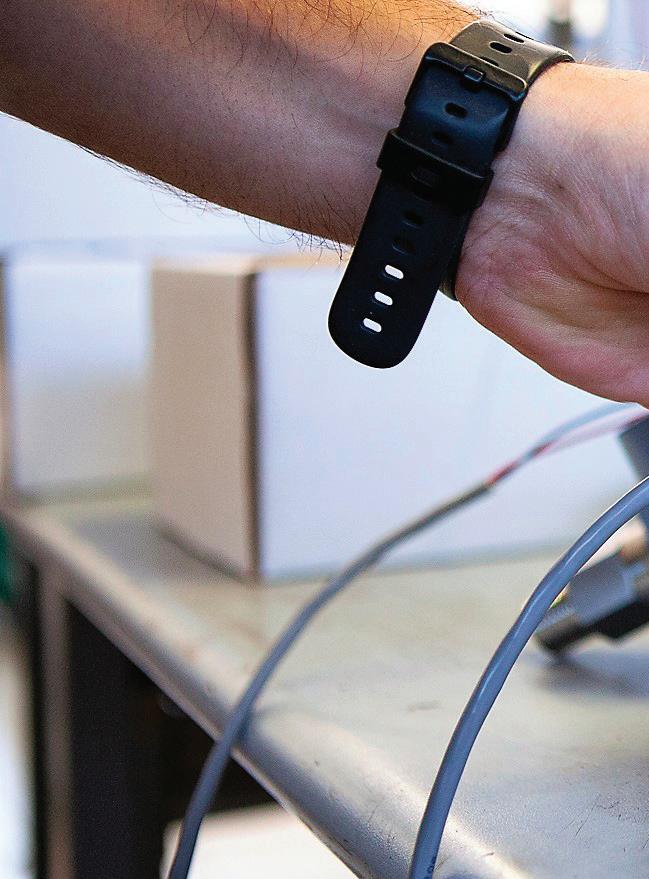
11 minute read
NUOVE PROSPETTIVE PER L’INDUSTRIA DI PROCESSO
SPECIALE
Advertisement
PER L’INDUSTRIA
DI PROCESSO
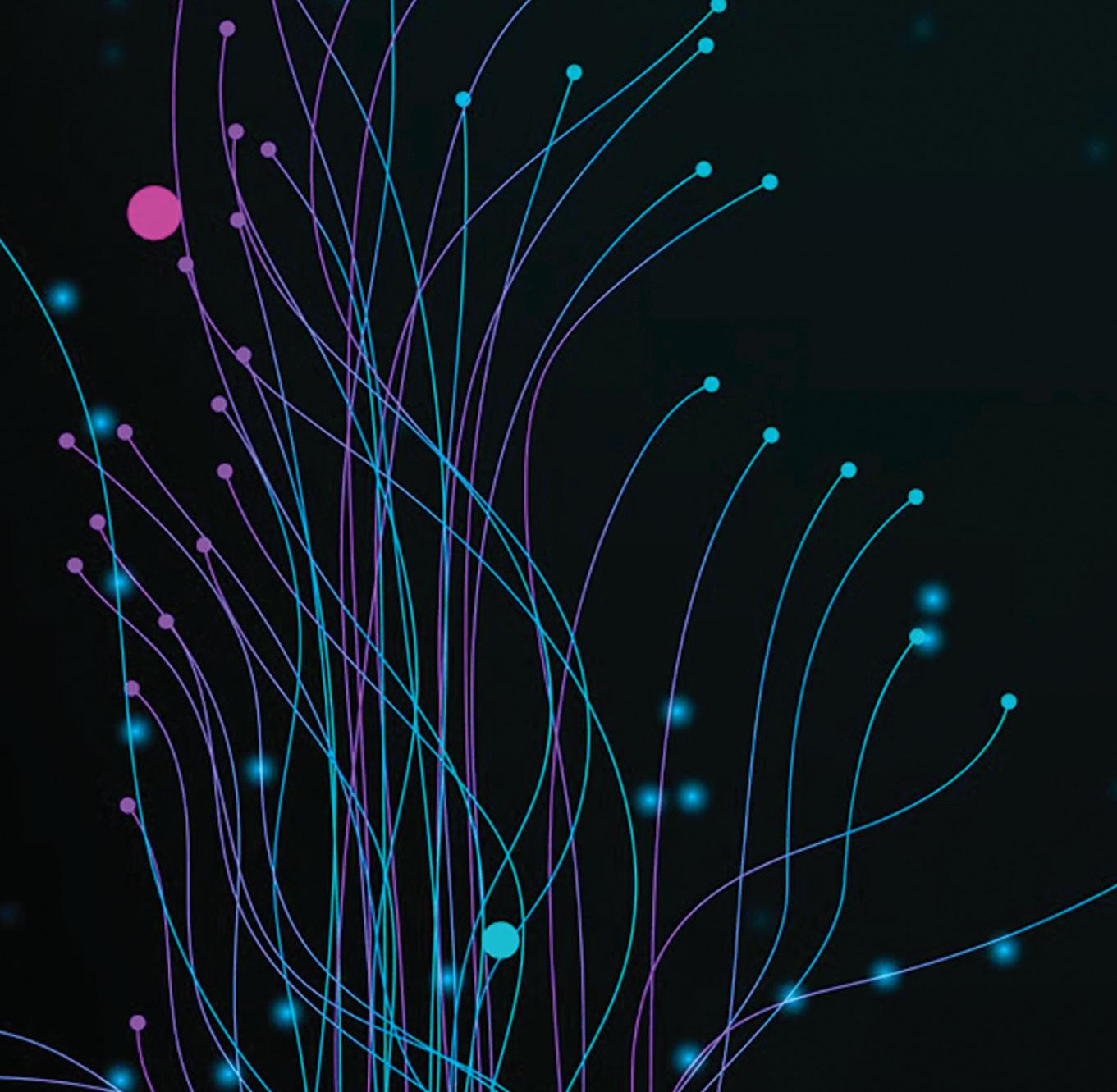
LA PRODUZIONE DI COMPONENTI E STRUMENTAZIONE PER L’INDUSTRIA DI PROCESSO, IL SETTORE NEL QUALE SI MUOVE TERRANOVA INSTRUMENTS, MOSTRA ALCUNE TENDENZE PREVALENTI, PRIME FRA TUTTE LE CRITICITÀ NEGLI APPROVVIGIONAMENTI E L’EVOLUZIONE VERSO NUOVI STANDARD INDUSTRIALI. VEDIAMO COME L’AZIENDA SI È ORGANIZZATA PER RISPONDERE A QUESTE SOLLECITAZIONI, AVVIANDO NEL CONTEMPO UN SIGNIFICATIVO PERCORSO DI RINNOVAMENTO INTERNO E RIORGANIZZAZIONE SUL MERCATO
Chimica Magazine: Che cosa significa per voi il concetto di “innovazione” e come lo avete declinato nella vostra realtà?
Sergio Valletti: Il primo significato di innovazione per noi riguarda il prodotto, con numerosi piani di rinnovamento avviati già da diverso tempo, anche se, a dire il vero, l’innovazione di prodotto che avevamo in mente non è stata pienamente raggiunta, per quello che è successo negli ultimi due anni. Terranova Instruments produce strumentazione elettromeccanica: il nostro prodotto è composto sia da parti meccaniche che da parti elettroniche, quindi si può dire che siamo stati colpiti in tutte le direzioni. I microprocessori su cui si basano le nostre schede elettroniche sono gli stessi utilizzati nel settore automotive, facendo ricadere anche su di noi gli effetti della scarsità di componenti e