Italiana La Metallurgia
International Journal of the Italian Association for Metallurgy
n. 09 settembre 2024
Organo ufficiale dell’Associazione Italiana di Metallurgia. Rivista fondata nel 1909
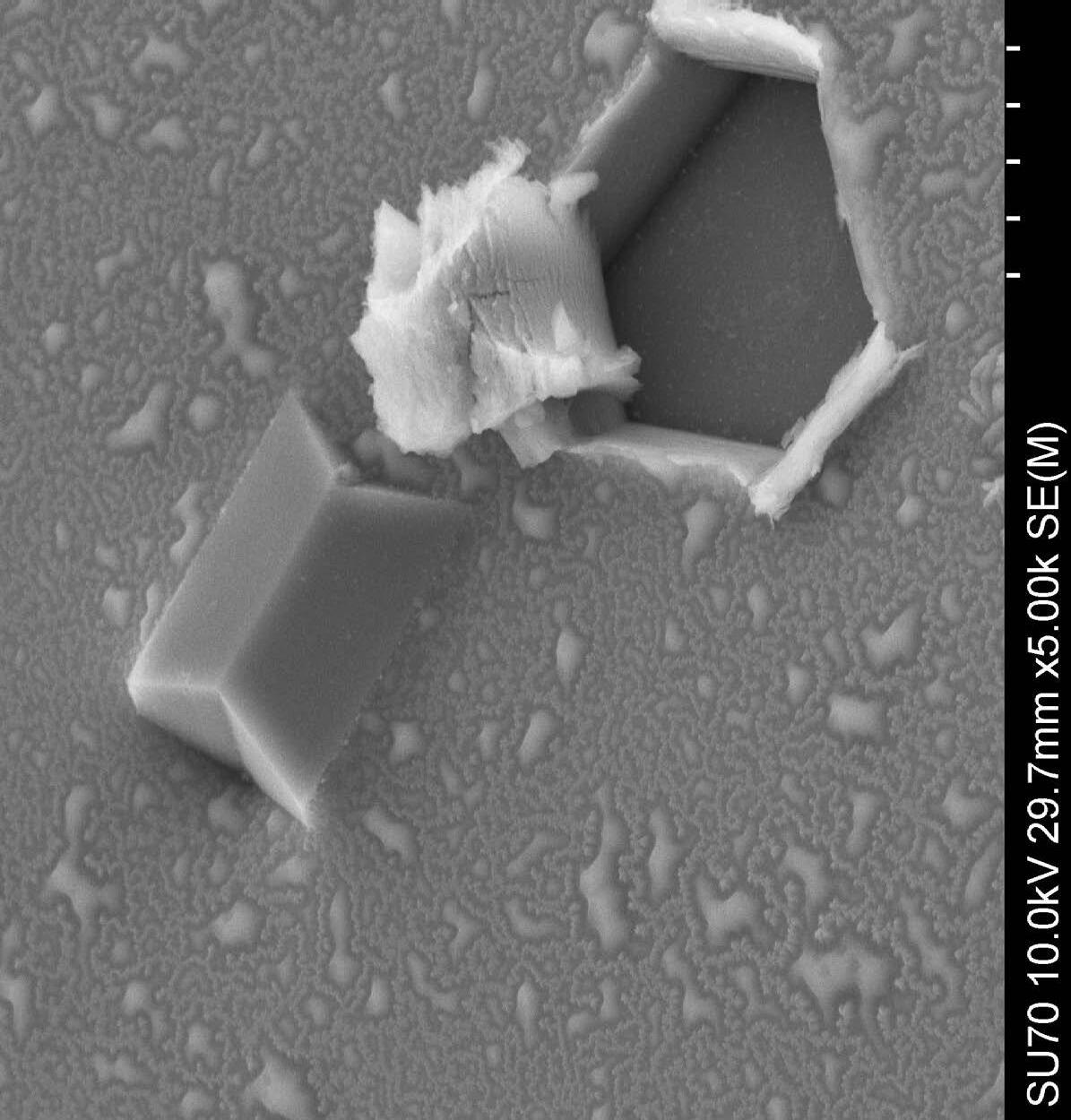
International Journal of the Italian Association for Metallurgy
n. 09 settembre 2024
Organo ufficiale dell’Associazione Italiana di Metallurgia. Rivista fondata nel 1909
International Journal of the Italian Association for Metallurgy
Organo ufficiale dell’Associazione Italiana di Metallurgia. HouseorganofAIMItalianAssociationforMetallurgy. Rivista fondata nel 1909
Direttore responsabile/Chiefeditor: Mario Cusolito
Direttore vicario/Deputydirector: Gianangelo Camona
Comitato scientifico/Editorialpanel: Marco Actis Grande, Silvia Barella, Paola Bassani, Christian Bernhard, Massimiliano Bestetti, Wolfgang Bleck, Franco Bonollo, Irene Calliari, Mariano Enrique Castrodeza, Emanuela Cerri, Vlatislav Deev, Andrea Di Schino, Donato Firrao, Bernd Kleimt, Carlo Mapelli, Denis Jean Mithieux, Roberto Montanari, Marco Ormellese, Mariapia Pedeferri, Massimo Pellizzari, Barbara Previtali, Evgeny S. Prusov, Dario Ripamonti, Dieter Senk
Segreteria di redazione/Editorialsecretary: Marta Verderi
Comitato di redazione/Editorialcommittee: Federica Bassani, Gianangelo Camona, Mario Cusolito, Carlo Mapelli, Federico Mazzolari, Marta Verderi, Silvano Panza
Direzione e redazione/Editorialandexecutiveoffice: AIM - Via F. Turati 8 - 20121 Milano tel. 02 76 02 11 32 - fax 02 76 02 05 51 met@aimnet.it - www.aimnet.it
Reg. Trib. Milano n. 499 del 18/9/1948. Sped. in abb. Post. - D.L.353/2003 (conv. L. 27/02/2004 n. 46) art. 1, comma 1, DCB UD
Immagine in copertina: Dettaglio della superficie di un campione di AlSi10Mg, utilizzato in test di laboratorio, con cristallo di Al2O3 (di circa 5 micron) e distacco parziale."
Gestione editoriale e pubblicità Publisher and marketing office: siderweb spa sb Via Don Milani, 5 - 25020 Flero (BS) tel. 030 25 400 06 - fax 030 25 400 41 commerciale@siderweb.com - www.siderweb.com
La riproduzione degli articoli e delle illustrazioni è permessa solo citando la fonte e previa autorizzazione della Direzione della rivista. Reproduction in whole or in part of articles and images is permitted only upon receipt of required permission and provided that the source is cited.
siderweb spa sb è iscritta al Roc con il num. 26116
n.09 settembre 2024
Anno 115 - ISSN 0026-0843
Editoriale/Editorial
Memorie scientifiche / Scientific papers
Metallurgia Fisica / Physical Metallurgy
Trattamento termico su componenti magnetici prodotti attraverso manifattura additiva
A. Di Schino, G. Stornelli, B.R. Rodriguez Vargas, R. Montanari, A. Varone, M. Sgambetterra, G. Zucca ............ pag.08
Influenza dei difetti di solidificazione e della grafite degenerata sulle proprietà meccaniche statiche di getti di grande spessore in ghisa sferoidale ferritica ENGJS-400-15
G. Di Egidio, A. Morri, P. Ferro ...........................................................................................................................
Ottimizzazionedelciclodiproduzionedialettecorrugatebrasatesupiastrecladin legaENAW3003:l’effettodelladimensionedeigrani
F.Bravaccino,A.W.Ipock,C.Sinagra-LaminazioneSottile,Caserta...........................................................................pag.25
Effettodelladensitàdienergiaedelladirezionedicostruzionesulla microstrutturadicampioniinlegaAl-Si10-MgprocessatiperSelectiveLaser Melting
P.Leo,G.Renna,A.A.DeLuca,N.Soni,R.Nobile,C.Mele,S.Bagheri......................................................................pag.32
LegheadaltaentropiaperThermomagnticEnergyHarvesters:sintesie caratterizzazione
E.Colombini,E.LassinanttiGualtieri,P.Veronesi,F.Cugini,G.Garulli,M.Solzi,L.Gallo,F.Albertini,G.Trevisi...pag.40
Caratterizzazionedellaresistenzameccanicaedellaresistenzaacorrosionedifuni ibrideacciaioinossidabile/fibradicarbonio
A.Meleddu,J.Ferino,S.Hecht,W.Frick,M.N.Amin,M.Meleddu,E.Kraemer,L.Pezzato,M.Ricotta,M.Dabalà,K.Brunelli..........................................................................................................................................................................................pag.50
Atti e notizie / AIM news 2024 FEMS Master Thesis Awards ...................................................................................... pag.58
Eventi AIM / AIM events ...................................................................................................... pag.60 Normativa / Standards ....................... pag.62
MILANO | 15-16-22-23-29-30 OTTOBRE 2024
L’iniziativa di formazione si rivolge a chi lavora con i materiali metallici e sovente non ha potuto ricevere in tempo opportuno le basi metallurgiche necessarie.
Il Corso si sviluppa in sei giornate, suddivise su tre settimane consecutive, per garantire continuità e, nel contempo, limitare assenze prolungate dalle aziende. I docenti, scelti tra esperti noti in Italia e all’estero, di estrazione sia accademica che industriale, assicurano un mix di competenze difficilmente raggiungibili in altra sede.
Il Corso è dedicato a persone non coinvolte in attività che richiedono una preparazione avanzata nei vari settori metallurgici, ma alle quali è sufficiente la conoscenza, l’interpretazione e la spiegazione della metallurgia nei più svariati settori tecnologici, applicativi, selettivi, ispettivi e di collaudo.
“Metallurgia per non metallurgisti”, con un linguaggio per “non addetti ai lavori”, è rivolto a manager, personale di vendita e di acquisto, progettisti, ispettori e in generale a tutti coloro che devono lavorare e utilizzare materiali metallici, senza avere necessariamente una preparazione universitaria. Il programma fornisce sia pure succintamente, e lezione per lezione, le principali indicazioni riguardanti i diversi argomenti trattati nel Corso. Le lezioni, si susseguiranno tra loro in modo da fornire al partecipante una conoscenza panoramica a trecentosessanta gradi dell’ampio settore metallurgico.
Docenti del Corso
Paolo Albertelli - Politecnico di Milano
Silvia Barella - Politecnico di Milano
Marco Belfi - Politecnico di Milano
Francesca Bisaglia - RTM Breda, Cormano
Francesca Bonfanti - Fomas Group, Osnago
Mattia Bosatra - Fondinox, Sergnano
Giovanni Maria Caironi - F.I.A.S., Gorla Minore
Alessandro Caironi - F.I.A.S., Gorla Minore
Enrique Mariano Castrodeza - Politecnico di Milano
Chiara Colombo - Politecnico di Milano
Mario Cusolito - Consulente, Lecco
Fabrizio D’Errico - Politecnico di Milano
Paola Demitri - A.Benevenuta & C., Forno Canavese
Andrea Gruttadauria - Politecnico di Milano
Nora F. Lecis - Politecnico di Milano
Vincenzo Loconsolo - Consulente, Milano
Carlo Mapelli - Politecnico di Milano
Davide Mombelli - Politecnico di Milano
Fabrizio Montagnoli - Leonardo Helicopters
Alberto Morini - Fondinox, Sergnano
Tommaso Pastore - Università di Bergamo
Dario Ripamonti - CNR ICMATE, Milano
Adriano Tavasci - Tenaris. Dalmine
Segreteria organizzativa
Via F. Turati, 8
20121 Milano
Tel. +39 0276397770
e-mail: met@aimnet.it www.aimnet.it
Organizzato da
con il patrocinio di
Coordinatori del Corso
Silvia Barella Politecnico di Milano
Carlo Mapelli Politecnico di Milano
"L'industria metallurgica, attualmente, è alle prese con la duplice sfida di soddisfare la domanda globale di materiali metallici che denotino sempre più elevate prestazioni e di ridurre l'impatto ambientale."
“Themetallurgicalindustry iscurrentlygrappling withthedualchallenge ofmeetingtheglobal demandforincreasingly high-performancemetallic materialsandreducing environmental impact.”
Il 40° Convegno Nazionale dell’Associazione Italiana di Metallurgia, che si è tenuto a Napoli dal 11 al 13 Settembre 2024, nell’anno delle celebrazioni degli 800 anni dalla fondazione dell’Università degli Studi di Napoli Federico II, prima università “pubblica” laica al mondo, potrebbe aver segnato una tappa significativa nel percorso verso l’utilizzo di pratiche industriali “sostenibili” nel settore metallurgico. La metallurgia, elemento essenziale della produzione industriale, è stata storicamente associata a una notevole impronta ambientale e realisticamente, molti processi industriali denotano, a tutt’oggi, un significativo impatto sull’ambiente. L'industria metallurgica, attualmente, è alle prese con la duplice sfida di soddisfare la domanda globale di materiali metallici che denotino sempre più elevate prestazioni e di ridurre l'impatto ambientale. In questo contesto, il ruolo delle tecnologie innovative e sostenibili non è mai stato così cruciale. Come accennato, i processi metallurgici tradizionali, pur essendo efficaci ed indispensabili al contesto pro-
The 40th National Conference of the Italian Association for Metallurgy, held in Naples from 11 to 13 September 2024, in the year of the celebration of the 800th anniversary of the founding of the University of Naples Federico II, the world's first ‘public’ secular university, may have marked a significant milestone on the path towards ‘sustainable’ industrial practices in the metallurgical sector.
Metallurgy, an essential element of industrial production, has historically been associated with a significant environmental footprint, and realistically, many industrial processes still have a significant impact on the environment. The metallurgical industry is currently grappling with the dual challenge of meeting the global demand for increasingly high-performance metallic materials and reducing environmental impact. In this context, the role of innovative and sustainable technologies has never been more crucial. As mentioned, traditional metallurgical processes, while efficient and indispensable in the global manufacturing
duttivo mondiale, spesso comportano costi ambientali significativi, tra cui l’utilizzo di combustibili fossili, un elevato consumo energetico, emissioni di gas serra, etc.. In risposta, l’Accademia e l'Industria stanno tentando un cambiamento trasformativo verso metodologie più pulite ed ecologiche.
La dimostrazione del cambiamento in atto, si è avuta nel 40° Convegno Nazionale dell’Associazione Italiana di Metallurgia in cui un numero rilevante di presentazioni (circa il 36% del totale), proposte da ricercatori universitari e da esponenti del mondo industriale, hanno esposto argomenti di estremo interesse ed attualità con uno stretto nesso con le problematiche ambientali come, ad esempio, lo sviluppo di leghe di alluminio da fonderia a ridotto impatto ambientale, l’applicazione di controllo di processo con termocamere e microdosaggio di acqua per ridurre il consumo, i trattamenti superficiali “green” di componenti ottenuti tramite tecnologia additive, il recupero di metalli preziosi e semi preziosi senza utilizzare le soluzioni acquose estremamente dannose per l’ambiente e la salute delle maestranze. Altre hanno riguardato le problematiche inerenti al trasporto e allo stoccaggio di idrogeno ed il suo utilizzo per il riscaldo dei forni. Mentre altri ancora hanno proposto l’utilizzo del forno elettrico quale unità produttiva chiave per la produzione di acciaio ‘carbon-neutral’. Alcune presentazioni, inoltre, hanno anche fornito esempi di applicazione dell'intelligenza artificiale, dell'apprendimento automatico e dell'automazione per creare pratiche metallurgiche più efficienti e sostenibili. In questa cornice ci pare importante porre in risalto che la relazione introduttiva in sessione plenaria, tenuta dall’Ing. Renato Benintendi, ha proposto come tema di discussione: “I materiali metallici: sfide ed opportunità alla luce della transizione energetica e dello sviluppo sostenibile” ripercorrendo la sua visione sul futuro sviluppo del settore.
Il Convegno ha avuto un ampio successo, come spesso accade a questa manifestazione, ed ha visto la presenza
environment, often entail significant environmental costs, including the use of fossil fuels, high energy consumption, greenhouse gas emissions, etc. In response, academia and industry are attempting a transformative change towards cleaner and more environmentally friendly methodologies.
Demonstration of the change taking place was given at the 40th National Conference of the Italian Association for Metallurgy in which a significant number of presentations (about 36% of the total), proposed by university researchers and representatives of the industrial world, illustrated topics of extreme interest and topicality with a close link to environmental issues such as, for example the development of aluminum alloys for foundries with reduced environmental impact, the application of process control with thermal imaging cameras and micro-dosing of water to reduce consumption,‘green’surfacetreatmentsofcomponents obtained through additive technology, and the recovery of precious and semi-precious metals without using aqueous solutions that are extremely harmful to the environment and the health of workers. Others dealt with the problems inherent in the transport and storage of hydrogen and its use for reheating furnaces. While still others proposed the use of the electric furnace as a key production unit for the production of ‘carbonneutral’ steel.
Some presentations also provided examples of the application of artificial intelligence, machine learning and automation to create more efficient and sustainable metallurgical practices.
In this context, we feel it is important to emphasise that the introductory plenary session report, given by Engineer Renato Benintendi, proposed as a topic for discussion: ‘Metallic materials: challenges and opportunities in the light of the energy transition and sustainable development’, retracing his vision of the future development of the sector.
The Conference was a great success, as often happens
di 250 delegati quasi equamente suddivisi tra Accademia ed Industria. Questo ci pare un altro dato rilevante a dimostrazione della vitalità e dell’interesse del settore. Allo stesso modo, ci pare interessante mettere in risalto che 54 dei 235 iscritti (circa il 25%) è costituito da Soci Junior, a testimonianza che anche il “futuro” del settore è “garantito”.
Il 40° Convegno Nazionale dell’Associazione Italiana di Metallurgia non è stato un incontro accademico, ma un chiaro richiamo a un impegno collettivo per la sostenibilità. Riflettendo sulle intuizioni e sulle innovazioni presentate, è chiaro che il futuro della metallurgia risiede nella sua capacità di adattarsi ed evolversi in risposta agli imperativi ambientali. Abbracciando pratiche sostenibili e promuovendo la collaborazione tra le discipline, il settore metallurgico può indirizzarci verso un futuro più sostenibile.
Un caro saluto ed un arrivederci al prossimo 41° Convegno dell’Associazione che si terrà nel settembre 2026.
at this event, and was attended by 250 delegates almost equally divided between Academy and Industry. This seems to us to be another relevant fact demonstrating the vitality and interest of the sector. Similarly, it seems interestingtoustohighlightthat54ofthe235registered members (around 25%) were Junior Members, proving that the ‘future’ of the sector is also ‘guaranteed’.
The 40th National Conference of the Italian Association for Metallurgy was not an academic meeting, but a clear call for a collective commitment to sustainability. Reflecting on the insights and innovations presented, it is clear that the future of metallurgy lies in its ability to adapt and evolve in response to environmental imperatives. By embracing sustainable practices and promoting collaboration across disciplines, the metallurgical sector can steer us towards a more sustainable future.
Greetings and goodbye until the next 41st Association's Conference in September 2026.
A. Di Schino, G. Stornelli, B.R. Rodriguez Vargas, R. Montanari, A. Varone, M. Sgambetterra, G. Zucca
La manifattura additiva (AM) rappresenta una valida alternativa per la produzione di nuclei ferromagnetici in acciaio FeSi ad alto contenuto di Si. In questo lavoro, è stata utilizzata la tecnologia laser a letto di polvere (LPBF) per produrre campioni di acciaio FeSi, con contenuto di Si del 3.0 wt. % (FeSi3) e 6.5 wt.% (FeSi6.5). Su entrambi gli acciai è stato studiato l’effetto del trattamento termico di ricottura (1150 °C per 1 ora) sull’evoluzione microstrutturale. Dopo la stampa, l’acciaio FeSi3 presenta grani colonnari con orientazione [100] lungo la direzione di stampa. Invece, nel caso del FeSi6.5, la microstruttura risulta essere mista, composta da grani colonnari ed equiassici con dimensioni medie di 11.3 ± 0.6 μ m, circa un ordine di grandezza inferiore rispetto a FeSi3 (103.1 ± 5.2 μ m). Dopo il trattamento di ricottura, nel FeSi3 la microstruttura non cambia significativamente, al contrario si assiste ad una crescita significativa del grano nel FeSi6.5 (81.2 ± 4.1 μ m) senza alterazioni della tessitura. I risultati indicano che i trattamenti termici ad alta temperatura possono essere sfruttati per migliorare le proprietà elettro-magnetiche degli acciai FeSi prodotti mediante AM in modo da raggiungere proprietà simili a quelle tipiche degli acciai commerciali.
