
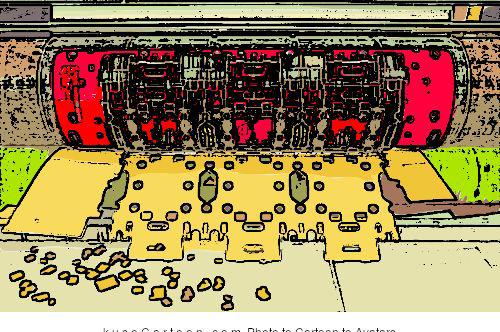
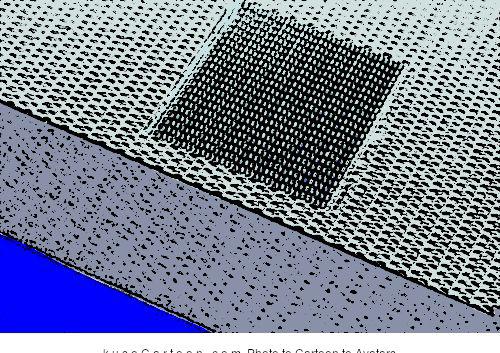
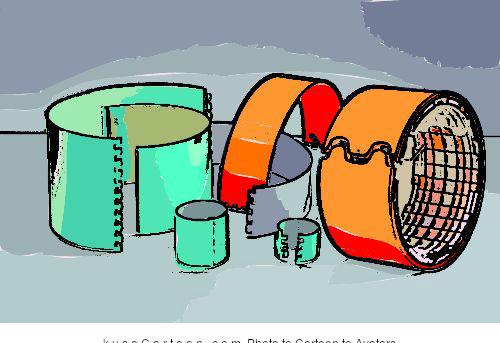
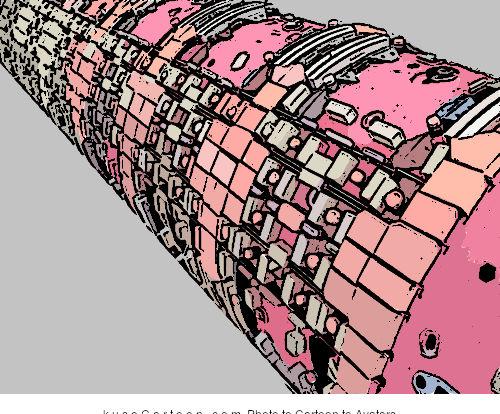
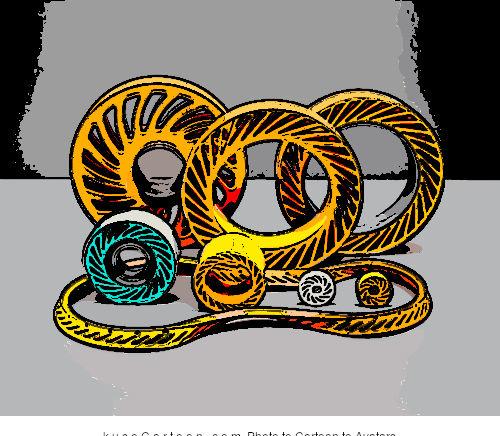
#cartiflex
Jimi Hendrix
packaging impreso & cartón ondulado julio - agosto 2020
"Cuando el poder del amor sobrepase el amor al poder, el mundo conocerá la paz"
Jimi Hendrix, fue un guitarrista y cantante estadounidense. A pesar de que su carrera profesional solo duró cuatro años, es considerado uno de los guitarristas más influyentes de la historia del rock. El Salón de la Fama del Rock and Roll lo describe como «Indiscutiblemente uno de los músicos más grandes de la historia del rock». Las influencias musicales de Hendrix se inspiraron en el rock and roll y blues eléctrico de Estados Unidos. Es conocido por usar amplificadores con distorsión, alto volumen y ganancia, además de que fue un innovador en aprovecharse de los acoples generados por la guitarra. También ayudó a popularizar el uso del pedal con wah-wah y fue el primero en utilizar efectos phaser estereofónicos en sus grabaciones. Hendrix fue pionero en el uso del instrumento como una fuente de sonido electrónico. Los guitarristas anteriores a él habían experimentado con acoples y distorsión, pero Hendrix convirtió esos efectos y otros en un vocabulario controlado y fluido igual de personal que el blues con el que comenzó
EDITA
Alabrent Ediciones, S.L.
DIRECCIÓN Jordi Arnella jordi@alabrent.com
PUBLICIDAD
Glòria Arnella marketing@alabrent.com
REDACCIÓN Javier López javier@alabrent.com
PRODUCCIÓN Jorge Martínez jorge@alabrent.com
196
Miembros de
Cartiflex no se identifica necesariamente con las opiniones de sus colaboradores y entrevistados © Cartiflex 2020 para todas las fotos y textos elaborados por la redacción de la revista
Obtener la máxima calidad en impresión flexográfica: Eso es realmente artístico. Con DuploFLEX® está en la posición adecuada. Porque DuploFLEX® es la cinta para aquellos que realmente se preocupan por la calidad. Lohmann no solo aporta la cinta óptima, sino también el mejor asesoramiento. Especialmente cuando las cosas se complican, nuestros FLEXperts ponen a su disposición toda su experiencia y le ofrecerán soluciones que son dignas de su obra de arte.
Lohmann Spain, S.A.
C/ Miquel Torello i Pagés 38
Polígono Industrial El Pla
08750 Molins de Rei (Barcelona)
Teléfono: +34 93 666 71 01
graphics@lohmann-tapes.com
www.lohmann-flexperts.com
Todos reconocemos la importancia de acertar en la incorporación de nuevos empleados en la empresa por lo que supone de compromiso, influencia en la producción, relación con los empleados existentes, etc. No obstante, a pesar de ello, en general se incorporan nuevos empleados en una forma excesivamente ligera. Conocidos, parientes, personas que nos han sugerido, etc.
por Jaume Casals de RCC Casals Consultants, S.A.Además, acostumbramos a no definir adecuadamente las funciones y puestos de trabajo y, en realidad, adaptamos todo eso a las características de la persona que hemos podido captar.
No parece que esto sea coherente con la importancia que reconocíamos al principio. ¿Qué deberíamos hacer en realidad? Lo primero deberá ser un análisis de la causa de esa nueva incorporación. Puede ser la iniciación de una nueva actividad en la empresa, la adquisición de una nueva tecnología, el intento de solución de un cuello de botella, el reconocimiento de un exceso de problemas en la productividad o en la calidad, una reorganización para atender al crecimiento sostenido, un crecimiento horizontal de la producción, etc.
En cualquiera de los casos, lo más importante es asegurarse que no existe alguna forma para poder simplificar los procesos existentes y liberar alguna persona que pudiera hacerse cargo de ese puesto que se desea cubrir. Aunque ello supusiera, en cierto grado, una actualización o adaptación de los conocimientos de esa persona.
En otras ocasiones, el planteamiento puede suponer la sustitución de una persona existente y su reubicación en otra tarea en la que puede ser más efectiva.
En la práctica no deberíamos precipitarnos a la hora de definir la necesidad de un nuevo puesto de trabajo. Esto exige una reconsideración del conjunto de la estructura de la empresa y de su posible evolución en un futuro inmediato. Una de las mayores causas de falta de competitividad estriba en unos procesos que exigen demasiada mano de obra y, con ello, unos costes de producción que pueden exceder a los que existen en el mercado.
Esto significa que, como decíamos antes, se ha reconsiderar el conjunto de personal que se tiene y compararlo, a través de información adecuada (benchmarking), con lo que existe en el mercado o, aún mejor, en los líderes del mercado. Esto nos puede hacer descubrir la necesidad de una readaptación del número de personas existente en otros departamentos.
Pero, al margen de reconsiderar la necesidad del nuevo puesto de trabajo, se debe, evidentemente, mejorar la forma que se utiliza para encontrar y elegir la persona adecuada. ¿Cuál es el proceso recomendable en estos casos?
Idealmente, deberíamos saber seguir el siguiente itinerario:
1. Asegurar que se tiene una buena definición de la estructura organizativa. En caso contrario, convendría aclarar dependencias, definir funciones y con-
firmar que todos saben de quién dependen y quiénes dependen de él o de ella.
2. A continuación debería identificarse el hueco que se pretende cubrir, sea por ampliación de actividad o por nueva actividad, asignando las funciones correspondientes a ese lugar. Esto supone, además, deducir las características o preparación ideal que esta persona debería tener.
3. Definir claramente el perfil de la persona que se busca, no sólo en lo que se refiere a la función a realizar sino a su formación y a sus características personales.
4. Poner en marcha el proceso de selección. Obviamente se puede encargar este proceso a una empresa especializada pero, si se hace en la propia empresa, conviene dedicar la atención y los recursos necesarios para asegurar un buen resultado. Sabemos que es muy difícil encontrar la persona perfecta para cada lugar de trabajo pero no por eso se debe intentar hacer todo lo posible para encontrar, dentro de las obtenibles, la más adecuada.
5. Para evaluar correctamente una persona y juzgar su adecuabilidad al puesto de trabajo necesitamos definir el perfil del puesto de trabajo y, correspondientemente, los atributos que debe cumplir la persona a proponer.
Entre estos atributos sugerimos aspectos tales como:
• Formación personal.
• Formación técnica.
• Idiomas necesarios.
• Experiencia en el lugar de trabajo.
• Conocimientos necesarios para el puesto de trabajo como pueden ser computación, calidad de productos gráficos, procesos de producción, etc.
• Nivel necesario de facultades de organización.
• Nivel necesario de facultades de decisión.
• Posibilidades de crecimiento pensando en la evolución del puesto de trabajo en el futuro.
• Conveniencia en el desplazamiento.
• Expresión verbal.
• Etc.
Por otra parte, convendrá también extrapolar las exigencias de ese puesto de trabajo hacia un tipo de personalidad necesaria en aspectos tales como:
• Preponderancia de la actividad sobre la meticulosidad o no.
• Conveniencia de ponderación o de impulsividad.
• Exigencias de dotes de mando.
• Exigencias en el trato social.
• Importancia de la objetividad.
• Necesidad de extroversión.
• Nivel de cooperativismo que se precisa.
• Etc.
En tercer lugar, no se podrá tampoco menospreciar las aptitudes naturales o adquiridas del candidato con respecto a lo que precisa en el puesto de trabajo, como pueden ser:
• Nivel de inteligencia necesario.
• Razonamiento abstracto o razonamiento lógico.
• Exigencia de aptitud numérica.
• Exigencia de comprensión del lenguaje.
• Nivel requerido de fluidez de expresión.
• Razonamiento técnico.
• Etc.
6. Supongamos que hemos podido escoger entre un número relativamente amplio de candidatos el que mejor se adapta a las exigencias de ese puesto de trabajo. Seguro que no cumplirá satisfactoriamente con todos los requisitos necesarios. Por tanto, nos deberemos plantear aquí la conveniencia de una preparación previa para completar sus conocimientos o su información.
En general, es preferible escoger aquella persona que cumple con los rasgos innatos, culturales, etc, que son difíciles de adquirir o cambiar. Debería preocupar menos el conocimiento de detalles o de aspectos que son adquiribles sobre el puesto de trabajo.
7. Deberemos pasar entonces a una preparación conveniente del entorno donde ha de trabajar. Nos referimos a que esté bien definido el puesto de trabajo, que disponga de los recursos necesarios, que haya una conciencia colectiva de su inserción, que haya quién le pueda atender durante el periodo de adaptación, etc.
8. En el momento de entrar, se le deberán dar unos objetivos específicos relativos al puesto de trabajo y que deberán servir para autoevaluar el pro-
greso y para saber hasta qué nivel de cumplimiento ha llegado después de un periodo determinado de tiempo. Y los objetivos no deberían ser únicamente primarios, específicamente de lo que está haciendo, sino que deberían incluir también sus consecuencias y lo que se pretende, al final, en el producto o en el servicio, con su intervención.
9. Durante un periodo que puede oscilar entre un mes y tres meses, convendrá un seguimiento cercano para corregir las desviaciones y explicar adecuadamente cómo se quiere que se haga la tarea y las consecuencias que pueden existir al hacerlo de otro modo. Esto no necesariamente deberá ser hecho por una persona totalmente involucrada en decisiones importantes sino que lo lógico sería que su inmediato superior o, porque no, un compañero, se hiciera cargo de este seguimiento o tutela.
10. Y, finalmente, algo que aconsejan todos los sistemas de gestión de la calidad total; la evaluación periódica. Este acto, que debería realizarse por el inmediato superior una o dos veces al año, no es solamente aplicable a los nuevos empleados sino que debería estar generalizado a todo el conjunto de la plantilla. Nos referimos a una revisión de la conducta de cada operario con respecto a sus propias funciones y objetivos, la opinión del jefe sobre cómo se podría mejorar el rendimiento correspondiente y, además, la identificación de formación o de recursos prácticos que la persona puede necesitar para aumentar su eficacia.
En definitiva, la incorporación de nuevos empleados en la empresa es una técnica que consideramos fundamental en la consolidación y crecimiento continuado de la productividad a la vez que ayuda a reconsiderar la estructura organizativa general, las funciones individuales y las dependencias jerárquicas.
La empresa debe tener como norte el crecimiento continuo, aunque sea poco, y esto exige un análisis y replanteamiento del mejor flujo de funciones y de responsabilidades bajo el prisma de la simplificación, la eficacia y el rendimiento progresivamente mayor.
Las empresas que hemos visto con mayor rendimiento por operario son aquellas que cumplen con estos requisitos.
La evolución de las organizaciones industriales hacia la Industria 4.0 plantea una serie de desafíos a la gestión. La interconexión CPS (sistema ciber físico) supone la creación y el intercambio masivo de datos en tiempo real procedentes de la fábrica, que fluyen gradualmente a los responsables de tomar decisiones. Los datos son el núcleo de la Industria 4.0. La gran cantidad de datos dentro de las empresas sin tratamiento y análisis en lugar de ser beneficiosos no tiene ningún uso. Antes de tomar cualquier decisión, los datos necesitan una transmisión, limpieza, tratamiento, clasificación y almacenamiento efectivos.
La recopilación de datos implica la existencia de una infraestructura de red y una captura de datos adecuada del equipo (a través de su detección). Teniendo en cuenta la gran cantidad de datos producidos e intercambiados, las tecnologías de "Big Data" son de fundamental importancia. No obstante, la generación, la comunicación y el reemplazo adecuado de los datos del proceso organizacional es solo una condición necesaria, pero no suficiente, para la creación de valor en la Industria 4.0. En este sentido, los datos deberían servir no solo para crear procesos para la autonomía en la toma de decisiones a lo largo de la cadena de valor, liberando gradualmente a los empleados y a los tomadores de decisiones de las tareas de toma de decisiones que requieren mucho tiempo y que requerirían una gran cantidad de tiempo para el análisis y la consideración, pero también para hacer predicciones y decisiones óptimas en consecuencia, lo que lleva a un ahorro de recursos y una mayor calidad.
SISTRADE tiene la herramienta adecuada para llevar a su empresa a la cuarta revolución industrial, optimizando, automatizando y controlando su línea de producción. Una de las aplicaciones clave de Sistrade es el Sistema de ejecución de fabricación (MES), que ofrece soluciones para planificar, recopilar datos, supervisar y controlar el proceso industrial. SISTRADE ofrece
soluciones para generar información para un rápido soporte de decisiones, incrementando la productividad.
Dentro del espectro de adquisición y procesamiento de datos en el taller, una de las principales soluciones que ofrece SISTRADE es el control de supervisión y la adquisición de datos: SCADA, que es un software basado en la web, que recupera automáticamente
datos de operadores, sensores de máquinas, PLC (controladores lógicos programables) y varios dispositivos dentro de una planta. SCADA tiene la capacidad de presentar una planta 3D de todas las máquinas, operadores y procesos en tiempo real, lo que permite reducir el tiempo improductivo.
Es importante comprender por qué la recopilación automática de datos es beneficiosa para las empresas. Entre los principales beneficios, reconocemos el aumento de la confiabilidad de los datos, ya que la intervención humana se minimiza, lo que también minimiza la posibilidad de un error. Las empresas también obtienen un mejor control de la velocidad de la máquina y tienen un registro de datos confiable sobre los tiempos de inactividad en el taller.
¿Cómo puede lograr el objetivo de reducir los costos y aumentar las ganancias, así como reducir el desperdicio en la empresa si analiza la información de producción del pasado, basando su decisión en la información que está desactualizada? La mayoría de las veces, para garantizar un buen control, los gerentes necesitan la información correcta aquí y ahora. La adquisición automática de datos permite que las decisiones relacionadas con la gestión de la producción tengan una base sólida en los datos más recientes y actualizados, que provienen directamente de las máquinas y los operadores, lo que garantiza la máxima eficiencia de la producción.
Con el sistema automático de adquisición de datos a la mano, puede recuperar datos sobre el estado de la máquina, la velocidad instantánea y promedio, conoce el tiempo de confi-
guración y producción, así como el material consumido y las cantidades de producción. Para garantizar un mantenimiento de activos efectivo y entregas oportunas, se proporciona la información sobre los tiempos de inactividad. El acceso a toda esta información en tiempo real no solo contribuye a un mayor rendimiento industrial, sino que también hace que el control de calidad sea mucho más fácil de monitorear, respaldando el compromiso de su empresa de cumplir con los más altos estándares de calidad.
