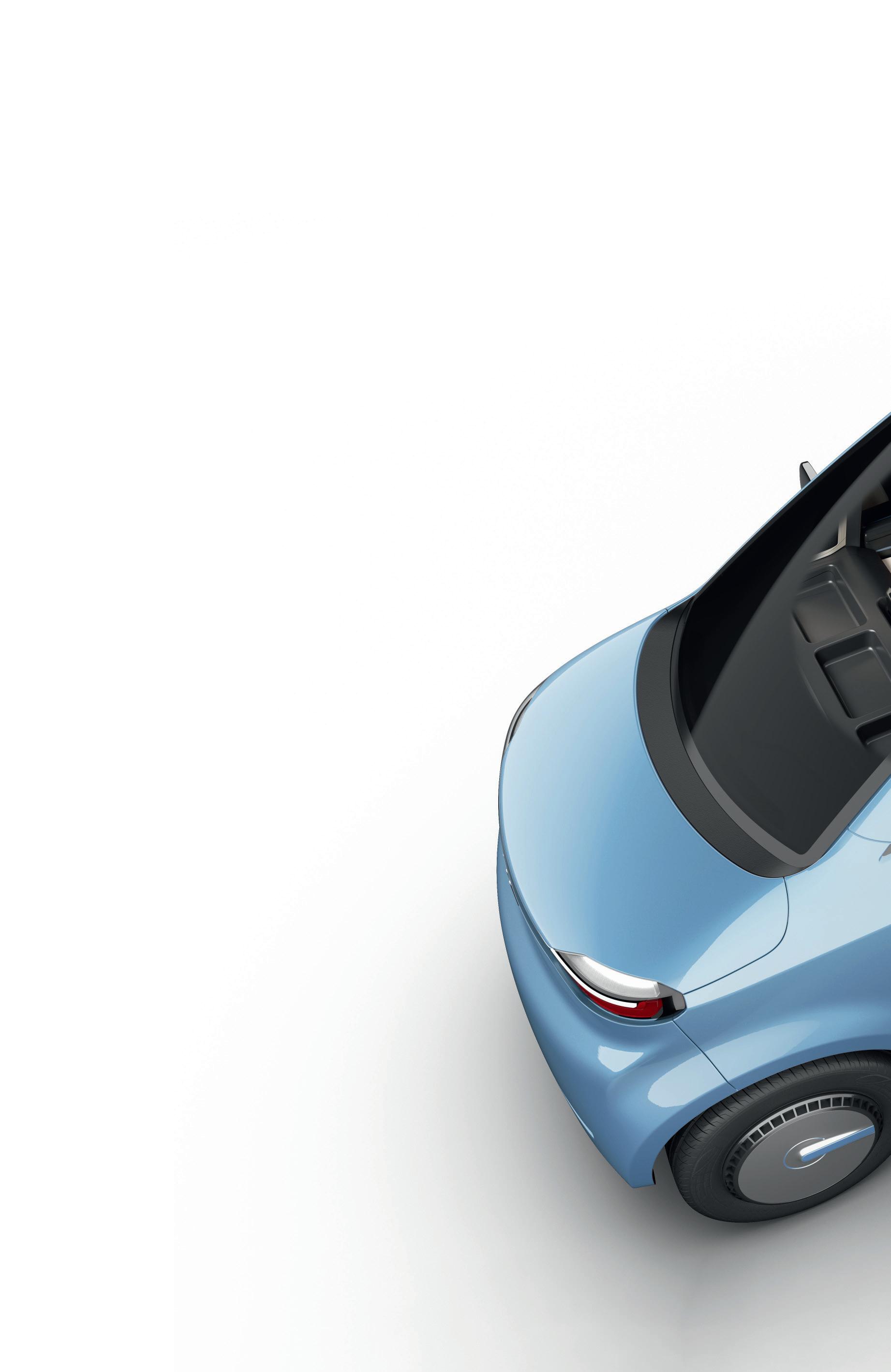
DESIGN POINTS
Designed using Autodesk Fusion, the team behind Eva is pushing hard on the software’s capabilities, using FEA simulation and other additional modules
DRIVER WELLBEING
As an enclosed vehicle, the Eva offers protection from the weather and pollution, while the added security also helps users feel safer when travelling alone
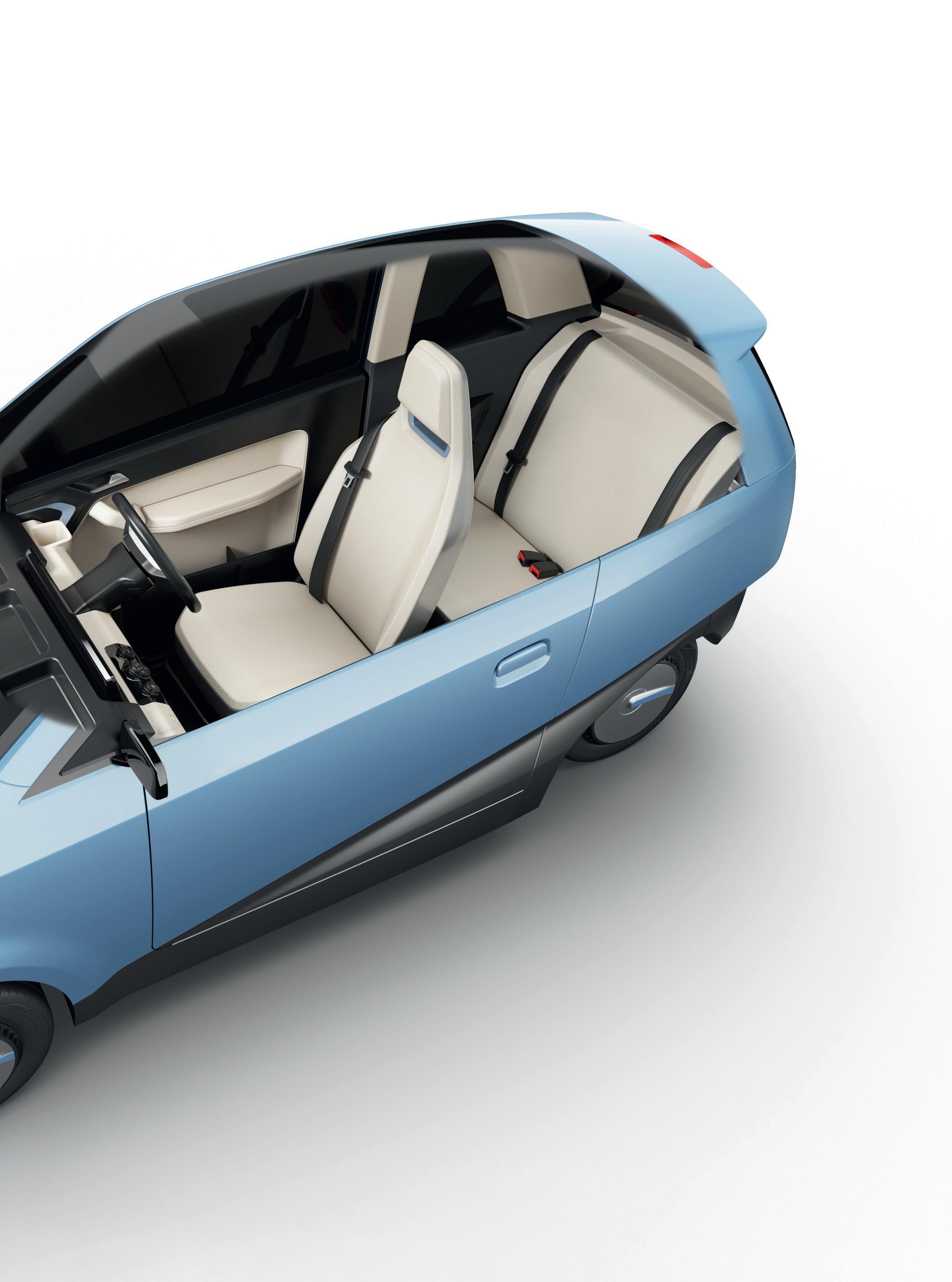
SPACIOUS STORAGE
50 litres of storage space can be found around the driver, while the rear seat can be folded flat, offering an additional 150 litres of hold space
NEAT NAVIGATION
The narrow two-wheel configuration at the rear assists with manoeuvrability. Designed for dense urban centres in India, Southeast Asia and Latin America, the Eva targets everyday journeys of 10 to 15 miles per day
The Eva is due to be launched at the Delhi Auto Expo in January 2025. Price: $6,000 www.evayve.com
FREE FLOW
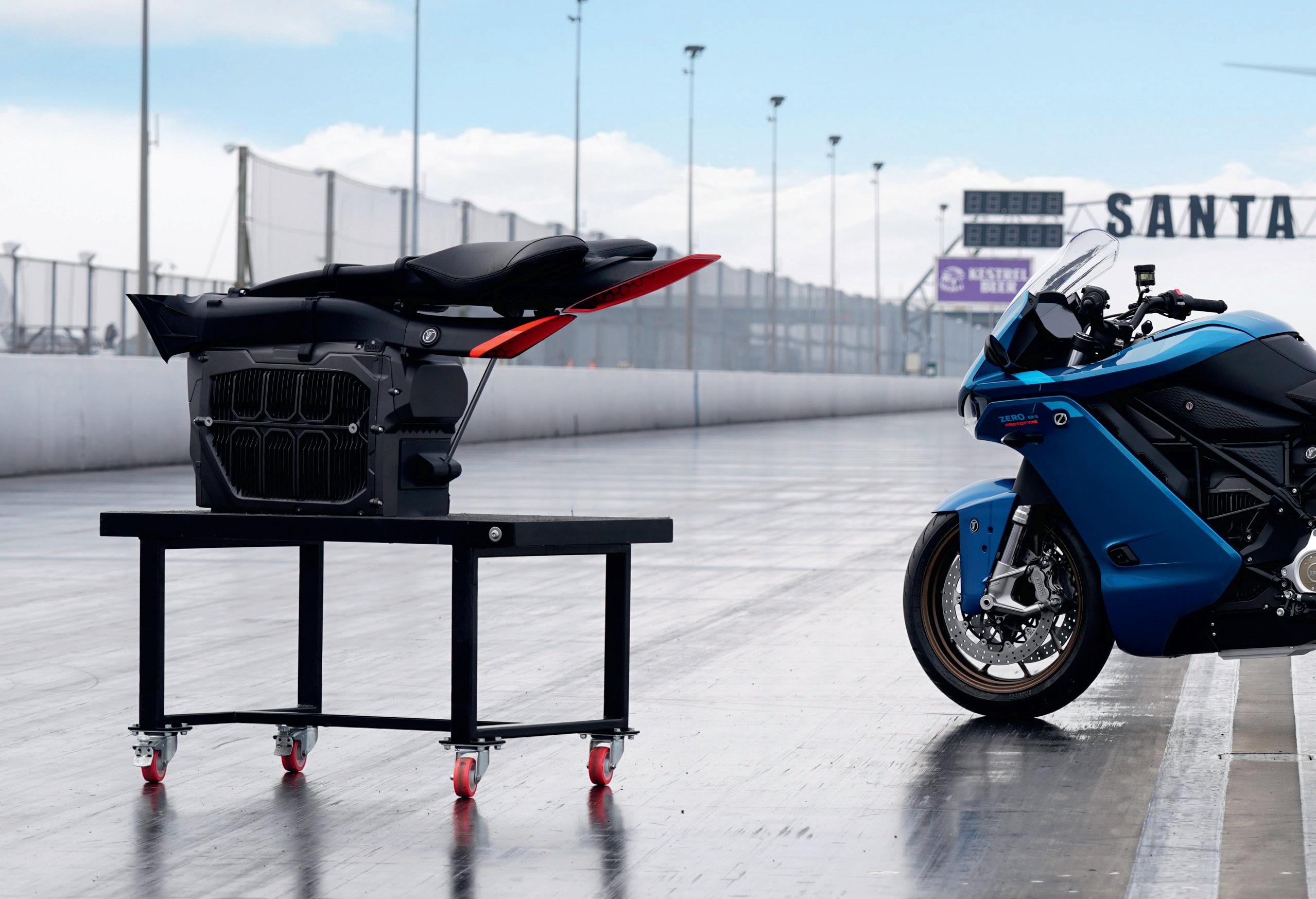
Cars have come a long way since the first Ford Model T was built back in 1908, with modern-day counterparts quite obviously larger and more curvaceous. With motorcycles, that’s not so much the case. Today’s motorbikes follow many of the same design and engineering principles as their early twentieth century predecessors.
Aerodynamics, in particular, have not been given the same consideration in motorcycle design as they have been in car design, which is big on drag coefficients and slippery forms that cut through the air.
The lightweight build and power offered by a motorbike, by contrast, means there has been little
need to tinker with the design formula, and fairings are frequently created to look fast but add little in terms of airflow around them.
With electrification, however, that’s starting to change. There’s a major need for shapes that offer both the performance and range that riders crave and deliver an endorphin rush when it comes to accelerating out of a corner or expertly navigating a winding mountain pass.
“At 60 miles per hour, a bike uses 80% of its power to overcome air resistance,” notes Ian Hird, commercial director at White Motorcycle Concepts (WMC). Unlike a car, he adds, where the ‘blob’ – in other words, the driver – is encased within a steel structure that can be made more aerodynamic, the ‘blob’ on a motorbike is clearly located on the outside of the structure.
» The motorcycle industry faces the huge technical and commercial challenge of producing electric sports bikes that offer performance equivalent to their petrol-fuelled counterparts. Stephen Holmes learns how White Motorcycle Concepts is blending aerodynamics and innovation to take journeys further

WMC boasts over 22 years of top-level motorsport experience, collaborating with the best technical specialists in F1, sports cars and MotoGP, and is now on a mission to revolutionise electric motorcycle design.
One of its first targets is duct technology, which funnels air from the front of the bike via a specially configured channel. This runs from behind the front wheel through the heart of the chassis and expels air over the rear wheel.
“Duct technology is very simple. It’s a fairing,” Hird explains. “There’s not a lot to go wrong. It doesn’t add a lot of weight to the bike and it doesn’t need maintenance. It performs the same on Day One as it does on Year Five, and it doesn’t degrade over time, whereas batteries do.”
But by reducing resistance, and thus easing the burden on batteries, a fairing can have a real impact not only
on an electric motorbike’s range, but its top speed as well. The more aggressively a bike is ridden, the better the duct’s performance – the opposite situation from a battery, which drains quickly if pushed hard.
Motorbike batteries, meanwhile, present a problem, because their size is limited by the form factor. (With cars, by contrast, the design can be bulked out to accommodate larger batteries.) But battery energy density can be expected to keep rising and this shift will open up greater volumes of space within a bike’s structure to fit a larger duct.
MIND THE GAP
Appraising WMC’s first public example of its innovative take on duct technology – incorporated in the WMC250EV – Hird acknowledges that the gaping duct
Having impressed with its electric world speed record bike (right), White Motorcycle Concepts has now developed its duct technology to fit an existing EV sports bike, the Zero SR/S
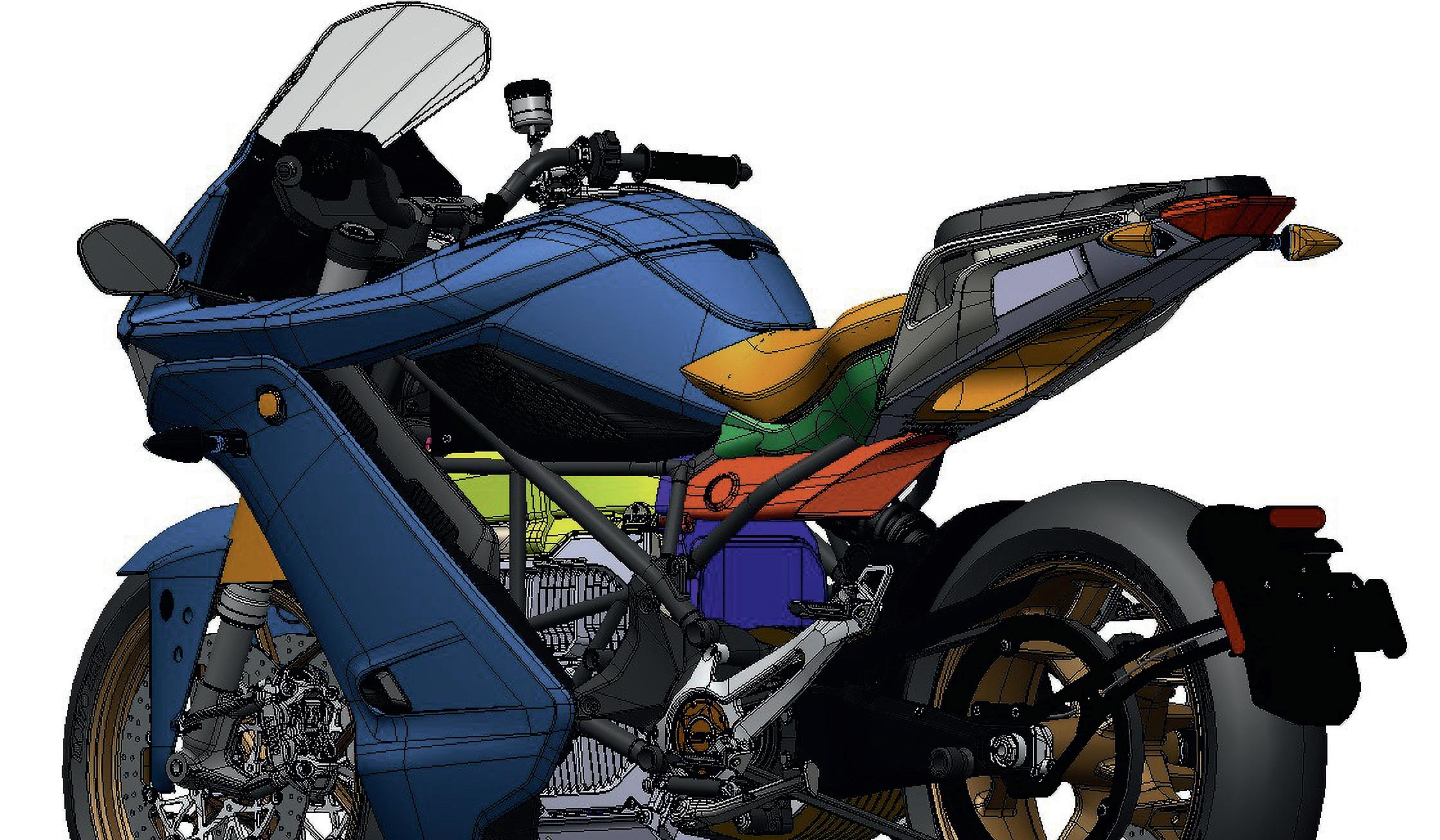
that flows the full length of the bike is a pretty unmissable feature. “It’s relatively difficult to hide a hole!” he jokes.
But as a result, the WMC250EV is capable of twice the mileage on the same electric charge as compared to competitors. It’s also designed as a world speed record EV bike, capable of achieving more than 250 miles per hour.
“It’s quite copyable,” he says, but points out that WMC has a broad patent in place that covers two-, threeand four-wheeled motorcycles in the UK, US, Japan and Europe.
This protection is vital, given that the company’s goal is not to produce bikes, but to work as a supplier to major motorcycle OEMs, and in that way, act as a catalyst for innovation across the industry.
“Ultimately, we’re not going to compete with a Honda or something like that. We will never win that war, so we position ourselves as a technology provider. What we wanted to do was get some proof points and build our credibility before we then start full-throttle engagement with the OEMs to incorporate the technology,” he explains.
Once WMC had got the attention of these big-name OEMs, the next task for the company to tackle was to help ‘draw the dots’, by translating a land speed-record design into a mainstream model, and demonstrate a working proof of concept.
The team began this work by looking at the other end of the spectrum, hunting for an existing bike, currently available in the market, which could offer the kind of space that WMC’s duct would need. The best candidate was judged to be the Yamaha Tricity, a 300cc three-wheel urban bike, which comes with a large under-seat storage bin designed to hold two helmets.
To this machine, WMC’s team managed to add its duct and create a hybrid working in conjunction with Northamptonshire Police. From there, they worked with Mahle Powertrains to redevelop the Tricity as a fully electric, three-wheeled motorcycle with a 100mile range, intended to serve the needs of police and emergency first responders.
DESIGN DELIBERATIONS
With this success under its belt, WMC subsequently partnered with US-based EV bike company Zero to tackle a two-wheeled fully electric sports bike project with a reengineered SR/S. The team explored over 39 duct designs and eight front fender designs in order to optimise the bike’s aerodynamics.
The first step, Hird explains, was defining where the intake hole might best be placed. With the land speed bike, the highest air pressure was found on the nose of the bike.
But with aero rake testing – a method similar to that used by Formula 1 teams – the nose cone area proved relatively aerodynamic. In fact, it showed that a bigger problem was air getting trapped behind the front wheel and being pushed under the bike before hitting the rear tyre and creating drag.
“It’s not just a case of putting a hole through the bike and there you go – you’re off! It’s about looking at everything and how it all has an impact,” says Hird. “Air is inherently lazy. It just does the easiest thing, so you have to guide it and manage it.”
This finding led to a lot of work around the bike’s existing fairings and around the duct openings. On its back side, a lip was added to the front fender to flick air up and into the duct aperture, while shrouds were added to the front forks to help smooth the air.
The bifurcated exit, meanwhile, fires clean air effectively into the turbulence created behind the rider, further reducing drag.
Overall, the design delivers a 10% increase in aerodynamic efficiency, equating to a 9% increase in range at highway speeds.
The duct itself passes through the internal architecture of the bike via the cleanest path possible, but it still has obstacles to navigate, including the battery.
Unable to change such a feature meant that the WMC team had to guide the airflow along a less-than-optimal route – but as Hird explains, even a subtle change to
● 1 WMC used Solidworks to decide on the optimal channel through an existing bike architecture
‘‘ What we wanted to do was get some proof points for our technology, before we then start full-throttle engagement with the motorcycle OEMs
Ian Hird, commercial director, White Motorcycle Concepts ’’
something like the battery casing’s shape could provide a further 3% boost in efficiency.
“The 10% that we’ve got is compromised, because there are certain points that are fixed in the bike that we can’t move. We can’t break into the battery casing, for example,” he says.
“The other bit we didn’t do, because we ran out of time, was to chase around the rest of the bike and look at how other parts could be made more aerodynamic. Just from a finger in the air [appraisal], we reckon there’s maybe a further 3% to 5%, maybe even 6%, gain from looking at external parts as well. So we’d like to get to 20%.”
THE ROAD AHEAD
In future, the key to achieving greater efficiencies will be to implement the duct technology from the earliest stages of design, where WMC will work alongside engineers from a bike manufacturer. In theory, that should prove simpler than retrofitting a channel through an existing bike package.
Hird estimates that nearly 4,000 hours of engineering went into optimising the Zero SR/S ducting within the packaging constraints of the existing bike.
Zero works with Solidworks on its 3D modelling, so the WMC team adopted Solidworks too for the SR/S project.
“For us, we’ll go native! We’re happy and our design engineer had good previous experience with Solidworks.”
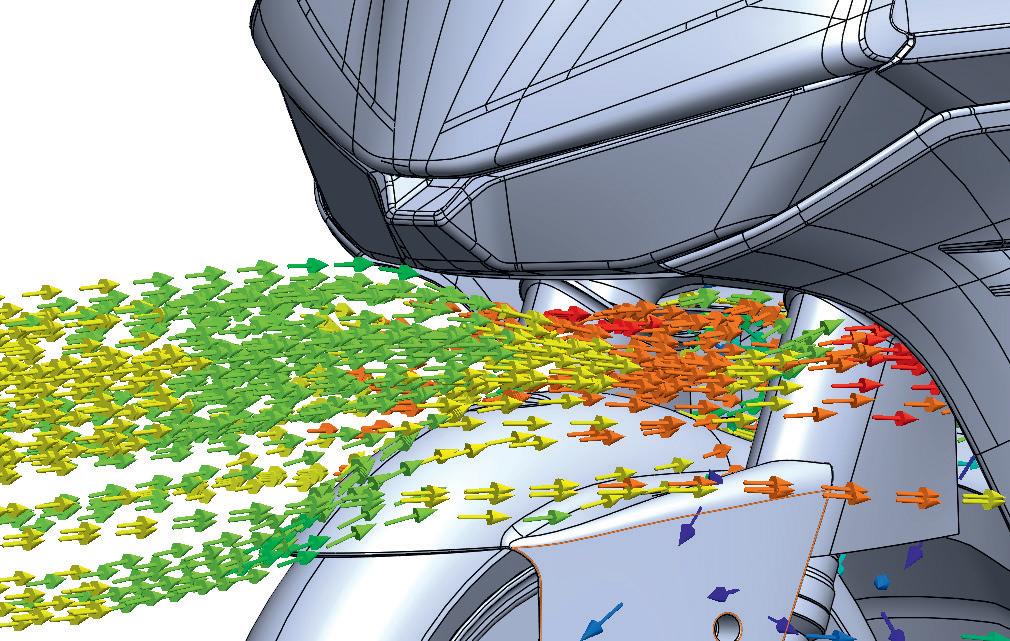
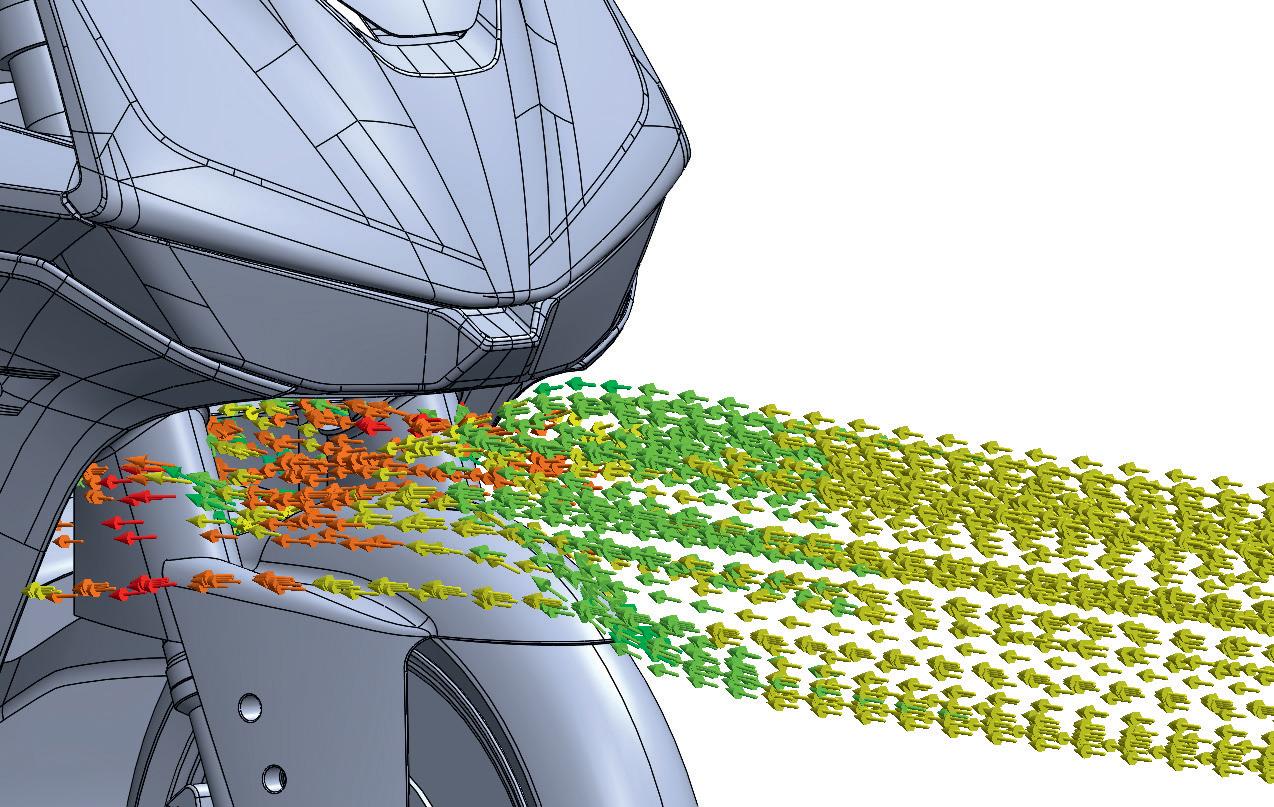

Using Solidworks Simulation, some initial digital analysis was run, to corroborate the real-world analysis derived from the aero rake testing. After that, more stringent loops of CFD analysis were undertaken.
WMC is proud of the extended network of partners that it has built up over the past five years that helps it deliver projects to an OEM standard. A critical contact is Catesby Projects, part of the TotalSim engineering group, which is dedicated to CFD analysis for the automotive and motorsports sectors.
Key to its process is the blending of CAD data with real-world scan data to get the full picture, which in the scenario of a motorcycle, needs to include a rider.
For this, an Artec Leo scanner was used to capture as much detail as possible, before the rider hopped off and Catesby team scanned key sections of the bike in reverse order of assembly, removing parts as it went along, exposing more elements of the bike.
“That’s to try and build up the most accurate model that we can,” says Jon Paton, managing director at Catesby Projects. “The saying ‘rubbish in, rubbish out’ is used a lot in this space. It’s really important to get the scan nice and accurate, because the simulation just doesn’t work if you’re making bits up, or the accuracy is not good enough.”
The data is then passed through Artec Studio, where it is pieced together, before being imported into Geomagic for tidying and repair. Gaps may exist in areas the scanner could not access, like a rider’s armpit, for example. For surfaces that need to be redrawn, Autodesk Alias is used to produce smooth surfaces.
CFD simulations run by Catesby Projects are based on software from its sister company, Bramble CFD.
“Bramble is basically aimed at making the tricky bit of setting up the simulations easy,” says Paton, highlighting the time-consuming process of meshing models and setting up boundary conditions.
“Bramble’s aim is to try and make that workflow as simple as possible. So, we drop the geometry in [as an STL file], and the boundary conditions are set for you. We set up a kinematic model for the whole project. And effectively, it’s then one click to set simulations up. If we want to change speed, yaw, corner radius, or make it follow another vehicle, for example, it’s one click away.”
When a new design iteration of the duct came through, Paton explains, it was just a case of dropping in a new STL file of the CAD into the set up and pressing start, this being one of Bramble’s big benefits over traditional CFD tools.
Having worked together since the initial land speed bike project, WMC and Catesby quickly built up an understanding of how the duct performs on a bike and how to get the best from it.
“I think on the land speed bike, we did about 120 runs in CFD to get to the optimum,” says Hird, explaining that this figure dropped to around 50 runs for the SR/S.

