Italiana La Metallurgia
International Journal of the Italian Association for Metallurgy
n. 03 marzo 2025
Organo ufficiale dell’Associazione Italiana di Metallurgia. Rivista fondata nel 1909
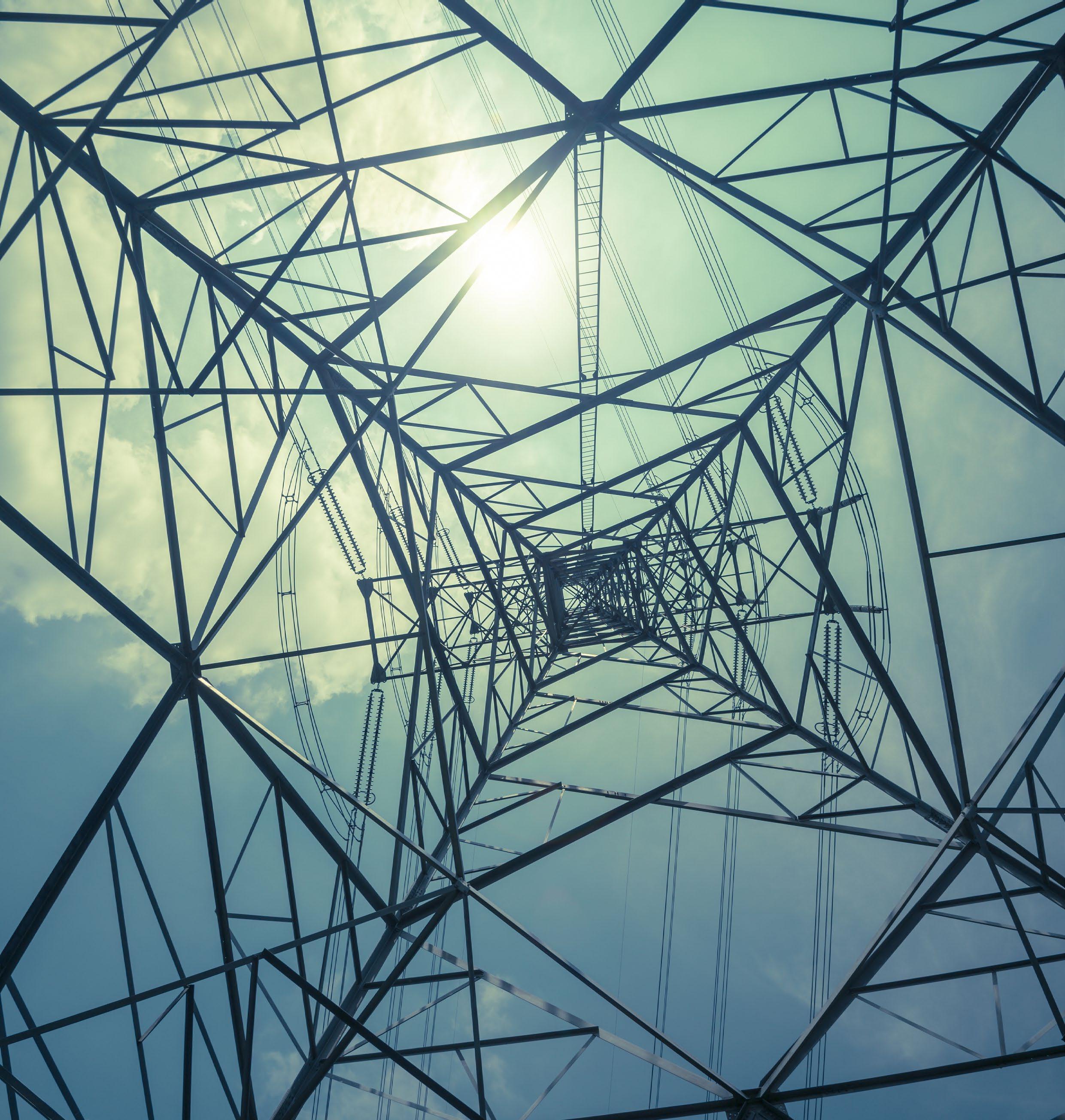
International Journal of the Italian Association for Metallurgy
n. 03 marzo 2025
Organo ufficiale dell’Associazione Italiana di Metallurgia. Rivista fondata nel 1909
International Journal of the Italian Association for Metallurgy
Organo ufficiale dell’Associazione Italiana di Metallurgia. HouseorganofAIMItalianAssociationforMetallurgy. Rivista fondata nel 1909
Direttore responsabile/Chiefeditor: Mario Cusolito
Direttore vicario/Deputydirector: Gianangelo Camona
Comitato scientifico/Editorialpanel: Marco Actis Grande, Silvia Barella, Paola Bassani, Christian Bernhard, Massimiliano Bestetti, Wolfgang Bleck, Franco Bonollo, Irene Calliari, Mariano Enrique Castrodeza, Emanuela Cerri, Vlatislav Deev, Andrea Di Schino, Donato Firrao, Bernd Kleimt, Carlo Mapelli, Denis Jean Mithieux, Roberto Montanari, Marco Ormellese, Mariapia Pedeferri, Massimo Pellizzari, Barbara Previtali, Evgeny S. Prusov, Dario Ripamonti, Dieter Senk
Segreteria di redazione/Editorialsecretary: Marta Verderi
Comitato di redazione/Editorialcommittee: Federica Bassani, Gianangelo Camona, Mario Cusolito, Carlo Mapelli, Federico Mazzolari, Marta Verderi, Silvano Panza
Direzione e redazione/Editorialandexecutiveoffice: AIM - Via F. Turati 8 - 20121 Milano tel. 02 76 02 11 32 - fax 02 76 02 05 51 met@aimnet.it - www.aimnet.it
Reg. Trib. Milano n. 499 del 18/9/1948. Sped. in abb. Post. - D.L.353/2003 (conv. L. 27/02/2004 n. 46) art. 1, comma 1, DCB UD
Immagine in copertina: Shutterstock
Gestione editoriale e pubblicità Publisher and marketing office: siderweb spa sb Via Don Milani, 5 - 25020 Flero (BS) tel. 030 25 400 06 commerciale@siderweb.com - www.siderweb.com
La riproduzione degli articoli e delle illustrazioni è permessa solo citando la fonte e previa autorizzazione della Direzione della rivista. Reproduction in whole or in part of articles and images is permitted only upon receipt of required permission and provided that the source is cited.
siderweb spa sb è iscritta al Roc con il num. 26116
n. 03 marzo 2025 Anno 116 - ISSN 0026-0843
Editoriale / Editorial
Giorgio Gavelli - Consulente . pag.05
Memorie scientifiche / Scientific papers
Materiali per l’energia / Materials for energy
Risposta al trattamento termomeccanico dell'acciaio EUROFER97: microstruttura e proprietà meccaniche
G. Stornelli, A. di Schino, D. Croccolo, G. Olmi, R. Montanari, A. Varone, C. Testani ............................................ pag.08
Studio dei processi di coating per il rivestimento in ferrite di materiali SMC
E. Poskovic, L. Ferraris, F. Franchini, M. Actis Grande ......................................................................................... pag.17
Green steel initiatives supported by CERO Waste Refractory Concept, enhanced slag engineering and using circular metallurgical additives
F. Kek, K-M. Zettl, N. Tanasic, P. Stahl, D. Giunta, P. Trezzi ............................................................... pag.27
AI-based monitoring of steel scrap properties for improved utilization in scrap based steelmaking
B. Kleimt, Z. Kargar, V. Peiss, A. Arteaga Ayarza, D. Mier Vasallo, M. Ferrer Prieto, I. Unamuno Iriondo ................. pag.35
Current state of grinding sludge recovery in the bearing industry: a review
M. Dehghanpour Abyaneh, R. Sesana, M. S. Javadi, S. Lamparelli, S. Rizzo ...................................................... pag.45
Atti e notizie / AIM news
Eventi AIM / AIM events pag.57 Comitati tecnici / Technical Committees pag.60 Normativa / Standards .................................................................................................... pag.64
Palaexpo Veronafiere
www.aimnet.it/estad2025
in collaboration with with the support of sponsored by
The knowledge and the development of the new ideas enhance progress. With the 7th European Steel Technology and Application Days 2025 (7th ESTAD 2025) AIM offers attendants and visitors the opportunity to meet, exchange their ideas, perform fruitful discussion and create new professional relationships involving technology providers, suppliers, producers and customers.
The meeting will be focused on the technological advances, changes of the supply chain involving the raw materials and energy sources, transformation of the production processes and plants to accomplish the twin transition (ecological and digital) and the new perspective of steel applications.
The registration is open. Registration fees are available on the ESTAD 2025 Conference website: www.aimnet.it/estad2025
Monday 6 October 2025 (16:00-18:30):
Early Congress registration and new on-site registration (pick-up of Conference material; possibility for speakers to upload their presentation at the slide centre)
Tuesday 7 October 2025: Opening/plenary session | Technical sessions | Get-together
Wednesday 8 October 2025: Technical sessions | Conference dinner
Thursday 9 October 2025: Technical sessions | Closing session
The Conference will be enhanced by an Exhibition at which companies will have the opportunity to inform all delegates of their latest developments.
Moreover, together with our partner Siderweb, we would be pleased to offer you a sponsorship package tailored to suit your own needs.
You can find on the Conference website more information together with the already present exhibitors.
Via Filippo Turati 8 | 20121 Milano MI | Italy
Email: estad2025@aimnet.it Phone: +39 0276021132 www.aimnet.it/estad2025
“"Un equilibrio tra crescita demografica, sviluppo economico-tecnologico e cambiamenti climatici richiede una transizione energetica radicale, pena conseguenze catastrofiche."
“A balance between demographicgrowth, economic-technological development and climate changerequiresaradical energy transition, on penaltyofcatastrophic consequences.”
Giorgio Gavelli Consulente
La discussione sui materiali per l'energia comporta una riflessione sull’energia stessa, in particolare sul modo in cui viene prodotta (o meglio, convertita), trasportata e utilizzata. Come affermava Vaclav Smil, l'energia è l’unica "moneta universale", essenziale per ogni attività e fondamentale per la vita. L’uomo ha imparato a utilizzare i flussi energetici disponibili e modellato lo sviluppo della sua civiltà di conseguenza, passando dai combustibili fossili all’energia nucleare al fotovoltaico. La domanda energetica crescerà rapidamente a causa della crescita demografica, dello sviluppo economico-tecnologico (si pensi all’impatto dell’intelligenza artificiale, che secondo alcune stime già adesso consumerebbe circa l’1% dell’energia prodotta) e dei cambiamenti climatici. Un equilibrio tra questi fattori richiede una transizione energetica radicale, pena conseguenze catastrofiche. In questo contesto, i materiali sono cruciali per affrontare le sfide della transizione: l'intermittenza delle rinnovabili (fotovoltaico, eolico), l'accumulo elettrochimico (terre rare), la produzione e lo
Talking about materials for energy involves thinking about energy itself, in particular how it is produced (or rather,converted),transportedandused.AsVaclavSmil stated, energy is the “only universal currency,” essential for all activities and fundamental to life. Humans have learned to use available energy flows and shaped the development of their civilization accordingly, moving from fossil fuels to nuclear energy to photovoltaics. Energy demand will rapidly grow, because of demographic growth, economic-technological development (let us think about the impact of artificial intelligence, which according to some estimates is already responsible for the consumption of about 1% percent of the energy produced) and climate change. A balance between these factors requires a radical energy transition, on penalty of catastrophic consequences. In thiscontext,materialsarecrucialtomeetthechallenges of the transition: the intermittency of renewables (photovoltaics, wind), electrochemical storage (rare earths), and hydrogen production and storage.
stoccaggio di idrogeno.
Questi fattori aumentano enormemente le esigenze dei materiali, sia in termini di caratteristiche che di quantità. È prevedibile un rilancio del nucleare, soprattutto con gli SMR (Small Modular Reactor), che potrebbero sopperire all’aleatorietà delle rinnovabili risultando socialmente più accettabili rispetto agli impianti nucleari di grossa taglia. La transizione richiederà enormi quantità di materiali, ad esempio per sostituire 4 TW di capacità fossile con eolico, fotovoltaico o nucleare, 1,4 miliardi di motori termici con batterie o combustibili non fossili, e mezzo miliardo di caldaie a gas con pompe di calore.
Se si confronta il fabbisogno di materiali, in tonnellate per MW di capacità di generazione, si osserva come quello delle turbine a gas (macchine efficienti, compatte e flessibili) sia di circa 30 t/MW, quantità che pare rappresenti solo il 6% del materiale per MW generato richiesto da una turbina eolica.
La complessità della situazione ha spinto l'Agenzia Internazionale dell'Energia (IEA) ad analizzare il mercato dei Minerali Critici, che ha evidenziato un forte aumento della domanda di litio, cobalto, nichel, rame e terre rare a causa dell’impiego di questi materiali nelle fonti rinnovabili.
È significativo che un’Agenzia che tradizionalmente si occupa più di combustibili abbia ritenuto di porre l’accento sul mercato dei Minerali Critici, che hanno innescato una forte competizione fra grandi potenze. La cronaca internazionale ne descrive gli sviluppi
These factors greatly increase material requirements, both in terms of characteristics and quantity. A revival of nuclear power can be expected, especially with SMRs (Small Modular Reactors), which could make up for the randomness of renewables by being more socially acceptable than large nuclear plants. The transition will require huge amounts of materials, for example to replace 4 TW of fossil capacity with wind, photovoltaic or nuclear, 1.4 billion thermal engines with batteries or non-fossil fuels, and half a billion gas boilers with heat pumps.
When comparing the material requirements, in tons per MW of generation capacity, it can be seen that it is about 30 t/MW for gas turbines (efficient, compact and flexible machines), an amount that appears to represent only 6 percent of the material per MW generated required by a wind turbine.
The complexity of the situation prompted the International Energy Agency (IEA) to analyze the Critical Minerals market, which highlighted a sharp increase in demand for lithium, cobalt, nickel, copper and rare earths due to the use of these materials in renewable sources.
It is significant that an agency that has traditionally been more concerned with fuels has chosen to emphasize the Critical Minerals market issues, which triggered strong competition among major powers. International news reports describe the dynamics.
International Workshop Carlo Longaretti on Digital Tools for the Metallurgical Industry
BERGAMO . ITALY . 27-28 NOVEMBER 2025
International Workshop Carlo Longaretti on Digital Tools for the Metallurgical Industry
DTMI 2025, the International Workshop Ing. Carlo Longaretti on Digital Tools for the Metallurgical Industry, will be an international meeting of excellent level for sharing knowledge and results about the applications of Artificial Intelligence, Machine Learning, Computational Simulation and Data Protection in the metallurgical fields. Theory, methodology, results and further potentialities will be dealt with. The aim of the Workshop is to provide a platform where researchers and practitioners from both academia will meet and share cutting-edge development about the aspects that are ruling the digital transitions.
Authors are invited to contribute to the Workshop by submitting presentations that illustrate research results, projects, surveying works, successful histories and industrial experiences that describe significant advances in the areas of computer science, engineering and applications applied to the Metallurgical sector.
The Workshop will be performed through invited presentations and on the basis of the selection of the abstracts sent by authors and companies interested in sharing their updated knowledge on the following topics.
• Artificial Intelligence Tools and Application
• Data Mining and Machine Learning Tools
• Computational simulation and modeling
• Simulations of metallurgical phenomena
• Improvement of the process efficiency
• Digital Twins Application of digital tools for quality assurance
• Innovative computational approach
• Control and simulation of Plastic Deformation
• Control and simulation of Melting and Solidification Process
• Control and simulation of the Thermal Treatments
• Simulation of Microstructural Evolution
• Robotics
• Recent Trends and Developments
• Succeful and promising applications of the digital tools in the metallurgical fields
BERGAMO . ITALY . 27-28 NOVEMBER 2025
Prospective speakers wishing to present are invited to submit a tentative title and an abstract of about 400 words (in English) to the Organising Secretariat (conference@aimnet.it).
The abstract should provide sufficient information for a fair assessment. Two ways to submit papers will be available:
• to send the title and the abstract, together with the requested information (Name and Surname, Affiliation, Mailing Address, Phone and e-mail) by e-mail to: conference@aimnet.it
• to fill in the form on the International Workshop page at www.aimnet.it
All participants will receive the pdf presentations in digital format at the Workshop. Authors interested in writing full papers for publication on “La Metallurgia Italiana - International Journal of the Italian Association for Metallurgy” (the scientific journal of AIM, which is covered in the Science Citation indexed by Clarivate Analytics (formerly Thomson Reuters), and in Scopus by Elsevier B.V) are invited to inform the Editorial Secretariat (met@aimnet.it) best while submitting their abstract.
The Workshop language will be English.
EXHIBITION & SPONSORSHIP OPPORTUNITIES
All information will be available at www.aimnet.it in the next months.
The Workshop will be held in Bergamo at the Congress Center Giovanni XXIII, Viale Papa Giovanni XXIII, 106 (www.congresscenter.bg.it).
Via Filippo Turati 8 20121 Milano - Italy
t. +39 0276021132 or +39 0276397770 conference@aimnet.it - www.aimnet.it
G. Stornelli, A. di Schino, D. Croccolo, G. Olmi, R. Montanari, A. Varone, C. Testani
L’acciaio EUROFER97 è l’acciaio di riferimento Europeo per la realizzazione di parti strutturali nei futuri reattori a fusione nucleare. In questo lavoro è stata condotta un'estesa campagna sperimentale con lo scopo di migliorare la resistenza senza ridurre la duttilità. L'idea alla base del presente studio è quella di raggiungere l'obiettivo attraverso l'affinamento del grano, mediante laminazione a freddo e successivo trattamento di ricottura. La sperimentazione ha previsto la combinazione di cinque rapporti di riduzione a freddo (CR) (20%, 40%, 50%, 60% e 80%) e otto temperature di trattamento termico da 400 °C a 750 °C, per 1 ora. I risultati hanno mostrato che con CR: 80% e temperatura di 650 °C, si ottiene una struttura completamente ricristallizzata con grani sub-micrometrici (dimensione media dei grani 600 ± 60 nm). Tale microstruttura garantisce un incremento del limite di snervamento e del carico massimo, rispettivamente del 18% e del 5 %, e un allungamento uniforme doppio rispetto a quello dell'acciaio EUROFER97 standard. Per quanto riguarda il comportamento a fatica i test di fatica ad alto numero di cicli indicano caratteristiche simili.