materia prima, quali semiconduttori, resine e così via. Queste condizioni non hanno facilitato il raggiungimento degli obiettivi di innovazione su alcuni prodotti che noi avevamo impostato da circa tre anni a questa parte ed è ancora difficile, in questo momento, capire quando potremo riprendere questo percorso. Ad esempio, erano previste nuove release di prodotto a partire da fine 2021, ma in questo momento il lead time per i microprocessori di cui abbiamo bisogno è a 52 settimane. Per le aziende del nostro settore, parliamo di uno scenario davvero pesante. Detto questo però, di fronte a questa grande crisi che riguarda gli approvvigionamenti, abbiamo cercato di migliorare il più possibile quello che possiamo chiamare “l’esistente”, andando oltre un’ottica di breve periodo e rapportandoci con quelle che saranno le principali evoluzioni tecnologiche del nostro settore, che riguardano in particolare i protocolli di comunicazione. Cerchiamo insomma di sfruttare questo tempo per orientare i nostri prodotti attuali in vista di questo passo ulteriore, riprogettandoli in modo che possano incorporare sia le modifiche che abbiamo già messo in programma dal punto di vista tecnico, sia quelle che sono in via di definizione e sviluppo da parte dell’industria. E questo riguarda tutti i nostri prodotti, anche quelli presenti e am-
A COLLOQUIO CON:
Sergio Valletti , Managing Director di Terranova Instruments

piamente consolidati sul mercato praticamente da decenni.
