
www.nzmanufacturer.co.nz
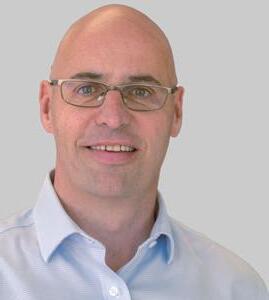
SMART MANUFACTURING
Rethinking workforce development for a competitive future.
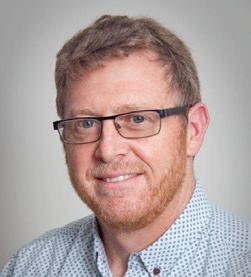
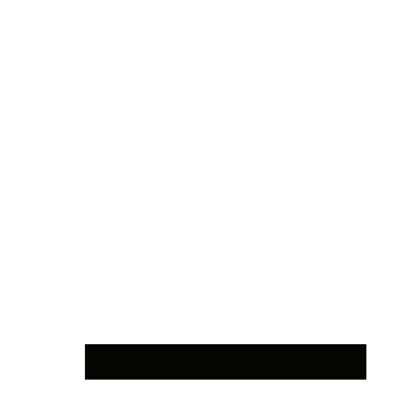
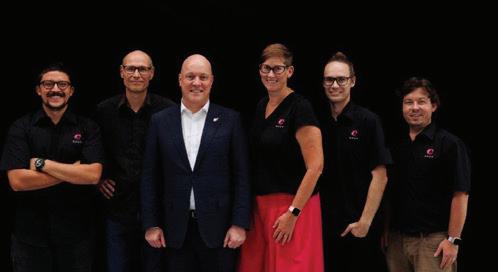
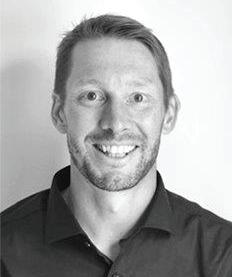
ANALYSIS Can we be world class leaders? SMART
www.nzmanufacturer.co.nz
Rethinking workforce development for a competitive future.
ANALYSIS Can we be world class leaders? SMART
A new multimillion dollar green logistics facility in South Auckland will help boost access to steel construction materials needed for New Zealand’s major infrastructure and renewable energy projects.
Latest Government data shows more than $120 billion has been forecast to be spent on infrastructure by the Crown, Crown entities and KiwiRail over the next five years.
The investment is designed to address New Zealand’s infrastructure deficit and prepare the country for future challenges, including population growth and climate change. Key areas of investment include transport, regional infrastructure, resilience and emergency preparedness, public buildings and schools.
Dean Brown, CEO of Asmuss Group, says with over 1,400 infrastructure projects valued at $10 million or more planned in the coming years, improving the construction industry’s supply chain capacity will be critical to the efficient delivery of these projects.
He says the new $25 million, 15,400m2 purpose-built logistics facility at Drury South Crossing can store over 12,000 tonnes of steel, around 2.1 times the steel volume used in the Auckland Harbour Bridge.
“Most of New Zealand’s structural steel needs
are met by overseas suppliers and developing the capability to manage the rapid distribution of large volumes of these materials will help ensure that materials are sourced, transported, and utilised effectively to avoid delays.
“The operating model at the new facility has been designed to move high volumes of steel across multiple bays simultaneously, significantly improving operational efficiency and customer service deliveries.
“In practice, this could see us unload 1,000 tonnes of steel, around 42 truckloads, from the port in a matter of days. By introducing greater redundancy and reducing any supply chain bottlenecks we can help support the development of New Zealand’s infrastructure in a shorter timeframe,” he says.
Brown says seven high-capacity, 32-metre-wide anti-sway gantry cranes can move large quantities
of steel safely and over 35% more efficiently than their previous warehouses, eliminating operational constraints.
He says the new facility, which will consolidate several of their logistics sites into one location, is now fully operational.
Brown says Asmuss has enjoyed solid growth in recent years with the Drury DC being one of several investment projects across the Group and they are projecting the demand for steel to grow from next year onwards as new commercial and infrastructure projects commence.
“The new South Auckland location was chosen from over 20 sites around the region however modelling showed Drury was the optimal area, strategically positioned to drive transport efficiencies within the golden triangle.
Secure supply of energy and data to moving industrial equipment.
• Large size range
• Vertical travels
• Energy tubes
• Hygienic chains
• Solutions for long travel
• Guide troughs
• Readychain
• Robotic, 3D
• Circular movement
HUGE range of high quality flexible cables
• Control cables
• Single cores
• Data cables
• Sensor/Actuator
• Intrinsically Safe
• VSD/EMC cables
• Halogen Free cables
• High temperature
• Harsh Conditions
• Crane cables
• Profibus cables
• Bus/DeviceNet
• Solar cables
• Instrumentation
• Flat cables
• Curly cords
Largest range of flexible conduits for cable protection
• Conduits
• Conduit fittings
• Divisible systems
• Jumbo systems
• Conduit Accessories
• Braided cable protection
• Fire barrier solutions
• Food and beverage
• EMC systems
• Ex, ATEX, IEC EX
Industrial connectors for many industries
• Rectangular multipole connectors from ILME
• Single pole Powerline connectors from TEN47
• EPIC connectors from Lapp Group
• M23 circular connectors from Hummel
• Circular connectors specifically for the entertainment/stage lighting industry from Socapex
Safety engineering solutions from EUCHNER
• Multifunctional Gate Box MGB
• Transponder-coded safety switches
• Electromechanical safety switches
• Magnetically coded safety switches
Sensor technologies for automation
• High-Precision Laser Distance Sensors
• Ultrasonic Sensors
• Inductive Sensors
• Fluid Sensors
South Auckland logistics facility to support future infrastructure projects.
BUSINESS NEWS
Can your business afford to waste resources amid escalating costs?
The inherent risk to NZ’s brand from commoditised food exports.
SMART MANUFACTURING
Arohia Trailblazers set to forge path to global markets.
EMA
Holidays Act reform.
SMART MANUFACTURING
Beyond the status quo: Rethinking workplace development for a competitive future.
Innovative Kiwi businesses unlock global opportunities with AI.
ANALYSIS
Can we be world class leaders?
REGIONAL DEVELOPMENT: NORTHLAND
Fiona Bycroft, CEO,Naut.
Matt Woodley, CEO, Donovan Group.
SMART MANUFACTURING
Embracing Digital Transformation: A Strategic Roadmap for Argus ManuTech Ltd.
PRODUCTIVITY
Frank Phillips, MD, Fulcrum.
2024 KIWINET AWARD WINNERS
Deep tech heroes turning science into impact.
COMPANY PROFILE
Cetogenix: Building renewable futures — with no waste left behind
DEVELOPMENTS
Free mental health resources for business owners
New Christchurch specialist trades school.
WORKSHOP TOOLS
Green hydrogen production on Kite ships with cynapse gearboxes.
Fire suppression technology protects plant and operators.
CyroMill MS20- a dependable and versatile shoulder milling.
ANALYSIS
Addressing climate change through technology.
THE LAST WORD
Water-Energy Efficiencies: The Catalyst to Semiconductor Sustainability.
Ian Walsh
Ian is a Partner, Argon & Co. NZ, a master black belt improvement specialist and global lean practitioner. He is passionate about improving productivity and helping to create world class New Zealand businesses.
Dr Barbara Nebel CEO thinkstep-anz Barbara’s passion is to enable organisations to succeed sustainably. She describes her job as a ‘translator’ – translating sustainability into language that businesses can act on.
oodward
Is Managing Director of Connection Technologies Ltd, Wellington and is passionate about industry supporting NZ based companies, which in turn builds local expertise and knowledge, and provides education and employment for future generations.
Mark Devlin
Having owned food manufacturing and distribution businesses for a decade, Mark Devlin now runs Auckland public relations agency Impact PR. Mark consults to several New Zealand manufacturing firms including wool carpet brand Bremworth, aircraft exporter NZAero and cereal maker Sanitarium.
Insa Errey
Insa’s career has been in the public and private sectors, leading change management within the energy, decarbonisation, and sustainability space. Insa holds a Chemical and Biomolecular BE (Hons) from Sydney University. She is a member of the Bioenergy Association of NZ and has a strong passion for humanitarian engineering, working with the likes of Engineers Without Boarders Australia.
Insa is a member of Carbon and Energy Professionals NZ, been an ambassador for Engineering NZ's Wonder Project igniting STEM in Kiwi kids and Engineers Australia Women in Engineering, increasing female participation in engineering.
Jane Finlayson is Head of Advanced Manufacturing at the EMA, and has 25-years’ experience in business and economic development. She is passionate about empowering businesses to grow, innovate and embrace Te Ao Māori.
PUBLISHER
Media Hawke’s Bay Ltd, 121 Russell Street North, Hastings, New Zealand 4122.
MANAGING EDITOR
Doug Green
T: +64 6 870 9029
E: publisher@xtra.co.nz
CONTRIBUTORS
Holly Green, EMA,
Business East Tamaki, Ian Walsh, Adam Sharman, David O’Connor, Mark Devlin, Nicholas Russell, Jane Finlayson, Frank Phillips, Geerten Lengkeek, Ross Thompson, Eric Lai
ADVERTISING
T: + 64 6 870 9029
E: publisher@xtra.co.nz
DESIGN & PRODUCTION
:kim-jean: E: kim.alves@xtra.co.nz
WEB MASTER
Julian Goodbehere
E: julian@isystems.co.nz
PUBLISHING SERVICES
On-Line Publisher
Media Hawke’s Bay Ltd
DIGITAL SUBSCRIPTIONS
E: publisher@xtra.co.nz Free of Charge.
MEDIA HAWKES BAY LTD
T: +64 6 870 9029
E: publisher@xtra.co.nz
121 Russell Street North, Hastings NZ Manufacturer ISSN 1179-4992
Vol.16 No.9 October 2024
Copyright: NZ Manufacturer is copyright and may not be reproduced in whole or in part without the written permission of the publisher. Neither editorial opinions expressed, nor facts stated in the advertisements, are necessarily agreed to by the editor or publisher of NZ Manufacturer and, whilst all efforts are made to ensure accuracy, no responsibility will be taken by the publishers for inaccurate information, or for any consequences of reliance on this information. NZ Manufacturer welcomes your contributions which may not necessarily be used because of the philosophy of the publication.
All we want for Christmas is a further RBNZ cut. Not too much to ask, seeing there is movement up in the economic mood. Let’s keep it going!
On Page One we bring you news of a new $25 million, 15,400 square metres purpose-built logistics facility at Drury South Crossing that can store over 12,000 tonnes of steel, around 2.1 times the steel volume used in the Auckland Harbour Bridge. The new facility is now fully operational.
Thia facility will help build access to steel construction materials needed for the country’s major infrastructure and renewable energy projects.
Latest Government data shows that $120 billion has been forecast to be spent on infrastructure by the Crown, Crown entities and KiwiRail over the next five years.
The New Zealand food industry is a major export player and Mark Devlin (Page 7) looks at why the drive to grow export volumes need to be tempered with an understanding of the risk associated with a disproportionate focus on commodified food exports.
Heard of Arohia Trailblazers? Callaghan Innovation is to support seven trailblazing NZ companies – Basis NZ Ltd, Emrod Limited, Fabrum Solutions Limited, Toku Eyes Limited, Zincovery Process Technologies Limited and Zenno Astronautics Limited – as they set their paths to conquer global markets. (Read full article on Page 9.)
Winners of the 12th annual KiwiNet Research Commercialisation Awards were honoured at a gala event in Auckland last week (Page 20).
