Italiana La Metallurgia
International Journal of the Italian Association for Metallurgy
n. 01 gennaio 2025
Organo ufficiale dell’Associazione Italiana di Metallurgia. Rivista fondata nel 1909
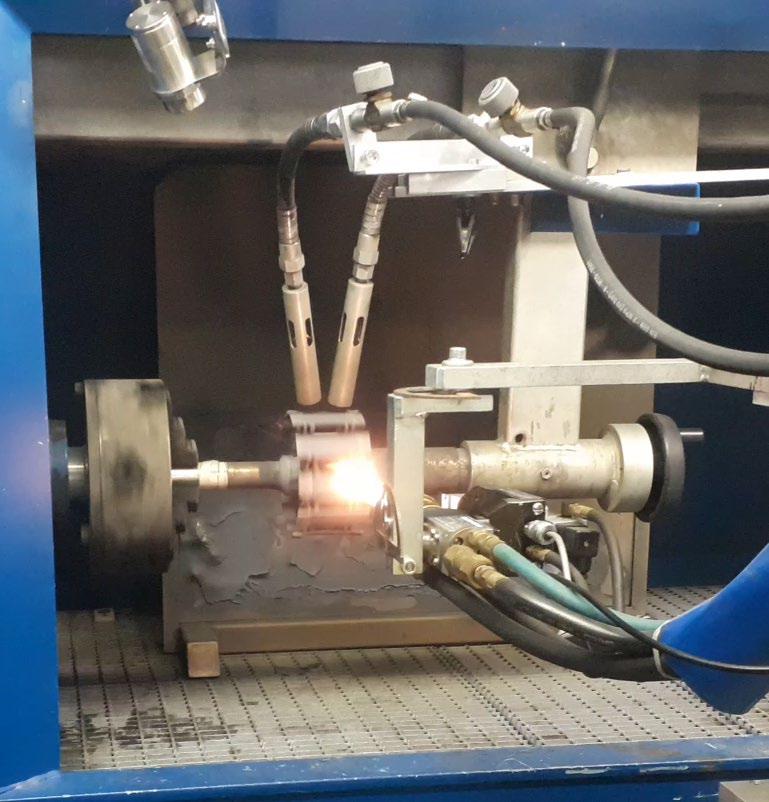
International Journal of the Italian Association for Metallurgy
n. 01 gennaio 2025
Organo ufficiale dell’Associazione Italiana di Metallurgia. Rivista fondata nel 1909
International Journal of the Italian Association for Metallurgy
Organo ufficiale dell’Associazione Italiana di Metallurgia. HouseorganofAIMItalianAssociationforMetallurgy. Rivista fondata nel 1909
Direttoreresponsabile/Chiefeditor: MarioCusolito
Direttorevicario/Deputydirector: GianangeloCamona
Comitatoscientifico/Editorialpanel: MarcoActisGrande,SilviaBarella,PaolaBassani,ChristianBernhard,MassimilianoBestetti,Wolfgang Bleck,FrancoBonollo,IreneCalliari,MarianoEnriqueCastrodeza,EmanuelaCerri,VlatislavDeev,Andrea DiSchino,DonatoFirrao,BerndKleimt,CarloMapelli,DenisJeanMithieux,RobertoMontanari,Marco Ormellese,MariapiaPedeferri,MassimoPellizzari,BarbaraPrevitali,EvgenyS.Prusov,DarioRipamonti, DieterSenk
Segreteriadiredazione/Editorialsecretary: MartaVerderi
Comitatodiredazione/Editorialcommittee: FedericaBassani,GianangeloCamona,MarioCusolito, CarloMapelli,FedericoMazzolari,MartaVerderi,SilvanoPanza
Direzioneeredazione/Editorialandexecutiveoffice: AIM-ViaF.Turati8-20121Milano tel.0276021132-fax0276020551 met@aimnet.it-www.aimnet.it
Reg.Trib.Milanon.499del18/9/1948. Sped.inabb.Post.-D.L.353/2003(conv.L.27/02/2004n.46) art.1,comma1,DCBUD
Immagineincopertina:
GiovanniBolelli
Daattivitànell'ambitodelprogettoHorizonEurope"CoBRAIN"(GA101092211)
Gestione editoriale e pubblicità
Publisher and marketing office: siderweb spa sb
Via Don Milani, 5 - 25020 Flero (BS) tel. 030 25 400 06 commerciale@siderweb.com - www.siderweb.com
La riproduzione degli articoli e delle illustrazioni è permessa solo citando la fonte e previa autorizzazione della Direzione della rivista. Reproduction in whole or in part of articles and images is permitted only upon receipt of required permission and provided that the source is cited.
siderweb spa sb è iscritta al Roc con il num. 26116
n. 01 gennaio 2025 Anno 116 - ISSN 0026-0843
Editoriale / Editorial
a cura di Giovanni Bolelli – Università degli Studi di Modena e Reggio Emilia . pag.05
Memoriescientifiche/Scientificpapers
Rivestimenti/Coatings
Caratterizzazionediunrivestimentomultistrato(Ni-P+DLC)applicatosu componentiinlegaPBF-LBAlSi10Mgcostituitidageometriecomplesseestrutture reticolari
G.DiEgidio,C.Martini,A.Morri,L.Tonelli,L.Ceschini,M.Tocci,M.Gelfi,A.Pola,A.Martucci,M.Lombardi.......pag.08
TrattamentoelettrochimicodianodizzazionedellalegadimagnesioWE43perapplicazionibiomedicali
A.Acquesta,F.Desiderio,T.Monetta,G.Stornelli,A.DiSchino......................................................................pag.18
Saldatura / Welding
An innovative industrial approach of SFSW technology on AA6061
M. Sadeghi, H. Sabet ......................................................................................................... pag.26
The Effect of Activated flux and shielding gas mix of Argon-Nitrogen on the bead geometry of Duplex Stainless Steel 2205 Gas Tungsten Arc Welds
R. Sasidharan, S.R. Koteswara Rao, S.Vijayan .................................................................................
Le Aziende di AIM / AIM’s Companies
La sostenibilità ambientale - politiche nazionali e certificazione del contenuto di riciclato
Stefano Incrocci - IGQ ....................................................................................................... pag.51
Atti e notizie / AIM news
Eventi AIM / AIM events ......................................................................................................
/ Technical
ANCONA . 25-27 GIUGNO 2025
Organizzate da
con il patrocinio di
Sponsorizzate da
AIM, APCE, AMPP Italy Chapter e Università Politecnica delle Marche vi invitano al più importante evento nazionale dedicato alla corrosione e protezione dei metalli! La XVI edizione delle Giornate Nazionali sulla Corrosione e Protezione si terrà in presenza ad Ancona nei giorni 25, 26 e 27 giugno 2025, presso la Facoltà di Ingegneria dell’Università Politecnica delle Marche.
Le Giornate rappresentano l’evento di riferimento a livello nazionale per la discussione e il confronto sulle questioni scientifiche, tecnologiche e produttive, nell’ambito della corrosione e protezione dei materiali. In particolare, il Convegno prevede la presentazione dei risultati raggiunti da vari gruppi di studio e da numerose aziende del settore, in forma orale e poster.
Presentazione di memorie
Gli interessati a presentare memorie scientifiche e tecniche dovranno inviare titolo, nomi degli autori con relative affiliazioni ed un breve riassunto alla Segreteria organizzativa, entro il 31 gennaio 2025
Le memorie potranno essere proposte: · compilando il form online dedicato all’evento, sul sito www.aimnet.it inviando i dati richiesti all’indirizzo info@aimnet.it
Segreteria organizzativa
Via Filippo Turati 8 · 20121 Milano tel: +39 0276397770 · +39 0276021132 info@aimnet.it www.aimnet.it
"I trattamenti di superficie sono uno dei metodi principali per mitigare le problematiche tribologiche."
“Surface treatments are one of the main methods to mitigatetribologicalissues.”
Nella tecnologia moderna, le problematiche connesse alla tribologia, e quindi relative ai fenomeni di usura, attrito e lubrificazione, sono di centrale importanza. Il celebre “rapporto Jost”, col quale, come ricordato ad esempio in [1], veniva coniato nel 1966 il termine stesso “tribologia”, stimava che un miglioramento delle conoscenze relative a usura e attrito e una loro corretta applicazione industriale avrebbero potuto permettere all’economia del Regno Unito un risparmio dell’1% del proprio PIL. Varie stime di questo genere si sono poi succedute negli anni e, quasi a rispecchiare un’ottica di miglioramento continuo in cui i progressi della conoscenza tecnica e scientifica rendono possibile l’ottenimento di risultati sempre più ambiziosi, un recente studio del 2017 [2] ha indicato che tuttora i benefici che si potrebbero ottenere dall’applicazione dei più recenti progressi nel settore della tribologia potrebbero portare a risparmi sostanziali in termini di consumi energetici ed emissioni di CO2, stimando che ben il 23% del con-
In modern technology, issues related to tribology, and thus related to the phenomena of wear, friction and lubrication, are of central importance. The famous “Jost report,” by which, as recalled for example in [1], the term “tribology” itself was coined in 1966, estimated that improved knowledge about wear and friction and their proper industrial application could save the UK economy 1% of its GDP. Various such estimates have since followed over the years and, as if reflecting a view of continuous improvement in which advances in technical and scientific knowledge make it possible to achieve ever more ambitious results, a recent 2017 study [2] indicated that even now, the benefits that could be gained from applying the latest advances in tribology could lead to substantial savings in energy consumption and CO2 emissions, estimating that as much as 23% of global energy consumption is related to wear and friction issues.
Closely related to the topic of tribology are those of
sumo globale di energia sia legato alle problematiche di usura e attrito.
Strettamente connesso all’argomento della tribologia sono quelli dei rivestimenti e, più in generale, dei trattamenti di superficie, che sono uno dei metodi principali per mitigare le problematiche tribologiche. Un materiale massivo, infatti, difficilmente può soddisfare i numerosi requisiti di resistenza strutturale a carichi statici e/o affaticanti, di lavorabilità, di rapporto costo/prestazioni, e contemporaneamente avere anche le proprietà superficiali, come elevata durezza, inerzia chimica, bassa energia superficiale, ecc., necessarie a controllare il comportamento tribologico. Inoltre, non va mai dimenticato che la tribologia non è una proprietà di un singolo materiale, ma una molto più complessa risposta di un sistema a cui contribuiscono entrambe le superfici accoppiate, l’ambiente circostante, eventuali “terzi corpi” presenti, e le condizioni operative (velocità relativa, pressione di contatto, configurazione di moto relativo, ecc.). La modifica della superficie di un componente deve quindi essere sempre fatta sulla base di considerazioni legate all’insieme di tutte le condizioni operative, rendendo spesso necessaria l’individuazione di soluzioni “ad hoc” per ogni situazione.
Su queste premesse si fonda buona parte dell’attività del Comitato Tecnico “Rivestimenti e Tribologia” dell’Associazione Italiana di Metallurgia, di cui questo numero della Metallurgia Italiana presenta un piccolo “spaccato”. Le memorie presentate spaziano infatti dallo studio di materiali massivi a quello di rivestimenti e trattamenti di superficie. Fra questi ultimi, troviamo sia un esempio di un processo di modifica chimica delle caratteristiche superficiali del materiale-base, sia un esempio di deposizione di riporti. Quest’ultimo, illustrando bene le possibilità offerte dalla tecnologia più recente, mostra come sia possibile, combinando fra loro alcuni dei moltissimi processi di ricoprimento oggi disponibili, ottenere caratteristiche e prestazioni altrimenti non raggiungibili. Un ulteriore filo conduttore che accomuna due dei tre lavori qui presentati sono le tecnologie di manifattura
coatings and, more generally, surface treatments, which are one of the main methods of mitigating tribological issues. A massive material, in fact, can hardly meet the manyrequirementsofstructuralresistancetostaticand/ or fatiguing loads, workability, cost/performance ratio, and at the same time also have the surface properties, such as high hardness, chemical inertness, low surface energy, etc., necessary to control tribological behavior. Furthermore, it should never be forgotten that tribology is not a property of a single material, but a much more complex response of a system to which both coupled surfaces, the surrounding environment, any “third bodies” present, and operating conditions (relative velocity, contact pressure, relative motion configuration, etc.) contribute. Modifying the surface of a component must therefore always be done on the basis of considerations related to the totality of all operating conditions, often making it necessary to find “ad hoc” solutions for each situation.
Much of the activity of the Italian Association for Metallurgy's Technical Committee “Coatings and Tribology” is based on these premises, of which this issue of La Metallurgia Italiana presents a small “crosssection.” Indeed, the papers range from the study of massive materials to that of coatings and surface treatments. Among the latter, we find both an example of a process of chemical modification of the surface characteristics of the material-base, and an example of the deposition of coatings. The latter, illustrating well the possibilities offered by the latest technology, shows how it is possible, by combining some of the very many coating processes available today, to achieve characteristicsandperformanceotherwiseunattainable. A further common thread linking two of the three papers presented here are additive manufacturing technologies. Their peculiarities, including the ability to produce geometries of extreme complexity and the “near-net-shape” nature that minimizes material losses typical of “subtractive” machining (e.g., by chip removal), indeed make them of particular interest in so
additiva (“additive manufacturing”). Le loro peculiarità, incluse la possibilità di produrre geometrie di estrema complessità e la natura “near-net-shape” che minimizza le perdite di materiale tipiche delle lavorazioni “sottrattive” (es. per asportazione di truciolo), le rendono infatti di particolare interesse in tanti campi dell’industria, e la ricerca su questi materiali sta crescendo a un ritmo esponenziale. Fra le problematiche che devono essere affrontate, vi sono ovviamente anche quelle di modifica delle superfici, che, nella fattispecie di componenti “additive”, presentano sfide particolari, legate ad esempio alla peculiare topografia superficiale o alla stessa complessità geometrica.
In conclusione, le memorie presentate in questo numero dimostrano come il settore dei rivestimenti e della tribologia stia affrontando le molteplici sfide e i nuovi filoni di ricerca che si stanno aprendo con un approccio dinamico e interdisciplinare.
[1] J. Williams, The Invention of Tribology: Peter Jost’s Contribution, Lubricants 12 (2024) 65. https://doi.org/10.3390/lubricants12030065
[2] K. Holmberg, A. Erdemir, Influence of tribology on global energy consumption, costs and emissions, Friction 5 (2017) 263–284. https://doi.org/10.1007/s40544-017-0183-5.
many fields of industry, and research on these materials is growing at an exponential rate.
Among the issues that need to be addressed are, of course, those of surface modification, which, in the case of “additive” components, present special challenges, related, for example, to the peculiar surface topography or geometric complexity itself.
In conclusion, the papers presented in this issue demonstrate how the field of coatings and tribology is addressing the many challenges and new lines of research that are opening up with a dynamic and interdisciplinary approach.
[1] J. Williams, The Invention of Tribology: Peter Jost’s Contribution, Lubricants 12 (2024) 65.
https://doi.org/10.3390/lubricants12030065.
[2] K. Holmberg, A. Erdemir, Influence of tribology on global energy consumption, costs and emissions, Friction 5 (2017) 263–284. https://doi.org/10.1007/s40544-017-0183-5.
Caratterizzazione
G. Di Egidio, C. Martini, A. Morri, L. Tonelli, L. Ceschini, M. Tocci, M. Gelfi, A. Pola, A. Martucci, M. Lombardi
Le strutture reticolari in lega AlSi10Mg prodotte mediante tecnologia Powder Bed Fusion – Laser Beam (PBF-LB) presentano un’elevata resistenza specifica e un ottimale rapporto superficie/volume. Tuttavia, nella condizione as-built esse sono caratterizzate da un’alta rugosità che ne può peggiorare le prestazioni. Per risolvere questa problematica, è stato depositato un rivestimento multistrato costituito da (i) un interstrato in Ni-9%P per via chimica autocatalitica, utile a compensare i difetti superficiali e ottimizzare la topografia superficiale, e (ii) un rivestimento a base di carbonio amorfo idrogenato (DLC a-C:H) via PA-CVD (Plasma Assisted-Chemical Vapor Deposition). Le caratteristiche del sistema rivestito sono state valutate mediante: (i) profilometria ottica, (ii) osservazioni al FEG-SEM/EDS, (iii) prove di durezza su micro/nanoscala e (iv) scratch test. Sulla base dei risultati ottenuti, sono state quindi individuate le principali problematiche legate alla deposizione del rivestimento multistrato Ni-P+DLC su componenti critici in lega PBF-LB AlSi10Mg, in modo da ottimizzare l'intero ciclo post-stampa e garantire un’adeguata funzionalità del rivestimento multistrato.