INTRODUZIONE
EUROFER97 è l’acciaio di riferimento per la realizzazione di parti strutturali nel futuro reattore a fusione nucleare DEMO e nei reattori a fissione di IV generazione [1,2]. La composizione chimica di questo acciaio è stata sviluppata per garantire una ridotta attivazione da irraggiamento neutronico. In particolare, alcuni elementi chimici, tipici degli acciai commerciali ferritici-martensitici contenenti Cr e Mo, sono stati sostituiti con elementi chimici metallurgicamente equivalenti e caratterizzati da ridotti tempi di decadimento radioattivo [3]. L’acciaio EUROFER97 viene prodotto mediante una fusione a induzione a vuoto (VIM) seguita da una rifusione in vuoto (VIR). Viene quindi colato un lingotto, omogeneizzato mediante forgiatura e, in seguito, laminato a caldo a partire da 1250 °C. Infine, il laminato segue 3 passaggi di trattamento termico: austenitizzazione a 980 °C per 30 minuti, tempra in aria e rinvenimento a 760 °C per 90 minuti [4]. Alla fine di tale processo la microstruttura è quella tipica di una martensite rinvenuta. L’ acciaio mostra una buona saldabilità ed eccellenti proprietà meccaniche alle alte temperature [5]. Tuttavia, in seguito ad irraggiamento neutronico l’acciaio
Giulia Stornelli, Andrea di Schino
Department of Engineering, University of Perugia, Perugia, Italy
Dario Croccolo, Giorgio Olmi
Department of Industrial Engineering (DIN), University of Bologna, Bologna, Italy
Roberto Montanari, Alessandra Varone
Department of Industrial Engineering, University of Rome “Tor Vergata”, Rome, Italy
Claudio Testani
CALEF-ENEA CR-Casaccia, S. Maria di Galeria, Rome, Italy
EUROFER97 ha buone prestazioni meccaniche solo in un intervallo limitato di temperatura (350 – 550 °C) [6] e, numerosi sono gli studi scientifici condotti per ampliare tale finestra operativa. Per incrementare il limite superiore di temperatura operativo fino a circa 650 °C, una possibile soluzione è quella di utilizzare una versione dell’acciaio EUROFER97 di tipo ODS, rafforzato mediante alligazione meccanica di ossidi di Y (Y2O3) di dimensioni nanometriche, con la funzione di inibire la crescita del grano e lo scorrimento a bordo grano alle alte temperature [5]. Riguardo al limite operativo inferiore a 350 °C, questo è principalmente connesso alla perdita di duttilità indotta dai difetti reticolari prodotti dall’irraggiamento neutronico. Si assiste ad una perdita di tenacità e allo spostamento della temperatura di transizione duttile fragile verso temperature maggiori di quella ambiente [7]. Per quanto riguarda il comportamento a fatica a basso numero di cicli (LCF) questo è stato ampliamente studiato fino alla temperatura di 550 °C [8, 9], valutando anche l'effetto di diversi cicli di carico. Petersen et al. [10] hanno studiato anche l'effetto dell'irraggiamento sulla resistenza meccanica statica e a fatica a basso numero di cicli. La sperimentazione è stata condotta con flusso di neutroni veloci di 1.8 × 1015 n/cm2s, temperatura < 340 °C, 15 e 30 dpa, evidenziando che, con l'aumento del danno da irraggiamento (dpa), si assiste ad una drastica riduzione dell'allungamento uniforme sotto carichi statici. Analogamente, si ha una riduzione dell'allungamento totale a fatica. L’allungamento totale a fatica raggiunge valori inferiori all'1% con un aumento del numero di cicli fino alla rottura, proprio a causa della perdita di duttilità causata dall'irraggiamento.
Per ottimizzare la resistenza dell’acciaio EUROFER97 a T < 350 °C, una possibile strategia è quella di tendere all’ottenimento di un grano ultra-fine. In genere, un affinamento del grano incrementa la resistenza meccanica e migliora la resistenza all’irraggiamento ma induce una riduzione della duttilità a causa dell’aumento della densità di dislocazioni. In letteratura, sono stati condotti numerosi studi che sperimentano diversi metodi di affinamento della
microstruttura dell’acciaio EUROFER97 [11-14] che mostrano effetti benefici sulla resistenza all’irraggiamento. A tal proposito, lo scopo di questo lavoro è stato quello di sviluppare un trattamento termo-meccanico, aggiuntivo a quello tradizionale, per affinare la microstruttura e rafforzare il materiale, senza perdere in duttilità.
La composizione chimica nominale dell'acciaio EUROFER97-3, oggetto di questo lavoro, è 9Cr–1W–0,07Ta–0,2V–0,11C–0,4Mn (wt.%) [4]. Una lamiera di acciaio EUROFER97 tradizionale (spessore 14 mm) è stato laminato a freddo e trattato termicamente combinando cinque rapporti di riduzione a freddo (CR) (20%, 40%, 50%, 60%, 80%) e otto trattamenti termici a diverse temperature (in campo ferritico [15]) nell'intervallo 400-750 °C (incrementi di 50 °C) per 1 ora. Sui campioni così trattati sono state condotte analisi microstrutturali mediante microscopia elettronica a scansione ad alta risoluzione (FE-SEM-Zeiss, Gemini Supra 25, Jena, Germania) dotata di un rilevatore EBSD (C Nano Oxford Instruments), con passo di scansione di 0,02 μm e diffrazione dei raggi X (XRD-PW 1729, Philips, Eindhoven, Paesi Bassi). Le osservazioni al SEM sono state effettuate dopo lucidatura meccanica e attacco chimico mediante reagente Vilella. Un'analisi d’immagine per la determinazione della dimensione media del grano è stata eseguita sulle mappe EBSD utilizzando il software dedicato AlexaSoft X-Plus.
Gli spettri XRD sono stati ottenuti utilizzando la radiazione Mo-Kα (λ= 0.070926 nm) nell’intervallo angolare 2θ 10° - 60° (profilo di precisione con passo di scansione 0.005° e tempo di conteggio per passo di 5 s). Per tutti i picchi è stata ricavata la larghezza a metà altezza (βT) che può essere descritta come la somma di due contributi, β D dovuto alla dimensione dei domini coerenti di diffrazione (D) e βε dovuto alle micro-deformazioni (ε) dipendenti principalmente dalle dislocazioni:
dove θ è l’angolo di Bragg. I due contributi, β_D and β_ε, sono stati valutati mediante la procedura di Cauchy [16].
Dal valore di ε è stata calcolata la densità di dislocazioni ρ mediante la relazione di Williamson-Smallman [17]:
dove Ξ = 16.1, F ≈1 e b = 0.248 nm il modulo del vettore di Burgers.
Le proprietà meccaniche sono state studiate mediante prove di durezza Vickers (carico di 5 kg) e, in casi selezionati, mediante prove di trazione e di fatica ad alto numero di cicli. Le prove di trazione e fatica sono state eseguite su provini piatti, estratti lungo la direzione trasversale alla laminazione. Le prove di trazione sono state condotte in accordo con la norma ASTM E8 utilizzando una macchina di trazione servomeccanica (MD 100, MAYES). Le prove di fatica sono state eseguite mediante una macchina risonante (capacità di 20 kN, Rumul, Svizzera) in controllo di carico, sottoponendo il provino ad un ciclo in trazione, con un rapporto di sollecitazione R = 0.2 e frequenza f = 113 Hz. Il numero massimo di cicli di fatica (Run-out) è stato fissato a 107 cicli. Ulteriori dettagli sulla sperimentazione svolta sono riportati in [18].
RISULTATI E DISCUSSIONE
I valori di durezza dell’acciaio EUROFER97 dopo i trattamenti termo-meccanici sperimentati in questo lavoro sono riportati in Figura 1 e sono confrontati con il valore di durezza dell’acciaio EUROFER97 tradizionale (201.6 ± 1.9 HV [19]). Come mostrato nel grafico, la durezza è fun-
(2)
zione sia del tasso di laminazione CR sia della temperatura di trattamento termico. Dall’osservazione SEM della microstruttura dei campioni così trattati si riscontra che il trattamento termico porta a completa ricristallizzazione per tutti i tassi di laminazione. Le strutture allungate, tipiche del materiale incrudito, tendono progressivamente a riorganizzarsi in strutture con grani equiassici di dimensioni sub-micrometriche. A titolo di esempio, nelle Figure 2 e 3 sono messi a confronto, rispettivamente per i casi estremi CR: 20% e CR: 80%, le strutture del materiale incrudito e ricristallizzato. Per il tasso di laminazione del 20 % la ricristallizzazione è completa alla più alta temperatura sperimentata (750 °C). Al contrario, per CR: 80%, si ha completa ricristallizzazione a circa 650 °C. La frazione dei grani ricristallizzati dipende dal trattamento termico ma è fortemente legata al tasso di incrudimento. Dall'analisi XRD la densità di dislocazioni ρ aumenta all’aumentare del tasso di riduzione a freddo e, per l'80% di deformazione è circa due ordini di grandezza maggiore rispetto a materiale standard passando da 7.2 × 1010 cm-2 a circa 1.2 × 1012 cm-2. Questo, a seguito del trattamento termico, comporta una diversa evoluzione microstrutturale e di conseguenza diverse proprietà meccaniche.
Fig.1 - Effetto del trattamento termo-meccanico sulla durezza dell'acciaio EUROFER97 / Effect of thermomechanical treatment on the hardness of EUROFER97 steel.
Fig.2 - Micrografie SEM dell'acciaio EUROFER97 laminato a freddo con CR: 20% allo stato incrudito (a) e trattato termicamente a 750 °C per 1 ora / SEM micrographs of cold-rolled EUROFER97 steel with CR: 20% in the work-hardened state (a) and heat treated at 750 °C for 1 hour
Fig.3 - Micrografie SEM dell'acciaio EUROFER97 laminato a freddo con CR: 80% allo stato incrudito (a) e trattato termicamente a 650 °C per 1 ora / SEM micrographs of cold-rolled EUROFER97 steel with CR: 80% in the work-hardened state (a) and heat treated at 650 °C for 1 hour
Sulla base dei risultati delle prove di durezza, i campioni con le migliori prestazioni meccaniche sono stati sottoposti a prove di trazione, e i risultati, in termini di resistenza allo snervamento (YS), carico massimo (UTS), allungamento uniforme (AU – in corrispondenza del carico massimo UTS) e allungamento totale (AT – in corrispondenza del carico di rottura), sono riportati in Figura 4, e confrontati con l’acciaio EUROFER97 standard [20, 21].
Dopo trattamento termico a 600 °C, i valori di YS e UTS sono tutti molto alti rispetto a quelli dell’EUROFER97 standard, tuttavia, a tale rafforzamento corrisponde una consistente perdita di duttilità. Un reale miglioramento della duttilità, unito al rafforzamento del materiale, è visibile solo per il campione sottoposto ad un tasso di laminazione dell’80% e temperatura di trattamento a 650 °C per 1 ora. A tale condizione di trattamento termo-mec-
canico corrisponde un incremento dei YS e UTS rispettivamente del 18% e 5%. AT è paragonabile (23%) rispetto all’EUROFER97 standard mentre l’aspetto più rilevante è che AU è più che doppio (13.4% vs. 6.5%).
Fig. 4 - YS (a), UTS (b), AT% (c) e AU% (d) di alcuni campioni di acciaio EUROFER97 sottoposti a trattamento termo-meccanico / YS (a), UTS (b), AT% (c) and AU% (d) of some EUROFER97 steel samples subjected to thermo-mechanical treatment.
L’analisi microstrutturale del campione ottimizzato (CR: 80%, 650 °C) rivela che la combinazione migliore tra rafforzamento e duttilità corrisponde ad un materiale completamente ricristallizzato con grani equassici di dimensioni sub-micrometriche (dimensione media del grano 600 ± 60 nm) (Figura 5a). Tale temperatura rappresenta una soglia di trattamento, infatti, per temperature più alte (700 e 750 °C) la microstruttura risulta essere fortemente disomogenea con dimensione dei grani su diverse scale, micrometrica e sub-micrometrica. Il campione a 750 °C presenta una dimensione media del grano maggiore di 1 micron, con alcuni grani che superano i 15 micron (Figura 5b). Tale risultato è in accordo con quanto osservato in [14]. La combinazione tra l’intrinseca mobilità dei bordi grano e la presenza di instabilità microstrutturali locali (dislocazioni e coalescenza dei precipitati M23C6) favorisce
entrambi i fenomeni di crescita normale e abnorme del grano.
I risultati delle prove di fatica ad alto numero di cicli sono riportati in Tabella 1. Come descritto in un precedente lavoro [18], il modello lineare è il più adeguato a riprodurre la distribuzione di dati così ottenuti. In genere, i dati di letteratura disponibili per l’acciaio EUROFER97 tradizionale fanno riferimento alla resistenza a fatica sotto carico simmetrico alternato [8, 9]. Inoltre, per confrontare il comportamento dinamico-meccanico dell’acciaio tradizionale con quello proposto in questo lavoro, è necessaria una conversione utilizzando lo strumento del diagramma di Haigh e l’applicazione della relazione della retta di Goodman [18]. Dal confronto delle curve così modificate è emerso che i valori di resistenza a fatica sono molto vicini, con una dif-
ferenza massima dell'ordine del 5% (350 MPa a 105 cicli per EUROFER97 tradizionale e 335 MPa alla stessa durata dopo CR:80 % e 650 °C). Pertanto, si può concludere che il trattamento termo-meccanico proposto in questo lavoro porta a miglioramenti significativi dal punto di vista del comportamento meccanico statico di EUROFER97, con elevata duttilità e carico di snervamento, e non peggiora la risposta a fatica.
direzione di laminazione
Fig.5 - Mappe EBSD di EUROFER97 deformato con CR dell'80% e trattato termicamente per 1 ora a 650 °C (a) e 750 °C (b) / EBSD maps of EUROFER97 after 80% deformation heat treatment for 1 hour at 650 °C (a) and 750 °C (b)
Tab.2 - Trattamenti eseguiti sui campioni e relativi codici.
Memorie scientifiche - Materiali per l'energia
Per ottenere maggiori informazioni sull'evoluzione del grano in seguito alle prove di fatica dei campioni laminati con CR:80% e trattati a 650 °C, sono state condotte delle analisi EBSD esaminando le zone prossime alla frattura. Ad esempio, la Figura 6a mostra la mappa EBSD del campione #13. Dopo la prova di fatica, la dimensione media del grano è maggiore (873 ± 53 nm) rispetto al campione prima della prova (600 ± 60 nm) e si verificano alcuni cambiamenti di struttura. Inoltre, dalle analisi delle mappe EBSD la frazione relativa di bordi grano a basso angolo (LAGB) diminuisce da 0.45 ± 0.01 (materiale originale) a 0.36 ± 0.05. Dunque, l'EBSD mostra principalmente che i LAGB diventano instabili per effetto del carico ciclico nelle prove di fatica. A tale evoluzione microstrutturale corrisponde una variazione della durezza (Figura 6 b).
In Figura 6b i valori di durezza misurati nei campioni dopo la prova di fatica sono riportati in funzione di Δσ: anche se si osserva una certa dispersione dei dati, la durezza tende a diminuire all'aumentare di Δσ. Inoltre, dal confronto con i valori di durezza del campione non sottoposto a sol-
lecitazione di fatica, si osserva una variazione di durezza fino all'8%. I valori di durezza riportati in Figura 6b sono stati rilevati in prossimità della zona di frattura. I bordi di grano, in particolare i LAGB, possono migrare a causa del movimento collettivo delle dislocazioni indotto dalla sollecitazione applicata durante le prove di fatica. In letteratura è stato riportato solo un caso di crescita del grano in seguito a sollecitazione di fatica a temperatura ambiente nella lega di Al 7075 [22]. Pertanto, il fenomeno osservato nel presente lavoro rappresenta una novità di grande interesse; indagare e valutare quantitativamente la stabilità microstrutturale di questo acciaio è di notevole importanza per le applicazioni nucleari. Nel lavoro si osserva che la struttura ultrafine dell’acciaio EUROFER97 tende ad evolvere a seguito di sollecitazione ciclica mentre il problema più generale della stabilità microstrutturale dell’acciaio riguarda soprattutto la possibile evoluzione in temperatura (ad esempio durante l’impiego) e in una condizione di grano verosimilmente non ultrafine.
Fig.6 - Campione #13: mappa EBSD (a), durezza dei campioni sottoposti a prove di fatica rispetto a Δσ /
Sample #13: EBSD map (a), hardness of samples submitted to fatigue tests vs. Δσ (b).
Questo lavoro ha indagato l’evoluzione microstrutturale e delle proprietà meccaniche dell’acciaio EUROFER97 dopo trattamento termo-meccanico innovativo, con l’obiettivo di migliorare la resistenza meccanica mediante un affinamento della microstruttura, senza introdurre effetti dannosi alla duttilità. A partire dall'acciaio EUROFER97 standard, sono stati ottenuti un gruppo di 40 campioni, combinando diverse condizioni di laminazione a freddo (tassi di laminazione CR: 20, 40, 50, 60 e 80 %) e otto diverse temperature di trattamento di ricottura (da 400 a 750 °C per 1 ora). I principali risultati possono essere riassunti come segue:
- La ricristallizzazione avviene in tutti campioni laminati a freddo e trattati termicamente, con cinetiche dipendenti sia dalla temperatura di trattamento sia dal tasso di incrudimento.
- Il trattamento termo-meccanico corrispondente a CR dell'80 % e trattamento termico a 650 °C dà origine ad
una microstruttura completamente ricristallizzata con una popolazione di grani equiassici di dimensioni sub-micrometriche (600 ± 60 nm). Tale condizione porta ad un incremento di YS e UTS (rispettivamente del 18 % e 5 %) rispetto all’ acciaio EUROFER97 standard e ad un AT pressoché invariato (23%). Tuttavia, di rilevante interesse è l’incremento dell’allungamento uniforme di oltre il doppio (13.4 % vs. 6.5 %).
- La resistenza a fatica dell'acciaio sottoposto al nuovo trattamento termomeccanico è paragonabile a quello dell’acciaio EUROFER97 standard.
- I campioni sottoposti a fatica subiscono un aumento della dimensione media dei grani, da attribuire all’intrinseca instabilità dei LAGB durante la sollecitazione di fatica. Il collasso di alcuni confini porta alla riorganizzazione delle dislocazioni e alla coalescenza dei grani. A tale evoluzione microstrutturale corrisponde una variazione della durezza fino all’8%.
