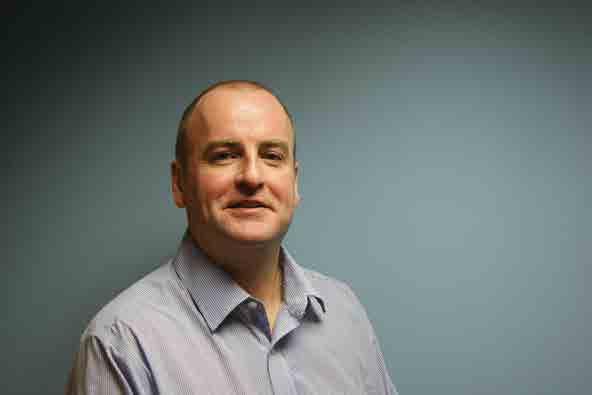
11 minute read
Pressure for perfection Avure
and other coolant handling applications.
The products offered include technically advanced convoluted hoses with stainless steel rings to absorb the relative movement between engine and intercooler. Specially developed convolutes minimise resistance to flexing and loads transferred to connection spigots. The company has its own in-house testing facilities to carry out load movement trials, accelerated dynamic testing to approve functional integrity, and so on.
For high-pressure applications, James Dawson’s cuffless clamping system can provide an effective seal to existing metalwork – at the same time allowing the full hose length to absorb any offset or movement. It has also developed a special fluorocarbon based compound to cope with gas components at temperatures of up to 275° C, helping to enable the reduction of exhaust outputs.
In the area of organic rubber hoses, the company can offer a range of different options, including one-piece hoses, legged hoses, large bore hoses and hoses with inserts. Finally, its range of ductings constructed from recyclable thermoplastic elastomer (TPE) offers high standards of flexibility and durability with resistance to ozone, weathering and engine compartment oil splashing, to name just a few of its benefits.
“All our products are bespoke,” adds Mr Edwards. “At our company there is no such thing as standard lines. Instead, we collaborate with customers as early as we can in the engine design to make the products they need to fit their machines.”
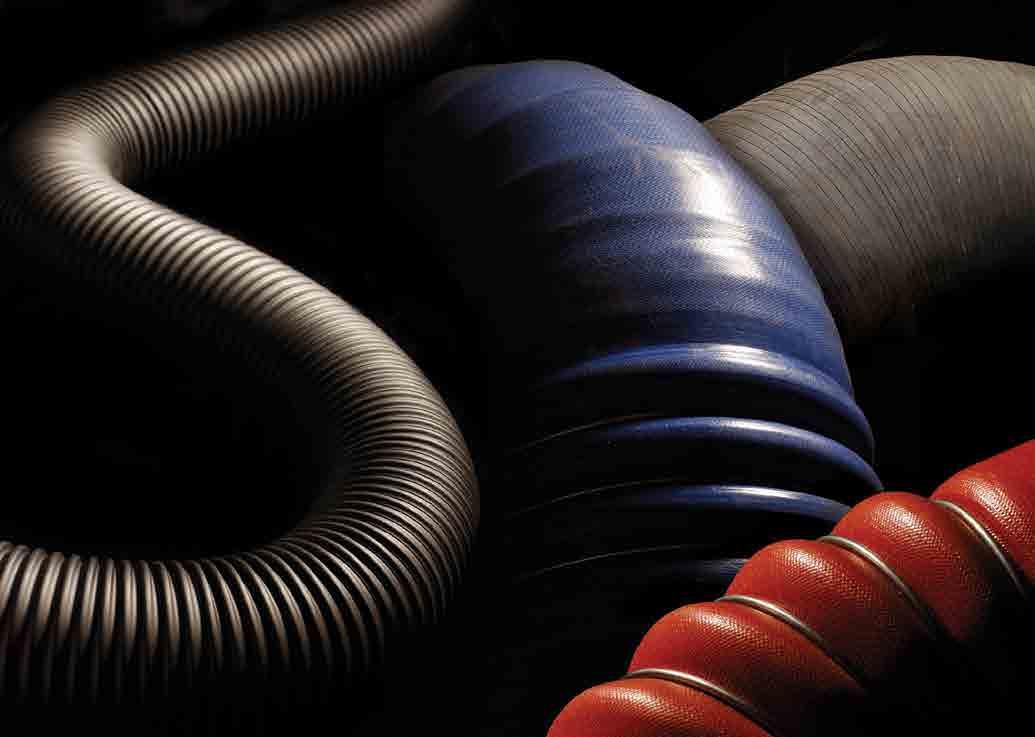
New focus on development
The above point leads us on to an important shift of focus currently taking place at the company. Up until recently, the collaboration between James Dawson and its clients would work as follows: the client would send a drawing of their design to the company. Its material scientists would then choose the right material for the application, and its technical specialists would look at ways to create the product using existing processes. But this is changing.
