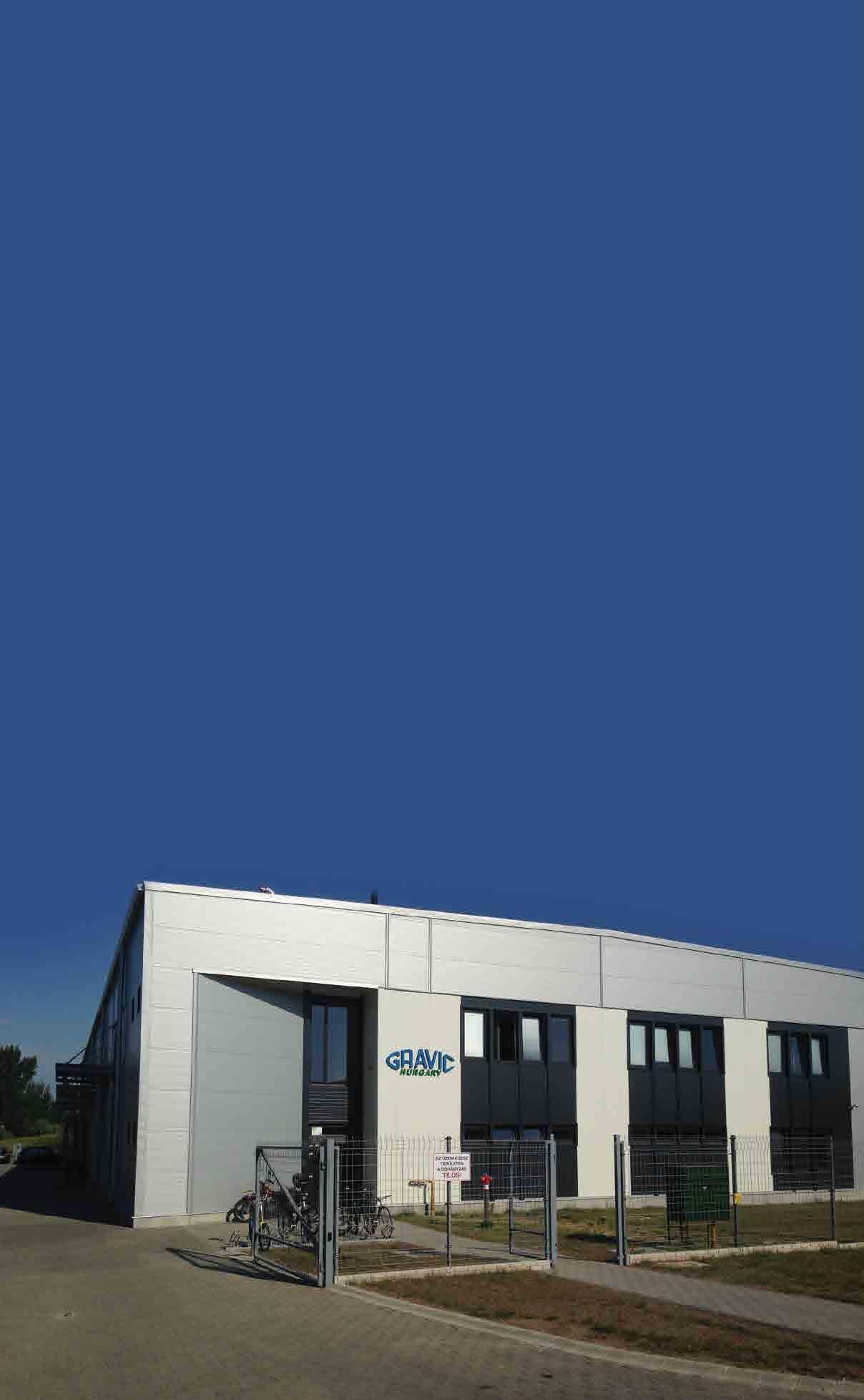
11 minute read
The 3D printing revolution Materialise
around 17 per cent of the business of Gravic Hungary is with the auto industry. We supply it with products such as identification labels for components, protective films and electronic interface materials.”
