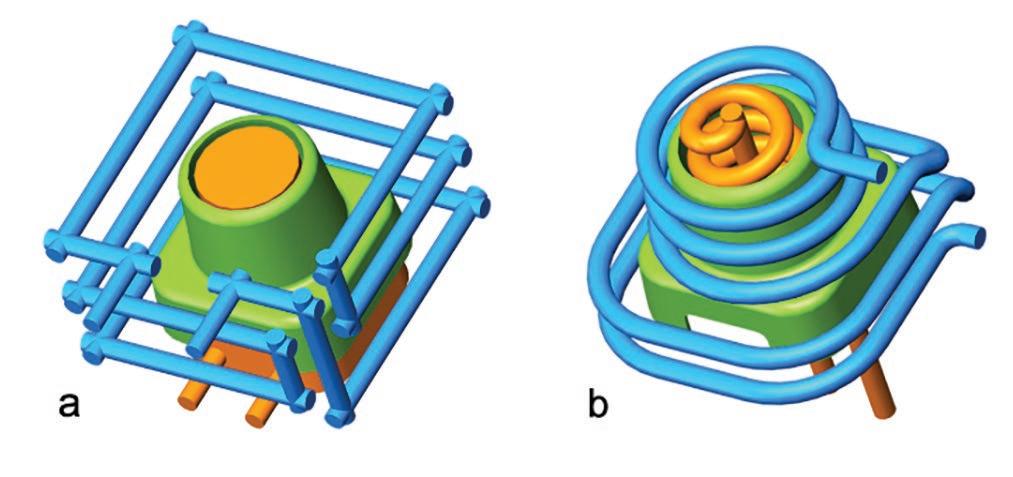
9 minute read
COMPARAÇÃO DE TEMPO E CUSTO ENTRE MOLDES CONVENCIONAIS E HÍBRIDOS PARA A INJEÇÃO DE DISSIPADORES DE CALOR POLIMÉRICOS
from Molde N.º 137
by CEFAMOL
1 -IPC - Instituto de Polímeros e Compósitos, Departamento de Engenharia de Polímeros, Universidade do Minho;
2 - DONE Lab - Advanced Manufacturing of Polymers and Tools, Universidade do Minho;
Advertisement
3 - BOSCH Car Multimedia S.A..;
4 - Lab2PT, Escola de Arquitetura, Universidade do Minho
Introdu O
A moldação por injeção é um dos processos mais utilizados no fabrico de peças plásticas, devido aos seus inerentes maiores níveis de produtividade e precisão, e à facilidade de obtenção de produtos de alta qualidade para campos de aplicação mais distintos. Na produção de moldes de injeção, são amplamente utilizados métodos de produção subtrativos que utilizam ligas de aço como material de construção. Estes moldes de injeção permitem produções em larga escala na ordem dos milhares, centenas de milhares ou mesmo milhões de unidades de peças plásticas [1,2].
No entanto, hoje em dia, o mercado é altamente competitivo e exige novos modelos de desenvolvimento de produtos customizados para satisfazer as necessidades dos consumidores. Portanto, um produto deve atender aos requisitos do cliente, mas também com tempo e custos de desenvolvimento e produção reduzidos. Nesse sentido, algumas empresas enfrentam o desafio de fabricar moldes para pequenas quantidades de peças plásticas. Numa abordagem para resolver esta questão, surgiu o conceito de moldes híbridos que combina tecnologias alternativas de fabrico, como por exemplo, tecnologias de Fabrico Aditivo (FA) com métodos de fabricação convencional [3,4], como a fabricação subtrativa.
As tecnologias de FA permitem a criação de modelos físicos baseados na aplicação de camadas consecutivas de material, ou seja, depositando o material camada a camada para gerar toda a forma da peça pretendida. A designação de moldes híbridos resulta da diversidade de materiais e técnicas empregues simultaneamente num molde. Deste modo, os métodos convencionais são normalmente aplicados para produzir toda a estrutura do molde, exceto os insertos moldantes que são produzidos por tecnologias de FA, conforme mostrado na Figura 1 [5].
As principais vantagens associadas aos moldes híbridos incluem uma maior eficiência na redução de desperdícios e consumo de energia, na redução do time-to-market e na facilidade de personalização de layouts para o sistema de controlo de temperatura, proporcionando uma maior eficiência no controlo térmico durante o processo de moldação por injeção [6]. Esta liberdade de design é uma das vantagens inerente aos processos de FA que permite aos projetistas e engenheiros analisar a melhor estratégia de projeto para os canais do sistema de controlo de temperatura, de forma que os canais sejam posicionados o mais próximo possível da peça, melhorando assim, a eficiência térmica do sistema, contribuindo para a otimização do processo de moldação por injeção. Este tipo de configuração é mais vantajoso ao recorrer a tecnologias de FA baseadas em metal e é tradicionalmente referido como canais de controlo de temperatura ou canais de arrefecimento conformados (Figura 2b) [7]. Uma vez que a fase de arrefecimento representa uma grande parte do tempo total do ciclo de injeção (normalmente cerca de 70-80 %), o recurso a este tipo de configuração de arrefecimento otimizado pode levar a poupanças significativas (até 33 %) que se traduzem num aumento da produtividade no processo de moldação por injeção. Além disso, com uma distribuição de temperatura controlada na superfície da peça, é possível prevenir certos defeitos que podem ocorrer no processo de moldação por injeção, como contração, empeno e chupados, garantindo a qualidade das peças moldadas [7-9]. No entanto, apesar dessas vantagens, a matéria-prima e a própria tecnologia apresentam custos elevados quando comparados com os métodos convencionais [7]. Portanto, é importante entender quando se deve aplicar o FA e soluções de arrefecimento conformado num molde de injeção e, como isso se reflete, em comparação com um molde totalmente convencional, no tempo e nos custos gerais para obter um produto de alta qualidade.
