
6 minute read
GUARNIZIONI: UNA NUOVA REALTÀ PER NUOVI MERCATI
PRESENTE NEL SETTORE DELLE GUARNIZIONI DA 25 ANNI, CAAST STA PERSEGUENDO UN APPROFONDITO PERCORSO DI RINNOVAMENTO AZIENDALE, FUNZIONALE AD OBIETTIVI DI GRANDE PORTATA: CRESCITA SUL MERCATO E SVILUPPO DI NUOVI SETTORI APPLICATIVI. A QUESTI RIVOLGE LA SUA CAPACITÀ DI ANDARE SEMPRE OLTRE I CONFINI DEL PRODOTTO STANDARD, PARTICOLARMENTE INTERESSANTE AD ESEMPIO PER AGGREDIRE AREE DI MERCATO CHE OGGI PRATICAMENTE ANCORA NON ESISTONO – È IL CASO AD ESEMPIO DEL VASTO AMBITO DELLA TRANSIZIONE ENERGETICA - MA PER LE QUALI AZIENDE E START UP STANNO GIÀ METTENDO ALLA PROVA LA VALIDITÀ DEI FORNITORI
SPECIALE
Advertisement
DIGITAL TRANSFORMATION e INDUSTRIA SMART
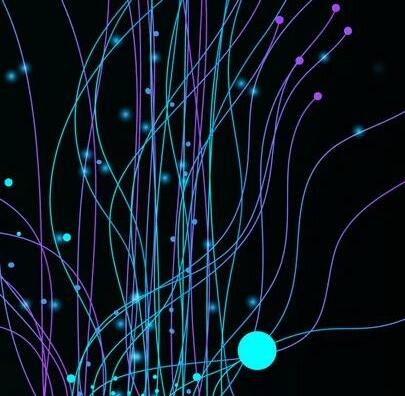
«Quella delle guarnizioni è una nicchia di mercato. Una nicchia sottovalutata, però. La guarnizione è l’ultima cosa a cui pensa un impiantista ma è anche la cosa che può fare più danni. Con la guarnizione sbagliata, l’impianto non funziona» afferma Lorenzo De Lorenzi, direttore commerciale di Caast, descrivendo il core business dell’azienda che da sempre è rappresentato dalle sealing solutions: guarnizioni, sistemi di tenuta in generale e tutti i dispositivi a corredo. Si tratta di componenti critici che sono realizzati in accordo con le sempre più esigenti specifiche richieste dai mercati di oggi.
Caast produce internamente tutte le tipologie di guarnizioni da lavorazione meccanica, con riferimento a due grandi famiglie di materiali componenti, plastici o termoplastici ed elastomerici, passando per tutte le possibili varianti, quali ad esempio polimeri fluororati (Viton), HNBR (NBR idrogenati), fino ad arrivare ai materiali PTFE per applicazioni più particolari. Nella gamma Caast vi è anche la divisione dedicata agli o-ring, quasi esclusivamente realizzati in mescole speciali. Altra linea di prodotto è quella delle guarnizioni energizzate (spring energized), specifiche e spesso customizzate per il settore oil & gas; un prodotto che ha richiesto forti investimenti nella ricerca e sviluppo, per gestire correttamente il calcolo strutturale delle spinte date dalle molle interne in relazione alle prestazioni e alla tenuta della guarnizione. A completamento della gamma prodotti, a copertura delle applicazioni critiche ci sono le guarnizioni metalliche che l’azienda fornisce in modalità rivendita: è questa la fascia di prodotto più critica in assoluto, dato che il metallo subentra laddove tutti i materiali plastici visti fin qui non sono più sufficienti, per questioni di temperatura, di pressione, di compatibilità o di dimensioni dell’applicazione. Anche in questo caso però l’azienda garantisce una competenza specifica, supportata da partnership di lunga data con i propri fornitori specializzati.
