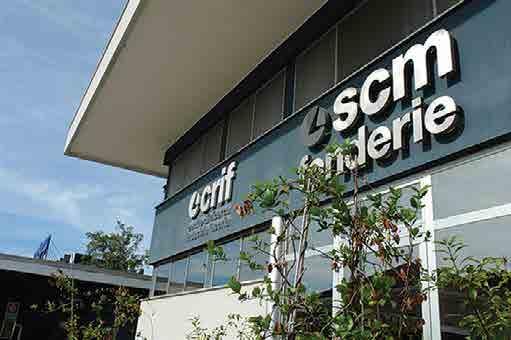
9 minute read
A new leader in surface solutions Oerlikon Balzers
EKW GmbH was established in 1903 and set up its Italian branch, EKW Italiana, in 1967 with the aim of consolidating and increasing the presence of its products (refractory materials) in Italy.
The company, which today has changed its name to EKW Italia, is not just a distributor, but also plays an active role in coating design, assembling, sintering and delivery of ‘turn-key’ systems, thanks to a technical and commercial team available 24/7 and flanked by skilled assembling staff using own equipment.
The admin staff is available to fulfil customers’ bureaucratic and commercial needs. Moreover, by availing itself of skilled foundry technicians, the company is able to support its clients with the best technical application solutions concerning castings feeding systems.
EKW Italia S.r.l. Via del Lavoro, 21, 20863 Concorezzo (MB) Tel: +39 (0)39628031 Fax: +39 (0)396280322 E-mail: info@ekw.it
Rimini-based SCM Foundries belongs to the SCM Group, whose origins go back to 1932, when Nicola Gemmani and Lanfranco Aureli set up a factory specialising in the production of agricultural machines and a foundry for iron castings. A major change of direction took place in 1952, when woodworking machine manufacturing commenced. Based on a design by newly qualified engineer Giuseppe Gemmani, the first cast iron combined multi-purpose woodworking machine was produced: L'invincibile B4. It was the first in a considerable series of innovations, which together with a strong propensity towards exports and the development of an impressive world-wide distribution network, in just a few years made the company an international leader. Today the group is a leader in woodworking machines and systems catering for both industrial clients and traditional joineries. Originally SCM Foundries specialised in the production of woodworking machinery components, mainly serving the other companies of the group. Its activity evolved during the years and today 90 per cent of its turnover derives from products for external customers, to whom it mainly supplies rough components, as well as being able to provide finished products when this is demanded. While the design and specifications are supplied by customers, SCM offers a co-engineering service, advising clients on the best way to fulfil their product needs, thus optimising the production process, quality and value for money.
