
6 minute read
De la mano con la transformación digital
En las plantas de procesamiento, los espacios de mejora apuntan a aumentar la eficiencia de este proceso, para lograr mayor seguridad para los trabajadores, asegurar la continuidad de la producción y también, la confiabilidad de las operaciones. En el contexto global que se vive actualmente, la transformación digital juega un rol crucial, y aplicado en la industria minera, un mecanismo de relevancia con miras a la eficiencia es la digitalización. Para esto, los actores del sector se encuentran desarrollando numerosas acciones que buscan dar soporte a dicho proceso. Los expertos consultados por MINERÍA CHILENA coinciden en que las mejoras que se prevén para esta área de la minería, están relacionadas a la inteligencia artificial y automatización, orientada a la optimización de procesos, control y monitoreo remoto de las operaciones.
Mejora continua
En cuanto a las tecnologías que han aparecido en plantas de procesamiento, la académica de la Universidad de Chile, Pía Lois, señala que “hemos visto mejoras en la captura de datos, por ejemplo, los procesos de caracterización de material de cabeza ya han incorporado análisis granulométricos, elementales e incluso mineralógicos en las correas transportadoras y mejores analizadores de elementos de interés en los flujos aguas abajo”. Desde un punto de vista de equipos -agrega la académica-, “se han diseñado e implementado equipos de molienda que en teoría consumen menor energía generando una mejor liberación del mineral tales como el HPGR o el VeRo Liberator; se han desarrollado incluso prototipos de reducción de tamaño por electricidad (HVP). Hoy día se entiende que los mecanismos rios virtuales inmersos en la realidad operativa de la planta, entregando apoyo a operadores y metalurgistas para diversos fines, tanto de entrenamiento como de optimización operacional”.
Nuevas tendencias
La minería chilena se encuentra en plena transformación digital, es por esto que, según Opazo, “la digitalización, automatización y control han mostrado ejemplos claros y
Plantas de procesamiento: De la mano con la transformación digital
de quiebre afectan de manera distinta a las distintas menas”. En el ámbito de los simuladores dinámicos de plantas de procesamiento, el gerente senior de Servicios Expertos de Metso Outotec, Juan José Opazo, destaca el reciente lanzamiento de la plataforma Geminex. “Gemelo digital que combina datos operativos y de diseño de equipos, creando escenaexitosos de implementación en salas de control operadas remotamente por compañías de la gran minería, explotando con ello el uso de la información en la analítica de negocios. El desafío actual se encuentra en seguir creando un ecosistema de colaboración entre los productores mineros y la red de proveedores que permita crear sinergias con un enfoque en productividad y eficiencia”.
Monitoreo en tiempo real, automatización e inteligencia artificial son algunas de las tendencias que marcan el progreso en esta área.
Plataforma Geminex, gemelo digital de Metso Outotec.
Esta afirmación es complementada por la académica de la Universidad de Chile, quien afirma que “se ha avanzado mucho, hoy se pueden instalar sensores en cada flujo y tener un balance casi en línea. Además, de tener información cada segundo de que pasa por cada punto de la planta, lo que permite predecir y anticiparse a problemas operacionales e incluso reducción en la calidad del producto. Sin embargo, aún existe una desconexión con lo que pasa en la mina, ya que perdemos el track del mineral en la zona de acopio, además de la caracterización (mineralógica y metalúrgica) que nos sirven para predecir el comportamiento del mineral en planta están, por lo general, muy espaciados en el espacio dentro de la mina. Nos falta conectar la información que viene de la mina, para tener una mejor planificación y poder predecir con mejor certeza el producto a generar en una cierta condición operacional. La integración de la información mina-planta es necesaria para una optimización total del proceso productivo”.
