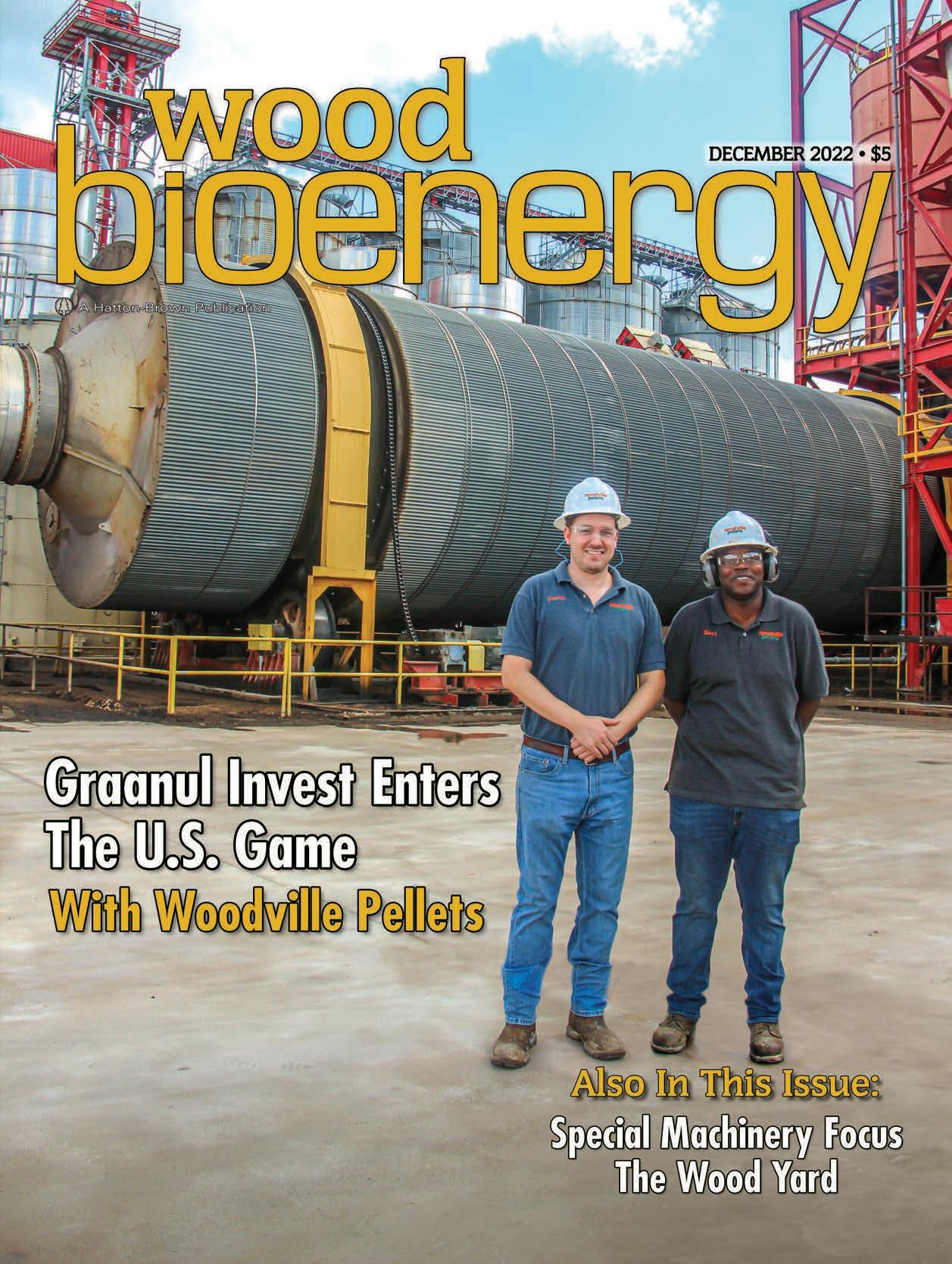
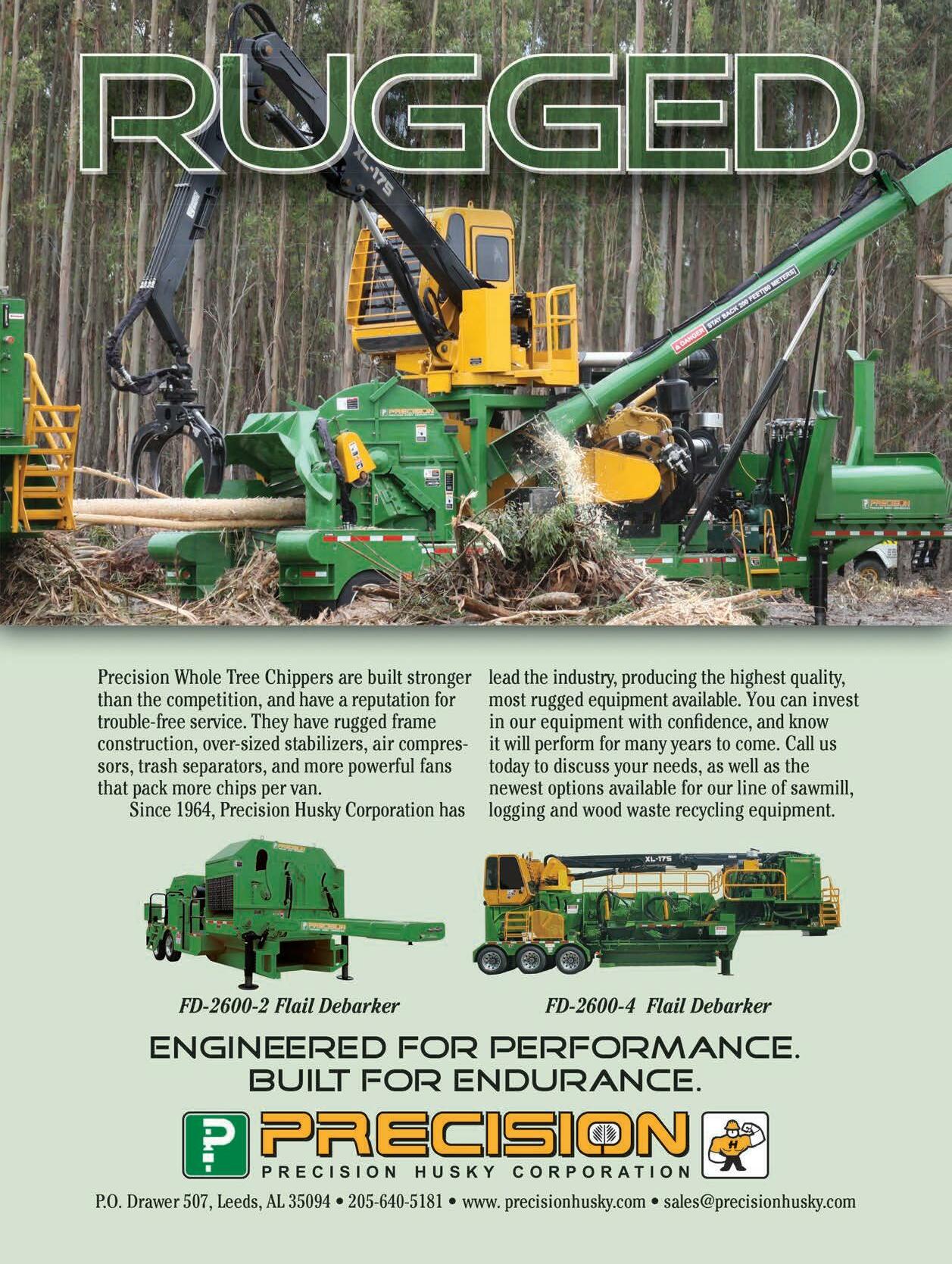
The news that Strategic Biofuels in Louisiana is working with the Forest Service and other groups on biomass standards is big. Developing a Renewable Fuel Standard (RFS) system to make it easier to incorporate forestry feedstock into biomass and green energy initiatives and projects by ensuring raw materials meet sustainability standards is going to make utilization of woody biomass more attractive—and that’s good for the wood bioenergy industry.
Having such a system is yet another tool to aid in the increased utilization of wood as a sustainable energy source. Strategic Biofuels is taking the lead in developing an auditable system to track feedstock qualification, source-origin and chain of custody data to support its Louisiana Green Fuels project that will use woody biomass to produce renewable diesel and naphtha.
While the Louisiana facility is expected to break new ground with a negative carbon footprint and also incorporate well-based carbon sequestration technology, the use of woody biomass as a biofuel feedstock is an encouraging sign.
The EPA is required under the Clean Air Act to set RFS volume requirements each year. There are four renewable fuel standards—conventional renewable fuel, advanced biofuel, cellulosic biofuel, and biomass-based diesel.
Traditionally, biofuel has been the province of big agriculture: “Conventional renewable fuel” is mostly corn ethanol; “advanced biofuel” uses mostly non-food crop ag residues and industrial waste as feedstock; “cellulosic biofuel” uses mostly corn stover and similar products; and “biomass-based diesel” has seen soybean oil as its biggest feedstock.
Julie Tucker, National Wood Innovations Program Manager of Bioenergy, Biofuels, and Bioproducts, U.S. Forest Service, notes that “Historically, forest residuals have been a disposal challenge. The Renewable Fuel Standard helps change that by giving the renewable energy sector a financial incentive to convert these unwanted forest residuals to high value biofuels and renewable electricity.”
Tucker adds that EPA must ensure that forest residuals receiving credit under the RFS are qualifying feedstock: “We also want them to be sustainably sourced. This initiative with Strategic Biofuels is an exciting opportunity to do that.”
With large amounts of forest residue volumes available in timber-rich regions of the U.S., it’s important to see timber-based biomass standards set and met. This is especially true in areas where forest health issues and projects create large amounts of biomass available for utilization.
While the development group is being led by the Forest Service and Strategic Biofuels and the full team is still being assembled, members will include representatives from the National Assn. of State Foresters and the American Loggers Council as well as groups representing industrial and non-industrial landowners, tribal interests and others.