BIBLIOGRAFIA
[1] Chen X, Bhattacharya A, Sokolov MA, Clowers LN, Yamamoto Y, Graening T, Linton KD, Katoh Y, Rieth M. Mechanical properties and microstructure characterization of Eurofer97 steel variants in EUROfusion program. Fusion Eng Des 2019;146:2227-32
2] Stornelli G, Montanari R, Testani C, Pilloni L, Napoli G, Di Pietro O, Di Schino A. Microstructure refinement Effect on EUROFER 97 steel for nuclear fusion application. Mater Sci Forum 2021;1016:1392-7
3] Tavassoli AAF, Alamo A, Bedel L, Forest L, Gentzbittel JM, Rensman JW, Diegele E, Lindau R, Schirra M, Schmitt R, et al. Materials design data for reduced activation martensitic steel type EUROFER. J Nucl Mater 2004;329-333:257-262
4] Rieth M, Schirra M, Falkenstein A, Graf P, Heger S, Kempe H, Lindau R, Zimmermann H. EUROFER 97 Tensile, Charpy, Creep and Structural Tests. Report FZKA6911, Eurofusion programme. 2003
5] Lindau R, Moslang A, Rieth M, Klimiankou M, Materna-Morris E, Alamo A, Tavassoli AAF, Cayron C, Lancha AM, Fernandez P, Baluc N, Schaublin R, Diegele E, Filacchioni G, Rensman JW, Shaaf BVD, Lucon E, Dietz W. Present development status of EUROFER and ODS-EUROFER for application in blanket concepts. Fusion Eng Des 2005;8:75-9
6] Coppola R, Klimenkov M. Dose dependence of micro-voids distributions in low-temperature neutron irradiated Eurofer97 steel. Metals 2019;9:1-12
7] Zinkle SJ, Möslang A. Evaluation of irradiation facility options for fusion materials research and development. Fus Eng Des 2013:472482
8] Marmy P, Kruml T. Low cycle fatigue of Eurofer 97. J Nucl Mater 2008;377(1):52-8
9] Roldan M, Leon-Gutierrez E, Fernandez P, Gomez-Herrero A. Deformation behaviour and microstructural evolution of EUROFER97-2 under low cycle fatigue conditions. Mater Charact 2019;158:109943
10] Petersen C, Povstyanko A, Prokhorov V, Fedoseev A, Makarov O, Walter M. Tensile and low cycle fatigue properties of different ferritic/martensitic steels after the fast reactor irradiation. J Nucl Mater 2009;386-388:299-302
11] Cristalli C, Pilloni L, Tassa O, Bozzetto L. Mechanical properties of several newly produced RAFM steels with Tungsten content in the range of 2 wt%. Nucl Mater Ener 2020;25:100793
12] Pilloni L, Cristalli C, Tassa O, Salvatori I, Storai S. Grain size reduction strategies on Eurofer. Nucl Mater Ener 2018;17:129-136
13] Cristalli C, Tassa O, Bozzetto L, Pilloni L. Achievement of Ultrafine Grain structure by means of recrystallization treatments. J Nucl Mater 2022;568:153852
14] Oliveira VB, Sandim HRZ, Raabe D. Abnormal grain growth in Eurofer-97 steel in the ferrite phase field. J Nucl Mater 2017;485:23-38
15] Stornelli G, Di Schino A, Mancini S, Montanari R, Testani C, Varone A. Grain refinement and improved mechanical properties of eurofer97 by thermo-mechanical treatments. Appl Scien 2021;11:10598
16] Cullity BD. Elements of X-ray Diffraction, Second Edition. Addison-Wesley Publishing Company, INC. 1977
17] Williamson GK, Smallman RE. III. Dislocation densities in some annealed and cold-worked metals from measurements on the X-ray Debye-Scherrer spectrum. Philos Mag 1956;1:34-46
18] Croccolo D, Di Schino A, Montanari R, Olmi G, Stornelli G, Testani C, Varone A. High cycle fatigue response of grain refined EUROFER97. Int J Fatig 2024;108442
19] Schuring EW, Hofmans HE. Metallographic characterization of EUROFER97 plate and bar materials. Report ECN Library 2000
20] Qiu GX, Zhan DP, Cao L, Jiang ZH. Review on development of reduced activated ferritic/martensitic steel for fusion reactor. J Iron Steel Res Int 2022;29:1343 – 56
21] Lindau R, Moslang A, Rieth M, Klimiankou M, Materna-Morris E, Alamo A, et al. Present development status of EUROFER and ODSEUROFER for application in blanket concepts. Fusion Eng Des 2005;75 – 79:989 – 96
22] Goswami R, Feng CR, Qadri SB, Pande CS. Fatigue-assisted grain growth in Al alloys. Nat Sci Rep 2017;7:10179
EUROFER97 steel is the European reference steel to manufacture structural parts in future nuclear fusion reactors. In this work, an extensive experimental campaign was carried out aiming to improve strength without reducing ductility. The main idea behind the present study is to achieve such result through grain refinement obtained by cold rolling and heat treatment. The combination of five cold reduction (CR) ratios (20%, 40%, 50%, 60% and 80%) and eight heat treatment temperatures from 400°C to 750°C, for 1 hour, have been examined. The treatment consisting of CR = 80% and heating at 650 °C induces a fully recrystallized structure with sub-micrometric grains (average grain size 600 ± 60 nm). This microstructure guarantees an increase of the yield stress and ultimate tensile strength of 18% and 5%, respectively, and a uniform elongation nearly double than that of standard EUROFER97 steel. Furthermore, the results obtained from high cycle fatigue tests evidenced a similar behavior.
KEYWORDS: EUROFER97 STEEL, THERMO-MECHANICAL TREATMENTS, RECRYSTALLIZATION, MICROSTRUCTURE, MECHANICAL TESTS;
E. Poskovic, L. Ferraris, F. Franchini, M. Actis Grande
I materiali magnetici trovano sempre più applicazione in diversi settori industriali, i quali richiedono diverse proprietà magnetiche con basse perdite nel ferro e design sempre più complessi. In tal ottica la ricerca ha portato a nuovi materiali, come ad esempio i Soft Magnetic Composites (SMC). I principali vantaggi derivanti dall’utilizzo degli SMC al posto degli acciai laminati sono: correnti parassite inferiori, possibilità di geometrie complesse, percorso del flusso magnetico 3D, comportamento efficiente alle alte frequenze. La bassa resistenza meccanica a temperatura ambiente rappresenta un limite, che può essere superato adottando strati in grado di lavorare oltre i 600 °C e sopportare quindi trattamenti termici che possano conferire più solidità meccanica. In questo lavoro, è stato studiato un coating inorganico con particelle di nano-ferrite, adottando diversi particolari processi per rivestire le particelle ferromagnetiche e sono stati considerati tre tipi di ambienti di trattamento termico. La caratterizzazione degli SMC prodotti è stata eseguita attraverso misure di resistività elettrica e coercitività con l’obiettivo di selezionare il processo migliore.
CHIAVE: MATERIALI MAGNETICI
TURBULA MIXER, MULINO A PALETTE, COERCITIVITÀ, RESISTIVITÀ ELETTRICA, ANALISI METALLOGRAFICHE, FERRITE DOLCE;
INTRODUZIONE
I materiali magnetici trovano sempre più applicazione in diversi settori industriali [1]. Ad esempio, nelle macchine elettriche, i magneti permanenti (materiali magnetici duri) vengono utilizzati per produrre il flusso magnetico, mentre gli acciai laminati (materiali magnetici dolci) per realizzare il nucleo magnetico. Anche i dispositivi elettronici, induttori e filtri EMI sono preparati con materiali magnetici dolci [2, 3]. I magneti sono anche molto comuni nella sensoristica.
I materiali magnetici dolci possono essere suddivisi in varie famiglie: leghe ferro-silicio, leghe ferro-cobalto-vanadio, ferriti dolci, materiali magnetici amorfi, ecc. È importante abbinare un'elevata permeabilità magnetica a basse perdite nel ferro e forme di design innovative. In tal ottica, la ricerca ha portato a nuovi materiali, come ad esempio i Soft Magnetic Composites (SMC) [4, 5]. I materiali SMC sono preparati per compattazione di particelle ferromagnetiche, isolate da specifici layer che possono essere di natura organica o inorganica [6]. I principali vantaggi derivanti dall’utilizzo degli SMC al posto degli acciai laminati sono: correnti parassite inferiori, possibilità di geometrie complesse, percorso del flusso magneti-
Emir Poskovic, Luca Ferraris, Fausto Franchini
Politecnico di Torino, Dip. Energia, Italia
Marco Actis Grande
Politecnico di Torino, Dip. Scienza App. e Tecn., Italia
co 3D, comportamento efficiente alle alte frequenze. Le basse resistenze meccaniche, tuttavia, rappresentano un limite, che può essere superato adottando strati di layer isolante in grado di resistere oltre i 600 °C [7]. In sostanza, in seguito alla pressatura, vengono effettuati trattamenti termici di stress relieveing al fine di ridurre le perdite per isteresi magnetica e le sollecitazioni meccaniche di trazione presenti sulla superficie dei materiali pressati. Tuttavia, la maggior parte dei rivestimenti adottati commercialmente e nel settore della ricerca, vanno incontro a un degrado dovuto al trattamento di stress relieving oltre i 600°C, perdendo le loro caratteristiche di isolamento. In questo lavoro è presentato lo studio di una tipologia di coating inorganico realizzato con particelle di nano-ferrite a copertura di micro particelle ferromagnetiche di Fe [8-10], adottando cinque differenti processi per rivestire la polvere ferromagnetica. Inoltre, sono state utilizzate tre differenti atmosfere durante il trattamento termico di stress relieving: in aria, vuoto e vapore. Lo studio, focalizzato sul trattamento termico, è atto a stabilire quali siano le migliori condizioni di trattamento a parità di tipologia di coating. Il numero di campioni testati in questo lavoro è molto numeroso, e per tale motivo l’efficacia del coating è stata valutata solamente attraverso delle caratterizzazioni preliminari, omettendo le misure delle perdite magnetiche (perdite d’isteresi e correnti parassite) e dei cicli d’isteresi, in quanto dispendiose in termini di tempo e necessarie solo nel caso in cui i test preliminari abbiano esito positivo. In tal ottica, la caratterizzazione è stata eseguita attraverso misure di resistività elettrica e misure di coercitività, parametri che risultano essere direttamente proporzionali rispettivamente alle perdite per correnti parassite e d’isteresi, con l’obiettivo di selezionare il processo di rivestimento e termico migliori. A supporto delle valutazioni dei campioni, saranno effettuate delle osservazioni delle polveri post miscelazione tramite microscopia ottica.
La polvere ferromagnetica deve soddisfare alcuni requisiti per poter essere impiegata; principalmente la polvere deve presentare un elevato grado di purezza e ottima comprimibilità, nell’ottica dell’ottenimento di un’elevata ripetibilità nella produzione dei campioni tramite compattazione della polvere. Per questo motivo, si è scelto di
usare una polvere di ferro denominata commercialmente Fe ABC100.30, prodotta tramite atomizzazione ad acqua e avente dimensione media della polvere di circa 100-150 µm. Un'altra importante peculiarità di questa tipologia di polvere è il basso tenore di ossigeno, il quale risulta da datasheet di 0,04 wt%. Le altre impurezze (C ed H) sono altrettanto trascurabili.
Per quel che concerne il materiale di rivestimento usato come isolante elettrico da inserire tra le particelle ferromagnetiche, si è adottata la polvere di ossido di ferro Fe2O3, comunemente definita come polvere di ferrite. Le dimensioni della polvere di ferrite, notevolmente inferiori rispetto a quelle della polvere ferromagnetica, sono nell’ordine di 100 nm. In aggiunta all’elevato isolamento elettrico, la polvere Fe2O3 presenta anche il vantaggio di consentire l’esecuzione di trattamenti termici a diversi intervalli di temperatura. Un’ulteriore peculiarità nella scelta della ferrite come layer di rivestimento è che tale polvere è un materiale magnetico dolce, e in quanto tale presenta delle proprietà magnetiche. Tali proprietà risultano essere interessanti nell’ottica della produzione di un materiale magnetico composito, poiché esso avrà, quindi, una frazione magnetica il più elevata possibile. Per finire, l’additivo ceroso Kenolube P11, prodotto dalla ditta Höganäs, viene utilizzato come lubrificante per migliorare la processabilità della miscela di polveri e mantenere una elevata densità del compatto ottenuto.
I processi di rivestimento studiati sono cinque, al fine di produrre due combinazioni di miscele di materiale composito, variando la quantità dello strato isolante: Fe ABC100.30 con 1 wt% e 0,2 wt% in peso di Fe 2O3; inoltre, il Kenolube è stato mantenuto a 0,3 wt% in tutte le miscele. Inizialmente, la polvere ferromagnetica Fe ABC100.30 viene vagliata tramite dei settaci in tre intervalli granulometrici, per poi essere rimescolata con una nuova frazione granulometrica (vedi Tab. 1) in grado di fornire migliori risultati magnetici [11]. Per ottenere le miscele composte sono state adoperate due diverse tecniche: la miscelazione tramite la “Turbula Mixer” e quella eseguita con il mulino a palette. Entrambe le strategie sono di natura meccanica. I cinque processi di rivestimento sono delle combinazioni delle due tecniche. Inoltre la tecnica a mulino a palette viene successivamente suddivisa in due diversi sotto-processi, come illustrato nella Fig. 1.
Tab. 1 - Composizione granulometrica in percentuale di peso della polvere ferromagnetica Fe ABC100.30 originale e ricomposta / Granulometric composition in weight percentage of the original and recomposed Fe ABC100.30 ferromagnetic powder. DENOMINAZIONE DELLA DISTRIBUZIONE
Fig.1 -Schema dei passaggi principali dei relativi processi di rivestimento / Scheme of the main steps of the related coating processes
La miscelazione con Turbula avviene in un tempo di 30 min; la polvere di ferro, isolante inorganico e lubrificante sono inseriti direttamente in mixer senza nessun precedente passaggio. Questa tecnica permette di raggiungere una buona uniformità in tempi relativamente brevi, rendendo questo metodo particolarmente efficiente. Nel caso del mulino a palette [12], inizialmente l’omogeneizzazione del composto viene effettuata inserendo solo la ferrite e le frazioni granulometriche ricomposte S1 e S2, per evitare che le particelle più piccole appartenenti all’intervallo S3 vadano a ricoprire quelle più grandi, creando così alcune aree non isolate elettricamente. Le polveri vengono processate nel mulino a palette per un tempo pari a 1 min. Al completamento di questa fase, la miscela viene poi unita alla frazione granulometrica S3 e al lubrificante Kenolube, e la miscelazione finale viene completata in Turbula per 30 min.
Questo metodo, tuttavia, introduce un incrudimento delle particelle e la produzione di una polvere finissima (< 1
µm) dovuto agli urti delle palette del mulino con le particelle di polvere. La deformazione plastica delle particelle rende più difficile il movimento dei domini magnetici causando di conseguenza ad un aumento delle perdite per isteresi magnetica. Si ipotizza, inoltre, che la componente fine della polvere di ferro possa andare a ricoprire le particelle più grandi influendo sull’uniformità del rivestimento isolante. In tal ottica, sono state predisposte delle varianti di processo di rivestimento con il mulino a palette. Per fare fronte all’incrudimento delle polveri metalliche è stato inserito un passaggio tra l’omogeneizzazione nel mulino a palette e quella nella Turbula. La miscela viene sottoposta ad un trattamento termico di distensione a 450 °C per 30 min, trattamento che può essere svolto in aria o in vuoto [13]. Infine, per rimuovere le particelle di polvere finissime (< 1 µm) è stata eseguita un’ulteriore variante del processo di rivestimento con miscelazione ottenuta da mulino a palette con i seguenti passaggi: dapprima sono state messe nel mulino solo le frazioni granulometriche
rimescolate S1 e S2 e sono state processate per 1 min. Successivamente, la miscela ottenuta è stata setacciata con una maglia di 1 µm e reintrodotta nel mulino a palette insieme alla ferrite e rimescolata per un totale di 30 s. La miscela finale è stata poi ottenuta in Turbula seguendo la procedura dei processi spiegati in precedenza. Una volta ottenute le miscele composte si procede con la compattazione green che avviene tramite pressatura uniassiale a freddo a 800 MPa. I campioni vengono pro-
Memorie scientifiche - Materiali per l'energia
dotti in forma di parallelepipedo 55x10x3 mm come in Fig. 2. Solitamente questa forma viene usata per una caratterizzazione magnetica tramite il metodo Single Sheet Tester (SST) [14-16] e per le prove meccaniche a flessione. Al fine di migliorare le proprietà dei campioni analizzati, questi sono stati sottoposti a tre tipologie di trattamenti termici di stress relieving: in aria, in vuoto ed in vapore. I trattamenti sono effettuati a 600 °C per 15 min.
Fig.2 - Campioni dopo vari trattamenti termici di stress relieving / Samples after various stress relieving heat treatments
ANALISI METALLOGRAFICHE
L’osservazione delle polveri è stata effettuata attraverso microscopia ottica in luce polarizzata. In Fig. 3 e Fig. 4 sono mostrate le polveri SMC contenenti lo 0,2 wt% di strato isolante. In Fig. 3-A si può osservare che la quantità di ferrite introdotta come isolante nel processo Turbula mixer (che appare in un color rosso vivo) non è sufficiente a rivestire le particelle, e solo alcuni granuli di polvere appaiono completamente ricoperti. Nel caso del mulino a palette (Fig. 3-B), la ferrite viene agglomerata al lubrificante: sono infatti visibili particelle sferiche di Kenolube totalmente rivestite di ferrite. Il rivestimento sulle polveri ferromagnetiche è discontinuo. In Fig. 3-C, è mostrato il processo di rivestimento con l’adozione del mulino a palette con post-trattamento in aria. Le polveri appaiono
ossidate (aventi colorazione molto scura) e solo scarsamente rivestite, mentre la ferrite riveste le particelle fini ed il Kenolube.
Nel caso di post-trattamento in vuoto (Fig. 4-A) la polvere appare ossidata, di colorazione scura, ed è evidente la quasi totale assenza del rivestimento di ferrite (in rosso). L’assenza di ferrite, in questo caso, è imputabile all’aspirazione della pompa a vuoto, che ha aspirato le nano particelle, evidenziando l’inefficacia del rivestimento. Infine, in Fig. 4-B è mostrato il rivestimento con mulino a palette senza polveri fini. In questo caso, la polvere appare uniformemente rivestita dal coating di nano ferrite.
Fig.3 - A processo di rivestimento con solo Turbula Mixer / Coating process with only Turbula Mixer; B processo di rivestimento con Mulino a Palette - Coating process with Impact Mill e C processo di rivestimento con Mulino a Palette con Post-trattamento in Aria - Coating process with Post-Air treatment Impact Mill (a) (b)
(d)
(e)
Fig.4 - A processo di rivestimento con Mulino a Palette con Post-trattamento in Vuoto / Coating process with Post-Vacuum treatment Impact Mill e B processo di rivestimento con Mulino a Palette Mulino a Palette senza FiniCoating process with Dustless Impact Mill
Le misure di coercitività vengono eseguite tramite il coercimetro (vedi Fig. 5), che effettua misure a bassissima frequenza (inferiore a 1 Hz). I valori dei campioni al verde dopo la pressatura sono riportati in Fig. 6-A dove si evince che i post trattamenti distensivi durante le fasi di rivestimento mostrano valori più elevati, soprattutto nel caso di processo in aria a 450 °C. Per quanto concerne il trattamento termico di stress relieving a 600 °C in aria, illustrato in Fig. 6-B, la riduzione della coercitività è più accentuata nei processi a mulino a pallette con posttrattamento rispetto al caso green (massima differenza del 41%). Anche i valori minimi sono riferirti al processo di rivestimento con il post-trattamento a vuoto. Nel caso di trattamento termico di stress relieving a 600 °C in vuoto (vedi Fig. 7-A) si nota una riduzione rispetto al verde di circa il 50%. Per tutti processi di rivestimento si ha una
diminuzione percentuale pressoché uniforme, e il valore minimo è ottenuto per il processo con la Turbula. Per concludere, il trattamento termico di stress relieving a 600 °C viene mostrato in Fig. 7-B. La differenza percentuale più ampia è stata misurata con il processo di rivestimento con mulino a pallette con post-trattamento in aria. Tuttavia, per altri processi di rivestimento, la riduzione è intorno al 30%, dimostrando che il trattamento termico in vapore risulta il peggiore per quanto concerne la riduzione della coercitività. Per quanto riguarda la quantità dello strato isolante, per maggior parte dei casi la frazione minore allo 0,2 wt% risulta avente coercitività minore rispetto all’1 wt%. Comunque, le differenze in termini di coercitività al variare del contenuto di rivestimento in ferrite, nella maggioranza dei casi, sono dell’ordine di qualche percento, raggiungendo al massimo il 10%.