CM: Di quali evoluzioni tecnologiche si parla?
SV: Principalmente dell’introduzione dello standard di comunicazione Ethernet APL, che apre per noi delle prospettive molto interessanti, in rapporto al mondo dell’IoT e con il resto del mercato. I nostri competitor, che sono le grandi multinazionali tedesche, americane o giapponesi, stanno gradualmente orientando il nostro settore verso un nuovo protocollo di comunicazione, in sostituzione dei tipici bus di campo che sono sempre stati utilizzati nella nostra industria, come possono essere ad esempio Hart, Fieldbus, insomma la tipica uscita che consente al dispositivo di comunicare in un sistema di automazione. Rispetto a questi protocolli molto specifici per il mondo industriale, avremo invece lo standard Ethernet APL, che consente l’utilizzo di un normale cavo LAN per la connessione di qualsiasi dispositivo, come già avviene negli ambienti più consumer dell’informatica o della domotica. Ecco, le aziende stanno operando per far sì che questo protocollo possa essere implementato anche nell’industria: un percorso abbastanza rivoluzionario perché in questo contesto bisogna tenere conto di regole molto più stringenti rispetto a quelle domestiche o civili, in termini di sicurezza o di vincoli ambientali. Parliamo ad esempio di certificazioni di sicurezza intrinseca, di standard relativi ad emissioni, irradiazioni o disturbi elettromagnetici, e allo stesso tempo della necessità di garantire la stabilità del segnale, un aspetto fondamentale per garantire la qualità dei processi, cosa indispensabile in qualsiasi tipo di industria. Tutto l’installato dovrà essere aggiornato alla luce di questa evoluzione, per impattare il meno possibile sull’economia degli impianti esistenti. E tutto questo comporta uno studio accurato sulle caratteristiche del prodotto, che noi abbiamo incorporato nel nostro sviluppo e che stiamo portando avanti adesso in modo da arrivare pronti, quando sarà il momento, con una gamma prodotti totalmente in linea con la nostra concorrenza.
CM: Che impatto avrà questa evoluzione sul mondo dell’automazione?
SV: Renderà l’accesso agli impianti più facile e fruibile, anche nel rispetto di tutti i protocolli di sicurezza che saranno emessi dalle varie legislazioni nazionali o europee. È lo stesso percorso virtuoso della standardizzazione, che abbiamo visto in tanti altri ambiti dell’elettronica. Normalizzare linguaggi diversi, che storicamente hanno senso in quanto nati in mo-
SPECIALE
DIGITAL TRANSFORMATION e INDUSTRIA SMART
menti o in luoghi diversi, puntando invece all’integrazione, ad una comunicazione uniforme, dà sempre un risultato positivo: forse non arriveremo all’esperanto, che rimane una chimera, ma potremo almeno intenderci in inglese, che è già un risultato adeguato. In questo nuovo scenario, il linguaggio dei sistemi di automazione potrebbe essere veicolato anche tramite device standard quali PC, tablet o smartphone. Diciamo che questo filone si inserisce in pieno nel solco dell’Industria 4.0, in quanto contribuisce a realizzare il concetto di Internet of Things. Posso prendere un device da campo e metterlo in comunicazione – ad esempio – con il forno di casa, perché serve solo un’interfaccia tra i due sistemi ma il linguaggio di comunicazione è già lo stesso: devo semplicemente farli incontrare.
