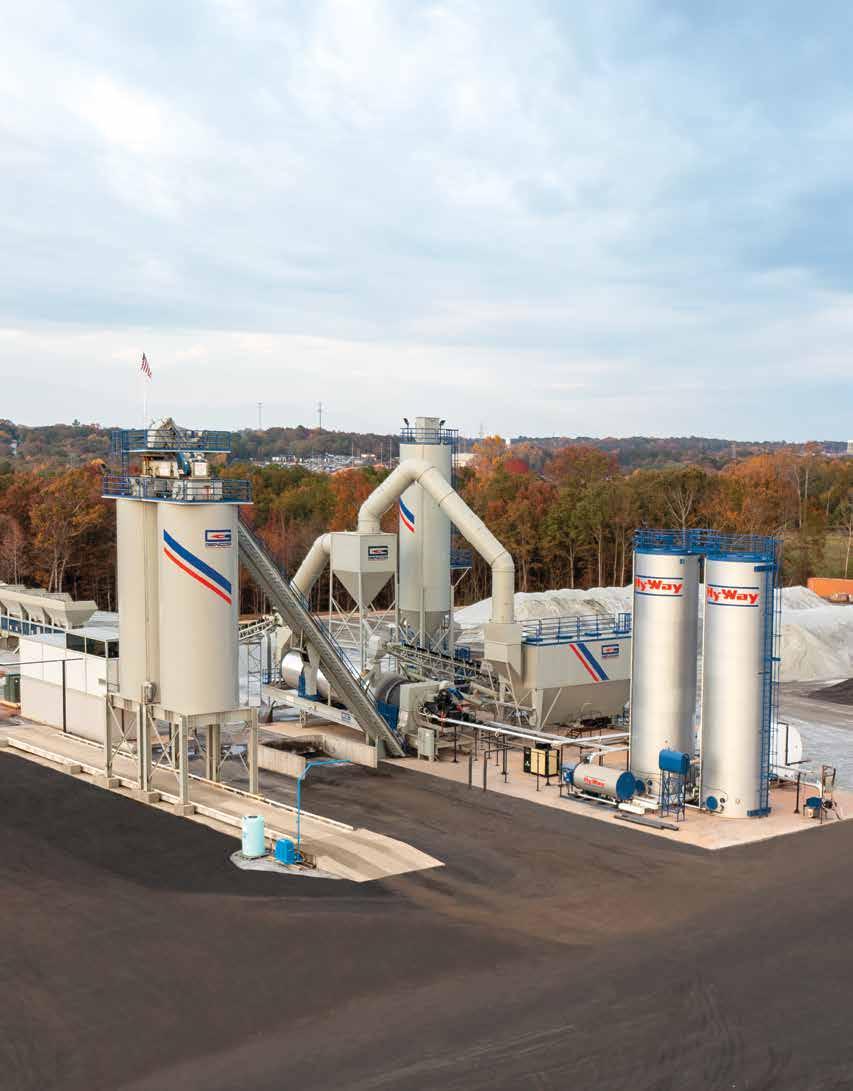
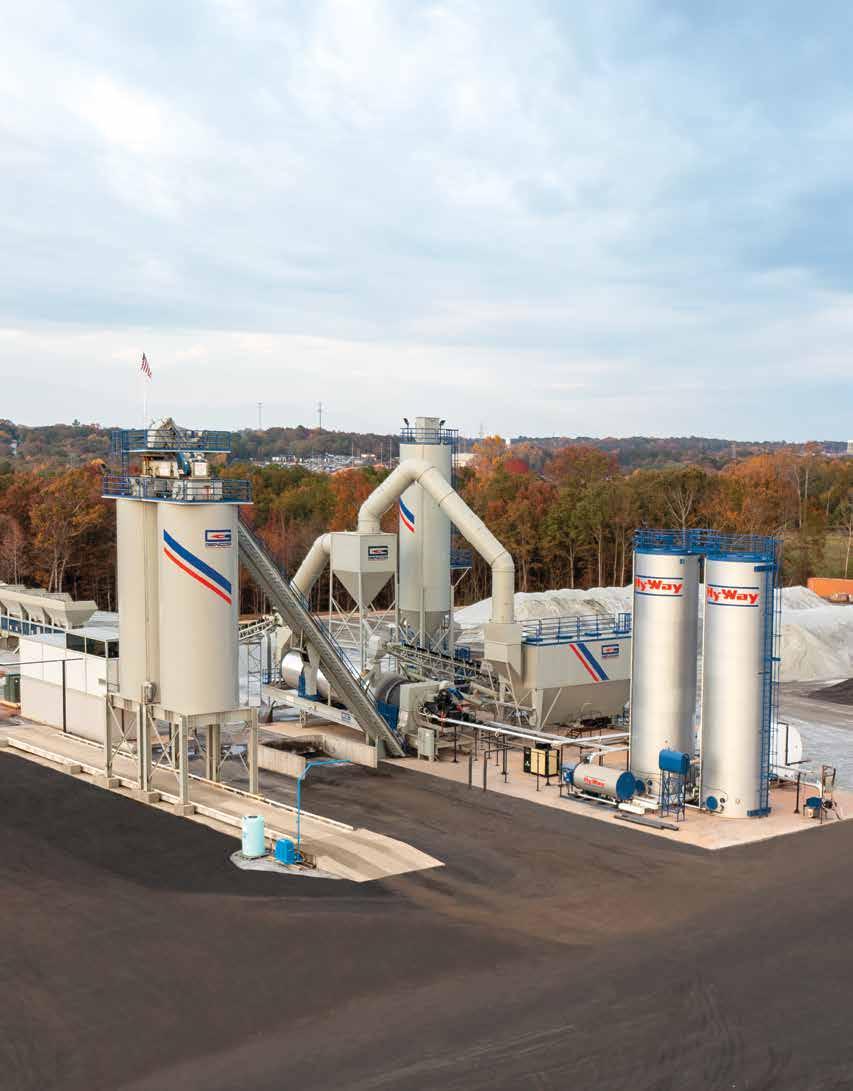
BUILT TO CONNECT
Sustainable Innovation
As a decades-long leader for asphalt plant innovation, Astec has introduced numerous products contributing to sustainability. From the Double Barrel® dryer/mixer introduced in 1988 to the debut of the high RAP Double Barrel XHR in 2016. In addition to these industry-changing products, Astec also leads in sustainability with our warm mix system, the V-PAC stack temperature control system, low emission burners, and blue smoke systems.
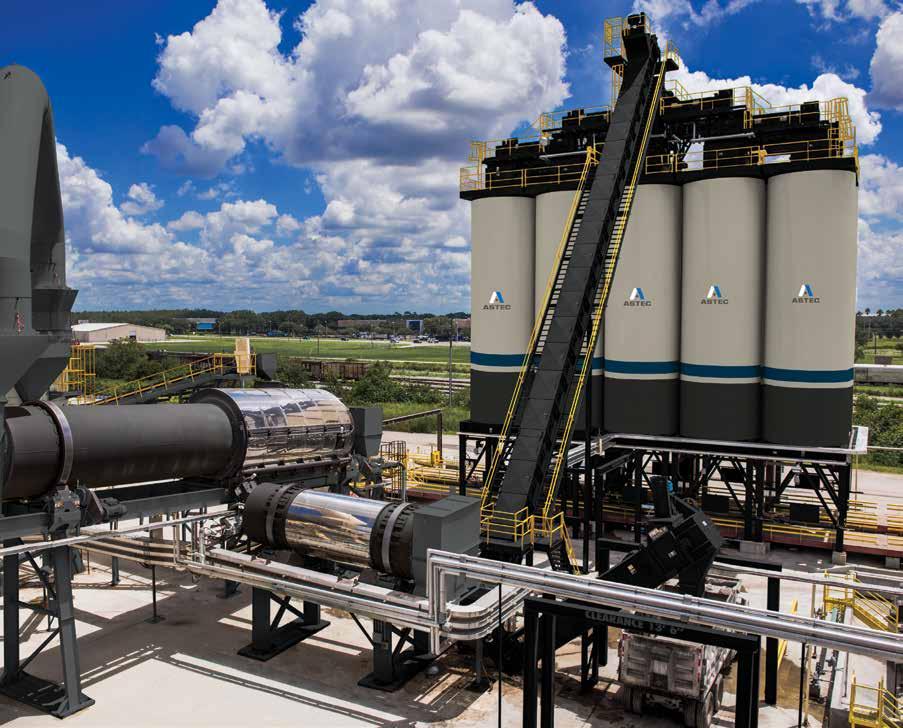
Astec is well-equipped to carry our culture of innovation into the future. Our dedication to sustainability includes new product development teams and an on-staff product manager for sustainability.
Reach out to learn more about how we can help you meet your asphalt plant sustainability goals.

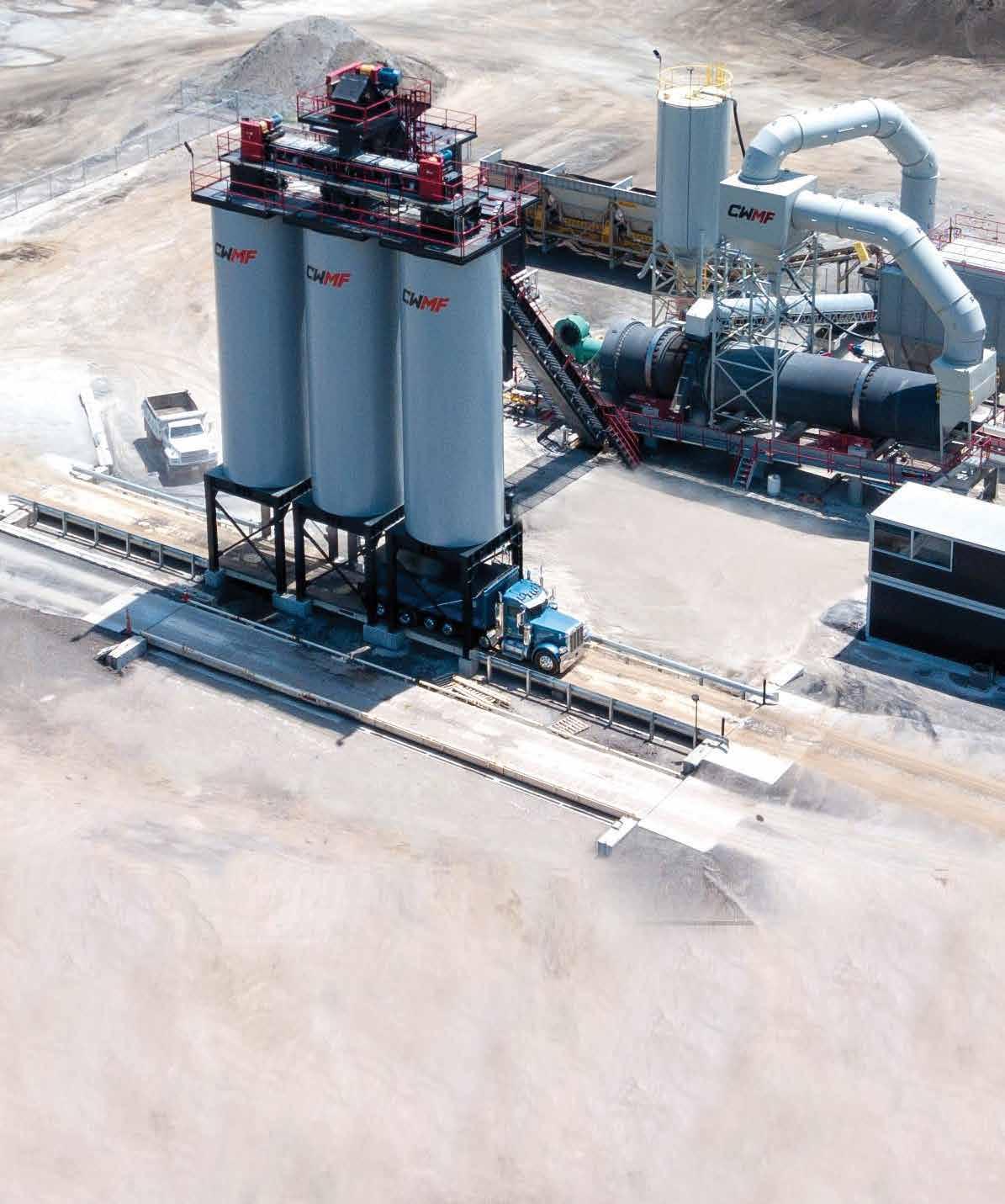
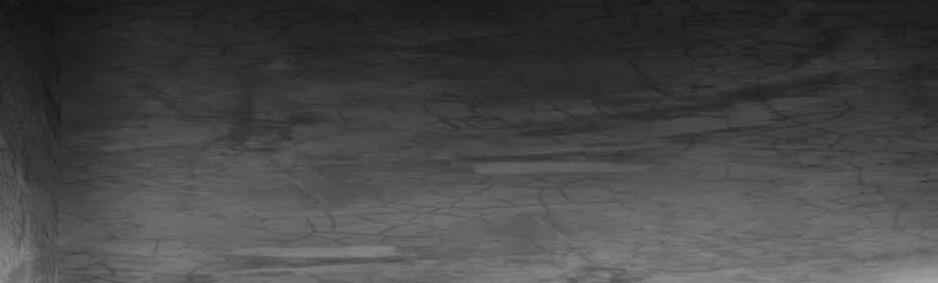
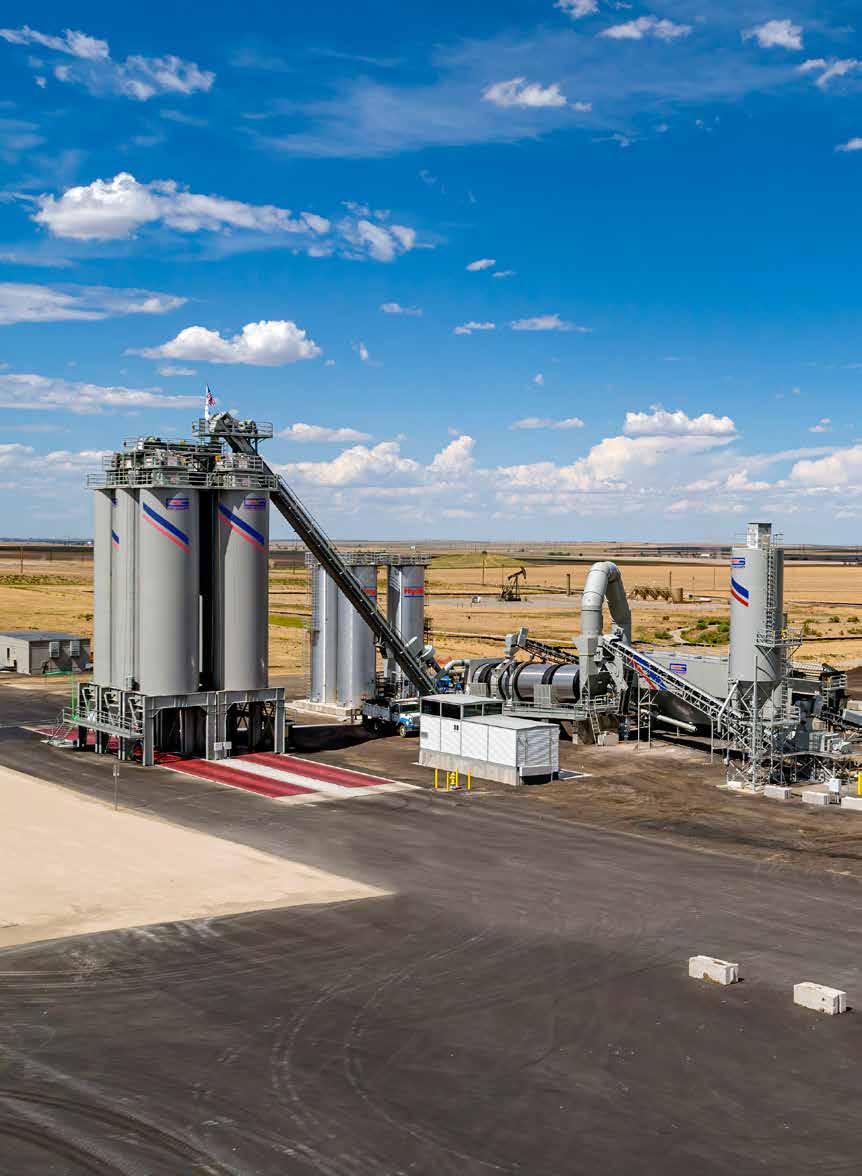
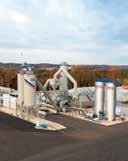
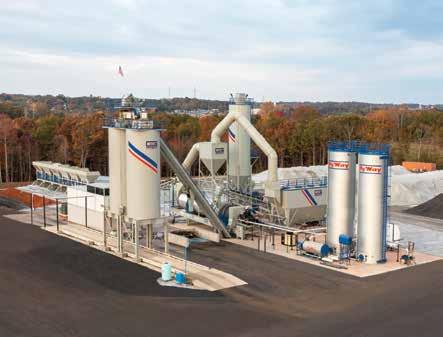
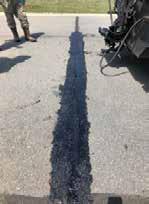
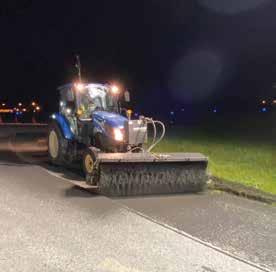
What Are You Doing About It?
IIt feels almost like a cop-out to write about workforce development here. I’m not telling you anything new by saying, depending on the region of North America you’re in, you're probably struggling to find laborers, estimators, office workers or something in between.
What I’ll say instead is we have oodles of ideas in this industry for finding workers to fill jobs. You may be tasked with training the individual you hire into the construction workforce, but the humans are out there, and we need to attract them. We’ve got articles about that on TheAsphaltPro.com to help. Visit your local chamber of commerce, state asphalt pavement association, AGC regional association, and so on, for even more ideas.
Now let’s talk about what we should be doing to attract the next generation. Not necessarily the kids in high school whose guidance counselors are falling asleep at the wheel. I’m talking about our grandkids. (In my case, this would be my nieces and nephew, all of whom have been inundated with random gifts of adorable construction stress-relief squishies and construction t-shirts over the years.)
About a decade ago, AsphaltPro Magazine and EZ Street teamed up to create a children’s activity book titled “Asphalt Lane,” in which Chip—a young haul truck—learns about paving. From safety in construction to how the plant works to how a road is paved, kids in elementary school learn alongside Chip. (You can order copies in bulk quantities to hand out at open house events, zoning meetings, Girl Scout campouts,
first day of school, and so on. Visit TheAsphaltPro. com/asphalt-lane/.)
Recently, IUPAT union member Marisa L. Richards released a children’s book that teaches girls they can grow up to build in our world. Her colorful hardcover features 16 construction “jobs” anyone can take on if they aren’t afraid of “a little hard work,” but she targets young ladies for our future in “Girls Who Build.” Each page has a rhyming couplet to catch kids’ attention while you read to them, too. If you’ll grant me a moment of personal privilege, I posted a review of the book on my BookTube channel, which you can watch here: https://youtu.be/HGk2eVQLoRk.
At press time, you can preorder the book on Amazon; it’s available after June 1. I highly recommend it for young elementary school kids. It’s another one that’s great to hand to a teacher for the first day back to school.
All this leads to a question. What are you doing to attract the next generation to our workforce? I know for a fact Ajax Paving Industries of Florida invited a Girl Scout troop to one of their facilities and gave the girls an awesome opportunity to see our industry up close. I bet you have some ideas, whether you’ve had the chance to implement them yet or not. You’ll see this post on LinkedIn and Facebook. I encourage you to get in on the discussion and to share ideas for recruiting now and into the future.
Stay Safe, Sandy Lender
602 W. Morrison, Box 6a Fayette, MO 65248 (573) 823-6297 • www.theasphaltpro.com
GROUP PUBLISHER