SISTRADE tiene la herramienta adecuada para llevar a su empresa a la cuarta revolución industrial, optimizando, automatizando y controlando su línea de producción.
El objetivo principal de nuestra solución es reducir la intervención humana en los registros de datos de producción y al mismo tiempo mejorar significativamente la confiabilidad de los datos. La adquisición de datos desde el taller puede realizarse mediante el uso de tarjetas de adquisición patentadas, así como PLC estándar (por ejemplo, Omron o Siemens), también utilizamos protocolos estándar como el servidor OPC o XML y la base de datos relacional: SQL Server. Existen diferentes plataformas que se pueden implementar de acuerdo con los requisitos de cada proyecto.
¿Qué puede darle una mejor comprensión de cómo su empresa puede mejorar con la ayuda de dicho sistema que un ejemplo real de la solución del sistema Sistrade ya implementada en la empresa en el mercado turco? Por lo tanto, traemos un estudio de caso que describe la implementación de un proyecto de "Conveyor - Transportador". El marco de este proyecto consiste en la instalación de tres cintas transportadoras entre el taller y el almacén. El área de producción prepara el palé para enviarlo al almacén y el operador coloca cada palé en la cinta; luego, el sistema lee el código de barras del pallet y realiza la transferencia automática al almacén. Todo este proceso de transferencia garantiza una mayor fiabilidad, donde cada paleta se puede controlar a través de las pantallas, conociendo la referencia y la ubicación exacta. No hay intervención humana que disminuya la posibilidad de errores.
Como resultado, el software Sistrade® permite a las organizaciones automatizar sus procesos de producción, optimizar sus líneas de producción y transformarse en una fábrica inteligente. El concepto de Industria 4.0 se está convirtiendo gradualmente en una realidad, generando ganancias comprobadas en eficiencia, economía y agilidad para reaccionar a los cambios del mercado, permitiendo a las empresas extraer el mayor valor de sus procesos y recursos. La industria de la impresión y el embalaje también podría adoptar esta realidad, aprovechando las soluciones de software de gestión para la Industria 4.0 que ofrece SISTRADE.
Esko, un proveedor global de soluciones integradas de hardware y software para los sectores de impresión y embalaje, ha presentado su cámara de imágenes de un solo cabezal más rápida, la nueva Optics 100v2, que ofrece un aumento del 25% en la productividad de las impresores de placas corrugadas. La opción de velocidad y calidad es la última incorporación a la gama Esko CDI que presenta una tecnología láser dividida única y patentada de "cabezal único".
Exclusivo de las plataformas CDI Crystal y CDI Spark, el innovador Optics 100v2 presenta una nueva configuración de imagen que permite a los fabricantes de planchas obtener una hoja completa de 5080 (50 pulgadas x 80 pulgadas o 127 cm x 203 cm) más por hora de su CDI y lograr un notable 100% de aumento en la productividad en planchas parciales.
"Hemos desarrollado Optics 100v2 para abordar los principales problemas que enfrenta la industria", dijo Pascal Thomas, Director de Flexo Business en Esko. “La presión de los costos está aumentando en todos los ámbitos y una gran cantidad de mano de obra calificada y experiencia está involucrada en la fabricación de planchas flexo-
gráficas para la producción de impresión de cartón ondulado.
"Esta última innovación significa que los operadores de preimpresión ahora pueden trabajar más rápido, produciendo una plancha más por hora y mejorando de manera importante la eficiencia de operación en un 20%", explicó Pascal. “No solo eso, sino que todos sabemos que, dado que los materiales de plancha pueden ser muy caros, es necesario utilizar la mayor cantidad de material recortado posible para minimizar el desperdicio.
“Tradicionalmente, ha tomado 15 minutos o más para obtener una imagen de una plancha parcial para evitar el desequilibrio de la máquina, pero ahora con Optics 100v2 es significativamente
más rápido, en menos de siete minutos para un corte de 1 m2. Los fabricantes de planchas pueden reducir el desperdicio, usar menos energía y minimizar el aporte del operador para reducir costos y aumentar la eficiencia operativa ”
El aumento general de la productividad conduce a una mejora del 20% en la eficiencia operativa, mientras que la capacidad de obtener 5080 hojas más por hora significa 5080 hojas adicionales por turno típico.
"Este es, con mucho, el sistema de cabezal óptico más rápido del mercado actual", dijo Pascal. “El sistema de un solo cabezal elimina el problema de pegar o unir dos cabezales en el medio de una imagen, y además, la nueva configuración de imágenes permite el
uso de la velocidad máxima en planchas parciales independientemente del grosor, a diferencia de cuando se usan varios cabezales. El diseño también reduce la vibración y optimiza la formación de imágenes de planchas gruesas, que son las típicas de la industria del cartón ondulado.
"Esto permite imágenes significativamente más rápidas en planchas parciales gruesas y crea libertad para que los operadores preparen la siguiente plancha mientras esperan, aumentando aún más la productividad y la eficiencia", dijo Pascal.
Optics 100v2 es solo una de una serie de nuevas características innovadoras y actualizaciones que Esko ha
presentado como parte de su cartera de software integrado, Esko Software 20. Los nuevos y significativos desarrollos aportan aún más innovación y funcionalidad al conjunto de soluciones de software más vendidas de Esko. Parte de su impulso continuo para brindar mejoras de eficiencia operativa a la cadena de valor del embalaje junto con un valor sobresaliente para los clientes. Disponible desde el 15 de junio de 2020 en adelante, y gratis para los clientes de Esko Software Care Plan, la última versión del software incorpora soluciones como ArtiosCAD 20, Automation Engine 20, Studio 20 y actualizaciones de eficiencia para Share & Approve y el galardonado
Asistente de control de impresión . Disponible para todos los materiales de plancha de fotopolímero certificados, los usuarios pueden obtener más información sobre el lanzamiento de Optics 100v2 utilizando el nuevo Esko Innovation Hub (www.esko.com/innovation) que ha sido diseñado para proporcionar a los usuarios una visión única de la cartera de innovaciones que Esko trae al mercado en 2020. Los usuarios pueden navegar por las últimas soluciones integradas de hardware y software de Esko, en su propio tiempo, acceder a conocimientos e información técnica, así como aprender nuevas formas de aumentar la productividad, la eficiencia y la rentabilidad del negocio.
Gráficos de prueba mejorados, pantallas de cristal para flexografía y optimización de tinta blanca para envases flexibles son algunas de las innovadoras funciones incluidas en la nueva versión del software Print Control Wizard de Esko, galardonado en varias ocasiones.
El proveedor global de soluciones de hardware y software integradas para los sectores de impresión y de envases ha lanzado la última versión del innovador software Print Control Wizard 20.0.
“Desarrollamos Print Control Wizard para responder a las peticiones del sector de simplificar la implementación de tramas y curvas de ganancia de punto, y queríamos continuar con nuestro éxito inicial con esta nueva versión”, explicó Robert Bruce, RIP & Screening Product Manager en Esko. “Por eso hemos añadido herramientas de administración de color integradas y un nuevo proceso de implementación. Por ejemplo, mientras que los estándares globales piden tres pruebas de prensa para llevar a cabo un proyecto de flexografía, que abarcan la optimización con tests de trama única, la caracterización con administración de color y la huella de máquina para la ganancia de punto, los usuarios de Print Control Wizard 20.0 ya pueden pasar directamente al paso de huella de máquina. Esto permite reducir considerablemente los costes y el tiempo de prensa.”
Print Control Wizard 20.0, que se ha lanzado incluye una serie de funciones nuevas y atractivas diseñadas para impulsar la eficiencia, como:
- Diseño mejorado del gráfico de prueba: la cantidad de pruebas de prensa necesarias para crear tramas y curvas para proyectos de flexografía se ha reducido a una. Con esto se logra un análisis más rápido de una nueva condición de impresión y se consigue una mayor eficiencia. El asistente incluye ahora un gráfico de prueba con 4 colores, permite a los usuarios crear gráficos de huella de máquina, e incluye un modo de digitalización rápido para la calibración del punto mínimo, lo que reduce el tiempo dedicado en cada trabajo.
- Mejoras en la galardonada interfaz de tipo asistente: la nueva interfaz de Color Engine Pilot no solo incluye una nueva vista de tramas y curvas, sino que también permite a los usuarios acceder a todos los recursos de tramas de Esko desde una sola aplicación.
- Asistente para confección de planchas: se trata de una ubicación central de almacenamiento para la
instalación de Esko CDI. Esta nueva herramienta usa guías integradas para facilitar la instalación del equipo de exposición de planchas CDI, lo
las funciones de administración de
que garantiza el mejor rendimiento en el menor tiempo posible.
- Informes: los nuevos informes de huella de máquina totalmente automatizados y personalizables ahora están disponibles con solo pulsar un botón.
- Nuevas pantallas de cristal para flexografía UV: con una misma interfaz de usuario centrada en el proceso para envases flexibles y flexografía UV, este módulo totalmente nuevo ofrece las funciones de Print Control Wizard de manera simplificada y las tramas personalizadas para flexografía UV, con compatibilidad para CDI Pixel+ y sin Pixel+.
- Optimización de tinta blanca para envases flexibles: mejora las prestaciones de las tintas más empleadas en envases flexibles (que también son las más caras). Con Print Control Wizard 20.0, la opacidad, el moteado y el peso de la tinta blanca se controlan y optimizan automáticamente, lo que mejora la calidad de impresión y la reproducción de imagen, y además reduce los costes de consumo de tinta.
Lanzado por primera vez el año pasado, Print Control Wizard fue diseñado especialmente para mejorar el proceso de confección de planchas para flexografía y la calidad de impresión en flexografía mediante pantallas de cristal. Adopta un enfoque simplificado y estandarizado para el uso de los parámetros del proceso, como la tinta, la prensa de impresión, el sustrato y el anilox, en la creación de tramas y curvas. El resultado es un conjunto de pantallas de cristal y curvas
“Desarrollamos Print Control Wizard para responder a las peticiones del sector de simplificar la implementación de tramas y curvas de ganancia de punto, y queríamos continuar con nuestro éxito inicial con esta nueva versión”, explicó Robert Bruce, RIP & Screening Product Manager en Esko.
que se usan para la exposición de las planchas en un dispositivo CDI Crystal XPS, logrando así la mejor calidad de impresión en flexografía.
“Nuestro propósito era proporcionar a los expertos en flexografía las herramientas para estandarizar y simplificar la creación de tramas y curvas, que les permitiera conseguir los mejores resultados de calidad sin necesidad de añadir pasos y comprobaciones adicionales al proceso,” comentó. “Después de que Print Control Wizard fuera premiado con varios de los galardones más importantes del sector, hemos seguido trabajando sin cesar para desarrollar estas nuevas mejoras. Ahora estamos entusiasmados por lanzar esta nueva versión para seguir apoyando el trabajo de los especialistas en impresión y envases de todo el sector.”
Print Control Wizard 20.0 es solo una de las muchas actualizaciones y funciones innovadoras que Esko ha dado a conocer como parte de su catálogo de productos de software integrado, Esko Software 20. Los nuevos e importantes avances son aún más innovadores y añaden más fun-
ciones al conjunto de aplicaciones de software de Esko más vendido, como parte de su esfuerzo continuo por impulsar la eficiencia de las operaciones en la cadena de valor del envasado, además de su incomparable valor para los clientes. Disponible a partir del día 22 de junio del 2020 (y gratuito para los clientes que dispongan actualmente de un Esko Software Care Plan) esta nueva versión de software incluye soluciones como ArtiosCAD 20, Automation Engine 20, Studio 20 y actualizaciones que mejoran la eficiencia en Share & Approve.
Si desea saber más sobre Print Control Wizard 20.0, visite el nuevo Esko Innovation Hub (www.innovation.esko.com), un entorno virtual centralizado para ofrecer a los usuarios información exclusiva sobre la variedad de innovaciones de Esko Software 20. Allí podrá conocer las soluciones de software y hardware integradas más recientemente de Esko, a su propio ritmo, así como consultar información útil y datos técnicos, además de aprender nuevas maneras de potenciar la productividad, la eficiencia y la rentabilidad.
“Nuestro propósito era proporcionar a los expertos en flexografía las herramientas para estandarizar y simplificar la creación de tramas y curvas, que les permitiera conseguir los mejores resultados de calidad sin necesidad de añadir pasos y comprobaciones adicionales al proceso”
Asahi Photoproducts, empresa pionera en el desarrollo de planchas flexográficas de fotopolímeros, participa en un importante proyecto con Comexi y otros socios del sector. Como parte de este proyecto llave en mano, Asahi instalará una procesadora de lavado con agua Asahi AWP™ 4835 P y planchas procesadas al agua Asahi AWP™ con tecnología CleanPrint en el Centro Tecnológico Manel Xifra Boada de Comexi en Girona (España). El proyecto está diseñado para concienciar a los impresores de embalaje flexible sobre el valor de la producción propia de planchas flexográficas y demostrar lo fácil que resulta hacerlo con la tecnología actual.
“Estamos orgullosos de participar en este proyecto tan importante junto a nuestro socio Comexi”, señala Philip Mattelaer, director de ventas de Asahi Photoproducts. “Cada vez son más los impresores de flexografía que internalizan la producción de planchas con el objetivo de impulsar la eficiencia y mejorar la calidad. Este proyecto demostrará al mercado flexográfico lo fácil que es producir planchas, fortaleciendo la cadena de valor en el punto de producción de la impresión. Además de mejorar la eficiencia y la calidad, este proyecto también demuestra cómo los proveedores de impresión pueden aumentar la sostenibilidad incorporando la tecnología Asahi CleanPrint".
Soluciones innovadoras integran la preimpresión y la impresión en las instalaciones del cliente.
Las planchas flexográficas CleanPrint de Asahi Photoproducts han sido especialmente diseñadas por los ingenieros químicos de Asahi para transferir toda la tinta restante al soporte impreso, reduciendo los tiempos de puesta a punto y las paradas de limpieza de la máquina en comparación con otros sistemas de producción de planchas, al tiempo que ofrecen una calidad excepcional. Las planchas flexográficas Asahi CleanPrint también son ideales para la impresión con paleta de colores fija, un método que se usa cada vez más para ahorrar tiempo y dinero, manteniendo el nivel de calidad que esperan las marcas. Esto es posi-
La procesadora AWP™ 4835 P está pensada para atender las necesidades exigentes de impresores que usen un formato de plancha máx. de 90 x 120 cm. Para los impresores de banda ancha, la nueva procesadora de planchas AWP™ 4260 PLF es la solución más indicada gracias a su formato de plancha de 106,7 x 152,4 cm (42 x 60 pulgadas). Reduce al mínimo el consumo de agua, por lo que es una solución sostenible para producir planchas flexográficas.
ble gracias al registro preciso de las planchas procesadas al agua CleanPrint de Asahi. La gama AWP de planchas y procesadoras convierte la producción de planchas flexográficas en un proceso respetuoso con el medio ambiente, minimizando el consumo de agua, eliminando productos químicos nocivos y trazando un futuro más limpio para la industria flexográfica.
La producción propia de planchas
flexográficas también se traduce en una mayor disponibilidad de planchas, lo que, a su vez, redunda en una mayor eficiencia general de los equipos (OEE). Este es uno de los factores que impulsa la internalización de la producción de planchas, la misma tendencia que experimentó la industria de la impresión offset offset hace años. El proyecto llave en mano de Comexi abarcará también la organización de eventos
periódicos para los clientes, en los que se demostrará el potencial de agruparlo “todo bajo un mismo techo”.
La producción propia de planchas flexográficas también se traduce en una mayor disponibilidad de planchas, lo que, a su vez, redunda en una mayor eficiencia general de los equipos (OEE)
“Los visitantes del proyecto quedarán gratamente sorprendidos viendo la rapidez y la limpieza con que se producen las planchas procesadas al agua Asahi AWP con CleanPrint, y tendrán acceso a expertos que pueden ayudarlos a emprender su propio camino CleanPrint hacia un futuro que se caracterice por una impresión flexográfica más limpia”, añade Mattelaer. “La clave para controlar la calidad y los niveles de servicio en la impresión flexográfica es controlar la preimpresión, y el proyecto
llave en mano de Comexi muestra a los visitantes la facilidad con la que pueden hacerlo. Combina hardware, software, instalación, optimización, formación y
soporte de producción para garantizar una transición fluida hacia un futuro limpio para los impresores de flexografía de todos los tamaños”.
I n n o v a t i o n | C r e a t i v i t y | F l e x i b i l i t y
Dentro de su compromiso de mejora continua, un compromiso adquirido hace más de 35 años con los clientes y que se renueva cada año, Gestión21 ha incorporado una serie de nuevas funcionalidades específicas para el sector del packaging.
Este sector ha sido siempre piedra referencial para Consultores Asociados SL dentro de las artes gráficas, como así lo atestigua el hecho de que desde los orígenes de su erp, un elevado porcentaje de clientes ha pertenecido al mismo. Este hecho, junto con la cada vez más predominante posición del envase dentro de nuestras vidas, junto con la impresión de etiquetas, ha hecho que se acentúe cada vez mas la incidencia del porcentaje de clientes tanto de packaging como de etiquetas dentro del parque de usuarios de Gestión21.
