

SPEED IS THE ESSENCE
Stewart-Haas Racing’s formula for NASCAR success
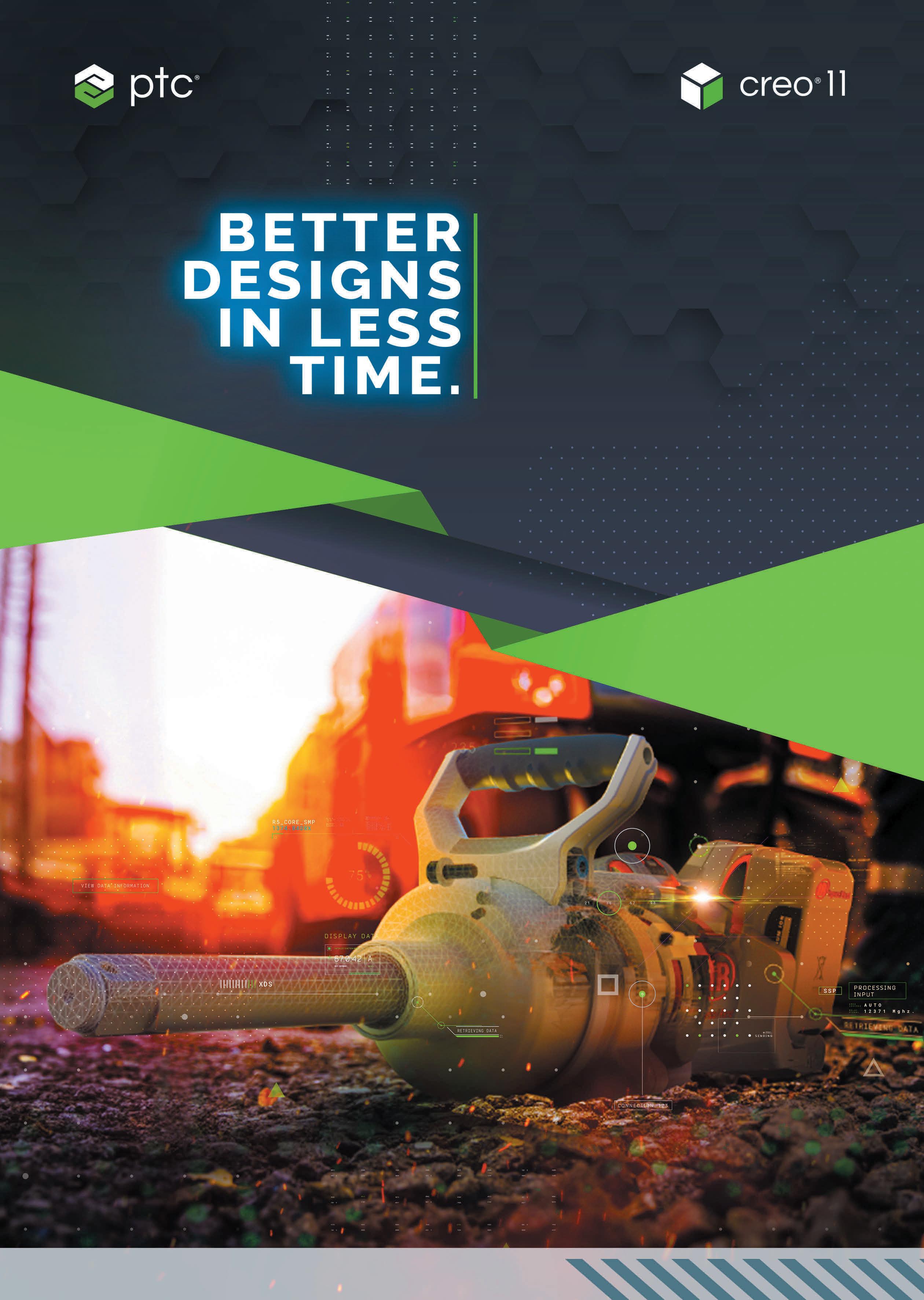
Industrial workers rely on Ingersoll Rand for powerful, durable impact wrenches. Ingersoll Rand relies on PTC for award-winning CAD performance. To learn more about Creo 11 go to http://www.ptc.com/creo11
EDITORIAL
Editor
Stephen Holmes
stephen@x3dmedia.com
+44 (0)20 3384 5297
Managing Editor
Greg Corke
greg@x3dmedia.com
+44 (0)20 3355 7312
Consulting Editor
Jessica Twentyman jtwentyman@gmail.com
Consulting Editor
Martyn Day martyn@x3dmedia.com
+44 (0)7525 701 542
Staff Writer
Emilie Eisenberg emilie@x3dmedia.com
DESIGN/PRODUCTION
Design/Production
Greg Corke
greg@x3dmedia.com
+44 (0)20 3355 7312
ADVERTISING
Group Media Director
Tony Baksh tony@x3dmedia.com
+44 (0)20 3355 7313
Deputy Advertising Manager Steve King steve@x3dmedia.com
+44 (0)20 3355 7314
US Sales Director Denise Greaves denise@x3dmedia.com
+1 857 400 7713
SUBSCRIPTIONS
Circulation Manager
Alan Cleveland alan@x3dmedia.com
+44 (0)20 3355 7311 `
ACCOUNTS
Accounts Manager Charlotte Taibi charlotte@x3dmedia.com
Financial Controller Samantha Todescato-Rutland sam@chalfen.com
ABOUT
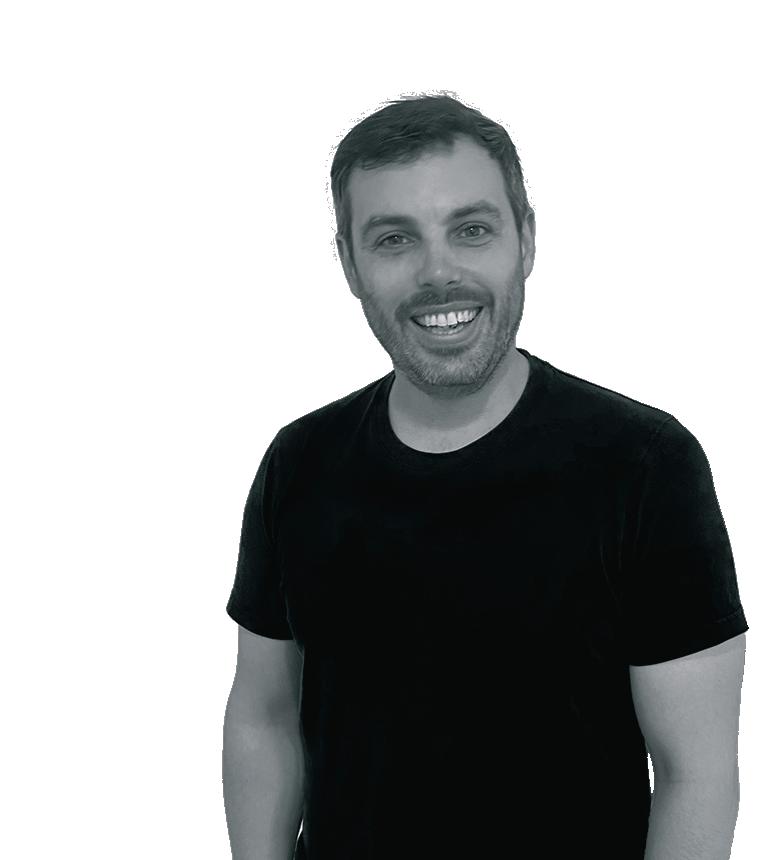
Ihave to admit that my recent visit to a NASCAR team was unlike any other motorsport experience I’ve ever had. Above all, it struck me that this is a sport that is far more open to its fans than many others.
I watched as members of the public arrived at Stewart-Haas Racing in their droves, popping into the building’s atrium to peer through the glass at real cars being assembled for race day and then leaving via the gift shop. It bore no resemblance to visits I’ve made to Formula 1 teams or similar.
That’s not to say that NASCAR in any way lags its fancy F1 cousins –not least because this is a team that actively supports its cousin, Haas F1. No, the key difference here is the desire to keep the experience inclusive.
This issue also sees two giants of the CAD world – PTC and Siemens – take their places on the starting grid for a new season. In a market where the differences between CAD packages is dwindling, it’s interesting to see what each supplier is doing to differentiate its products in the minds of buyers.
We also dip a toe in the topic of sustainable hydropower, with a look at Energyminer and its schools of Energyfish generators, which are powered by river and canal waters, before zipping over to India, to learn how Ather Energy is finetuning its designs for the batteries that power its electric scooters.
Elsewhere, Greg investigates the rise of extended reality, or XR, and considers how it is likely to impact graphics requirements. He also reviews new hardware from Scan and Nvidia.
Finally, we’re thinking about accessible design. In my Last Word column, I ponder how inclusive the product design and engineering industry really is, especially when you consider that the success of an accessible product is often closely tied to the input and advice of people with disabilities during the research and conceptual stages. And, also on that subject, we take a look at eVita, Callum Designs’ concept for an wheelchair-accessible electric chair.
So start your engines for a packed issue!

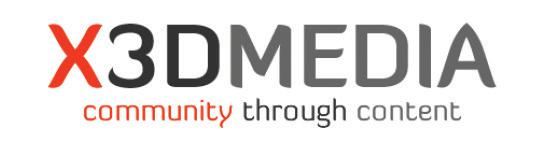
DEVELOP3D is published by X3DMedia 19 Leyden Street London E1 7LE, UK
T. +44 (0)20 3355 7310
F. +44 (0)20 3355 7319



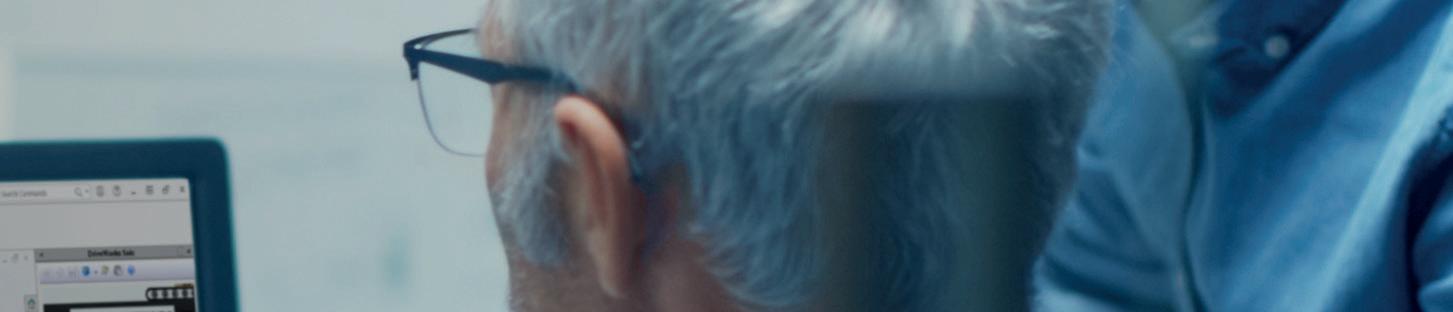
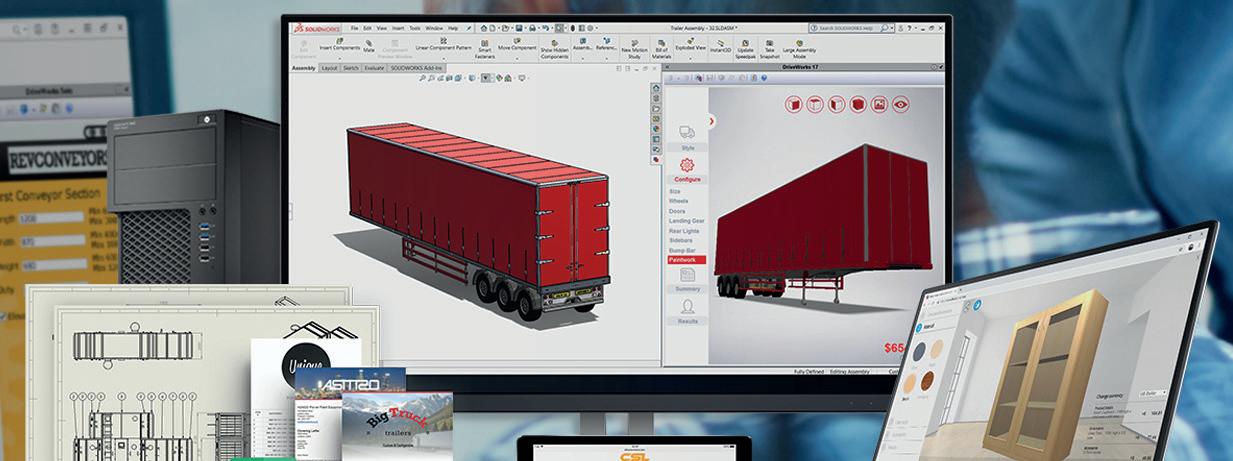

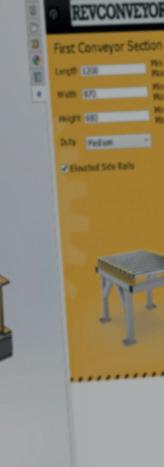
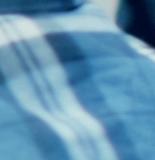

Automate SOLIDWORKS manufacturing processes & sell digitally using DriveWorks
DriveWorks is flexible and scalable. Start for free, upgrade anytime. DriveWorksXpress is included free inside SOLIDWORKS or start your free 30 day trial of DriveWorks Solo.
DriveWorks Pro
30DAY FREETRIAL
DriveWorksXpress
Entry level design automation software included free inside SOLIDWORKS®
Entry level SOLIDWORKS part and assembly automation
Create a drawing for each part and assembly
Find under the SOLIDWORKS tools menu
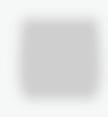

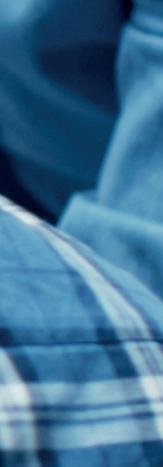
One time setup
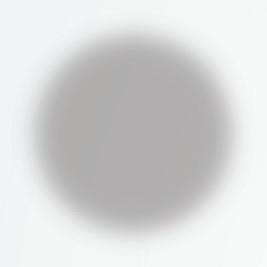
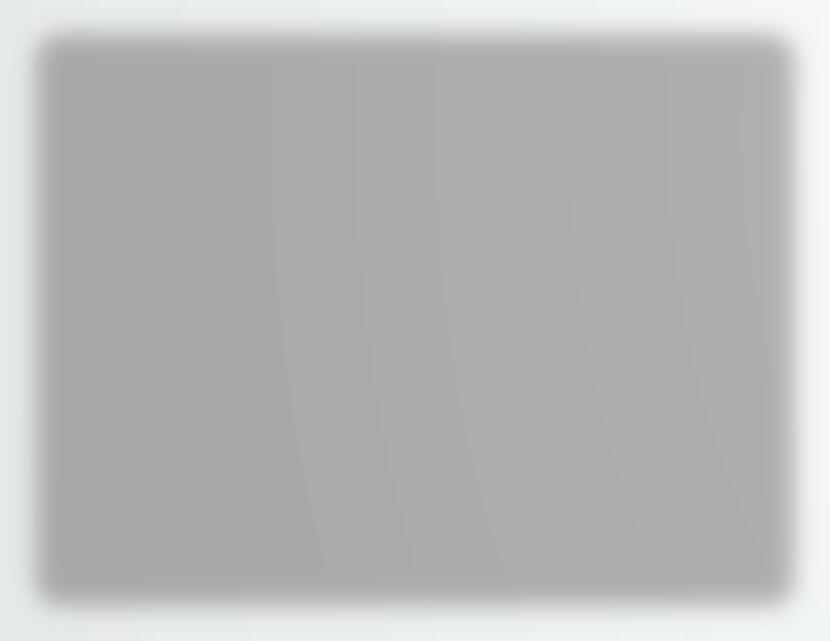
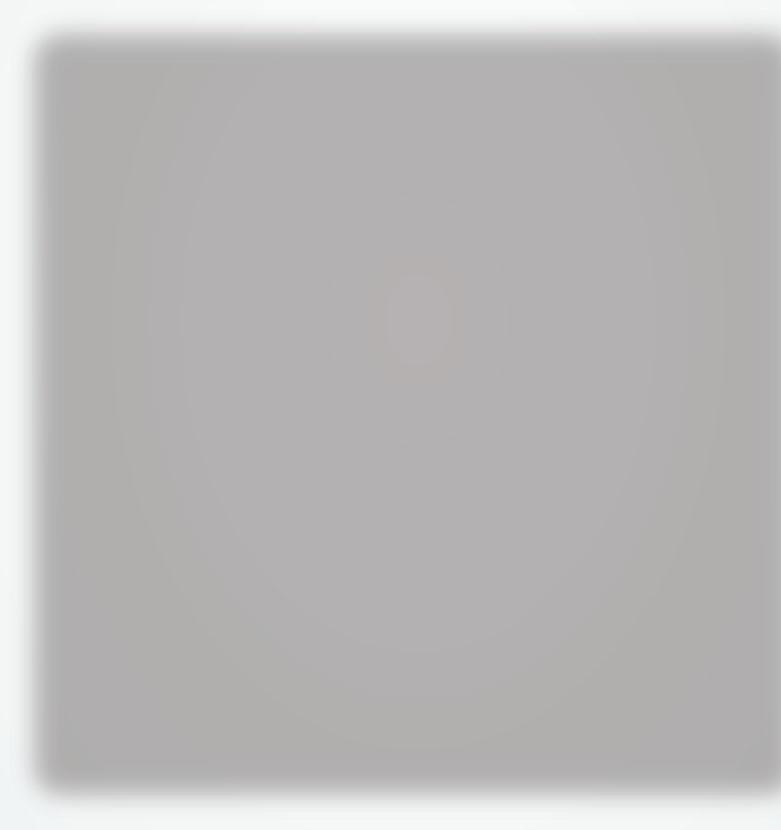
Modular SOLIDWORKS® automation & online product configurator software

DriveWorks Solo

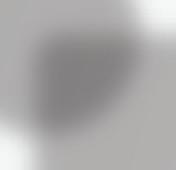
SOLIDWORKS® part, assembly and drawing automation add-in
Automate SOLIDWORKS parts, assemblies and drawings
Generate production ready drawings, BOMs & quote documents automatically Enter product specifications and preview designs inside SOLIDWORKS
Free online technical learning resources, sample projects and help file
Sold and supported by your local SOLIDWORKS reseller
examples online
Set up once and run again and again. No need for complex SOLIDWORKS macros, design tables or configurations.
Save time & innovate more
Automate repetitive SOLIDWORKS tasks and free up engineers to focus on product innovation and development.
Eliminate errors
DriveWorks rules based SOLIDWORKS automation eliminates errors and expensive, time-consuming design changes.


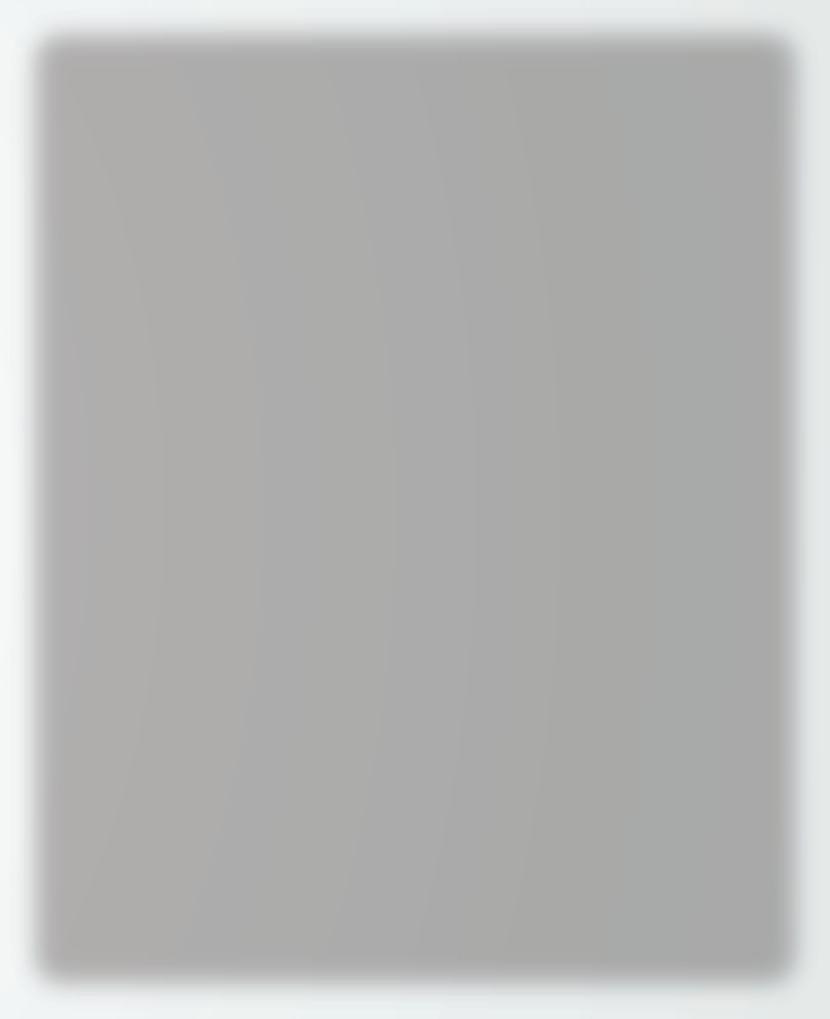
Complete SOLIDWORKS part, assembly and drawing automation
Automatically generate manufacturing and sales documents
Configure order specific designs in a browser on desktop, mobile or tablet
Show configurable design details with interactive 3D previews
Integrate with SOLIDWORKS PDM, CRM, ERP, CAM and other company systems
Scalable and flexible licensing options
Sold and supported by your local SOLIDWORKS reseller
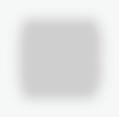
Connect sales & manufacturing
Validation ensures you only offer products that can be manufactured, eliminating errors and boosting quality.
Integrate with other systems
DriveWorks Pro can integrate with other company systems, helping you work more efficiently and effectively.
Intelligent guided selling
Ensure your sales teams / dealers configure the ideal solution every time with intelligent rules-based guided selling.

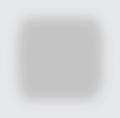
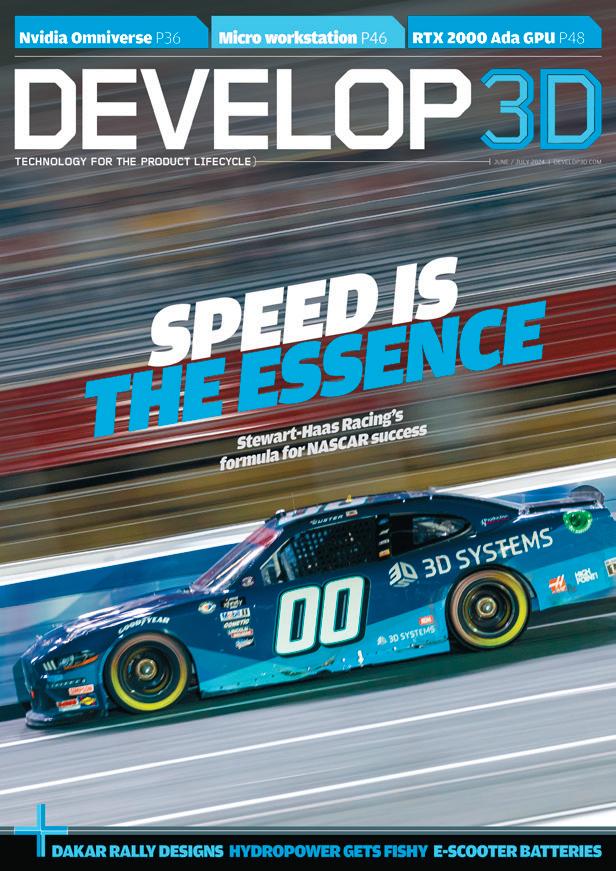
NEWS
Siemens Xcelerator expands its offerings, PTC unveils Creo 11, Xencelabs launches Pen Display 16, and more
FEATURES
Comment: Laurence Marks on meshless simulation
Comment: SJ’s heartfelt message to a 3D printing bureau
Visual Design Guide: Callum Designs’ eVita concept car
COVER STORY Stewart-Haas Racing at full speed
Q&A: PTC’s Paul Sagar on new Creo 11 enhancements
Extended reality (XR) - the rise of streaming
Event report: Autodesk Automotive Innovation Forum
Event report: Siemens Realize 2024
New heights: Inside Nvidia Omniverse’s Cloud APIs
Go with the flow: Sustainable hydropower at Energyminer
Dune racer: Prodrive’s Dakar Rally 3D scanning strategy
Ather Energy’s mission to achieve e-scooter dominance
Fully charged: Fine-tuning battery design at KTM
REVIEWS
Scan 3XS Small Form Factor (SFF) workstation
Nvidia RTX 2000 Ada Generation GPU
THE LAST WORD
Accessible product design can make a huge difference for people with disabilities, writes Stephen Holmes, but is the product design and engineering industry inclusive enough to get them more deeply involved?
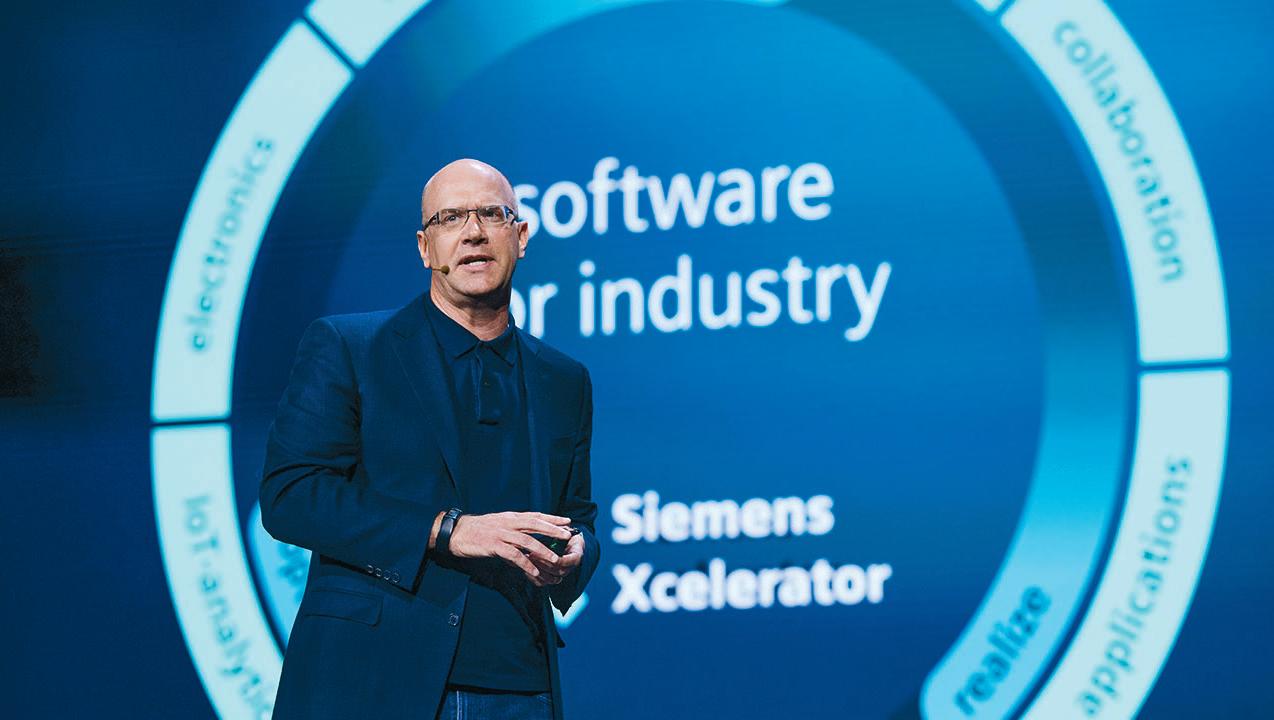
SIEMENS
XCELERATOR EXPANDS TO OFFER NEW CLOUD VERSIONS OF NX AND SIMCENTER
» Company executives claim that software-as-a-service versions of popular Siemens packages give customers greater freedom of choice and reduced IT requirements
Siemens Digital Industries Software has announced it is expanding its Xcelerator SaaS portfolio, introducing more capabilities from its comprehensive software portfolio and allowing users to tailor their choices according to their specific requirements.
Billed as “flexible, modular solutions run on the industry’s most robust interoperable data backbone”, these SaaS solutions provide a wide range of capabilities, designed to underpin workflows spanning conceptual design work to manufacturing production.
NX X is Siemens’ new cloud-based solution for product engineering that delivers industry-leading product design capabilities on an as-a-service basis.
This SaaS approach, company executives claim, will allow customers to free up resources and instead focus on achieving greater scale and innovation. Centralised cloud license management, configuration and provision of capability should also simplify IT requirements. The software can be installed on desktops or streamed via AWS cloud services as preferred, providing flexibility for distributed teams.
Additionally, Siemens executives say that NX X provides fully integrated and secure data management capabilities with
every license, so that users can handle product data, change management and release workflows, as well as conduct collaborative reviews with view/mark-up and commenting in real time, directly from the NX X interface.
Based on data and lifecycle management capabilities originating in Siemens’ Teamcenter X software, NX X has been designed to offer a route to adopting PLM.
The SaaS version of NX also delivers cloud-based, ad hoc data sharing and collaboration with external collaborators through the Teamcenter Share app.
Simcenter X, meanwhile, is a cloud-based version of the capabilities of Simcenter’s portfolio of simulation and test solutions.
The initial release is focused on Simcenter STAR-CCM+ and is delivered as part of Siemens Xcelerator.
Simcenter X enables engineers in companies of all sizes to access a cloud-based virtual engineering desktop environment for modelling and postprocessing, combined with a highly scalable high performance computing (HPC) environment.
Another offering is Teamcenter X Essentials, which is being marketed as an affordable way for customers to access Teamcenter’s PLM capabilities, helping them to begin the transition to digital methods faster and to adopt PLM rapidly.
Other additions to the Siemens Xcelerator SaaS portfolio include Opcenter X, a new SaaS solution for manufacturing operations management (MOM); and the Zel X engineering app, designed for streamlining manufacturing and shop floor operations.
Joe Bohman, executive vice president for PLM products at Siemens Digital Industries Software, recently spoke about the innovation surrounding Siemens Xcelerator in his presentation at Siemens’ Realize Live user event in Las Vegas (see event report on p. 34).
“The cloud market will surpass $1 trillion in 2026 and every CIO I talk to is intensely interested in what we’re doing with the cloud,” he told attendees.
“What we’re doing is Siemens Xcelerator as a Service. We’re offering our full set of solutions as SaaS solutions, designed using our digital thread methodology so it all connects together. We’re building out-of-the-box SaaS solutions that are secure, personalised and customisable with Mendix, and it brings together expert communities, giving people the ability to talk and work together.”
According to Siemens’ own research, its customers claim they are 33% faster to market using this approach and rack up 60% lower IT costs. www.sw.siemens.com
Teams
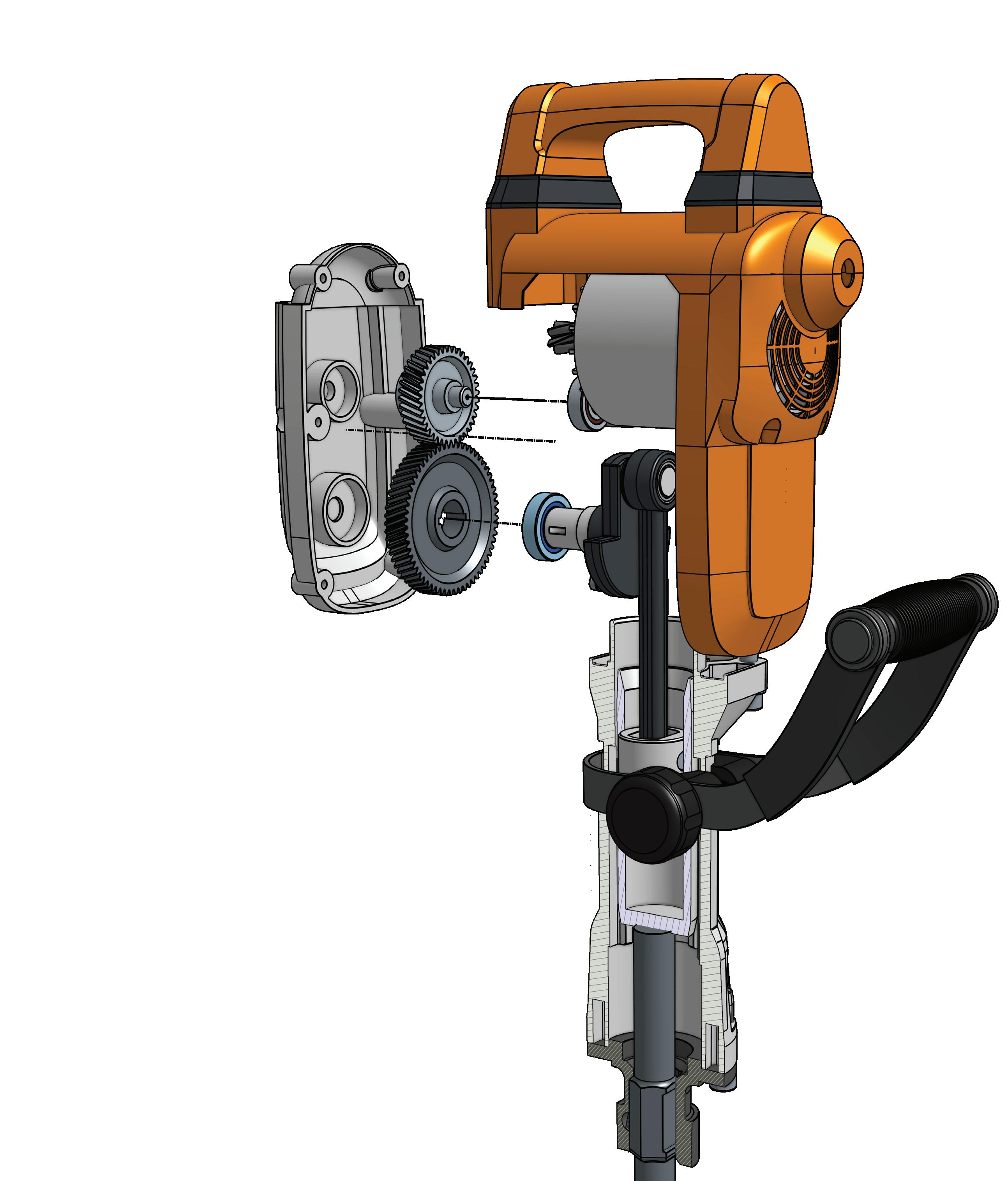
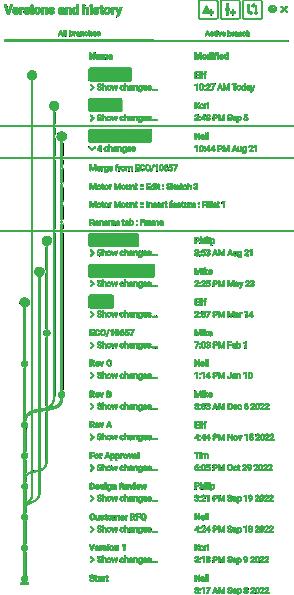
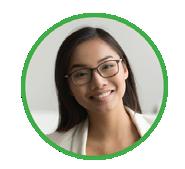
From the founders who created SOLIDWORKS, Onshape is the most widely used cloud-native CAD & PDM system on the market with over 3 million users.
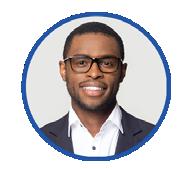
Built-in PDM - a single source of truth for design data with robust version control.
Real-Time Collaboration - users across the globe can simultaneously view and edit parts, assemblies, and drawings.
Zero IT Overhead - Onshape runs in a browser anytime, anywhere, and on any device. No costly workstation required.
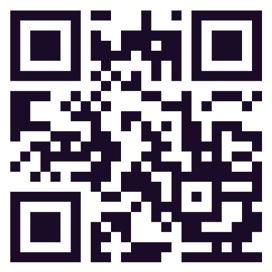

PTC EMPHASISES USABILITY AS IT LAUNCHES CREO 11
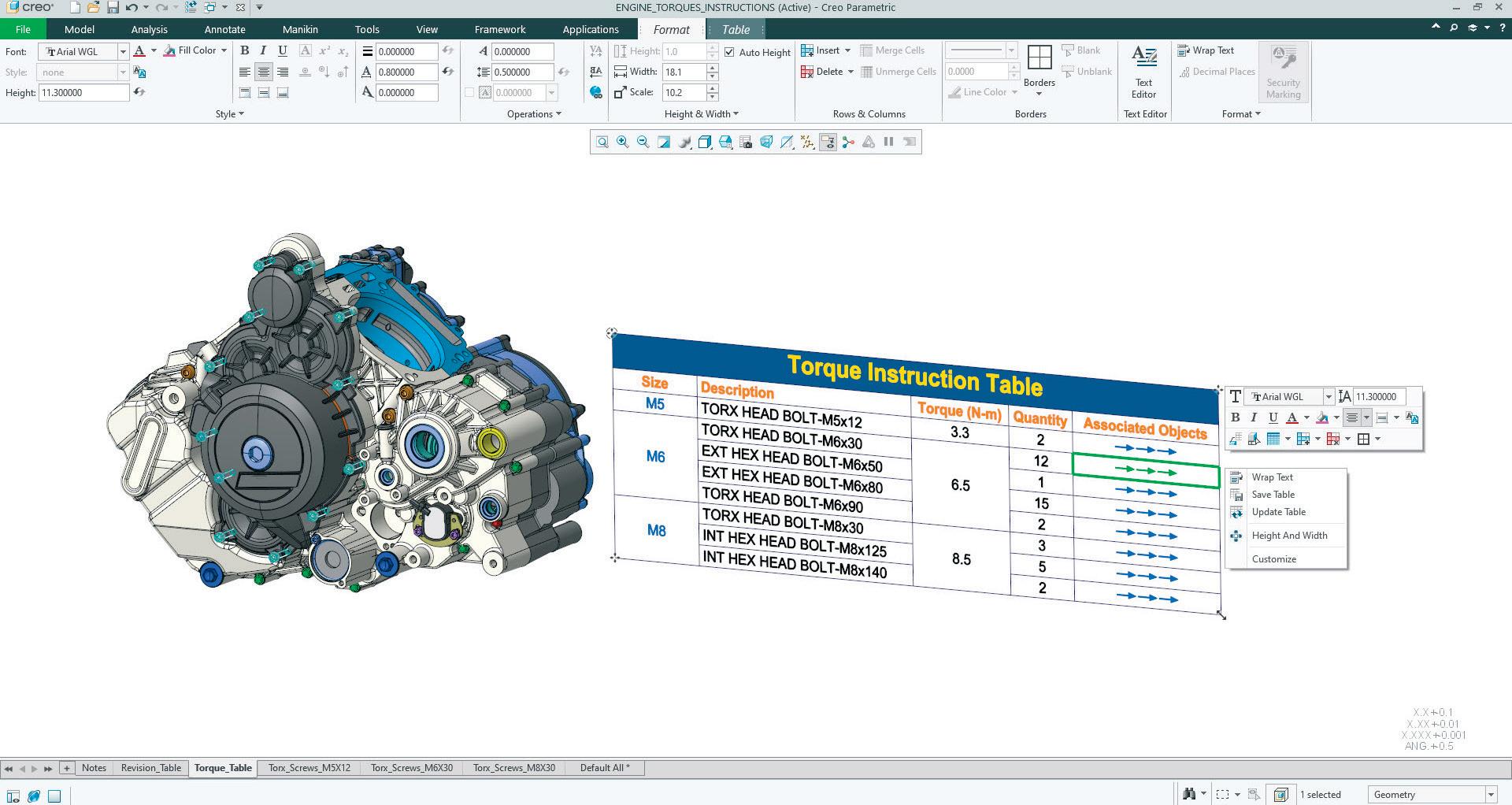
PTC has launched Creo 11, introducing a wide range of enhancements for electrification, composites, model-based definition, simulation-driven design and advanced manufacturing – but a conspicuous absence of AI dominating the release. Instead, Creo 11 is looking to simplify user workflows with an unbroken chain of design, adding everyday productivity enhancements and building on recent additions.
The new release now supports multibody concepts for designs containing multiple sheet metal and regular bodies, allowing users to better design sheet metal parts in context. In addition, solid bodies from parts of an assembly can be transferred into a single multibody part using a shrinkwrap feature.
Creo 11 also features an enhanced enclosure volume feature, to optimise and calculate the minimum bounding box of a part or assembly for packaging optimisation.
Other improvements include further composites design and manufacturing capabilities, such as transitions, laminate sections and draping simulations. MBD tools have been improved to provide greater clarity with less effort.
Simulation has taken a step forwards, with new simulation-driven design capabilities for better design ideation, guidance and validation.
Generative design has also been improved with the introduction of minimum feature size constraints, bearing load support and planar symmetry constraints. www.ptc.com
Model-based definition tools in Creo 11 enable users to organise design data into simple tables
Fall in number of women engineers
New data from EngineeringUK reveals that the number of women working in engineering and technology fell between 2022 and 2023.
The proportion of women working in this sector shrunk to 15.7% in 2023, from 16.5% in 2022. By contrast, women make up 56.1% of the total UK workforce.
The majority of women working in engineering and technology during 2023 were between the ages of 16 and 34, suggesting that many join straight from education and then leave the industry during their mid-thirties. www.engineeringUK.com
Infinitform makes its debut
InfinitForm has emerged from stealth mode and launched its debut software offering. This takes advantage of GPU processing power and promises to transform the design for manufacturing (DFM) process, by delivering highly optimised designs that can be CNC machined with maximum speed and efficiency.
“Generative design solutions work well for additive, but they don’t work well for traditional manufacturing,” explained Infinitform founder and CEO Dr Michael Bogomolny. www.infinitform.com
Xencelabs Pen Display 16 offers new portability
Xencelabs has announced the release of the Pen Display 16, a 4K OLED fanless display with edge-to-edge super-AG etched glass.
Compared with the Pen Display 24, which weighs 6 kg and is 1.4 inches thick, the Pen Display 16 is 1.22 kg in weight and 0.47 inches thick, making it easier to transport.
The pen display features five factorycalibrated colour spaces: Adobe RGB (98%), P3-DCS (98%), sRGB (99%), Rec 2020 and Rec 709.
It has an aluminium back, resulting in heat dissipation without any fan noise and can connect to any compatible PC or laptop via a USB-C to USB-C cable. All necessary cables, as well as two different Xencelabs pens and a mobile easel, are included in the bundle.
In terms of the two pens offered, the 3-button pen has a wider barrel, with three customisable buttons for keyboard shortcuts. The Thin Pen creates the effect of a real pencil or a thin brush and has two buttons for keyboard shortcuts. Both are pressure-sensitive and come with pressure-sensitive erasers. www.xencelabs.com
Weighing in at just 1.22 kg, the Pen Display 16 is Xencelabs' most portable design yet

