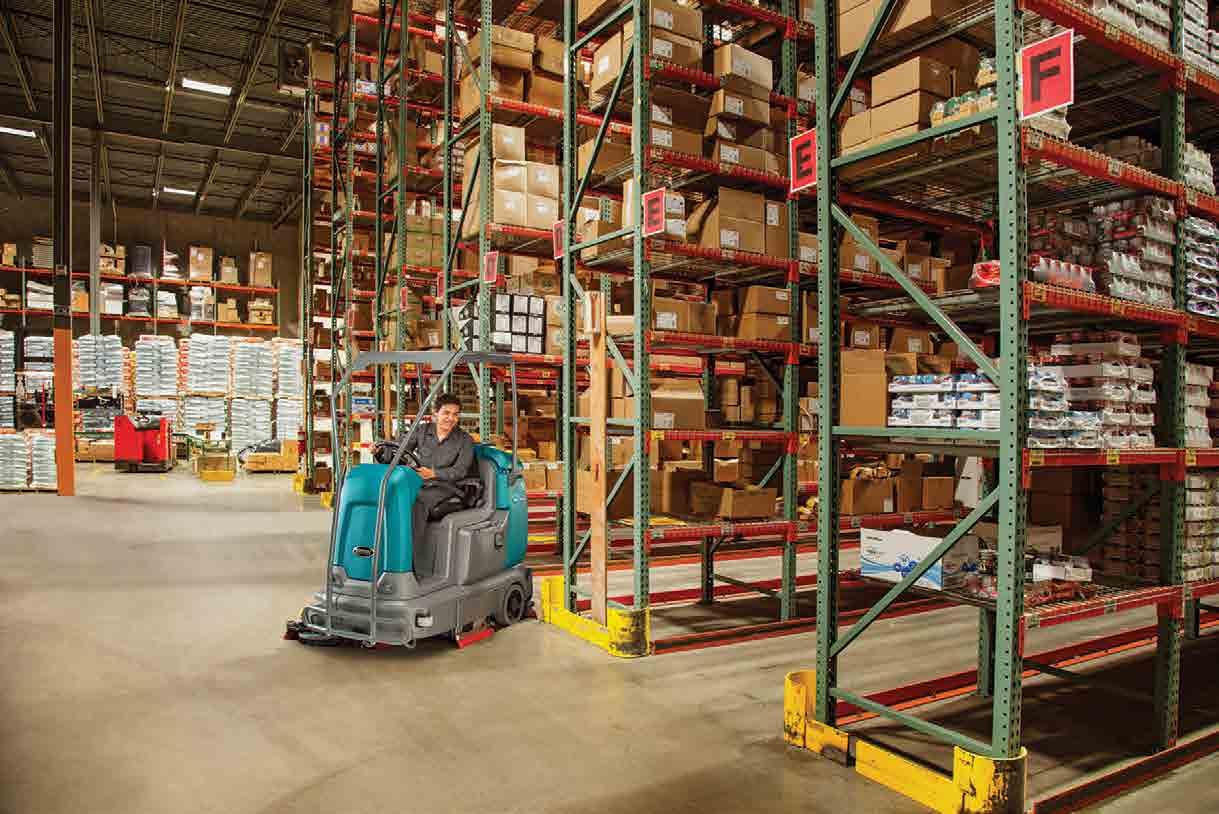
6 minute read
Transforming power efficiency Kolektor Etra

cleaning solution that works with most existing cleaning equipment and methods. The Orbio 5000-Sc cleaning solution cleans most soils, including fats, proteins and organic oils. It aims to match or exceed the performance of most conventional cleaners so customers can replace many costly, potentially harmful chemicals from their cleaning programs with just one cleaning solution.
More productive
In 2013 Tennant introduced the T12 compact scrubber rider, which had been developed following in-depth customer research.
The T12 was designed to clean effectively, save money, increase safety and reduce environmental impact with optional chemicalfree ec-H2O technology. It can clean floors from edge-to-edge with optional scrubbing side-brush and offers a 28 per cent wider scrub path.
The move from the 7000-100 scrubber to the T12 saw major investment at Tennant. There has also recently been a move to bring the manufacture of plastic body components in-house, resulting in a total investment of $1 million at the Netherlands Facility.

