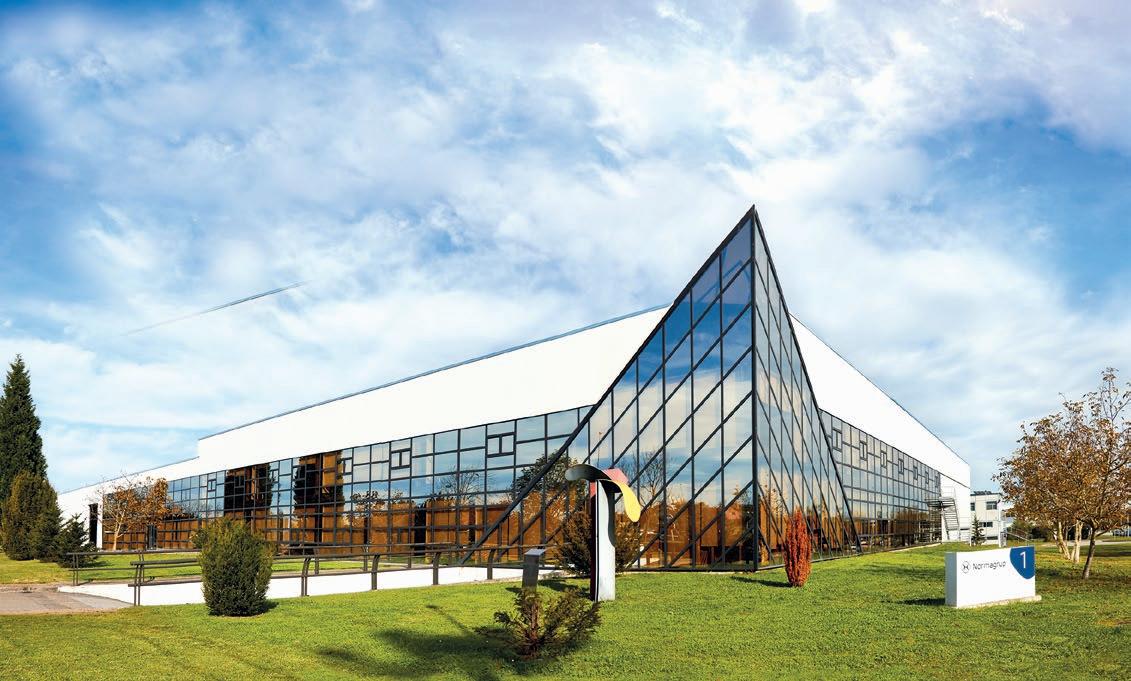
7 minute read
Fabricación de soluciones de iluminación en Asturias: Normagrup
La redacción de la revista tuvo la oportunidad de conocer de primera mano las instalaciones que Normagrup tiene en el Parque Tecnológico de Asturias, próximo a Oviedo. Un complejo de más de 40.000 metros cuadrados que engloba líneas de producción automatizadas, área de I+D+i y laboratorio de iluminación, entre otros recursos. Con un volumen de producción aproximada de entre 8.000 y 9.000 luminarias por día, “todos los procesos se hacen dentro de la empresa”.
Normagrup comenzó su trayectoria empresarial en 1971 con una luz de emergencia que se desarrolló de manera casi artesanal, utilizando un molde de madera y un horno casero. Aquel pequeño dispositivo ya contenía en su interior una tecnología avanzada.
Tras más de 50 años, hoy en día la empresa cuenta con una plantilla de casi 200 empleados y unas instalaciones punteras con más de 40.000 metros cuadrados, situadas en el Parque Tecnológico de Asturias (próximo a Oviedo). Además, la compañía ha adquirido recientemente una nueva nave en el mismo Parque, que se dedicará a tareas logísti- cas, lo que hace que el complejo de Normagrup sume unos 60.000 metros cuadrados, englobando a las cuatro divisiones del grupo: Normalux, NormaLit, Normadet, Norclinic, con sus diferentes líneas de producción.