Hexagon 3D scans go wireless
Hexagon has announced the launch of two new wireless 3D scanners that have been designed for measuring parts in a wide range of inspection environments.
The handheld Atlascan Max and Marvelscan devices do not need a PC or cables to operate and are batterypowered, making measuring surfaces in outdoor environments or in confined spaces far more practical.
Users can switch between Fine mode, for scanning detailed surfaces at high resolution, and Standard mode, for scanning open surfaces. Data collected using either mode can be combined as a single point cloud. www.hexagon.com
FYOUS PROMISES WASTE-FREE TOOLING WITH NEW TECH
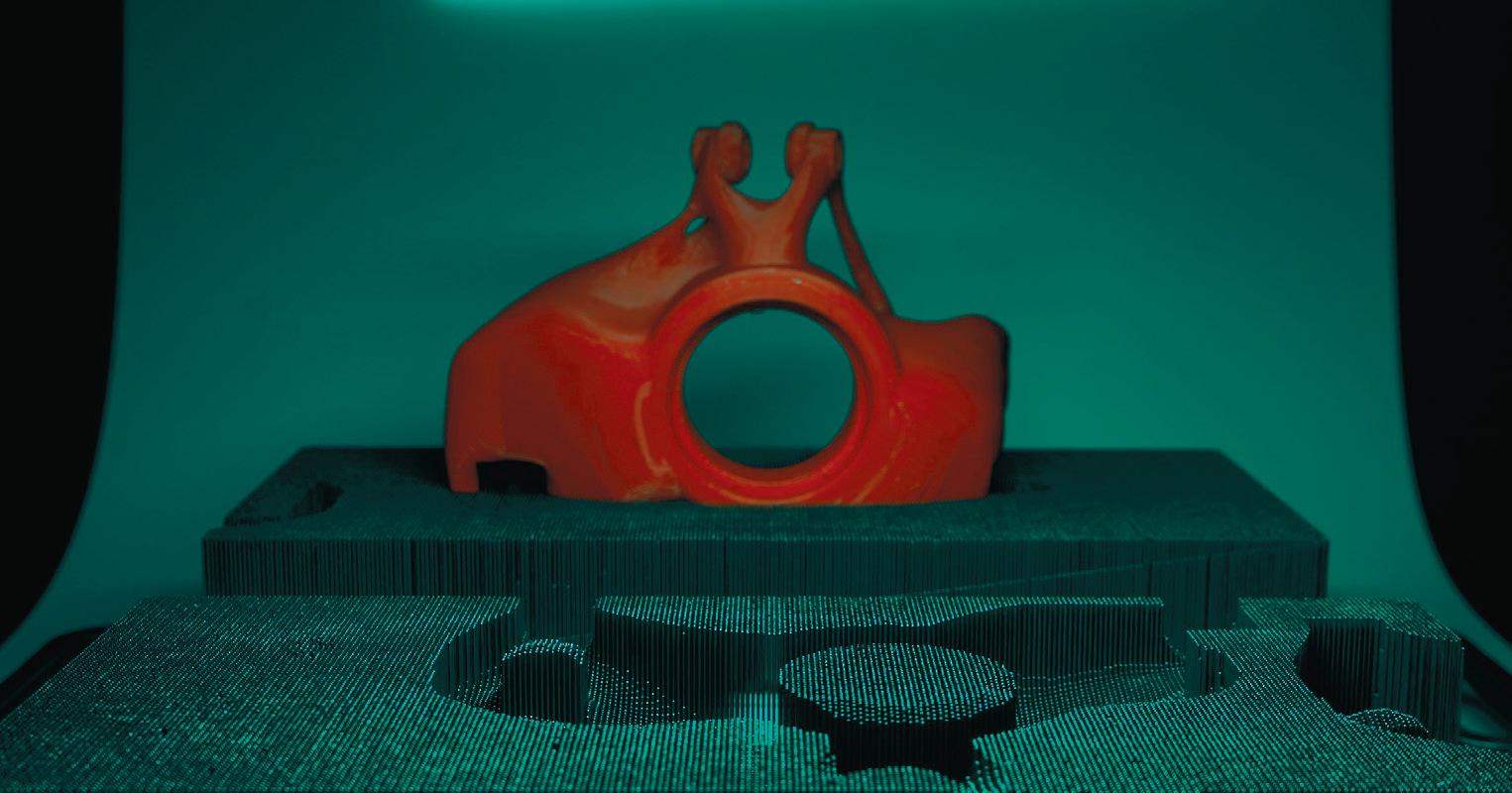
Sheffield, UK-based Fyous has announced the commercial launch of its polymorphic moulding technology, an alternative to 3D printing that it claims is 20 times faster.
Polymorphic moulding is an automated pin tool moulding technology, whereby a mould can be infinitely reconfigurable and reused in minutes. This enables Fyous to replicate mass manufacturing of custom parts economically and to rapidly prototype new designs. The patentpending technology supports a wide array of materials and processes, including moulding, casting, vacuum forming and composite lay-up.
Fyous executives have explained that the pin tool shape shifts automatically in under 20 minutes using a provided 3D model, altering the 334 pins per square
inch – the
as a 50p
and capable of holding 6 tonnes of pressure in its current configuration. Stable at temperatures of 150°C and more, currently the max part size is 155 x 350 x 100 cm. New moulds create zero waste. Affordable customisation, according to co-founder Joshua Shires, is “crucial for applications that require interfacing with the human body, from dental appliances to medical devices and sports equipment.”
Fyous has actively pushed the technology in the footwear sector, so that custom shoes for diabetic patients can be made in more attractive styles. It is now actively seeking new partnerships, from across a wider range of industries, in order to further develop and deliver its polymorphic moulding technology to market faster.
www.fyous.com
Landr FDM 3D Printer takes off
Landr, a spin-off from digital manufacturing expert Ryse 3D, has launched its first FDM 3D printer, which claims to handle engineeringgrade materials at one-tenth the costs associated with competing machines.
Featuring a 500 x 500 x 500mm build volume, the Landr 500 offers a 100°C heated chamber, a 500°C hot end, a 140°C heated print bed, and reported speeds of around 500 mm/s, even when printing with nylon-carbonfibre filaments.
A Bondtech LGX extruder, double-skin, gold-reflective insulation, built-in camera and auto nozzle wipe and nozzle purge, along with a heated filament dryer, all come as standard on a printer costing £11,398.80 including VAT.
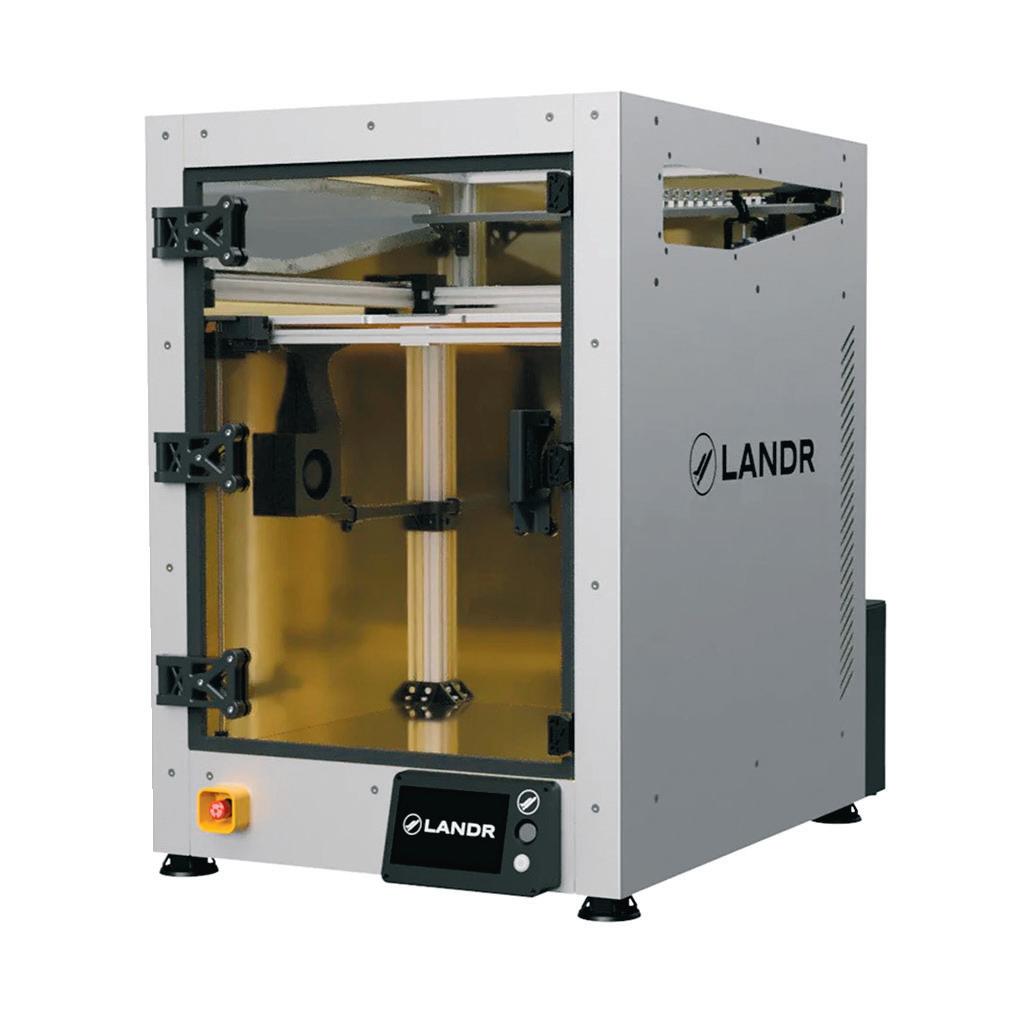
Landr CEO Mitchell Barnes claims that the printer’s closest competitor is ten times the cost, three times the weight and twice the size – a challenge for cramped shop floors. Ten Landr 500 3D printers are already deployed at Ryse 3D and have so far clocked up over 30,000 hours of use. www.landr3d.com
ROUND UP
New integrations between Authentise Threads, Plyable and Google Docs aim to increase the efficiency of mould development, along with delivering streamlined engineering processes, enhanced collaboration and a faster path between ideas and manufactured parts www.authentise.com
can be infinitely reconfigurable and reused in minutes, say Fyous' founders
The spacious build platform of the Landr 500 makes it well-suited to handle largeformat jobs
WAAM3D’s new MiniWAAM system offers the company’s proprietary end-effectors and its sensing hardware and software in a competitively priced package, in a bid to attract more companies to the world of wire-fed direct energy deposition (DED) 3D printing for metal parts www.waam3d.com
Cadence Design Systems has completed its acquisition of Beta CAE, a move that company executives claim will accelerate its Intelligent System Design strategy, by adding some highly complementary products focused on structural analysis to its existing multiphysics analysys suite www.cadence.com
Markforged has announced a software update for its Mark Two and secondgeneration Onyx Pro 3D printers that adds a ‘turbo function’ to its FDM additive layering process, resulting in print speeds up to two times faster, while offering the same surface finish quality www.markforged.com
The Engineering Design Revolution, a history of CAD and summary of the CadHistory.net website, has been republished by Shapr3D on its site as a way of protecting the writings of its author, the late David E Weisberg, and with the approval and permission of Weisberg’s family www.shapr3d.com
LIQUID COOLED THREADRIPPER PRO WORKSTATION LAUNCHES
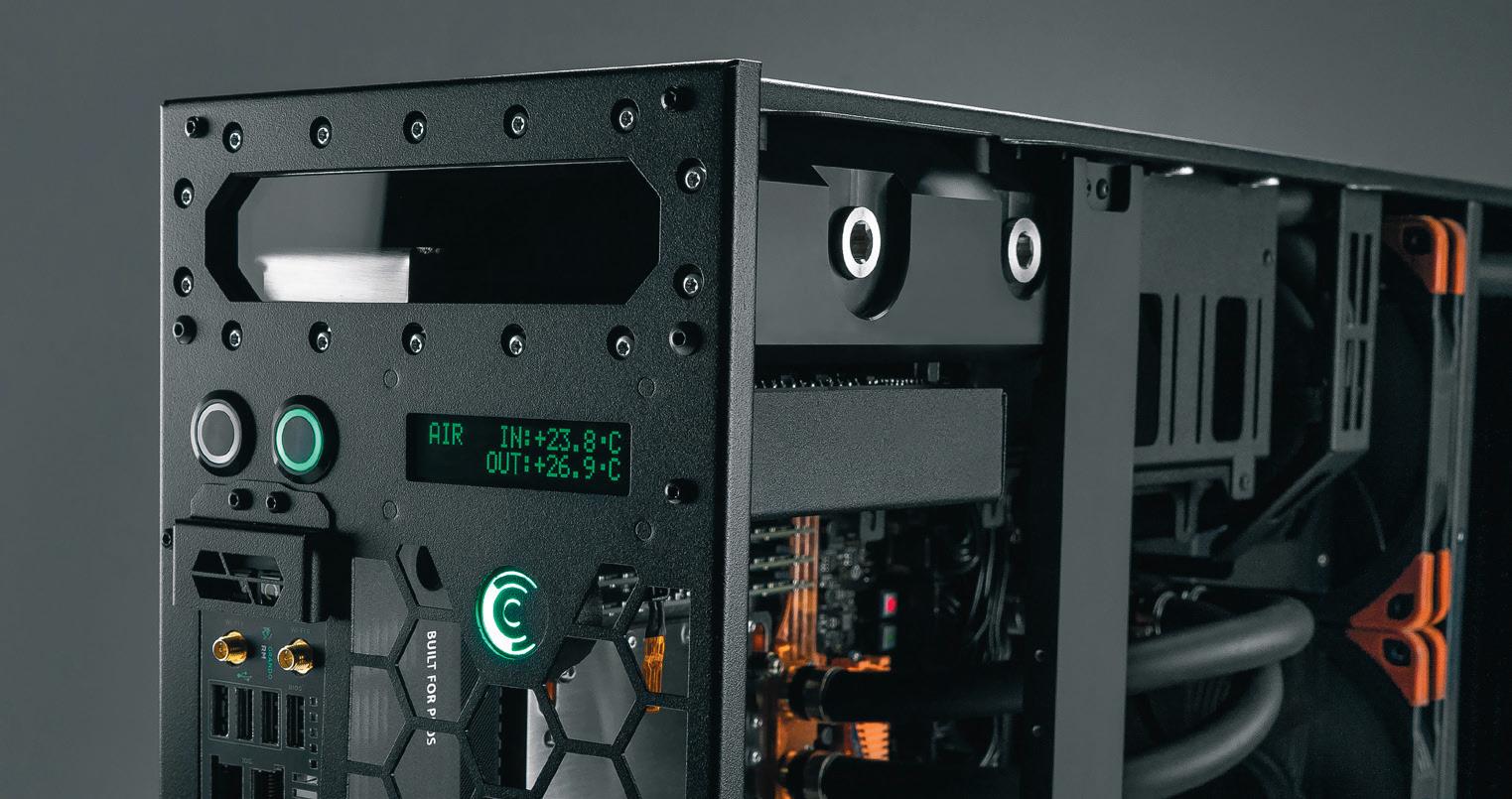
Comino, a specialist in liquid cooled workstations and servers, has updated its Comino Grando ‘hyper performance’ workstation, offering the AMD Threadripper Pro 7000 Series processor with up to 96 cores.
The workstation can be configured with up to four high-end GPUs. This includes traditional graphics-focused boards, such as the Nvidia RTX 6000 Ada Generation (48 GB), Nvidia RTX GeForce 4090 (24 GB) and AMD Radeon Pro W7900 (48 GB), plus those designed for AI workflows and highperformance computing (HPC), such as the Nvidia A100 (80 GB), Nvidia H100 (80 GB) and Nvidia L40S (48 GB).
The Comino Grando is different to most desktop workstations in that the CPU, GPUs and VRM modules on the motherboard are cooled with Comino’s
custom liquid cooling technology.
According to the company, it makes the workstation significantly quieter and cooler than standard workstations and prolongs the lifespan of the hardware. It also allows Comino to push more power into the AMD Threadripper Pro processor compared to an air-cooled workstation and therefore maintain significantly higher all-core frequencies.
According to Alexey Chistov, Comino CTO, the Threadripper Pro 7995WX (96 cores) can reach 4.5GHz @ 900W and the Threadripper Pro 7985WX (64 cores) can reach 5.0GHz @ 900W, compared to 2.53.5GHz for an air-cooled workstation.
Comino manufactures its own highperformance waterblocks out of copper and stainless steel. For GPUs, the slim water block takes up a single PCIe slot. www.comino.com
Water cooling is said to make the workstation significantly quieter and cooler than others
Lenovo updates ultra portable P1
Lenovo has introduced the ThinkPad P1 Gen 7, the latest version of its ‘ultra-portable and high-performance’ mobile workstation. The 16-inch pro laptop features an Intel Core Ultra processor with an integrated neural processing unit (NPU) and a choice of Nvidia RTX Ada Generation GPUs, both of which can be used for AI processing.
According to Lenovo, the integrated NPU is dedicated to handling light, continuous AI tasks, while the Nvidia RTX GPU with Tensor Core technology is meant for more demanding day-to-day AI processing, including AI inferencing and training.
Beyond AI, most designers and engineers will likely use the laptop for CAD and entry-level visualisation workflows, taking advantage of the ray-tracing, and graphics capabilities of the Nvidia RTX GPU. www.lenovo.com
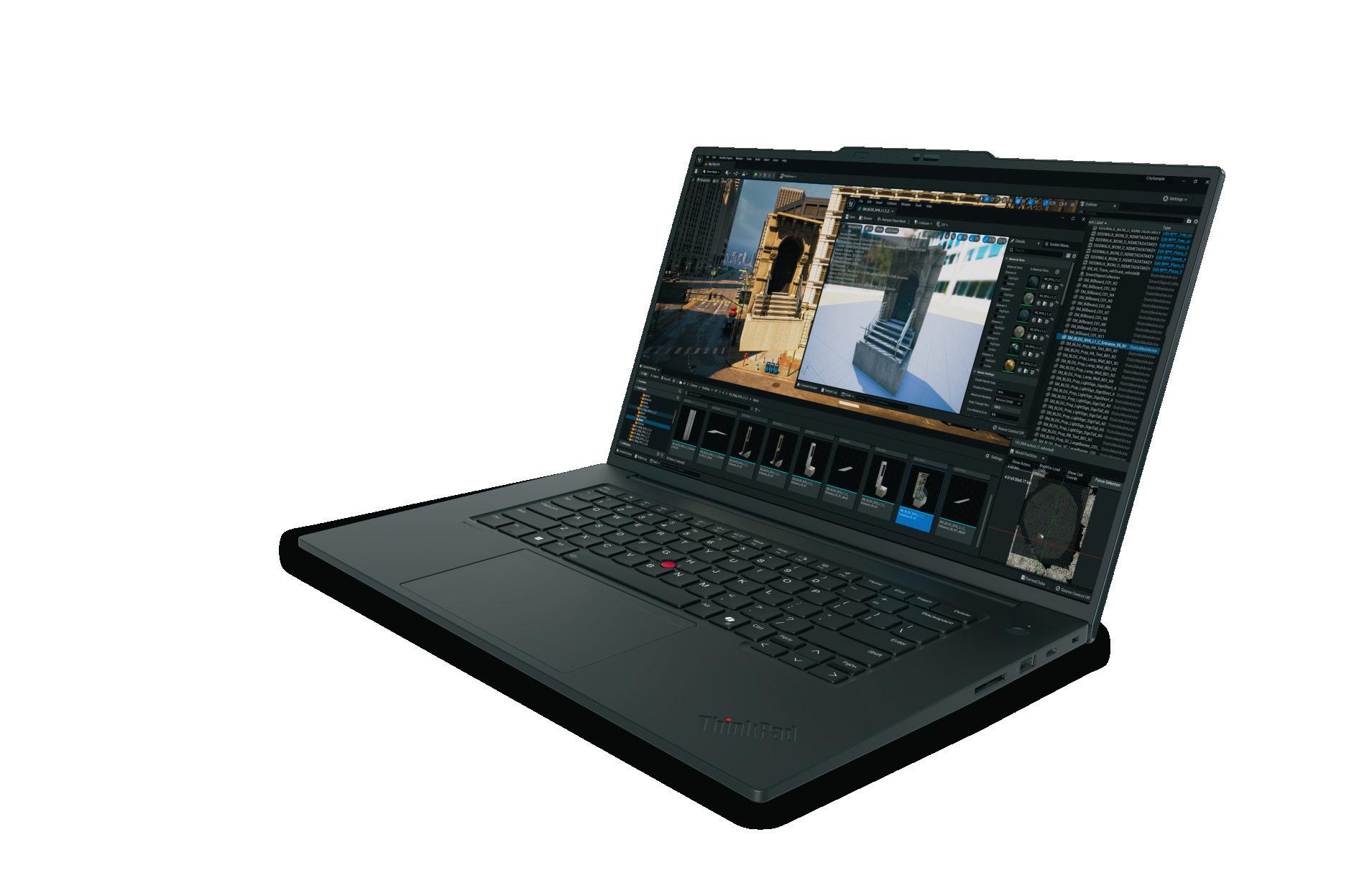
Nvidia finally brings RTX to entry-level
Nvidia has launched the first entry-level pro desktop GPUs to feature RT cores for ray tracing and Tensor cores for AI.
The Nvidia RTX A400 (4 GB) and RTX A1000 (8 GB) are built on the Nvidia Ampere architecture, which was first introduced in 2020, and not the Nvidia Ada architecture used in its most recent Nvidia
The Nvidia RTX A1000 is said to deliver over 3x faster generative AI processing for tools like Stable Diffusion compared to the previous generation

RTX 2000, 4000, 4500, 5000 and 6000 class professional GPUs.
According to Nvidia, the new GPUs have AI processing capabilities that surpass traditional CPU-based solutions, enabling professionals to run AI applications, such as intelligent chatbots and co-pilots, directly on their desktops.
With 72 Tensor cores, the Nvidia RTX A1000 is said to deliver over 3x faster generative AI processing for tools like Stable Diffusion, compared to the previous generation Nvidia T1000, which only had CUDA cores. Stable Diffusion is used for conceptual design.
Both GPUs also offer ray tracing capabilities for next generation CAD software and entry-level viz tools and will likely be predominantly sold in compact workstations like the HP Z2 Mini G9. www.nvidia.com
External box gives GPU boost
Zotac has unveiled a new external GPU Box that plugs into a compact desktop or mobile workstation to boost GPU performance for rendering, AI and other workflows.
The ZBox Pro External GPU Box features an embedded workstationgrade MXM 3.1 Type-B form factor Nvidia RTX Ada Generation laptop GPU (2000, 3500 or 5000) that is typically used in mobile workstations. It connects to the workstation via Thunderbolt 3, and can be used for shared GPU access amongst small to midsized teams. www.zotac.com
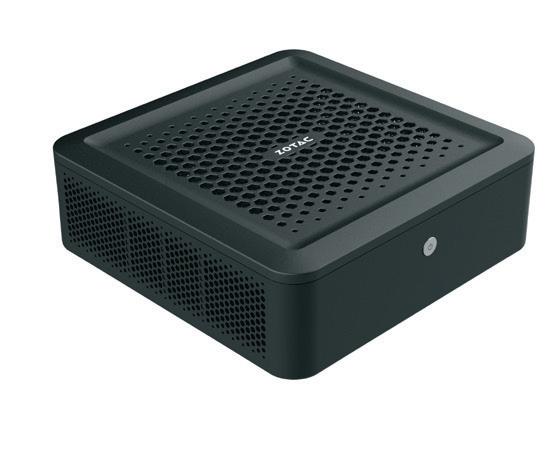
LENOVO THINKPAD P14S GEN 5 AMD GETS AI BOOST
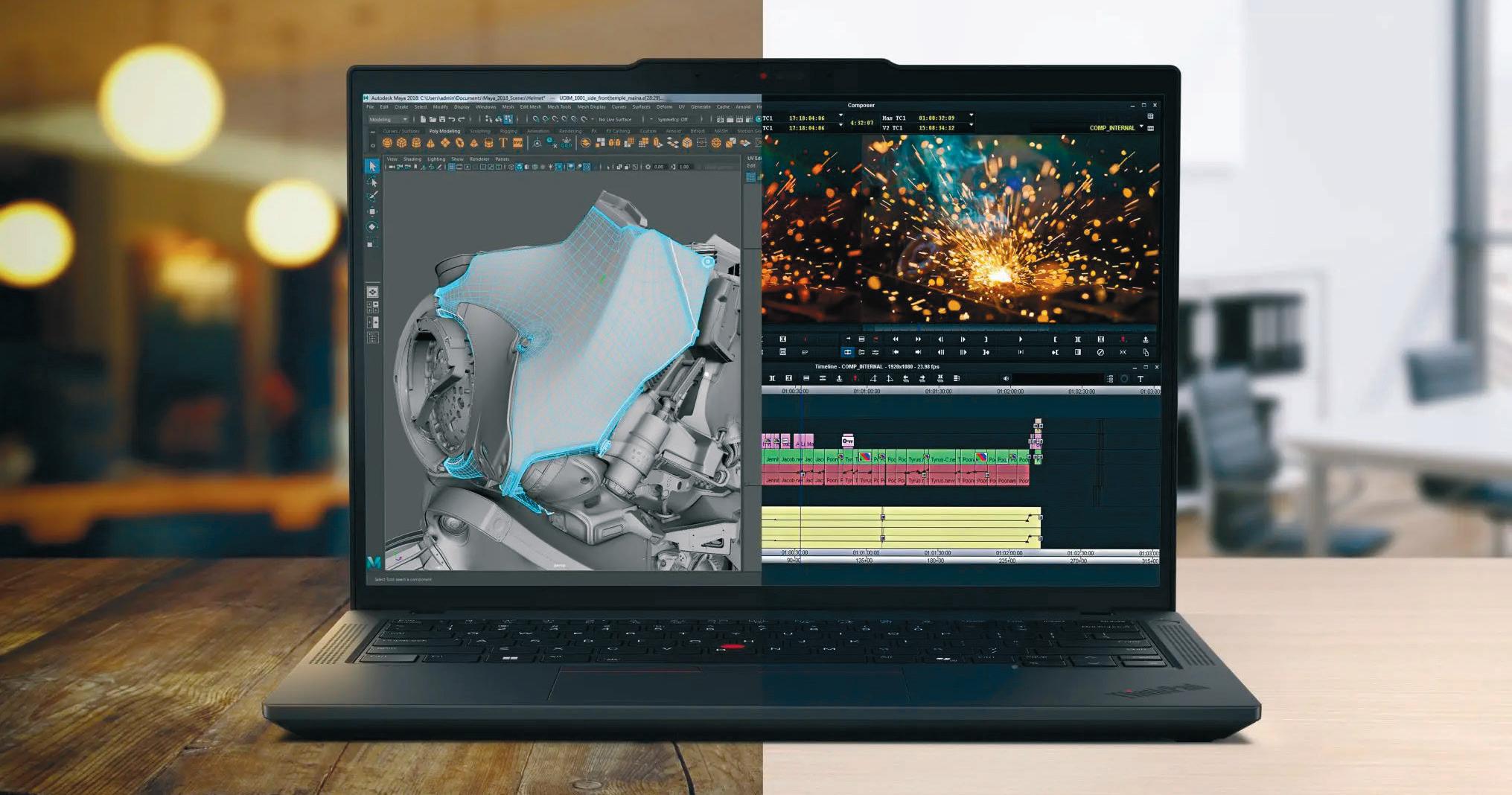

Lenovo has launched the ThinkPad P14s Gen 5 AMD, a 14-inch mobile workstation powered by the new ‘ultra efficient’ AMD Ryzen Pro 8040 HS-Series processor.
The new pro laptop does not appear to be that different to the previous Gen 4 edition. The new AMD processor, which has CPU, GPU, and NPU (Neural Processing Unit) built into the same silicon, has almost identical specs to its predecessor, the AMD Ryzen Pro 7040 Series.
For instance, the new laptop’s top-end AMD Ryzen 7 Pro 8840HS processor has the same AMD Radeon 780M GPU with pro graphics driver, plus 8 cores, 16 threads, and a max frequency of 5.1 GHz.
However, it’s a different story when it comes to AI processing, with the NPU said to deliver 39 AI TOPS, almost 3.5x that of
the previous generation.
The Lenovo ThinkPad P14s Gen 5 AMD comes with a range of independent software vendor (ISV) certifications and, on paper, looks well suited to running CAD tools such as AutoCAD, and Solidworks. The laptop also offers ThinkShield security features and, according to Lenovo, passes comprehensive MIL-SPEC testing for durability.
Other primary specs include up to 96 GB DDR5 memory up to 2TB PCIe SSD, and a choice of 14-inch 16:10 displays, up to a 2.8K OLED (2,880 x 1,800) anti-glare 400nit IPS panel with 100% DCI-P3, and X-Rite FCC. Additional features include Wi-Fi 6E and optional 5G WWAN, and a choice of 39.3Whr battery or customer replaceable 52.5Whr battery.
Elsewhere, it looks like Lenovo has shaved a few millimetres off the chassis. www.lenovo.com
The new Lenovo ThinkPad P14s Gen 5 AMD features a beefed up NPU (Neural Processing Unit) for general purpose AI tasks
WHAT WE THINK
On paper, the Lenovo ThinkPad P14s Gen 5 AMD looks to be a great pro laptop for CAD workflows. It shares the same fundamental processor technology and pro graphics driver as the ThinkPad P14s Gen 4 AMD, which has plenty of performance to run CAD tools like Solidworks, as illustrated in the April / May 2024 Edition of DEVELOP3D Magazine.
Also, with this AMD processor, if you run out of GPU memory, you can borrow more from system memory without the performance penalty you’d typically get from the traditional combination of CPU and discrete GPU.
The ThinkPad P14s Gen 5 AMD might not bring much new to the table in terms of primary processing, but the significantly faster NPU should make the laptop more future proofed.
While we’ve yet to see CAD software developers extract real value from NPUs, with many preferring to use processors in the cloud, designers should certainly derive benefits from NPUs when running general local software, such as Microsoft Copilot and Zoom. Of course, for more intensive AI workflows, such as using Stable Diffusion for concept design, powerful discrete Nvidia RTX GPUs will likely be faster. However, as the ThinkPad P14s Gen 5 AMD has the CPU, GPU and NPU all on the same chip, which can potentially access a whopping 96 GB of memory, far more than you get on a discrete laptop GPU, this could present some interesting workflow opportunities for AI in the future.
AMD Radeon Pro W7900 Dual Slot professional GPU launches
AMD has slimmed down its flagship professional workstation GPU, the AMD Radeon Pro W7900, introducing a new dual slot version of the board.
The new AMD Radeon Pro W7900 Dual Slot (DS) looks to be identical in terms of specifications – 48 GB of GDDR6 ECC memory, 123 TFLOPs of FP16 peak half precision performance and a total board power of 295 W. However, the new design overcomes one of the major limitations of the original triple slot card – that of density in workstations.
In many workstations, even those that can take multiple dual slot GPUs, it was only possible to add a single board, effectively ruling out the Radeon Pro W7900 as an option for those seeking multi-GPU configurations.
With the new AMD Radeon Pro W7900 Dual Slot, AMD says it has qualified the use of up to four cards in a single workstation chassis.
AMD is pitching the Radeon Pro W7900 DS as a cost-effective alternative to the Nvidia RTX 6000 Ada Generation GPU, which also comes with 48 GB of memory.
Priced at $3,499, AMD claims the GPU offers close to 2x performance per dollar in digital content creation (DCC) applications including Autodesk 3ds Max and DaVinci Resolve.
AMD is also highlighting the GPU’s credentials for Generative AI workflows. With the forthcoming AMD ROCm 6.1 open compute software stack for Radeon GPUs, AMD says it will be possible to develop for more AI frameworks, thanks to the addition of TensorFlow. ROCm 6.1 also supports multi-GPU and comes with beta
support for Windows.
To learn more about the AMD Radeon Pro W7900, read our in-depth review in the June / July 2023 DEVELOP3D Workstation Special Report. www.amd.com/radeonpro
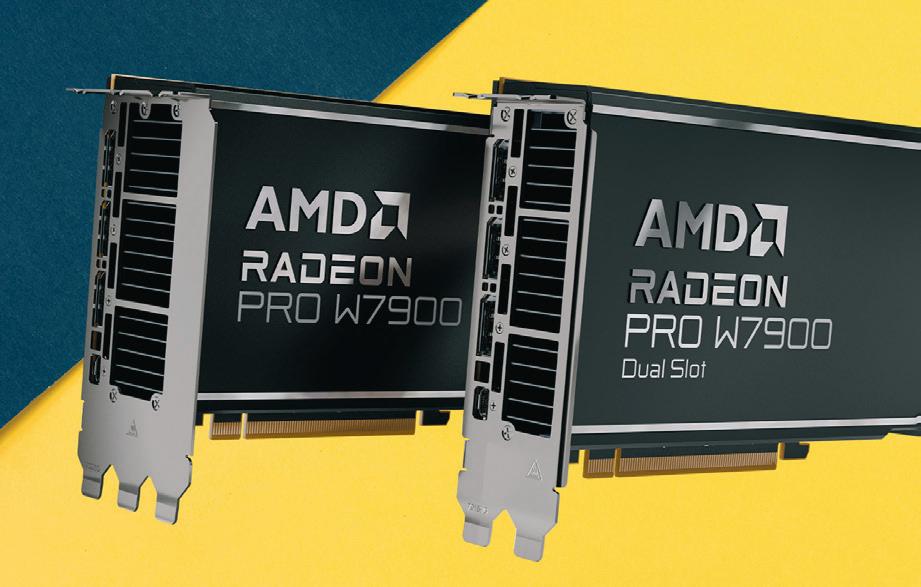
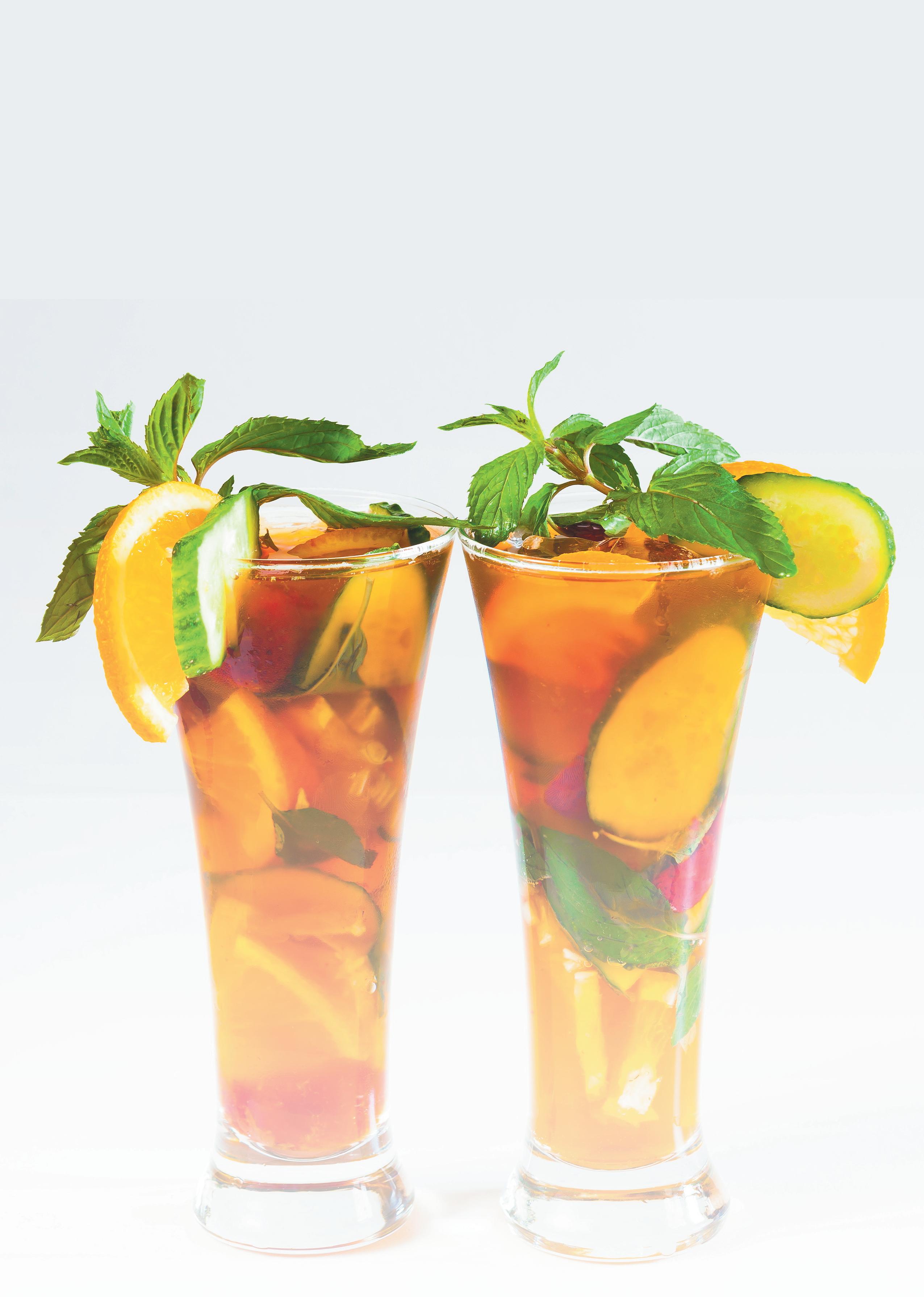
Meshless simulation has experts
impressed, but can it really deliver a successful merger between the worlds of simulation analysis and product design? It’s doubtful, according to regular contributor Laurence Marks
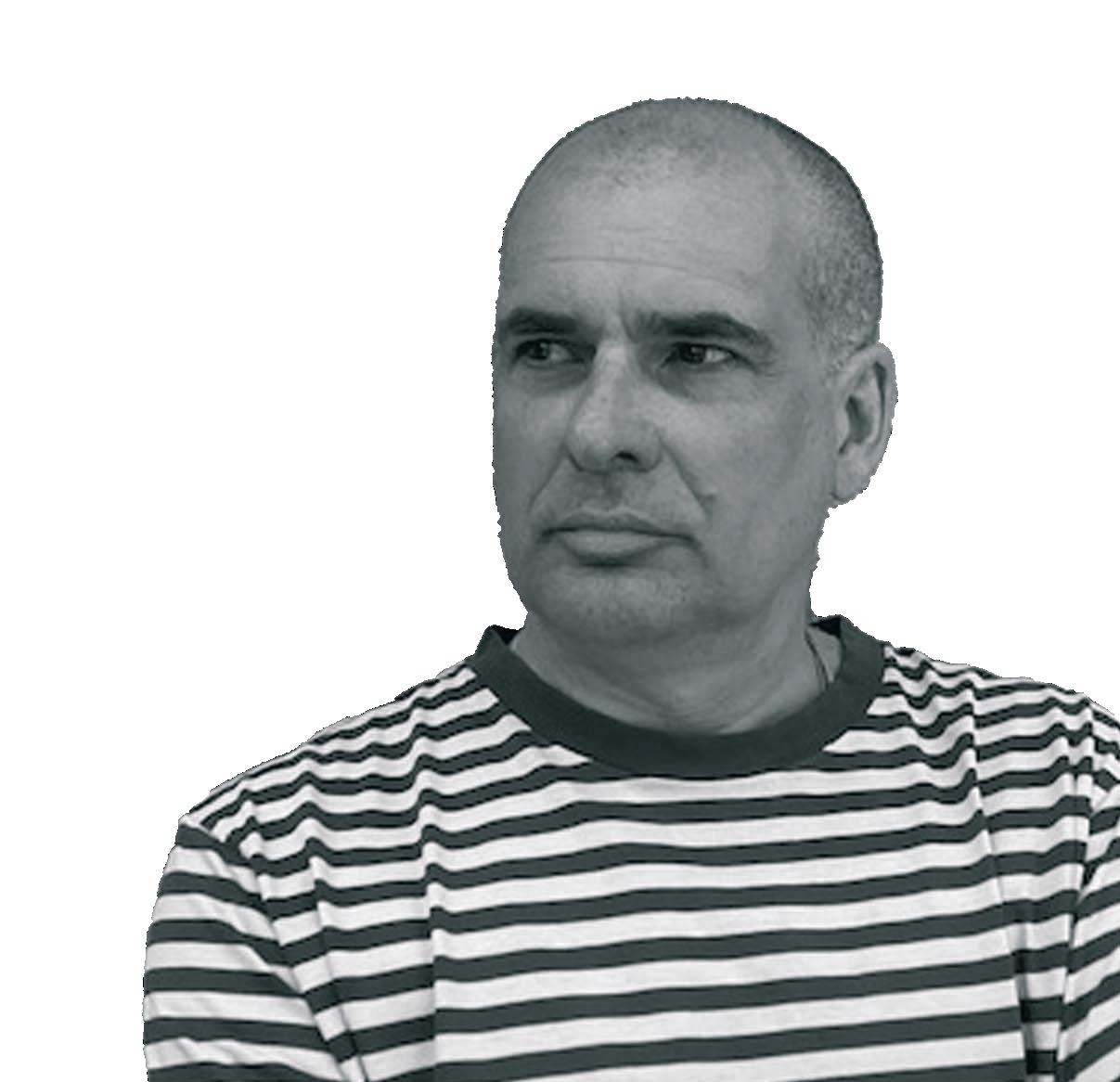
For years, people have talked about meshless simulation as the future. Various systems have entered the market, in various guises, all waving the meshless banner. But it’s fair to say that none of these have so far had much impact on the average designer or engineer’s view of the world.
Yet things seem to be changing. Superexperienced simulation analysts now report great advances in meshless technologies – and if there was a group you might expect to be all about the meshing, it’s them.
So, what are they saying? Well, they say you can set up models in a super-quick time; that automatic set-up on interfaces is reliable; and that you can get a credible solution very rapidly. And don’t forget that these are the sort of people who check this stuff to the nth degree.
Obviously, the software has evolved from ‘promise-high, deliver-low’ solutions to systems that actually work, even in the demanding and ubercynical world of the professional analyst.
This has got me thinking about products from the 1990s, and in particular, the new CADintegrated simulation tools such as Rasna, CosmosWorks, Designspace that were greeted with restraint by the expert community.
night, selling a system like this?”, during a NAFEMS conference Q&A session.
These calamities largely didn’t occur. Some near-disasters did happen, but not because designers could finally get results themselves from a finite element analysis. What actually transpired was that designers bought these systems but then avoided using them in critical solutions, because for all sorts of really good reasons, they didn’t feel comfortable or empowered to make critical decisions.
They generally left these to the experts, who are now finding many of the benefits of this sort of UI methodology, now powered and enabled by meshless.
DO IT YOURSELF?
Where things may have changed is in the actual understanding of the solver technology by users. During the 1990s, I got so sick of others boasting of how they had written their own solver that I simply got on and wrote my own. It was a lot of work just so that I could say “So did I,” – but it was worth it. I’m that sort of person.