La linea di prodotto nella quale l’azienda si distingue maggiormente è però quella delle grandi dimensioni: Caast infatti è in grado di produrre guarnizioni con diametro anche di oltre tre metri. Si tratta di una competenza importante soprattutto in vista dei nuovi mercati aperti dalla transizione energetica: tali misure infatti sono tipicamente richieste dai sistemi di produzione di energia che sfruttano fonti naturali quali gas, acqua oppure vento. Nel settore idroelettrico, ad esempio, le valvole che regolano l’entrata dell’acqua nelle turbine possono raggiungere i quattro o cinque metri di diametro. Si tratta in particolare, in questo caso, di un settore anche piuttosto datato, nel quale può succedere di dover sostituire vecchi prodotti magari a base di gomma telata, con nuove soluzioni realizzate con materiali termoplastici oppure elastomerici. Un esempio di sviluppo particolarmente innovativo, legato anch’esso alle grandi dimensioni, riguarda i prodotti forniti per una turbomacchina che convoglia il gas nei gasdotti – un mondo che oggi è sotto i riflettori per le questioni legate alla Russia, ma che indubbiamente rappresenta una parte ancora molto importante del nostro futuro energetico. L’azienda cliente utilizzava sistemi di tenuta di tenuta ad anello chiuso di circa tre metri di diametro, caratterizzata da notevole complessità nelle fasi di montaggio e adattamento. In questo caso, Caast ha sviluppato una guarnizione di grandi dimensioni e divisibile