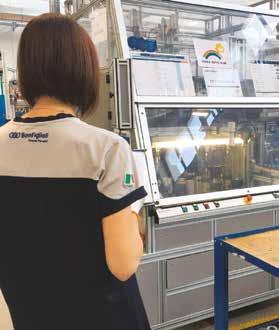
5 minute read
Bonfiglioli un modello per la “fase 2
La multinazionale non ha mai chiuso il nuovo stabilimento in Polo Meccatronica, tra rigidi protocolli di sicurezza frutto dell’esperienza maturata a Shanghai e una solida rete territoriale.
PER Bonfiglioli Mechatronic Research di Rovereto la “fase 2” è iniziata due mesi fa. Il nuovo stabilimento operativo dallo scorso gennaio in Polo Meccatronica, l’incubatore hi-tech di Trentino Sviluppo, non ha infatti mai interrotto la produzione di motori a magneti permanenti e correlati componenti per la trasmissione del moto, dedicati alla compressione del palloncino AMBU all’interno dei sistemi per ventilatori polmonari destinati agli ospedali. Il management, facendo tesoro dell’esperienza di altri stabilimenti del Gruppo che avevano anticipato i piani di sicurezza richiesti dal contenimento del Covid-19, in particolare il plant Bonfiglioli di Shanghai in Cina,

ha da subito messo in campo un’articolata serie di sistemi e comportamenti di prevenzione che hanno permesso di conciliare salute e produzione, sicurezza dei lavoratori ed aspetti economici. Misura della temperatura corporea all’ingresso, gel sanificante, mascherine e guanti, pulizie e sanificazioni intensificate. Il lavoro dei 99 dipendenti, prima articolato in un unico turno, è stato riorganizzato su due turni sfalsati di venti minuti, in modo da ridurre del 50% i contatti. Bonfiglioli, azienda multinazionale nata a Bologna nel 1956, è a Rovereto dal 2011. Dal 2020 opera nel nuovo stabilimento di Polo Meccatronica affacciato su via Unione con quasi 100 dipendenti e sviluppa un volume d’affari di 23 milioni di euro. Sedi, filiali e stabilimenti Bonfiglioli sono sparsi in diversi continenti (Europa, Asia, Nord e Sud America) per un totale di oltre 3.700 dipendenti e 960 milioni di euro di fatturato nel 2019. “Per noi, come gruppo – sottolinea Marco Bertoldi, responsabile dello stabilimento Bonfiglioli di Rovereto – non può esserci lavoro senza sicurezza. Perciò abbiamo applicato, quasi da pionieri tra gli stabilimenti italiani ed europei, fin dall’inizio dell’emergenza, rigidi protocolli per conciliare produzione e tranquillità per i dipendenti che desidero ringraziare
Anche il gruppo Armani a sostegno della sanità trentina
La Giorgio Armani Operations Spa, una delle sedi produttive del Gruppo Armani, sita a Mattarello nella Valle dell’Adige, fa parte di quelle imprese che hanno deciso di riconvertire la propria produzione per sostenere il Paese e far fronte alle nuove esigenze determinate dall’epidemia da Covid-19. Dopo una prima fase di chiusura, in quanto rientrante nella categoria delle cosiddette “attività non necessarie” individuate dal Consiglio dei Ministri, l’azienda, nota in tutto il mondo per il prestigio dei suoi capi, ha scelto di rendersi utile al territorio convertendo la propria produzione nella realizzazione di camici utili al personale dell’Azienda Sanitaria Trentina. Il tutto ha avuto inizio quando l’Apss, trovandosi di fronte a una carenza di Dpi, si è rivolta a Confindustria Trento chiedendo aiuto nel reperimento di questi dispositivi. Il Presidente dell’Associazione degli Industriali Trentini, Fausto Manzana, ha subito lanciato un appello alle aziende del settore tessile trentino, chiedendo di valutare la possibilità di riconvertire la produzione, allo scopo di far fronte alla mancanza in regione di camici e mascherine per il personale sanitario. A rispondere all’appello anche Renato Meneghello, Direttore dello Stabilimento di Trento Sud, che non ha esitato un solo istante ad acconsentire alla proposta del progetto di riconversione dell’impianto produttivo in seguito esteso, per volontà di Giorgio Armani, a tutti gli stabilimenti. Le attrezzature, una volta superata l'emergenza, non potranno essere riutilizzate per la produzione originale dell'azienda. Un investimento, dunque, non