Además de esta infraestructura, un elemento fundamental en este complejo es el Normagrup Tech Center (NTC), un espacio que, tal como definen en la empresa, está diseñado “para investigar, experimentar y aprender”. Dispone de 6.000 metros cuadrados donde se albergan los laboratorios, el departamento de I+D y un auditorio con capacidad para 60 personas, utilizado para presentación de novedades, cursos de formación y otras acciones.
Además, el edificio del NTC alberga un innovador showroom con 1.000 metros cuadrados de exposición, donde se han instalado 2.500 luminarias que están controladas con el software propio de control de iluminación Normalink. Este espacio de showroom muestra distintos entornos de aplicación (tienda de ropa, alimentación, oficinas, etc.), donde se puede ver de manera muy práctica las posibilidades de la regulación de la iluminación para distintos usos, jugando con la temperatura de color, el flujo luminoso, reproducciones cromáticas y otros parámetros. Se puede comprobar también la aplicación de soluciones Tunable White o blanco dinámico.
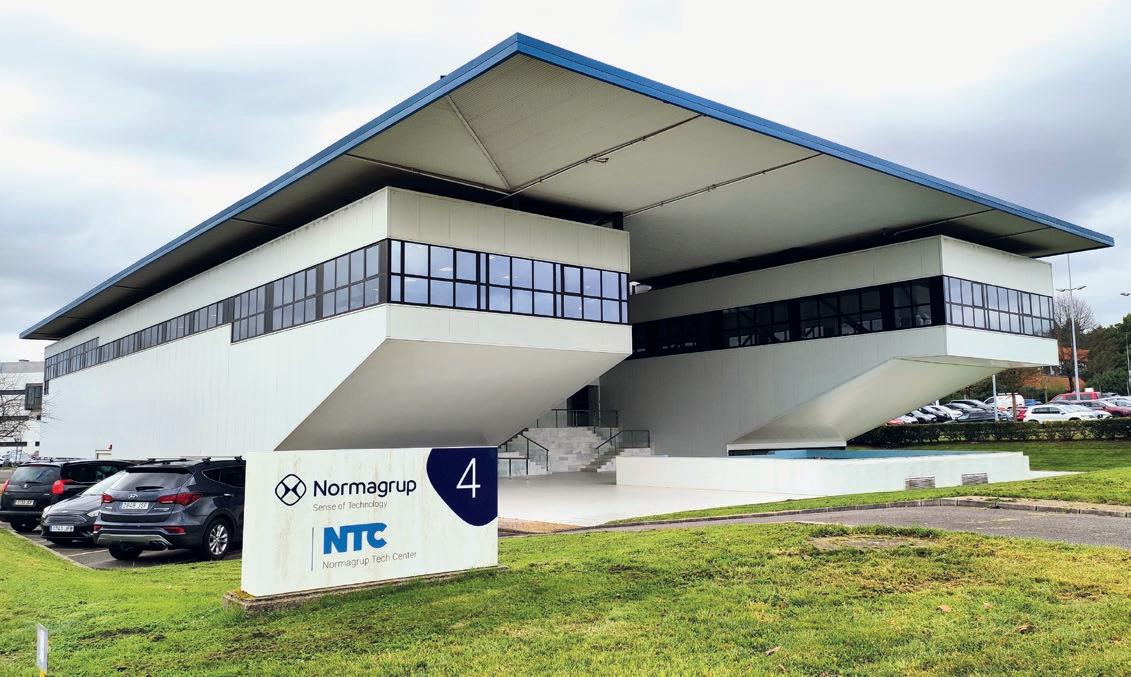
Gran volumen de fabricación con logística avanzada
Normagrup dispone en estas instalaciones de líneas de fabricación de electrónica, Pick and Place (SMD), donde se realiza una trazabilidad total de los componentes y su verificación mediante sistemas de visión artificial y pruebas eléctricas del 100 % de las placas fabricadas. La empresa produce más de 1,5 millones de placas electrónicas al año para las luminarias que fabrica. El diseño de la electrónica se lleva a cabo dentro de la propia empresa, en el área de I + D, que está compuesta por 22 ingenieros.
