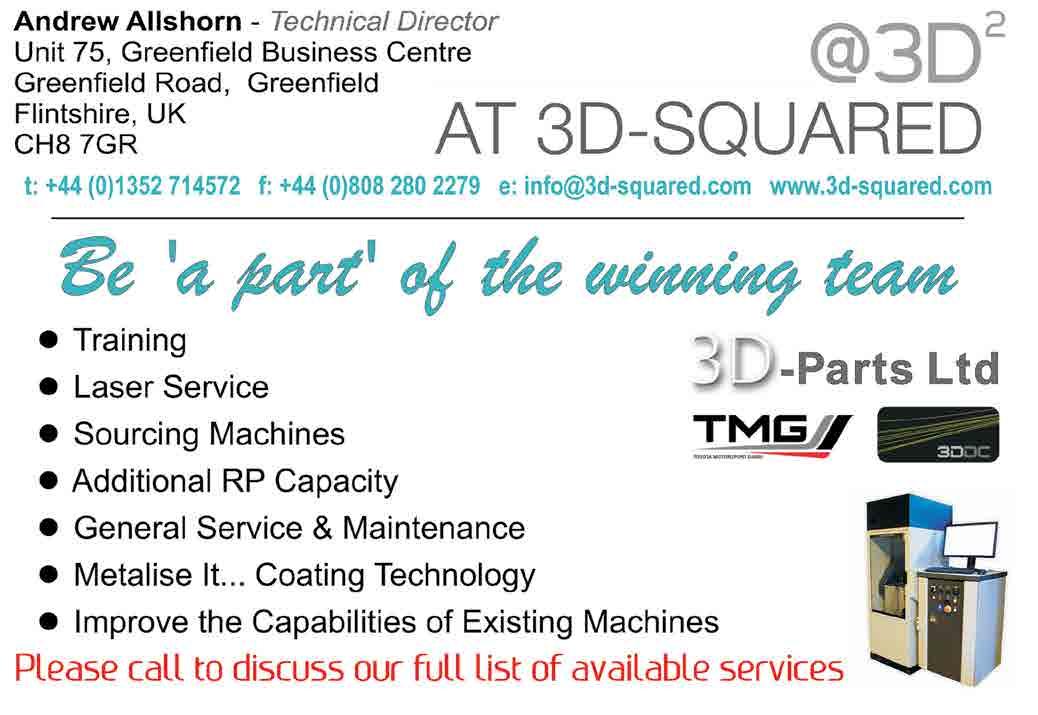
4 minute read
Polymer production solutions Mikrosan
it has been developing software for the automatic design of personalised hearing aid shells as far back as 2001. In fact, Mr Van der Schueren points out that by 2008 almost all custom hearing aids are now 3D printed.
There are many examples of Materialise’s pioneering work in the biomedical field. One recent high-profile case was that of a 15 year-old Swedish girl facing a lifetime in a wheelchair owing to a congenital disease that had left her with a severely deformed left hip joint. In 2012 the case was brought to the company’s Mobilife medical products division. A custom implant was designed to reconstruct the joint, and almost immediately after surgery she was pain-free. Today she is able to walk without crutches.
Mr Van der Schueren tells us: “What we are doing is creating scaffold structures between the bone and the titanium implant. The bone has a natural affinity with titanium so it will grow surprisingly rapidly once the implant is in place.”
And in fact, the company is taking this kind of implant technology one step further: “One of the things that maybe hasn’t been ideal with existing implants in the market is that they are too strong, if anything. A consequence of this is that the implant doesn’t load the bone anymore which doesn’t encourage new growth.
Nikon Metrology handheld 3D Scanner - additive manufactured series of housings




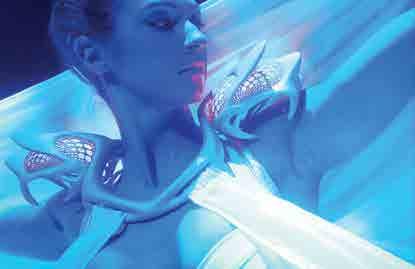
Anouk Wipprecht, Niccolo Casas and Materialise - Cirque Du Soleil © Liana Bandziulyte Mammoth machine park @ Materialise - capable of building large parts in one piece
Nikon Metrology handheld 3D Scanner - additive manufactured series of housings
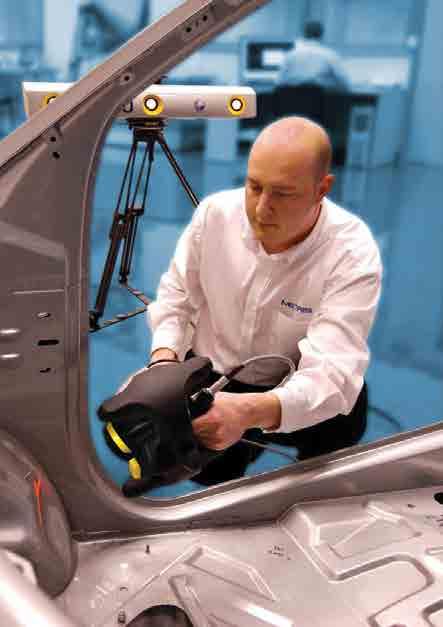

