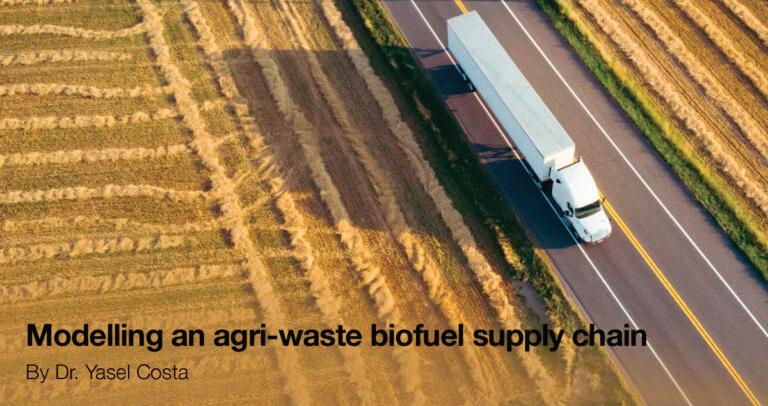
7 minute read
OTTIMIZZARE LA SUPPLY CHAIN DEI BIOCARBURANTI DA SCARTI AGRICOLI
COME DIMENSIONARE CORRETTAMENTE UNA CATENA DI APPROVVIGIONAMENTO DEI RIFIUTI AGRICOLI PER LA PRODUZIONE DI BIOCARBURANTI, GESTENDO ADEGUATAMENTE TUTTI GLI ELEMENTI DI INCERTEZZA DI QUESTA COMPLICATA FILIERA? UN GRUPPO DI RICERCATORI DI UNIVERSITÀ COLOMBIANE, GUIDATI DAL PROF. YASEL COSTA, DELLO ZARAGOZA LOGISTICS CENTER, PROPONE UN MODELLO MATEMATICO PENSATO PER INTEGRARE LE NUMEROSE VARIABILI DI QUESTA CATENA, GENERANDO UN PIÙ REGOLARE E ADATTO AD UNA PRODUZIONE INDUSTRIAL
di Yasel Costa
Advertisement
Professor, Zaragoza Logistics Center
La coltivazione di un terreno finalizzata alla produzione di biocombustibile anziché di prodotti alimentari non è vantaggiosa, né dal punto di vista economico, né da quello ambientale. Quando invece si tratta di convertire in biocarburanti gli scarti e i residui di colture già esistenti, il discorso cambia. Tuttavia, ottimizzare una catena di approvvigionamento per questi rifiuti, in modo che funzioni in termini ambientali, economici e sociali, non è semplice, come io stesso ho scoperto, in questo studio realizzato in collaborazione con i colleghi colombiani Marcela María
Morales Chavez (Universidad Libre Seccional Pereira) e
William Sarache (Universidad Nacional de Colombia).
I flussi che abbiamo modellizzato provengono dalle piantagioni di caffè, ma le problematiche che abbiamo analizzato sono adattabili a molti flussi originati da rifiuti reali e potenziali. I rifiuti agricoli in questione sono generati, di solito, al momento del raccolto, anche se con alcune colture possono essercene altri, ad esempio come nel caso ci siano cicli di potatura o di diradamento. Il momento della raccolta è incerto: dipende dalle variazioni climatiche durante la stagione di crescita e, in alcuni casi, dalle condizioni del terreno; per il caffè, l’altitudine è un fattore determinante. Anche

la resa (del raccolto e degli scarti) può variare in base alle condizioni di crescita della stagione. Ma per una produzione di biocarburanti efficace dal punto di vista dei costi, i convertitori, le raffinerie e la distribuzione al dettaglio a valle richiedono un flusso equilibrato e costante di materie prime durante la “campagna”. (Una raffineria può, ovviamente, lavorare altri scarti di altre colture in periodi diversi dell’anno).
Dobbiamo quindi pianificare un flusso costante di materiale verso la raffineria per garantire che quest’ultima lavori al massimo dell’efficienza il più a lungo possibile. Ma non possiamo limitarci ad accumulare il materiale: questo ha i suoi costi e gli scarti possono deteriorarsi.
Non si tratta solo di un singolo flusso. In genere, si cerca di raccogliere e pre-trattare i rifiuti, ad esempio essiccandoli e compattandoli per rendere più efficiente il trasporto. L’ideale sarebbe trovarsi vicino all’azienda agricola o alla piantagione, ma “vicino” è un termine flessibile e può comportare il trasporto di rifiuti non trattati per molti chilometri, magari attraverso terreni difficili. Le modalità di trasporto e i veicoli che trasportano dall’azienda agricola al pre-trattamento e da quest’ultimo alla raffineria possono variare: potrebbe non essere possibile, ad esempio, utilizzare camion di grandi dimensioni in zone montuose (la qualità del caffè si degrada se le temperature sono troppo calde, quindi le migliori piantagioni, almeno in Sud America, si trovano in genere ad alcune migliaia di metri sul livello del mare). Ci siamo quindi posti la sfida di creare un modello per le filiere dei biocarburanti basati sui rifiuti agricoli. Questo modello avrebbe tre obiettivi interconnessi: ottimizzare l’ubicazione (e il numero) dei centri di raccolta/prelavorazione e delle bioraffinerie; garantire un flusso adeguato di materiale per soddisfare la domanda in ogni fase e affrontare la pianificazione del percorso per una flotta di veicoli inevitabilmente eterogenea. Questo problema di localizzazione-inventario-indirizzamento (LIRP) è ben noto e diffuso.