It’s critical to have a wide range of stakeholders involved, including wood bioenergy interests, to help develop such a system that has national implications for increased biomass utilization—and help ensure the wood bioenergy industry’s concerns are heard as biomass
Hatton-Brown
Publisher/Adv. Sales Manager ■ David H. Ramsey Chief Operating Officer ■ Dianne C. Sullivan
Editor-in-Chief ■ Rich Donnell Managing Editor ■ Jessica Johnson Senior Editor ■ Dan Shell Senior Editor ■ David Abbott
Publisher/Editor Emeritus ■ David (DK) Knight
Art Director/Production Manager ■ Cindy Segrest Ad Production Coordinator ■ Patti Campbell Circulation Director ■ Rhonda Thomas Online Content/Marketing ■ Jacqlyn Kirkland
North American Sales Representative
Susan Windham ■ P.O. Box 2268
Montgomery AL 36102-2268 334.834.1170 ■ Fax: 334.834.4525 E-mail: windham.susan4@gmail.com
International Sales
Murray Brett ■ 58 Aldea De Las Cuevas, Buzon 60 Benedoleig 03759, (Alicante) Espana +34 96 640 4165 ■ Fax: +34 96 640 4048 E-mail: murray.brett.aba@abasol.net
Classified
Bridget DeVane ■ Tel: 334.699.7837 ■ 800.669.5613 E-mail: bdevane7@hotmail.com
Advertiser
Air Burners 17 772.220.7303
Airoflex Equipment 36 563.264.8066
Baker Rullman Manufacturing 38 920.261.8107
Bio360 32 +33 03 84 86 89 30
BM&M Screening Solutions 35 800.663.0323
CPM-Roskamp Champion 19 800.428.0846
CW Mill Equipment 37 800.743.3491
Evergreen Engineering 36 888.484.4771
Fagus GreCon 22 704.912.0000
FMW North America 29 706.829.3337
Fulghum Industries 10 800.841.5980
Hallco Industries 7 800.542.5526
Kice Industries 23 316.744.7151
Metal Detectors 29 541.345.7454
Mid-South Engineering 34 501.321.2276
MoistTech 35 941.727.1800
Morbark 40 800.831.0042
Nestec 8 610.323.7670
Precision-Husky 2 205.640.5181
Rawlings Manufacturing 38 866.762.9327
Schaeffer Oil 39 800.325.9962
Stela Laxhuber GmbH 15 +49 8724 899 0
Timber Products Inspections 37 770.922.8000 TSI 31 425.771.1190
U.S. Blades 34 800.862.4544
Vermeer Manufacturing 16 641.628.3141
West Salem Machinery 11 800.722.3530
Wolf Material Handling Systems 9 763.576.9040
Wood Bioenergy (ISSN 1947-5306) is published six times annually (February, April, June, August, October, December) by Hatton-Brown Publishers, Inc., 225 Hanrick St., Montgomery, AL 36104. Wood Bioenergy is free to qualified readers in the United States, including owners, managers, supervisors and other key personnel. All nonqualified U.S. subscriptions are $50 per year, Canadian subscriptions are $60 and foreign subscription are $95 per year (U.S. funds). Subscriber Inquiries and Back Issue Orders—TOLL-FREE: 800.669.5613. Fax 888.611.4525. Subscribe or renew online: www.woodbioenergymagazine.com and click on the “Subscribe” button. When requesting change of address, please specify both old and new. Periodicals postage paid at Montgomery, Ala. and at additional mailing offices.
Member, Verified Audit Circulation
Managed By HattonBrown Publishers, Inc.
Postmaster: Please send address changes to: Wood Bioenergy, P.O. Box 2419, Montgomery, AL 36102-2419
All advertisements for Wood Bioenergy are accepted and published by Hatton-Brown Publishers, Inc. with the understanding that the advertiser and/or advertising agency are authorized to publish the entire contents and subject matter thereof. The advertiser and/or advertising agency will defend, indemnify and hold any claims or lawsuits for libel violations or right of privacy or publicity, plagiarisms, copyright or trademark infringement and any other claims or lawsuits that may arise out of publication of such advertisement. Hatton-Brown Publishers, Inc. neither endorses nor makes any representation or guarantee as to the quality of goods and services advertised in Wood Bioenergy. Copyright ® 2022. All rights reserved. Reproduction in whole or part without written permission is prohibited. Printed in USA.
“Productivity improvements across our manufacturing facilities, including debottlenecking, asset utilization increases, and the capacity expansions we have underway, are resulting in production rates that we expect to translate to over 6 million tons next year, and when combined with our improving supply chain conditions and the constructive pricing environment, particularly in Europe, are expected to not only provide modest opportunities in fourth-quarter 2022 to drive incremental margin and cash flow, but also set the stage for substantial growth in 2023 and beyond,” comments Thomas Meth, President and CEO of Enviva, in the company’s third quarter report.
goula cluster in Bond, Miss., subject to receiving the necessary permits. It will have the capacity to produce more than one million MTPY of wood pellets, and, similar to the Lucedale and Epes plants, will export from the Enviva terminal at the Port of Pascagoula.
Enviva is evaluating the timing of a fourth wood pellet production plant in its Pascagoula cluster and anticipates making a decision around year-end 2022. The company is also in the process of securing sites in Georgia and South Carolina and will continue the evaluation process in the coming months to determine which is most suitable for a new greenfield project in Enviva’s “Savannah cluster.”
Enviva recently appointed Mark Coscio as Executive Vice President and Chief Development Officer to lea corporate development and construction functions.
The acquired fee lands contain 7.5 million tons of merchantable timber inventory, or 54 tons per acre, 66% of which consists of higher-value grade products. Average plantation age of the acquired fee lands is 18 years.
The acquisitions are expected to generate an average annual harvest volume of approximately 860,000 tons over the next 10 years. No wood supply agreements encumber the properties, thus enhancing operational flexibility.
As of September 30, Rayonier owned or leased under long-term agreements 2.7 million acres of timberlands located in the U.S. South (1.79 million acres), U.S. Pacific Northwest (486,000 acres) and New Zealand (417,000 acres).
The report states that Enviva is progressing well through the early stages of its growth plan to more than double wood pellet production capacity over the next four to five years, from 6.2 million MTPY to 13 million MTPY. Enviva’s Lucedale, Miss. plant, the first plant in its “Pascagoula cluster,” continues to ramp production, and is on track to reach nameplate capacity of 750,000 MTPY by the end of 2022. In July 2022, Enviva commenced construction of the 1.1 million MTPY plant in Epes, Ala., the second plant in its Pascagoula cluster.
Enviva also announced plans to build the third plant in its Pasca-
Rayonier Inc. entered into two agreements to acquire 172,400 acres of high-quality commercial timberlands in Texas, Georgia, Alabama and Louisiana for $474 million from Manulife Investment Management, a timberland investment manager. The acquisitions comprise well-stocked and highly productive timberlands located in some of the strongest timber markets in the U.S. South. Approximately 80% of the acquisitions consist of fee ownership, and the remaining 20% consist of a longterm lease.
Rayonier believe portions of the acquisitions are well-positioned to capitalize on emerging ecosystem services, natural climate solutions opportunities, including bioenergy, biofuels, and carbon capture and storage.
Of the acquired fee lands, 72% are plantable with an average expressed site index of 73 feet. This translates to an expected sustainable yield of 670,000 tons per year, or 4.8 tons per acre per year.
Drax has agreed to a Memorandum of Understanding (MoU) with the carbon finance company, Respira, which could see the largest volume of carbon dioxide removals (CDRs) traded so far globally.
Respira will reportedly be able to purchase up to 2 million tonnes of CDRs from Drax over a fiveyear period, under the terms of the MoU. The creation of the CDRs would be linked to the future deployment of BECCS by Drax in North America.
Drax already aims to invest more than £2bn in its UK BECCS project and its global supply chain by 2030, to remove 8 million tonnes of CO2 from the atmosphere each year. In addition to this it is developing investment plans for BECCS projects outside the UK, including in North America, which could remove a further 4 million tonnes of carbon dioxide from the atmosphere each year.
Will Gardiner, Drax Group CEO, comments, “This agreement with Respira will play a pivotal role in the development of voluntary carbon markets globally and the deployment of BECCS. The
clear demand that we are seeing for engineered carbon removals, alongside the policies being developed by progressive governments in the U.S. and UK to support BECCS, will enable the investment needed to kickstart a vital new sector of the economy, creating tens of thousands of jobs, often in communities which need them the most.”
Ana Haurie, Respira International CEO and co-founder, adds, “Rising global temperatures underline that it is absolutely vital for corporates to augment existing carbon emissions strategies with further solutions to address the climate emergency. This partnership with Drax marks a new and exciting development for Respira as it is our first engineered carbon removals project.”
Under the terms of the MoU with Drax, Respira would be able to purchase CDRs produced by Drax in North America, receiving up to 400,000 tonnes of CDRs a year over a five-year period to sell on a voluntary carbon market. This would enable buyers, such as corporations and financial institutions, to achieve their own carbon emissions reduction targets.
Five-hundred fifty global scientists have signed off on a letter to the presidents of the European Commission, European Parliament, and European Council that outlines numerous climate benefits of woody biomass and sustainable forest management.
“Obviously forests are at increasing risks from climate change, while at the same time they have the capacity to mitigate climate change and increase biodiversity with proper management and use of its products to secure a bioeconomy and renewable energy supply in Europe,” the letter states.
The letter points out that in many European countries a high level of growing wood stocks has
already been reached and further accumulation of biomass appears risky under climate warming. “Without harvesting, the forest volumes will saturate. The carbon sink will approach zero, as it is visible in the old-growth areas in the Ukraine pristine forests.”
The climate benefits of wood products are multiple, and these follow sustainable management, the letter adds. Use of wood as building material is not only an additional storage for CO2, but additionally secures urgently needed affordable housing, reduces energy demand of buildings and creates sustainable employment in all European regions.
“Additionally, manufacturing wooden products will also result in residues like cuttings, shavings and sawdust that are suitable for producing energy. The energy content of remnants and residues of wooden products at the end of their life cycle should be recovered ideally by using BioEnergy with Carbon Capture, Use and Storage (BECCS). It has been argued that wood is inefficient for energy production due to its low energy density compared to fossil fuels. However, this comparison is unfair. Fossil fuels will not be available in near future. When the energy transition in Europe has been successfully achieved, biomass-based carbon capture and storage technologies have also the ability to produce hydrogen and biochemicals.”
Strategic Biofuels has announced that the Louisiana Community Development Authority’s (LCDA) Executive Committee voted unanimously to adopt a resolution granting final approval for the issuance of up to $1.1 billion of its revenue bonds to finance a portion of the Louisiana Green Fuels project (LGF) in Columbia, La. The utilization of waste materials to produce fuels enables the LGF project
to utilize these tax-exempt municipal bonds. Citigroup Global Markets Inc., the investment bank and financial services company, has been engaged to serve as the underwriter of the bonds and will be responsible for marketing the bonds to investors.