The global manufacturing sector is experiencing a major transformation fuelled by rapid technological advancements and an increasing demand for efficient, sustainable, and data-driven operations. Adam Sharman, LMAC, describes (Page 17) the approach Argus Manutech Ltd took to maximise their opportunities.
-Geerten Lengkeek, Managing Director, Productivity
As input costs for electricity, labour, and materials continue to rise, businesses across New Zealand are feeling the squeeze. Whether you’re in industry, small business, or a residential consumer, the current electricity crisis is impacting everyone.
Combined with the lingering effects of the pandemic on labour and materials costs, businesses now face yet another formidable challenge.
The recent news of Winstone Pulp International, a major industrial player in the Central North Island, halting its operations is a stark reminder of the challenges ahead. It could well be the first sign of more difficulties to come.
For exporters aiming to establish or expand in foreign markets, these escalating costs present a significant competitive disadvantage. Similarly, businesses focused on the domestic market must contend with increasing pressure from lower-cost imports.
Consider this: New Zealand continues to fall further behind its trading partners in key productivity measures. According to the latest Stats NZ data:
• Labour productivity fell by 0.9% last year.
• Capital productivity declined by 3.8%.
• Multifactor productivity, which accounts for technological advances, efficiency gains, and economies of scale, dropped by 2.2%.
If your business is grappling with rising costs, how do you stay competitive? The structural infrastructure deficits in our country, particularly in electricity generation, are major obstacles to productivity. While addressing these issues lies within the purview of government, businesses can and should still take action.
Boosting productivity means doing more with the same resources, and one key strategy is to eliminate waste. With the cost of electricity, labour, and materials on the rise, can your business afford to be inefficient?
If you’re not actively working to improve productivity and reduce waste, you risk falling behind in the market.
Fortunately, many businesses in New Zealand have adopted structured approaches to enhance their productivity and competitiveness. They understand that wasting precious resources is not an option – and neither should it be for your business. A productivity resurgence for Aotearoa is essential to securing a prosperous future for the next generation.
So practically, what are some examples of what these successful businesses have done to raise productivity? It’s common sense that is unfortunately not always common practice. Here are three examples:
• Ensuring information and materials are easy to
access, correct and unambiguous – by organising the physical and virtual workplace using Lean practices such as 5S (“a place for everything, and everything in its place”).
• Studying the internal and external defects and eliminating these to root cause, thereby creating a ‘right first time’ mindset and reducing rework and scrap costs.
• Streamlining and load-levelling the work to ensure staff are maximising their time on value-adding tasks, eliminating waiting times and increasing their utilisation and therefore their productive output.
If you’re just beginning your productivity journey, the most important step is to understand what improvements are both beneficial and achievable for your organisation. The question isn’t where to start, but when – and the answer is now.
New Zealand’s agricultural sector has been tasked with doubling food exports over the next decade. NZ Manufacturer business advisor and co-founder of Auckland public relations agency Impact PR co-founder,Mark Devlin, looks at why the drive to grow export volumes should be tempered with an nderstanding of the risk associated with a disproportionate focus on commoditised food exports.
With around $4 billion in annual revenue from more than 164 million trays of produce, Zespri is the world’s largest producer of green, gold, and now, red kiwifruit.
And with the NZ-EU Free Trade Agreement now in effect, eliminating the 8.8% tariff (around $47 million annually) on kiwifruit exports to Europe, the future for this single-desk seller looks increasingly promising.
The macro lens on this is attractive by any measure but from the consumer perspective how does this manifest at the point of sale?
For an FMCG marketer, foreign supermarkets offer fascinating insights into local retail cultures. Large-scale populations create the right environment for greater diversity and choice.
No matter where in the world you go, however, Zespri kiwifruit is the one ubiquitous constant appearing on supermarket shelves.
Case in point - during a recent trip to Austria, I visited a local supermarket to explore new food product innovations.
As you can see from the image, there are three different kiwifruit offerings on the shelf.
The first is a paper-wrapped Argentinian brand “Bio-Kiwis”. The second is “Zespri Sungold” and the third is a generic “Budget Kiwi”.
This noticeable contrast between the packaging and price of the South American product and the cellophane-wrapped New Zealand offerings raised questions for me - specifically around the level of control Zespri had over the retail sale and presentation of its produce.
I approached Zespri about this and they advised their product is shipped in bulk to Europe and from there is repacked according to customer and market needs, following one of the options below:
1. Fruit is sold to customers in bulk and remains as such until it reaches consumers in store (loose fruit)
2. Fruit is repacked into Zespri branded pre-packs, either from Zespri at one of our hubs, or their customers’ facilities. In both cases, Zespri fully controls both the packaging type and brand/design of the packaging
3. Fruit is sold to service providers – which pack the fruit in line with the retailer’s branding. In this instance, Zespri does not control the final packaging type or packaging design.
I was informed that what I had seen in Austria (considered an emerging market for NZ kiwifruit) fell into the third category, however, this was more the exception as the organisation gains a foothold in this country, and most European retailers are using fully branded Zespri packaging.
While Zespri has said they are dedicated to improving packaging sustainability in its global channels unfortunately for many Austrians (and other similar markets), this kiwifruit is their only exposure to New Zealand exports - so what message does this send them about us?
Zespri has done an exceptional job at growing our offshore earnings, however, this retail presentation gap underscores the inherent problem with commoditised food exports. When a strategy is centred on clearing larger and larger volumes of products, sometimes this scale will come at the expense of the brand. W
When country of origin labelling shows this product is from New Zealand, this has repercussions for that brand too.
If we circle back to the Government’s objective of doubling our food exports by 2034, we need to consider how this accelerated growth programme can be managed strategically and in line with the image we have invested so heavily in building as a nation.
The reality is that achieving this goal is not going to be possible by simply doubling the amount of fresh produce we send offshore. The sector needs to look at increasing the proportion of added-value products, particularly those that have a high dollar value-to-weight ratio, as we look to mitigate the geographical barriers we face accessing the borders of our largest trading partners.
This is where organisations like the New Zealand Food Innovation Network (NZFIN) come in.
NZFIN is a Crown-funded applied science and commercialisation collaboration between the government, industry, research and education providers, it is unique as the only Government-supported national innovation network that develops and commercially manufactures added-value food and beverage products to open new consumer markets.
Food producers and manufacturers bring their concepts and challenges to NZFIN’s team of food scientists, who then develop value-added ingredients, extracts, or consumer products tailored for both domestic and export markets.
The organisation was established in 2010 from the realisation that we need to focus on exporting value-added food and beverage innovations, internationalising New Zealand’s innovation by using our country for pilot scale commercialism of food systems and attracting co-investment from international partners to support its distribution to reach globally significant production volumes.
One of the more interesting fields that NZFIN is working in is the upcycling of waste into new added-value products. It is a similar approach to Fonterra’s historic shift from using whey protein as animal feed to unlocking its nutritional benefits as a functional food for the multi-billion dollar health and sports food industries.
Fast forward to today and more than 1,000 companies around the country have worked with NZFIN to develop new products to support growing global demand. The reality is that innovation is critical to our export growth, and we need to do more to support our food manufacturers of all sizes in accessing these development pathways that enable them to create high-value, market-ready products to meet global needs.
Callaghan Innovation will support seven trailblazing Kiwi businesses with bold ideas to succeed in global markets, while forging new pathways for like-minded Kiwi innovators.
Minister for Science, Innovation and Technology, Judith Collins announced the Ārohia Trailblazer grant recipients at the New Zealand Aerospace Summit in Christchurch.
Callaghan Innovation has allocated $17.5 million in co-funding to Astrix Astronautics, Basis NZ, Emrod, Fabrum Solutions, Toku Eyes, Zincovery Process Technologies and Zenno Astronautics. The Ārohia Trailblazer
Innovation Grant supports businesses that are benefiting the Aotearoa New Zealand innovation ecosystem, and have global potential.
“Congratulations to these Kiwi innovators who have developed these impressive, and ambitious innovations with the potential for success here and in global markets.
“We look forward to following their success as they inspire and enable other, like-minded ambitious innovators,” says Callaghan Innovation Chief Product Officer, Brett Calton.
“These trailblazers represent diverse sectors, including HealthTech, CleanTech and aerospace, that are growing and have the potential to make a bigger impact globally.”
Astrix Astronautics Astronautics | Auckland | astrix.space
Astrix Astronautics design unique, reliable high performance power systems for small satellites using
continued from Page 1
a state-of-the art inflatable deployment mechanism that delivers solar power to mega-constellations.
Basis NZ Limited Cleantech | Auckland | wearebasis.com
Basis has developed the world’s first residential Smart Panel, enabling homeowners to reduce their electricity costs, make their homes dramatically safer and lower barriers to adopting electrification technologies (EV, battery & solar).
Emrod Limited
Hi-tech Engineering | Auckland | emrod. energy
Emrod is pioneering the transition to a wireless, global energy network. Its technology is hardware for wirelessly sending large amounts of power over long distances, safely and efficiently. Just as the internet transformed communication, wireless power will transform the world’s ability to generate and use energy.
Fabrum Solutions Limited
Hi-tech Engineering | Christchurch | fabrum.nz
The fundamental technologies that Fabrum has developed leverage over 20 years of composite and cryogenic discovery. The company has developed a very desirable library of patents and trade secrets, including cryocoolers, refuelling technologies, liquefiers and storage systems for hydrogen, nitrogen, oxygen and LNG. Fabrum operates around the globe
with 80% of its product made in New Zealand and exported globally.
Toku Eyes Limited
Healthtech | Auckland | tokueyes.com
Toku has developed a product that can identify individuals with elevated chronic kidney disease risk (CKD) using retinal fundus images only. Commercialisation of this AI medical device will remove the need for blood and urine test to identify high-risk CKD individuals, enabling preventative care to avoid costly debilitating kidney failure.
Zincovery Process Technologies Limited
Cleantech | Christchurch | zincovery.com
Zincovery is looking to bring the first 100% recycled, low carbon and high purity zinc product to the market. This is enabled by their innovative zinc recycling technology that avoids the use of fossil fuels, reducing emissions by up to 95% and processing costs by 45%.
Zenno Astronautics Limited
Astronautics | Auckland | zenno.space
Zenno is building the future of agile and sustainable operations in space. They have developed a patented technology based on superconducting magnets that enables spacecraft operators to reduce their costs while also increasing their mission value.
For more information visit: arohia.govt.nz
“As funding conditions improve we are expecting infrastructure activity to increase on the back of Government fast-tracking legislation to stimulate investment.
“Asmuss is playing a crucial role in supplying industries that are the engine room to New Zealand’s economic recovery. We are committed to doing our bit to support the future growth across construction, infrastructure, manufacturing, and emerging markets such as renewable energies.
“We are positioning ourselves to meet this growth with the investment in the new logistics hub, which will help us to expand our capacity to supply major
infrastructure and construction projects,” he says.
Stephen Hughes, CEO of Drury South Crossing the country’s largest mixed-used development, says there is a trend towards centralisation of distribution among large-scale operators.
He says the development is rapidly becoming one of the largest distribution centres in the Auckland region.
“What we are seeing is a growing number of businesses looking to consolidate their distribution facilities into one major hub and reduce their operational costs.
“The construction of specialised facilities like the 5 Green Star Asmuss building, which is one of the most sustainable and structurally strongest of its kind in the industry, requires a greenfields site to allow for this level of customised design.
“The demand for this type of development has seen over 70ha sold to large-scale operators, with hundreds of millions of dollars set to be invested in new facilities to supply the region.
“Businesses opening in the area are also accessing a local workforce that doesn’t want to travel into Auckland,” he says.
