
8 minute read
OBRAS CENTENARIAS / LA FERRERÍA DE PIEDRAS AZULES, DURANGO
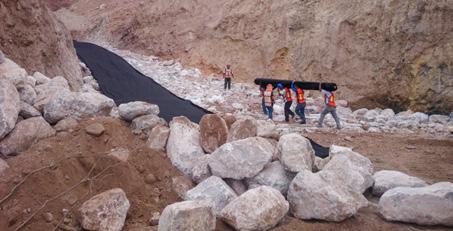
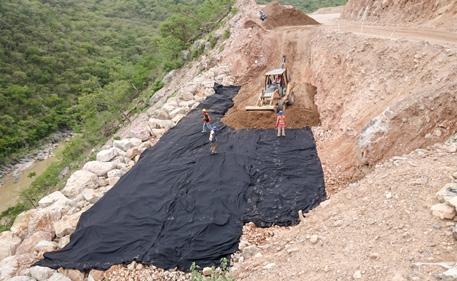
Advertisement
Figura 5. Colocación de geotextil para evitar migración de finos al pedraplén.
En el suministro del material seleccionado para la conformación del pedraplén, previamente se deben generar las condiciones del sitio de vertido, de forma que sea posible asegurar que tan sólo se suministren los fragmentos de roca sin suelo (véase figura 3). En su conformación se debe incorporar una proporción de agua, con la finalidad de que las aristas de los fragmentos pierdan resistencia y cedan a una mayor trabazón.
En la conformación del pedraplén, deben colocarse los fragmentos de roca en toda la superficie, ya sea la correspondiente a la del nivel de desplante o la de la capa previa en una posición en contrainclinación respecto a la horizontal, en un espesor del tamaño máximo de los fragmentos de roca colocados, y estrictamente debe ser bandeada la capa con la maquinaria pesada en más de 10 pasadas en toda la superficie.
Se debe garantizar la configuración geométrica del pedraplén, para lo cual resulta indispensable precisar las actividades que deberá desarrollar el operador del equipo, y éste deberá ser asistido por una persona que le indique la colocación del material, con la finalidad de que los fragmentos de roca de mayor tamaño entre capa y capa no coincidan (véase figura 4), es decir, el fragmento superior debe estar apoyado por lo menos sobre dos fragmentos, y viceversa; deben identificarse los espacios entre los fragmentos, que deberán ser reducidos en lo posible con elementos de menor tamaño, y deberá darse seguimiento topográfico para confirmar su alineamiento e inclinación definidos en el diseño.
Al finalizar la construcción del pedraplén, es indispensable realizar el monitoreo topográfico recomendado con la periodicidad necesaria, en puntos bien referenciados que permitan corroborar la estabilidad de la estructura y se haga registro de los posibles asentamientos previstos en el diseño.
Otras aplicaciones
Los pedraplenes sin suelos con estas consideraciones pueden ser aplicables en otros requerimientos, como es el caso del mejoramiento de terreno natural para la construcción de obras de drenaje, apoyo de estabilización al pie de taludes de corte inestables, capas drenantes, etc. Esto por efecto de que, ante las condiciones geomecánicas de los materiales que lo integran y el proceso estricto de construcción, permite aportar mayor resistencia del terreno natural, además de ser una estructura que permite el drenaje de escurrimientos superficiales o subsuperficiales y aporta un peso considerable en sitios que se requieran, además de que hace posible proteger materiales de relleno o terreno natural contra las acciones ambientales. Es preciso mencionar que en la alternativa de pedraplenes sin suelo, y cualquiera de sus aplicaciones, es indispensable el análisis correspondiente para garantizar una estructura segura y estable
u Para declararse que se tienen las condiciones propicias para la elección de pedraplenes sin suelo, es indispensable que los materiales seleccionados cumplan con ciertas características y que se encuentren disponibles, esto es, los materiales que integren la estructura deben ser analizados para predecir en lo posible sus parámetros de resistencia y compresibilidad, con objeto de determinar el modelo geomecánico de la estructura propuesta para su análisis de estabilidad y de asentamientos, de manera que se garantice en su diseño una estructura satisfactoria y funcional.