Mr Edwards explains: “Moving forward we would like to be working with our customers from the very start of the product development stage. We will be focused on product optimisation to get just the right balance between quality and price. It’s a strategy of increased customer integration and more focused innovation. So much so that rather than our current tagline of ‘James Dawson – Global Hose Specialists’, in the future it will be ‘James Dawson – Engineered Hose Solutions’.
To this end, the company has been focusing investments on R&D and creating unique solutions. This year it purchased a new lab mixer in order to explore the capabilities of advanced compounds with a view to bringing ground-breaking new products to the market. September 2014 will see the appointment of a new Head of Innovation & Technology to lead James Dawson’s new R&D team.
The basis of the new strategy will be formed of three interlinked concepts, according to Mr Edwards. “The first of these will be customer integration. This means working with customers very closely at an early stage so we can produce fit-for-purpose, optimised products.”
The second concept revolves around ‘focused innovation’: developing new materials or working on ways to solve the problems customers experience with exisitng products. “For example, a customer recently came to us wanting to use a silicone hose in applications at up to 550° C. We thought

that was a step too far, but it got us thinking about how we could develop an existing product to make it withstand greater heat.
“The result is that we are now developing a hose that can withstand temperatures in excess of 300° C (the previous upper limit being 275° C). This will enable customers to run their engines hotter – and with emissions legislation getting tougher, running the engine hotter means you can burn off more toxic emissions so they run much cleaner. We are also looking at how clients can use more lightweight metals, such as titanium, within their engine designs. This product is currently in the testing phase and we are already seeing some initial interest from customers.”
The third major arm of the new strategy is focused on operational excellence on a global level. This, as Mr Edwards explains, will mean an increased emphasis on an ‘optimal global footprint’.

Meeting future challenges
For James Dawson, this drive to achieve excellence on a global level is a way of meeting one of the biggest challenges for any company in this sector: increasing competition from highquality Asian producers. “This is why our new strategy of customer integration is so important to differentiate us,” says Mr Edwards. “If we can become a partner as well as a supplier it means we can work with clients on creating top quality products that are fitted specifically to our existing processes. This makes it more cost effective for them overall because we don’t have to adapt their own designs to fit our technology.”
Finally, James Dawson may also consider looking into other applications for its products at some time in the future. “All we do at the moment is linked to diesel engine applications so we may one day look to branch out into aerospace or oil & gas, to name just two examples. However, this is not something we will be working on in the immediate future because we feel it’s better to focus our energies on the possibilities for our existing markets. If we were to see a downturn in these sectors – always a possibility – then we could look at this more carefully. It’s always important to have options like this in the pipeline.”
