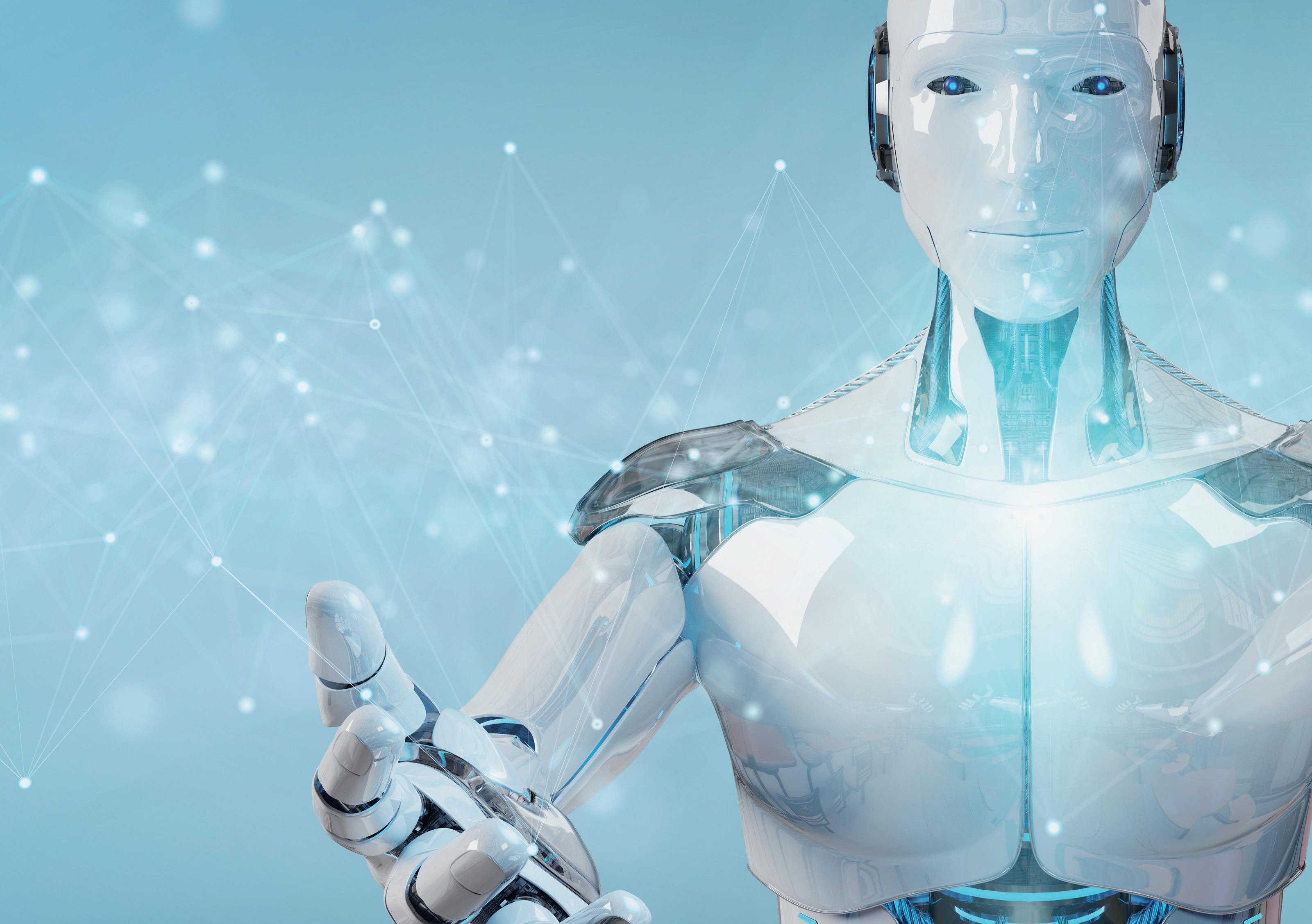
18 minute read
STORIA DI COPERTINA
LA FABBRICA SMART È PIÙ RESILIENTE
Il ruolo della tecnologia sarà fondamentale non solo per la reazione alla crisi provocata dal lock-down, ma anche per accelerare un processo di trasformazione digitale sempre più necessario alle imprese manifatturiere per aumentare l'efficienza e la flessibilità.