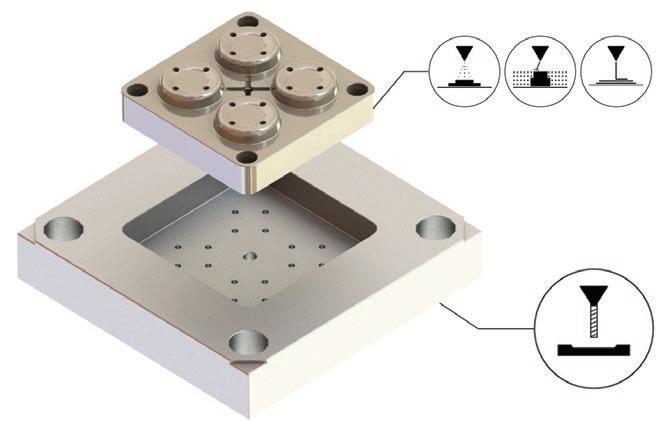
1.1. CASE STUDY
A Bosch Car Multimedia S.A. é uma empresa que fabrica dispositivos eletrónicos para sistemas multimédia para a indústria automóvel. Em determinadas aplicações, é necessário um housing para conter e proteger uma série de componentes com diferentes funções e finalidades, que serão posteriormente montados no automóvel. Tradicionalmente, a Bosch Car Multimedia S.A. utiliza housings de base metálica devido às suas vantagens inerentes em garantir proteção de blindagem eletromagnética e gestão térmica eficiente.
No entanto, as soluções à base de metal são mais pesadas, o que leva ao aumento do consumo de combustível e do impacto ambiental. Devido a estas questões, a Bosch Car Multimedia S.A. visou o desenvolvimento de um conceito totalmente novo de housings eletrónicos mais leves que permitem ao automóvel tornar-se ambientalmente mais sustentável. Este conceito inovador, denominado Lightweight Electronic Enclosure (LEE) é inteiramente construído com materiais plásticos compósitos com propriedades específicas. A Figura 3a) mostra a versão metálica de um housing enquanto que a Figura 3b) apresenta as alterações realizadas ao seu design para ser produzida em material compósito de base polimérica mais leve e, na Figura 3c) é mostrada uma vista explodida de todo o conjunto do housing
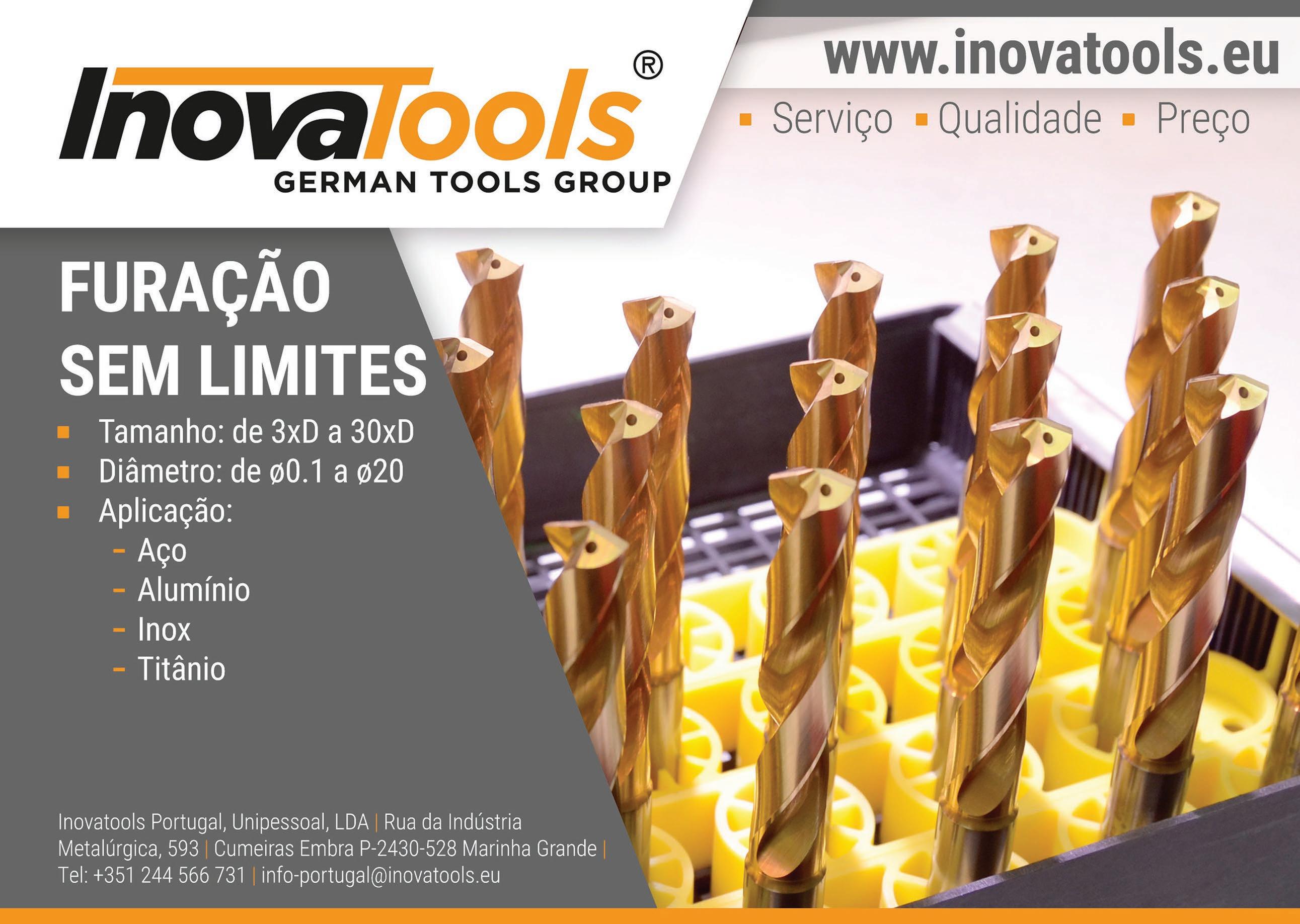
Neste quadro, este estudo descreve as etapas experimentais para o projeto e fabrico de dois moldes de injeção por moldação, com base nas abordagens convencional e híbrida, para a produção de três diferentes dissipadores de calor que integram o housing eletrónico de base compósita (Figura 4). O material do processo de moldação por injeção selecionado para os dissipadores de calor consiste num Polibutadieno Tereftalato (PBT), condutor de calor com 68 % de fibras de carbono incorporadas, maioritariamente grafite e alguns óxidos. Os parâmetros do processo de injeção e os custos de fabrico de todas as estruturas e acessórios para cada molde foram registados, permitindo fazer uma análise comparativa entre as duas metodologias. de construção. Em seguida, um varrimento a laser é refletido por um sistema de espelhos galvanométricos, fundindo seletivamente os pós metálicos sobre a cama de pó. Este processo é então repetido permitindo a criação de uma peça, camada a camada.