But at the moment it seems there is plenty of scope for James Dawson to reach the next stage in its evolution as an engineered solutions provider for its current markets. We will watch with interest to see how this develops over the next year. n
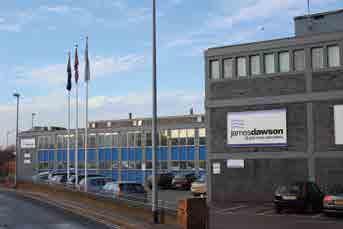
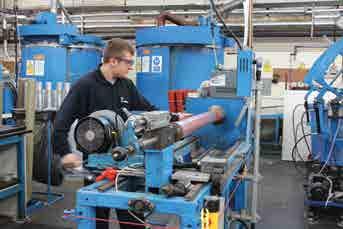
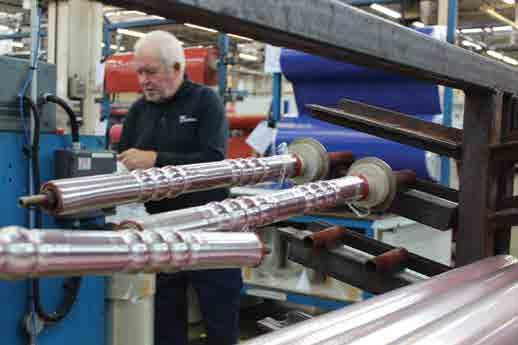
Valmiera Glass is an international manufacturer of glass yarns and woven fabrics for a wide variety of applications from automotive and thermal insulation to coated products and composite materials.
We are a fully accredited Aerospace supplier, and wish continued success to James Dawson and its associated companies.
Valmiera Glass UK Ltd +44 (0)1935 813 722 www.valmiera-glass.com www.atex-membranes.com
Ever since it found a way to turn carbon into synthetic diamonds 60 years ago, Avure has been using high pressure technology to produce innovative and costeffective solutions for metal processing and forming. Peter Mercer reports.
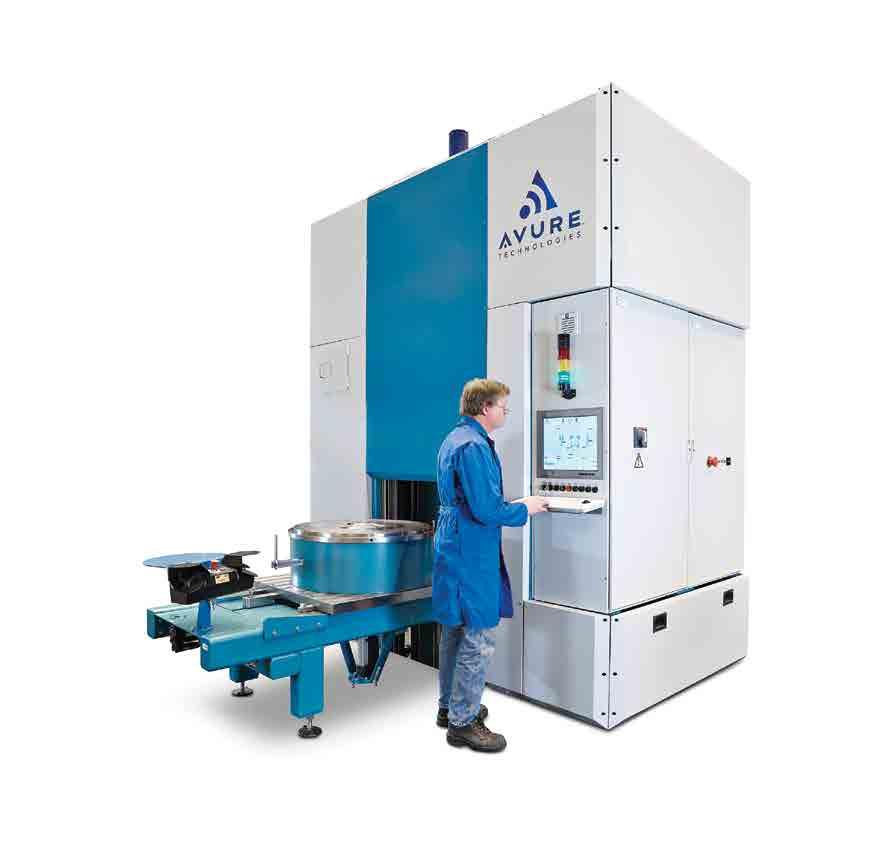
PRESSURE FOR PERFECTION
For nearly six decades engineers and scientists at Avure Technologies have led the world in the design and construction of high pressure processing systems to meet the needs of many industries. The company’s isostatic processing equipment has opened up a whole new world of possibilities in metallurgy and ceramics and its Flexform sheet metal forming systems have enabled customers to create complex shapes while saving up to 90 per cent in tooling costs as well as significant savings in man hours thanks to a reduction in the need for grinding / manual correction. Its high pressure technology has also been extended to the pasteurisation of food products such as seafood, vegetables and beverages.