The LCDA is a statewide Conduit Issuer of revenue bonds and is authorized to issue bonds to finance economic development, industrial and manufacturing facilities, and a variety of projects on behalf of local governmental entities throughout the State of Louisiana. Although the State of Louisiana authorizes the issuance of the bonds, they are not guaranteed by the State or the LCDA nor are taxpayer dollars involved.
To date, Strategic Biofuels has received $450 million in total bond allocations—$200 million for 2020 and $250 million for 2021. The company anticipates receiving substantial additional allocations over the next two years.
Velocys plc, a sustainable fuels technology company, announced that its proposed facility Bayou Fuels in Natchez, Miss. has been re-optimized for maximum decarbonization to a negative carbon intensity of -375g CO2e/MJ (previously -144g CO2e/MJ), abating the carbon emissions from the equivalent of 1.1 million return economy trips from San Francisco to London per annum.
The significant improvement in negative carbon intensity has the potential to increase future revenue for Bayou Fuels and enhance the attractiveness of the project for third party project funding. In particular it will allow the Bayou Fuels project to derive maximum benefit from the 45Z tax credits under the Inflation Reduction Act of 2022, which incentivizes the total amount of avoided carbon instead of the volume of sustainable fuel supplied, thus prioritizing those technologies which offer routes to negative carbon intensity fuels.
The Bayou Fuels project, which is expected to enter production in 2026, will now use renewable energy derived from sustainable biomass power instead of solar power This will approximately double the carbon savings for its aviation customers, thereby enabling maximum carbon abatement from the Velocys conversion pathway. The Bayou Fuels SAF (Sustainable Aviation Fuel) prospective carbon intensity of -375 g CO2e / MJ avoids more than 15 times as much CO2 as a typical HEFA SAF gallon from soybean oil.
Velocys carried out preliminary boiler engineering evaluations, identified the most appropriate carbon capture system, confirmed the availability of sustainable biomass and re-evaluated the layout of the overall facility in order to validate the use of biomass power at the plant.
Henrik Wareborn, CEO, comments, “The Inflation Reduction Act means that future SAF production must
focus on the number of tonnes of avoided carbon and not gallons of fuel produced. The use of biogenic feedstock, biomass power and CCS at our project in Mississippi equates to a yearly reduction of 1.8 million tonnes of carbon and means our technology is ideally positioned to benefit from the SAF tax credits of the IRA.”
The facility will be first of its kind and Velocys’ agreement with Oxy Low Carbon Ventures, LLC (OLCV) will take these environmental benefits a step further through CCS, whereby Bayou Fuels CO2 will be captured before it enters the atmosphere. This combination of CCS-ready technology and OLCV’s expertise in storing CO2 will enable the Velocys’ facility to produce net negative carbon intensity fuels.
Enviva Inc. has announced that Thomas Meth, Enviva’s President, has been appointed the Company’s Chief Executive Officer and will become a member of Enviva’s board of directors, while retaining his title as President.
This announcement comes at the same time Enviva announced
that John Keppler, Chairman and CEO, is expected to assume the role of Executive Chairman, consistent with the succession plan developed by the Board. Prior to doing so, Keppler will be stepping down from his responsibilities to pursue medical and surgical treatment to address a cardiac valve issue. Enviva expects Keppler, who co-founded the company in 2004 with Meth, to remain available to the company, and return in the active Executive Chairman role early in 2023. Ralph Alexander, who has been a member of the Board since 2013, will fulfill Keppler’s duties as Chairman of the Board until Keppler’s return, when Alexander is expected to become Lead Independent Director.
“After careful consideration, I have decided with my medical team and family to step back and focus on my heart condition,” Keppler comments. “The Board and I are delighted that Thomas Meth will serve as our next CEO. Thomas has been my closest business partner in building Enviva into the great company it is today, and I know he will continue to excel in leading Enviva’s growth trajectory as we execute our plan for the future.
Thomas is an exceptionally skilled leader who has full command of all
facets of the company and has earned the respect of our employees, customers, investors, and other key stakeholders.”
Thomas Meth says, “All of us at Enviva wish John the best as he prioritizes his health and full recovery, and we look forward to his return as Executive Chairman. We are laserfocused on executing the previously announced business plan and are on track to deliver results for 2022 in line with the expectations we outlined recently on our third-quarter earnings call. The world wants costeffective, ready-to-deploy bio-based alternatives to fossil fuels, from secure sources, and that’s exactly what we offer.”
A multidisciplinary team of researchers at the University of Georgia and two partner institutions have been awarded a $15.8 million grant over five years from the U.S. Dept. of Energy to reengineer poplar trees to be used as a sustainable energy source.
The researchers will use state-of the-art biotechnology approaches to breed the trees as a multipurpose crop that can be used for bioenergy, biomaterial and bio-
product alternatives to petroleumbased materials.
“Poplars are among the fastest growing trees in the U.S. and are important for both carbon sequestration and global carbon cycling,” says Robin Buell, principal investigator on the grant and the GRA Eminent Scholar Chair in Crop Genomics at the Center for Applied Genetic Technologies in the College of Agricultural and Environmental Sciences.
The team will start by measuring mRNA transcripts in single cells—mRNA transcripts are portable strands of RNA that encapsulate the information contained in a gene—and will look at how the 3D DNA changes in single cells. From this, they will create a cell type-specific gene expression and regulatory map of poplar that will provide new information on gene function.
Ultimately, the project aims to
fabricate new types of poplar through genetic modification.
“What we propose is to genetically engineer poplar to make it a multipurpose crop by changing its architecture and engineering it to produce different things in the leaves and wood,” Buell says, adding that the team will try to engineer several different types of poplar trees in the study to take advantage of different plant materials—such as the wood or the leaves—for different uses.
Through biotechnology, plant materials harvested from the reengineered architecture of the tree will be used to create products that have the potential to replace petroleum-based products.
A research team in Auburn University’s College of Forestry, Wild
life and Environment (CFWE) is working to find solutions to an increasing threat to pine forests needle blight. Through a $2.1 million U.S. Forest Service grant, Lori Eckhardt, a professor of forest health, and her team members in the college— Joseph Fan, associate professor of forest ecology and statistics; Lana Narine, assistant professor of remote sensing and modeling; and Janna Willoughby, assistant professor of population and conservation genetics—are aiming to determine the impacts on productivity and biological causes of needle blight.
Insect pests and fungal diseases are a great concern to the forest industry, as costs associated with damage caused by non-native pests and pathogens within forests throughout the U.S. were estimated to be valued at approximately $4.2 billion annually.
Historically, the disease has only infected longleaf pines, or Pinus palustris, but in the last few years, the disease also has begun to infect loblolly pines, or Pinus taeda, in young and mature stands.
Alabama Forestry Commission (AFC) notes the first sign of infection is discoloration of the needles. Infected needles will contain circular lesions with a brown spot surrounded by a yellow halo. Over time, the infected area will turn brown with a dark red or dark green border. The discoloration begins in the lower portion of the crown and moves up as the disease spreads by rain and wind events. An easy way to identify the disease is if the pine needles look as if they have been scorched by fire, even though there has been no burn.
The cause for this change in behavior of the disease has yet to be determined, but it can be speculated that it may be a new sub-species that has evolved from the original fungal pest, according to AFC.
“An investment in mitigating forest pests, such as those associated with needle blight, requires adaptive management geared to prevention and remediation that provide economically sound solutions,” says
Eckhardt, team leader, CFWE professor of integrated forest pathology and entomology and director of the Forest Health Cooperative.
Through their research, landowners and forest managers may be able to predict future timber revenues more precisely from affected stands and adjust management activities accordingly.
“We hope to determine the distribution and movement of the needle pathogens, determine if their appearance is due to more aggressive strains and understand the disease cycle and the environmental factors that drive their emergence and distribution,” adds Eckhardt.
University of Arkansas at Monticello (UAM) hosted a ribbon-cutting ceremony for the Arkansas Center for Forest Business, housed
in the UAM College of Forestry, Agriculture and Natural Resources building on the Monticello campus, October 3, 2022. Approximately 200 people attended the ceremony, where Arkansas Governor Asa Hutchinson served as the keynote speaker.
The center was created to provide market-based economic solutions to forest resource issues. It aims to improve business practices for forest enterprises and enhance the economic competitiveness of Arkansas’ forests in a global economy. Gov. Hutchinson provided seed funds of $450,000 to establish the center in June 2021.
Dr. Matthew Pelkki, professor, and George Clippert Chair of For estry in the UAM College of For estry, Agriculture and Natural Resources, serve as the directors of the Arkansas Center for Forest Business. During the ceremony, Dr. Pelkki highlighted the origin of the
center, explaining, “About 12 years ago, Dean Emeritus Phil Tappe and I came up with a simple concept: healthy forests, healthy forest economy, healthy forest businesses, and vibrant rural communities are really complementary. They all work together, and it is a win-win-win situation for the forest, the people, and the economy, so we put together a proposal for the Center for Forest Business with the help of a long list of people.”
Dr. Peggy Doss, chancellor of UAM, said the center will partner with programs at the UAM Colleges of Technology in Crossett and McGehee to provide additional educational opportunities to those pursuing forestry-related careers.
For the ribbon cutting, Gov. Hutchinson landed a blow from a sledgehammer on the end of a precut log, knocking free a wooden cookie to reveal the Arkansas Center for Forest Business logo.
WOODVILLE, Tex.
Plagued by never-ending drama—from financing to fire—the former Texas Pellets facility here and its nearby port facility never saw the consistency that many other industrial wood pellet operations in the pine-rich U.S. South have experienced over the last decade. Instead, it battled engineering issues, machinery issues, staffing concerns and then finally a bankruptcy. When Baltics-based Graanul Invest, one of the world’s largest and most reliable wood pellet producers, purchased the mothballed six-year-old plant at auction in 2019, to be blunt, the facility was a mess. But it had an untapped potential. But first, some of the lingering legal messes had to be cleared by the administration. Then the familiar song of COVID-related delays killed some of the company’s timelines for re-start. But, as they say, the past is the past and the future, well, the future for Woodville Pellets, as the operation is now called, is bright.