If you aren’t old enough to remember that far back, it was thought that these tools could be responsible for aircraft falling from the air, for cars failing at critical moments, and for meltdowns at nuclear power stations – all sorts of calamities. A career highlight for me was being asked, “How can you sleep at
The point here is that any betterthan-average FEA user in the 90s could probably have written some form of FEA solver. Not a great one, to be sure – but they’d have known where to start and how to finish.
But a meshless solver? That’s not something an average FEA user could start, finish or even contemplate writing. And recognising this gives you a very different perspective on the technology and how you use it.
The meshless bit really is the enabling technology. After all, it’s not the core technology that matters. As long as it
Meshless technologies have evolved from ‘promise-high, deliver-low’ solutions to systems that actually work, even in the demanding world of the professional analyst
works, it’s relevant and therefore useful. It’s how that technology integrates with the overall simulation and design workflow that is ultimately the true metric of success.
Does this spell the end of the nearubiquitous automatic tetrahedral mesher and sparse iterative solver technology? And does this mean that the world of the professional analyst is merging with that of the designer? The answer, in both instances, is almost certainly not.
One thing I’ve learned in the world of simulation is that big shifts in technology are rarely followed quickly by equivalent levels of adoption or changes in roles. And for some reason I’ve never really understood, people are typically happy fighting with an inferior but familiar technology, even when altogether better solutions are readily available.
Meshless simulation software packages, such as Altair SimSolid, eliminate geometry simplification and meshing, the two most time-consuming and expertise-heavy tasks carried out in traditional FEA
Overall, this highlights one aspect about simulation, simulation engineers, and their role within projects and organisations –and that’s that progress with software is often not about software at all. Instead, it’s about understanding real-world structures and real-life ‘pull it until it breaks’ materials. If you don’t have that understanding, then the choice between mesh and meshless is irrelevant.
ABOUT THE AUTHOR: Laurence Marks built his first FEA model in the mid-1980s and his first CFD model in the early 1990s. Since then, he’s worked in the simulation industry, in technical, support and management roles. He is currently a visiting research fellow at Oxford Brookes University, involved in a wide range of simulation projects, some of which are focused on his two main areas of interest: life sciences and motorsports.
Relationships are tricky and can go through some rocky
patches – especially the relationship that a company has with its additive manufacturing bureau.
Here, our regular columnist SJ lays their feelings on the line
Dear AM bureau, l am writing to say that I feel like the vibes have been off lately. I’m picking up what you’re putting out. You need me – and your other customers –to be more demanding.
Like, when we’re on a high, and requesting quotes for quantities in the thousands, the vibes are immaculate. Communication is on point, email responses are prompt, home visits are super-friendly. The frequency of our calls may be lower, but the quality of those calls is much higher.
But, when we’re in our lows, it’s chaotic. I give you the news that we were outbid by a competitor, or that the programme wants to stick with a safer, more conservative manufacturing method, and instead of comforting me and acknowledging my feelings, you go on and on about how I never come through for you and how I put your business at risk with false hopes and expectations. Like, come on – what did you expect? We’re both grown adults here!
I mean, don’t get me wrong, I’m totally into you. But, like, not exclusively. You know how ‘vendor lock’ really cramps my style. When you’ve got that rizz, being tied down to just one partner gives you the ick.
I know it’s really hard to put in all the work that you do to make me happy and then see me out at conferences talking to someone else, acting like I don’t know you, like I wasn’t just at your site just the week before, like I’m not in your DMs right that second asking for even more quotes. But you’ve gotta give me some breathing room.
Our current relationship just isn’t working anymore. In the beginning, you were so happy to do the little one-off jobs for me. Now, all you ever want is production. And, babes, I’m so happy to give you production – but you’ve got to upgrade your quality system, to invest in it. It has to eat and leave no crumbs if we ever want to be making qualified, flight-ready hardware together.
TIME FOR A RETHINK
I guess what I’m trying to say is that I’m starting to question if this is what I really want. I mean, the highs are amazing, but the lows are just too much sometimes. And I don’t know if I can keep living like this, wondering if we’re always going to make it through the next financial quarter or if it’s gonna be the end of us.
I’m not saying we should break up or anything – but maybe we need to take a step back and re-evaluate things, because I don’t want to be stuck in a toxic cycle forever, you know?
I’m out here grinding, making moves, and I need a supportive partner by my side. I need you. Because without you, I wouldn’t be able to order parts.
Without you, I wouldn’t know my way around a build plate. I couldn’t even speak DFAM until you showed me the right angles, the max hole sizes, the best aspect ratios, the difference between a watertight wall and one that’s pressure-proof. And who can forget all those late-night rushed emails we had around support designs?
It took multiple meetings for you to explain that supports were just fancy lattices. I never told you this, but I really appreciated you letting me come over to your house to show me how supports are removed and the whys and hows of that. My respect for you grew considerably.
Especially when you showed me the variety of printers and materials you had to offer me. It was an impressive spread and I was touched by your generosity. In the spirit of that, I want to be more honest with you. I was all rough edges and no contour until your process parameters lasered their way through my heart.
REACHING A COMPROMISE
Maybe, we can compromise? I’m more than willing to open up a couple of tolerances for you, if you can promise me better quality on the post-process side. And we can talk more about bringing down material testing costs

Perhaps we can find a compromise? I’m more than willing to open up a couple of tolerances for you, if you can promise me better quality on the postprocessing side
if you’re willing to get on board with sharing in-situ monitoring data on the machines. I can’t reign in my overbearing and costly inspection requirements, but I can move those requirements to be for specified classes of parts and give you a different, less intense inspection process for low risk/ non-critical product lines.
Does that sound do-able on your end? Are you willing to meet me in the middle here?
The key to a successful partnership is one where we make efforts to grow together and to support each other in our shared goal: a healthy and sustainable manufacturing industry.
I need someone who’s gonna hold it down for me, not someone who’s gonna bring me down. I hope you understand where I’m coming from. Anyway, I just needed to get this off my chest. Let’s talk about it sometime, yeah?
Your (toxic) customer, SJ
P.S. Have you even read the ‘RevC_Final_ FinalDrawing_thisone.dwg’ that I sent over last night at 3am?
P.P.S. Well, obviously I’m still sending model updates after you’ve started the print file, babe. That’s who I am. Didn’t we discuss that you wanted me to be more demanding?
ABOUT THE AUTHOR: SJ is a metal additive engineer aka THEE Hottie of Metal Printing. SJ’s work involves providing additive manufacturing solutions and 3D printing of metal parts to help create a decarbonised world.
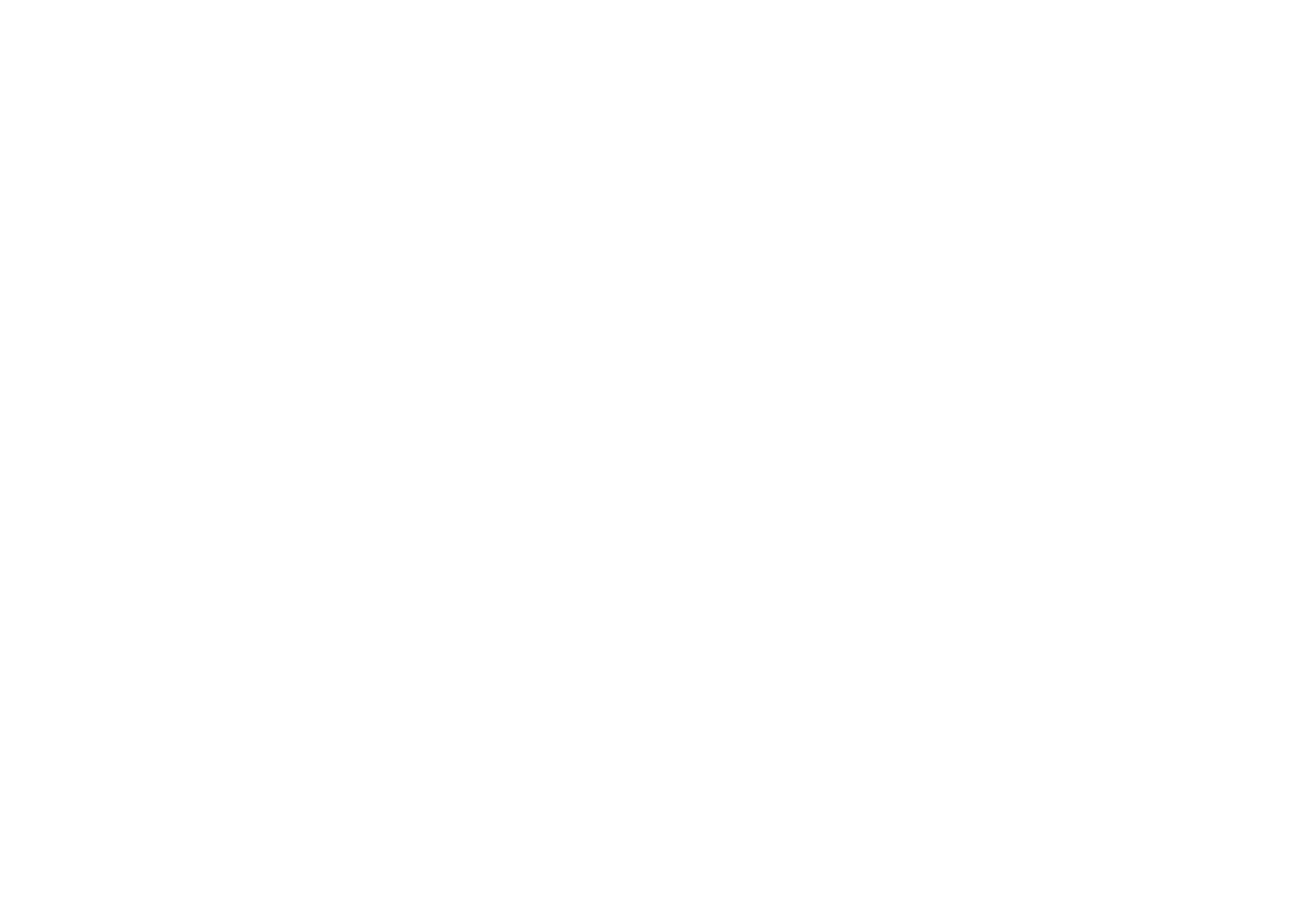
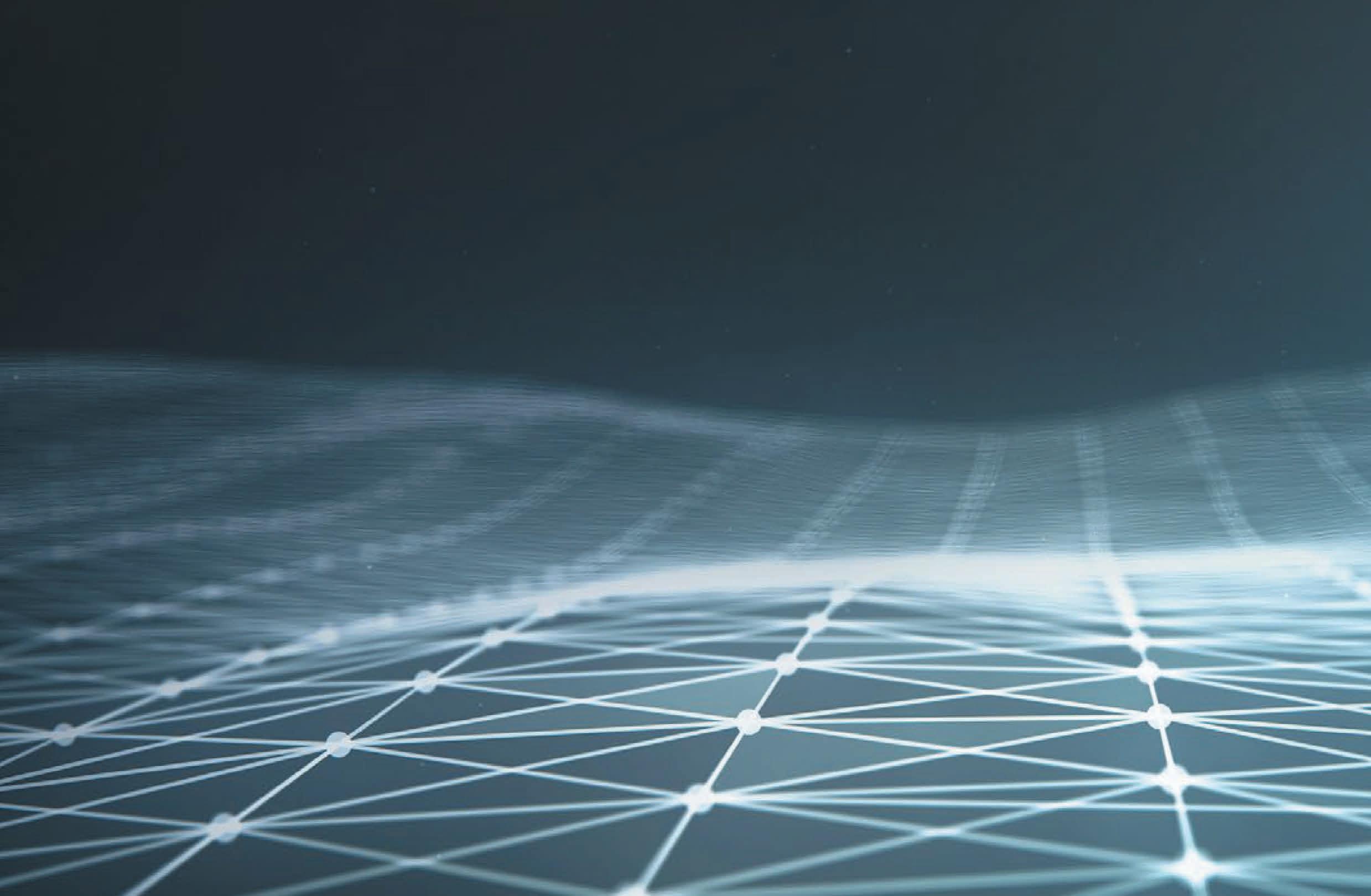
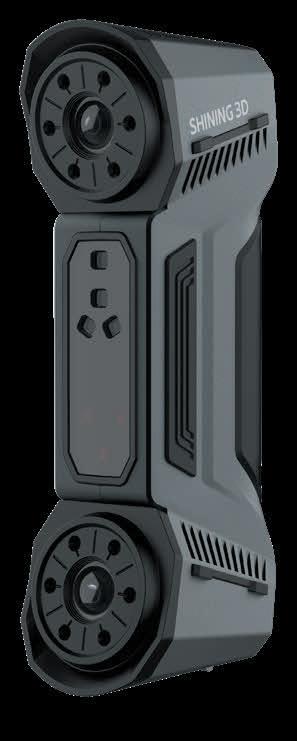
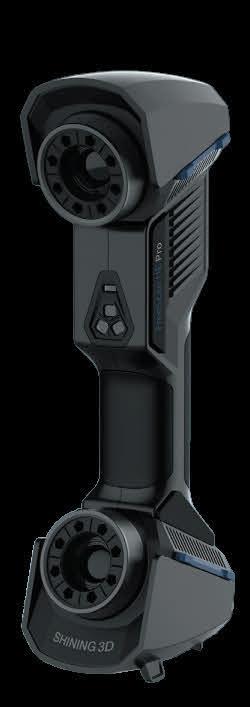
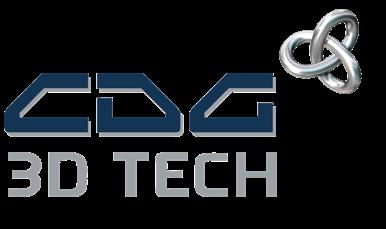

VISUAL DESIGN GUIDE CALLUM DESIGNS EVITA
Callum Designs has partnered with Motability Operations to create a functional and accessible electric vehicle designed for wheelchair users
CHARGING UP
Two charging points mean ease of access for users. One is found on the vehicle’s nearside and the other is mounted on its front
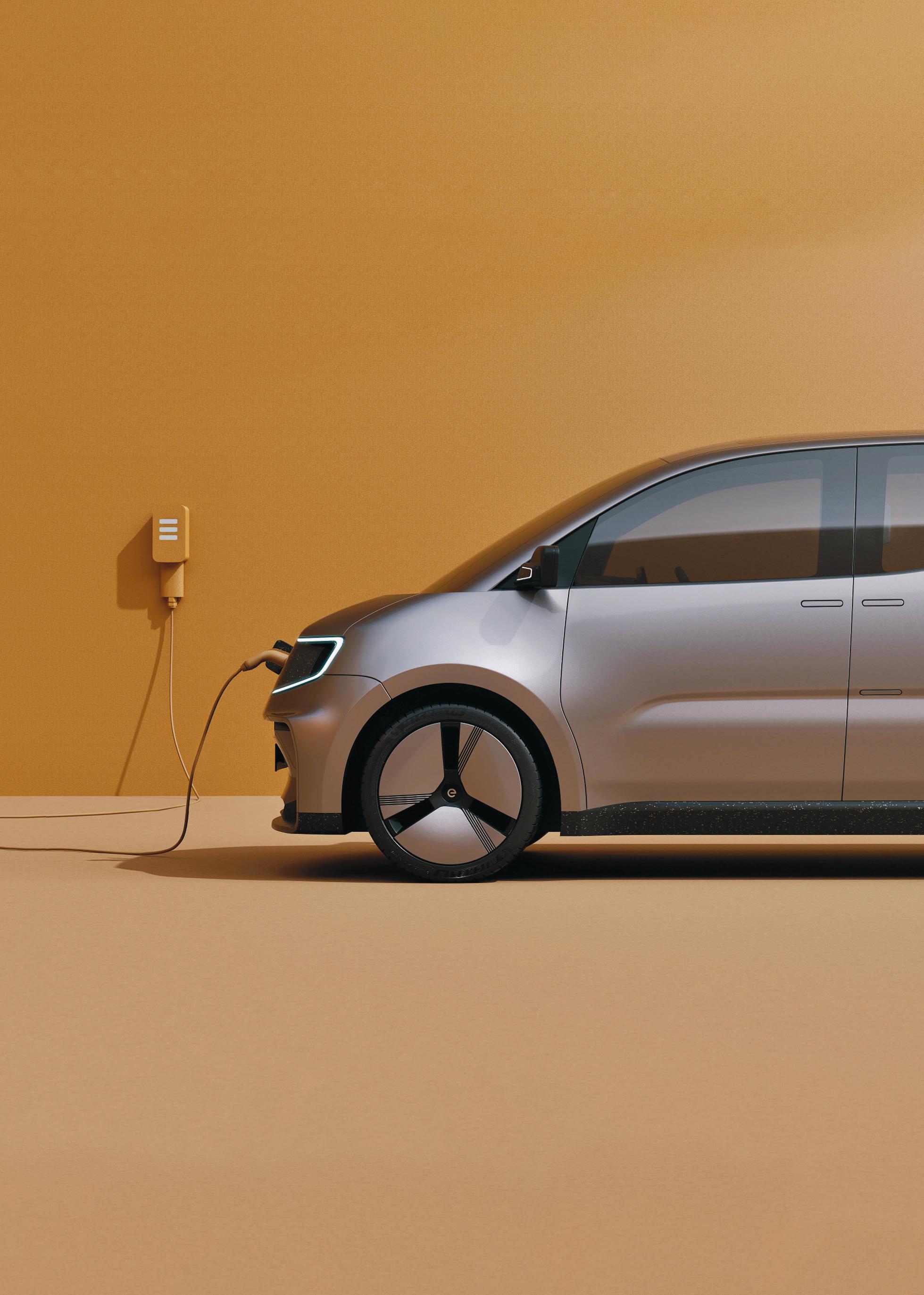
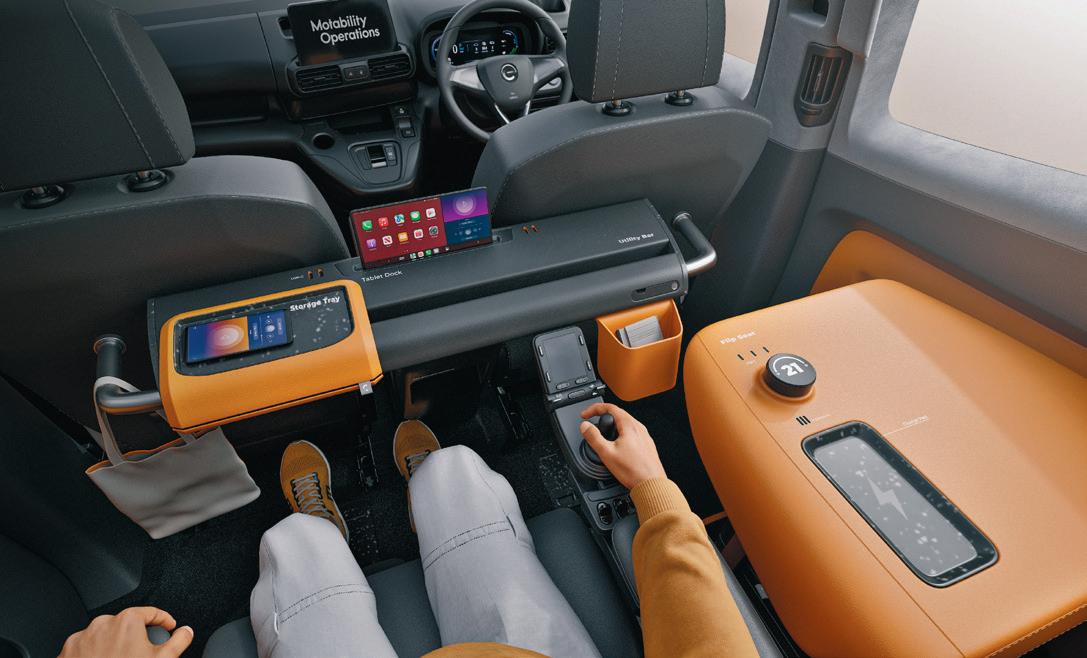
LOW TO GO
A lower seating position in the cabin gives wheelchair users more headroom, improved visibility and the ability to sit at the same height as other passengers
STAYING IN CONTROL
A utility bar in the back of the car means that the passenger can control heating and air conditioning, charge devices and store belongings
KEEPING THINGS EVEN
The eVita’s EV battery has been repackaged to reduce size, allowing it to be positioned under the floor behind the first row of seats without intruding on the space needed to allow wheelchairs to easily enter the vehicle
REACHING OUT
The upper section of the split tailgate acts as an extension to the roof, keeping passengers dry in wet weather when entering and exiting the vehicle using the automatic ramp
LIGHT AS A FEATHER
Lightweight materials have been used everywhere possible in the eVita, in order to offset the added weight of onboard equipment
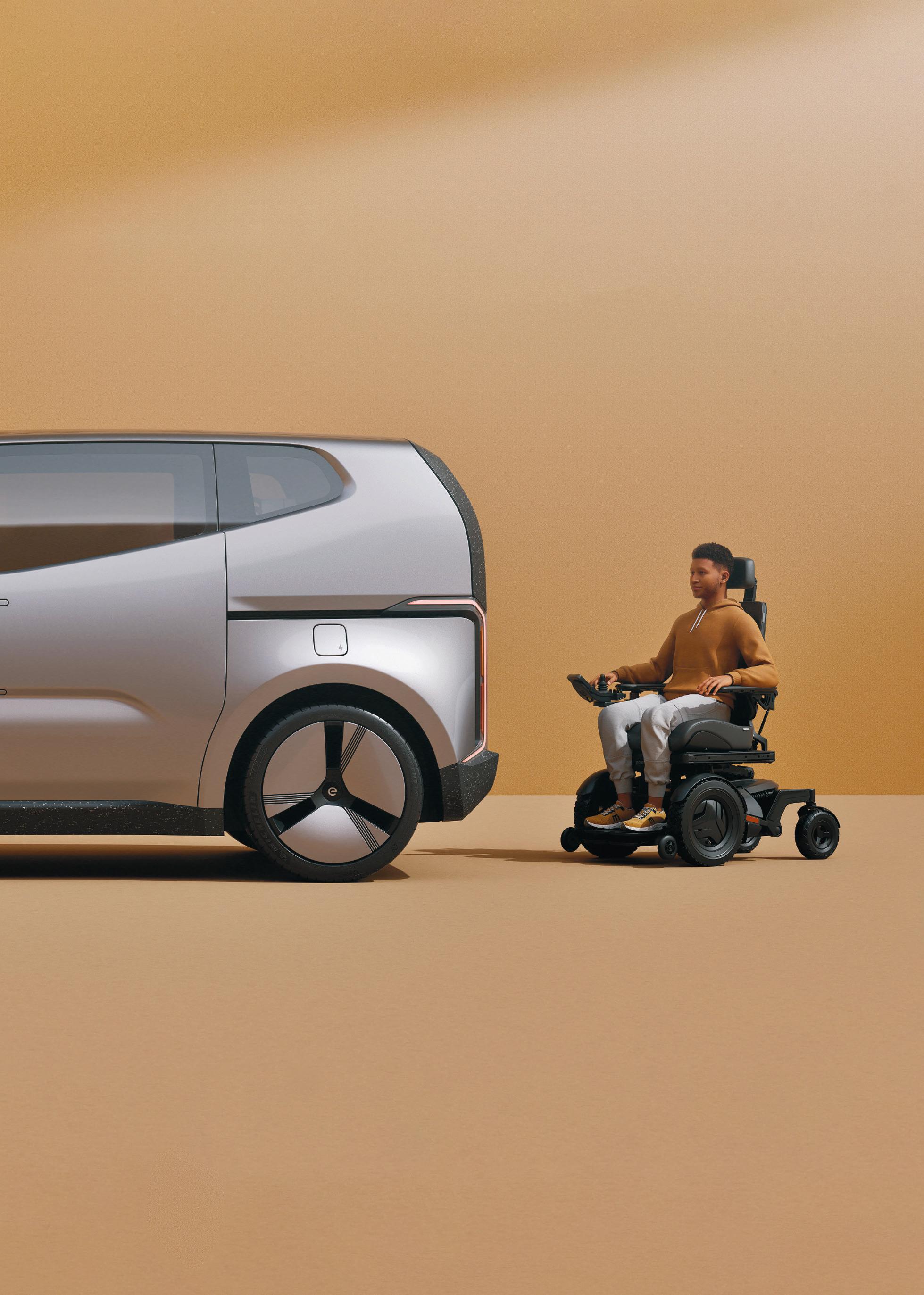
SMOOTH SAILING
Highly damped rear suspension means predictable handling and roll-minimising control to reduce bumps when navigating roundabouts and over potholes

EVITA is a concept vehicle designed to showcase potential advancements and spark innovation within the automotive industry. It is not currently available as a production vehicle www.callumdesigns.com
LIGHTING UP
An energy-efficient LED puddle light projects the space required for the extended ramp onto the ground when parking
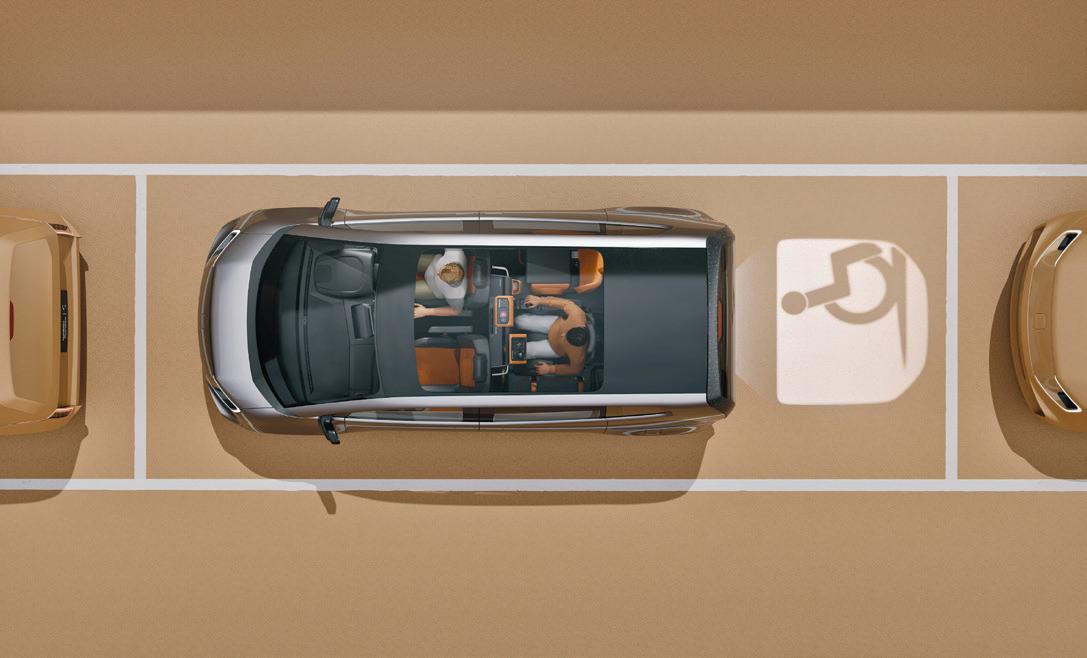
STARTYOURENGINES

YOURENGINES
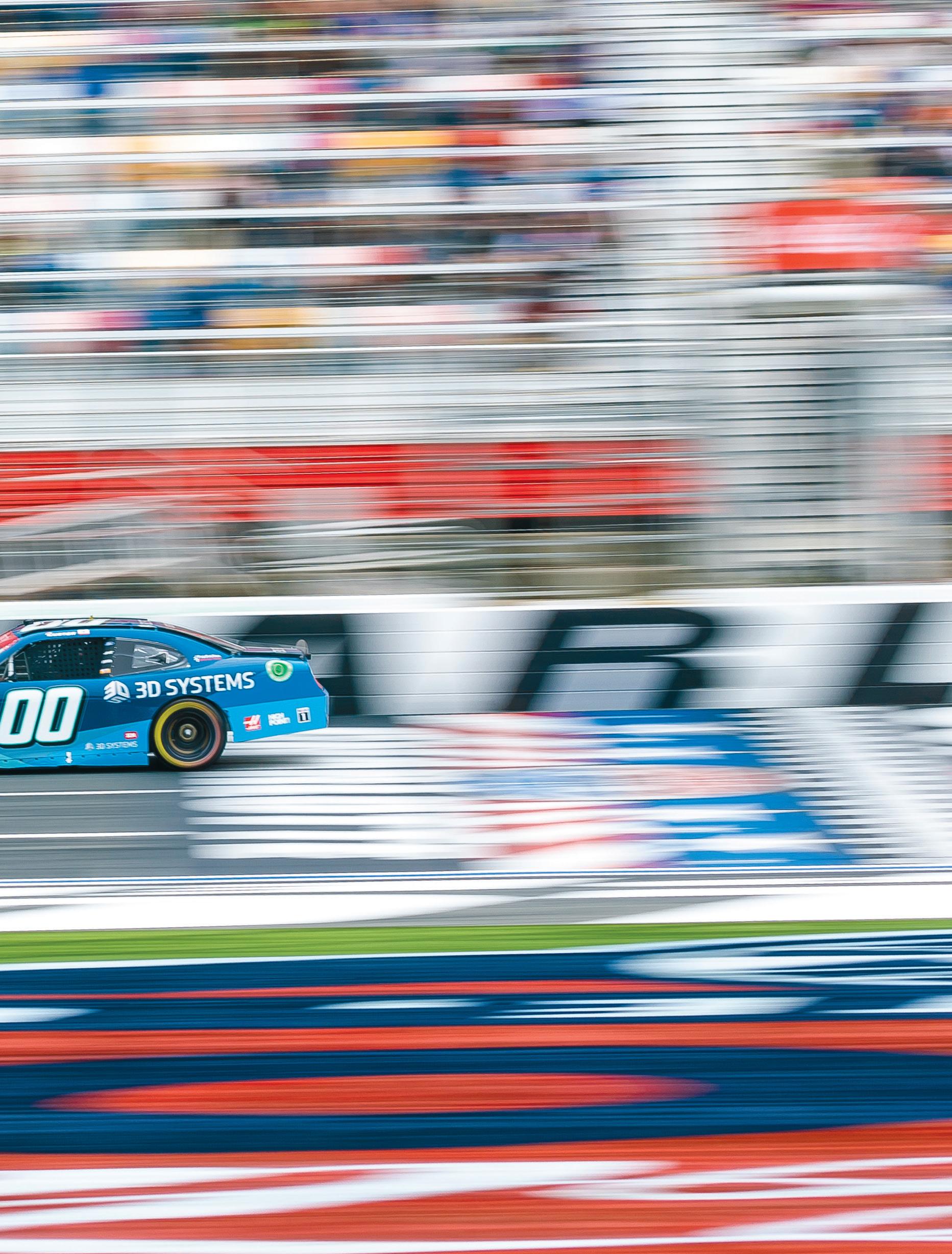
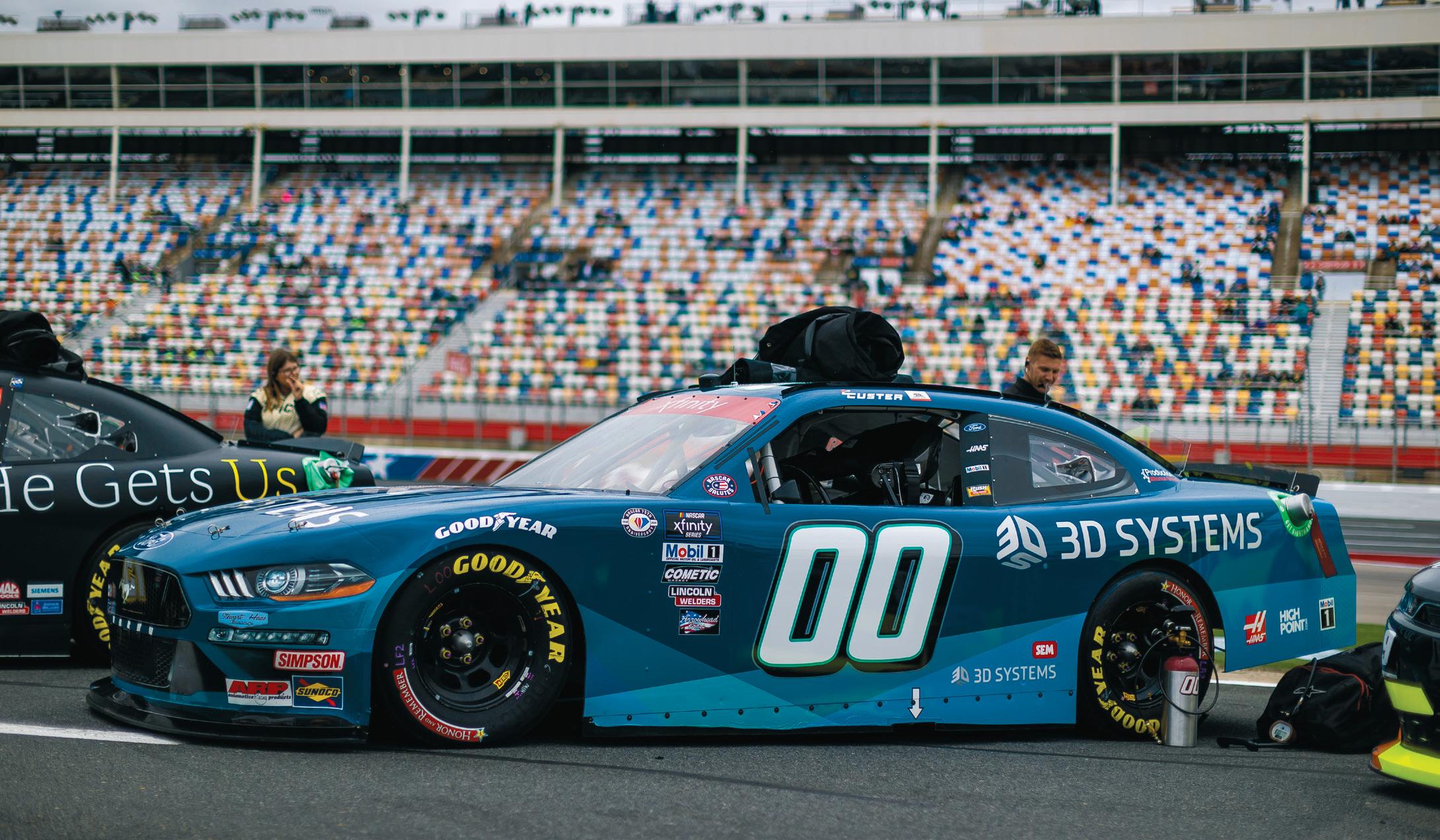
» Stewart-Haas Racing is a hub where smart mechanics, cutting-edge aerodynamics and ingenious engineering all come together. Stephen Holmes ventures to the heartland of NASCAR development to find out what it takes to cross the finish line first
The huge main hall at StewartHaas Racing is a hive of energy.
Mechanics and engineers swarm around four NASCAR Cup cars in the final stages of assembly, as the clock ticks down to the next race.
Heads are buried deep in engine bays, trolleys rattle along filled with parts, and vital measurements are taken, ready for the cars to be loaded into specially built haulers and driven to the racetrack for the fast-approaching weekend. This team has experienced the kind of success you’d expect from one co-owned by three-time NASCAR Cup Series champion Tony Stewart and Gene Haas, an automotive obsessive and founder of Haas Automation, one of the world’s largest CNC machine tool builders. Starting out with two Cup cars in 2009, Stewart-Haas
Racing has now won over 70 races across the Cup and Xfinity series. Today, it has four cars in the Cup series, two in Xfinity. All of the drivers – each with their own car, engineers, mechanics and race staff – share the facility in Kannapolis, North Carolina, elbow-to-elbow with their race day rivals. Located a short sprint north of the Charlotte Motor Speedway track, the area is home to many NASCAR teams and the beating heart of the sport.
The cavernous main garage of Stewart-Haas Racing is flanked by numerous workshops and storage facilities, with an annexe for the shorter and lighter Xfinity cars, a pit crew training area and storerooms filled with row after row of components and spares.
Giant pennants dangle above the main atrium where the Cup cars are fettled and fixed. Acknowledgements of two Cup titles, two Xfinity championships and victories that include globally known races such as the Daytona 500 and Brickyard 400 hang from the rafters alongside many others.
‘‘
We don’t just build one car and race it all season. Every weekend, there’s a new track and new cars to race on that track Reneau Van Landingham, Stewart-Haas Racing
“We like to hang banners here in our shop,” says Reneau Van Landingham, production manager at Stewart-Haas Racing, pointing to the ceiling. “We are literally measured by the performance that we have throughout the race. That’s why we’re all here. We’ve got an engineering group and the fabricators that are all working together towards that end.”
While the entrance lobby and gift shop that overlook the main garage are open to the public, NASCAR is as secretive as any other motorsport. At Stewart-Haas Racing, high-level CFD simulation and engineering work happens very much behind the scenes, in an upstairs room overlooking the garage floor. Mirrored glass, reflecting the winners’ banners hung opposite, keeps even the keenest eyes from prying.
MEASURE UP
Car specifications are governed by NASCAR’s rulebook, yet each track that the drivers face is unique, varying in length, banking angles and climate. That means that every car must be designed and built specifically to tackle it.
“We don’t just build one car and race it all season. Every weekend, there’s a new track and new cars for that track. And when the cars come back here after the race, they’re completely torn down and rebuilt for the next race,” says Van Landingham.
With races running from February through to early November, the Xfinity Series races take place 33 times a
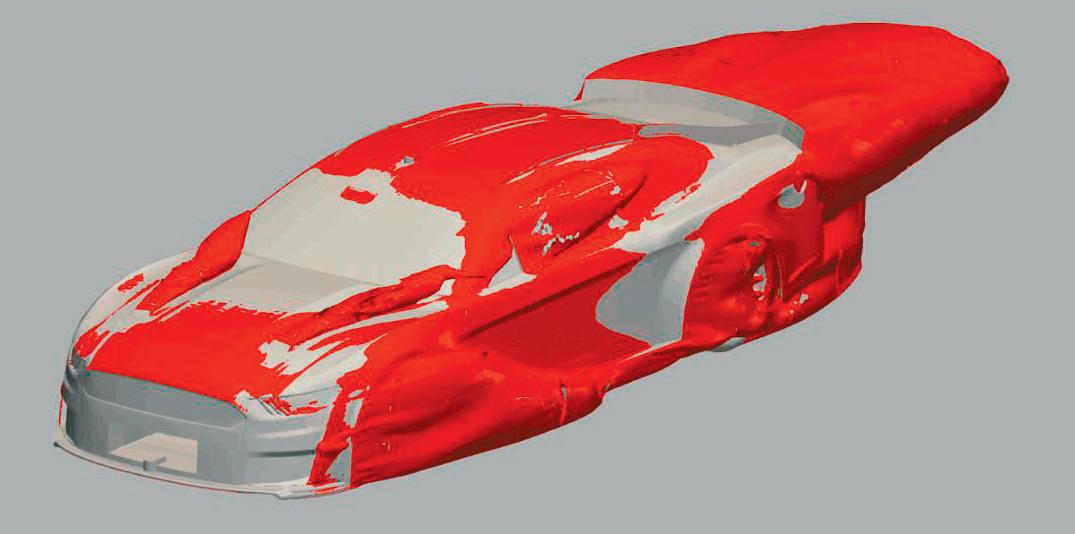
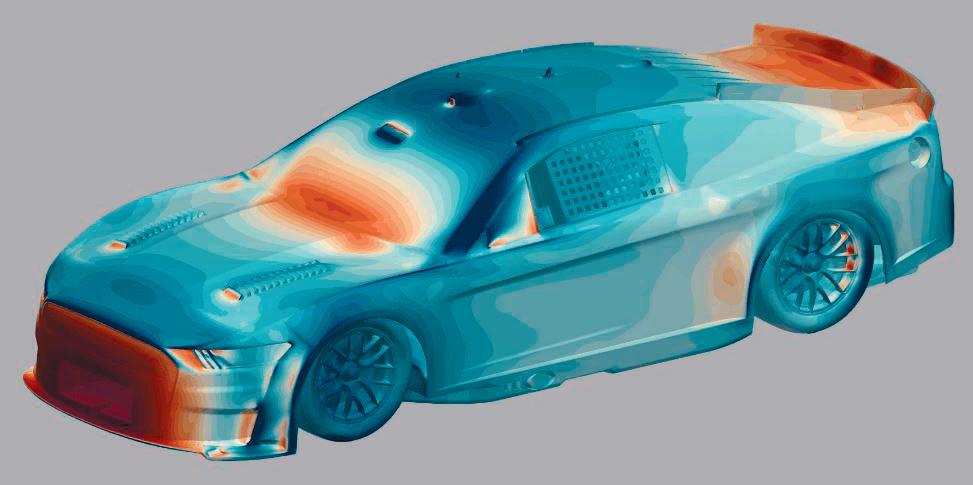
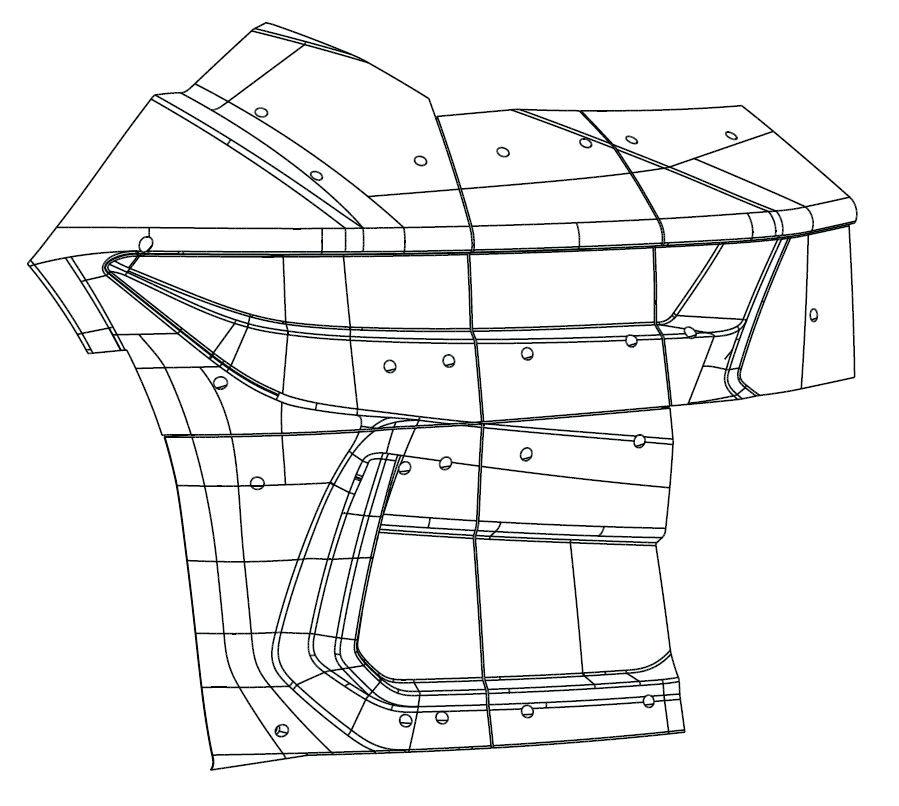
year, with five or six weekends off. The Cup Series boasts 40 races in a season, including a 30-race stretch of racing every weekend. By way of comparison, Formula 1 teams typically race bi-weekly, 24 times a year.
Stewart-Haas engineers responsible for preparing the cars also head out to the tracks, so any race delays due to adverse weather severely impact the cars’ development schedule.
Aerodynamics is a big component of the performance equation, with body panels assembled precisely and fixed to cars to enable the best possible performance. Short tracks have different specifications compared to longer tracks, and a Speedway track will be different to a road course, so every millimetre of the car’s surface is optimised to suit.
All the body panels used in NASCAR are made from carbon fibre-reinforced plastic that provides more race durability and cost savings than the stamped steel of old, with Stewart-Haas working with a specialist fabricator to turn around parts in time for each race.
Each panel, its placement and how it’s mounted on the car has to comply with a NASCAR-specified range, giving teams room to play with that amounts to just 300/1000ths of an inch – or 7.62mm.
Cars are scanned throughout the build process, with portable Hexagon Romer Arms being used to capture individual part data, and then in the team’s optical scanning station, using a replica of NASCAR’s on-track Hawkeye system, meaning that every car should make it to the starters flag without a snag.
NEXT TIME FASTER
In preparation for the 2024 season, Stewart-Haas Racing’s aerodynamic engineering team played a critical part in determining the best performance design for the Ford Mustang car that all Ford-badged teams race.
The Ford Mustang Dark Horse project needed not only to reflect the key sponsor’s latest roadgoing vehicle incarnation, but also to be able to handle the requirements of NASCAR racing and meet the race authority’s guidelines.
For submission projects, the Stewart-Haas Racing team works alongside Ford’s industrial designers and the styling group to get a preview of what the next year’s Ford Mustang will look like. “We usually say, ‘Wow, that looks really great! But it’s not going to perform the way we need it to perform on the track at 185 miles per hour!’” laughs Van Landingham.
It’s down to the designers and engineers at StewartHaas Racing to encapsulate the spirit of the new Mustang, retaining the many distinctive lines and angles of its styling, while adapting it for the aerodynamic demands of stock car racing.
The whole process can last for months, with back-andforth discussions, designing and testing prototype parts both in CFD and in the wind tunnel that can improve downforce on the car.
‘‘ We
don’t have a ton of sensors on the cars. NASCAR doesn’t allow it. The driver is the only one who can tell the team what’s going on Cole Custer, StewartHaas Racing
’’
What’s vital is that the end result of that process still retains and reflects the Mustang’s unique style. As Van Landingham puts it, Ford wants its cars “to win in the races on Sunday, and for people to go and buy those Mustangs on Monday.”
With that in mind, once CFD analysis has identified the most favourable designs and configurations, engineers then convert the CFD surface meshes into solid CAD models, before dividing designs into large tiles that can be 3D printed using a 3D Systems ProX 800 SLA 3D printer.
Once printed and assembled, the tiles are designed to be attached to the sub-frame chassis of a full-scale car before being tested in Haas Automation’s Windshear wind tunnel, based at nearby Concord airport.
SPRINT TO THE FINISH LINE
Travis Jack is a mechanical engineer from the aerodynamics department who runs the team’s 3D printing lab. Overseeing a range of 3D printing technologies, including the ProX 800 SLA and a Figure 4 Standalone unit also from 3D Systems, he has FDM machines and more at his disposal.
To develop the Dark Horse Mustang parts, Jack used 3D Systems’ 3D Sprint software to orientate the CAD models to be printed, optimising print speed, quality and quantity per build platform.
Working with Accura 25 resin allows for fast and accurate parts, he says, while the ProX 800 build volume allows for the largest parts possible to be produced.
“It’s just a great tool for doing this type of thing,” adds Van Landingham standing next to the large 3D Systems ProX 800 machine.
“Then we know that the shape of a headlight is a good one, or we didn’t really like it and we want to change the radius to improve the performance. And we’ll do the whole process again.”
For this project alone, more than 2,000 parts were produced over a seven-month timeframe, with the help of Ford’s engineers in Dearborn, Michigan.