Label technology
Gravic itself began operations in 1967 in Antibes, on the Cote d’Azur, making printed circuits and metal plates. It moved to its current French headquarters at Mouans Sartoux in 1981, by which time it was specialising in technical labels and front panels (printed display and control panels for electronic and household appliances). In 1986 the company established Gravic Roll, which specialised in the fabrication of technical labels in rolls for use in large-scale production. This operation was merged with Gravic itself in 2008 and the whole company became Gravic Europe. In 1999 a subsidiary production operation, Tunitec Labels, was established in Tunisia, followed five years later by Gravic Hungary. The core of Gravic’s business remains the fabrication of blank and pre-printed labels on all kinds of substrates, adhesive or non-adhesive. These can be produced in large, medium or small scale volumes and in units, in rolls, in sheets, in folded sheets or in just about any specified format. The company also produces a wide range of other products such as front panels, 3D badges, information plates, protective films and insulators. As well as serving the automotive industry, it also supplies products for computers, household electronic appliances, medical devices, aerospace components and even cosmetic packaging.
In serving suppliers to the auto industry, Gravic is involved in three core activities - industrial marking by silk screening, fitting together multi-layer components and cutting technical pieces to shape. These skills are used to produce printed labels, dashboard panels, backlight filters, meter components, foam gaskets and cut-to-size technical pieces.
“Essentially we buy substrates from suppliers such as Avery Dennison, print on them and cut them to size,” says Vincent Zink. “For car dashboards, for example, we silk screen print on materials such as polycarbonate or transparent polyester and then supply the product cut to the customer’s exact specifications. We also now supply thermal interface films that help to diffuse the heat that is generated by the high power LED lights that are common on cars today.
“In fact we have a huge product range. Every week at Gravic Hungary we are involved in an average of 20 new projects and we typically deal with around 700 different part

numbers each month for customers in the household appliance, medical, transport and medical appliance industries as well as in the auto industry. All three Gravic plants supply the same kind of products for different geographical markets. However Gravic Hungary actually deals with most of the group’s overseas customers because our sales and service people here speak English and most of those at Mouans Sartoux do not.”
Fast responses
Last year Gravic Hungary moved into a new 1,800 m2 plant at Debrecen (two and a half times the size of its original facility) and it is planning a further major investment of more than €1m in new machines and new technology at the end of this year. Mr Zink reports that current growth is running at some 20 per cent year on year; sales to Hungarian customers currently account for 40 per cent of turnover while 60 per cent is in export business not only to neighbouring countries such as Germany, Slovakia, Poland, Italy and Austria but all over the world, from Mexico to Singapore.
“We are quite a small team here in Hungary and some of our competitors are huge, with thousands of people, but we believe we are much more flexible and responsive than they can ever be,” he says. “It’s not unusual, for example, to have a customer who has taken a product right through to the production stage and then finds the label has been overlooked. We can work quickly to put that right. We have a lot of specialised experience in our team and our staff turnover is very low so we can offer expert advice in choosing the appropriate material and so on.
