
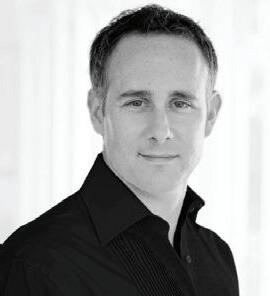
Navigating a Reputation Crisis.
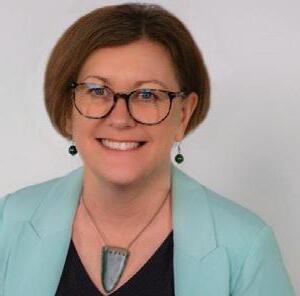
EMA
Fixing manufacturing’s billion dollar harm problem.
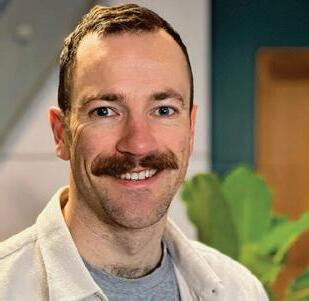
SMART MANUFACTURING
Tech isn’t the Hero, it’s the plucky sidekick.
Navigating a Reputation Crisis.
EMA
Fixing manufacturing’s billion dollar harm problem.
SMART MANUFACTURING
Tech isn’t the Hero, it’s the plucky sidekick.
-Sean Doherty, Product Manager, Callaghan Innovation
The advent of Industry 4.0 has been a game-changer for the manufacturing sector and can deliver real returns for New Zealand businesses, through increased efficiency, productivity, and innovation. However, many manufacturers remain hesitant to embrace these technologies. This reluctance often stems from persistent myths that cast doubt on the practicality and benefits of Industry 4.0.
Based on Callaghan Innovation’s experience working with New Zealand manufacturers who are on their Industry 4.0 journey, we’re keen to dispel some of these common myths and provide some evidence-based solutions to encourage Kiwi manufacturers to confidently step into the future with Industry 4.0. ...
The Reality: Industry 4.0 is not exclusive to large manufacturers. Small and medium-sized enterprises (SMEs) can also leverage these technologies to enhance their operations.
Indeed, as a nation of SMEs, this is where Industry 4.0 technologies arguably have the most potential to boost this country’s productivity and economic output.
Companies like Nautech Electronics, Gyro Plastics and Oasis Engineering, are all great examples of SMEs deploying Industry 4.0 technologies to good effect.
The key is to start small and scale up. For instance, SMEs can begin by implementing IoT sensors and use data analytics to optimise their existing processes. Retrofitting new hardware systems to older equipment can be a cost-effective way to integrate Industry 4.0 technologies without the need for significant upfront investment in new machinery.
The Reality: While initial investments may seem daunting, the long-term benefits of Industry 4.0 technologies can lead to substantial cost savings and increased efficiency.
Several McKinsey and Company case studies show manufacturers gaining a 10-20% increase in efficiency, between 10-15% improvement in quality and cost reductions of up to 30%.
continued on Page 19 7 11 18 22
Secure supply of energy and data to moving industrial equipment.
• Large size range
• Vertical travels
• Energy tubes
• Hygienic chains
• Solutions for long travel
• Guide troughs
• Readychain
• Robotic, 3D
• Circular movement
HUGE range of high quality flexible cables
• Control cables
• Single cores
• Data cables
• Sensor/Actuator
• Intrinsically Safe
• VSD/EMC cables
• Halogen Free cables
• High temperature
• Harsh Conditions
• Crane cables
• Profibus cables
• Bus/DeviceNet
• Solar cables
• Instrumentation
• Flat cables
• Curly cords
Largest range of flexible conduits for cable protection
• Conduits
• Conduit fittings
• Divisible systems
• Jumbo systems
• Conduit Accessories
• Braided cable protection
• Fire barrier solutions
• Food and beverage
• EMC systems
• Ex, ATEX, IEC EX
Industrial connectors for many industries
• Rectangular multipole connectors from ILME
• Single pole Powerline connectors from TEN47
• EPIC connectors from Lapp Group
• M23 circular connectors from Hummel
• Circular connectors specifically for the entertainment/stage lighting industry from Socapex
Safety engineering solutions from EUCHNER
• Multifunctional Gate Box MGB
• Transponder-coded safety switches
• Electromechanical safety switches
• Magnetically coded safety switches
Sensor technologies for automation
• High-Precision Laser Distance Sensors
• Ultrasonic Sensors
• Inductive Sensors
• Fluid Sensors
Aotearoa’s Industry 4.0 journey.
BUSINESS NEWS
EMA partners with ASB for manufacturers workshop.
Navigating a Reputation Crisis.
SMART MANUFACTURING
5S – Not That Old Chestnut
Global campaign for world-first drone set to boost NZ’s screen sector.
EMA
Fixing manufacturing’s billion-dollar harm problem.
SMART MANUFACTURING
Miraka milk company invests in the future with Flex ERP technology.
Driving demand for green hydrogen.
Building digital capability and fluency:
Empowering the future of New Zealand’s manufacturing sector.
COMPANY PROFILE
Primero Profiles ANALYSIS
Finding your true competitive edge.
SMART MANUFACTURING
Tech isn’t the Hero, it’s the plucky sidekick.
COMPANY PROFILE
Empowering energy sovereignty.
SUSTAINABILITY
How manufacturers can prepare for the ESPR.
WORKSHOP TOOLS
Bearings and e-mobility.
Efficient refrigerant dryer sets standards.
DEVELOPMENTS
2024’s SCNZ Excellence in Steel Awards.
THE LAST WORD
NZ is encouraging the use of AI.
Ian Walsh
Ian is a Partner, Argon & Co. NZ, a master black belt improvement specialist and global lean practitioner. He is passionate about improving productivity and helping to create world class New Zealand businesses.
Dr Barbara Nebel CEO thinkstep-anz
Barbara’s passion is to enable organisations to succeed sustainably. She describes her job as a ‘translator’ – translating sustainability into language that businesses can act on.
oodward
Is Managing Director of Connection Technologies Ltd, Wellington and is passionate about industry supporting NZ based companies, which in turn builds local expertise and knowledge, and provides education and employment for future generations.
Mark Devlin
Having owned food manufacturing and distribution businesses for a decade, Mark Devlin now runs Auckland public relations agency Impact PR. Mark consults to several New Zealand manufacturing firms including wool carpet brand Bremworth, aircraft exporter NZAero and cereal maker Sanitarium.
Insa Errey
Insa’s career has been in the public and private sectors, leading change management within the energy, decarbonisation, and sustainability space. Insa holds a Chemical and Biomolecular BE (Hons) from Sydney University. She is a member of the Bioenergy Association of NZ and has a strong passion for humanitarian engineering, working with the likes of Engineers Without Boarders Australia.
Insa is a member of Carbon and Energy Professionals NZ, been an ambassador for Engineering NZ's Wonder Project igniting STEM in Kiwi kids and Engineers Australia Women in Engineering, increasing female participation in engineering.
Jane Finlayson is Head of Advanced Manufacturing at the EMA, and has 25-years’ experience in business and economic development. She is passionate about empowering businesses to grow, innovate and embrace Te Ao Māori.
PUBLISHER
Media Hawke’s Bay Ltd, 121 Russell Street North, Hastings, New Zealand 4122.
MANAGING EDITOR
Doug Green
T: +64 6 870 9029
E: publisher@xtra.co.nz
CONTRIBUTORS
Holly Green, EMA,
Business East Tamaki, Ian Walsh, Adam Sharman, David O’Connor, Mark Devlin, Nicholas Russell, Jane Finlayson, Frank Phillips, Sean Doherty, Nathan Cooper, Amanda Turnbull
ADVERTISING
T: + 64 6 870 9029
E: publisher@xtra.co.nz
DESIGN & PRODUCTION
:kim-jean: E: kim.alves@xtra.co.nz
WEB MASTER
Julian Goodbehere
E: julian@isystems.co.nz
PUBLISHING SERVICES
On-Line Publisher
Media Hawke’s Bay Ltd
DIGITAL SUBSCRIPTIONS
E: publisher@xtra.co.nz Free of Charge.
MEDIA HAWKES BAY LTD
T: +64 6 870 9029
E: publisher@xtra.co.nz
121 Russell Street North, Hastings NZ Manufacturer ISSN 1179-4992
Vol.16 No.10 November 2024
Copyright: NZ Manufacturer is copyright and may not be reproduced in whole or in part without the written permission of the publisher. Neither editorial opinions expressed, nor facts stated in the advertisements, are necessarily agreed to by the editor or publisher of NZ Manufacturer and, whilst all efforts are made to ensure accuracy, no responsibility will be taken by the publishers for inaccurate information, or for any consequences of reliance on this information. NZ Manufacturer welcomes your contributions which may not necessarily be used because of the philosophy of the publication.
Sean Doherty, Callaghan Innovation, tells us (on Page1) that Industry 4.0 has been a game changer for our manufacturing sector. However, many manufacturers remain reluctant to embrace these technologies, because of myths that cast doubts on its practicality and benefits.
These attitudes need to change if maximising business opportunities is what your company is all about. Nautech Electronics, Gyro Plastics and Oasis Engineering are examples of companies using Industry 4.0 to good effect,
Elsewhere in November issue, EMA is partnering with ASB Bank (Page 6) for the upcoming Manufacturing Workshop series, ‘The Impact of Industry 4.0 on Your Business”. Ian Walsh (Page 9) reminds us about 5S, a practice that was developed at Toyota in the 1960s.
Mark Devlin (Page 7) discusses Navigating a Reputation Crisis; Adam Sharman (Page 17) explains how companies who take decisive action during downturns often emerge stronger when the economy recovers.
Frank Phillips (Page 18) tells us that Tech is not the Hero; it is the plucky sidekick.
Now, about the Indo Pacific 4, comprising New Zealand, Australia, Japan and South Korea. It is probably the group of friends you would bring home to meet your mother. A group of like-minded countries working closely together.
And this group is a part of the reason New Zealand has an FTA with the European Union.
Trade is expected to increase with the European Union by up to 30%. In the first three months since the FTA came into being, goods to the EU were $1.52bn, of which $463m was in fruit and $301.1m in meat. Up from $1.27b, which includes $334.63m in fruit and $271.46m in meat, for the same period a year earlier.
Other good news is that European investment in New Zealand could increase by 80% via the FTA. Currently the EU investment is $18b.
NZ Manufacturer Media Kit 2025 is now available. Email publisher@xtra.co.nz to receive a copy. Plan your year ahead.
Doug Green
Publisher
The EMA is delighted to announce a partnership with ASB Bank for the upcoming Manufacturers Workshop series, ‘The Impact of Industry 4.0 on Your Business’.
ASB Bank is committed to improving productivity in New Zealand businesses, and its support underscores its dedication to helping manufacturers stay one step ahead in business with the use of technology and process improvements.
