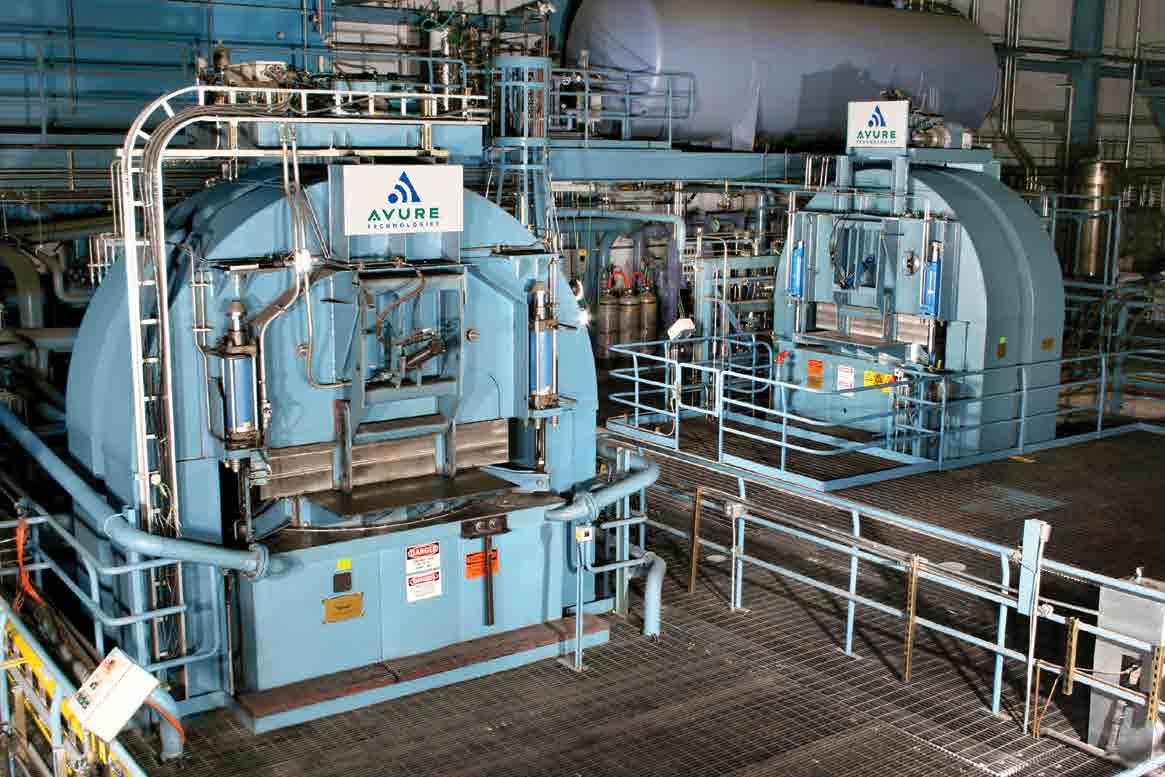
10 minute read
Celebrating 40 years of high technology Fidia
more than 100 Flexform systems in operation at the plants of major aircraft manufacturers such as Airbus, Boeing, Bombardier, Cessna, Embraer, Alenia, BAE Systems, EADS and Mitsubishi.
The aerospace industry began using fluid cell pressing more than 50 years ago as a replacement for the rubber pad forming technique that had been in use as an economical method of forming sheet metal parts since the advent of metal aircraft (multi-piece metal tooling was too expensive for the small volume of aircraft parts). The advantages offered by Flexforming include better part definition and more complex shapes thanks to the higher forming pressure, deeper and more intricate shapes, better productivity and larger parts. At high pressure, parts can also be formed to their final shape in one forming operation, eliminating the need for downstream manual corrections.
Testimony to these advantages is offered by J.J Rousse, of the French aerospace company Daher-Socata: “For many parts, hand correction of incompletely-formed shapes has been completely eliminated. Even very large parts can now be formed to tolerance in a single pressing. We have documented cost savings of 25 to 42 per cent on sampled parts thanks to fewer required cycles and reduced manual rework”.
