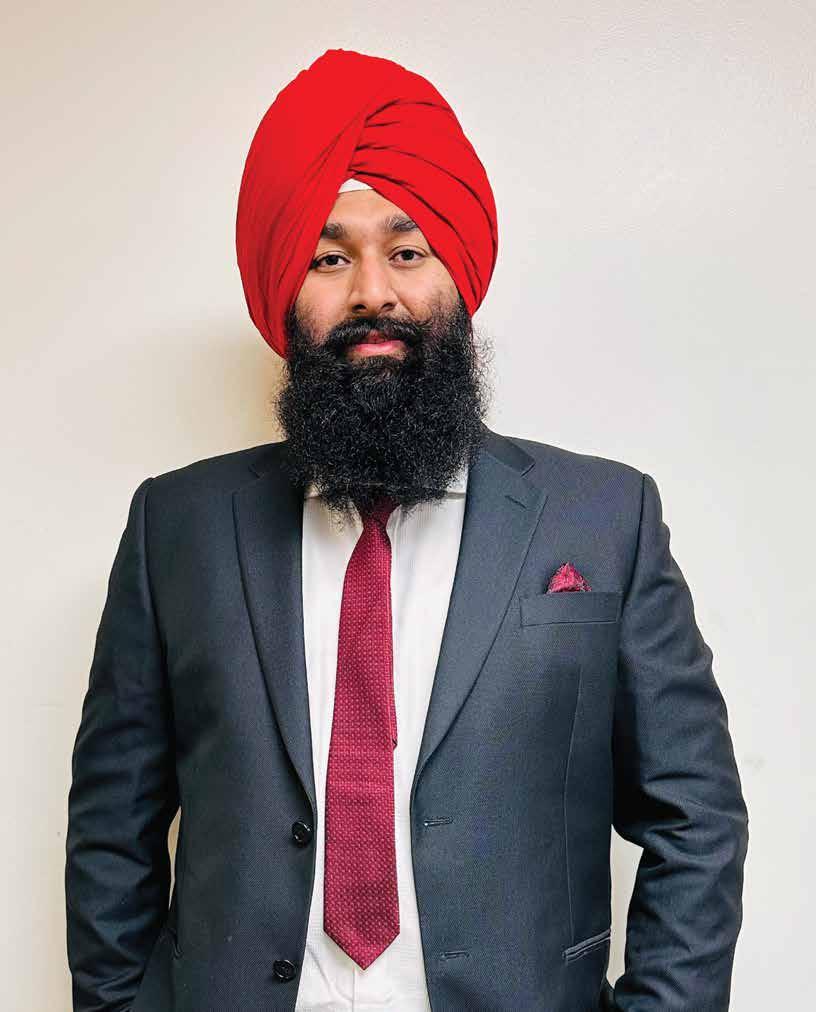
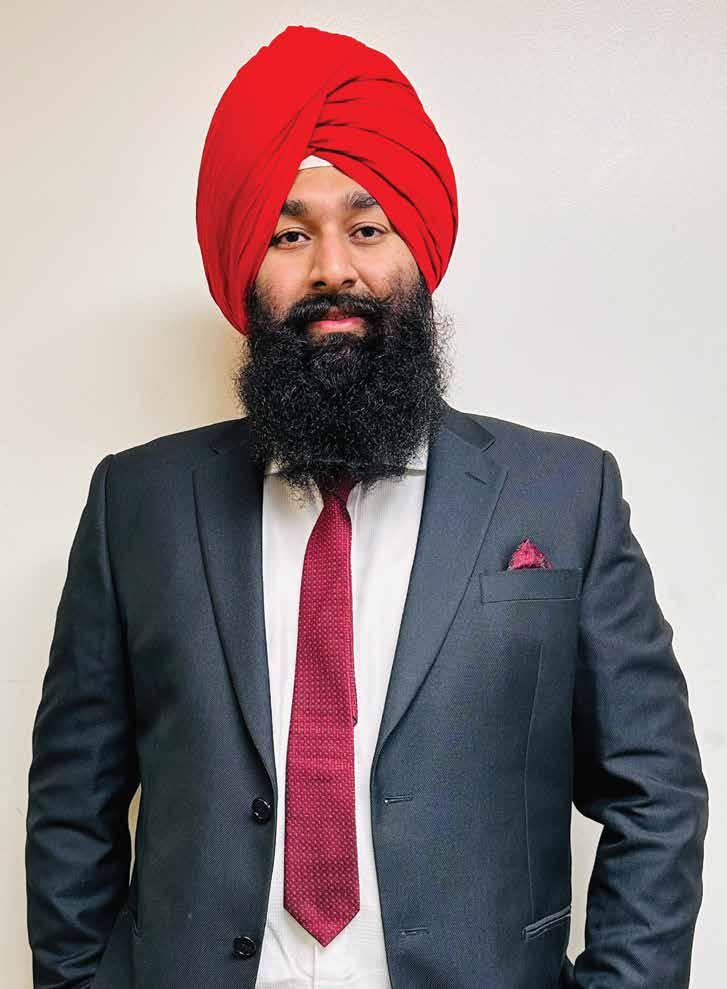
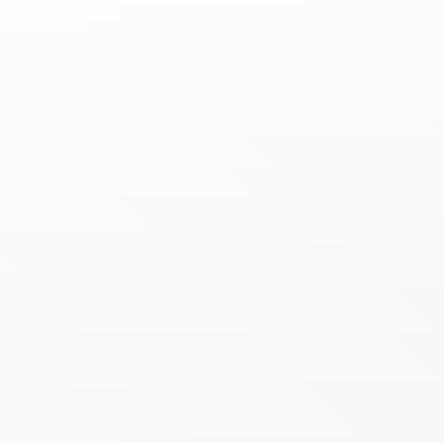
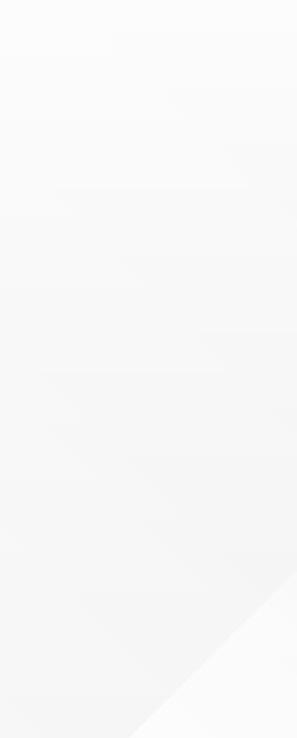
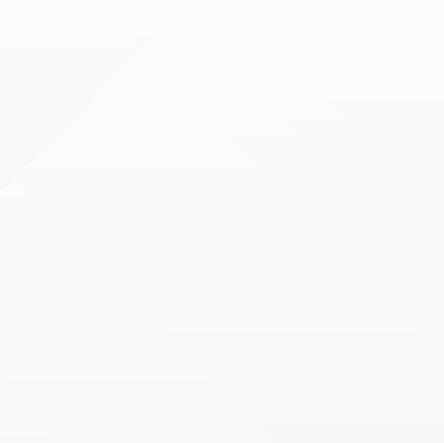
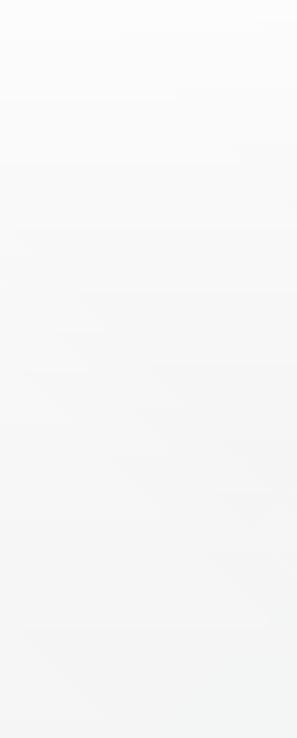
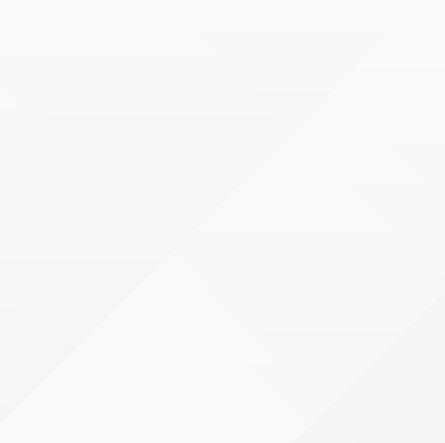
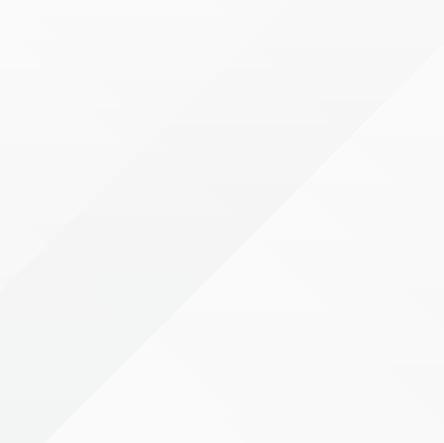
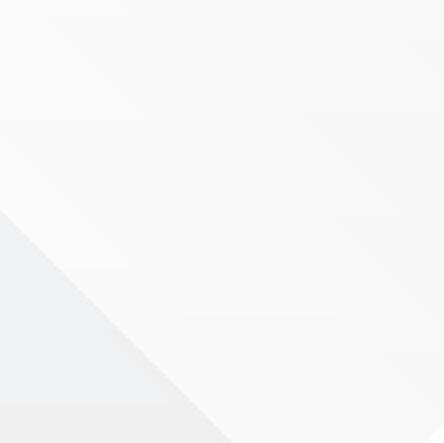
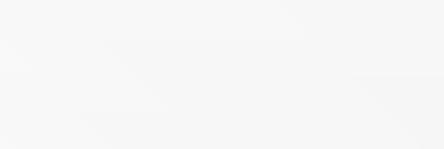
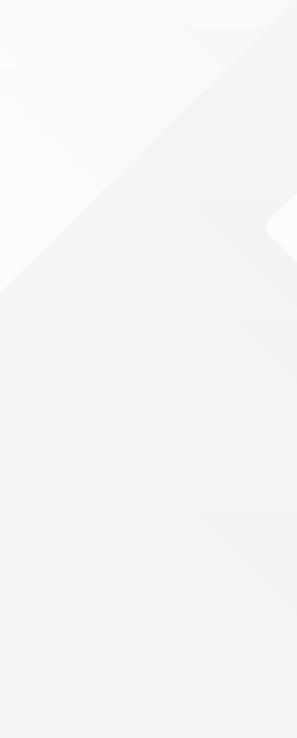
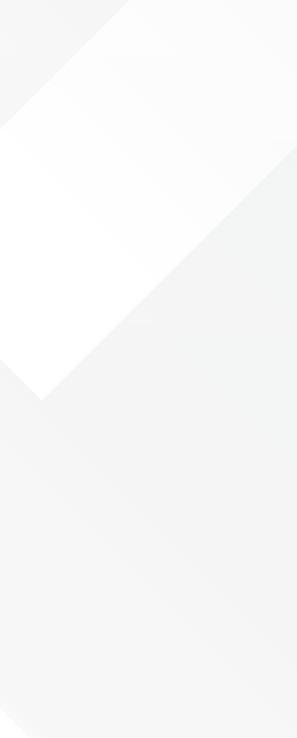

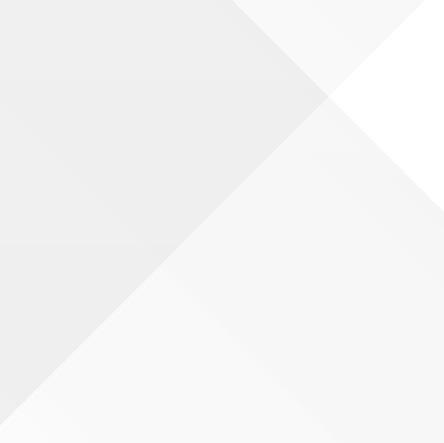

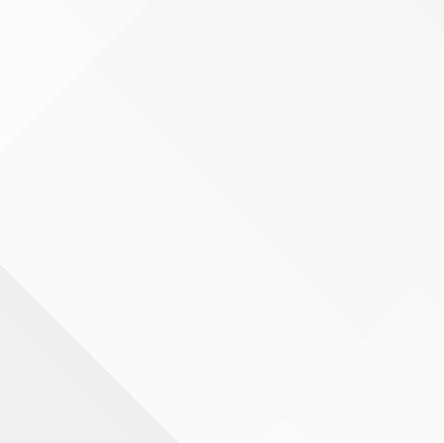

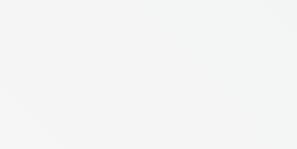
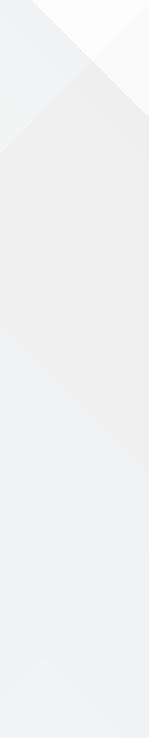
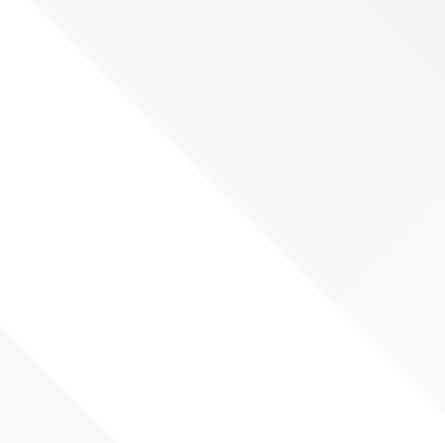
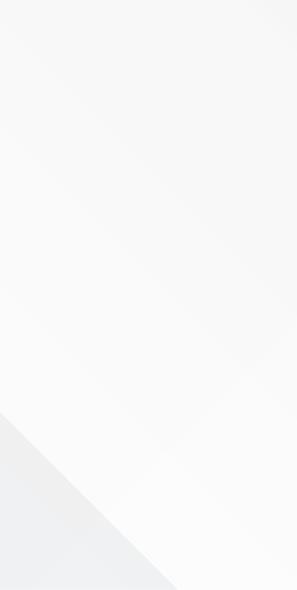
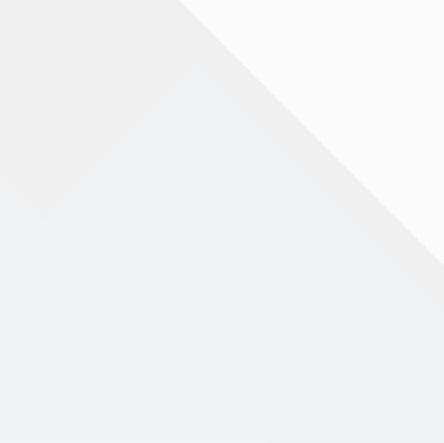
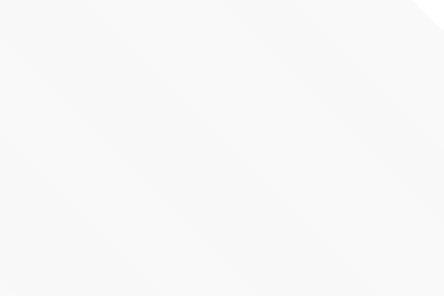

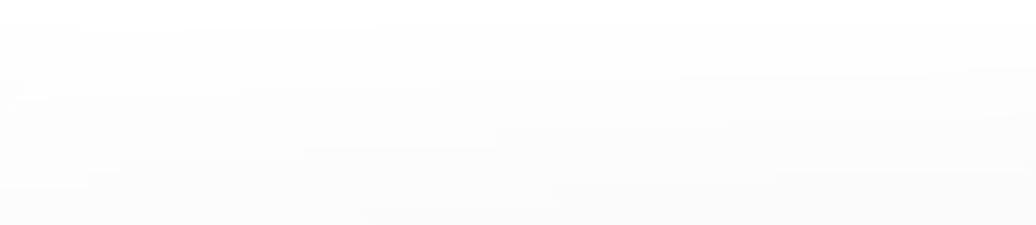
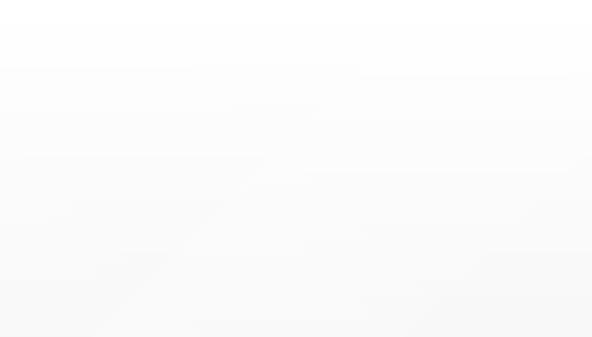
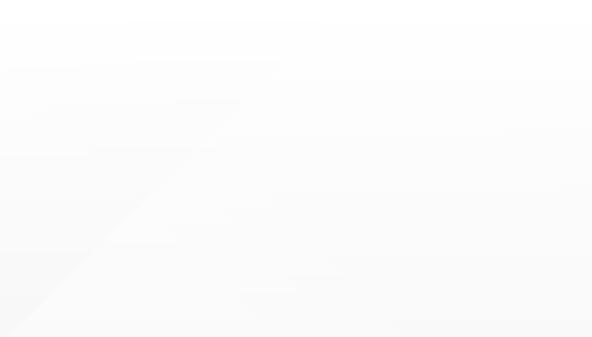
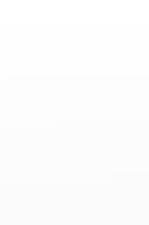

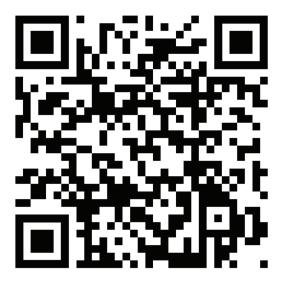


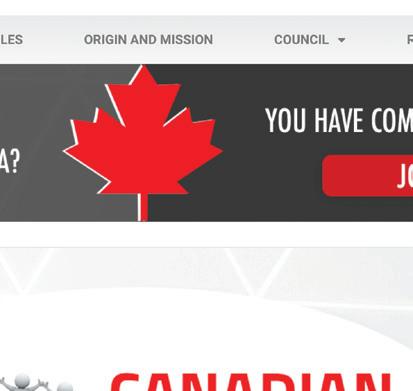
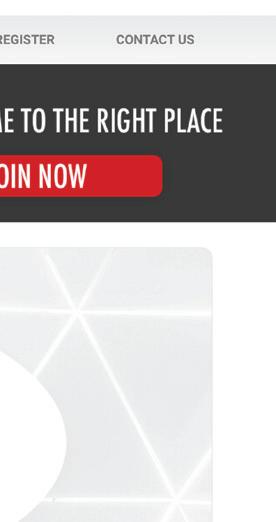


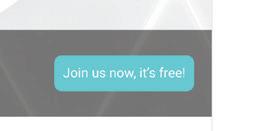
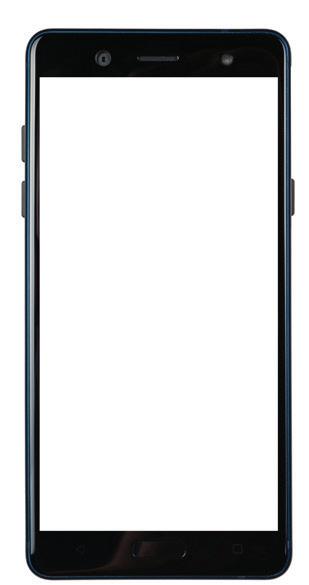

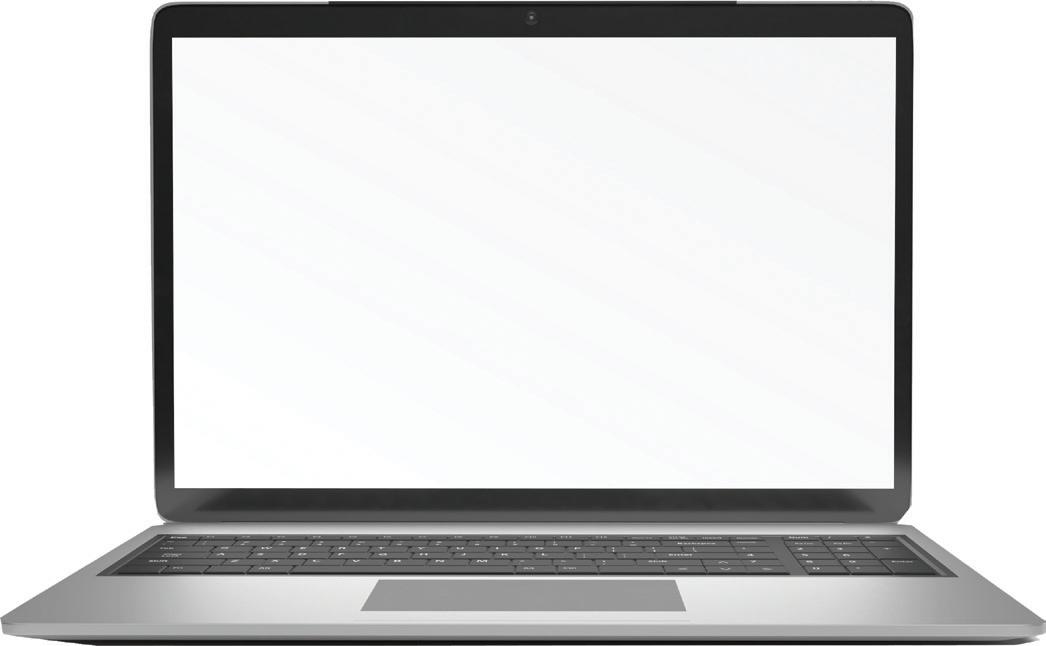
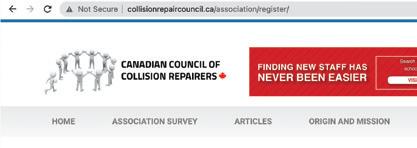
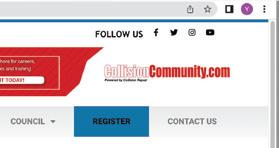
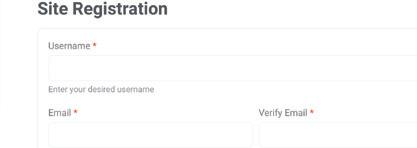
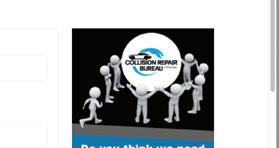

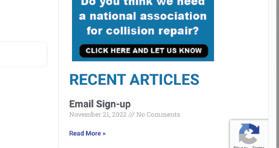


Canadian industry legend Sam Mercanti wrote a book—and we’ve got exclusive excerpts. Find out how to get your hands on a copy today.
We know you’ve been waiting. See how repairers graded Canadian insurers in terms of payment, conflict management and relations in the annual Insurer Report Card.
Plenty has happened since this initiative first started. To provide initial direction and guidance, an Advisory Board was created. It includes 20 Canadian collision centres; independents, network affiliates and MSOs.
The first action item on the agenda was to pick a name. The group is now called the Canadian Council of Collision Repairers (CCCR). It was also decided that this group should, for the time being at least, only include shop owners/ operators. See below for a sample of the comments and rationale.
The group will be dedicated to representing repairers by identifying and prioritizing business concerns and issues, education and information sharing. The goal is to provide a positive, inclusive and nurturing platform to develop the best course of action to provide positive
solutions for issues concerning its members. The mandate and mission are still a work in progress and are always open for discussion. The list of members will not be made public; nor will the members of the Advisory Board. This will remain so until such time the group decides differently.
Our next step is to have an open Zoom meeting open to all shop owners, managers and operators. There will be registration, but in the meeting, there will be an option to remain anonymous. The CCCR will determine their needs and share their concerns about the industry in a safe and anonymous—if desired—environment.
Joining this group is as simple as filling out a form on the website. The only requirement at this time is a desire for repairer professionalism and credibility among the consumer-driving public and all other key players in the industry.
“I feel this needs to be a council directed and run by collision shop owners and management. WITH influence involved we would start with a lopsided perspective.“
“I Would like to have more shop accountability in proving they are properly equipped with properly trained/ qualified staff to perform safe repairs. With that being related to proper compensation from insurance companies.”
“We need to be our own voice and not amalgamate with others who have their own motives and boards / members to appease. there has been NO VOICE for the collision repair industry as a whole (let’s be honest with ourselves!)”
“It’s been A long time since we have had something like this.”
“let’s Set a clear message and goal for the organization. I would also like to see the group work one issue at a time until it is resolved. I worry that if we dilute our cause with too many concerns at once, it will go nowhere. A small progression of one topic at a time might be our best opportunity for development in the industry.”
“Thanks for spearheading this as it’s crucial to our industry and sustainability within our shop networks (even though many do not really understand what that entails). This should not be a platform for complaining rather a group for the better of our industry that drives results.”
Unless you speak up, the status quo will never change. The Canadian Council of Collision Repairers is ready to be your voice.
By DARRYL SIMMONSThere’s nothing more exciting than getting together a group of shop owners and managers. They sure are a passionate group. Since we first started talking about a national association for shops only, the groundswell has progressed at a rapid pace. It’s obvious; the time for such a movement is now. There never was a wrong time, but it’s needed more now than ever.
A survey conducted by Collision Repair had nearly a hundred responses stating a clear need for some sort of association for collision repairers … and only for the owner/operators. Key issues identified were the standard ones often bandied about: professionalism, industry relations, parts and materials, attraction and retention. But underlying was one key point—profitability.
Profitability is essential. Profitable shops buy more products, hire more people, get more training, provide more efficient service etc. Everyone in the supply chain (auto repair economy) benefits.
by others so there will be no fear of retribution. Help create a strong message and ensure that message is heard. Silence means consent. And that should not be the only option.
Right now, the group has just under a hundred members and well on its way to get hundreds more. Once this happens, the voice is not of a particular shop or person, but of the collective. And this is when people can start speaking a lot more freely with no fear of retribution.
The next steps will be to include the consumerdriving public to be aware of what is needed to conduct safe repairs and who is capable of performing them.
PUBLISHER
Darryl Simmons publisher@collisionrepairmag.com
ASSOCIATE PUBLISHER
Orest Tkaczuk | orest@mediamatters.ca
EDITOR Allison Rogers | allison@mediamatters.ca
ART DIRECTOR Yvonne Maschke | yvonne@mediamatters.ca