Ben Speedy, ASB’s General Manager of Commercial Banking, said: “We are excited to be working with the EMA to deliver the Manufacturers Workshop Series to Kiwi businesses across the country. Our research has found that investing in innovation now will unlock benefits and choice for New Zealand, with the potential to raise real GDP to $500 billion by 2045.
“At ASB, we have the financial tools and insights to empower our customers to make the right decisions for their business, ranging from our self-serve tools on ASB’s Business Hub website, to tailored guidance and advice. Through these workshops, we look forward to supporting business growth and accelerating the progress for all New Zealanders.”
The ASB Manufacturers Workshop series, ‘The Impact of Industry 4.0 on Your Business’ will demystify Industry 4.0, breaking it down to the nuts and bolts of what it means for your business in a practical sense.
The workshop is delivered by the EMA and the experienced team at LMAC, who work alongside
many NZ manufacturers to make the most of Industry 4.0.
“It is all about making smart choices about your business and manufacturing processes going forward - this is a good place to have these conversations and find out about the range of ways to achieve improvements,” says Jane Finlayson, Head of Advanced Manufacturing at the EMA.
Join other manufacturers, for an in-depth exploration of Industry 4.0 technology and its transformative potential for your business.
The ASB Manufacturers Workshop: The Impact of Industry 4.0 on Your Business is designed for decision-makers - operations managers, finance teams, business owners, and managers - who are ready to embrace digitisation and automation to build their business’s competitiveness.
This is the first step to find out what others are already doing and how a range of different technologies is making their businesses more productive.
Key Highlights:
• Discover how other manufacturing businesses are harnessing more advanced technologies to boost productivity, streamline operations, and drive growth.
• See practical applications of Industry 4.0 such as ‘ERP’ and ‘MES’ systems along with ‘co-bots’, which paid for themselves in six months.
• Talk through why a clear roadmap for implementation is important.
• Discover where to go for the next steps to adopt some innovative solutions into your existing processes.
Featuring The Smart Factory Showcase with Kiwi Manufacturer Nautech Electronics, facilitated by experienced consultants from LMAC. Manufacturers have found that bringing a few of their team along, to gain a wider understanding of digital tools and automation opportunities and their implications for manufacturers, is a great way to get momentum in their business.
The EMA is committed to helping manufacturers, who form the largest membership group of the EMA, improve productivity and reap benefits such as enhanced efficiency, improved health and safety management, energy savings, and lower carbon output.
Don’t miss this opportunity to equip yourself with the knowledge and strategies needed to lead your business into the Industry 4.0 era.
Event Details:
• Auckland: Thursday, 14 November 2024, from 1:00pm-4:00pm at EMA Business Hub, 145 Khyber Pass Road.
• Whangarei: Wednesday, 20 November 2024, from 1:00pm-4:00pm at Distinction Hotel Whangārei, 9 Riverside Drive.
For more information and to register, visit the ASB Manufacturers Workshop events page.
When Small Business and Manufacturing Minister Andrew Bayly admitted to calling someone a “loser” during a winery visit recently, he triggered a media storm that lasted for weeks. His comment not only raised questions about his judgement but also illustrated the importance of a well-managed public relations (PR) response to quickly navigate and resolve an issue. Director of Auckland public relations agency Impact PR Mark Devlin discusses how manufacturers can navigate a crisis in front of the media.
Business leaders rarely expect a reputation crisis, but these situations do arise, often attracting media scrutiny. Facing media inquiries in challenging times can be daunting, particularly when potential brand damage is involved.
For many businesses, lacking a crisis response plan means CEOs and senior leaders might struggle to manage a sudden call from a journalist or an impromptu press conference. Some executives opt for a “no comment” response, which can imply a lack of transparency or unwillingness to address issues directly.
In most cases, declining to comment isn’t the best strategy. Although there may be rare instances where silence is justifiable, generally, it’s more effective to respond with honesty, offering information where possible.
The key to successfully managing media during a crisis is having a pre-existing plan, pinpointing potential crisis scenarios, and identifying who will address reporters’ questions. This spokesperson must be well-prepared and trained in media engagement to deliver a clear, impactful message.
Preparation is the best defence against negative press. Most can recall a situation where a CEO’s or spokesperson’s mishandled responses amplified a crisis, but there are also cases where skilled media handling turned potential setbacks into reputation-building moments.
The company’s most senior leaders, especially the CEO, should ideally be the face of media responses during a crisis, signalling that the situation is taken seriously. The CEO’s presence shows the company values the matter and is ready to act, as they are seen as the ultimate authority who can credibly commit to solutions or offer a genuine apology.
Whoever is chosen to interact with the media must understand how to positively influence both the interviewer and the broader audience. An interview is an opportunity to convey the company’s stance clearly and concisely, and it’s important to provide what the journalist needs for their story.
Before an interview, preparation is vital. Effective delivery involves clear, calm, and authoritative speech, especially for broadcast media. In radio interviews, a warm tone can be just as critical; listeners pick up on friendliness through voice, even if they can’t see the speaker.
Whatever the issue, honesty is paramount. Passion for the business should come through naturally, avoiding overly rehearsed statements. Practising responses to difficult questions can help maintain composure during high-stakes interactions.
Journalists are likely to engage better with someone who is open and committed rather than overly polished or rehearsed. It’s also essential not to overload interviews with excessive information. Focus on two or three key points and avoid jargon, giving the journalist a concise and authentic narrative.
Since journalists work on tight schedules, getting your main message across from the start is crucial, as interviews often end sooner than expected. Having key messages prepared can keep the conversation on track and prevent unnecessary tangents, which may suggest evasiveness.
With the right planning and calm preparation, businesses can represent themselves effectively in public, turning potential crises into moments of positive exposure. CEOs and senior leaders should treat media interviews as a top priority, ensuring they’re as prepared as possible to make the best impression.
Professional crisis preparation is your insurance against media derailing your business overnight. The team at Impact PR have represented brands during dozens of crises over the past two decades. Give us a call today to ensure you are ready to weather any risk to your reputation.
Here are ten key lessons from how Andrew Bayly’s recent crisis was handled, with insights into where improvements could strengthen public perception and brand management.
1. Own the Mistake Quickly: Acknowledging the issue as soon as it becomes public is crucial. In Bayly’s case, addressing the “loser” comment immediately and offering a sincere apology might have shown accountability and limited speculation.
2. Show Genuine Remorse: In any situation involving a personal remark, sincerity is essential. PR experts suggest that conveying empathy and regret openly builds credibility. Bayly’s approach could have benefitted from a more personal, transparent response.
3. Avoid Justification or Excuses: Attempting to rationalise or downplay a negative remark risks undermining the apology itself. Effective crisis management involves accepting responsibility without excuses, which can shift public focus away from perceived defensiveness.
4. Centralise Messaging Early: It’s essential for spokespeople to keep responses consistent. By defining a singular, cohesive message and sticking to it, the public response becomes clear and dependable. Any mixed messaging could have been avoided by this strategy.
5. Contextualise with Positive Actions: Shifting focus from a negative incident to positive contributions is a common strategy in crisis PR. By spotlighting Bayly’s other professional efforts, the narrative could have been reframed more constructively.
6. Involve a PR Expert for Sensitive Issues: For situations involving personal remarks, a PR professional’s guidance can be invaluable in creating responses that align with the public’s expectations for accountability and respect.
7. Utilise Body Language and Tone in Apology Videos: Where a public apology video is possible, tone and body language are critical. Using a sincere, calm demeanour to emphasise remorse. In Bayly’s case, this might have added a layer of perceived sincerity to his response.
8. Engage Stakeholders with Follow-Up Actions: After an apology, proactive steps to repair relationships with key stakeholders or affected parties can be a powerful way to rebuild trust.
9. Leverage Supporters Carefully: Positive testimonials or endorsements from trusted allies can sometimes help restore credibility. However, it’s important to be cautious with endorsements to avoid perceptions of damage control that may seem insincere.
10 Commit to Improving Professional Conduct: Publicly committing to specific, professional improvements can help manage future expectations. Bayly’s crisis management approach could have benefited from explicitly stating how he intends to ensure similar incidents don’t happen again, showing growth and respect for public sentiment.
Ian Walsh, Partner, Argon & Co NZ
I was reflecting recently on how many business owners have started an improvement program with 5S and failed. Before I talk about the “why” and the “how” 5S implementations fail in these businesses, and for those who haven’t come across 5S before, allow me to briefly explain what 5S is.
5S is a practice that was developed at Toyota in the 1960s. 5S consists of 5 “S’s” based on Japanese words and the associated anglicised word:
1. Seiri (Sort) – Eliminate unnecessary items from the workplace.
2. Seiton (Set in Order) – Organize the necessary items so they are easy to use and accessible.
3. Seiso (Shine) – Clean the workplace and keep it clean.
4. Seiketsu (Standardise) – Standardise the best practices within the workplace.
5. Shitsuke (Sustain) – Ensure discipline and commitment to maintain the 5S processes.
All the business leaders that I’ve talked to about failed 5S implementations were unable to maintain the “standardise” and “sustain” the initiative. After a period of time, standards slipped and then eventually (or quite quickly) returned to the previous level with a few artifacts remaining. Most of these leaders said “we tried that, it didn’t work”.
This needs a deeper analysis. There are examples across the globe of world-class companies that rely on 5S as a core practice and have succeeded in sustaining the practice. On that evidence, surely it’s not that 5S itself fails, but that particular implementations fail?
Many of these business leaders I talked to stated that they were told something along the lines of “if you can’t do 5S you can’t do anything”, and so they started their improvement journey with 5S, usually with help from a “mentor”.
Typically, they would do a 5S exercise in an area in 1-2 days and then move into the sustain part of the process.
Of course this misunderstands the point of 5S. Yes, it is about making work flow and making the business more productive. But more than that it’s about setting a standard and holding the team to that standard, and establishing teamwork and accountability. The actual saying was “if you can’t master 5S, forget the rest” but it’s not really about 5S itself. The point is that if you can’t engage a workforce in sustaining a standard in their workplace, then that workforce won’t be able to hold any standard or follow any process consistently, and this will limit the business’ ability to drive an improvement culture.
The last S (sustain or shitsuke) actually has two meanings. At the beginning of an implementation it means directed discipline; that change has to be led from the top, with leaders requiring teams to adhere to a new standard.
As teams mature the meaning is more about self-discipline; it has become embedded in the culture. As such each “S” should be followed with some “standardise” and “sustain”, and a period of leaders’ support to ensure the new standard is achieved and sustained. Once this is done the next “S” can be tackled.
It’s like most successful change implementations: a combination of top-down and bottom-up efforts executed well can form the base of a team culture of achieving and sustaining standards, and as a platform for further improvement.
A key piece of advice is to choose an area to start which is big enough to make a real difference through reduced waste and rework, but not so big that it absorbs more resource than the team can afford. Bite off just what you can chew.