“Ninety per cent of our sheet metal forming equipment business is concerned with the production of structural aluminium parts for the aerospace industry,” explains Mats Sjostedt. “There can be as many as 7000 different such parts in each aircraft and our Flexform systems are ideal for their costeffective low volume (2000 to 3000 units per year) production.”
The latest orders for Avure’s fluid cell presses include a hydroform deep-draw press for Kale Pratt & Whitney, the joint venture between Pratt & Whitney of the USA and Kale Holding of Turkey. The press will enable the Turkish facility to produce high quality sheet metal engine components with great accuracy, repeatability and lower costs. A new Avure high pressure fluid cell press has also just been installed at the Ohio plant of Jones Metal Products Co; it will provide JMP with economical parts-forming solutions to customers in industries such as aerospace, defence, medical, rail, lighting and power generation where there is zero margin for error.
Avure offers application support in the form of training courses and tool design consultancy services in order to help its customers get the best result from the Flexform process. This also helps them to understand where they can make improvements in their businesses, focusing on the complete process from determination of materials blank to the final pressed part.
Auto applications
Flexform is also widely used in the automotive industry for fast, low-cost prototyping, validating tools and parts and saving time in new model development. And although auto-making, unlike aerospace, typically involves very high volumes, there are parts of the industry where Flexform is the preferred method for parts production too. These include limited edition cars, buses, trucks and farm and construction equipment. Formed automotive components include bumpers, doors, bonnets, roof and floor panels, pillars and support beams. In fact in the auto industry, Flexform is considered to be economically viable for parts with production volumes up to several thousand parts per year,
Avure has supplied Flexform solutions for decades to major auto OEMs such as Ford, Daimler-Benz, Volvo, BMW, GAZ and Saab.
Total service
Over nearly six decades Avure engineers have installed high pressure systems for customers worldwide, with many of these presses
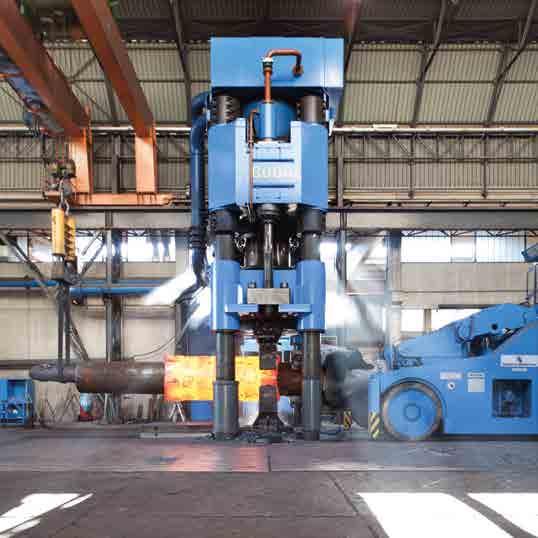
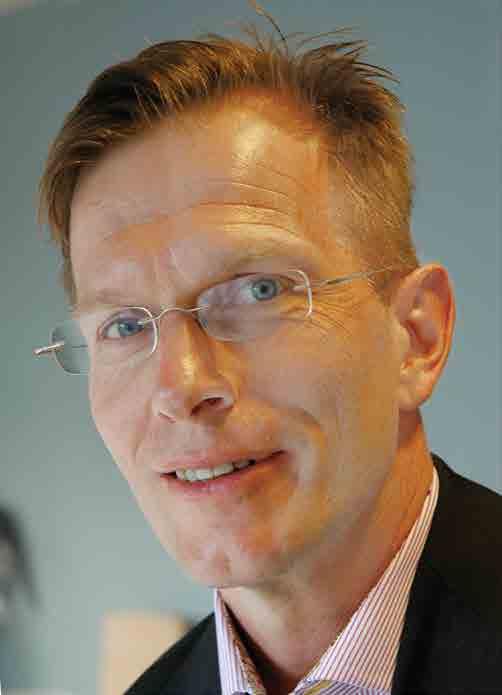
being in service for more than 40 years and with some exceeding one million cycles under high pressure. To keep all these units in peak operating condition, the company employs a full-time team to provide global technical support. These experts can identify and correct any abnormalities in the pressure system that might compromise safety or operating efficiency and ensure that customers’ systems keep working like new.