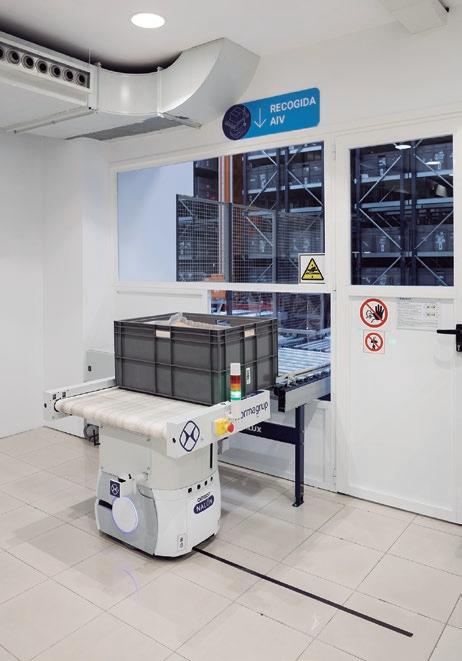

En esta línea de producción, la compañía realiza un control de calidad con visión 3D mediante la realización de cientos de fotografías, con el fin de determinar que todos los componentes de la luminaria se han colocado y soldado de manera correcta. También se lleva a cabo, en otra parte del proceso industrial, una verificación eléctrica y electrónica de la luminaria mediante software. Con ello el índice de posibles fallos técnicos se reduce al mínimo.

Posteriormente, en la línea de fabricación automatizada de alumbrado de emergencia, se efectúa una inspección para comprobar que la luminaria de emergencia funciona con la batería, gracias a una máquina diseñada por el propio departamento de Ingeniería de la empresa. Por último, se realiza una verificación adicional final, donde se aplica el marcado láser final con la indicación normativa. Las emergencias pasan en ese punto a la línea de embalado automático, donde se introducen iluminando.
En suma, la planta dispone de cuatro líneas de fabricación de electrónica: una para las luminarias de emergencia, una para la producción de placas electrónicas de equipos más complejos y dos más dedicadas a las gamas de Normalit.
“Normagrup apuesta claramente por la automatización de los procesos e incrementando año tras año la plantilla”, pone de relieve Juan Ramón Santos, director de marketing de Normagrup. De esta manera, el equipo de investigación y desarrollo ha crecido con más técnicos y en estos momentos el área de I + D está compuesta por 22 especialistas de distintos perfiles.
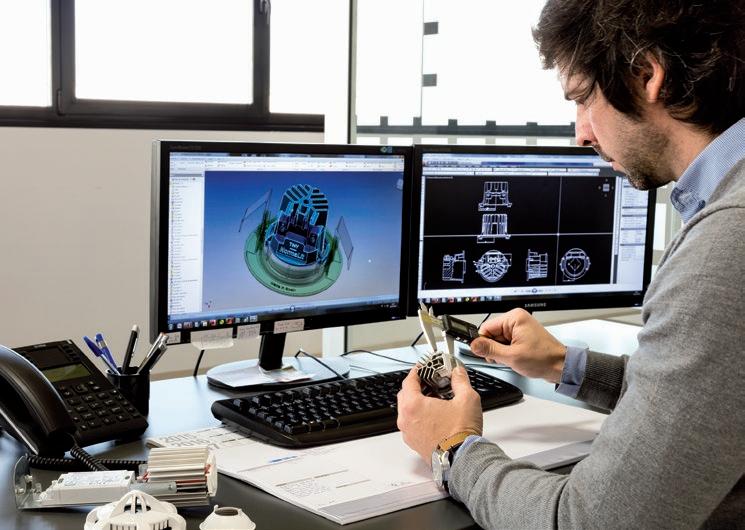
El volumen de producción que puede alcanzar la línea de producción de emergencias es 3.000 luminarias por turno. Si hablamos de tres turnos, podríamos estimar que se producen entre 8.000 y 9.000 luminarias al día en estas instalaciones.
En el caso de las líneas de fabricación de la gama Normalit, las máquinas de producción cuentan con mejoras de automatización y robotización que han sido desarrolladas e implantadas por el departamento de Ingeniería de la casa.