in due parti, che semplifica tali fasi riducendo il tempo di installazione da oltre tre ore a trenta minuti.
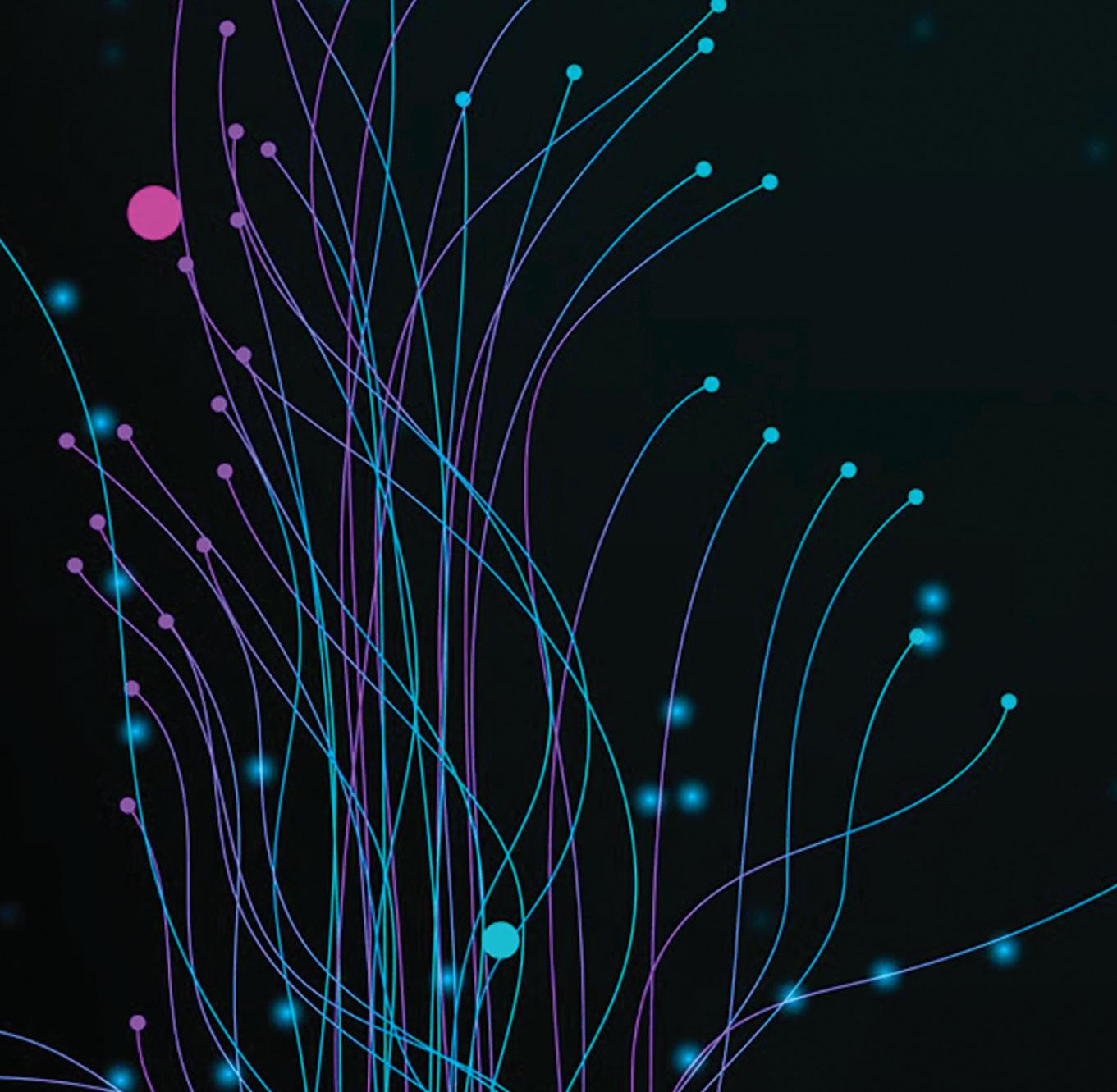
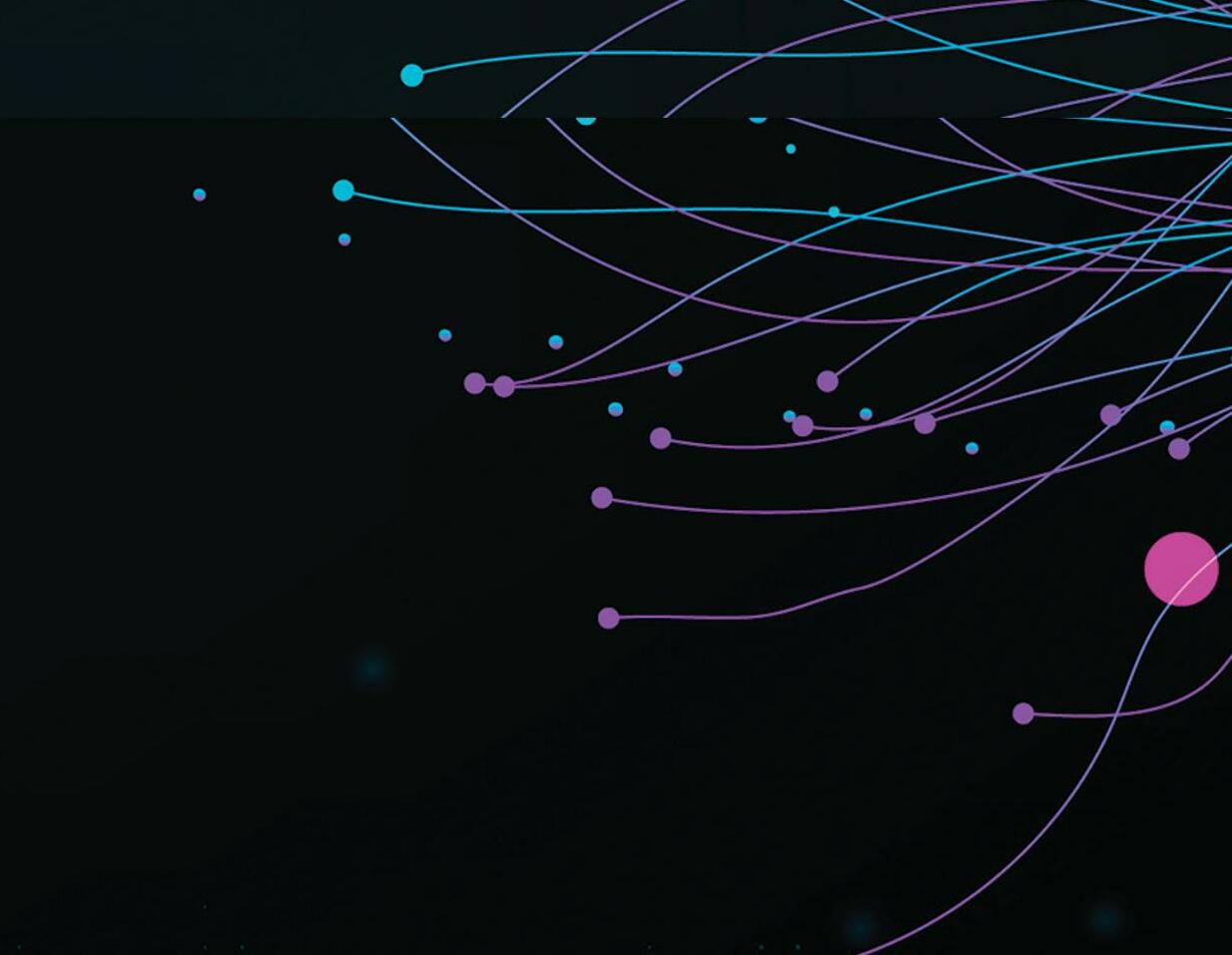
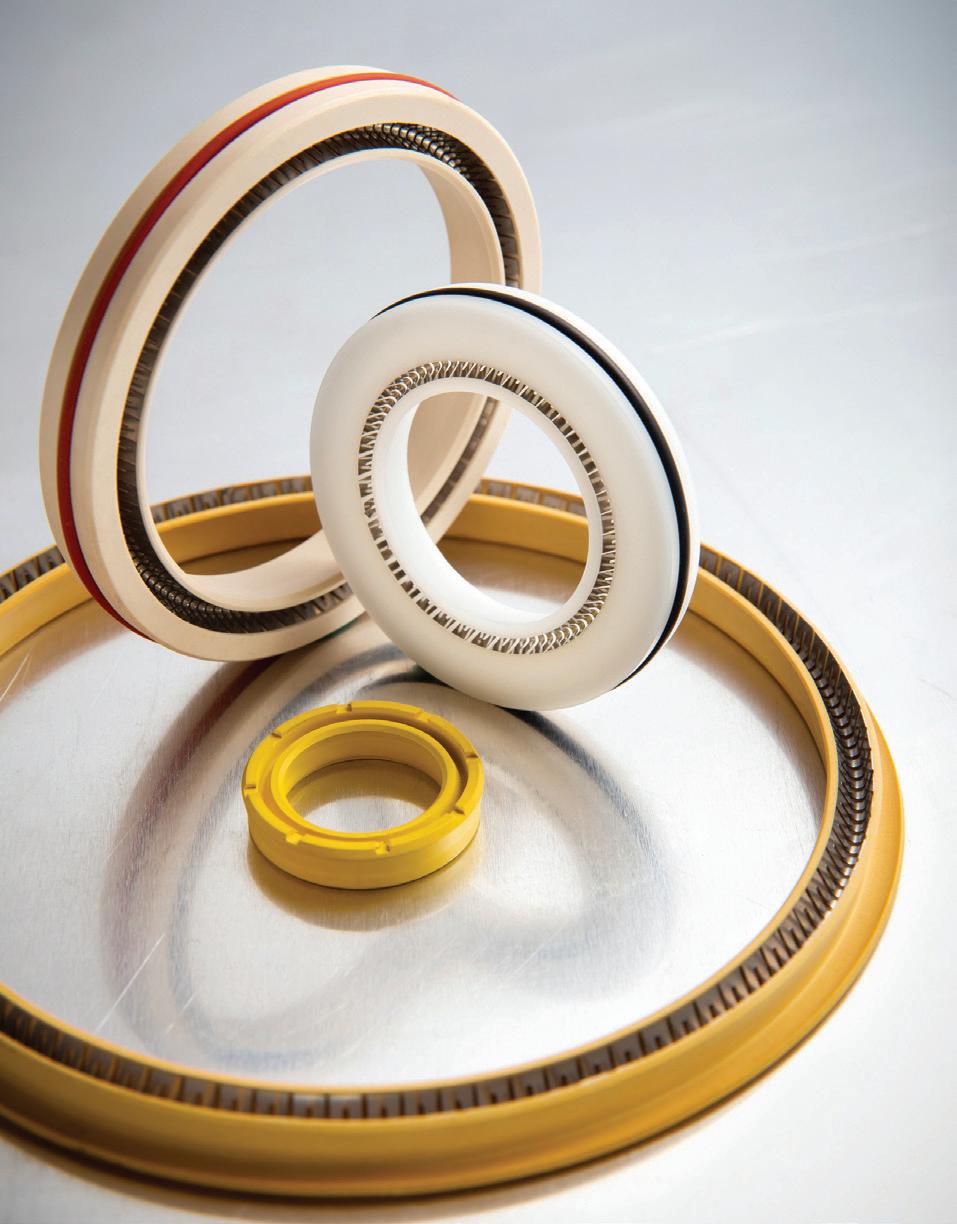
I REPARTI PRODUTTIVI: DALLA TORNITURA ALLA SALA METROLOGICA
L’area produttiva di Caast presenta innanzitutto un magazzino semilavorati, che contiene le billette dei materie termoplastiche, plastiche oppure elastomeriche (parte delle quali conservate in una