“Our service offer begins from the moment a unit is ordered,” says Mats Sjostedt. “We understand that each customer has a need to produce a specific part and so we don’t just sell them a machine but use our wealth of experience and knowledge to help them find the optimum solution; we then follow through with expert installation, machine set-up and continuous staff training as well as our equipment, services (including spare parts, service engineers, inspections and trouble shooting) and application support. This is then backed up by preventative maintenance, high quality service, efficient parts inventory and continual system improvement.
“Global leaders are defined by their track record and in the demanding business of ultra-high pressure systems, Avure’s record is second to none.” n
Forgiatura Mamé and Forge Monchieri have pursed the winning decision of renouncing the individualism of their entities in favour of one single strength founding M&M Forgings, the strategic Alliance born to represent the global center of excellence in the forging industry. It is an extraordinary and ambitious business project conceived as an integrated high technical capacity industrial project, with the aim to create a wider operating future.
Thanks to the experience and professionalism gained by Forgiatura Mamé and Forge Monchieri in over a century of business, the competitive advantages of M&M Forgings are:
• On stop shop • Forgings from 1 to 120 tons • Heat treatments • Fast Track and contracts • International presence • Cladding
Thanks to more than 10 years of experience and to the excellent partnership built during these years with Avure, Forgiatura Mamé has supplied forgings in fully machined conditions for food presses, isotactic presses and sheet metal forming presses, has guaranteed a constant supply chain of products such as jokes, cylinders, columns, lower and upper closures and has become a very key supplier for Avure.
For further details, visit our NEW websites at:
www.mm-forgings.com www.monchieri.it www.forgiaturamame.it
This year Fidia is celebrating 40 years of high technology in mechanics, having started its business in 1974. Barbara Rossi speaks to Rudy Piliego and Enrico Tamburini - respectively Communication & Area Manager for the High Speed Milling division and Software Marketing Manager - about the interesting developments that have taken place since their last conversation with Industry Europe and current strategies for the future.
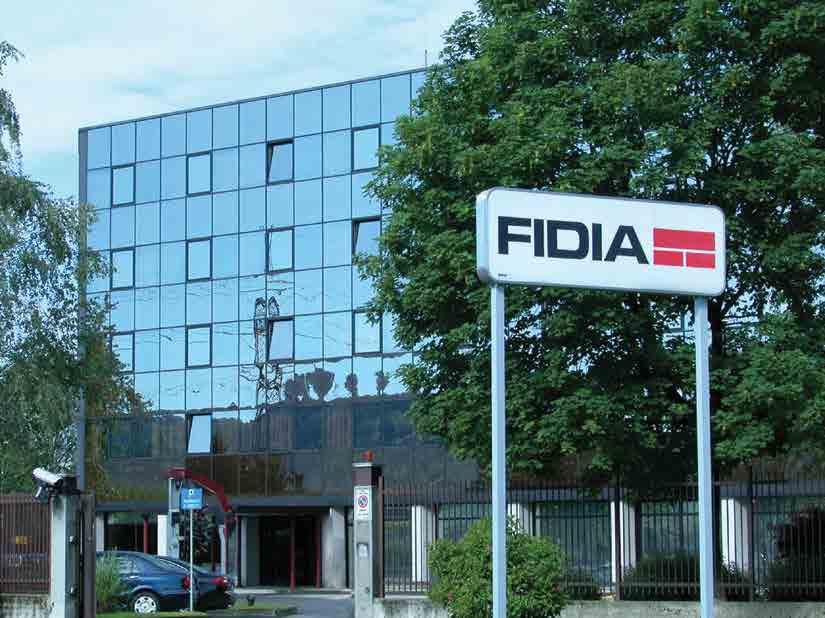
CELEBRATING 40 YEARS OF HIGH TECHNOLOGY
Fidia’s operations are organised in different business units, namely High Speed Milling (HSM Division) and Numerical Control (CNC Division). As well as producing high speed milling machines, the HSM division (which generates about 70 per cent of Fidia’s turnover) also manufactures proprietary 5-axes and 3+2 axes milling heads, which as well as being incorporated in the machines are also distributed independently, for instance for revamping purposes. The CNC Division produces the electronic and the real-time software aboard the Fidia’ Numerical Controls, as well as accessories and digital drives. One of the main Fidia distinguishing features, truly the basis of its value added products, is the vertical integration of its offer, as customers can be supplied with complete systems, from the mechanic to the electronic up to the software aboard the Fidia’s HSM machines.