“We are very optimistic about the future. The auto markets in Central and Eastern Europe are continuing to grow and we are investing substantially to meet this growth. Currently 17 per cent of our output is for the auto market and we would like to take that to 30 per cent. It is a very competitive market but we have the strengths to succeed and to continue to be valued, long-term partners with our automotive customers.” n
THE 3D PRINTING REVOLUTION
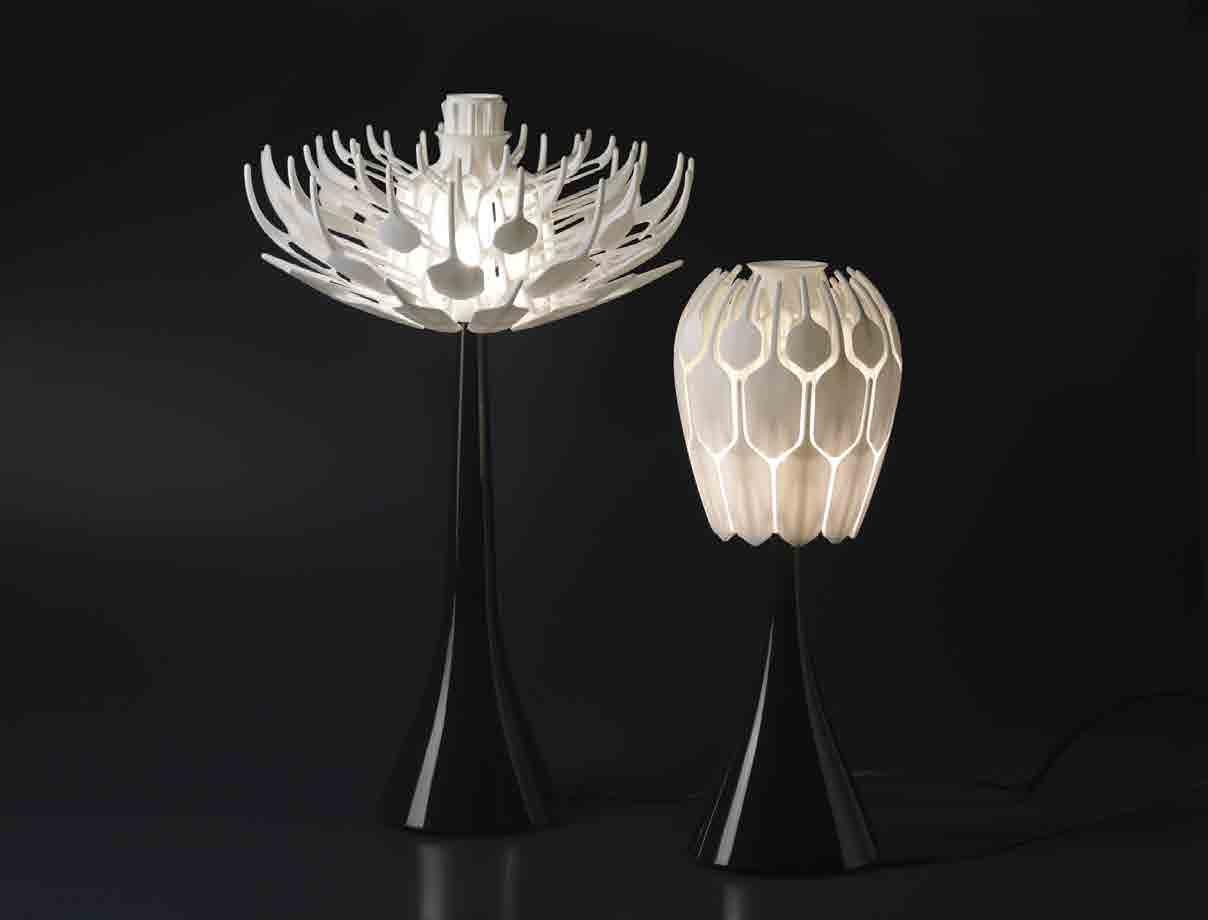
As a leading player in the area of 3D printing, Belgium-based company Materialise is equipped with worldclass design, manufacturing, prototyping, consultancy and manufacturing capabilities. Victoria Hattersley talks to Bart Van der Schueren, vice-president of Industrial Production, to find out more about the company’s activities and the future possibilities for this growing market sector.
For more than 24 years Materialise has been active in 3D printing, or additive manufacturing to give it its other widely used name. It has the largest capacity for additive manufacturing in Europe as well as a global reputation as a provider of innovative software solutions. Today its state-of-the-art modeling software and manufacturing capabilities are applicable to a wide range of markets and industries, from automotive and machining to aerospace, biomedical and consumer goods.