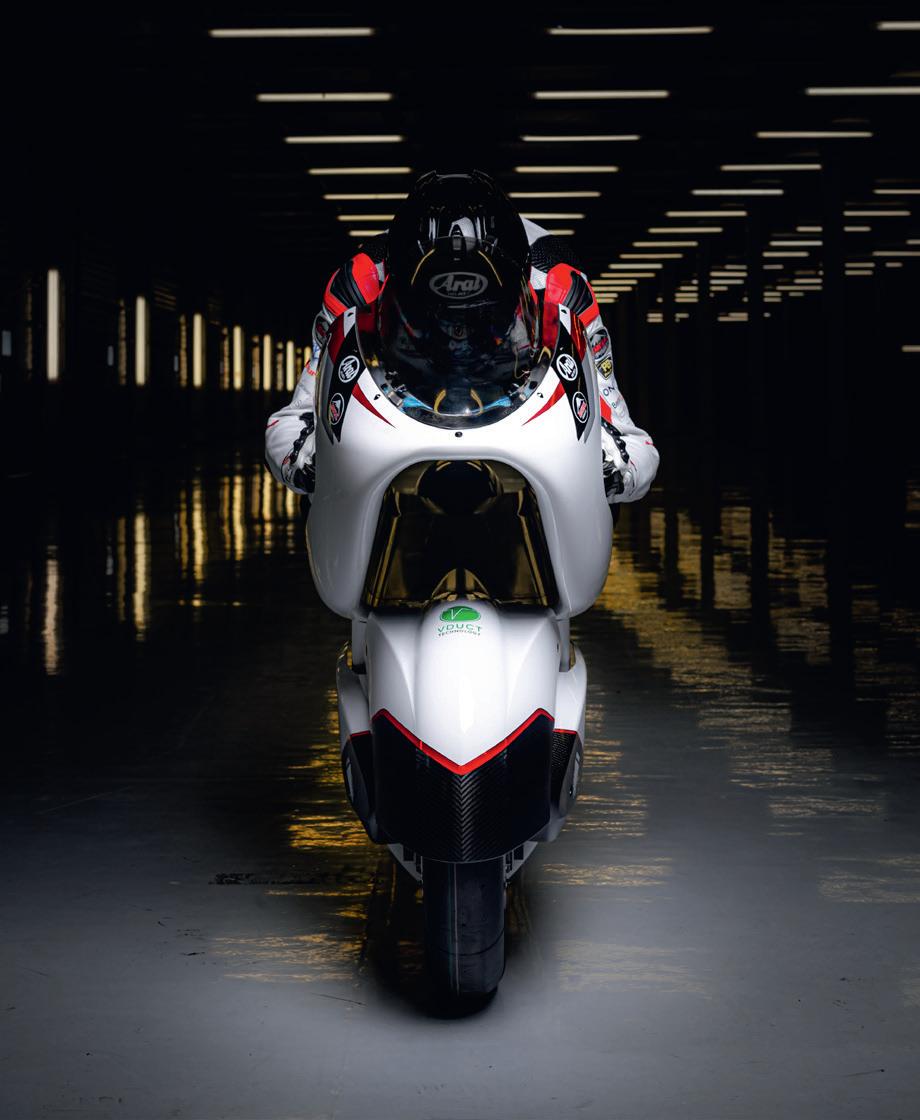
“[This approach] allows us to do fewer CFD runs, because we’ve got to the 90% mark much quicker.”
The optimised design for the SR/S was then physically built using WMC’s in-house Stratasys F370 FDM 3D printer. The parts were limited by the machine’s 355 x 254 x 355mm print bed, meaning the prototype duct had to be printed and assembled in pieces.
It’s not always rapid prototyping in a conventional, next-day sense, he stresses, as some prints take 50 hours. But having a physical prototype that can be put in front of potential clients and users is massively important, he adds, because the aim is to create prototypes that look like they came from a factory. It’s what will help sell this duct as a ‘real’ product, ready today – and not just some half-baked idea.
FUTURE FLOW
Beyond improved aerodynamics, WMC’s duct technology has the potential to introduce further benefits for future bikes. Electric motorcycles have a top speed and what’s known as a ‘top speed sustained’. As Hird explains, “That’s all about clipping the temperature to make sure that the batteries don’t overheat.”
By reducing resistance, WMC’s ducts already ensure batteries don’t need to work so hard, but with a sustained flow of air moving through the bike, elements like cooling fins might be added to the battery design to work with this in-built cooling channel, helping to manage temperatures.
Another element of WMC’s patent includes an aerofoil, positioned in neutral while moving, but which can close to act as an air brake. With growing legislation around brake dust particulates and pollution, the ability to reduce physical brake pad wear, and even potentially recharge the battery via a form of regenerative braking, would introduce further, welcome effi ciencies to a bike’s design.
For now, the main goal is to canvass opinions on the design. “When somebody sees it for the first time, there’s always a double take, like, ‘Are there mirrors in there?’ Or, ‘Is it a magic trick?’, because the viewer can see through to the other side!” he laughs.
“If you ask people, ‘What will a futuristic bike look like in 30 years?’, then they’ll draw you some mad space thing. The reality is that it will look similar, but the technology will be better,” he concludes. And maybe, if WMC’s design meets with widespread approval, it will also have a hole through the middle.
www.whitemotorcycleconcepts.com www.totalsimulation.co.uk
‘‘ It’s very important to get the scan really accurate, because otherwise, the simulation just doesn’t work Jon Paton, managing director, Catesby Projects ’’
A prototype duct was built in-house using a Stratasys F370 3D printer
The WMC250EV’s duct shows what can be achieved when new tech is built into a design from its earliest stages ● 7 The SR/S design is not just about adding the air channel, but also aerodynamically optimising other areas around it

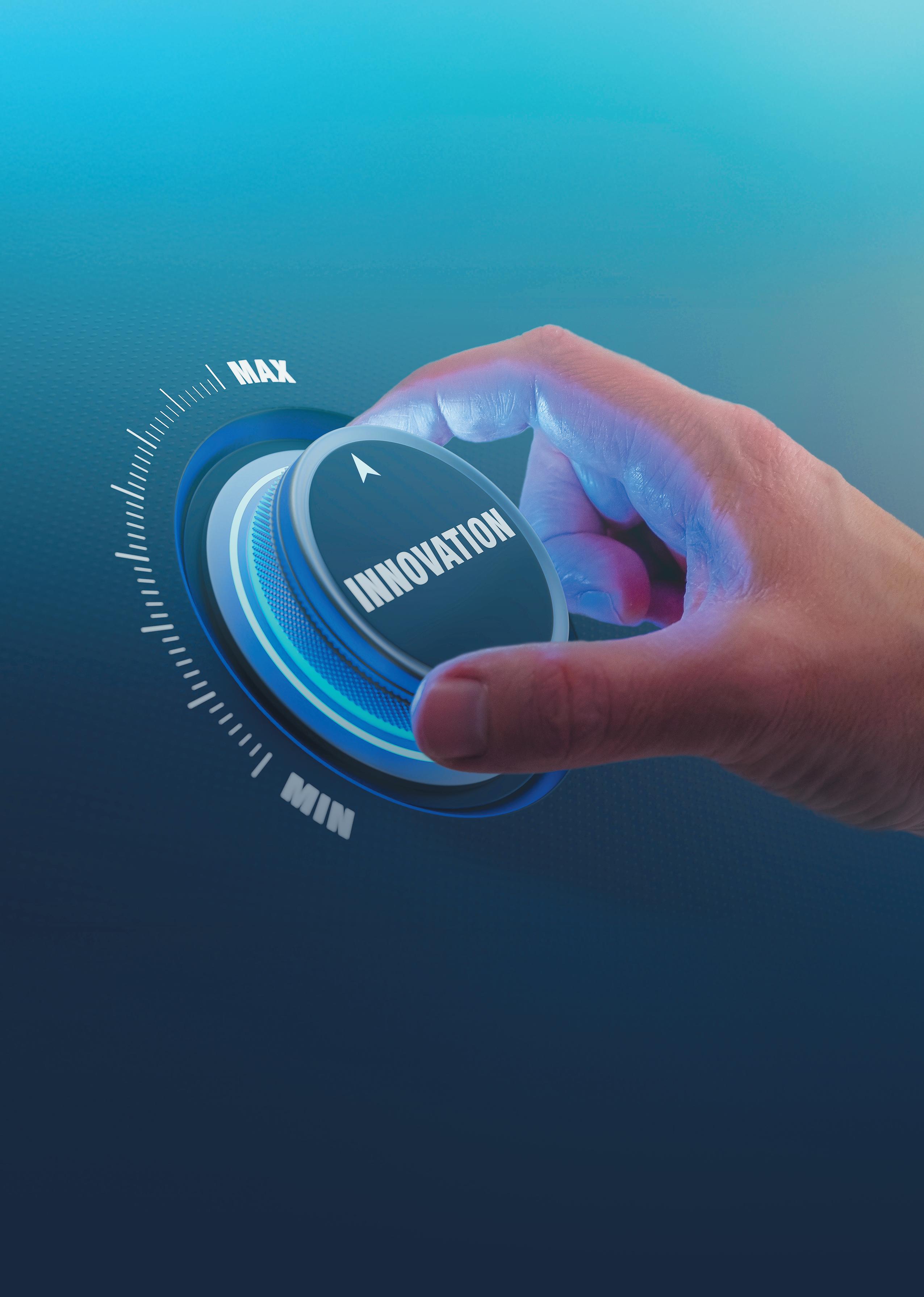
Native Instruments Empowers DJs and Musicians Worldwide with Autodesk Fusion and Fusion Manage
Discover how Native Instruments leverages Autodesk Fusion and Fusion Manage to revolutionize music production equipment. By:
Emily Suzuki
Over the past two decades, the music production experience has been digitalized with incredible capabilities. From electronic keyboards to mixers, musicians now have more options than ever for bringing their creativity to life.
For over 25 years, Native Instruments has been at the forefront of this sonic innovation, developing integrated audio, hardware, and software solutions to inspire and enable DJs, musicians, producers, and engineers to express themselves. Today, the Berlin-based company provides a vast array
of music equipment through its extensive list of software products (libraries, instruments, etc.) and hardware products (controllers, keyboards, etc.).
Komplete Kontrol, for example, is its nextgeneration MIDI keyboard controller. It’s available in 49, 61-semi-weighted, or 88 fully-weighted hammer action options and features a highresolution screen to browse and tweak music options directly on the keyboard. “When you turn it on for the fi rst time, the lights come on and the interface comes alive,” says Johannes Schroth, lead industrial designer.

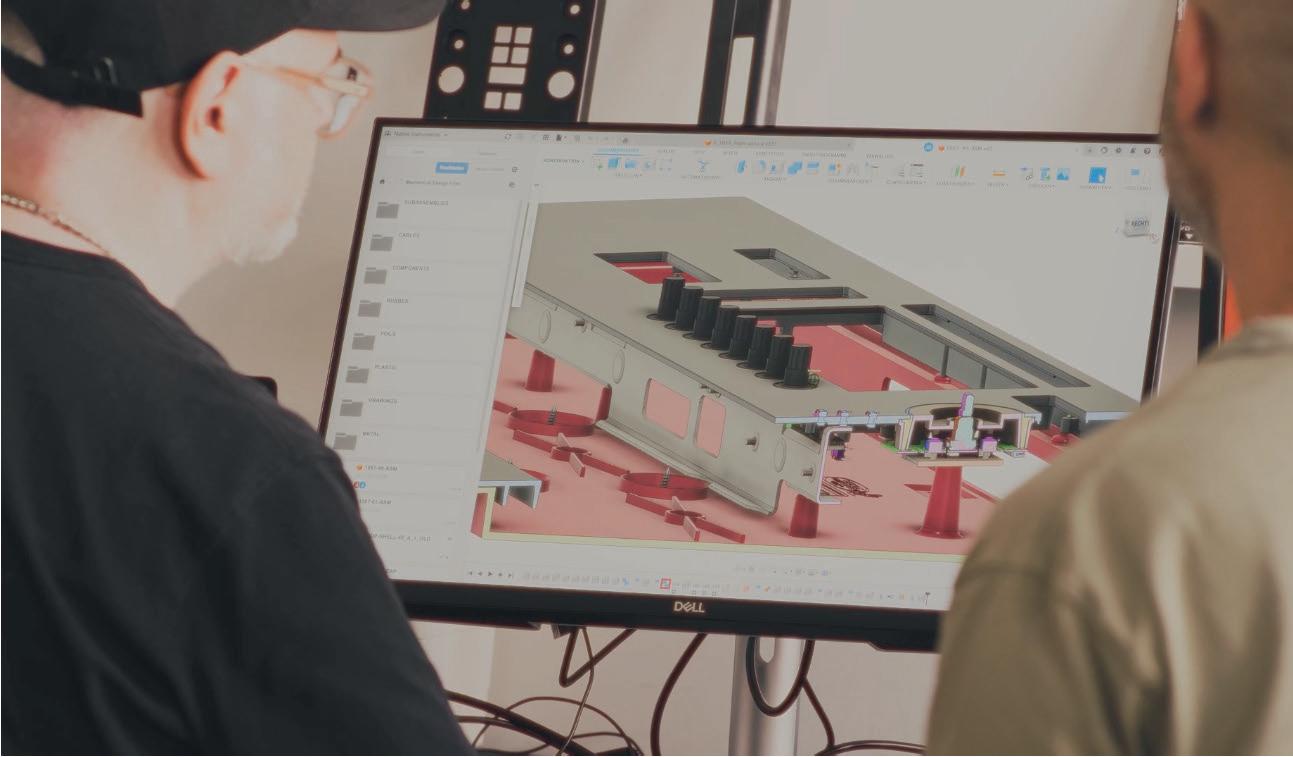



Collaboration takes the lead ,
By switching to Autodesk Fusion from SolidWorks and Creo and by leveraging Fusion Manage, Native Instruments has completely transformed its design and engineering workflows, manufacturing, and product lifecycle management for the better.
Fusion now brings industrial designers and mechanical engineers together to work seamlessly in one shared platform, reducing the complexities of using different design tools and increasing efficiency when working in other locations. These new collaboration opportunities were especially apparent with the design of Komplete Kontrol.
“We had very tight space constraints, especially in the center console where we’re really packing [things in] tight,” Schroth says. “It’s important for us to come together because there’s a negotiation that happens. It’s really cool to be on the same platform with Autodesk Fusion to move things around and discuss the specifics of how to solve problems in these tight spaces.”
Unlocking effi ciencies with connected, centralized data
A crucial part of Native Instruments’ workflow improvements was ensuring that all teams had access to the most up-to-date information. As a cloud-based PLM system, Fusion Manage serves as a central platform for specifications, data sheets, and other critical documents.
Michal Dudzik, senior purchase and supply chain specialist at Native Instruments, works with engineers, product managers, and suppliers to determine the right components to go inside the products—and make sure they arrive on time and at a competitive price.
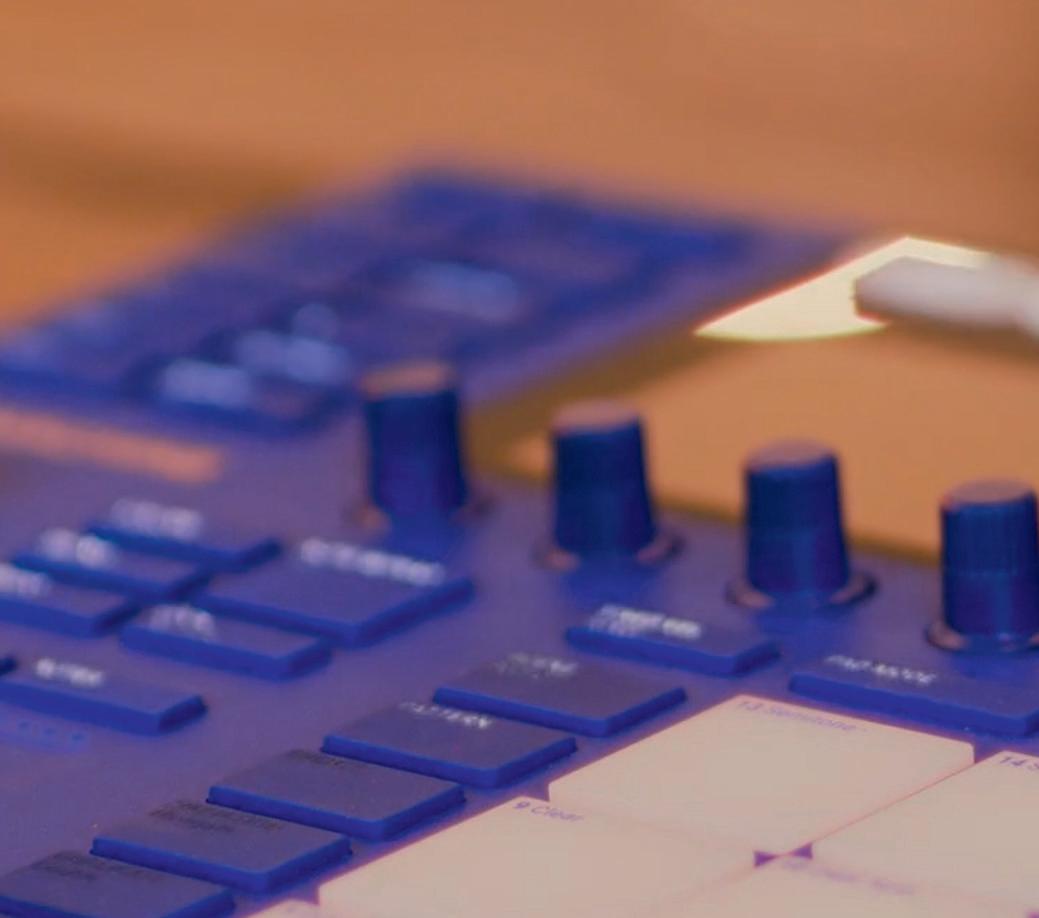
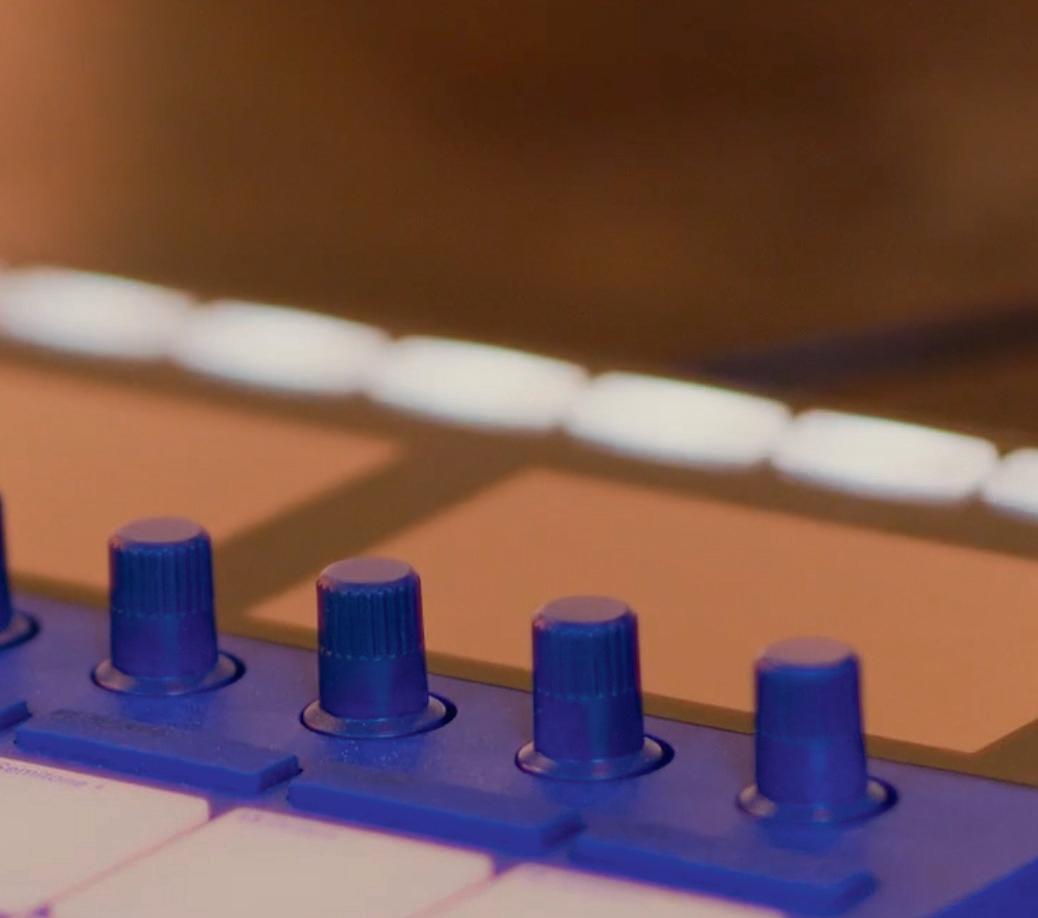
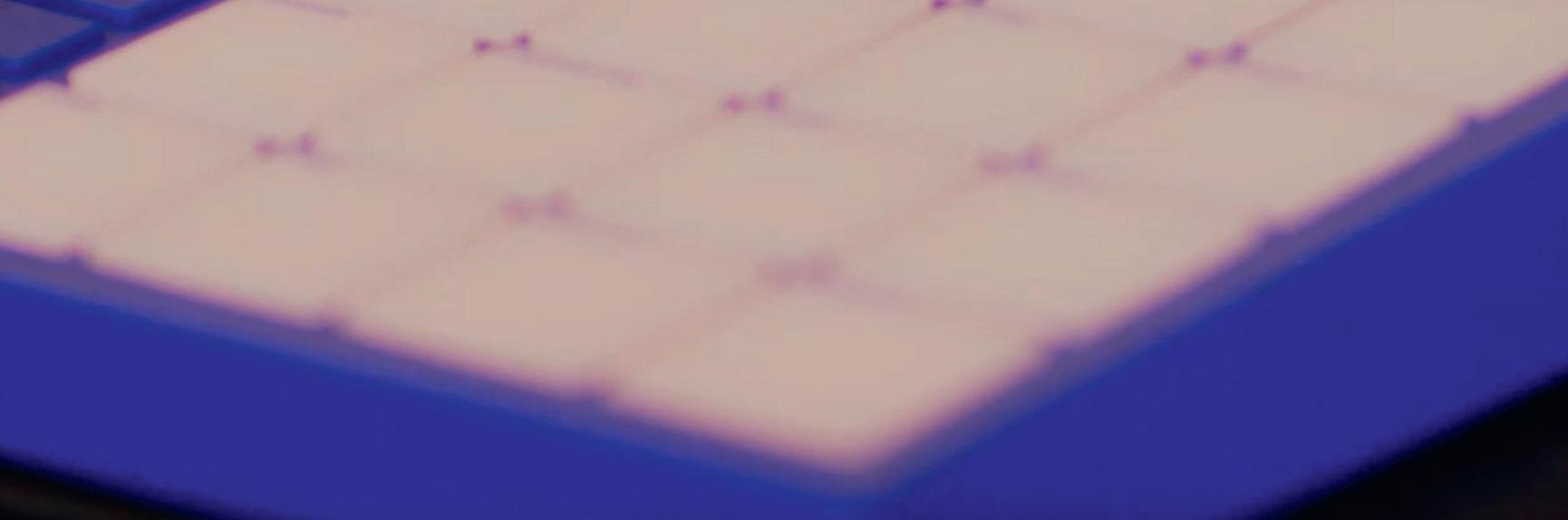
“I’ve been with Native Instruments for almost four years. Before we used Fusion Manage, we had a home-written command line-based tool that was very difficult to use,” Dudzik says. “It was also very errorprone with duplicate components and wrong prices, and it was difficult to keep accurate revisions.”
“With Fusion Manage, we found a tool that helped us have one centralized database of components,” he continues. “We can always release the correct revision of our design to external partners and collaborate internally, so our products get manufactured at the right quality and cost.”
New designs manufactured in record time Native Instruments recently celebrated its 25th anniversary. To commemorate this huge milestone, they decided to create a special, limited edition of almost every product line. But they only had three months to get the designs done and manufactured.
“We had more than 500 customized parts, and it was only possible to do this with Fusion Manage,” Schroth says. “We created branches of the products with new artwork and color, material, and finish (CMF) files that were pushed to manufacturing partners in China to send us samples.”
“A complex system like this manually would have been a huge cause of errors and difficult to mitigate within the limited time we had,” he continues. “It was really cool to have a centralized platform and repeatable workflows for everything.”
Ensuring the accuracy of final tested products
As a senior QA engineer at Native Instruments, Hannah Borland is focused on testing to see how
a product comes together, as well as its intent, compliance, and more. “We start testing early, even at raw component levels,” she says. “We either create our own specifications or, if we’re buying parts, start testing against specifications. Then we upload to Fusion Manage.”
Durability tests alone can run into thousands and even millions of test repetitions. Fusion Manage helps Borland ensure all the final tested products are universally communicated and used.
Prioritizing instrument longevity & sustainability One of Native Instrument’s core tenets is to build products that last. But, just like restringing a guitar or reskinning a drum kit, repairs may be needed over time. By focusing on access to easy repairs or replacement parts, Native Instruments can be more sustainable and keep customers sampling, composing, and mixing for years to come.
“Usually, customers ask us to ship a spare part that they need to repair their own instruments,” says Matthias Geserick, senior customer care agent, Native Instruments. “Fusion Manage enables me to just find it directly in the database and send it to the customer with all the specs they need.”
Creativity—and the music—comes first
From the beginning of initial or updated designs to engineering, testing, procurement, manufacturing, and finally helping ensure a long lifecycle, Native Instruments continues to take the use of Fusion and Fusion Manage to the next level. But, at the end of the day, it’s all about the music.

Wecomefromaworldwhere industrialdesignersworkwith theirtoolsandmechanical engineersworkwithdifferent tools.Forus,thenext transformativestepwasto gotothesameplatform. AutodeskFusionreally helpeduscometogether.
NativeInstruments

SOLIDWORKS 2025 Q+A WITH STEPHEN ENDERSBY
DEVELOP3D spoke with Stephen Endersby, director of product portfolio management for Dassault Systèmes/Solidworks, in order to get his perspective on the recent Solidworks 2025 release and find out where he believes the software will most effectively push back boundaries for design workflows
Q (DEVELOP3D): Solidworks 2025 is a new release, but would it be fair to say that things have changed at Solidworks, in terms of how release cycles now work?
A (Stephen Endersby): This is the twenty-first release of Solidworks in which I’ve been involved. And what’s interesting for me is that, in the last few years, like many other vendors, we’ve changed the way we release software.
In the past, you’d have a major release with all the new functionality, and then you’d have service packs for bug fixes. In recent years, we started dropping functionality into the service packs, with the idea being to get new functionality out to the users fast.
this release, it’s more a celebration of all the
If a customer finds an issue, it comes back to the developer while it’s still fresh in their mind - not a year later. So, when we look at what’s new for this release, it’s more a celebration of all the functionality that has happened in the last 12 months.
Q: With that in mind, there are over 200 new functions and updates in this release. Which of these stand out for you the most?
machine learning model to help you, based on previous behaviours of the wider Solidworks audience. It can deduce from what you’re selecting whether you’re looking to perform an extrude, revolve or whatever, and help guide you.
Q: But is something like that really going to be of help to the experienced Solidworks user?
A: Maybe, when performing some odd or uncommon tasks – but it’s definitely going to help new users coming in. These are not just students, but also people who are moving from another CAD system to Solidworks. Because if I’m coming from another CAD software, I know how to extrude, but maybe I don’t know where the button is in the Solidworks user interface. So this is really about helping people go faster. It comes down to the fact that we’re not doing AI for AI’s sake. We’re doing it where we feel there’s a positive impact. It’s about enabling the user, as opposed to it being a magic wand.
‘‘ This is about helping people go faster. We’re not doing AI for AI’s sake. We’re doing it where we feel there’s a positive impact ’’
A: It’s a very personal view, based upon how I use Solidworks (because I actually do use it myself), how the customers I’ve seen use Solidworks, and which of the features I believe are going to solve real problems for them. In this release, there is an AI command predictor that uses a

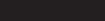

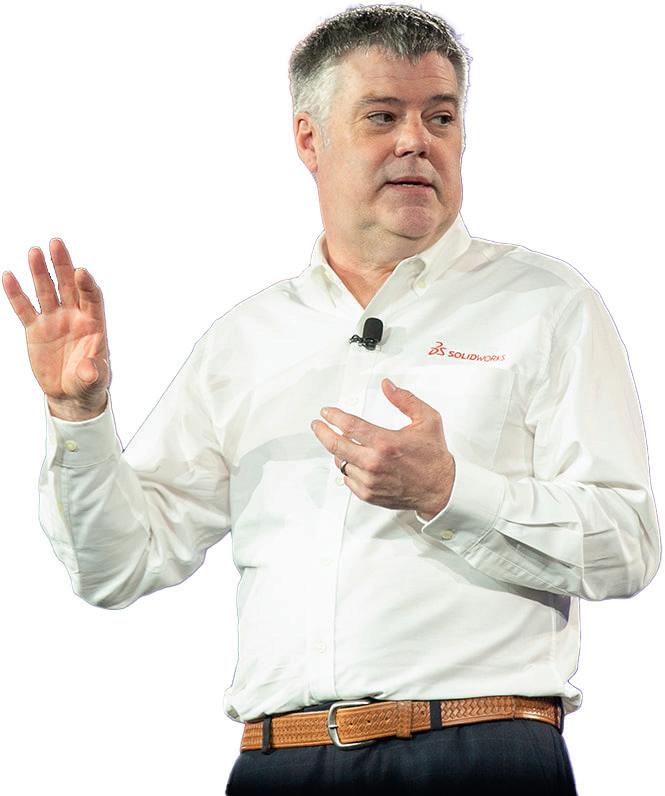
Q: On that subject, what wider impacts do you see AI having on the Solidworks platform?
A: I think there are defi nitely some tools out there that would really benefi t from AI. And I think, over the next year or so, you’ll see a lot more becoming what I would call ‘production ready’ and really ready to go. It’s not something that’s a core focus for Solidworks right now, but I think in the future, we’ll see a lot more of it.
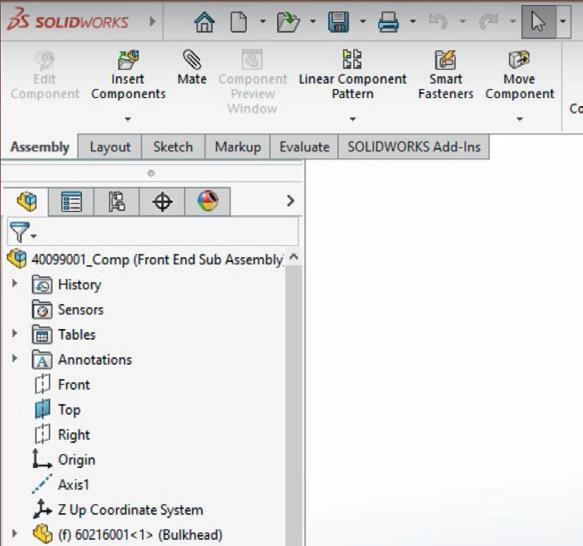
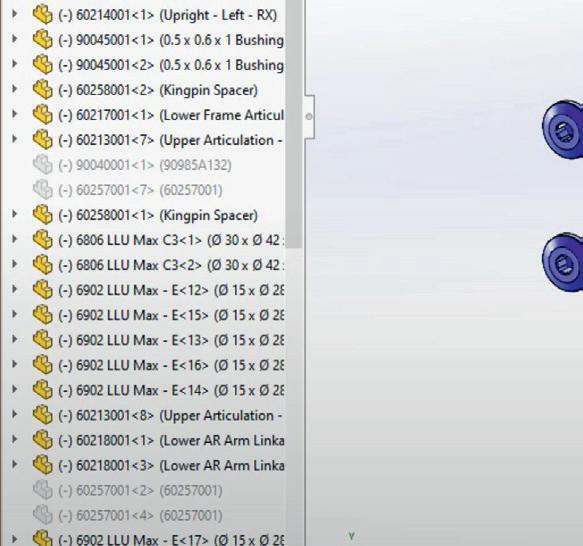
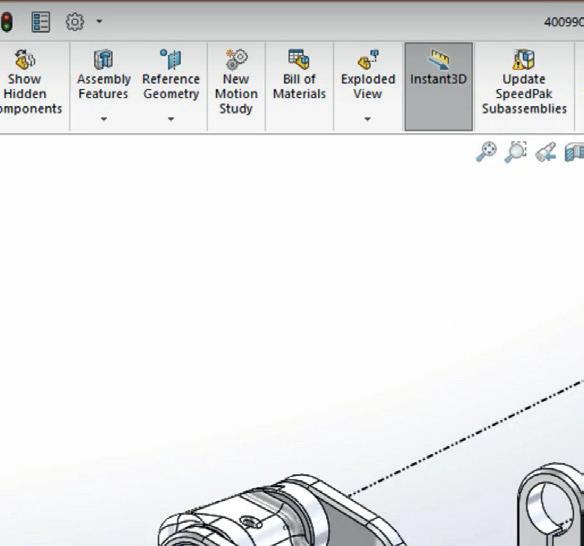
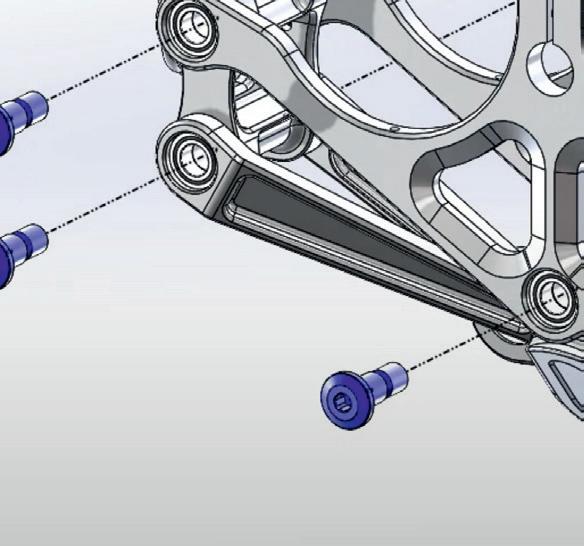