By EMA Head of Advocacy and Strategy Alan McDonald
It’s hard to think of a piece of legislation that has needed reform for as long as the Holidays Act.
Successive governments have been aware of longstanding concerns over the Act among workers, employers and payroll providers alike and promised to fix the issues. But they have also largely failed to deliver any meaningful change.
Businesses have long been calling for the Holidays Act to be scrapped and rewritten, saying it’s too complicated and is costing businesses time and money. Unfortunately, the approach to addressing those issues has been largely to ignore the main problems and tinker with existing legislation, adding further complexity.
The main issue for many employers was how the Act calculates annual leave, public holidays, sick days, and bereavement leave.
With the rise of different styles of work, it was challenging to accurately figure out how much workers were owed.
The previous government had a go at reforming the legislation, and in March 2020, Cabinet endorsed in full the 22 recommendations for improvements to the Act made by a tripartite Holidays Act Taskforce. However, the draft bill was far too complicated and didn’t see the light of day.
Now, the coalition government is attempting to reform the legislation and an exposure draft on the Holidays Act Bill was released for targeted consultation in September.
The EMA was one of the organisations tapped to review the exposure draft and provide feedback. We’ve worked with select members of the EMA to make sure we canvassed a range of opinions across the business community.
We also recently tested out thinking with around 500 members on a webinar and they largely agreed with the direction of our approach as it provides something efficient and simple for employers to operate.
We have been under a non-disclosure agreement as we reviewed the draft, but we can reveal the broad direction of travel that the government plans to take.
The exposure draft has suggested an hours-based accrual system from day one for annual leave. The EMA strongly supports that approach to annual leave, possibly also using IRD earnings to calculate the total value of the leave.
But the current proposals then approach sick leave allocation on a days-based entitlement and a system for pro-rating part-time work under the draft.
The EMA and many of our members always opposed the blanket entitlement of 10 days’ sick leave to all staff as it has never made sense that someone working one shift a week gets 10 days’ sick leave while someone working five days a week gets the same. This change is also welcome.
However, taking the above approach means we still have two different ways of calculating different leave entitlements and the EMA and the members continued on Page 11
“Beyond
David O’Connor, Head of Emerging Markets, The Learning Wave
As a nation, we take pride in our innovation and adaptability. However, when it comes to workforce development, we still find ourselves lagging behind.
The challenges are clear: a widening skills gap, ongoing productivity issues, a growing need for both transferable and technical skills, and businesses struggling to meet global competition demands.
Are we ready to push boundaries and adopt effective solutions for today’s workforce and tomorrow’s needs? Or are we content to tinker at the edges of a broken system? Recent conversations suggest the latter.
So, what can we do? It’s easy to blame outdated educational structures, funding issues, inter-agency hurdles, and slow policy changes. But are we truly held back by the system, or are we reluctant to challenge the status quo?
Current structures, though well-intentioned, often miss the mark when it comes to evolving business needs. We need a shift towards flexibility, continuous learning, and strong industry partnerships. We must stop waiting for the government to solve the skills gap; we require more business-led initiatives.
Relying solely on government action is unrealistic and short-term thinking. Instead of waiting for mandates or funding schemes, the government should incentivize businesses with tax breaks for upskilling and training their staff.
The business community must lead the way.
continued from Page 10
Organisations can - and should- drive change by partnering to source and fund necessary skills training. Many companies recognize the value of investing in their workforce, and there’s an opportunity to create a coordinated, industry-wide effort that harnesses the best training available.
Small businesses often claim they can’t make an impact, but we can transform isolated successes into a nationwide movement.
Collaboration among businesses is key to creating a more agile and responsive training ecosystem that meets the needs of both employers and their workforce. We need to reconsider how we approach skills training, moving away from rigid standards and qualifications.
While traditional educational pathways are valuable, they are not the only route to developing a skilled workforce.
We must prioritise a broad range of transferable skills and invest in practical, sector-relevant training that can be quickly updated. There’s a growing demand for short, stackable micro-credentials and on-the-job training, which are seen as more flexible and relevant than conventional qualifications. Businesses will invest in what they value, and training providers must deliver programs that are accessible and valuable to both employers and workers.
As part of this revolution, we need a flexible, open
market that quickly responds to business and learner needs. Moving away from one-size-fits-all training, a dynamic system would allow businesses to access specific skills on demand while enabling workers to upskill or reskill throughout their careers. This approach would foster competition and innovation among training providers, offering diverse, tailored options that drive continuous improvement.
If we want real change, we must think differently. We need to be bold, willing to challenge existing structures, and invest in solutions that may not fit the traditional mould but deliver the skilled workforce we need.
New Zealand’s future competitiveness depends on it. The business community must step up and take responsibility for leading this transformation. Instead of being tied to traditional institutions, learners should have diverse options tailored to their specific career goals and employer needs.
This will create a competitive environment where training providers are incentivized to continuously improve and innovate.
Let’s not wait for permission–- let’s start building the workforce of the future today.
Holidays Act reform – let’s get it done once and done right
we worked with all preferred an hours-based accrual system across all types of leave, to avoid having different approaches.
That could also mean sick leave being accrued on an hours basis from day one, with a 10-day maximum for full-time staff. We’d also want to see a more disciplined approach around the uses and granting of medical certificates for sick leave and how the return-to-work process is managed.
Bereavement leave has been a difficult area for many employers to navigate, particularly due to the changing nature of the workforce and cultural needs. The exposure draft has suggested a broader definition of what constitutes a ‘close family member’.
We prefer a different approach where the law does not try to define what constitutes a close family member. Instead, we think there should be a cap on days of bereavement leave, with some employer discretion in granting leave in difficult circumstances. Once that cap is used up, it’s down to family and friends if they need to take leave, but that will be unpaid. After that time, leave can be taken unpaid at the discretion of the employer. But that is also an approach we will need to refine further in the next round of consultation on the new legislation draft. In our submission on the exposure draft we have asked that other forms of leave be revisited.
New Zealand’s domestic violence leave law puts the onus on workplaces for paid support to staff affected by family violence. While take-up rates for domestic violent leave are very low – less than 1% – our view has always been that payment should sit within the welfare system rather than with employers.
In addition, we believe the hourly accrual system should help to iron out many issues that have come up around accruing leave while on paid parental leave, ACC or jury service. Under this simplified system, you accrue leave based on hours worked.
Unfortunately for those already struggling with the current Holidays Act, the impact of the EMA’s approach may be to slow down introduction of a new Act.
We understand that Ministry of Business, Innovation & Employment officials are already working on how to implement what is outlined in the exposure draft. But, in our view, that only solves half of the issues and we’ve recommended moving to hours-based accruals for all forms of leave – which is basically a fresh start to the complete Act, rather than a 50% fix.
Considering how long we have put up with this current problematic legislation, let’s get a new Holidays Act done once and done right.
Submissions on the exposure draft ended in early October and the EMA has presented its feedback.
The next step will be the introduction of the new legislation for its first reading to the House by the end of the year or early 2025. Once this first public draft has passed through the house, it will go out for submissions and employers will also have an opportunity to appear before the select committee on the changes.
We anticipate the final legislation will be passed by mid-2025, with a 12- to18-month delay before implementation as new software will need to be written by payroll system suppliers and employers will need to upgrade their payroll systems.
We also want a grace period against prosecution of 12 to 18 months while employers bed in their new systems and smaller employers become fully aware of their new obligations and familiarise themselves with those new much simpler systems.
Sandra Lukey
Sandra Lukey is the founder of Shine Group, a consultancy that helps science and technology companies accelerate growth. She is a keen observer of the tech sector and how new developments create opportunity for future business.
Mike Shatford
is an expert in the field of technology development and commercialisation. His company Design Energy Limited has completed over 100 significant projects in this vein by consulting for and partnering with some of New Zealand’s leading producers.
Among Mike and his team’s strengths are industrial robotics and automated production where the company puts much of its focus.
Sean O’Sullivan
Has a B Com (Hons) Otago University. In 20002001 introduced PCs on the workshop floor and job and staff tracking and a productivity software App to Fletcher Aluminium Group and 100 manufacturers NZ nationwide. Founding Director Empower Workshop Productivity & Scheduling Software App.
Iain Hosie
Iain is a Director and Founder of Nanolayr Ltd, Director for the NZ Institute for Minerals and Materials Research, Commercial Director for Fabribotics Ltd, and Executive Council of BiotechNZ.
Catherine Lye
Is the first Chief Executive Officer of the newly formed cross-sector incorporated society, Advanced Manufacturing Aotearoa (AMA).
Catherine has been Head of Manufacturing and Export Communities at the 7,100-member Employers and Manufacturers Association for the past two years. As part of that she has guided the Advanced Manufacturing and Industry 4.0 initiatives.
Adam Sharman
Is a Senior Partner at Dsifer. With a background in technology implementation, manufacturing and strategy, Adam and the team at Dsifer are on a mission to support New Zealand’s manufacturing sector transform using technology, data and analytics to outcompete on the world stage. Combining expertise in data engineering, data science & analytics and visualisation.
Patrick McKibbin
CEO – Hutt Valley Chamber of Commerce
Patrick joined the Hutt Valley Chamber of Commerce in September 2021. His passion is identifying and connecting with manufacturing & technology businesses, other businesses, local government, central government and industry associations.
Two innovative startups show how AI can enable ingenious Kiwis to develop new products for global markets, says Callaghan Innovation Chief Executive, Stefan Korn.
Prosaic and Script Sense showcased very different use-cases at the AI Activator launch. Script Sense is an award-winning AI platform that helps pharmacists to overcome workforce challenges, enhance efficiency, and improve patient care.
“AI has opened up a world of opportunities for Script Sense to innovate in the pharmacy sector,” says co-founder Kieran Erasmuson. “By harnessing AI, we’ve created a platform that not only addresses the pressing issue of pharmacy workforce shortages in New Zealand but also has the potential to transform healthcare operations globally.
“Our AI-driven approach allows pharmacists to focus on what truly matters –patient care – while improving efficiency and safety. As a Kiwi company, we’re excited to showcase how AI can enable us to develop world-class solutions that can compete on the global stage,” he says.
Prosaic is an AI-powered app that uses AI and open banking to help small businesses, sole traders and their accountants to automate the process of finding deductible expenses and income tax credits.
“AI enables startups to solve old problems in new and innovative ways – especially when combined with emerging technology like open banking.
“Using AI to automate time consuming tasks – in our case identifying and categorising thousands of business transactions instantly – not only translates into immediate, positive impacts for Kiwi business users, but opens opportunities for a wave of AI-native startups from New Zealand to export new solutions to the world too. It’s a pretty exciting time,” says Prosaic Co-founder, Nick Houldsworth. Designed to boost economic growth and exports via the rapid adoption of AI, the AI Activator is a Callaghan Innovation collaboration with partners NZTE and NIWA.
“We are delighted to be working with NZTE and NIWA to support innovative, and ambitious startups to use the transformative power of AI to develop world-leading products, find a competitive edge, or boost productivity,” says Stefan Korn. Recent research commissioned by the AI Forum found that 67 per cent of Aotearoa New Zealand businesses surveyed are using AI, with most of these using generative AI.
The AI Activator supports founders and companies with the rapid adoption of AI to boost productivity and create a competitive advantage for New Zealand businesses in global markets. Led by Callaghan Innovation, in partnership with New Zealand Trade and Enterprise (NZTE) and the National Institute of Water and Atmospheric Research (NIWA), the AI Activator provides access to AI experts, R&D resources and capabilities, AI tools for businesses and interactive learning modules.
Modelled after the successful Callaghan Innovation Healthtech Activator, the AI Activator aims to rapidly increase the overall AI usage and talent base across New Zealand to accelerate growth and global competitiveness.