PAROLE CHIAVE: PBF-LB, ALSI10MG, STRUTTURE RETICOLARI, GEOMETRIA CRITICA, INDENTAZIONE STRUMENTATA, PROVE DI ADESIONE, ANALISI TOPOGRAFICA
Il grande interesse della comunità industriale e scientifica rivolto alla tecnologia Powder Bed Fusion - Laser Beam (PBF-LB) è legato al suo peculiare metodo di progettazione e produzione, che consente di abbassare l’emissione di CO2 attraverso la riduzione del peso dei componenti, delle fasi ad alto dispendio energetico, e dei materiali di scarto [1]. In questo contesto, le leghe Al-Si prodotte mediante tecnologia PBF-LB stanno avendo un successo significativo, specialmente nella produzione di componenti per veicoli elettrici [2]. Questo è dato dalla possibilità di ottenere un significativo alleggerimento strutturale e una maggiore efficienza energetica dei componenti prodotti, grazie ad un ottimale rapporto superficie/volume raggiungibile mediante un’efficace ottimizzazione topologica. La lega Al-Si ad oggi maggiormente impiegata in ambito PBF-LB è la lega AlSi10Mg grazie all’ottima resistenza specifica e alla notevole conducibilità termica, oltre all’elevata riciclabilità e al basso costo, che la rendono ideale per la produzione di parti leggere di forma complessa,
G. Di Egidio, C. Martini, A. Morri, L. Tonelli, L. Ceschini
Università di Bologna
M. Tocci, M. Gelfi, A. Pola
Università degli Studi di Brescia
A. Martucci, M. Lombardi
Politecnico di Torino
quali scambiatori di calore ad alta efficienza [3]. Tuttavia, la scarsa finitura superficiale dei componenti as-built e i fenomeni di usura legati alla bassa durezza relativa della lega PBF-LB AlSi10Mg possono portare a una rapida riduzione delle prestazioni dei componenti. Una soluzione a questa problematica può essere l’applicazione di trattamenti di modifica superficiale e/o rivestimenti, in modo da estendere significativamente la vita utile e sfruttare appieno tutti i vantaggi dei componenti additive. Attualmente queste soluzioni non sono state ancora studiate in modo sistematico in letteratura su componenti realizzati mediante PBF-LB, ponendo l’attenzione invece sul ruolo della microstruttura e dei trattamenti termici [4,5], o su trattamenti di conversione come l'anodizzazione [68].
Il rivestimento multistrato Ni-P+(a-C:H) DLC (costituito da un interstrato in lega Ni-P depositato per via chimica autocatalitica da fase liquida, seguito da un rivestimento in carbonio amorfo idrogenato simil-diamante depositato da fase vapore) si inserisce molto bene in questo contesto. Questa soluzione garantisce la piena compatibilità delle condizioni di deposizione (tempo e temperatura) del rivestimento multistrato con la microstruttura metastabile della lega PBF-LB AlSi10Mg [9], l’integrazione con eventuali cicli di trattamento termico per l’ottimizzazione delle proprietà meccaniche del substrato [9], e una buona adesione e continuità indipendentemente dall'orientamento di stampa [10]. In applicazioni quali gli scambiatori di calore, il rivestimento Ni-P presenta il vantaggio di poter rivestire uniformemente anche i canali interni nelle strutture reticolari prodotte mediante PBF-LB [11] grazie all'elevato potere penetrante della deposizione chimica autocatalitica [12]. Al tempo stesso, la deposizione di un topcoat quale (a-C:H) DLC può garantire un miglioramento delle proprietà tribologiche grazie alle sue peculiari caratteristiche [13]. Come dimostrato in un precedente lavoro [9], questa soluzione può essere applicata con successo sulla lega PBF-LB AlSi10Mg, garantendo una buona adesione su superfici lavorate e migliorando la resistenza a fatica del materiale. Il rivestimento Ni-P+DLC può permettere di superare le limitazioni microstrutturali e topografiche indotte dal processo PBF-LB, quali l’alta rugosità superficiale e l’elevata densità di difetti presenti in superficie, che
influenzano negativamente il comportamento tribologico dei componenti PBF-LB AlSi10Mg [6]. Al tempo stesso, la riduzione ottenibile del coefficiente di attrito e del tasso di usura nei componenti rivestiti porterebbe ad un minore consumo di energia e, quindi, minori emissioni di CO2 in servizio, nonché ad una maggiore durata dei componenti rivestiti e quindi ad un minore consumo di risorse. Partendo dai risultati riportati in [9,10], ottenuti su campioni di geometria semplice e lavorati alle macchine utensili, questo studio si pone l’obbiettivo di analizzare l’integrazione del rivestimento multistrato Ni-P+DLC con la realizzazione di geometrie complesse ottenibili con tecnologia additiva. A tal fine, sono stati realizzati diversi prototipi/dimostratori di forma complessa e con strutture reticolari tramite tecnologia PBF-LB, in modo da prendere in esame le principali criticità geometriche per la deposizione del rivestimento multistrato Ni-P+(a-C:H) DLC. Dopo il processo di stampa, i campioni sono stati dapprima sottoposti a burattatura per migliorare la qualità superficiale prima della deposizione dell'interstrato Ni-P. Sebbene la buona adesione dell'interstrato Ni-P su superfici lavorate e piane della lega PBF-LB ALSi10Mg sia stata dimostrata in lavori precedenti [9,10], l'identificazione di un processo di finitura superficiale alternativo compatibile con la complessità geometrica dei componenti additive potrebbe ampliarne i campi di applicazione. Successivamente alla deposizione del rivestimento Ni-P, è stato depositato un topcoat (a-C:H) DLC tramite tecnologie di deposizione in fase di vapore (PA-CVD). Lo studio ha analizzato la qualità del rivestimento in termini di omogeneità dello spessore e di adesione, sia per il singolo strato di Ni-P che per il multistrato Ni-P+(a-C:H) DLC, mediante l’osservazione di sezione trasversali dei componenti e test macro-, micro- e nanomeccanici (Mercedes test, scratch test e nanoindentazione). Inoltre, la rugosità superficiale prima e dopo la deposizione di ogni strato (Ni-P e DLC) è stata valutata tramite profilometria ottica.
I provini dimostratori in lega PBF-LB AlSi10Mg sono stati prodotti mediante un sistema di stampa industriale EOSINT M270 Dual Mode, prevedendo diverse tipologie di geometrie che includono aspetti potenzialmente critici
nella fase di rivestimento (foro cilindrico in testa, foro romboidalenelcorpo,strutturereticolari,comemostrato in Fig. 1). Le geometrie sono state distinte in: (i) “critica”, dove i sopracitati aspetti di criticità sono estremizzati e (ii) “non critica”, in cui sono più smorzati. La stampa è avvenuta in atmosfera controllata (Ar ad alta purezza con livello di O2 inferiore allo 0,1 vol.%), utilizzando una piattaforma riscaldata (100 °C) in modo da ridurre gli effetti delle tensioni residue. Per la produzione dei provinièstataadottataunastrategiadiscansioneastrisce parallele con rotazione di 67° tra layer successivi, oltre ai seguenti parametri di stampa: (i) potenza laser: 195 W, (ii) velocità di scansione: 800 mms-1, (iii) spessore
del layer: 30 μ m, (iv) spaziatura tra strisce adiacenti: 170 μ m. La scelta dei parametri di stampa è stata rivolta a massimizzare la qualità superficiale del pezzo e ottenere un'elevata tolleranza dimensionale. Allo stesso modo, la scelta di orientare dei provini perpendicolarmente alla piattaforma di stampa e l’ottimizzazione delle strutture di supporto è stata effettuata al fine di facilitare il distacco dei componenti dalla piattaforma e ridurre le sollecitazioni residue. Successivamente alla stampa, i provini sono stati sottoposti ad un trattamento di distensione (1,5 ore a 270 °C, rampa di riscaldamento a 5 °C/min e raffreddamento in aria) in modo da prevenire il rischio di distorsione nel distacco dalla piattaforma mediante elettroerosione.
Rivestimento As-built
Condizione Burattato
Designazione B
Geometria non critica
Geometria critica
Geometria non critica
Geometria critica
Fig.1 - Dimostratori in PBF-LB AlSi10Mg - PBF-LB AlSi10Mg prototypes. / From left to right, barrel finished, Ni-P non-critical geometry, Ni-P critical geometry, Ni-P+DLC non-critical geometry, Ni-P+DLC critical geometry.
La composizione chimica e le dimensioni delle polveri impiegate sono riportate in Tabella 1.
Tab. 1 - Intervallo dimensionale e composizione chimica (% in peso) delle polveri AlSi10Mg, fornite dal produttore / Size range and chemical compositions (wt%) of as-supplied AlSi10Mg powder
Intervallo dimensionale (µm)
- 63 µm
Composizione chimica (% in peso)
Il rivestimento Ni-P a medio fosforo (9% in pesoISO4527-03) è stato depositato dopo processo di burattatura in ambiente industriale. Similmente, il topcoat DLC (carbonio amorfo idrogenato, a-C:HISO20523-17) è stato depositato mediante tecnologia PA-CVD (Deposizione Chimica da fase Vapore assistita da Plasma) mediante processo industriale (temperatura di deposizione compresa fra 150 e 180°C). La finitura superficiale dei campioni è stata valutata
mediante profilometria ottica (NANOVEA JR25), utilizzando una griglia 3x3 di linee di scansione (lunghezza di campionamento: 5 mm, step di scansione: 5 µ m, cutoff ( λ c): 0.8 mm) su una superficie piana dei provini, in accordo alla BS EN ISO 4288:1998 (Tabella 2). Il leggero incremento di rugosità riscontrata nei campioni rivestiti è dovuto alla tipica morfologia superficiale a cavolfiore del rivestimento Ni-P, completamente replicata dal topcoat DLC.
Tab. 2 - Rugosità superficiale, µ m / Surface roughness, µ m
As-built
La spettroscopia di emissione ottica (GD-OES) è stata utilizzata per verificare la composizione chimica del multistrato Ni-P+DLC secondo ISO 14707:2015. La valutazione dello spessore del rivestimento depositato è stata svolta su sezioni metallografiche parallele alla direzione di stampa dei provini, inglobate in resina epossidica e in resina conduttiva per le sezioni più critiche. Le superfici sono state levigate con carta abrasiva fino a 2500 grit e infine lucidate con panni e sospensioni diamantate da 9 a 1 µ m, secondo la normativa ASTM E3. Un microscopio elettronico a scansione con sorgente ad emissione di campo (FEG-SEM) e spettroscopia a raggi X a dispersione di energia (EDS, Brucker Quantax 200/30 mm 2) è stato utilizzato per valutare la morfologia delle superfici e lo spessore dei rivestimenti tramite osservazioni della sezione trasversale. L'analisi EDS è stata utilizzata per un’analisi semiquantitativa localizzata della composizione. L'adesione del singolo strato di Ni-P è stata valutata mediante Mercedes test (osservazione delle modalità di delaminazione al microscopio ottico dopo indentazione HRC, seguito dalla classificazione in classi di adesione da 0 (HF1) a 3 (HF4)), secondo ISO 26443-23. L’adesione del topcoat DLC è stata valutata mediante scratch test (Revetest Xpress, CSM Instruments), secondo normativa ASTM G171, utilizzando un penetratore Rockwell (raggio della
punta sferica: 200 μ m, con carico normale crescente da 1 a 100 N, velocità di carico: 100 N min−1, velocità lineare: 10 mm min−1, lunghezza di prova 10 mm) e operando sulle facce piane esterne del corpo dei provini. I valori di carico critico (Lc), mediati su 5 ripetizioni, sono stati determinati secondo la normativa ISO 20502-15. I valori di durezza (H) e di modulo elastico (E) dell'interlayer Ni-P e del topcoat DLC sono stati analizzati mediante test di nanoindentazione (NANOVEA PB1000) con penetratore Berkovich (angolo linea centrale-faccia, α = 65,27°, modulo di Young, Eo = 1141 GPa, coefficiente di Poisson, ��o = 0,07). I test di nanoindentazione sono stati effettuati con 100 mN min-1 di velocità di carico e 5 s di tempo di mantenimento al carico di picco. Il carico massimo è stato posto pari a 20 mN per il DLC e 300 mN per il Ni-P in accordo ai differenti spessori nominali, 4 µ m e 20 µ m, rispettivamente, e alla morfologia superficiale (morfologia a calotte dovuta all’interstrato Ni-P). Per ciascuna condizione è stata effettuata tramite una matrice 4x4 di indentazioni equidistanti in step di 50 µ m.
I rivestimenti depositati sono costituiti da: (i) lega Ni-P (in media 9% in peso di P, quindi appartenenti alla categoria “medio fosforo” più diffusa per via del buon compromes-
so fra resistenza a corrosione e proprietà meccaniche/tribologiche [14]), con spessore medio pari a circa 20 µm; (ii) rivestimento DLC costituito da un bond layer a base di Cr e un top layer a base di C amorfo idrogenato (spessore complessivo pari a circa 4 µm nelle zone ottimali). Gli spessori del solo rivestimento Ni-P e del rivestimento multistrato Ni-P+DLC sono stati valutati nelle zone più critiche dei dimostratori (Figura 1), ovvero il foro cilindrico presente sulla testa (Figure 2- 4), la struttura reticolare (Figura3)eilforopassanteromboidalepresenteall’internodelcorpo(Figura4),inmododavalutarelospessoredi deposizionedeisingolistrati. Le analisi morfologiche del fondo dei fori sulla testa dei dimostratori mostrano l’influenza della geometria (rapporto diametro-profondità del foro (R)) sull’efficacia di deposizione del multistrato Ni-P+DLC (Figura 2). Per la condizione “non critica” DLC-GNC (Figura 2(a)), caratterizzata da un R pari a 5, il rivestimento Ni-P+DLC sembra essere distribuito in maniera omogenea sia nella zona centrale(Figura2(b)),caratterizzatadaunasuperficiesulla quale le irregolarità derivanti dal processo PBF-LB sono state smussate grazie al processo di burattatura, sia nella
zona periferica (Figura 2(c)), la quale presenta una superficie più ondulata data la difficoltà degli elementi utilizzati in burattatura nel raggiungere aree in prossimità delle pareti verticali. Il rivestimento è stato in grado di seguire molto bene la morfologia superficiale del fondo del foro, riuscendo a depositarsi anche all’interno dei lack-of-fusion (LoF) superficiali (Figura 2(b)). Al contrario, la condizione “critica” DLC-GC (Figura 2(d)), caratterizzata da un R pari a 0,9, mostra i limiti del rivestimento Ni-P+DLC. In particolare, il fondo del foro ha evidenziato il distacco (Figura 2(e,f)) del rivestimento dal substrato lungo un’ampia zona anulare (aree chiare), la quale presenta una superficie estremamente corrugata a causa della maggiore difficoltà di accesso da parte degli elementi burattanti in prossimità del fondo delle pareti verticali.
Fig. 2 - Morfologia del rivestimento Ni-P+DLC all’interno del foro di testa (immagini FEG-SEM: DLC-GNC (a,b,c); DLC-GC (d,e,f) / Morphology of the Ni-P + DLC coating on the bottom of the head hole (FEG-SEM images): DLCGNC (a,b,c); DLC-GC (d,e,f)
Fig. 3 - Analisi dello spessore del rivestimento Ni-P all’interno del foro di testa (immagini FEG-SEM retrodiffusi) per i provini Ni-P-GNC (a,b,c,d,e) e Ni-P-GC (f,g,h,i,j,k), e per la struttura lattice del provino Ni-P-GC (l,m,n,o) / Ni-P coating thickness analysis inside the head hole (backscattered FEG-SEM images) for the Ni-P-GNC (a,b,c,d,e) and Ni-P-GC (f,g,h,i,j,k) samples, and for the lattice structure of the Ni-P-GC sample (l,m,n,o)
Fig. 4 -Analisi dello spessore del rivestimento multistrato Ni-P+DLC (immagini FEG-SEM in elettroni retrodiffusi): DLC-GNC foro di testa (a) e cavità nel corpo centrale (c,d); DLC-GC foro di testa (b) e cavità nel corpo centrale (e,f). Lo spessore riportato per le superficie esterne è solo indicativo della presenza del rivestimento: l’evidente sovrastima risente degli effetti di curvatura dovuti alla geometria del componente. / Analysis of multilayer Ni-P+DLC coating thickness (backscattered FEG-SEM images): DLC-GNC of head hole (a) and body hole (c,d); DLC-GC of head hole (b) and body hole (e,f). The thickness reported for the external surface is only indicative of the presence of the coating, as it is overestimated due to the geometry of the component.
Per comprendere le cause della scarsa adesione del topcoat, è stata valutata dapprima la profondità di penetrazione dell’interlayer Ni-P all’interno del foro di testa (Figura 3), per poi analizzare nel dettaglio anche l’efficacia della deposizione del topcoat DLC (Figura 4). La condizione Ni-P-GNC è caratterizzata da una deposizione uniforme del rivestimento Ni-P su tutta la superficie del foro, sia sulle pareti verticali che sul fondo (Figura 3(b-e)), di spessore pari a circa 20 µ m, riuscendo a penetrare all’interno di LoF collegate alla superficie (Figura 3(d)). Per la condizione critica Ni-P-GC (Figura 3(f)), invece, lo spessore si riduce all’aumentare della profondità (Figura 3(g)). In particolare, fino a 2 mm di profondità (R = 5) lo spessore del rivestimento Ni-P rimane pari a circa 20 µ m (Figura 3(h)), come osservato per la condizione Ni-P-GNC. Proseguendo all’interno del foro, ad una profondità di 4 mm (R = 2,5), il Ni-P raggiunge uno spessore pari a circa 7 µ m (Figura 3(i)), mentre proseguendo fino a 6 mm di profondità (R = 1,7) lo spessore scende ad un valore di circa 1,5 µ m (Fi-
gura 3(j)). Scendendo ulteriormente all’interno del foro, e quindi al ridursi del rapporto R, il rivestimento appare discontinuo,comeriscontratosulfondodelforo(R=0,9) (Figura 3(k)). Un’altra zona tra le quelle critiche analizzate èlastrutturareticolarenelcorpodeicampionirivestitidal solo Ni-P (Figura 3(f)). In questo caso, nella condizione piùrestrittiva(posizionecentraledelreticolo(Figura3(l)), lo spessore del rivestimento è apparso uniforme e pari a circa 20 µm (Figura 3(o)). È interessante notare come il rivestimento Ni-P riesca a seguire in maniera estremamente dettagliata sia la morfologia del reticolo che le polveri e gli spatter adesi alla superficie (Figura 3(m)). Tuttavia, queste zone risultano estremamente difficili da raggiungere per i media della burattatura, causando una minore adesione del rivestimento di Ni-P e la formazione di unostratoporosochesiinterponetrailNi-Peilsubstrato AlSi10Mg(Figura3(n))incuisiaccumulanoicontaminanti nonasportaticompletamenteprimadelladeposizionedel Ni-P.