So why do most businesses fail? If change is done to a team or at them, rather than them owning it, they will wait for the leadership to fail so they can go back to their old ways.
It requires a significant conscious effort to make team members feel that it’s their process, and have them embed that process into their ways of working. In most cases this effort is unable to be maintained, and the team returns to their previous state. Fundamentally, you can’t change a culture in a day. It requires ongoing reinforcement and discipline to set a new standard, and holding yourself and your team to account until the standard has been achieved. Leaders must support the team through change, and address team members who are undermining the change or not complying with the new standard. As a successful change process plays out in a team, and once the standards can be sustained, only then should you move to the next level.
If you need help with this, or perhaps have “failed” 5S previously, I’m keen to chat.
New Zealand’s international profile as a destination for global productions and development of new drone technology is set to rise following the filming of a new campaign for the world’s first 8K flying action camera in Canterbury.
Industry experts say the campaign which required 70 scenes to be shot across mountain snow, forest and beach locations in two days could not have been made elsewhere in the world in the same time frame and with the level of scenic diversity found here.
Latest data from Stats NZ shows the country’s screen industry, which includes the production of films and TV series, generates $3.5 billion in annual revenue. Attracting international productions to this market can also help promote tourism, boost employment, improve technology transfer to other industries and increase international recognition of the New Zealand brand.[1]
The new campaign for HoverAir, makers of the X1 drone range, raised more than US$1 million in just over two hours when the NZ shot commercial was posted on crowdfunding site Indiegogo - one of the fastest ever to reach this milestone.
Nick Hyne, Diaries Downunder director and former professional snowboarder, says New Zealand’s dramatic landscape provided the perfect backdrop for the commercial with the ability to go from snow to surf in less than two hours.
He says the new advert will continue to enhance Christchurch’s international reputation as a hub for campaign production, with the city already enjoying growing interest from global brands wanting to film here.
HoverAir’s COO Emily Wang says tech entrepreneur Mengqiu (MQ) Wang founded the company having graduated from Otago University with a postgraduate degree in Computer Science before completing his PhD at Stanford University. She says in addition to enhancing ultra high-definition camera content productions New Zealand has significant potential as a destination for testing and development of new drone technologies. Wang says the commercial has already been seen by millions of viewers in more than 75 countries as
diverse as Andorra, Brunei, Cambodia, Liechtenstein, and French Guiana and it was their CEO’s experience of New Zealand that saw him want to return and have the content shot here.
“We wanted to create an advertisement that introduced these new 8K flying action cameras to the market, we wanted to leverage New Zealand’s dynamic landscapes to bring these drones to life.
“The quality of the content created here was well beyond what we had hoped for and we were able to generate millions of dollars in financial backing from around the world within hours of posting the video. This would not have been achievable without New Zealand’s scenic range and the experience of the local production team.
“The diverse environments here also gave our technical team the perfect conditions to test new features and refinements at altitude, in high winds and through forest and coastal locations. This field data was relayed back to our developers in our head
office in real time who will utilise it in creating new modes and future product innovations.
“Our technical research team believes the country has the potential to become an international hub for new product development in the drone space as well as content creation,” she says.
Hyne says mountain specialists were part of the crew of 14 who shot footage in locations including; Mt Hutt, Bottle Lake Forest, Banks Peninsula, and New Brighton beach.
“One of the things that was really unique about this shoot is that we were able to have the product in an environment from both a first and third-person viewpoint. This was really important for the client as they wanted to show real footage plus what the product also looks like as it’s very small and fits into your pocket. We were also able to get some unique angles and a couple of the flight modes on the drone, which was really fun to capture.”
- Jane Finlayson, EMA Head of Manufacturing
Harm in New Zealand manufacturing is unacceptably high and urgent action is needed.
The good news is that through a recent partnership between the Accident Compensation Corporation (ACC) and the Employers and Manufacturers Association (EMA), help is on the way.
ACC claims costs for the manufacturing sector have skyrocketed, exceeding $165 million annually, with weekly compensation costs doubling from $51 million to $109 million between 2015 and 2024.
Health and safety regulator WorkSafe estimates that chronic harm results in a staggering loss of 5,000 disability-adjusted life years each year, contributing to an economic burden of approximately $1.23 billion.
The breakdown of this burden is alarming: 27% of injuries stem from musculoskeletal disorders, 17% from mental health issues, 16% from cancers, and 15% from respiratory problems.
In a significant stride towards addressing this harm, ACC appointed the EMA to lead a by industry for industry project to create a harm reduction action plan. The EMA stood up Project Whakahaumaru, which translates to ‘safeguard’ or ‘protect’, and gathered the perspectives of around 200 stakeholders from the manufacturing sector, health and safety professionals, and WorkSafe via focus groups, one-to-one interviews, co-designed workshops and surveys.
EMA Head of Manufacturing
Jane Finlayson says the recently released results of this discovery phase have been sobering.
“We embarked on this journey to safeguard our industry, and the findings highlight a pressing need for change,” Finlayson says.
“Injuries are not just numbers; they represent lives affected, families impacted, and potential futures altered.
“We cannot ignore the implications of these injuries – not only for the workers but for businesses and the economy as a whole.
“These figures are a call to action.”
Over the past year, the EMA has worked with stakeholders across the sector to develop the Project Whakahaumaru Harm Reduction Action Plan, which it believes can foster change.
Finlayson says this multi-pronged approach is desperately needed. Despite the manufacturing sector comprising 10% of New Zealand’s workforce – approximately 227,000 employees – it has lagged continued on Page 19
Sandra Lukey
Sandra Lukey is the founder of Shine Group, a consultancy that helps science and technology companies accelerate growth. She is a keen observer of the tech sector and how new developments create opportunity for future business.
Mike Shatford
is an expert in the field of technology development and commercialisation. His company Design Energy Limited has completed over 100 significant projects in this vein by consulting for and partnering with some of New Zealand’s leading producers.
Among Mike and his team’s strengths are industrial robotics and automated production where the company puts much of its focus.
Sean O’Sullivan
Has a B Com (Hons) Otago University. In 20002001 introduced PCs on the workshop floor and job and staff tracking and a productivity software App to Fletcher Aluminium Group and 100 manufacturers NZ nationwide. Founding Director Empower Workshop Productivity & Scheduling Software App.
Iain Hosie
Iain is a Director and Founder of Nanolayr Ltd, Director for the NZ Institute for Minerals and Materials Research, Commercial Director for Fabribotics Ltd, and Executive Council of BiotechNZ.
Catherine Lye
Is the first Chief Executive Officer of the newly formed cross-sector incorporated society, Advanced Manufacturing Aotearoa (AMA).
Catherine has been Head of Manufacturing and Export Communities at the 7,100-member Employers and Manufacturers Association for the past two years. As part of that she has guided the Advanced Manufacturing and Industry 4.0 initiatives.
Adam Sharman
Is a Senior Partner at Dsifer. With a background in technology implementation, manufacturing and strategy, Adam and the team at Dsifer are on a mission to support New Zealand’s manufacturing sector transform using technology, data and analytics to outcompete on the world stage. Combining expertise in data engineering, data science & analytics and visualisation.
Patrick McKibbin
CEO – Hutt Valley Chamber of Commerce
Patrick joined the Hutt Valley Chamber of Commerce in September 2021. His passion is identifying and connecting with manufacturing & technology businesses, other businesses, local government, central government and industry associations.
Maori-owned sustainable milk company, Miraka, is investing in Plex by Rockwell Automation as a company-wide ERP system.
Rockwell Automation has announced a new partnership with
Maori-owned dairy business, Miraka, the world’s first dairy processor to be powered by renewable geothermal energy.
Miraka will be using Plex, by Rockwell Automation, to enhance the company’s business and operations with a business-wide enterprise resource planning (ERP) system.
In announcing the partnership, Miraka CEO, Karl Gradon, said “We’re delighted to be partnering with Rockwell Automation, the largest company in the world that is dedicated to industrial automation and digital transformation.”
“As part of our strategic planning, Miraka will be using Plex ERP software. In real time, Plex will seamlessly integrate and manage all of our transactions and systems from the farm, to factory, to customer. It will help us to become even more efficient, resilient, agile and, sustainable,” he said.
“Miraka has always taken a long-term, intergenerational view about everything we do. We’re focused on success and partnering with businesses which share our values. We look at where we’ve come from, where we are now, and where we want to be in the future.”
Rockwell Automation regional director, South Pacific, Anthony Wong, said,
“What sets Plex apart is that it was designed by manufacturers and processors with deep knowledge of these industries. Companies like Miraka can use these intuitive ERP tools to gain efficiencies across their operations.”
“Plex is also a modular system, so it can grow and adapt as needs change in the future, allowing companies like Miraka to remain agile and stay ahead of the competition,” he said.
Miraka chief financial officer, Robert Bell, who is leading the project, said “Miraka has made big strides since establishment in excellence and innovation – both are core Miraka values which underpin this phase of work. Plex is an integrated suite of tools that will drive efficiency in our production, supply chain, financial, quality control, HR and customer relationship management.”
“To be the best requires investment in both people and financial resources. We’re investing heavily in our future to remain an industry leader, with the capacity to deliver the outcomes our shareholders and stakeholders expect.”
“Plex will streamline the way we operate and will link into the existing Rockwell automation in the plant. It is next level integration, and we expect it will provide beneficial outcomes for our team, our dairy farmers and customers,” said Mr Bell.
Miraka is New Zealand’s, and the world’s, first dairy processing company to use renewable geothermal energy, giving us one of the lowest manufacturing carbon emissions footprints that there is globally.
www.miraka.co.nz
Hydrogen is widely regarded as a key pillar in a future clean energy ecosystem. Green hydrogen, produced by the electrolysis of water, has a key role to play in decarbonising numerous industries.
One of the key challenges in its adoption is waste when transferring liquid hydrogen from one vessel to another, or during its storage.
Fabrum’s newest pieces of technology will enable customers in a broad range of sectors to transition to zero-loss liquid hydrogen handling and storage. The result is a potential 25% cost reduction per kg, helping to drive demand for green hydrogen and associated technologies, along with a reduction in emissions.
Christchurch based Fabrum was formed in 2004 by two Canterbury University engineering students, Hugh Reynolds and Christopher Boyle.
For twenty years they’ve been developing small to medium liquefaction systems and composite cryogenic vessels used globally in heavy transport, mining and aviation industries. They operate around the globe with 80% of their product made in New Zealand and exported globally.
Their two decades of hard work has resulted in an impressive library of patents and trade secrets, along with a product catalogue that includes cryocoolers, refuelling technologies, liquefiers and storage systems, for hydrogen, nitrogen, oxygen and LNG.
They have a clear, bold mission: to create technology that enables humanity to do more, using less, and for longer.
The main impact of Fabrum’s project is a reduction of the cost of green hydrogen. A reduction in
cost not only increases demand, but also creates new opportunities for other businesses to create associated technologies.