Mr Maffei explained, “Our offer includes a wide range of grey and nodular iron castings, from those featuring high mechanical resistance to their more ductile counterparts performing well at low temperatures, which are increasingly demanded by some sectors such as the rail and wind power industries.”
The company has two production sites, at Rimini (also the location of its headquarters) and at nearby Villa Verucchio. The Rimini site has two green sand moulding plants equipped with a hot blast cupola oven and an electric holding furnace. This site specialises in castings with weights ranging from 1kg to 500 kg, produced in medium series. Situated 15 km away, the Villa Verucchio plant is dedicated to manual moulding with resin bonded sand and can avail itself of two methane rotary furnaces. Its specialism is castings with weights between 200kg and 4,000kg, produced in small to
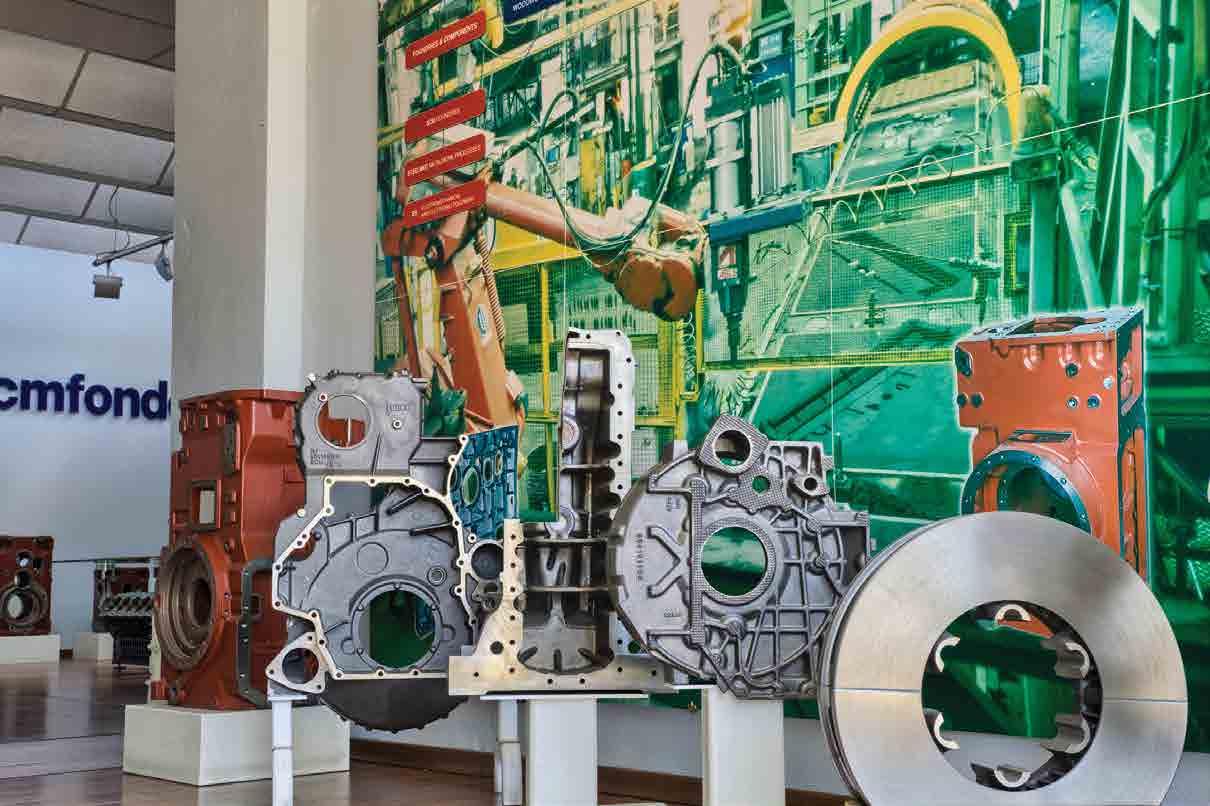
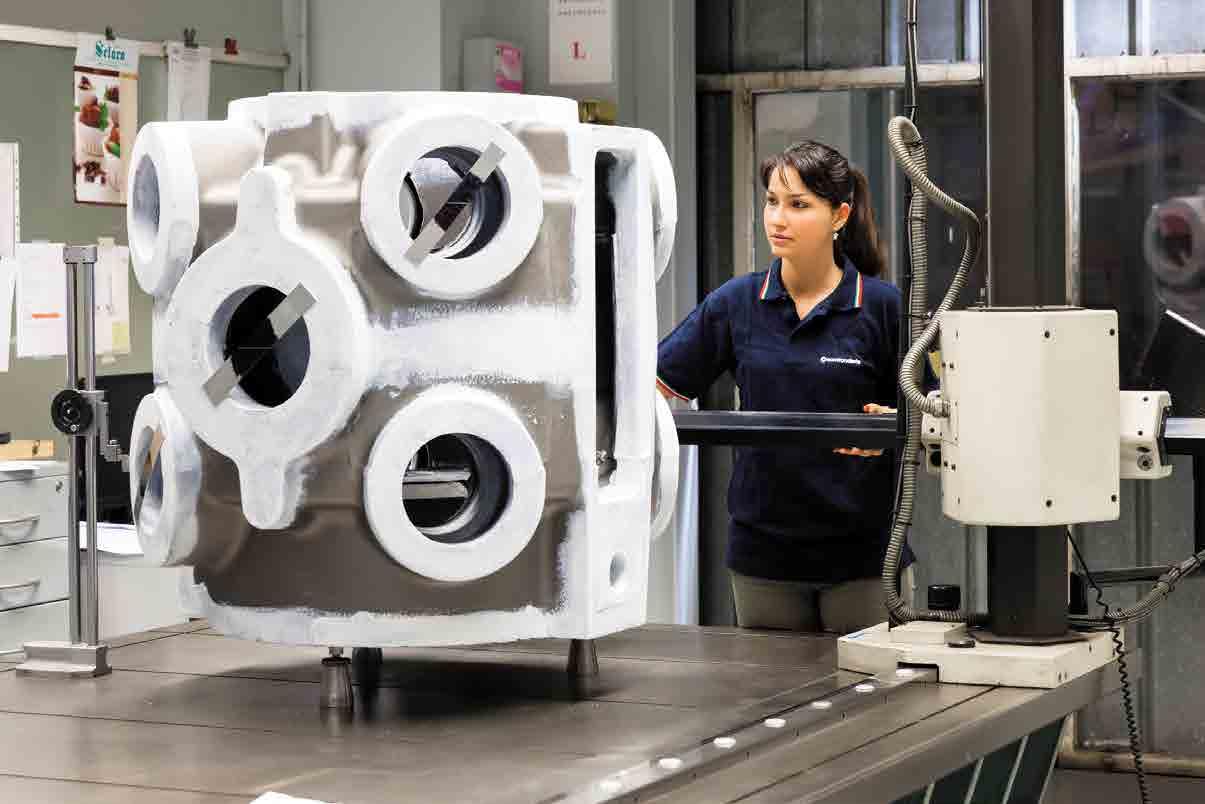
medium series. “Our annual production capacity is 35,000 tonnes, but one of our future aims is that of widening the range that we offer to our customers, so as to include castings of larger dimensions, up to a weight of 10,000 kg. We are planning to do this because our clients are moving towards larger components, for instance with regard to compressors.”
“We invest regularly to modernise and improve our existing plants to optimise the process and service on offer. For instance, recently in Rimini, there has been the revamping of the 12 tons/h cupola oven and one of the two automatic moulding systems, whilst in the summer of 2014 we are going to replace the electric holding furnace. Furthermore, we are currently considering some important innovations for the strengthening of the melting department to increase the flexibility of our offer. Our Villa Verucchio facilities have undergone a phase of great change, starting with a true revolution in the melting department, thanks to the replacement of the cold blast cupola oven with two 20 tonnes oxy-fuel rotary furnaces. Moreover, we have been able to increase the maximum weight that can be processed, thanks to the addition of a new remote manipulator and a new sandblasting system for castings of up to 4 tonnes. Significant investments have also been made in the core department in terms of a new no bake core production systems. In the near future we plan to widen our moulding department, including no bake processing for the production of castings of up to 10 tonnes. Last, but not least, we have continuous investments targeted at increasing environmental friendliness and health and safety at work, obviously matters of priority for our company.”
