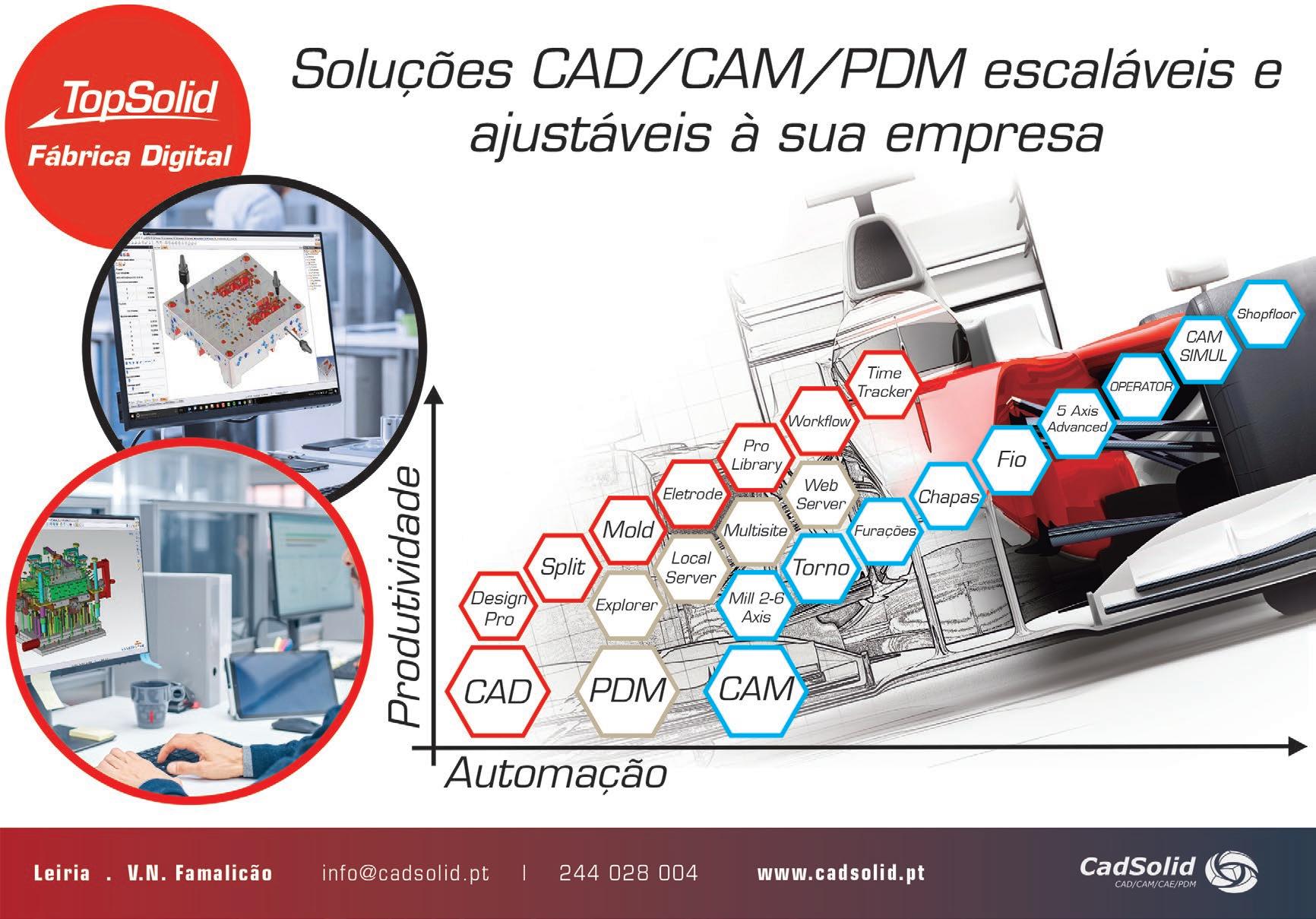
7 minute read
PROJETO – MELHORIA DA EFICIÊNCIA
from Molde N.º 137
by CEFAMOL
António Pina 1, José Morais 2, Liliana Chaves 2 1 – Anibal H. Abrantes, 2– Lexus-Consultores, Lda.
