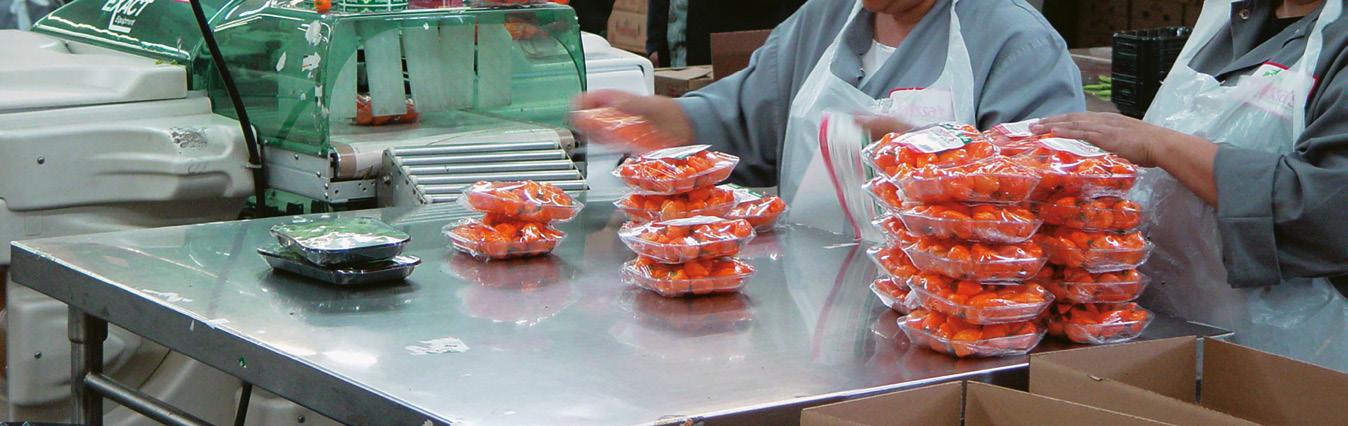
15 minute read
Fine linea - Ridurre i costi e aumentare i profitti durante la crisi Covid-19 nell’in dustria alimentare - Nuove tecnologie digitali per maggiore flessibilità - Sistemi di confezionamento efficienti e sostenibili
Ridurre i costi e aumentare i profitti durante la crisi Covid-19 nell’industria alimentare
L’impatto del Coronavirus sulla filiera alimentare nazionale ed internazio nale ha posto le aziende del settore di fronte a sfide senza precedenti. In questo contesto, il miglioramento dell’efficienza e la riduzione del costo totale di produ zione e distribuzione sono fondamentali. Roberto Sca nu, Business Area Manager Product Inspection Division presso Mettler Toledo, spiega come le più recenti soluzioni per l’ispezione dei prodotti alimentari possano contribuire al raggiungimen to di questi obiettivi.
In un mercato globalizzato ed estremamente competitivo come quello odierno, i produttori di alimenti confezionati sono sempre alla ricerca di metodi nuovi e più completi per ridurre i costi e ottimizzare i profitti. L’impatto della pandemia Covid-19 sull’approvvigionamento e sul commercio alimentare a livello globale ha reso ancor più fondamentale la necessità di migliorare l’efficienza operativa e ridurre i costi. Tradizionalmente, indicatori come il costo totale di proprietà (TCO) hanno costituito un mezzo comprovato e affidabile per valutare le decisioni di investimento. Basandosi sul TCO, ovvero tutti i costi direttamente correlati a una macchina, ad esempio la spesa di acquisto e di manutenzione, si possono effettuare analisi sull’approvvigionamento e valutare accuratamente il valore a lungo termine di un nuovo acquisto.
Tuttavia, il TCO si basa su un insieme relativamente limitato di dati ed è quindi utile fino a un certo punto. Un calcolo finanziario più dettagliato è rappresentato dal costo totale di produzione e distribuzione (Total Delivered Cost, TDC), che quantifica il modo in cui tecnologie come le soluzioni per l’ispezione dei prodotti possono contribuire a ridurre le spese necessarie alla produzione e alla distribuzione degli alimenti confezionati. Il TDC è più completo rispetto al TCO, perché tiene conto di tutti i costi di gestione, compreso il prodotto fisico e fattori come il confezionamento, la manodope-
ra, i controlli qualità, lo spreco di prodotto e il trasporto.
Per aziende come Mettler Toledo, che produce strumenti come rivelatori di metalli, sistemi a raggi-X, controllo peso e ispezione visiva, il crescente utilizzo del TDC nel settore degli alimenti confezionati si è tradotto in una maggiore attenzione alle caratteristiche che aiutano i clienti a eliminare sprechi e inefficienze.