And it starts with recent industry veteran hires Jason Ansley as Vice President of U.S. Operations and Earl Herndon as General Manager of both the Port of Port Arthur facility (which was included in the purchase) and the Woodville site. The pair, having worked together for another manufacturer, have an easy comradery and clear vision of what they want the facility to achieve. Both see what the plant can be and want to get there—while also recognizing the process will take some time.
“The path we are on is going to be bumpy. There are things that will be up and down. We’re going to find something we didn’t expect,” Ansley says of the process to bring the facility to Graanul’s world-leading standards. But he’s quick to point out the team in place is going to help them get there together.
Herndon echoes him by saying that with all transitions there are pain points, and turnover happens, but the knowledge base with the 78 employees, some of whom have been with the facility since commissioning, is unmatched. And the team will stay focused and reach its aspirations as long as everyone, including the two at the top, don’t get overwhelmed.
Adding, “It’s always going to be about people; that triggers everything else. You focus on people and you get everything else done.” Herndon has only been on the job since late summer, but putting people first has already helped the plant actualize some of its goals.
Herndon is also incredibly invested in the team because this is his first facility to manage. He says he had gotten out of the industry when Ansley came calling to chat. Once his steel toes hit the ground and the sweat
started coming, he knew he wanted in.
“I love the energy of the facility, but I also love the ability to be active here. You can affect real change here,” Herndon says. “You’re on the ground floor, but there’s also Jason’s leadership. He is really understanding if we want to change something or try something different. He will talk with us about it, get the details and let us go do it.” This perspective and open line of communication has brought the team success in data reporting and becoming much more aware of possible maintenance and processes that can help the plant run more efficiently, and strive to reach its nameplate capacity of 500,000 tons annually.
While Ansley and Herndon are leading the way in Texas, they are not on an island, and are definitely not without support from their head office in Estonia.
Although Graanul Invest is a relative newcomer to the North American landscape, the company is well-established as the second largest pellet producer in Europe with 11 pellet plants and six combined heat and power plants operating in Estonia, Latvia and Lithuania. The U.S. facility brings Graanul’s pellet production capacity to 2.7 million metric tons. Ansley reports that Graanul has a good balance in that the team overseas is willing to help out, send people over, pick up the phone and support the U.S. team, but also is willing to allow the U.S. operation to take point and work through the process and get things done on their own. Herndon says the Graanul teams in Europe are very conservative in their thinking, and like to think things all the way through before making suggestions—an approach he respects deeply.
Ansley, who has spent time at the European plants, says the culture that Graanul has worked hard to build is evident. Employees are methodical in their approach to the care and upkeep of the plant’s machinery and structures and invested in the work the company is doing. Exactly the way he wants Woodville’s culture to become. He says, “You can tell it was not an overnight process, they invested time and money in getting it right and now culturally, they are invested in sustaining it.”
Herndon was not able to make the trip abroad, but from talking with other managers, watching videos Ansley and others have taken, he says he got a good feel for the operations, and loves the way they are organized. He echoes Ansley that it was clearly not an overnight process but something he certainly wants to reach in Texas—even if that means moving deliberately and recognizing the discipline needed to get to the point where everything doesn’t have to run full-speed all the time. Instead, Herndon is having the team focus on small pieces of the single points of failure that have been identified, or areas that need cleanliness attention, get them handled and reach sustainability. Then move on to the next portion of the process. For Herndon and Ansley, it’s all about the sustainability of the plant—a
plant they’ve only been working with for right around six months as a team, and a plant that Graanul has only had control over for three years.
“It’s an interesting spot to be in. This plant is nearly 10 years old. It obviously went through a bankruptcy. Graanul has only owned the facility for three years. In the grand scheme of things, that is not a whole lot of time,” Ansley says. “The facility has good bones with the layout and equipment.” Woodville has to get the right people in place, the right systems in place and then strategically invest in upgrades where it makes sense, he adds.
The European plants put more emphasis on stability, Ansley notes, than on just throwing around investments. “They do not run around and just tape something up and hope that it lasts for six months. They stop and fix it. They have redundancies built in. Earl and I are going through a list of where our single points of failures are and working through that. But it is too early to commit to next steps on projects. Because they are definitely out there and the company is very supportive of investing in the success of the plant.”
Ansley reiterates that this will not be an all at once process. There have been several projects that have been completed since the purchase, including air emissions control enhancement and upgrading the wet hammermills. The single most obvious project done by Graanul is pouring concrete and building a maintenance shop that wasn’t previously on site. Herndon and Ansley also added stairs to the Port of Port Arthur. Herndon says these projects aren’t, on face value, going to get the company more tons, or reduce costs. But it is about helping people do their jobs and making a better working environment. And that goes a long way culturally in the plant.
The facility operates four shifts, which gives staff plenty of time to transition from day to night. This includes giving staff every other weekend off, with two weeks on days and then back to nights. “This way you can get your internal clock in order instead of constantly switching shifts. And you always have time to run errands and get those kinds of things done, while still having your weekends back,” Herndon says of the shift change Ansley made.
The changes to the shifts is part of the bigger emphasis Herndon and Ansley put on employee experience. Herndon explains, “We made some key internal moves. A lot of people have been here for years, through the ups and downs. They are really dedicated. If I have a question about a part, Keith Mahaffey has the knowledge. We want to invest in them and make their jobs easier. We want to turn this plant around and we want to sustain it.”
Herndon is an electrical engineer by trade and selfproclaimed super nerdy dude, but he’s not afraid to get his hands dirty. He believes the best way to get buy-in is to show he’s willing to do the work. He admits, laughing, that sometimes the employees don’t want him in the thick of it, but he still shows up anyway: “The only way we get to where we want to be is by us all working together, not me and Jason sitting in the high tower yelling down direction about something. It is us on the ground floor, walking the plant, looking at things and making sure people are staying safe.”
Another culture-focused change Ansley and Herndon have implemented is War Room meetings, where each area manager is responsible for reporting their data, written on a white board, and reported on to other man-
agers during a fifteen-minute stand-up meeting. In these meetings, upcoming changes and ideas are discussed and managers are given equal say in what happens— with a twist.
Herndon says one of the area managers, Sonny Patrick, was always coming up with different ideas, so one day Herndon gave him the go ahead. But he told Patrick he only had this amount of time to complete the action, a little good-natured competition between the areas, as another area was also trying out an idea that day. Herndon gives cushion for the ideas he thinks are better than others. Explaining, “So, when we are in the War Room, and they say this is how long this action is going to take, if they’ve had a great idea, I will give them a little more buffer. They love that because it makes it a little more lighthearted instead of ‘gotta go do this or gotta go do that.’ Any of these ideas, I look at it from an engineering perspective. I am all about trying different things as long as it is not going to violate OEM constraints that will lead to other issues.”
Ansley loves Herndon’s approach to management, and says they are on the same page at (nearly) most turns. Implementing two-hour reporting, KPIs, and daily War Room meetings are things both were accustomed to at other facilities and helps give better visibility in the process and by using them in Woodville help take this plant to the next level.
Ansley points out that the Estonian head office did a really good job of giving Woodville a good foundation and providing good business systems that are automated. As Graanul has a very lean corporate staff, and each plant staff is relatively small, the company has put considerable time and effort into putting systems together that help operators do their job. Graanul has service programs for PM routes that are integrated onto tablets; items that help automate the scale house, tons tracking, fiber procurement, where typically if you were to come into a situation like this—taking a plant out of bankruptcy—there would be lack of organization. Fortunately, Graanul has already set the foundation for a digital factory, and now it is on the staff at Woodville to use those systems and leverage them.
Woodville operates on a 50/50 mix of lower value stemwood to pre-processed material, 100% southern yellow pine, of which 40% is residual chips from local sawmills, 10% is dust. Once trucks are received through the scale house, they are either dumped by a Phelps dumper to the chip pad or unloaded to the stemwood yard using a Caterpillar 990 wheel loader or LogPro crane. Fuel from the dumper goes onto a reversing belt from the chip pad. Lower quality stemwood is debarked using a LogPro drum debarker and chipped by a CEM chipper.
The chip pad is outfitted with an FMW stacker-reclaimer with screw to rake the pile. Chips are conveyed
to another belt, where the pulverized material goes to the Champion wet mill island, complete with Vecoplan pre-screeners that are currently being tweaked to reach operational level, then to the dryer island. Woodville’s dryer island is a dual line TSI system. This includes the heat energy system
and dryers as well as the emission control system for the dryers, the wet ESP and RTO. The system was originally supplied over 10 years ago as the first of the new generation of TSI dryer islands that featured Sigma Thermal furnaces and TSI single pass recycle dryers along with newly intro-
from a single source.
Currently, dry material does pass additional processing, with four Vecoplan pre-screeners to help reach targeted chip size of between 88-92% 2 mm chips for producing smaller industrial pellets.
After the Champion dry mills, two Tank Connection dust silos act as more of a buffer between process islands. Part of the redundancy built in to help handle maintenance, these silos allow the facility to perform work without stopping the press hall. The silos are able to feed both lines of the press hall, which is broken up as line one with CPM presses
The wood pellet manufacturing process is not kind to regenerative thermal oxidizers (RTO). The process air flow downstream of the dryers contains a significant amount of moisture, particulates and other contributing factors that make life difficult for the owners and operators of these required emissions control systems. The question most deal with is not if, but when, an RTO requires a significant repair or rebuild. To complete this type of project, it requires two of the most feared words for any manufacturing facility: Money and downtime.
But, do not lose all hope. Each day presents an opportunity to recoup both. Everything done during the life cycle either reduces or buys back more time from the moment a repair or rebuild is required.
A well-developed preventive maintenance program? Buys back more time. Consistent bake-outs? There’s a few more weeks. Poor specification of materials of construction during the last rebuild project? Expedites your next major service to the next plant outage.
Choosing the right components for your process stream and a proper maintenance schedule will have long lasting, encouraging effects on overall system operation and uptime.
Rebuilding an RTO is not a small investment. In addition to capital costs for material and onsite installation services, end users accrue hours of internal costs working with suppliers, subcontractors and others in development. The most efficient route is to work with a company that has significant experience rebuilding RTOs and can cover nearly all aspects of the design, fabrication, project management, installation and commissioning. Having one point of contact for all aspects of a rebuild will lead to a more complete and successful project.
Regardless of the company you choose, the best approach is to follow a series of strategic steps.
What is the end goal? If capital costs are limited or the longer-range plan is to completely replace the RTO system at some point, smaller repairs may be the best approach. If returning the existing RTO to a like-new condition with plans for another decade or more of operation is the goal, the plan should include a full rejuvenation of the RTO unit, using updated media arrangements, materials of construction and other new components.
