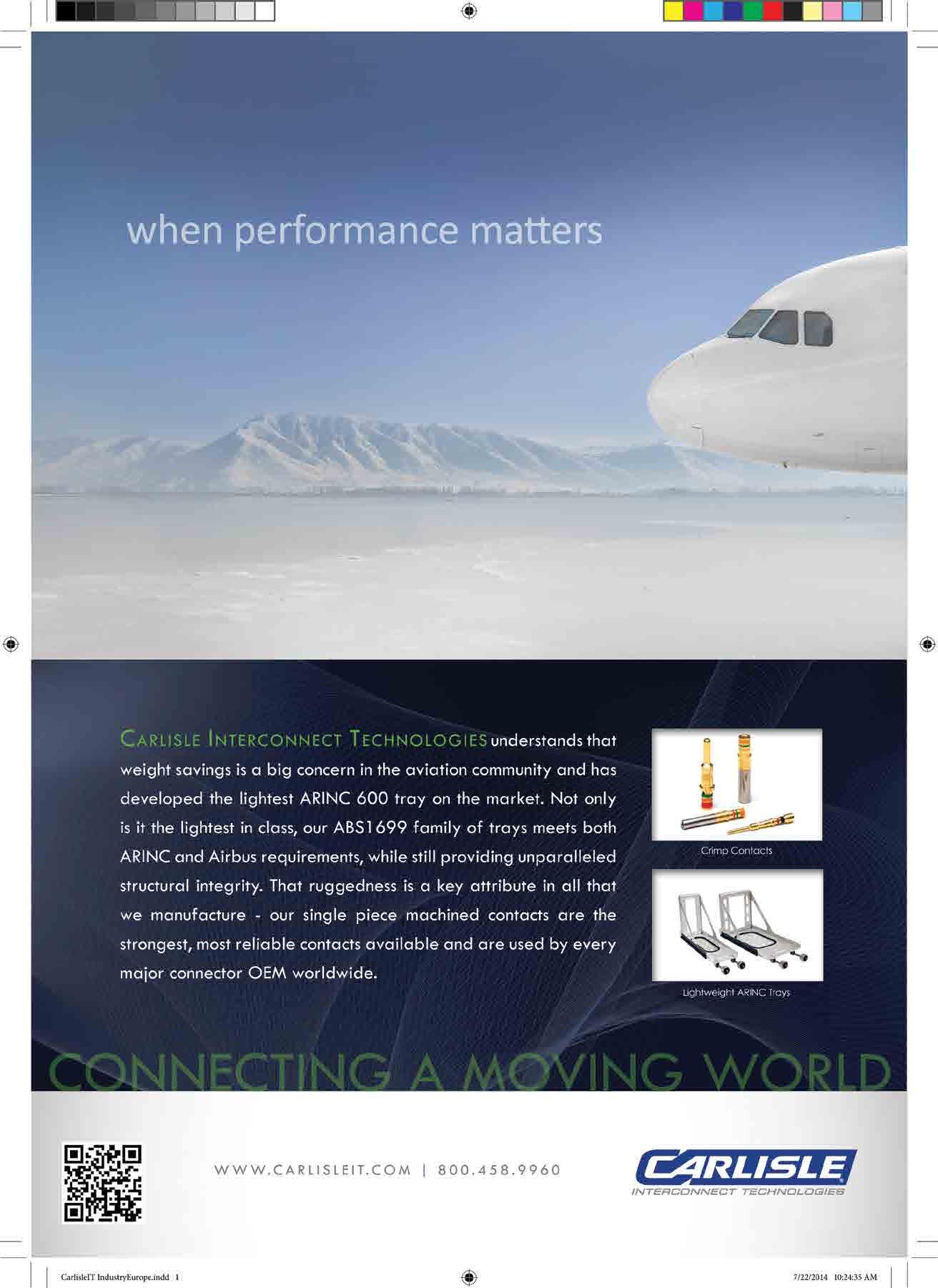
3 minute read
Experts in assembling automotive parts
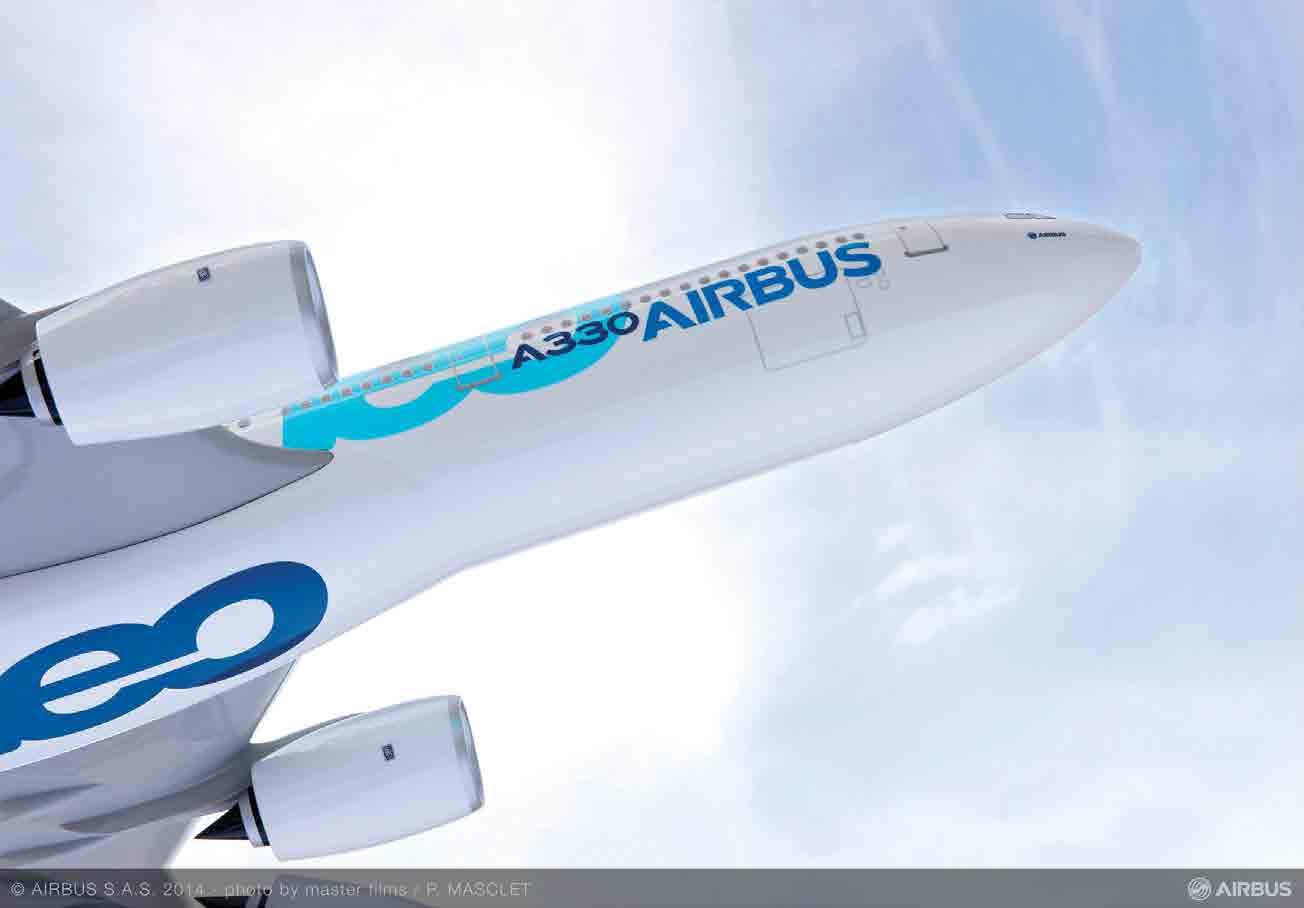
readiness for the ongoing aircraft production ramp-up and the development of a world-class supply chain for the future.
As the group says: “Aircraft are complex products, integrating hundreds of thousands of components.” Collaborating with the entire supply chain is vital to ensuring that each aircraft delivered meets the highest applicable environmental standards. Environmental criteria are included when selecting suppliers and environmental requirements are further introduced in contractual agreements. “Airbus suppliers are therefore expected to comply with the company’s environmental policy and to provide reliable environmental data on the products delivered,” says the group.
In his early 2014 statement, CEO Fabrice Brégier described the steps taken to improve efficiency and the organisational changes that had given more empowerment to local teams, especially in the plants. He promised further improvements in Airbus’s global competitiveness, efficiency and effectiveness and said the focus would also be on incremental innovation that is ‘simpler, less risky, less costly and comes faster to market’.