Passando all’analisi delle zone critiche dei dimostratori rivestiti mediante Ni-P+DLC (Figura 4), si osserva che la penetrazione del topcoat DLC appare maggiormente influenzata dal valore di R rispetto al Ni-P, fenomeno riconducibile alla differente tecnologia di deposizione (PA-CVD vs. deposizione autocatalitica). Per il provino DLC-GNC (Figura 4(a)) è osservabile sulla superficie esterna della testa e sul fondo del foro uno spessore complessivo pari a circa 4 µ m. Tuttavia, sulla parete laterale del foro, lo spessore riscontrato scende a circa 2 µ m, mentre nel vertice inferiore del foro, il topcoat appare estremamente discontinuo se non assente, presumibilmente a causa di effetti di shadowing, tipici dei processi da fase vapore [14].
Passando alla geometria DLC-GC (Figura 4(b)), questo effetto viene amplificato sia a causa del minore valore di R, come già osservato per i campioni rivestiti Ni-P (Figura 3), sia per un’amplificazione dell’effetto legato all’angolo di deposizione; infatti, solo in alcuni punti è stato possibile rilevare il rivestimento DLC. Ciò è probabilmente dovuto al fatto che l’inefficienza del processo di burattatura nel livellare le superfici in questi recessi ha causato i problemi di adesione del Ni-P precedentemente descritti, compromettendo l’integrità dell’intero multistrato. Il foro romboidale passante nel corpo dei dimostratori (con un rapporto area/profondità al centro A/P=16 mm2/ mm per la geometria non critica e 4 mm2/mm per quella critica) mostra alcune differenze in termini di spessore del rivestimento tra le due geometrie esaminate. Per la condizione DLC-GNC, il multistrato Ni-P+DLC è perfettamente osservabile (Figura 4(c)). Tuttavia, a causa della curvatura della superficie nel punto in cui il foro emerge, gli spessori sono sovrastimati. Sulla sezione interna, posta ad una distanza dalla superficie esterna pari a 12,5
mm, è possibile constatare l’elevato potere penetrante dellanichelaturachimica;infatti,ancheaquestaprofondità, lo spessore di Ni-P si mantiene sui 20 µm. Di contro, il processo di deposizione direzionale PA-CVD non riesce a raggiungere queste profondità in maniera adeguata; di conseguenzasonoosservabilisolotraccediscontinuedel rivestimento DLC. La geometria critica amplifica ulteriormente questo effetto (Figura 4(e,f)): mentre lo spessore del Ni-P è sempre comparabile a quello osservato nella condizione DLC-GNC, nel DLC-GC il topcoat è presente solo in tracce sull’interlayer Ni-P. Soffermandosi sui fori romboidali, è molto interessante osservare come il Ni-P riesca a replicare superfici estremamente articolate, sia nella geometria critica che in quella non critica. Inoltre, in tutte le condizioni analizzate (DLC-GC e DLC-GNC), il Ni-PhamostratolacapacitàdirivestireancheLoFprofondi ma collegate alla superficie, colmandole parzialmente. Questo risultato è di estremo interesse considerando gli effetti negativi dei LoF sulle caratteristiche meccaniche, legatiall’intensificazionedeglisforziindottadaidifettisuperficialiacuti.
IlrivestimentoinNi-Pinoltrehamostratounabuonaadesione al substrato (classe di adesione 1 (HF2), con limitate cricche radiali ma assenza di delaminazione). Anche i risultati delle prove di scratch realizzate sul DLC hanno mostratounabuonaadesionediquest’ultimosuNi-P(Tabella 3). In particolare, il DLC non ha mostrato fenomeni di delaminazione, bensì solo la formazione di cricche conformi. I dati relativi a durezza (H) e modulo elastico (E) ottenuti mediante prove di indentazione strumentata hanno permesso di ricavare risultati confrontabili a quelli riportatiinletteraturaperilNi-Pnontrattatotermicamente[15,16]eperiltopcoat(a-C:H)DLC[17,18].
Tab. 3 - Risultati della caratterizzazione micro- e nanomeccanica / Micro and nanomechanical characterization data
7,4 ± 0,7 LC2 [N] 33,9 ± 1,6
137,3 ± 6,8 LC3 [N] 39,6 ± 2,2
27,0 ± 5,6
151,9 ± 62,5
I risultati di questo studio hanno permesso di evidenziare le principali criticità nella deposizione di un rivestimento multistrato Ni-P+(a-C:H) DLC su prototipi/dimostratori in lega AlSi10Mg caratterizzati da geometrie complesse e strutture reticolari ottenute con tecnologia additiva. In particolare:
• il rivestimento Ni-P è risultato efficace nel rivestire le geometrie più critiche, quali fori profondi, cavità passanti e strutture reticolari, grazie all’elevato potere penetrante intrinseco della deposizione autocatalitca: tuttavia, fattori estrinseci come la difficoltà nel realizzare un’appropriata preparazione del substrato in zone geometricamente critiche (es. nei fori cilindrici ciechi con un rapporto diametro-profondità minore di 5, solo parzialmente accessibili durante la burattatura) hanno impedito il raggiungimento dellospessorenominale(20 µm)nellezonepiùprofonde. Tuttavia,ilNi-Pèrisultatoefficacenelcompensareidifetti superficiali,spessopresentineicomponentiadditive.
•Iltopcoat(a-C:H)DLChamostratoinvecemaggioricriticità. Lo spessore del rivestimento è apparso non omogeneoancheall’internodellecavitàmenocritiche(rapporto diametro foro-profondità (R) pari a 5), anche a causa di un’orientazione delle pareti verticali spesso non ottimale rispetto all’angolo di deposizione. Di contro, nelle cavità critiche (foro sulla testa caratterizzato da R < 5 e cavità romboidale con un rapporto area cavità-profondità (A/P) inferiore a 16 mm2/mm), lo spessore del topcoat appare disomogeneo o pressoché assente, per via dei noti effetti di shadowing. Tuttavia, questo lavoro ha permesso di
quantificare i fattori geometrici critici R ed A/P.
• Infine, la caratterizzazione meccanica del rivestimento multistrato (Mercedes test, scratch test e nanoindentazione) ha mostrato risultati promettenti, indicativi della qualità del rivestimento nelle zone non critiche: il topcoat DLC ha mostrato un netto incremento della durezza rispetto all’interlayer Ni-P (+ 265 %). Questo, unito alle ottime proprietà tribologiche del DLC e alla capacità del Ni-P di coprire i difetti superficiali e di supportare il topcoat, permetterà di migliorare sensibilmente la vita utile dei componenti additive, aumentandone la resistenza ad usura e aprendo interessanti scenari in termini di aumento della resistenza a fatica.
Gli autori desiderano ringraziare il Dott. Francesco Lavalle e l’Ing. Paolo Lavalle di STS Srl – Cellatica (BS) per la definizione dei fattori geometrici e la deposizione dei rivestimenti esaminati. Questo lavoro è stato svolto nell’ambito del progetto Proof of Concept “ALuminium alloy COmponents produced by additive Manufacturing: improvement of performance by multilayer coatings (ALCOM)” finanziato nel contesto dei bandi a cascata dello Spoke 11 MOST (https://www.centronazionalemost.it/, finanziato dall'Unione europea – NextGenerationEU: Centro Nazionale Mobilità Sostenibile, CN00000023, Decreto MUR n. 1033 - 17/06/2022, SPOKE 11 Materiali Innovativi & Alleggerimento).
BIBLIOGRAFIA
[1] W. GAO, Y. ZHANG, D. RAMANUJAN, K. RAMANI, Y. CHEN, C.B. WILLIAMS, C.C.L. WANG, Y.C. SHIN, S. ZHANG, P.D. ZAVATTIERI, The status, challenges, and future of additive manufacturing in engineering,Comput. Aided Des. 69, 65-89 (2015).
[2] D. SCHUMANN; C. ROCKINGER; M. MERKEL; D.K. HARRISON, A Study on Additive Manufacturing for Electromobility. World Electr. Veh. J. 13, 154 (2022).
[3] J.Y. HO, K.C. LEONG, T.N. WONG, Additively-manufactured metallic porous lattice heat exchangers for air-side heat transfer enhancement, Int. J. Heat Mass Transf.150, (2020).
[4] A.K. MISHRA, R.K. UPADHYAY, A. KUMAR, Surface Wear Anisotropy in AlSi10Mg Alloy Sample Fabricated by Selective Laser Melting: Effect of Hatch Style, Scan Rotation and Use of Fresh and Recycled Powder, ASME. J. Tribol. 143(2), 021701 (2021).
[5] R.S. NANJUNDAIAH, S.S. RAO, K. PRAVEENKUMAR, T.R. PRABHU, A.K. SHETTIGAR, M. PATEL G C, E. LINUL, Fretting wear behavior on LPBF processed AlSi10Mg alloy for different heat treatment conditions, J. Mater. Res. Technol. 30, 4330-4346 (2024).
[6] L. PEZZATO, M. DABALÀ, S. GROSS, K. BRUNELLI, Effect of microstructure and porosity of AlSi10Mg alloy produced by selective laser melting on the corrosion properties of plasma electrolytic oxidation coatings,Surf. Coat. Technol. 404, (2020).
[7] E. DALLARI, M. BONONI, A. POLA, M. TOCCI, P. VERONESI, R. GIOVANARDI Pulsed Current Effect on the Hard Anodizing of an AlSi10Mg Aluminum Alloy Obtained via Additive Manufacturing. Surfaces 6, 97-113 (2023).
[8] L. LORENZETTI, L. TONELLI, I. BOROMEI, L. CESCHINI, P. SHASHKOV, C. MARTINI. Anodizing by Electrochemical Oxidation (ECO) of the Laser Powder Bed Fusion-processed A357 aluminium alloy: microstructural characterization and dry sliding behaviour. Prog Addit Manuf 8, 629–648 (2023).
[9] G. DI EGIDIO, L. CESCHINI, C. MARTINI, A. MORRI, Influence of Ni-P + DLC multilayer coatings on the tensile properties of the AlSi10Mg alloy produced by Laser-based Powder Bed Fusion,Procedia Struct. Integr. 47, 337-347 (2023).
[10] G. DI EGIDIO, C. MARTINI, L. CESCHINI, A. MORRI, Influence of Electroless Nickel—DLC (Diamond-like Carbon) Multilayer Coating on the Mechanical Performance of the Heat-Treated AlSi10Mg Alloy Produced by Powder Bed Fusion-Laser Beam, Materials 16, 3313 (2023)
[11] H. FAYAZFAR, J. SHARIFI, M.K. KESHAVARZ, M. ANSARI An overview of surface roughness enhancement of additively manufactured metal parts: a path towards removing the post-print bottleneck for complex geometries. Int J Adv Manuf Technol 125, 1061–1113 (2023).
[12] D.W. BAUDRAND, Electroless nickel plating, in: ASM Handbook 5, ASM international, 2002. ASM Intern.
[13] C. DONNET, A. ERDEMIR (Eds.), Tribology of Diamond-like Carbon Films. Fundamentals and Applications. New York (US): Springer, (2009)
[14] B.G. MELLOR, (ed.) Surface Coatings for Protection against Wear, Cambridge, UK. Woodhead Publishing, (2006)
[15] A. SALICIO-PAZ, H. GRANDE, E. PELLICER, J. SORT, J. FORNELL, R. OFFOIACH, M. LEKKA, E. GARCÍA-LECINA. Monolayered versus multilayered electroless NiP coatings: Impact of the plating approach on the microstructure, mechanical and corrosion properties of the coatings. Surf. Coat. Technol. 368,138-146 (2019).
[16] A.M. PILLAI, A. RAJENDRA, A.K. SHARMA, Electrodeposited nickel–phosphorous (Ni–P) alloy coating: an in-depth study of its preparation, properties, and structural transitions. J. Coat. Technol. Res. 9, 785–797 (2012).
[17] M.H. STAIA, E.S. PUCHI-CABRERA, A. IOST, A. ZAIRI, S. BELAYER, A. VAN GORp, Tribological response of AA 2024-T3 aluminium alloy coated with a DLC duplex coating, Tribol Int 85, 74-87 (2015).
[18] BS EN ISO 14577-4:2016 Metallic materials. Instrumented indentation test for hardness and materials parameters. Test method for metallic and non-metallic coatings (2007)
AlSi10Mg alloy lattice structures produced by Powder Bed Fusion - Laser Beam (PBF-LB) technology show high specific strength and an optimal surface/volume ratio. However, in the as-built condition they are characterized by a high roughness that may worsen their performance. To address this issue, a multilayer coating consisting of (i) electroless Ni-9%P interlayer, to compensate surface defects and optimize the surface topography, and (ii) PA-CVD hydrogenated amorphous carbon (DLC a-C:H) topcoat was deposited. The features of the coated system were evaluated by: (i) optical profilometry, (ii) FEG-SEM/EDS observations, (iii) micro/nanoscale hardness tests, and (iv) scratchtest.Basedontheresults,themainproblemsrelatedtothedepositionoftheNi-P+DLCmultilayercoatingon the PBF-LB AlSi10Mg critical components were identified, in order to optimize the whole post-printing cycle and guaranteeadequateperformanceofthemultilayercoating.
KEYWORDS: PBF-LB, ALSI10MG, LATTICE STRUCTURES, CRITICAL GEOMETRY, HYDROGENATED AMORPHOUS CARBON (A-C:H) DLC COATING, ELECTROLESS NI-P COATING, INSTRUMENTED INDENTATION, ADHESION TESTS, TOPOGRAPHIC ANALYSIS
A. Acquesta, F. Desiderio, T. Monetta, G. Stornelli, A. Di Schino
Il magnesio e le sue leghe sono promettenti candidati come materiali biodegradabili per applicazioni biomediche, grazie alla loro scarsa resistenza alla corrosione e alla loro biocompatibilità. Tuttavia, il processo di degradazione è troppo rapido e comporta lo sviluppo di idrogeno e l'alcalinizzazione dell'ambiente circostante. Pertanto, per migliorare la resistenza alla corrosione, sono necessari trattamenti superficiali o leghe realizzate ad-hoc. Il processo elettrolitico al plasma è un trattamento elettrochimico superficiale semplice ed ecologico, che consente la crescita di un rivestimento a base di ossido, molto aderente al substrato. La struttura dell'ossido, e di conseguenza le sue proprietà chimico-fisiche, possono essere influenzate da diversi parametri adottati durante il trattamento. In questo lavoro, si propone di studiare l'influenza della densità di corrente applicata durante l'ossidazione elettrolitica al plasma sulla microstruttura e sulle proprietà di corrosione della lega di magnesio composta da terre rare, WE43. La morfologia dei rivestimenti è stata analizzata attraverso la microscopia elettronica a scansione (SEM) e il microscopio confocale a scansione laser. Inoltre, sono state effettuate misure di microdurezza. Le proprietà elettrochimiche sono state studiate attraverso test di polarizzazione potenziodinamica e spettroscopia di impedenza elettrochimica in soluzione di Hanks a 37 °C. I risultati ottenuti hanno rivelato una particolare morfologia dell'ossido, nonché la possibilità di diminuire e controllare la velocità di corrosione della lega in esame.
INTRODUZIONE
Il magnesio è il più leggero dei metalli strutturali e questa proprietà lo rende un ottimo candidato per un'ampia gamma di applicazioni [1], ma a causa delle sue scarse proprietà meccaniche, deve essere legato con altri elementi che sono solubili in esso [2], ad esempio l'aggiunta di terre rare migliora la resistenza alle alte temperature e al creep. Le leghe di magnesio hanno l'enorme vantaggio di avere proprietà meccaniche e modulo di Young molto simili a quelle dei tessuti ossei [3] e questo permette di ridurre drasticamente il fenomeno del c.d. stress shielding. Tuttavia, il magnesio è molto reattivo e ha una scarsa resistenza alla corrosione, che diminuisce ulteriormente se viene messo a contatto con un ambiente acquoso ricco di ioni cloruro, proprio come l'ambiente biologico [4]. Inoltre, il problema principale da tenere in considerazione riguarda la formazione di idrogeno gassoso durante la corrosione ed è quindi essenziale poter ridurre o controllare la quantità di gas rilasciata durante la degradazione dell'impianto. Infatti, i trattamenti superficiali delle
Annalisa Acquesta, Fulvia Desiderio, Tullio Monetta
Dipartimento di Ingegneria Chimica, dei Materiali e della Produzione Industriale, Università degli Studi di Napoli Federico II
Giulia Stornelli, Andrea Di Schino
Dipartimento di Ingegneria Industriale, Università di Perugia annalisa.acquesta@unina.it
- Coatings
leghe di magnesio per applicazioni biomediche mirano a migliorare il comportamento alla corrosione e a garantire l'integrità e la durata del sistema nei tempi richiesti dalle applicazioni specifiche [5]. L'ossidazione elettrolitica al plasma (PEO) è un trattamento elettrochimico controllato di ossidazione della superficie metallica, simile all'anodizzazione ma che utilizza potenziali più elevati per formare uno strato di ossido. In seguito al trattamento PEO effettuato sulle leghe di magnesio, si osserva un miglioramento della resistenza alla corrosione. In letteratura, sono numerosi i lavori sullo studio del trattamento elettrochimico al plasma sulle leghe a base di zinco ed alluminio. Pochi,
invece, sono gli studi del medesimo trattamento effettuato sulle leghe di magnesio a base di terre rare, come la lega WE43. L'obiettivo del presente lavoro è studiare l'influenza di diversi valori di densità di corrente erogate durante la PEO sulla morfologia e risposta elettrochimica del rivestimento anodico accresciuto.