These discussions should happen internally and with
RTO projects don’t have to mean lost time and money.
an expert in RTO rebuilds. To better assess the situation, ask potential rebuild partners for potential highlevel budgetary costs.
It’s important to evaluate existing information related to the design and operation of your RTO system. Providing data about the process is helpful when choosing ceramic heat exchange media, materials of construction, insulation, etc. The following items are normally requested:
Upstream process data: It’s imperative to have data about air constituents, moisture levels, temperature and other operating conditions. Knowledge of corrosioncausing agents guide materials of construction decisions and mitigate premature degradation of the newly rebuilt system.
Recent test reports: Destruction efficiency tests or particle loading assessments provide knowledge of what is in the process and how the RTO has been operating.
Maintenance reports: It is important to have your RTO inspected annually. Providing a baseline of the health of your equipment over the years helps reduce the chance of future operational failures.
RTO drawings: To expedite pre- and post-contract processes, provide existing drawings of the equipment and your site. General arrangements and component details provide valuable information.
A great first step is to bring in a system expert to complete a full assessment or inspection of the RTO. This RTO unit review will confirm existing issues and may uncover additional items that require attention.
In the long run, identifying a broader scope initially will mitigate any unexpected future shutdowns and remobilizations. A detailed report should highlight the items required as part of the rebuild.
At this point, a decision about what to include in the rebuild project needs to be solidified. If destruction efficiency is of concern, now is the time to replace the worn valves. If the process fan is operating at maximum capacity, a change in ceramic media will reduce wear, while providing additional air flow capacity. Once a budget has been established, a complete scope of work can be developed to ensure the vendor can quote accurately and efficiently, and price effectively. Furthermore, let the vendor know the amount of downtime you have available. While the scope of work requested cannot always be completed in that time frame, using multiple crews, around-the-clock shifts, and onsite pull ahead work before the RTO shuts down can mitigate downtime.
The goal of any major rebuild is to make the system last long term. As a result, the vendors should be cognizant of the proper materials of construction for the job. Improperly selecting components for the application could lead to a rebuild situation 12 to 18 months later. The following items generally make up the largest purchased equipment costs and are most affected by your air process stream:
l Cold faces: These structures provide the structural support for the ceramic heat exchange media bed.
High moisture or chlorides in your process stream can contribute to premature degradation of these structures and lead to a catastrophic failure. While 304 stainless steel and 304L have very similar structural similarities, 304L contains less carbon, which makes it more structurally capable in corrosive environments. Furthermore, the addition of more beams, bars and perforated plates will increase the likelihood of a long-term solution. Invest more initially or invest even more later as a result of component failure.
l Air flow dampers: Improving or replacing these apparatuses is crucial to the overall destruction performance of the RTO unit. It‘s worth the investment to consider a more robust design or include air seals for better performance.
l Ceramic heat exchange media: Switching from a random packing ceramic media to a more modern structured block could significantly increase process air flow capacity without major modifications to your fan or variable frequency drives. Also, using a mix of different styles of ceramic block can relieve the organic particulate plugging that is carried over from your dryers, without sacrificing thermal efficiency and experiencing higher utility bills.
Rebuilding RTOs is never convenient. Even if planned well in advance, the size and scope of the project still takes away from what these companies do best—producing wood pellets. But, by following the above steps and considering all of the factors discussed, operators can reduce downtime and achieve long-term RTO sustainability.
Greg Thompson is key account manager in the Clean Technology Systems division of Dürr Systems, Inc., located in Southfield, Mich. He earned a B.S. from Eastern Michigan University in Ypsilanti, Mich. and has 19 years of experience in the emissions control industry. This article and photos were submitted by Dürr as part of their Wood Bioenergy Conference gold sponsorship package.
Ctime in years to discuss the state of bioenergy and its future potential.
Around 200 industry insiders gathered for the Wood Pellet Assn. of Canada (WPAC) conference in Vancouver, September 20-21. Speakers from coast to coast assembled to tackle questions surrounding fiber supply security, local economic development, public perceptions, climate change mitigation, and plant safety.
WPAC president Vaughan Bassett, a senior vicepresident for Drax, welcomed attendees with a summary of the association’s activities over the pandemic years. Membership grew despite the supply chain disruptions and communication challenges. The association’s leadership, led by executive director Gordon Murray, made strides in the government relations and policy fronts, safety, domestic outreach, and marketing.
Both federal and B.C. provincial governments took the stage to address the industry and layout their policy priorities.
Monique Frison, the director general of Trade, Economics and Industry branch of the Canadian Forest Service, summarized the federal outlook on Canada’s forest landscape and the role of bioenergy. “Biomass and pellet companies play a very clear role using the material that 20 to 30 years ago was a waste product,” she said.
The Canadian Forest Service conducts an internal pellet mill survey, she said, encouraging producers to
of declining annual allowable cut (AAC)—a growing challenge for the entire B.C. forest industry. As many have heard before from the Canadian government, the solution they see is in shifting the forest sector from high volume to high value.
MacDougall said their figures estimate four to six million megatons of greenhouse gas (GHG) emissions are lost to slash pile burning in the province. Pellets are among the opportunities to further utilize slash pile residuals, especially in indigenous communities where they can convert to wood energy, she said.
Bioproducts are another area of focus for the province, she said, highlighting project examples including FPInnovations’ testing of lignin-containing asphalt and the University of British Columbia’s research on bio-fabric made from softwood kraft pulp. Pellets can address challenges with the transportation and processing of harvest residuals, and the creation of a standardized feedstock, to make these projects sustainable, MacDougall said.
“Now is the time for B.C. to lead in the bioproducts sector,” she said.
A panel formed to discuss wood pellets’ role in communities and local economic develop took the stage next, with speakers representing a pellet producer, Indigenous development corp., supplier and policy planner.
Diane Collins, general manager with the Kitsumkalum Economic Development Group, spoke first
and outlined the Indigenous values that center their development in the forest industry: Only take what can be used; use everything taken; all things are connected in the chain of life, and we must support the ability for all living things to thrive.
The Kitsumkalum community is a small First Nations village just west of Terrace, B.C. The Nation works closely with Skeena Sawmills and Skeena Bioenergy.
Skeena president Roger Keery said they work with more than 20 First Nations, most of which have active forestry operations.
Their sawmill and pellet plant are located within the town limits of Terrace, B.C. Community support is a critical cog in their business wheel. “The community and company succeed or fail together,” he said. Every business decision they make must balance their financial success with the priorities of the community.
Focus turned next to Atlantic Canada communities with presentations from Jonathan Levesque from Biomass Solutions Biomasse (BSB)—a division of Groupe Savoie in New Brunswick that supplies biomass boilers, and Paula Cook, a senior energy engineer with the Government of Nova Scotia.
Both addressed provincial policy developments to support bioenergy in their provinces. Cook outlined a study she led in Nova Scotia to understand the emission reductions and cost comparisons of various heating options for replacing oil boilers in public buildings.
Based on the study’s conclusions, Cook said, “Wood heat is an excellent scenario, especially when we have aging assets.”
The next three presentations fell under the session title of “Setting the record straight.”
Senior communications consultant Karen Brandt, who has been working closely with WPAC to share key messages for the wood pellet industry, outlined ways companies can help share their brand message. One tip: “Don’t get stuck on the hamster wheel,” Brandt said. In other words, don’t spend the majority of your effort correcting misinformation. Instead, she said, focus on doing the right things and “walking the talk.”
The next presenter, Phillippe Theriault with Tsi Del Del Enterprises, spoke directly to feedstock harvesting on the Tsideldel First Nation forest licenses, west of Williams Lake, B.C. Tsi Del Del Biomass formed in 2018 to focus on biomass and hog fuel recovery from their logging operations in order to use all of the fiber they were harvesting for solid wood products.
Nearly one million cubic meters of fiber has been recovered for biomass purposes since the company formed—diverting what would have been burned in slash piles to products such as pellets or hog fuel for Atlantic Power. Theriault made the point that without favorable biomass policy in B.C., larger forest product companies may choose to invest in other areas of
North America, but First Nations cannot. They need support for their activities that enable the full use of their resources.
Tsi Del Del partners frequently with the Forest Enhancement Society of B.C. (FESBC) to move biomass projects forward. Executive director Steve Kozuki spoke next to explain how their organization’s early focus on social license meant that they’re an active advocate and storyteller for the biomass industry.
Since being formed in 2016, FESBC has funded 263 projects to the tune of $238 million. Many of these projects supported First Nations companies like Tsi Del Del.
Kozuki shared an example of a wildfire reduction project in which the community’s priority was to thin a section of forest that would allow for reintroduction of native berry plants for berry picking.
The final three presenters of day one addressed climate change mitigation from biomass, beginning with FutureMetrics president William Strauss.
Strauss focussed on carbon accounting in the biomass power sector, noting that if sourced from harvest residuals of sustainably managed forests and mill residuals, wood pellets are carbon neutral in combustion, minus the carbon emitted during production/transportation, as with any fuel. A necessary condition of this is that the annual harvest rate across the managed forest landscape must be less than or equal to the annual growth rate.
Ann Burton, Drax’s new build BECCS projects international lead, outlined an even more optimistic future for the pellet industry’s carbon footprint: Bioenergy carbon capture and sequestration, or BECCS. The technology would see Drax capture and store underground the CO2 produced from the generation of electricity from biomass. The result would be the removal of carbon from the atmosphere.
Drax is pioneering the technology and aims to be commissioning their first plant in 2028, to create the world’s first carbon removal power station by 2030. The international potential of the technology could see the decarbonization of local energy grids.
Continuing the look at decarbonization, Fahimeh Yazdan Panah, WPAC’s director of research and technical development, updated the audience on developments to marine biofuels and wind assist to reduce ocean shipping emissions. Yazdan Pannah noted there is no silver bullet to reduce emissions, but that liquid and gaseous biofuel pathways are short- to mid-term solutions to bring the marine sector closer to its targets.
Day two of WPAC was all about safety, with five speakers taking the stage to outline best practices and ongoing projects to enhance the safety of pellet operations across Canada.
WPAC members take part in monthly safety meetings to check in on research developments and lessons learned. Bill Laturnus, a senior safety advisor with the BC Forest Safety Council, said members should consider themselves lucky to have access to these meetings.
“I really don’t think another industry has anything like that,” he said. Referring to his work with the pellet industry to implement a safety process called bowtie analysis and critical control management, he said the safety meetings, “S et the stage to have the commitment and support from industry before we started the process.”
