
5 minute read
Visión LEAN Manufacturing
Por Jorge Enrique Randolph Guerra Director General en Randolph Manufacturing
Don Juan tenía razón, pues nadie lo habría percibido, de no ser por un detalle: todos los pobladores pensaron e hicieron lo mismo, con tal de no perder esa jarra de vino de su producción”.
Más allá de las libertades que toma la ficción —como el hecho de que es prácticamente imposible que un país elimine los impuestos o que surja un vino exquisito luego de mezclar los mejores vinos de una región—, este relato nos muestra el perjuicio que pueden provocar las malas prácticas, por un lado, a los buenos acuerdos o alianzas estratégicas que se consolidan en un momento determinado y, por otro, a las propias actividades que llevamos a cabo en nuestras empresas o proyectos personales. Esta historia es, digamos, una versión libre del cuento que aparece en Recuentos para Demián, de Jorge Bucay, y que el propio autor, a su vez, tomó del Libro de los enxiemplos del conde Lucanor et de Patronio, escrito hacia el año 1340 por el infante Don Juan Manuel, en el que narra diversas enseñanzas que el conde Lucanor recibe de su siervo Patronio, cada una de ellas contada a manera de ejemplos, con el propósito de ofrecer una enseñanza y que ahora me será de utilidad para explicar el concepto de LEAN manufacturing.
Una filosofía de mejora continua
La manufactura esbelta o LEAN manufacturing, consiste en un conjunto de herramientas diseñadas para eliminar todas aquellas prácticas y acciones que no agregan valor a los procesos, productos y servicios de una empresa u organización. Bajo esta dinámica también se busca reducir el desperdicio de recursos, tiempo, materiales y energía, además de erradicar todo lo que no se requiere, con el propósito de mejorar las operaciones de la compañía. Todo esto en un entorno en el que prevalece el respeto por los trabajadores.
En la actualidad, el término LEAN manufacturing es ampliamente utilizado en la industria, en virtud de que se asocia a la excelencia y a la competitividad en el mercado global. Así, la visión LEAN manufacturing se basa en principios de mejora continua, colaboración interdisciplinaria, compromiso con el cliente y sostenibilidad.
Esta visión surge en la filosofía Kaizen, un palabra de origen japonés que significa ‘moverse hacia algo mejor’, como lo expresan las dos partes que conforman esta palabra: 改, kai, ‘cambio’, y , zen, ‘bueno’ o ‘mejora’. Básicamente, esta filosofía propone implementar pequeñas, pero constantes mejoras, en el entendido de que esta constancia se traducirá en beneficios a largo plazo para una empresa u organización.
Al tratarse de una palabra de origen japonés, podríamos pensar que la filosofía Kaizen se desarrolló en el país del sol naciente; sin embargo, surgió en Estados Unidos de América con el nombre de Training Within Industry, durante los programas de entrenamiento en la industria. En un segundo momento, el concepto se implementaría en Japón, donde finalmente se consolidó para luego expandirse a distintas partes del mundo.
Para poner en contexto la historia del LEAN manufacturing, en la segunda mitad del siglo XX, Japón se encontraba en la ruina, debido a la Segunda Guerra Mundial. Este escenario sometió al país a una impresionante falta de recursos y a condiciones precarias. Paradójicamente, este panorama sería propicio para el florecimiento de la filosofía Kaizen, pues postulaba pequeños cambios en todos los niveles, en especial, en lo económico y en lo social, bajo la perspectiva que exigía ese momento: optimizar recursos. Para lograrlo, esta filosofía se basa en cuatro ejes de acción:

1. Planeación , un eje que se entiende como el momento en que se fijan objetivos o se impulsa el desarrollo de soluciones y mejoras.
2. Realización, es decir, un eje que coincide con el momento en que se ponen en marcha las acciones para alcanzar los objetivos que se establecen durante la planeación.
3. Comprobación, concebida como el proceso enfocado a analizar las soluciones propuestas o el objetivo a alcanzar.
4. Actuación, un eje que se correlaciona con los resultados alcanzados, esto es, mantener los procesos y estrategias para implementar soluciones, o bien, alcanzar los objetivos.
En conjunto, estos mecanismos minimizan las pérdidas y maximizan el valor añadido al cliente. Gracias a la filosofía Kaizen, en un lapso de aproximadamente 15 años después de que terminara la Segunda Guerra Mundial, Japón comenzó a recuperar su salud financiera y económica, al grado de posicionarse como uno de los estados más estables a nivel mundial, puesto que aún conserva en la actualidad. Esta afirmación pudiera generar dudas en la actualidad, pues Japón es el país más endeudado a nivel mundial, debido a que lleva décadas impulsando el gasto interno para mantener su economía en marcha. Lo anterior como consecuencia de que sus ciudadanos y empresas, cuyo papel es clave en el crecimiento económico, son muy reacios a consumir, de ahí que el estado se vea obligado a gastar por ellos (Orgaz, 2023). A pesar de esto, el país genera una profunda confianza y posee una gran reputación, y es por tal que los inversionistas sigan pensando en Japón como un buen lugar para confiar su dinero.