Mentre il calcolo del TCO è più strettamente incentrato su questioni direttamente correlate alla risorsa, come l’affidabilità e la produttività, il TDC amplia la visuale sul valore, includendo fattori come la riduzione dei tempi di configurazione, la riduzione dei falsi scarti e il miglioramento dell’efficienza energetica. Si tratta di sviluppare strumenti più rapidi e semplici da usare e che producono meno sprechi. Tutto ciò aiuta le aziende a ridurre i costi.
Soluzioni per la riduzione del TCO
In che modo, quindi, le soluzioni per l’ispezione dei prodotti possono aiutare i produttori di alimenti confezionati a ridurre il TDC? Utilizziamo l’esempio concreto di un’azienda statunitense che utilizza quattro linee identiche per la produzione di uno snack a base di cereali. Il prodotto viene confezionato in sacchetti di pellicola metallizzata con confezionatrici a sigillatura verticale (Vertical Form Fill Seal, VFFS) a una velocità di 100 confezioni al minuto. Il ricavo della vendita di ciascuna confezione è di $ 1,50. Il tipico costo della manodopera per una fabbrica è di $ 12 all’ora e lo stabilimento prevede 2 turni da 12 ore, 260 giorni all’anno.
L’azienda in questione ha installato un rivelatore di metalli con sistema automatico di verifica (ATS) sulla confezionatrice VFFS per verificare la presenza di contaminanti appena prima del confezionamento. Subito dopo la confezionatrice VFFS, è stato implementato un sistema di controllo peso dinamico e, a seguito dell’inscatolamento a valle, un sistema di ispezione a raggi-X verifica la presenza di altri contaminanti non metallici, grumi di sostanze aromatizzanti e l’assenza/presenza di inserti promozionali. Ogni due ore, il rivelatore di metalli e il sistema a raggi-X vengono testati manualmente per garantire che le prestazioni di rivelazione rimangano costanti e che venga soddisfatta la conformità agli standard di sicurezza dell’industria alimentare.
In questa fase del processo produttivo, il prodotto in caduta viene ispezionato da un rivelatore di metalli per confezionatrici verticali, indicato per contaminanti ferrosi, non ferrosi e in acciaio inox.
Una parte essenziale della procedura di garanzia di qualità è quella di assicurare che il rivelatore di metalli sia in grado di individuare continuativamente i contaminanti al livello di sensibilità richiesto. Per riuscirci, è necessario eseguire le regolari verifiche, ov

Il costo totale di produzione e distribuzione (Total Delivered Cost, TDC) quantifica il modo in cui tecnologie come le soluzioni per l’ispezione dei prodotti possono contribuire a ridurre le spese necessarie alla produzione e alla distribuzione degli alimenti confezionati.
vero un processo molto lungo che influisce anche sulla disponibilità della linea di produzione, riducendo la produttività.
La frequenza dei test di monitoraggio delle prestazioni richiesta da alcuni rivelatori di metalli può essere ridotta fino all’80% con l’introduzione della tecnologia chiamata “Modalità Test ridotto”. Ciò assi

La frequenza dei test di monitoraggio delle prestazioni richiesta da alcuni rivelatori di metalli può essere ridotta fino all’80% utilizzando la tecnologia chiamata “Modalità Test ridotto”.
cura che il sistema operi continuamente a un livello di sensibilità superiore a quello necessario per rivelare i contaminanti. Se il livello di rivelazione del sistema comincia a variare, l’operatore riceve immediatamente un segnale di allarme in modo che lo strumento venga verificato prima che sia raggiunta la soglia minima consentita. In questo modo, il produttore di snack ha la certezza che il rivelatore di metalli soddisfi o superi costantemente lo standard di ispezione desiderato. In questo caso specifico, la Modalità Test ridotto ha permesso di limitare la frequenza della verifica da due a sei ore, richiedendo quindi solo due test per ogni turno da 12 ore. Ciò ha consentito inoltre di migliorare l’efficienza della produzione e ridurre i costi di gestione, dato che l’operatore non deve più fermarsi sulla linea e verificare lo strumento con la stessa frequenza di una volta.
“In questo caso, il vantaggio della Modalità Test ridotto si è tradotto in un aumento dei ricavi delle vendite pari a $ 78.000 a linea, per un totale di $ 312.000”, ha spiegato Niall McRory, Global Key Account Manager della Divisione Ispezione Prodotti di Mettler Toledo. “Si tratta di un risparmio notevole, che potrebbe avere un impatto significativo sul TDC”.
L’uso di un sistema automatico di verifica (ATS) per condurre i testi di monitoraggio delle prestazioni dei rivelatori di metalli offre ulteriori opportunità per ridurre i costi di gestione. Da sempre, i produttori impiegano un metodo che richiede agli operatori di lavorare in quota, accanto al sistema di pesatura, per introdurre nel flusso di produzione tre campioni di contaminanti in metallo di cui si conoscono dimensioni e materiali.