A implementação deste projeto apresentou dois momentos fundamentais. Um primeiro, em que consistiu na realização de formação no modelo EFQM 2020 (Figura 1) e na realização da autoavaliação da AHA, de acordo com o modelo EFQM, e na priorização e seleção das ações de melhorias. O segundo momento baseou-se na concretização das ações de melhoria selecionadas, através das várias sessões de trabalho junto dos seguintes elementos: Diretor de Fábrica, Responsável de Produção, Responsável da Qualidade, Responsável de Bancada e Responsável Maquinação.
A implementação deste projeto teve como base sessões de trabalho, normalmente estabelecidas, com a equipa de trabalho definida, no apoio à implementação das ações, de forma a que, após a conclusão do projeto, estivesse apta para sustentar e, melhorar se necessário, as ações executadas.
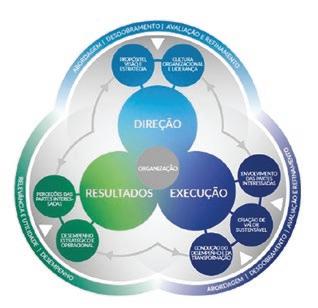
Na sequência da ação que visa a melhoria da eficiência produtiva, foram implementadas determinadas ferramentas, como por exemplo, ferramentas Lean, incidindo na caracterização atual da AHA, na procura de pontos críticos de ineficiência e na implementação e avaliação do impacto das medidas de melhoria.
A eventual fragilidade na comunicação e a falta de gestão visual resultam em vários problemas, nomeadamente, atrasos frequentes na entrega, ou entre secções das organizações, ou até mesmo, ao cliente e, por isso, cada vez mais é carecedor de um acompanhamento mais próximo do planeamento. Também, é importante ouvir as dificuldades que surgem ou que poderão surgir, por forma a conseguir cumprir os prazos determinados pelo planeamento, e fomentar uma abordagem de atuação pela prevenção, ao invés de atuação pela correção. primeiro ensaio do molde, sobre os problemas detetados no molde em análise, com vista a identificar ações mais eficazes, alcançando assim, a redução, ou até a eliminação dos respetivos problemas já no ensaio subsequente.
Para tal, instituiu-se a seguinte prática: stand-up meetings ou, em português, realização de reuniões curtas diárias juntamente com ferramentas visuais, como por exemplo, o Quadro de Melhoria.
O objetivo destas reuniões consiste em organizar um encontro diário, num local definido e no mesmo horário, no qual os integrantes desta reunião estão de pé, a trocar ideias e discutir as atividades inerentes à empresa, bem como a sua priorização.
Neste tipo de reuniões deve ser respeitado o prazo de duração, que é bastante curto, máximo 15 minutos. Todos ficam de pé para criar um senso de celeridade, estimulando um brainstorming mais objetivo e focado no que realmente é mais importante. Para tal, foi necessário construir o Quadro de Melhoria (Figura 2), ferramenta visual, para dar início a esta nova prática de realização de curtas reuniões diárias entre os responsáveis de Projeto, Maquinação e Bancada, juntamente com o Comercial, Responsável de Qualidade e de Produção e, pontualmente, a presença do Diretor de Fábrica.
