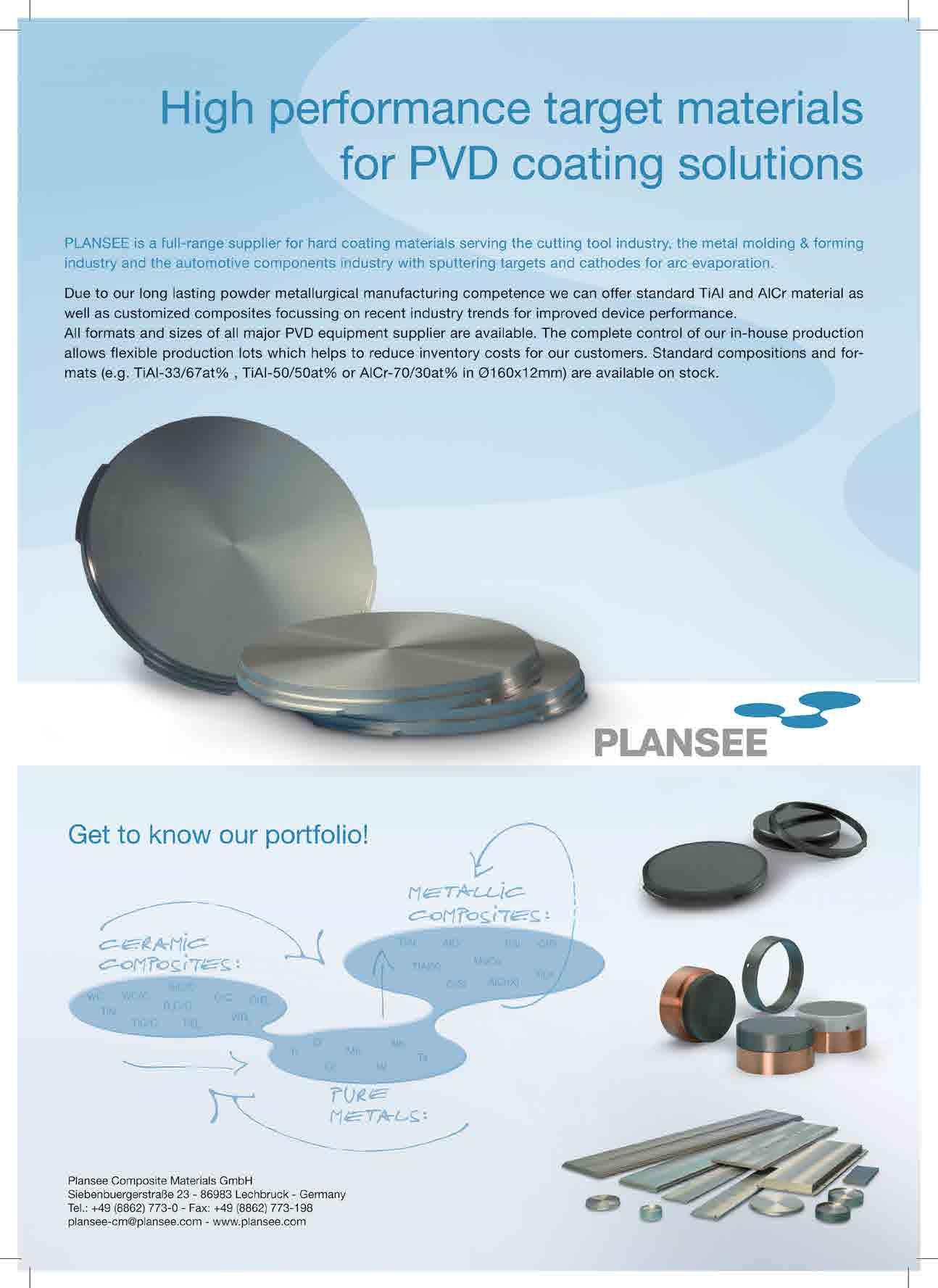
4 minute read
Diversity in metals Zucchetti Mario Forging
smooth yet dense and hard coatings to be manufactured reliably and efficiently for the first time. The application potential for this technology is wide-ranging in a large number of fields.
“Dense, hard and highly adhesive coatings, with a controlled microstructure, are extremely important for the coating of tools in order to increase productivity. For many years physical vapour deposition (PVD) – using arc evaporation technology – has proven able to deliver these properties and for a decade researchers tried to combine this technology with the sputtering process to achieve extremely smooth surfaces,” says a company spokesperson.
“Oerlikon Balzers has managed to overcome all of the limitations of the previous approaches and expanded the parameter range in several dimensions independently of one another. The technology is protected by multiple patent applications and is now ready for production.”