Chris Harrison chris@ theasphaltpro.com
PUBLISHER
Sally Shoemaker sally@theasphaltpro.com (573) 823-6297
EDITOR
Sandy Lender sandy@theasphaltpro.com (239) 272-8613

DIGITAL EDITOR
Sarah Redohl
sarah@theasphaltpro.com (573) 355-9775
MEDIA SALES
Cara Owings
cara@theasphaltpro.com (660) 537-0778

ART DIRECTOR Kristin Branscom
BUSINESS MANAGER
Susan Campbell (660) 728-5007
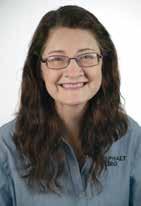
AsphaltPro is published 11 times per year. Writers expressing views in AsphaltPro Magazine or on the AsphaltPro website are professionals with sound, professional advice. Views expressed herein are not necessarily the same as the views of AsphaltPro, thus producers/contractors are still encouraged to use best practices when implementing new advice.
SUBSCRIPTION POLICY: Individual subscriptions are available without charge in the United Sates, Canada and Mexico to qualified individuals.
One year subscription to non-qualifying Individuals: United States $90, Canada and Mexico $125.00. For the international digital edition, visit theasphaltpro.com/subscribe/
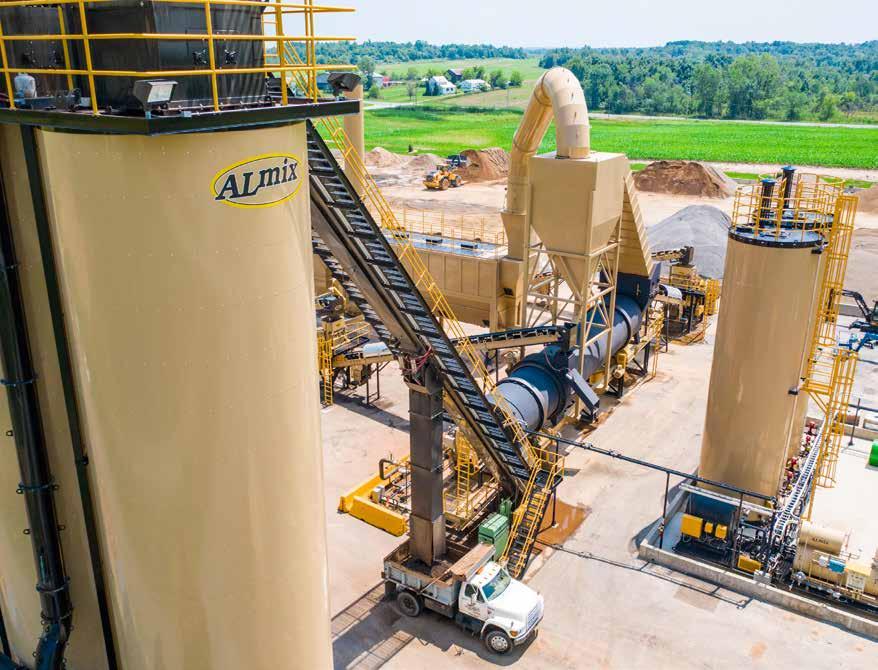
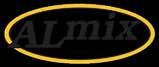
How to Handle Asphalt Burns
BY ASPHALTPRO STAFFNo matter how many hours of safety training the asphalt tank farm manager, sealcoat laborer, or other paving professional undergoes, accidents can happen in an industry where materials are stored and applied at high temperatures.
Rick Stone, the business development manager for Maxwell Products Inc. has been in the pavement maintenance market for over four decades and has found evidence that most asphalt burns happen to workers who have less than a year of experience or more than 10 years of experience. The first category of worker is new to the job and prone to mistakes. The second category of worker grows complacent in the day-to-day routine. While the industry can learn from these statistics and beef up safety training for all, we can also look at what to do when someone is burned by hot material.
HOW TO AVOID THE BURN
First and foremost, recognize that hotmix asphalt (HMA) is just that—hot. That sounds simplistic but it’s easy to become complacent when you work with the material day in and day out.

Workers coming into the industry must be told what temperatures and materials they’re working with. You can’t expect that they’re reading the safety data sheets pinned to the bulletin board where they clock in or in the break room. They must be told that hot liquid asphalt cement (AC) has the potential to explode when other substances are introduced to it. If you stop and think about it, we foam liquid asphalt with water to create specific pavement mixes, but we do this in a controlled manner within a contained apparatus. If you allow water to splash into heated asphalt, it could bubble up and explode to dangerous effect.
Teach this to new workers; remind veteran workers.
In its “Asphalt Worker Safety” series of safety manuals, the Occupational Safety and Health Administration (OSHA), spells out a number of back to basics, common sense practices for avoiding burns during asphalt work. What we have to remember is these are only “back to basics” for veterans of the industry. It’s all new to a worker who’s nev-
er been introduced to something that has a flashpoint above water’s boiling point.
The personal protective equipment (PPE)—such as thermally insulated safety gloves and a plexiglass face shield—you give the new worker represents common-sense protective measures against burns but feels foreign to him at first. He needs to hear; these gloves keep 300-degree liquid from burning your hands and harsh solvents from soaking into your skin. This face shield keeps 300-degree asphalt from splashing onto your face, sticking there, and scarring you for life.
Six Safety Minimums
• Avoid splashing water or other additives into heated asphalt.
• Avoid smoking near asphaltic materials or additives.
• Avoid inhaling hot fumes.
• Always wear thermally insulated safety gloves.
• Always wear long sleeves and long pants.
• Always wear safety glasses; add a face shield to that in the lab.
HOW TO TREAT THE BURN
Once an accident happens, you must take fast action. We’re not talking about reacting to an explosion. We’re talking about a burn on the skin. If what you have is a 375-degree drop of sealer the size of a dime that has dripped onto your hand or forearm, “it’s still going to hurt like hell,” Stone said. But that single drip is not necessarily going to stop production.
Paving Consultant John Ball has seen workers get a splash of hot tack on their wrist or hand and the steps to help them are immediate. He said, “We shove their arm in the ice container right off to kill the pain.”
If the area was small enough, those workers wrapped the wound in gauze—which OSHA does not recommend—and went back to work the rest of the shift. For more severe burns or those that cover more area, the worker needs to be treated in an emergency room. Ball recommended the crew
have a discussion during the pre-construction meeting that includes:
• What is the closest hospital?
• What’s that hospital’s phone number?
• Who is the designated driver in the event of an emergency?
• Where is this information written on the day’s job report?

N.B. West’s Steve Jackson reminded readers that you need to include the site’s emergency address. For example, the address you give to the haul truck driver to come pick up mix may not be the address emergency personnel would use to find your team if a worker is down with a chemical burn. Know what address you are to give to the 911 dispatcher whether you’re out on a highway project, at a commercial lot, or at the asphalt plant.
At the paving site, each morning’s toolbox talk should include a “this is where we are today” moment when the foreman points out the cross streets or nearest mile marker. Have workers repeat the name of the street or the mile marker so you know they can say it to a dispatcher on a 911 call. Few dispatchers will be able to direct emergency responders efficiently to “the back of the tack truck in that work zone out on I-95.” Do all EMTs know what a tack truck looks like? Maybe not. It’s best if your personnel can say, clearly, “We’re at mile marker 79 Southbound on I-95.”
Don’t forget that an emergency will put the human mind and body into fight/flight/ freeze/focus mode. That means the members of the crew witnessing a colleague screaming in pain may not react as they are supposed to. Even though they know they need to plunge the injured person’s arm into a bucket of ice water and call the emergency number
KNOW WHAT ADDRESS YOU ARE TO GIVE TO THE 911 DISPATCHER WHETHER YOU’RE OUT ON A HIGHWAY PROJECT, AT A COMMERCIAL LOT, OR AT THE ASPHALT PLANT.


SAFETY SPOTLIGHT
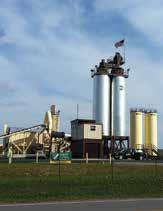
for help, their prefrontal cortex has transferred “action” to the lizard brain. When this happens, you want their instinct to be the right actions. You want them to be so well trained in the right steps to take that they have no choice but to help their co-worker properly. That means you need to practice emergency safety training.
Ball suggested practicing to help a burned co-worker during a rainy day, at the tailgate talk, or during annual safety day seminars. Or at all three. By practicing what to do in the event of an emergency, your team is more likely to respond to the emergency properly.
Check out the poster from Asphalt Institute—available for purchase through the National Asphalt Pavement Assocation (NAPA) online store—titled: “First Aid for Asphalt Burns Poster.” The NAPA store also features “First Aid for Asphalt Burns Wallet Cards.” Both of these properties have an area where the purchaser (you) writes in the appropriate emergency number in your immediate region/county to call for help. Both of these properties stress the importance of immediate cooling care for the burn victim at the scene, but address the need to ensure the victim is breathing clearly.
Step 1. Immediately assess the victim’s breathing and circulation.
Step 2. Immediately begin the cooling process. Run cool water over the affected area. If water isn’t immediately available, you “can” place an ice pack or a cold pack on the area while someone brings water to the site.
Step 3. Let others know what’s happening. Get help. Don’t try to do this alone.


Step 4. Call for emergency help, whether that’s 911 or the local emergency number. Notice these steps do not include covering the affected area with gauze or a bandage or any other wrapping. All current sources indicate you must leave the burn uncovered. Get the victim to help instead. Notice these steps do not include trying to remove the asphalt from the skin. All sources indicate this step is for medical personnel in an emergency room or other medical setting to undertake; even those sources are divided on best substances for asphalt removal from skin to prevent irritation, infection and potential poisoning from the substance being used. Let a medical professional handle that task. Get the victim to help instead.
Reminder from Robert Redford
While smoking cigarettes has its own health risks, doing so near asphalt or flammable additives can cause an explosion. You might not see vapors, but they could be around the ember of your cigarette, about to catch fire.
Members of this audience might be familiar with the 1975 Robert Redford movie “The Great Waldo Pepper,” in which a World War I non-fighter pilot sought fame and fortune on the state fair airshow circuit. In that film, one of Pepper’s fellow stunt pilots crashed in front of an excitable crowd of looky-loos who rushed onto the scene with their cigarettes hanging from their lips and fingers. Of course, their ashes caught the leaking fuel vapors afire, and Pepper’s friend died a horrible death
Let that scene burn into your memory and the next time you need a smoke break, take that break far from the asphalt action.
In fact, if the victim wears contact lenses and has liquid AC in his eyes, it is recommended that trained emergency personnel be the ones to remove the lenses. You will flush the eyes with cool water for at least 20 minutes, but a trained medical professional should handle the difficult task of saving the victim’s sight.
Common sense dictates burns that incorporate the eyes, face or other sensitive area will require more immediate emergency care than a burn to an arm or leg, but all burns should be treated with immediate, cooling care. But the best way to treat an asphalt burn is to avoid it. Train your workers how to respond to an accident, but above all, train them how to avoid the accident in the first place. Show them how and why to use PPE and how to be safe around hot materials.
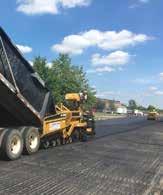
THE ASPHALT PLANT SOLUTIONS PROVIDER


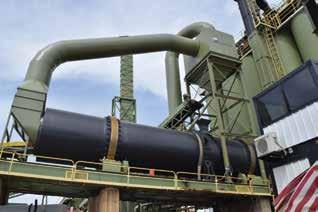
Whether you are planning to keep your asphalt plant for three years or 30 years, we would appreciate the opportunity to partner with you to help fine-tune your operation and assure that you meet your hotmix production demands.
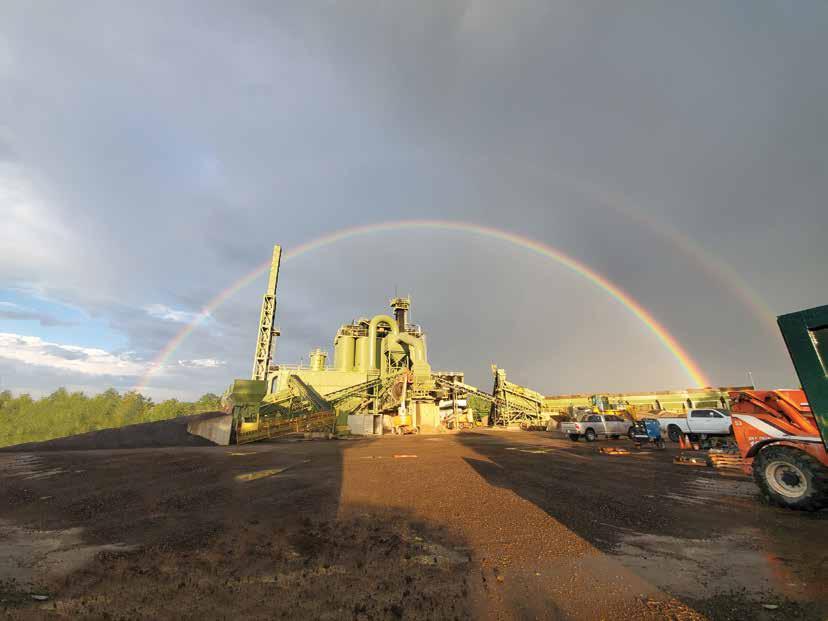
We are all about taking the time to talk with you and assess your unique situation. It is our goal to evaluate every job differently and give recommendations based on the best way to solve your problem.
EQUIPMENT USED EQUIPMENT
The only Full Service Custom Integrator of ALL BRANDS of asphalt plants. INTEGRATION is achieved by combining existing plant components with new components, used equipment or re-engineering plant parts and pieces to yield a fully functioning hotmix asphalt plant facility.
As an OEM, our parts are engineered and designed to make your plant run better. Our industry experts, from all backgrounds, specialize in retrofits and duplication of any type, brand or manufacturer of asphalt plants. We can provide you with anything for your asphalt plant.
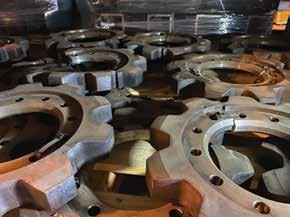
We are here to assist in helping you sell your used asphalt plant equipment for the best price on the market. In addition, sometimes a used component can solve your issue as well as a new one for a much lower price. We will advise you on the best option for your particular situation.
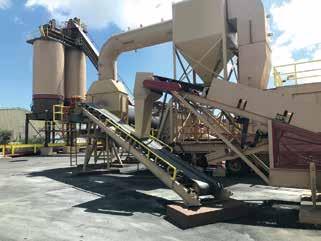
Recycle, Remove Safely
BY ASPHALTPRO STAFFAcontractor in the Midwest found the crew faced with tearing out multiple driveways, sidewalks, flares and pavement edges before the team could settle into paving. As you can see in the problematic pictures on this page, some of the sections of existing pavement were broken into slabs and removed with the skid steer. There’s nothing wrong with this concept. The execution here requires some discussion.
As you can see in the pictures on this page, a skid steer bucket was employed on this project for transferring broken slabs of cracked pavement to a haul truck for removal from the site.
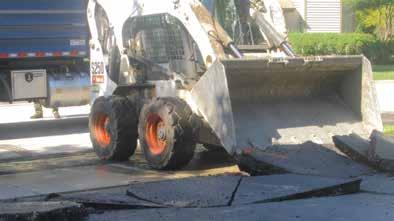
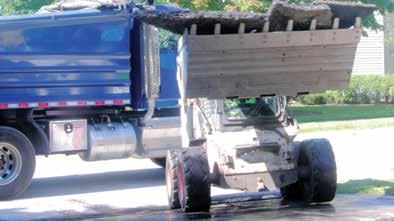
Using the skid steer bucket to remove rubble from the site would be a perfectly acceptable practice if the crew had been given adequate time to break up the pavement and turn it into rubble. They weren’t given the opportunity to make safe, manageable chunks.
If your crew will be required to remove pavement from tight quarters or from areas where a utility size milling machine isn’t welcome, a jack hammer or pavement saw is your next best option to get the material down to a size that doesn’t pose a hazard to workers or passing motorists/pedestrians.
What ideas can you share for safe and efficient transfer of material on a tight project? What type of excavator or attachment would you recommend for this residential application? Share your ideas with one another on the AsphaltPro Facebook page when this article goes live in June and help keep colleagues safe.
1. Before the skid steer operator began scooping large material into the bucket, the crew should have broken or cut the chunks down further.
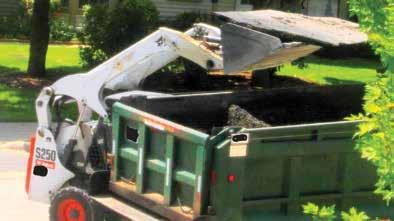
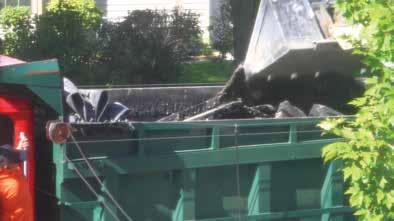
2. This situation is precarious at best. The team might believe they’re saving time or manpower by moving large chunks of material with the bucket, but they are placing workers in danger.
3. Which of those chunks will fit nicely through the tailgate at the truck’s destination?
4. All it takes is one bump and the skid steer operator can be badly injured. If he miscalculates any part of this haul, the truck driver or any worker nearby could be badly injured. This is an unsafe practice that can be avoided with a little elbow grease and better planning on the front end of the project. Photographer and contractor information withheld
LEADING THE WAY
Weiler Material Transfer Vehicles lead the way with proven innovations to provide the lowest cost per ton of operation.
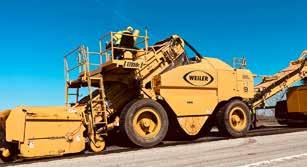
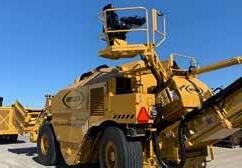
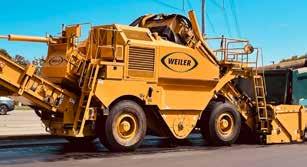