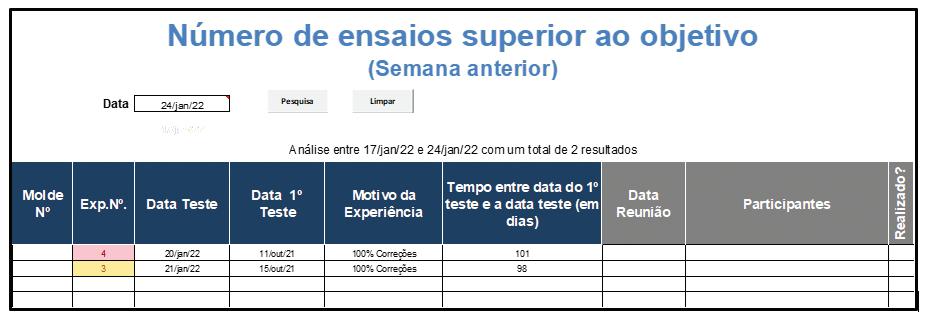
Os elementos constituintes do Quadro de Melhoria foram, ao longo do tempo, revistos e ajustados às necessidades da empresa. Atualmente, o Quadro de Melhoria Diário é composto pelas seguintes componentes:
• Planeamentos dos Moldes (relativos à Programação, Projeto, Maquinação e Bancada) e os respetivos pontos críticos;
• Indicadores a monitorizar: (i) Taxa de Ocupação Semanal das Máquinas; (ii) Taxa de Ocupação Diária das Máquinas; e, (iii) Número de ensaios superior ao objetivo definido realizados na semana anterior. A monitorização das taxas de ocupação diária e semanal permite aos responsáveis de secção ter a quantificação, em percentagem, da real utilização face à capacidade da máquina. No que diz respeito à monitorização do número de ensaios, um dos objetivos consiste em reduzir o número de ensaios dos moldes. Este indicador foi criado com base num registo de dados já existente, que posteriormente, realizou-se um desenvolvimento de forma a obter, de uma forma célere, uma listagem dos moldes ensaiados da semana anterior, que ultrapassa o objetivo definido. Todas as segundas-feiras, é afixada esta informação no Quadro de Melhoria (a título de exemplo, Figura 3), sendo a mesma analisada, selecionando qual o molde que irá ser alvo de estudo e, posteriormente, dever-se-á agendar uma reunião, juntamente com as pessoas determinantes, para avaliar os relatórios de ensaios e, caso exista, comentários dos clientes, para definir ações mais eficazes. Detetou-se também que se estava a atuar nos problemas do molde após vários ensaios numa fase posterior. Neste sentido foi proposto a realização de uma reunião após o
• Boas práticas: tem como objetivo manter e divulgar boas práticas existentes. Neste momento, esta área, face ao exercício de brainstorming no decurso de um workshop sobre as TARP (Técnicas de Análise e Resolução de Problemas) realizado pela Lexus, está preenchida no Quadro de Melhoria, com as boas práticas para tornar reuniões produtivas;
• Área de comunicação: este é um campo livre, preparado para a partilha de qualquer assunto que se pretenda comunicar. Neste caso, possui informação sobre a última encomenda realizada na AHA, permitindo a tomada de conhecimento de todos. Também possui a informação relativa à caixa de sugestões, ideia essa explicada posteriormente, contendo um fluxograma e um impresso para o colaborador preencher a sugestão de melhoria.
Para um melhor entendimento do envolvimento e atitude dos colaboradores da AHA, realizou-se uma auscultação por questionário, anónimo e confidencial, cujas respostas foram apenas utilizadas para efeitos de estudo. Este questionário foi parte integrante do projeto, no qual se compreende a atitude dos trabalhadores dividida em três dimensões relacionados com a eficiência. Procedeu-se ao apuramento dos resultados e à divulgação dos mesmos através do Quadro de Melhoria para todos os colaboradores da AHA.