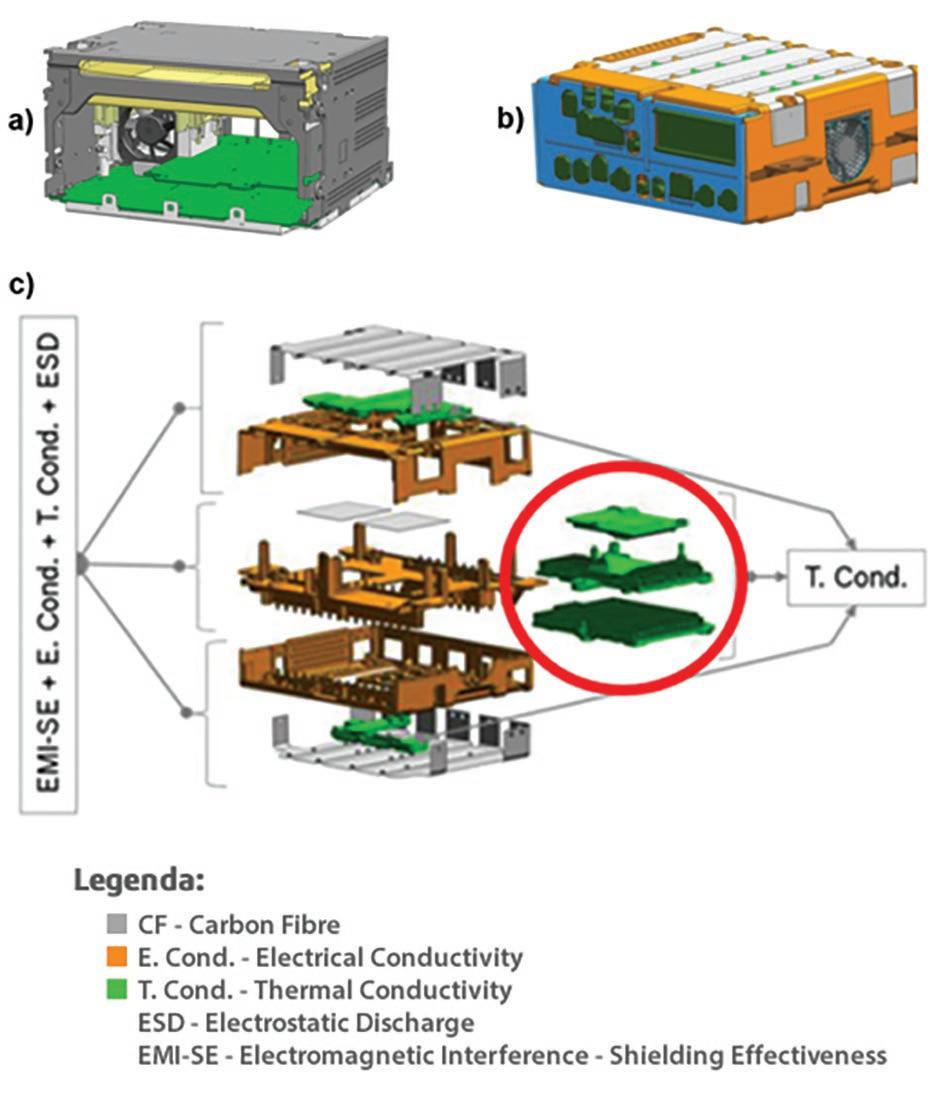
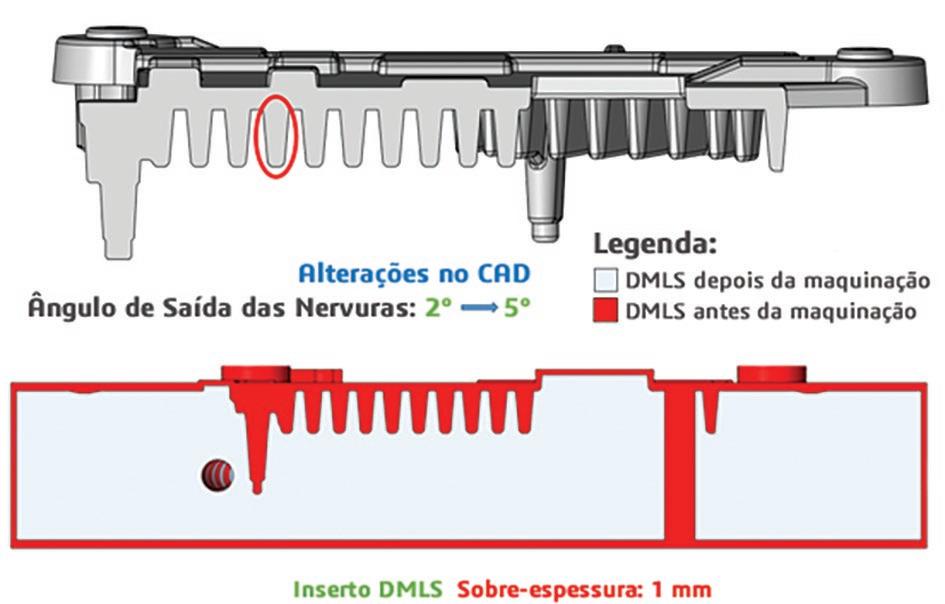
Os insertos moldantes para o molde híbrido foram produzidos pelo equipamento Concept Laser M2 Cusing, utilizando a liga de alumínio comercial CL31AL da Concept Laser GmbH (AlSi10Mg), como material de construção. Foi realizado um pós-processamento para melhorar o acabamento superficial da bucha e da cavidade, que incluiu uma etapa de maquinação CNC. Para esse efeito, foi considerada uma sobre espessura de 1 mm em ambos os insertos moldantes tendo em conta o posterior acabamento superficial da maquinação (Figura 7).