Non è tempo di previsioni. O, per meglio dire, sarebbe tempo, visto che le previsioni dovrebbero essere più utili proprio in regime di incertezza, ma al momento in cui scriviamo non si conosce ancora l’impatto della “seconda ondata” della pandemia, che già vede in Francia e Spagna, ad esempio, un numero di contagiati giornalieri simile a quello che poi portò al lock-down di marzo. Quello che alcuni analisti, subito dopo il lock-down,
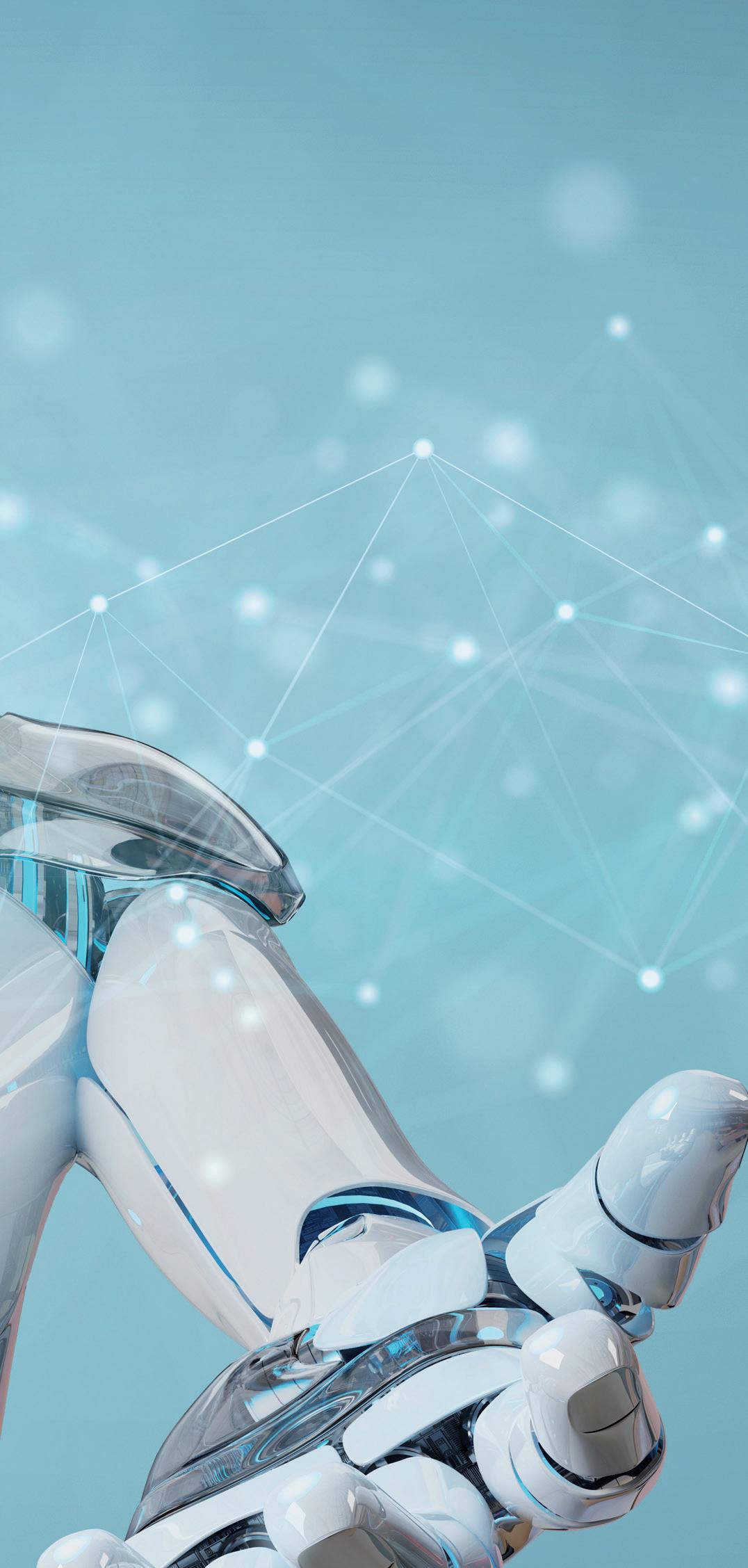
hanno chiamato “golfo dell’incertezza” è quindi ancora molto ampio, e non consente di fare stime attendibili. Limitiamoci quindi a qualche indicatore utile. Più che il Pil, le cui proiezioni si base annua sono state parecchio altalenanti (a seconda del periodo e della fonte della stima), concentriamoci sul Pmi (Purchasing Manager’s Index), che nella zona di Eurolandia (anche qui, meglio circoscrivere il campo) ha toccato un minimo di 33,4 (l’indice si considera positivo, cioè indicherebbe una crescita del mercato degli acquisti, quando è superiore a 50) a maggio, mentre prima dell’arrivo del Covid-19 “viaggiava” tra 52 e 60. Bene, il Pmi a fine agosto è tornato a toccare i 52 punti, segno, almeno nelle intenzioni dei direttori acquisti delle aziende europee, che ci sarebbe una timida fiducia nella ripresa e, soprattutto, la concreta volontà di acquistare beni e servizi. L’indice Pmi fornisce un’indicazione interessante sullo stato di salute del comparto manifatturiero e sulla crescita della produzione; gli operatori finanziari lo tengono in considerazione perché i responsabili degli acquisti di solito hanno un accesso privilegiato ai dati relativi alle prestazioni delle loro aziende, che possono diventare un indicatore chiave della prestazione economica nel suo insieme. Cambiando ottica e analizzando la situazione da un punto di vista più qualitativo, si può dire che il settore manifatturiero è stato colpito in modo molto diverso da altri comparti. Alcuni (trasporti, turismo, ristorazione) a causa della pandemia sono stati investiti da un vero e proprio tzunami. Il manifatturiero ha subito invece un contraccolpo più complesso da analizzare, in