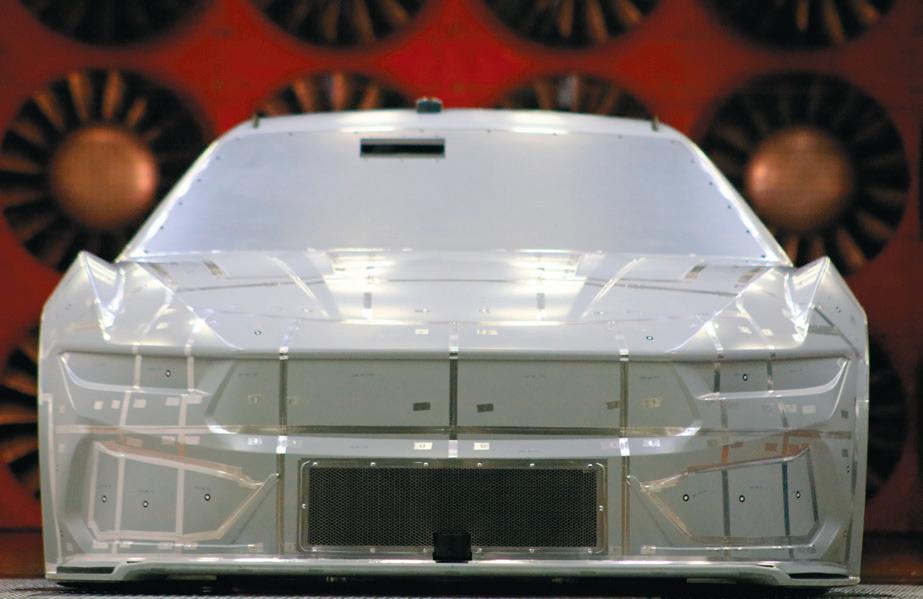

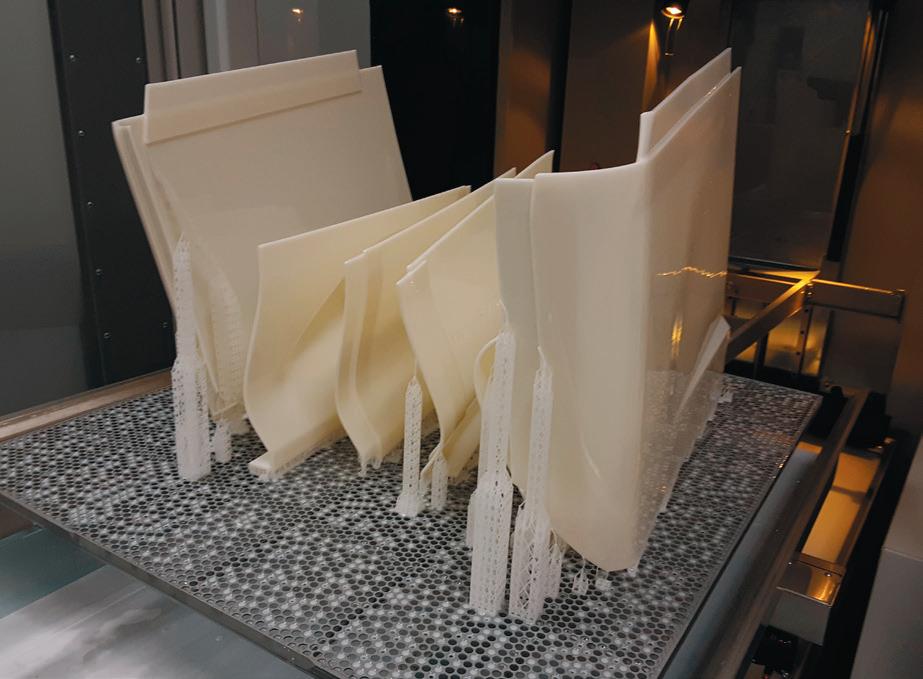
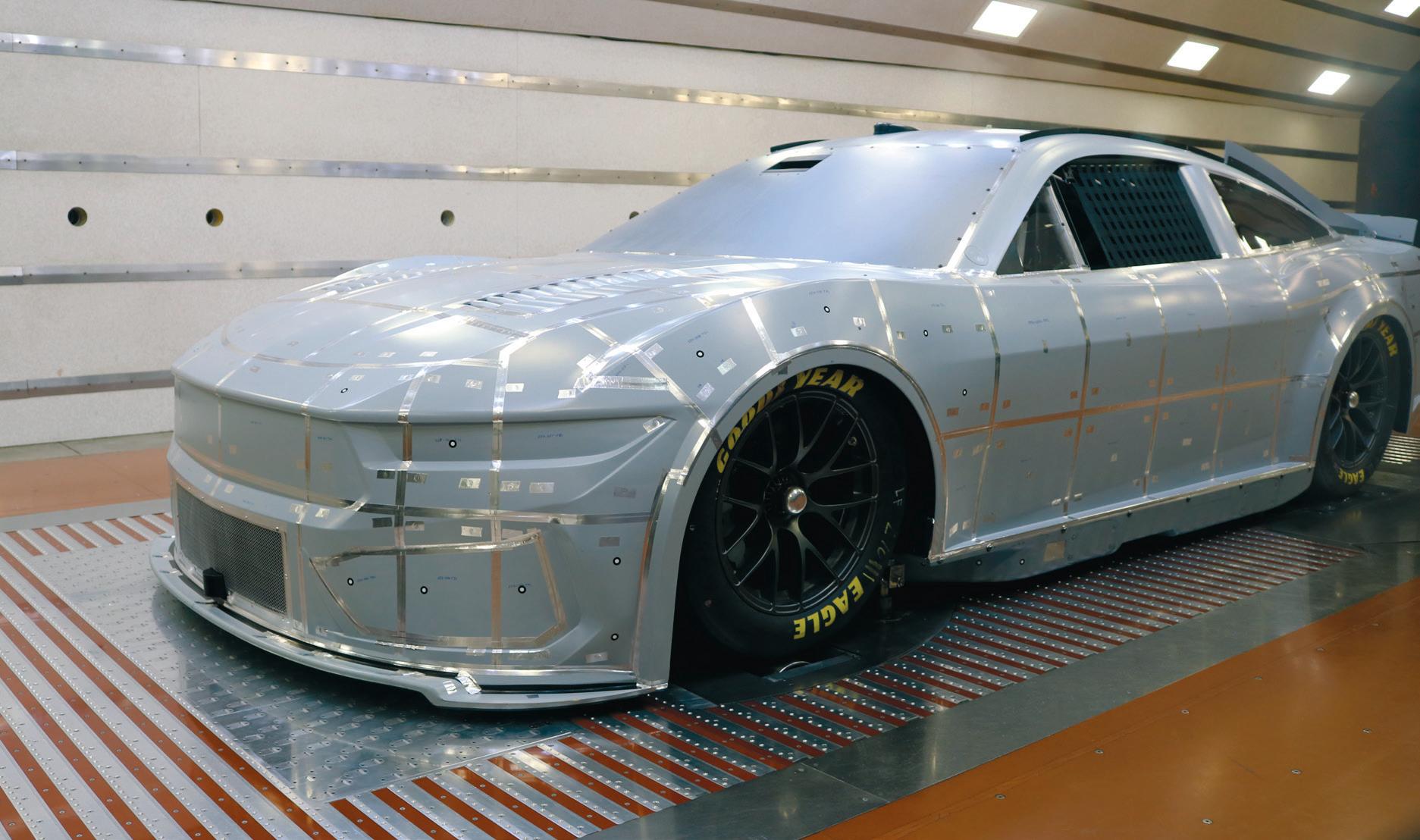
Van Landingham explains that the team has become so reliant on 3D printing that the numbers continue to stack up. “It’s no longer hundreds of parts, it’s thousands of parts,” he says. “It’s a well-ingrained tool that we use now – it’s no longer novel. It’s a critical part of our development process and all the engineers leverage it. We get uneasy if a weekend’s coming up and there’s nothing to print!”
FIRST CUT
Even for a team with strong links to its founder’s CNC machining empire, and all the metal cutting technologies you’d expect as a result, 3D printing polymers is still a “huge” part of the workflow, according to Joe Custer, Stewart-Haas Racing’s team president.
Historically, he says, engineers would dream up a part for a race car, put all their effort into it, machine the first article and then find there was a problem. As with most engineering tasks, producing a perfect part takes multiple iterations, and 3D printing a prototype early on is what helps the team achieve that perfect part faster.
“What’s happened now is that it’s almost instantaneous from designers,” Custer says of 3D printing a part. With rapid prototyping, a good idea travels further than just the design office. “Crew chiefs working with us, they understand now. The guys at the track have learned that this is unbelievable. If they truly work with our resources, they can get parts on their car way ahead of some of our competitors. The whole previous structure is out the window.”
Van Landingham adds: “Rapid prototyping means we can print the parts really quick, check the size and shape, and then we can go to machine the parts, because that generally does take longer and usually it’s more expensive, depending on the material.”
In effect, he adds, this means that, “within a one to two-week timeframe, we’re doing design, engineering, [wind tunnel] testing, fabrication, production, and it goes onto the car on the track.”
It’s a “race between the races”, he continues, with engineering groups from each team competing against each other to get parts on their respective cars faster.
This urgency comes further into perspective when you speak to drivers. “We only get 20 minutes when we show up and you really can’t change a ton [of stuff],” says Cole Custer, son of Joe, driver of Car 00 and reigning champion of the NASCAR Xfinity Series.
Following Covid, organisers recognised that television audiences didn’t miss the practice sessions, so whereas previously, teams had two or three hours to finetune cars at the track, now they get 20 minutes. “Everything has to be exactly right when you show up to the track,” says Cole Custer.
“We don’t have a ton of data on the cars that we can look at on the weekends. We don’t have tire pressure sensors. We don’t have load sensors. NASCAR doesn’t allow it.
The driver is the only one who can tell the team what’s going on. So, you try and give as much good feedback as you can to him, to try and make it better and interesting,” he says, pointing to Van Landingham.
Car 00 has an advantage in that it is also sponsored by 3D Systems, part of a technical partnership between the team and the 3D printing giant.
His father Joe Custer goes on to explain that, sometimes, if there’s a significant cost attached to trying a new technology or material, management might put the brakes on trying it.
“But with a partner like 3D Systems,” he trails off, smiling widely, acknowledging the benefits. “They’re down the road, so there’s the personal relationship and that trust – and then turning [our engineers] loose with their menu!”
Anybody can buy a 3D printer, he adds, but when you have a 3D printer company as your technical partner, that adds substantial value, including early access to technologies, he suggests. “Even if it might just be a few months ahead, our competitors will look and wonder ‘How do they do that?’”
In racing, few advantages last for long. You might only have as long as it takes for a rival to figure out your engineering secret. But if that advantage holds up long enough for you to win that weekend’s race, that’s plenty in the fast-moving world of NASCAR.
www.stewarthaasracing.com
The Future of Farming in Japan: Final Aim and Yamaha Motor’s Co-Created Concept EV
See how Final Aim leveraged generative AI and Autodesk Fusion to design an electric farming vehicle that blends kawaii with function
Throughout his career as an industrial designer and entrepreneur, Yasuhide Yokoi has always taken bold approaches with technology. He was even one of the first people to use Autodesk Fusion in Japan more than 10 years ago. Now as co-founder and Chief Design Officer at Final Aim, Yokoi and his team aren’t just looking at what’s on the horizon with blockchain and generative AI. They are actively working to incorporate it and reap the benefits today.
Collaborating with Yamaha Motor on a unique design brief Recently, the Final Aim team landed a unique opportunity to design a new electric vehicle concept
and prototype for Yamaha Motor. But it wasn’t just any EV—it needed to be specifically designed for the agriculture industry and light farm work. Yokoi wasn’t familiar with the industry or even what would make a difference in the design. So, the team turned to generative AI and started asking questions.
“We first used text-to-text AI to see the potential for the design concept and gain a broader perspective about the future of agriculture in Japan and the world,” Yokoi says According to Yokoi, the features proposed by AI were refreshing and a completely different experience than how he would usually sit down to start a design. A key design driver and audience surfaced during the AI research.

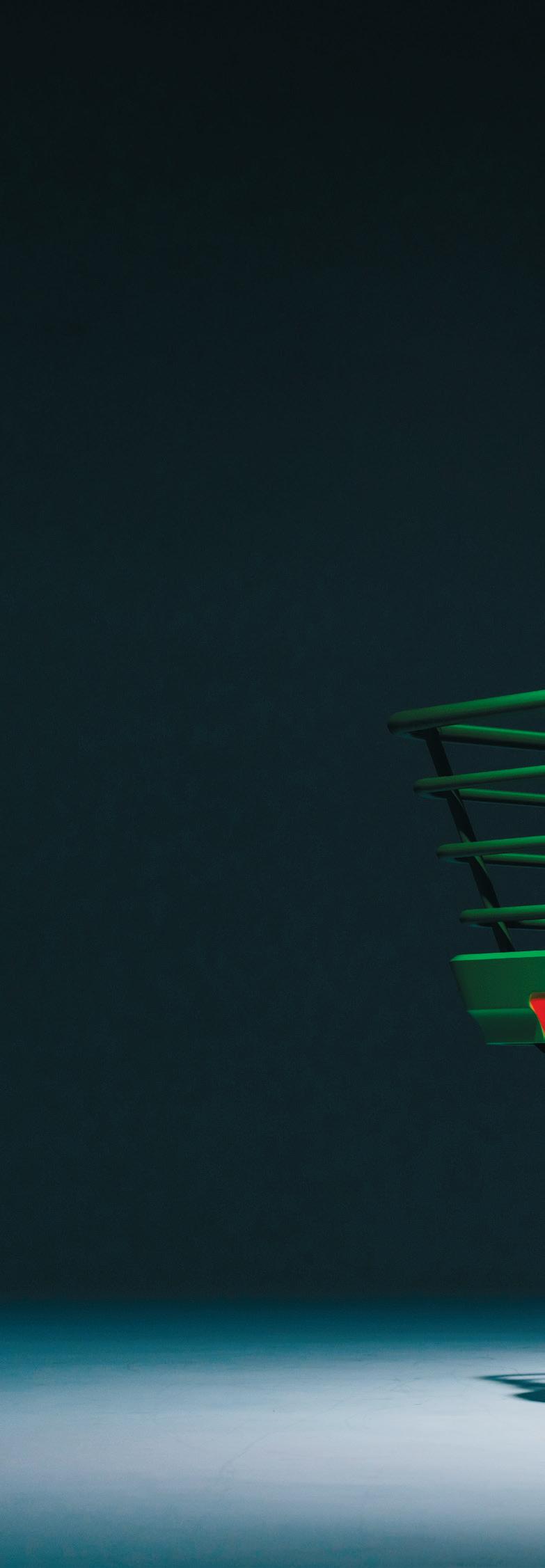
“I don’t have any agricultural background, so I was able to catch up with the industry very quickly and efficiently,” he says. “In Japan, the average agriculture worker is 65-years-old. From this information, I understood how younger workers would need to enter the industry. We had to create a design and features that would appeal to them.”
Once the initial research was completed, Yokoi and the team took their findings and began using generative AI for visual concepts. “We broke down the answers to explore the technical features and aesthetics,” he says. “Using generative AI, we ideated more than 2,400 different design images in just a couple of weeks. From there, we narrowed it down to a couple that we wanted to pursue.”
Final Aim turned an AI vision into reality with Fusion
The timeline for the project with Yamaha Motor was only about two months, culminating with an appearance at the recent Tokyo Auto Salon. While the ideation and design concept were rapidly accelerated
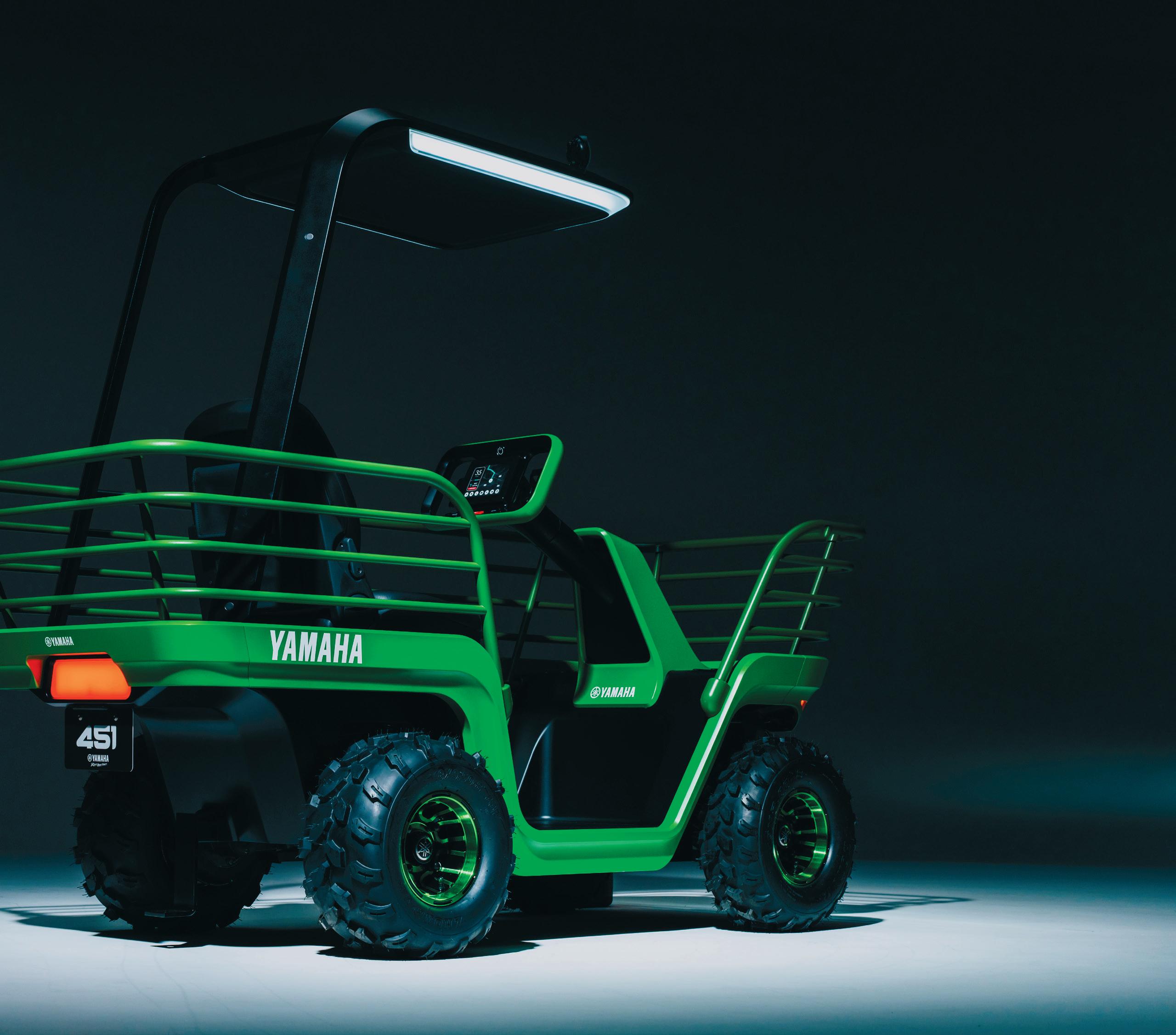
with AI, Yokoi recognized that could only take them so far. The design needed to be functional, validated, and manufacturable. They began building a 3D model in Autodesk Fusion that would work in the physical world. Once the 3D model was complete, they needed to hand it off directly to the manufacturer. “The handoff process through cloud features was a big advantage when using Fusion,” Yokoi says.
“We use Fusion because it enables quick development and communication between a lot of stakeholders,” he continues. “Even here in Japan, the team was distributed between Yamaha Motor in Shizuoka close to Mount Fuji, the manufacturer in Kyoto and Osaka, and myself in Tokyo. We could meet this very tight deadline with a fully developed design as well as actual manufacturing.”
It’s OK to call it cute
The final design of “Concept 451” is a quintessential blend of functionality and kawaii.
The pipe-frame structure evokes a certain boldness, and visibility is increased with the
removal of the typical front pillars. For Yokoi, calling it cute is a compliment and means that it’s achieving the design goals for a younger generation entering the industry.
“It was an exciting moment to see the response from the visitors, the market, and the media,” he says. “We got a lot of ‘kawaiis’ and some very helpful feedback on features to add or expand.”
The project also fulfilled a key goal for Yamaha Motor and taking a completely different approach to traditional design and product development. Their EV platform is a standard base, so a vehicle could technically run on a road the very first day. Using generative AI and Fusion, Final Aim and Yamaha Motor could experiment with a new, agile process to quickly prototype, share it with the market, and get real-time feedback.
“With Fusion, we’re taking a deeper look at the feedback and applying that on the next version,” Yokoi says. “We’re excited to see the potential users and the market for the future of EVs in the agriculture industry.”
Fusionprovidesaccesstothe cloudandcomprehensivedesign featuresthataren’taccessiblewith other3DCADsoftwaretools.For allofourprojects,wecanrelyon Fusionandtapintotheincredible usercommunityandeven Autodeskitselfforknowledge. YasuhideYokoi,Co-founderand ChiefDesignOfficer,FinalAim
Q&A: PTC CREO 11
» DEVELOP3D spoke to Paul Sagar, VP of CAD product management at PTC, to get his insights on the newly launched Creo 11 and hear where the software is pushing workflows most in this release
Q (DEVELOP3D): A good place to start is how does Creo 11 stack up against the last few releases we’ve seen?
A (Paul Sagar, PTC): It’s a big one for new features and updates. Creo 11 has over 150 enhancements in this release – that’s a pretty significant chunk! For reference, I think that in Creo 9, we added about 120. In Creo 10, it was somewhere around 130. A lot of those 150 enhancements are really customer-driven, based on feedback we’ve had from talking with our customers
Some of those are relatively small improvements and tweaks – we’re always looking to make the product easier to use and improve general features like core modelling and general assembly work. Others are pretty significant.
Q: There are some strong updates for composites design in the new release. Given the tools were only added in Creo 10, how far have they developed over the past year and what’s guiding the direction PTC is taking with them?
A: We’ve gone out to all different markets – not just ‘big aerospace’ – and asked them about what they need. We work closely with customers that build boats, bicycles, race cars, wind turbines and, of course, airplanes. We got a very large group of these customers together and went through all their requirements. Some of these overlap, some of them are unique to certain industries. And what we’ve done is taken those capabilities and put them into the product.
With Creo 11, we’ve tried not to focus too much on a specific industry, because what we want to do is make sure our solution is broadly applicable to all industries, so we looked at three main areas.
The first was to expand on what we did in Creo 10 and streamline the UX for that, and then we’ve introduced the notion of Zones and Zone Stacks. Zones allows really big models made up of hundreds or thousands of composite plys to be broken down into sections and really investigated. With Zone Stacks, you can apply your ply stacks to individual Zones. So it’s a much faster way of building a large number of ply stacks very, very quickly.
We’re also focused on the downstream manufacturing of composites, not just the designer’s finished ply structure, so there are tools for improved draping, extension of boundaries and creating laser projection files using LAP and Virtek systems.
Q: Model Based Design (MBD) has continued to grow in importance over past releases, helping communicate critical model information to stakeholders. How is it shaping up in Creo 11?
A: The whole MBD initiative really falls into a couple of categories: efficiency, in terms of reducing the inordinate amount of time it takes documenting 2D drawings; and removing misinterpretation.
Because MBD is controlled by the 3D model with all its semantic awareness, the system can guide you. So, as long as the user has defined those critical elements, there’s never a risk of something being missed.
This release brings tables to the fore. In a 2D drawing, there’s typically lots of tables that support a number of different things. Although, once you hand that drawing to somebody else, you’re breaking the chain of the digital thread. That 2D drawing might be out of date, right?
So, in Creo 11, there’s a full semantic relationship between the table and the 3D model, and if you do a query on the table, it will highlight on your 3D model exactly what that is referring to. It feeds the traceability of your designs. We’ve also expanded our GD&T advisor capabilities in Creo, to help guide the user through adding GD&T onto their model and validate that the model conforms to the appropriate standards.
Q: The partnership with Ansys for simulation tools as part of Creo continues with the new release, right?
A: There’s a lot of new abilities across both Creo Simulation Live, our real-time simulation capability, and in Creo Ansys Simulation, the more traditional higher fidelity simulation.
A nice new feature in Live is its ability to predict the heat transfer between solids and fluid flow (excellent for predicting heatsink abilities early on), as well as being updated to the latest solvers from Ansys.
‘‘ With Creo 11, we’ve tried not to focus too much on a specific industry, because what we want to do is make our solution broadly applicable to all industries ’’
For Creo Ansys Simulation, I’d highlight the new Transient Structure ability, which allows users to understand the impact on the structural integrity of a part over time.
From a generative design perspective, there are three main improvements: the introduction of a minimum thickness control to control the amount of ribbing on a part, for example; there’s added support for bearing, so now you can specify that as an input for your optimisation; and finally, when we reconstruct a shape as full
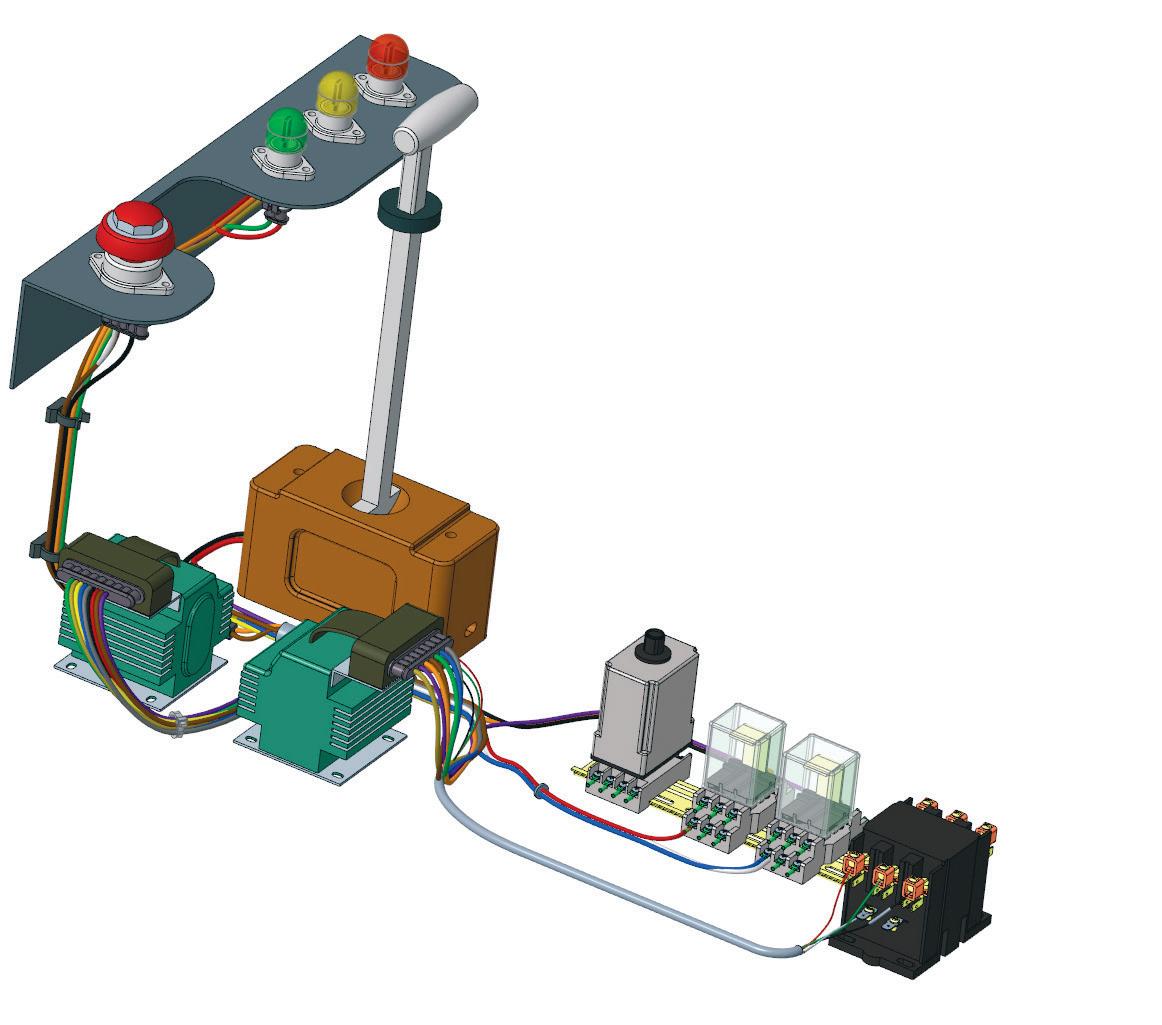
● 1 Cabling and ECADMCAD collaboration capabilities boost circuitry designs
● 2 Creo 11 offers expanded composites design, simulation and manufacturing capabilities
● 3 Improvements for machining include high-speed machining and 4-axis turning
● 4 Models can now feature multiple sheet-metal bodies as well as solid bodies
geometry, there’s the ability to take into account if there was planar symmetry.
Q: There are some interesting new tools for additive processes in there, especially around lattices. Is this something you’re seeing customers adopt more?
A: Lattices now are starting to be used more as part of the design process, so they actually have a purpose, they’re not there to lightweight a design. And we have tools in there to be able to simulate and optimise those designs. What we’re seeing is customers rethinking the design process and what they can do to take advantage of lattices – things like impact absorption, or gyroid lattices for more efficient heat exchangers, built as a single part. A key new feature in Creo 11 for lattices is the ability to connect multiple, disconnected volumes of beam-based lattices with a seamless flow that joins them.
Q: High-speed machining features prominently in the Creo 11 release notes. How do you see user requirements evolve with regards to machining?
A: We’ve been heavily investing in expanding our subtractive manufacturing capabilities, and what we’re seeing is a shift where everybody is interested in high-speed machining. Just the little tweaks that it allows you to make –taking a couple of seconds off a toolpath, for example, when you’re making that toolpath 1,000 times a day. It all adds up. With this release, we’ve started to shift some focus towards turning, expanding and modernising some of our capabilities for four-axis turning. A lot of the work we’ve done around machining is focused on customer needs and driven by the types of interactions we have with them for what they need, based upon the latest innovations in manufacturing.
Q: What aspect of Creo 11 do you expect to receive the most attention?
A: Probably the one that will get the most love, based on the positive beta testing feedback we’ve had, is the addition of multiple sheet metal bodies. Back in Creo 7, we introduced Multibody Design capabilities where you could build a model that had multiple solid bodies in it. What we’ve done in 11 is expand that, so you can do that with multiple sheet metal bodies. Users can now have a part that has multiple solid bodies and multiple sheet metal bodies in it as well. It spans the use case for looking to build multi-thickness sheet metal parts, or the same thickness sheet metal parts, and it just expands the usability and simplicity of building those parts.
Q: What’s the part of Creo 11 that excites you most?
A: I would say it’s the composites! It’s only 12 months old, but the breadth of capability we now have for composites is something I’m very, very proud of. In one-and-a-half releases, we’ve gone from having no solution to having an offering that I would say competes head-on with the other composite software out there in the market. Typically, if you’re introducing a new product, it’s going to take you two, three, four, maybe even five releases before you get to a point of being a leader in that space. So, to be up there with the other leaders so quickly, I think, is pretty impressive.
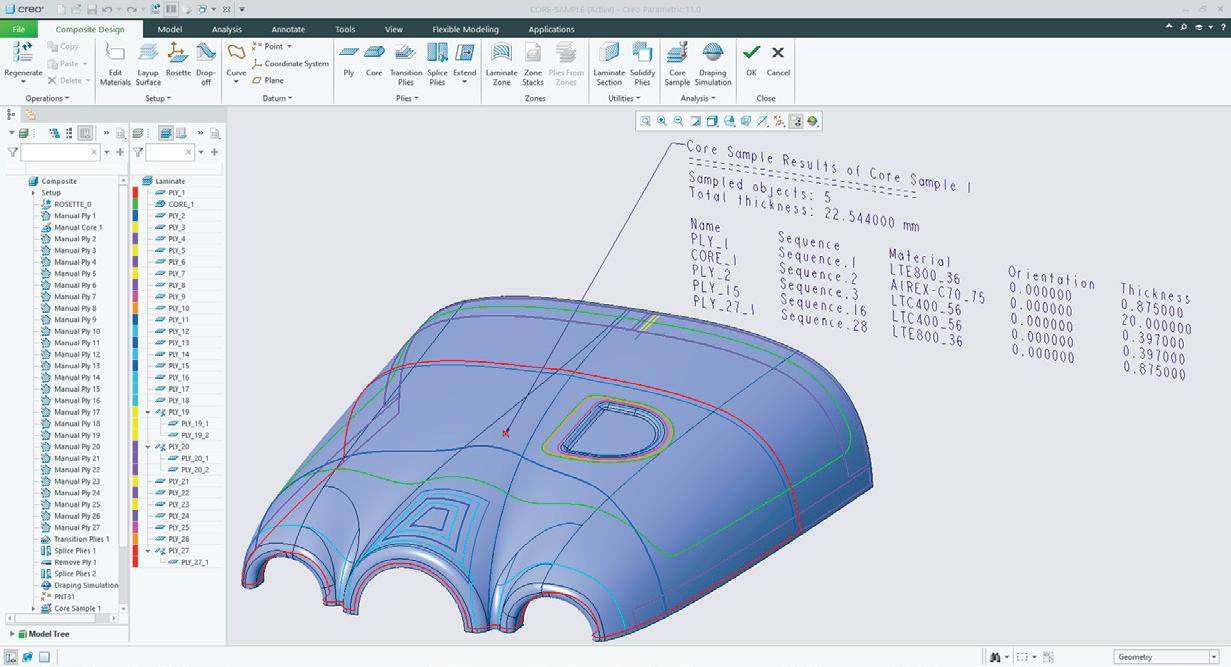
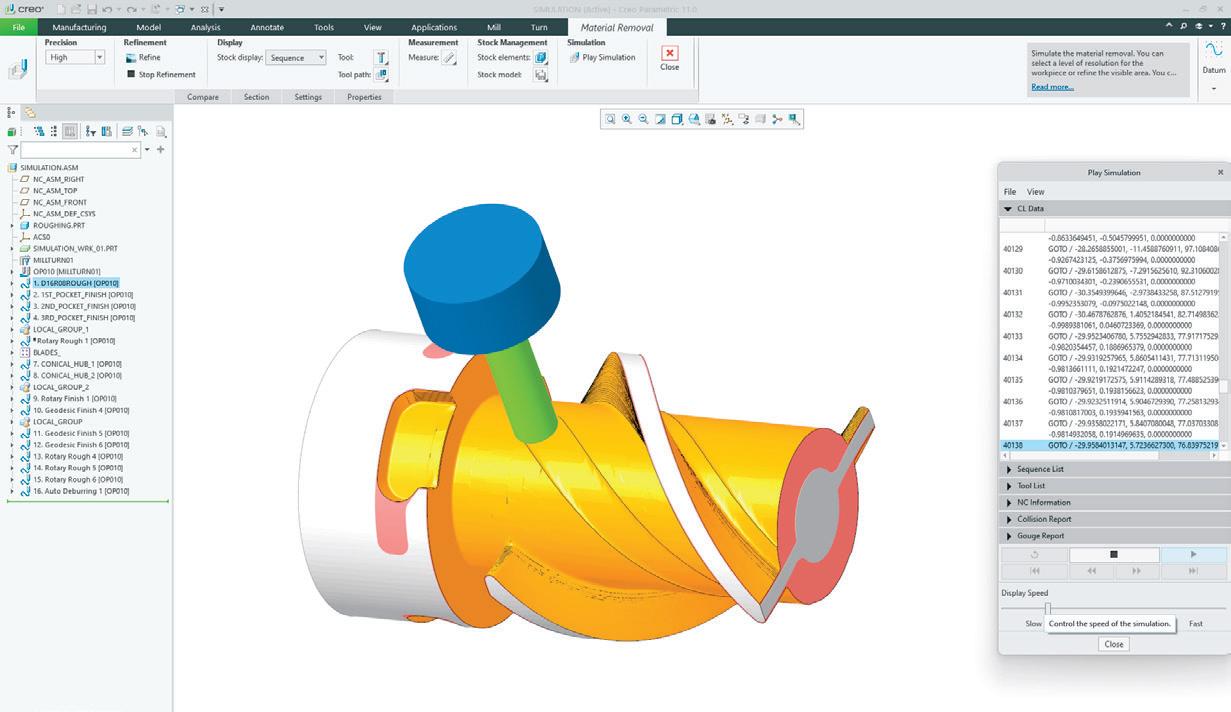