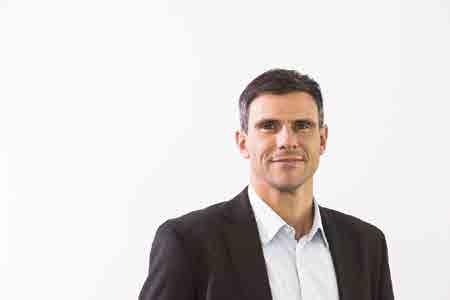
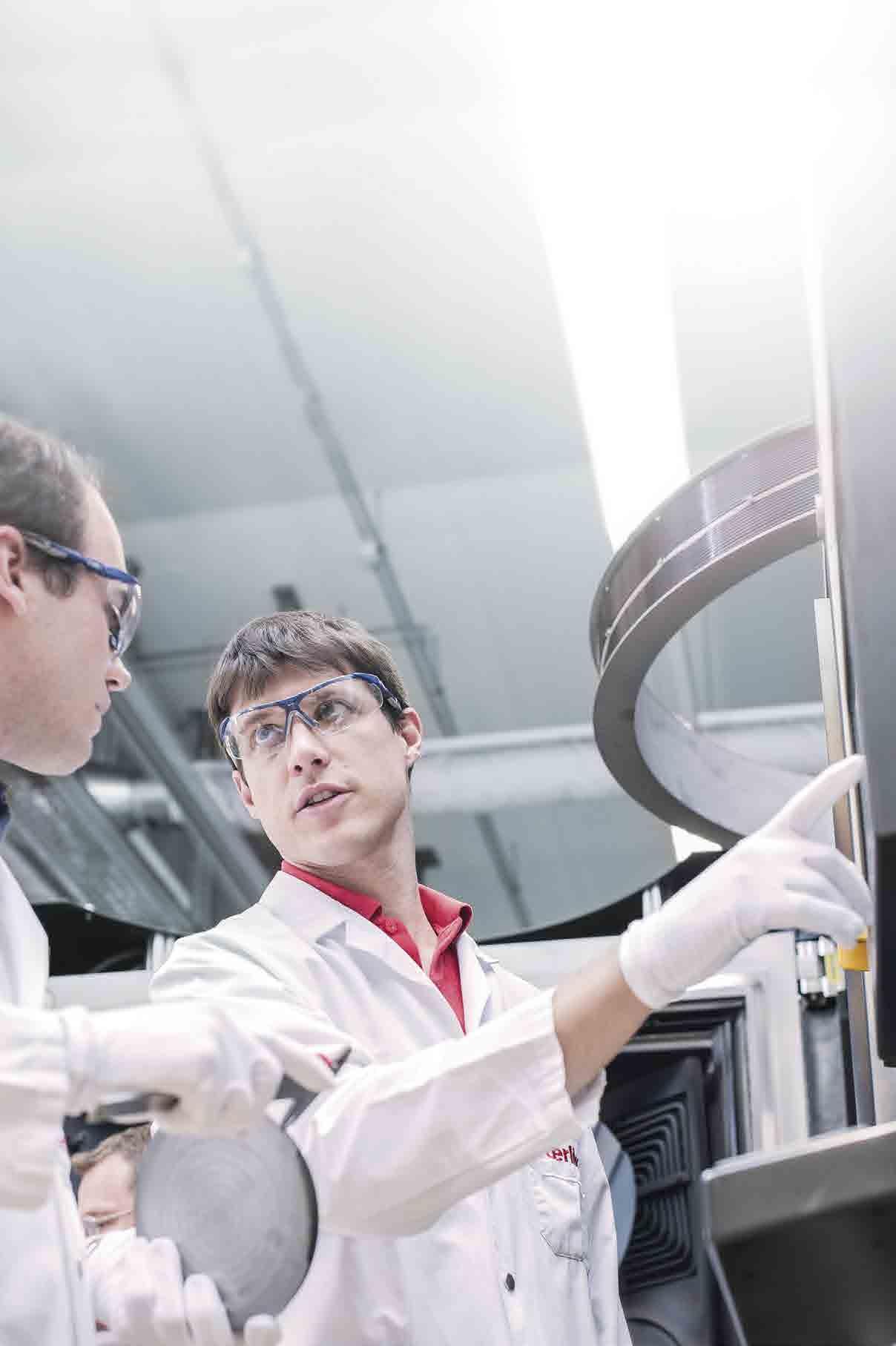
Greener options
Following a pilot in Germany, the first ePD™ (embedded PVD for Design Parts) technology centre in the world was opened at the Suzhou location, China. In contrast to traditional procedures, the low-emissions, eco-friendly ePD™ technology for the metallisation ofplastic parts does not use any environmentally damaging materials, such as chromium VI. ePD™ offers innovative functional features, such as radar-transparent metallisation for distance sensor systems, lightweight construction and a greater variety of design possibilities.