Innovative and reliable operator friendly features such as paver hopper management system with distance to paver, storage hopper management and auto chain tensioning.
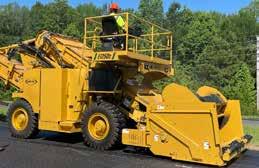
Variable speed elevator and conveyors meet production requirements with the minimal amount of wear.
Clam shell doors and full width drop down floors provide unmatched access for cleanout.
The evolution of chains, sprockets and augers are retrofittable to all machines and provide increased wear life.
How to Get the Best Crack Seal
BY ASPHALTPRO STAFFDuring the National Pavement Expo (NPE) in Charlotte this past January, the presentation titled “Comparing and Contrasting: Hot Pour Crack Sealing with Hot Pour Mastics” offered Friday morning attendees a look at different options for their businesses. Maxwell Products Inc.’s Rick Stone shared decades of knowledge with the audience.
Today’s crack-sealing contractor doesn’t have the same headaches we had back in the day. In the mid-1970s, a contractor might have been using roofing asphalt to fill cracks merely to create a flexible waterproof seal. In the early days, the early hot pour sealants were usually asphalt and crumb rubber mixes that took three to four hours to heat up in a 200-gallon tank and tended to clog the applicator hoses. We had cheap boxes that weren’t always easy to open.
We’ve come a long way, but our goal is the same. For crack sealing, we want to create a watertight seal. For crack filling, we’re simply replacing the void; waterproofing isn’t necessarily taking place.
To protect the pavement and help it last longer, the goal is to keep water out. Thus, our developing sealant industry came up with performance requirements, classifications for sealant types, and performance specs. ASTM, AASHTO, and states came up with standards and specs for manufacturers to adhere to.
Your classifications for hot pour sealants fall into these categories:
• Mineral filled
• Asphalt rubber
• Asphalt & fibers
• Polymer modified
• Polymer hybrid
• Jet fuel resistant
This means you can expect your hot pour sealant to extend the pavement life two to eight years. It’s giving you a quick application, so it’s often used to enhance other surface treatments. It’s usually used to prevent further deterioration of the existing pavement.
What the hot pour sealant won’t do for you is improve ride quality, restore structural integrity or fix structural deficiencies of the pavement.
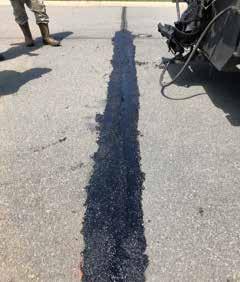
If your customer has asked you to seal cracks on his parking lot—whether that’s prior to a sealcoat or stand-alone repair work—there are some ideal surfaces and some not-so-ideal surfaces for crack sealing. Remember that compatibility of processes is important in the pavement preservation industry.
Pavement candidates for crack sealing are those with well-defined single cracks or new cracks that have appeared within the
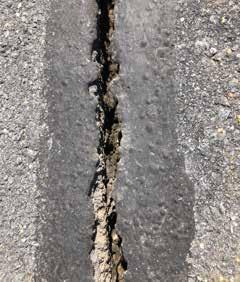
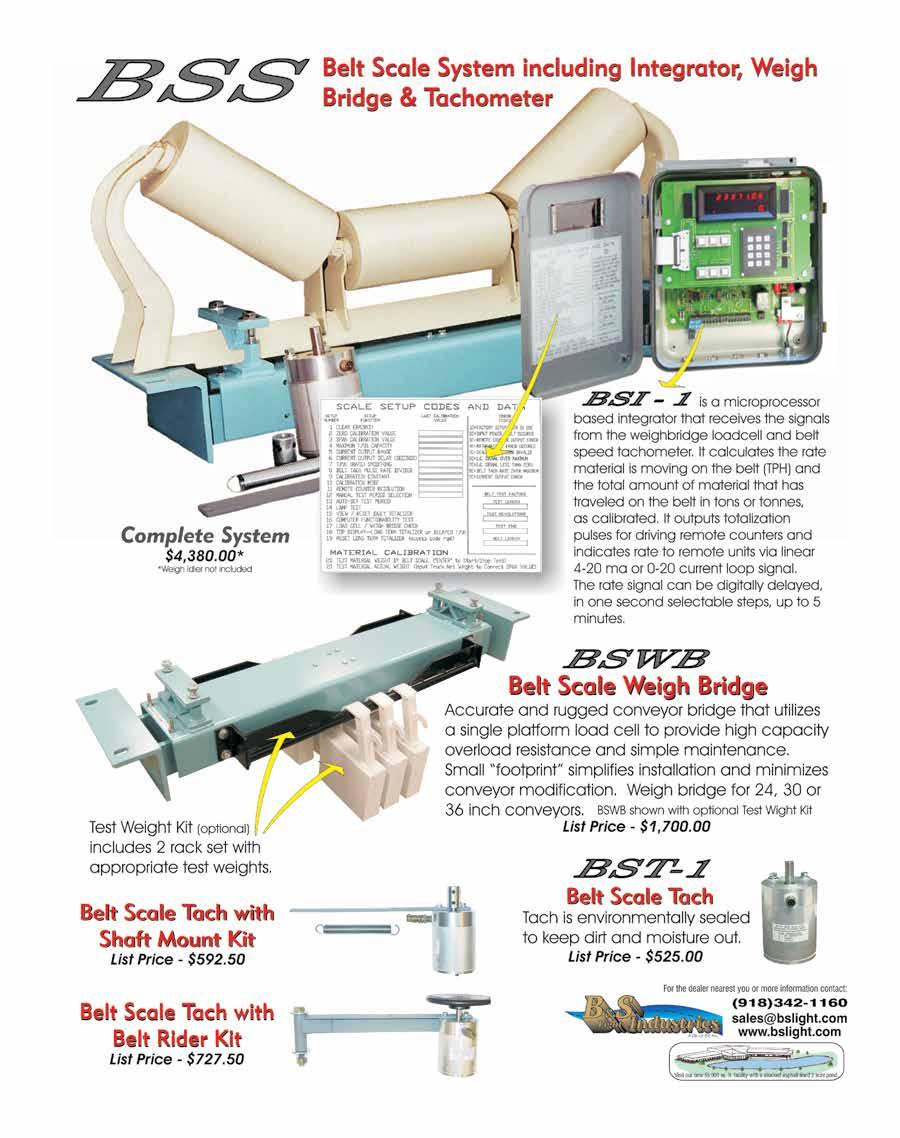
PAVEMENT MAINTENANCE
first 18-36 months of the structure’s life. You want to bring out the tape measure for some of these and make sure the cracks are within 1/8- to 1-inch wide. You’re looking for pattern cracking—longitudinal and transverse—but not an excessive amount. Also, perimeter sealing around utility cuts is ideal for crack sealing.
Hot pour mastics are designed to be a bit more robust. They return structural integrity to voids in the pavement while waterproofing yet remain flexible. They can improve ride quality and are typically used as a standalone repair or prior to another surface treatment. Again, think of compatibility of processes.
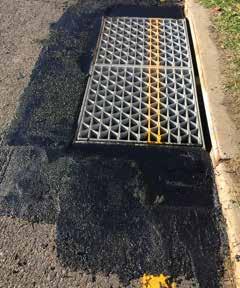
Some good candidates for using hot pour mastics include those pavements with wide, deep cracks (greater than ¾-inch wide, 1-inch deep). The aggregates must penetrate the bottom of the void. If you need to repair a pavement distress, fill a pothole, cap a utility cut, repair the joint failure between a pavement and shoulder, perform skin patches where alligator cracking is taking place, repair raveled pavements, fill in around raised manholes or drains, even up ruts or adjoining pavements, level a bridge approach and so on, the hot pour mastic is a fine choice.
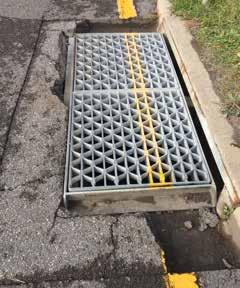
The next National Pavement Expo is set for Jan. 23-25, 2024, in Tampa. Visit https:// nationalpavementexpo.com/.
There is a minimum standard of performance for mastics, but the ASTM D8260 sets the bar fairly low. This means you may see different performance characteristics from manufacturer to manufacturer, even if the product meets ASTM’s standard. In other words, every mastic is a little bit different. You’ll want to talk to the manufacturer’s rep about the limits of their products. Find out what type, size and quantity of aggregate is incorporated in the product.
Keep in mind, our industry is maturing in the use of hot pour mastics. Improvements in uniformity are coming and will allow the crack-fill contractor to make better estimates and give better results to customers.
When you’re looking at cost comparisons, keep in mind what your workforce will have to do to prepare the product and surfaces as well as what installation equipment you’ll need to apply the product. While most hot pour sealants are priced by the pound, it’s easier to compare mastics when pricing by the gallon. Look at the anticipated life cycle of sealant versus mastic as well as the availability of materials in your region.
REMEMBER THAT COMPATIBILITY OF PROCESSES IS IMPORTANT IN THE PAVEMENT PRESERVATION INDUSTRY.Mastics also work well to fill in around raised manholes or drains, as seen in this example.

