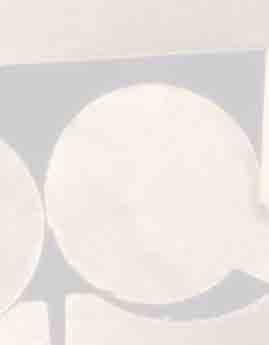
7 minute read
Experts in technical labels Gravic Hungary
Metallurgica San Marco has being working as well as customising brass for three generations. Today the company is one of the leading producers of extruded and drawn brass at a European level.
Since 1968 Metallurgica San Marco has been producing brass semi-finished products, in complex copper-zinc alloys and copperzinc-lead alloys, both standard range rectangular, square bars, hexagonal and round rods, and extruded and drawn profiles for the personalized solutions.
The company exports in more than 30 countries in Europe, North and South America, Middle and Far East.
At Metallurgica San Marco you will fi nd the most common sizes of extruded and drawn products in a variety of standard alloys for machining and forging applications.
Besides our standard alloys CW614N and CW617N, we can provide rods in dezincification-resistant alloys, as well as low-lead and leadfree alloys. Such alloys retain the excellent workability properties of standard brass, guaranteeing at the same time hygienic drinking water applications as well as the compliance to the newly introduced legislations for potable water.
Numerous sizes of standard rods are available from stock, allowing customers to place orders on a short-term planning.
Customer centrality, product quality and high service have been our main priorities for a long time.
We continuously renew our equipment and production processes and promote the activity of material recycling, in order to reduce the environmental impact of our activity.
We offer advice to all of our clients on the feasibility, alloy, measures, processing and application of the semi-finished products. We carefully listen to each one of them to identify and develop new solutions and solve their specific needs.
We can respond to the new demands of the market thanks to our versatility and ductility and to the commitment of our staff to providing high-quality products and excellent customer services.