Ci è parsa emergere un’ulteriore complicazione. Tutti i modelli devono fare delle ipotesi semplificative e la maggior parte della modellazione convenzionale del LIRP presuppone che le varie strutture di elaborazione siano fisse, per quanto riguarda la loro capacità fisica, la loro ubicazione e i tempi in cui sono operative. Nessuna di queste ipotesi è necessariamente vera o ottimale: un determinato flusso di rifiuti di solito aumenta, raggiunge picchi e diminuisce nell’arco di settimane o mesi, quindi non c’è alcuna ragione per cui un particolare impianto all’interno di una rete debba essere operativo all’inizio della campagna, o debba continuare fino alla fine, o non debba ridurre o aumentare la propria capacità durante la stagione. (Anche se non abbiamo considerato specificamente questo caso, è possibile che le strutture di pre-elaborazione, in particolare, possano essere mobili, spostandosi da un’azienda agricola all’altra man mano che il raccolto si sviluppa a diverse altitudini o climi. Potremmo esaminare questo aspetto in un lavoro futuro).
Ci sono quindi molte variabili, molte delle quali sono “stocastiche”, nel senso matematico: ovvero pur non essendo strettamente casuali, possono essere modellate come se lo fossero. L’approccio classico è quindi quello della programmazione non lineare a integrazione mista.
Ma c’è un problema: un approccio di questo tipo, per un problema di questa portata, richiede un’enorme quantità di potenza di calcolo e, cosa forse più importante, di tempo: non c’è alcun vantaggio nel ricavare una soluzione matematicamente ottimale per il raccolto dell’anno scorso - abbiamo bisogno di un’approssimazione vicina per la situazione di quest’anno. Abbiamo quindi sviluppato una strategia per convertire il nostro modello originale in una formulazione di programmazione lineare, con la capacità di essere efficiente in termini di tempo di esecuzione e di essere altamente competitiva, in termini di qualità della soluzione, con gli approcci di “metodo esatto”.
Il modello è necessariamente complesso, ma crediamo di aver colto l’essenziale nel modo seguente: abbiamo le quattro fasi di produzione (aziende agricole, centri di raccolta, bioraffinerie, impianti di miscelazione), molteplici tipi di rifiuti agricoli (da colture alternative, o perché i rifiuti possono essere generati sia al momento del raccolto, sia separatamente se la coltura ha una fase di potatura o diradamento), infine molteplici periodi di tempo. I fornitori (aziende agricole) non sono legati a una specifica stazione di raccolta, né a una specifica raffineria. Le decisioni che riguardano lo stoccaggio riflettono i requisiti delle raffinerie per le materie prime, ovviamente, ma anche la deperibilità o degradazione dei rifiuti in attesa di lavorazione e la capacità di stoccaggio dei centri di raccolta. Il modello riconosce anche il valore temporale del denaro e il fatto che l’aumento della capacità delle stazioni di raccolta o delle bioraffinerie può non produrre economie di scala, anzi, i costi fissi e variabili della lavorazione possono aumentare. Questo è uno dei motivi principali per cui questo problema essenzialmente non lineare deve essere “linearizzato”.
Per i matematici, il nostro modello di ottimizzazione è definito “NP-hard” (o NP-difficile), quindi abbiamo utilizzato un approccio euristico in due fasi. Abbiamo progettato una serie di 15 problemi o scenari su piccola, media e grande scala. Nella prima fase abbiamo definito la struttura della rete basata sull’apertura, la variazione della capacità e la chiusura di impianti di raccolta/prelavorazione e bioraffinerie. Poi abbiamo ottimizzato le variabili relative al flusso dei materiali, della biomassa come input e del biocarburante come output. Ciò include la gestione dei livelli di inventario nelle stazioni di raccolta/prelavorazione e l’ottimizzazione del percorso dei veicoli per la raccolta dei rifiuti dalle fattorie/piantagioni, tra le stazioni di raccolta e le bioraffinerie e da queste alle stazioni di miscelazione (perché i biocarburanti sono raramente utilizzati “puliti”).
Possiamo quindi confrontare i nostri risultati con le soluzioni “esatte” per gli scenari specifici per vedere quanto ci avviciniamo al “vero” optimum, tenendo presente che la vita reale e la stagione del raccolto sono troppo brevi per calcolare soluzioni esatte per ogni possibile combinazione di valori delle variabili, soprattutto perché stiamo cercando di ottimizzare fattori ambientali e sociali, oltre che puramente economici - emissioni di carbonio, occupazione rurale e così via.
La nostra modellazione si è rivelata molto competitiva sia in termini di tempo di calcolo che di approssimazione ai risultati calcolati “esatti”.
Forse la scoperta più importante è che una strategia dinamica degli impianti, in base alla quale i centri di raccolta e le bioraffinerie possono aprire, espandersi, contrarsi o chiudere a seconda dei casi all’interno della campagna, se può essere adeguatamente modellata e gestita, facilita davvero una maggiore produzione di biocarburanti, una supply chain più redditizia, la creazione di un maggior numero di posti di lavoro e un migliore utilizzo del territorio, in modo che la produzione di biocarburanti occupi quanto meno terreno agricolo possibile, lasciandone spazio di conseguenza alla produzione alimentare.
Allo stesso tempo, abbiamo anche cominciato a familiarizzare con l’impatto dell’incertezza – quella derivante dalla disponibilità di scarti agricoli – sulle performance economiche delle supply chain basate sul biocarburante che deriva dai rifiuti. Questo suggerisce alcune linee di ricerca per il futuro, in particolare per coprire le aree di input che oggi sono particolarmente carenti di dati, come ad esempio la domanda di mercato verso i biocarburanti o i tassi di conversione dei carburanti in generale.