Memorie scientifiche - Materiali per l'energia
Fig.6 - Misura di coercitività: A green e B dopo il trattamento termico in aria a 600°C / Coercivity measurement A green and B after heat treatment in air at 600°C
Fig.7 - Misura di coercitività dopo il trattamento termico in vuoto A e in vapore B a 600°C / Coercivity measurement after heat treatment in vacuum A and steam B at 600°C
I valori della resistività elettrica sono stati ricavati tramite la misura della resistenza elettrica. Per ottenere le misure di
resistenza è stato utilizzato un multimetro connesso ad una pinza, come mostrato in Fig. 8. In Fig. 9 -A vengono riportati i valori della resistività elettrica per il compatto in ver-
de. Si nota che solo il processo con il mulino a palette con post-trattamento in aria ha valori elevati di resistività, dovuto alla considerevole ossidazione. Inoltre, solo il mulino a palette senza particelle fini si avvicina alla soglia di almeno 200 µ Ω m. Questo conferma che il processo di rivestimento è stato il più uniforme. Tuttavia, si è osservata un’anomalia: con l’aumento della percentuale dello strato di isolante in ferrite, la resistività in generale diminuisce anziché aumentare. Questo inconveniente è inoltre da associare al comportamento inatteso e controproducente del lubrificante, che agglomera le particelle di nano-ferrite impendendo loro di rivestire il ferro, come osservato nelle diverse immagini in microscopia ottica. Il trattamento termico di
stress relieving a 600 °C in aria, mostrato in Fig. 9 -B, ha un effetto negativo sulla resistività, la quale è ridotta ai valori unitari di µ Ω m. I valori di resistività risultano ulteriormente diminuiti, al livello frazionario di µ Ω m, per i trattamenti termici di stress relieving a 600 °C in vuoto (Fig. 10-A) e in vapore (Fig. 10 -B). Considerando la quantità dello strato isolante, i risultati migliori si ottengono nel caso di 1 wt% di Fe2O3 per quasi tutti i trattamenti termici di stress relieving. Questo è in controtendenza rispetto ai valori ottenuti con il green. Per tale motivo, sarebbe necessaria un’analisi dettagliata tramite microscopia elettronica a scansione SEM.
Fig.8 - Misura della resistenza elettrica / Measurement of electrical resistance
e B dopo il trattamento termico in aria a 600°C / Resistivity measurement A green and B after heat treatment in air at 600°C
Fig.10 - Misura di resistività: e dopo il trattamento termico in vuoto A e in vapore B a 600°C / Resistivity measurement after heat treatment in vacuum A and steam B at 600°C
Dalle osservazioni al microscopio ottico, si evince che il processo di rivestimento più efficiente risulta essere il mulino a palette senza le particelle fini; tuttavia, dai dati di coercitività il miglior processo risulta essere quello con la turbula mixer. Inoltre, il trattamento termico di stress relieving a 600 °C in vuoto risulta la soluzione migliore per ridurre la coercitività. Nel caso dell’uso del mulino a palette con post-trattamento in aria la considerevole ossidazione delle polveri aumenta la resistività elettrica ma al contempo la coercitività risulta troppo elevata. Un buon risultato di resistività elettrica è ottenuto con il processo di rivestimento a mulino a palette senza le particelle fini. Tuttavia dopo vari trattamenti termici di stress relieving nessun risultato può essere considerato soddisfacente dal punto di vista dei valori di resistività. Inoltre, sono state riscontare delle problematiche con l’uso del lubrificante Kenolube insieme alla ferrite nanometrica e difficoltà ad adoperare il vuoto durante la distensione delle polveri
RIFERIMENTI
per i processi di rivestimento con il mulino a palette. In sostanza, il processo di rivestimento in turbula mixer può essere migliorato riducendo il quantitativo di Kenolube e aggiungendo maggiore quantità di ferrite, in modo tale da ricoprire un numero maggiore di particelle ferromagnetiche, tuttavia sarebbe poi necessario sviluppare un metodo per asportare il quantitativo in eccesso di ferrite nanometrica. La stessa considerazione sulle problematiche del lubrificante Kenolube può essere fatta per il rivestimento con il mulino a palette senza le particelle fini. Tuttavia, durante l’attività con il mulino a palette un attento controllo di tempi e quantitativi di ferrite da aggiungere di volta in volta necessita ancora ulteriori approfondimenti. Inoltre si è notato che la ferrite utilizzata non risulta la più adatta, essendo soggetta ad una transizione di fase tra 450 °C e 500 °C. In futuro si potrà pensare di utilizzare altri tipi di ossido di ferro più stabili o con transizioni di fase a temperature maggiori.
[1] J. M. SILVEYRA, E. FERRARA, D. L. HUBER, T. C. MONSON, “Soft magnetic materials for a sustainable and electrified world”, AAAS Science, 362, October 2018, doi: 10.1126/science.aao0195.
[2] M. KĄCKI, M.S. RYLKO, J.G. HAYES, C.R. SULLIVAN, “Magnetic material selection for EMI filters”, IEEE ECCE Conf., Cincinnati (USA), 1÷5 October 2017; Conf. Proc. pp. 2350–2356, doi: 10.1109/ECCE.2017.8096456.
[3] J. HE, H. YUAN, M. NIE, H. GUO, H. YU, Z. LIU, R. SUN, “Soft magnetic materials for power inductors: State of art and future development,” Materials Today Electronics, 6, 2023, 100066, ISSN 2772-9494, https://doi.org/10.1016/j.mtelec.2023.100066
[4] E. A. PÉRIGO, B. WEIDENFELLER, P. KOLLÁR, J. FÜZER, “Past, present and future of soft magnetic composites”, AIP Applied Physics Reviews 5 (2018).
[5] R. BUREŠ, M. STREČKOVA, M. FABEROVA, P. KOLLAR, J. FUZER, “Advances in powder metallurgy soft magnetic composite materials”, Arch. of Metallurgy and Materials, 62, 2017, pp. 1149-1154.
[6] E. POŠKOVIĆ, F. FRANCHINI, L. FERRARIS, E. FRACCHIA, J. BIDULSKA, F. CAROSIO, R. BIDULSKY, M. ACTIS GRANDE, “Recent Advances in Multi-Functional Coatings for Soft Magnetic Composites”, MDPI Materials, 14 (22), November 2021, doi: 10.3390/ ma14226844.
[7] E. POŠKOVIĆ, L. FERRARIS, F. FRANCHINI, R. BIDULSKY, M. ACTIS GRANDE, “Novel SMC Materials with the Insulating Layer Treated at High Temperature”, EPMA EURO PM2019, Maastricht (Netherlands), 13÷16 October 2019, Conf. Proc..
[8] J. FÜZER, M. STREČKOVÁ, S. DOBÁK, Ľ. ĎÁKOVÁ, P. KOLLÁR, M. FÁBEROVÁ, R. BUREŠ, Y. OSADCHUK, P. KUREK, M. VOJTKO, “Innovative ferrite nanofibres reinforced soft magnetic composite with enhanced electrical resistivity”, J. of Alloys and Compounds, 753, 2018, pp.219-227.
[9] K. J. SUNDAY, F. G. HANEJKO, M. L. TAHERI, “Magnetic and microstructural properties of Fe3O4-coated Fe powder soft magnetic composites”, J. of Magnetism and Magnetic Materials, 423, 2017, pp. 164-170.
[10] B. MENG, B. YANG, X. ZHANG, B. ZHOU, X. LI, R. YU, “Combinatorial surface coating and greatly-improved soft magnetic performance of Fe/Fe3O4/resin composites,” Mater. Chem. Phys. 2020, 242, 122478, https://doi.org/10.1016/j.matchemphys.2019.122478.
[11] EMIR POŠKOVIĆ, LUCA FERRARIS, FAUSTO FRANCHINI, MARCO ACTIS GRANDE; The effect of particle size on the core losses of soft magnetic composites. AIP Advances 1 March 2019; 9 (3): 035224.
[12] E. POŠKOVIĆ, F. FRANCHINI, F. CAROSIO, M. ACTIS GRANDE, L. FERRARIS, “Application of impact mill technique for the production of soft magnetic composite materials,” In Proceedings of the AIM 2020, Naples, Italy, 20 January 2021
[13] G. ZHAO, C. WU, M. YAN, “Enhanced magnetic properties of Fe soft magnetic composites by surface oxidation”, J. of Magnetism and Magnetic Materials, 399, 2016, pp. 51-57.
[14] C. APPINO, E. FERRARA, F. FIORILLO, L. ROCCHINO, C. RAGUSA, J. SIEVERT, T. BELGRAND, C. WANG, P. DENKE, S. SIEBERT, Y. NORGREN, K. GRAMM, S. NORMAN, R. LYKE, M. ALBRECHT, X. ZHOU, W. FAN, X. GUO, M. HALL, “International comparison on SST and Epstein measurements in grain-oriented Fe-Si sheet steel”, International J. of Applied Electromagnetics and Mechanics, 48, 2015, pp. 123–133.
[15] E. POŠKOVIĆ, F. FRANCHINI, L. FERRARIS, F. CAROSIO, M. ACTIS GRANDE, “Rapid Characterization Method for SMC Materials for a Preliminary Selection”, MDPI. Appl. Sci., 11 (24), December 2021, doi: 10.3390/app112412133.
[16] Z. GMYREK, "Single Sheet Tester With Variable Dimensions," IEEE Trans. Instrum. Meas., 65 (7), pp. 1661-1668, July 2016, doi: 10.1109/TIM.2016.2540839.
Magnetic materials are increasingly being used in various industrial sectors, that require different magnetic properties with low iron losses and increasingly complex shape designs. From this perspective, the research has led to new materials, such as Soft Magnetic Composites (SMC). The main advantages deriving from using SMCs instead of laminated steels are lower eddy currents, the possibility of complex geometries, 3D magnetic flux path, and efficient behavior at high frequencies. However, a low mechanical strength at ambient temperature represents a limit, which can be overcome by adopting layers capable of working over 600 °C, and thus withstand thermal treatments, which could add better mechanical strength. In this work, an inorganic coating with nano-ferrite particles was investigated; adopting several particular processes to coat the ferromagnetic particles and three types of heat treatment environments were considered. The characterization of the obtained SMC was performed through electrical resistivity and coercivity measurements with the aim of selecting the best process.
KEYWORDS: SOFT MAGNETIC COMPOSITE MATERIALS, POWDER METALLURGY, TURBULA MIXER, IMPACT MILL, COERCIVITY, ELECTRICAL RESISTIVITY, METALLOGRAPHIC ANALYSIS, SOFT FERRITE;
The 4th WCCM will take place on August 25-28, 2026, at NH Milano Congress Centre, Milan, Italy. The primary objective of the World Congress on Condition Monitoring (WCCM) is to facilitate the global exchange of research and applications in Condition Monitoring (CM) and related areas, with a strong emphasis on scientific and technological advancements, industrial applications and international cooperation. The Congress serves as a worldwide platform for scientists and professionals from both academia and industry to share knowledge and insights. The event is organized in collaboration with condition monitoring and NDT societies worldwide.
• 2017: WCCM 2017 London, UK
• 2019: WCCM 2019 Singapore
• 2024: WCCM 2024 Beijing, China
The congress technical programme includes:
• Plenary keynote presentations
• Distinguished overview presentations
• Invited and contributed presentations, including case study presentations
• Industrial sessions for major industrial sectors
• Workshops/tutorials on advanced topics in condition monitoring, led by recognised scientists and engineers
• Expert panel session on hot topics in condition monitoring and related areas
• Exhibition, vendor presentations and a plenary spotlight session for exhibitors and sponsors
• Deadline for abstract submission: January 30, 2026
• Notification of abstract acceptance: February 28, 2026
• Deadline for submission of full papers (Optional): April 30, 2026
• Notification of full paper acceptance .................................... May 31, 2026
• Deadline for registration and payment for early bird: June 10, 2026
• Standard Registration Deadline: July 31, 2026
NH Milano Congress centre. Address: Strada 2, 7, Assago (MI) - Italy. NH Milano Congress Centre is located in Assago, Milan business district just 15 minutes away from the city center and nearby the vibrant Navigli area.
The detailed exhibiting and sponsorship packages will be available on the WCCM 2026 website in the following months. In the meantime, companies interested in taking part in the Exhibition or sponsoring the event may contact the organizing secretariat.
Prof. Dr. Len Gelman
The University of Huddersfield, UK
Prof. Dr. Hamid Reza Karimi Politecnico di Milano, Italy
For inquiries, contact:
• E-mail: conference@aimnet.it
• Phone: +39 02-76021132
• Website: www.aimnet.it/wccm2026
Social media
Follow us for updates:
F. Kek, K.-M. Zettl, D. Giunta, N. Tanasic, P. Stahl, M. Lin, P. Trezzi
In the pursuit of a sustainable refractory and steel industry, the circular economy offers the most resilient answer. RHI Magnesita and MIRECO close the loop by engaging the producer, user and recycler of refractories, extending their services to the Italian market. Integrating Reffratari Trezzi’s innovative solutions and expertise, even greater value can be delivered to clients and customers. In addition to the CERO Waste Concept, this approach also involves a slag engineering solution and circular metallurgical additives. The CERO (Continuous Economic Recycling Optimization) Waste Concept encompasses the collection, sorting, reuse assessment and disposal, as well as legal management of refractory material. This concept generates circular minerals serving as alternatives to primary raw materials for circular refractory products and green metallurgical additives, thereby maximising refractory recycling rates, reducing CO2 emissions, and minimising landfill use. A metallurgical consultancy service for slag engineering provides deep insights into process optimisations, the application of green metallurgical additives and slag compatibility with refractory linings. Three studies on electric arc furnaces, basic oxygen furnaces and secondary metallurgy ladle treatments illustrate opportunities with circular metallurgical additives and address challenges such as MgO saturation, slag foaming, desulphurisation and alloys saving. These studies, using e-tech slag modelling tools, highlight the added value in metallurgical, refractory and circular economy knowledge for a steel plant’s green steel strategy.
KEYWORDS: CIRCULAR ECONOMY, CERO WASTE, REFRACTORY RECYCLING, CIRCULAR METALLURGICAL ADDITIVES, SLAG ENGINEERING, METALLURGICAL CONSULTANCY;
Reducing greenhouse gas emissions is an urgent priority across industries, with the steel sector facing significant pressure due to its energy-intensive processes and aim to reduce emissions to zero or almost zero by the middle of the century. Many steelmakers already monitor emissions across their product life cycles through Product Carbon Footprints (PCFs), a method that tracks emissions from the initial stages of production up to the factory gate – also known as the “cradle to gate” approach. Environmental Product Declarations (EPDs) expand this scope by incorporating additional environmental impacts, establishing PCFs and EPDs as essential tools for tracking climate-friendly product performance. Despite these advancements, a consistent framework to classify and evaluate “Green Steel” based on emissions remains underdeveloped. The International Energy
F. Kek, K.-M. Zettl
RHI Magnesita, Austria
D. Giunta
RHI Magnesita, Italy
N. Tanasic, P. Stahl
MIRECO, Germany
M. Lin
RHI Magnesita/MIRECO, Austria
P. Trezzi
Reffratari Trezzi, Italy
Agency (IEA) has established baseline thresholds for emissions, defining standards for Low Emission Steel and Near Zero Steel in both integrated- and electrical steel
mills (Table 1). They create a basis for climate-friendly products to be explicitly favoured, for example in public tenders. [1,2].
Tab.1 - Emission thresholds for “Green Steel” product declaration [1,2].
Slag additives play a vital role in reaching these emission thresholds, as their own PCFs – due to calcination and premelting – significantly contribute to the overall PCF of steel. Consequently, steel producers are increasingly interested in circular refractory management and sustainable additives.
MIRECO, a joint venture between RHI Magnesita and Horn & Co., provides crucial support to steelmakers adopting green steel practices according to the abovementioned demands. The joined forces of a circular refractory manufacturer with a strong R&D backbone and
metallurgical expertise, and a refractory recycler with decades of experience in terms of sorting, processing, material and waste management offer an all-in-one tailored solution to meet the unique requirements of each steel plant.
MIRECO’s platform spans Europe and features multiple recycling sites in Germany, Sweden, Poland, Kosovo, and Austria, along with on-site solutions at steel plants in Duisburg, Bremen, Dillingen, and Dunkirk. Their recent expansion into the Italian market, aided by Reffratari Trezzi, brings further innovations in recycling and refractory management to local customers. In Figure 1, a map of all MIRECO locations is pictured, highlighting the new site near Milan.
MIRECO offers a comprehensive range of sustainable additives for the steel production process, facilitating the reintegration of used refractory products into the supply and value chain. In addition to direct sales, the CERO Waste service is also available, enabling customers to benefit from MIRECO’s expertise and implement closed-loop recycling to significantly decrease CO2 emissions. The approach complies with the European Waste Framework Directive and focuses on optimising refractory collection material sorting, and recycling to minimise landfill [3]. Furthermore, a slag engineering solution giving insights into metallurgical process optimisations, the application of sustainable additives and slag compatibility with refractory linings can be provided [4,5,6].
MIRECO’s circular approach involves three core services:
• CERO Waste Concept
Supports closed-loop recycling, minimising landfill waste and reducing CO₂ emissions.
• Circular Metallurgical Additives
Provides recycled, sustainable additives directly for the steelmaking process.
• Slag Engineering Solutions
Offers consulting for optimal slag management, refractory compatibility and specific metallurgical optimisations.
Traditional refractory materials often follow a linear lifecycle, with products being discarded after use. Refrac-
tory producers, steelmakers and their decisions against products containing circular raw materials are the reason for this significant waste accumulation and the loss of potentially valuable materials. The alternative opportunity is following MIRECO’s circular CERO Waste approach, unlocking these material potentials by using circular refractory products and circular metallurgical additives.
Figure 2 pictures the trinity: Customer, MIRECO and RHI Magnesita, within the CERO Waste circle. The customer at the top provides used refractory material to MIRECO in a clockwise direction. There, the material is sieved, sorted and cleaned, leading to two main material types: the finer fraction for non-refractory circular raw materials (CRMs) and the coarser fraction for CRMs for refractory products. Non-refractory CRMs are converted into circular metallurgical additives, i.e., slag conditioner supplied in a counterclockwise direction back to the customer. These sustainable additives and their impact on steelmaking will be elaborated on in this article. CRMs for refractory products are provided to a refractory producer, in first instance to RHI Magnesita, manufacturing new circular refractory products the customer is supplied with. In this way, the circle of refractory lifetime is closed, the most added value is taken out of each material stream and landfilling is decreased to less than 2% [3].
MIRECO designed a promotional video [3], giving a detailed overview about the four steps CERO Waste provides to a steel plant with products and services to
Fig.3 - CERO Waste Concept and its 4 steps of continuous sustainability [3].
So far, MIRECO has enabled over 30 European customers to achieve a more efficient circular economy, providing more than 100,000 tonnes of CRM products and additional services annually. MIRECO has introduced a Sustainability
close the circle of refractory life. Figure 3 illustrates the four respective steps of the concept.
1) Collection Point Management
In this first step, the complete refractory material flow is drawn out between all involved stakeholders, starting from lining via demolition to the final material destination. This procedure needs time and a transparent and open steelmaker.
2) Material Sorting
Second, in order to maximise the yield of recyclable raw materials, the different spent refractory qualities are sorted into the required qualities. Sorting manually and with laser technology is the core competence of MIRECO.
3) Reuse
During the third step of the concept – the creative part – all possible ways of reusage are evaluated, together with the producer and the user of the refractory. In this step, the highest impact on CO2 and landfill reduction is achieved.
4) Disposal
In this step, MIRECO takes care of the disposal process and the responsible and legal handling of waste products.
Award to recognise the success of its customers in terms of annual CO2 savings. This award was presented to GMH Gruppe and Swiss Steel Group in 2023, each with annual CO2 savings of around 10,000 tonnes – see Figure 4 [7].
[7].
Metallurgical additives from primary raw material sources in general serve crucial functions in iron and steelmaking, where slag chemistry directly impacts refining processes like dephosphorisation, desulphurisation and slag foaming. Additives are generally classified into basic and fluxing oxides, with the former aiding in CaO and MgO saturation and the latter in fluidising the slag [5].