MATERIALI E METODI
La lega di magnesio utilizzata in questo lavoro è la WE43 (50 mm x 20 mm x 2 mm), la cui composizione chimica nominale è riportata nella Tabella 1.
Tab. 1 - Composizione chimica nominale della lega di magnesio WE43 / Chemical composition of the WE43 magnesium alloy.
Preparazione dei campioni
I campioni sono stati sottoposti a due trattamenti consecutivi: mordenzatura in un bagno di acido cloridrico (HCl) 0,15 M per 10s e ossidazione elettrolitica al plasma (PEO).
Inoltre, per avere una superficie iniziale replicabile, tutti i campioni sono stati lappati manualmente con carta abrasiva al carburo di silicio (SiC) di grana P320, poi lavati con etanolo in un bagno a ultrasuoni per 10 minuti e asciugati all'aria. Infine, è stato utilizzato del nastro isolante per mascherare i campioni, lasciando esposta un'area di 1 cm2 .
Ossidazione elettrolitica al plasma Il trattamento di ossidazione elettrolitica al plasma è sta-
to eseguito applicando due valori di densità di corrente (15 mA/cm2 e 30 mA/cm2) per 20 minuti in una soluzione composta da 5 g/L di silicato di sodio (Na 2SiO3) e 2 g /L di idrossido di sodio (NaOH), mantenendo la temperatura costante a 18°C con l'ausilio di un bagno termico e agitando la soluzione. Durante il processo, una lamina di platino è stata considerata come catodo. Dopo il trattamento, i campioni sono stati lavati con etanolo in un bagno a ultrasuoni per rimuovere ogni residuo di soluzione. La nomenclatura utilizzata per i diversi campioni è la seguente:
Tab.2-Nomenclaturautilizzataperidentificareicampioni/Nomenclatureofthesamples
CAMPIONE DESCRIZIONE
WE43_UT lega di magnesio WE43 non trattata
WE43_PEO15 lega di magnesio WE43 trattata con PEO applicando una densità di corrente 15 mA/cm2
WE43_PEO30 lega di magnesio WE43 trattata con PEO applicando una densità di corrente 30 mA/cm2
CARATTERIZZAZIONE
L'analisi morfologica dei rivestimenti PEO è stata eseguita con un microscopio a scansione elettronica (F.E.I.
Quanta 200 FEG) dopo aver metallizzato il campione con una sottile lega di oro-palladio; le osservazioni sono state raccolte operando in alto vuoto a una tensione di 30 kV.
Per misurare lo spessore del materiale metallico è stato utilizzato un misuratore di spessore (DUALSCOPE® MP0R, Fischer). Le misure di rugosità sono state eseguite mediante microscopia confocale a scansione laser (Lext 5100, Olympus Evident) e tra i diversi parametri di rugosità sono stati considerati: Sa (altezza media aritmetica); Sq (altezza quadratica media); Ssk (skewness come misura della distribuzione dell'altezza); Sku (Kurtosis come misura dell’acutezza del profilo, si riferisce alla geometria della punta di picchi e valli); Sdr (rapporto di area interfacciale sviluppata). Le prove di microdurezza Vickers sono state effettuate sui campioni sia prima che dopo il rivestimento PEO, utilizzando un microdurometro (HX-10000 Remet). Le proprietà elettrochimiche dei campioni sono state analizzate in una soluzione fisiologica (i.e, Hanks) a 37 °C eseguendo test di polarizzazione potenziodinamica e spettroscopia di impedenza elettrochimica (EIS) utilizzando un potenziostato (Gamry Instruments, Pennsylvania, USA). Per questi test, i campioni di magnesio trattati e non sono stati utilizzati come elettrodo di lavoro, un elettrodo al calomelano saturo (SCE) come elettrodo di riferimento e un filo di platino come controelettrodo. Dopo la misura dell'Open Circuit Potential (OCP), che consente al sistema di raggiungere un potenziale di equilibrio, è stato avviato il test di polarizzazione potenziodinamica. L'analisi EIS è stata eseguita in un intervallo di frequenza
compreso tra 105 e 10-2 Hz e registrata per un periodo di 14 giorni di immersione.
RISULTATI
Curve di potenziale-trattamento nel tempo L'andamento della tensione nel tempo e l'evoluzione delle microscariche sulla superficie del campione consentono di schematizzare il trattamento PEO in quattro diverse fasi. Nella prima fase, il potenziale aumenta rapidamente a causa della rapida passivazione del magnesio a contatto con la soluzione alcalina, e contemporaneamente si verifica la rottura dello strato di ossido anodico.A seguito di ciò, sulla superficie del campione iniziano a formarsi piccole e fitte scintille bianche, visibili a occhio nudo, seguite da emissioni acustiche, indicative della rottura delle aree più deboli del film di ossido con conseguente formazione di pori. Nel terzo stadio si verifica un cambiamento nella colorazione delle scintille, da bianche ad arancioni, la velocità di variazione del potenziale diminuisce e le emissioni acustiche diventano stridenti. Infine, nell'ultima fase, l'andamento della tensione si riduce ampiamente, le scintille diventano ancora più grandi e la loro densità sulla superficie diminuisce significativamente. Di seguito sono riportate le curve potenziale-tempo registrate durante il trattamento.
Fig.1-Curvedipotenziale-durataregistrateduranteiltrattamentoPEO/Potential-durationtreatmentcurverecorded duringthePEO
Il trattamento di ossidazione elettrolitica al plasma (PEO) è stato eseguito in corrente continua (DC) e utilizzando due valori di densità di corrente: 15 mA/cm2 e 30 mA/cm2
In particolare, la tensione di rottura di 200 V è stata raggiunta in minor tempo dal campione WE43_PEO30 rispetto al campione rivestito applicando una minore densità di corrente (WE43_PEO15). Inoltre, per quest’ultimo, il terzo stadio è iniziato con un ritardo significativo, mentre dopo neanche 3 minuti WE43_PEO30 è passato al quarto stadio, misurando una tensione superiore a 400 V. Sebbene il valore della densità di corrente applicata sia diverso, per entrambi i campioni è stato osservato un valore di potenziale finale comparabile.
AnalisiMorfologica
Per il campione non trattato, il solo trattamento di mordenzatura ha rimosso parzialmente le tracce della precedente pulizia meccanica, mentre al contrario, i campioni trattati con PEO hanno mostrato uno strato di ossido poroso, bianco, uniforme e compatto. In particolare, il cam-
-
pione trattato con una minore densità di corrente è ricoperto da numerosi pori di piccole dimensioni, distribuiti in modo casuale su tutta la superficie del campione, mentre il campione a maggiore densità di corrente presenta pori più grandi ma in quantità minore e distribuiti in modo casuale con preferenza lungo i bordi dell'area considerata. Attraverso le osservazioni al SEM, riportate in Fig.2, si è osservato che entrambi i campioni, pur essendo stati trattati con densità di corrente diverse, hanno uno spessore simile ma una morfologia diversa. Infatti, il campione WE43_PEO15 ha uno spessore di circa 12 µm e presenta una struttura stratificata, costituita, partendo dal substrato, da: un sottile barrier layer, uno strato intermedio striato e uno strato esterno con struttura porosa. Inoltre, se osservato in sezione, presenta una morfologia scanalata fatta di canali aperti che si estendono fino al barrier layer. Il campione WE43_PEO30, invece, presenta la classica struttura porosa, con un evidente barrier layer, seppur nanometrico, e uno spessore di 11 µm.
SEM dei campioni a) WE43_PEO15 e b) WE43_PEO30 / SEM images of the samples a) WE43_ PEO15 and b) WE43_PEO30
- Immagini SEM dei campioni visti dall’alto a) WE43_PEO15 e b) WE43_PEO30 / Top view SEM images of a) WE43_PEO15 and b) WE43_PEO30
Misuredirugosità
La diversa morfologia del rivestimento PEO dei due campioni rispetto al campione non trattato è stata
ulteriormente evidenziata dalle seguenti immagini 3D delle misure di rugosità.
Un confronto delle misure di rugosità tra i tre campioni mostra che i parametri Sa e Sdr sono significativamente più alti nei due campioni anodizzati, a seguito della particolare morfologia porosa che comporta il trattamente PEO, mentre il parametro Ssk è negativo per tutti i campioni, indican-
do che la superficie ha una prevalenza di valli. Infine, il parametro Kurtosis, che fornisce informazioni sulla morfologia dei picchi, è maggiore di 3 in tutti e tre i casi e indica una superficie caratterizzata da picchi acuti.
Tab.3 - Risultati delle misure di rugosità / Results of the roughness measurements
Microdurezza
Le misure di microdurezza, effettuate mediante microtester, hanno evidenziato una significativa differenza tra la lega WE43 allo stato nudo e i campioni trattati con PEO. Il valore medio di durezza della lega WE43_UT è di 110 HV, mentre i campioni WE43_PEO15 e WE43_PEO30 mostrano
valori di durezza molto più elevati, rispettivamente 482 HV e 494 HV. Questa differenza è attribuibile alla formazione di un film ceramico nei campioni anodizzati, che aumenta notevolmente la resistenza meccanica e la durezza superficiale.
Fig.5 - Valori di microdurezza dei campioni: WE43_UT; WE43_PEO15; WE43_30 / Microhardness values of the samples: WE43_UT; WE43_PEO15; WE43_30
Polarizzazione potenziodinamica
Il comportamento elettrochimico è stato analizzato mediante test di polarizzazione potenziodinamica (PD) e spettroscopia di impedenza elettrochimica (EIS) immergendo i campioni nella soluzione di Hanks a 37 °C [6]. Come illustrato nella Fig. 6, la curva di polarizzazione potenziodinamica del campione di magnesio non trattato ha presentato la più alta densità di corrente di corrosione, pari a 1,25 x 10-5 A/cm2 e l'anodizzazione ha ridotto la velocità di corrosione. Il campione WE43_PEO15 ha registrato un potenziale di corrosione, Ecorr, come quello non trattato, ma ha presentato un breve intervallo di pseudo-passività tra -1,56 e -1,66 V vs SCE. Il campione WE43_PEO30 ha
presentato un potenziale di corrosione più basso rispetto ai campioni precedenti, suggerendo una maggiore tendenza termodinamica ai fenomeni di corrosione, ma un intervallo più ampio di pseudo-passività, tra -1,56 e -1,75 V vs SCE. Poiché lo spessore dei rivestimenti PEO era simile, la diversa risposta elettrochimica potrebbe essere attribuita alla loro diversa morfologia, come evidenziato dalle osservazioni al SEM. Entrambi i campioni anodizzati hanno registrato il potenziale di transpassività, il potenziale al quale avviene la rottura del rivestimento di ossido, a -1,56 v vs SCE, secondo quanto riportato in letteratura [7].
Fig.6 - Curve di polarizzazione potenziodinamica dei campioni WE43_UT, WE43_PEO15 e WE43_PEO30 / Potentiodynamic polarization curves of the samples WE43_UT, WE43_PEO15 and WE43_PEO30
CCaratterizzazionedellaspettroscopiadiimpedenza elettrochimica
Il comportamento dei campioni WE43 non trattati e anodizzatièstatoverificatoripetendoiltestperunperiododi 14giorni.
Il magnesio nudo, all'inizio della prova, ha presentato un andamento della curva del modulo di impedenza, caratterizzato da un comportamento resistivo alle alte e basse frequenze e da un comportamento capacitivo nell'intervallo di frequenza intermedio, registrando un modulo di impedenza alla frequenza più bassa di 1,43 x 103 Ω cm2
Dopo 24 ore di immersione non sono stati rilevati cambiamenti. Nel resto del tempo di immersione è stato registrato un aumento e una diminuzione alternati del modulo d’impedenza, suggerendo una continua formazione e dissoluzione dello strato di ossido sulla sua superficie. In particolare, dopo 168 ore l'aumento del modulo Z ad alta frequenza indica la formazione di uno strato protettivo, dovuto all'interazione del substrato con l'ambiente fisiologico.
- Grafico di Bode del campione WE43_UT / Bode plot of the sample WE43_UT
L'anodizzazione ha comportato una diversa risposta elettrochimica rispetto al campione non modificato. Il campione WE43_PEO15 ha mostrato un comportamento capacitivo a partire dalla gamma delle alte frequenze con un cambiamento di pendenza nell'intervallo intermedio per registrare un comportamento resistivo alle frequenze più basse, in cui il modulo di impedenza ha raggiunto un valore di circa 1,2 x 105 Ω cm2, due ordini di grandezza maggiori rispetto al campione non trattato. Un leggero miglioramento del modulo di impedenza alla frequenza più bassa è stato registrato fino a due giorni di immersio-
ne. Dopo 168 ore, è stata rilevata una piccola diminuzione di Z, che è rimasta stabile fino ad altri 7 giorni. Un tempo di immersione di circa 500 h ha comportato una riduzione del modulo di impedenza di circa un ordine di grandezza. La vicinanza delle curve attesta la stabilità del rivestimento di ossido anodico sotto esame. Invece il campione WE43_ PEO30, pur mostrando lo stesso andamento del campione precedente, ha registrato valori più bassi del modulo di impedenza, pari a 6,5 x 104 Ω cm2 e 2,8 x 103 Ω cm2, all'inizio e alla fine, rispettivamente, delle osservazioni temporali.
Fig.8 - Grafico di Bode dei campioni WE43_PEO15 e WE43_PEO30 / Bode plots of the samples WE43_PEO15 and WE43_PEO30
CONCLUSIONI
Il presente lavoro mirava a studiare l'influenza della densità di corrente applicata durante l'ossidazione elettrolitica al plasma sulla microstruttura e sulle proprietà di corrosione della lega di magnesio composta da terre
rare, WE43. La morfologia dei rivestimenti, analizzata attraverso la microscopia elettronica a scansione (SEM), è risultata essere diverse per le due tipologie di campioni. Infatti, il rivestimento ottenuto applicando una densità di corrente più alta presentava la classica tipologia di rive-
stimento porosa attesa, a differenza di quello ottenuto applicando una densità di corrente più bassa che ha mostrato una tipologia di pori passanti. Le misure di rugosità hanno dimostrato una rilevante estensione dell’area reale nelcasodeirivestimentianodizzati.Unamaggioredurezza dei rivestimenti ceramici è stata mostrata dalla misura di microdurezza. Le proprietà elettrochimiche, effettuate attraverso test di polarizzazione potenziodinamica e spettroscopia di impedenza elettrochimica in soluzione di Hanks a 37 °C, hanno mostrato un miglioramento delle proprietà elettrochimiche dei campioni anodizzati. In
particolare, il rivestimento ottenuto a minore densità di corrente ha mostrato una maggiore stabilità nel tempo, rispetto a quello accresciuto applicando densità di corrente maggiori. Quindi, tale studio ha confermato che la densità di corrente, come parametro di processo, ha un’influenza sulla morfologia del rivestimento, ma soprattutto ha dimostrato che applicare una densità di corrente di corrosione pari a 15 mA/cm2 è sufficiente se non migliore per allungare la durabilità della lega in esame, quando utilizzato in fluidi simulanti quelli biologici.
[1] Dewidar, M.M.; Yoon, H.-C.; Lim, J.K. Mechanical Properties of Metals for Biomedical Applications Using Powder Metallurgy Process: A Review. Met. Mater. Int. 2006, 12, 193–206.
[2] Handbook, A.S. Magnesium and Magnesium Alloys. ASM Int. 1999, 106–118.
[3] Zheng, Y. Magnesium Alloys as Degradable Biomaterials. 2015.
[4] Makar, G.L.; Kruger, J.L. Corrosion of Magnesium. Int. Mater. Rev. 1993, 38, 138–153.
[5] Narayanan, T.S.; Park, I.-S.; Lee, M.-H. Surface Modification of Magnesium and Its Alloys for Biomedical Applications: Opportunities and Challenges. Surf. Modif. Magnes. Its Alloys Biomed. Appl. 2015, 29–87.
[6] Carangelo, A., Acquesta, A.Monetta, T. Durability of AZ31 magnesium biodegradable alloys polydopamine aided. Part 2: Ageing in Hank's solution, J. of Magnes. Alloys, 2019, 7(2), 218–226.
[7] Tekin, K.C.; Malayoğlu, U.; Shrestha, S. Electrochemical Behavior of Plasma Electrolytic Oxide Coatings on Rare Earth Element Containing Mg Alloys. Surf. Coat. Technol. 2013, 236, 540–549, doi:10.1016/j.surfcoat.2013.10.051.
Magnesium and its alloys are promising candidates as biodegradable materials for biomedical applications due to their low corrosion resistance and biocompatibility. However, the degradation process is too rapid and results in the development of hydrogen and the alkalinisation of the surrounding environment. Therefore, ad-hoc surface treatments or alloys are required to improve corrosion resistance. The electrolytic plasma process is a simple and environmentally friendly electrochemical surface treatment, which allows the growth of an oxide-based coating that is very adherent to the substrate. The oxide morphology, and consequently its chemical-physical properties, can be influenced by various parameters adopted during the treatment. In this work, it is proposed to study the influence of the current density applied during electrolytic plasma oxidation on the microstructure and corrosion properties of the rare-earth magnesium alloy, WE43. The morphology of the coatings was analysed by means of scanning electron microscopy (SEM) and laser scanning confocal microscopy. Additional microhardness measurements were carried out. Electrochemical properties were investigated through potentiodynamic polarisation tests and electrochemical impedance spectroscopy in Hanks' solution at 37 °C. The results revealed a peculiar morphology of the oxide layer, as well as the possibility of decreasing and controlling the corrosion rate of the alloy under investigation.