INTRODUZIONE
Le esigenze energetiche per il raggiungimento dei rigorosi obiettivi di riduzione delle emissioni di CO2 hanno richiesto negli ultimi anni lo sviluppo di materiali innovativi, nell’ambito di diversi settori industriali (petrolchimico, aerospaziale e automobilistico). In questo contesto, la diffusa richiesta di motori elettrici dal mercato automobilistico ha evidenziato la necessità di migliorare l’efficienza dei dispositivi di conversione energetica [1,2]. L’acciaio FeSi rappresenta il riferimento tra i materiali magnetici dolci [3] per quanto concerne le applicazioni elettro-magnetiche più comuni (nuclei ferromagnetici di motori, generatori e trasformatori elettrici). In generale, gli acciai al Si con contenuto di Si compreso tra 2.0 e 7.0 wt.% garantiscono buone proprietà magnetiche. E noto, inoltre, che un contenuto di Si del 6.5 wt.% offre le migliori proprietà magnetiche in termini di ridotta magnetostrizione, bassa anisotropia magneto-cristallina ed elevata resistività elettrica [4-6]. Tuttavia, nella pratica industriale i dispositivi magnetici commerciali vengono prodotti con lamierini sottili di acciaio al Si (3.5-4.0 wt.%) [7]. La strategia di utilizzare lamierini sottili di spessore
Andrea Di Schino, B.R. Rodriguez Vargas, Giulia Stornelli
Department of Engineering, University of Perugia, Perugia
Roberto Montanari, Alessandra Varone
Department of Industrial Engineering, University of Roma Tor Vergata, Roma
Mirko Sgambetterra, Guido Zucca
Italian Air Force - Aeronautical and Space Test Division, Pomezia
0.2-0.8 mm, isolati da strati di dielettrico, consente di ridurre le perdite per correnti parassite. Con questo approccio vengono realizzati componenti con buone proprietà magnetiche. Tali proprietà non risultano comunque essere le ottimali, causa il ridotto contenuto di Si in lega. La limitazione nella possibilità di produzione di acciai a più alto tenore di Si (contenuto di Si > 4.5 wt.%) è dovuta all’intrinseca fragilità e scarsa lavorabilità di tali leghe. Il progressivo infragilimento degli acciai al Si all'aumentare della quantità di Si è dovuto alla tendenza di tali materiali verso la formazione di strutture reticolari ordinate (B2 e D03) [8-10]. È noto che il moto delle dislocazioni all'interno di una fase ordinata forma bordi di anti-fase [11,12] con conseguente aumento di durezza e fragilità [11]. Dunque, risulta irrealizzabile la produzione di lamierini sottili di acciai FeSi ad alto contenuto di Si [4]. Negli ultimi decenni la manifattura additiva (AM) si è consolidata come una potente tecnologia in grado di superare alcune limitazioni imposte dai convenzionali processi produttivi [13-15]. Anche nel caso degli acciai FeSi, la tecnologia AM rappresenta una valida alternativa produttiva in quanto le elevate velocità di raffreddamento, tipiche del processo AM, consentono di limitare la formazione di fasi ordinate negli acciai FeSi, rendendo possibile la produzione di componenti con un elevato contenuto di Si [16-18]. Inoltre, la capacità di produrre componenti con geometria complessa consente di ottimizzare le prestazioni magnetiche dei nuclei ferromagnetici e l’alleggerimento dello stesso componente. Ad oggi, la ricerca scientifica sulla produzione di materiali e componenti magnetici tramite AM fa riferimento a leghe FeSi con un contenuto di Si fino al 6.9 wt.%, con principale attenzione al raggiungimento degli ottimali parametri di processo. La progettazione metallurgica, la scelta del processo produttivo e la capacità di modificare la microstruttura mediante trattamento termico, rappresentano gli elementi chiave per l'ottimizzazione di componenti per applicazioni elettro-magnetiche. In questo studio, la tecnologia laser a letto di polvere è stata impiegata per produrre campioni utilizzando due tipi di acciai FeSi: una variante con contenuto di Si standard (3.0 wt.% - FeSi3) e l'altra con contenuto di Si elevato (6.5 wt.% - FeSi6.5). In particolare, è stato investigato l'effetto del trattamento
termico sull’evoluzione microstrutturale e della tessitura, caratteristiche che influenzano fortemente le prestazioni magnetiche. Il comportamento magnetico è stato studiato per entrambe le leghe FeSi3 e FeSi6.5 [18] e confrontato con quello di un acciaio FeSi3-50H230 commerciale [19].
Per stampare i campioni con la tecnologia LPBF sono state utilizzate due polveri di acciaio FeSi con contenuto di Si del 3.0 wt.% e 6.5 wt.% (FeSi3 e FeSi6.5). Le polveri sono state prodotte mediante atomizzazione a gas e le loro composizioni chimiche sono rispettivamente 3Si-0.009C0.0001O-Fe (wt.%) e 6.5Si-0.008C-0.0001O-Fe (wt.%).
Per entrambi gli acciai sono state utilizzate delle polveri con morfologia prevalentemente sferica con alcuni satelliti. La dimensione media delle polveri è di circa 30 μ m e 25 μ m rispettivamente per gli acciai FeSi3 e FeSi6.5. Successivamente, le polveri sono state processate utilizzando un sistema con tecnologia LPBF (EOS-M290). La temperatura della piattaforma è stata mantenuta a 200 °C e il processo è stato condotto in un'atmosfera di Ar con un contenuto di ossigeno inferiore allo 0.4%. Per ogni acciaio sono stati realizzati dei campioni di dimensioni 5 mm x 5 mm x 10 mm, con il lato lungo nella direzione di costruzione (BD) e ogni strato è stato stampato con una rotazione di 67° rispetto al precedente. L'energia laser specifica E, la velocità di scansione v e la potenza laser P utilizzate per produrre i campioni sono rispettivamente E = 250 Jm-1, v = 1 ms-1, P = 250 W per l’acciaio FeSi3 ed E = 200 Jm-1, v = 0.835 ms-1, P = 167 W per l’acciaio FeSi6.5. Dopo il processo di fabbricazione, i campioni sono stati trattati termicamente in atmosfera di Ar a 1150 °C per 1 ora. Il campione prima del trattamento termico (as-built) è stato analizzato come confronto. I campioni sono stati lucidati e attaccati chimicamente con reattivo Nital2%, lungo un piano parallelo alla direzione di costruzione (BD). Per determinare la struttura e la sua evoluzione dopo i trattamenti termici, sono state eseguite misure EBSD con un passo di 5 μ m, tramite FEG-SEM (Ultra-Plus Carl-Zeiss-Oberkochen Germania con rilevatore EBSD C-Nano Oxford Instruments, UK). La tecnica EBSD è stata utilizzata per determinare la dimensione media dei grani, la tessitura e la distinzione della tipologia di bordi grano a basso angolo (LAGB) e ad alto angolo (HAGB). Inoltre,
sul campione as-built in FeSi6.5 è stata condotta l’analisi DSC fino a una temperatura di 750 °C con una velocità di riscaldamento di 10 °C/min, al fine di valutare la presenza di fasi ordinate.
Secondo il diagramma di stato [11] mostrato in Fig. 1 (a), quando il contenuto di Si supera il 5.3 wt.%, la soluzione solida disordinata (fase α ) inizia a trasformarsi in B2 a temperatura minore di 500 °C mentre, la fase ordinata D03 si forma se il tenore di Si è superiore al 6.0 wt.%. Oltre agli effetti dannosi sulla duttilità, la presenza di fasi ordinate modifica anche le proprietà magnetiche dell'acciaio FeSi, in particolare l'anisotropia magnetica diminuisce con la crescita di B2 mentre D03 diminuisce la magnetostrizione e la forza coercitiva [20].
Dall’analisi DSC riportata in un precedente lavoro [21], si osserva che per le polveri e i campioni as-built di FeSi3 non vi è alcuna trasformazione in fasi ordinate mentre, per l'acciaio FeSi6.5, lo scenario è diverso. Infatti, come visibile dalla curva DSC in Fig. 1 (b) per il campione FeSi6.5 sono visibili due caratteristiche: la trasformazione di ordinamento e la trasformazione magnetica. Riscaldando il materiale si assiste ad una reazione esotermica nell’intervallo tra 380 e 550 °C, che può essere attribuita alla trasformazione da soluzione solida α a fasi ordinate B2 e D03 e alla conseguente diminuzione dell'entropia man mano che gli atomi si dispongono con un ordine
periodico. Questo però non accade nei campioni di FeSi6.5 preparati per AM in quanto l’elevata velocità di raffreddamento (~106 °C/s) limita notevolmente i fenomeni diffusivi responsabili della formazione di fasi ordinate. Questo trova riscontro in misure di diffrazione dei raggi X eseguite su campioni stampati di FeSi6.5 [19]. La differenza tra quanto si osserva con la diffrazione dei raggi X e le prove DSC dipende dai diversi tempi di permanenza dei campioni nell’intervallo di temperatura dove le reazioni di ordinamento possono avere luogo e, conseguentemente, dal diverso libero cammino medio degli atomi. Va inoltre ricordato come DCS abbia una grande sensibilità e capacità di rilevare fenomeni che interessano anche piccoli volumi del campione esaminato. Dunque, a differenza dei processi produttivi convenzionali, i rapidi raffreddamenti caratteristici dei processi di manifattura additiva congelano la lega in soluzione solida disordinata α garantendo la fabbricazione di campioni ad alto contenuto di Si. La trasformazione tra lo stato ferromagnetico e quello paramagnetico inizia attorno ai 660 °C con temperatura di picco di circa 690 °C. In Figura 1a e 1b si nota una minima variazione nella determinazione della temperatura di Curie TC dovuta alle differenti velocità di riscaldamento/raffreddamento coinvolte nei due casi.
Fig.1 - (a) Diagramma di fase Fe-Si (Si > 5wt.%). B2 e D0 3 sono le fasi ordinate mentre α è la soluzione solida disordinata. T c è la temperatura di Curie. Ridisegnato da [11] (b) Curva di riscaldamento DSC per il campione asbuilt dell’acciaio FeSi6.5 / (a) Fe-Si phase diagram (Si > 5 wt.%). B2 and D03 are the ordered phases while α is the disordered solid solution. T c is the Curie temperature. Redrawn from [11] (b) DSC heating curve for as-built sample of FeSi6.5 steel.
In Fig. 2 e 3 sono riportate le microstrutture dei campioni as-built degli acciai FeSi3 e FeSi6.5 lungo la BD, dalle quali è evidente un diverso comportamento di solidificazione tra i due acciai. Per quanto riguarda l'acciaio FeSi3 dopo processo di stampa, la microstruttura è costituita da grani colonnari grossolani orientati lungo BD (dimensione media del grano 103.1 ± 5.2 μ m). Ciò è dovuto alla crescita epitassiale degli strati a partire da quello sottostante, già solidificato. Il materiale così costruito presenta una orientazione dei grani con la direzione [100] lungo la BD e, una prevalenza di bordi grano a basso angolo rispetto a quelli ad alto angolo (LAGB: 63% vs. HAGB: 37%). Invece, per quanto riguarda l’acciaio FeSi6.5, la microstruttura risulta essere mista e costituita da grani colonnari orientati lungo la BD e alcune colonie di grani equiassici. La dimensione media del grano è 11.3 ± 0.6 μ m, notevolmente ridotta rispetto all’acciaio FeSi3. La presenza di un mix di grani colonnari ed equiassici è evidenziata più chiaramente dalla mappa EBSD ad alto ingrandimento. Come precedentemente osservato nel caso del FeSi3, anche per la lega FeSi6.5 i grani sono orientati con la direzione [100] lungo la direzione di costruzione del campione. Invece, per quanto riguarda la tipologia dei bordi grano, per il FeSi6.5 si ha prevalenza di bordi grano ad alto angolo (HAGB: 96%).
Tali differenze microstrutturali possono essere spiegate
partendo dai diversi parametri di processo utilizzati per ottenere le due leghe mediante tecnologia LPBF, in particolare la potenza del laser (250 W per FeSi3 e 167 W per FeSi6.5). È noto che l'aumento della potenza del laser favorisce la solidificazione epitassiale con grani colonnari [22,23]. Inoltre, essendo l'inerzia termica degli acciai pressoché simile (3.50 J/Kcm3 per FeSi3 e 3.44 J/Kcm3 per FeSi6.5), l'utilizzo di maggiore energia specifica nel caso del FeSi3 comporta il raggiungimento di una maggiore temperatura dal materiale e un più lento raffreddamento, con conseguente formazione di grani grossolani. Il maggiore sotto-raffreddamento nel caso dell’acciaio FeSi6.5 favorisce la nucleazione di nuovi grani e ne rallenta la crescita dando origine, oltre che a grani colonnari, ad una popolazione di grani di piccole dimensioni e orientazioni casuali. Un'altra differenza rilevante tra i materiali indagati è la tipologia del bordo grano con una prevalenza di LAGB nel FeSi3 e di HAGB nel FeSi6.5. Come mostrato in [24], la formazione di LAGB deriva da fattori di instabilità in fase di fusione e stress termici indotti dal continuo riscaldamento/raffreddamento. La conduttività termica del FeSi3 (23.08 W/mK) è maggiore di quella del FeSi6.5 (17.5 W/ mK), quindi il volume influenzato dal calore e i gradienti termici risultano essere maggiori per il FeSi3. Ciò spiega la formazione di una maggiore densità di dislocazioni che poi si organizzano per formare i LAGB.
La microstruttura iniziale dei materiali as-built influenza notevolmente la loro evoluzione dopo i trattamenti termici. In Fig. 4 sono riportate le mappe EBSD dopo il trattamento termico a 1150 °C per 1 ora. Nell’acciaio FeSi3 la dimensione e la forma dei grani non cambiano notevolmente dopo il trattamento termico, la dimensioni medie dei grani risulta essere di 123.8 ± 6.2 μ m con la stessa tessitura mentre per l’acciaio FeSi6.5 si verificano variazioni rilevanti. La popolazione e le dimensioni dei grani equiassici aumentano dopo il trattamento termico a 1150 °C che diventano prevalenti rispetto a quelli colonnari. Una possibile spiegazione della diversa risposta ai trattamenti termici dei due acciai al Si è legata alla natura dei bordi di grano, ovvero la differenza nella prevalenza di LAGB nel FeSi3 e di HAGB nel FeSi6.5. È noto che la mobilità dei LAGB è significativamente inferiore a quella degli HAGB
[25] quindi i grani crescono più velocemente nel FeSi6.5. Tuttavia, ciò non comporta un indebolimento dell'orientazione cristallografica preferenziale che resta cubica [100]. Come noto, le prestazioni magnetiche dei materiali magnetici dolci dipendono fortemente dalla dimensione dei grani e dalla tessitura [26], in particolare le tessiture cubica [100] e Goss [110] favoriscono una facile magnetizzazione del componente mentre, l'effetto opposto è dato dalla tessitura [111]. Dall'analisi EBSD si osserva che la tessitura [111] di difficile magnetizzazione non è presente lungo la BD dei campioni as-built e trattati termicamente di entrambi gli acciai. Ciò è abbastanza promettente per le applicazioni magnetiche.
Va ricordato inoltre che le misure di diffrazione dei raggi X non rilevano fasi ordinate in FeSi6.5 anche dopo il trattamento termico [19].
- Mappe EBSD degli acciai FeSi3 e FeSi6.5 dopo trattamento termico di ricottura a 1150 °C per 1 ora / EBSD maps of FeSi3 and FeSi6.5 steels after annealing heat treatment at 1150 °C for 1 hour.
In Tab. 1 sono state riportate a confronto le proprietà magnetiche di un acciaio commerciale FeSi3 di grado 50H230 (a grani non orientati) [27] con quelle dei campioni con forma toroidali in FeSi3 e FeSi6.5, ottenuti mediante tecnologia additiva LPBF e trattati termicamente a 1150 °C per 1 ora, come riportato in [18]. Le perdite specifiche corrispondono alla somma delle perdite dovute all'isteresi e alla circolazione delle correnti parassite. Dai valori riportati in Tab. 1 è evidente come il FeSi6.5 mostri una magnetizzazione M maggiore e una perdita di potenza inferiore (oltre il 50%) rispetto al FeSi3, stampato e trattato termicamente nelle stesse condizioni. Inoltre, la lega FeSi6.5 presenta delle prestazioni magnetiche non troppo lontane da quelli della lega commerciale, che presenta ancora le migliori prestazioni. Dunque, le proprietà magnetiche riportate nella Tab. 1 pei i campioni ottenuti mediante AM, unitamente alle caratteristiche
microstrutturali (dimensione media dei grani, tessitura e tipologia di bordi grano) in seguito ai trattamenti termici, mostrano chiaramente la superiorità del FeSi6.5 e suggeriscono la necessità di un’ ulteriore miglioramento dei trattamenti termici per garantire caratteristiche paragonabili o migliori rispetto al FeSi3 commerciale.
Tab.1 - Confronto delle perdite specifiche e della magnetizzazione M di campioni toroidali di FeSi3 e FeSi6.5 da tecnologia LPBF, trattati termicamente a 1150 °C per 1 ora [18], con quelli di un acciaio commerciale FeSi3 di grado 50H230 [27]. Le perdite specifiche sono state misurate con f = 50 Hz e B = 1 T, invece la magnetizzazione M con 800 e 1700 A/m / Comparison of the specific losses and of the magnetization M of toroidal samples of FeSi3 and FeSi6.5 from LPBF technology, heat treated at 1150 °C for 1 hour [18], with those of a commercial FeSi3 steel grado 50H230 [27]. The specific losses were measured with f = 50 Hz and B = 1 T, meanwhile the magnetization M with 800 and 1700 A/m.
In questo lavoro è stata studiata la possibilità di produrre nuclei ferromagnetici in acciaio FeSi ad altro tenore di Si attraverso tecnologia additiva LPBF. Sono state prese in esame due leghe con diverso tenore di Si (3.0 wt.% e 6.5 wt.%). Per entrambi gli acciai è stata studiata l’evoluzione microstrutturale in seguito al trattamento termico di ricottura a 1150 °C per 1 ora con l'obiettivo di valutare le migliori prestazionali ottenibili attraverso un approccio produttivo alternativo e gli eventuali benefici forniti dai trattamenti termici. Le conclusioni possono essere riassunte come segue:
- La tecnologia additiva rappresenta una promettente alternativa per la produzione di acciai ad alto contenuto di Si. Infatti, dall'analisi DSC risulta che il campione as-built dell’acciaio FeSi6.5 mostra una struttura cristallina disordinata, caratteristica confermata da una analisi ai raggi X sui campioni stampati. La rapida solidificazione coinvolta nel processo di manifattura additiva sopprime i fenomeni diffusivi che controllano la formazione di strutture ordinate B2 e D03, garantendo così la processabilità di tali leghe.
- Per entrambe le leghe, FeSi3 e FeSi6.5, la microstruttura di solidificazione mostra grani colonnari con la direzione [100] parallela a BD. Tutti i grani del FeSi3 sono colonnari mentre nel caso del FeSi6.5 la
microstruttura è mista con grani colonnari ed equiassici.
- La dimensione media dei grani del FeSi6.5 as-built è 11.3 ± 0.6 μ m, circa un ordine di grandezza inferiore a quella del FeSi3 (103.1 ± 5.2 μ m). Nel FeSi3 as-built c'è una grande prevalenza di LAGB (63 %) mentre la loro frazione è molto bassa (4 %) nel FeSi6.5 as-built.
- Dopo il trattamento termico a 1150 °C per 1 ora, la dimensione e la forma dei grani del FeSi3 non cambiano significativamente, mentre nel FeSi6.5 la dimensione dei grani aumenta fino a 81.2 ± 4.1 μ m. Nonostante la crescita del grano, la tessitura cubica [100] viene preservata dopo il trattamento termico.
- La lega FeSi6.5 mostra proprietà magnetiche migliori rispetto alla lega FeSi3, con maggiore magnetizzazione M e ridotte perdite di potenza (oltre il 50%). Inoltre, i valori di FeSi6.5 risultano essere confrontabili con quelli di una lega commerciale FeSi3-50H230.
Il progetto è stato finanziato dalla Regione Umbria nell’ambito del “Piano Sviluppo e Coesione FSC ex DGR n. 251/2021—Avviso ricerca 2020–codice CUP I39J20002770008”.