Grazie all’ATS, tre campioni di prova vengono inseriti nell’apertura del rivelatore di metalli all’interno di tubi separati, per simulare la presenza di un contaminante nella posizione più difficile, ovvero la linea centrale del tubo di alimentazione dei prodotti. Dal punto di vista della qualità, questo processo è molto più affidabile rispetto all’inserimento manuale di campioni che potrebbero passare erroneamente più vicini al lato dell’apertura in cui sarebbero più facili da rivelare. In termini di operatività, il tempo di verifica viene notevolmente ridotto e si registra un incremento della sicurezza, dato che l’ATS rende superfluo il lavoro in quota per l’esecuzione del test.
Riduzione dei falsi scarti
Con i sistemi a raggi-X, il TDC viene ridotto in altri modi tangibili, soprattutto grazie all’uso di un software avanzato che permette di ridurre la percentuale di falsi scarti (FRR). Nella produzione di alimenti confezionati, i costi legati a un elevato valore di FRR sono potenzialmente enormi, per via della necessità di nuove verifiche, rilavorazioni o lo smaltimento di confezioni “buone” erroneamente valutate come contaminate. Tradizionalmente, viene usata una piccola serie di algoritmi integrata nel software di ispezione per verificare la presenza di variazioni inaccettabili nell’immagine a raggi-X su un intervallo ampio. Ora, un avanzato software di ispezione a raggi-X come ContamPlus definisce automaticamente il miglior livello possibile di rivelazione dei corpi estranei. L’uso di un maggior numero di algoritmi, in grado di verificare singolarmente le anomalie dei prodotti in un intervallo più ridotto, aumenta l’accuratezza dell’ispezione e la tolleranza alle variazioni naturali nella confezione, riducendo al minimo il valore di FRR. In questo modo, il produttore può evitare i costi legati a sprechi e rilavorazioni e proteggere i profitti. Ciò crea un maggiore livello di fi

ducia nella capacità dello strumento di proteggere la reputazione del produttore di snack e la salute dei consumatori.
“Nel caso del produttore di snack statunitense, il vecchio sistema a raggi-X generava almeno quattro falsi scarti all’ora, pari a circa 7 confezioni su 10.000”, ha spiegato McRory. “Un addetto alla garanzia di qualità pagato $ 12 all’ora trascorreva in media quattro minuti a esaminare e documentare i risultati di ogni evento legato al falso scarto. Con il passaggio a un sistema a raggi-X dotato di software avanzato, il valore di FRR si è ridotto ad appena 2 confezioni su 10.000, limitando così i costi di gestione per il produttore. Il vantaggio finanziario totale derivante dall’uso del software avanzato ammontava a circa $ 70.000 all’anno.
“Nel frattempo, la possibilità di automatizzare completamente la configurazione del prodotto sui moderni sistemi a raggi-X ha permesso al produttore di snack di incrementare la flessibilità e di introdurre nuove linee di prodotti a una velocità molto maggiore incrementandone inoltre la disponibilità”.
Offrendo un’accuratezza comprovata a velocità di produzione elevate, anche i sistemi di controllo peso permettono di ridurre il TDC e di limitare lo spreco di prodotto. Nel caso del produttore di snack, il sistema di controllo peso è stato collegato a un circuito di retroazione affinché potesse comunicare con la macchina riempitrice destinata al confezionamento, permettendo di controllare in modo affidabile il peso medio per ridurre ulteriormente lo spreco di prodotto. “Ciò ha contribuito significativamente alla riduzione del TDC”, ha proseguito McRory.
Il TDC consente di prendere decisioni ponderate
In ultima analisi, l’impatto che le soluzioni per l’ispezione dei prodotti possono avere nella riduzione del TDC dipende dalle specifiche circostanze correlate ai processi produttivi e al tipo di prodotto. Prima di implementare un nuovo strumento di produzione o di ispezione prodotti, si consiglia ai produttori di alimenti confezionati di preparare una checklist e richiedere calcoli tangibili sulle riduzioni dei costi. È necessario tenere in considerazione percentuale di falsi scarti, tempistiche di configurazione del prodotto, frequenza di controlli qualità/validazione, consumo energetico e tempi di creazione dei report. Altri fattori comprendono i costi di manodopera e manutenzione. Ciascuno di questi elementi può avere un impatto significativo sulla riduzione del TDC.
Grazie al software avanzato in grado di limitare al minimo la percentuale di falsi scarti (FRR), i sistemi a raggi-X possono contribuire a ridurre il TDC.
