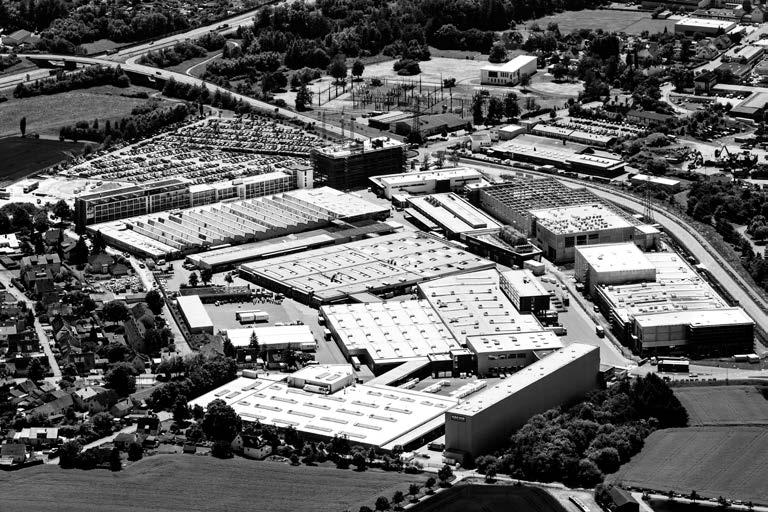
4 minute read
Erfolgsfaktor digitales Maschinen-Management: Kaeser Kompressoren
from Denkraum 4
Erfolgsfaktor digitales Maschinen-Management
Welche Möglichkeiten stecken in der Industrie 4.0? Das Unternehmen Kaeser Kompressoren hat jetzt ein innovatives Geschäftsmodell vorgestellt, das erst durch die umfassende Digitalisierung ermöglicht wird.
Advertisement
von Herbert Lechner
// Kaeser ist ein typischer „Hidden Champion“, außerhalb seiner Branche nur wenigen bekannt, aber dafür in seinem Segment weltweit führend. Durch eigene Tochtergesellschaften und exklusive Vertragspartner ist der Kompressorenspezialist heute in über 100 Ländern aktiv. Das traditionsreiche Familienunternehmen, mit seiner Zentrale im oberfränkischen Coburg angesiedelt, hat schon immer die Zeichen der Zeit erkannt – und gezielt genutzt. Zunächst produzierte Firmengründer Carl Kaeser feinmechanische Ersatzteile für die aufkommende Autoindustrie, spezialisierte sich aber bald zunehmend auf Sondermaschinen für die Thüringer Glasindustrie.
Als die Belieferung dieses Marktes nach dem Zweiten Weltkrieg und der Teilung Deutschlands nicht mehr möglich war, erweiterte Carl Kaeser junior die Produktion um Druckluftkompressoren, die schnell zum Erfolgsrezept werden sollten. Zum Produktionsprogramm der Kolbenkompressoren kamen Anfang der 1970er-Jahre innovative Schraubenkompressoren, die sich durch ein neuartiges Läuferprofil, dem sogenannten Sigma Profil, auszeichnen. Und nach der Übernahme des französischen Kompressorenherstellers Compresseurs Bernard in Lyon entwickelte Kaeser ein erfolgreiches Programm fahrbarer Schraubenkompressoren für die Bauindustrie („Mobilair“).
Contracting für Druckluft Doch nicht nur in der Hardwarekonstruktion beschritt Kaeser immer wieder neue Wege. Eine spannende Erweiterung der umfangreichen Serviceleistung des Technologieführers bildet ein Contracting-Modell, das sich bereits seit rund 30 Jahren international bewährt: Kaeser bietet nicht nur den Kauf der Kompressoren, sondern auch die Druckluft! Gerade für kleinere Betriebe, die keinen kontinuierlichen Bedarf haben, eine interessante Alternative zur Investition in die Geräte. Doch auch für bestehende Kunden kann diese Lösung bedeutende Vorteile bringen. Diese sogenannten hybriden Leistungsbündel kombinieren technisch innovative Produkte mit intelligenten Dienstleistungen aus dem Bereich Engineering. So umfasst das Contracting-Paket außer der Sicherheit, stets die neuesten, und das heißt besonders energieefiziente, Kompressor- und Steuerungsausführungen zu erhalten, auch die laufende Überwachung aller Kaeser-Komponenten. Regelmäßige War tungsintervalle und die Überprüfung möglicher Verschleißfolgen werden zentral gesteuert – und entsprechende Maßnahmen von Kaeser durchgeführt.
