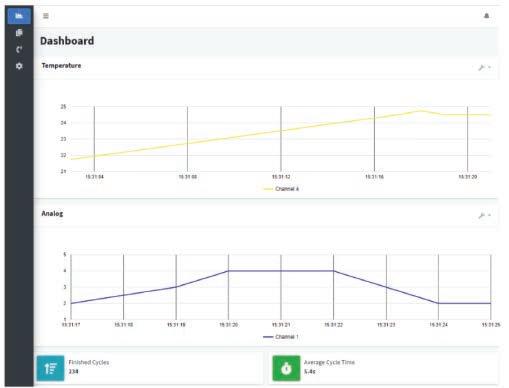
11 minute read
Sistema de validação da garantia de moldes
70 SISTEMA DE VALIDAÇÃO DA GARANTIA DE MOLDES
João Alves *, Lino Ferreira **, Sérgio Silva ***
* Instituto Politécnico de Leiria/ESTG
É extremamente importante para os fabricantes de moldes de injeção saberem se os moldes que fabricam e vendem são devidamente utilizados, não sendo violadas as condições estabelecidas nos contratos de garantia. O sistema desenvolvido, denominado de Sistema de Validação de Garantia de Moldes, permite cumprir este objetivo de forma automática, ultrapassando as limitações dos sistemas atuais, baseados em contadores que apenas contabilizam o número de ciclos de utilização dos moldes. O sistema proposto adquire e armazena diversa informação sensorial relacionada com a utilização dos moldes, como por exemplo o número de ciclos de utilização, valores de temperatura, de pressão na cavidade, vibrações, ressonância, entre outros. E, em função de regras e pressupostos técnicos adequados, determina automaticamente e alerta em tempo real se a garantia de um determinado molde de injeção já não é válida. A informação recolhida possibilita, complementarmente, a monitorização automática do processo de fabrico no sentido de o otimizar, e ainda o apoio nos processos de manutenção.
1. INTRODUÇÃO
Para não incorrerem em despesas adicionais associadas a garantias de fabrico, é pertinente que os fabricantes de moldes de injeção conheçam as condições em que estes estão a ser utilizados. Atualmente, a validação da garantia de um molde é feita com base na contabilização dos ciclos de utilização de abertura e fecho do molde, levados a cabo por simples contadores digitais [1] e mecânicos [2] [3]. Tipicamente, estes contadores só contam até um determinado número máximo de ciclos e não possibilitam qualquer reinicialização. Além disso, os contadores mecânicos, sofrem desgaste inerente ao processo de abertura e fecho de um molde. Contudo, existem ainda outros fatores que podem influenciar o ciclo de vida de um molde, como por exemplo a temperatura e a pressão a que este é sujeito, que os contadores não “contabilizam”.
Mais recentemente, têm vindo a ser utilizados paulatinamente outros sistemas [4] [5] [6], com a possibilidade de adquirir e registar dados sensoriais inerentes ao processo de fabrico de peças através de processos de injeção. O propósito destes sistemas é monitorizar e otimizar o processo de fabrico e a qualidade das peças. Alguns destes sistemas baseiam-se apenas na contagem de ciclos de utilização do molde, outros já usam sistemas sensoriais mais complexos. Contudo, estes sistemas não se focam na questão da validação da garantia de um molde, a sua perspetiva de utilização é direcionada para o benefício do utilizador do molde, não salvaguardando, portanto, os interesses do fabricante.
Portanto, considera-se pertinente monitorizar automaticamente a utilização de um molde de forma a ser possível verificar a validade da garantia não apenas por excesso de ciclos de utilização. Para de alguma forma validar este pressuposto, foi realizado um estudo de mercado, direcionado para empresas portuguesas fabricantes de moldes, com o objetivo de se perceber a utilidade e o nível de aceitação de um sistema deste tipo. Das empresas inquiridas, foram obtidas 109 respostas, em que mais de metade delas revelaram a pertinência de um sistema deste tipo e o interesse na sua aquisição.
Face ao interesse neste tipo de produto no sector, foi projetado e desenvolvido um sistema para validação da garantia de moldes. No capítulo seguinte será descrito o sistema desenvolvido, no qual será dada ênfase à sua constituição, às características e funcionalidades e, para finalizar, ao processo de instalação.