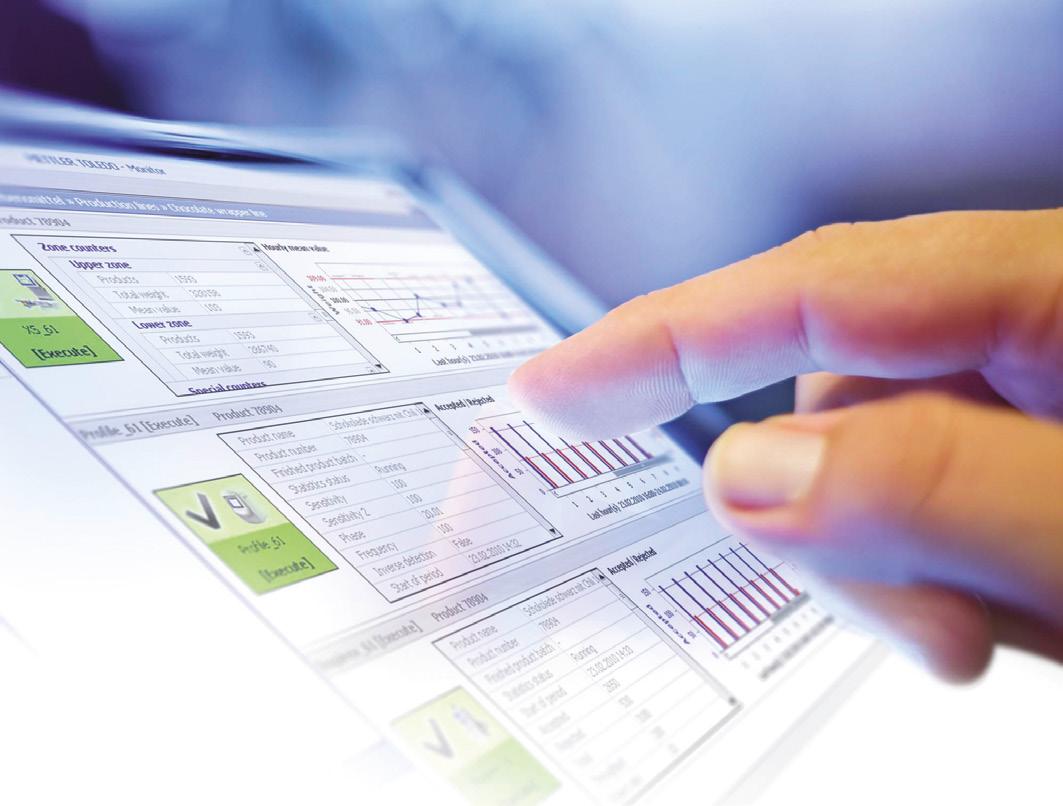
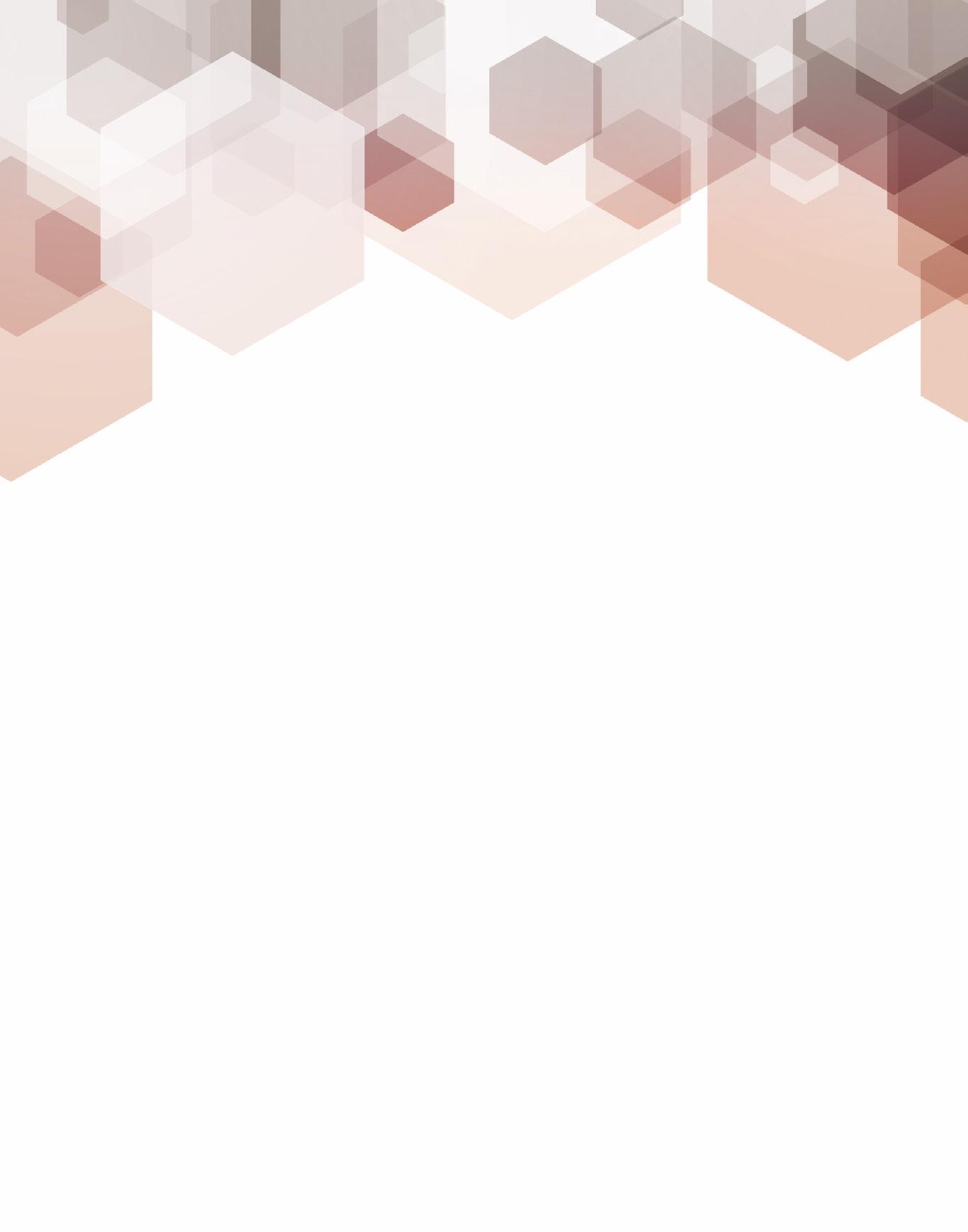
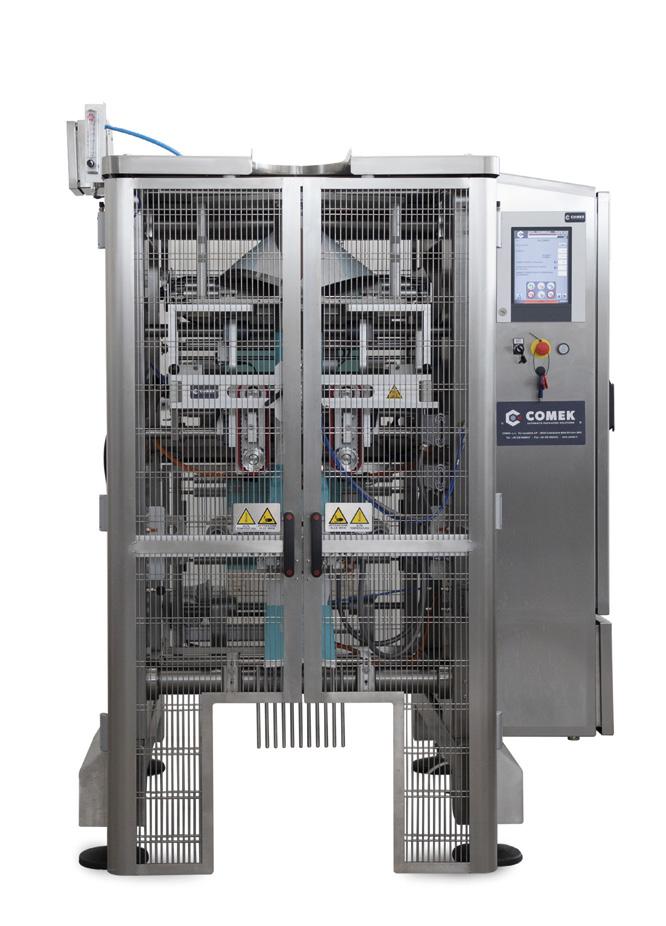

Più veloce, più flessibile, più sostenibile: il settore del packaging attualmente si trova davanti a diverse sfide che richiedono ai produttori un processo di confezionamento economico ed ecologico. Per realizzarlo sono necessarie macchine altamente flessibili e processi efficienti e costanti. Con il sistema modulare combinabile dei suoi impianti TLM, la Schubert offre già oggi un vantaggio che il gruppo aziendale continua a sviluppare proponendo nuovi robot e nuove soluzioni digitali. Per assecondare le nuove tendenze come la richiesta di materiali di confezionamento alternativi, nella costruzione dei nuovi impianti l’azienda si concentra sulle possibilità di impiego flessibili e testa direttamente sulle proprie macchine i nuovi materiali, per giudicarne la qualità e la loro idoneità al processo meccanizzato. Per soddisfare il settore del confezionamento che tende sempre più spesso a lanciare sul mercato nuovi formati, la Schubert offre macchine che utilizzando le tecnologie più avanzate danno la possibilità di eseguire velocemente il cambio di formato e sono in grado di fornire risultati produttivi immediati privi di errori e senza curva di partenza.