KEYWORDS:
M. Sadeghi, H. Sabet
In the present study, an innovative industrial approach of submerged friction stir welding (SFSW) technology on AA6061 was investigated. This state-of-the-art nano-submerged FSW method is applied to advanced manufacturing and industrial sectors to enhance weld strength. The solid-state joining of aluminum alloy plates of AA6061 reinforced with titanium dioxide nanoparticles via SFSW butt welding was performed. Nano-SFSW meticulously considers the addition of TiO2 nanoparticles into the abutting edges of the base material. The tool traversing speed played a predominant role in improving the mechanical properties of the joints. The tool rotational speed ( ω ) and transverse speed ( ϑ ) were varied from 1000 to 1200 rpm and 25–40 mm/min, respectively. Two different pitch welding conditions, nano SFSW and SFSW, were evaluated. Mechanical testing illustrated that hardness and tensile strength were enhanced, with the highest tensile strength reported as 284 MPa and hardness as 165 HV. Microstructural and metallurgical studies revealed that the weld nugget grain size diminished, and SEM and TEM microstructures showed very fine grains and uniform distribution of TiO2 nanoparticles. This development in welding technology, particularly for clean energy processes, facilitates various joints, especially non-homogeneous joint nanocomposites.
KEYWORDS: SUBMERGED; FRICTION STIR WELDING; NANO-PARTICLES; TITANIUM-DIOXIDE
Welding is the most widely used fabrication technique in the manufacturing industry, Rajak et al. briefly explaining their mechanisms to show a comparison between friction welding (FRW) and friction stir welding (FSW) [1]. FSW was invented by Thomas WM at TWI UK in 1991 to overcome the fusion welding problems. Shahabuddin et al. have been indicated that submerged friction stir welding is a latest technique which is widely acceptable in the industries like Aerospace and Shipbuilding for joining of different aluminum alloy series such as (6xxx,7xxx,8xxx) due to the light weight and high strength. It is very difficult to weld these alloys by using fusion method so, friction stir welding is introduced and it is widely taken into consideration for performing such welding process [2]. Sabry and El-Kassas have been illustrated that four stages during friction stir welding (FSW) have been carried out: the plunging stage, the dwelling stage, the welding stage, and the escape or retracting stage of the tool. The FSW procedure is essentially carried out by plunging a spinning FSW mechanism unit through the interface of two rigidly clamped sheets before the shoulder meets the surface of the material being welded [3]. Wahid et al. have been studied that the travel of the unit progresses
Sadeghi.m2024@gmail.com h-sabet@kiau.ac.ir
along the weld line allowing the material to displace from the advancing side to the retracting side. Meanwhile, the tool shoulder consolidates the material at the back of the pin, resulting in a stable state [4]. El-Kassas and Sabry, compared to other conventional welding processes, FSW process uses a significant amount of energy. The absence of flux or cover gas makes the process environmentally safe [5]. As well as Sabry et al. have been described that they are critical in producing heat generation, forging strain, the flow of material, welding appearance, and performance. As an outcome of dislocation density increase, the nugget area has high stiffness at higher speeds [6]. After this, Kucukomeroglu et al. and Imam et al. investigated the area of FSW research is broadening, and their excellent performance either in the joining of similar material or dissimilar material documented [7,8]. Magalhaes et al. and Meng et al. explored that FSW successfully used in various industries, including railway, automobile, defence, aerospace and renewable energy [9,10]. Kumar et al. have studied the parametric control of rotation speed, transverse speed, and pin length during underwater friction stir welding (UW-FSW) on aluminum AA6063 and indicates that the proposed optimization module efficiently controls the varying process parameters to achieve conflicting response values. It is highly efficient to manufacture high-efficiency welded joints and is recommended for optimum joint qualities [11]. Meikeerthy et al. observed the pure titanium welded joints produced by underwater FSW was evaluated and the mechanical properties such as yield strength, tensile strength, and hardness are improved in UW-FSW when compared with conventional FSW. As well as the effect of other prominent ceramic nanoparticles like Alumina (Al2O3), TiC, TiO2 as reinforcement in the FSW process also has been reported by several researchers [12]. Singh et al. examined the effect of Al2O3 and TiO2 nanoparticles reinforcement in the FSW of AA6061-T6. It can be observed that Al2O3 reinforced joints, nanoparticles distribution, are more uniform with no surface defect. While in the case of TiO2 reinforced joints, agglomerated nanoparticles observed in the heat-affected zone on the advancing side, which is attributable to a reduction in heat transfer between the tool and deformed plasticized materials [13]. Fragmentation, in the case of TiO2 reinforced joint is fewer than that of Al2O3 reinforced joints have been
described by Derazkola and Simchi [14]. Vimalraj and Kah demonstrated that homogeneous distribution of carbide nanoparticles (i.e., SiC and TiC) in joints requires slow traverse speed and high rotation speed; however, in the case of oxide nanoparticles (TiO2), an increase in number of passes is required [15]. Manjunath et al. performed that double pass FSW-friction stir welding on 6061 T6 and 7075 T651 alloys of aluminium matrix reinforced with nano h-BN have been analyzed and deploying a range of welding parameters specifically tool spindle speed, tool traverse feed, and tool profile [16]. Singh and Singh et al. indicated that the solid-state joining of AA6061-T6 Al2O3 and TiO2 nanoparticles via friction stir welding was done. Results reveal that the weld without nanoparticle welded at many FSW conditions, while in the case of weldments With Al2O3 Nanoparticle (WAL) and With TiO2 Nanoparticle (WTI)), the working window was narrower [17,18]. The welds reinforced with Al2O3 and TiO2 nanoparticles were inspected visually and at macroscale level for outward imperfections that depend on the flow behaviors, localized heat input intensity, and welding parameters Singh et al.[19]. The surface appearances of the TiO2/FSW weld reveals the non-homogenous rough surface with the flash formation in the advancing side (AS) and retreating side (RS) of the weld. This was attributed to the inadequate heat generation and fast cooling rate occurred due to stiffer TiO2 particles that provide more restriction against the movement of the FSW tool in the transverse direction Gangil et al. [20].While the surface appearance of Al2O3/FSW weld shows the smooth well forged surface appearance with no visually inspected particle agglomeration on either side of the weld zone (NZ) representing the perfect defect-free weld. Singh et al. are considered while the Al 2O3 and TiO2 nanoparticles agglomerations were observed when the tool rotational speed was further increased with the decrease in traverse speed. Despite the difference in nanoparticles, the particle distribution is not inherently sensitive to the particle type. Such that the type, size, volume fraction, and shape are all significant to determine the properties of nanocomposites or welds. [21,22]. Sufian et al. microhardness results reveal that appreciable enhancement in material strength for WTI weldment is ascribed due to a decrease in nanoparticle size according to the Hall-Petch relationship. [23]. No previous study on nano-submerged FSW processing of
AA6061/TiO2 welds has been reported. This research fills that gap by evaluating the microstructure, metallurgical, and mechanical properties of nano-submerged FSWed AA6061/TiO2 joints.
MATERIALS AND EXPERIMENTAL PROCEDURES
Thin sheets of AA6061 aluminum alloy were selected as the parent material. TiO2 nanoparticles (rutile-reinforced)
with 99.9% purity and an average particle size of 30 nm were used as reinforcement. Rutile is a low-cost, readily available mineral with superior mechanical properties, corrosion resistance, wear resistance, and higher thermomechanical properties. The schematic of SFSW Al 6061 with TiO2 reinforcement and the isolated pin tool location are shown in Fig. 1.
- (a) Schematic of the Nano-SFSW (b) The location of TiO2 nano-particles.
The quality of FS welded joints is influenced by several factors, including rotational speed, tool traverse speed, axial force, tool geometry, material, tilt angle, backplate material, and workpiece material. This work identified three process variables: rotational speed, tool traverse speed, and welding condition (Nano-SFSW and SFSW).
Process Steps:
1. Simulate a seawater environment
2. Design special tools for SFSW
-The SFSW and dimensions (a) The nano SFSW(b) Tool pin (a) (b) a) b)
3. Improve tool properties via heat treatment for water environment use
4. Add TiO2 nanoparticles to abutting edges of the base material
5. Cut weld samples for mechanical testing
6. Observe weld microstructure using optical microscopy and SEM
Fig. 2 illustrates the aluminum alloy joint welded simulation and pin tools.
Tools made of H13 low-alloyed carbon tool steel were heat treated to improve properties. The novel technique was applied to Al 6061 strips (150 × 65 × 5 mm3) in butt welding positions, with the chemical composition shown in
Table 1. For the first time, 0.2% TiO2 (30nm) reinforcement particles were used in submerged FSW. The tool rotational speed ( ω ) and transverse speed ( ϑ ) were varied, with different welding conditions given in Table 2.
Tab. 1 – Chemical composition of AA6061 (Wt.%)
2 – Welding conditions for different samples
Figs. 3 scheme of mechanical and microscopy samples and the tensile specimens after wire cut from the weld joints.
Fig.3 -(a) Scheme of mechanical and microscopy samples(b) The tensile specimens.
Mechanical tests, including hardness and tensile strength, were conducted on different samples. The tensile tests followed ASTM-E8M-11 at ambient temperature with a cross-head velocity of 2 mm/min. Microhardness profiles were evaluated using a Vickers microhardness tester (OMNITECH). Weld zone microstructures were analyzed using optical microscopy and scanning electron microscopy (SEM) with energy dispersive spectroscopy (EDS).
RESULTS AND DISCUSSION
The microstructure and mechanical properties of the
base material were examined before SFSW. The volume fraction of nanoparticles was determined using Clemex image analyzer which comes out to be 0.2%. The microstructure of Al 6061 base material was shown in Figs.4 The characterization of the base material was depicted in optical microstructure of Al 6061 base material reveals and Transmission electron microscopy (TEM) images of TiO2 nanoparticle have similar morphology of spherically shape irregular patterns, and mean grain size of 30 nm was evaluated using the William- Son-Hall method.
(a) (b)
When the Nano-SFSW samples are compared with SFSW sample, the Nano-SFSW sample is without cracks and defects, and the quality of the welding surface is similar to each other.
The Nano-SFSW sample are free of cracks and defects and surface quality specimens similar as another sample that welded in SFSW. Table 3 Given the mechanical test of different samples. It can be seen that by increasing the pitch welding (ω /ϑ ), the hardness, yield and tensile strength of weld metal in SFSW and Nano-SFSW condition increased. In addition, the hardness, yield strength and tensile
strength of weld metal in Nano-SFSW as higher than the SFSW condition. The tensile strength of joints formed in Nano-SFSW is higher than those of SFSW and the highest tensile strength was reported as 284 MPa.Microhardness of the friction stir welded aluminum alloy joints was directly related to the amount of reinforcing TiO 2 nano-particles and grain size. The highest microhardness of nugget in the absence of TiO2 nano-particles was HV110, which significantly increased to HV165 in the presence of TiO2 nano-particles, for the 1000-1200 rpm specimen.
The microstructure weld metal by optic microscopy (OP) shown in Figs. 5. In SFSW condition with 30 and 40 grain size 82μ and 60μ were gained when two microstructure
nuggets compared in Nano-SFSW condition with 30 and 40 pitch welding grain size 63μ and 47μ therefore grain size in Nano-SFSW condition has been decreased.
-Optical microstructure nugget weld (a) SFSW 30 pitch welding, grain size 82μ(b) SFSW 40
In figs. 6 the microstructure of weld metal result illustrated that scanning electron microscopy (SEM) microstructure approved that very fine grains and nano-TiO2 particles uniformly mix between the base materials.
Fig.6 -Scanning electron microscopy (SEM) nugget weld (a) SFSW 30 pitch welding, grain size 82μ(b) SFSW 40 pitch welding, grain size 60μ(c) Nano- SFSW 30 pitch welding, grain size 63μ(d) Nano- SFSW 40 pitch welding, grain size 47μ.
When considering microstructural formation, nanoparticles reinforcement in Al joints tends to reduce the grain size. With TiO2 nanoparticles, the grain size in the joint has been reduced compared with grain sizes in joints without nanoparticles. By using TiO2 nanoparticles with a single pass, the grain size has been slightly reduced compared to the grain size attained without nanoparticles. However, the grain size was further reduced by increasing the number of passes on the joints with TiO 2 nanoparticles.
Nano-SFSW the grain sizes in the weld nugget with the TiO2 nanoparticles further grain size reduction (50μ) when compared to SFSW the TiO2 nanoparticles (88μ). This could be due to the size of the TiO2 nanoparticles in SFSW (20–25 nm) and the size of the TiO2 nanoparticles in Nano-SFSW (5–10 nm). Moreover, no agglomeration of TiO2 nanoparticles was found in the joints, as shown in (Fig. 7).
Nano-SFSWed samples exhibited better tensile properties than SFSWed joints due to enhanced grain refinement and uniform TiO2 distribution. The highest tensile strength and hardness were observed at a higher tool rotational speed ( ω =1200 rpm) and traverse speed ( ϑ =40 mm/min).
CONCLUSIONS
• Nano-SFSWed AA6061 joints exhibited enhanced mechanical properties compared to conventional SFSWed joints.
• Uniform distribution of TiO 2 nanoparticles contributed
This study explored an innovative industrial approach of SFSW technology on AA6061. The incorporation of TiO2 nanoparticles led to significant improvements in mechanical properties. The following conclusions can be drawn:
to increased hardness and tensile strength.
• Optimal welding conditions for the highest mechanical properties were identified as ω =1200 rpm and ϑ =40 mm/ min.
The findings suggest that Nano-SFSW is a promising technique for improving the mechanical properties of aluminum alloy joints in various industrial applications.
The author wishes to acknowledge to the Islamic Azad University, Karaj Branch for the Postdoctoral research facilities and their support.
[1] Rajak D.K., Pagar D.D., Menezes P.l. and Eyvazian A., “Friction-based welding processes: friction welding and friction stir welding”, J. Adhes. Sci. Technol., 34(24), 2613–2637, (2020). https://doi.org/10.1080/01694243.2020.1780716 .
[2]. Shahabuddin, Dwivedi V. K., Sharma A., “Experimental investigation of the mechanical properties and microstructure of AA 7075-T6 during underwater friction stir welding process”, Int. J. Eng. Advance Tech., 8(4), 1289-1293, (2019).
[3]. Sabry. I and El-Kassas. A.M., (2019), “A new quality monitoring system for friction stir welded joints of aluminum pipes”, Int. J. Eng. Tech., 11(1), 78-87. http://dx.doi.org/10.21817/ijet/2019/v11i1/191101040 .
[4]. Wahid M.A., Khan Z. A. and Siddiquee A.N. “Review on underwater friction stir welding: A variant of friction stir welding with great potential of improving joint properties”, Trans. of Nonferr. Meta. Soc. China., 28, 193-219, (2018). http://dx.doi.org/10.1016/S10036326(18)64653-9 .
[5]. Sabry. I and El-Kassas. A.M. ,(2017), “A comparison between FSW, MIG and TIG based on total cost estimation for aluminum pipes” J. Adv. Eng. Tech., 4(3), 158-163.
[6]. Sabry I., Mourad I. and Thekkuden D., “Comparison of mechanical characteristics of conventional and underwater friction stir welding of AA 6063 pipe joints”, Int. Rev. of Mech. Eng., 14(1), 64, (2020). http://dx.doi.org/10.15866/ireme.v14i1.17483 .
[7]. T. Kucukomeroglu, Aktarer S. M., Ipekoglu G., Cam G., “Microstructure and mechanical properties of friction-stir welded St52 steel joints”, Int. J. Min. Met. Mater. ,25, 1457-1464, (2018). http://dx.doi.org/10.1007/s12613-018-1700-x
[8]. Imam, M., Racherla V. Biswas K., Fujii H., Chintapenta V., Sun Y., Morisada Y., “Microstructure-property relation and evolution in friction stir welding of naturally aged 6063 aluminium alloy”, Int. J. Adv. Manuf. Technol. ,91, 1753-1769, (2016).
[9]. Magalhaes V. M., Leitao C. and Rodrigues D. M., “Friction stir welding industrialisation and research status”, Sci. Technol. Weld Join. ,23, 400-409, (2017). https://doi.org/10.1080/13621718.2017.1403110
[10]. Meng X, Huang Y., Cao J., Shen J., dos Santos J., “Recent progress on control strategies for inherent issues in friction stir welding”, Prog. Mater. Sci. ,115 ,1-183, (2021). https://dx.doi.org/10.1016/j.pmatsci.2020.100706 .
[11]. Kumar J., Majumder S., Kumar A., Rajesh M., Verma K., “Influence of rotation speed, transverse speed, and pin length during underwater friction stir welding (UW-FSW) on aluminium AA6063: A novel criterion for parametric control”, Int. j. lightweight mater. manuf., 5, 295-305, (2022). https://doi.org/10.1016/j.ijlmm.2022.03.001
[12]. Meikeerthy S., Ethiraj N., Neme I., Masi Ch., “Evaluation of pure titanium welded joints produced by underwater friction stir welding”, Adv. Mater. Sci. Eng. ,2023, 1-12, (2023). https://doi.org/10.1155/2023/2092339
[13]. Singh T., Tiwari S.K., Shukla D.K., “Mechanical and microstructural characterization of friction stir welded AA6061-T6 joints reinforced with nano-sized particles”, Mater. Char. ,159, 11-47, (2020). https://doi.org/10.1016/j. matchar.2019.110047
[14]. Derazkola A., Simchi.H, “A new procedure for the fabrication of dissimilar joints through injection of colloidal nanoparticles during friction stir processing: proof concept for AA6062/PMMA joints”, J. Manuf. Process., 49, 335-343, (2020). https://doi.org/10.1016/j. jmapro.2019.12.008
[15]. Vimalraj C., Kah P., “Experimental review on friction stir welding of aluminium alloys with nanoparticles”, Metals., 11(3) ,1-26, (2021). https://doi.org/10.3390/met11030390 .