Fabrum are planning to establish a hydrogen test facility – the first in Aotearoa. The facility will be highly sought after by academia, as well as a broad range of businesses from across the globe with a vested interest in hydrogen systems.
Additionally, they’re looking to establish new high volume manufacturing capability.
Alongside the new facilities, the team will be forming a centre of excellence, which will act as a hub for collaboration and knowledge sharing, directly enhancing the capabilities of local engineering and manufacturing firms.
As the project contributes to the setting of regulatory benchmarks, the team will be stepping up their efforts to share knowledge with policy makers, as well as other private firms and research institutions.
rohia funding will aid Fabrum in setting up their new facilities, as well as implementing cutting-edge data-led manufacturing technologies.
The team will grow in size thanks to recruitment of new key roles and their supply chain will be optimised.
All of this will ensure Fabrum can rapidly scale up production from 4 to 50 units per annum, achieving a greater speed to market, and securing first-mover advantage.
What does your company do?
We are a steel product manufacturer. .
How long have you been in business?
41 years this month.
products do you make?
We manufacture our own Roadsign Supports brand range of highway sign pole systems for the NZ market primarily. This includes motorway signage, and urban signage on single post units called Monopoles which are our main products. We are also involved in special electronic poles for bus and congestion management.
How are you finding business at present?
We have been steady this year but sales volumes are a bit down. I am getting good enquiries, however, and am confident about next year.
We source all our materials locally from merchants and utilise second-tier suppliers such as profile cutters and galvanisers. Suppliers such as profile cutters and galvanisers. We try to source NZ AUS material as much as possible.
The roads of national significance and associated new highway projects announced by National mean we have a long-term future with the products we make. The electronics industry is also exciting, and we are right there with many new project solutions with our good client partner.
David O’Connor, Head of Emerging Markets, The Learning Wave
The World Economic Forum highlights that a “digital mindset” goes beyond simply understanding technology. It’s about cultivating curiosity, creativity, problem-solving, empathy, flexibility, and sound judgement to thrive in today’s fast-changing, tech-driven world.
It’s no surprise that these skills are vital for thriving in today’s rapidly changing workplaces. Data from the international Survey of Adult Skills reveals that New Zealand faces a significant gap in this area, with a staggering 55% of adults lacking problem-solving skills in technology-rich environments.
This gap presents a serious challenge for our workforce, leaving many workers unprepared and ill-equipped to use modern digital tools. As a result, their ability to leverage emerging technologies is limited, potentially leading to low engagement and poor performance at work.
While basic computer tasks may be within reach for most, more advanced digital skills are crucial to fully unlocking the potential of today’s smart technologies. These tools can significantly boost efficiency, productivity, and safety in our manufacturing workplaces. However, without a digitally capable workforce, many of these benefits may remain untapped.
As smart technologies continue to reshape our workplaces, businesses that prioritise the digital upskilling of their workforce will be the ones to thrive. Those that fail to invest in developing these capabilities risk falling behind, leaving both their people and their
operations at a disadvantage.
So why does Digital Capability matter so much for Manufacturing?
For manufacturers, digital capability is not just about implementing the latest software or automating production lines. The end goal should be to build a workplace and culture that fosters innovation, agility, and forward-thinking. A digitally fluent workforce can drive innovation, optimise production, and improve supply chain efficiency - ultimately aligning technology and talent to transform operations, enabling manufacturers to become world-class.
Building digital capability requires more than just teaching technical skills. It starts with unlocking the digital mindset first and foremost, and then building confidence and competence across these eight keys elements.
1. Cultural - Understanding how to behave in digital environments.
2. Cognitive Knowing how to use digital tools effectively.
3. Constructive - Using technology to create new value.
4. Communicative - Mastering digital communication tools for collaboration.
5. Confident - Cultivating confidence and belonging in digital spaces.
6. Creative - Leveraging technology to innovate and solve problems.
7. Critical - Evaluating digital information to make
We’re all using more electricity than ever before. But, the household switchboard isn’t designed for our modern demands. Nor does it offer the control or insights expected of modern household electrical goods.
Basis has developed the world’s first residential smart panel – designed to replace the old-school switchboard. It enables homeowners to reduce their electricity costs, make their homes dramatically safer and lower barriers to adopting important electrification technologies, such as EV, battery and solar.
Basis was borne more out of pure frustration than inspiration. It all began at a casual BBQ, where co-founders Danny Purcell and Julyan Collett met and discovered their shared frustration at the energy sector and desire to change it for the benefit of both people and the planet.
Within months, they quit their jobs and set out to build the world’s first true smart panel. Since the business was formally founded in 2020, the team has grown to 90 full-time staff split between Auckland & Christchurch. Their first-generation smart panel, and accompanying app, has achieved IEC (International Electrotechnical Commission) compliance and the team are gearing up for production and soft-launch.
Their ultimate goal is to get their panels into every household across the globe.
Benefits to the innovation ecosystem
Basis’ technology has the potential to disrupt the energy and electricity ecosystem, and create numerous opportunities for other businesses, particularly around electricity usage data and insights. But rather than fragment the sector, key players in the field see the opportunity for a more aligned and collaborative industry.
The team are planning on building a testing facility in Aotearoa, which they intend on opening to other customers, as well as new cloud-based platforms to benefit a wide range of groups via API Basis’ technology has not only captured the attention of many other NZ ventures, but also attracted impressive overseas talent to join the company.
The award of the rohia Trailblazer grant comes at an ideal time for Basis as they enter what’s normally a tricky phase for all hardware startups. In their case, it’s additionally complex due to strict electrical safety regulations.
The funding means they will be able to improve the overall quality of the panel and increase the speed of delivery.
Outside of the manufacture of their panel, the funding will also help establish key sales and commercial functions and further refinement of marketing collateral.
The rohia Trailblazer grant will help Basis bring their world-first Smart Electrical Panel to homes across New Zealand and the world. This support enables them to empower homeowners with better energy management, enhance safety, and lower barriers to adopting clean technologies like EVs and solar.
informed decisions.
8. Civic - Understanding how to engage and participate in the digital economy.
These eight elements go well beyond simple technical or systems know-how. They represent a more comprehensive approach to digital fluency, empowering workers to navigate the complexities of the digital work-world with greater confidence.
For manufacturers, this means enabling employees not only to use technology, but also to think critically and apply digital solutions in ways that enhance teamwork, boost overall productivity, and, of course, ensure safety while doing their mahi.
By investing in the right training and upskilling for your workforce, businesses can better prepare their employees for the demands of the digital workplace.
The good news? The Learning Wave is on a mission to help bridge that gap.
We offer a free Digital Skills Assessment designed to provide a clear picture of where your workforce stands in terms of digital fluency. This assessment helps to identify areas for improvement and tailor a training programme that will enhance the organisation’s capabilities, enabling teams to thrive in the modern digital workplace.
Don’t let your organisation fall behind. Take the first step towards building a digitally fluent workforce today. Contact us now to schedule your free digital skills assessment.
https://vimeo.com/816734925
Advertising Booking Deadline – 5 December 2024
Advertising Copy Deadline – 5 December 2024
Editorial Copy Deadline – 5 December 2024
Advertising – For bookings and further informa
Media Hawkes Bay Limited 06 870 9029
Articles to be sent to: publisher@xtra.co.nz www.nzmanufacturer.co.nz
Primero Profiles processes and distributes steel profiles (flat steel products that have been cut, and when needed, folded or rolled) to a broad range of fabricators in the manufacturing and construction industries across New Zealand.
The business has one of the most experienced teams in steel plate processing –with processing capability up to 24 hours a day across three manufacturing hubs in Auckland and Tauranga. Directors Rob Hunt and Vaughn Clark lead the team of approximately 100 people.
With a diverse spread of customers across manufacturing and construction, Primero Profiles has witnessed a decline in demand across these industries over the past couple of years. However, Vaughn Clark explains that diversification has helped the company successfully navigate the current economic cycle.
“Across the verticals we serve, we haven’t experienced a uniform rise and fall of demand. Instead, we’ve seen each vertical experience its own peaks and troughs, which has shielded us from the potential full force of the recent market downturn.
“Overall, we’ve seen annualised decreases in tonnage demand of up to 25% within the verticals we operate in, over the past two years. Now, we’re seeing a stabilisation and turn of those trends. Our daily metrics are showing that enquiry volumes have picked up, and those requests are increasing in size and scale,” says Vaughn.
Based on recent conversations with customers, Vaughn says that there is certainly positivity starting to flow through, and the consensus is that New Zealand is now at the end point of this current cycle.
“Our customers are pleased with the relief coming through following the Reserve Bank’s recent cuts, and project financing is changing, removing many of the barriers for capital developments to proceed.
“But it’s not yet a clear path ahead, and many are waiting to see the strength of the rebound. The green shoots are there, with our rising enquiry levels a clear example, but we haven’t seen them convert yet into locked-in orders,” Vaughn explains.
Vaughn adds that in a traditional industry such as theirs, where demand is often influenced by the economy, it’s important for Primero to continue to adapt its business operations accordingly, as the country passes through constriction and growth periods.
His fellow Director Rob Hunt agrees, and sees the economic upturn not only bringing relief, but also challenges.
“The biggest challenge will be expanding Primero to match the rate of demand growth. We need to ensure we have the team on board to deliver our product and supply chain, to order to maintain the required product volumes to match increased capacity.
“With inflation only just reaching the desired range, the concern is also that we see another ‘boom and bust’ cycle, rather than steady, considered investment in critical areas like infrastructure,” says Rob.
As part of that adaptation focus, Rob says that they are always looking for ways to increase efficiencies through innovation investments. Constantly updating machinery is key, as is their digitalisation journey.
“For the past three years, we’ve been heavily digitalising the whole business, creating interconnected systems and upgrading traditionally manual processes. Now, the customer still gets the same end product, but the delivery path has changed drastically.
“ IT platforms are a critical part of success in anything that you do. With 80% of the journey complete, the next year ahead for us is completing the full digitalisation programme.”
Rob has no doubt that a fundamental part of Primero’s success leveraging new digital systems involves recruitment, and enabling their current team through upskilling initiatives.
“In our business, the team is broadly split in two: those who work closely with our customers, and those that deliver the product. So as we gain momentum, we know we’ll need to scale our sales team slightly, but the more significant resourcing requirements will be in expanding our production team. We’re always thinking about who we bring on for the next round of growth,” Rob says.
“Our digitalisation push is all about giving our people the tools to better serve our customers. Looking forward to the next five years, our aim is clear - to not have a piece of paper go onto our production floors, so we’re planning for the innovation spend required to achieve this goal.”
-Adam Sharman, CEO LMAC Group, APAC
Throughout 2024 we have heard the mantra ‘survive to ‘25’ across a number of businesses and sub-sectors of our industry. In challenging economic times, manufacturing businesses face unique pressures from all directions – supply chain disruptions, decreased demand, and tightening credit markets.