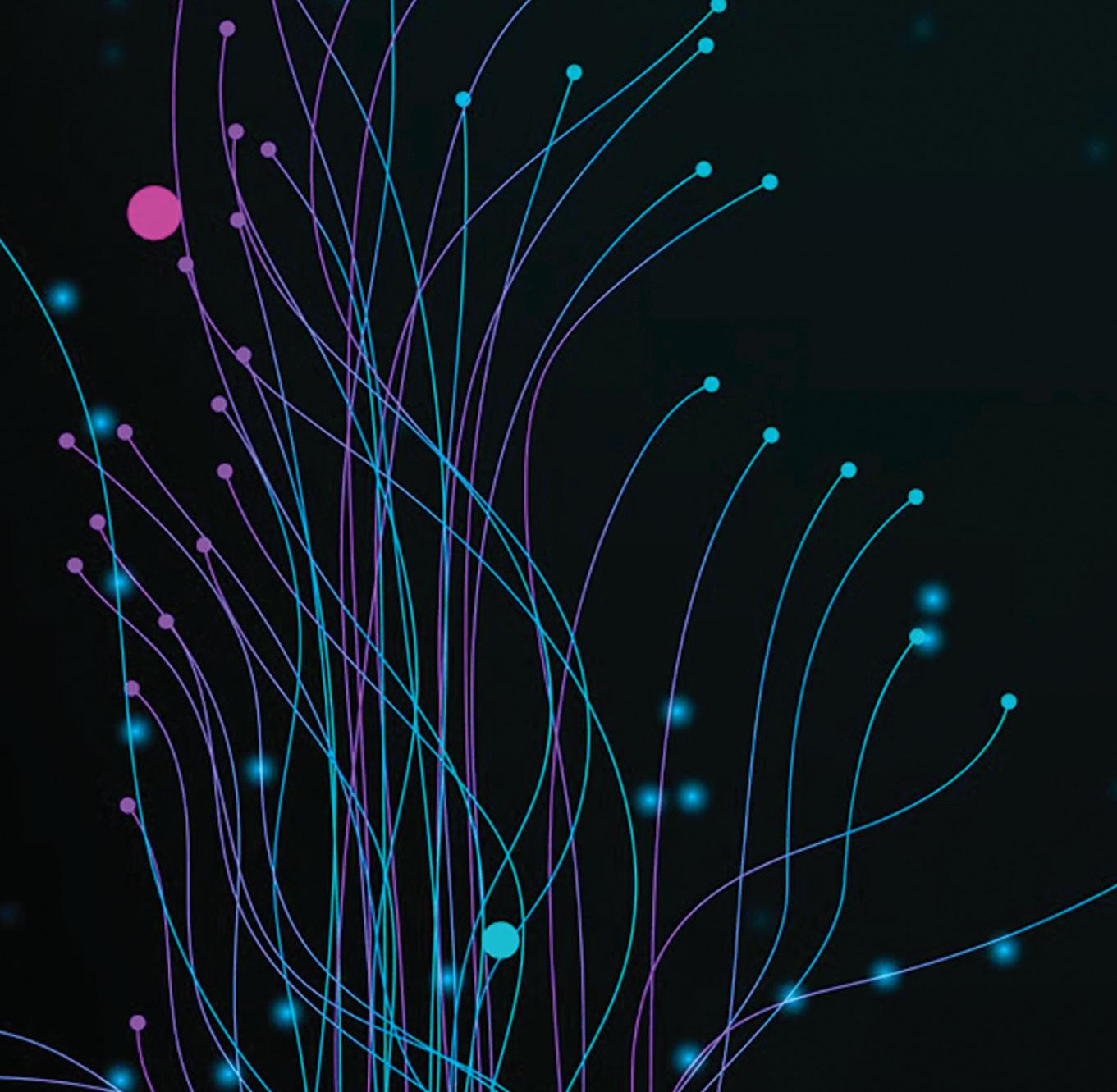
CM: Torniamo, invece, al tema della supply chain e alle difficoltà di approvvigionamento. Come le avete affrontate?