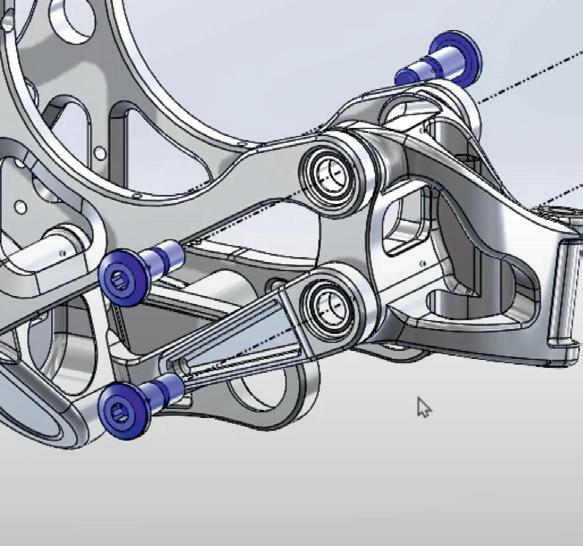
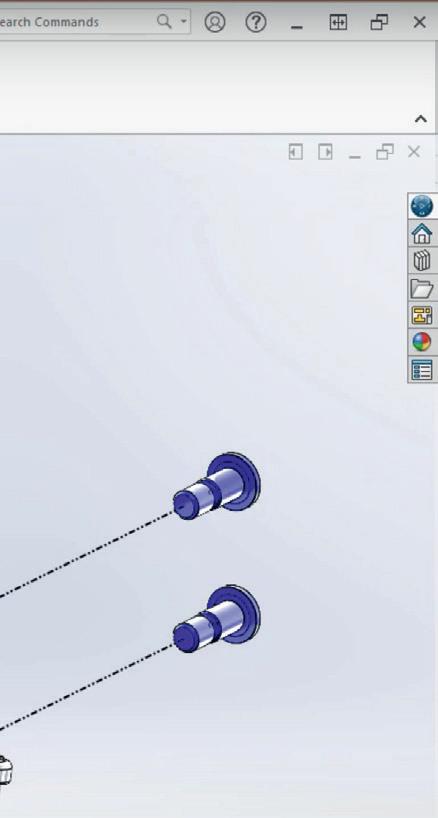
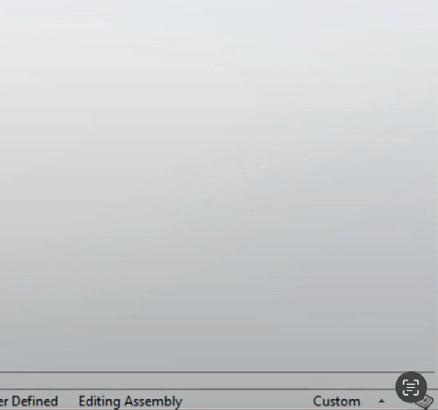
Q: Collaboration tools and ECAD have both seen some upgrades this release. What can you tell us about the thinking behind that?
A: Collaboration is key, and we started that game a long time ago with eDrawings. People were sending eDrawings files and marking them up. Now, we’re moving more towards using 3DSwym communities that you can access from directly inside your CAD system, so you have a really tight understanding and a tight communication chain with whoever you’re working with. I think that’s the future need. In fact, it’s a future necessity!
With ECAD, meanwhile, we’ve got a lot of our customers now working with ECAD-MCAD workflows. So we’ve changed the way we handle data exchange to IDX, which is a much richer format, and done a lot of work with CircuitWorks to enable that workflow. There’s lots and lots of things going on in here.
Q: When you look at this latest release, is there one particular tool that you feel has gone to a whole new level, functionality-wise?
A: I think if I was to choose one thing that’s now a really strong tool, I would probably say it’s the xShape app for sub-D modelling. There are a lot of new tools in xShape, helping not only to control a shape in the context of something else, so it has to marry up and match up. There’s a lot of work in there to ensure users have the connectivity they need.
So maybe the majority of your design is going to be in traditional Solidworks, but you want to develop an organic shape. Using 3D Sculptor or xShape is the way to do that. I think people who maybe looked at xShape in the past and thought it was not quite there yet should take another look at it. I think it’s a really, really strong tool and we’ve got quite a few customers using it. They are
already asking questions and pushing us to develop it even further.
Q: Is there any aspect of the 2025 release that in your opinion will provide a particularly good fit for smaller businesses?
A: If you’re a user at a smaller organisation, one of the benefits of the platform is that it allows you to punch above your weight with access to a lot of tools, just like the big boys use. But the challenge for a small company is that they’ve maybe got 10, 15 or even 20 years of legacy in what – for 90% of our users – would be Windows folders.
So they’ll be asking: ‘How do I get my stuff from here to there? Do I even need to get myself from here to there?’ We’ve done a lot of work on the sorts of tools that will help people move their data from where it is currently to the 3DExperience platform. From there, they can use the platform to work in a global way, taking advantage of all these communities and collaboration tools to work as part of a larger organisation.
I think that’s one of the main things that we’re trying to achieve here - to create a platform to help smaller companies work with global organisations and pitch anywhere around the world.
Q: A lot of the most attention-grabbing aspects of the Solidworks 2025 release are not just about creating geometry, but also focus on online collaboration and cloud file management. How do you view that shift?
A: I think that if you’ve used OneDrive or if you use Dropbox, you can use the 3DExperience platform in much the same way – if you choose to do that. But if you then take that one step further, then its benefits magnify with each small step forwards. I think it’s now the case that, in a couple of years’ time, people will wonder what the fuss was all about? Because it’s obvious that this is how we should work.
Solidworks is going beyond annual updates to get new functionality out to users faster
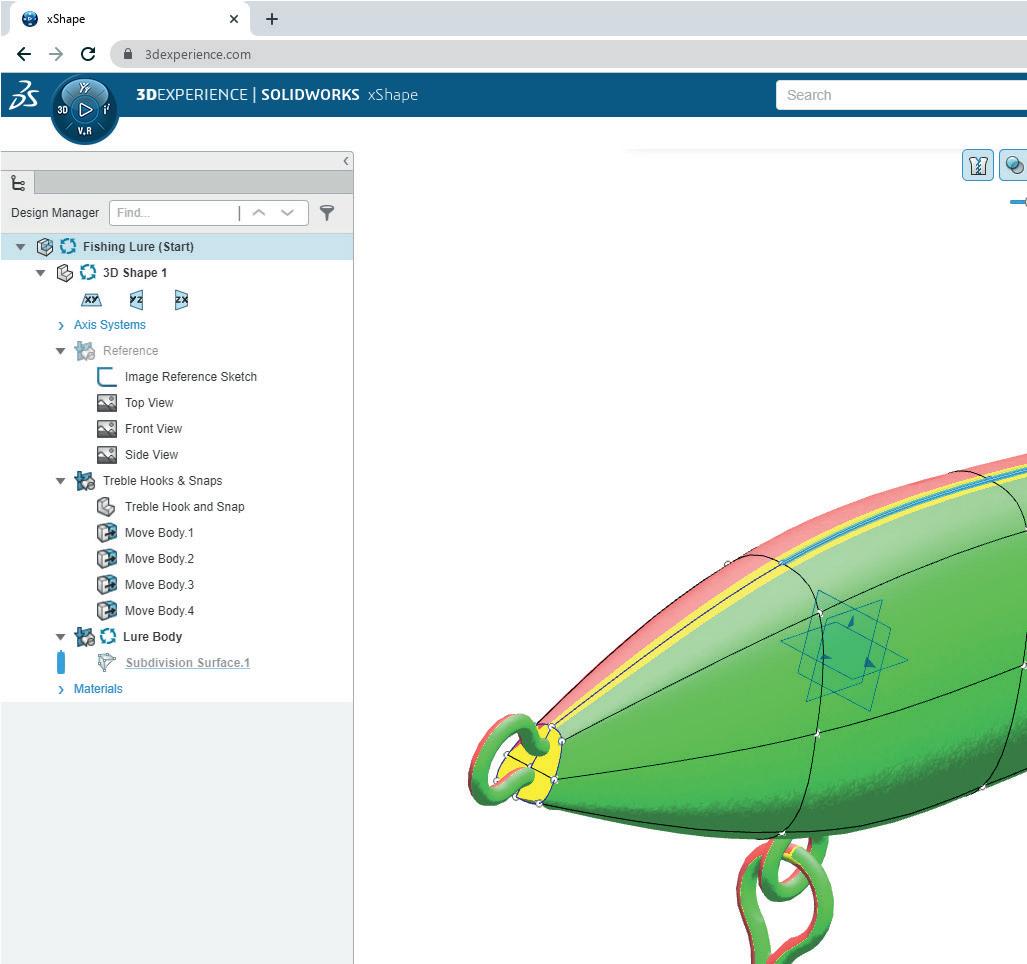
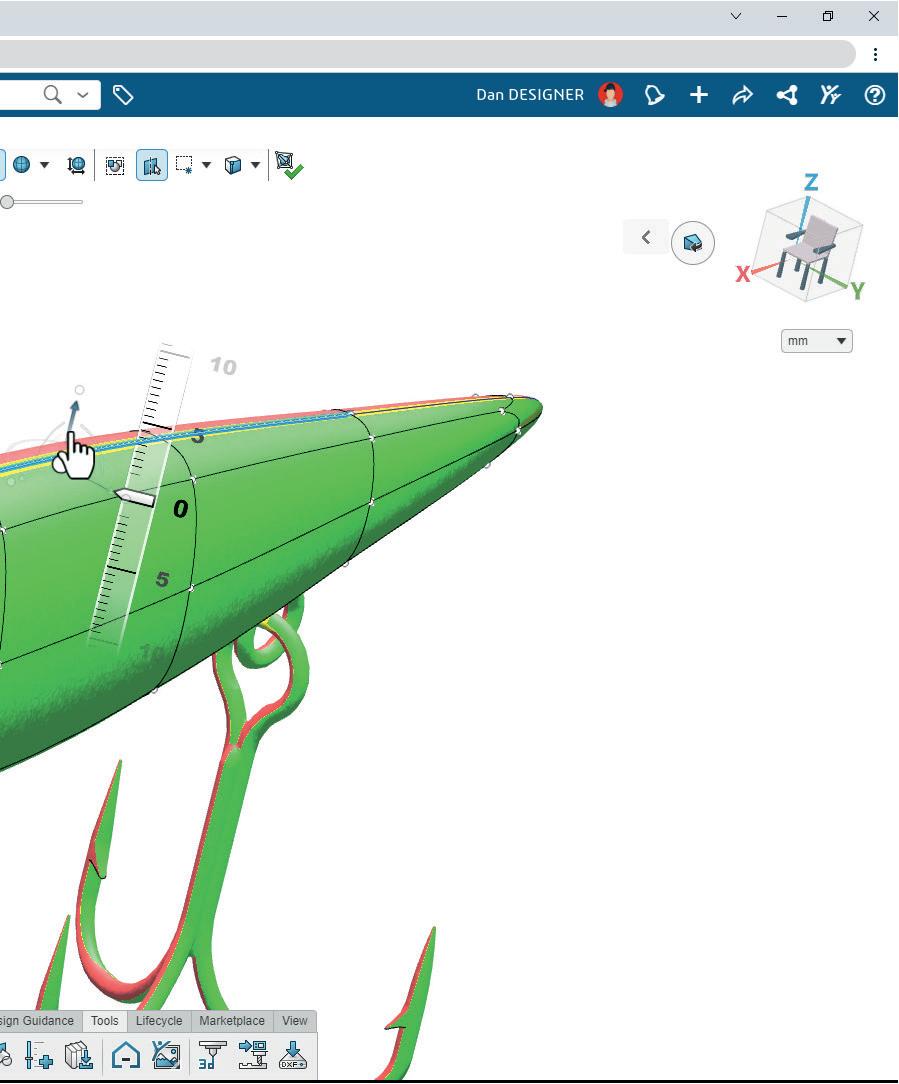
The other day, I had to find an old demo set that I had saved to an old external drive. I eventually found it in a box in the loft and, in the end, it turned out that the drive was corrupted. That’s days of productivity lost. And then I remember thinking, ‘I wonder how much data I’ve lost over the 20 years I’ve been working?’ If I was the owner of a business, I wouldn’t want my team using on-premise external hard drives. It’s just too risky. I think it’s a generational thing.
I think the next step is to use the cloud, not just for storage for data, but also as a central point for the whole ideation workflows that we want to see. And what’s interesting is that different industries have different ways of approaching this.
Aerospace is probably leading the way. Automotive is not that far behind. And then lagging a long way behind is probably the AEC industry. For companies in that sector, the paper is the legal document – but cloud is still going to happen.
We can see these trends coming, but what we want to be sure of is that our customers have the opportunity to make the switch and not be forced to make it. I think their own business opportunities will drive that process.
I think as more and more tools become online, not installed-only, this trend will continue. I don’t think people today fear the cloud as a fast storage, data management, collaboration platform, as much as they did five years ago. I think it’s become more normal.
Q: Two years ago, the xApps solutions were packaged with the Solidworks licence. Has that generated a rise in users and is it helping to drive development of those tools?
A: Yeah, I think it is. We’re seeing an uptick in people using this. In fact, we’re seeing a lot more of this sort of merged, hybrid model, that combines desktop and online tools. And we’re seeing newer, younger companies coming in and starting to compete in the X world. I think
it’s a trend we’ll see more and more over time.
Personally, I would rather sit in the full online world, because I think to myself: ‘Well, where have I been where I’ve been unable to get online?’ But I think for a lot of customers who have invested in infrastructure, having access to xWorks is a happy middle ground that enables them to start the transition whenever they want.
If I’m a company and I’ve invested in Solidworks for the last 10 years, and I’ve got a lot invested in PDM, and I’ve got inspection, and I’ve got simulation and whatever – it’s OK. I know this works. My business works well on this.
So I think that just by having access to this hybrid world, it will allow users to dip their toes in the water. They might decide that, for their next project, they’ll try using it. And if it doesn’t work for them, then they can always roll back and continue in their established way. I think it’s a case of enabling people to make the change when they actually want to make that change.
You know, the old adage of users using just 20% of functionality isn’t far wrong, in my experience. It’s one of the reasons why we built the online apps. We’re trying to create tools that allow users to focus on the task at hand – and ultimately, to help them design better parts, faster and more efficiently.
www.solidworks.com
Stephen Endersby is director of product portfolio management at Dassault Systèmes. He manages a team of product managers dedicated to delivering innovative solutions to the Solidworks user base across traditional desktop and SaaS platforms.
I don’t think people today fear the cloud as a platform as much as they did five years ago. I think it’s become more normal ’’
The xShape app for sub-D modelling features new tools designed to give users more control
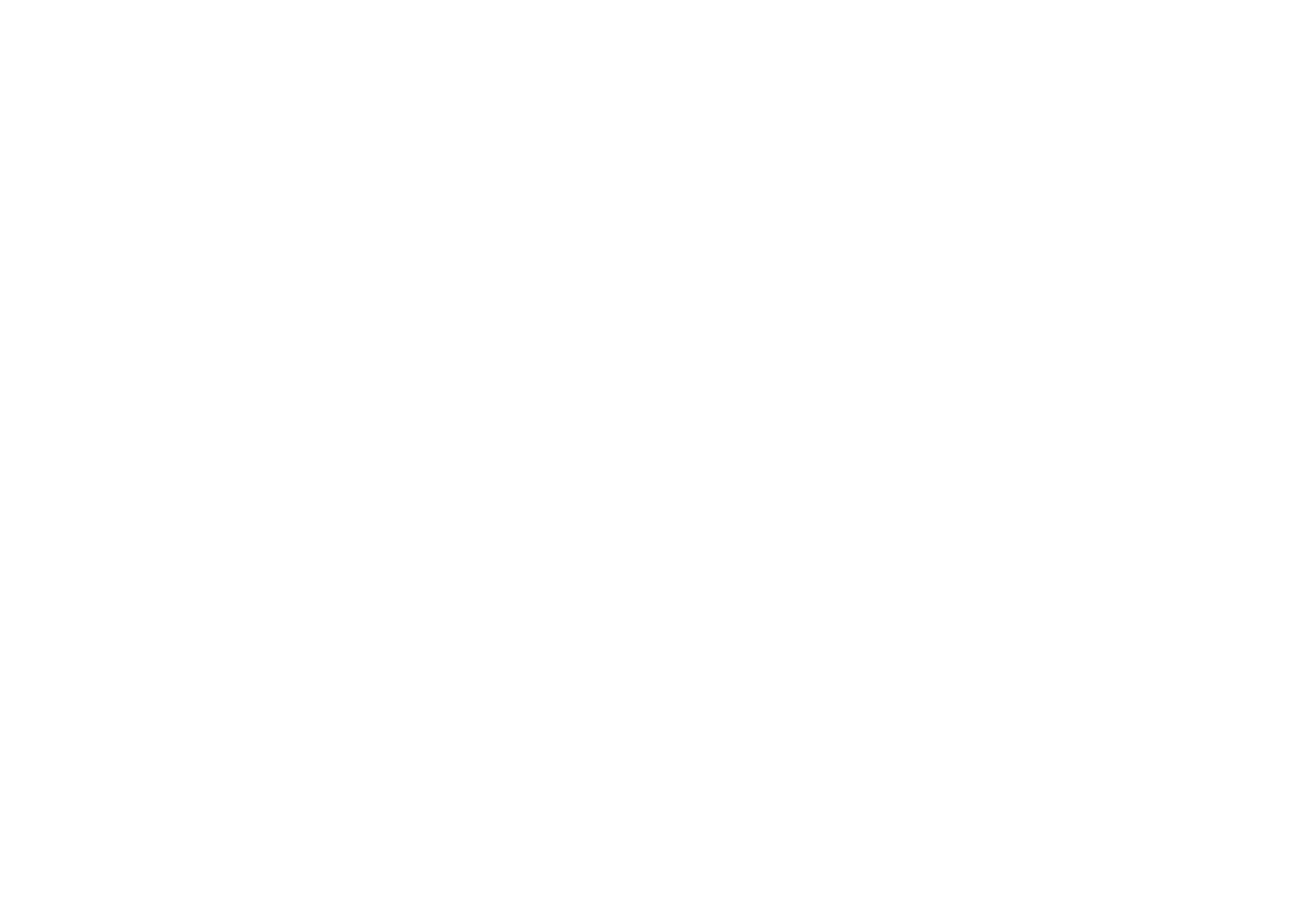

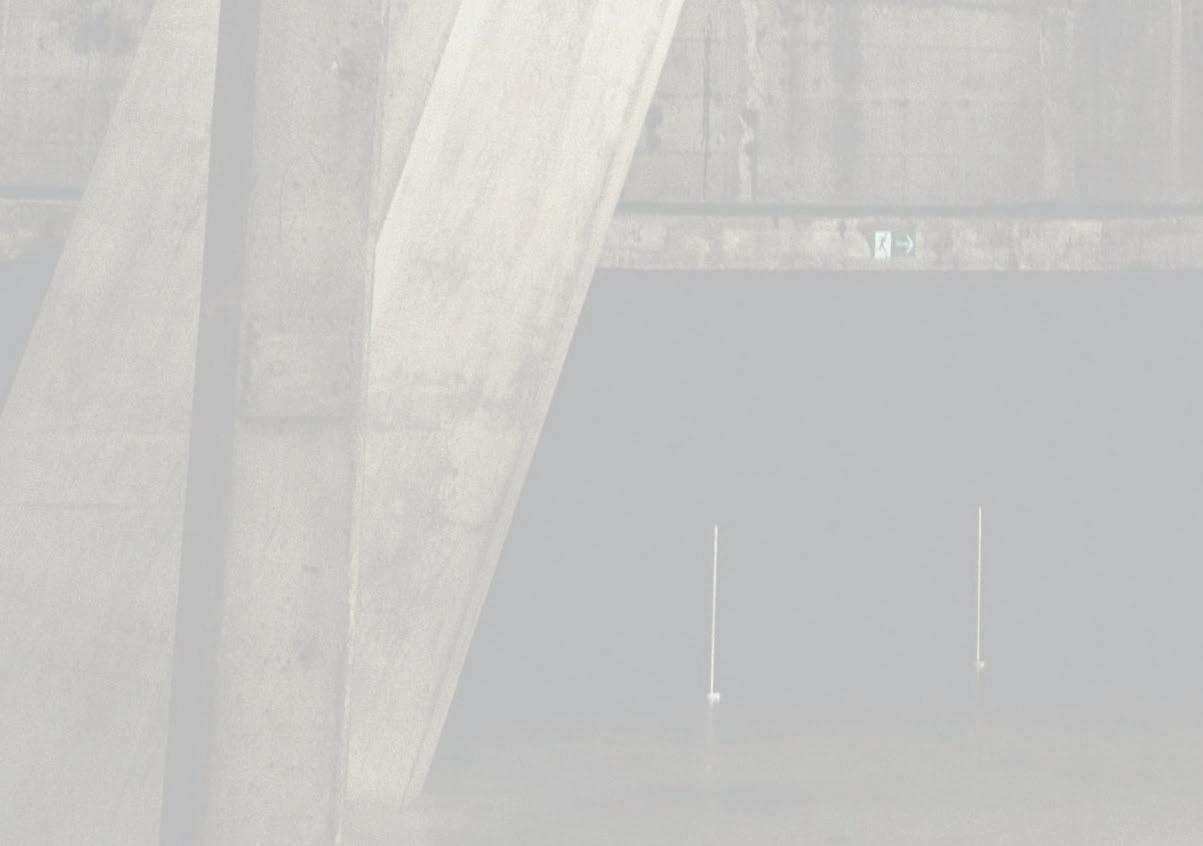
G5 Ultra Desktop 3D printer
G12 Industrial XL 3D printer
Largest choice of materials
Super-fast print speeds
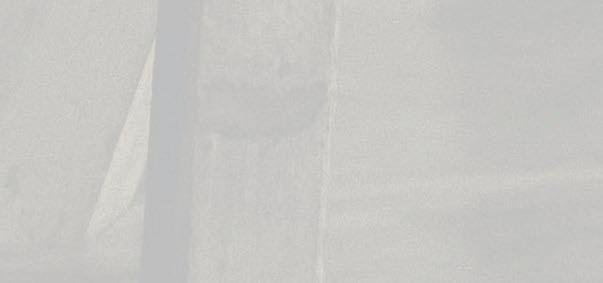
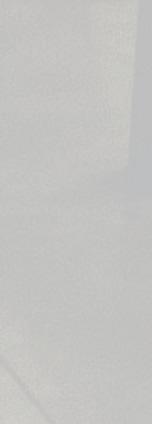

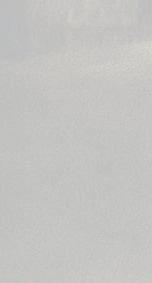
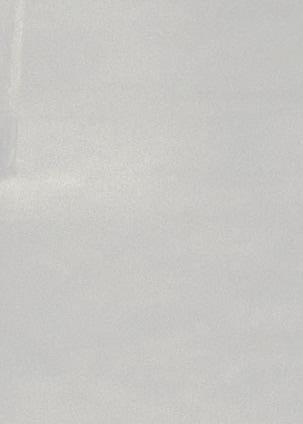
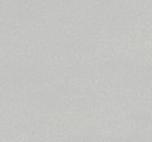
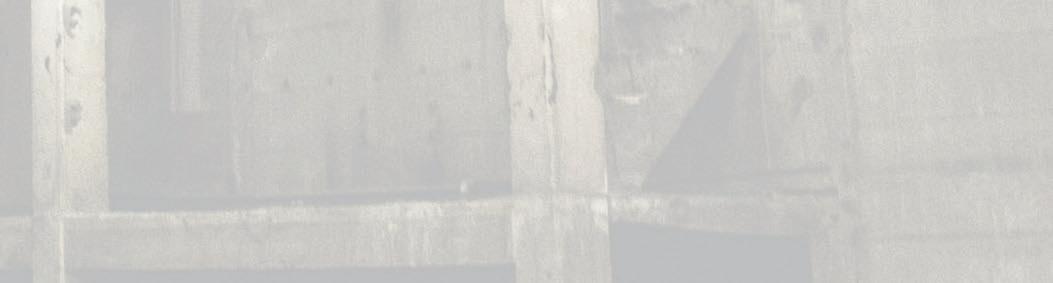
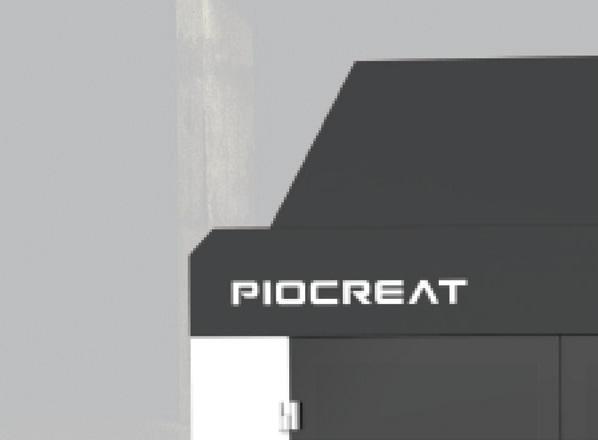
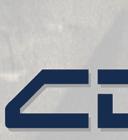
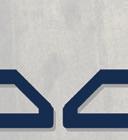

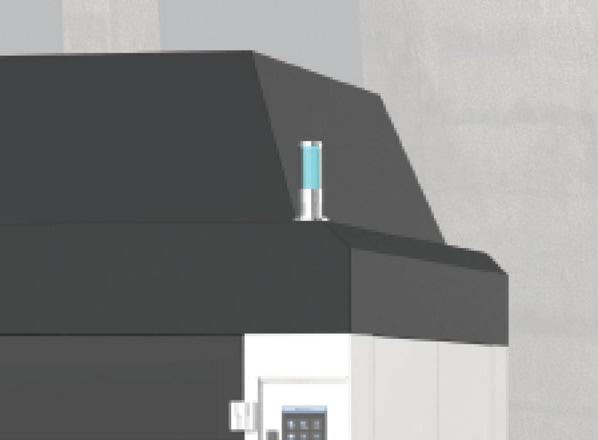
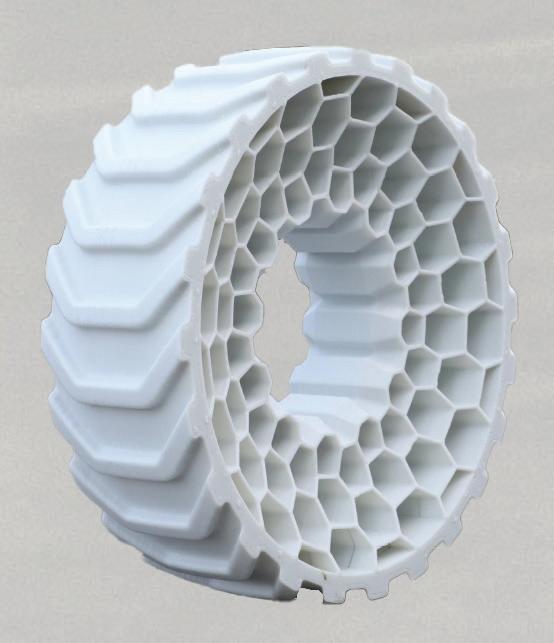

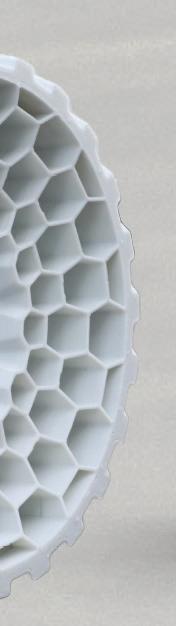
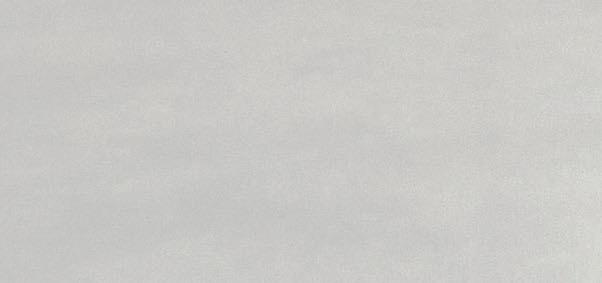
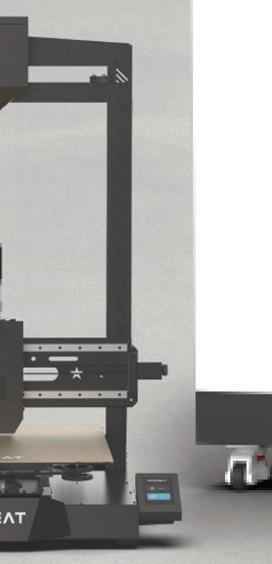
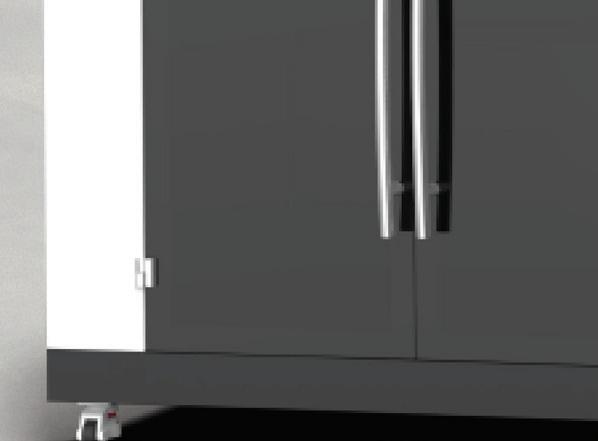