However, history shows that companies taking decisive action during downturns often emerge stronger when the economy recovers.
In these times, organisation must be clear on what it is that sets them apart, in order to prioritise investment of time and resources in those activities that will accelerate their competitive advantage as markets recover.
But how many truly understand what sets them apart? A genuine competitive advantage isn’t just about being better—it’s about being different in ways that matter to customers and are difficult for competitors to replicate.
Traditional thinking often leads manufacturers to focus on standard metrics like price, quality, or delivery times. While these factors matter, they rarely constitute a sustainable competitive advantage. Every serious player in manufacturing strives to optimise these elements, making them table stakes rather than differentiators.
The key lies in identifying unique combinations of capabilities that create lasting value. Consider Toyota’s revolutionary production system—it wasn’t just about efficiency, but rather a holistic approach combining worker empowerment, continuous improvement, and waste reduction that took decades for competitors to understand, let alone replicate.
Start by mapping your customers’ entire value chain, not just their immediate needs. What challenges do they face upstream and downstream? A manufacturer of industrial fasteners discovered their true advantage wasn’t in the products themselves, but in their ability to provide engineering support that helped customers optimise their entire assembly process.
Document every customer touchpoint and gather data on:
• Problems customers face that they haven’t explicitly mentioned
• Inefficiencies in their operations that your company might be uniquely positioned to address
• Long-term trends affecting their industry
Conduct a thorough analysis of your organisation’s capabilities, focusing on:
• Proprietary processes or technologies
• Unique combinations of skills within your workforce
• Intellectual property and trade secrets
• Established relationships and network effects
• Historical knowledge base and institutional memory
The goal isn’t to list everything you do well, but to identify capabilities that meet three crucial criteria: they create demonstrable value for customers, are difficult for competitors to copy, and can evolve as market conditions change.
For each potential advantage identified, ask:
• How long would it take a well-funded competitor to replicate this capability?
• What barriers protect this advantage?
• How might technological changes affect this advantage?
• Does this advantage strengthen or weaken as we scale?
Using this approach, a New Zealand based electronics business was able to identify that their greatest competitive advantage was not price, as previously though, but security of product and supply chain.
By doubling down on this dimension of their service, this company was able to win contracts in the defence and automotive industry away from cheaper, overseas manufacturers, significantly increasing their revenue and market reach.
Many manufacturers stumble by:
• Confusing operational effectiveness with strategic positioning
• Focusing on advantages that are easily replicable in the market (or in overseas markets)
• Failing to invest in maintaining and evolving their competitive edge
• Not aligning their entire organisation around their core advantage
A true competitive advantage isn’t static—it must be continuously reinforced and evolved. Consider creating a dedicated team responsible for:
• Monitoring changes in customer needs and market conditions
• Identifying emerging threats to your competitive position
• Exploring ways to strengthen and expand your advantages
• Ensuring organisational alignment around your core differentiators
To begin this analysis:
1. Assemble a cross-functional team including operations, sales, and customer service
2. Conduct in-depth interviews with your most valuable customers
3. Map your capabilities against customer needs and competitor offerings
4. Identify gaps between current positioning and desired competitive advantages
5. Develop an action plan to strengthen or acquire needed capabilities
Remember, the goal isn’t to be marginally better at everything, but to be significantly different at something that matters. Your competitive advantage should be as unique as your company’s DNA— impossible to copy because it’s intrinsically tied to your organisation’s history, culture, and capabilities.
In manufacturing, sustainable success comes not from winning every battle, but from choosing the right battles to fight—those where your unique advantages give you the best odds of success.
-Frank Phillips, Director, Fulcrum NZ
The Tale of Two Manufacturers
Imagine two companies, both manufacturers here in New Zealand, standing on the brink of change. Company A embraced digital technology not just as a solution but as a stepping stone to reshape their operations. They invested in data analytics, IoT, and automation, with a clear vision to enhance their product offerings.
They didn’t see tech as a shiny new toy; they saw it as a tool to make existing processes more efficient, reliable, and insightful. As a result, they grew sustainably, adapting each new piece of tech to complement their strategy.
Company B, on the other hand, rushed into the world of digital with stars in their eyes and a sense of FOMO. They adopted everything from machine learning to augmented reality but hadn’t mapped out where these would fit into their overarching business vision.
Within two years, they were drowning in tech debt and bloated processes, with digital “solutions” that solved nothing but looked impressive in investor presentations.
The difference? Company A used tech as a supportive actor, not the main character. Company B? They gave tech top billing without considering how it fit into the wider story. The lesson here? Industry 4.0 should be the sidekick in your journey—not the destination.
It’s tempting to make Industry 4.0 your main strategy—after all, the tech is exciting! But if you’re all about tech and not about your business goals, you might end up with a whole lot of digital flash and little substance. In manufacturing, the real heroes are efficiency, quality, and customer satisfaction. Industry 4.0 tech—be it sensors, AI, robotics, or data analytics—is just the toolkit to help us get there.
For New Zealand manufacturers, it’s about knowing that “the “cool factor”
should come with a purpose. If the tech doesn’t directly improve how you serve customers, lower costs, or improve product quality, maybe it’s just noise.
There’s one big exception to this rule, and it’s a fascinating one. If you’re looking to pivot your whole business model—from selling products to selling services based on those products—then, yes, technology might become more central.
This trend, known as “servitisation,” transforms manufacturers into service providers. Think about the shift from selling machines to selling “machining hours,” where clients pay for output rather than buying the equipment.
For instance, some global manufacturers are now selling hours of machine operation or even monitoring equipment to provide predictive maintenance. Instead of a one-off sale, they’ve created ongoing revenue streams.
Imagine New Zealand machinery companies transitioning to leasing out cutting-edge equipment with embedded IoT sensors that alert customers about potential failures before they happen. In these cases, the technology is integral to creating the new value proposition itself.
For most manufacturers, the goal should be a measured, thoughtful approach. Here’s how to make Industry 4.0 work with your strategy, not as your strategy:
1. Know Your Endgame: Start with the business goals, not the tech specs. What problem are you solving? Better throughput? Lower waste? Happier customers? Find out, then look at tech solutions that help achieve that.
2. Don’t Overcomplicate the Machine: The beauty of Industry 4.0 is its scalability. You can start small—say, with IoT sensors on a few critical pieces of equipment— before diving head-first into full automation. This lets you test ROI without betting the farm.
3. People Over Pixels: Digital transformation can bring as much disruption to your people as it does to your products. Make sure your team is on board, properly trained, and understands why the changes are happening.
4. Focus on Incremental Value: Tech that doesn’t add immediate value to the production line or improve your core offerings is probably best left to the shelf.
The trick is to set clear expectations with a tech roadmap aligned to your goals. Think of it as a map for growth, not just a showcase of what’s possible. Set timelines, assess which new technologies will fit seamlessly, and budget for iterative improvements.
You’ll avoid the “shiny object syndrome” that ensnared Company B and make tech an enabler for strategy, not the strategy itself.
In the fast-paced world of Industry 4.0, tech has a crucial role, but it’s just that—a role. For New Zealand manufacturers, the path forward is about leveraging Industry 4.0 tech to align with your values and objectives, not as a one-size-fits-all solution.
So, don’t let tech take the wheel of your strategic vision; let it be the co-pilot, guiding you to higher efficiency, customer satisfaction, and growth.
If you start with the right mindset, you’ll find that technology will work for you— not the other way around.
continued from page 1
A PwC study found that companies can expect to reduce operational costs by 3.6% annually, while increasing efficiency by 4.1% annually, on average, by embracing Industry 4.0.
The Reality: Automation does not necessarily equate to job elimination. Instead, it often leads to the creation of new roles and opportunities.
A classic example of this from the world of manufacturing is the introduction of the assembly line by Henry Ford in 1913. It reduced the amount of time it took to build a Model-T Ford from 12.5 hours to 1.5 hours. It led to more production, increased sales, and expanded employment.
Similarly, Industry 4.0 is generating demand for new skill-sets, such as those of data scientists, software engineers, and specialist machine operators, offering new opportunities for employees to upskill.
The Reality: While integrating Industry 4.0 technologies can be complex, it is by no means insurmountable.
New Zealand companies such as Silver Fern Farms, Fisher & Paykel Healthcare, and Bostock, have discovered that integrating these technologies as pilot projects can lead to them being scaled up to be used more widely.
The Reality: There are numerous success stories locally and around the world that showcase the tangible benefits of Industry 4.0.
continued from Page 11
My advice to help manufacturers to get past these myths and get started, is to consider the following evidence-based solutions.
• Start with education: Callaghan Innovation has a wide range of New Zealand case studies from local manufactures sharing best practice. The World Economic Forum is another go to website with hundreds of global case studies as part of its Manufacturing Lighthouse network.
• Consider the Smart Factory Assessment Program at Callaghan Innovation: This is working with an industry expert to find the best opportunities for improvement in process, organization and technology. It also has the benefit of being a global benchmark against your global competitors.
• Start small and scale: Begin with pilot projects that address specific pain points identified in the assessment and gradually expand as confidence and expertise grow.
• Focus on training and upskilling: Invest in training programs to equip your people with the necessary skills to work alongside new technologies.
• Leverage partnerships: Collaborate with technology providers and industry experts to navigate the complexities of implementation.
• Stay Informed: Keep abreast of industry trends and success stories to understand the evolving landscape and potential applications of Industry 4.0.
By addressing these myths with clear, evidence-based solutions, manufacturers can confidently adopt Industry 4.0 technologies and secure their place in the competitive manufacturing landscape of the future.
behind other industries such as construction and agriculture in adopting coordinated safety measures.
Small to medium businesses experience the highest incidence of injury claims in the sector. Additionally, certain demographic groups face significantly higher risks. Older workers (60+) account for a much higher share of the lifetime costs of harm and younger workers (under 25) are also at heightened risk.
For staff, factors such as lack of training, poor communication and actions only taking place after incidents occur have been major concerns.
For business owners, complex regulations and generational and cultural divides have been identified as problems.
“We see that Māori and Pacific people are disproportionately affected by workplace harm. This is unacceptable, and we must address these disparities head-on,” says Finlayson.
“Our commitment to a ‘by industry for industry’ approach is crucial as we work to reduce harm in manufacturing.”
To tackle these challenges, Project Whakahaumaru focused on evidence-based interventions to develop the Harm Reduction Action Plan. It sought perspectives from a wide audience, through virtual workshops, interviews, and digital surveys. HS practitioners, WorkSafe inspectors, academics, business association members, trade unions and Māori and Pacific groups all contributed.
“We’re looking to leverage advances in technology, workplace design, and leadership development to create safer working environments,” Finlayson says.
“This isn’t just about compliance; it’s about fostering a culture that prioritises the health and safety of every worker.”
The Harm Reduction Action Plan includes the appointment of a kaiwhakatere (navigator) to oversee the implementation of this strategy.