-Ian Walsh, Partner, Argon and Co
Recently, I had the opportunity to work with business leaders on New Zealand’s productivity performance and, how it compares to key trading nations and OECD members.
Over the past 50 years, New Zealand’s ranking has fallen from being in the top five to the bottom five. It’s a tough reality, but more interestingly, the discussion centred around why Scandinavian countries and Ireland excel while we continue to struggle.
Many attribute New Zealand’s lagging performance to factors like distance to market, limited access to capital, and the small size of our domestic markets. Undoubtedly these do play a role, but they are largely beyond a business’s control.
No matter how efficient we become, we still face the challenge of shipping goods across the globe. If we focus on these external factors alone, we will continue to run the risk of overlooking the most crucial areas where we can improve - leadership and people management.
Studies show that New Zealand consistently underperforms in these areas compared to other OECD nations, and this is not a recent development. Over the last 40 years, other countries have systematically invested in cultivating great leaders, while New Zealand seems to have fallen into five fatal assumptions about leadership.
The Five Fatal Assumptions About Leadership in New Zealand:
1. Promoting the best operator to leader will work out
Many workplaces fall into the trap of promoting the best operator to leadership roles. While they are often respected for their technical skills, they
By David Epstein.
What is the best way to pursue excellence? Should you focus all your time, energy, and attention on a single pursuit? Or would it be wiser to dabble in several before committing to one?
In his book Range: Why Generalists Triumph in a Specialized World — an instant New York Times bestseller — David Epstein digs into the evidence looking for answers. A former Sports Illustrated staffer, Epstein begins in familiar territory, comparing the stories of two elite athletes: Tiger Woods, the golf champion, and Roger Federer, the tennis star. Woods was practically born with a golf club in his hands and was encouraged by his parents to go all in when they recognised his precociousness; Federer tried out a number of sports — swimming, skiing, skateboarding — before committing to tennis. So which method is best, the Roger or the Tiger? Epstein makes a strong case for the Roger. Research shows that “it takes time — and often forgoing a head start — to develop personal and professional range, but it is worth it,” Epstein writes. Furthermore, “highly credentialed experts can
may lack the ability to manage people effectively. This can result in the loss of a great operator and sometimes even a demotivated team. Leadership requires a different skill set—one that needs to be developed, not assumed.
2. Leaders are born, not made
The belief that leadership is innate is misleading. Being respected for one’s technical abilities is not the same as having the ability to lead others. If leadership were truly an inborn trait, large multinationals wouldn’t invest heavily in leadership development programs. Instead, they’d simply identify these “natural” leaders. The reality is that leadership can be taught, and the best organisations know this.
3. I know how to develop and mentor leaders
There’s a “number 8 wire” mentality in New Zealand where people believe they can mentor others simply because they’ve been through the ranks themselves. However, mentoring requires more than experience—it requires skill and a structured approach.
If no one in your organisation is truly qualified to develop leaders, it’s time to get external help.
4. Leaders will learn by doing the job
This assumption is equivalent to giving a learner driver a Ferrari and hoping for the best. In reality, people will often entrench the habits they already have; habits that may need to be unlearned later. Leadership development requires structured training combined with hands-on mentorship.
Without ongoing support and feedback, new leaders are likely to repeat the same mistakes, limiting their effectiveness and harming the organisation in the process.
5. We can recruit good leaders from the market
The idea that the market is awash with good leadership talent is flawed. Studies show that New Zealand has some of the lowest levels of leadership capability in the OECD.
If most businesses aren’t investing in leadership development, where is this mythical pool of great leaders supposed to come from? The talent simply isn’t there unless we create it ourselves.
New Zealand’s decline in productivity isn’t because we’ve become worse. It’s because other countries have gotten better. Nations at the top of the OECD rankings invest heavily in leadership development and people management, which drives the industries of the future.
While geography and population offer them some advantages, their real edge comes from having better leaders who make better decisions.
Imagine a business where every leader is competent, teams work on the right things with purpose, and first-level leaders can resolve most issues on their own. Senior leaders are freed from day-to-day firefighting and can focus on growth and strategy. If that sounds like an improvement over the current situation, the answer is clear: start developing better leaders.
become so narrow-minded that they actually get worse with experience, even while becoming more confident — a dangerous combination.”
In true generalist fashion, Epstein examines several disciplines to support his argument, highlighting exemplars from art, science, education, and business. For example, Nintendo’s all-time most influential video-game innovator, Gunpei Yokoi, had no specific life plans when he took the job. His advantage emerged from his experiences as a hobbyist, inventor, and tinkerer.
Epstein also advocates for late bloomers, among them Vincent van Gogh, who only started painting in earnest at age thirty-three, and former Girl Scouts CEO Frances Hesselbein, whose professional career began when she was in her mid-fifties. Though Epstein’s defense of dabbling is convincing, he also shows us that the approach doesn’t work equally well in every field. In a chapter on chess masters, Epstein points out that a devotion to the game from early childhood onward can be helpful, because chess tests the skills of a person working
in an isolated rule-based system. Conversely, less technical domains that demand flexible thinking, like film and literature, reward creative types.
Epstein suggests, for example, that Haruki Murakami’s early musical aspirations fueled his fresh approach to literary fiction.
It makes sense that Epstein was keen to explore this topic, since his own career has taken some turns — he studied environmental science and journalism at Columbia and coauthored a paper on Arctic ecology while writing for Sports Illustrated — and his book shines when he makes personal connections to a topic.
His key point seems to be that getting lost can land us in wonderful places — certainly a worthwhile message, and one that many will welcome.
What does naut specialise in?
Naut enables customers to head out on the ocean or lakes, have an amazing day doing everything they usually would, and sometimes more, and return home leaving nothing but wake! We do this by providing electric propulsion systems that fit into the boat of the users choice with the final drive of the users choice, be that stern drive, jet unit, or the Naut outboard.
A key difference between a Naut system and a conventional system is the reduction of noise, fumes and pollution and higher reliability.
A key difference between the Naut system and other electric systems is the power – the Naut system is 350hp+ and can easily get a boat planing.
How is Naut finding current business conditions?
Naut has technology that is ready to go to market. Like any new tech, it needs those early adopters to come on board to demonstrate the technology in different sectors and use cases. Naut is excited about where the conversations are going with these early adopters, so watch this space (or maybe I should say watch the waterways near you)
Are there export opportunities for your products?
Absolutely! We are keen to see more systems sold to NZ based individuals or companies first, and then Australia and USA are natural next markets. However we have already received interest from a number of other countries, and are always open to talking to either boat builders or boat users from around the globe.
How easy is it to find the right staff members?
Because we are doing exciting work, it is easy to attract highly capable people. As we are a small team with a physical product that we manufacture,
we are expecting people to spend quite a bit of the week working out of our Whangarei based office.
While Whangarei is an amazing place to live, work and raise a family, people outside of the region aren’t necessarily aware of this. So we are finding that people with school aged children are a little more resistant to relocating, and therefore we can’t always bring on the people that do apply.
Saying this, we have also had at least one amazing person that is either local or happy to travel or relocate, for all roles we have advertised to date!
the marine industry are you seeing growth?
We consider two users in the boating market: the recreational boater and the commercial operation. For the recreational market, we are hearing there has been a large downturn in orders which has impacted many players in the boat building or retail market. There are still some sales in the higher price market, which in the boating world is $500k and upwards. The recreational market is by far the biggest sector (compared to commercial) and so it is this segment that has really affected the decline in boat sales.
Within the marine industry, electric boating is a new market, and this absolutely is seeing growth. New Zealand as a keen boating country, has many innovations to offer in the electric boating sector and there is success to be seen across all companies in this sector.
As it is relatively new technology, users tend to underestimate what is actually possible right now, let alone what will be possible as the technology continues to improve. We have found that a ride on our demonstration boat converts even the most pessimistic resistor to electric boats.
The key aspect that drives the performance of the system is the battery packs. The battery packs are what provide the power and energy to the system and are the largest aspect of the system both in terms of weight and size. We have selected battery packs that have passed incredibly high safety tests and come with an international marine certification.
Absolutely yes. There are the industries that we want to sell in to – tourism and aquaculture industries are perfect for electric boating. We are also keen to work with adjacent tech in the industry. Because electric propulsion means having electrical energy stored on boat, this can be used for a range of purposes other than propulsion.
How is your company finding present business conditions?
Challenging. The recession and tightening economic conditions impact on construction is well document. While overall volume in construction is down year on year, we have been able to take advantage and implement improvements in our design software, manufacturing plant and equipment and several processes improving our overall efficiency.
What are you working on at present?
We are continuing to serve our Coresteel and Kiwispan national distributor networks with world class design, engineering and manufacturing or portal frame metal buildings. Additionally, we have established a new light gauge steel frame business, MODNframe, which is providing light steel frame and truss to our networks and the industry nationally.
How difficult is it to find good staff these days?
Difficult in skilled trades and professional roles such as engineering.
Where do you see future growth for your company?
We have recently welcomed an additional two Kiwispan distributors (Bay of Islands / Far North
and Mid-Canterbury) and have additional Coresteel territories available too. Our growth will continue across both Kiwispan and Coresteel brands.
Plus, MODNframe provides additional growth in residential and commercial construction projects. Further to this we are exporting under licence our patented Donobrace rod tension bracing system to the US and Canada.
Additionally, we are exporting our Airbuildr software for metal buildings design, visualisation and qualification in the USA and Canada through our Donovan Group Technologies North America business.
What one thing would make business better for you?
What will development look for your company in the near future?
We continue to develop increasingly efficient design and manufacturing processes. Adiditonally our focus is strongly on export market development of licensed hardware and software products.
The number of businesses in Northland Region was up 1.4% for the year to June 2024, reaching an annual average of 23,122, up from 22,795 in the previous 12 months.
Business units have continued to rise, up 1.5% in the year to June 2024 despite the difficult economic environment for businesses. Growth bounced back, up 0.5 percentage points from the almost 3-year-low in March, although remaining lower than the strong growth in 2022.
High borrowing rates, input costs and low consumer spending, combined with limited ability to pass these costs on through price increases, make for difficult conditions for new businesses.
However, a weakening labour market will provide
more uncertainty for potential business creators as we will likely see subdued spending as a result.
The number of EV registrations in Northland Region decreased by 26% in the year to June 2024, compared to a year earlier. The decline was the same as in New Zealand (26.0%).
The number of EV registrations in Northland Region reached an annual total of 338 in the year to June 2024, down from 457 in the year to June 2023 and 391 in the year to June 2022.
A stronger domestic economy and improved roading infrastructure connecting northland to the rest of NZ.
plans?
Donovan Group construction technology export growth.
The newly released ISO standards for circular economy provide clear guidance on transforming your business model – and avoiding greenwashing. This article builds on last month’s introduction of an MBIE study that showed circular opportunities for New Zealand’s manufacturing sector.
As sustainability becomes a central focus in global markets, understanding and adopting the ISO 59000 series standards will help New Zealand manufacturers stay competitive, reduce waste, and align with global sustainability expectations.
Manufacturing relies on many unique resources. MBIE published in September its draft list of critical minerals for consultation. It comprises 35 minerals that it considers essential for many applications across the New Zealand economy, including healthcare, agriculture, electronics, transport, and construction.
These minerals are vital for the low-carbon technologies we need and underpin most of our manufacturing value. They are also subject to supply disruptions resulting from monopolistic supply chains, resource nationalism, conflict and climate change impacts.
We need to become better stewards of these materials and prevent them from being wasted. The circular economy offers a solution by promoting the more efficient use of resources, reducing waste, and encouraging innovative approaches to design, production, procurement and use.