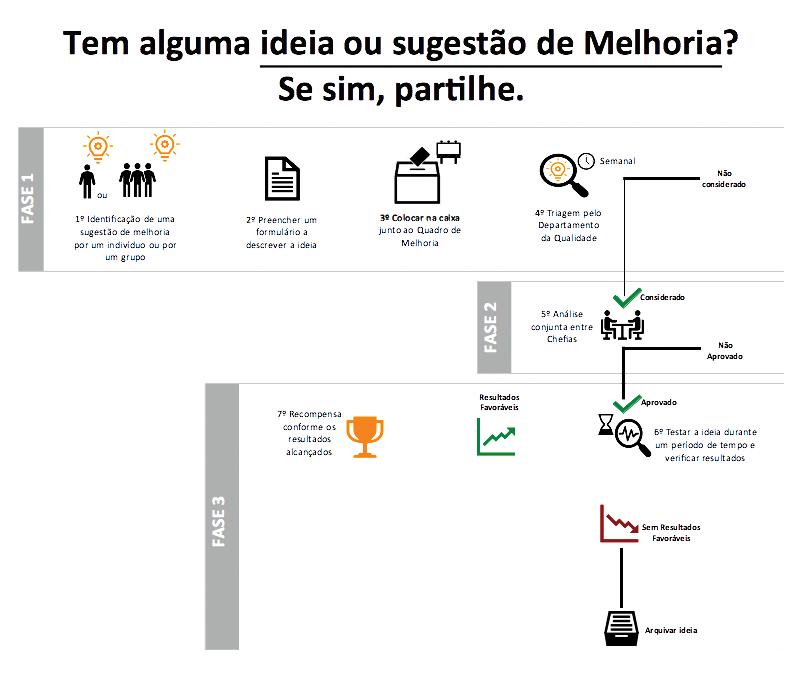
Os resultados alcançados na atitude dos trabalhadores foram a alavanca para a dinamização do sistema de sugestões de melhoria. Esta dinamização não se restringiu à criação de uma caixa para o efeito e de um fluxograma (Figura 4) sobre o funcionamento da caixa de sugestões, mas sim na otimização do registo e tratamento das sugestões de melhoria (Figura 5). Este conteúdo encontra-se afixado no Quadro de Melhoria, na componente da “Área de Comunicação”, permitindo uma maior visibilidade e clareza no sistema de sugestões de melhoria.
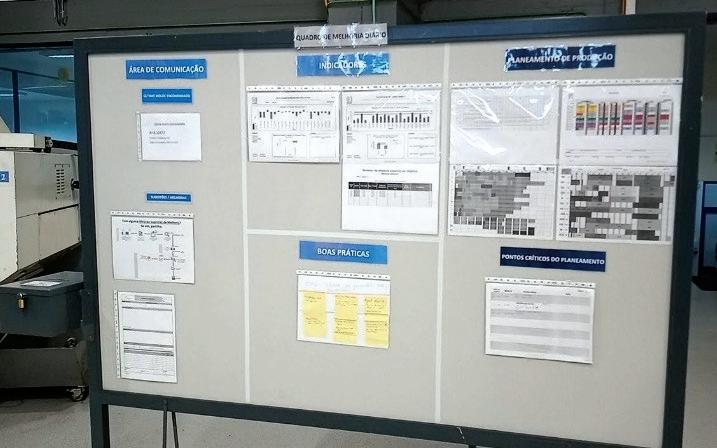
Após esta implementação, constatou-se uma evolução significativa na apresentação do número de sugestões entre 2021 e 2022, um incremento de 300 %.

No decorrer do projeto, foram realizados vários fluxos para análise dos circuitos das peças principais, cavidades e buchas, e dos respetivos tempos de operação. Para tal, foram analisados moldes concluídos, previamente selecionados pela equipa de trabalho. A primeira análise efetuada consistiu no desenho, recorrendo ao layout das instalações, de todo o percurso efetuado pelas peças de cada molde, nomeadamente as máquinas utilizadas e respetivos tempos efetivos de trabalho, os quais estão apresentados como exemplo, a peça 200, na Figura 6.
A segunda análise englobou a criação de Diagramas de Gantt, ferramenta visual na compreensão e observação do cronograma real das diversas operações, no qual se cruzaram os registos de operações associadas às correções face aos relatórios de ensaios, conforme ilustrado na Figura 7.