alcuni casi simile al maremoto (pensiamo all’automotive o al fashion) in altri invece molto più sfumato (l’industria Ict, ad esempio, e alcuni segmenti direttamente coinvolti nella reazione all’emergenza, come la logistica, il medicale, l’alimentare o il tessile). In più, il manifatturiero è caratterizzato da un ciclo di vita molto diverso da quello dell’erogazione dei servizi: c’è il mondo dell’indotto, della realizzazione di componenti e parti di prodotti più complessi, c’è il grande settore delle infrastrutture che ha tempi più lunghi rispetto ai cicli della pandemia. Insomma, alcuni imprenditori hanno dovuto “fermare le macchine”, altri hanno potuto continuare a ritmo serrato. La vera incognita è la “seconda ondata” non tanto del virus (che comunque incombe minacciosa, con ipotesi funeste di un eventuale ulteriore lock-down totale o parziale) quanto della crisi macro-economica conseguente a una contrazione di tutto il comparto economico-finanziario (i paventati licenziamenti di massa delle grandi compagnie multinazionali, il blocco del settore immobiliare, il cambiamento globale delle abitudini di acquisto e consumo). Come vedremo nelle pagine seguenti, nelle opinioni degli addetti ai lavori, prevale una moderata soddisfazione per la tenuta del comparto manifatturiero durante la crisi ma anche un lieve timore per il breve-medio termine. C’è, infine, una considerazione di carattere più sociale che economica: le fabbriche, grandi o piccole, sono, rispetto agli ambienti d’ufficio, luoghi dove il “social distancing” è per molti versi più facile rispetto ad altre realtà, e dove le modalità di smart working, se possibile, sono ancora tutte da sperimentare. Da una parte, la spesso indispensabile presenza fisica del personale pone un serio problema di pianificazione e tutela dei lavoratori (le macchine, invece, lo sappiamo, possono essere vulnerabili ai virus informatici ma non al Coronavirus), dall’altra potrebbe rilanciare le fabbriche come vero luogo di aggregazione sociale, un ruolo che in alcune realtà più innovative (dal punto di vista della tecnologia ma anche dell’organizzazione del lavoro) è già una realtà.