Extending the service life of products and reusing critical components enables valuable resources to be recovered, lowering costs and creating opportunities for new businesses linked to recovery and remanufacturing.
While recycling undoubtedly has a role, many critical minerals are lost or diluted through the recycling process. The supply chains that turn recycled materials back into products are often offshore.
The Intergovernmental Panel on Climate Change estimates that about half of the environmental problems we need to solve are linked to how we make and use products while the other half comes from the types of energy we use.
Greenwashing happens when companies make false or exaggerated claims about their environmental efforts. This is a growing concern as consumers become more environmentally conscious.
The ISO standards help you
avoid greenwashing by providing a clear, verifiable framework for circular practices.
For example, ISO 59020 requires manufacturers to measure their resource flows and recycling rates, ensuring that their “sustainable” or “circular” claims are based on solid evidence.
This helps build trust with consumers and regulators and protects businesses from accusations of greenwashing.
1. Staying competitive globally: The ISO standards are recognised internationally, giving you an edge when exporting products to markets where consumers demand circular and sustainable solutions. Having robust, traceable data on sustainability or circularity claims will soon be a legal requirement for placing products on the EU market under the Ecodesign for Sustainable Products Regulation (ESPR) that has just come into force.
2. Meeting regulations and reducing risk: Environmental regulations are becoming stricter worldwide. The ISO standards can help you to align with these regulations, reducing the risk of fines and legal challenges. By adopting these practices early, you can stay ahead of regulatory changes and avoid potential disruptions.
3. Driving sustainable growth: Circular economy practices can create new opportunities for growth. By rethinking how products are made, used, and reused, you can lower costs, explore new business
models like leasing or product-as-a-service, and tap into new markets.
4. Innovation and collaboration: The ISO standards emphasise working together across industries to achieve circularity. New Zealand manufacturers can collaborate with others to find new ways to reuse materials, redesign products, and close the loop in production processes.
The ISO 59000 series provides a framework to help businesses adopt circular economy principles. These standards are particularly relevant to manufacturers and offer a step-by-step approach to transitioning to more sustainable practices. Here’s a quick overview:
ISO 59004 sets the foundation for the circular economy, providing clear definitions and principles. This helps businesses speak the same language when discussing circularity.
It encourages you to think about how you can reduce waste and improve resource efficiency at every stage of your production
ISO 59010:
This standard provides guidance on how you can shift from a linear model (using resources once and then discarding them) to a circular one. It helps you to set goals, plan strategies, and make changes to your operations to reduce waste and improve resource reuse. Importantly it starts from the economic rationale behind the transition, enabling you to develop a sound business case.
One challenge businesses face when adopting circular economy practices is knowing how to measure their success. ISO 59020 gives you the metrics to benchmark your performance and track your progress. Importantly, it looks beyond recycling and enables other circular strategies, such as durability, reuse, remanufacturing, and nature-based solutions, to be compared on an equal footing. www.thinkstep-anz.com
Argus ManuTech is a new name, but it has over 50 years of experience as an industry-leading manufacturer of electrical products. It specialises in cable and harness assemblies, viscous reheating products, and electrical medical devices. It has a rich history of supplying local and global customers from its facility in Christchurch.
The global manufacturing sector is experiencing a major transformation fuelled by rapid technological advancements and an increasing demand for efficient, sustainable, and data-driven operations.
Recognising the opportunities these changes presented, Argus ManuTech set out to tackle key challenges such as improving productivity, optimising supply chains, and remaining competitive despite rising labour costs.
To address these issues, the company developed a clear roadmap for its digital manufacturing transformation.
Argus ManuTech’s digital transformation strategy was developed through an initial two-step assessment process. Initially, a business survey was conducted with all employees to understand their challenges and needs regarding their work and the opportunities for the organisation.
This survey proved invaluable in shaping the transformation strategy and identifying key insights and themes. Nathan Hay, General Manager, says, “I can’t stress enough how impactful and important it was to engage with staff before developing any strategy.”
The second step involved using the Smart Industry Readiness Index (SIRI) framework to guide Argus ManuTech in prioritising initiatives for digital transformation initiatives.
The SIRI framework, an Industry 4.0 diagnostic tool facilitated for Argus ManuTech by LMAC’s certified assessors, was employed to evaluate the current digital state of Argus ManuTech’s factories. This framework addresses three fundamental aspects of Industry 4.0: Process, Technology, and Organization.
Based on this assessment, four high-impact areas were identified for ManuTech to focus its resources on: vertical integration, shop floor automation, shop floor intelligence, and inter and intra-company collaboration.
Using these impact areas, Argus ManuTech developed a digital transformation roadmap.
1. Vertical Integration: This strategy aims to refine decision-making processes, reduce manual tasks, and improve forecasting and inventory management through data-driven solutions.
Partnering with Dsifer and LMAC, Argus ManuTech established a data lake to aggregate unstructured and structured information into a single data source for manufacturing and organisation insight and system integration.
2. Shop Floor Intelligence: Using technology and the data available through the data lake, ManuTech partnered with Dsifer to develop a visual shop floor with real-time information feedback, enhancing decision-making processes and overall operational improvement.
This includes implementing digital work instructions, real-time production dashboards, and machine data collection. Nathan Hay says, “This transformation has been a game-changer, enabling our operations teams to identify problems and potential areas for improvement promptly, preventing issues before they escalate.”
3. Shop Floor Automation: Argus ManuTech recognised the opportunity for automation to enhance safety, maximise efficiency, improve productivity, and drive innovation in the manufacturing process.
The automation strategy involved partnering with Design Energy to identify automation opportunities, prioritise them based on potential ROI, and involve shop floor team members in the scoping, selection and implementation process.
4. Inter and Intra-Company Collaboration: Argus ManuTech recognised that team engagement and capability building are crucial for a successful digital transformation. This strategy focuses on driving transformational change through improved collaboration between and within teams and business units.
A digital lean training program was established through partnerships with the Learning Wave and LMAC to foster collaboration and continuous improvement and build digital skills in the workforce.
Underpinning these focus dimensions, Argus ManuTech developed a comprehensive change management strategy to support team engagement around an aligned purpose.
Branded, the Argus Improvement Mission (AIM), a programme was developed to provide deliberate focus on organisation identity, values and mission to create a one-team culture of support, innovation and improvement.
Through this holistic approach to digital transformation, combining technology, data, automation, and people focuses, Argus ManuTech has seen a significant uplift in production performance, moving from 80% efficiency in 2023 to 93% in 2024. The data-driven approach to production planning and forecasting, combined with production efficiency uplift, has resulted in a $1.6m inventory savings in the same period.
Perhaps, most importantly, Argus ManuTech has seen a significant shift in culture, resulting in an all-of-team approach to continuous improvement, with new ideas being generated from all areas of the business.
Nathan Hay says, “The reason we have the traction we have is that many of the new initiatives are being driven by the teams themselves, not by management”.
Argus ManuTech Ltd.’s digital transformation journey is a testament to the company’s commitment to innovation and operational excellence. By engaging the whole organisation, leveraging the SIRI framework and focusing on key areas such as automation, vertical integration, and collaboration, Argus ManuTech is well-positioned to navigate the challenges of Industry 4.0 and emerge as a leader in the manufacturing sector.
Argus ManuTech has proven how it is possible to manufacture in NZ competitively. And how this valuable capability is shared by providing competitive manufacturing services to their contract manufacturing clients. The strategic roadmap outlined in this article provides a comprehensive guide for other companies looking to embark on their own digital transformation journeys.
We have all heard of our ‘productivity problem’. Adopting proven and well understood technology – not the bleeding edge risky stuff – will be key to tackling it.
Anyone in manufacturing who has tried to search for technology solutions to solve a particular challenge knows the rabbit hole it can become. The associated lack of confidence in vendors (particularly when there’s no in country support) follows; so it goes in the too hard basket and progress stops.
All this in a nation where Number 8 wire pedigree and ‘build it yourself’ solutions start to proliferate. This distracts from core business focus and can be a black hole of investment to develop and maintain.
We save time; give confidence and ultimately help manufacturers get stuff done!
Fulcrum connects New Zealand manufacturers to New Zealand technology partners. Part of this is a simple self-service platform, but we also act as your part time CTO, prioritising and advising to make sure the right things get done by the right partners.
In New Zealand we have all the skills, knowledge and technology for manufacturing to thrive, but we often don’t do a great job of talking about it!
Fulcrum works with manufacturers and primary industries of all sizes. We often find that our on-boarding and follow up sessions allow us to act as an unofficial ‘part time CTO’ - helping manufacturers to prioritise, build the foundations of their digital transformation and work with the right partners to deliver it.
We’ve been conscious when onboarding Technology partners that their can be a right size fit to consider. A specialist contractor working independently may be the right fit for one manufacturer in agility and cost, but not right for another where long term support agreements are needed.
Not always, our background in manufacturing brings with it a huge amount of pragmatism, we will just as often guide manufacturers away from a technology solution for certain things (knowing theirs a cheaper or simpler way)!
A lot is written about Digitisation / Industry 4.0 / Digital transformation (and I’m guilty!); in reality, many of the technologies delivered by Fulcrum Technology Partners are well known and proven. Although the hardware and system architectures that support them have evolved (just think of the move to cloud based software), the outcomes for manufacturers are still hugely valuable.
For example, manufacturers have been getting live data from their machinery for decades, how this is achieved now will look different. Potentially using IIoT instead of traditional networks.
Automation suggests brand new, freshly painted machinery being installed. And this is important, for productivity and attracting talent to the industry. In a broader sense it includes removing manual and time-consuming tasks from admin, sales, reporting and many more.
It probably pays more to look at the virtuous circle; with automation freeing up talent to focus on the next big win, or strategic project. Retaining and attracting great people for innovation.
The ultimate example of these working in harmony are the ‘reshoring’ success stories, where the total cost of ownership has actually become cheaper to process in New eland than traditional offshoring locations.
Our growth and focus short term will come for the
manufacturing side of the platform, with 22,000+ manufacturers in the country, the majority of which will be looking at some form of technology to support their business in the next 12 months. We want to engage and support them with our really accessible model.
The opportunities long term really varied; expanding to other partners that manufacturers might wish to be connected to such as auditing, Health & Safety and R&D specialists for example. There’s already examples of this with Digital Skills Training and other complimentary services being listed on the platform. Alternatively, taking the platform overseas, either as a white label product for other countries to adopt, or giving New Zealand based technology partners an avenue into other markets.
How are you finding the current business climate?
Now’s probably not the time to be starting a new boot strapped venture from reading and listening to the media!
There are two sides to Fulcrum: Technology Partners & Manufacturers.
Technology Partners have been receptive so far, and we’ve focussed on this side of the market first to build the platform. Ultimately we’re providing an edge over, particularly international, competition.
For manufacturers, it’s early days. The true test was our launch on the 7th October, so watch this space.
Has Fulcrum found a niche to work within?
We are trying something new for the industry. In a way we’re trying to create a niche.
Whilst Fulcrum is new to the scene, we are certainly not. We know the value connecting with the right technology partner can have, first hand.
How we facilitate this here in New Zealand is morphing continually. We’re always keen to talk to more manufacturers and technology partners about what we do and how we solve the productivity problem using New Zealand skills & technology, and this will shape our niche for us.
The role of every leader is to make valuable agreements for the organisations they serve. Whether recognised or not, every conversation, where an agreement is required, is a negotiation. These agreements extend to employees, shareholders, stakeholders, customers, communities and yourself.
The leaders who succeed set themselves apart by embodying essential values— values that enhance their emotional intelligence and define their character.