Expanding customer base
The company’s foundries serve hundreds of clients operating in various sectors of the mechanics industry. The castings manufactured by SCM Foundries are mainly employed for applications such as gear motors, robots, large compressors, pumps, tractors and rail sector products. Other segments served, among many, are urban lighting, industrial handling and woodworking machinery.
Geographically, 90 per cent of turnover derives from the domestic market, with the remainder mainly being generated in Europe (for instance in Germany, France, Switzerland, Romania, Croatia and Slovakia). On one occasion SCM Foundries also supplied components for high-speed trains in China. Although most of the company’s direct clients are based in Italy, after being processed and assembled by customers, SCM components are exported all over the world. “Our future strategy is going to be oriented towards increasing foreign-based direct clients, with a particular focus on Europe, and Germany, in particular. We plan to grow organically, strengthening our existing facilities, widening our range of casting in terms of weight and continuously improving our service. Fundamental factors necessary for our future development are an increase in flexibility and ever more complex and sophisticated products at a technological level. We are also developing castings for niche sectors, which require value-added products and might offer interesting business opportunities. A higher level of technological sophistication is a must in order to be able to successfully face competition. Another must for success is diversification, which we have been undertaking for a number of years and which has protected us from downturns in some market segments.”
SCM Foundries holds a number of certifications, including UNI EN ISO 9001:2008, UNI EN ISO 14001:2004 Lloyd’s Register, Germanischer Lloyd and AIA (Environment Integration Authorisation). In 2013 the company established its research centre for the casting industry (CRIF) which works with SCM Foundries and is dedicated to research, testing and trials of new materials and products and, in general, all matters relating to cast iron castings. “In terms of R&D we are currently engaged in three new projects for energy efficiency, environmental sustainability and foundry automation.”