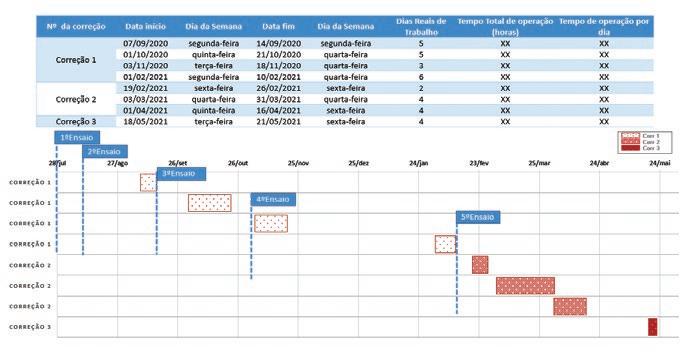
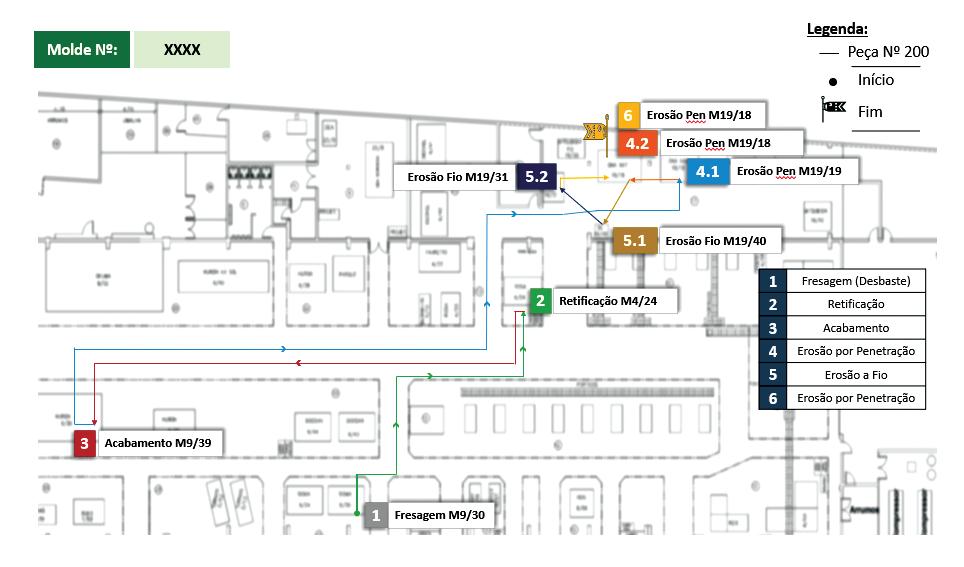
Este tratamento permitiu à equipa de trabalho analisar a sequência das operações e as máquinas utilizadas e, ainda, o tempo de operação real em cada máquina. Aquando da análise dos relatórios de ensaios, verificou-se que alguns dos desvios poderiam ser combatidos pelo correto preenchimento das checklists, sendo operacionalizadas determinadas ações, conforme Figura 8. Neste sentido e, após análise, foi sugerida a revisão das checklists da Montagem e do Projeto e posteriormente, partilhadas e acordadas pelas empresas do Grupo. As mais valias da aplicação eficaz de uma checklist baseiam-se na prevenção de riscos e falhas. Por forma a cumprir a correta utilização das checklists definiram-se práticas, não só de um maior acompanhamento e sensibilização do preenchimento, mas sim na ótica de promover a autorresponsabilidade dos operadores. consumido por atividade e molde, tempo consumido por operário e categoria ou atividade, entre outros.