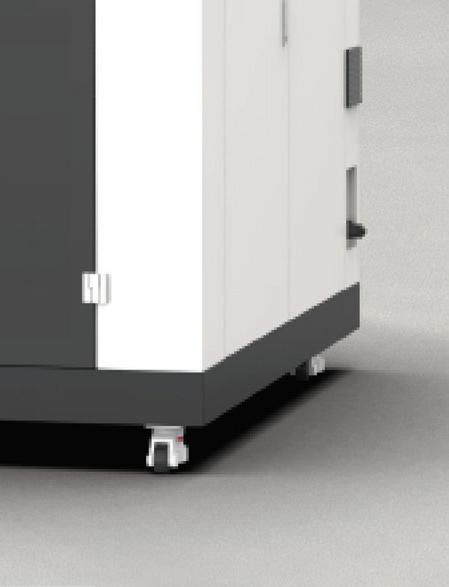

THE ANALYSIS OF
With the 2024 acquisitions of Ansys and Altair, the simulation technology landscape is shifting again, says Laurence Marks. Mainstream CAD integration may have boosted useability at the sacrifice of true advancement, but there’s still plenty of creativity to be found in a new generation of simulation tools
Growth in simulation, in terms of sales volume – or more interestingly, in terms of models run per year – has in recent years defined the evolution of product engineering.
This growth has been far from uniform across different industry verticals and individual companies, in my opinion. It’s my hunch that much
of the growth has come from big increases in spend and model creation at larger organisations, rather than further down the food chain. Either way, it means that the eff ects of the current market consolidation is felt diff erently by diff erent groups of users.
It’s not the first time this has happened, although we saw a different picture in the twentieth century, as CAD companies acquired the then big CAE companies.
>> FIFTEEN SIMULATION TOOLS TO WATCH

Our quick guide to some of the latest and perhaps under-theradar simulation tools from developers around the world, which are not only changing how analysis is conducted and the speed at which it can happen, but also unlocking analyses that might have been too slow or costly to perform in the past
1

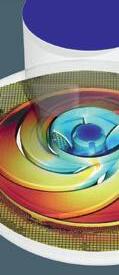
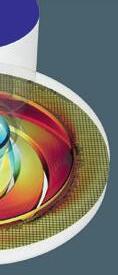
CONVERGE CFD
CONVERGENT SCIENCE WISCONSIN, US
After years as a CFD consultancy focused on building meshes for clients, Convergent Science pivoted in 2008 to become a developer of its own CFD software. The company’s flagship product Converge CFD offers autonomous meshing capabilities that eliminate the grid generation bottleneck from the simulation process. Converge CFD Version 4 includes new solver options for speed and accuracy, new modelling capabilities, and tools that expand the software’s functionality and improve user experience. In 2024, the company upgraded its cloud computing platform, Converge Horizon, enabling users to submit and monitor jobs, while giving them access to real-time billing and usage data. Converge Horizon further streamlines the set-up process, with expanded collaborative capabilities, such as groups with shared storage spaces. www.convergecfd.com
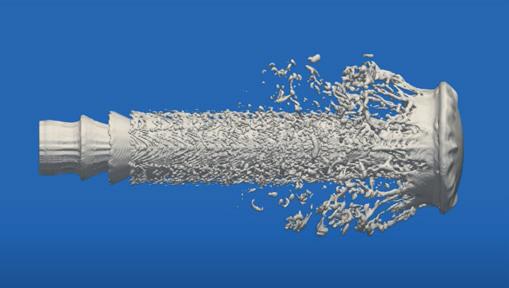
2

WILDKATZE
DIGITAL SOLUTIONS CO HIROSHIMA, JAPAN
Japan-based Digital Solutions Co launched its Wildkatze CFD software package in 2018, utilising robust Finite Volume and Finite Difference solvers, a pre-processing module and multiphysics models for a wide range of industrial problems. Flexibility and advanced solver customisation through user algorithms and C++ coding lie at the heart of its success, enabling users to set up different physics models that utilise different schemes in different regions of flow to enhance the reproducibility of physical phenomena and quality of analysis. For example, it is possible to set up an LES model in one region and k-omega turbulence model in another region. Users can incorporate their own physics models into Wildkatze for conducting advanced research. www.digital-sol.co.jp/wildkatze
3
Smoothed Particle Hydrodynamics (SPH) simulation is at the core of this browser-based CFD software founded in 2018. SPH opens up new avenues for simulation in applications like gearbox lubrication, electric motors, sealing and water ingress, while the meshless nature means set-up is fast, offering more time for experimenting. By uploading an .stl file and with few clicks on its simple user interface, Dive lets users observe fluid behaviour and analyse wall properties like wetting and stress characteristics. A partnership with Microsoft Azure allows users to choose where they want their computations hosted, using servers in the US and EU. Included in subscriptions is “personalised and continuous guidance” from Dive’s team of CAE expert engineers. www.divecae.com
SIMULATION
In the beginning, simulation companies were set up by individuals and small groups, and the customer base they served was similarly small technical groups. The links between CAD and simulation weren’t close, or particularly happy.
PTC went quickly into the game, buying Rasna in the 1990s. Dassault Systèmes purchased HKS and its Abaqus product. Siemens snapped up CD Adapco, LMS and others.
It wasn’t just the CAD companies that caught the acquisition bug. The larger simulation companies started buying smaller players, too, with Ansys buying Fluent and Ansoft, for example, thus widening its offer across physical domains as well as growing ever larger.
These software groups eventually created a series of mainstream CAD-integrated products for the wider market, but migration from the CAD simulation space to more traditional simulation tools and activities has
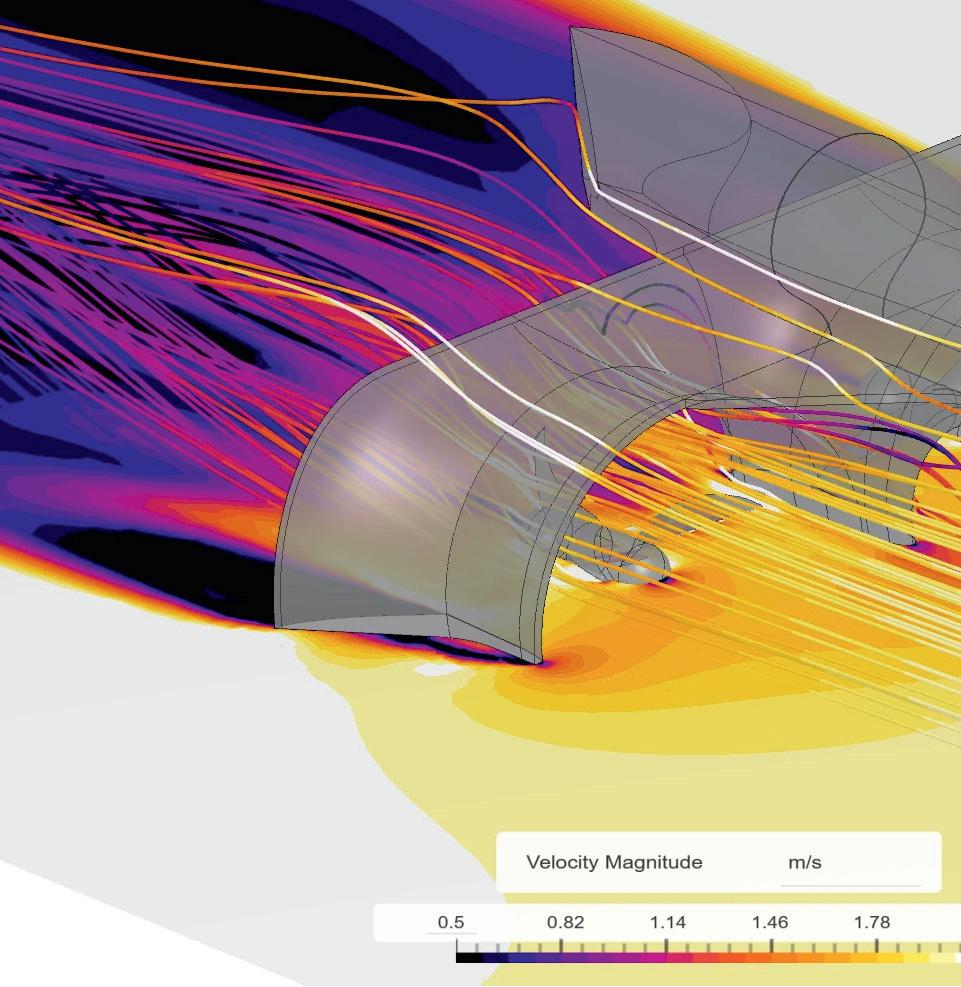

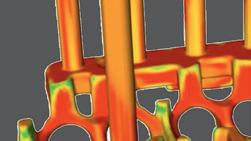
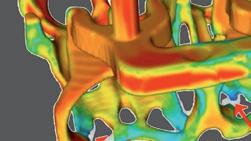
4
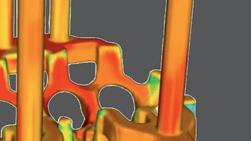

FLOW-3D FLOW SCIENCE NEW MEXICO, US
Founded back in 1980, Flow Science’s flagship CFD software
Flow-3D is a powerful tool for complex fluid modelling problems using accurate simulations of free-surface flows provided by its proprietary TruVOF form of the volume-of-fluid technique. Applicable to a wide range of industrial applications and physical processes, Flow-3D also offers a range of specialised versions for areas like investment casting (featuring 11 process workspaces), welding and additive manufacturing with laser powder bed fusion and DED. Its general-purpose CFD software is used for a broad range of applications, including water and environmental, microfluidics, inkjets, consumer products and energy. www.flow3d.com

5
LUMINARY CLOUD LUMINARY CLOUD CALIFORNIA, US
A simulation-as-a-service highfidelity CFD solver with cloud-based compute power, Luminary Cloud promises improved scalability, superior speed, better scale and more accurate data generation when compared to traditional software. With no downloads or installs, the process is secured via an ITAR-compliant platform that directly imports CAD, automating healing and mesh generation. Whether used for a single, large simulation or for numerous parallel simulations, Luminary combines modern AI/ ML techniques with physics-based constraints for much faster predictions and simplified workflows that can then be shared as a link to collaborators. Founded in 2019 by Jason Lango, an expert in HPC and cloud computing, and Juan Alonso, an expert in computational physics and aerospace engineering, Luminary Cloud was incubated at Sutter Hill Ventures, coming out of stealth in March 2024. www.luminarycloud.com

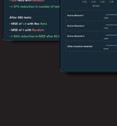
6
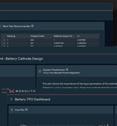

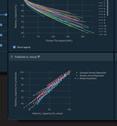

MONOLITH MONOLITH LONDON, UK
Monolith was founded in 2016 by Dr. Richard Ahlfeld, directly born from his PhD research at Imperial College London and NASA and boosted by an accelerator programme in 2018. With its own proprietary algorithms for handling 3D data, Monolith partnered with universities like Imperial, Cambridge and ISAE-Supaéro to develop its AI capability. Offered on a software-as-a-service basis, Monolith uses no-code AI to build pipelines and interactive ‘notebooks’ that load, explore and transform data for AI. This enables users to train and evaluate self-learning models and quickly find the best fit, while offering purpose-built tools for engineering and test-specific applications. Looking to accelerate AI adoption, Monolith allows users to train and upskill teams with inproduct tutorials, online learning tools and custom training options. www.monolithai.com
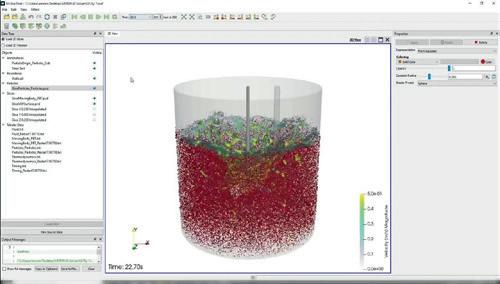
7
US
Pairing modern Lattice Boltzmann algorithms with up-to-the-minute GPU architectures, M-Star CFD software was built from the ground up to run millions and billions of lattice grid points. Founded in 2014, M-Star became part of Dotmatics’ science R&D software platform in 2024. Being designed for a more powerful computer architecture, M-Star uses Large-Eddy Simulations (LES), particle and bubble tracking, pushing what users can glean outside of the traditional Reynolds-averaged NavierStokes (RANS) based tools. Capable of simulating CFD-DEM, Non-Spherical Particles, Reacting Particles, Particle Breakup and Mixing Rules, the number of pharmaceutical manufacturers that use this product gives a sense of the trust levels engendered by its calculations, which can run on-premise or on the cloud via AWS.
www.mstarcfd.com
Simulation tools such as SimScale help designers to optimise new product ideas
been patchy at best. And this evidence alone signposts where the market could be heading.
LIMITS OF CONSOLIDATION
The process of consolidation in the market has probably gone about as far as it can go now, with Ansys becoming part of Synopsys, Altair joining Siemens, and MSC being bought up by Hexagon a while back.
So, what will the simulation market look like in 2025? Well, one thing is sure: it will look nothing like it did in the 1980s and 1990s, when every new software release really did contain ‘significant enhancements’ and represented a significant move forwards in the art of the possible.
With consolidation, the pace of technical change has relaxed. Or, as the rate of technical change has relaxed, the pace of commercial consolidation has accelerated. I, for one, can’t tell which it is – although I guess both are probably inevitable and interlinked.
Today, we find ourselves in a world where simulation products are mass-market offerings, with customers and developers probably further apart from each other than they’ve ever been. Which is fine, if you want to apply slick integrated products to established workflows.
If, like most people who work in simulation full-time, the motivation is applying creative simulation techniques
to interesting problems and challenging physics, where do you look now? Because, at first glance, you might think that the options are distinctly limited.
While LinkedIn seems to have become a showcase for people who have copied and stolen other people’s work (OK, I mean my work), or who are prematurely showing off an as-yet unmarked student project (please don’t do that), it is still probably the best place to research and observe what could almost be described as a renaissance in the standalone simulation market.
TWO DISTINCT CAMPS
The new developments seem to be split into two distinct camps. You want traditional FEA? PrePoMax leads the way and happens to be free. And there are others in the free space, including first-into-the-field Openfoam. I’m not sure that the availability of these products is as significant as some think. They are great for what you pay, but do they stack up in the commercial environment of their users? I’d say that this isn’t clear yet, but sticking my neck out, I would also say that they won’t be replacing paid-for products any time soon.
In the second camp, more critically for the future of simulation, there are many new ‘real’ products on the market. These generally don’t look like the traditional FEA and CFD products of the 1980s and 1990s, or even
>> FIFTEEN SIMULATION TOOLS TO WATCH
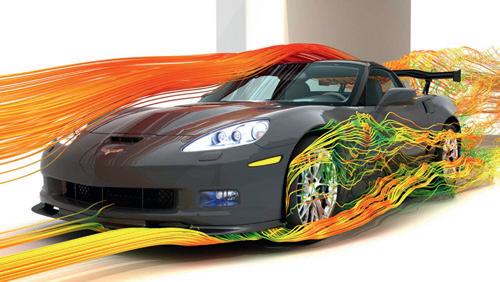
NEURAL CONCEPT NEURAL CONCEPT LAUSANNE, SWITZERLAND
Founded in 2018 at EPFL, the Swiss Federal Technology Institute, Neural Concept’s platform aims to bring together data scientists, CAE and CAD designers on a single platform for deep-learning simulation capabilities. Users can swap quickly between different AI models, establishing model training and retraining strategies to harness the large amount of engineering data available within an organisation. A collaboration with Nvidia sees Neural Concept’s software deployable on nearly all of its GPUs and CUDA software. It is compatible with Dassault Systèmes Catia and Solidworks, PTC Onshape, Spaceclaim, Siemens NX, STAR-CCM+ and Simcenter. For example, Simcenter users can execute Simcenter CFD simulations with HPC power. Neural Concept is deployable on-premises, air-gapped, or via a SaaS or public cloud application. www.neuralconcept.com 8

9
PACEFISH NUMERIC
SYSTEMS
MUNICH, GERMANY
Pacefish is focused on analysing and optimising the complex aerodynamics of vehicles using transient LatticeBoltzmann Method (LBM) simulation. Its transient modelling considers timedependent effects like vortex streets and dynamic vortex shedding, as well as pressure and velocity fluctuations. In addition to the Smagorinsky LES model, the software offers hybrid uRANS-LES (SST-DDES and SST-IDDES) as well as uRANS (K-Omega-SST) turbulence models. Capable of using up to 16 GPUs operating at almost ideal scaling, it can tackle simulations beyond one billion cells, with Pacefish reporting models of more than 100 million cells achieving turnaround times of just a few hours. Founded in 2016 by aerospace engineer Eugen Riegel, Pacefish can be used as an on-premise application using an organisation’s own hardware, or through SimScale as a web- and cloudbased application in a browser. www.numeric.systems/pacefish

10
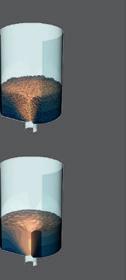
AI4SIMULATION NXAI LINZ, AUSTRIA
Founder Sepp Hochreiter is already noted for his contributions in the fields of machine learning, deep learning and bioinformatics and NXAI has a strong grounding for building AI systems. Founded in 2023, its AI4Simulation toolset, headed by former Microsoft researcher Johannes Brandstetter, is launching with particle-based simulations for modelling multi-fluid systems and fluid-material interactions. AI4Simulation’s first simulation project, NeuralDEM, is an end-to-end, deep learning alternative for modifying industrial processes such as fluidised bed reactors or silos. Aimed at scaling industrial and manufacturing processes, NeuralDEM captures physics over extended time frames. With deep learning, AI4Simulation looks to scale to millions of particles, but has an eye on the future, involving models of scales that surpass human understanding, marking the importance of AI-driven simulation technology. www.nx-ai.com

Laurence Marks built his first FEA model in the mid-1980s and his first CFD model in the early 1990s. Since then, he’s worked in the simulation industry, in technical, support and management roles. He is currently a visiting research fellow at Oxford Brookes University, involved in a wide range of simulation projects, some of which are focused on his two main areas of interest: life sciences and motorsports
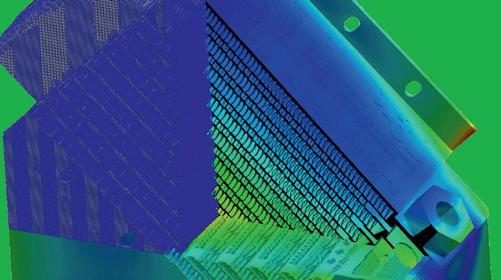
11
This voxel-based FEA simulation software was launched in 2022, lead by Dr Pan Michaleris and some of the team originally involved in Autodesk’s Netfabb Simulation. PanX’s voxelbased meshing allows for featureaware meshing that maintains fine details where needed, but allows for coarsening in bulkier areas that are less critical. Where traditional additive simulation tools solve the first few layers very quickly, before slowing to a crawl as elements are added, PanX eliminates that slowdown, letting models run faster over the entire solve on a typical mobile workstation toting 8 cores and 64Gb. It has varied uses across several 3D printing workflows, from optimising print surfaces to preventing overheating during LPBF builds, all with a focus on improving part quality and consistency. www.panoptimization.com
the mainstream products now sold by the megacorps.
New CFD codes based in Lattice-Boltzmann Method (LBM) technologies, like Pacefish, and new particle-based codes like Dive and ParticleWorks, are carving a niche in the more specialist reaches of the CFD application space.
The hunt for new entrants into the market also uncovers an interesting point. You quickly become aware of the technologies and companies that you already knew existed, but which have kept a low profile and haven’t yet become some minor division of any IT megacorp.
Here, I’m thinking of products like Converge CFD, which is both established and highly technically competent. There are still significant players in the sim space that haven’t joined the headlong charge into the corporate big time and which still seem to maintain a steady focus on technology.
AI OUTLOOK
This leads me on to the topic of what AI means in the simulation space. It’s too big a subject for here and now, largely because I think the CAE companies are sending out messages that could at the very least be called ‘mixed’. I’m not certain what I think the role of AI in simulation is going to be at this stage, but it’s pretty obvious that it isn’t faster CFD runs.
Presenting at the NAFEMS UK conference, I followed the PhysicsX team onstage, and from what I learnt, this
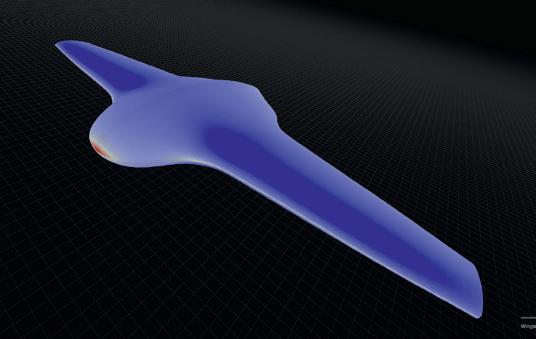
12
LGM-AERO PHYSICSX LONDON, UK
Born out of numerical physics and Formula One, PhysicsX was founded in 2019, came out of stealth in 2023, and joined the AWS Generative AI Accelerator in November 2024. Once set up, PhysicsX claims its tools can simulate complex systems in seconds, automatically iterating through millions of designs to optimise performance, while respecting manufacturing and other constraints. LGM-Aero is a geometry and physics model pre-trained on more than 25 million meshes, representing more than 10 billion vertices, and a corpus of tens of thousands of CFD and FEA simulations, generated using Siemens Simcenter STAR-CCM+ Nastran software. LGMAero demonstrates the creation of geometry and the assessment of physics performance in under one second, compared to the multiple hours required for traditional simulations. www.physicsx.ai
is an organisation doing something truly creative using AI in the simulation space, and what’s more, it’s doing so outside of the usual CAE megalith organisation. That company is one to watch, I’d say.
So where does all this get us? Nothing ages as quickly as opinions about the future, but it looks to me like we’ll end up with two CAE streams: one that is integrated into mainstream CAD and CAE in a limited way; and another more fully integrated group. And by loosening the connection, we’ll end up with the rebirth of the ‘point solution’.
Technical products that solve a problem earn their keep by generating and enhancing IP without forming a key part of a slickly integrated whole. The big CAE vendors will still continue to supply the vast chunk of the simulation space, and they will do that effectively, with products that perform at levels we could not have dreamed of years ago. But small teams of simulation and physics specialists will continue to drive creativity, via a new generation of more focused applications.
The winners in this space look likely to be those people who can interact and optimise their work using tools like Python. So rather than mass extinction, we might in fact be looking at a new beginning, driven by consolidation in the wider market. Or perhaps not – but I certainly know which scenario I hope to see.
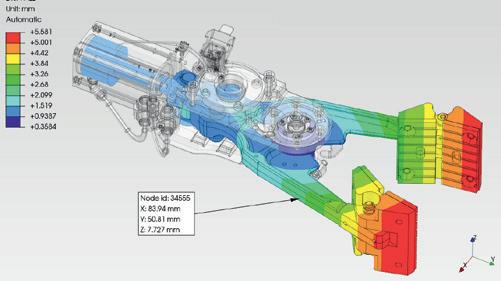
13
PREPOMAX
PREPOMAX MARIBOR, SLOVENIA
PrePoMax is an open-source preand post-processor for the Calculix FEM solver, based on a modern user interface to speed up workflows. Developed predominantly by Matej Borovinsek, assistant professor of mechanical engineering at the University of Maribor in Slovenia, PrePoMax allows users to import geometry from various CAD formats and .stl files, using support from the open-source Open Cascade platform. Users can mesh a solid or a shell-based geometry using linear and parabolic finite elements. The product also supports an import of a file’s finite element mesh or uses the open-source Netgen library to perform meshing. PrePoMax results can be shown as animations and uses 2D plotting tools to represent history outputs. https://prepomax.fs.um.si
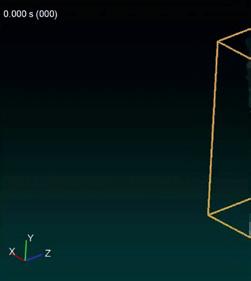
14
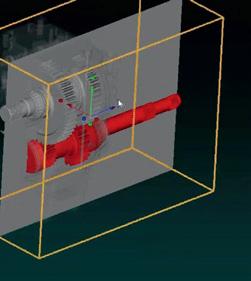
PARTICLEWORKS
PROMETECH TOKYO, JAPAN
Particleworks uses the Moving Particle Simulation method developed by Professor Seiichi Koshizuka of the University of Tokyo, from which the company was spun out in 2023. Moving Particle Simulation excels in simulating liquid and multi-phase flows, offering a straightforward process for complex geometries with moving parts. The meshless solver and an intuitive interface make the simulation process simple and fast even for complex geometries with moving parts, like gears and shafts in a complete transmission or in an engine. The software leverages GPU computing power for fast and efficient simulations, while Particleworks is integrated with Ansys Workbench (Mechanical and Fluent) as well as with Romax, to help streamline simulation workflows. A partnership with European simulation software reseller EnginSoft provides support for customers. www.particleworks.com/en
‘‘ Technical products that solve a problem earn their keep by generating and enhancing IP without forming a key part of a slickly integrated whole ’’
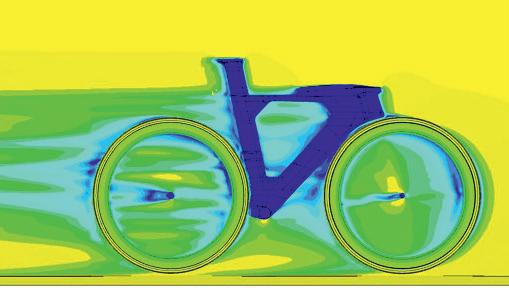
15
With its browser-based platform, SimScale covers a broad range of physics simulation capabilities, including structural mechanics, fluid dynamics, thermodynamics and electromagnetics. Founded in 2012, its goal of high-fidelity engineering simulation on any hardware with instant access anywhere, anytime has since come to fruition, and today, SimScale has practically no limits when it comes to simulation size. Integrations with PTC Onshape and Autodesk Fusion have seen its popularity grow in recent years. A more recent partnership with Hexagon sees its Marc solver directly accessible through SimScale’s interface, putting advanced nonlinear structural analysis onto the cloud. SimScale has integrated AI capabilities, including an AI copilot that aids model set-up. A constantly learning AI model also helps select the best HPC compute infrastructure for each simulation automatically. www.simscale.com
LIGHT AS
Using a simulation-led design for additive manufacturing workflow and advanced multi-laser metal 3D printing technology, Airbus is achieving 75% lightweighting, multi-part consolidation and precise geometric tolerances. Stephen Holmes speaks to the team behind hefty changes that add up to lighter designs
The team at Airbus Operations set out to redesign the fuel air separator for the company’s A330 aircraft with a good idea of all the benefits that additive manufacturing might bring to their work. They knew that the technology could be used to lightweight the part, consolidating many connecting parts within the system, and that it would enable them to make that part in a way that could be qualified to fly.
All the same, they weren’t fully prepared for the striking results that they actually achieved.
The fuel air separator is a large and complex component, which removes air from the auxiliary power unit (APU) fuel feed system, ensuring that the APU can power essential aircraft systems when the main engines are off.
Typically, this part is fabricated from more than 30 individual components that require manual welding and
A CAD model of the original fuel air separator, comprising over 30 individual parts
assembly. This makes for a labour-intensive production process, as well as being prone to supply chain challenges.
However, the higher-level objective for redesigning the air separator in a prototyping project was to reduce CO2 emissions over the lifespan of an aircraft. Weighing in at 35kg, a typical system also requires a substantial mounting rack that adds further weight to the aircraft. So it was a cause for considerable celebration that the system was able to be consolidated as a single part weighing less than 8.8kg – some 75% lighter than the original.
BIG METAL, FINE MARGINS
The new fuel air separator was built on the Nikon NXG XII 600 3D printer, a large metals SLS system boasting 12 lasers and a build area of 600 x 600 x 600mm, and capable of building the new design in 68 hours.
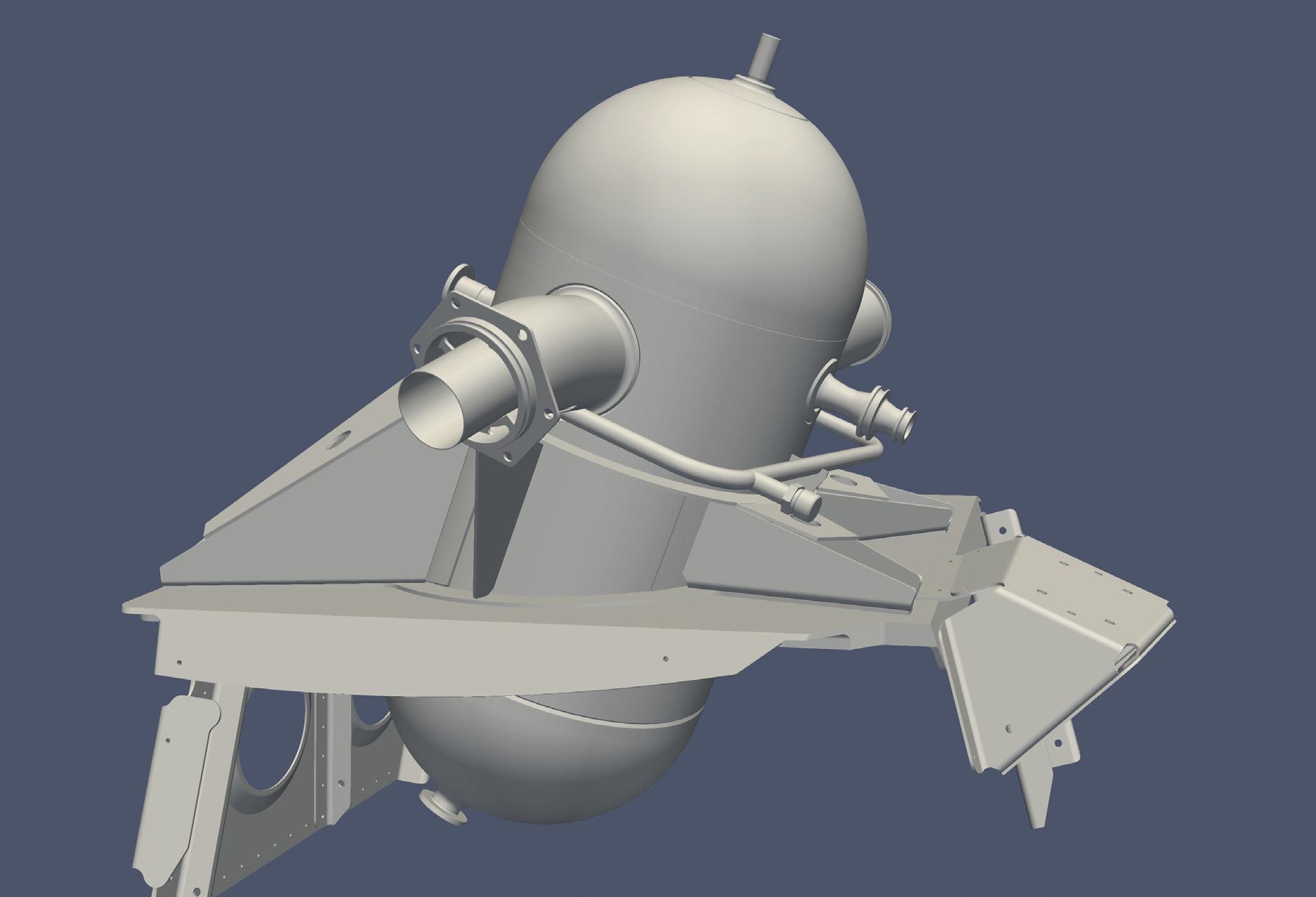
‘‘ This hybrid approach is used in cases where you have complex geometry, risk of distortion and tight tolerances ’’
AIR
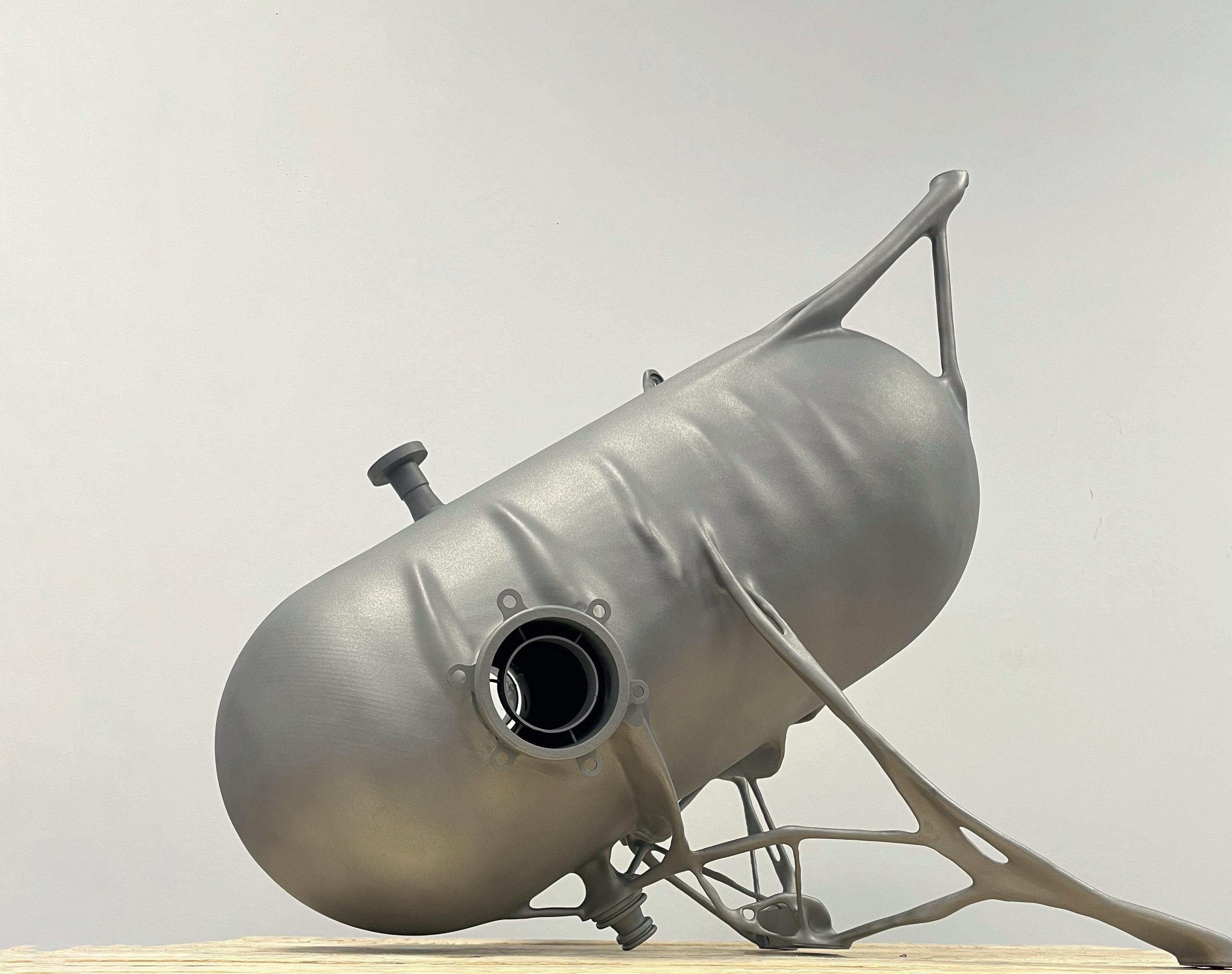
While still a lengthy process, which also requires several hours of post-processing and heat treatments, this method still beats the conventional approach hands-down.
“In terms of cost, we don’t have a very precise breakdown, but expect it to be cost-competitive as well, due to the complexity of the original design and the work in assembly,” adds Mathieu Pérennou, global director of additive manufacturing solutions at Hexagon’s Manufacturing Intelligence division.
Tackling a part of such scale and complexity was not straightforward. In fact, without advances in software from project partner Hexagon, the air separator could not have come close to the tolerances required.
The consolidation of elements and lightweighting of the overall form utilises topology optimisation within Hexagon Apex Generative Design, but that is only the first step.
Key to this project was developing a process to mitigate all the manufacturing risk, given that physical builds on large-scale metals 3D printing systems are costly in terms of time, resources and money.
The build process for aligning the part on the Nikon NXG XII 600 3D printer was quickly derived using Hexagon AM Studio. After that, the risk-reduction work really began, with in-depth process simulation taking into account all factors relating to the machine and the materials used.
Process simulation is used for two things, explains Perennou. First, it’s used to mitigate manufacturing issues – risks like recoater interference, supports
separating, or cracks appearing due to the stress levels in the build. But once you can simulate a process with no manufacturing problems, you still need to consider the impact this simulation will have on the shape of the part.
“With titanium especially, you’re going to have distortions,” he says. “There are going to be shrinkage distortions. And then the next step is to use simulation to try to make a part within tolerance.”
Using Hexagon Simufact Additive, the team was able to virtually print the part and compare this model to the nominal, determine the differences between the two, and then morph the nominal into a distortion compensation model that, when printed, builds a part within tolerances.
Yet for large, complex aerospace parts with tight tolerances like the fuel air separator, simulation results can still lead to real-world headaches.
To take this a step further, Hexagon has developed an advanced compensation module for an approach Perennou calls ‘second time right’. Here, a simulation gets you very close to the end result. You print that first part and then 3D scan it, allowing you to compare that data capture to your nominal once more, showing you where the differences lie.
The 3D data capture measurements can be added into Simufact, compensating the printable mesh based on the measured deviations from an optical or CT scan and address localised distortions for more accurate compensation.
Airbus redesigned the A330 fuel air separator in partnership with Hexagon and Nikon