Q: And finally, we can’t leave without mentioning Creo+. When can we expect all the new features of Creo 11 to appear in the SaaS version?
A: All of these new capabilities in Creo 11 will be automatically pushed out to our Creo+ customers around a month or so after the launch. As well as these latest capabilities, there are a few other improvements that we’ve made that are specific to Creo+ as well.
Bio: Paul Sagar is vice president of CAD product management at PTC. In this role, Sagar is responsible for understanding broad customer requirements for Creo, Creo Elements Direct and Mathcad; for developing short- and long-range product release plans; and for communicating those plans across PTC’s wider development organisation.
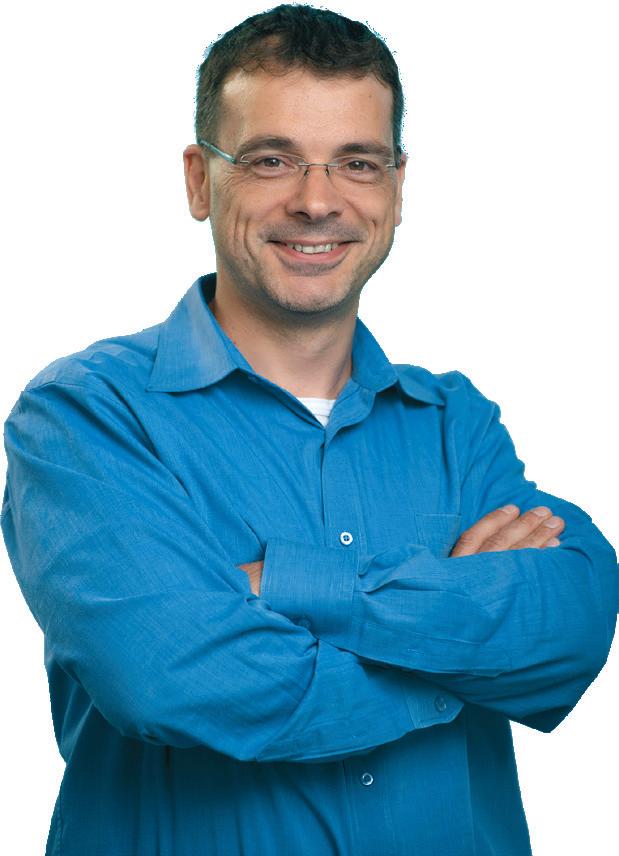
ENTERPRISE XR
STREAMING TO A HEADSET NEAR YOU SOON
All-in-one XR headsets have proved very popular for geometrical design review. But to add realism and complexity, 3D models must be processed externally, and pixels streamed in. Greg Corke reports on a growing number of XR technologies that do just that, from cloud services to local appliances
The first wave of VR headsets - the Oculus Rift and HTC Vive - were tethered, so all the graphics processing was done on a workstation with a powerful GPU. But cables can be restrictive, and external processing can add complexity and cost, which is why all-in-one headsets like the Meta Quest have proved so popular in the architecture, engineering, and construction sector. But relying on a headset to process 3D graphics has its limitations - in terms of the size and complexity of models it can handle and, especially, the realism it can convey.
In AEC, this hasn’t proved such an issue for BIMcentric design/review, where simply rendered geometry is adequate for ironing out clashes and issues before breaking ground. But when more realism is required, for product design, automotive design, or to place manufactured products in the real-world context of where they will be used, visual fidelity and model scale and complexity are considerably more important. The ultimate goal of XR is to make the virtual indistinguishable from the real.
Graphics processing on XR headsets has been steadily improving over the years. The new Apple Vision Pro has a tonne of compute on the device, but it’s still not enough to handle huge models with millions of polygons.
The answer, according to Nvidia, is to offload the processing to a powerful workstation or datacentre GPU and stream the pixels to the headset. In March, the company introduced a new technology that allows developers to beam their applications and datasets with full RTX real-time physically based rendering directly into Apple Vision Pro with just an internet connection. It uses Nvidia Omniverse Clouds APIs to channel the data through the Nvidia Graphics Delivery Network (GDN), a global network of graphics-optimised data centres.
“We’re sending USD 3D data into the cloud, and we’re getting pixels back that stream into the Vision Pro,” explains Rev Lebaredian, vice president, Omniverse and simulation technology at Nvidia. “And working with Apple’s APIs on the Vision Pro itself, we adjust for the latency, because there’s a time between when we ask for the pixels, and it comes back.
“In order to have a really great immersive experience you need to have those pixels react to all of your movements, locally. If you turn your head, the image has to change immediately. You can’t wait for the network, so we compensate for that.”
Nvidia is one of many firms streaming XR content
from the cloud for use by AEC and manufacturing firms. Hololight offers a range of services based around Hololight Hub, which it describes as an enterprise streaming platform for spatial computing. It can run on public cloud, private cloud, or on-premise.
The platform supports a variety of headsets - Magic Leap, HoloLens, Meta Quest 3, Lenovo ThinkReality VRX, as well as iOS tablets and Windows for desktop apps. For streaming, Hololight Hub can use Nvidia CloudXR or the bespoke Hololight Stream technology, which also supports AMD and Intel GPUs. To address latency from the cloud, Hololight has developed several mechanisms including ‘frame skipping and reprojection algorithms’.
The company recently launched an integration with Nvidia Omniverse and OpenUSD, which provides an environment for real-time 3D collaboration.
Innoactive is another specialist that offers XR streaming from the cloud. Through its Innoactive Portal, it works with a range of tools including Twinmotion, Enscape, VREX and Bentley iTwin (beta), as well as apps built on Unreal Engine and Unity.
More recently, the company combined its Innoactive Portal with Omniverse and Cesium, allowing users to combine Universal Scene Description (OpenUSD) projects of buildings with contextual geospatial data and visualise both in real time.
OpenUSD projects can be streamed to a standalone VR headset, such as Meta Quest, HTC Vive XR Elite, Pico 4E or Lenovo ThinkReality VRX, or to a web-browser on an office PC. Innoactive Portal is available through AWS and can also be self-hosted.
EXTENDING THE REACH OF XR
Thanks to cloud technology, BMW Group has dramatically extended the reach of XR within the automotive firm. With a bespoke platform hosted on AWS, using Nvidia GPUs for acceleration, and Nvidia CloudXR for streaming, over 200 BMW Group departments across the world, from design, engineering and production to sales and marketing, can now get near instant access to XR. BMW is using the platform for CAD visualisation, collaborative design review, and factory training.
BMW’s solution, the ‘3D AppStore’, provides easy access to
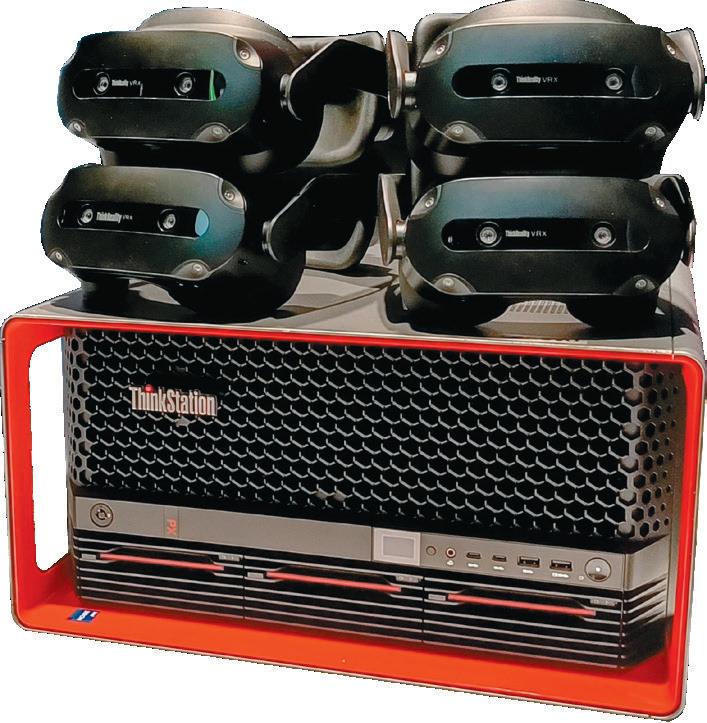
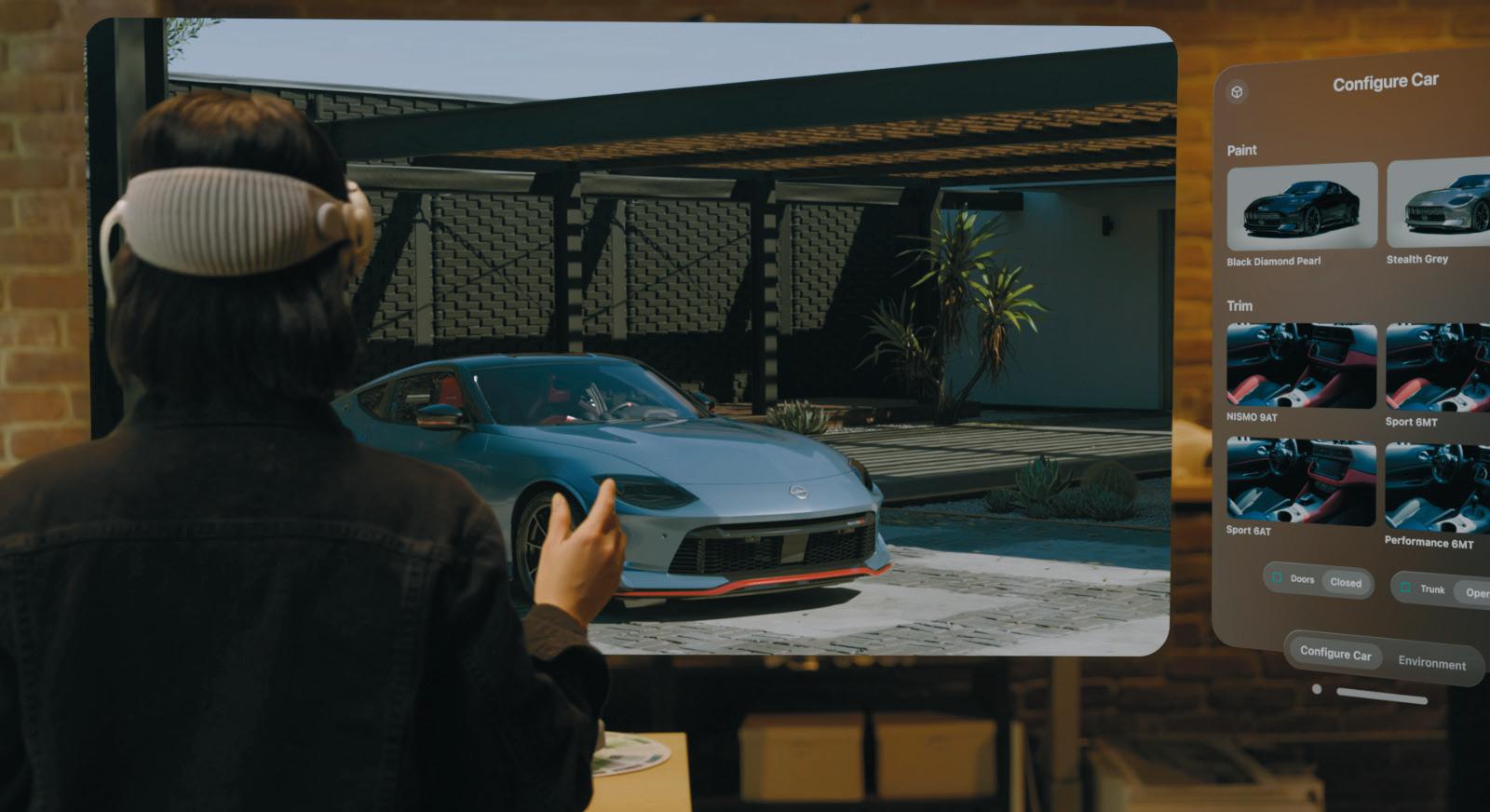
content through a user-friendly web-based portal. Users simply select the headset they want to use (Meta Quest or Vive Focus), click the application and dataset, and it starts an GPU-accelerated instance on AWS.
LOCAL DELIVERY
Of course, streaming doesn’t have to be from the cloud. Design and manufacturing firms can use local workstations or servers equipped with one or more pro GPUs, such as the Nvidia RTX 6000 Ada Generation (48 GB), which are typically more powerful than those available in the public cloud. What’s more, keeping everything local has additional benefits. The closer the headset is to the compute, the lower the latency, which can dramatically improve the XR experience.
At Nvidia’s recent GTC event, Nvidia gave a mixed reality demonstration where a realistic model of a BAC Mono road-legal sports car rendered in Autodesk VRED could be viewed alongside the same physical car.
The Autodesk VRED model was being rendered on a local HP Z Workstation and streamed to an Nvidia CloudXR application running on an Android tablet with pass-through enabled.
Nvidia also showed the potential for natural language interfaces for immersive experiences, controlling certain elements of Autodesk VRED through voice commands via its API.
“VRED doesn’t have anything special that was built into it to support large language models, but it does have a Python interface,” explains Dave Weinstein, senior director of XR at Nvidia. “Using large language models, using some research code that we’ve developed, we’re able to simply talk to the application. The large language model translates that into commands that VRED speaks and through the Python interface, then issues those commands.”
Practical applications of this technology include a car configurator, where a customer could visualise the precise vehicle they want to buy in their own driveway - changing paint colours, trim and wheels, etc. Also in collaborative design review, voice control could give
non-skilled users the ability to interact with the car and ask questions about it, hands free, when wearing an immersive VR headset.
Nvidia’s natural language research project is not tied to XR and could be used in other domains including Product Lifecycle Management (PLM), where the language model could be trained to know everything about the car, and present information. One could query a product, pull up a list of parts, etc. It seems likely the technology will make its way into Nvidia Omniverse at some point.
THE COLLABORATIVE PACKAGE
Lenovo has an interesting take on collaborative XR for design review with its new Spatial Computing Appliance.
The desktop or rack-mounted solution enables up to four users to collaborate on the same scene, at the same time, using a single workstation, streaming pixels with Nvidia CloudXR over a WiFi 6E network.
The ‘fully validated’ reference architecture comprises a Lenovo ThinkStation PX workstation, four Nvidia RTX 6000 Ada Gen GPUs, and four Lenovo ThinkReality VRX headsets. It supports Nvidia Omniverse Enterprise, Autodesk VRED, and other XR applications and workflows.
Lenovo’s Spatial Computing Appliance works by carving up the workstation into multiple Virtual Machines (VMs), each with its own dedicated GPU. Lenovo uses Proxmox, an open-source hypervisor, but will work with other hypervisors as well, such as VMware ESXi.
Four users is standard, but the appliance can support up to eight users when configured with eight single slot Nvidia RTX 4000 Ada Generation GPUs.
The Nvidia RTX 4000 Ada is nowhere near as powerful as the Nvidia RTX 6000 Ada and has less memory (20 GB vs 48 GB), so it won’t be able to handle the largest models at the highest visual fidelity.
However, it’s still very powerful compared to a lot of the GPUs offered in public cloud. BMW, for example, uses the equivalent of an Nvidia RTX 3060 Ti in its AWS G5 instances, which on paper is a fair bit slower than the Nvidia RTX 4000 Ada.
‘‘
Relying on a headset to process 3D graphics has its limitations, both in terms of the size and complexity of models it can handle, and the realism it can convey ’’
FEATURE
With eight VMs, firms may find they need more bandwidth to feed in data from a central server, Omniverse Nucleus, or data management system. To support this, a 25Gb Ethernet card can be added to the workstation’s ninth PCIe slot.
The Lenovo ThinkReality VRX is an enterprise-level all-in-one headset, offering 2,280 x 2,280 resolution per eye. The headset largely earns its enterprise credentials because it works with Lenovo’s ThinkReality MDM (mobile device management) software.
It means IT managers can manage the headsets in much the same way they do fleets of ThinkPad laptops. The headsets can be remotely updated with security, services and software, and their location tracked. The appliance will work with other VR headsets, but they won’t be compatible with the Lenovo ThinkReality MDM software.
Of course, these days IT can be flexible. No firm needs access to XR technology 24/7, so the ThinkStation PX can be reconfigured in many different ways - for rendering, AI training, simulation and more.
To help deploy the Spatial Computing Appliance Lenovo is working with partners, including Innoactive. The XR streaming specialist is using the Lenovo technology for on-premise XR deployments using Nvidia CloudXR. At NXT BLD 2024 (a conference hosted by DEVELOP3D’s sister publication AEC Magazine) in London on 25 June (www.nxtbld.com), the company will be giving demonstrations of streaming VR from a ThinkStation PX to multiple users running tools including Enscape, Omniverse, and Bentley iTwin.
PHYSICAL ATTACHMENT
Despite big advances in streaming technology, for the ultimate XR experience, headsets still need to be tethered. To deliver its hyper-realistic ‘human eye’ resolution experience the Varjo XR-4 must maintain stable and fast data transfer rates. This can only be achieved when physically connected to a workstation with USB C and DisplayPort cables.
For rendering you need an exceedingly powerful GPU like the Nvidia RTX 6000 Ada or Nvidia GeForce RTX 4090, which can help deliver photorealism through real time ray tracing.
But that doesn’t necessarily mean you’ll always need cables. “We’re still working on that on Varjo,” said Greg Jones, director of XR business development at Nvidia, at Nvidia GTC recently.
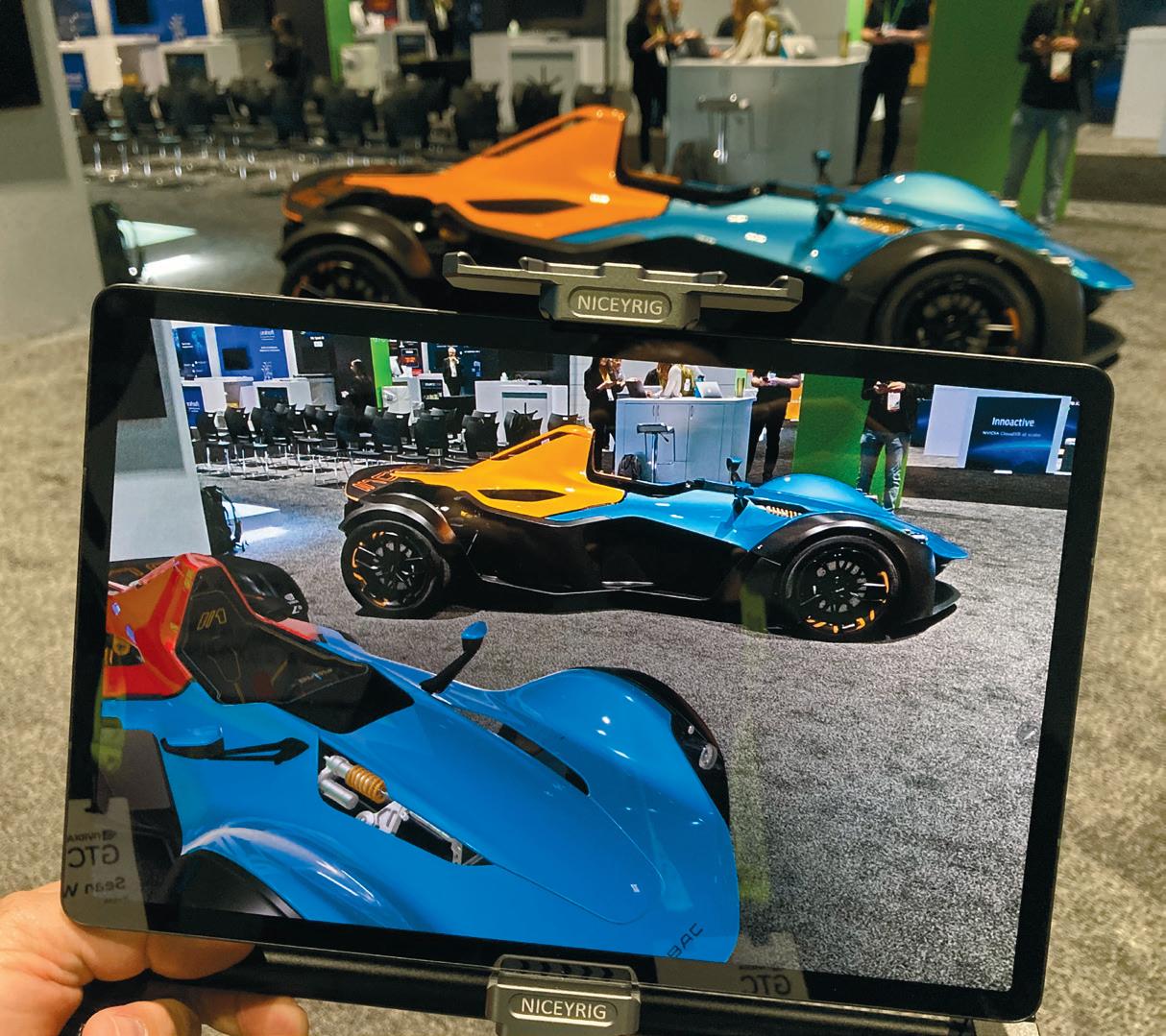
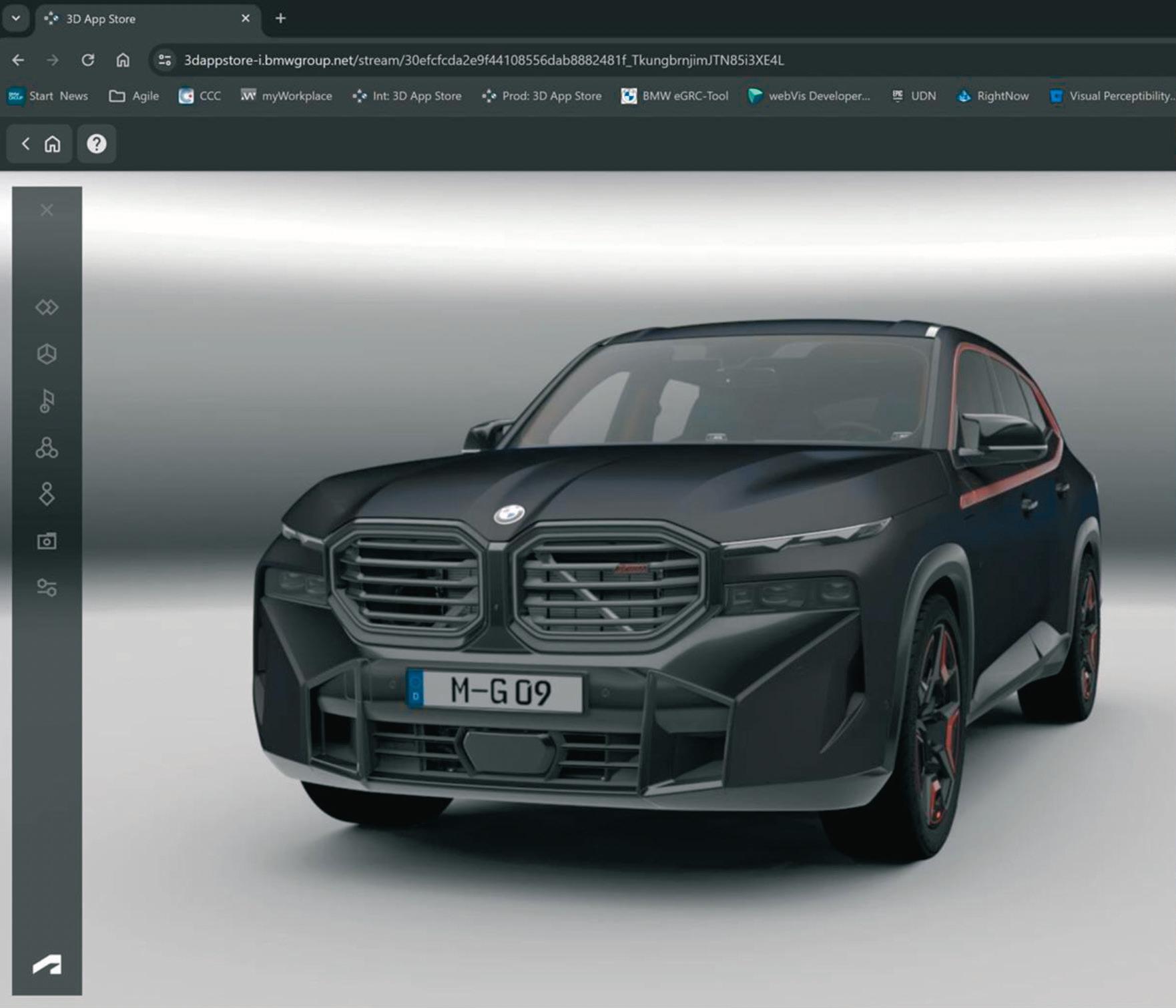
1 Realistic 3D model of a BAC Mono sports car
SONY AND SIEMENS PIONEERING XR FOR DESIGN

and Sony are gearing up for the late 2024 release of a new XR headset, the SRH-S1, designed using Siemens
The SRH-S1 headset features 4K OLED microdisplays, delivering a resolution that Sony says is comparable to the visual precision of the human eye for precise capture of form, colour and texture.
The controllers — a ring with a gyro sensor and a pointing controller for object modelling — are specifically designed for ‘intuitive interaction’ with 3D objects. The headset is powered by a Qualcomm
XR2+ Gen 2 chip but can also be tethered. The most interesting thing about the SRH-S1 is the software integration. It’s a fundamental component of the forthcoming NX Immersive Designer, an integrated solution based on Siemens NX which is intended for mixed reality design. Preview videos show the head-mounted display being used with virtual monitors, similar to Apple Vision Pro, and the user ‘effortlessly moving’ between real and virtual spaces by flipping up the display.
Creo 11: Design The Way It Should Be
Creo 11® helps you build better products faster, by accelerating innovation, reusing the best of your design and replacing assumptions with facts.
Try Creo 11 Today: For Free
Unleash the power of Creo 11 in your organisation. Maximise productivity without sacrificing innovation. Visit bit.ly/creo-free-trial or scan the QR code to receive your free trial.

DRIVING CHANGE IN AUTOMOTIVE
»
AI is everywhere in product development right now and took centre stage at the Autodesk Automotive Innovation Forum 2024, as Andy Shaw reports from the event held in Darmstadt, Germany in May
The tools we use on a day-to-day basis are undergoing huge changes with the adoption of AI. So when I attended the Autodesk Automotive Innovation Forum 2024, I was keen to see how the company plans to navigate the opportunities that AI presents. This promised to be an intriguing event.
After all, managing design programmes and deploying new vehicles for our clients, both OEMs and start-up companies, is our studio’s bread and butter. At Vital Auto, any new software (or indeed, hardware) developments that promise us a competitive advantage are worth further investigation. With this in mind, I was keen to see what Autodesk has planned.
The event is an opportunity for Autodesk to showcase its latest technologies and was taking place in downtown Darmstadt, a German city about 30 minutes south of Frankfurt and a well-established hub of automotive manufacturing. As a consequence, it’s home to many local design studios that work for large OEMs including KIA, Opel and Chery, among others.
One of the most important functions of the event for Autodesk is to get user feedback on its new introductions and future plans, a process that is ongoing over the two days. The upside for attendees, meanwhile, is the opportunity to get stuck into software features with the experts, to learn about best-in-class workflows and, perhaps most importantly, to network with their peers and share a drink or two.
MAKING BETS ON AI
The relaxed atmosphere of the Autodesk Automotive Innovation Forum enabled us to get straight into the flow of things, which kicked off with an impressive keynote from Maks Giordano, a corporate advisor on the topic of generative AI.
Giordano’s presentation really set the tone for the event. The range of AI tools discussed and detailed deserves a deeper dive, but the main takeaway for me was that Autodesk seems to be making a series of bets based on investigating the potential of neural network-enhanced functionality within the software (Alias and VRED), as well as supporting research projects with automotive OEMs such as KIA.
I am sure that I wasn’t the only person to suggest that some of the menial tasks we regularly perform – such as flipping surface normals – could be AI-powered in the
future. That’s maybe not as exciting as 3D form generation, but it would surely be a time-zapping solution.
In conversation with Thomas Heermann, vice president for Alias and VRED at Autodesk, and director of product development Marek Trawny, I asked how AI research programmes can be run alongside traditional programmes when advances in AI technology happen at such a breakneck speed?
Their answer was that they have established an internal AI think tank that is agile enough to make decisions quickly. This is coupled with customer feedback and workshop sessions, which help keep the team focused.
A good answer, but it left me with further questions. For example, how can Autodesk guide smaller companies through the rapid changes brought about by emerging AI tools, and what can be done to bridge the gaps in workflow between traditional and AI tools?
NAVIGATING THE WILD WEST
In many ways, AI feels like the Wild West. And no single software creator – including Autodesk – can yet offer designers the most proficient, or indeed adaptable, workflow.
It should be noted that, individually, certain previously elaborate cross-programme functions such as Sub-D modelling are going from strength to strength within Alias. That’s boosting productivity, thanks to the thought that has clearly been paid to the contextual use of the tool. It’s evident, for example, in elements such as mesh modelling while generating NURBS output geometry.
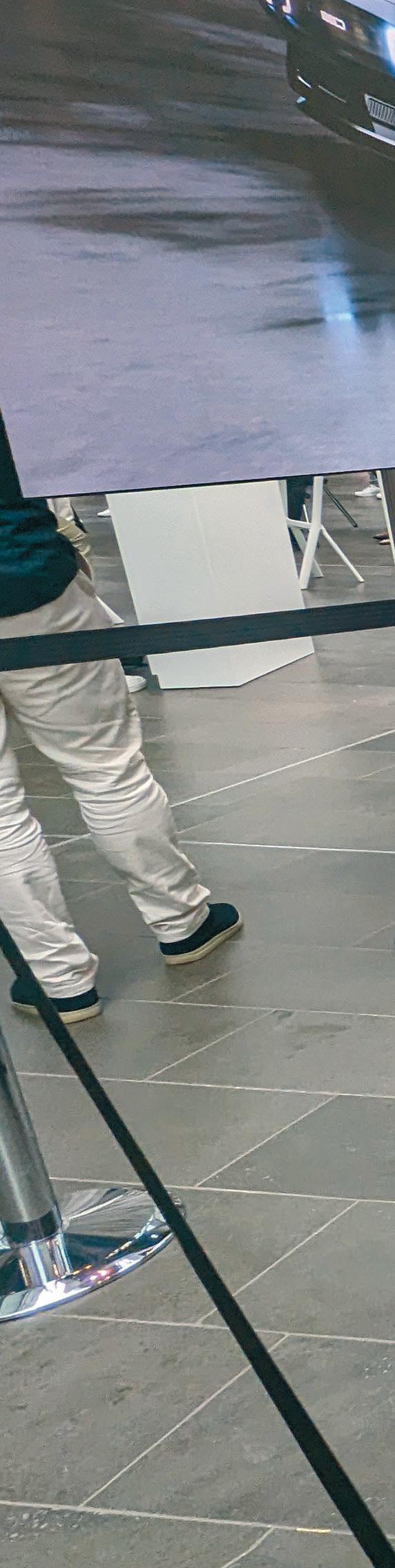