Transformación digital
La transformación digital ha avanzado a pasos agigantados. En base a esto, Lois expone que “hoy se pueden instalar sensores en cada flujo y tener un balance casi en línea. Además, de tener información cada segundo de que pasa por cada punto de la planta, lo que permite predecir y anticiparse a problemas operacionales e incluso reducción en la calidad del producto. Sin embargo, aún existe una desconexión con lo que pasa en la mina, ya que perdemos el track del mineral en la zona de acopio, además de la caracterización (mineralógica y metalúrgica) que nos sirven para predecir el comportamiento del mineral en planta están, por lo general, muy separados en el espacio dentro de la mina. Nos falta conectar la información que viene de la mina, para tener una mejor planificación y poder predecir con mejor certeza el producto a generar en una cierta condición operacional. La integración de la información mina-planta es necesaria para una optimización total del proceso productivo”. Por su parte, Opazo agerga que “el avance ha sido sostenido. Podemos ver cómo los productores mineros se han enfocado en crear la in-
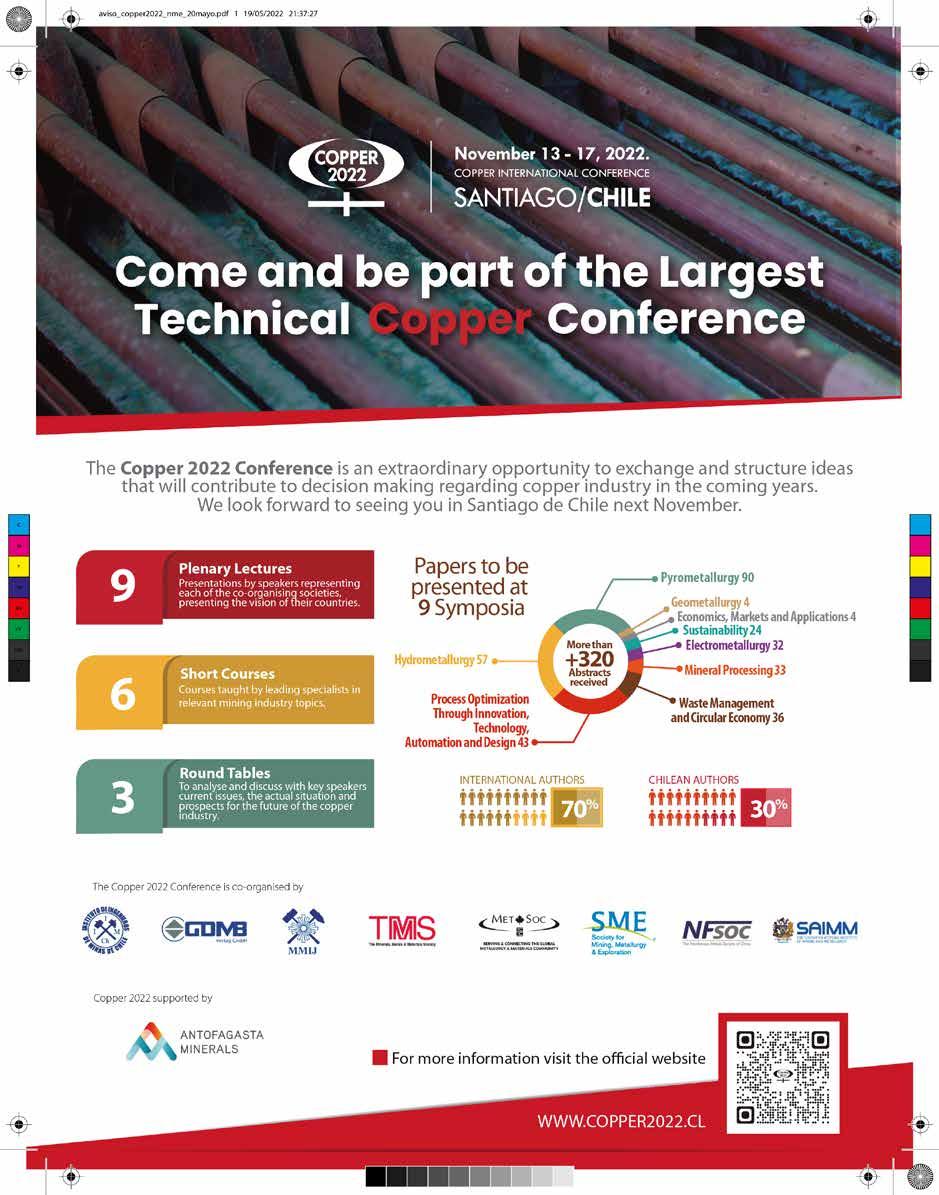
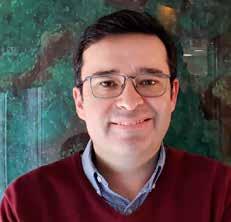

fraestructura y plataformas requeridas para un uso extensivo de datos. Ejemplos de aplicación muy visibles han ocurrido en flotas mineras, logrando autonomía operacional tanto en minería de cielo abierto como en minería subterránea. Por el lado de las plantas de procesamiento, también se ha podido ver un desarrollo en la sensorización, con una mayor oferta de instrumentos del tipo avanzado, la incorporación de gemelos digitales y las plataformas de simulación, tendencia que ha sido una constante. Muchos cambios están pasando en un corto plazo y muy probablemente nos sorprenderemos en los años venideros de los avances logrados con claro valor adherido al negocio minero”.
Otras soluciones