STAFF WRITERS
Max Reid | max@mediamatters.ca Kate Ng | kate@mediamatters.ca
GRAPHIC DESIGN INTERN Cynthia Lee | cynthia@mediamatters.ca
VP OF INDUSTRY RELATIONS & ADVERTISING
Gloria Mann 647.998.5677 | gd.mann@rogers.com
DIRECTOR OF BUSINESS SOLUTIONS
Ellen Smith 416.312.7446 | ellen@mediamatters.ca
What started as an ember has been fanned into flame. The key now is to keep things moving so it doesn’t get any chance at all to burn out.
But, according to a vast number of respondents, shops today are doing more work for less money. And it’s not just one big item, but a plethora of little ones: such as increased admin time, missing line items, rising material costs, delayed payments and the list goes on. It’s obvious to anyone in the industry that things can’t continue as is.
The Canadian Council of Collision Repairers is open to all shop owner-operators, be it independent, network-affiliated or dealer-owned. What started as an ember has been fanned into flame. The key now is to keep things moving so it doesn’t get any chance at all to burn out. This is why your help is needed.
The CCCR is getting very close to a critical mass of credibility and negotiating strength. In a group of a dozen, there is no anonymity—there’s a looming fear of sticking your neck out and being in the spotlight. But in a group of hundreds, the collective overshadows the individual and there is no more fear of retribution for speaking on issues that some may deem as sensitive. There is also no chance of being ignored by “business partners” or having issues you feel important swept under the rug, or worse: put on hold until they are forgotten altogether.
This group is not anti-anything. It’s just that it is pro-shop. If you are an owner or manager, your opinion matters. And hopefully, it will be shared
This is the voice of the repairers. It’s not that insurers, manufacturers, suppliers, network head offices and other ancillary services are less important, but they already have platforms from which they are being serviced. Perhaps in the future, there will be a seat at the table for them, but right now owner-operators need to crystallize their vision in terms of a concrete mission, a clear message and a target audience.
Collision Repair magazine is the ideal communications vehicle to facilitate as our mandate is to serve as the informational, educational and inspirational platform for repairers.
CCCR’s goal is to promote open and honest communication amongst each other to build a credible voice to speak with external stakeholders. All comments, positive and negative, are welcome as members must be able to speak out without fear of rebuke or retribution.
Please help get as many shop owners/operators, regardless of the type of shop, to sign up at www.collisionrepaircouncil.com
Building trust amongst members is a key first step. And it’s a big one. It’s a strong tide that raises all boats, so it is to your advantage to share your opinions, even if your competitor is in the same room. By focusing on general issues in a positive way, change can take place.
Change is what is needed, and it must start someplace. Why not let it start with you?
INDUSTRY RELATIONS ASSISTANT Wanja Mann 647.998.5677 wanjamann1@gmail.com
AUDIENCE ENGAGEMENT MANAGER James Kerr | james@mediamatters.ca
DIGITAL OPERATIONS MANAGER Cassie Doyle | cassie@mediamatters.ca
CONTRIBUTORS
Jay Perry, Tom Bissonnette, Stefano Liessi, Greg Horn
SUBSCRIPTION
Single edition $7.99 One-year $39.95 ( 6 issues)
Collision Repair ™ magazine is published bimonthly, and is dedicated to serving the business interests of the collision repair industry. It is published by Media Matters Inc. Material in Collision Repair™ magazine may not be reproduced in any form without written consent from the publisher. The publisher reserves the right to refuse any advertising and disclaims all responsibilities for claims or statements made by its advertisers or independent columnists. All facts, opinions and statements appearing in this publication have been compiled and included with the permission, though not necessarily the endorsement, of the editor, or of independent columnist contributors, and are in no way to be construed as those of the publisher, or as endorsements of them.
Fix Network has announced the promotion of Sylvain Seguin to the president of Fix Network Canada, effective September 26. Seguin has been with Fix Network Canada since 2018 when he joined as vice president of operations. In that role, he had oversight of the operations teams for all brands in Canada which include Fix Auto, ProColor Collision, NOVUS Glass and Speedy Auto Service. In 2020, he was promoted to executive vice president of Fix Network (Canada). He has more than 30 years of experience in automotive aftermarket services.
Joern Stoever will serve as the interim manager of SATA Canada following the departure of John Turner, who held the role since 2016. “The board thanks Mr. Turner for his great commitment to SATA Canada and we wish him all the best in his personal endeavours,” wrote the company in its press release. Stoever has worked closely with the Canadian market for the last 11 years, said SATA. “With his intimate knowledge of the conditions found in the Canadian market, SATA Canada will provide absolute continuity in your dealings with us.”
Collin Welsh will now serve as the zone director for CARSTAR Canada’s Ontario operations, the company announced on September 27. Previously the senior director of franchise development, Welsh will continue to build the CARSTAR brand and develop relationships with company franchisees in his new, Ontario-focused role.
Simplicity Car Care made some changes to its senior leadership team early in December, announcing that Domenic Prochilo has been promoted to the role of COO. According to a statement provided to Collision Repair, Prochilo, in his new role, “will work closely with the senior leadership team of Simplicity Car Care, franchise partners and industry stakeholders to execute Simplicity’s growth plans and launch vertical business lines to complement the Simplicity brand.” He will also work with the business development team to develop campaigns focused on attracting independent repair facilities to the Simplicity network.
Agreat deal of newsprint has been used over the past two years highlighting how the current supply chain problem is disrupting businesses globally. I am not speaking only about major multinationals being affected, but also small and medium entrepreneurs, whose daily operations have almost come to a standstill.