In Europe, approximately 170 million tonnes of steel are produced annually, with 45% coming from integrated steel mills and 55% from electrical steel mills. Taking an average specific slag amount of 200 kg per tonne of steel implies a significant slag volume and thus a huge demand of slag forming additives [8].
MIRECO sources spent refractories through CERO Waste. Due to handling and processing, even pre-separated materials contain a significant percentage of fine particles. The whole material is sieved, sorted and cleaned in the same way. The coarser fraction is converted into CRMs for new refractory products and the finer fraction – i.e., nonrefractory CRMs – is converted into circular metallurgical additives. With a roughly 1:1 ratio of fine to coarse fractions, both depend strongly on each other. Under European waste legislation’s “No-Out, No-In”-rule, recycling spent refractories requires maintaining a balance between these two fractions. Unlike mined primary raw material availability, those circular raw materials and circular metallurgical additives and their availability always depend
on the other material type and its use, respectively. Circular metallurgical additives contribute to environmentally friendly steel production as the PCF of these materials can be <10% of commonly used slag formers (Table 2) and is detailed in the technical data sheet [9]. Additionally, these sustainable products are characterised by their cost competitiveness, as they do not require calcination or premelting and are not dependent on fuel price volatilities. They offer a price advantage of approximately 10%. In terms of chemistry, the MgO content protects a basic refractory lining from corrosion, while carbon is an energy source as well as a reducing and/or slag foaming agent. When compared to synthetic premelted slags, recycled alumina products have the advantage of containing accompanying oxides that lower the melting point and a specific surface area ten times higher than common additives, making them a competitive alternative for calcium aluminate slags or even a CaF2 substitute [5,6]. As circular metallurgical additives are applied in significant quantities and with high frequency, the resulting carbon emission savings can be substantial. This is why an increasing number of steel plants are eager to adopt these sustainable additives. MIRECO provides a general portfolio (see Table 2), showing standard grades of basic and fluxing oxides that can be customised to the steel plants demands accordingly. Currently, more than 100,000 tonnes of circular metallurgical additives are sold on the European market every year. The split in terms of basic and fluxing oxides is two-thirds to one-third.
When considering the use of circular metallurgical additives, it is important to address existing biases against reclaimed materials, the sensitivity to freight costs, and the need for effective dissolution. However, both laboratory and industry studies have shown that circular MgO additives have good solubility in electric arc furnace (EAF) and basic oxygen furnace (BOF) processes, even in MgO-oversaturated slags [4,5]. Additionally, industrial trials demonstrated good solubility and no impact on desulphurisation capacity when ladle furnace (LF) slags were fluxed with circular alumina carriers instead of premelted slag, even reducing CaF2 to zero [6].
Various showcase trials testing circular metallurgical additives in different steelmaking units, combined with RHIM’s metallurgical expertise, have led to a new offering that supports the circular economy approach: a slag engineering solution. This solution provides customers with comprehensive metallurgical consulting to optimise their slag engineering. It includes access to e-tech slag modelling tools, offering detailed insights into specific slags and helping to enhance the overall metallurgical process.
The e-tech platform is a collection of online slag modelling tools available in RHI Magnesita’s Customer Portal, the secure online environment enabling access to data including order tracking, refractory performance reports, scope 3 CO2 emissions from consumed refractory products, and gunning consumption figures. The e-tech tools are used to determine potential process improvements; they were applied in the showcase studies “Quickfoam” for EAF and BOF processes, and “Slag Optimisation” and “Kinetic Desulphurisation” for the LF process [10,11], which are described in the following section.
Three case studies – one for each steelmaking unit: the EAF, BOF and LF processes – highlight the positive impacts of MIRECO’s solutions on green steel production.
The following saving ranges for an average steel plant being provided with MIRECO’s services can be assumed:
• Up to 20% less specific refractory consumption
• € 0.3-1.0 of savings per produced tonne of steel
• 10-15 kg CO2 savings per produced tonne of steel
• EAF – MIRECO’s circular MgO and carbon containing additives were applied to the EAF process via injection equipment, evaluating the most efficient time slot for enhanced slag foaming and most lining protection.
• BOF – Circular additives were tested in a BOF environment, addressing the challenge of MgO saturation. Trials showed that circular additives dissolved effectively, ensuring slag compatibility and maintaining process efficiency.
• LF – In secondary metallurgy, circular alumina products replaced traditional calcium aluminate slags, enhancing desulphurisation performance while reducing CaF₂ dependency. The high surface area of these additives facilitated better integration, with e-tech modelling confirming the improved efficiency.
The following Table 3 shows an overview matrix of the three studies conducted, each published in an RHI Magnesita Bulletin article – see literature [3,4,5].
The shift towards sustainable practices in the steel industry is essential to reducing environmental impact and aligning with global climate goals. MIRECO’s initiatives, including the CERO Waste Concept, slag engineering solutions and circular metallurgical additives, represent significant advancements in achieving a circular economy within steel production. By promoting closed-loop recycling, optimising slag chemistry and introducing low-carbon alternatives to traditional additives, these innovations reduce CO₂ emissions, minimise landfill waste, and offer economic benefits for steel plants. Through incorporating Reffratari Trezzi organisation, MIRECO is extending its impact in Italy and across Europe, demonstrating the
feasibility and advantages of integrating circular materials into steelmaking.
Case studies illustrate that circular materials maintain or enhance process efficiency in electric arc, basic oxygen and ladle furnaces. The development of tools like the e-tech platform further aids steel plants in optimising their operations and maximising the value of recycled materials. By addressing challenges such as raw material variability and biases against recycled products, MIRECO is paving the way for a more sustainable steel industry. As steelmakers increasingly adopt these practices, the industry moves closer to realising its green steel goals, setting a strong foundation for a climate-friendly future.
[1] T. Sach, P. Creutzburg - Leitmärkte für klimafreundliche Grundstoffe Wissenschaftliches Begleitdokument im Auftrag des Bundesministeriums für Wirtschaft und Klimaschutz, 2024.
[2] IEA; Achieving Net Zero Heavy Industry Sectors in G7 Members, 2022.
[3] https://www.mireco.com/de/cero-waste.php
[4] F. Kek, T. Griessacher, C. Bauer, B. Zocratto, R. Krump, and C. Koubek, Refractory Waste to Slag Engineering Solution—Metallurgical Consulting Supports Steel Plant’s Circular Economy Strategy. RHI Magnesita Bulletin. 2022.21–28.
[5] F. Kek, M. Kirschen, F. Lopez, P. Souza and P. Stahl, Sustainable Slag Engineering in the Basic Oxygen Furnace Using Circular Metallurgical Additives and Modelling Tools, RHI Magnesita Bulletin, 2023.
[6] F. Kek, A. Horn, P. Souza, F. Lopez, N. Lechner and P. Stahl, Green Steel Initiatives Supported by Enhanced Slag Engineering Using High Alumina Circular Metallurgical Additives. RHI Magnesita Bulletin. 2024.
[7] https://www.linkedin.com/company/mireco-minerals-recovery/posts/
[8] World Steel in Figures 2024, World Steel Association, 2024.
[9] M. Joos-Bloch, L. Rechberger, C. Haider, W. Moulin-Silva, J. Wucher and T. Drnek, Product Carbon Footprint of Refractory Products. RHI Magnesita Bulletin. 2023. 39-44.
[10] Souza, D., López, F., Moggee, H. and Lamare, C. A Toolbox of Slag Modelling and Metallurgy in Your Pocket. RHI Magnesita Bulletin. 2021, 72–77.
[11] Souza, P., Freitas, C., Arth, G., Penido, G., Zettl, K., Bolognani, J., Lamare, C., Lammer, G., Moser, G. and Hoffert, A. Next Level of Digital Refractory Contracts. RHI Magnesita Bulletin. 2022, 52–59.
Punta a soluzioni refrattarie su misura
Scegli un partner di eccellenza per i refrattari nel trattamento termico dell’acciaio
> Una gamma completa di refrattari di alta qualità
> Progettazione, produzione, supervisione in loco
> Soluzioni per ridurre la tua impronta di carbonio
> Qualità senza compromessi
B. Kleimt, Z. Kargar, V. Peiss, A. Arteaga Ayarza, D. Mier Vasallo, M. Ferrer Prieto, I. Unamuno Iriondo
Scrap-based steelmaking in the Electric Arc Furnace (EAF) allows to produce high quality steel grades on the basis of secondary raw materials. However, due to the fluctuation and quality impairment a tight control of the properties of steel scrap is required.
In the framework of the EU-funded project “Artificial Intelligence Technologies for European Process Industry digital transformation (s-X-AIPI)”, an intelligent, AI-based system for continuous monitoring of scrap properties, directly coupled with a scrap mix optimisation for steel qualities to be produced was developed and implemented at the Sidenor Electric steelmaking plant in Basauri, Spain. The system is designed to enhance the selection process of the charge materials for EAF steelmaking through the integration of a self-managing AI framework. Predictive machine learning models are used to improve the reliability and precision for characterisation of scrap properties like metallic yield, composition and specific energy requirements from historical and most recent production data, to provide upto-date information to a scrap mix optimization calculation. When significant deviations between predicted and actual liquid steel composition occur, an autonomous event handler initiates a retraining of both the prediction models and the scrap characterisation tools, to adjust the scrap property parameters, the predictive AI models, and/or the scrap mix optimizer constraints. Supported by a knowledge base, this AI framework ensures consistent and reliable scrap management under varying and changing process conditions.
KEYWORDS: ELECTRIC ARC FURNACE, SCRAP CHARACTERISATION, SCRAP MIX OPTIMISATION, PREDICTIVE AI MODELS, SUPERVISION;
The Electric Arc Furnace (EAF) is the most important aggregate for steelmaking by recycling of secondary raw materials. The scrap used as charge material in the EAF is characterised by a high variability in metallic yield, chemical composition and melting behaviour. Although the European scrap types are standardized, it is difficult to ensure the quality aspects of some of the scrap types due to the heterogeneity of the materials origin. This is essential to be considered in context with online monitoring and control of the EAF process. Within the framework of the Horizon Europe project “Artificial Intelligence Technologies for European Process Industry digital transformation” (s-X-AIPI), for the steel use case at Sidenor Aceros Especiales in Spain a supervision and decision support tool was developed, which allows on the one hand side to characterize the properties of the different scrap types in use and monitor their evolution over time, and on the other hand to use this information
Bernd Kleimt, Zeinab Kargar, Vera Peiss
VDEh-Betriebsforschungsinstitut GmbH, Düsseldorf, Germany bernd.kleimt@bfi.de
Asier Arteaga Ayarza, Diana Mier Vasallo, Maria Ferrer Prieto
Sidenor I+D S.A., Basauri, Spain
Inigo Unamuno Iriondo
Sidenor Aceros Especiales, Basauri, Spain
for scrap mix optimization of the EAF process. The overall target of this supervision and decision support tool is to reliably achieve the quality specific target composition of liquid steel produced in the EAF process, and to facilitate as much as possible the use of low-quality scrap types for the production of high-quality steel grades. These aspects contribute to the aims of the Green Deal of the EU, reducing the CO2 emissions of steel production and strengthening at the same time the circular economy. Even more, the scrap use is expected to increase due to the decarbonization strategy of EU steelmaking, and thus more pressure is expected on the scrap markets. The development of this supervision and decision support tool was based on previous work of the authors in different areas:
A statistical modelling approach for characterising the properties of the steel scrap in use by means of a multilinear regression was first developed within the project FLEXCHARGE [1], which was funded in the European RFCS steel research fund. Within this project, also the first version of a scrap mix optimization software based on a simplex optimization was developed. It is evident that a scrap mix optimization allows to reduce the EAF production costs and to improve steel quality and environmental impact at the same time [2, 3]. The developed solutions were based on Matlab stand-alone applications, whereas within the Horizon 2020 project REVaMP [4, 5] a user-friendly web-based solution with direct data base access was developed. Also, this multilinear regression calculation approach was extended towards an on-line supervision of scrap properties, to detect significant deviations in expected scrap quality on a short-term basis [6, 7].
The multi-linear regression calculation provides accurate results for those elements which do not react with oxygen, as e.g., copper, nickel, tin and molybdenum. However, for prediction of those elements which react with oxygen, e.g., Phosphorus, Manganese or Chromium, a non-linear approach is required. A fully dynamic process model using all relevant cyclic and even-driven input data, is of course able to predict the analysis of liquid steel regarding all chemical elements. This has been proven in the above-mentioned project REVaMP, where for example the phosphorus content could be predicted with
excellent accuracy [5]. However, the effort to implement such a dynamic model is rather high. In contrast to that, AI-based non-linear models offer a solution for prediction of the element concentrations which can be implemented with a significantly lower effort.
Within this paper, the results of the s-X-AIPI project work for the steel use case are presented with respect to an AI-based supervision and decision support tool, which combines classical solutions for scrap characterisation with AI-based prediction models to detect deviations in the scrap properties and to react on them by providing up-to-date information to the scrap mix optimization for the EAF.
Characterisation of steel scrap
The main charge material at the electric steelmaking plant of Sidenor is steel scrap from three different origins:
• Post-consumer scrap: Old scrap from the demolition of the metal structure of industrial buildings, machinery, railway and naval scrap, used cars etc.;
• Pre-consumer scrap: Industrial or new scrap that is generated in processing industries that use steel as raw material in their manufacturing processes
• Internal recoveries: Scrap generated along the steelmaking process itself, in melt shops, rolling mills and other processes inside the Sidenor plant.
Pre-consumer scrap is usually very clean in its chemical composition and its variability is lower compared to post-consumer scrap. However, its use is limited due to the high price. Well managed, internal recoveries can also provide a stable chemical composition that can lead to huge savings on ferroalloys additions, however the available amounts are not very high. The critical scrap types are the post-consumer scraps with only roughly known composition and high variability in their properties. As a first step, multi-linear regressions were performed based on historical process data regarding used scrap types, achieved meltdown analysis and tap weight, with the objective of visualizing statistically the variability of the 11 scrap grades currently in use at Sidenor. In Figure 1 is shown as example the copper content of each of the 11 scrap types, visualized as a so-called violin diagram with average contents and their statistical distributions.
Especially the post-consumer scrap types D and E show high Cu contents with a large variability. Similar figures were created for all other important elements included
in the scrap, as Mn, Cr, P, etc., as well as for the overall metallic yield.
These investigations of Sidenor were the basis for VDEhBetriebsforschungsinstitut (BFI) to develop a webbased tool for easy and comfortable assessment of scrap properties (metallic yield, element composition, specific meltdown energy requirement) on the basis of a data
base access for the above-mentioned process data. The calculation of the scrap properties is based on finding the optimal solution for the two overdetermined systems of linear by the least square method:
To rule out unreasonable solutions, appropriate constraints for metallic yield and element concentration are defined.
In order to predict the energy required in the EAF process for processing the individual heats, it is necessary to de-
termine the specific meltdown energy demands for the individual scrap types. Assuming a linear dependence, the amount of energy required for any heat with given scrap masses is described by the following approach: (Eq.3)
Figure 2 shows exemplarily the Graphical User Interface (GUI) for selection of the evaluation period via heat numbers. A multi-linear regression calculation determines the properties of the different scrap types with mean value and standard deviation. The accuracy of the characterisation is visualised by a graph plotting the
predicted versus the measured respectively analysed values of tap weight, steel analysis and electrical energy consumption. The latter one is shown in the graph of Figure 2. Also, mean values and standard deviation of the prediction error and the R² correlation value are provided.
Fig.2 - GUI for selection of heats to be evaluated and accuracy of prediction (a) and evaluation results for electrical energy consumption (b) of the web-based tool for scrap type characterisation
Furthermore, the timely evolution and the statistical distribution of the different scrap properties are determined and displayed by applying the multi-linear
regression in moving window calculations with selectable window and step size. Exemplary results for the copper content of the scrap types are shown in Figure 3.
(b)
Fig.3 - GUI for displaying the timely evolution (a) and the statistical distribution (b) of the scrap types in use.
Prediction of element concentration in liquid steel
The multi-linear regression calculation provides accurate values for the scrap composition for those elements, which are more noble (Cu, Sn, Ni and Mo). For these elements, the correlation between predicted and analysed concentration in liquid steel is good, as can be seen in Figure 4a. However, for those elements which are partly oxidized during the EAF process (P, Mn, Cr), the
correlation is rather weak (see Figure 4b). Thus, the values for scrap composition determined by the multi-linear regression are not reliable enough. Further process data besides the charged amounts of scrap like the amount of injected oxygen and carbon and the addition of lime have to be considered to achieve a better correlation.
Fig.4 - Prediction accuracy of the multi-linear regression for copper (a) and for phosphorus (b). (a) (b)
As for Sidenor especially the phosphorus content plays a critical role to produce high-quality steels, its prediction based on the scrap properties needs to be improved.
To consider the effect of the metallurgical reactions of dephosphorisation, relevant operational process data had to be involved:
• amount of injected oxygen in relation to the injected carbon
• amount of lime addition via the 5th hole
• amount of injected lime
The surplus of injected oxygen creates FeO in the slag, which promotes in combination with lime additions the dephosphorisation reaction. To avoid the effort to implement a fully dynamic model for dephosphorisation within the EAF process, as it has been demonstrated in [5],
a non-linear regression approach based on AI methods was selected. The best performance was achieved by a Random Forest Regression method. A Random Forest Regressor is an ensemble method that builds multiple decision trees and combines their predictions for higher accuracy and stability. It handles non-linear relationships, is robust to outliers, and provides feature importance scores to identify key variables [8]. This AI-based nonlinear regression method has already been applied to evaluate the energy efficiency parameters of an Electric Arc Furnace [9].
As shown in Figure 5, by consideration of the abovementioned additional process data the correlation coefficient R² can be improved significantly.
The above-described AI-based model is applied to predict for every produced heat the final content of quality critical elements with focus on the copper and the phosphorus content. The prediction result is compared to the analysis of a steel sample which is taken for every EAF heat before tapping. Figure 6 shows this comparison exemplarily for the phosphorus content. In general, it
can be observed that the prediction result of the Random Forest Regressor is in line with the analysed results, with a scatter in the range which has been shown in Figure 5. Higher deviations between measured and predicted contents indicate that the properties of the charged scrap types may have changed.
Fig.6 - Application of a non-linear Random Forest Regressor to improve the prediction accuracy for the phosphorus content.
When the deviation between measured and predicted element content is higher than a predefined threshold for several heats in a row (see in Figure 7 for the phosphorus content), a dedicated software tool, the so-called Autonomic Manager (AM) creates an alarm that possible
anomalies in the scrap type properties have been detected. The Autonomic Manager functions as an autonomous coordinator of the AI data pipeline and acts as the primary decision-maker [10]. Within the s-X-AIPI project, it also has been applied to the Aluminium sector [11].
Fig.7 - Deviation between measured and predicted Phosphorus content with application of a threshold
Consecutively, a supervision procedure automatically activates an update of the scrap characterisation calculation to determine new and more accurate property values for the scrap types which are currently in use. A plant expert with metallurgical background knowledge checks if the new property values are reasonable and decides if they can be accepted to be used in the scrap mix
optimisation calculation for the following heats, so that further violations of quality restrictions can be avoided. At the same time, a re-training of the AI-based prediction model is initiated, so that it will also be adapted to the new properties of the scrap types. This supervision of the model results is also an elaborated checking procedure of the scrap properties, useful to monitor the evolution
of different scrap types in a changing market. The whole interaction between the different software modules is
illustrated in Figure 8.
Fig.8 - Overall concept for AI-Driven supervision of scrap utilisation.