SV: Per quanto riguarda la parte elettronica, la parola chiave è senz’altro scouting, almeno dove è stato possibile. In pratica abbiamo dovuto dividere in modo netto quello che poteva essere ricercato da quello che non poteva essere ricercato. I componenti elettronici o microprocessori sono sostanzialmente prodotti da ST Microelectronics oppure da aziende cinesi per ST. Di conseguenza, abbiamo cercato questi componenti ovunque, trovandoli dove possibile, ovviamente a prezzi lievitati perché la domanda è diventata molto superiore all’offerta. Altra possibile soluzione sarebbe stata quella di trovare prodotti alternativi, ma questo per noi significherebbe rifare tutto il progetto relativo al nostro dispositivo, perché ogni nostro strumento si basa sulla logica del suo microcontrollore. E anche risolvendo questo aspetto, non sempre questi potenziali fornitori erano in grado di darci garanzie di approvvigionamento per i due, tre, cinque anni successivi, tali da poter avviare una nostra produzione. Su questi fronti ci siamo dovuti fermare, mentre abbiamo proseguito le ricerche presso stockisti, broker, trader di vario tipo per limitare i danni ed evitare di rimanere senza componenti critici, piuttosto pagandoli un po’ di più. La scarsità dei materiali si è fatta sentire anche per quanto riguarda la parte meccanica, più precisamente gli acciai speciali, quelli realizzati con leghe specifiche: anche in questo caso abbiamo dovuto fronteggiare difficoltà di approvvigionamenti e prezzi lievitati anche di tre o quattro