Without a doubt, it is a real test of nerves. While the aftermarket industry was largely resilient to the economic uncertainty surrounding the COVID-19 pandemic, the ensuing after-effects are now proving to be major headaches for the industry, and it is unlikely that a long-term solution will be found any time soon.
There are lots of challenges associated with running businesses these days – from the global supply chain disruption
to possible large increases in logistical costs, unprecedented consumer demand, and ongoing turmoil in the markets providing critical raw materials for automotive components. Those challenges also affect the automotive aftermarket business, an essential service that needs to keep running all the time.
The aftermarket industry sources raw materials for components and other critical items from different countries. Over time, that supply has been squeezed, leading to longer delays. For example, the difficulty in procuring a semiconductor chip (typically costs between $5 and $15) has brought the automotive industry to its knees. The same is the situation with almost everything associated with the business – from EV batteries to paint solutions, from urethane for windshields to sheet metal and other parts for electrical components.
The global supply chain disruption is one of the major challenges affecting the automotive aftermarket industry. Sylvain Seguin advises how shops can plan ahead to prepare for the inevitable.
In its latest Fall 2022 “State of the Industry” Report, released recently, the Specialty Equipment Market Association (SEMA) points out that inflation and supply chain issues are raising costs for the industry. SEMA’s survey of more than 1,900 industry stakeholders concluded that there hasn’t been any significant drop in business despite the current operating climate.
I share your concern about the ongoing business environment – almost everyone has been affected in some way or the other. The silver lining though is that there are important discussions taking place across Canada and the globe to resolve the issue. At Fix Network, we are speaking to almost every stakeholder across the industry to identify pain points and propose solutions. Our industry-wide engagement includes everyone – from parts suppliers to insurance providers, from paint manufacturers to lawmakers, industry bodies and franchisees.
Collision repair is a tough business, and shops always look to manage their operations efficiently, with minimum cost and maximum returns. As the industry looks for workable solutions, here are some ways how you can manage the current challenges for your shop:
Set realistic expectations on deadlines: Most customers are aware of the supply chain issues taking place around the world and understand your challenges. However, it’s best to advise them about impending delays if you are waiting on spare parts or any specialty items.
Train your staff: Customer service teams – the first point of contact with the customer – should be trained with the
right relationship management skills and be as transparent as possible with clients to give them a complete picture of the situation. The teams should be trained to understand the client requirements and always communicate clearly, especially if there are any foreseeable delays. We need to remember that we are an essential business and that we are in the customer service business.
Collaborate closely: This will also be a good time for you to work proactively with your team and with suppliers to address immediate priorities. Engage with multiple suppliers if necessary.
Monitor the situation regularly: There is no clear picture of when the situation will improve but it’s best to look at the ongoing trends and developments with advice from your peers or organizations like Fix Network, to understand any developments that may impact your business.
Order efficiently: This will be perhaps the right time for you to combine cost-efficiency with profitability. Ensure that you have enough of the right components, accessories and materials, without the risk of over-stocking. Having more items in your inventory than necessary may leave you burdened with items that you don’t need when the situation improves.
As we close the year with an ambition to remain resilient, let’s hope and pray that the coming year brings in more opportunities for all of us to survive those challenges.
Sylvain Seguin is President of Fix Network (Canada).
The federal government is reportedly set to introduce subsidies for the production costs of large EV battery producers in hopes it will convince the parties to build plants on Canadian soil. The new measures—dubbed a “game changer” for Canada’s industrial policy—could see Ottawa fund the operating expenses of battery and battery component manufacturers through subsidies linked to the number of units produced. Previous government programs have been based on one-time capital expenditures. The measures could act as a counter to the recently adopted American law, the Inflation Reduction Act, that experts say poses a threat to the Canadian industry as it allocates US$270 billion in climate and clean energy investments. Canadian industrial and manufacturing experts say the U.S.’s ambitious plan could trigger a wave of investment toward States-based manufacturing.
Recent data from the Society of Collision Repair Specialists (SCRS) contradicts the belief of some OEMs that blending can be completed in half the time as creating a new coat. On Oct. 30, five North American coating companies presented study findings at the Collision Industry Conference (CIC), where they concluded that on average, blending took 31.6 percent more time than a full refinish. The study results conclude that the existing 50 percent formula may not accurately represent the difference between the two tasks, which reduces the compensation for labour and materials during a refinishing.
The Automotive Industries Association of Canada (AIA) and a team of 20 associates across Canada were in parliament on Oct. 18, bringing the Right to Repair issue to Ottawa. The association’s message was clear: “give Canadian consumers a choice when it comes to auto repair.” AIA Canada was supported by executives from numerous automotive companies operating in Canada, including representatives from collision repair banners. Twenty-five MPs arrived for an all-party panel discussion before association members broke off to meet one-on-one with the local riding representatives to discuss the specifics of how consumers can attain greater choice on a community level.
Dealerships beat out the aftermarket in revenue this year, according to J.D. Power’s 2022 Canada Customer Service Index, which shows that dealer repairs captured more than half of the industry revenue from its competition. The study found that dealership-based service centres accounted for 47 percent of all service visits and captured 58 percent of industry revenue this year, reversing the market share gains of aftermarket shops reported in 2021. The average per-visit spend for dealership customers in 2022 is $394. For aftermarket visits, the average cost sits at $247–nearly $150 cheaper. Customers appear to have equal faith in the quality of both dealership and aftermarket work. The percentage of aftermarket customers who said all service work was completed right the first time was 95 percent in 2022; down two percent from 2021. The dealership segment reported 94 percent of customers citing service completion upon first visit; like the prepandemic levels of 2019.
The Canadian Collision Industry Forum (CCIF) is set to return to Toronto this Feb. 2 and 3 at the Delta Hotels by Marriot Toronto Airport and Conference Centre. The first day will feature a workshop and networking events, while day two will dive into industry programming from aftermarket leaders like Stefano Liessi, Collision Repair columnist and I-CAR trainer. Visit ccif.ca/events-meetings for more information on the forum.
The automotive aftermarket appears to be leading among the many other industries seeking out highly in-demand skilled trades workers, as the latest employment report from DesRosiers Automotive Consultants Inc. (DAC) shows that employment in the sector is up 4.2 percent since June 2021. “The aftermarket especially continues to show strength, with employment count increases for both repair facilities and parts stores,” said the managing partner of DAC, Andrew King. Auto dealers and repair facilities now boast total workforces of more than 150,000 and 111,000 employees respectively, according to DAC’s research—figures far surpassing those of other industry sub-sectors. DAC said that in the year between June 2021 and 2022, the Canadian auto industry’s workforce expanded from 651,100 to 667,5000 employees.
Tesla’s recent decision to stop using ultrasonic sensors (USS) in its cars will reportedly save the electric automaker roughly US$114 per vehicle, said Mike Lane, an analyst from Munro & Associates. While the figures have not been verified by Tesla, Lane said each Tesla comes equipped with about a dozen USS, at US$8 each. That brings the cost of sensors to US$96, said Lane. The automaker also spends on eight heat-staked brackets at $0.15 apiece; installation and labour add another US$1.80 per car. Each vehicle requires two wire harnesses for the fascia at US$2.20 each: two wiring connectors for the dash, costing US$0.40 and two integrated circuits at US$5 each. Tesla plans to build more than two million cars next year, potentially saving more than US$200 million in 2023 alone.
out USS could save Tesla up to US$114 per vehicle, according to recent reports.
AkzoNobel has released its Q3 2022 financial results, reporting strong revenue gains thanks to price hikes outpacing expected losses from lower volume, higher material costs and global inflation. Specifically, the company increased revenue by 19 percent by increasing prices by 13 percent, justified by similar increases in raw material expenses and other variable costs. Additionally, volume was lowered by five percent due to weaker demand for decorative and performance coatings in Europe and lower market demand in China. Ultimately, the company saw returns on sales of 6.4 percent, which AkzoNobel says comes “from lower volumes and higher raw material and freight costs, as well as inflation on operating expenses.”
A camera is mounted above the rear license plate.
Ultrasonic senors (if equipped) are located in the front and rear bumpers.
A camera is mounted in each door pillar.
Three cameras are mounted to the windshield above the rear view mirror.
A camera is mounted to each front fender.
Radar (if equipped) is mounted behind the front bumper.
A strategic investment from General Motors into Quebec-based Lithion Recycling will see the companies partner to build a circular supply chain for key battery materials. The partnership reportedly seeks to validate Lithion’s recovered battery materials for the production of new batteries in addition to developing a recycling process for EV batteries. Lithion says its technology allows up to 95 percent of battery components to be recovered, treated and reused again by OEMs. The process has the potential to “reduce greenhouse gas emissions by over 75 percent and water usage by over 90 percent compared to mining battery materials,” said the company, citing third-party lifecycle analyses.
Canada’s largest pension fund, in terms of assets, has significantly reduced its holdings in electric vehicle companies in recent months—namely in Tesla and Chinese automakers NIO, Xpeng and Li Auto. As of June 30, the Canadian pension fund held 230,061 Tesla shares; which increased to 690,183 shares following the company’s three-for-one stock split in late August. But, according to a regulatory filing from Sept. 30, the Canadian pension fund held 368,867 Tesla shares—dropping nearly half of its stake in Tesla in Q3. A report from TheStreet.com claims the Canadian pension plan dropped “virtually all its stake” in Chinese EV makers NIO, Xpeng and Li Auto during Q3, but did not specify the number of shares still held in each.
A Toronto man alleges that his Tesla battery died under suspicious circumstances after he refused to pay $26,000 for an OEM replacement battery pack. Mario Zelayna said in a TikTok video he uploaded that he was locked out of the car after fluid leaked from the vehicle’s air conditioning system and into the battery, effectively stopping him from accessing the interior of the vehicle. A follow-up video posted the next day showed the vehicle turning online after a prospective buyer boosted the vehicle. Inside, the vehicle’s heads-up display indicated that the battery was flat and required servicing. According to Zelayna, this is one example proving that the vehicle was remotely disabled and claims that the vehicle previously held a charge of 300km. Transport Canada is aware of the incident, but has yet to comment on the ongoing investigation.
A member of the Forbes Technology Council warns that modern roads may need to be reworked to suit the needs and capabilities of autonomous vehicles. CEO of machine learning company Blyncsy, Mark Pittman says autonomous vehicles could mistake fallen construction barrels or crooked paint lines as warning barriers or exceptionally narrow lanes—uncommon events easily understood by human drivers but absolutely confounding for the average autonomous system. This challenge comes from the current state of autonomous driving, where roads in autonomous-safe areas are manually programmed—meaning, people arrived on-site to scan and survey roads ahead of AV deployment. Going forward, Pittman suggests a future with roads autonomously communicating with autonomous vehicles, guided by increasingly advanced AI—manual surveying may soon be an obsolete approach.
Tesla has removed Full-Self Driving (FSD) beta restrictions from Toronto’s downtown core, following complaints among drivers that much of the city’s urban centre is geofenced off by the software. This was confirmed in a tweet by FSD tester Chansoo Byeon who posted a photo of his Tesla driving itself along Toronto’s famously clogged Yonge Street. When the FSD beta was first expanded to Canada in March, much of Toronto’s downtown area was restricted, with Elon Musk explaining that the autonomous system was not ready for one particular city’s iconic streetcars. He said at the time that the software just did not know how to respond to streetcars, given their tendency to perform frequent stops in the middle of the road for passengers to embark and disembark.
A flying car startup backed by Google co-founder, Larry Page, will wind down operations after 12 years of work to develop an affordable electrical aircraft capable of vertical takeoff. Startup KittyHawk announced on LinkedIn that the company would be shutting its doors, but had yet to work out the details for what’s coming next. While the reasons for closure have not been released, it appears that KittyHawk’s people and technology may continue in a different capacity. Wisk, a joint venture between KittyHawk and Boeing will continue.
The Insurance Bureau of Canada (IBC) says the Insurance Corporation of British Columbia is on track to record a financial loss of $298 million for 2022. Vice president of IBC’s western and Pacific regions, Aaron Sutherland, called this update from the ICBC “incredibly disappointing” and said that taxpayers will likely face the brunt of this poor performance. Sutherland’s chief complaint with ICBC is that despite recent changes made by the insurer, such as the no-fault claims system designed to streamline processes and save money, the corporation continues to bleed financially. “After years of financial turmoil, the introduction of no-fault was supposed to help stabilize ICBC’s financial situation by eliminating the right to sue in most cases and introducing strict limits on the care and recovery benefits it provides. As a result, the first year of no-fault saw ICBC spend 30 percent less helping accident victims recover from their injuries. Despite this, ICBC is once again forecasting a financial loss,” he said.
The Insurance Bureau of Canada (IBC) will have a new CEO and president effective Jan. 1 as Celyeste Power assumes the role. Power is currently the executive vice president of strategic initiatives and advocacy at IBC and will take over the helm from Don Forgeron, who will retire from his post at the end of 2022. Power is known to be an advocate for diversity, equity and inclusion and is an active member of the Insurance Supper Club Canada, which supports the advancement of women to senior positions across the insurance sector.
“I’m thrilled about the opportunity to lead one of Canada’s preeminent industry associations,” said Power. Heather Masterson, president and CEO of Travelers Canada, said the insurer was “pleased” with the announcement and that Power will bring “a wealth of experience” to the role.
Automakers are struggling to get on track to achieve net-zero emissions by 2050, according to a recent report by the Capgemini Research Institute.The academic think tank explains that investment in sustainability initiatives has fallen to less than one percent in 2022, compared to 1.22 percent in 2019. At current investment levels, greenhouse gas emissions by 2030 will be reduced by 24 percent—a far cry from the goal of a 45 percent reduction. These reductions were accomplished by less than 10 percent of companies in the industry actively working towards sustainability strategies, meaning that over 90 percent of companies failed to make the necessary adaptations.
Several false advertising lawsuits have been levelled against Tesla recently, leaving the OEM with the possibility of class action lawsuits taking shape in California and Florida. In California, Cotchett, Pitre & McCarthy, LLP announced a class action lawsuit alleging that Tesla misled the public regarding its autopilot and full self-driving (FSD) technology, saying that the OEM made untrue and misleading statements while having yet to produce a fully self-driving car. Meanwhile in Florida, a Palm Beach County court has set a date in February for the first in a series of autopilot collision trials.
The Out of Spec Detailing team used a paint protection film to cover scratches, and highlighted vinyl wrapping as another possibility.
As of late September, Transport Canada has authorized Rivian to sell vehicles in Canada. The news came days after Drive Tesla Canada reported that Rivian in fact, did not receive certification, following its application to Transport Canada earlier this month. The electric automaker reached out to the site a day later to clarify that it never failed the application; the OEM was simply required to provide supplemental information to finalize its certs. To meet Transport Canada’s certification requirements, Rivian had to meet specific standards in speedometer units of measure, certain labels, immobilizer requirements for anti-theft, pass-by noise standards and more. Collision Repair can confirm that the OEM has visited collision centres in several Canadian city centres, though the nature of those meetings was not specified.
An American vehicle detailing shop has made an interesting discovery—the OEM coating on a new Lucid Air Grand Touring is so thin that polishing can damage the paint. According to a Youtube video by Out of Spec Detailing, the Lucid Air’s Grand Touring paint was too thin to even polish. In fact, paint thickness measurements regularly scored below 3mm and went as low as 2.24mm. For context, most vehicle coatings vary between 4 millimetres to 7 mills—enough for a polishing abrasive material to polish scratches away.
Have you ever removed a rebar rod from a body? A Prince Edward Island shop had quite the project after a local event volunteer turned up with a rebar rod lodged in his vehicle’s trunk. The poor volunteer had been working since 4 a.m. and returned to their vehicle to find a metal pole, originally used to prop up temporary fencing, embedded deep into his vehicle’s trunk.
Officers from the Ontario Provincial Police (OPP) experienced a glitch in the matrix this fall after members of the force responded to calls reporting a floating car. Thankfully, the scene was not part of a ritual gone wrong—just a car stuck on a wire.
Bodywork meets arts and crafts with the University of Tokyo’s latest project: a pair of motorized eyes for autonomous vehicles (AVs), intended to alert pedestrians to whether they’ve been seen by the vehicle. Unlike today’s vehicles, future AVs may not have human drivers, and require the ability to telegraph “driver” intent to pedestrians. Researchers created scenarios in a virtual reality environment, where nine male and nine female pedestrians decide whether it was safe to cross the road. In half the tests, the AV would wait for the pedestrian, while the other half drove through. Half featured googly eyes; half without.