Il compito della tecnologia
In questa auspicabile “reazione al Covid-19” del settore manifatturiero la tecnologia, e più in generale l’innovazione, giocano un ruolo importantissimo. Tornando ai dati certi (il Pmi, citato in precedenza, è “solo” un indicatore), la sfida è da far tremare i polsi. Il Centro
Studi Confindustria, ha rilevato una diminuzione della produzione industriale del 33,8% in maggio (rispetto a maggio 2019) e del 44,3% in aprile. Gli ordini in volume sono invece diminuiti del 51,6% annuo (dato riferito a maggio). Premesso che tutti gli analisti sono concordi nel prevedere che, se non ci sarà un secondo lock-down, la ripresa sarà importante ma non riuscirà ovviamente a compensare lo stop dei mesi più bui, l’intensità della reazione dipenderà anche molto dalla volontà di manager e imprenditori di mettersi in gioco, con tecnologie e processi nuovi. Sotto questo profilo, come si usa dire spesso, la disgrazia del Covid-19 potrebbe essere vista come una grande opportunità di cambiamento (così come lo è già in parte stata in alcuni settori dei servizi, che hanno banalmente scoperto l’efficacia e il risparmio di un vero smart working). Il cambiamento dovrebbe coinvolgere i processi: una nuova organizzazione del lavoro, una diversa supply chain, con una differente collocazione (reshoring) dei fornitori per non dipendere troppo da aree geografiche troppo distanti e non controllabili in caso di pandemia, nuovi modelli di business e di go to market. Ma anche nuove tecnologie, come ad esempio i digital twin, l’Iot, la manutenzione predittiva, la manutenzione da remoto sfruttando la Augmented Reality, gli analytics e la manifattura additiva. Un altro punto cardine di uno sviluppo in ottica smart manufacturing è la convergenza tra tecnologie It (Information Technology) e Ot (Operational Technology). Le prime portano in dote, ad esempio, una pratica più avanzata di trasmissione e trattamento dei dati e un’esperienza di cyber-sicurezza che ha già fatto i conti con una casistica purtroppo numerosa di attacchi e incidenti. Insomma, la trasformazione digitale, che nel manifatturiero aveva fino all’arrivo del Coronavirus un altro passo e un’altra accezione rispetto agli ambienti d’ufficio, sarà determinante per costruire un nuovo modello di manifattura, quella costituita da fabbriche smart, più resiliente in tutti i sensi (quello della continuità della produzione ma anche quello del business). Le politiche e le strategie che saranno adottate a livello nazionale (non vorremmo tornare a parlare di Industria 4.0 ma non si può non citarla) saranno altrettanto determinanti. La speranza è che il Governo e gli organi preposti

al disegno e al supporto delle politiche industriali non si concentrino solo sui settori più direttamente colpiti (sacrosanto aiutare turismo e ristorazione) ma riescano a guardare anche più avanti, al nuovo ruolo che il nostro Paese, che così bene ha reagito alla pandemia (con ovvie e deprecabili eccezioni), può assumere partendo dalla sempre considerevole (e spesso dimenticata) posizione di seconda potenza manifatturiera d’Europa.
Emilio Mango
DIALOGO IT/OT E DIGITAL TWIN SONO GLI ELEMENTI PER USCIRE DALLA CRISI
Technopolis ha intervistato Franco Megali, vice presidente e Ceo di Siemens Digital Industries Software Italia e Mea, per capire quali sono gli strumenti a disposizione delle imprese per reagire alla fase di stallo generata dal lock-down.
A che punto siamo con la ripresa nel manifatturiero? Il settore del manufacturing non sta andando bene, i dati che abbiamo a disposizione segnalano una decrescita di 18 punti percentuali rispetto all’anno scorso, su base mensile. Certo, bisogna dire che c’è un’Italia che vediamo tutti i giorni sui mass media e c’è un Italia più “vera”, sottotraccia, dove le aziende fanno parte di filiere globali importanti, esportano, costituiscono comunque un ecosistema che in Europa è tra i più attivi. Siemens opera in tutto il mondo e possiamo dire che, come tutti sanno, la pandemia non è ancora vinta; in Italia siamo un po’ più avanti ma io penso sia decisamente presto per parlare di “rinascita”. Sicuramente ci sarà una ripresa, che avrà più le sembianze di una “L” che di una “V”. Le imprese, guidate più da imprenditori che da manager, hanno bisogno di certezze e di sostegno da parte del Governo. In compenso, le grandi organizzazioni, che hanno intrapreso un impegnativo percorso di digitalizzazione (anche grazie alle nostre soluzioni) già da una decina di anni, gestiscono i loro cicli produttivi con strumenti digitali da molto prima della pandemia, e il Covid-19 ha solo accelerato il processo di trasformazione.
