
5 minute read
Kirby Lumber Company LaunchesHuge Hardwood Institution
For the past tw,enty-two yeers the Kirby Lumber Company has ,been one of the largest manufacturers of Yellow Pine in the South and notwithstanding the fact that this com,pany still has some four 'billion feet of standing pine stumpage, it is now commencing the rnanufacture of hardwood upon a lartge scale.
Two years ago in a settlement of its stumpage contract with the Houston Oil Company, the Kirby Lumber Company acquired all of the h,ardwood owned by that company, and this stumpage, in addition to the stumpage then owned by the KirblLumber Company, gives it hardw,ood holdings of conside.rably over one billion feet. These figures are based on estimates of expert hardwood m,en who have cruised the timber and includred in their estimates onlv high grade hardwood stumpage. The Kirby Company now owns all of the pine and hardwood timber on approximately one million four hundred thotrsand acres.
The main stand of this hardwood tim.ber is in t'he Neches River Valley, and'throughout the entire holding 1gd gum predominates. Approximate,estimates of the relative quantities of various species of hardu'ood indicate 'about 60 per cent red lgu'm,r lg per cent 1r'hite oak, 5 per cent red oak, 5 per cent red cypress and 10 per cent m'iscellaneous such as ,ash, tupelo, beech. magnolia, and so forth. Because of the predominance of red gum the Kirby hardwood operations will feature as their specialty in the h,ardwood trade, "Neches Valley Red Gum." This gum is extra large in size and of particularly fine quality.
Pine and Hardwood Segregated
When the question of manufacturing this hardwood stumpage was approached, Kirby officials at once recognized the, necessity of completel,v segregating the yellow prn,e and hardwood operations, realizing that the logging, manufacture and sale of hardwood is an entireiy different business from yellow pine, and the only point in contact between the pine and hardwood operations exists in the instructi,ons to pine logging superintendents to cut and ship to the Voth mill only'the very finest hardwood logs,gonvenient to yellow pine logging operations. Separate hardwood logging operations were, immediately arranged for in strictly hardwood territory as a main sourc€ of Jupply. for the hardwood nr{ills. . Foi the operation of the hardivood mills a complete hardwood crew from general manager to water Fy has been organized, so that from the outset every foot oJ hardwood lumber manufactured' will be handled bv people'fully acquainted with the hardwood business etim,,inating all experiment. This principle will be ,rigidly adhered to.
.At_ the present time the Voth Hapdwood Company, which is a subsidiary of the Kirby Lumber Company, is operating a double band mill at Voth, Texas. preient plans of the company include the building of two more mills similar to the mill now in operation, ihe installation, of one or two veneer units, the building of a hardwood flooring plant, ari.d billet mills for the manufacturing of hickory tim'ber, as well as ten small rntills designed to-cuit ties from the small and rough timber. Some of these tie mills will follow the ,h,ardwood logging operations and clean up the woods, as only the high grade logs will be sent to the large mills, while other mtills will be put into scat- tered hardwood tracts cutting the low ,grade tim,ber, th'e select logs being sent to the large mills as accumulated.
Exclusive of.the capacity of the tie mills these plans call Ior a hardw,ood production of s'eventy-five million feet per year by the end ol 1924.
Mill Is Modern and Up-to-Date
The mill at Voth is onet of the most modern and up-todate hardwood plants in the United States, and in its -construction and operation incorporate a number o{ unusual featu.res which are w,orthy of revierv.
The mill itself is equipped throughout with Filer ct Stowell machinery havin'g two eight foot ,band, mills; an eight foot bancl resaw; two double edgers; a ten saw trimmer; slab slashers ; fu,el hog and butting saw for the trimrming of tim'bers. The daily capacity is one' hundred' thousand feet. The mill has been runn,ing three and one half months, and during the month of Novernbet' ,average d better than ninety-one thousand feet per day, with the best day's cut of one hundred and six thousand feet.
From the mill the lumber passes to a double-deck sorting table two hundred feet lon,g, the sixteen foot lengths passing over the upper deck, the shorter stock going to the lower d,eck. On the sorting table the lurnber is separa'ted, each kind, grade, length and thickness going into a separate package of uniform width and height. i
These packages are picked up by an "Industrial Works" eighteen ton, specially built locomotiv,e crane an,d, loaded on flat cars set fore and aft of the crane, each flat car carrying seven packages. Each packaig'e rests on two pieces of three by three o'ak, ,about six inches longer than the width of the package. These, bearings fit int,o stirrups on the crane chains. Packages from the upper deck are picked up direct, while'those from the lower deck are run out on to ,a transfer car.
The crane conveys these bulk packages to the stacking platform which is provided with fifteen separate track- ways. Six of thes,e are built with a slight incline toward the stacking table atr the rear. The crane places the bulk packages on short dry kiln trucks. These packages are run to the stacking table as .requi,red, and th.e empty trucks returned to the front. There are six stacking tables, two nnder each shed, which are so arranged thatl the stacked lumber may go to the dry, kilns or to the yard for air d'rying as desired. Two men work at each stacking table.

