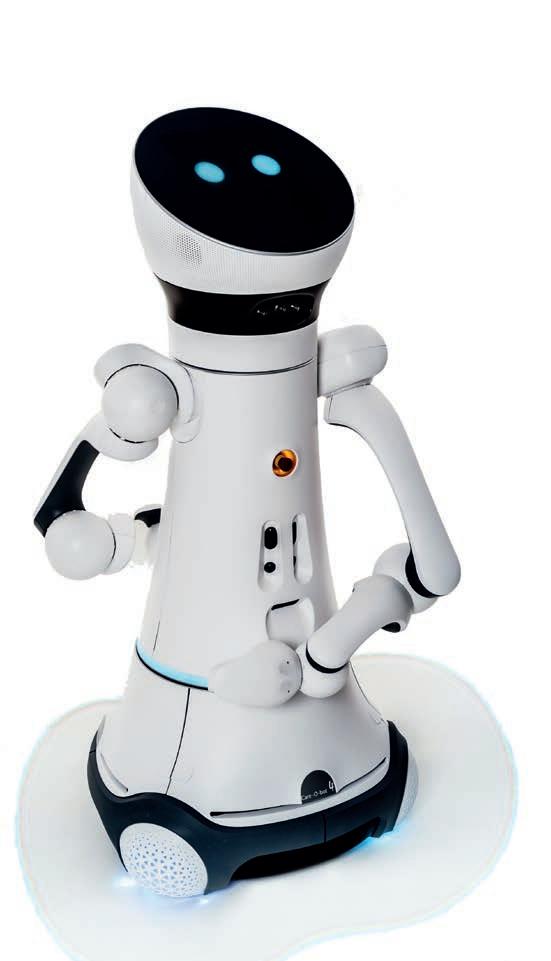
7 minute read
Digitalisierung – heute und in Zukunft Big Data, Industrie 4.0, Einkauf 4.0, Internet der Dinge, Künstliche Intelligenz. Vor einem fundamentalen Wandel
from Denkraum 4
Digitalisierung – heute und in Zukunft
von Christine Klein und Florian Steinkohl
Advertisement
Digitalisierung ist derzeit ein Buzzword und medienbestimmendes Thema. Schlagworte wie Big Data, Industrie 4.0, Einkauf 4.0, Vernetzung, Internet der Dinge, Künstliche Intelligenz werden gern unter diesem Begriff zusammengefasst. Die Technologie selbst ist nicht so neu. Sie begann ab den 1970er
Jahren, als nach Erfindung der Mikroprozessoren die Speicherung und digitale Verarbeitung von Daten fortlaufend zunahm. Für jeden von uns sind viele Tätigkeiten und
Prozesse bereits heute vollkommen selbstverständlich digitalisiert. Wir benutzen Textverarbeitungsprogramme oder senden Sprachnachrichten über Messenger-Dienste. In Unternehmen wird IT seit 50 Jahren eingesetzt. Seit 30 Jahren arbeiten auch Roboter und Maschinen in der industriellen Fertigung computergesteuert.
Was kennzeichnet die Digitalisierung bis heute? Die wesentliche Grundlage der „digitalen Revolution“ – Industrie 3.0 – ist das Moore’sche Gesetz aus dem Jahr 1965. Die Anzahl der Komponenten auf einem integrierten Schaltkreis pro Flächeneinheit verdoppelt sich alle zwei Jahre. Paradoxerweise ist das ursprüngliche Moore’sche Gesetz bald aus physikalischen Gründen – es kann nicht mehr noch kleiner gebaut werden – dem Ende geweiht. Allerdings ist zu erwarten, dass herkömmliche Schaltkreise durch neue Technologien ersetzt werden und das Moore ’sche Gesetz dadurch weiter seine Gültigkeit behalten wird.