Two hydrogen fuel cell electric buses were on display at the Edmonton Electric and Hydrogen Vehicle Expo from Sept. 24 to 25, where one official decided to prove how clean the tech is by drinking straight from a bus tailpipe. The two buses—Xcelsior models manufactured by New Flyer—use a Ballard fuel cell electric engine, which releases water and heat instead of greenhouse gas emissions. The verdict? It quenches.
These buses are part of Alberta’s $9.8 million Zero Emissions Hydrogen Transit initiative to cut greenhouse gas emissions. Edmonton’s energy transition strategy aims to cut emissions by 35 percent, compared to levels recorded in 2005. The province looks to achieve this by 2025 and cut a further 50 percent by 2030, striving for zeroemissions by 2035.
As a part of the CSN network, you’ll become part of a genuine collision repair community. Whether you’re ascending the industry’s peak, or just leaving base camp – we know your business. At CSN we give you the freedom, choice, and support needed to grow and perform. Visit csncollision.com/join for more information!
Remote work just isn't for everyone!
To run Town Autobody, it takes a village
It can be easy to get a big head in an industry like collision repair.
When nearly every conversation covers what credentials you do and don’t have, which OEMs you are and aren’t certified for, a simple chat between fellow business owners can devolve into high school level posturing quickly.
Yet, if you really think about it, we are all (for the most part) traveling down the same path, often pursuing the same certifications and pieces of equipment as our so-called competition.
And if all things going into the repair are considered relatively equal, both the equipment and skill of the repairer, what sets facilities apart besides the colour of the sign on their building?
For the customer, their decision then comes down to the not-so-simple choice of which local collision shop manager they will entrust with their means of transportation, not to mention a fair chunk of hard-earned income as well.
These are people that the average customer has likely never met before, or at least not outside of a collision-induced crisis, and “going with your gut” or blindly following the word of their insurer does little to give consumers an educated basis from which to decide.
Well, allow us at Collision Repair to make that decision a little bit easier—assuming you live in Winnipeg, of course.
If you want a young, energetic business leader with proven management skills, backed up by a talent for auto body repair tempered right on the shop floor, Shamsher Singh Gaidhu is your man.
If you want a young, energetic business leader with proven management skills, backed up by a talent for auto body repair tempered right on the shop floor—Shamsher Singh Gaidhu is your man.
Shamsher took the reins of what would become Town Autobody back in 2014, thanks to a connection from his older brother Amandeep, who was also working in the local collision industry at the time.
His entry into the industry came on hard and fast—Shamsher only graduated from
high school in 2012 and wasn’t even a full Red Seal technician by the time Town Autobody first opened its doors—but financial difficulties within his family made him grow up quick, both in terms of his skills as a repairer, but also as a burgeoning young manager in an industry he was only just starting to get a grasp on.
“When we moved from India to Canada, it was a tough situation,” Shamsher said, over the phone with Collision Repair.
“I never push our technicians to do the work in two hours… our first priority is always quality work.”
– Shamsher Singh Gaidhu, owner | Town Autobody
“My brother couldn’t get a higher education because we didn’t have the funds due to loans and everything like that.”
Amandeep eventually found a path forward in the world of collision repair, and on the advice of their father Hardev, a former Jeep assembly line worker back in India, his younger brother followed suit.
“I did my apprenticeship at a CARSTAR shop in Winnipeg, where I did my Level 1 and Level 2 [training],” said Shamsher. He was also enrolled in a pre-collision course at the local Red River College campus in Winnipeg around that time.
When the owner of Amandeep’s shop told him that he had plans to retire and was open to offers on the shop, the Gaidhus got together and came up with the idea to start a family business.
To say that Town Autobody’s early days did not come easy would be an understatement, as Shamsher and his family found themselves thrust into a world of persistent advancement, and in turn, persistent investment of both
time and money into the many certifications and qualifications a modern repair facility must satisfy.
“When we first bought the shop, we had no idea how quickly everything moves,” said Shamsher.
“I did some I-CAR training and production manager training, but at the same time I was working at a KFC as a manager, so I did at least have some basic management skills going into it.”
Shamsher says that with every day he spends at Town Autobody, he learns something new, and rest assured, dear reader—he did eventually get his Red Seal.
In fact, if you take your car in for repairs, there is a good chance that Shamsher will have a hand in the work at some point down the line, as he makes a point of playing an active role in all aspects of his shop’s operation.
“I’m in the back, on my feet, all day,” he said. “If I need something welded, I will do the welding.”
This quite literal hands-on approach to processing repairs, in addition to daily morning and afternoon meetings with staff, are the ingredients to the open lines of communication that have built so much of Town Autobody’s success.
Success that Shamsher says he often sees manifested right before his eyes, in the form of a strong word-of-mouth reputation informed by the mantra that “doing quality business will never let you down.”
“We haven’t done much advertisement over the past two years, and we haven’t needed to, because we have so many customers coming back with their relative and friends.”
Customers come from all corners of Winnipeg to visit his family’s north-end shop, according to Shamsher.
“I never push our technicians to do the work in two hours…our first priority is always quality work.”
To say that quality equipment for his staff comes as an afterthought for Shamsher would be far from accurate, however, as being an
active technician in his own right, he ensures that the technicians on his team have access to industry-leading tools in their 10,000 square-foot production space.
“We use the PPG Aquabase paint line, a Spanesi Touch machine to measure vehicles, and several spot welders. I am also certified to repair air conditioners as well,” said Shamsher.
Town Autobody is also a proud holder of I-CAR Gold Class certification, as well as a partner to Manitoba Public Insurance and the Manitoba Car and Truck Rental Association.
For all the success the Winnipeg community has given Shamsher, his family and his business, he says he makes a point of returning the favour by contributing to several local charities, as well as by presenting the benefits of a life in the trades to students at nearby high schools, when the opportunity to do so arises.
Shamsher’s trajectory in this industry is highly unique and nothing short of admirable.
Honestly, how many people do you know who immigrated to a new country, graduated high school and opened up their own body shop in the span of less than ten years?
“It is because of my family’s support,” he said. “That’s why we are here right now.”
For Shamsher, it really is as simple as that.
In the same way that his father supported him and his brother in opening Town Autobody, Shamsher supports the technicians under him who are developing their skills, giving them opportunities to grow as tradespeople in a truly collaborative, family-oriented business environment.
Should you find yourself in Winnipeg and in need of body repair, or in desire of an industry colleague to pick your brain, you can rest easy knowing that there is at least one shop in town where the owner can deliver.
“If I need something welded, I will do the welding.”
– Shamsher Singh Gaidhu, owner | Town Autobody
The North American automotive aftermarket industry’s biggest show was back and in full form this year, as the team from Collision Repair ventured out to Las Vegas for the SEMA Show 2022, from Nov. 1 to 4.
After speaking with literal hundreds of members of our industry, the consensus was clear that the aftermarket is excited and motivated to get back out into the world and take on its challenges head-on. Check out what was on display at this year’s show!
Veterans of the SEMA Show are well aware of the fact that, while the crowds of the show floor are great and exciting, and the cars and products are neat—AIA’s Canada Night is truly the place to be during the first week of November. Coinciding with the opening day of the SEMA Show, the Automotive Industries Association of Canada always kicks off the annual Vegas affair with a memorable night of camaraderie for members of the Canadian aftermarket, and this year’s event did not disappoint.
This year’s Canada Night celebration saw some of the Canadian auto industry’s biggest names mixing and mingling at the Venetian Resort, including Joern Stoever, interim general manager of SATA Canada, Daryll O’Keefe, senior v-p of Fix Network Canada, and Ryan Bruno, CEO of CSN Collision Centres, among many others.
Join Collision Repair for a look back at that exciting night in Las Vegas!
Fix Network hosted its annual Network Conference in late September, where company franchisees, industry stakeholders and Fix executives gathered in Quebec City for two days of speaker sessions, a trade show, networking activities and a semi-formal gala.
The event kicked off on the afternoon of Sept. 29 with an opening address from the newly named President of Fix Network Canada, Sylvain Seguin.
Next up was a keynote address from Hod Lipson, a professor of engineering and data science at Columbia University and automotive AI expert. Lipson co-authored the award-winning books “Fabricated: The New World of 3D printing” and “Driverless: Intelligent cars and the road ahead,” cementing him as one of the top minds in auto industry development.
The afternoon continued with more sessions from Nicky Woerner, who discussed OE Connection and OEM certifications, as well as a talk on perseverance from former CFL safety Etienne Boulay, who won the Grey Cup alongside the Alouettes in 2009 and 2010, and again with the Toronto Argonauts in 2012.
A reception with a silent auction concluded night
one—but the festivities kicked off bright and early again on the following Friday.
Ryan Mandell of Mitchell International launched day two’s lineup of speakers, where he talked about current trends around electrification and how the repair industry can prepare for a shifting work mix.
The Cartier Agency then treated audiences to a presentation on leveraging search engines and online reviews to garner the best possible image of your brand on the web.
A discussion on recruiting and company culture was led by Debbie McCarthy, followed by a panel also focused on attracting and retaining staff, which concluded day two’s presentations.
Attendees were then let loose around Quebec City for a scavenger hunt, before getting dressed to the nines for the red carpet, gala dinner with a live auction where thousands of dollars in donations were generated for the Ronald McDonald House Charities.
The gala dinner was followed by an awards presentation.
Let us know if you spot any familiar faces in Collision Repair mag’s photos from the event!
Cleanup after a big event is never a fun ordeal, but its hard not to catch yourself smiling if you knew the big national conference you just held gave more back to the environment than it took.
Simplicity Car Care can officially take pride in the fact that its September National Growth Conference in Niagara Falls was climate positive; the first North American aftermarket event to ever achieve such a feat.
Despite all the heat generated by its impressive lineup of guest speakers and industry influencers, the collision repair consolidator managed to remove twice the amount of greenhouse gas emissions than were generated over the two-day event, from Sept. 15 to 17.
“Right now we must all take responsibility for our contribution to the climate crisis which will affect every single living being on our planet,” said Dominic Napier, managing director at Carbon Neutral Repair and featured guest at Simplicity’s conference.
“Bringing the Simplifiers together is critical to their continued vision in making affordable vehicle repair available for everyone, but it is not acceptable to not acknowledge the impact any conference has on the environment.”
The company considers its commitment to environmental sustainability as just another way Simplicity supports its franchisees and their well-being.
“Franchisee support continues to receive significant investment as we experiment with data-based learning models to customize development for each strategic franchise partner,” said Domenic Prochilo, Simplicity COO.
Attendees to the event were treated to a keynote address from the former vice president of Disney’s Magic Kingdom, Dan Cockerell, who asked of the enthralled conference audience, “How’s the Culture in Your Kingdom?”
Cockerell spoke in-depth on how businesses can establish a culture that fosters success for
all members of the team, while also generating quality solutions for customers.
Speaking to the importance of the event as a whole, Simplicity CEO Paul Prochilo said in his opening address, “This is a celebration of Simplifiers [as he called those in the network], a celebration of your commitment, perseverance, and leadership, and a celebration of our B2B partners and customers who trusted us and worked with us to help fuel or vision of making car care simple and affordable for every vehicle owner in the world!”
Consolidated Collision Services (CCS) held its National Network Meeting in conjunction with the Automotive Convention Expo (ACE) this October, where more than 80 CCS members partook in a full day of thoughtful presentations, discussion and general merriment.
The network spent a full day celebrating its top-performing partners and CCS’s continued growth, while also serving up several educational updates and sessions for the dedicated crew of collision centre managers.
Aviva Canada, OEConnection, Auto+
Performance and BFA Group were among presenters, while BASF, 3M and Enterprise offered sponsor support.
The CCS team also awarded some of the most prestigious awards the company has to offer that day—the President’s award, given to the eight members that first believed in CCS’s cause—the inaugural facilities to join the network.
Recipients included Highland GM Centre in Aurora, Ont.; Bennett GM Collision Centre in Cambridge, Ont.; Heffner Toyota Lexus Collision Centre in Kitchener, Ont.; Raceway Chrylser Collision Centre,
Mississauga, Ont.; Imperial Collision Centre in Sudbury, Ont. and Premier Chevrolet Collision Centre in Windsor, Ont.
Next, the organization announced the winner of the BASF Leadership Award, in recognition of the CCS location that has demonstrated itself as the clear and definitive market leader in the community that they serve.
The award went to Performance Collision Grimsby.
The group honoured Sandy Liguori with a surprise award, which was met with humble gratitude from the industry leader.
After lunch with a gorgeous view of the Falls, an industry panel of CCS members discussed some prevailing topics in the collision industry—HR, profit, parts, OEM certification and more.
Trent Dayton of South Pointe Collision and Glass; Michael St. Germain of Mercedes-Benz Oakville Collision Centre; Sandy Liguori of Woodchester Auto Group; Daniel Segretto of Scarborough Toyota Collision Centre and Bing Wong, the managing director of Canadian Hail Repair, co-founder of Collision Builders Inc. and managing partner at E-Sheets.
The CCS meeting concluded with more award presentations, with Trent Dayton of South Pointe Collision claiming the 3M Innovation award; the team from Imperial Collision from Sudbury, Ont. snagged the top net promoter score award; and Danny Zita of Eastside Old Mill Collision Centre received honours for recording the lowest LOR–the only CCS facility to do so this year, said Beier.
To conclude the meeting, CCS delivered the Facility of the Year award, which went to Capital Collision out in Mount Pearl, N.L.
Hundreds of honky-tonk-seeking Canadian industry members were in Nashville over American Thanksgiving as CSN Collision Centres held its twentieth anniversary conference at the Omni Hotel.
The network made a point to honour some of its top performers during the event—including the much-coveted Shop of the Year award. The honour went to CSN Chatham, which weathered several severe storms in the past year, yet remained resilient, streamlined and, of course, passionate about seeing the centre succeed.
“We can’t believe it,” Chris Jones, co-owner of CSN Chatham and Apex Autogroup, told Collision Repair immediately after the win. “This is truly such an honour—we have no words.”
In true industry fashion, both Jones and partner Tammy Johnson Blake were greeted by peers after accepting the award.
• CSN Elite (Customer Service award — British Columbia)
• CSN Reflections (Customer Service award — Alberta & Saskatchewan)
• CSN Dundas Valley (Customer Service award — Ontario)
• CSN Collision Clinic (Customer service award — Atlantic & Quebec)
• CSN Springfield (Sales Growth award — British Columbia)
• CSN Autolab (Sales Growth award — Alberta & Saskatchewan)
• CSN Walkerton (Sales Growth award — Ontario)
• CSN Keizer’s (Sales Growth award — Atlantic & Quebec)
“I’ve never won anything in my life!” exclaimed the top-prize raffle winner, who went home with two fully paid airfare tickets to anywhere WestJet flies.Mike Gilliland, AutoHouse Technologies. Jason Arnott, CSN with Cameron Clark, CSN Cam Clark; Al McNeil, CSN. Allison Rogers, Media Matters, and Jenica Bennett, AutoHouse Technologies. Two teams went head-to-head during the CSN Family Feud. Bianca Salimis and Connor Jameson, CSN Elite, and CSN’s very own in-house Family Feud host. The Bodyshop Connect crew. PPG crew Emmanuel Souply, Scott Spike, Norman Angrove
Parr Auto Body touts quite the reputation in Saskatoon. The facility opened its doors in 1952 under the leadership of Ken Scissons, who named the business after a nearby golf course.
Seventy years down the production line, the business continues to thrive under the leadership of Chelsea Stebner, Brayden Neufeld, David Sather and Shane Desrosiers. The company has formed longstanding and loyal relationships within its own team, the Saskatoon community and beyond.
An anniversary like this is nothing to scoff at—particularly for an independent facility. Most would expect the Parr team to throw a celebratory bash, fit with all the trimmings, but that’s not really the collision centre’s style.
After all, success is that much sweeter when shared with your friends and family. The idea of community is rooted in the business’s founding values; it’s a mindset that’s been carried through the company’s 70-year history.