The navigator will play a crucial role in resourcing and supporting sector partners, enhancing collaboration, and ensuring that safety initiatives are effectively communicated and executed.
Key interventions planned include improving workplace culture and leadership, providing access to health and safety best practices, and promoting what ACC
calls ‘effective recovery at work’. This latter intervention is based on research that shows the sooner an injured person gets back to work and everyday life, the better it is for their health, wellbeing and recovery.
“By prioritising the physical and mental well-being of our workers, we can drive significant improvements in safety and productivity,” Finlayson says.
“The ultimate goal of Project Whakahaumaru is to create a manufacturing industry that values and protects its workforce while enhancing overall productivity.
“By investing in our people and fostering collaboration, we can create a safer and more sustainable future for manufacturing in New Zealand.”
Next steps involve securing investment funding from ACC to progress to the next phase of Project Whakahaumaru, resourcing the navigator, and moving the Harm Reduction Action Plan from conception to implementation.
“It’s essential that we act quickly and decisively,” Finlayson says. “This is a critical moment for our industry, and we have the opportunity to turn these findings into actionable solutions that will benefit our workers and our economy.
“Together, we can make a difference. This initiative represents a turning point for the manufacturing sector, and I urge every business leader to engage with this process.
“Let’s ensure that we are not only talking about safety but taking the necessary steps to create a culture that prioritises the well-being of our workforce.”
To support manufacturers to better understand the current levels of harm and how their business is performing relative to others, the EMA is now hosting an online dashboard that collates reported accidents and groups them by manufacturing sub-sector.
The information is anonymised, but it will allow businesses to map, track and benchmark their rates of harm to better understand the risk factors in their sector and how they measure up.
The Harm Reduction Action Plan and dashboard can be found at ema.co.nz/ manufacturing.
The EMA is hosting a webinar on Thursday, 21 November, to discuss the findings and next steps. If you want to know more, visit learn.ema.co.nz.
Mackwell & Co. are a Christchurch based engineering firm established by Founder and Chief Engineer Sam Mackwell in 2016. The company is developing biomass fueled steam engines for off-road transport and mobile power applications.
Biomass is an abundant resource across many regions but until now there has been no effective means to have it generate useful work in a clean and safe way. The patent-pending Mackwell safety boiler emits 96% less CO2e than an equivalent diesel engine, and 90-99% less CO than other biomass boilers, and can offer significant lifetime savings for operators.
The Mackwell & Co. Mission is to empower energy sovereignty: the right of conscious individuals, communities, and peoples to make their own decisions on energy generation, distribution, and consumption in a way that is appropriate within their ecological, social, economic, and cultural circumstances, provided these do not affect others negatively.
To deliver on this mission Mackwell & Co. has successfully grown its crew in the last 18 months, from a more research-focused operation to now include a range of talented engineers, designers and business specialists.
Six people work full-time from THE Christchurch facility, conducting R&D, planning production and manufacturing, building internal business systems, engaging stakeholders and developing business opportunities. This is complemented by experienced contractors in finance, human resources, and design and programming work when required.
Mackwell & Co. believe in quality, skilled workmanship, and building relationships with trusted suppliers to achieve manufacturing efficiency. One example of this is the decision to use paper based systems where appropriate, keeping the cost and complexity of digital systems to a minimum: engineers produce hand drawings in the design office before taking copies directly to the workshop for machining and test fitting.
It has been found that placing more importance on each step of the in-house process increases awareness of the task at hand and reduces the chance of small but potentially costly errors.
As a result of this skills first approach, Mackwell & Co. staff retention exceeds averages. For an early stage business this is essential to maintaining talent and
avoiding the costs associated with employee turnover. Finding and training the staff to develop novel technology takes time, but attracting values-aligned individuals has proven a good strategy for us.
The vision for the future of Mackwell & Co. is to continue growing the business to deliver on the company mission. In the near term we will look to establish a production facility for our small engine range that will become an important source of revenue.
This will in turn enable reinvestment in the design and build of large, high industrial equipment for sectors such as forestry and large scale carbon dioxide removal. The company will target both domestic and offshore markets, and in July we delivered our first export - a set of four combustion chambers to Australia for commissioning in one of the largest biochar projects globally.
As the technology can be deployed anywhere with a sustainable biomass supply, the commercial opportunity extends to primary industries throughout temperate and tropical regions worldwide.
The development of off-road transport solutions comes with its challenges, most notably its capital intensive nature. Increasing investment opportunities in New Zealand that support early stage innovators with larger capital requirements would potentially see many more valuable manufacturing businesses reach commercial success. Long term projects require long term thinking, and potential returns for years to come.
Looking for a marketing edge?
70% of licence holders say signing on has positively affected sales.
As global sustainability regulations evolve, New Zealand manufacturers must stay ahead of the curve to maintain their competitive edge, especially with upcoming policies like the European Union’s Ecodesign for Sustainable Products Regulation (ESPR). But what is the ESPR, and how can manufacturers in New Zealand prepare for it?
is the ESPR?
The ESPR is a new EU policy aimed at making products more sustainable and circular throughout their lifecycle, supporting the EU’s 2050 climate goals. The ESPR applies to products sold within the EU, setting specific sustainability requirements for design, use and disposal. It applies to most products sold in the EU, except for some like food and medicines. Non-compliant products may face fines or bans.
Although it took effect in July 2024, the detailed rules will be developed over the next year. The regulation aims to make products more durable, reusable, repairable, and recyclable, while banning the destruction of unsold goods like electronics and textiles.
A digital product passport will also be required, giving consumers direct access to sustainability data and exposing brands to greenwashing claims under the Green Claims Directive.
Why should New Zealand manufacturers pay attention to ESPR?
For manufacturers exporting to the EU or intend to:
➔ Failure to prepare for the regulations could result in loss of market access, fines, or even prosecution.
➔ Your products will face stricter comparisons on sustainability and circularity, which could impact your market share positively or negatively.
Even if your business doesn’t currently export to the EU, the trends set by the ESPR are likely to influence regulations and purchasing decisions in other markets
➔As supply chains globalise, multinational corporations may enforce ESPR-style standards on all their suppliers, no matter where they are located.
➔ With more sustainability and circularity data available, products without this data risk being left behind, even in domestic markets.
Preparing for the ESPR can also offer benefits beyond regulatory compliance. As consumers and investors increasingly prioritise sustainability, early adopters of sustainable practices can enhance their brand reputation, reduce costs through resource efficiency, and innovate with new products that meet the growing demand for more sustainable alternatives.
Steps New Zealand manufacturers can take to prepare for ESPR
1. Start gathering the necessary data
Sustainability data needs to conform to international
standards and may need to be verified to avoid claims of greenwashing. A Life Cycle Assessment (LCA) or Environmental Product Declaration (EPD) can help you understand and communicate the environmental impact of your products, from raw material extraction to disposal.
Circularity data is now supported by new standards, ISO 59020 describes the minimum data requirements for quantifying the circularity of your products. Tools like the Material Circularity Indicator (MCI) or the Circular Transition Indicators (CTI) can help you to apply this standard to benchmark and report your circularity alongside your LCA or EPD.
Start gathering and verifying the necessary data well in advance. This process can be resource-intensive, so early preparation is key to a smooth transition.
2. Engage with your supply chain
Both your operations and supply chains must meet sustainability standards. Start by mapping your supply chain to find areas for improvement.
3. Invest in circular design
Circularity is at the heart of the ESPR. Start by benchmarking your operation’s circularity with ISO-compliant metrics. Focus on redesigning products to use fewer materials, last longer, and be easier to repair or recycle.
Shifting from a linear “take, make, waste” model to a circular economy is essential. Consider take-back schemes, repair options, and effective recycling as part of your product stewardship strategy.
4. Strengthen eco-innovation
The ESPR’s push for sustainable product designs gives
businesses investing in eco-innovation a competitive edge. Whether it’s creating sustainable materials or improving production efficiency, innovation will be crucial for meeting ESPR standards and staying competitive in the global market.
5. Stay informed on regulatory developments
It’s crucial to stay updated on the latest developments. Engaging with industry groups can help you understand the impact on your business. Being proactive, rather than reactive, will enable you to adapt your operations more strategically.
6. Embrace digital tools for compliance
Choosing the right Digital Product Passport (DPP) platform is essential, with several leading platforms already working on interoperability and standardisation. Since DPPs must meet EU requirements, developing a home-grown solution could be challenging.
These tools are key for meeting ESPR’s data needs, including traceability, recyclability, and environmental performance. Investing in the right technology will help your business meet regulatory demands efficiently.
Getting ready for the ESPR may seem daunting, but it’s also an opportunity for New Zealand manufacturers to innovate, enhance their sustainability credentials, and future-proof their business in an increasingly eco-conscious world.
By understanding the ESPR’s requirements and adopting proactive measures, you can meet compliance and unlock new business opportunities in global markets.
www.thinkstep-anz.com
~ Smart bearings provide critical data for predictive maintenance of EV components ~
It’s clear that the shift to e-mobility is happening now, rather than in three-to-five years’ time. Every component in a vehicle — from, major body structures down to individual bolts and screws — has an integral role in keeping it running sustainably. That includes bearings.
Here, Chris Johnson, managing director at SMB Bearings, explains the vital role smart bearings will play in today and tomorrow’s electric vehicles (EVs).
The race is on to build lighter, more efficient EVs and to maximise vehicle range per charge. Smaller and lighter bearings are needed as EV parts also become less heavy and more compact for example, due to improvements in battery energy density that enhance the driving range of vehicles.
That’s why vehicle developers are looking closely at every bearing location in EVs. They must ensure that each bearing helps optimise friction performance, reduces energy expenditure and yields the highest levels of electromobility performance.
Bearings in EVs will remain essential across the vehicle itself steering columns, motor shafts, wheels, wipers and electric mirrors, windows and seats will all rely on bearings. And there are the drive trains and chassis systems, which rely on Electric motor bearings designed for very low noise and low vibration applications.
In all cases, these bearings must enable smooth, fluid motion — for instance, while turning the steering wheel or adjusting the wing mirrors. A quality bearing must be optimally-sized for a given application and able to withstand high stress and loads. In other words, automotive bearings should be chosen carefully.
EV motors provide up to 15,000 revolutions per minute (rpm) compared with less than 8,000 rpm for ICEs, and consumer cars usually provide less than 6,000 rpm. The higher rpms of electric motors are a major selling point in terms of performance, and also eliminate the need for heavy and expensive transmissions. But this puts higher quality demands on components throughout the powertrain.
Automotive bearings undergo a great deal of stress, wear and tear, depending on the application. They must withstand higher centrifugal forces with minimal self-heating caused by rapid rotation. Aside from wear on the bearings themselves, design engineers must also consider the life of the vehicle, which must perform reliably over hundreds-of-thousands of miles decades into the future.
When choosing bearings for automotive engineering, there is a lot to consider. Not just the specifications of size and material, but also the choice of lubricant and choosing a reliable supplier.