Come la tecnologia può aiutare le imprese manifatturiere nella ripresa? Grazie al digitale c’è oggi la capacità di simulare non solo la progettazione del prodotto ma anche il suo funzionamento. È il concetto esteso di “digital twin” con
Franco Megali
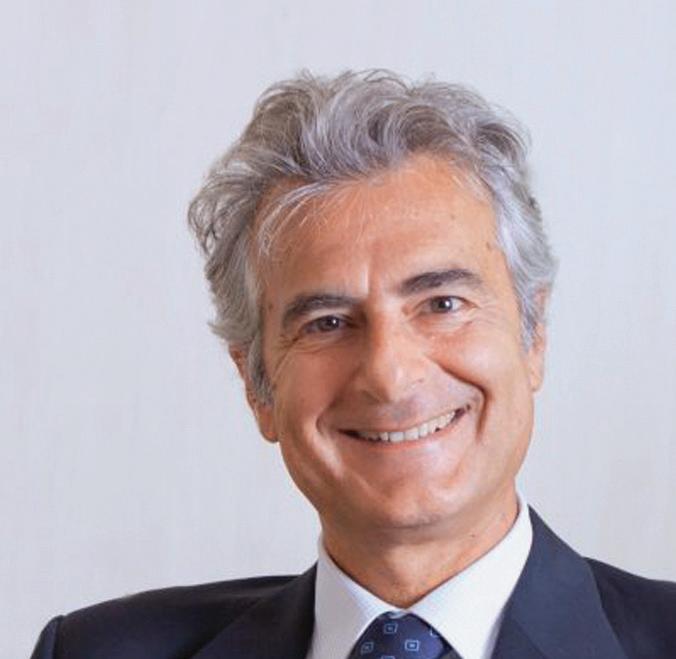
cui molti si riempiono la bocca ma che nella pratica è, appunto, una simulazione. In Siemens lo chiamiamo “Comprehensive Digital Twin” perché riguarda tutto il ciclo di vita del prodotto: dall’analisi di mercato che consente di impostarne i requisiti alla simulazione del funzionamento. Ovviamente parliamo di un prodotto complesso, non solo composto da parti meccaniche, ma un insieme di componenti anche elettriche ed elettroniche, che devono funzionare in armonia. Poi c’è la fase vera e propria di manufacturing, dove posso simulare la costruzione del prodotto, e infine il virtual commissioning. Alla fine parliamo di almeno tre “digital twin”, che diventano quattro se consideriamo poi l’analisi dei dati e le simulazioni che si possono fare sfruttando le tecnologie IoT. Insomma, è una sorta di “closed loop” che coinvolge il prodotto dal concepimento alla manutenzione. Tutto questo aiuta le aziende a essere più efficienti, e quindi a reagire meglio anche alle crisi come questa. I concetti di closed loop in realtà non sono nuovi, ma il Covid-19 ne ha accelerato la diffusione, estendendola a figure non tecniche, come quelle manageriali, che ora possono comprenderne i vantaggi di business.
Quindi c’è speranza? Siemens mette a disposizione strumenti estremamente potenti, che potrebbero permettere alle aziende di fare un salto importante in termini di competitività, costi, efficacia ed efficienza. Quello che però ancora vedo è un gap tra quello che sarebbe possibile implementare e quello che nella realtà viene fatto. Un gap che non dipende tanto da un fattore culturale (che, ripeto, la pandemia ha in qualche modo migliorato) ma proprio dalla messa a terra di progetti di trasformazione digitale. Quest’ultimo processo ha subito un ulteriore stop a causa del Coronavirus: se fino a febbraio vedevo aziende che investivano in innovazione, con la pandemia per molte imprese le priorità sono cambiate, sono state ad esempio l’accesso a supporti come la cassa integrazione. Speriamo che con la fine dell’emergenza il percorso di trasformazione riprenda.
Quanto è importante il dialogo tra It e Ot? Il dialogo tra It e Ot è essenziale. Non è un caso che Siemens abbia deciso di acquisire Mendix, una società di sviluppo software specializzata nel low-coding che ora è diventata strategica per accelerare tutti i processi di integrazione in ambito manufacturing. E.M.
L’AUTUNNO PORTERÀ UN RINASCIMENTO INDUSTRIALE?
Guido Porro, managing director Euromed di Dassault Systèmes, prova a tracciare il percorso e a identificare gli elementi che potrebbero portare le imprese italiane a uscire dalla crisi.