Die Industrie 3.0, die die Automatisierung ganzer Bereiche vorangetrieben hat, ist durch eine hierarchische Systemarchitektur – die sogenannte Automatisierungspyramide –
Unternehmensstrategie Vision Mission
Unternehmensleitebene
Betriebsleitebene
Prozessleitebene
Steuerungsebene
Feldebene/ physikalische Ebene Internet der Dinge in der Cloud Unternehmensstrategie
gekennzeichnet. Sie ist in fünf Ebenen unterteilt: Feldebene, Steuerungsebene, Prozessleitebene, Betriebsleitebene und Unternehmensleitebene. Durch die Bereitstellung leistungsfähigerer Rechenleistung und wachsender Speicherkapazitäten konnte jede dieser Ebenen laufend optimiert werden. Beispielsweise kann dies in der Steuerungsebene für SPSProgramme und Technik, die zur Steuerung und Regelung von Produktionsanlagen dient, beobachtet werden. Auch die Verbesserung der Leistungsfähigkeit von ERP-Systemen in der Unternehmensleitebene kann über die letzten Jahrzehnte nachvollzogen werden.
Die Automatisierung in jeder Ebene schreitet stetig voran. Allerdings gibt es bis heute keine zufriedenstellende Lösung, um die einzelnen Ebenen miteinander zu verbinden, da die Datenspeicherung jeweils innerhalb der getrennten Systeme erfolgt. Konsequenzen daraus sind aufwendige Übergabeprozeduren zwischen den einzelnen Systemen und eine nur eingeschränkte übergreifende Datenverfügbarkeit. Zwar kommt es immer wieder zu Verbesserungen innerhalb der einzelnen Systemebenen, doch das Problem der Schnittstellen und der mangelnden Datentransparenz bleibt weiterhin ungelöst.
Wie Industrie 4.0 unsere Arbeit verändert Die Industrie 4.0 basiert im Wesentlichen auf drei neuen Ideen. Zum einen baut sie auf einer komplett neuen Systemarchitektur auf. Anstelle des hierarchischen Aufbaus werden vernetzte dezentrale Steuerungen eingesetzt. Die einzelnen Hierarchieebenen verschwinden und damit auch die Schnittstellenprobleme. Der zweite Ansatz besteht aus der Schaffung eines gemeinsamen Datenraums – der Cloud. Der Zugriff auf alle Daten in unterschiedlichen Verarbeitungsstufen ist dadurch möglich.
Vision Mission
Verarbeitung von Daten Weitergabe von Daten Datenspeicher Dienste
Daten zur Steuerung Daten zur Analyse/ Erhebung Feldebene/physische Objekte mit digitalem Zwilling
Der dritte zentrale Bestandteil von Industrie 4.0 ist die Geburt des „digitalen Zwillings“. Damit ist gemeint, dass alle physikalischen Objekte in der Produktion wie Maschinen, Behälter oder Produkte zugleich als virtuelle Objekte angelegt werden. Diese digitalen Zwillinge werden intelligent. Sie sind durch entsprechende Algorithmen in der Lage, Daten aus Sensoren und der Umwelt zu bewerten, um eigenständige Entscheidungen zu treffen. Beispielsweise kann ein Transportbehälter über seinen Standort und Füllstand Auskunft geben oder auch automatisiert eine Nachbestellung anstoßen.
Die Daten aller vernetzten Komponenten laufen im Internet der Dinge zusammen. Durch die dezentrale Steuerung ist eine hohe Flexibilität der Anlagen zu erreichen. So wird es unter anderem möglich, Produkte in beliebigen Mengen zu produzieren oder mit geringem Aufwand neue Fertigungsroboter in den Produktionsablauf zu integrieren. Was einen deutlichen Mehrwert bringen kann, ist die nun mögliche Analyse und Auswertung des gesamten Datenraums. Praktisch bedeutet das für die Prozesse auf der Unternehmensleitebene, die bisher weit weg von der physikalischen Ebene waren, dass der Zugriff auf die Datenbasis aus der Fertigung aktueller und genauer ist, womit Reaktionszeiten deutlich verkürzt werden können. Das wird den Unternehmen helfen, noch effizienter zu planen und zu produzieren.