finalizzato a un mero ritorno economico, ma che nasce dal desiderio di fornire un reale contributo al nostro Paese. In pochissimo tempo, grazie anche alla preziosa collaborazione di Giancarlo Bizzarri dell'Apss, lo stabilimento, dotato di nuovi macchinari e attrezzature per una linea produttiva inedita, ha potuto intraprendere la sua nuova missione. “Un progetto – racconta Meneghello – di alta valenza solidale, partito dal signor Armani in persona per confezionare tanti camici e fatti bene, con la stessa professionalità che viene impiegata per il confezionamento di capi di alta moda”. Attualmente il Gruppo Armani è in grado di realizzare mille camici al giorno, dei quali 400 realizzati nell’impianto produttivo trentino. La sensibilità dimostrata dai vertici aziendali nei confronti dell’esigenze del nostro territorio si riscontra anche nei dipendenti dell’impresa, che su base volontaria hanno deciso di rientrare al lavoro per il confezionamento dei camici. “C’è tanto entusiasmo -spiegano dall'azienda- il sentimento comune è di far parte di qualcosa che possa dare concretamente un aiuto al personale sanitario. L’adesione è stata pressoché totale”.
personalmente. Soluzioni che ora sono un riferimento anche per gli altri stabilimenti del gruppo e non solo”. “I lavoratori hanno recepito con grande senso di responsabilità i nuovi protocolli e le nuove modalità di lavoro – aggiunge la responsabile della sicurezza, Martina Sparano Aveta – e abbiamo fornito “device” e indicazioni ergonomiche anche per lo smart working. Abbiamo avuto fin da subito mascherine e gel grazie al supporto di Confindustria Trento”. Il centinaio di dipendenti è stato distanziato nelle postazioni, sia negli uffici che sulle linee produttive: “Affinché i due gruppi non si incontrino, abbiamo creato due turni di lavoro separati di 20 minuti: dalle 6 alle 13.50 e dalle 14.10 alle 22”, racconta il responsabile di produzione, Valter Grifoni, che spiega anche le nuove produzioni. “Per un cliente italiano abbiamo già realizzato 500 riduttori per ventilatori polmonari, ma anche componenti per sistemi che azionano macchinari per la produzione di farmaci iniettabili, per realizzare blister di compresse e per la movimentazione dei pazienti in ospedale”. “La vita è cambiata – conclude il direttore Marco Bertoldi – ma il lavoro in sicurezza è possibile. Nuove soluzioni intelligenti sono state stimolate dall’emergenza pandemica: l’industria 4.0 sta già lavorando su maggiore automazione, tecnologie sanitarie, nuovi sistemi di packaging per evitare contatti con le merci, e le tecnologie per la sanificazione subiranno un’accelerata e saranno sempre più robotizzate”. Anche i pasti, dopo la chiusura della mensa interna all’incubatore di Trentino Sviluppo, vengono consumati in azienda grazie al servizio di consegna in fabbrica organizzato dalla cooperativa Risto3: in piccoli gruppi, con il personale distanziato in aule e sale che riportano scritto in chiaro, appeso agli ingressi, il numero massimo di persone che vi possono entrare.
La tua salute è importante! Proteggila con i nostri sistemi e prodotti igienizzanti
STAND IGIENIZZANTE MANI La soluzione versatile, dal design elegante per mettere a disposizione gel alcolici mani in modo pratico e sicuro.
HYGIENIC STAZIONE IGIENIZZANTE MOBILE SYSTEM In un unico spazio di contenute dimensioni e con un design che si adatta a qualsiasi ambiente, tutti gli strumenti necessari per adempiere alle nuove esigenze.
PRONTA CONSEGNA
Contattaci e scopri la vasta gamma di prodotti per la disinfezione e sanifi cazione per allontanare il rischio
CORONAVIRUS
PIÙ IGIENE E SICUREZZA Nasce la gamma Defend Tech: una selezione delle migliori ed esclusive tecnologie per innalzare gli standard di igiene dei prodotti in carta, dispenser, saponi e gel. Soluzioni all’avanguardia a supporto della prevenzione quotidiana. Vieni a scoprire tutti i prodotti su www.ressmultiservices.it