* La normativa para carreteras considera únicamente la construcción de terraplenes, estructuras que pueden estar conformadas con material compactable o no compactable; este último es un material cuya compactación no puede verificarse, está conformado por fragmentos de roca y suelos con tamaño máximo de 75 cm y debe colocarse en capas de un espesor mínimo tal que permita el máximo tamaño del material empleado; se debe aplicar un riego de agua a razón de 150 l/m3 y debe bandearse al menos con tres pasadas con un tractor de 36.7 t. Puede decirse que existe cierta similitud, pero su exigencia en cuanto a calidad no se compara con el material al que se hace referencia en este artículo. En el caso de los puertos, está normada la construcción de estructuras denominadas enrocamientos, formadas con material pétreo para resistir la acción del oleaje o de las corrientes marinas.
¿Desea opinar o cuenta con mayor información sobre este tema? Escríbanos a ic@heliosmx.org
La ferrería de Piedras Azules, Durango
Los orígenes de la industria del hierro en México se remontan a 1805 con la finalidad de atender los reclamos de abasto de hierro de las empresas mineras novohispanas. Antes, todo el hierro empleado en la Nueva España provenía de Europa, en especial de Inglaterra, Alemania y España.
El hierro constituye uno de los materiales más utilizados en la industria de la construcción. Es un mineral abundante en la corteza terrestre (aproximadamente 4.5%), la mayor parte en forma de óxido. Aun así, se sabe que el hierro se aprovechó en la prehistoria, aunque en una muy reducida escala y, ciertamente, no en la construcción. Los primeros utensilios de hierro fundido datan del siglo V antes de nuestra era (a.n.e.), y los descubrieron arqueólogos en la región conocida hoy como Jiangsu, en China. Es resistente a la compresión, pero no a la tensión. El hierro fundido se inventó en China en el siglo V a.n.e. Entonces se vertía en moldes para fabricar arados y vasijas, así como armas y pagodas. Se introdujo en Inglaterra alrededor de 1500. En América, los primeros talleres de fundición se establecieron sobre el río James, en Virginia, hacia 1619. A finales del siglo XVIII el hierro fundido comenzó a utilizarse extensamente en Inglaterra en la construcción de puentes y otras estructuras. El primer puente metálico de Europa se construyó en Ironbridge, sobre el río Severn, en 1799; se utilizaron 400 toneladas de hierro fundido (véase figura 1).
Los orígenes de la industria del hierro en México se remontan al establecimiento de la ferrería de Coalcomán, Michoacán, en 1805 por acuerdo del Real Tribunal de Minería. La finalidad era atender los reclamos de abasto de hierro de las empresas mineras novohispanas. El hierro ha sido un elemento indispensable para la ejecución de diversas actividades productivas, agrícolas, industriales y de la propia explotación minera. Antes de la creación de la ferrería de Coalcomán, todo el hierro empleado en la Nueva España provenía de Europa, en especial de Inglaterra, Alemania y España. Ese flujo lo interrumpió el conflicto bélico, ocurrido durante el reinado de Carlos IV, entre Inglaterra y España. La principal razón se relacionó
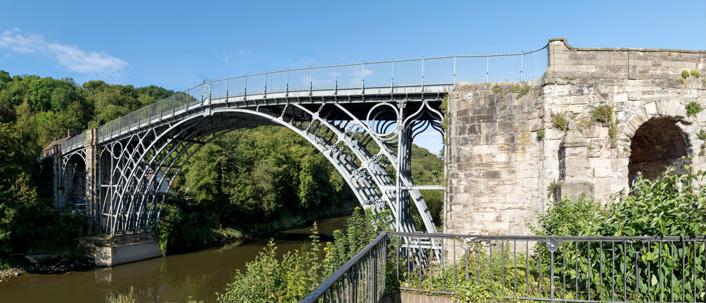
Figura 1. Vista del puente Ironbridge.