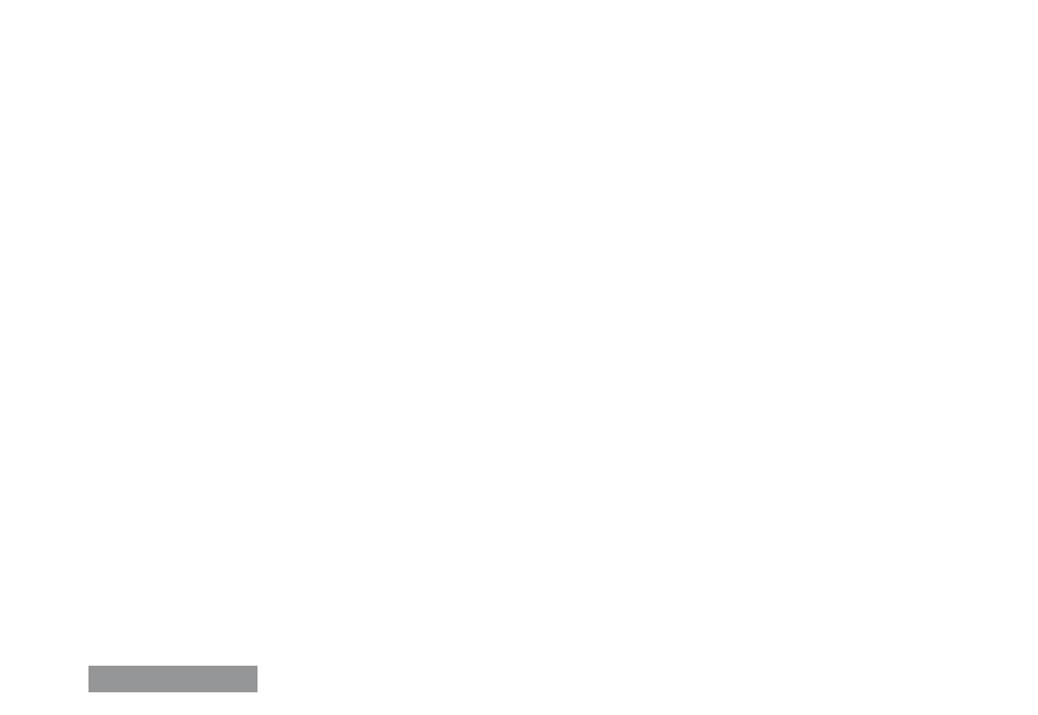

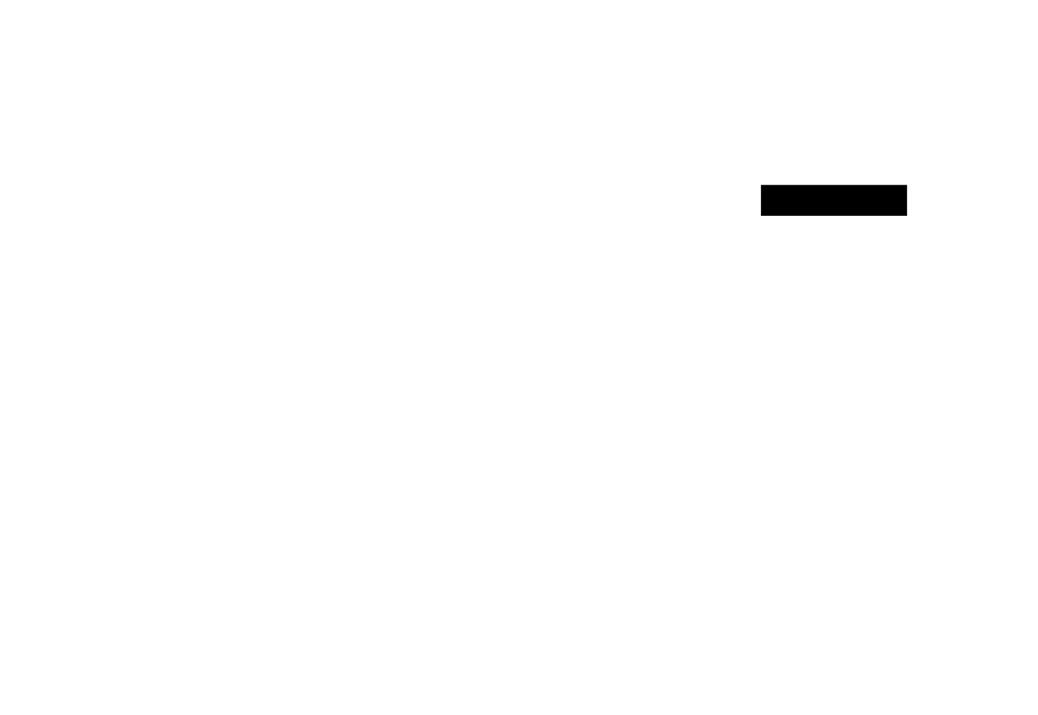
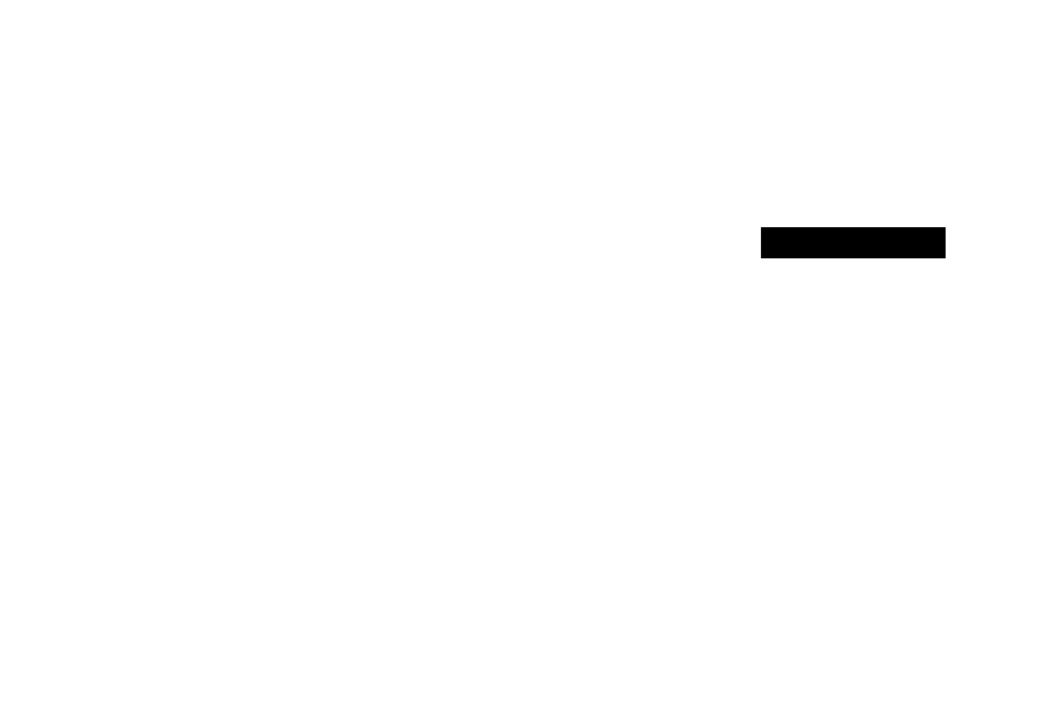
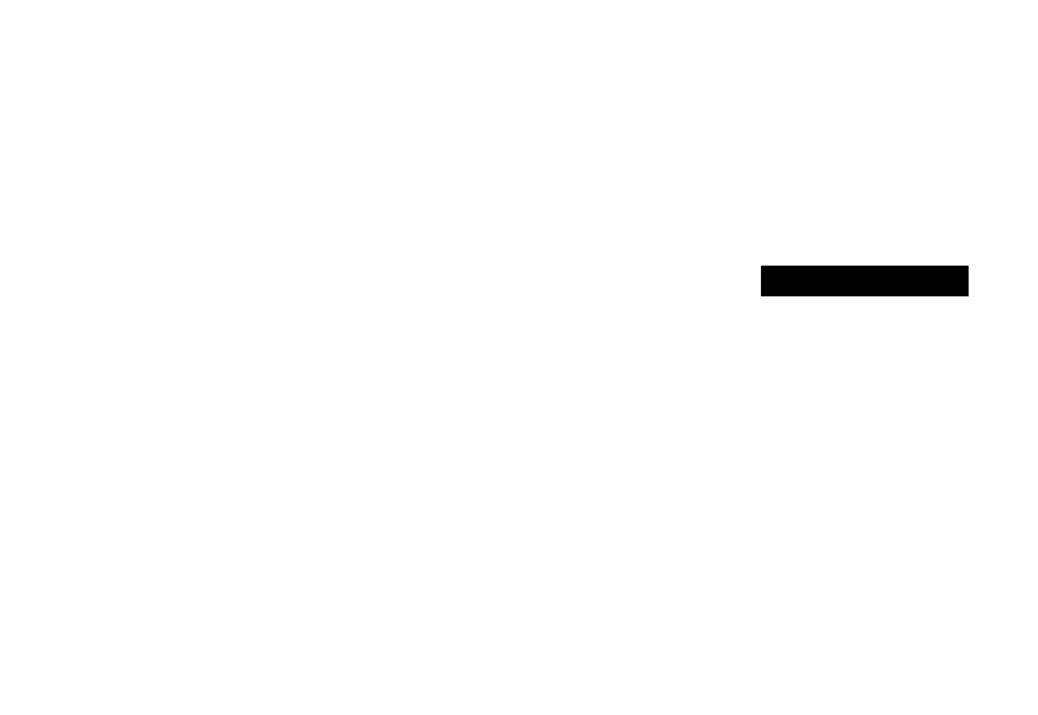
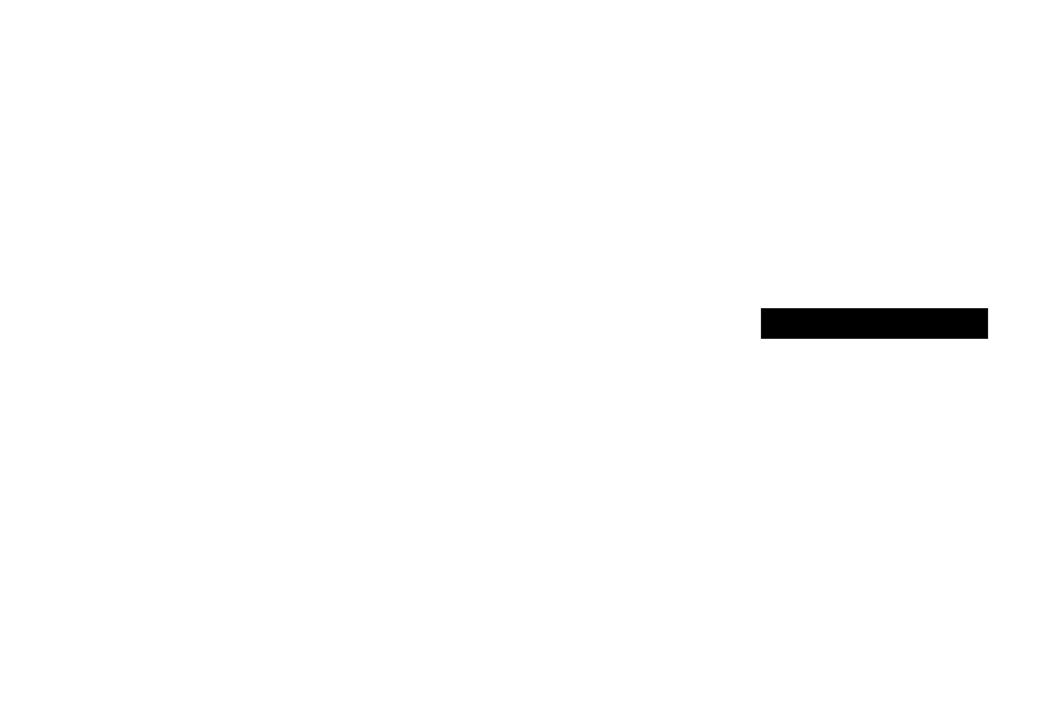
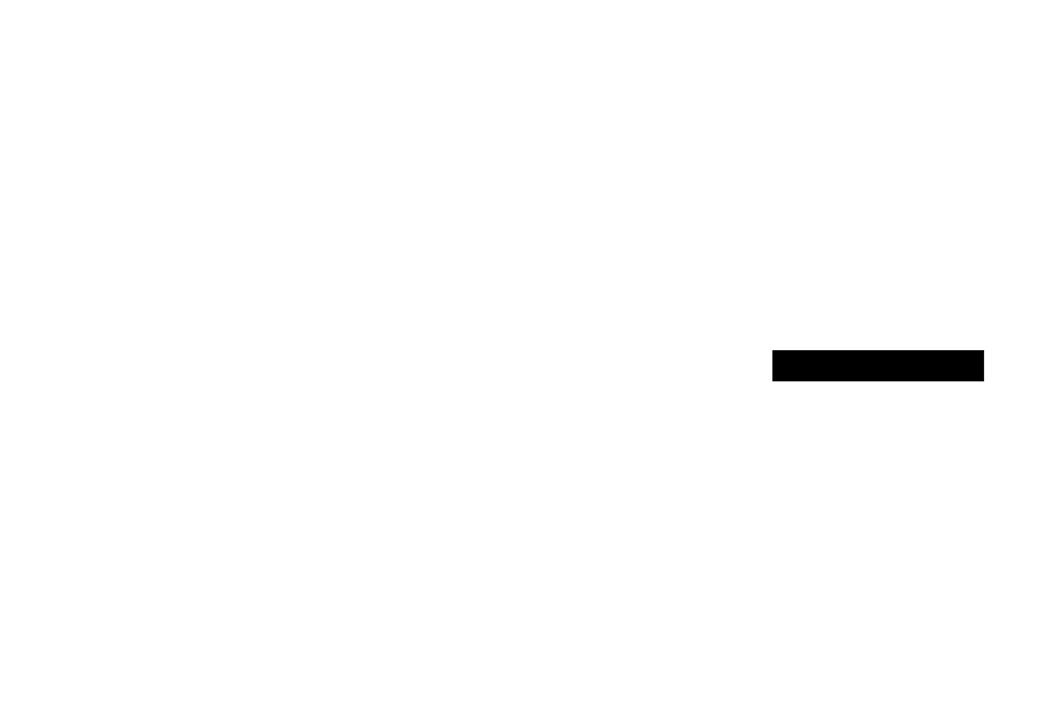
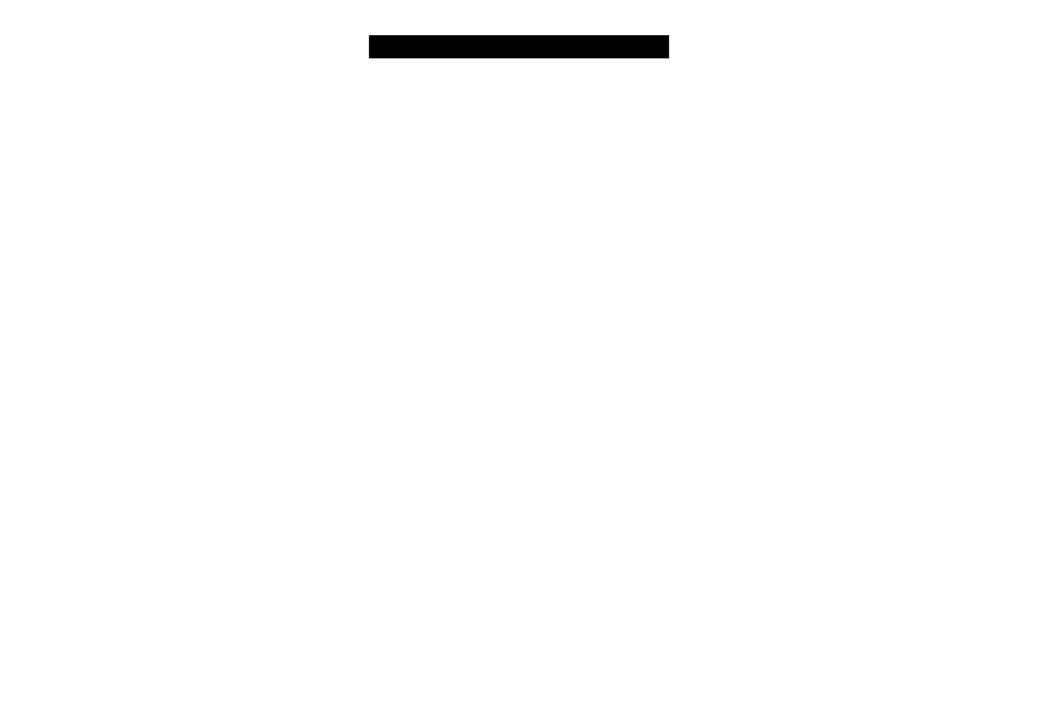
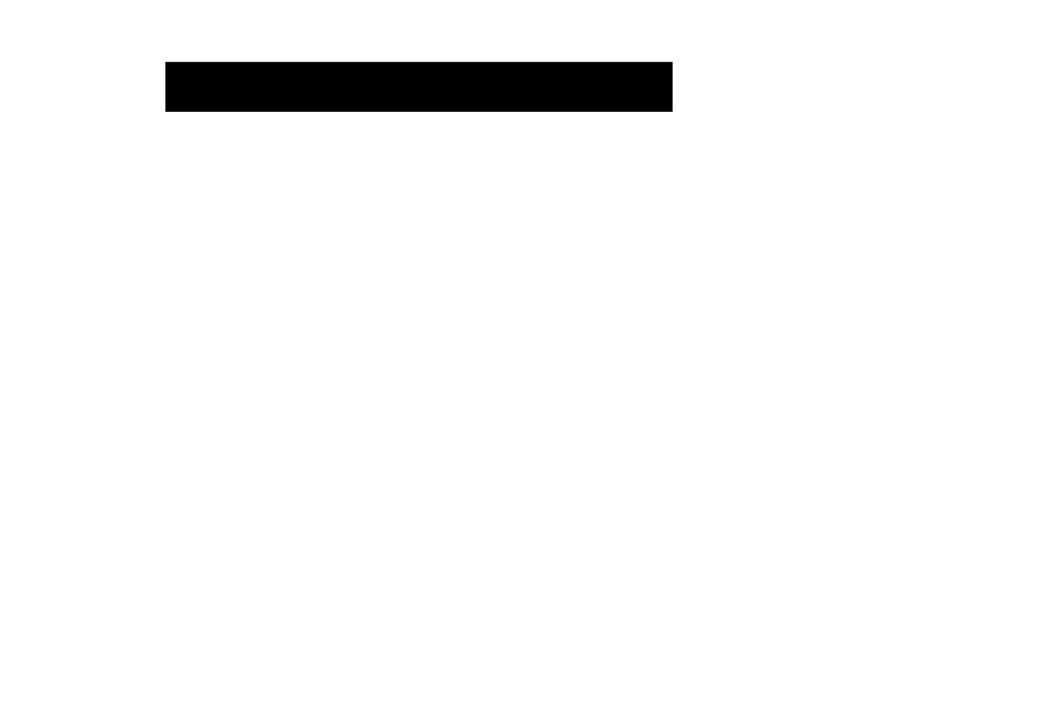
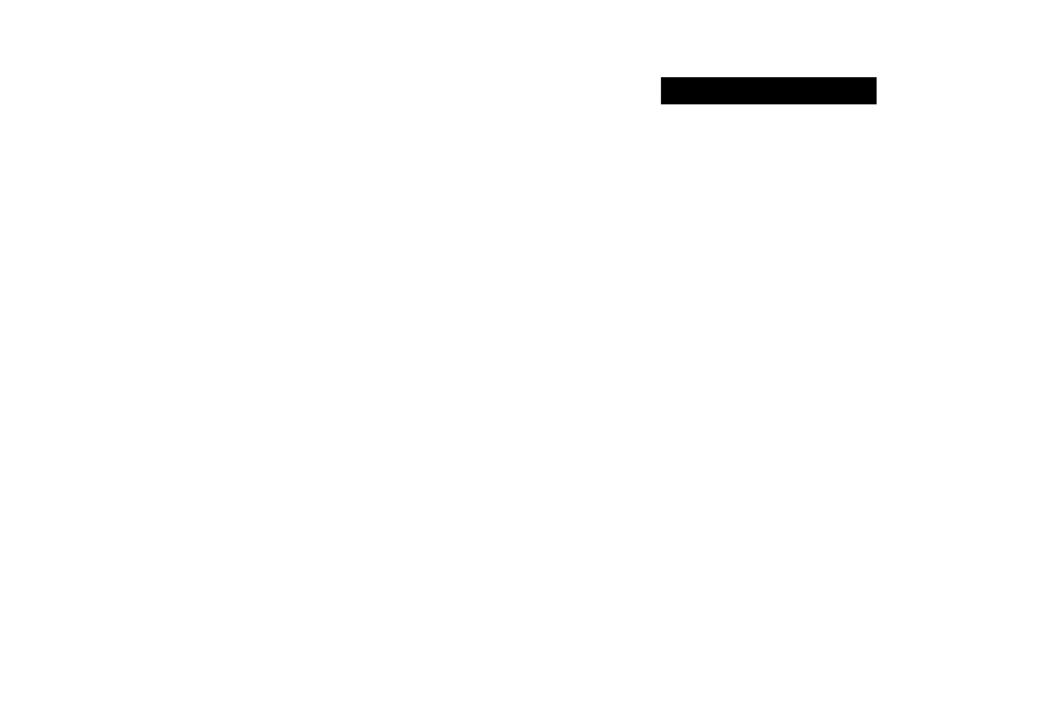
“There are major benefits to producing these parts ourselves,” says Mr