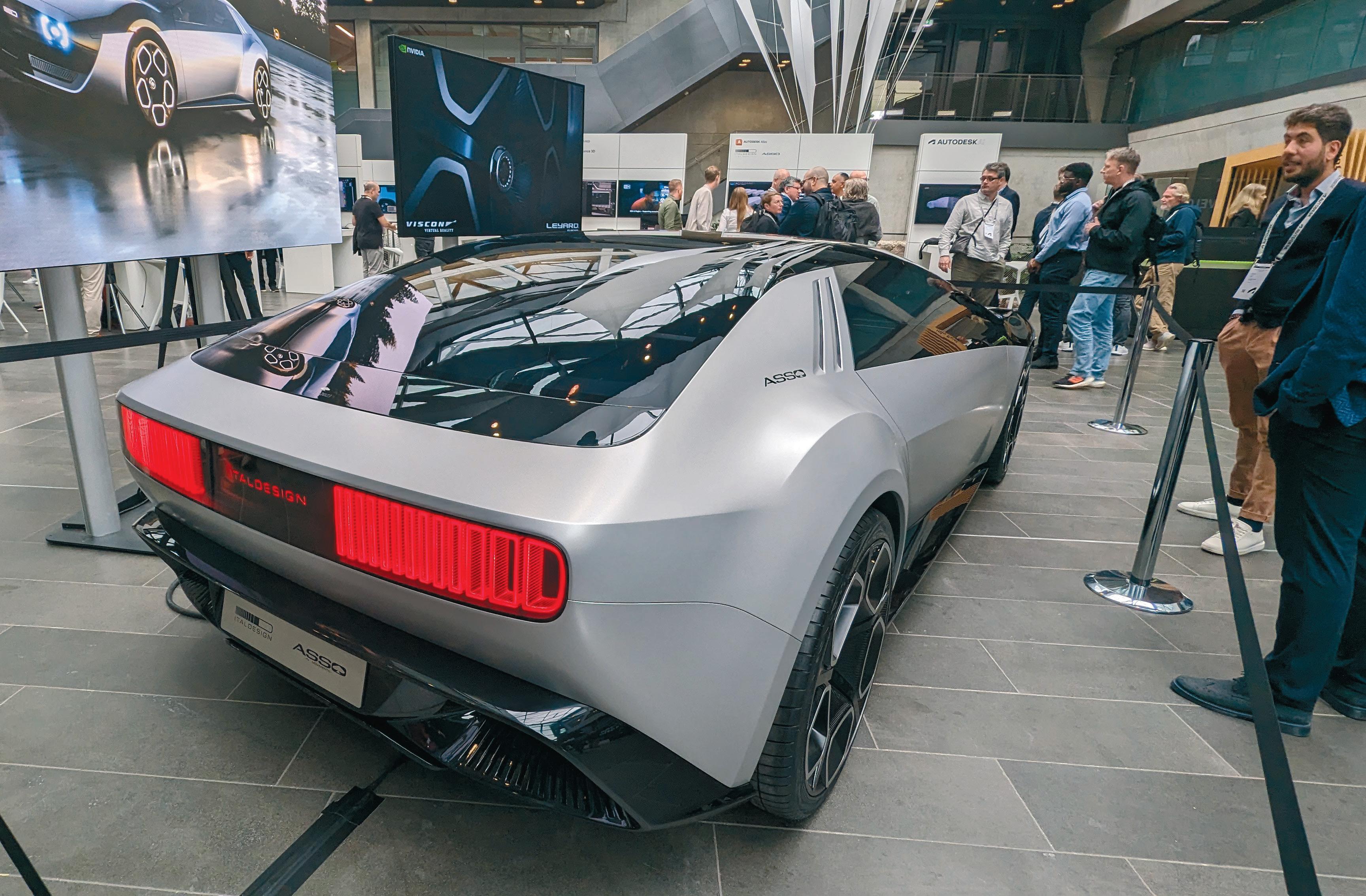
(Above) Forum attendees admire Italdesign’s Asso di Picche concept car
(Below) Maks Giordano, CEO of consultancy Juuman’okudo, opens the event
However, some of the more creative tools seem misplaced on a CAD screen, feeling more at home on the tip of a biro. And some of the detailed engineering functions that are now appearing in VRED seem to be targeted at Class A surfaces and visualisation teams, who may not be best-placed to act on the engineering tolerance guidance provided.
In fact, there are so many functions in Alias today that one of the most often-used tools in the set is actually the ‘tool finder’ function. I kid you not.
Just because we as designers ask for a clever feature in the software does not always mean that we should be given it. This isn’t an Autodesk issue, but rather a wider design issue.
Many software vendors seem to push the idea that the entirety of the design process should be digital – but ultimately, a designed product will exist in the real world (usually). As a result, delaying physical realisation until much later in the process, deleting clay and snapshot models (which are not that expensive when compared to the required digital manpower and licensing costs) may be risky. After all, as we get closer to production deadlines, the freedom to make changes steadily dissolves.
On a more optimistic note, it feels like we designers are increasingly empowered to find our own way in all of this, and that Autodesk is willing to listen and act. In the time that’s passed since the early May event, we’ve seen the release of a new multimodal version of OpenAI’s ChatGPT,
which at this rate, may further displace the whole design ecosystem rather quickly.
Being able to navigate AI tools and reap its benefits across different platforms may be a necessity for any designer in the coming months.
Either way, this is a hugely exciting time to be involved in the design industry. I’m already keen to see what developments the Autodesk team will bring to next year’s event and how impossibly far beyond today’s trajectory we will have taken our workflows.
ABOUT THE AUTHOR
Andy Shaw is director and co-founder at Vital Auto, a global leader in physical and digital automotive prototyping based in Coventry, UK. From design programmes to prototype vehicles and engineering deployment, Vital works discreetly with OEMs and start-ups to develop new vehicles. Shaw holds an MA in Automotive & Transport Design from Umeå University in Sweden.
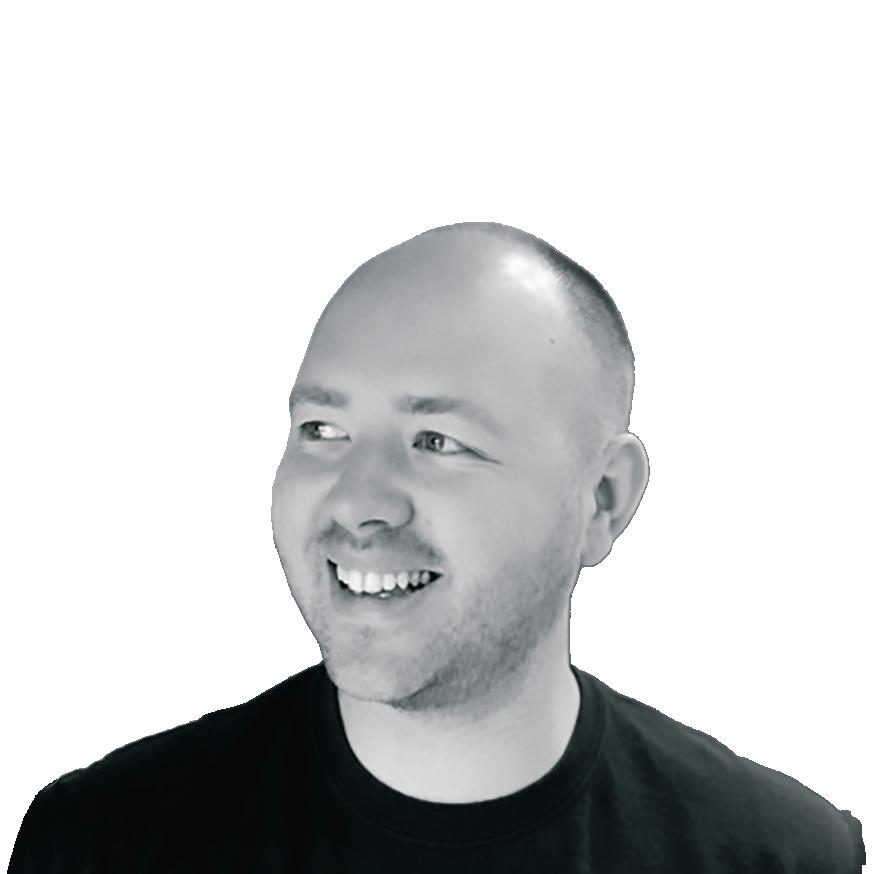
‘‘
Just because we as designers ask for a clever feature in the software does not always mean that we should be given it. This isn’t an Autodesk issue, but rather a wider design issue ’’
SIEMENS: REACHING FOR THE CLOUD
» Siemens is looking to the future, which fuelled plenty of conversation about AI and SaaS that users can embrace at its recent Realize Live 2024 Americas event in Las Vegas, as Emilie Eisenberg reports
Artificial intelligence (AI) was at the forefront of every presentation and conversation at Realize Live Americas 2024, as conference host Siemens Digital Industries Software looks to AI integration to make every process quicker and easier for its users.
At this huge user event, CEO Tony Hemmelgarn didn’t hold back on his plans for AI and his vision of it playing a role in every software package that customers use, from acting as a CAD co-pilot to speeding up simulation analysis.
“You may think that many things have been overhyped, but when it comes to AI, this feels different,” he said. “It feels different because we’re seeing immediate business value for our customers, and frankly, the possibilities are endless when you think about what can happen.”
It’s when a customer sees the true benefits that they understand how it will make a difference to their business, he continued, “and it requires us to think a little bit differently.”
Hemmelgarn then went on to explain that Siemens sees AI’s impact in three areas: analyse, optimise, and generate.
The key element, analyse, involves AI co-pilots built into Siemens software that allow users to interrogate design, engineering and manufacturing data to create the data needed with a simple prompt.
Optimise is about using AI to finetune everything from a manufacturing production schedule to reconfiguring a factory floor for the best business results.
Finally, generate is about looking to use AI to automatically create design specifications, manuals, or even geometry.
Uses for AI-enabled engineering, as explained by Siemens learning architect Jody Crossfield, range from domain-based user interaction models to guidance on sustainability and manufacturability predictions.
AI can anticipate the results of any decision made by the manufacturer, whether that decision is related to manufacture or traceability. It also acts as an intelligent search engine with optimised results.
In Crossfield’s keynote on using predictive AI in NX X, the new SaaS-based version of NX, he demonstrated live how the AI industrial co-pilot can speed up design processes and eliminate the need for manual selection in CAD. According to Crossfield, NX X’s AI can identify similar shapes, faces and areas, making editing less timeconsuming and has a 94% accuracy rate so far.
When it comes to Siemens’ simulation software, combining physics-based predictions with AI-based inferences can help augment the frequency and lower the turnaround time of simulation results, explained JeanClaude Ercolanelli, senior vice president of simulation and test solutions.
Using AI to predict a product’s life cycle leads to increased sustainability, with long-lasting materials chosen and the environmental impact of the product anticipated and reduced long before the product is manufactured and sold – particularly important when manufacturing transport such as cars and aeroplanes.
CLOUD THINKING
AI-enhanced solutions were also on the table when Siemens’ partnership with Microsoft was showcased on the main stage. The continuation of a 35-year partnership with Microsoft currently means that the Siemens Xcelerator as a Service portfolio can be run through Microsoft Azure and be integrated with Azure’s generative AI.
The expansion of the Xcelerator portfolio into Siemens Xcelerator as a Service was announced at the event by executive vice president for PLM products Joe Bohman, who outlined the new set of solutions that are available through the cloud.
The cloud market will surpass $1 trillion in 2026, Bohman said during his presentation, and it’s clear that Siemens wants a big slice of that market.
NX X, Teamcenter X, Simcenter X, Opcenter X, and the Zel X engineering app are just some of the software packages that are now available through the Siemens Xcelerator as a Service portfolio.
Billed as “flexible, modular solutions that run on the industry’s most robust interoperable data backbone”, the software available can fit workflows from concept to manufacturing.
“It brings together expert communities, giving people the ability to talk and work together,” said Bohman.
The Siemens Xcelerator as a Service portfolio also gives NX X users access to over 100 available products through the cloud, making it easy to run occasionally needed products without having to make a separate purchase.
The user experience is of the quality of NX, but with additional means of collaboration that aren’t possible without the SaaS-based update.
It also makes tools like NX more accessible for more occasional users, with NX Command Prediction focused on making the customer more efficient and productive, and taking away the learning curve associated with getting someone up and running on NX, said Jeff Miller, director of customer success marketing.
Advances in realistic, immersive visualisation also aim to help users conquer the learning curve – something that is especially important when you consider that the new generation of incoming product designers have grown up surrounded by video games and other forms of graphic design.
Bob Haubrock, senior vice president of product engineering software, delivered a session on the importance of effectively connecting the real and digital world using immersive tools.
Siemens says it has improved its multi-discipline collaboration, graphics and colour to make the design process more seamless for a “gaming-level experience”, even without a headset.
However, much of the opening keynote session was devoted to Siemens’ partnership with Sony. In particular, the SRH-S1 headset developed to work in harmony with NX Immersive Designer was unveiled to the audience.
The Sony XR head-mounted display is designed specifically for use with NX and can be used to view and interact with models, providing a more immersive and authentic experience than looking at them on a desktop. When announcing the release of the headset, Seiya Amatatsu, head of Sony’s XR technology development division, claimed that it has already improved the productivity of the company’s own internal design team by 25%. The headset will be available later this year.
OUT ON THE FLOOR
There was much to see in the Solutions Centre at the event, where Siemens customers get the opportunity to experience first-hand new products and technologies. A popular focus was low-code app development platform
Mendix, bought by Siemens in 2018 and included in the Xcelerator portfolio.
Using Mendix, Siemens customers can view their manufacturing systems and workflows, build apps and share data through the cloud, reducing costs and the necessity of travel.
In a customer session, Applied Materials India outlined how it used Mendix to develop its Material Product Manager Console App, for managing bills of materials and product costs. The BOM data was centralised from Teamcenter and from its deployment of the open-source Java framework Hadoop.
Siemens also showcased the Maintenance Aware Design Ecosystem, or MADe, which identifies and mitigates technical risk and optimises design for engineering systems.
This system, created by PHM Technology as a solution to potential risk in engineering systems, proposes to replace traditional, manual methods of risk-checking, which are no longer practical as systems become rapidly more complex.
MADe supports digital transformation by digitising risk and maintainability analysis, in keeping with the slogan of Realize Live 2024: “Where your digital transformation gets real. Fast.”
As Marlene Haag, a pre-sales solution consultant with Siemens Digital Industries Software put it: “The importance of maintaining a digital system is often overlooked. But risk management is essential, especially when relying on the cloud.”
Digital transformation might require some risk management, but at Realize Live, we glimpsed the beginnings of Siemens’ cloud-based and AI-supported future.
It’s a move that the company claims will democratise its software portfolio and make it available to a wider range of companies. At the very least, it opens up a world of new possibilities for what product development technology can become.
www.sw.siemens.com
‘‘ AI feels different, because we’re seeing immediate business value for our customers, and frankly, the possibilities are endless ’’
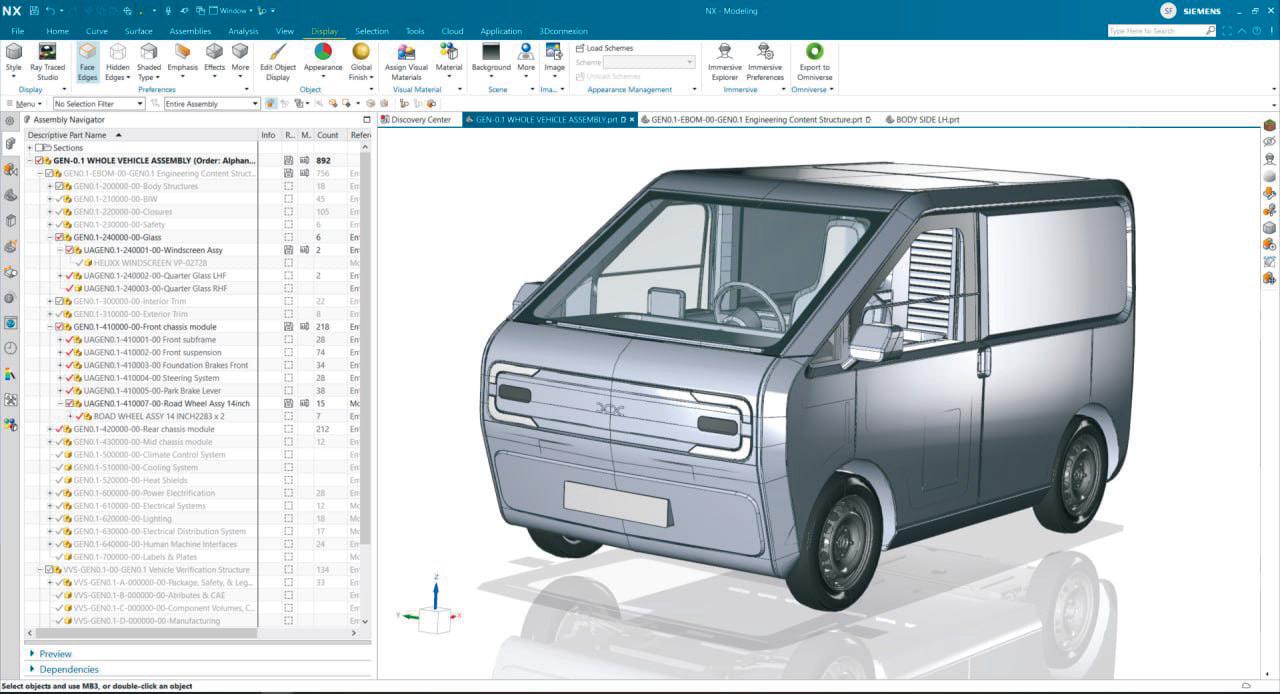
NVIDIA OMNIVERSE
» Nvidia is extending the reach of Omniverse with new Cloud APIs that put visualsation and simulation into the hands of many more users, writes Greg Corke
Nvidia Omniverse has been instrumental in bringing USD, the 3D scene description originally developed by Pixar for content creation and interoperability between tools, into the world of design and manufacturing.
Since its launch in 2020, Omniverse has had a significant impact in industrial digital twins. Firms including BMW are using the platform for virtual factory planning, to optimise layouts, and simulate robotics and logistics systems before production starts. BMW is also connecting domain-specific software tools for multi-user live collaboration across locations, on any device.
Omniverse is not just for simulation and collaboration, however. It provides a powerful environment for visualisation. Powered by Nvidia RTX GPUs on desktop or in the cloud, design and manufacturing firms have ready access to technologies including real time ray tracing for photorealistic rendering, and one click VR/AR.
THE CLOUD ATTRACTION
In product development, many firms have established workflows for Product Lifecycle Management (PLM) or Product Data Management (PDM). The CAD software developers also have long-term strategies to move their customers to their respective cloud platforms. Autodesk has Fusion, Solidworks has the 3DExperience Platform. There are several others.
Each platform is not just about centralising data; it’s about building optimised collaborative workflows around that data and, in the future, using AI to obtain valuable insights from that data.
Of course, software developers ideally want customers to
remain in their platform as long as possible. Furthermore, manufacturing firms don’t necessarily want to build workflows around multiple platforms or tech stacks.
To some extent, Omniverse pushes against this. In order for Nvidia to play a bigger role as these cloud platforms grow in stature, the company recently released a series of Omniverse Cloud APIs, coming first to Microsoft Azure.
Rather than making Omniverse the centre of everything, Nvidia is enabling software developers to integrate key Omniverse technologies into their respective platforms. It means their users can continue to work in a familiar environment, workflows remain the same, and data is stored in one central repository.
In its simplest form, software developers can embed Omniverse-powered viewports into their platforms, delivering ‘instant’ real-time physically based rendering – processed on GPUs in the cloud with pixels streamed to a client device. Software developers can also use the APIs to connect Generative AI tools into their existing apps, as well as a range of workflow tools for OpenUSD data.
Several software developers have already come on board with Omniverse Cloud APIs, including Ansys, Cadence, Dassault Systèmes, Hexagon, Microsoft, Rockwell Automation, Siemens, and Trimble. Some Omniverse API developments are at a more advanced stage than others, and details are still thin on the ground.
DEVELOP3D caught up Siemens to find out more.
MAKING VISUALISATION PERVASIVE
Siemens has been working closely with Nvidia on Omniverse for a couple of years now, so it’s no surprise to see the company embracing the new Cloud APIs.
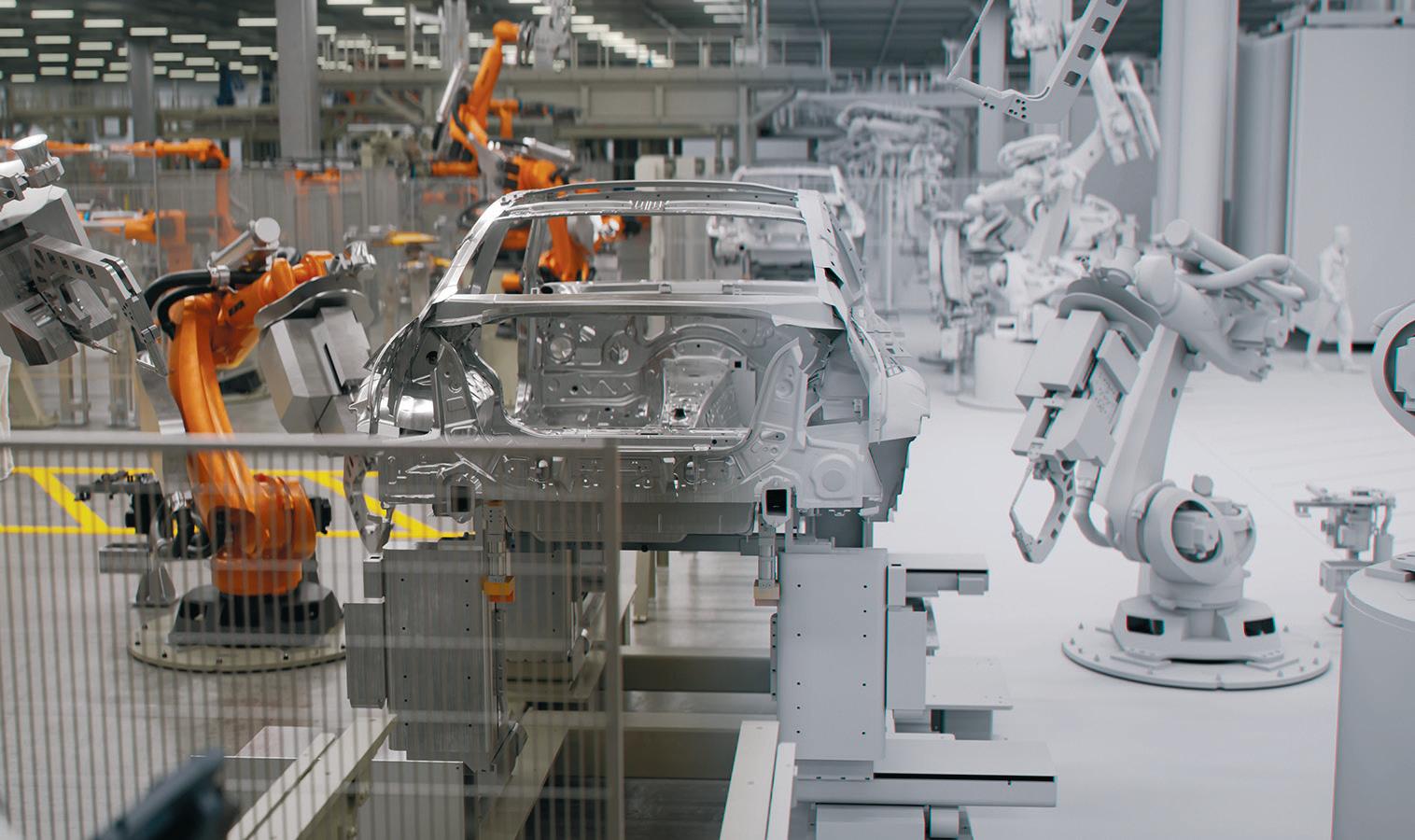
● 1 BMW is using Omniverse for virtual factory planning, to optimise layouts, and to simulate robotics and logistics systems before production starts ● 2 Omniverse RTX rendering is available directly inside Siemens Teamcenter X, the cloud-based PLM platform, so massive engineering datasets can be visualised interactively and photo-realistically with real time ray tracing
SPREADS ITS WINGS
Siemens is starting with Teamcenter X, offering Omniverse RTX rendering directly inside the cloudbased PLM platform, so users can visualise massive engineering datasets, interactively and photo-realistically with real time ray tracing.
At Nvidia’s GTC event in March 2024, Siemens gave a demonstration of a colossal 7-million-part ship model from HD Hyundai, visualised in real time, powered by GPUs in the cloud. The demo also showed the use of Generative AI, using text prompts, such as ‘atlantic ocean waves, remote photography, ocean, sea, morning sky’ to generate 3D objects or HDRi backgrounds to visualise the model in context.
The interesting takeaway here is that PLM software needs to be used by all different types of users. Providing a beautifully rendered viewport with buckets of GPU acceleration from the cloud, on-demand, instantly makes 3D model data accessible to everyone and not just those with powerful local workstations.
With Omniverse RTX rendering, you also get the ability to create beautiful visualisations relatively easily. This can massively aid communication and understanding, at all levels - right down to the shop floor. In theory, it could also mean marketing departments can create their own visuals, rather than having to rely on a designer or engineer powering up NX Ray Traced Studio, the visualisation tool that works with Siemens NX.
Siemens has plans to extend Omniverse APIs into other tools, including Siemens NX which was recently made available as a cloud service (Siemens NX X). Siemens NX X can be deployed in two ways: on the desktop, where it uses local CPU and GPU processing, and in the cloud
where it runs on cloud workstations and pixels are streamed to the local device.
Siemens is currently working with Omniverse Cloud APIs to put an Nvidia RTX-powered viewport directly into Siemens NX X, delivering real time ray tracing on-demand, powered by cloud GPUs. The RTX viewport will co-exist alongside the current OpenGL viewport, so Siemens will not have to completely re-architect the software using modern graphics APIs like DirectX 12 or Vulkan, which would be a huge undertaking.
THE CLOUD FUTURE
With Omniverse Cloud APIs, Nvidia is extending the reach of its Omniverse platform, putting RTX visualisation into the hands of many more users, especially those that previously would have been excluded because of underpowered local hardware. The emphasis is on photorealism, but with powerful GPUs in the cloud, far outpacing those in your average desktop, laptop or tablet, Omniverse Cloud APIs could also help all different types of users view larger, more complex 3D models in general.
Of course, cloud processing doesn’t come cheap and software firms like Siemens will need to pass on costs to customers. If demand is there, however, paying for GPUs on demand could be a more cost-effective way of extending the reach of valuable 3D assets, the alternative being providing everyone with powerful workstations, which may be underutilised a lot of the time.
For Nvidia it looks like a win, win. More use of Omniverse, a gateway into the broader Omniverse platform, and more use of GPUs, wherever they might be. www.nvidia.com/omniverse

‘‘ Siemens is currently working with Omniverse Cloud APIs to put an Nvidia RTX-powered viewport directly into Siemens NX X, delivering real time ray tracing on-demand, powered by cloud GPUs
GO WITH THE FLOW
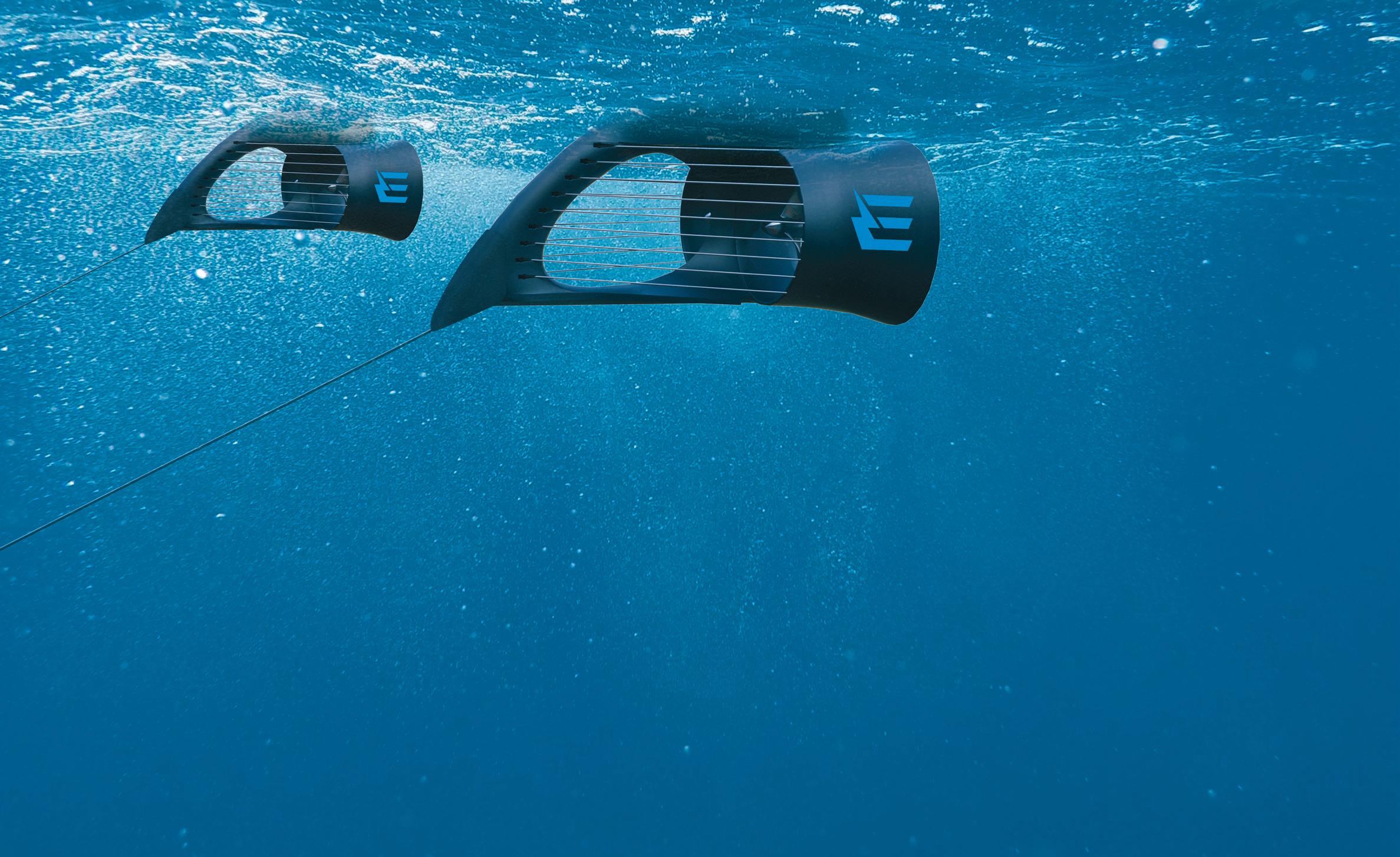
» Generating power from flowing water is nothing new, but Energyminer is looking to do it without dams or weirs that interfere with nature. Stephen Holmes learns how simulation technology is enabling it to test its Energyfish power plant across multiple rivers in a fraction of the time than would otherwise be required
Hydropower is one of the primary sources of renewable energy at work today, producing over 60% of all sustainable energy, but its deployment comes with some limitations. Building weirs and dams is expensive, resource-intensive and can have negative environmental consequences.
But many of us live and work close to moving bodies of water, be they rivers or man-made canal networks – so what if removable and replaceable energy generators could be deployed in such locations, acting as convenient sources of electricity?
That’s the thinking behind clean energy start-up Energyminer, where founders had the goal of creating a hydrogenerator far more versatile in terms of placement than more traditional approaches. The idea was to instead build energy ‘fish’ – small generators, to be anchored in a stretch of waterway, with ‘schools’ of up to 100 fish deployed. Each Energyfish is small enough that it doesn’t take up much space in the river, keeping the environmental impact low.
Based in Munich, Energyminer’s two founders Dr Richard Eckl and Dr Georg Walder began discussing
the concept back in 2020. In 2023, Chantel Niebuhr, a specialist in hydraulics and fluid mechanics for civil engineering, joined the team as CTO.
One of Energyminer’s first tasks was to assess where its fish should swim, prompting an analysis of German rivers.
As Niebuhr explains: “You need to choose the size of your power plant according to what you have available, because you want to be able to utilise as many resources as possible. So that set out the design parameters.”
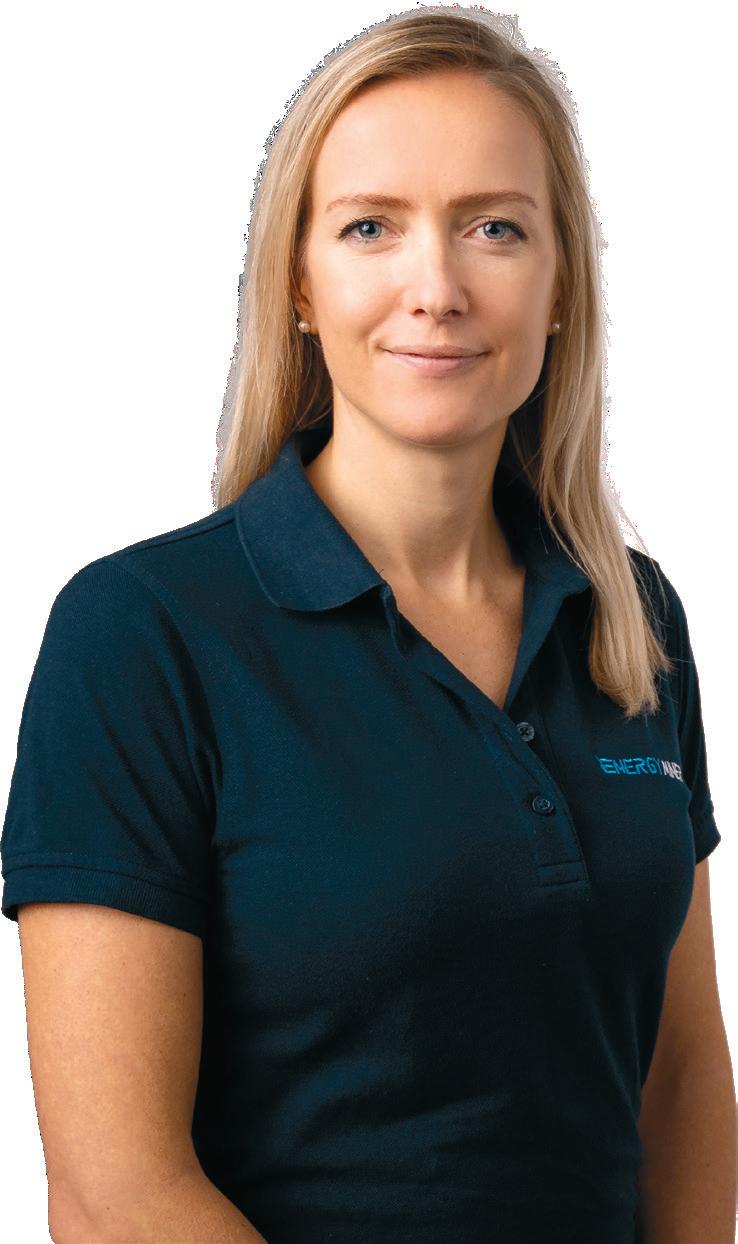
Questions asked included: How deep are most of the rivers in Germany? How deep is a typical river section? Where might Energyfish be most effective in size, so that a deployment could be scaled laterally in terms of arrays, but not require a massive turbine that only fits some 5% of river sections?
Key to this initial research was an academic study that looked at how best to fully utilise hydrokinetic energy in river sections. Niebuhr suggests that much of the time, links between academia and industry aren’t used to good effect, but Energyminer sourced the latest knowledge available, bringing new findings into its concept design process to create the most efficient design.
As a result, the design package for the Energyfish was limited to the size of a small car, allowing it to be transported on a normal
CFD analysis performed using SimScale indicates the turbulent flow field around the turbine
●
4 In this analysis, the colour of the flow lines indicate their velocity as they pass through the device
truck, reducing installation demands and limiting environmental impact. “You never want to use up a lot of the cross-section of the river, so we always want to use only the first metre depth. And that’s why the Energyfish is shaped and built the way it is,” says Niebuhr.
CURRENT THINKING
The form of the Energyfish is governed by basic hydrodynamic principles; these include considerations such as increasing the pressure over or around the blades to adjust buoyancy and achieving optimum flow velocity in slower river sections.
“Water flow is not something that’s so simple to analyse,” says Niebuhr, “and it gets very complicated, especially when you have rotating components.”
The first step to optimising the flow was to build an initial prototype, building a 3D model in Onshape, before the team got more hands-on, producing a working proof of concept that shows Energyminer’s hardware components working together with other electromechanical components within the structure.
With that first success under its belt, the process of optimising the design began. For this, Energyminer’s team turned to SimScale’s cloud-based CFD tools.
“Cloud gave us a very big advantage, because CFD is usually very expensive,” says Niebuhr. “A lot of people can’t do simulation themselves or use external consultants to do it. So we had a big advantage where we could do a lot of that in-house and that gave us a lot of information.”
Using a digital twin of the Energyfish, the team greatly reduced the need for live laboratory testing, and could compare a wide range of scenarios from different German rivers and canals, at different times of year. With physical testing, this would have been almost impossible.
“We could take all this complexity and actually analyse it in terms of our hardware,” says Niebuhr, explaining that this process answered many important questions: “How does it affect our housing? Where do we need more strength? Where do we need to maybe look at other materials? We can analyse all of that without even [building] another prototype, which is just extremely expensive.”
No two rivers are the same. Using SimScale allowed Energyminer to test its design in multiple flow conditions, in different river sections and then tweak
designs in Onshape to create a product applicable to a wider range of water bodies.
“Working with those two together was just a perfect workflow for us,” says Niebuhr. “You can change something in Onshape, and then it’s imported directly into SimScale, and you can run a simulation again, and then see, ‘Okay, maybe we need to vary this a little bit’.”
LIFE ON THE WATER
The team’s latest prototype has been operating for over a year in a river flowing through central Munich, sending power to the grid via its low-voltage connection to a land box and validating much of the company’s simulation data at the same time.
When 1,000 kg per metre cube of water comes down a river section, even at 1 metre per second, that’s a lot of force to contend with – so it’s here that the team learnt what to expect from fluid structure interaction simulations.
Rivers and canals, after all, are rarely free of debris such as tree branches, other vegetation, rubbish, even quite large objects.
In fact, the pilot project in Munich proved prone to unusual debris. “Everything gets thrown into this canal,” says Niebuhr. “There’s also a zoo upstream, so we have some wonderful biofilm growth, snails and interesting plants! It was a really good test for us and a big thing that we had to address.”
As a result, the Energyfish has been designed to be as debris-deflecting and self-cleaning as possible. It can also dive down out of harm’s way during floods or periods of faster flow.
“That’s just a question of buoyancy. When you have a certain pressure change or force on the structure, then it dives down, so it’s not sitting in this upper region, where all the branches and debris are floating in a flood event.”
Production is already underway and next steps involve installing a school of Energyfish in Germany, allowing Energyminer to test how a group works together in a typical river.
With over 4,000 rivers in Germany alone, it is hoped that these swimming generators of clean energy will soon produce greener hydropower while allowing nature to remain unspoilt.
www.energyminer.eu
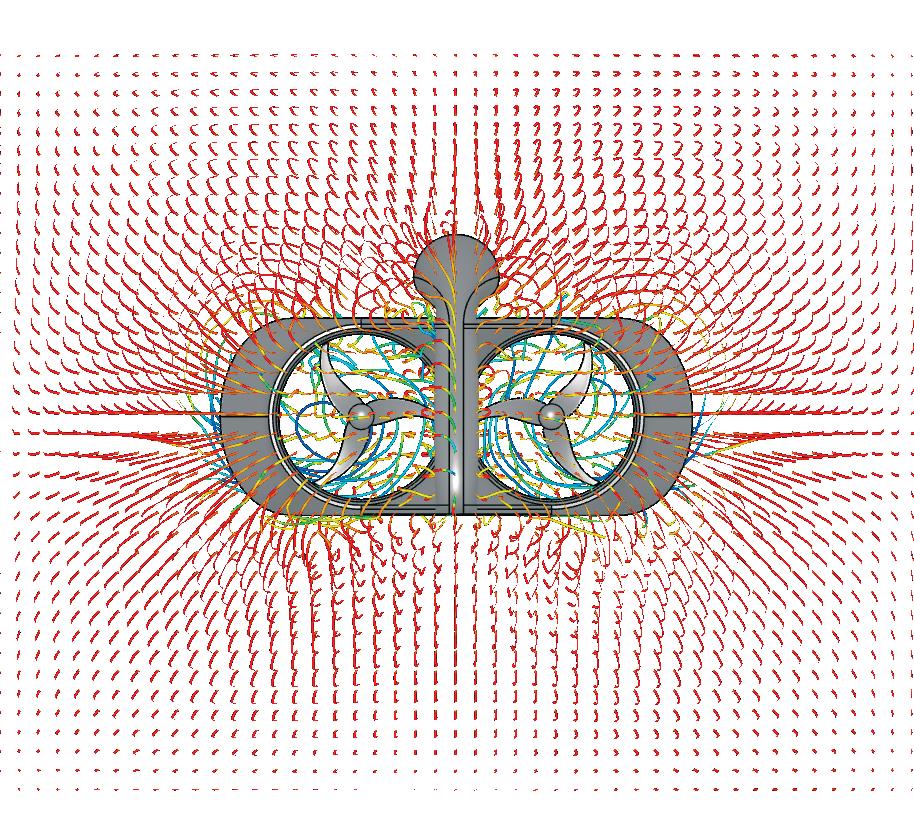
‘‘ Water flow is not something that is simple to analyse –it gets very complicated, especially when you have rotating components ’’
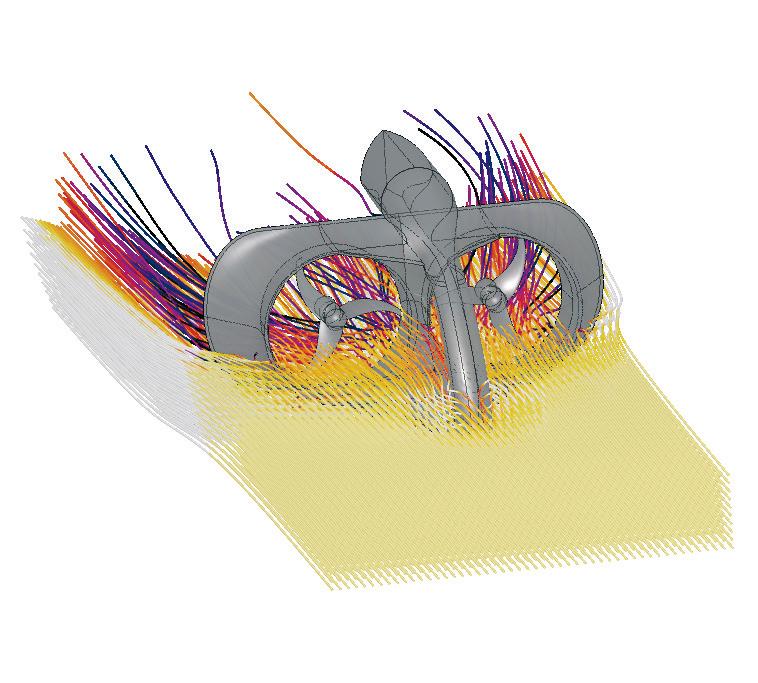
DUNE RACER
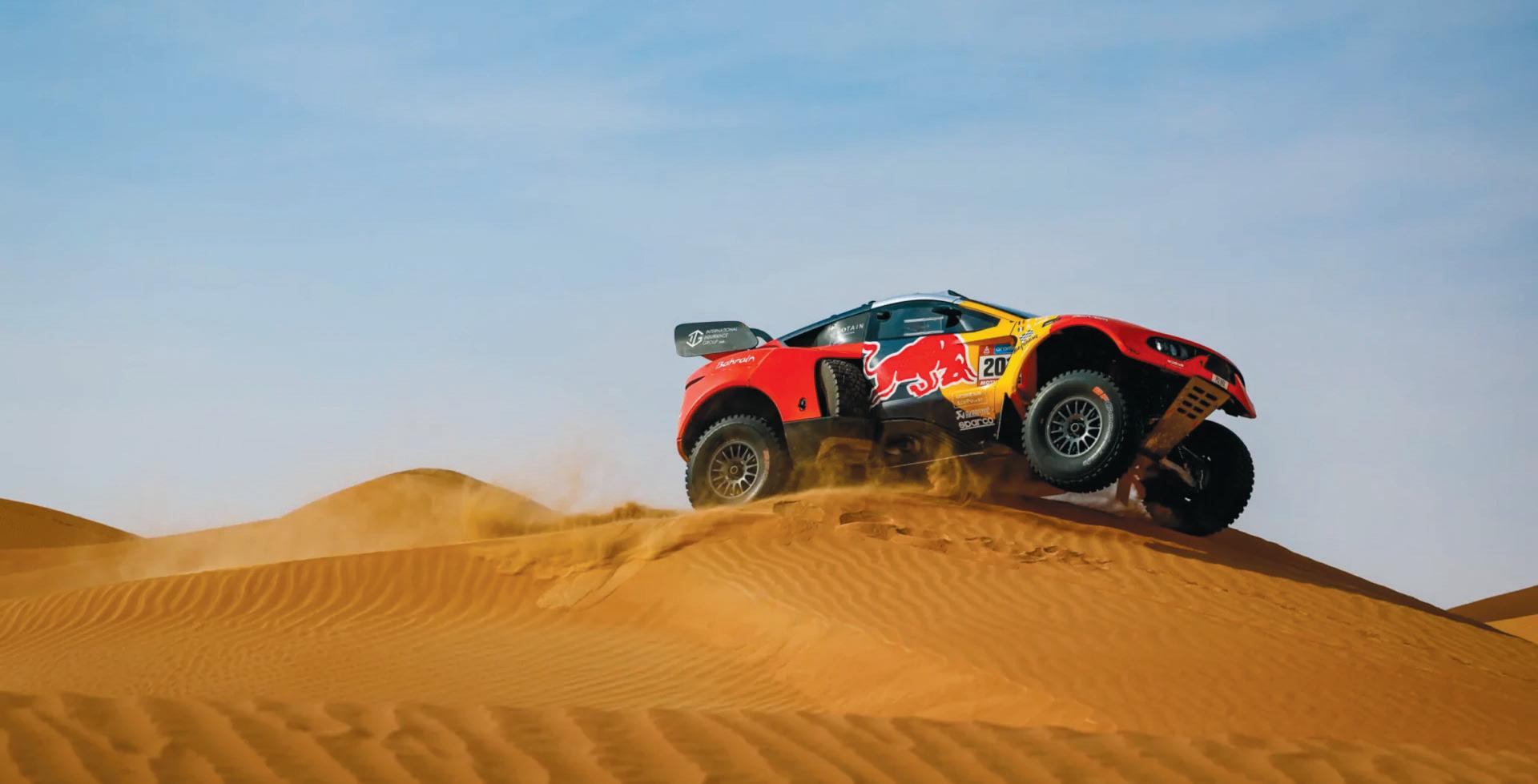
» The Dakar Rally is one of the toughest races in the world, for both drivers and their vehicles. Prodrive uses 3D scanning to improve its chances in races and maintain its winning streak when it comes to putting drivers on the podium
The annual Dakar Rally, one of the most famous races in the world, covers over 8,000 km of deserts, mountains and savannahs and tests participants and their vehicles to their limits.
In January 2024, only 239 out of 340 vehicles finished the race, with incredibly tough terrain and weather conditions cementing the Dakar Rally’s reputation as a one-of-a-kind endurance event.
What was originally a race from Paris, France to Dakar, Senegal, has been relocated several times and took place this year in the desert of Saudia Arabia, beginning in AlUla and finishing on the shores of the Red Sea.
Prodrive is no stranger to the challenges posed by this race. Headquartered in Banbury, UK, the company is a British brand with an exceptional pedigree, having tuned cars for a variety of race teams, including Subaru, BMW and Porsche, since 1984.
It first entered the Dakar Rally in 2020. In 2024, it unleashed the Prodrive Hunter, its first all-terrain hypercar, which secured the top three positions on the podium and retails at a cool £1.25 million.
On mountainous terrain, Prodrive’s priority is making sure that cars aren’t destroyed and that drivers remain safe. In an effort to improve its cars each year, the company has employed the help of The 3D Measurement Company’s (T3DMC) Trackscan-Sharp.
STRUCTURAL INTEGRITY
The structural integrity of a vehicle is extremely important in the difficult racing conditions presented by the Dakar Rally, and is often the determining factor when it comes to whether or not a team will finish. Prodrive conducts post-rally 3D scans of its cars to collect data about how the vehicles have coped with the conditions.
The Trackscan is a handheld 3D scanning system which has a tracking distance of up to 8 metres. It uses optical tracking technology and high-resolution cameras to create accurate, fast scans of large-scale objects. In other words, it’s ideal for cars. A 49 metres cubed measurement volume allows for a complete surface scan of the car’s shell frame without needing to reposition
the tracking system. With dot-free 3D scanning and an accuracy up to 0.025 mm, seven parallel blue laser lines and 25-megapixel cameras capture every small detail, with the data processed onboard the device.
After the scanning process, the resulting STL file is imported into inspection software for side-by-side comparison with CAD models of the car’s frame. The results of this inspection are used when designing future models, to ensure durability and high performance.
Regular scans of cars mean that potential issues can be identified early on, extending a vehicle’s lifespan and reducing the possibility of malfunctions during the race. Post-rally inspections provide information about how the vehicle withstands the harsh conditions of the Saudi Arabian desert.
“The terrain would smash any normal car to bits. What we need to do is monitor the health of our vehicles, in particular the space frame,” says Prodrive vehicle director, Paul Doe.
Prodrive also uses the Simscan, also from T3DMC, as a smaller, portable scanner, which allows for single-handed operation and more detailed scanning, with accuracy up to 0.020 mm and 2.8 million measurements per second. It offers dual measurement volume for scanning both large and small areas.
“With both of these items in our armoury, we’re able to do things at such a higher level and very fast,” says Doe.
Looking ahead to the 2025 Dakar Rally, Prodrive has announced a partnership with Dacia to compete in the World Rally-Raid Championship, which culminates in the Dakar.
With the help of 3D scanning, Prodrive and Dacia have the potential as a partnership to create cars that revolutionise the Dakar Rally, and have three teams lined up for Dakar 2025, pushing the limits of what’s possible in the world’s toughest race.
www.prodrive.com