2. SISTEMA DESENVOLVIDO
O sistema desenvolvido carateriza-se por ter diversas funcionalidades, sendo composto por um conjunto de elementos, cada um com um papel importante para a execução das mesmas. O sistema deverá ser instalado corretamente, de modo a poder-se usufruir totalmente das suas funcionalidades.
2.1. CONSTITUIÇÃO O sistema compreende os seguintes elementos: • Unidade microcontroladora de coordenação do funcionamento global do sistema; • Relógio em tempo real; • Sensores para recolha de informação; • Dispositivos de sinalização luminosa; • Dispositivo de armazenamento de dados; • Dispositivos de comunicação de dados com e sem fios; • Fonte de alimentação principal; • Fonte de alimentação redundante.
A unidade microcontroladora apresenta um funcionamento cíclico, posterior a uma configuração inicial e à configuração dos outros dispositivos, adquirindo, processando e registando os dados provenientes dos sensores instalados no sistema. Encontra-se programada para alterar automática e momentaneamente o seu funcionamento cíclico na presença de anomalias, do sistema e do molde, em que ativa a respetiva sinalização luminosa e o seu registo, e também para responder no momento em que é detetado um pedido de reconfiguração, um pedido de exteriorização de dados, ou a determinação se a garantia dada pelo fabricante de um molde foi violada em função de regras e pressupostos técnicos definidos.
O relógio em tempo real permite identificar o tempo preciso em que houve uma ocorrência (dados recolhidos, anomalias) e cronometrar o tempo de duração dos ciclos, assim como o seu início e fim.
Os sensores de recolha de informação obtêm informação do molde relacionada com a temperatura, a pressão, o número de ciclos de abertura e fecho e impactos mecânicos.
Os dispositivos de sinalização luminosa encontram-se interligados com as restantes partes integrantes do sistema, assinalando anomalias do sistema e do molde e o funcionamento dos dispositivos de comunicação com e sem fios.
O dispositivo de armazenamento de dados é capaz de guardar os dados adquiridos, processados e registados pelo sistema e armazenar outras informações relevantes tanto para o funcionamento geral do sistema, como para a análise de validade da garantia do molde.
Os dispositivos de comunicação de dados com e sem fios possibilitam a exteriorização dos dados para dispositivos externos.
A fonte de alimentação redundante garante o funcionamento contínuo do sistema no caso de falha da fonte de alimentação principal, durante um tempo limitado.
2.2. CARACTERÍSTICAS E FUNCIONALIDADES A mais valia deste sistema, que o torna distinto de outros análogos que envolvem aquisição, processamento e registo de dados industriais, prende-se com a grande facilidade de automaticamente determinar se a garantia dada pelo fabricante de um molde foi violada.
Os dados típicos que o sistema adquire são referentes ao número de ciclos, à temperatura e à pressão de funcionamento de um molde. Para este efeito, são utilizados sensores apropriados em número e tipo, de acordo com as características do molde. Podem também ser incorporados outros sensores para a aquisição de outros dados não tão típicos, como por exemplo referentes a impactos mecânicos associados ao manuseamento e ao funcionamento de um molde.
O número e tipo de sensores utilizados, a quantidade média de amostras recolhidas por ciclo e as condições que invalidam a garantia do molde, são configuráveis e reconfiguráveis pelo fabricante do molde, a partir de um ficheiro de configuração onde são definidos esses parâmetros.
As condições típicas que podem originar o fim de garantia são o excesso de número de ciclos de utilização, valores máximos e mínimos excessivos de temperatura ou de pressão e a utilização do molde sem o sistema estar ligado a uma fonte de energia. Mesmo que se verifique alguma condição que implique o fim da garantia do fabricante, o sistema continua a adquirir, processar e registar dados de forma contínua, de acordo com a configuração definida. A única condição de paragem do registo de dados típicos é a falta permanente de energia para alimentar o sistema. Portanto, é da responsabilidade do utilizador do molde garantir que o sistema está devidamente alimentado pela fonte de energia principal quando o molde está em utilização. Porém, dispondo de um sistema de alimentação redundante, a validação poderá continuar a funcionar normalmente durante um período de tempo limitado. Assim, poderá ser comprovado que o molde foi utilizado nesta situação, podendo tal ser motivo para a violação do contrato de garantia.