Por todo esto, el departamento de desarrollo de la empresa ha realizado una serie de mejoras que vienen a incrementar las ya existentes para el sector del packaging. El trazador de estuchería, una potente herramienta que permite no sólo tener almacenados los estuches que utiliza la organización basándonos en los modelos FEFCO, sino también calcular la optimización de la imposición tanto en troquel como en el pliego, incorpora ahora la posibilidad de realizar búsquedas inteligentes de estos estuches, así como establecer sistemas de aviso que nos permiten reutilizar la información de estuches ya creados en otros nuevos. Además, gracias al módulo de B2B de Gestión21, cada vez son mas los usuarios del sistema que incorporan dicho módu-
lo con el objeto de permitir a sus clientes interactuar en tiempo real para realizar pedidos, calcularse ellos mismos los precios, acceder a la información de facturas, ordenes de fabricación, almacén, etc.
Para Mario Temprano, Director General de Consultores Asociados, “Desde nuestros inicios fueron muchas las empresas de packaging que confiaron sus negocios en Gestión21 para gestionar su día a día. Gracias a esa confianza y a sus sugerencias fue como hemos ido implementando en el sistema esas mejoras. A día de hoy seguimos mejorando con nuevas funcionalidades que sin duda hacen de
Gestión21 el sistema referencia dentro del sector del envase”.
Gestion21 es un ERP especializado en el sector gráfico cuya misión es gestionar los flujos de información y trabajo de las empresas gráficas con el objeto de que estas ahorren tiempo en las labores administrativas y a su vez obtengan información a nivel de gestión en los distintos departamentos de las mismas. Las áreas que cubre esta herramienta van desde Presupuestación , Producción, Taller, Facturación, Almacén, Compras, Planificador de Producción, Contabilidad, Gestión Comercial, Área de recursos Humanos, etc.
El software de gestión de color GMG les ayuda a los proveedores de impresión a hacer exactamente eso: ofrecer un alto grado de previsibilidad del color, ya sea para la producción de impresión de empaques complejos, trabajos de gran formato o para pruebas de color. GMG ofrece
soluciones para la estandarización y simplificación de flujos de trabajo de gestión de color para lograr colores consistentes en todos los sustratos y en cualquier proceso de impresión.
"Estamos muy entusiasmados por colaborar con HP y ofrecer productos de gestión de color GMG para
integrar al Suite HP One Package", dice Darrian Young, gerente de asociación global. "Creemos que podemos ayudar a quienes trabajen con las prensas corrugadas HP al proporcionar una forma de mejorar la precisión de color de sus clientes".
El tercer sistema de impresión UTECO Sapphire EVO M para la producción de packaging flexible inició su viaje hasta las instalaciones del cliente pocos días después de superar la prueba de aceptación en fábrica. Esta rotativa de inyección de tinta está destinada a una compañía de Norteamérica que la utilizará para aplicaciones que requieren un alto número de trabajos de tirada corta. Ya hay otros sistemas de impresión Sapphire EVO M funcionando con gran éxito en impresores de packaging flexible de Italia y Japón.
El nuevo cliente eligió el sistema de impresión Sapphire EVO M porque ofrece el mejor ciclo de carga de cualquier sistema de impresión digital de bobina mediana y permite una producción más económica de volúmenes de hasta 20.000 m2 en comparación con los procesos analógicos.
El sistema de impresión Sapphire EVO M es un desarrollo conjunto del Grupo Uteco y Kodak. Este sistema de impresión digital de bobina mediana permite a los impresores de packaging migrar trabajos de los procesos de impresión tradicionales a la tecnología digital y disfrutar así de unos resultados de alta calidad, además de enormes ahorros de tiempo, preparación y costes. Gracias a la tecnología de inyección continua de tinta KODAK Stream y a las tintas de pigmento de base acuosa de bajo coste de Kodak, este sistema de impresión digital proporciona una excelente calidad de impresión CMYK sobre toda una variedad de
papeles y materiales de película plástica. El Sapphire EVO M admite un ancho de bobina máximo de 650 mm y un ancho de impresión de 620 mm. Con velocidades de producción de más de 150 metros por minuto, es más rápido que cualquiera otra solución digital para sustratos flexibles.
El nuevo cliente eligió el sistema de impresión Sapphire EVO M porque ofrece el mejor ciclo de carga de cualquier sistema de impresión digital de bobina mediana y permite una producción más económica de volúmenes de hasta 20.000 m2 en comparación con los procesos analógicos. Otro beneficio clave del Sapphire EVO M desde el
punto de vista del cliente es que mejora enormemente su tiempo de salida al mercado. Mientras que la producción basada en procesos analógicos convencionales suele requerir dos semanas o más, se estima que será posible ejecutar los trabajos con el nuevo sistema de impresión de inyección de tinta en apenas dos días.
«Este último éxito comercial demuestra claramente que los sistemas de impresión Sapphire EVO con tecnología de inyección continua de tinta a alta velocidad y tintas de base acuosa de Kodak están en vías de convertirse en las soluciones líderes mundiales para la impresión digital de packaging
flexible»,
indica Randy Vandagriff, Vicepresidente Senior de Impresión de Eastman Kodak Company.Este sistema de impresión digital de bobina mediana permite a los impresores de packaging migrar trabajos de los procesos de impresión tradicionales a la tecnología digital y disfrutar así de unos resultados de alta calidad, además de enormes ahorros de tiempo, preparación y costes
Aldo
Peretti, Presidente y Director General del Grupo Uteco, agrega:«Estamos encantados de que nuestro sistema de impresión Sapphire EVO M
esté pronto en acción con diferentes aplicaciones de packaging flexible en tres continentes. Ofrece a los impresores de packaging y convertidores una forma asequible de satisfacer la cre-
ciente necesidad de una producción rápida, rentable y de alta calidad con tiradas cortas y medianas entre los propietarios de marcas».
“No tenemos miedo de desafiar a nuestros clientes. Para nosotros, es una parte muy importante del establecimiento y el mantenimiento de una relación, así es como descubrimos nuevas formas de trabajo.” Quien habla es Chris Rigby, y la empresa de la que habla es Pulse Media, con sede en Stockport (Reino Unido), que fue galardonada con el Premio de Plata en los Global Flexo Innovation Awards de Miraclon el año pasado, un premio que reconocía su eficiencia en los flujos de trabajos y la conversión de procesos del offset a la flexografía.
Siempre que es necesario, Pulse desafía a sus clientes en varios puntos de la cadena de suministro del embalaje flexográfico, habiendo desarrollado una cartera de servicios que abarca desde el diseño inicial, pasando por la gestión de la marca y el color, hasta la asistencia a las pasadas en prensa, la gestión de proyectos y la consultoría. Está muy lejos
de la fabricación de planchas litográficas escalonadas y repetidas que fue la única oferta de Pulse cuando comenzó su trayectoria en 1982. En ese momento, los clientes eran impresores locales; hoy en día, Pulse se posiciona como una agencia de gestión de impresión que sirve a marcas globales de productos de consumo masivo.
La presencia de la empresa en el sector de FMCG se remonta a finales de la década de los 80 y al auge de productos de “marca propia” de minoristas. Rigby, director técnico de Pulse, afirma: “Los clientes necesitaban proveedores que pudieran garantizar que el embalaje fuera consistente en todos los formatos: cartón litografiado, bolsa flexográfica, caja de
cartón corrugado o etiquetas UV. Pulse vio la oportunidad y la aprovechó, y 30 años después de lograr esta consistencia sigue siendo el centro del negocio.”
En el centro de un triángulo
Rigby describe a Pulse como una “agencia de gestión de impresión. Nos posicionamos en el centro de un triángulo formado por diseñadores, propietarios de marcas e impresores, y nuestro trabajo es asegurar la consistencia de la marca. Para que funcione, las tres partes tienen que confiar en nosotros y en nuestra experiencia y actuar en su mejor interés para obtener los mejores resultados.” El trabajo que ganó el Premio a la Innovación de Pulse es un buen ejemplo de esta relación de colaboración. Las cajas de cerveza ya habían sido impresas en litografía, con resultados poco satisfactorios, y el desafío de Pulse era mejorar tanto la calidad de impresión del conjunto del envase como la consistencia del color. Un equipo técnico formado por Pulse, el impresor, el proveedor de planchas y un técnico de tintas revisó el diseño para decidir el mejor enfoque, considerando factores como las divisiones de color, etc.
“No tenemos miedo de desafiar a nuestros clientes. Para nosotros, es una parte muy importante del establecimiento y el mantenimiento de una relación, así es como descubrimos nuevas formas de trabajo”
Rigby sigue contando: “El día en el que se iniciaba la impresión, con el trabajo en la fase de registro, el cliente aprobó la primera tirada, lo que permitió una puesta a punto más rápida. En general, la versión flexográfica mostró un registro mejorado, un mejor control de los puntos de realce, una alta densidad de sólidos y una mejor consis-
tencia de impresión, en una gran superficie y durante toda la tirada. ¿El resultado? La marca decidió que otros tres diseños se realizarían con flexografía y no con litolaminado.”
Gracias a éxitos como este, Pulse está creciendo a pesar de estar en un mercado que Rigby describe como “muy duro”, y en el que lo que él llama “compras basadas en el precio” son demasiado habituales. Con 50 empleados en sus oficinas centrales, más cinco que trabajan en las instalaciones de los clientes, dice que Pulse “encaja perfectamente en la categoría de pequeñas y medianas empresas, por lo que no tenemos el poder adquisitivo de los grandes.” En cambio, tenemos que competir en calidad y servicio, y captar regularmente nuevos clientes que vienen rebotados de proveedores más baratos y que buscan un proveedor que pueda ofrecer una buena relación calidadprecio.”
También ayuda el hecho de que Pulse opere en un sector de la industria (la flexografía) que Rigby describe como “el más emocionante de la industria de impresión de embalajes hoy en día, el sector que más innovaciones ha vivido y en el que se ha visto un mayor aumento de la calidad en la última década.” Gran parte del mérito de todo ello se lo da a Kodak Flexcel
NX. “Hace diez años era difícil para la flexografía igualar la producción de huecograbado y offset, pero NX supuso un gran avance, entre otras cosas porque animó a otros fabricantes a invertir en el proceso de flexografía, mejorando aún más la calidad, el control de la prensa y las tintas. Igual de importante fue la voluntad de los impresores de comprometerse y ponerse objetivos más ambiciosos”.
A corto y medio plazo, esta ambición está poniendo en juego tecnologías como la gama de colores extendida (ECG) y la paleta de colores fija (FCP), ya que las marcas buscan reducir tanto los costes como la huella de carbono mediante la reducción del color. Dado que la sostenibilidad es cada vez más importante para los consumidores, se está prestando gran atención a los materiales reciclables, especialmente los plásticos, y Pulse participa actualmente en una serie de ensayos sobre nuevos sustratos. “La flexografía está experimentando un gran impulso”, dice Rigby. “Dada la calidad y la consistencia que podemos lograr, además de la reducción del tiempo de comercialización, cada vez hay menos argumentos para seguir con el huecograbado para los embalajes flexibles. A menudo la única razón es la duración de las tiradas, pero las tiradas se reducen año tras año, e incluso esa ventaja percibida será menos importante a medida que pase el tiempo”.
El mercado de los embalajes se encuentra inmerso en una profunda transformación. Los propietarios de marcas demandan una comercialización más rápida y soluciones más sostenibles. Para hacer frente a estas necesidades, BOBST anuncia el lanzamiento de EXPERT RS 6003, una nueva generación de rotativas de huecograbado, que permitirá a las empresas de conversión afrontar los retos actuales del mercado.
La flexibilidad y la productividad son las palabras clave de la EXPERT RS 6003, que puede alcanzar la velocidad máxima de 500 m/min y puede configurarse con cilindros de impresión con o sin eje.
«En BOBST llevamos siempre más allá la tecnología destinada a mejorar constantemente el rendimiento de los equipos y procesos para cumplir los requisitos actuales y futuros del mercado —explicó Jonathan Giubilato, director de línea de productos de huecograbado en Bobst Italia.— El mercado de los embalajes flexibles cada vez demanda más poder producir tiradas cortas, versionar packagings, optar por soluciones más ligeras, más finas y reciclables y una consistencia cromática global, así que estamos listos para apoyar a nuestros clientes dedicados a la conversión con unas soluciones que les permitan comercializar rápido sus productos, con mayor calidad, productividad, agilidad y seguridad. Y la tec-
nología del huecograbado no es una excepción.»
La flexibilidad y la productividad son las palabras clave de la EXPERT RS 6003, que puede alcanzar la velocidad máxima de 500 m/min y puede configurarse con cilindros de impresión con o sin eje.
Las opciones de configuración incluyen la elección del sistema de entintado, para garantizar los mejores resultados de calidad según los requisitos de producción. El sistema de entintado estándar MPI (Multi-Purpose Inking) o el opcional HSM (High Speed Metering) ofrecen una impresión consistente y repetible de alta calidad en cualquier condición y con todos los tipos de tintas y disolventes.
Para que la preparación de la impresora y los cambios de trabajos resulten más fáciles y rápidos, BOBST ha utilizado un nuevo sistema innovador exclusivo en la EXPERT RS 6003. El Flex Trolley es como un carro de servicio que puede quedar colocado durante la impresión o eliminarse una vez configurada la impresora. De este modo se reduce considerablemente el número mínimo de carros necesarios para el funcionamiento de la impresora y ofrece la máxima flexibilidad durante las operaciones de cambio de trabajos.
El sistema de secado incluye muchas de las proezas técnicas de la tecnología de secado de BOBST, que se han renovado para garantizar la eficiencia de secado necesaria con una
longitud de cámara de secado más corta. Esta solución acorta considerablemente la longitud de banda en la prensa con la consiguiente reducción del desperdicio, aproximadamente un 30 % al principio y durante los cambios de trabajos en comparación con las cámaras de secado convencionales.
La impresora permite imprimir a alta velocidad con tintas a base de disolventes y a base de agua, y es compatible con oneECG. BOBST ha liderado el uso de la gama de colores extendida (ECG) en huecograbado con su solución oneECG, que abre las puertas al mundo digital del huecograbado para descubrir una nueva forma de seguir el ritmo de los requisitos actuales del mercado.
En línea con la visión de BOBST, donde la conectividad, la digitalización, la automatización y la sostenibilidad son las piedras angulares de la producción de embalajes, nuestros clientes disponen de aplicaciones de supervisión y BOBST Connect, que proporcionan una conectividad y un soporte totalmente remotos.
«Con nuestros últimos avances en huecograbado, reinventamos el proceso y recuperamos las ventajas del hue-
cograbado de un modo que responde con hechos a la pregunta de si el huecograbado es capaz de evolucionar con la transformación actual del mercado para garantizar un crecimiento futuro y sostenible a los usuarios —comentó Jonathan Giubilato,.— Tenemos ya
las herramientas (equipos, procesos y flujos de trabajo digitalizados) que darán un giro a la estrategia de la industria de huecograbado y sentarán las bases de un buen futuro para nuestros clientes de impresión por huecograbado » concluyó.
Flint Group ha colaborado con socios clave de la industria para ofrecer un seminario web sobre la última tecnología disponible para ofrecer una impresión de gama extendida (EGP).
Con imágenes en vivo de la última prensa flexográfica inteligente SOMA Optima² CI en acción en el Centro de Tecnología SOMA en Lanskroun, República Checa, el equipo imprimió un diseño EGP ecológico, de alta definición y reverso impreso en una película de polipropileno.
El diseño se centró en la impresión de gama ampliada HiQ de 80 lpcm (203 ppp), demostrando la impresión en un grupo de diez extensiones impresas en diferentes colores de marca. El trabajo utilizó anilox de bajo volumen y tintas de alta intensidad en CMYK, así como verde, violeta y un blanco de alta opacidad, con resultados sobresalientes con alta vitalidad y detalle.
Thomas Strohe, director senior de segmentación y estrategia de productos de Flint Group, dio una idea de las contribuciones de Flint Group al proyecto. “En línea con nuestra visión de sustentabilidad, que se enfoca en apoyar los mercados de embalaje con productos construidos de manera responsable y soluciones sustentables diseñadas para economías circulares, el seminario web fue una oportunidad fantástica para demostrar el desempeño y los beneficios ambientales de nuestras soluciones EGP".
“La demostración en vivo mostró a la audiencia nuestra cartera única de fundas, planchas y tintas a base de solvente y, al ser el único proveedor global con certificación EGP a través de una solución completa que cubre tanto planchas como tintas, pudimos demostrar nuestra capacidad para llevar la calidad de impresión al siguiente nivel".
“Estamos escuchando las necesidades de nuestros clientes de simplificación, innovación, confiabilidad y, por supuesto, sustentabilidad. EGP es la representación perfecta de esta estrategia. Ofrece a los impresores la oportunidad de ofrecer resultados de impresión fantásticos y, al mismo tiempo,
El diseño se centró en la impresión de gama ampliada HiQ de 80 lpcm (203 ppp), demostrando la impresión en un grupo de diez extensiones impresas en diferentes colores de marca.
simplificar sus rangos de tinta, reducir los costos y, lo que es más importante, brindar numerosos beneficios para el medio ambiente”.