Airbus was, he said, ‘well on track with a clear roadmap for a successful 2014’. n
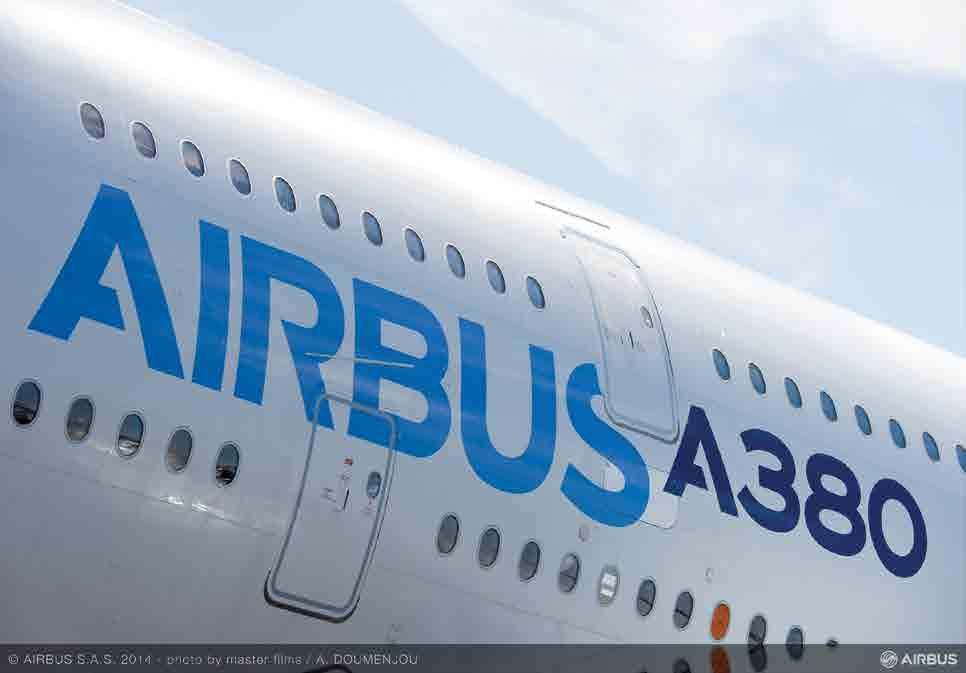
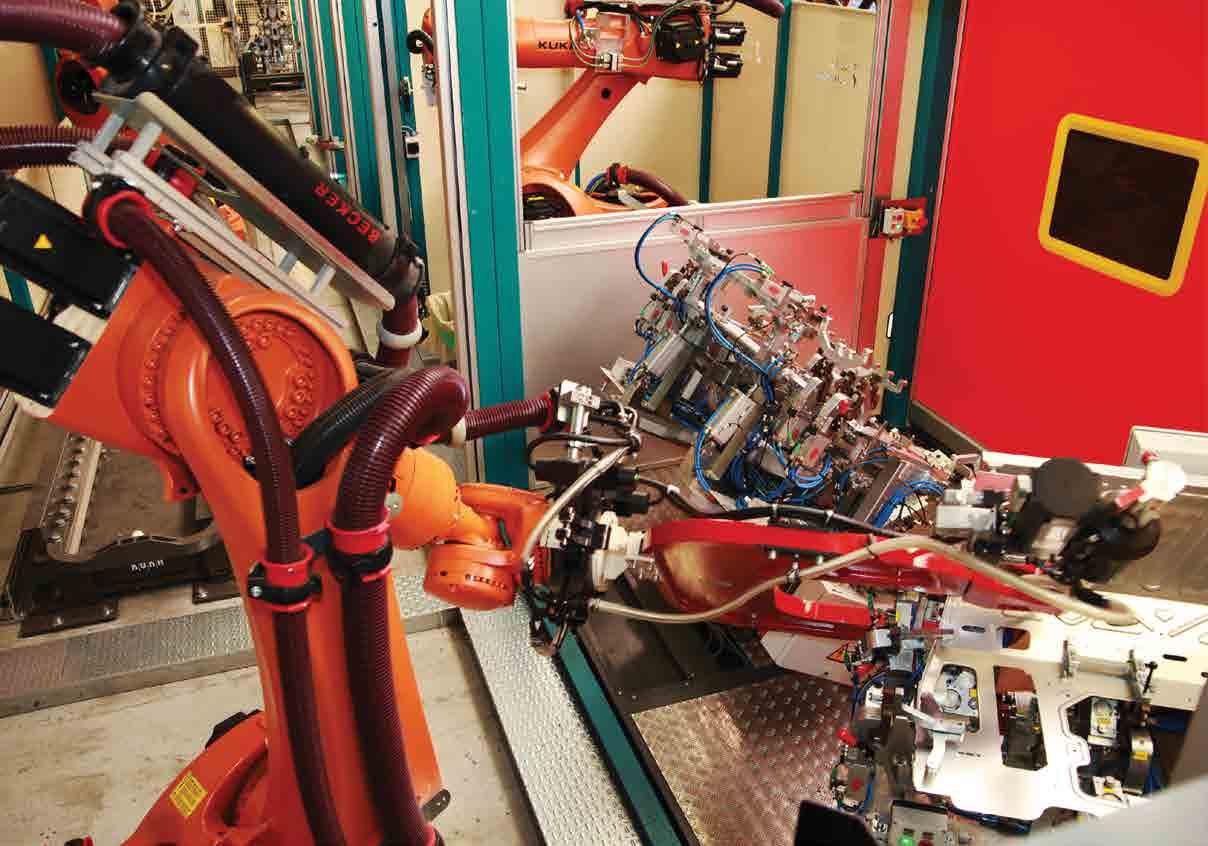
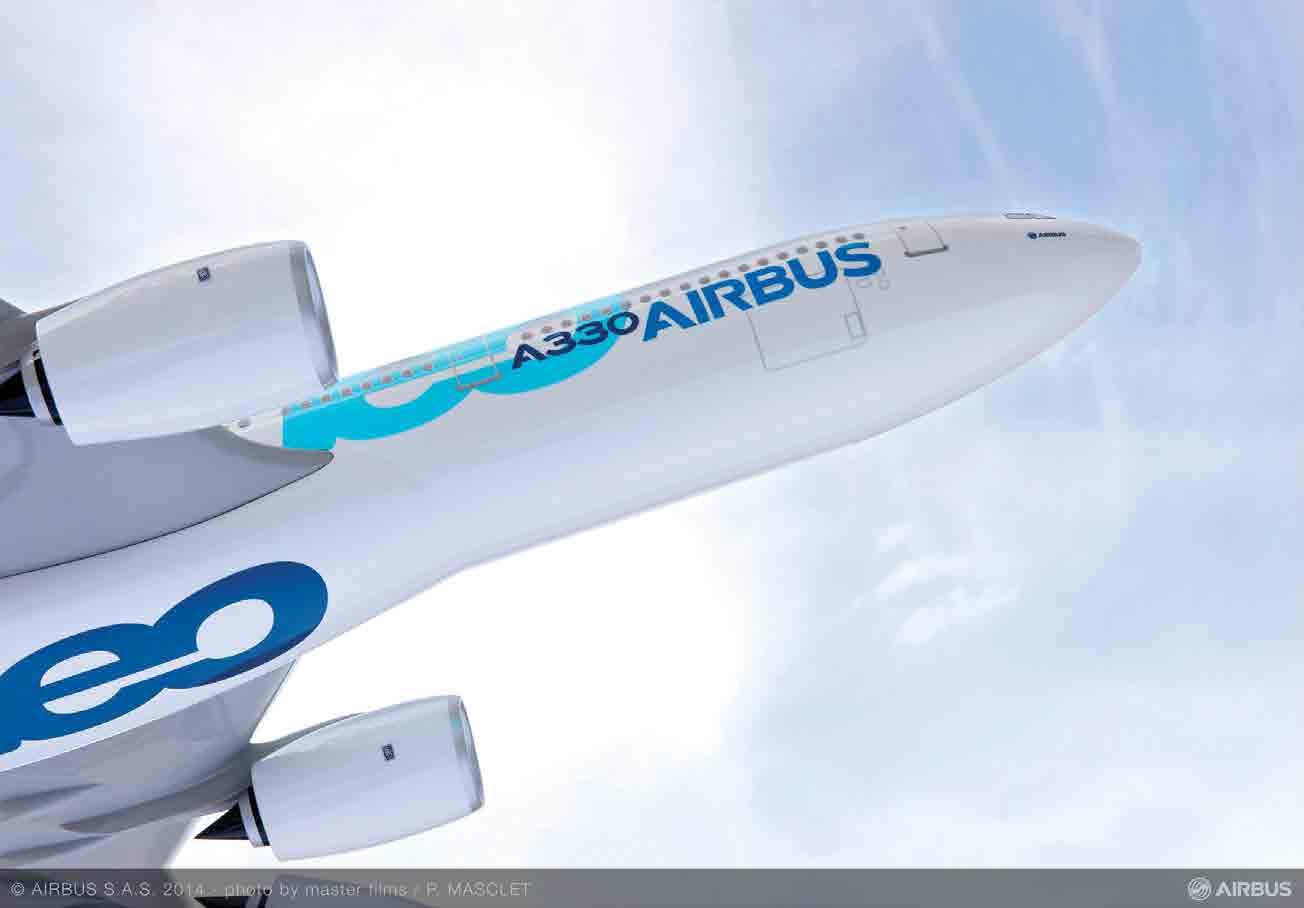
GEDIA Poland Assembly, a company from Nowa Sol, Poland, is a part of GEDIA Automotive Group. As the first company in the group it has focused on the assembly of parts and now highly complicated assembling for the automotive industry is its specialization.