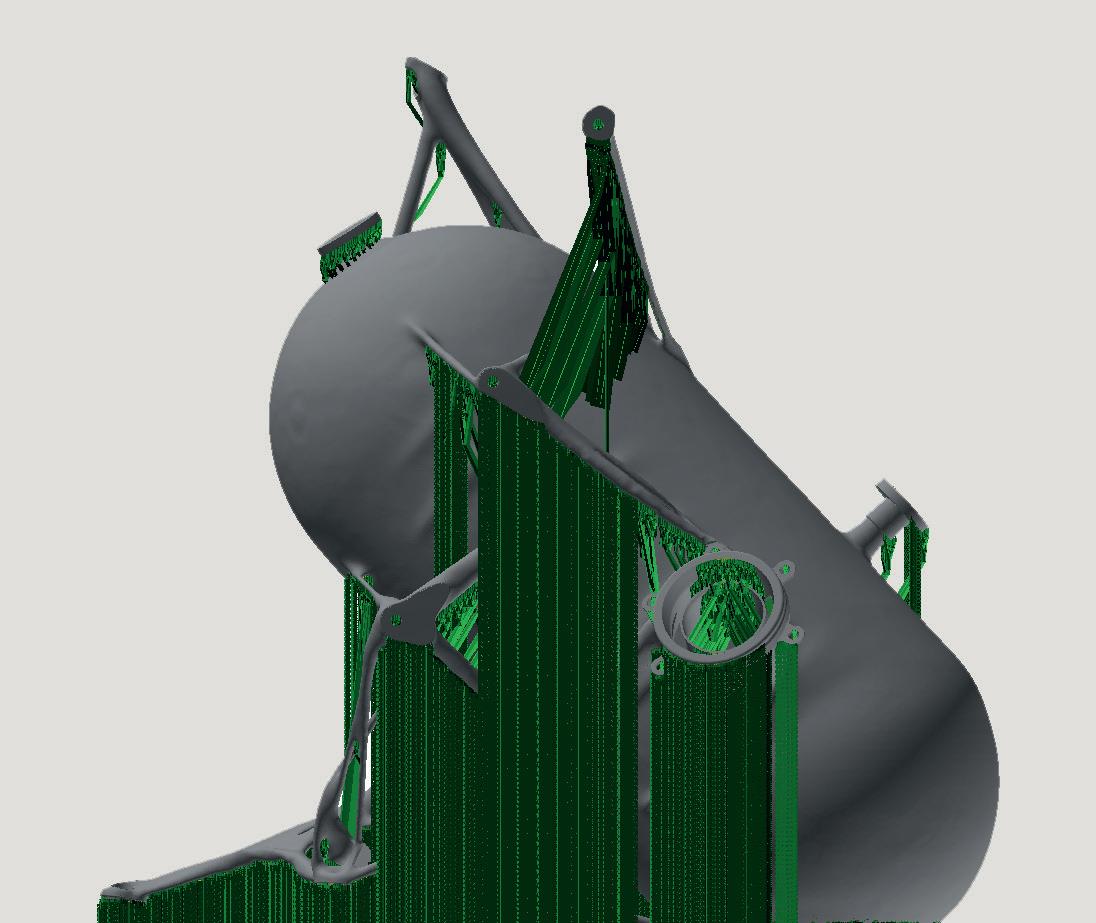
THE EDGE OF ACCURACY
With parts like the air separator, you’re starting to approach the edge of accuracy in terms of what simulation can achieve, says Perennou. So, you’re probably better off just printing the first part and compensating it based on its measurements.
“This hybrid approach – using the two-step approach that we’re talking about – is used in cases where you have a complex geometry that distorts a lot, and you have tight tolerances.”
Simulation alone might mean 90% of the geometry meets tolerances, but there remains a lot of trial and error to defi ne that last 10% by tuning it via multiple physical builds.
Hexagon executives say the company is enabling this by using elements from its VG Studio Max product –better known for CT scan analysis and adding them into Simufact, making it more forgiving of gaps in scan data and letting Simufact Additive users perform metrologybased compensation with whatever data capture technology they have to hand.
“The idea is really to reduce the [physical] iterations as much as possible,” explains Perennou. Because of this new process, some Hexagon aerospace customers are taking on projects that might otherwise be deemed too risky and too expensive, with too many builds needing to be scrapped.
The next level is Hexagon’s drive to define macro scale elements of additive parts in Simufact, by looking at the quality of the part from a material standpoint and simulating potential defects – what Perennou calls ‘ virtual CT scanning’ – to find where porosities and defects in a part might arise.
Having defined all the process parameters for machine and materials in Simufact, users are presented with a ‘heat map’ that flags up any potential cure risks that could cause porosity.
While your initial process model could be within the right parameters, factors like heat building up over a build lasting several days means that errors could arise. Perennou explains that Simufact Additive constantly calculates parameters during the simulation, adjusting it to the thermal conditions of the path when it’s being printed, showing where the failures might occur.
“Here, we do it layer by layer, and then you can really see the scanning patterns, how the temperature evolves and the kind of results you can get.” This ability bleeds into another area of Hexagon’s expertise: quality assurance.
“Sometimes you don’t have all the freedom you want,” adds Perennou. “So at least you know where there is a risk of defects. You know where you want to scan your part, so you can save time in the quality inspection process, by not having to scan a complete part.”
With the ability to inspect CT Scans of parts in Hexagon VG Studio Max, users can complete the loop to verify their simulation data with that of the end part – feeding any further tweaks back into the process.
By taking away the guesswork and diving deep into the details before a part has even been sent to a 3D printer, Hexagon hopes that this de-risking of the process will allow more ambitious projects to see the light of day.
In industries such as aerospace, having processes defined in such detail early on will mean more pioneering builds like Airbus’ air separator, enabling more qualified and sustainable parts to take off. www.airbus.com | www.hexagon.com
NEW CAMPUS, NEW OPPORTUNITIES
Emilie Eisenberg attended Hexagon Live: Manufacturing Intelligence in Eindhoven, Netherlands, to witness the opening of Hexagon’s new Experience Centre and learn how the company plans to continue successfully collaborating with customers
At the opening of its new Experience Centre at the Brainport Industries Campus in Eindhoven, Hexagon ceded the floor to customers from a wide range of industries.
A number of speakers from Hexagon also highlighted how the company’s recent successes in a number of different sectors have led to the opening of the Experience Centre and means that its collaborations with several major brands will continue to flourish.
Hexagon’s vice president and president of the EMEA region Stephen Chadwick highlighted current trends in manufacturing, including those taking place at new aerospace start-ups. He also stressed the role that additive manufacturing is playing as an essential part of many workflows, especially when it comes to electrification in vehicles.
Traditional barriers between manufacturers are breaking down, he said, with electronics companies manufacturing electric cars, for example. Companies using Hexagon’s digital twin model, he claimed, are able to stay ahead of the curve by shortening the time to market from years down to months.
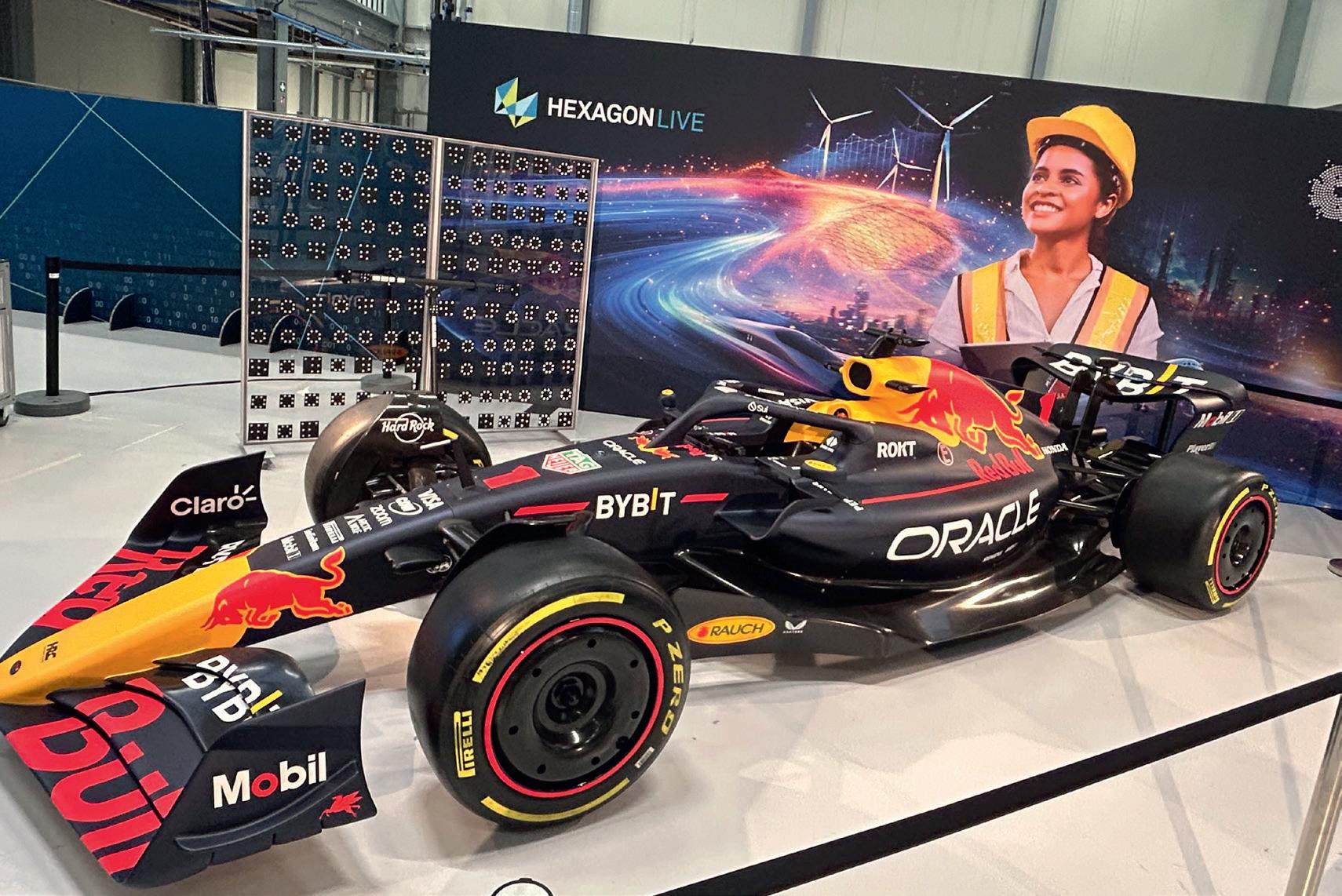
Hexagon’s interpretation of the digital twin concept is not a CAD file or a simulation, but a set of information and data that allow engineers and product designers to digitise and simulate components. The result is that they can better predict how a product’s manufacturing process and lifespan is likely to play out.
Stephen Graham, executive vice president and general manager of Nexus, Hexagon’s open digital reality platform,
spoke on the importance of cloud-based collaboration between engineers. Nexus is currently available for Hexagon customers, and there are plans to expand it as a purchasable add-on. It can link an unlimited number of different software platforms together, including those from third parties, as well as from Hexagon.
Nexus offers real-time visual collaboration between both engineering and
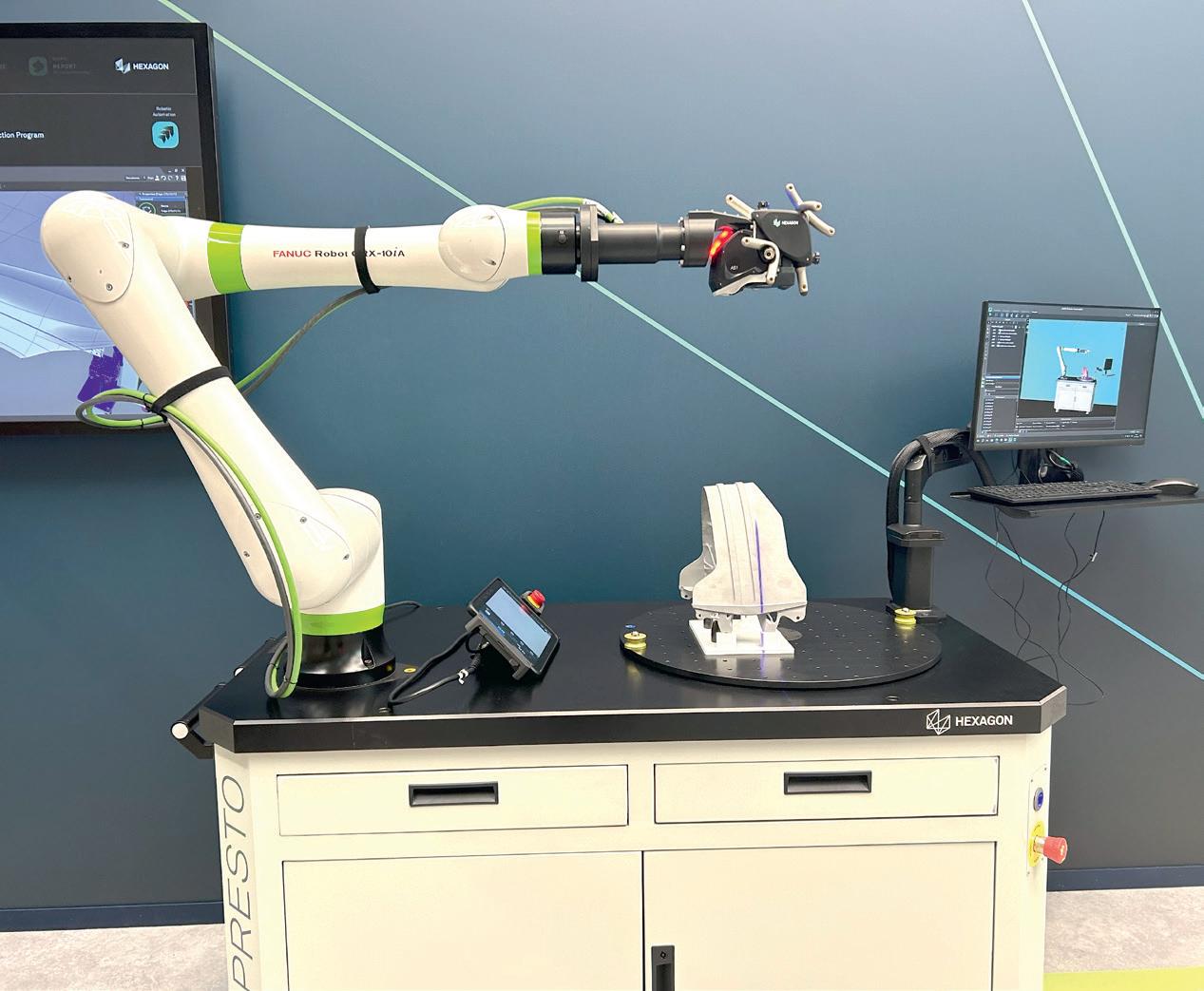
manufacturing, and customer and supplier. In particular, it is a powerful tool for linking the platforms used by different generations of engineers. After all, recently graduated engineers may prefer to use different software platforms from their colleagues who have been working for several decades on another platform.
Introducing artificial intelligence (AI) into Nexus means that it can learn from data derived from multiple databases, making it possible to automate machines on the shop floor, which Graham anticipates will save 75% more time.
Despite the concerns some designers have about AI, Graham is confident that the technology should be viewed as just another update to software, rather than a radical change.
Nexus is a project developed in partnership with Microsoft Azure, and uses Microsoft’s data centres. “It was Microsoft who coined the phrase ‘copilot’ for its AI large language model (LLM), and it is just that – a co-pilot,” said Graham.
RAINFOREST REVOLUTION
Erik Josefsson, president of R-Evolution, demonstrated how Hexagon’s 3D scanners – typically used in the automotive and aerospace industries, among others –can be used for environmental purposes and in the important work of saving the planet.
R-Evolution has scanned 125 million cubic metres of rainforest, including the La Gamba biological corridor in Central America, using Hexagon’s Leica CountryMapper Hybrid Airborne Sensor alongside handheld scanners. These methods of scanning allow R-Evolution to scan the rainforest in layers, down to the soil, and even to scan underwater rainforests.
Morgan Maia, partnerships manager at Oracle Red Bull Racing, discussed how the team’s use of Hexagon’s technology will become more important than ever in 2026, with the release of Red Bull Powertrains. Currently, approximately one million parts are scanned and verified by Hexagon’s technology each year, ensuring that Red Bull’s cars can be verified by FIA standards. Starting in 2026, however, this quantity will rise closer to three million.
The opening of the Experience Centre places Hexagon in the centre of the EMEA area, and connects the company directly with some of its biggest customers in Eindhoven. The event provided insight into the range of companies using Hexagon software and hardware, leaving the impression that Hexagon is driving to succeed in all these markets.
brainportindustriescampus.com
Red Bull Racing plans to launch its own powertrains in 2026 with help from Hexagon
Hexagon’s data capture technology is used across a wide range of industries
5 THEMES FROM
» The world’s foremost 3D printing event, held in Frankfurt, Germany in November 2024, was as busy as ever, despite market uncertainty and a wave of mergers and acquisitions. Stephen Holmes reports on his key takeaways from the event
1FOCUS ON SUSTAINABILITY
Since its earliest days, proponents of 3D printing have frequently hailed it as more sustainable than subtractive methods – but companies in this market still feel they have more work to do in promoting it as a green manufacturing technology.
At almost every stand on the Formnext exhibition floor, suppliers were showcasing their latest sustainability enhancements, from new materials to new ways to reuse previously processed powders.
EOS, for example, introduced its HighReuse materials line, including ALM PA 950 HD and PA 2220, which boast recycle rates of up to 80% and 70%, respectively.
Stratasys went one step further with a new SAF ReLife software upgrade for its H series machines. This works alongside the company’s thermal controls for its SAF (Selective Absorption Fusion) process and enables Stratasys H350 machines to use waste PA12 powder which might otherwise be discarded, from any 3D printing process, including SLS and MJF.
Even more niche materials have seen improvements. Flame retardant PA12FR from Evonik, for example, is now capable of 50% reusability with HP Multi-Jet Fusion 3D printers. The polymer is also cost-effective, offering an alternative to injection moulding parts like electronics housings and battery holders.
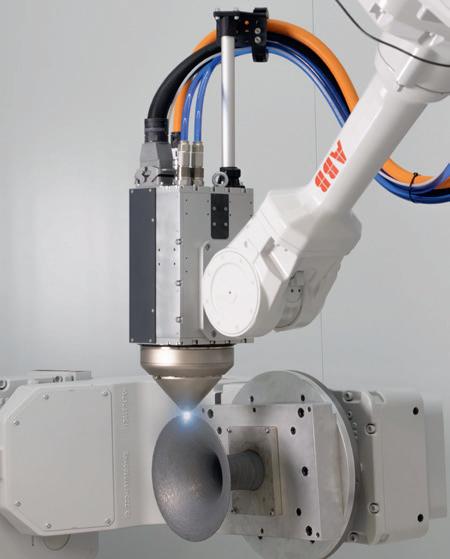
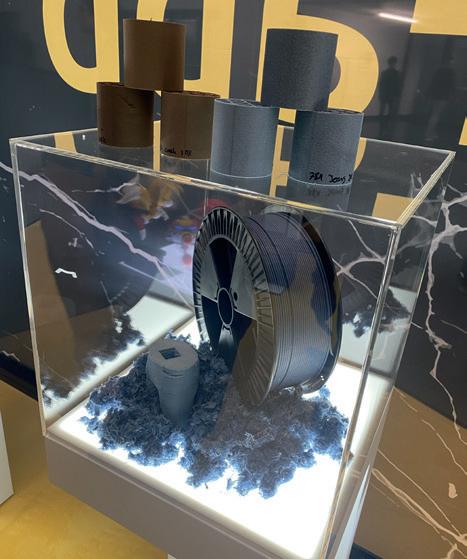
2GETTING THE SPARK BACK
With the dust starting to settle from a flurry of mergers and acquisitions – some that happened, some that very publicly did not – big names in the industry are getting back to the important business of adding more innovative technology to their platforms.
The large Stratasys stand, for example, was full of upgraded tools and materials, from a new filament drying cabinet for longer FDM prints on its Fortus F900 machine, to over 30 new materials for the Origin P3 resin platform.
● 1 (Left) Meltio’s blue laser technology consumes 30% less power, while ColorFabb (Right) is developing materials that use waste products, such as scraps from the denim industry
● 2 3D Systems’ new PSLA 270 is a highspeed, projectorbased SLA 3D printer
● 3 Ultimaker’s Factor 4 is intended for use on the factory floor rather than the design studio
● 4 VoxelDance’s tech shows temperature build-up, but the company felt the heat at Formnext from customs officers
● 5 Packaging expert Baralan worked with Stratasys to develop a process for 3D printing in full colour on glass containers




Most notable were the materials from ColorFabb, a company already known for its wide range of colour FDM fi laments, but also for using waste products in its materials, such as bamboo and cork.
3D Systems, meanwhile, unveiled the PSLA 270, a highspeed, projector-based SLA 3D printer, which drew a great deal of interest from the crowd and is supported by the now mature Factor 4 materials portfolio.
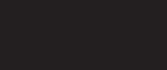
The Dutch brand fi nds use in industrial waste and fully

The Dutch brand fi nds use in industrial waste and off cuts, and this year showcased fi laments made from denim jean fi bres and used polystyrene packaging, as well as from a fully biodegradable material. Given the wide range of choices it off ers, ColorFabb is a name to note by anyone with a professional interest in ESG (environmental, social and governance) issues or CMF (colour, material, fi nish) matters.
Even power-hungry elements like lasers are evolving 4L quality represented by the Formlabs brand.


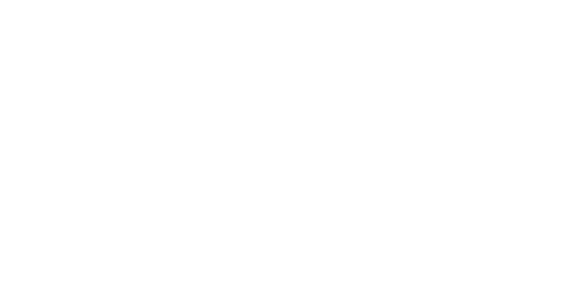

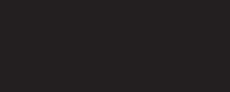
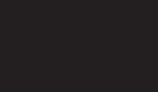
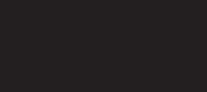
There was also a scrum around the Formlabs stand, with attendees keen to see the Form 4 and Form 4L printers. While there were plenty of other lower cost desktop SLA printers on show at Formnext, it was clear that professional users really value the design and build
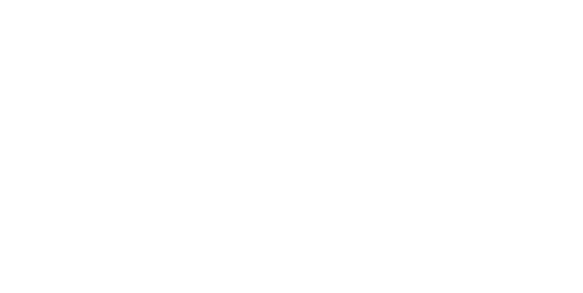
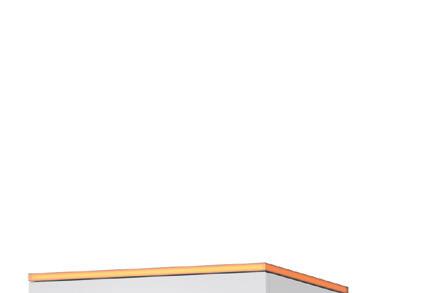
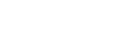
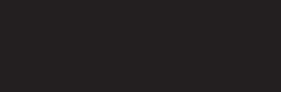
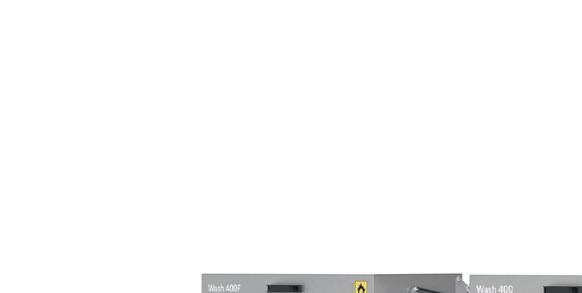


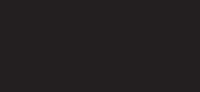
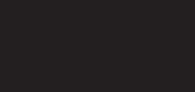
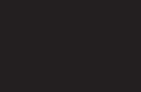
Even power-hungry elements like lasers are evolving in an environmental direction, with bright sparks like Meltio adding new blue laser technologies that consume 30% less power, while also reducing the weight of the robot arms and gantries on which lasers are mounted. Smaller, lower power units are the way forward, it seems.