Las tintas de embalaje de Flint Group demostraron una impresión EGP perfecta
Las tintas FlexiPrint MV de Flint Group son tintas a base de nitrocelulosa modificadas que se han optimizado para la impresión de superficies flexográficas o laminadas de alta calidad en una amplia variedad de películas.
Las tintas brindan una excelente resistencia al frote, al agua y al calor, junto con una calidad de impresión superior a altas velocidades, también tienen poco olor. Las tintas FlexiPrint
MV se prueban de acuerdo con los estándares de certificación OK Compost, lo que las hace adecuadas para una amplia variedad de películas y aplicaciones de embalaje compostables. Diseñado para circularidad, FlexiPrint MV de Flint Group Packaging Inks está aprobado por CADEL DEINKING para el destintado a base de agua para respaldar el proceso de reciclaje de material de embalaje a base de plástico.
Con una intensidad de color maximizada y tonos específicos para respaldar el trabajo de proceso multicolor HiQ y Expanded Gamut, estas tintas están específicamente modificadas para impresión de alta velocidad y estabilidad mejorada de la prensa, mejorando la eficiencia general del equipo.
CHROMA CUT RDC 2100 2400 2800
LA TROQUELADORA ROTATIVA CON SERVOMOTORES HBL
PARA IMPRESIÓN FLEXO DE ALTA CALIDAD www.celmacchgroup.com
TECNOLOGÍA TOP
COMPONENTES DE PRIMERA CLASE MADE IN ITALIA
Chroma Cut combina la más avanzada tecnología de impresión de la serie Chroma Print con la máxima precisión de la troqueladora rotativa, para proporcionar una productividad excepcional a largo plazo.
SERVOMOTORES HBL CON PUESTA EN MARCHA RÁPIDA
TECNOLOGÍA DE SERVO ACCIONADORES SIEMENS
SISTEMA DE RASQUETAS DE FIBRA DE CARBONO
CILINDRO TROQUELADOR CON ENGANCHE RÁPIDO DEL TROQUEL
SERVO ACCIONADORES CON SISTEMA DE RECTIFICADO
CONTROL DE REGISTRO Y TECNOLOGÍA 0 DEFECTOS
Comexi, especialista en soluciones para la industria de la impresión y conversión del envase flexible, anunció proyectos para un nuevo Centro Tecnológico (CTec) en la nueva sede de la compañía en los Estados Unidos, en Miami (Florida). Con las nuevas oficinas de ventas y servicio al cliente ya terminadas, la instalación del CTec de 1.400 metros cuadrados, con un gran stock de repuestos centralizado, está programada para completarse en noviembre de 2020.
La nueva sede de la compañía en los Estados Unidos ofrecerá formación in situ en flexografía, laminación, corte, mantenimiento, gestión del color y preimpresión, así como pruebas industriales.
Los clientes y partners de Comexi pueden realizar, en el CTec USA, formación especializada en flexografía, laminado, corte, mantenimiento de equipos, gestión del color y procesos de preimpresión. El centro también permitirá a los clientes probar y ensayar materiales utilizando maquinaria in situ. Miami es el tercer Centro Tecnológico de la empresa en todo el mundo.
“El Centro Tecnológico Manel Xifra Boada, Comexi CTec, está totalmente integrado con nuestras instalaciones en Riudellots de la Selva. En la actualidad, creemos que es hora de avanzar con la creación de nuestro tercer centro tecnológico, con el fin de ofrecer nuestros servicios de formación, asesoramiento y soporte técnico del proceso para la industria de la impresión y conversión del envase flexible. Gracias al CTec USA, Comexi podrá dar una respuesta
más eficaz a las necesidades de nuestros clientes americanos”, explica Albert López, responsable del Comexi CTec.
Cuando esté finalizado, el CTec USA tendrá un laminador sin disolvente SL2 completamente operativo, una cortado-
ra de banda ancha S2 DT y una prensa flexográfica híbrida F2 MP. La laminadora Comexi SL está diseñada para todo tipo de laminados sin disolventes, lo que hace de esta máquina una perfecta solución sostenible. La cortadora
Comexi S2 DT cuenta con un sistema de rebobinado de doble torreta que proporciona una excelente calidad y productividad. La F2 MP 60” de Comexi es una impresora flexográfica de 10 colores altamente versátil diseñada para una amplia gama de producción de impresión de calidad.
La primera formación técnica en el nuevo centro tendrá lugar en el cuarto trimestre de 2020, para un curso de 3 días sobre gestión de color. El curso cubrirá sesiones prácticas y teóricas sobre el control de procesos basado en mediciones, la implementación de la gama de colores extendida, la gestión del color y el de control de calidad. En el segundo trimestre de 2021 se ofrecerá capacitación sobre impresión de alto valor, laminación y mejora de la producción de corte. El registro estará disponible online.
Según Olof Buelens, vicepresidente y director de operaciones de Comexi en Norteamérica, “la nueva sede y el CTec en Miami es una inversión significativa de Comexi para ofrecer mejores y más amplios servicios en términos de capacitación, calidad, procesos, sistemas I+D+I y pedidos online a nuestros clientes en América. La creación de un stock de repuestos ampliado también ayuda a garantizar una distribución mejor y más rápida de las piezas de repuesto a los clientes de Estados Unidos y Canadá".
Actualmente, Comexi North America cuenta en su plantilla con técnicos a tiempo completo para garantizar el soporte oportuno a los clientes desde América del Sur hasta Canadá, además de un equipo de especialistas para brindar soporte técnico las 24 horas, los 7 días de la semana.
Siempre aplicando tecnología punta para brindar un mejor servicio a los clientes, Comexi presentó recientemente Comexi Cloud, la plataforma de servicio digital más completa del mercado para visualizar, compilar, analizar y almacenar todos los datos. Los clientes también se benefician del soporte remoto de Comexi con el sistema de comunicación Smart Glasses, un programa de mantenimiento operativo, un programa de servicio personalizado, capacitación y consultoría.
A partir del pasado 1 de julio, Christian Apenberg fue nombrado director de marketing regional de EMEA para soluciones de imagen. En esta función, Christian Apenberg definirá e implementará estrategias e iniciativas para los segmentos de Flexo y Tintas digitales en el Equipo de liderazgo de ventas regional y en cooperación con la Dirección de marketing global.
Después de más de 14 años en las áreas de investigación y desarrollo y servicio técnico, más recientemente como líder tecnológico en soluciones de imagen EMEA, está cediendo la responsabilidad del área técnica a Michael Louis Weber.
Michael Louis Weber, especialista en servicio técnico de Image Solutions EMEA, ha sido nombrado director de servicio técnico de Image Solutions EMEA a partir del 1 de agosto. Tiene muchos años de experiencia en investigación y desarrollo y servicio técnico.
Tanto Christian Apenberg como Michael Louis Weber están ubicados en la oficina de DuPont en NeuIsenburg, Alemania.
Mondi, líder global en el mercado de papel y soluciones de embalaje, ha desarrollado el primer soporte siliconado de papel kraft recubierto de polietileno (PCK) sostenible y lo presenta ahora a escala mundial.
Este tipo de soportes son indispensables para transportar y proteger los productos adhesivos sensibles a la presión (PSA). Actualmente, lo normal es desecharlos una vez se han utilizado los productos PSA a los que acompañan. NextLiner de Mondi utiliza una base de papel reciclado con un recubrimiento que proviene de fuente sostenibles. Usar fibras recicladas y materiales renovables puede tener un impacto positivo para reducir la huella en el medio ambiente de NextLiner utilizado en artes gráficas, cintas adhesivas y otras aplicaciones industriales.
“Nuestra meta es apostar por diseños sostenibles. Hemos innovado para crear NextLiners que sean respetuosos con el medio ambiente y apoyen los objetivos de sostenibilidad de nuestros clientes. Usar fibras recicladas y resinas renovables es un paso más que nos acerca a hacer las cadena de suministro de PSA más sosteni-
ble”, señaló Stefan Schönberger, Director de Productos Sostenibles Mondi Release Liner.
Cada vez se usan más soportes siliconados (release liners) - el consumo de papeles policubiertos es cercano a 9 billones de metros cuadrados anualmente, siendo un 16% destinados a la fabricación de release linersasí que disponer de alternativas ecológicas es fundamental. El lanzamien-
to de NextLiner es un importante primer paso en el desarrollo de soportes siliconados sostenibles. Mondi, en su compromiso de contribuir a la conservación del planeta, lleva a cabo continuamente tareas de I+D destinadas a encontrar alternativas más sostenibles para los release liners (tanto de PCK, como de papel y film) y mejorar las tecnologías relacionadas con el reciclaje.
El Centro Tecnológico Manel Xifra Boada, Comexi CTec, especializado en formación, asesoramiento y soporte técnico del proceso para la industria de la impresión y conversión del envase flexible, ha incorporado en su portfolio un nuevo servicio que tiene como objetivo integrar el proceso de preimpresión en las plantas de sus clientes, partiendo desde cero. Este proyecto llaves en mano cuenta con la colaboración de distintos partners altamente cualificados como Esko, Asahi y DuPont, y culmina cuando el cliente produce su propia preimpresión bajo todos los estándares de calidad definidos.
“El control de la preimpresión es un elemento clave para el proceso, tanto por su eficiencia como por la calidad del producto final. Tenerlo bajo control es indispensable para ser competitivos”, explica Albert López, responsable del Centro Tecnológico, que añade que “la evolución de la tecnología de producción de planchas hacia una respuesta de tiempo de entrega bajo premisas de sostenibilidad comporta que los convertidores integren cada vez más la preimpresión como parte de su proceso propio de producción”.
Para que la transición sea lo más fácil posible en coste y en tiempo, el conocimiento es vital. Comexi CTec dispone de los recursos necesarios para ofrecer a sus clientes la posibilidad de integrar todo el flujo de trabajo de preimpresión mediante un proyecto llaves en mano. La propuesta
tecnológica de la compañía comporta la integración de un departamento de preimpresión partiendo de cero, e incluye el hardware, el software, la instalación, la optimización, la formación y el acompañamiento en producción hasta que el cliente es autónomo de forma eficiente. El tiempo estimado para culminar el proyecto
es de seis meses, aproximadamente. La propuesta tecnológica cuenta con un sistema de exposición con un procesado de planchas sin solventes y de producción rápida. La tecnología de procesado puede ser al agua o térmica, y la plancha puede estar lista para entrar en producción en menos de 50 minutos.
Zanders continúa el desarrollo de su exitosa gama de papel para envasado de alimentos: el Zanbarrier NGR mejorado ("resistente a la grasa natural") ofrece la barrera 100% natural contra el aceite y la grasa sin el uso de ningún químico y ahora con una densidad aún mayor. Consistente en nada más que fibra virgen pura, Zanbarrier NGR es 100% biodegradable y la elección perfecta para evitar cualquier material no natural en el envasado de alimentos. El grado respetuoso con el medio ambiente se produce en la PM3 de 6.6 m de ancho de Zanders, la máquina de papel más grande y eficiente para papeles de barrera en Europa.
La mayor densidad del Zanbarrier NGR mejorado abre nuevas posibilidades de aplicación. Es ideal para innumerables formas de embalaje flexible del sector de alimentación que requieren resistencia al aceite, a la grasa y a la humedad, por ejemplo comida rápida como doner kebab o patatas fritas, bolsas de panecillos, envoltorios para mantequilla, cajas de pizza y confitería o bolsas de galletas. "La excelente opacidad combinada con excelentes propiedades de impresión y conversión per-
miten cualquier tipo de procesamiento, desde micro flauta hasta laminación", dice Michael Berner, gerente de ventas de envases de alimentos en Zanders. El uso de fibras 100% vírgenes y la certificación ISEGA aseguran la idoneidad para el contacto directo con los alimentos.
Michael Berner ilustra el proceso de producción único de Zanbarrier NGR: “Las fibras de celulosa se someten a un proceso de molienda increíblemente intenso en varias etapas de refinación. Tratadas de esta
manera, las fibras forman una estructura de lámina reticulada fuerte y apretada, creando así una barrera completamente natural para el aceite y la grasa. Gracias a la calidad excepcional, Zanbarrier NGR desempeñará un papel similar en el envasado flexible de alimentos como Chromolux, por ejemplo, en el mercado del papel de etiquetas”.
El coste total de la producción de etiquetas está determinado por tres factores clave: calidad, coste y productividad. Estos no deben considerarse de forma aislada, lo que sin embargo ocurre debido a la complejidad en la práctica. Si bien existen ideas claras sobre la calidad y los costes alcanzables de una máquina de impresión de etiquetas antes de cualquier decisión de inversión, la productividad en consideración de la variabilidad del proceso a menudo recibe muy poca atención al tomar una decisión de compra. En el siguiente ejemplo se muestra cuán grande es la influencia de este criterio en los costes operativos totales.
En la planificación de inversiones, los segmentos de mercado en los que se utilizará la máquina se encuentran al comienzo de un análisis detallado. El análisis en este ejemplo muestra que el mercado y la estructura del cliente consisten esencialmente en clientes en los segmentos de cosméticos, vinos y licores, medicamentos (sin receta), así como pedidos en impresión de seguridad, p. timbres fiscales para el tabaco. Esto da como resultado los segmentos de mercado potenciales para los que está configurada la máquina. Estamos buscando un sistema de máquina que cumpla con los requisitos específicos de estos segmentos del mercado. También debe tenerse en cuenta que todos los segmentos de mercado mencionados se caracterizan por longitudes de tiradas pequeñas a medianas, así como por largas tiradas, es decir, una gran cantidad de trabajos con muchos sustratos y procesos de impresión diferentes.
Para cumplir con la amplia gama de requisitos identificados, se requiere un sistema de máquina libremente configurable y expandible con un alto grado de automatización. En el mercado, tales sistemas de máquinas son ofrecidos por varios fabricantes. Para ilustrar esto, dos de los tipos de máquinas más utilizados se utilizan como referencias en el mercado.
La máquina del fabricante A tiene un máx. ancho de impresión de 430 mm (17") con una velocidad de máquina especificada de máx. 160 m / min., la máquina del fabricante B tiene un ancho de impresión máximo de 410 mm (16") y un máx. velocidad de la máquina de 170 m / min.
Ambas máquinas se pueden configurar individualmente o en combinación con todas las unidades de impresión, como la impresión offset, flexográfica y rotativa, estampado en caliente e impresión en frío, para los requisitos de los segmentos de mercado mencionados anteriormente. Cada uno está equipado con un control de tensión de la banda, que también es adecuado para laminados de tubos de hasta 450 μm en el sector de la cosmética.
Ambas máquinas se pueden configurar adicionalmente con unidades de impresión de huecograbado y cumplen con los requisitos de calidad de impresión y facilidad de uso en una prueba de comparación. Tienen un alto grado de automatización para el ajuste dinámico de alimentación, el preajuste de la longitud y el registro cruzado y para los trabajos repetidos, los ajustes de la máqui-
na se pueden recuperar de la memoria principal además de tener también unidades de lavado automático.
En pocas palabras, desde un punto de vista técnico, hay equipos de máquinas comparables, pero las máquinas difieren en términos de costes de adquisición. El precio de la máquina B es aproximadamente un 20% más bajo que el precio de la máquina A, lo que en consecuencia influiría en una decisión de compra, teniendo en cuenta los criterios enumerados, claramente a favor de la máquina B.
Los tiempos de cambio de proceso tiene una influencia significativa en la eficiencia económica de un sistema de máquina en impresión.
Un cambio de proceso, es decir, cambiar una unidad de impresión a otra, requiere menos de 5 minutos para que la máquina esté "lista para imprimir".
¿Qué influencia tiene la variabilidad del proceso?
Los segmentos de mercado como los cosméticos y las etiquetas de vino requieren una gran cantidad de cambios de proceso por turno en la impresión de etiquetas. Para las etiquetas de vino, la regla son 4 cambios de proceso por turno, a veces incluso hasta 7 cambios de proceso. Por esta razón, los tiempos de cambio para un cambio de proceso están a la vanguardia de un análisis de rentabilidad. Con la máquina A, por ejemplo, los cambios de proceso pueden tener lugar mientras la máquina está en funcionamiento, es decir, las unidades de impresión que no son necesarias para el trabajo actual ya pueden prepararse para el trabajo de seguimiento.
Si, como en la estructura de orden dada, se requieren muchos cambios de proceso, es decir, se intercambian unidades de impresión de diferentes procesos de impresión, la suma de los tiempos de cambio de proceso tiene una influencia significativa en la eficiencia económica de un sistema de máquina en impresión de banda estrecha.
Los tiempos de cambio de proceso tiene una influencia significativa en la eficiencia económica de un sistema de máquina en impresión
Con respecto a los tiempos de cambio de proceso en sí mismos, que a menudo se subestiman en una decisión de inversión, las dos máquinas de referencia difieren significativamente. El tiempo de cambio para un cambio de proceso es de 5 minutos para la máquina A, sin separar la banda y con una configuración completamente automática utilizando un carro de cambio, mientras que es de 30 minutos para la máquina B. Con el número correspondiente de cambios de proceso, esta diferencia afecta claramente la rentabilidad de un sistema de máquina.