[1] Cardelli E, Faba A, Pompei M, Quondam Antonio S. Magnetic losses in Si-Fe alloys for avionic applications. AIP Adv. 2017;7:056112
[2] Boglietti A, Cavagnino A, Krings A. New Magnetic Materials for Electrical Machines and Power Converters. IEEE Trans. Ind. Electron. 2017;64:2402-2404
[3] Garibaldi M, Ashcroft I, Simonelli M, Hague R, Metallurgy of high-silicon steel parts produced using Selective Laser Melting. Acta Mater. 2016;110:207-16
[4] Lemke JN, Simonelli M, Garibaldi M, Ashcroft I, Hague R, Vedani M, Wildman R, Tuck C. Calorimetric study and microstructure analysis of the order-disorder phase transformation in silicon steel built by SLM. J Alloys Compd. 2017;722:293-301
[5] Cullity BD, Graham CD. Introduction to magnetic material: John Wiley & Sons; 2011
[6] Ninomiya H, Tanaka Y, Hiura A, Takada Y. Magnetostriction and applications of 6.5% Si steel sheet. J Appl Phys. 1991;69:5358
[7] Babuska TF, Wilson MA, Johnson KL, Whetten SR, Curry JF, Rodelas JM, Atkinson C, Lu P, Chandross M, Krick BA, Michael JR, Argibay N, Susan DF, Kustas AB. Achieving high strength and ductility in traditionally brittle soft magnetic intermetallics via additive manufacturing. Acta Mater. 2019;180:149-57
[8] Ustinovshikov Y, Sapegina I. Morphology of ordering Fe-Si alloys. J Mater Sci. 2004;39:1007-16
[9] Cava RD, Botta WJ, Kiminami CS, Olzon-Dionysio M, Souza SD, Jorge AM, Bolfarini C. Show more Ordered phases and texture in spray-formed Fe-5 wt%Si. J Alloys Compd. 2011;509:S260-4
[10] Jang P, Lee B, Choi G. Effects of annealing on the magnetic properties of Fe-6.5%Si alloy powder cores. J Appl Phys. 2008;103:5-8
[11] Shin JS, Bae JS, Kim HJ, Lee HM, Lee TD, Lavernia EJ, Lee ZH. Ordering-disordering phenomena and micro-hardness characteristics of B2 phase in Fe-(5-6.5%)Si alloys. Mater Sci Eng. 2005;407:282-90
[12] Gonzalez F, Houbaert Y. A review of ordering phenomena in iron-silicon alloys. Rev Metal (Madr). 2013;49:178-99.
[13] Di Schino A, Stornelli G. Additive manufacturing: a new concept for end users. The case of magnetic materials. Acta Metallurgica Slovaca. 2022;28(4);208-211
[14] Ridolfi MR, Folgarait P, Di Schino A. Laser Operating Windows Prediction in Selective Laser-Melting Processing of Metallic Powders: Development and Validation of a Computational Fluid Dynamics-Based Model. Materials. 2020;13:1424
[15] Stornelli G, Ridolfi MR, Folgarait P, De Nisi J, Corapi D, Repitsch C, Di Schino A. Studio di fattibilità della fabbricazione di nuclei ferromagnetici attraverso tecniche di Manifattura Additiva. La Metallurgia Italiana. 2021;113: 50-63
[16] Garibaldi M, Ashcroft I, Simonelli M, Hague R. Metallurgy of high-silicon steel parts produced using Selective Laser Melting. Acta Mat. 2016;110:207-216
[17] Goll D, Schuller D, Martinek G, Kunert T, Schurr J, Sinz C, Schubert T, Bernthaler T, Riegel H, Schneider G. Additive manufacturing of soft magnetic materials and components. Add Man. 2019;27:428-439
[18] Stornelli G, Faba A, Di Schino A, Folgarait P, Ridolfi MR, Cardelli E, Montanari R. Properties of Additively Manufactured Electric Steel Powder Cores with Increased Si Content. Materials. 2021;14:1489
[19] Di Schino A, Montanari R, Sgambetterra M, Stornelli G, Varone A, Zucca G. Heat treatment effect on microstructure evolution of two Si steels manufactured by laser powder bed fusion. Journal of materials research and technology. 2023;26;8406-8424
[20] Narita K, Enokizono M. Effect of ordering on magnetic properties of 6.5-percent silicon-iron alloy. IEEE Trans Magn. 1979;15:911-5
[21] Stornelli G, Rodriguez Vargas BR, Folgarait P, Ridolfi MR, Sgambetterra M, Di Schino A. Development of FeSi steel with increased Si content by laser powder bed fusion technology for ferromagnetic cores application: Microstructure and properties. MRS Advances. 2023;8:1195-1199
[22] Niendorf T, Leuders S, Riemer A, Richard HA, Treoster T, Schwarze D. Highly anisotropic steel processed by selective laser melting. Metall Mater Trans B. 2013;44:794-796.
[23] David SA, Vitek JM. Correlation between solidification parameters and weld microstructures. Int Mater Rev. 1989;34:213-45.
[24] Chuang LC, Maeda K, Morito H, Shiga K, Fujiwara K. Origin of small-angle grain boundaries during directional solidification in multicrystalline silicon. Materialia (Oxf). 2018;3:347-52
[25] Humphreys FJ, Hatherly M. Recrystallization and related annealing phenomena. 1st ed. Pergamon; 1995.
[26] Beckley P. Electrical steels for rotating machines. London: The Institution of Engineering and technology; 2002.
[27] Nippon steel catalogue, non-oriented electrical steel sheets. Transportation Safety Board of Canada; 2019.
- KILOMETRO ROSSO | 5 NOVEMBRE 2024
La Giornata di Studio dedicata alla digitalizzazione in Pressocolata mira a esplorare le nuove frontiere tecnologiche che stanno trasformando il settore.
Perché dobbiamo digitalizzare in fonderia? La digitalizzazione rappresenta un passaggio cruciale per le fonderie che desiderano rimanere competitive in un mercato in rapida evoluzione. Integrando tecnologie avanzate, possiamo migliorare i processi produttivi, ridurre i tempi di produzione e aumentare la qualità.
Perché digitalizzare in Pressocolata conviene? Investire nella digitalizzazione offre numerosi vantaggi economici. Le fonderie che adottano soluzioni digitali possono ottenere una maggiore efficienza operativa, riducendo gli sprechi e ottimizzando l’uso delle risorse. Inoltre, la digitalizzazione consente di monitorare in tempo reale i processi, facilitando l’identificazione e la risoluzione rapida dei problemi, con un conseguente risparmio di costi.
Questa giornata di studio è rivolta ai responsabili di Processo, ai responsabili di Produzione, ai General Manager, e rappresenta un’opportunità unica per approfondire queste tematiche, conoscere gli strumenti digitali che abbiamo a disposizione e capire quali competenze sono necessarie per sfruttarli al meglio, confrontarsi con esperti del settore e con altre fonderie che hanno già intrapreso il viaggio verso la digitalizzazione. Sviluppare una mentalità orientata all’innovazione e alla risoluzione dei problemi e implementare e gestire efficacemente le nuove soluzioni digitali permette di trasformare la Pressocolata, rendendola più efficiente, competitiva e pronta ad affrontare le sfide future.
Le rivoluzionarie scoperte della fisica del ‘900 hanno permesso di sviluppare nuove tecniche di indagine dei materiali, che abbracciando l’inarrestabile progresso tecnologico degli ultimi anni, ci hanno regalato nuovi strumenti, sempre più raffinati, per la caratterizzazione dei materiali.
Obiettivo della giornata di studio è offrire una carrellata su molte delle tecniche che coinvolgono l’uso dei raggi X nei laboratori, sia spiegando i principi di base delle tecniche stesse, che esponendo casi pratici di applicazione al settore metallurgico.
Coordinatore:
Giantonio Toldo Omega Test
Organizzata da
con il patrocinio di Coordinatori
CMYK: 0, 0, 0, 100
Flavio Cecchetto – Motultech Baraldi
RGB: 0, 0, 0
Marcello Furlati – SIT
CMYK: 0, 75, 84, 5
Piero Parona – Motultech Baraldi
RGB: 197, 87, 52
Gianluca Pialorsi – Pialorsi Stampi
Tiziana Tronci – Gefond
FONT: Helvetica Condensed Regular
Lorenzo Valente – Ecotre Valente
Organizzata dal Centro di Studio Controllo e Caratterizzazione del Prodotti della
Sponsorizzata da
G. Di Egidio, A. Morri, P. Ferro
L’eccellente colabilità e le ottime proprietà meccaniche hanno permesso alle ghise sferoidali di assumere sempre maggior rilevanza nel settore dei trasporti pesanti e delle energie rinnovabili. I lunghi tempi di solidificazione che interessano i getti di grande spessore possono portare alla degenerazione degli sferoidi di grafite e alla formazione di difetti di solidificazione, influenzandone negativamente le proprietà meccaniche. In questo studio sono stati analizzati gli effetti di lunghi tempi di solidificazione (dalle 3 alle 20 ore) in diverse zone di cubi di lato pari a (i) 350 mm, (ii) 700 mm, e (iii) 1000 mm. È stato osservato un netto calo delle proprietà meccaniche all’aumentare dei tempi di solidificazione, riconducibile ad un aumento dei difetti di solidificazione e dei fenomeni degenerativi che interessano gli sferoidi di grafite. Questi risultati sono di grande rilevanza per valutare il comportamento meccanico e i meccanismi di rottura di getti in ghisa sferoidale di dimensioni non standard in relazione alle diverse condizioni di solidificazione che si verificano al loro interno.
INTRODUZIONE
Le ghise duttili (GD) a matrice ferritica sono ampiamente utilizzate dai progettisti per la loro eccezionale combinazione tra proprietà tecnologiche (bassa temperatura di fusione e di colata, elevata colabilità, ed economicità) e meccaniche (buona tenacità a frattura, resistenza statica e a fatica). Queste caratteristiche le rendono molto adatte alla produzione di getti di grandi dimensioni impiegati nei settori dell'energia rinnovabile e del trasporto pesante, favorendo uno loro rapida ascesa nella produzione di turbine eoliche e contenitori per lo stoccaggio di scorie nucleari [1].
Tuttavia l'attuale assenza di una normativa che definisca le caratteristiche microstrutturali e le proprietà meccaniche minime per getti in ghisa duttile di grande spessore (GDGS) di sezione superiore a 200 mm rappresenta un limite per la loro progettazione e diffusione. Inoltre, l'elevata qualità richiesta a questi componenti critici contrasta con la difficoltà dei fonditori nel controllare la
G. Di Egidio, A. Morri
Dipartimento Ingegneria Industriale, Università di Bologna P. Ferro
Dipartimento di Tecnica e Gestione dei Sistemi industriali, Università di Padova
microstruttura all’interno di getti GDGS. In particolare, le lunghe fasi di solidificazione e raffreddamento dovute alle grandi dimensioni di questi componenti influiscono negativamente sulle caratteristiche microstrutturali dei getti GDGS (nodularità della grafite, densità e dimensione dei noduli, vuoti da ritiro, dimensione e disomogeneità della matrice ferrosa), portando di conseguenza ad un peggioramento significativo delle proprietà meccaniche [2]. In un precedente lavoro, Ferro ed altri [3] hanno osservato un netto calo del carico di rottura e dell’allungamento a rottura nei getti GDGS a causa della presenza di grafite chunky, rispettivamente del 15% e del 70%. Come riportato da Wang ed altri [4], infatti, la diminuzione delle proprietà meccaniche nei getti GDGS sembra essere direttamente proporzionale ad una riduzione della nodularità e ad un aumento dei fenomeni di degenerazione della grafite. Questi fenomeni sono più significativi quando gli spessori delle pareti dei getti raggiungono i 100 - 200 mm, a causa dei fenomeni di segregazione di elementi minori e di un ridotto sottoraffreddamento.
In assenza di una regolamentazione adeguata a guidare la progettazione di getti GDGS, la letteratura ha affrontato questo argomento analizzando le variazioni nelle proprietà meccaniche all'aumentare dei tempi di solidificazione [5,6]. Tuttavia indagare l'effetto delle anomalie microstrutturali sulle proprietà meccaniche dei getti GDGS derivanti dai lunghi tempi di solidificazione non è semplice; infatti i campioni per i test meccanici vengono solitamente estratti da blocchi Y o da piccoli lotti di fusione di laboratorio, tenendo così conto solo parzialmente della microstruttura eterogenea tipicamente riscontrata nei componenti reali. Mentre la microstruttura finale può essere controllata in modo efficiente in campioni relativamente piccoli, in componenti reali di grandi dimensioni il lento avanzamento del fronte
di solidificazione e il ridotto sottoraffreddamento introduce nel materiale difetti difficilmente replicabili in piccole fusioni. Di conseguenza, l’analisi delle proprietà meccaniche delle fusioni ottenute in condizioni di produzione standard è di fondamentale importanza. In questo lavoro vengono riassunti i risultati relativi ad uno studio inerente la correlazione tra condizioni di solidificazione e proprietà meccaniche statiche di una GD ferritica EN-GJS-400-15, svolto con l’obbiettivo di colmare le attuali lacune presenti in letteratura e nelle normative relative alla progettazione di getti GDGS. Cinque diverse fonderie sono state coinvolte nella produzione di cubi di lato pari a 350 mm, 700 mm, e 1000 mm, in modo da fornire dati affidabili per ampliare il know-how tecnico nel campo delle GDGS. È stata svolta un’ampia caratterizzazione microstrutturale e meccanica su campioni caratterizzati da diverse condizioni di solidificazione relative a tempi (3, 10 e 20 ore) e zone di solidificazione (zona di transizione e centro termico) in modo da correlare microstruttura, proprietà meccaniche e condizioni di solidificazione. I risultati riportati nel presente lavoro potranno essere di grande importanza per i progettisti che affrontano il problema della progettazione di getti GDGS le cui dimensioni non sono coperte da normative.
Cinque fonderie italiane sono state coinvolte per produrre in modo indipendente i cubi da cui estrarre I campioni per i provini di trazione, identificati e testati attraverso una procedura in doppio cieco in modo da garantire la validità dei risultati. La composizione chimica nominale del materiale impiegato è riportata nella Tabella 1: per ciascun getto è stata verificata dalle singole fonderie su provini estratti mediante carotaggi.
Tab.1 -Composizione chimica (% in peso) della ghisa EN-GJS-400-15 secondo la normativa EN 1563 / Chemical composition (wt.%) of EN-GJS-400-15 cast iron according to EN 1563 standard.
Ciascuna fonderia ha realizzato tre fusioni corrispondenti a cubi di lato pari a 350 mm, 700 mm e 1000 mm, in modo da riprodurre i tempi di solidificazione previsti
dai modelli di colata preliminari con una tolleranza di ±10%. In particolare sono stati analizzati quattro differenti condizioni di solidificazione, come riportato in Tabella 2.
Tab.2 - Condizioni di solidificazione analizzate / Analyzed solidification conditions
Nomenclatura
Le dimensioni dei cubi sono state progettate tramite simulazione numerica agli elementi finiti mediante il sotware Magmasoft® per riprodurre un tempo di solidificazione(TS)nelcentrotermicodeigettiparia3,10 e 20 ore. Inoltre, per il cubo di lato 1000 mm, i campioni sono stati estratti sia nel centro termico (TS pari a 20 ore) sia in una posizione laterale intermedia, tra il centro e la superficiedelgetto,caratterizzatadaunoTSparia10ore. Aciascunafonderiaèstataassegnatalastessatemperatura (1340 °C), e sistema di colata, mentre il trattamento di inoculazione è stato lasciato all’esperienza di ciascuna fonderia. Alla lega sono stati aggiunti 25 ± 5 ppm di Sb nellacolata delcubo da350 mme 50 ± 10 ppmdi Sbnelle altre colate in modo da limitare la degenerazione della grafite. È stata impiegata sabbia silicea per lo stampo in quantità minima per coprire la colata, impedendo al contempol’impiego di raffreddatori e canali di colata. Le staffe sono state rimosse al raggiungimento di una temperatura superficiale di 400 °C. Sonostatirealizzatiproviniditrazionecilindrici(lunghezza tratto utile, 70 mm, lunghezza calibrata, 84 mm, diametro tratto utile, 14 mm, in accordo alla UNI EN 1563:2009) da porzionidimaterialeestrattenelleposizionipresceltedei cubi.Leproveditrazionesonostateeseguiteatemperatura ambiente secondo la ISO 6892:2016 (metodo A). Per ciascuna condizione sono stati testati venticinque provini per ottenere risultati rappresentativi delle condizioni di solidificazione. Le prove di durezza Brinell (HB30) sono state eseguite su campioni metallografici estratti dai codoli dei provini di trazione secondo la ASTM E10-18 (sfera di acciaio da 2,5 mm, carico di 187,5 kg e tempo di
permanenza di 20s). I campioni metallografici sono stati incorporati in resina conduttiva e preparati mediante tecniche metallografiche standard secondo la ASTM E3. Il reagente impiegato per l’attacco chimico è stato il Nital al 4% (4 mL HNO3 - 96 mL alcol etilico) in accordo alla ASTM E407. Sono state effettuate analisi microstrutturali mediante microscopia ottica su tutti i provini al fine di valutare la nodularità N (%), la densità dei noduli DN (mm-2), l'area media dei noduli NA (mm2), la percentuale di degenerazione della grafite GD (%), la dimensione del grano ferritico FG (numero di intercette/mm-1), e la percentualediareaperliticaPA(%).Consideratal'assenza di normative per la caratterizzazione metallografica della grafite in getti GDGS di spessore maggiore di 200 mm, è stata eseguita seguendo laddove possibile la BS ISO 945-4:2019. L'analisi d’immagine mediante software ImageJ è stata svolta su tre immagini di dimensione 3,2 mm x 5,7 mm, per un'area di analisi totale per ciascun campione di trazione di circa 55 mm2. Per eliminare eventualierroridimisurazioneintrodottidagraffi,rumore e piccoli pori, sono considerare solo particelle di grafite didiametrodiFeretsuperiorea30 μm(classe6oinferiore secondo la BS ISO 945-4:2019), escludendo la grafite lungo i bordi. La densità dei noduli è stata misurata su particelledigrafiteconunvaloreminimodiroundnesspari a 0,6 (secondo la normativa BS ISO 945-1:2019). La grafite degenerata è stata conteggiata manualmente per valutare la percentuale di degenerazione della grafite ed esclusa dalle immagini per facilitare l'analisi automatizzata dei noduli. La dimensione del grano ferritico è stata valutata con il metodo dell'intercetta secondo la normativa
ASTM E112-13 (2021), ovvero numero di intercette (ni) dei bordi grano per la lunghezza d’analisi. La frazione di area perlitica è stata valutata come percentuale di area all'interno della microstruttura. La caratterizzazione frattografica è stata inoltre realizzata mediante analisi al microscopio elettronico in scansione (FEG-SEM), dotato di spettroscopia a dispersione di energia (EDS).
In Tabella 3 sono riportati i valori di durezza (HB30) e le proprietà meccaniche statiche (tensione di snervamento (Rp0,2), carico di rottura (Rm), allungamento a rottura (A%)) ottenuti sui provini caratterizzati da diverse condizioni di solidificazione: tempi (3 ore, 10 ore e 20 ore) e zone di estrazione (transizione (T) e centro termico (C)). Le proprietà meccaniche sono state confrontate con le caratteristiche meccaniche nominali della ghisa EN-GJS400-15 in relazione allo spessore del getto (s, in mm), come riportato nella normativa BS EN 1563:2018 in relazioneacampioniestrattidagetti(EN-GJS-400-15C).
Tab.2-ConfrontotralecaratteristichemeccanichenominalidellaghisaEN-GJS-400-15Cconle caratteristichemeccanichedellediversecondizionidisolidificazione:(i)3-C,(ii)10-C,(iii)10-Te(iv)20-C/
ComparisonbetweenthenominalmechanicalpropertiesoftheEN-GJS-400-15Ccastironwiththe mechanicalpropertiesofthedifferentsolidificationconditions:(i)3-C,(ii)10-C,(iii)10-Tand(iv)20-C
Come descritto in letteratura [6] per spessori inferiori a 200 mm, le proprietà meccaniche diminuiscono in maniera significativa all'aumentare di TS, eccetto la durezza la quale perde solo il 5% dalla condizione più favorevole (3-C) a quella meno favorevole (20-C). Tra le condizioni di solidificazione analizzate è interessante notare come per TS fino a 3 ore, le proprietà meccaniche sono in linea con quanto richiesto da normativa (Tabella 2), men-tre per le condizioni più severe (10-C, 10-T e 20C) solo Rp0,2 si mantiene al di sopra dei valori riportati in normativa.
Di contro, Rm e A% risultano al di sotto dei valori minimi, sia nei provini estratti dal cubo di lato 700 mm (10-C) che in quelli estratti dal cubo di lato 1000 mm (10-T e 20-C). È bene tuttavia sottolineare come i valori riportati in EN 1563:2018 siano più conservativi, riferendosi a spessori, e quindiatempidisolidificazione,inferiori(<200mm).