RÍO TUNAL ESTRUCTURA HIDRÁULICA ALTO HORNO
PRESA DERIVADORA LA FERRERÍA CARBONERA
Figura 2. Plano del conjunto de la ferrería de Piedras Azules.

Figura 3. Cortina de la presa derivadora.

Figura 4. Vista exterior de los restos del alto horno.
con que casi siempre las fundidoras se ubicaron en sitios cercanos a los yacimientos ferrosos, y que además dispusieran de agua y recursos forestales suficientes para el abasto de materiales y combustible indispensables para su funcionamiento. Hoy, las fundiciones se distribuyen por los estados del norte, occidente y centro del país.
Además de la ferrería de Coalcomán, funcionaron otras cinco fundiciones instaladas entre 1825 y 1850 en los actuales estados de Michoacán, Jalisco y Durango. Tales establecimientos constituían empresas pequeñas, unidades productivas relativamente frágiles, puesto que para el trabajo del fierro dependían del abastecimiento de mineral de hierro o chatarra ajenos; además, dependían de los productores de carbón vegetal para alimentar los hornos de fundición y no poseían transportes propios; por lo tanto, estaban obligados a pagar fletes caros debido a la falta de caminos adecuados.
Al principio, las ferrerías funcionaban con tradicional tecnología de las forjas catalanas. Éstas, como es bien sabido, cuentan con una larga historia, sobre todo en la industria siderúrgica española, de donde pasó a México. Modesto Bargalló considera que “un taller de forja o forja catalana constaba de uno, a veces de dos y en casos excepcionales hasta de tres hornos; trampa de agua para el soplo de aire; un martillo o martinete movido por rueda hidráulica. Podía tener otros martillos más pequeños para un segundo o ulterior forjado del hierro obtenido en el horno. Grabados de horno, e incluso del horno con su trampa, eran corrientes en las obras de metalurgia, en los textos de Química y hasta en diccionarios enciclopédicos” (Sánchez Díaz, 2009, p. 15).
Según el mismo autor, las llamadas ferrerías menores –como las que funcionaron en México en la primera mitad del siglo XIX– “eran unos edificios muy similares a las ferrerías mayores: utilizaban energía hidráulica para mover los mazos y fuelles y su combustible era el carbón vegetal. Su función era transformar y reducir los tochos de fierro (materia prima base) procedentes de las mayores barras, es decir, en piezas semielaboradas, en hierros comerciales de forma y tamaño diversos, según la demanda del mercado; bien para los herreros que las empleaban para fabricarlos en las fraguas” (Sánchez Díaz, 2009, p. 16).
Respecto de la tecnología siderúrgica del alto horno, se tiene noticia de que algunos experimentos practicados al finalizar la primera mitad del siglo XIX resultaron fallidos. Debe quedar claro que “la tecnología utilizada por las ferrerías en la primera mitad del siglo fue básicamente el método catalán para producir fierro. Las forjas catalanas tenían entre uno y tres hornos, los cuales eran alimentados con carbón vegetal. Se contaba además con una o dos trampas de aire y algunos martillos de gran peso movidos por ruedas hidráulicas. Uno de los grandes problemas que se tenían que vencer era el poco poder calorífico del carbón vegetal, ya que en las forjas no se alcanzaba a fundir el hierro por la insuficiente temperatura (Sánchez Díaz, 2009, p. 16).
La ferrería de Piedras Azules, situada en Durango, fue la primera instalada en México después de consumarse la independencia. Perteneció a la Compañía Unida de Minas Mexicanas y contó con el apoyo de Lucas Alamán. Construida en 1826, entre sus fundadores figura Santiago Baca Ortiz, entonces gobernador de Durango,
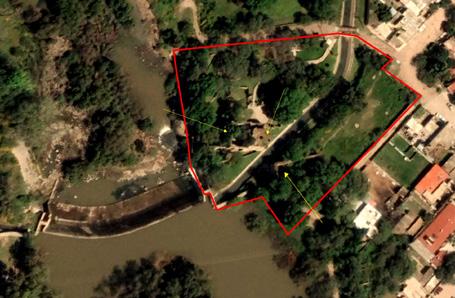