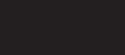
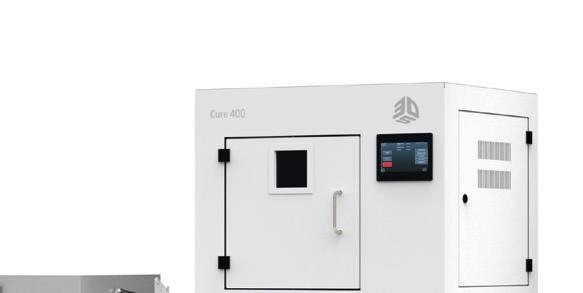


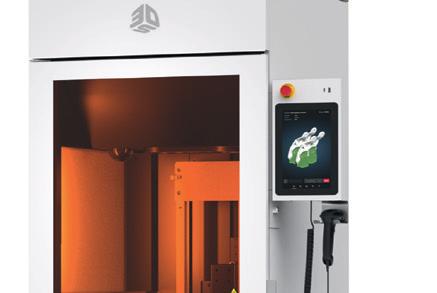
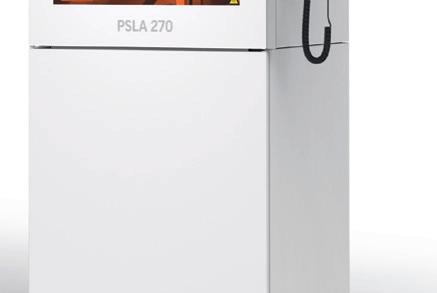
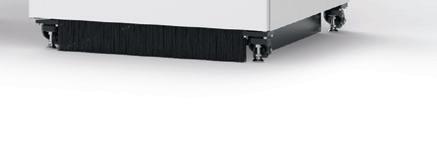
FROM FORMNEXT
3HAS DESKTOP FDM PEAKED?
In a swamped market characterised by both a headlong rush to offer lower prices and an uptick in performance and output quality from brands that include (but are by no means limited to)
Bamboo Labs and Prusa, desktop FDM machine development appears to be slowing.
Brands such as UltiMaker - which combines the work of two former pioneers of small-format FDM - may continue to offer high-end desktop machines, but its sights seem to be set on more industrial customers with its Factor series. The Factor 4 offers all the bells and whistles you’d expect from a machine in this industrial category – something it has in common with many of the other medium-sized FDM 3D printers we saw at Formnext, which are targeted more at factor floors than design studio workbenches. Tellingly, there were no new desktop FDM launches at this year’s show, at least not from the major western brands, which suggests that customer interest in this sector may have peaked.
4SLICKER SOFTWARE
Formnext 2024 was a great showcase for a healthy number of software options for additive manufacturing, designed to help users handle design, process control and simulation, among other tasks. There were demos from newer brands like Synera, which builds software for automating workflows and for connecting diverse tools, and Cognitive Design Systems, which focuses on generative design and automated build process screening.
High levels of interest in software demonstrated a shift in the Formnext attendee demographic, from those just there to kick the tyres of physical machines to those looking to gain real competitive advantage from additive manufacturing. The printer manufacturers were also keen to tout their partnerships with innovative software providers, with names like nTop, Hexagon and Altair prominently displayed on their stands.

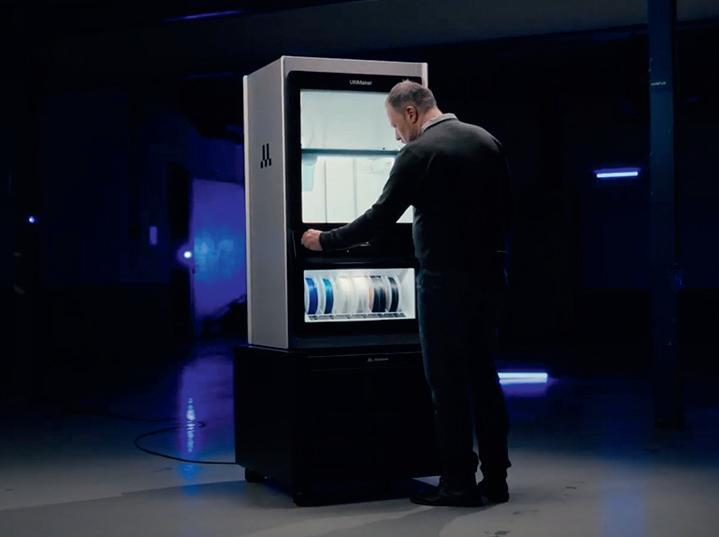
5FRESH ATTEMPTS TO DELIVER ON EARLIER PROMISES
Brands at Formnext showed a renewed determination to deliver on elements such as colour parts and 3D printed electronics, helping additive shift from prototyping to real-world parts. Stratasys showed off how it has been working alongside Italian packaging expert Baralan, so that its PolyJet technology can be used to create forms more commonly associated with traditional manufacturing methods - such as glass perfume bottles - and bring new textures and full-colour designs into play. Enabled by a specially developed primer and protective coating, Baralan sees this technology as an exciting way to add bespoke details to luxury products and support short production runs.
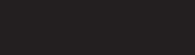
- such as glass perfume bottles - and bring


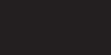

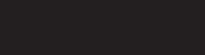
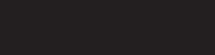

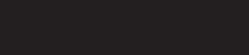

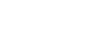
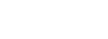
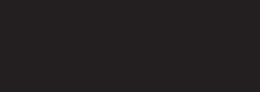


A Stratasys rival in the colour 3D printing stakes, Mimaki, drew crowds with the lifelike realism of its prototyping and display models and its dedication to achieving industrystandard, repeatable colours in the additive space.
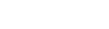
demonstrations to a halt. It remains to be seen how this skirmish
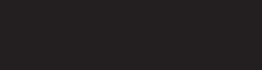
There was drama surrounding China-based software company VoxelDance, which was at Formnext to show off an all-in-one pipeline that incorporates implicit modelling, build preparation and simulation. Accusations of IP infringements, however, brought German customs investigators to the company’s stand and product demonstrations to a halt. It remains to be seen how this skirmish will play out and what wider impact any legal dispute will have.
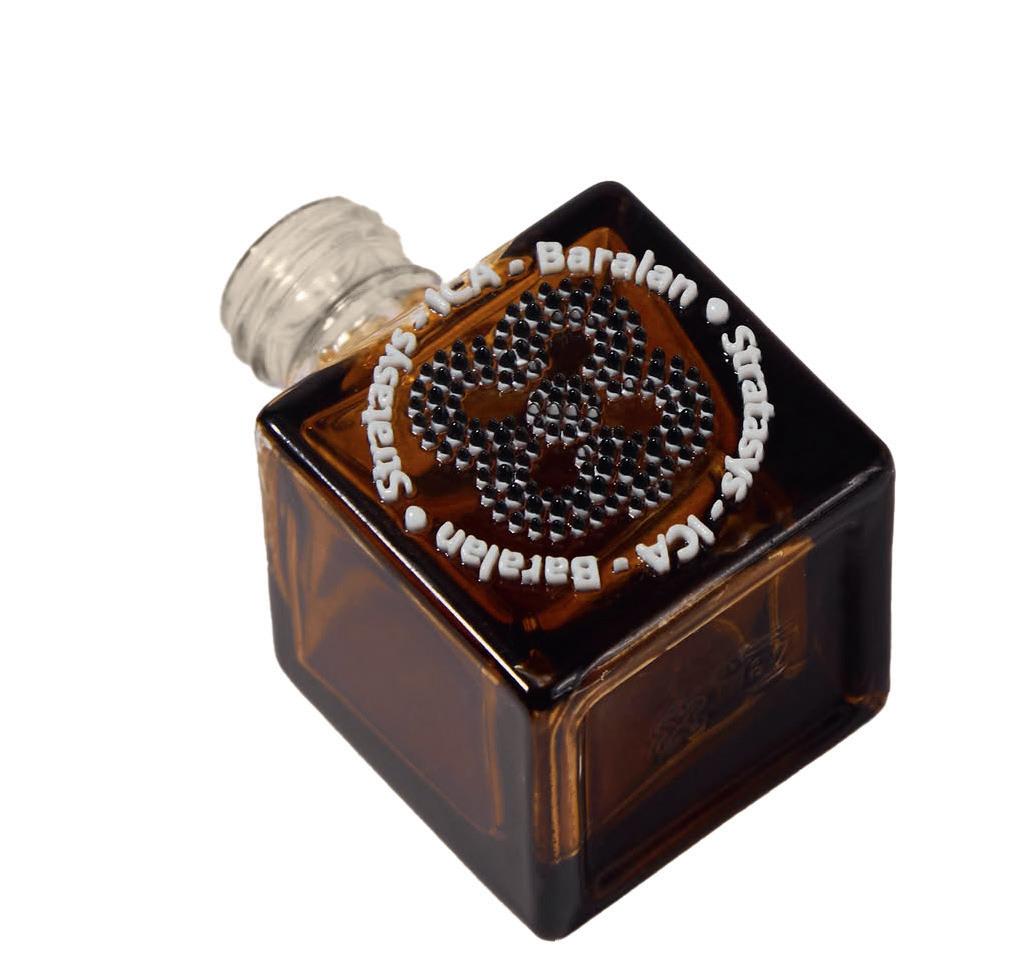


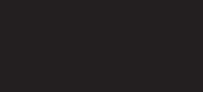
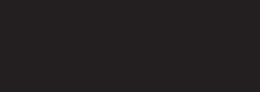
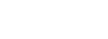

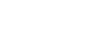
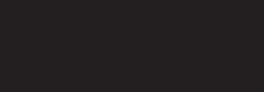

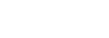



Names familiar from the CAD world were there, too, including Catia, Onshape, Siemens and Autodesk, using Formnext to explain how additive workfl ows are now fi rmly entrenched in their software packages as they increasingly aim to whittle away at the infl uence of specialist software fi rms such as Materialise, with its Materialise Magics product.
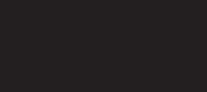



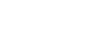
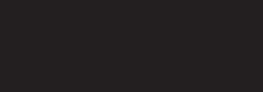

There was greater software support, too, for the printer makers. Executives from Tech Soft 3D were eager to

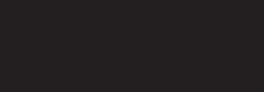

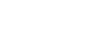
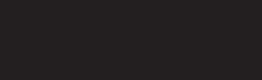

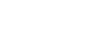
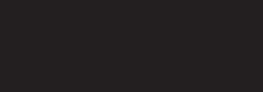
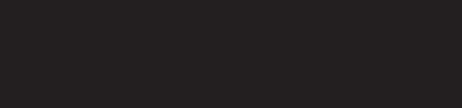
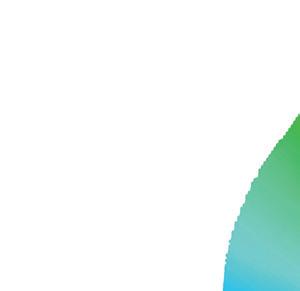
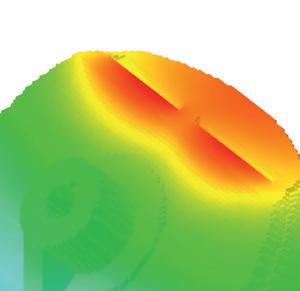


A big highlight of the event for many, however, was to be found at the Nano Dimension stand. Having hit the headlines over the past year for its acquisitions of Markforged and Desktop Metal (among others), Nano Dimension execs impressed attendees with the company’s Dragonfly 3D printed electronics and micro 3D printing capabilities. In particular, Dragonfly’s use of conductive inkjet 3D printing is capable not only of producing one-off PCB prototypes, but also an array of end-use parts. Fully working 3D-printed motors, embedded electronic drone chassis and compact aerials made the Nano Dimension stand look like a scene from a James Bond movie set in Q’s laboratories.
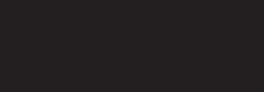


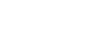

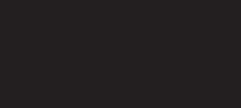
There was greater software support, too, for the printer makers. Executives from Tech Soft 3D were eager to highlight that their product is a backbone to many tools and services found in additive workflows, while those from Australia-based Visionware 3D were promoting the company’s turnkey services and support aimed at building everything from custom 3D printing engines to control systems for vendors.

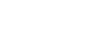


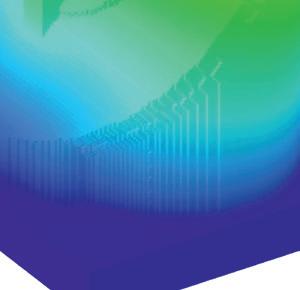
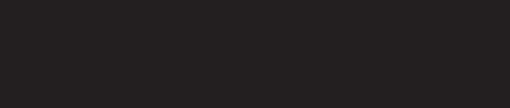
working 3D-printed motors, embedded electronic drone
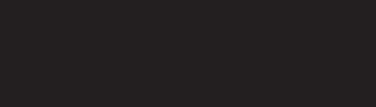
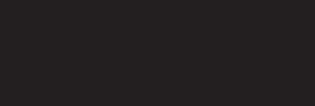

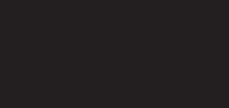
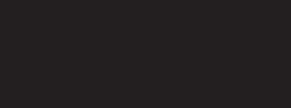
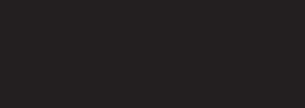
While all this activity prompts many to wonder about Nano Dimension’s long-term intentions, it’s clear that a world unshackled from 3D PCBs and wiring looms is one that many Formnext attendees would welcome.

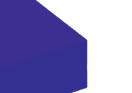

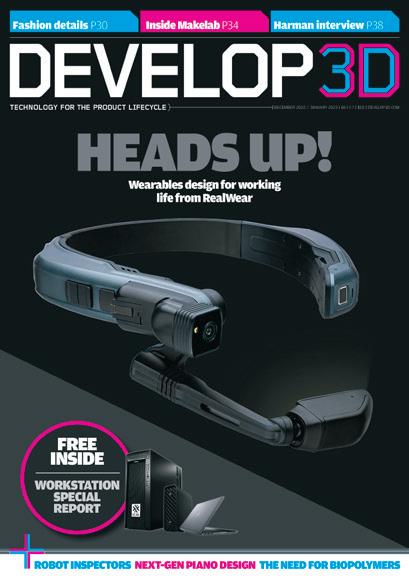
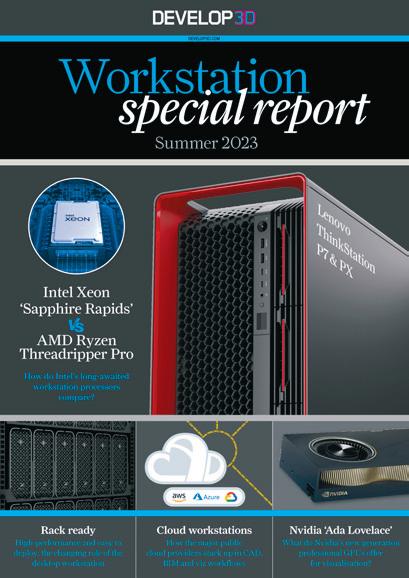
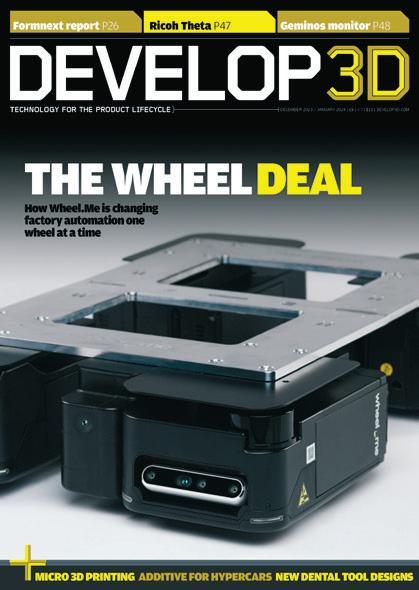

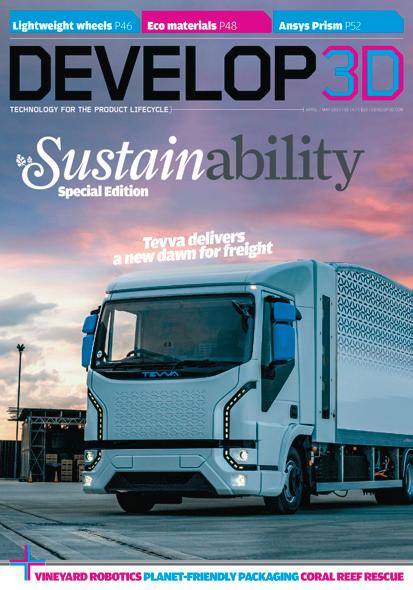
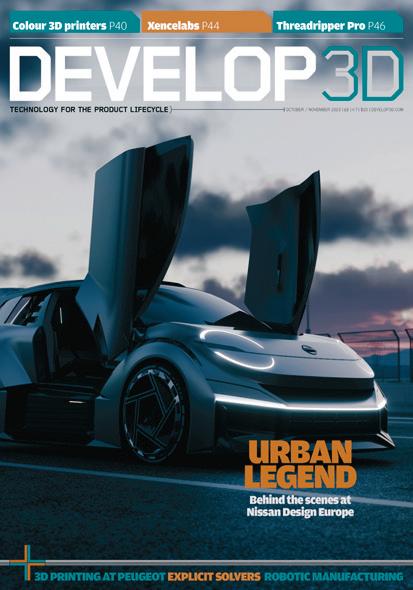

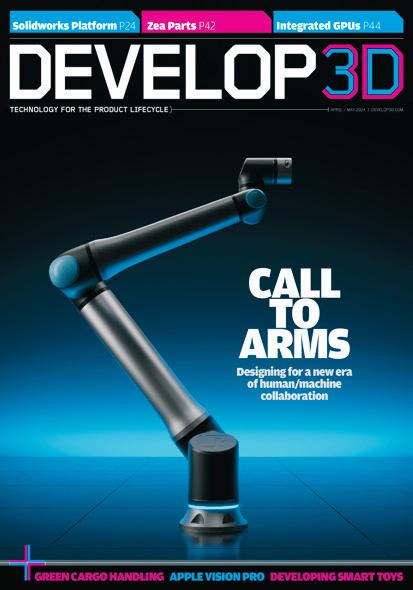
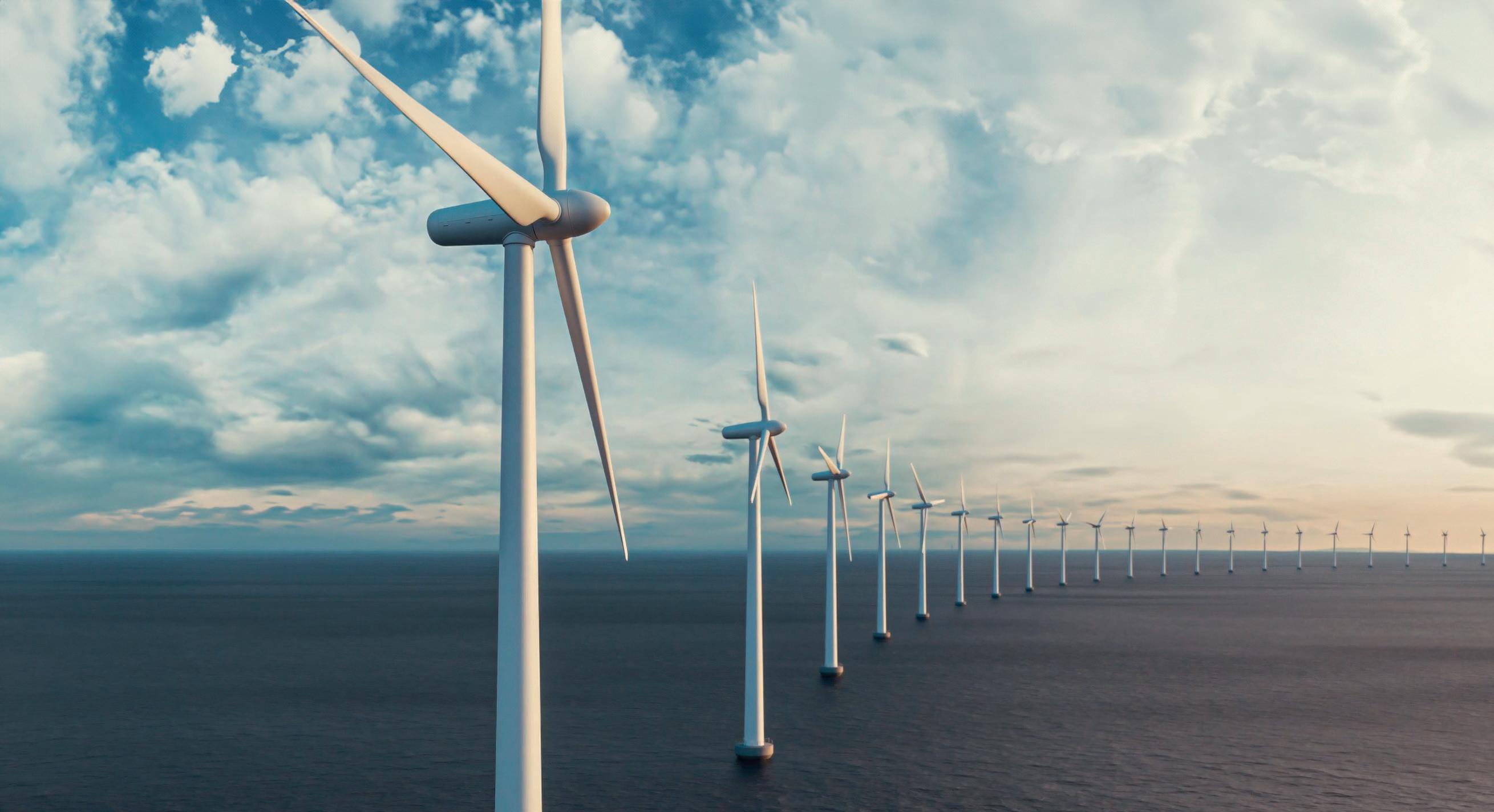
WIND SPEED CHALLENGE
» Using Stratasys SLA technology, Gulf Wind Technology designs and tests its wind turbine rotors in a fraction of the time it used to take, as Emilie Eisenberg reports
Gulf Wind Technology has been manufacturing wind turbine rotors since 2021, with a team of specialised engineers improving wind turbine design across North America from its factory in Mississippi.
As America’s only independent wind turbine rotor technology solution provider, Gulf Wind Technology prides itself on its state-of-the-art equipment and facilities.
A recently announced partnership with 3D printing company Stratasys has seen the introduction of additive manufacturing to its arsenal, in order to test and improve rotor models.
In particular, the company is implementing Stratasys Neo stereolithography (SLA) technology, with the goal of reducing the design and fabrication cycle for wind tunnel models, from between 30 to 40 days to just three to four days.
Introducing additive manufacturing technology to the workflow also allows for the creation of specialised features such as pressure taps for real-time airflow data, which were previously difficult or impossible to execute using conventional manufacturing methods.
TEST MODELS
With additive manufacturing, engineers can design internal structures and pressure taps directly into test models. These models are produced using the Somos Perform Reflect material, which offers high strength, stiffness and temperature resistance, all of which are important in wind tunnel testing. They can then be used for testing aerofoil shapes and rotor designs more rapidly, resulting in the maximisation of wind energy efficiency.
The team at Gulf Wind Technology was inspired by the use of additive manufacturing in Formula 1 racing, where teams print precise parts in order to save time, which they can then spend making countless adjustments to the cars before they are shipped to each race.
“Our work with Gulf Wind Technology demonstrates how manufacturers are adopting additive manufacturing where it makes the most sense for their business,” says Rich Garrity, chief business unit officer at Stratasys.
“Gulf Wind Technology can rapidly prototype and test complex designs, greatly improving its efficiency and ability to innovate. This is a perfect example of how 3D printing is expanding its place on the manufacturing floor alongside traditional methods.”
www.gulfwindtechnology.com
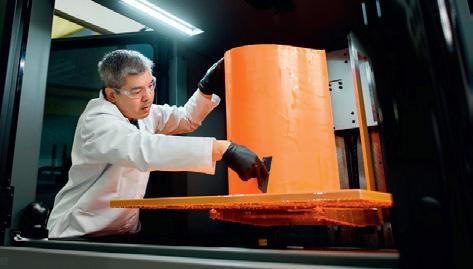
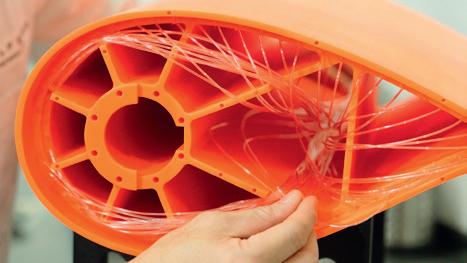
(Above) Wind turbines working hard to generate energy in the Gulf of Mexico (Below) Test models are vital to achieving maximum energy efficiency in turbines
(Bottom) With 3D printing, engineers can build internal structures directly into test models
DEPENDABLE DELIVERY
» In order to coordinate the development of commercial electric vehicles across three US sites, Workhorse is relying on technology from the Siemens Xcelerator portfolio
Built to carry last-mile deliveries along North American roads, the Workhorse W56 not only offers 210 kWh battery capacity and a range of up to 150 miles, but also 1,000 cubic feet of cargo space.
With a robust chassis that can be stripped back, the company’s flagship model is sufficiently flexible to support custom body builds, enabling the W56 to be configured as a delivery van, a utility truck or some other kind of specialised vehicle.
That has great appeal for customers looking to transition to zero-emission commercial vehicles – among them, global logistics giant FedEx. In September 2024, FedEx placed an order for 15 Workhorse W56 models. More recently, Workhorse announced that it had secured orders for seven W56 models from three parcel delivery independent service providers in the 30 days following its participation at the FedEx Forward Service Provider Summit.
Each truck, according to the company, is made with durable EV components and intuitive technical features, with a view to making “every job smarter, safer and more productive than before.”
CLOSE COORDINATION
Delivering on the promise of dependable flexibility involves significant complexity for design, engineering and supply chain teams at Workhorse. In response, they have standardised on the Siemens Xcelerator portfolio, in a bid to streamline their cross-functional activities and, along the way, boost production rates while reducing costs.
And, as Workhorse CIO Jeff Mowry points out, the combination of NX and Teamcenter X from that portfolio is able to support close collaboration between colleagues from the company’s engineering and technical design centre in Wixom, Michigan, its production hub in Union City, Indiana, and its engineering teams in Sharonville, Ohio.
“Previously, our multi-CAD environment was costly and required extra resources,” he says. “With Siemens, we’ve eliminated these inefficiencies and can focus on building complex electric trucks more effectively.”
By adding Teamcenter X Software-as-a-Service (SaaS), and working in collaboration with Siemens partner Prolim, Workhorse was able to get full PLM up and