[16]. Manjunath.M, Pillappan.SS and Kurse.S, “Process parameter analysis of double pass friction stir composite welds”, Int. J. of mater. Manuf. Processes. ,38, 1213-1230, (2023). https://doi.org/10.1080/10426914.2023.2190380
[17]. Singh T., “Processing of friction stir welded AA6061-T6 joints reinforced with nanoparticles”, Results in Materials. 12 .1-10, (2021). https://doi.org/10.1016/j.rinma.2021.100210 .
[18]. Singh T., Tiwari S.K., Shukla D.K., “Production of AA6061-T6/Al2O3 reinforced nanocomposite using friction stir welding”, Eng. Res. Express. ,1, 025-52,(2019).
[19]. Singh T., Tiwari S.K., Shukla D.K., “Effect of nano-sized particles on grain structure and mechanical behavior of friction stir welded Al-nanocomposites”, Proc. Inst. Mech. Eng. Part L. J. Mater. Des. Appl. ,234 (2), 274–290, (2019).
[20]. Gangil N., Maheshwari S., Siddiquee A.N., “Multipass FSP on AA 6063-T6 Al: strategy to fabricate surface composites”, Mater. Manuf. Process. ,33 (7), 805–811, (2018).
[21]. Singh T., Tiwari S.K., Shukla D.K., “Novel method of nanoparticle addition for friction stir welding of aluminum alloy”, Adv. Mater. Process. Technol, 8 (1), 1160-1172,(2022). https://doi.org/10.1080/2374068X.2020.1855397 .
[22]. Singh T., Tiwari S.K., Shukla D.K., “Preparation of aluminum alloy-based nanocomposites via friction stir welding”, Mater. Today. Proc. ,27 (3), 2562–2568, (2020).
[23]. Sufian R., Mohd Ridha M., Mohd Fadzil J., Farazila Y., “A review on nanomaterials reinforcement in friction stir welding”, J. Mater. Res. Technol., 9 (6), 164591-16487,(2020). https://doi.org/10.1016/j.jmrt.2020.11.072
R. Sasidharan, S.R. Koteswara Rao, S.Vijayan
Gas Tungsten Arc Welding (GTAW) is widely used to fabricate duplex stainless-steel structures. While the process offers clean welds, it is difficult to achieve full penetration in flat butt joints thicker than 3mm, that are common in pipe welds. This study aims at obtaining single pass full penetration welds in 6 mm thick plates with flat butt joint configuration, which can avoid use of filler material and minimize edge preparation. Use of activated flux and addition of nitrogen to the shielding gas have been employed to obtain single pass full penetration autogenous welds on 6mm thick plates. The effect of welding current, welding speed, arc gap and gas flow rate have been studied while using Activated flux and nitrogen addition.
In this investigation the effect of shielding gas argon and argon plus nitrogen are studied on the bead geometry of Activated flux assisted GTA welds of Duplex Stainless Steel 2205, 6 mm thick plates. The ATIG process parameters were optimized using Taguchi L16 orthogonal array. Current (A), Welding Speed (mm/min), Gas Flow Rate (L/min) and Arc Gap (mm) are the input process parameters considered while the depth of penetration is the response to be maximized. It has been concluded that the welding speed and current are the dominant parameters affecting the response with and without the inclusion of nitrogen in the shielding gas respectively. Nitrogen addition seemingly reduced the depth of penetration.
KEYWORDS: DUPLEX STAINLESS STEEL (2205), ACTIVATED FLUX GTA WELDING, TAGUCHI L16 OPTIMIZATION, BEAD GEOMETRY
A novel variation of the TIG welding procedure known as the Activated flux ATIG welding technique was initially created for the welding of titanium by Paton Institute of Electric Welding to boost penetration capability by up to 200% when compared with conventional welding. TIG welding makes use of a non-consumable tungsten electrode to form the weld. To prevent oxidation and contamination, the arc is shielded by an inert gas such as argon or helium.
ATIG welding is like TIG welding, except it adds an extra gas, usually nitrogen, to the welding arc. This active gas increases weld penetration and improves the mechanical qualities of the weld joint. In ATIG process, just prior to welding, an active flux is applied and deposited on the workpiece surface by brushing or spraying the flux layers onto the workpiece's surface. Welding happens when the surface has been dried and layer deposition is finished. The flux helps in arc striking and arc stability.
R.Sasidharan
Department of Mechanical Engineering, Tagore Engineering College, Chennai, India
S.R. Koteswara Rao, S.Vijayan
Department of Mechanical Engineering, Sri Sivasubramaniya Nadar College of Engineering, Chennai, India
The slag produced will shield the weld bead, cover the arc gap, and prevent damage to the molten metal. Deeper penetration is accomplished due to ATIG's improved arc penetrating capabilities. ATIG welding is similar to TIG welding, except it adds an extra gas, usually nitrogen, to the welding arc. This active gas increases weld penetration and improves the mechanical qualities of the weld joint [1]. TIG welding offers precise control and clean welds, but it may not penetrate thicker materials, whereas ATIG welding improves penetration and productivity while enhancing mechanical qualities, albeit at higher cost and complexity. Material thickness, desired weld quality, and available resources all plays a role when choosing what approach should be employed [4 &5].
One of the primary problems with welding duplex stainless steels is the production of weld metals with an excessive quantity of ferrite due to the rapid cooling that takes place during welding. The problem is often resolved by altering the weld metal composition or heat input to obtain the correct phase balance. Nitrogen has a larger heat capacity than other gases, therefore it can absorb and release heat more efficiently. Heat is evenly spread over the workpiece by introducing nitrogen gas flow during the welding process, which prevents localised overheating and minimises distortion [7-10]. This improves control over the perimeters, which leads to precise and appealing welds. The use of nitrogen gas in welding and metal manufacturing can considerably reduce post-weld cleanup time. Nitrogen, being an inert gas, inhibits oxides and scale from forming on the weld surface, minimising the need for considerable cleaning and surface preparation. This saves time and decreases the usage of chemicals and abrasive materials commonly used to remove weld spatter and scale. The cleaner welds achieved with nitrogen gas also make subsequent processes easier, such as painting applications, because they give a smoother and more uniform surface for adhesion [2].The use of duplex stainless steels, which offer excellent resistance to stress corrosion caused by chloride and strong mechanical properties, can help to lessen this problem in pipelines. The metallurgical characteristics of duplex stainless steels, however, pose a variety of technical difficulties during the welding process [21-23]. In welding pipes, the depth of penetration needs to be carefully controlled.
Puren et al analyses the stress corrosion cracking behaviour of 2205 duplex stainless steel welded joints when hydrogen,
corrosive media, and stress are combined. The results reveal that the presence of hydrogen causes the fracture to transfer from the base material to the heat affected zone and commence pitting, which leads to crack initiation and stress corrosion fracture [25].The impact of Post Soldering heat treatment (TTPS) parameters 25 s 1050 °C on autogenous TIG welds of UNS S31803 DSS strips, modifies the microstructure which enhances higher corrosion rates observed with higher ferrite content and nitride precipitation [26].The multi-layer multi-pass welding of low-alloy steel and duplex stainless steel, ER2209 welding wire was single-layer single-pass deposited on the surface of Q345B hot-rolled plate using gas metal arc welding (GMAW). The "tongue-shaped" morphology formed due to arc energy and the width of the heat affect zone in the welded joint, affects the corrosion performance of the welded joints [27].
The austenite content in DSS deposits increases with increasing deposition energy, with Ar+2%N2-protected deposits having much greater content than Ar+2%CO2protected deposits. DSS deposits with balanced phase content (austenite concentration of 48.4%) were achieved at a line energy of 600 J/mm for DED-arc under Ar+2%N2 protection. Unlike the nitrogen loss in Ar+2%CO2protected samples, Ar+2%N2 shielding gas introduces more nitrogen elements into DSS samples. Ar+2%N2 protected samples contain more austenite and exhibit a more homogenous microstructure, resulting in solid solution strengthening and a significant reduction in the anisotropy of the tensile characteristics [28].Microstructure characterisation of Plasma Arc Welding linked on SDSS 2507 at a thickness of 10 mm characterisation reveals significant changes in austenite content, ranging from 68.9% in weld metal (WM) to 32.1% in the heat-affected zone (HAZ). The oxide inclusions in the WM increase the hardness of the welded joints, but also provide a channel for crack development, reducing its impact toughness. HAZ has a complex microstructure that forms ferrite and a variety of austenite, including grain boundary austenite (GBA), intragrain austenite (IGA), and Widmanstätten austenites (WA). HAZ contains minor amounts of secondary austenite (γ2) and chromium nitride, which considerably reduces its corrosion resistance [29]. This paper attempts to optimize the TIG and ATIG welding process's process parameters and their effect on depth of penetration using the Taguchi technique.
Duplex Stainless Steel (2205) plates of 6mm thickness 200X100 mm size are edge prepared to form flat butt joints. The chemical composition of the Duplex Stainless Steel (2205) is listed in the table 1. The joints were autogenously welded using an automatic GTA welding machine. The process parameters considered for study are: Welding Current (A), Welding speed (mm/min), Gas Flow rate (L/ min) and Arc gap (mm) [6]. The response variable is Depth of Penetration and width of the weldment. ATIG welding
experiments using different shielding gases of Pure argon and mixture of Argon + 2% Nitrogen are carried out by varying the arc gap in the range of 1.8 to 2.4 mm, the gas flow rate in the range of 10–16 litres/min, the welding current in the range of 150–180Amps to and the welding speed in the range of 100–130 mm/min. The process parameters considered are summarized in Table 2. The electrode material and tip angle are kept constant. Taguchi L16 orthogonal design is used for designing the experiments and the experimental layout is shown in Table 3.
Based on the Taguchi design the experiments were conducted and subjected to metallographic observation. Specimens were polished and etched using kalling’s reagent No.2 for metallographic observations at mid length of the weld. For each weld, depth of penetration and weld face width were measured using an image analyzer.
To the given heat input, the weldments should have maximum penetration and minimal face width, however in case of activated GTA welds, the presence of activated flux changes the temperature gradient to positive value
i.e. dσ /dT>0. This positive temperature gradient presents centripetal marangoni convection which in turn directs the flow toward pool center resulting in deeper and narrow weld pool than the normal TIG welds. In Activated TIG optimization is done to maximize depth of penetration. Depth of penetration falls under higher the better-quality characteristic and the corresponding loss function is expressed by Equation 1. The overall loss function of depth of penetration is further changed into the s/n ratio by Equation 2. In Taguchi method, S/N ratio is used to find out the deviation of the quality characteristics from the preferred value [3,12&24].
The average S/N ratio for all the responses (depth of penetration: DOP) values of all levels are calculated and listed in Table 4.
Analysis of variance (ANOVA) is performed on the S/N ratio using a commercially available software package
for both ATIG and ATIG+N based results. The results are provided in Tables 5& 6.
R-Sq = 96.89% R-Sq(adj) = 84.43%
(mm)
R-Sq = 94.1% R-Sq(adj) = 70.4%
In ATIG welding of duplex steel 2205 with and without of nitrogen as a shielding gas, the current and welding speed plays a major role in deciding the depth of the penetration
of the weld. The contribution of the levels of arc gap is not predominant in affecting the responses considered. The corresponding regression equations are:
With C: Current, WS: Welding speed, GFL: Gas flow rate and AG: Air gap.
EFFECTS OF PROCESS PARAMETERS:
The effects of the process parameters of Activated TIG welding on welding duplex stainless steel Using Argon and Argon + Nitrogen as shielding gas is obtained by plotting the main effects of the process parameters to the response considered are shown in response Tables 7 & 8 and plotted as response graphs in Figure 1 and 2 respectively.
Tab. 7 – Response table S/N ratio for depth of penetration ATIG (larger the better)
1 – Main effects of S/N ratio for ATIG welds – depth of penetration
Tab. 8 – Response table S/N ratio for depth of penetration ATIG+N (larger the better)
The optimum setting is A4B1C2D4
The welding current directly influences the heat input to the weld. Higher currents result in more heat input, which can improve penetration and fusion but can also cause excessive heat-affected zones (HAZ). Duplex stainless steels require a balanced microstructure of ferrite and austenite. High current levels can increase heat input, which promotes grain growth and may increase ferrite content. This can upset the balance, resulting in a greater amount of ferrite. Optimal current levels are required to preserve phase stability and prevent the production of undesired phases such as sigma or chi phases, which can be caused by excessive heat input and prolonged high-temperature exposure. The ideal current for ATIG welding duplex stainless steels should be determined by the material's thickness, joint configuration, and required weld qualities. It is typically necessary to fine-tune to get the optimal mix of penetration, microstructure control, and overall weld quality.
The current is the heat source of the process exhibits a linear relationship with the depth of the penetration and the area of the weld. The depth of penetration as well as the area of the weld increases with increase in the welding current is clearly visualized from both statistically as
well as the weld macrostructure. The minimization of the aspect ratio is also achieved in increasing the welding current. The desired level of current in achieving maximum penetration and minimum aspect ratio is level 4 ie., 180 Amps for ATIG and ATIG+N.
Welding speed effects cooling rate; greater speeds generally increase cooling rate, resulting in a larger ferrite content. Slower speeds, on the other hand, allow for greater time at higher temperatures, which promotes the development of austenite.
Proper welding speed contributes to the mechanical integrity of duplex stainless steel. High welding speeds may result in a higher ferrite content, increasing strength but decreasing toughness. Slow speeds might cause excessive austenite, weakening strength.Faster welding speeds typically produce narrower and shallower weld beads, which may not be sufficient for complete penetration welds in thicker materials. Slower speeds can improve penetration but may result in broader beads and an increased risk of overheating.
Excessive welding speeds might compromise weld pool stability, potentially resulting in porosity and incomplete
fusion defects. In contrast, extremely slow rates can result in excessive heat input, creating weld metal dilution and increasing the danger of hot cracking. The ideal welding speed for duplex stainless steels must be carefully selected depending on the material thickness, welding technique, and desired weld qualities. The function of the welding speed is to concentrate the heat source to a particular point. In order to maximize the depth of penetration and the area of the welds, the welding speed should be low as possible. The welding speed exhibits an inverse function with respect to the depth of penetration concerned. And it is clearly captured from the experiments. The minimization of the aspect ratio is also achieved in decreasing the welding speed. Thus, the welding speed at level 1 is the desired level for the responses considered i.e., the welding speed is to be set at100 mm/min for ATIG welding of duplex steel.
The gas flow rate is one of the significant factors in ATIG welding process. The gas rate should not be low or so high, but a moderate gas flow rate is essential in determining the weld geometry and depth of penetration. The desired rate of gas flow is at second level for the responses considered i.e., the gas flow rate is to be set at 12 lit/min for ATIG welding of duplex steel.
The air gap is one of the important factors in ATIG welding process. In our investigation the air gap doesn’t affect the
responses significantly. It should be inferred that within the selected range of process window it can be fixed at any level to get a desired output.
Nitrogen is essential in ATIG welding duplex stainless steels because it stabilises the austenite phase, increases corrosion resistance, improves mechanical characteristics, reduces porosity, and controls the heat-affected zone. Proper nitrogen level management is critical for producing high-quality welds with the necessary characteristics. Insufficient nitrogen can result in increased ferrite content, whilst too much nitrogen can induce porosity and other weld defects. The penetration of the weldments were reduced and controlled by the presence of nitrogen in the shielding gas mixture as well as the its governs the bead geometry of the welds by maintaining a good aspect ratio of the weld.
Macro structures of all the ATIG and ATIG+N welds (16 welds each) are shown in Figure 3 & 4. The macrostructure study shows the effect of various welding parameters on depth of penetration. It can be noticed from these macrographs that for ATIG and ATIG+N welds even small variations in current (Amps) and welding speed (mm/min) can affect the depth of penetration significantly and also points out the head of optimization of process parameter in order to achieve full penetration welds.
4 – Macrostructures of Bead Geometry (ATIGL9 – ATIGL16)
Duplex stainless steel (DSS) contains approximately equal proportions of body centered cubic ferrite (α) and facecentered cubic austenite (γ). Austenite stabilizers, such as nickel and nitrogen, promote the formation of austenite (γ phase), while ferrite stabilizers, such as chromium and molybdenum, promote formation of ferrite (α phase)
respectively[17].The DSS base material microstructure and sem image is shown in Figure 5 ac & b which has Ferrite-Austenite dual phase banded structure. During welding the weld pool solidifies as ferrite, which on further cooling partially transforms to austenite.
Fig. 7 – Microstructures of base material and welded joints: (a) Optical microstructure; (b) SEM micrograph; (c) ATIG;(d) ATIG + N
In Figure 5 c and d shows the microstructure of ATIG and ATIG +N welds. The ferrite content in the different weld zones were ATIG – 63% and ATIG+N – 55% whereas 54% ferrite is observed in the Base Metal is shown in table 9.
All duplex stainless steel weld metals solidify primarily as ferrite and, in the subsequent solid-state transformation, part of the ferrite transforms to austenite[7-9]F. This ferrite-to-austenite transformation takes place over a range of temperatures starting at the solvus temperature. However, the transformation cannot attain equilibrium on account of the rapid cooling, so that more ferrite remains untransformed than under equilibrium conditions. The
transformation of ferrite to austenite during the welding of duplex stainless steel is similar to that in low carbonsteel weld metals where austenite transforms to ferrite on cooling. In low-carbon steels, first the proeutectoid ferrite forms at the prior-austenite grain boundaries; then the Widmanstätten side-plates nucleate at the grain boundaries and grow inward; and finally, the intragranular acicular ferrite forms in the regions partitioned by the side-plates.