Soffermandosi sui risultati ottenuti dai provini estratti dal centro termico (3-C, 10-C, 20-C), all'aumentare del TS l’A% diminuisce fino all’78%, mentre il rapporto Rp0,2/Rm tende a 1, sintomo di un aumento della fragilità della ghisa. Al contempo, le proprietà resistenziali statiche, Rp0,2 e Rm, calano rispettivamente del 11% e del 27%. Considerando 10 ore di TS, è osservabile una differenza in termini di proprietà meccaniche tra i campioni estratti da zone diverse in cubi di diverse dimensioni, ovvero le condizioni 10-C (cubo 700 mm, centro termico) e 10-T (cubo 1000 mm, zona di transizione). In particolare, l'A% è risultato il parametro più sensibile alla zona di estrazione dei provini a parità di TS, con una riduzione di circa il 26%. Di contro, le proprietà resistenziali hanno mostrato un calo meno significativo, pari al 4% e al 11% rispettivamente, per Rp0,2 e R m
La variabilità delle proprietà meccaniche risulta relativamente bassa nella condizione 3-C, mentre tende a crescere per le altre condizioni (10-C, 10-T, e 20-C). Questo andamento è legato alla maggior disomogeneità microstrutturale, come verrà discusso successivamente, sia in termini di matrice ferrosa che di sferoidi di grafite. Al fine
di comprendere i risultati appena esposti è opportuno osservare sia le superfici di frattura che le microstrutture dei provini più rappresentativi, ovvero le cui caratteristiche sono comparabili al valor medio (“Medio”) e ai valori più bassi (“Peggiore”) per le singole condizioni (Figura 1).
meccaniche
Fig.1 - Frattografie (immagini in retrodiffusi e secondari) e microstrutture nelle diverse condizioni di solidificazione: (a,b) 3-C; (c,d) 20-C; (e,f) 10-C; (g,h) 10-T. Il dettaglio in (g) è riportato nella figura successiva / Fractography (backscattered and secondary images) and microstructures of the different solidification conditions: (a,b) 3-C; (c,d) 20-C; (e,f) 10-C; (g,h) 10T. Detail in (g) is reported in next figure
Le superfici di frattura riportate in Figura 1 mostrano caratteristiche piuttosto diverse. Nei provini 3-C la grafite sferoidale è uniformemente distribuita nella matrice ferritica,
in cui sono presenti anche isolate aree perlitiche dovute a fenomeni di segregazione. Questo porta ad una rottura duttile caratterizzata dalla presenza di dimples equiassici
che circondano ciascun nodulo di grafite (Figura 1(a)), il qualeèassimilabileadunvuotonellamatriceferriticache cresce con la deformazione del provino. La coalescenza tra vuoti adiacenti produce creste che delineano i grandi dimplesequiassici,sullequaleèpossibileosservaredimplesdidimensionicircaunordinedigrandezzapiùpiccoli dei dimples primari. A parità di caratteristiche microstrutturali,sono le cavità da ritiro piuttosto chei fenomenidegeneratividellagrafitearidurreRmeA%nellacondizione 3-C,lecuidimensioni,analizzatesullasuperficiedifrattura, possono superare 1 mm2 (Figura 1(b)). Passando alla condizione più critica, 20-C, l’influenza della grafite degenerata rispetto ai ritiri di solidificazione sulle proprietà meccaniche dei getti GDGS è evidente. In particolare, laddove i provini sono caratterizzati da una buona nodularità (Figura 1(c)), le superfici di frattura mostrano grandi dimples equiassici che circondano sia i noduli che la grafite esplosa, Allo stesso tempo, sono osservabili piani di clivaggio tipici di una modalità di frattura transgranulare (Figura 1(c,d)) dovuti a fenomeni di forte deformazione
localizzata causati sia dalla maggior presenza di aree perlitiche, caratterizzate da una plasticità inferiore rispetto alla matrice ferritica, che dall’intensificazione degli sforzi dovuta alla morfologia irregolare della grafite esplosa e chunky [3,4]. D'altro canto, nel campione mostrato in Figura 1(d), l’estesa presenza di grafite chunky che copre ampiamente la superficie fratturata riduce notevolmente la continuità della matrice, favorendo una deformazione plastica localizzata e la prematura rottura del materiale,
Ciò avviene secondo un meccanismo già discusso in [4]: in presenza di zone con grafite degenerata, la cricca penetra al loro interno attraversando le aree ferritiche interconnesse, mentre, nel caso di grafite sferoidale, essa propaga muovendosi attorno al perimetro dei noduli all'interfaccia con la matrice. Un ulteriore fattore che favorisce la frattura per clivaggio nella matrice ferritica è la presenza di carburi complessi a base di Ti, V, e Zr di dimensioni rilevanti (diametro di Feret ≈ 100 μ m) che si formano nelle aree perlitiche a seguito di fenomeni di segregazione (Figura 1(d) e Figura 2(a)),
Fig.2 - Immagini in retrodiffusi e secondari e analisi EDS delle superfici di frattura della ghisa EN-GJS-400-15 nelle condizioni: (a) 20-C; (b) 10-T. / Backscattered and secondary images and EDS analysis of the fracture surfaces of the EN-GJS-400-15 cast iron in the conditions: (a) 20-C; (b) 10-T. (a) (b)
Le condizioni 10-C e 10-T (TS pari a 10 ore al centro termico e in zona di transizione, rispettivamente) da un lato presentano caratteristiche microstrutturali e meccaniche “intermedie” rispetto alle condizioni 3-C e 20-C, ma con differenze significative, fra loro, in termini di Rm e A%. In entrambi i casi l’aumento della frazione di grafite degenerata e la conseguente diminuzione della nodularità ha portato ad una significativa riduzione di Rm e A% (Figu-
ra 1(f,h)). In entrambe le condizioni è stato possibile osservare con maggiore facilità la presenza di macroritiri di solidificazione nei provini caratterizzati da un’elevata nodularità (Figura 1(e,g)). Di contro, provini caratterizzati da una minore nodularità (Figura 1(f,h)) hanno mostrato ampie aree caratterizzate da grafite degenerata, facilitando l'interazione tra i vuoti all’interfaccia grafite/matrice in fase di deformazione, il rapido aumento del volume dei vuoti per coalescenza e, di conseguenza la riduzione dell’A% dei provini. Inoltre, come osservato per i provini 20-C, la grafite degenerata è stato un fattore di intensificazionedegli sforzi per fenomeni di intaglio, favorendo la nucleazione e propagazione di cricche, e causando sia una riduzione della duttilità che un aumento della variabilità dei dati. Viste la similarità tra le superfici di frattura e i va-lori di nodularità nei campioni analizzati, le differenti pro-prietà meccaniche tra la condizione 10-C e 10-T non sono attribuibili a questo parametro. Come descritto in [4-7], leparticelle di grafite nella GD possono essereconsideratecomecavitàoinclusioninellamatrice, data la minor resi-stenza della grafite rispetto alla matrice e la scarsa forza dilegame tra particelle di grafite/matrice ferrosa.Diconse-guenza,maggioreèladimensionedegli sferoidi di grafite, maggiore sarà la velocità con cui avvengono i fenomeni di coalescenza tra i vuoti e di conseguenza la rottura del campione. Al contrario, un piccolo diametro iniziale degli sferoidi di grafite determina una minore crescita dei vuo-ti, per cui un maggior allungamento a rottura. Parallela-mente, un affinamento del grano ferritico della matrice porta ad un miglioramento complessivo delle proprietà meccaniche. Considerando quindi come il cubo più gran-de (1000 mm3) necessiti di un tempo più lungo per rag-giungere i 300 °C in superficie rispetto al cubo intermedio (700 mm3), rispettivamente 200 h e 131 h, i meccanismi di diffusione in soluzione solida al di sotto della temperatura eutettica si protraggono per tempi più lunghi. Questo porta ad un ingrossamento microstrutturale sia in termini di noduli che di matrice ferrosa in misura maggiore nella condizione 10-T rispetto alla condizione 10-C a parità di TS, come evidenziato dall’analisi microstrutturale, e può essere considerato come uno dei fattori principali della differenzadiproprietàmeccanicherilevata.
Infine come evidenziato dal focus in Figura 1(g), riportato in maggior dettaglio in Figura 2(b), le condizioni che presentano tempi più lunghi di solidificazione (10-C, 10-T, e
20-C) presentano ampie zone di clivaggio non solo dovute alla presenza di perlite, carburi o grafite degenerata, ma anche a inclusioni non metalliche quali ad esempio composti MgO formatisi dall’interazione del Mg impiegato come nodularizzante e l’O. Le inclusioni non metalliche agiscono come punti di intensificazione degli sforzi, riducendo significativamente le proprietà meccaniche del materiale. È interessante notare come i composti MgO si trovino al centro di ampie zone di clivaggio circondate da particelle di grafite e grafite degenerata, la cui formazione è favorita proprio dalla presenza di O [8], L’azione dell’O quindi è doppiamente negativo: da un lato intrappola il Mg e favorisce la formazione di grafite degenerata, mentre dall’altro forma composti non metallici che peggiorano la duttilità dei getti.
Questo lavoro cerca di colmare le lacune attuali relative ai getti in ghisa duttile di grande spessore, svolgendo un’approfondita caratterizzazione microstrutturale e meccanica su getti di spessore maggiore di 200 mm. In particolare sono stati analizzati gli effetti di tempi di solidificazione lunghi, dalle 3 alle 20 ore, e in diverse zone, centro termico e di transizione, all’interno delle fusioni. Come previsto, le proprietà meccaniche, in particolare il carico di rottura e l’allungamento a rottura hanno risentito sensibilmente dell’aumento degli spessori dei getti e quindi dei tempi di solidificazione, a causa dell’aumento dei fenomeni degenerativi della grafite e dell’ingrossamento del grano della matrice ferritica. In particolare, maggiore sono i tempi di solidificazione, più la grafite degenerata sembra assumere un ruolo dominante rispetto alle cavità di ritiro di solidificazione nel ridurre la duttilità del materiale. A questo si aggiungono i difetti derivanti da fenomeni segregativi, quali carburi ed inclusioni non metalliche, più comuni al crescere delle dimensioni del getto e quindi dei tempi di solidificazione, i quali riducono ulteriormente la duttilità del materiale, favorendo la rottura per clivaggio transgranulare. Tali risultati sono da considerarsi molto utili per la progettazione di componenti in ghisa duttile di grandi dimensioni, in quanto forniscono informazioni fondamentali per attuare le contromisure necessarie al fine di limitare la formazione dei difetti più pericolosi all’interno dei getti a seconda delle dimensioni del componente.
[1] W, BAER Graphite in Ferritic Spheroidal Graphite Cast Iron: Formation, Prevention, Characterization, Impact on Properties: An Overview, Inter Metalcast 14, 454–488 (2020),
[2] P, FERRO, A, FABRIZI, R, CERVO, C, CAROLLO, Effect of inoculant containing rare earth metals and bismuth on microstructure and mechanical properties of heavy-section near-eutectic ductile iron castings, J, Mater, Process, Technol, 213 (9), 1601-1608 (2013)
[3] P, FERRO, L, LAZZARIN, F, BERTO, Fatigue properties of ductile cast iron containing chunky graphite, Mater, Sci, Eng, A 554, 122–128 (2012)
[4] ZH, WANG, X, ZHANG, FL, XU, KC, QIAN, KM, CHEN Effect of nodularity on mechanical properties and fracture of ferritic spheroidal graphite iron, China Foundry 16, 386–392 (2019),
[5] M, BENEDETTI, V, FONTANARI, D, LUSUARDI, Effect of graphite morphology on the fatigue and fracture resistance of ferritic ductile cast iron, Eng, Fract, Mech, 206, 427-441 (2019),
[6] T, BORSATO, P, FERRO, F, BERTO, C, CAROLLO Effect of Solidification Time on Microstructural, Mechanical and Fatigue Properties of Solution Strengthened Ferritic Ductile Iron, Metals 9(1):24 (2019),
[7] A, GHAHREMANINEZHAD, K, RAVI-CHANDAR, Deformation and failure in nodular cast iron, Acta Materialia 60(5) 2359-2368 (2012)
[8] R, KÄLLBOM, K, HAMBERG, M, WESSÉN, L,-E, BJÖRKEGREN, On the solidification sequence of ductile iron castings containing chunky graphite, Mater, Sci, Eng, A 413–414, 346-351 (2005),
Excellent castability and mechanical properties have led ductile irons to gain increasing importance in the heavyduty transport and renewable energy sectors. Long solidification times involving heavy-section castings can lead to degeneration of graphite spheroids and the formation of solidification defects, negatively affecting their mechanical properties. In this study, the effects of long solidification times (from 3 to 20 h) were investigated in different zones of cubes with sides of (i) 350 mm, (ii) 700 mm and (iii) 1000 mm. An important decrease in mechanical properties was observed with increasing solidification times, attributable to solidification defects and degenerative phenomena affecting graphite spheroids. These results are of great relevance to evaluate the mechanical behavior and failure mechanisms heavy-section ductile iron castings of non-standard dimensions in relation to the different solidification conditions occurring inside them.
KEYWORDS: HEAVY-SECTION CASTINGS, FERRITIC DUCTILE IRON, MICROSTRUCTURE, SOLIDIFICATION DEFECTS, GRAPHITE DEGENERATION, MECHANICAL PROPERTIES
F. Bravaccino, A.W. Ipock, C. Sinagra, A. Acquesta, T.Monetta, A. Ferrarese, S. Legnani
Nella produzione di laminati di alluminio e sue leghe si definiscono cicli di lavorazione tali da assicurare una struttura con grani di dimensione fine ed omogenea che determina le proprietà meccaniche necessarie per la realizzazione di numerose tipologie di manufatti. In alcuni casi, però, l’esigenza può essere completamente diversa. La lega ENAW3003 può essere impiegata per la produzione di alette di raffreddamento che devono essere brasate sulle piastre dello scambiatore di calore utilizzati per la produzione di impianti di condizionamento. Esse sono costituite da laminati di alluminio clad composti da un tri-layer 4XXX/3000/4XXX. In questi casi, al fine di ottenere una corretta brasatura, è necessario aumentare la dimensione dei grani, ed allo stesso tempo, garantire il persistere di buone proprietà meccaniche al manufatto. Lo scopo del lavoro è stato quello di determinare quali variazioni di composizione della lega 3003 e/o di processo bisogna attuare per ottenere una buona brasatura. I test effettuati riducendo la quantità di affinanti nella lega 3003, che sembrava la soluzione più logica, non ha determinato risultati soddisfacenti. Un nuovo approccio al problema è stato valutato variando la concentrazione del ferro, silicio e manganese nella lega. Questa soluzione, unita alla riduzione del rapporto di incrudimento del materiale dal 40% al 30%, ha permesso di ottenere dimensioni dei grani adeguate al fine di ottenere una efficace brasatura.
INTRODUZIONE
Nella produzione di scambiatori di calore del tipo tube/ fins è necessario brasare gli elementi costituenti la piastra (tube), prodotta con materiale cladd (tri-layer 4XXX/3000/4XXX), con le alette corrugate un-clad prodotta, normalmente, con la lega EN AW 3003 come da immagine in figura 1.
Fig.1 - Tipica sezione di uno scambiatore tube/fins ottenuto per saldobrasatura e particolare dell’aletta brasata.
Francesco Bravaccino, Anthony W. Ipock, Ciro Sinagra
Laminazione Sottile, Caserta
Annalisa Acquesta, Tullio Monetta
Università degli studi di Napoli Federico II, Napoli
A. Ferrarese, S. Legnani
IBS Technology S.p.A. – R&D Dpt Tradate, Varese
Tenere sotto controllo la struttura del laminato in lega AW EN 3003 e la dimensione del grano è importantissimo per ottenere una buona saldatura tra tube (piastra) e fins (aletta corrugata). In particolare, contrariamente a tante applicazioni (ove al fine di ottenere delle buone caratteristiche meccaniche del laminato si tende ad una struttura metallurgica a grani di piccole dimensioni) per questo processo non bisogna avere una struttura troppo fine. La realizzazione degli scambiatori di calore prevede una serie di fasi di processo che partono dalla lavorazione della materia prima fino al collaudo dell’elemento finito. Lo scambia-
La realizzazione dei singoli componenti prevede l’uso di materia prima in formato di nastri, lamiere o barre che prevedono una serie di fasi di lavoro per raggiungere il formato finale. Le masse radianti, in particolare, sono realizzate manualmente assemblando, un componente dopo l’altro, l’intero elemento centrale dello scambiatore. La giunzione tra le varie parti viene effettuata attraverso un processo di brasatura. Il sistema è poi contenuto all’interno di due telai in acciaio, per garantire un peso costante nel processo di brasatura e stabilità all’insieme, vincolandolo con delle fascette in acciaio per tenere i compo-
tore di calore è realizzato interamente in alluminio ed è costituito da diverse componenti interconnesse tra loro attraverso processi di formazione di giunti di brasatura e saldatura. Un esempio della struttura di uno scambiatore di calore prodotto da IBS Technology è riportato nella Fig. 1.
structure of a heat exchanger.
nenti in posizione fino al successivo trasporto al forno. La massa radiante viene brasata per consentire che le diverse placche brasanti, collocate tra un canale e il successivo, permettano la formazione dei giunti di brasatura sull’intero elemento, collegando tra loro i singoli componenti in un blocco unico di materiale.
Lo schema di flusso del processo di lavoro per la realizzazione dello scambiatore è così costituito dagli step riportati nel seguito:
Fig.3 - Schema di flusso del processo di lavoro per la realizzazione dello scambiatore / Flow diagram of the work process for the construction of the exchanger.
Le masse radianti sono realizzate manualmente assemblando un componente dopo l’altro l’intero elemento centrale dello scambiatore di calore. Il sistema è poi contenuto all’interno di due telai in acciaio, per garantire un peso costante nel processo di brasatura e stabilità all’insieme, vincolandolo con delle fascette in acciaio per tenere i componenti in posizione fino al successivo trasporto al forno.
Al forno CAB, le masse radianti sono collocate su delle gabbie (rack) verticali per essere trasportate all’interno del processo di brasatura. Qui, attraversando le diverse camere di processo del forno – 2 Dryer, Vacuum Loading Chamber, Pre-Heat, Brazing, Vacuum Cooling Chamber, Air Cooling Chamber – la massa radiante viene brasata permettendo che le diverse placche brasanti collocate tra un canale e il successivo permettano la formazione dei giunti di brasatura sull’intero elemento, collegando tra loro i singoli componenti in un blocco unico di materiale. Successivamente si effettua una lavorazione meccanica di fresatura meccanica sui bordi per realizzare le sedi di
contatto tra le vaschette e le masse che dovranno essere saldate. Effettuata un’operazione di puntatura manuale per tenere in posizione le parti da saldare, attraverso l’uso di robot di saldatura vengono unite le vaschette di raccolta del fluido alla massa radiante.
Lo scambiatore così completato è poi sottoposto ad un controllo ad una fase di collaudo finale. L’elemento è messo in pressione con aria compressa alla pressione richiesta dal cliente finale (in funzione del sistema su cui sarà installato e delle condizioni di esercizio a cui dovrà essere sottoposto) e immerso in vasche d’acqua per assicurarci che non ci siano perdite nel circuito. Il controllo è eseguito tramite ispezione visiva da parte di operatori qualificati.
Le specifiche richieste al laminato di alluminio in lega EN AW3003 e le specifiche meccaniche richieste sono qui di seguito riportate (tabella 1):
Tab.1 - Limiti di specifica per la lega EN AW 3003 secondo la UNI EN 573 / Specification limits for alloy EN AW 3003 according to UNI EN 573.
PROPRIETÀ MECCANICHE RICHIESTE:
Tab.2 - Limiti di specifica delle caratteristiche meccaniche su materiale finito di laminazione in stato fisico H14 e dopo ciclo di brasatura a 600°C per 1h. / Specification limits of mechanical properties on finished sheets in temper H14 and after brazing simulation cycle at 600°C for 1h in oven.
ID spessore (mm) UTS (N/mm2) YS (N/mm2)
Spec. 0.200 – 0 / +0,024
Sono stati quindi progettati due cicli di lavoro per due diversi master coil:
MASTER COIL A
• Laminato a caldo a spessore 6mm
• Laminato a freddo fino a spessore 0.35mm
• Ricottura di riscristallizzazione completa (400°C per 5 ore) a spessore 0.35 mm
• Laminazione a freddo a spessore 0.21mm
MASTER COIL B
• Laminato a caldo a spessore 6mm
Dopo simulazione brasatura a
• Laminato a freddo fino a spessore 0.50mm
• Ricottura di riscristallizzazione completa (400°C per 5 ore) a spessore 0.50 mm
• Laminato a freddo fino a spessore 0.30mm
• Ricottura di riscristallizzazione completa (400°C per 5 ore) a spessore 0.30 mm
• Laminazione a freddo a spessore 0.21mm
ANALISI CHIMICA
Tab.3 - Composizione chimica dei due master coil adoperati per i cicli di lavoro A e B / Alloy chemical composition of the two master coils used for the metalworking cycles A and B.
Tab.4 - Caratteristiche meccaniche a trazione dei due master coil A e B nelle due direzioni parallela e ortogonale alla direzione di laminazione e dopo test di brasatura / Tensile strenght mechanical testing of the two master coils A and B in the two directions (parallel and orthogonal to Rolling direction) and after brazing test.
Analisi metallografica a spessore 0.21mm CAMPIONE A
Fig.4 - Metallografia in cross section del campione A in stato H14 dopo attacco barker sotto luce polarizzata / Metallographic picture in cross section of sample A in temper H14 after barker etching under polarising light.
STRUTTURA A SPESSORE 0.21mm prima della brasatura – attacco fluoborico luce polarizzata – x100
- Brasatura aletta prodotta con campione A – non idonea / Brazed fin made with sample A – not suitable for heat exchangers.
Fig.8 - STRUTTURA A SPESSORE 0.21mm prima della brasatura – attacco fluoborico luce polarizzata – x100 / Metallographic picture in cross section of sample B in temper H14 after barker etching under polarised light –100x
- Brasatura dell’aletta fatta con campione B – idonea / Brazed fin made with sample B – suitable for heat exchangers.