As Qantas faces the backlash of its former CEO’s agreements, we are reminded of the huge cost when these essential values are lacking. In negotiations, values act as shortcuts to remember who we aspire to be, guiding our behaviour and reminding us of the impact we can choose to have. Observing these values ensure we remain on the right side of power versus force, leading to outcomes that are both positive and sustainable.
Making valuable agreements is impossible without creativity. Although we are encouraged to think outside the box, our work environment, risk appetite and often narrow perspectives limit our ability to discover new possibilities. Embracing creativity helps us to transform challenges into shared rewards, avoid deadlocks and fosters positive, sustainable outcomes.
By leveraging diverse perspectives, brainstorming, and remaining flexible, we can turn our obstacles into opportunities, ensuring all parties achieve their goals in new and effective ways.
Connection goes beyond just building rapport; it involves recognising our shared humanity and understanding how small acts of disconnection, like failing to communicate properly, can lead to dehumanising behaviour. When we neglect the value of connection, we risk damaging relationships, tarnishing our reputation and compromising our integrity.
Valuing connection means treating others respectfully and closing any open loops (not ghosting) with those we interact with. When we value relationships over transactions, we strengthen our connection with ourselves, our leadership and elevate the standards of communication we give and accept from others.
The most effective CEOs excel in asking pertinent questions that help gather information and make decisions. This is equally vital in negotiation. High self-regard and emotional intelligence allow us to focus on asking vital questions that reveal underlying problems and facilitate optimal solutions.
Curiosity doesn’t just help with problem-solving; it helps us suspend judgement and prevents us from jumping to conclusions based on false assumptions. In conflict situations, choosing curiosity over judgement promotes understanding rather than quick judgements, it means we explore deeper to solve smarter.
Compassion in negotiation is often misunderstood. While empathy is essential for understanding the needs and interests of others, compassion can sometimes be seen as a vulnerability, especially in competitive environments.
Yet, integrating compassion brings a critical dimension to negotiations - when we drive every deal with understanding it’s compassion that turns our empathy into practical steps that enhance outcomes for both ourselves and others. Compassion is actionable empathy which elevates our humanity and fosters better long-term outcomes.
Have you ever pushed for results over nurturing your relationships with colleagues and stakeholders? In negotiations, genuinely caring means valuing both the results and the relationships you cultivate. This balanced approach is crucial because, while results are measurable, relationships are the foundation of long-term success.
Achieving results in a way that respects and considers all parties involved is just as important as the outcomes themselves. In negotiation, care is the art of valuing results as much as relationships — both are non-negotiable.
We often experience our greatest sense of value when we perceive our actions as contributing meaningfully to something greater than ourselves. In successful negotiations, the same holds true. There’s a significant difference between just showing up and making a real impact. Contribution is about how you present yourself in those critical moments under pressure.
By embodying the value of contribution, you aim to be impactful through your interactions, not just involved. This approach doesn’t just change the outcomes of the negotiation—it transforms you, as a person.
Being a contributor means looking beyond your immediate desires and considering how you can help shape a better future for everyone.
It’s about creating a legacy of positive change where your actions speak volumes. In negotiation this is more than altruism—making a contribution in the way you interact and give value to others creates more sustainable and profitable outcomes over the long term.
Negotiation, after all, isn’t just something you do but an expression of who you are through the process. By integrating these six values into your negotiation strategies you will not only transform the value of the agreements you make but transform you and your business.
Glin Bayley, author of The Negotiation Playbook is a negotiation specialist, a non-exec board director, author and speaker.
Visit www.thevaluenegotiator.com
Winners of the 12th annual KiwiNet Research Commercialisation Awards were honoured at a gala event in Auckland last week for their success in transforming scientific discoveries into new technologies, businesses and real-world solutions.
Winners’ innovations include animal-free dairy proteins, high protein oat milk powder, a plant-based polystyrene replacement, medtech AI for eye exams, and advanced engineering innovations for health and building resilience. KiwiNet’s Commercialisation Icon and Commercialisation Rising Star were also honoured.
The KiwiNet Awards celebrate deep tech heroes from across New Zealand, including research entrepreneurs, innovators and commercialisation professionals who are driving significant economic and societal benefits for Aotearoa by creating innovations emerging from outstanding research within New Zealand’s universities, Crown Research Institutes and other research organisations.
The 2024 KiwiNet Research Commercialisation Awards winners are:
• Emma Arvidson – Teiny/ Te Whare Wananga o Waitaha | University of Canterbury: High protein oat milk powder with impact
Sprout Agritech Breakthrough Innovator Award
• Emily McIsaac - Daisy Lab/ Te Kunenga ki Pūrehuroa Massey University: Making dairy proteins - without the cows
Researcher Entrepreneur Award
PhD student Jessie Fitzjohn with Geoff Chase
• Distinguished Professor Geoff Chase - Te Whare Wananga o Waitaha | University of Canterbury: Engineering better medicine and a more resilient New Zealand
KCA Commercialisation Rising Star Award
• Ben Pearson - UniServices: Building connections and collaboration for exceptional outcomes
CEO Sarah Heine.
• ZealaFoam® - AgResearch/ Plant & Food Research/ Scion: Breaking the mould with sustainable plant-based polystyrene replacement
AJ Park Commercialisation Impact Award
• Toku Eyes and Waipapa Taumata Rau, University of Auckland: Medtech AI: Using the eye as a window to our health
• Melissa Yiannoutsos, Booster NZ: A transformative leader in New Zealand’s science and commercialisation ecosystem
The Commercialisation Icon is KiwiNet’s highest honour. It is awarded to a champion of New Zealand’s research commercialisation community who has made an outstanding impact on the ecosystem and advanced the commercialisation of publicly funded research within New Zealand.
KiwiNet CEO Dr James Hutchinson says,: “Our 2024 winners are shining examples of how New Zealand’s public research, combined with exceptional commercialisation leadership, can drive both economic growth and meaningful solutions to global challenges. The KiwiNet Awards do more than recognise outstanding projects—they celebrate the collective strength of our innovation community. As our sector matures and momentum builds, we must keep pushing forward to amplify the impact of New Zealand’s science on the world stage.”
The 2024 KiwiNet Awards judging panel comprised Cather Simpson – CEO of Orbis Diagnostics and Partner at Pacific Channel; Greg Sitters – Managing Partner at Matū Group; Guy Royal – Director of Tuia Group; Suse Reynolds – Angel Investor; and Olivia Ogilvie – CEO and co-founder of Opo Bio.
The Kiwi Innovation Network (KiwiNet) is a consortium of 19 universities, Crown Research Institutes, an Independent Research Organisation and a Crown Entity established to boost commercial outcomes from publicly funded research by helping to transform scientific discoveries into new products and services.
The 2024 KiwiNet Awards are supported by MBIE, PwC NZ, Sprout Agritech, BNZ, KCA, Campus Plus and AJ Park as well as Return On Science, Momentum, and Matū, the sponsor of the Momentum Student Entrepreneur.
KiwiNet is the combined power of 19 of New Zealand’s universities, Crown Research Institutes, and other research organisations, working together to transform early-stage discoveries into products and services that will have social, environmental, cultural, and economic impact for NZ.
Through PreSeed Accelerator funding from MBIE, training programs, support, and industry connections, KiwiNet helps commercialisation teams and entrepreneurial scientists take their discoveries from the lab to the world. To date, KiwiNet organisations have invested $65.7M in PreSeed Accelerator Funding with 87 start-up companies established, and 787 employment opportunities generated or sustained in NZ. Our PreSeed projects since 2003 have created over $640m in known revenue to NZ.
https://kiwinet.org.nz
Each year, the world produces more than 100 billion tonnes of carbon-rich waste from food production, agriculture, sewage treatment and industrial manufacturing.
Cleantech startup Cetogenix, a 2024 KiwiNet Research Commercialisation Awards finalist, has found a way to harness the untapped potential of organic waste to generate renewable energy and other circular economy products.
The company’s Ceto-Boost™ system breaks down organic wastes and transforms them into valuable products like biomethane, fertilizers and biomaterials. Their patented process uses hydrothermal oxidation — leveraging temperature, pressure and air without any additional chemicals — to deconstruct waste with remarkable efficiency. This novel approach reduces organic waste volumes by 95% and eliminates contaminants like microplastics and pathogens. Globally, it’s estimated Ceto-Boost™ could replace up to 12% of fossil natural gas production and cut greenhouse gas emissions by 884 million tonnes of CO2e annually.
Ceto-Boost Prototype with Cetogenix engineer George Estcourt
The foundation of this innovation lies in over a decade of science and engineering research while the Cetogenix co-founders were working at Scion. They formed Cetogenix in July 2022 via a successful NZ$4.8 M capital raise with co-investment from Pacific Channel Limited, Angel HQ, Enterprise Angels, and Icehouse Ventures.
Since launching, Cetogenix has grown to a team of twelve, who complement strong domestic and international R&D and commercialisation relationships. Within one year of founding, Cetogenix scaled up to a prototype Ceto-Boost™ pilot system in Rotorua, where they still maintain a strong collaborative research partnership with Scion. The company is initially focusing on the global municipal wastewater and agricultural biogas markets and has confirmed pilot trials with end-users in New Zealand and the United Kingdom. Maintaining application flexibility and aligning their technology development and intellectual property with evolving market needs has proven crucial for success.
With its sustainable waste-to-resource technology, Cetogenix offers a powerful solution to the world’s reliance on fossil carbon — paving the way for a cleaner, greener future.
NZ Manufacturer talks with Cetogenix CEO and co-founder Trevor Stuthridge:
Cetogenix CEO and co-founder Trevor Stuthridge
How are you finding interest in your Ceto Boost system?
Our development of Ceto-Boost™ coincides with major global drivers related to energy security (i.e., finding alternatives to fossil energy, such as natural gas), circularity (i.e., better re-use and upcycling of waste streams), and climate change (i.e., adopting technologies that lower greenhouse gas emissions from source – such as organic wastes – or in supply chain – by replacing fossil carbon with bio-based alternatives).
Given that Ceto-Boost™ effectively addresses each of the elements, we have had considerable interest in our technology, especially as it is seen as a more effective solution to those of a number of potential competitors.
is interest coming from?
Interest is coming from both domestic and international parties in the municipal wastewater treatment, agricultural/horticultural sectors, and industrial manufacturing space. For municipal stakeholders, our capacity to eliminate solid waste disposal to landfill or via land application is of the greatest importance – and forms the basis for a significant partnership with the UK water sector. For agricultural stakeholders, our capacity to increase biogas production of their adopted anaerobic digestion systems – whilst capturing significant value from the nutrients as replacements for synthetic fertilisers – has been compelling – and we collaborations in New Zealand, Australia and Europe in that space.
Finally, several large global corporates are working with us to help deliver their zero-carbon strategies by addressing their own requirement to better upcycle
their own organic wastes from manufacturing –as well as supporting primary producers in their supply chain to adopt best practice waste-to-value opportunities.
you are doing is a big deal; universally, cutting emissions must give you enormous pride
We are immensely proud that innovation from New Zealand has the potential to make a substantial difference to global sustainability. It has been a long journey from the original invention of the IP by the Cetogenix co-founders – and one that required us to “wait” until the market conditions aligned best with our value proposition.
What is particularly exciting is that, in a number of cases, internationally substantive end-users are reaching out to us to engage, having assessed their options and determined that Cetogenix has a unique technology offering.
This is particularly satisfying because we deliberately adopted a set of “sustainable design” principles from the very beginning in creating this technology – like the concept of “no waste left behind” – and these are being embraced by these end-users.