2. FABRICO DO MOLDE
2.1. MOLDE CONVENCIONAL
A estrutura do molde convencional foi construída com aço de liga 1.1730, e os insertos moldantes (bucha e cavidade) foram fabricados em aço temperado 1.2738.
Para a construção do molde convencional foram utilizados dois processos de maquinação: por Comando Numérico Computadorizado (CNC) e pelo processo de Eletroerosão (EDM). As placas moldantes foram maquinadas por forma a integrar as buchas e cavidades correspondentes aos três dissipadores de calor. No entanto, foi definida uma válvula no sistema de alimentação que direciona o polímero fundido para a cavidade desejada possibilitando a injeção de apenas uma peça de cada vez, peça que é definida pelo operador ao ajustar a válvula antes da injeção processo. Em relação ao sistema de controlo da temperatura (Figura 5), o diâmetro dos canais é de 8 mm, tanto para a bucha como para a cavidade. O molde de injeção tem um sistema de alimentação por canais frios. O lead-time para a construção do molde convencional foi de 12 semanas.
Outras considerações de design para o processo DMLS incluem um aumento do ângulo de saída das nervuras de 2.º (molde convencional) para 5.º, de forma a otimizar o processo de maquinação e pósprocessamento, além de facilitar a extração das peças.
Além disso, como o material de construção dos insertos moldantes para o molde híbrido é um material mais macio do que o material de construção selecionado para os insertos moldantes do molde convencional, essa consideração de design evitará o desgaste precoce causado pela abrasão durante a injeção do material compósito.
2.1. MOLDE HÍBRIDO
A estrutura do molde híbrido também foi fabricada por maquinação CNC com aço de liga 1.1730. O sistema de alimentação definido foi por canais frios, tal como o molde convencional (Figura 6).
Os insertos moldantes (bucha e cavidade) foram produzidos através do processo Direct Metal Laser Sintering (DMLS). Resumidamente, DMLS é um processo de fabrico aditivo no qual um recoater distribui a quantidade de pó metálico para uma espessura de camada predeterminada, enquanto espalha o material sobre uma plataforma
Um sistema de arrefecimento por canais conformados foi definido para cada dissipador de calor em estudo (Figura 8), considerando um desempenho ótimo e, tendo em conta a regra de distância mínima entre os canais do sistema de controlo de temperatura e as peças moldadas ou componentes metálicos, como extratores. O diâmetro dos canais varia entre 6 a 8 mm para garantir essas distâncias de segurança aos elementos críticos.