Quali sono le ricadute della pandemia? La crisi ha insegnato molto, ha accelerato una strutturazione di progetti e creatività anche tra le Pmi, che si sono interrogate su quali business model più resilienti possono essere implementati, e quindi su come riconfigurare i sistemi di produzione secondo una logica, appunto, di resilienza, di sostenibilità e di agilità. Cosa non meno importante, sempre a causa del Covid-19, le imprese hanno dovuto rivedere anche le modalità di interazione umana e sociale all’interno delle aziende. Vorremmo vedere anche i lati positivi di quello che è stato un dramma di enorme portata per persone e imprese: le aziende italiane hanno mostrato nonostante tutto una buona vitalità. Questa fase così particolare ha portato alla luce la necessità di virtualizzare i processi di marketing e vendite per seguire i temi di mass customization e continuare a essere vicini ai clienti, magari proprio partendo dai dati 3D che sono disponibili in azienda: presentare i propri prodotti a migliaia di chilometri di distanza con le tecniche di Augmented Reality e Virtual Reality, siano esse applicate a un singolo componente o a un’intera linea produttiva, è ad esempio una sfida che oggi può affrontare ogni imprenditore.
Quali sono gli strumenti tecnologici che possono aiutare la ripresa? La piattaforma 3Dexperience di Dassault Systèmes sta diventando uno standard nel mondo del manufacturing, ed è molto richiesta anche dalle Pmi. La maturità del prodotto in versione cloud è tale da dare la possibilità anche alle aziende meno strutturate di avvantaggiarsi di questi nuovi strumenti digitali. Inoltre, il tema dell’innovazione digitale, e in particolare dei digital twin, è stato finalmente compreso dalla maggioranza delle imprese, anche se quelle con forte vocazione all’export ovviamente hanno reagito meglio. Questo che potremmo definire un nuovo rinascimento industriale potrebbe iniziare da subito, perché ha basi già consolidate. Il centro di questa trasformazione possono essere le piattaforme come 3Dexperience, che coinvolgono gli ingegneri che progettano, gli uomini della finanza che tengono sotto controllo i costi e gli uomini di marketing che devono determinare il pricing del prodotto finito. Queste piattaforme aiutano a fornire lo stesso alfabeto a tutti i soggetti coinvolti, creando una massa critica di persone che interagiscono in rete.
Ci sono casi già concreti di adozione di questo approccio “a piattaforma”? In Italia abbiamo esempi molto interessanti, uno tra i tanti Geico, leader nel settore della verniciatura delle scocche di automobili; il mercato dell’automotive, tra l’altro, vede una domanda crescente di prodotti “made to order” di grande qualità a costi sostenibili. Per arrivare a questo risultato sono neces
Guido Porro
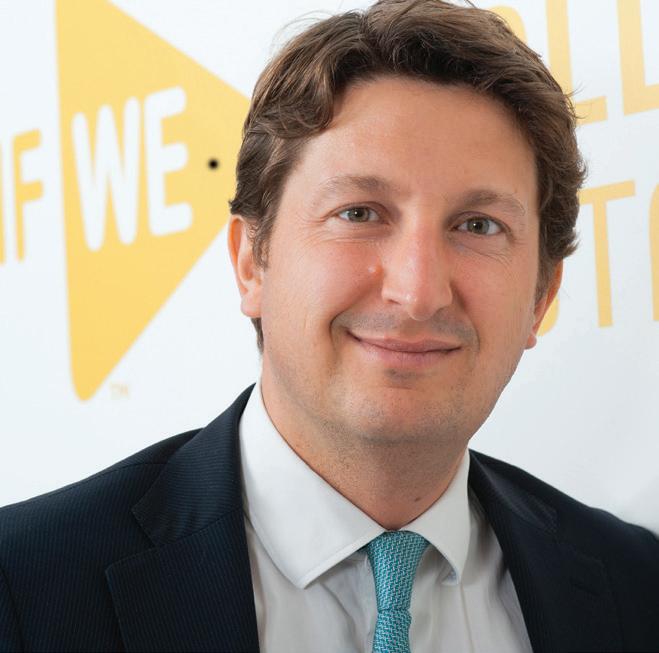
sari modelli di produzione estremamente flessibili.