Mr Maffei concludes, “We have excellent relationships with our clients. I would like to mention some of them, for instance Rossi, Bonfiglioli and Dinamic Oil for gear units, Same Deutz Fahr, Argo Tractors and CNH for agricultural vehicles, Siad for large compressors, Comau for robotics, Parker Hannifin for hydraulic motors, and Alstom, G.E. Tranportation and CMS for the rail sector.” n
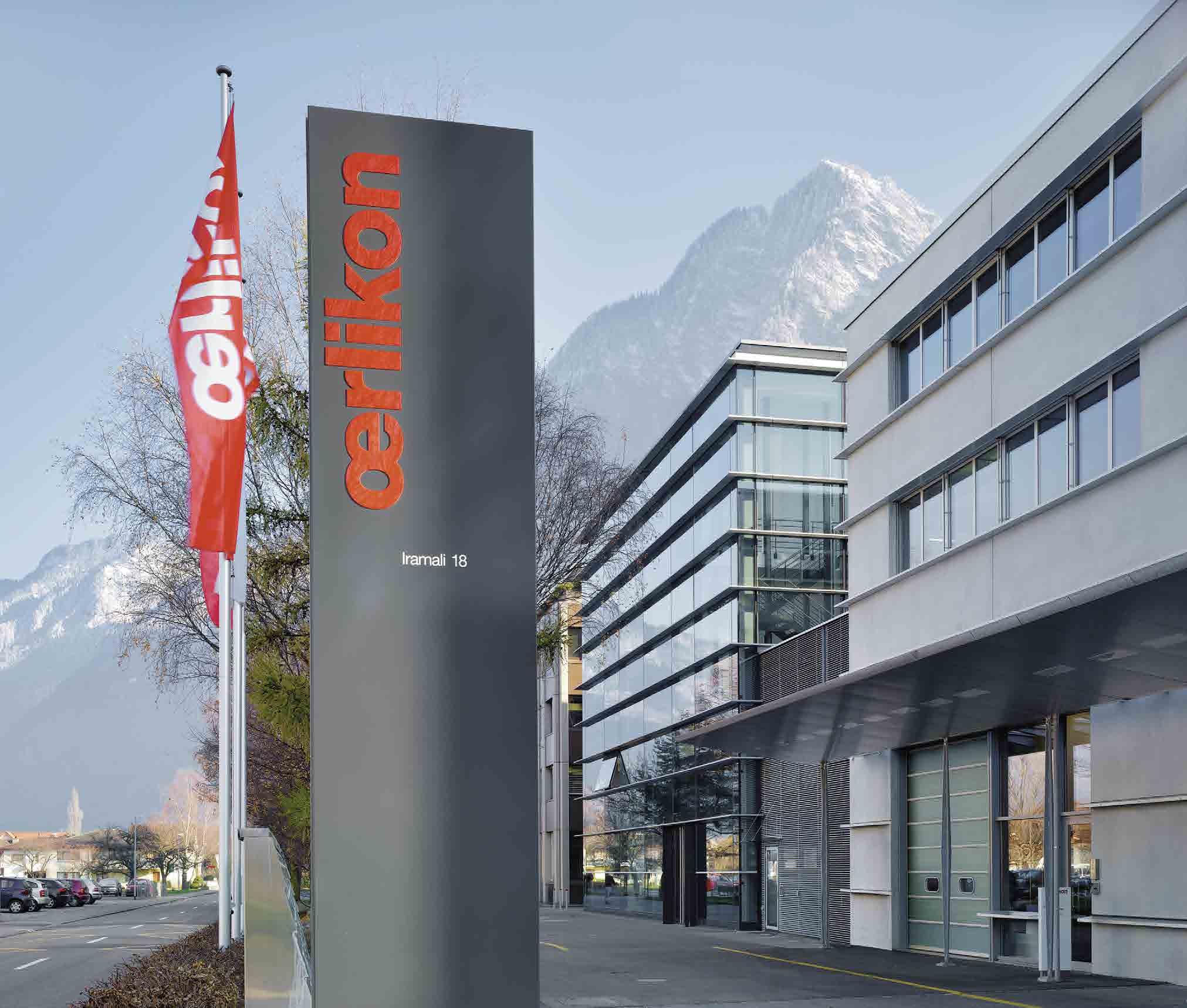
A NEW LEADER IN
SURFACE SOLUTIONS
Oerlikon Balzers is the leading global provider of thin-film coatings to improve the performance and longevity of precision components and tools. This year the group embarked upon a process of transformation with the acquisition of Sulzer Metco, in order to create a global technology leader in surface solutions.