volte negli ultimi mesi. D’altra parte, invece, tutto questo ci ha anche portati ad aprire nuove porte, magari con fornitori che prima non venivano considerati semplicemente per rapporti di fidelizzazione già in essere o piani di consegna concordati.
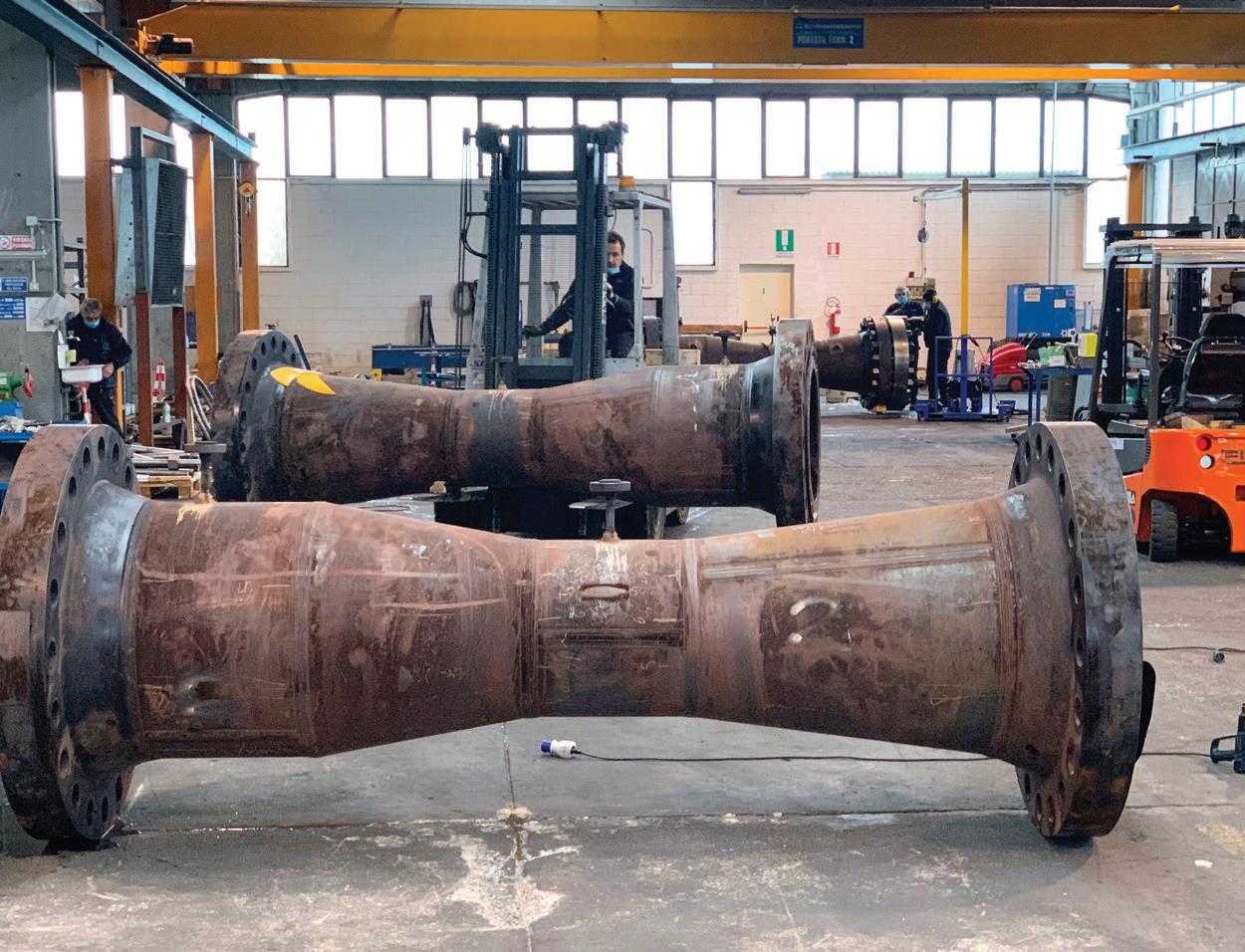
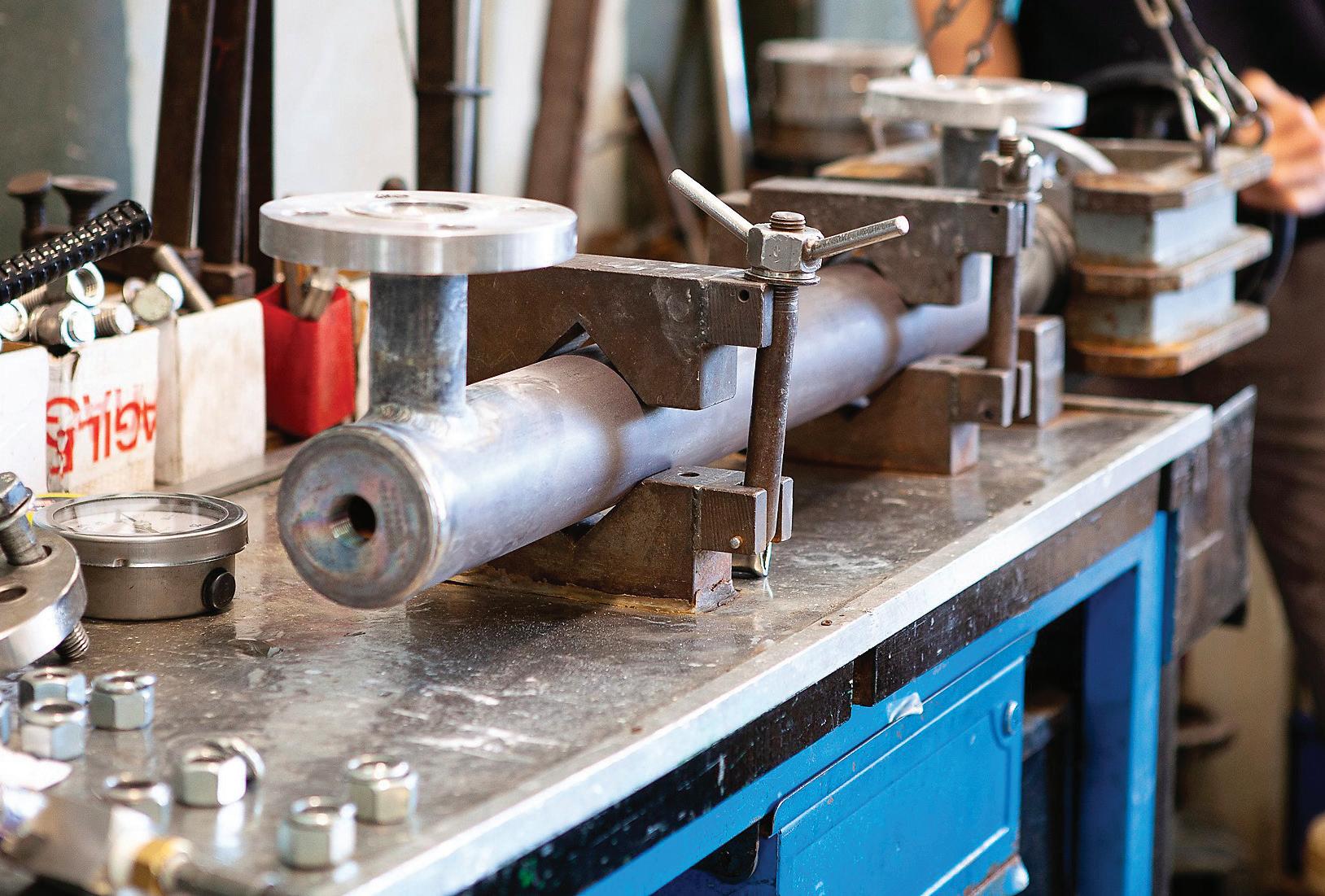
CM: Lo shortage è sicuramente una delle tendenze di cui si è parlato di più ultimamente, ma ve ne sono anche altre, come ad esempio la sostenibilità ambientale. Questo obiettivo rientra nel vostro percorso di innovazione e se sì come?
SV: Sì, innanzitutto dal punto di vista del contenimento dei consumi. E questo punto di vista viene introdotto in tutte le fasi progettuali che riguardano non solo il prodotto in sé, quindi il suo funzionamento, ma anche tutto quanto comporta la sua lavorazione e più a monte la sua supply chain, a partire dagli approvvigionamenti. Questo orienta anche la scelta dei fornitori e non necessariamente a parità di costo: in pratica cerchiamo di scegliere il fornitore più idoneo fra quelli più vicini a noi, anche se risultano un po’ più costosi. Oggi insomma non possiamo più ignorare la variabile “distanza” nella scelta dei fornitori. Le aziende ci sono ed è compito nostro trovarle, che siano sia vicine che capaci di lavorare bene come serve a noi.