CONCLUSIONI
Le prove condotte con presenza di titanio consentivano una dimensione dei grani che è apparsa insufficiente per garantire una brasatura con caratteristiche qualitative
[1] ASM Specialty HandbooK – Alliminum and Alluminum Alloys
[2] Manuale dei materiali per l’ingegneria Aimat - McGraw-Hill
[3] Alluminium Alloy Structures M. Mazzolani - E & FN SPON
[4] Manuale di fonderia d’alluminio C.Panseri - Ulrico Hoelpli
adeguate. Le prove eseguite con la lega modificata conducono ad una dimensione granulare con un esito positivo in brasatura.
[5] I processi di raffinazione per la produzione di leghe per getti di qualità A.Alti – Alcan - Alluminio
[6] Il controllo di qualità nella produzione di laminati sottili di lega di alluminio: un fattore fondamentale per il loro sviluppo tecnologico e applicativo C.Sinagra – XII International Metallurgy Congress
[7] Fenomeni di attrito ed usura durante la laminazione dell’alluminio C.Sinagra – Lamiera n. 10/90
[8] Uno sguardo all’interno dell’alluminio D. Altenpohl – Tecnomedia
Processing cycles to produce rolled aluminium and its alloys are identified in such a way as to ensure a alloy structure showing fine and homogenous grain size that determines the mechanical properties required to produce numerous types of manufactured products. In some cases, however, the requirement may be completely different. Alloy ENAW3003 can be used to produce cooling fins that must be brazed onto heat exchanger plates used in the production of air conditioning systems. They consist of aluminium clad laminates composed of a 4XXX/3000/4XXX tri-layer. In these cases, to achieve a correct brazing, it is necessary to increase the grain size, and at the same time, ensure that good mechanical properties persist in the part. The aim of the work was to determine what changes in 3003 alloy composition and/or process must be implemented to achieve good brazing. Tests carried out by reducing the amount of refiners in the 3003 alloy, which seemed the most logical solution, did not lead to satisfactory results. A new approach to the problem was evaluated by varying the concentration of iron, silicon and manganese in the alloy. This solution, combined with a reduction in the work hardening ratio of the material from 40% to 30%, resulted in adequate grain sizes for effective brazing.
KEYWORDS: HEAT EXCHANGERS, BRAZING, GRAIN SIZE, EN AW 3003
P. Leo, G. Renna, A. De Luca, N. Soni, R. Nobile, C. Mele, S. Bagheri
In questo studio è stato analizzato l’effetto della densità di energia e della modalità di costruzione sulla qualità di parti in lega Al-Si10-Mg processate per Selective Laser Melting. Parallelepipedi a base rettangolare sono stati processati in direzione verticale (campioni V) e orizzontale (campioni H) cioè, con il loro asse longitudinale rispettivamente parallelo e perpendicolare alla direzione di applicazione del fascio laser. A parità di parametri di processo, la modalità di costruzione verticale induce un ingrossamento della microstruttura. All’aumentare della densità di energia la microstruttura e proprietà dei campioni V evolvono significativamente mentre le caratteristiche dei campioni H rimangono più simili tra loro. Alla minima densità di energia il campione H esibisce un maggior numero di vuoti a morfologia non circolare. Le differenti microstrutture e difettosità non comportano significative differenze nella risposta a corrosione dei campioni H e V che risulta comunque migliorata dal trattamento superficiale di Ultrasonic Peening (UPT).
PAROLE CHIAVE: FUSIONE LASER SELETTIVA, MICROSTRUTTURA, DIFETTOSITÀ, CORROSIONE, TRATTEMENTO DI ULTRASONIC PEENING
INTRODUZIONE
Le leghe alluminio-silicio (Al-Si), che rappresentano l'85-90% della produzione di getti in alluminio, sono particolarmente apprezzate per la loro elevata colabilità, favorita dalla presenza del silicio [1]. Oggigiorno, la fusione laser selettiva (Selective Laser Melting - SLM) offre un'alternativa innovativa per la produzione di componenti in queste leghe, permettendo di realizzare geometrie complesse e di ottenere proprietà meccaniche superiori. Questo processo impiega un fascio laser ad alta energia per fondere completamente una polvere metallica depositata in strati successivi, all'interno di una camera ad atmosfera controllata. Il metallo fuso solidifica rapidamente, creando la geometria del componente desiderata strato dopo strato [2]. Nonostante i numerosi vantaggi di questa tecnologia, i componenti prodotti
P. Leo, G. Renna, A. De Luca, N. Soni, R. Nobile, C. Mele, S. Bagheri Università del Salento
via SLM presentano ancora significative limitazioni in termini di finitura superficiale e porosità. Questi fattori compromettono le prestazioni complessive del componente [3-5]. Per ovviare a questi problemi, vengono spesso impiegati trattamenti superficiali postproduzione come ad esempio la sabbiatura, pallinatura, elettrolucidatura e Lapping (lucidatura meccanica). Tra i varitrattamentisuperficialipost-produzione,lapallinatura ultrasonica (UPT) si configura come una promettente alternativa per migliorare la rugosità superficiale, le proprietà meccaniche e la resistenza alla corrosione [6]. Inoltre, l'orientamento di costruzione nei componenti prodotti con SLM introduce anisotropia ed eterogeneità microstrutturali, influenzando significativamente le proprietà meccaniche. Studi come quello di T. Maconachie et al. [7] analizzano l'effetto dell'orientamento di costruzione (orizzontale, verticale e 45°) sulle proprietà meccaniche di campioni in lega AlSi10-Mg prodotti con una densità di energia volumetrica (VED) di 54 J/mm³. Gli autori osservano una riduzione significativa della duttilità nei campioni costruiti verticalmente, senza cambiamenti rilevanti nella resistenza a snervamento e nella resistenza ultima a trazione. Sebbene la duttilità sia fortemente influenzata dall'orientamento di costruzione, la resistenza alla corrosione, essenziale per la vita utile dei componenti, sembra essere meno sensibile a questa variabile. Come riportato da A. Tiwari et al. [8], per le leghe Al-Si10-Mg prodotte con SLM, l'orientamento di costruzione (orizzontale o verticale) ha un effetto trascurabile sulla resistenza alla corrosione, a parità di VED e dimensioni deicampioni.
In questo studio è stato analizzato l'impatto della densità dienergiavolumetrica e dell'orientamento di costruzione sulla microstruttura e sulla qualità di componenti in lega
Al-Si10-Mg realizzati tramite Selective Laser Melting (SLM). Sono stati prodotti campioni parallelepipedi (base 50 mm², altezza 100 mm) con due orientamenti: verticale (campioni V) e orizzontale (campioni H), corrispondenti a un allineamento dell'asse longitudinale rispettivamente parallelo e perpendicolare alla direzione del fascio laser. L'analisi microstrutturale è stata condotta utilizzando microscopia ottica e microscopia elettronica a scansione. Mentre la qualità dei componenti è stata valutata mediante analisi di immagini utilizzando il software Image J. Inoltre, al fine di ottimizzare la finitura superficiale e favorire una maggiore resistenza alla corrosione, i campioni prodotti in entrambe le orientazioni (H e V) sono stati trattati con pallinatura a ultrasuoni.
MATERIALIEMETODI
I campioni sono stati prodotti mediante stampa 3D utilizzando il processo di fusione a letto di polvere laser (Laser Powder Bed Fusion, LPBF) con una macchina Renishaw AM 400. È stata utilizzata una polvere di AlSi10Mg, ottenuta tramite atomizzazione da gas e con una granulometria media di 40 μm, la cui composizione è riportata nella Tabella 1. È stata adottata una strategia di scansione denominata Meander, con i parametri di processo riportati nella Tabella 2. Per ridurre le tensioni residue, la camera di costruzione è stata preriscaldata a 250°C.Tuttiicampionihannounaformadiparallelepipedo (5x10x100 mm) ma si differenziano per l'orientamento della sezione di costruzione (XY) rispetto al fascio laser: trasversalelunga(campioniH)etrasversalecorta(campioni V).
- Composizione (in massa) della polvere AlSi10Mg / Powder Composition ( weight %).
Fig.1 - Direzione di costruzione per i campioni SLM / Building Mode for SLM parts.
Tab.2 - Parametri di processo / Process Parameters.
Per valutare le differenze microstrutturali indotte dalle diverse orientazioni di costruzione (H e V), sono state effettuate analisi al microscopio ottico (Nikon Ephiphot 200 OM) ed elettronico a scansione (Zeiss EVO SEM). La durezza Vickers è stata misurata utilizzando uno strumento digitale Affri Wiky 200JS (Affri, Varese, Italia) applicando una forza di 0,5 Kg per un tempo di indentazione di 15 s (HV0.5/15).
Per i campioni processati a 250 W e costruiti con orientazione H e V, è stata condotta un'analisi approfondita dei difetti utilizzando microscopia ottica e il software ImageJ. In particolare, sono stati quantificati parametri come numero, distribuzione, morfologia, dimensione media e percentuale di area dei difetti rispetto alla sezione di costruzione.
Per tutti i campioni, la resistenza alla corrosione è stata valutata nella sezione centrale del lato longitudinale (sezione XZ) su un’area di 10 mm². Prima delle misurazioni, la superficie esposta è stata levigata con carta abrasiva in SiC da 2000 grit. Le misure sono state effettuate a temperatura ambiente utilizzando un potenziostato Gamry
Potentiostat 1010E (Gamry Instruments, Warminster, PA, USA) in una soluzione acquosa di NaCl al 3,5%, in condizioni di aerazione naturale. Durante i test è stata adottata una configurazione standard a tre elettrodi: contro elettrodo a rete espansa di grafite, elettrodo di riferimento Ag/AgClecampionicomeelettrododilavoro.
Un trattamento di pallinatura ultrasonica (UPT) è stato applicato per 1 minuto sulla superficie longitudinale dei campioni V e H (sezione XZ - 10 mm²), allo scopo di migliorare la finitura superficiale. Il trattamento è stato effettuato con un dispositivo Sintes UP 600, utilizzando un punzone di diametro 3 mm e una frequenza di vibrazione di20kHz.
Infine, utilizzando un conduttivimetro Sigmatest D 2,068 Fo-erster e un rugosimetro MahrSurf PS10, sono state determinate rispettivamente la conducibilità elettrica e la deirugositàcampioni.
RISULTATI E DISCUSSIONE
La microstruttura dei campioni H e V, processati alla minima e massima densità energetica, è stata analizzata nella
sezione longitudinale a metà altezza dopo la preparazione metallografica e l'attacco chimico (Fig. 2). È evidente la caratteristica geometria delle pozze fuse, determinata dal meccanismo dominante di trasporto del calore, cioè la conduzione. Inoltre, è anche possibile osservare che nei campioni H, nonostante la notevole differenza nella densità di energia (Fig. 2 c, d), le microstrutture appaiono più simili tra loro mentre, nei campioni V (Fig. 2a, b) si osserva una più significativa differenza. In particolare, nel campione V processato alla massima densità di energia (Fig. 2b) si osserva un significativo aumento delle dimensioni, in
particolare della profondità delle pozze fuse. La differente microstruttura potrebbe essere correlata all’accumulo preferenziale di calore che risulta favorito per i campioni V a causa della minore area di scambio di calore della sezione di costruzione che è pari a 50 mm2 mentre nei campioni H è pari a 500 mm2 [9]. Così, sebbene l’incremento della densità di energia sia lo stesso per le differenti direzioni di crescita, l’effetto sulla microstruttura e relative proprietà è particolarmente significativo per i campioni costruititi verticalmente (campioni V).
Fig.2 - Micrografie ottiche per i campioni V (a,b) e H (c, d) processati a 250 W (a,c) e 350 W (b,d) / Optical micrographs for the V (a,b) and H ( c,d) parts processed at 250W (a,c) and 350W (b,d)
Poiché un maggiore accumulo di calore nel substrato favorisce sia un maggiore volume di materiale portato a fusione che una velocità di raffreddamento più contenuta, in accordo ai principi di solidificazione, laddove la pozza fusa esibisce dimensioni maggiori, anche la microstruttura sarà più grossolana e quindi la durezza delle parti processate subirà un decremento. A conferma di quanto sopra, in Tabella 3 sono riportati i valori di microdurezza HV0,5/15 rilevati nelle sezioni trasversali dei campioni H e V. Si osserva che, all’aumentare della densità di energia la riduzione della durezza è particolarmente significativa per i campioni verticali (V) mentre è più contenuta per gli orizzontali (H), in accordo a quanto osservato dal punto
di vista microstrutturale. Per ulteriore verifica, la conducibilità elettrica è stata valutata a metà altezza nei campioni verticali (V) processati a 250 W e 350 W. I rispettivi valori sono riportati in Tabella 4. Nel campione verticale processato alla massima densità di energia (V-350W), si osserva un leggero incremento della conducibilità elettrica. Questo incremento è attribuibile principalmente alla ridotta sovrassaturazione della matrice e alla microstruttura più grossolana, che facilita il passaggio della corrente elettrica.
Tab.3 - Microdurezza Vickers per le sezioni trasversali campioni H e V processati a 250W e 350W / Microhardness evaluated for the H and V samples at 250W and 350W.
Campioni HV0,5/15
V - 250W 138 ± 3
H - 250W 145 ± 4
V - 350W 126 ± 2
H - 350W 139 ± 4
Tab.4 - Condicibilità elettrical (60Hz) per i campioni V processati a 250W e Microdurezza 350W / Electrical Conductivity for the V samples at 250W and 350W.
Campioni Conducibilita media [µS·m]
V - 250W
V - 350W
La microstruttura dei campioni orizzontali e verticali processati a 250W è stata inoltre caratterizzata mediante microscopia elettronica a scansione (Fig. 3). È possibile
19,7 ± 0,1
21,1 ± 0,1
osservare che in prossimità della zona di rifusione la microstruttura appare a grani equiassici, mentre all’interno delle pozze le dendriti assumono morfologia allungata.
Fig.3 - Micrografie SEM per i campioni H (a) e V( b) processati a 250W. / SEM micrographs for the H(a) and V ( b) parts processed at 250W.
Inoltre, dall’analisi al SEM il campione costruito verticalmente (V) sembrerebbe caratterizzato da una microstruttura più grossolana (Fig. 3b), compatibile con il maggior accumulo di calore che caratterizza le sezioni ad area ridotta a parità di densità di energia. Tuttavia, i valori di microdurezza in Tabella 3 evidenziano come i valori di microdurezza dei campioni H e V a 250 W siano molto simili. Tali valori potrebbero essere influenzati quindi da altri fattori, quali la difettosità. Per tale ragione l’analisi dei vuoti è stata effettuata mediante software Image J nelle sezioni trasversali a metà altezza dei campioni H e V. Il risultato della caratterizzazione dei vuoti ha fatto emergere interessanti caratteristiche come
risulta dalla Figura 4 e dalla Tabella 5. La percentuale e numerosità dei vuoti è molto superiore nel campione H (Tabella 5). Inoltre, dalle distribuzioni dei vuoti in Fig. 4 si rivela che il campione H esibisce vuoti di dimensioni maggiori e a bassa circolarità riconducibili a vuoti da mancata fusione (Fig. 4b). Tale risultato è correlabile a un accumulo di calore favorito nel campione V, a parità di densità di energia. Inoltre, spiegherebbe anche i valori di durezza confrontabili per i campioni V e H, nonostante la microstruttura più fine rilevata per il campione H, a causa della maggiore occorrenza di difettosità nel campione costruitoorizzontalmente(0,6%percampioneHVs0,2% perilcampioneV).
Fig.4 - Distribuzione dei vuoti nelle sezioni trasversali del campione V( a) e H (b) processati 250W / Voids distributions for the H(b) and V ( a) parts processed at 25.
Tab.5 - Percentuale di area dei vuoti e densità dei vuoti per i campioni processati a 250W / Area voids (percentage) and voids density for H and V samples processed at 250W.
Campioni Vuoti [%] Densità dei vuoti [N°vuoti/µm²]
V Trasversale 0,2
H Trasversale 0,6
Il comportamento a corrosione (Figura 5) non rileva significative differenze per i campioni H e V, in accordo a quanto riportato in letteratura [8]. Per entrambi i campioni, l’applicazione del trattamento superficiale di UPT, determina solo una leggera riduzione della corrente di corrosione. L’ottimizzazione dei parametri del trattamento superficiale potrebbe ulteriormente migliorare la risposta
5,996E-06
1,139E-05
a corrosione dei campioni processati via Selective Laser Melting. Le ragioni di tale miglioramento sono in genere imputate a riduzione di rugosità, ad un affinamento della microstruttura e all’introduzione di tensioni residue di compressione. Successivi studi interesseranno la verifica di tali effetti e l’ottimizzazione dei parametri di processo del trattamento superficiale.
Fig.5 - Curve potenziodinamiche per le sezioni longitudinali del campione H (a) e V(b) processati 250Wprima e dopo l’applicazione del trattamento superficiale / Potentiodynamic curves for H(a) and V (b) parts processed at 250.
Di seguito le principali conclusioni raggiunte in questo studio sull’ effetto della densità di energia e della direzione di costruzione sulla microstruttura di campioni in lega Al-Si10-Mg processati via Selective Laser Melting:
1) Incrementando la densità di energia volumetrica da 67 J/mm3 a 84 J/mm3 si osservano modifiche significative nella microstruttura e proprietà dei campioni verticali mentre per i campioni orizzontali la microstrutturaeproprietàrimangonopiuconfrontabili.
2) A parità di densità di energia (67 J/mm3) la microstruttura del campione verticale risulta più grossolana rispetto a quelladel campione orizzontale. Mentre i valori di durezza per i due campioni non differisconosignificativamente.
3)Aparitàdidensitàdienergia,neicampioniprocessatia250Wsiosservalamassimaoccorrenzadivuotiper il campione H. In particolare nel campione H si osserva una maggior incidenza di vuoti di mancata fusione. Tale maggiore numerosità e dimensione media dei difetti nel campione orizzontale speigherebbe i valori di durezza confrontabili per i campioni H e V nonostante la microstruttura piu fine rilevata nel campione oriz-
zontale.
Le precedenti conclusioni sono correlabili ad un accumulo preferenziale di calore per i campioni verticali a causa della minore area di scambio della sezione di costruzione, Come conseguenza si osserva una minore incidenza dei vuoti da mancata fusione e una microstruttura più grossolana e caratterizzata da minore durezza.
4) La resistenza a corrosione non varia in maniera significativa in relazione alla direzione di crescita
5) Il trattamento superficiale UPT si è rivelato efficace nel ridurre la corrente di corrosione per entrambe le direzioni di costruzione dei campioni processati alla minima densità di energia. L’ottimizzazione dei parametri di processo per l’UPT potrebbe indurre ulteriori miglioramenti nella risposta a corrosione e sarà oggetto di studi futuri.
[1] Smith, W.F. Structure and Properties of Engineering Alloys, 2nd ed.; McGraw-Hill: London, UK, 1993; pp. 218–223.V.
[2] J. Zhang, B. Song, Q. Wei, D. Bourell, Y. Shi, A review of selective laser melting of aluminum alloys: Processing, microstructure, property and developing trends, Journal of Materials Science & Technology 35 (2019) 270–284.
[3] I. Maskery, N.T. Aboulkhair, M.R. Corfield, C. Tuck, A.T. Clare, R.K. Leach, R.D. Wildman, I.A. Ashcroft, R.J.M. Hague, Quantification and characterisation of porosity in selectively laser melted Al–Si10–Mg using X-ray computed tomography, Materials Characterization 111 (2016) 193–204.
[4] S. Beretta, S.A. Romano, Comparison of fatigue strength sensitivity to defects for materials manufactured by AM or traditional processes, Int. J. Fatigue 94 (2017) 178
[5] Avi Leon, Eli Aghion. Effect of surface roughness on corrosion performance of AlSi10Mg alloy produced by Selective Laser Melting (SLM), Materials Characterization 131 (2017) 188–194.
[6] L. Li, M. Kim, S. Lee, M. Bae, D. Lee Influence of multiple ultrasonic impact treatments on surface roughness and wear performance of SUS301 steel, Surf. Coat. Technol. 307 (2016) 517-524
[7] Tobias Maconachie, Martin Leary, Jianjun Zhang, Alexander Medvedev, Avik Sarker, Dong Ruan, Guoxing Lu, Omar Faruque, Milan Brandt. Effect of build orientation on the quasi-static and dynamic response of SLM AlSi10Mg. Materials Science and Engineering: A. Volume 788, 24 June 2020, 139445
[8] Tiwari, A.; Singh, G.; Jayaganthan, R. Improved Corrosion Resistance Behaviour of AlSi10Mg Alloy due to Selective Laser Melting Coatings 2023, 13, 225.
[9] G. Mohr, S.J. Altenburg, K. Hilgenberg, Effects of inter layer time and build height on resulting properties of 316L stainless steel processed by laser powder bed fusion, Addit. Manuf. 32 (2020), 101080.