Alto grado de autonomía en todos los procesos
En las instalaciones centrales, además de la fabricación de la electrónica se realiza también la inyección de plásticos, con alimentación directa de materia prima desde silos centralizados, y con la extracción de piezas fabricadas mediante robots).
“Se diseña y fabrica todas y cada una de las piezas que componen una luminaria”, señala Santos a este medio.
La empresa tiene un taller propio de matricería para la fabricación y mantenimiento de moldes de inyección, tanto para inyectar plástico como para aluminio. “Actualmente tenemos activos más de 600 moldes. Como ejemplo, solo en 2022 se han fabricado unos 70 moldes”.
Aunque no fabrican todos los moldes, en esta área se encarga de realizar correcciones, ajustes y mantenimiento de todos los moldes que se utilizan. “La idea es depender lo menos posible de proveedores externos y controlar todos los procesos”. Por ello, cuentan con una máquina de 16 toneladas para fabricar moldes y también con un equipo industrial con dos compresores para producir nitrógeno, necesario en algunos procesos de la fabricación.
Otra nave del complejo en el Parque Tecnológico de Asturias está dedicada a la línea de pinturas. Se utilizan pinturas electrostáticas (con carga) para no usar disolventes perjudiciales para el medio ambiente; ofrecen una cubierta uniforme y con ello se desperdicia menos material. Esta línea de pinturas aporta flexibilidad y se puede aplicar la pintura que desee el cliente.
Además, disponen también de un horno para fundir el aluminio. “El horno para fundir aluminio es algo excepcional en nuestro sector, que nos diferencia de nuestra competencia. Nos permite mantener un elevado grado de autonomía a la hora de manejar y aplicar este material en los equipos, sobre todo porque este metal ha sufrido notables incrementos de su coste en los últimos meses”, detalla Juan Ramón Santos.
Soluciones para el entorno sanitario y residencias
Dentro del complejo de Normagrup también se encuentran las líneas de fabricación más avanzadas de sistemas de hospi- talización Norclinic. En esta sección cuentan con una línea de mecanización para fabricación de perfiles metálicos: se pueden diseñar y producir perfiles metálicos de diferentes tamaños, aportando una personalización de este tipo de productos muy apreciada por los clientes.
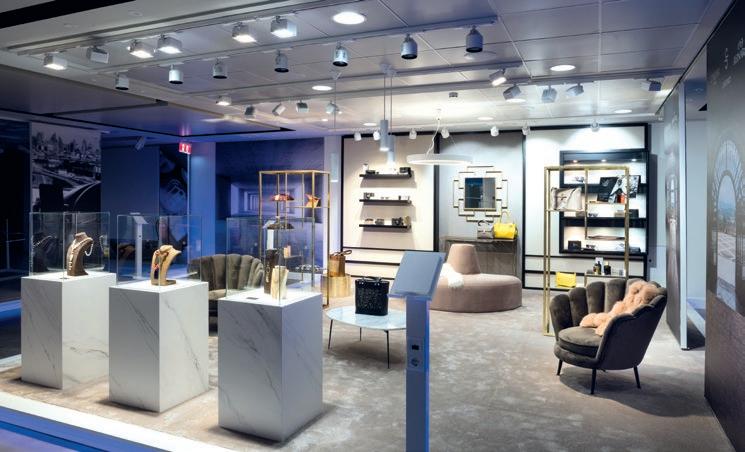
Ejemplos de aplicación donde se han instalado soluciones Norclinic, equipos que cuentan con certificado sanitario, son el hospital Álvaro Cunqueiro de Vigo o el Hospital General de Asturias en Oviedo. Esta clase de desarrollos que se comercializan en España también encuentran salida en otros mercados con un alto volumen de exportación.
En Normalit disponen de un catálogo de más de 2.000 referencias activas. El departamento de Ingeniería, junto con el área de I+D+i, Producción y Comercial son capaces de encontrar la solución adecuada a cada necesidad en este campo; “se pueden ajustar tensiones, tamaños, lúmenes, colores y demás parámetros para producir el equipo que nuestro cliente necesita en cada momento”.