A Figura 9 mostra os insertos moldantes do molde híbrido antes da maquinação CNC e ainda presos à plataforma de construção pelo material de suporte e, após a maquinação CNC onde é notória a melhoria da qualidade superficial da bucha e cavidade de cada inserto moldante. O lead-time para toda a construção do molde

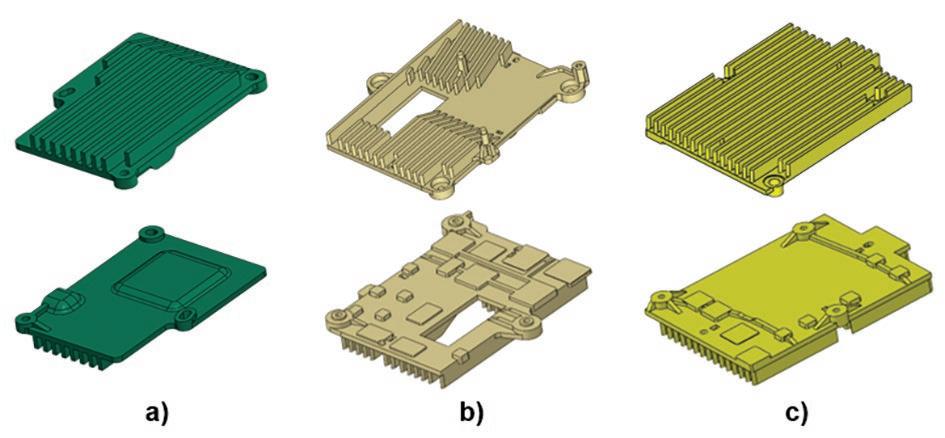
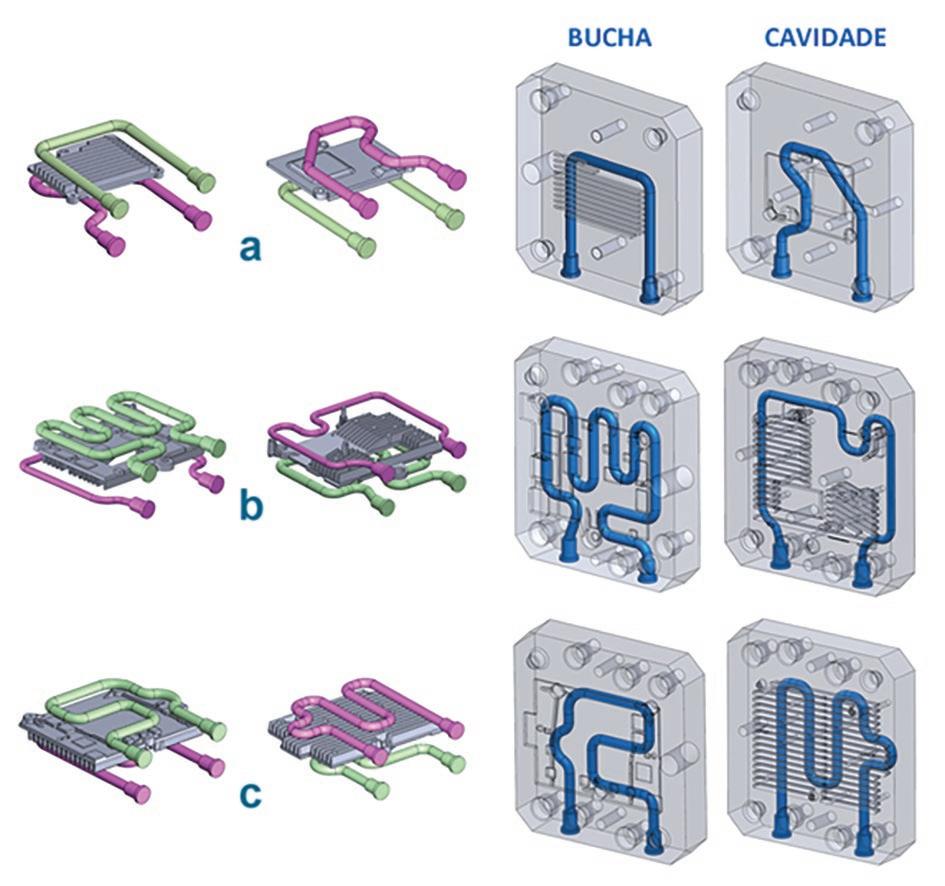
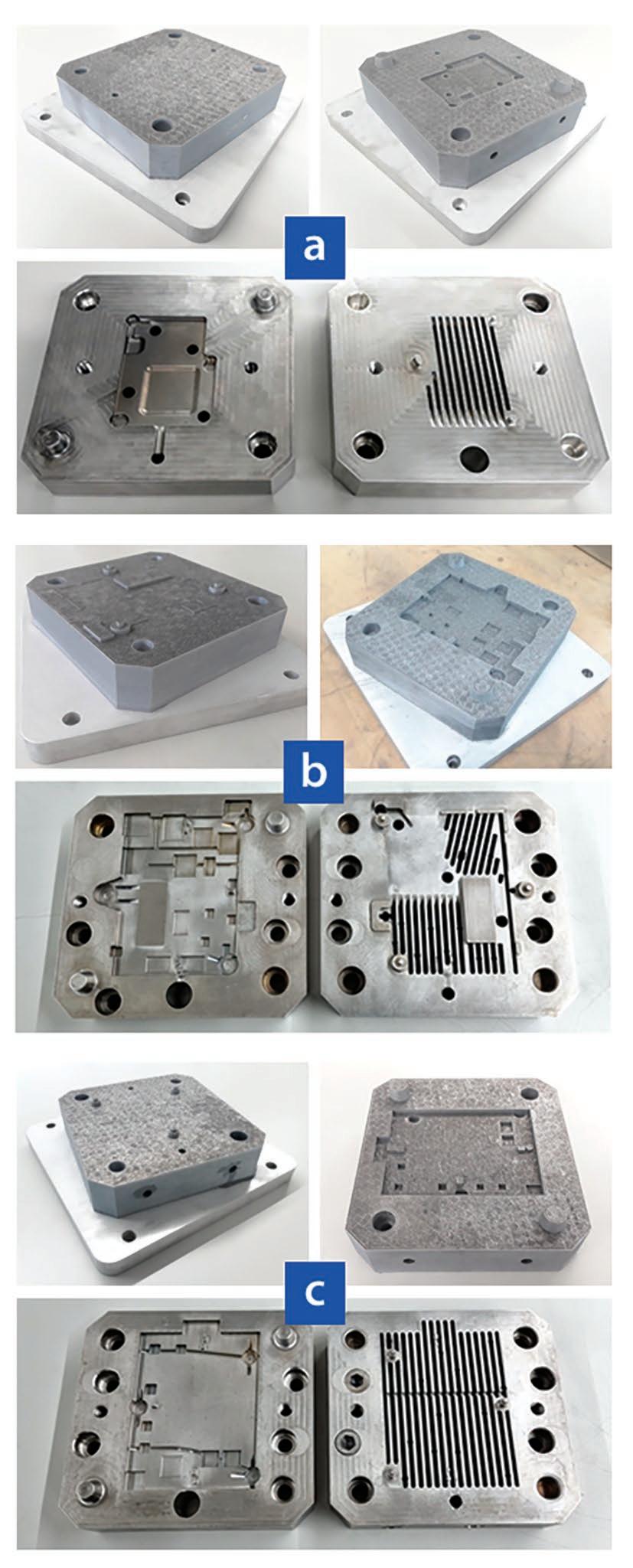
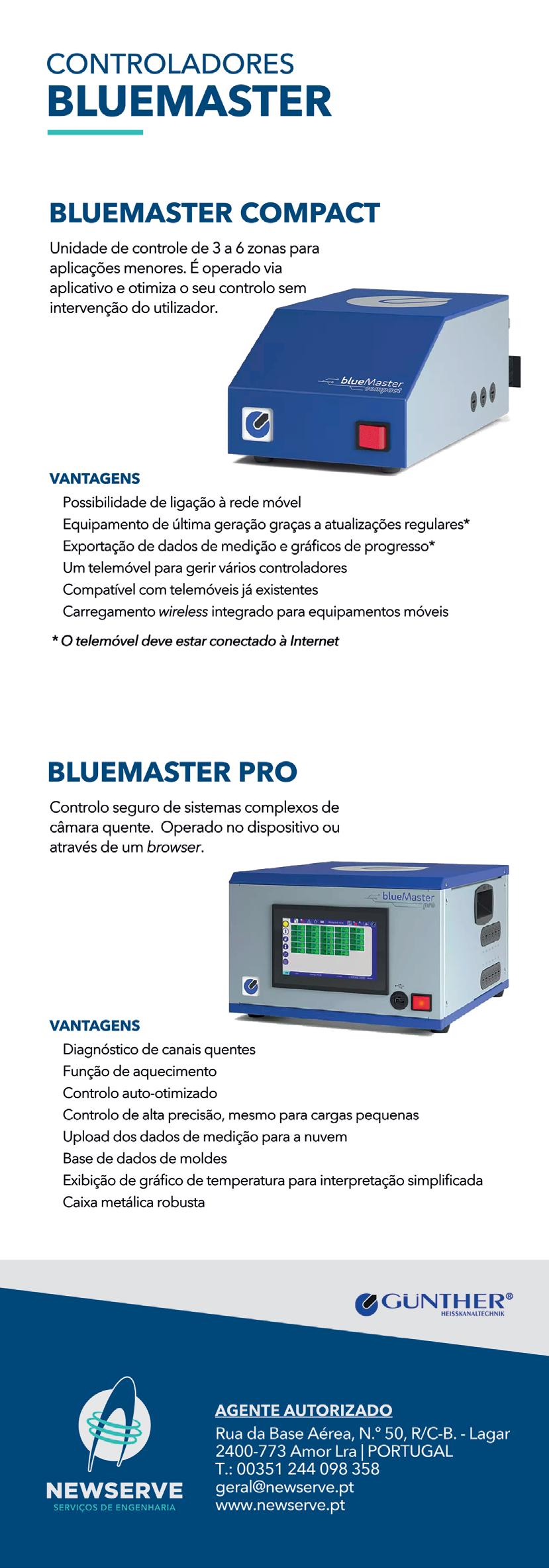
3. PROCESSO DE MOLDAÇÃO POR INJEÇÃO
Os parâmetros do processo de moldação por injeção foram otimizados para cada molde desenvolvido (Tabela 1). Para a definição do perfil de temperaturas do processo de injeção (Figura 10), devido ao fenómeno de dissipação viscosa causado pelo material condutor, foi definido que a maior temperatura seria na zona de transição e não no bico de injeção, para melhor garantir