Os dados adquiridos, processados e registados internamente pelo sistema, assim como as anomalias detetadas e registadas, podem ser exportados através de comunicações com fios, para dispositivos de dados, e sem fios, enviando-os por notificações SMS (Short Message Service) e para uma base de dados num servidor.
Com o dispositivo de dados conectado são descarregados, para o mesmo, todos os registos de dados e anomalias guardados no dispositivo de armazenamento do sistema, assim como outras informações relevantes do seu funcionamento. É também possível fazer a reconfiguração do sistema, colocando previamente um ficheiro de configuração no dispositivo, realizando-se a reconfiguração no momento da conexão do mesmo com o sistema.
As mensagens SMS são enviadas para os contactos telefónicos guardados no dispositivo de armazenamento, após a ocorrência de uma anomalia que pode invalidar a garantia do molde. A mensagem contém informações detalhadas sobre a ocorrência e a identificação do molde.
Os dados exportados para a base de dados, podem ser acedidos e analisados num servidor web, sendo uma das páginas exemplo apresentada na Figura 1.
/ / Figura 1 – Página do servidor web
O servidor pode ser acedido a partir de qualquer dispositivo que tenha capacidade para aceder à Internet. Para aceder ao servidor é necessário realizar a autenticação utilizando credenciais que identificam o utilizador. No servidor é possibilitada a análise dos dados, a partir de gráficos como a evolução da temperatura e da pressão da cavidade do molde e é apresentada informação relevante, como o número de ciclos concluídos e o seu tempo de duração médio.
É também permitido o acesso a todos os registos de dados recolhidos pelos sensores e o registo das anomalias detetadas, podendo ser descarregada uma cópia e/ou eliminar os mesmos. Por fim, é possível realizar uma reconfiguração do sistema, (alterar o número e tipo de sensores, número médio de amostras, etc.) e também alterar ou adicionar os destinatários das notificações SMS.
Para além das anomalias serem registadas internamente com a respetiva data e hora, são também sinalizadas através de dispositivos de sinalização luminosa. O seu intuito é fornecer uma informação simples e intuitiva ao utilizador de modo a garantir e certificar o correto funcionamento do sistema global. Estes dispositivos de sinalização luminosa sinalizam as seguintes anomalias e ocorrências: • Falha na ligação de sensores; • Falha na fonte de alimentação principal; • Valores máximos e mínimos pré-definidos excedidos (de temperatura, de pressão e de ciclos de utilização do molde); • Falha ou sucesso na comunicação de dados com dispositivos externos; • Perda de garantia do molde.
É também armazenada internamente informação relativa às peças desenhadas, dados técnicos do molde e ainda o contrato de garantia, mas o seu propósito é distinto, assentando apenas na consulta do utilizador do molde.
O funcionamento do sistema resume-se, portanto, nos seguintes pontos: 1. O sistema é configurado em função do ficheiro de configuração presente no dispositivo de armazenamento de dados; 2. Inicializa os módulos de comunicação sem fios; 3. Adquire, processa e armazena dados; 4. Verifica a ocorrência de anomalias, registando-as se for o caso; 5. Exterioriza dados ou reconfigura o sistema, caso seja pedido.
É de notar que a partir do ponto 3 o funcionamento é cíclico.
Na Figura 2 é apresentada a esquematização simplificada do funcionamento do sistema e a sua interação com o exterior.