Asimismo, SaLUZ es el proyecto que ha desarrollado la compañía para la iluminación saludable de las personas. Basándose en estudios científicos, la gama SaLUZ adecua automáticamente la luz e intensidad al momento del día en que nos encontramos, inspirándose en la luz del sol para adaptarse a los ciclos biológicos naturales, permitiendo crear ambientes saludables, confortables y eficientes.
Futuro de la iluminación: bienestar y economía circular
La fábrica es un elemento estratégico para dar a conocer todo el know-how y potencial de la compañía, por ello las visitas de clientes son fundamentales. “Tras finalizar la pandemia volvimos a retomar las visitas y tenemos una media de 2 visitas a la semana (excluyendo periodos vacacionales). Podemos estar hablando de unos
600 profesionales al año, entre distribuidores, ingenierías, arquitectos, instaladores, entre otros perfiles”, explica Juan Ramón Santos.
En este sentido, hay tres aspectos que despiertan mayor interés entre los profesionales. El primero sería descubrir una fábrica automatizada, donde se diseña, se fabrica tanto la electrónica como los envolventes, se montan los equipos y se envían a los clientes. El segundo sería comprobar cómo se trabaja en el área de I+D y los laboratorios. Y por último, “descubrir el showroom y ver en la práctica la importancia de una buena iluminación, y cómo influye en los proyectos constructivos, o incluso en el estado de ánimo y la salud de los usuarios finales”.
Desde Normagrup ponen de relieve que el futuro de la iluminación pasará por aspectos relacionados con la salud visual de las personas: “vivimos y trabajamos la mayor parte de nuestra vida bajo luz artificial”, y también por los temas vinculados con el medio ambiente y la economía circular.
En el primer caso, la empresa ha desarrollado la gama SaLUZ, con la iluminación centrada en las personas, ciclo circadiano, reducción de azules, etc. Y en el segundo caso, “estamos adaptando nuestros procesos de diseño de producto dándoles un enfoque integral hacia aspectos medioambientales, con criterios de ecodiseño, menor uso de materias primas y energía en su fabricación, rediseño de embalajes y nuevas gamas de producto con fuentes de luz intercambiables”.
A esto se une, y es importante, que todo ello contribuye a generar una menor huella de CO2 en la logística, “a lo que contribuye el que seamos un fabricante local y cercano”, concluye finalmente Juan Ramón Santos.
LABORATORIO DE LA LUZ
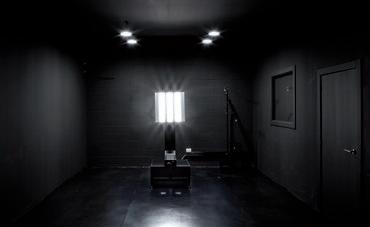
Dentro del edificio del NTC, Normagrup cuenta con recursos tecnológicos muy avanzados para llevar a cabo comprobaciones y test de sus productos, y controlar su trazabilidad, aportando así una total garantía del cumplimiento de las normativas. “Todo lo hacemos dentro de la empresa”, subraya Juan Ramón Santos.
Los recursos y equipamientos que utiliza el equipo de ingenieros en este auténtico laboratorio de la luz son los siguientes:

◗ Fotogoniómetro (para efectuar curvas lumínicas o fotométricas).
◗ Espectrofotómetro (coordenadas cromáticas de la luz, temperatura de color, CRI,...).
◗ Doble monacromador (para la seguridad fotobiológica).
◗ Esfera de Ulbricht (flujo luminoso).
◗ Sala de IP de líquidos (de IP X1 a IP X8).
◗ Cámara de estanqueidad para polvo.
◗ Martillo de impacto (del IK 1 al IK 10).
◗ Máquina del hilo incandescente (autoextinguibilidad de las envolventes).
◗ Testeador de Bus DALI.
◗ Testeador de baterías.
◗ Túnel de humo y calor.