THE POWER
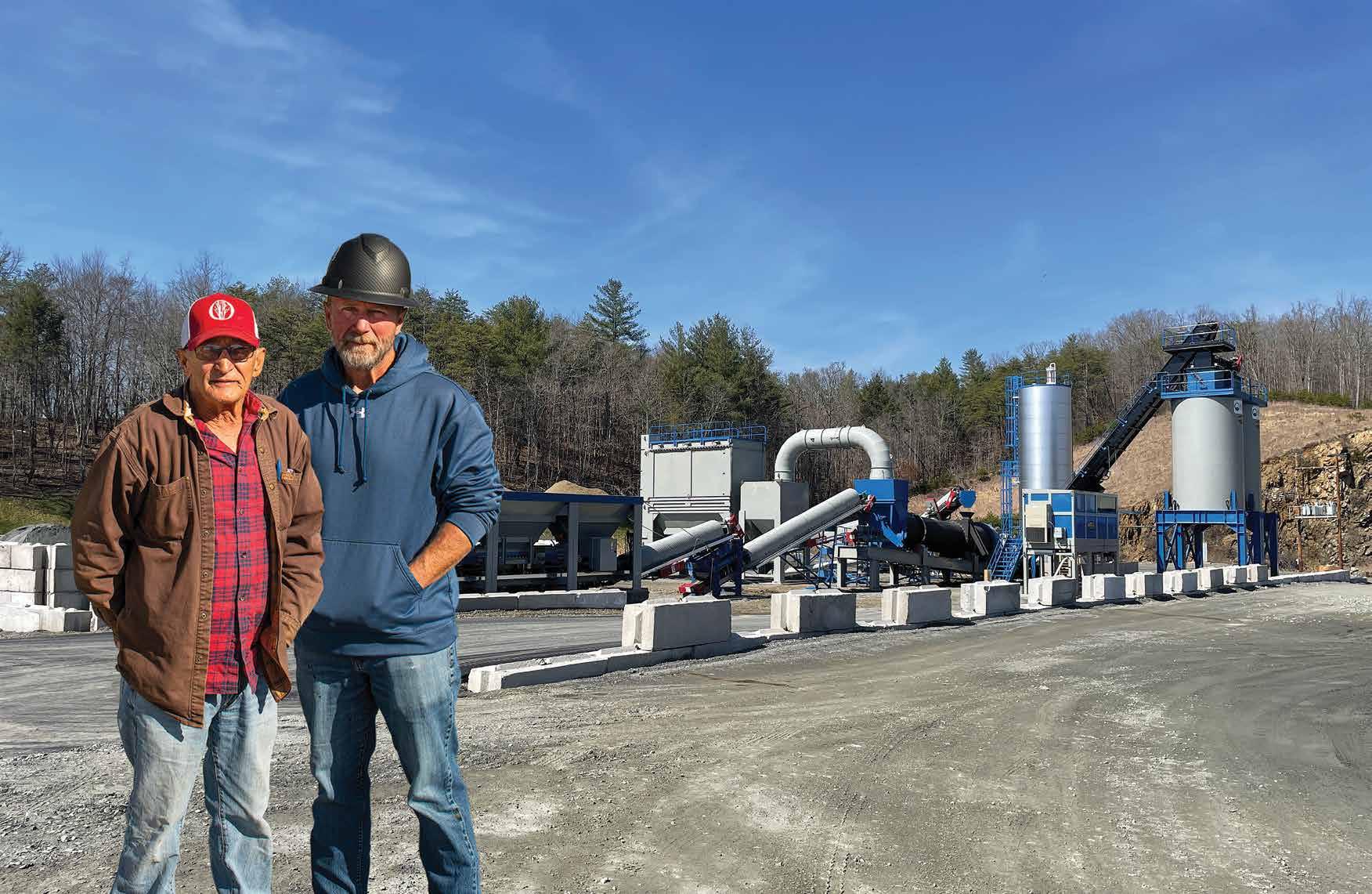
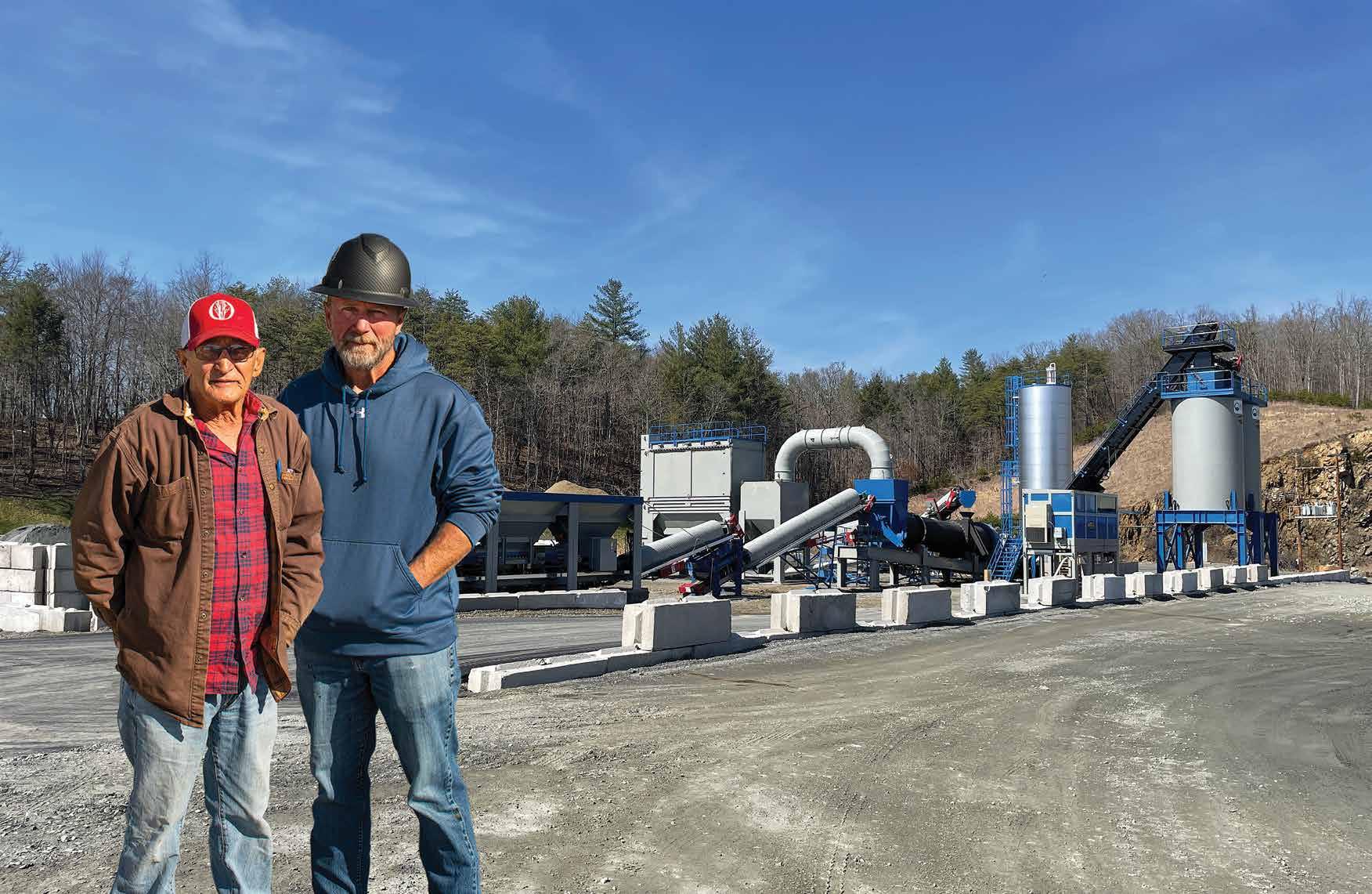
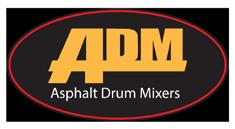
PALMETTO COMPLETES SUCCESSFUL BUILDS
PALMETTO COMPLETES SUCCESSFUL BUILDS
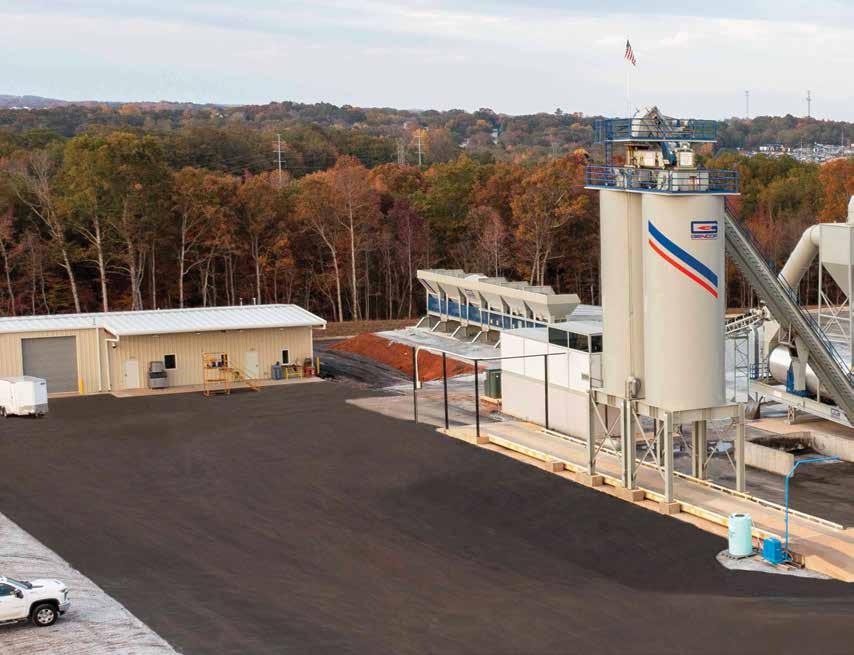
TThe team at Palmetto Corporation, headquartered in Conway, South Carolina, has managed steady growth over the years. When management saw opportunity in the market at the outset of the 2020s, they reached out to long-time partner Gencor Industries, Orlando, to get the ball rolling on updates and ideas. Among the results of that partnership is the new plant installation creating jobs and facilitating infrastructure development around the city of Greer, South Carolina.
MARKET FORCES
Ray Mothershead is the manager for all the plants for Palmetto and he spoke of the leadership that brought the Greer plant to life. His words
portrayed nothing but respect and admiration for Shawn Godwin, CEO and owner of Palmetto Corp., and the person he commended for finding the spot.
“We knew where we wanted to go,” Mothershead said. “We had that confidence. Shawn said this is the market we want to go to. He lays out the vision and we follow it. We have relationships with customers and the DOT around the area and he saw that in the market.”
Godwin spoke of the area as well. “South Carolina is a great place to live and do business. We have known this for years but now the rest of the world is starting to see the potential. This has led to remarkable economic growth, specifically in the Upstate market. Our new asphalt plant in Greer will allow us to service this area.”
Having relationships means taking care of the community, even before you arrive with the iron. “Do your community awareness before you buy,” Mothershead suggested. “Get out there in your community and do your due diligence. We just gotta be a good neighbor.”
Part of being a good neighbor is letting the community know you’re there for them. Mothershead said, “We hire their sons and daughters. Shawn gives to the local baseball teams.” Other examples he shared included having local elementary school kids come to the plant for field trips, which gives teachers, children and parents the chance to learn more about the positive job source in the community.
UPDATES AND CAPACITY INCREASES
Other projects getting updates while the Greer plant was underway included the Orangeburg property for Palmetto. Gencor’s Mark Spicer, who is based in Ocala, Florida, visited the Orangeburg site with Mothershead to assess what the team required there.
Around December 2020, the teams rebuilt a used plant out of Michigan for the Orangeburg site, Spicer said. He listed the drum, baghouse, cold feeds, recycle bins and drag as used components that came from the existing Michigan plant; the liquid asphalt cement (AC) tanks, silos, control house and cables were components that were required to complete the plant that Gencor supplied. These were the remaining components that Palmetto ordered through one person in the Gencor parts department so everything would be under one code and not overwhelming for either party.
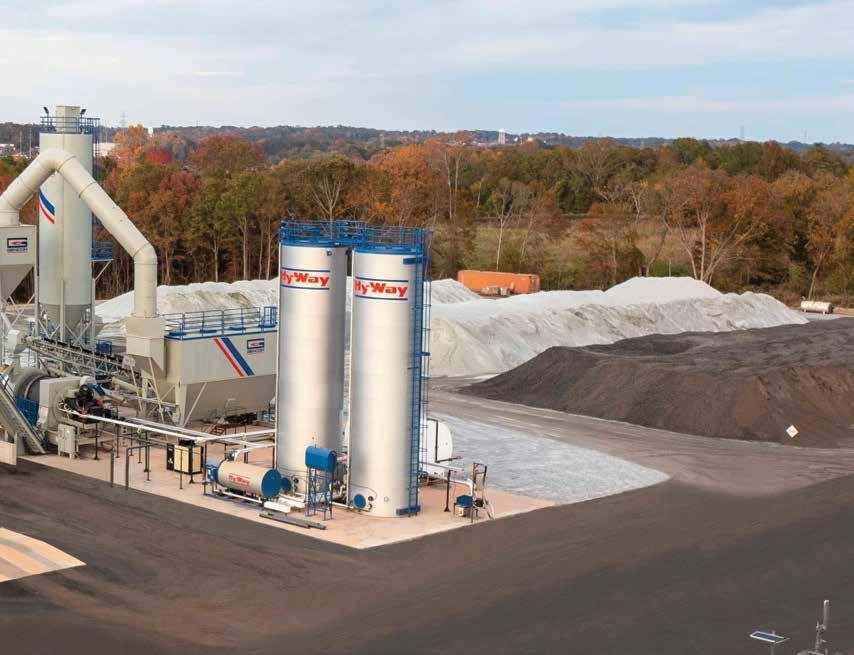
Spicer said they had everything evaluated and ready to order by April 2021. “All the manufacturers were way out on delivery by then,” Spicer said. “We needed about eight months for the new pieces.” By January 2022, the Orangeburg plant was ready to set up.
“We started to put the Orangeburg plant up in January [2022],” Mothershead said. “We ran it in March.” He stated that “getting the transformer was a problem,” and the team ran into the same delay with that component when working on the final elements of the Greer plant installation.
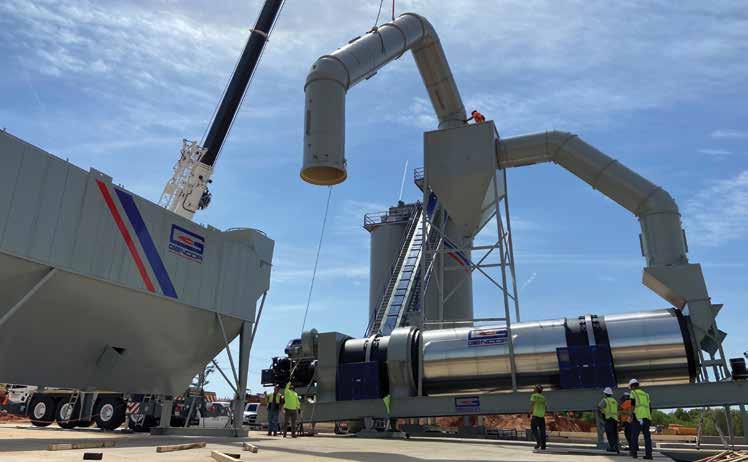
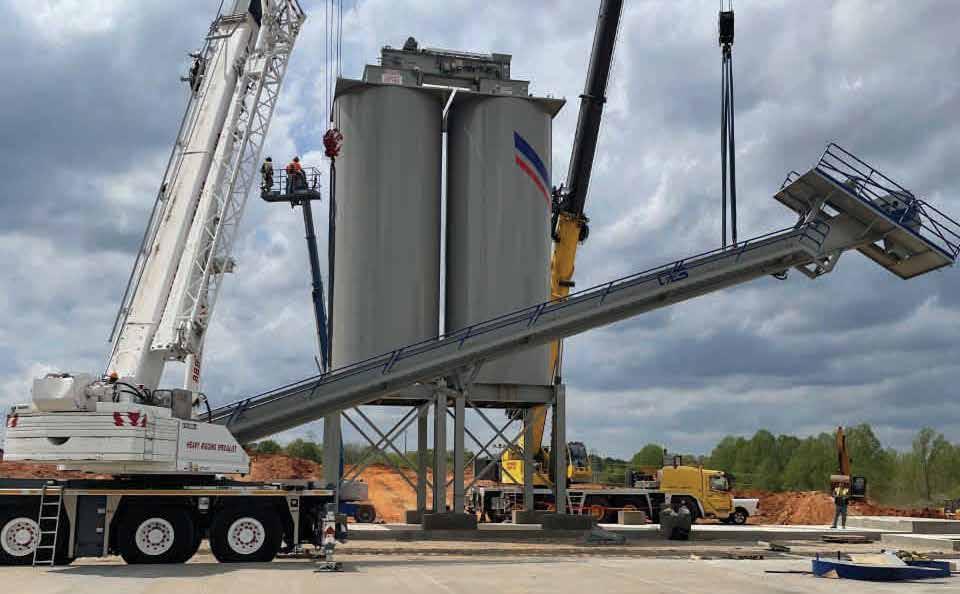
“They [transformers] take time to get in because of the current supply chain,” Mothershead warned. And that’s something to be mindful of these days.
NEW PLANS, NEW PLANT, NEW CREW
Something else to watch out for is extraneous permit requirements. While both Spicer and Mothershead explained the building permit was not in hand when Palmetto ordered the Greer plant in August of 2021, the process would be straight-forward. Mothershead spoke of the process as almost “easy if you do your due diligence,” but also said the process started “right after we bought the plant.” There was no waiting around to get the permitting process off the ground.
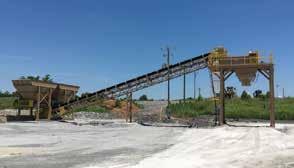
“The permitting process is no different than any other phase of the project,” Godwin shared. “It always takes a team effort to get to the finish line. Wade Kennard spearheaded the permit process and pulled in other resources as needed. The permit process took about nine months.”
Mothershead listed other team members who were integral to the process. “There were other people who didn’t go to the city council meetings but helped out, like Eric Faulk and Mark Nye.”
“Make sure that the land you’re buying really is heavy industrial,” Mothershead cautioned. “When you’re going to buy a piece of land, buy as much of it as you can and make yourself a buffer. Follow the policy to the letter. We’ve got a great team here with great relationships. As long as you meet the criteria, you can get the permit.”
With the building permit in hand, and the plant going up, the Palmetto team faced an interesting twist from the city. “You can buy the property and do the sitework and start erecting the plant, but you still need the operational permit,” Mothershead said. “The control tower has to have an engineer sign off on it. Gencor thinks ahead and already did that. We never encountered that because we put plants up in a county. This was scrutinized by the city of Greer. But the control tower? Gencor already knew about it.”
The plant will also need utilities to operate. As mentioned above, getting a physical transformer in place took a bit of time due to the supply chain challenges we’ve seen lately. “It sat waiting for utilities; just needed gas and power for getting it turned on,” Spicer said.
They achieved the operating permit from the city in July, ran test mix, and were making mix by August 2022. That bit of delay gave way to a stellar new installation for Palmetto—one that shows off the teamwork of a blended crew.
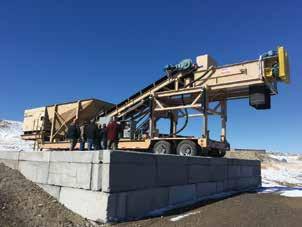
Sources spoke proudly of the team at Palmetto. “Their own inhouse maintenance crew did the install,” Spicer said. “Gencor was
We’ve been designing and manufacturing custom mixing solutions in Tennessee for nearly 40
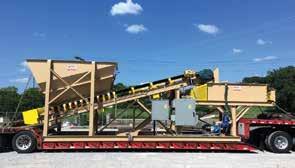
“MAKE SURE THAT THE LAND YOU’RE BUYING REALLY IS HEAVY INDUSTRIAL. WHEN YOU’RE GOING TO BUY A PIECE OF LAND, BUY AS MUCH OF IT AS YOU CAN AND MAKE YOURSELF A BUFFER.”—RAY MOTHERSHEAD
TOP: In this image, you can see the attention to detail that Gencor’s Mark Spicer commended the Palmetto team on. Piping around the plant included insulation that will keep fuel use down. Not only is this a nod to good long-term cost management, but it’s also another way to manage one’s overall carbon footprint. BOTTOM: The control center is a split-level design allowing the operator a 360-degree view of the entire plant. The motor control center is situated on the lower level of the unit. All control centers are pre-wired from the factory for fast setup and operation, and that proved handy for the Greer facility when it came time to grab the final operational permit.
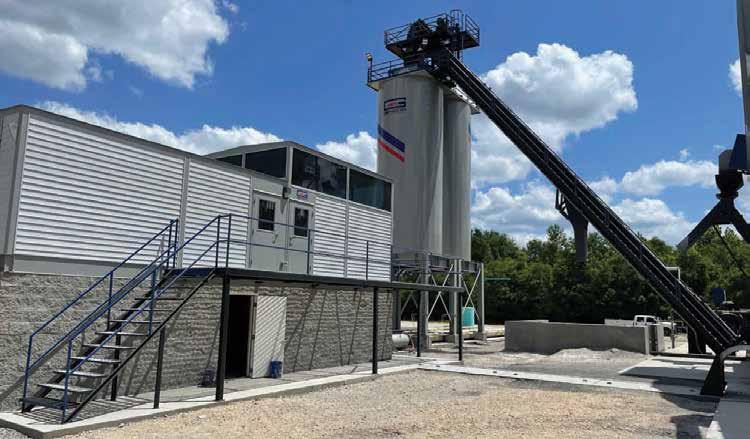
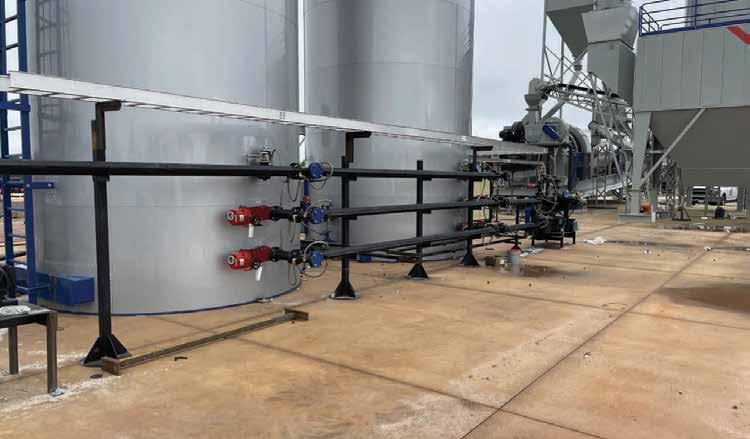
there for putting the iron up and for setup, but their [Palmetto’s] people did the install.”
He said they did it the right way, too, taking the time and spending the money “upfront” to handle details such as insulating all the piping. By insulating and jacketing piping around the tank farm and elsewhere, the Palmetto crew minimizes heat loss and keeps fuel consumption—thus costs—down for the future.
“One goal with the Greer build was to do it better than the one before,” Mothershead said. “We wanted to be more efficient...and we were. And we brought some new people on board and they did great. They help fulfil our company’s needs.”
Mothershead is a self-proclaimed asphalt fan who loves this industry. He looks for people who know how to work together for the good of the industry, the good of the company and the good of each other. “The guys we brought on worked great. They’re a great bunch of guys working it out. There’s gotta be a bridge between family and work. We hire great people with skills. Building strong relationships with team members. Bringing everyone’s skills to the project.
“I’m very proud of the men and women who work in the plants with me. They’re the ones who do the work these days.”
END GOALS
At the end of the day, the Palmetto team overcame supply chain hiccups and a twist from the city with the help of their long-time partner and succeeded in a new plant installation. They have a new Ultradrum® plant from Gencor rated at 300 tons per hour with two silos with a storage capacity of 400 tons.
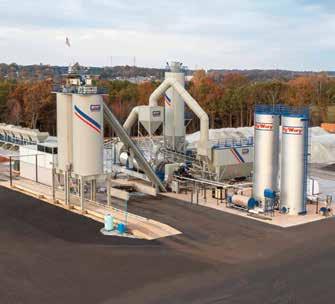
“We don’t put asphalt plants up to sell mix,” Mothershead said. “We put up asphalt plants to support our crews.” He shared the plants feed both customers and Palmetto crews with about 80% supplying all their work from their plants.
The end goal, he said: “Be efficient, get the mix out the door and get paid for every drop of it.”
After two years of testing the top asphalt rejuvenators in mixes with 40% RAP, Invigorate beat the competition by 300%.
For more information on the results, call us at 1-888-663-6980.
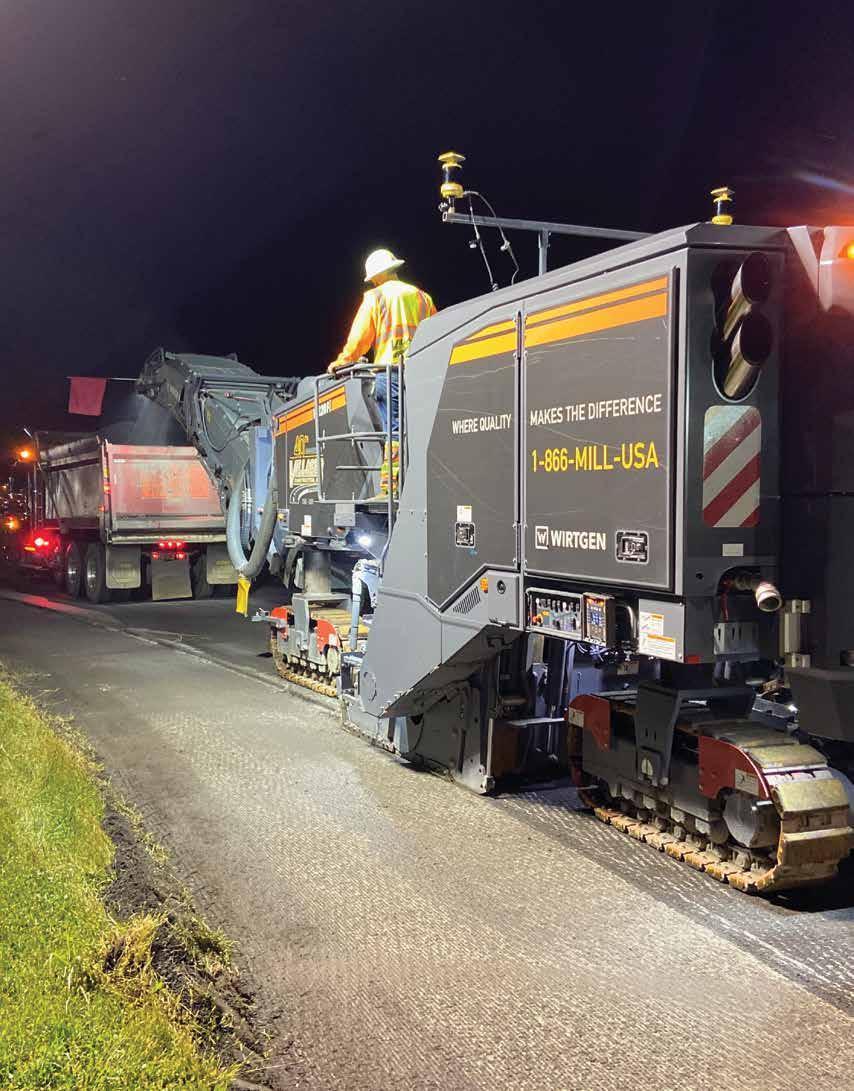
FINE AIRPORT GRIND
GPS milling solution proves speed and accuracy are not mutually exclusive
BY LARRY TROJAKU
Urgency drives most any airport resurfacing effort. Even in cases when the facility has the luxury to totally shut down for the duration of the resurfacing, the pressure is on to reopen and restore flight traffic. For times when contractors don’t have that luxury, and work is done in a segmented fashion between temporary closings, steady production is key.
On a recent taxiway resurfacing project at Albany International Airport (ALB), general contractor Rifenburg Construction, Troy, New York, faced some of those daunting logistical challenges as it worked to mill and pave one of the facility’s main taxiways. Aided by the use of a 3D machine control system controlling both milling machines on the project—including the first Wirtgen 210 Fi in North America to be so outfitted—the company and its subcontractor easily handled the profile milling effort and completed the project on time with excellent results.
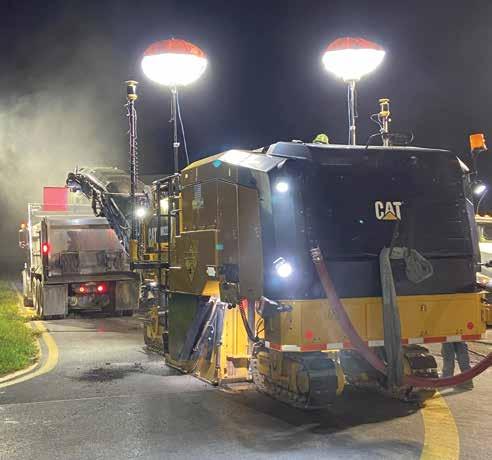
THE SETUP
Located just north of downtown, ALB serves as the major air center for New York State’s Capital Region, as well as the northeastern part of the state, and Western New England, handling roughly 1.5 million passengers annually. Built in 1908, ALB is the first (and still the oldest) municipal airport in the United States. While much has changed since then, the very numbers that confirm its success also dictate the difficulty of scheduling regular maintenance on its runways and taxiway surfaces.
“One of the real challenges after winning the bid for the Taxiway ‘A’ Rehab Project, as the job is known, was getting the necessary work done in a severely constricted time frame,” said Darin Cooper, Rifenburg’s superintendent. “We were limited to performing between 10:00 p.m. and 5:00 a.m. In that time, we had to get out to the area being resurfaced, set up, do all the required milling, clean out the area after milling, tack it, pave it, get it striped, and move off. That’s a whole lot of activity to complete in such a short period.”
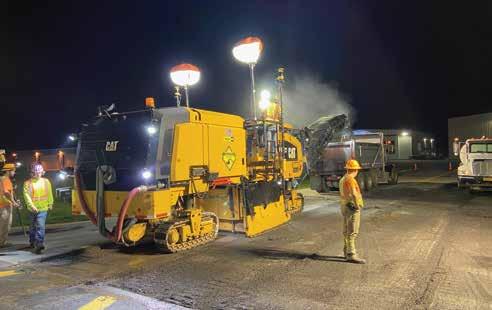
Considering it took 20 to 30 minutes each for setup and breakdown, he added,
ABOVE: Here you can easily see the receivers atop the CAT PM822 as it prepares to mill with 3D milling precision. AT LEFT: The team said this was the first W 210 Fi to be outfitted with the Topcon 3D machine control system in the United States, showcasing the two OEMs’ compatibilities. They installed a valve switching unit to control the electronic automation on the CAT PM822.
the crew was actually only left with about six hours to do everything mentioned above. “It was an exercise in efficiency, for sure,” Cooper said.
IT TAKES A VILLAGER
While Rifenburg counts milling as one of its core strengths, for the ALB airport job, because of equipment availability, it found it necessary to subcontract out a portion of the milling effort to Villager Construction, Fairport, New York. With nearly 30 machines at work throughout New York State and up and down the east coast, Villager is a milling force to be reckoned with. Under normal circumstances, using a sub of that caliber would have been a straightforward arrangement. At ALB, however, additional factors had to be considered, according to Mike Momrow, a Topcon professional services manager.
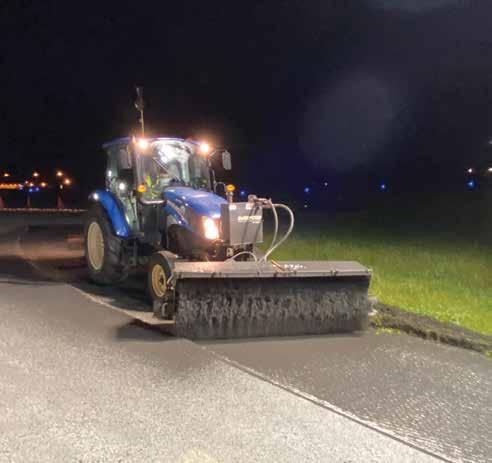
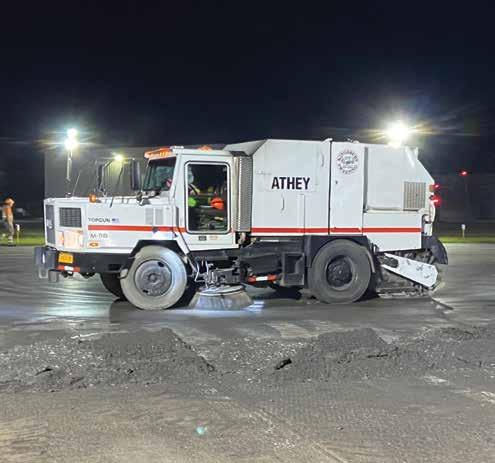
“Rifenburg decided early on that a profile milling approach would be best to correct a number of surface irregularities that had been identified in the initial survey design,” he said. “So, well before the project started, we met with representatives from Villager to discuss ways in which the Topcon Millimeter GPS solution could work with a new Wirtgen 210 Fi they’d just purchased. At the same time they were using that machine, however, Rifenburg would also be milling with a Cat unit, so there was a compatibility concern to address.”
For some, integration difference between the two machines could have presented problems. However, the combination of the Wirtgen unit’s CAN interface and the plug-andplay design of the Millimeter GPS solution resolved any concerns about “playing nice with others.” For Rifenburg’s Cat PM822 machine, Momrow said, a relatively old-school approach solved the compatibility concern.
“TO GET THE NECESSARY GRADE CORRECTIONS, WE WERE MILLING ANYWHERE FROM LESS THAN AN INCH IN SOME SPOTS TO AS MUCH AS 5 INCHES IN OTHERS, ALL WHILE TRYING TO MAINTAIN A 1:1.5 SLOPE TO THE EDGES.”
—BRIAN MCGRATH
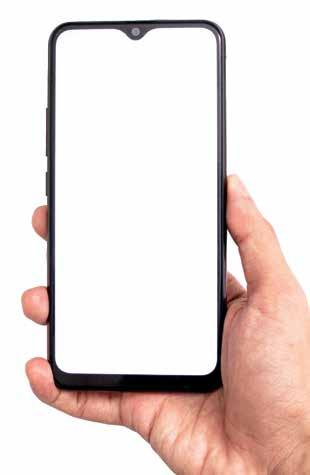
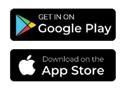