Stebner and the current leadership team credit much of Parr’s success to Tom Bissonnette, the director of the Saskatchewan Association of Automotive Repairers and longtime owner of the business. Frequent readers of Collision Repair will know of his time with the business well—he’s spent the last year writing columns on his trials and successes in the collision repair realm.
While Bissonnette passed many nuggets of knowledge to the present team, Stebner says the fearless leader always ensured they
understood the importance of giving back to its community.
“My parents were always actively volunteering when I was a kid, so I’ve always been raised on the idea of philanthropy,” she said. “Tom is more of a quiet philanthropist—he’s always said, ‘let’s spend donation dollars instead of advertising dollars.”
“If you don’t understand our business values, you probably won’t mesh with the team,” admits Stebner.
Each year, Parr takes half of its donation budget and gives a lump sum to a local cause. The rest of the funds are committed to a cause chosen by the collision centre’s team.
“We always donate to a cause that means something to our team. This year felt different, though. It didn't feel right to host a big party after all we'd been through during the pandemic."
When it comes to selecting a cause for annual fundraising efforts, the whole Parr team puts their heads together.
“We want to make sure the team feels connected with what we’re supporting. The Parr Auto Body family has a personal connection to youth mental health, so it’s very special we’re able to support the Dube Centre this year.”
The facility is well-versed in community contributions: the team has supported several local sports programs, homeless shelters, food banks and the Ronald McDonald House and more via other charitable partnerships.
“We’ve taken part in a lot of different initiatives. Ronald McDonald House—we love helping out there whenever we can. We also volunteer with the Sherbrooke Community Centre, a long-term care home in our community.”
The team also makes a point to celebrate its own successes accordingly. The team hosts frequent BBQs in the summer and baked goods are often traded in the break room.
“We’ve also done partnerships with local businesses, in the past.”
As the facility steps into its seventy-first year of operation, Stebner says she has no doubt they’ll continue to hold the same values tight.
“Community is engrained in our values—always has been, and always will be. It’s what makes Parr Auto Body the facility we love to call our workplace.”
Many people enter the collision repair industry for some sense of excitement; a career where they know that no day will be exactly like the one that came before. As a daily news outlet, we here at Collision Repair understand that sentiment intimately.
While most collision centres do what they can to market themselves as fixtures in their local communities in the hopes that steady business will follow, some opt to take some of the randomness out of the equation and seek out clients directly.
Enter the world of fleet-based collision repair, where specialty repairs and corporate networking reign supreme.
A star example of a facility that operates on the business-to-business side of our industry is Revline Industries in Montreal.
Helmed by the dynamic duo of president Frank Dias and vice president of business development, Maria Rossetti, this shop deals with some of the most high-profile corporate clients currently operating in Quebec, including grocery delivery chains, telecommunications companies and numerous other mobile services with fleets needing regular repair.
Part of the appeal of working with corporate fleets, according to Rossetti, is that certain amenities that consumer-facing repair centres must facilitate, such as rental cars for clients, can largely be dispensed with and therefore, more of the shop’s overall focus can be placed on completing repairs.
“It’s really just about taking care of the client and making sure the repair gets done and in a timely manner—the process is a lot quicker,” she said, over the phone with Collision Repair.
From a repair perspective, Dias says that working with fleets allows technicians to really hone in on their skills on a number of highly-specialized commercial models that traditional repair facilities would likely be unequipped to deal with.
“They are a special type of client, and certain clients—they’re really special, in the sense that some of these vehicles that we take on in fleets are not your standard Ford pickup truck or standard Volvo car,” said Dias.
“Some of these vehicles are specially equipped with custom boxes, in some cases, and so when they have collisions you really need a body shop that has a real expertise in that repair, because now you’re playing with plastic, carbon fibre and fibreglass.”
There are many occasions where the technicians at Revline work directly alongside their corporate partners when, for example, a vehicle with a refrigeration component is sent in and third-party specialists are needed to assist.
The experience both provides clients a one-stop-shop for the entire repair process, in addition to giving the staff exposure to the many converging technologies that may be present on a specialized commercial vehicle.
“When you’re catering to these people, and you get to know their product well—some of these are refrigerated units, some are for servicing tools—that’s the beauty of fleets. When they come to us, we very quickly get to know their vehicles,” said Dias.
These sorts of business partnerships don’t simply spawn out of thin air, nor do corporate fleet managers go door-to-door offering up contracts to strangers—Dias and Rossetti put in the legwork to earn the business of their partners, no doubt about it.
As a former marketing consultant for several Fortune 500 companies in the past, including recent stints with two paint giants, Rossetti is a master networker when it comes to creating value for her business partners
and has helped elevate Revline’s operations immeasurably.
“It’s about establishing relationships within fleet management companies. Sometimes it’s also about dealing directly with the customers and doing research in the market to see who big corporations are dealing with, who manages their fleet, who does their collision management,” said Rossetti.
“Once you’re in, it’s about being very service-oriented.”
Dias says that the part of Rossetti’s presentation to prospective partners that captures the room's attention is when she asserts that a deal with Revline means a 60 percent reduction in repair downtime for your fleet, while still remaining well within budget.
One rather unfortunate bridge between the consumer and corporate collision repair worlds, however, is the issue of labour retention. Like their counterparts on the consumer side of the industry, Dias and Rossetti have had to put a large part of their business’ focus on securing staff to work Revline’s busy production floor.
For several years now, the shop has thrived on the talent of automotive technicians
sourced from abroad and conditioned into the Revline way of doing things.
“I have a fella out of Moldova here. He’s a great guy and really knows his stuff; one of the best metal refinishers I’ve seen in this industry,” said Dias, a man with a keen eye for talent, paired with a marked distain for sloppiness, disorganization, and most of all—dust in the shop.
“The one problem with him in the beginning was that we knew he was used to working in body shops back in the 70s—absolute dirt pits. It took about two years of getting his work cleaned up, but now he understands that this is how Uncle Frank works.”
All this is to say, the corporate fleet repair world is by no means immune from the woes that affect traditional neighbourhood repair shops; it simply requires a slightly different set of skills.
Where one manager may have an encyclopaedic knowledge of their local community, its culture and its politics, a fleet repair manager has a keen understanding of a wider corporate climate and the strategies that inform the operational decision-making processes of these large companies.
are using digital locks to create their own networks—and consumers are fighting back
Story by KATE NGWhile repairability in the past was dictated by the tooling at your disposal and your knowledge, digital locks have quickly created an impassible barrier for the average person. A security expert might find workarounds, given enough time and effort—but not many people have the time to become security experts to fix a phone or faulty printer.
This has allowed certain corporations and a considerable number of OEMs to create artificial barriers preventing qualified repairers from accessing their products. The technology and repair know-how are there, but the software stops them, given the risk of “bricking” the product.
In a meeting between the Automotive Industries of Canada (AIA Canada) and policymakers on Oct. 18, association members emphasized how current legal conditions allowed OEMs to consolidate repairs to a limited number of facilities–only their own repair centres have the codes to disable software locks.
This leaves small businesses at the mercy of larger OEMs, who can easily gatekeep repair and diagnostic information. This isn’t an attempt to ensure that only qualified repairers can access the data—case studies and expert testimony suggests this is an effort at market consolidation by larger OEMs.
These are a few of the testimonials from industry representatives and individual shops.
While the idea of having the option to repair and maintain a product that you own would be common sense in the pre-digital age, this concept has eroded with the advent of digitally based software locks.
For all intents and purposes, most commercially installed digital locks were created to deter most consumers from using their software in ways that the OEM did not intend.
As you probably know from living in 2022,
this can wildly vary from OEMs protecting software source codes to forcing customers to get products repaired directly at the OEM. This has been the landscape in modern consumer rights for the past two decades, with right to repair aiming to update legislations around the world to ensure that customers have the right to choose who repairs their device—whether fixing it themselves, taking it to the OEM, or a third-party shop.
Feb 22, 2021 - Bill C-272 is proposed. If passed, it will allow anyone to bypass program protection and encryption for maintaining, diagnosing and repairing products with embedded protection software.
It also allows for the manufacture, import and provision of devices and components to circumvent said protection measures, as long as the design and use exclusively pertains to diagnosis, maintenance and repairs.
AIA Canada is a representative association for Canada’s automotive aftermarket supply chain and service industry and has petitioned for the right to repair as far back as the 2021 federal election.
The organization has heard one clear message from shops since then–OEMs did not voluntarily provide repair information as suggested by information Canadian Automotive Service Information Standards (CASIS), and that legislation making such information mandatory was required.
According to Alana Baker, senior director of government relations with AIA Canada, this is an extremely common problem. On a Zoom call, Alana recalled a case which she says is not uncommon in the slightest.
One collision centre AIA spoke with reported having all the tools and software to replace a vehicle’s engine control module on a customer’s Honda but needed the immobilizer code to begin repairs. Upon logging onto the OEM’s official website, they discovered that the
One repairer with direct experience on regionally locked security codes is Jamie Holmes, co-founder of the Master Mechanic franchise in Ontario. He has years of auto service experience under his belt, specializing in diagnostic systems.
Specifically, he cites Honda and Toyota as examples who's American models have accessible repair codes for repairers but not Canadian models, despite identical mechanical or diagnostic faults.
Holmes believes that this stems from the desire for OEMs to control the service aftermarket, allowing them to direct customers to OEM repairers, or charge independent auto shops for the privilege of accessing diagnostic information.
While citing the example of a fellow repairer in Toronto who pays $10,000 for a yearly subscription to a diagnostic tool
code was exclusive to American customers.
Essentially, this single line of code meant the repairer could repair a vehicle purchased from an American dealership, but not an identical model sold by a Canadian dealership.
Ultimately, the customer was forced to tow their vehicle to a dealer to begin repairs—not only did the business lose a prospective customer and a few hours of work, it also resulted in the OEM poaching said customer and risking the shop’s reputation in the process.
“Despite the independent shop having all the proper equipment, credentials, and knowledge to carry out the repair, stories like these are all too frequent,” Baker explained.
“Automakers must share vehicle data with anyone the consumer chooses, which would remove the current practice where many automakers are making it more difficult, more expensive and sometimes impossible to access repair information and tools,” AIA Canada wrote in its press release.
for Mercedes-Benz vehicles, his issue has more to do with the progressive nickle-and-diming that quickly adds up, even with fees that may seem more reasonable at first glance.
“Granted, companies do offer shorter subscriptions, but it's still $140 or so.”
Ultimately, this slow economic bleed hurts small shops the most and will eventually harm the OEM’s reputation through a lacklustre aftermarket service experience.
“OEMs need the aftermarket to be able to fix their vehicles. There was a study done in the 1960s—if you purchased a brand-new car and you weren't happy with it, there was a chance the client would come back despite the bad experience. When that study was done in the early 2000s, the chances of another purchase was (nearly) zero,” Holmes concludes.
June 2, 2021 – Bill C-272 is accepted by the House of Commons during its second reading.
Sept. 20, 2021 – The 2021 federal election is called. Bill C-272’s development unofficially ceases due to a change in cabinet. Legally, it currently is awaiting a committee consideration.
Feb 4, 2022 – Bill C-231 (44-1) calls for OEMs to make diagnostic and repair information available to independent repairers, in addition to offering service parts.
These must be offered to independent repairers “in the same manner as the manufacturer makes the information and parts available to authorized repair providers.”
“For a truly open and fair and competitive automotive aftermarket, consumers need to be protected by legislation that reflects the new reality of vehicles. Right to repair is about the preservation and protection of consumer choice.”
– Alana Baker, right to repair advocate
“Despite having (the) clearances, what's odd is we can get that information for any US built vehicle, but not any Canadian market vehicle,”
- Jamie Holmes, current VP of Master Mechanic
It’s not just costs and the potential to lose customers that shops face. Mark Lemay, co-owner of Auto Aide Technical Services, highlights one important point: even if the shop has all the money in the world, OEMs might simply drop the ball on providing shops with their purchased or requested information in a timely manner.
“Around the end of June, we had a car come in, a Mercedes B-200. I went through the application process, which is extremely clunky and off-putting, but I did it all right,” said Mark.
He believes this may stem from OEMs seeing other service shops as competitors, rather than part of the greater aftermarket ecosystem.
“I don't think they have a vested interest in the aftermarket at all, having worked in dealerships at the service manager level myself. Other than its place to sell parts, the aftermarket is a competitor.
“I think it's something they wish would just go away.”
While opinions on OEMs differ, one possible consolation for the auto repair industry is that Canadians from other industries and parts of society overwhelmingly favour right to repair thanks to its visible impact across all ages and income groups.
Bryan May is Canada’s member of parliament representing Cambridge, Ont. and the mind behind Bill C-272’s proposal. For him and his constituents, right to repair is a return to an age where products could be repaired if you had the relevant parts and knowledge, due to the lack of digital locks.
“Growing up, there was a television repair (business) in my neighborhood that doesn't exist anymore,” he recalls. “All of a sudden, something you would normally and intuitively be able to repair yourself has a digital lock.
“If we do get a true framework, it’ll have an economic impact and you'll see a resurgence of those types of businesses.”
While similar legislation has been proposed in other countries as early as 2012, this remains significant as Canada’s first proposal addressing right to repair in an era where software locks are universal across multiple industries.
“We must recognize that manufacturers are not breaking any laws. In the case of Canada, the Copyright Act was written decades ago to do something…[it] was never intended [for],” said May.
From a political perspective, this is a non-partisan issue that revolves around updating outdated legalisation, rather than a conflict between small and big businesses.
“Every party in the house has a reason to get behind it. Conservatives see the value for the agriculture sector. The Bloc [Quebecois] were very keen on the idea of fighting planned obsolescence, and of course, the NDP and the Liberals are really focused on the environmental impact.”
Feb 8, 2022 – Bill C-244, whose wording is nearly identical to Bill C-272, is proposed. Rather than a proposal which builds on Bill C-272, this is effectively a revived version of the same bill – albeit with a new cabinet.
In practice, this is the same bill starting from the absolute
beginning of the legal process. Not as good as finishing what was already started, but better than leaving right-to-repair in the dust.
However, these two bills are largely focused on consumer level electronics with easily available fixes and diagnostics.
“I submitted that around June 25. I think I got access on July 27. Meanwhile, the customer’s car is sitting on my lot. We've had to send cars to the dealer because we couldn't get what we needed.”- Mark Lemay, automotive repair industry veteran of 36 years.
“In such a small piece of legislation, everybody can find an angle that they can support”
- Bryan May, Member of Parliament representing Cambridge, Ont.
The SATA RPS (Rapid Preparation System) multi-purpose cup system performs four functions: mixing, painting, refilling, storing. The handling of SATA RPS is so easy because it consists of only three parts: cup, lid and sieve.
SATA RPS fits directly onto your SATA spray gun with QCC connector (Quick Cup Connector) without any adapters. It makes a technician's life much easier, considerably increases productivity and drastically reduces the consumption of cleaning solutions and solvents.
Bendable – allows the painting of sill areas or wheel arches "overhead" Stable – due to the screw connection between cup and lid, the cup always remains on the lid and gun even when touching obstacles.
Easy removal of the lid in case of emergency – without soiling the working area.
Clean removal of the cup – by pressing the cup in, vacuum is created, which empties the material passage when pulling the trigger.
Constant material flow – helps the painter to achieve perfect coating results just like child's play.
Very quick colour change – cleaning becomes a minor matter
Available in 3 cup sizes: 0.3 l, 0.6 l and 0.9 l
Also available as UV version: 0.6 l
SATA Canada Inc. 125 Buttermill Avenue Vaughan, ON L4K 3X5
www.sata.com/sata-rps-multi-purpose-cup
Phone: +1 905 660 1101 Toll-free: +1 844 554 SATA (7282) Fax: +1 905 760 1250 contact@sata.ca www.sata.com
READ
Many in the global collision industry recognize the name Sam Mercanti.The Italian-born businessman came to Canada with his family as a child.. He was raised in a bodyshop setting and, in adulthood, went on to helm one of Canada’s most successful collision repair franchises.
But there’s far more to Sam’s story.
His upcoming memoir, tells the story of a young Italian kid who came to Canada with nothing, dropped out of high school, worked in his family’s bodyshop sweeping floors, and went on to revolutionize the collision industry in Canada.