Su un altro fronte, quello della produzione di energia, stiamo cominciando a perseguire nuovi e interessantissimi settori di mercato. Ad esempio, abbiamo cominciato a produrre una nuova linea di trasmettitori di livello a immersione, dispositivi che misurano il livello di pozzi, falde, o altro tipo di bacino, specificatamente progettati per gli impianti di gestione delle biomasse. Si tratta in pratica di cisterne che raccolgono il percolato che si genera dai rifiuti: i nostri trasmettitori sono in grado di rimanere immersi in questo tipo di liquido, che è particolarmente aggressivo, per misurarne il livello e quindi per migliorare l’efficienza della gestione di queste vasche, utilizzate nella produzione di energia da fonti di recupero. Dal nostro punto di vista è un settore di mercato totalmente nuovo: fino al 2020 per noi neanche esisteva, quest’anno invece è stato messo a budget perché comincia a rappresentare una parte rilevante anche nella nostra produzione. C’è poi tutto il fronte dell’idrogeno, che abbiamo ben presente e sul quale ci stiamo documentando continuamente, anche presenziando alle fiere internazionali nel settore energia e oil&gas. In questo caso però il nostro ruolo è di supporto: facciamo praticamente quello che siamo in grado di fare da sempre, fornire tecnologia adeguata per resistere ai parametri di questo processo in termini di pressione, temperatura, resistenza agli ambienti e alla corrosione, che in un sistema di produzione o utilizzo di idrogeno possono essere anche molto gravosi. In un certo senso non stiamo vivendo questa evoluzione da protagonisti, d’altro canto però siamo già totalmente in grado di supportarla con una gamma di strumentazione adeguata ai suoi vincoli di processo.