This allows the company to be the sole supplier for the whole system, offering customers the advantage of having a counterpart which takes sole responsibility for all the crucial components of the machine. All the components are designed, developed and manufactured in the company’s own plants. The whole production process takes place in Italy (Turin and Forlì) while abroad there is a network of foreign branches and service centres in order to be close to clients, providing them with assistance and services.
Mr Piliego explains, “Our high level of vertical integration is recognised as a real asset by our clients: SME as well as major companies appreciate the benefit of a high-end machine serviced in a more efficient manner than competitors adopting market hardware.
It also allows us to participate in and win numerous bids at the international level.
We serve many large clients world-wide (90 per cent of Fidia’s products are exported in more than 40 Countries) in the automotive and aerospace sectors, our two main outlet markets, which have become even more important for us in the last decade. We are extremely successful in our bidding and our vertical integration plays a key role in this. Our value added offer is already highly appreciated by the Chinese market as well as in the consolidated Western market, from USA to Europe. The fact that we are currently involved in two aerospace sector bids at the national level (both for Alenia Aermacchi) is further proof of this. Furthermore, this happens even if (or maybe I should say because) we supply proprietary numerical control systems, which may run against the trend with an innovative and more efficient, custom-tailored technology.”
As well as supplying complete packages, the company is also able to offer individual products or components. One of these is the registered ViMill® software, as Mr Tamburini explains, “We are in the process of patenting (currently we have reached the internationalisation phase). The product is also registered in all the countries where we operate, including Europe, North America, Brazil, China, Japan, Turkey, the Russian Federation and India. ViMill® can be offered as a stand-alone product, especially for use in a CAM environment”.
Keeping an open house
The company held an open house event at one of its Forlì sites in mid-May, where it showcased some of its main products to its customers.
The “stars” presented at the recent open house event were three models of 5 axes high speed fully operative Gantry machines: GTF3212/LC-6000, GTF3214/QA-4200 and GTF3514/MA-2200. The first of these three belongs to the L series and features a large size welded steel gantry structure meant for light materials applications as composite, full size car design models in resin, or aluminium precise-and-large aerostructures or car masters. It is equipped with a HSK63A - 56 Nm spindle, reaching a 24,000 rpm speed and 35kW. The second model, belonging
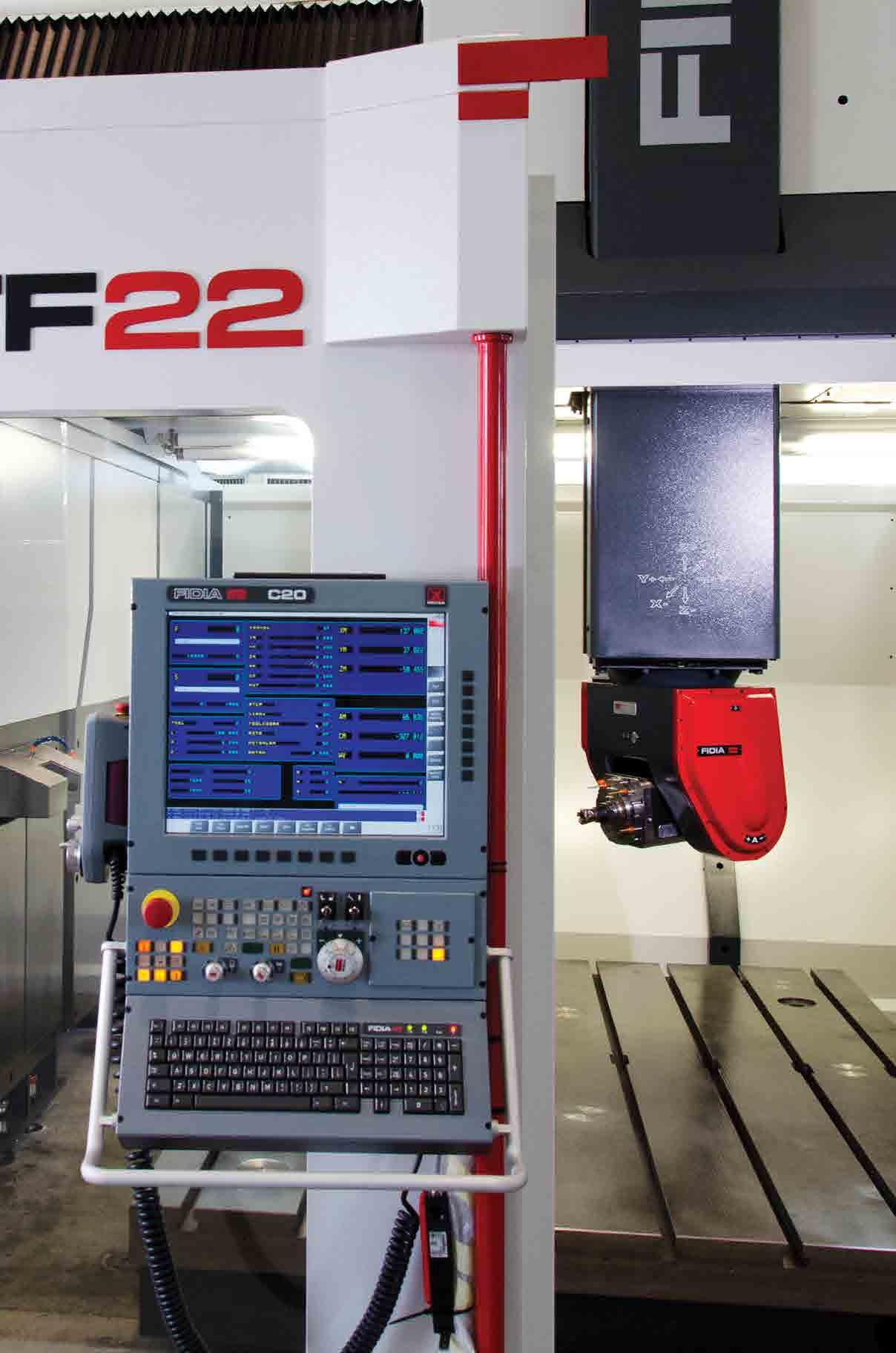
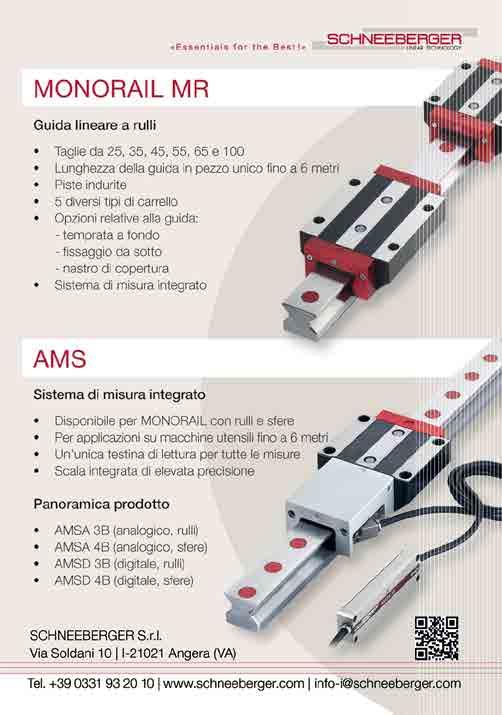
Since 1984 Tecnomesa S.a.s. has been engaged in a wide and diversified range of production activities inherent to mechanical processes: from construction of mechanical components to special equipment, from structures to trial and testing services.