◗ Impresoras 3D, con las que los técnicos e ingenieros crean y fabrican moldes, prototipos y versiones preliminares del producto.
◗ Analizador de espectros electromagnéticos.
◗ Cámara climática.

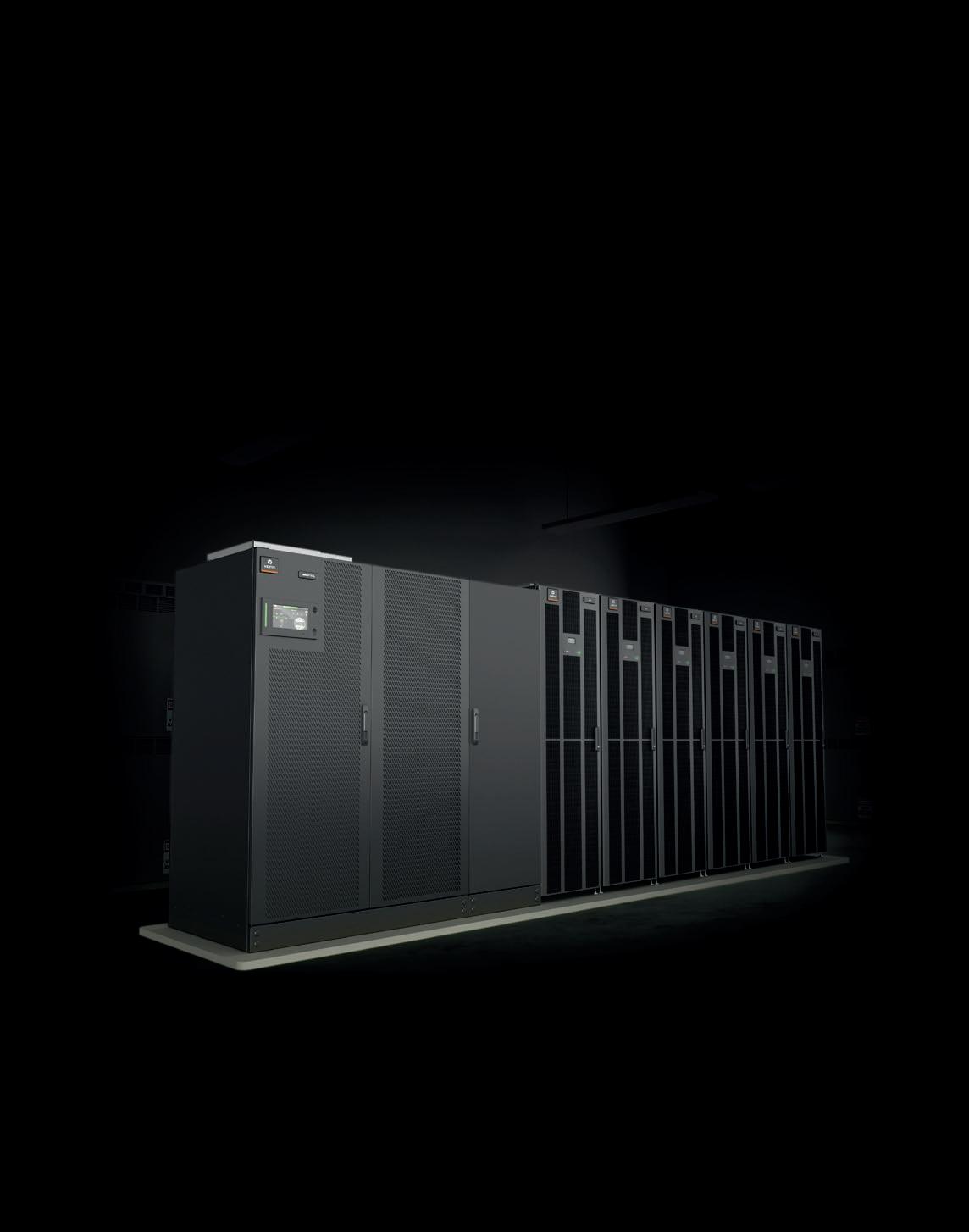