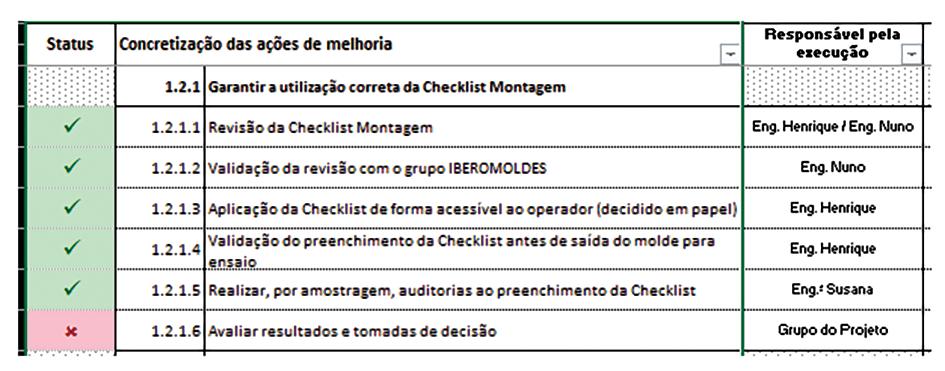

No âmbito das Não Conformidades, identificou-se a necessidade de melhorar o controlo estatístico sobre as mesmas, resultando na sensibilização da revisão da metodologia utilizada, nomeadamente o tratamento dos dados aquando do registo, permitindo um apuramento / análise das causas e dos custos, mais real e “fino”, através da visualização gráfica, como apresentado abaixo (Figura 9).
Com vista a identificar eventuais ineficiências no chão de fábrica, este projeto recorreu à Metodologia 5S, com aplicação em todas as secções, e a Diagramas de Esparguete, na secção da Maquinação. A Metodologia 5S, apesar de já ser do conhecimento de toda a fábrica, considerou-se apropriada a ser reaplicada em todas as secções, visto ter sido aplicada no passado. Para tal, foi elaborada uma lista de verificação para a realização de “Auditoria 5S” e utilizada em dois momentos. O primeiro consistiu numa auditoria inicial e fotografias do “antes” nas áreas a intervencionar e, o segundo momento baseou-se numa 2.ªAuditoria, aplicada após a implementação das ações de melhoria com as respetivas fotografias do “depois” nas áreas intervencionadas. A título de exemplo, a secção da Erosão, obteve um resultado inicial de 60 % e, após implementação de um conjunto de ações de melhoria, obteve um resultado final de 80 % (Figuras 11 e 12).
No âmbito do projeto, o Responsável do Projeto considerou relevante analisar os tempos real de trabalho nas atividades de projeto (Figura 10), com a finalidade de identificar as atividades críticas atuais, e definir respetivas medidas de melhoria. Neste tratamento, conseguiu-se obter uma série de informação como o tempo total (valores absolutos ou convertidos em percentagens) por atividade em horas, geral e por categoria definida pela secção (Artigo, Molde, Peça e Vários), tempo
Dado que a movimentação desnecessária é considerada como um tipo de desperdício, isto é, resulta em trabalho que não acrescenta valor (NVA) para o cliente, foram elaborados Diagramas de Esparguete, ferramenta Lean, visual, utilizada para mapear as movimentações de colaboradores. Desta forma, foi realizado um levantamento nesta área, quantificando e, identificando o impacto a médio e longo prazo. Assinalando-se as situações críticas, conforme ilustra a Figura 13, obtendose um total de 132 horas ano destinadas a movimentações que poderiam ser reduzidas. Em resultado desta ação, procedeuse à redefinição da afetação das pessoas às máquinas.