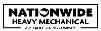
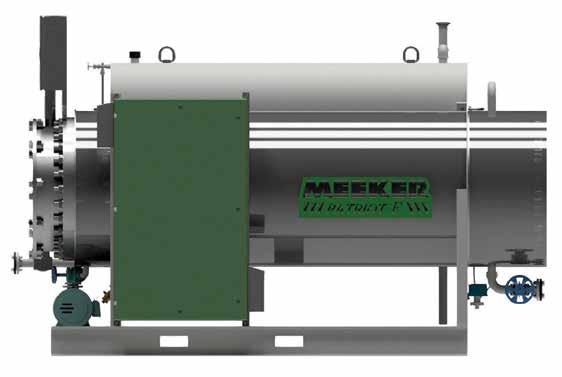
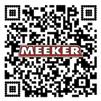
“For the Cat [machine], we installed a valve switching unit to control the machine’s electronic automation,” he said. “So, while the two platforms were completely different, they were both able to work off the same digital model and get equally impressive results. It worked like a charm and, despite being new to the technology, Villager’s crew really took to it after just a couple basic sessions on operation.”
LONG OVERDUE
If the Albany Airport project had a theme, it might have been “It’s about time.” In addition to aptly describing the tight work window faced every night, it also summed up the taxiway’s overdue need for repair. While the 01/19 runway was resurfaced in 2015—a project Rifenburg also headed up—the adjacent taxiway was not. The need for improvement was showing in many areas, according to Brian McGrath, Rifenburg’s survey manager.
“There were many cracks in the taxiway surface, some of which had grass growing through them—that’s never a good thing,” he said. “And, based on some areas that had standing water after a heavy rain, there were also some grade issues that needed to be corrected. So, it wasn’t a typical ‘mill-and-fill’ where we could just track the existing surface, mill 2 inches and put back 2 inches. It needed a profile-based solution, which played perfectly to the strengths Millimeter GPS brings.”
VARIABLE DEPTH
The solution the crews of both Rifenburg and Villager drew upon—Millimeter GPS—augments the benefits of GPS positioning technology with a zone laser reference to improve the vertical accuracy of the milling machine. Working off an initial survey design, Rifenburg simply ran a minus 2-inch offset from proposed grade and both units milled to that design grade.
“Running off that model made all the difference on the taxiway project,” McGrath said. “I’m sure there’d been some basic mill-andpave resurfacing in the past—without any changes for grade issues. Now, however, in order to get the necessary grade corrections, we were milling anywhere from less than an inch in some spots to as much as 5 inches in others, all while trying to maintain a 1:1.5 slope to the edges. Without the Millimeter GPS solution, it would have been extremely difficult.”
The benefits realized through use of Millimeter GPS were many. In addition to bringing the taxiway up to standard and correcting the long-standing drainage issues, the solu-
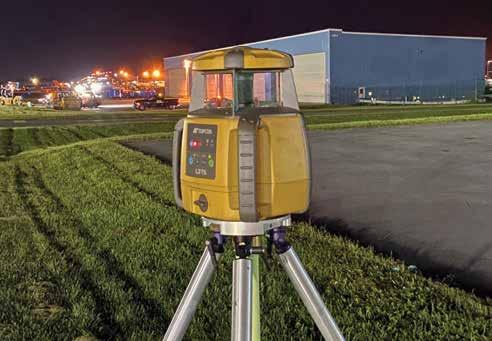
tion both streamlined the milling process and resulted in material savings.
“Profile milling with Millimeter GPS results in a much higher degree of accuracy,” Cooper said. “Because the accuracies are so tight to the design, the amount of asphalt needed to get back to grade is reduced, saving the owners money. On a project in which we paved anywhere from 500-650 tons per night, material savings are welcome.”
Though Rifenburg Construction is a seasoned user of Topcon millimeter-grade mill-
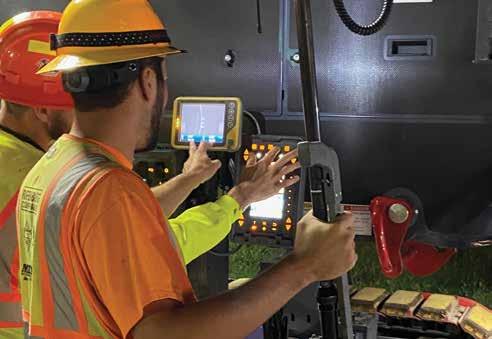
ing and paving solutions, this was Villager’s first foray into the 3D realm. According to Momrow, the company’s status as a major milling services provider added an element of interest to the Albany project.
“Villager owns and operates more than two dozen machines up and down the east coast,” Momrow said. “Until now, they’ve never made a commitment to adding 3D control to one of their machines. So, we wanted to make sure they realized the full benefits our solution can provide, and I know we did.”
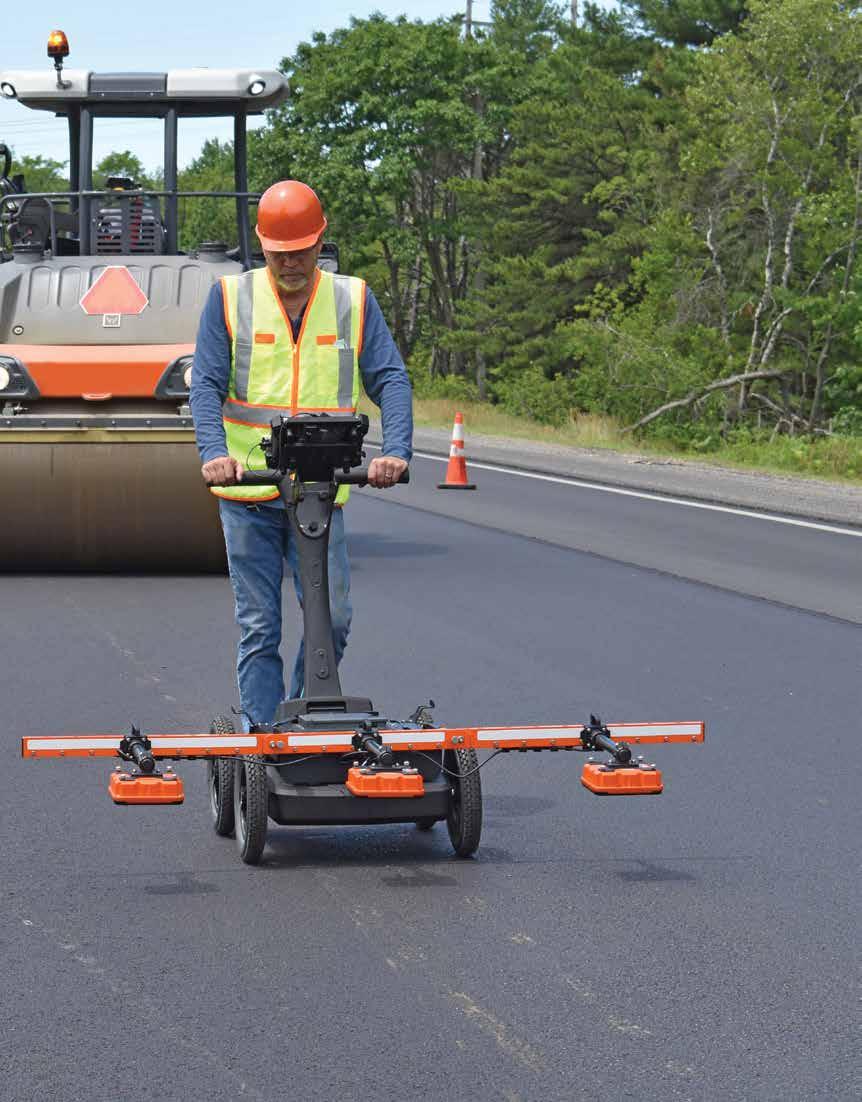
Meet a Woman of Asphalt: Superior Asphalt Materials’ Beth Conley
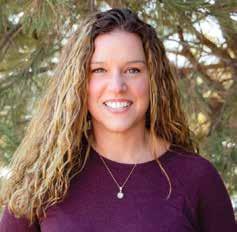
Beth Brusveen Conley has been in the construction industry about 26 years and brings a deep knowledge and understanding of asphalt production to her current role as sales manager for Superior Asphalt Materials in Aurora, Illinois. That’s because she worked as a manager at Builders Asphalt LLC in Elburn, starting in 2006, where she oversaw the plant and crusher and handled sales. Conley shared that even the mechanical side of the asphalt plant shows the heart of our industry. All the belts and components working together to make the final product showcase the reliance we all have upon one another for our best success.
“The asphalt plant is an allegory for a team working together, with the operator as the leader,” Conley said.
She serves on the Women of Asphalt of Illinois board and is the president of the Women Road Builders of Illinois, which is a non-profit in the Chicagoland area for all engineers, contractors, professional services and the like. Conley is a force for teamwork and pulling together to accomplish great things for the group. With a busy season start-up and CONEXPO-CON/AGG 2023 schedule, she made the time to share her story and encourage others as a woman of asphalt.
AsphaltPro: What did you find interesting or fulfilling as a manager with Builders Asphalt? (What do you think about that role would be attractive to other women joining our industry?)
Beth Conley: My work in asphalt in the beginning was all new and interesting. I always loved a good challenge. I was very familiar with the office side of things on concrete, but asphalt is much different, plus I was dealing with the field side of things. Ev-
ery day was something new. The guys were great and very helpful. We were a new plant and starting from scratch. I had some great mentors, some real old school guys that helped me along the way. I am very thankful.
AsphaltPro: You have degrees in political science and government, with minors in math, business and international studies. Could you share with the readers how your education prepared you for the ups-anddowns of managing asphalt and crushing plants as well as materials sales?
Beth Conley: I feel like politics are a part of every avenue in our lives. There are a lot of politics in construction in our area. I’ve learned to be more objective and see both sides of a situation. As my Poly Science professor said, life is about choices. We all make them. Some are tough and some are easy, but they all have ramifications. You can make a decision that is in your best interest or the interest of the greater good. I feel like this applies to everything we do.
AsphaltPro: We know the asphalt industry doesn’t require a four-year college degree
to jump in and excel, but you mentioned some great courses available in Illinois, like the Level III in asphalt, the 5-day aggregate certification and the Level III in concrete, for anyone wishing to level up to quality control manager. Could you share with readers an experience you found invaluable from those courses?
Beth Conley: Yes, the State of Illinois Department of Transportation has a great set of classes anyone can take through Lakeland College to help you advance in the asphalt industry. I was encouraged to take the classes early on.
They are all 3- to 5-day classes. Upon completion, you receive a certificate that allows you to work as QC or as QA on any construction site, quarry or plant in different capacities. They have aggregate, asphalt and concrete levels 1 through 3. I have completed my 5-day aggregate class and have a Level 3 in concrete and asphalt. The classes have been very helpful in problem solving and discussing specifications with our customers. Plus, you can meet a lot of good people. Many of the connections I made back then, I still work with today.
AsphaltPro: Could you share with the readers what your job as a sales manager for Superior Asphalt Materials requires of you?
Beth Conley: In my role as sales manager, I am in charge of the customer experience from beginning to end. I work with the customer on bidding and pricing. Then when the job starts, they will call me to get their order set up. I usually visit their job site to make sure everything is going well. In the billing process, I review their invoices to verify their billing matches their quote and follow up with them if necessary on payment. I’d like to think our customer experience is the reason they continue to come back.
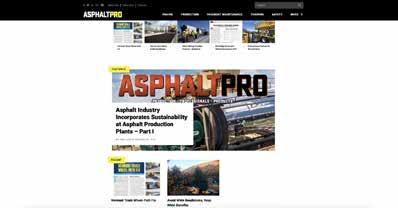
AsphaltPro: Does your role ever involve bringing potential buyers to a plant site prior to a big project to go over mix designs or production schedules, etc.? Could you share with the readers what is intriguing (or stress-inducing) about pre-planning like that?
Beth Conley: We have lots of projects that are a cooperative effort between Quality Control, the plant and the customer. We are very lucky that our guys like to work together for the greater good and the customer’s happiness. There are lots of jobs we send mix designs for approval, get start dates and verify materials for mixes. There is a lot of planning. Sometimes our internal jobs overlap with customer jobs, but we have gotten good at making everyone happy.
AsphaltPro: What about your role with Superior Asphalt Materials is “most cool” to you?
Beth Conley: One of the best parts of my job is watching the company grow. Before me, there was very little outside sales. They brought me in to grow business in outside sales. The numbers are tangible, and it is great to see the progress, but it is also rewarding to see the guys push outside of their comfort zone to grow with the possibilities.
AsphaltPro: What do you think is the most important skill you’ve brought to your position as a sales manager? (And how would you encourage other women entering the industry to hone a similar skill?)
WOMEN OF ASPHALT
Beth Conley: The most important skill is to see the greater picture. What you do affects someone else’s position. I feel women are great problem solvers and see a larger picture. When you put it all together you are limitless.
AsphaltPro: What would you say was the most challenging “obstacle” you, as a female in the construction industry, had to overcome in the past 26 years, and how DID you overcome that obstacle? How do you think other women in the industry can incorporate that skill or habit into their workdays?
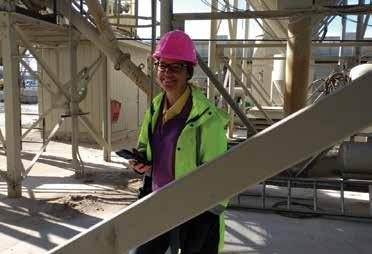
Beth Conley: The most challenging obstacle is being a woman. There are so few of us, you work with a large majority of men on a daily basis. I’ve been lucky that most of the men I work with want to help and be helpful. The best part of our industry is the people. I’ve met some great ones.
I would say the best way to overcome this obstacle is to take the time to get to know your people. When you work as a team the possibilities are endless.
Also, it has been a catalyst for us starting Women Road Builders. We are a 501c3 charitable organization built to promote and support women in infrastructure. We have a powerhouse of women on our board, and we are working endlessly to support the women in our industry.
AsphaltPro: What is the most rewarding aspect for you of being in the asphalt industry?
Beth Conley: The most rewarding aspect has been the people. I have met some of my
best friends in the industry. Most of my customers have become friends. We are an industry of good people. I have met some good ones along the way and I am truly grateful for their guidance. It has been priceless.
AsphaltPro: Will you tell us about a person who served as a mentor for you and how they have encouraged you?
Beth Conley: My parents were my first mentors. They always said I could do anything.
In my career, there are three mentors that stand out. Sam “Junior” Palumbo, Tom Crook, and Anne Bigane Wilson, PE. They all helped in different ways.
Junior was a senior mentor who always pushed me to go farther. He always encouraged me through his knowledge and experience. He was an old school part of my experience. His knowledge was endless.
Tom Crook was our panel operator when I first started in the industry. He always took the time to answer all of my questions no matter how big or small. He showed me all of the possibilities in the industry. He taught me all about asphalt plants and how they worked, showed me how to load trucks when needed, and taught me about asphalt plant maintenance.
Lastly Anne Bigane Wilson, PE, showed me what women are capable of in our industry. She’s very determined and established. Anne has taken time to discuss with me some of her obstacles in the industry and has shown that you can overcome them. Also, that you are not alone.
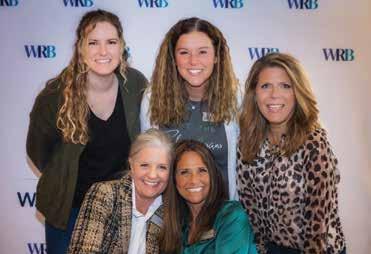
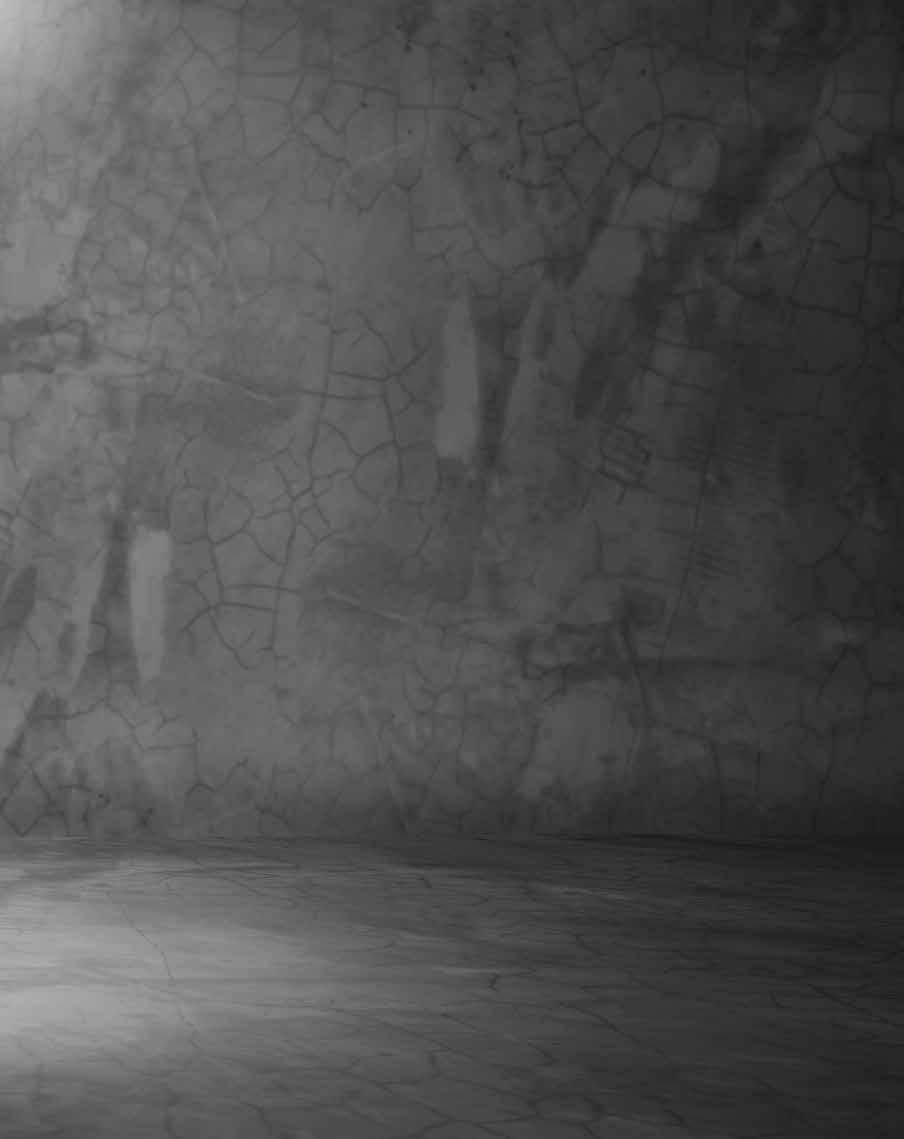
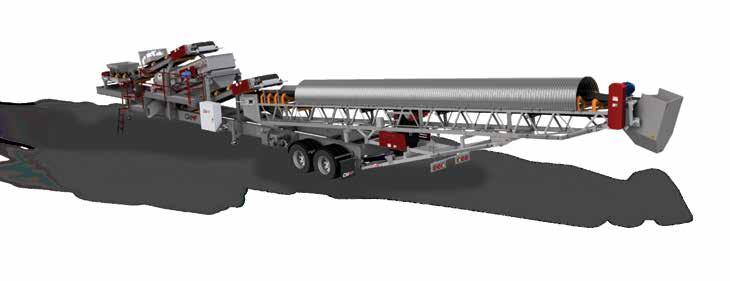
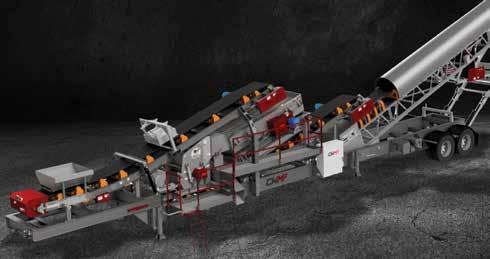