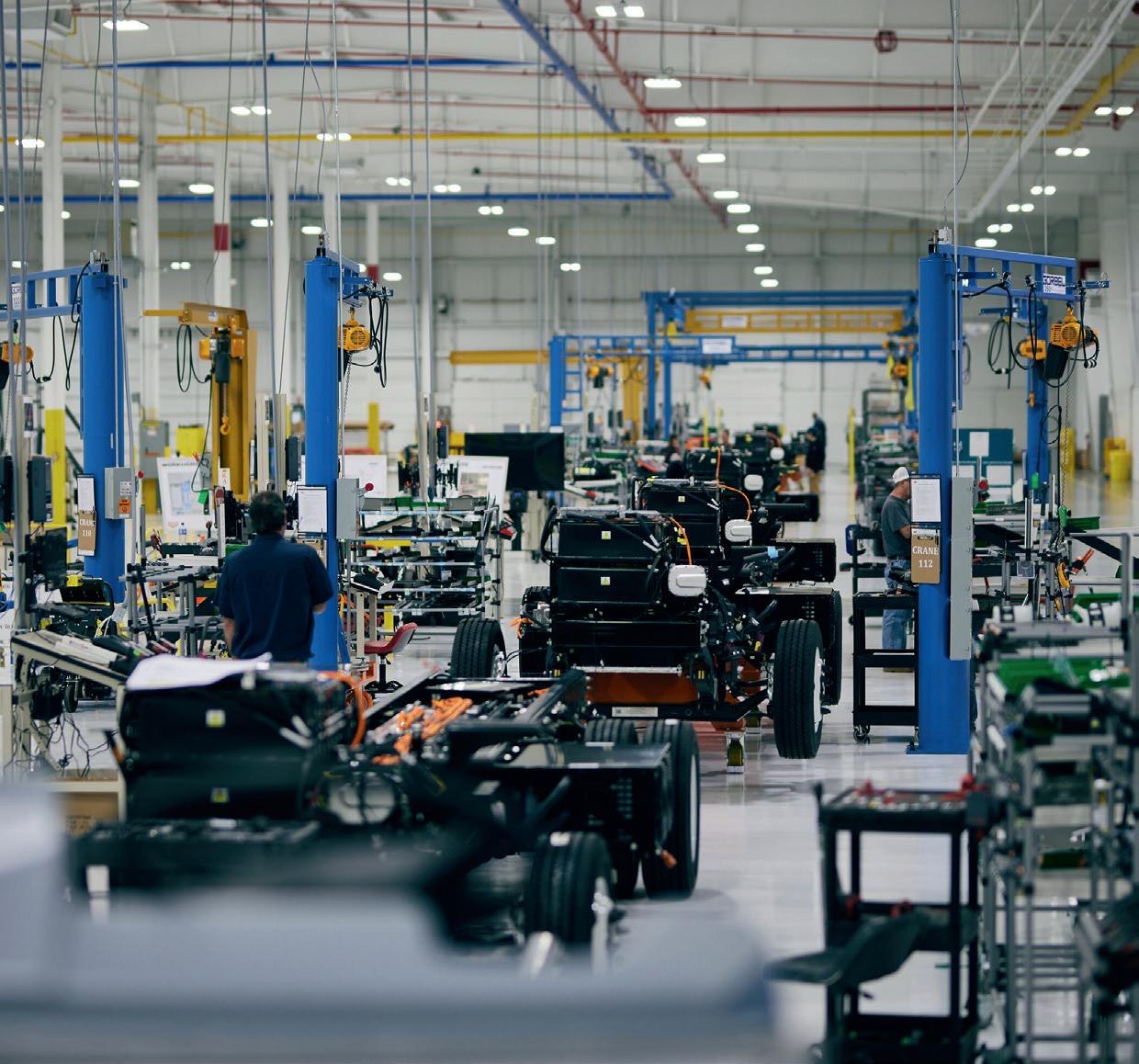
running for its production processes, using dramatically fewer IT resources than required by traditional onpremises legacy solutions.
“Using Siemens’ tools, we are able to effectively manage our intricate bill of materials and engineering change notices, which is key given the dynamic nature of electric vehicle production,” Mowry added. “This strategic move has not only lowered our operational costs, but also strengthened our ability to protect intellectual property and ensure cybersecurity.”
Looking ahead, employees at Workhorse are already exploring ways to expand the company’s use of Siemens’ software, with plans that include the implementation of a configurator module to handle more complex product variations and a supply chain module to improve supplier collaboration.
www.workhorse.com
BEST FOOT FORWARD
» Asics is racing head with customisable designs for its best-selling trainers, using Dassault Systèmes Catia to create comfortable, long-lasting products, as Emilie Eisenberg reports
Like many other apparel companies, sportswear giant Asics is looking to stand out from the rest of the field when it comes to creating personalised, environmentally friendly footwear. Addressing individual needs in such a vast market is no easy feat. To conquer the challenge, Asics has partnered with Dassault Systèmes, opening a personalisation studio and smartphone app that combine technologies in order to enable individual customers to tailor individual products to their precise needs and preferences.
In particular, Asics uses Dassault Systèmes’ 3D CAD software Catia to create custom insoles for trainers, deploying virtual twins to ensure that each insole provides the perfect match for a customer’s foot.
“No two people have the same foot shape,” points out Genki Hatano, lead researcher in the Green Manufacturing Team at Asics. “Now, to provide all our customers with products that deliver a new level of comfort and satisfaction for both mind and body, we are considering more customisation options, such as foot beds that support the underside of the foot, and customisable shoe components.”
LEAPS AND BOUNDS
First, an app is used to scan and capture the foot shape. The data is then imported into the Catia 3DExperience platform, where the scan is converted into a neutral shape using Visual Scripting, Catia’s no-code algorithmic approach to parametric design. This step ensures that an insole can be designed with as much flexibility as possible.
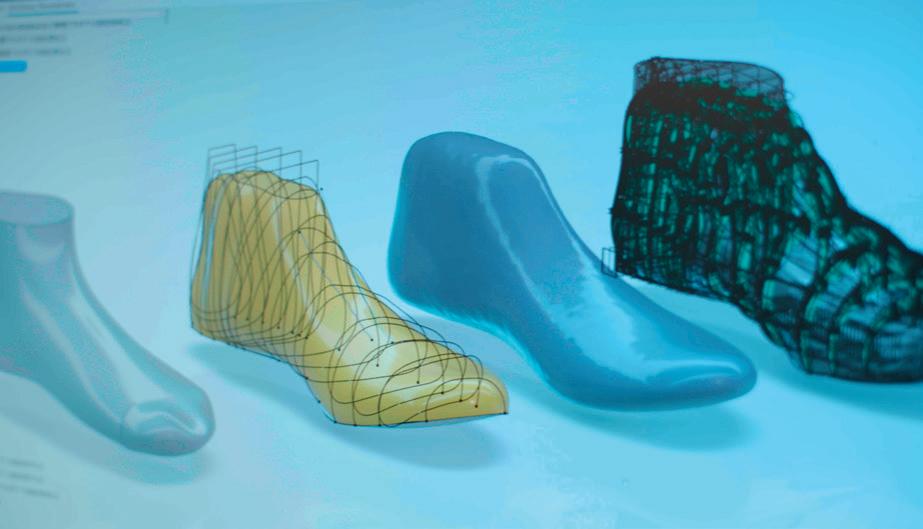
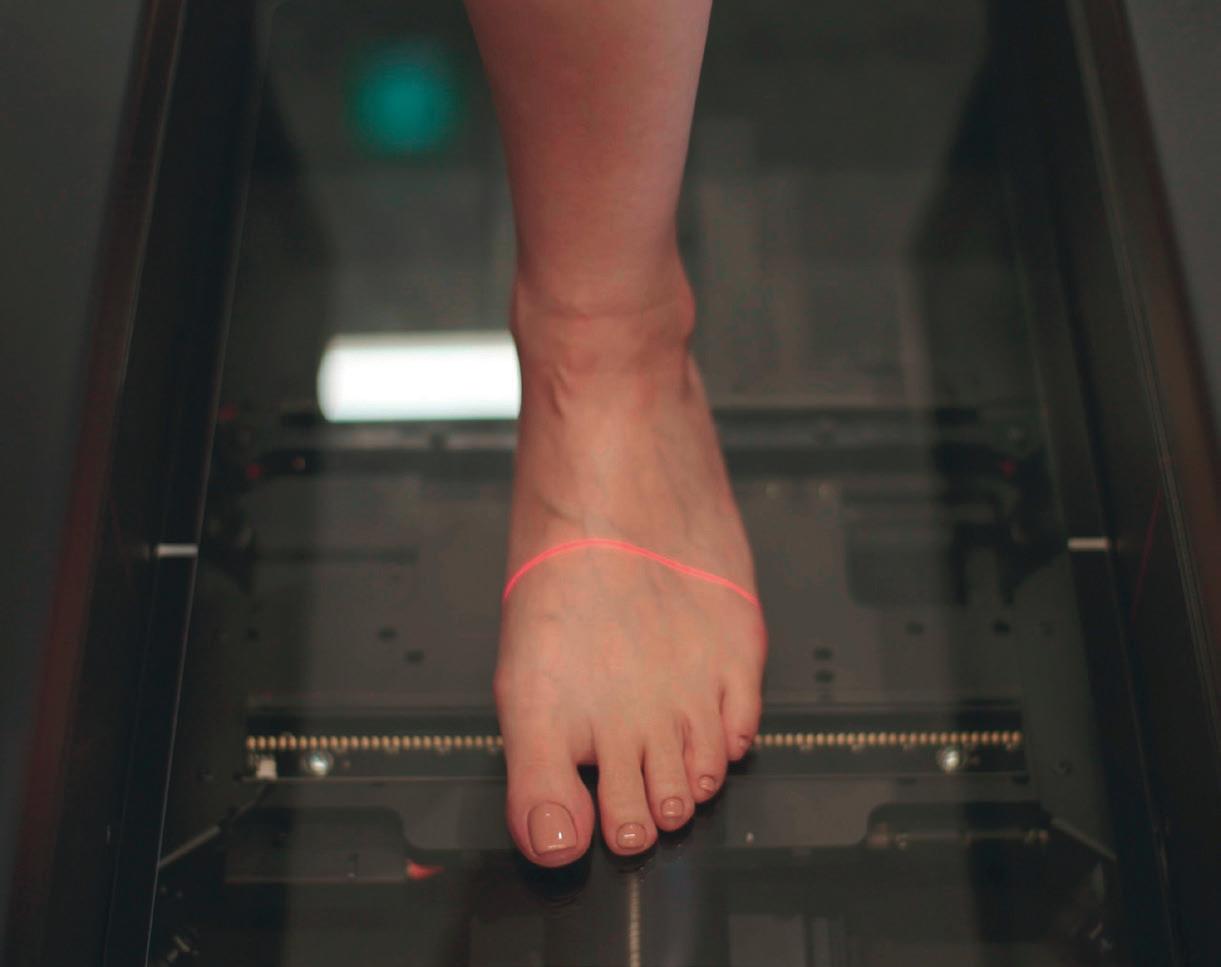
The infill for the insole design is created using Catia Lattice Design, giving a designer control over the thickness of the lattice structure, down to minute details. Multiple contributors are able to collaborate and share models of personalised lattices, using Catia’s Visual Scripting on 3DExperience.
The process is monitored through Delmia Apriso, Dassault Systèmes’ manufacturing operations management (MOM) software. To keep design as sustainable as possible, Asics automates lifecycle assessment studies, using Catia Eco Designer at the earliest possible stage. Eco Designer creates a live representation of the material composition of a virtual twin and calculates the environmental footprint for each product.
“Personalisation and sustainability are a very important combination,” says Hatano.
Made-to-order shoes reduce waste and water consumption, he points out, and a lifecycle assessment before the manufacturing process begins results in shoes that last longer.
Following the success of its personalised insoles, Asics plans to expand this technology to develop entire shoes customised to individual customers’ feet, and is collecting data and feedback from users in order to develop its production line further.
The company also plans to continue its collaboration with Dassault Systèmes, incorporating virtual twin technology into future customisation projects and helping it to stay one step ahead of its competitors. www.asics.com
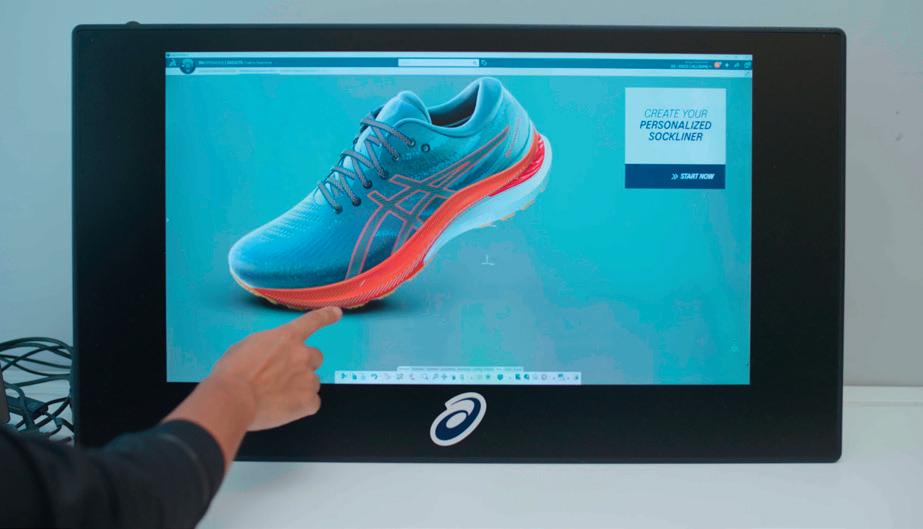
‘‘ No two people have the same foot shape. To provide comfort and satisfaction, we are considering more custom options ’’
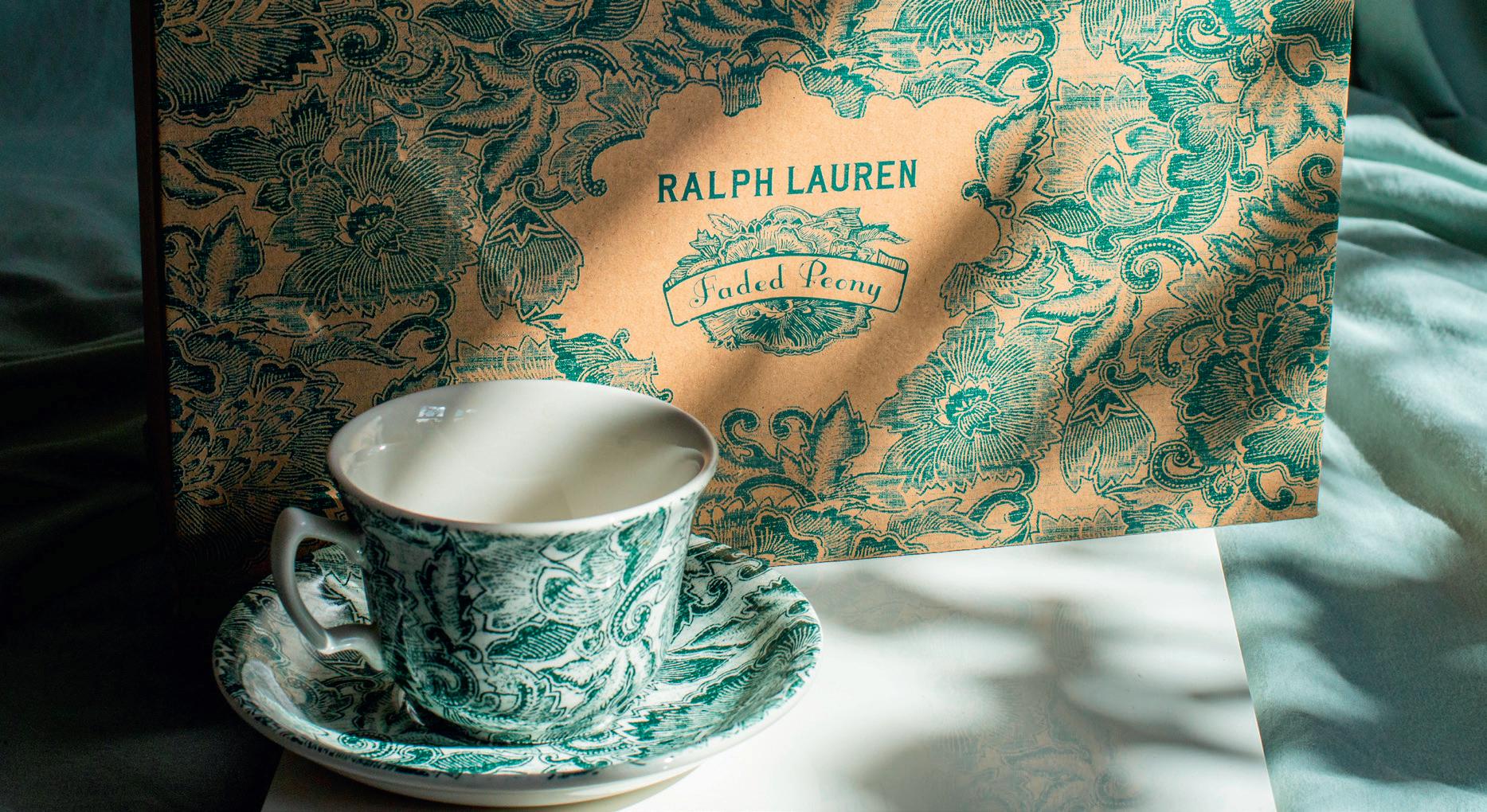
BOXING CLEVER
» Emilie Eisenberg learns how British packaging designer Think Tank is using 3D design to elevate its work for clients
Thinking of gifting some perfume this Christmas? Or maybe you’ll be handed a free T-shirt at some event, or splash out on a scarf that shows your support for a particular football team? If so, Think Tank might well be involved somewhere along the line.
Since 1999, the company has produced high-end packaging for brands that include Ralph Lauren, Ted Baker, Formula One, Coca-Cola and Manchester City. In 2024, Think Tank marked its 25th anniversary and the team there has much to celebrate.
“At the heart of our company’s ethos is our name,” says head of creative production Nick Seston. This, he explains, brings together ‘think’, symbolising the realm of ideas and creativity, and ‘tank’, representing an engine that brings ideas to life, “through coordination with suppliers and streamlined logistics.”
Each project is designed alongside the relevant client, in a process that includes researching existing designs, new materials and current trends. The goal: to develop packaging that will intrigue and entice customers.
ALL WRAPPED UP
Designs built in Rhino 3D are subsequently moved into 3D renders and videos using Keyshot, in order to demonstrate to the client how the final product will look.
By opting for rendering instead of prototyping, designs can be edited and changed as many times as a client likes, tweaking small features until they are 100% satisfied.
A final prototype is then made, using the client’s choice of materials. This might range from card and paper to organic textiles. What’s important is that the prototype accurately demonstrates what the final product will look and feel like. Before manufacturing begins, further edits and new prototypes may be made.
Due to the company’s commitment to sustainable packaging, Think Tank encourages clients to opt for recycled or biodegradable materials where possible, Seston says. “Over the past few years, we have seen a noticeable shift towards paper, card and organic textures, as companies become more concerned about their impact
on the planet. We have also made a pronounced effort to move away from designs that require large moulds, as this process produces far more waste than other methods.”
He continues: “We always advise recycled content options and urge clients to avoid using plastics in laminations, as well as other unsustainable processes, such as foam fitments. To ensure manufacturing is as sustainable as possible, Think Tank only uses accredited factories with which it has long-standing relationships.”
SMART SUPPLY CHAINS
Manufacturing a wide range of products, Think Tank works directly with suppliers in order to maintain quality control. A core supply chain produces card, paper, packaging and textiles in various locations, both in the UK and in other locations around the world, depending on client requirements.
“The long-term relationships we have fostered with our suppliers are vital to creating top-quality products and packaging, so this is the best way to ensure we never have to compromise on quality,” says Seston.
The length of a manufacturing process will vary. Initial prototypes can be produced within a week, followed by an open-ended consultation period. Urgent print work can be completed in a few days, and larger orders can be completed in under 12 weeks.
Think Tank is already looking towards the future with the launch of its SMART packaging format, which blends physical packaging with digital content by using digital access codes that can be activated using a smartphone.
“It’s a really exciting moment, as SMART formats will help our clients elevate their packaging design and boost their commercial reach,” Seston explains.
For now, guiding customers to more sustainable solutions is one of Think Tank’s main priorities. The team may not be able to reveal what’s currently in the works – its projects are kept under wraps until they hit the shelves – but it’s more than likely that SMART formats will add some extra excitement to this company’s highly visual packaging solutions. www.thinktankcreative.london
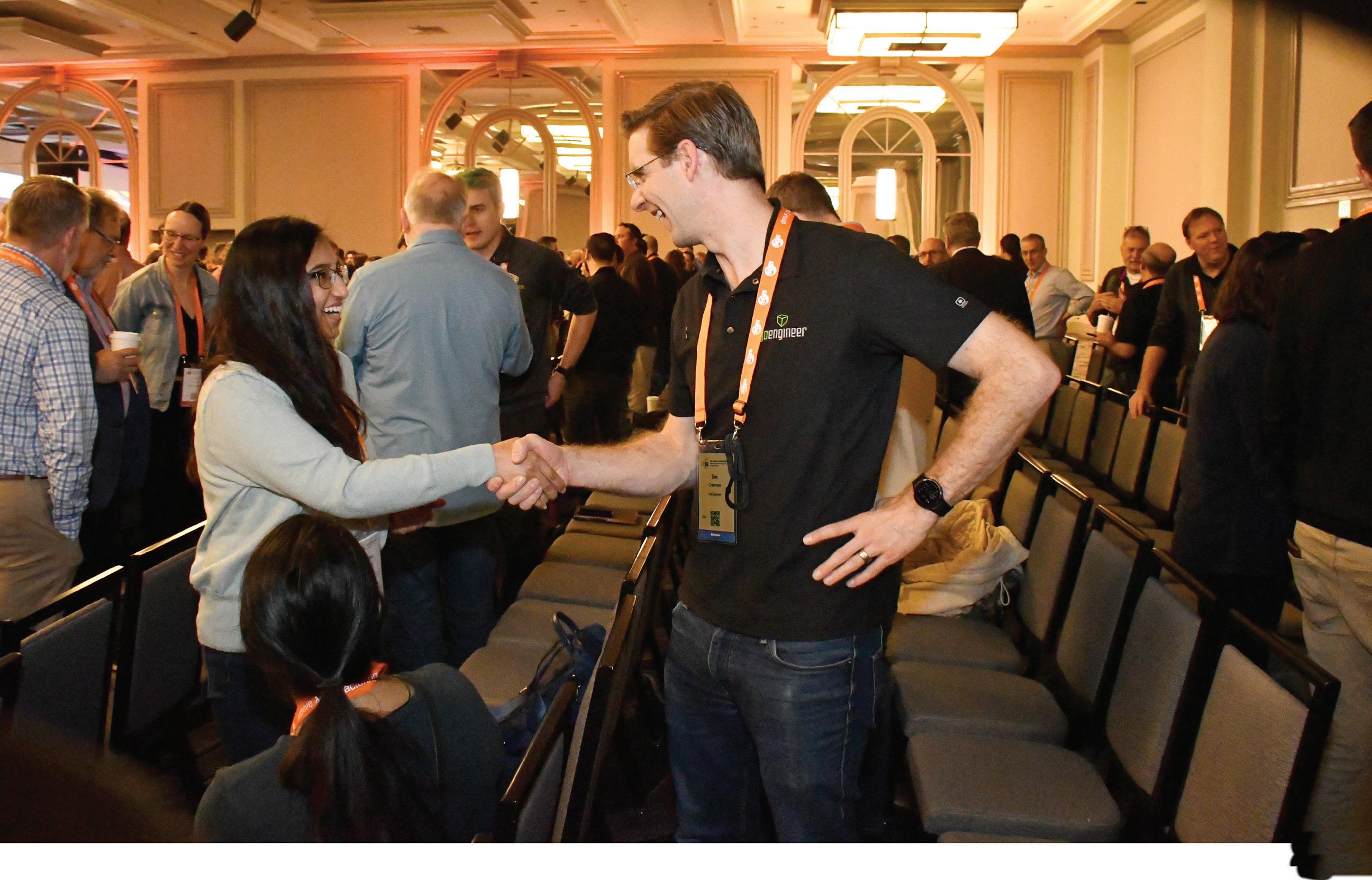
Expertise
Gain practical knowledge through proactive participation and handson experience
n Become more productive through AMUG’s community of problem solvers
n Learn and share expertise, best practices, challenges, and application developments
Network
Impactful networking without any agendas
n Embrace the camaraderie and enjoy effortless networking
n Form meaningful connections through casual conversations
Value
Get the most value of any conference with an ALL-INCLUSIVE program
n 4-day conference
n Hands-on workshops
n Technical competition
n AMUGexpo
n Meals and entertainment throughout

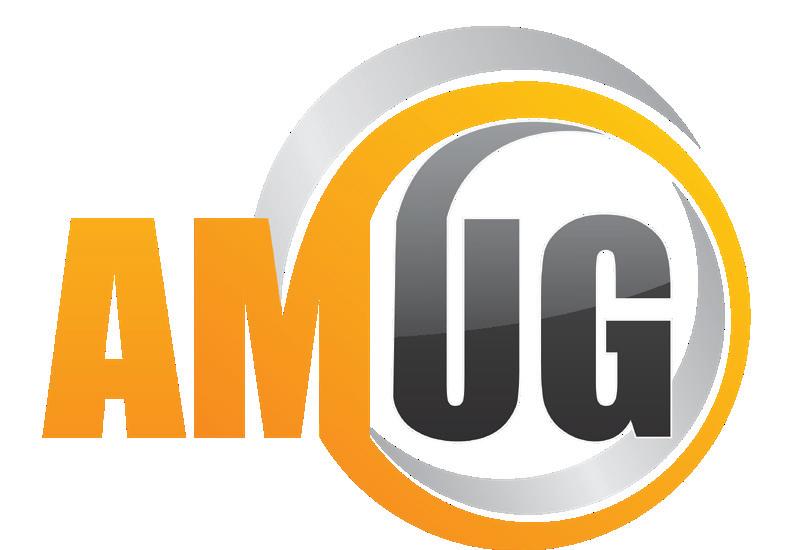

DRAFTSIGHT 2025
» Solidworks once had issues working with DWG files, so it licensed a DWG clone and gave it away for free. Over time, this product evolved into professional CAD tool, DraftSight. Martyn Day looks at the latest release
The defining CAD system of the 1980s was DOS-based AutoCAD and its proprietary DWG file format, which has dominated the market ever since. However, the secrets of the DWG file format are now common knowledge and there are tens of drawing tools which all speak the same interchangeable language of lines, circles, arcs, text and so on.
Several tools are owned by long-standing CAD software companies, including Hexagon (BricsCAD), Gräbert (Ares) and Dassault Systèmes (DraftSight).
DraftSight offers a lot more than basic 2D CAD functionality. It supports LISP APIs, point clouds, drawing compare, and shortcuts. The software comes in Professional, Premium and Network (licence) versions. Premium includes a sheet set manager, PDF import and batch printing, advanced 2D tools with 3D modelling, meshing and 2D parametric constraints. The Network version allows enterprise deployment with simultaneous usage and built in compliance, enabling cost savings.
The latest release – DraftSight 2025 – provides a range of new and updated capabilities that cover all the drawing and output bases, such as PDF export settings, Batch and Print settings and a Lasso Selection. It offers both menu and ribbon bar interfaces simultaneously, and some other highlights, listed below.
Dimensioning: A new auto dimension feature makes complex dimensioning tasks simple with minimal input. In addition to manual dimensioning, DraftSight’s Smart Dimensioning tools figure out the best dimension type based on the entity selected.
Table management: Tabular information can now organise data better, automating formulas, adding
consistent formatting, grips for manipulating tables, and support for breaks and block insertion.
File formats: A new STEP file import feature integrates externally created 3D models into 2D drawings. The IMPORTSTEP command can bring in complex mechanical parts. The new EXPORTDGN command lets users convert DWG drawings to Bentley Systems’ DGN format to aid those working in infrastructure.
Flatten: For those with drawings that have entities spread over the Z depth, the flatten command brings everything down to zero. This enables the easy clean-up of files which may have artifacts in 3D space.
Block management: The new Block Structure Palette helps designers see nested blocks and complex hierarchies more clearly (preview, isolate). The palette also organises design elements better and reduces time spent looking through complex block relationships.
Visual style options: The Visual Style Manager offers multiple viewing choices – wireframe and realistic rendering, conceptual and sketch appearances, X-ray visualisation. Using custom presentation styles, users can select how and which entities appear within a single block. There is also more visual control with a fill visibility for various entities including polylines, solids, traces, hatches and gradients.
CONCLUSION
DraftSight 2025 provides practical workflow improvements with overall better performance on loading, views and stability with big drawings. There are also usable upgrades to file management, block structure control, and dimensioning systems, together with
WHY DOES AUTOCAD STILL COST SO MUCH?
With software budgets being squeezed, many design, engineering and architecture firms are questioning why AutoCAD still costs so much — especially when it’s no longer cutting-edge technology. At time of writing, AutoCAD costs £1,986/year. Meanwhile, BricsCAD Pro (Mac or PC)
is £484/year, DraftSight Professional £249/year, DraftSight Premium (Mac or PC) £499/year, and Gräbert Ares Commander (web, mobile or desktop) £300/year. Of course, there’s also the cut-down version – AutoCAD LT – which costs £486⁄year. But AutoCAD LT has limited API, 3D,
automation and collaboration capabilities.
On a pure like-for-like basis, at today’s prices, it’s possible to get four seats of DWG, equivalent drafting to one full AutoCAD seat. That even goes up to eight to one on yearly subscriptions. Some vendors also offer the design director’s
favourite – network licensing
– where users can share a pool of licences.
Of course, it’s important to point out that users of Autodesk’s Suite/Collection bundles for vertical markets deliver better value, where AutoCAD is one of many commonly used Autodesk
industry tools. However, the cost of these bundles will be going up in the near future and there will an end to the 2-for-1 perpetual to subscription 8-year deal. All of this is giving design and engineering firms plenty of food for thought, as they reevaluate their software estates.
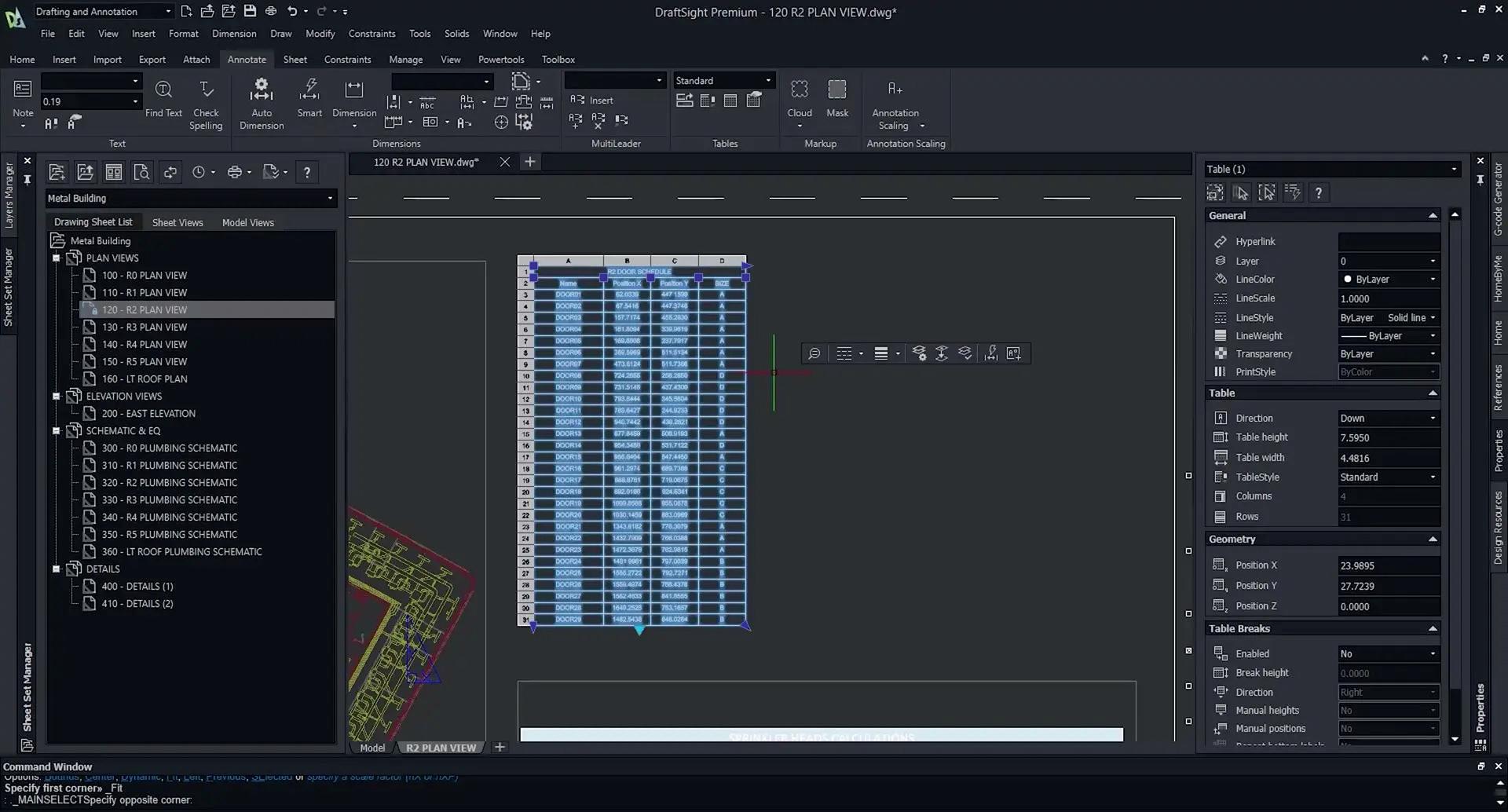
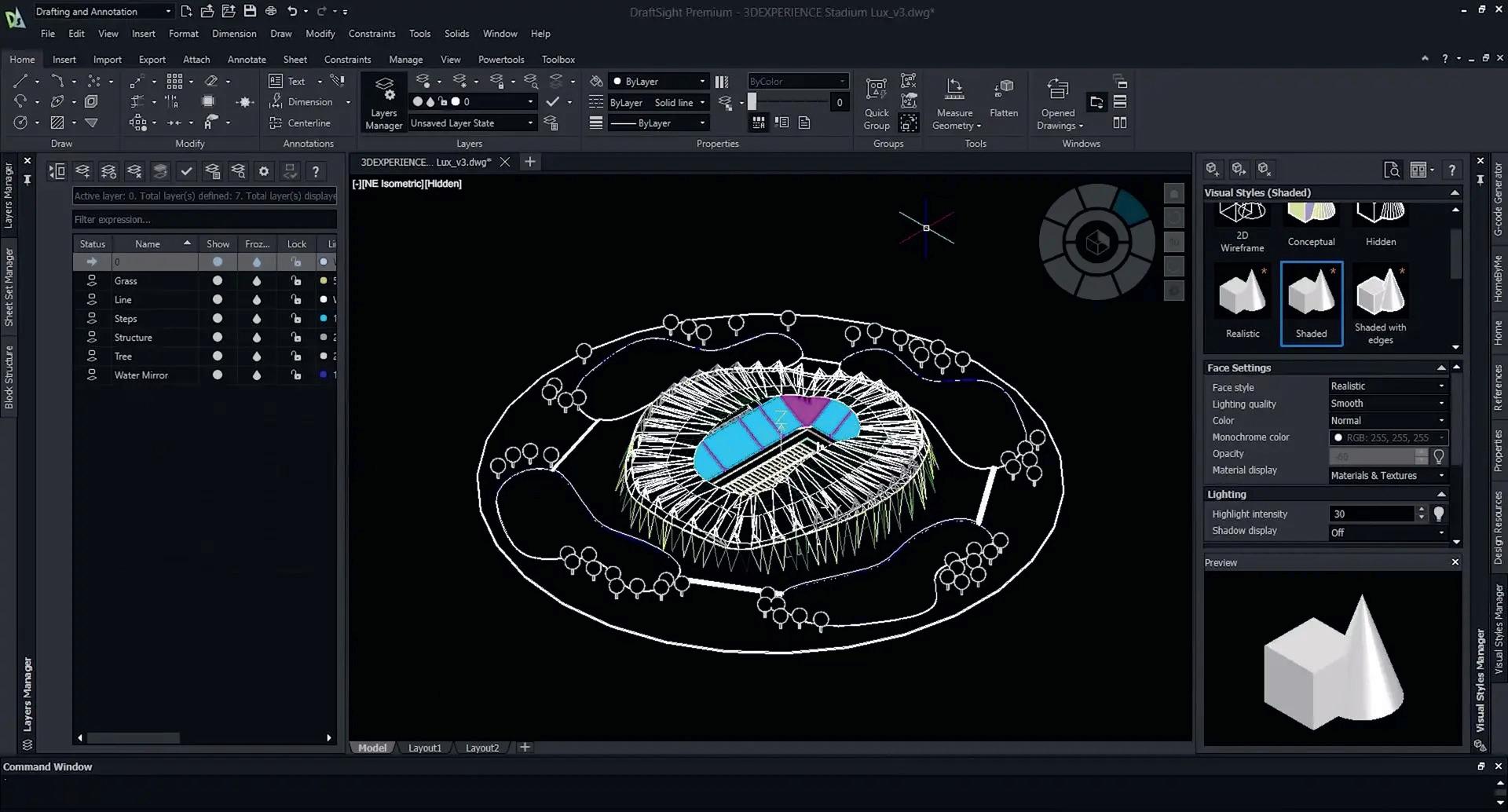
expanded file support with STEP (for MCAD models) and DGN export – useful for users in the architecture, engineering and construction (AEC) sector.
As DS licenses its core technology from Gräbert, it also has access to Gräbert’s evolving auto drawing capabilities, which were demonstrated at NXT DEV (www.tinyurl. com/Grabert-NXT), an event organised by DEVELOP3D’s sister publication, AEC Magazine.
In the next release of DraftSight, if not sooner, we expect to see some particularly useful assistance in batch autogenerating drawings from MCAD and BIM models, as DS turns its focus to additionally cater more for AEC users. www.draftsight.com
The
secrets of the DWG file format are now common knowledge and there are tens of drawing tools which all speak the same interchangeable language of lines, circles, arcs, text and so on
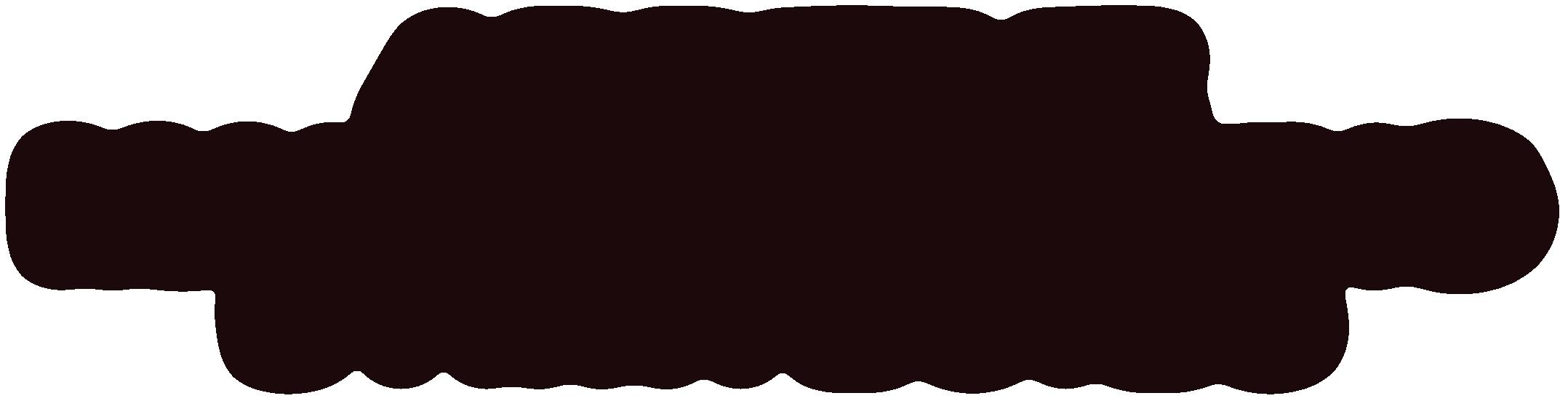