Derycke. “We can now react much faster to peaks in demand and have responsibility for quality checks.”
In 2014 Tennant has launched a further nine new products already, including the T17 battery-powered rider scrubber and walk-behind battery-operated burnishers that are emission-free and deliver high performance gloss results.
Future growth
As Tennant Company moves forward, the emphasis will continue to be for innovation, both in terms of product development and the way the company operates. The company will continue to look at improving its access to customers and, while municipal cleaning has taken a downturn along with the economy, expects to see growth in the area in the future.
“We will also maintain our focus on service contracts and the after-market,” says Mr Derycke. “This is an important part of listening to our customers and making sure they get everything they want. If our global vision is to transform, we have to keep looking at all these areas.” n
LINAK
The LINAK Group is divided into 5 divisions organized as individual business units. This ensures that customers within the various business areas will always be serviced by a team of experts with immense relevant insight and experience.
LINAK is globally recognized for high quality, technically advanced, innovative solutions that reach the marketplace as cutting edge products giving both us and our customers a strategic advantage.
With more than 7,000 different articles, no one else in the industry offer a wider range of actuator systems than LINAK. Our complete selection includes actuators, lifting columns, control boxes, controls and a wide range of accessories.
80% of our products are customized solutions, and we take pride in being a strong partner in the development of new applications.