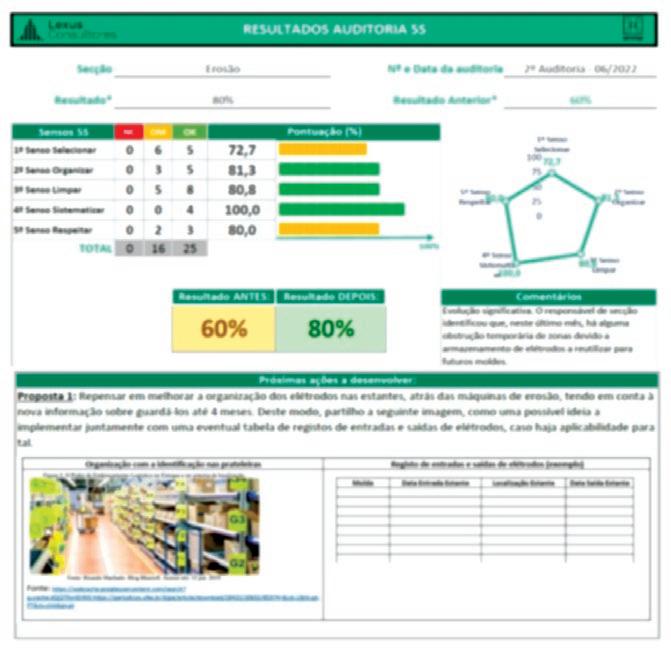
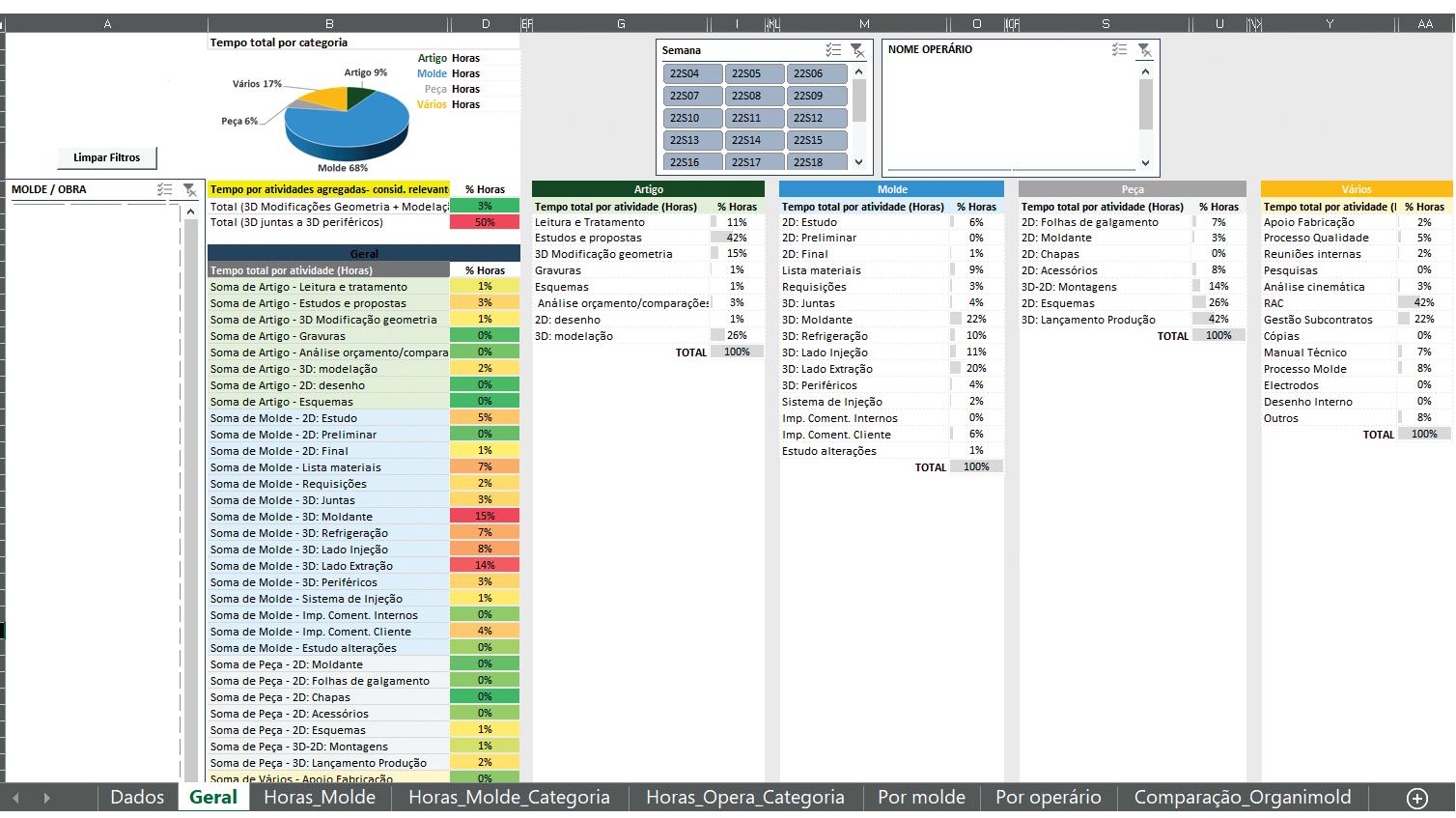
De acordo a definição do ecossistema da AHA (Figura 14) propuseram-se ações das quais os detalhes não podem ser incluídos no contexto deste artigo.