Additive manufacturing is the process of making a three-dimensional object from a digital model. One of its many benefits is the speed of development it offers: without the need for moulds or dies, parts and prototypes can be created on-demand. This also means lower costs and the freedom to modify a design quickly and easily.
From a sustainability perspective, this technology will allow for the creation of lighter components. As an added advantage for end users in sectors such as machining, this will also speed up the manufacturing process. Finally, as it is a relatively affordable technology it is hoped that it will be brought to wider use outside the sphere of manufacturing in offices, classrooms and homes in the coming years.
Mr Van der Schueren explains how the sector has evolved – and how Materialise has remained at the forefront of development: “One of the most important changes in 3D printing in recent years is that we have moved from simply prototyping to actually manufacturing and using the products.
“Our company had anticipated this change as far back as the 1990s but the technology has taken a long time to really enter the mainstream. It is really only in the past three years that industry has seriously recognised this technology for the purposes of manufacturing. Now customers can come to us with an idea for a product that could be made using 3D manufacturing, and we can work with them to make it a reality.”
But Materialise has long been aware of the possibilities for 3D manufacturing. As far back as 2003 it established its MGX brand, initially to produce high-end lampshades. This has now expanded into other kinds of furniture including jewellery, stools and even haberdashery.
Production base
With manufacturing now playing such a key role in the world of 3D printing, Materialise has been active in establishing a strong production base of its own. Therefore, in addition to its design and prototyping software it now also has four production locations in total. The largest is at its headquarters in Belgium, another is in the US, one is in the
First 3D Printed Race Car - by - Formula GroupT 2012 Areion Car MachinePark@Materialise

Flexible Material - TPU 92A-1 - squeezing

Czech Republic, where it has been present since 2004, and one in Poland.
“We already produce a large number of end-use goods at our facilities. We run over 100 professional standard 3D printers. In fact, in Belgium alone more than 50 per cent of our output consists of end-use goods.”
In recent years Materialise has observed that there is a trend towards manufacturing moving from the Far East to eastern Europe. Therefore, to boost its eastern Europe presence even further, in February this year (2014) it acquired a Polish company, e-Prototypy, a leading provider of rapid prototypes and 3D printing. “We believe in the potential of eastern Europe so it makes sense for us to establish a strong base here to anticipate this production shift. Because a production shift also means that product development will shift.”

Technological capabilities
Another key strategic reason behind this recent acquisition is Materialise’s conviction that product development needs to happen as close to manufacturing as possible. When asked why this is so important, Mr Van der Schueren explains: “For one thing, prototyping has to be fit for purpose. But the second point is that it has to be fit for production itself. And if the actual manufacturing is carried out far away from where product development takes place it becomes difficult to develop a product that can actually be produced in a cost effective way. With our 3D Printing we are ideally placed to produce the prototypes that are required in the product development.
Materialise works mainly with plastic when it comes to manufacturing, although for biomedical applications such as hip implants it can also work with metals. The technologies it uses fall broadly into three main categories: powder based manufacturing (including laser sintering); resin based; and FDM (fused deposition modeling), which works by laying down material in layers.
Complete software solutions
Whilst it would be hard to list every one of Materialise’s many solutions here in great depth, it is safe to say that it is able to offer a product to help its clients every step of the way through the rapid prototyping and additive manufacturing processes. For design, for example, its 3-matic solution offers modification, simplification, 3D texturing, remeshing, forward engineering and much more. When it comes to manufacturing there is the abovementioned MGX brand as well as i.materialise, both of which are well established on the market and offer cutting-edge possibilities for turning customers’ ideas into a reality.
For prototyping, Materialise’s range of Magics software solutions allow users to import data and prepare platforms, whilst its revolutionary Streamics product provides them with a user-friendly server based system to centralise their customer project data and facilitate full traceability of the additive manufacturing process.