Collision Repair magazine was lucky enough to receive an advance copy of RISEN From the Shop Floor: Lessons from an Entrepreneur by Sam Mercanti.
We attached two standout excerpts on these pages but, but we've got more in our digital version on www.collisionrepairmag.com. Or scan the QR code on this page to purchase your own copy today!
If you ask Canadians from outside the prairies about Saskatchewan, many will give the misguided response that it’s so flat out there that there is nothing to see.
Any born and bred Saskatchewan resident knows it to be the opposite—there’s plenty to see and do with fantastic parks and lakes throughout the province! Known as the Land of Living Skies the wide-open spaces provide breathtaking sights.
The Saskatchewan Association of Automotive Repairers (SAAR) is boldly putting its province on display, proudly espousing a life of flexibility and affordability for auto body technicians who may be considering having a lifestyle rather than just making a living. Home ownership is easily attainable with a nice home starting in the $300,000 range!
In this debut Saskatchewan Shop Spotlight, readers will get a glimpse into the communities of Melfort and Swift Current, Saskatchewan; both bustling small cities outside of the urban sprawl that offer affordable housing, youth sports and picturesque views of nature, all within a short drive’s distance.
Any technicians out there looking for a change of pace, and less strain on their wallet, ought to consider a future in either of these thriving Saskatchewan communities.
Helmed by owner Mitch Holtvogt, Vern’s Paint and Body sets itself apart from the competition with what its own shop foreman refers to as an “unending commitment to quality.” A life at this Melfort, Saskatchewan collision repair facility can bring with it a place in a vibrant and welcoming community that can support tradespeople with wages comparable to larger city centres.
The city of Melfort provides numerous affordable opportunities for your children’s recreational pursuits in sports like hockey, soccer and baseball plus an excellent school system that will allow them to easily walk or bike to school.
Vern’s Paint and Body is currently looking to hire a journeyman auto body technician and journeyman refinish technician, as well as front office staff and wash bay/support staff. Send your resumes in to mitch@vernspb.com
Henry Klassen says the people of Swift Current, Saskatchewan love their local Junior Hockey Club, the Swift Current Broncos, but there are numerous recreational options for all ages at an affordable price.
The city of a little more than 16,000 has anything a prospective employee could ever want, all within a ten-minute drive. Whether it be for Swift Current’s picturesque parks and canals or the two 18-hole golf courses nearby, life in the city comes with a small slice of paradise.
The shop is currently looking for detailing and auto body technicians to join the team. Anyone interested is encouraged to email their resume to hklassen@csnklassen.com.
As a host of economic hurdles continue to put pressure on Canada's repair shops, what other revenue streams could you explore?
For most of the body shop industry's recent history, the struggle has been how to bring more and more services in-house—first paint, when it was a separate department, then the advent of in-house mechanics in body shops and now ADAS calibration, which has become a full-fledged department in some cases.
But what if you want to do the opposite? How could you position yourself to offer some of these services on your customers' terms, at their homes or businesses?
There's a long, unwritten list of do's and don'ts from managers who have offered mobile repair services in the past—some have seen their businesses reach new heights and solidify their position in the community— while others have been overwhelmed by the unforeseen complexities that can accompany these services.
The first aspect of the mobile industry that managers tend to overlook is the issue of liability. Taking what is usually a highly
regulated and controlled procedure, such as a dent removal for example, and bringing it to a complete stranger's driveway poses a whole host of challenges to be met and overcome.
Technicians don't normally have to deal with issues such as bad weather or a lessthan-ideal workspace when working from their home shop, but when these services are offered on the road, anything is possible.
Vern Gervais, national director of glass operations for NOVUS, says some of the body shop industry's biggest competitors have entered the mobile services arena.
"When we look at the largest competitors in the industry, [mobile repair] is a significant part of their business. The reality is that it's an industry standard, so you must decide if you want to be in the industry or if you want to be someone who watches the industry from the sidelines.
"There are many elements to [NOVUS'] mobile strategy—direct customer contact is only one part of the business. That aspect of the business, as we approach automation, will become more difficult," Gervais told Collision Repair.
"The flip side of mobile is business-to-business, where we go to our commercial customers, fleets, transportation companies —companies where it's difficult to get those vehicles to us. That opens the door for an existing franchisee to solicit different types of work from their customers."
Other questions include how a shop determines which technicians work in the field and which work in-house.
Having your top technician on the road meeting with customers seems like an intriguing idea at first, but when it comes time to check the books at the end of the month, you may find that less work was done by that technician, due to the time spent traveling to job sites, and perhaps your internal metrics even start to change to reflect the workflow of a different team.
Also, with gas prices soaring over the past year, the prospect of spending both
labour hours and gas money on repairs that are generally low stakes can be a tough pill to swallow for a collision center manager in 2022.
Liability is another consideration, but no more so than in your own production shop.
"Every one of our commercial operators, they're all insured for every potential scenario that could happen," Gervais said.
"There's nothing we would do in your driveway that would be different than what we would do on the shop floor. Our equipment is safe, our safety procedures are the same, our repair processes are the same.
"Fortunately, glass removal and installation is a clean operation. There is a multitude of new equipment that allows for one-person installation. I don't see it being a big challenge and I can tell you anecdotally that never in all the years I've been in this business have I encountered a problem in a private residence."
It takes two to make a thing go right. It also takes two to make it outta sight. And, in our case, it takes two parties to ensure a customer leaves the repair centre with a safe, reliable, pre-accident condition vehicle.
Collision Repair magazine has witnessed plenty of industry anticipation regarding this year’s annual Insurer Report card. Below are some of our key findings, based on more than 120 submissions from collision centres across the country.
For the third straight year, Collision Repair’s Insurer Report card has recognized the Co-Operators as the highest-scoring insurer, receiving an A grade for the second year in a row. In 2020, the Co-Operators took the crown with an overall grade of B+.
The Co-Operators was not alone at the top this year, though. Saskatchewan Government Insurance (SGI) grabbed clean As in every category—contrary to the Co-Operators A-, A and A+, respectively. The two insurers are tied for top scorer in our 2022 report.
Economical scored Fs in all categories—the only party to do so. The insurer also received an F-grade overall in last year’s report.
The industry certainly recalls RSA’s integration with Intact, which started in June 2021 when the latter acquired RSA. RSA had scored a B in last year’s Insurer Report card; Intact a D. The integration resulted in an overall letter grade of D+ for Intact; a small improvement over 2021’s results. The insurer scored an F in the bodyshop relations category.
The Co-Operators and Saskatchewan’s crown insurer were the only two parties with overall clean A-grades, though Wawanesa claimed an A-. Its lowest score was in dispute management practices, claiming a modest B grade.
In terms of top performers per category, two crown insurers came out on top where quick payment is concerned. SGI and MPI touted the top grades in the category with two As.
The Co-Operators and SGI can be commended for their dispute management practices; both insurers scored As for the category. The Co-Operators went one step further to claim an A+ for its bodyshop relations—the only A+ in the entire report.
*Note: Collision Repair magazine has edited some submitted opinions for clarity and length.
“It's hard to tell clients something good about their insurance company when they don't communicate with their customers what’s been trending. Betterment has become a huge issue and having bodyshops explain it to customers is backwards. We have no information on their policy and shouldn’t be educating them about it.”
“The expectations the insurers put on shops during COVID were massive. Volume dropped—the industry lost staff. We need a huge increase in rates in order to attract and hire staff. Not to mention equipment. The repairers need to stand together and make the changes this industry needs.”
“The timeline to have estimates approved/ reviewed by insurers has increased dramatically.”
“The use of photo desks and the reduction of field adjusters/appraisers has improved the relationships in the industry. Conversely, DRP programs continue to support and have a negative impact on the quality of repairs and satisfaction to the customer.The use of algorithms in establishing R&R and R&I labour times continues to erode the labour pool—it favours insurance carriers unfairly. Although conflicts can be resolved with the use of the DEG process, it continues to place a burden on the repair shops. Technicians and management continue to absorb the time lost for this process without compensation.”
“Insurance companies, who post profits every year, are so slow to pay. It’s not a great way to treat a partner, especially when we put out thousands of dollars for repairs and have to constantly call to be paid. Bodyshops are not the bank.”
“The only reason SGI got a lower grade in bodyshop relations [in the 2021 report] is that they do just enough to stay ahead of the rest of the insurance companies. If we could get all companies to raise their game, I’m sure SGI could be A+ across the board.”
We ask the industry for their honest comments* on the graded insurers. Here’s what they said.
“Many insurance companies have made it very clear and apparent that the quality of customer repairs has nothing to do with the claim or who repairs the vehicle.”
“Phrase of the year: 'we no longer pay for that operation'.”
“Customer pay is slowly becoming the dominant source of income. We without dispute receive more than the average insurance company is willing to pay from our customer pay repairs; $20.00 per hour for labour, an additional $4.50 for paint and materials and $2.00 for supplies.”
“Record inflation and no labour rate increases. [Insurers] need to pay us more so we can be sustainable, not to mention profitable.”
“Most insurers are dragging their feet when it comes to labour rates and material rates.”
“If I talk I will be punished and won’t have any work.”
“We
mandate that image desks are I-CAR Platinum Certified, at the very least, or have taken Vale National Estimating and passed, or a 310B Licensed Tech. Not just click-happy discount specialists that do not understand a
“The SGI lot…they drink an economically impactful amount of complimentary coffee pods.”
“This should be an interesting year as more technicians retire and the pool of repair work increases. We are scheduling four weeks out, on average, and expect LOR to increase. The days of low hourly rates and dictating are coming to a head. Is that honest enough?”
“Insurers appear less concerned about shop challenges.”
“Aviva’s reps are very humble, though they have much to be humble about.”
need to
thing about repairing damaged vehicles.”
“Collision centres are the only party in the collision repair process where you have to fight to survive.”
As Einstein is attributed to have said, “Doing the same thing over and over expecting a different result is the definition of insanity.”
He didn’t really say it, but I believe he believed it.
Leaders fall into the trap of continuing to do the same thing because they have achieved successes in the past that can give them confidence that they have figured out the superior way of being. This is a sense of hubris that is immediately squashed by reality.
Today, that reality is the cost of labour and shortage of workers available.
how money isn’t the only thing workers want. Of course, it is important that you pay people in accordance to their worth. What else is important is that you engage with them, provide opportunity for growth and development and create a culture that has people wanting to be on your team.
One of the more progressive clients has provided the opportunity for their people to move around between jobs that interest them in their career development. Another forward-thinking client is in the midst of a career path strategy that will advertise careers not just jobs. This move makes sense because
IF YOU PAY ATTENTION TO THE REASONS WORKERS GIVE FOR LEAVING AN EMPLOYER, MORE TIMES THAN ANY OTHER THEY CITE A TOXIC ENVIRONMENT AS THE MOTIVATOR.
Einstein did say, “The measure of intelligence is the ability to change.” He was preaching humility. We must have humility if we wish to be great in our leadership. Humility allows us to examine “the way we have always done it” and stop protecting the status quo.
Leaders must develop humility above all else. This is what allows them to accept the notion that maybe there is a better way. They must listen to messages from near and far, weigh the potential and be brave to change when they see that potential.
Listen to what workers are saying. In a recent BDC newsletter, an article outlined
good people are hard to find, so when you find one—hang on to them! Create a desire to want to stay with you because they see the opportunity.
If you pay attention to the reasons workers give for leaving an employer, more times than any other they cite a toxic environment as the motivator. It is no longer enough to provide a clean, safe workspace. People want more satisfaction from a place they are spending almost a third of their time. They want to belong to an organization that has a cause—beyond just money—can see them as an individual and supports their ambitions.
That requires leaders thinking differently than we have been.
I have met employees that have had degrees and certifications paid for by their employers. I still hear things like, “what if I pay for the education and they leave?” This kind of small thinking is what will sink the ship. Not seeing the need to invest in better equipment or better education is a death knell.
Get to know your people and what they prize, then start delivering it! That’s the way you can stay the one who’s driving!
Looking to retirement but want to be sure your team is taken care of? Sell your business to another local owner!
CARSTAR is a collision repair network made up of independent owners, most of them being long running family businesses. They join CARSTAR because they want to keep
providing premier auto body repair services to the communities they work and live in, but need support competing with large national chains in their market.
Contact Dave Foster today if you want to sell your business to another local owner at dfoster@carstar.ca
In the past six years I have seen more change to the collision industry than I ever did in my first 30 years. I am not sure that I would be enjoying the business as much now as I did a short time ago.
The amount of administration and technical issues that have been downloaded to collision centres for the labour rates they’re paid is getting to be totally ridiculous. What I could do with 15 people six years ago now takes 20 people and with parts becoming a much bigger part of every work order, the gross profit is simply not there to sustain most body shops.
Admittedly shops with large sales volumes are somewhat protected from the increased costs but the smaller, mainly rural, shops are really feeling the pinch. As our businesses
try to compete with other four-year trades, or industries like mining and oil, to attract and retain employees, we find we simply cannot compete.
To make matters worse, in our province the government insurance company, SGI, continues to hire some of our best and brightest young technicians as appraisers. To be fair, SGI is aware of this issue, and they are taking steps to no longer take our young journeyman technicians.
It used to be that a collision centre could afford to pay its employees more than the insurance companies could, but not anymore. The days of the flat rate technician pounding out 300 hours a month is fast becoming a thing of the past in our province. We are required to follow OEM procedures and document
them with photos—if we do not, we don’t get paid for some labour operations and we most certainly will have the job audited by our insurance company. If we make a mistake our insurer can and does call the customer back in, explain where we went wrong and completely re-do the work that was not done according to OEM guidelines.
Every job requires that the technician supplies a digital copy of the OEM procedures to the insurance file and numerous photos at every step of the repair to confirm that these procedures have been followed to the letter—unless our insurance partner feels the OEM procedure is not totally necessary and standard industry operating procedures will suffice—it usually means they want it repaired cheaper.
It’s time for serious change—are you in?
Aftermarket parts continue to be a challenge for our facilities. The extra gross margins hardly pay for the extra time pre-fitting parts or spending extra time to make these parts fit. Sure, some of these parts are fine but we really don’t know for sure until we try them on the vehicle.
In our province we have spent the last five years working on the Safe and Quality Auto Repair Program (SQARP). Our insurance partner requires all certified shops to be either I-CAR Gold Class or have OEM Certifications. All facilities are also required to have the proper equipment to properly fix today’s vehicles and the training to use them properly. I would not be exaggerating to suggest that the average business had to spend the better part of $250,000 to meet the SQARP Certification.
In Saskatchewan we have not had a labour rate increase since 2016, when we were at just over $92 per hour. Every year since then our insurance partner has refused to give a rate increase with the justification that we have the highest labour rate in the country. The challenge for our shops is that we got that labour rate so that we could compete with other four-year trades for employees and most shops gave their staff significant
What
I could do with 15 people six years ago now takes 20 people.
wage increases. Since then, our profitability has been eroded with the increased costs previously mentioned and with the latest up tick of inflation it has simply gotten worse.
Over the last few years SGI has made a truly admirable effort to connect with the collision industry, discover our pain points and then work with our shops to eliminate as many as possible. We are not where we want to be but thank goodness we are not where we used to be. I for one really appreciate SGI’s willingness to engage in conversations with our collision centres—they have set a standard that other insurance companies seriously need to consider. My experience is that we have both benefited from these conversations.
So, what is a fair labour rate?
Generally, the rule of thumb is that a shop needs to make at least 40 percent gross profit after all direct costs—and that could be in question as we now see parts sales outstripping labour sales in our market. Just the same, let’s do the math.
Currently we are paying our journeyman technicians anywhere from $30 to $35 an hour, add 30 percent for benefits—holidays, training, uniforms, group insurance, CPP, UIC etc.—and we are paying anywhere from
$39 per hour to $45.50 for a 40-hour work week. Overtime, which is plentiful due to a lack of qualified help, adds another 50 percent to that cost. Using a 60 percent gross margin, assuming your technician is at least 100 percent efficient—let’s face it, some are higher, some are lower, we need to look at the average technician—a shop would need a labour rate of at least $100 per hour to $120. If you consider the overtime that most shops have to pay I believe that $120 an hour is the minimum and $150 per hour is more realistic.
Our challenge in Saskatchewan: all the other province’s labour rates are far too low, and they are keeping us down. I honestly don’t know how you make it work. If not, why not? Who made the vehicle? Should they not know the proper way to repair it?