It’s essential to select high quality bearings that offer the best performance, longest component life and to avoid parasitic losses at all costs.
While the shift to e-mobility gathers pace, designs of bearings have remained consistent for decades, despite some evolutions in the materials used as in ceramic bearings However, a major change has been digitalisation especially the use of bearings within the context of Industry 4.0. Digital technologies like advanced diagnostics and machine-to-machine communications have changed how maintenance is executed.
Smallest CO2 footprint and lowest power consumption – BOGE is setting new standards with the development of the innovative DT refrigerant dryers.
The frequency-controlled cooling compressor and the speed-controlled fan are merely two of the clever features ensuring ideal operation that is adapted to the actual requirement. Furthermore, the new models are particularly environmentally friendly. This energy balance is unique – with the expansion of its DT refrigerant dryer series, the compressed air specialist from Bielefeld eclipses similar products. The established refrigerant dryers DT 4 to DT 140 that guarantee a constant dew point of 3 °C at a free air delivery of 0.4 to 14 m³/min, are now complemented with new models that provide a free air delivery of 18 to 75 m³/min.
They are available as fixed speed or frequency-controlled models and with water cooling as an option.
A key component of the new generation is the hermetically enclosed cooling scroll compressor which, from a flow rate of 18 m³/min, is also available as a frequency-controlled version (DT 180 F).
The DT series cooling scroll compressor allows operation low in vibrations and noise. With the frequency-controlled version, BOGE is now making a strong statement with regard to energy efficiency. This dryer flexibly adjusts energy consumption to the thermal load as well as flow quantity of the refrigerant and requires low start-up currents, thus reducing power consumption, especially in partial load. Requirement-dependent adjustment leads to minimisation of energy costs, which has a positive effect on Total Cost of Ownership.
Frequency control ensures that, even when there is little demand, the drying capacity remains ideal and the pressure dew point is stable. Five operating modes allow individual configuration. “By selecting the relevant operating mode, the operator can prioritise maximum energy savings or the ideal pressure dew point“, explains In the 5th operating mode, the refrigerant dryer automatically switches between the individual modes to guarantee the perfect results. Another savings effect: If the flow rate falls below 20%, the control can turn off the cooling compressor altogether.
In particular, digitalisation has heralded a move away from reactive maintenance towards predictive maintenance. Industry 4.0 technologies like sensors can be fixed to automotive components, gleaning real-time data on their condition and performance which is then relayed to manufacturers’ or engineers’ supervisory control and data acquisition (SCADA) systems.
These developments include Industrial Internet of Things (IIoT)-compatible smart bearings, which are able to self-diagnose impending faults and failures. Because they are typically located in the heart of all rotating applications, smart bearings are ideally-placed to help engineers adopt a predictive approach to maintenance. Crucial data on bearing speed and direction, or on the rotational speeds, forces and vibrations impacting upon the bearing and other components, allow for advanced diagnostics to be performed.
Every part in an electric vehicle, big or small, has an integral role in keeping a car running, and this goes for specialist bearings, too. To this end, early warnings about any deterioration in bearing condition can also be accessed. This data can be transferred to the cloud and accessed by engineers in real-time and, as part of a predictive maintenance strategy, help EVs run optimally and for longer distances.
The condensate in the heat exchanger then cools the compressed air until the dew point exceeds the target value. Only once this happens does the cooling compressor come back on. The frequency-controlled fan also reduces energy consumption. Frequency control results in precise monitoring of the cooling capacity, leading to ideal temperature management and drying efficiency.
The refrigerant dryer features a large display which shows all values clearly – from the utilisation of the frequency-controlled compressor, electronic expansion valve and speed-controlled fan to individual parameters such as temperature, evaporation and condensing pressure. Consistent collection of data is the foundation of process optimisation and it supports trouble-shooting. Maintenance cycles can also be planned more effectively. Using numerous interfaces, the DT refrigerant dryers offer ideal connectivity and can therefore be integrated perfectly into existing infrastructure.
As standard, the DT series uses the environmentally friendly and future-proof R 513 A refrigerant that boasts low global warming potential. The cooling circuit is hermetically sealed, rendering annual leakage tests by certified refrigeration engineers unnecessary.
The demands placed on EMC cable glands are multifaceted: they must not only effectively dissipate electromagnetic interference fields, but also undesirably high shield currents.
Furthermore, compact dimensions are needed to fit them in limited installation spaces. In response to market requirements, EMC cable glands also need to be simple, quick and dependable to install.
Addressing these needs, the new UNI Dicht TRI from PFLITSCH combines the top EMC bonding capabilities of the TRI spring – familiar from the blueglobe series – with the compactness and individuality of the UNI Dicht modular system.
The UNI Dicht TRI achieves maximum screening attenuation across the entire frequency range, facilitated by its patented triangle spring that enables 360° bonding with the cable shield over a large area. The mechanical separation of the shield contacting from the sealing element guarantees constant and enduring EMC properties for the UNI Dicht TRI.
A further advantage is the very high current carrying capacity that reliably dissipates undesirably high shield currents thanks to the large contact area of the solid stainless steel TRI spring.
The assembly process is both straightforward and reliable. All the user needs to do is to remove the cable sheath at the contact point where the shielding braid is to be bonded.
The TRI spring reliably bonds the cable shield as soon as the cable is inserted in the cable gland – even with out-of-round or off-centre cables. Importantly, this bonding method from PFLITSCH means that the cable shield only needs to be exposed at the actual connection point inside the control cabinet.
As the shielding braid remains fully intact, maximum screening attenuation is achieved and the useful signals are transmitted without being unnecessarily affected by interference signals.
The interlocking of the double nipple and sealing insert prevents the cable from twisting when the pressure screw is tightened. This feature makes the UNI Dicht TRI particularly suitable for applications where the cable is already bonded, for example connectors and sensors.
Huge screening ranges ensure a reliable EMC connection.
The UNI Dicht TRI is available in sizes from M16 to
M25 for cable diameters from 4.0 mm to 20.5 mm. Thanks to its large sealing ranges, wide diameters can be reliably sealed with IP 68. The huge screening range of the UNI Dicht TRI furthermore ensures a reliable EMC connection.
For example, in the M25 very thin shield diameters from 3 mm up to 17 mm can be bonded. The large sealing area in PFLITSCH cable glands prevents constriction of the cable sheathing to guarantee durable and safe installation. The UNI Dicht TRI made of nickel-plated brass or stainless steel is approved for the temperature range from –40 °C to +130 °C with a TPE sealing insert and from –55 °C to +200 °C with a silicone sealing insert.
PFLITSCH EMC cable glands are an important element of the EMC protection concept for electrical systems, safeguarding against interference and failures.
Sandvik Coromant has upgraded the damping mechanism for Silent Tools turning adaptors for an even more consistent performance and improved surface finish during internal turning operations at long overhangs. The new adaptors integrate seamlessly with the new generation of CoroTurn SL cutting heads, which feature side-oriented internal through coolant.
With close to 50 years of experience in preventing vibration, tool-holding system Silent Tools has aided machining at long overhangs by effectively damping vibrations. Now 33 cylindrical and Coromant Capto items from the turning adaptor range (diameters
16–25 mm and –1 inch) have been improved and equipped with an overhauled and refined damping mechanism.
The damping mechanism has been substantially upgraded compared to the former generation of Silent Tools. The damper body, previously requiring manual fine-tuning, is now calibrated and assembled by a machine.
This automation results in a highly precise and predictable frequency area, perfectly matched to each adaptor’s intended overhang and application. This means that Silent Tools turning adaptors are more efficient at countering vibration forces at long overhangs than ever before.
Thanks to the upgrade, Silent Tools turning adaptors will ensure improved consistency and machining repeatability over all available length-to-diameter ratios, for a more reliable and high-performing product.
Silent Tools and CoroTurn SL — the perfect combination
To further ensure optimal performance and boost productivity, a new generation of CoroTurn® SL
cutting heads for small diameters (sizes 16 and 20) featuring side-oriented internal through coolant has been developed to integrate with the upgraded turning adaptors.
CoroTurn SL cutting heads benefit from Silent Tools technology, which provides improved stability performance. These two products work together to enhance component quality, increase machining process stability, reduce scrap and unnecessary rework, as well as minimise unplanned machine stops.
Furthermore, downtime will be reduced due to better chip control, which is one of the main issues when boring long overhangs in small diameters.”
The upgraded Silent Tools turning adaptors in sizes 16 and 20 mm ( and ¾ inch) seamlessly integrate with the new generation of CoroTurn SL cutting heads in sizes 16 and 20, which feature side-oriented internal through coolant. Additionally, Silent Tools turning adaptors in size 25 mm (1 inch) are a perfect fit for existing CoroTurn SL cutting heads in size 25 with high precision coolant. When combined with the corresponding adaptors, these cutting heads provide all the same benefits mentioned above.
David Moore, Managing Director of Grayson Engineering, is the 2024 recipient of the prominent Steel Construction New Zealand (SCNZ) Chair’s Award. The annual award recognises individuals who have made a significant and lasting contribution to New Zealand’s structural steel industry.
SCNZ Chair and MJH Engineering Managing Director Malcolm Hammond presented Moore with the award at a gala dinner in Rotorua last night.
Hammond described Moore as humble and genuine, and commended Moore’s selfless service to SCNZ over many years. “He is not only focused on his own business, he is also dedicated to giving back to the industry and helping it to raise the bar.”
Hammond said that Moore is well regarded by his peers,and is very approachable and supportive.
“David has maintained an open-door policy, assisting fabricator members to achieve SFC certification and providing additional capacity to support other fabricators when needed.”
As SCNZ Treasurer post-COVID, Moore successfully
helped SCNZ to navigate the volatile period, said SCNZ General Manager Darren O’Riley. He also noted Moore’s advocacy efforts for SCNZ. “David is a longstanding HERA [Heavy Engineering Research Association] board member who represents our industry. And he has always made himself available to meet with ministers to advocate on behalf of our sector.”
Moore is also passionate about futureproofing the structural steel industry by encouraging support for young, emerging talent, and he has served as a judge for the SCNZ Apprentice of the Year award for eight years.
SCNZ and the structural steel industry have greatly benefited from Moore’s invaluable contributions.
The structural steel sector has celebrated the bright new talent in the industry with the Apprentice of the Year and Young Achiever of the Year awards.
The Steel Construction New Zealand (SCNZ) awards acknowledge the growing number of highly capable individuals emerging in the structural steel industry, and celebrate those whose skills, drive and willingness to learn have helped them to achieve outstanding outcomes.
They recognise well-rounded people who demonstrate not only talent and a good attitude, but display traits important to the industry –commitment, innovation and agility.
Apprentice of the Year Winner:
Reegan Glass, Foster Engineering
More than 10 percent of the total workforce employed by local structural steel contractors are in a training programme, and 70 percent of structural steel contractors employ an average of five apprentices.