In che modo esattamente si ottengono costi più sostenibili? Il sistema è flessibile e può essere customizzato fino a diventare, nel caso di Geico, un vero e proprio “custom paint shop” che, grazie all’analisi dei dati in real time, può implementare attività di manutenzione predittiva migliorando l’efficienza di produzione. In più, le aree che prima erano viste in modo frammentato oggi convergono in un’unica piattaforma Smart, che copre le attività dalla manutenzione al marketing.
E i digital twin? Quella del Virtual Twin è una tecnologia che noi proponiamo con successo: consente di virtualizzare gli impianti in una logica di process planning e manufacturing execution system. Dal nostro punto di vista, avere la possibilità di sbagliare (a costo zero) e avere un grado minore di fallimenti è non solo un tema tecnologico ma anche culturale. E.M.
LA REALTÀ AUMENTATA AIUTERÀ LA RIPRESA
Iniziamo dalla classica fotografia della situazione post-covid. Partiamo dai dati che tutti possiamo leggere: il calo della produzione industriale, tra meno 30 e meno 50%, e l’indice Pmi (Purchase Management Index) che in Italia ha toccato durante il lockdown un minimo di 31 punti. È fuori di dubbio che siamo di fronte alla peggiore recessione dal dopoguerra, e l’onda sarà abbastanza lunga, proiettando una ripresa più a “U” allargata che a “V”. I settori impattati sono tutti e correlati, per questo l’inerzia sarà importante. Detto questo, vedo un re-start a due velocità: le aziende più grandi e strutturate da una parte, quelle piccole dall’altra. Se invece guardo le vendite di nuovo software, devo piacevolmente constatare che siamo in un trend sicuramente meno drammatico del previsto; all’inizio del lock-down il nostro presidente aveva prospettato tre scenari possibili per il secondo trimestre: molto negativo (-50%), negativo (tra il -20 e il -30%) e blandamente negativo (-20%). Ebbene, i risultati sono stati superiori alle aspettative e il terzo trimestre fa ben sperare. Anche in Italia, dopo un rallentamento in Q2, quando le aziende avevano altre priorità, si assiste a un deciso miglioramento. In definitiva, quest’anno, nonostante tutto, proiettiamo un aumento del fatturato (grazie al recupero in Q3 e Q4) ma senza una crescita sensibile dei nuovi contratti.
Che tipo di reazione si sta verificando? Il “new normal” porta due sfide importanti: la gestione di una “asincronia” tra domanda e offerta e una ridefinizione
Paolo Delnevo

Paolo Delnevo, vice president Southern Europe di Ptc, spiega come le nuove tecnologie, tra cui la connettività e l’Ar, potranno aiutare le imprese ad agganciare un trend positivo dopo la pandemia.
dei piani strategici (diversi a seconda del settore industriale) che devono per forza portare a una maggiore agilità delle linee produttive. Abbiamo visto una buona reazione delle aziende alla crisi, anche grazie allo smart working, ma naturalmente non ci sono state nuove assunzioni e quindi nuove risorse per piani strategici. Diversa è la situazione per le aziende più grandi e strutturate, che parallelamente alla crisi hanno potuto godere di una riduzione dei costi vivi. Abilitare le persone a lavorare da remoto ha aiutato anche ad accelerare il percorso verso la digitalizzazione e la “smart production”.
Quali sono gli elementi di innovazione più importanti? Le aziende manifatturiere stanno investendo nello shop floor e in progetti di Augmented Reality perché devono recuperare efficienza a fronte del calo dei volumi di produzione. Resilienza, robustezza e agilità sono i tre obiettivi che devono essere raggiunti grazie alla tecnologia; in questo senso la tecnologia è fondamentale ma si spiega anche, ad esempio, la tendenza al reshoring. La connettività e l’AR, tornando al digitale, sono le due tecnologie che generano al momento maggior valore, perché abilitano, tra l’altro, il distanziamento sia nello shop floor sia in fase di manutenzione.
Che contributo può dare Ptc alla ripresa? Insieme a Rockwell e Microsoft abbiamo deciso di sviluppare soluzioni pronte all’uso che mettono insieme software, cloud e servizi. Già in autunno saranno disponibili le nuove versioni di questi pacchetti che saranno declinati in quattro diverse varianti, due più orientate agli analytics e due all’AR: Real-time Production Performance Monitoring, Asset Monitoring and Utilization, Connected Work Cells e Digital and Augmented Work Instructions. Grazie a queste soluzioni chiavi in mano le aziende potranno raggiungere più facilmente gli obiettivi di velocità e scalabilità che sono indispensabili per la ripresa. E.M.