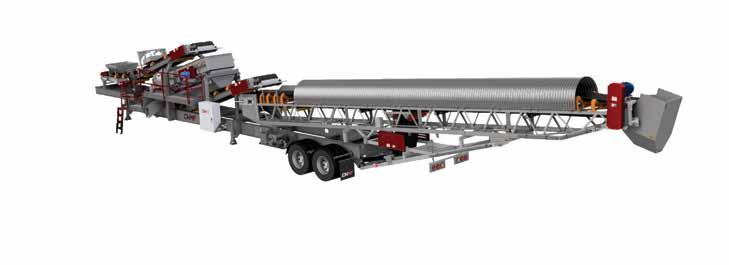
Pave, Maintain Safely
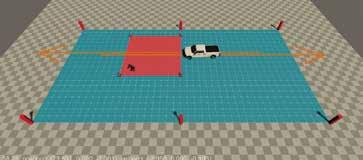
FROM ASPHALTPRO STAFF
While the June product gallery department will continue AsphaltPro Magazine’s focus on iron and services for the paving and pavement maintenance contractor launched around the CONEXPO-CON/AGG 2023 tradeshow and conference in Las Vegas, we’ve seen some important releases between the March event and press time. For example, the researchers at University of Houston and Durham School of Architectural Engineering and Construction, University of Nebraska-Lincoln, published in a recent Applied Sciences journal, “ViPER+: Vehicle Pose Estimation Using Ultra-Wideband Radios for Automated Construction Safety Monitoring.”
Those scientists—Alireza Ansaripour, Milad Heydariaan, Kyungki Kim, Omprakash Gnawali and Hafiz Oyediran—found the ViPER+ safety monitoring system for construction sites accurately tracked workers’ locations on job sites. Here’s part of the press release they shared with media April 20.
“The point of our research project was to enhance safety of workers and equipment on a construction site by tracking their location,” said Ansaripour, a computer science doctoral student at UH and first author of the study. “By tracking their location, we can monitor location-based policies related to the safety of workers and equipment in construction sites.”
These location-based safety policies are created during the planning stage of the construction site such as when Internal Traffic Control (ITC) plans are made. These policies define safe areas for workers and equipment or define a safe distance between them when equipment is operating in the construction site. ViPER+ automates the monitoring of these policies and detects any violations of the policies while workers and equipment are working.
ViPER+ uses ultra-wideband technology for location tracking. “These radios use large bandwidths to communicate, which enables them to perform location tracking more accurately compared to other wireless radios,” Ansaripour said. “This was the technology we used to track the locations of workers and equipment.”
The team’s ViPER+ system overcomes non-line of sight situations. These are instances in which trucks, construction loaders and other equipment block the signal between the transmitter and receiver in ultra-wideband radio transmissions.
Ansaripour and his colleagues implemented a correction method in their localization, or location tracking algorithm to reduce the error caused by non-line of sight.
TESTING VIPER+ IN CONSTRUCTION ZONES
ViPER+ is an updated version of the group’s initial system ViPER. The greatest difference between the two is the enhanced location tracking on ViPER+, which is more accurate in non-line of sight situations.
The team tracked locations through tags and anchors. Tags are small ultra-wideband radio transmitters, mounted to workers and vehicles to monitor their locations. Anchors are ultra-wideband receivers that receive signals from tags. The researchers then collected data from anchors to their computer server and estimated the location of vehicles and people in a construction site.
They tested their system twice in actual construction zones in Houston that were cordoned off for their experiment. But instead of real construction workers, students had to play that part.

“In our evaluation, all four construction workers had tags mounted. We also had one vehicle, either a truck or bulldozer with multiple tags on it, and another static vehicle was used to create a nonline of sight situation.”
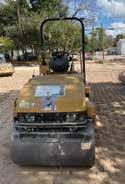
The first evaluation was in 2019 when researchers set up tags in an area measuring about 8,600 square feet called the tracking zone. Four students operated as workers in the tracking zone while Ansaripour was managing the data flow of the system and made sure the experiment ran smoothly. In 2022, a similar scenario was set up but at a different construction site.
“Alireza is one of those students with brilliant ideas and the work ethic to see these ideas to fruition,” said Gnawali, associate professor of computer science at the UH College of Natural Sciences and Mathematics and co-author of the study. “Having that combination is important to get these technical projects to be successful.”
FUTURE IMPROVEMENTS
Future changes to the system include ironing out user design issues such as alerting construction workers when they are too close to moving machinery.
“We also have an issue creating a tracking zone that covers all of a construction site, not just a portion of it,” Ansaripour said. “There are still some improvements that need to be made for this to become a commercial product, but our work provides insight on how a real-time safety monitoring system can be used for safety tracking in construction sites.”
Other authors of the study include UH’s Heydariaan, and from the University of Nebraska-Lincoln, corresponding authors Kim and Oyediran. This research project was funded through the National Cooperative Highway Research Program (NCHRP) Idea of the National Academy of Sciences under the award NCHRP-206.
ASTEC
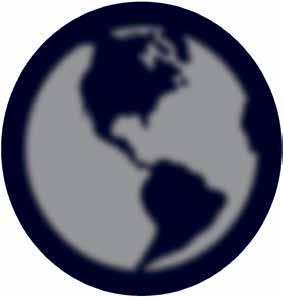
The team at Astec Industries, Chattanooga, displayed its newest generation of tracked highway class paver—the RP-175 and RP-195 F series—at its CONEXPO-CON/AGG 2023 booth. A spokesperson listed increased production, simpler maintenance, increased visibility and reduced noise as some of the focuses for the new 8-foot and 10-foot pavers.
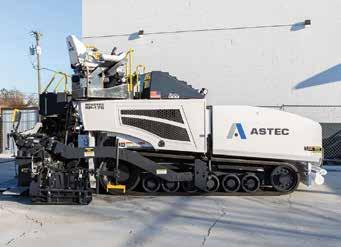
Keith Hagy, the product manager for paving, explained that the company seeks dealer input from customer advocacy groups, and learned that areas for enhancement in past paving equipment included noise reduction and serviceability.
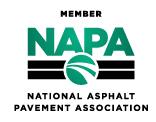
“We've gone from a single fan cooling system to a dual system, moved to the top of the machine, blowing away from the operator and away from the ground crew.” This improved the cooling efficiency about 15%, Hagy said, and the net result of moves and changes is a 20% reduction in noise.
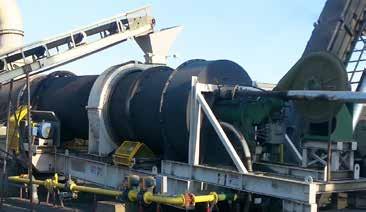
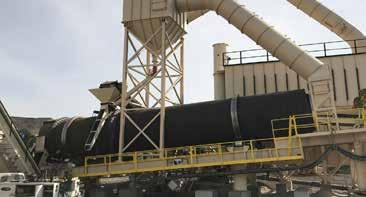
New lightweight hoods are designed to make accessing daily maintenance areas quick and easy, with no need for hydraulics. Hagy explained, “We've transitioned to a composite design with our side doors and hoods. Now one person can easily raise the hood and access the engine area without any need for extra hydraulics.”
The new F-model series has a State V engine, meeting the most stringent emission limitation required in the global market. Hagy said, “With the RP-175 we’ve upgraded to an engine
block that is smaller and more compact, but still provides the same commanding torque and horsepower.”
The RP-175 and RP-195 have a redesigned track system for improved durability and ease of maintenance. When it comes to hydraulics, the new track pavers have fewer connection points, easing maintenance tasks.
For more information, visit https://www.astecindustries.com/products/details/roadtec-rp-175-highway-class-asphalt-paver
BOMAG
BOMAG Americas, Ridgeway, South Carolina, offers the BOMAP Connect networked control and documentation program for all rollers working at the jobsite. All compaction data collected by BOMAP Connect is cloud-based, so compaction documentation can be quickly accessed from a computer or mobile device from anywhere an internet connection is available.
An operator activates the BOMAP app from an Android tablet or smartphone from a BOMAG roller, and the app connects with the machine’s interface and registers its parameters. All compaction passes are then automatically recorded. If required by job specification, the interface can connect with BOMAG’s Joblink via Bluetooth, and in addition to roller passes, the system also records the Evib value, asphalt temperature, and vibration frequency and amplitude of the BOMAG rollers, and adds the data to the documentation.
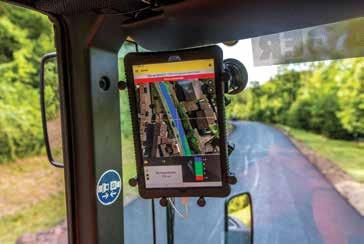
For other roller brands in the fleet connected to the networked jobsite, BOMAP Connect logs and transmits the number of passes, generating a pass map for the entire site. By equipping the rollers with an optional high-precision antenna, GPS reception is maximized to further increase documentation accuracy.
All rolling data collected from the site are combined in real time in the cloud application and displayed as a colored map in Google Maps. The colored areas indicate where compaction has already been achieved and where it is still necessary.
BOMAP Connect enables all roller operators to achieve optimum compaction in the minimum number of passes. BOMAP Connect enhances parallel planning of different projects within BOMAP, including construction site planning. Using 3D planning data combined with online map services, the system makes it possible to spec-
PRODUCT GALLERY
ify all relevant core project parameters and to plan the construction process in detail. Project planners can input compaction specification details and the deployed rollers display these project parameters when connected.
At the push of a button, BOMAP Connect transmits the final project parameters to the mobile devices of the roller operators, foremen and site managers. Project changes can be uploaded to the program and quickly be transmitted to the field in real time.
For more information, visit at https://www.bomag.com/us-en/technologies/overview/bomap/bomap-connect/.
CASE
CASE Construction Equipment announced its new E Series compact vibratory rollers with both double drum and combination (front drum and rear pneumatic tires) configurations. The rollers are designed with a high curb clearance, no overhangs and narrow drum widths ranging from 39 to 54 inches, depending on the model, to accommodate smallto mid-size compaction applications such as driveways, walking paths, commercial developments and existing structures.
The E Series features seven models and replaces the previous CASE compact vibratory roller line. Primary enhancements include a redesigned operator interface for intuitive operation and improved ergonomics. New control features include an electronic travel lever with an extended range of functions at the operator’s fingertips, including RPM settings, drive settings, sprinkler system controls, parking brake and more. An automated sprinkling system reduces water use when the machine is in neutral.
Operators can also choose between automatic or manual vibration engagement to meet their preference and to help avoid damage to the asphalt during starts and stops, while the offset tapered drums reduce asphalt tearing during operation around curves.
E Series rollers are compatible with the CASE ACE Force intelligent compaction system—a technology designed to improve compaction quality while requiring fewer passes to reach target specs. ACE Force also generates reports for applications where exacting specs and records of compaction performance are required.
A new operation mode selector allows the operator to select loading, working or transport to maximize machine performance and fuel efficiency. Operators are also able to choose between soft drive that delivers a smooth ride during asphalt compaction applications, and an optional hard drive setting that allows the operator to make swift turns. An optional rear differential lock function is available on combi models.
ROAD WIDENER
Road Widener LLC, Delafield, Wisconsin, displayed its patented FH-R material placement attachment during CONEXPO-CON/ AGG 2023. The remote-controlled attachment connects to most skid steers, compact track loaders, road graders and wheel loaders, operating off the host machine’s engine and hydraulics. It is available in left, right or dual dispensing configurations. The attachment is designed to streamline a variety of tasks including backfilling, road widening, road shoulder repairs, remediation and aggregate placement. The material is poured into the hopper at the top of the FH-R and then dispensed via remote control in adjustable lay-down widths from 1 to 6 feet. The attachment dispenses up to 20 tons of material in under 10 minutes, according to the manufacturer.
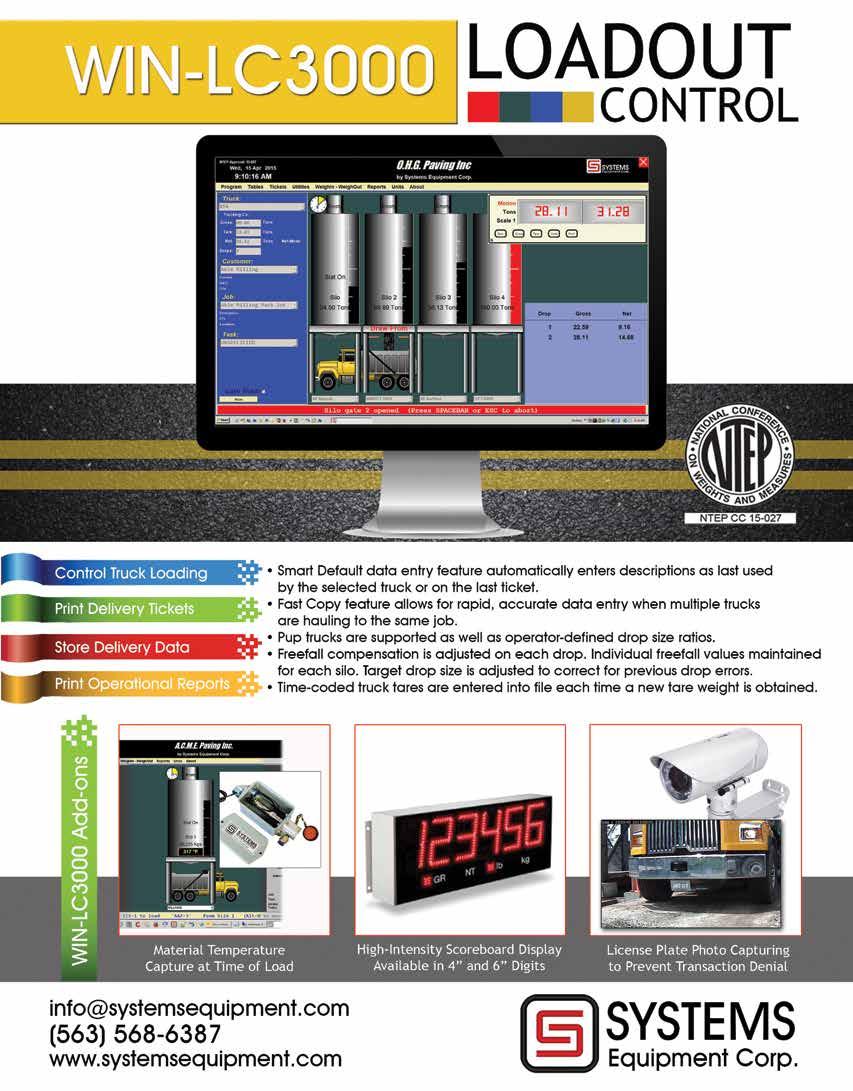
SCHWARZE
Schwarze Industries, Huntsville, Alabama, unveiled its 100% electric M6 Avalanche EV prototype sweeper at CONEXPO-CON/AGG 2023. The company stated: “It’s clear that electric sweepers present a great opportunity for the sweeping industry going forward—with their superior efficiency and zero emissions offering significant benefits for both operators and the environment alike.”
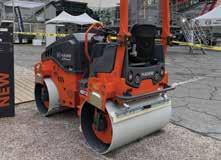
The manufacturer pointed to an upcoming decrease in the cost of electric sweeper machines as an expected advancement. “Whereas current models are still relatively expensive due to battery costs, the prices are projected to go down substantially with advances in battery technology and increased production. Governments worldwide are
TANDEM ELECTRIC COMPACTION
Two of the OEMs who introduced battery-operated machinery during CONEXPO-CON/AGG 2023 were BOMAG Americas, headquartered in Ridgeway, South Carolina, and Wirtgen Group, with American headquarters in Antioch, Tennessee. Of the offerings at their booths, attendees could’ve seen tandem rollers with that “e” designation.
Bomag’s compact BW 100 AD e-5 electric tandem roller hits the 2.5ton class commercial roller market with a 39.4-inch rolling width and is designed for parking lot, driveway, asphalt repair and soil compaction work. It features a low-voltage, 48V system with 25-kWh Li-Ion batteries. With its recuperative system, energy is recovered during braking, converting mechanical energy back into electrical.
The new tandem roller’s e-PERFORMANCE system is equipped with two electric motors—one dedicated to travel and the other for steering and vibration. A 26.8-hp electric motor propels the front and rear driven drums at working speeds of 0-3.1 mph and travel speeds reaching 6.2 mph. When traveling, the roller only uses one motor to conserve energy consumption.
The roller offers two vibration frequencies of 3,900 and 3,360 vpm (64 and 54 Hz) with a single
implementing EV policies such as tax credits and subsidies that can further reduce purchase costs.”
The manufacturer also pointed to improved efficiency via faster charging times and longer operating ranges as another positive development in electric sweepers.
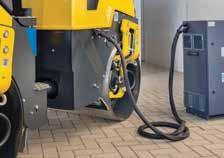
TAKEUCHI
Thursday, April 13, 2023, Takeuchi-US celebrated a significant milestone when the 1000th compact track loader—a TL12R2 model—rolled off the assembly line at the manufacturer’s facility in Moore, South Carolina. This 156,000-square-foot production facility, Takeuchi’s first in North America, officially began assembling compact track loaders Sept. 22, 2022.
LEARN MORE
amplitude of 0.20 inch, generating 7,194 and 5,395 pounds (32 and 24 kN) centrifugal force. Its intelligent vibration control (IVC) helps operators to know when compaction has been optimized to save on passes.
For more information, visit https://www.bomag.com/us-en/ machinery/categories/asphaltrollers/bw-100-ad-e-5-88075/.
The team at the Wirtgen booth shared information about its new HD 10e and HD12e tandem roller, saying, “Hamm delivers the first fully electric, battery-driven, tandem rollers. The models form part of the HD compact line series.”
A spokesperson explained that the series follows other roller family trends with drum configuration flexibility. “Some models are fitted with oscillation drums including the world’s first e-combination roller featuring oscillation. Not only is compacting with these emission-free, it’s also ultra quiet.”
Product specialist Tim Kowalski spoke further about the drum configurations, reminding us the equipment can compact forward with vibration on the front drum and oscillation on the back, then change modes with the flip of a switch so the machine still provides vibration on the leading drum and oscillation on the trailing drum as the operator rolls in reverse.
The new HD 10e and 12e feature a 48V lithium battery, hydraulic pumps, and all electric motors. The machines have been released in Europe first and are set to be made available in North America later in 2023.
For more information, check with your local Hamm equipment dealer.
“We started out with just 10 employees at this facility a few short months ago,” said Ralph Wabnitz, director of manufacturing for Takeuchi-US. “Today, we have 117 on staff, with a goal of 140 by the end of 2023. Our plan is to assemble all Takeuchi CTL models here in Moore by the end of 2023. I’m very proud of what our team here has accomplished, and I look forward seeing what new milestones we’re able to achieve in the months and years ahead.”
WESTERN GLOBAL
Western Global has introduced two diesel exhaust fluid (DEF) storage solutions, the DEF Cube and Top Tote, to its lineup. The DEF Cube is a stand-alone storage tank designed for large quantities of DEF. The Top Tote can be attached to the top of a TransCube Global fuel tank for a 2-in-1 diesel and DEF solution. Both the DEF Cube and the Top Tote provide a commercially available universal solution for DEF storage and offer an option to help operations meet DEF requirements for Tier 4 Final engines.
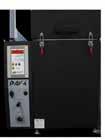
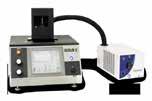
The DEF Cube has a blue, cube-shaped design and a capacity of 132 gallons. This can be situated next to on-site fuel storage tanks so operators can fill equipment with both fluids at the same time. This DEF storage tank has the same features of the TransCube Global, including four-way forklift pockets for easy transport, lockable compartments for enhanced security and a stackable design.
The Top Tote has a low-profile design to keep the overall height below 6 feet to eliminate ladder or harness use to access the ports.
This DEF storage solution has a capacity of 110 gallons and can attach to three models of TransCube Global fuel tanks—the 20TCG, 40TCG or 50TCG. This creates a 2-in-1 storage solution that holds both DEF and diesel at the same time. Additionally, Top Totes can be daisy-chained on the 40 and 50 TransCube Global to maintain the proportional relationship of approximately 10% of DEF per gallon of diesel. The Top Tote also includes a reusable nylon Micro Matic RPV valve, which is designed to pair with RSV/RPV couplers to provide closed liquid transfer.