apposita area climatizzata). La produzione per Caast avviene prevalentemente per tornitura e asportazione di truciolo, mediante macchinari e soluzioni specificatamente dedicate a questo tipo di prodotti, quindi
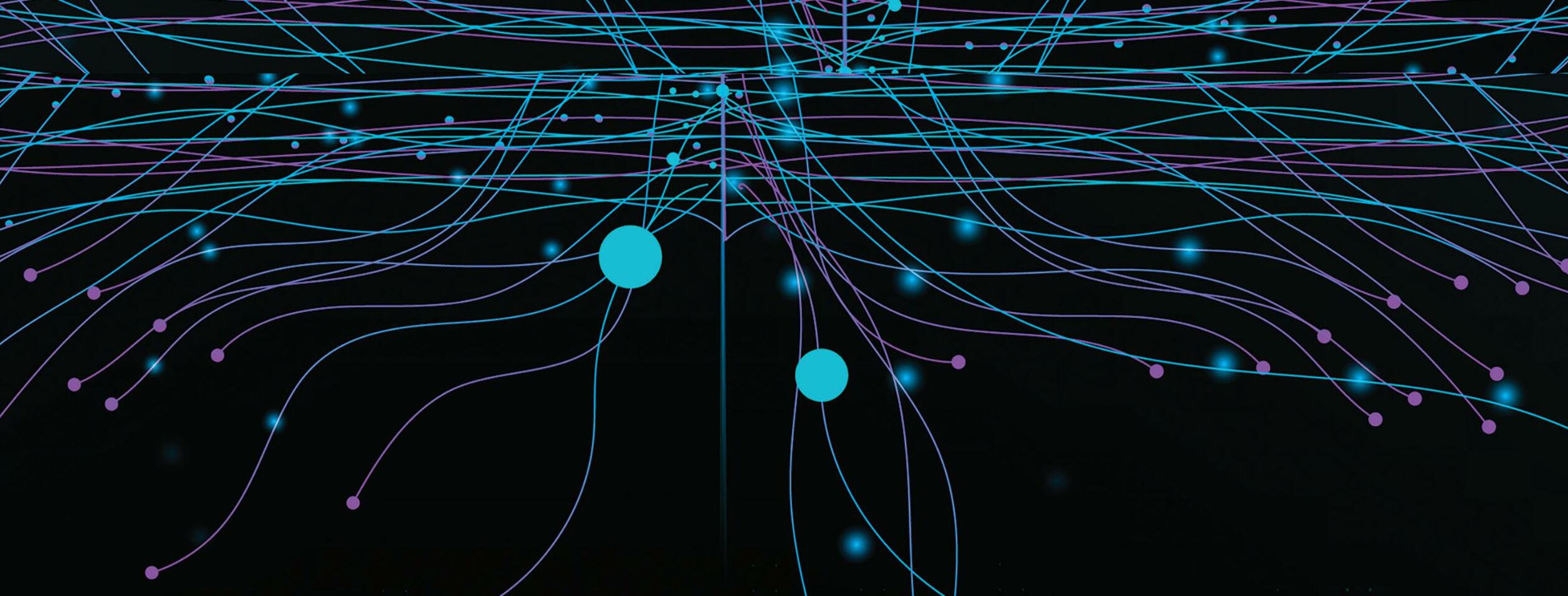
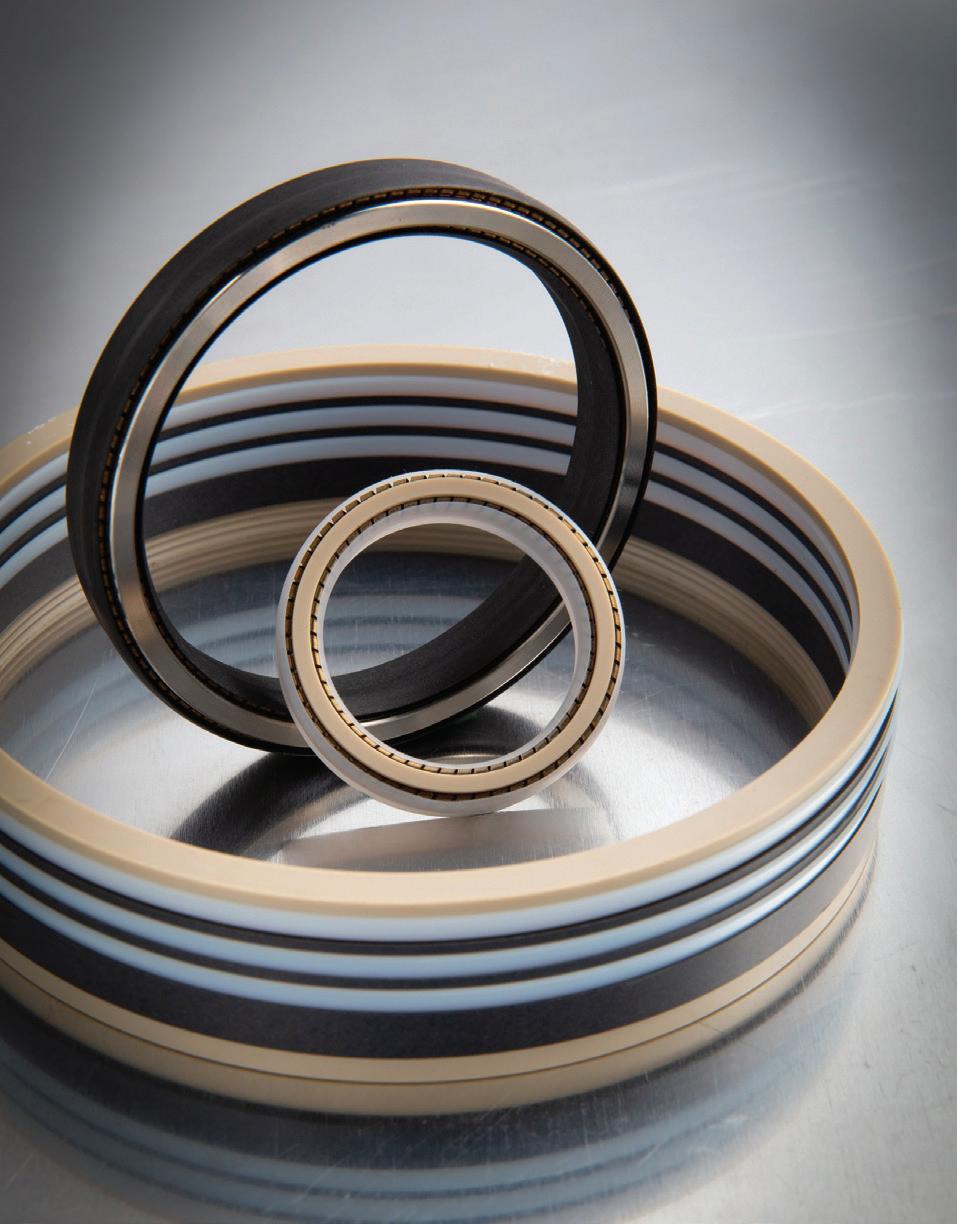
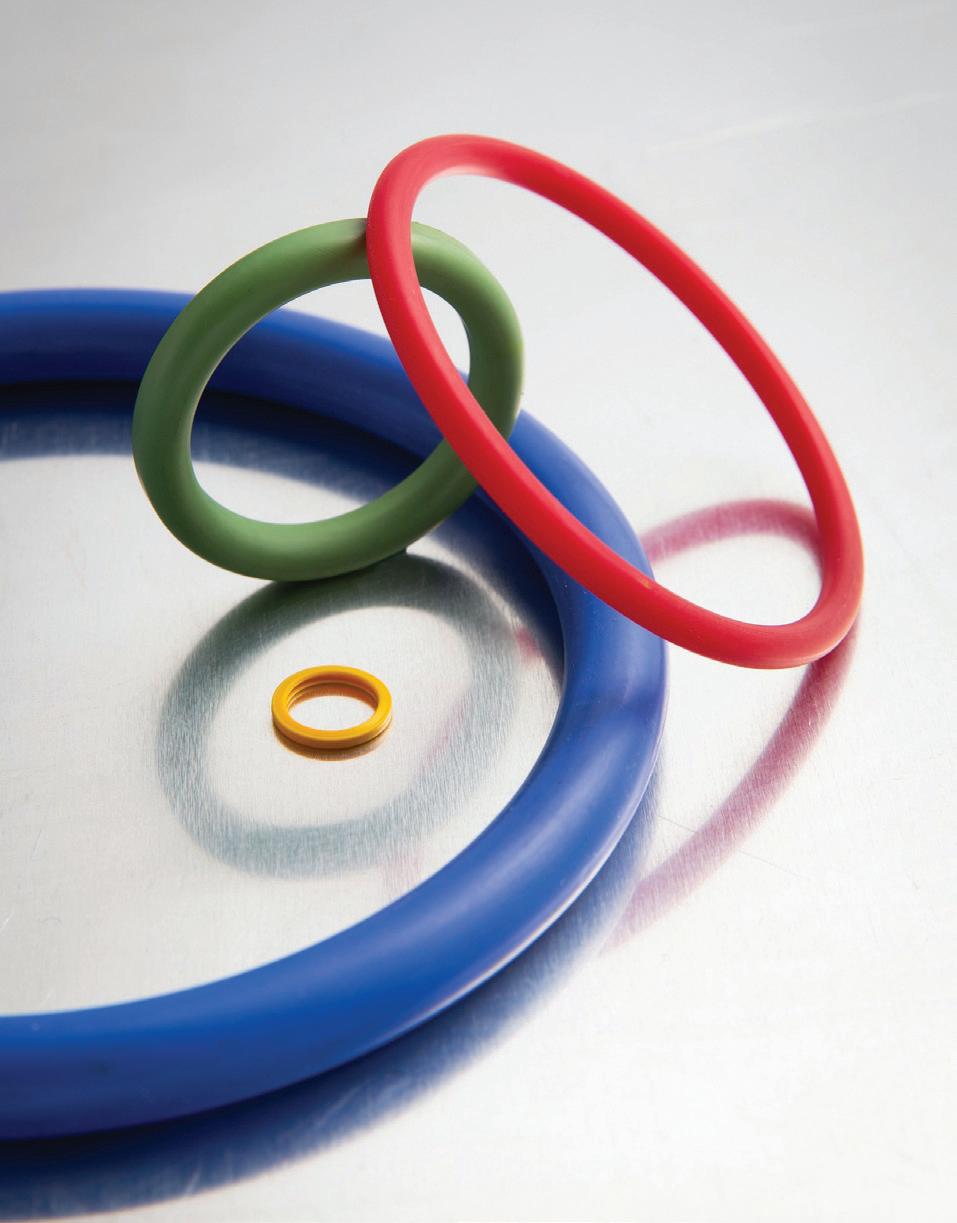
con utensili e sistemi di rotazione fatti apposta per lavorare la plastica e la gomma. Di fatto, la guarnizione che esce da queste macchine presentano finiture superficiali paragonabili ai prodotti ottenuti per stampaggio, nel rispetto delle tolleranze richieste per questo tipo di materiali. Questo per quanto riguarda i prodotti soggetti a tornitura; nel caso di prodotti realizzati mediante stampaggio (proposti da Caast anche in collaborazione con fornitori specializzati) si parte invece dal granulato e dalla formulazione della mescola di base, che vengono formati in appositi stampi. Altre tecnologie utilizzate sono estrusione e vulcanizzazione.