Deciding the awards was no easy feat due to the high calibre of finalists in both categories, and all are deserving of an accolade, said the judges. The
standard of apprentices continues to be high and the winner and finalists are each a great reflection of the tradespeople coming through the industry.
And the young achievers all possess leadership skills beyond their years and are strong ambassadors for the industry now and into the future.
The 2024 winners and finalists are:
Reegan Glass joined Te Rapa-based Foster Engineering straight from school and rapidly became a valued member of the team, known for his positive attitude, reliability and collaborative nature. He further impressed with his attention to quality and safety, and his contributions to problem-solving.
Among his achievements, Glass recently completed a challenging supply-and-install staircase project. Despite the job’s technical difficulties, such as building off site to match existing steelwork and handling complex panel balustrades, he executed the project largely unaided. “This project stands out as a milestone in Reegan’s transformation from apprentice to tradesman,” said Fletcher.
The judges also noted Glass’ strong drive and can-do attitude, along with the pride he takes in his work.
Apprentice of the Year finalists:
- Kele Setefano, Black Steel Mobile (Runner-up)
- Cameron Bone, Black Steel Mobile (Highly Commended)
- Max Meffan, Farra (Highly Commended)
Winner: Aki Liyanage, Beca
Aki Liyanage’s recent attainment of Chartered Status with Engineering New Zealand Te Ao Rangahau is a
testament to his dedication to engineering and his efforts to develop sought-after solutions for Beca’s clients and the built environment.
Liyanage has displayed resilience in facing design challenges, such as navigating consultations with clients on critical decisions like removing existing structures to streamline project designs.
His ability to collaborate effectively under pressure reflects his maturity and a capacity to overcome obstacles. Liyanage’s calm manner has helped to balance competing priorities and arrive at solutions that are ‘best for project’ rather than just a narrow discipline-specific focus.
Judges were impressed with Liyanage’s resilience, communication skills and ability to solve challenging problems.
Liyanage’s sound technical skills in structural steel design, combined with his determination and genuine enthusiasm for achieving project outcomes, make him an asset to Beca. Particularly notable is Liyanage’s skill in fostering connections and empowering others; through his infectious enthusiasm for engineering, he aspires to inspire those around him.
finalists:
- Kelan Attwood, Cut Fold NZ (Runner-up)
- Katie Golieb, Farra (Runner-up)
- Ricardo Maximo, All Steel Services (Highly Commended)
- Mengdi Li, Mott MacDonald (Highly Commended)
- Jacob Mills, John Jones Steel (Highly Commended)
- Rajeshwaran Nagendran, John Jones Steel (Highly Commended)
Steel Construction New Zealand (SCNZ) is pleased to announce the results of 2024’s SCNZ Excellence in Steel Awards. The winners were announced in Rotorua recently, where close to 300 structural steel industry leaders and specialists gathered to celebrate the best of the best at an event that showcases the sector’s commitment to innovation, best practice and collaboration.
Each year, the task of judging becomes increasingly difficult. This year, 24 finalists were selected from a pool of more than 50 outstanding submissions across an impressive array of structural steel applications. Together, they reflect the endless possibilities of structural steel, demonstrating the remarkable design and execution possible when steel is the primary construction material.
“This year’s entries have once more showcased our industry’s ability to produce remarkable work,” says SCNZ Chair Malcolm Hammond. “We are a progressive industry that continues to add significant value to projects through our unparalleled knowledge of steel construction, and our appetite to collaborate with our clients and design teams.”
“It has been the most hotly contested awards to date and, anecdotally, has produced some of the highest and closest scores ever seen in the SCNZ Awards,” says SCNZ General Manager Darren O’Riley. “It is a reflection of the industry’s continued evolution and sophistication.”
• Supreme Winner and Standalone Residential Category Winner: Grayson Engineering for Geo Domes
and formed heavy universal column and beam sections.
Measuring 42m by 42m and 7.5m high in the centre, the larger dome is comprised of 110 tonnes of steel. Steel was the only viable material for the domes, offering the required strength, durability, quick on-site assembly and cost-effectiveness to meet the design specifications.
Coordination between the steelwork and the builder, along with the temporary works required to support this complex organic form during the build, was extensive.
• Over $3M Category Winner: D&H Steel Construction for University of Auckland Recreation and Wellness Centre
This substantial new facility showcases engineering on a grand scale, pushing the boundaries for clear spaces and high suspended loads.
Comprising eight levels on a 3,600sqm footprint, the vertically stacked amenities include an underground swimming pool, sports halls, elevated running track, fitness studios, rooftop outdoor plaza and turf field. A full-height perimeter steel diagrid bracing system serves as both an architectural feature and a structural element.
The expansive spaces were achieved through a range of innovative structural steel solutions, totalling 6,000 tonnes.
• $1.5M-$3M Category Winner: PFS Engineering for Peacocke Cycle Bridge
The architecturally stunning 71m-long pedestrian and cycling bridge is a prominent gateway (waharoa) to the new Waikato River crossing. The geometrically complex structure comprises five sections with nearly 200 tonnes of weathering steel.
Two 25m-high taurapa (steel masts) feature twin skins with the external skin showcasing Māori artwork. The bridge employs a simple box-beam structure, supported by stiffeners and diaphragms, which form the outer skin and deck.
Steel shrouds enclose the earthquake bearings and joints, connecting them to the reinforced concrete cantilever beam and pier.
• Earthquake Strengthening Category Winner: Petone Engineering for Lambton House Diaphragm Retrofit
Strengthening was completed on the main structure of Lambton House in 2012 to achieve a rating of 80 percent of the New Building Standard. Unfortunately, the work did not address the prestressed floor units’ seating or the level-four diaphragm transfer.
The solution was to install circular hollow section members, connected to the exterior and interior reinforced concrete beams, and to the underside of the precast system slab.
The innovative use of new technology achieved a high degree of accuracy for the fabricated
structure and the exposed steel is a feature of the level-four car park ceiling.
• $500K-$1.5M Category Winner: Lewis Bradford Consulting Engineers and Acme Engineering for Touchdown Sculpture
Stunning in its elegance, simplicity and complexity, ‘Touchdown’ is a large-scale ‘feather’ sculpture constructed from structural steel with a 4m-long fibreglass quill tip.
It weighs 22 tonnes, and measures 21m long, 11m wide and 17m high. Located on a remote site at the on top of a hill, it sits lightly on the ground with just one cantilevered support point.
Challenges included the site’s high wind and seismic loads, the requirement to fabricate the feather with no visible connections, and design intricacies such as the main quill section tapering in two directions as it curves along a constant arc.
• Under $500K Category Winner: PFS Engineering for Spiral Staircase
The spiral steel staircase is a focal point for Made Market, Hamilton’s newest urban precinct near the Waikato River.
A key feature of the sculptural staircase is the balustrade, which supports the stair treads. The soffit beneath the treads forms steel ‘petals’, creating a segmented, curved and smooth surface.
The central column of the stairway serves as the primary structural support, for both the stairway and the deck above. This allowed the use of lighter steel materials in the stairway and façade, ensuring more efficient resource use while preserving the strength and stability of the assembly.
the
but it’s largely
As investment in generative AI continues to grow globally, New Zealand’s government has been implementing its use across the public sector and encouraging businesses to embrace the technology’s potential.
But the environmental, social and governance risks and costs of AI remain under-investigated.
In particular, the energy-hungry computations generative AI requires mean an ever-expanding carbon footprint for this technology at a time when countries are expected to make more ambitious commitments to cut emissions at the upcoming United Nations climate summit (COP29) next month.
We argue that questions around AI’s environmental and social impact need to be part of the conversation about the role it should play in New Zealand society.
Currently, the global use of AI gobbles up as much energy as a small country. This rate is expected to double by 2026. Increasingly sophisticated AI is also projected to double the number of data centres in the next four years.
This ever-expanding reliance on data centres brings sustainability worries. The average data centre already uses about 40% of its power for cooling, often relying on local water supplies.
AI also brings social risks to employees and users. Its capabilities may result in job displacement and the wellbeing of staff who train AI could be affected if they are repeatedly exposed to harmful content.
Governance pitfalls include concerns about data privacy, breaches of copyright laws and AI hallucinations. The latter refers to outputs that sound right but are incorrect or irrelevant, but nevertheless affect decision making.
Like other countries, Aotearoa is rapidly adopting generative AI, from business to the courts, education and the work of government itself.
A recently announced collaboration between Microsoft and Spark Business Group means New Zealand will enter the hyperscale data centre trend. Hyperscale data centres allow for vast data processing and storage needs.
Once completed, a new hyperscale cloud region promises to enable New Zealand businesses to scale up locally, all powered by 100% carbon-free energy provided through an agreement with Ecotricity.
For the moment, many of the environmental and social costs of New Zealand’s growing use are being borne elsewhere. The issue for New Zealand right now is one of global entanglement.
Asking ChatGPT a question in New Zealand means relying on overseas data centres, using a lot of electricity from their municipal grid and likely their water for cooling.
Data centres are scattered across the world and many are located in developing countries. Even where data centres use renewable electricity sources, this diverts supply from other priorities, such as the electrification of public transport.
This is ethically problematic because other (often poorer) countries are shouldering the burden of New Zealand’s AI use. It may also be legally problematic. As a developed country and party to the Paris Agreement,
New Zealand is committed to taking a lead in addressing climate change. This means setting progressively more ambitious emissions reduction targets (known as nationally determined contributions).
Last year’s United Nations global stocktake on climate action confirmed that countries’ total efforts are insufficient to limit temperature rise to well below 2°C above pre-industrial levels. New Zealand’s contribution is also falling short.
The tension between increasing use of generative AI and meeting climate goals is one that climate change minister Simon Watts and his team will be wrestling with as they prepare for next month’s climate summit in Azerbaijan.
To press on with New Zealand’s commitment to address climate change, we need to focus on entangled solutions to deal with the growing environmental, social and governance costs of generative AI.
“Digital sobriety” is a concept that encourages reduced technology use. It is one approach to thinking about the tensions between AI use and its escalating impacts.
This is similar to our approaches to reducing water consumption and waste. It also involves asking ourselves whether we really need the latest smart device or bigger data plans.
Another potential remedy is to scale down slightly and make use of small language models instead of data-hungrier large language models. These smaller versions use less computational power and are suitable for smaller devices.
Integrating sustainability into AI guardrails would also help to balance some of the environmental impacts of generative AI.
Guardrails are filters or rules that sit between inputs and outputs of the AI to reduce the likelihood of errors or bias. Currently, these safeguards are mainly focused on fairness, transparency, accountability and safety.
As the Paris Agreement acknowledges, adopting sustainable patterns of consumption plays an important role in addressing climate change. Careful thinking now about how we adopt hyperscale generative AI in New Zealand in sustainable ways could help steer the country towards a more responsible relationship with this powerful and swiftly developing technology.