By this procedure, which includes automatic functions but also Humans in the Loop (HITL), it is ensured that the scrap mix optimization always uses up-to-date values regarding the scrap properties, which significantly affect the optimization results and thus the suggestions which scrap types with which amounts shall be charged. Consequently, it shall be ensured that a minimum of violations regarding the quality restrictions occur, and that on the other hand low-quality scrap types are used with the maximum allowable amount.
The task of the scrap mix optimiser is to calculate the cost and quality optimal scrap mix for each steel grade to be produced. The optimization calculation not only considers the scrap purchase costs, but also the costs for meltdown energy, which have been determined by the scrap characterisation. If accessible, also the direct CO2
emissions caused by the use of the different scrap types can be considered. This accounts to the fact that a scrap type which may be cheap on the scrap market can turn out to be an expensive scrap type when considering the costs for the required meltdown energy.
Figure 9 shows the user interface of the scrap mix optimization. The selected scrap types of the optimal scrap mix with their amounts are displayed numerically and as a pie chart on the left-hand side. The maximal allowable element concentrations for the produced steel grades are read from a data base and compared in a table with the concentrations which are predicted form the suggested scrap mix in the right-hand part of the user interface. Charging restrictions for the different scrap types like minimum or maximum amounts are defined in a separate screen.
Statistical models for scrap characterisation provide reliable and up-to-date information on the properties of the scrap types in use. The data are directly and dynamically fed into a scrap mix optimization for decision support and control of the scrap mix to be charged. As properties of scrap types in use vary with EAF operating conditions and scrap suppliers, a close monitoring of deviations and appropriate short-term reactions are required. A comprehensive AI-based supervision and decision support system has been developed to react on detected anomalies in process and model performance caused by variations in scrap properties. Detection, diagnosis and self-repair modules support the operators and engineers to ensure an optimal performance of the EAF charge mix control tools. The whole decision support system has been implemented at the EAF plant of Sidenor Aceros Especiales in Spain and is currently tested in this industrial environment. Within a first test application of the scrap mix optimization Sidenor already identified cost savings of up to 12 €/t by increasing the percentage of low-cost scrap types in the charge mix [4].
This work has been supported by the project "self-X Artificial Intelligence for European Process Industry digital transformation" (s-X-AIPI), which has received funding from the European Union’s Horizon Europe research and innovation program under grant agreement No. 101058715. Views and opinions expressed are however those of the authors only and do not necessarily reflect those of the European Union. Neither the European Union nor the granting authority can be held responsible for them.
[1] Malfa, E., Nyssen, P., Fillipini, E., Dettmer, B., Unamuno, I., Gustafsson, A., Sandberg, E., Kleimt, B.: Cost and Energy Effective Management of EAF with Flexible Charge Material Mix. BHM (2013) Vol. 158 (1), 3-12
[2] Gyllenram, R., Westerberg, O.: The impact of scrap upgrading on EAF production cost and environmental performance. Stahl&Eisen 136 (2016), Nr. 1, 32-36
[3] Bets, S., Cesareo, E., Rolando, A., Venturi, F., Fontana, P., Mazarrello, B.: OPTIMET: An advanced Charge Optimizing Model for EAF steelmaking. 11th European Electric Steelmaking Conf., May 2016, Venice, Italy
[4] https://revamp-project.eu/
[5] Kleimt, B., Krieger, W., Mier Vasallo, D., Arteaga Ayarza, A., Unamuno Iriondo, I.: Model-based Decision Support System for EAF online Monitoring and Control. Metals 2023, 13, 1332. https://doi.org/10.3390/met13081332
[6] Sandberg, E.: Improved material efficiency utilizing cloud-based novel tools for on-lien supervision of EAF raw materials properties. 12th European Electric Steelmaking Conf., Sep. 2021, Sheffield, UK
[7] Kleimt, B., Mier, D., Maza, D: Early detection of deviations in charge material properties and adjustment for optimal scrap usage in the EAF. 5th European Steel Technology and Application Days, ESTAD 2021, Sept. 2021, Stockholm, Sweden
[8] https://scikit-learn.org/stable/modules/generated/sklearn.ensemble.RandomForestRegressor,
[9] Manojlović, V., Kamberović, Ž., Korać, M., & Dotlić, M. (2022). Machine learning analysis of electric arc furnace process for the evaluation of energy efficiency parameters. Applied Energy, 307, 118209.
[10] Quadrini, W., Cuzzola, F. A., Fumagalli, L., Taisch, M., De Luca, G., Calderaro, M., ... & Marguglio, A. (2024). A reference architecture to implement Self-X capability in an industrial software architecture. Procedia Computer Science, 232, 446-455.
[11] Angosto Artigues, R.; Gregores Coto, A.; Torrez Herrera, J.; Lou Tomas, F.; Verardi, S.; Marzano, M.; Fernandez Martinez, A. An AIDriven User-Centric Framework reinforced by Autonomic Computing: A case study in the Aluminium sector. In Proceedings of the Human Interaction and Emerging Technologies (IHIET 2024). AHFE Open Access, 2024, pp. 196–206. https://doi.org/10.54941/ ahfe1005478.
M. Dehghanpour Abyaneh, R. Sesana, M. S. Javadi, S. Lamparelli, S. Rizzo
Sludge generation worldwide yearly amounts to about 12 million tons. One of the hazardous waste products generated during iron and steel manufacturing is sludge. The industrialization of developing countries and the manufacturing of steel are expected to drive these figures even further upward. Sludge and slag waste management is challenging due to its value, unpredictability, and huge quantities produced at different sites. Another problem is the current frequent practice of landfilling. Since steel sludge is essentially constituted of iron, this study aims to investigate scalable, practical recycling methods currently used in present industrial processes. Among the methods to manage large volumes of sludge and provide immediate use are mechanical treatments, powder metallurgical, hydrometallurgical, and creative techniques. This review paper on sludge grinding in the bearing industry emphasizes the possibilities of bearing and transmission steel technology to turn low-value waste into valuable resources. It provides reasonably priced, ecologically acceptable approaches for industrially recycling metal waste. These processes not only promote industrial sustainability goals but also reduce environmental hazards for resource recovery by leveraging transmission steel technology, thereby providing a feasible road forward.
KEYWORDS: SLUDGE GENERATION, STEEL PRODUCTION, RECYCLING METHODS, MECHANICAL TREATMENTS, POWDER METALLURGY, HYDROMETALLURGY, BEARING INDUSTRY;
Advancements in manufacturing processes and the current situation are undoubtedly worthy of recognition. Its idea and philosophy changed from the Stone Age, when the first weapon was most likely developed to kill animals. Later on, the production processes evolved through many phases, adding and using more modern ideas and technological advances; therefore, we are about to enter Industry 4.0. The first industrial revolution came with the creation of steam-powered machinery in the 18th century; since then, it has been always changing. Further, the core of Industry 3.0 is the mass production and usage of conveyor belts, which brought Industry 2.0 and the development of computers and electronic systems. This is the backbone of automation. Industry 4.0 originated with the introduction of a cyber-physical system like information and communication technologies and robots to give greater flexibility, adaptability, and improved production system productivity [1-4].
Industry 5.0 uses a human-cyber-physical environment to probably reinterpret people as the core of operations. Two insightful thoughts stand out in this context. One
Mohsen Dehghanpour Abyaneh
Department of Mechanical and Aerospace Engineering (DIMEAS), Politecnico di Torino, Italy - TN ITALY, Global Manufacturing Organization, Italy mohsen.dehghanpour@polito.it mohsen.dehghanpour@Tsubaki-Nakashima.com
Raffaella Sesana
Department of Mechanical and Aerospace Engineering (DIMEAS), Politecnico di Torino, Italy raffaella.sesana@polito.it
Mohammad Sadegh Javadi
Department of Mechanical Engineering, Amirkabir University of Technology, Iran javadims@aut.ac.ir
Stefania Lamparelli, Sebastiano Rizzo
TN ITALY, Global Manufacturing Organization, Italy
stefania.lamparelli@tsubaki-nakashima.com sebastiano.rizzo@tsubaki-nakashima.com
of them may be regarded as the duration between the industrial revolutions is much shorter, reflecting the fast contemporary technical development. The second observation relates to technical developments spanning the second to the fourth industrial revolution. These
historical patterns indicate that during the next ten to twenty years the fifth industrial revolution will center on the mix of human, computer, and physical systems [5-8]. Figure 1 shows clearly the industrial revolutions with their different themes.
In past years, manufacturing was seen as turning raw resources into valued items to satisfy human needs. As life develops in many spheres, the rising need for sophisticated and advanced technologies to produce premium goods has grown as well [9-13]. As Figure 2 shows, industrial technology may be divided into four primary divisions in the current period [14-17].
Among the previously listed manufacturing categories, subtractive and transforming classes are used frequently in manufacturing. The main difficulty for the manufacturing sector is industrial competitive pricing as much waste sludge is involved in these operations. One of the usually utilized techniques for giving the components their final form and size is grinding. Steel sludge disposal greatly
influences grinding bearings in the steel sector. Until 2035 in this field, the worldwide demand for steel and thus the quantity of produced trash is predicted to keep increasing [18].
The majority of sludge ends up in landfills, which is hazardous to the environment. With over 3% oil in the sludge, it should be disposed of in specific landfills
costing more than 1200 € per ton [19]. Thus, sludge and waste material recovery not only promote environmental sustainability but also helps to save expenses. Developed following subtractive and transforming procedures for over a century, special recovery steel technologies have been widely documented and used in sectors [20-24]. The growing environmental rules and the need for sustainable waste management techniques have made sludge recovery
a vital subject of study and development. Particularly in the metallurgical and manufacturing industries, the sludge produced from several industrial operations includes valuable elements that may be collected and used again [24, 25]. Figure 3 shows the most recent developments in sludge recovery techniques in industry, so this review article seeks to provide a summary of them.
Sludge recycling is now a major component of industrial waste management as cost-effectiveness and sustainability for the environment define it. Particularly in the metallurgical and manufacturing industries, industrial operations produce large volumes of bearing steel sludge, a byproduct including precious metals. Sludge recovery, arranged from industrial and scholarly points of view, is the process by which waste products are turned into useful resources. From an industry standpoint, the focus is on scalable, pragmatic ideas easily applied to current procedures. Important techniques falling under this area consist:
• Mechanical Treatments
• Powder Metallurgical
• Hydrometallurgical
• Novel techniques
Mechanical treatment methods assist in recovering sludge by reducing moisture content, improving sludge properties, and preparing it suitable for future use or processing. These techniques increase sludge management's efficiency and efficacy by use of separate mechanical procedures. Enhanced briquetting, ball drumming, and dry screening are the major techniques used in this scheme. Every technique contains characteristics and variables that aid in maximizing sludge recovery in industrial-scale operations.
Borowski et al [26] investigated an affordable approach to treat ball-bearing manufacturing metal waste. Their goals were to find appropriate binders, ascertain the physical-chemical characteristics of the waste product, and examine variables influencing briquette strength.
The technique called for pre-treated sludge with an initial humidity of 25% utilizing both stamp presses and roll presses. This test plan has as its variable’s unit pressure, kind of briquetting machine, usage of molasses instead of non-bio additives, and briquette seasoning. Sludges' mechanical performance improves more if they are seasoned for around 120 hours. Molasses adds much
to the sludge's stickiness. For producers of steel mills, achieving sludge moisture levels ranging from 4.5% to 6.5% was acceptable. Figure 4 shows the suggested method for an industrial operation on a large scale wherein the wastes are air-dried on a sludge-drying bed. Additionally shown in their research was the schematic of the process line with thermal waste drying.
According to the findings of the studies, the briquettes could be recycled in furnaces used in steel-making. Other garbage-related businesses can benefit as well from the apparently universal approach suggested to solve this kind of waste management issue. Additions made during the stage of the briquette consolidation operate, inter alia, as iron oxides reducing agents in steelmaking operations producing a decrease in slag foaming [26-28].
Using carbon-containing briquettes derived from stainless steel manufacturing waste, YANG et al. [29] examined smelt reduction in an electric arc furnace (EAF). Under a 3.5 kg load, laboratory simulations showed that briquettes resisted heating at 1,186°C without disintegrating and could be added to the melt without causing any splashing. Briquettes laden with slag formers provide high-carbon concentration zones for the best metal recovery. To maximize carbon reduction of metal oxides and achieve efficient recycling in EAF or induction furnaces, the research revealed that silicon concentration near briquettes should be decreased. Figure 5 provides the test setup for this study.
Deng et al. [30] developed a novel rotating-drum drying technique using hot steel balls (FIG. 6). Waste heat of metallurgical slag heated steel balls. This test plan used Drummer Rotating Speed, Steel Ball Diameter, Sludge
Mass, and Steel Ball Temperature as its variables. Under this approach, the sludge was dewatered in drums containing hot steel balls. This method reduced the water content by around 15%, therefore producing less than 5% of sludge.
The key element of this approach was to use sludge with 15% to 20% coolant. To get the necessary starting conditions, pre-processing methods like filter-press, briquetting, or dry-screening were thus combined. According to the results, this suggested technique is practical and effective. Reducing the sludge treatment mass, raising the steel ball temperature and diameter, and choosing a suitable drum rotating speed helped sludge drying to be better. Thus, this method tackles the limitations of conventional technologies by having cheap costs, great efficiency, and complete drying.
Although there have not been any study studies on this technique, it seems that few businesses provide indirect
low- and high-temperature dry screeners creating dried sludges with less than 5% coolant concentration. SHINCCI, a Chinese company, is one of these ones. A sophisticated technique for lowering sludge volume, stabilizing, sterilizing, and reusing sludge waste is the sludge dryer. The sludge drying process's overall layout is shown in Figure 7. Running effectively 24/7 with little control, the dryer lowers sludge moisture content from 80% to 10%, volume by 67%, and weight by 80%. Eliminating supplementary water treatment and lowering odor emissions are two advantages of this system. Figure 8 presents the sludge drying system's schematic mechanical concept [31]
Tab.1 - he typical technical knowledge about SHINCCI company's supplied dry screener [31].
screener
Structure Assembled Set
Cooling Method
Water Cooling SL (Δt=12℃)
Refrigerant R134a
Drying Temperature
Control System
Powder Metallurgical (PM) Treatment includes creating metal samples from powdered metals by mixing, compacting, and heating them while regulating the volume and quality of the components, resulting in complicated geometries with minimum waste. Authors [32] suggested a sustainable PM technique using residual lubricant and abrasive particles as secondary raw material to recycle tool steel grinding sludge. Publications on recycling different materials, swarf, and scrap have been investigated stressing the efficiency, waste reduction, and quality improvement in manufacturing different metal components on the laboratory level [21, 23, 32-34].
Two main techniques relevant to recycling in the industrial setting are solid-liquid phase sintering (SLPS) and hot isostatic pressing (HIP). These techniques are fit for large-scale production operations as they provide dependable and effective ways to generate premium metal components from powdered materials.
Hankel et al. [35] proposed a feasible recycling method for recovering metallic components of industrial sludge produced from cold work tool steel grinding. According to this approach, the completely dried sludge particles sinter in vacuumed sinters using the SLPS process. Grain sizes of powders offered a benefit relevant to PM technology. The criteria in this process were sintering temperature, pretreatment scenario for powder, and sintering time. At 129 ℃, a sintering temperature, a maximum density of 76 vol% was recorded. Reusing swarf as a precursor for SLPS
48~56℃ (recycle air)/ 65~80℃ (supply air)
Touch screen + PLC programmable controller
has thus shown encouraging effects.
Jäger et al. [36] noted and published a methodology based on powder metallurgy called HIP. The authors focused on produced samples from HIP and SLPS. Unlike previous sintering techniques, the SLPS method required no prepressing of the powder to a green body and then sintering. Rather, sintering started right from the powder spill. Figure 9 shows the schematic sintering procedures of an SLPS system. The aim of the HIP approach was to evaluate the HIP process using sludge powder and a combination of 100Cr6 gas-atomized powders. Figure 10 shows the usual methods. The variables of this process were single powder and mixed powder, pre-pressing against non-pressing, sintering time, and sintering temperature. With 100 MP of pressure at 105℃, authors found up to 84% of low sample density using argon gas in 4 hours. Consequently, in this paper, the produced samples from SLPS and HIP revealed quite big pores and a low sample density (SLPS: 86.02% and HIP: 84.00%). With much lower pores of smaller size, the treated mixtures produced denser samples (SLPS: 98.00% and HIP: 98.00%).
Iron was extracted from the swarf via hydrometallurgy, which included leaching with hydrochloric acid and then precipitating and filtering the resulting iron chloride solution to remove metal impurities. Each stage of the process was planned and adjusted to discover simple but flexible solutions to make the recycling process economically viable and capable of dealing with changes in the grinding swarf [37].
Chen et al. [38] reported that for manufacturing sectors, large-scale equipment made of stainless steel has remarkable performance and durability. This approach studied hydrometallurgical techniques, including chemical precipitation, solvent extraction, and acid leaching. Alloys were extracted from the pre-treated sludge using several kinds of acids under varied process
conditions and then by an extractor. Water was removed using a muffle furnace (LE 6/11, Naberthem, Lilienthal, Germany) for pretreatment oil; the residue was pulverized by a ball mill at 260 rpm for 24 h and sieved with a 100mesh screen to enhance the leaching percentages of iron, nickel, and chromium. Different acids (HCL, H2SO4, HNO3), extractant pH value, extractant concentration, aqueousorganic ratio, and reaction time were the guidelines of this process. Figure 11 shows the whole process of the experiment.
Fig.11 - The process of iron, nickel, and chromium recovery systems from stainless steel sludge [38].
After eight hours of calcination at 300 °C, the sludge was leached by 4 mol/L HCl. Of iron, nickel, and chromium, the leaching percentages were correspondingly 97.6%, 98.1%, and 95.7%. By means of 0.1 mol/L bis(2- ethylhexyl) phosphate (D2EHPA), Fe (III) was efficiently recovered in the two-stage solvent extraction method with an aqueous or organic ratio of 1 over 10 min at pH 1.5. Nickel's and chromium's recoveries at last were, respectively, 99.5% and 75%, thanks to chemical precipitation.
A 2016 publication by Roslan et al. [39] basically reported the results of laboratory studies on the substitution of cement substitutes in concrete from electric arc furnace steel slag and steel sludge (byproducts from steel manufacturing companies). Their approach tested a combination of varying doses of completely dry sludge powder with cement. Flexural strength analysis, pozzolanic, thermogravity and mechanical properties assessment were measured in the study. This process included sludge dosage and cement dosage as its variables. Compressive strength increased when 15% and 20%
steel sludge and steel slag were added correspondingly. Controlling the mix, especially at later curing ages, helped to provide stronger results.
Alwaeli [40] stated that replacing raw sand in a concrete building with scale and steel chip waste may be ecologically friendly. The impact of various percentages of these wastes on concrete characteristics like compressive strength and radiation attenuation was examined in this work. According to the findings, the concrete combined with steel chips increases its strength. In this research, the average utilization of 25% replacement came out to be. The results also underlined the possibilities for improving material qualities and fostering sustainability by means of industrial waste used in concrete manufacturing. It was found that the approaches included in this review article effectively satisfied industry-scale demands and controlled environmental sustainability simultaneously. Sludge recycling has interesting future prospects and calls for thorough attention on enhancing and maximizing the given techniques as well as on finding fresh ideas. Table 2 lists the important books on sludge recovery methods in mass industrial production.