I nuovi robot pick-and-place con maggiore potenza specifica
Per chi ha bisogno soprattutto di una grande portata in piccoli spazi oppure di più movimento nel trattamento dei prodotti Schubert propone i robot specializzati T4 e T5, che completano i ben collaudati robot F4 già impiegati in numerose linee picker e linee di imballaggio dell’a
Con la nuova piattaforma Part-Streaming si possono stampare, direttamente in produzione, i pezzi di formato 3D più disparati per gli utensili dei robot (Schubert).
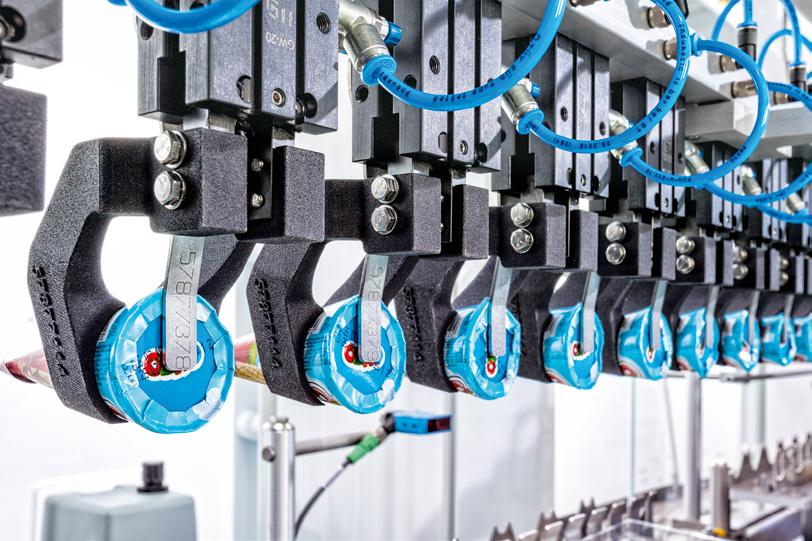
zienda tedesca. La costruzione di questi nuovi robot pick-and-place si basa sui ben conosciuti robot di tipo Delta. La loro area di lavoro limitata a un rettangolo li rende predestinati a lavorare con alte portate e con un ingombro limitato. Infatti, in un unico telaio TLM, possono lavorare contemporaneamente fino a sei robot di questo nuovo tipo T4 a quattro assi. Un’altra nuova possibilità per i processi meccanizzati è costituita dalla variante T5 che dispone di un quinto asse con cui si possono orientare e rovesciare i prodotti.
Magazzino ricambi virtuale con la stampa 3D on demand
La stampa 3D rivoluziona non solo le macchine, ma anche la gestione del magazzino. In pochi secondi i dati costruttivi elettronici possono essere richiamati “on demand“ in tutto il mondo. La Schubert rende ora possibile l’accesso ai dati stampa collaudati e certificati con la nuova piattaforma Part-Streaming della sua azienda affiliata Schubert Additive Solutions. Il magazzino virtuale è veloce, affidabile ed economico e costituisce un grande passo avanti per garantire la produzione sicura e flessibile. I ricambi immagazzinati digitalmente sono disponibili ovunque, relegando al passato i lunghi tempi di attesa e di consegna. Con la piattaforma Part-Streaming, oltre ai semplici pezzi di ricambio e alle parti soggette a usura, si possono stampare i pezzi di formato 3D più disparati per qualsiasi utensile di robot. Anche per i mezzi e i dispositivi di produzione continuamente in uso vengono offerte
numerose possibilità. Uno dei collegamenti dati più sicuri tra la stampante del cliente e la nuova piattaforma è rappresentato dal gateway industriale GS.Gate della Schubert. Il gateway digitale offre inoltre nuove opzioni per produrre in modo più economico e senza fermi per guasti, grazie all’acquisizione mirata dei dati macchina.
La nuova moneta si chiama big data, anche nell’industria del packaging. Ma la memorizzazione dei dati macchina non è sufficiente. Chi vuole veramente godere di tutti i vantaggi ha bisogno di eseguire l’analisi oculata dei valori indicativi più importanti e la sicurezza assoluta contro gli attacchi hacker provenienti da Internet. La Schubert ora offre questi due vantaggi di serie, integrando in tutti gli impianti TLM il gateway industriale GS.Gate. Con il gate si possono scaricare le analisi dettagliate sulla produttività dell’impianto. I risultati sono consultabili sulla piattaforma clienti GRIPS.world oppure sul terminale di comando della macchina. Da tale analisi si possono dedurre il potenziale e le possibilità dell’impianto come i valori indicativi OEE (Overall Equipment Effectiveness) che permettono di migliorare lo sfruttamento del valore aggiunto.