This study investigates the effect of the building modes and surface treatments on the quality of Al-Si10-Mg parts processed by Selective Laser Melting (SLM). The same geometry of the samples was built but the section to be grown (the perpendicular one to the laser beam) has been chosen respectively as the long transversal section (designed as horizontal samples or H) and the short transversal section (designed as Vertical samples or V) of the parts. For the sake of simplicity, we have named the different built samples as Horizontal samples (H) and Vertical samples (V). The different building modes induced a coarser microstructure in the V samples at set process parameters. The microstructural features of the V samples are more sensitive to the increasing of Energy density with respect to the H samples. The corrosion behavior does not differ significant for all the parts. Finally, the UPT surface treatment was found to improve the corrosion resistance of all the parts leading a significant decrease in the corrosion current.
KEYWORDS: SELECTIVE LASER MELTING, BUILDING MODE, MICROSTRUCTURE, DEFECTS, CORROSION RESISTANCE, ULTRASONIC PEENING TREATMENT
E. Colombini, E. Lassinantti Gualtieri, P. Veronesi, F. Cugini, G. Garulli, M. Solzi, L. Gallo, F. Albertini, G.Trevisi
Circa il 70% di tutta l'energia prodotta dall’umanità viene dissipata come calore, pertanto lo sviluppo di nuove tecnologie per catturare l'energia termica dispersa convertendola in energia riutilizzabile è essenziale per promuovere la transizione verso un’economia circolare e sostenibile. I generatori termomagnetici (Thermo-Magnetic power Generators TMG) sono ecologici sistemi di conversione dell’energia in grado di affrontare questa sfida. Scopo del presente lavoro è lo sviluppo di materiali avanzati che possano essere sfruttati come elementi attivi per la raccolta di calore e la produzione di energia elettrica su piccola scala. Fra i materiali disponibili la ricerca si è focalizzata sulle Leghe ad Alta Entropia (HEA) grazie alle loro peculiari proprietà. Le HEA sviluppate sono prive di terre rare con metalli 3d di transizione non critici, facilmente accessibili, stabili e riciclabili, come Fe, Ni e Mn. Partendo dalla HEA di composizione equimolare FeCoNiCrAl è stata variata la stechiometria degli elementi Ni e Cr al fine di valutare l’effetto della variazione composizionale con la temperatura di transizione. Le HEA sono state ottenute sia per alligazione meccanica sia per sinterizzazione FAST (Field Assisted Sintering Technologies). Le composizioni ottenute sono state studiate mediante analisi strutturali, microstrutturali e tecniche di caratterizzazione magnetica. Sono stati eseguiti trattamenti termici per modificare la struttura cristallografica e magnetica ed il grado di ordine atomico. Il risultato porta all’identificazioni di importanti considerazioni sulla relazione fra microstruttura e proprietà magnetiche.
INTRODUZIONE
Sfruttare le proprietà termomagnetiche dei materiali ferromagnetici per convertire l'energia termica in energia elettrica è un principio noto dal XIX secolo, ma solo di recente la ricerca sulla refrigerazione magnetica ha portato alla scoperta di materiali che mostrano un’ampia variazione di magnetizzazione intorno alla temperatura ambiente, favorendo così la possibilità di realizzare generatori in grado di recuperare il calore di scarto a temperature inferiori a 100°C per generare energia elettrica da piccole differenze di temperatura. Lo sviluppo di materiali avanzati che possano essere sfruttati come elementi attivi per la raccolta di calore e la produzione di energia elettrica su piccola scala risulta essere un argomento di interesse tecnologico. I materiali investigati fino ad oggi sfruttano come materiale attivo il Gd , ma la Comunità Economica Europeea nel 2018 all’interno del “Report on Critical Raw
E. Colombini - E. Lassinantti Gualtieri, P. Veronesi
Dipartimento di Ingegneria “Enzo Ferrari”, Modena
F. Cugini
Dipartimento di Scienze Matematiche, Fisiche e Informatiche, Università degli Studi di Parma - Istituto IMEM-CNR, Parma
G. Garulli
Dipartimento di Scienze Matematiche, Fisiche e Informatiche, Università degli Studi di Parma
L. Gallo, S. Fabbrici, F. Albertini, G.Trevisi Istituto IMEM-CNR, Parma
M. Solzi
Dipartimento di Scienze Matematiche, Fisiche e Informatiche, Università degli Studi di Parma - Istituto IMEM-CNR, Parma
Materials and the Circular Economy” ha identificato le terre rare come materiale a rischio pertanto ha incentivato lo sviluppo di soluzioni per il riciclo delle terre rare e di materiali privi di terre rare.
L’innovazione di nuovi materiali è considerata quindi essere la chiave per lo sviluppo di nuove tecnologie nel mondo moderno. In questo contesto si inseriscono le ormai note leghe ad alta entropia (HEAs) appartenenti al gruppo delle complex concentrated alloys (CCAs). Esse possiedono un’ampia variazione delle proprietà fisiche grazie alla variazione composizionale che possono ricoprire. Per questi motivi in letteratura sono ormai molteplici i lavori sulla comprensione degli effetti che composizione e microstruttura hanno sulle proprietà fisiche e meccaniche.
In quest’ottica si inserisce quindi l’idea di utilizzare queste leghe ad alta entropia per ottenere sistemi con le proprietà magnetiche desiderate, in particolare prive di terre rare. Fra le famiglie di HEAs quelle contenenti metalli di transizione come Fe, Cu, Co, Ni o Mn sono promettenti materiali magnetici dolci. Diversi studi mostrano come la variazione del contenuto di Al, nel tradizionale sistema FeCoNiCrAlx, modifichi la microstruttura della lega variando la microstruttura da FCC a FCC+BCC (0.5<x<0.9) a completamente BCC con conseguente variazione del campo coercitivo Hc. Inoltre, recentemente si è valutato l’effetto dei precipitati nanofasici BCC uniformemente distribuiti in una matrice di fase B2 dimostrando come si riduca notevolmente l’effetto coercitivo delle HEA e concludendo come si possano modificare le proprietà magnetiche di una lega modificando la dimensione della seconda fase. Indagini sul sistema FeCrCoNi-based suggeriscono che una struttura BCC abbia una temperatura di Curie (TC) superiore alle strutture FCC, questo probabilmente da imputare al momento magnetico medio degli elementi che è maggiore nel sistema BCC rispetto al FCC. Infatti, alcuni studi confermano che elementi ferromagnetici quali Fe, Co e Ni presentano un momento magnetico maggiore nella struttura BCC rispetto alla FCC e che le fasi BCC/B2 posso presentare un più forte magnetismo. In queste indagini viene sottolineato come la struttura cristallina influenzi il campo coercitivo (HC) della fase ferromagnetica. Esso può essere aumentato anche mediante modifica della microstruttura, aumentando la densità di
difetti quali dislocazioni, vacanze e bordi grano, che vanno a creare punti di pinning per il moto delle pareti dei domini magnetici. Nello studio sfruttano il Cr per ottenere una lega resistente a corrosione e Al per modificare la struttura delle fasi ottenendo una lega (Fe2.25Co1.25Cr)94Al6 completamente BCC con buone proprietà anticorrosive. Il Cr dovrebbe portare a un ampio cambiamento del momento magnetico, da un momento magnetico di c.a 0.8 µ B nella struttura FCC a un momento magnetico nullo nella struttura BCC. Gli autori ripostano come le proprietà magnetiche siano influenzate dalla temperatura e dalla struttura del sistema e quindi dal metodo di sintesi. Una recente review mostra come la maggior parte delle leghe abbia una microstruttura bifasica FCC/BCC ma evidenzia come microstruttura, macrostruttura e distribuzione delle fasi sia fortemente influenzata dal metodo di sintesi scelto per produrre la lega confermando come HEAs prodotte con diversi metodi di sintesi abbiano diverse proprietà magnetiche. Inoltre, conferma l’ormai noto effetto dell’aggiunta di elementi come Al, che forza la struttura a diventare BCC o del Si che aumenta le proprietà meccaniche. Gli autori riportano un esaustivo elenco delle diverse HEAs sintetizzate attraverso diversi metodi e si nota come l’alligazione meccanica sia usata in pochi sistemi FeCoNiMnV, AlFeMgNiTi, CoCrFeNiMn, e FeCoAlNiCr con 30 ore di macinazione. Lo studio evidenzia la formazione di una unica fase BCC, con parametro reticolare 2.88 ± 0.01 Å, dopo alligazione meccanica per 30 ore e la formazione di una fase NiAl B2 e Ni3Al L2 con la formazione di fase σ nella lega dopo sinterizzazione a 900°C. Sebbene sia dimostrato il grande potenziale delle HEAs nelle applicazioni magnetiche ci sono alcuni interrogativi non ancora risolti. Per esempio, nonostante molte leghe contenenti Al formino una fase ordinata B2, l’effetto della formazione della fase e della suddivisione fra B2 e BCC sulle proprietà magnetiche non è ancora spiegata. Alcuni autori notano l’aumentare della saturazione magnetica all’aumentare della quantità di BCC e al diminuire della fase FCC, ma l’origine di tale effetto non è ancora compreso. Pertanto, nel cercare di rispondere a questi quesiti gli autori sviluppano una HEA in cui si varia il rapporto Fe/Cr e dimostrano come la variazione di questo rapporto nel mantenere una struttura BCC sia la chiave per progettare HEA con i metalli di transizione. La modifica delle proprietà magnetiche in funzione della
composizione chimica di questi sistemi è nota, il metodo di sintesi più utilizzato passa per la fase liquida nonostante ci siano dei noti svantaggi come la segregazione e la microstruttura disomogenea. D’altro canto, la metallurgia delle polveri presenta diversi vantaggi: l’estensione della solubilità allo stato solido in sistemi non miscibili, processi a temperatura ambiente, riduzione della segregazione chimica, e sintesi di leghe con una struttura molto fine (grani ultrafine o nanocristallini). Gli autori riportano uno studio in cui il sistema FeCoAlNiCr sottoposto a diversi trattamenti termici mostri una variazione delle proprietà magnetiche. Altri studi mostrano come SPS possa modificare la transizione magnetica della lega CoCrFeNiMn ottenuta per alligazione meccanica. In letteratura è noto che più di 150 composizioni siano state studiate in particolare la loro microstruttura e le proprietà meccaniche. Ma una indagine sistematica delle proprietà fisiche e chimiche non è ancora completa. Gli autori evidenziano come l’alta densità di difetti causata dalla presenza di diversi atomi all’interno della struttura cristallina determini proprietà magnetiche diverse e ricordano come queste strutture possano essere significativamente modificate da trattamenti termici e metodi di sintesi. La comprensione dei meccanismi di questi cambiamenti strutturali darà la possibilità di modificare le proprietà dei sistemi e creare nuovi materiali funzionali.
Tutto questo porta nuovamente a sottolineare il motivo del crescente interesse nei sistemi HEA: modificando
composizione e sintesi si possono ottenere leghe con proprietà predeterminate in base alla microstruttura ottenuta. Inoltre si possono modificare le proprietà magnetiche dei sistemi modificando la struttura cristallina dei sistemi aumentando la densità di difetti quali dislocazioni, vacanze e bordi grano, che vanno a creare punti di pinning per il moto delle pareti dei domini magnetici e fra tutti i metodi di sintesi l’alligazione meccanica potrebbe essere una tecnica molto performante, ma i risultati in letteratura relativi alle proprietà magnetiche di sistemi ottenuti per alligazione meccanica sono pochi, per questo motivo lo studio presentato studia un sistema noto come FeCoAlNiCr sintetizzato sia per alligazione meccanica che per Spark Plasma Sintering e valuta l’effetto della variazione del rapporto Ni/Cr nel sistema alligato meccanicamente.
Nel presente studio sono state analizzate diverse composizioni ottenute per alligazione meccanica partendo dalla composizione equimolare FeCoAlNiCr. In particolare, è stato variato il rapporto Ni/Cr e la composizione equimolare è stata poi confrontata con composizione ottenute per sinterizzazione per Spark Plasma Sintering. Il rapporto Ni/Cr è stato variato con la seguente sequenza: 0.5, 1, 2, 3 e 18.
Le polveri vergini sono fornite da Sigma Aldrich, le cui caratteristiche sono riportate nella tabella sottostante.
Tab.1 - Composizione delle polveri di metallo (BCC=cubico corpo centrate; FCC= cubico a facce centrate: HCP= esagonale compatto) / Composition of the metal powder used (BCC=body center cubic; FCC=face center cubic; HCP=Hexagonal closed-packed arrangement)
Le alligazioni meccaniche (MA – mechanical alloying) sono state eseguite in un mulino planetario (PM100, Retsch GmbH, Haan, Germany) equipaggiato con una giara da 250 mL e biglie di diversa dimensione (4-10 mm) in acciaio. Le polveri sono state accuratamente pesate usando una bilancia analitica e raccolte nella giara con le biglie e 1% wt. di acido stearico come agente di controllo di processo (process control agent PCA). Il BPR (ball to powder eight ratio) è 20:1, con rotazione di 400rpm. Lo strumento è stato programmato per avere 10 min di fermo alternati
a 15 min di movimento in modo da ridurre al minimo la formazione di calore con conseguente effetto cold welding delle polveri, per un totale di 10 ore di macinazione attiva. Tutte le operazioni che vedono la manipolazione delle polveri sono state eseguite in una glove box con atmosferadiArgonperevitarelacontaminazionedaossigeno.Sullepolverialligateèstatoquindicondottountrattamento termico in forno tubolare elettrico con atmosfera protettivadiArgonper4orea600°C,temperaturavalutata dopoanalisiDSC(SDTQ600V20.9Build20).
La composizione equimolare semplicemente miscelata è stata poi sintetizzata anche mediante tecnica di Spark Plasma Sintering (SPS) a due diverse temperature mediante DR.SINTER® SPS1050 (Sumitomo Coal & Mining, now SPS Syntex, Inc.) con stampo e pistone in grafite. I campioni hanno geometria cilindrica con altezza di 5 mm ediametro20mm. Lasintesièstata condottaadue diverse temperature massime nominali, i.e 1000 °C e 1250 °C (misurata con una termocoppia inserita in un foro cieco a contatto con la parete) applicando una pressione uniassiale di 60 MPa. La velcoità di riscaldamento è 100°C/min finoa950°Ce500°C/minfinoallatemperaturaimpostata di sinterizzazione. La temperatura massima e la presione sono mantenute per 5 minuti prima di riportare il forno a temperaturaambiente.
Il comportamento magnetico di tutte le composiizoni è statovalutatomediantemisuredisuscettivitàmagneticae magnetizzazion in funzione della temperatura. La suscettivitàmagneticaabassocampoèstatamisuratainfunzione
della temperatua in un ThermoMagnetic Analyzer (TMA) mediante un campo magnetico alternato di ampiezza 5 10-4 T. Misure di magnetizzazione in basso (10 mT) e alto campo (1T) sono state effettuate in un magnetomtero ad estrazione (Maglab2000 System della Oxford Instruments) nel range di temperatura 100-340 K.
Per ognuna delle composizioni è stata valutata la transizione magnetica ad alto e basso campo e sono state eseguite analisi microstrutturali, in particolare diffrazione e microscopia ottica.
Le indagini microstrutturali sono state condotte mediante diffrazione X-ray Diffraction, XRD Empyrean da Malvern Panalytical (serie III multicore) Geometria Bragg-Brentano. Rilevatore PIXcel 3D allo stato solido (technologia Medipix3). CuK α 40 kV e 40 mA, Specchio multistrato, una slitta divergente programmabile, una slitta soller e una mascera (1/4 °, 0.04 rad e 6 mm, rispettivamente. I diffrattogrammi sono stati raccolti nel range angolare da 10 a 120 °2Theta.
A completamento dei dati raccolti mediante diffrazione sono state raccolte le immagini mediante microscopia elettronica: Scanning electron microscopy (SEM- ESEM Quanta-200, FEI company) equipaggiato con Energy Dispersive X-ray Spectroscopy (EDS, INCA-350 energy-dispersive X-ray spectroscopy detector -Oxford Instruments) e FEI and SEM/FEG Nova NanoSEM 450 – FEI sempre equipaggiato con energy dispersive spectrometry (EDS). Per semplificare la lettura in Tab. 2 vengono definiti i nomi che verranno date alle diverse leghe sviluppate
Tab.2 - Nomenclatura adottata nello studio per identificare le leghe / Name attributed at each composition.
Composizione
Ni/Cr Nome 18 HEA1
FeCoAlNi30Cr10 MA 3 HEA2
FeCoAlNiCr MA 1 HEA3
FeCoAlNi27Cr13 MA 0.5 HEA4
FeCoAlNi0.5Cr0.03 MA @600°C 4h 17 HEA1TT
FeCoAlNi30Cr10 MA @600°C 4h 3 HEA2TT
FeCoAlNiCr SPS @1000°C 1 SPS1
FeCoAlNiCr SPS @1250°C 1 SPS2
RISULTATI
Tab. 3 mostra le composizioni in peso (wt%) e i relativi
calcoli molari delle singole composizioni realizzate per il presente lavoro
Tab.3 - Composizione in peso delle miscele di polvere sottoposte ad alligazione meccanica e SPS / Weight compositions of the powder mixtures subjected to mechanical alloying and SPS.
Peso (wt.%) dei singoli elementi nelle miscele di polvere
Al fine di determinare un possibile trattamento termico da eseguire sulle polveri si è eseguita una calorimetria differenziale a scansione, il cui risultato è riportato in Fig. 1. La misura determina la presenza di un picco a bassa temperatura (ca 310°C) probabilmente dovuto alla presenza di acido stearico, usato come agente di processo duran-
te alligazione meccanica. Successivamente si evidenzia il picco di cristallizzazione intorno ai 600 °C per poi trovare i picchi caratteristici della fusione che appaiono come tre picchi sovrapposti intorno ai 1300°C. Si è quindi scelto 600°C come temperatura per eseguire i trattamenti termici.
Fig.1 - DSC campione HEA2 / DSC analysis on HEA2 sample.
I diffrattogrammi raccolti sono mostrati in Fig. 2 e Fig. 3, dove vengono confrontate rispettivamente le leghe ottenute per alligazione meccanica a diverso rapporto Ni/Cr (HEA1, HEA2, HEA3 e HEA4) e le leghe dopo trattamento termico (HEA1TT e HEA2TT). Tutte le composizioni ottenute per sola alligazione meccanica presentano un certo
grado di amorfismo dovuto alle specifiche tecnologiche proprie del processo di macinazione. Le composizioni estreme HEA1 e HEA4 (rispettivamente con rapporto Ni/ Cr 18 e 0.5) mostrano entrambe predominanza di struttura BCC, mentre le composizioni intermedie (HEA2 e HEA3) sono bifasiche con predominanza di FCC. I diffrattogram-
mi raccolti mostrano che tutte le composizioni che hanno subito un trattamento termico ((HEA1TT, HEA2TT, SPS1 e SPS2), sia esso semplice trattamento termico o la sinterizzazione mediante SPS, presentano quindi un maggior grado di cristallinità rispetto alle polveri alligate. Indipendentemente dalla composizione la struttura che si ottiene è una struttura mista FCC/BCC con presenza di intermetallico γ -NiAl, a conferma di quanto osservato dagli stessi autori in lavori precedenti e come riportato in letteratura. A parità di composizione la diversa tempera-
tura di trattamento (SPS 1 e SPS2) non porta a modifiche strutturali, mentre a parità di temperatura di trattamento le due diverse composizioni (HEA1TT e HEA2TT) mostrano un comportamento singolare: la composizione HEA1TT (rapporto Ni/Cr 18) mantiene la struttura BCC mentre la composizione HEA2TT (con rapporto 3) mostra una predominanza di fase BCC rispetto alla fase FCC. Questi risultati sono confermati dalla letteratura dove si conferma i lunghi tempi, fino a 100 ore, per rendere termodinamicamente stabili le HEAs.
Fig.2 - Diffrattogrammi delle composizioni ottenute per alligazione meccanica / X-Ray pattern of mechanical alloying compositions.
Fig.3 - Diffrattogrammi delle composizioni dopo trattamento termico / X-ray pattern of treated samples.
Indipendentemente dalle diversità riscontrate nei diffrattogrammi tutte le composizioni mostrano complessivamente una buona omogeneità microstrutturale di tutti i
campioni confermando grazie all’analisi EDS la corretta stechiometria dei campioni, come riportato in Tab. 4
Tab.4 - Analisi EDS dei campioni realizzati / EDS analysis of samples.