Since January 2014, Oerlikon Balzers has been offering its wear-protection solutions for large forming tools in China and Japan. The Pulsed-Plasma Diffusion (PPD) process developed by Balzers is an efficient and clean replacement for the hard chrome plating typically used in the automotive industry. The tools for skin parts only require a single treatment which uses no harmful chemicals. This technology therefore makes a significant contribution to promoting environmentally friendly production processes for the global automotive industry.
Onwards and upwards
In the future, the company expects to see organic growth across all the industries in which it is involved but the medical and aerospace industries are likely to be particularly interesting. For example, its centre of competence in France is focused on aerospace applications.
As the company grows, it will also continue to pursue its strategy of following its customers and the developing markets. n

Plant of ZMF Forging Ideas
DIVERSITY IN METALS
Zucchetti Mario Forging, today better known as ZMF, is an Italian company specialising in forging non-ferrous, multi-alloy metals. Sales and marketing manager Andrea Seroldi talks to Barbara Rossi about the company’s production facilities, its diversification process and future growth prospects.
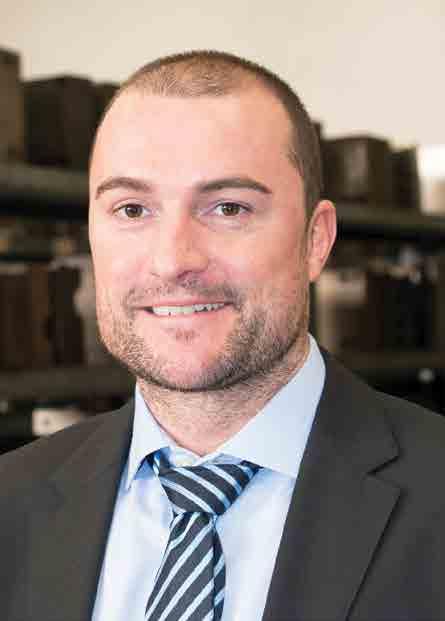
Andrea Seroldi, sales and marketing manager of ZMF Forging Ideas
ZMF started its business in 1975 as a company specialising in hot brass forging. It is part of Zucchetti Holding, which has three companies all based in northern Italy. In 1996 the company obtained the UNI EN ISO 9001 certification and in 2001 it introduced aluminium processing alongside its traditional brass forging activity. This was further developed in 2006 when an innovative finite elements simulation system was introduced, allowing the company to evolve from hot forging for taps and fittings to specialising in forging non-ferrous, multi-alloy metals, with a number of value-added services.
The company, which is the second largest in the Zucchetti holding group, operates from a single 25,000m2 covered plant in Antegnate, 50km from Milan. Today, as well as brass and aluminium, its range of alloys includes copper, bronze (including nibral) and titanium. “As well as offering traditional brass and other alloys, we have low-lead and lead-free alloys. We have a lot of experience with these metals both in terms of forging and machining. There is increased demand for these types of materials, owing to legislation prescribing their use for drinking water pipes,” Mr Seroldi explains.
New Press FO 10000S, a 1000-ton Recent development
Over the past few years, the historic Zucchetti Mario company has not only renewed its corporate image – changing its brand and name to ‘ZMF forging ideas’ – but also equipped itself with advanced machines and presses which are able to combine boring with technology-based forging. ZMF can therefore offer highly complex products in collaboration with the finite element simulation system (FEM); these include hubs forged in aluminium, multi-way valves for special applications, and even bodies for solenoid valves up to 3” (about 20kg).
Several years ago, the company purchased the FO 10000S, a 1000-ton hollow punching press which is equipped with a forging tool to bore medium and large sized pieces up to a maximum weight of 20kg of brass components, and round billets with a diameter ranging from 40 to 140mm. For normal-sized parts, with a weight of around 3–4kg, a remarkable production rate can be achieved. Thanks to this purchase, ZMF is able to manufacture products of greater weight and complexity, significantly expanding its already rich offer whilst at the same time achieving a high level of efficiency and competitive prices.
The FO-10000S not only performs well in terms of efficiency and accuracy, but also allows users to operate in a healthy environment. The fact that it is secure, fully monitored and has a relatively low noise level means that it provides the best possible working conditions. The loading of parts is carried out automatically, using a special 4-axis arm, which allows the operator to put the pieces in any desired position. In addition, in terms of loading there is the option of carrying out L-forms and similar bending up to a diameter of 50mm.
Given the considerable size of the press, which can produce heavy pieces even in flexible batches, a semi-automatic system of