YANMAR
Yanmar Compact Equipment, Grand Rapids, Minnesota, launched a new line of compact track loaders—the TL65RS, TL75VS, TL80VS and TL100VS—during CONEXPO-CON/AGG 2023. The new compact track loaders range from 67 to 103.5 horsepower.
The loaders incorporate Yanmar’s optional SmartAssist telematics from the company’s mini excavator line. Features range from error detection and notification to real-time operational status updates and daily work reports. SmartAssist also includes integrated theft protection, allowing the machine’s owner to set a range from a specific location and trigger an alert if that range is exceeded. A state-of-the-art, touchscreen 7-inch color display also comes standard with each of the new compact track loaders for improved convenience on the jobsite.
ASPHALT BINDER TESTING
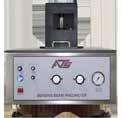
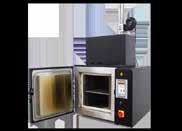
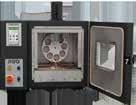
How to Find Your Next Paving Foreman
BY SANDY LENDERWhile you can bring a novice into the asphalt industry to serve as a laborer on the crew—teaching him or her the ropes alongside veteran workers—you won’t hire an intern for the summer to be the crew’s foreman. That’s not a wise business move for a number of reasons. The foreman for a paving, maintenance, milling or other asphalt-related crew should come from the experienced crewmembers you have on hand.
That’s easier to type out for a how-to article than it is to put into practice, so let’s have the experts talk about it for a minute.
In today’s climate where skilled workers are worth their weight in gold, you may hesitate to move a skilled paver operator or excellent breakdown roller operator from their post into the foreman role. John Ball, the proprietor of Top Quality Paving & Training, Manchester, New Hampshire, shared that he was tasked with finding his successor when he wanted to move up to foreman when working at Pike Industries back in the day.
“I was running the paver and was ready for the next responsibility,” Ball said. “I asked [my boss] what I had to do to get that promotion. He told me to find my replacement first. So, I had to train the guy on the screed to take over running the paver before I could move up.”
Melissa (Missy) Paulus, the asphalt paving and equipment pool manager, Maintenance Operations Division for the Seattle Department of Transportation (SDOT), takes on the responsibility of building up the person who will fill in. For example, she mentored and promoted a senior raker on the paving crew to crew chief. That made him the boss and would have left a hole in the crew, but she hired another raker to succeed him.
“I like to mentor and help my employees grow in new directions,” Paulus said. “If I see an employee, and I believe they have other skill sets, I will mentor them to reach skills to fill upward mobility.” She then promotes the next person in line that has teachable skills to fill in for the dump guy or equipment operator she’s moved up.
MORE THAN PAVING SKILL
There’s more to becoming a foreman than knowing how to operate equipment. Bryce Wuori, CEO of Pavewise, Bismarck, North Dakota, looks for a willingness to listen, the ability to be a leader, and effective communication skills in the person he’d promote into the foreman role, accentuating the worker’s understanding of the equipment the people on his crew are operating.
“I believe the paving foreman should concentrate on the paving equipment, crews and operations,” Wuori said. He shared that it can be a negative if the foreman “gets in the mix of running equipment too much.” This can be distracting. “They can lose concentration on the paving operations. If there is one specific tool they should understand, it should be the paver and screed.”
Randy Blount, the CFO of BuildWitt and formerly president of Blount Contracting, put a high degree of importance on personal accountability for the foreman he looks for in the company. You want a person who is accountable to themselves and their team, he said.
“When you move into a new role, you will certainly make mistakes and a good leader will own up to those mistakes and improve,” Blount said. “This leader’s example of accountability will help them as they hold their team members accountable.”
This will also be someone who “knows what they don’t know,” Blount continued. “I want
someone that is humble enough to ask the crew or their boss for help or advice.”
Blount also looks for someone who concentrates on the people.
“People are what makes a crew. I want someone that understands it is not the equipment but the people that deliver safety, quality, production, etc. People want to know they matter and they contribute (are
Traits You’re Looking For
The next great paving foreman could be standing right in front of you. Our experts shared some of the traits they look for—although this isn’t an exhaustive list—in a person who would move up and take on more responsibility with the paving crew.
• Accountability
• Asphalt knowledge
• Communication
• Conflict-resolution skills
• Good attitude
• Leadership potential
• Open-mindedness (ability to change)
• Paving equipment knowledge
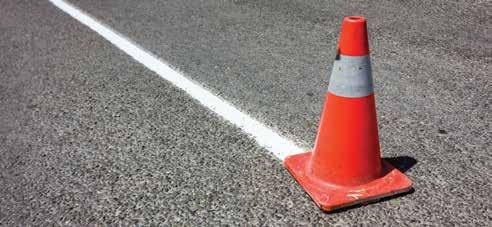
• Planning ability
• Respect for new guys & co-workers
• Willingness to teach (and learn)
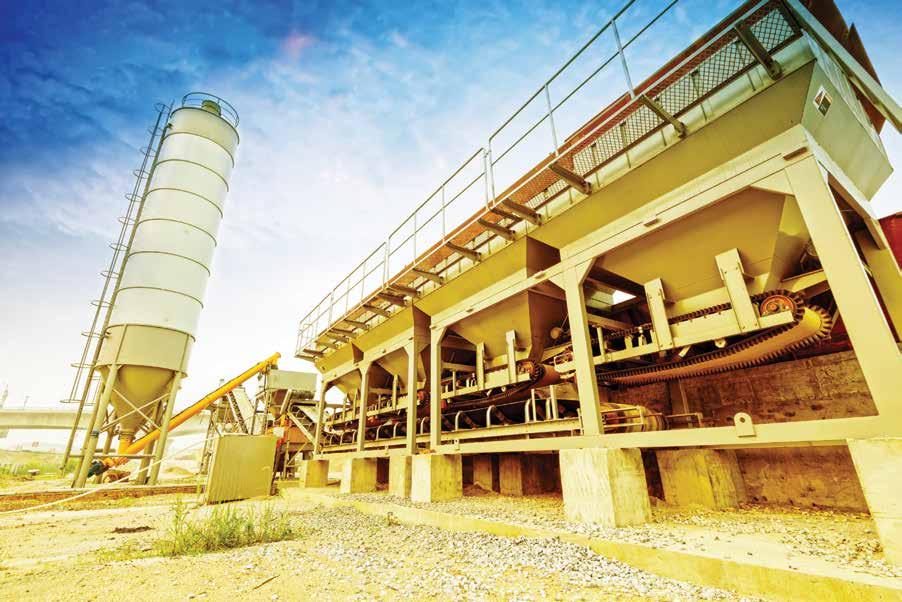
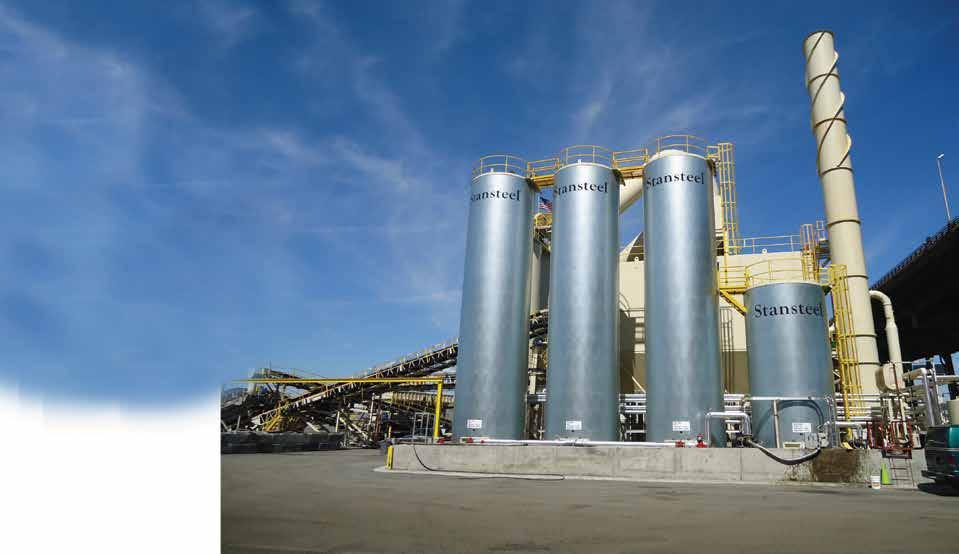
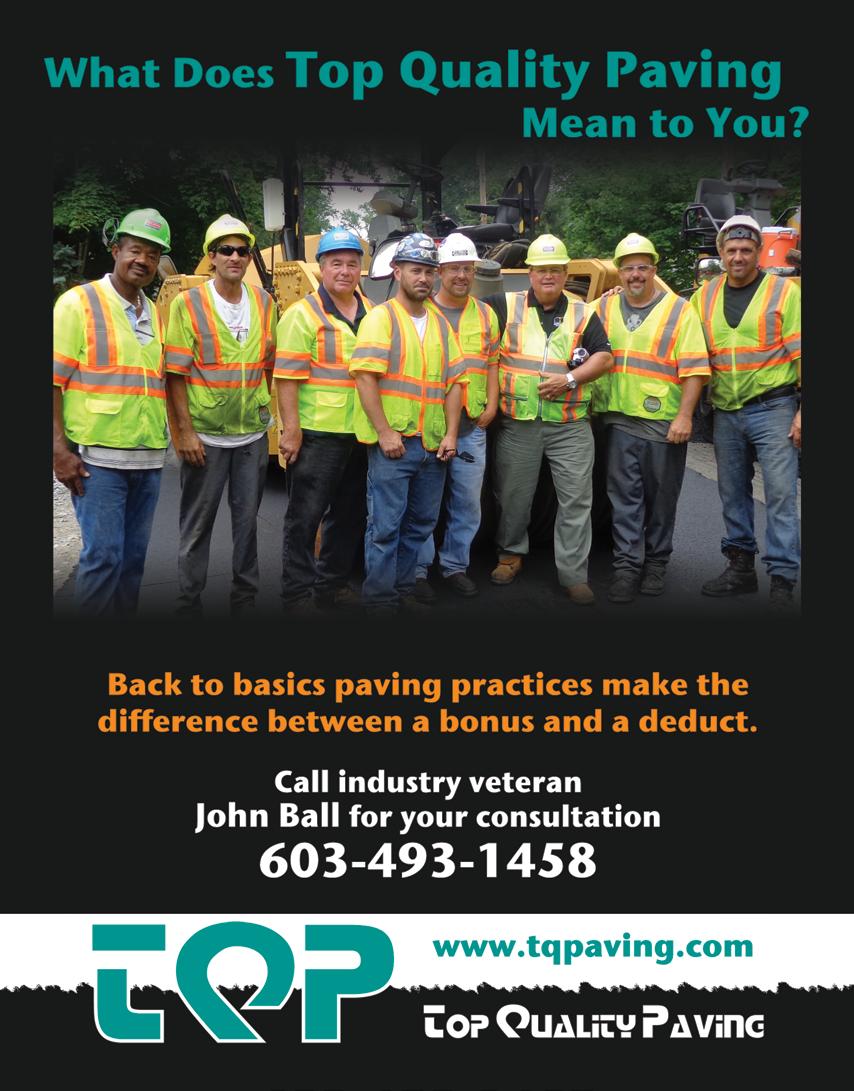
valued). I think the ideal leader has demonstrated that while on a crew.”
The experts in the field have seen their share of great foremen over the years.
“I’ve seen a lot of equipment operators work up the ranks to foreman and superintendent and one of the most important things they must do is communicate effectively and understand how to delegate tasks to others,” Wuori said. “It’s difficult to move operators into these positions when they are good at their jobs but if they are the leaders we expect them to be they will teach a new employee the ropes. Steve Haugen from Northern Improvement is one top notch supervisor and Jeff Momerak from Mayo Construction is another one that has worked his way up and is an amazing superintendent. Communication is key in these positions.”
“My foreman is Paul Pablo,” SDOT’s Paulus shared. “He is key to my success. He’s Mr. Organized. He plans down to the T.” She said Pablo always holds a pre-construction meeting with his senior rakers and is very knowledgeable about asphalt paving and all it entails. “I have also mentored him, so he now fills in for me as asphalt manager as well. It’s a big win to have that kind of employee trust and knowledge.”
PREPARE YOUR NEXT FOREMAN FOR SUCCESS
Echoing the earlier example Paulus gave of promoting a senior raker, Blount’s advice suggests your next foreman could be anyone on the crew and it’s best to keep your eyes and mind open to the possibilities.
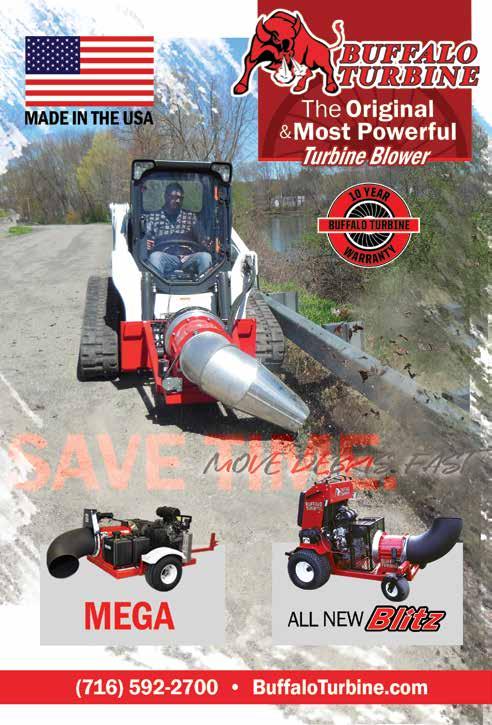
“I’m not sure promoting the best operator is a wise prerequisite,” Blount said. “Operating equipment is an incredible skill and some people that operate equipment have leadership characteristics and some don’t. I am looking for who is leading, teaching, putting the team first and learning from their mistakes. I would make sure everyone on the crew knows these are what you see as keys to moving into a leadership role. There might be a laborer doing all these things and I’m going to start having conversations with that person about how to develop them into a foreman.”
Blount reminded readers that a person can lead others without being a supervisor and shared: “If we are focused on build-
ing more capable leaders in all levels of our company, then there will be more people who are able to take on a leadership role. As humans we want to win and often the reservation around additional responsibility is the fear of failure. Failure can look like: working so many hours that your family life suffers, your friends no longer want to talk or work with you because you don't treat
them right as the ‘boss,’ the additional stress makes it hard to enjoy building, etc.
“Preparing people for this new role before they arrive is key. People can't show up to a marathon race without training and be successful. Why do we think we can promote someone into a leadership role without lots of preparation and expect them to be successful?”
Teach Your Crew What it Takes to Pave a
Bonus-Worthy Mat
AsphaltPro magazine joined forces with hall-of-fame paving consultant John S. Ball III of Top Quality Paving & Training to bring you the newest online training resource for your crew: Asphalt Paving 101.
The course is available on any device, anytime, anywhere to train your entire crew. Your single subscription to the best curriculum of all time gives you access to train all of your employees, each time you bring in a new hire.
Asphalt Paving 101
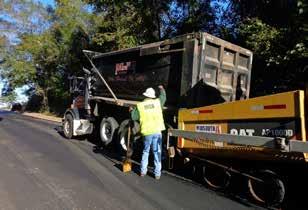
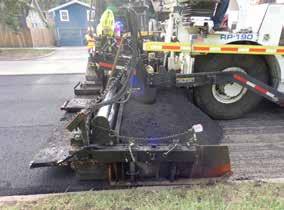
In this course, your crew will learn:
• How to stay safe on the job site
• How to build a takeoff ramp
• How to determine fluff factor
• How to determine yield
• How to prep for real paving in the real world