Il cobot: il prossimo livello di automazione
Con i robot cooperativi che lavorano senza gabbia di sicurezza si possono automatizzare e ottimizzare notevolmente i processi di confezionamento dei piccoli lotti. Per il suo nuovo modulo cobot la Schubert sta sviluppando un sistema completo. I nuovi robot cooperativi della Schubert verranno presentati alla Interpack 2021 che si terrà dal 25 febbraio al 3 marzo 2021 a Düsseldorf.
Sistemi di confezionamento efficienti e sostenibili
Dato il rinvio di Interpack 2020, Syntegon Technology espone online numerosi sistemi orizzontali senza soluzione di continuità in uno spazio virtuale, dove spiccano tre soluzioni complete per barrette, biscotti o cracker e prodotti da forno che hanno in comune flessibilità e numerosi vantaggi in termini di sostenibilità.
Nell’imballaggio primario, le innovazioni della tecnologia Syntegon facilitano l’avvolgimento dei prodotti in flow-pack con mono-materiali e carta. La nuova formatrice Kliklok ACE realizza cartoni e vassoi senza colla mentre l’incartonatrice con carica dall’alto Sigpack TTM e l’inscatolatrice Elematic 2001 utilizzano rispettivamente cartone riciclato e di fibra d’erba.
Il sistema di confezionamento continuo seamless ad alta velocità per barrette realizza tutti i passaggi dalla tecnologia di processo fino all’inscatolamento, dove il
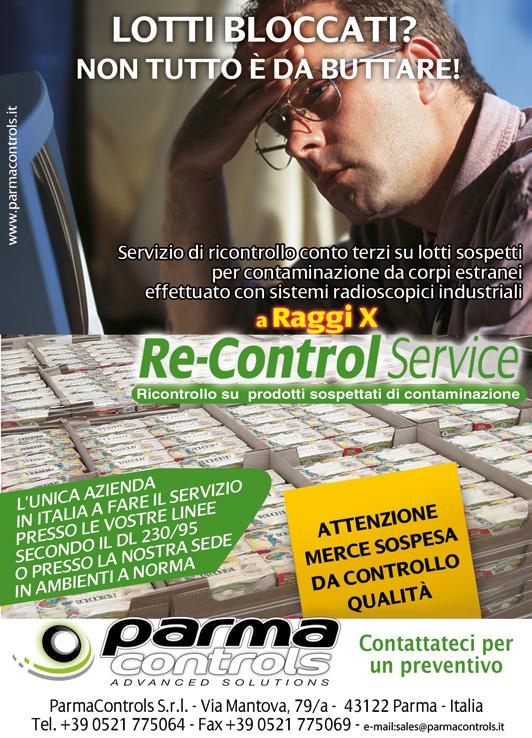
nuovo rullo di compressione WRW Flex consente di regolare l’altezza e la larghezza delle strisce di massa che costituisce le barrette durante la produzione con la massima flessibilità e precisione, riducendo al minimo gli sprechi di prodotto. Una volta tagliate e smussate, le barrette vengono confezionate con avvolgimento flow-pack dall’unità Sigpack HRM, alimentata dal sistema di alimentazione Sigpack FIT senza contatto, flessibile e compatto con tecnologia a motore lineare XTS. La confezionatrice HRM presenta il nuovo kit di retrofit paper-on-form in combinazione con la tecnologia di saldatura a freddo, la prima del suo genere a realizzare imballaggi di carta senza compromettere la velocità e la sicurezza del prodotto.
Il sistema senza giunzioni viene fornito con la comprovata incartonatrice Sigpack TTM. Il modulo di alimentazione delicata Sigpack FWV assicura che lo strato barriera sensibile dell’involucro di carta rimanga intatto, anche alle massime velocità. Inoltre, la macchina tratta con la massima precisione cartoni realizzati con fibre riciclate al 95%. Nella fase finale, l’Elematic 2001 racchiude i cartoni in scatole e si distingue per l’uso efficiente dei materiali di imballaggio e la capacità di gestire fino a 100 diversi modelli di scatole alla velocità massima di 40 scatole al minuto.
Per i prodotti da forno come i cupcake, invece, Syntegon Technology propone un sistema di confezionamento a tutto tondo, con la stazione di distribuzione pullnose a deposito diretto, il nuovo Pack Feeder 4 e il wrapper a flusso orizzontale Pack 403. La flow-wrapperPack 403 è inoltre dotata del kit di retrofit su modulo on-paper per il confezionamento in carta. A differenza del sistema per le barrette, la Pack 403 utilizza la termosaldatura combinata con l’unità di formatura della carta che realizza saldature efficaci, anche con materiali cartacei altamente isolanti. Una volta confezionate le tortine nell’involucro di carta, la soluzione robotica pick and place Paloma le organizza per la formatura del vassoio a valle. Il sistema di confezionamento è completato dalla nuova formatrice di cartoni e vassoi KEklok ACE che opera senza colla.