In the case of a higher Nitrogen content welds like AuTIGN and AuATIGN, the areas of ferrite phases were surrounded by Austenite phase in large amounts. The weld specimens
show only dual phase structure of α ferrite and γ austenite [10,12-15]. Weld metals which experience Faster cooling rates result in higher ferrite and lower austenite compared to parent material. Figure 5 c and d shows the
microstructure of ATIG and ATIG +N welds. The ferrite content in the different weld zones were ATIG – 63% and ATIG+N – 55% whereas 54% ferrite is observed in the Base Metal is shown in table 9.
The effects of the process parameters of ATIG welding on welding duplex stainless steel is clearly shown by plotting the main effects of the process parameters to the concern response considered. And it is summarized below for each process parameter. Based on the L16 experiments,
the optimum level settings for depth and aspect ratio are A4B1C2D4 and A4B1C2D4respectively.)The average values of the factors at their levels are taken from the Table 5 and the predicted value of the response is given in the table 10 [12 &24].
Tab. 10 – Predicted optimal levels for confirmation run (ATIG & ATIG+N)
S.No.
1 Depth of penetration
2
The confirmation experiments were carried out by setting the process parameters at optimum levels for different responses considered. At the optimum settings
full penetration of the welds is achieved and the values obtained in the confirmation run are shown in Table 11. The macrostructures of the confirmation runs are shown in Figure 6.
Tab. 11 – Predicted and confirmation run values for ATIG & ATIG+N S.No.
1 Depth of penetration
2
mm
mm
Fig.8 – a) Macrostructure of bead geometry for confirmation run (DOP) ATIG: b) Macrostructure of bead geometry for confirmation run (DOP) ATIG+N
The Activated flux significantly increases the Depth of penetration for a given current value for full penetration, 180 A was found to be sufficient against 250A required for welding DSS plates without flux.
It has been found that Autogenous ATIG welding with Argon + 2% Nitrogen as shielding gas can be used to produce sound welds on 6mm thick 2205 DSS plates in single pass.
Current and Welding Speed plays a vital role in heat input of the process and is highly significant in influencing the Depth of penetration of the weld. As well as both the parameters are highly significant in affecting aspect ratio of
the welds in both ATIG and argon, nitrogen mixture ATIG welding.
The presence of nitrogen in the shielding gas mixture lowers and controls the weld penetration while also governing the bead shape of the welds by keeping a proper aspect ratio.
The authors thankfully acknowledge the financial support for this research provided by All India Council for Technical Education (AICTE) – Research Promotion Scheme (RPS), Government of India, under the Grant No. AICTE/ RIFD/RPS(POLICY-III)32/2012-13.
[1] Chern, TS, Tseng, KH & Tsai, HL 2011, ‘Study of the characteristics of duplex stainless steel activated tungsten inert gas welds’, Materials and Design, vol. 32, pp. 255-263 DOI:10.1016/j.matdes.2010.05.056
[2] Chuan-Ming Tseng 2003, ‘The influence of nitrogen content on corrosion fatigue crack growth behavior of duplex stainless steel’, Materials Science and Engineering, vol. A 344, pp.190-200.
[3] Fisher, RA 1925, ‘Statistical methods for research worker’, Olive and Boyd, London, UK.
[4] Fujii, H , Sato, T, Lu, S P, Nogi, K, ‘Development of an advanced A-TIG AA-TIG, welding method by control of Marangoni convection’, Materials Science and Engineering A 495 2008, pp. 296-303 DOI:10.1016/j.msea.2007.10.116
[5] Huang, HY, Shyu, SW, Tseng, KH & Chou, CP 2005, ‘Evaluation of TIG flux welding on the characteristics of stainless steel’, Science and Technology of Welding and Joining, vol. 10, no. 5, pp. 566-573 DOI:10.1179/174329305X48329
[6] Huang, HY, Shyu, SW, Tseng, KH & Chou, CP 2006, ‘Effects of the process parameters on austenitic stainless steel by TIG-flux welding’, Journal of Materials Science & Technology, vol. 223, pp. 367-374
[7] Huang, L, Deng, X, Liu, J& Wang, Z 2016, ‘Relationship Between Retained Austenite Stability and Cryogenic Impact Toughness in 0.12 C-3.0 Mn Low Carbon Medium Manganese Steel’, Acta Metall. Sin., vol. 53, pp. 316-324.
[8] Iris Alvarez-Armas 2008, ‘Duplex stainless steels: brief history and some recent alloys’, Recent Patents on Mechanical Engineering, vol. 1, pp. 51–57.
[9] Karlsson, L 1994a, ‘Welding duplex and super duplex stainless steels’, Svetsaren, vol. 48, no. 2, pp. 5-10.
[10] Karlsson, L 1994b,’ Welding of modern duplex stainless steels’, Proceedings of the Pre-assembly Symposium on Welding, Joining, Coating and Surface Modification of Advanced Materials, Dalian, China, pp. 49-60.
[11] Koil Raj, M, Vijayan, S & Rao, SRK 2012, ‘Friction stir welding of dissimilar aluminum alloys: AA2219 to AA5083 – Optimization of process parameters using Taguchi method’, Materials and Design, vol. 42, pp. 1-7 DOI:10.1016/j.matdes.2012.02.016
[12] Kokawa, H, Kuwana, T & Okada, J 1993, ‘Nitrogen absorption and microstructure of duplex stainless steel weld metal’, Welding International, vol. 7, no. 5, pp. 384-389.
[13] Kokawa, H, Okada, J & Kuwana, T 1992, ‘Nitrogen absorption and microstructure of duplex stainless steel weld metal’, Q Journal of Japan Welding Society, vol. 10, no. 4, pp. 496-502.
[14] Kokawa, H, Okada, J & Kuwana, T 1993, ‘Effect of nitrogen on tensile properties of duplex stainless steel weld metal’, Q Journal of Japan Welding Society, vol. 11, no. 4, pp. 531-53.
[15] Kokawa, H, Yomito, M, Kuwana, T 1995, ‘Effect of nitrogen on impact toughness of duplex stainless steel weld metal’, Welding International, vol. 9, no. 3, pp. 8-14.
[16] Lu, SP, Li, DZ, Fujii, H & Nogi, K 2007, ‘Time dependant weld shape in Ar-O2 shielded stationary GTA welding’, Journal of Materials Science and Technology, vol. 23, no. 5, pp. 650-654.
[17] Nilson, JO 1992, ‘Overview- super duplex stainless steels’, Materials Science and Technology, 8.8, 685-700.
[18] Ogawa, T, Aoki, S, Sakomoto, R &Zaizen, T 1982, ‘The weldability of nitrogen-containing austenitic stainless steel: Part 1 – chloride pitting corrosion resistance’, Welding Journal, vol. 61, no. 5, pp. 139-148.
[19] Okagawa, RK, Dixon, RD, Olson DL 1983, ‘The influence of nitrogen from welding on stainless steel weldmetal microstructures’, Weld journal, vol. 62, pp.204-208.
[20] Sathiya, P, Aravindan, S & Noorul Haq, A 2006, ‘Optimization for friction welding parameters with multiple performance characteristics’, International Journal of Mechanical Material Design, vol. 3, pp. 309-318, DOI:10.1007/s10999-007-9037-z
[21] Stephenson, N 1987, ‘Welding status of duplex stainless steels for offshore Applications’, Part I. Welding & Metal Fabrication, pp. 159-164.
[22] Still, JR 1994a, ‘The use of duplex Stainless steel in the offshore and oil and gas industry – Part I’, Welding & Metal Fabrication, pp. 293-296.
[23] Still, JR 1994b, ‘The use of duplex Stainless steel in the offshore and oil and gas industry – Part II’, Welding & Metal Fabrication, p. 331-339.
[24] Sasidharan, R, Rajendra Boopathy, S, Vijayan, S & Koteswara Rao, SR 2016, ‘Optimization of bead geometry for duplex stainless steel GTA welds using the Taguchi approach’, Materials Testing, vol. 58, no. 4, pp. 312-318, DOI 10.3139/120.110854.
[25] Puren Liu, Ming Liu, Qing Zheng, Lining Xu, Lijie Qiao, Yu Yan,"Study on the failure mechanism of the heat-affected zone in 2205 duplex stainless steel weld-joints induced by hydrogen,"Corrosion Science,Volume 244,2025,112657,ISSN 0010-938X,https://doi. org/10.1016/j.corsci.2024.112657.
[26] Flávia Wagner Pinheiro, Lucas Menezes de Souza, Elaine Cristina Pereira, Sergio N. Monteiro, Afonso R.G. Azevedo, “Effect of solubilization heat treatment on microstructure and corrosion resistance of joints welded with the autogenous TIG process duplex stainless steel," Journal of Materials Research and Technology," Volume 26,2023, Pages 1527-1536, ISSN 2238-7854.https://doi. org/10.1016/j.jmrt.2023.08.014
[27] Guangnan Ge, Shawei Tang, Jin Hu, Yan Huo, Caimeng Qi, Kuiliang Zhang, Yi Liu, Jing Li,Influence of arc energy on the microstructure and corrosion behavior of ER2209 duplex stainless steel deposited on Q345B low-alloy steel by GMAW,Materials Today Communications,Volume 41,2024, 110778,ISSN 2352-4928, https://doi.org/10.1016/j.mtcomm.2024.110778.
[28] Kanglong Wu, Chen Shen, Peizhi Xu, Jianwen Xin, Yuhan Ding, Lin Wang, Wenlu Zhou, Gang Ruan, Yuelong Zhang, Fang Li, Man-Tai Chen, Xueming Hua,Revealing the evolution of microstructure and mechanical properties with deposition energy and shielding gas
to achieve phase-balanced directed energy deposition of 2205 duplex stainless steel,Materials Science and Engineering: A, Volume 915,2024,147197,ISSN 0921-5093,https://doi.org/10.1016/j.msea.2024.147197.
[29] Qi Wang, Guochao Gu, Chuanbao Jia, Kan Li, Chuansong Wu,Investigation of microstructure evolution, mechanical and corrosion properties of SAF 2507 super duplex stainless steel joints by keyhole plasma arc welding, Journal of Materials Research and Technology, Volume22, 2023, Pages355- 374,ISSN22387854,https://doi.org/10.1016/j.jmrt.2022.11.107
La sostenibilità in ambito economico, ambientale e sociale è definita come la caratteristica di un processo o di uno stato che può essere mantenuto a un certo livello in maniera costante e indefinita. Negli ultimi anni questo concetto ha assunto un ruolo sempre più rilevante, nonostante esso inizi a concretizzarsi a partire dai primi anni ’70. È in quegli anni che ha iniziato a svilupparsi la coscienza che l'utilizzo umano delle risorse naturali stesse raggiungendo il limite e che questa tendenza, piuttosto che diminuire, stava raggiungendo un livello di allarme. Negli ultimi decenni, inoltre, questo concetto si è ulteriormente evoluto e dalle sue basi si sono sviluppate iniziative globali di sostenibilità ambientale.
La sostenibilità ambientale può essere identificata come il processo nel quale lo sfruttamento delle risorse, l'orientamento dello sviluppo tecnologico e le emissioni di inquinanti sono in sintonia tra loro e valorizzano il potenziale attuale e futuro al fine di far fronte ai bisogni e alle aspirazioni dell'uomo. Il significato di sostenibilità ambientale non è sempre chiaramente identificabile, si tratta di un concetto che presenta tantissime sfaccettature e comprende un’ampia gamma di princìpi e aspetti.
Analizzando le attività dell’uomo, è intuitivo identificare il settore industriale come uno dei principali responsabili quando si parla di impatto ambientale. Nell’ottica di uno sviluppo sostenibile, è pertanto necessario cercare di riorientare un modello economico lineare – nel quale le materie prime vengono trasformate per essere consumate e poi diventano rifiuto – verso il modello di economia circolare, che cerca di ridurre al minimo i rifiuti, favorendo al massimo i processi di riciclo, riutilizzo e ricondizionamento dei materiali, reintroducendoli sul mercato. Attuare strategie che valorizzano aspetti di sostenibilità ambientale non comporta solo oneri, ma può apportare anche potenziali vantaggi di riduzione dei costi di produzione derivanti, per esempio, dall’impiego di materia prima seconda a costi più contenuti, oppure da una riduzione della spesa energetica che spesso il riciclo dei rifiuti può comportare: da tutto questo può conseguire una sensibile riduzione delle emissioni di CO2.
PROCUREMENT AI CRITERI
AMBIENTALI MINIMI
Al fine di fornire una guida per la gestione delle iniziative nel campo della sostenibilità ambientale, e in accordo con le indicazioni della Commissione
Europea, il Ministero dello Sviluppo Economico in collaborazione con gli altri ministeri competenti ha contribuito all’elaborazione del Piano Nazionale d’Azione sul Green Public Procurement (PAN GPP).Introdotto nel 2008 a carattere volontario, con la pubblicazione del D.Lgs 50/2016 “Codice degli appalti pubblici e dei contratti di concessione”, il Green Public Procurement ha assunto valore cogente in Italia.
Il Green Public Procurement (GPP) è uno strumento di politica ambientale volto a indirizzare le procedure di acquisto della Pubblica Amministrazione, integrando considerazioni di carattere ambientale e contribuendo al raggiungimento degli obiettivi delle principali strategie europee, come l’uso efficiente delle risorse o l’approccio all’Economia Circolare.
In particolare, il Green Public Procurement (GPP) si pone come obiettivo quello di orientare la spesa pubblica verso l’efficienza energetica e il risparmio nell’uso delle risorse, con attenzione alla riduzione delle emissioni di CO2, dell’uso di sostanze pericolose e della produzione di rifiuti. Il Piano individua categorie di prodotti e servizi di interesse prioritario per volume di spesa e per impatti ambientali rispet-
to alle quali definire “criteri ambientali minimi” (CAM), ossia requisiti di natura ambientale collegati alle diverse fasi della procedura di appalto, da implementare nelle ordinarie procedure di acquisto pubblico. L’applicazione di tali requisiti è divenuta obbligatoria con l’entrata in vigore del Decreto Legislativo 56 del 19/4/2017.
I Criteri Ambientali Minimi (CAM) sono requisiti di tipo sociale, ambientale ed economico, volti a indirizzare le scelte della Pubblica Amministrazione, premiando quei prodotti e servizi a più elevato valore di sostenibilità sotto il profilo ambientale e lungo il ciclo di vita. I CAM mirano a raggiungere un buon equilibrio tra prestazioni ambientali, considerazioni sui costi e disponibilità del mercato.
Tenendo presente la distinzione fra criteri base e criteri premianti, le amministrazioni possono scegliere – in base alle loro esigenze e al livello di ambizione – di includere tutti o solo determinati requisiti, rendendo così modulabili i criteri stessi. Sono detti minimi in quanto si prendono in considerazione gli elementi di base che dovrebbero caratterizzare le procedure di acquisto preferibili da un punto di vista ambientale. La loro implementazione garantisce che la politica nazionale in materia di appalti pubblici “verdi” sia efficace non solo nell’obiettivo di ridurre gli impatti ambientali, ma anche al fine di promuovere modelli di produzione e consumo più sostenibili e circolari.
Coinvolgendo i prodotti e i servizi soggetti alla pubblica amministrazione, al momento sono disponibili 19 Decreti CAM pubblicati in Gazzetta Ufficiale. Tuttavia, riguardo i prodotti che
più generalmente trovano impiego nel campo delle costruzioni, i decreti di maggiore interesse sono il Decreto CAM Edilizia e il Decreto CAM Infrastrutture stradali.
I Decreti CAM definiscono al loro interno i requisiti che un appalto della Pubblica Amministrazione deve rispettare sotto tutti gli aspetti: dalla definizione del progetto all’approvvigionamento dei materiali, o per la rilevazione dei costi. In particolare, per la definizione delle caratteristiche di sostenibilità ambientale e con particolare interesse alla quantificazione dei contenuti di materiale riciclato e/o recuperato e/o sottoprodotto nei materiali coinvolti, sono state individuate specifiche certificazioni che rispondono a questa richiesta in modo adeguato. In particolare, per quanto riguarda i Decreti CAM rivolti ai settori delle costruzioni, questo parametro di valutazione può essere dimostrato attraverso la presentazione, nel fascicolo dell’appalto, di una delle seguenti certificazioni (per ogni materiale coinvolto):
• una dichiarazione ambientale di Prodotto di Tipo III (EPD), conforme alla norma UNI EN15804 e alla norma UNI EN ISO 14025;
• certificazione “ReMade in Italy®” con indicazione in etichetta della percentuale di materiale riciclato, oppure di sottoprodotto;
• una certificazione di prodotto, basata sulla tracciabilità dei materiali e sul bilancio di massa, rilasciata da un organismo di valutazione della conformità, con l’indicazione della percentuale di materiale
riciclato o recuperato, oppure di sottoprodotti;
• una certificazione di prodotto, rilasciata da un Organismo di valutazione della conformità e in accordo alla prassi UNI/PdR 88 "Requisiti di verifica del contenuto di riciclato e/o recuperato e/o sottoprodotto, presente nei prodotti", qualora il materiale rientri nel campo di applicazione di tale prassi;
• marchio “Plastica seconda vita” con indicazione della percentuale di materiale riciclato;
• per i prodotti in PVC, una certificazione di prodotto basata sui criteri 4.1 “Use of recycled PVC” e 4.2 “Use of PVC by-product”, del marchio “VinylPlus” Product Label, con attestato della specifica fornitura.
I Decreti CAM considerati, inoltre, inseriscono una specifica per quanto riguarda le asserzioni ambientali auto-dichiarate conformi alla norma ISO 14021. Allo stato attuale le asserzioni non possono essere accettate come documenti a sé stanti con finalità CAM, dal momento che generalmente hanno una validità annuale e i Decreti specificano che tali attestati, qualora fossero stati validati da un organismo di valutazione della conformità, potrebbero essere accettati solo nel caso in cui fossero in corso di validità alla data di entrata in vigore del Decreto (dicembre 2022) e fino alla loro scadenza.