El ejecutivo de Metso sostiene que, en la compañía “hemos estado focalizados en desarrollo de Inteligencia Artificial, empaquetando conocimiento experto de nuestras tecnologías en algoritmos que monitorean en tiempo real el funcionamiento de nuestras máquinas. Todo esto ocurre desde nuestro Performance Center, centro de monitoreo donde nuestros especialistas supervisan mediante herramientas analíticas y el apoyo de estos algoritmos la salud de los equipos. Con ello, podemos asistir a nuestros clientes en tiempo real y darles soporte con conocimiento especializado”. Por otro lado, la académica de la Universidad de Chile manifiesta que “principalmente en los sistemas de control de procesos y se ha visto un aumento sostenido en la cantidad de datos disponibles en todos los flujos de planta, al menos en la gran minería. Es de esperar que la mediana y pequeña minería, sigan ese camino. En algunos centros de investigación incluso se han desarrollados gemelos digitales que planta, que nos permitirían observar en línea la operación, tal como si estuviéramos in situ”. Finalmente, Lois complementa que “entre las proyecciones a largo plazo, esperaría un full automatización y digitalización de las plantas que permitan una operación automatizada, eso es casi una realidad en varias mineras de gran escala. Sin embargo, creo que aún estamos al debe con la integración minaplanta que nos permita una mejor planificación anticipada y también con el desarrollo tecnológico que nos permita generar una molienda más selectiva y un proceso de separación a escala más gruesa (y/o una lixiviación de sulfuros). Creo que solo con un cambio tecnológico disruptivo y mayor integración de procesos podremos reducir considerablemente el material a tratar y por tanto los consumos energéticos, insumos y por supuesto, el mayor pasivo de la minería, los relaves”.
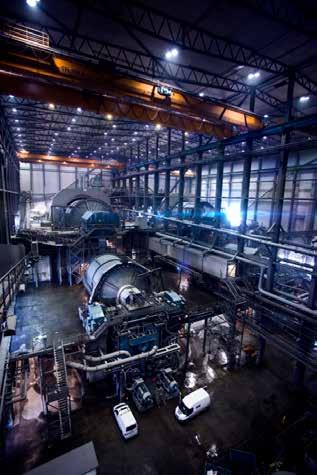
Arriba de Izq. a Der.: Juan José Opazo, gerente senior de Servicios Expertos de Metso Outotec. Pía Lois, académica de la Universidad de Chile. Planta de procesamiento, gentileza Metso.