I know Darryl Simmons authored an article called The Tipping Point and I believe he is right; it is time for body shops across Canada to stand together and demand fair compensation for the highly technical work we are performing.
their insurer is not allowing some OEM repair procedures to be performed on their vehicles? Do they understand that in some cases going to an insurance preferred shop may not be beneficial for them?
How about advocating for the body shops? Just because some insurance companies pay insufficient labour rates do they all have to follow suit? Is it fair to insist that body shops discussing door rates is an act of antitrust, yet most insurance companies are within spitting distance of each other’s door rates? Could a national association speak on behalf of body shops to our elected officials and the Insurance Bureau of Canada?
What should this national association look like? I can’t say for sure, but it starts with having a conversation and I know that Collision Repair magazine is asking the industry to bring their ideas forward. If enough owners come forward, I believe we could form a national association to educate consumers, governments and insurance companies of the dire situation our industry finds itself in.
TOM BISSONNETTE
is the director of the Saskatchewan Association of Automotive Repairers (SAAR). Tom’s Tales is a series of Collision Repair magazine articles chronicling his journey through the collision industry, since 1982. Besides telling his story, Tom hopes that today’s shopowners and manager can learn from his victories—and his mistakes.
Could we initiate a national association that would advocate for the consumer and the body shops?
Does the consumer know we are installing non-factory-approved parts on their cars? Do they understand the concept of diminished value when their vehicle is in a significant collision? Do they realize that
Don’t wait for the other guy, send your ideas in to allison@mediamatters.ca and let’s see what happens.
Our challenge in Saskatchewan: all the other province’s labor rates are far too low, and they are keeping us down.
The AAPEX/SEMA Show is one of the largest automotive trade shows in the world. Held annually in Las Vegas, Nev., it consistently draws a crowd of more than 100,000 car enthusiasts and industry insiders. If we narrow in on the collision industry, I will hazard a guess that it is the largest in the world for our specialty.
In this opportunity comes a plethora of collision eye candy; new welders, frame racks, measuring and fixture systems, spray equipment and consumables, to name a few tooling options. Part of the tools of the trade also includes components such as software and management applications that also work in conjunction with business ideologies that sometimes promise all the answers to your problems—sign here on the dotted line. The trade show is a salesperson’s paradise with a captive audience that is removed from its day-to-day business with the intent of being there to shop.
Everyone—and no one—was selling the one most sought-after item: the answer to your business problems. The magical solution to the destination of profitability. How do you turn
the monstrous amount of cash flow into profit, effortlessly and guaranteed, one might ask?
What do I mean by “everyone and no one?”
Simply put, each person I encountered had a product or idea far superior to the competition and insisted I will see the benefits immediately. But, each year, operators come back full of energy, wisdom, ideas, and even equipment that fizzles out after the rush is gone, further
demonstrating that no one actually had the solution.
There is no magical answer; there is no such thing as overnight solutions. Get-rich-quick schemes are precisely that—a scheme. Now it’s not all doom and gloom; as I stated, no “magical”
solution is available at SEMA; however, there are many opportunities to help you get to that profitability, just not in the form of an elixir. I looked at some fantastic welders and incredible new systems used in dent repair; the glue pull repair is a definite game-changer. Access to OEM information with software to aid in adding your line items, universal jig setups and measuring systems are becoming so advanced that it is almost…ALMOST impossible not to repair vehicles correctly. Most of what I saw was, in actuality, very beneficial to a business’ success and credibility.
Here is my so-called magical formula; start using the equipment and processes you brought back from SEMA and stick to it, do not back down, and do not become complacent in your old ways or the status quo. You only change your outcome by implementing the change to get there. You have spent money in the past to advance your facility, to meet some form of certification, and now you need to utilize that investment to its fullest. I see far too many facilities invest in this equipment only to leave it in the corner as a coffee cup holder or parts
drying rack. Remember the day you saw that piece of equipment at SEMA and how you were told it could do all these things to help your business and fix vehicles correctly? Well, it can only do that if you use it properly. Each time you choose not to utilize that shiny show purchase from SEMA or another source, you leave cash on the table.
I have heard countless excuses and justifications for NOT utilizing the equipment or processes. Here is the catch, the OEs are giving you every opportunity to start using it right now—they have for decades. Looking through the OE procedures, there is a clear and definite direction to implement the use of the equipment in the procedures—after all, you are certified. There will be sections that tell you that you must measure, you must use silicone bronze, you must STRSW, you must set up and destructive test your welds, and so on. So why would you not do this? You can account for everything you do; every item
is a line item. This sets your KPIs on track and balances out your WIP, providing actual usable data for your management system, and tracking a return on the investment you made. As far as I know, if you provide service, charge for service, pay expenses, the leftover is profit. This is business practice 101, unless something has changed over the years that I am unaware of. Nowhere does it say to throw money at it and wait.
Yes, I can hear you right now. As I said, I have listened to it all, regardless of what your situation is, agreements, deals, and organizations. At the end of the day, in my opinion, and you are entitled to my opinion, the magical elixir is the traditional model of providing the full service, utilize the tools at your disposal (equipment, software, etc.) and account for everything you are doing.
A job well done correctly should never cost you money; a job done incorrectly will cost you your business.
Averages can be very misleading when used to compare different, or when there are numerous outliers in the data. The problem is that the collision industry has historically measured performance in averages: Average paid claim severity, average percentage of parts dollars by part type and average part price.
Before the pandemic, I spoke with a collision repairer who was told he was at risk of being dropped by an insurance DRP partner because his average paid claim
severity was higher than their other shops in his area. His was a smaller shop, with no ‘fast lane’ for minor repairs. I told him that may be his problem, if a larger shop that had the space to complete same day bumper repairs, with an average repair cost of a few hundred dollars, they would have a much lower average paid severity for that insurance carrier.
The same applies for a very common metric in our industry: measuring parts performance by average percent of
parts dollars. A simple example is that if you have $1,000 in parts on an estimate, and one of those parts is a $200 aftermarket part, using this metric means your aftermarket utilization is 20 percent. If you find a less expensive aftermarket part, say for $100, your spend goes down to $900 and your aftermarket utilization 900/100 is now 11 percent.
Average part price is another common, and very flawed, metric to measure parts performance.
The actual claims in the exhibit below left, show that there isn’t a tight correlation between average part price and alternate parts performance. Averaging the part price of collision repair parts on an estimate where a molding clip is $0.45 is in the same population as a $450 hood illustrates why average part price is so misleading. A fairer and more accurate measure of parts performance is the discount from the OEM MSRP list. It precisely measures
each part performance against OEM MSRP and accounts for OEM price matching, where part measure by part type does not.
With the inflation in claims costs, the accuracy of true measuring parts performance is more critical than ever and hopefully it is now clear that using averages can yield very flawed results. When you look at your collision repair key performance indicators, how many employ the “flaw of averages?”
The Women’s Industry Network has a mission to support and enhance the role of women in the collision repair industry, promoting education, professional advancement and networking.
The all-volunteer group represents various collision industry segments, including repair facilities, suppliers, consultants, information providers, insurance companies and more.
For those unfamiliar with the not-for-profit, WIN works with many women—and men—in management roles; individuals seeking strategies on how to improve retention for female employees and attract more women to the sector. Through the organization’s focus, WIN aims to sustain a healthy dialogue that continues to advance the marketplace as a whole.
The organization sponsors several programs aside from its annual conference, including sponsorships for female apprentices in the automotive space
WIN also fosters the Most Influential Woman program, an award established in 1999 to recognize women in the aftermarket whose leadership and commitment to excellence have enriched the collision repair industry.
After what felt like an eternity of COVID-19 restrictions, FinishMaster B.C. was finally able to hold its twenty-second annual trade show over the second week of September, as more than 250 guests gathered for the festivities and returned home with armfuls of gifts and prizes.
The automotive refinishing company held their annual celebration at the Grand Villa Casino Hotel and Conference Center in Burnaby on Sept. 7, where attendees were treated to a wide selection of food across multiple chef stations, product demos and spotlights, prizes, as well as swag bags for guests to take home.
The province of British Columbia is proud to announce more details in its plan to re-launch the provincial certification process for skilled tradespeople, under the name SkilledTradesBC.
The province says the new organization, renamed from the Industry Training Authority, will work to “raise the profile of skilled trades, modernize trades training and implement skilled trades certification.”
A stakeholder advisory working group narrowed down the ten initial trades that will be focused on certification, with rollout to be carried out in two phases. Phase one will concern mechanical trades and electrical trades, with a deadline set for Dec. 1, 2023, while phase two will address automotive trades and have a further out deadline of some time in 2024.
Uncertified trade workers will be required to register as an apprentice or pass a certification exam before their respective deadlines. “We are excited by our expanded mandate to implement skilled trades certification, and our new name will make it easier for people to understand who we are and what we do,” said SkilledTradesBC CEO, Shelley Gray.
“SkilledTradesBC will focus on educating tradespeople and employers about skilled trades certification. We will provide online assessment tools and low-cost exam preparation to help workers get certified.”
The province currently projects that more than 85,000 jobs will open in the next ten years, and many of them will be in skilled trades sectors. B.C. eliminated certification requirements for skilled trades workers in 2003.
High costs of living are causing many British Columbia drivers to hold on to their aging vehicles just a little while longer, according to a recent survey conducted on behalf of the British Columbia Automobile Association (BCAA).
The survey, carried out by Leger, found that 70 percent of B.C. drivers intend on keeping their vehicles “much longer than they planned,” and will make the investments needed to keep it on the road, even when money is tight, just to avoid buying a new vehicle.
It was also found that 49 percent of drivers have skipped repairs and maintenance in the past due to high costs, but going forward, 83 percent report that they won’t take the risk of a mechanical breakdown and having to go without a vehicle.
To that point, 93 percent of respondents said that vehicle maintenance is worth it, despite the costs.
About 78 percent of drivers reported that they have already had their vehicles in for winter servicing or are scheduled to do so soon, which the BCAA considers a positive step forward for general driver preparedness.
“We’re seeing people we haven’t seen in a long time, and they’re telling us that their days of skipping regular vehicle servicing are over,” said Keith Berry, regional manager for BCAA auto repair and maintenance.
The province may be famous for flatness, but Saskatchewan leads the way in new Canadian vehicle sales this past August, according to recent stats from DesRosiers Automotive Consultants (DAC).
While most provinces saw light vehicle sales decrease in August 2022, the prairie province recorded an estimated 3.5 percent increase in sales for the month. Saskatchewan leads the Canadian new vehicle sales market year-to-date, as well; the province’s sales were down 6.8 percent for the year, compared to a nationwide decrease of 12.7 percent.
Newfoundland was also found to have outperformed the market with a 6.2 percent sales decrease, despite showing the largest year-todate sales drop of 20.6 percent. Alberta reported the lowest decrease at 7.1 percent, while British Columbia had the largest decrease at 18.5 percent.
The Saskatchewan Association of Automotive Repairers (SAAR) is known for its undying dedication to its members across the province of Saskatchewan. Another thing SAAR will now be known for is a shaky grasp of when seasons are, as the association announced that its Spring Conference will be running from Feb. 10 to 11 in Moose Jaw.
Though who are we kidding, the only difference between February and March in Saskatchewan is the size of the snowbank you found your car in that morning.
Anyway, the Saskatchewan Association of Automotive Repairers is gearing up for yet another meeting in the new year, where members will gather at the Temple Gardens Hotel and Spa in Moose Jaw to hear the latest issues affecting the province’s highly unique collision repair industry.
Few details have been shared at this point, however, organizers are calling on association members to mark their calendars for this can’tmiss conference.
Southern Alberta Institute of Technology’s (SAIT) auto body program is among three training institutions in the province due to receive a boost in classroom funding, thanks to an investment announced on Sept. 23.
In addition to NAIT, Portage College and its many campuses, SAIT’s auto body technician and automotive service technician programs are due to receive $187,810 of a total $1.37 million investment earmarked for opening up additional seats in classrooms.
The Alberta government says this investment is part of a three-year plan to inject $15 million into apprenticeship education programs at post-secondary institutions across the province.
SAIT’s auto body technician and automotive service technician programs are due to receive $187,810 of a total $1.37 million investment earmarked for opening up additional seats in classrooms.
Maaco held its 2022 convention in November, where the Driven Brands-owned network awarded two honours to Alberta-based franchisees. One of Maaco’s top award honours, the Terry Taylor Award, went to Peter Flannigan of Maaco Airdrie in Alberta.
“Flannigan has a longstanding reputation for giving back to his community,” wrote the network in its award announcement. “Whether it’s going the extra mile on the paint job on a classic car; pitching in with a community effort to help someone in need, or making generous donations to local charities, [Flannigan] goes above and beyond.”
Maaco also noted Flannigan’s role as an “engaged franchisee” as an Advisory Council member and supportive colleague.
The Mirante family of Maaco Edmonton also received an honour during the conference: a Regional Cup marking outstanding performance in car count, sales and operational excellence.
Torontonians and West Coasters be warned; there are Albertans looking to convince you to work in the Wild Rose province, and they may have lassos.
Following the lead of Saskatchewan and Nova Scotia, Alberta is several months into its own recruitment effort, aiming to convince residents of two of Canada’s most expensive cities that everything they could ever need is available and cheaper in Alberta.
According to Canadian Real Estate Association (CREA) data, the average home sale price over the last three years in Edmonton was $383,000—34 percent of the price of a home in Greater Vancouver and 38 percent of the price of a home in Greater Toronto, respectively.
The Alberta is Calling campaign is expected to cost the province $2.6 million as it rolls out billboards, radio and newspaper ads and social media initiatives across the two cities.
While much of the nation sits in a state of powerlessness regarding catalytic converter theft, a triple-threat partnership between the province, the police and Winnipeg Crime Stoppers has greatly curbed theft rates in Manitoba, and its efforts are becoming more expansive.
As per a series of amendments to the Scrap Metal Act, the province of Manitoba mandated that automotive recyclers buying scrap metal are required to detail every transaction involving scrap metal and hold these records for two years.
The Scrap Metal Act was first introduced in December 2021 to curb a 450 percent increase in catalytic converter theft between 2021 and 2022. Between January and September, the province found that converter thefts dropped from a peak of 353 thefts in April, to 19 reported thefts in September
The Manitoba government attributes this decrease in thefts to Winnipeg Crime Stoppers’ catalytic converter engraving programs, where drivers may engrave their vehicle’s VIN engraved so it could be traced back to its owner in the event of a theft.
In the fight to attract new skilled trades workers to Canadian industry, the Ontario government has announced the launch of a new travelling, skillsfocused, career fair geared toward students from Grades 7 to 12.
With its debut event at Mississauga’s International Centre, Ontario’s labour minister is not mincing words, saying “Ontario is facing the largest labour shortage in a generation, which means when you have a job in the skilled trades, you have a job for life.”
The fair is slated to visit cities across Ontario including London, Sudbury, Ottawa and Thunder Bay, where young adults will get hands-on exposure to all 144 recognized skilled trades and presentations from industry professionals and local employers.
Students interested in attending one of the Level Up! fairs are encouraged to reach out to their school’s Ontario Youth Apprenticeship Program (OYAP) representative, or a teacher or guidance counsellor for assistance in registering.
The office of Ontario’s Auditor General released its 2022 Annual Report on Nov. 30, where more light was shed on the province’s growing disparity between low crash frequency rates and high auto insurance premiums.
Penned by Auditor General Bonnie Lysyk, this year’s report found the average Ontario auto insurance premium rose by 14 percent from 2017 to 2021, totalling an annual rate of about $1,642, despite the fact that the province often records the lowest crash frequency nationally.
The report laid out several suggestions for initiatives that could work to make Ontario’s auto insurance industry more efficient, affordable and equitable for the province’s many drivers.
“Like Alberta, Ontario could develop more protocols to treat automobile accident injuries instead of providing cash for those injured to seek their own treatment,” read an excerpt of the report.
“Ontario could also follow British Columbia and Saskatchewan in implementing a mandatory licensing or certification regime for automobile repair businesses to protect consumers against poor repairs and fraud.”
Tropicana Employment Services recently hosted its long-anticipated Collision Repair and Auto Body preapprenticeship graduation, where the non-profit honoured three classes of now-working apprentices.