Le asserzioni ambientali secondo ISO 14021 possono essere utilizzare nella qualifica dei contenuti di
materiale riciclato nei prodotti per cui è richiesta una certificazione LEED a livello internazionale. Inoltre, dato che la certificazione EPD fornisce una fotografia dell’impatto ambientale di un prodotto in termini di anidride carbonica equivalente (CO2e), ma non sempre include i valori del contenuto di materiale riciclato, queste dichiarazioni sono spesso integrate all’interno di una certificazione ambientale di Prodotto di Tipo III (EPD), laddove l’azienda abbia fatto richiesta di esplicitare tale valore.
Vista l’ampia scelta di metodologie di certificazione e qualifica a cui ci si può appoggiare per dimostrare i requisiti di sostenibilità ambientale, in particolare per la vasta gamma di prodotti che ricadono sotto i requisiti dei Decreti CAM, si ritiene importante che il fabbricante di un prodotto operi adeguate valutazioni. Deve per prima cosa inquadrare correttamente il suo prodotto rispetto al metodo di qualifica disponibile, rivolgendo ad esempio la propria attenzione verso certificazioni di settore ove queste siano disponibili. Definire chiaramente qual è il requisito principale che vuole andare a verificare, che si tratti dell’impatto generale del prodotto ad esempio definito in termini di emissioni di CO2 o che siano altri aspetti di natura sociale, ambientale o economica. Valutare la propria disponibilità economica in termini di costi e tempi di ottenimento di tale certificazione; alcune delle certificazioni citate possono infatti richiedere lunghe tempistiche di valutazione data la mole di dati che prendono in considerazione, oltre a ingenti spese per la loro raccolta ed elaborazione. Accertarsi se il
prodotto possa trovare impiego negli appalti della Pubblica Amministrazione e quindi verificare che il metodo di qualifica scelto risponda correttamente a quanto previsto dal Decreto CAM di riferimento.
Considerazioni di questo tipo sono indirizzate in particolare per le piccole realtà, dove le risorse per sostenere certificazioni particolarmente onerose in termini di costi e tempistiche possono essere limitate. In questi casi si ritiene consigliabile rivolgere la propria attenzione verso certificazioni di prodotto mirate e rilasciate da organismi di valutazione della conformità (come le certificazioni in accordo alla UNI PdR 88:2020).
Infine, per quanto le politiche nazionali stiano ponendo i requisiti di sostenibilità ambientale su un piano sempre più rilevante, in particolare per i prodotti per le costruzioni per cui è prevista la marcatura CE, tale requisito inizierà a essere richiesto a carattere cogente quando, a partire da gennaio 2026, partirà ufficialmente il processo di conversione delle attuali norme armonizzate verso quelle aggiornate al nuovo Regolamento Prodotti da Costruzione (CPR). Nel nuovo Regolamento sono infatti inseriti dei nuovi requisiti essenziali di sostenibilità ambientale che dovranno essere valutati e certificati dai competenti organismi preposti. Per procedere con la certificazione di tali aspetti, si renderà però necessario che la norma di un prodotto per cui è previsto l’impiego nel settore delle costruzioni e per cui è richiesta la marcatura CE, sia aggiornata al nuovo Regolamento Prodotti da Costruzione
(CPR). Il processo di revisione potrà essere avviato solo dopo che saranno conclusi i termini previsti per la chiusura dei lavori di revisione delle norme già in atto, ovvero fine dicembre 2025. L’apertura dei nuovi tavoli di discussione e revisione delle norme vedrà quindi il via con l’inizio del 2026, ma richiederà in ogni caso ancora del tempo prima di poter avere disponibili delle norme armonizzate con la definizione del processo di certificazione dei requisiti di sostenibilità ambientale.
Giornata di Studio TRIBOCORROSIONE
Modena c/o Università degli Studi di Modena e Reggio
Emilia – 4 febbraio 2025
>> SCOPRI DI PIÙ
Giornata di Studio
ADDITIVE MANUFACTURING E MATERIALI PER APPLICAZIONI BIOMEDICALI
Lecco c/o Politecnico di Milano - campus di Lecco6 febbraio 2025
>> SCOPRI DI PIÙ
Scuola
TECNICHE ELETTROCHIMICHE PER LA CORROSIONE II edizione
Ferrara - 11-13 febbraio 2025
>> SCOPRI DI PIÙ
Seminario
NORMATIVA NEL CAMPO DEI TRATTAMENTI TERMICI
Webinar - 26 febbraio 2025
>> SCOPRI DI PIù
Giornata di Studio
TRATTAMENTI TERMICI E FORMAZIONE METALLURGICA
NEL MONDO DELLO STAMPAGGIO DEGLI ACCIAI
Ivrea c/o Confindustria Canavese - 6 MARZO 2025
>> SCOPRI DI PIÙ
Giornata di Studio
SOSTENIBILITA’ DELLE LEGHE DI ALLUMINIO
Bergamo c/o Kilometro Rosso, 12 marzo 2025
>> SCOPRI DI PIÙ
13th International Tooling Conference TOOLING 2025
Trento, 24-27 March 2025
>> SCOPRI DI PIÙ
Corso modulare Metallografia
Milano - maggio-giugno-settembre
>> SCOPRI DI PIÙ
Giornate Nazionali CORROSIONE E PROTEZIONE - XVI ed. Ancona, 25-27 giugno 2025
>> SCOPRI DI PIÙ
7th European Steel Technology and Application Days 2025
7th ESTAD 2025
Verona - Palaexpo VeronaFiere - 6-9 October 2025
>> SCOPRI DI PIÙ
DIGIMET 2025 - International Workshop ing. Carlo Longaretti on Digital Tools for the Metallurgical Industry Bergamo - 27-28 November 2025
>> SCOPRI DI PIÙ
ESTAD will take place for the seventh time after Paris 2014, Düsseldorf 2015, Vienna 2017, Düsseldorf 2019, Stockholm 2021 and Düsseldorf 2023.
ESTAD 2025 will be hosted by AIM, the Italian Association for Metallurgy, in Verona – Italy on 6-9 October 2025.
The knowledge and the development of the new ideas enhance progress. With the 7th European Steel Technology and Application Days 2025 (7th ESTAD 2025) AIM offers attendants and visitors the opportunity to meet, exchange their ideas, perform fruitful discussion and create new professional relationships involving technology providers, suppliers, producers and customers.
The meeting will be focused on the technological advances, changes of the supply chain involving the raw materials and energy sources, transformation of the production processes and plants to accomplish the twin transition (ecological and digital) and the new perspective of steel applications.
Costituito nel 1951, il Centro sviluppa tutte quelle attività che contribuiscono al progresso ed al perfezionamento della tecnica di fabbricazione degli acciai ed abbraccia le tematiche relative alle materie prime, all’estrazione dei metalli dai minerali, alla gestione energetica, alla fusione, affinazione e solidificazione ed impatto ambientale delle operazioni siderurgiche.
Presidente: Carlo Mapelli
Politecnico di Milano
Vicepresidente: Gianpaolo Foglio
Feralpi Siderurgica SpA
Segretario: Silvia Barella
Politecnico di Milano
Il Comitato Tecnico Acciaieria ha recentemente focalizzato la propria attività formativa e di disseminazione delle conoscenze in relazione alla corretta gestione energetica e delle materie prime nell’attività siderurgica, vista la criticità di tali tematiche nell’attuale contesto produttivo. Oltre a tali attività, che risultano particolarmente sentite nell’attuale congiuntura economica si mantiene la focalizzazione sulle aree di interesse tradizionalmente trattate relative all’innovazione e alla gestione dei forni elettrici, dei sistemi di siderurgia secondaria e alla pratica di solidificazione mediante colata continua e produzione dei lingotti.
Tra le iniziative in programma, si evidenziano il Corso itinerante sulla Macchina di Colata Continua, previsto nei mesi di maggio/giugno 2025. La settima edizione del congresso internazionale ESTAD (European Steel Technology and Application Days 2025), in programma a Verona nei giorni 6-9 ottobre 2025.
Chiuderà l’anno l’International Workshop ing. Carlo Longaretti Digital Tools for the Metallurgical Industries, che si svolgerà a Bergamo n ei giorni 27-28 novembre 2025.
Il CT Acciaieria sta inoltre lavorando alla realizzazione di un’iniziativa dedicata all’Inserimento del personale femminile con ruoli operativi nella produzione siderurgica ed a una Giornata di Studio focalizzata sulla Manutenzione.
Il settore siderurgico nazionale risulta ben posiziona-
to dal punto di vista della patrimonializzazione e della dotazione tecnologica, ma sta attraversando una congiuntura economica particolarmente sfidante caratterizzata da un calo della domanda, un incremento dei costi energetici e vincoli ambientali progressivamente più stringenti soprattutto in termini di emissioni di gas serra. L’ampio utilizzo di sistemi fusori elettrici operato già nel corso del XX secolo rendono la dotazione siderurgica italiana molto avanzata rispetto a quella dei concorrenti internazionali, ma l’attività di formazione del personale ed innovazione dei processi e dei prodotti risulta fondamentale per affrontare la transizione digitale e ambientale che stanno investendo anche il comparto siderurgico. Per tale ragione oltre alle tematiche tradizionalmente trattate, una particolare attenzione verrà dedicata nel prossimo futuro all’applicazione di sistemi digitali (nuove tecniche di modellazione matematica dei processi, intelligenza artificiale generativa, automazione e robotizzazione di operazioni pericolose) e a tecniche produttive a basso impatto ambientale (diminuzione dell’impronta carbonica dei prodotti, utilizzo di risorse biogeniche, sistemi di sequestro della CO2, corretta gestione dei scorie e dei sottoprodotti ecc.).
Fondato nel 1955, il Comitato Tecnico Corrosione si interessa del degrado dei materiali metallici in ambienti naturali ed industriali e delle metodologie di prevenzione, controllo, monitoraggio e protezione. Una particolare attenzione viene rivolta al comportamento in
Nel corso del 2024, il Comitato Tecnico Corrosione ha organizzato il Corso modulare di corrosione nel periodo gennaio-marzo, coordinato dai prof. Andrea Balbo e prof. Tiziano Bellezze.
Il Corso si è svolto in 4 moduli:
• MODULO I Aspetti generali, metodi di indagine e monitoraggio;
• MODULO II Corrosione nell’atmosfera e nel calcestruzzo;
• MODULO III Corrosione nei terreni e nelle acque;
• MODULO IV Corrosione in ambito industriale.
I partecipanti, una trentina per ogni modulo, hanno espresso nei questionari di soddisfazione giudizi in generale positivi.
Il CT Corrosione ha partecipato attivamente al 40° Convegno nazionale AIM (Napoli settembre 2024), con la presentazione di 12 lavori, suddivisi in due sotto-sessioni. Una selezione dei lavori sarà pubblicata sulla rivista “Metallurgia italiana” durante il 2025.
Il CT Corrosione collabora, inoltre, con altri Comitati Tecnici dell’Associazione Italiana di Metallurgia nell’organizzazione di Giornate di Studio e Corsi; a titolo di esempio negli ultimi anni con i CT Metallurgia Fisica e scienza dei Materiali, Materiali per l’Energia, Controllo e Caratterizzazione dei Prodotti e Storia della Metallurgia. La collaborazione per l’organizzazione delle iniziative si è allargata anche ad altre associazioni quali il CTA
Presidente: Fabio Bolzoni Politecnico di Milano
Vicepresidente: Marina Cabrini
Università di Bergamo
Segretario: Tiziano Bellezze
Università Politecnica delle Marche
(Collegio dei tecnici dell’acciaio), AMPP Italian Chapter (in precedenza NACE Milano Italia section) e APCE (Associazione per la protezione dalle corrosioni elettrolitiche).
Il CT Corrosione collabora attivamente con la EFC (European Federation of Corrosion). AIM, federata nella EFC, nomina il rappresentante italiano nell’assemblea generale della EFC, attualmente il prof. Fabio Bolzoni. Nel Board of Administrators della EFC è stato eletto il prof. Lorenzo Fedrizzi, mentre nello Scientific and Technical Advisory Committee è presente la dott. Pierangela Cristiani, in qualità di presidente del Working Party (WP) numero 10 “Microbial Corrosion”. Vari componenti del CT Corrosione sono vice-presidenti o segretari dei gruppi di lavoro (WP) della EFC. I ricercatori che partecipano al CT Corrosione sono in generale molto attivi anche nella partecipazione al convegno internazionale Eurocorr, principale evento organizzato dalla EFC (https://efcweb.org/index.html).
Nel 2025, si svolgerà la seconda edizione della Scuola “Cecilia Monticelli” Tecniche elettrochimiche per lo studio della corrosione (Ferrara 11-13 febbraio), con il coordinamento del prof. Andrea Balbo, prof. Tiziano Bellezze e prof. Fabio Bolzoni. La Scuola si rivolge principalmente agli studenti di dottorato di ricerca, ma anche a giovani ricercatori, assegnisti, borsisti di ricerca e ad esperti del settore che intendano approfondire le loro conoscenze sulle tecniche elettrochimiche utili alla comprensione dei fenomeni di corrosione. (https://
www.aimnet.it/manifestazione.php?id=876&idc=2).
Si terranno inoltre le Giornate Nazionali sulla Corrosione e Protezione - XVI edizione (Ancona 25-27 giugno 2025), EFC event no. 525, presiedute dal prof. Tiziano Bellezze e organizzate in collaborazione con l’Università Politecnica delle Marche, l’Associazione per la Protezione dalle Corrosioni Elettrolitiche (APCE) e l’AMPP Italy Chapter. La manifestazione è supportata da numerose associazioni. Le Giornate Nazionali sulla Corrosione e Protezione si sono tenute per la prima volta a Milano nel 1992 e attualmente hanno una cadenza biennale. Rappresentano l’evento di riferimento a livello nazionale per la discussione ed il confronto sulle questioni scientifiche, tecnologiche e produttive nell’ambito della corrosione e protezione dei materiali. Nel corso della conferenza sarà presente uno spazio per espositori e sarà conferito un premio riservato a giovani ricercatori (studenti di Dottorato di ricerca o giovani ricercatori post-dottorato) in memoria della Prof. Cecilia Monticelli. (https://www.aimnet.it/manifestazione. php?id=852&idc=3)
Si segnala poi il Convegno internazionale EMCR 2025 (Venezia 15-19 giugno) organizzato dall’Università di Udine con il patrocinio di AIM, con coordinatori il prof. Francesco Andreatta ed il prof. Lorenzo Fedrizzi. (https://emcr2025.uniud.it/).
Norme pubblicate e progetti in inchiesta (aggiornamento al 31 dicembre 2024)
Norme UNSIDER pubblicate da UNI nel mese di dicembre 2024
UNI EN 10216-2:2024
Tubi di acciaio senza saldatura per impieghi a pressione - Condizioni tecniche di fornitura - Parte 2: Tubi di acciaio non legato e legato per impieghi a temperatura elevata
Norme UNSIDER ritirate con sostituzione da UNI nel mese di dicembre 2024
UNI EN 10216-2:2020
Tubi di acciaio senza saldatura per impieghi a pressione - Condizioni tecniche di fornitura - Parte 2: Tubi di acciaio non legato e legato per impieghi a temperatura elevata
Norme UNSIDER pubblicate da CEN e ISO nel mese di dicembre 2024
EN ISO 13503-2:2024
Oil and gas industries including lower carbon energy - Completion fluids and materials - Part 2: Measurement of properties of proppants used in hydraulic fracturing and gravel-packing operations (ISO 13503-2:2024)
EN 15266:2024
Stainless steel pliable corrugated tubing kits for gas installation pipework with an operating pressure up to 0,2 MPa (2 bar)
EN ISO 4937:2024
Steel and iron - Determination of chromium content - Potentiometric or
visual titration method (ISO 4937:2024)
EN 10344:2024
Malleable cast iron fittings with compression ends for steel pipes
ISO 10855-1:2024
Offshore containers and associated lifting sets — Part 1: Design, manufacture and marking of offshore containers
ISO 10855-2:2024
Offshore containers and associated lifting sets — Part 2: Design, manufacture and marking of lifting sets
ISO 10855-3:2024
Offshore containers and associated lifting sets — Part 3: Periodic inspection, examination and testing
ISO 10803:2024
Design method for ductile iron pipes
ISO 6331:2024
Chromium ores and concentrates — Determination of chromium content — Titrimetric method
Progetti UNSIDER in inchiesta prEN e ISO/DIS – gennaio 2025
prEN – progetti di norma europei
EN ISO 19905-1:2023/prA1:2024
Oil and gas industries including lower carbon energy - Site-specific assessment of mobile offshore units - Part 1: Jackups: elevated at a site - Amendment 1 (ISO 19905-1:2023/DAmd1:2024)
ISO/DIS – progetti di norma internazionali
ISO/DIS 19901-2
Oil and gas industries including lower
carbon energy — Specific requirements for offshore structures — Part 2: Seismic design procedures and criteria
ISO/DIS 16650
Bead wire
ISO 377:2017/DAmd 1
Steel and steel products — Location and preparation of samples and test pieces for mechanical testing — Amendment 1
Progetti UNSIDER al voto FprEN e ISO/FDIS – gennaio 2025
ISO/FDIS – progetti di norma internazionali
ISO/FDIS 24204
Oil and gas industries including lower carbon energy — Bulk material for offshore projects — Design for architectural supports
ISO/FDIS 19901-4
Oil and gas industries including lower carbon energy — Specific requirements for offshore structures — Part 4: Geotechnical design considerations