Keeping an eye on quality Metallurgica San Marco has a management system for its product and service quality which is ISO TS16949, for the automotive sector. The company also holds a OHSAS 18001:2007 certification for health & safety at work.
For further information and enquiries:
Metallurgica San Marco S.p.A. Via Statale 11, 132/134 25010 Ponte San Marco - Brescia – Italia Tel: +39.030.963174 Fax: +39.030.9969973 E-mail: marketing@metallurgicasanmarco.it Web: www.metallurgicasanmarco.it
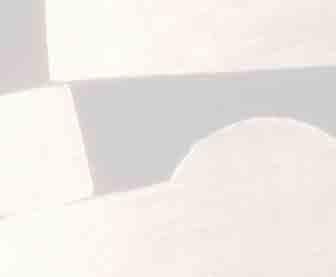
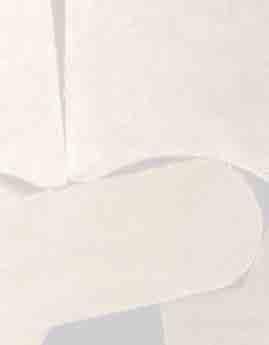
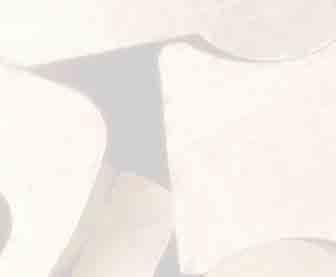
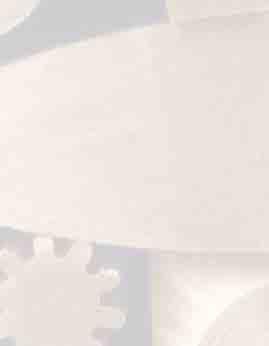
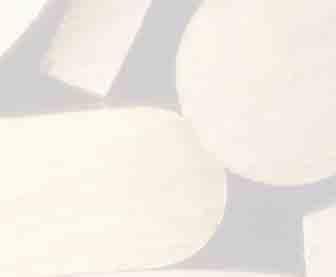

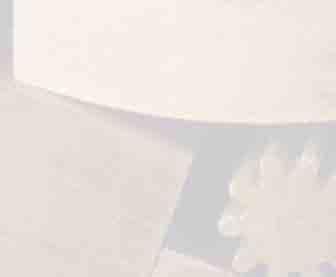
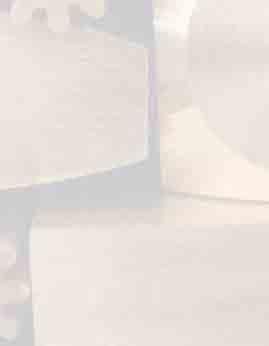



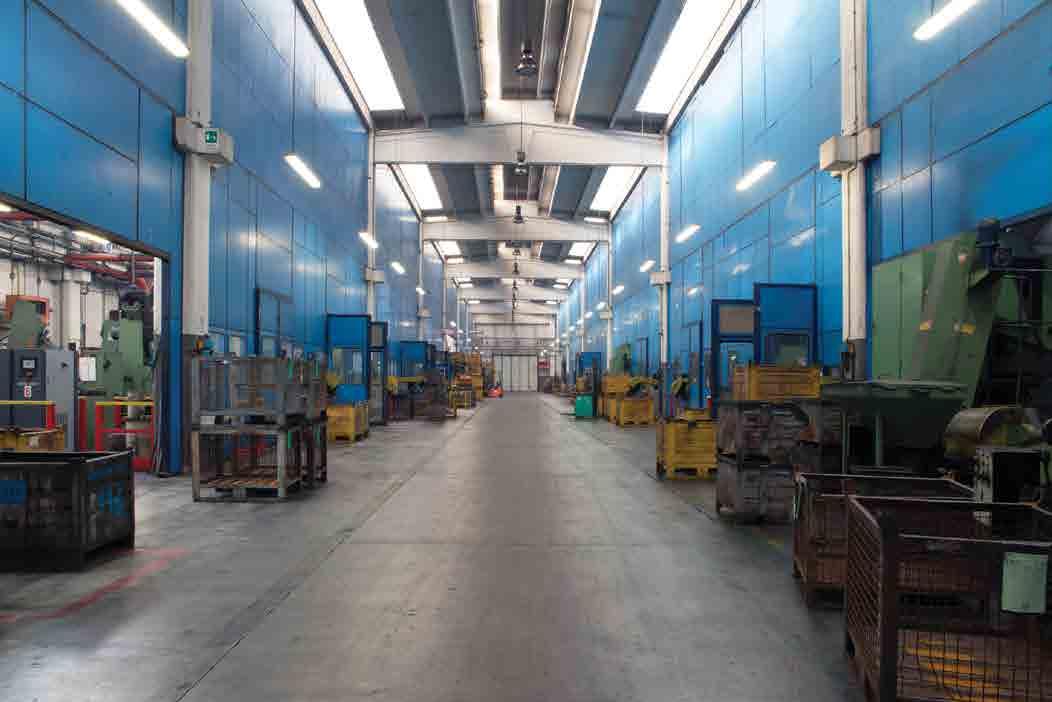
Forging department of ZMF Forging Ideas
Metallurgica San Marco
Metallurgica San Marco has a wide range of extruded and drawn brass products, round rods, hexagonal and square rods, flat bars, as well as shapes and profiles.
We manufacture round rods for hot stamping from diameter 10mm up to 150mm, round rods for free cutting and machining from diameter 6mm up to 80mm, hexagonal bar from 8mm to 70mm, square bar from 8mm to 80mm, flat bar from a minimum thickness of 2mm up to a maximum width of 150mm.
For further information about our products or for inquiries: marketing@metallurgicasanmarco.it
quick mould change (and then item change) has been devised.
The plant is also equipped with a belt oven which can heat billets with diameters up to 150mm and lengths up to 350mm, and is also suitable for aluminium heating. An oven belt, made of special steel mesh for high temperatures, was chosen because it gives the option of using different shaped pieces, such as billets, discs, squares and preformed parts. In this way, very heavy pieces (from 23 to 25kg) can be automatically placed on the belt.