Der wirklich radikale Umbruch in der Industrie 4.0 steht jedoch erst an, wenn Daten von Lieferanten, auch Vorlieferan
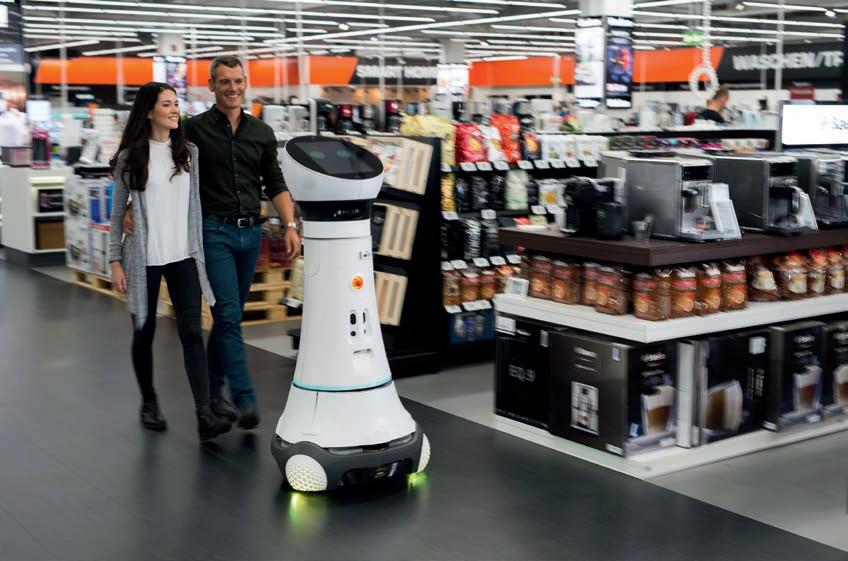

Roboter Paul begrüßt die Kunden bei Saturn in Ingolstadt, begleitet sie zum gewünschten Produkt, plaudert übers Wetter und ruft per VoiP seine menschlichen Kollegen zur Kundenberatung. Den Care-O-bot®4-Prototyp hat das Fraunhofer Institut für Produktionstechnik und Automatisierung (IPA) ursprünglich als Assistenzroboter zur Unterstützung in Haushalt, Hotel, Pflegeheim oder Klinik entwickelt. An dieser vierten Generation haben die IPA-Forscher zusammen mit Phoenix Design und der Firma Schunk drei Jahre gearbeitet, die Vorgänger wurden seit 1989 konstruiert.

ten, Produzenten und Kunden in einem gemeinsamen Datenraum, eben in der Cloud, zugänglich gemacht werden. Denn hierdurch können sehr früh verfügbare Kapazitäten, drohende Engpässe oder andere kritische Ereignisse identifiziert und analysiert werden. Allein das Wissen über diese Daten wird einen zusätzlich handelbaren Wert darstellen und zum Beispiel die Produktion der Unternehmen noch weiter flexibilisieren. Aber auch damit nicht genug. Aus dieser immensen Datenbasis lassen sich neben den bisher möglichen Standardabfragen auch Prognosen unter geänderten Rahmenbedingungen erstellen. So können Szenarien für einen Lieferantenwechsel, für Produktionssteigerung oder Standortverlegungen simuliert und bewertet werden.
Ermöglicht und gestützt werden die Entwicklungen der Industrie 4.0 durch die weiterhin stark wachsende Rechnerleistung. Erst dadurch ist es möglich, Konzepte der künstlichen Intelligenz wie wissensbasierte Systeme oder neuronale Netze – sogenanntes Deep Learning – zur Analyse dieser riesigen Datenmengen einzusetzen und damit brauchbare Ergebnisse zu erzielen.