Fike Canada’s Jeff Mycroft summarized the findings from WPAC’s Belt Dryer Working Group, urging producers who operate or are considering purchasing a belt dryer to read their document to help inform their decisions. The study tackles safety issues and hazards related to direct heated dryers, Mycroft said, but the takeaways are applicable to most dryers used in the wood processing industry.
Kayleigh Rayner-Brown, principal with Obex Risk, shared her work advancing process safety management (PSM) in pellet plants in partnership with WPAC, Dalhousie University, the BC Forest Safety Council and
Dust Safety Science. Her conclusions found that “explicit and effective” integration of PSM in wood pellet plants can help in prevention and mitigation of loss of control incidents.
Mike Tasker, occupational safety officer with WorkSafeBC, outlined the role his organization took on to implement bowtie analysis in the pellet industry with partners like the BC Forest Safety Council. Initial momentum was slow but, he said, but companies have since made significant capital investments to improve processes and lower risk.
The conference wrapped up with a much-anticipated keynote from B.C. political columnist Vaughn Palmer. The seasoned journalist shared his ballot predictions following B.C. Premier John Horgan’s planned exit, and the likely result on forest policy.
Responding to questions from the audience about facing down well-funded and organized ENGOs, Palmer said the fiber study is a significant stand to address a major point in their criticisms. “Your industry, though small, is not alone,” Palmer said, referring to the strides made across the forest industry to address social license.
First printed by Canadian Biomass and reprinted here as part of an ongoing collaborative effort between Canadian Biomass and Wood Bioenergy. It has been edited for length.
Airoflex has been building equipment since 1947 and has dumpers still in operation after 35 plus years. No other company can make that claim. When you purchase an Airoflex standard pivot or extended arm truck dumper, trailer tipper, receiving hopper, or hydraulic cylinder, you know you are buying proven quality.
Airoflex dumpers and hoppers have 100% bolted connections, pre-fit and match marked in our shop to ensure ease of installation. This attention to detail significantly reduces installation costs, time, and resources. The bolted connections allow for easy field replacement in the event of damage or wear. We also employ a highly trained crew of AWS certified welders and in-house quality inspectors that monitor fabrication processes to ensure compliance with our customers’ product specifications.
After-sale customer service is our commitment. Airoflex offers start-up and commissioning services, a large inventory of spare parts, service legs for ease in maintenance, cylinder rebuild and repair, and inspection and testing assistance when required. Search our large, in-stock inventory for pins, pin eyes, pusher pins, pivot bearings, sleeves, adjustable packing glands, packings, and replacement cylinders for the main dumper, backstop, pit doors, and wheel locks.
Airoflex products have been installed throughout the U.S., Canada, Mexico, Central America, South America, and in the Middle and Far East for industries such as biomass, pulp and paper, energy generation, co-generation, rendering, and recycling industries.
CW Mill Equipment Co., Inc. has been building grinders for over 40 years, and strives to advance its best grinder status through added efficiency, torque, proven production, reliability, visible quality, durability, solid value, and customer service.
CW originally began building hay grinders for the agriculture industry but as we began to see the shift in government regulation for landfills, burn bans, etc., we saw the need for a higher quality heavier duty industrial wood grinder. We’ve been responding to the wants and needs of several industries ever since such as the wood waste industry, disaster recovery, biomass fuel industry, and scrap tire industry. When it came to industrial wood grinding, we started from the ground up with a specific goal to take on the toughest applications. We knew that our goal would drive us to manufacture the most reliable, highest capacity tub and horizontal grinder on the market, and we did it with the creation of HogZilla.
HogZilla Grinders are used for waste reduction, recycling, disaster recovery after storms, land clearing, construction demolition debris, tires, or any other tough grinding application.
HogZilla tub and horizontal grinders have been continuously improved over the years, and CW now offers over 20 HogZilla grinder models for buyers to customize ranging from mid-sized to massive including self-propelled track driven and self-loading units and can be powered by either diesel or electric power.
As the cost of diesel fuel has increased, electric powered grinders have become the grinder of choice for an increasing number of grinding professionals over the past several years. If your operation can be laid out and organized around a centralized location, you certainly owe it to yourself to research an electric powered HogZilla.
Of course, there are operations where a stationary machine simply will not work. Portable wheeled machines along with track mounted HogZilla grinders are available with numerous options and are built specifically how you want the machine built. A portable wheeled machine is simple to move around a job site.
We know customers businesses depend on a reliable machine with increased efficiency, reduced maintenance, heavy duty construction, and simplicity. Our customer service and parts support speak for itself, and our customers can attest to that.
For more than three decades, Evergreen Engineering has offered the best possible range of knowledge and capabilities to address retrofit, expansion, and new construction for wood processing projects. We design new safety systems, develop new environmental controls, install power generation and distribution, and improve processes, helping mills across North America remain competitive with greater safety, recovery and speed.
Our projects have included a sawmill upgrade that involved a new stacking system, new head rig infeed system, log yard layouts, new scanning layout, and preliminary design bark and bucking system; a sawmill redesign involving a rebuilt log processing system, additional re-saws and edgers, and a total reconfiguration of the mill waste system; and a log yard optimization project.
For this project, we installed a large and small log high recovery merchandising system and a whole log chipping system. The systems supported both a random length sawmill and a stud mill. The systems included large log, small log, and chip log infeed decks; log processing optimization; residual conveying and chip production; and chip screening and storage systems.
Evergreen’s project scope included civil, structural, and mechanical design and drafting for the log optimization area, chip log infeed deck, chip log handling system, and residual conveying system for the optimization and chip log area. Miscellaneous foundations and structures, such as foundations for a gantry crane and pneumatic conveyor support structures, were also included.
Evergreen is a full-service consulting engineering company, serving the wood products industry since 1985. Our staff comprises mechanical, civil/structural, electrical/controls, environmental, and chemical engineers, designers, and drafters. We can deploy all project phases from planning through construction, including scheduling, feasibility studies, preliminary engineering, capital estimates, detail engineering, process design, environmental permitting, purchasing, commissioning and start-up assistance, and project management.
At FMW, we believe that process consistency creates process efficiency. It is a fact that mills benefit when maximizing consistency at the beginning of the process. The homogenization provided by blended-bed stacker/reclaimer technology contributes benefits that are unheard of in other means of chip handling. The result is a high return for your investment and years of exemplary process benefits.
The blended-bed stacker/reclaimer is the flagship of FMW’s product line. Having developed this pioneering technology in the 1970s, FMW has delivered more machines than all other suppliers combined. Recognized as the world’s undisputed leader for the supply of chip storage and reclaim systems, many of the most respected companies in the forest products industry are FMW repeat customers.
To maintain our technological lead, FMW works relentlessly to improve its products. These product enhancement efforts are led by dedicated R&D engineers whose sole function is continuous improvement. We routinely work with industry partners to evaluate ideas under actual production conditions. Everything that we learn from these efforts, and through the experience of our installed systems, is immediately incorporated into the latest generation of FMW stacker/reclaimers.
In 2020, FMW North America was incorporated with the goal of simplifying the customer-supplier interface while providing our customers with local and immediate support. Later that year, we opened our new parts and service center to better meet our customer needs for the quick and reliable delivery of parts. These developments, along with our team of North American and European service engineers, have made our responsiveness even better than you have come to expect.
There is so much more to say, but the fact is that FMW has developed an outstanding reputation for innovation, engineering, quality, and customer service during its 60 years in business. When considering chip handling projects, whether individual machines or complete systems, give us a call. At FMW, we are your engineers of progress.
For over 65 years, Fulghum Industries has provided quality equipment to the forest products industry. Our organization has endeavored to meet the needs of the forest products market by constantly paying attention to detail, quality and innovations in technology.
Our first product, the rosserhead debarker was the result of the lumber industry’s need for effective debarking to convert slabs and edgings into usable wood fiber. This simple machine has forever changed the operation of sawmills and pulp mills alike by providing economical furnish from what was once waste.
Soon after the first rosserhead, Fulghum realized the industry’s need for a high-quality chipper. Today, Fulghum chippers are recognized worldwide as among the very best in the industry.
In the mid 1970s, Fulghum recognized a need to revamp its product line. This heralded the development and manufacture of the Fulghum drum debarker and log handling crane.
From this beginning our organization has grown to provide a diverse product line including equipment ranging in size and purpose from 48-in. chippers to 175 ft. radius log handling cranes.
Our innovation and expansion have never stopped. Along with updates in our product line, Fulghum has been keenly aware of concept evaluation and testing. In 1965, Fulghum was among the first to recognize the need for remote chipping facilities. This requirement was met by a succession of early experimental concepts that developed into the Fulghum satellite chip mill. Examples of these systems are now in operation for such widely known organizations as Georgia-Pacific, International Paper, Weyerhaeuser, WestRock, Nelson Pine Ltd. (New Zealand), and Forico (Tasmania), among others.
The Fulghum 45-ton log crane is our latest effort to expand our offerings to the forest products industry. This new crane, combined with our 14 ft. drum debarker and 120 in. 14 knife chipper has created a higher production system incorporating the same Fulghum standards and economies realized in our time-tested systems. Today, as always, Fulghum Industries stands committed to providing the finest degree of goods and services to the forest products industry.
Metal Detectors, Inc. (MDI) has strived to create superior technology and exceed expectations in the industrial metal detection sector for nearly 60 years. A family business four generations strong, we continue to set the industry standard while simultaneously expanding into different fields of application.
One of the oldest metal detector manufacturers in North America, MDI has a reputation for superior, long-lasting and effective metal detection equipment. Our professional sales and service staff have over 150 years of combined experience in metal detecting solutions.
MDI designs and manufactures metal detectors for industrial applications and process solutions; primarily protecting expensive machinery and ensuring product purity, in the effort to optimize line efficiency. An MDI system will help to prevent costly downtime and repairs due to tramp metal entering a product line or conveying system, quickly paying for itself and more.
We are proud to highlight our newest line of metal detectors, the 5000-X Series systems. These systems have the tried and true characteristics of our previous models but feature our latest innovations in metal detection technology. One such advancement is our MDI View-Link technology that allows for remote start-up assistance, programming and troubleshooting for any MDI metal detector that it accompanies.
With over 45 years of experience in the forest and sawmill related industries, Rawlings Wood Hogs have delivered a reputation for durability, high performance and reliability. As proven leader in wood grinding technology, Rawlings assists our customers with the design of custom wood recovery systems to meet our client’s specific processing needs and budget.