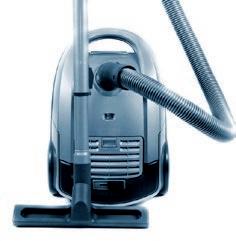
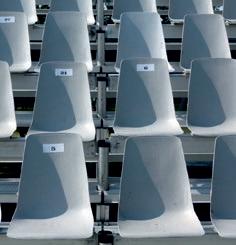
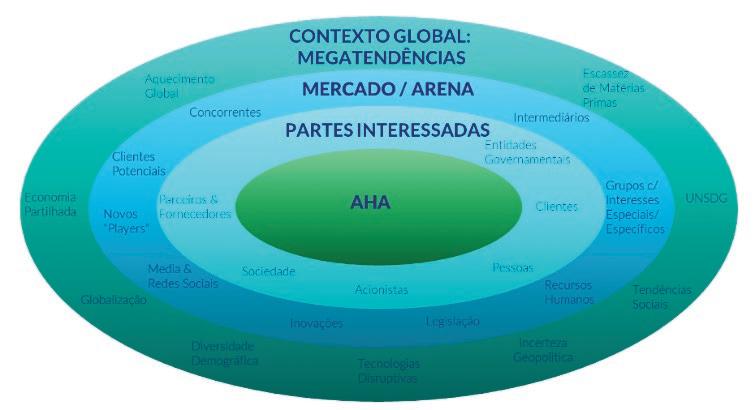
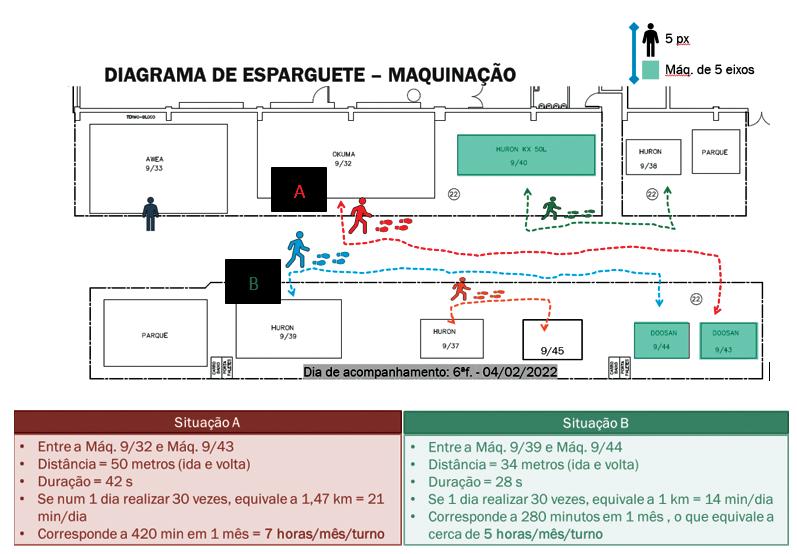

Apesar de as abordagens de melhoria e dos respetivos resultados do projeto já se encontrarem implementados, considerou-se que, numa perspetiva de consolidação, continuidade e maturidade, seria útil “embebe-las” no Sistema de Gestão da Qualidade, para que as mesmas, possam, assim, ser objeto de monitorização e auditoria regular.