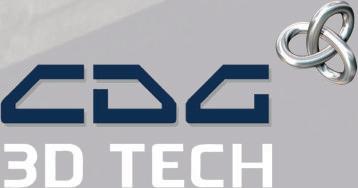

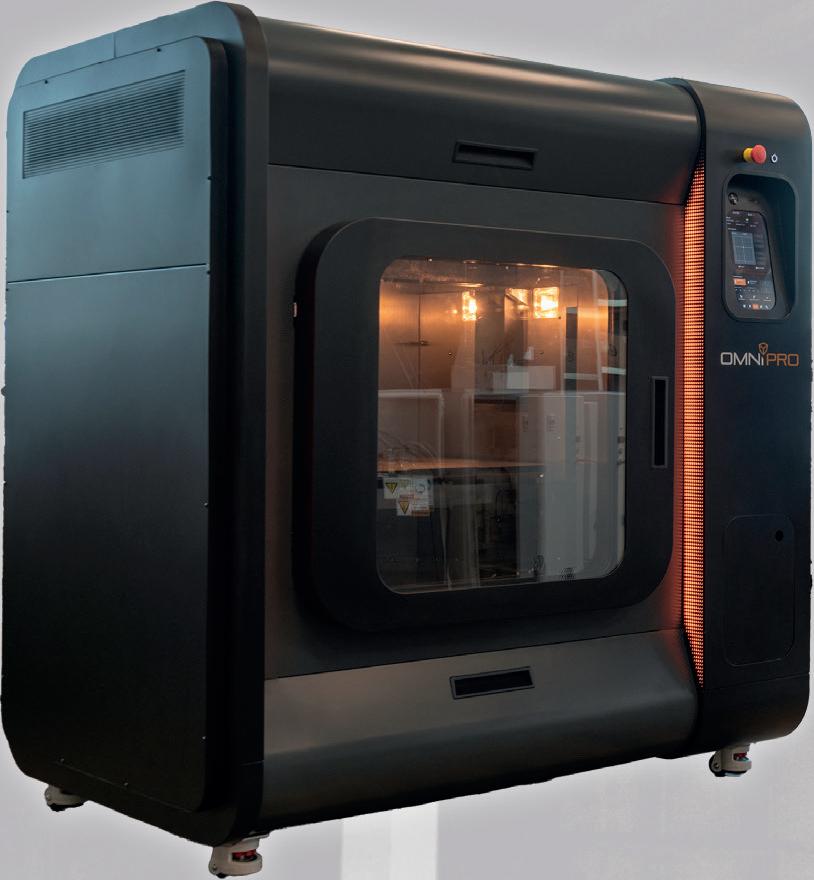
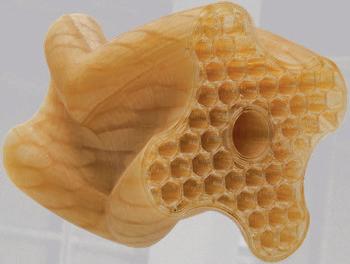
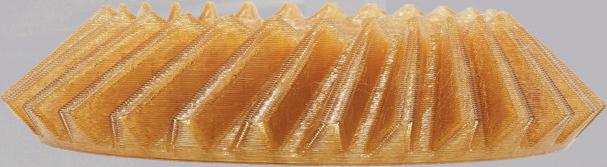
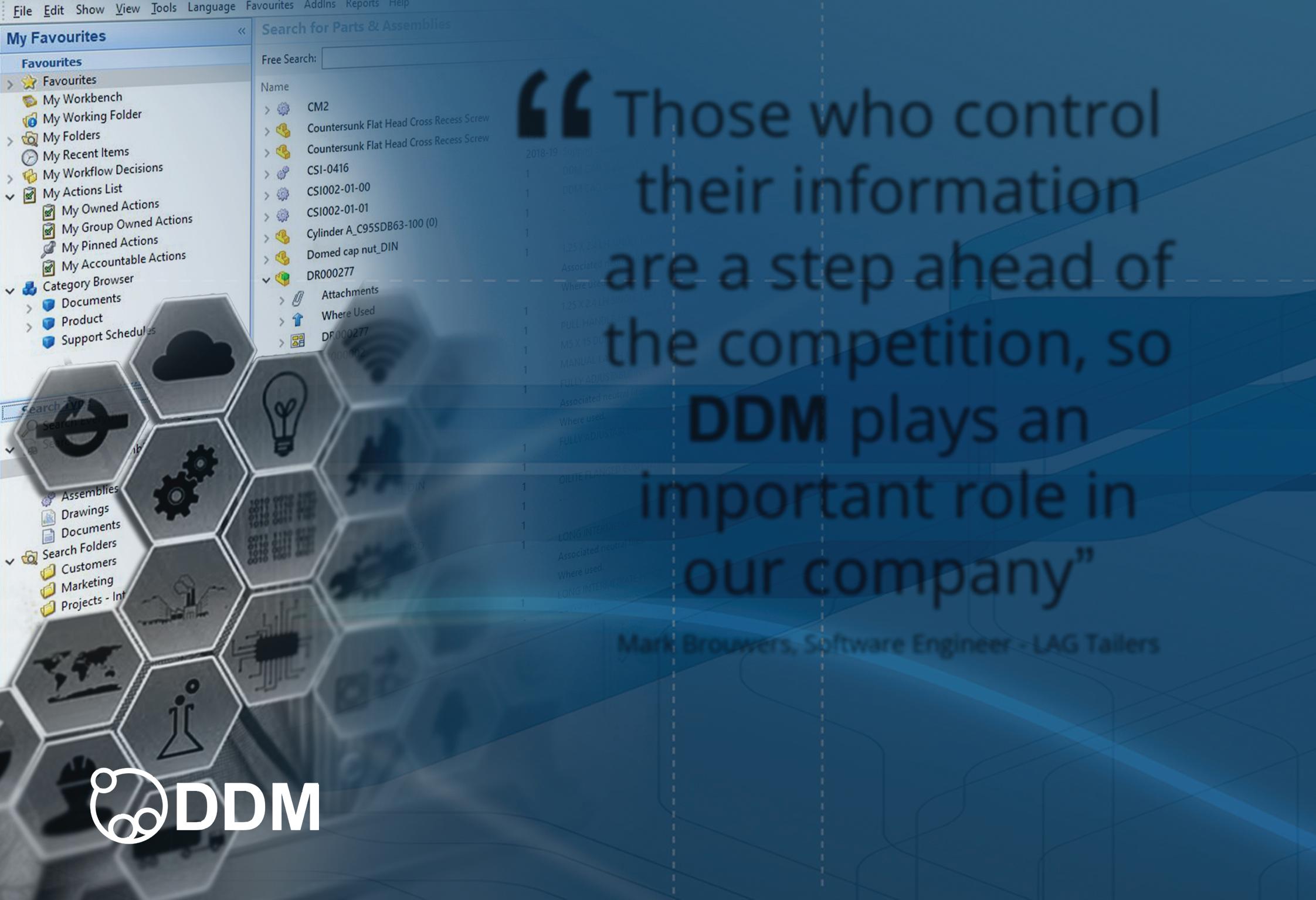
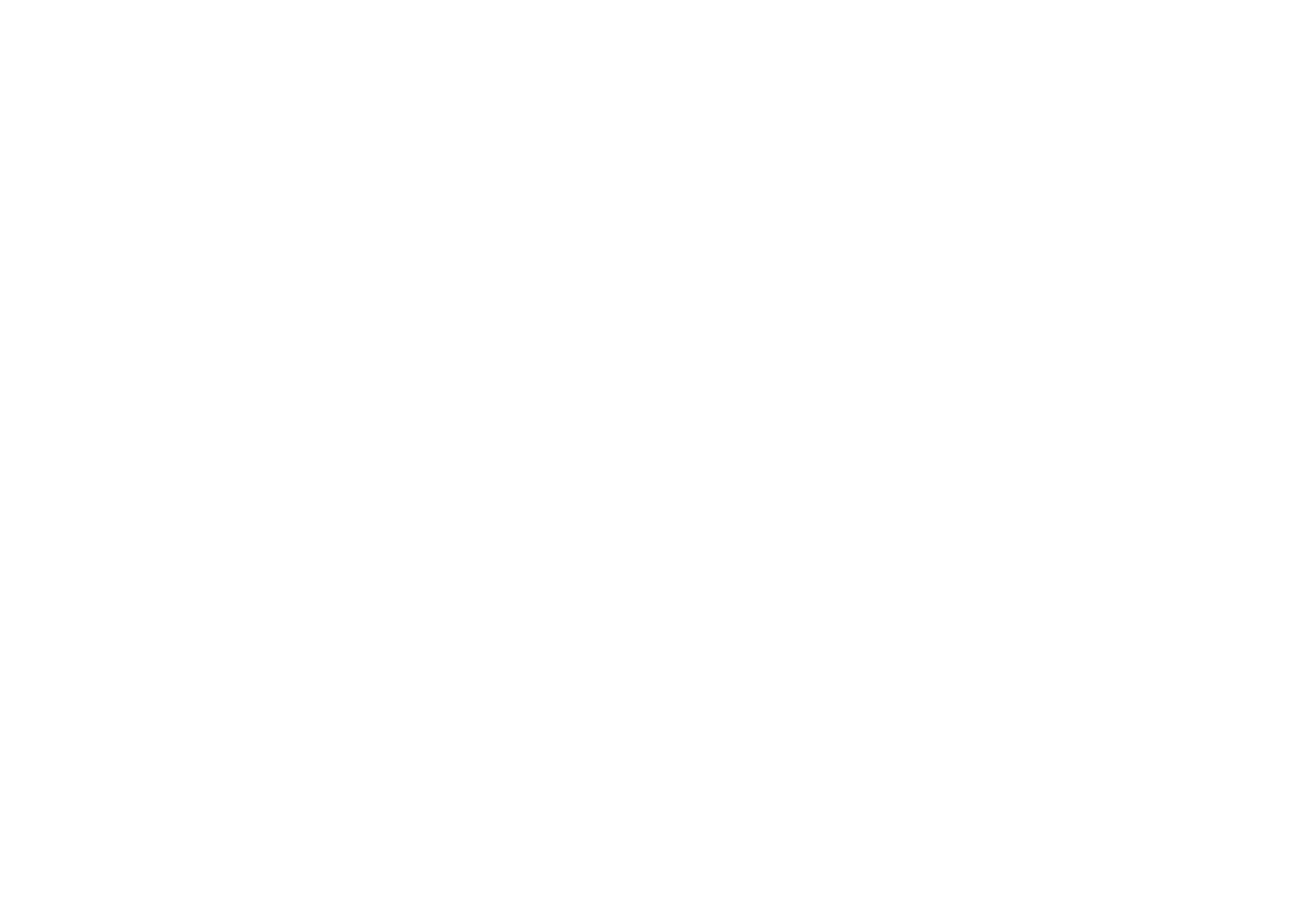
POWER OF TWO
» Ather Energy, a nimble start-up in the Indian electric vehicle market, is using the Siemens Xcelerator platform to fast-charge new product development and engineering of more sustainable two-wheelers
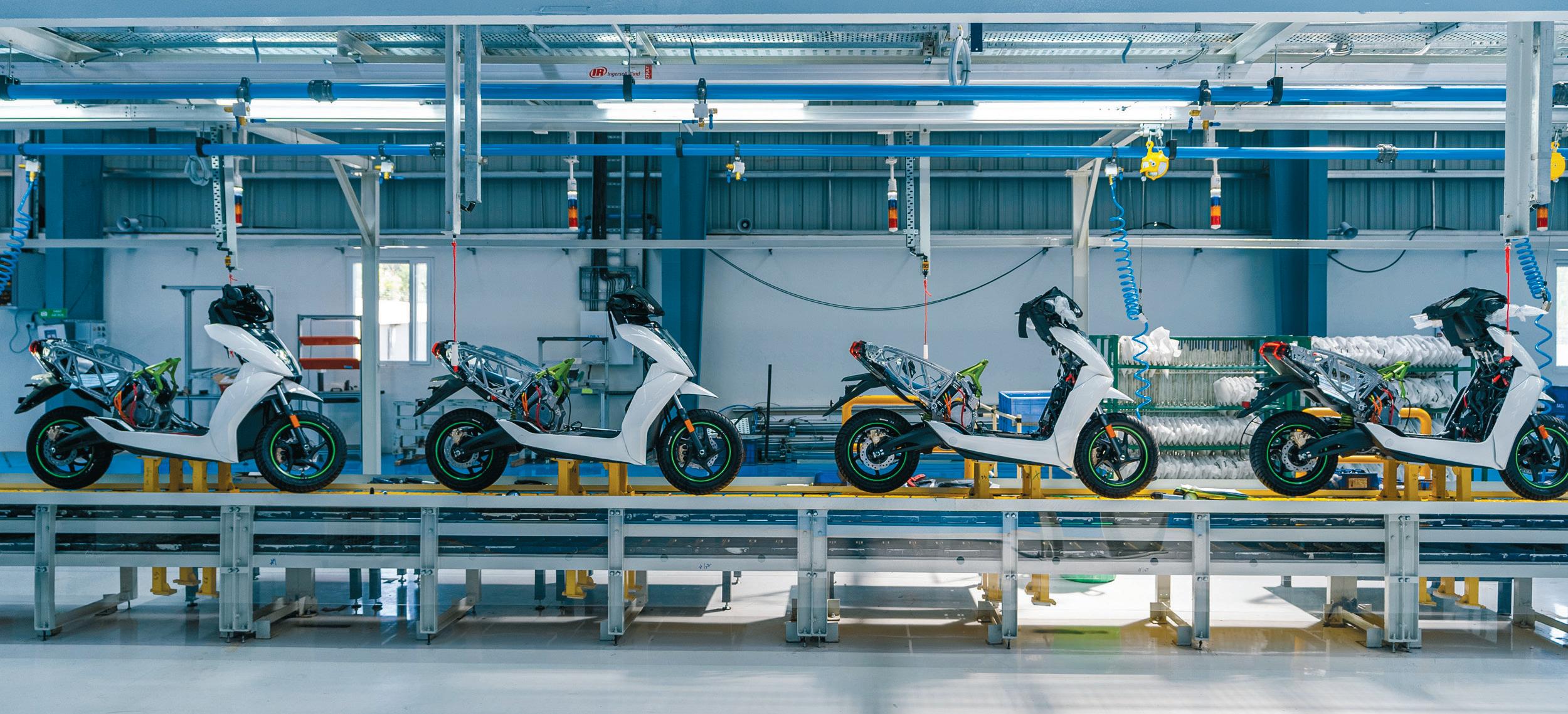
Over the coming decade, the global electric scooter market is projected to surpass $59 billion, providing an accessible form of transportation to the masses that also benefits from renewable energy.
India is seen as one of the key markets for such products, with a vast population keen to jump on the electric twowheeler trend. As a result, electric scooters are forecast to make up some 70% of Indian vehicle sales by 2030.
Ather Energy is already a leading brand in the sector, offering a range of eye-catching machines and running a comprehensive charging network. Founded in 2013 by Indian Institute of Technology (IIT) Madras alumni Tarun Mehta and Swapnil Jain, it launched India’s first truly intelligent e-scooter, the Ather 450, back in 2018.
Variants of the 450 have since followed, from the sporty Apex model to the family-focused Rizta. All models benefit from the 1,600-plus charging points across India that make Ather Grid one of India’s largest fast-charging networks.
“In the fast-evolving EV industry, speed to market is an important lever to succeed,” says Jain, whose roles at Ather include that of Chief Technology Officer.
Ather Energy originally adopted Siemens Teamcenter software for its PLM capabilities, in order to drive down time to market. According to Jain, this helped reduce the company’s design and engineering cycle times, with the removal of design iterations and the adoption of a ‘right first time’ approach.
Since then, the Ather Energy team has adopted the Siemens Xcelerator portfolio, taking advantage of Simcenter Star-CCM+ software for CFD analysis of bikes and batteries. Simcenter plays a key role in the company’s
in-house testing regime for factors including durability and noise, vibration and harshness (NVH).
Most recently, the Ather Energy vehicle engineering team moved to Siemens’ NX, helping it to build CAD models for new product development and engineering and shift away from its legacy system for all existing and new vehicle platforms.
“The simulations and virtual testing we perform using Siemens’ tools enable us to crush timing and provide us with great savings in resources and money spent on repeating testing,” says Jain.
“The stack-up analysis enables us to get a design right the first time and avoid engineering changes. We are looking at expanding the Siemens tools into controlling the manufacturing processes by introducing the management of a Bill of Processes.”
Ather Energy is moving forwards in as nimble a manner as its EV scooters navigate Indian roads. Evidence of its success includes a partnership with Hero MotoCorp, the world’s largest two-wheeler manufacturer, which wishes to benefit from Ather’s fastcharge network.
With further growth yet to come, Ather Energy has built out a product development platform that looks set to provides an ideal launchpad for its bold sustainable transport ambitions.
www.atherenergy.com

Full Colour 3D Print
It’s All Over
Your search for a 3D printer capable of producing complex & creative models in up to 10,00 0,00 0 colours is over T he new Mimaki 3DUJ-22 07 delivers extraordina r y detail in full colour.
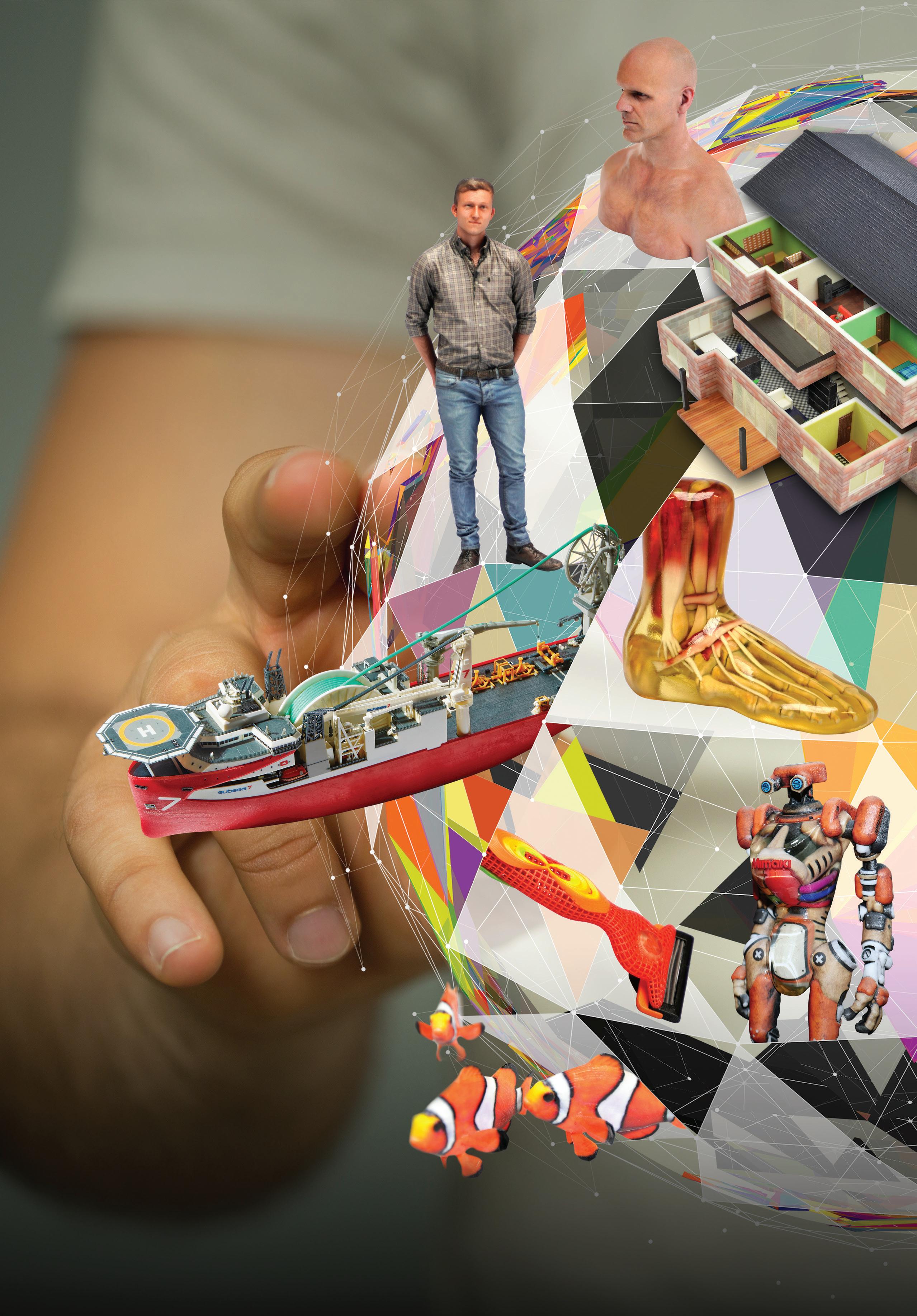
E xplore a wor ld of colour for just
3 4,995

» E-bikes are in high demand, but reliable batteries are essential to make them both safe and sustainable. KTM has worked with Ansys and CADFEM to push its batteries to their limits, as Emilie Eisenberg reports
Adirt bike is built for the back roads, to scramble over gravel and dirt as the undisputed off-road speed machine.
KTM aims to heighten the dirt bike’s appeal by matching its agility with expert electric power delivery, lower fuel costs, decreased maintenance and a significantly smaller carbon footprint.
A key component in this mission is the battery. Here, KTM uses simulation technology to test batteries according to the various situations that a dirt bike might encounter.
Working with German simulation expert CADFEM, KTM’s engineers looked to optimise its battery design’s thermal properties. A well-designed battery offers faster charging times, a slower ageing process through better temperature distribution, and crucially, will not overheat.
To meet these needs, KTM developed a simulation workflow using Ansys Twin Builder. This consisted of three submodules that all exchange input and output data simultaneously.
HEAT GENERATION
An electrical lumped element model was used for heat generation to test each cell’s temperature and its state of charge. Resulting values were then fed into a compact thermal model derived from 3D finite element method (FEM) models, which calculated the battery’s temperature distribution.
A third sub-module was created based on computational fluid dynamics (CFD) analysis to calculate thermal dissipation of the battery housing resulting from convection and radiation.
KTM used Ansys Mechanical via CADFEM for model order reduction and imported the reduced order model into Twin Builder. CADFEM’s tool Model Reduction Inside Ansys was then used for accelerating computation times during reduced order model extraction without a loss of accuracy.
Reduced order model verification within the battery pack was accomplished using simulation of a 3D model of the battery to track the accuracy of, and determine the optimal parameter settings for, model order reduction.
KTM conducts all its cell testing in-house and the testing for the new e-bike battery created the need for a cell database containing every option for each project. It used the Battery Wizard toolkit in Twin Builder to generate Equivalent Circuit Model (ECM) lookup tables from all the test data in its database.
This system gave designers the ability to analyse cell data easily and quickly. Once single-cell ECM tables were created, the wizard connected cell ECMs in parallel according to specifications to configure an accurate electrical model for the battery module.
Matching the simulation model against experimental test data involved current and dynamic discharge measurements. In a single cell, the predicted output voltage showed an error of less than 20 millivolts.
For the entire battery pack model, a temperature deviation of less than 2 degrees Celsius was achieved for certain drive cycles, resulting in a stable battery pack design.
(Above) All the exhilaration of dirt biking, without the environmental impact (Below) KTM works with Ansys and CADFEM to build batteries that can boast low temperature deviation
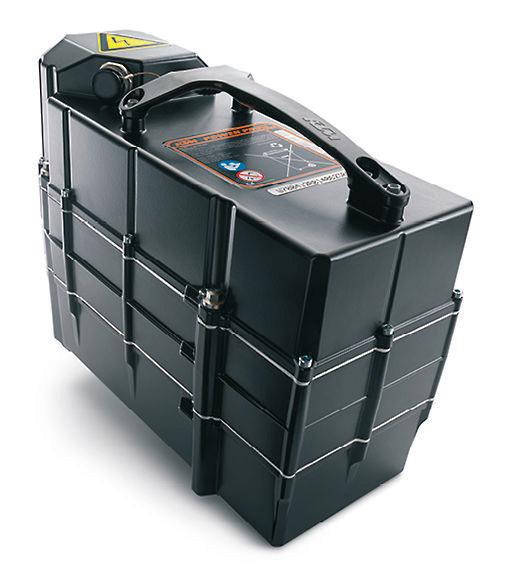
Once implemented in Twin Builder, KTM’s model of the battery pack could simulate real-world drive cycles, predicting results and heat transfer. With the virtual model, KTM can evaluate the qualities of different design proposals, optimising the airflow around the battery.
By creating the best battery packs possible, KTMs dirt e-bikes can ride harder and faster for longer with many more recharges yet to come. www.ktm.com
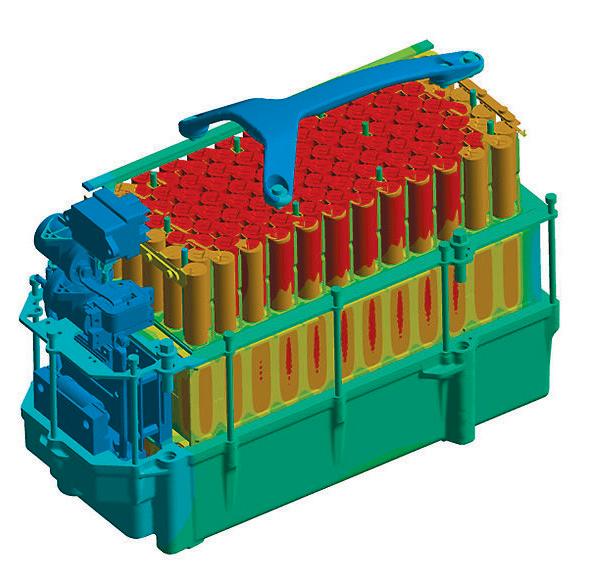
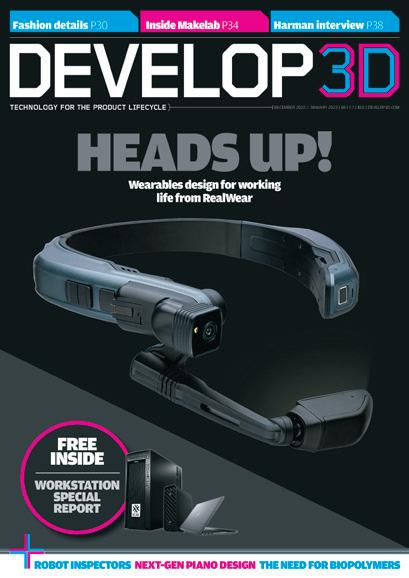
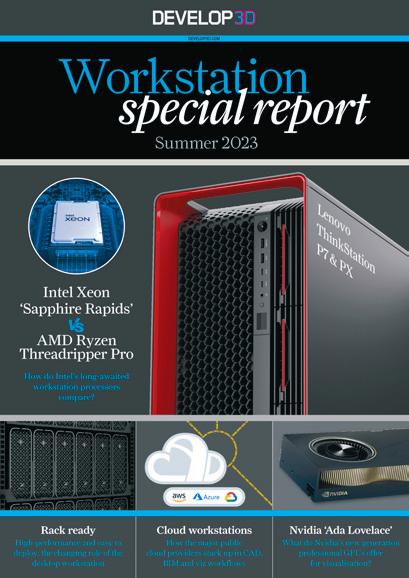