The new press, made specifically for ZMF by Aida, is therefore able to produce several pieces with a wide range of weights in almost automatic mode, offering operator safety and the guarantee of maintaining a high standard of production. This 9-metre high press weighs 60 tons and, although it employs hollow technology typical of brass, can also forge other non ferrous alloys and metals such as aluminium, bronze, copper alloys and nibral. This allows ZMF to serve value added markets. Diversification, innovation and flexibility
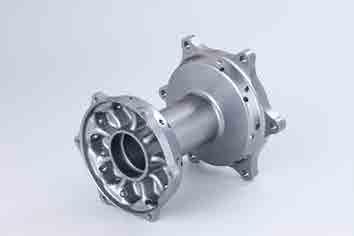
ZMF, which holds the UNI EN ISO 9001 certification, carries out its R&D internally and designs its products in collaboration with its clients. “Our strength is that we begin with a customer’s idea and produce a semi-finished product ready to be assembled, taking care of forging, mechanical processing and surface treatment. Today we are able to manage a series of surface treatments for aesthetic effect or protective purposes. Some of these, namely sandblasting for brass, steel and stainless steel, are carried out in-house. The rest – including nickel plating, chrome plating, tin plating, anodising and PVD – are outsourced to skilled and reliable external suppliers.”
The company has expanded its activities in recent years, so that nowadays its serves a range of industries, including valves and fittings, marine equipment, automotive, electrical components, plant and machinery and taps. Currently 55 per cent of its turnover is derived from products for the heating, plumbing and sanitary fittings industry, while the remaining 45 per cent is divided among the other sectors. In terms of metals, 65 per cent of its turnover is generated from brass, 25 per cent from aluminium and 10 per cent from other non-ferrous metals and alloys. 65 per cent of production is for Europe, in particular Germany, the Netherlands, Luxembourg, France, Spain and Scandinavia. Other markets offering good growth prospects include the US and Canada.
Future growth is expected to focus on both geographical market development and specific product development, in order to further establish the company at a global level. “We have realised that market globalisation and product diversification go hand in hand and are therefore key to our future development and success. In the near future we are going to start manufacturing products for the accessories, sports equipment and aerospace sectors. We do not want to identify with a particular type of product: in fact, because of the wide range of sectors we serve, we are really six or more companies in one.” n


EXPERTS IN TECHNICAL LABELS
Ten years ago the French label specialist Gravic set up an operation in Hungary to serve the region’s growing markets. Today Gravic Hungary is a major supplier to the automotive industry and is active in export markets across the world. Peter Mercer reports.
Gravic Hungary was established in 2004 in Debrecen, a university city in the east of the country. For its parent company, Gravic Europe, which was headquartered in Mouans Sartoux in the south of France, the new location offered the strategic advantages of being in the heart of Central Europe, 30km from Romania, 100 km from Slovakia and 110 km from Ukraine. This was particularly important for Gravic at that time because a large part of its business was the production of technical labels for mobile phones (for SIM cards, batteries etc) and other products of the consumer electronics industry. Much of the production of these devices was moving to Central Europe – Nokia, for example, had a large plant in Hungary – and there were clear advantages in establishing production close to the company’s major customers.
“In those early years, we were supplying labels not only for mobile phones (including Nokia and Blackberry products) but also to electronic component manufacturers such as Flextronics and it was expected that more and more of this business would move to neighbouring countries such as Romania and Ukraine so Hungary was an ideal growth opportunity for Gravic,” explains Vincent Zink, Managing Director of Gravic Hungary, “However, it was not long before the consumer electronics market became even more competitive, with a lot of production moving to China and other parts of Asia, and the remaining business became less profitable and less stable – contracts were commonly for three months only.