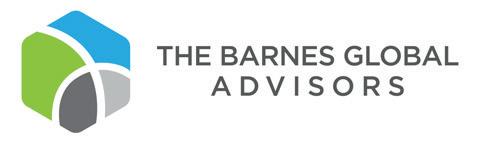
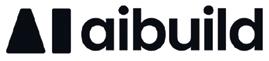
Lexip PU94
» With a 360-degree internal pivot and even more tricks up its sleeve, Lexip’s mouse is built for navigating 3D worlds single-handedly, which makes it an exciting option for manipulating CAD models too, writes Stephen Holmes
The sheer variety of gaming mice available offers CAD users a great opportunity to find the perfect fit for work, but the Lexip PU94 brings yet another dimension to the table.
The mouse’s top shell can pivot, allowing you to control a 360-degree spin around your 3D model with your resting palm. Typically, designers have become accustomed to using a puck in their second hand to control this rotation in the 3D space, but Lexip packs this feature and much more into its premium offering.
As well as featuring a total of six buttons and 12 programmable macros, the PU94 also features a thumb-controlled mini joystick – perfect for zooming in.
At this price point, the mouse is clearly intended for hardcore gamers, but as a result, is blissfully ergonomic for use over long hours driving CAD models. It has only marginally more heft than other mice, and this is offset by the ease with which it glides across the desk or Lexip’s B5 mouse mat (more on this below).
SMOOTH MOVES
Its slickness of movement is enabled by the PU49’s six ceramic feet. While normal mice move on plastic, the Lexip ceramic pads make this easily the smoothest mouse we’ve ever used.
Regardless of how you appraise its other features for your use, the feet alone may make you seek an upgrade. In fact, Lexip sells its feet pads separately, so you can retrofit to a wide range of mice. It’s definitely worth making the swap.
Such nimble movement is targeted at fast-paced gaming accuracy, which is at the core of the PU94. This easily translates to more stately daily tracking across CAD user interfaces. Equipped with a high-performance ADNS-9800 laser sensor, it can track with a speed/ acceleration ratio of 150 FPS/30g and the handset includes two separate accelerometers.
It’s a solid product, with a plastic construction capable of withstanding drops. Its braided USB cable can be unplugged to aid initial installation or make
Product
» Lexip PU94
€99.90
www.lexip.co
Specifications
» Sensor - Laser
ADNS-9800
» Controls - 360° Internal Pivot, Thumb Joystick, Six buttons
» Weight - 157g
» Software requirementsWindows 10, 11
» ConnectivityBraided USB-A wire
» Warranty – five years


it easier to throw into a bag without damage. It offers excellent tactility, clicking and scrolling with nice resistance, even down to the slightest notching on the thumb-joystick rotation, helping you to maintain control.
Issues with the PU94 are minimal, and mostly linked to software. The Lexip Control Software application allows you to assign buttons and even the RGB colours of the handset but is a little clunky. Thankfully, set-up is quick via drop-down menus, and you shouldn’t need to delve into it too often.
The second issue is that you might find that Lexip doesn’t yet support drivers for your chosen software. However, the list at time of publication is healthy enough, featuring Autodesk Fusion and Inventor, Dassault Systèmes Solidworks and Catia, and Siemens Solid Edge. Meanwhile, Rhino3D, Blender, Unreal Engine and Unity are supported in some form, and Lexip continues to
look to add more partners as professional adoption increases.
The aesthetics of gaming mice can be like Marmite, eliciting a ‘love it or hate it’ feeling among users. But the design of this mouse is more subtle than many in the space and the ability to control its glow, dialling it down from a teenager’s bedroom look to something more fitting for a sedate professional space, will appeal to many.
Being able to pack so much control into one device at first led to fears of overworking my hand, but I eventually settled well into using it. The PU94 is a great product and an excellent option for those on the go. Having full control via a single peripheral means less kit to take on your travels and reduced real estate necessary to work comfortably. It’s also a great option if you struggle with using both hands conjunctively, or for anyone lacking dexterity or digits for whatever reason.
With a five-year warranty included, any worries about how the unique pivoting mechanism might hold up to daily grind should be quashed, letting you find a way to flit across the screen more smoothly than ever before.
Jaguar’s recent rebrand
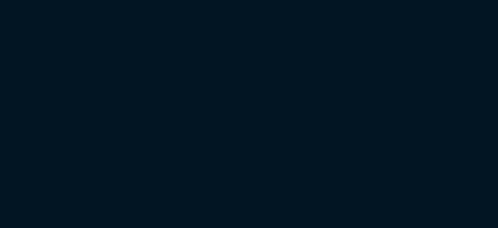
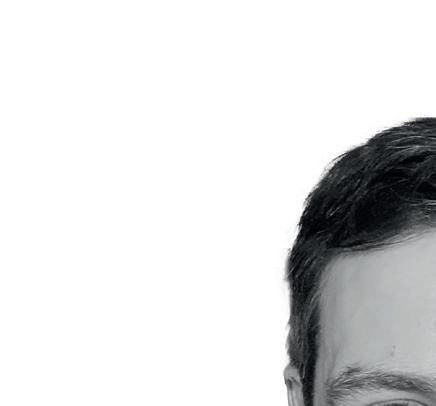
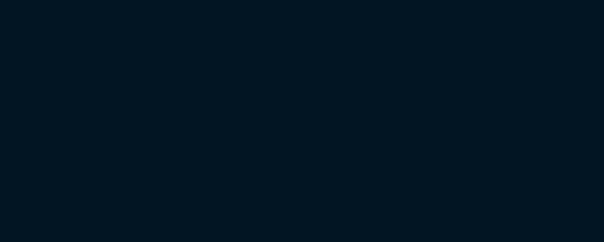

has got many industry commentators in a total fluster, revealing a side to the business that doesn’t fit well with the serious task of delivering on electrification,

writes Stephen Holmes
When it comes to writing a column for every issue of this magazine, it can sometimes be a painful process to find a suitable inspiring topic to cover. So imagine my joy when the stately brand of Jaguar, so reminiscent of red trousers and tweed jackets in the Waitrose car park, was boldly reimagined as something more likely to don a vividly coloured tutu, frilly sleeves and a balaclava.
Design is so infrequently in the headlines that when it does finally pop up (and this definitely popped), then I’m reluctant to simply walk on by – even if you’ll be reading my thoughts some time after the main commotion has subsided.
However, my opinion on its new colour palette, its artsy, fashionista video, the binning of an ugly bonnet badge and the eventual unveiling of a concept car that looked ‘a little bit Jaguar’ in any case is frankly of little interest compared to the kerfuffle that unfolded on everyone’s most/least favourite social media platform.
Opinions are like arseholes – everyone has one. And LinkedIn, in particular, is full of them. For weeks, my feed on that platform was drowning in hot takes about Jaguar’s ‘woke’ rebirth.
It launched a myriad of ‘thought pieces’, written by everyone from CEOs to students. If product designers were the Army in this narrative, rushing to the frontline to thoughtfully explore its practical possibilities, then the marketing mouthpieces were clearly the Navy, leaning heavily into why Jaguar should never have sailed into such choppy waters. Graphic designers, meanwhile, were the Air Force, wafting around in the clouds, wailing about a capital G and possibly imagining the shock that would ensue if Biggles were to rebrand in such a similarly radical manner.
It was almost as if a Blue Peter competition to design the next big British
coupe had been launched by smiling presenters on a cheery sofa, and the entire industry couldn’t resist submitting an entry.
Felt markers were uncapped, charcoal was brandished in anger and AI renders were pumped out at volume, with thousands of people screaming and ideating into the void.
STRONG EMOTIONS
I’ve spoken many times before about how even the most inane products can conjure strong emotions. Cars are perhaps the biggest offenders in the sense of generating a huge degree of audience passion.
But in a segment undergoing radical technological change, where vehicles are becoming more like appliances, it’s clear that huge innovation is necessary for brands to stay ahead and to stay relevant.
The resurrection and reimagining of automotive brands is big business, of course, with many car companies checking down the back of the sofa for any badges to which they might still own the rights.
In 2024, Italy’s government began proposals to sell dormant Italian automotive brands to companies that wanted to invest in the country or move their manufacturing activities there, rather than lose out to Chinese start-ups.
That last point is key. I was recently the first customer to sit in the back of ‘Frankfurt’s first Nio taxi’, as its beaming Uber driver owner enthusiastically told me.
My passenger experience in the back of this Chinese EV was one of the loveliest I’ve had outside of a Bentley. And this is just a regular car – not some high luxury brand.
If marques like Jaguar are to exist in the future, change isn’t something they can just slip on like an old pair of comfortable slippers. They need upheaval – and fast.
But the emphasis should be on new automotive designs that beautifully capture changes in technology and market tastes, not from automotive executives crowdsourcing styling tips on LinkedIn.
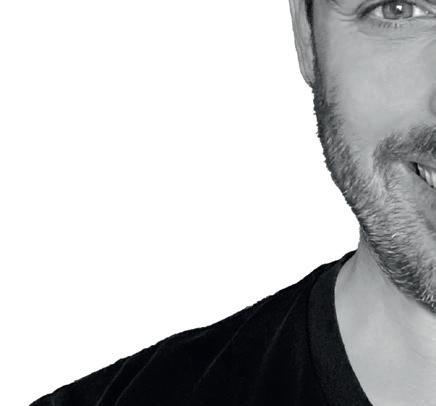
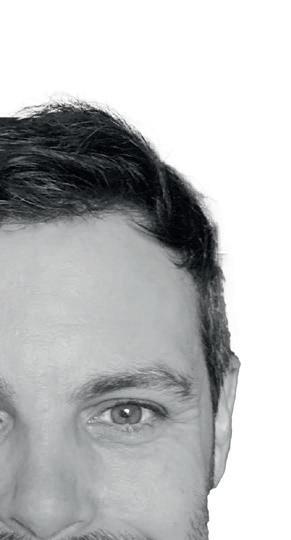
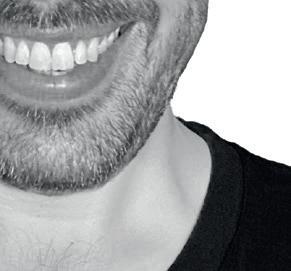
Pioneering new power electronics, energy storage and other next-gen technologies is a critical part of building a desirable automotive product, upon which styling and branding can then be layered
ELECTRIC DREAMS
Electrification is going to radically shift our expectations of transport. If all cars can go from 0-60 mph in silly seconds, and in relative silence and comfort, then what is there to set a brand like Jaguar apart?
Will it be exterior lines, CMF, interior comfort, the entertainment system? Definitely. But there’s more to EVs than the physical and digital architecture in which they’re wrapped. New engineering and new electronics platforms are still not as sexy to most people as a front three-quarter view of a new sports car.
Jaguar Land Rover knows all this. According to those in the know, it’s software team is not far behind that of Tesla in terms of scale and capability. Its electricals/electronics team is pushing not just to compete, but to lead in this highly competitive market.
Pioneering new power electronics, energy storage and other next-gen technologies is a critical aspect of building a desirable product, upon which styling and branding can be layered.
After all, no car looks good being towed on the back of a flatbed, whether it’s Miami Pink, London Blue, or some other so-called ‘woke’ colour entirely.
GET IN TOUCH: After a recent trip in the back of Chinese EV that practically drove itself, silently, while heated massage seats worked their magic, Stephen has been wondering when the Gatwick Express will catch up. On Twitter, he’s @swearstoomuch
DEVELOP3DSERVICES
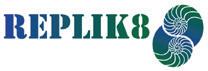
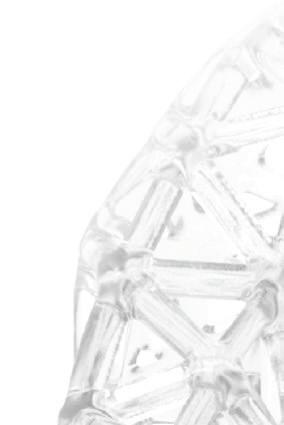
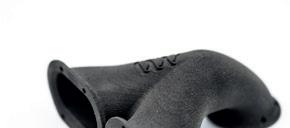
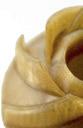
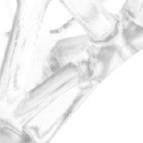
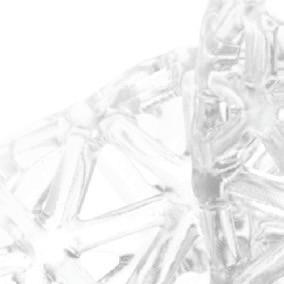
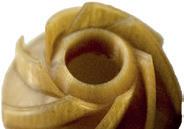
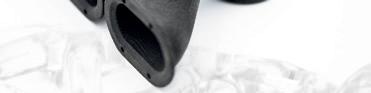

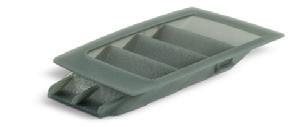
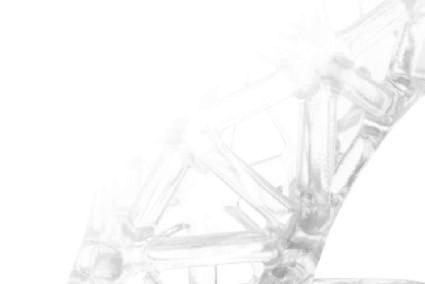

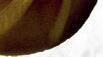



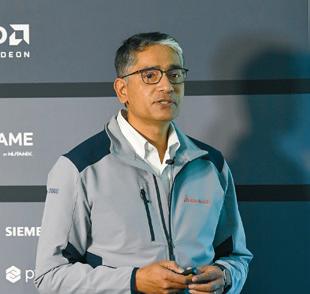


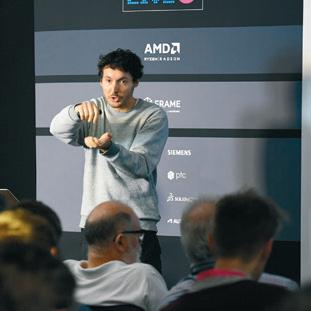

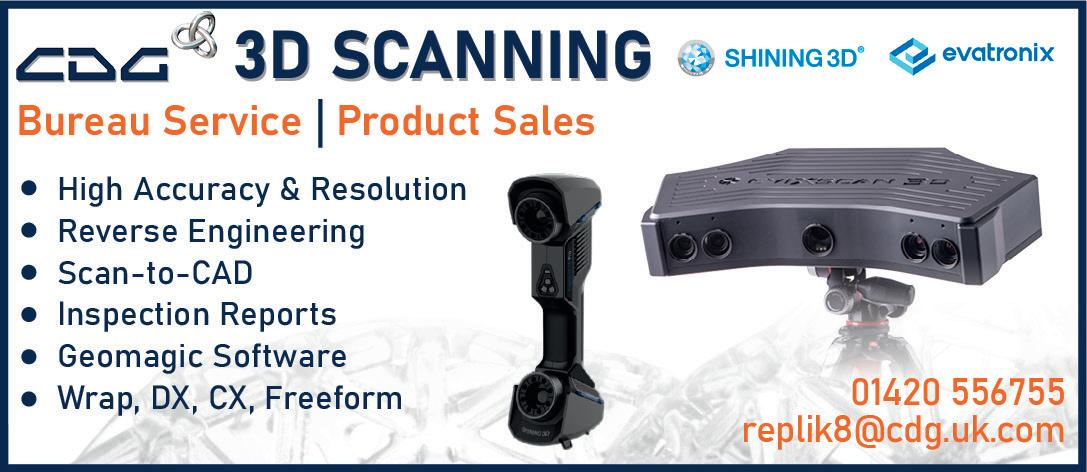
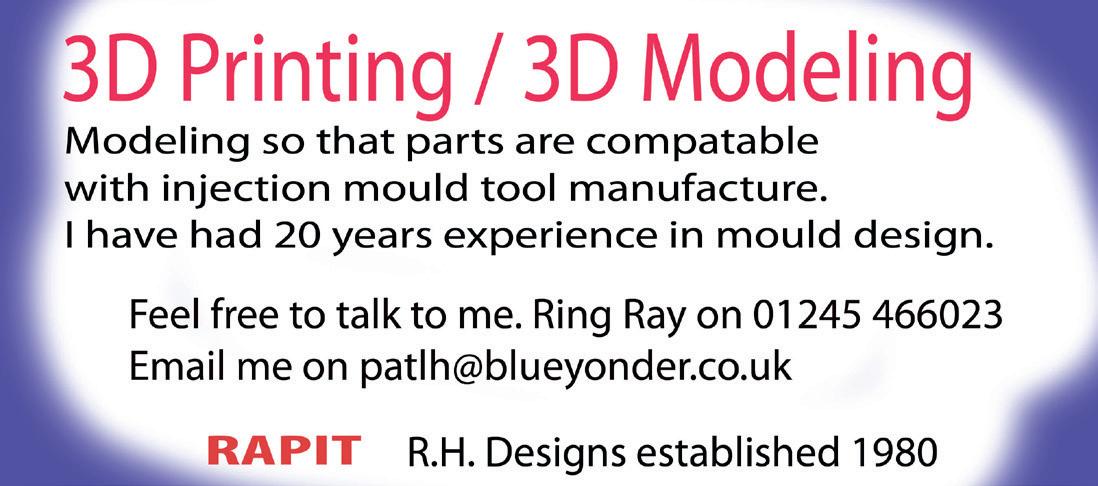



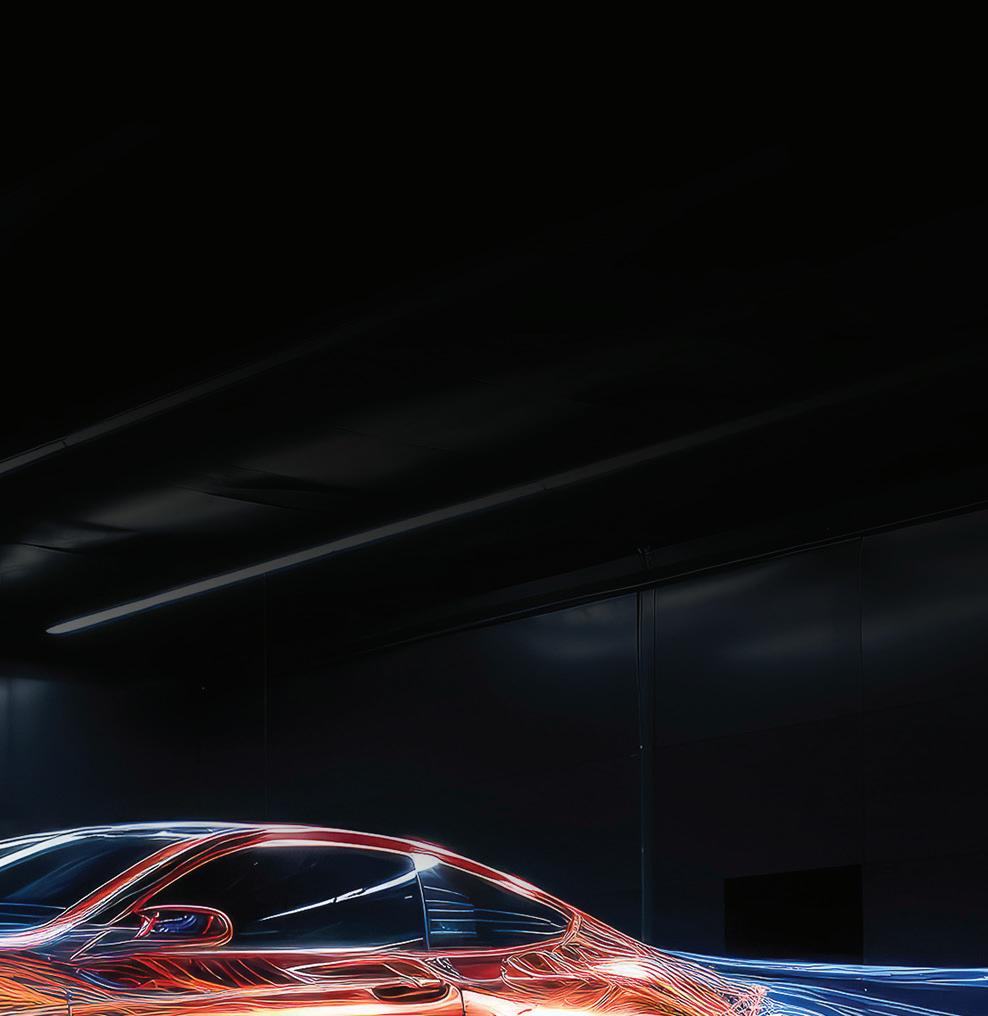
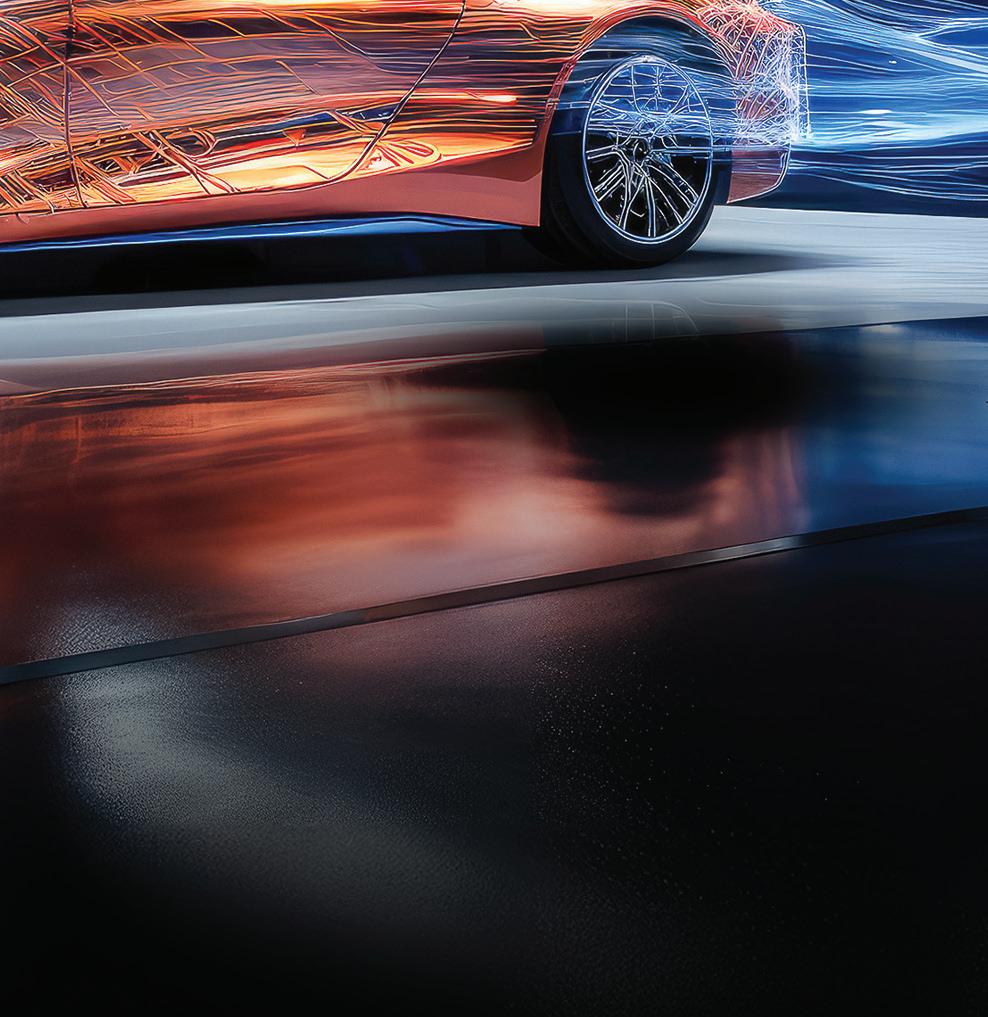
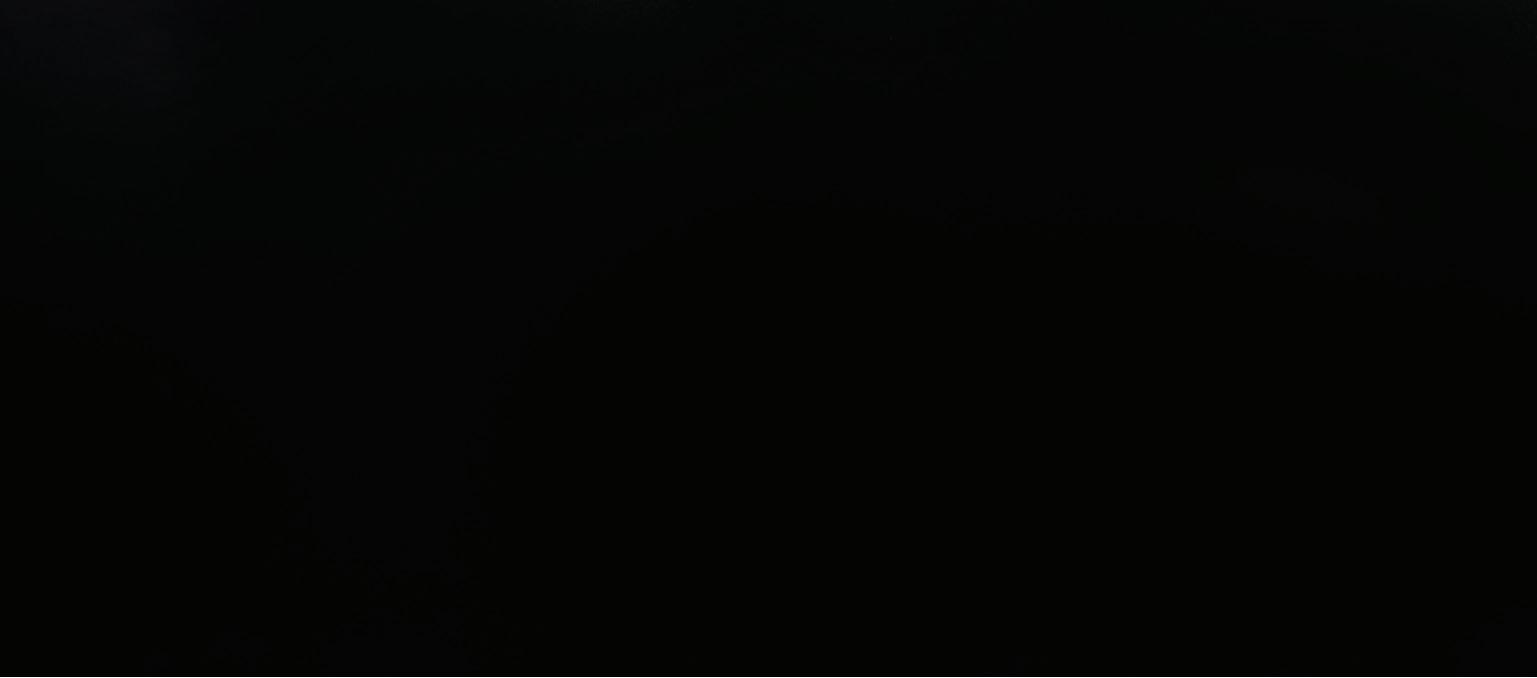
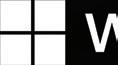
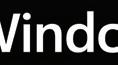

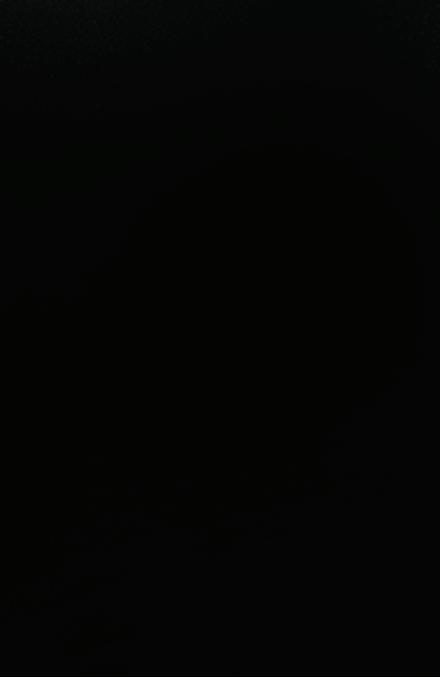