Rawlings Wood Hogs come in all shapes and sizes, we offer a complete line up of different sizes of both vertical and horizontal hogs to fit any application; from simple stand-alone vertical hogs, to complete multi-dimensional grinding systems. Add a wide variety of available options, and you’ve got the flexibility to customize the perfect wood recovery system. Each system can be designed with work platform decks, choice of belt, chain, vibrating in-feed and out-feed conveyors, metal or magnet protection and product screening that allows the customer to protect their investment while producing a high- quality consistent end product. recognized in the industry as the “Green Monster Hog” and provides the crushing and shearing power needed to handle really tough jobs like green waste, cypress, redwood, cedar, black spruce, poplar and a wide range of other stringy and fibrous material. Each machine is equipped with the Rawlings Super Hi-Inertia solid steel rotor. With the increased inertia of the solid steel rotor our machine runs at lower RPMs than our competitors resulting in overall savings of electricity and maintenance costs. The machines are tolerant of contaminants, rocks and metal without catastrophic maintenance costs if metal enters the grinding chamber.
To help reduce the likelihood of major machine damage caused by certain metal contaminants entering the hammermill, Vermeer has introduced the damage defense system—an option now available for tub and horizontal grinders. If the mill comes in contact with metal while grinding, damage defense system will alert the grinder control and automatically initiate the shutdown process. The system idles the engine down, reverses the infeed or tub and disengages the clutch. Once the contaminant is cleared, normal operation can resume.
“The optional damage defense system is ideal for any tub or horizontal grinder operation that may encounter metal mixed in their incoming material,” says Jeff Bradley, product manager for recycling and forestry equipment at Vermeer. “The system can be factory-installed on new Vermeer grinders, and is available as a refitted option for many older Vermeer grinder models.”
The Vermeer Damage Defense system uses exclusive technology to reduce the possibility of severe damage when large metal objects enter the hammermill, and operators can easily adjust the sensitivity settings for jobsite conditions to help reduce nuisance shutdowns. It is integrated into the grinder’s controls system, and features robust components and a weather-resistant box.
West Salem Machinery (WSM) is a leading manufacturer of grinding, crushing, milling, and screening machinery for biomass fiber, fuel preparation, and other processing applications. Superior componentry and maintenance friendly features deliver the tough, severe-duty equipment that plant managers rely on to keep their facility operating.
l WSM Horizontal And Vertical Grinders/Crushers: Made of the highest quality materials with severe-duty construction for primary and secondary processing of biomass and waste materials. Built to provide a long wear life with low maintenance. Design features insure maximum production with minimum maintenance expense. Full range of machine sizes with capacities ranging from 1-150 TPH.
l WSM Super Shredders: These machines are truly massive shredding machines designed for the highest capacity processing requirements. Mill-duty construction delivers 24/7 operation while producing premium quality feedstock. High tip-speed for consistent fiber sizing, increased screen area for maximum through-put, and flexible/interchangeable tooling with replaceable tips. Super Shredders are efficient and durable, built for the toughest applications.
l WSM 4400 Series Hammermills: Widely used by some of the largest pellet producers to create finished fiber in dry milling applications. Field-proven and reliable, these high capacity milling machines provide superior “fine grind” processing and uniform particle sizing. Rugged design and construction provide reliable operation, low maintenance and long machinery life.
l WSM Screens: Our complete line of screening machines includes disc screens, vibrating screens, oscillating screens, and our revolutionary Titan trommel screens. A full range of screening machines provide the best screen for every classification requirement.
l WSM Systems: WSM can supply metering bins, magnetics, support structures, access platforms, discharge conveyors, and fully integrated systems. In-house design and engineering services ensure complete system integration. Along with engineered systems, we offer project management and start-up assistance.
As a family owned and operated business for over 75 years, WSM has a long reputation for supplying rugged and reliable processing machinery, proudly manufactured in the U.S.
Wolf Material Handling Systems is a leading designer and supplier of fuel yard systems for the biomass power and conversion, pulp and paper, power generation, gasification, resource recovery, mining, chemical, manufacturing & recycling, and other industries that require material handling. Wolf MHS provides complete in-house design, engineering, manufacturing, assembly, and installation for systems using conveyance, stacking, reclaiming, truck dumpers, receiving hoppers and ash/biochar receiving, handling, storage, and removal.
Wolf understands the challenges required to handle biomass and its by-products, and provide the complete process from fuel receiving, sizing, storage, reclaim and boiler feed. With a long history of delivering performance and innovation, Wolf is often considered, not just a material handling systems provider, but a technology partner in the development of projects, by providing complete inter-disciplinary systems and support beginning with the conceptual phase through commissioning.
Wolf MHS has successfully supplied the complete material handling systems for several of the largest biomass power projects in the U.S. Past projects for Wolf include a 115 MW wood waste feedstock biomass power plant (named the 2012 Biomass Project of the Year by Power Engineering) and a 100 MW wood waste feedstock biomass power plant (named a finalist for Power Engineering’s 2013 Bioenergy Project of the Year). In addition, previous projects have included wood waste, agricultural residues and other feedstocks for power generation ranging from 20 to 65 MW.
With 45 years of experience, Wolf MHS systems and equipment maximize process and production efficiency with consistent and reliable flow of materials. Each system is designed to reduce labor and maintenance costs thus consuming less power per mass unit than other alternatives. Wolf MHS is committed to offer each client a material handling solution for their specific site and process requirements. Wolf MHS’s in-house capabilities include consultation for scope definition, system design, equipment engineering, detail drawings, fabrication, assembly, inspection, start-up, and commissioning.
In 2021, the EU remained the global leader in wood pellet production—followed by the U.S. and Canada—reaching an output of almost 20 million tonness, representing around 48% of the global production, according to a Policy Brief from Bioenergy Europe. In 2021, European production capacity increased by 6.2% and production by 8.9% compared to the previous year.
In 2021, the EU consumption of pellets reached 24.5 million tons, growing by 18% over the previous year. The residential and commercial sectors accounted for 66.1% of the European pellet consumption, while “industry” took the remaining 33.9%. Industrial consumption (for electricity and CHP) is the main driver for the Netherlands and Denmark. In Italy, Germany and France it is the residential heating sector that leads wood pellet consumption. However, it should be noted that use of pellets for heat takes place practically all over Europe and new markets—like the Polish one— exhibited tremendous growth rates in 2021.
Founded in 1990, Bioenergy Europe is a non-profit, Brussels-based international organization bringing together more than 40 associations and 90 companies, as well as academia and research institutes from across Europe. Its goal is to be the leading player in ensuring that sustainable bioenergy is a key pillar in delivering a carbon neutral Europe.
A key factor behind the increasing popularity of wood pellets is their cost-competitiveness compared to other energy carriers: Natural gas, electricity, oil. Toward the end of 2021, industrial wood pellet prices were actually lower than coal, potentially representing a game changer for industries that have traditionally relied on solid fossil fuels for their energy production. However, increasing energy prices are also impacting the pellet sector, affecting pellet prices, a trend which has intensified in 2022 also due to the increase in its demand.
Following the crisis of COVID-19, to which the wood pellet sector demonstrated remarkable resilience, Europe has entered a turbulent time with the onset of the energy crisis in the second half of 2021. The pellet sector is negatively affected from a variety of sources: Increased production costs (primarily of electricity), raw material shortages due to slowdown in the sawmilling industry and market tightness due to increased demand for pellets, but also due to lower supply following the EU sanctions over Russia and Belarus in 2022. For many years, wood pellet prices have remained much more stable compared to electricity and natural gas, but now wood pellet prices—like those of all energy products—are reaching record levels, according to Bioenergy Europe.
The ongoing energy crisis should not reverse the EU’s decarbonization efforts. Heating and cooling make up for almost half of the EU’s energy consumption and the majority (around 80%) is still fossil based.
The use of pellets for heat takes place practically all over Europe, including by the Drax power station, shown here.
It is essential not only to reach carbon neutrality by 2050, but also to reduce reliance on imported fossil fuels and to help households stay warm at an affordable cost. Wood pellets, along with other sustainable biomass sources, are already a proven and cost-effective renewable solution and can successfully contribute to the decarbonization of the heating sector, the organization states, adding:
l A stable policy framework is essential to provide a long-term perspective to companies to further invest in pellet production capacity, fostering European pellet production and thus ensuring adequate supply along with promoting climate mitigation efforts.
l Measures to ensure that wood pellet prices remain at acceptable levels for consumers should be implemented. VAT reductions—in line with other energy carriers—are suggested, while measures for reducing costs in pellet production (like net metering for pellet producers) should be promoted.
l Instead of subsidizing fossil fuels, EU and national funds should be directed to consumers that wish to switch from fossil fuel appliances, or older and less efficient wood fired ones, to modern and efficient wood pellet solutions. This will accelerate the deployment of renewables, reduce air pollutant emissions, improve resource efficiency all while shielding vulnerable consumers from energy poverty.
l A progressive ban of fossil fuels for heating is also a very effective policy to consider in order to achieve a fast energy transition.
According to Bioenergy Europe’s Statistical Report, in many regards 2021 was a year of records for the pellet industry, with both production and consumption experiencing significant growths. The short-lived recovery
after the COVID-19 induced lockdowns contributed to increased energy in general, including pellets. In addition, the heating season of 2020-2021 was longer than normal due to a longer period of cold temperatures, increasing the demand on the residential pellet market. Finally, national initiatives to phase out heating oil and for promotion of renewable heating sources have contributed to impressive growth rates, both in emerging markets, such as Poland, as well as in established ones, such as Austria. And on the global level, new players in Latin America, Asia and elsewhere have started the process of establishing vibrant pellet markets—both for domestic consumption and for export.
Then came late summer 2021. Foreshadowing Russia’s war in Ukraine, new hurdles in the supply of Russian fossil energy to Europe started to emerge and the energy market entered an extend period of constant price growth that impacted every sector of the economy. Naturally, the pellet sector was not immune to this situation, and pellet prices also increased due to higher costs for raw materials, electricity and transportation.
Despite these increases, pellets managed to maintain or even improve their competitive position versus most other energy carriers, which saw sharper price increases. In the industrial market, wood pellets have emerged as the most competitive fuel source for thermal power generation, cheaper than both coal and natural gas. In the residential and commercial sector, fears of disruptions in the natural gas flows, as well as extraordinary natural gas prices, are prompting more and more consumers to switch to locally available, renewable and cheaper heating sources—which obviously include pellets.