a temperatura pretendida durante a injeção, evitando que fique a “babar” à saída do bico. Este fenómeno ocorre devido à composição do material, que, por apresentar uma maior percentagem de cargas termicamente condutoras, potencia um aumento da temperatura do fundido durante o avanço no interior do cilindro da injetora. Este aumento da temperatura deve-se ao aquecimento por dissipação viscosa, devido ao atrito entre as cargas que compõem o fundido e as paredes internas do cilindro de injeção.
Além disso, ao trocar os housings eletrónicos de metal para material compósito de matriz polimérica, foi possível reduzir aproximadamente 305 gramas (Figura 13) ao peso total do conjunto.
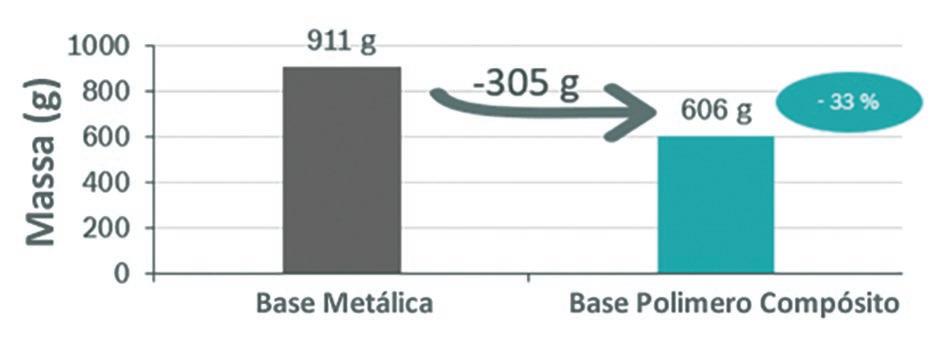
Os dissipadores de calor foram injetados com sucesso em ambos os moldes de injeção desenvolvidos, apresentando excelente qualidade superficial (Figura 11).