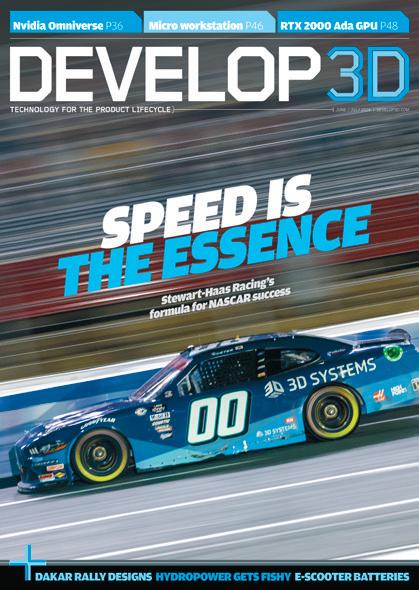
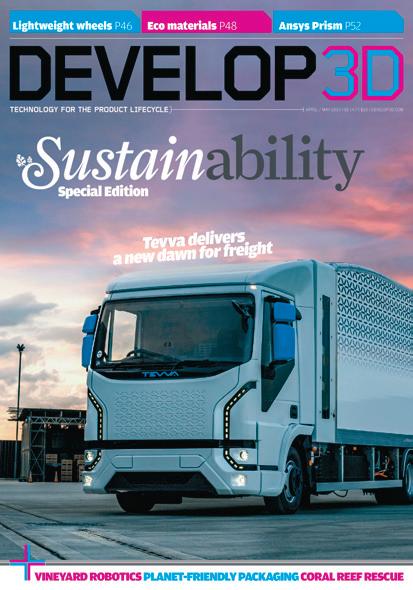
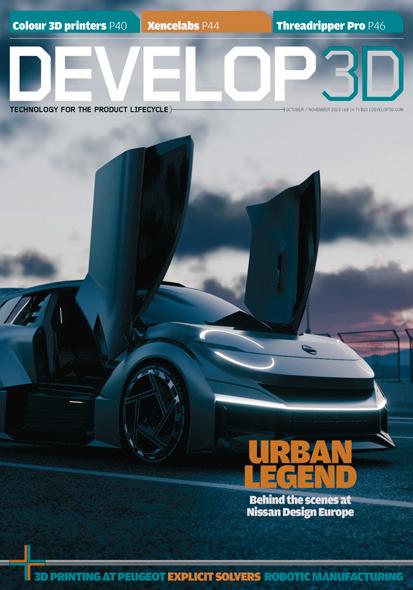
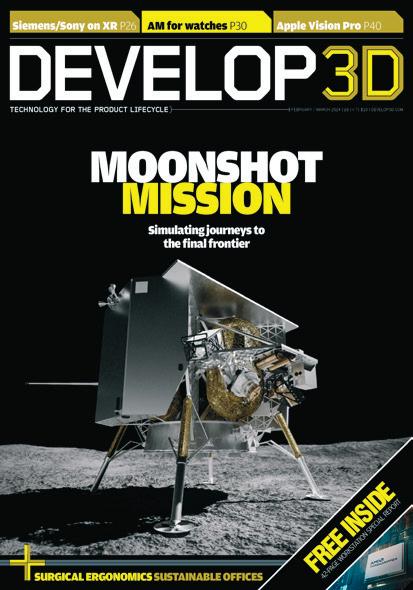
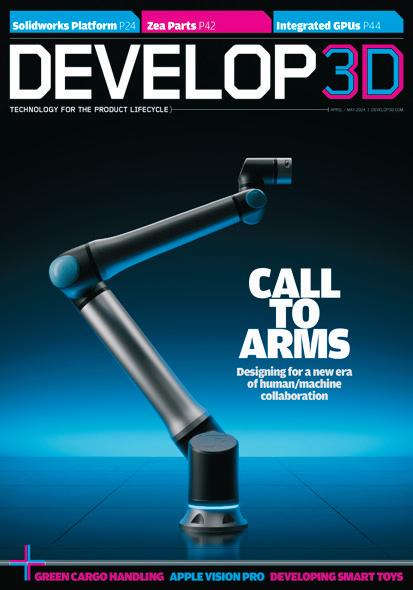
Scan GWP-CAD A124R Micro
» Compared to the
major OEMs,
this compact 8-litre
workstation
might not bring much new to the table in terms of chassis, but it’s hard to not take notice when the price is so aggressive, writes Greg Corke
» AMD Ryzen 9 Pro 7945 processor (3.7 GHz, 5.4 GHz boost) (12-cores, 24 threads)
» Nvidia RTX 2000 Ada Generation GPU (16 GB)
» 32GB (2x 16GB) Corsair Vengeance DDR5 5,200MHz memory
» 1TB Solidigm P41 Plus NVMe PCIe 4.0 SSD
» Asus Pro A620M-CCSM motherboard
» 95 x 327 x 266mm mini chassis
» 300W CWT, 80PLUS Bronze PSU
» Microsoft Windows 11 Pro
» 3 Years – 1st Year Onsite, 2nd and 3rd Year RTB (Parts and Labour) warranty
£1,292 (Ex VAT) www.tinyurl.com/scan-micro
Bolton-based Scan is renowned for its quality desktop workstations, but most of the machines we’ve reviewed over the years have been built around sizable towers.
That’s to be expected for high-end workstations, aimed at visualisation, simulation, AI, or other demanding workflows. After all, high core count CPUs, multiple dual slot GPUs and buckets of memory need plenty of space for housing and cooling. But for CAD/BIM workflows, where the computational
and ultra-compact workstations from major workstation OEMs like Dell, HP, and Lenovo, plus the trend towards smaller offices and home working, it’s surprising that it’s taken Scan so long to shake up its workstation portfolio.
Last year, the company added a small form factor (SFF) micro-ATX workstation to its line-up, specifically designed for CAD users. The 95 x 327 x 266mm chassis has a volume of just 8 litres, versus 60 litres for a typical mid tower, or 150 litres for a full tower, the type that Scan uses for its high-end AMD Threadripper Pro
Compared to the competition, it’s more like an HP Z2 SFF, than the smaller HP Z2 Mini or Dell Precision 3280, which can be VESA mounted on the back of a display.
THE COOLING CHALLENGE
As small workstations have grown in popularity, manufacturers have had to deal with significantly bigger power demands from processors, which has presented significant challenges for cooling.
Recent top-end Intel Core processors, which are ideal for CAD as they deliver the highest single core frequencies and impressive Instructions Per Clock (IPC), are rated at 125W, but draw up to 253W at peak. Most compact workstations simply can’t get rid of the heat that a chip like
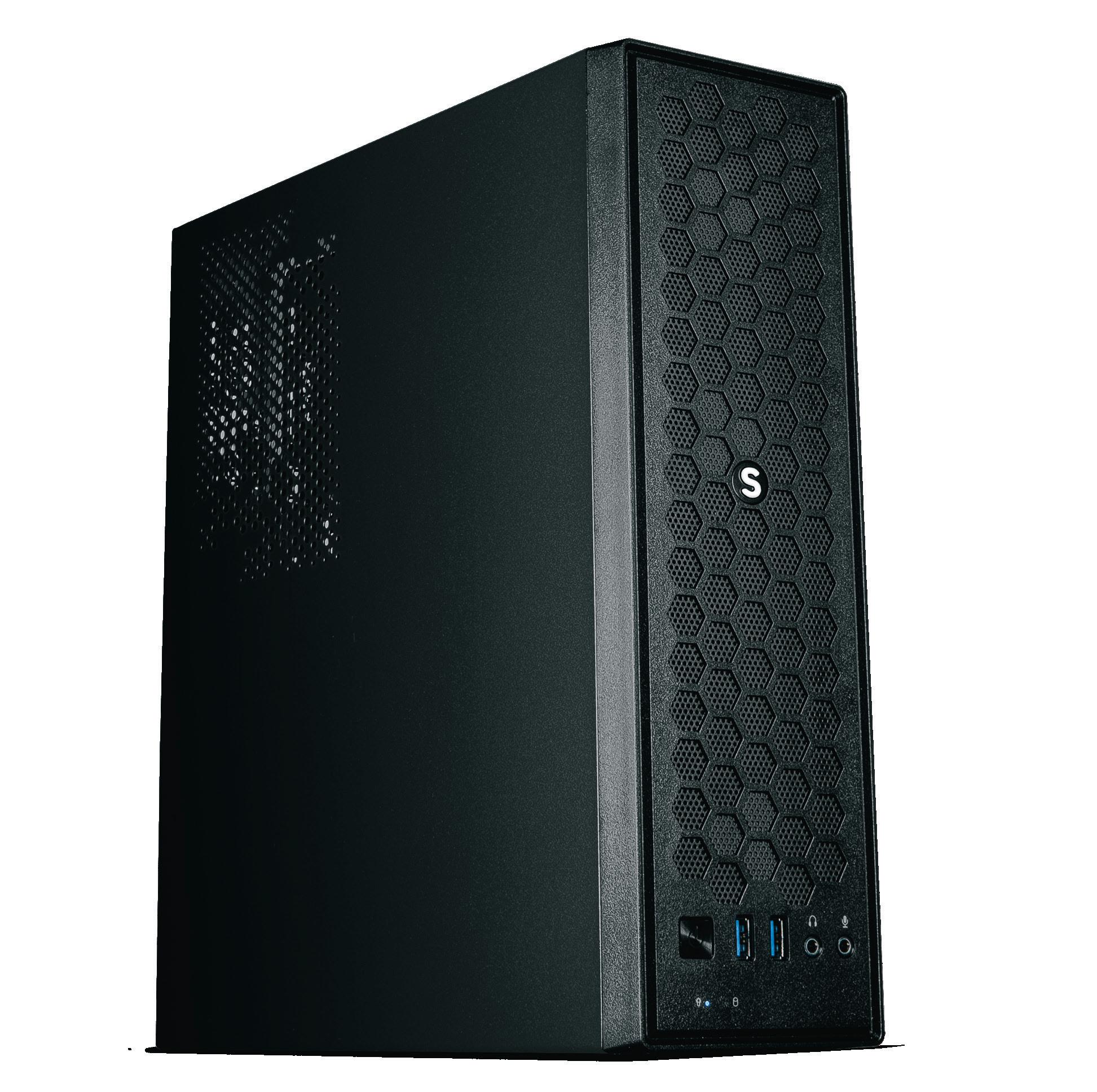
To deliver what it describes as the best balance of performance and energy efficiency, Scan has configured its new Scan GWP-CAD A124R Micro workstation with a 65W AMD Ryzen 9 Pro 7945 processor. According to Scan, the processor draws 121W less power than an equivalent Intel Core i7 under maximum load. The chip has 12 cores, 24 threads and a max boost clock of 5.4 GHz.
With Ryzen Pro, together with the Asus Pro A620M-C-CSM motherboard, you also get enhanced security and manageability, compared to a consumer
The slim chassis means the Scan GWP-CAD A124R is limited to a lowprofile graphics card. In years gone by these were only really suited to CAD , but the latest models from Nvidia are significantly more powerful, and some are ideal for entry-level visualisation. Our test machine came with the new Nvidia RTX 2000 Ada pro GPU, a replacement for the Nvidia RTX A2000 which originally launched in 2021. It’s not only more powerful than its predecessor but boasts more memory – 16 GB compared to 12 GB (or 6 GB with the original version of the card).
32 GB (2 x 16 GB) of Corsair Vengeance DDR5 5,200MHz RAM should be fine for entry-level to mainstream CAD . However, for more demanding workflows, especially those that fill up the Nvidia RTX 2000 Ada’s 16 GB of GPU memory, we’d
For storage, there’s a 1TB Solidigm
P41 Plus NVMe PCIe 4.0 SSD, which is rated at 4.1 GB/s read and 2.9 GB/s write. Additional storage is available via a second free M.2 NVMe SSD slot on the motherboard. Scan can also squeeze in a 3.5-inch Hard Disk Drive (HDD) or two 2.5inch drives, so there’s plenty of options. 1GbE Ethernet, a single USB Type C at the rear and a total of seven USB Type A ports, including USB 3.2 round out the specs.
THE CAD WORKHORSE
CAD is a bread and butter workflow for a workstation of this type. The AMD Ryzen 9 Pro 7945 delivered good performance in 3D CAD software Solidworks, hitting 5.2 GHz in many of its single threaded workflows. However, compared to the Intel Core i9-14900K, our CAD performance processor of choice, it’s a fair bit off the pace – between 10% and 41% slower in the SPECapc for Solidworks benchmark. But when it comes to small form factor workstations this is a bit of a moot point. With the Intel chip drawing 253W at peak, you’re unlikely to ever find one in a machine of this size. And even if you do, it’s likely to be throttled.
Of course, the AMD Ryzen 9 Pro 7945 is all about power efficiency. In rendering benchmark Cinebench 2024 it drew a mere 44W on the single core test and 90W on the multi-core test. This leaves plenty of headroom for the Nvidia RTX 2000 Ada GPU, which draws 65W at peak. Even in the most demanding of workflows — CPU rendering in Cinebench and GPU rendering in Solidworks Visualize — we observed a peak total power of 220W at the socket. Amazingly, the Scan GWP-CAD A124R didn’t even break into a sweat, maintaining an all-core CPU frequency of 4.6 GHz for well over an hour. This is all done with air-cooling too, using two fans — one attached directly the CPU heatsink, and another to push air over the GPU and SSD.
THE VISUAL AID
One of the trade-offs of power efficiency is fewer CPU cores. The AMD Ryzen 9 Pro 7945 comes with 12 cores, four less than a top-end Ryzen 9 processor with 16 cores, typically used in larger towers.
Despite this gap, the AMD Ryzen 9 Pro 7945 still does a good job in multithreaded workflows. When rendering, it was only between 30% and 50% slower than the Intel Core i9-14900K, which has 16 P-cores and 8 E-cores but consumes around three times as much electricity!
Of course, these days for visualisation, it’s often the GPU that does most of the heavy lifting. Tools including Twinmotion, Unreal Engine, and Solidworks Visualize rely entirely on GPU processing, and the Nvidia RTX 2000 Ada is a good entry-level option for product designers. It doesn’t deliver anywhere near the same level of performance as
a high-end pro GPU like the Nvidia RTX 5000 Ada, but it can still do a good job for CAD-centric visualisation. Importantly, it has 16 GB of on-board memory, which should be plenty for mainstream viz datasets, and enough to play with earlystage ideation or concept design using Generative AI tools like Stable Diffusion.
From our testing the Nvidia RTX 2000 Ada GPU looks best suited to real-time viz at FHD resolution. At 4K, frame rates in our Unreal Engine and Enscape scenes were too slow for a smooth real-time experience. Of course, you can always upgrade to the Nvidia RTX 4000 SFF Ada with 20 GB of memory, but this will add £625 + VAT onto the price of the machine. Scan has also yet to qualify this top-end low-profile GPU, but it should be available as an option soon. You can read more about the Nvidia RTX 2000 Ada GPU in our in-depth review on page 48.
CONCLUSION
It’s become the accepted norm that if you want a small workstation, you must give up some performance. And with mainstream desktop processors
‘‘ Compared to the competition, it’s more like an HP Z2 SFF, than the smaller HP Z2 Mini or Dell Precision 3280, which can be VESA mounted on the back of a display ’’
now burning through more watts than ever, this has never been more true. But shrinking things down also turns the conversation to energy efficiency. And with a careful choice of processor, and a maximum total power draw of 220W, Scan looks to have found a good balance here. With HP, Dell and Lenovo all investing heavily in tiny desktop workstations there’s certainly an appetite for these types of machines. Scan’s latest offering doesn’t really bring anything new to the table in terms of chassis design — the OEMs have been doing this for years — but it really shines on price/performance. At £1,292 + VAT it’s considerably cheaper than the equivalent from Dell, HP or Lenovo. And none of those manufacturers are yet to offer the new Nvidia RTX 2000 Ada as an option.
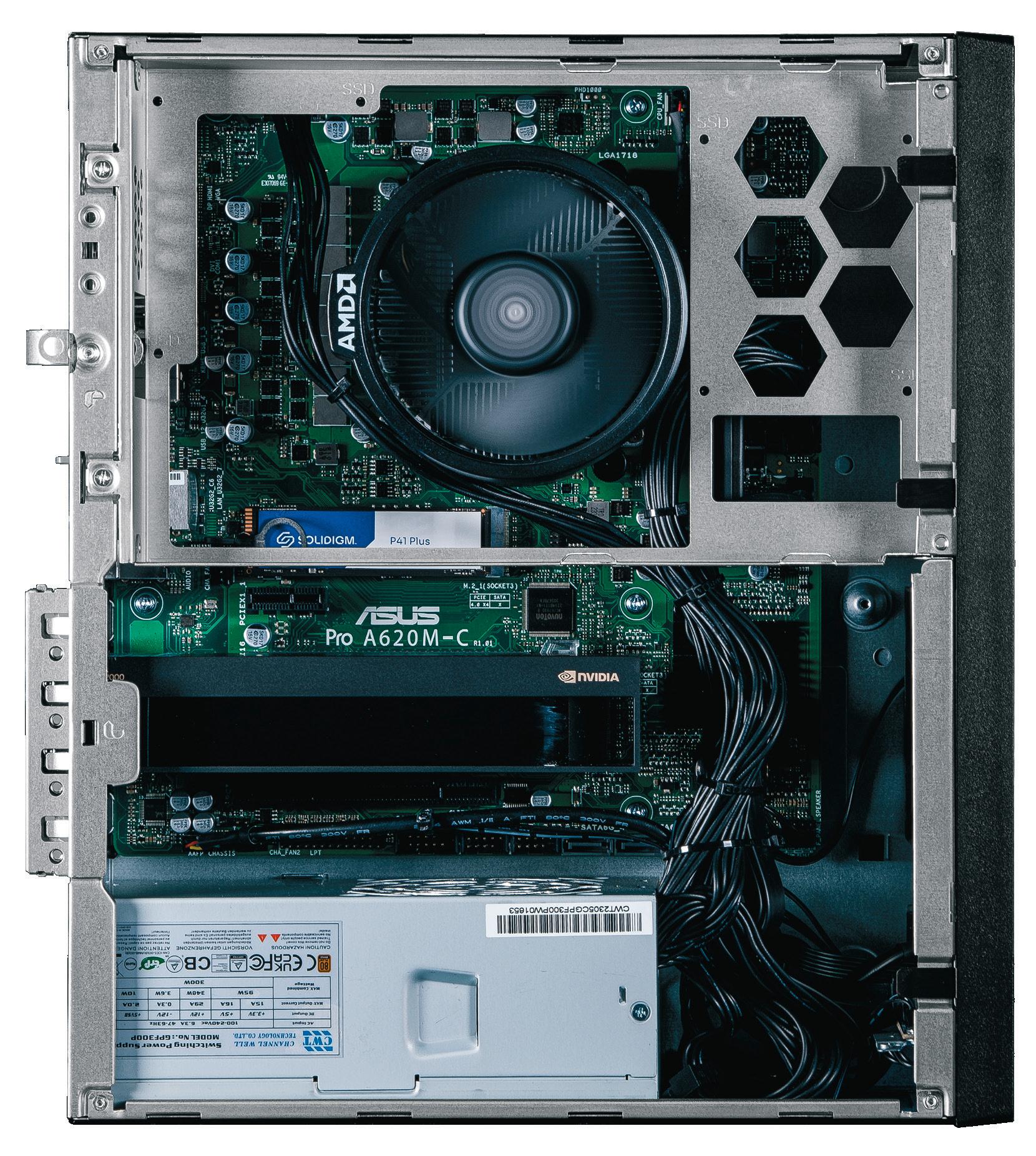
Nvidia RTX 2000 Ada Generation
» This entry-level pro viz GPU is a great option for small workstations. Thanks to the Ada Generation architecture it gets a boost in all the right areas, including ray tracing and AI, but also receives an important memory uplift, writes Greg Corke
Small form factor (SFF) and Ultra Compact workstations are big business these days. They are among the biggest sellers at Dell, HP and Lenovo. And as you will see on page 46, specialist system builders like Scan are also getting in on the action.
Small workstations need small GPUs. They require a special low-profile form factor, a compact GPU design with a shrunk down circuit board and a half height bracket for space efficiency.
Half of Nvidia’s recent pro graphics introductions are low-profile boards. There are four models: two take up a single slot on the motherboard, the Nvidia RTX A400 (4 GB) and the Nvidia RTX A1000 (8 GB), and two take up two slots, the Nvidia RTX 2000 Ada (16 GB) (the focus of this review) and the Nvidia RTX 4000 SFF Ada (20 GB).
While the single slot cards are mostly targeted at CAD and BIM workflows, the dual slot cards are much more powerful. They are ideal for designers and engineers that want to push their workflows beyond the likes of Solidworks, Autodesk Inventor, and PTC Creo, into the realms of KeyShot, Twinmotion, and Solidworks Visualize for visualisation.
The Nvidia RTX 2000 Ada launched in February 2024 as part of a staggered roll out of Ada Generation GPUs. However, the card is only now starting to become available in the channel through PNY. Expect to see it in OEM workstations soon.
The Nvidia RTX 2000 Ada is not to be confused with the Nvidia RTX A2000, which
» Product: Nvidia RTX 2000
Ada Generation
» Supplier: Nvidia / PNY
Price: £556 + VAT www.nvidia.com www.pny.com/professional
Ada comprises three different types of cores: Nvidia Ada Lovelace CUDA Cores for rasterisation and general-purpose processing, fourth-generation Tensor Cores for AI compute and third-generation RT Cores for ray tracing.
On paper, the Nvidia RTX 2000 Ada represents a big step up from the Nvidia RTX A2000. It boasts 12.0 TFLOPs vs 8.0 for single precision performance, 27.7 TFLOPs vs 15.6 for RT Core performance and 191.9 TFLOPs vs 63.9 for Tensor performance.
Tensor performance is important for generative AI, the importance of which is likely to grow in the coming years. Text-to-image tools like Stable Diffusion, for example, are gaining interest for ideation and concept design. According to Nvidia, the Nvidia RTX 2000 Ada will deliver 1.6 times better performance in Stable Diffusion compared to the Nvidia RTX A2000.
The Nvidia RTX 2000 Ada also adds more memory to the board. It has 16 GB of GDDR6 compared to 12 GB or 6 GB, in the Nvidia RTX A2000. 16 GB is significant as it should provide a good platform for most CAD-centric viz workflows.
RTX 2000 VS 4000 SFF ADA
With the Nvidia RTX 2000 Ada (16 GB) and Nvidia RTX 4000 SFF Ada (20 GB) it’s the first time that Nvidia has had two viz capable low-profile GPUs from the same GPU architecture.
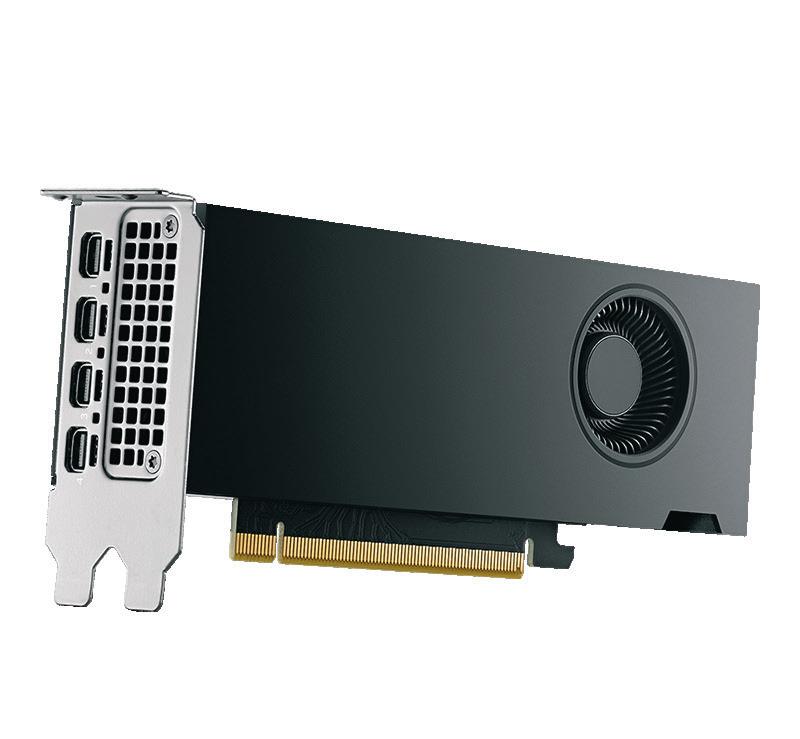
To the untrained eye, both GPUs look identical. Both are rated at 70W, so draw all their power from the motherboard’s PCIe slot. Both have four mini DisplayPort connectors, and both can be fitted with a half-height or full-height ATX bracket, so can be used in SFF workstations or full sized towers.
Naturally, the Nvidia RTX 4000 SFF Ada has a more powerful GPU (19.2 TFLOPs single-precision performance, 44.3 TFLOPs RT Core performance and 306.8 TFLOPs Tensor performance) and slightly more memory (20 GB). It also has more features, including support for Nvidia Quadro Sync II for display walls and 3D stereo for immersive 3D. As a result, it costs more than twice as much as the Nvidia RTX 2000 Ada — £1,160 + VAT versus £556.
It’s important to point out here that the Nvidia RTX 4000 SFF Ada has a full-height sibling, the Nvidia RTX 4000 Ada, that can
only fit in full sized tower workstations. Both GPUs have the same core specs, but the Nvidia RTX 4000 Ada can draw twice as much power (130W), so you get significantly more performance out of the same silicon. They also cost exactly the same, so there’s little point in putting an Nvidia RTX 4000 SFF Ada in a tower workstation unless you’re extremely focused on energy efficiency.
NVIDIA RTX 2000 ADA ON TEST
For testing, we compared the Nvidia RTX 2000 Ada (16 GB) with two other cards in the Ada Generation family: the low profile, dual slot Nvidia RTX 4000 SFF Ada (20 GB), and the full height, single slot Nvidia RTX 4000 Ada (20 GB).
We also included two previous generation Ampere GPUs: the low-profile, dual slot Nvidia RTX A2000 (12 GB), and the full height, single slot Nvidia RTX A4000 (16 GB).
Here, it’s important to state that our benchmark comparisons are not perfect, as not all GPUs were tested in the same machine. For the Nvidia RTX 2000 Ada and Nvidia RTX A2000 we used the latest 552.22 driver inside an AMD Ryzen 9 Pro 7945-based workstation from Scan.
For the other two GPUs, benchmark data was taken from previous lab tests. The Nvidia RTX 4000 SFF Ada and Nvidia RTX A4000 with 536.25 driver were tested inside an AMD Ryzen 9 7950X3D-based workstation from Armari. The Nvidia RTX 4000 Ada with 537.7 driver was tested in an Intel Core i9-14900KF-based workstation from Workstation Specialists.
We would expect the Nvidia RTX 4000 Ada benchmark scores to be elevated a little in 3D CAD, as the Intel Core i914900KF is faster in single threaded and lightly threaded workflows and CAD is typically CPU limited for 3D graphics. However, in graphics intensive real-time viz tools, the partner CPU shouldn’t make as much difference and, in GPU rendering, very little at all.
All benchmark scores can be found at www.tinyurl.com/D3D-RTX2000.
For CAD, the Solidworks benchmark data only really tells part of the story. The reality is, we found the Nvidia RTX 2000 Ada able to easily handle the largest of assemblies, including the colossal 8,000+ component MaunaKea Spectroscopic Explorer telescope model. The visualisation benchmarks gave
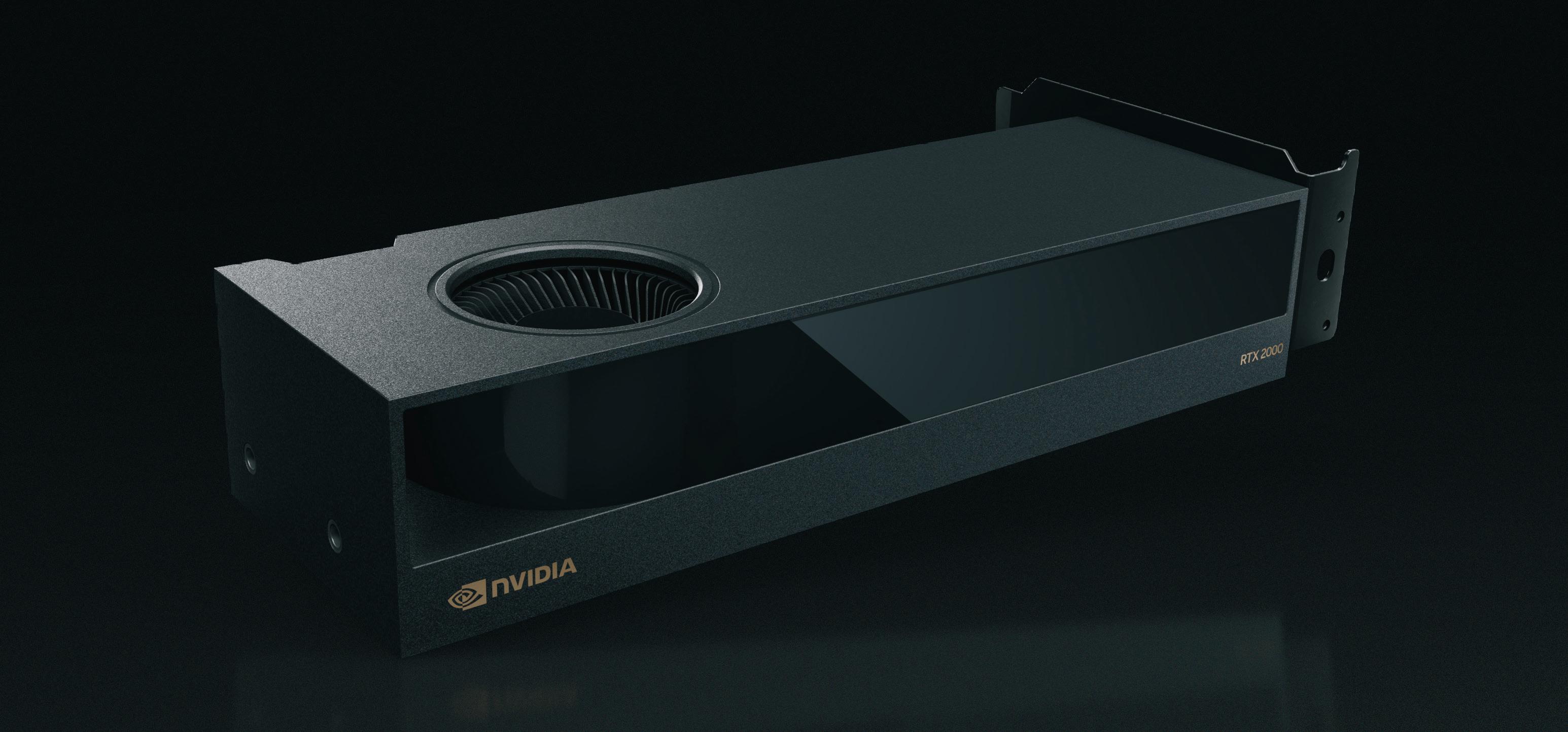
greater insights into the capabilities of the Nvidia RTX 2000 Ada. For real time 3D we saw a performance bump of around 30 percent over the Nvidia RTX A2000. However, our Unreal Engine and Enscape tests indicate the card is probably better suited to working at FHD resolution. When working at 4K, frame rates dropped below that golden 20 frames per second (FPS) threshold. However, this is of course dependent on the types of models you work with. With less complex datasets, especially with real-time ray tracing disabled in Unreal Engine, performance at 4K may be perfectly acceptable. Either way, moving up the range to the Nvidia RTX 4000 SFF Ada will give you a significant boost, but only choose this GPU if your heart is set on a compact workstation. For the same price, you can have the Nvidia RTX 4000 Ada in a tower – although you can also fit this full height GPU in the slimlime HP Z2 SFF G9 workstation thanks to a riser card that rotates the GPU through 90 degrees. In Twinmotion and Lumion, the Nvidia RTX 2000 Ada delivered batch renders between 27% and 37% faster than the Nvidia RTX A2000. This went up to 45%
in KeyShot and 51% in Vray, both of which lean much more heavily on ray tracing, so take full advantage of the Nvidia RTX 2000 Ada’s far superior RT Core performance. With the Nvidia RTX 4000 SFF Ada, you’ll get an additional 26% out of Lumion, 33% out of Vray and 39% out of KeyShot.
THE VERDICT
The Nvidia RTX 2000 Ada is another great pro graphics card from Nvidia that hits the price / performance sweet spot for CAD-centric visualisation. For most design and engineering firms it’s hard to justify giving every CAD user with a viz requirement a workstation with a highend GPU. But at £556 + VAT, the Nvidia RTX 2000 Ada is certainly affordable, and provides a great starting point for tools like Twinmotion, KeyShot and Solidworks Visualize. We’re not just talking frame rates and render times here though. The GPU also has enough memory to load up some fairly sizeable datasets.
Energy consumption also deserves a mention. With a peak power of 70W, the Nvidia RTX 2000 Ada uses significantly less electricity than its full height siblings and produces less heat. With many firms
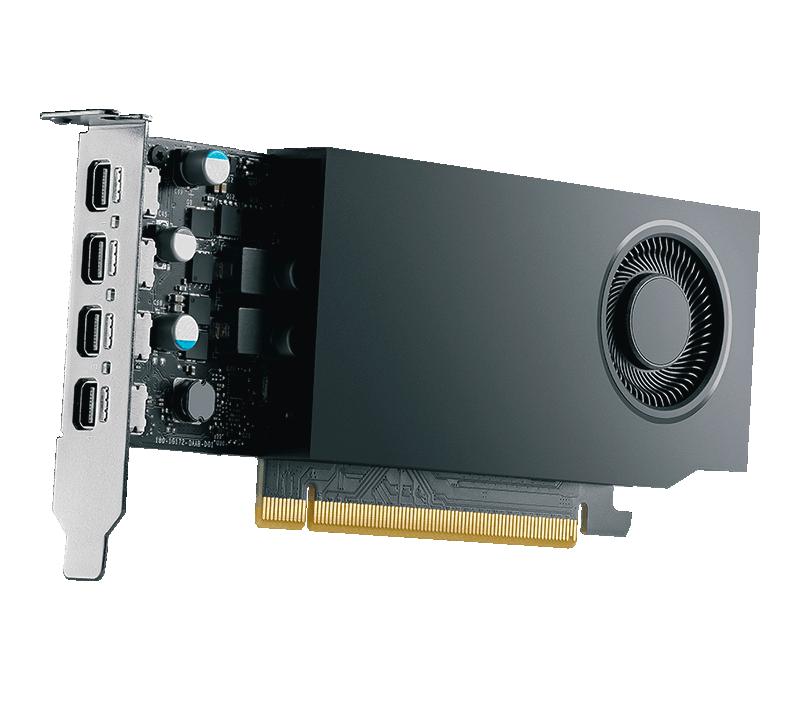
If budgets are tight and design visualisation isn’t part of your day to day workflow, you should consider the Nvidia RTX A1000, based on the older ‘Ampere’ architecture. This new single slot, low-profile GPU is nailed on for 3D CAD and entry-level visualisation
‘‘ The Nvidia RTX 2000 Ada is another great pro graphics card from Nvidia that hits the price / performance sweet spot for CADcentric viz ’’
workflows. And with RTX capabilities — a first for a ‘1000’ class desktop Nvidia GPU — it also has RT and Tensor cores, both of which will likely become more important in the coming years (RT cores, if ray tracing finally makes it into the viewport of modern BIM / CAD tools, and Tensor
@
under pressure to hit sustainability targets, this is more important than ever.
The Nvidia RTX 2000 Ada might be primarily designed for small form factor / compact workstations, but it’ll be just as at home in a standard tower. Unlike the Nvidia RTX 4000 SFF Ada, there’s no full height equivalent.
We expect the Nvidia RTX 2000 Ada will start to be available in OEM workstations like the HP Z2 Mini G9, HP Z2 SFF G9, Lenovo ThinkStation P3 Ultra, and Dell Precision 3280 soon. For now, you can get it through the channel via PNY, and in custom workstations like the extremely price competitive Scan GWP-CAD A124R Micro, which we review on page 46.
Cores for AI processing).
With only 8 GB of memory, the Nvidia RTX A1000 is unlikely to be that useful for text-to-image Generative AI with tools like Stable Diffusion, but it could be a great companion for general PC tasks, such as background blurring or noise suppression in
Teams, using the efficient Tensor cores to do the heavy lifting, rather than having to rely on general purpose Nvidia Cuda cores or Intel / AMD CPUs.
The card has four Mini DisplayPorts and a max power of 50W and comes in at £333 + VAT, more than £200 cheaper than the Nvidia RTX 2000 Ada.
Accessible product design makes a big difference to users with disabilities, writes Stephen
Holmes, but this industry still has many barriers to break down before it can truly be considered inclusive

On separate occasions over the past few weeks, I’ve been lucky enough to catch up with Jude Pullen and Ross Atkin, both talented design engineers. It’s been a good reminder of The Big Life Fix, the excellent reality TV series in which they both participated.
Originally aired in 2020 on BBC2, The Big Life Fix focused on tailored design solutions for people with disabilities. If you’ve not seen it, then you should try to hunt it down on some streaming platform or other. The show not only blended marvellous ingenuity with a feelgood payoff, but also provided a terrific showcase of why so many enter this profession: to make a difference.
Increasing numbers of young people, many of whom will have graduated in recent weeks, are now looking for roles in which they can effect change.
And there are many people out there, including Pullen and Atkin, who help advise corporations on, among other topics, designing more accessible products. Many work in studios with commendable track records of positive impact. Many graduates will want to join them, eschewing more traditional career pathways in order to join a company making a tangible difference.
designers is the ability to ‘shape-shift’ – to understand the experience of the people for whom they are designing, to take on their viewpoint, to dive deeply into the details.
All of this makes me proud of the type of people designers and engineers tend to be, and you should be too.
But however brilliant they might be at creating products for others and their lives, no research will ever be quite as good as first-hand, lived experience.
For that reason, it seems to me that there is a very strong argument that more people with disabilities should be employed as designers and engineers.
And that, in turn, raises the question: How accessible, really, is this industry, its workplaces and its tools?
As an industry, product design and engineering is struggling to achieve the kind of inclusivity seen in some other industry sectors
In total, there are some 1.8 billion people with disabilities in the world, more than the total population of China. In the UK, over two million people live with some level of sight loss and over half a million use wheelchairs. An estimated 15% to 20% of the UK population is thought to be neurodivergent.
I could sit here, reeling off numbers all day long. But I strongly feel that, as an industry, product design and engineering is still struggling to achieve the kind of inclusivity seen in other industry sectors and that needs fixing.
A WHOLE NEW APPROACH
SHAPE-SHIFTING SKILLS
In the previous issue of DEVELOP3D, I met Tatum Robotics, company developing a tactile robotic hand that DeafBlind people use to communicate. I was impressed to see how closely its designers worked with members of the DeafBlind community.
In fact, I think that a key skill for
Most business leaders now recognise that, when it comes to accessibility, their websites need redesigning, their offices need retrofitting, their facilities need to be improved. There’s a lot to consider and a lot of work to do. It’s not just a case of putting in a wheelchair-accessible toilet and then patting themselves on the back.
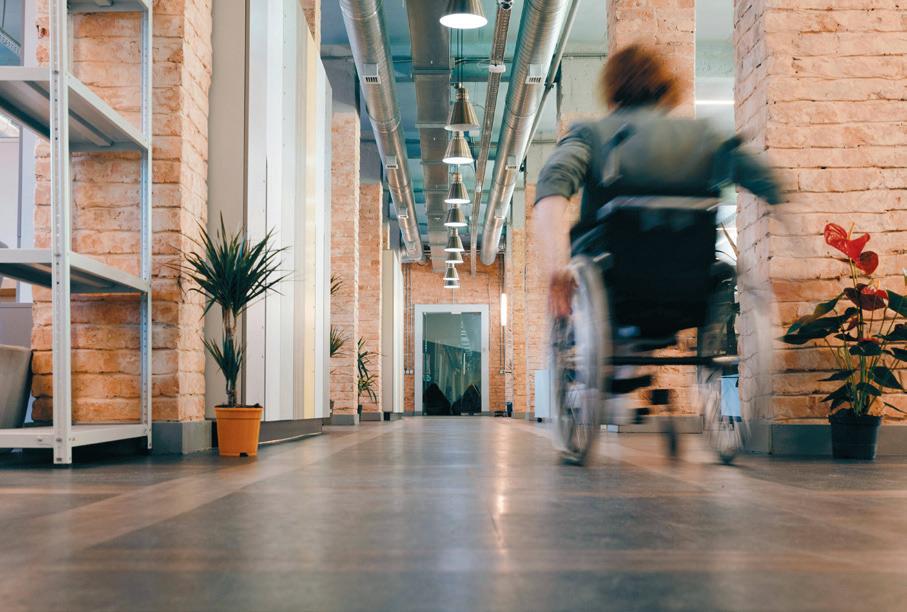
It was recently explained to me that if you cannot navigate a business’s website using just the keyboard, then some people won’t be able to navigate it at all.
So what about the main tool of our trade, complex 3D CAD software? AI might yet provide a solution here, with voice prompts acted upon by AI-enabled assistants to carry out modelling tasks. But it’s safe to say that a working solution is some way off.
Everywhere we go in our industry, there are barriers to inclusivity. Some will remain firmly in place until technology advances. Others could quite easily be removed tomorrow, if only the problems they present were more widely recognised.
At a recent trade show, for example, I realised that the fixed user interface screens on some 3D printers are situated way too high up to be read by someone under 5 foot tall or sitting in a wheelchair.
As we increasingly strive for equality, accessibility may be the next big social revolution — and maybe as designers and engineers, a long, hard look at our own workplaces and tools might be a very good place to start.
GET IN TOUCH: As new product review samples roll in, Stephen is surrounded by Bluetooth-connected digital peripherals that free the user to move and work as they please. That’s leading him to question how long it can possibly be until all design studios relocate to the beach? On Twitter, he’s @swearstoomuch
DEVELOP3DSERVICES
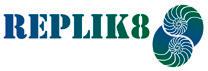


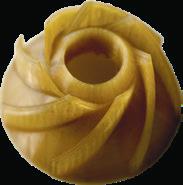

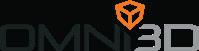
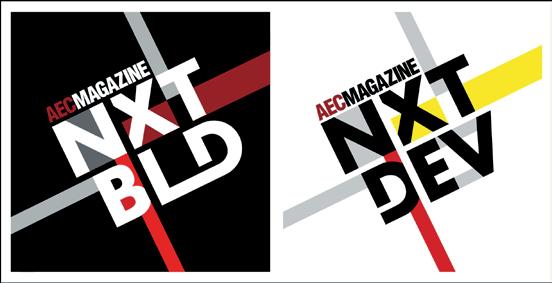

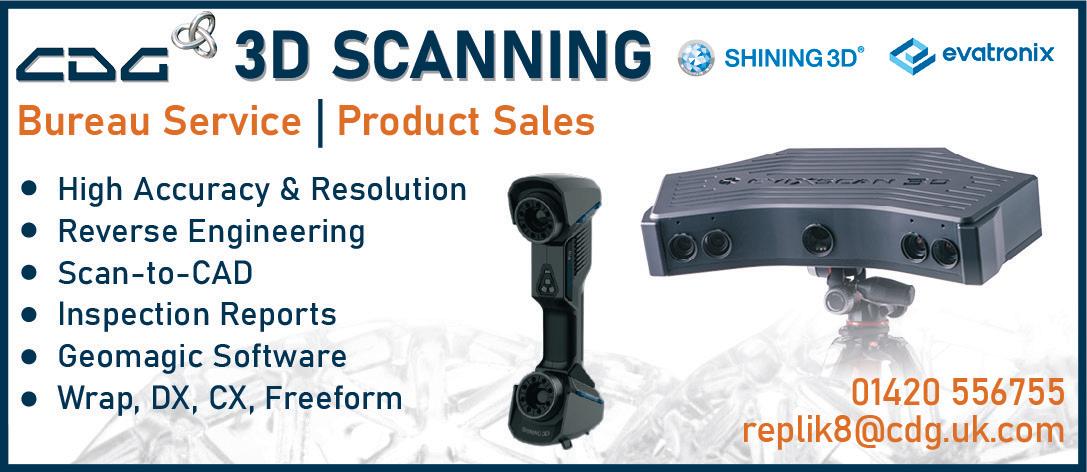
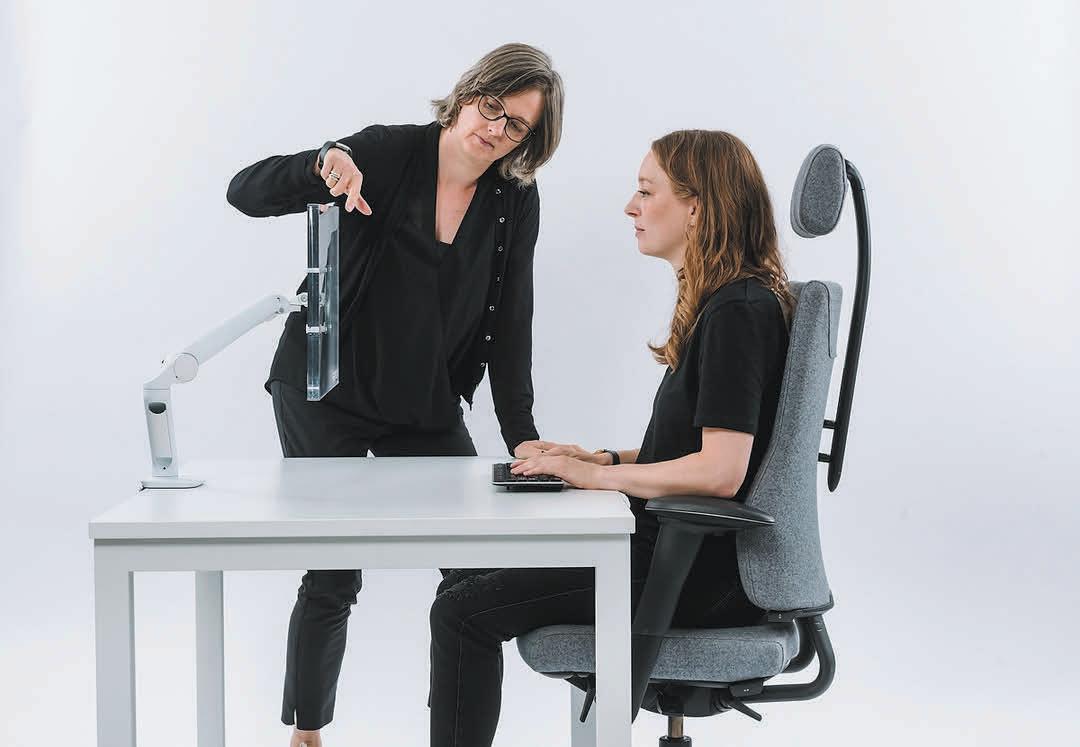

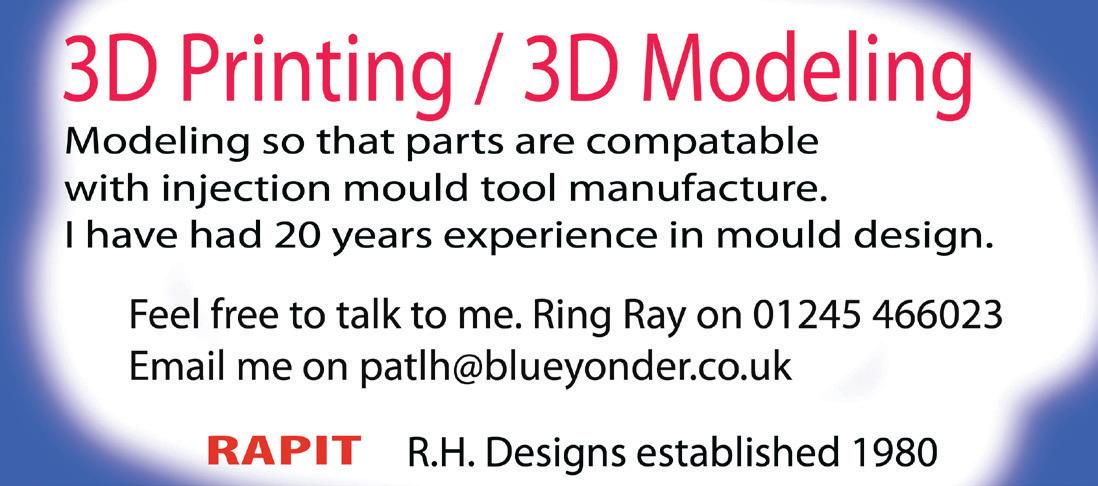


now for your free trial
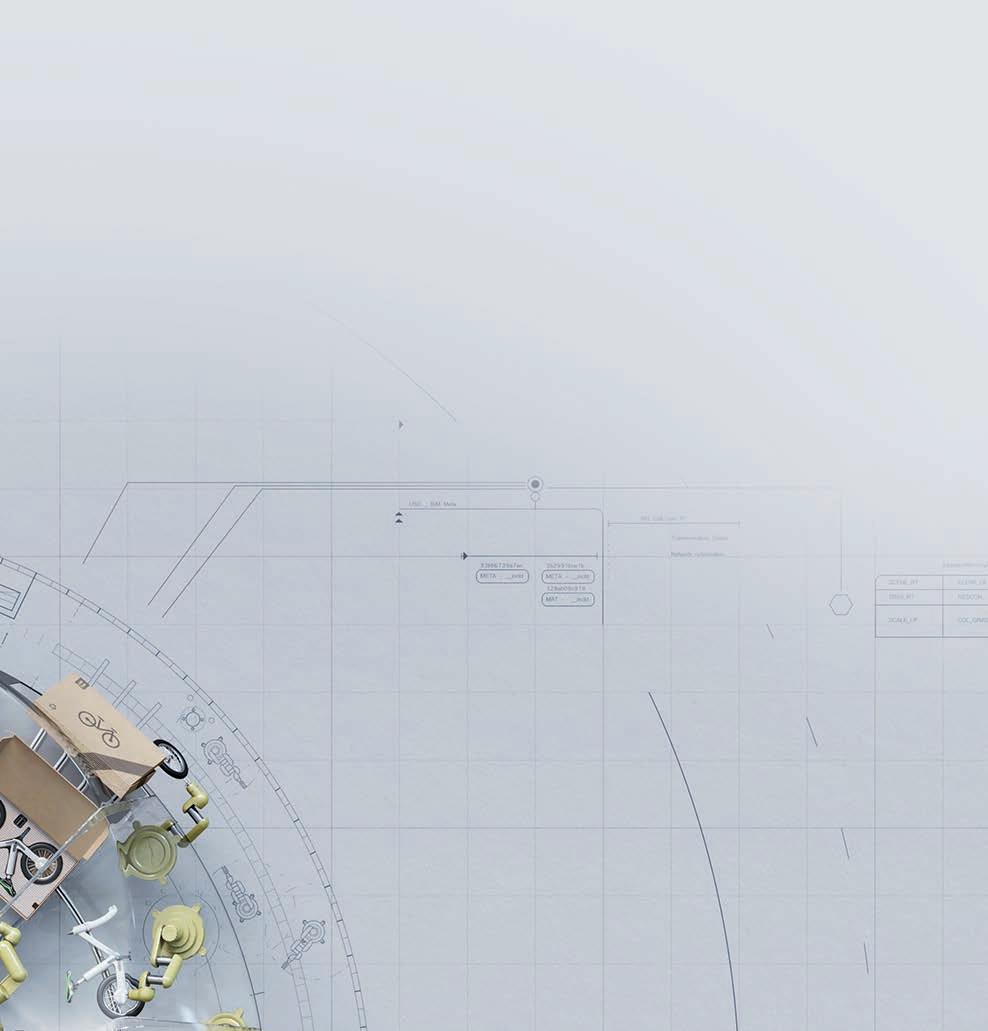

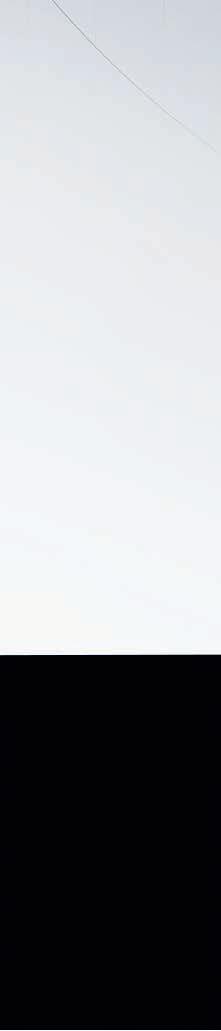
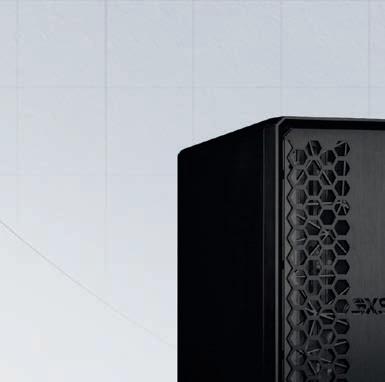

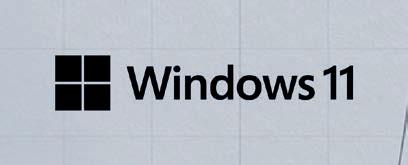
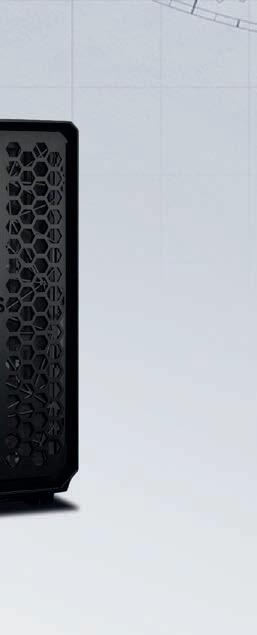
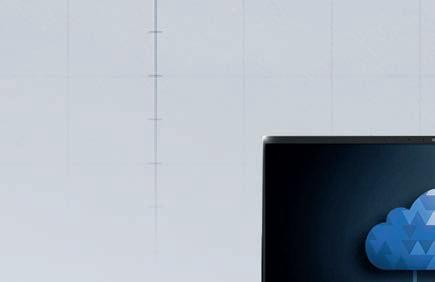


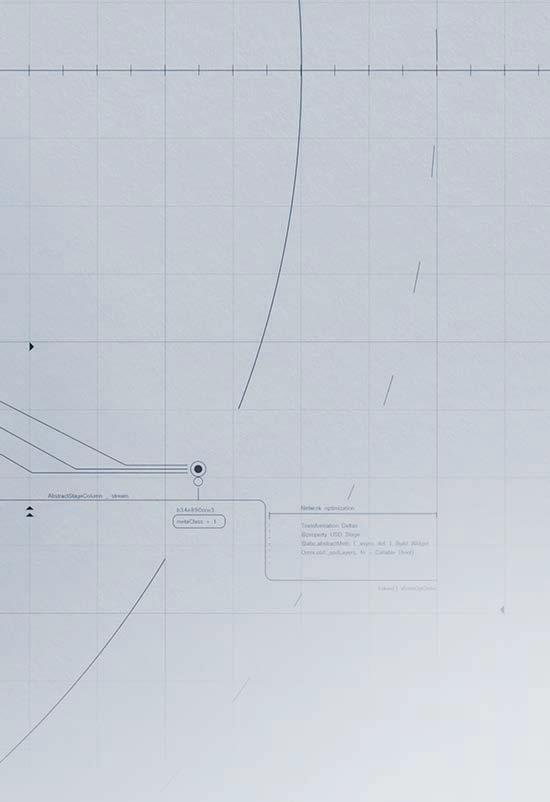
3XS Workstations
Tested and compatible with NVIDIA Omniverse


Cloud Solutions
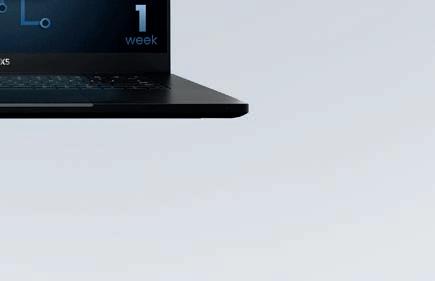
The power of 3XS workstations now in the cloud
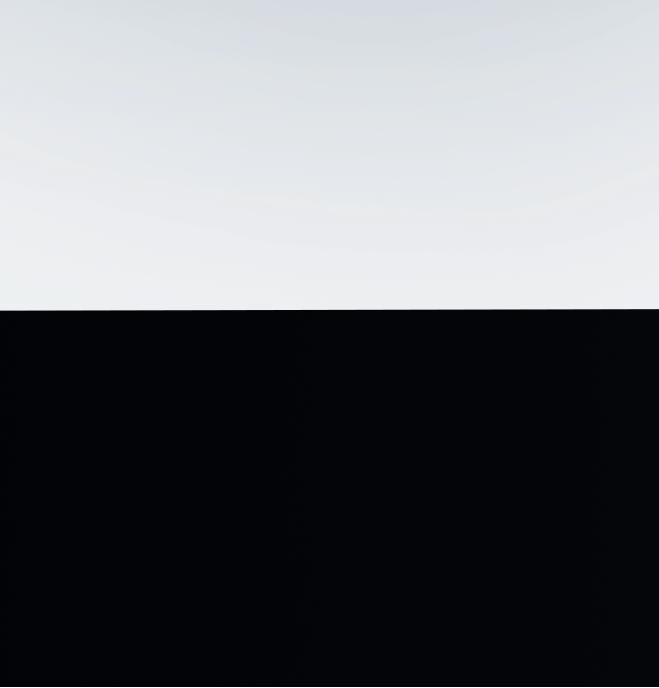
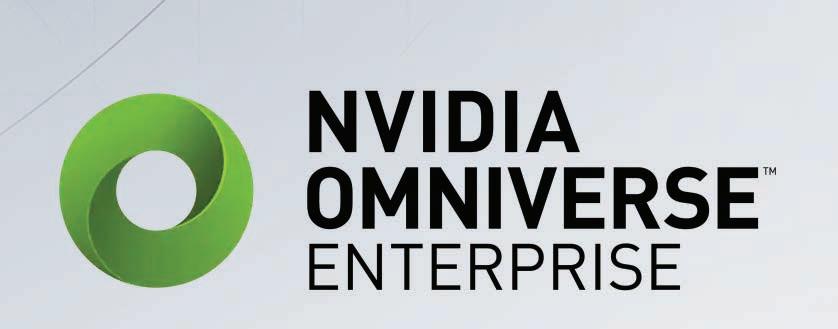
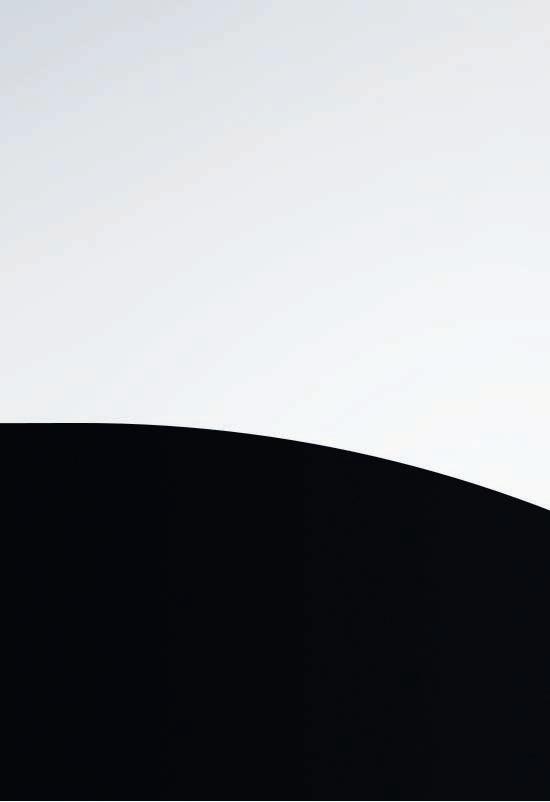
Omniverse Licenses
Enhanced features and enterprise-class support