Search for quality
Customer care, targeted at achieving full client satisfaction, is at the foundation of our activity, along with a constant search for quality at every level, which is pursued through continuous improvement of technological and productive know-how, as well as continuous technical updating of the means of production.
A trustworthy company
Many important companies, such as FIDIA, have already given us their trust. Tecnomesa S.a.s. is ready to fulfil any requirements. Phone: +39 0121 501436
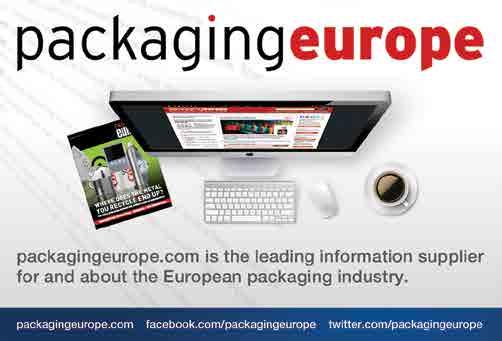
to the Q series, has a structure based upon epoxy concrete columns and is suitable for applications in automotive moulds & dies, as well as aeronautical structural components. Its HSK63A 88 Nm spindle can reach the same speed of its previous counterpart while developing 55kW power. The model belonging to the M series serves the same types of application as the Q series model also offering a 15.000 rpm, HSK100A spindle. GTFM differs in that it has a self-supporting cast-iron structure which saves the cost of the traditional foundation usually required by machines offering similar cutting capacity.
One of FIDIA’s products shown at the open-house event, in the accessory range, was HMS, a head/table measuring and calibration device system. This is an accessory solely available for Fidia numerical control systems, of which the company is particularly proud. “The fact that a company of medium size such as ours - with a turnover of €45m and 350 employees at global level- is able to compete with much larger players highlights our quality and commitment to R&D and original high technology solutions” Mr Piliego and Mr Tamburini adds.
With regard to software, the open house showcased the previously mentioned ViMill® - anti-collision 3D simulator, the first on-board machine virtual look-ahead software on the market, capable of supporting the machine tool operator in preventing and avoiding collisions. ViMill® forecasts any possible 3- and 5-axes movement, automatic and manual, stopping the machine when such movement implies a collision between movable parts, tool and the workpiece.
Just as for the HMS, also this unique ViMill® SW (patent pending) is exclusively available from FIDIA.
All the machines were equipped by the V5 –Look-ahead, which provides new algorithms for tool path control with 3 and 5 interpolated axes, including optimisation of the dynamic behaviour of the machine.
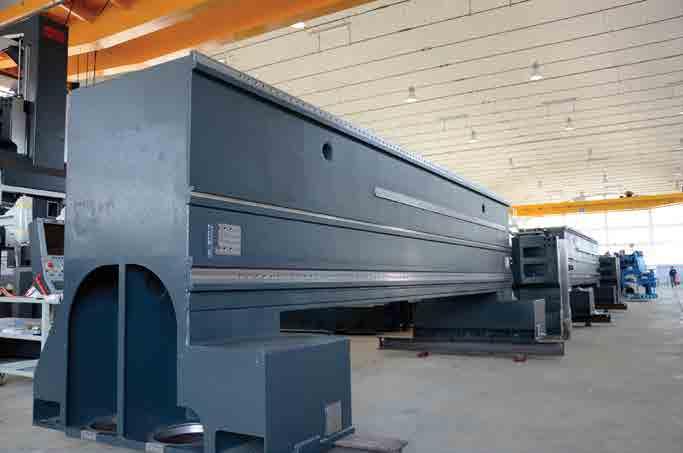