Utilizando una calculadora de coste
La variabilidad de los procesos es uno de los factores clave del costo total de la propiedad.
En este ejemplo, todas las unidades de impresión offset pueden reemplazarse por unidades de impresión flexográfica, unidades de serigrafía, unidades de troquelado o unidades de lámina caliente. También es posible el intercambio con unidades de fabricantes OEM.
Un mayor número de cambios de proceso por turno acorta el período de recuperación del precio adicional de la máquina. En el caso de cinco cambios de proceso, por ejemplo, el precio adicional en una operación de tres turnos se amortiza después de aprox. 1,5 años (basado en 20 días hábiles /mes a una tarifa por hora de la máquina de 183 EUR /h).
total de propiedad (TCO), que el fabricante de la máquina aplica para la comparación de costes, se puede determinar qué sistema de máquina con sus costes de adquisición específicos en la estructura de pedido determinada y el número promedio supuesto de 4 cambios de proceso por turno tiene la más alta eficiencia. Esto muestra que incluso un precio de compra más alto de una máquina se amortiza en un tiempo relativamente corto si el tiempo de cambio de proceso del sistema de la máquina es más corto.
Si, por ejemplo, el precio de compra de las máquinas difiere en 400,000 EUR, los costes de adquisición más altos se amortizan mediante ahorros en los cambios del proceso en la operación diaria en este ejemplo después de dos a un máximo de tres años de operación, dependiendo de si una máquina se opera dos o tres turnos. El requisito previo para lograr este período de amortización es la plena utilización de la imprenta.
Una ventaja adicional es que con la máquina A, la banda de material no tiene que separarse al cambiar el proceso, lo que significa un ahorro adicional de material. Con un promedio de 12 m de tela perdida por cambio de proceso,
4 cambios de proceso por turno dan como resultado un ahorro adicional de aprox. 7,000 EUR por año en operación de tres turnos. Estos ahorros de material por sí solos también reducen significativamente el período de amortización del costo adicional de la máquina A.
Cuanto más complejo es un producto de impresión, más frecuentemente se necesitan cambios en el proceso de producción, porque dependiendo de los requisitos del trabajo, una aplicación requiere el uso de las unidades de impresión en diferentes posiciones. Los cambios de proceso más comunes en el segmento de belleza son principalmente flexografía a serigrafía y viceversa, pero también una unidad de impresión offset a menudo tiene que ser reemplazada por una flexografía, serigrafía o una unidad de estampado en caliente. La serigrafía se utiliza, por ejemplo, para blanco opaco, letras finas o para depositar blanco. La impresión flexográfica representa la aplicación rentable de tintas y recubrimientos, así como la impresión de colores planos.
Un análisis más detallado revela que la máquina A y la máquina B solo se pueden comparar a primera vista. El factor decisivo en una inversión no es solo la inversión total y la calidad alcanzable, sino también el rendimiento general.
En este contexto, además de los aspectos cualitativos, la variabilidad del proceso del sistema de la máquina es esencial, especialmente con los cambios frecuentes del proceso. La razón es simple: los cambios rápidos de proceso y los tiempos de configuración tienen una influencia decisiva en los costos operativos totales.
A medida que las órdenes se hacen más pequeñas, esta influencia se vuelve cada vez más fuerte. Especialmente en el caso de una estructura de pedidos con muchos cambios, vale la pena invertir en un sistema de impresión de etiquetas altamente automatizado y flexible a pesar de los costes iniciales más altos. La máquina aparentemente más cara demuestra ser la solución más económica en estas condiciones generales.
El mercado de soluciones de etiquetado automático industrial alcanzará un volumen de negocio de 13 millones de euros en 2020 en nuestro país, lo que supone un incremento del 20% respecto a 2019, año en el que se vendieron unos 850 sistemas de este tipo, sumando un parque total superior a 6.000 equipos.
Según un análisis de Toshiba Tec en España, este crecimiento se debe al notable incremento de la demanda de estas soluciones registrado en el primer semestre de este año y que prevé se mantendrá en el segundo, por la necesidad de reducir el manipulado manual de productos, como medida de prevención sanitaria, y de aumentar la productividad y reducir los errores ante el auge del e-commerce.
De hecho, Toshiba ha registrado un crecimiento del 147% de la demanda de este tipo de soluciones durante el primer semestre del año, con respecto al mismo periodo del año anterior. Asimismo, la compañía lidera este segmento, con una cuota de mercado del 20% en el sector industrial, con su solución APLEX4.
La compañía señala además que la automatización del etiquetado reduce los errores un 98% y aumenta un 30% la productividad, al optimizar procesos, eliminar errores de inventario y reducir incidencias en los envíos al cliente final.
El APLEX4 es una solución flexible cuya implementación no exige una gran inversión y tiene uno de los mejores costes de propiedad (TCO) del mercado. La solución de Toshiba cuenta con un diseño que permite su adaptación a las líneas de producción existentes. Además, frente a la integración personalizada y costosa de otras soluciones, su instalación es muy sencilla gracias a su sistema Plug & Play («enchufar, conectar y usar»).
El módulo APLEX4 está equipado con impresoras de la serie B-EX4 con tecnología de emulación incorporada para trabajar con flujos de datos de otros fabricantes, permitiendo mejorar las etiquetas sin modificar el software instalado.
La solución puede imprimir y aplicar etiquetas de 25 x 25mm a 110 x 200mm desde cualquier ángulo de rotación requerido. Su alta productividad permite imprimir hasta 1.800 etiquetas a la hora de un tamaño 100 x
100 mm y dispone de una gran autonomía gracias al uso de cintas de impresión de hasta 800 metros.
Por último, la serie de impresoras B-EX4 dispone de la tecnología ecológica de Toshiba que permite el ahorro automático de cinta de impresión, utilizándola sólo en las zonas a imprimir, y reduce un 70% el consumo de energía en modo stand-by en comparación con anteriores generaciones.
El
negocio de 13 millones de euros en 2020, un 20% más que en 2019
HIGH SPEED FLEXO FOLDER GLUER
Colorscan Imaging Products Ltd. ha dado un importante paso adelante en su expansión dentro del mercado de las etiquetas tras invertir en una impresora inkjet UV single-pass Tau 330 RSC E y en una solución software de Durst, fabricante de tecnologías avanzadas de impresión y producción digital.
Tras instalarla a principios de agosto de este año, Keith Forster, propietario y director general de la empresa familiar Colorscan, opina: “Nuestro negocio se entra principalmente en el suministro de material impreso para la industria cervecera. Aunque obviamente el sector también se resintió durante el confinamiento, nuestra línea de negocio de impresión de etiquetas realmente se incrementó durante este período. Hemos comprado la máquina en el momento preciso. Sin duda vemos un gran margen de crecimiento en el campo de las etiquetas”.
“Antes de la pandemia provocada por el coronavirus, siempre estudiábamos la posibilidad de actualizar nuestras máquinas, porque la tecnología no para de avanzar. En este caso, llevamos a cabo un estudio en el que valoramos las opciones de siete proveedores, para lo que realizamos una cantidad sustancial de pruebas. La propuesta de Durst destacó rotundamente como la mejor impresora industrial, ofreciendo tanto una elevada productividad como una extraordinaria calidad de impresión (1200x1200 dpi de máxima resolución)”.
La impresión digital de etiquetas a precios asequibles ya es una realidad para Colorscan gracias a su inversión en la tecnología Durst Tau 330 RSC E
“No existe nada parecido en términos de calidad y fiabilidad. La Durst Tau 330 RSC E sustituye dos máquinas y aumenta de manera espectacular nuestra capacidad, funcionando significativa-
“No hay nada comparable en términos de calidad y confiabilidad”, dice Keith Forster (en la foto a la derecha) frente a la Tau 330 RSC E con el Gerente de Desarrollo Comercial de Durst, Peter Jones.
mente más rápido que las dos máquinas a las que reemplaza. Esto significa que nuestros costes operativos se han reducido sustancialmente, además de que este equipo permite también un considerable ahorro en el consumo de tinta por metro lineal. Por otro lado, es importante mantener el flujo de trabajo adecuado, y esa fue otra de las razones para elegir Durst”.
Desde sus instalaciones de casi 4.000 metros cuadrados en Burton-onTrent, Staffordshire (Reino Unido), Colorscan lleva más de 25 años fabricando y suministrando al mercado cervecero. Fabrica clips y fijaciones para tiradores, insignias y placas para barriles, y produce etiquetas informativas sobre alérgenos para envases de ali-
mentos y botellas de vino y cerveza. Sus especialidades dentro del segmento de las etiquetas son los recubrimientos metálicos, transparentes, brillantes, mates y en PET.
Peter Bray, Director General de Durst UK & Ireland, señala: “La impresión digital de etiquetas a precios asequibles ya es una realidad para Colorscan gracias a su inversión en la tecnología Durst Tau 330 RSC E, y se suma a las muchas otras empresas que ya disfrutan de un paquete integral que ofrece alta calidad, el mejor servicio posible y la consiguiente fiabilidad en producción, así como un importante ahorro en costes. Estamos entusiasmados de que esto les ayude a dar el gran salto en el mundo de las etiquetas”.
Tan solo dos años después de su aplaudido lanzamiento, Durst celebrará la instalación número 100 de su plataforma tecnológica Tau RSC, que ha cosechado un enorme éxito y ha demostrado su calidad en el mercado.
En las próximas semanas, un importante convertidor de etiquetas europeo instalará la unidad número 100 de la serie de impresoras de etiquetas inkjet UV single-pass, Durst Tau 330 RSC. Muy pronto, la máquina estará imprimiendo etiquetas de alta calidad, con unos niveles de productividad y un tiempo de funcionamiento inigualables.
La Tau 330 RSC suscitó un gran interés cuando Durst la presentó, por primera vez, en la Labelexpo 2017 en Bruselas, Bélgica. Tanto los visitantes, como los otros proveedores de soluciones de impresión, quedaron sorprendidos por lo que la tecnología RSC de Durst prometía en términos de calidad de impresión y rendimiento de productividad, con una resolución de 1200x1200 dpi y una velocidad de
impresión de 80 metros lineales a todo color.
Nueve meses después, y tras un exitoso test beta de esta nueva y revolucionaria tecnología de impresión, Durst comenzó a distribuir las primeras impresoras Tau 330 RSC. Desde entonces, un número creciente de convertidores de etiquetas de pequeño, mediano y gran tamaño optaron por la nueva plataforma, que ya se ha convertido en un referente en soluciones inkjet UV con su solución Durst Tau 330 RSC y el modelo ‘entry label’, Tau 330 RSC E, o con la nueva Tau RSCi.
Desde mediados de este año, Durst ha continuado su avance con la instalación de las primeras impresoras de etiquetas Tau RSCi 330 / 420 / 510, que conforman la ampliación más
reciente del catálogo de impresoras de la plataforma Tau RSC de Durst.
Helmuth Munter, director del departamento de etiquetas y envases flexibles de Durst, afirmó: “Ya desde su presentación hace dos años, la Tau 330 RSC y la Tau 330 RSC E han marcado un nuevo estándar en la impresión de etiquetas. Hoy, con 100 instalaciones en todo el mundo, nos sentimos honrados por la confianza que los usuarios satisfechos de la plataforma Tau RSC han depositado en Durst. Tenemos la seguridad, y así lo confirman los continuos comentarios positivos de los clientes, de que nuestra plataforma actualizada Tau RSC seguirá siendo todo un referente para el futuro de la impresión digital inkjet en la industria de las etiquetas y el embalaje”.
Xeikon anuncia el lanzamiento de su nueva unidad de adorno Fusion: Xeikon FEU. Esta última incorporación a su ya amplia cartera de equipos digitales para etiquetas, se basa en la ambición de la empresa de proporcionar y equipar a los impresores y convertidores de etiquetas con la cartera más completa de innovadores equipos digitales para el amplio alcance de la fabricación de impresión de etiquetas.
“No hay nada comparable en términos de calidad y confiabilidad”, dice Keith Forster (en la foto a la derecha) frente a la Tau 330 RSC E con el Gerente de
Xeikon FEU ofrece a los impresores y convertidores de etiquetas la máxima flexibilidad para satisfacer las demandas de los propietarios de marcas y diseñadores que se esfuerzan por lograr etiquetas de alta calidad, llamativas, únicas, entretenidas y creativas. Con capacidades completas de acabado y embellecimiento digital, la FEU de Xeikon se basa en la tecnología MGI y proporciona barniz UV puntual, barniz táctil, laminado, texturas 3D y hologramas en una amplia gama de sustratos, incluido transparente sobre transparente, BOPP común y caras de papel hasta estructura natural documentos. La Xeikon FEU estará disponible comercialmente en Europa y América del Norte a partir de octubre de 2020.
Filip Weymans, vicepresidente de marketing de Xeikon, dice: “En un mundo de consumismo en constante evolución, estamos viendo cambios significativos y continuos en los patrones de comportamiento. Los consumidores son más exigentes y los propietarios de marcas exigen más de sus diseñadores e impresores. En el envasado y el comer-
cio minorista, existe una creciente presión por la innovación creativa y niveles más altos de productividad. Con ese fin, Xeikon se ocupa ante todo de las necesidades de sus clientes. Seguimos adaptándonos a las tendencias actuales y con el lanzamiento de la Xeikon FEU estamos ofreciendo a nuestros clientes las máximas oportunidades. La integración del flujo de trabajo construida alrededor de nuestro Vectorizador X-800 proporcionará a nuestros clientes todo lo que necesitan para avanzar de manera efectiva hacia la fabricación total de impresión de etiquetas digitales”.
Utilizando la unidad de embellecimiento Fusion de Xeikon, los impresores de etiquetas con una cartera de clientes dedicados al vino, cerveza premium, comida gourmet, licores, etiquetas de salud y belleza podrán lograr pruebas fáciles y rápidas de nuevos diseños con tiempos de comercialización más rápidos. Sin necesidad de herramientas y con tiempos de preparación reducidos, esta solución económica ofrece niveles superiores de acabado de calidad en volúmenes más pequeños de etiquetas.
Con la tecnología de inyección de tinta, cualquier área de etiqueta definida puede recibir automáticamente barniz UV puntual con o sin efectos de textura 3D. De manera similar, para aplicaciones opacas, el área de las etiquetas digitales pueden recibir láminas controladas digitalmente con o sin efectos 3D con complejidad limitada en comparación con la analógica.
FEU de Xeikon es una solución independiente. Esto le permite embellecer materiales impresos procedentes de diferentes tecnologías. También es capaz de preimprimir láminas sobre sustratos, satisfaciendo así las muchas necesidades nuevas de los propietarios de marcas para los diseños de etiquetas actuales. Opcionalmente, la FEU de Xeikon se puede equipar con una unidad de troquelado semirrotacional para que entregue etiquetas totalmente adornadas y acabadas. Si bien el enfoque actual de Xeikon está en las aplicaciones de etiquetas, la nueva FEU tiene el potencial de abordar otras aplicaciones con el tiempo.
Weymans concluye: “El objetivo a lar-
go plazo de Xeikon es ofrecer a sus clientes la gama más amplia de productos que aborden la transformación digital de la impresión. Los socios industriales bien establecidos, como en este caso las tecnologías digitales MGI, a menudo cuentan con productos probados que se integran muy bien en este proceso de digitalización. Con esta últi-
ma incorporación a nuestra cartera, uno de los beneficios más importantes para nuestros clientes es la disponibilidad de tecnologías digitales integradas, todas proporcionadas y respaldadas por el proveedor, que garantizan la máxima productividad en todo el proceso de fabricación. La provisión combinada de impresión digital y embellecimiento digi-
tal permitirá a los impresores de etiquetas ejecutar trabajos de gama alta, de tamaño corto a mediano a costos sustancialmente reducidos con un tiempo de comercialización más corto. Xeikon continúa liderando el camino como asesor y proveedor de confianza de sistemas digitales innovadores para la comunidad mundial de etiquetas".
La nueva Prati Saturn Digi se caracteriza por ser un equipo polivalente para acabados de flexografía y digital, permite flexibilizar la producción poniendo más recursos dónde se necesita en cada momento y solucionando los retos de los convertings con más eficacia.
Este equipo de la marca Prati Company permite reducir fácilmente los tiempos de entrega y completar los pedidos mucho más rápido. Se trata de un equipo flexible, con el que se podrá aprovechar al máximo todo el potencial del equipo para laminar, barnizar, troquelar, inspeccionar, cortar y rebobinar etiquetas autoadhesivas y embalaje flexible. Además, la Prati Saturn Digi cuenta con una gran novedad, ya que incorpora troquel semi-rotativo y troquel rotativo al mismo tiempo además de registro en el troquel y un doble eje. Etibérica , cuenta con sus instalaciones en Almería y es especialista en la producción y comercialización de etiquetas para el sector agroalimentario y vinícola. Rufino y Jose Manuel, dueños de Etiberica, nos cuenta su experiencia desde la instalación en marzo de la nueva Saturn Digi.
¿Qué necesidades de producción os llevaron a elegir una Prati Saturn?
Al ser una empresa de reciente creación buscábamos una máquina versátil, con capacidad tanto para la producción de etiqueta anónima como de troquelado de etiqueta impresa en digital. Para esto último era imprescindible un troquel semi-rotativo y con Prati encontramos las solución más satisfactoria, ya que podemos producir etiqueta anónima de forma muy productiva y también tenemos la posibilidad de troquelar etiqueta impresa en digital con una exactitud total.