Furthermore, Mr Van der Schueren explains that software development is likely to become an increasing focus for the company in the years to come: “More and more production companies are likely to have 3D printing machines in their own production environments. This means they will need complementary software to help run them in the same way they needed it to control their CNC, injection moulding capabilities and so on. Over the past few years, we have been developing our Streamics software to run as a control system alongside production. This will help with traceability, liability checks and so on.”
Growth in biomedicals
Of particular note has been Materialise’s work in the biomedical sector, for which
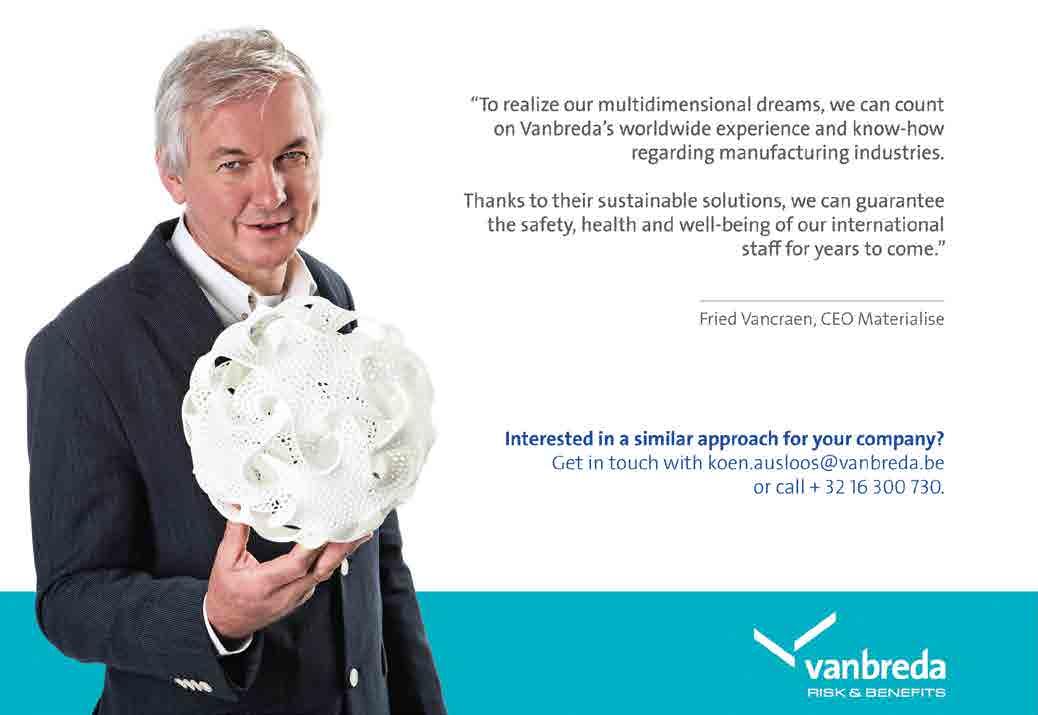
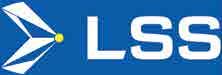
For more than 12 years, LSS GmbH has operated as an independent, pan-European Support and Service Provider in the field of Selective Laser Sintering (SLS) and Stereolitography (SLA). Beside of our service activities LSS delivers state of the art upgrades and customized solutions, distributes SLS & SLA materials and provides application support. Our success is based on a highly motivated and flexible acting service team combined with solid technical experience in rapid prototyping and manufacturing equipment with focus on systems from DTM / 3D Systems Inc. and EOS GmbH* .
Product/Service Summary: LSS GmbH supports their customers in the following areas of Selective Laser Sintering (SLS) and Stereolithography (SLA): • Field Services , standard and customized packages • System upgrades and customized solutions • Distribution of SLS and SLA materials • Sales of revised and upgraded systems
*DTM / 3D Systems Inc. and EOS GmbH are registered trademarks.