The celebration honoured three graduating classes—the classes of 2020 and 2021 had their originally scheduled ceremonies cancelled due to the pandemic—and was held at Centennial College’s event centre.
Tropicana also gave honours to students particularly keen on their studies. The Toyota Canada Scholarship, facilitated through the Black Business and Professional Association (BBPA), went to Chanice Camille Dwyer. Through this two-year scholarship, Dwyer can access funds to further their education and training toward obtaining a Red Seal Ontario Apprenticeship in the trade of Auto Body and Collision Damage Repairer 310B Apprenticeship.
Graduates Medhi Tirafkan, Justice Kirby-Black, Tariji Herd and Tre MatosasAdderley all took home $500, Tropicana Community Services Bursary awards, which will go toward their Level 2 administrative fees if they continue their career path in collision repair.
Initial estimates by the Insurance Bureau of Canada (IBC) indicate that Hurricane Fiona has caused at least $660 million in insured damage, according to the Catastrophe Indices and Quantification Inc.
According to IBC, Hurricane Fiona is the costliest extreme weather event recorded in Atlantic Canada, and the tenth worst in Canada when measured by insured damages.
Nova Scotia suffered more than $385 million in insured damage, with Halifax being noted for a particularly high number of trees falling on cars.
Prince Edward Island suffered more than $220 million in insured damages and suffered significant damage to housing, infrastructure and power lines.
New Brunswick suffered more than $30 million in insured damages, thanks to being on the fringe of the storm’s path. Nevertheless, power outages occurred across the province.
Quebec suffered more than $11 million in insured damage, with extensive flooding and erosion in Ilesde-la-Madeleine and the Gaspé Peninsula coast.
Newfoundland and Labrador suffered more than $7 million in insured damages, largely from destroyed homes between Burgeo to Port aux Basques.
Given that the exact damages are still being tallied, a breakdown of the auto insurance is unavailable. However, publicly available images and videos depict auto damage ranging from scratches and dents to extreme structural warping.
CSN Demers is the latest addition to CSN Collision in Quebec.
Acquired in 2010 by Bemac Autobody and owned by Joe and Danny Frangione, CSN Demers is a part of a 60-year legacy built on quality repairs, honesty, and professionalism. The challenges brought by new innovations create opportunities for them to continuously improve their craft, with customer service always at the forefront. CSN Demers employs the most skilled technicians in the area, building a culture of trust and service with their staff.
The Bemac group expanded to Quebec to provide the best possible collision repair experience to all their customers, as they do currently with their eight locations in Ontario. CSN Collision Centres says it has supported the Bemac shops since 2007 and will be a part of the company’s growth for years to come.
Quebec facilities—you’re about to see a whole lot more inquiries from Honda owners. The law firm representing a class of dissatisfied Honda Civic owners announced in November that the six-month period to receive reimbursement for early paint degradation is now open, following a judgment from the Superior Court of Québec to approve the settlement in the Daunais Class Action.
From Sept. 30, 2022, to March 31, 2023, owners of 2006 to 2013 Honda Civic and 2006 to 2011 Acura CSX vehicles purchased in Quebec who has experienced paint degradation are entitled to a settlement of up to $2,675.
The firm representing the Daunais Class Action against Honda Canada, CBL and Associés out of Granby, Que., listed the following possibilities for settlement: receive up to $2,550 to have your affected vehicle repainted by an authorized auto body shop; obtain cash compensation of a maximum of $1,530, or 60 percent of the amount allowed to have your vehicle repainted; get reimbursed up to $2,550 if the vehicle has already been repainted due to early paint degradation; or obtain compensation of up to $1,530 if the vehicle was resold at a loss due to early paint degradation.
As the one-year mark on several overhauls to Ontario’s towing industry approaches tow truck operators looking to reapply as OPP-requested services are on the hook to complete their own electronic criminal record checks following a series of updates to the provincial program. This is a new addition to the application specifying which police detachment they wish to partner with, due Oct. 15. Operators outside the borders of the GTA tow zones will see no changes to the way dispatching works, with the exception that only TSSOs on the OPP’s request list will receive calls from police for assistance, rather than the previous free-forall. Documentation to apply as an OPP-requested TSSO can be found on the OPP website.
Tow truck operators outside the borders of the GTA tow zones will see no changes to the way dispatching works, with the exception that only TSSOs on the OPP’s request list will receive calls from police for assistance, rather than the previous free-for-all.
Alberta RCMP recently learned that tow truck operators were paid to refuse their requests to help clear a highway blockade near a federal border crossing during the 2022 “Freedom Convoy” protests, according to evidence revealed during the Emergencies Act inquiry. A written testimony from a high-ranking security official in Alberta suggested that the RCMP officers faced challenges when they tried to recruit tow trucks to move vehicles used in blockades. An Alberta assistant deputy minister told the Emergencies Act inquiry that tow truck operators were “reluctant” to sign up to help after protesters blockaded the highway; he also said some truckers told the police they were paid to not assist law enforcement.
While the deputy minister did not say who paid the operators to refuse their services, he did confirm the province was able to hire private sector tow trucks to aid RCMP efforts.
Details from an internal investigation from the Ontario Provincial Police’s (OPP) Professional Standards Unit have uncovered that two Mississauga, Ont.-based police officers, were arrested for allegedly giving preferential treatment to certain tow truck operators within the GTA. The two officers had been on paid suspension since January 2021 while an investigation, first spawned from a February 2019 internal complaint, was carried out to determine their culpability. The pair were released on undertakings and are scheduled to attend a Brampton court next year.
www.spanesi-americas.com Spanesi®’s
e Multibench Workstation from Spanesi® is the technician’s solution to e cient vehicle repairs. Boasting a load capacity of over 3,100kg and a pulling column capacity of 10 tons, this system is ideal for cars, mid-size SUVs, and small commercial vans. e Multibench allows technicians to li vehicles directly from the wheels removing the need for bu ers. With a small footprint and a total lowered height of under 35mm, the Multibench takes up very little room in the shop, allowing technicians to utilize the bay for other repair operations. Multibench has a li ing height of over 1450mm.
www.hunter.com
www.LKQCanada.ca
The Hunter ADASLink® Full Diagnostic Scan Tool offers Dynamic (driving) ADAS calibration coverage. The static (fixture) ADAS calibration system is available with DAS 3000. The product is FCA secure gateway compatible and pre- and post-scan ready. It allows users to look at installed systems and associated codes for comprehensive use in any bay, without Hunter aligner. The full scan tool is not limited only to ADAS.
https://herkules.us
In 1985, Herkules revolutionized the body shop industry by creating the Paint Gun Washer. Made in the USA, every model of paint gun washer still offers a significant productivity increase by reducing the hours spent per day cleaning spray guns, cups, and accessories to just minutes. Our line of solvent or waterborne paint spray gun washers offers hands-free washing and push-up nozzle for one-handed washing and rinsing and a flow-through adjustable controlled brush, simplifying washing. Wash and waste are separated, reducing hazardous waste with solvent recovery that reduces costs on solvent purchases that creates an environmentally friendly solution.
LKQ’s Pro Series Body Fillers are available in four different finishes.
1. Pro Series Premium Lightweight Autobody Filler FIB1004; 3.0L/0.8 Gallons
2. Pro Series Lightweight Finishing Putty and Hardner FIB1024; 1.5kg/3.3lbs
3. Pro Series Lightweight Autobody Filler FIB2004; 3.0L/0.8 Gallons
4. Pro Series Fiberglass Reinforced Autobody Filler FIB3112; 3.0L/0.8 Gallons
For more information, contact your local LKQ location or call 866-557-2677
www.carbeat.com
Optimize shop production and communication with Carbeat.® It helps you optimize your body shop’s production and communication flow, and so much more. Carbeat is a patented software system combined with a large digital touch-screen that is customized to suit your business, operated by your own associates. As an interactive tool, CarBeat provides a detailed look at your production in each independent phase of the repair. Plus, with built-in departmental analysis and reporting of cycle times and bottlenecks, it helps you better control production and process flow and increases your shop’s profitability and efficiency.
www.motivatedreps.com
https://herkules.us
a high gloss level and is a multi-substrate.
Boss Lifts™–Speeding shop processes with powerful, efficient, and ergonomic lifts. Herkules™ offers Automotive Lift Equipment to a wide variety of customers, including auto dealerships, service garages, fleet operations, hobbyists, and do-it-yourselfers. The BossLifts™ product line features automotive lifts and air jacks that support shop efforts and speed processes. Developed with safety, efficiency, and ergonomics in mind, the BossLifts™ product line’s lifts use domestic steel and are manufactured in Michigan, USA. Leveraging the engineering knowledge and experience gained through developing our popular customized industrial lifts, BossLifts™ provide quality, strength, and versatility to any shop.
www.astech.com
asTech simplifies the repair process by providing access to OEM and OEMcompatible diagnostic tools, ADAS insights, calibrations, and programming capabilities all from a single device for a more streamlined workflow. With asTech, you get:
• The power to choose the right scan type for the job (remote OEM or local OEM-compatible)
• Identify and perform more ADAS calibrations
• Support from 400+ certified technicians
• Seamless estimatic integration and reporting
• Scans covered by our warranty
The Automotive Recyclers Association of Atlantic Canada (ARAAC) welcomed the fall season by hosting its 2022 convention—marking the organization’s first official gathering since pre-pandemic days.
Despite Hurricane Fiona’s sweep of the Maritimes—which occurred just days before the convention—50 dedicated recycling industry stakeholders made it to the first ARAAC Convention at the Inn on Prince in Truro, N.S.
Guests witnessed a variety of presentations covering on-trend topics for auto recyclers, like boosting core and catalytic converter
profitability; the impending opportunities in recycling electric vehicle batteries and insights on using your financials as strategic assets.
Next year’s event is already set and scheduled, said Steve Fletcher, managing director of the Auto Recyclers of Canada (ARC). He told Canadian Auto Recyclers that the 2023 convention will be the biggest ARAAC event ever, as the organization partners with the Auto Recyclers of Canada (ARC) and the Canadian Association of Recycling Industries (CARI) in Halifax from June 8 to June 12, 2023.
This
Recycling delegates from all corners of the globe gathered in Orlando, Florida, in September for the annual Automotive Recyclers Association (ARA) Convention and Trade Show. With almost 1,000 in attendance, this was the world’s largest auto recycling event for auto recyclers.
One of the highlights from the event came from eBay Motors, which announced a new airbag program wherein only certified auto recyclers will be allowed to list airbags. The virtual marketplace with cover certification and member costs–click here for more information.
Certification was a big conversation topic, said Steve Fletcher, managing director of the Automotive Recyclers of Canada (ARC). The ARA has had its certified auto recycler program in place for many years longer than the ARC–but less than 20 percent of
Standard Auto Wreckers owners Ken and David Gold were recently presented with an appreciation certificate, courtesy of Markham, Ont. mayor Frank Scarpitti, for the company’s work alongside the Markham Fire crew.
The Golds accepted the honour at Standard’s Toronto location alongside Fire Chief Brad Sterling and the rest of his crew.
“I want to say thank you to Dave and his team here because they give our firefighters the opportunity to come in and train on these vehicles. It speaks to another great value–sustainability and ensuring that we use the resources we have accordingly,” explained Scarpitti. “This is a very important initiative. It may look like a simple training exercise, but what happens here saves vital seconds on the scene.”
“Dave from Standard Auto has been phenomenal with us,” said Sterling. “He gives us the opportunity to create car accidents that we feel resemble real-life scenarios. A
ARA members are certified, compared to 100 percent of ARC members. With these eBay benefits in place–and more on the way–the goal is to get every ARA member certified. Canada has certainly seen the benefits of certification and look forward to sharing how to achieve this goal.
Handling electric vehicles (EVs) was another heady subject.
Ryan Mandell from Mitchell International was present to speak on collision industry trends around repairing EVs, where he focused on parts utilization, delivery delays and other industry trends affecting the repair or totaling of insured electric vehicles.
One audience member compared EV battery recycling with catalytic converter recycling 20 years ago. Mirrored by the current confusion around EV recycling, catalytic
converters, too, were once a product avoided by many recyclers.
“Information was scarce, then,” said Fletcher. “Today there are hundreds of [catalytic converter] buyers, and the data exchange is significant such that they add very nice profit for every auto recycler.”
Approximately 20 Canadian companies were in attendance, represented in both exhibitors and industry delegates.
“For sure the highest number [of people] from a country outside the United States,” said Fletcher.
Team Canada’s presence at the event will surely be remembered–if not for their passion to learn, then certainly for their big win during the awards banquet trivia contest.
“We made sure they heard from us there,” said Fletcher.
few weeks ago, we had a real incident with a late-model car. We were highly successful in that scenario because we train at Standard every Wednesday.”
“Thank you all for these kind words,”
remarked Gold. “The nicest thing to be able to do is give back to our community. To be part of the community where many of us live, and to give back and understand the importance of this training–for us, that’s all we need.”
The source for forward thinking practices and environmentally conscious programs, this fully bilingual magazine offers a comprehensive look at the recycling industry with up to 100 pages of content as well as exclusive articles on parts, the environment, association updates, the mechanical sector, a directory and much, much more.
ADVERTISER INDEX
3M 11
AkzoNobel 92
Arslan Automotive 07
asTech/Repairify 93
Axalta 100
Carcone’s Auto Recycling 79
Cardinal Couriers Ltd 10
Caroliner 31
Car-Part.com 75
CARSTAR Canada 71
Color Compass Corp 87
Consolidated Collision 99
CSN Collision Centres 25
Dominion Sure Seal 17
Fix Auto Canada 40
GoProMobile 90
Hail Specialist Canada 84
Herkules 92,93
Hunter Engineering 92
IBIS 77
IAA cover flap, 02,03
Keystone (LKQ) 04,91
Motivated Reps 93
ProColor 12,13,43
ProSpot International Inc 23,91
Rexall Solutions 21
Sata Canada 59
Simplicity Car Care 45
Spanesi Americas Inc. 19,91
Thorold Auto Parts 88
United Catalyst 73
We Buy Key Fobs 15
It’s time to get the transformation train moving
By ALLISON ROGERSWe are part of an industry with many moving parts, several connecting checkpoints and numerous verticals, in which effective conversations are required for the deal, job—the entire relationship—to go smoothly.
It’s integral, as the industry nears an unavoidable intersection, that we work together with minimal conflict, from the first notice of loss through delivery and beyond.
A commonly-addressed theme in my conversations from this past year has been
Let’s get the change train finally moving.
We’re a pretty smart industry. We are capable of creating initiatives that lead toward more open, productive conversation between parties of all verticals, on all levels. There are plenty of ways to get involved in advocacy— and they all start in the same place, with a conversation. Discuss the challenges we’re facing as an industry as casually as what you had for dinner last night. Partake in industry groups—I hear there’s a pretty cool association
Scream into your pillow, then leave that pillow in 2022. We’re about optimism in 2023.
contained in a word the collision repair sector likes to toss around liberally during speaker presentations, keynotes, training sessions and the like: change.
The industry is always talking about what’s changed; what’s changing at the minute and what’s bound to change at some indiscernible date in the future. Sometimes it feels like we spend so much time reminiscing about the past or dreaming about the future that we forget we’re able to take action on challenges in the present moment.
At this very moment, this industry has no shortage of frustrated folks. They think it may be too late to alter the course the collision repair sector is headed on. We’ve been talking about tackling change for the last 20 years, they say. There’s nothing that can be done.
If you’re of that mind, do this magazine a favour: scream into your pillow, then leave that
gaining traction…wink-wink. Check out Darryl’s publisher’s page at the front of the book for more on that.
This year’s Insurer Report Card received an overwhelming amount of comments. One of the most unfortunate themes, repeated in nearly a dozen testimonials, spoke to the fear of speaking out. There are members of this industry that feel they must stay silent on long-persisting issues, lest their livelihood be challenged.
But this isn’t about one party in particular. We’re not aiming to engage in a tug-o-war. Every role in the industry can play a part in shifting course.
Another calendar flip is before us. Let’s quit discussing change and move forward to a revolutionized, modernized industry for all.
Happy New Year from Collision Repair magazine.
Collision Repair magazine.
She can be reached at allison@mediamatters.ca.