ANALYTICS E MACHINE LEARNING PER FABBRICHE PIÙ EFFICIENTI
Le nuove tecnologie si possono mixare sapientemente con pratiche collaudate come la computer vision per realizzare soluzioni di manutenzione predittiva o per incrementare la sicurezza dei lavoratori. L’esperienza dell’italiana Iconsulting.
Iconsulting si occupa da vent’anni di trasformare i dati grezzi in informazioni utili; ha quindi percorso tutta la strada che dalla business intelligence ha portato agli analytics e che ora si fonda sui pilastri dei big data e del machine learning per aiutare le aziende rendere più efficienti i propri processi. In ambito manifatturiero, la società bolognese ha creato un’area di eccellenza nell’ambito della object detection analytics e della computer vision, tecnologie che oggi utilizzano soluzioni di frontiera ma che poggiano su una solida base di esperienza perché in voga da parecchi anni. “Le immagini, siano esse statiche o in forma di video”, dice Alfredo Formisano, senior manager di Iconsulting, “catturano sempre un dato che ha due caratteristiche: quella di essere geolocalizzato (analisi geo-spaziale), e quella di descrivere un fenomeno. Tanto per fare un esempio, in ambito manifatturiero, possiamo rilevare l’assembramento di oggetti o di persone in uno spazio”. I campi di applicazione della computer vision, una tecnologia forse meno “sexy” di altre che oggi godono di maggiore visibilità, sono tanti. Uno dei più noti è la manutenzione predittiva, cioè la possibilità di capire in anticipo quando è il momento di intervenire su un macchinario in modo da anticipare un eventuale guasto e il conseguente blocco della produzione. “Possiamo capire se una macchina si sta per guastare”, dice Formisano, “in due modi: analizzandone i parametri e tenendo sotto controllo gli eventi, una strada percorribile ma complicata, oppure attraverso soluzioni di computer vision, una modalità decisamente più agnostica perché indipendente da persone e processi: monitorando una linea produttiva posso capire se e quando gli oggetti prodotti si accumulano, ad esempio su un nastro trasportatore, rivelando un collo di bottiglia che magari prelude a un blocco, e intervenendo preventivamente”. Un secondo caso d’uso piuttosto frequente è legato alla sicurezza sul lavoro. Negli impianti produttivi moderni, basati sui concetti di ergonomia e salvaguardia della salute dei lavoratori, analizzare l’ambiente operativo che circonda gli operai è fondamentale. Attraverso la computer vision si possono monitorare i movimenti del personale, valutandone la congruità con i livelli di confort e sicurezza desiderati. Un terzo ambito, estremamente attuale, riguarda le procedure anti-Covid-19, come ad esempio l’utilizzo dei dispositivi di sicurezza (mascherine) e il rispetto delle distanze: la computer vision riesce agevolmente a monitorare entrambe le situazioni. “Il fattor comune di queste soluzioni”, dice Formisano, “è l’analisi dei dati provenienti dalle videocamere attraverso algoritmi di deep learning, quindi con l’utilizzo di reti neurali. I sistemi vengono istruiti dando loro in pasto un gran numero di immagini e non attraverso un
Alfredo Formisano

programma software. In pratica creiamo una black box di algoritmi statistici che consentono alla macchina di imparare in base alle informazioni che riceve”. Oggi le tecnologie permettono di non avere più limiti in termini di capacità di memorizzazione, e quindi una volta salvati i dati è possibile elaborarli in modalità “batch” (in un secondo momento) in ottica analytics e geospaziale, per costruire ad esempio mappe di calore che forniscono valutazioni statistiche di fenomeni nel corso del tempo. Allo stesso tempo è possibile implementare soluzioni di tipo real time (Streaming Analytics), che operano appena il dato viene reso disponibile, ad esempio per segnalare un dipendente che non indossa le protezioni o un malfunzionamento di una macchina; il tutto rispettando la privacy (le immagini sono anonimizzate). “Questo tipo di approccio”, conclude Formisano, “è interessante anche perché è indipendente, agnostico, rispetto alla tecnologia utilizzata (che può essere Google, Microsoft, Amazon), è l’insieme della soluzione che costituisce il vero valore aggiunto”. E.M.