Tab.2 - The list of studies documenting many facets of industrial-scale sludge recovery
Citations Components Technique
Borowski et al. [26]
Fine-grained grinding sludge Briquette-making
YANG et al. [29] stainless steel sludge Briquette-making
Deng et al. [30] converter sludge Ball drumming
Hankel et al. [35] steel grinding sludge SLPS
Jäger et al. [36] Metallic grinding swarf SLPS and HIP
Ottink et al. [37] Steel swarf
Chen et al. [38]
Hydrochloric acid leaching
Stainless steel sludge Acid leaching
Roslan et al. [39] Steel slag and sludge As cement replacements.
Alwaeli [40] Steel chips
Significant results
Briquetting sludge to recycle ball bearing manufacturing metal waste.
Investigating effects of operating circumstances on metal recovery rates.
Using a suggested rotating-drum-drying method helps to optimize operational parameters for drying.
Showing excellent and creative reusing strategies.
Concentrating on the swarf's performance characteristics and recycling path
Obtaining abrasive and metal selective separation from cutting fluid.
Developing a better recovery mechanism and maximizing the extraction effectiveness.
Evaluating in concrete the performance of steel slag and steel sludge.
As a substitute for sand Using scale and steel chip waste helps to improve concrete properties.
Research results draw a variety of knowledge. Some addressed articles derived from quantitative data, including sludge volume or extraction efficiency. These outcomes allow us to evaluate many approaches to recovery based on past studies. This information helps us to determine how to implement scholarly results in useful industrial environments, thus optimizing largescale manufacturing. Table 3 contains the papers about the recovery of steel sludge from various recycling procedures using different waste sources.
Tab.3 - Metals recovered from stainless steel waste using various recycling procedures.
Citations Components Technique Significant results
Zhang et al. [41] Pickling sludge Reduction and magnetic separation
Liu et al. [42] Stainless steel dust
Wu et al. [43] Pickling sludge
Carbon-thermal reduction
Direct reduction and magnetic separation
Extraction efficiency: Fe 70.1%, Ni 60.3%, Cr 53.7%.
Extraction efficiency: Fe 79.7%, Ni 83.6%, Cr 90.7%.
Extraction efficiency: Fe 95.3%, Ni 97.5%, Cr 88.7%.
Chen et al. [38] Stainless steel sludge Chemical precipitation Extraction efficiency: Fe 99.9%, Ni 99.5%, Cr 75.1%.
Chen et al. [38] Stainless steel sludge Acid leaching Extraction efficiency: Fe 97.6%, Ni 98.1%, Cr 95.7%.
Ottink et al. [37] Steel swarf
Hydrochloric acid leaching
Leaching: 24.600 mg/l Fe, 150 mg/l Mn, 12 mg/l Ni and <1 mg/L Cr and Mo.
Jäger et al. [36] Metallic swarf SLPS and HIP Densification: SLPS: 98.00 % and HIP: 98.00 %.
Hankel et al. [35] Steel sludge SLPS Metal recovery: Up to 50 wt%.
Zhang et al. [41] Pickling sludge Reduction and magnetic separation
Extraction efficiency: Fe 70.1%, Ni 60.3%, Cr 53.7%.
In industrial uses, mechanical sludge treatment and recovery techniques include improved briquetting, ball drumming, and dry screening. Every technique has different advantages; thus, the level and type of their parameters in every method are computed to maximize sludge recovery. While ball drumming offers notable dewatering and dry screening, which shows promise for production, enhanced briquetting enhances sludge characteristics and adhesion; minimal academic study was noted in this situation.
By powder metallurgical treatment, steel grinding sludge may be recycled sustainably and effectively. Two exciting and high-potential treatments used in industrial sectors which recycle up to 85% of sludge are HIP and SLPS. Through the conversion of industrial sludge into useful raw materials, both attractive techniques improve the quality of the final sample. Through acid leaching and solvent extraction, hydrometallurgy studies efficiently remove iron, nickel, and chromium from swarf and stainless-steel sludge. High recovery rates were found in hydrometallurgical techniques by optimizing parameters including acid type,
concentration, and extraction conditions. These methods so show the performance of hydrometallurgical methods in manufacturing processes. For building applications, one of the creative recovery methods combines slag and steel sludge with concrete producing positive results. In this example, the studies showed that adding 15–20% steel sludge and slag improves compressive strength, especially at later curing stages, supporting sustainability in this sector, and thereby emphasizing the possibilities of industrial waste sludge in concrete structures.
This publication is also part of the project PNRR-NGEU which has received funding from the MUR-DM117/2023 for one of the writers (MD), [Project No: MUR DM 117/ Tsubaki Nakashima – Recovery, reuse and reduction of waste sludge in the production of balls and rolls for rolling bearings] (Nov. 2023- Oct. 2026), which is gratefully acknowledged.
[1] Kishore, K., et al., A comprehensive review on the grinding process: advancements, applications and challenges. Proceedings of the Institution of Mechanical Engineers, Part C: Journal of Mechanical Engineering Science, 2022. 236(22): p. 10923-10952.
[2] Yin, Y., K.E. Stecke, and D. Li, The evolution of production systems from Industry 2.0 through Industry 4.0. International Journal of Production Research, 2018. 56(1-2): p. 848-861.
[3] Nardo, M., D. Forino, and T. Murino, The evolution of man–machine interaction: The role of human in Industry 4.0 paradigm. Production & manufacturing research, 2020. 8(1): p. 20-34.
[4] Esmaeilian, B., S. Behdad, and B. Wang, The evolution and future of manufacturing: A review. Journal of manufacturing systems, 2016. 39: p. 79-100.
[5] Barata, J. and I. Kayser, Industry 5.0 – Past, Present, and Near Future. Procedia Computer Science, 2023. 219: p. 778-788.
[6] Chen, X., et al., A human-cyber-physical system toward intelligent wind turbine operation and maintenance. Sustainability, 2021 13(2): p. 561.
[7] Adel, A., Future of industry 5.0 in society: human-centric solutions, challenges and prospective research areas. Journal of Cloud Computing, 2022. 11(1): p. 40.
[8] Xu, X., et al., Industry 4.0 and Industry 5.0—Inception, conception and perception. Journal of manufacturing systems, 2021. 61: p. 530-535.
[9] Singh, M., et al., In situ micro-observation of surface roughness and fracture mechanism in metal microforming of thin copper sheets with newly developed compact testing apparatus. Materials, 2022. 15(4): p. 1368.
[10] Leksycki, K. and J.B. Królczyk, Comparative assessment of the surface topography for different optical profilometry techniques after dry turning of Ti6Al4V titanium alloy. Measurement, 2021. 169: p. 108378.
[11] Niesłony, P. and W. Grzesik, Optimization procedures for machining operations on CNC machine tools. Pomiary Automatyka Kontrola, 2011. 57(2): p. 224-227.
[12] Gupta, M.K., et al., Cutting forces and temperature measurements in cryogenic assisted turning of AA2024-T351 alloy: An experimentally validated simulation approach. Measurement, 2022. 188: p. 110594.
[13] Koch, J., et al. Cycle management for continuous manufacturing planning. in Enabling Manufacturing Competitiveness and Economic Sustainability: Proceedings of the 5th International Conference on Changeable, Agile, Reconfigurable and Virtual Production (CARV 2013), Munich, Germany, October 6th-9th, 2013. 2014. Springer.
[14] https://web.archive.org/web/20240808085130/https://www.novaoneadvisor.com/report/additive-manufacturing-market
[15] https://web.archive.org/web/20240808084132/https://www.grandviewresearch.com/industry-analysis/additive-manufacturingmarket.
[16] https://web.archive.org/web/20240808105535/https://www.marketsandmarkets.com/Market-Reports/cnc-market-195192631. html
[17] https://www.databridgemarketresearch.com/reports/global-additive-manufacturing-market.
[18] Moszkowicz, J., Steel Demand Beyond 2030-Forecast Scenarios-Presented to: OECD Paris. 2017.
[19] Fu, H., M.A. Matthews, and L.S. Warner, Recycling steel from grinding swarf. Waste Management, 1998. 18(5): p. 321-329.
[20] Chang, J.I., et al., Recycling oil and steel from grinding swarf. Resources, conservation and recycling, 2006. 49(2): p. 191-201.
[21] Singh, A., et al., Production, characterisation and utilisation of grinding swarf/feedstock for synthesis of metal matrix composite through powder metallurgy process: a short communication. Sādhanā, 2022. 47(3): p. 160.
[22] Ruffino, B. and M.C. Zanetti, Recycling of steel from grinding scraps: Reclamation plant design and cost analysis. Resources, conservation and recycling, 2008. 52(11): p. 1315-1321.
[23] Rane, K. and P. Date, Sustainable recycling of ferrous metallic scrap using powder metallurgy process. Journal of Sustainable Metallurgy, 2017. 3: p. 251-264.
[24] Milton, I.P.H., P. Sakthivel, and E. Sivasenthil, A reuse approach of grinding sludge: Analysis of corrosion and mechanical properties of oxyacetyline torch melted Fe and Cu alloy. Cleaner Engineering and Technology, 2023. 16: p. 100674.
[25] Das, B., et al., An overview of utilization of slag and sludge from steel industries. Resources, conservation and recycling, 2007. 50(1): p. 40-57.
[26] Borowski, G. and J. Kuczmaszewski, Investigation of briquetting of metal waste from the bearing industry. Waste Management & Research, 2005. 23(5): p. 473-478.
[27] Paknahad, P., M. Askari, and S.A. Shahahmadi, Cold-Briquetted Iron and Carbon (CBIC), investigation of steelmaking behavior. Journal of Materials Research and Technology, 2020. 9(3): p. 6655-6664.
[28] Borowski, G. and J. Kuczmaszewski, Utilization of Fine-Grained Metal Waste. Wydawnictwo Politechniki Lubelskiej: Lublin, Poland, 2005.
[29] Yang, Q.-x., et al., Briquette smelting in electric arc furnace to recycle wastes from stainless steel production. Journal of Iron and Steel Research, International, 2015. 22: p. 10-16.
[30] Deng, S., et al., Converter sludge drying in rotating drum using hot steel balls. Applied Thermal Engineering, 2021. 197: p. 117368.
[31] Available from: https://web.archive.org/web/20240808110406/https://shincci-global.com/
[32] Großwendt, F., et al., A novel powder-metallurgical eco-friendly recycling process for tool steel grinding sludge. Journal of Cleaner Production, 2023. 392: p. 136329.
[33] Rane, K. and P.P. Date, Recycling potential for finely divided ferrous metallic scrap using powder technology. Recycling, 2018. 3(4): p. 59.
[34] Ryabicheva, L., A. Tsyrkin, and N. Beloshitskii, Powder produced from steel 40Kh10S2M grinding sludge. Powder Metallurgy and Metal Ceramics, 2007. 46: p. 298-302.
[35] Hankel, J., S. Jäger, and S. Weber, Development of a recycling strategy for grinding sludge using supersolidus liquid phase sintering. Journal of Cleaner Production, 2020. 263: p. 121501.
[36] Jäger, S., S. Weber, and A. Röttger, Potential of the recycling of grinding sludge by various powder metallurgical processes. Procedia CIRP, 2021. 104: p. 893-899.
[37] Ottink, T., et al., Novel approach to recycling of steel swarf using hydrometallurgy. Resources, Conservation and Recycling, 2022. 185: p. 106450.
[38] Chen, W.-S., Y.-C. Chen, and C.-H. Lee, Hydrometallurgical recovery of iron, nickel, and chromium from stainless steel sludge with emphasis on solvent extraction and chemical precipitation. Processes, 2022. 10(4): p. 748.
[39] Roslan, N.H., et al., Performance of steel slag and steel sludge in concrete. Construction and Building Materials, 2016. 104: p. 16-24.
[40] Alwaeli, M., The implementation of scale and steel chips waste as a replacement for raw sand in concrete manufacturing. Journal of Cleaner Production, 2016. 137: p. 1038-1044.
[41] Zhang, L., Y. Liu, and F. Duan, Metal recovery and heavy metal migration characteristics of ferritic stainless steel pickling sludge reduced by municipal sludge. Waste Management, 2022. 144: p. 57-66.
[42] Liu, P., et al., New understanding on metal recovery of Fe, Ni and Cr during carbon-thermal reduction of stainless steel dust. Advanced Powder Technology, 2021. 32(11): p. 4273-4285.
[43] Wu, M.-T., et al., Harmless treatment and resource utilization of stainless steel pickling sludge via direct reduction and magnetic separation. Journal of Cleaner Production, 2019. 240: p. 118187.
Giornata di Studio
ADDITIVE MANUFACTURING: IL GIOIELLO NASCOSTO DEL SETTORE
DELLA MODA E DEL LUSSO
Padova presso Palazzo della Salute, 10 aprile 2025
>> SCOPRI DI PIÙ
Giornate di Studio
IL MAGNESIO DA FONDERIA
LEGHE, PROCESSI E CARATTERISTICHE
Torino, 14-15 maggio 2025
>> SCOPRI DI PIÙ
Corso modulare METALLOGRAFIA
Milano, 15-21-22-28-29 maggio - 5 giugno - settembre
>> SCOPRI DI PIÙ
Giornata di Studio
ACCIAIO IN EVOLUZIONE: ESPLORANDO LA DEFORMAZIONE A CALDO E LE SUE IMPLICAZIONI E CONSEGUENZE
Brescia, 16 maggio 2025
>> SCOPRI DI PIÙ
Giornata di Studio
TITANIO: PRODUZIONE, TECNOLOGIE E MERCATO Aggiornamento alla luce dell'attuale situazione politico- economica mondiale
Milano - 20 maggio 2025
>> SCOPRI DI PIÙ
Corso
ANALISI CHIMICHE - VI EDIZIONE Milano c/o Fast - 17-18 giugno 2025
>> SCOPRI DI PIù
Giornate Nazionali
CORROSIONE E PROTEZIONE - XVI ed. Ancona, 25-27 giugno 2025
>> SCOPRI DI PIÙ
7th European Steel Technology and Application Days 2025
7th ESTAD 2025
Verona - Palaexpo VeronaFiere - 6-9 October 2025
>> SCOPRI DI PIÙ
DTMI 2025 - International Workshop ing. Carlo Longaretti on Digital Tools for the Metallurgical Industry Bergamo - 27-28 November 2025
>> SCOPRI DI PIÙ
Il Centro desidera porre l’attenzione sulla tecnologia di forgiatura dei metalli e delle leghe ferrose e non ferrose. Si propone inoltre di considerare anche aspetti trasversali che concorrono allo sviluppo ed all’evoluzione dei processi nel contesto in cui si trova ad operare.
Presidente: Alessandra Saleri
Forge Fedriga Srl
Vicepresidente: Alessandra Lissignoli
NLMK Verona
Segretario: Cristian Viscardi
Ecotre Valente
Negli ultimi anni, l’attività del Comitato Forgiatori dell’Associazione Italiana di Metallurgia ha registrato una crescita significativa, sia in termini di numero di componenti che di partecipazione alle iniziative promosse. Questo sviluppo testimonia il ruolo sempre più centrale del CT nella diffusione della cultura metallurgica e nella promozione dell’eccellenza del settore della forgiatura a livello nazionale e internazionale.
Tra gli eventi di maggiore rilievo organizzati dal CT nel 2024, si ricordano:
Giornata di Studio sulle Superleghe a base Nichel –Tenutasi il 22 febbraio 2024 presso il Museo Nazionale della Scienza e della Tecnologia Leonardo da Vinci, questa giornata ha rappresentato un’importante occasione di confronto su metallurgia, fabbricazione e applicazioni dei prodotti forgiati. La straordinaria partecipazione di aziende leader del settore e di utilizzatori finali ha confermato l’interesse e la necessità di approfondire tematiche di frontiera nella forgiatura.
Corso Forgiatori 2024 – Coordinato dall’Ing. Gabriele Rampinini, il corso, svoltosi il 6-7-13-14 marzo 2024, ha riscosso un successo tale da rendere necessaria la chiusura anticipata delle iscrizioni per il raggiungimento del numero massimo di partecipanti. L’iniziativa ha offerto un’opportunità unica di formazione specialistica, affiancando alle lezioni teoriche visite presso primarie realtà industriali del settore, con l’obiettivo di rafforzare la connessione tra conoscenza accademica ed esperienza pratica.
IFM-2024 – International Forgemasters Meeting –
Evento di portata internazionale, tenutosi dal 27 al 30 maggio 2024, che ha visto la partecipazione attiva del CT. Alcuni membri hanno avuto l’opportunità di presentare studi, approfondimenti e risultati innovativi a una platea di esperti provenienti da tutto il mondo, consolidando il ruolo del comitato come punto di riferimento nella comunità globale della forgiatura. Grazie all’impegno e alla professionalità dei suoi componenti, il CT ha saputo costruire un percorso di crescita e di valorizzazione delle competenze tecniche e scientifiche, contribuendo in modo significativo allo sviluppo del settore. L’obiettivo per il futuro è quello di consolidare questi risultati, ampliando ulteriormente le collaborazioni, promuovendo nuove iniziative di alto profilo e rafforzando la rete tra aziende, istituti di ricerca e professionisti della forgiatura.
Nel corso del 2025, il Comitato Forgiatori vuole continuare il suo percorso di crescita e consolidamento, partecipando attivamente a iniziative intersettoriali e rafforzando il dialogo con altri comitati. L’obiettivo è quello di valorizzare sempre più il ruolo della forgiatura all’interno della filiera siderurgica e metallurgica, contribuendo con competenze e approfondimenti tecnici di alto livello.
Le iniziative già definite e in fase di preparazione includono:
7th ESTAD 2025 (Verona, 7-9 ottobre 2025) – Evento di riferimento per le tecnologie dell’acciaio in Europa, dove il CT Forgiatori intende promuovere il contributo essenziale della forgiatura nella produzione di componenti ad alte prestazioni, sottolineando il
legame tra innovazione metallurgica e processi di trasformazione avanzati.
DTMI 2025 - International Workshop Carlo Longaretti on Digital Tools for the Metallurgical Industry (Bergamo, 27-28 novembre 2025) – Iniziativa focalizzata sugli strumenti digitali applicati alla metallurgia, un tema di grande rilevanza anche per la forgiatura, dove la digitalizzazione sta trasformando processi e controlli qualitativi. Il CT Forgiatori si propone di portare il proprio contributo su questi aspetti, esplorando l’integrazione delle tecnologie digitali nelle operazioni di forgiatura.
Giornata della Manutenzione (Secondo semestre 2025) – Organizzata dal CT Acciaieria, questa giornata di studio si concentrerà sulle tematiche legate alla manutenzione negli impianti siderurgici. Il CT Forgiatori si propone di partecipare attivamente con almeno un intervento specifico sulle sfide manutentive nel settore della forgiatura.
Giornata di Studio sull’Impiego delle Risorse Femminili in Ambito Siderurgico e Metallurgico (In fase di analisi) –Considerata la crescente presenza di donne in posizioni apicali all’interno delle aziende siderurgiche, si sta valutando l’organizzazione di una giornata dedicata alla condivisione di esperienze, opportunità professionali e prospettive future. Il CT Forgiatori intende sostenere e promuovere l’iniziativa, riconoscendo il valore della diversità e della competenza femminile nel settore della metallurgia e della forgiatura.
Attraverso queste attività, il CT Forgiatori conferma il proprio impegno nel rafforzare la sinergia con gli altri attori del settore e nel promuovere il ruolo strategico della forgiatura all’interno dell’industria metallurgica globale.