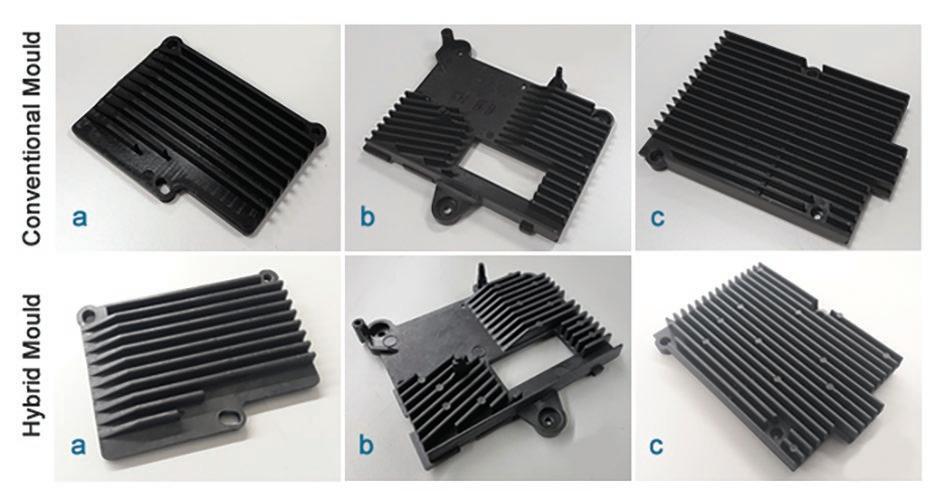
4. RESULTADOS E CONCLUSÕES

A Tabela 2 reúne as principais informações referentes a custo, leadtime e também aos tempos relacionados com os parâmetros de processamento (tempo de arrefecimento e tempo médio de ciclo), para os dois tipos de moldes de injeção em estudo, convencional e híbrido. Com base nessas informações, algumas observações podem ser feitas:
- Embora o custo de fabrico do molde híbrido (€ 33.182) tenha sido ligeiramente superior (aproximadamente 5 %) ao do molde convencional (€ 31.500);
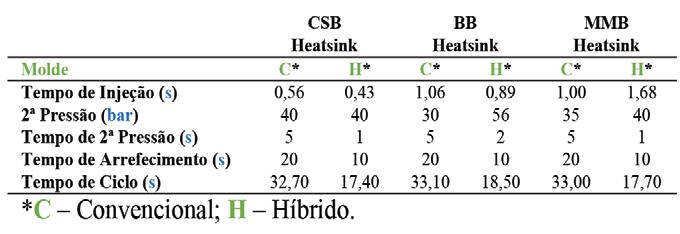
- houve um notável ganho de lead-time para o molde híbrido, com uma diferença de 8 semanas a menos (um terço do tempo) em relação ao molde convencional;
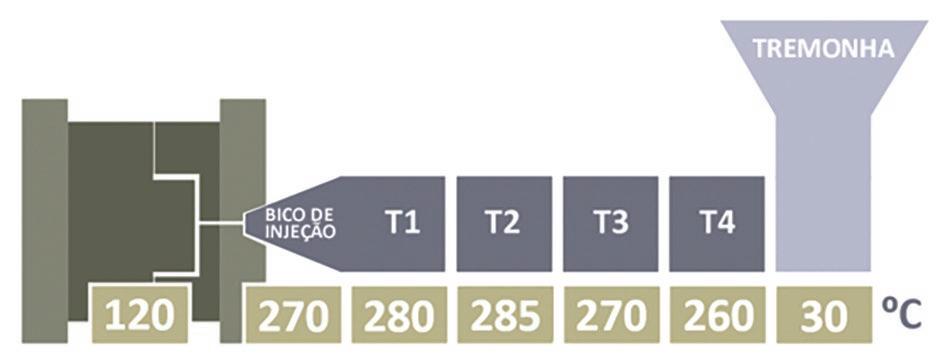
- Além disso, o molde híbrido, devido aos canais de arrefecimento conformados, permitiu reduzir o tempo de arrefecimento para metade, em comparação com o molde convencional resultando, consequentemente, num menor tempo médio de ciclo e maior produtividade do processo.
Considerando os resultados obtidos, é possível concluir que, apesar de o custo ser um pouco maior, ainda é rentável optar por uma solução de molde híbrido, pois as peças injetadas foram obtidas com qualidade semelhante ao molde convencional e com uma taxa de tempo de comercialização mais rápida.
Os dissipadores de calor foram então inseridos na placa de circuito impresso e o Lightweight Electronic Enclosure foi totalmente montado (Figura 12). Os sistemas foram avaliados e todas as peças produzidas, quer por molde convencional e por molde híbrido, apresentaram um desempenho semelhante em testes eletrónicos, mecânicos e dimensionais.
Agradecimentos
Este trabalho foi apoiado por: Fundos Europeus Estruturais e de Investimento na componente FEDER, através do Programa Operacional de Competitividade e Internacionalização (COMPETE 2020) [Projecto nº 039334; Referência de Financiamento: POCI01-0247-FEDER-039334], e pela FCT - Fundação Portuguesa para a Ciência e Tecnologia, Referências UIDB/05256/2020 e UIDP/05256/2020.
5. REFERÊNCIAS
1. Pontes, A. J., Queirós, M. P., Martinho, P. G., Bártolo, P. J., and Pouzada, A.S. - “Experimental Assessment of Hybrid Mould Performance.”2010. International Journal of Advanced Manufacturing Technology 50 (5–8): 441–48. https://doi.org/10.1007/s00170-010-2546-1.
2. Pouzada, A. S. - “Hybrid Moulds: A Case of Integration of Alternative Materials and Rapid Prototyping for Tooling.” – 2009. Virtual and Physical Prototyping 4 (4): 195–202. https://doi. org/10.1080/17452750903438676.