Was macht die Zukunft möglich? Drei Megatrends sollen kurz dargestellt werden:
1. Künstliche Intelligenz (KI) Von KI spricht man, wenn ein Computer dazu gebracht wird, menschenähnliche Intelligenz nachzubilden, um infolgedessen eigenständig Probleme bearbeiten und lösen zu können. Die Anwendungen sind sehr vielfältig. Algorithmen von Suchmaschinen wie Google oder Time line in Facebook versuchen stets, unter Verwendung von künstlicher Intelligenz, aus dem Verhalten des Nut zers zu lernen, welche Interessen diese Person genau hat und welche Suchergebnisse dementsprechend am bes ten zu ihr passen. Auch Spracherkennungs- und Sprachsteuerungsprogramme wie Siri, Google Now und Cortana nutzen KI. Das Expertensystem Watson von IBM, automa tische Muster- und Bilderkennung, aber auch maschinelle Übersetzung sind nur einige weitere Anwendungsfelder.
2. 3D-Printing Die Ersatzteilbeschaffung oder auch die Produktion kompletter Teile können durch den 3D-Druck deutlich vereinfacht werden. Sofern es einen digitalen Zwilling zu einem Bauteil gibt, kann dieser per 3D-Druck an einem beliebigen Ort zu einer beliebigen Zeit hergestellt werden. Die Abhängigkeiten von Lieferanten und Logistik werden reduziert. Da es bei der Herstellung eines Werkstücks im 3D-Druck unwesentlich ist, ob es einmal oder 100.000-mal gefertigt wird, können auch kleinste Stückzahlen angefertigt werden. Dabei kann insbesondere verstärkt auf kundenindividuelle Anforderungen eingegangen werden.
Das Moore’sche Gesetz gilt noch immer
Die Rechenleistung eines Computerchips wird sich weiterhin alle zwei Jahre verdoppeln. Um dieses exponentielle Wachstum zu veranschaulichen, sollten wir uns folgender Tatsache bewusst werden: Würde sich die Rechenleistung nicht alle zwei Jahre, sondern lediglich alle fünf Jahre verdoppeln, so hätten, beginnend 1968, die heutigen Chips ein 15 Millionstel ihrer Rechenleistung, sie wären also ungefähr so schnell wie die Chips des Jahres 1981! Und das Smartphone (ab 2007) gäbe es dann erst im Jahr 2104. Daraus lässt sich erkennen, in welcher Dimension das exponentielle Wachstum steigt.
3. Virtuelle Realität Die Wirklichkeit lässt sich virtuell abbilden, um Entwick lungen zu testen und erlebbar zu machen. Einsatzmöglichkeiten gibt es heute schon bei der Pilotenausbildung in Flugsimulatoren, sie können aber beliebig ausgedehnt werden, etwa zur Produktentwicklung, zum Bau von Prototypen, zu Visualisierungen in der Architektur, in der Städteplanung und Medizin. Auch der Einsatz im Einzelhandel, zum Beispiel das virtuelle Anprobieren von Kleidungs stücken oder das Einrichten der Wohnung im virtuellen Raum, ist denkbar. Von dort kann nahtlos zur individuellen Fertigung von Kleidungsstücken oder Möbeln mittels 3D-Druck übergegangen werden.
Wie werden wir auf den Umbruch reagieren? Sicherlich werden durch fortschreitende Digitalisierung und den Umbruch zur Industrie 4.0 gewisse Berufsfelder verschwinden. Das ist keine neue Entwicklung, sondern war stets eine Begleiterscheinung technologischer Neuerungen. Die allgegenwärtige Digitalisierung lässt sich nicht aufhalten und auch nicht abschotten, sie wird Basis des globalen Wettbewerbs. Es ist also keine Ja/Nein-Entscheidung zur Digitalisierung – die Frage lautet vielmehr: Wie setzen wir sie intelligent ein? Wir können vom Nutzen der Digitalisierung profitieren und müssen versuchen, mögliche negative Begleiterscheinungen zu minimieren. Wichtig für jeden Einzelnen sind eine offene und flexible Grundhaltung, die Bereitschaft zur Weiterbildung und die Neugier, andere Wege auszuprobieren. Dann können wir optimistisch einer faszinierenden, weltverändernden digitalen Zukunft begegnen. //