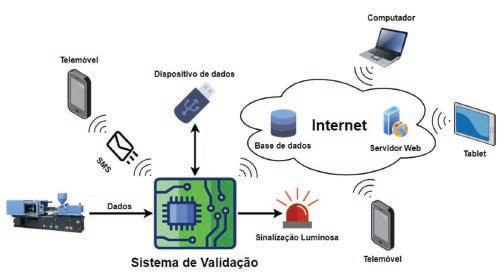
/ / Figura 2 - Esquematização do sistema desenvolvido
O sistema desenvolvido garante ainda a robustez necessária para o funcionamento em permanência, independentemente das adversidades às quais o molde é exposto durante o processo de fabrico das peças. Além disso, também garante que o sistema não é alvo de qualquer forma de intrusão que possa originar o seu mau funcionamento ou um acesso indevido aos dados registados. O invólucro do sistema desenvolvido é feito de um material que garante a proteção dos componentes eletrónicos face a temperaturas elevadas e choques mecânicos e, além disso, a sua abertura implica a sua destruição.
2.3. INSTALAÇÃO O sistema é acoplado à parte fixa de um determinado molde. Isto pode ser realizado por parafusos ou por meio de atração magnética. Na Figura 3 encontra-se um exemplo da instalação do sistema num molde de injeção.
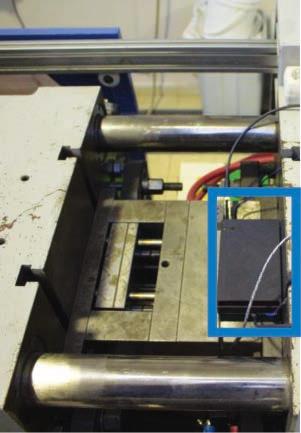
/ / Figura 3 - Sistema desenvolvido acoplado a um molde
Os sensores de temperatura e de pressão são colocados dentro da cavidade do molde e os sensores indutivos de contagem de ciclos são instalados de forma a detetar o fecho e abertura do molde. Neste caso apenas se utilizou um sensor de cada tipo, embora o número, o tipo e a localização dos diversos sensores possam ser ajustados de acordo com as especificações do molde e as condições definidas pelo seu fabricante. O sistema possui também uma ficha de alimentação para ligação a 230VAC.
3. CONCLUSÃO
Graças à sua conectividade, o sistema desenvolvido permite ao fabricante de um determinado molde de injeção estar permanentemente informado sobre o estado da sua garantia, independentemente do local onde se encontre. Além disso, toda a informação automaticamente recolhida sobre o funcionamento do processo pode ser visualizada graficamente e processada no sentido de se explorarem oportunidades de melhoria ao nível da produção e da qualidade das peças. O conceito que está na base do desenvolvimento deste sistema pode também ser aplicado noutros processos de fabrico semelhantes. No momento da escrita do presente artigo, o sistema apresentado encontra-se patenteado.
Este trabalho foi financiado pelo INOV C 2020 - Projetar a região enquanto referência nacional na criação de novos produtos e serviços resultantes de atividades de I&D. SAAC - CENTRO-46-2016-01 – Projeto nº5625
4. BIBLIOGRAFIA
[1] “Sistemas de contagem digital,” Hasco, [Online]. Available: https://www.hasco.com/ pt/Cat%C3%A1logo-do-produto/Z/T%C3%A9cnica-de-medi%C3%A7%C3%A3o/ Sistemas-de-contagem/Digital/c/PIM03070301. [Acedido em novembro 2020]. [2] “Sistemas de contagem mecânico,” Hasco, [Online]. Available: https://www.hasco. com/pt/Cat%C3%A1logo-do-produto/Z/T%C3%A9cnica-de-medi%C3%A7%C3%A3o/ Sistemas-de-contagem/Mec%C3%A2nico/c/PIM03070302. [Acedido em novembro 2020]. [3] “Contador de batidas,” [Online]. Available: https://www.directindustry.com/pt/prod/ hengstler/product-5789-873445.html. [Acedido em novembro 2020]. [4] “Monitor de Moldes CVe,” Progressive, [Online]. Available: https://www.casafer.com.br/ produto/monitor-de-moldes-cve/. [Acedido em novembro 2020]. [5] “ComoNeo - Process Monitoring System,” Kistler, [Online]. Available: https://www.kistler. com/en/product/type-5887a/?application=17. [Acedido em novembro 2020]. [6] “MouldBox - A PROCESS MONITORING SYSTEM,” Formteknik, [Online]. Available: https://formteknik.com/mouldbox/. [Acedido em novembro 2020].