Winding process on horizontal winding machine
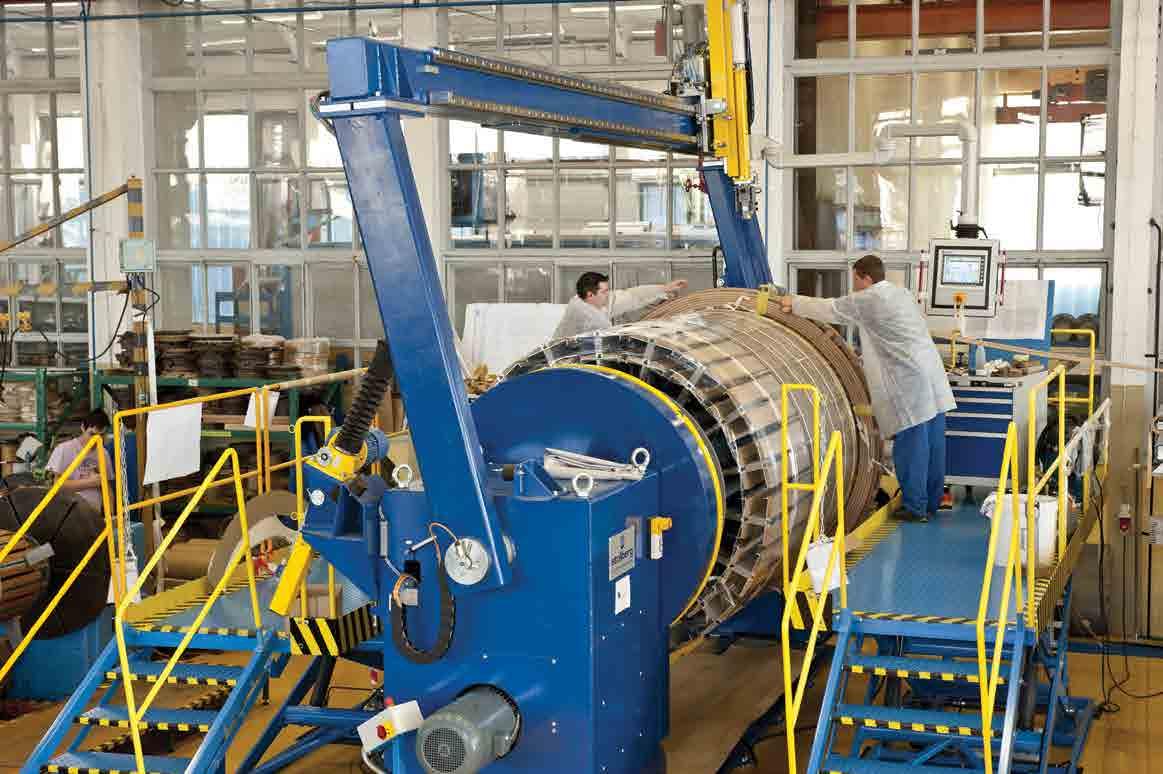
TRANSFORMING POWER EFFICIENCY
Kolektor Etra is a leading European manufacturer of high-voltage power transformers. Philip Yorke talked to Peter Novak, the company’s Executive director for Sales and Procurement about the advances made in its production capabilities and move into new markets.
IN 1933 a company was formed in Slovenia to provide servicing for small transformers and the manufacturing of components for power distribution. The company was ”EMD” (Elektromehanične delavnice Črnuče)’ and is known today as Kolektor Etra, after KOLEKTOR GROUP purchased 75 per cent of its shares in 2010. In 2012 the company invested in an extensive purpose-built, state-of-the-art facility that is capable of manufacturing high-power transformers of 500 MVA rated power and 420Kv rated voltage to meet individual and specific customer requirements. Today Kolektor Etra is a modern, lean and innovative company that has facilities extending to more than 45,000m2 of which over 20,000m2 is devoted to state-of-the-art manufacturing processes. The company currently employs over 290 people and in 2013 recorded sales of more than €56 million.
Increased capacity
In 2011, a major strategic investment decision was made and a new building programme was embarked upon that was designed not only to upgrade the existing facilities, but to take the company to an entirely new level. Traditionally Etra produced transformers and components for products up to 200MVA. However, as the demand for power has increased worldwide the need for much higher rated transformers became evident. There was therefore a strategic and economical imperative to design and produce highly-efficient transformers of up to 500MVA and with rated power of up to 420kV or more.