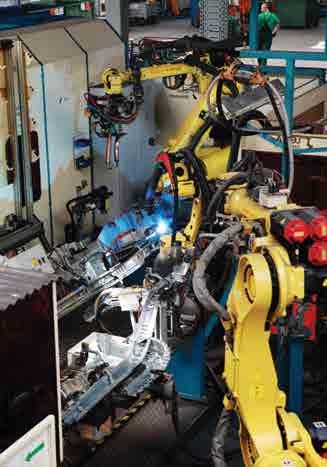
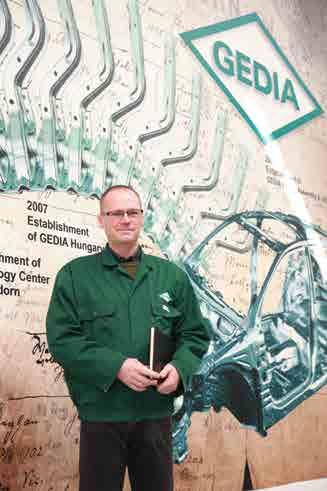
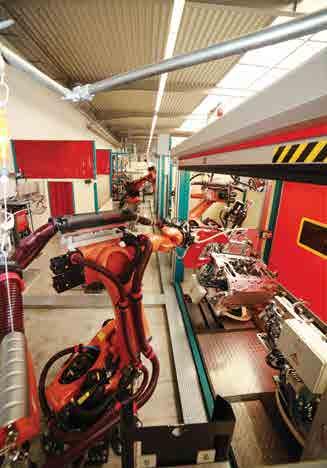
GEDIA Automotive Group is a global, privately owned company with headquarters in Attendorn, Germany. Its core operations include the development, production and distribution of body components for the global automotive industry. GEDIA has specialised in the development of body press parts and welding components for cars and trucks.
The group’s annual turnover in 2013 is estimated at more than €400 million. It employs about 2,500 people worldwide. GEDIA Automotive Group includes locations in such countries as Poland, Spain, Hungary, and China. It has joint ventures in Mexico and the USA, and engineering centres in France and Sweden.
In 1998 it built its first production plant in Nowa Sol, Poland, which specialized in cold and hot forming. Ten years later GEDIA opened its second production unit in Nowa Sol - GEDIA Poland Assembly (GPL2). GM was behind it
“The construction of this plant was an important event in the life of the whole group”, says Mr. Andrzej Marcinek, the GEDIA Assembly Poland Managing Director. “First of all, it was the group’s first facility built entirely for one large project commissioned by a client (GM). It was also the facility that started a new path of the group’s development, namely the assembling of parts. “By this time GEDIA’s main business was focused on the pressing and assembling of smaller parts. The idea for creating GPL2 was to switch to more demanding projects. We managed to do this. Attracting new, more complex projects and implementing such new technologies as laser welding were other milestones in the company’s history. One of the main current trends in the automotive industry is to produce lighter cars. Light cars use less fuel and are less polluting. To meet these needs the group has implemented such technology as hot forming. At GPL2 we have learned to laser weld light alloys such as aluminium.”
