
2 minute read
MOLDES DE INJEÇÃO: MAIS EFICIENTES, OTIMIZADOS OU INTELIGENTES?
from Molde N.º 137
by CEFAMOL
INEGI - Instituto de Ciência e Inovação em Engenharia Mecânica e Engenharia Industrial Simoldes Aços
OS MOLDES DE INJEÇÃO PRODUZEM MILHÕES DE PEÇAS PRATICAMENTE IDÊNTICAS E ENTRE ELAS EXISTEM PEÇAS PLÁSTICAS COMPLEXAS.
Advertisement
Estima-se que, em 2021, o mercado global de moldagem por injeção corresponda a US$ 261,8 biliões, prevendo-se um crescimento anual de 4,8 % entre 2022 e 2030. Espera-se que o crescimento do mercado seja impulsionado pela crescente procura pela produção em massa de milhares de componentes idênticos a custos mais reduzidos, a par da procura pela flexibilidade de desenho e precisão que vários sectores valorizam, como embalagens, medicina e eletrónica.
Porém, a produção por injeção é um processo complexo, multivariável, não linear e variável no tempo, dificultando a otimização dos parâmetros do processo. Existem muitos fatores que afetam a qualidade da injeção. Entre eles, a estrutura do molde é a que rege o tempo de arrefecimento no ciclo de moldagem e a qualidade dos produtos. Um sistema de refrigeração adequado é necessário para transferir o calor do molde e manter uma taxa de arrefecimento estável, garantindo produtos finais de maior qualidade. Portanto, a otimização da estrutura do molde é um meio importante para prevenir defeitos e melhorar a qualidade do processo.
INEGI DESENVOLVE UM FRAMEWORK PARA OTIMIZAR A QUALIDADE E REDUZIR O TIME-TO-MARKET DE MOLDES DE INJEÇÃO
O projeto i-Tool, promovido pelo consórcio Simoldes Aços com copromoção da Simoldes Plásticos e do INEGI, responde eficazmente a um desafio permanente de integração de ferramentas, software e fases de desenvolvimento de moldes (expertise, design e desenvolvimento, desenvolvimento 3D, definição de estratégia de fabrico, produção) utilizando técnicas e algoritmos baseados em ciências computacionais.
O projeto i-Tool, alavancando uma importante inovação de produto, tirando partido dos mais recentes desenvolvimentos associados à ciência e aos dados computacionais dos algoritmos, teve implicações positivas nas fases de conceção, desenvolvimento e fabrico do molde, culminando num molde otimizado que é mais leve. Estes benefícios estão associados a: (i) menores taxas de rejeição e impacto ambiental, (ii) menores tempos de arrefecimento nos ciclos de injeção de moldes, (iii) aumentos na capacidade de produção, (iv) uso de menor tonelagem das máquinas, redução dos custos de energia e, finalmente, (v) um time-to-market mais curto de peças plásticas. Este último responde especificamente às necessidades e exigências da indústria automóvel e dos OEM, uma vez que podem potencialmente aceder a maiores volumes de produção de peças injetadas, a um preço competitivo, com níveis de qualidade superiores, em prazos mais curtos e com rentabilidade reforçada e sustentada. Estes benefícios são complementados por vantagens competitivas em termos de eficiência energética, redução de resíduos e emissões de CO2
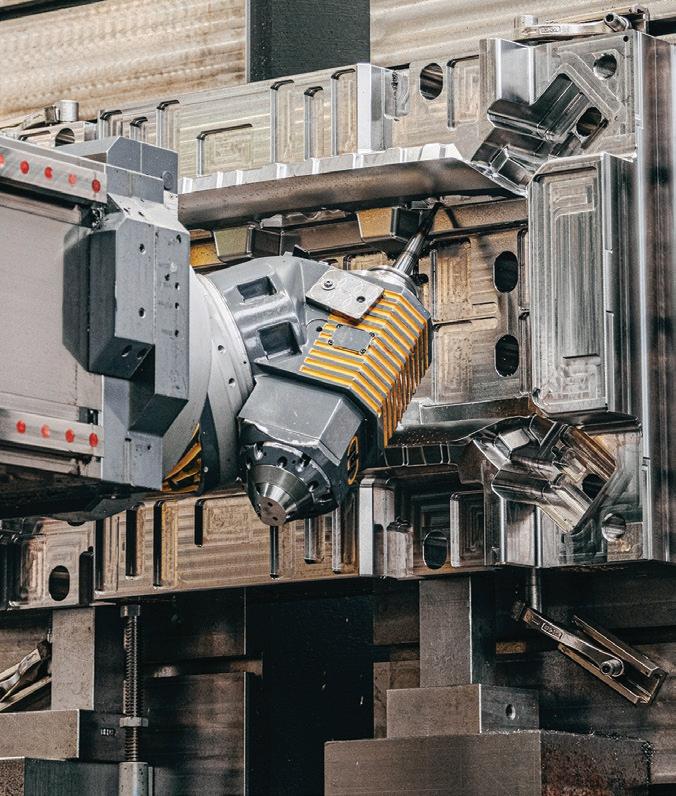
Entre os resultados a destacar, salienta-se que o consórcio conseguiu uma redução de massa de cerca de 20 % num molde otimizado, e uma redução do time-to-market. Como? Vejamos:
Otimiza O Estrutural E T Rmica De Moldes
Os moldes possuem diversas partes com diferentes níveis de importância para otimização estrutural e térmica. Por isso, no âmbito do projeto i-Tool, definimos como objetivo identificar as partes do molde com maior relevância, bem como analisá-las e otimizá-las com base em duas técnicas. Inicialmente, os moldes foram analisados estruturalmente considerando melhorias em três sectores: (1) desenho dos blocos de travamentos; (2) otimização dos pilares; e (3) otimização dimensional do molde. Os travamentos são desenhados de forma a garantir que uma folga máxima entre a cavidade e a interface do macho, resultante da pressão interna, seja respeitada, obtendo-se um produto de maior qualidade e uma menor taxa de rejeição dos produtos finais. A otimização de pilares considera o controlo da flexão nos blocos do molde. Por fim, a otimização dimensional do molde tem influência direta no volume do mesmo. Em comum, estas três etapas têm como objetivo a minimização da massa dos componentes envolvidos, reduzindo o peso do molde com base nos resultados de análises computacionais.