Ardjusta'ble Gate Insures Even Stacks
Uniform stacking has long been desired and under the arrangements at the Voth plant it comes very near realization. A gate that can be ,raised or lowered to fit the height of the stack, carries slots spaced on, two foot centers for the placing of t,he sticks, e.ach gate carrying two
STACKING PLATFORM. \
sets of slots, one perpendicular for kiln stacking, the other slightly inclined for yard stacking. Eight foot stock is stacked with the sixteen foot, and six foot with, the 'twelve foot, with a doublihg of sticks occurring at the center of each stack. so as to leave no loose ends. Each stack rests on two pieces of three by three oak, and these in, turn rest on shsrt dry kiln trucks. Each stack or package is exactly four feet wide, and contains, thirty-three layers of inch boards for the yard stock, or forty-eight layers when stacked for the kilns, and is an absolutely perpendicular stack for the kilns, or with a "lead" for the yard. A single cover of number three boards is placed on each package of number two and better. The sticks in the slots eliminate guess work and the sticks are always in a uniform line. Stacked packages are built on tracks having a slight inclin'e toward the main yard line.
When a package has been stacked it goes to the transfer car, if for the kilns, which transfer is made direct without any crane lift. If the package is for the yard it id rolled back to the track end of the platform, where it ig again. picked up by the crane and transferred to flat cars. So far only two bearirrgs h'ave been found necdssary fbr inch lumber, and there has been no trouble about sticks dropping out, even with 'sixteen foot stock.
When the'two flat cars have been loaded, the crane proceeds to the yard with its cars, traveling under its own power at the rate of eight miles per hour. drriving here, iach packagp is pickdd up in turn |and. set onr its prroper: foundation, or on the top of the ploper uncompleted stack, three un,its making a com,plete stack. The two bea.ring sticks remain as they were, and three more are added to afford proper base support. When a package rests on another in the yard two pieces ten feet long.are used fore and aft, as a tid bar for two stacks. Views of the yard show that it is possible to build th'ese packages so as to have a stack with uniform pitch and "pull" fromt top to bottom. Int shipping from the yard this process is mlerely reversed, the crane handling each package as before, and conveying it to the shipping dock, wher'e the inspector . (Continued on Page 42)
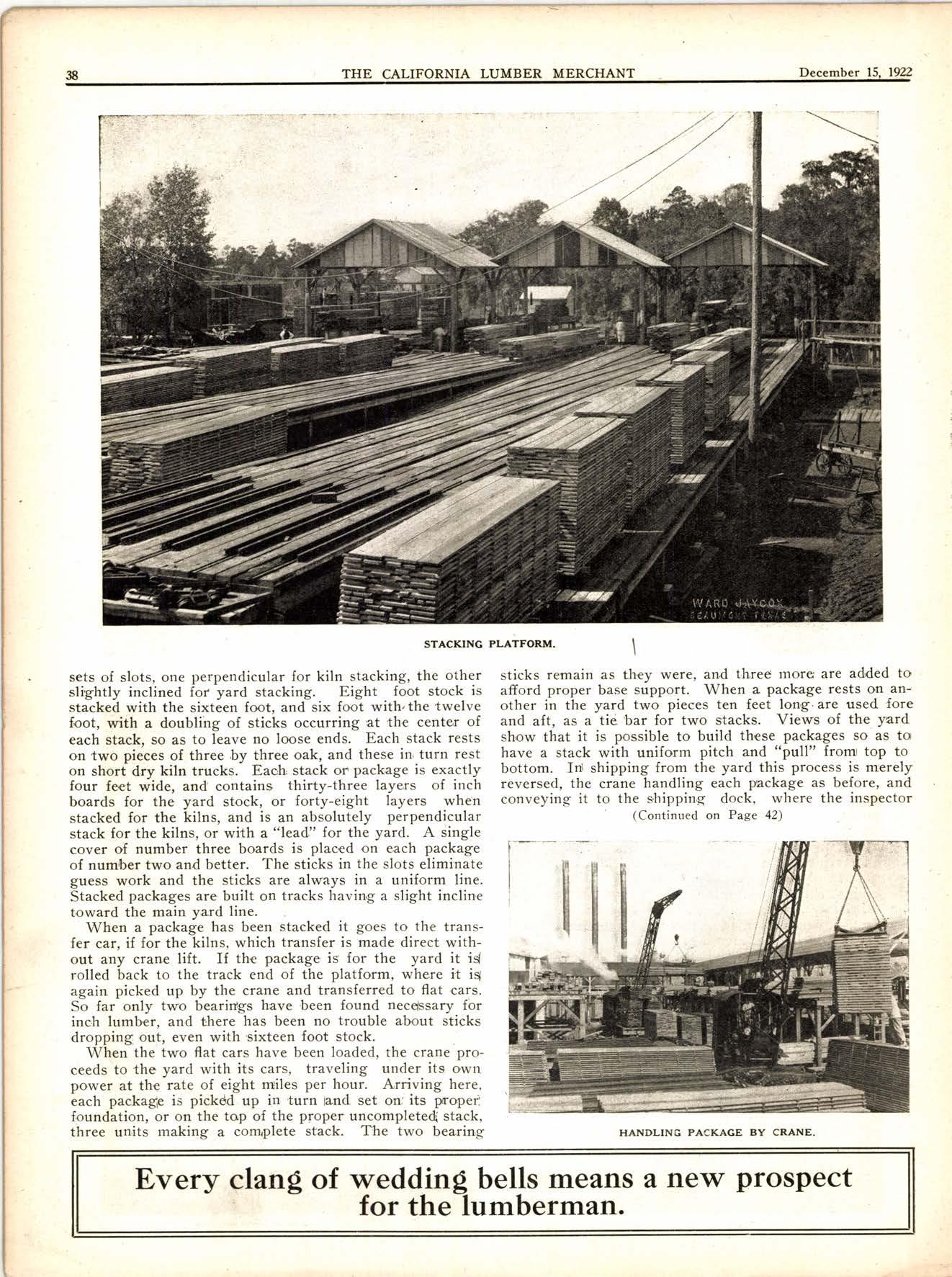