Avure’s history goes back to the mid-1950s when the Swedish electrical power company ASEA began to commercialise isostatic pressure technology. In fact, ASEA was one of hte first companies in the world to create systems to produce synthetic industrial diamonds, employing pressures of nearly 1 million psi. In the 1960s it introduced isostatic presses and Flexform sheet metal forming presses to the industrial market and these were further developed when ASEA became part of Sweden’s ABB. In 1999 the high pressure business unit of ABB was acquired by Flow International of the USA who subsequently took forward the expansion of its high pressure technology into the food preservation market under the Avure brand. In 2009 Avure Technologies was sold to the privately-owned US company Milestone Partners. Then, in 2013, the company was divided into two stand-alone divisions – Avure Food, headquartered in Middleton, Ohio, and Avure Industry, headquartered in Vasteras, Sweden, where 90 per cent of current industrial production and assembly takes place. Avure Industry also has a facility in Columbus, Ohio, which takes care of projects in the North and South America regions and customer serivce for North and South America.
Today Avure Industry is focused on two high pressure technologies – isostatic presses for advanced material densification and Flexform presses for sheet metal forming.
QUINTUS
“After it had successfully developed systems that could withstand the huge pressures required to transform carbon into industrial diamonds, ASEA realised that the same technology could be used to compress other metallic or ceramic powders. The problem, however, was how to ensure the safety and reliability of containment systems with pressures of 1 million psi that would be in regular
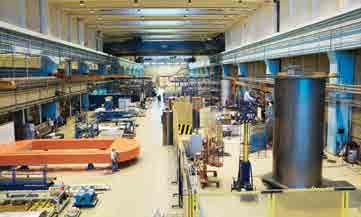

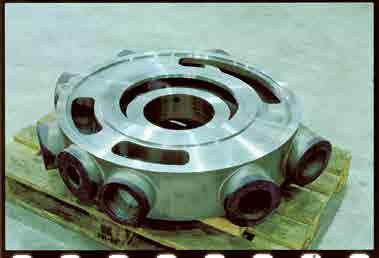

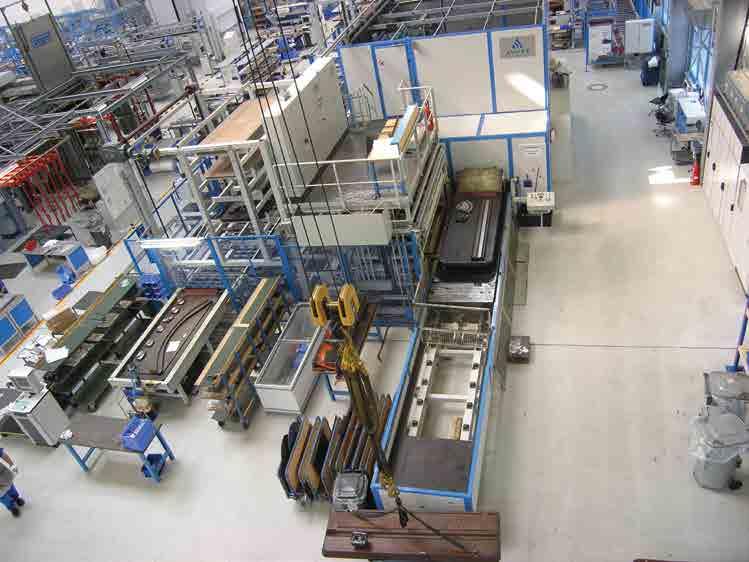
industrial use,” explains Avure Industry Sales and Business development Director Mats Sjostedt. “The solution was the development in the early 1960s of the QUINTUS wirewound pressure vessel, which is still considered to be the safest and most reliable pressure containment system ever designed.”