Le misure termomagnetiche eseguite sulle diverse leghe sono riportate nelle immagini Fig. 4 e Fig. 5. I grafici riportano le misure di suscettività magnetica normalizzata in funzione della temperatura. Fig. 4 riporta le misure di leghe ottenute tutte per alligazione meccanica con diverso rapporto Ni/Cr. Al variare della composizione per le leghe ottenute per alligazione meccanica si nota un incremento della temperatura di transizione all’aumentare del rapporto Ni/Cr. Passando dal range 150-350 K per i rapporti Ni/Cr 1 e 3, fino a oltre 600K per Ni/Cr 17. A parità di composizione invece prima e dopo trattamento termico a 600°C per 4 ore la transizione tende ad un aumento della temperatura fino a circa 700K. Anche questo comportamento potrebbe essere dovuto al diverso grado di cristallinità dei due sistemi analizzati. HEA1 mostra un alto valore di temperatura di transizione come confermato da letteratura grazie alla sua struttura BCC, mentre HEA4 nonostante sia maggiormente BCC la sua transizione è influenzata dalla presenza di una piccola percentuale di FCC, come evidenziato dai diffrattogrammi precedentemente discussi (Fig. 2). Fig. 5 riporta le misure di suscettività magnetica per le composizioni sottoposte a trattamento termico in particolare la composizione equimolare trattata con SPS a due diverse temperature (SPS1 e SPS2) e le leghe con diverso rapporto Ni/ Cr ottenute per alligazione meccanica e successivo trattamento termico a 600°C (HEA1TT e HEA2TT). Come si può notare il metodo di ottenimento della lega influenza la
temperatura a cui avviene la transizione magnetica tra una fase ordinata e una fase paramagnetica ad alta temperatura. Infatti, se le leghe SPS1 e SPS2 mostrano una transizione intorno a 250 K abbastanza netta, la lega ottenuta per sola meccanosintesi a parità di composizione (HEA3) mostra dopo alligazione una transizione molto più ampia ad un intervallo di temperatura inferiore (c.a 150-250 K). A parità di trattamento la temperatura non influenza molto la temperatura di transizione, i.e SPS1 e SPS2 hanno un simile comportamento; mentre a parità di temperatura di trattamento invece la composizione della lega influenza molto la transizione, i.e. HEA1TTe HEA2TT. Questo potrebbe essere imputabile alla diversa microstruttura dei campioni che passano da uno stato molto amorfizzato nel caso della alligazione a una struttura cristallina dopo SPS o trattamento termico.
Fig.4 - Misure di suscettività magnetica dei campioni ottenuti per meccanosintesi al variare del rapporto Ni/Cr / Magnetic susceptibility of samples obtained by mechanical alloying as different Ni/Cr ratio.
Fig.5 - Misure di suscettività magnetica al variare del trattamento termico / Magnetic susceptibility of samples treated a differente heat treatment.
Lo scopo del presente lavoro è quello di ottenere materiali che mostrino una transizione magnetica regolabile nell'intervallo di temperature 290-350 K con un’ampia variazione della magnetizzazione, favorendo così la possibilità di realizzare generatori in grado di recuperare il calore di scarto a temperature inferiori a 100°C per generare energia elettrica da piccole differenze di temperatura. Sulla base della ricerca bibliografica per questo studio si è quindi scelta una stessa famiglia di HEA, i.e FeCoAlNiCr, con diverso rapporto fra Ni/Cr e due diversi metodi di sintesi: SPS e alligazione meccanica. Dai risultati emerge come non solo la composizione chimica ma anche il metodo di sintesi scelto possa influenzare la temperatura di transizione magnetica. Se da un lato alligazione meccanica offre vantaggi come l’estensione della solubilità allo sta-
to solido in sistemi non miscibili, processi a temperatura ambiente e riduzione della segregazione chimica, dall’altro determina la formazione di strutture fortemente amorfe e instabili termodinamicamente. Sicuramente anche a formazione di sistemi bifasici rende complessa la comprensione di quale sia il meccanismo predominante nella determinazione della temperatura di transizione magnetica. In quest’ottica quindi una più approfondita indagine della frazione di una fase rispetto all’altra potrebbe aiutare in tale compressione. Sviluppi futuri riguarderanno quindi non solo l’uso di tecniche di indagine per quantificare le fasi ma anche un’ulteriore variazione del rapporto Ni/Cr e della temperatura di trattamento al fine di ottenere una lega con transizione fra 290-350 K visto che le leghe fin ora indagate risultano avere transizione in un range leggermente inferiore.
[1] T. Borkar, Acta Mater. 116 (2023)
[2] J.Cieslak Journal of Alloys and Compounds 740 (2018)
[3] Colombini et al., Materials Chemistry and Physics 210 (2018)
[4] E. Dastanpour, et al., Journal of Alloys and Compounds 939 (2023)
[5] D. Dzekan, et al., APL Mater. 9 (2021)
[6] J. Duan, Sci China Materials 66 (2023)
[7] T. A. Edison, Pyromagnetic Generator, US-Pat. 476983 A, 1892
[8] European Commission, Report on Critical Raw Materials in the Circular Economy, 2018
[9] V. Franco, et al., Progr. Mater. Science 93 (2018)
[10] F. Gong et al., Acta Materalia 256 (2023)
[11] M. Gueltig, et al., Adv. Energy Mater. 7 (2017)
[12] W. Ji et al., Intermetallics 56 (2015)
[13] C. Jung Acta Materialia 171 (2019)
[14] Y.F. Kao Journal of Alloys and Compounds 488 (2009)
[15] P. Kumari, Journal of Magnetism and Magnetic Materials 554 (2022)
[16] S.R.Larsen et al., Journal of Alloys and Compounds 861 (2021)
[17] J.Y. Law, V. Franco, Journal of Materials Research (2022)
[18] C.M. Lin and H.L. Tsai, Mater. Chem. Phys. 128 (2011)
[19] Y.Ma et al., Adv. Mater 33 (2021)
[20] P. Martin et al., Metallurgical and Materials Transactions A 52A (2021)
[21] N.A. Morley et al., Scientific Reports (2020)
[22] Munitz et al., Journal of Alloys and Compounds 683 (2016)
[23] Perrin, JOM The Minerals, Metals & Materials Society (2017)
[24] E.J. Pickering et al., Mater Sci. Eng A 645 (2015)
[25] E.J. Pickering et al., Scr. Mater. 113 (2016)
[26] V. Shivam et al., Journal of Alloys and Compounds 832 (2020)
[27] V. Srivastava, et al., Adv. Energy Mater. 1 (2010)
[28] N. Tesla, Pyromagneto Electric Generator, US-Pat. 0428057 A1, 1890
[29] J.M. Torralba et al., Powder Metall, 62 (2019)
[30] S.Uporov, Intermetallics 83 (2017)
[31] T. Yang et al., Mater. Sci. Eng 648 (2015)
[32] Y.F. Ye, Mater. Today 19 (2016)
[33] C. Zhao, J. Mater Sci Tech 73 (2021)
[34] Q. Zhang et al., J. Alloy. Comp 693 (2017)
[35] K. Zhang J. Alloy. Compound 502 (2010)
At least 70% of all energy produced by humanity is dissipated as heat, therefore the development of new technologies to catch thermal energy for converting into reusable energy is essential to promote the transition towards a circular and sustainable economy. Thermomagnetic generators (Thermo-Magnetic power Generators TMG) are environmentally friendly energy conversion systems capable to address this challenge. The aim of this work is the development of advanced materials that can be exploited as active elements for heat harvesting and small-scale electricity production. Among the available materials, research has been focused on High Entropy Alloys (HEA) thanks to their peculiar properties. The developed HEAs are rare earth-free thus containing non-critical, easily accessible and recyclable 3d transition metals, such as Fe, Ni and Mn. Starting from the HEA of equimolar composition FeCoNiCrAl, the stoichiometry of the elements Ni e Cr was modified in order to evaluate the effect of the compositional changing with the transition temperature. The HEAs were obtained both by mechanical alloying and by FAST sintering (Field Assisted Sintering Technologies). The obtained compositions were studied using structural, microstructural analyzes and magnetic characterization techniques. Thermal treatments were performed to modify the crystallographic and magnetic structure and the degree of atomic order. The result leads to the identification of important considerations on the relationship between microstructure and magnetic properties.
KEYWORDS:
A. Meleddu, J. Ferino, S. Hecht, W. Frick, M.N. Amin, M. Meleddu, E. Kraemer, L. Pezzato, M. Ricotta, M. Dabalà, K. Brunelli
Lo sviluppo di materiali ad alta resistenza e basso peso risulta essere di sempre maggiore rilevanza in svariati settori industriali tra cui quello delle funi. Il presente lavoro ha come obiettivo quello di presentare alcuni dei risultati ottenuti nell’ambito del progetto europeo FIRST-WIRE, finanziato dal Research Fund for Coal and Steel – RFCS 2019. Obiettivo del progetto era quello di sviluppare e caratterizzare funi ibride con un guscio in acciaio inossidabile (acciaio super austenitico X1NiCrMoCuN25-20-7) e un cuore di fibra di carbonio (trefoli di fibre pre-impregnate). Oggetto del presente lavoro è la caratterizzazione della resistenza meccanica e della resistenza a corrosione dei singoli fili costituenti la fune. Nel dettaglio, sono state eseguite analisi della resistenza a trazione statica e a fatica del materiale ibrido e prove di pull out ottenendo risultati soddisfacenti in termini di resistenza e di allungamento e ottimi in termini della resistenza dell’interfaccia fibra-guscio. Per quanto concerne la resistenza alla corrosione sono state ottenute ottime caratteristiche di resistenza al pitting e non si sono riscontrate problematiche di corrosione per contatto galvanico mentre sono stati individuate possibili problematiche relative alla corrosione sotto sforzo.
INTRODUZIONE
Nel mercato delle funi metalliche, l'elevato rapporto prestazioni/peso delle funi d'acciaio presenta sfide significative per le applicazioni onshore/offshore come linee di ormeggio per piattaforme offshore, attrezzature di sollevamento per operazioni minerarie in acque profonde o ponti strallati/strutture strallate su larga scala. In questi scenari vengono adottate con successo le funi convenzionali in acciaio. Nelle linee di ormeggio (es.: per piattaforme galleggianti) le funi d'acciaio dimostrano robuste proprietà di resistenza e rigidità elastica superiore, mentre estensione e isteresi non pongono problemi significativi. Tuttavia, sono soggette a corrosione e la loro massa intrinseca presenta vincoli per campate estese nelle applicazioni in acque profonde. Attualmente il peso proprio delle funi convenzionali in acciaio ad alte prestazioni rappresenta una limitazione nel raggiungimento di grandi profondità marine per il sollevamento di applicazioni offshore. Per la maggior parte degli operatori leader a livello
A. Meleddu, J. Ferino
Astarte Strategies SrL, Italy
S. Hecht, W. Frick
University of Stuttgart, Germany
M. N. Amin, M. Meleddu
Teufelberger-Redaelli, Italy
E. Kraemer
Cunova GmbH; Germany
L. Pezzato, M. Ricotta, M. Dabalà, K. Brunelli
University of Padua, Department of Industrial Engineering, Italy
mondiale, questo limite è di circa 2.000 m.
Attualmente gli studi per ridurre il peso proprio delle funi metalliche ad alte prestazioni hanno recentemente proposto l’utilizzo di materiali compositi ibridi acciaio/CFRP [1,2] che prevedono l’impiego di fili di acciaio e fili di CFRP per formare funi più leggere.
Nell'ambito del programma di finanziamento EU RFCS, il progetto FIRST-WIRE [3] mira a sviluppare un filo ibrido in acciaio e fibra di carbonio per corde e cavi con prestazioni migliorate e peso ridotto. Nel presente lavoro viene brevemente descritto il concetto di filo ibrido sviluppato e i risultati sperimentali ottenuti nella caratterizzazione del prodotto. I risultati ottenuti hanno dimostrato che è possibile ottenere fili e funi leggeri ad alte prestazioni, convalidando pienamente il concetto di materiale ibrido proposto.
Produzione dei fili Ibridi
Il concetto di filo ibrido sviluppato nel presente lavoro prevede un guscio in acciaio inossidabile (con un diametro compreso tra 3 e 5 mm e uno spessore di 0,3-1,0 mm) che racchiude un nucleo costituito da fibre di carbonio ad alte prestazioni. Uno schema che illustra questo nuovo concetto di filo ibrido si trova in Fig.1. Questa innovazione è in fase di brevetto da Redaelli [4]. Le prestazioni finali del filo sono determinate sia dal guscio in acciaio inossidabile che dal nucleo in fibra di carbonio. In particolare le prestazioni sia dal punto di vista della resistenza meccanica che da quello della resistenza a corrosione dipendono dalla scelta del materiale costituente il guscio ed il nucleo.
I fili ibridi sono stati prodotti dall’azienda Cunova mediante processo di laminazione, per formare il tubo esterno con una saldatura continua longitudinale mediante tecnica
TIG. Le anime in fibra di carbonio sono state introdotte all'interno del tubo durante la laminazione prima della chiusura finale e della saldatura. Per il tubo in acciaio inox costituente il guscio esterno protettivo attorno al nucleo in fibra di carbonio è stato scelto un nastro di acciaio inossidabile super austenitico AISI F44/6Mo (X1NiCrMoCuN25-20-7). Matasse di fibra di carbonio ad alta resistenza pre-impregnate (Hyosung carbon fiber tows /7/ H2550 (12k/24k)) sono state scelte per andare a costituire il nucleo.
Caratterizzazione della resistenza meccanica e della resistenza a corrosione dei fili
La resistenza meccanica e a corrosione dei fili è stata valutata su fili ibridi di diametro 5.16 mm. La resistenza
meccanica dei fili ibridi è stata valutata mediante prove di trazione statica, prove di fatica e prove di pull-out. Tutte le prove di resistenza meccanica sono state eseguite con una macchina 100 PSA Schenk Hydropulse con cella di carico fino a 100 kN. Le prove sono state eseguite utilizzando un sistema di afferraggio dedicato (Fig.2) che blocca il filo in due piastre di acciaio con una scanalatura appositamente progettata della stessa dimensione dei fili. Le viti sono state chiuse con una chiave dinamometrica con un carico di 35 Nm. Per evitare scivolamenti tra il tubo e le fibre, i campioni sono stati testati con la parte finale opportunamente deformata per bloccare le fibre nei tubi. Le prove di fatica sono state realizzate in modalità trazione/ trazione con R=0.1. La resistenza alla corrosione per pitting è stata valutata mediante un test potenziodinamico (ASTMG61 in soluzione 3.5%NaCl), utilizzando il campione come elettrodo di lavoro, un elettrodo al calomelano come elettrodo di riferimento e un elettrodo di platino
come contro elettrodo. La corrosione per contatto galvanico (ASTM G71 in soluzione 3.5% NaCl e 9% NaCl) è stata valutata misurando la corrente passante tra un campione costituito dalla fibra di carbonio e un campione costituito dall’acciaio inossidabile in un rapporto di area 1
a 1. La corrosione sotto sforzo (ASTM G123/G36) è stata valutata mediante immersione dei campioni di filo (dritti oppure piegati a 90° per indurre uno stato di tensione) in soluzione di MgCl2 bollente e successiva osservazione dei campioni per individuare la possibile presenza di cricche.
Fig.2 - Geometria dei campioni utilizzati nella valutazione della resistenza meccanica e afferraggi sviluppati / Geometry of the samples and of the clamping systems employed for the mechanical characterization of the wires.
Caratterizzazione della resistenza meccanica dei fili I risultati delle prove di trazione statiche, eseguite su fili ibridi di diametro Φ 5,16 mm, sono riportati in Fig.3 a sinistra. La lunghezza iniziale dei campioni era di 250 mm. I test sono stati eseguiti alla velocità di 1 mm/min. Dai risultati riportati la combinazione del nucleo in fibra di carbonio e del guscio in acciaio inossidabile consente di ottenere un filo ibrido caratterizzato da elevata resistenza a trazione e buon allungamento. La resistenza alla trazione calcolata sulla zona esterna del filo è di circa 1200-1400MPa. È stata eseguita anche un’analisi frattografica SEM dei campioni dopo le prove di trazione e dai risultati (Fig.3 a destra) si può osservare la presenza di superficie di frattura duttile, tipica degli acciai inossidabili a temperatura ambiente. I test di pull out sono stati eseguiti su fili ibridi con diametro 5,16 mm. Un provino da 50 mm è stato inciso circonferenzialmente per l'intera profondità del guscio in acciaio in modo che i due semitubi vengano separati scorrendo sul nucleo in fibra di carbonio. Il test è stato eseguito staticamente ad una velocità di 1 mm/min. La parte vuota del tubo è stata afferrata per una lunghezza di 12 mm. La lunghezza del tubo contenente la fibra era quindi pari a 50-12=38 mm. I risultati riportati in Fig.4 a sinistra permettono di evidenziare come, dopo una prima rampa, lo
sforzo si avvicini ad un plateau di circa 4MPa. Il risultato è molto interessante perché mostra che, sebbene non sia stato applicato alcun trattamento specifico all’interfaccia fibra-tubo, la forza di attrito richiesta per estrarre le fibre è sufficientemente elevata da garantire una buona sinergia di entrambi i componenti all’interno del filo ibrido. I risultati sono confermati dall'analisi SEM dei campioni dopo il test di pull out (Fig.4 a destra), che mostra come le fibre si stacchino e si rompano parzialmente durante l'estrazione, ciò indica una forte forza di attrito tra le fibre e il tubo durante i test.
Fig.3 - Risultati delle prove di trazione statiche (a sinistra) e analisi della superficie di frattura dopo il test (a destra) / Results of the static tensile tests (left) and fracture surface (right) after the tests.
Fig.4 - Risultati delle prove di pull out (a sinistra) e analisi SEM del campione dopo il test (a destra) / Results of the pull-out tests (left) and SEM analysis of the samples after the test (right).
Considerando i test di resistenza a fatica la Fig. 5 mostra i risultati dell'analisi statistica nell'ipotesi di distribuzione log-normale del numero di cicli a rottura Nf e dispersione costante rispetto al livello massimo di carico applicato raggiunto nel ciclo di fatica. Considerando i dati sperimentali disponibili, la resistenza a fatica di riferimento valutata a 200'000 cicli è risultata pari a Fmax=3,86 kN per P. S.=50%, pari a 3,55 kN per P. S.=90% e pari a 4,19 per P. S.=10%, come riportato nella Tab.1
Fig.5 - Risultati delle prove di fatica / Results of the fatigue tests .
Tab.1 - Risultati delle prove di fatica / Results of the fatigue tests.
Caratterizzazione della resistenza a corrosione dei fili
Per quanto concerne la resistenza alla corrosione sono state innanzi tutto effettuati test di contatto galvanico tra il tubo in acciaio superaustenitico e le fibre di carbonio in modo da comprendere se il concetto stesso di filo ibrido fosse compatibile con un utilizzo in ambiente marino. I risultati dei test, effettuati sia in soluzione 3.5% che 9%
NaCl, sono riportati in Tab.2. Come si può osservare in entrambi i casi le correnti galvaniche che fluiscono tra i campioni sono estremamente basse, fatto che permettere di escludere l’insorgenza di corrosione per contatto galvanico tra il nucleo in fibra di carbonio e il guscio in acciaio inossidabile.
Tab.2 - Risultati delle prove di contatto galvanico in soluzione 3.5% e 9% NaCl / Results of the galvanic corrosion tests in solution 3.5% and 9% of NaCl
Current density [A/cm2]
3,5% NaCl 9% NaCl
Stainless steel Tube/Carbon Fibers
È stata valutata anche la resistenza alla corrosione per pitting del filo ibrido ed in particolare del guscio in acciaio inossidabile che viene a contatto con l’ambiente esterno.
A tale scopo sono state effettuate analisi potenziodinamiche e i risultati sono riportati in Fig.6 e in Tab.3. Dall’analisi
dei risultati e in accordo con l’elevato PREN del materiale si può riscontrare una notevole resistenza alla corrosione per pitting del materiale costituente il guscio esterno del filo ibrido.
Fig.6 - Risultati delle prove potenziodinamiche in soluzione 3.5%NaCl / Results of the potentiodynamic polarization tests in 3.5%NaCl.
Tab.3 - Valori della corrente e del potenziale di corrosione e del potenziale di pitting, estrapolati graficamente dalle prove potenziodinamiche / Values of the corrosion potential and corrosion current and of the pitting potential extrapolated from the potentiodynamic polarization tests E corr [V] I corr [A/cm2] Epitt [V] Stainless steel Tube -0,524 1,12 10-7 0,609
Sono state effettuate prove di corrosione sotto sforzo secondo la norma ASTM G36 – 94. Sono stati preparati sei campioni piegandone la metà a 90° per produrre uno stato di tensione. Successivamente, i campioni sono stati immersi in cloruro di magnesio bollente per 1 ora e poi osservati al SEM al fine di identificare la possibile presenza di cricche che risultano indice di suscettibilità a corrosione sotto sforzo. I risultati dell’osservazione al SEM sono riportati in Fig.7 per il campione non piegato e in Fig.8 per il campione piegato a 90°. I risultati delle osservazioni al SEM hanno dimostrato la notevole
suscettibilità del filo ibrido alla tensocorrosione (SCC). Sia i campioni piegati (Fig.8) che quelli non piegati (Fig.7) presentano un numero significativo di cricche lunghe e profonde in particolare nelle immediate vicinanze delle zone saldate. La presenza di cricche anche nei campioni non piegati risulta indicativa del fatto che la suscettibilità alla corrosione sotto sforzo risulta legata non solo alla presenza di una sollecitazione esterna ma anche alla presenza di tensioni residue all’interno del filo (come successivamente dimostrato mediante analisi XRD).
Fig.7 - Risultati delle osservazioni al SEM dei campioni non piegati dopo test di corrosione sotto sforzo (a) 200X; (b) 1000X; (c) 2000X / Results of the SEM observation of the unstressed samples after SCC tests (a) 200X; (b) 1000X; (c) 2000X.