Mit solchen Lösungen im Bereich der Drucklufterzeugung wurde eigentlich die Basis für Industrie 4.0 bereits vor Jahren gelegt. Dank der rapiden Steigerung der Datenverarbeitung und neuer kommunikativer IT-Möglichkeiten können solche Dienstleistungen nun noch mehr verfeinert und verbessert werden.
Vorausschauende Wartung Bei Industrie 4.0 geht es bekanntlich um die effiziente Vernetzung und Kommunikationsfähigkeit der Maschinen. Auf der diesjährigen Hannover Messe zeigte Kaeser eindrucksvoll, welche Chancen die neue Dimension der Datengewinnung und des permanenten Datentransfers eröffnet.
Diese reichen von einer exakten Analyse des Druckluftbedarfs, der Konzeption der optimalen Druckluftversorgung über die regelmäßige Wartung und Instandhaltung, die Nutzung im Rahmen eines Energiemanagements bis zur Planung von Erneuerungen, Erweiterungen oder Ersatzinvestitionen. Und das während des gesamten Lebenszyklus einer Druckluftstation.
Der neueste Coup begeistert Kunden wie Entwickler: Das Zauberwort lautet „Predictive Maintenance“, also zu Deutsch vorausschauende Wartung. Das bedeutet nicht weniger, als dass die Datensammlung auf mögliche Störungen hinweisen kann, bevor diese überhaupt auftreten! Die Echtzeitüberwachung zahlreicher Sensordaten ermöglicht nicht nur die unmittelbare Reaktion auf außergewöhnliche Betriebszustände, sie ist auch Grundlage für eine optimale Serviceplanung. Dank
Das Kaeser-Firmengelände im oberfränkischen Coburg – Zentrum eines Global Player mit weltweit 5.500 Mitarbeitern
intelligenter Prognosetools wird man zukünftig schon im Voraus wissen, was tatsächlich in der Druckluftstation passieren wird. Damit können Fehlzeiten des Maschinenparks drastisch vermindert werden.
Big Data der Maschinenkommunikation Voraussetzung dafür ist allerdings, dass alle Komponenten so ausgestattet sind, dass sie einerseits in einem Verbund effizient steuerbar sind und zugleich relevante Betriebsdaten für eine Echtzeitüberwachung gewinnen und an übergeordnete Systeme weitergeben. Moderne Kompressoren und Komponenten zur Druckluftaufbereitung besitzen deshalb interne Steuerungen auf Industrie-PC-Basis, die diese Daten mittels Schnittstellen einem übergeordneten System zur Verfügung stellen können.
So gehen die Daten, die laufend von den Komponenten generiert werden, erst an eine übergeordnete Steuerung, die eine Doppelfunktion hat: Sie ist Managementsystem zur Steuerung der Druckluftstation und Knotenpunkt zur Weiterleitung der gewonnenen Daten. Ein solches Managementsystem muss in der Lage sein, unter Berücksichtigung von Schaltverlusten, Regelverlusten usw. die Kompressoren effizient und insbesondere auch vorausschauend zu schalten. Kommt es zu Auffälligkeiten, wird automatisch im Servicecenter eine Information generiert, sodass präventiv entsprechende Maßnahmen erfolgen können, ohne dass ein Stör- oder Ausfall auftreten wird. Die erforderlichen Datenmengen sind gewaltig. Dies erfordert eine außerordentlich komplexe Struktur zur zeitnahen Analyse und eine entsprechend investitionsintensive Ausstattung im IT-Bereich.
Basis künftiger Innovationen Positiver Zusatzeffekt dieses Aufwands für das Unternehmen und seine Kunden: Diese Daten werden natürlich nicht nur von den Service-Technikern genutzt, um die Anlagen der Kunden zu optimieren, sondern ebenso von den Mitarbeitern in Forschung & Entwicklung. Können doch durch diese minutiöse Kontrolle bestimmte Verhalten von Produkten vor einem Störfall beobachtet und analysiert werden und Muster bzw. Gründe dafür erkannt werden, was zu einem möglichen Ausfall führen könnte. Auf dieser Basis lassen sich auch die Komponenten selbst weiterentwickeln und optimieren. Ja sogar ganz neuartige Anlagenkonzepte sind dadurch denkbar.
Störungen und Fehlfunktionen werden sich nie völlig ausschließen lassen. Doch mit den digitalen Mitteln der Industrie 4.0 besteht die Chance, sie auf ein Minimum zu reduzieren. //