Like all start-ups, we are constantly looking for investment to support our strategic direction and scale up our technology. We were very privileged to have an initial set of investors support us in 2022. We are currently raising additional investment to ensure we can accelerate our technical and commercial programs—especially important given our strong alignment to market forces.
We believe Cetogenix is creating the “new normal” for advanced sustainable technologies in our chosen market spaces. In five years, we hope to see a large number of our modular systems installed as retrofits into existing plants in Europe and elsewhere.
We also expect to see our technology fully integrated into new-builds via partnerships with leading waste-to-renewables companies at a global level. Overall, this will mean we are offering tangible and meaningful impacts on climate change metrics, value creation, and sustainable production of energy and biomaterials.
Whilst our own largest markets are certainly international, it would be great to see New Zealand also adopting our technology across a number of key sectors – especially agriculture – where greenhouse emission reduction, replacement of fossil-based products, and demonstrable low-carbon production are critical to their global customers.
Schneider Electric a leader in the digital transformation of energy management and automation, has announced that Oliver Hill will commence as New Zealand Country President on 29 October 2024.
In this role, Hill joins the Pacific Zone Leadership Team, reporting directly to the Pacific Zone President of Schneider Electric, Colette Munro. He will lead the company’s New Zealand team to deliver sustainable, innovative solutions across software, services, and energy management for various industries and partners, for both Schneider Electric and PDL.
“I’m thrilled to work alongside Oliver and see him lead the New Zealand team through this next phase,” said Pacific Zone President Colette Munro.
“Since rejoining Schneider Electric in February, I’ve regularly visited New Zealand, where I’ve had the pleasure of meeting our talented teams, engaging with customers, and identifying growth areas in the market. I look forward to seeing what Ollie’s technical and channel expertise will bring to our customers based on the opportunity that I’ve seen here.”
With a proven track record of delivering results and building high performance teams, Hill brings over 20 years of experience working within outsourced managed services, partner management, and enterprise account management, before leading the commercial channel, printing systems channel, and enterprise teams. Most recently, he served as Managing Director, HP, New Zealand.
Hill expressed his enthusiasm for his upcoming role, saying, “Schneider Electric has a strong reputation for delivering innovative and sustainable solutions across various industries. I am excited to be leading the talented New Zealand team as we strive to introduce new opportunities to a well-established business.
“My focus will be on deepening relationships with customers and partners while adding to a culture of collaboration and inclusivity. I’m passionate about the role we can play in shaping the future of energy
management and sustainability in Aotearoa.”
In addition to his breadth of experience, Hill is an advocate for sustainability, actively serving as a board member of TechCollect NZ. Ollie’s advocacy and his commitment to developing inclusive, collaborative teams that are innovative and drive positive change are a feature of the leadership style that he will bring to this role.
The Government and Auckland Business Chamber have entered a memorandum of understanding which will enable mental health and wellbeing resources for business owners to be freely available, Small Business and Manufacturing Minister Andrew Bayly says.
“As a former business owner, I know first-hand the toll running a business can take on your mental health. Business owners up and down the country are doing it particularly tough right now as they battle challenging economic conditions. With Mental Health Awareness Week now underway, it is a timely reminder that business owners need all the support they can get.
“We know that many Kiwis find it difficult to talk about their mental health and do not know where or how to access help when they need it.
“First Steps is an online platform populated with resources designed to support business owners
with their mental health and connect them with approved professionals who can provide counselling and therapy, as well as services like nutritional advice, leadership training, business mentorship and guidance on digital literacy.
“In the past year alone, the resources were used more than 750,000 times.
“First Steps is all about supporting business owners to take the first step in a series of actions. The intention is to crack open the door and provide some basic tools and information to start that journey.
“The online on-demand content is designed for
business owners who are often time poor and struggle to take time off work but is freely available for all New Zealanders across the country to use.
“Under the memorandum of understanding, the resources, which were developed by the Ministry of Business, Innovation and Employment, will be managed and updated by the Auckland Business Chamber.
“It is great that the business community sees the value of the resources and will assume responsibility for managing First Steps’ content, taking a by-business-for-business approach.”
An industry-leading trades training facility opened by Hon Shane Jones in Ōtautahi Christchurch will create exciting new opportunities for aspiring electrical and plumbing trades in the region.
The first of its kind in Canterbury, the Skills Group Skills Hub will incorporate a three-trades model. It will house the Group’s three specialist trades brands—Etco for apprentice and electrical training, E-tec for advanced electrical training, and—new to Christchurch—Industry Connection for Excellence (ICE) for plumbing, gasfitting, and drain laying (PGD) apprentice training.
The newly modernised Hornby campus is located in the former Placemakers building, and its state-of-the-art facilities will supercharge trades training for 360 electrical apprentices, 80 pre-trade students, a number of PGD apprentices and 250 learners enrolled in industry short courses in the region.
Skills Group Director of Specialist Trades, Ben Stevens, says the Group is delighted to support Christchurch and the Canterbury area by giving South Island-based apprentices and their employers more training choices, with less travel.
“This is a real positive for the region and will
help meet the significant apprentice training demand across the South Island,” says Stevens. “It’s great to have a presence here and create something new, something modern, using the best quality gear and technology so that we can equip our apprentices for success.”
Ben believes the extensively renovated campus offers purpose-built training facilities with industry-standard equipment, including large roofed drain laying pits, modular bathroom pods, new hand and battery tools, new workshop equipment, multiple 4+ assessment sets for each task, large bright touch-enabled displays, and class sets of laptops.
AI will also be front and centre.
have extensive on-the-job experience, ensuring apprentices gain all the skills they need to succeed in the sector.
Skills Group is closer to its vision of changing the landscape for South Island tradies; the Christchurch hub follows the Group’s opening of a three-trade school in Dunedin in August.
“The online component of our programmes includes additional learning activities featuring videos, animations, and interactive scenarios to support trainees’ knowledge development,” explains Russell. “We are also initiating a new project to explore the potential of augmented reality devices for gathering evidence during on-the-job assessments.”
Tutors will come directly from industry and
“We are thrilled to be moving another step ahead in our long-term vision of being the leader in providing quality specialist trades training. Our world-class South Island hubs will more effectively support our apprentices, employers and the industry,” said Stevens.
The Hub is located at 69 Shands Road, Hornby.
Looking for a marketing edge? 70% of licence holders say signing on has positively affected sales.
When wind energy is harvested for electrolyzing seawater directly on board, these power-dense, intelligent and communication-enabled hypoid gearboxes, from Wittenstein, perform important functions controlling the four up to 1200 meter-long ropes of the Kite Propulsion system’s 60 square meter kite.
OceanEnergy opted for a reliable, future-proof technology comprised of robust TPK+ gearboxes and their cynapse functionality, i.e. with integrated sensors, logic and an IO-Link data interface in the gearboxes. These smart gearboxes will supply essential operating and status data, while the energy ships that produce green hydrogen in the six permanent oceanic trade wind zones will be smartly navigated there according to the wind forecast.
Kite Hydrogen Ship – inspired by kitesurfing
It was kitesurfing that provided the inspiration for the Energy Ships.The basic idea was to harness the forces acting on the kite that pull the kite’s ropes and convert them into electricity. At the heart of the Kite Hydrogen Ship concept is the patented K1 Kite Propulsion system, which can be imagined as a green power socket for the on-board electrolysis process. The challenge for the smart hypoid gearboxes is to control the kite’s four frequency converter-driven ropes as they generate electricity during the harvesting journey by launching and pumping the kites. A large part of the energy that is generated in
this way by the K1 Kite
system is utilized directly on board for the production of green hydrogen.
A hydrogen plant of this kind is designed to produce around 1000 tons of green hydrogen during its eight-week harvesting journey. That adds up to a good 6000 tons per year – enough to supply about 40,000 hydrogen cars or power an Airbus for almost twelve months.
The aim of the energy ship fleet now in the pipeline is to produce green hydrogen costing just 2 euros per kilo by 2035 – in other words, significantly more economically than with any other green technology known to date.
Dynamic wind loads of up to four tons per rope – no problem for a TPK+ hypoid gearbox
Hypoid gearboxes from the TPK+ series were selected to control the four steering ropes while pumping the kite based on simulation and application data. Their right-angle design is central to the ultra-space-saving principle of the entire K1 Kite Propulsion system and its integration into a seaworthy container. These size 300, two-stage gearboxes have a ratio of i=100 and are characterized by high torsional rigidity, low torsional backlash and greater absorption of external forces. The high-quality hypoid teeth simultaneously ensure high torque and exceptionally smooth running.
www.treotham.com.au
Immediately-responsive 24/7 fire suppression technology has been installed by Hydraulink for the leading heavy equipment Porter Group’s first BOMAG BC1173RB-5 refuse compactors to be introduced to Australasia.
The fluorine-free Muster F3 foam system features its own bult-in electrical power system and self-maintenance features to ensure it functions whenever and wherever it is needed, either at work, parked on-site or based in its user’s workshop.
Regardless of when and where this valuable plant is located, its fire suppression technology offers immediate protection to owners and operators. Importantly, it is engineered to curtail fire hazards before they spread, preventing any hazard becoming
more unsafe and damaging to personnel, machine, and surrounding facilities.
The Muster fire suppression system used is tailored to markets where safety and operational compliance are paramount, including particularly underground mining and tunnelling as well as steel and metals processing, highway and roads, agricultural, forestry, waste management, construction, defence, and anywhere that machinery works could lead to a fire and damage equipment, stock, or put lives in danger.
The muster fire suppression systems are designed to detect and activate automatically in the case of fire. They feature manual activation via a remote actuator that can be placed anywhere appropriate on your site for maximum safety.
Hydraulink Fire Suppression, which services all of New Zealand, specifies Fluorine-free F3 foam on all new pre-engineered fire suppression installations, because it is more environmentally friendly, and safer for workers and machinery operators.
The fire suppression system engineered for the BOMAG refuse compactors had to be up to the engineering standards of compactors that are some of the most advanced of their type in New Zealand and Australia.
Their design is engineered to advance environmental objectives by achieving the best possible use of landfill volume, and at the same time offer ideal and homogeneous compaction. This ensures the optimum stability of a landfill site.
The fire suppression system has to be rugged and versatile, because the BOMAGs from Porter Group can be used on landfill sites of all sizes and types, regardless of whether the refuse is industrial, household, bulky, or construction waste.
The BC 1173s are packed full of advanced time saving and efficiency technology, such as BOMAG TELEMATIC computerised remote monitoring, which provides location and operating data by the click of a mouse at any time to manage fleets more efficiently.
Automatic reports provide full transparency on fuel consumption, idle times, and the potential for fleet optimisation. BOMAG TELEMATIC also includes real-time monitoring of pending maintenance and service history.
To complement the advanced technology built into the BC1173RB-5s being introduced by Porter Group, engineered into them was a Muster fire suppression system that integrates perfectly with the 24/7 monitoring and automation of the vehicle and provides a gold standard of protection and compliance for advanced machinery that increasingly is automated and digitised.
All Muster systems installed by Hydraulink are AS5062 compliant.
Hydraulink Fire Suppression utilises Linear Heat Detection (LHD) to further minimise costs and downtime for customers. The major advantage of using LHD, is that there is no leakage of gas through the system.
Socomec, a leading manufacturer of electrical equipment with strong expertise in critical energy applications, has entered into a new exclusive distribution partnership with NHP for its energy management portfolio in Australia and New Zealand.
NHP – an Australian company specialising in power distribution, motor control and automation systems – already has a longstanding relationship with Socomec, and has been the distributor for Socomec’s Power Control and Safety (PCS) range for 20 years.