CM: Ci sono altre soluzioni che fungono da abilitatori per le vostre innovazioni? Anche finanziarie, ad esempio con l’accesso a contributi per lo sviluppo tecnologico, magari legati ai fondi del PNRR?
SV: Dal punto di vista finanziario, abbiamo alcuni progetti in corso: la nostra amministrazione sta infatti valutando dei contributi legati all’adozione di nuove tecnologie per migliorare il processo interno. Fra le tecnologie che stiamo valutando vi sono ad esempio dei marcatori ottici, in pratica delle telecamere intelligenti che si possono collegare direttamente con il sistema di gestione della produzione. Questo progetto dovrebbe rientrare in un’area di finanziamento che potrebbe sbloccarsi nel giro dei prossimi mesi. E come questo abbiamo altri progetti in corso per il rinnovamento dei nostri processi produttivi. ìDal punto di vista delle nuove tecnologie, guardiamo con attenzione all’area del 3D non tanto per la prototipazione, cioè per la produzione di prototipi in modalità additiva, quanto piuttosto dal punto di vista del software, quindi con soluzioni di tipo vettoriale che noi utilizziamo specificatamente per la progettazione. In questi anni abbiamo investito tantissimo su soluzioni quali Inventor o Autocad per portare tutto ciò che era disegno su tavola, quindi bidimensionale, in un ambiente software tridimensionale. In questo modo oggi sviluppiamo non solo i pezzi meccanici ma anche l’insieme dei pezzi meccanici con quelli elettronici, verificando le tolleranze e il funzionamento sul campo, in un ambiente tridimensionale completo. Che tra l’altro è sempre più richiesto anche dal nostro cliente, che per primo vuole vedere il nostro device all’interno del suo impianto o del suo skid, simulando totalmente la sua performance reale. La stampa 3D, tuttavia, potrebbe risultare utile per valutare i prototipi di custodie o housing, ma va anche detto che proprio grazie alla progettazione in 3D e alla prototipazione che questa consente, la fase di produzione stessa risulta enormemente più precisa, in quanto le tolleranze di errore sono ridotte al minimo. Fra gli abilitatori di tipo tecnologico e i progetti di innovazione sulla gamma dei prodotti devo poi aggiungere un’operazione importante, effettuata alla fine dell’anno scorso: l’acquisizione di TM Tecnomatic, azienda con sede a Cremona che dagli anni Sessanta produce una gamma di strumenti di misura di elevata qualità e del tutto complementari alla nostra. Questa operazione ci consente di innovare rapidamente dal punto di vista del portafoglio prodotti e delle sinergie che si possono avviare a livello di produzione. Non siamo nuovi a questo tipo di operazioni, dato che già oggi la gamma di Terranova Instruments include altri tre brand, frutto di analoghe acquisizioni condotte nel corso degli anni, quali Valcom, Spriano e Mec-Rela. Da quest’ultima acquisizione ci aspettiamo di migliorare ulteriormente la nostra posizione sul mercato, con soluzioni più integrate che in quanto tali sono molto più apprezzate dal punto di vista dei clienti. L’accordo con TM Tecnomatic dimostra infine che, nonostante le complessità che stiamo vivendo negli ultimi tempi, e anche di fronte alle interruzioni che abbiamo dovuto subire da alcuni punti di vista, non ci siamo lasciati fermare e abbiamo anzi espresso le nostre capacità, anche finanziarie, su altri aspetti, come quello delle strategie e degli obiettivi futuri. L’operazione inoltre rafforza la nostra compagine aziendale, con altre venti persone di alto profilo che si aggiungono alle nostre quaranta, e consolida ulteriormente uno dei nostri maggiori punti d’orgoglio: la produzione interamente made in Italy, un aspetto strutturale della nostra storia sul quale puntiamo fortemente anche per il nostro sviluppo futuro.