QUINTUS wire-wound vessels combine unmatched strength with a light, compact structure. Unlike conventional forged steel mono-block vessels they are pre-stressed and wound completely with high tensile cold-rolled spring steel ribbon. Pre-stressing causes the forged steel vessel wall to remain in residual compression even when subjected to maximum loads and the wire winding is not only much stronger than forged steel but more layers of wire can always be added to increase the strength. QUINTUS wire-wound vessels are typically half the weight of conventional presses and will leak before they break, so avoiding the catastrophic failures that can occur with mono-block vessels and the frequent and expensive inspection procedures that are required to prevent such failures. They also have a working life that is typically twenty times that of conventional designs.
Material densification
Avure’s Hot Isostatic Pressing systems (HIP) use compressed high pressure gas to produce parts that have excellent isotropic material properties and show the highest possible density of all available compaction methods. HIP Castings presses are widely used to completely remove internal porosity in castings. The HIP-ing of casted parts results in parts with a better fatigue and strength and provides more uniform properties in various metals such as aluminium, titanium, nickel-based super alloys and stainless steel. Hip’s unique ability to densify castings is crucial to the production of components such as turbine blades, joint implants and engine parts. The removal of potential initiators of failure, such as shrinkage defects, pores and voids, significantly improves the strength and durability of cast components.
The use of HIP also widens the range of titanium alloy compositions possible for castings in comparison with wrought systems. Significant cost savings can also be achieved with investment casting and HIP in comparison to machining parts from solid.
“Avure’s material densification systems are widely used for refining castings in the aerospace, automotive, bio-medical, energy and consumer electronics industries,” says Mats Sjostedt. “In essence you put a cast part into a hot isostatic press and all the cracks and other defects just disappear, resulting in parts with highly accurate tolerances and very long lifetimes. A critical advantage of HIP is that parts for aircraft or automobiles, for example, no longer have to be over-designed to ensure their strength, which means they can weigh less and cost less. Reducing weight is essential in new-generation, fuel-efficient airplanes and with an estimated 35,000 new airplanes required by 2035 and 137,000 engines the potential demand for Avure’s HIP casting systems in immense.
“In the automotive industry too the drive towards reducing the weight of cars and trucks means increasing use of aluminium parts. But aluminium is a low viscosity metal and it is easy to get cracks in castings. With HIP, defect-free aluminium castings can be guaranteed for critical applications such as engine blocks and costs reduced thanks to much lower scrap rates. And in the energy industry the expansion of deep-sea oilfields and the likely demand for up to 500 new nuclear reactors over the next 20 years will also drive the increase in demand for our HIP systems.”
Avure’s HIP technology is also widely used in powder metallurgy. The hot isostatic pressing of encapsulated powder metals produces net or near net shape parts with special particle properties. HIP treated PM parts are isotropic and deliver significant savings in materials and lead times compared to wrought components. HIP also enhances the versatility and design flexibility inherent in powder metallurgy by allowing, for example, freedom in chemical composition, particle size, distribution, form and even permitting graded structures.
HIP PM parts are increasingly used in the oil and gas producing industries for valves, pumps and drilling components, where they reduce the need for costly frequent inspections, and as components for solar panels, electrodes for steel production and, of course, in the aerospace industry. The technology is also critical to the fast-growing 3D Printing industry, where parts such as hip implants need to be structurally perfect.
Flexform
Avure’s solutions for metal forming are centred on its Flexform fluid cell forming system. Introduced by ASEA in the 1960s, Flexform employs a soft rubber diaphragm filled with highly pressurised fluid to press flat metal blanks uniformly into and around a lower tool half, which can be a punch or die. It is a highly versatile solution for manufacturing highly defined prototype components, particularly in industries where speed and lower costs are crucial in reducing time-to-market and staying globally competitive. Flexform is also ideal for low volume parts production.
Today Avure is the leading fluid cell press supplier to the aerospace industry, with