“We believe NHP is an ideal fit for our Energy Management portfolio, and by consolidating both business lines into one cohesive channel, we can further enhance the experience for customers across Australia and New Zealand,” said James Fraser, Managing Director – ANZ, Socomec.
Socomec is a global organisation with more than 4,200 employees across 30 subsidiaries on all five continents, including Australia and New Zealand.
“We have seen the exceptional results NHP has achieved with our PCS portfolio, so we are confident they will enhance our well-established position in the market by taking on our Energy Management line,” added Fraser.
“NHP has outstanding technical competencies, a strong local stocking capacity, extensive local project references, and a history of quality product management, so they are an ideal fit to be our distribution partner in the region.”
NHP CEO, Stephen Coop, says Socomec’s Energy Management line is a natural fit which enhances NHP’s existing power distribution portfolio.
“By expanding our partnership with Socomec, we can provide enhanced connectivity utilising latest technology tailored for the local Australian and New Zealand markets. This expanded partnership will bring additional growth opportunities for both organisations as we move towards a more energy efficient and sustainable future,” he said.
The new exclusive distribution partnership will become effective from 1st January, 2025.
“With both Australia and New Zealand focusing on building sustainability, energy management solutions are becoming increasingly sought after by companies looking to meet ESG (Environmental, Social, and Governance) targets and other regulations,” says Fraser.
“You have Green Star building ratings, NABERS (National Australian Built Environment Rating System), NCC (National Construction Code) requirements, and different Government regulations, all demanding more sustainable building usage,” he says.
“To comply with Standards and regulations, it is essential to measure energy consumption and use
smart technologies to reduce usage and optimise performance. Electrical contractors, switchboard manufacturers, environmental managers, consulting engineers, and a range of other key stakeholders will now have access to the full Socomec energy management range through NHP.”
Another driver for energy management solutions is the increasing prevalence of Electric Vehicles (EVs) in Australia and New Zealand.
“EVs require charging stations that draw large amounts of power, so it’s essential that the right technologies are in place to make sure power is being taken at optimal times,” says Fraser.
From Sandvik Coromant is the CoroMill MS20, a true 90-degree shoulder milling solution. Thoroughly designed for roughing to finishing in stainless steel and heat-resistant super alloys, it ensures uncompromised security, versatility and productivity.
CoroMill MS20 is a single-sided, two-edge solution for true 90 degrees shoulder milling applications in ISO M and ISO S materials, particularly suited for the aerospace and oil and gas industries. Being versatile, CoroMill MS20 excels in repeated shoulder milling, face milling, linear and helical ramping, full slotting, and plunging applications.
One of the standout features is its optimized geometries tailored for different ISO materials, ensuring higher edge line security. The reliability of
the CoroMill MS20 inserts exhibit a predictable and gradual wear pattern on the cutting edge, even in demanding applications.
Premium assortment, premium results
The combination of high-quality cutter bodies and inserts ensures excellent surface finishes and optimal wall quality (without any steps) in repeated shoulder milling applications.
The robust cutter body boasts high levels of dimensional control, closely matching the nominal diameter with tighter tolerances on axial and radial runout. This results in improved component quality, fewer rejections, and extended insert tool life.
Manufactured using a new pressing technology, the inserts offer superior dimensional accuracy, further
enhancing component quality and insert tool life. The high accuracy of the direct-pressed CoroMill MS20 insert enables it to replace periphery ground geometries with similar performance.
The assortment encompasses cutter bodies in the range of 15.8–84 mm (with inch equivalent cutters), along with inserts featuring optimized geometries for stainless steel and HRSA applications.
By Ross Thompson CEO, Greenbox
Manufacturers across the Asia Pacific region – from Singapore to Sydney, Adelaide to Auckland – are central to decarbonisation. If Australia and its business ecosystem doesn’t ride the opportunity winds to its 2050 net zero target, don’t expect too much wealth and health to flow through the Australian economy in the years ahead.
Current events and latest polls tell us that Federal & State Policies have taken too long to implement. Meanwhile, a majority in our households and the workplace are thinking ‘just get on with it.’
As the presidential election approaches in the US, should the Democratic Party keep its control, it is likely that significant investment into cleantech will continue off the back of President Biden’s administration signing into law the largest clean energy investments in America’s history.
Add to this that the globally agreed target limit of 1.5C to avoid damaging climate change impacts was recently breached across an entire year for the first time, according to the European Union’s climate service, and it seems clear we need to take action – and soon.
How we create and use technology is the biggest lever to manage climate change. The International Energy Agency estimates that 35% of the emissions cuts needed to meet 2050 climate goals will have to come from technologies not yet available.
The window will close as governments and firms jostle for gamechanger tech in this great clean energy economy.
Given the enormity of the task at hand to decarbonise Australia, there will always be pressing trade-offs as Australia looks to leverage its abundance of gas reserves as the transitional fuel towards its 2050 net zero targets (latest policy, backing gas until ‘2050 and beyond’).
Aussie smarts should and must supply the inexorable demand created by the global transition to a net zero economy.
The good news is our climate tech sector has some momentum. Globally, compared with a few years ago, there is now a clear market for climate technology. Australian climate tech players span sectors ranging from renewables, carbon markets and agri-food through to storage, mobility, built environment, data and finance, and circular economy.
Our circularity focus here at Greenbox includes repurposing existing tech hardware to reduce e-waste.
Australian cleantech is powering up everything from EV charging and hydrogen solutions to virtual
power plants, vertical and smart farming, and soil carbon removal. Climate Salad’s 2024 Australian Climate Tech Industry Report identifies 689 climate tech companies with 49% already operating internationally.
Key takeaways include that Australian climate tech can create both domestic and international impact, 80% of companies aim to raise capital in the next 12 months, and market conditions continue to make raising capital challenging.
Climate tech founders are looking to the government’s recent 15B National Reconstruction Fund Corporation for financial support targeted at high-value industry transformation. Some are scratching their heads, however, and the fund has been under fire for being slow out of the blocks.
Climate tech addresses complex challenges, so this deep tech activity is naturally capital-intensive and a good number of Australian climate tech start-ups are struggling in the soft market for funding.
Positively, Q2 2024 venture capital data from Cut Through Ventures showed that Climate Tech/ CleanTech, along with Fintech and Biotech/Medtech “remained the most consistently supported sectors by investors, maintaining their positions atop the best-funded segments.” Long term, there is unquestionable demand for climate tech.
Australia’s energy transition is everyone’s challenge, but it is technology that will deliver it. Tech, AI and data analytics can see and rapidly think across, inside and forward to drive innovation, efficiency and productivity that is low-carbon, low-waste and regenerative.
Tech roles in every company should be highlighting efforts to bring their organisation and supply chains into the Australian circular economy. It’s about digital leadership but also taking responsibility given the ongoing deep environmental and social footprint attached to resourcing the infrastructure and hardware of this extraordinary digital era.
Importantly, you don’t have to be a climate tech company to impact climate change. There are quick and impactful decarbonisation wins for all Australian companies through technology.
The obvious one is reuse of devices like laptops,
desktops, smartphones and monitors: around 15% of a company’s climate emissions come from its ICT equipment and 80% of an ICT product’s emissions take place when it is being produced. Circular ICT procurement delivers huge gains.
In a circular economy you have accessibility without necessarily buying, owning and discarding. The whole non-linear point is to keep products and materials circulating so materials don’t become waste and nature is regenerated.
On top of widespread tech-led business decarbonisation actions, we need the Australian government to step it up on climate policy. Business leaders should advocate for more financial support and incentives for renewables and low emission technologies and activities.
Climate tech companies do our heavy lifting for the transition, and they need a bit more help.
To get to this green future first, we need commitment, capital and collaboration on a whole new level. Let’s get on with it and create the jobs, companies and country of the future.
Ross Thompson is Group CEO of sustainability, data management and technology asset lifecycle management market leader Greenbox. With facilities in Brisbane, Sydney, Melbourne, Canberra, Auckland, Wellington, and Christchurch.
-Eric Lai, Senior Regional Sales Director for Industry APAC
Fuelled by the explosive growth of emerging markets like AI and electric vehicles, the semiconductor industry – which manufactures the essential materials that power these technologies – is poised to grow into a massive trillion-dollar industry by 2030 .
At the very heart of this growth lies Southeast Asia, as markets in the region actively pursue opportunities to capture higher value-add positions within the burgeoning global industry. In fact, Singapore’s Minister of State of Trade and Industry called for efforts for the state to sharpen its competitive edge in the semiconductor industry as it aims to double its manufacturing sector’s value by 2030 .
However, despite the semiconductor industry’s immense potential for economic growth, its notorious thirst for water and energy stand at direct odds with Southeast Asia’s climate ambitions, wherein most countries across the region have committed to carbon neutrality by 2050.
How can the growth of semiconductor manufacturing be reconciled with these climate targets to achieve balanced and sustainable long-term development?
Intensifying climate events around the globe have brought the semiconductor industry’s immense resource consumption to the fore. Growing concerns about global water shortages have placed the sector’s water usage under scrutiny, while its substantial electricity consumption remains a focal point of concern.
However, discussions about these resources tend to occur in silos, with limited focus on the water-energy nexus – which refers to the interdependent relationship between both resources. For instance, considerable energy is required to treat and move water in semiconductor fabrication plants (fabs); conversely, water is critical for the energy generation processes that power these facilities.
To truly drive sustainability in this sector, there needs to be a concerted effort to move beyond traditional energy reduction to target the energy-intensive water processes central to the water-energy nexus.
Firstly, all fabs require mammoth volumes of ultra-pure water (UPW) to cleanse their silicon chips. In fact, estimates show that an average fab uses about 37.8 million litres of UPW daily to ensure the quality of their output . To obtain UPW, however, fabs undergo a rigorous purification process that consists of energy-intensive steps like reverse osmosis and distillation, which contribute significantly to the plant’s overall energy consumption.
Furthermore, producing high-quality chips demands a significant cooling capacity. This involves effectively managing the flow of water throughout the manufacturing process. It’s not just the cleanrooms that require strict control over temperature, pressure, and humidity. Many processes and dedicated machines within the plant generate a substantial amount of heat during operation, for instance, in wafer fabrication, etching, and deposition. Cooling towers play a crucial role in regulating the temperature of the circulating cooling water for these processes and machines, ensuring optimal performance and efficient heat dissipation.
When optimising equipment processes, engineers typically focus on overall equipment effectiveness (OEE) , which looks at an equipment’s overall productivity and efficiency – an approach that tends to deprioritise energy consumption metrics. To drive water and energy efficiencies, there first needs to be a mindset shift that encourages prioritising energy efficiency from the get-go, rather than focusing solely on OEE.
For existing plants, conducting a comprehensive, measurement-based analysis of current processes and performance can uncover the critical areas that offer
the most potential for energy savings, ensuring that any changes enacted are targeted and effective in driving impact.
Additionally, digital solutions are a pivotal avenue for manufacturers to attain operational efficiencies, as they enable us to understand demand and intuitively manage supply, ensuring we only use what we need. The good news is that these technologies already exist – manufacturers just need to make the switch to achieve improved water and energy efficiencies.
For instance, Grundfos has helped manufacturers across various industries optimise their cooling systems and towers by implementing real-time monitoring and automating adjustments to pump speeds and fan operations, resulting in up to 60% energy savings and 20% reduction in water loss.
Ultimately, creating more water and energy-efficient processes are not just beneficial for sustainability purposes; they are also a strategic business priority that allow companies to minimise operational costs and align with the growing demand for environmentally responsible supply chains.
By prioritising environmental impact as they seek to establish themselves in the global semiconductor arena, Southeast Asian countries can find a way to harmonise their economic ambitions with their climate goals to chart the path for a sustainable future.