Durante a otimização térmica do molde, os circuitos de refrigeração são desenhados com base numa análise computacional térmica. Uma melhor configuração dos circuitos de refrigeração (parâmetros de fluxo e localização dos canais) leva a uma distribuição da temperatura final mais uniforme. A técnica utilizada neste procedimento também leva a um arrefecimento mais uniforme da zona de moldagem e da peça plástica.
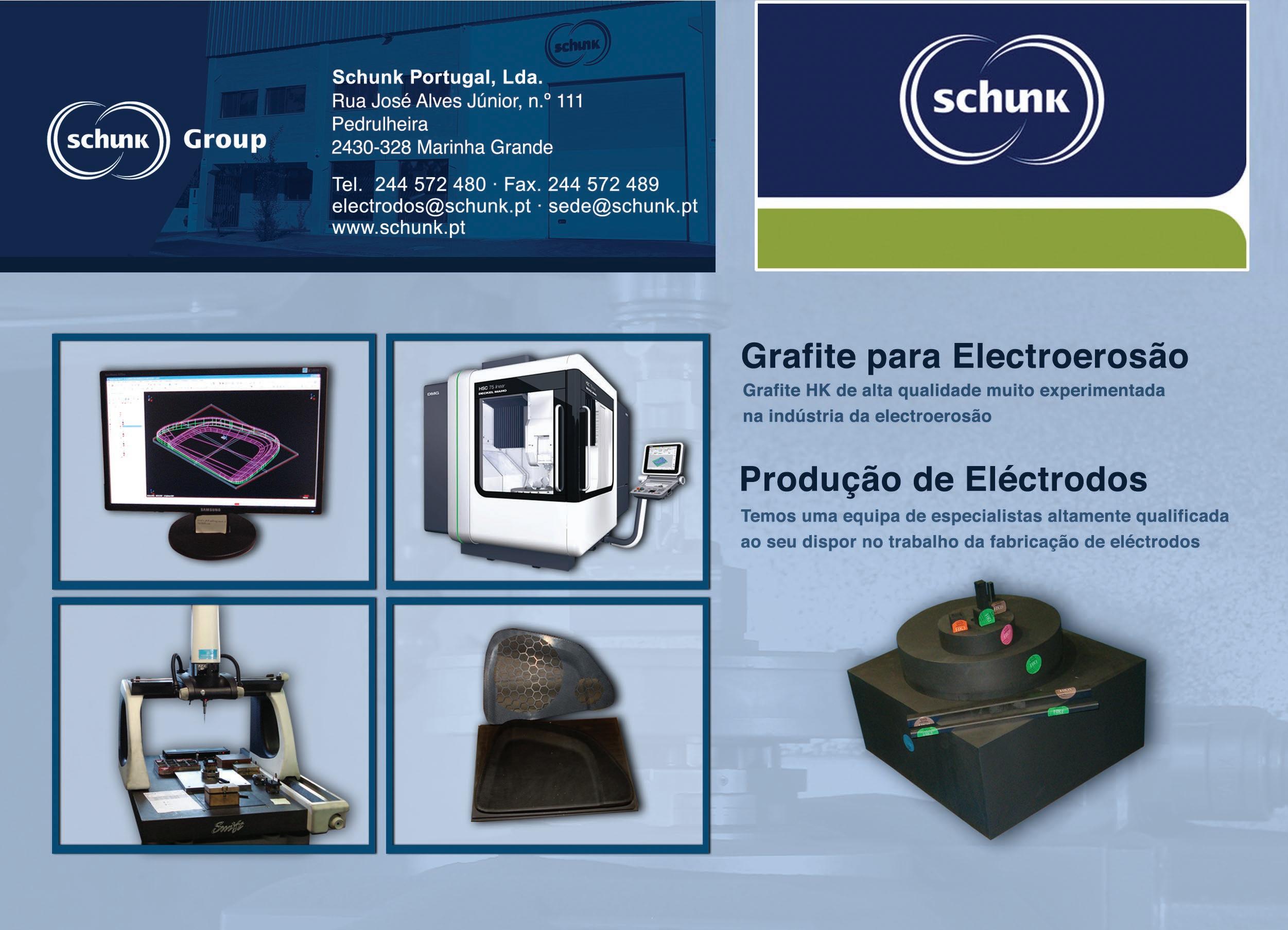