¿Por qué Etibérica ha confiado en la marca Prati para ampliar su línea de producción?
Cuando tomamos la decisión de invertir en maquinaria para la producción de etiquetas aprovechamos que se celebraba la Labelexpo para poder ver la más amplia gama de maquinaria. Tras analizar detenidamente todo lo visto en
la feria llegamos a la conclusión de que con Prati obtendríamos la seguridad de tener una máquina robusta, fiable y con un gran servicio técnico, lo que nos garantizaría poder contar con el mínimo de paradas técnicas y poder obtener así el máximo rendimiento y una productividad lo más alta posible.
¿Unos meses después de la instalación, cumple el equipo con vuestras expectativas?
Tras el breve período de adaptación que toda maquinaria nueva conlleva, la productividad que estamos obteniendo sobrepasa con creces la que nos habíamos imaginado, por lo que no sólo cumple sino que sobrepasa nuestras expectativas. La precisión en el troquelado es máxima y la velocidad inmejorable (llegamos a troquelar a 70
m/min en semi-rotativo). Además, es muy versátil al poder cambiar de semirotativo a rotativo para las producciones que lo requieren.
¿Consideráis que la experiencia con Esagraf ha sido buena?
La experiencia con Esagraf ha sido muy satisfactoria. La fecha prevista para la instalación coincidió con el período de estado de alarma decretado a causa del Covid-19, pero el equipo de Esagraf hizo todo lo posible para llevar a cabo la instalación a pesar de las restricciones de movilidad impuestas por el gobierno.
En Esagraf estan muy agradecidos por el esfuerzo realizado, en un momento tan delicado para todas las empresas debido al Covid-19.
Screen ha convertido la necesidad en una virtud, poniendo a disposición su nueva impresora de etiquetas Truepress Jet L350UV SAI para realizar demostraciones a distancia desde su Centro de Tecnología en Amstelveen.
La nueva tecnología de impresión de etiquetas de SAI amplía significativamente las capacidades de la impresión digital para aplicaciones de etiquetas y packaging de banda estrecha. Y los clientes actuales y potenciales pueden ahora ver esto "de primera mano" con demostraciones remotas pero completas de la nueva máquina.
"Son capaces de dejar que imprima etiquetas según sus especificaciones, ver la máquina funcionar desde diferentes ángulos y obtener explicaciones detalladas de su operador. Luego pueden inspeccionar el resultado de la impresión en imágenes de primer plano en sus computadoras en casa o en la oficina. SCREEN envía copias impresas de las pruebas a través de un mensajero, lo que permite una inspección 'real' de las pruebas en 24 horas", explica Carlo Sammarco, Director de Desarrollo de Negocios.
Es probable que las demostraciones a distancia sigan siendo pertinentes y mantengan su demanda después de la pandemia del Covid-19
"Las pruebas remotas han despegado desde que instalamos la L350UV SAI hace poco tiempo", dice Sammarco. "Es una solución a las restricciones de viaje debido a Covid-19. También es un tremendo ahorro de
costes y tiempo para nuestros clientes actuales y potenciales, que están repartidos por toda Europa, el Medio Oriente y África". Pensamos que estas sofisticadas demostraciones remotas muy probablemente continuarán siendo relevantes después de la pandemia del Covid-19."
SCREEN ha invertido significativamente en el equipo necesario para dar vida a estas demostraciones en línea, y el equipo de aplicaciones ha perfeccionado sus habilidades de presentación para hacerlas atractivas y convincentes en un entorno virtual.
Por supuesto, el sitio de Amstelveen también está abierto para aquellos que aún pueden viajar para hacer demostraciones en persona.
El Truepress Jet L350UV SAI se basa en una nueva tecnología que proporciona una gama mejorada de precisión de color y vitalidad. Además de las tintas CMYK, se pueden pedir dos colores más - naranja y un azul único - que pueden solicitarse a fábrica o actualizar en casa del cliente a posteriori.
Domino ha puesto en marcha un nuevo Programa de Leasing. De esta manera, los propietarios de impresoras de etiquetas, independientemente de su envergadura, pueden incorporar con una facilidad sin precedentes la impresora inkjet UV digital líder en la producción de etiquetas a su gama de tecnologías de impresión.
La impresión digital adquiere cada vez mayor importancia. Actualmente, los propietarios de impresoras de etiquetas comprenden más que nunca el valor de contar con sistemas digitales en su arsenal. Dado que los propietarios de las marcas están aumentando sus SKUs, versiones y personalización, y además exigen plazos de entrega más cortos, una reducción del inventario y una calidad de impresión superior para diferenciar sus productos, los propietarios de impresoras de etiquetas están percatándose de que los equipos digitales no son deseables, sino que son necesarios para que sus empresas puedan ser competitivas, retener a los clientes, acceder a nuevos mercados y aumentar la actividad comercial.
Chris Gleis, presidente de Factor Forms & Labels Niagara, Ltd., comenta: «La impresora N610i de Domino nos va a permitir seguir creciendo con porcentajes de dos cifras al año. Esta tecnología es la mejor de su clase y nos permitirá imprimir con la mejor calidad posible».
El programa de leasing de Domino permite a los clientes pagar su nueva impresora de etiquetas inkjet UV digital N610i de Domino durante un período de tiempo, normalmente entre tres y cinco años, por medio de mensualidades fijas.
«El tipo de leasing que ofrecemos es el llamado leasing de capital o leasing
financiero; es, en esencia, una compra de capital cuyos pagos se efectúan a lo largo de un período de tiempo determinado. Al final de este período, el cliente pasa a ser el propietario de la impresora», declara Mark Herrtage, director financiero de Domino Digital Printing Solutions.
Sin grandes desembolsos iniciales, es más fácil
«El programa de leasing es una forma sencilla para que nuestros clientes adopten esta tecnología. Y lo mejor es que para empezar a trabajar no es necesario un gran desembolso inicial», afirma Barry Wendell, gerente de cuentas de Domino Digital Printing Solutions en Norteamérica.
Patrick Wafer y Ryder Fyrwald, pro-
pietarios y codirectores generales de Alros Label explican: «Una de las grandes ventajas del programa de financiación de Domino es que podemos invertir en otras áreas… Ventas, marketing, contratar nuevos empleados, esas son las formas de hacer que la empresa crezca, y la financiación nos permite hacerlo. Nosotros no tenemos el dinero en efectivo necesario para comprar una de estas máquinas. Así que poderlas financiar e irlas pagando con el tiempo, con unos tipos de interés muy atractivos, hizo que la decisión fuese muy fácil».
Mark añade lo siguiente: «Nuestros programas de leasing están destinados a todo tipo de empresas, tanto las pequeñas que puedan necesitar algo de ayuda financiera nuestra, como las grandes que tan solo quieren proteger su liquidez para invertir en otras cosas. Les ayudamos a hacerlo».
Los propietarios de impresoras de etiquetas verán que el programa de leasing interno de Domino ofrece tipos de interés competitivos que, por lo general, son inferiores a los que ofrecen los bancos o terceras empresas de alquiler. Además, tratarás directamente con Domino, y no necesitas avales personales. Christopher Stoehr, presidente de Southwest Label & Printing, señala: «Se pusieron en contacto conmigo, trajeron los contratos, lo revisamos todo, y enseguida quedo todo hecho. Fue perfecto. Tratarás directamente con Domino. Sin bancos de por medio. La relación con Domino, no solo en lo que se refiere al equipo, sino también el
Una de las cosas buenas del programa de leasing de Domino es que está respaldado por nuestros programas de recompra. Si lanzamos un nuevo producto y deseas adquirirlo, nos quedaremos con la antigua impresora y volveremos a generar un nuevo alquiler. Sí, tenemos un gran programa de recompra.
alquiler y la financiación, van de la mano y, en mi opinión, así unido funciona mejor. Todo lo gestiona una misma empresa. Creo que es la mejor elección que podía haber hecho».
El leasing incluso puede estructurarse con pagos aplazados que permitan al cliente «poner en marcha» su actividad digital… e ir conformando su cartera de encargos asociados a la impresora Domino… antes de realizar el pago de la primera mensualidad. «Incluso tenemos un programa para el leasing de la impresora sin pagar los primeros seis meses, mientras se pone en marcha la producción. Los clientes tan solo pagan las tintas. Y pasados los seis meses, pueden empezar a pagar la impresora con los márgenes que obtengan de las ventas generadas del uso de la Domino N610i», declara Mark. Emily Kroll, gestor de cuentas de Domino, apunta lo siguiente: «Aceleramos la puesta en marcha de la producción para que puedas ganar dinero cuanto antes».
Con los programas digitales incluidos en el plan, tendrás «todo tu negocio en un solo sitio»
Emily afirma: «Siempre me preguntan: "¿Por qué comprar una impresora digital?". Con el programa de leasing de Domino, la pregunta sería: "¿Qué razón hay para no comprarla?". Incluye mantenimiento, reparaciones, formación y cabezales. Para los clientes, esta cuota mensual fija es perfecta. No hay
incertidumbres». «Con el programa de leasing de Domino las cuotas mensuales no solo cubren las amortizaciones de capital de la impresora, sino también los contratos de mantenimiento completo. Y podemos incluir programas de soluciones digitales.
Por unos pocos dólares, libras o euros más, puedes incluir mucho más en tu plan», apunta Mark.
A lo que Barry añade: «Ofrecemos todos los recursos para formar a tus operarios. Si quieres formar al personal de ventas, nosotros podemos formarles; enseñaremos a la dirección a gestionar los activos digitales y al personal de atención al cliente a hacer estimaciones de los equipos digitales. Es básicamente todo tu negocio en un solo sitio».
Programa de recompra y garantía de futuro, toda una revolución
«Una de las cosas buenas del programa de leasing de Domino es que está respaldado por nuestros programas de recompra. Si lanzamos un nuevo producto y deseas adquirirlo, nos quedaremos con la antigua impresora y volveremos a generar un nuevo alquiler. Sí, tenemos un gran programa de recompra», dice Mark. Emily pone énfasis en el principal beneficio de este programa: «En mi opinión, la principal ventaja del programa de leasing de Domino es que permite a tu empresa crecer utilizando los avances de la tecnología digital. Lo digital es el futuro, y la N610i de Domino y el programa de leasing que hemos preparado son revolucionarios».
El Fogra Research Institute for Media Technologies certifica que la serie LabelStream 4000 de Canon es la primera impresora digital con gama de 6 colores (blanco + CMYK + naranja), de acuerdo con las especificaciones de PSD PrintCheck. Con este reconocimiento, se ratifica la capacidad del equipo para lograr una consistencia del color y tirada óptimos, así como para garantizar el control de la uniformidad visual y nitidez de los detalles.
los artefactos desde una inspección visual. . La evaluación de la gama de colores de LabelStream supera, por lo tanto, la de muchas impresoras de etiquetas digitales de 7 colores disponibles actualmente en el mercado.
Acerca del ProcessStandard
Digital (PSD) de Fogra
La serie LabelStream 4000 utiliza los robustos y acreditados cabezales industriales de inyección de tinta UV, Xaar 2001+ UV, que ofrecen una alta carga de pigmentos y una mayor capacidad de deposición de la tinta para aumentar el abanico de colores. Asimismo, LabelStream posee una cobertura de la gama de tonos del 96 %, con un valor Delta E 2000 inferior a 2. En definitiva, LabelStream ofrece etiquetas de alta calidad, colores de marca exactos y una producción
consistente en un stock de etiquetas estándar.
La evaluación reveló que la gama de colores, la homogeneidad y la consistencia de LabelStream permiten lograr unos resultados de impresión de nivel A (la puntuación más alta) según el ProcessStandard Digital (PSD) PrintCheck del Fogra (basado en la norma ISO/TS 153112). El PSD PrintCheck certifica la fidelidad del color, la consistencia del color y uniformidad, la resolución, y
AntiTac es un nuevo recubrimiento especial para los rodillos de máquinas de etiquetado, cuya principal característica es su gran capacidad antiadherente.
Su utilización está cada vez más extendida entre los impresores y algunos fabricantes de maquinaria de etiquetado ya equipan sus máquinas de origen con rodillos AntiTac de Westland.
El AntiTac ha sido desarrollado con la tecnología de microestructura de
Westland. Se consigue una superficie exenta de poros, como la de una hoja de loto, reduciendo la parte en la que el material adhesivo pueda quedar pegado. Esto facilita la impresión de las etiquetas y la limpieza del rodillo. Además es muy resistente a los solventes y por tanto al inflado.
Fogra ofrece a todas las empresas, sean miembros o no, la oportunidad de obtener el certificado de acuerdo con el ProcessStandard Digital Printing (PSD), basado en la norma ISO/TS 15311. Con este certificado, las empresas de impresión y medios de comunicación garantizan la calidad y la capacidad de producción sin problemas. Esta garantía de calidad que otorga el PSD comprende la evaluación del resultado final de impresión, es decir, «lo que el cliente obtiene». Son el objeto de la familia de normas ISO/TS 15311, que define los requisitos para la impresión de producción digital en la norma ISO/ TS 15311-2, que actualmente se basan en tres niveles de calidad diferentes (tipos de calidad A, B y C).
La serie LabelStream 4000 está disponible para demostraciones virtuales y puede verse en el Customer Experience Center en Poing, Alemania.
Saico es una fábrica de cajas que, convertida en una realidad histórica de Umbría en el sector de la producción de embalajes industriales de cartón ondulado y con el paso del tiempo, ha crecido en tamaño y participación en el mercado gracias a inversiones continuas y prudentes. El cambio del sistema informático de gestión y la llegada de las soluciones de software de RTS fue el último paso decisivo hacia una producción inteligente y 4.0.
El cambio del ERP de gestión, que es el corazón de una empresa en crecimiento en términos de tamaño, volúmenes de producción y facturación, nunca como en este caso había sido tan decisivo para enfrentar un período complicado como este que estamos experimentando debido a la emergencia del Covid-19. Aunque estamos en Umbría, una región afortunadamente apenas afectada por el virus, las consecuencias de la emergencia también han sido sufridas por empresas como Scatolificio Saico. La oportunidad fue crucial para dejar al personal adminis-
trativo y comercial en Smart Working que, gracias a la transición al nuevo sistema de administración RTSv8, permitió a la compañía administrar las actividades sin ningún problema en particular.
Pero vamos en orden, hemos acudido virtualmente a Città di Castello, en la provincia de Perugia, para escuchar, de manos de Francesca Polveroni, hija del fundador y propietario de la empresa, los detalles de esta última inversión que, de hecho, decreta la entrada de Saico al mundo de los grandes del cartón ondulado.
El software de gestión RTS, del sueño a la realidad
«La compañía fue fundada por mi padre en 1971, con 5 colaboradores. Servimos principalmente a las fábricas de muebles en el área, grandes distribuidoras, ropa, y somos socios de referencia para las industrias cartotécnicas de la zona. Estamos equipados para cumplir con cualquier tipo de requisito de embalaje de cartón ondulado, desde tiradas pequeñas hasta las más grandes. Estando en la industria por más de 30 años, conozco RTS y sus soluciones
Instalciones de Saico en Città di Castello, en la provincia de Perugia (Italia).de software que siempre he considerado como un objetivo a alcanzar. A lo largo de los años he tenido la oportunidad de trabajar con sistemas de otras empresas de software competidoras, sin embargo, siempre he considerado a RTS como el mejor para el sector del cartón ondulado y un día soñé con tenerlo también en mi empresa, confiando en que habría sellado un camino de crecimiento comercial que hoy podemos decir que hemos logrado», comienza Francesca Polveroni, subrayando también que hoy, para una empresa que tiene 40 empleados, con diferentes líneas de producción, es absolutamente necesario tener un software de gestión capaz de soportar la fábrica de cajas en cada departamento. Scatolificio Saico es un negocio familiar, Francesca cuenta con el apoyo de su esposo y su hijo Luca, quien junto con Maichol Grilli, ha dado el impulso decisivo para enfrentar el paso hacia una gestión cada vez más inteligente y orientada a 4.0.
Scatolificio Saico opera en una sede de aproximadamente 7.500 m2, y gracias a las continuas inversiones en tecnología, hoy cuenta con un parque de máquinas que consiste en una casemaker de 4 colores EMBA instalada hace unos cuatro años y gracias a la cual se estableció un doble turno de trabajo, a la que se suman otras 4 casemakers completas con sistema de movimiento, un plotter de corte digital y una troquladora automática. La próxima instalación es una encoladorade 4 ángulos que fue confirmada por la Sra. Polveroni.
La compañía también puede contar con un sistema de logística automatizado con lanzadera 4.0 para llevar los palets al almacén, listos para entregas garantizadas por los 8 camiones de transporte propios que permiten a Scatolificio Saico ser extremadamente flexible en la entrega a los clientes.
Cara a cara con Francesca Polveroni, propietaria de Scatolificio Saico
Su relación con RTS acaba de comenzar, ¿puede decirnos cuándo y por qué confió en RTS como socio para la gestión del software de sus procesos comerciales?