As a result of this dramatic increase in the demand for higher rated transformers, the company constructed a state-of-theart, purpose-built facility that would match the capabilities of any western European
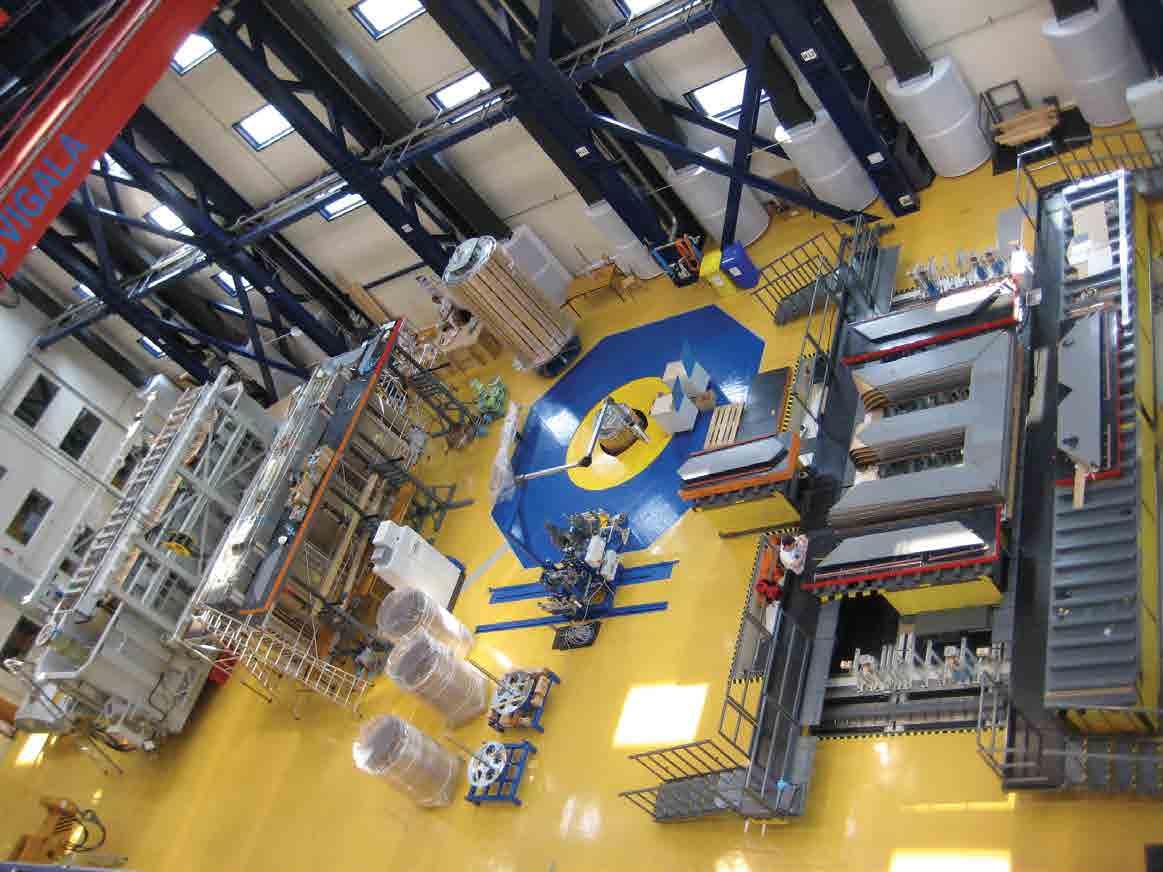
ART 350000-420 kV, TS Stupava, SEPS, Slovakia, 2013, ready for energizing RT 300MVA -400 kV, TS Okroglo, ELES, Slovenia, 2013, putting on foundation
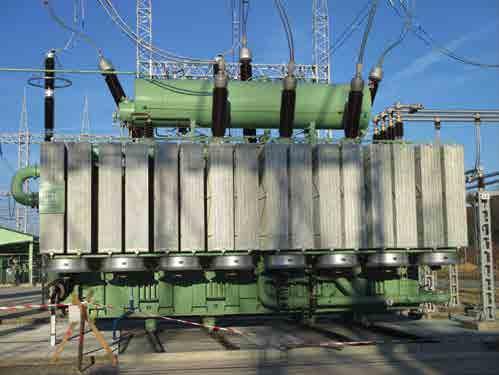
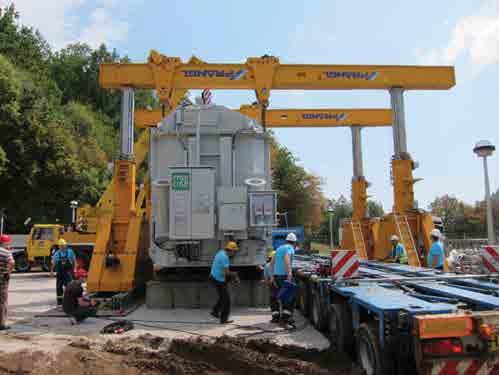
manufacturer. The new plant includes advanced manufacturing facilities for drying and oil treatment and machinery for the cutting and stacking of core sheets. In addition new equipment was commissioned for the winding and treatment of different kinds of windings. Furthermore, ETRA’s new highvoltage laboratory for transformer testing is equipped with the most advanced and precise measuring equipment whose sensitive instruments are regularly calibrated by European authorised institutions.
The company’s new facility also offers full repair and maintenance services for transformers that are not only produced by Etra, but also by any other manufacturers. These services can be carried out either on-site or at ETRA’s own workshops. The company guarantees a fast and efficient service with professional inspection and diagnosis and within the agreed time lines.
Tailor-made innovation
In today’s fast growing and demanding power distribution market, the quality of transformers is becoming even more relevant. This is in order to guarantee consumers and manufacturers an optimised, high-quality, efficient and reliable service. Novak said, “It was imperative that we positioned ourselves to meet the increasing and changing demands of world markets. We have therefore invested heavily to increase our production capacity, as well as the efficiency of both our products and our manufacturing processes. We have to be able to produce more complex and bigger transformers in order to meet the new power market requirements. This means that we now operate the most modern transformer factory in Europe, which includes hermetically sealed clean-room facilities that meet all the current EU standards and legislation. In the