Eventuale sintesi sull’andamento del settore cui il CT afferisce
Il comparto della forgiatura in Italia è tra i più importanti in Europa e rappresenta un’eccellenza riconosciuta a livello internazionale. Negli ultimi trentanni, l’adozione di tecnologie avanzate nella deformazione dei metalli, lo sviluppo di laboratori altamente specializzati all’interno delle aziende e l’introduzione di strumenti di collaudo sempre più sofisticati hanno permesso alla forgiatura italiana di rafforzare il proprio ruolo nella realizzazione di componenti critici per settori strategici.
Oggi, uno dei principali fattori trainanti per la forgiatura è il settore della generazione di energia, con particolare attenzione alle turbine per il Power Gen e alla ripresa dell’Energia Nucleare. In questi ambiti, la qualità, l’affidabilità e la sicurezza dei prodotti forgiati risultano indispensabili per garantire il funzionamento efficiente e duraturo degli impianti. Parallelamente, visto il contesto internazionale si potrà assistere ad una crescente domanda di forgiati ad alte prestazioni per applicazioni militari e aerospaziali, dove la necessità di materiali con caratteristiche meccaniche eccezionali è fondamentale.
L’industria della forgiatura sta inoltre assumendo un ruolo
centrale nella transizione energetica, contribuendo con componenti essenziali per l’infrastruttura delle energie rinnovabili e delle tecnologie a idrogeno, che saranno determinanti per il futuro della sostenibilità industriale. Tuttavia, il settore si trova anche ad affrontare nuove sfide, tra cui l’aumento dei costi energetici, la necessità di processi sempre più sostenibili e la crescente competizione globale.
Per mantenere la propria leadership, la forgiatura italiana deve continuare a investire in innovazione, digitalizzazione e formazione del personale, garantendo standard qualitativi elevati e consolidando il proprio ruolo di partner chiave per l’industria del futuro.
Eventuali temi di interesse per il settore di riferimento su cui il CT sta iniziando a sviluppare iniziative
Uno dei principali temi di interesse per il settore della forgiatura è l’applicazione dell’Intelligenza Artificiale (AI) in supporto agli uffici tecnici e ai reparti produttivi, con l’obiettivo di gestire problematiche sempre più complesse senza sostituire le competenze umane, ma potenziandole.
L’AI può fornire un contributo significativo nella corretta interpretazione delle specifiche tecniche di prodotto richieste dai clienti, analizzandole in profondità e mettendole in relazione con gli standard internazionali di riferimento citati nella documentazione. Questo permette di ridurre il rischio di errori interpretativi, velocizzare la fase di studio e garantire un allineamento più efficace ai requisiti di qualità e prestazione richiesti.
Inoltre, l’AI può supportare l’ingegneria di prodotto nella preparazione del processo di fabbricazione, suggerendo le migliori strategie produttive sulla base dell’analisi di grandi quantità di dati storici, ottimizzando così i parametri di deformazione e trattamento termico per ottenere un prodotto finale conforme alle aspettative.
Un ulteriore ambito di applicazione riguarda il monitoraggio del processo di fabbricazione tramite analisi di immagine, che consente di seguire l’intero ciclo produttivo in tempo reale. La raccolta sistematica dei dati di produzione, combinata con il confronto con i risultati del collaudo finale, permette di identificare eventuali anomalie o aree di miglioramento, garantendo un’ottimizzazione continua della qualità del prodotto.
L’integrazione dell’AI nella forgiatura rappresenta dunque un’opportunità strategica per aumentare l’efficienza operativa, migliorare la sicurezza dei lavoratori e consolidare la competitività del settore nel panorama industriale globale.
Il CT si propone per questo specifico argomento di richiedere la collaborazione del nuovo comitato AIM recentemente costituito e dedicato specificatamente ai processi di AI.
Il Centro di Studio CoMET (Coordinamento della Ricerca e della Didattica Universitaria in METallurgia) è stato costituito nel 2013. È la Comunità accademica cui aderiscono i docenti italiani di Metallurgia (Settore Scientifico Disciplinare IIND-03/C), distribuiti in 26 diverse Sedi Universitarie. Il CoMET costituisce la sede di confronto e discussione su ogni argomento di interesse generale dei docenti di Metallurgia, in relazione alle attività didattiche e di ricerca e alla loro organizzazione nel sistema universitario nazionale. CoMET promuove l'interesse della Comunità accademica per i progetti e le iniziative didattiche e di disseminazione in ambito europeo. Stimola inoltre il confronto e la discussione con il mondo industriale rappresentato in AIM per quanto riguarda le iniziative didattiche delle Università e i loro esiti in termini di formazione ed occupazione.
CoMET agisce in sinergia con i Settori Scientifico-Disciplinari della Progettazione Meccanica e Costruzione di Macchine (IIND-03/A) e del Disegno e Metodi dell’Ingegneria Industriale (IIND-03/B), nell’ambito di un Grup-
Coordinatore: Franco Bonollo - Università di Padova (sede di Vicenza)
po di Lavoro Intersettoriale nell’Additive Manufacturing (AM), denominato CoCoAM. CoCoAM ha come obiettivo la promozione ed il sostegno di progetti e iniziative scientifiche, didattico-formative, di ricerca e di disseminazione della cultura dell’Additive Manufacturing. Si occupa quindi di progettazione e costruzione di componenti e sistemi, sviluppa e ottimizza materiali, metodi e strumenti per la concezione e lo sviluppo di prodotti, e studia le caratteristiche e le prestazioni dei prodotti, i processi di trattamento dopo fabbricazione e di finitura dei prodotti, il controllo dei materiali metallici per AM. Il CoCoAM intende inoltre promuovere il confronto con l’industria, nell’ottica di sviluppare ricerca e innovazione ma anche favorire iniziative didattiche delle Università indirizzate alla formazione dei futuri ingegneri.
La Comunità accademica del CoMET consiste di oltre 100 docenti di Metallurgia, tra professori ordinari, associati e ricercatori, distribuiti in 26 Sedi Universitarie. L’attività CoMET viene coordinata da una Giunta, costituita da una decina di docenti, che si riunisce con periodicità bimestrale.
CoMET ha organizzato nell’estate del 2024 la “Summer School Metal Additive Manufacturing”, evento internazionale di formazione sulle tematiche interdisciplinari dell’Additive Manufacturing, riservato a dottorandi e a giovani laureati dipendenti di aziende metallurgiche. Con oltre 40 partecipanti, l’evento ha contribuito a costruire una comunità di giovani ricercatori, universitari e industriali, attenta a sviluppare le tematiche maggiormente innovative nel campo della Metallurgia. La Summer School, che ha confermato negli anni la sua attrattività, passerà dall’originale cadenza biennale ad una periodicità di diciotto mesi.
La Giunta CoMET ha recentemente elaborato il documento Metallurgia 2040, volto a delineare le prospettive future della didattica e della ricerca in ambito metallurgico. Il documento offre alcuni spunti di riflessione per quello che riguarda la didattica metallurgica, che dovrà sempre più sviluppare i concetti di trasversalità e inter-disciplinarietà, valorizzando le numerose collaborazioni di ricerca tra i docenti di Metallurgia e l’industria
La didattica e la ricerca universitarie si trovano in un momento di profonda evoluzione, caratterizzato da approcci trasversali e multi-disciplinari e dalla necessità di stimolare sempre più l’efficienza dei processi di appren-
dimento (learning efficiency).
In questo contesto, una continua integrazione tra Università e Industria è un elemento qualificante nei percorsi formativi in ambito ingegneristico e scientifico. La centralità della metallurgia troverà sempre più affermazione grazie allo sviluppo di profili professionali (neo-laureati, ma anche professionisti inseriti in un contesto di formazione permanente) in grado di agire da “esperti del dominio metallurgico”.
Per rispondere alle sfide e alle competizioni globali, è necessario lavorare alla costruzione del profilo professionale del “metallurgista del futuro”, pienamente consapevole degli scenari generali delle transizioni ecologica e digitale, dotato di solide conoscenze dei fenomeni e dei processi che coinvolgono le leghe metalliche, capace di interpretare ed elaborare moli crescenti di informazioni e di individuare, proporre, validare soluzioni tecnologiche sostenibili e affidabili.
È a questa costruzione che CoMET, in sinergia con il contesto industriale metallurgico, sta lavorando.
“METALLURGIA A FUMETTI”
Al fine di premiare la creatività e il talento al servizio della divulgazione tecnico-scientifica, l’Associazione Italiana di Metallurgia propone il Premio METALLURGIA A FUMETTI concorso per la realizzazione di tavole/strisce a fumetti, legato alla metallurgia ed in particolare alla produzione, trasformazione e applicazione dei materiali metallici
REQUISITI
La partecipazione è GRATUITA. È possibile iscriversi singolarmente o come gruppo. Sono ammesse anche opere proposte da organizzazioni (case editrici, scuole di fumetto…) o già finanziate, premiate ecc.
TEMA
METALLURGIA #metalli #scienza dei materiali metallici #siderurgia #forgiatura #corrosione #trattamenti termici #rivestimenti e ingegneria delle superfici #saldatura #ambiente e sicurezza #manutenzione #pressocolata #fonderia #lavorazione plastica dei metalli #additive manufacturing
SPECIFICHE TECNICHE
Per partecipare al concorso sarà necessario realizzare una storia a fumetti di minimo 1 tavola legata al tema del concorso. Le tavole dovranno essere in formato ISO A3 (297x420 mm) o A4 (210x297 mm), con il lato più lungo come altezza, con risoluzione 300 dpi in formato CMYK, e dovranno essere inviate in formato PDF con una DIMENSIONE MASSIMA dei Files di 10 MB ciascuno.
Potranno essere eseguite con qualsiasi tecnica, in b/n o a colori, a mano o digitale. Il lettering dev’essere in lingua italiana e/o inglese. Le opere dovranno essere completamente inedite e personaggi e universo narrativo non dovranno essere coperti da diritto d’autore.
ISCRIZIONE E SCADENZA
Per partecipare al concorso è necessario inviare le tavole unicamente utilizzando un servizio di file sharing gratuito (es. wetransfer), entro il 30 giugno 2025, all’indirizzo di posta met@aimnet.it
DOCUMENTAZIONE
Assieme alle tavole è necessario inviare:
1) Scheda di partecipazione compilata in ogni sua parte e firmata QUA, da allegare in formato .pdf
2) Breve biografia dell’autore (o del gruppo) e sinossi dell’opera di max 1000 battute, da inviare in formato .doc o .pdf
GIURIA
La commissione che valuterà le opere sarà composta dal comitato di redazione de La Metallurgia Italiana: provvederà a selezionare dieci opere finaliste. Il giudizio espresso sarà insindacabile.
Le opere vincitrici e selezionate verranno inoltre pubblicate sulla rivista dell’Associazione Italiana di Metallurgia La Metallurgia Italiana ed esposte presso la sede dell’Associazione.
PREMI
1° Classificato: 1.500 euro lordi
2° Classificato: 1.000 euro lord i
3° Classificato: 500 euro lordi
Norme pubblicate e progetti in inchiesta (aggiornamento al 28 FEBBRAIO 2025)
Norme UNSIDER pubblicate da UNI nel mese di febbraio 2025
UNI 11967-1:2025
Prodotti in acciaio per calcestruzzo armato - Armature - Parte 1: Armature non assemblate
UNI EN 10335:2025
Acciaio per imballaggio - Prodotti piani di acciaio destinati all'utilizzo a contatto con gli alimenti, i prodotti e le bevande per il consumo umano e animale - Acciai non legati rivestiti per via elettrolitica di cromo e di ossido di cromo
UNI EN 10205:2025
Prodotti per l’imballaggio laminati a freddo – banda nera
UNI EN 10334:2025
Acciaio per imballaggio - Prodotti piani di acciaio destinati all'utilizzo a contatto con gli alimenti, i prodotti e le bevande per il consumo umano e animale - Acciaio non rivestito (banda nera)
UNI EN ISO 20182:2025
Preparazione dei provini refrattariPannelli refrattari spruzzati con lancia miscelatrice pneumatica
UNI EN ISO 4937:2025
Acciai e ghise - Determinazione del cromo - Metodo mediante titolazione potenziometrica o visiva.
Norme UNSIDER ritirate con sostituzione da UNI nel mese di febbraio 2025
UNI EN 10335:2005
Acciaio per imballaggio - Prodotti piani di acciaio destinati all'utilizzo a contatto con gli alimenti, i prodotti e le bevande per il consumo umano e animale - Acciai non legati rivestiti per via elettrolitica di cromo e di ossido di cromo
UNI EN 10205:2017
Banda nera laminata a freddo per la produzione di acciaio per imballaggi
UNI EN 10334:2005
Acciaio per imballaggio - Prodotti piani di acciaio destinati all'utilizzo a contatto con gli alimenti, i prodotti e le bevande per il consumo umano e animale - Acciaio non rivestito (Banda nera)
UNI EN ISO 20182:2008
Preparazione dei provini refrattariPannelli refrattari spruzzati con lancia miscelatrice pneumatica
UNI EN 24937:1992
Acciai e ghise Determinazione del cromo. Metodo mediante titolazione potenziometrica o visiva.
Norme UNSIDER pubblicate da CEN e ISO nel mese di febbraio 2025
EN ISO 19901-4:2025
Oil and gas industries including lower carbon energy - Specific requirements for offshore structures - Part 4: Geotechnical design considerations (ISO 19901-4:2025)
EN ISO 13628-1:2025
Oil and gas industries including low carbon energy - Design and operation of subsea production systemsPart 1: General requirements and recommendations (ISO 13628-1:2025)
EN ISO 23779:2025
Shot blasting machinery - Safety and environmental requirements (ISO 23779:2024)
CEN ISO/TS 6892-5:2025
Metallic materials - Tensile testing - Part 5: Specification for testing miniaturised test pieces (ISO/TS 6892-5:2025)
EN 10379:2025
Steel sheet piles - Test methods
ISO 19901-4:2025
Oil and gas industries including lower carbon energy — Specific requirements for offshore structures — Part 4: Geotechnical design considerations
Progetti UNSIDER in inchiesta prEN e ISO/DIS – marzo 2025
prEN – progetti di norma europei
prEN ISO 14720-2
Testing of ceramic materialsDetermination of sulfur in non-oxidic ceramic raw materials and ceramic materials - Part 2: Inductively coupled plasma optical emission spectrometry (ICP-OES) or ion chromatography (IC) after burning in the oxygen flow (ISO/DIS 14720-2:2025)
prEN ISO 14720-1
Testing of ceramic materials -
Determination of sulfur in non-oxidic ceramic raw materials and ceramic materials - Part 1: Infrared measurement methods (ISO/DIS 14720-1:2025)
prEN ISO 10280
Steel and iron - Determination of titanium content - Diantipyrylmethane spectrometric method (ISO/DIS 10280:2025)
ISO/DIS – progetti di norma internazionali
ISO/DIS 10280
Steel and iron — Determination of titanium content — Diantipyrylmethane spectrometric method
ISO/DIS 4967
Steel — Determination of the non-metallic inclusion content — Micrographic method
Progetti UNSIDER al voto FprEN e ISO/FDIS – marzo 2025
FprEN – progetti di norma europei
FprEN ISO 12747
Oil and gas industries including lower carbon energy - Pipeline transportation systems - Requirements and guidance for pipeline life extension assessment (ISO/ FDIS 12747:2025)
ISO/FDIS – progetti di norma internazionali
ISO/FDIS 22504
Oil and gas industries including lower
carbon energy — Pipeline transportation systems — Onshore and offshore pipelines pig traps design requirements
ISO/FDIS 12747
Oil and gas industries including lower carbon energy — Pipeline transportation systems — Requirements and guidance for pipeline life extension assessment
ISO/FDIS 5002
Hot-rolled and cold-reduced electrolytic zinc-coated carbon steel sheet of commercial and drawing qualities
ISO/PRF 4997
Cold-reduced carbon steel sheet of structural quality
ISO/PRF 3575
Continuous hot-dip zinc-coated and zinc-iron alloy-coated carbon steel sheet of commercial and drawing qualities
BANDO DEL PREMIO - ed. 2025
L’Associazione Italiana di Metallurgia è lieta di indire il bando del prestigioso Premio Aldo Daccò - edizione 2025, con l’obiettivo di stimolare i tecnici del settore e contribuire allo sviluppo e al progresso delle tecniche di fonderia e di solidificazione con memorie e studi originali.
L’Associazione invita tutti gli interessati a concorrere al Premio, inviando a mezzo email il testo di memorie inerenti le tematiche fonderia e solidificazione, unitamente al curriculum vitae dell’autore concorrente, entro il 3O novembre 2025
Saranno presi in considerazione e valutati i lavori riguardanti le varie tematiche di fonderia e di solidificazione, sia nel campo delle leghe ferrose che in quello delle leghe e dei metalli non ferrosi.
Il premio, pari a Euro 5000 lordi, è offerto dalla Fondazione Aldo e Cele Daccò, istituita dalla signora Cele Daccò, per onorare la memoria del marito Aldo Daccò, uno dei soci fondatori dell’AIM e suo encomiabile Presidente per molti anni.
Le memorie verranno esaminate da una Commissione giudicatrice designata dal Consiglio Direttivo, il cui giudizio sarà insindacabile.
Nel giudicare, la Commissione terrà conto, in particolar modo, dell’originalità del lavoro e dell’argomento in relazione alla reale applicabilità dei risultati. Non sono ammesse candidature da chi abbia già ottenuto riconoscimenti, anche per lavori diversi, dalla Fondazione Aldo e Cele Daccò.
Le memorie premiate e quelle considerate meritevoli di segnalazione, potranno essere pubblicate sulla rivista La Metallurgia Italiana.
La cerimonia di premiazione con la consegna della medaglia avrà luogo in occasione del 41° Convegno Nazionale AIM.
I vincitori del Premio Aldo Daccò
...dal 1975 al 2024
1975 M. Remondino - F. Pilastro - E. Natale
1979 A. Goria - M. Mischiatti
1981 E. Borghigiani
1982 R. Medana
1983 R. Medana
1984 E. Borghigiani - F. Belletti
1986 R. Medana
1987 L. Piras - L. Lazzaro
1989 P. Fumagalli
1990 F. Cavalleri - G. Tosi - A. Pedaci
1991 R. Roberti - A. Bianchi - F. Pedrotti
1992 R. Maspero - B. Calzolai
1993 E. Gariboldi - G. Caironi
1994 G. Zaramella
1995 G.P. Marconi - A. Boccardo
1996 R. Medana
1997 R. Nada
1998 C. Bolner
1999 A. Gregori
2001 C. Mapelli
2002 L. Battezzati - P. Ferro
2003 R. Venturini - S. Baragiola
2004 E. Liotti - F. Piasentini - F. Bonollo - A. Tiziani
2005 C. Viscardi
2006 D. Baldissin - M. Di Sabatino
2007 G. Timelli - A. Manente
2008 A. Arrighini
2009 M. Merlin
2010 A. Morri
2011 E. Zanini - G. Timelli
2012 D. Casari - C. Soffritti
2013 R. Carli - M. Alloni
2014 D. Gelli
2015 L. Rovatti - J. Lemke
2016 F. De Antoni - M.T. Di Giovanni
2017 M. Cavallini
2018 S. Toschi
2019 A. Fortini - L. Lattanzi
2020 L. Tonelli - M. Galbiati
2021 A. Mantelli - F. Di Giovanni
2022 G. Scampone - Ö. Gürsoy
2023 E. Fracchia
2024 A. Bongiovanni - C. Morales Bazaldua
Per informazioni e candidature:
Via Filippo Turati 8 · 20121 Milano
Tel. +39 02-76397770 · +39 02-76021132
E-mail: info@aimnet.it www.aimnet.it