«RTS siempre ha sido un punto de
Todas nuestras máquinas están conectadas al nuevo sistema de gestión, lo que nos permite tener bajo control en cualquier momento todos los eventos de producción
referencia para mí y he seguido, incluso como no cliente, la evolución de sus productos. Para nosotros era solo cuestión de esperar el momento adecuado para dar el gran paso, una inversión que sin duda es importante, pero en solo unos meses de operación, ya nos está dando resultados increíbles.
Ahora todo está más ordenado e incluso en producción, nuestros colaboradores han aceptado este cambio con gran entusiasmo, sobre todo porque han podido apreciar las ventajas también para su trabajo. Desde la entrada de los productos en el almacén, la trazabilidad de los productos a lo largo de las diversas etapas del proceso, hasta la facturación final, ahora todo está bajo control y automatizado. Los informes que este software puede procesar, la cartera de pedidos, los datos disponibles y fácilmente comprensibles, son herramientas indispensables para la gestión de una fábrica de cajas moderna equipada con múltiples líneas de producción.
Aunque la fase de implementación de los módulos aún no está terminada, esta-
mos muy satisfechos con RTS y esperamos poder explotar plenamente su potencial para fin de año. Ahora el trabajo ya se ha aligerado, somos más puntuales con las entregas. También estamos en red con los productores de cartón ondulado del que usamos y que también usan el sistema RTS, aprovechamos al máximo la sinergia. Ya estábamos convencidos de RTS antes de la compra y desde las primeras reuniones nos dimos cuenta de los beneficios de la inversión».
¿Cuáles son las características que más aprecias en las aplicaciones RTS?
«El análisis de costes fue uno de los primeros elementos que nos afectó favorablemente. Todas nuestras máquinas están conectadas al nuevo sistema de gestión, lo que nos permite tener bajo control en cualquier momento todos los eventos de producción. Hemos eliminado todo el papel inútil de nuestros escritorios y hemos conseguido una comunicación eficiente entre nosotros y hacia los clientes y proveedores. Además, en este período de confiamiento, gracias al nuevo sistema de gestión, algunos puestos de oficina pudieron trabajar desde casa, sin ningún problema para acceder a los datos esenciales de la empresa para el desempeño de su trabajo. Hoy, gracias al conocimiento preciso de todos los costes comerciales y de producción, hemos podido establecer una especie de sistema gratificante para nuestros colaboradores, a quienes se les anima a hacerlo cada vez mejor».
Instalar e iniciar un nuevo sistema tan estratégico para la empresa habrá sido un desafío. ¿Le gustaría decirnos cómo lo manejó y cómo RTS lo apoyó y lo siguió apoyando?
«El trabajo más exigente fue transferir datos del sistema antiguo al nuevo, con algunas dificultades en los meses en que utilizamos los sistemas simultánemente. Después de este período, desde el 1 de diciembre de 2019 comenzamos con el nuevo sistema de gestión sin ningún problema en particular. El apoyo de RTS ha sido preciso y puntual desde los primeros momentos y hemos encontrado en Marco Trastu un consultor muy competente, capaz de adaptarse a nuestra realidad empre-
sarial y guiarnos en esta transición. Incluso mi hijo y Maichol, que han seguido todo el proceso de instalación e inicio del sistema, están entusiasmados con las nuevas posibilidades que RTS nos ofrece».
¿Qué otros beneficios pretendes alcanzar a plena capacidad?
«El siguiente paso del proyecto será instalar Easystock para la gestión automática del producto terminado y los almacenes de materias primas. De acuerdo con la metodología RTS, este paso se implementará una vez que todos los datos necesarios para explotar plenamente su potencial estén presentes».
En 2021, Scatolificio Saico celebrará 50 años de actividad, y la esperanza de Francesca y su familia es poder cele-
brar este importante hito con una agradable fiesta junto con los colaboradores, clientes y proveedores una vez que hayan salido de la etapa de emergencia.
BOX: El nuevo sistema de gestión para soportar la red de ventas
Riccardo Maraldi representante comercial para Romagna celebra este año 10 años de actividades en Scatolificio Saico y el propietario de la compañía le agradece la valiosa colaboración mostrada durante todos estos años. A partir de ahora también para Maraldi, con la llegada del software RTS será más fácil gestionar clientes, gracias a la cartera de pedidos que recibe diariamente, con el control diario de los envíos y todas las alertas que forman parte de RTS.
Cartonajes Santorromán, uno de los principales proveedores de envases y embalajes de cartón ondulado en España, ha anunciado la adquisición de la prensa digital HP PageWide C500, que permitirá ofrecer la primera solución digital de cartón ondulado a escala industrial con tintas base agua.
Como una de las principales empresas en el mercado de los embalajes para vino, bebidas y productos agrícolas, la seguridad alimentaria es un factor clave en la estrategia de embalaje de Santorromán. La adquisición de la nueva Prensa Digital tiene como objetivo proporcionar una solución de embalaje segura para los alimentos y productos sensibles para las marcas, así como poder afrontar campañas de embalaje con tiempo de respuesta rápidos. Santorromán también ofrece soluciones avanzadas de Displays y de Punto de Venta.
"Como líder en innovación de soluciones de embalaje, estamos invirtiendo para trasladar a nuestros clientes los beneficios y las ventajas que ofrece la impresión digital con calidad offset. En particular, las tintas base agua de la HP C500 nos permitirán producir embalajes para nuestros clientes que sean seguros para los consumidores", ha declarado Leopoldo Santorromán, consejero delegado de Cartonajes Santorromán. “Además de esta enorme ventaja, esta nueva prensa de producción nos permitirá reducir el tiempo de entrega y las cantidades mínimas de
pedido para apoyar una campaña de cualquier tamaño, ayudando así a optimizar la cadena de suministro de cartón ondulado de nuestros clientes”.
Santorromán tiene previsto iniciar la instalación de la HP PageWide C500 a principios de 2021 en su sede de fabricación ubicada en Calahorra, La Rioja, donde suministra embalajes de cartón ondulado a todo el mercado ibérico. La incorporación de la HP PageWide C500 a escala industrial se basa en la experiencia digital de la empresa, que ya funciona con una HP Scitex Corjet desde 2001.
“El poder de la impresión digital de calidad offset con tintas base agua en el mercado de los embalajes de cartón ondulado en la Península Ibérica es ahora una realidad, gracias a un líder innovador como Cartonajes Santorromán", ha señalado Mark Rowland, director de ventas de HP PWI Corrugated para la región EMEA.
La revolucionaria tecnología HP
PageWide C500
La PageWide C500 emplea la tecnología patentada de inyección de
“Thermal Inkjet” de HP, diseñada para obtener una alta calidad de impresión en entornos de producción exigentes, imprimiendo a 75 metros lineales/min en una resolución de 1200 dpi con un millón de “nozzles”. La tecnología exclusiva Corrugated Grip de sujeción de cartón ondulado de la C500 ofrece una manipulación precisa de los cartones de calidad industrial para una producción sin problemas, mientras que la tecnología Virtual Belt ofrece un movimiento preciso de los soportes.
La prensa HP PageWide C500 ofrece textos y códigos de barras nítidos, tran-
siciones de tono suaves y colores vivos. Las tintas base agua de HP son inodoras y no contienen sustancias químicas que reaccionan a los rayos UV, lo que permite una amplia gama de aplicaciones de embalaje, incluidos los embalajes primarios y secundarios para usos sensibles como los alimentos y el cuidado personal, sin necesidad de barreras adicionales. Las tintas base agua de HP pueden cumplir con los estrictos requisitos de seguridad alimentaria como la guía de Nestlé, la Ordenanza Suiza, EuPIA y la norma 21 CFR de la FDA del USA.
Signode fabrica una amplia gama de productos específicamente diseñados para ser utilizados en la industria del cartón ondulado desde flejadoras-escuadradoras y mesas de expulsión, hasta flejadoras automáticas con prensa para palets y máquinas automáticas de aro para film estirable. Todos los equipos de Signode están diseñados para trabajar independientes, así como para integrarse en líneas de otros fabricantes de equipos utilizados en la industria del sector, ayudando a proporcionar el máximo tiempo de actividad, rendimiento y eficiencia. Las máquinas de Signode están respaldadas por nuestra experiencia, resultado de años de dedicación en la industria del cartón ondulado, lo que nos permite comprender sus problemas y brindarle la mejor solución posible.
El embalaje diseñado y fabricado por DS Smith Tecnicarton para el transporte de líquidos a granel, Tecnitank®, está validado por el 3H ISTA para el transporte de graneles, lo que garantiza la calidad del embalaje y su seguridad durante toda la cadena alimentaria.
El protocolo ISTA 3H asegura que, tanto el producto como su proceso de fabricación, se han desarrollado cumpliendo los más altos estándares de calidad. Para conseguir esta validación, el producto ha sido sometido a rigurosos ensayos y pruebas que determinan su efectividad para transportar y albergar grandes cargas; su resistencia ante fuertes movimientos o condiciones extremas, así como que dicho embalaje garantiza la inocuidad de los alimentos durante toda la cadena de suministro.
La compañía dispone de un sistema propio de calidad que permite certificar y garantizar la seguridad de sus embalajes durante toda la cadena alimentaria
La empresa DS Smith Tecnicarton dispone de un sistema propio de calidad que permite certificar y garantizar la seguridad de sus embalajes, con el objetivo de aumentar la eficiencia y reducir los costes, sin mermar la calidad; consiguiendo mejorar, así, la satisfacción de los clientes.
Como explica el director del área de Calidad de DS Smith Tecnicarton, Jorge García, “es imprescindible contar con unos protocolos de actuación muy claros para poder garantizar la seguridad a través de toda la cadena alimentaria. El embalaje es uno de los componentes que intervienen en ésta y, por este motivo, es necesario que cumpla todos los requisitos en tema de seguri-
El Tecnitank® es un embalaje de cartón ondulado que permite transportar hasta 1.000 litros de líquidos y que resulta óptimo para el transporte marítimo.
dad alimentaria y disponga de unos sistemas de control eficaces para detectar posibles riesgos a tiempo, antes de que entrañen un peligro para la salud”.
La certificación oficial para el desarrollo y comercialización de nuevos productos es una necesidad para las empresas y, en este sentido, la validación del Tecnitank® ofrece la seguridad al cliente de que sus productos contarán con el mejor embalaje y que las mercancías llegarán a su destino en óptimas condiciones.
El Tecnitank® es un embalaje de cartón ondulado que permite transpor-
tar hasta 1.000 litros de líquidos y que resulta óptimo para el transporte marítimo gracias a la resistencia del material utilizado.
Para los operarios de cargas, se trata de un embalaje fácil de usar gracias a su punto de descarga efectivo que permite un vaciado fácil y rápido y, desde el punto de vista medioambiental, evita el riesgo de contaminación, ya que dispone de una bolsa isotérmica que no necesita limpieza ni desinfección.
Además, otra de las ventajas de las que dispone Tecnitank® es su capacidad para aguantar el apilamiento en dos alturas durante el tránsito y hasta tres alturas en almacenamiento con contenido. Tiene un valor de compresión superior a 8.000 kilogramos y está diseñado para evitar abultamientos.
Desde hace más de 60 años Topazzini ha sido una referencia en el suministro de embalaje de cartón ondulado en el noreste italiano para numerosos sectores entre los que destacan mobiliario, alimentos y bebidas y metal-mecánico.
La sede en Villanova di San Daniele (Udine), con sus 48 mil metros cuadrados de superficie, cuenta ahora con unos 150 empleados y con una facturación que alcanza los 50 millones de euros.
«Para la gestión de nuestros procesos comerciales, a principios de la década del 2000, decidimos confiar en las soluciones de software de RTS, una empresa líder y con un profundo conocimiento del negocio y los problemas relacionados con nuestro sector específico.
RTS demuestra conocer muy bien todo lo que gira en torno a la producción, la ficha técnica y los problemas relacionados con la Industria 4.0. RTS tiene una sólida historia detrás, representa el presente y tiene en su cajón proyectos interesantes para el futuro. Estamos muy satisfechos con esta asociación y reconfirmamos la elección realizada».
Marco Dittaro, Resp. IT Toppazzini SpaSaica Paper, la división de negocio del Grupo Saica que fabrica papel reciclado para cartón ondulado, amplía los gramajes del producto Nature Kraft desde 115 g/m2 a 245 g/m2
Nature Kraft, un papel 100% reciclado, supone una alternativa a los kraftliners tradicionales por sus altas prestaciones físico-mecánicas y un aspecto similar al de la fibra virgen. Esta ampliación supone una apuesta por aportar soluciones sostenibles e innovadoras que satisfagan la creciente demanda de productos respetuosos con el medio ambiente al mismo tiempo que aportan una alta calidad de impresión.
La ampliación de gramajes es el resultado de un laborioso trabajo de innovación tecnológica para aportar nuevas soluciones a un mercado en continuo cambio, atendiendo a la necesidad de impulsar envases sostenibles y de calidad que ayuden a avanzar en los objetivos de la economía circular.
Estos papeles responden a los requisitos medioambientales de los clientes finales, ayudando a reforzar su imagen al mismo tiempo que se avanza hacia un desarrollo sostenible y respetuoso. La gama Nature Kraft se caracteriza por:
- Buen rendimiento productivo en las máquinas de cartón ondulado.
- Apto para contacto en seco con alimentos.
- Papel certificado FSC®.
- Calidad de impresión óptima, permitiendo todo tipo de acabado y personalización del embalaje.
Los nuevos gramajes son aptos para aplicaciones más complejas, pudiendo ser destinados a sectores de la agricultura. Por otra parte, el
papel de 115 g/m2, muy utilizado en el sector alimentario y de la distribución, permite una mayor optimización de los recursos, dado que consigue aligerar sustancialmente el peso del embalaje proporcionando igual o mejor rendimiento que otros papeles de gramajes superiores.
En su planta de producción de Mannheim, DS Smith garantiza la calidad de la impresión con el sistema de inspección al 100% en línea CartonSTAR de ISRA VISION, un proveedor líder a nivel mundial en el área de los sistemas de inspección de superficies. El sistema distingue de manera fiable y segura entre los defectos técnicos de la impresión relevantes para la calidad y las estructuras no homogéneas de la superficie del cartón ondulado. Además, el control continuo de la calidad y del proceso de obtención de la imagen impresa reduce permanentemente los costes de producción y garantiza un uso sostenible de los recursos.
El cartón ondulado impreso adquiere cada vez más importancia como material de embalaje. Esto se debe en gran medida al aumento creciente de la venta online que hace uso de envases de cartón ondulado, frente a los cuales apenas existen otras alternativas. El rapidísimo crecimiento del sector está estrechamente ligado a este
fiable material de embalaje.
DS Smith es uno de los proveedores líderes mundiales de envases de cartón ondulado. La empresa, con sede central en Londres, se dedica al desarrollo y a la fabricación de soluciones de embalaje sostenibles en 37 países. En Alemania y Suiza, la empresa cuenta con más de 2.900 trabaja-
dores en un total de 21 ubicaciones. En su planta de producción de Mannheim, DS Smith produce diversos tipos de cajas y bandejas para alimentos, productos tecnológicos y artículos de higiene, los cuales se imprimen en la línea de producción Mitsubishi EVOL100 recién instalada mediante la técnica de flexografía.
La empresa solicitó un sistema de monitorización de la imagen impresa que tuviera en cuenta los estándares de calidad internos. La instalación de un sistema de inspección es prácticamente un estándar en el sector, por lo que se trataba de una absoluta necesidad. La experiencia positiva de los compañeros de la planta de Arnstadt hizo que los responsables de la Packaging Division de DS Smith se interesaran por ISRA.
El sistema de inspección CartonSTAR goza de una aceptación muy elevada entre los operarios de Mannheim. Se trata de una solución de dos cámaras dotada de iluminación LED Backline de alto rendimiento. Son sobre todo los usuarios que trabajan directamente en la máquina quienes más se benefician de este sistema, ya que el riesgo de errores de impresión se minimiza debido al control ininterrumpido de las imágenes impresas.
El control al 100% de la imagen impresa reduce considerablemente el número de reclamaciones, aun si las exigencias de los clientes son cada vez mayores. Las planchas de cartón con defectos en la imagen impresa son detectadas de forma segura y expulsadas antes de que sean posteriormente procesadas. El sistema es capaz de “ignorar” la estructura superficial no homogénea del cartón ondulado, a la vez que identifica de forma segura todos los defectos importantes para la calidad, incluso a velocidades muy elevadas de hasta 18.000 planchas por hora. Todos los defectos se
CartonSTAR de ISRA VISION es capaz de identificar con seguridad todos los defectos de impresión relevantes para la calidad, incluso a velocidades muy elevadas de hasta 18.000 planchas por hora.
clasifican de forma precisa. En palabras del jefe de producción Daniel Malolepszy: “Esta particularidad del sistema CartonSTAR permite separar los defectos relevantes de los no relevantes, lo que contribuye de manera decisiva a su éxito comercial”. Especialmente el hecho de que la clasificación pueda efectuarse de forma rápida y sencilla para cada cliente hace que la productividad del proceso de impresión aumente de manera considerable. Esto permite calcular claramente las ventajas del uso del sistema de inspección en base a la mejora de la productividad y al ahorro de costes de reclamación.