Porous Titanium Skull Implant - OBL Paris
This means the bone is just resorbing or not growing anymore. We design our implants in such a way that some of the load is transferred to the bone structure and enables it to grow. Using 3D printing techniques we can develop and create complex shapes for each individual implant.”
Future prospects and challenges
When it comes to other key industry sectors, Materialise has also been seeing very strong growth in aerospace and machine building. In the aerospace industry in particular, the potential for creating more customised, lightweight parts makes additive manufacturing very attractive.
He acknowledges that despite the many benefits we are already seeing, there are still plenty of challenges for the industry to face. The first of these, he says, is making the technology more accessible when it comes to the kinds of materials that can be used and so on.
When it comes to manufacturing, he tells us that the major focus for development will be on improving machine performance. In order for this technology to be used more widely it is essential that professional 3D printers produce goods which are repeatable and predictable when it comes to quality. “Not only this, but the speed of the machines will need to increase as they are still relatively slow compared to other forms of manufacturing.”
To illustrate this last point, he gives the example of making an extremely common plastic component – the back of a mobile phone. “Today, if you use injection moulding then it will take a few seconds to make. If it’s 3D printed it will take about 5–10 minutes so we need to find a way to speed things up in the coming years. With rapid prototyping you can develop and create a product in a matter of days, but when it comes to rolling out to manufacturing there is still a gap between the two that needs to be closed.”
Indeed, Mr Van der Schueren doesn’t believe that the growth of additive manufacturing technology should necessarily be focused on replacing conventional manufacturing techniques. He acknowledges that these may always be more suited for mass production, and certainly for the next 20 or 30 years. Rather, it’s a case of 3D finding its own specific niche in the market for specialised products in smaller runs. And this is where we have really seen it come into its own over the past three years. It will be fascinating to see what the next few years hold for this dynamically developing sector. n

Mikrosan Makine ve Kalıp Sanayi A.Ş. is a Turkish manufacturer of machines for the production of polymer-based products. Vanja Švačko discussed the company’s operations in Turkey and beyond with Mr Rauf Rustamov, a Commercial Director of Mikrosan Company.
POLYMER PRODUCTION SOLUTIONS
Since its establishment in 1978 Mikrosan Makine has been acting as a solution partner to companies within the plastics industry. In the beginning it was plastic processing machinery that the company started with and today it has a much diversified product range as a result of comprehensive market analyses.
Mikrosan’s portfolio is generally divided into three main categories of products: pipe extrusion, profile extrusion and granule extrusion, with major revenue coming from the first two production lines. Each line is part of a highly professional engineering project and manufactured using the most advanced technolo-
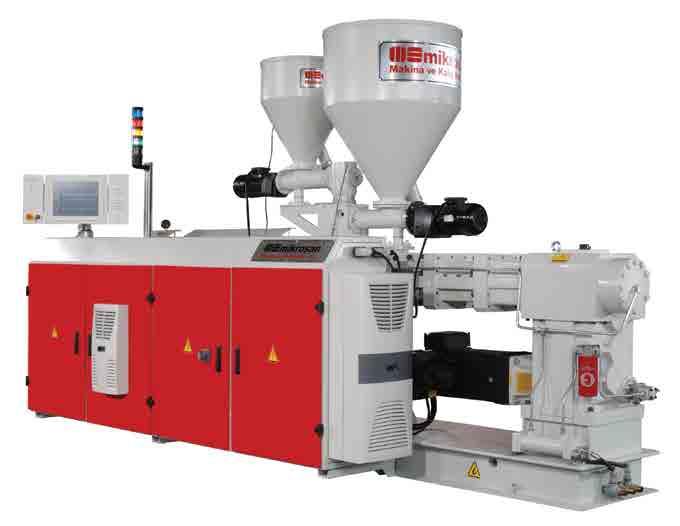