“Consequently we took the decision to develop longer-term supply partnerships with the automotive industry – both OEMS and component suppliers – in Hungary and in neighbouring Germany. Germany is obviously the most important auto producing country in Europe and there have been many major investments by German auto makers in Hungary too – the huge Audi plant at Gyor is the most well-known of these. This business is much more stable for us – contracts are typically for at least four years – and today
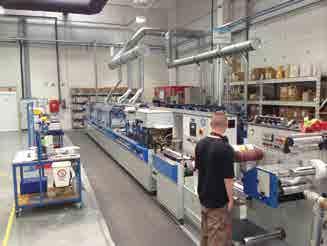
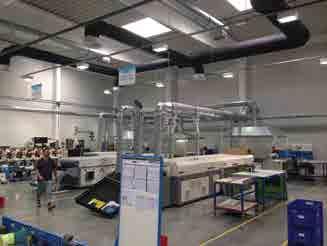
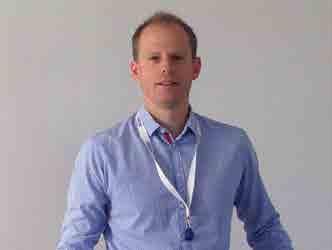
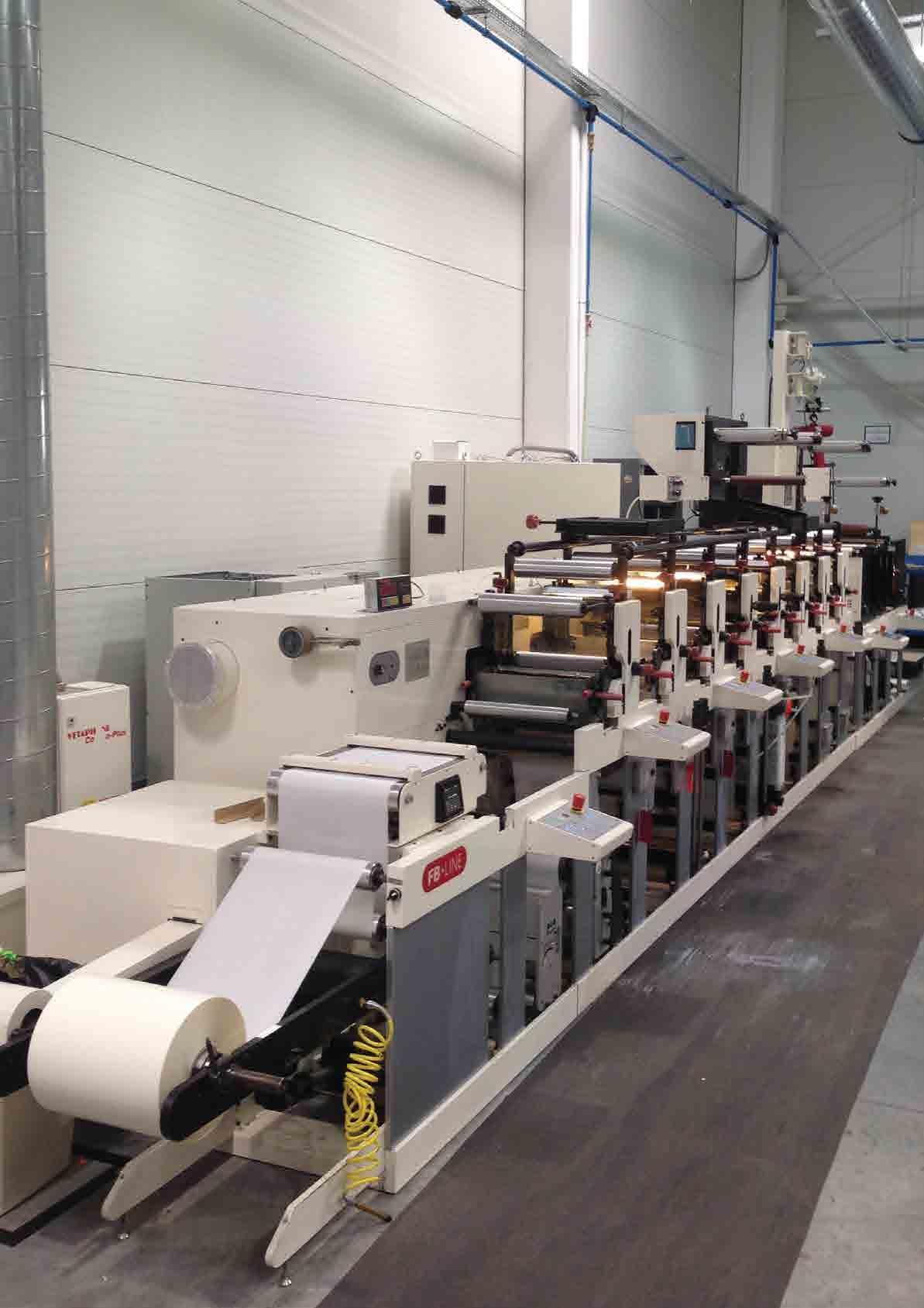