Fig.8 - Risultati delle osservazioni al SEM dei campioni piegati dopo test di corrosione sotto sforzo (a) 200X; (b) 1000X; (c) 2000X / Results of the SEM observation of the stressed samples after SCC tests (a) 200X; (b) 1000X; (c) 2000X.
CONCLUSIONI
Il presente lavoro riporta i risultati relativi allo sviluppo e alla caratterizzazione di un innovativo filo ibrido costituito da un guscio esterno in acciaio inossidabile e un nucleo interno in fibre di carbonio per la realizzazione di funi e cavi leggeri ad alte prestazioni. La produzione di fili ibridi basata sulla laminazione di nastri con saldatura continua (TIG), ha dimostrato la fattibilità del processo di produzione su larga scala. La caratterizzazione meccanica dei fili
ha permesso di evidenziare ottime caratteristiche di resistenza e allungamento in rapporto al peso del filo mentre il comportamento a fatica deve essere ulteriormente indagato al fine di indagare il reale contributo delle fibre. I test di pull out hanno permesso di evidenziare la formazione di una forte interfaccia fibra/guscio inox anche in assenza di trattamenti specifici. Per quanto concerne il comportamento a corrosione è stata esclusa la possibile insorgenza di fenomeni di corrosione per contatto galva-
nico tra guscio in acciaio e nucleo di fibre di carbonio ed è stata altresì verificata l’elevata resistenza al pitting garantita dalla presenza del guscio in acciaio inossidabile. È stata inoltre riscontrata una suscettibilità alla corrosione sotto tensione che dovrà essere opportunamente ridotta andando a modificare alcuni step del processo produttivo. In conclusione i risultati risultano essere estremamente promettenti per la realizzazione di funi ad alte prestazioni in filo ibrido acciaio inox/fibra di carbonio anche se alcuni aspetti del processo produttivo andranno modificati al
fine di aumentare la resistenza a fatica e ridurre la suscettibilità alla corrosione sotto sforzo.
Questa ricerca è stata cofinanziata dall'Unione Europea nell'ambito del programma Fondo di ricerca per il carbone e l'acciaio – RFCS CALL 2019, Project: “FIber Reinforced STeel WIREs for high performance lightweight ropes and cables operating in demanding scenarios” N. Project 899299.
[1] Xiong W, Cai CS, Xiao R, Deng L. Concept and analysis of stay cables with a CFRP and steel composite section. KSCE Journal of Civil Engineering. 2011; 16. 10.1007/s12205-012-1152-1.
[2] Cai H, Aref AJ. On the design and optimization of hybrid carbon fiber reinforced polymer-steel cable system for cable-stayed bridges. Composites Part B: Engineering, 2015; 68: 146-152
[3] https://firstwire.eu/
[4] Redaelli Patent WO 2013/065074 A1: Composite Wire with Protective External Metallic Mantle and Internal Fiber
The development of highly resistant and lightweight materials is becoming increasingly important in various industrial sectors including the ropes sector. The objective of this work is to present some of the results obtained in the European FIRST-WIRE project, financed by the Research Fund for Coal and Steel - RFCS. The objective of the project was to develop and characterize hybrid ropes with a stainless-steel shell (super austenitic steel X1NiCrMoCuN25-20-7) and a carbon fiber core (pre-impregnated fiber bundles). The object of this work is the characterization of the mechanical and corrosion resistance of the single wires constituting the rope. In detail, analyses of the static tensile and fatigue resistance of the hybrid material and pull out tests were carried out, obtaining satisfactory results in terms of resistance and elongation and excellent in terms of the resistance of the fibre-shell interface. As regards corrosion resistance, excellent resistance to pitting was obtained and no problems of corrosion due to galvanic contact were encountered while possible problems relating to stress corrosion cracking were identified.
KEYWORDS:
Organizzate da
con il patrocinio di Sponsorizzate da
AIM, APCE, AMPP e Università Politecnica delle Marche vi invitano al più importante evento nazionale dedicato alla corrosione e protezione dei metalli!
La XVI edizione delle Giornate Nazionali sulla Corrosione e Protezione si terrà in presenza ad Ancona nei giorni 25, 26 e 27 giugno 2025, presso la Facoltà di Ingegneria dell’Università Politecnica delle Marche.
Le Giornate rappresentano l’evento di riferimento a livello nazionale per la discussione e il confronto sulle questioni scientifiche, tecnologiche e produttive, nell’ambito della corrosione e protezione dei materiali. In particolare, il Convegno prevede la presentazione dei risultati raggiunti da vari gruppi di studio e da numerose aziende del settore, in forma orale e poster.
Presentazione di memorie
Gli interessati a presentare memorie scientifiche e tecniche dovranno inviare titolo, nomi degli autori con relative affiliazioni ed un breve riassunto alla Segreteria organizzativa, entro il 13 dicembre 2024
Le memorie potranno essere proposte:
· compilando il form online dedicato all’evento, sul sito www.aimnet.it
· inviando i dati richiesti all’indirizzo info@aimnet.it
Segreteria organizzativa
Via Filippo Turati 8 · 20121 Milano tel: +39 0276397770 · +39 0276021132 info@aimnet.it www.aimnet.it
La dr.ssa Sara Scolari, dottoranda del Politecnico di Milano – Dipartimento di Meccanica, nominata da AIM per il 2024 FEMS Master Thesis Awards, si è classificata al terzo posto con la presentazione della sua tesi magitrale Agglomeration of integrated cycle steel plant by-products through several organic binders.
Il conferimento è avvenuto in occasione del FEMS Junior EUROMAT organizzata dalla IOM3 a Manchester nei giorni
15-18 luglio.
Il riconoscimento, istituito nel 2018, mira a premiare le migliori tesi di laurea magistrale sulla scienza e l'ingegneria dei materiali, presentate in qualsiasi istituzione accademica del paese di una qualsiasi associazione membro FEMS.
Corso METALLURGIA PER NON METALLURGISTI
Milano, 15-16-22-23-29-30 ottobre 2024
>> SCOPRI DI PIÙ
ECIC 2024 - 9TH EUROPEAN COKE AND IRONMAKING CONGRESS
Bardolino, 16-18 ottobre 2024
>> SCOPRI DI PIÙ
Giornata di StudioINNOVAZIONE E DIGITALIZZAZIONE IN PRESSOCOLATA: VERSO IL FUTURO DELLA PRODUZIONE
Kilometro Rosso - Stezzano BG - 5 novembre 2024
>> SCOPRI DI PIÙ
Giornata di Studio MICROSCOPIA ELETTRONICA APPLICATA ALLA FAILURE ANALYSIS
Campogalliano MO c/o Tec Eurolab - 7 novembre 2024
>> SCOPRI DI PIÙ
L’elenco completo delle iniziative è disponibile sul sito: www.aimnet.it (*) In caso non sia possibile svolgere la manifestazione in presenza, la stessa verrà erogata a distanza in modalità webinar
Giornata di Studio FUTURO SOSTENIBILE E COMPETITIVO DELLA METALLURGIA DELLE POLVERI TRADIZIONALE
Maerne VE c/o Pometon - 14 novembre 2024
>> SCOPRI DI PIÙ
Corso PROVE NON DISTRUTTIVE
Milano c/o Fast - 21-22 novembre 2024
>> SCOPRI DI PIÙ
Giornata di Studio Tecniche analitiche derivate dai raggi X
Milano c/o Fast - 28 novembre 2024
>> SCOPRI DI PIÙ
International Meeting on CIRCULAR METALLURGY - Raw Materials, By-products & Recycling
Bergamo, 28-29 novembre 2024
>> SCOPRI DI PIÙ
www.aimnet.it
Norme pubblicate e progetti in inchiesta (aggiornamento al 31 agosto 2024)
Norme UNSIDER pubblicate da UNI nei mesi di luglio e agosto 2024
UNI EN 1561:2024
Fonderia - Getti di ghisa grigia
UNI EN 10178:2024
Acciai - Determinazione del niobioMetodo spettrofotometrico
UNI EN 10179:2024
Acciai - Determinazione dell'azoto (tenori in tracce) - Metodo spettrofotometrico
UNI EN 10188:2024
Acciai e ghise - Determinazione del contenuto di cromo - Metodo mediante spettrometria di assorbimento atomico nella fiamma (FAAS)
UNI EN 10251:2024
Materiali magnetici - Metodi di determinazione delle caratteristiche geometriche di lamiere e nastri magnetici di acciaio
UNI EN 16079:2024
Fonderia - Getti di ghisa a grafite compatta (vermicolare)
UNI EN ISO 8840:2024
Materiali refrattari - Determinazione della massa volumica apparente del materiale in granuli
UNI EN ISO 16961:2024
Industrie del petrolio e del gas compresa l'energia a basse emissioni di CO2 - Rivestimento protettivo interno e
rivestimento dei serbatoi di stoccaggio di acciaio
UNI EN ISO 21068-2:2024
Analisi chimica delle materie prime e dei prodotti refrattari contenenti carburo di silicio nitruro di silicio, ossinitruro di silicio e sialon - Parte 2: Determinazione della perdita alla combustione del carbonio totale, del carbonio libero e del carburo di silicio, della silice totale e libera e del silicio totale e libero
UNI EN ISO 15544:2024
Industrie del petrolio e del gas - Impianti di produzione offshore - Requisiti e linee guida per la risposta alle emergenze
UNI EN ISO 21068-1:2024
Analisi chimica delle materie prime e dei prodotti refrattari contenenti carburo di silicio nitruro di silicio, ossinitruro di silicio e sialons - Parte 1: Informazioni generali, terminologia e preparazione del campione
UNI EN ISO 21068-3:2024
Analisi chimica delle materie prime e dei prodotti refrattari contenenti carburo di silicio, nitruro di silicio, ossinitruro di silicio e sialon - Parte 3: Determinazione dell'azoto, dell'ossigeno e dei componenti metallici e ossidanti
Norme UNSIDER ritirate con sostituzione da UNI nei mesi di luglio e agosto 2024
UNI EN 10178:1990
Analisi chimica dei materiali ferrosi. Determinazione del niobio negli acciai. Metodo spettrofotometrico.
UNI EN 10179:1990
Analisi chimica dei materiali ferrosi.
Determinazione dell'azoto (tenori in tracce) negli acciai. Metodo spettrofotometrico.
UNI EN 10188:1992
Analisi chimica dei materiali ferrosi. Determinazione del cromo negli acciai e nelle ghise. Metodo mediante spettrometria di assorbimento atomico nella fiamma.
UNI EN 10251:2015
Materiali magnetici - Metodi di determinazione delle caratteristiche geometriche di lamiere e nastri magnetici di acciaio
UNI EN 16079:2012
Fonderia - Getti di ghisa a grafite compatta (vermicolare)
UNI EN 993-18:2003
Metodi di prova per i prodotti refrattari formati densi - Determinazione della massa volumica apparente del materiale in granuli (metodo dell'acqua)
UNI EN ISO 16961:2015
Industrie del petrolio, petrolchimiche e del gas naturale - Rivestimento protettivo interno e rivestimento dei serbatoi di stoccaggio di acciaio
UNI EN ISO 21068-2:2008
Analisi chimica delle materie prime e dei prodotti refrattari contenenti carburo di silicio - Parte 2: Determinazione della perdita alla combustione del carbonio totale, del carbonio libero e del carburo di silicio, della silice totale e libera e del silicio totale e libero
UNI EN ISO 15544:2010
Industrie del petrolio e del gas naturale - Impianti di produzione offshore -
Requisiti e linee guida per la risposta alle emergenze
UNI EN ISO 21068-1:2008
Analisi chimica delle materie prime e dei prodotti refrattari contenenti carburo di silicio - Parte 1: Informazioni generali e preparazione del campione
UNI EN ISO 21068-3:2008
Analisi chimica delle materie prime e dei prodotti refrattari contenenti carburo di silicio - Parte 3: Determinazione dell'azoto, dell'ossigeno e dei componenti metallici e ossidanti
UNI EN 1561:2011
Fonderia - Getti di ghisa grigia
Norme UNSIDER pubblicate da CEN e ISO nei mesi di luglio e agosto 2024
EN 16482:2024
Founding - Continuous cast iron bars
EN 13480-2:2024
Metallic industrial piping - Part 2: Materials
EN 13480-1:2024
Metallic industrial piping - Part 1: General
EN 13480-4:2024
Metallic industrial piping - Part 4: Fabrication and installation
EN 13480-3:2024
Metallic industrial piping - Part 3: Design and calculation
EN 13480-8:2024
Metallic industrial piping - Part 8: Additional requirements for aluminium and aluminium alloy piping
EN 13480-6:2024
Metallic industrial piping - Part 6: Additional requirements for buried piping
EN 13480-5:2024
Metallic industrial piping - Part 5: Inspection and testing
EN ISO 10714:2024
Steel and iron - Determination of phosphorus contentPhosphovanadomolybdate spectrophotometric method (ISO 10714:2024)
EN 10248-2:2024
Hot-rolled steel sheet piles - Part 2: Tolerances on dimensions and shape
EN 10249-2:2024
Cold formed steel sheet piles - Part 2: Tolerances on dimensions and shape
EN 12560-1:2024
Flanges and their joints - Dimensions of gaskets for Class-designated flangesPart 1: Non-metallic flat gaskets with or without inserts
EN 1514-1:2024
Flanges and their joints - Dimensions of gaskets for PN-designated flangesPart 1: Non-metallic flat gaskets with or without inserts
ISO 15590-1:2024
Oil and gas industries including lower carbon energy — Factory bends, fittings and flanges for pipeline transportation systems — Part 1: Induction bends
ISO 10714:2024
Steel and iron — Determination of phosphorus content — Phosphovanadomolybdate spectrophotometric method
ISO 4941:2024
Steel and iron — Determination of molybdenum content — Thiocyanate spectrophotometric method
ISO 10427-1:2024
Oil and gas industries including lower carbon energy — Equipment for well cementing — Part 1: Casing bow-spring centralizers
ISO 6338-2:2024
Calculations of greenhouse gas (GHG) emissions throughout the liquefied natural gas (LNG) chain — Part 2: Natural gas production and transport to LNG plant
ISO 643:2024
Steels — Micrographic determination of the apparent grain size
ISO 642:2024
Steel — Hardenability test by end quenching (Jominy test)
Progetti UNSIDER messi allo studio dal CEN (Stage 10.99) – agosto e settembre 2024
EN ISO 19905-1:2023/prA1
Oil and gas industries including lower carbon energy -” Site-specific assessment of mobile offshore units -” Part 1: Jack-ups: elevated at a site -” Amendment 1
prEN ISO 7799 rev
Metallic materials -” Sheet and strip 3 mm thick or less -” Reverse bend test
prEN ISO 20482 rev
Metallic materials -” Sheet and strip -” Erichsen cupping test
prEN ISO 14310 rev
Oil and gas industries including lower carbon energy ” Downhole equipment ”
Packers and bridge plugs
prEN ISO 15136-2 rev
Oil and gas industries including lower carbon energy ” Progressing cavity pump systems for artificial lift ” Part 2: Surfacedrive systems
prEN ISO 21809-1 rev
Petroleum and natural gas industries ” External coatings for buried or submerged pipelines used in pipeline transportation systems ” Part 1: Polyolefin coatings (3-layer PE and 3-layer PP)
Progetti UNSIDER in inchiesta prEN e ISO/DIS – agosto e settembre 2024
prEN – progetti di norma europei
prEN 15979
Testing of ceramic raw materials and ceramic materials - Direct determination of mass fractions of impurities in powders and granules of silicon carbide by optical emission spectrometry by direct current arc excitation (DCArc-OES)
prEN ISO 19901-1
Oil and gas industries including lower carbon energy - Specific requirements for offshore structures - Part 1: Metocean design and operating considerations (ISO/DIS 19901-1:2024)
prEN ISO 14577-1
Metallic materials - Instrumented indentation test for hardness and materials parameters - Part 1: Test method (ISO/DIS 14577-1:2024)
prEN ISO 14577-2
Metallic materials - Instrumented indentation test for hardness and materials parameters - Part 2: Verification and calibration of testing machines (ISO/ DIS 14577-2:2024)
prEN ISO 14577-3
Metallic materials - Instrumented indentation test for hardness and materials parameters - Part 3: Calibration of reference blocks (ISO/DIS 145773:2024)
prEN ISO 26203-1
Metallic materials - Tensile testing at high strain rates - Part 1: Elastic-bar-type systems (ISO/DIS 26203-1:2024)
prEN 10338
Hot rolled and cold rolled non-coated products of multiphase steels for cold forming - Technical delivery conditions
ISO/DIS – progetti di norma internazionali
ISO/DIS 14577-3
Metallic materials — Instrumented indentation test for hardness and materials parameters — Part 3: Calibration of reference blocks
ISO/DIS 5490
Steel — Rating and classifying nonmetallic inclusions using the scanning electron microscope
ISO/DIS 4940
Steel and cast iron — Determination of nickel content — Flame atomic absorption spectrometric method
ISO/DIS 26203-1
Metallic materials — Tensile testing at high strain rates — Part 1: Elastic-bar-type systems
ISO/DIS 19901-1
Oil and gas industries including lower carbon energy — Specific requirements for offshore structures — Part 1: Metocean design and operating
considerations
ISO/DIS 14577-1
Metallic materials — Instrumented indentation test for hardness and materials parameters — Part 1: Test method
ISO/DIS 14577-2
Metallic materials — Instrumented indentation test for hardness and materials parameters — Part 2: Verification and calibration of testing machines
ISO/DIS 5872
Oil and gas industries including lower carbon energy — Pipeline transportation systems — Terms and definitions
Progetti UNSIDER al voto FprEN e ISO/FDIS – agosto e settembre 2024
FprEN – progetti di norma europei
FprEN ISO 20182
Refractory test-piece preparation - Gunning refractory panels by the pneumatic-nozzle mixing type guns (ISO/ FDIS 20182:2024)
FprEN ISO 23779
Shot blasting machinery - safety and environmental requirements (ISO/FDIS 23779:2024)
FprEN ISO 10855-1
Offshore containers and associated lifting sets - Part 1: Design, manufacture and marking of offshore containers (ISO/FDIS 10855-1:2024)
FprEN ISO 10855-2
Offshore containers and associated lifting sets - Part 2: Design, manufacture and marking of lifting sets (ISO/FDIS 108552:2024)
FprEN ISO 10855-3
Offshore containers and associated lifting sets - Part 3: Periodic inspection, examination and testing (ISO/FDIS 108553:2024)
FprCEN/TR 1591-6
Flanges and their joints - Design rules for gasketed circular flange connectionsPart 6: Background information
FprEN ISO 23063
Foundry machinery - Safety requirements for high pressure die casting machines (ISO/FDIS 23063.2:2024)
FprEN 15266
Stainless steel pliable corrugated tubing kits for gas installation pipework with an operating pressure up to 0,2 MPa (2 bar)
FprEN 10265
Magnetics materials - Specification for electrical steel strip and sheet with specified mechanical properties and magnetic polarization
FprEN 10216-2
Seamless steel tubes for pressure purposes - Technical delivery conditions - Part 2: Non-alloy and alloy steel tubes with specified elevated temperature properties
ISO/FDIS – progetti di norma internazionali
ISO/FDIS 17650
Low-alloyed steel — Determination of Mn, P, Cr, Ni, Mo, Co, Cu, V, Ti, As and Sn — Inductively coupled plasma atomic emission spectrometric method
ISO/FDIS 5124
Loading and unloading of liquefied natural gas (LNG) tank wagons and containers
ISO/FDIS 10855-1
Offshore containers and associated lifting sets — Part 1: Design, manufacture and marking of offshore containers
ISO/FDIS 10855-2
Offshore containers and associated lifting sets — Part 2: Design, manufacture and marking of lifting sets
ISO/FDIS 10855-3
Offshore containers and associated lifting sets — Part 3: Periodic inspection, examination and testing
ISO/FDIS 10803
Design method for ductile iron pipes
ISO/FDIS 7801
Metallic materials — Wire — Reverse bend test
BERGAMO 28-29 NOVEMBER 2024
Prospective authors wishing to present are invited to submit a tentative title and an abstract of about 400 words (in English) to the Organising Secretariat. The abstract should provide sufficient information for a fair assessment.
Two ways to submit papers will be available:
• to fill in the form on the International Meeting website at www.aimnet.it
• to send the title and the abstract, together with the requested information (Name and Surname, Affiliation, Mailing Address, Phone and e-mail) by e-mail to: aim@aimnet.it
ORGANISED BY WITH THE SUPPORT OF
6-9 OCTOBER
IRONMAKING
STEELMAKING
ROLLING OF FLAT AND LONG PRODUCTS, FORGING
STEEL MATERIALS AND THEIR APPLICATION, ADDITIVE MANUFACTURING, SURFACE TECHNOLOGIES
HYDROGEN-BASED STEELMAKING, CO2-MITIGATION, TRANSFORMATION /ENVIRONMENT /ENERGY
DIGITAL TRANSFORMATION
Organised by