Hacer más con menos
El modelo de gestión de LEAN manufacturing está diseñado para minimizar las pérdidas y maximizar el valor agregado para los clientes. Como mencioné antes, es un sistema que tiene su origen en la industria automotriz, pero que poco a poco encontró aplicaciones en otras empresas, industrias y sectores. Dicha visión ha sido particularmente exitosa en lo que se refiere a mejorar la competitividad empresarial, entendida como la capacidad de una empresa para ofrecer un producto o un servicio que cumple o supera las expectativas de los clientes, a través de un manejo más eficiente de los recursos, en contraste con otras empresas del mismo sector (García, 2015). Por tanto, la visión LEAN manufacturing es un valor fundamental para la permanencia y trascendencia de las organizaciones.
Ahora bien, la pregunta que surge es una: ¿cómo lograr que funcione? En un entorno altamente competitivo, las empresas intentan minimizar los costos para operar con mayores márgenes de beneficio y ofrecerles una mejor relación calidad-precio a sus clientes. Para implementar esta visión en una empresa, es necesario identificar aquellos procesos que provocan desperdicios de tiempo, materiales y recursos, como lo pueden ser las actividades que demandan mucho tiempo, los desperdicios en el flujo de materiales, el inventario excesivo y los equipos obsoletos. Lo anterior significa que la organización debe evitar a toda costa que los procesos interrumpan el flujo de producción, al mismo tiempo que ponen en marcha mecanismos para minimizar los retrasos y los procesos redundantes, pero también para agilizar las tareas necesarias.

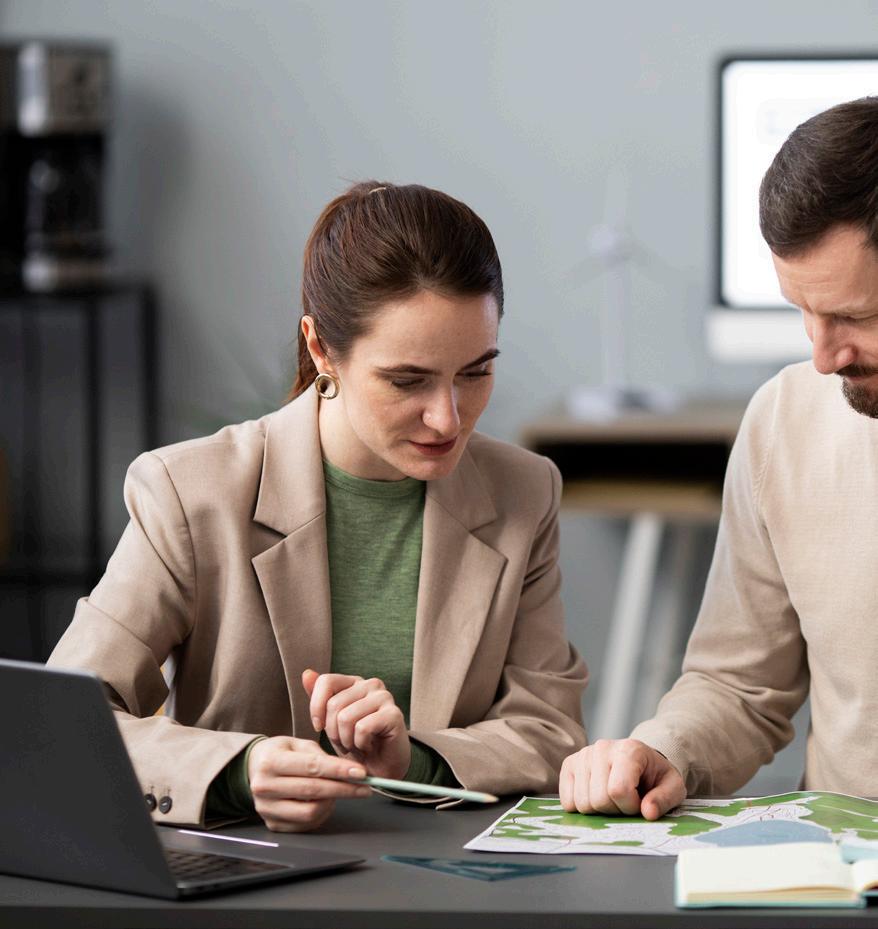
En consecuencia, la visión LEAN manufacturing es una filosofía de mejora continua: a medida que se optimiza un aspecto, también debemos considerar los próximos pasos a optimizar en aras de alcanzar una mayor eficiencia. Para llegar a resultados más notables, lo ideal es ejecutar pequeños cambios, con el propósito de reducir las prácticas que interrumpen o entorpecen el flujo de trabajo. Estos cambios pueden ser de distinto tipo, desde los más complejos o ambiciosos, como optimizar o automatizar procesos en el diseño de una línea de producción, hasta los más sencillos, como lo sería promover una mejor coordinación entre las áreas de la empresa, aunque para muchas empresas pudiera ser a la inversa: lo complejo pudiera ser mejorar la comunicación entre áreas y no tanto la optimización o automatización de las líneas de producción. Por supuesto, sea en el polo de los cambios sencillos o en el polo de los cambios complejos, se requiere dedicar una notable cantidad de tiempo para poner en marcha los cambios, pero los beneficios que se obtendrán serán igualmente notables.