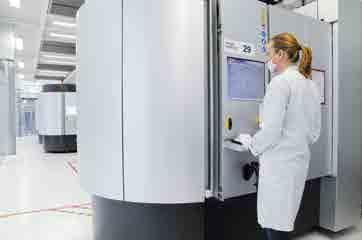
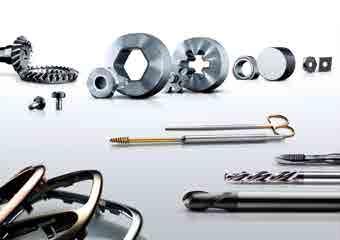
The company, which is a segment of the Switzerland-based Oerlikon Group, is a leading global supplier of PVD coatings and other surface technologies for precision components as well as metalworking and plastics processing tools.
Oerlikon’s announcement in January 2014 of its acquisition of Sulzer Metco is an exciting step forward for the company. The combination of Metco with Oerlikon’s existing coating segment has created a world technology leader in Surface Solutions. It has a unique global footprint with more than 100 coating centres worldwide.
Following a process of restructuring and portfolio shaping, this important step is the first major transaction to expand Oerlikon’s business inorganically. Oerlikon Balzers CEO Dr Hans Brändle said of the acquisition: “The combination of Balzers and Metco under one umbrella is a perfect fit of technologies, business models, R&D activities and market access for the benefit of our customers.”
In the area of surface treatment, Oerlikon’s new PRIMEFORM solution is a plasma supported treatment system through which a diffusion layer with a surface hardness gradient is produced. With this treatment, the wear and corrosion protective properties of the base material are improved.
An expanding footprint in coatings
When it comes to coatings, its other main business area, Oerlikon develops and manufactures solutions that significantly improve the performance and longevity of precision components and tools. Marketed under the Balinit® brand name, these coating are extremely thin and exceptionally hard. They significantly reduce friction and wear.
The company also develops processes, manufactures and sells systems and production facilities, and offers contract coating services through a dynamically growing network. Under the technology brand ePD™, it develops integrated services and solutions for the metallization of plastic parts with chrome effects.
“We have over 90 coating centres in 33 countries across Europe, the Americas and Asia – and this footprint is constantly expanding. The year 2012 saw expansion in Malaysia, India and China and our plan now is to continue expansion in new countries in South East Asia and eastern Europe, as well as expanding capacity and strengthening our footprint in places such as Turkey and the US.”
As part of its ongoing strategy to extend its coatings footprint, in April this year Oerlikon expanded its coatings facilities still further with the opening of a second coating centre in Austria. This will allow the company to meet the growing demand in Europe for innovative coating solutions for tools. The new centre is based in Ohlsdorf, a town in Upper Austria located between Salzburg and Linz. It specialises in coating solutions for shaft tools and indexable inserts.
Key applications
The company’s solutions are used in a broad range of applications in the automotive and machine industry, in food and packaging, medical technology and increasingly in aerospace. Leading tool manufacturers and automobile manufacturers count among Oerlikon Balzers’ customers. It has over 20,000 customers around the world and processes more than 200 million precision tools and components every year, ranging from items as small as watch pins up to dies for entire car bodies.
The largest area of application for physical vapour deposition (PVD) hard material coatings is precision tools for metal cutting (drills and cutters), forming tools, plastics processing and metal die casting as well as low friction coatings for automotive applications. A relatively new but rapidly growing area of focus is the coating of precision components in order to reduce friction and improve durability.
Other industries in which PVD hard material coatings are used include general machinery industries, the aircraft industry, motor racing and the medical and hygiene technology industry. PVD coatings are also being increasingly used in the luxury goods industry (watches, cell phones) – for aesthetics and practicality.
New technologies
One major area of focus at the moment for Oerlikon Balzers is the industrialisation of S3p™ and ePD™ technologies. Both were launched in 2011 and are now set to propel the company into further growth.
S3p™ - also referred to as ‘scalable pulsed power plasma’ enables extremely