The company’s main customer is General Motors Manufacturing Poland at Gliwice. GPL2 has specialized in assembling longitudinals for the Opel Astra IV which carry the whole structure of the car chassis. GPL2 is GM’s first external supplier commissioned by Opel to make this part. “We managed this very well and in recognition of our high quality we have been awarded with GM’s Supplier Quality Excellence Award and included in GM’s top 5 per cent of suppliers”, adds Mr. Marcinek. “It is our know-how and high quality that make us different from our competitors and are the reasons for the satisfaction of our customers. GEDIA Group has a wide
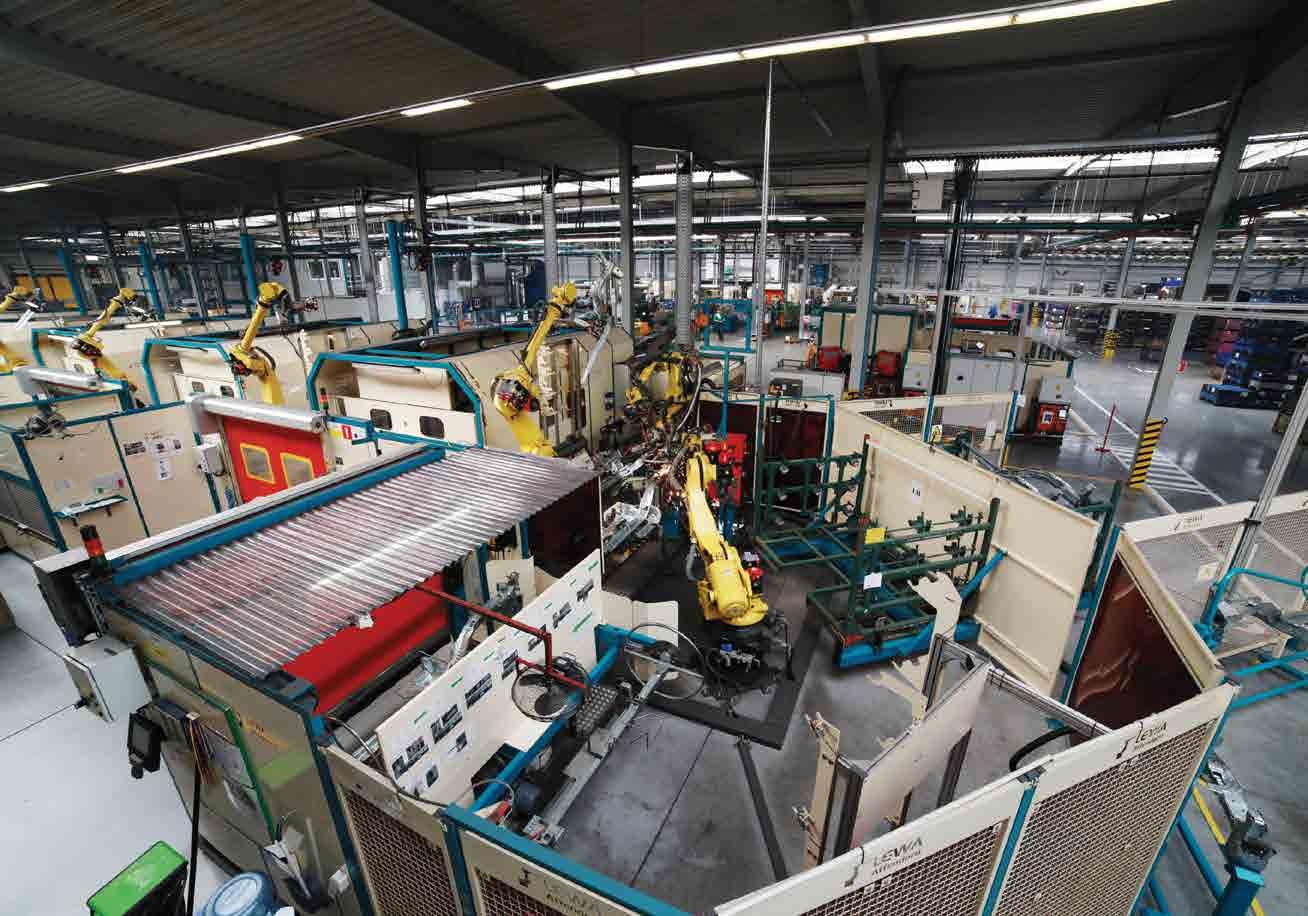