Di Syntegon Technology ricordiamo infine una soluzione compatta e ad alta velocità per il confezionamento di biscotti e cracker in film mono-materiale completamente riciclabili, capace di garantire velocità elevate e ottima qualità di saldatura. Essa si compone della confezionatrice flow-pack Sigpack HCS equipaggiata con la più recente tecnologia di saltatura termica amplificata (AHS), mentre per la manipolazione e il conteggio dei prodotti viene impiegato il nuovo modulo Sigpack FGMT (FGM-Turbo).

Sistema di confezionamento ad alta velocità per barrette (Syntegon).
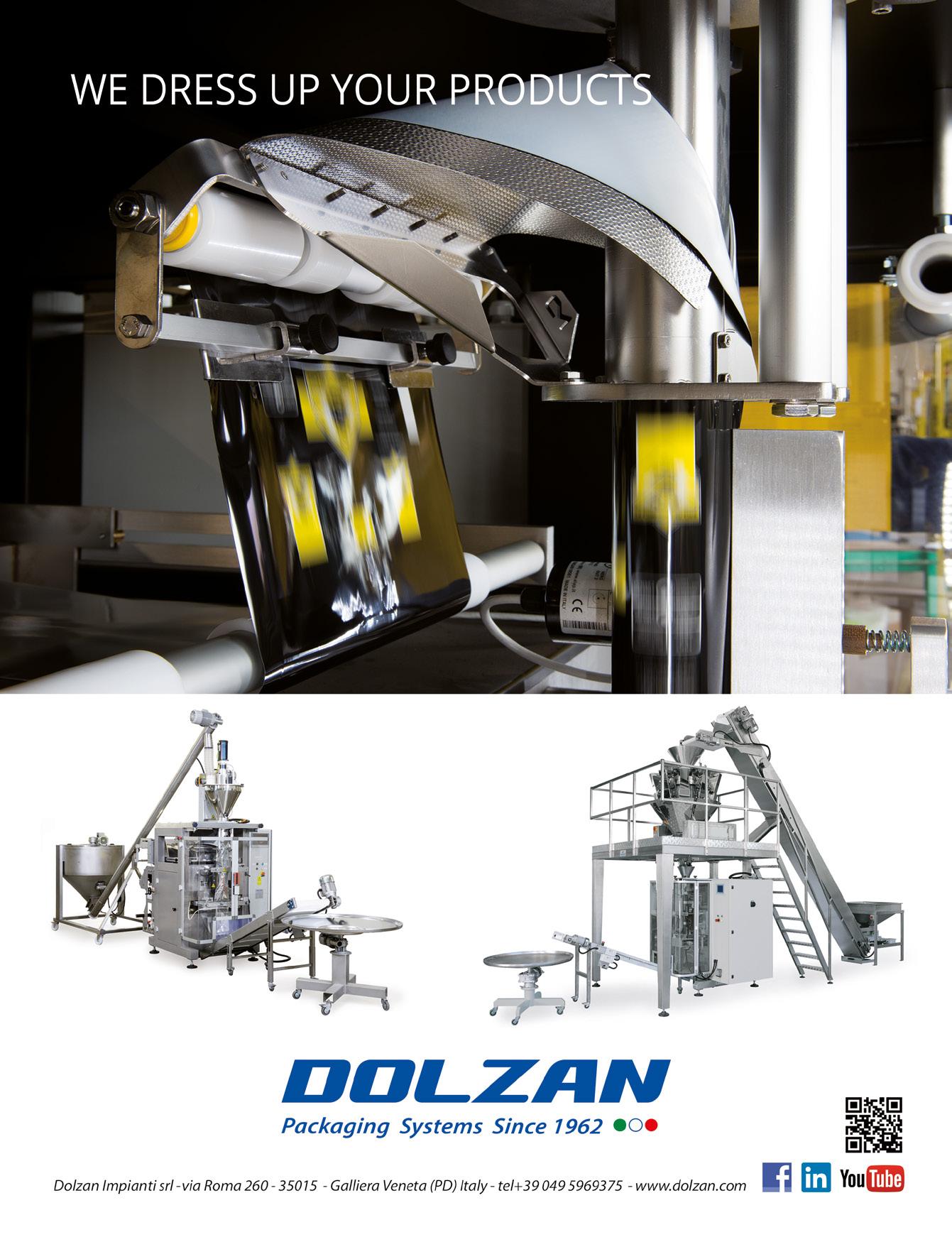