3. Martinho, P. G., Bártolo, P. J., and Pouzada, A. S. - “Hybrid Moulds: Effect of the Moulding Blocks on the Morphology and Dimensional Properties.” – 2009 - Rapid Prototyping Journal 15 (1): 71–82.
https://doi.org/10.1108/13552540910925081.
4. Rosochowski, A., and Matuszak, A.. “Rapid Tooling: The State of the Art.” - 2000. Journal of Materials Processing Technology 106 (1–3): 191–98.
https://doi.org/10.1016/S0924-0136(00)00613-0.
5. Pontes, A. J., Gago, P., Bártolo, P. J., Soares, R., and Pouzada, A. S. - 2005. “HIBRIDMOLDE.Pdf.” https://doi.org/10.1016/j.matpr.2021.02.126. https://doi.org/10.1016/j.addma.2016.03.004. https://doi.org/10.1007/s12541-011-0009-8.
6. Hänninen, J. - “DMLS Moves from Rapid Tooling to Rapid Manufacturing.” – 2001. Metal Powder Report 56 (9): 24, 26–29.
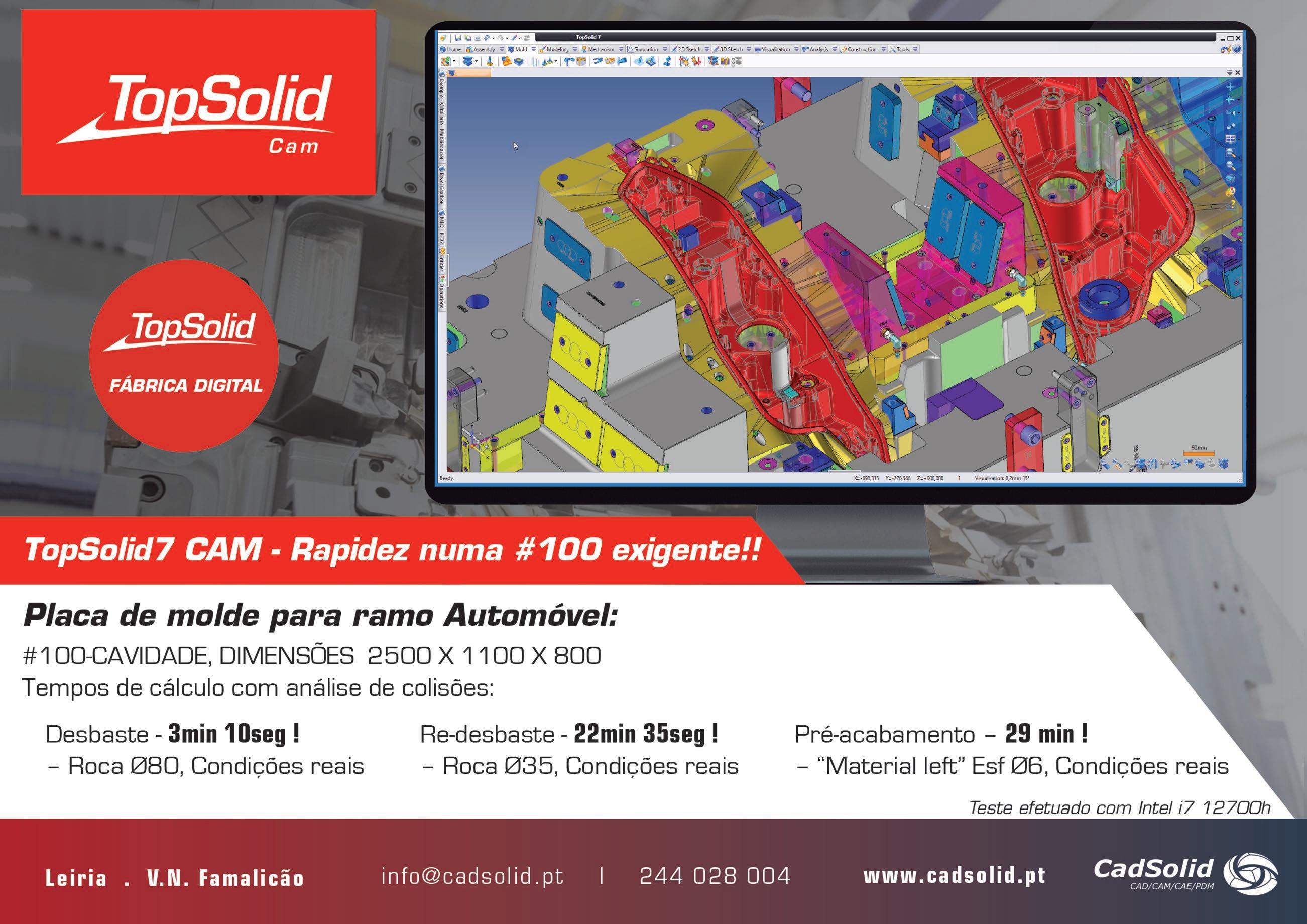
7. Chan, Lun, Y., Diegel, O., and Xu, X. - “Evaluation of Bonding Integrity of Hybrid-Built AlSi10Mg-Aluminium Alloys Parts Using the Powder Bed Fusion Process.” – 2021. Materials Today: Proceedings 46: 1277–82.
8. Brooks, H., and Brigden, K. - “Design of Conformal Cooling Layers with Self-Supporting Lattices for Additively Manufactured Tooling.” –2021. Additive Manufacturing 11: 16–22.
9. Dang, Phuong, X., and Park, H. S. - “Design of U-Shape Milled Groove Conformal Cooling Channels for Plastic Injection Mold.” - 2011. International Journal of Precision Engineering and Manufacturing 12 (1): 73–84.