Laser Sinter Service GmbH Gottlieb-Daimler-Strasse 12, D-59439 Holzwickede, Germany Phone: +49 2301 91323-0 • Mail: office@lss-europe.com www.lss-europe.com
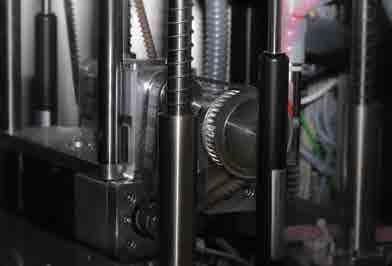
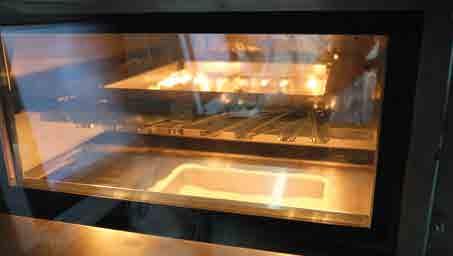
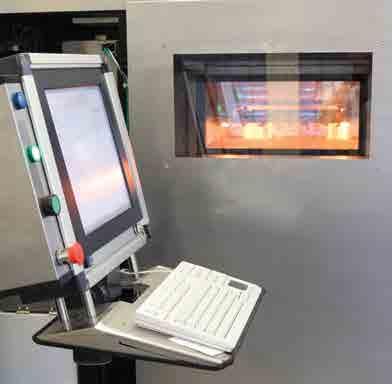

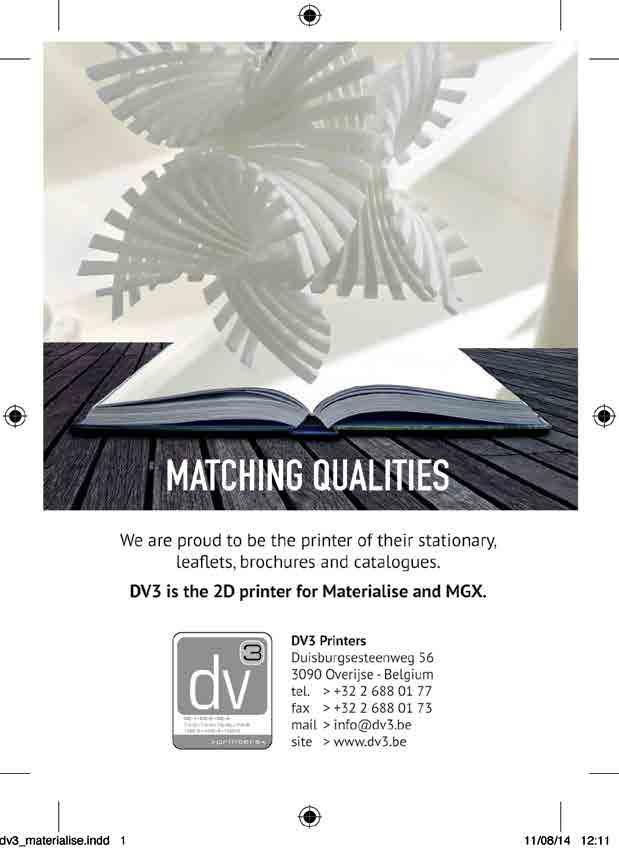
DSM
Becoming a publically traded company is no small feat — and neither are the great strides in innovation that are made by Materialise. Their dedication to making the world better and healthier through Additive Manufacturing is truly inspirational.
DSM’s Somos® materials are honored to work with such an amazing company in developing breakthrough materials for Additive Manufacturing. The new applications that have opened up thanks to this technology have been able to do everything from saving lives to creating works of art.
DSM believes that 3D printing is a major change agent for the world creating brighter lives for people today and generations to come. Somos® Materials is dedicated to customer growth in the ever-changing world of 3D Printing and promotes this growth through continuous material and application development, encouraging industry collaboration and maximizing customer asset value by providing continuous information and support. To learn more, visit us at: www.dsm.com/somos