• How to maintain equipment the right way
• Job responsibilities for each paving crew member
• and so much more…
Purchase your access to the course at: training.theasphaltpro.com
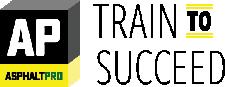
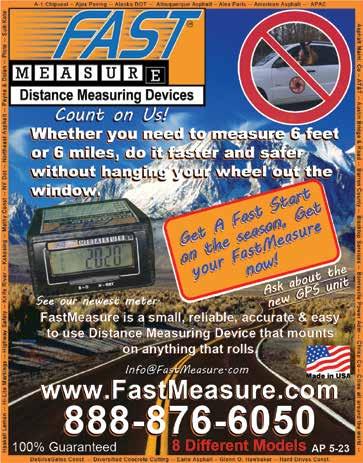
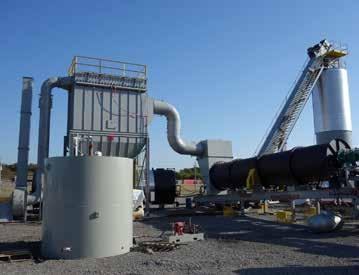

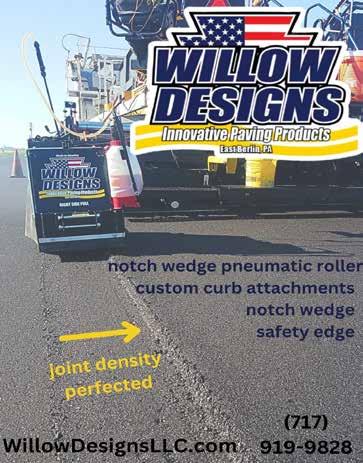
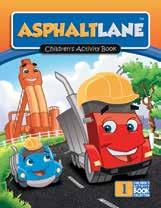
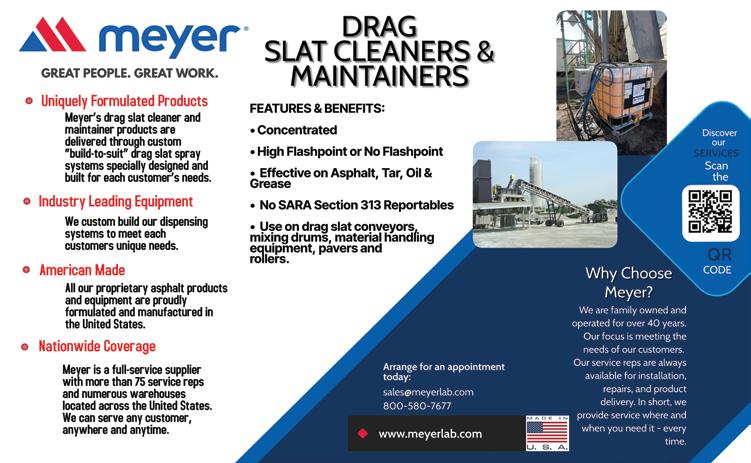
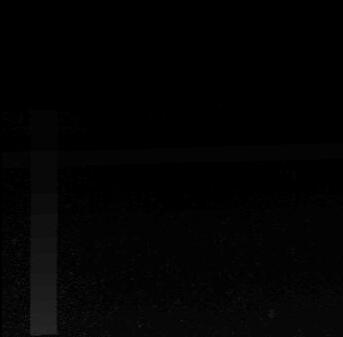

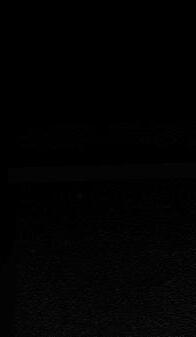
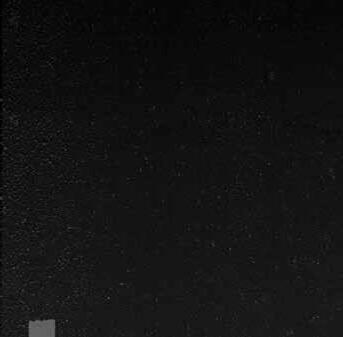
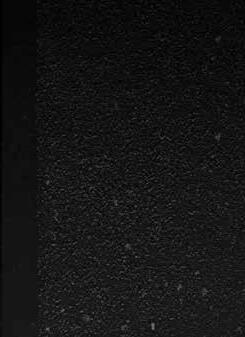
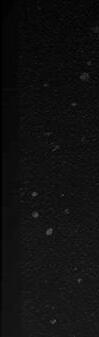

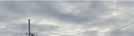

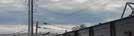

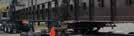

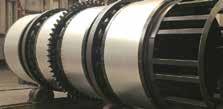
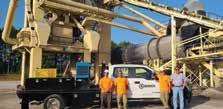
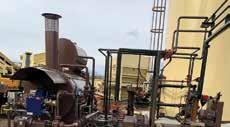
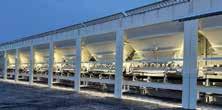

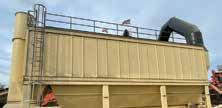
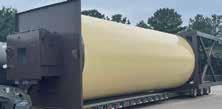
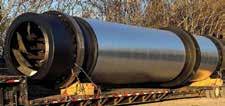
App Connects Crew Mental Wellness
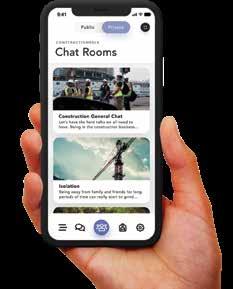
The team at iRel8.org recognized the disturbing trend toward an increased risk for mental health issues such as depression, anxiety and substance abuse in the construction industry and created an environment within its iRel8 app specifically for our industry. “ConstructionRel8, within iRel8, is live today and available free to anyone who downloads the app and uses the code ‘construction’ when they sign up,” shared Dion Gonzales, co-founder of iRel8.org.
iRel8 currently serves individuals, first responders, active military, veterans, state governments, charities, and now the construction industry. Co-developed with Microsoft, iRel8’s enterprise technology is positioned to help promote mental wellness globally. The app is designed to offer companies a platform where workers can log in—anonymously, if they wish—and communicate with colleagues about the stressors affecting their everyday lives. They have the opportunity within the app to share trials and triumphs, find support, and offer encouragement for one another.
One additional offering to companies within the app is the use of short-form video, which the team has named Peeroic. This is a user-generated video platform that integrates with the anonymous chat apps without selling or tracking data. And the team works to protect users against negative trolling.
“Anyone can post videos to Peeroic; however, ConstructionRel8 users can target their videos to others in the construction industry based on their initial signup using the “construction” partner code,” Gonzales shared. “We have multiple layers of moderation built into the platform including community-based, a moderation bot, and human oversight.”
Gonzales shared that the community-based moderation is highly effective because people are using the app for the right reasons. “We’ve only removed one user from our app ecosystem in 5+ years.”
Within the app, professional counselors are available as well. “We definitely have licensed professionals who are in the app, either actively chatting or as a resource when someone is ready to talk with a professional,” Gonzales shared. “Since the app is based on chatting confidentially with others who have ‘been there, done that,’ we don’t offer professional services directly in the app; that said, users can find professional resources in the app and then contact them.”
Although resources are made available, users aren’t inundated with advertisements. “We don’t have “advertisers” per se in the app, but we do allow qualified companies to be in the marketplace and/or resources section where users can see products/services and purchase. We have a recommendation engine that pops up qualified companies based on the user’s request. For instance, if someone types a message saying, ‘I’m having trouble sleeping,’ the recommendation engine will search companies and resources and show a few options to the user to select (or not select from). This, in combination with peer driven recommendations, en-
CONSTRUCTION
sures a human-first connection supported with best-in-class technology.”
The app is designed to allow a company freedom to protect and help workers. For example, the company could limit access to only its employees or could elect to give access to its employees plus those of subcontractors and others in a region or network.
Gonzales explained: “We accommodate both situations. Some companies who are large enough want a white label app or a private section in iRel8. A private section allows members to chat privately (and anonymously) with invite only members from the same company, plus they can connect with any other construction professional from any other company around the world—though primarily in the United States right now.”
iRel8 supports 54 different languages.
A prime contractor for a large, multi-year project could grant access to subcontractors and vendors. “This is certainly something we support; a prime could set up an invitation only group in the app and invite subs and vendors to be part of that group,” Gonzales said. “Since the group is invite-only, it acts as an exclusive section. The phrase ‘your organization and those you serve’ is meant for larger organizations that understand the critical importance of mental wellness and want to provide the app to their employees, members or those they serve.”
For more information, visit iRel8.org.
“27% OF
WORKERS REPORTED SYMPTOMS OF DEPRESSION, COMPARED TO 13% OF WORKERS IN OTHER INDUSTRIES.”—OSHAThe ConstuctionRel8 app is based on chatting confidentially with others who have ‘been there, done that,’ in the construction industry with the goal of prioritizing the mental health of workers.
ROCK TO ROAD
What’s Next In Paving
Introducing the new Roadtec RP-195 and RP-175 highway class pavers. These tracked pavers are optimized for usability with an innovative layout that significantly decreases noise, maintains visibility and runs cooler. Modern controls are right at your fingertips and a solid cast undercarriage design translates to easier maintenance and increased durability. Keep things running smoothly with the unparalleled material handling and mat quality you expect from Astec.
See the new RP-195 highway class paver.
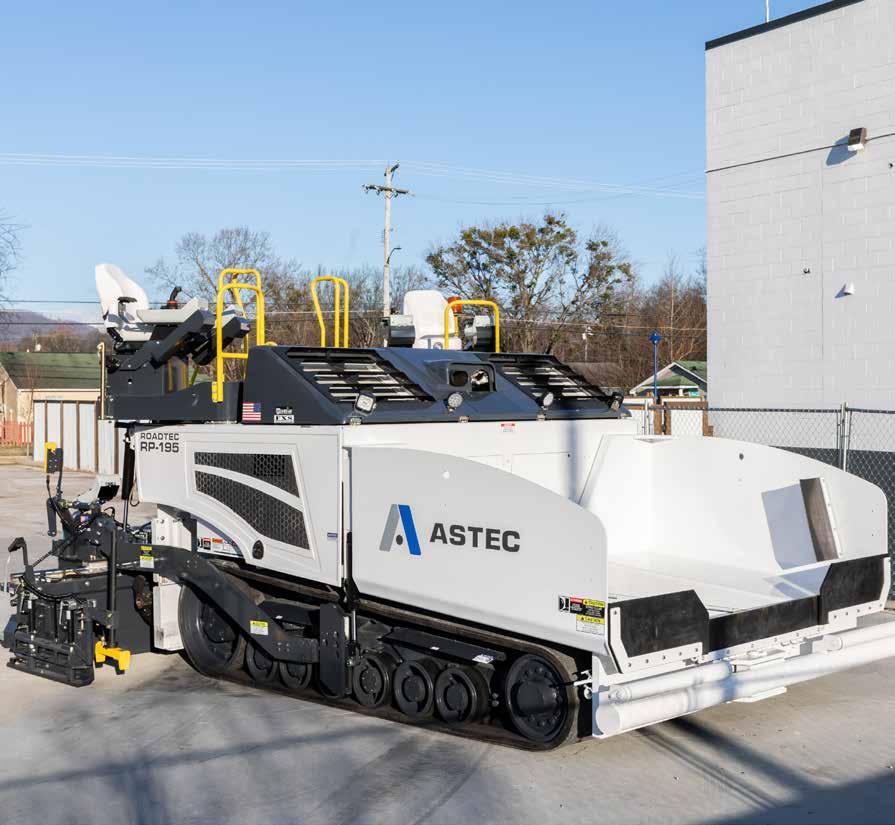
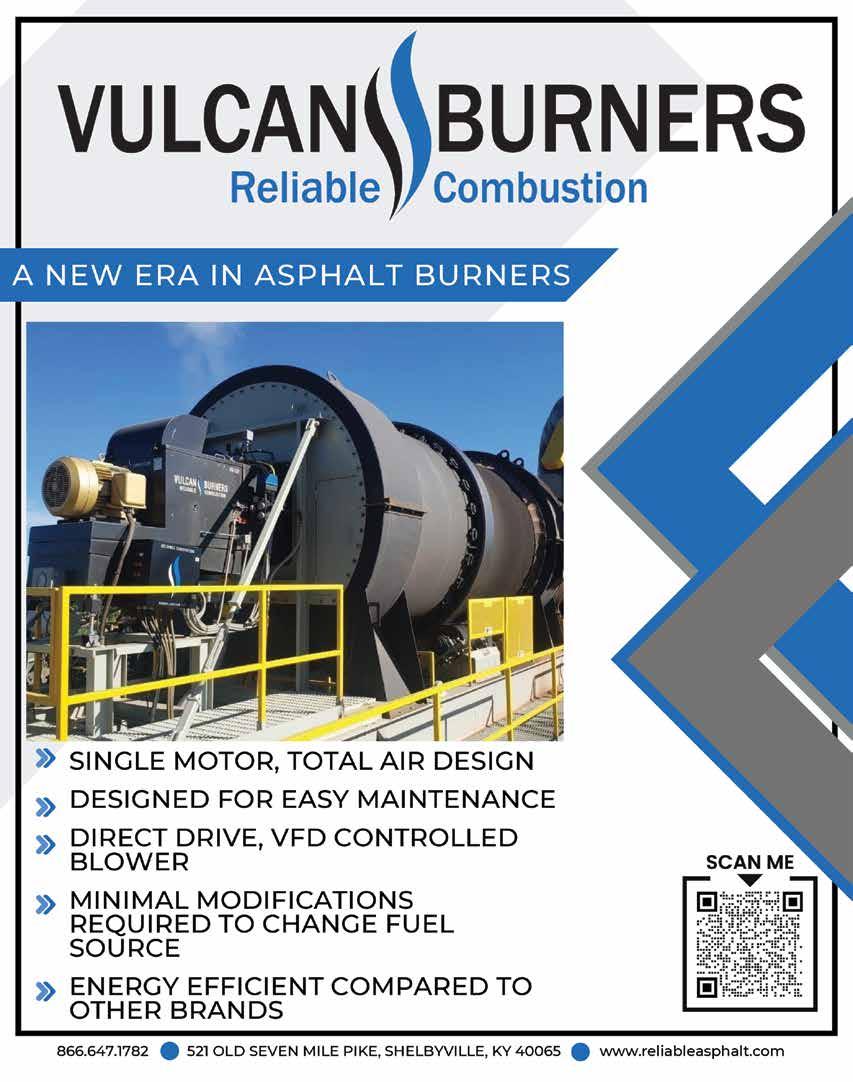