Un asset importante della produzione Caast è rappresentato dalla sala metrologica, allestita con svariate soluzioni per tutte le attività di misurazione o collaudo finale dei prodotti e per la prova delle caratteristiche meccaniche dei materiali. La sala, a temperatura controllata, è dotata di svariate strumentazioni, da quelle più tradizionali quali durometri, micrometri, calibri digitali e così via, una stazione per le prove meccaniche, di trazione e allungamento, densità, durezze, fino ad arrivare a macchine a visione ottica di nuova concezione. L’ultima arrivata in particolare, fiore all’occhiello della gamma Keyence, è in grado di effettuare gran parte delle misurazioni necessarie in modalità sostanzialmente automatica, semplicemente richiamando il disegno del prodotto, controllandone parametri e tolleranze in tempi rapidissimi. Altra soluzione metrologica Keyence è un profilometro, un proiettore laser in grado di misurare il profilo dei prodotti senza doverli sezionare materialmente, utile soprattutto in caso di cavità interne.
«Ci troviamo in una fase di mercato molto particolare, nella quale ci chiedono anche soluzioni per applicazioni che oggi non sono ancora veramente partite: è il caso ad esempio dell’idrogeno. Le aziende ancora non sanno che cosa dovranno gestire, e nemmeno come, ma già devono disporre di soluzioni di tenuta e solo dopo, con i prodotti che forniamo loro, possono effettuare i test di compatibilità» prosegue Lorenzo De Lorenzi. «Questo è uno degli estremi a cui ci porta il mercato di oggi, complice anche la situazione geopolitica: prodotti sempre all’avanguardia, in tempi zero. Ma è qui che possiamo far emergere tutto il nostro valore, che si basa sull’elevata qualità del prodotto, sulla profonda competenza di settore, sul servizio tecnico capillare».
Fra le certificazioni di qualità conseguite dall’azienda, che è ISO 9001 fin dal 2006, vi è anche il sistema AS9100 per il settore aerospazio e difesa, un traguardo raggiunto sempre con l’obiettivo di entrare in nuovi settori applicativi interessanti e coinvolgenti. «Un percorso complicato, non solo per la severità della norma, ma anche per il modo in cui essa è formulata» conclude Lorenzo De Lorenzi. «La certificazione 9100 infatti richiede che l’azienda riceva un ordine entro i primi due anni, pena la perdita della qualifica; ma i clienti di questo settore – compresa l’azienda per la quale abbiamo cominciato la procedura – possono acquistare solo prodotti già certificati. L’azienda in questione aveva avuto una rottura di stock per un o-ring destinato ai propulsori degli aerei, un elastomero che doveva arrivare a 320 °C di temperatura. Nel giro di un mese e mezzo abbiamo preso un nostro prodotto ancora non omologato ed effettuato i test necessari per soddisfare tutti i parametri richiesti. Un errore in questa fase non era ammissibile perché ci avrebbe estromessi per sempre dal settore. I test sono riusciti perfettamente e ora ci muoviamo in modo sempre più solido anche in quest’area, con diversi clienti internazionali».