This increased interest in pellets—coupled with the financial support offered by the aforementioned national fuel switching initiatives—are also stimulating the market for pellet heating appliances, both boilers and stoves, with numerous producers reporting large increases in production capacities.
However, Russia’s invasion of Ukraine in February 2022 turned the energy market upside down, sending energy prices skyrocketing. The European Pellet Council reacted swiftly to condemn the invasion by suspending ENplus certificates for pellet producers located in Russia and Belarus in April 2022. By summer 2022, wood products—including wood pellets—have been included in the list of EU sanctions over Russia.
Three main factors are contributing to an unprecedented situation of market tightness: increased pellet demand (which also includes overstocking driven by fears of future pellet shortages), reduced pellet supply due to the cutting-off of Russian and Belarusian markets, and to a lesser extent, years of slower pellet production capacity growth compared to the growth of pellet consumption restricting the ability of existing producers to absorb/adjust to/respond to this shock.
The current energy crisis is a more fundamental threat and in anticipation of the 2022-2023 heating sea-
son, the whole of Europe enters very murky waters, according to the report. Trends in European policy developments—the European Parliament’s introduction of the term “primary woody biomass” and potential restrictions on its use in REDIII along with the very low priority for bioenergy in REPowerEU—are not helpful in establishing framework conditions that foster the development of the sector.
In 2021, the EU27 saw once again its total pellet production increase significantly, by about 9%. When looking at the world’s top producers, seven of the top 10 countries are from the EU. Besides Germany and Lithuania, countries such as Sweden, France, Poland, Austria and Estonia are among the biggest producers worldwide.
The rest of Europe (outside the EU27) also saw a significant increase of around 15% between 2020 and 2021.
North American production between 2020 and 2021 increased by about 4%, which represents an absolute increase of just over 500,000 tonnes. An important point to note is that this increase is almost exclusively due to production growth in Canada, where production increased by 15% or 490,000 tonnes. U.S. production only increased slightly by less than 1%. However, the U.S. still leads the global production of pellets, with approximately 9.3 million tonnes produced in 2021.
From The Editors
Restoration Fuels Offers Torrefaction Solution Page 6
Enviva Names Meth As President Page 8
Bioenergy ’22 The Stage Is Set Page16
Engineering Firm Becomes Owner/Operator Page 18
Wood Bio Guide Products, Manufacturers Pages 22-39
Dryer Island Page 40
APRIL
From The Editors Welcome Back Baby! Page 6
Drax, Enviva Make Key Announcements Page 8
Wood Bio Conference Gears Up For Atlanta Page 14
Page 30
From The Editors
It Was Literally All There Page 6
Enviva Will Build Pellet Mill In Bond Page 8
Conference Recap Wood Bio Speakers Present The Big Picture Page 14
In-Woods Harvesting Page 22
Biotreatment Of VOCs And Contaminants In Exhaust Gases And Wastewater Page 26
Restoration Offers Torrefied High Carbon Opportunities Page 14
Conference Recap Equipment Companies Reveal Latest Developments Page 18
Energy Technology Page 24
From The Editors Show Daze Page 3
Arbios Bio-Oil Project Gains New Name Page 6
Three Men & A Chipper Page 14
Asset Protection Page 18
Wrapping It Up Wood Bio Conference Page 22
From The Editors Building Demand Boosting Utilization Page 3
Enviva Moves Forward With Expansion Plans Page 6
Graanul Breathes Life Into Woodville Page 12
Determining The Best Path Forward RTO Rebuild Pays Off Page 18
Reconnecting, Refocusing: WPAC Conference Page 20
The Wood Yard Page 24
Bioenergy Europe Pushes Wood Pellets Page 30
one through six and line two with CPM presses seven through twelve. Each press uses 70 mm dies, with a capacity of 5.5 tons/hour maximum. Herndon admits that on good days the facility is reaching 5 tons/hour, saying this is truly a year to dive into the reliability of the process.
There is one cooler for each pair of presses, to help cure pellets. Shaker screens remove fines, dropping to a conveyor that re-enters the process. Accepted pellets travel on a bucket elevator into one of four Chief pellet silos.
Load out is carried via another bucket elevator to the truck load out building. All production is hauled via truck to the Port of Port Arthur, just an hour and a half away from Woodville, mainly using company owned trucks.
Kice Industries’ Process Group engineered and designed dust collection and process air systems required for the wood grinding and pelleting. This work included designing various dust collection pick-up points, laying out duct runs to various points, overall dust collection manifolds, and dust collection equipment layout of the various baghouse filters.
Kice’s complete engineering package included construction drawings of each system as well as installation and startup.
Kice-manufactured centrifugal fans were employed as the air movers along with the Kice CR and VR Series baghouse filters used to capture the dust. Kice airlocks and PD blowers were integral to these and other processes throughout the facility. Any material not big enough for the baghouses goes to an airlock, screw and back into the process.
Additionally, a Nestec RCO treats VOCs off the process—adding a layer of redundancy in VOCs control with both the Nestec RCO and TSI RTO. The facility utilizes a GreCon fire detection system.
The team is making a concerted effort to address leakage—if something needs to be fixed, it’s taken down and fixed. Herndon says this is in line with his desire to bring more pride to the plant and create excellent, clean working conditions. Adding, “I want everyone to feel good when they come to work. Their tools are in the right place. All that stuff is rolled into helping us be safe and do a good job. We’re continuing to work on it.”
The facility has basic policies and procedures to keep everyone safe, and the plant in the best condition it can be. Ansley and Herndon are in the process of reviewing and refreshing the safety programs, to make sure everything is handled in a safe manner. They’ve also rolled out safe work practices that are more orientated toward the pelletizing industry.
Ansley says that anyone can say safety is a core value, but for him, it is more than just expecting someone to do something specifically. Instead, he draws it back to equipping employees with the right tools to do their jobs—whether it be a literal tool handed to them or a program to report near misses or a service program to put in work orders and work requests. Things that he believes might not on the surface level seem like “safety” but is part of the safety culture that will drive change to the organization.
He believes, “These changes are what leads to a highly reliable facility because you focus on fixing problems that can lead to safety issues. It all ties together. Earl and I know what this plant can be. We’re on a path; it’s getting there. For the people that have been here for 10 years, it’s getting them to a spot where they see it and see it come to fruition. I am excited about the journey and where we are going.”
Morbark, LLC, and its affiliated brands, Rayco and Denis Cimaf, have selected Brandt Tractor Ltd., a wholly-owned subsidiary of the Brandt Group of Companies, as the exclusive, authorized dealer for their tree care (brush chippers, stump cutters, articulated wheel loaders), forestry/biomass (whole tree drum chippers, Chiparvestors, flails), recycling (horizontal and
tub grinders), and Rayco Forestry/ Denis Cimaf (forestry mulchers and mulching attachments) equipment lines in Canada.
“For Morbark, it was an easy choice to sign Brandt as our exclusive dealer in Canada,” says Michael Stanton, vice president of sales and marketing. “Their 56 full-service locations will provide our Canadian customers with the complete support they need and deserve.”
Brandt was founded in 1932 as
a small electrical contractor in Regina, Saskatchewan, Canada. After nine decades of impressive growth, the company has become the world’s largest John Deere dealer, owning and operating a total of 120 full-service equipment dealerships in Canada, Australia, and New Zealand. Since executing the contract, Brandt sales and service teams have been busy preparing to support Morbark, Rayco, and Denis Cimaf customers by participating in sales
and service trainings and building their inventory of equipment and aftermarket parts.
l Additionally, Morbark, LLC, has announced that Maverick Environmental Equipment is the new, exclusive dealer of Rayco Forestry mulchers in Ohio. With two branches in Newbury and Bremen, Maverick is also an authorized dealer for Morbark’s industrial equipment product lines, which include horizontal and tub grinders, whole tree drum and disc chippers, and flails.
Maverick began operations in 2016 when equipment industry veterans Tim Smith and Charlie Stahl joined forces to build their own company. The company focuses on providing machinerybased solutions for environmental applications, including aggregate processing, waste recycling, forestry and biomass.
“We are dedicated to bringing
our customers the highest quality products. This means partnering with top-tier manufacturers, like Rayco and Morbark, whose products work hard and take on the toughest materials,” says Tim Smith, managing partner, Maverick Environmental Equipment. Maverick Equipment recently displayed a Rayco C120 Forestry mulcher with a Denis Cimaf mulching head (FM120-6CF) at the 2022 Paul Bunyan Show in Cambridge, Ohio. They also demonstrated a Morbark 6400XT Track Wood Hog horizontal grinder.
Robert “Bob” Lee Vermeer, who drove the growth of Vermeer Corp. and its line of whole tree chippers and other wood processing equipment, died on August 17. He was 78. His vibrant love of people,
passion for Christ, distinct laugh and desire to put others first is what those who knew him will remember most.
Born in Oskaloosa, Ia. to Gary and Matilda Vermeer, Vermeer grew up on a family farm near Pella, Iowa where his love for the outdoors, animals and life on the farm was evident.
From an early age, he loved spending time with his parents and two siblings, Stan and Mary. They grew up watching their father and founder of Vermeer, Gary Vermeer, build a company based on values while innovating better ways to do work on the farm.
After high school, Bob attended Dordt College for a two-year degree. He transferred to Central College, graduating in 1966. His first job out of college was working at Marion County Bank, working there until 1973.
In 1968, Vermeer married Lois
DeJong and they raised three children—Daniel, Heidi and Allison— in Pella.
Bob joined Vermeer in 1974 and held multiple roles that drove the business strategy and long-term growth of Vermeer, including as CEO beginning in 1989 and later Co-CEO in 2003. He also served as
Chair of the Board from 1989 through 2014. It was during his tenure that the business grew to more than 60 countries on six continents. On the family side, Bob was a leader in promoting succession planning to transition the business to future generations of the Vermeer family.
Ponsse North America, Inc has expanded its operations to Midway, Fla. right outside of Tallahassee. The main factors that influencedthis development are the growing demand for cut-tolength wood and an increase in machine sales in the South, according to Ponsse.
“Forestry is our focus and all we do. We are extremely excited about our expansion to the South because of the number of mill investments with new facilities opening, reopening of shutdown mills and capacity increases.
It is time for cut-to-length to be more dominant in the South like it is currently in the northern part of the U.S.” states Pekka Ruuskanen, President and CEO of Ponsse North America, Inc.