El sistema registra además todos los acontecimientos producidos y hace posible una gestión comprobable de la calidad. Gracias a la inspec-
ción durante el propio proceso de impresión, DS Smith se asegura la monitorización continua de la imagen impresa y de la calidad del material. Para el usuario, CartonSTAR es un “sistema absolutamente inteligente”. A esto hay que añadir las buenas experiencias en el trato con el personal de mantenimiento de ISRA. Con la solución de inspección de ISRA, DS Smith incrementa la calidad de sus productos, reduce permanentemente los costes de producción y garantiza un uso sostenible de los recursos. Además, su empleo asegura el control integral del proceso. El sistema refuerza la posición de la empresa en el mercado y le proporciona una decisiva ventaja competitiva. El retorno de la inversión se alcanza generalmente en un plazo de doce meses.
El grupo alemán vuelve a confiar en Pasaban para el diseño y fabricación de la que será una de las piezas fundamentales de la renovada sala de acabado de su fábrica de cartón reciclado, la cortadora KB 1700.
Junto con una KB2400 totalmente automática suministrada en 2017, la nueva cortadora juega un papel clave en la mejora de la sala de acabado de la fábrica. Dispone 2 desbobinajes, cambio automático de pila y está configurada para cortar una amplia gama de gramajes desde 150 a 500 g/m 2 a una velocidad operativa de
350 m/min.
“La cortadora KB es la solución óptima para aquellos clientes que precisan una alta capacidad de producción. Ofrece un alto nivel de precisión de corte y una excelente calidad de producto final”. Carlos Muriel, Director Comercial de Pasaban.
Con una capacidad superior a 1
millón de toneladas al año, el grupo alemán lidera el ranking de producción de cartón laminado para el sector de packaging de alimentos y comercial.
"Estamos orgullosos de continuar ofreciendo máquinas de alta tecnología a los principales fabricantes y manipuladores de papel y cartón a nivel mundial".
Martin Leonhard, nos habla sobre la nueva Gallus Labelfire “Carton Edition”, especialmente diseñada para combinar la impresión de etiquetas con la impresión de cartón plegable.
Imprimir etiquetas y cajas plegables con un solo equipo: la máquina híbrida de banda estrecha Gallus Labelfire también puede utilizarse para imprimir y procesar aplicaciones de cartón y cajas plegables. Hemos hablado con Martin Leonhard, Business Development Digital en Gallus Ferd. Rüesch, sobre el desarrollo de este nuevo equipo, el mercado del cartón plegable - con sus requisitos especiales, y cuándo es el mejor momento para invertir en este sistema de impresión híbrido.
¿Por qué Gallus ha decidido crear un equipo híbrido como Gallus Labelfire, apto tanto para la producción de etiquetas autoadhesivas como para packaging de cartón plegable?
La propia demanda del mercado y la petición expresa de una de las marcas líder del sector, fueron los factores decisivos que dieron el tiro salida al desarrollo del proyecto. Las soluciones disponibles para aplicaciones de cartón y cajas plegables todavía no estaban a la altura de los requisitos que nos exigía el cliente. Después de un análisis cuidadoso de nuestras capacidades, todo nuestro equipo llegó a la conclusión de que podíamos ofrecer un sistema de máquina que fuera capaz de imprimir cartones plegables digitalmen-
te con una alta calidad de impresión y que, además, fuera capaz de aplicar acabados y embellecimiento, manteniendo, al mismo tiempo, la capacidad de impresión de etiquetas original.
¿Cuáles son los métodos habituales para imprimir cartón plegable?
Este tipo de producto está dominado por la impresión en huecograbado (por ejemplo, las cajetillas de tabaco se imprimen en hueco), lo que lleva a tiempos de preimpresión extensos y altos costes de herramientas. A este sistema le siguen el offset y la impresión litográfica.
El mercado de la impresión de cajas plegables tiene sus propias reglas ¿podría nombrar las tres tendencias
más relevantes en la actualidad?
Las tendencias más relevantes son similares a las del mercado de etiquetas: agilidad, productividad con una sola pasada y producción al momento. Al contrario que el mercado de etiquetas, el mercado del cartón plegable es un mercado mucho más maduro. En un futuro próximo, el propio sector desarrollará procesos más industrializados, combinados con producción de tres / cuatro turnos, habrá una creciente e intensa competencia y, en consecuencia, los márgenes empezarán a bajar.
¿Estas tendencias, están relacionadas entre sí?
¡Absolutamente! La agilidad en el
mercado está estrechamente vinculada a la producción al momento y ‘justo a tiempo’. Con la creciente presión de los costes, la producción en línea genera cada vez más problemas. El mercado del tabaco exige los más altos requisitos de productividad (parcialmente 24/7), calidad de impresión y acabados muy atractivos (barnices de todo tipo y efectos metálicos). En este sentido, y dados todos los datos de los que disponemos ahora, tenemos que pensar en la tecnología digital. Con esta clase de impresión, pueden imprimirse una amplia gama de sustratos de forma rápida, es fácil de usar y es altamente versátil. Para cualquier taller que trabaje con esta tecnología, el uso de la impresión por inyección de tinta significa:
- Capacidad para imprimir tiradas cortas (en el mercado de cajas plegables, de 50.000 a 60.000 se considera una tirada corta). Menor tiempo de comercialización.
- La impresión con lote extendido (mismo sustrato y línea de troquelado) es la forma más rentable de imprimir un trabajo con muchas versiones diferentes.
- No se necesitan otras herramientas y es fácil de operar.
¿Existen desafíos especiales a la hora de imprimir y armar cajas plegables en comparación con las etiquetas autoadhesivas?
Sin duda. Imprimir cartones plegables es un mundo completamente diferente a la impresión y producción de etiquetas. El mercado del cartón plegable es más grande y, por lo tanto, la inversión de tiempo y activos requeridos es mayor. "Fuerza industrial", fiabilidad y disponibilidad de las máquinas. Consideraría esas dos palabras, clave. Los cartones plegables a menudo se usan, especialmente en el segmento de tabaco, como embalaje primario, pero esta clase de sustrato no posee propiedades de barrera. Por esta razón, las tintas deben cumplir con los requisitos de alto cumplimiento del fabricante de productos de tabaco, ya que éstos deben cumplir con los requisitos de la legislación alimentaria. En este sentido, también es esencial la seguridad del producto, antes de habilitar cualquier nuevo proceso o tecnología. En pocas palabras: ¡es un mercado emocionante pero también muy exigente!
¿Cómo está siendo la demana de Gallus Labelfire “Carton Edition”?
La "Carton Edition” de Gallus Labelfire ya se está usando con resultados exitosos en la producción de uno de los mayores propietarios de marcas de tabaco del mercado. Por ahora, ya cuentan con cuatro equipos Gallus Labelfire, tres de los cuales, produciendo cajas plegables en la actualidad.
En su opinión, ¿valió la pena modificar un equipo Gallus Labelfire con las nuevas aplicaciones para cartón plegable?
Sin duda, la adaptación de la primera Gallus Labelfire para imprimir en un sustrato como cartón plegable fue un desafío, pero valió la pena. Al cumplir con los requisitos de los nuevos clientes, Gallus sentó las bases para abordar un nicho dentro del mercado del cartón plegable. Ahora, podemos ofrecer un equipo que es capaz de imprimir etiquetas autoadhesivas y cajas de cartón plegables, incluso cuando hablamos de dos sustratos que no se pueden comparar de ninguna manera. Tenemos curiosidad por ver cómo será el desarrollo y, sobretodo, por ver si la inyección de tinta finalmente consigue el éxito en el mercado del cartón plegable.
La combinación de las nuevas tecnologías visionarias de BOBST aportará niveles de automatización y transformación digital sin igual para las empresas de conversión de cartón plegadizo que buscan una mayor agilidad y eficiencia en las operaciones de troquelado. La troqueladora plana, MASTERCUT 106 PER, junto con la novedosa herramienta de gestión de recetas digitales, TooLink, encarnan la nueva visión de BOBST presentada en junio, que consiste en proporcionar un sistema de producción de embalajes totalmente conectado.
MASTERCUT 106 PER es una troqueladora de última generación con un mayor grado de automatización y una capacidad de producción que superan a su antecesora, que ya era líder en el mercado.
Bodo Junge, Director de Marketing de producto de cartón plegadizo de BOBST, explicó: “Hemos identificado la conectividad, la digitalización, la automatización y la sostenibilidad como los pilares de la producción de embalajes ahora y en el futuro. Nuestra visión para el sector consiste en última instancia en permitir a las empresas de conversión adaptarse y responder rápidamente a los propietarios de marcas cuyos requisitos cambian constantemente.”
“Con estos cuatro pilares en mente, BOBST pretende crear una cadena de suministro de embalajes eficiente donde las máquinas y herramientas se
comuniquen entre sí para proporcionar una calidad y un rendimiento óptimos, y a la vez reducir los errores, el desperdicio y los costes en todo momento. La introducción de nuevos sistemas inteligentes, como nuestra plataforma de flujo de trabajo en la nube, BOBST Connect, y TooLink, complementan y refuerzan la automatización de las plantas y las máquinas a unos niveles sin precedentes.”
MASTERCUT 106 PER es una troqueladora de última generación con un mayor grado de automatización y una capacidad de producción que superan a su antecesora, que ya era líder en el
mercado. Su nuevo diseño la convierte en la troqueladora más automatizada y ergonómica, y va acompañada de una gama de características innovadoras que apoyan la visión de BOBST.
Es la única troqueladora del mundo que puede configurarse desde un solo punto de control y la automatización de sus funciones y su configuración, desde el «alimenrador hasta la salida», reduce al mínimo la necesidad de intervenciones del operador durante su funcionamiento. Las herramientas de expulsión y colocación de poses están ahora totalmente automatizadas gracias al nuevo sistema Matic Plus, que
utiliza cámaras para medir la posición de las herramientas y, a continuación, las alinea automáticamente en el registro con la hoja impresa. La detección y la configuración de atascos también se han automatizado en esta nueva máquina, al igual que el sistema de bastidores sin paradas en la sección de salida.
Bodo Junge añadió: “La MASTERCUT 106 PER demuestra un nuevo nivel de automatización único. Las nuevas funciones hacen posible una reducción considerable del tiempo de configuración de 15 minutos, permitiendo una preparación más rápida, tan crítica para las líneas de producción hoy en día. Su nivel excepcional de automatización convierte a esta máquina en el equipo de troquelado más productivo para tiradas cortas y largas, permitiendo a los fabricantes de embalajes aceptar todo tipo de trabajos con tiradas de cualquier longitud.”
MASTERCUT 106 PER incluye TooLink, una plataforma que conecta la troqueladora con las herramientas para aunar todo el proceso de conversión. Esta tecnología única influye positivamente en la flexibilidad de producción, los plazos de entrega de los trabajos y la productividad.
La troqueladora cuenta con un chip de datos con la tecnología TooLink, que crea un ID digital único que permite el reconocimiento instantáneo a tra-
vés de la IHM de la máquina. Las herramientas equipadas con chip son detectadas automáticamente por la máquina y se suministra una receta de trabajo lista para producir, lo que permite reducir el desperdicio y ahorrar hasta 15 minutos durante los cambios de trabajos. Este sistema exclusivo permite recuperar automáticamente los trabajos sin ninguna intervención del operador.
“TooLink conecta, digitaliza y automatiza la conversión” —indicó Alex Volery, director de la división de herramientas en BOBST. — Crea un auténtico ecosistema de conversión que trata
los problemas de producción clave en materia de eficiencia, control, velocidad, calidad y sostenibilidad. Con TooLink y su serie de aplicaciones IoT, los fabricantes de embalajes tienen una visión completa de sus troqueles, recetas e historiales de trabajos y acceso a un mayor nivel de datos e información sobre la producción.
“Esta combinación de excelentes tecnologías materializa la visión de BOBST. Para los fabricantes de embalajes, es una excelente oportunidad para preparar sus operaciones de cara al futuro, ante una demanda del mercado muy cambiante.”
Los grandes eventos no encajan en la nueva normalidad. La expansión del coronavirus en Europa obligó a cancelar o posponer los encuentros multitudinarios en primavera y ahora, tras un verano en el que los contagios por Covid-19 vuelven a estar al alza, continúa el efecto dominó de cancelaciones o retrasos de ferias.
Si la situación evoluciona favorablemente, 2021 vendrá cargado de eventos que buscan facilitar los negocios entre expositores y visitantes. Las garantías sanitarias son fundamentales para poder celebrarlos, pero son sin duda un motor fundamental para la reactivación de la economía, tan castigada en este contexto de pandemia.
La última ha sido ALL4PACK París 2020, dedicada al mundo del envase y la logística, cuya organización ha decidido trasladar el evento a noviembre de 2022 dada la evolución de la pandemia. “Fieles a nuestra misión, nuestra intención es estar en contacto con la profesión y apoyar la recuperación y la transformación de los actores del sector del packaging y la logística”, afirma Olivia Milan, directora de ALL4PACK.
Como ella, otros grandes eventos del sector gráfico, de los envases y las etiquetas se han visto obligadas a retrasar sus ediciones de este año. Una de las primeras ferias afectadas fue Interpack
2020, que se iba a celebrar a principios de mayo de este año pero que se pospuso del 25 de febrero al 3 de marzo de 2021. “La feria vive de los encuentros personales y del intercambio entre personas del mundo entero. Esto solo es posible si no existen riesgos para la salud”, explicó Christian Traumann, presidente de Interpack 2020.
La feria Drupa, uno de los grandes eventos del sector que se celebra en la ciudad alemana de Düsseldorf y que estaba programada inicialmente del 16 al 26 de junio de este año, se celebrará finalmente del 20 al 30 de abril de 2021.
“La decisión se ha tomado después de
consultar con nuestros órganos asesores y las asociaciones de patrocinadores”, afirmó Werner M. Dornscheidt, presidente del consejo de dirección de Messe Düsseldorf GmbH, cuando se hizo pública la decisión. También en Düsseldorf se celebra Glasstec, dedicada a la industria del vidrio y el cristal, que ha trasladado su edición de 2020 a 2021, del 15 al 18 de junio.
En España, Graphispag, Hispack y C!Print Madrid son los tres mayores eventos de estos sectores. Graphispag e Hispack son bienales y celebraron sus últimas ediciones el año pasado, por lo que sus reubicaciones han sido más
sencillas, aunque han tenido que ajustarse a un calendario cargado con los eventos pospuestos al año que viene. La primera se celebrará del 23 al 26 de marzo de 2021 y la segunda tendrá lugar del 19 al 22 de octubre, ambas en el recinto de Fira Barcelona.
C!Print Madrid, feria anual centrada en el sector de la comunicación visual, sí ha tenido que renunciar a su edición de 2020. Todavía no se han publicado las nuevas fechas, pero la organización está preparando el lanzamiento de una plataforma virtual, C!Print Sourcing, que ya está en marcha en Francia. Se trata de una aplicación de búsqueda dedicada al mercado nacional de la impresión y la comunicación visual y que funciona como una extensión del salón físico.
Los eventos de los sectores clientes de las industrias de la comunicación visual, packaging y etiquetas no son ajenos a la situación sanitaria. La feria Alimentaria Barcelona, uno de los salones de alimentación y bebidas más importantes del mundo tendrá lugar del 17 al 20 de mayo de 2021 y el Salón
Gourmets se celebrará del 12 al 15 de abril. En el sector de la farmacia, Infarma Madrid, prevista del 10 al 12 de marzo de este año, trasladó su celebración a marzo de 2021, del día 23 al 25. Farmaforum ha sido aplazada a los días 17 y 18 de marzo del año que viene.
A estos eventos del sector hay que sumarles los que ya estaban previstos inicialmente para 2021, como Labelexpo Europe, el mayor encuentro del sector de
las etiquetas que tendrá lugar del 21 al 24 de septiembre de 2021 en Bruselas.
Si la situación evoluciona favorablemente, 2021 vendrá cargado de eventos que buscan facilitar los negocios entre expositores y visitantes. Las garantías sanitarias son fundamentales para poder celebrarlos, pero son sin duda un motor fundamental para la reactivación de la economía, tan castigada en este contexto de pandemia.
Suministradores de maquinaria para la producción de etiquetas:
Offset Semirotativo ∞ Flexo ∞ Estampación Serigrafía ∞ Acabados para Digital Rebobinadoras / Inspeccionadoras Extracción Desperdicios
Camisas de flexografía, huecograbado y laminación, Anilox, cerámicos, planchas de barniz, portaclichés, limpiadores
918 859 577 ventas@boettcher-systems.com
Lohmann Spain S.A. c/Miquel Torelló i Pagés, 38 P.I. El Pla 08750 Molins de Rei (Barcelona) /Spain www.lohmann-tapes.com
Lohmann Spain S.A.
c/Miquel Torelló i Pagés, 38 P.I. El Pla 08750 Molins de Rei (Barcelona) /Spain www.lohmann-tapes.com
Servicio de corte y entrega a medida
Cut service and tailor made delivery
our confidence open us a world of possibilities Y
u confianza nos abre un mundo de posibilidades S
comartsa.com
MB PRIME FBB BRIGHT
MB PRO FBB BRIGHT
MB CLASSIC FBB
¡NUEVAS REFERENCIAS, DESCÚBRELAS!